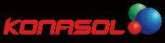
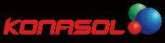
KONASOL


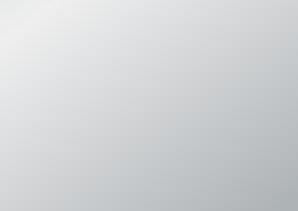


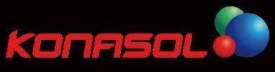
To make people happy with nanotechnology
KOREA NANO SOLUSION
KO : Korea
NA : Nano
Korea’s Leading Position in the world, Pursuing the World Top 5 from the poorest country, Realized High-Speed Growth in short period of time, The Image of Most Successful Country
Achieved the Highest level of National Brand, A Country of Cultural Advancement with K-POP including BTS, K-CULTURE, and K-FOOD
Nano Science Technology, Nano Material
Material component with one-hundredth of a millionth of the thickness of a hair The core technology of 4th industrial revolution developing Nano Technology and its utilization
A Scientific Technology of future material creating higher value scientifically and engineeringly
SOL : Solution
Provide Solutions to the problems of human being and customers’ Technical Difficulties (Solution Provider)
Provide Solutions to difficult problems in each field.
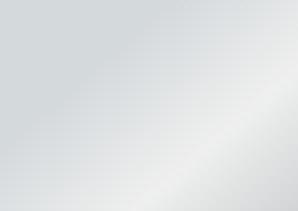
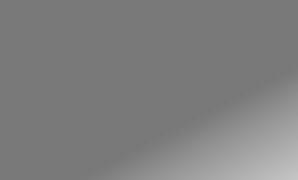


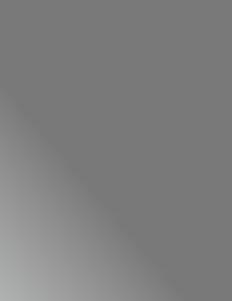
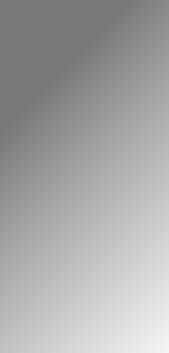






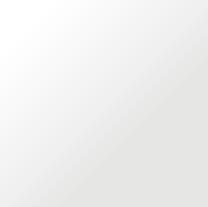
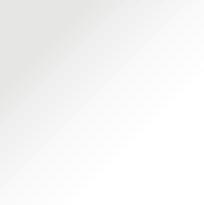


Powder Metallurgy
Alloy Steel


Casting RESISTARⓇ





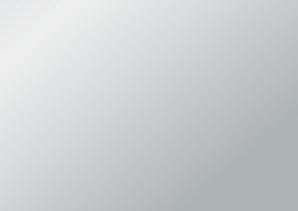
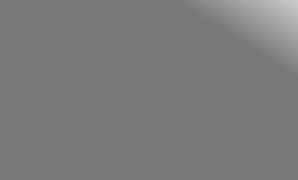
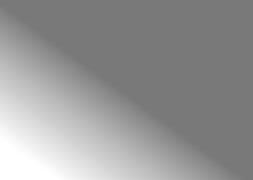
Company overview
MAIN BUSINESS
Alloy-TiC, powder steel, rolling mill, guide roll, tube mill, transfer rate, mold, extruding grinding, construction facility component, heating furnace, roll, transfer, control facility, magnet for industrial purpose, scrap steel cut, vehicle component, piston pin
HEAD OFFICE
17-60, Saneopdanji-gil, Myeoncheon-myeon, Dangjin-si, Chungcheongnam-do, Republic of Korea
Tel. +82-41-359-6600
Fax.+82-41-359-6609
17-60, Saneopdanji-gil, Myeoncheon-myeon, Dangjin-si, Chungcheongnam-do, Republic of Korea
HWASEONG PLANT
711-63, Mannyeon-ro, Jeongnam-myeon, Hwaseong-si, Gyeonggi-do, Republic of Korea
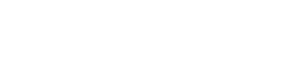
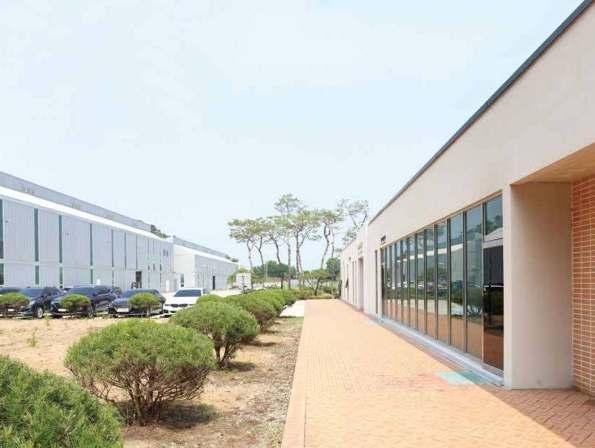
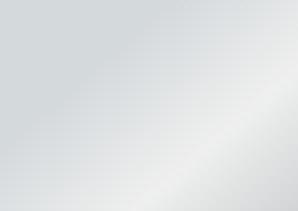

Founded Myeong Jun Industry
Changed to Alloytic Co., Ltd.
Appointed as a corporation for special cases on military service, business venture
Designated as a corporation eligible for export support
Established a company-affiliated research institute
Qualified for ISO 9001:2000 certification, EM Mark(quality certification)
Patent qualification(No. 0340800), selected as an expert company in component material
Patent qualification(No. 10-0587495), promising export company, INNO-BIZ
Renamed Daehwa Alloy Tech Co., Ltd. as a result of M&A with Daehwa Precision Manufacturing Co., Ltd.
Selected as a company of innovative management(No. 080501-01086)
KOTRA-guaranteed brand(Seal of Excellence) certification qualification
Awarded the 3 Million Dollar Export Tower Award
Patent application(complex hammer bits/composite rolling mill/vessel engine nozzle)
Install HIP(Hot Isostatic Pressing)(maximum size in Korea)
Patent application(piston pin for vehicle /nano lubrication additives) dispersion)
Promoted as a middle standing company by the Federation of Korean Industries
(10 out of 4,000 companies designated)
Awarded the 10 Million Dollar Export Tower Award
Certification of vehicle non-engine oil driving to be the longest record in Korea (Korea Record Institute)
(Add nanorex - obtain new record from the existing 837Km to 1,309Km)
Relocated head office / first factory to Dangjin Myeoncheon Industrial Complex
Awarded the Minister of Trade, Industry, and Energy Prize
Selected as a youth-friendly small hidden champion(Ministry of Employment and Labor
Confirmed as root company, increased investment from external institutes (2.8 billion won of capital)
May - Renamed DAT Advanced Material Co., Ltd.
July - Established 100% self-sufficient powder for our company at the Daejeon factory
Products selected by Korea Energy certified
Awarded the Minister of Trade, Industry, and Energy Prize(Nano Korea 2020)
Awarded by Korea Prime minister for Machinery and Robotic Development
Selected as a specialized company in material, parts and equipment by Korea Government
New Company Name of KONASOL

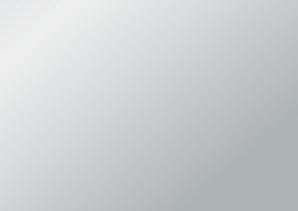
Products
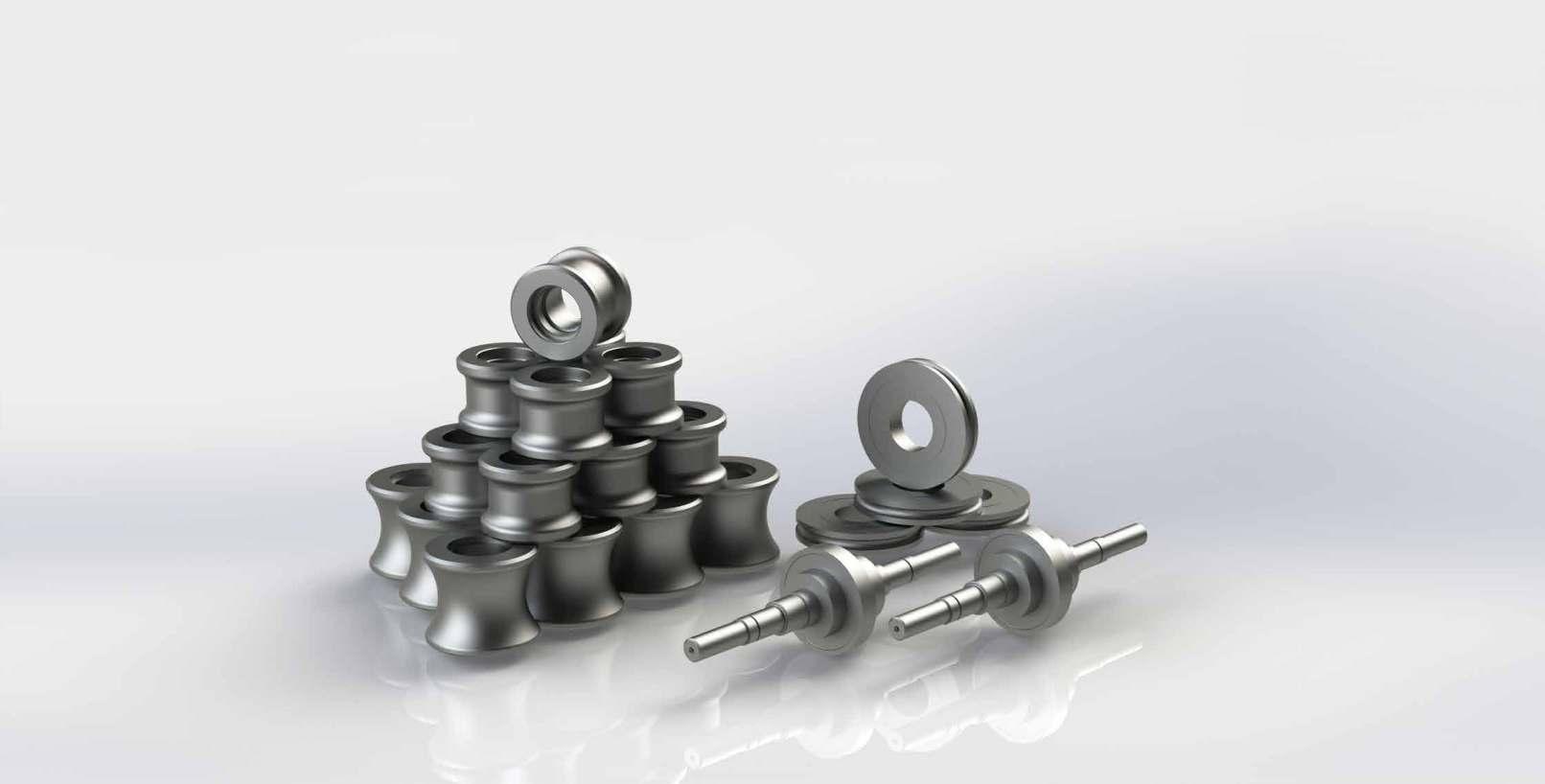
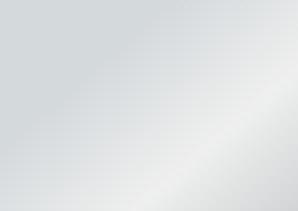

