M52 n AUG/SEP 2022 n € 15 SEVEN SEAS FIVE OCEANS ONE VOICE SAAM TOWAGE Expert maritime towage services in the Americas WIGHT SHIPYARD CO A powerhouse of the fast ferry sector DANN OCEAN TOWING Fifth-generation tugboat company voyaging into greener waters inside ( ( MARINE i M ANDTOWAGEWORKBOATSSALVAGE The push and pull
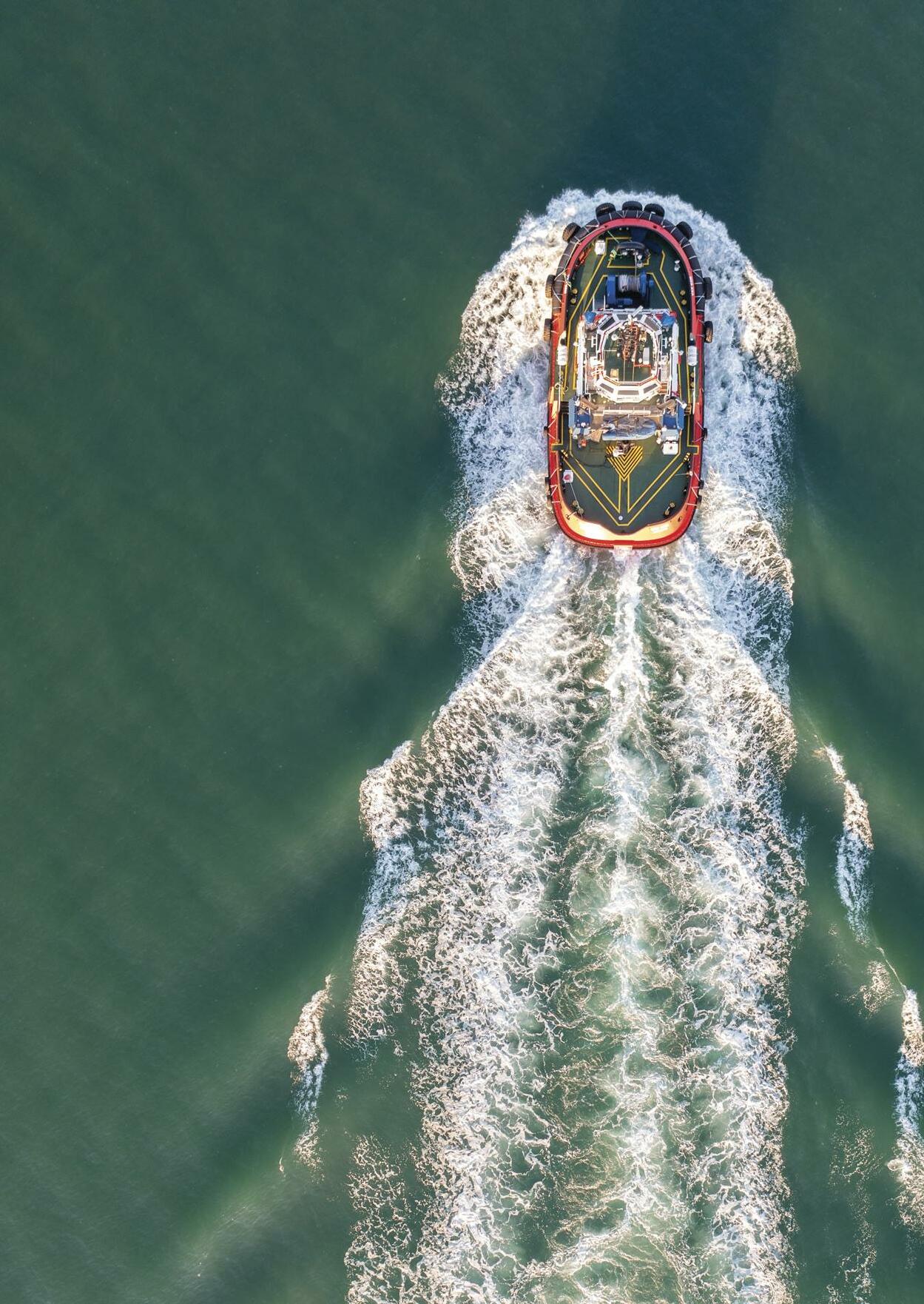
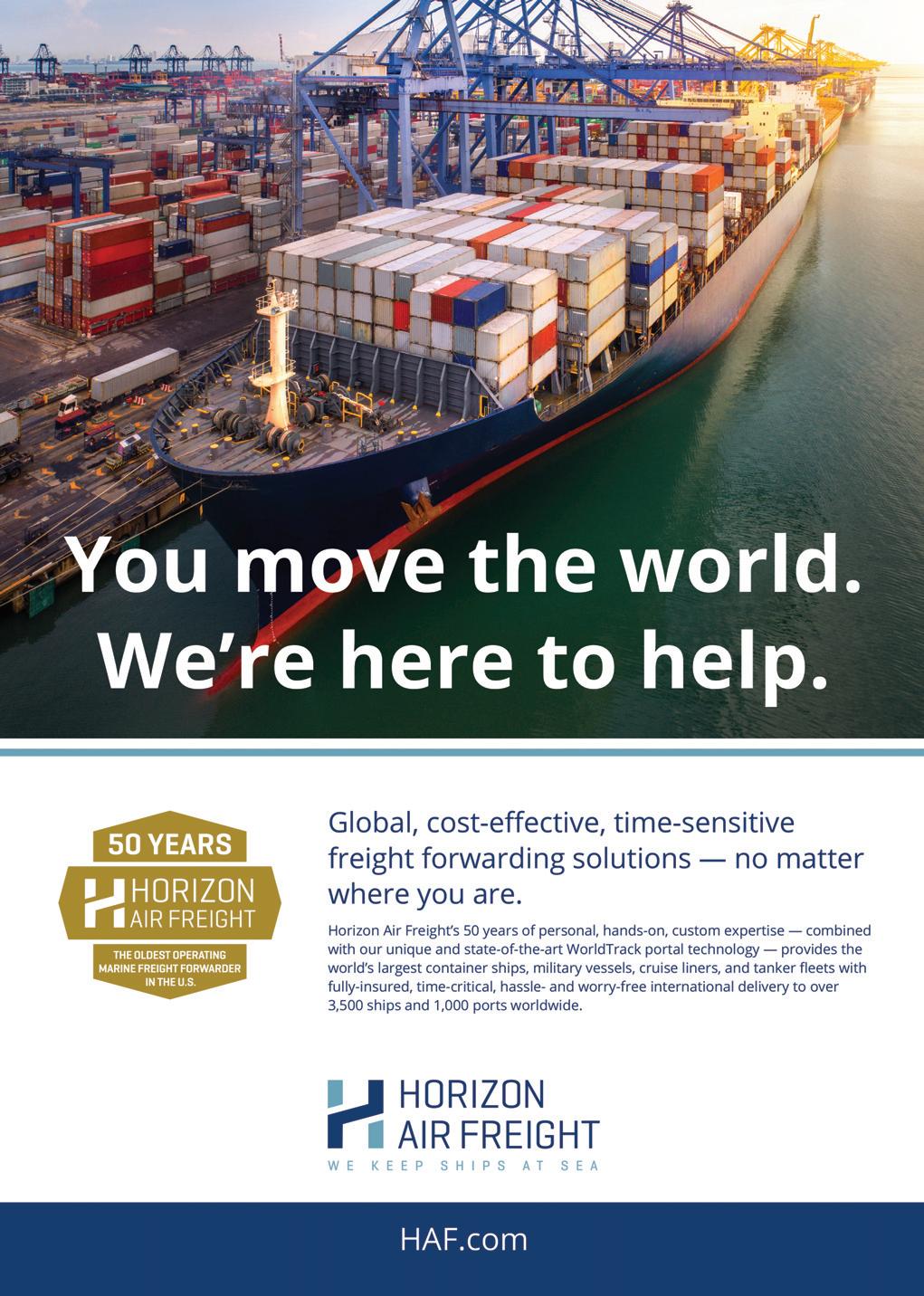
John White Managing Director
((
Now these are not the sort of workboats that we tend to focus on so much these days, instead, interestingly out at sea themselves during the race and emerging from the same harbour, were many work boats that attend the local offshore wind farms. It was fascinating to observe the old and new at sea at the same time.
Welcome dear reader to your latest edition of Inside Marine. With a focus in this edition on workboats, towage, and salvage, I would like to share with you a pleasant experience I had this weekend. Following a hearty full-English working breakfast with my business partner at a café near Lowestoft seafront, we noticed a large crowd gathering at around eight that morning on the seafront in and around the town’s historic fishing port. Upon investigation, we found out from members of the crowd that there was to be an old fishing smack (fishing boats that are around 100 years old!) race along the coast to Great Yarmouth and back. Watching these wonderful old sailing vessels crewed by vol unteer crews of eight was a glorious sight and doubtless a nostalgic trip down memory lane for some of the older crowd members who will have recalled their parents having worked on them when they were crammed into the port of Lowestoft. Indeed, my grand father went to sea on them in his youth so I must confess that it brought a tear to my eye.
Inside Marine 3
Therefore, this edition is dedicated to those seafarers and the companies that operate these busy working vessels. They graft, day in, day out, wearing overalls, boots, and hardhats rather than deck shoes, shorts, and baseball caps. Their industry is a busy one the world over and any mariners I am sure will join me in acknowledging their efforts. As always, I hope you enjoy the many news items, company profiles, advertise ments, and event previews that this edition brings you, and like I have, I hope you find time in your busy schedules to read about these not so glamourous but certainly hard working commercial marine sectors. I will sign off now as whilst typing this I have just realised that as it is a hot day, I am sat at my desk wearing soft deck shoes, a pair of leisure shorts and a stripy blue and white casual shirt…. all I am missing is a baseball cap that has ‘Captain’ written on it. My grandfather would role his eyes up at that, I have no doubt! n
Lowestoft sadly no longer has much of a fishing industry, certainly not in the capacity that it had in the first half of the last century, however, it remains a busy commercial port with workboats, salvage and towage vessels operating alongside many other types of commercial and leisureWhilstcraft.onthe subject of old fishing ves sels, the inner harbour at Lowestoft is full of old vessels that, either damaged irreparably at sea or simply past their best, ended up being towed into the inner stretch of river to be salvaged, stripped of any useful parts and either sunk or semi buried in the riverbanks. In fact, most are hardly visible anymore as they have become part of the riverbank and harbour walls! Visitors to Lowestoft will notice the many yacht basins we have, including the Royal Yacht Club close to the harbour entrance. There are some glorious vessels, both sail and power, to behold.
IT’S NOT GLAMOROUSALL PLAIN SAILING
Managing Director John White doffs his captain’s hat to the tough working boats and their crews.
Send us your feedback
Your input matters to us and we take all feedback on board to help our readers enjoy the magazine now and for years to come.
Arguably less glamourous but still sharing the quayside with them, are a selec tion of commercial craft reminding all that Lowestoft, like many ports and harbours of the world, is an operational commercial port and not simply a playground for the leisure craft and crews.
Your feedback matters, email us: media@insidemarine.com inside MARINEi M
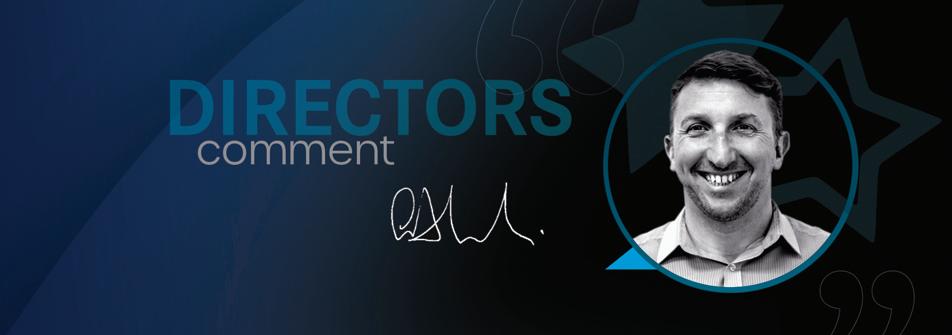
Managing Director John GeorginaSarahDanielDesignersMichaelWebmasterPhilipArtIanArtCallumDavidChrisKymTonyDarrenProjectHelenSalesRichardSalesKainCallumClareGinelleBeckyJeffAdamJasmineJudiResearchRichardRomanaLauraAndyColinFilomenaProfilePhilJordanEditorialDanielEditorialWhiteManagerBarnesAssistantYallopNichollsWritersNardiChineryProbertWatlingMoaresHaganEditorsWheaton-MarsLodgeWhiteJohnsonScrivensLorenzoBishopSmithMcBarron&MarketingDirectorBrightmoreManagerLeisiManagersFoiretIngrouilleHamiltonRenicarEarlRobbDirectorSpencerEditorWhiteStampO’MalleyJonesHarrisTelephone:+44(0)1493445121+44(0)1502576953Email:media@insidemarine.comWebsite:www.insidemarine.comCompanyRegNo:06783092CompanyVATNo:167675757©InsideMarine2022Nopartofthispublicationinanyformforany purpose, other than short sections for the purpose of review, must be reproduced without prior consent of the publisher. 4 Inside Marine inside MARINE(( Introduction 3 Director’s comment It’s not all glamorous plain sailing Events 6 Marine events Upcoming events in the industry Inside marine minds 8 Inside Marine asks the experts about their personal experience in the industry In light of current global events, how is your company ensuring that its longterm relationships with suppliers remain as strong as possible? Country focus 10 Scotland New Grangemouth container route launches as demand increases for a Scottish express service into Europe 11 Taiwan Yang Ming adds 11,000 TEU ship YM Tutorial to transpacific service 12 USA WETA awarded $14.9m to develop electric ferry network in San Francisco 13 Singapore PIL opens new centre for maritime efficiency 2022 best builds 16 Bon voyage! Inside Marine takes a look at a number of the industry’s most impressive new builds and refits News 20 Marine news in brief Latest news from the marine industry Matter of fact 26 Did you know? Interesting and unusual marine facts from around the world For the executive 28 A passion for haute horology F.P. Journe Workboats, towage & salvage 32 Towing power across the Americas SAAM Towage 40 The power behind the towing Dann Ocean Towing P16 P40
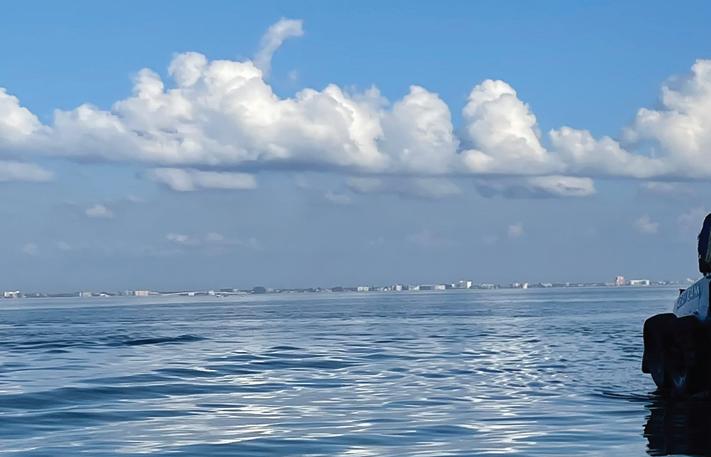
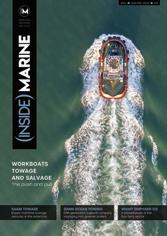




Inside Marine 5 Contents 46 Are you sailing from Scarborough fair? Mainprize Offshore Ltd 52 Launching a maritime legacy Miller’s Launch 58 A century of salvage Otto Wulf Shipyards 66 All aboard exhilaratingtheWight Express Wight Shipyard Co 74 Colombia’s favorite shipyard marks 50 years Astivik Shipyard 80 One name, two locations, four decades of exceptional service Cernaval Group 86 This Whitby Endeavour Parkol Marine Engineering Ltd 92 Redefine, convert, explore! ICON Yachts 98 Building a shipbuilding legacy Blount Boats 104 The push and pull of boat building and repair Senesco Marine 108 Expansion adds to shipyard’s flexibility Hat-San Shipyard Ports 114 The darling of West Coast container shipping Port of Portland 118 Gateway to Caribbean’sthetwin islands Port Authority of Trinidad and Tobago 122 A port of change for the better Port of Long Beach Owners, managers & agencies 130 Celebrating four generations of shipping history Maritimex 138 Maritime management masters of the Middle East Dockendale Ship Management 144 Beating the queues with bulk cargo Eastern Car Liner Americas 150 Always prepared for the extra mile OL Shipping Group 156 A bespoke yachting odyssey Variety Cruises Design & engineering 164 Designing the future Deltamarin 168 Plasma-Green for a clean future Weihe Equipment & services 176 Generating growth in electronic propulsion OSWALD Elektromotoren 182 Casting a spell on diesel machinery Merlin Diesel Systems 186 The signs of safety at sea T-ISS 190 Taking AIME at maritime innovation Ocean Craft Marine 194 The technology within Precision Products (UK) Ltd P66 P150
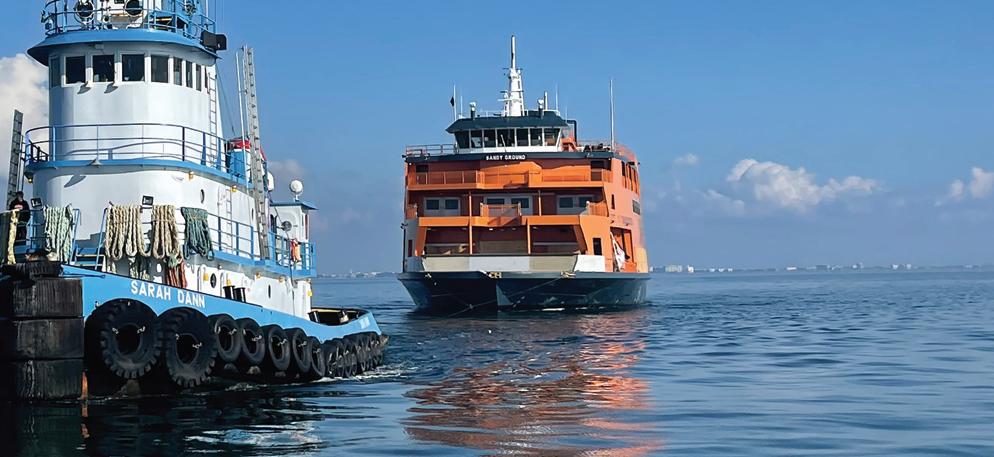
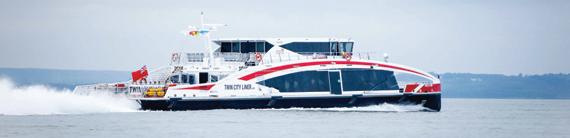

Marine UpcomingEventsevents
Breakbulk Americas is the event for all those involved in the project cargo and breakbulk industry.
Focused on companies and projects from Canada down to the tip of Argentina and the Caribbean, this is the place to expand your operations in one of the most promising regions of the world. In addition to meeting more than 200 exhibitors, you’ll find a full conference agenda featuring industry leaders, including shippers, global project forwarders, leading carriers, and more. You will hear perspectives and lessons learned from major project participants, informa tion that you won’t find anywhere else.
Breakbulk Americas 27-29 September 2022
www.americas.breakbulk.com
in the industry events upcoming SMM 2022 6-9 September 2022
Digital transformation, as well as climate change and the maritime energy transition all take centre stage at the 30th SMM. With an expanded spectrum of key areas and addi tional presentation formats, the leading international trade fair for the maritime industry accompanies the change at close quarters. Maritime industry professionals from all parts of the world will get the complete overview of innovations from all sectors, and of course they will finally enjoy again the opportunity for live encounters on the exhibition ground as well as in the high-profile trade conferences.
www.smm-hamburg.com
6 Inside Marine
The show features everything the leisure marine industry has to offer. Ranging from paddle boards to superyachts, and all the products and services you need to enjoy life in, on or around the water – you’ll find it at the show. Show favourites, new exhibitors and exciting attractions make sure there’s a lot to see and do: From kayaks to catamarans, SUPs to superyachts, there’s a boat for everyone.
www.southamptonboatshow.com
Southampton International Boat Show 16-25 September 2022
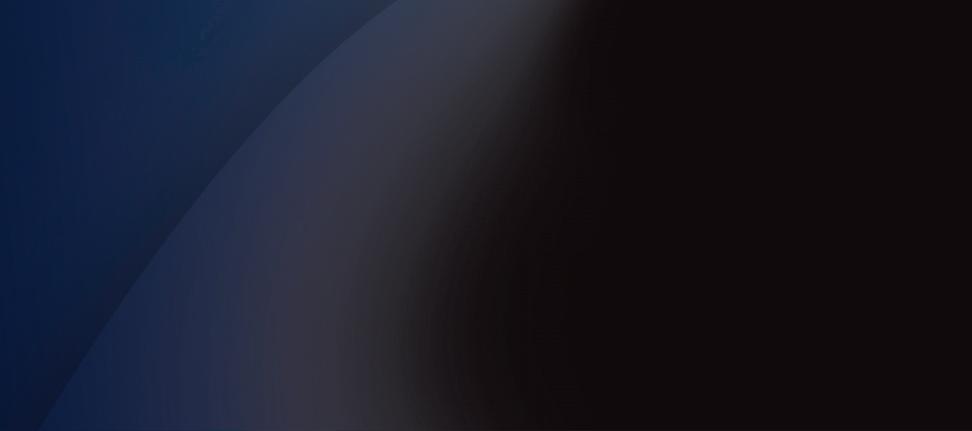
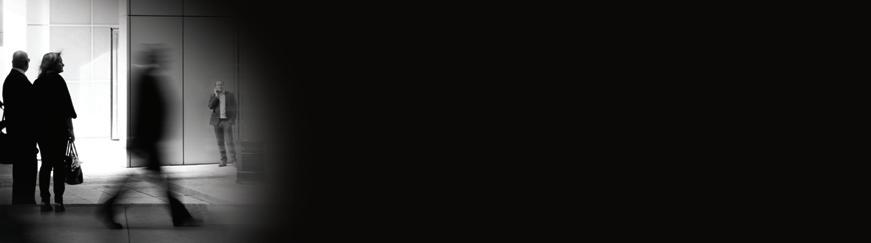
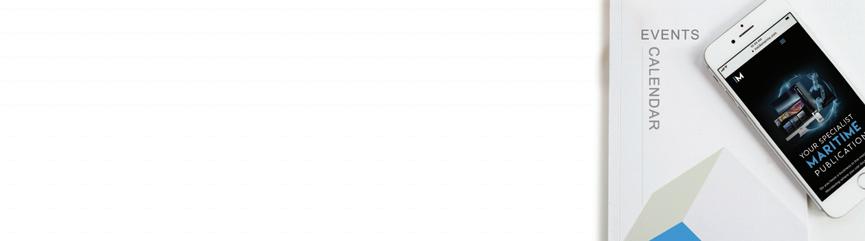
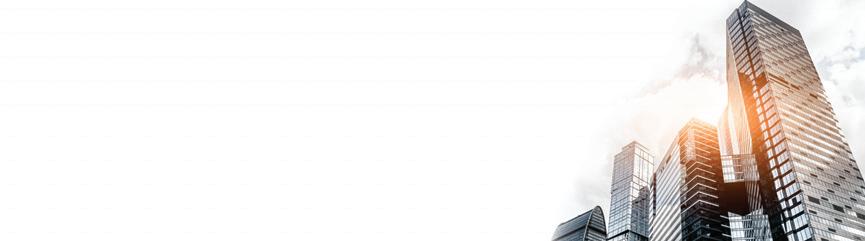



The Monaco Yacht Show is world-renowned for the exceptional quality of its superyachts and their impressive length: among the +100 units on display, +40 new models are unveiled as world pre mieres each year. The fleet has an average length of 50m and mega yachts exceeding 100m.
METSTRADE 15-17 November 2022
FROM HITCH KNOTS TO Monaco Yacht Show 28 September – 1 October 2022
After two years of industry change, port technology advancement and digital acceleration, TOC Asia will connect the port and container supply chain community across the APAC region. Hear from change-makers within the global container supply chain and discover the latest innovations within terminal operations. Alongside a first-class conference, visitors will also benefit from a global port technology exhibition and the return of TOC’s famous social programme. TOC Asia will enable you to identify and leverage the key market opportunities that are waiting for you. Visit TOC Asia for solu tions, powerful learning and the long overdue networking that only face-to-face events can bring.
The show has become an emblematic event for private visitors who come to discover an out standing concentration of superyachts available for purchase or charter and to meet the industry experts in the festive and glamorous atmosphere of the Principality of Monaco.
www.monacoyachtshow.com
The METSTRADE Show is the world’s largest trade exhibition of marine equipment, materials and systems. Labelled as the only truly international B2B exhibition for the marine leisure industry, METSTRADE has served as a platform for innovation, market developments and networking since launching in 1988. In addition to the overall leisure marine industry, METSTRADE caters for three specialist sectors, namely superyachts, marinas and yards and construction materials through three specialised pavilions, each offering a smaller self-con tained show within the larger METSTRADE Show context. www.metstrade.com TOC Asia 29-30 November 2022
www.tocevents-asia.com
Inside Marine 7 WINDSOR KNOTS
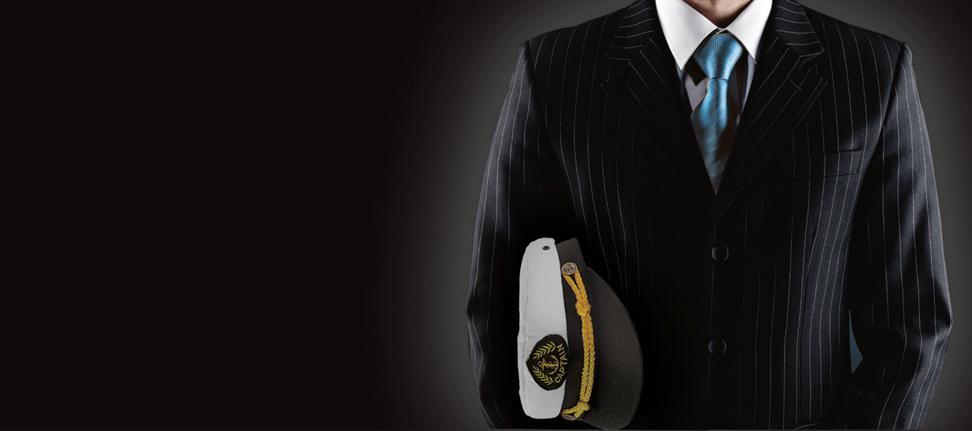
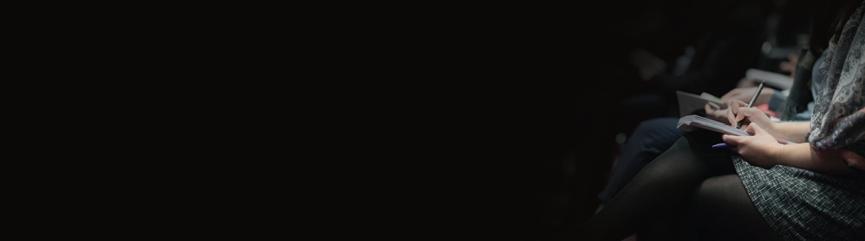
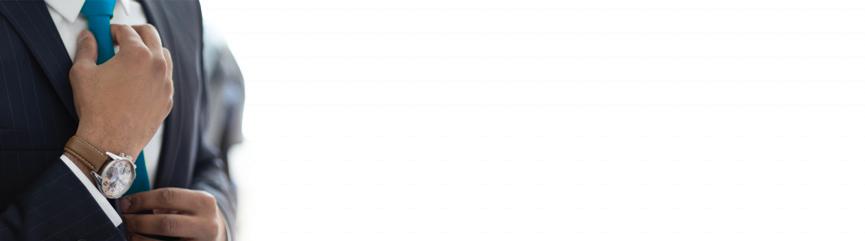




Cristian Eversbusch, Director, Maritimex “
Toby BusinessMumford,Development Manager, Wight Shipyard Co “ As with any relationship, the key is consis tency and reliability. This is what we’re doing to maintain our long-term relationships; be consistent and reliable. That’s what keeps rela tionships intact and strong throughout this dif ficult global atmosphere. You need people who you can count on and who can count on you.
Bill Christ, Executive Vice President and COO, Eastern Car Liner Americas “ “ We maintain open, direct and transparent relations with clients, never seeking to take advantage of them during difficult times.
Edward Snyder, President and CEO, North Atlantic Ship Repair “ “ All we can do is to continue building high-quality vessels on time, on budget and being as open as possible in communications with both suppliers and clients.
Marcia Blount, President, Blount Boats “ “ We share with them our longterm visibility on orders, materials as well as our plans, new products and investments in order to grow. Being transparent is the only way to have real partnerships and to underpin a business’ success.
Through open communication. They know that they can pick up the phone and get me any time they need me. Every business experi ences good and bad times but we maintain the same level of communication regardless. We answer the call no matter whether it’s good times or bad. Communication is therefore so important. Any one of my vendors, I can pick up the phone and I know that they’ll be there for me.
“ “ “ 8 Inside Marine Inside marine minds Inside Marine asks the experts about their personal experience in the industry mindsmarineinside
Lydia Doussopoulos, General Manager, Seamar Management “
Fabio Planamente, CEO, Cantiere del Pardo “ “ The aim is to keep communications open, be honest and transparent to ensure the supply chain remains strong, and that deadlines and budgets remain on track for customers. It is challenging and we don’t know what to expect as prices are now starting to spiral.
“ We maintain deep ties with many vendors. We do occasionally go out for quotes but we’ve worked with many of them for many years. They’ve been very cooperative with us especially in terms of pricing and scheduling.
In light of current global events, how is your company ensuring that its long-term relationships with suppliers remain as strong as possible?
Özgün RepairsOruç,Division, Marketing Manager, Hat-San Shipyard “ We consider them to be part of our family. We do what we can to ensure that their finances are healthy so that they can render great services to us; we really try to look after them. We also prefer not to request credit facilities from them or pass any financial burdens to them. We prefer that they’re happy so that they can provide great services and products to us.
Question:
Alexis Philandrianos, Sales and Strategy Director, Couach Shipyard “ “ Our relationships are very long-term and respectful in both directions, between vendor and customer. It’s part of our company culture and philosophy and always has been. It’s perhaps even more so, during these turbulent times, that we must respect those relationships. That goes to the ports and the agents we work with, as well.
If we have availability at the ship yard, we are always flexible to their demands and accommodate them as much as we can.

“ “
inside (( MARINE
Hernán Gómez, Managing Director, SAAM Towage “
Jeroen Mulder, Managing Director, Newthex “
Captain Eberhard Koch, owner, OL Shipping Group “
db@insidemarine.com Get Involved i Mwww. insidemarine .com
We place a lot of emphasis on making timely payments to our vendors, it proactively solves a lot of problems and ensures that trust is maintained. We ensure that whatever we’ve promised or committed to, especially in terms of payment, we act on time. We never renege on promised payments.
We would love to hear your answers, so send an email over to our Editorial Manager, Daniel Barnes, and share your thoughts to all our readers.
Satish Kumar, Managing Director, Dockendale Ship Management “ Our suppliers are the result of long-term relationships, they’re companies we’ve known for many years. We will continue the relation ships by always being upfront with each other, having an open dialogue and solving problems together.
“ We know that change is the only thing you can count on. So we work closely with our stakeholders to ensure close relationships and open lines of communication at all times.
Dr Noel Hacegaba, Deputy Executive Director, Port of Long Beach “ “ We like to create partnerships that will endure hardships, and we do this through maintaining regular contact with our suppliers. We have in-person meetings when we can as well, which is really the key for us because it builds trust. I firmly believe that if you can’t trust the man’s handshake, then you can’t trust his signature.
Michael Richards, Bulk & Breakbulk Manager, Port of Portland “ Our scale has allowed us to develop arecentlyourselves.vendorsareagreementslong-termthatgoodforourandforWesignedglobalagreement with CAT for the maintenance of the CAT engines in our fleet. The contract standardises the way we can work in each country and it makes the contract measurable across the board, despite different agents and vendors being involved. We believe it will have positive results. We’ve taken the same standardisation with the shipyards we work with, to ensure that we have good new-build relationships with them.
“ We ensure that they’re not suppliers, but partners in building our projects. Partnerships are very important for us and so we try to keep those relationships very close. It means that you have to share things, and I’m not afraid to do so. The only thing that multiplies by division is knowledge.
A successful supply chain requires coopera tion throughout all the links in the chain, and that’s our main goal.
Inside Marine 9
“ We need to work together with all possible players in the shipping industry and in general. I believe our people in the OL Group are key players in this diffi cult global game and are already leaders providing solutions, coop eration, and excellent services to customers and suppliers.
Nick Miller, Vice President, Miller’s Launch “
“

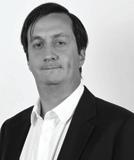

Within and around the Firths of Forth and Tay, Forth Ports manages and operates an area of 280 square miles of navigable waters, including two specialised marine terminals for oil and gas export and pro vides other marine services, such as towage andTheconservancy.PortofGrangemouth operates Scotland’s largest container port and han dles in excess of 155,000 containers per annum. More than £6 billion worth of goods passes through Grangemouth each year including steel plate, timber, paper and equipment for the oil and gas industry. There are regular container services from Grangemouth with frequent daily sailings to Rotterdam, Antwerp, Felixstowe and Hamburg. Most of the major lines utilise these feeder services to link with mother container vessels plying between the world’s major ports. n
The Port of Grangemouth, which handles 30% of Scottish GDP, will be a strategic site for a new Forth Green Freeport which will help to transform the port into a major logistics, manufacturing, renewable energy hub and R&D centre for the Scottish and UK economies.
“We are committed to supporting eco nomic growth within the areas we operate, and I am looking forward to continuing to work alongside Forth Ports as we expand our service offering in Scotland.”
The arrival of the Skylight container vessel into Scotland’s key strategic freight hub at the Port of Grangemouth marks the maiden call of a new Scottish Express (SCX) service secured with the CMA CGM Group, a global player in sea, land, air and logistics solutions, and its subsidiary, Containerships, the leader in intra-European multimodal transport. New Grangemouth container route launches as demand increases for a Scottish express service into Europe We are committed to supporting economic growth within the areas we operate, and I am looking forward to continuing to work alongside Forth Ports as we expand our service offering in Scotland “ “
About Forth Ports Forth Ports Limited owns and operates eight commercial ports in the UK – Tilbury on the Thames, Dundee on the Firth of Tay and six on the Firth of Forth – Leith, Grangemouth, Rosyth, Methil, Burntisland and Kirkcaldy.
An important addition to the Scottish market
The SCX service rotation is a weekly route to mainland Europe, from Grangemouth via Teesport to Rotterdam, and will be capable of handling around 20,000 containers per annum through the port.
James Leeson, General Manager at CMA CGM UK, said: “We are delighted to announce the launch of our new SCX ser vice at the Port of Grangemouth. This is an important addition to the Scottish market with a fixed day weekly service and increases Scotland’s connectivity to mainland Europe and beyond.
The new service, which calls into Grangemouth each Thursday, has been launched to principally support growing exports from Scotland’s largest exporters who transport produce from Leven and Shieldhall through Grangemouth and into Europe to service worldwide destinations.
10 Inside Marine Scotland Country Focus Reporting on the latest developments from the Scottish maritime sector
The SCX service provides export and import customers with a regular addi tional call into mainland Europe each week through Scotland’s largest container port, increasing shipping capacity to meet the demands of the Scottish market.
Commenting on the new service, Derek Knox, Head of Operations at Scottish Ports, said: “The new Scottish Express service is great news for Grangemouth and for Scotland. The Port of Grangemouth plays a key role in Scotland’s logistics and freight sector and this new weekly call will increase the frequency of vessels connecting to main land Europe and we welcome the team from CMA CGM and Containerships to our con tainer“Theterminal.additional shipping capacity created from this new direct freight service to Europe will play a key role in fulfilling the demands of the Scottish market trading with European and international destinations. This further supports our ambitions to deliver a Forth Green Freeport where one of the key objec tives of the policy is to develop trade.”
He added: “We are continuing to deliver our investment programme in Grangemouth with new equipment, an expanded container terminal and ware housing complex, linked freight rail terminal and over 400 reefer connections securing the Port of Grangemouth as Scotland’s freight hub of choice.”

