
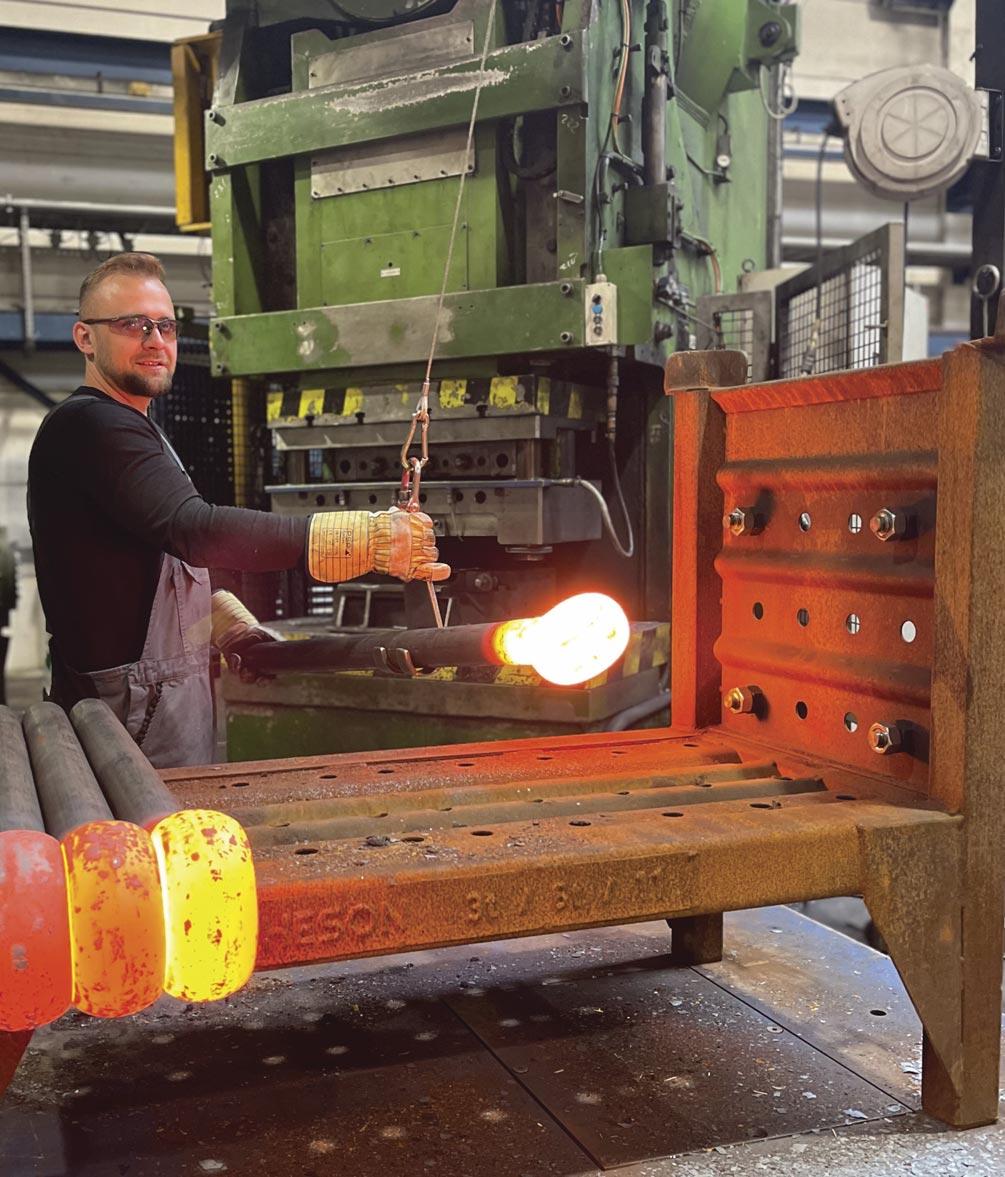
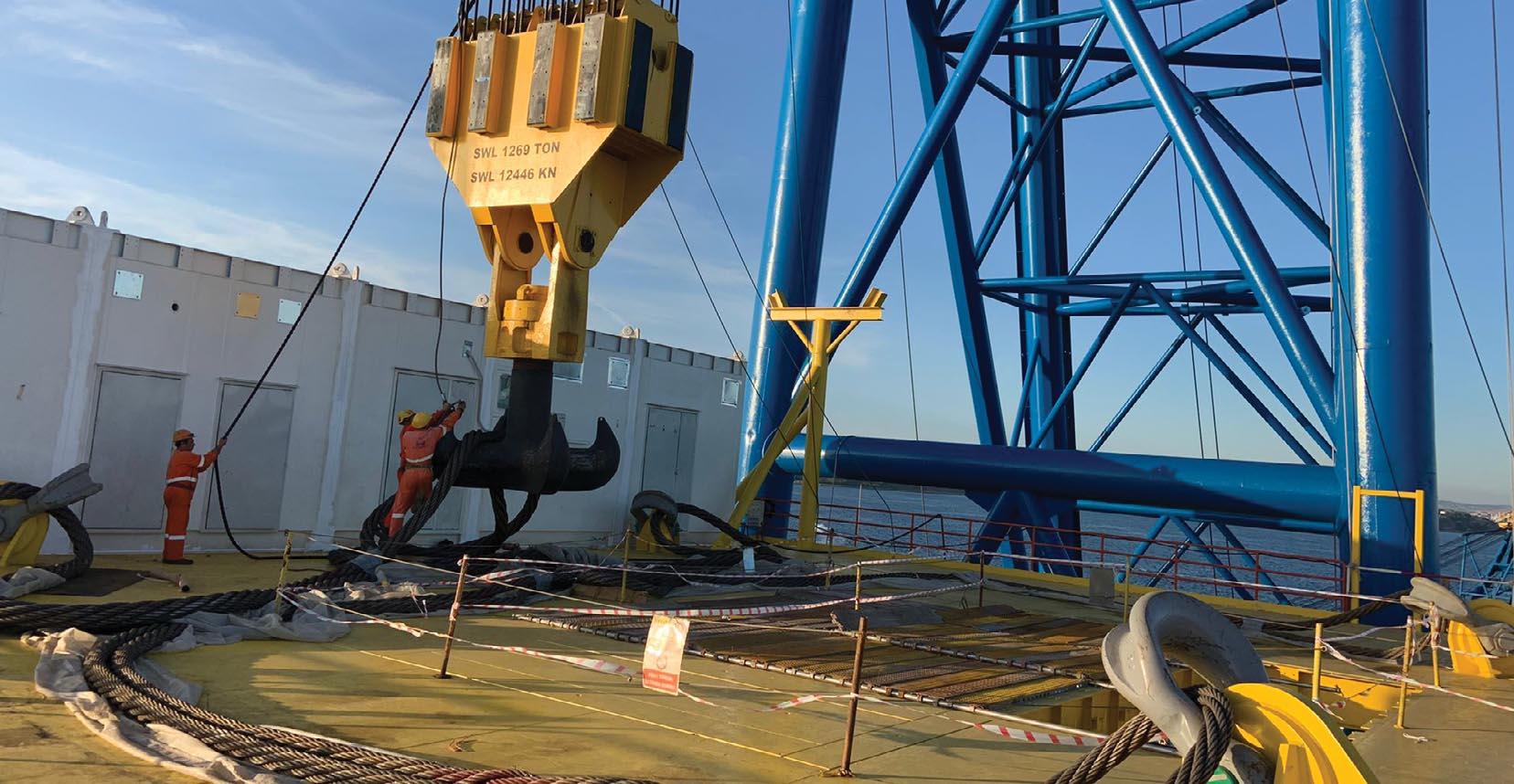

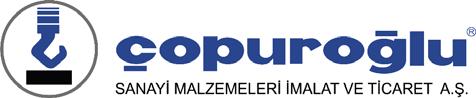
When things need to be lifted, customers all over the world call Royal Van Beest. Known for its premium quality lifting equipment, Royal Van Beest’s impressive portfolio of lifting, lashing and mooring fittings is trusted on the world’s most demanding work sites. Having just celebrated its centenary, this Dutch family-owned company is more optimistic about the future than ever before. Heavy Lifting Sales & Export Manager Rifat Cevahir got Richard Hagan hooked on the lifting industry.
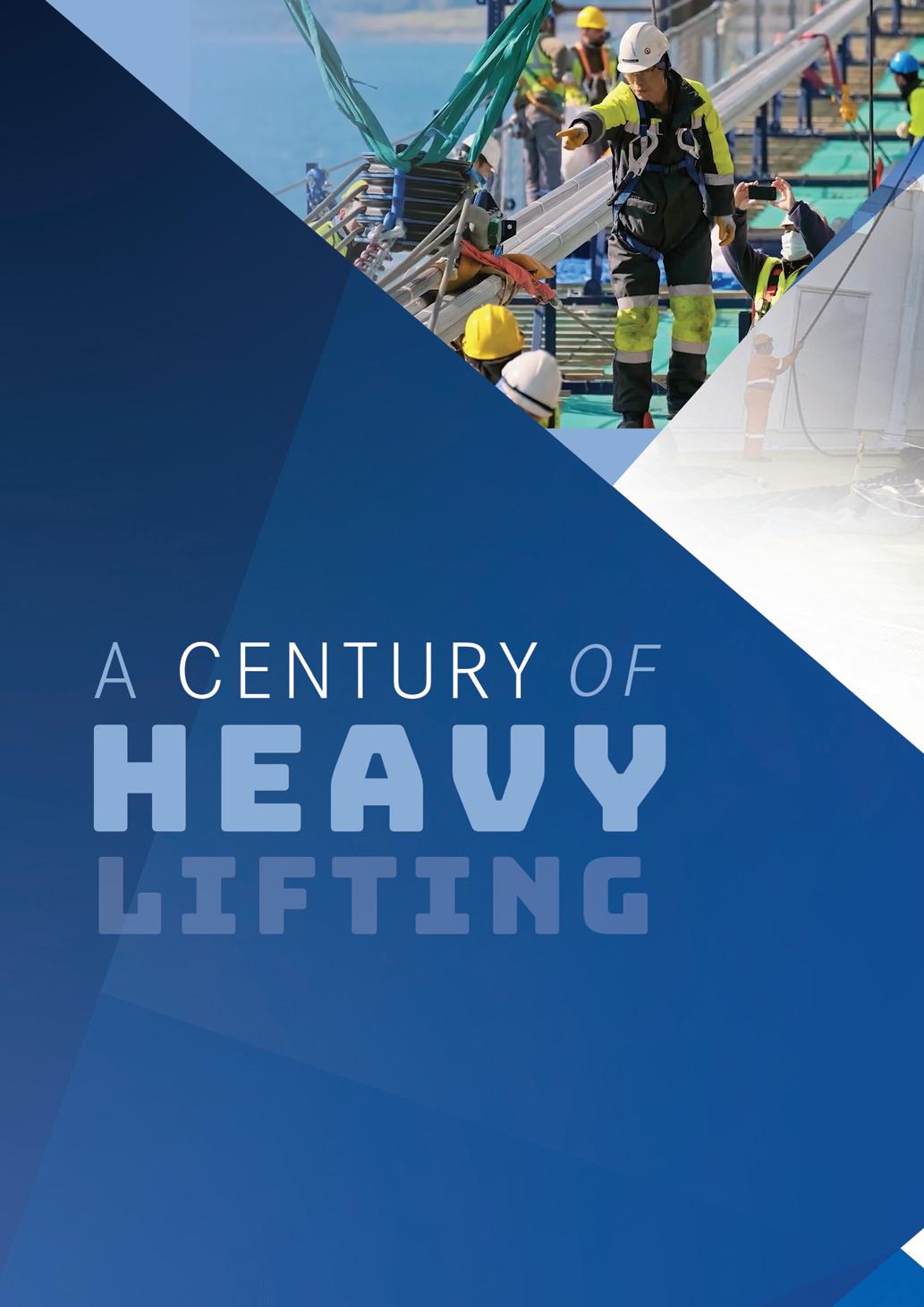
Since 1922, Royal Van Beest has been manufacturing premium quality lifting equipment and today, thanks to its commitment to excellence, quality and customer service, it has climbed to the top of the demanding, high stakes lifting game. It is deservedly now the world’s leading manufacturer of lifting, lashing and mooring fittings – such as shackles, hooks and remotely operated vehicle (ROV) accessories.