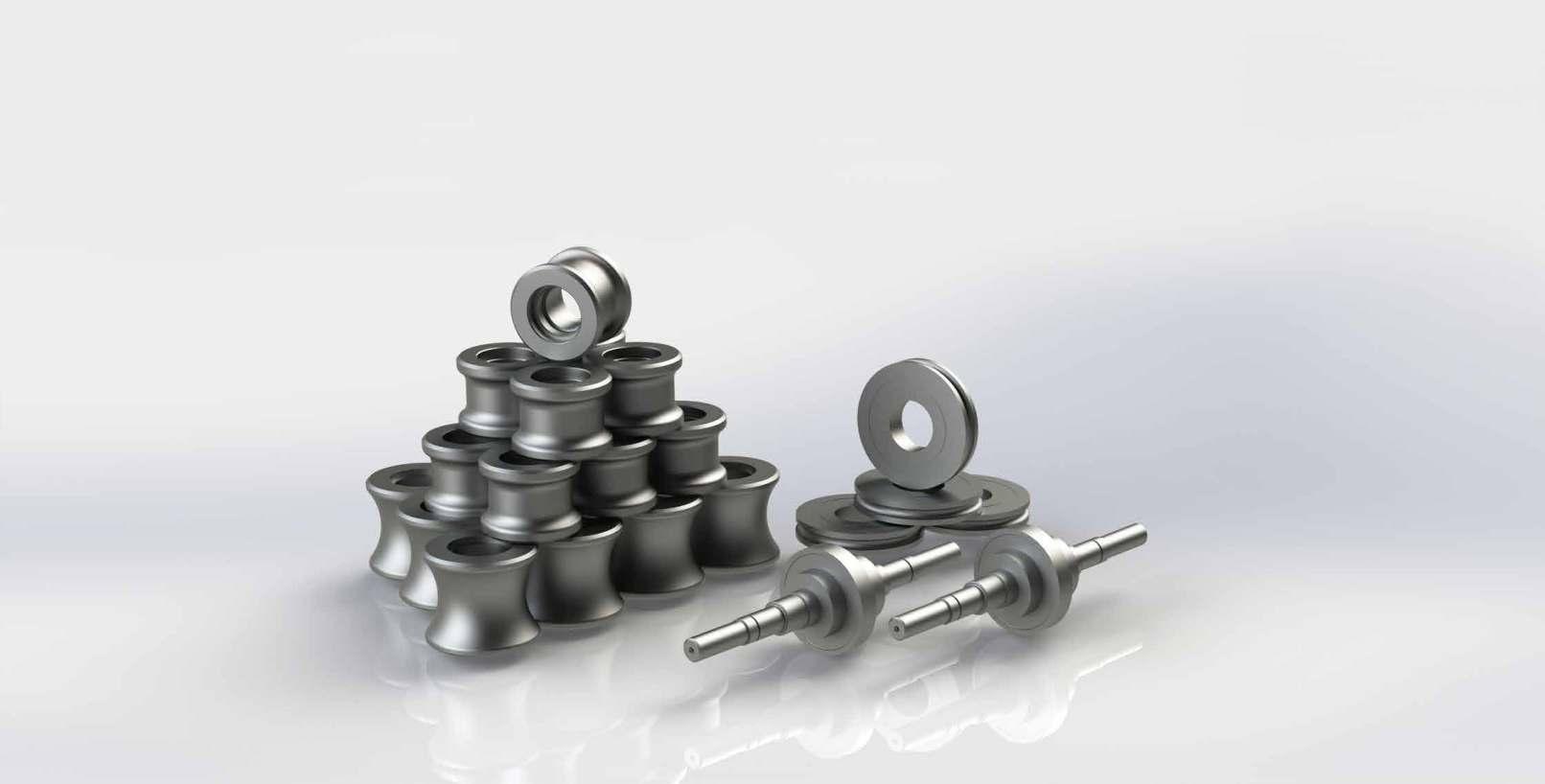
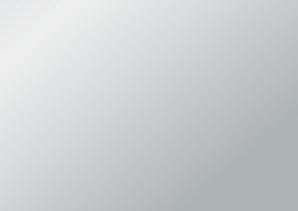



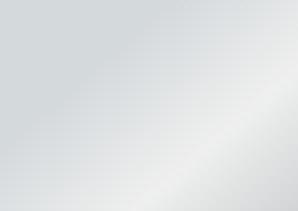
Alloy-TiCⓇ
Overview of Alloy-TiC®
Alloy-TiC is one of the metal matrix composites having TiC (titanium carbide) as raw material and high hardness, with minute circular titanium carbide sprayed uniformly all over the alloy steel. Alloy-Tic is produced after mixing and molding the alloy steel and TiC powder and sintered in a vacuum furnace and then processed to HIP. The TiC (Hv:3,200) particle shows over 30% higher hardness than WC (Hv:2,400) particle, but Alloy-TiC can be racked, milled, and polished in annealing state, which is advantageous for the hardening process of up to HRc 68-72.
Advantages of Alloy-TiC®
1. Excellent wear resistance
Wear resistance is one of the widely known advantages of Alloy-TiC. The TiC particle on a surface after wrapping and polishing is a circular HRc92 with 30% or higher hardness and lower friction coefficient than WC hardness; hence the minimized pick-up, galling, and chipping phenomena and little or no wear loss upon contact with other metals.
2. Low density of Alloy TiC offers cost reduction effect
Alloyteel (6.5g/cm3) has relatively low ratio than WC hard metal (14.5g/cm3) or tool steel (8g/cm3) that, if applied to the same volume as WC hard metal or tool steel, it is cheaper in price and, if used instead of WC hard metal, the maintenance and change costs of components are relatively low.
3. Alloy-TiC is the only machinable carbide composite
Alloy-TiC can be processed with general machining process with HRc43-45 in annealing state, becoming hard metal of HRc68-72 after heating process. In addition, before and after the heating process, its size strain is relatively stable.
4. Alloy-TiC is zero-defect sintered carbide composite
Alloy-TiC is zero-defect composite without bubbles inside thanks to the HIP process.
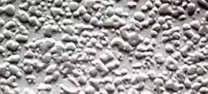
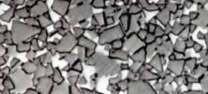

Alloy-TiCⓇ FT-1
Characteristic
Alloy-TiC FT-1 is a sintered product after spraying approximately 45% of high-hardness circular TiC (Titanium Carbide) particle, which has hardness within the powder matrix of steel alloy as HRc 92; thus it is a hard metal available for mechanical process that can endure severe repetitive friction
• Excellent wear resistance using high hardness(HRc 02) circular TiC particle
• Friction during the drawing process due to the excellent lubrication property of TiC particle
• Minimally improve quality(prevent picking up, scratch)
• Easy to process with common mechanical process prior to heating process
• Size stability before and after heating process(strain ±0.0002mm)
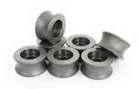
• Heat proof, impact resistance, and corrosion resistance can be added by the composite of steel alloy
• Can contain up to 70% TiC to improve wear resistance and can have higher hardness by nitriding
• Same with Ferro-TiC CM
Composition







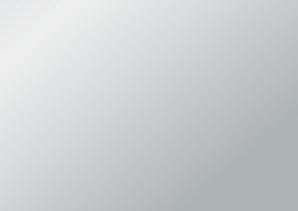

Alloy-TiCⓇ FT-2
Characteristic
Alloy-TiC FT-2 is a product with 45% of TiC (Titanium Carbide) circular particles with high hardness of HRc 92 within the powder matrix of stainless 400-type alloy spread and sintered; thus, it is a hard metal available for general mechanical process that can endure extreme repetitive friction
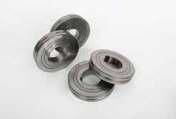
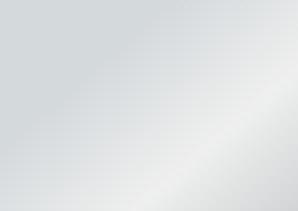
• Excellent wear resistance using TiC circular particles with high hardness(HRc 92) - 5- to 20-fold wear resistance compared to Stainless Steel/ Monel
• Excellent corrosion resistance with Stainless 400 type
• (US) FDA-certified material
• Easy to process with common mechanical process prior to heating process
• Minimize friction due to excellent lubrication of TiC particles(prevent picking up, scratches)

Alloy-TiCⓇ FT-4
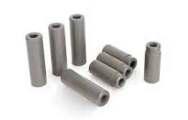
• Same as Ferro-TiC C, applied at tool, die, and worn components, excellent oscillation damping during annealing state.
• Alloy-TiC FT-4 is widely used for general mechanical tools, gauges, and other wear resistance components.