Yang Ming has taken delivery of twelve vessels since 2020; eleven of which have been deployed on the company’s transpa cific routes to meet customer needs and maximise capacity utilisation. These newbuildings will lower the average age of Yang Ming’s global fleet, reduce unit cost and achieve energy efficiency. In addi tion, these ships will accelerate fleet optimi sation to proactively cope with the challenges and stricter environmental regulations faced by the fast-changing shipping industry.
Taiwanese shipping company Yang Ming Marine Transport Corp (Yang Ming) has welcomed its newest 11,000 TEU class container vessel, YM Tutorial. The vessel is chartered from Shoei Kisen Kaisha Ltd and built by Imabari Shipbuilding Co Ltd.
YMTutorial was named at a ceremony held at Imabari Hiroshima Shipyard on June 17th and entered into Yang Ming’s transpa cific West Coast route PS6 on July 15th. To further strengthen Yang Ming’s mid-to long-term operational efficiency, the com pany ordered a total of fourteen 11,000 TEU newbuildings through long-term charter agreements with ship owners. YM Tutorial is the 12th vessel in the series. These vessel types have a nominal capacity of 11,860 TEU and are equipped with 1,000 plugs for reefer containers. With a length of 334m, a width of 48m and a draft of 16m, these vessels are designed to cruise at a speed of up to 23 knots. The containerships incorporate various environmental features including scrubbers, water ballast treatment plant and alternative marine power systems.
Inside Marine 11 Taiwan Country Focus Reporting on the latest developments from the Taiwanese maritime sector
The port rotation for the first voyage of YM Tutorial in PS6 begins in Qingdao, before port calls in Ningbo, Pusan, Los Angeles and Kobe, before returning to Qingdao.
Yang Ming adds 11,000 TEU ship YM Tutorial to transpacific service
Yang Ming to launch Far EastLatin America service SA8 Following the news of the company’s latest newbuild delivery, in July 2022 Yang Ming announced the launch of its latest Far East - West Coast of Latin America (FE-WCSA, Loop code: SA8) service. The new service will offer customers broader service cov erage and ensure more reliable services in FE-WCSA trade.
Increased manoeuvrability With shorter length and beam, the ship is easier to manoeuvre during berthing or departure. The optimal dimensions enable the ships to call at major ports worldwide and pass through the new Panama Canal with little restriction, thereby facilitating greater flexibility in vessel deployment.
The new SA8 service is jointly operated by Yang Ming, WAN HAI LINES and Pacific International Lines Pte Ltd (PIL). A fleet of eight 2,400-3,700 TEU vessels will be deployed on the weekly service; two of them are from Yang Ming. The first sailing of the SA8 service commenced from Ningbo on 13th July, 2022 with a round trip scheduled to take 70 days. The SA8 port rotation leaves port at Ningbo before heading to Shanghai, Qingdao, Pusan, Manzanillo, Lazaro Cardenas, Puerto Quetzal, Buenaventura and Valparaiso before returning to Ningbo.
Yang Ming Marine Transport Corporation (Yang Ming) was established on December 28th 1972. As of June of 2022, Yang Ming operated a fleet of 93 vessels with a 7.684 million DWT and an operating capacity of 683,000 TEUS, specialising (not exclusively) in container ships.
The vessels in this newbuild project adopt the twin-island design to increase loading capacity and navigational visibility to ensure greater efficiency and safety. The ship design and build also includes hull form opti misation, which will further increase energy savings and reduce overall emissions.
n
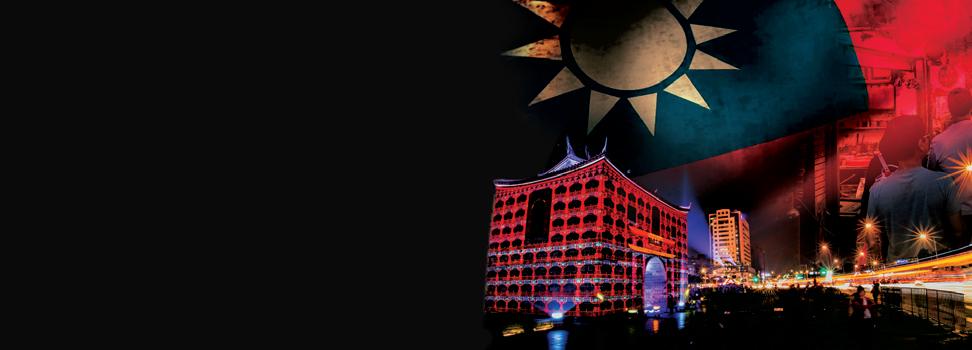

The grant will fund the construction of ferries and shoreside charging infras tructure to support the San Francisco Clean Ferry Network, which will use zeroemission ferries to connect waterfront San Francisco neighbourhoods including Downtown, Treasure Island and Mission Bay.
“San Francisco’s waterfront is home to some of the region’s fastest-growing new neighbourhoods and this grant will help reduce traffic and improve air quality by connecting workers and residents with the country’s first high-speed, zero-emission ferry service,” said WETA Board of Directors Chair Jim Wunderman. “We owe thanks to Governor Gavin Newsom, CalSTA Secretary Toks Omishakin, our tireless Bay Area Legislative Caucus, and our strong support coalition for sharing our vision for a world class clean ferry network for the region.”
The San Francisco Clean Ferry Network will be a major milestone in WETA’s tran sition to a zero-emission ferry service. The agency is currently completing a twopronged study investigating both clean marine propulsion technology and shore side infrastructure needs that will inform policy decisions going forward. Ferries aging out of San Francisco Bay Ferry ser vice will be replaced with new zero-emis sion vessels. WETA may also convert some current ferries to zero-emission propulsion systems over the next decade.
“As we rebuild ridership we’re doing everything we can to make it as simple as possible to buy a ferry ticket,” said WETA Executive Director Seamus Murphy. “This is a simple one-stop shop for all your San Francisco Bay Ferry ticket needs. The new ticketing system improves the passenger experience and streamlines the system by bringing all non-Clipper forms of payment under oneWETAumbrella.”isontrack to launch its real-time ferry information system soon. Real-time predictions and service notifications will be built into the SF Bay Ferry app. Integrations into popular third-party apps including Transit and Google Maps have begun. WETA is also building tools to improve its website experience using realtime information.
This grant, which was awarded through CalSTA’s Transit and Intercity Rail Capital Program (TIRCP), is the latest in a series of grant awards that have been secured to sup port the new service. In 2020, WETA was awarded $9 million from CalSTA to design and build its first zero-emission ferry along with shoreside infrastructure. In early 2022, WETA won a $3.4 million Federal Transit Administration (FTA) grant to add an addi tional battery-electric vessel to the network. This $14.9 million award funds construc tion of a third vessel for what will eventually be a four-vessel network. The grant also includes funds for the charging infrastruc ture needed to operate the service.
New systemticketingapplaunched
Built on Hornblower Cruises’ Anchor platform, the ticketing system allows passengers to purchase ferry tickets for regular service as well as special event service to Oracle Park and Chase Center right from their smartphones in the new San Francisco Bay Ferry app or San Francisco Bay Ferry’s website at sanfranciscobayferry.com . Anchor now powers the ferry system’s paper ticket system as well. San Francisco Bay Ferry encourages local and frequent passengers to use Clipper, the regional multi-agency transit fare product. Mobile and paper tickets can be an alternative solution for families and travellers visiting from outside the Bay Area, as well as to provide timed reserva tions for San Francisco Bay Ferry’s popular special event service.
12 Inside Marine USA Country Focus Reporting on the latest developments from the USA’s maritime sector
Following the above news, on July 19th, WETA launched a new integrated ticketing system and smartphone app for San Francisco Bay Ferry to improve and streamline the fare pay ment system for passengers.
More than 3 million passengers rode WETA’s San Francisco Bay Ferry service in 2019. WETA has delivered eight new ferries with a combined 3,255 seats since 2017, with three more vessels under construction. Under WETA’s Pandemic Recovery Program, San Francisco Bay Ferry’s ridership in June 2022 reached 63% of pre-pandemic levels.
n
On July 15th, the San Francisco Bay Area Water Emergency Transportation Authority (WETA) had announced it has won a $14.9 million grant from the California State Transportation Agency (CalSTA) to develop a high-frequency network connecting some of San Francisco’s fastest growing neighbourhoods with battery-electric ferries.
Transition to a zero-emission ferry service
WETA awarded $14.9m to develop electric ferry network in San Francisco
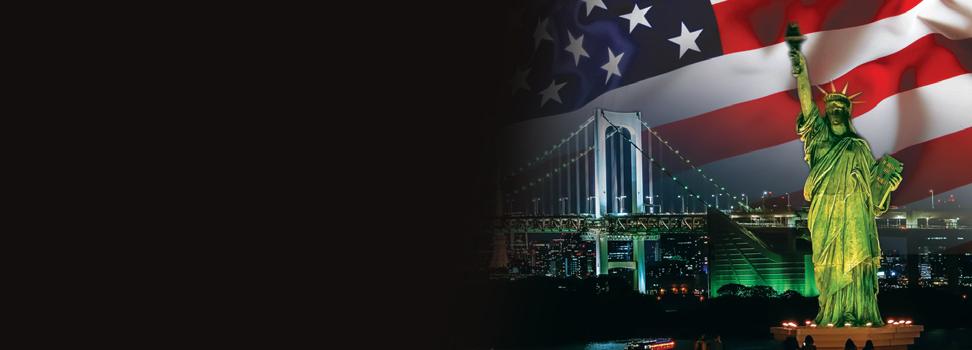
With the new CME, PIL said it will reap a number of benefits. These will include a reduction of greenhouse gas (GHG) emis sions generated from its operations, enhanced fleet safety and security, the max imisation of cost-effectiveness through effi cient traffic and route-based management of PIL’s fleet, and the provision of more training berths for the company’s seafarers designed to act as a ship-to-shore career path.
MoU with the Centre of Excellence in Maritime Safety
“By equipping them with the necessary tools, knowledge and autonomous tech nologies to safely manoeuvre highly volatile conditions, we will raise the standard of maritime safety for the larger maritime community.”
The CME will be equipped with a state-ofthe-art digital system that houses all rele vant operational data and applications in a single platform to facilitate comprehensive, centralised and efficient coordination.
Pacific International Lines (PIL) said its two new initiatives would further enhance the company’s operational efficiencies and strengthen the capabili ties of its sea crew in navigation safety.
PIL opens new centre for maritime efficiency
“At the end of the day, we aim to deliver quality service and good connectivity to our customers, who are increasingly expecting container shipping services to be nimble and flexible to meet their evolving needs.”
PIL and CEMS will jointly explore the effectiveness of using immersive, simula tion and remote technology to deliver safetyrelated and ship navigation training in demanding traffic and sea states. The data and knowledge collected from this project will be utilised for research and collabora tion between the two partners towards the objective of strengthening the standards of maritime safety.
Lars Kastrup, CEO, PIL, said: “The rolling out of this new Centre for Maritime Efficiency is timely as we forge ahead to become a more efficient shipping line committed to reducing our carbon foot print. This is also aligned with our aim to better leverage technology and digitalisa tion in our operations for enhanced opera tional effectiveness.
Pacific International Lines (PIL) has opened its new Centre for Maritime Efficiency and signed a MoU with Singapore Polytechnic’s Centre of Excellence in Maritime Safety (CEMS). The devel opments are both aimed at cutting the Singapore based shipping company’s carbon footprint.
The first initiative launched is the opening of its new Centre for Maritime Efficiency (CME). The key role of the CME is to enable PIL to grow its competencies in managing ship and fleet energy-efficiency performance as part of PIL’s commitment to lowering its carbonHelmedfootprint.byateam of seven with extensive seafaring experience and leveraging on digi talisation, the CME’s responsibilities include traffic optimisation and route analysis aimed at minimising energy usage by PIL’s fleet.
“PIL is indeed pleased to collaborate with Singapore Polytechnic, a leading institute of higher learning in maritime education and training,” commented Mr Kastrup. “We have over 4,000 seafarers working with PIL and their safety, health and wellbeing are of utmost importance to us. “The long-running pandemic has also made us more cognizant of the crucial role that seafarers play in ensuring the smooth running of the global supply chain. We are confident that this partner ship with Singapore Polytechnic will contribute towards strengthening our seafarers’ ability to conduct safe naviga tion and Georginaoperations.”Phua,Deputy Principal (Development), Singapore Polytechnic, said: “Through this strategic capability-building partnership, our Centre of Excellence in Maritime Safety will team up with Pacific International Lines to leverage on our com bined extensive domain knowledge and expertise in the maritime sector to conduct and deliver meaningful research into tech nology-enabled navigational and operational safety training for our seafarers.
Inside Marine 13 Singapore Country Focus Reporting on the latest developments from Singapore’s maritime sector
PIL recently inked a Memorandum of Understanding (MoU) with Singapore Polytechnic’s Centre of Excellence in Maritime Safety (CEMS) to collaborate on a ‘Training with Technology’ project.
About Pacific International Lines and Singapore Polytechnic Incorporated in 1967, Pacific International Lines is ranked 12th among the world’s top container shipping lines. From a modest ship-owner in Singapore, PIL has developed into a global carrier with a focus on China, Asia, Africa, Middle East, Latin America and Oceania. Together with its sister companies Mariana Express Lines (MELL) and Malaysia Shipping Corporation, PIL serves customers at over 500 locations in more than 90 countries worldwide with a fleet of around 100 container and multipurposeEstablishedvessels.in 1954, Singapore Polytechnic (SP) offers 30 full-time diploma courses and three common entry pro grammes for more than 13,500 students. n
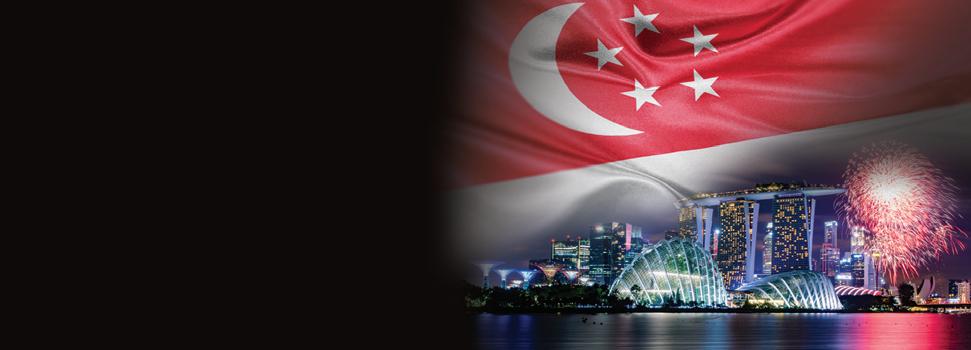
14 Inside Marine
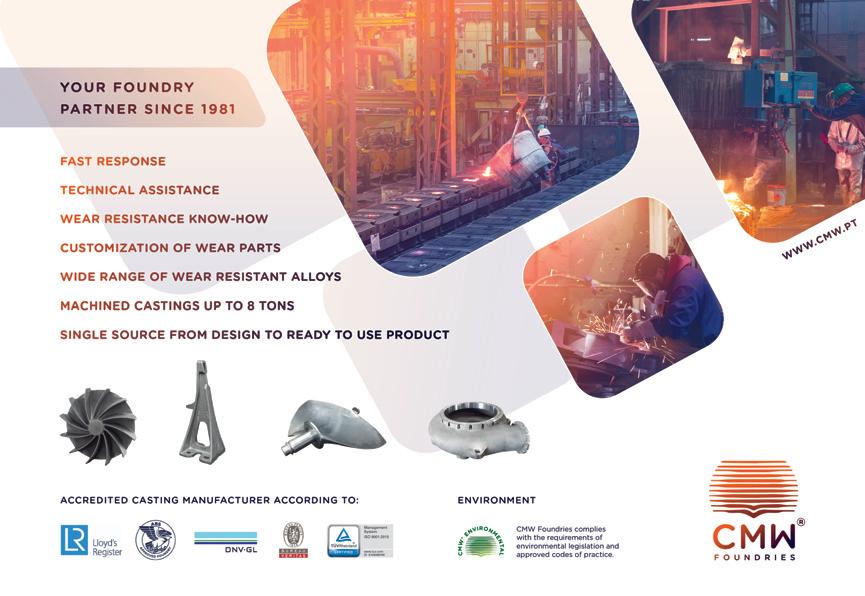

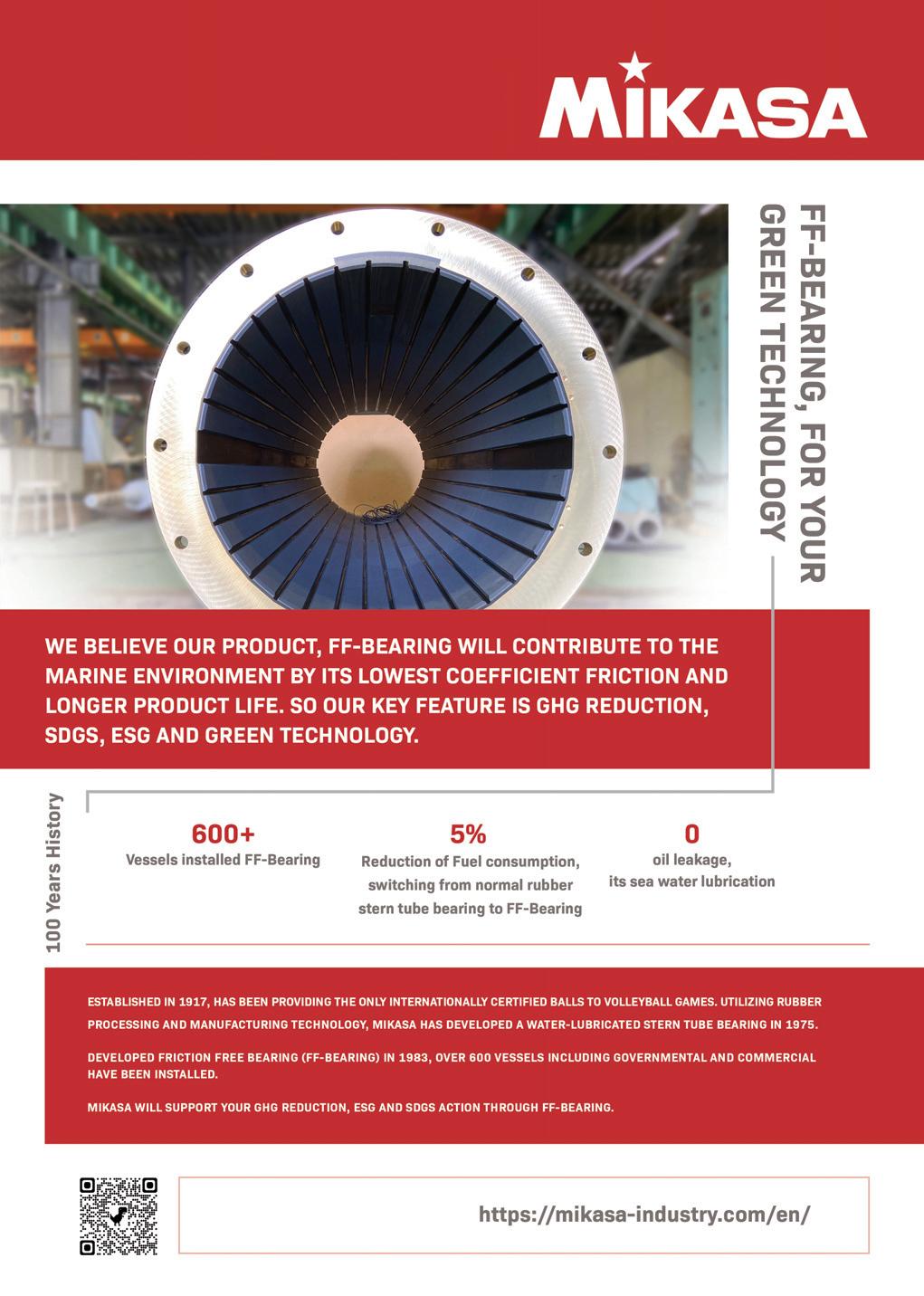
16 Inside Marine voyage!bon Inside Marine takes a look at a number of the industry’s most impressive new builds and refits 2022 Best Builds 1 2 3 4 5 6

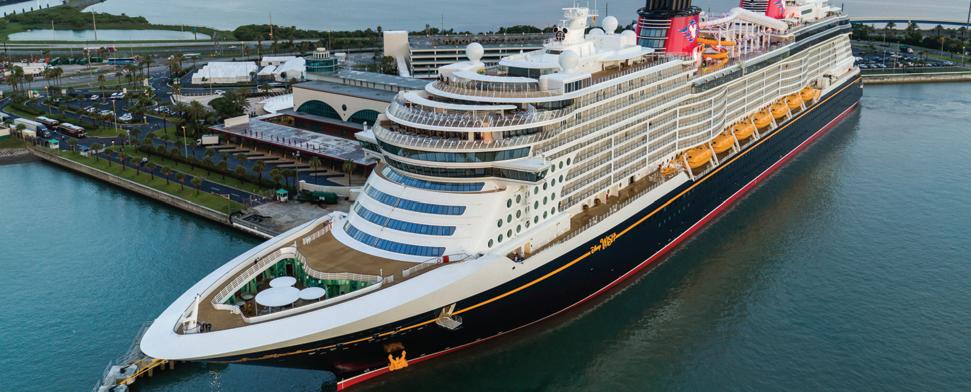
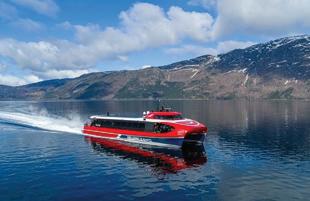
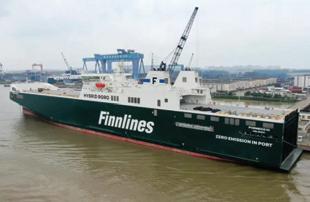
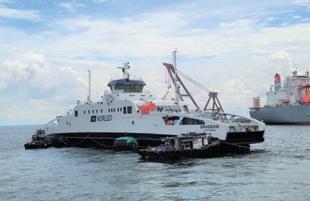

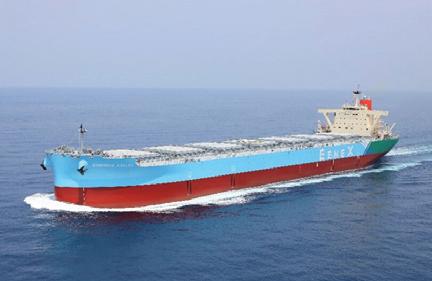
Aero 1 Highspeed
Owner: Finnlines Builder: China Merchants Jinling Shipyard (Jiangsu) Vessel Type: ro-ro vessel Length: 238m Info: Finneco III is the third and last of three Eco class ro-ro vessels ordered by Finnlines. The vessel will enter Finnlines’ Biscay line, where it will join the sister vessels, Finneco I and II. The ships each have a cargo capacity of 5,800 lane metres and can carry 400 trailers per voyage – a 40% cargo carrying capacity increase on the previous largest vessels in Finnlines’ fleet. “Through our ambitious investment we can bring to our customers, not only the economies of scale and increased frequency, but a green and well scheduled infrastructure in the Baltic Sea, the North Sea and the Bay of Biscay,” said Emanuele Grimaldi, Chairman of the Board, Finnlines.
Owner: Disney Cruise Line Builder: Meyer Werft Vessel Type: Cruise liner Length: 341m Info: Disney Wish is the fifth ship in the Disney Cruise Line fleet, and according to its owner, is filled with one-of-a-kind entertainment and innovation from bow to stern. These include family dining adventures themed to Frozen and Marvel, an immersive tour of the Star Wars galaxy, interactive virtual quests, original stage productions, signature fireworks at sea, imaginative clubs for kids of all ages, and an expanded collection of experiences exclusively for adults. “We’re pushing the boundaries of what’s pos sible with awesome new entertainment and experi ences and combining them with Disney Cruise Line fan-favourite offerings,” said Josh D’Amaro, Chairman, Disney Parks, Experiences and Products.
The Energia Azalea is the third in the EeneX series of next-generation coal carriers based on the Japanese shipbuilding industry's accumulated know-how and technology in development and construction of coal carriers, along with MOL’s expertise in operating these vessels. Adoption of a double-hull structure eliminates the need to fill cargo holds with ballast water, reducing the risk of marine pollution and min imising cargo contamination with salt and rust. Disney Wish Energia Azalea
Owner: Norled Builder: Sembcorp Marine Vessel Type: Ro-Pax ferry Length: 82m Info: Norwegian ferry operator Norled has taken delivery of the second of three identical batteryoperated Ro-Pax ferries from Singapore shipbuilder Sembcorp Marine. The zero-emission vessel was designed by Sembcorp Marine’s LMG Marin sub sidiary and features lithium-ion batteries that will be charged using green hydroelectric power. Operating at a service speed of ten knots, the ferry can operate on a combined battery-diesel hybrid backup mode if needed. Features of the multi-deck and double-ended ferry include quick-connection shore charging plugs, auto-mooring and auto-cross capabilities, and efficient hull, propulsion and heat recovery systems. It has a capacity for carrying 300 persons and 80 cars, or a combination of up to ten cars and ten trailer trucks.
Finneco III Dragsvik
Owner: MOL Builder: Oshima Shipbuilding Vessel Type: Coal carrier Length: 235m Info: As a vessel built especially to serve Chugoku Electric Power, the Energia Azalea will transport coal from overseas to its power stations, along with the Energia Centaurus already in service, to contribute to a sustainable and stable supply of electricity.
Inside Marine 17 1 2 3 4 5 6
Owner: Attica Group Builder: Brødrene Aa Vessel Type: fast catamaran Length: 36m Info: Greek coastal shipping company Attica Group has announced the delivery of the Aero 1 Highspeed catamaran, constructed at Norway’s Brødrene Aa shipyard. The Aero 1 Highspeed is the first of the three Aero Catamarans ordered in January 2021, totalling €21 million, that will replace ships sailing in the Saronic islands. The vessel has a maximum speed of 32.2 knots and a carrying capacity of 150 passengers. The new aerodynamic vessels are built from extremely light carbon fibre, contributing to the reduction of fuel consumption and air emissions, and thus to the mitigation of Attica Group’s carbon foot print. In an effort to further improve its energy effi ciency, Attica equipped the vessel with solar panels which will generate the energy required for all lighting and energy consumption of the accommodation area.
Stena Pro Marine
Owner: Proman Stena Bulk Builder: Guangzhou Shipyard International Vessel Type: Chemical/oil products tanker Length: 186m Info: Stena Pro Marine has been delivered to Proman Stena Bulk, a joint venture between methanol pro ducer Proman and Stena Bulk. It follows the recent delivery of sister ship, Stena Pro Patria. Both 49,990 DWT IMOIIMeMAX dual-fuel mid-range tankers are expected to consume 12,500 tonnes of methanol per annum, which virtually eliminates local pollutants, cuts NOx emissions by 60% and reduces CO2 emis sions by up to 15% on a tank to wake basis versus conventional marine fuels. Anita Gajadhar, MD of Proman Shipping, Marketing and Logistics, said: “Stena Pro Marine demonstrates to shipowners and policymakers that the industry can take proactive and immediate steps on the decarboni sation pathway.”
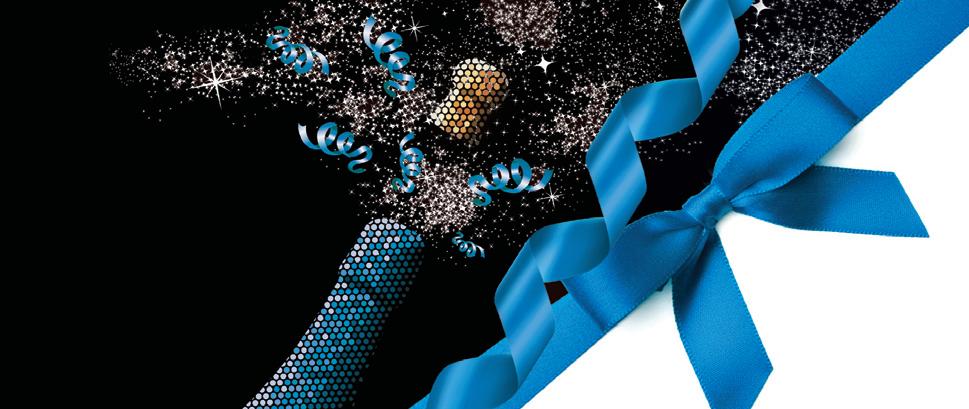
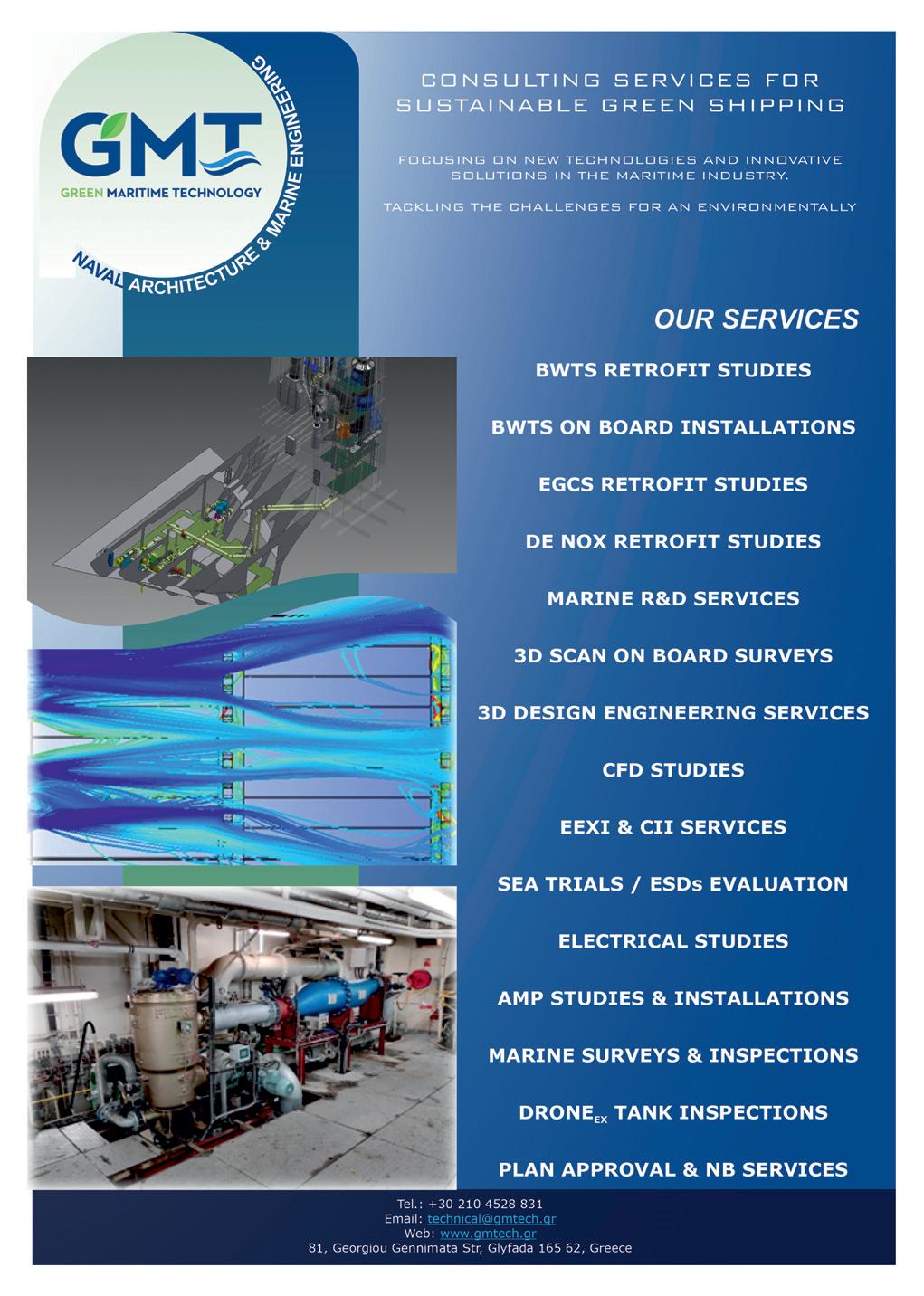
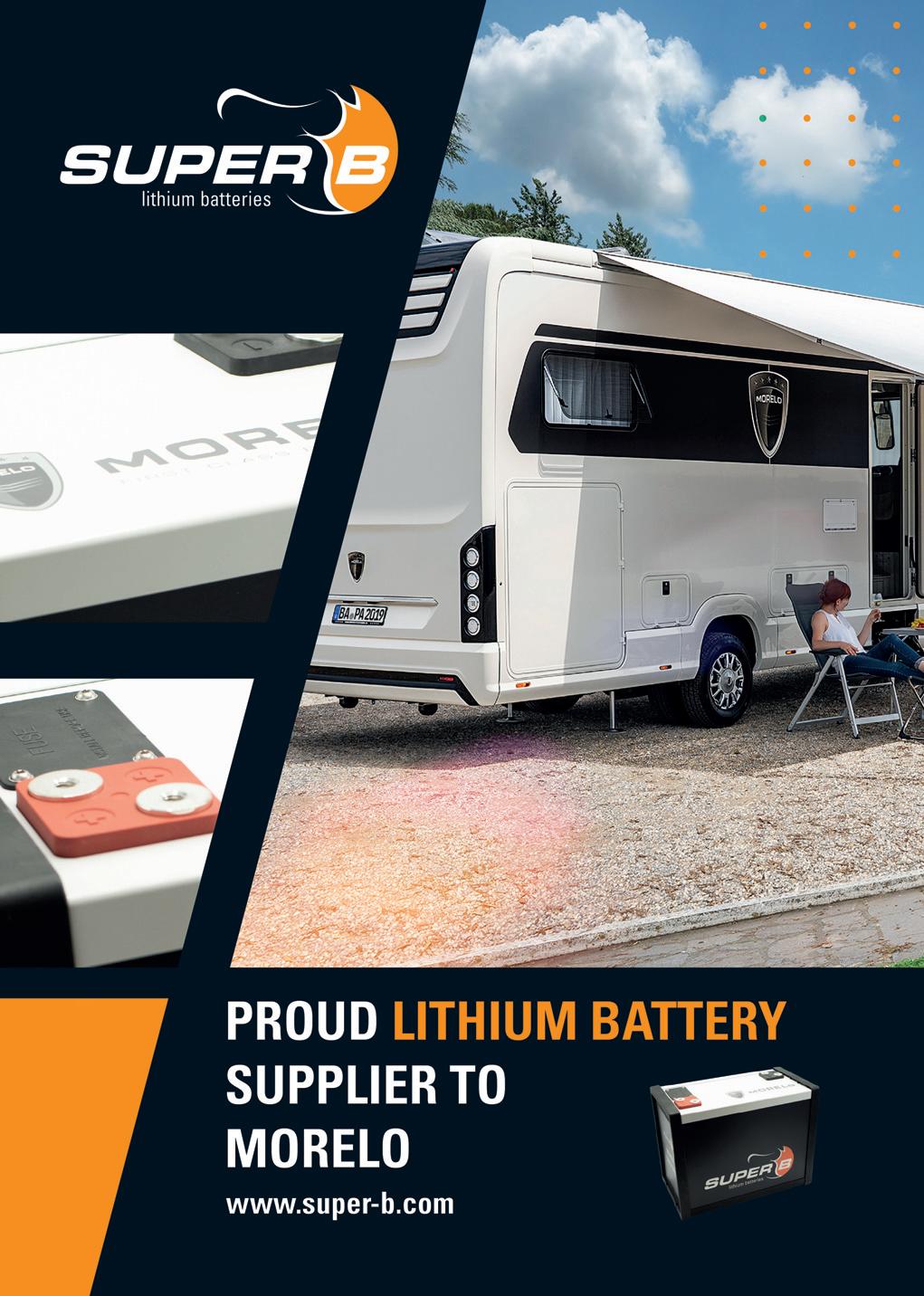
Image © Brittany Ferries
Navigating busy ports and berthing are two of the most chal lenging aspects of ferry operations. Increased vessel size, intro duced in line with ‘safe return to port’ regulations, and challenging weather conditions mean the margin for error during these manoeuvres is tiny. The SPECS super-wide cameras will give the crew a 360° view, from the edge of the hull to the horizon, streamed directly to the bridge in real-time. Live distance indications to objects around the vessel reduce risks of a collision, protecting passengers, crew and the ferry, while improved visi bility helps captains navigate rough seas. With busy schedules to keep, minutes used manoeuvring on each side of a voyage can also quickly increase costs. The efficien cies achieved thanks to the assistance of the SPECS system can maximise trading time and minimise fuel consumption. By saving fuel, Brittany Ferries is also reducing its greenhouse gas emis sions, advancing the company’s sustainability strategy.
“It is also encouraging that Brittany Ferries shares our vision of a high-tech future for bridge systems and is excited about, not only the benefits SPECS can bring today, but also how tech nology will advance and develop into the future. SPECS provides the core situational data that will make this vision a reality and we are delighted to be partners with Brittany Ferries on this dig italSPECSjourney.”also enables a host of other functions. Processed data can be exported for use in simulation and training.
Brittany Ferries plans to use the data to show other crew how manoeuvring can be performed in specific conditions and ports. Export to simulation facilities can also allow for close investigation into any vessel incidents and thus reduce the risk of similar occurrences.
W ärtsilä Voyage’s Smart Panoramic Edge Camera System (SPECS) will be used by Brittany Ferries to improve the safety and efficiency of its passenger ferry operations. SPECS will be first installed onboard the Salamanca – the 214.5m, 1,015 pas senger ferry which started operations between Portsmouth and Bilbao in March 2022.
Sasha Heriot, Head of Product, Assistance Systems, Wärtsilä Voyage, commented: “SPECS will help the crew of the Salamanca augment their situational awareness whilst also enabling Brittany Ferries to improve operational safety and efficiency. The com pany’s proactivity in adopting cutting-edge technology is impres sive and will ensure it remains one of the leading cross-channel ferry operators.
Brittany Ferries’ Salamanca passenger ferry uses Wärtsilä’s SPECS camera system for more efficient and safer operations
Arnaud Le Poulichet, Director of Engineering and Maintenance, Brittany Ferries, said: “When the captain is confident in manoeu vring it improves safety, saves time and fuel. This clear and strong return on investment makes adopting SPECS an obvious decision.
“ But there is more to embracing digitalisation. Using the latest technology also plays an important role in attracting highquality crew. By having innovative technology onboard, we make sea faring attractive to a new generation of seafarers – who we must engage in the industry.”
Marine News Latest news in the marine industry 20 Inside Marine
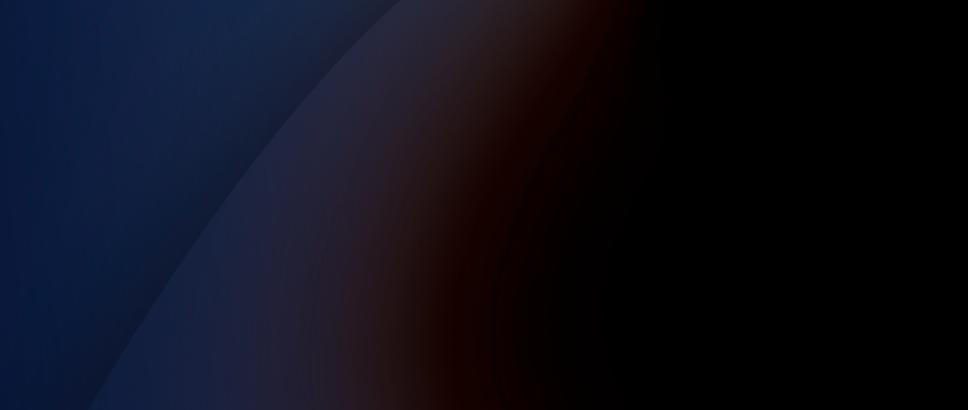
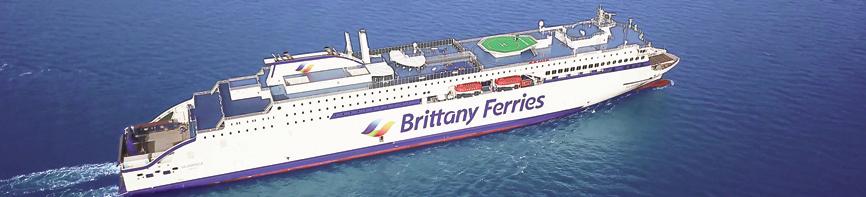
A .P. Moller - Maersk (Maersk) has reached an agreement to acquire Martin Bencher Group, a Denmark-based project logistics company with premium capabilities within non-con tainerised project logistics. Martin Bencher was founded in 1997 and is an asset-light logis tics provider that specialises in project logistics. Martin Bencher’s core capability is designing end-to-end project logistics solutions for global clients, and the company’s competitive strengths include deep industry expertise, a solid track record, long-term stake holder relationships as well as a highly skilled organisation.
– including detailed planning, orchestration, and sequencing of end-to-end shipments from suppliers to destination sites. Such service requires managed transportation capabilities with deep technical specialist knowledge around specific supply chain elements such as the handling of oversized and special lift cargo, conducting road surveys, and delivery planning as well as offload and assembly of the equipment on sites.
“Martin Bencher will be an excellent fit to Maersk and our inte grator strategy, strengthening our ability to provide project logis tics services to our global clients,” said Karsten Kildahl, Regional Managing Director in Europe, Maersk. “When Martin Bencher joins the Maersk family, we will be able to deliver project logistics services with a high degree of reliability, a proven track-record, and a strong focus on Health, Safety, Security and Environment (HSSE). In addition to supporting our existing customers’ project logistics needs, we will also be able to provide a more comprehen sive offering to a wide array of industries.”
Martin Bencher Group is headquartered in Aarhus, Denmark, and has a presence in key locations globally through 31 offices in 23 countries, with almost 170 employees. us your news We welcome all your important updates and company news. If you wish for us to share your press releases with our readers please send it to us today. Send to: media@insidemarine.com
inside (( MARINE Send
i M
Project logistics is not new to Maersk, as the company already has niche competencies based mainly in Europe and North America. However, in order to expand and mature the service offering, existing activities will be consolidated into a global product offering.
“We are thrilled to become an integral part of Maersk, which we see as an ideal fit for our people and clients,” commented Peter Thorsoe Jensen, CEO of Martin Bencher. “Clients requiring project logistics are aware of the constraints and challenges facing them and are seeking strategic partners with sufficient ambitions and strength to handle their entire global supply chain now and in the years to “Togethercome.with Maersk, we will have the scale, commitment, and capabilities to handle the entire logistics scope of work for clients around the world – as well as expand into new industries.”
With the intended acquisition of Martin Bencher, Maersk will also introduce a new product, Maersk Project Logistics. Project logistics is a specialised service offering within the global logis tics industry that covers the combination of solution design, special cargo transportation, and project management services
Inside Marine 21 Send your latest news media@insidemarine.comto:
A.P. Moller - Maersk buys Danish project logistics company Martin Bencher Group of project logistics
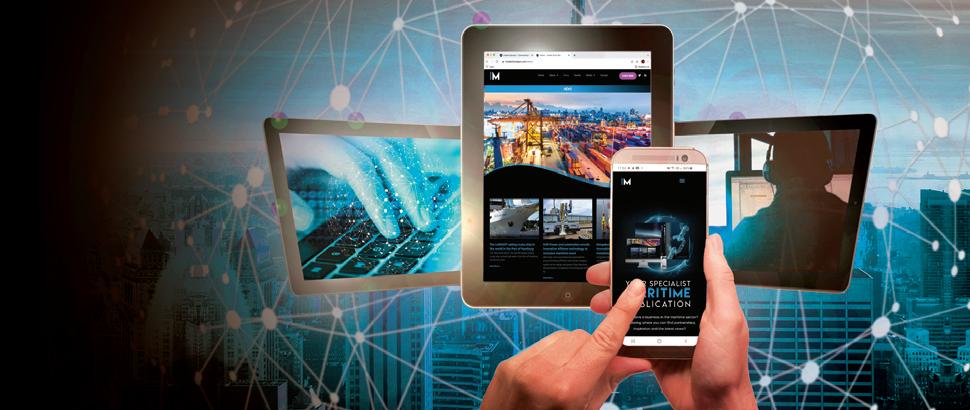
22 Inside Marine
Cedar Marine specialises in assessing the complete energy, fuel and emissions impact of a customer’s entire business operations. The company’s Carbon Management Plan allows the customer to establish benchmarks, continuously assess their performance, and demonstrate improvements over time.
Chris Huxley-Reynard, Managing Director, Reygar commented: “As an industry, we’re all hugely aware of the importance of moving towards more sustainable, and less carbon intensive operations. But we can only make positive changes if we truly understand at a really granular level the emissions and sustain ability challenges across our businesses. “That’s why we chose to collaborate with Cedar to offer what we think will be a really valuable and innovative service to cus tomers; combining our skills in data gathering and processing, with Cedar’s broad experience of carbon monitoring and naval architecture insight.”
Reygar and Cedar Marine collaborate to deliver carbon reduction for fleet operators of project logistics
“As
In the current climate of rising oil prices and pressures to reduce carbon footprints, fleet operators are increasingly focused on identifying ways to reduce fuel and energy use, as well as to demonstrate their environmental credentials to customers and stakeholders.
an industry, we’re all hugely aware of the importance of moving towards more sustain able, and less carbon intensive operations. But we can only make positive changes if we truly understand at a really granular level the emissions and sustainability challenges across our businesses” Marine News Latest news in the marine industry
Included in the service, and drawing on the naval architec ture experience of its founding team, Cedar Marine provides insight into specific measures a customer can take to reduce their fuel/energy costs and emissions, based on the measured vessel performance data supplied by BareFLEET in line with architectural and operational characteristics for each vessel in the customer’s fleet. Such an approach marries big data with human experience and insight, offering customers actionable choices with quanti fied benefits based on solid and directly relevant data, to improve theirOwenperformance.Preece,Managing Director, Cedar Marine commented: “Since vessel fuel burn is the major contributor to maritime emissions, combining accurate BareFLEET fuel, speed and oper ational data with our understanding of the broader emissions profile from other aspects of customers’ business operations allows us to offer the best possible combination of data and insight to drive real operational evolution and change across our customer base.”
M aritime remote monitoring business Reygar, and carbon reduction and sustainability specialist Cedar Marine, have partnered to provide an integrated service for monitoring and reducing fuel, energy use and carbon emis sions, across vessels and business operations of firms in the marine industry.
The integrated subscription service utilises measured fuel consumption and emissions data from Reygar’s industry-leading BareFLEET remote monitoring product, in combination with addi tional information gathered by Cedar Marine on other aspects of a customer’s operations, for a holistic and encompassing overview of the business-wide carbon emissions profile. This provides the customer with a comprehensive and accu rate picture of their energy and fuel use and emissions based largely on measured data, providing a full and accurate picture of carbon liabilities across operations.
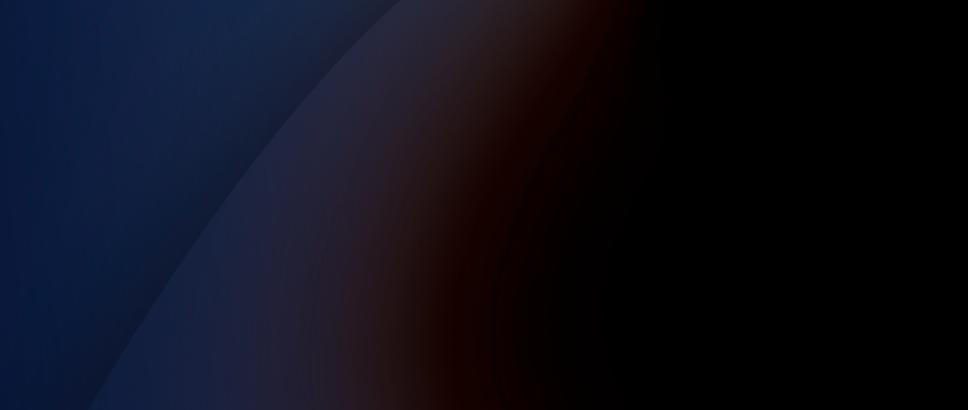
Eminox releases latest white paper on emissions regulations in the global shipping industry
To access the full white paper visit: https://eminox.com/downloads/
Send your latest news media@insidemarine.comto:
Exploring the latest regulations and legislation and the myriad of implications for the global shipping industry, the paper supports all sectors to understand what is required and how compliance can be “Thisachieved.isperhaps one of the most ambiguous sectors for emis sions requirements, and often feels counterintuitive against the backdrop of driving the highest standards possible across all geo graphical regions,” said Dr David Phillips, Engineering Director, Eminox. “Raising awareness of current legislation, presenting solutions to achieve compliance, and tackling the future regula tions head-on will help everyone, from engine manufacturers and shipbuilders to operators and compliance bodies, understand how we can help the marine industry become a leader in tackling global emissions.”
Master Boat Builders to construct new tugboat for Suderman & Young Towing Company
With over 90% of world trade transported by sea, it is not sur prising the emissions generated by the shipping industry makes it one of the world’s largest producers of air pollution.
A leading designer and manufacturer of emissions technolo gies and solutions has released its latest white paper which tackles the challenges of compliance and emissions regulations in the global shipping industry.
M aster Boat Builders has signed a contract to build a new tugboat in its Coden, Alabama yard for Suderman & Young Towing Company of Houston, Texas. Master Boat Builders cur rently has three tugs under construction of a different design for Suderman & Young. “We at Master Boat Builders take pride in our work and are heart ened by this vote of confidence from the team at Suderman & Young,” said Garrett Rice, President of Master Boat Builders. “Suderman & Young is one of the premiere tugboat operators in the United States and we are excited to continue partnering with them to provide another quality tugboat to serve the western Gulf Coast ports.” Naval architect and marine engineering firm Robert Allan Ltd designed the tugboat, which will meet United States Coast Guard Sub-M regulations and will be classed through the American Bureau of Shipping. The tugboat will have an overall length of 30m, a beam of 13m and produce a bollard pull of over 80 metric tonnes. The vessel will fea ture two Caterpillar main engines (3516E), EPA Tier 4 certified and each producing 3500 HP, along with two Schottel Z-Drive thrusters (SRP 510FP), and a Markey Machinery Company bow winch (DEPSF48-100).
Inside Marine 23
“Reducing marine emissions remains a global focus, and it is essential that as an industry we deliver solutions which will enable us to meet the IMO target of 50% reduction in GHG by 2050,” said Dr Phillips. “To achieve this we need stronger legis lation, applicable to both the original installation and retrofit of marine vessels, to accelerate emissions reduction. Importantly, there is also an urgent need for the harmonisation of global marine“Becauselegislation.Eminox understands the need for systems which are compact, easily controlled, and compatible with a range of marine and stationary/power generation engines, we can use our expertise, global understanding and manufacturing capabilities to deliver future proofed compliance.”
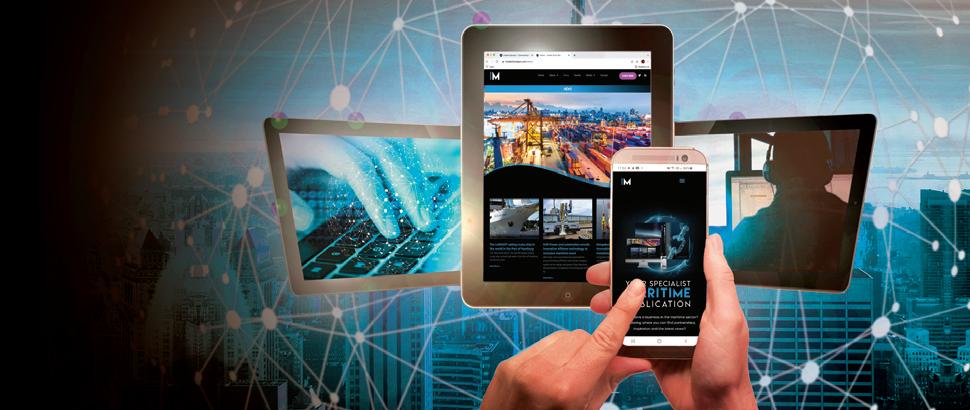
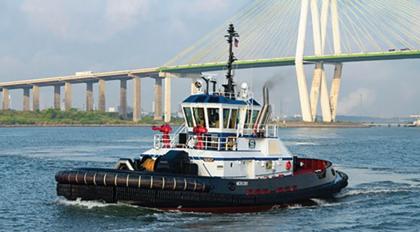
Falmouth Harbour aims to appoint a builder in October with a view to having the new, 16–18m dedicated coded pilot vessel operational in 2024.
“This long-awaited procurement represents a very exciting time for us as an organisation,” said Falmouth Harbour CEO Miles Carden. “The new vessel will be a significant step forward in technology, fuel efficiency and sustainability and will mod ernise Falmouth Harbour’s pilotage service, securing safe and efficient operations for the future benefit of the port and its many“Thisstakeholders.isaconsiderable investment in the future of our harbour and potentially allows us to modernise our operations so we are absolutely fit for purpose and can realise future opportunities around technologies such as Floating Offshore Wind (FLOW). This is a generational investment of over £1 million in our future sus tainableFalmouthoperations.”Harbour’s two current all-weather coded pilot boats operated by the Pilot Service are Arrow, a 16.7m Halmatic built modern pilot vessel built in 2006, and the LK Mitchell, a 17.5m Nelson 56 pilot vessel. A twoboat operation, with the vessels oper ated in rotation, is essential to ensure complete coverage of the area and allow for vessel downtime and maintenance.
The new vessel will replace the LK Mitchell which was built in 1978 and has been operating as a Falmouth pilot boat ever since.
24 Inside Marine Marine News Latest news in the marine industry
Falmouth Harbour is looking to the UK’s network of builders to receive proposals which make full use of modern advances in fuel-saving technology, safety and crew welfare. The value of the project is expected to be between £1.1 to £1.4 million and will take up to three years to complete. When in commission the new vessel will be one of the UK’s greenest and most efficient vessels of its type.
Falmouth Harbour (FH) is inviting boat builders around the UK to tender for the construction of a clean, green, fuel-efficient pilot vessel to join a fleet operating 24/7, 365 days a year and completing more than 1,000 boardings and landings per year within the Falmouth Pilotage Area.
“At 44 years old, LK Mitchell is fast approaching a point where she is no longer economically viable to operate to the standards required of a 24/7 operation in Falmouth,” said Mr Carden. “She has been a loyal servant to our port but the time to replace her has come. We will outline this vessel’s future in the coming months and we hope to redeploy her in a second, less demanding commercial life.”
Falmouth Pilot Services (FPS) is a service arm of Falmouth Harbour Commissioners and Falmouth Harbour is the pilotage authority for the Falmouth Pilotage Area which spans from Black Head to the Dodman including Falmouth Bay, the Helford and Percuil rivers, the Carrick Roads and the River Fal. FPS provides pilotage services to Falmouth Dock operators A&P Falmouth and Cornwall Council which runs the Ports of Truro and Penryn under an agency agreement. Falmouth Pilot Services has the remit to supply safe and efficient pilotage for this whole area on behalf of the many businesses and organisations that operate within it. The service operates 24/7 and 365 days a year across the full weather range in which shipping movements can take place within the area.
HarbourFalmouthcredit:Photo
Falmouth Harbour invites UK tenders to build “greenest, most efficient” £1m+ pilot boat
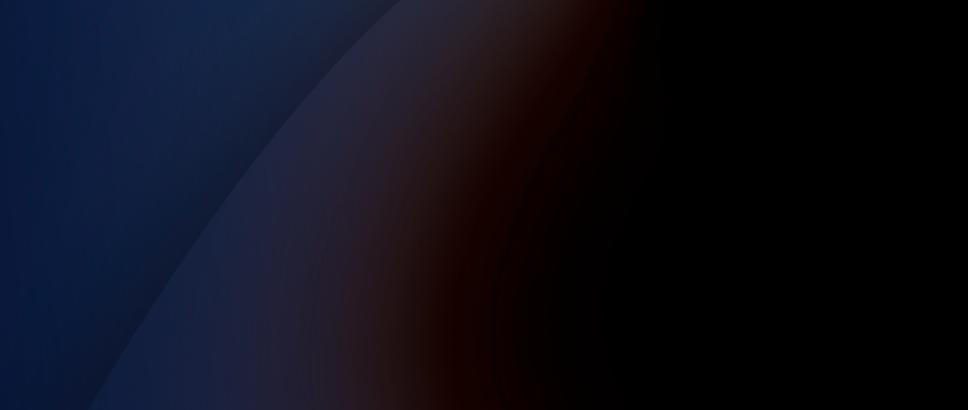
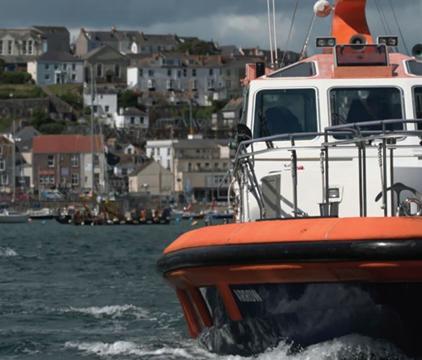
Inside Marine 25 Send your latest news media@insidemarine.comto:
Austal USA has been awarded a $156 million fixed-price incen tive contract option from the United States Navy for the con struction of two Navajo-class Towing, Salvage, and Rescue Ships (T-ATS 13 and 14). With the award, the company is now under contract for four TATS, having received awards for T-ATS 11 and 12 in October 2021.
Austal Limited CEO Paddy Gregg said the latest contract award reaffirmed the United States Navy’s great confidence in Austal USA’s capabilities as a steel shipbuilder, following the recent start of con struction on T-ATS 11.
“It’s a great sign of confidence by the Navy, in the Austal USA team’s ability to deliver both steel and aluminium ships simultane ously, that they have awarded a contract for another two vessels.
Austal USA awarded contract option for two additional towing, salvage and rescue ships for the United States Navy
“Congratulations to the Austal USA team on yet another multiple steel vessel contract, which will go even further to demonstrate the company’s diverse capabilities, in aluminium andT-ATSsteel.”is an ocean-going tug, salvage, and rescue ship designed to support the United States Navy’s fleet operations, with a multimission common hull platform capable of towing heavy ships. The ships are capable of supporting a variety of missions, including oil spill response, humanitarian assistance, search and rescue andAustalsurveillance.USAwill utilise its proven ship manufacturing processes and innovative methods that incorporate lean manufacturing prin ciples, modular construction, and moving assembly lines, all housed under the company’s state-of-the-art enclosed steel produc tion facility. This unique production capability positions Austal USA to meet the ongoing, growing demands of both the Navy and CoastConstructionGuard. on T-ATS 13 and 14 will commence in the second half of 2023 and first half of 2024; with delivery planned for the second half of 2025 and first half of 2026, respectively. In addition to T-ATS, Austal USA is currently constructing the United States Navy’s Independence-variant Littoral Combat Ship and Spearhead-class Expeditionary Fast Transport and is under contract for the construction of a 211 metre steel Auxiliary Floating Drydock Medium. The company was also recently awarded a contract for up to 11 steel Offshore Patrol Cutters for the United States Coast Guard, worth up to US $3.3 billion.
NavyUScopyright:Image
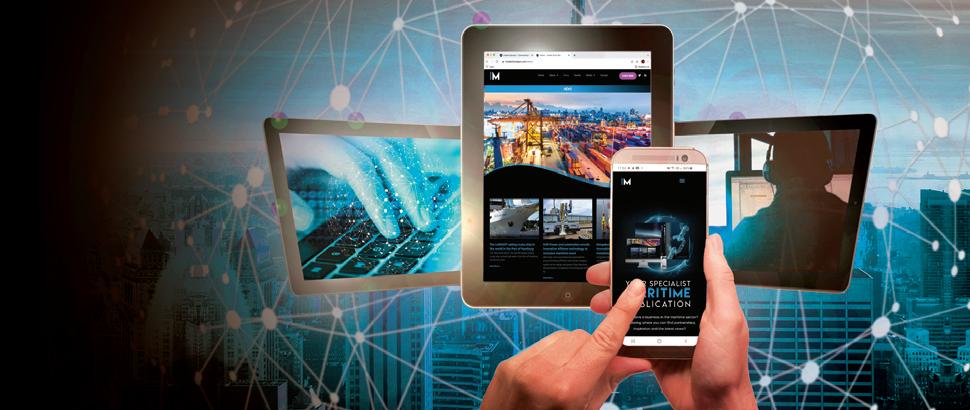
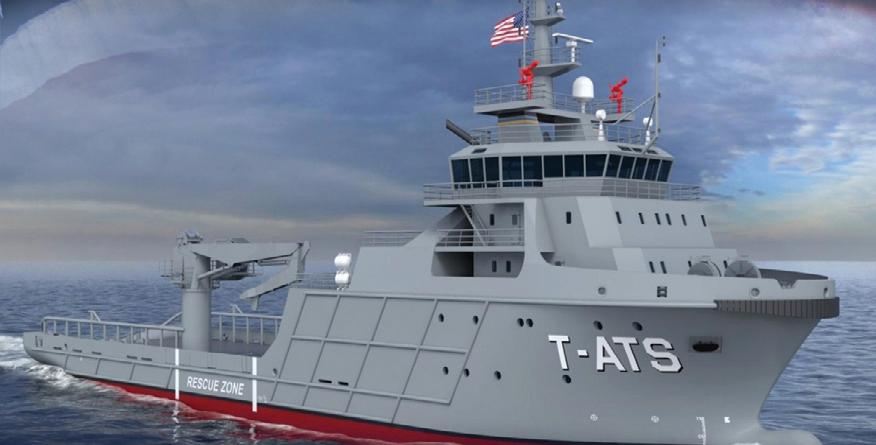
Copyright: Konecranes
The Port of San Diego will be the first in the Americas to operate two eco-efficient Generation 6 Konecranes Gottwald Mobile Harbour Cranes. Planned to be opera tional by mid-2023, the cranes plug into the mains power, then operate on internal battery packs for extensive travelling time around the port.
26 Inside Marine
Norwegian ferry operator Norled operates MF Hydra, the world’s first liquid hydro gen-powered ferry. The double-ended MF Hydra was designed by LMG Marin and built at the Westcon shipyard in Norway. MF Hydra is 82.4m long, with capacity for 300 passengers and 80 cars
While only 6.4km long, the Corinth Canal between the Gulf of Corinth and the Saronic Gulf in the Aegean Sea holds the record for being the deepest canal in the world, with a depth of 8 metres.
Interesting and unusual marine facts from around the world fact
Matter of fact
matterof
Hybrid service vessel Northern Skagerrak, oper ated by Northern Energy & Supply around the port of Gothenburg, saves 680 tonnes of CO2 with elec tric power and an auxiliary engine powered by hydrotreated vegetable oil. Northern Skagerrak further supports the environment by collecting sludge and slops from vessels for safe disposal.
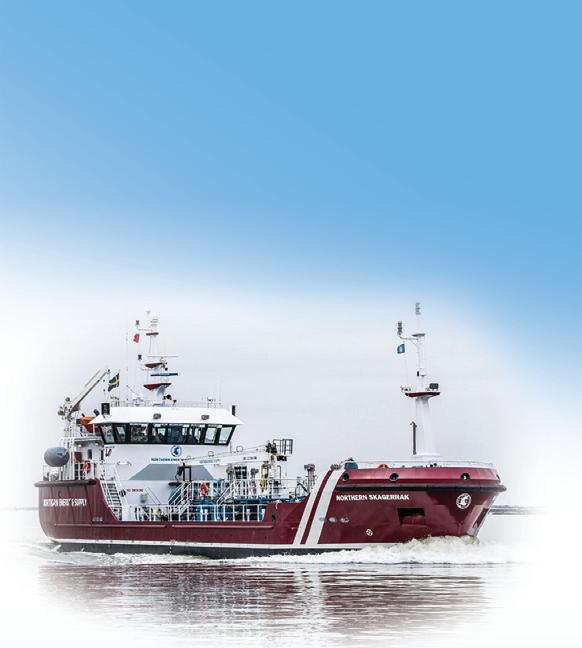
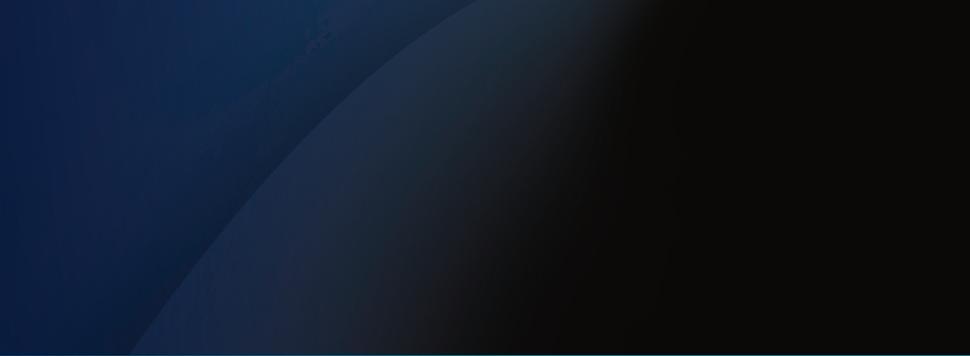

