PORTS AND TERMINALS
The industry contained
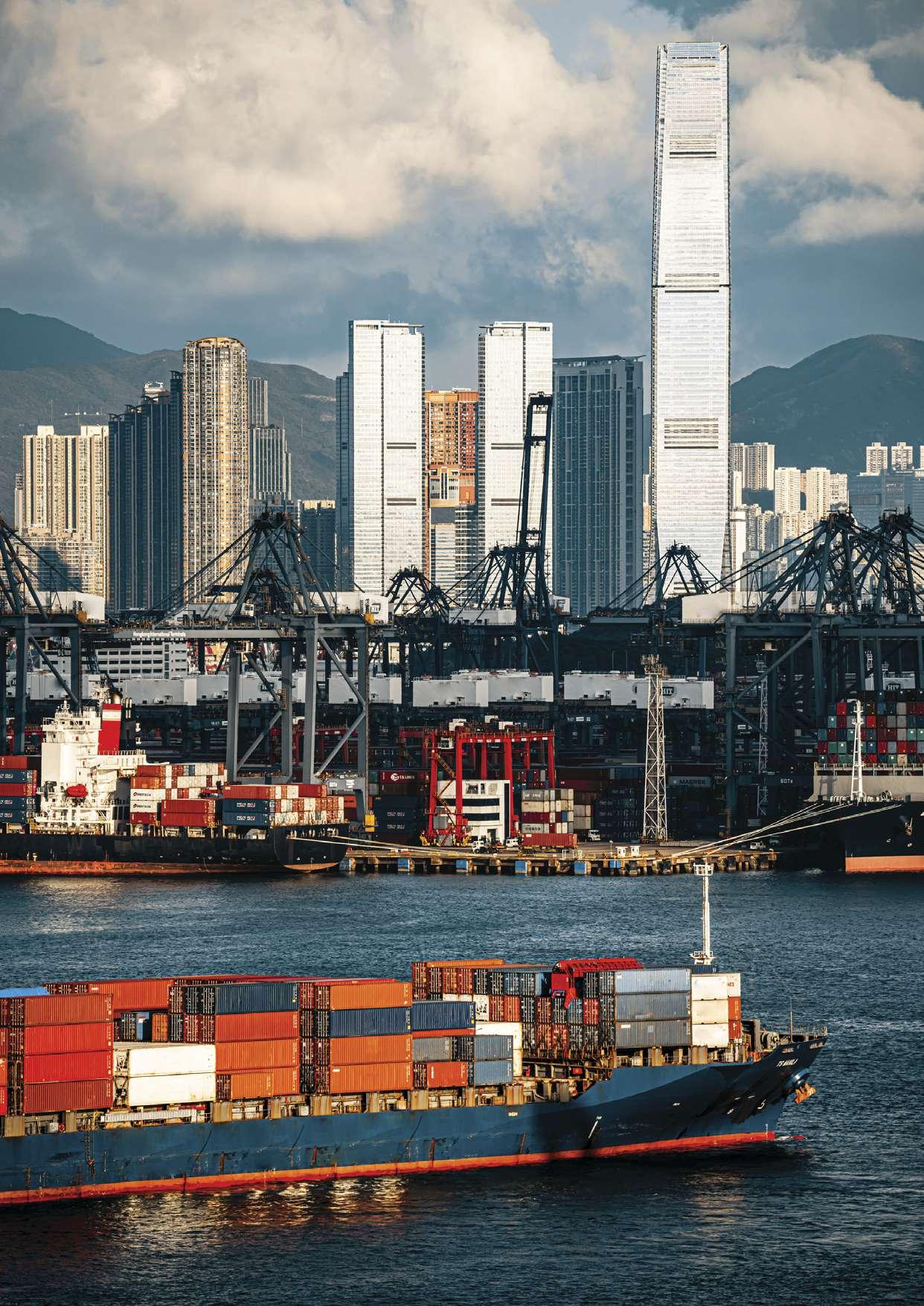
ATLANTIC TOWAGE
Ireland-based marine services company
NIEDERSACHSEN PORTS
The largest operator of German public seaports
CHEMGAS SHIPPING
A leading transporter of LPG


John White Managing Director
The industry contained
ATLANTIC TOWAGE
Ireland-based marine services company
The largest operator of German public seaports
A leading transporter of LPG
John White Managing Director
Managing Director John White discusses the importance and benefits of plotting the best course across the oceans and seas of 2023.
Welcome, Dear Reader, to your latest, and first of 2023, edition of Inside Marine. Although this is now being circulated to you all in January of 2023, much of the content was finalised as we all put 2022 to bed, and what a year that was for most of us. Working so closely with many of you for well over a decade, it is always interesting to hear about the changes that you have gone through in a relatively short space of time.
One of the biggest impacts on us all has been a concerted effort to introduce sustainability into dictionary. Of course, being the forward thinking and smart bunch that you are, most of you have been addressing this issue for a number of years now. Indeed, some of you are market leaders and influential trend setters for others to follow. Inside Marine is no different. We are proud to say that throughout 2022, we have actively worked towards reducing our carbon footprint without suffering a detrimental effect on our productivity or the quality of service you expect from us.
Indeed, we were proud to launch a new title last year; Inside Sustainability, as the name suggests, focusses on what multiple industry sectors have done in this field. It is already a popular magazine, as companies are justifiably proud to discuss their activities and share with our global readership these best working practises for the greater good. Inside Sustainability (formerly Inside Industry) covers all industry sectors, promotes their businesses with articles, advertisements, news, views and events, as does the more niche sector of Inside Marine.
However, one of the major changes was introducing Inside Sustainability as a dig -
ital-only magazine that moved away from a hard copy. Inside Marine will follow suit after this edition, as will all our other titles. Along with the reduction of our carbon footprint, adopting the digital model means that you benefit from even greater exposure to the global marketplace than the original hard copy and digital package enjoyed.
With the new digital-only version, we have greater scope in terms of readability, user interaction, creativity and availability on multiple platforms. In addition to the digital magazine that is circulated to our readers, the magazine will now also be published on our website for all to see. When we add to that the additional coverage afforded by our social media channels, the content of each edition now reaches a truly staggering number of key decision makers within the maritime community.
So, thrilling news for you all, I trust. We are certainly excited by this upgrade, as our duty is to serve you and deliver as much coverage as possible for your products and services. There are additional gains that this
transition will open up for us all, but more on that topic as the year unfolds.
So, what does this edition have for you? Well, a great deal, is the short answer. For a lengthier one, rather then listen to me prattle on, I suggest you simply flick through the pages and enjoy finding out for yourself. Or use the index to take you directly to the sections that interest you more. However, a quick overview for those of you that are kindly still on this page with me; informative articles, tantalising advertisements, the latest news and comments, forthcoming event previews and, hopefully, a little something for everyone. There is a focus on the bustling world of ports and terminals, an area that is close to us all here as we are based near the busy ports of Lowestoft and Great Yarmouth on the east coast of England, and their access to the ever-busy nautical highway of the North Sea and English Channel.
I will sign off now by wishing you a happy new year, and may it prove to be a productive and enjoyable one for all. n
42 A gateway to the future
La Spezia Container Terminal
48 Port that plays to its strengths Port of Rijeka
54 A port like no other Port of Milford Haven
58 Energy transition on the North Sea coast Niedersachsen Ports
Owners, managers & agencies
64 Carrying the pressure along inland waterways and across the sea Chemgas Shipping
78 The titans of heavy lift GPO Heavylift
86 Steering the sustainable energy sector in Taiwan Dong Fang Offshore
92 The bulk of Singapore’s shipping industry Seatrek
98 A match made in maritime heaven LD Tide
104 Navigating the waters of automobile transportation
Neptune Lines
110 The secret to project flexibility and agility
Varamar Group
116 Building bridges for a better industry
Landbridge Ship Management
122 A boundless sense of adventure SunStone Ships
128 Shipping at the crossroads Pyxis Tankers
134 Shipping that never sleeps Capramar Ship Management
138 Barges that are always running
Rán Offshore
142 Laying the groundwork for a brighter future
Bayu Maritim Berkah
146 Offshore quality and speed in Mexico
Naviera Integral
Engineering
152 Maintaining strong links
DMT Marine Equipment
160 Pioneers of rope production since 1936
Katradis Marine Ropes
166 Experts in refit, repair & manufacturing
All Points Boats
170 Crane specialist extends reach with new contracts payload Allied Systems
174 Turbocharging Chile’s maritime industry
Turbodal
178 The one-stop heat exchange shop
R.W. Fernstrum and Company
Shipping & decommissioning
184 Veering to the future
Baltic Workboats
190 The reliable partner to build your vessels
Marsun Shipyard
196 Shipyard breathes again Penzance Dry Dock
202 Holding tight to ship decommissioning ambitions
Atlas Decommissioning
Logistics, supply & services
208 Taking Chile’s technical services to new heights
Ancora Chile
214 Just like coming home
Frank Weber
220 The RoRo cube rolls out
Goodpack
Towage & salvage
228 Taking salvage and towage in new directions
Atlantic Towage & Marine
234 Working ‘Tug-Ether’ to supply America’s ports with reliable vessels
Ultratug
An interactive 3-day conference known for its high-profile thought-leaders and in-depth discussion points. For the 37th edition, the key topics include State of the Industry, Decarbonisation & Alternative Energy, Freight Markets, Digitalisation, Finance, Salvage & Wreck Removal, Integrated Logistics and Finance. Meet 80+ world class exhibitors on the expo floor and explore the latest solutions and technology in the maritime industry. The expo hall will showcase leading technology, maritime equipment, fuel and lubricant, safety and sustainability suppliers, ship repair, navigation and communication, software solutions, energy, salvage and emergency response solutions providers, insurers, and maritime recruiters. https://informaconnect.com/cma-shipping/
Nor-Shipping is at the centre of the oceans. This is where the maritime and ocean industries meet every two years – a natural hub for key decision makers from across the world to con nect, collaborate and do deals to unlock new business opportunity. Nor-Shipping is the meeting place for globally leading maritime players, technology innovators, investors, and all the stakeholders interested in realising ocean opportunities. An inter national arena for building cross industry partnership, business and sustainable ocean development. This is the arena for ocean solutions. https://nor-shipping.com/
The largest event in the world for the project cargo and breakbulk industry. Breakbulk Europe has become the global gathering for the industry with more than 120 countries represented. Exhibitors and sponsors include cargo owners, ocean carriers, freight forwarders, ports/terminals, heavy haulers, equipment companies and more. The parallel conferences will take place on two stages: the Main Stage and the Innovation Stage, complemented by a Discovery Zone in Hall 1. The 2023 event in Rotterdam brings an unprecedented opportunity to reconnect with colleagues, new business partners and project cargo decision-makers. https://europe.breakbulk.com/Home
Marine Interiors, the Cruise and Global Expo powered by SMM. Europe's first stand-alone trade fair for interior design, equipment and technology for passenger ships returns with thousands of industry professionals on the exhibition floor and renowned speakers in the conference area. Powered by SMM, the event benefits from the organisation and networking strength of the world’s leading trade fair for the maritime industry. Moreover, the co-location with Seatrade Europe provides additional attention from the “who’s who” of the cruise industry. Success factors which will remain in place for 2023. www.marineinteriors-expo.com
London International Shipping Week (LISW) is one of the most important international shipping and maritime events in the world. Having grown consistently since its conception in September 2013, LISW is set to become an even bigger event in 2023. LISW23 will play host to the maritime world, with hundreds of events attracting thousands of international industry decision-makers into London during the week. Competition is already heating up among sponsors eager to organise the most attractive networking events at the most glamourous venues in London. https://londoninternationalshippingweek.com/
Running for over 40 years, Marintec China has become renowned as the most authoritative B2B platform for the International Maritime Industry. Organised with the professional expertise of China’s largest trade exhibition organiser–Informa Markets– in conjunction with the Shanghai Society of Naval Architects & Marine Engineers (SSNAME), Marintec China connects businesses and distills insight for Asia’s maritime industry. The 2019 edition of this biennial event hosted 2,200 exhibitors and 71,700 professional visitors from 100 countries, breaking all previous records. https://www.marintecchina.com/
In late 2022, as part of a commitment to being a global integrator of logistics, A.P. Moller –Maersk opened a new warehouse in Cajamar, part of the state of Sao Paulo, Brazil. This new facility is part of Maersk’s transformation journey in Latin America, connecting and simplifying customers’ supply chains to help clients grow and thrive.
Maersk aims to better connect Latin America with the world by expanding its end-to-end warehouse and distribution footprint and regional consolidation/deconsolidation network with innovative solutions that address customers’ needs.
“By the end of 2022, we will have a 350,000-square-metre warehouse footprint in Latin America,” explained Robbert van Trooijen, President of Maersk in Latin America. “We have a great ambition for the years to come. As we combine these strategically located warehouses and a broad portfolio of services, we aim to offer more value-added, agile solutions to our customers.”
Spread over 19,400sqm, the Cajamar warehouse is located close to the main economic centres of the southeast region and is strategically set up near the main markets for fastmoving consumer goods, retail, technology and electronics, plus fashion and lifestyle, among others. The facility is situated 50km from the main airports of Brazil, 120km from the port of Santos and 30km from Sao Paulo, with quick access to the main highways.
“This new facility adds to our six existing facilities in Brazil,” said Karin Schoner, Managing Director of Maersk on the East Coast of South America, “and is part of the plans Maersk has for the country to support our customers and their domestic and international supply chain needs. Maersk has transformed into a full-service, end-to-end
logistics services provider, and our warehouse and distribution solutions take advantage of our shared global network operations to help optimise our customers’ supply chains.”
This is one important step on Maersk’s journey into being a global integrator of container logistics. The new facility in Brazil is part of an investment in the east coast of South America to build up the warehousing and contract logistics business.
The new facility offers supply chain management services, including order fulfilment, the receipt and storage of goods, inventory management, the picking and packing of pallets or cases, and more. The warehouse has a racking structure to store up to 21,000 pallet positions and 22 docks, 6-ton floor capacity, J4 sprinklers capacity, and 12m clear height.
This ‘green facility’ helps customers reach their sustainability goals with end-to-end low-emissions logistics solutions. The new site is certified LEED Platinum, and features rooftop solar panels, rainwater recapture, waste management system, felt thermal insulation and lithium battery material-handling equipment.
Maersk’s strategic priorities of environmental, society and governance (ESG) and increased focus on technology can help customers move closer to achieving net zero supply chains. Maersk is growing in
We have
“ “
a great ambition for the years to come. As we combine these strategically located warehouses and a broad portfolio of services
volume and footprint in Brazil and the Latin America region, placing warehouses strategically to carry out the integration of dis tribution capabilities.
Increasing complexity in global supply chains is making them inefficient, vulnerable and unsustainable. At Maersk, the strategic vision is to become the Global Integrator, offering truly integrated logistics solutions that connect, protect and simplify customers’ supply chains.
Global logistics underpins development and growth. An endless choreography of goods and services, it supports economies, partnerships and the whole global society. When the connections become weak, so does the world’s ability to grow, and thrive, together.
At Maersk, the vision is to transform the flow of the foods, goods, data and materials that sustain people, businesses and economies the world over. This vision is intended to enable the exchange of ideas, culture and trust for a truly integrated world where value is created for everyone. n
GoodShipping and the Port of Rotterdam
‘Switch to Zero’ campaign to reduce carbon emissions
Companies that import or export their freight by vessel generally have little influence on the container shipping company’s fuel choice. GoodShipping aims to change this with the ‘insetting’ concept. The Port of Rotterdam Authority and GoodShipping are conducting a joint campaign to inform companies of this concept so they can have part, or all of their sea freight transported via sustainable fuel.
The aim of the ‘Switch to Zero’ campaign is to recruit 20 sea freight shippers.
Swinkels Family Brewers, known for brands including Bavaria and Cornet, and Dille & Kamille are the first to announce their participation in this campaign. They will have some, or all of their containers shipped using sustainable fuel next year.
Insetting does not involve achieving carbon reductions through compensation (offsetting by planting trees, for example), but through shipping using sustainable fuel. Shippers often transport small numbers of containers on different vessels and can use insetting to purchase a certain amount of carbon reduction via GoodShipping. GoodShipping ensures that this is achieved by providing a vessel with sustainable fuel. This does not need to be the same vessel on which the containers are transported.
As part of their drive to promote CO2 savings in the logistics sector, GoodShipping and the Port of Rotterdam Authority aim to find 20 sea freight shipping companies that wish to use this service. The campaign makes it easy to get involved and deliver a concrete contribution to reducing carbon emissions. The aim is for joint vessel bunkering with these shippers to reduce the amount of carbon released into the atmosphere by 2,023 tonnes. This is comparable to the amount of carbon released
when transporting 15,000 TEU containers between Rotterdam and Gothenburg.
“We’ve seen a huge acceleration in the pace of the energy transition brought about by shippers over the past two years,” said Dirk Kronemeijer, CEO of GoodShipping, “which is why we want to give more companies the opportunity to have their freight shipped sustainably. The Port of Rotterdam aims to be the world’s most sustainable port, and it was an obvious choice for GoodShipping to support that. With the ‘Switch to Zero’ campaign, we’re making it easy for companies to enhance the sustainability of their transport without complex supply chain adaptations.”
“Shipping is not yet on schedule to be carbon neutral by 2050,” explained Allard Castelein, Port of Rotterdam Authority CEO. “We are working with partners to develop a range of initiatives to help make logistics more sustainable: from battery-powered inland shipping to shore power for sea-going vessels, and from bio-kerosene production
for aviation to so-called Green Corridors for sea-going vessels. The 2,023-tonne reduction through sustainable fuel use is just the start. We want to show that it can be done and start the discussion, with the aim of scaling up and reducing carbon emissions even further. The transition tempo needs to step up.”
Shipping is responsible for approximately 3% of global carbon emissions but, at the same time, is a complex sector that fell outside the international climate agreements for a long time. The chain is also fragmented because companies often only ship just a few containers on a vessel.
Dutch company GoodShipping is a global market leader in insetting, the service for shippers and producers to enable sea-going freight to be transported using sustainable fuels instead of traditional fossil fuels. This form of insetting accelerates the energy transition in the transport sector. The initiative does not lie with shipping companies, but with freight owners.
GoodShipping already works for companies including DHL, IKEA, BMW, Tony’s Chocolonely, Beiersdorf and Kings of Indigo. The fuel is produced from certified sustainable flows including frying oils and animal fats that are labelled as 100% waste and cannot be used in higher grade products.
Ingeteam’s converters increase the efficiency of the ship, also making it a ‘green ship’. This order came from Hyundai Global Service, a South Korean firm specialising in the provision of maritime services and power generation.
Ingeteam has recently completed the supply and commissioning of its equipment for a smart electric ship for the company Hyundai Global Service, a South Korean firm specialised in the provision of maritime services for shipbuilding. This ship is South Korea’s first smart electric passenger ship. Ingeteam has been working on the project for the last year.
Specifically, Ingeteam supplied and commissioned its converter Ingedrive LV400 DC Grid type, which enables a more efficient grid by reducing the number of power conversion stages and allows variablespeed generation of the gensets, thus operating at peak efficiency. As a result of this, and Ingeteam’s technology, the vessel can be considered a ‘green ship’, increasing its added value.
With a capacity of up to 375 passengers, the ship will shortly begin service. Specifically, it will sail the Whales Sea Travel Line near Jangsaengpo, a port in the southern area of
Ulsan, South Korea’s seventh largest city with a population of 1.1 million.
The ship has a length of 89.2 metres, a breadth of 12.8 metres and will sail at a maximum speed of 16 knots. Construction of the ship began last year at the Hyundai Mipo Dockyard in Ulsan. The vessel uses the latest information and communication technologies, making it a smart electric ship.
The equipment supplied by Ingeteam is fully redundant in case of failure of any of the converter outputs. Ingeteam’s system is a DC grid and can, therefore, serve directly as the ship’s power plant.
Ingeteam, is a group of more than 4,000 people in 24 countries, with more than 80 years of experience. The company provides creative solutions to specific problems to electrify society in an innovative and sustainable way through cutting-edge tech -
nology, specialising in the conversion of electrical energy.
The company aims to consolidate its position as leaders in renewable generation (wind, photovoltaic and hydroelectric), storage and in the intelligent transport network. Ingeteam enables the efficient and clean consumption of electrical energy through electric vehicle chargers, converters, generators and motors. These applications are suitable for the traction, marine, iron and steel industries, mining, for the production of green hydrogen, submersible motors and water pumps.
Ingeteam has supplied 25GW of solar photovoltaic power with its solar inverters, over 54GW to the wind industry with converters and Indar generators. The company has more than 10.5GW of total installed power in the hydropower sector with Indar generators, more than 12,000 Indar submersible pumps and motors worldwide and more than 6,000 electrical substations are automated with its equipment. In addition, 1.6GWh accumulated in electrical storage facilities and Ingeteam is the world leader in the provision of operation and maintenance services in renewable energy plants, with more than 18GW of power maintained.
In terms of efficient consumption, it is worth highlighting the more than 12,500 chargers for electric vehicles, the supply of equipment for 700 electric trains, or for the more than 600 ships that are equipped with Ingeteam technology, enabling an evolution towards hybrid and full electric naval propulsion systems. n
Maritime UK launched in November its national awards programme for 2023, celebrating a sector worth over £116bn to the UK economy and supporting over 1 million jobs. The Maritime Minister Baroness Charlotte Vere and Industry Minister Nusrat Ghani MP are both expected to attend.
Awarded for the first time in September 2019, the Maritime UK Awards are run by the industry for the benefit of the industry. From a judging panel of internationally recognised maritime leaders to an awards evening at the DoubleTree by Hilton Hull, the Maritime UK Awards are a unique and impactful way to showcase business, and collectively, to celebrate a thriving sector, worth £116bn to the UK economy.
Each year the Maritime UK Awards rotate around the UK, having visited Plymouth, Portsmouth and Glasgow so far, the 2023 Awards will visit Hull. The portal for submissions opened in November.
The Maritime UK Awards are open to organisations from across the breadth of the maritime sector and its component shipping, ports, services, engineering, science, and leisure marine industries. Since the launch of Maritime 2050 in 2019, which set out the government’s vision and ambitions for the future of the sector, the award categories are designed to mirror its themes.
In the past year, since the sector came together in Glasgow, Maritime UK has published its 2022 State of the Maritime Nation report which revealed the £116bn economic impact of UK maritime, supporting over 1.1 million jobs and paying 30% more than the national average. The sector has seen significant activity and progress in recent months, with the launch of the National Shipbuilding Strategy, the third round of the Clean Maritime Demonstration Competition and the development of Freeports.
March 2022’s awards were held in Glasgow, where the winners included: Onboard Maritime, Serco, Babcock LGE, Cavendish Nuclear, Artemis Technologies, Plymouth Boat Trips, Solent Local Enterprise Partnership, CyberOwl, Port of Cromarty Firth, Cowes Enterprise College, FrazerNash Consultancy, PD Ports, Blackpool and The Fylde College, and Peel Ports.
The fourth Maritime UK Awards will be held at the DoubleTree by Hilton Hull, on Thursday 9th March 2023. With over 800 years of seafaring history, Hull was chosen as the host for the 2023 awards to shine a light on a city that can be considered a powerhouse for trade and one cementing its position at the heart of a new green industrial revolution. Associated British Ports have been announced as Diamond Sponsors for the 2023 Awards.
Maritime UK announced the first six category sponsors as Nautilus International (Bevis Minter Award), Trinity House (Future Skills Award),
Offshore Renewable Energy Catapult (Clean Maritime Innovator), Associated British Ports (Clean Maritime Operator) the Department for Transport (Maritime 2050 Award), Lloyd’s Register (Clean Maritime Enabler) and Port of London Authority (Innovation Award).
“We are hugely excited that Hull will host the Maritime UK Awards,” said Sarah Kenny, Maritime UK Chair. “These awards shine a spotlight on different parts of our maritime nation. In Hull, and the Humber as a whole, we have an incredibly compelling maritime proposition as one of the UK’s largest ports complex, the fourth largest trading estuary in Northern Europe and a strong focus on the offshore renewable energy sector.
“2022 has been a year of significant activity for the maritime sector, and there is real momentum across the sector as we target our Maritime 2050 ambitions. The 2023 awards will, therefore, be a fantastic opportunity to showcase and celebrate the growing number of world-leading projects, developments and initiatives helping to ensure the UK’s position as the most innovative, competitive, and sustainable maritime centre by the middle of this century.”
Maritime UK is the umbrella body for the maritime sector, bringing together the shipping, ports, services, engineering and leisure marine industries. Maritime UK also has responsibility for the coordination and delivery of industry recommendations within Maritime 2050.
Named by the Royal Institute of Naval Architects as one of the most influential women of the past century, Danielle Doggett is Founder and CEO of Veer Group. Veer is developing an innovative wind-powered solution for cargo shipping. Questions by Phil Nicholls.
By way of introduction, could you please share a brief history of Veer?
Veer is the culmination of my 20 years in sailing. Combining 12 years’ experience sailing cargo with an obsession for achievement, I went back to the drawing board to create the ideal solution for end users. After all this time, not a single company was listening to the client. I focused my attention on understanding the needs of clients and coupled them with cutting-edge clean-energy systems that are ready.
Can you please outline the sustainable shipping solution from Veer?
Veer directly leads to healthier, more resilient oceans and coastal systems by critically examining myriad factors that negatively affect these zones - and producing innovative solutions that can be tested and proven today. Veer is an intrepid, breakthroughcompany that is scalable and replicable, proving to stakeholders that achieving greater ocean health is safe, reliable and ready.
Some of the factors that Veer addresses are greenhouse gas emissions (including sulphur), heavy air pollution, oil spills, fracking, bio-acoustic pollution, invasive species, barriers to access of small island nations, rights of coastal community members and crew, and more. These factors are quantifiable contributions which improve the health of the oceans and many other systems.
The most eye-catching feature of the Veer ships are the DynaRig sails. Please share with our readers the benefits of returning to wind-powered shipping.
The benefits of returning to wind-powered shipping are the sustainable nature of the resource, the lack of contribution to climate change, and, for our clients, a reliably priced product that doesn’t fluctuate with oil prices.
The Veer container ships will be 100 metres long, so what levels of performance will the sails deliver?
The high-performance sailing rig will be able to power 100% of the propulsion requirements of the vessel when there are prevailing good conditions.
The ships are designed to go 12-18 knots - which is on par with, or faster than, what current international authorities expect of oil cargo ships. While traditional container ships can go up to 20-25 knots, the marginal deficiency in oil use is cost and resource prohibitive, so they regularly sail at between 8-12 knots.
I understand that these ships will also feature green hydrogen fuel cell engines. Can you please explain your reasoning for adopting a hybrid wind/hydrogen model?
Yes - this design of vessel will have a 750kW engine, powered by green hydrogen fuel cells. This system will be coupled with a battery bank, which will allow for peak-shaving (improving energy balance).
In harbour and port, as well as on calm days, it is essential to have a reliable back-up power source. Knowing we wanted these
ships to be 100% clean, we needed an energy source that was efficient and effective - hydrogen fuel cells are just that. It is proven technology that works.
While sailing in good conditions, the vessel will have the option to generate electrical energy by using the propeller as a turbineeffectively capturing the kinetic energy (forward motion of the ship as driven by the wind and sails) and converting it to direct use or stored electrical energy.
In subsequent iterations of this design, we may choose to have an electrolyser onboard - an investment which would allow for green hydrogen generation onboard the ship.
October 2022 brought Approval in Principle for the project from the American Bureau of Shipping. How has this achievement assisted the development of the Veer Voyage project?
Having the Approval in Principle granted to Veer from the American Bureau of Shipping sets our project apart - there are so many ideas and concepts out there today, it can be hard for stakeholders to know which project has the potential to be realised - this is a major indicator of our ability to make these
ships a reality. When stakeholder confidence is increased, it creates enabling conditions for them to support further development, which has a positive-feedback effect.
We have what we need to bring to shipyards for the builds to begin. Others will be looking at paper for a long time, we will be looking at our steel hulls in a short time.
Your stated mission is to be a ‘clean shipping generation leader’. Do you believe that this can only be achieved through wind-powered shipping?
I believe that wind is a solution at our fingertips that is not being harnessed. For me, my path as a shipping leader at this moment is with wind. Through my work with wind, I hope to inspire others into creating - or generating - other projects within clean shipping. There are so many emerging technologies in the energy space, I wouldn’t use the word ‘only’ - recurring themes in clean shipping are stakeholder collaboration, blended capital and hybrid energy approaches. We are not at a turning point with energy, we are at a starburst.
What are the biggest challenges you face for the next step of the project?