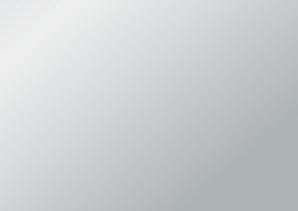

Alloy-TiCⓇ FT-5
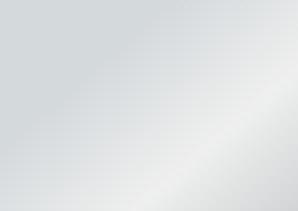
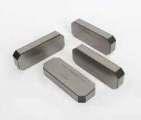
Alloy-TiC FT-5 is a precipitation reinforcement-type nickel base high heat resistance alloy and is a product where high-hardness TiC circular particles are spread and sintered at the matrix, which can be applied to the tool steel used for general use or to other materials such as in a situation of corrosion and oxidation at high temperature. This product can be used up to 980ºC regardless of strength loss at approximately 700ºC.
In addition, because of the circular particles of TiC, it has low friction coefficient, resulting in excellent wear resistance after pick-up, galling, chipping, and related phenomena occurring upon contact at high speed or high temperature due to low friction coefficient as friction works are minimized.

Alloy-TiC FT-5 and Inconel X-750 comparison
Inconel X-750 property comparison
Inconel X-750 is a precipitation reinforcement-type Ni-base superalloy with high temperature strength, corrosion resistance, and oxidation resistance. Its use is for jet engine and rocket components. It can be used up to 700ºC regardless of strength loss at approximately 650ºC.
Comparing the mechanical properties between Alloy-TiC FT-5 and Inconel X-750 as shown in picture 1, Alloy-TiC FT-5 shows 1.7-fold hardness compared to Inconel X-750 at 650ºC; thus, as shown in picture 2, it has 2-fold wear resistance. Therefore, if it is applied to the same extruding die, lifespan is expected to increase 2-fold compared to Inconel.







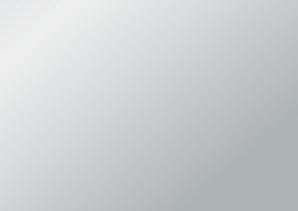

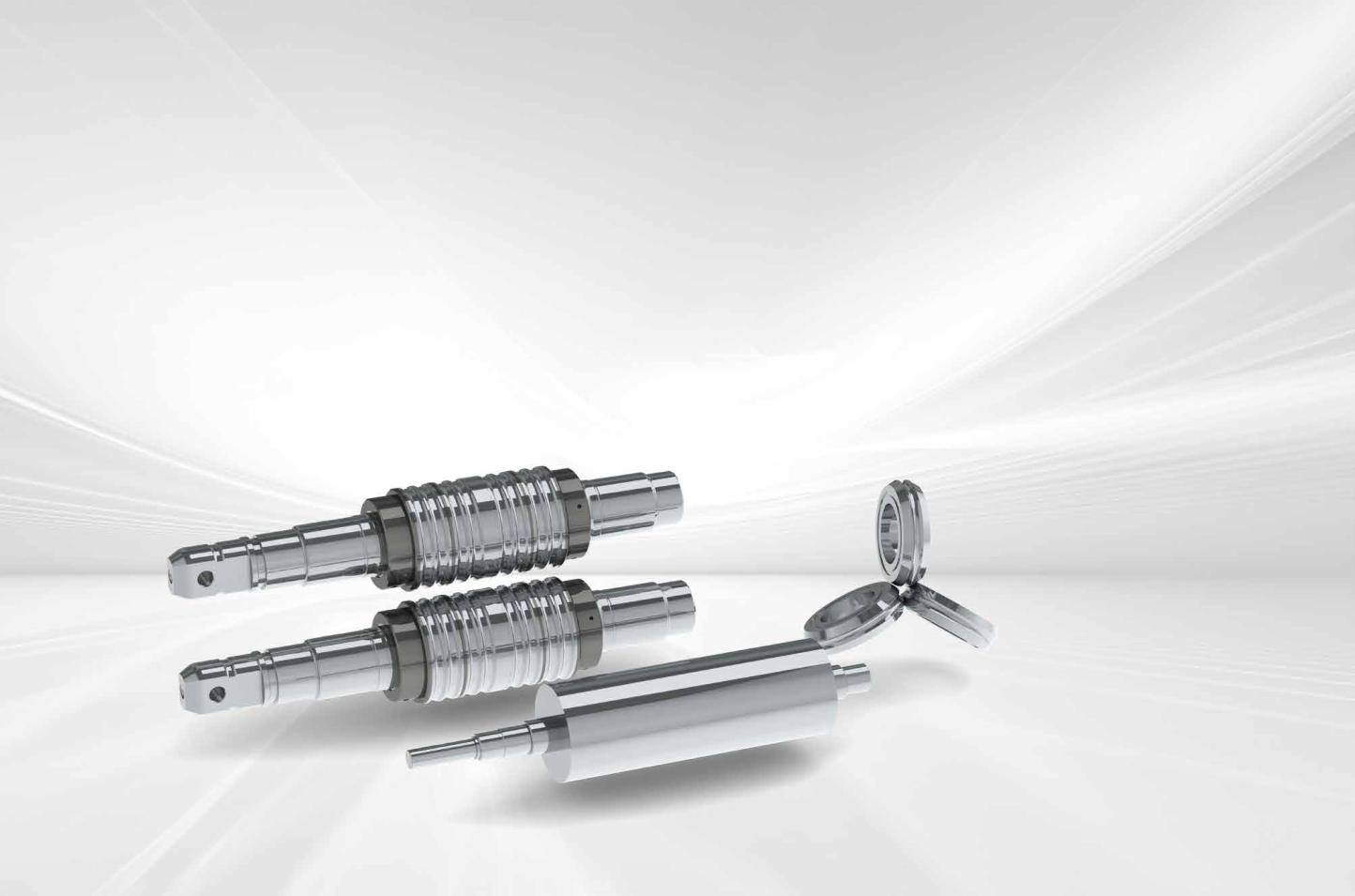
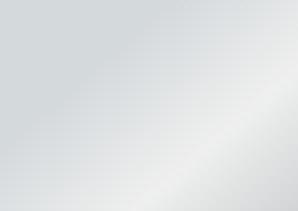
Alloy-TiCⓇ Applications
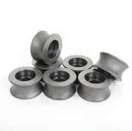

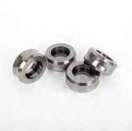

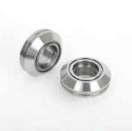
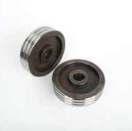
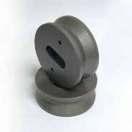
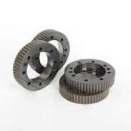
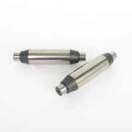

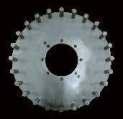
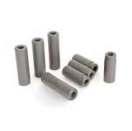
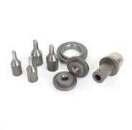
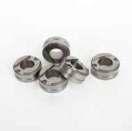
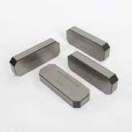
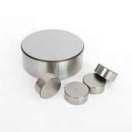
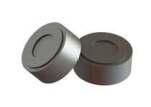
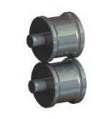