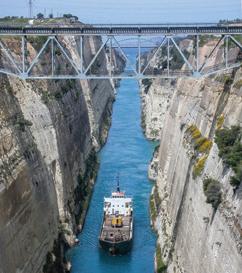
Inside Marine 27
The Alphenaar is the first electric inland shipping vessel in the Netherlands, powered by ZES rechargeable batteries mounted in shipping containers. Alphenaar sails canals between Alphen aan den Rijn and Moerdijk carrying ship ments of Heineken beer.
According to housing specialists Heat, Space and Light Ltd, the best way to recycle shipping containers in the housing market is to melt down the steel container into screws and use them to build up to 50 timber-frame houses suit able for human habitation.
The Port of Newcastle in Australia is the world’s largest coal export port, but from 2022 it is now 100% powered by renewable energy, saving almost 5,000 cubic tonnes of carbon emissions. The world’s longest yacht race was the Volvo Ocean Race 2017-8, which covered 45,000 nautical miles around the world. After a race lasting 126 days, the winning margin was only 16 minutes.
The 109m motor yacht Bravo Eugenia was built with a focus on hydrodynamics. Her refined hybrid propulsion system deliv ers up to 30% less fuel consumption compared to conventional superyachts of the same length.
The oldest shipyard still in operation is the Haliç shipyard in Istanbul, which was founded in 1455. Every problem is a gift we would not grow without problems “ “ Anthony Robbins
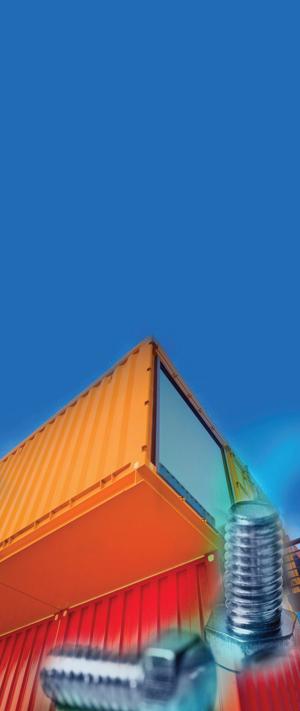
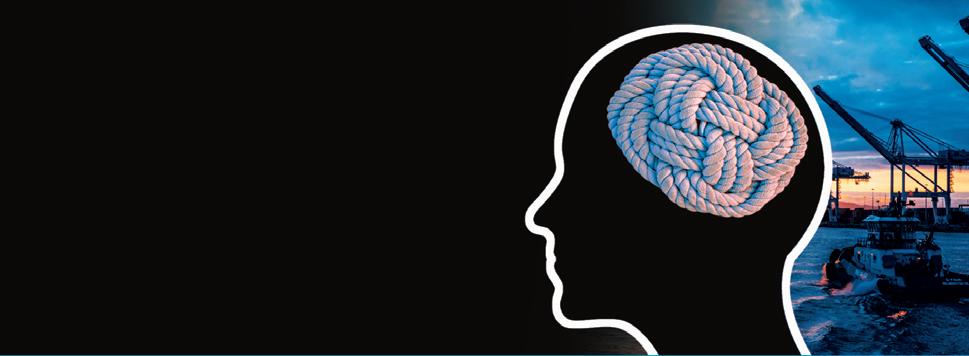
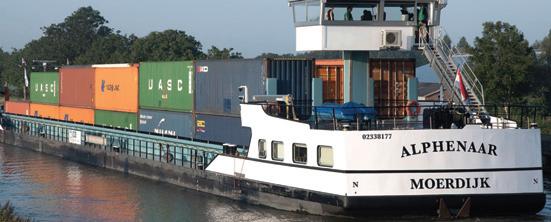
Journe has been inventing and making watches for over 40 years. He draws on his historical knowledge and expertise to face the most daring horological challenges, demonstrating a timeless consis tency in research and innovation with a single goal: make each mechanical timepiece as accurate as possible. FOR HAUTE HOROLOGY A F.P.JOURNE I PROFILE
28 Inside Marine
François-Paul
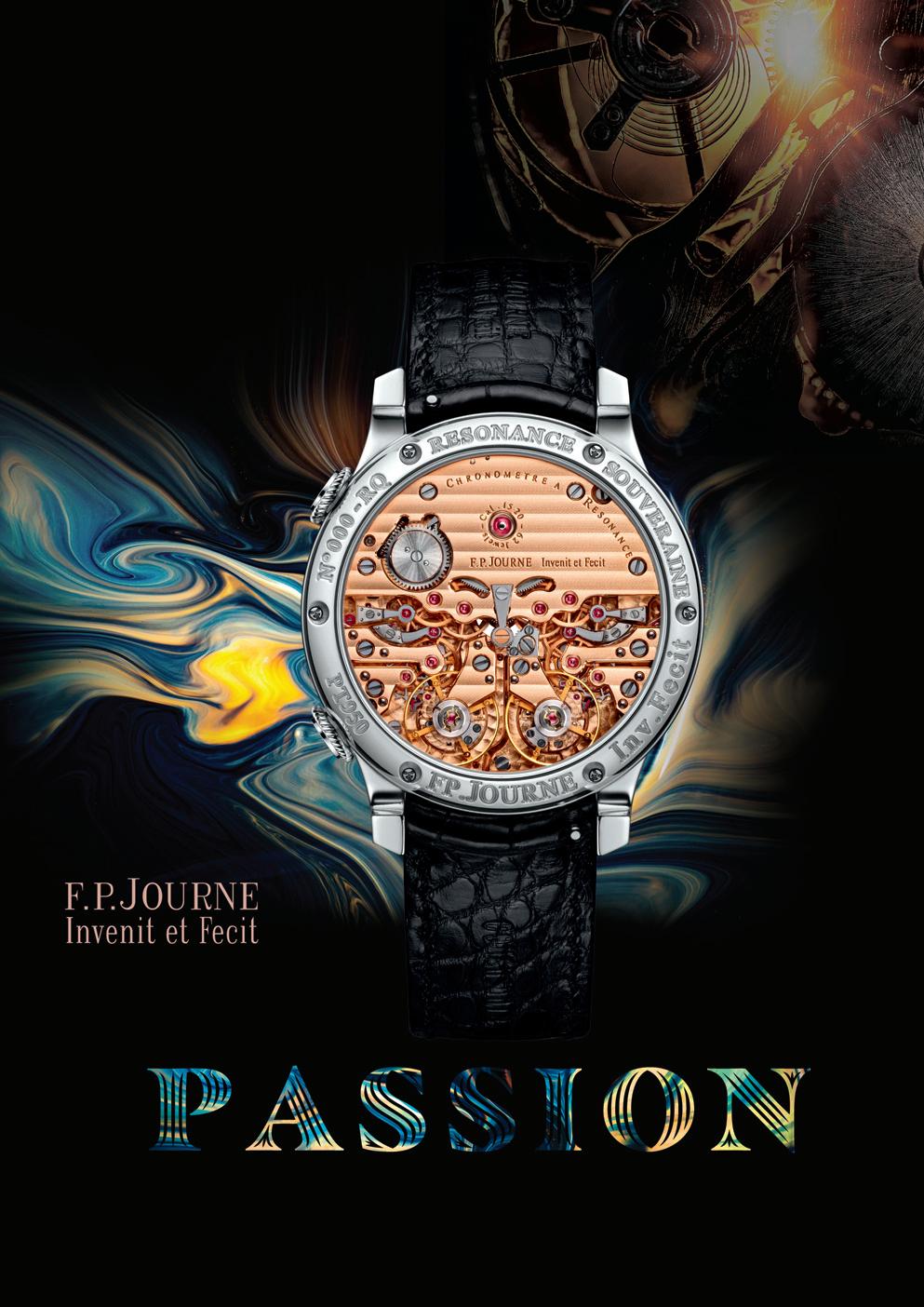
The exceptional F.P.Journe high horology creations have spanned over decades, showcasing an exceptional watch pedigree from the astounding Sonnerie Souveraine, the ultra slim Répétition Souveraine, the emblematic Chronomètre à Résonance, the Chronomètre Optimum, the amazing Octa automatic caliber with a 160 hours power reserve, to the Astronomic Souveraine, an ultra-complicated watch with 18 functions andTheseindications.exceptional creations have granted F.P.Journe the awarding of the most important international watch prizes throughout the world: seven distinctions at the GPHG in Geneva, from which three times it has received the ultimate dis tinc tion of the Golden Hand. And numerous times its creations have been awarded W atch of the Year accolades in Japan, China, United States, Switzerland and Mexico. François-Paul Journe has also been decorated with the title of Chevalier des Arts et des Lettres by the French Minister of Culture.
Inside Marine 29 xcellence and precision are the essence of an F.P.Journe watch, as well as authenticity and chronometry.
Because the exceptional F.P.Journe time pieces of watchmaking art deserve to be brought out to their true dimension, the brand opened a network of 10 boutiques in Geneva, Paris, Tokyo, Hong Kong, New York, Los Angeles, Miami, Beirut, Kiev and Dubai. At each destination, visitors may dis cover the pieces of the Classique, lineSport and élégante by F.P.Journe collections in the brand’s exclusive universe, as well as special editions that are reserved solely for them such as the Black Label collection or the Boutique Anniversary Centigraphe. n E
F.P.Journe produces all its movements in 18K Rose Gold, a first in the watch world and a unique feature of the brand. Signed with the label Invenit et Fecit (invented and made), each F.P.Journe exclusive movement guarantees a manu facture calibre, entirely invented, con structed, and assembled in the Geneva workshops.
In the 18th century this inscrip tion used to be engraved on watches manufactured by prestigious French master-watchmakers upon their accep tance by the Royal Academy of Sciences. At the crossroad between arts and haute horology, the independent F.P.Journe Manufacture is a world in itself, embodying excellence, know-how and innovation, in the respect of the haute horology tradition from which FrançoisPaul Journe is the proud guardian. It was founded with one principle in mind: inno vate and uphold, if not outrival the high standards of haute horology. Every effort was made to verticalize the production in order to produce inside its walls, almost all the components necessary for the making of F.P.Journe watches. It includes the cre ation and production of all its dials and watch cases which echo with the move ment in perfect harmony. The modernity of machines and instru ments is essential to reach the expected level of perfection, but it is also paramount to maintain craft tradition, since many operations are still done manually, with an infinite precision, tirelessly repeated until flawlessness. In his manufacture, François-Paul Journe is the master watchmaker and that differentiates the brand from other watch companies. With unmatched tech nical and watchmaker skills, he makes a point of honour to design and manufac ture mechanical watches one by one and in small series. Honouring artisanal work With a limited production of less than 900 mechanical timepieces per year, the sanc tuary of the F.P.Journe manufacturing process honours artisanal work. It prides itself in maintaining a genuine watch maker’s art. Each certified watchmaker is reacquainting with state-of-the-art haute horology, making a specific watch according to his technical sensitivity, and performing all production stages from beginning to end without anyone inter fering in the process, including the deli cate rating, casing-up and testing.
Boutiques across the world
FPJOURNE.COM
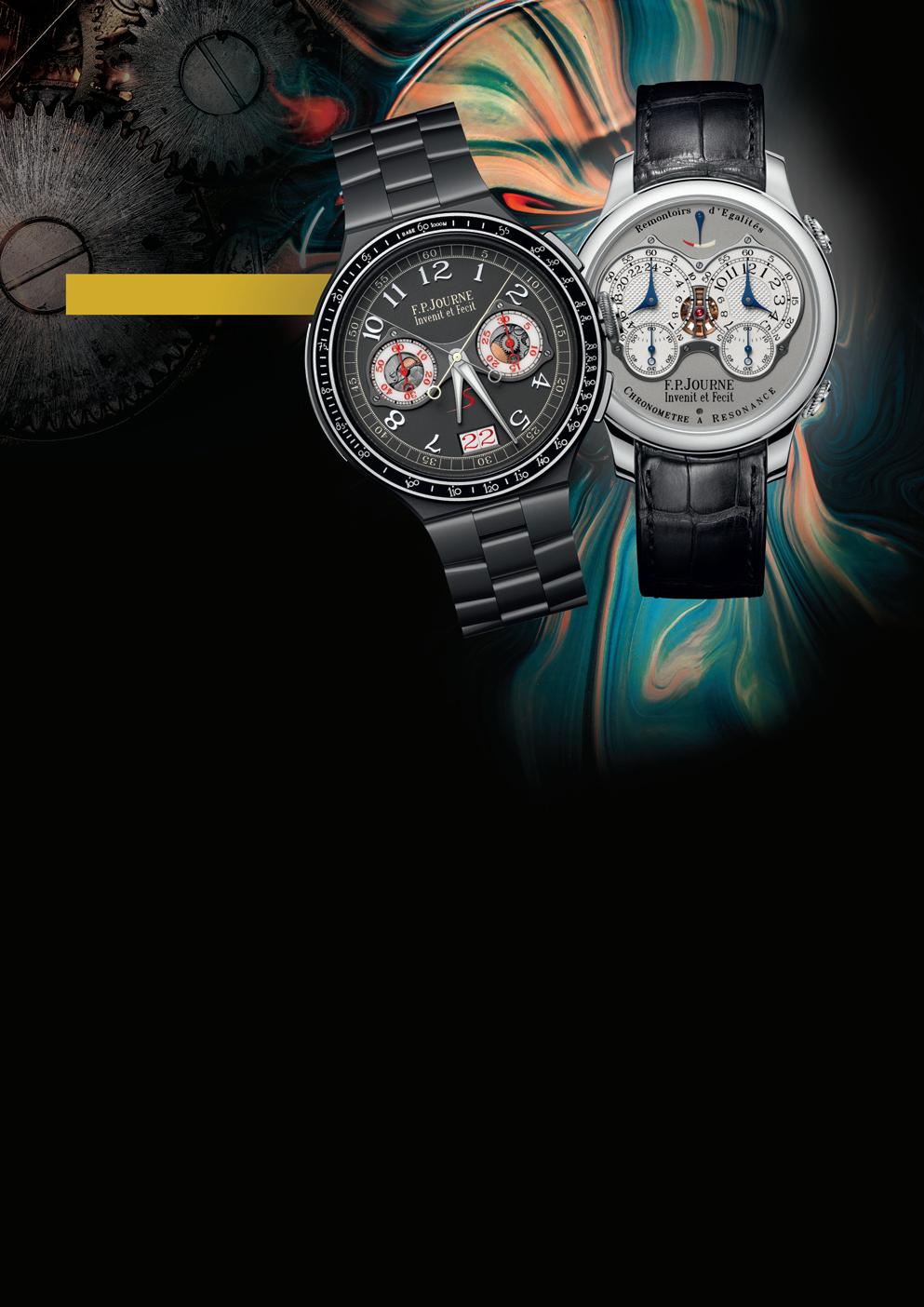
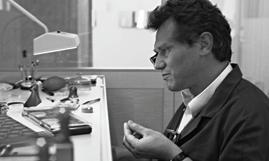
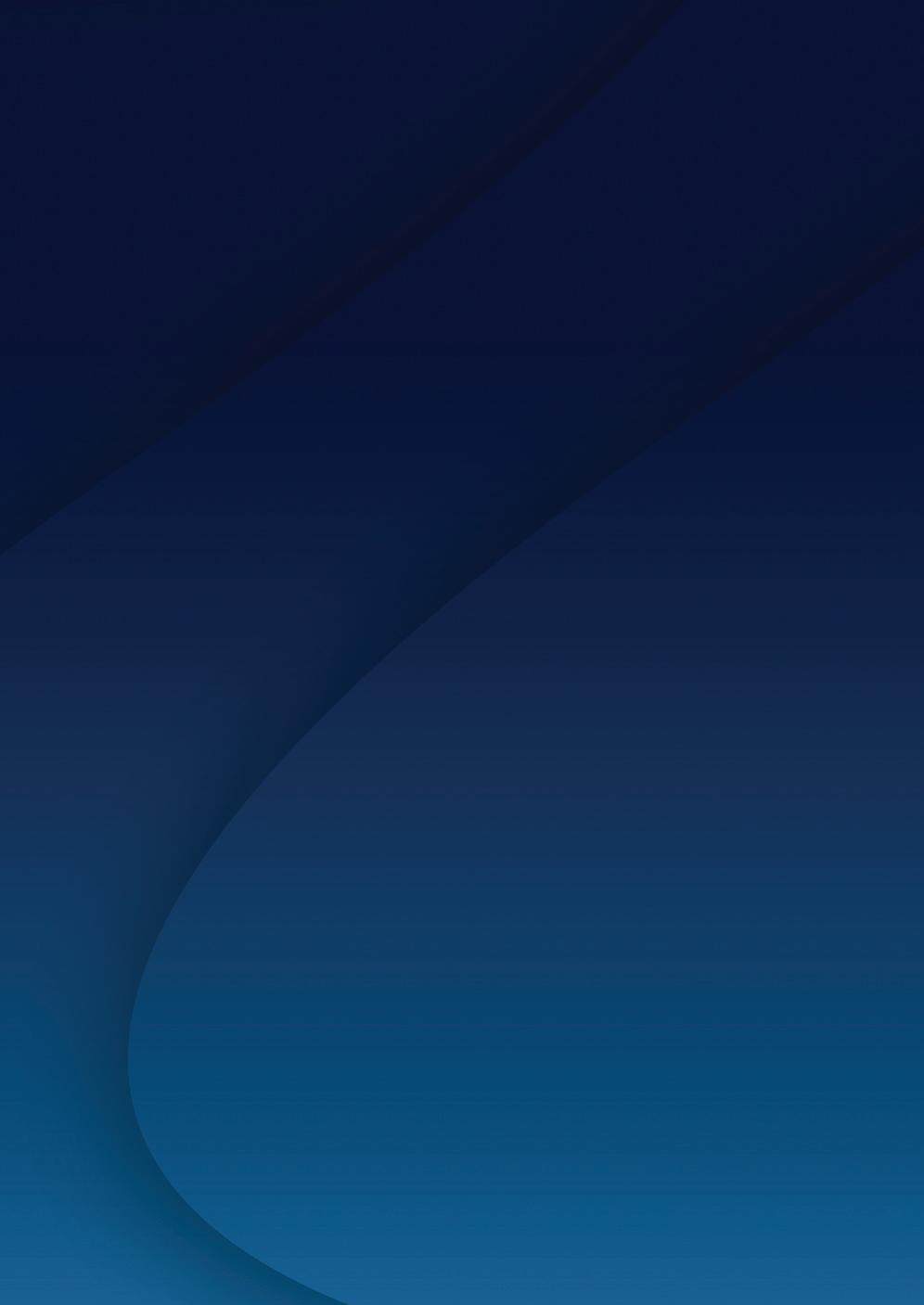
TOWAGEWORKBOATS,&SALVAGE seven seas, five oceans, one voice saam towage dann ocean towing mainprize offshore miller’s launch otto wulf i M

SAAM TOWAGE I PROFILE 32 Inside Marine
power
With substantial assets and robust operational capacity spread throughout the Americas, SAAM Towage is the region’s largest and most important provider of expert maritime towageThanksservices.toitsconstant focus on evolution, customer service and careful reinvestment, the company has enjoyed ongoing organic and inorganic growth for the past 20 years. Hernán Gómez, SAAM Towage Managing Director, discussed the company’s growth strategies and vision with Richard Hagan.
Towing across the Americas
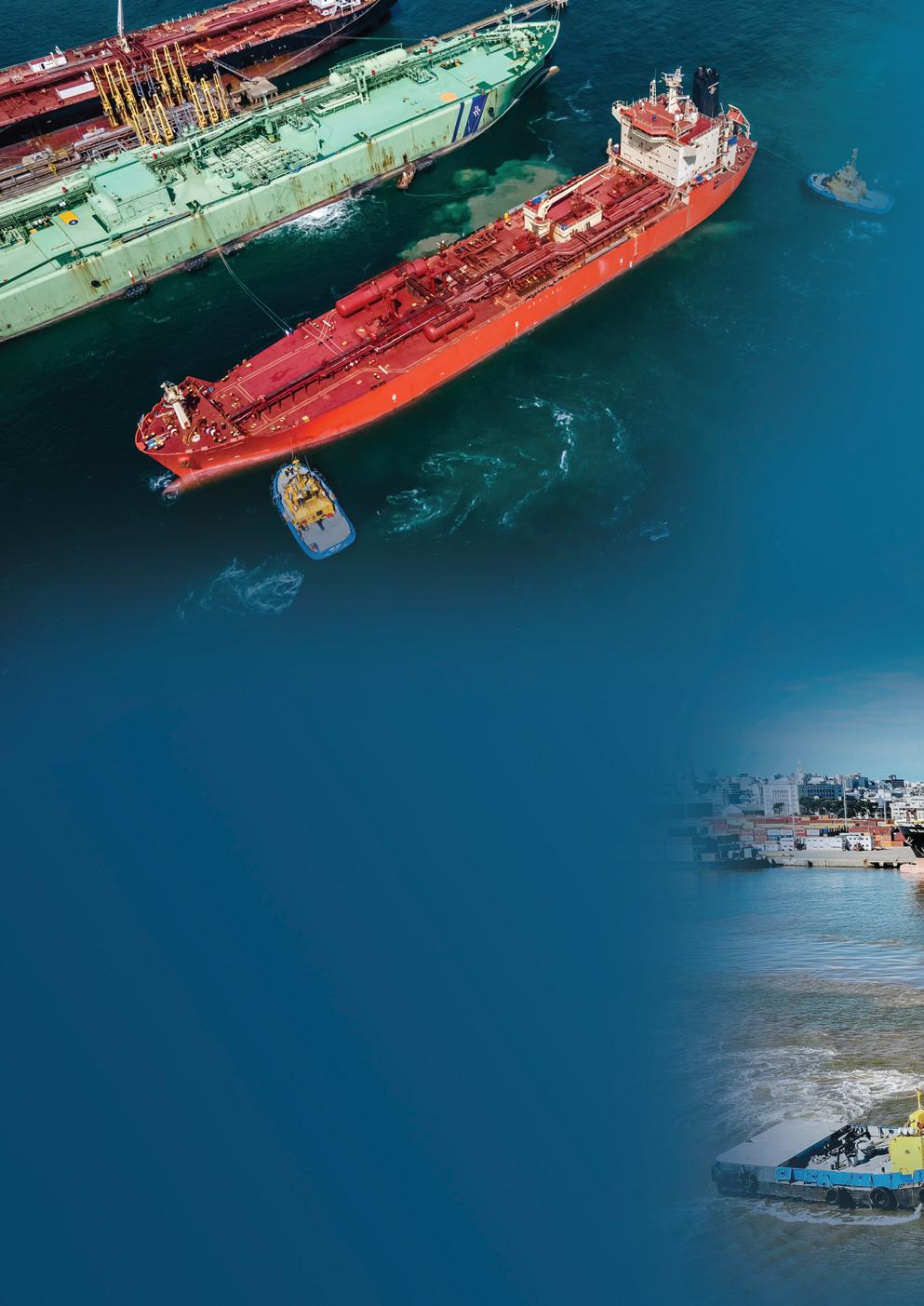
A modern tugboat service provider SAAM Towage provides cargo and terminal towage operations across the Americas, with an operational and asset footprint spanning from Chile to Canada. Customers include all the large liner companies, as well as numerous large oil and gas companies and many large portTheauthorities.company’s services include both the terminal and harbour towage segments and also special services. Harbour towage refers to the services provided by its tugboats to ships that are tradition ally from the container shipping lines and other shipowners and customers. For this service category, SAAM Towage would typi cally have several vessels deployed in any given port, and within the port, they’ll assist these large vessels with berthing and unberthing manoeuvres.
The second category, terminal towage, sees SAAM Towage estab lish direct contractual relationships between itself and a terminal project. In terms of these agreements, SAAM Towage would pro vide dedicated towage services for the berthing and unberthing of vessels calling a particular terminal for a longer duration, but generally on a lower frequency basis than those provided as part of a harbour towage agreement.
Altogether, SAAM Towage owns over 180 modern tugboats that are crewed and managed by a staff complement of almost 2,000 people. Of those, the bulk of its staff – about 80% – are seafarers and 20% are onshore personnel. The company follows a careful strategy of ongoing reinvestment in its vessels. Of its fleet of 180 vessels, 35 have been added to the fleet since 2015. Since 2010, the company has added a minimum of two or three vessels to its portfolio each year. SAAM Towage’s latest vessel, the 29m Mataquito II, features 82 tonnes of bollard pull and constant tension and was delivered to SAAM Towage in May 2022. Thanks to this large and growing asset portfolio of modern, capable tugs, SAAM Towage is able to handle a wide spectrum of vessels, including large container ships, ro-ro ships, oil, chemical and LNG tankers as well as bulk carriers, reefer ships and general cargo vessels.
Beginning life in 1961 as a subsidiary of shipping line CSAV, SAAM’s present form came into focus 50 years later in the early 2010s when it was spun off from its parent and became a fully independent, publicly traded company.
Tugs provided in terms of terminal towage contracts are generally required to meet high safety standards, especially relating to fire fighting capability and overall response to emergencies capabilities.
Inside Marine 33
Towing throughout the Americas

34 Inside Marine
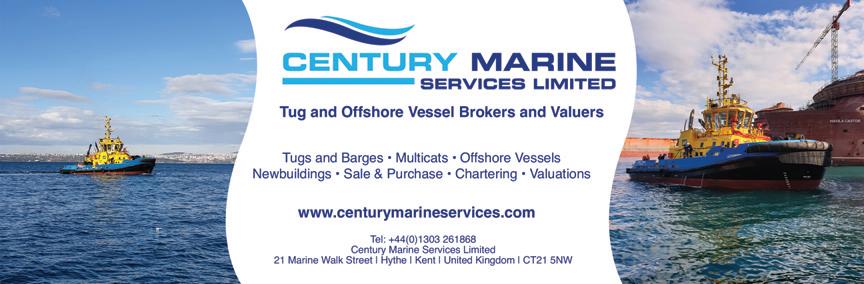
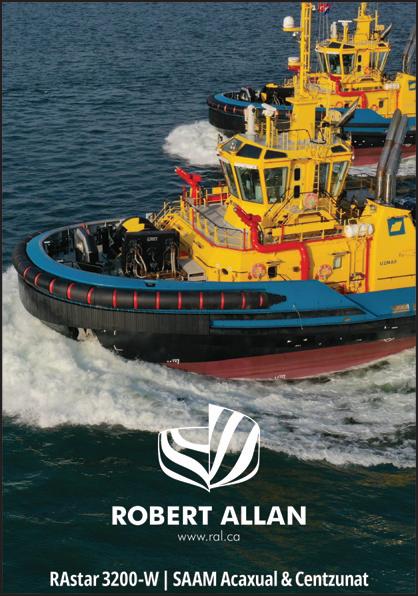

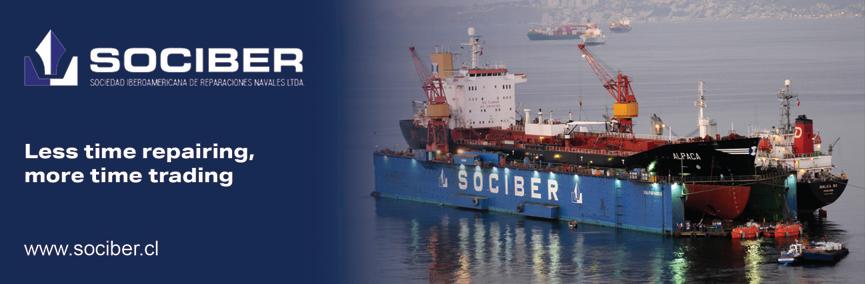



He added: “We believe the cost-efficiency and operational smoothness that we gain from this project will keep us competi tive and that it will attract future growth. It’s a very transforma tional internal project with a lot of implications for us.”
“We invest with a long-term view in our fleet, and we maintain partnerships with shipyards and equipment providers which have all put us in a very good place,” Mr Gómez confirmed. “We have a very strong balance sheet that allows us the flexibility, in this capital-intensive industry, to pursue growth opportunities when they“Allarise.”ofthis gives both existing and potential clients the peace of mind that we’re a reliable company that will be there to service our contracts and agreements.”
The company is headquartered in Santiago, Chile, while its fleet is operational throughout South and Central America and also in Canada where it has a long-term presence in British Columbia
Pushing partnerships and growth
In recent years, SAAM Towage has enjoyed strong, sustained growth, particularly in the five years between 2017 and 2022. Its growth strategy comprises a combination of organic growth, acquisitions and the creation of new companies to service its customers’ needs in new countries.
Its physical footprint is also impressive, with offices in Brazil, Canada, Chile, Colombia, Costa Rica, Ecuador, El Salvador, Guatemala, Honduras, Mexico, Panama, Peru and Uruguay. Of those, SAAM Towage’s biggest and busiest territory is Brazil, where it currently operates 51 tugs and provides services in almost every port in the country.
“We’ve invested in a lot of work around our operational processes,” said Mr Gómez. “One project will standardise our maintenance, procurement and operational processes across all of our opera tions, including invoicing. Building this new system has taken us just over two years and will ensure that we have all of our compa nies running on the same systems. It’s central to our strategy.”
Strategic partnerships and fleet reinvestments feature promi nently in the company’s growth strategy as well. Conversely, careful financial management is equally important.
SAAM TOWAGE I PROFILE 38 Inside Marine
To ensure that all of these moving parts remain united, the company has recently invested in some impressive new collabo ration processes.
“SAAM Towage’s leadership, with the largest fleet of tugboats in the Americas and highly specialized crews, is at the service of foreign trade,” said SAAM Towage Managing Director Hernán Gómez.