Celebrating the centenary
Van Beest was established in Sliedrecht, (near Rotterdam), in 1922, by Dirk Van Beest, after whom the company is named. Initially, all of the company’s forged products were mainly sold to Dutch dredging companies, such as Boskalis and Van Oord, who are nowadays still major clients.
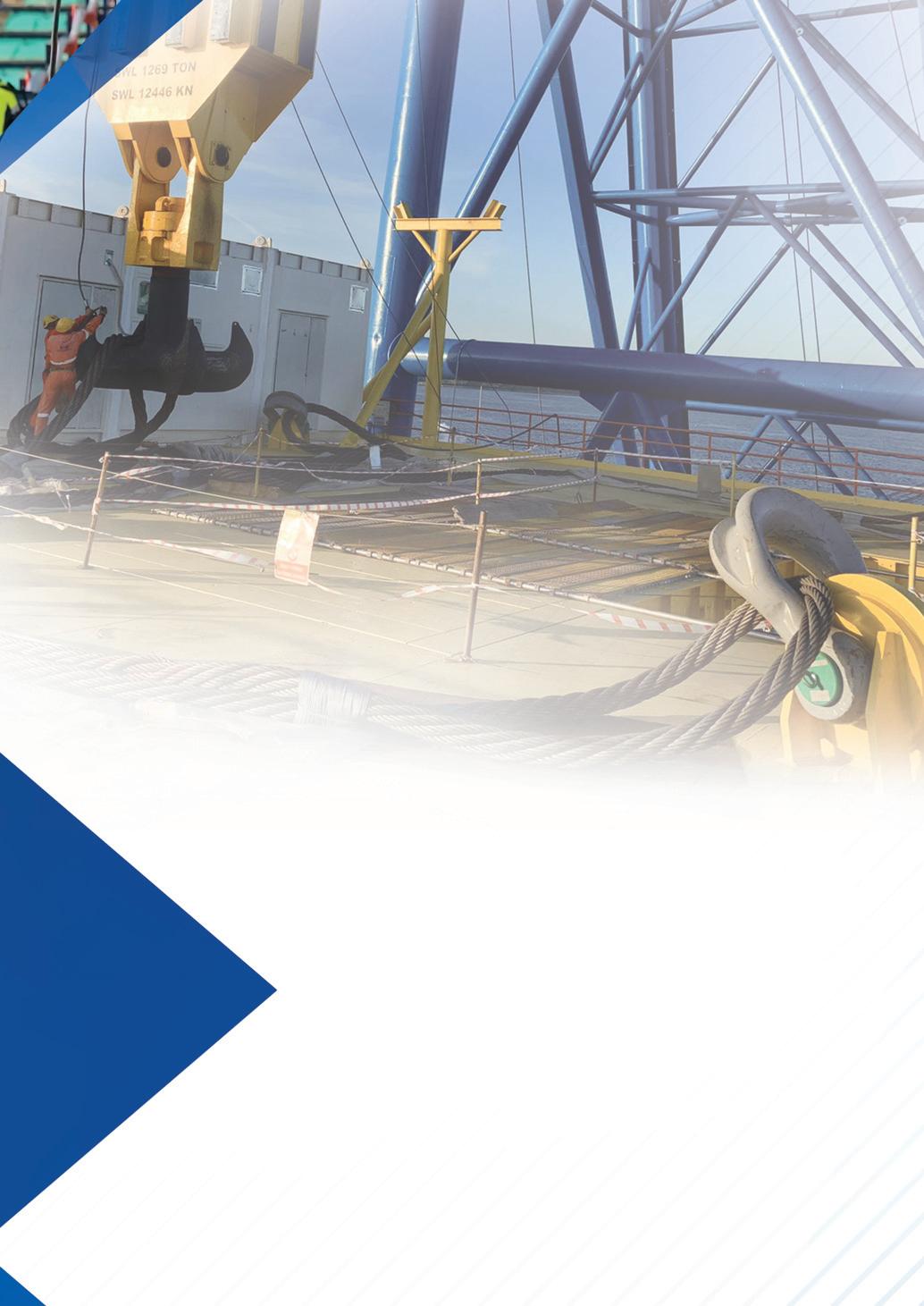
The family ownership and the company’s living connection to the original Van Beest family remain a key part of the company’s modern identity and a proud aspect of its heritage.