Currently, we are about to submit our bid packages to shipyards. Finding the right partner to build with us is imperative. This has also never been done before, so anytime you head into unknown territory, you must be ready for anything. What those challenges will be, I do not know, but we will face them head on. I chose the partners I work with for that reason, they are world-renowned leaders in their industry. I have no doubt that together, whatever comes our way, we will be successful.
Do you have a timeframe for when we are likely to see these amazing ships?
In our communications with the shipyards to manufacture the ships, we expect 7-12 months for hull completion, 18 months for the DynaRig sails/masts. As the combination of DynaRig, hydrogen systems and a new hull design has not been done before, Veer will build the first two ships simultaneously or consecutively in Europe. 2024 will be the year we start shipping.
What aspect of your job excites you personally? What makes you eager to walk into the office each morning?
My desire to see these ships on the water excites me. They are going to be so beautiful and so functional. The fact that I know it is possible, I know it is achievable, gives me an inspired determination to succeed. Running a start-up is so exciting, every day brings new challenges and opportunities… there’s never a dull moment!
Is there anything not covered by the above questions that you would like to share with our readers?
I believe that this shift to clean shipping will be powered by end users, by private markets - not by rules or regulation. Just like disruptive start-ups Airbnb and Uber, clean shipping companies like Veer will be the driver of those rules. With the support of major clients such as LUSH, Café William and more, the regulators will find themselves rushing to catch up to regulate the new playing field.
The Solent Freeport has been announced as one of the first UK Freeports to be fully approved by Government.
“This is the news we've been looking forward to, and I’m grateful to our partners across the public and private sectors for their commitment and vision in bringing about a freeport for the Solent which will benefit our communities for generations to come,” said Brian Johnson, Chair of the Solent Freeport.
“The strong business case we put forward has resulted in the Solent Freeport being one of the first officially designated by Government.
“The Solent Freeport really is a once-in-a-generation opportunity – an investment in our future which will ensure local people benefit from job creation and increased prosperity, regenerating our communities.”
The announcement follows formal Government designation of the tax sites within the Solent Freeport, where investment is underway. Tax sites offer occupiers business rates relief and other incentives to support capital investment, skills and employment. Business rates growth generated at the tax sites can be retained locally and reinvested in the area.
Designation of the Solent Freeport will help accelerate and enhance investment already underway at key locations. This includes a package of investments at the ABP Port of Southampton to enhance operational efficiency and capacity for new warehouse and distribution units. Additional container
storage areas; new HGV driver welfare facilities; improved marine access as well as enhanced rail provision to support businesses right across the UK will also be constructed as part of the investment.
The new 500,000sqft of business space at Navigator Quarter, adjacent to the runway at Southampton Airport, and part of a 75-acre site as part of the Solent Freeport is another investment benefitting from Solent Freeport’s designation. The project is being delivered by AGS Airports Ltd in partnership with blocwork, a Network Rail JV Company, and expected to be completed in 2024. The Navigator Quarter site is ideally placed to benefit from excellent air, road, sea and rail connectivity. Phase one will deliver over £120m GVA to the UK economy.
The Solent’s ambitious bid for Freeport status was one of eight in England shortlisted by the Government in the Spring 2021 budget. As an important part of the UK's economic recovery, freeports are areas that benefit from incentives to encourage economic activity.
The Solent Freeport is a widely supported proposal which will transform Solent productivity, create more than 15,000 jobs in the Solent and a further 15,000 throughout the UK. It is expected that the Solent Freeport will attract £1.35 billion of private sector investments in the area, and because of the Solent’s existing trading links, an additional £1.75 billion GVA is forecast to be generated for the UK as a whole.
Bureau Veritas (BV), a world leader in testing, inspection, and certification, has delivered certification to Nexans, a global player in electrification, for its risk management system for subsea power cables. Nexans and BV have announced the first outcome of their partnership to reduce risk and promote best practices for turnkey project delivery of high voltage power cables used for connecting offshore wind farms to onshore grids. Bureau Veritas has developed a protocol, leading to certification, to help minimise risk for Subsea Power Cables.
The subsea power cable market is going through unprecedented expansion, encouraged by major investments in offshore wind. At the same time, insurers’ studies confirm that high voltage power cables are among the most critical elements of offshore wind farms. Reliability of high voltage power cables, including installation, becomes an essential enabler for the current and the next generation of cables required to capture energy in deeper water. Hence, removing risks from new products, technologies and implementation methodologies is essential for the sector.
Due to the lack of any international or statutory certification scheme, Nexans engaged in a voluntary approach to ensure its risk management tools and processes are assessed and tested by an independent third-party body. The goal was to validate the
methodology in place that helps identify potential hazards, associated risks and evaluates the level of protection that may be afforded to the cable.
As a result, BV established solid protocol and certification guide lines to review Nexans’ risk management system in line with international standards ISO 21502:2020 (guidance on project management) and ISO 31000 (risk management). The BV certification covers any phase of a development project from conceptual phase, design, procurement, manufacturing, transportation, installation and commissioning/start-up.
“Managing risk is an important and integrated part of the Nexans management system for delivering Subsea Power Cable Projects,” said Anne Fossen-Helle, QHSSE & Risk Director at Generation & Transmission Business Group at Nexans. “By having our risk management system and projects validated against recognised standards by an independent certification company, we believe this is a trusted route to deliver stakeholder confidence showing that risks have been understood and minimised.
“Together with Bureau Veritas, we have certified the Nexans ‘way’ of managing EPCI projects and risks, developed new standards for the offshore wind farm and interconnection industry, reduced the risk profile of such projects and developed improved standards.”
INtheface of external uncertainties over the past six years, the OCEAN Alliance continuously optimised the service network, enhanced the capacity deployment, and gained the acclaim from customers with high-quality and stable services.
The launch of the OCEAN Alliance DAY 7 Product in 2023 ushers in a new chapter for the development of the alliance. Going forward, it will continue to uphold the customer-centric principle. Boasting 353 vessels with an aggregate capacity of 4.62 million TEUs, OCEAN Alliance provides customers with a variety of service options.
The OCEAN Alliance is always committed to the ‘green and lowcarbon’ concept and attaches great importance to regulatory compliance. The DAY 7 products were officially launched in January 2023, in tandem with the implementation of the IMO's new environmental rules, which demonstrates the OCEAN Alliance’s commitment and determination to fulfil the carriers’ social responsibilities.
The OCEAN Alliance DAY 7 products launched in 2023 cover 40 shipping routes and one Non-OA Transatlantic loop: 7 Far East - North
Europe services, 4 Far East - Mediterranean services, 21 TransPacific services (including 13 West Coast North America services, 8 East Coast North America and U.S. Gulf services), 3 Trans-Atlantic service (including one Non-OA loop), 4 Middle East services, 2 Red Sea services and 7 Far East – North Europe services.
The OCEAN Alliance will provide 7 North Europe direct services, including 4 upgraded loops. With an emphasis on the ‘green shipping and low-carbon’ principle, the OCEAN Alliance will optimise port rotation and vessel deployment to increase the vessel energy efficiency and the schedule reliability of its services. These loops offer direct services to 18 Asian ports and 15 North European ports along with around 100 port-pair coverage, thereby providing customers with high-frequency and comprehensive shipping services.
Leveraging COSCO SHIPPIING’s transhipment hubs like Zeebrugge, Rotterdam, Gdansk and its own feeder network, its services will be further extended to Spain, Ireland, Sweden, Denmark, Poland and Finland.
Fast Offshore Supply Pte Ltd, Asia’s largest offshore crew boat operator, has signed an MOU to jointly develop an Energy Storage System (ESS) with Terasaki Electric Co, Shift Clean Solutions Ltd and RINA for the FOS Fleet as part of FOS ‘Green Initiative and Sustainability Programme’ to cut vessel carbon emission.
The ESS system will be a containerised version where it will have a ‘Plug and Play’ connection to connect with the vessel's Electrical System. Terasaki Electric Co will provide the in-depth know-how to upgrade the existing vessel MSB and PMS for the vessel electrical system, while Shift will provide its latest state-of-the-art marine approved batteries and operational software (OnWatch) for the FOS’s ESS system. RINA will be reviewing the ESS systems and will provide the ‘approval-in-principle’.
“FOS’s ‘Go Green Attitude’ is absolutely amazing! The way they talk about decarbonisation and how to help the environment really thrilled us,” Ryo Katsuki of Terasaki Electric Co said. “With this project, we are determined to show our commitment to working towards a better, healthier and sustainable environ -
ment. We are happy to work once again side by side with Shift Clean Energy and RINA to support FOS’s ‘Green Initiative and Sustainability Programme’.”
“We are thrilled to work with Terasaki, RINA and Fast Offshore Supply to electrify these advanced crew transfer vessels,” said Brent Perry, CEO and founder of Shift Clean Solution. “It is a privilege to join forces with forward-thinking organisations and we know that this is only the beginning of an impactful, exciting project and the wider mission to decarbonise the marine industry as a whole.”
“The shipping industry faces unprecedented challenges as environmental regulations tighten,” said Simone Manca, RINA’s Regional Senior Director, Asia. “RINA is honoured to work with like-minded partners FOS, Terasaki and Shift Clean Solution in providing a way to comply with the regulations and contributing to reduction of carbon emission in shipping. We are excited to be part of the MOU to create a sustainable future for the benefit of all maritime stakeholders and the environment.”
The oldest ferry route in continuous operation is the Mersey Ferry from Liverpool to Birkenhead, in northern England. Benedictine monks began the service following the establishment of an abbey at Birkenhead in 1150CE.
Tugboat strength is measured in terms of bollard pull. The world’s most powerful tug is the Norwegian Island Victory with a bollard pull of 477 metric tonnes.
Jeddah Light watches over Jeddah Islamic Port on the Red Sea coast of Saudi Arabia. At 133 metres, it is the tallest lighthouse in the world.
Containerised shipping has a long history. The story began in 1766 in England when James Brindley’s box boat “Starvationer” featured 10 wooden containers for the transportation of coal from Worsley Delph to Manchester, via the Bridgewater Canal.
Every problem is a gift we would not grow without problems “ “
– Anthony Robbins –
The ocean appears blue because water absorbs the colours in the red part of the light spectrum. Acting like a filter, this process leaves only colours in the blue part of the light spectrum, which is what we see.
The most remote port in the world is Edinburgh of the Seven Seas, on the Atlantic island of Tristan da Cunha. The island is 2,400km (1,500 miles) from the nearest human settlement on Saint Helena.
MV Yara Birkeland is the world’s first fully electric, autonomous container vessel with zero emissions. With a cargo capacity of 120 TEU, Yara Birkeland operates in Norway, sailing between Horten and Oslo.
By tonnage, the busiest port in the world is Shanghai, handling over 47 million TEU in 2021.
The tidal bore on the Amazon River, known as the Pororoca, can reach a height of 3.6 metres. The wave is generated 15km out in the ocean, before travelling 800km up the Amazon.
What’s new in the marine industry?
From simple ideas to engineering feats
Ocean Signal announces Cospas-Sarsat approval for world’s most advanced
The Ocean Signal rescueME EPIRB3 and SafeSea EPIRB3 Pro beacons feature integrated AIS (Automatic Identification System), NFC (Near Field Communication) technology for use with the free Ocean Signal mobile app, and compatibility with Return Link Service (RLS) alerting. The slim, lightweight beacons, with 10-year battery life, also include GNSS (Global Navigation Satellite System) positioning, 406 MHz Cospas-Sarsat distress signal with MEOSAR compatibility and 121.5 MHz local homing signal.
Local Fuel Ltd, fuel expert and port tenant, is generously sponsoring a Seabin at Shoreham Port within the canal. The Local Fuel Seabin is installed to collect plastics and litter from their marine environments. Created by the Seabin Project, the award-winning device is a floating rubbish bin attached to a pontoon. A pump sucks water through a catch bag inside the Seabin, leaving litter and debris held inside. A single Seabin can collect over one tonne of litter each year – and can even capture microplastics as small as 2mm.
Elliott Bay Design Group (EBDG) has designed an innovative harbour power and charging barge, offering ports and harbours a high-performing option to minimise emissions from large vessels both pier side and at anchor. Delivering 7 megawatts (MW) of continuous power generated by methanol, this floating mobile platform is capable of cold ironing even the most demanding vessels, both at the pier and at anchor, for up to two weeks before refuelling.
Zelim is an Edinburgh-based start-up pioneering unmanned search & rescue solutions. In December 2022, the company secured a £2.3m equity investment, with lead investors Kero Development Partners and Aberdeen-based I7V.
Zelim aims to make the ocean a safer place to work by
Safety and survival specialist ACR Electronics introduced the new CospasSarsat approved ResQLink AIS Personal Locator Beacon, the most comprehensive communication set on the market for the rapid response and rescue of boaters. Featuring multiple levels of integrated signal technology in one compact package, the advanced ACR PLB with integrated AIS Man Overboard (MOB) alert combines the global response of the 406 MHz CospasSarsat satellite rescue services with the transmission of AIS signals for local assistance from nearby vessels.
Styled as a raised pilothouse model the 108 is offered as a long-range, full displacement steel/aluminium construction, or a semi-displacement aluminium version offering max speeds of 22-23 kts with a range of approaching 2500 nm. With a large volume interior offering a five-stateroom layout with a crew compliment of five, the StellarONE108 has a full-beam main deck master stateroom with lower deck accommodation comprising two equal-sized queen staterooms, a VIP suite with king-size bed and a twin stateroom. Send us your innovation
We welcome all your latest innovations and product releases. If you wish for us to share these with our readers please send them to us today.
Cruise vessel Marella Celebration was recently pictured during dry dock work in Cádiz. COLUMBIA Cruise Services (CCS), an affiliate COLUMBIA company, is solely dedicated to managing cruise and expedition vessels. Operating out of Hamburg, Germany, CCS offers the full range of services required to achieve long-lasting customer satisfaction.
To learn more about CCS, please visit: www.columbia-cs.com
seven seas, five oceans, one voice
rotterdam short sea terminals la spezia container terminal port of rijeka port of milford haven niedersachsen ports
Rotterdam Short Sea Terminals is Europe’s largest dedicated short sea terminal. It was established in 1997 and celebrated its 25th birthday at the end of 2022. RST has experienced significant growth since it was founded, especially following its takeover in 2021. According to CEO Arno Storm, the acquisition has given new energy to the development of RST. He explained more to Hannah Barnett.
Since its takeover by shareholders Blue Ocean Capital and Crestline Investors, Rotterdam Short Sea Terminals is going through what CEO Arno Storm called ‘a professionalisation of all functions and capabilities.’ This has meant an upgrade in facilities, people and even the way its employees work.
“A whole investment pipeline was put in place,” Mr Storm said. “We are currently introducing a lean way of working, with all employees following lean training. And what we have seen is that the entrepreneurial spirit has grown significantly.”
‘Lean’ working is a philosophy of work which emphasises the eradication of as
many inefficient activities as possible, with the principle that it is wasteful to expend resources for any goal other than the creation of value for the end customer. Accordingly, RST is now the sort of port which focuses on its efficiency.
With 64 hectares of terrain, 2,800 metres of quay space, 640 reefer connections, 14 ship-to-shore cranes, 12 straddle carriers, five reach stackers, six empty container handlers and 15 terminal tractors, Rotterdam Short Sea Terminals is well equipped for purpose.
And it needs to be, to transfer 800,000 containers per year and for the range of services on offer. As Mr Storm said: “We handle seagoing vessels, barges with inland connections, trucks and rail. We also provide storage depots, repairs and reefer services.”
Further investment in the port facilities is an ongoing project.
“In 2021, we invested heavily in reach stackers and acquired five new ones,” Mr Storm said. “We refurbished the pavement of the terminal, which is not very glamorous, but quite costly. That was a million or so. Upgrading the terminal
infrastructure and upgrading the gantry rails of several cranes, was also hugely costly.
“Currently we are working on a complete renovation of our technical building. And we fleet, which means that the first batch of six carriers will be ordered in 2023. And we are looking at replacing several older cranes.”
As a short sea terminal, it is crucial to be highly efficient. “We have the fastest ship-to-shore cranes available in the market,” Mr Storm said. “We have a unique operational setup in which the import stacks and
the export stacks are divided separately, and the cranes can swiftly interchange containers between the different stacks.”
This sort of functionality is reflective of the requirements of a short sea port.
“It means we are very flexible and efficient,” explained Mr Storm. “Our terminal operating software, where we manage all the container flow coming in and going out, is specially designed. This means our customers can bring in a container at the last minute, just before departure of the vessel, which is quite different to what you see in long-haul terminals.”
The terminal has invested in the efficiency of its connections, too. “There was a need to update the interchange between us and the rail terminal, adjacent to ours,” continued Mr Storm. “So, we set up a lean improvement project. We increased shunting time between the two sites, up
to a standard of more than 99% on-time shunting, within 24 hours. That is a stable product right now. The next step is to reduce the 24 hours to a faster standard, as quick as possible.”
Since its takeover, the terminal has been able to use the movements of the market to its advantage and make the best of turbulent periods.
“We anticipated the huge issues with the global logistical supply chain in 2022 and created an ‘extended gate’ product at our old dockyard facility,” Mr Storm said. “We were able to serve several customers with long-term storage for containers, which were not being taken out due to the congestion in the supply chain in the hinterland.
“This whole entrepreneurial mindset, which was not there in the past, has grown into the company. Now we're always looking for opportunities across the industry. And
in the spot market, where we've been quite successful too.”
Mr Storm also emphasised the significance of working closely with suppliers in order for RST to operate smoothly.
“'We’ve got an array of companies who support us,” he said. “For our rolling equipment, we have lease contracts in place. We've got several contracts with companies who do maintenance and repair to our cranes. Our software suppliers are important, because the terminal container business is all about data exchange nowadays, and they need to be swift and reliable. We work in a synergetic way with our main software supplier who provides the terminal operating system; their staff and our staff are co-located at our terminal.”
One of the strongest examples of quantifiable progress at RST is the automation of the gate facility, which serves 800 to 1,200 trucks a day and previously had a turnaround
time of 90 minutes, on average. Mr Storm said that this has been shaved down to 50, thanks to automation.
“That’s 35 to 40 minutes of increased efficiency,” he continued, “which is good for our customers, because waiting time needs to be paid for, there's nothing free in this world. What we also see is that the flow of trucks is smoother. And the experience for the truck drivers, and our own staff, is better. The whole stream throughout the terminal has improved.”
RST runs the gate alongside several other companies located in the same basin, as part of the Rotterdam City Terminal complex.
“The gate setup is quite efficient,” Mr Storm explained. “It's a joint investment with the other companies and the port authorities of Rotterdam. There is an internal lane which connects us all. I think that is also one of the big advantages of RST, we have a very good relationship with
our neighbours. And we've got efficient software, so everything is connected through Portbase, the common port community system.”
As a company fully invested in progress, it is no surprise that the terminal is also investing in hydrogen solutions and facilities for electric vessels. It has already decreased its carbon footprint per-container by 20% this year. The CEO acknowledged that becoming more sustainable is not without its challenges, but, as he said, ‘that’s a good thing.’ That’s because these measures mean more to RST than ticking a box, or even making a shrewd investment.
“We believe in sustainability, not only for the purpose of doing business,” Mr Storm said. “We believe in our role in society. So, we look at it not only from a CO2 reduction point of view, but also as our duty to our employees, to the people of Rotterdam and the planet.” n
La Spezia Container Terminal (LSCT) is a regional gateway container terminal in La Spezia, northern Italy. It has been in operation since 1971, following the founding of Contship, its parent company, two years earlier. The Contship Group is now a behemoth in maritime terminals and intermodal transport services and LSCT is a key asset. Alfredo Scalisi is CEO at the terminal. He explained his philosophy of ‘continuous improvement’ to Hannah Barnett.
There are plenty of comings and goings at La Spezia, the first private container terminal in Italy. Offering direct connections to global markets, access to central and northern Italy, and what it calls an ‘increasingly smart option’ for southern Europe. The LSCT terminal serves railway companies that connect the port of La Spezia with the various inland terminals of the country. Among the railway companies there is also Hannibal European rail network, which is dispatched from Rail Hub Milano, both of which are Contship subsidiaries. This enables fast and seamless cargo transfer by rail or lorry.
There is no denying it is a large operation. LSCT is managed directly by about 630 people and indirectly involves over 10,000. According to CEO Alfredo Scalisi, the terminal was initially formed to meet the “growing need for maritime transport via containers destined for the vast geoeconomic areas of northern Italy and southern Europe; a type of service that was not yet available in the historic ports of the northern Tyrrhenian Sea.” Mr Scalisi went on to explain what makes La Spezia stand out from the pack is the matching of its efficiency with “reliability, availability and versatility.”
Appointed to his post as CEO two years ago, Mr Scalisi set out his vision of why the company must strive for ‘continuous improvement’: “Being the most efficient terminal is not enough. We must always gain and maintain a competitive advantage by continuously studying, adapting and testing every single process, and by starting the same procedure all over again. Continuous improvement means that the terminal can offer a level of customer service that is ever closer to the needs of those who choose to come to La Spezia.”
Contship was started by Angelo Ravano in 1969 with fully containerised ships and the slogan “We Bring the Ship to Your Factory.”
The company was born in the early days of containerisation, the shipping method in which a large amount of merchandise is packaged into large, standardised containers Offering a wide range of integrated services, Contship is now seen as something of a pioneer in Italy and across Europe. Its end-toend business model was ‘adopted by others 40 years later,’ explained Mr Scalisi. As its subsidiary company, and founded only two years later, LSCT is clearly a significant cornerstone from the early days.
Contship has since evolved into a modern organisation with a long tradition of success and is now ready to accommodate the latest generation of container carriers.
The company is not only versatile however; it keeps innovating. Mr Scalisi explained that in 2021, the Contship group launched Drive My Box, a digital all-in-one platform for container shipments in road transport. Its expressed mission is to bring the handling of containers by lorry into the digital world. “Contship once again proved
itself, as a forerunner in its field by providing a completely digital service to the market,” as Mr Scalisi put it.
As well as its numerous ports, of which La Spezia is one, Contship is present in land logistics through its subsidiary Sogemar which owns both inland terminals and transport companies for rail and lorry. With a company of this size, how does one hand know what the other is doing? “The synergy between the Group's concepts is guaranteed by the presence of two CEOs, one for each macro business area, united by a shared vision,” explained Mr Scalisi.
The Group's companies include other maritime terminals in Italy, TCR (in Ravenna) and SCT (in Salerno), and two Moroccan terminals: EGT and TAT (in Tangier). Mr Scalisi cites North Africa as a particularly active growing market. And the company’s international scope extends furthe: according to Mr Scalisi, all the main shipping companies in the world pass through La Spezia: “Connections range from the east coast of the United States to Australia via the Middle East and the coasts of North Africa. From La Spezia we can look at the entire globe.”
Mr Scalisi recognised that the company has faced and continues to face an element of adversity, along with much of the rest of the industry. “In this post-pandemic period, and with the current international situation, the global market is volatile and definitely struggling to settle down,” he said.
But he was also confident that the recovery of LSCT is stronger than its competitors, who must rely on the government National Recovery and Resilience programme, the PNRR, that followed Covid. “Other container terminals are growing mainly thanks to the help of PNRR funds,” Mr Scalisi said, “And by implementing a supply-chain verticalisation strategy which involves help from separate shipping companies. Nowadays, in Italy there are only a few terminals that are financially independent like ours.”
The general success and dominance of the terminal has had a direct impact on the surrounding area. A significant percentage of the GDP produced in the Liguria region is generated by LSCT ‘contributing to the economy of the entire territory’ according to Mr Scalisi.
The company is also dedicated to several local schemes. ‘Among the most important’ Mr Scalisi highlighted the Porto Lab, an initiative that involves all the comprehensive schools in the area, giving the opportunity to primary school children to come into direct contact with the running of the terminal. As he put it, the benefits of the scheme allow the next generation “to live it closely, observe it, understand it. Children represent the future, and we believe that the future passes through the eyes of a child.”
The future may well pass through the eyes of a child, but LSCT has a ‘very challenging’ development plan that aims to reach a capacity of about 2,000,000 TEU and a rail transport capacity of 50% by the end of 2024. ‘The terminal of the near future’ will be automated, and processes digitised, with the aim of a further growth in efficiency.
Mr Scalisi is optimistic about the future, locating it in the work of the company and the people who run it, all undercut by his ‘continuous improvement’ strategy. “Continuous improvement is not only aimed at business-related processes, but also, and above all, at our staff who represent the real asset of the terminal.” He concluded, “Through specific processes we identify and train talented people, to ensure managerial continuity as well as to comply with our founder’s motto: ‘A company is made out of people, and its success is due to them.’”
Situated in the Kvarner Gulf of Croatia, the Port of Rijeka is well connected to the Danube region and Central Europe. One of its greatest assets is its advantageous location and knowing how to use it. The port offers solutions for maritime traffic, port services and the storage of cargo. The history of the port stretches back centuries; it was first mentioned in written texts in 1281. These days, its focus is on expansion, growth and adaptability, and its longevity may be down to its intelligent use of resources. Duško Grabovac, President of the Management Board, explained more to Hannah Barnett.
ANadvantage of the Port of Rijeka, (and of North Adriatic ports in general), over those in the North Sea or Baltic is that they provide a short link between Europe and Asia. With that in mind, the Port of Rijeka has an exceptional geo-traffic position that it uses to its full advantage. “We are the closest and most cost-efficient transfer location for rail and road,” said Duško Grabovac, President of the Management Board at the Port of Rijeka. With 646 employees, the port is positioned across several sprawling sites and terminals. It is becoming better equipped and modernised with ongoing work. The draught depth is above 18m and allows
access to large ships. The depth will be increased to 20m with the construction of new facilities.
Mr Grabovac gave a clear impression of the scale and scope of activity: “Our port is capable of accepting any type of cargo. Others are more specialist. From the cattle terminal to the wood business unit, we can accept everything.”
The cattle terminal is situated in the Raša Port Basin and offers a multi-purpose site for reception and transhipment of live cattle, timber and bulk cargo. The sea depth along the wharf is eight metres. The maximum
annual capacity at the terminal is 600,000 tonnes and there are vets on hand to control cattle. It has berth facilities for two ships and storage facilities for approximately 1,000 head of large livestock.
The wood business unit, on the other hand, offers one-time storage capacity of timber between 35,000 and 50,000 cubic metres, depending on the type of timber. The unit has a sea depth of ten metres and a favourable climate for the drying of sawn timber.
These are just two of the wide range of services the port has to offer. Mr Grabovac was particularly enthusiastic about another arm of the operation. “One of the most
significant resources we have is the huge inland terminal,” he said. “It is a facility we use to our advantage. It is almost 500,000 square-metres, located in Škrljevo, about 10km from the Rijeka Basin and 3km from Bakar. And the terminal is one of our key advantages against our competitors.”
The terminal is certainly a major strategic asset for the port. Boasting eight modern warehouses, it is excellently equipped as a hinterland terminal and multipurpose logistics centre, intended for warehousing and handling containers and timber, plus general and bulk cargo.
Like much of the port’s facilities, the space is well connected to railway and highways and has six rail tracks with a total length of 3,500 metres.
Expansion continues at the port. Work is ongoing on the reconstruction of railway tracks and roads, as well as the communal infrastructure in the Rijeka basin. The goal of the project is to increase the efficiency of cargo handling and to enable better connectivity with the Trans-European Transport Network. The investment is worth €28.5 million, before tax.
Mr Grabovac emphasised the significance of this project: “We are in the full process of renewing the railways and road infrastructure in the Port of Rijeka. This is partly financed by European funds. We have finished our period of renovation of the infrastructure in Bakar and we are not far from the end of the same thing here in Rijeka. We will finish this process at the end of 2023, and then we will have really good, robust road infrastructure.”
Investment into the improvement of resources paid dividends for the company in 2022. “We had a very good first three
quarters,” Mr Grabovac said. “We increased cargo by 21%. We have had a very good year and that is a consequence of several things.
“We renewed our Refrigerated Cargo terminal so the frigo cargo increased. Silo also made very good results in the last year. Our maximum annual capacity of silo is 1 million tonnes. And the port has also had very good results for iron ore and coal in 2022.”
The road ahead
Looking ahead, Mr Grabovac was realistic that there are challenges facing the port, as for any other company any other company operating in the global market. He emphasised that maintaining strong part -
nerships with the port’s network of partners will be one way to safely navigate any approaching turbulence.
“Very unpredictable times are coming,” he reflected. “That is because we don’t know the price of the electricity, the price of fuel. There is so much inflation. These are the things that are problematic at the moment. But we are
working closely with our partners about how to face the future.”
The company has developed strong partnerships with clients and suppliers in order to establish a stable market position, in Croatia, as well as abroad. But Mr Grabovac was clear that more growth and investment is needed for the port to really flourish and reach its full potential.