Gómez,Hernán DirectorManagingTowageSAAM
Meanwhile, in early April 2022, the company announced its acquisition of Standard Towing in Canada which will provide it with three new tugboats. Simultaneously, it welcomed a new tug boat to its fleet in Peru, a territory the business only recently re-entered in late 2021, by signing an agreement to acquire the towage operations of Ian Taylor Peru, increasing its fleet in this country to 10 vessels. Also, in 2022 the company received two new state-of-the-art tugboats for its operations in Chile. The latest milestone achieved by SAAM Towage for its Towage Division is signing an agreement with the Brazilian company Starnav to acquire 17 tugs currently operating in Brazil. The deal also involves the purchase of four additional tugs presently under construction.
Opportunity blowing in the wind SAAM Towage is eyeing new growth opportunities further afield, beyond its traditional markets. One of these is the rapidly growing windfarm market.
Mr Gómez concluded with his vision for the company’s future regional“Goingparticipation.forward,we need to ensure that we can participate in the coming volume with the shifts in the energy industry, ensuring that we are able to expand geographically into regions in which we’re not currently operating. Within the next three years, by 2025, we hope to have a foothold in a different region of the world or in a different project.” n
Inside Marine 39
Developing a sustainable future
“We’ve already invested in initiatives to reduce fuel consumption across the fleet, and now we’re starting to work on alternative propulsion. We’re well-equipped to manage that process.”
The shipping sector has increasingly been targeted globally for emissions reduction measures as part of worldwide global warming reduction efforts. SAAM Towage is alive to its responsibilities in terms of emissions reductions and as Mr Gómez highlighted, the company wants to be an industry leader in terms of its own efforts.
“We expect to see some news in 2022 about the changes we will be making in our fleet, but it’ll be a gradual process,” he continued.
“We have a relevant position in the market in our region and we want to be a driving force in environmental responsibility trends. We have a corporate environmental strategy in terms of which the next few years will be about ensuring that we make progress around the indicators we’ve identified and that we start investing in alternative propulsion solutions.
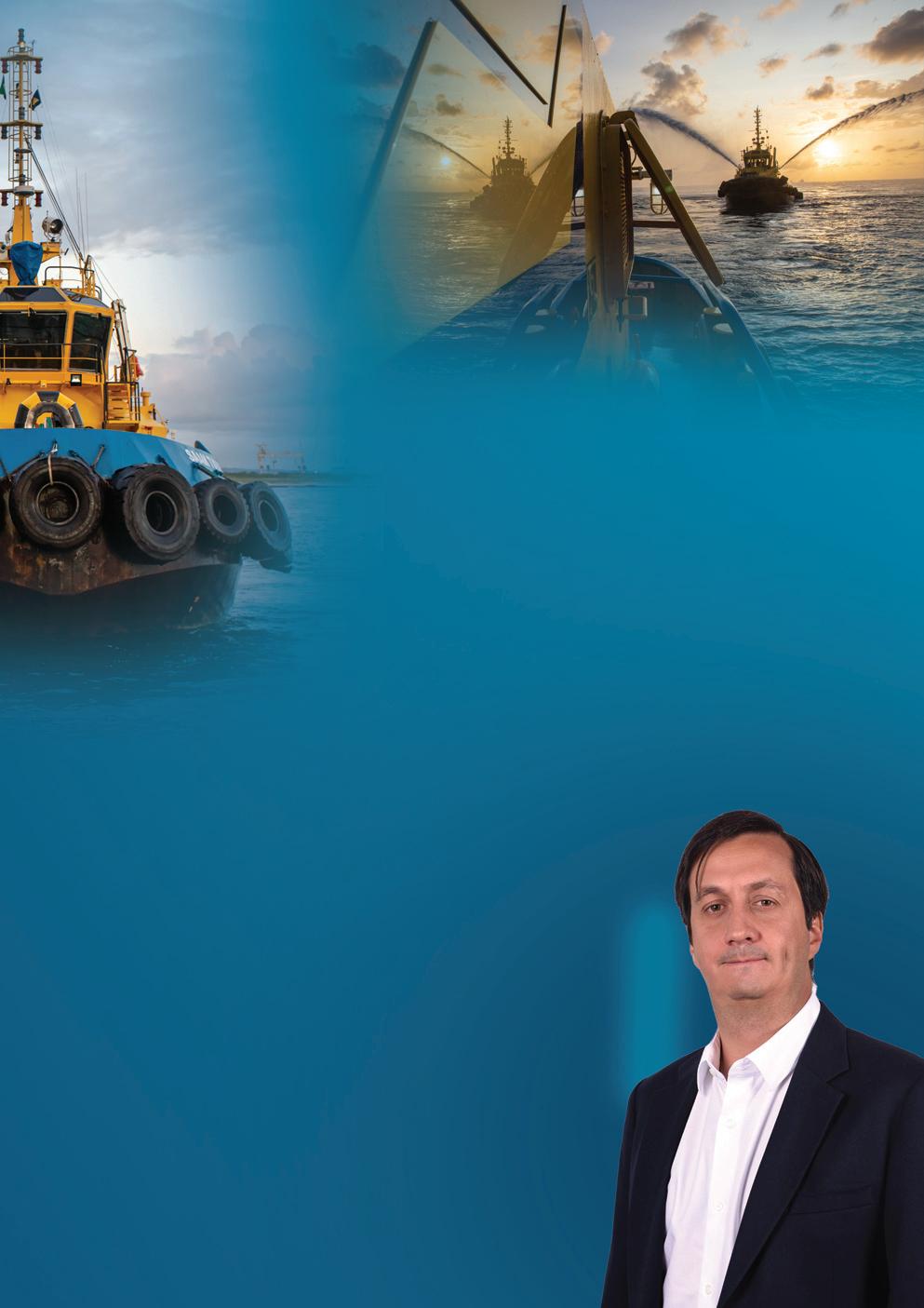
DANN OCEAN TOWING I PROFILE 40 Inside Marine The POWER Dann Ocean Towing has over 60 years’ experience as a leading provider of marine towage and turnkey project management serving the eastern seaboard of the United States, the Gulf of Mexico and beyond. Stephen Dann, President, related the latest news to Phil Nicholls. BEHIND THE TOWING

Diversification at Dann Ocean Towing sees the company manage stevedore crews operating pneumatic cement loaders for customers in Tampa, Fort Lauderdale, New York, Providence and Rhode Island.
The most iconic ferry in the United States is, arguably, the Staten Island route operated by the New York City Department of Transportation. Dann Ocean Towing had the honour of towing the new Ollis class ferries built by the Eastern Shipbuilding Group, shepherding the new vessels from Florida to New York.
Dann Ocean Towing is a fifth-generation tugboat company with a history stretching all the way back to Captain Clay Johnson’s paddle-wheel steamboats in the 1860s. Dann Ocean Towing Inc was officially founded by Rodney H Dann, Jr in 1960. From this beginning, the company steadily grew with a wide portfolio of services. Today Dann Ocean Towing has a fleet of 17 twin-screw ocean tugs ranging in size from the 74ft (22.5m) Captain Willie Landers to the 119.9ft (36.5m) Helen. With 150 employees, Dann Ocean Towing is based in Tampa, on the Gulf Coast of Florida. The company conducts a lot of business along the eastern seaboard of the US, so maintains dock space in Brooklyn, New York, and a mooring buoy at Bay Ridge in New York Harbor. The fleet at Dann Ocean Towing provides a broad range of marine towage services around the east coast and the Gulf of Mexico. Contract towing projects might take Dann Ocean tugs across the Atlantic, down to Central or South America, or across to Europe. Occasional voyages take them into the Pacific to China or Japan, but around 90% of the voyages are much closer to home.
Cool and iconic towing
For a company like Dann Ocean Towing, each day brings a fresh challenge. Few such challenges are as iconic as the con tract with Eastern Shipbuilding Group of
Inside Marine 41
Dann Ocean Towing believes a company is only as good as its crew. The company is proud of its roster of experienced, welltrained crews who are dedicated and com mitted to the industry.
“We do a wide variety of things,” said Stephen Dann, President. “We are ocean going, we’re a power provider to a lot of different industries, including a lot of bulk cargo barges. We’re involved in dredging and marine construction, salvage opera tions in general, and we keep our hand in with the general towing.”
“One of our strengths is our ability to retain employees,” explained Mr Dann. This experience in depth is a central plank of the company’s USP, along with its agility within the market. “We are multi-faceted; we provide the power and can move with market trends.”
Salvage, rescue and barge towing contracts are regular parts of the busi ness alongside harbour assist, oilfield support and anchor handling projects.
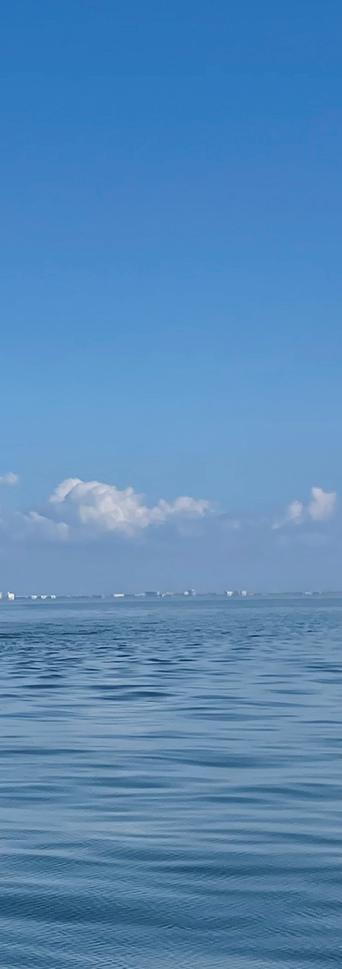
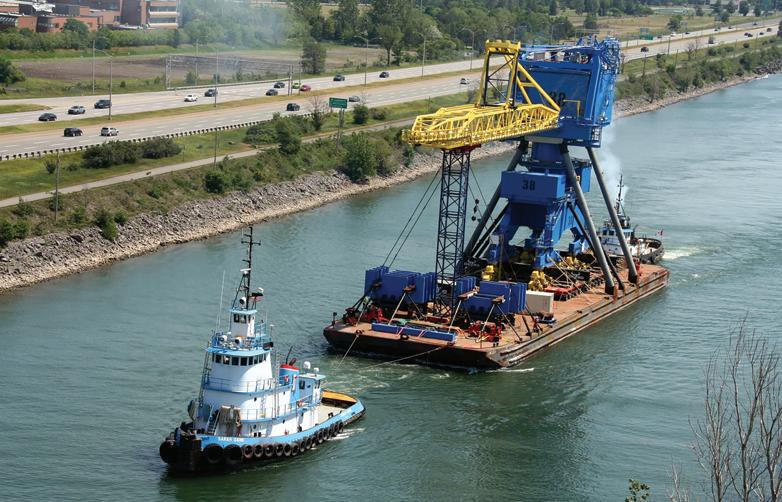

42 Inside Marine
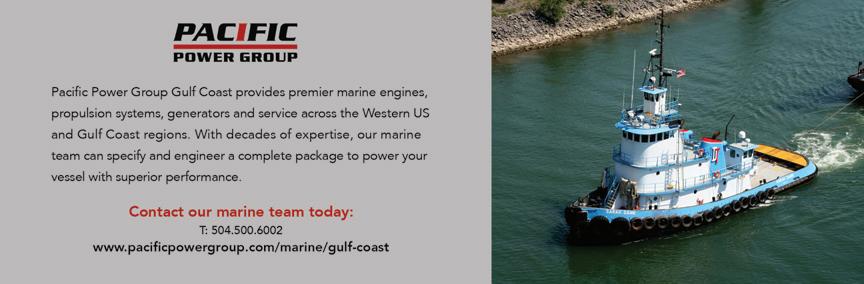
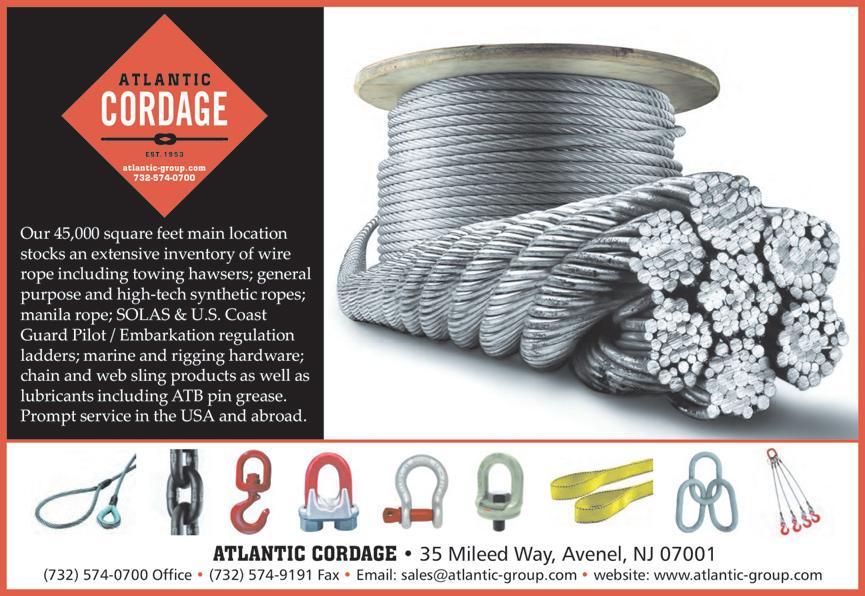
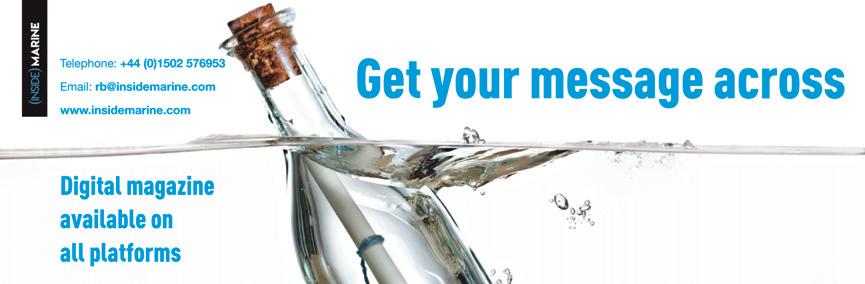
Inside Marine 43
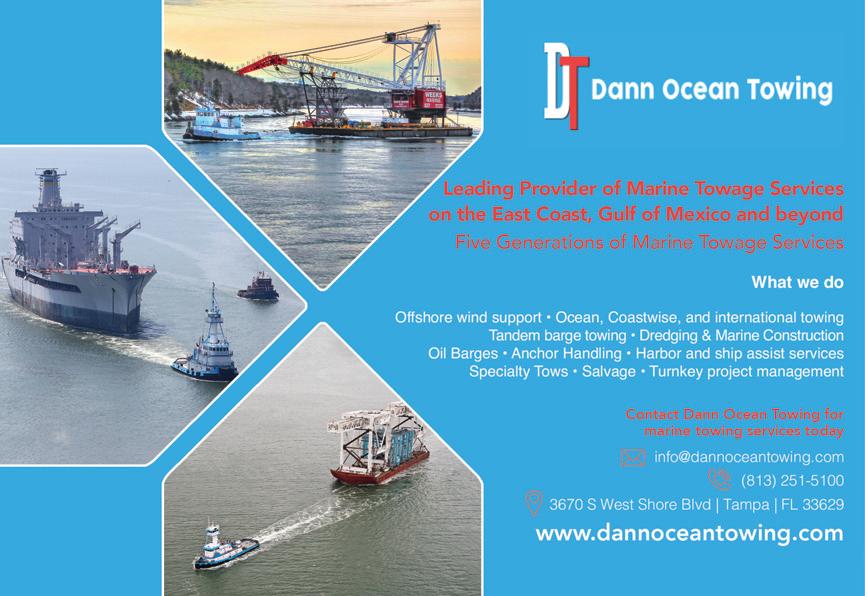
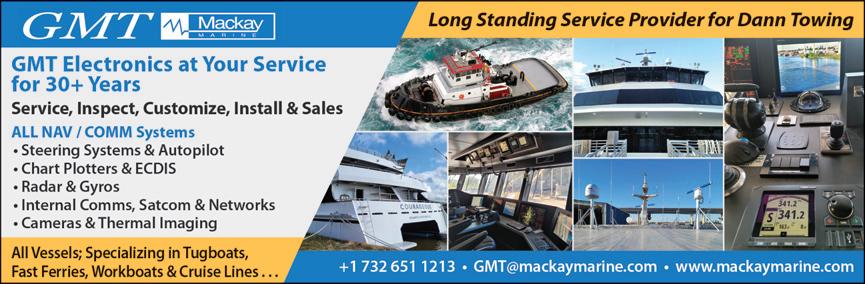

KNOLL MARINE SERVICES
44 Inside Marine editorial mention
Knoll Marine Services is committed to providing the best marine sur veying and consulting services to the maritime industry by perform ing our job safely, with prompt and accurate reporting. We know tugs, barges, and the value of uptime. We take a hands-on, practical approach to risk management.
Panama City in Florida. Eastern are in the process of building three new Ollis class Staten Island ferries. These new vessels combine the traditional double-ended design of the ferry with a capacity of 4,500 passengers and an overall length of 320ft (98m). First built was the Michael H Ollis, named after the Staten Island native Army Staff Sergeant Ollis, who was killed at the age of 24 while on his third tour of duty in Afghanistan. Fittingly, this was towed to New York by Dann Ocean Towing’s tug Colonel. The Sandy Ground was the next build off Eastern’s slipway and was towed by Dann Ocean Towing’s tug Sarah Dann to New York in December 2021, a voyage which took 14 days. Other projects for Dann Ocean Towing take the company back to Captain Clay
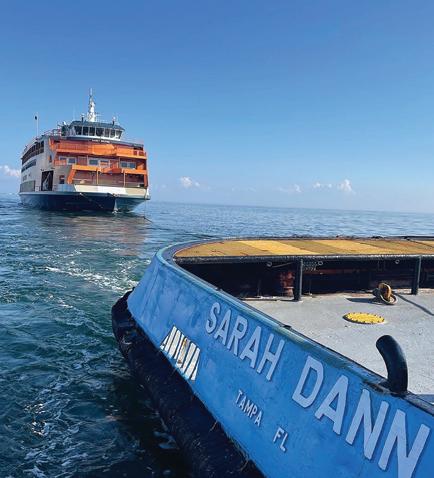

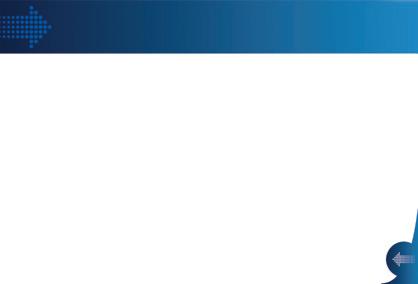
Dann Ocean Towing were entrusted with towing this $55 million crane across the Great Lakes and through the St Lawrence Seaway. The journey proceeded through the Atlantic to Portsmouth Naval Shipyard in Kittery, Maine. The ‘Big Blue’ crane will double lifting capacity for the US Navy in Kittery.
The newly delivered Staten Island Ferries have the fairly simple task of travelling back-and-forth between the St George Ferry Terminal in Staten Island to the Whitehall Ferry Terminal in Manhattan. In contrast, the Dann Ocean Towing fleet of tugs continue to visit new ports and customers around the United States and beyond.
n Inside Marine 45
From Dann Ocean Towing’s base in Florida, federal and state agendas for the environment are not always in alignment. Additional instability in the US political system from the rolling calendar of elec tions every two years pours further oil on troubled waters. In an ideal world, Mr Dann would seek a consistent message from the government , with a clear agenda and precise targets. The implementation of environmental regula tions in a business takes time and money, so any new legislation should have suffi cient lead-time to allow businesses to plan the necessary upgrades. Sadly, the current political climate does not afford Dann Ocean Towing the desired certainty for the Instead,future.Dann Ocean Towing must focus on those elements of the future it can con trol. Alongside planning for the growth of wind farms in the northeast, Mr Dann is also exploring additional partnerships with Moran Towing Corporation moving bulk barges. Further potential diversification will come from the development of more cargo operations and support services.
Winning market share In such a varied sector, Mr Dann must keep a close eye on market trends: “Everyone is gearing up in the northeast of the US for wind farming: we believe that will lead to a lot of opportunities for towing and anchor work.”
Johnson’s paddle-wheel steamboat ori gins on the Kissimmee River and Lake Okeechobee. Such a nostalgic project was the contract with Broadwind Heavy Fabrications and Konecranes in Port of Manitowoc, Wisconsin. This involved towing ‘Big Blue’, a crane capable of lifting 140 tonnes and the 2021 winner of ‘The Coolest Thing Made in Wisconsin’ award from Wisconsin Manufacturers & Commerce and Johnson Financial Group.
Voyaging into greener waters
Eager to maintain its market share, growt h within the sustainable energy sector is one opportunity to secure additional business, although Mr Dann remained cautious about the potential. The planned windfarms in the northeast will offer additional work for tugs, but possibly not “an oil field type of Asbonanza.”anestablished player in the field, Mr Dann takes a traditional view of building relationships with clients. “I treat people fairly and honestly. I still operate using a lot of handshakes sealing a deal with people that I’ve done business with before. When I tell someone, I can do a job, they trust me.”
All segments of the marine industry are working towards a more sustainable future. “We’ve done a number of re-powers to bring our engines up to compliance,” Mr Dann said. “If there’s a cleaner, safer, more efficient engine out there, then we’re interested in getting our boats up to speed.” Mr Dann identified the overlapping government jurisdictions as a hindrance towards advancing progress in this area.
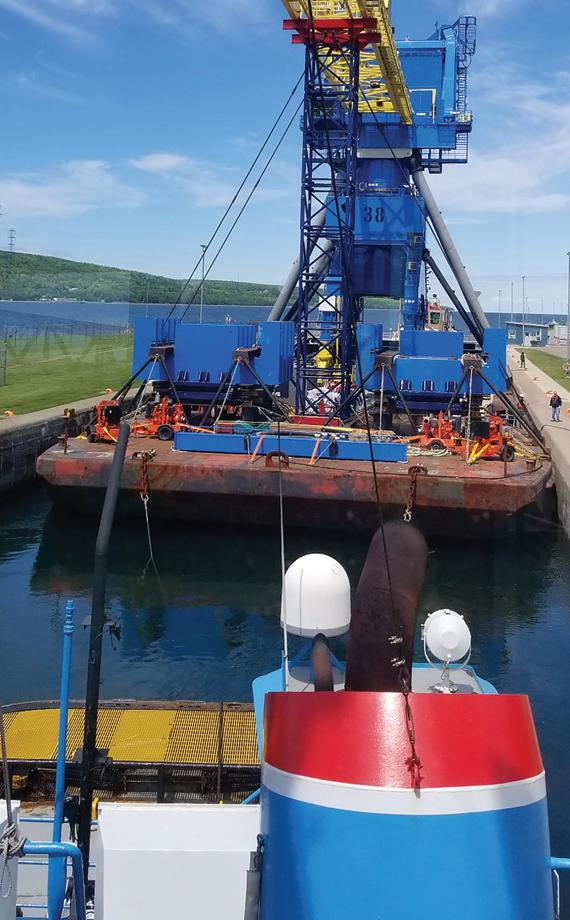
MAINPRIZE OFFSHORE LTD I PROFILE 46 Inside Marine
Mainprize Offshore became the new name for this company in 2011, as the business evolved from trawling to offshore renew ables. Developing the fleet over the fol lowing years was a key feature of the growth of the company. Mainprize quickly built up a fleet of five vessels developed to meet the specific needs of the offshore windfarm industry. The company is headquartered outside Scarborough, Yorkshire, on the northeast coast of England. All its vessels currently
Mainprize Offshore Ltd has 12 years’ experience providing offshore crew and cargo transfers within the renewable energy industry. General Manager Steve Evans, Finance Director Steve Wilcockson and Operations Manager Colin Thompson discussed the company and its fleet expansion. Report by Phil Nicholls.
“We pride ourselves on the performance of our boats,” Finance Director Steve Wilcockson explained. “They are oper ating in what is typically the harshest environment in Europe.”
The fleet of specially designed CTVs at Mainprize Offshore Ltd is almost doubling in size with four vessels under construction. These new builds will further enhance the company’s reputation for efficient and innovative ships delivering a professional and reliable service.
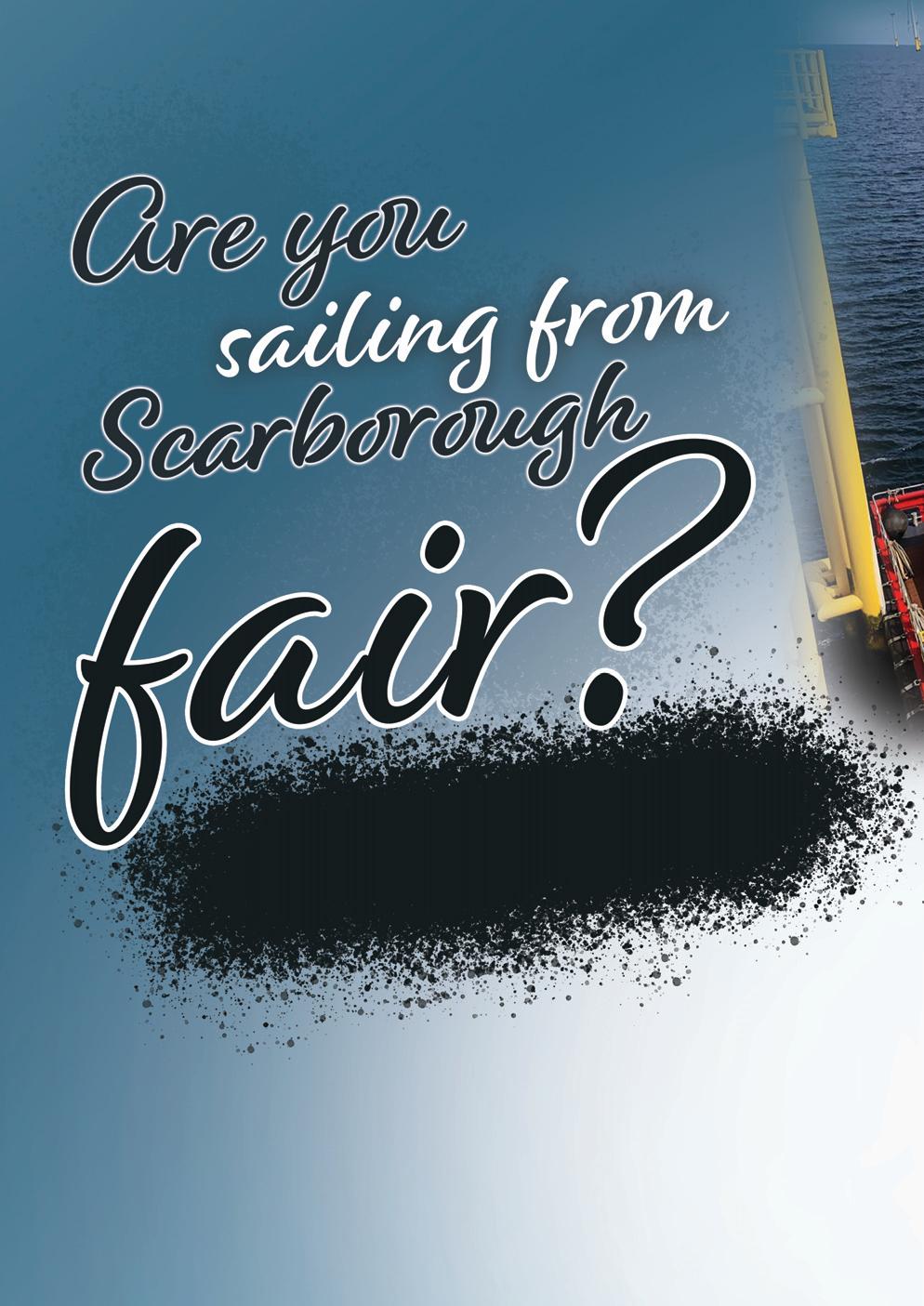
Each of the MO series of boats is built to a different set of specifications; they are all flexible vessels capable of fulfilling the broad range of Mainprize services. The core of these duties is crew transfer, heavy cargo operations and offshore bunkering. Additional services offered by Mainprize include subsea survey, dive support oper ations and marine consultancy.
“We can make the F1 analogy again in terms of the crew,” Mr Wilcockson said. “We’re looking for the Lewis Hamiltons and Max Verstappens because only the best crews can properly handle these boats.”
Incremental gains
“We own the IP for the designs of our boats,” agreed Mr Wilcockson. “The best analogy I can give is that we go into an F1-level of detail; we look at the nuts and the bolts. If we can save 0.1% of weight by using a dif ferent method, then we’ll do that. It’s all for the incremental gains.”
The careful design of the fleet is only one strand of Mainprize’s ability to secure and maintain long-term contracts delivering high levels of customer satisfaction. The caring family culture at Mainprize unites the best crews with its efficient vessels.
“This ship was the tipping point into the top echelon performance of our vessels,” General Manager Steve Evans said. “ MO 5 was a pivotal project for Mainprize.
The current Mainprize fleet of five ships are all designed to serve the offshore wind farm industry. The 25m, twin hulled MO1 and her sister MO2 were both designed by Teknicraft, a New Zealand firm specialising in catamarans. The other three ships, all with twin hulls, were designed in collaboration with Walker Marine Design, UK.
“We’re not a company who just sits in Scarborough,” Mr Thompson explained, “We visit the boats on a regular basis and frequently take the crews out for dinner. This is all part of our family culture, the crews actually feel wanted and part of a team, rather than just a number.”
The MO series of boats are at the heart of Mainprize’s USP. Operations Manager Colin Thompson outlined what makes these vessels so special: “Our careful design cre ates fantastic boats. A lot of time goes into research and development, looking at really fine details down to flow lines, rudders, propellers, thrust-to-weight ratios: all of that is incorporated into making our boats what they are.”
Inside Marine 47 operate in and around the North Sea. Mainprize is steadily building up its work force to 60 to crew the additional vessels.
This strong family culture valuing the workforce is the first of Mainprize’s three core values. Secondly, Mainprize embraces change as it pushes the boundaries of innovation and adapts to evolutions in the market. Finally, the company prides itself on achieving high levels of customer satis faction through reliability, proven excel lence, and dedication to providing the very best service. Elite vessels The latter two core values are evident in the story of MO 5.
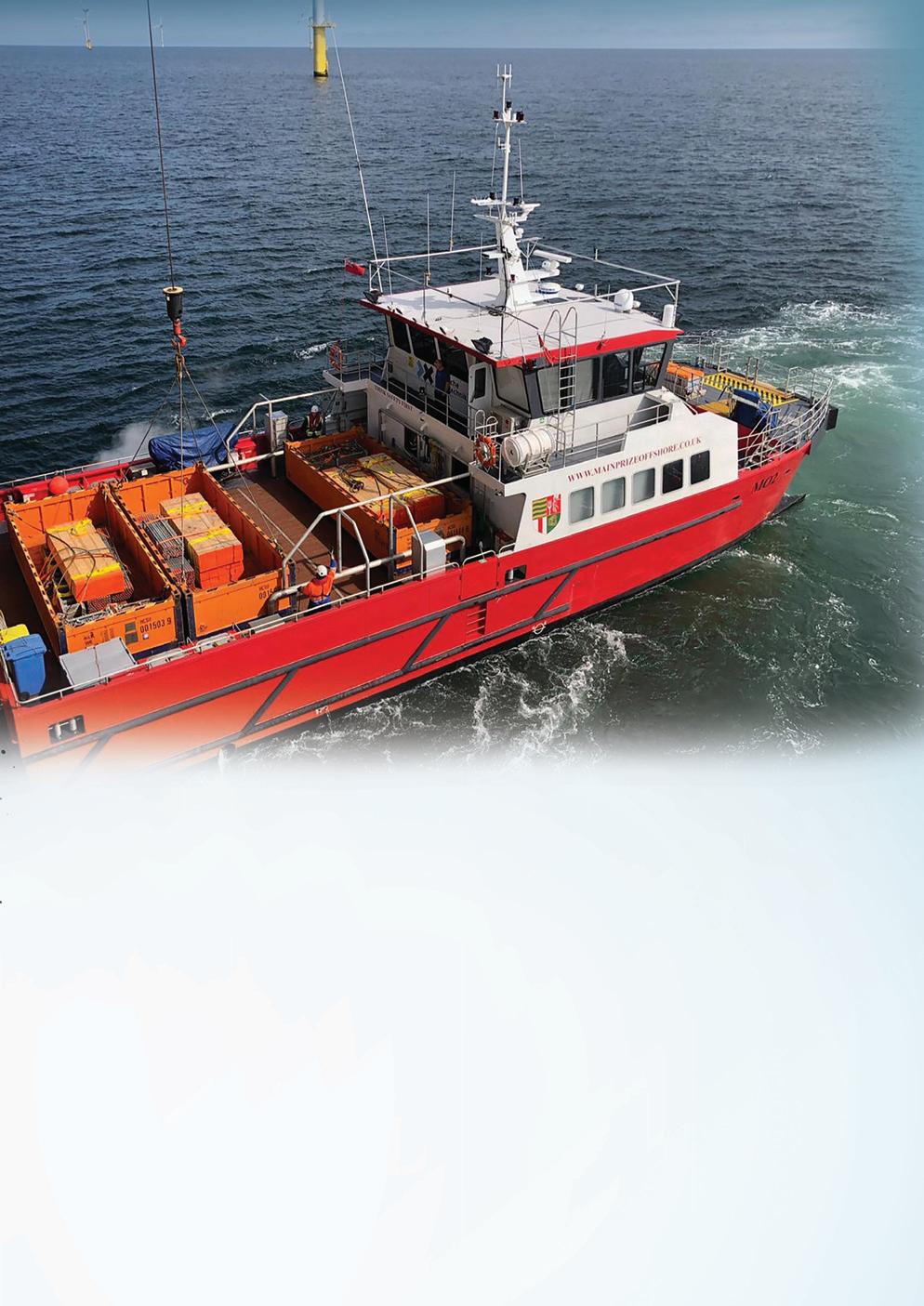
48 Inside Marine
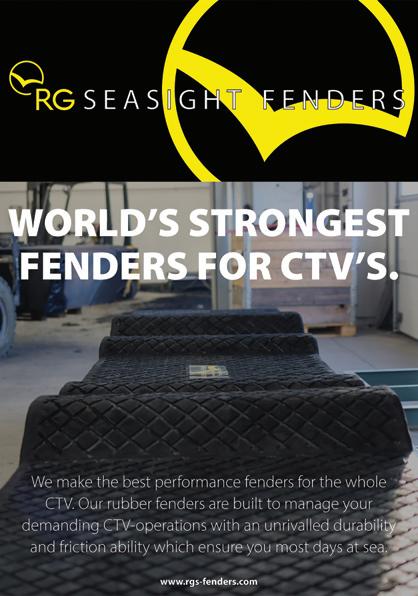