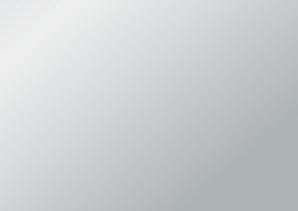

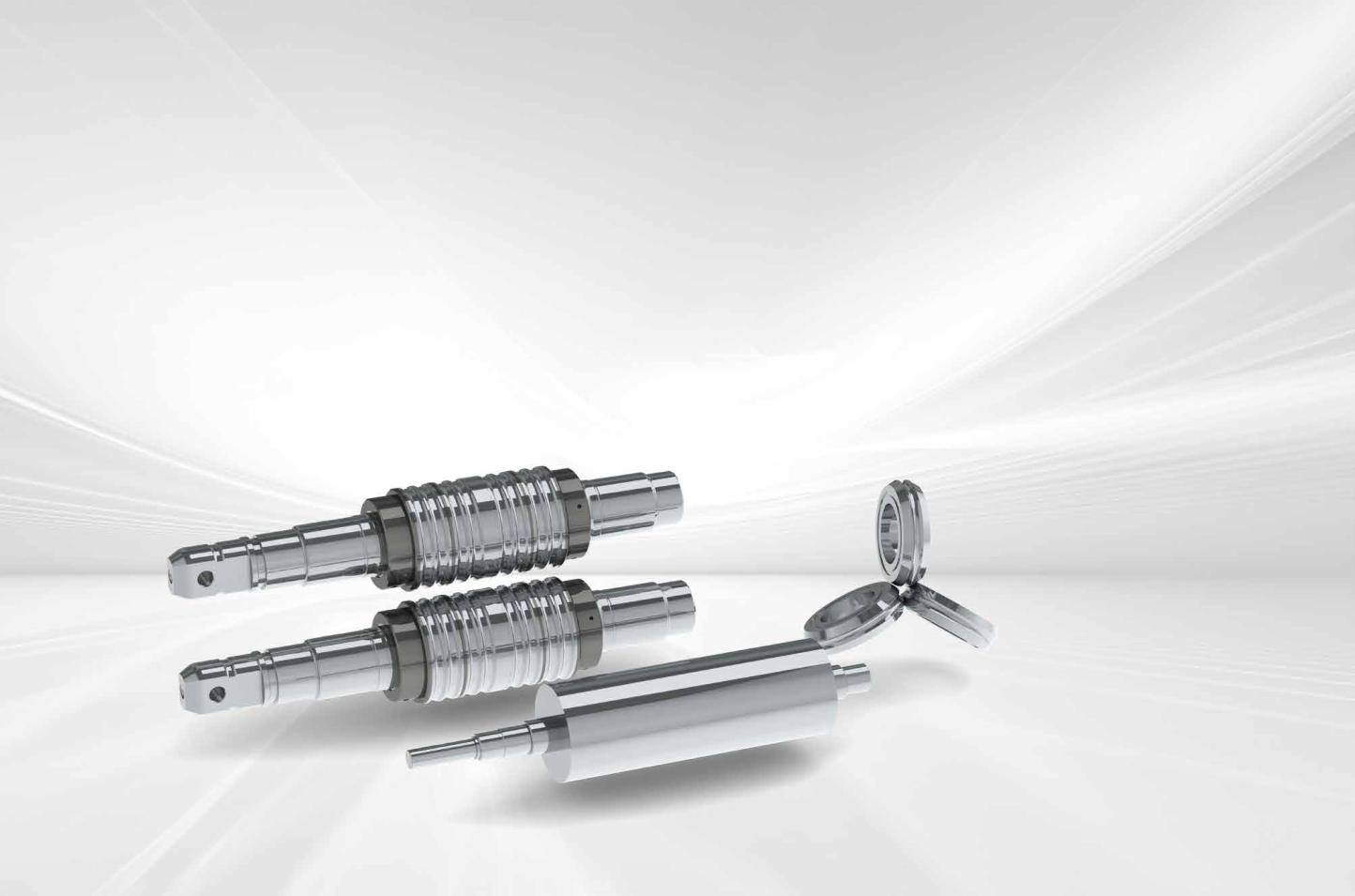
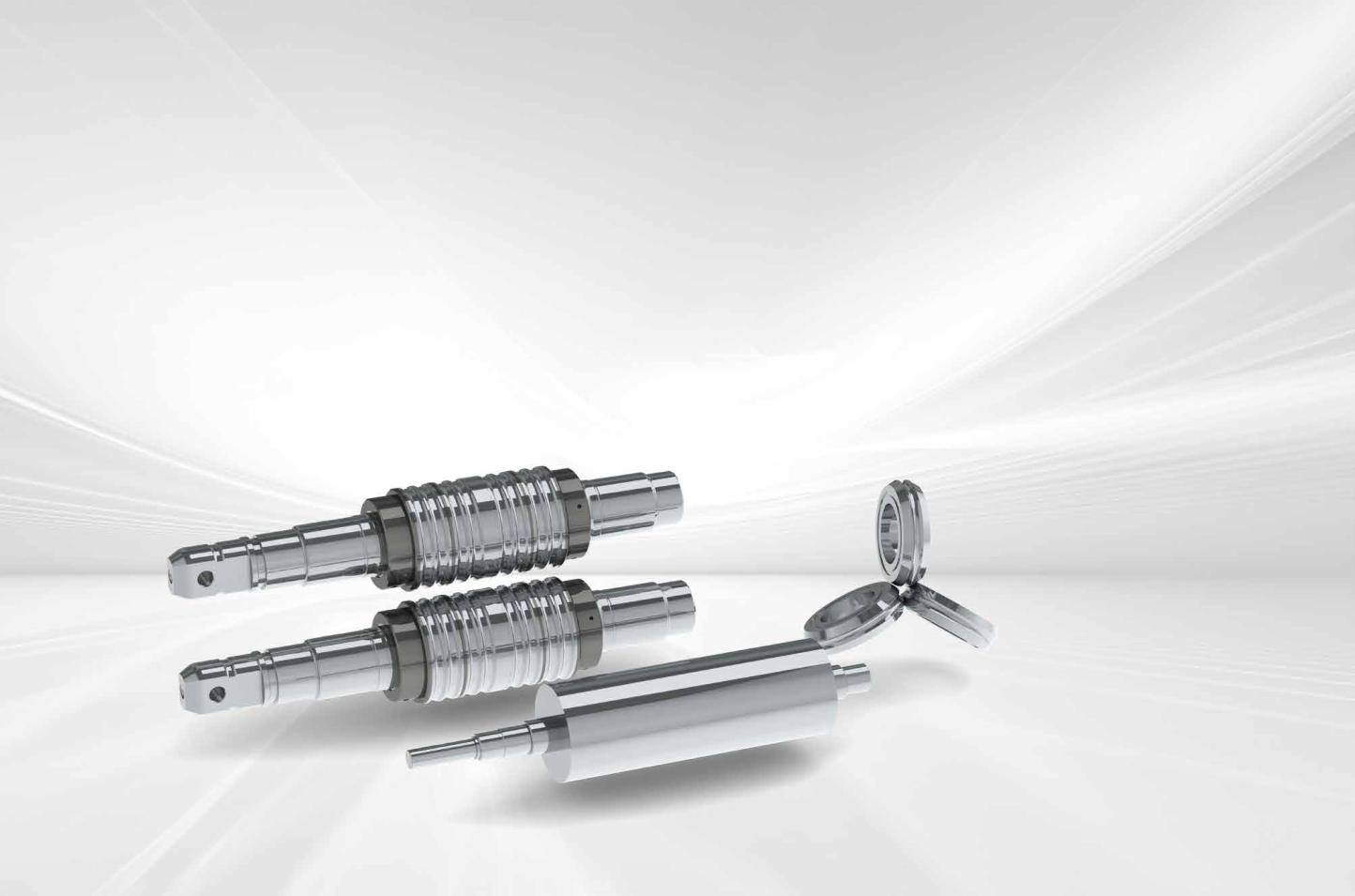
Powder Metallurgy Alloy Steel
FT-9 FT-10 FT-23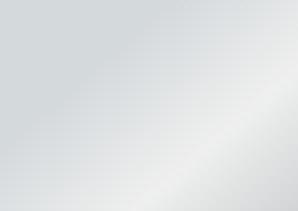
P/M FT-9
Characteristic
FT-9 is an excellent material with excellent wear resistance and toughness by spreading minute carbide evenly after being manufactured with powder alloy method and is adequate for molding during which severe wear occurs. In particular, the product has low heat expansion coefficient and aging change and has high wear resistance that it is highly suitable for semiconductor molding material.
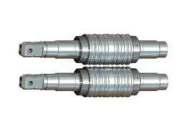
• Spray minute vanadium carbide (VC) uniformly → high toughness and yield strength and good wear resistance
• Minute carbide → easier to reproduce and refurbish than casting high-speed steel(improve by approximately 15%)
• Manufacture into alloy-type powder → prevent one-sided wear and roll marking
• Maintain wear resistance, toughness, and hardness up to 500ºC, minimize crack occurrence
• Similar to casting high-speed steel for heating process conditions, but better with toughness and wear resistance. (improve wear resistance and lifespan by about 30% or more compared to casting high-speed steel)
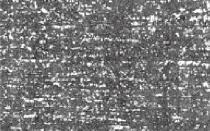
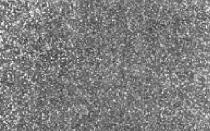
Composition
Properties
Wear resistance test results








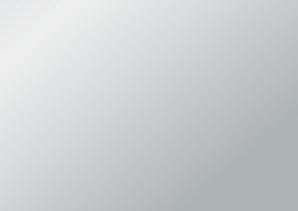

P/M FT-10
Characteristic
FT-10 is a material with excellent wear resistance and toughness by spraying minute carbide uniformly after being manufactured with the powder alloy method, which is adequate for molding during which severe wear occurs. In particular, this product is highly suitable for semiconductor molding material due to low thermal expansion coefficient and aging change extent and high wear resistance.
• Spray minute vanadium carbide (VC) uniformly → high toughness and yield strength with good wear resistance (improve by 50% compared to the SKD11 type)
• Minute carbide → easy for polishing(improve by approximately 15%)
• Manufacture alloy-type powder → prevent one-sided wear and roll marking
• Maintain wear resistance, toughness, and hardness up to 500ºC, minimize crack occurrence
• Low heating process strain and thermal expansion coefficient and low aging change extent(compared to ASSAB ASP23)
• Improve 2-fold compared to casting high-speed steel 3.5-fold compare to SKD11, improve wear resistance and lifespan
• Show same properties with CPM 10V and low cost compared to imported products