In 2022, Van Beest celebrated its centenary with the simultaneous announcement that it had successfully applied for the title
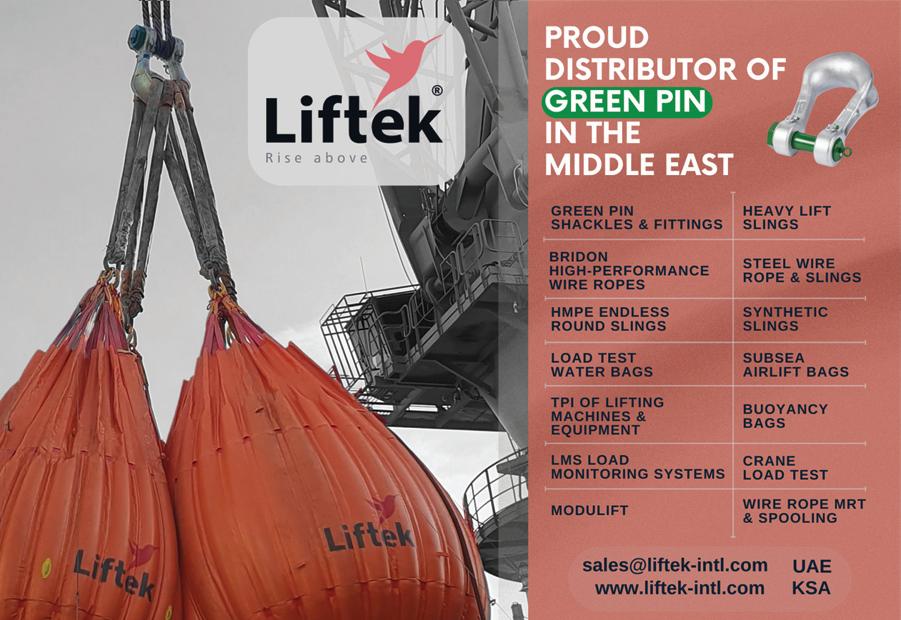
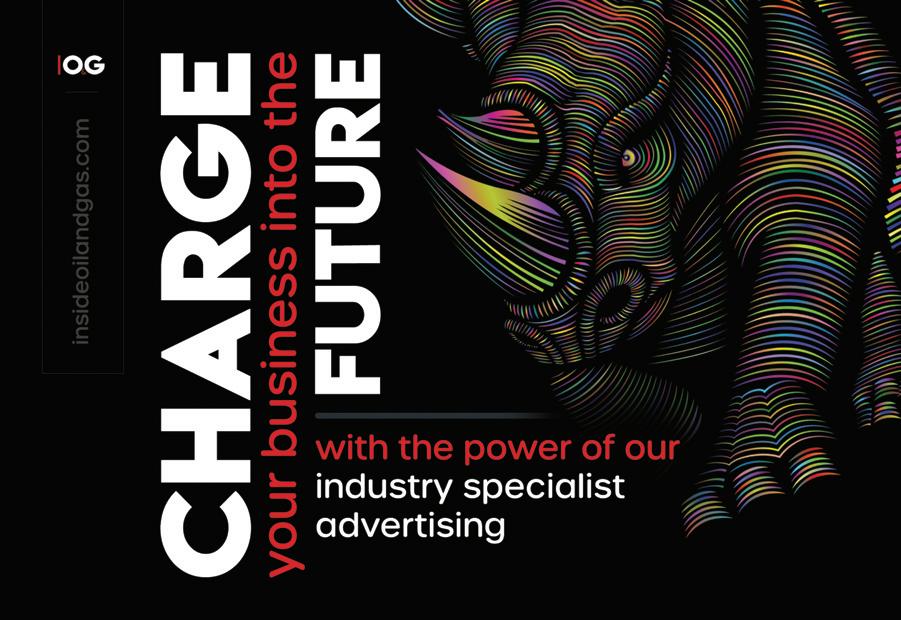
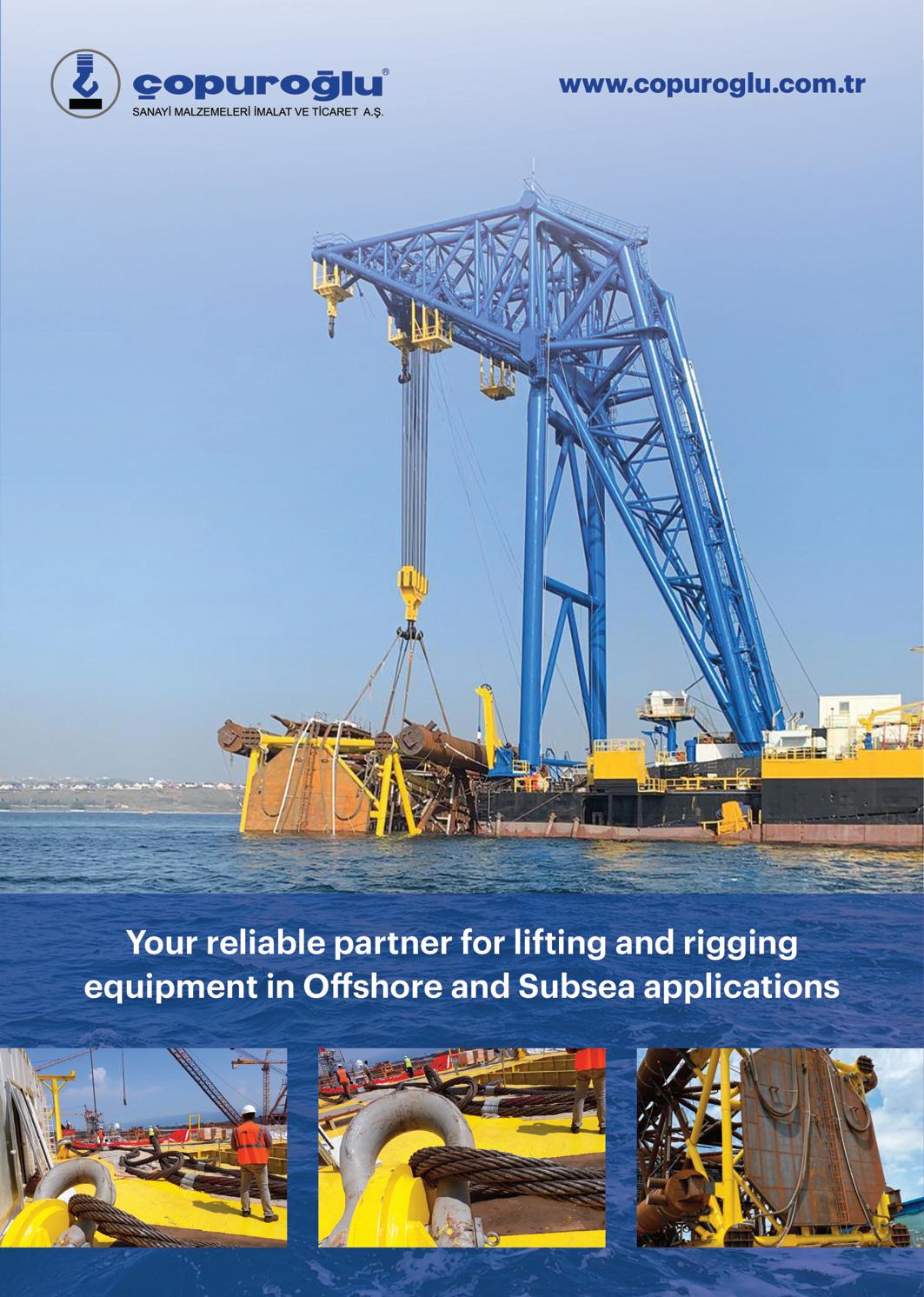
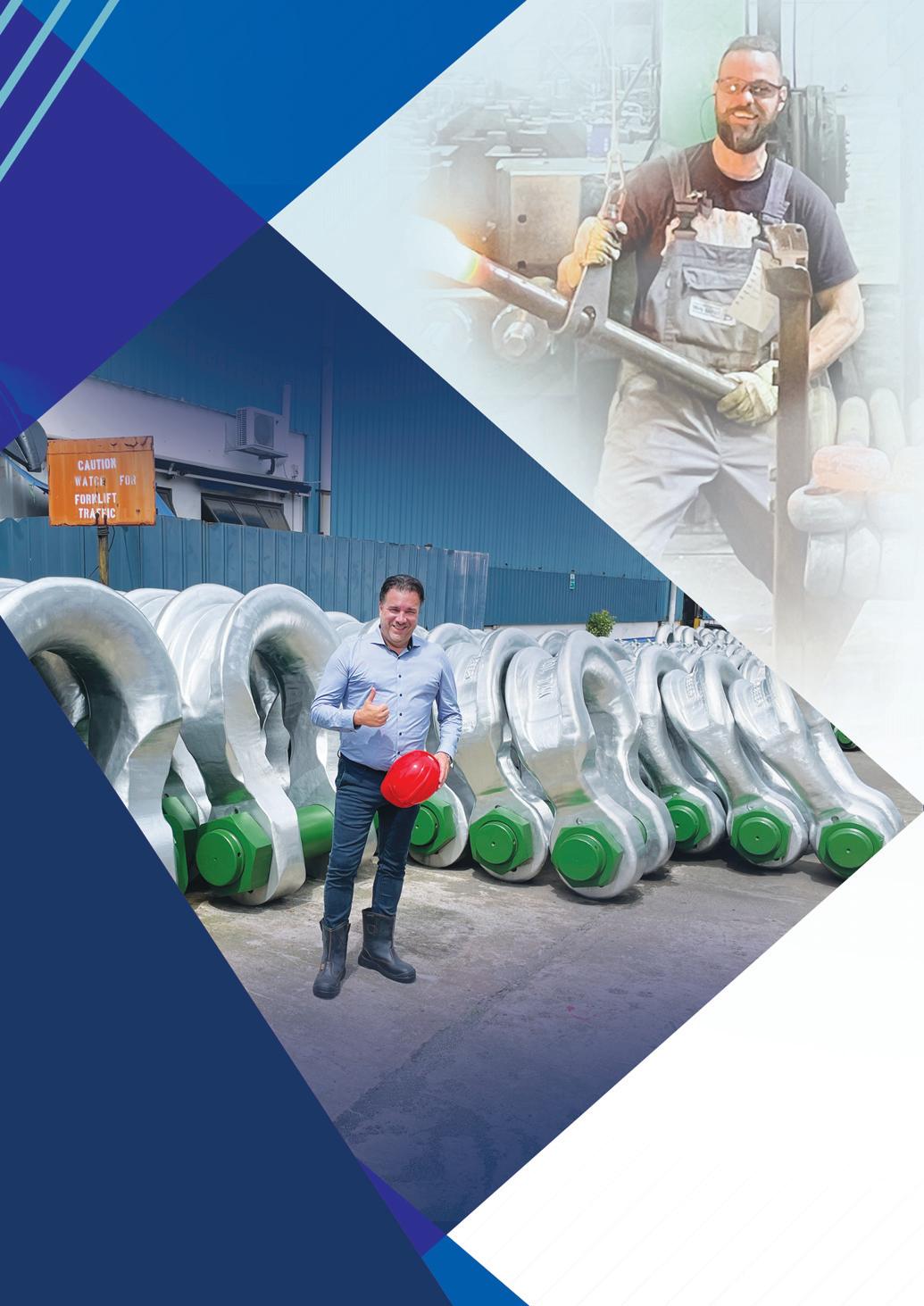
of Royal. The application process with The Netherlands’ Royal House began in 2021 and took over a year, involved detailed audits of the company’s current and historical business practices, ownership and management. All of its past directors were also investigated. Meanwhile, the Royal House even sought the Mayor of Sliedrecht’s advice on the application.
Having successfully completed the process, Van Beest changed its name to Royal Van Beest. The Royal title reflects the company’s reliability, integrity and ambition and further adds to the company’s credibility.
Doing the heavy lifting
Royal Van Beest remains headquartered in Sliedrecht in the Netherlands, but today, its reach goes far beyond the town’s borders. The Green Pin ® shackles are often used in major oil and gas projects and recently contributed to ADNOC’s Lightning project in the UAE, the Margin Oil Field Development in Saudi Arabia and the Northfield East LNG project in Qatar. Royal Van Beest has also supplied projects in the Caspian Sea, Brazil and the US. Shackles have been used for topside installations, platforms or installation on the seabed.
This is only possible thanks to its network of 900 distributors spanning 94 countries, Royal Van Beest efficiently serves customers around the world, including ADNOC, ARAMCO, Shell, BP, ENI and Total.