Inside Marine 49

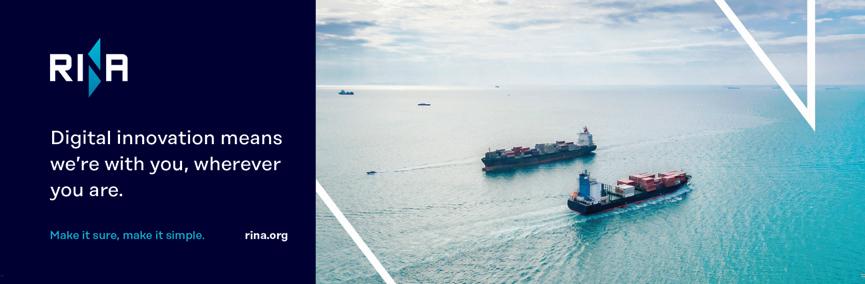

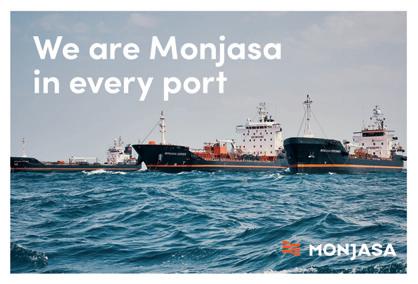
MAINPRIZE OFFSHORE LTD I PROFILE 50 Inside Marine MO 5 involved extensive modelling in the testing tank. We spent a tremendous amount of money on R&D. All our newer vessels are design improvements on top of MO 5.” The next four additions to the Mainprize fleet are under construction, designed by Walker Marine Design in the UK. MO 6, MO 7 and MO 8 are due to be launched in Q4 of 2022; these multi-role catamarans are able to transfer personnel in 2m wave height. They feature exceptional cargo capabilities with 190 sqm deck space and 41-ton pay loads. The fleet expansions continues with the addition of MO 9 to the fleet in Q2 2023. Most of the Mainprize fleet operate under long-term contracts reliant upon the company’s close relationship with business partners.
“We have a core of long-term suppliers and partners,” noted Mr Thompson. “It’s all based on communication, trust and loy alty. We are very loyal to people who serve us well.” In turn, Mainprize serves its cus tomers well, such as with the MO 5 declared the best boat in the client’s operation.
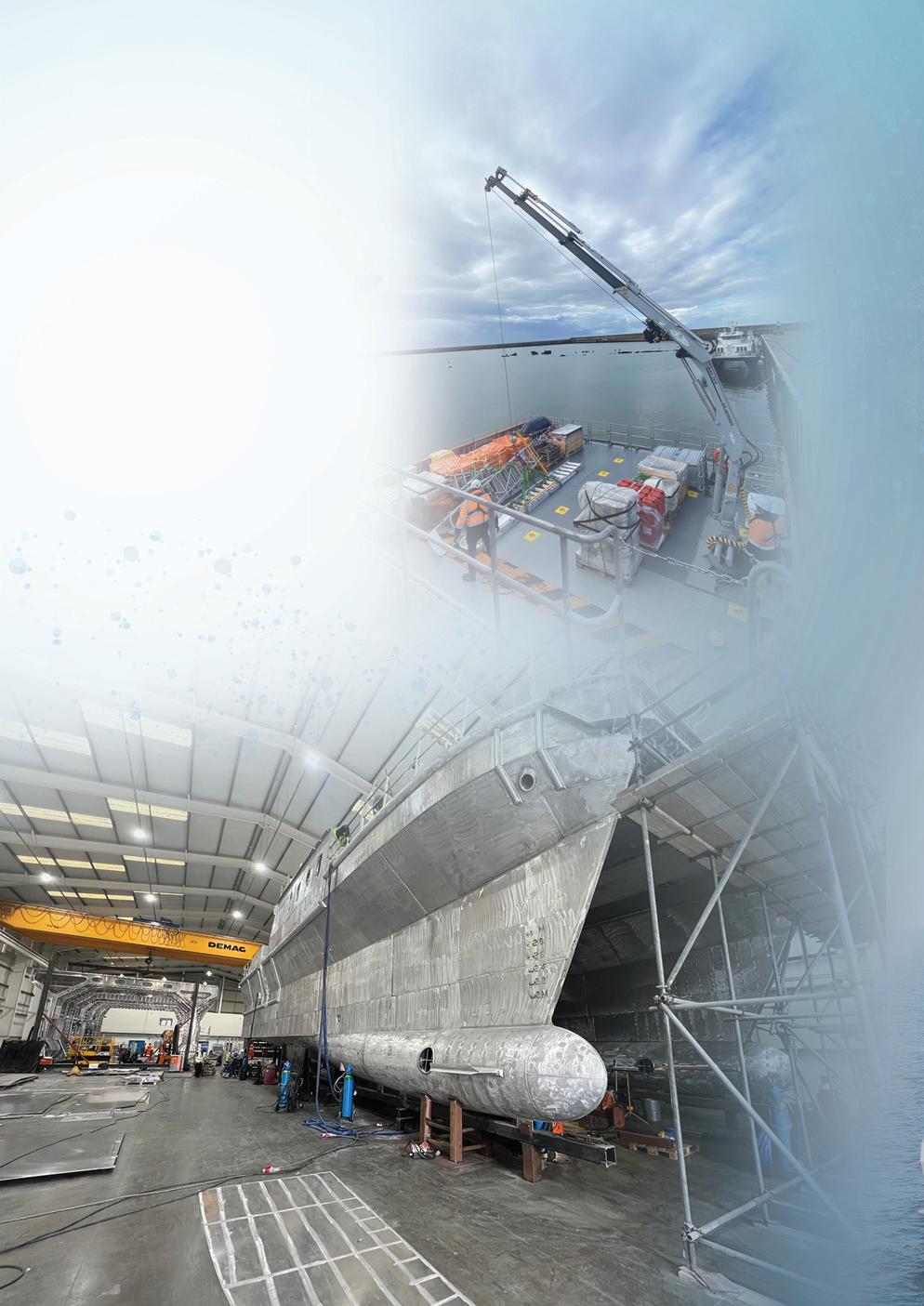
“ There’s always a challenge,” said Mr Thompson, explaining why Mainprize Offshore is a fantastic place to work. “The challenge varies in magnitude: it might just be a simple crew move at the last minute, or a mad dash to the airport to look at some thing that’s happening on one of our ves sels. It’s an absolutely great company and an ongoing success story.” n
The team at Mainprize face several chal lenges as they adjust to the demands of the expanding fleet.
Inside Marine 51
“Crewing is our biggest hurdle at the moment,” Mr Thompson said. “And it’s all down to availability. Another challenge is how to recruit the very best crew, but they’re just not out there at the minute. We have a massive training plan ongoing, and we will recruit the best folks out there , then partner them with our vessels to create a high performing package.”
The current four boat expansion to the Mainprize fleet is not the end of its plans. MO 10 and MO 11 are listed on the website with a potential move into hybrid technology, but the exact designs are in a state of flux. Mr Wilcockson outlined the many fac tors affecting the design parameters for these later vessels: “The demand for boats, specifically our boats, is absolutely massive We need to juggle the huge demands for our boats with the ability to deliver them suc cessfully. Our boats solve our customers’ problems, so they are built to perform the roles the client needs.” Thus, until the clients’ requirements are fixed, the capabilities of MO 10 and MO 11 remain undetermined. The design process for Mainprize boats involves a lot of backand-forth with the client to ensure that the final boat will efficiently fulfil the require ments of the contract.
Schrödinger’s catamarans

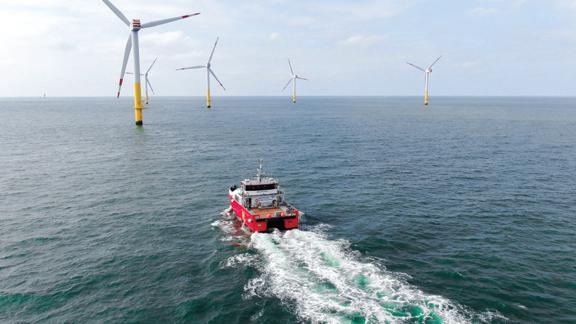
LAUNCHING A MARITIME LEGACY
Vice President Nick Miller spoke to Richard Hagan about his family’s company’s illustrious service record across the US East Coast.
T he owners of family-run Miller’s Launch are part of a long lineage of seafarers with a deep connection to the sea. The daily scheduling unpre dictability and the adventure of tackling the challenges of nature and winning, are second nature to them.
As the self-proclaimed ‘Swiss Army Knife of the Atlantic Ocean’, Miller’s Launch offers its clients a spcialised toolbox of maritime support services tailored to meet any and every need at sea.
“We all have some saltwater in our blood here,” commented Nick Miller, Vice president at Miller’s Launch. “You have to like the adventure of working here. It’s a lifestyle. Schedules change at a moment’s notice, and you have to deal with nature. It’s not like making widgets in a factory.”
MILLER’S LAUNCH I PROFILE 52 Inside Marine
From its base in New York Harbour, the company operates an impressive catalogue of floating assets ready to go at a moment’s notice, no matter the time of the day or night.
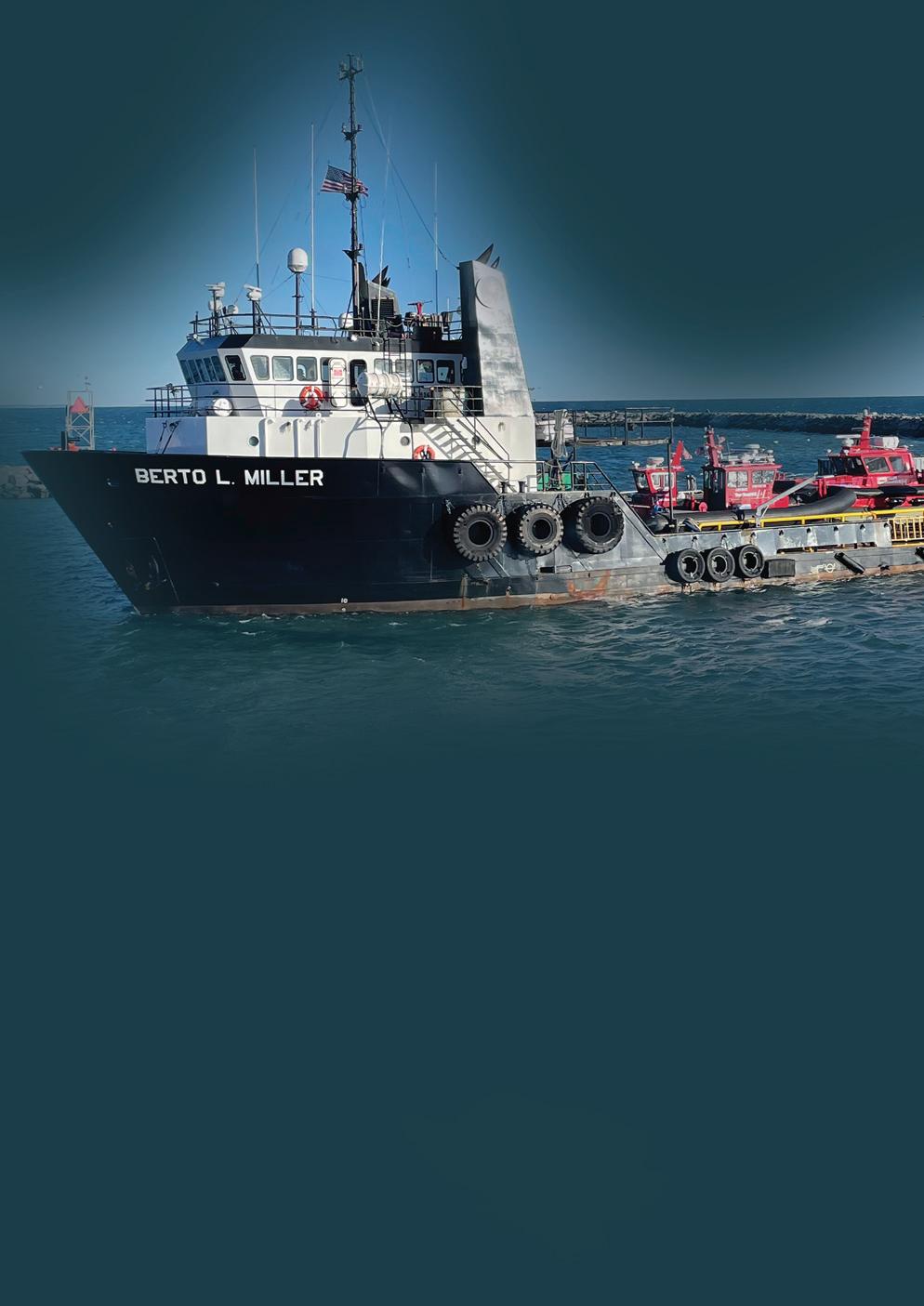
With a portfolio of around 70 pieces of equipment on the water, maintained and operated by a roster of 100 staff across all of its divisions, Miller’s Launch has the machinery, manpower and capacity to tackle any customer’s challenge. And as Mr Miller revealed, those challenges are“Wemany.provide marine support to various operations, including everything from offshore wind, to emergency and oil spill response and film industry needs, as well as construction barges, towing, offshore marine research, and lightering. You name it, we’ve probably touched it at some point in our history.”
“Ourwater.main ideology of the business is that we like to say yes to interesting marine problems and then come up with creative solutions to them,” Mr Miller explained.
The answer is yes Miller’s Launch has established a formidable reputation for being not only willing but also able to tackle any challenge, anywhere on the
Inside Marine 53
All of these services have developed from the company’s original ‘bread and butter’ offering of providing launch services to visiting commercial vessels. These include crew transfers, provisioning and other ser vices, all of which continue to form a core part of the company’s portfolio. In fact, not only are they still running, but the

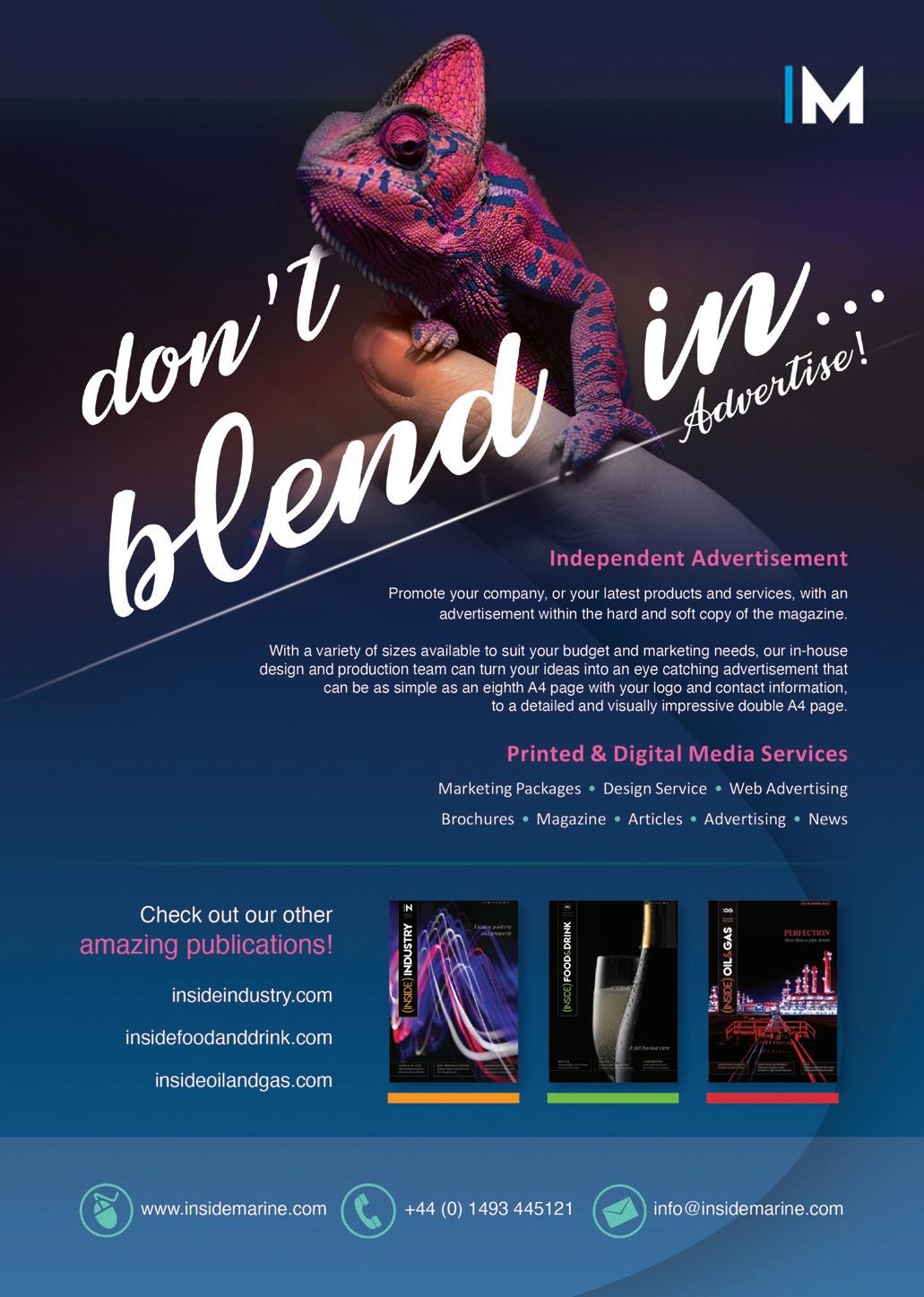
Inside Marine 55



MILLER’S LAUNCH I PROFILE 56 Inside Marine company’s launch services vessels are the busiest in its fleet.
“The launch side of the business runs 24/7, 365 days a year all the time for the past 40 years,” said Mr Miller. “Except for once when we had to shut down for a few hours in the middle of Hurricane Sandy.”
“We are one-hour responders for oil pol lution incidents,” Mr Miller revealed. “We open and close booms during oil transfers at terminals. From there, we provide ser vices across New York and New Jersey for both government and private entities.”
While the company’s material assets are important, its crews are more so, Mr Miller “Anybodyhighlighted.intheworld can go out and buy a vessel, but I want to help my cus tomers accomplish whatever they’re trying to do. Whether that’s building a school on Roosevelt Island or an offshore wind farm, I have a responsibility to provide not only the correct vessel but also the best captains, deckhands and fabricators who eat and breathe this lifestyle. One whole half of my business revolves around how good my captain is and how well he knows the local area.”
The breadth and variety of Miller’s Launch’s operations are unique for the“Weregion.really have a niche business here in New York that not a lot of other people can provide. We have a reputation in New York Harbor and amongst our vendors that if someone has a unique problem that nobody can solve, the solution is to go call Miller’s – they’ll figure it out,” he said with a chuckle.
The company’s experienced crew operate a fleet of vessels that include five tugs, a fleet of harbour launches, and large
A unique armada The company’s main facility is its head quarters located in New York Harbor in New York City, where it is sandwiched between the Navy Pier and the famous St George Ferry. Most of its operations take place at and from this location. Its second facility is located on Staten Island, where it enjoys a three-acre plot with water access. From there, Miller’s Launch mainly operates its offshore wind buoy division. A little-known aspect of Miller’s Launch is its ownership of a franchise of the famed TowBoatUS company. That facility is located in Atlantic Highlands in New Jersey, from which all of its towboat operations are run. Staying in New Jersey, the company also owns a business that primarily provides booming operations for the oil industry and oil-related emergencies.
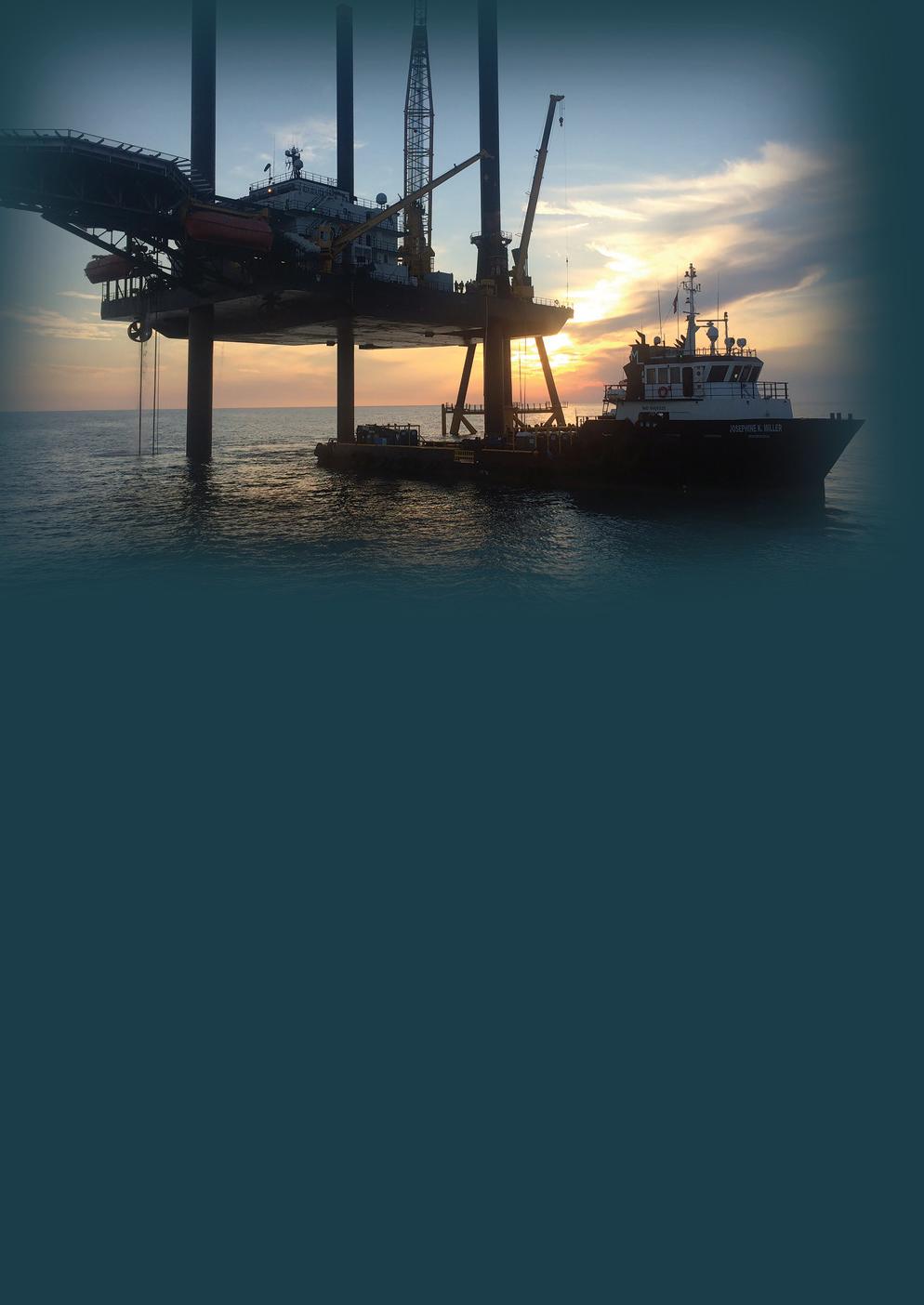

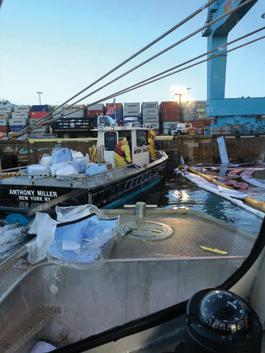
Mr Miller added: “I have a 30-tonne A-Frame capable of doing a variety of different work, ranging from surveys and research to construction and maintenance work. That really sets us apart.”
Local knowledge powering offshore construction
With multiple large wind farm installa tions already approved for imminent con struction off the US’ north east coast, Miller’s Launch anticipates surging demand for its specialist wind farm ser vices for which it has long been revered within the industry.
“For the permitting phases, you must have people who are trained to sit offshore and ensure that there are no endangered species of marine life that will be affected by the work that is underway.” In this sce nario, the company would provide the vessels and other platforms required for the PSO work to be undertaken.
The local knowledge of Miller’s Launch’s seafarers, added to its reputation for cre ativity and flexibility, is set to propel the company’s fortunes for years to come as it prepares to meet the demands of the surging offshore wind power sector.
“The people who are in offshore wind services should really talk to us,” Mr Miller added. “We’ve surprised a lot of people with our portfolio of work and the capacities we have to offer. We’re Jones Act com pliant. We’ve got dynamically-positioned vessels with A-Frames right here in New York Harbor.”
“The government and developers are looking to push local content for these projects, but there’s not a lot of knowl edge, experience and people here in the north east who can undertake that kind of work,” Mr Miller highlighted. “We are on the ground floor of an industry that in my lifetime is only just beginning to take off. The north east coast is really posi tioned to provide some of the best locations on earth for offshore wind farms. Our local knowledge means that we will be involved in projects from the pre-installation phase where we’ve already made a name for ourselves, all the way up through the con struction phase to the maintenance and operations phase, and eventually to the tearing down phase. I see a bright future.”
With a world-class schedule of constant maintenance and reinvestment, Miller’s Launch is looking forward to an actionpacked future. Whether it’s in New York Harbor ferrying crew or supplies to a ship, or supporting the installation of wind turbines dozens of miles offshore, Miller’s Launch has a boat, a crew, and the resources to tackle any challenge. n
Miller’s Launch has an existing résumé of offshore wind projects and naturally, it is leveraging its experience, talent and equipment in this field to ensure the com pany benefits from the large planned pro jects in its operational area. While he will certainly be looking for appointments in the various construc tion and maintenance phases, Mr Miller revealed the company will also be seeking appointments for PSO (protected species observer) services.
Inside Marine 57 offshore support vessels featuring spe cialised equipment including A-Frames.
A gadget for every future occasion Ultimately, Miller’s Launch is client-focused and passionate about finding solutions. The staff have even invented a tongue-in-cheek word to describe their skill in developing creative solutions: “We’re always inter ested in building the next ‘gizoroni’ for the next job,” said Mr Miller with a hearty chuckle. “Our passion is helping people solve
“Whetherproblems.it’s building whatever package t he client needs, or whether it’s an A-Frame or a crane for deploying an offshore buoy, we have a boat for that. And most of all, our local knowledge really sets us apart from the competition.”
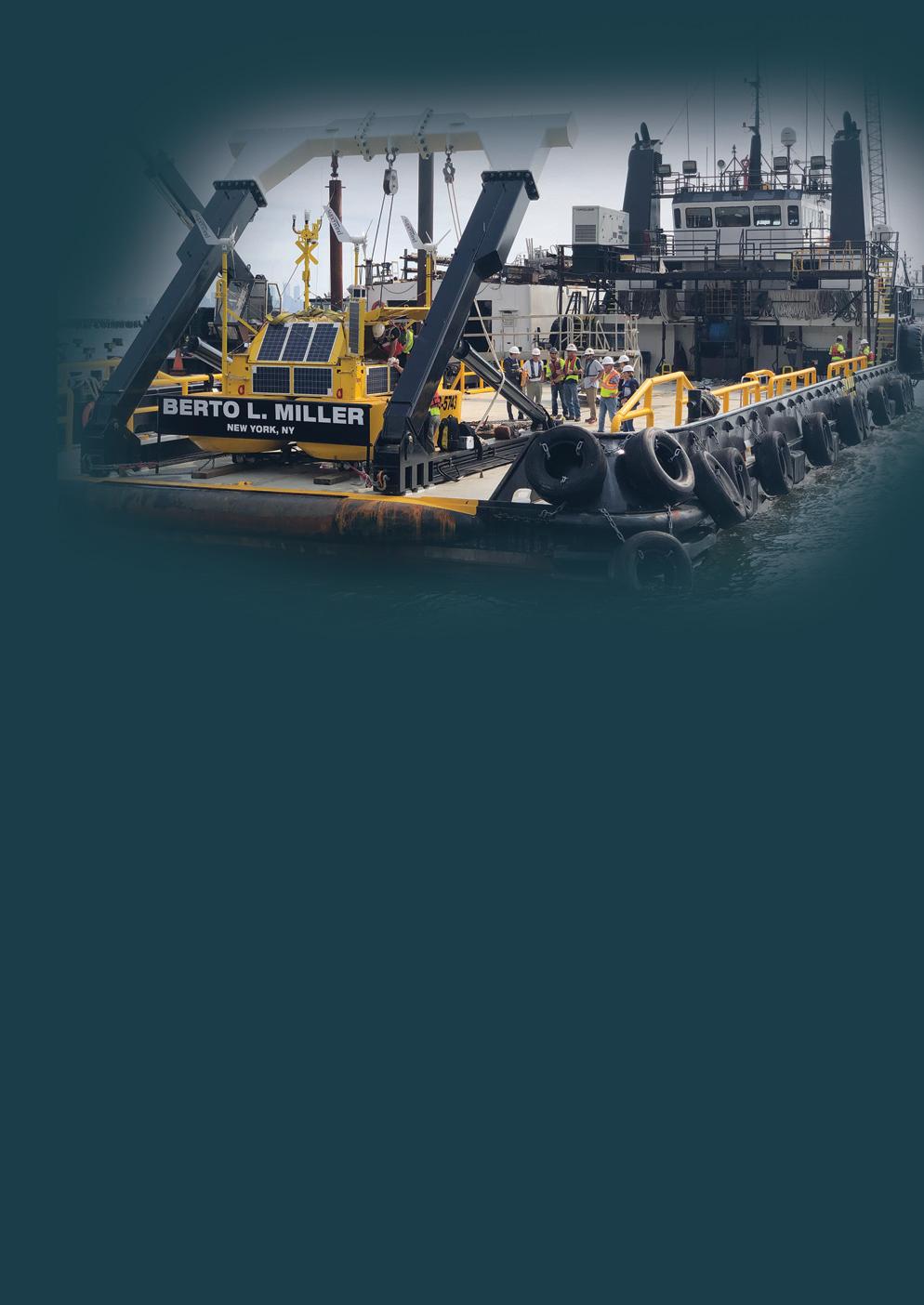
OTTO WULF I PROFILE 58 Inside Marine
A century of T
he storied history of Otto Wulf GmbH began in 1922 when Otto Wulf formed a salvage company. Captain Wulf leveraged his extensive knowledge of the Cuxhaven coast and River Elbe into a knack for finding lost anchors. This expanded into salvaging chains and smaller vessels which ranPost-waraground.expansion meant a bustling shipbuilding industry in Europe. Otto Wulf offered port assistance services, but also saw an opportunity transporting larger components like the hull or superstruc ture. This began with chartered barges, then expanded into operating its own barge fleet. By being based in Cuxhaven in north west Germany, Otto Wulf was perfectly positioned to serve the North Sea oil industry. The Mittelplate oil field was discovered in 1981 off the German North Sea coast on the southern edge of the Schleswig-Holstein Wadden Sea. Production began at Mittelplate in 1987 and represented a busy time for Otto Wulf. German reunification in 1990 lead to Otto Wulf opening an office in Rostock, estab lishing a base of operations for the Baltic. Otto Wulf was an early entrant in the wind industry, both on- and offshore. The com pany transported blades and towers for the operation in 2003 along with the offshore Nordsee One wind farm. Transporting wind farm components was a challenge when it came to the monopiles weighing 1,300 tonnes, as co-owner Sören Wulf explained: “What was special for us at that time was that we were really the first ones who had the guts to roll-on and rolloff these monopiles, instead of basically lifting them onto the barge with a crane.” This innovative solution using wheeled trailers meant the contractor avoided the 2022 sees Otto Wulf cele brating 100 years of maritime services in the North Sea and beyond. Owners Sören Wulf and Andreas Wulf discussed the company’s illustrious history and exciting future plans with Phil Nicholls.
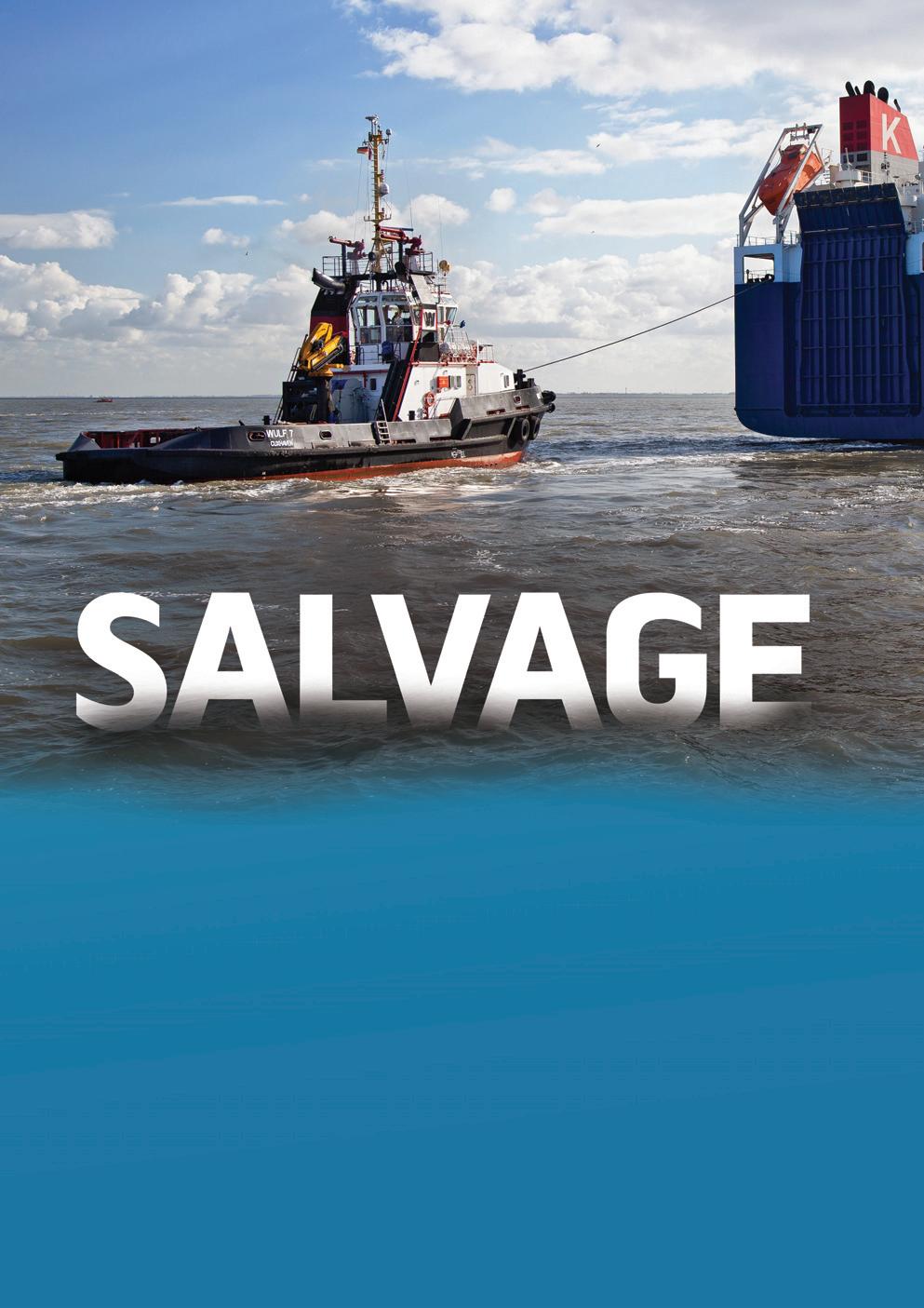
A global reach Growth and creativity are constant fea tures at Otto Wulf. As well as the estab lished office in Rostock, in 2012 Otto Wulf bought the Polish tug company Zakład Usług Zeglugowych based in Szczecin.
After almost ten years of operation, Otto Wulf sold on its investment, then formed Otto Wulf (UK) Limited in Edinburgh in 2021. Another new project sees Otto Wulf operating a charter for Qatar Energy in the Persian Gulf. Further growth is coming to the head quarters in Cuxhaven where the company plans to acquire a large dockside ware house as logistical storage options for the offshore wind industry and other partners.
A contract with Airbus brought fur ther challenges for Otto Wulf, carrying sections of aircraft between factories. Otto Wulf began with a conventional tug and barge operation, then commissioned the Ro-Ro cargo vessel MV Kugelbake, launched in 2009 with a capacity of 1,868 gross Kugelbaketonnage.remains operational, running a regular service between Hamburg and Nordenham, near Bremerhaven. She joins the Otto Wulf-owned fleet of six tugs, a 50m barge and an 86m pontoon. To operate this fleet, the company has 60 employees.
The 100-year history of Otto Wulf is a varied story of flexibility and innovation. The current owners are preparing to cele brate this milestone with a written his tory of the company which will be published at the end of September.
Managing Director Sören Wulf was clear about the benefits of following this Otto Wulf tradition: “We started as a pure sal vage company, grew into ship assistance, followed the building and dredging industry after World War II to rebuild and renew the destroyed ports in Germany, went on with the transport of large sections also for the growing shipbuilding industry, con tinued with the oil industry in German waters to the offshore wind projects in northern Europe. We keep on going to find for almost every case the right eco nomical and technical solution.
Inside Marine 59 additional costs for cranes at either end of the journey.
.
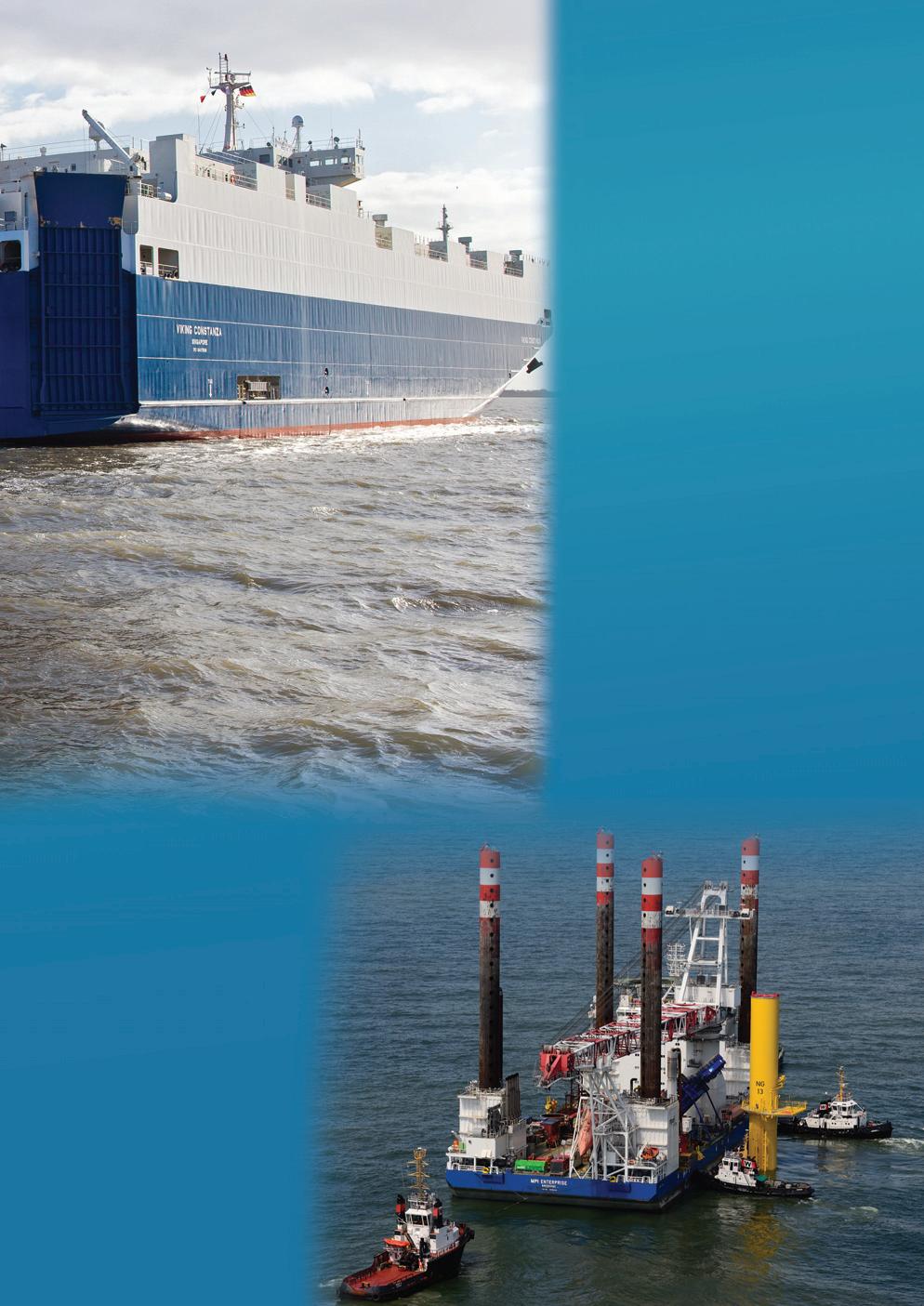
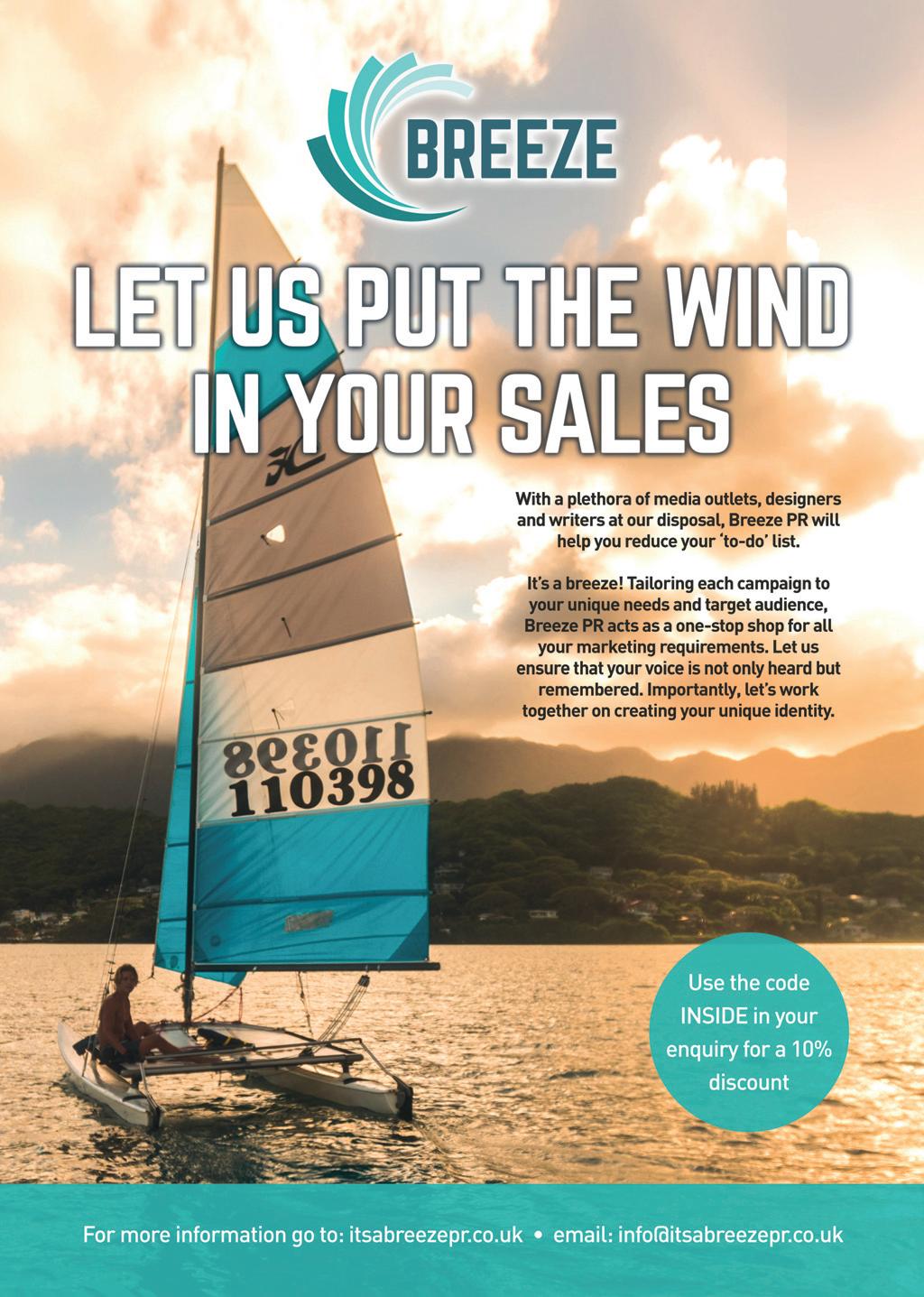
Inside Marine 61
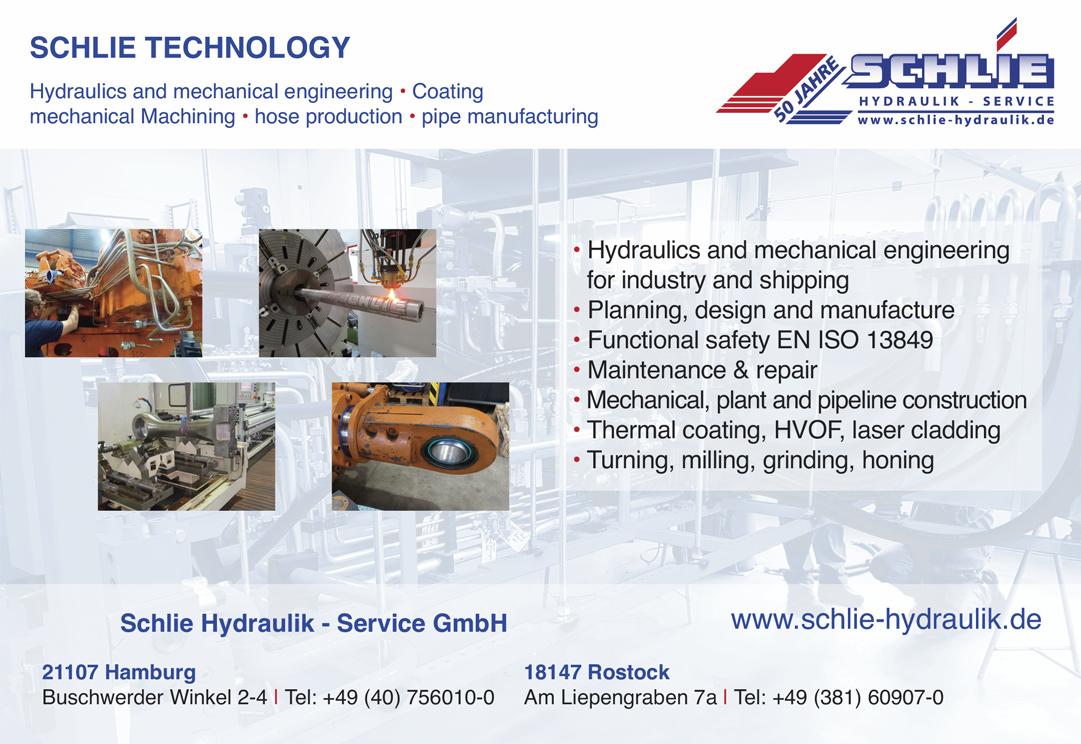
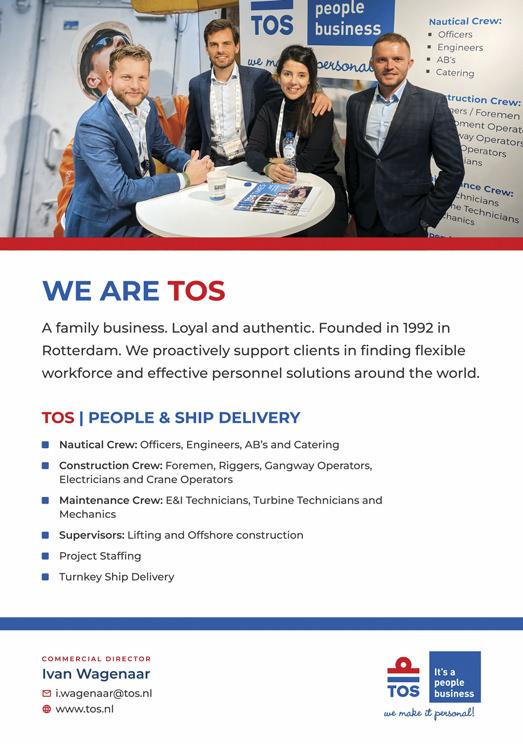