He laid out his vision for the next few years: “After the current process of renovation, we need a serious investment into facilities. First of all, in Bakar, we need to invest in cranes, in forklifts, in other types of infrastructure. We have bought two new cranes and several forklifts, but we need more. More investment. That way we will be more competitive, and our performance will be better.”
The Port of Rijeka, while adept at using its strengths, is not a company which rests on its laurels. Instead, the port constantly strives for improvement, growth and development. n
The Port of Milford Haven is a leading UK port handling over 30 million tonnes of cargo annually. That’s not all though the bustling site in Pembrokeshire, South Wales provides expert solutions in marine renewables, freight and passenger ferry services, fisheries, leisure and retail. Commercial Director Steve Edwards and Tam Bardell, Energy Development Manager, described some of the most exciting enterprises the company is involved in. Report by Hannah Barnett.
Though the Port of Milford Haven was officially founded 65 years ago in 1958, the history of commerce and shipping in the Milford Haven waterway stretches back centuries. These days much of the focus at the port is dedicated to how it can contribute to a greener future. There are multiple sustainability initiatives on the go, set to benefit not only the port, but the wider Welsh community too.
Leading by example, the Milford Haven Waterway Future Energy Cluster wants to strengthen the UK’s energy independence. This is a local coalition of energy companies, renewable developers, green technology innovators, the council and the Port of Milford Haven. The initiative has set a low-carbon vision for the area by backing a South Wales Celtic Freeport bid and a South Wales Floating Offshore Wind proposition. One of the aims of the cluster is to help increase the region’s renewable energy capacity by 10 GW by 2030.
Steve Edwards, Commercial Director for the Port of Milford Haven, explained the main objective of the cluster: “I thought it was important that we galvanise a collaborative energy vision for the Haven. There is vast potential for marine renewables to
decarbonise not only the industrial sector across South Wales, but also the UK more generally. The launch of the cluster is a pivotal moment for us.”
Mr Edwards said he hopes the project will help the decarbonisation process of the region’s largest emitters through the South Wales Industrial Cluster. “You’ve got Tata Steel, Valero, RWE, all in South Wales. The port has been part of that industrial group from its early stages as well.”
As Mr Edwards acknowledged, the Port of Milford Haven is known as the UK's largest energy port. This is partly because the port has certain strategic advantages like the ability to handle vessels with draughts of up to 22 metres. It also has valuable proximity to Atlantic trade routes.
The port has transported LNG since 2009. Mr Edwards identified this as a ’significant milestone’ because the Port of Milford Haven now carries, on average, 20% of the UK’s LNG, serving the South Hook LNG and Dragon LNG companies.
To give a sense of the scale of activity, Mr Edwards added: “In 2020, Milford Haven transported around 65% of all the freight
passing through Welsh ports, 33.5 million tonnes. That’s dominated by LNG and oil cargoes. And in 2019, pre-Covid our twicedaily ferry service saw 327,000 passengers travel between Ireland and Milford Haven. We've already supported over 1,000 vessels into the Haven over the last nine months. I think these are extraordinary stats.”
It is no surprise that, as the UK’s largest energy port, the company was a significant player in the Milford Haven: Energy Kingdom Project, a £4.5 million initiative completed in 2022.
The project explored what a decarbonised local energy system could look like for the Milford Haven area and the potential of producing zero-carbon hydrogen alongside other renewables. Central to the project is a commitment to engage with the community and local industry, providing insight and opportunities for economic growth.
Tam Bardell is Energy Development Manager and played a key role in the project. He explained how it came about:
“We are the UK’s largest energy port and we have some very significant energy infrastructure here. We need to think about how it’s all going to be used to decarbonise and transi tion to a net-zero future in all energy vectors - heat, power and transport.
“The technology is already there to decarbonise, it’s more about creating market levers, investment and infrastructure to do so; That's what this project sets out to do, to explore how you create that seed demand for renewables and hydrogen, and how that will aid a larger scale transition to net-zero within the region. It's clearly established the vision to redefine the Port of Milford Haven as a hydrogen hub. It's also identified local investment propositions to catalyse the market.
“As part of the project, we demonstrated the world's first smart hydrogen hybrid heating system. That's an air-source heat pump paired with a boiler and smart con -
trols which can react to local conditions. We put a hydrogen boiler in and tested hydrogen combustion through the heating system. We believe we are the first in the world to do that with a hybrid system. We also put in a hydrogen-electrolyser and refueler right down in the front of Milford Waterfront, where we get a lot of footfall, including school visits. So, it’s really in the public’s eye there.”
The port had this world-class marine engineering recognised, along with its potential for further innovation, when it was awarded over £28 million in funding from the Swansea Bay City Deal in June 2021.
The funding is to create a base for decarbonised energy production and marine renewables like offshore wind, wave and tidal, all as part of the Pembroke Dock Marine project. It also provided a substantial upgrade to the port infrastructure, with £13m invested directly by the Port of Milford Haven.
The deal has been ‘ground-breaking’ Mr Edwards said: “Having the LNG facility, then this funding, not only secured our role in the energy system today but started to lay the groundwork for us becoming a major marine energy hub.”
The Swansea Bay City programme is expected to generate £73.5 million a year for the regional economy, across all of its nine recipients.
With so much sustainable activity already ongoing, a recent pledge by the Crown Estate to deliver a new leasing opportunity for floating offshore windfarms in the Celtic Sea provided an ideal opportunity for Milford Haven.
“We are the closest UK port to the Celtic Sea,” Mr Edwards said. “By 2050, we hope to have put more than 1,000 wind turbines there. There are estimates that the supply chain value of that could be upwards of £80 billion.”
Mr Bardell added: “We are looking at the supply chain’s capability to support new and emerging industries around the Celtic Sea. We’re involved in project mapping the
skills gaps here in the local community and thinking about how we can engage local people to move into the sector.”
Paving the way for a renewable future is evidently essential at the Port of Milford Haven. The company is conscious of its place in the wider community. In recognition of that, it recently won an award for its sustainability from the British Port Association.
Mr Edwards reflected on the wider significance of investing so much into sustainability: “We are at the beginning of introducing a brand-new sector of energy that can help deliver Wales’ ambitious net-zero plans. Under the energy cluster that we’ve now formed, I think our vision is the most exciting opportunity facing not only the port of Pembrokeshire, but also Wales.” n
by
With a total of 15 port locations around Lower Saxony, Niedersachsen Ports is the largest operator of public seaports in Germany. The future of energy security in Germany has moved into the centre of the public debate since the devastating war in Ukraine. Climate change is also forcing everyone to rethink energy supply in the long term.
Ports play an important role in the energy transition because they have always been important transhipment points for fuel sources. One goal of the energy transition is to increasingly replace fossil fuels with renewable energies.
For the seaports in Lower Saxony, the fields of action are determined by the import of energy, by optimising consumption, by supporting the expansion of renewable energies and by energy production in the port. These four fields of action offer diverse potential for the development of new energies and make a significant contribution to structural change through innovations, forward-looking investments and maintenance.
A full 70% of energy is now imported. The proportion will be at least as high in the future. Ports offer the ideal conditions for importing off-grid energy sources. One example is LNG (Liquified Natural Gas), which is considered an important bridging technology for the energy transition. Two ports –Wilhelmshaven and Stade – that are part of Niedersachsen Ports (NPorts) are in greater focus because of their favourable conditions for gas terminals. Starting from LNG, the feeders can later be used for other liquefied gases such as green hydrogen or ammonia. A new import infrastructure must be developed for this to work.
“NPorts is well prepared for these requirements,” explained Holger Banik, Managing Director of Niedersachsen Ports GmbH & Co KG and JadeWeserPort Realisations GmbH & Co KG. “With its existing infrastructure, the port of Wilhelmshaven is able to handle all future ships at short notice. Imported green energy sources in liquid or gaseous form can be made available from there via grids and storage facilities.”
Several import terminals for LNG and green energy sources are conceivable in Wilhelmshaven, in different areas of the port. This location in particular is regarded as a true energy hub, which is the
most obvious example of structural change. This gives Wilhelmshaven the opportunity to position itself as a leading location in Germany for new energies.
Wilhelmshaven proved to be the ideal site for a liquefied gas terminal, since a corresponding jetty was already present. The existing bridge has undergone a step-by-step refurbishment and is now efficient and ready for operation. After a mere 194 days, an LNG jetty was created here. Adding to the existing cargo handling facility, a docking platform and dolphins with rubbing paunches as well as mooring dolphins were constructed for the berth. This is the location where the FSRU, a Floating Storage and Regasification Unit, can be docked. This way, Wilhelmshaven will contribute to ensuring the energy supply for Germany. In the future, various gases will be handled, synthetic climate-neutral gases such as hydrogen and ammonia, as well as liquefied natural gas (LNG). These gases will be required in the transitional period - until complete climate neutrality is achieved.
At the port of Stade, after two years of intensive preparation, the application for approval for the construction of another liquefied gas feeder is approved. Construction of this jetty began in January 2023.
Alongside importing fuels, the energy transition also requires the correct handling of the necessary energy in ports. Ports are large consumers of power, so the energy requirement must be significantly reduced through efficiency measures. When less energy is used, less energy needs to be replaced with valuable renewables.
In addition, port consumers must become more electrified and use alternative fuels. Electric engines in particular offer the possibility of using energy most efficiently. NPorts is already implementing many different energy efficiency measures, including lighting, buildings and heat generation, plus working on constantly reducing its own CO2 footprint.
The vehicle fleet, handling equipment and ferries in the ports of Lower Saxony are also gradually being electrified. Shore power is available at selected points to power ships in port. The first alternative fuels were already available in ports in 2015. Emden and Cuxhaven were the first locations in Germany to bunker LNG. Various research projects are also dedicated to the efficient use of electricity and alternative energy supply in NPorts.
The locations of the port group Niedersachsen Ports are part of a supply chain for power generation components. This includes the produc tion and assembly of components for wind turbines (onshore and offshore). A wide variety of wind turbine parts are handled at almost all NPorts locations. The sites are also important for the maintenance and repair of offshore wind farms, especially Emden and Norddeich.
The Cuxhaven location is considered the German offshore industrial centre and has seen positive development in recent years. With its heavy-duty quays specially designed for efficient production and storage capacities, Cuxhaven is the hub of the German offshore industry.
The future prospects are also promising. Offshore wind power capacities will increase significantly to at least 30 GW in 2030, 40 GW in 2035 and 70 GW in 2045. For 2030 alone, this means the installation of 2,000 new wind turbines. The NPorts location in Cuxhaven is ready to react immediately to this development. The construction of the new offshore berths could start immediately.
NPorts’ locations offer ideal conditions for generating green energy. Electricity from wind and sun can be used directly or stored in the form of other energy sources if required.
At the Emden site, for example, large onshore wind turbines are in operation. Further potential can still be tapped in the future with small wind turbines. The solar potential is also great. The
first roof areas on NPorts buildings are already generating green electricity in the port. A solar park on NPorts sites is currently being planned in Emden.
Furthermore, hydrogen is playing an increasing role as an alternative energy source that can be obtained from green electricity. At different locations, the hydrogen issue is being approached with specific projects. Ports offer good conditions for this, because locally generated energy can be stored on site in the form of hydrogen. Ports are often landing points for offshore electricity. They are therefore ideal locations for the production of hydrogen. NPorts is currently supporting the planning and construction of hydrogen filling stations in Emden, Brake, Wilhelmshaven and Cuxhaven.
Favourable framework conditions are needed to ensure that ports play their role in the best possible way. The port company Niedersachsen Ports can make a variety of contributions through its many locations.
The first course has been set; the first steps have been taken. Nevertheless, NPorts are still at the very beginning of a social, market and technical transformation. In order to achieve the goals of the energy transition and security of supply, it needs suitable framework conditions. This applies in particular to ports and the social areas involved in the implementation of the energy transition in order to be able to set the course at an early stage.
“If the framework conditions are favourable,” concluded Mr Banik, “NPorts and its ports can make a significant contribution to this in the short term. This results in a wide range of opportunities from which not only our seaports but also our coastal region and the entire economy will benefit." n
seven seas, five oceans, one voice
chemgas shipping gpo heavylift dong fang offshore seatrek ld tide neptune lines varamar group landbridge ship management sunstone ships pyxis tankers capramar ship management rán offshore bayu maritim berkah naviera integral
With almost 60 years’ experience in the shipping industry, Chemgas Shipping is a market leader in the transportation of fully pressurised LPG. Manager of New Building and Projects Taco Terpstra spoke in-depth about the company’s latest investments – aiding its plans for expansion – and the importance of hardworking crews to the success of Chemgas, in conversation with Imogen Ward.
Chemgas Shipping has recently focused its sights on innovation and creativity. With a desire to impact prominently on the build process of its new ships, the company invested heavily into a New Building Programme.
“The reason we have created the New Building Department is partly due to the specialised nature of the gas shipping trade,” Manager of New Building and Projects Taco Terpstra said. “Diversifying
into this side of the business allows us to keep our knowledge within the company and gives us an opportunity to implement this expertise into our ships.
“Our cargo handling systems are also unique to us and by providing this in-house department we can ensure our products retain Chemgas’ standard of excellence.”
From the get-go Chemgas innovated the transportation of liquefied petroleum gas (LPG). Formed from a joint venture between
Van Ommeren and Vulcaan, Chemgas was established in 1965 as a specialist in the shipping of LPG along inland waterways.
With a history of firsts in the industry (including being the first tanker company to operate vessels with larger cargo tanks), Chemgas has created a reputation of reliability and upstanding values that are renowned across the globe.
Chemgas is constantly researching new ways to improve its vessels: In 2019, the company invested in three gas tankers that feature Van der Velden FLEX Tunnels. This installation ensures propellers are performing at peak capacity regardless of the depth of the ship’s draught. Gas tankers are typically heavier than other vessels and, therefore, require larger propellors. Due to this increase in size, the tankers need higher water levels to maintain optimal performance. With the retractable
FLEX Tunnels in use, Chemgas ensures its tankers continue to sail in the most cost-effective and efficient manner.
The topic of carbon emissions has been in the spotlight at Chemgas. In the next few years, the company is looking to phase out its older generation of inland waterway vessels. This will move the company away from using black fuel. As a result, Chemgas is currently in talks with a ship recycling company to work out the most environmentally and socially responsible way to decommission these ships.
Going forward, all Chemgas vessels will be retrofit-ready when the time comes to transfer over to fully-renewable fuel sources. Until then, the company is working hard to reduce fuel consumption on all vessels and will invest in clean engines.
Chemgas’ headquarters is based in Rotterdam, the maritime capital of The Netherlands, and its technical department is located between the busy ports of Rotterdam and Antwerp, making delivery of spare parts and ship maintenance more routine. This quick turn-around helps to minimise the
effects of global supply issues. Another challenge that is affecting the shipping industry is the shortage of qualified personnel:
“During Covid, I think a lot of people went into quiet retirement,” Mr Terpstra said. “Perhaps the understaffing is an even bigger threat to the economy than global supply issues.”
Thankfully, Chemgas has a long-standing relationship with all its employees: a bond that ensured the company did not suffer a loss of staff, or a reduction in chartering capabilities.
This long-standing relationship with our crews is what distinguishes us from our competitors “ “
90% of the 300 seafarers that charter with Chemgas are permanently employed by the company; on the topic Mr Terpstra explained: “This long-standing relationship with our crews is what distinguishes us from our competitors. These people have strong loyalty to Chemgas. We like to ensure the wellbeing of our employees, and part of that is to ensure they get a good salary package.”
Not only does Chemgas offer a warmhearted approach to all its crews, but the company also supports trainee workers to ensure their passion for sailing continues to thrive.
“What we are doing now,” Mr Terpstra said, “is approaching schools and universities to offer students apprenticeships and internships to introduce them to the industry. Even if they go on to work for one of our competitors, that’s fine; we are more than willing to team up with other companies to be more proactive approaching young people to promote sailing on a ship.”
Over the years, Chemgas has built a remarkable rapport with its suppliers. These relationships formed an organic supply chain that Chemgas is now looking to grow. With the implementation of its New Building Programme, the company is talking to shipyards and other suppliers in the hopes of creating an equal professional stewardship.
“Part of my responsibility as the Manager of New Building and Projects is to expand our network of designers and ship makers,” Mr Terpstra said. “In the past, we had one design office for multiple projects, which could create a bottleneck effect. So, I am working hard to expand that. I am also talking to shipyards, preselecting them based on various criteria including their capabilities, their engineering knowledge and their company culture.”
After such immense success, Chemgas’ plans for the future do not disappoint. The company’s main goal will result
in the acquisition of more vessels. Chemgas has purchased four LPG tankers from Gas and Heat in Italy. With two already acquired, and the final two being delivered by January 2023, Chemgas has successfully diversified its capabilities. Previously, the company led the way in fully-pressurised LPG vessels; the acquisition of these four semi-refrigerated ships will expand its product portfolio – to enable shipment of other industrial gases.
Chemgas’ exciting plans do not stop there. “Next year, we are expecting the delivery of a third new build tanker,” Mr Terpstra said, “which is the final ship in a trilogy of new builds that we invested in. Parallel to that, we are already planning our next new build. Despite market circumstances – which look challenging –we have confidence in the future and are supported herein by the vision and longterm commitment of our General Director and Owner Dr Gunther Jaegers.”
We plan to continue investing in new ships, especially ones that have more luxurious accommodation for our crew members; their welfare is extremely important to us “ “
T hese LPG tankers comply with the latest emission restrictions and aid the company’s goals of CO2 reduction. The incorporation of this engine type will also make future transition to other renewable fuels smoother for the company.
As part of this investment, Chemgas has been heavily involved in the design and build of these vessels via its New Building Programme. Following the success of these new builds, the company plans to develop this programme further
with the building of new inland waterways tankers.
Pushing forward, Chemgas aims to continue its path as a market leader of the shipping industry. “Of course, we would like to retain our market share,” Mr Terpstra concluded. “We plan to continue investing in new ships, especially ones that have more luxurious accommodation for our crew members; their welfare is extremely important to us.
“We wish to diversify into shipping different kinds of products, making us more appealing to our customers. We will also continue to look for appropriate fuel alternatives and approach our clients for their opinions on this. We really believe that renewable energy is the way forward, and we want our clients to know this. Now is the time to act.”
Founded in 2014, Norway’s GPO Heavylift manages a fleet of bespoke, semi-submersible heavy lift vessels. The company specialises in carrying massive cargo loads across oceans to all corners of the globe. It is a difficult and specialised job requiring specialist people, specialised skills and, of course, a fleet of capable vessels. CEO Dagfinn Thorsen spoke to Richard Hagan about what it takes to carry the cargo that nobody else can.
When it’s time to move very large cargo across an ocean, you need GPO Heavylift and its fleet of custom-designed, semi-submersible heavy lift ships.
The company was established in 2014 by a group of Singaporean investors with experience in the offshore category. That same year, GPO Heavylift commenced the construction of its four bespoke semisubmersible heavy lift vessels. The fleet
was specially designed by CEO Dagfinn Thorsen, together with a captain who is a long-time colleague, to suit the company’s specific needs.
Mr Thorsen, a 40-year veteran of the maritime industry, immediately established the commercial viability of the new ships when he secured a transport contract for the first vessel even before any steel was cut. “The contract was to move an Aibel platform to the Johan Sverdrup Phase 2 project
owned by Equinor, from Thailand to Norway,” he recalled. “They required the same service again two years later and, based on our successful completion of the first one, we were awarded that contract, too.”
The four vessels were delivered starting with the first vessel in July 2017, while the second arrived in March 2018. The third was delivered in December 2019 and the fourth and final one was completed in October 2021. The fleet has the distinction of being the only four purpose-built semi-submersible vessels of equal design presently in operation in the world.
G PO Heavylift’s facilities span three sites and about fifteen staff. Its Singaporean office is responsible for the company’s financial administration, while its office in Oslo - with about six staff - is focused
on chartering, engineering and operation. Technical Management and crewing are handled by Wilhelmsen Ship Management - also in Oslo, Norway.
Within its staff complement, GPO Heavylift boasts three highly experienced loadmasters with decades of combined experience. The loadmasters are responsible for travelling to the ships and supervising the loading and discharge operations.
Mr Thorsen recalled how the pandemic and all its travel restrictions had forced the company to find new ways of conducting its business, particularly in the loading process. “We learned to do remote loading supervision. We even brought a company in to install video cameras both on the ship and on the quayside so that we could watch the loading operation from anywhere. We managed to conduct a loadout with people sitting in different places around the world,
communicating remotely with the on-site crew and the yard. That was a new experience that we’d do again, but only if need be!”
The CEO highlighted the fact that while the amount of work that goes into the loading process would surprise many casual observers, the first thing that often catches inexperienced people by surprise is a semi-submersible vessel’s operation in preparation for loading. “Some people are relatively surprised when they see the vessel begin submerging. We’ve even seen people ring the alarm system because they think that the ship is sinking!” he said with a chuckle.
With the typical understatement of a seasoned professional, Mr Thorsen described the process of loading 25,00030,000 tonne cargo as, “interesting,”
adding: “Each and every project we’re involved with is different from previous projects. Even when you’re loading the same cargo at the same place, it’s still treated as totally new, every time.”
Given the massive size of some of the cargo being loaded on to GPO Heavylift’s vessels, preparation and constant attention to the smallest detail is absolutely imperative. “You have to begin by preparing the ship to receive the cargo,” Mr Thorsen explained. “This involves going through all of the drawings of the cargo and ensuring that the information therein is all correct. That said, these days it’s a bit easier because we’re able to request photos of the cargo ahead of time, to verify our preparations correctly.”
The next step is a big one and it involves preparing the GPO Heavylift vessel’s deck to receive the load. “We fit timber cribbing to the main deck in a pre-designed pattern so that it lines up with the bottom structure of the cargo. We have to land the cargo directly on top of the cribbing. There’s absolutely no room for error here because the positional tolerance is relatively small – normally not more than +/- 5cm.”
To further ensure precision and security of the cargo, two massive guideposts are also welded to the vessel’s deck. These help to guide the cargo into exact position and to hold it in place.
“Once we see that the cargo is in position, we de-ballast the vessel and begin the lifting process. This can be quite challenging and very specific ballasting procedures have to be prepared in advance,” Mr Thorsen emphasised.
GPO Heavylift undertakes, on average, four to six transport jobs per ship per year. The shipment durations necessarily vary depending on complexity and length. Larger loads - for example a drilling rig - are too big for transiting canals and must be carried across the oceans, adding to the contract duration. But as Mr Thorsen highlighted, the versatility and safety of a heavy lift transit are proving to be irresistible for an increasing number of customers.
“There aren’t too many alternative means to carry the loads that we transport,” the CEO noted. “But it depends on the project.
For example, if a drilling rig needs to be transported across the open sea for more than five or seven days, then there aren’t too many options. Jackup rigs don’t have any alternatives to heavy lift, but selfpropelled rigs can sail by their own power Still, some companies prefer a dry tow (on the deck of a heavy lift vessel) because it’s safe and fast and they can save some money on insurance and crew. But all in all, almost everybody prefers to use a heavy lift vessel nowadays.”
GPO Heavylift’s managed fleet, namely GPO Grace, GPO Amethyst, GPO Sapphire and GPO Emerald, are identical in specification and feature an impressive length of 225m and a breadth of 48m. Of that, 183m of their length is available for loading, as is the complete breadth of 48m. All four vessels weigh in at 64,000 tonnes dwt and can submerge to a depth of 15 metres water above the deck.
The vessels feature fully redundant propulsion systems consisting of four 8,000 kW engines, as well as two 1,750 kW bow thrusters and two 1,000 kW stern thrusters. The vessels are also equipped with a DP2 dynamic positioning system
Of course, the fleet’s cargo lifting capacity is the centre of attention, and those numbers are impressive to say the very least. The fleet can lift Jackup rigs of up to 35,000 tonnes, and semi drilling rigs of up to 40,000 tonnes. A non-floating module of up to 25,000 tonnes can alternatively be carried, as can a spar-buoy.
Mr Thorsen pointed to the identicality of the company’s fleet as a major selling point for larger projects. “Serious clients like the fact that our setup features four identical vessels. Our fleet is fast, they feature strong decks and reliable machinery matched to a unique ballast system. They’re much more versatile than most of the competition.”
Looking into his metaphorical crystal ball, the CEO was justifiably optimistic about the company’s prospects. “The offshore wind energy business has really taken off, so it’s become an increasingly interesting market for our vessels. In fact, all four vessels will be busy in offshore wind
throughout summer 2023, carrying cargo from Europe to the US East coast, sailing back and forth a few times
“It’s such an active market that I hope to build more identical vessels,” he continued “We’re discussing with the vessels’ owner the possibility to build more vessels and hope we can proceed in due course.”
He concluded with some remarks about the business. “I’ve spent all my life in this industry; I like it so much that I work basically every day including weekends and public holidays. And I love my staff - I have really good people working here in GPO. I follow the ships online every day. The job is a huge part of my daily life.” n
Dong Fang Offshore has aided the offshore wind industry in Taiwan, with an impressive and diverse fleet since its establishment in 2019. The company has reached some impressive milestones over the past few years, including its acquisition of the Orient Adventurer –soon to be Taiwan’s first cable laying vessel (CLV). Chief Operating Officer Ben Darrington discussed this achievement and the company’s next steps, in conversation with Imogen Ward.
Dong Fang Offshore maintains exceptional standards within ship management. Based in Taiwan, the company follows the highest industry specifications to ensure the safety of its crews. “What really sets us apart from our competition,”
Chief Operating Officer Ben Darrington said, “is our willingness to embrace international industry standards. We incorporate these principles wherever we can to deliver a high-quality service in a market that is very remote from the usual supply chain for offshore wind.”
As a thriving subsidiary of Hung Hua Construction Group, Dong Fang Offshore continues to make history in the Taiwanese offshore wind industry. The company began operating in 2019 with an impressive fleet of CTVs (all manufactured at Damen). Since then, the fleet expanded and diversified to meet the needs of the wind farm industry.
Several key areas of the renewables sector are supported by the c ompany, including commissioning and surveyance activities, operations and maintenance (general upkeep and repair work), and the installation of offshore cables and foundations.
After being established for the support of the wind industry, Dong Fang Offshore made the conscious decision to improve its sustain -
able practices. The company’s strong love for the sea inspired it to remove single-use plastics from all its ships. This action helped contribute to a reduction of plastic in the ocean.
As a further homage to the renewable energy sector, the company actively acquires clean vessels that do not emit harmful waste into the water.
The use of renewable power sources for its fleet is also on the cards at Dong Fang Offshore (it is currently considering implementing batteries as a short-term bid to improve sustainability).
The fleet currently consists of 12 youthful vessels, that helped
the company gain several impressive accolades: Dong Fang Offshore is currently the largest owner and operator of CSVs and CTVs in Taiwan.
On top of this impressive accomplishment, the company is also adapting its latest acquisition (the Orient Adventurer) into Taiwan’s first CLV. This conversion should be completed by the middle of 2024.
In Dong Fang Offshore’s portfolio are five modern CTVs that aid the wind farm industry in the transportation of personnel and components. These vessels carry up to 20 tonnes of cargo on an impressive 90 square metre deck. The majority of these CTVs are Damen-built FCS 2710, providing extra space and an independent suspension system in every seat (dampening the impact of rough seas) for optimal comfort.
“Our CTVs are busy throughout the summer, and increasingly throughout the winter too,” Mr Darrington said. “This is because our customers recognise the CTVs ability to achieve high productivity in the colder months. Our vessels can work through difficult weather conditions due to the quality of parts and equipment we order in from our European contractors.”
Three AHTS vessels are a vital element of Dong Fang Offshore’s fleet. These tugs are used for towing barges and structures, providing surveyance and offering guard services to the offshore industry too. Each vessel is manned with over 20 experienced crew members to always ensure smooth operations.
The last vessel in the line-up is the Orient Constructor, a CSV that specialises in geotechnical surveyance and is designed for use as a walk to work vessel. “We purchased the Orient Constructor in 2021,” Mr Darrington said, “and it is our first construction support vessel. This was a huge milestone for Dong Fang Offshore.”
More recently, Dong Fang Offshore relied on the support of its outstanding suppliers. The company holds these relationships in the same regard as its customers – they are equally important to the continuation of the business.
“Our suppliers are key to our success,” Mr Darrington explained. “We regard them as partners. So, it is very important that we can continue working with these suppliers to create and deliver projects that are a success. We need the support of our suppliers, not just for equipment, but also as subcontractors; to help solve problems, to deliver solutions in a difficult and remote market, and to ensure the completion of projects.”