Royal Van Beest is able to fulfil demand uniquely efficiently thanks to its substantial
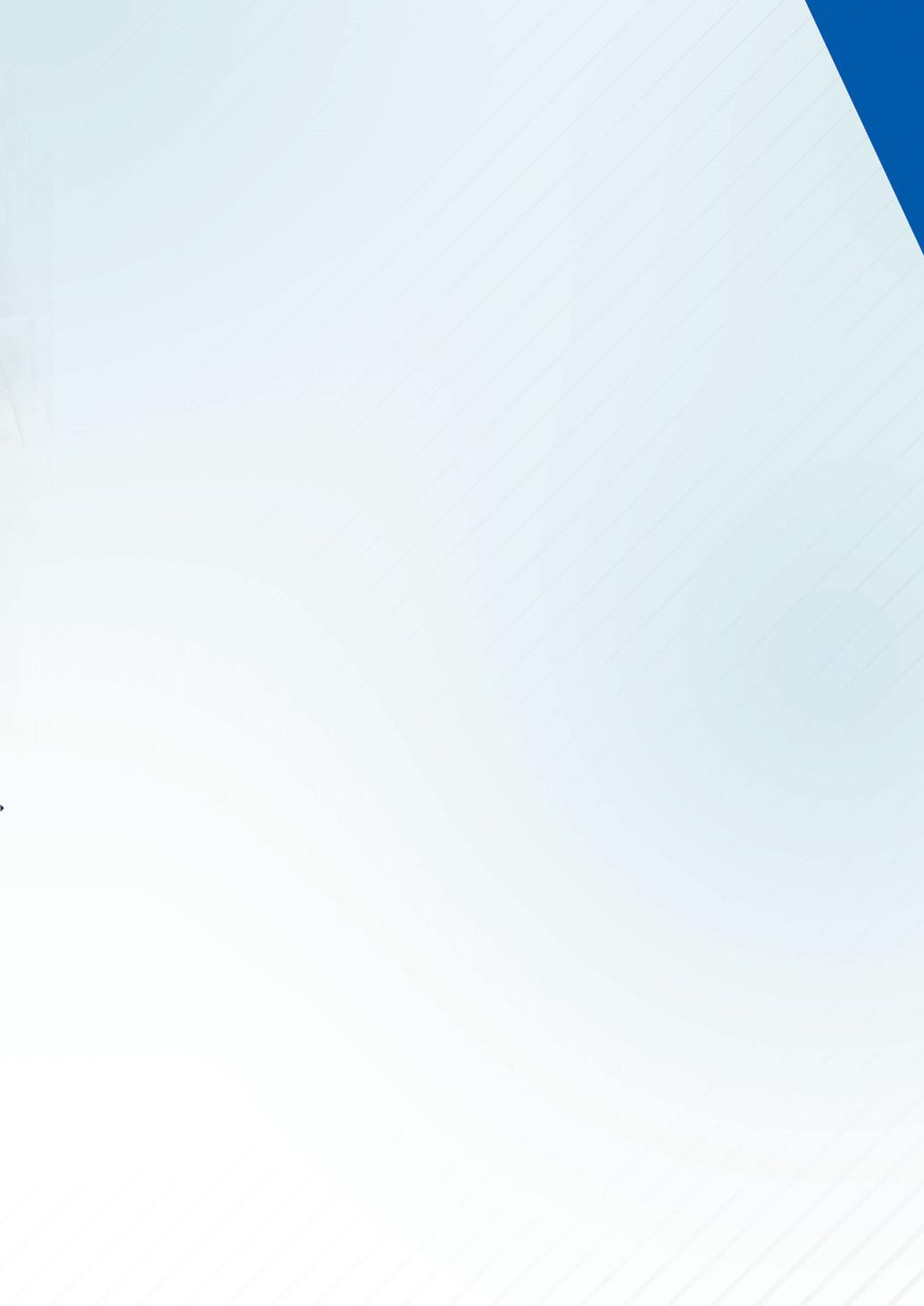
stockholding. “We carry the largest stockholding in the world,” Heavy Lifting Sales & Export Manager Rifat Cevahir revealed. “Our mindset has always been to put money into material rather than in the bank, because when times are tough, such as during the high demand for energy and gas due to the war between Ukraine and Russia, then our distributors must be able to trust that they’ll be able to source their product from us no matter what.”
Royal Van Beest’s stock is securely held in its own warehouse, which features 13,000 pallet places for a combined stock value of €50 million. This stockholding capacity ensures that Royal Van Beest has 97-98% stock availability at all times.
The company is staffed by 250 employees located worldwide, including workshop teams, office and sales staff.
Forging a new path
Over its 100 years in business, Royal Van Beest has constantly evolved not only its product range, but, crucially, also the way the shackle range is manufactured.
One of the key changes it has made is in its switch from standard forging to a method known as upset forging. While forging is traditionally a process that involves physically hammering or pressing a product into shape, upset forging (also known as ‘free forming’) is an automated process that involves locally heating a metal bar and then applying pressure to the end of the bar in the direction of its
axis, to bend it into its final shape –a shackle body.
Parts produced using upset forging exhibit better levels of strength and soundness, while resisting deformation and breakage during use. These characteristics make such shackles ideal for applications where high performance is critical – such as the heavy-lifting industry.
Shackles make up fully 80% of Royal Van Beest’s turnover, of which the standard range of shackles is manufactured in Holland in a specialised, highly automated production line.