Sören Wulf conceded that the largest challenge facing the company is the impact
A diverse future Sailing into the next 100 years, Otto Wulf has embraced sustainability. “We try to improve here all the time,” Andres Wulf outlined. “Our carbon foot print is getting smaller, but it has to be in a way which makes sense for us.”
OTTO WULF I PROFILE 62 Inside Marine Andreas Wulf, also an active captain, is proud of the company’s crews onshore and on board the vessels. They often do more than only their job and they manage to make the customers smile when a job is finished as planned.
Funded by the European Union’s Horizon 2020 Research and Innovation Programme , the project explores the aquaculture options around wind farms within the challenging conditions of the German Bight. “You have on one side, five universities and institutes who are theoretically bril liant,” Andreas Wulf explained. “And when we come to the practical task our experi ence from the offshore activities is very valuable. We are asked questions like ‘how big should the be anchors for the positioning of various nets?’, ‘how strong is the cur rent?’, ‘which anchor should we use on that ground, chain or steel wire?’ and so on. Sometimes we are out there with trial and error at the end of the day. This is what our business is all about: a project which we really like, we participate, try to bring in our ideas and most of the time it works out.”
A strong partnership with suppliers is a keystone in Otto Wulf’s long history. “We are loyal to our suppliers as well as our customers, but especially to our sup pliers,” said Sören Wulf. “We have some partners for 40 years in this business,” Andres Wulf agreed. “Which is quite unique, because this relationship with older companies gives us a fair rep utation in the market.”
Solar panels in the roof of the Cuxhaven offices provide electricity for the building and as supplemental power for moored ships. The MV Kugelbake has been given a fresh coat of silicone paint, offering 10% savings in fuel. Additionally, two new pro peller blades will be installed to generate even more efficiency.
The benefits of experience A recent project which epitomised Otto Wulf’s flexibility is the UNITED research into growing seaweed, blue mussels, eels , and clams around an offshore wind farm.

Inside Marine 63 of larger companies in the industry, who he said are “Fighting each other on such low margins, that we are a little bit con cerned that they are basically squeezing the market rates so far down that it also affects us.”
In contrast, Andres Wulf took a more light-hearted view of the future: “The chal lenge for all of the midsize companies is growing bureaucracy and rules. Sometimes I think that when human beings have no ideas, they make new rules!”
The next chapter of the Otto Wulf story includes plans to renew part of the fleet, retiring the older vessels. The current pro ject in the Persian Gulf may also be a clue for where Otto Wulf is heading. Despite the broad range of services already offered, Otto Wulf is exploring options for even greater diversity. As the fifth generation of the Wulf family are being trained, the company is prepared to meet the needs of customers anywhere in the world. n
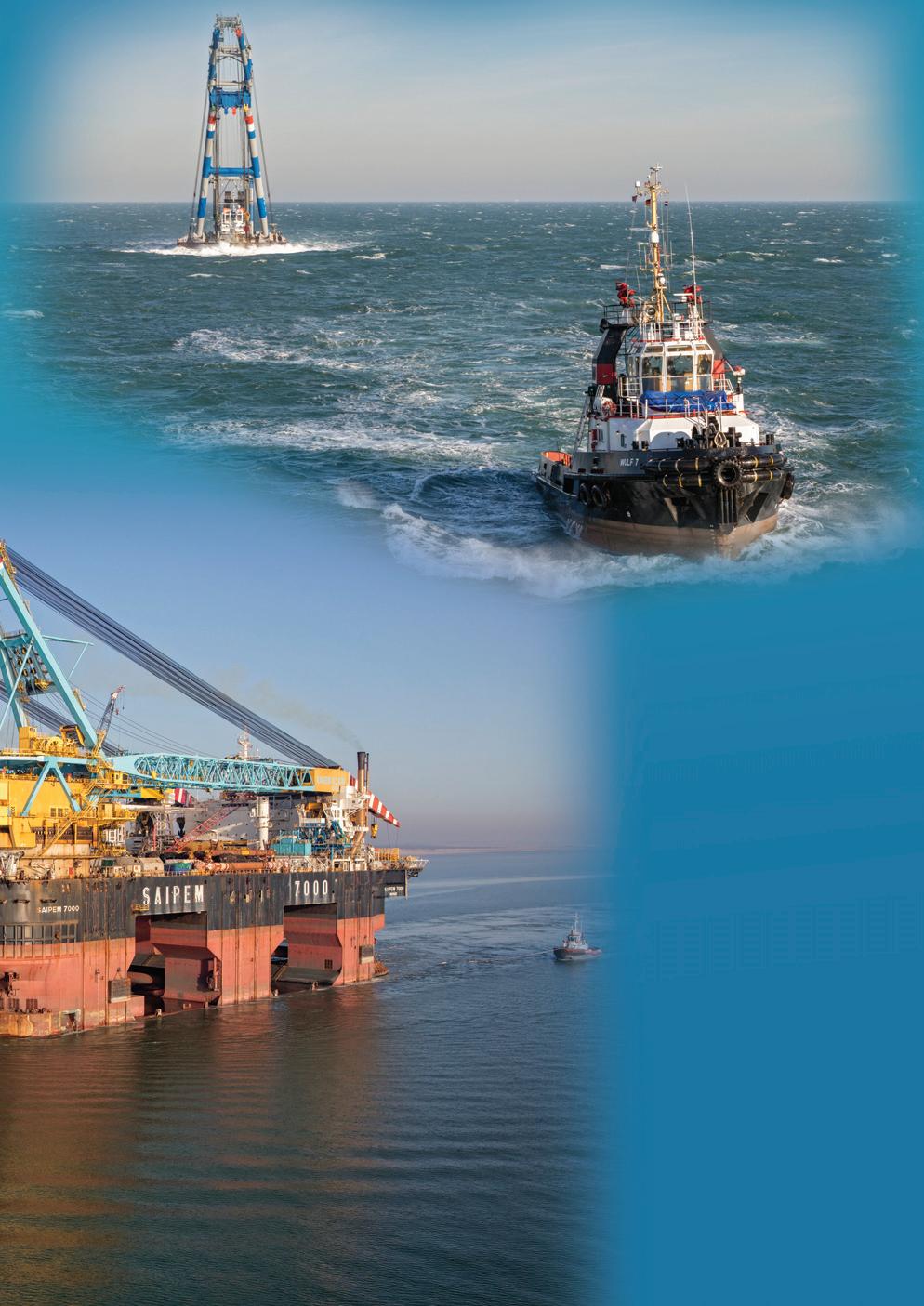
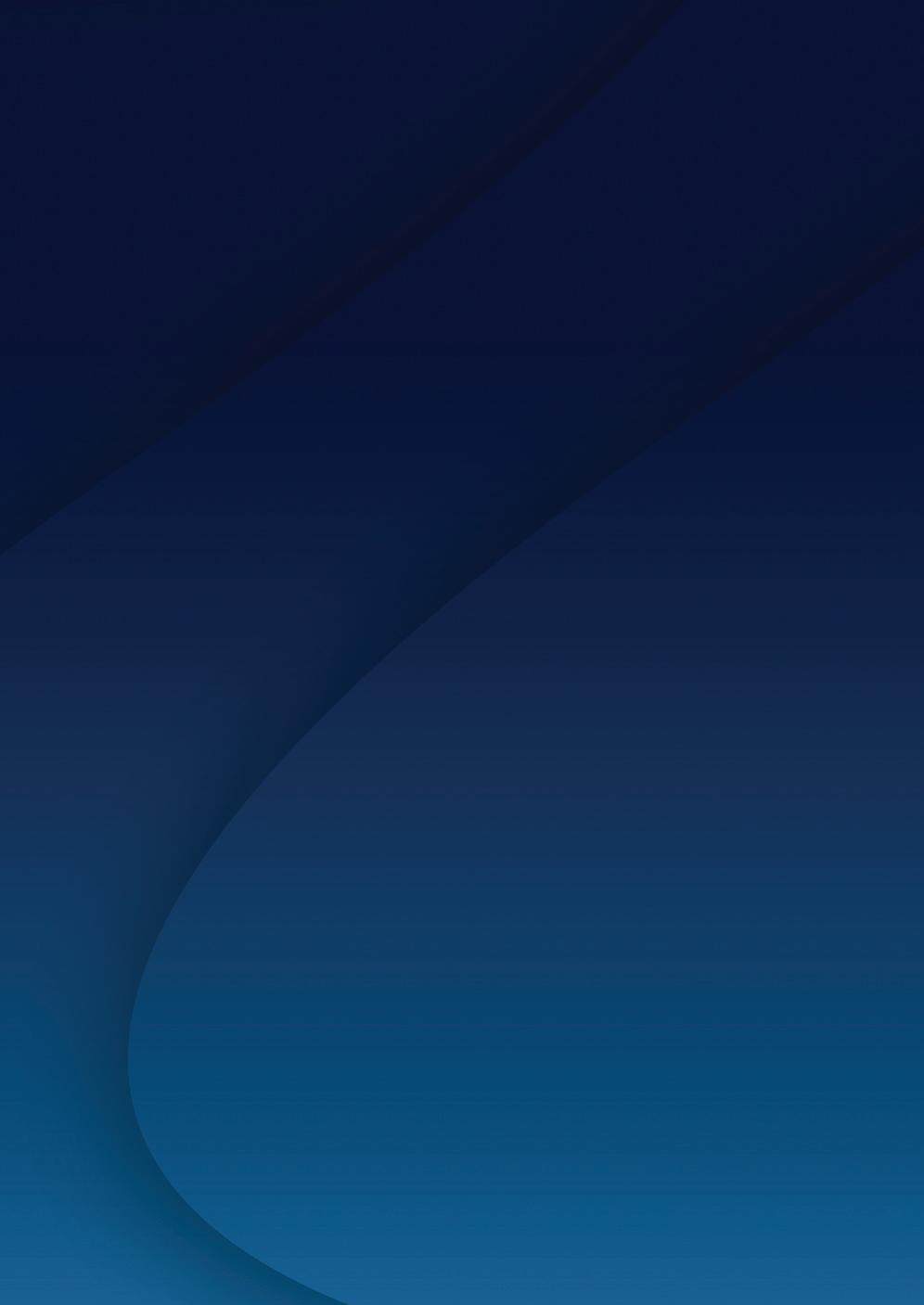
SHIPYARDS seven seas, five oceans, one voice wight shipyard co astivik shipyard cernaval group parkol marine engineering icon yachts blount boats senesco marine hat-san shipyard i M

WIGHT SHIPYARD CO I PROFILE 66 Inside Marine
“We have been working with OCEA on several projects, and it was clear from the outset we complemented each other in skills and experience. Going forward, both companies can benefit from the synergies and opportunities that this deal presents.
Transformational deal Reflecting on the merger, WSC’s Founding Member Peter Morton emphasised: “This is a transformational deal for WSC and the Isle of Wight, confirming the resurgence of the UK’s shipbuilding industry.
All aboard the exhilarating
As a powerhouse of the fast ferry sector, Wight Shipyard Co is pretty much an unstoppable force at the moment. A key merger, investment, new projects, and a Queen’s Award for Export are propelling the company ever forward. By Andy Probert. W ight Shipyard Co (WSC) con tinues to rapidly move at full bore through an ever-changing business landscape. While 2021 was historic, 2022 will prove highly influen tial in taking this dynamic company to newBritain’sheights.leading and one of Europe’s foremost high-speed craft and aluminium shipbuilders is looking to the future with even greater confidence, following a recent merger with French-based multinational shipbuilder OCEA. The deal will see the Isle of Wight con cern grow in size, capitalise on the fast ferry and offshore renewable markets, and provide significant employment opportuni ties at its historic shipyard in East Cowes.
“We have enjoyed a first-class working relationship with OCEA to produce ves sels and solutions to the highest stan dards, pushing the boundaries of fuel efficiency, the environment and modern shipbuilding practices.”

Clippers returned to the newly-styled WSC with a £6.3 million order for two new 170-capacity passenger boats, the largest fast passenger ferry deal for a British ship yard in more than 25 years.
Following the merger, the group will share resources whilst operations in East Cowes will ramp up significantly, helping the Isle of Wight to ‘level up’ with the creation of much-needed employment opportunities.
Rebranded as Wight Shipyard Co, WSC focused on the construction and refit of fast ferries and aluminium vessels, and SMS on steel vessel construction and motor yacht restoration.
Mr Morton said: “For East Cowes and the Isle of Wight, this is a step-change regarding future employment and secu rity for the WSC team. We will be able to bring in more high-skilled shipbuilders and technicians and provide career path ways all through the production chain. It is transformational for East Cowes as the epicentre of aluminium shipbuilding in the UK.”
Inside Marine 67
Queen’s Award The merger follows WSC receiving a Queen’s Award for Enterprise for International Trade in 2021. The award recognised the com pany’s outstanding short-term growth in the export market. Around 50% of WSC’s revenue is generated from exports.
Based at Les Sables d’Olonne, OCEA is an innovator in the aluminium vessel market with high quality builds for maritime secu rity, passenger vessels, multipurpose work boats, transoceanic yachts and hydrographic researchEmployingmarkets.over 500 skilled operators at facilities in France, the Caribbean and the Philippines, the strength of OCEA’s international export market has driven its multinational expansion. Both companies have complementary expertise in supporting the offshore renewable energy sector. Together, they will produce a global aluminium ship building operation with an order book that offers business security and sustain ability into the future.
WSC has rapidly built a considerable reputation in the fast-ferry market, selling its high-tech, environmentally friendly vessels domestically and internationally.
Mr Morton said: “We are delighted to accept this prestigious award on behalf of everyone at the yard, who are very much part of the re-birth of the British shipbuilding industry.”
The operators of the four million passenger commuter and tourist river bus service in London provided it with more work, with an order to refit three river ferries.
WSC was borne out of restoring Shemara, a classic gentleman’s motor cruiser for Sir Charles Dunstone, one of the country’s leading entrepreneurs and whose family office is the main backer of the yard. Following a three-year, one mil lion man-hour project to restore the mag nificent motor yacht, the business has grown exponentially. It acquired the repair and marine engineering business Southampton Marine Services (SMS).
Project success Following that project’s successful com pletion, discussions began with owners of Red Funnel about the construction of the new Red Jet fleet of fast catamarans servicing the Isle of Wight. Red Jet 6, a 275-passenger hi-speed catamaran for Red Funnel’s Isle of Wight–Southampton service, marked Britain’s first high-speed ferry construction for 16 years. With ground-breaking levels of reli ability, safety and passenger comfort, Red Jet 6 was a game-changer for the shipyard. Orders quickly followed for two Thames Clippers, with the yard proving its capabili ties in a high-tech aluminium construction.

We are pleased to see one of our long-serving partner’s efforts being deservedly recognised. Scania’s association with Wight Shipyard Company goes back many years and covers numerous different projects. We’ve worked collab oratively on many wonderous vessels, turning them from a blueprint into a reality, including the Twin City Liner.
68 Inside Marine
And our story won’t end there. We’re just at the beginning. The future has many exciting projects on the horizon, whether it’s focused on being more sustainable, or transitioning towards a cleaner future with modern hybrid and electric powertrains. We can’t wait to see what the next chapter of this story will be.
SCANIA GB LTD editorial mention
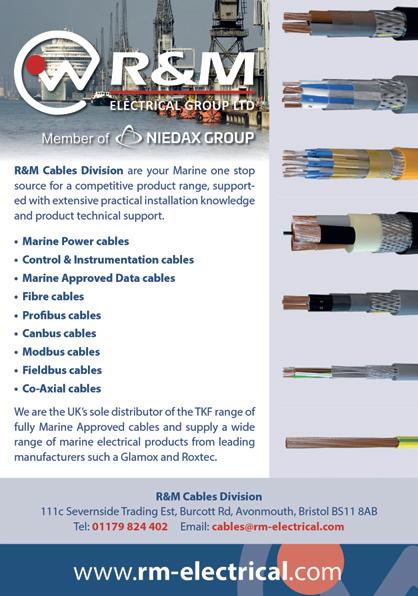
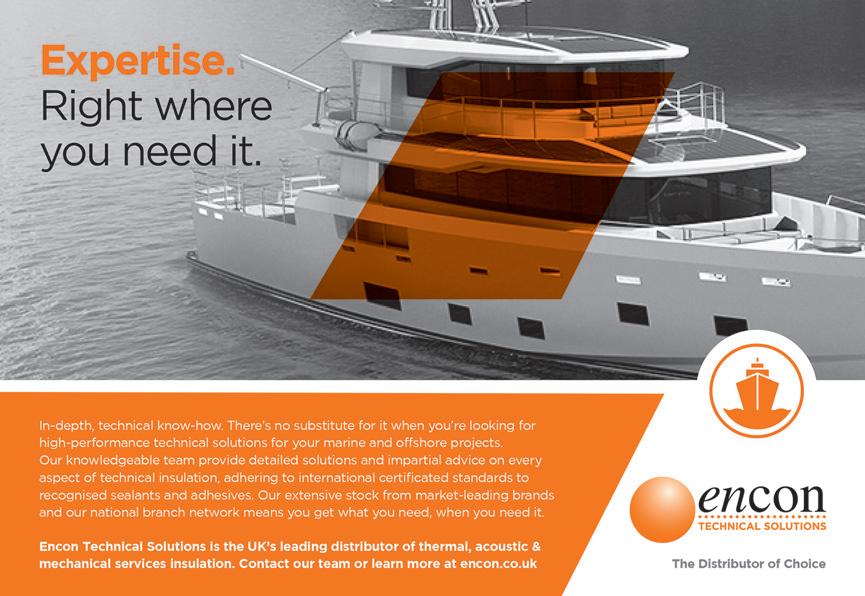
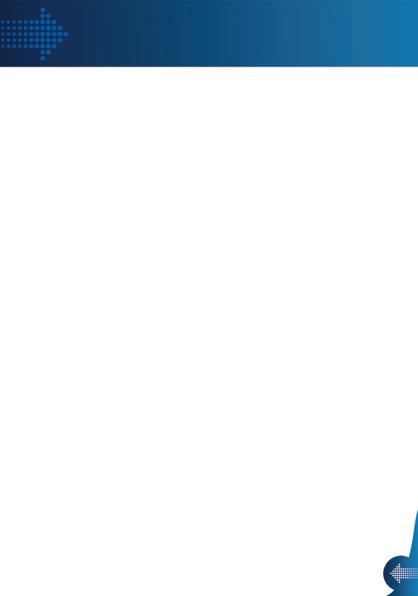
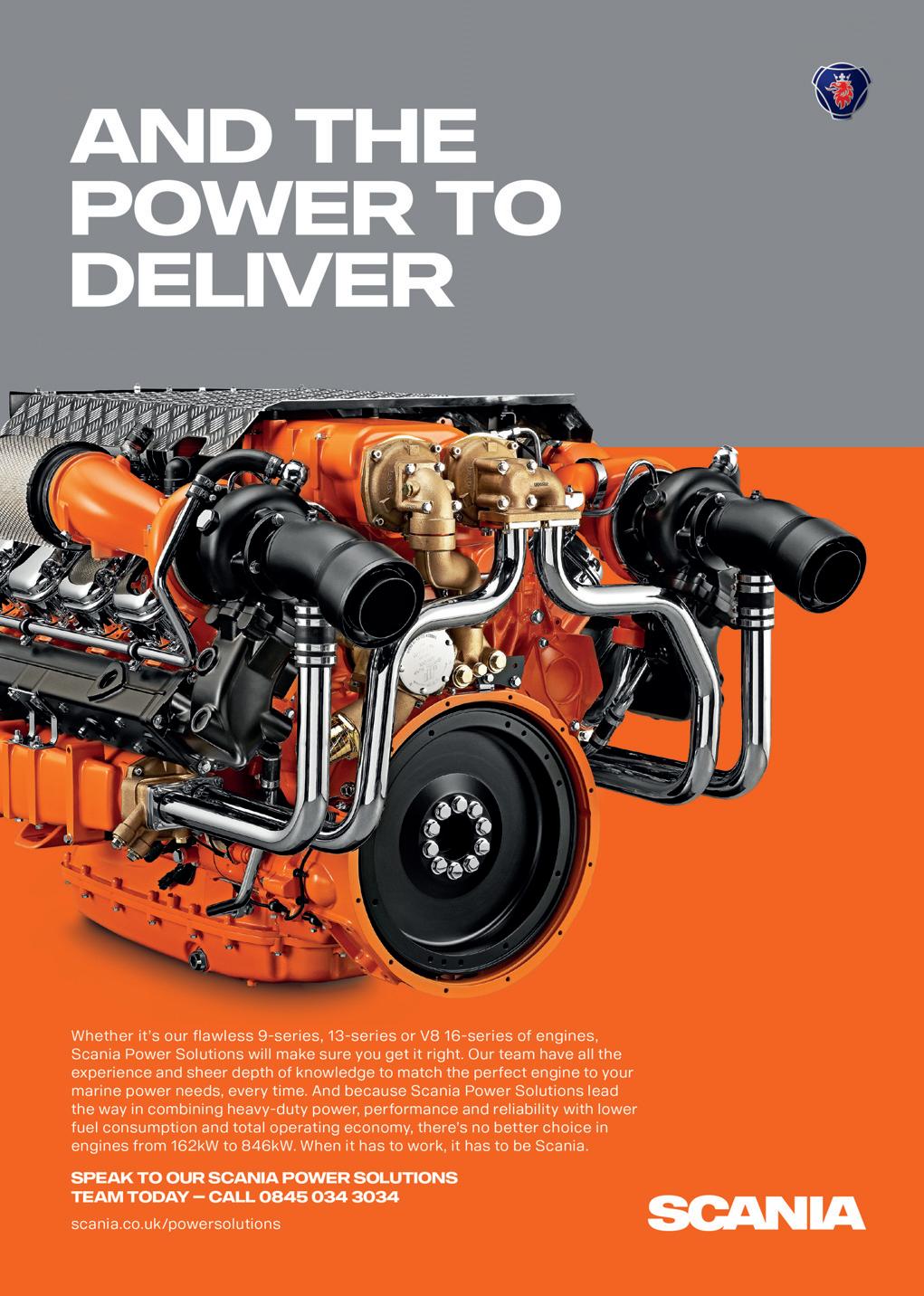
The yard recently signed an order for two more high-speed ferries, two 24 metre aluminium explorer vessels alongside building and delivering a hybrid wind farm support vessel capable of signifi cant speed advantages and fuel savings.
While utilising island suppliers wher ever possible, (supporting over 100 local companies of varying sizes), the yard has, continued to thrive, commented Toby Mumford, Business Development Manager. This includes the upcoming launch of a training school in the yard for apprentices to develop skills in welding. New investment is primed for the building of a new dock for a new travel hoist, increasing capacity from 70 tonnes to 260 tonnes, that will enable WSC to expand its work scope and do more refits on a wider range of vessels.
Additional orders have included two 37m high-speed ferries for Mexico’s largest ferry operator, Ultramar, a 40m vessel for Austria, four vessels for Malta, and a 39m 250-passenger speed river catamaran for services on the Danube between Vienna and Bratislava.
70 Inside Marine
“During the pandemic, the ferry manu facturing industry went very quiet, so we decided to diversify into the cruise transfer vessel and the superyacht explorer mar kets,” explained Mr Mumford. This led to the creation of CWind Pioneer, the world’s first hybrid surface effect CTV offering a greener, more efficient alternative to traditional SOVs and CTVs for the offshore wind industry. The vessel has a hybrid diesel and battery electric power system which enables it to operate purely on battery power while in harbour or at standby in the wind farm.
Mr Morton reflected: “We have the strongest pipeline of work since inception, and things look set to go from strength to strength. We have a bright future oper ating at the cutting-edge of aluminium construction and carbon reduction.”
“The vessel is one part of WSC’s drive to create a greener shipping environ ment, and she is a perfect demonstration of that,” added Mr Mumford. Three years ago, British boat builder Arksen unveiled its vision for a new con cept in sustainable marine adventures. The ambitious project has rapidly gained momentum with the sale of the second Arksen 85, Project Pelagos.
Strongest order pipeline Commissions continued to roll in for WSC with Red Funnel’s second 41m high-speed passenger ferry, Red Jet 7, becoming one of the greenest ships in its fleet, while Scotland’s Jacobite Cruises ordered a 21m cruise catamaran for Loch Ness.
CWind Pioneer is over 20% more fuel efficient than conventional CTVs.
WIGHT SHIPYARD CO I PROFILE
The 24-passenger CWind Pioneer can operate at speeds exceeding 43.5 knots, and transit and transfer safely in sea states in excess of 1.8m Hs, while min imising motion and acceleration through its air cushion motion control system.
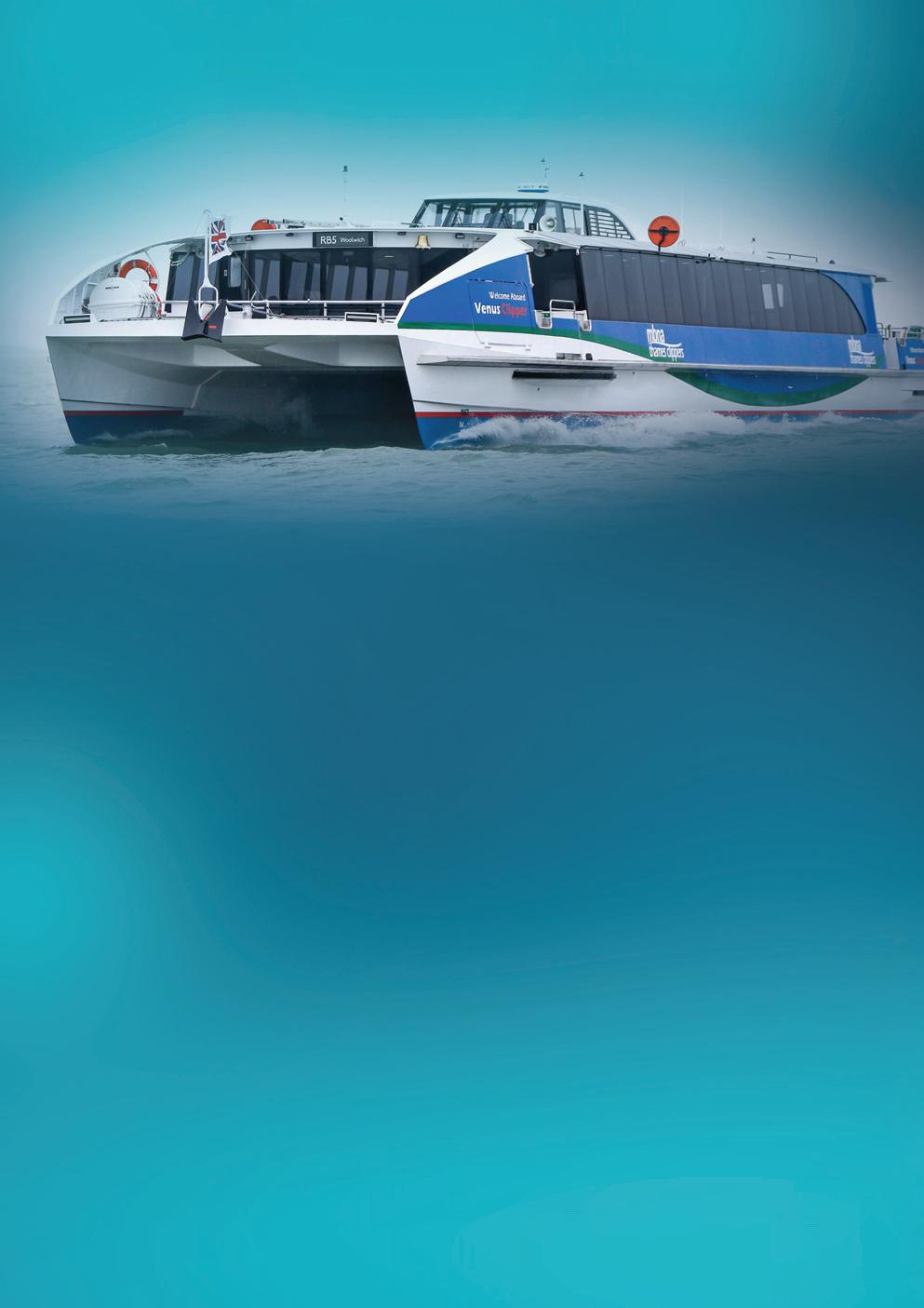