Picture 1 shows the minute grain of casting high-speed steel and FT-10. In the case of (a), the size and distribution of carbide are not uniform. In the case of (b), minute VC is distributed uniformly.
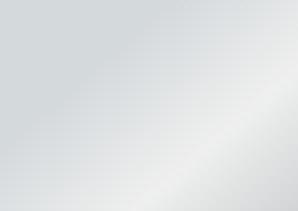
Picture 2 shows the cutting edge and wear shape of casting high-speed steel and FT-10.
In the case of (a), minute chipping occurs, which not only makes the cutting surface dull but also wields adverse effects on the cutting surface quality of cut surface matter due to wear phenomena caused by stress.
In the case of (b), the cutting surface is very sharp, and minute chipping does not occur; thus preventing burr, etc. of cut surface matter occur to improve the quality of cutting surface.
Properties
Wear resistance test results








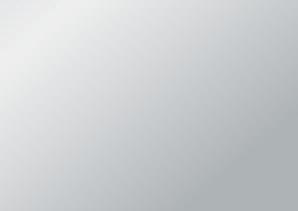

P/M FT-23
Characteristic
FT-23 is a material with outstanding wear resistance, toughness, and strength by spraying minute carbide uniformly after being manufactured with the powder alloy method. In addition, the advantage of this alloy is having low strain during the heating process with good polishing. The alloy is adequate for cooling molding due to high wear resistance and extruding strength.
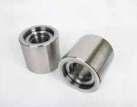
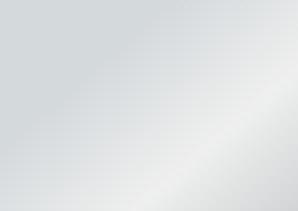
• Spray minute carbide uniformly → high wear resistance, toughness, and yield strength
• Minute carbide → easy polishing (improve by approximately 15%)
• Manufacture alloy-type powder → prevent one-sided wear and roll mark
• Maintain wear resistance, toughness, and hardness up to 500ºC, minimize crack occurrence
• Low heating process strain and thermal expansion coefficient, low level of aging change extent(compared to ASSAB ASP23)
• Same properties as ASP23 as same powder is imported and ASP23 is used for manufacture
• Lower cost that ASP23 import products
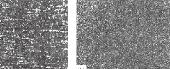
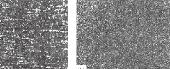
Picture 1 shows the minute grain of casting high-speed steel and FT-23
- In the case of (a), the size and distribution of carbide are not uniform
- In the case of (b), minute carbides are uniformly sprayed
P/M Manufacturing Process

















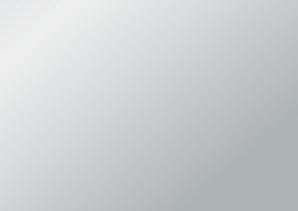

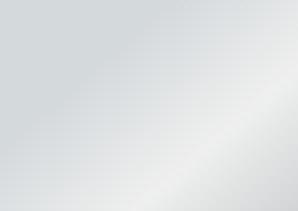
P/M Applications


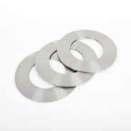
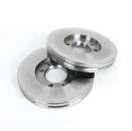
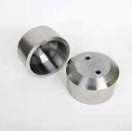
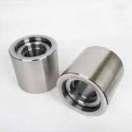
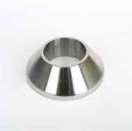
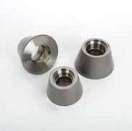
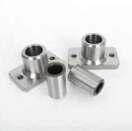

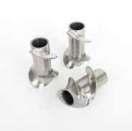
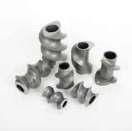
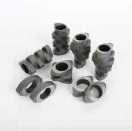
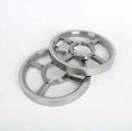
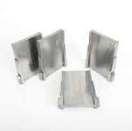
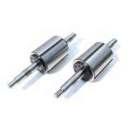
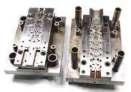
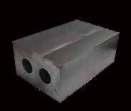
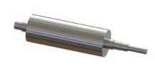








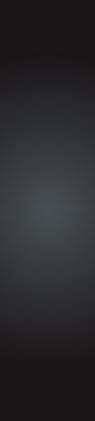
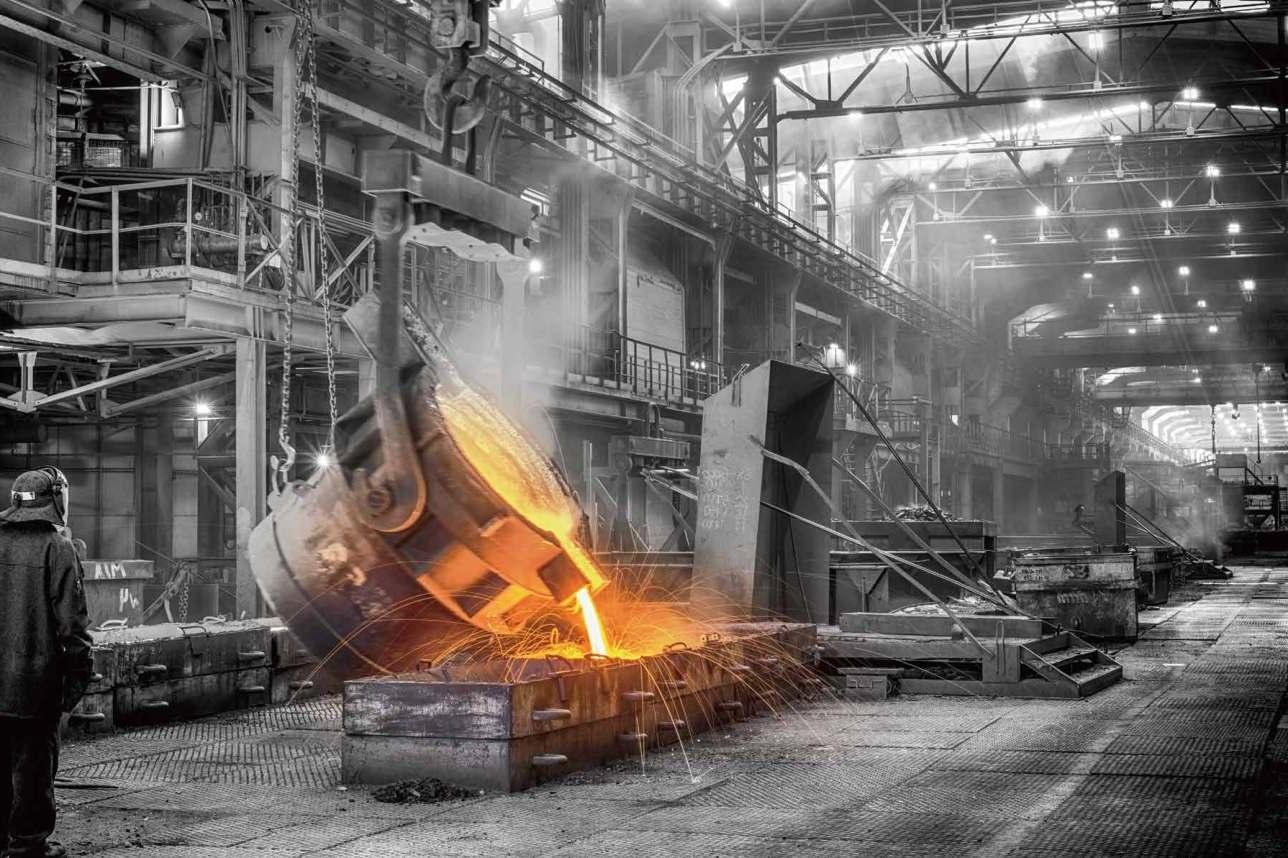
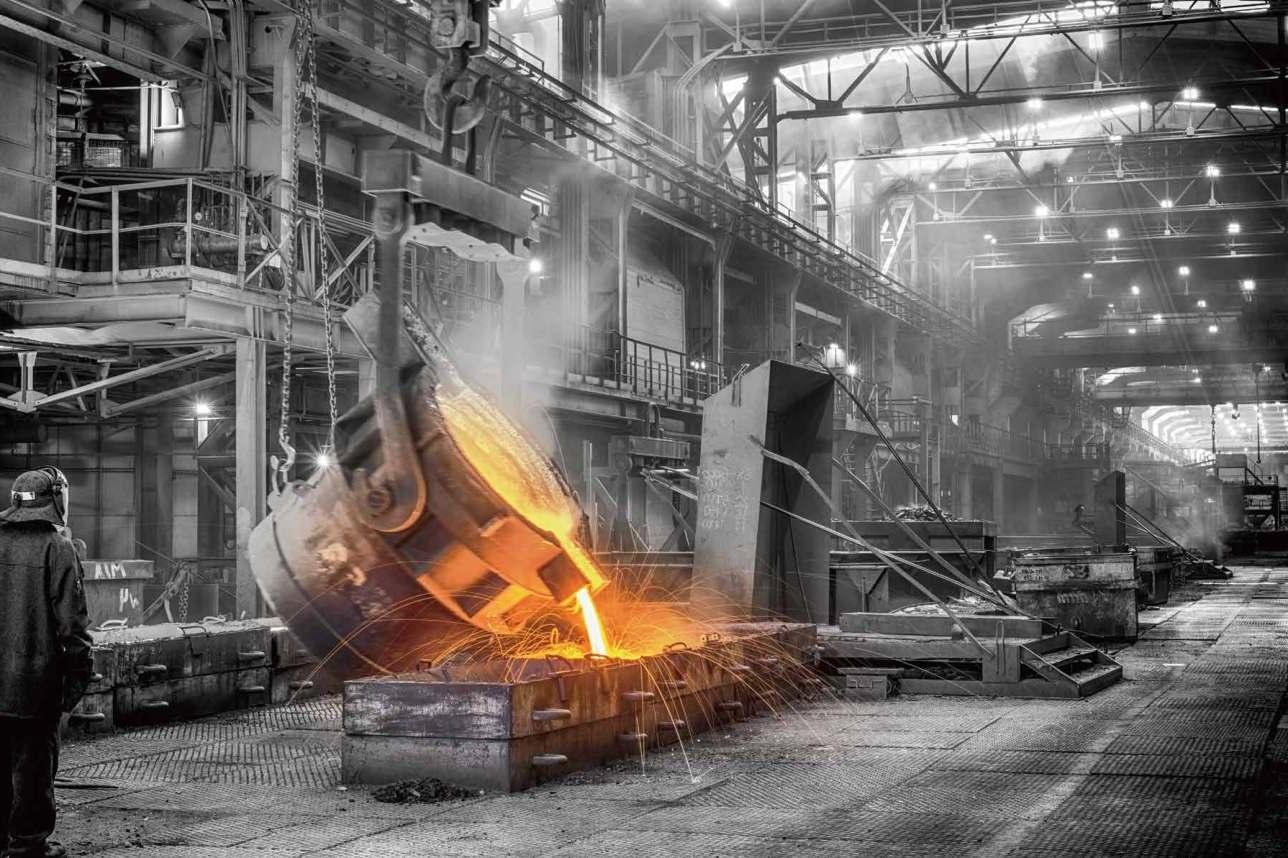
Casting RESISTARⓇ