To nurture these relationships, Dong Fang Offshore is also committed to supportive structures, including long term partnership agreements, enabling the companies to work side-by-side in the exploration of potential business opportunities. Dong Fang Offshore also encourages its suppliers to keep more products in stock (to minimise the effects of the global supply issues and ensure the company continues working with the highest standard of products).
One relationship that the company has developed is with Damen – a reputable shipyard based in the Netherlands – providing high-specification newbuild CTV vessels to Dong Fang Offshore.
Dong Fang Offshore has exciting prospects lined up for the future, planning to further expand its fast-developing fleet.
“Expansion is our focus,” Mr Darrington said. “We also aim to expand into other countries in the region. These would include Japan, Korea, Vietnam and Australia. Currently, offshore wind is quite a limited industry in these countries. They do, however, have a lot of potential. So, we would be extremely interested in expanding outside of the region of Taiwan and into the greater Pacific Ocean.”
To achieve these goals, the company will continue providing luxurious and modern vessels for the offshore wind industry –offering the best support for the maintenance of wind turbines.
“We are very excited to continue offering our customers the best engineered solutions,” Mr Darrington concluded. “Owning the first support vessel and CLV under the Taiwan flag, we continue to grow and expand our repertoire, pushing ourselves to perform and deliver a renowned standard of service. Through our hard work and dedication, we are accelerating the development of the offshore wind industry and delivering clean and sustainable energy to the Taiwanese community.” n
Seatrek is a leading dry bulk carrier and vessel owner in the marine shipping industry. With over 20 years’ experience, the company serves more than 100 destinations. Founder and Managing Director, Asifur Chowdhury is an expert when it comes to the shipping industry. He discussed Seatrek’s extensive history and his hopes for the future in conversation with Phil Nicholls and Imogen Ward.
Asifur Chowdhury’s hard work and experience, Seatrek began in 1999 Originally working for Atlas, his father’s first ship-owing company in Bangladesh, Mr Chowdhury decided to create his own business venture in Singapore.
He maintained a strong connection to his Bangladeshi roots, working closely with several clients within the country as well. Employee numbers at Seatrek at one point sat at 40 in a total of six offices spanning the globe.
Boasting a range of 200-350 operational vessels per year pre-Covid, the company continued to expand its fleet with the addition of three new tankers in 2018. Diversifying its range meant Seatrek was able to enter the tanker market and expand its reach in the shipping industry. However, out of concern for crew safety as well as adverse effects commercially, these numbers were scaled back during the pandemic.
Due to his experience at Atlas and expertise in inland riverine barging experience in Bangladesh, Mr Chowdhury secured several c ontracts with major cement manufacturing companies including Holcim, Cemex, Lafarge and Heidelberge.
Holding a long and prosperous relationship, Holcim and Seatrek’s history began with Holcim’s desire to invest into Bangladesh’s markets, providing its services to the country via Seatrek’s ocean transportation and barging services to Holcim’s cement manufacturing plant. This relationship continued to grow as Seatrek secured its first COA with Holcim. Seatrek also developed a similar partnership with Cemex and as a result, a two-year contract was agreed by the two companies to move cement between Thailand and Bangladesh as the first COA with Cemex.
When Cemex wished to expand export out of their APO Cement plant in Cebu, Philippines, Seatrek confidently applied
its previous experience to the contract.
“They had never exported before,” Asifur Chowdhury, Founder and Managing Director of Seatrek said, “so we used our expertise to start the exportation process.
“We actually used the same process that we had previously implemented in Chittagong, which meant we were able to successfully export the cement clinker out of Cebu.”
Mr Chowdhury felt his extensive experience within the shipping industry helped to secure these contracts. His knowledge of Bangladesh was also a crucial aid to Holcim and Cemex’s investment plans.
Seatrek has also completed several joint ventures with Lafarge, chartering and operating vessels for Lafarge’s third-party trades. Focusing again on Bangladesh, Lafarge wanted to expand its market presence within the country.
To penetrate this market, Lafarge felt the need to take a risk and set its clinker prices competitively. Seatrek very nobly offered to offset this risk by investing as a joint-venture scheme. This allowed both companies to share the outcome of the venture – whether the results were positive or not.
Another appeal of choosing to charter with Seatrek is its CQD (Customary Quick Despatch) service. This gives charterers added security when calculating loading and discharging rates which could lead to potential demurrages exposure to charterers. Seatrek has ensured that as shipowners, the charterers would not have to pay demurrage due to Seatrek’s CQD service.
The company’s close relationship with clients is vital to both current and potential future customers, according to Mr Chowdhury: “We have a direct relationship with our clients. That means whenever they have an issue, they can come straight to us.”
The chance to create this kind of relationship exclusively with Holcim Trading occurred in 2000. As the only shipping company trusted to work with Holcim without a shipbroker, Mr Chowdhury felt that this opportunity contributed greatly to Seatrek’s overall success. This relationship continued for 16 years until Holcim and Lafarge merged.
After overcoming challenges relating to the current economic climate, Mr Chowdhury is positive about the future of Seatrek. The company is currently working towards a focus on long-term chartering. Seatrek plans to take on contracts with a minimum of five years’ duration, freeing up time and money for other projects.
One of the projects Mr Chowdhury hopes to complete includes building special barges for Bangladesh. Due to the presence of mangrove swamps, these barges must be custommade. This is to ensure that no dust or debris affects these delicate swamp ecosystems. This customisation, therefore, requires a larger dedication of time and money.
The commitment to longer charters will also allow Mr Chowdhury to focus his attention on more humanitarian efforts outside of shipping.
Asifur Chowdhury Managing Director
A major health scare led Mr Chowdhury to feel inspired to give something back to the world. Focusing on several projects, the Founder of Seatrek has set out a plan to dedicate time and money to charitable acts.
Green ship recycling – a method of safely dismantling and disposing of an old ship –is an EU compliance not currently available in the India sub-continent, including Bangladesh. Mr Chowdhury has committed to working with Bangladesh in an attempt to install EU regulations compliance into the country’s scrapyards. The fundamental aim of the project is to reduce harmful waste from decommissioned vessels. This extraordinary accomplishment will mean higher safety standards for all workers within the yards as well as recycling the scrap materials in a green manner.
As an avid food enthusiast, Mr Chowdhury has also invested into Singaporean vertical farming, offering his advice to the business. This has also given him the opportunity to learn more about this innovative way of farming: “I was very impressed,” he said, “the difference between vertical farming and the greenhouse optimisation is very good. It’s completely organic. I was not even aware of the incredible tech that it uses.”
Furthering this exploration into the food and beverage industry, Mr Chowdhury hopes to commit more time to his restaurant. He established his fine dining Spanish restaurant, Binomio, ten years ago to bring the tastes of Spain closer to home.
One of his philanthropic endeavours is his scholarship fund for Bangladeshi students from poor economic backgrounds. This feat will enable these students to go to school and gives them better future prospects. Mr Chowdhury also started an initiative which empowers young women with sewing skills, thereby creating employment opportunities in the country’s garments industry.
Finally, Mr Chowdhury is also invested in keeping young people’s dreams alive. He plans to conceptualise final year projects into reality and reward the creators with 70% free equity of the business. By doing this, he hopes to set the students up with a financial support system and grant them vital experience in the industry.
“Once they graduate and look for jobs,” Mr Chowdhury said, “their dreams often fade away. We want to find those students and see whether we can conceptualise those dreams.” n
LD Tide is a joint venture between the French-owned Louis Dreyfus Armateurs (LDA) and the British-run Tidal Transit. The former has almost 170 years of experience in various maritime solutions, recently expanding into renewables. The latter offers transit services for the marine industry and is recognised as a specialist in offshore power. Gaël Cailleaux is Managing Director for Renewables at LDA, and Leo Hambro is Commercial Director at Tidal Transit. They explained to Hannah Barnett how LD Tide is putting the wind in the sails of the offshore industry.
Situated off the coast of Brittany, the Saint-Nazaire wind farm is set to supply approximately 20% of the domestic electricity consumption of the Loire-Atlantique region for the next 25 years. Following an international call for tenders, developer Eolien Maritime France (EDF-RE & Enbridge) and GE contracted LD Tide to produce three innovative Crew Transfer Vessels (CTVs) for the farm. They will transfer technicians between the coast and the farm for maintenance of the electrical substation and of the wind turbines in their operating phase.
Though LD Tide is an Anglo-Franco endeavour, it is also fundamentally French. “We managed to have a French design and a French shipyard to deliver the boat,” said Gaël Cailleaux, LDA’s Managing Director for Renewables.
The CTVs sail under the French flag and their innovative design was entrusted to Mauric, a naval architecture firm based in Nantes.
Construction was carried out by French shipyard OCEA, a market leader in the production of aluminium ships.
Mr Cailleaux said that this regional focus was beneficial in securing the bid: “We had a plan to develop activities locally. All our crew are from the area. We’ve managed to do that because we’ve secured long-term contracts of more than five years. That gives us visibility. We said if we have a long contract, we can commit to develop local activities with local people. And that is what we did. We have an integrated innovation and engineering team within LDA who worked closely with the ship designer and shipyard.”
One of the strengths of the LD Tide project has been the tools brought to the table by both sides of the venture.
“We felt that our experience in renewables in the small boat market would help bring LDA further into this industry,” said Leo Hambro, Commercial Director at Tidal Transit. “And then it
started to gel, we had some really fruitful conversations about our experience. Tidal Transit has predominantly worked with Equinor, RWE and Siemens. We have excellent coverage of the market in terms of existing contracts.”
Similarly, LDA subsidiary Louis Dreyfus TravOcean, which specialises in cable trenching, was able to contribute expert knowledge at the production stage.
“They’ve developed an innovative solution for the Saint-Nazaire wind farm,” Mr Cailleaux said. “The sides were too rough for jetting or mechanical trenching, so we laid the cable with mechanical protection. We provided this alternative solution and delivered the project earlier this year, ahead of schedule. It’s a great success. We’ve gained the confidence of new customers with our capability to provide them with pioneering, cost-effective solutions. This is how we’ve entered the renewables market as EPCI contractor, after many years of operating as trenching services provider.”
Operating the Saint-Nazaire wind farm are some of the world’s biggest energy firms. One CTV vessel is contracted to French-based
energy conglomerate EDF, the other two by GE. According to Mr Cailleaux, they proved very valuable clients: “Both have been very supportive and assertive on some of the features of the vessel. They were thorough about quality and performance. They’ve also offered long-term contracts, which allowed us to take risks on the design.”
And there is plenty about the CTVs design that is cutting-edge. Mr Hambro explained that LD Tide vessels are ‘not a standard commoditised CTV design’, but something that reflects years of experience in the market.
“At Tidal Transit we’ve had MAN engines in our in our boats since we started,” Mr Hambro said. “We’ve even gone out and bought second-hand boats because they had MAN engines in them. We wanted to make sure that the CTVs continued to use MAN engines because they have been bulletproof for us; not only reliable but extremely efficient.
“These boats are diesel hybrids with options to further decarbonise when the availability and density of batteries increases. But they already have the ability to charge the battery.”
As well as considering its long-term sustainability, LD Tide is also taking the immediate environment of the CTVs into account.
“We’re dealing with the Bay of Biscay, which is not the nicest of places to have to sail every day,” Mr Hambro explained. “The weather conditions are much rougher than the coastal environ -
ments in the North Sea. We've had to build something that's stronger, more capable than other CTVs in the market. So that's why we've gone for a tank of a model. And to make the tank efficient, we have the hybrid engine and the Foil Optimisation and Stability System which is a key part of the Mauric design. This increases not only comfort for passengers, but also the efficiency of the vessel.”
Being adaptable has proved a key element in the LD Tide venture. “Our business in the UK uses fixed pitch propellers and water jets,” Mr Hambro said; “Whereas going into the French market and the Bay of Biscay, we've looked into Controllable Pitch Propellors (CPPs). We've combined the best engines with the most advanced CPP system and made life a bit more complicated for ourselves, rather than using the more standard fixed pitch propulsion systems.”
Both Mr Cailleaux and Mr Hambro were excited about the future of the industry, and LD Tide’s place within it.
“Every time I open a paper, I see something about offshore wind,” Mr Hambro said. “We're selling shovels into a market that produces the real goods. The potential for growth in the vessel sector is enormous. There are about 320 CTVs in the market, with the projection of getting to 550 by 2035. And by 2050 they're talking about 800 or so.”
This is a very exiting environment for innovation, Mr Cailleaux added: “We have an electric hybrid solution ready to go, and a more advanced design to push further the operating limits. The hull, the material, the propulsion, the fuel (Methanol or Hydrogen), all aspects of these vessels are innovative. This is the future. By providing these types of solutions, we hope to convince the customer that the extra pennies they pay now will be a solid foundation to save on future operations and their CO2 emissions.”
As this is also an initiative that began at the start of the Covid pandemic, it does not seem too extreme to suggest the sky is now the limit for LD Tide.
“During the first lockdown we managed to win tenders with GE and EDF for 12- and five-year charters respectively,” Mr Hambro recalled. “We managed to negotiate with the shipyard, get the design work agreed with the naval architects and the clients, and get the money together to start delivering. It’s been a phenomenal couple of years. If we can endure what we have endured, then I’m very excited about the potential of what we can achieve in this market.”
Neptune Lines has over 45 years of experience as a leading finished vehicle logistics provider. The family-owned business has been offering transportation and shipping solutions to manufacturers and shippers of cars since 1975. Chief Operating Officer Nikos Paterakis discussed the company’s operation with Hannah Barnett.
The name alludes to the Roman God of the Sea, so it is no surprise that Neptune Lines has a strong and long-term presence in the maritime industry. The company boasts more than 500 employees, offering short sea transportation solutions of cars, plus high and heavy cargo. Operations are focused on the Mediterranean, north europe, the Black Sea and recently the Far East, and the company currently operates 21 vessels, 19 of which it owns, with an aggregate capacity of 75,000 units. Neptune Lines has some of the world’s largest automobile manufacturers among its clientele.
Chief Operating Officer, Nikos Paterakis, described how the company grew into a major player within the industry from the small seed of an idea: “This was due to the foresight and hard work of its founder, Nikos Travlos: ‘All you need is a vision and the willpower to make it happen,’ he used to say. Mr Travlos put all the different market parameters together and the result was an agile, very customer-centric, focused company that never deviated from its course.”
The clear thinking and deep insight of Nikos Travlos brought Neptune Lines to where it is today. Starting as a cargo and shiphandling services business, it was his idea for the company to begin transporting automobiles in 1986. This intuition proved highly valuable, as by the 1990’s Neptune Lines was enjoying the recognition of leading car manufacturers.
In 1992, the Greek government provided incentives for the car industry to replace old cars with newer ones including catalytic converters, and Neptune Lines was able to capitalise. With boosted car sales and a subsequent increase in the maritime transportation of them, the company acquired two more vessel s to meet the demand.
In a practical sense, Neptune Lines’ later success was due to focusing on short sea trades in the Mediterranean, and according to Mr Paterakis, “an early reaction to the warning signs of costs rising, which was effectively tackled by building bigger vessels.”
Displaying profitable insight yet again, and irrespective of the stormy market conditions that followed the 2008 financial crisis, Neptune Lines embarked on a sizeable newbuild program in 2010. Doubling its carrying capacity proved a successful gamble, as the company was able to capitalise on the subsequent increase in new cargo volumes that new contracts brought.
The company’s activities start at sea but do not end there: Neptune Lines cooperates with a well-established and extensive agency network, ensuring quality service and smooth operations. As Mr Paterakis explained, understanding the needs of the automotive industry is crucial when forming an integral par t of the downstream supply chain.
Theshipping ofindustryrepresentssome3% globalCO2emissionsand thereisalwaysspace forimprovement “ “
Oceantransportationhasthe lowestCO2emissionsperthanvehicle-transported-kilometre transportation.anyotherformofvehicle
All these years of experience accrued in automotive logistics go hand in hand with the company’s responsible stance and long-time focus on sustainability – a challenge it is seizing head-on.
“We have an exigent responsibility to positively impact emissions in our sector while improving governance and societal aspects related to our business,” Mr Paterakis said. “Ocean transportation has the lowest CO2 emissions per-vehicle-transported-kilometre than any other form of vehicle transportation. The shipping industry represents some 3% of global CO2 emissions and there is always space for improvement. We have several projects running that look at alternative fuels, emission capture a nd storage systems that we hope can feature in the next gener ation of new vessel orders when that time comes.”
Digitalisation will play a significant role in Neptune Line’s efforts to monitor and analyse emissions data which now more than ever has become a crucial factor for managing the vessels in an efficient manner. Our energy efficiency
and data performance inhouse team is currently implementing solutions which will drive the reduction of our emissions towards 2030.
Protecting the environment remains at the core of company’s focus. To further reduce emissions and operate with energy efficiency, Neptune Lines company has in place various environmental performance measures – technical and operational - as applicable for each vessel's type (i.e. design, specifications, machinery and equipment). This programme has resulted in a 6.8% decrease in CO2 emission since 2010 and a 13.09% decrease in energy use onboard and at company premises since 2011.
The first ‘Eco-Design’ vessels were introduced in 2014. Built at the Hyundai Mipo Dockyard, the ships were fully equipped with the latest propulsion and environmental technologies. Maintaining focus on environmental compliance and innovation, in the years that followed, the Company completed the installation of hybrid-ready scrubber technology for most of its vessels. Currently, as Mr Paterakis said, “there are several promising projects under study for the reduction of its carbon footprint using alternative fuels and through the technical enhancements of the fleet.”
The company is certainly looking ahead to the demands of future generations. It proudly runs a Cadet Training Programme, currently employing at least two or three cadets on each ship, striving to achieve a balanced overall ratio of men and women
across all fleets. The cadets are trained on board its vessels, becoming the next generation of skilled seafarers.
Recent high inflation across Europe has heralded challenges , and like most industries, Neptune Lines was impacted by disruptions in the global supply chain. “We have experienced peaks and troughs of volume flows we have not encountered for some time,” said Mr Paterakis. “This creates a high degree of inefficiency in outbound supply chains, causing tremendous pressure on our capacity planning and resulting in overall poor asset utilisation.”
Turbulent resulting though the environment may sometimes be, Mr Paterakis is confident that Neptune Lines has overcome recent adversity for the better. Communication, he said, remained crucial: “We are in good dialogue with our customers to adjust trading conditions together and ensure we not only perform in the short to mid-term, but are also able to invest in a new and more environmentally efficient capacity for the future.”
It is a rapidly changing world, but as Neptune Lines continues to grow and adapt there is little doubt that its place in the industry is firmly secured. As Mr Paterakis said, while the need for mobility continues to grow, so will the demand for Neptune Lines: “The world’s population has a rising middle class, societies are developing at a fast pace and prosperity is increasing like we have never seen. Mobility, and therefore vehicles, being a key feature in that development makes us very confident that distribution of those vehicles will be needed for many generations to come.” n
Thanks to visionary leadership and a flexible business strategy, Varamar Group has enjoyed constant growth, with its Canadian office being the latest fruit of its hard work. But while its new office in Vancouver joins Varamar’s impressive and expanding global network of offices, the company hasn’t lost sight of the boutique-style service that continues to drive its success. Varamar Canada’s Director, Andrii Bondarenko, gave Richard Hagan an insight into the company’s unique customer service approach.
Varamar Group is an international project cargo carrier, specialising in the worldwide shipping of project, heavylift and breakbulk cargo. Alexander Varvarenko established the company in 2009 in Odesa, Ukraine, in a small office staffed by four people.
Varamar’s initial efforts revolved around a small trade of projects from the Black Sea to the Persian Gulf, a route which remains popular to this day. But the business got a major boost when Mr Varvarenko signed a contract to deliver equipment on a monthly basis from Romania to South Korea. Varamar’s handling of those relationships and this route proved to be so successful that the company has now established its Europe to Asia route as its backbone, ‘bread and butter’ business.
A dominant European network
Today, Varamar’s network of offices spans several countries and regions, with facilities in Vancouver, Hamburg, Genoa, Antwerp,
Shanghai, Ukraine and others. A Houston office is planned for opening in late 2023.
Before Feb 2022, Varamar’s operational headquarters was in Odessa, with the commercial headquarters situated in Antwerp. But due to the ongoing conflict in Ukraine, Varamar has had to react, protecting not only its business, but most importantly, its people.
“We had over 50 people in Odessa. When the invasion happened, our group organised transportation, and moved the Ukrainian staff and their families to other offices worldwide – mostly in Europe,” explained Varamar’s Director Andrii Bondarenko.
“It was a very hectic seven days when all of the moving started happening. But this highlights the company’s respect and support towards the staff we cherish. We try to keep the company mid-size specifically to maintain that personal relationship; we know the names of our staff’s families, which is important to us.”
Varamar offers its customers what it describes as boutique-style customer service and as Mr Bondarenko pointed out, it’s all about putting the customer’s specific needs first.
“I believe that it’s easy to sell freight but it’s difficult to sell ocean transportation solutions as we do,” he said. “For example, if you go to a very large shipping company, you’ll find that they are very qualified, experienced and smart, but they don’t have time to spend on customer service;
to talk with the customer and really understand how best to solve his problem.
“When customers come to Varamar, they receive a tailor-made solution,” he added. The company prides itself on its ability to find creative, cost-saving solutions to customers’ shipping needs. This may, for
example, involve using its fleet of shallowdraught vessels to collect or deliver cargo closer to its source/destination by navigating rivers or small ports that larger ships can’t reach, thus reducing the customer’s overall transport and insurance costs by eliminating road or rail transportation legs between major nodes.
“By learning where exactly the cargo is going to or coming from, you can solve the customer’s transportation needs at a lower cost,” Mr Bondarenko reiterated. “It’s eyeopening for the customer. This is what our boutique service is all about.”
all
Varamar’s highly flexible fleet arrangements are a key foundation of the company’s trademark flexibility in delivering customercentric solutions.
Its fleet will have grown to 20 by the end of 2022. All of these vessels are either on long-term charter to Varamar or under its commercial management. “This is a fleet size that we are comfortable in our ability to handle very well,” Mr Bondarenko noted.
The company’s approach to strategic growth is building a perfect mix between a time-chartered, commercially managed and, in the future, owned fleet. This mix should enable Varamar to remain flexible in the service offered to clients, as well as
on pricing. On the other hand, it should be the right approach to remain strong regardless of the market conditions.
Having developed a considerable footprint in Europe in the years following its establishment, Varamar decided to tackle the North American market and consequently opened its Vancouver office in 2019.
“Opening the Vancouver office gave us an opportunity to do business with a whole new market,” said Mr Bondarenko. “The clients we’ve spoken to thus far are very open to working with us; there’s definitely
an appetite for new players within the market. The incredible support we’ve received so far from the local Canadian community is evidence of that.”
The Vancouver office has seen the development of an impressive amount of business for Varamar, with routes bringing exported goods from Asia to the United States in particular but also to Europe and Africa. The US market is expected to be a star performer for Varamar in the coming years, as Mr Bondarenko revealed. “By the beginning of 2023, we expect that our trade route between Europe and North America will be our most profitable.”
Varamar Shipping has been involved in some exciting projects and Mr Bondarenko was keen to highlight two of them, beginning with a stadium-sized project in the Middle East in which Varamar carried 75% of the structures required for the World Cup Stadium in Qatar.
Another major cargo highlight came in the form of a massive structure that Varamar shipped across to Westfield World Trade Centre in New York City. Both visitors and Mr Bondarenko described the gargantuan structure, which has to be seen to be believed for its size to be appreciated, as looking almost like a giant dinosaur skeleton.
As interesting as both of those were, neither bore the complexity or impressive scale of a project Varamar completed for a German client exporting cargo to the Port of Kamsar in Guinea, West Africa. “The client was exporting a Bauxite conveyor
belt to Kamsar, with about 40,000 tons of equipment coming from China,” he explained. “The customer initially wanted to deliver the cargo between main ports using big bulk carriers. The customer had calculated that the project would take nine to ten months to deliver all of the cargo and for the port to build the conveyor belt.
“At that point, we came into the project,” he continued. “We suggested that the cargo should be delivered directly to the site where the cargo is needed. They told us that that would be impossible due to the shallow draught of the port. That sounded like a challenge to us,” he said with a grin.
Varamar’s team of specialists immediately got onto the case. They contacted the local ports, and then they identified and located the right vessels for the project. With the port’s assistance, they developed a docking plan and the project swung into action. “We put three or four vessels into China, each carrying 10,000 freight tons to this small berth in Kamsar, Guinea,” he recalled. “Ultimately, we delivered the cargo within three months instead of nine. We were the only company at the time who entered the bidding process having first developed a direct delivery service plan.
“This project proved once again that we have the time to listen to the customer and provide the right solution for them,” he emphasised.
A winning team with no limits Looking towards the future, Mr Bondarenko was excited by the potential that his Canadian office had already demonstrated and he looked forward to what they would achieve together in the coming years.
“The team that I work with is exceptional and I really love them,” he declared. “I’m also excited by the market that we’re in. We’re carrying project cargo, not bulk, so every shipment is different and every customer has their own story to tell. Our job is to listen and give them the right solution. Our huge customer retention numbers are ”90 proof that our approach is bearing fruit and delivering.
“Thanks to our owner’s vision, the company’s structured in such a way that senior management has a lot of authority within the group,” he said in conclusion. “I have no limits and so I’m open to any business development opportunity, for any sort of cargo and all possibilities. If you’re not limited, you’re not bored!”
As one of the foremost voices in the ship management industry, Captain Sanjeev Verma of Hong Kong's Landbridge Ship Management is leading calls for greater acceptance of technology among his peers. In conversation with Andy Probert, he also spoke about the impact a potential future shortage of seafarers could have.
ATthe helm of a young fleet of Very Large Crude Carriers (VLCC), Captain Sanjeev Verma has a unique 360-degree view of the ship management industry's changing tides, times and trends emerging post-Covid.
Not only has he seen the impact up close and personal on crews and onshore staff as Managing Director of Hong Kong's Landbridge Ship Management, but he also has an ear tuned in to the membership of the Institute of Chartered Shipbrokers (ICS).
The ICS, founded in 1911, is the only internationally recognised professional body in the commercial maritime arena and represents shipbrokers, ship managers and agents worldwide. It has 26 branches and 4,000 individual Members and Fellows.
As a member of the ICS Hong Kong branch, Capt Verma said: “One of the few positives to emerge from the pandemic's impact
is the greater inter-connectivity between people, through technology. No longer are we trying to juggle flights and schedules to speak to people. Jumping on Zoom or Teams is quick, effective and cost saving.
“Webinars have become the main mode of contact for our industry in reaching diverse audiences and helping enhance their knowledge. One of my tasks at ICS HK is to promote that shipping knowledge worldwide.”
A recent Inside Marine-supported ICS webinar about the forthcoming changes to tanker inspections by the Oil Companies
International Marine Forum (OCIMF) saw 300-plus attendees listen in.
“It sought to clarify a shift in the vessel inspection regime that has run for the last 25 years,” he said. “The OCIMF is overhauling the complete system to bring more of the human factor element into their inspection process.”
The webinar brought together ship owners, operators, crews, charterers and commercial operators, the OCIMF regulator and the project manager overseeing this new regime. “Overall, it was very successful in raising maximum awareness,” Capt Verma
explained. “Many sought to clarify doubts and listen to industry leaders about the new system. Certainly, we will host more webinars on different topics affecting our industry.”
Since its inception in 2018, Landbridge has been led by Capt Verma, a Master Mariner with 27 years in the shipping industry. Landbridge is part of the Landbridge Group, a private multinational group of companies from Shandong Province, China.
Under his tenure, Landbridge has asserted itself as one with an enviable reputation, with strong business links to oil majors
and traders. With 20 shore-based staff, it oversees a pool of 300 international seafarers to maintain the fleet of five 310,000 DWT VLCC tankers. These are chartered to global oil majors, traders and pool operators on either long-term or spot contracts, and there have been no accidents or spills to date.
Capt Verma said Landbridge was intent on expanding its platform and transitioning from an in-house ship manager to a third–party manager: “We are in talks with other ship owners interested in having us manage their assets. Our hope is to raise the bar and scale up to manage ships of different types.”
In the last year, a number of oil majors audited the company's processes and procedures. “They assessed any gaps in our procedures compared to industry best practices and how Landbridge could improve,” explained Capt Verma. “It was demonstrated how far the company has come in a short time.”
Capt Verma commented that the ship management industry was well aware of the challenges posed by environmental pressures and the need to drive down greenhouse gas emissions: “However, we, the managers and owners, cannot overcome these challenges alone,” he said. “I am glad more stakeholders, including shipyards, charterers and regulators, are now discussing these challenges.”
One change coming will be monitoring and rating a ship's emissions, a significant ‘cross-benching’ for the industry. “We will be able to categorise a ship by its performance,” Capt Verma continued. “As a comparison, look at the household electric products industry. For many years, you have been able to choose a product based on the ratings based on its gas emissions.