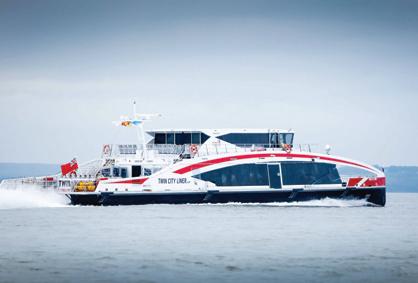

The Arksen 85, currently close to con struction conclusion at WSC, represents the flagship vessel within the Arksen Explorer Series. The Arksen 75 and Arksen 65, make up the other vessels of the Explorer fleet.
n
WIGHT SHIPYARD CO I PROFILE 72 Inside Marine
The hybrid design will allow the new Uber Boat by Thames Clippers vessels to operate solely on battery power to trans port commuters and sightseers along the Thames throughout the Capital’s central zone between the Tower Bridge and Battersea Power Station piers and recharge while using bio-fuel power outside of Central London. The technology is not reliant on shorebased charging, with the boats using excess power from the bio-fuel engines to recharge their batteries for the Central London stretch. Additionally, they will be among the quietest ever seen in the passenger boat industry and will stand as future-proofed examples of environmental excellence.
Project Pelagos, due to be released late 2022, provides 12 berths in a six-cabin configuration. The Arksen 85 offers robust build quality, excellent reliability and superb efficiency, combined with comfort, style and safety, as expected from a modern, long-range cruising vessel. The design of the trans-ocean going Arksen 85 and onboard systems allow for operation in a wide range of condi tions, including high altitudes, tropical climates and adverse weather, and extended periods in remote regions without external support.
Mr Mumford said WSC was further buoyed by news it had secured the contract for two new passenger catamarans for operation on the ever-growing Thames commuting and sightseeing line for Uber Boat by Thames Clippers.
The contract will see WSC build the next generation of Clipper-class vessels utilising the latest battery-power technology and recharging options.
Revolutionising the industry
Mr Morton added: “WSC is firmly on the side of forward-thinking owners and operators revolutionising the industry. Our employees have true global expertise in delivering on the net-zero challenge for
“Weshipbuilding.areveryproud of what is being achieved with our innovative and costeffective approach to modern shipbuilding: WSC is truly at the forefront of the alu minium shipbuilding industry.”
Mr Mumford concluded: “We are building the lightest, most fuel efficient ferries in the world. WSC is committed to building a diversified fleet of vessels for our growin g list of happy clients.”
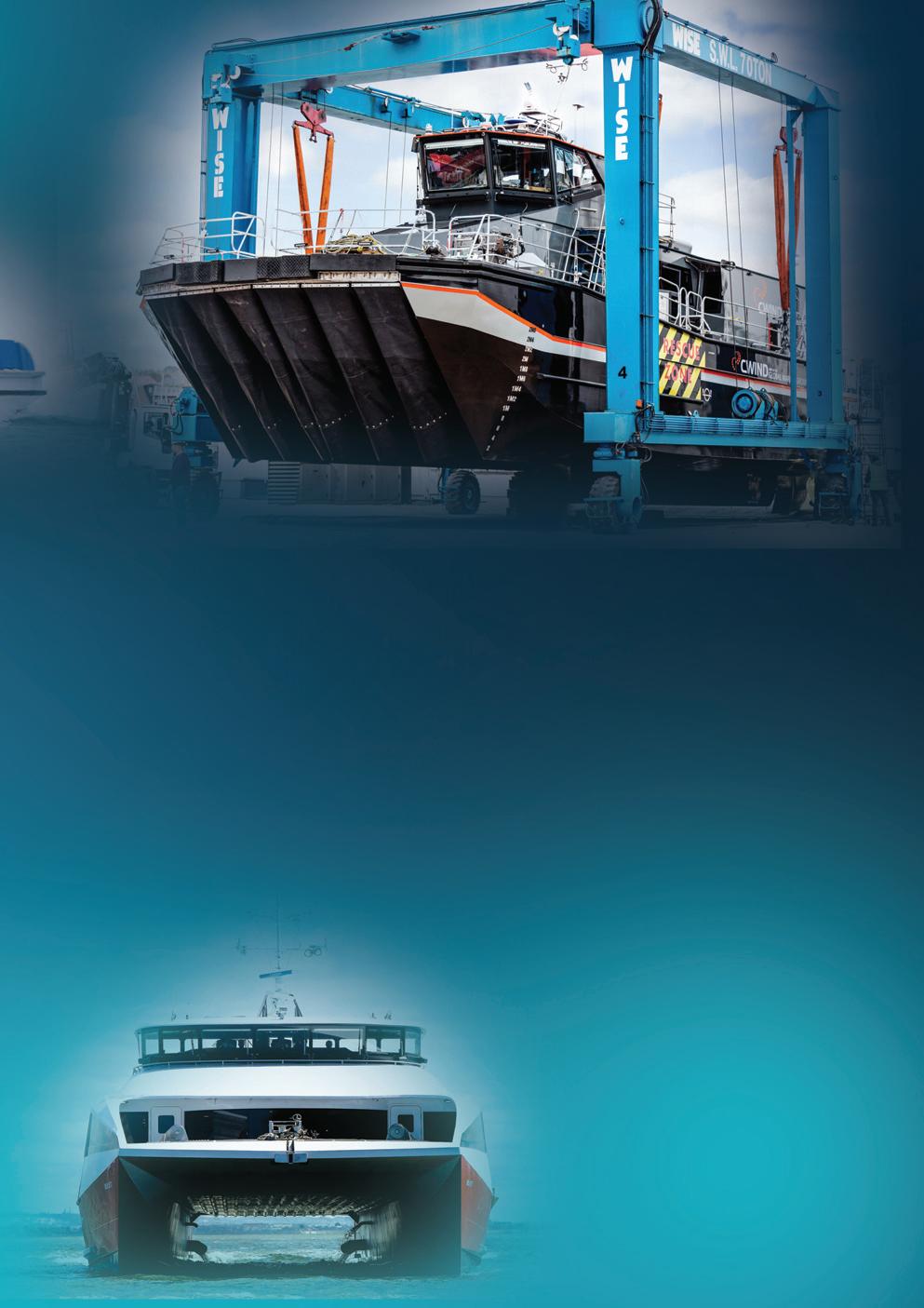
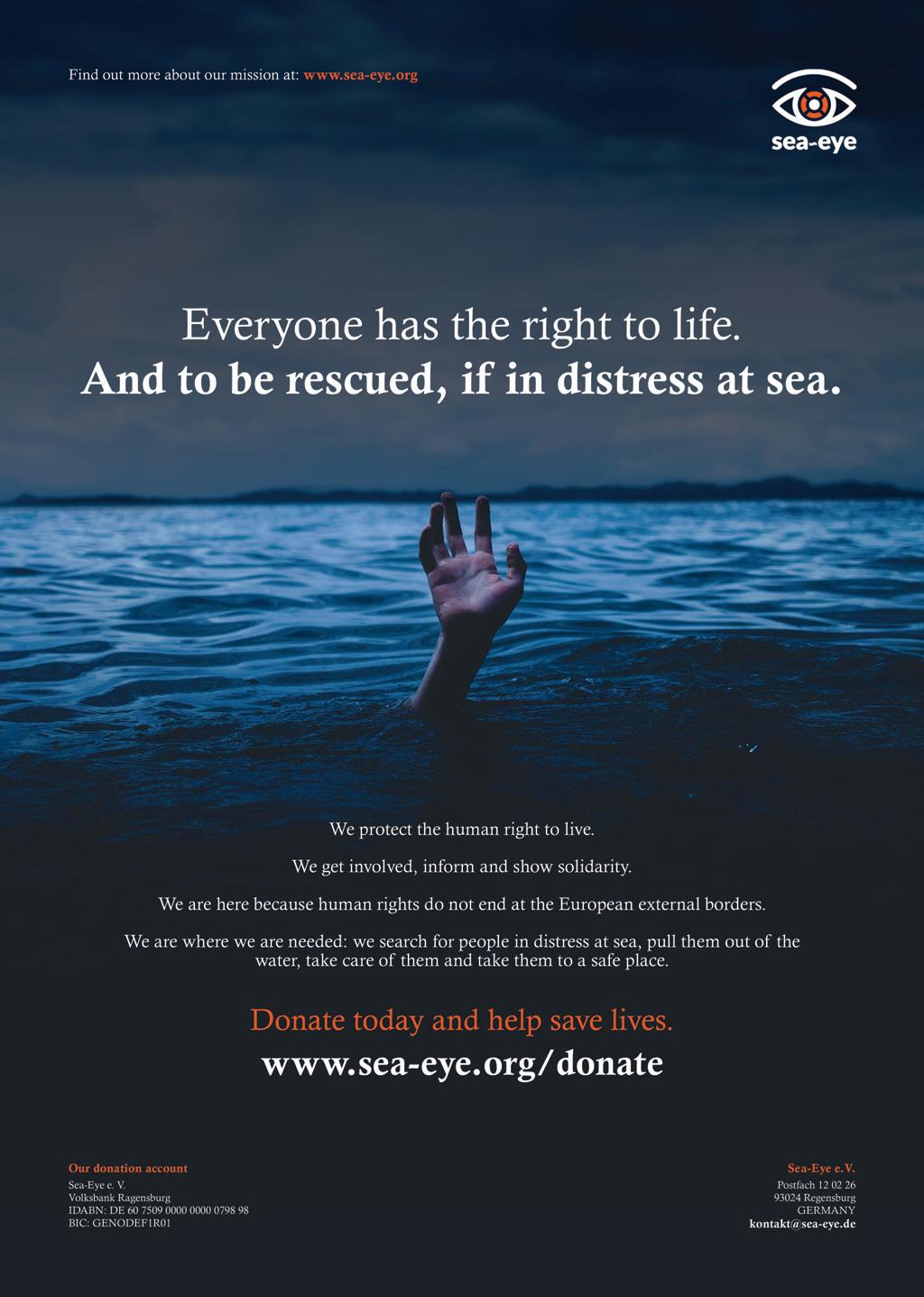
74
ASTIVIK SHIPYARD I PROFILE Inside Marine
Astivik Shipyard is located on Colombia’s Caribbean coast inside Cartagena de Indias protected bay. Celebrating 50 years of experience in the marine sector this year, Astivik now takes the crown for maximum lifting ability also within its homeland – with a capacity 4,000 tonnes. After starting out as a company created to provide maintenance for a fishing concern, Astivik now has customers both international and domestic and has grown to a business that, directly and indirectly, supports 2,500 jobs. Article written by Jordan Yallop.
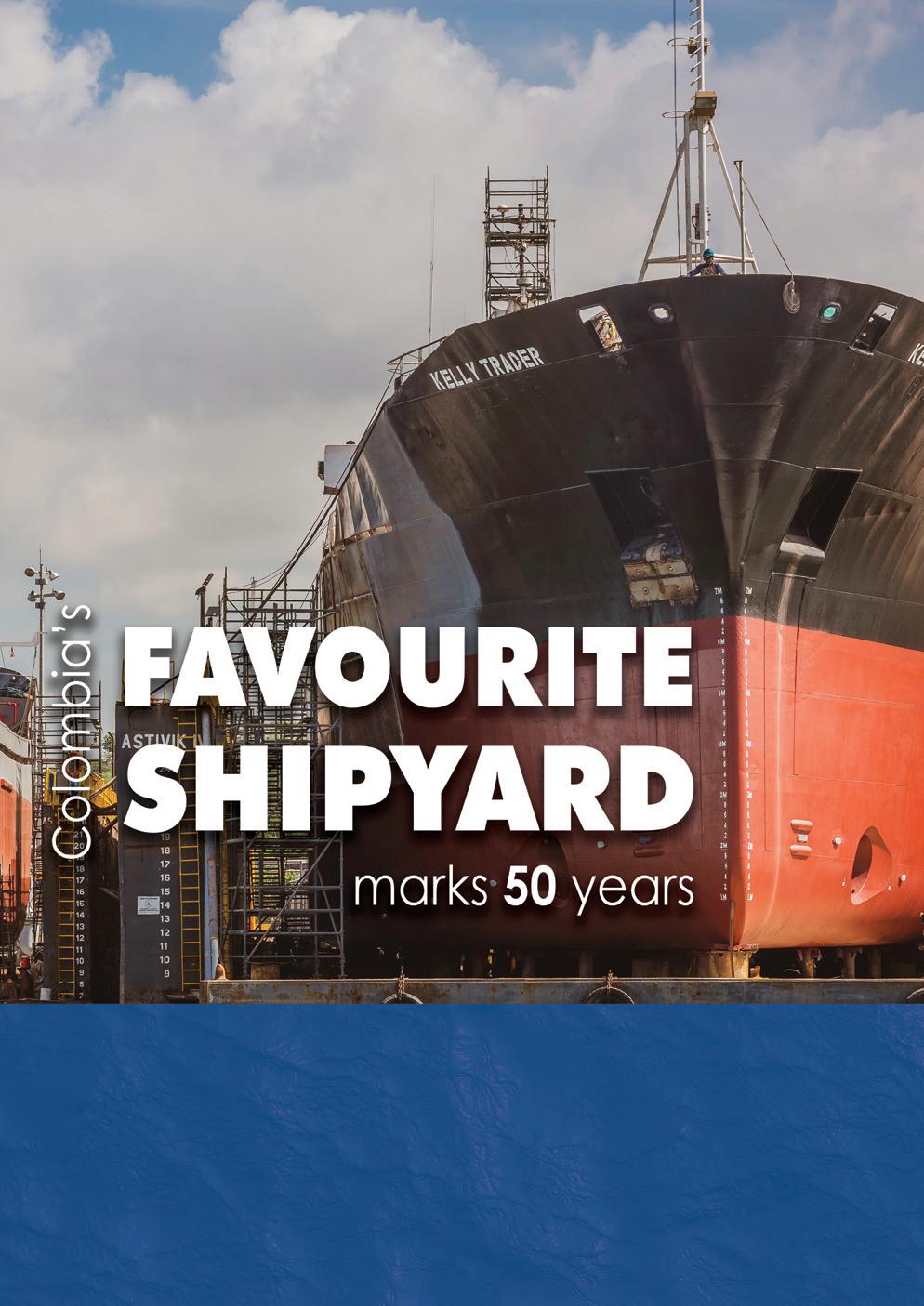
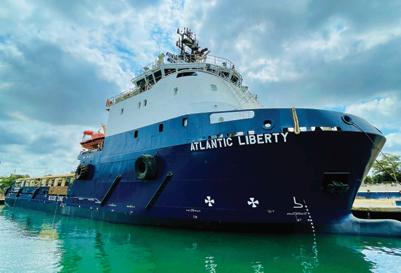
In the 1980s the company undertook its first constructions and began to provide services to the Colombian maritime sector. In 2004
“This is very evident when you have clients in the Pacific Ocean who prefer to sail more than 800 nautical miles passing through other shipyards and crossing the Panama Canal.” Keen to highlight the shipyard’s 50-year milestone, Mr Mar said Astivik will be celebrating with everyone that has made it possible.
Originally founded in 1972 as a part of Vikingos, a renowned Colombian fishing company, Astivik was originally created to solely provide maintenance and repair to its own fleet.
“Our team, collaborators and customers, all who we consider part of the Astivik family, will join us in celebrating our 50-year anniversary,” he said.
Astivik has a site that covers seven hectares, with a covered area of 2,155 sqm and three floating drydocks. Also, the company has an Airbag docking position to haul large barges, a high-performance slipway and a 984 ft pier.
Cristhian Mar, Business Development Manager said: “We have a wide portfolio of clients in more than 20 countries around the world. Customer confidence has been generated from the fulfil ment of our value promise that understands three main needs of the client – quality, time and fair prices.
In the same year, Vikingos sold Astivik to Carsun LLC, a North American company, and began serving foreign-flagged vessels.
Hectares of quality service
Jaime Sanchez, Vice President, said: “We have put a lot of effort into increasing our capacity to attend bigger vessels and by doing so, increasing the job opportunities in our region. Today we have created over 2,500 jobs between direct and indirect specialised and dedicated workers. We also support them through training and edu cation to help develop new skills for a rapidly changing industry.”
Now 50 years on, Astivik has consolidated itself as a company with trust from both national and international markets.
With a lot of effort and hard work, Astivik has established itself as one of the region’s most successful shipyards. Today it provides services ranging from ship repair, maintenance and design, to building, retrofit and equipment rental.
2011 saw the Astivik IV floating drydock built and with its total lifting capacity of 4,000 tonnes, it has cemented Astivik’s posi tion as Colombia’s premier shipyard. The financial figures back this up, too. The yard has made more than $20 million in export sales in the last two years alone and has used in excess of 2,000 tonnes of processed steel in the last three years.
Inside Marine 75
Astivik currently has clients in Panama, the Caribbean islands, Europe, Asia and the USA, which due to the Free Trade Agreement, permits US flag vessels to do maintenance and repair in Colombia.
Astivik built its first floating drydock with a capacity of 1,200 tonnes; it was the first of its kind to be both designed and built in Colombia.

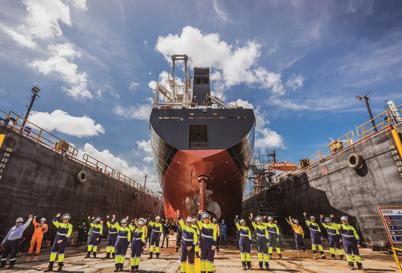
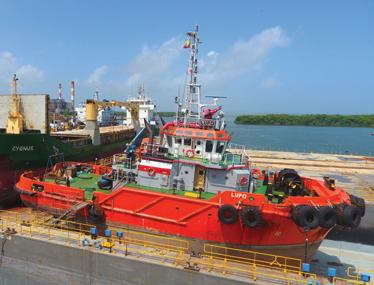
A strong link in the chain The ship repair and maintenance markets are an increasingly competitive ones. Customers not only expect good prices but the demand for quality is also increasingly high. Consequently, Astivik remains steadfast in its commitment to continually provide its clients a ser vice that exceeds their expectations by combining the themes of quality with prompt delivery times, competitive prices and safety. This ethos has not only allowed Astivik to 76
Mr Mar said: “As I stated, we have extensive experience in new builds, more than 40, for companies like Drummond, Glencore, Seacore, Impala/Trafigura among others. All have been constructed to be compliant with international standards such as ABS, Lloyd’s Register or Bureau Veritas regulations.”
Mr Mar underlined that customer service is one of the biggest factors to which Astivik pays special attention; the company under stands the criticality of these types of services within the sector.
Both foreign and domestic Astivik, considered by many to be the Caribbean region’s best option for ship design, repair, maintenance, and shipbuilding, has a wide portfolio including expertise in the maintenance and repair of azimuthal systems. Currently 70% of Astivik’s sales is from its export services. Mr Mar stated that this is not because the domestic market is unimportant, it is because it is limited, and Astivik currently already has 80% of the domestic market share.
As such Astivik aims to offer a bespoke, personalised service which pays special attention to delivery times and quality.
One such case study is the RR Dorada pusher, which at 3,300 bhp, is considered the most powerful river pusher ever designed and built in Colombia. Specially designed for the complex naviga tion of the Magdalena River, it was built in a record time of seven months by Astivik in 2015.
“Due to the demand, we have focused our efforts on maintenance and repair and we have achieved great results in this area. We have also developed some of the most important private newbuild pro jects in our country, ranging from barges, floating drydocks, bay tugboats, to the most efficient push boat navigating the Magdalena River,” said Mr Mar. Mr Sanchez added: “We would like to attend more newbuild pro jects, but in our country these are very limited and unfortunately, we cannot participate in defence vessel projects. But with our expertise we are very positive that soon we will participate in the foreign new build market.”
Inside Marine ASTIVIK SHIPYARD I PROFILE
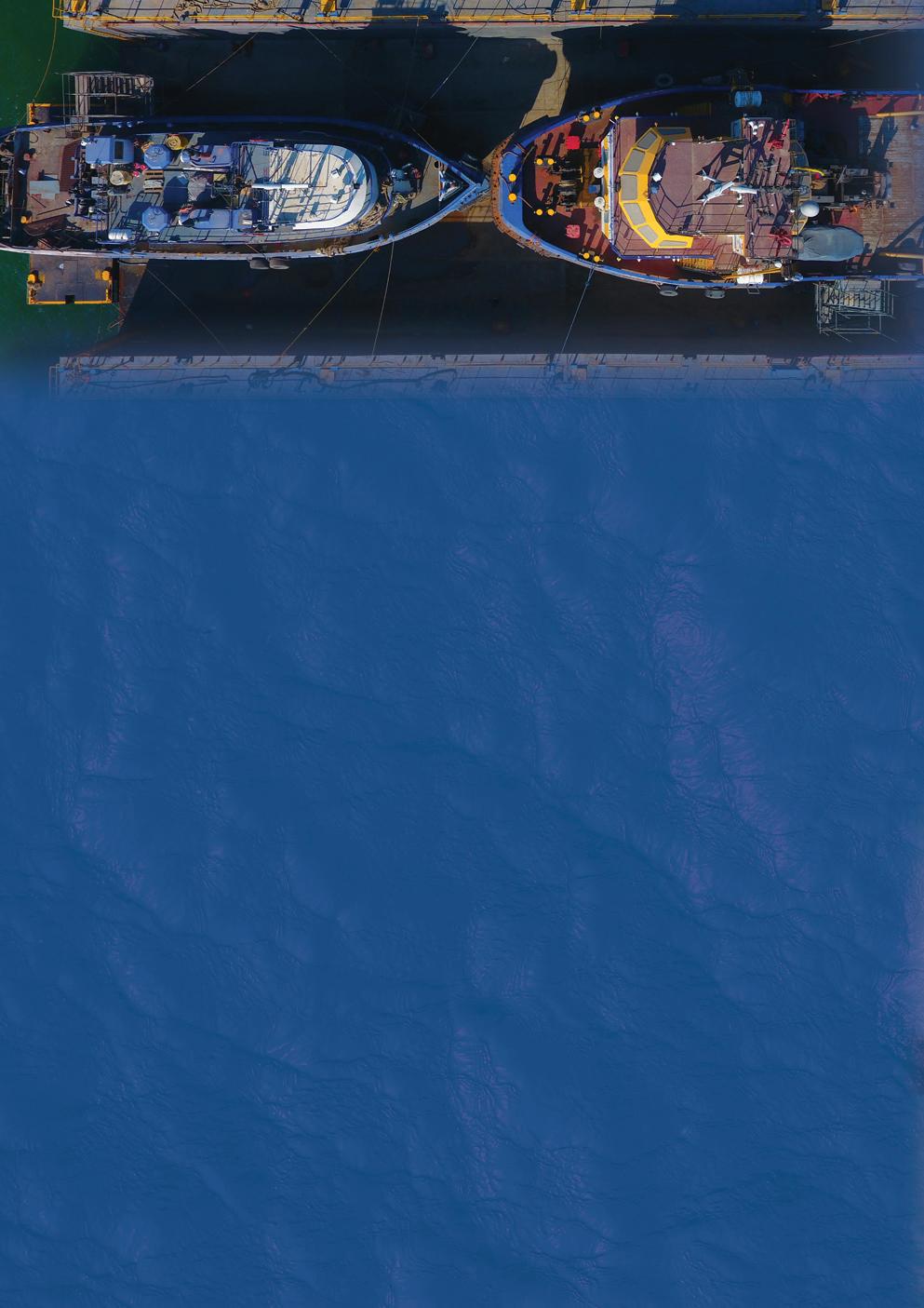

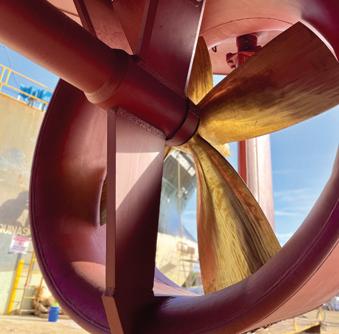
Inside Marine 77
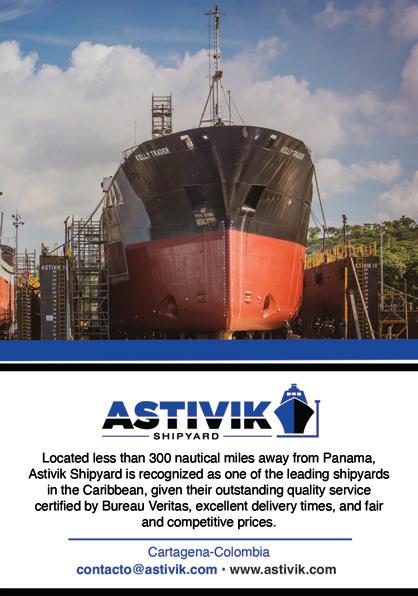
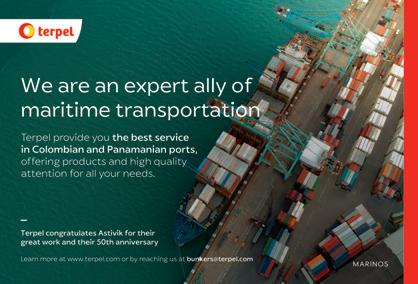
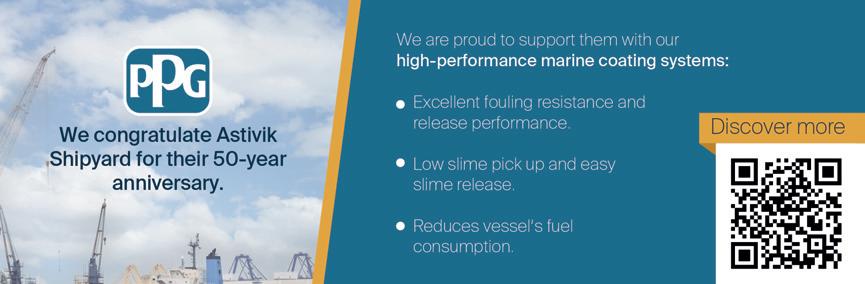

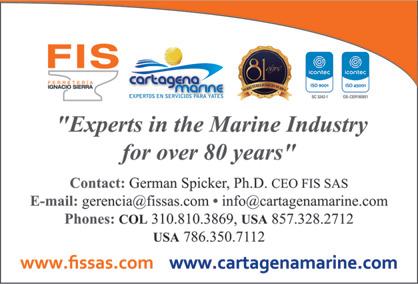
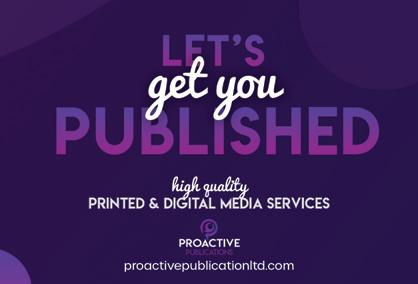
ASTIVIK SHIPYARD I PROFILE
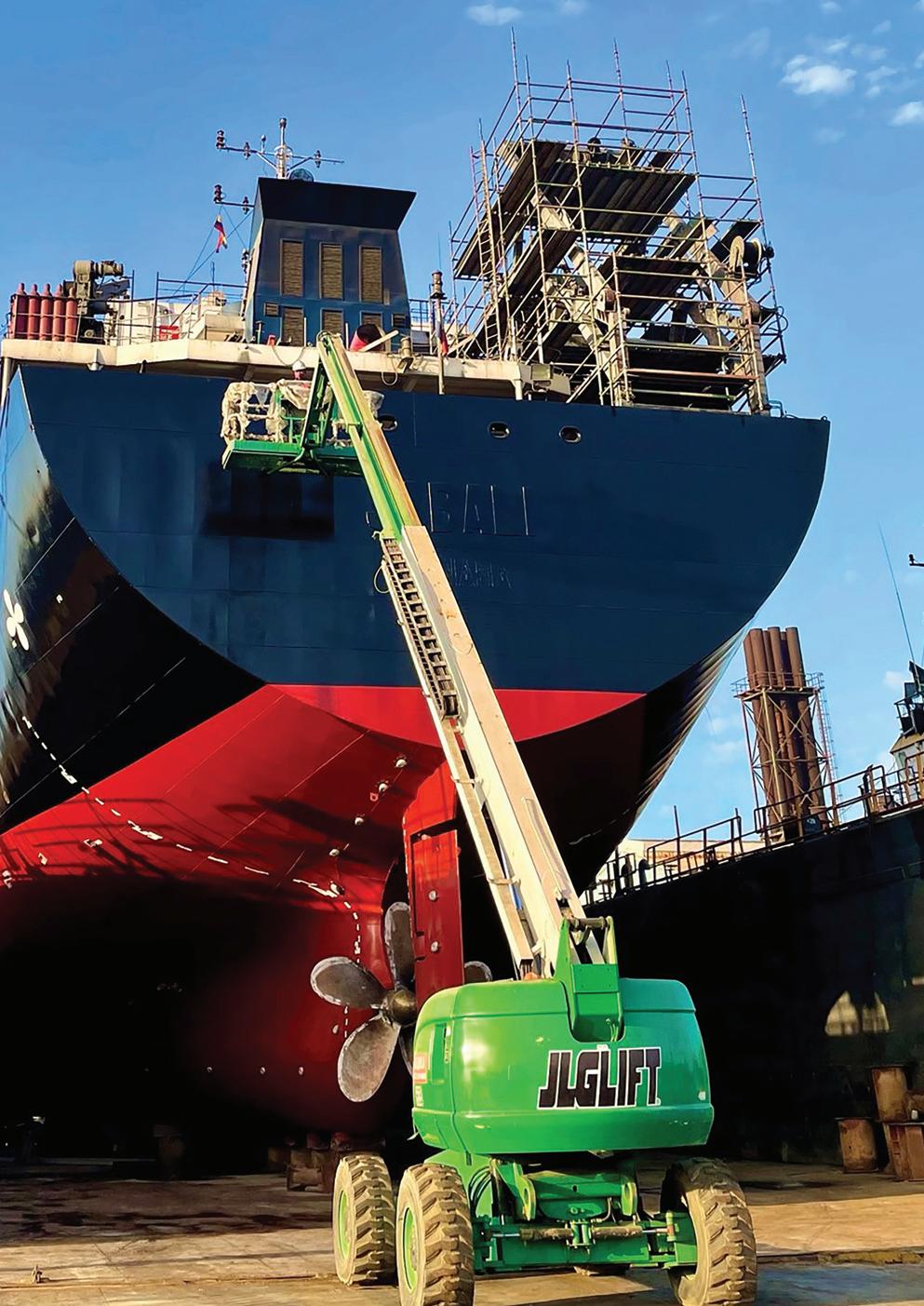
Mr Sanchez concluded: “We have been (and will remain) optimistic. The shipyard industry is known as one of the oldest, most open, and highly competitive markets in the world. Astivik has proven experi ence in surviving spikes and downturns in the economy and we will remain positive, and work towards the development of our company and the shipyard industry in our country.” n
For the past year, Astivik has continued the execution of its master plan, which also includes the modernisation of infrastructure and acquisition of new equipment. Further to this, the shipyard will begin the construction of a new floating drydock that will have a lifting capacity of 8,000 tonnes. These additions will help them position themselves within the tanker, cargo and fishing vessel segments.
As with almost every industry and sector, Astivik has seen some very challenging years, not just limited to the Covid pandemic and supply chain issues, but also constant increases in prices of raw materials, such as steel, paint and welding supplies which are cur rently rampant throughout the business world.
In light of this, Mr Mar was quick to reiterate that customer service is precisely what differentiates Astivik from other shipyards.
“We understand that vessels are the main assets of our customers. Our clients consider us their allies and their friends. Suppliers, too, are a fundamental link in our chain… without them it would have been impossible to celebrate our 50th anniversary.”
A positive future
Inside Marine 79 consolidate itself into its customers trust but also stabilising its position as one of the region’s main shipyards.
“These challenges have forced us to be more competitive, we have taken this time to focus on our people,” Mr Sanchez said. “Working on cultural transformation programs oriented to improve quality and efficiency; all this framed in safety and always with the goal of excel lence in our agenda. This ultimately has resulted in great service.”
Emissions and sustainability are two of the most important topics in the maritime world today and Astivik is addressing these within its 2025 Master Plan. The shipyard has set in motion the mitigation of its electrical energy systems by moving to solar derived energy, and simultaneously, staff are fully prepared for the installation of hybrid propulsion systems and scrubbers.
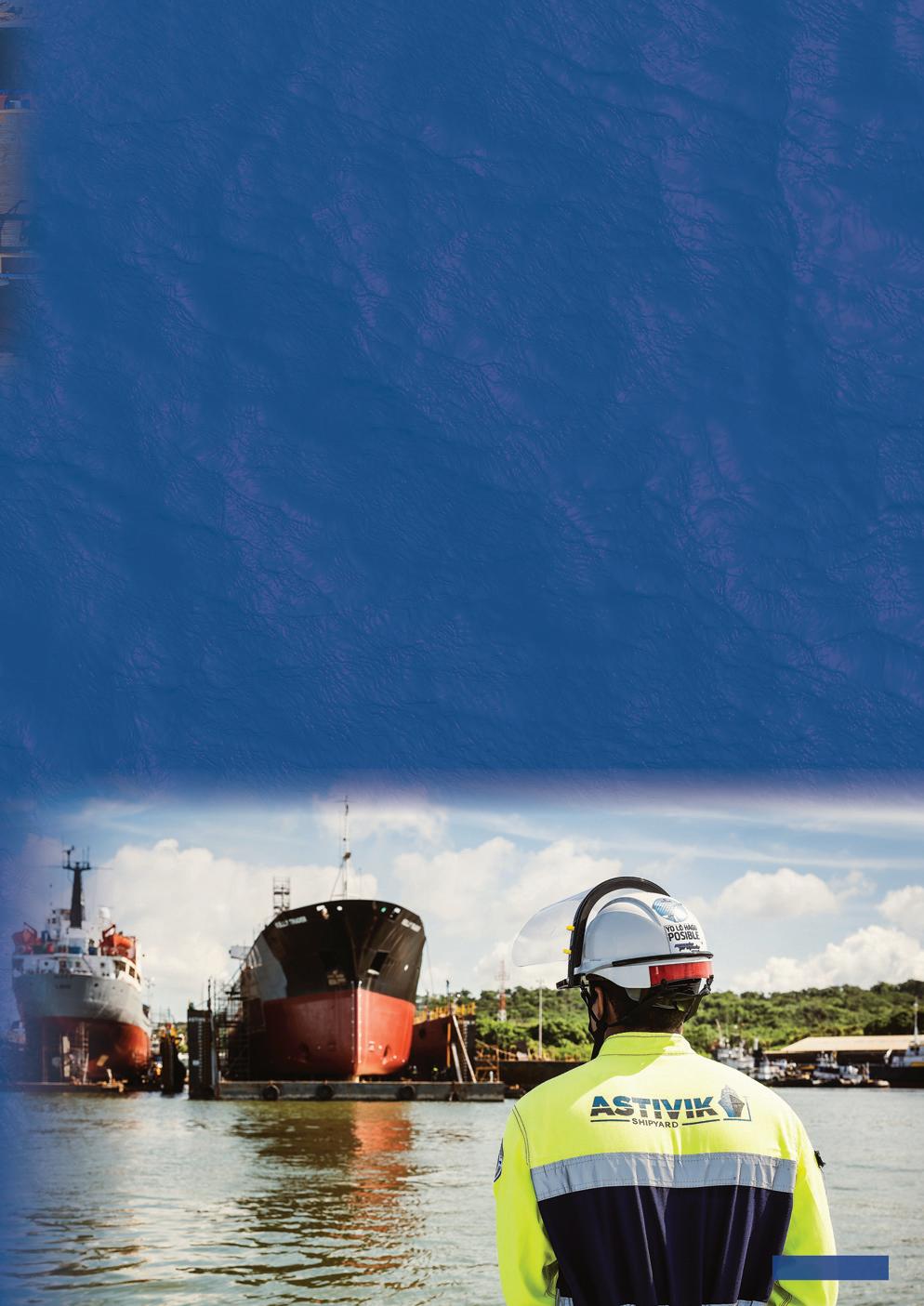
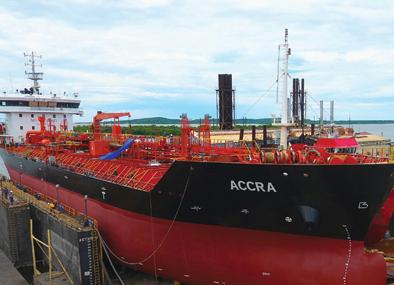
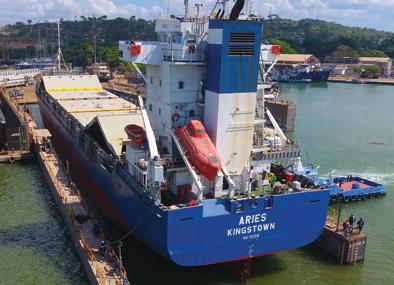
CERNAVAL GROUP I PROFILE 80 Inside Marine
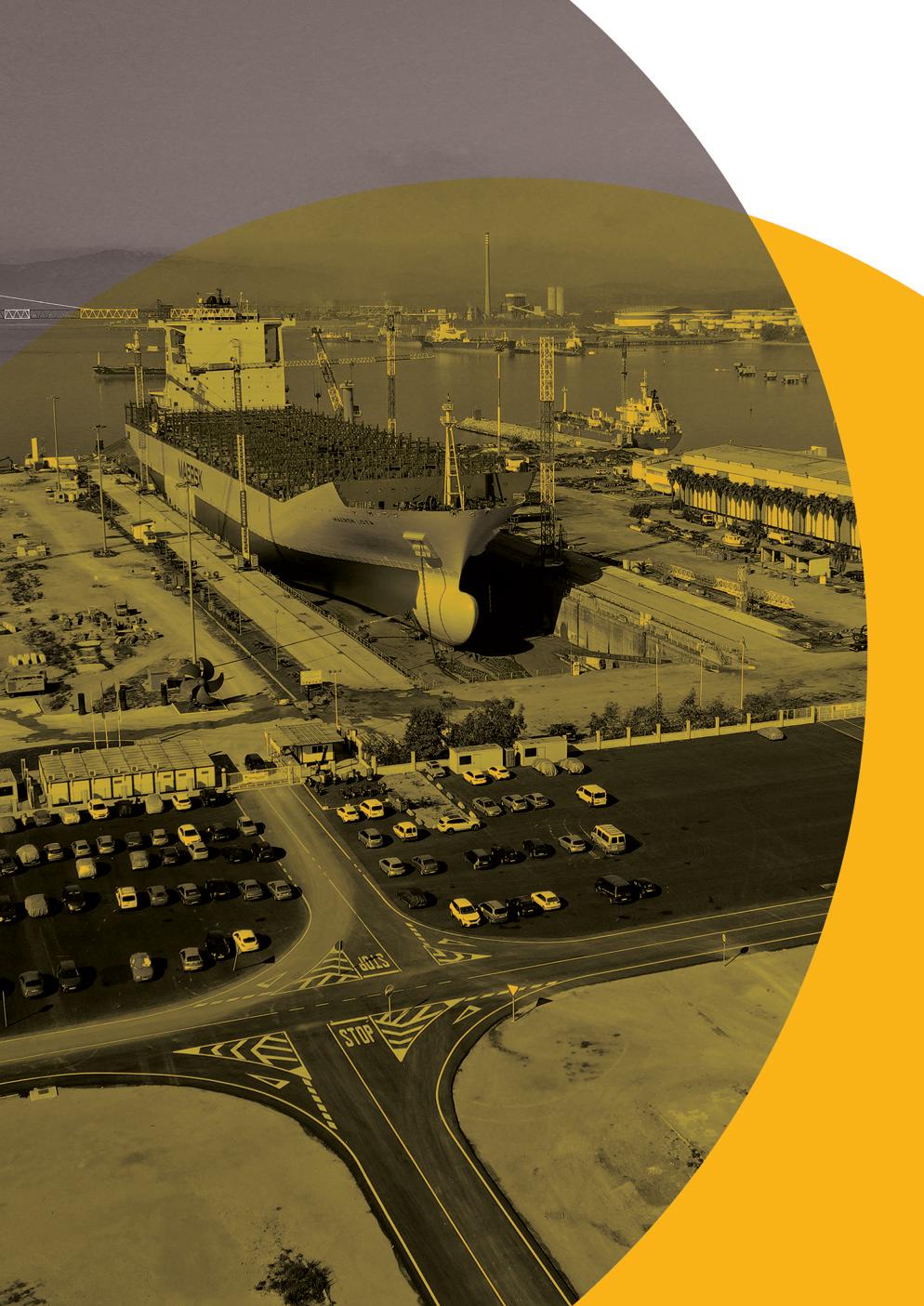
As the owner of shipyards in Malaga and Algeciras, the Spanish family-owned Cernaval Group has remained buoyant through the turbulent times of the maritime industry with a laser-focus on high-quality ship repairs and maintenance services. Timely investments in infrastructure and their logistical presence in the Straits of Gibraltar guarantee the shipyards are always busy. Commercial Director Enrique Perez spoke to Inside Marine’s Andy Probert about the group’s ambitions.
Enduring success Critical to the enduring success of the modern yards has been the foresight and careful investment of the Lopez family, which first stepped into the arena with the launch of the Mario Lopez Shipyard in the Port of Malaga in the mid-1980s.
Having ridden the lows and highs of the pandemic, the shipyards of the Cernaval Group have enjoyed complete occupation since late 2021, and there appears no let-up into 2022.
Inside Marine 81
“Welcome to my kind of crazy,” said Enrique Perez. This opening remark reflects his 14 years of working within the Cernaval Group, a highly successfully privately-owned company that runs shipyards at Malaga Port Bay and Algeciras Port.
For Mr Perez, Group Commercial Director, that kind of ‘good crazy’ is overseeing vessels from across the world calling in for requisite repairs, ballast water treatment system retrofits, and all manner of works that have marked the shipyards out as key reference points in the Mediterranean and Straits of Gibraltar for quality and high standards of workmanship. The yards are fully equipped for marine repairs and general ser vices ranging from electrical, heavy gears, propulsion, hatch covers, steel and mechanical works, pipe works and hull treatment.
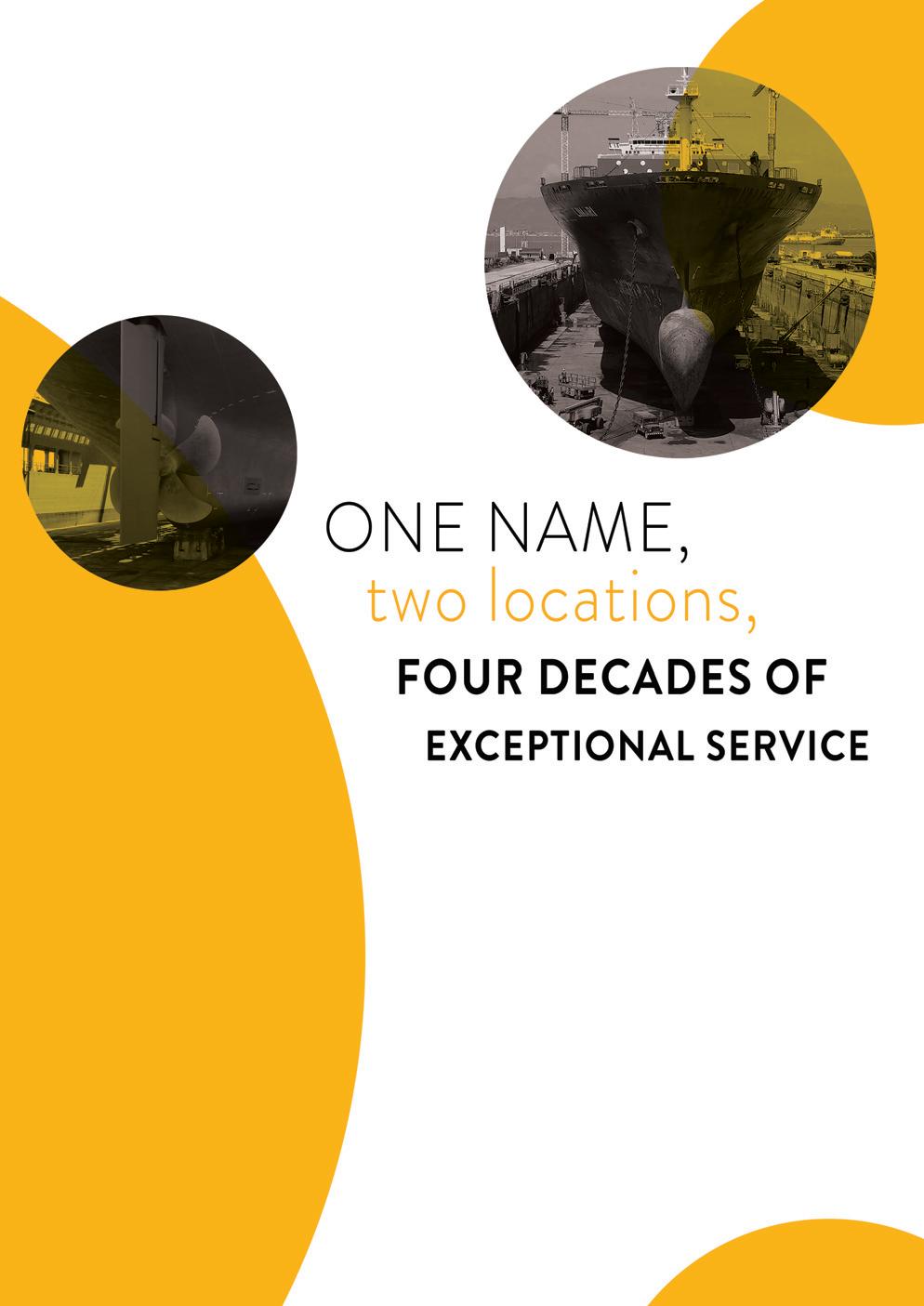
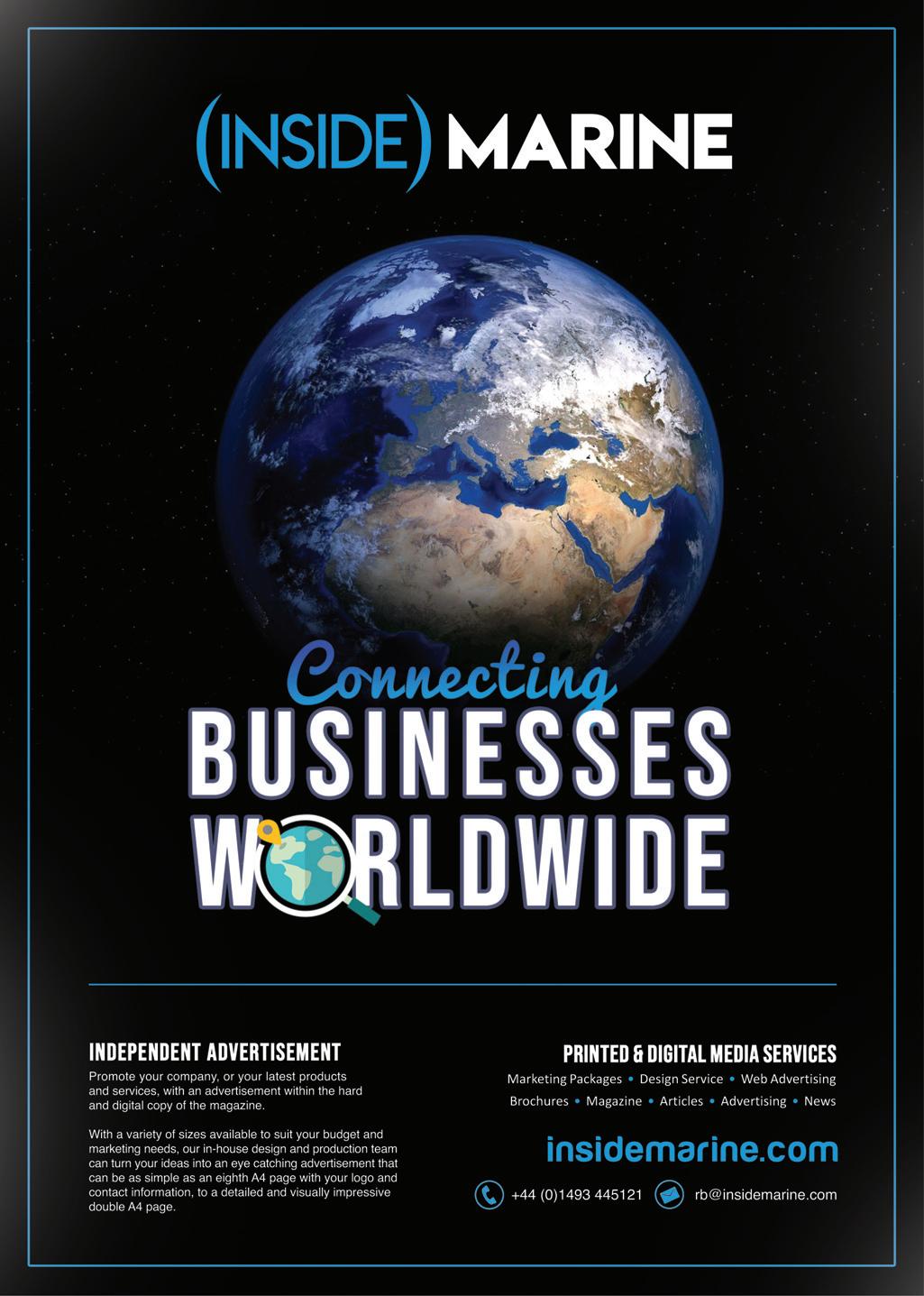
Inside Marine 83
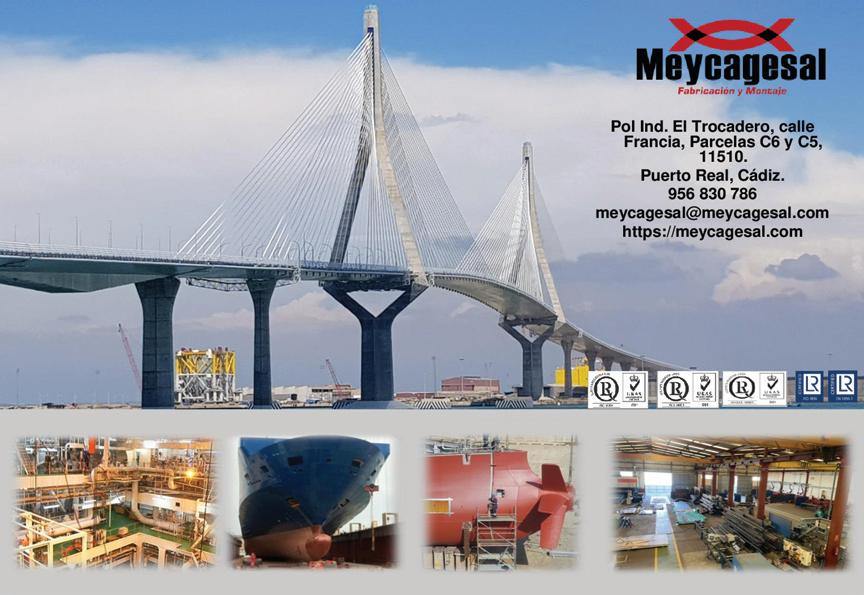
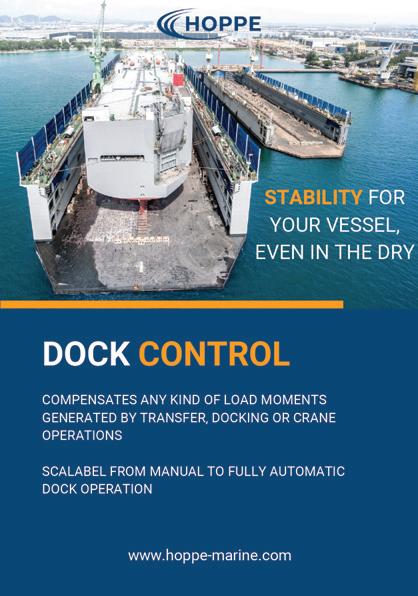