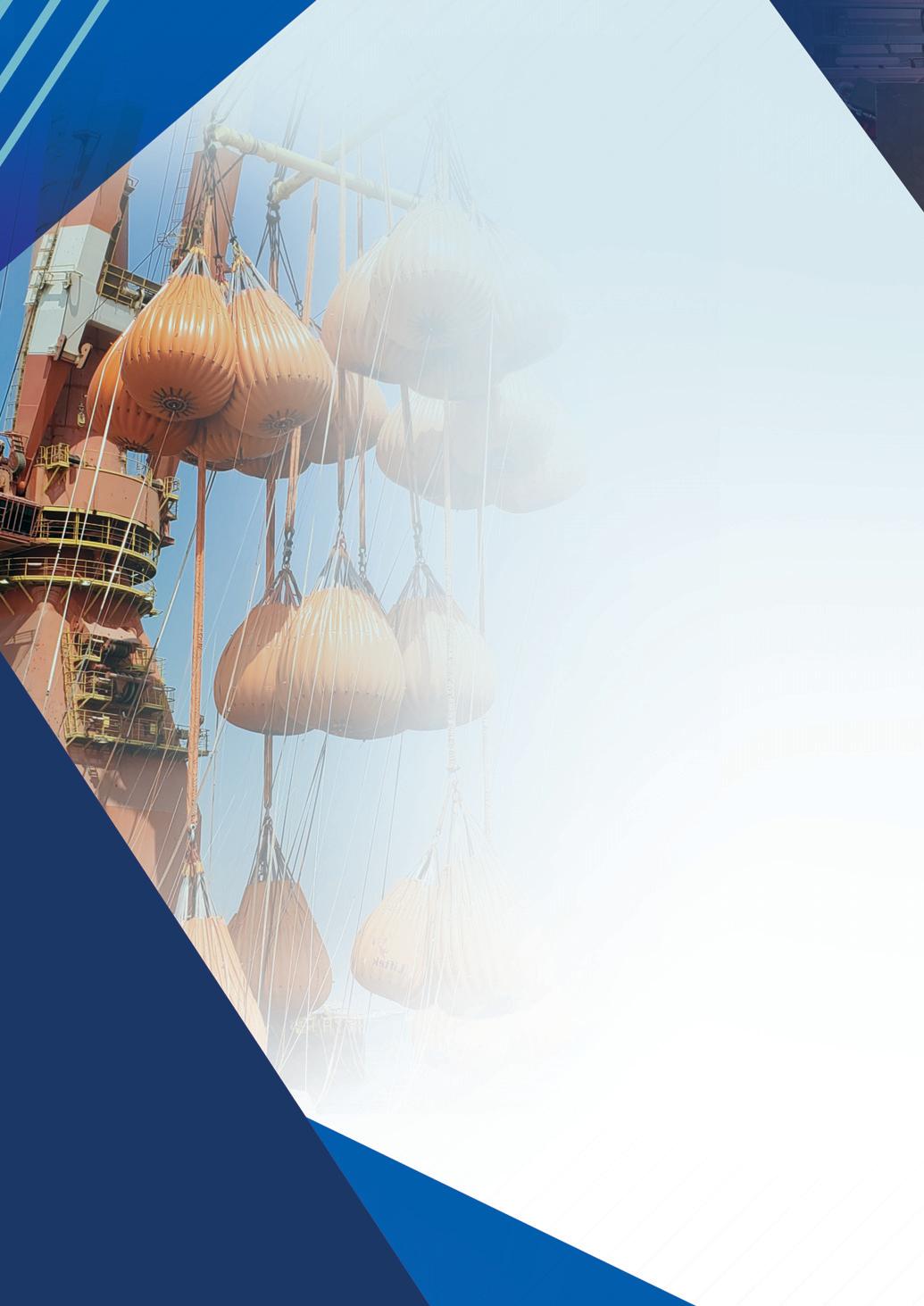
“Our upset forging line is quite unique: we have three forges that bend a solid shackle into shape, and from there we only have to drill the eye,” Mr Cevahir said. “It’s fully automated and involves minimal material loss leading to a very competitive price.”
The production lines include heat treatment and assembly, with automated inspections occurring throughout the process, ensuring that any flaws or imperfections are identified and resolved immediately. This process maintains Royal Van Beest’s extremely tight tolerance levels and it guarantees that sub-par products will never reach a customer’s warehouse.
Going green
While one of Royal Van Beest’s most active markets is the oil and gas industry, it is deliberately developing new business in the wind energy market, and it’s doing that through
smart investments in product development and in an exciting acquisition.
One of Royal Van Beest’s best-selling products is its Green Pin ® shackles. Regarded as the world’s leading brand for premium quality lifting and lashing equipment, The Green Pin ® range includes shackles, turnbuckles, hooks and fibre link chains. Easily identifiable thanks to their trademarked green colour pin, Gree n Pin ® shackles are built to international standards, are battle-proven and offer unrivalled performance and reliability.
In 2017 and late 2022, Royal Van Beest acquired Irizar Forge and Sling Supply International SA (Slingsintt), both based in Spain. Irizar Forge is the expert in forging heavy lifting hooks and crane blocks, while Sling Supply International is especially well-known for the lifting tools that it has developed for the global wind i ndustry and used in the lifting of nacelles, hubs, towers and blades.
Thanks to these acquisitions, Royal Van Beest is now able to counter every market’s demand, including wind farm contractors, a holistic lifting solution that features the company’s entire portfolio of li fting products from crane block to seabed Additionally, thanks to ongoing investments in its heavy lifting hooks as well as mooring equipment, Royal Van Beest is able to offer a range of seabed mooring products for floating wind farms.
“We expect that these products together could make us a one-stop shop f or our customers,” Mr Cevahir concluded “Where contractors who need to lift a nacelle may previously have had to sepa rate the product suppliers, we are now able to supply everything in one project.”