“The shipping industry has not had that benchmarking. But this carbon-index rating from 2026 will have sweeping changes.”
A lack of crew manpower has heavily impacted the industry, made worse by the conflict between Russia and Ukraine – two countries that account for about 15% of seafarers globally. “As we don't see an ending to the war in the short-term,” said Capt Verma, “we are looking at a massive shortage of qualified seafarers.”
Additionally, the prolonged lockdown in mainland China, another big source of manpower, is having an impact, according to Capt Verma: “It has also affected the intake of future seafarers, given the negative sentiments of other seafarers about the quarantine restrictions they encountered.
“Looking to the future, a lack of qualified seafarers could drive u p the cost of manpower. When that happens in poor market conditions, it will impact a ship’s running costs. Everyone could begin to chase the same pool of officers and seafarers to recruit.
“Those who are not so well-trained could get into the system to replace the vacuum created by this shortage. This could affect the safety of our industry. A tighter regime of checks and balances on potential staff is very much required in certain countries to give greater assurance.”
As a young company, Landbridge has established a shrewd IT infrastructure with a cloud-based platform, enabling its employees to work worldwide and seamlessly connect with its ships.
“When I look at us and compare with other ship management companies, yes, we are young and dynamic, but our IT-driven strategy in daily operations helps to heighten our transparency,” Capt Verma said. “That puts us in a different position from market leaders with traditional legacy systems.
“We use data and analysis to reflect and make decisions based on those findings. We believe technology can help you run your fleets smartly. The industry talks about emissions and changing fuel types. But why not talk about improving technology and a machine's efficiency?
“Crunch the datasets and improve the performance, rather than expending heavy investment into changing fuels or engines. A small
percentage could have great positives in optimising a ship’s performance and reduce carbon emissions.”
He concluded: “We are reaching a point where we need to change people's mindsets: technology is not an enemy to our industry; it can help change your operations. And change for the better is an improvement for all.” n
With decades of expertise and hands-on experience, SunStone Maritime Group A/S operates the world’s largest fleet of expedition vessels available on charter. Founder and Chairman Niels-Erik Lund outlined recent events and provided an overview of the fleet, in conversation with Phil Nicholls.
SunStone Maritime Group A/S is not a cruise company, but a provider of tonnage to cruise companies, tour operators and travel companies around the world. Developers of the award-winning Infinity class of vessels, SunStone is looking to the future with a fresh fleet.
“We have been working on our new line of ships for more than a year,” explained Founder and Chairman Niels-Erik Lund. “The Boundless series has all the same safety and comfort features as our Infinity class, only they’re a little bit bigger.”
With a history stretching back to 1990, recent events brought SunStone both the biggest positive and greatest negative. The Covid pandemic meant 18 months without cruise operations, delivering low income levels. This was balanced out by receipt of five ships in the Infinity series.
“Delivery of the ships was delayed,” said Mr Lund, “but in 2022 we were handed Ocean Odyssey and Sylvia Earle, with Ocean Albatros coming in 2023. So, that's all going well, and all ships are chartered out. We are very pleased with the progress.”
SunStone remains the largest operator of expedition cruise ships in the world, deploying a fleet of 12 vessels. Typically, these carry 100-200 passengers on destination cruises to explore remote locations around the world. Popular voyages include polar cruises or less-frequented islands in the Pacific Ocean.
The stars of the SunStone fleet are the Infinity class vessels with an impressive range of safety features developed by the company in-house. “We wanted to create a small expedition ship,” Mr Lund explained, “with all the safety and comfort features
Infinity class vessel five, delivered October 2022. Built by China Merchant Heavy Industries in Haimen, China.
Tonnage: GT 8500
Length: (LOA) 104.4m
Breadth: 18.4m
Draft: 5.1m
Speed: 15.5kn
Capacity: 160 passengers / 80 cabins
Registry: Nassau, Bahamas
Now sailing on long-term, year-round charter with Vantage Deluxe World Travel.
possible. So, as an example, we worked to ensure compliance with the SOLAS Safe Return to Port regulations, which is not a requirement for these ships.
“As our ships operate in remote areas, from a safety point of view, they need duplicate engine rooms, bridges and galleys. Whatever happens, these ships can bring the passengers safely back to the port. Maybe not at the usual speed, maybe not with a seven-course dinner. But we can still cook and serve food, we have engines running and vital systems working.”
Additional features include the zero speed stabilisers that keep a vessel stable, even when not moving. The dynamic positioning system ensures an Infinity vessel always sits in the water exactly as the captain requires, at the precise position, regardless of sea conditions and without dropping anchor. Most distinctive, however, is the X-BOW which gives the Infinity ships such a striking silhouette. Copied from offshore work boats, the X-BOW greatly enhances the stability of the Infinity vessels and translates into a significantly more comfortable voyage for passengers, as well as providing greater fuel efficiency.
While SunStone designed the specifications of the Infinity class ships, the company worked closely with its charterers on the interiors of the vessels. “They've been involved in how many cabins, or the size of a cabin,” said Mr Lund. “The charterers can choose how many restaurants, bars or lounges on a ship, or pick colour schemes and the type of furniture.
“From that point of view, they have been very much involved. But from the safety and comfort point of view? No, that's our expertise.”
SunStone deployed its expertise as naval architect when choosing the exact equipment to be fitted in its vessels. Everything from the main engines to the propellers, generators and thrusters were chosen by the SunStone team to ensure the finished ships exactly meet the company’s demanding requirements.
As ships are built as a series, SunStone easily establishes close relationships with suppliers. Uniformity across a series allows SunStone to secure better value from suppliers. Furthermore, this uniformity also means that crew trained on one Infinity ship can easily work on any other vessel in the fleet, as the equipment is duplicated across the series.
SunStone’s tight control on the equipment aboard the fleet also allows the company to apply the same exacting standards to its environmental impact. The company installs the least-polluting equipment possible in its ships. A modern fuel like LNG is not suitable for expedition cruises, where frequent refuelling depots are simply not available.
Yet SunStone deploys the cleanest engines and fuels it can find, while still allowing the ships to fulfil their role as expedition cruises. The Infinity class ships are fuel-prepared, ready to take advantage of new fuels as they reach the market.
The sustainability of the SunStone fleet is recognised by the Magellan Awards organised by Travel Weekly magazine. In 2021, Albatros Travel won the gold medal for Overall-EcoFriendly “Green” Cruise Ship with the Infinity ship Ocean Victory. This feat was repeated for SunStone in 2022, when Aurora Expeditions also won the gold medal for Overall-EcoFriendly “Sustainable” Cruise Ship with the Infinity ship Greg Mortimer.
The team at SunStone is not complacent and continues to build the company. One project is the new company office in Madeira. The fleet is slowly being moved to the Madeira flag and the team at this office is steadily growing to accommodate the new arrivals. The switch to this EU-based flag should not affect SunStone’s operations but makes clear the fleet’s continued performance within these tighter rules and regulations.
However, the main development of the company revolves around the new Boundless series of ships – expanding on the
Infinity series. The Boundless vessels will be fitted with all the safety features characteristic of SunStone ships, although there will be some differences.
“Instead of 104 metres, they're going to be 125 metres long,” explained Mr Lund. “The Boundless ships will be wider and with a capacity between 100 to 130 cabins. So, 200 to 260 passengers.”
SunStone will sign a framework agreement for up to ten Boundless ships, with four orders in the initial wave.
“We expect that the first ship would arrive in 2025,” Mr Lund continued, “and then two ships per year after that.
“Going forward, we plan to evolve the fleet further: by 2030, we will phase out all our older vessels. Then our strategy is to launch a new series of ships every five years.”
Reflecting on more than 50 years in the shipping industry, Mr Lund remained as enthusiastic as ever about SunStone and its potential for growth: “I'm so happy to see my two sons getting into the business, Carsten and his younger brother Christian. The shipping industry has been my entire life and I still love it. This is not really a job: it's a hobby.” n
Focused on medium range product tankers, Pyxis Tankers owns a modern fleet engaged in the seaborne transportation of refined petroleum products and other bulk liquids. CEO Valentios Valentis outlined the challenges and opportunities for the company and the broader industry, in a review with Phil Nicholls.
Recent global events have thrown a series of challenges into the path of the shipping industry. It takes an agile company to navigate these difficult waters and plot a safe course into an unknown future.
“Shipping is at the crossroads of major changes,” explained CEO Valentios Valentis. “Zero-emission shipping is on the way, which means strict new regulations and, of course, technological advancements. Therefore, we need to be ready to embrace change Our industry should stand united and collaborate closely to ensure a smooth transition for the benefit of all shipping companies, liners or tramp, big or small.”
Pyxis Tankers is no stranger to the challenges of the sector. Formed in 2015 through a reverse take-over of a small company, Pyxis immediately endured almost six years of difficult market conditions. Starting in early 2020, however, an operating and financial restructuring plan enhanced the company’s competitive position, which was subsequently boosted by a substantial improvement in the tanker chartering environment in 2022.
Headquartered in Maroussi, a northern suburb of Athens, Pyxis operates a fleet of five eco product tankers which carry a broad range of refined petroleum products and edible oils. These medium range product tankers (MR2s) were all built in South Korea and have an average carrying capacity of 50k dwt and an average age of 9 years.
“The number of our onshore personnel is small, given the size and nature of our operations,” Mr Valentis said. “International Tanker Management Ltd (ITM) is the technical manager of our fleet, providing crewing and on-board vessel operations. Overall, our operations are efficient and scalable.”
When attractive opportunities develop in the market, Pyxis expects to scale up the fleet by acquiring modern eco-efficient MR2s. This follows the recent sale of an old non-eco MR2 and two
non-core small tankers. Last year, Pyxis acquired 2013- and 2017-built product tankers. The ongoing fleet evolution will afford many operational benefits and meet growing customer needs.
Pyxis Tankers is publicly traded on Nasdaq (PXS). In the third quarter of 2022, the company generated net revenues of over $17 million, the adjusted EBITDA equating to about $8m and net income in the region of $5.3m.
These results were substantially better than the comparable period in 2021, primarily due to changes in fleet composition and dramatically higher spot charter rates. Chartering conditions continue to be strong for Pyxis, where the daily time charter equivalent rate (TCE) per MR increased from $29,062 in Q3 to a preliminary bookings rate of $36,800 for Q4, 2022.
“Our vessels operate worldwide and trade all designated MR routes,” Mr Valentis said. “The war in Ukraine, the upcoming winter season, low product inventory levels (especially in Europe), and the announced EU embargo of refined product exports from Russia starting in February 2023 - all these factors create dislocations in the global market.
“The result is higher charter rates, increased ton-mile demand and arbitrage opportunities. Everything points towards a high-rate environment, at least in the short term, but also higher volatility.”
Mr Valentis remains confident in the Pyxis business model operating in this volatile global market: “Pyxis owns and operates only Eco-MR2’s which are employed under a mixed chartering strategy of spot voyages and time charters. Spot voyages provide upside revenue opportunities in rising markets; time charters deliver stable, visible cash flows.
“Given the nature of Pyxis’ operations, the company has a long list of suppliers and service providers around the world. Many of these vendors have been supplying Pyxis for several years, frequently on a repeat basis”
“The company management owns around 55% of the outstanding common shares of Pyxis; we have continuously invested in our own company, in order to enhance shareholder value.”
Continued efficient operation in these circumstances requires close relationships with suppliers and partners. Given the nature of Pyxis’ operations, the company has a long list of suppliers and service
providers around the world. Many of these vendors have been supplying Pyxis for several years, frequently on a repeat basis.
Supported by these business partnerships, Pyxis is strongly positioned to weather the latest round of changes within the shipping industry, according to Mr Valentis: “The shipping industry is highly regulated under numerous international, national and local rules covering vessels, operations and maintenance. Moreover, our charterers, who consist of large integrated and national oil companies, major trading firms and
refiners, have rigorous vetting requirements for a vessel’s condition and operation.
“Industry regulations, especially environmental, are increasing. Pyxis Tankers is committed to good ESG standards. These are periodically reviewed by the Board, which is comprised of a majority of industry experienced independent members.”
Core to these industry-wide changes is a drive towards greater sustainability. The eco vessels operated by Pyxis deliver reduced fuel consumption, plus lower emissions and running costs. The company has installed ballast water treatment systems and upgraded its oldest vessel, built in 2009, by installing fuelsaving devices.
“Regarding the upcoming IMO environmental regulations,” continued Mr Valentis, “such as CII and EEXI, our studies are complete and our vessels will soon have the designated ratings in order to fully comply by January 1, 2023.”
The nature and complexity of the international seaborne transportation of refined petroleum products remains management intensive. The team at Pyxis has the requisite experience to handle a broad range of issues.
“In the short-term, product tanker industry conditions should remain robust,” Mr Valentis said. “Long-term supply/demand funda-
mentals look positive for the next couple of years, save a massive global recession. We try to mitigate risk by emphasising quality and reliability in operations and diversified chartering employment. Good financial controls and interest rate hedging are also important components of our company.”
Regarding the future, Pyxis plans to further improve its financial position in the short-term, allowing the company to take advantage of strategic opportunities as they arise. The recent significant appreciation in second-hand tanker values has proved a double-edged sword, as vessel acquisitions became very expensive, especially for modern tonnage. Pyxis looks forward to expanding as a company when the timing is judged right.
“I love ships,” concluded Mr Valentis, “and the freedom and entrepreneurial spirit of the marine business. Also, Pyxis being a publicly listed company has given me another responsibility and purpose - to ensure that shareholder’s interests are closely aligned with the management team and that value is created and enhanced. There is never a dull day in shipping!” n
Capramar Ship Management is an up-and-coming ship management company, who eagerly entered the shipping market at the start of 2022. The company already has an impressive fleet of ten vessels and hopes to expand this in the future. Co-Founder and Managing Director of Capramar Ship Management, Canatay Yilmaz discussed the company’s services, its current fleet numbers and its hopes for the future with Imogen Ward.
INearly in 2022, high-flyer, Capramar Ship Management has broken into the shipping market with an impressive accrual of ten vessels to its name. With headquarters in Istanbul, the company has 15 onshore workers, and an additional 250 out at sea.
The fleet, consisting of cargo ships and multi-purpose cell container ships, is full of life. With many years of future trading ahead, this company is a confident competitor within the maritime industry. All these ships are currently in operation, trading magnificently across the globe.
“We are a modern, forward-thinking ship management company,” Canatay Yilmaz, Co-Founder and Managing Director of Capramar Ship Management said. “We pride ourselves in being highly diverse in all aspects of our company.”
Capramar Ship Management carries out a vast number of incredibly important services, all of which are vital to the success and continuation of ship manning. Carrying out crucial inspections and audits has ensured that the company can maintain all of its ships effectively – keeping them in excellent, sea-ready conditions. Alongside this, Capramar Ship Management is already offering these services out to other companies too and hopes to provide even more companies with these valuable services in the future
Staff well-being is also paramount at Capramar Ship Management. Any accidents and incidents involving crew members onboard vessels are thoroughly investigated by the company. In addition, vigorous security assessments are continuously fulfilled by the team. These include the creation and implementation of vital ship security plans, ensuring that everyone aboard can work in the best environment.
The implementation of hull and machinery damage inspections also ensures that crew members are working safely. This is reinforced by extensive planning of dry docking, which enables the company to complete hull repairs effectively and safely without the risk of overlapping schedules or risk of ship damage.
The company also plans all budgeting for any repair work and dry-docking needs. This fore-planning ensures the most stable
A highly valuable cadet programme that promises to nurture any maritime skills and talents within the company is also a prominent part of these opportunities. All crew members are fully certified in STCW and meet all requirements of the Flag State and the MLC “ “
and reliable process possible. At all stages of repair, Capramar Ship Management has supervisors on hand to guarantee proper conduct and that regulatory processes are executed.
The company prides itself in versatility, Mr Yilmaz said: “We aren’t just a ship management company. Our motto is, ‘providing everything you need!’ We have a wide range of tailor-made services to meet customer needs.”
Crews at Capramar Ship Management are essential to the company’s success. To make sure that they have all the tools required to do their jobs effectively, the company has in place several top-quality training programmes. This includes both on-shore and off-shore job training.
A highly valuable cadet programme that promises to nurture any mar itime skills and talents within the company is also a prominent part of these opportunities. All crew members are fully certified in STCW and meet all requirements of the Flag State and the MLC.
Boasting technical management of the highest standard, Capramar Ship management ensures all ships are fully maintained, managed in line with promised operating price-points, and supplied with all required spare parts. The company operates in full compliance with all relevant rules, regulations, and codes – providing an efficient and safety-conscious service to all.
Capramar Ship Management is the place to go for maritime consultancy. All in-house, the company can offer technical and financial feasibility studies.
Another option is the company’s design review and plan approval process. With the team having previous experience of almost 20 years in the industry, those at the company know how to advise customers effectively. As a hands-on company Capramar Ship Management always offers to follow up on any project that has progressed into being operational, highlighting the company’s undeterred devotion to the industry.
Other appealing services that Capramar Ship Management i s dedicated to performing include S&P management. The company is committed to making the purchasing and chartering processes in shipping as stress-free as possible. Ship condition inspections are offered pre-purchase and pre-charter, requiring all ships to meet regulations and be damage free. This ensures complete and utter reliability for the customer.
Capramar can also offer a competitive insurance placement service; the company can do this consistently and assertively, using its team’s prior experience and knowledge within the industry.
The company has already established good relationships with suppliers and partners through the previous experience held by those at Capramar Ship Management. Going forward, it hopes to sustain these connections and develop new ones as the company matures.
For the foreseeable future, Capramar Ship Management sees the global energy crisis and the increase of inflation as continuous challenges to adapt to and overcome. More notably, there have been reoccurring disruptions in the supply chain: this, however has not deterred the company, and Capramar Ship Management is positive about what the future will bring.
With crew well-being high up in the company’s priorities, it is determined to maintain a safe, secure, and economical operation. Further objectives include the continual promotion of first-class safety and security awareness, alongside the paramount maintenance of safe working practices amongst all team members.
The company also wishes to fine-tune the current ‘two-way street’ communication system in place between onshore and offshore crews. This is vital for improved effectiveness and the minimisation of material wastage onboard all managed ships. In addition to this, Capramar Ship Management hopes to continue improving it’s training programmes, including safety-management skills. It also hopes to reinforce paramount preparation for emergencies related to staff safety and environmental protection.
Capramar ship Management is not afraid of competition within the maritime industry and is confident going forward within the market. “We are aware that our competitors bring quality,” Mr Yilmaz concluded. “Capramar however, is the epitome of quality.” n
Norway’s Rán Offshore is a highly effective performer in the international barge industry, offering its five-strong fleet primarily to the energy and offshore windfarm sectors to assist in the transportation of materials. Andy Probert catches up with CEO Lars Bjerke Tho and co-founder and Chartering Director Trym Lintoft about the company’s latest projects and ambitions.
Whether it’s a luxury yacht, components for offshore windfarms or transporting a pipe laying tower, the fleet of Rán Offshore is among the busiest and most versatile in the floating barge sector today. With its consistently high service levels and commitment to excellence in its client network, Rán Offshore has ensured its fleet of four North Sea barges and a ballastable 400ft barge are in continual demand from the North Sea to Gulf of Mexico and West Africa.
The company was founded as Greenway Shipping in 2011 by four work colleagues with an eye to tapping potential in the international barge market. This led to them commissioning the four new build 91m x 27m barges in 2012-13 from China’s Dalian Shipyard.
Today, CEO Lars Bjerke Tho and co-founder and Chartering Director Trym Lintoft remain at the head of the company, which was renamed Rán Offshore after the Norse Sea Goddess Rán in 2015. From the company’s Trondheim base, they oversee the fleet, which operates out of Rotterdam and Stavanger.
The modern ultra-deck strength flat top North Sea barges, known as the Greenbarges, each have a 9,025 DWT capacity and a deck strength of 25T/m2. The barges’ hull shape is improved for reduced water resistance, obtaining a higher towing speed with less fuel consumption. The barges were also the first in their sector to have ballast water treatment systems installed when they were built.
In addition to a 400 x 120 feet ballastable barge, Ranbarge 1, with a deck strength of 25T/m2 and 19,891 DWT, Rán Offshore acts as technical manager for two 50 x 18m flat top barges, commercially operated by the company Fundamentering (FAS).
Mr Tho said: “The international barge market is a niche area, and the North Sea s ector was initially our goal. It was a tough few years following the oil price collapse of 2015-16, so we’re proud to still be here having got through that period.”
Collectively with more than 50 years of experience serving within the marine industry, from shipowners to ship
equipment suppliers, Rán Offshore offers a complete service to clients from chartering of tugs and barges, daily reporting routines, ballast operators and procedures, related logistics, as well as engineering, port and agent services.
Rán Offshore barges are normally chartered to major contractors for projects in the offshore, energy and wind farm markets, or are operated with full-service provision, including transportation. “Around 70% of our business is pure barge rentals,” Mr Lintoft explained, “and the remaining 30% is transportation.”
Both confirmed that business has been “fairly static” in recent years, although challenges remain. Despite a slow start for their newest barge, Ranbarge 1, (which was acquired in 2018) it has been fully occupied throughout 2022 and potentially into 2023.
“The market for our Greenbarges in the North Sea has been very stable, with them being utilised for more than 50%
of the time, which is a key industry benchmark,” confirmed Mr Tho.
Rán Offshore is ISO 9001:2015 and ISO 14001:2015 accredited and holds an ISM Statement of Compliance for the operation of barges. Reassuringly, the Greenbarges were dry-docked in 2022 for inspection and given their 10-year operational class certification.
The fleet has been engaged in various energy projects, including ones in West Africa, between 2016 and 2018. Mr Tho said: “It was very important for us to get those contracts, as two barges were engaged for three years full-time.
“In summer 2022, two barges worked on a load-out operation on the Hinkley Point project in England, and that was concluded successfully for the client,” he added.
Ranbarge 1 was utilised to transport a large pipe-laying tower which was then lifted off by the world’s largest crane vessel , Sleipnir, and transferred to the pipe-laying vessel Amazon in Maasvlakte, Rotterdam.
Ranbarge 1 was also engaged on carrying materials for an oil and gas project in Mexico last year and is presently on duty for a major windfarm project off the coast of Scotland.
Mr Lintoft commented: “For the more unusual projects, our barges have been called on to trans-ship a big bridge to Gothenburg, a yacht from Rotterdam, a big hull section from Poland to Norway and a topside weighing 4,600 tonnes on the Greenbarges. They all show the capacity and versatility of our fleet, which are commonly split 50:50 between energy and offshore wind contracts.”
Mr Tho reflected how the rental of barges had been on “the low side for many years , but we are now seeing a slight increase in the rates, which is good for everyone. The barges are built for 25-30 years of operational life, and I think there is a good balance in the market.
“For the short to medium term, Rán Offshore is focused on maintaining its
position in the market, exceeding 50% usage for the barges in coming years and to continue delivering highly competent services by working closely with brokers and clients.”
Mr Tho said that Ran Offshore has a competitive advantage in the market as barges were their core focus: “Our barges are of high quality, and we try to respond quickly to clients as they need to be able to work quickly.
“We maintain good contacts with toptier EPCs who commonly work with oil majors. Our long-term relations are founded on transparency, trust and excellent communications. If you can offer good service and excellent assets, it isn’t rocket science that you can maintain fulfilling and effective relations across the market.”
Looking ahead, Mr Lintoft concluded: “For Rán Offshore, it is steady as she goes: picking up and exploring potential opportunities for our barges along the way, while maintaining our reputation in this market. Overall, we think we’re positioned well for the future.”
Supporting the oil and gas industry has enabled Bayu Maritim Berkah to build a solid reputation as one of the biggest providers of Accommodation Workover Barges in southeast Asia. The Indonesia operator is now contemplating an approximately US$60 million investment injection to increase fleet numbers, build a shipyard, and diversify its business offering. Andy Probert caught up with President and CEO Adi Agung Tirtamarta on the company's vision for expansion.
Established in 2011, Indonesia's Bayu Maritim Berkah has transitioned swiftly from agent to shipping owner and operator, providing 18 Accommodation Crane Workover Barges (AWBs) and Offshore Support Vessels (OSVs)
While its domestic and international reputation continues to grow as a safe and reliable partner to oil and gas majors, the company is set to take the biggest step in its relatively short history.
"We are planning a major expansion based on three core pillars: consolidation of our support services to the oil and gas sector, diversification into cable-laying and the establishment of a shipyard," explained President Director and CEO Adi Agung about the company’s US$60 million plans.
The fleet of 13 AWBs and five OSVs consists of AWBs with a capacity to handle between 100 and 424 people and are equipped with cranes from 100MT-300MT. It also owns various dynamic positioning vessels, anchor handling tug supply units, harbour tugs, diving support and multi-purpose support vessels.
However, the company plans to seriously upscale the fleet in 2023 with an additional three AWBs. One will be extensively refurbished to become a self-propelled pipe-laying vessel to handle up to 60inch diameter pipes.
Mr Adi explained: "We are in the market for second-hand units because the price of an AWB unit is $6-7 million compared to a new build of up to $22 million."
Two second-hand platform supply vessels (PSVs), with a minimum operational age of seven years, will be acquired. One will be allocated on operational duties in Southeast Asia in 2023. The other PSV will be converted into a cable-laying vessel and readied for the Indonesia Government’s plans to install 13,000 km of fibre-optic cabling to the country’s east and west areas in 2023.
Bayu Maritim Berkah also intends to acquire two second-hand Anchor Handling Tug Supply vessels (DP2) as they offer the potential to expand its business service offering in the region.
Mr Adi has also invested in 16 hectares of land formerly used as part of a power plant on the Island of Bintan, part of Indonesia's Riau Archipelago and with good proximity to Singapore. The area, equipped with a 250 metre long jetty, will become a smallscale shipyard to help repair and maintain the Bayu Maritim fleet. "We hold hopes of utilizing the yard in the future to build more specialist vessels. We will use some parts for a scrap business and build the yard to fully comply with the latest Hong Kong convention regulations.
"The heavy investment in the fleet is justified as we have identified many opportunities coming forward in 2023-2024 that require us to be forward-thinking, agile and geared up."
In particular, some AWBs will be stationed on short-term contracts to service oil and gas rigs offshore of Mumbai, India. These vessels are highly sought as they are equipped with lifeboats and conform to recent India Government guidelines requiring this type of ship to have a lifeboat aboard.
This feature emerged after the 2021 Cyclone Tauktae on India's west coast killed nearly 80 people, most of whom were on a barge carrying offshore workers that sank and 600 were rescued from offshore oil installations.
Mr Adi said: "What transpired is that most AWBs working in India, south-east Asia up to the Far East are not equipped with lifeboats. Ours are, so enabling us to work on continuous projects.
"We also see opportunities arising with ADNOC in the UAE who have opened contracts for five years but ask for the highest-spec in accommodation barges."
In Indonesia, due to the pandemic and the oil and gas crisis, some competitors are facing problems and may be forced to close, presenting Bayu Maritim in a strong position to pick up more work domestically.
The company is also contemplating retrofitting its oldest 90m barges into 300-person capacity AWBs to build greater flexibility for their contracts in Indonesia.
The decade-long success of Bayu Maritim and its ability to position itself firmly for the future is down to "being reliable, versatile and ever adaptable" to the changing circumstances of the oil and gas industry, according to Mr Adi.
After he became the President Director in 2011, Mr Adi manages the company as its CEO by first chartering barges and vessels to oil companies to support their activities in Indonesia and overseas. As one of the shareholders, he was determined the company become the leader in the accommodation barge business domestically, while building its foundation internationally.
It began with three AWBs and an OSV to meet the demands of Indonesian law, which effectively encouraged local vessels to work on government-issued tenders. Bayu Maritim worked with the likes of Chevron, CNOOC and Total and continued to expand its fleet to support workovers for drilling and platform work.
"Today, we are now the biggest owner of AWBs in Indonesia. We have several – around 65% - working domestically, while others have been on active contract in India for the last five seasons." Other vessels are on service in Myanmar, Malaysia and Thailand.
While the company saw turnover and work decrease by about 10%, it has seen a 15% bounce-back in 2022 as contracts continue to pick up and the oil and gas industry in the region emerge from the pandemic. Mr Adi said Bayu Maritim differentiates itself from the competition because "we are fully committed to providing the best services even if we are running at zero profit on contracts.
"With both suppliers and clients, we remain open, communicative and tell the truth. If they are happy, then we are happy. Ultimately, we want to partner with them for the long haul.
" We believe our expansion is well-timed,” Mr Adi concluded, “and will position ourselves very well for future gains as new opportunities come forward and boost our revenues in 2023 by 20%-25%."