RESISTARⓇ
Characteristic
RESISTAR of high-speed steel (HSS) type contains high-cost alloy components (Cr, Mo, W, Ni, Co, V etc.), maintains high wear resistance by minimizing hardness reduction at high temperature, and improves productivity by minimizing damages with its toughness property. In terms of client needs, its hardness is freely controlled, it has excellent performance as verified compared to conventional materials; it can also be exported to nations worldwide. In particular, it shows excellent performance in rolling mill, guide roller, and pinch roller and screw and paddles.
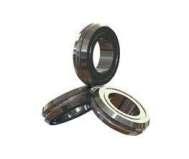




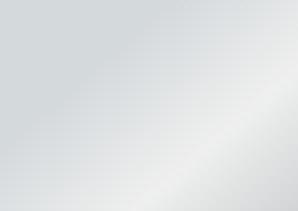
• Excellent mechanical property compared to general high-speed steel
• Increase in productivity due to excellent wear resistance
• Increase in component lifespan due to low grinding amount during reproduction
• Minimize surface pick-up phenomena
• Reduce idle time of changing components due to long lifespan



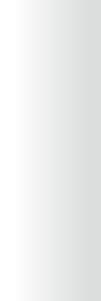


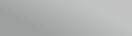







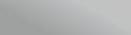



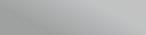



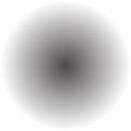
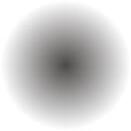
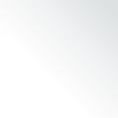
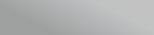




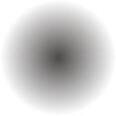
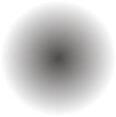
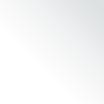







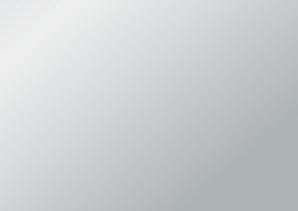

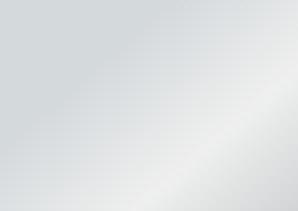
RESISTARⓇ Applications
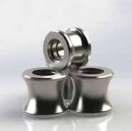


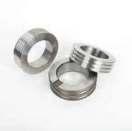
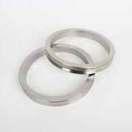

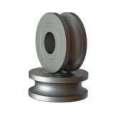
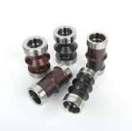
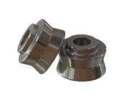

Other Applications
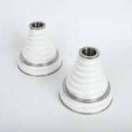
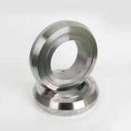
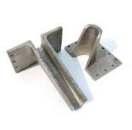
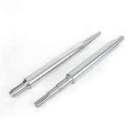


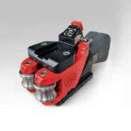
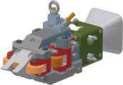







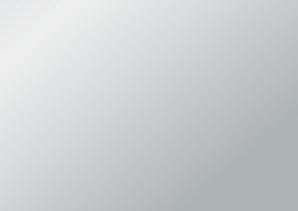

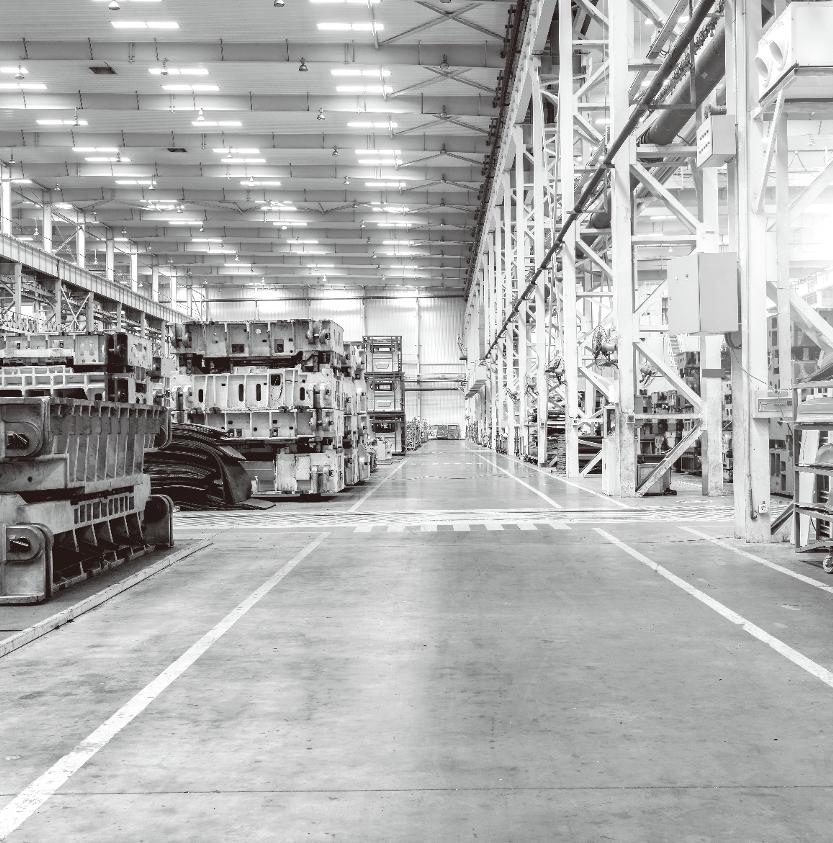
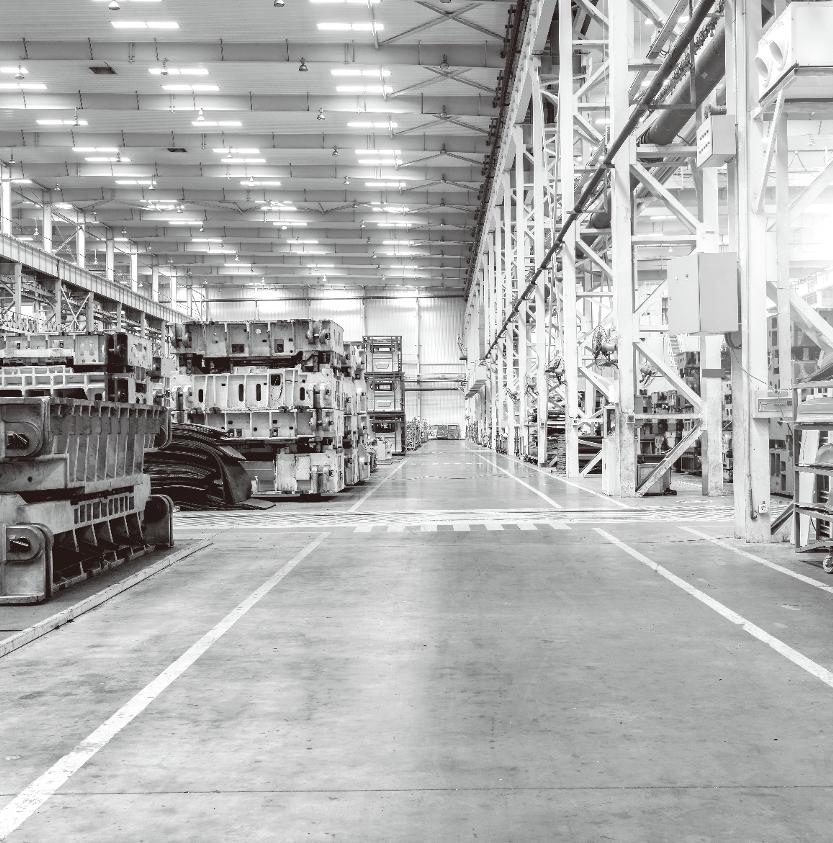
Hi-Max