Royal Van Beest attends the ADIPEC show in October every year and you are cordially invited to meet the Royal Van Beest team and discuss your lifting requirements. n
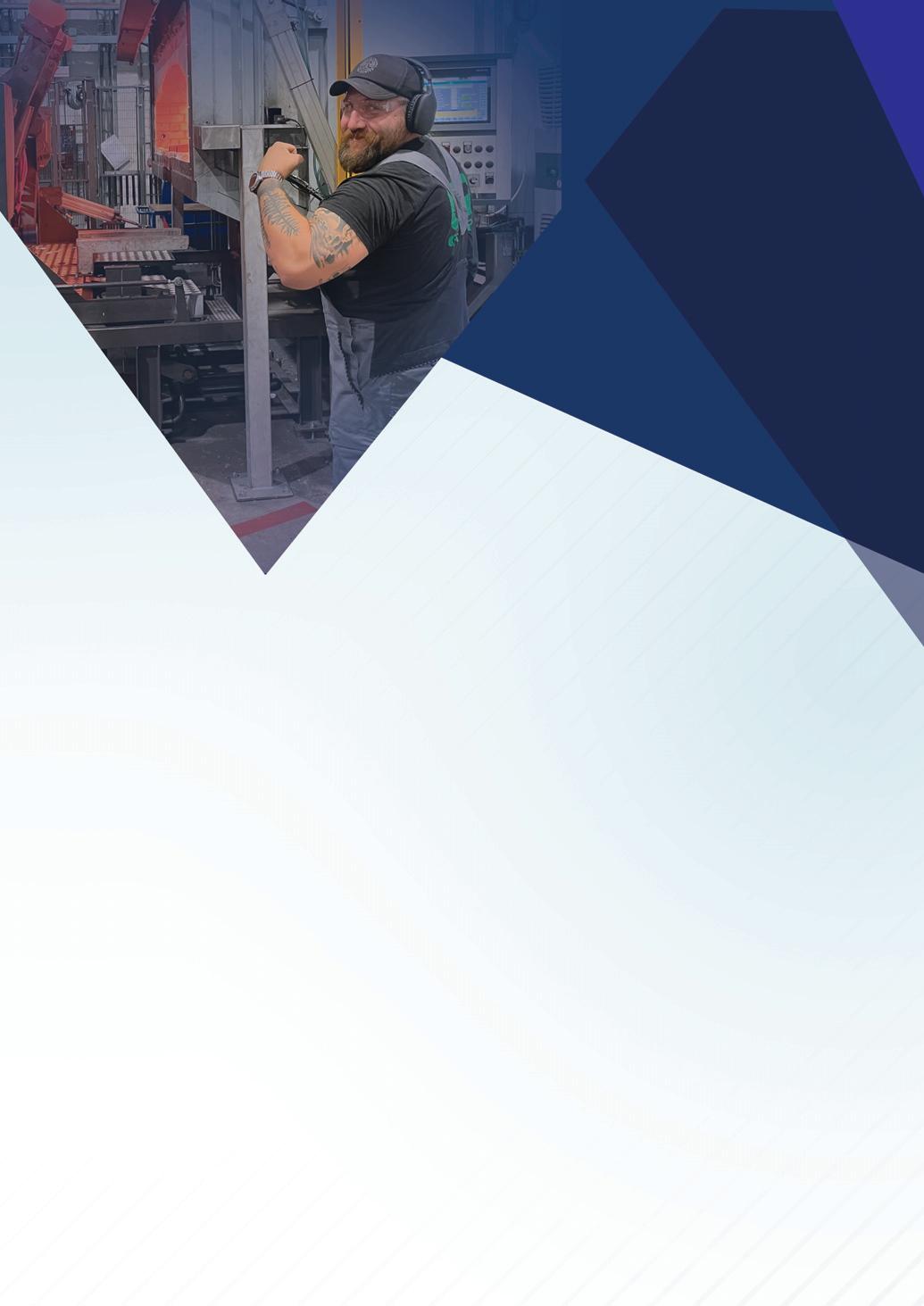
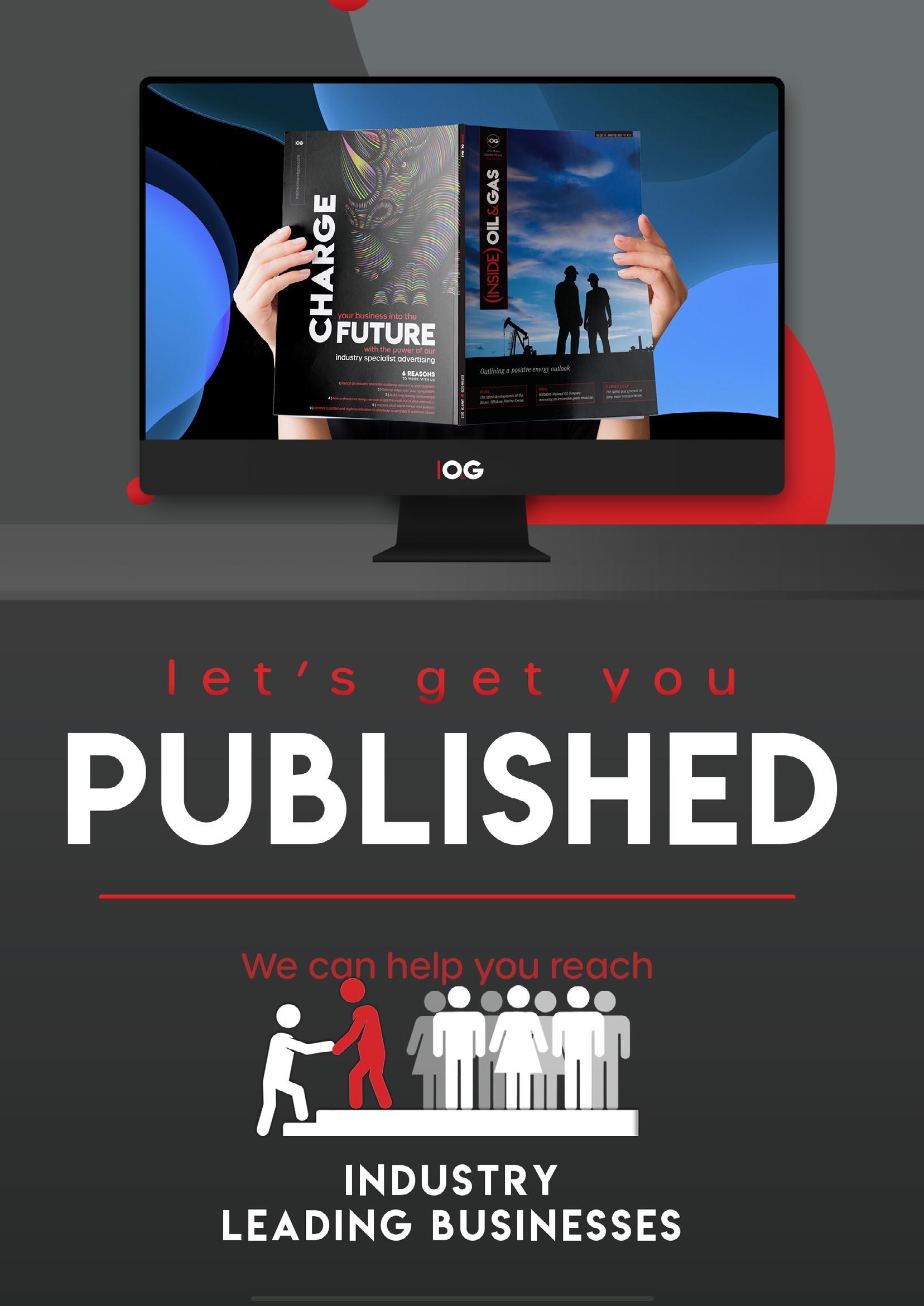