For the past 35 years, Mexico’s Naviera Integral has been faithfully serving the offshore oil sector in Mexico and Latin America. Having grown its fleet from a humble three boats to a veritable force of 37, the company has earned its position as one of the leading providers within the region’s offshore crewing and supply market. Chief Commercial Officer Cesar Vera Mendez chatted with Richard Hagan about the business of boating to and from offshore installations.
Based in Mexico City, Naviera Integral supplies vessel chartering and related services for the offshore energy sector in Mexico and locations throughout Latin America.
The company was established as far back as 1987 by Juan Pablo Vega Arriaga, who remains President and General Manager of Naviera Integral to this day. Mr Vega’s ambition was to create a company that would provide vessel chartering services to the highest safety and efficiency standards. He aimed to eventually become the supplier of choice within the sector. And by all accounts, that is precisely what he has achieved.
Starting with only three boats, Naviera Integral made an early decision to appoint the famed Dutch shipyard Damen to build out its fleet. This decision would later prove to be a key factor in the company’s success, as Chief Commercial Officer Cesar Vera Mendez pointed out: “Our collaboration with Damen became a long-term shared learning
experience, as we both learned about the Mexican offshore market’s specific needs. Every new ship we ordered from Damen incorporated design improvements based on the performance of the preceding vessels. It’s been a process of continuous innovation.”
Today, Naviera Integral owns 37 vessels, of which 97% were manufactured by Damen. The fleet consists of crew boats, fast supply vessels, and platform supply vessels. Crew boats do exactly what the name suggests: they specialise in the transfer of crew to and from offshore installations, and they’re also able to carry light cargo loads.
Fast supply vessels, often known as simply FSVs, are the express couriers of the offshore environment. Equipped with high-efficiency hulls, Naviera Integral’s FSVs provide a vital cargo and personnel transport service to and from offshore assets. Its platform supply vessels (or PSVs), meanwhile, are very large, very specialised deep-sea vessels designed specif ically to perform a variety of functions to support offshore installations. This includes bulk cargo and equipment delivery and even the transfer of liquids. PSVs and their specialised equipment are often also called on in case of an emergency to perform rescue and recovery operations.
Naviera Integral’s extensive experience in vessel design and specification was put on full display in 2020 when it initiated a pro -
ject to build a new, state-of-the-art FSV to provide greater levels of service quality to the deepwater sector. The one-of-a-kind vessel, named Leonardo was built by Damen and features a host of passenger comforts and high-tech, specialised equipment that make it and its sister ship, unique jewels in the Naviera Integral fleet, as Mr Vera explained: “Leonardo is built on a Damen 5009 Axe Bow which is designed for speed, efficiency, seakeeping and crew and cargo capacity.
“Though the hull design substantially reduces pitching while underway, we’ve also installed a VEEM Marine VG1000 SD gyrostabiliser which provides advanced stabilisation of the vessel. This significantly improves passenger comfort, particularly at zero speed, while also increasing overall safety significantly.”
The VEEM gyrostabiliser is not common on workboats of this kind but its inclusion on the boat speaks to Naviera Integral’s industry-leading commitment to exceptionally high customer service. The stabiliser’s performance has been so successful that scientific testing proved a roll reduction of 80% while at zero speed and 60% while underway. Thus, in combination with the pitch-reducing axe bow, Leonardo’s passengers can look forward to a significantly smoother journey versus competitor vessels.
In addition to its unique hull design and its gyrostabiliser, Leonardo also boasts
firefighting systems, rescue capabilities including a six-passenger tender with deployment crane, a Jason’s cradle (a special climbing net hung over the side for rescue operations), 150 lifejackets and blankets, and dynamic positioning systems. It also has a professional infirmary fully equipped for an emergency and permanently staffed by a physician.
Passengers are especially well cared for thanks to Leonardo’s guest facilities. They ride in total luxury in 35 fully-reclining business class seats equipped with advanced infotainment facilities. There’s also a fully stocked coffee and snack bar, but according to Mr Vera, the coffee and snack bar are seldom fully utilised: “The seats are so comfortable that the passengers don’t even notice the length of the ride - most people fall asleep!”
Leonardo has been such a success with Naviera Integral’s charter client to whom Leonardo is assigned, that the client has been able to reduce their usual costly fleet of Sikorsky transport helicopters from three down to the mandatory minimum of one.
Naviera Integral has upgraded Don Julio, a second Damen 5009 with similar specifications as Leonardo. Don Julio is currently assigned to a client in Suriname
A fleet of 37 vessels requires a lot of maintenance and in this respect, Naviera Integral has built robust maintenance and logistics infrastructure to ensure maximum uptime of its boats.
While Naviera Integral’s head office is located in Mexico City, its 700 staff are spread across the head office and its main operations centre, which is located in the middle of the offshore industry action at the port of Ciudad del Carmen in the state of Campeche. Here, Naviera Integral and its sister companies operate a waterfront space with a length of 100m - the largest for its sector.
Naviera Integral’s main service centre is located here, hosting the company’s certified Caterpillar, Cummins and Detroit Diesel mechanics. These highly skilled teams perform daily, regular maintenance on the company’s boats to keep them running at their peak.
“We are able to test entire engines on site, and we have a warehouse containing critical parts,” said Mr Vera. “Hence, we’re able to rapidly respond to unplanned maintenance issues. This results in technically zero downtime for our customers.”
The company is also very proud of its very low staff turnover, which Mr Vera attributed to Naviera Integral’s carefully managed staffing policies: “In a company as large as ours, you might expect to see some challenges with crew. But we’ve grown organically, and our personnel have grown from within and with us and thus we’re able to provide them with a career path. They’ve developed careers that allow them to operate
across any of our vessels with total confidence. Plus, our workforce is enriched by a constant flow of newly-graduated as well as mid-career naval engineers, captains, machinists and others.”
As with any fleet owner today, emissions reduction is a major focus at Naviera Integral and its efforts have borne promising fruit.
A particular example is its FSVs and their arrow-like wave-piercing hulls. “They’re designed to utilise smaller, more efficient engines,” noted Mr Vera. “A similarly sized FSV would use a 7,500hp engine arrangement, whereas our FSVs only need 6,000hp. That’s a huge reduction in emissions.
“All of our vessels also each have a magnetic particle aligner that results in a 4% reduction in fuel consumption,” he continued. “In the quest for additional improvements, we’ve incorporated electric motors, and are considering batteries and solar panels in our PSVs. We’re also carefully looking into hydrogen as a fuel source, but we have to be cautious because both
the technology and the fuel supply are not yet readily available for this to be a viable option right now. But we’re going in that direction.”
Meanwhile, Naviera Integral will implement an exciting social responsibility programme involving oyster farming. “It’s very socially beneficial for the community because it provides work opportunities and an overall economic benefit for them,”
Mr Vera said. “We’re still the main economic driver in our community, however, because while fishing used to be an important career path for the community, the fish stocks are no longer sustainable.
“The oyster farm is just one example of further projects that we plan to roll out,” he added. “We’re working on this as we speak.”
Mr Vera concluded our conversation by highlighting some of his favourite aspects of life at Naviera Integral: “I really enjoy my team in the commercial department, it consists of six professionals. They’re truly committed, caring people. Being part of what the company is doing is very exciting, too. And I love the fact that it’s a 100% Mexican company. We’re all part of an extended family!” n
seven seas, five oceans, one voice
dmt marine equipment katradis marine ropes all points boats allied systems turbodal r.w. fernstrum & company
DMT Marine Equipment has overcome a testing pandemic and landed one of the biggest contracts in its history. With innovation at its core, the company is relentlessly looking to reshape its industry with good design and quality principles. CEO and Company Founder Piet ter Schure discussed the company in conversation with Andy Probert.
Piet ter Schure is immensely proud his company's products do not simply come as standard. That defines DMT Marine Equipment's approach to business.
Its focus on innovation and continuous product development is intentional, said the CEO and Company Founder, because of where it positions DMT in the market: “We listen to our customers' needs and design their required solutions. Where our quality comes as standard, innovation never has, it’s exceptional! That's why we keep pushing the boundaries.”
This drive has secured industry recognition, with DMT taking the Best Deck Winch Supplier 2021 award for a second year. On the commercial front, it has won a significant contract to support the construction of one of Europe's most ambitious infrastructure projects, the Fehmarnbelt tunnel.
As much as Mr ter Schure is happy to acknowledge the positive, he is also reflective of a painful period the company endured during the pandemic: "2021 was challenging as we encountered supply chain problems with the delivery of electronics and overseas transport issues.
“We were super-positive for 2022. Everything looked good. Then, the Russian-Ukraine conflict erupted. For the past 18 years, we have had business entities in both countries.
“Purchase orders were 60%-70% higher, but then we had a 90% increase in steel prices. It was a new challenge. But we survived with good teamwork, believing in what we could do in-house and working with good partners. That was our focus: survival in highly unpredictable times.”
However, DMT has seen new market developments, such as in the liquid gas sector. “Liquid gas means tanker-transport in Europe,” Mr ter Schure said. “That means demand for specialised equipment that we can make. It is working well for us.”
Such confidence is born out of DMT winning a contract to supply 64 winches for the construction of the longest immersed tunnel in the world. The Fehmarnbelt tunnel will connect the Danish and German coasts through a 40m deep underwater road and rail link.
DMT will supply all winches for the subsea positioning of 89 prefabricated tunnel elements, weighing between 21,000 and 75,000 metric tonnes each. The winches will be placed on four immersion pontoons to work together. Mr ter Schure said: “It is a great honour and a major responsibility
With over 60 years’ experience in the marine world, Rotor is proud to take part in this project as a partner of DMT Marine Equipment, via the delivery of the winch motors for barges. We appreciate our daily cooperation with DMT on different projects. Our team is now working on the production of the motors for the Fehmarnbelt tunnel project, and we look forward to continuing this close cooperation with DMT and partners.
to bring our passion and know-how to the success of this project.”
The contract represents the peak of DMT's powers in a highly competitive marketplace and vindication for Mr ter Schure He launched DMT in Romania in 2001, with three colleagues from an office in a small apartment, and ploughed his last personal savings into four computers and two printers.
While headquartered in Romania, DMT now has offices in China, Holland, Russia, Turkey, the US and Ukraine, with a 300strong workforce. It operates three workshops across 5,400 sqm of workspace and plans to invest in a fourth.
Post-pandemic, DMT is fielding new orders and enquiries from designers, builders and owners from the global marine, civil and mining sectors as the market is reinvigorated. The high demands of towing winches led to a significantly increased worldwide presence of DMT equipment in this market. For these remarkable results, the company’s loyal customers in Turkey played a key role. DMT remained profitable despite 2021’s difficulties and is looking at 2023 with
growth potential of up to 60%, according to Mr ter Schure: “We need suppliers to help us manage this increase, and we have selected good partners. We have signed contracts for next year and are working on 2024. Substantial orders are from Europe, but we are looking to new markets and clients.
“We are highly respected for our specialist winch products. It has taken a long time to get this belief from customers, but it has paid off. DMT never intends to stand still, and by having these projects, we can invest in combined technologies which can be utilised in the future.”
He zeroed in on obstacles, including spiralling inflation and ensuring the flow of payments from clients: “The biggest challenge is to make the correct calculation for the client and us,” Mr ter Schure explained.
“For example, we thought the price of overseas transport was lowering, and we considered that problem solved, but then the price changed, it impacted many things. Change appears to be the only constant.”
Supply chain and lead times have also proved challenging, he added. “As winch builders, we want to focus on innovating and developing new products. We always want to evolve our portfolio and take it to the next level.”
According to Mr ter Schure, a major concern was taking care of DMT’s team: “It’s the biggest asset to us. At DMT, keeping the team happy, particularly in difficult times of high inflation and energy costs, is key. We have to do things more efficiently, smarter and use different calculation methods, such as optimal cutting times.”
Over the last 18 months, the company has focused efforts on reducing the environmental impact of its equipment and
production processes. It intends to invest in alternative energy sources, such as solar power, to become self-sustainable.
“We intend to be as green as possible,” said Mr ter Schure. “Reinvestment in people, facilities and innovation will help keep the business moving.”
As demand for greener products continues, DMT is focused on R&D: “We are looking at a particular area of winch products that traditionally consume a lot of energy,” he continued. “We want to achieve the same performance with less gasoline usage. We are close, and will look to introduce and test this product next year.
“But we will not make any concessions on quality as our products stand by their reputation for durability, reliability and longevity. Clients know they can perform in harsh environments and DMT will remain loyal to those principles.”
Mr ter Schure outlined how DMT’s after-sales support and commitment to a price-quality balance on products
remain differentiators: “I try to be loyal and honest and everyone who knows me can confirm that. Clients and suppliers know we stand for transparency, and that helps strengthen partnerships in the long run.”
Reinvestment in people, facilities and innovation will help keep the business moving “ “
Katradis Marine Ropes is an established manufacturer of quality sup- plies with a strong presence in the maritime industry. Its long course stretches well over eight decades and has granted Katradis a high degree of technical know-how and quality manufacturing expertise.
CEO Constantinos Katradis explained to Hannah Barnett how company has established itself as the preferred supplier of all major shipping companies around the world.
The long and distinguished history of Katradis Marine Ropes goes back to the first half of the twentieth century. That is when it was founded, in 1936, by Konstantinos Katradis, as a ship supplier specialising in high-quality mooring ropes.
The company continued in the field, producing innovatively designed, good quality mooring ropes to the present day. It has also made zinc and aluminium sacrificial anodes for corrosion protection of commercial vessels since 1968.
These days, the wider Katradis Group also supplies anchors and anchor chains for port development and deck equipment. This allows it to serve the marine industry as well as the sectors of offshore, aquaculture, fishing, and yachting. In recent years the company’s product line has expanded to include yachting ropes as well as fishing and aquaculture nets.
Constantinos Katradis is CEO of Katradis Marine Ropes and has been working in the industry for over 20 years. In a few choice words, he defined what sets the company apart from its competi -
tors: “Price. Quality. And an understanding of what the market needs.”
Mr Katradis oversees the company’s global network from its base in Greece, where it supplies more than 10,000 ships with Katradis mooring ropes and other marine products at ports around the world.
“Our factory is just outside Athens, and we have a presence in most major ports around the world, such as Rotterdam, Singapore and the UAE,” Mr Katradis said, painting a picture of an international operation.
It is as rope producers that the Katradis Group first made its name and rope where it continues to dominate the market. The company manufacture a wide range of synthetic mooring and steel wire ropes.
Katradis created its first braided ‘double-twisted’ rope in 1944 and continues to sell them today. Its 8-strand ropes are con -
“We stand out due to the high quality in competitive price and understanding of what the market needs”
structed using yarns of Nika steel double twisted fibres. The fibres are produced with a unique formula, which takes into account stretching ratios, material percentages, and stretching temperatures. As a result, they exhibit a much higher tenacity and abrasion resistance than most conventional fibres.
The double-twisting process also offers improved performance in dynamic and shock-loading conditions, while maximising resistance against internal and external abrasion. It is this combination of powerful fibres and the elaborate double twisting process that make the Nika cord 8-strand rope a jewel in company’s crown, and what it describes as its flagship product.
Everything the company makes is infused with the Katradis philosophy, though. This means ensuring ships are using the safest possible equipment to minimise the chance of accidents.
A good way of ensuring that is through splicing. Katradis manufacturing experts emphasise the importance of attention to detail when it comes to eye splicing and perform strength tests under strict quality control procedures. This ensures the efficiency and performance of the rope when used in mooring operations.
Another of the company’s signature products that emphasise high safety standards, is its snap-back rope.
A snap-back is the sudden recoil of a mooring line because
of its failure under tension. A snap-back zone on a mooring deck is the space where it is anticipated that the failed mooring line could recoil with great velocity.
As any mariner knows, snap-back zones are potentially very dangerous and mooring operations are one of the most critical activities a ship’s crew needs to perform. By following international reduced snap-back rope testing methods, the company has put its Nika steel fibres to use once again and developed mooring lines of reduced recoil in a ‘special polymer blend.’
Our RSB (Reduced Snap Back) ropes have been developed for safer mooring operations in the shipping industry. The research and development team created a mixture of superior mechanical properties compared to conventional polypropylene fibres. These properties allow for reduced recoil on a tense rope, giving ship’s staff valuable time to react and seek safety.
Manufactured and certified by international standards the ropes also offer reduced recoil effect by their unique inner-braid rope structure that enables the restraining of snap-back release in case of rope partition. To reassure rope longevity, the developers have also added UV stabilisation for increased protection against sunlight that normally affects all polymer materials. The snap-back rope can be used in mooring, anchoring, tow lines and STS operations.
Similarly impressive, the green revolution has extended to the rope business. Being an eco-conscious company, keen to promote sustainability, Katradis manufactures its products based on the highest safety and eco-friendly standards. Its new ‘eco-ropes’ are made from a production process which requires 59% less energy. The fibres are also specially designed to reduce CO2 emissions.
There is a reason the Katradis Group has been around for so long. Its products are cleverly designed and well sourced, from a network of suppliers it has been using for a long time. The company has a clear selling point, position in the market, and vast swathes of expert knowledge on its team.
Nonetheless, all industry has been affected by disruptions in the global supply chain in the last few years. Mr Katradis is reflective and cautiously optimistic about how the company has navigated the turbulence.
“We are certainly influenced by the global situation,” he said. “With the sort of economy that we are living in, we have seen a large increase in transportation costs. There has also been a very big fluctuation in energy costs and in the price of raw materials. So, there is a sense of instability in the global economy. We are optimistic about the future, but I think the next two or three years will be difficult for global markets in general.”
Going forward, the company hopes to continue at the top of its game. In the words of Mr Katradis, that means: “supplying the best customers, supplying the best quality products, trying to keep up with competition in the maritime industry.” n
All Points Boats (APB) has more than 25 years of experience providing metal fabrication and manufacturing services to the thriving yachting community in South Florida. President and Founder Nate Goodwin spoke to Andy Probert about the company’s commitment to innovation and diversity.
For Nate Goodwin, sailing is in his blood. Having raced sailing boats from a young age, he found himself in South Florida setting up a small business in 1997 to repair and outfit 60ft70ft motor yachts. Through a process of acquisitions, investments in cutting-edge equipment and employees, APB is now a leading comprehensive manufacturer and metal fabricator in the superyacht sector.
“Our business has evolved as the industry has grown over the past 25 years,” said Mr Goodwin, “and APB has built a well-earned reputation as a quality one-stop shop. Our core business is around vessel operating systems.”
Employing 65 skilled craftsmen at its 30,000 sqft workshop in Fort Lauderdale APB’s primary services include reverse engineering and refurbing damaged, corroded or deteriorated components through replicated construction back to original condition.
Services include class certified welding, plumbing, valve and pipe fitting, hydro static pressure testing, FRP repairs, and carpentry outfitting. The company is class-approved to perform repairs and modifications in stainless steel, aluminium, bi-metallic and coppernickel. Class-approved repairs are backed by ABS, Lloyds, Rina, MCA, and USCG.
APB also provides one-, five- and 15-year class surveys of vessels, along with valve inspections and testing for all class societies. As well as being an authorised dealer and service provider for Seakeeper, and SeaVision, it has a thriving composite business.
APB recently completed a $3 million infrastructure upgrade of its workshop, investing in a state-of-the-art CNC 5-axis FLOW waterjet, CNC 3-axis router, CNC plate rolling machine, high capacity metal shear, 3-axis CNC press brake, and two climate control spray booths.
The company’s CNC 4-roller plate rolling machine, which can be deployed to produce complex shapes, ovals, cones, ellipses, and any style tank or piping assembly, was recently used to fabricate a 6ft section of an ABS marine-grade pipe for a new ship’s sea chest.
Mr Goodwin said: “As overseas supply chains choke on material availability, APB is actively solving these problems by manufacturing quality components in-house. In the current market that has proved exceptionally beneficial.”
APB services facilities and clients on the U.S. East Coast, including BAE Systems Shipyards in Jacksonville. “While most of our clients are in the Fort Lauderdale area,” continued Mr Goodwin, “we also travel to assist them wherever they are, as we are fully mobile and set up to work in any facility.”
The company has a significant commercial undertaking in certified welding and emergency repairs for vessels entering ports. “Our teams also manufacture components for cruise lines and suppliers
to the cruise industry, and can make modular components ready to ship into a vessel,” Mr Goodwin added.
APB’s performance has been stable, including through the pandemic, as it remained open as an essential business.
He said: “We never stopped, kept a majority of staff, and found opportunities where we could in our manufacturing specialisms. During the pandemic, we made strategic decisions to reduce overheads and our teams took on extra responsibilities. APB came through stronger knowing it can do more with less.”
While the marine industry accounts for 80% of its business, APB diversified into commercial, industrial, architectural and residential work five years ago. “We do all engineering in-house,” Mr Goodwin said, “so we have programmed our CNC machines and do 3D modelling for prospective clients on new projects.”
On innovation, APB now rebuilds vessel sea chests using ABS-certified Wencon Epoxy. During a recent 10-year ABS annual inspection, APB’s certified applicators utilised Wencon’s state-of-the-art coatings to rebuild a sea chest and recondition a hull’s penetrating systems.
Mr Goodwin explained: “Wencon Epoxy is a revolutionary, environmentally friendly, non-hazardous, low CO2 emission epoxy coating system. It extends the lifespan of the substrates where erosion and corrosion are most prevalent. Using this superior technology, we can offer customers a quick and cost-effective way to repair deteriorated surfaces.
“APB partnered with Dantech Offshore and Marine Group to bring this product to Florida. We completed 12 months of testing
and are excited with the results.” The intention is to showcase Wencon Epoxy’s capabilities at boat shows, introduce the product to the U.S. market, and expand it to Canada and Mexico.
The company continues expanding and investing in cutting-edge equipment, leading the way for other companies and facilities to attempt to copy what APB does.
“It is standard in the industry for APB to pioneer techniques and repair services that others have picked up,” Mr Goodwin reflected. “The industry is evolving and adapting, and we must find ways to fix boats and achieve the unobtainable. The demand from clients is to be faster, cleaner and neater than ever.
“Our industry is heading in the way of aviation. More regulation will be applied and enforced as boats become bigger, and insurance liability will become more extensive. It means more complex navigation through the processes before we even do the work.”
APB’s aim over the next few years is to provide its manufacturing to a broader base of customers and industries, according to Mr Goodwin: “Where we see shortfalls is in supply from other countries. Lead times are quite extensive and challenging, so we are narrowing our focus on filling those voids by providing highquality parts with fast turnaround times.”
He emphasised that APB is keen to increase staff numbers, with continual training to ensure the quality of its end product remains high. “A key differentiator for us is that we do the right thing safely. Our hands-on experience, critical solutions and in-house expertise ensures we keep tight control on production quality.”
Mr Goodwin concluded: “We have built lifelong relations with suppliers and clients. In doing so, APB intends to continue to grow and expand its influence through creative thinking, highly motivated staff and value-added US-based services that fill the void that the global supply can’t.” n
Allied Systems, a US-based design and manufacturing hub for marine cranes and davits, is forging ahead, having secured its biggest-ever contract. Mr Hitesh Patel, VP of Sales and Marketing, spoke to Andy Probert about the company's commitment to client satisfaction and its extensive global support.
Cranes and davits are the silent workhorses of the maritime sector, hourly performing loading, unloading and handling tasks, then in critical moments, enacting rescue and boat deployments. For more than 40 years, Allied Marine Crane - a division of Oregon-based Allied Systems - has designed and developed cranes, davits, handling arms, winches and A-Frames to meet global demand.
Allied Systems is a veteran- and family-owned business operating from a 250,000 sq ft facility in Sherwood, Oregon. The company offers a full-service fabrication shop, a dedicated CNC shop with 13 CNC mills and lathes, and many other capabilities. These include a largescale paint and sandblasting section (one of the largest in Oregon), an 84,000 sq ft assembly facility, and critical test facilities.
“We proudly produce our products here in the United States, something that few of our competitors do,” said Mr Hitesh Patel, VP of Sales and Marketing. “We keep as many processes as possible here inhouse to ensure the highest-quality end-to-end control.”
Dedication to detail is never far from Allied. It has a 25-strong engineering team focused on designing and customising product.
“We specialise in highly-specified marine cranes, davits and handling systems designed and built to industry standards, including API, ABS, SOLAS and Lloyds Register among others.”
Their cranes are utilised on vessels for clients including the US Navy, US Coast Guard, oceanographic research vessels, and commercial customers worldwide. Clients include shipyards, vessel owners and operators. Allied’s handling systems are deployed on oceanographic research vessels for various needs including recove ring sediment samples from the seabed thousands of metres below the surface of the ocean, as well as measuring ocean water data at varying depths, including conductivity, temperatures, density, etc.
“Maintaining every aspect of our processes on-site, allows us to design to the exact specifications our customers’ need,” said Mr Patel. “That could be for a very high-sea state, extreme cold weather conditions or specific regulatory requirements. Designing purpose-built equipment is what differentiates us in our industry.”
He added: “One of our core values is our support. That is very important for clients. We have so many cranes in critical applications with customers, such as the US Navy, it is essential their equipment is always ready to run.”
Allied has a 15-strong team of service technicians that are deployed worldwide to handle crane issues for clients. The company also maintains a fully dedicated service parts warehouse that can ship globally 24 hours a day, 365 days a year.
“That support is the backbone of Allied and the core values we extend to clients,” Mr Patel said. “Many of our US customers appreciate that we are a US manufacturer.”
Within Allied's five different product lines, marine crane applications account for the largest portion of all turnover for the Sherwood-based business. But things are now moving fast for the company as it seeks to scale up employment from its current 200-plus workforce.
Mr Patel explained: “Allied is growing rapidly and continuing to pick up momentum. Sales growth is up 52%compared to last year, and 120% over 2020. Our major challenge is recruiting people fast enough to keep up with business growth.”
Underpinning that sterling performance is Allied securing its biggest-ever contract in 2019, worth $70 million, to design, manufacture and deliver Crash and Salvage Crane units for the US Navy.
The mobile rubber-tired cranes move aircraft with mechanical failures or battle damage out of the way on the flight deck of aircraft carriers, landing helicopter assault and dock vessels. “They
are critical equipment,” Mr Patel said, “as no flight operations are allowed without an operational Crash Crane running on standby.”
The Crash Crane design was pulled from Allied’s experience in designing and manufacturing its Wagner product line of rubbertired logstackers and chipdozers, and its skill in designing cranes for harsh marine environments.
“While it was our largest ever contract, it has also been the most challenging,” Mr Patel continued. “The US Navy wants to make sure that no matter what environmental conditions are present this crane is operational, otherwise they cannot conduct any flight ops off the carrier. You don't want a multi-billion aircraft carrier sitting dead in the water if our equipment isn't working.”
With a prototype close to completing exhaustive testing to ensure it can withstand extreme environmental and operational conditions, Allied has been greenlit to begin full production and that will continue for the next four years. The new crane is designed to support a fully-loaded F-35 Joint Strike Fighter, for which the previous model did not have the capability. Another challenge was reducing the machine's weight to meet strict deck loading requirements while increasing the load capacity.
Mr Patel confirmed lucrative contracts are in the pipeline, with negotiations ongoing with potential clients. Allied is also engaged in making new standardised crane product lines. Additionally, it has just released the new DX Series Davits range, a lightweight, ultra-compact, cost-competitive design intended to fit within tight deck envelopes.
The company is engaged in the push for environmentally friendly applications and offers eco-friendly oils for crane operation, according to Mr Patel: “We understand the importance of equipment being as environmentally safe as possible and continue to invest in research and development in those areas.”
Allied cranes are built for the long term, and he acknowledged that many were still working globally for 40-plus years. “That is a testament to our product longevity and the support we provide,” he said. “We want to ensure that we are placing customer support above all else. Support is the most valuable product we offer to our customers”
“Unique to us is that our support team is directly employed by Allied and are experts in our product. We provide direct and rapid engineering support to overcome client problems when there are challenges.”
Mr Patel concluded: “We understand how critical our equipment is to our customers. Our product is 100% tested before it leaves our factory. Our customers appreciate that they can trust that our equipment is safe to use, and they appreciate the support we provide over the life of the product, and we believe that leads to a mutually beneficial relationship.” n
Chile's Turbodal has powered its way to become one of South America's leading and most reliable providers of turbochargers to the maritime sector. Director Sergio Parada discusses expanding business opportunities, innovations and the realities of bringing sustainability to bear in ever-evolving times with Andy Probert.
Turbodal is a key fixture in Chile’s maritime industry, providing a range of world-class turbochargers to the nation’s shipyards and vessel owners. Given that the South American country’s aquaculture industry is the third largest in the world, making up 12% of global production, the company considers itself well-positioned to capture a wide net of future opportunities.