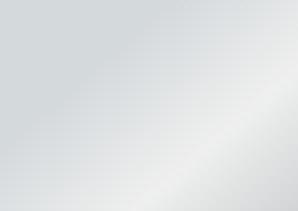
Hi-Max Technology
Powder Manufacturing Process
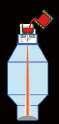
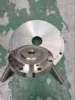


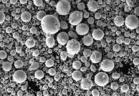

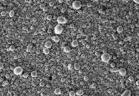
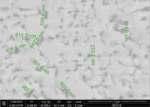


Hi-Max & FT-9 Characteristics Comparison
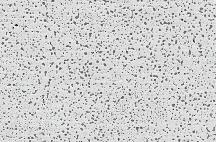
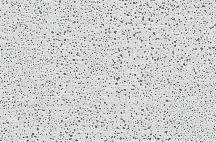
Hi-Max & FT-9 Characteristics Comparison
3.2 Microstructure observation results
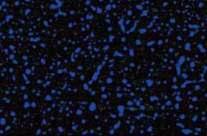
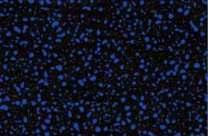







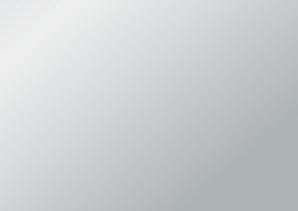

Hi-Max Technology
Hi-Max & FT-9 characteristics comparison
3.3 Low Cycle Fatigue Test Results
Low Cycle Fatigue Condition
• Load : 46, 56 kgf
• Frequency : 2 Hz
• Wave form : Sine
• Stress ratio(R) : 1
• Temperature : RT
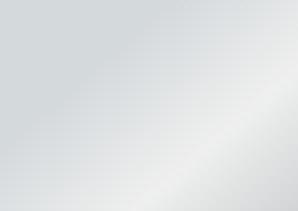
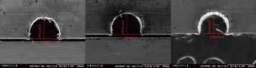
• Sample Size : 2.44x2.44x24 (Notch 0.3x0.27)
Low Cycle Fatigue Results : Lower Tendency of Hair Cracks
56kgfFT-9Hi-MaxIncrease (%) 1st 12,19715,57428%↑
Hi-Max & FT-9 characteristics comparison
3.4 Wear Resistance Test : Pin-on Disk
Test Condition
• Load : 10N
• RPM : 622
• Rotation diameter : 11.5mm
• Wear distance : 500m (667sec)
Wear Resistance Test : Hi-Max has 2.6 times higher wear resistance than FT-9

3.1. Microstructure observation results : Hi-Max has smaller carbide size
Comparison with Cast Iron rolls :
Hi-Max mill rolls have 4 - 5 times Longer Lifetime per Groove
Comparison with HSS roll :
Hi-Max mill rolls have 2 - 2.5 longer Lifetime per Groove




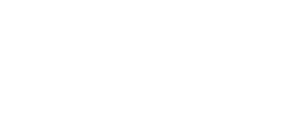



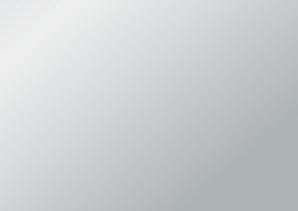

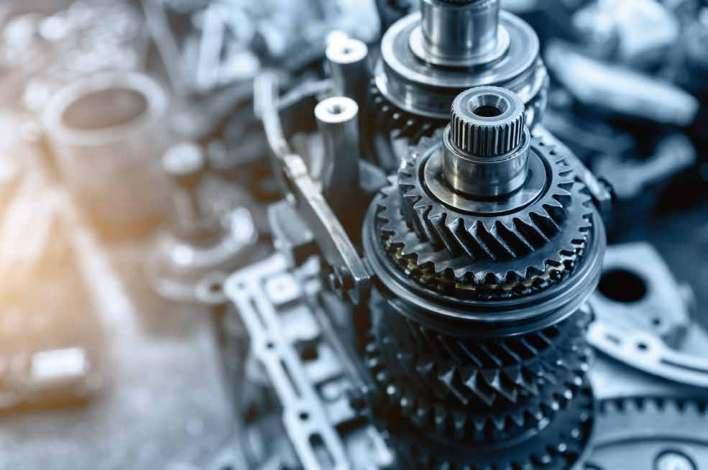
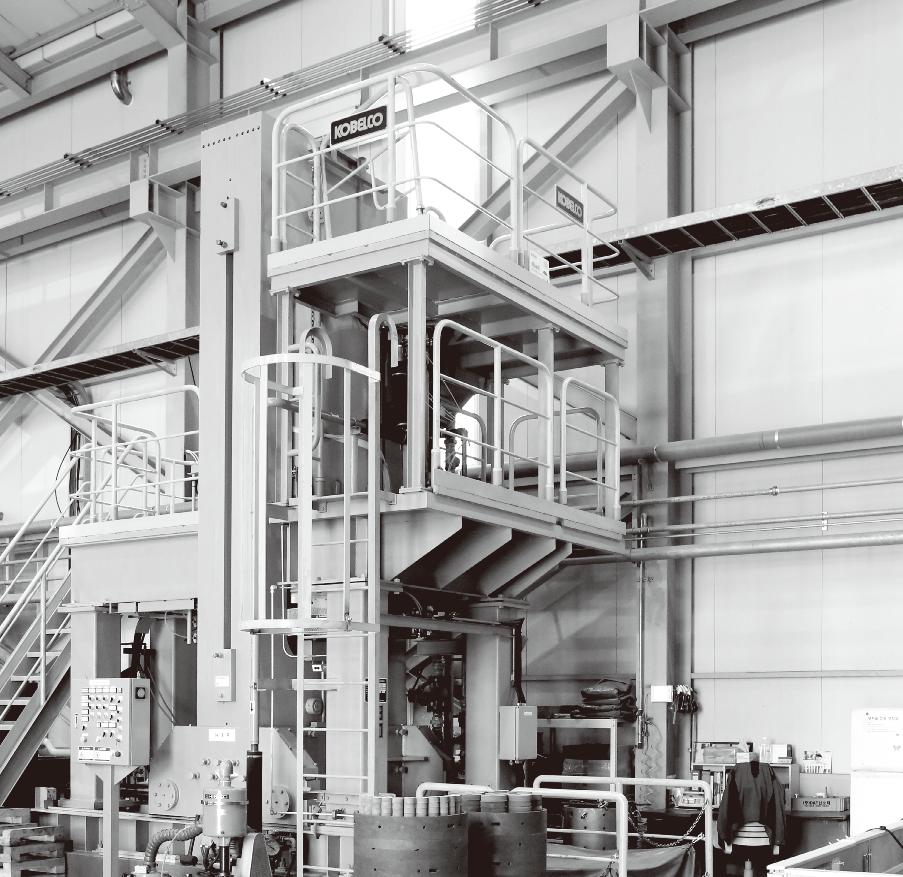
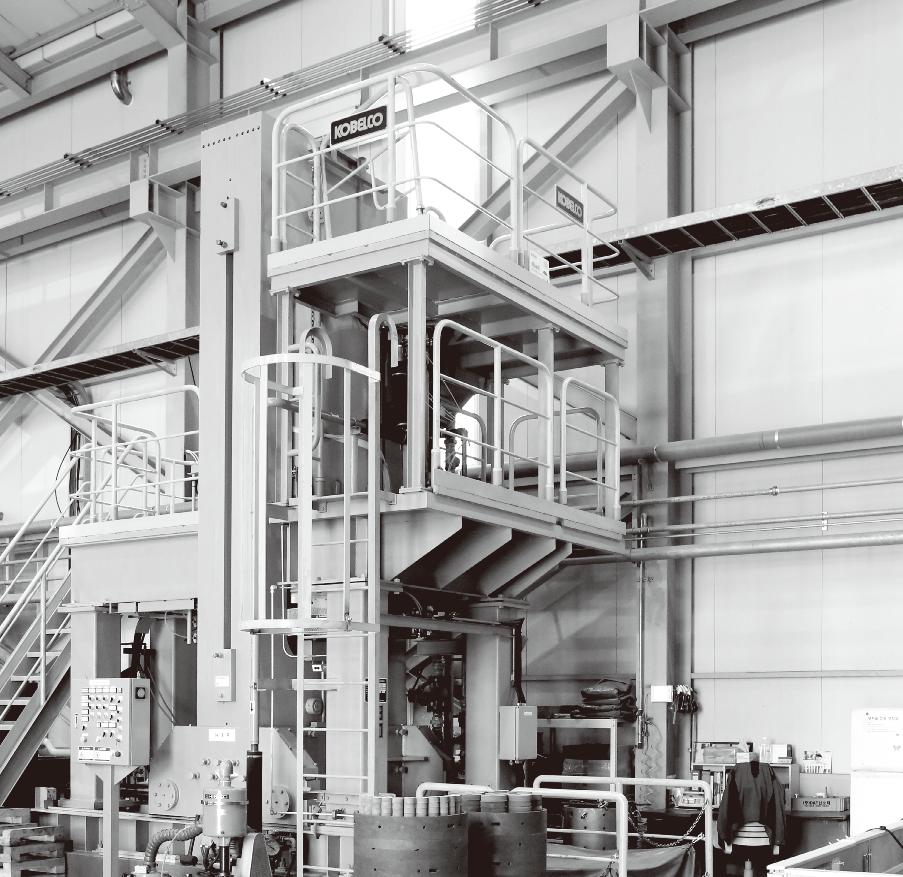
HIP (Hot Isostatic Press)