Established in 1980, Turbodal was a pioneer of its time in becoming the first dedicated turbocharger workshop in Chile. Over the decades, it has continued to evolve and is now considered one of the nation’s acknowledged leaders in the sales and servicing of turbochargers.
Turbodal, which employs 90 people and has annual sales of $10 million, is part of a larger group of companies with a 400-strong workforce and a $70 million turnover.
The parent company also has interests in sales and servicing mining machinery, trucks, bulldozers and engines. This is primarily focused on Caterpillar Engines and Komatsu brands. The parent company also has a similar set-up in Argentina that works with Caterpillar Injectors and is involved in a partnership with Japan’s Marubeni.
Turbodal is also highly regarded for its dedicated service provision, carrying out fault analysis and diagnosis, cartridge repairs, essential maintenance and cleaning.
“Today, Turbodal has ten branches across Chile. We are proud to be the dealers for the globe's main turbocharger brands and exclusive dealer in Chile to the Japanese engine maker Yanmar,” said Director Sergio Parada.
Turbodal works closely with both shipyards and operators whose vessels call into port. He said: “Chile has very good shipyards dedicated to small to medium vessels, in between 500 and 3,000 tonnes, and they mainly provide well boats and fish carriers to serve the burgeoning salmon farming industry.
“As a company, we are uniquely placed to serve both sectors due to our excellent support and vast knowledge, experience and support.”
Mr Parada spoke of Turbodal’s involvement with Yanmar as a “happy and virtuous conjunction” at a critical time for both companies. “We saw an important need for Yanmar marine engines in Chile, but the Japanese company previously lacked vital local support.
“The quality of their engines is quite extraordinary, but you still require sales and comprehensive servicing on the ground to maintain those engines for customers. That is where Turbodal comes into its own.”
Business growth of recent years for Turbodal has continued apace, increasing by an average of 7% per year despite the impact of the pandemic. It has sold around 20 engines, with a total of 20,000 KW output, in the last three years.
Mr Parada said that one highlight was Turbodal’s continued involvement in the expansion of the Patagon-named fish carrier fleet. In partnership with Yanmar, Turbodal supplied the main auxiliary engines for the Patagon 9, 10 and 11 vessels. These are 3,000ton vessels, owned by Patagonia Well Boat Company and built by Asenav Shipyard, to transport live fish as part of the nation’s salmon fishing industry.
He added: “We have also supplied engines into two new barges for different private companies and a vessel deploying buoys and signalling on behalf of the Chilean Navy. All these projects were completed in 2020 and 2021.”
Mr Parada added: “2022 and 2023 are looking very promising for Turbodal as new projects come online. More well boats are coming through, and we are gearing up to meet those demands.”
As part of its business expansion, Turbodal plans to open a new service facility in Puerto Montt, a port city in Llanquihue Province, southern Chile, which is vital to the salmon fishing industry there.
“It has been 20 years since Turbodal last opened a new facility in Chile,” commented Mr Parada, “however, we appreciate the business potential that Puerto Montt presents.
We detect opportunities for servicing that are not presently provided there by others.
“We will succeed as we are well-known for our service provision nationally. Puerto Montt will become an important focal point for Turbodal’s service support to clients using Yanmar and other branded engines. We are on track to open the new workshop in 2023.”
The main challenges to the company and its industry are the constant technology upgrades and the drive for lower emissions, according to Mr Parada: “These two challenge us, as we must be on top of both of them in order to provide proper customer support.
“We also invest a significant budget into R&D to overhaul and modify engines to ensure high performance, low emissions and minimal pollution. We adopt eco-friendly cleaning procedures using biological cleaners to care for industrial waste safely.”
The global turbocharger landscape has changed dramatically in the last 20 years, explained Mr Parada: “From very mechanical rotating pieces to the complex electronic controls and different phases of turbocharging today. But it is one of the most influential elements of an engine and key to lower emissions, so we have to evolve our education on both.
“Because of that, our teams are regarded as the leaders in Chile and South America and have won many awards from manufacturers because of their dedication and commitment.
“The most important aspect of our company is our orientation to customer service. This is backed by our experienced and skilled staff. We take pride in offering top-quality service, as the customer experience is of paramount importance. We are always honest and professional in our work, and these are the foundations for our longterm relations with our suppliers and clients.”
Mr Parada concluded: “The Chilean ship market remains very attractive because of the country’s long coastline, the shipyards building medium-sized vessels are very good and customers are always seeking good quality and service from engine manufacturers. These all present a wealth of opportunity for Turbodal to take advantage of in the future.”
Since 1948, R.W. Fernstrum and Company has provided the marine industry with advanced heat exchange systems. Being industry leaders of heat exchange, the company has maintained its reputation in the market as an innovative manufacturer. President Sean Fernstrum discussed the company’s current work scope and its exciting new partnership with Omega Thermo Products, in conversation with Imogen Ward.
R.W. Fernstrum and Company developed from the ingenious vision of Robert Fernstrum after he was tasked with the job of designing a cooling system for Navy landing craft. Taking this assignment in his stride, Mr Fernstrum designed and invented a successful prototype within six months. This innovative design is still used as a base for all Fernstrum products.
The company has a rich heritage with generation after generation taking the helm – leading the business into its next stage of life. This strong familial atmosphere spreads into every aspect of the company’s operation.
With employees from multiple generations, Fernstrum has created a welcoming and loving atmosphere for all involved. “We always want to ensure the work environment is safe and clean for our employees,” President Sean Fernstrum said, “and having that assurance pays off. Our people don’t leave, so we must be doing something right.”
When speaking on the topic of the company’s impressive turnover, Mr Fernstrum commented warmly: “People come to me and say, well, what kind of turnover do you have at your company? Well, I’ve got apple, I’ve got cherry, I’ve got blueberry!”
This convivial attitude is extended to the company’s customer base too. Fernstrum prides itself in maintaining long-lasting and profound client relationships. “We’ve got to be able to meet all our customers’ needs,” Mr Fernstrum said. “We want our company to expand, and the best way to do that is to keep doing the things that make us successful. We take care of our employees, our representatives, our customers; we make
sure we’re meeting all their needs and try to figure out what they may want – before they even realise what they need themselves.”
With 35 employees based in Menominee, Michigan and 18 international representatives, Fernstrum has covered all its bases. The company is proud to be a strong international contender. “The US Chamber of Commerce says that only 1% of businesses in the US operate internationally,” Mr Fernstrum said, “and that’s just in at least one international country. Only half of this 1% do business in more than one country.
“On average we do business in 50 different countries annually. We are this little place, tucked away in the upper
peninsula of Michigan, but we’ve got this global reach. We’re on every continent including Antarctica. You’ll find our products everywhere.”
The company’s products can be found in a huge range of products and places, including ferries, pumping stations and even autonomous buoys.
Fernstrum’s latest investment saw them partnering with Omega Thermo Products –a company whose family-centred philosophy aligns perfectly with Fernstrum’s ethos. The Omega Laser Plate is highly sophisticated in design and can be used in closed-circuit heating and cooling systems. The Laser Plates are always custom made to ensure the very best fit for clients – this includes adjustable welding patterns, plate cut-outs and plate shapes.
“The Laser Plate is such a refined product,” Mr Fernstrum said. “Not only does Omega make the heat exchangers, but they also build, design and engineer the CNC welding equipment that is used in the production of the laser plate exchanger. They really know how to dial in that laser technology to make the best use of it during production. They’ve got some highly skilled and knowledgeable metallurgists, in addition to their amazing engineers.”
Omega Laser Plates consist of two stainless steel sheets with a space between them; the edge of these plates is welded to a contour using Omega’s laser welder – the
hollow space is then used by a heating or cooling medium. The use of thinner materials and the implementation of Omega’s expert welding system makes this product highly adaptable to any space. With a highly successful entrance to the market, the product has received huge interest. Despite global supply issues, Fernstrum has ample resources to continue creating these systems. “We’ve been around a long time,” Mr Fernstrum said; “these aren’t the first supply chain issues we have witnessed. We learned in the past to always ensure we had material in-house; that’s why we don’t have the kind of shortages other companies have suffered with. We invested heavily in inventory to ensure we could cover any customer needs.”
The GRIDCOOLER® keel cooler is perhaps the company’s most well-known product. A first-class system, Fernstrum’s keel cooler is unmatched in design. Featuring rectangular tubes instead of the more conventional round tube, the Keel Cooler is
highly efficient – enabling the company to concentrate heat exchange effectively.
“We expect a minimum product operation time of 20 years,” Mr Fernstrum said. “Another positive aspect is our use of 90/10 copper nickel. By avoiding the 70/30 ratio of monel, we get a 30% boost in heat exchange. On top of that, our high copper content also provides a fantastic antifouling material, removing the need for coated heat exchangers. By incorporating 90% copper, we clear the 80% threshold that’s required for barnacles and other marine growth.”
The company also partnered with WEKA Marine to produce WEKA Boxcoolers. WEKA has the only 90/10 copper nickel boxcooler on the market. Similar in operation to a Fernstrum GRIDCOOLER® keel cooler with the added protection of a seachest, customers can have peace of mind that these systems will be secure and safe from any underwater obstacle.
Ever-flexible, Fernstrum is highly adaptive when it comes to customer needs. The company is always excited
to find the perfect solution to a customer’s problem. Whether it is a one-off product, or a solution that turns into a continuous product line, like their Z series flanges, Fernstrum will complete the request.
Exponential evolution
Fernstrum’s future is brimming with possibilities. With growth at the forefront, the company plans to expand into more countries whilst maintaining and finessing its current client relationships.
Renewable fuel sources are becoming more popular in the marine industry, because of this, the company has been looking into the best ways to further evolve its products; the move to renewable energy would require a different type of heat exchange. Fernstrum hopes to release systems for these vessels in the future. The company has also invested in a new CNC mill. This large machine is expected to arrive halfway through 2023 and will effectively ensure the continuous evolution of its products.
Whatever steps Fernstrum takes next, all decisions will be made with great care and attention, and with its clients in mind. Robert Fernstrum cared deeply about his customers and those around him – this legacy is still evident in the company’s ethos. “My grandfather started a scholarship fund in 1996,” Mr Fernstrum concluded, “giving out eight scholarships a year. Since then, we have given out over $1 million in multi-year scholarships and helped over 60 people get a degree. My grandfather really was quite a guy.” n
seven seas, five oceans, one voice
baltic workboats marsun shipyard penzance dry dock atlas decommissioning
toBaltic workboats has over two decades, experience in the shipbuilding industry. With an overwhelming expertise in ship building, the company has now turned its hand to electric boats – creating more sustainable vessels in the process. Head of Sales and Marketing Rimo Timm discussed this progression alongside the company’s latest projects and its ability to overcome adversity, in conversation with Imogen Ward.
ASbusy as ever, Baltic Workboats is continuously producing exceptional vessels. With a more recent focus on renewable energy sources, the company is doing everything to ensure a positive environmental impact Furthering this, the company currently has two windmills and an array of solar panels that fulfil the shipyard’s entire energy demands. Hoping to broaden the impact of its solar energy, the company is also
looking to expand its panel numbers –having previously installed these on the roofs of its shipyard buildings.
Known for its manufacturing quality, Baltic Workboats has a wide array of projects on the go. From diesel-powered workboats to the more recent demand for electric propulsion in ferries, the company is consistently adapting to any customer request.
With a varying portfolio, Baltic Workboats designs and manufactures ferries, patrol ships, pilot vessels, tugs and workboats. Each type of boat also comes in a range of models. This includes10 types of pilot boat that range from 12m to 24m, all of which include the company’s innovative, patented wave-piercing technology. This enables the vessels to cut seamlessly through high waves – making them extremely efficient when at sea.
The company’s flexibility also enables it to produce eight different types of ferries. These start at 16m and include
a triumphantly large electric ferry just shy of 100m. Featuring three electric models and one hybrid, Baltic Workboats is reinforcing its commitment to sustainability.
Since its last interview with Inside Marine , Baltic Workboats successfully overcame several global challenges. Undeterred by the limitations brought on by the pandemic – with 14 vessels being commissioned during this time – the company found itself adapting to Covid restrictions using Virtual Reality (VR).
“Our engineers were in communication with the commissioning committee for these projects,” said Head of Sales and Marketing Rimo Timm. “The equipment manufacturers in Germany instructed our engineers via the commissioning programme remotely, using the VR.”
Baltic Workboats also used this software to supply clients with vessel progress pictures. The company is now implementing this technology with further clients. This practice has enabled the completion of commissioning and trials on a remote basis After seeing how useful this technology is, the company has now committed to using VR after the pandemic. This has saved the customers and Baltic Workboats valuable time and money.
Forming a separate research and development department this year, Baltic Workboats has shifted focus toward innovation to ensure its products evolve with the times. Concentrating efforts on new platform technologies and investing time into reducing the ecological impact of its vessels, the company continues to expand its electric fleet.
Three fully electric vessels are currently in production, including a 30-metre catamaran and one 19-metre passenger ferry and one 12-metre pilot vessel. The company also experienced an increasing demand for electric pilot boats. With a top speed of 25 knots, these vessels are perfect for short journeys and charters that are focused more inland.
“We really see that there is a market requirement for these vessels,” said Mr Timm, “especially on rivers and lakes where the journeys are shorter, and charging is only required for a short time.”
More recently, Baltic Workboats signed its first ever contract in Canada. Agreeing to this exciting opportunity, the company will deliver a PILOT 17 WP boat to the Laurentian Pilotage Authority (LPA) in first half of 2023. This vessel will also feature an IMO III exhaust system, which ensures the
reduction of nitrogen oxide, effectively squashing LPA’s environmental impact even more.
“Baltic Workboats saw that it could offer a new product in Canada,” said Mr Timm, “and the technical requirements matched the company’s product range well. We are now working really hard to deliver top quality products to the Canadian market. Hopefully, in the future we can use this contract as a reference to gain more commissions in the area.”
The company is constantly improving its products and assessing current market availability. Because of this investment, Baltic Workboats is extremely flexible, quickly adapting to situations where necessary.
“We haven’t expanded the facilities at the moment,” Mr Timm said, “but we have all the permissions required if the opportunity occurred for building bigger vessels than our facilities can currently handle.”
Looking forward, Baltic Workboats has several plans in place to ensure its continuous success.
Baltic Workboats is considering packaging its integrated alarm, monitoring and control system (IAMCS) as a branded product for sale in the marine market. This investment is in response to huge interest during recent exhibitions. The company is experienced in the production of IAMCS, having developed the system over the past 10 years. Highly flexible, the system can be designed precisely to customer requirements, which is proving extremely popular with Baltic Workboats’ current customers.
Following such a successful year, the company also intends to put its research and development team to work on economical solutions. With a highly experienced and dedicated team, Baltic Workboats has been boosting its operations to curb the impact of inflation within the energy sector. The company is optimistic for next year, and more specifically the future of the supply chain, predicting an improvement on delays.
Very happy with current production figures, the company has successfully matched last year’s rates. The company has also filled up contract slots for 2023. Regardless of the current instability of the marketplace, Baltic Workboats is resilient and confident in its position.
Having dealt with recent supply issues –waiting upwards of four months for certain vessel parts – Baltic Workboats has depended greatly on its reliable suppliers. Ever loyal, the company is continuing to nurture these relationships. Working in partnership with vital suppliers, such as Volvo Penta, Kongsberg and ZF among others, Baltic Workboats conceptualises excellence and brings its pragmatic and effortless visions to life in all different forms.
“Our suppliers are so important to us,” Mr Timm concluded. “We are doing everything we can to maintain good relationships with our suppliers and are working in partnership with them to find solutions and get our deliveries to our customers as quickly as possible. It is so important to keep everybody in the loop to avoid any misunderstandings.” n
Established in 1980, Marsun Shipyard started out making small speed boats and passenger ferries in Thailand. But such humble beginnings did not last. These days the company makes naval patrol ships, yachts, and commercial vessels for the marine or offshore industries, as well as offering a repair service. According to Mr Wutthiwat Atthaseriruj, Vice President of Sales and Business Development, this is only the beginning. He explained to Hannah Barnett how Marsun is now hoping to take on the world.
Located near Bangkok, at the mouth of the Chao Phraya River i n Samut Prakan province, lies the Marsun Shipyard. The site covers an area of up to 50,000 square metres including the building and assembly workshop. It is capable of outfitting and launching vessels up to 80 metres in length.
After more than 40 years in the business, Marsun boasts an extensive roster of past vessels delivered, numbering over 330. The company has also provided consultation on design, construction, and repair to meet wide-ranging requirements for both domestic and international customers. It has produced more than 80 vessels for the Royal Thai Navy alone. The shipyard has also branched into the commercial sector, providing vessels into operation for renowned oil and gas companies including Chevron Thailand, PTT Exploration and Production, and Petronas.
Marsun has earned its reputation as a high-quality and wellproven shipbuilder. The company emphasises on-time delivery. Its vessels must meet strict stipulations and achieve a performance evaluation in both pre-delivery tests and during trial periods. Customer satisfaction is everything.
As Mr Wutthiwat, Vice President of Sales and Business Development, explained: “we are experts in building highperformance, high-speed, advanced vessels in aluminium and steel, for both governmental and commercial work.”
The quality of the in-house engineering at Marsun is one of the key elements that sets it apart, according to Mr Wutthiwat.
With over 40 experienced in-house designers specialising in different fields, the company can easily customise a vessel to clients’ requirements and provide a bespoke service. This allows Marsun to offer services from shipbuilding to ship interior design, for both the military and commercial offshore industries.
“Many of our designers are marine engineers. So, it’s well within our ability to do the design ourselves. We have all our knowledge on vessel design, and we can customise and tailor-make it for the client’s requirements,” said Mr Wutthiwat.
Marsun is keen to invest in the latest technology to increase the capabilities of engineering, manufacturing, and quality assurance among its workforce. The company says it encourages staff to study and research ship designs by themselves to maintain the highest efficiency and to ensure Marsun remains one step ahead of any competitors.
Mr Wutthiwat showed how this flexible approach can be beneficial: “Most of the military patrol boats that we built are our own design, but we have good connections and are open to work with any reputable designers worldwide for any vessel design for commercial workboat projects.”
The company will work from an external designer’s blueprint at first. “From that basic design until class approval,” he continued; “then we use our authenticity and credibility to do the detailed design, together with the outside designer.” This allows for what Mr Wutthiwat described as a ‘seamless and efficient’ design phase throughout the construction period.
It is not only old, failsafe, ship designs the company works with. One of the places these advanced design capabilities are being put to the test is with an ongoing project to build the very first High-Speed Craft Passenger Trimaran Crew Transfer Vessel (CTV) in Asia, for an offshore wind farm in Taiwan. The Trimaran CTV was partnered with WIND Naval Architects and One2Three Architects. “This is an advanced, really complicated and sophisticated design ,” said Mr Wutthiwat. “Likewise, to other advanced designs, we are willing to take on the challenge to build any innovative vessels.”
The company has an eye on the cutting edge of the market. As with many industries, that looks to be in the sphere of sustainable, renewable, electric vehicles and, in this case, vessels. “At the moment we are enabling innovation,” explained Mr Wutthiwat. “We are working on the development of new technology like unmanned surface vehicles for offshore oil, gas and survey applications. We are looking towards R&D in that area.”
Unmanned Service Vehicles (USV) are boats or ships that operate on the surface of the water without a crew. As Mr Wutthiwat said, Marsun has been investing in the IP of USV “for several years now.”
He expanded further on this burgeoning market: “Right now we're talking about drones and USV. So that's one thing that’s growing, and another is people are trying to develop the best solution for EV (Electric Vehicles). People are developing a lot of electric vessels for example, for offshore wind farms. A lot of developers give
subsidies to the ship owners, who provide a green and decarbonised net-zero type of vessel, that is the trend at the moment. We want to serve the customer in that sector and stay on top of the game.”
Marsun is clearly a future-facing company. Not only in its adoption of modern technology, but in its own endeavours too. The shipyard has hopes of expanding its products to service customer needs worldwide from Asia Pacific, Middle East and Europe to West Africa. Mr Wutthiwat considered this sort of move would make sense with the company’s established goal to move to achieve 30% of its sales from the domestic market and 70% from the international. It is a goal Mr Wutthiwat is staying focused on: “That is our future.”
There is no doubt it is an exciting time at Marsun Shipyard. Mr Wutthiwat spoke to Inside Marine as the company prepared to launch itself on the Thai stock market, hoping to gain momentum and investment from going public.
“We want to tell the world that we are here,” Mr Wutthiwat reflected. “We have a proven track record as a shipyard, especially in terms of high-performance, high-speed vessels, with a customercentric mindset. And right now, we are ready to service the commercial offshore industry. So to any shipbuilder, any operator, any player that's looking for a trustworthy, high-quality partner in Asia, to deliver the vessel anywhere around the world; we are the perfect partner, and we are ready to take on any challenge.”
Having worked in the offshore and marine industry internationally for his entire career, it is patently clear that Mr Wutthiwat is passionate about the venture. The Vice President of Sales and Business Development stated he has confidence in the company’s manufacturing capabilities and is passionate about helping Marsun Shipyard fulfil its potential in the world arena. “It is my calling,” he said. n
What is exciting about Penzance Dry Dock in Cornwall, is that it is a hybrid of old and new. It is a site of historical significance, steeped in maritime history, but it is also an up-and-coming company at the cutting-edge of new industrial developments. CEO Jamie Murphy is at the forefront of its growth. He described its illustrious past and bright future to Hannah Barnett.
Penzance Dry Dock was established in 1815. By 2021, after more than 200 years and with the decline of the shipping industry in the area, it faced closure.
That was where Linked Solutions stepped in. A manufacturing, marine engineering and consultancy business, its founder, Jamie Murphy, is a Cornwall native with four generations of family having worked at the dock. He is now the CEO of Penzance Dry Dock and made saving it a passion project that he was willing to go to any lengths for. “I put my house on the line to secure funding,” he said.
Penzance Dry Dock were the perfect fit for the recently formed Linked Solutions, and for Mr Murphy himself. “Industrial decline has been on my radar since I was a child,” he explained. “When I left the Navy, and I saw the state the industry was in across the UK, I started Linked Solutions. I use my personal relationships with suppliers and people who owned manufacturing companies.”
Since Linked Solutions took over, Penzance Dry Dock has quadrupled staff members, won a rising star of industry award, and launched the first apprenticeship scheme seen on-site in over 25 years.
Its location in the west of Cornwall makes Penzance Dry Dock a key strategic point for mariners crossing the Atlantic. When he took over, Mr Murphy was keen to utilise this potential, and attract all types of vessels ‘whether it's defence, commercial, or private yachts.’
Linked Solutions’ diversification was another significant aspect of the restructuring process. “We took the machinery that was only working at a 50-60% capacity,” Mr Murphy said, “and opened it to an element of industry that it hadn't been exposed to before. We commissioned a production line, which was the first one ever at Penzance Dry Dock We encouraged manufacturers to diversify, and it works.”
With one foot in the past and one eye on the future, Mr Murphy explained how the industrial revolution ‘started in Cornwall’ and continues today in a different form, with the ‘green energy’ offered by offshore wind farms.
He continued: “We are well equipped to offer logistical solutions and engineering support, like running crew transfer or support vessels. We are perfectly positioned to support every element of the industry.”
The company has also applied for a shared prosperity fund, to enable a complete refit of the site. After decades of neglect and mass dilapidations, it is vital to bring the yard up to an even playing field with other shipyards in the UK. “That's going to allow us to deliver with the full scope of the offshore wind project,” Mr Murphy said.
A hive of activity
Mr Murphy described Penzance Dry Dock as a now bustling site, with plenty of projects on the go, ’36 completed in our first year’ he said. There are around 40 full-time staff members, up from six at the time of takeover, including ‘labourers, fabricators, project
managers, team leaders’ as well as people working on projects up the coast, in London, or overseas.
Mr Murphy continued: “Our first year was the first time in decades that Penzance Dry Dock used all of the spaces available to it. We've got a UK Border Force vessel that's in the Wet Dock. There's not been a Border Force vessel that’s had a Penzance Dry Dock contract in over 30 years. We’ve got two ships in the Dry Dock. And we've got two mass fabrication projects going on in the workshops, one of which is the largest mass fabrication project the company has ever had since the yard’s formation in 1815.”
The scale of this growth is taking the company beyond Cornwall, to an international level. Mr Murphy revealed that the company hope to soon be building and developing a deep-sea fishing fleet in Zanzibar: “When this comes to fruition, we will be building 15 ships. It will be the largest commercial shipbuilding contract Cornwall has ever seen.”
The project will enable a collaboration with the well-established Tor Group shipbuilders, Macduff Ship Design, Kort Propulsions and Wills Ridley. “We're all in it together,” he said. “They can help us to deliver a build, by bringing their specialties, their products and their expertise to the table, to mitigate the risk.”
Everything that goes on at Penzance Dry Dock is a collaborative process to some degree and Mr Murphy was keen to emphasise that. From the relationships that helped save the dock in the
first place, to the everyday ones that keep the business afloat day-to-day and the future ones that are allowing for its expansion.
“It’s all about relationships, you've got to maintain relationships, whether that's your neighbours, or your nearby yards, or the people within your workforce,” he said. “We're in constant talks with other shipyards around the UK, to see how we can help each other. In modern Britain, we must focus on our own industry and become more self-reliant. We've all got to work together, right across the country.”
Unsurprisingly, with such an optimistic attitude, Mr Murphy was serene about tackling some of the challenges currently faced by all industries. “Communication is key,” he reflected. “You can't help the global crisis; you can't help the energy crisis. You just have to make sure you're communicating that the prices have gone up because of x, y, z to your client, as your suppliers do to you. Everyone’s in exactly the same situation.”
The company extends this partnership ethos to its own workforce. Mr Murphy said that saving Penzance Dry Dock has benefitted everyone involved ‘even the council.’ He continued: “It's having a huge knock-on effect. There is not a single member of staff who is on minimum wage. To be down in West Cornwall and have a job which isn't on minimum wage, is a gift from God, in a way.”
Additionally, Penzance Dry Dock incentivises its workforce by making it ‘part of’ the company itself: “We also offer a profit share: the better we do, the better the individual does.”
The horizon looks hopeful for the company. Mr Murphy said it wants to move into supporting the defence sector with government contracts, as well as doing more ship builds, continuing to diversify and to support the green energy sector.
As stories of triumphing over adversity go, Penzance Dry Dock has a good one. Perhaps most significant is the way the company’s success may also offer hope to the individual. Mr Murphy may be a CEO now, but he has worked his way to the top. As a result, he was keen to stress the significance of the company’s apprenticeship scheme: “It’s what I really care about. I started off as an apprentice many years ago. And now I’ve got two engineering companies. There is nothing to stop any of our apprentices from being sat at the top one day.”
All but abandoned for two decades, the UK’s largest dry dock is primed to become a decommissioning hub and centre of excellence. Despite recent setbacks, Mike Dixon, Managing Director of Atlas Decommissioning, remains convinced the need for such a project remains promising, if long overdue. Report by Colin Chinery and Andy Probert.
Inchgreen Dry Dock is a former Scottish shipyard that knows the majesty and the misery. The dry dock where the QE2 was fitted out in 1966 has lain idle for the last two decades; its cranes lost to the Clydeside skyline.
One of the largest dry docks in Britain is poised for regeneration as a global ranking, end-of-life decommissioning hub for vessels and marine infrastructure. But even that journey has not been without its frustrations.
“Our vision is to grow Inchgreen to become a centre of decommissioning excellence,” said Mike Dixon, Managing Director of Atlas Decommissioning. This Teesside company secured a long lease contract from Inchgreen Dry Dock’s owners, Peel Ports.
As well as the operating dry dock, the 25-acre facility in Port Glasgow includes an adjoining repair quay and direct access to very deep water. “I’d go as far to say it is unique in the UK; a fully functioning
dry dock with a great in and out access that will enable us to ship 30,000-tonne coasters to the Far East, for example,” said Mr Dixon.
Acknowledging Inchgreen as “a jewel in Scotland’s crown”, Peel Ports says it remains committed to bringing it back to full industrial use and sees the new project as a “game changer.”
Mr Dixon is keen to assuage ‘Scotland’s largest scrapyard’ misapprehensions.
“What we are doing here is essentially shipbuilding in reverse, requiring much of the same engineering excellence and expertise, with some transferable skills, often involving complex operations. The process is a lot cleaner when compared with shipbuilding processes.”
However, no path in business is straight and true. 2022 has proved frustrating for Atlas Decom, part of Atlas Commodities. In March, without having secured work, the
business was forced to let several workers go. This was further compounded in August with its biggest setback when the potential to decommission the Foinaven FPSO went to Denmark.