HIP(Hot Isostatic Press)
Characteristic

Advantages of HIP
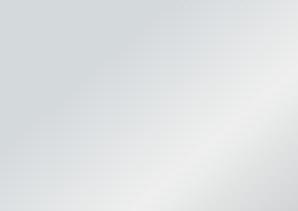
Maximum pressure
Heater, temperature zone
Maximum temperature
Applied gas
Applied space
What is HIP?
118Mpa(1,200kgf) graphite, region 3 1500℃
Ar(99.99%)
Ø560x1,300(mm)
HIP is equipment using the principle of pressurizing pressure from all directions after high pressure (1,000kg/cm2 ~ 2,000kg/cm2) is formed by gas expansion if temperature is leveled up to high temperature(Max. 2000ºC) after pressurizing constant pressure by using compressor with inert gas in the vessel(high-pressure container).
• Remove inner blowhole
• Reduce production and welding
• Improve production surface
• Lose directional properties
• Reduce defects by maintaining improvements due to high solid-state sintering
• High strength
• Improve mechanical properties
• Sinter or bond difficult in forming member
• Minute grain structure
• Improve fatigue life(2~12 folds)
• Recover scrap components
• Recycle scrap

Usage of HIP equipment - Sintering




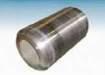




Usage
• Power HSS : difficult to produce by casting
• Iron-type/Non-iron-type alloy
• High melting point metal/ceramic/cermet
• High-purity target
• Complex material
Property
• Minute grain, isostatic property
• Same or better mechanical quality than rolling or forged products


• Available for high-quality component production even for difficult materials to produce
• Manufacture soft shape reducing stress concentration
• Manufacture net or near-net shape to reduce production fee
• Improve fatigue strength
• Bond 2 or more materials by using 1 or 2 or more powder
Usage of HIP equipment - blowhole reduction
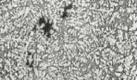
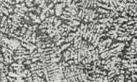
Usage
• Hard metal, cermet, ceramic, etc.
• Aluminum alloy, titanium alloy, heat-proof alloy
• Stainless cast product, resin, etc.
Property
• Improved wear resistance and flexural strength by removing air gap and minute blowhole.
• Hard metal in particular with excellent wear resistance is difficult to manufacture without air gap and minute blowhole due to its minute particles and low amount of cobalt.
• Tools, drawing dies, and rolling mills








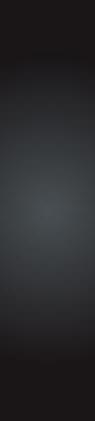
HIP(Hot Static Press)
Usage of HIP equipment - Diffusion Bonding



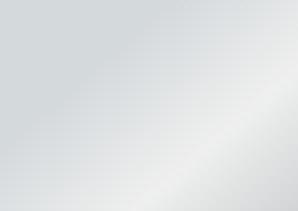




Usage
• Products difficult to manufacture with bracing or welding(example) heterojunction between metal and ceramic
• Components with complex 3-dimensional structure
• Bond between hetero metals
• Bond between metal block and powder
• Case of bonding with part of powder
• Manufacture complex material
Applications







Property
• Layer with improved wear resistance and corrosion resistance
• High bonding strength(homo and hetero bond: Metal to metal, ceramics to metal)
• Bonding part: Seamless grain structure
• Mechanical property-uniform minute structure → similar density : Solid, Powder
• Low-process temperature(HIP temperature) : 50~70% of MP flawless: no piece/solid crack







Q.A equipment
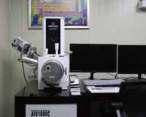
Scanning electron microscope (SEM, EDS)
• Measurement rate : X5000
• Component analysis : Equipped EDS
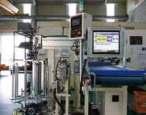
Automatic hardness detector (Rockwell)
• Measurement method : Rockwell
• Measurement value : HRc
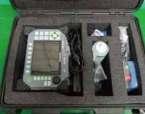
Nondestructive inspector
• Measurement method : UT
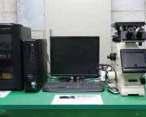
Metallographic microscope
• Measurement rate : X1500
• Manufacturer : Olympus
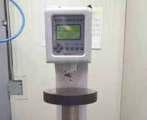
Hardness device(Rockwell)
• Measurement method : Rockwell
• Measurement value : HRc
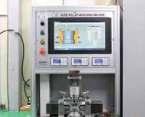
Automatic sizing measurer
• Measurement standard : ~ø60mm
• Measurement method
: contact method

Surface profile detector
• Measurement rate : ~50mm
• Measurement method : contact method
• Measurement value : Ra(μm)
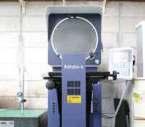
projector
• Measurement rate : X10







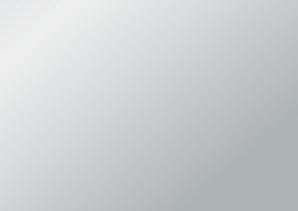

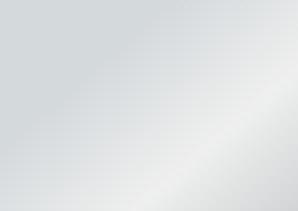
Facility & equipment status
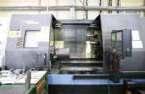
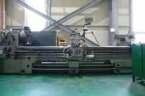

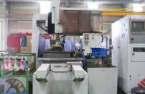
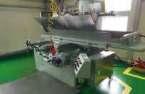
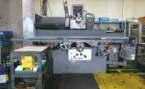
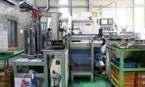
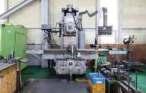
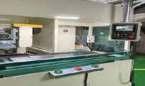
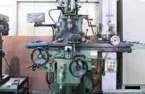

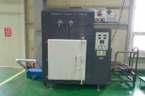

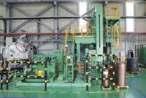
• Ø560 X 1,300

• 600W X 600H X 1300L
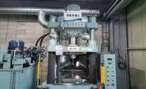
• Automatic 105 TON
• Manual 300 TON
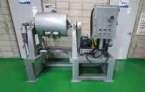
• 50 ~ 225kg

• Φ600 X 650

• 550W X 550H X 1200L
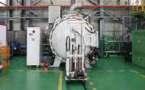
• 700W X 600H X 1200L
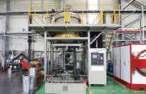
• Ø500 X 500L
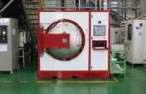
• Ø450 X 450H

• 650W X 650H X 1400L
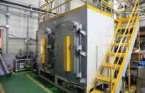
• Ø600 X 1100







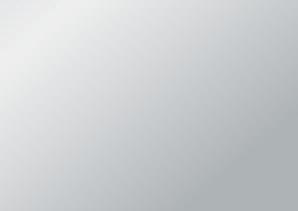

Certification
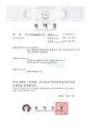
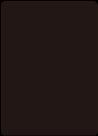
Manufacturing method of sintered alloy dispersed with titanium carbide within steel base by canning-hot isostatic pressing
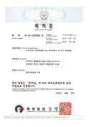
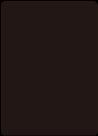

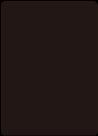
Wear resistance hard alloy steel bond and its manufacturing method
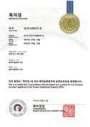
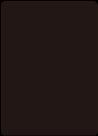
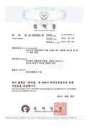
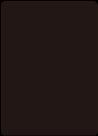
Wear resistance complex materials and engine piston made by the materials and its manufacturing method.
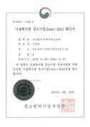
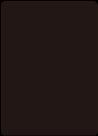
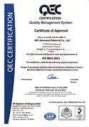
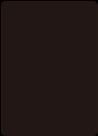
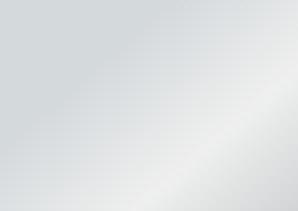
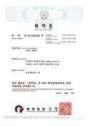
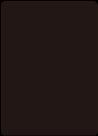
Complex roll for rolling
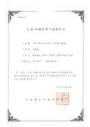
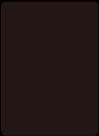
Materials and components expert business certification
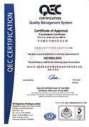
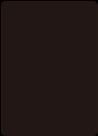

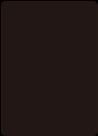

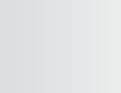








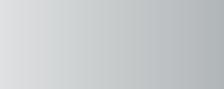












200 Domestic Customers110 Overseas Customers

SeAHFS
Dongkuk steel mill
ILJIN

SeAHbesteel














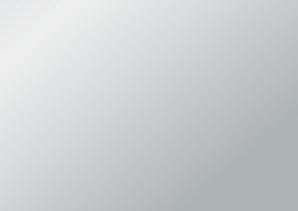

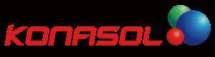
To make people happy with nanotechnology

Head Office 17-60, Saneopdanji-gil, Myeoncheon-myeon, Dangjin-si, Chungcheongnam-do, Republic of Korea
Hwaseong Plant 711-63, Mannyeon-ro, Jeongnam-myeon, Hwaseong-si, Gyeonggi-do, Republic of Korea
Tel. 041-359-6600 Fax. 041-359-6609 www.millroll.com