Mr Dixon commented: “We’re bitterly disappointed as we were engaged in that process for around 12 months. And to be engaged on that for so long and not be given the opportunity to showcase what we can do was deeply frustrating.”
He added: “Despite this, we are still actively pursuing oil and gas and smaller commercial vessels projects. We are also in the process of having our EU accreditation rubber-stamped. That’s another step forward.
“We are working closely with specific organisations with strong ESG policies to champion environmental solutions to dispose of these assets responsibly. We remain convinced Inchgreen is one of significant untapped potential, and we invite clients and partners to consider what we have to offer.
“We will turn the tide of frustration that we have experienced into one of positivity. Atlas Decommissioning remains alive to market opportunities.”
What Atlas Decom brings to the table is a partnership of niche engineering skills, processing, and the commodities market. “Our leaders are experts in shipping, metal processing, and commodities; a combination that is helping us to close the loop and maximise our market potential,” he added.
Offshore decommissioning has increased significantly over the last decade and is estimated to reach $8 billion by 2027, a projected 7.4% CAGR. The UK is poised to lead the way as operators increase spending on North Sea decommissioning work, according to research company Rystad Energy.
“It’s a huge opportunity for the future,” said Mr Dixon. “But with a lot of the a ctivity and work on the engineering side –ensuring wells are plugged and abandoned,
“ “
Our leaders are experts in shipping, metal processing, and commodities; a combination that is helping us to close the loop and maximise our market potential
for example, the end-of-life structure processing we undertake is only a small fraction of the money being spent.
“However, if we can maximise our capacity across different sites, and with our unique combination of both the shipping and commodities experience on board, we expect to be one of the front runners.”
Responsible and sustainable
Efficient decommissioning is long overdue for a global industry where a disregard for basic worker safety and shameless exploitation have attracted odium. More than 70% of end-of-life vessels end up in South Asia, where they are broken down under rudimentary conditions on the beaches of Alang- Sosiya in India.
The ship recycling industry has also long been under pressure to reform health and safety. Slow progress is finally being made to reduce deaths and serious
injuries, with Atlas Decom placed to become a leading example.
Metals are well suited for reuse and remanufacturing and are almost infinitely recyclable. China, the world’s biggest metal user, plans to boost steel scrap usage by 23% in the next five years.
The UK Research and Innovation, a non-departmental public body, also aims to make the UK fully circulate all its steel and aluminium, minimising or eliminating the extraction of raw materials and waste production.
“People now increasingly realise the importance of having an endless supply of steel – an opportunity to
recycle numerous times,” said Mr Dixon. “This will dictate where we send our materials, which will largely be mainland Europe or the Far East in the short to medium term.”
He added: “Inchgreen offers an excellent opportunity to bring the industry back to an area with a great shipbuilding tradition, maximise the site, and regenerate it as a centre of excellence. I don’t use that term lightly.
“We want to create a facility that allows end users and clients to want to bring their vessels and structures in for end-of-life disposal and bring economic regeneration to the area.”
Inverclyde’s economic woes are welldocumented: its 5.2% unemployment rate is a bleak counterpoint to its long, proud shipbuilding tradition. If the FPSO had come through, Atlas Decom had plans to create 60 local jobs.
In concluding, Mr Dixon confidently asserted: “Atlas Decom remains focused on responsible and sustainable decommissioning. We are at Inchgreen not just as a quick fix, but as a long-term solution over the next decade and beyond. Our ambition is to create a legacy. It’s what we intend to do and what we will be pushing for.” n www.atlasdecom.co.uk
seven seas, five oceans, one voice
ancora chile frank weber goodpack
Ancora Chile has become one of the mainstays of the support sector enabling the country’s aquaculture industry, primarily salmon, to continue meeting international demands. Now offering a diversified approach, the company represents 15 global brands, offering an unmatched service at a local level. Report by Andy Probert.
Ancora Chile may have been operational as an independent technical company since 2015, but it has more than three decades’ prior experience in delivering commercial services to the localised naval and fishing industries.
The workforce of 30 people represents 15 brands through its offices in Concepción and Puerto Montt, repairing and maintaining units such as azimuth systems, ship thrusters, gearboxes, transverse propellers, deck equipment, vacuum pumps, reverse osmosis plants, UV systems, sewage treatment plants and marine cranes amongst other equipment.
This multi-level, expert approach grew from a commercial department set up in the mid-1980s by Valdivia shipbuilder Astilleros y Servicios Navales (ASENAV),
primarily to serve the requirements of fishing vessel owners.
The commercial office rapidly expanded to cope with the economic boom of Chile’s fishing sector. By the 2000s, following the sector’s decline, the unit was based from a sole office and refocused on tugboat and ferry companies.
Further consolidation followed with a move from Talcahuano to Concepción, and a second office opened in 2006 in Puerto Montt to meet the demands of the aquaculture industry.
In 2015 ASENAV's Commercial Division began to operate independently under the name of Ancora Ltd. It immediately took charge of all representations of global
equipment brands serving the aquaculture and naval industries, and projects related to the aquaculture industry.
Ancora’s portfolio now includes a number of leading brands including Schottel propulsion systems, Reintjes gearboxes, marine cranes, boats and davits from Palfinger Marine, CanaVac fish pumps, Hamann AG sewage plants, Norwater fresh water generation systems, Bernoulli water filtrations, Deepchill liquid ice, Samson liquid ring vacuum pumps, Stranda Prolog fishing pumping solutions, Ultraqua UV disinfection systems, Winteb vent heads and Steen deck equipment.
“Utilising the quality products of these brands, we offer a world-class platform of unrivaled services for clients,” emphasised Juan Pablo Gómez, Ancora’s General Manager.
Another element of the Ancora business model is delivering solutions tailored to the client’s specific needs, primarily to the aquaculture market. It has extensive experience in Tanktainer-to-plant unloading systems, Tanktainer loading systems from ships, and fish pumping systems.
For on-site and on-board harvesting systems, Ancora has developed modular transportable pumping systems, either to suck live fish over the side of culture cages or the side of a wellboat and unload them onto a harvesting table.
Ancora Chile’s dockside Tanktainer loading system enables a vacuum pump to suck harvested fish from ponds into a barge before being loaded onto two tank trucks.
The company also manufactures power packs with vacuum pumps, stainless drain
tanks for fish pumps, electrical power and control panels, and water backwash systems in wellboats.
Ancora Chile’s knowledge of black and grey water treatment systems allows its teams to offer a specialised technical service in physical-chemical treatment systems.
In 2021, all the energies and experience of the Ancora team were combined to help the company supply and install part of a system for a primary salmon processing plant in the Puerto Natales area of southern Chile, which brought its turnover to a record compared to previous years.
In fact, one of the company’s main success stories of recent times was supplying Australis Seafoods, a Southern Chile-based company, with primary processing
plants from Norwegian-based Stranda Prolog. These include fish pumping systems, Helix ponds for fish cooling and bleeding, vacuum plants, sorting tables and dewaterers; essentially all high-tech equipment designed to promote the best hygiene standards and low environmental impact.
Mr Gómez said: “We continue to provide maintenance to 90% of the total equipment that we supply to clients in Chile, and are looking to provide these services to entities across South and Latin America as we have a lot of knowledge to offer.”
Ancora Chile also supplied a water treatment and purification system, the marine cranes, transverse thrusters, reactor UV and the fresh water generation system aboard the world’s first salmon processing vessel, the Owurkan, to treat common aquatic pests and diseases.
The ASENAV Shipyard-built vessel is equipped with a large reverse osmosis facility to provide 125 cbm of fresh water per hour for some treatments, and a continuous filtration system to remove sea lice.
Three years ago, another ASENAV build, the Magellan Explorer was developed specifically for Antarctic air-cruise operations, under the specifications of the Polar
Code. Ancora Chile supplied two Hamann sewage treatment plants; Palfinger marine cranes, boat davits and abandonment boats and a Reintjes reducing box.
With a capacity of 100 passengers, plus 60 crew, the Magellan Explorer has a Polar Ice Class PC6 classification, allowing it to navigate in frozen waters for long periods without calling at a port.
“It is with tremendous pride to have been part of these ground-breaking projects,” commented Mr Gómez. “We continue to work with clients, furthering their projects with the supply of world-class products represented by Ancora and to ensure their needs are always met.”
Meeting these demands is dependent on the company’s flexibility in overcoming the difficulties in meeting delivery time deadlines and supply chain issues, he said.
“Our competitors are generally global, but the supply of quality equipment into the aquaculture sector, for example, in Chile, generally comes down to Ancora Chile. That is a major advantage to us. We are global, but ultimately local, thanks to the experience and availability of our excellent technical service team here.
“This came to the fore during the pandemic as competitors who don’t have localised technical service units were hampered by travel limitations and flight restrictions. Clients increasingly turned to us to solve aftersales issues, warranty and service problems, and supply of spare parts.”
Mr Gómez concluded: “Clients see us as an essential partner. Undoubtedly, Ancora Chile’s representation of global brands has been a key and enduring factor in our successful business relationships for many years.” n
Frank Weber GmbH has owned Borkum Bunker Station for more than 25 years. A family-run business that offers a uniquely friendly and helpful attitude to all its customers, the bunker station is renowned with all who refuel there. Managing Director Frank Weber, Bunker Service Manager Petra Schnell, and Ilona Weber (who organises vessels and services) discussed the bunker station’s success and the different ways that they ensure customer satisfaction each and every day. Report by Imogen Ward.
Borkum Bunker Station is the epitome of hard-work and positivity. With a delightful team of enthusiastic individuals, the bunker station runs off the passion of these workers. They always go above and beyond to ensure the very best service for those refuelling at Borkum Island.
“You must love what you do,” Frank Weber said, “that is very important; if you make a business only about money, then it won’t be as strong as if you make it with heart. Borkum Bunker Station is our baby. When we first started, we worked 24/7 to ensure it would thrive. It’s much bigger now, but it’s still our baby. I think that essence really shines through to our customers.”
The welcoming atmosphere at Borkum Bunker is renowned throughout the shipping industry. The names Frank, Ilona, Petra and Bogdan pass from vessel to vessel, known as warm and friendly individuals who go the extra mile to help their customers.
Found in the idyllic setting of Borkum Island off the North Sea coast of north-western Germany, the bunker is located on the south pier of Borkum harbour. This family-run business is a hub of activity 365 days a year and has been since Frank Weber bought the company from his uncle 26 years ago.
With three trucks in-house (two 40 ton and one 16 ton), Borkum Bunker ensures swift delivery of fuel to its customers, as well as to the surrounding Island of Borkum. “We use our small truck for the island,” Bunker Service Manager Petra Schnell said, “to fill up our diesel filling station, and also as support for our larger trucks. When there is a large amount of fuel to transport, our 16-ton truck can cover the excess.”
The island has a regulation of 12 tons; therefore, the company utilises its smaller tanker for transportation of fuel around the island. This ensures that the bunker station can aid those residing on the island too, including anyone who moors near the beach.
As part of its promise of first-class service, Borkum Bunker has maintained a strong relationship with one fuel supplier. This decision ensures that the bunker station knows the durability of its goods. “We rely on a sole supplier for our fuel,” Mr Weber said. “If we have a problem, we know exactly where that stems from, whereas, if we had a whole slew of suppliers, it would make it much more difficult to locate the source of the issue.”
As a result, Borkum Bunker knows its vehicles are reliable and, hence, successfully minimises any risk of delivery delays that could negatively impact customers.
The bunker station’s latest investment in automatic overnight fuelling (11pm-6am), will also provide its commercial customers the highest quality of fuel 24 hours a day. This addition will be available to customers in 2023 and gives customers the option of self-service filling.
Over the past years alone, Borkum Bunker has supplied 200 different CTVs. “The number of vessels we see each month is really different,” Ms Schnell said, “it can range from 1 to 30 depending on the time of year.”
“Now, because of the wind farms nearby,” Ms Weber added, “it is normal for us to have a variety. Currently, we have ten because it is winter. Whereas, during 2020, with Covid, we saw 32 vessels refuelled daily in one month. Summer is always busier than winter too, because the contracts start around April / May and go through to October.”
To ensure that everyone arriving at Borkum Bunker gets the very best service, the bunker station works in partnership with Maritime Offshore Solutions (MOS) who offers repair services for ships refuelling at nearby Borkum. MOS has divers to perform underwater inspections and repairs, and engineers to fix any electrical faults relating to the onboard systems (including ship automation, navigation and hydraulics).
With an added touch of luxury, there is also a choice of accommodation on the island. The Borkum Hafen Immobilien offers all those who work in the offshore sector – technicians and crews –the opportunity to get a good night’s rest away from their vessel.
Borkum Bunker is extremely flexible when it comes to customers’ needs. The bunker station serves commercial and private boats, and also has an additional diesel filling station for trucks and cars. The company works in partnership with EPAS in Emden to ensure food, and any other provisions needed, arrive on time for the vessels.
On top of this service, Borkum Bunker goes above and beyond to make sure the crews onboard are being looked after too, “When the crews need food or other stuff,” Ms Schnell said, “we pick it up for them and bring it to the vessels. When they need something they cannot buy on the island, the crew have it delivered to our office, and we bring it to the vessel as soon as possible.
“Even the technicians on the windfarms, they order their parcels to us, we give it to the CTVs and then the CTVs bring it down to them. We have created a very good network here.”
This reinforces the company’s customer-first attitude – going the extra mile and maintaining an honest reputation.
The staff at Borkum Bunker always look forward to seeing their regulars arrive. With a familial atmosphere engulfing the bunker station, this extends to all new customers too. Frank, Ilona, Petra and Bogdan are always happy to meet new people and assist them.
“It is a great feeling for us to be able to say we are close to our customers,” Ms Weber concluded. “It’s so important to love what you do; it reinforces the success of a business. We are family here and that sense is reflected in our customers; every single person is important to us and we are always happy when we meet again; they say it’s just like coming home.” n
Based in Singapore, with a global network of depots, Goodpack has over 30 years’ experience delivering efficient, integrated supply chain solutions via a network of strategically located global depots and fleets of returnable containers. Chief Operating Officer Peet Leong Kok, Goodpack Korea Country Manager Chul Hee Chun, and Regional President, Northeast Asia and Global Business Director Synthetic Rubber, Chee Heng Sng, discussed Goodpack’s news and operations. A report by Phil Nicholls.
Disruptions to the global supply chain remain a challenge for almost every business. Logistics experts at Goodpack have developed the innovative RoRo Cube which enables customers to side-step many of the problems affecting the free movement of global trade.
“We have a partnership with Wallenius Wilhelmsen,” President Goodpack Korea Chul Hee Chun explained. “They provide us space on their RoRo vessels, we provide them with packaging solutions and transportation equipment. For example, there has been a lot of congestion in US container ports. However, they use their own terminals, or contracted terminals which are dif ferent from container ship terminals, so once the RoRo vessels arrive they can quickly release their cargo.”
Goodpack began in Singapore in 1990, focused on logistics for the rubber industry.
The company quickly expanded into a global network of supply chain solutions working across multiple sectors. Recent years were dominated by the Covid pandemic and its impact on businesses. Goodpack showed its agility by shifting supply chains to limit the impact on the business a successful process which enabled growth to continue throughout the pandemic.
As a global operation, Goodpack has 350 associates operating across 80 countries with over 5,000 delivery and collection sites spread through six continents. The company deploys over four million returnable bulk containers and supports close to seven million deliveries each year.
The RoRo Cube Goodpack delivers efficient, end-to-end supply chain solutions via this worldwide network of depots. At the heart of this
provision for customers lies innovative container solutions, such as the RoRo Cube
The business concept of RoRo Cube was developed alongside Wallenius Wilhelmsen, a global market-leader in RoRo shipping with a fleet of over 130 vessels operating on every ocean.
“We realised that a container box would be a good solution for a RoRo vessel,” Regional President, Northeast Asia and Global Business Director, Synthetic Rubber Chee Heng Sng said. “So, we looked at ways to work with Wallenius to find a product offering our customers an alternative to how they’re shipping things today. The result is the product we call the RoRo Cube.” Headquartered in the heart of southeast Asia, Goodpack began serving the rubber industry. As the company expanded, it became involved in the supply chain for a range of industries. Goodpack
containers can be fitted with hygienic food-grade packaging. This facilitates transport and storage solutions for food and liquid products.
Another sector for Goodpack is the transportation of chemical products, such as inks, paints and resins. The company’s focus on streamlined transport and storage solutions are also applied to the shipping of components and consumer goods around the world, all customers benefitting from digitisation, payload visibility and speed to market.
“Goodpack enjoys a close relationship with CEVA, the biggest automotive logistics company,” continued Chief Operating Officer Peet Leong Kok. “We’re working with CEVA in the tyre space, with a programme to develop TyreCubeTM to transform the supply chain, using our
container as the de facto movement medium for everything from intermediates – like compounds, bladders and tubes – to finished tyres.
“Our close relationship with Goodpack in developing innovative solutions for the tyre industry is a key factor for our tyre subsector growth strategy. Our ability to focus on automation, digitalization, and circular economy concepts is gaining the right momentum,” mentioned David Dudek, global automotive and tyre sector leader for Ceva.”
The development of new transportation options such as the TyreCubeTM is a crucial part of Goodpack’s growth strategy.
Goodpack relies upon its close partnership with the network of third-party logistics, suppliers, depot operators, trucking companies and freight forwarders. “We think of them as our arms and legs, executing our network,” Mr Kok said.
The company is proud of its sustainability credentials, according to Mr Kok: “Our container solutions have been tested by independent valuers and verification bodies; these containers will last more than 35 years. When compared with a single-use packaging solution, the Goodpack method is definitely much more sustainable in terms of carbon emissions.”
In parallel with the inherent benefits of reusing the containers, often shifting them between industry sectors to meet fluctuations in demand, Goodpack is also investing in eco-friendly improvements within the company. The network of depots is steadily switching over to energy-efficient LED lighting.
From an operational perspective, the greatest challenge facing Goodpack has been the Covid pandemic and the restrictions this imposed on international shipping. Similar limitations also reduced the opportunities for face-to-face meetings with clients, an important part of building strong partnerships. As these restrictions are
A returnable Intermediate Bulk Container made from galvanized metal. RoRo Cubes are suitable for many products, can be stacked safely on RoRo ferries, and are collapsible when not in use.
• Dimensions: 1.46m x 1.15m x 1.09m
• Capacity: Up to 1,500 litres
• Unladen weight: 131kg
now steadily lifting Goodpack can return to normal business practices, meeting clients and colleagues around the world.
Viewing these signs of the world steadily returning to normal, Mr Kok gave a cautiously optimistic assessment: “Economically, the world may be in a soft slowdown. We see good growth in food logistics, as people always need to eat. Goodpack is also looking at EV batteries as a growth market, at least in terms of sustainability and the automotive industry, as announced recently with Wallenius Wilhelmsen. We’re looking into that segment to see how we can be the industry-standard for the supply chain of EV batteries to our automotive customers.”
Alongside this expansion into the distribution of EV batteries, Goodpack is also investigating how to harness the accumulated data from seven million voyages annually. Every year, customers demand better service from their logistics partners and Goodpack believes this wealth of data can add value for its customers.
Goodpack continues to enjoy the strategic benefits of its location in Singapore. “This part of the world remains very exciting,” concluded Mr Sng. “China has been a growth engine for us in the region over the better part of ten years as it continues to grow. Goodpack is excited about the future, helped by being so close to both Japan and Korea. These two countries continue to be at the leading edge of the constant innovation and industrialisation that drives EV technology.”
seven seas, five oceans, one voice
atlantic towage and marine ultratug
Over the last decade, Atlantic Towage and Marine has increased its vessel fleet beyond its Irish south coast borders and is now primed for an addition, with a first-ever new build. Andy Probert spoke to Managing Director Sean Harrington about the company’s ambitions.
ASAtlantic Towage and Marine reaches its 15th anniversary with its founder and Managing Director Sean Harrington still at the helm, the company is looking to up the ante with a fleet addition.
The Ireland-based marine services company has placed its firstever order for a new build with Damen Shipyards for a MultiCat 2309, the latest addition to Damen’s range of highly versatile, multipurpose workboats.
Scheduled for delivery in 2023, it will play an essential role in Atlantic Towage’s expansion beyond Ireland, UK and mainland Europe – and further consolidate its presence.
A fleet of 14 tugs, dive support vessels, and multipurpose workboats, enables Atlantic Towage and Marine to offer a wide range of services, including salvage, ship handling/berthing, towage, surveys, buoy and mooring handing, and pollution response. It also works on various contracts for construction companies and insurance companies.
Based in Bere Island, in the sheltered waters of Bantry Bay on Ireland’s south coast, the majority of the company’s regular work comes from Zenith Energy’s oil storage facility at Whiddy Island, West Cork.
Atlantic Towage and Marine assists in maneuvering oil tankers as large as 300,000 tons but also offers tailored services to help with rig support, guard vessel duties, pilot and line boats, jetty services, and in-shore and shallow water work.
In more recent times – and where the new MultiCat 2309’s versatility will further spearhead its push – is the increasing contract work Atlantic Towage is picking up from the offshore renewables sector in European waters.
Mr Harrington said: “We have seen work increase in the renewables sector in the last 12 to 18 months. We support surveying work for the eventual laying of cables to the wind farms. The new MultiCat will be a warmly welcomed addition and help better cater to our clients’ future needs.”
To optimise the vessel for its role, Mr Harrington has specified a larger forward deck crane, AKC 185 HE4, and an aft deck crane, HS AK34 HE4, from HS Marine, plus a DP1 system from Kongsberg.
It will be the first in its range to operate with a Dynamic Positioning System, while additional customisations will enhance its operational profile and deliver better client service.
While the MultiCat 2309 comes IMO Tier II compliant, Atlantic Towage has selected the option that pre-prepares the engineering space to retrofit a Damen Marine Nox Reduction System. This uses selective catalytic reduction technology to deliver Tier III compliance and, with the space already available, can be fitted as and when.
“We chose Damen based on its reputation in the market, plus we already have a Damen vessel in our fleet which has performed well. We look forward to taking delivery next year and putting the MultiCat to work immediately,” acknowledged Mr Harrington.
Work has been completed on the superstructure at Damen Shipyards Ko ´ z le, and the MultiCat has now been taken to the Netherlands to be fitted out.
It has taken less than a decade for Mr Harrington’s fleet and workforce to more than double in numbers. That reflects the demand for Atlantic Towage’s multidisciplinary services across different marine sectors and Mr Harrington’s passion for working at sea.
Mr Harrington mastered his trade courtesy of his father’s ferry business. “I used to work on the ferries going out to the island. My father owns the ferry service, so I worked there when I was on summer holidays from school and on weekends for years,” he reflected.
This inherited desire to work on the sea is one of the reasons why Atlantic Towage and Marine has continued to expand. “I was brought up on boats. It’s what I’ve always done from a young age and what I will always do. I enjoy my job.”
This passion is the primary driving force that has motored Atlantic Towage into its position as one of the leading companies in its sector. Crews are highly experienced and trained in the towage and salvage industry. A professional onshore management team backs them up to ensure customers’ needs are met with the highest standards.
“We remain a forward-looking organisation that invests heavily to develop our fleet, equipment, and personnel to continue to provide the safest, best and most efficient services,” he said.
The company has also received ISO 90001, 14001, and 450001 and was accredited by DNV.
Keeping its competitive edge, Atlantic Towage boosted its fleet with the twin-engine MV Trojan, which underwent an extensive refit, and now coupled with a deck crane and hydraulic A-frame, its versatility is being deployed for towage and marine projects.
The company further added the Damen-built Tug Ocean Battler. The 19.5m vessel, with a Bollard Pull of 21t, was overhauled at the Macduff shipyard and was put straight to work on the construction works of the NnG Wind Farm on the Firth of Forth, Scotland. She then continued down to Fecamp where she spent the summer working on another renewable energy project.
Mr Harrington said the fleet’s work in recent months had also included salvage of a fishing vessel, buoy deployment and raising a sunken fishing boat outside Cork harbour. But towage, in general, still accounts for about 50% of its business.
The company has also provided vessels in Dublin Port to Zenith Energy for fire-fighting and oil spill response cover, and mooring operations.
Mr Harrington commented: “What sets us apart in the industry is that we are built on generations of experience using innovative technology and techniques, pay close attention to every detail, and if we say we will do it, we do.”
Looking ahead, he concluded: “We want to keep expanding, offering our services to the renewables sector and growing our operations and relevance in European waters. Our new MultiCat will undoubtedly help in that regard.” n
Ultratug is one of the leading tugboat suppliers within Latin America; it is part of the Ultranav shipping group, specialising in the operation of tug, salvage and offshore vessel fleets. With over 15 years’ experience at the group, CEO Cristián Lyon spoke in depth about the current economic climate within the tug and offshore vessel industry with Daniel Barnes and Imogen Ward.
Headquartered in Chile, Ultratug is a diligent, dependable vessel operator. It is currently operational in eight countries; this includes Brazil where it runs PSVs for the offshore sector under a joint venture with Wilson Sons. Ultratug has an impressive crew size of 1000 who operate a variety of vessels including tugs, pushers, barges, OSV´s, and pilot boats, in more than 45 ports across Latin America. The company also boasts an impressive 20 years’ experience specialising in terminal work.
Ultratug is a highly experienced vessel operator: this year alone it completed 30,000 manoeuvres.
The company is always looking to improve its environmental impact. As an example, Ultratug is currently offsetting its emis -
sions in Colombia via the purchase of green bonds. Coltugs has recently been certified as a Carbon Neutral company by Bureau Veritas (BV) with the ISO 14064 y PAS 2060: the first company in the maritime industry of Colombia that complies with the BV standard to measure greenhouse emissions, and offsets 100% of the national operation through green bonds to finance reforestation projects.
Looking to the future, Ultratug hopes to invest in the best renewable fuel source. To do this, the company is doing extensive research into the different new technologies regarding propulsion systems, ensuring that it chooses the most sustainable and reliable source possible.
Cristián Lyon, CEO of Ultratug, felt it would take a few years to have a good variety of new technologies available, but
for the moment it is interesting to analyse and develop a project involving engine producers, yards and clients where all parties will see benefits.
“We need to also take into account the fit between technologies and the operation profile of the port or region where the tug will be deployed,” said Mr Lyon. He continued that going for the second-hand market in conventional diesel tugs is a good idea, while waiting for the most reliable fuel source in an equally effective and sustainable package.
When discussing the options, Mr Lyon said: “Hybrids are particularly good when you have long navigations. Fully electric is continuing to improve – delivering more power and operational reliability each time, and some others are coming such as methanol, which is very interesting.
Like all sectors, the tugboat industry has felt the effects of the current economic climate. With inflation rates at an all-time high
and an increase in living cost, Ultratug has had to overcome several challenges.
The first challenge that the company faced was the potential cost of developing tugs that can process renewable fuels. The technology required for such an upgrade can be costly and would involve a greater commitment of investment funds and time.
There is also the previously mentioned decision of what fuel type to use going forward. Ultratug, however, has experienced change before when the market moved to ASD tugboats, so it is prepared to transition when the time is right.
The ability to replace boat parts has also been a challenge because of slow delivery times: this can lead to tugs being out of action. Therefore, Ultratug always works hard to maintain the relationships it has between shipyards, suppliers, and investors, ensuring that these companies are kept up to date with all vessel-related breakdowns.
To help maintain these relationships and gain a better understanding of what Ultratug’s investors and suppliers are
looking for, Ultratug attends various events and tradeshows throughout the year, including the ITS Convention in Istanbul.
Regarding the conference, Mr Lyon said: “it is a brilliant opportunity to see all the latest technology and witness first-hand the advancements that suppliers are making. Not just that, but it also allows us to gain a better understanding of them and continue to build those relationships.”
Ultratug also maintains a strong relationship with several shipyards for its fleet renewal and growth. This includes local and international alternatives – depending on availability, delivery time, design and, of course, quality.
Ultratug takes the wellbeing of its crews very seriously, especially when it comes to the safety and training of those onboard its vessels. The company sees its employees as its strongest asset; therefore, it continues
to implement structures that guarantee the wellbeing of all Ultratug workers.
During the pandemic, Ultratug ensured that the crews were as safe as they could be. If someone caught Covid, the company made sure all crew members would isolate at home and requested testing to minimise the spread of the virus. This of course came with its own set of challenges; short staffing resulted in tugs being non-operational for several weeks at a time.
Despite the tribulations brought on by the pandemic, Ultratug bounced back to pre-Covid operations, and is confident in the recovery achieved by the marine vessel market.
“The standards we implement are extremely high in terms of procedures, safety and maintenance,” Mr Lyon concluded. “We want to continue in the market, being known as the company with a strong and powerful fleet who are dependable and maintain the highest principles.” n