In 1995, the family took over the Campamento shipyard at Algeciras to enable the handling of bigger vessels and more complex works.
The group’s main focus of work is for vessels on their first or second special surveys, usually those that are five to ten years old rather than older-aged vessels.
Key location and investments
The group is also set to extend a 285m length pier to 510 metres. Mr Perez said: “This will be an excellent addition to the shipyard to be used for afloat repairs or for a vessel to wait from dock to berth.”
“The port authorities considered using the space at Algeciras as a container port, but that didn’t transpire, and it remained abandoned for about 20 years. Eventually, they invited Mr Lopez, our President, founder and owner, to look at the area, and he agreed to establish a shipyard. Since then, Cernaval’s name and reputation has grown on the world stage.”
“2020 was one of our best years. After July 2021, we have boomed and 2022 has started fantastically and while several factors can alter this trend, we remain optimistic for the rest of the year.”
Mr Perez said that since the addition of the graving dock at Algeciras in 2008, the company had shifted emphasis from a pre dominantly Spanish clientele to a more global approach.
“We have received vessels from main customers in Germany, the Netherlands, Greece, Spain, Hong Kong, Singapore, and even Ecuador and Cuba,” Mr Perez listed. Speaking of the client diversity, he reflected that the group had been ramping up its search for new markets and “to take advantage of the lack of facilities with big docks in America.”
Today, the 20,000 sqm Malaga base has four quays totalling 1,000m in length, with a 2,000 sqm workshop, warehousing and a 140m x 24m floating dock, with a lifting capacity of 7,500 tonnes. This is in marked contrast to the 300,000 sqm of available space in Algeciras, which accommodates workshops over 5,000 sqm, two lay berths of 510m and 240m in length, a 400m graving dock, a 230m x 39m floating dock, and a lifting capacity of 35,000 tonnes.
CERNAVAL GROUP I PROFILE 84 Inside Marine
Christened Crislaube, the floating dock embarked on a twomonth voyage on COSCO Heavy Transport’s semi-sub Xin Guang Hua and was received in Algeciras in May 2019. She was dry docked, inspected and modified before being placed in her new operational position. Pressed into service in April 2020, her first vessel was Maersk’s Safmarine Nakuru, a 35,137 DWT, 2,478 TEU container ship for essential works.
He added: “We have been trying to look for customers who need sizeable dry-docking facilities and repair works. Our quality of work, reputation and close contacts have helped us network and collaborate with brokers and clients.
“We have the same dedication and commitment whether smaller vessels, such as tug boats, barges and offshore, which go to Malaga, or if it’s mainly Aframax tankers, Capesize bunkers or con tainers, attended, to by Algeciras,” said Mr Perez.
A snapshot of the type of operations at Algeciras was offered when, in the summer of 2020, Cernaval was handling repairs and works on a RoRo cargo ship for Grimaldi Group, a Hapag-Lloyd container ship for afloat works, and a RoRo passenger vessel for Baleária. The yard also managed a self-discharge bulker for works and afloat repairs for several offshore units belonging to Archirodon Construction Group.
“We are exceptionally busy at the moment. From the second half of 2021 through to the first quarter of 2022, we saw a high number of vessels coming for repairs, and that will remain the case going forward in 2022.”
Mr Perez explained: “We sold our previous floating dock to a ship yard in Ivory Coast in 2017, and immediately after, we bought a much bigger one from South Korea.”
The group’s clientele originate from every corner of the globe, from Central and South America, Europe and Asia.
Exceptionally busy
One significant investment the Cernaval Group has reaped was acquiring a new 230m x 39m floating dock for Algeciras.
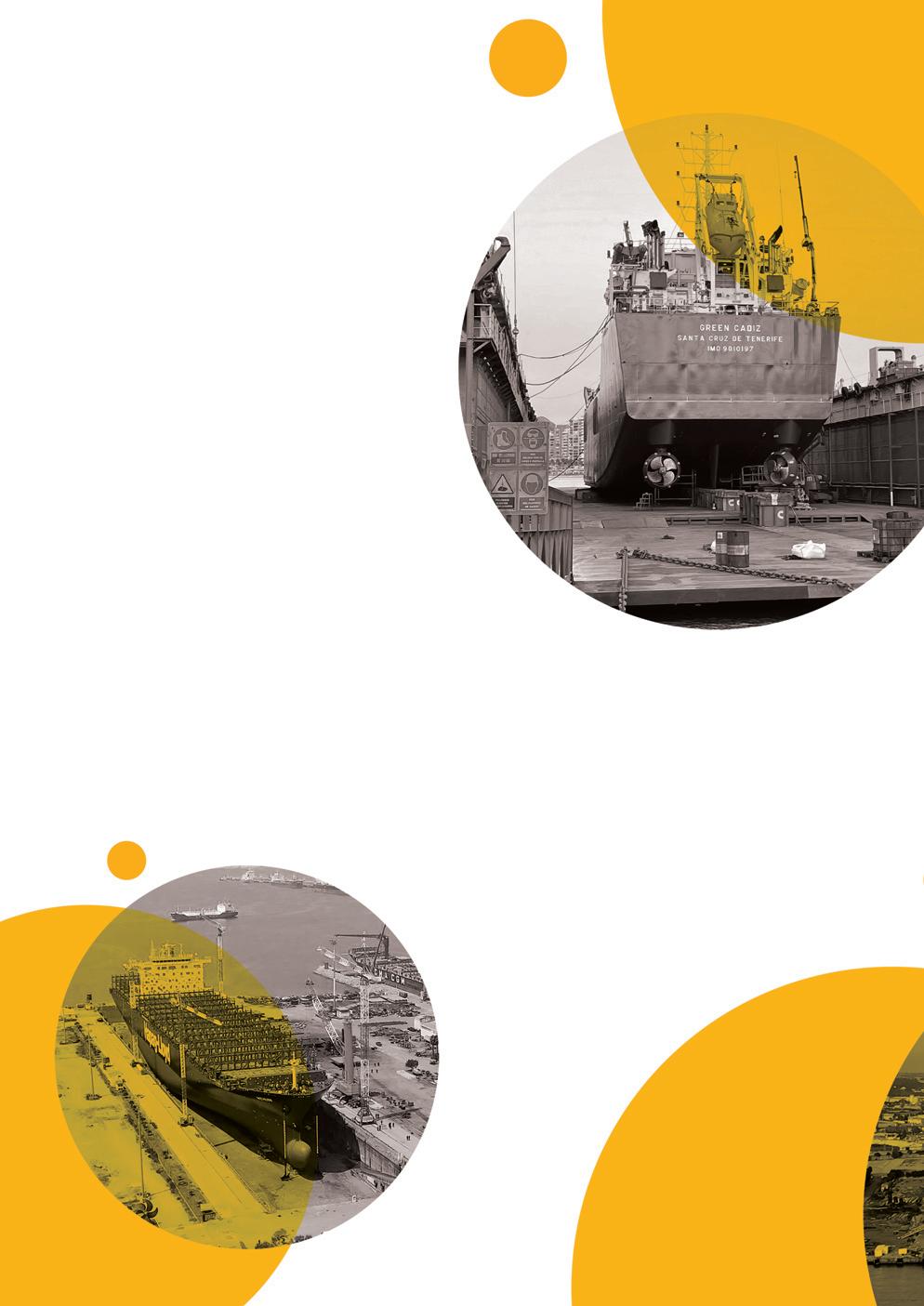
“Given our key location in the Straits of Gibraltar, we have con tinued to grow strongly in the last five years. The market believes we are doing very well, meeting delivery times, at a reasonable price, given we are in a Western European nation. Because of var ious factors, some shipowners have mobilised back to Europe for repairs rather than Asia.
“We decided to evaluate the market as we wanted to break the trend of vessel work going elsewhere and attract owners to Algeciras. We concluded by investing in a mobile crane for this hatch cover work.”
“We also benefit from the fact that Maersk and CMA CGM, two of the main players in containers ships, are located at Algeciras. In our favour, the distance from the terminal to our repair centre is practically zero.”
Employing between 150 to 170 workers, Cernaval can turn to external contractors, which can push that figure up to 250 people, depending on projects at any given time.
Inside Marine 85
“As a family-run, 100% private venture, this gives clients many advantages. We are flexible to their necessities; we can rapidly optimise the work and complete projects. Our structure is very direct and dynamic. Relationships with clients and suppliers are built on transparency, honesty and trust, allowing the profes sional relationship to become more personal and friendly.”
He said: “You can still find the owner, Mr Lopez, still coming into work every day. The Cernaval Group is second-generation run through his three daughters, with Cristina, the Financial Director.
A global but personal business
“The priority is to convince customers to test Cernaval’s capa bilities to see if we can put ourselves in front of competitors they have been using previously.”
He elaborated: “It is only recently that we have signed con tracts with these two important clients. This was due to the syn ergies between the community here, and they were hearing how well we were doing. And they knew where we were located. It is a matter of Accordingtrust.”toMrPerez, one of the tipping points in Cernaval’s favour was the work required to replace hatch covers on container vessels.
“Year-by-year, investment-on-investment, our reputation grows organically. This is because of the owner’s foresight to invest so that we can take on bigger vessels. As customers coming and contin uing to return for work are increasing, that fuels our optimism for future growth,” Mr Perez concluded. n
He added: “A major differentiating factor is our special location in the Straits of Gibraltar. Along with the Panama Canal, Suez Canal and Singapore, it is one of the four channels through which marine traffic has to pass. We are at the gateway of the Mediterranean and to the Atlantic. We have 150,000 vessels passing through the area, so we are in one of the right places in the world.
He said the group’s main ambition is to keep growing clientele and “make our relationships stronger, and ensure our reputa tion carries from mouth-to-mouth in the maritime industry. This business is global, but it is very personal.
Cernaval’s 400-tonne mobile crane was bought from a client in northern Spain and delivered in May 2021. It was in service less than two weeks later and has remained so ever since. He explained: “Now we can do everything in one day that a stan dard crane would take two-and-a-half days to do on hatch cover recovery on a 300-metre vessel. We can now match the speed of our competitors, and offer a very reasonable price.”
Another major factor in favour of Cernaval, said Mr Perez, is how quickly its staff can move between Malaga and Algeciras, facilities or vice versa depending on the projects.
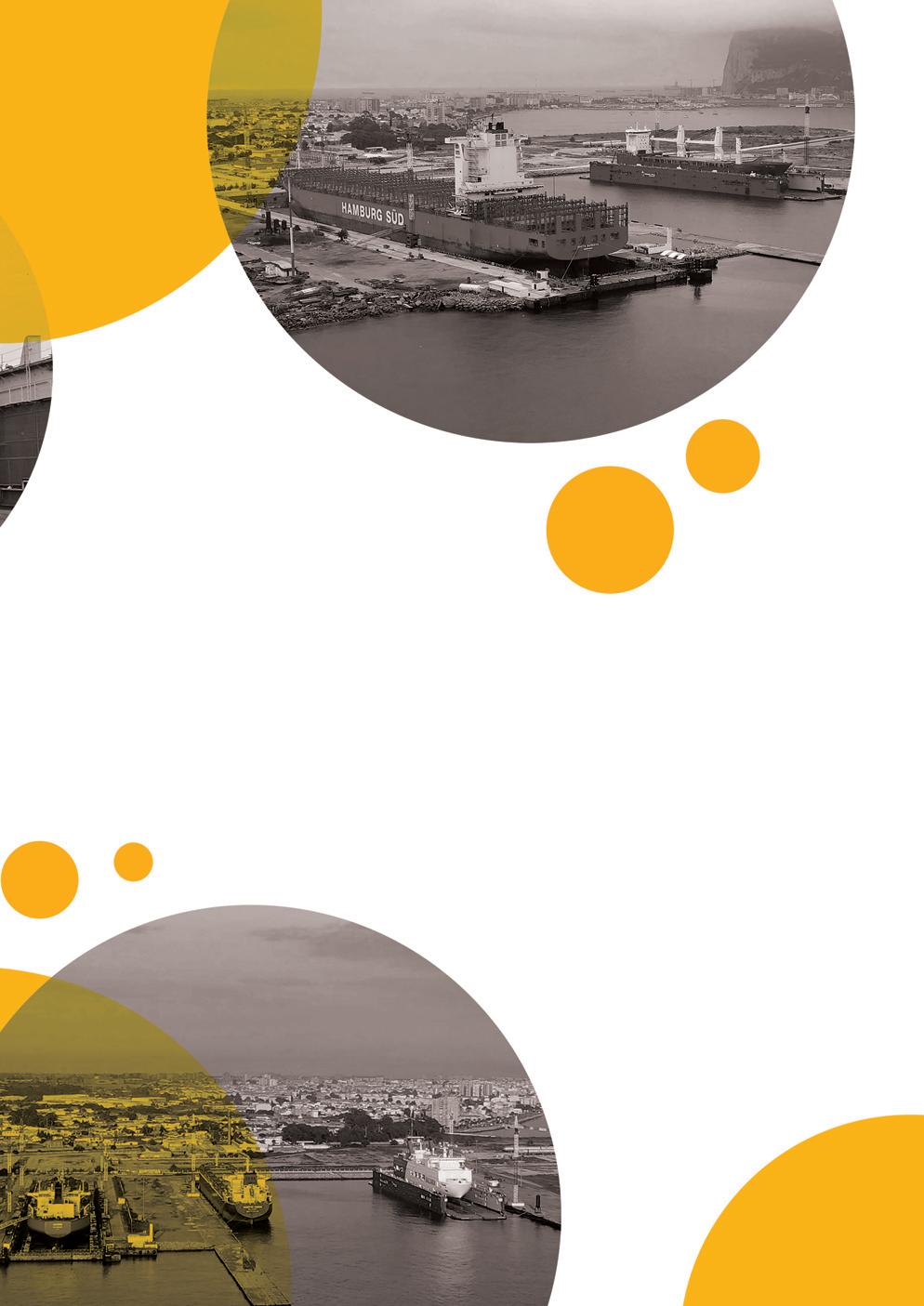
Parkol Marine Engineering Ltd builds and maintains innovative fishing vessels and other craft at Whitby and Middlesborough in the north of England. SallyAtkinson, Director and Project Manager, discussed the company’s history and projects with Phil Nicholls.
PARKOL MARINE ENGINEERING I PROFILE 86 Inside Marine
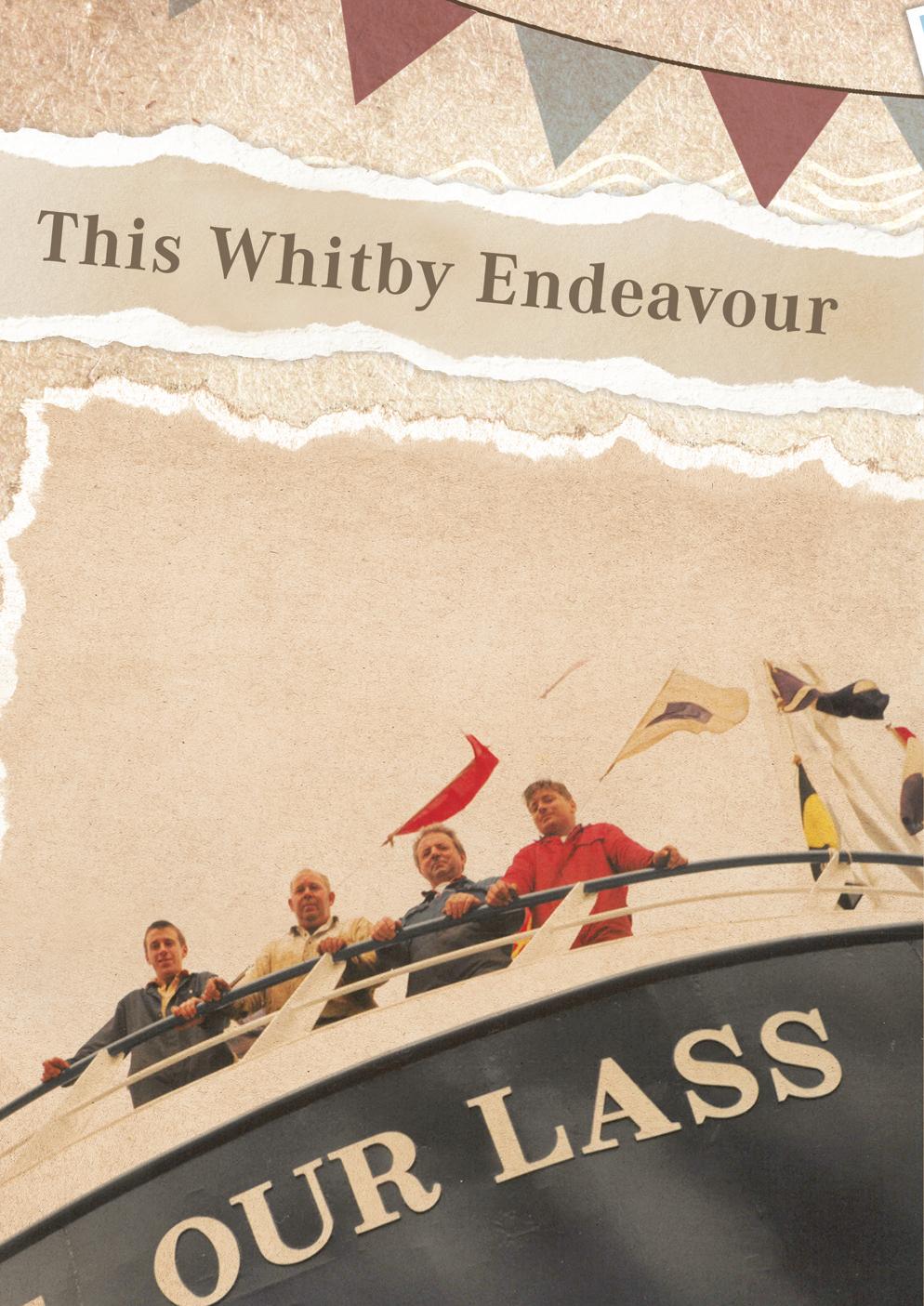
Parkol is one of only three companies building fishing boats in the UK in the under 24m registered size. While boats of this size are Parkol’s main area of activity, the company has a broad range of vessels on its books.
Inside Marine 87
“The different types of fishing boat tend to come in peaks and t roughs,” explained Sally Atkinson, Director and Project Manager: “A couple of years ago, we were building vivier crabbers. Then, for whatever reason, the market changes and we’ve not had many enquiries in that respect. At the minute, it’s mainly twin-rig trawlers we’re getting enquiries for.”
At the time of writing, Parkol recently completed a trawler, and the ships under construction include a vivier crabber, a twin-rig trawler, a beam trawler and a pelagic boat. Parkol also provides an after-sales service for its boats, along with re-fits and assorted maintenance services for local fishing boats.
Parkol’s flexibility is also present in the range of vessels built in the yard. Back in 2002, Parkol built a 40%-sized replica of HMS Endeavour, complete with oak frames, larch planking and Douglas fir decking. This new Endeavour measures nearly 14m long with 12m-high masts carved from Douglas fir. She works most days in Whitby harbour taking visitors for a tour. Other unusual Parkol projects include Havilah, a small cargo ship for a Shetland salmon
The North Yorkshire port of Whitby has a long maritime his tory, but in naval circles it is most famous for being where t he young James Cook learned his trade. When Captain Cook embarked on his exploration of the Pacific he sailed on HMS Endeavour, herself built in Whitby. Parkol Marine Engineering is keeping Whitby’s shipbuilding heritage alive. Parkol was established in 1971 by Ken Parker and John Oliver, combing their surnames to form the company name. Initially based in Spital Bridge in Whitby, the company moved to its cur rent home on the town’s Eskside Wharf in 1992. The company grew steadily but remains a family business. I n 2017, Parkol expanded to a second yard, this one at Middlesborough, about 50km north of Whitby. Across these two sites, the company has 80 employees and posts a turnover of £12 million.
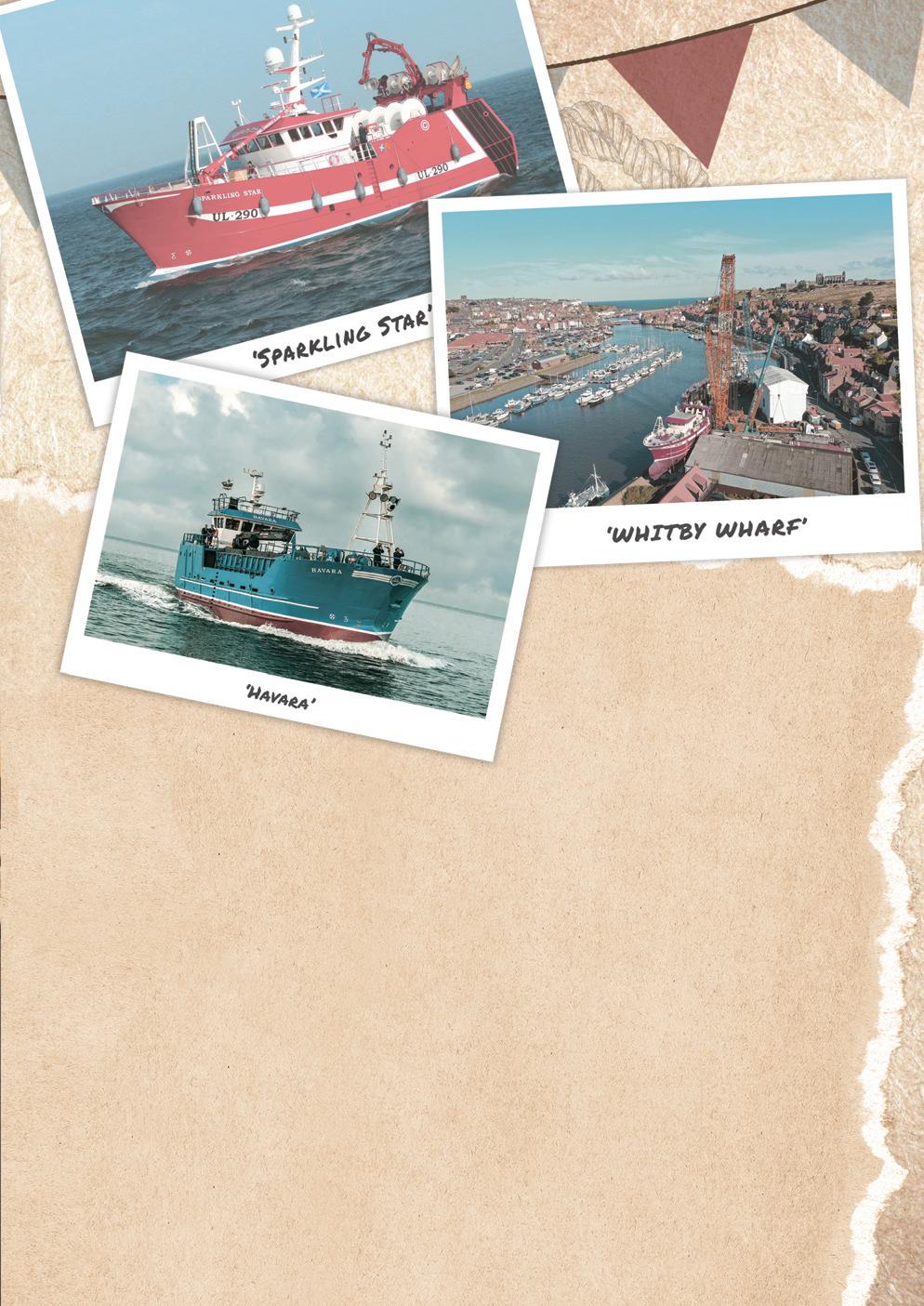
88 Inside Marine


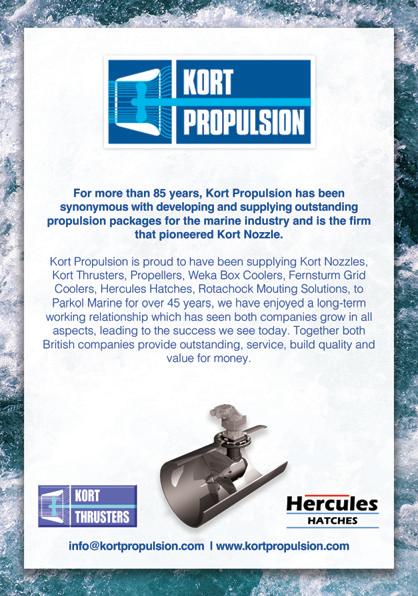

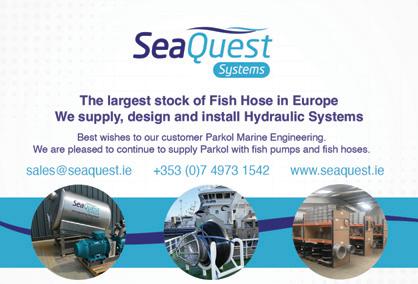
Inside Marine 89


“One of the selling points of Parkol is that the vessel designs are quite bespoke in terms of the customer requirements and how the final layout is customer-led.”
Efficient designs Ms Atkinson was clear on what distinguishes Parkol from the competition: “The difference compared to competitors is that we offer greater benefits in terms of vessel fuel efficiency, arising from the hydrodynamic design of the hull. Parkol builds round bilge hulls, and the steel kit parts for these hulls feature 3D forming of the steel plates, where we might have curves in threeThisdimensions.”workontheshape of hulls is part of Ian Paton’s drive to improve the fuel efficiency of Parkol’s vessels. “Over the last seven,
The process of building a boat can take from 20,000 to 40,000 hours, depending upon the size of the vessel. It is thus no surprise that Ms Atkinson cited the most rewarding part of her job was “the sense of satisfaction on the completion of a vessel.”
Yet the bulk of Parkol builds are fishing boats, built as bespoke designs for clients, as Ms Atkinson outlined: “It’s defi nitely a two-way process with the designer Ian Paton, our Technical Director and naval architect. After an initial enquiry, Ian produces an outline general arrangement drawing for the vessel. From this point, a back-and-forth discussion takes place where tweaks are made and bulkheads get moved to suit, depending upon how much space the client wants for rooms such as the galley, cabins, wash rooms, wheelhouse, engine room, and fish handling area.
“She’s the first scallop trawler of that size built in UK for over 20 years,” Ms Atkinson said, “Alcedo was a step up in terms of her requirements, such as quality assurance and materials testing, different grades of material required and basically higher spec machinery and hull. This was a good experience for Parkol in terms of learning those new skills and specifications.”
PARKOL MARINE ENGINEERING I PROFILE 90 Inside Marine farm; Able One, a 26.75m motor yacht; and a Foyboat to assist with mooring on the river Tees.
Two ambitious examples Examples of Parkol’s bespoke design process and build capabilities are evident in vessels such as Alcedo. Launched in January 2020, the 33.95m Alcedo is a beam scalloper rigged to fish both king and queen scallops and became the largest vessel built by Parkol when delivered. She is a steel-hulled motor fishing vessel with round bilge, transom stern, bulbous bow, soft nose stem, dredge tipping doors and catch handling conveyors for 18 dredges each side.
Another first for Parkol was the Ambitious II, the company’s first export to the Republic of Ireland. This multi-rig prawn trawler was built for David and Niall Kirwan of Clogherhead, County Louth. Ambitious II was constructed in accordance with the differing demands of the Irish regulations, further expanding Parkol’s repertoire.
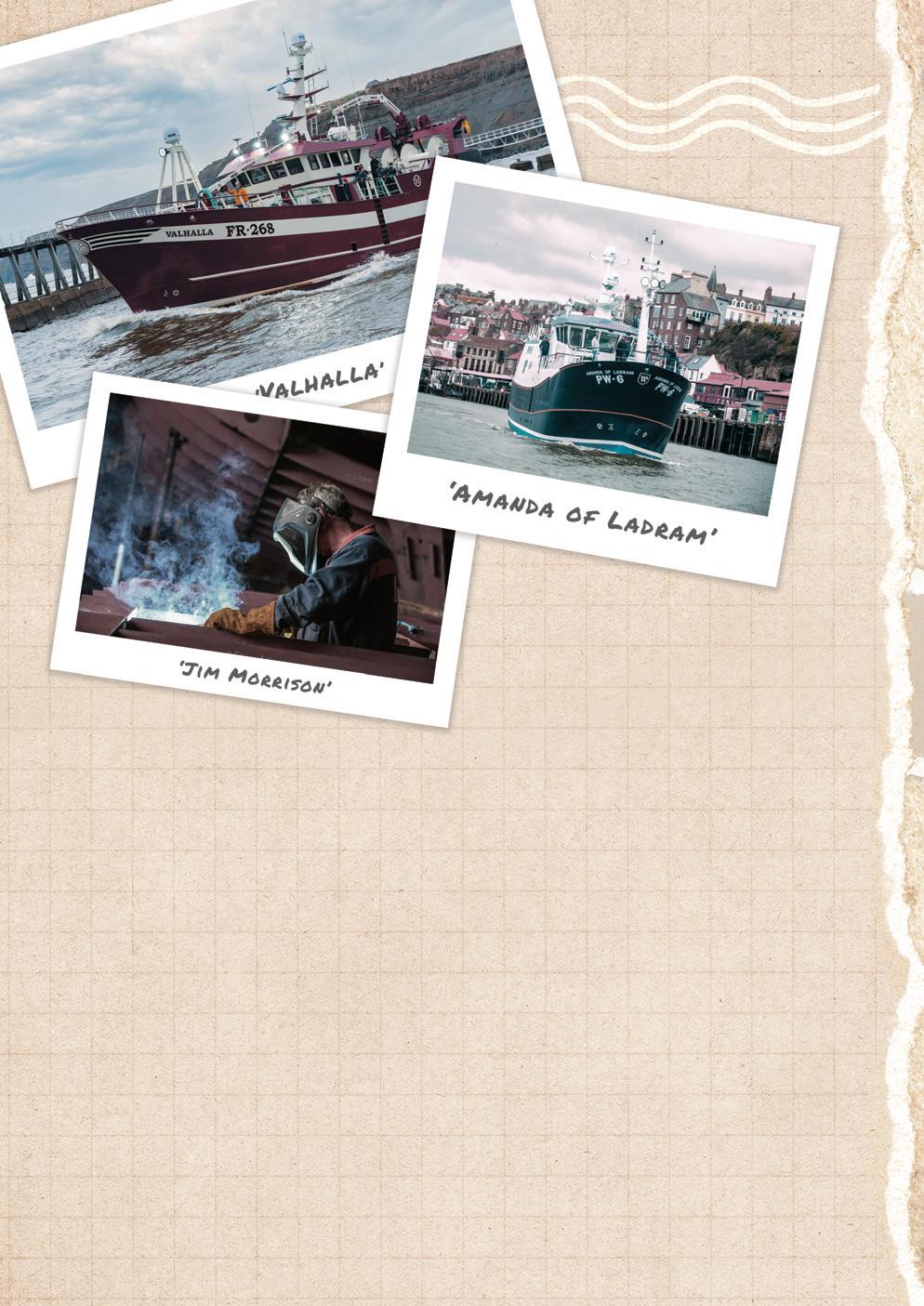
Parkol celebrated 50 years of Whitby ship building in 2021 and sails onwards into the future. In the future, the company hopes to expand its drydock capabilities. A larger floating drydock would help the company to slip larger vessels as this Whitby endeavour keeps the history of the port alive n
“Parkol has an approved supplier database and we are fortunate to have long-standing relationships with suppliers,” Ms Atkinson said.
Parkol thus works closely with its extensive selection of suppliers.
“In terms of the new build contracts, there are large sub-contracts for items like deck machinery and engine packages.”
Supply choices Ms Atkinson admitted she sees the impact of global supply issues “almost on a daily basis. This affects the new build side more than the repair side, because for the repairs we work on shorter-term contracts. For new builds, we have to be really pru dent before agreeing a build price, being aware of what prices could change and working with suppliers to fix quotes.”
Inside Marine 91 eight years,” Ms Atkinson said, “our Naval Architect has put a lot of r esearch into computerised fluid dynamics, modelling the hull in computer software and then running different scenarios/speeds of the vessel through the water. This enables the hull lines to be tweaked to make it more efficient.”
Yet, the specifics for each vessel are another customer-led aspect of the build, as Ms Atkinson highlighted: “Engineering Manager and Director Andrew Oliver advises and guides the customers on their machinery options, but ultimately it’s got to be their decision because they have to work and maintain the equipment over the vessel’s lifetime.”
Ian Paton also worked on the propeller design and nozzles to improve efficiency. Parkol is now seeing an increased number of enquiries relating to alternative fuels and diesel electric hybrid engines. The result of this research is an improvement in the effi ciency of the client’s vessel. A refit of the propulsion system can save a client 15-25% of fuel costs. A brand-new boat offers greater savings on an older vessel, delivering 20-25% savings.
“Parkol celebrated 50 years of Whitby ship building in 2021 and sails onwards into the future.In the future, the company hopes to expand its drydock capabilities. A larger floating drydock would helpthe company to slip larger vessels as this Whitby endeavour keeps the history of the port alive”

As a premium quality Dutch builder of bespoke superyachts, specialising in refit, conversion, and new builds, ICON Yachts prides itself on customer relations. This yacht builder is dif ferent from the norm and has solidified itself in the Conversion-Explorer market by keeping up with the market trends set by a new age of yacht owner. Taking advantage of the com paratively new expedition class of yachts, ICON Yachts has cemented its place in the sector by providing world-leading conversions to research and support vessels. Article co-written by Daniel Barnes and Jordan Yallop.
EXPLORE!CONVERT REDEFINE
ICON YACHTS I PROFILE 92 Inside Marine

“We are built on that experience, it brings in fresh air and new possibilities, and we also have a pragmatic business model with regards to our builds. ICON Yachts is increas ingly being recognised for being the leader in Conversion-Explorer projects through a unique approach and consistently building on this expertise.”
T he sight of a superyacht evokes the mental image of passengers sun bathing by the pool and all things hot and sunny. But a new cooler trend in supery acht destinations has been emerging in recentGreenland,years. Antarctica and the Arctic are the new – and adventurous – destina tions for those wanting a little something different from their time onboard a supery acht. Swap your snorkelling gear, jet skis and RIBs for snow scooters and submarines.
And these places with harsher conditions need vessels tough enough to handle all that is thrown at them – without sacrificing the elegant and high-end facilities, com fort and luxuries – such as large dining areas, state rooms, pools, steam rooms, saunas or wellness rooms, and bars – that superyacht owners expect.
ICON Yachts prides itself on its ability to deliver a unique custom-built superyacht to a client, built to the company’s exacting standard, within three years. The company has created a hyper efficient system that combines meticulous pre-planning and a smart modular construction technique. This innovation reduces the time of delivery and guarantees build quality, while also offering infinite variations to cater to the clients’ desires. ICON Yachts works closely with each client’s team to deliver outstanding
Friso Hylkema, Business Development Executive at ICON Yachts said: “One thing that helps define ICON Yachts is creativity and thinking outside the box. While we are a relatively young company, the people wh o work here have brought with them exten sive experience in the sector.
Founded in 2006, the Harlingen-based builder’s large dry dock (150m long, 50m wide and 10m deep) can accommodate four 70m vessels simultaneously – or up to six 50m yachts or two 90m yachts. With 500m of secure protected mooring in a sheltered deep-water harbour, it is a 2.5 mile sail, unrestricted by locks, dykes or bridges, into the North Sea.
Cornering the market
ICON Yachts carries on the proud Dutch yacht building heritage, with an emphasis on quality builds, craftman ship and reliability.
Inside Marine 93
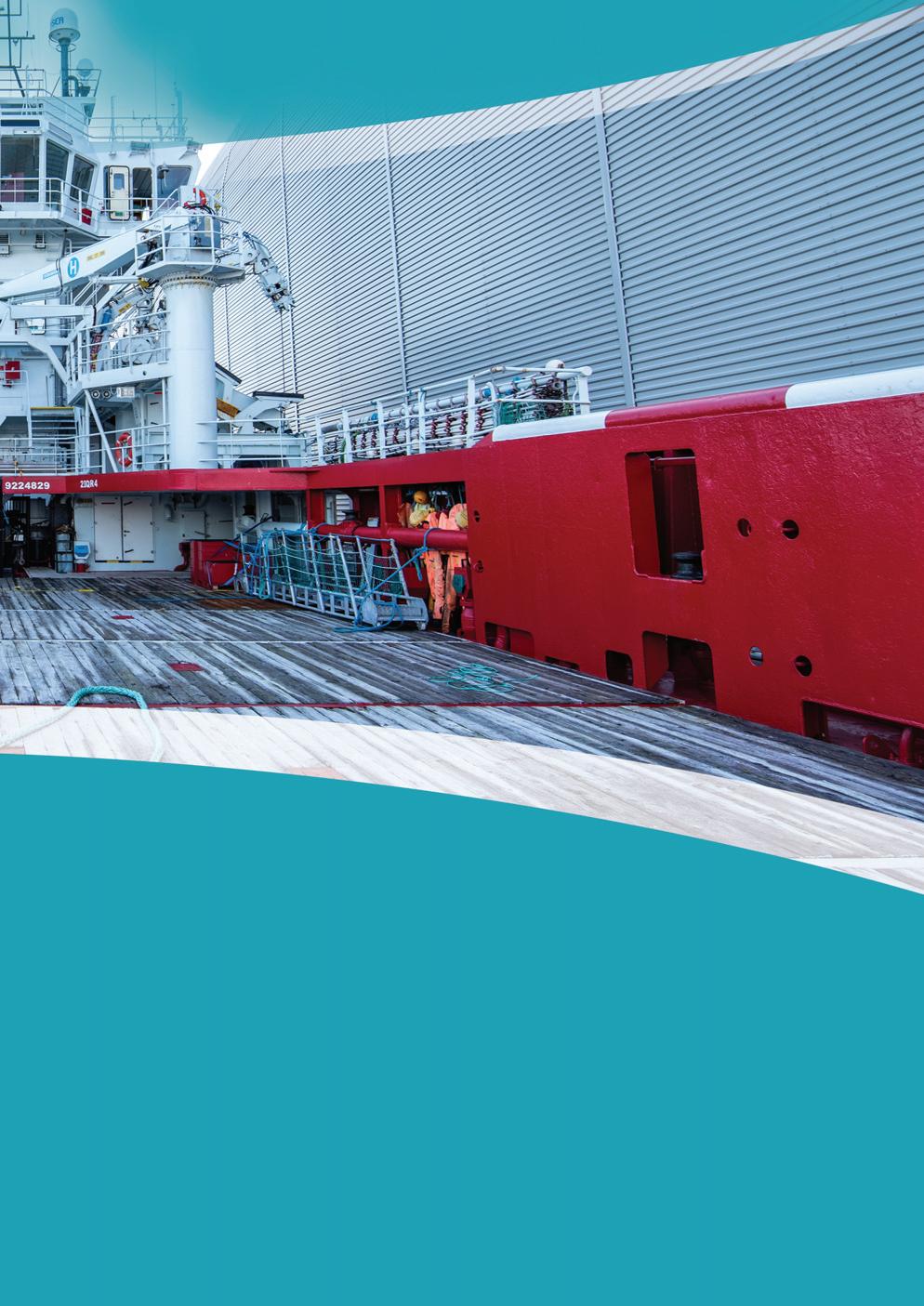
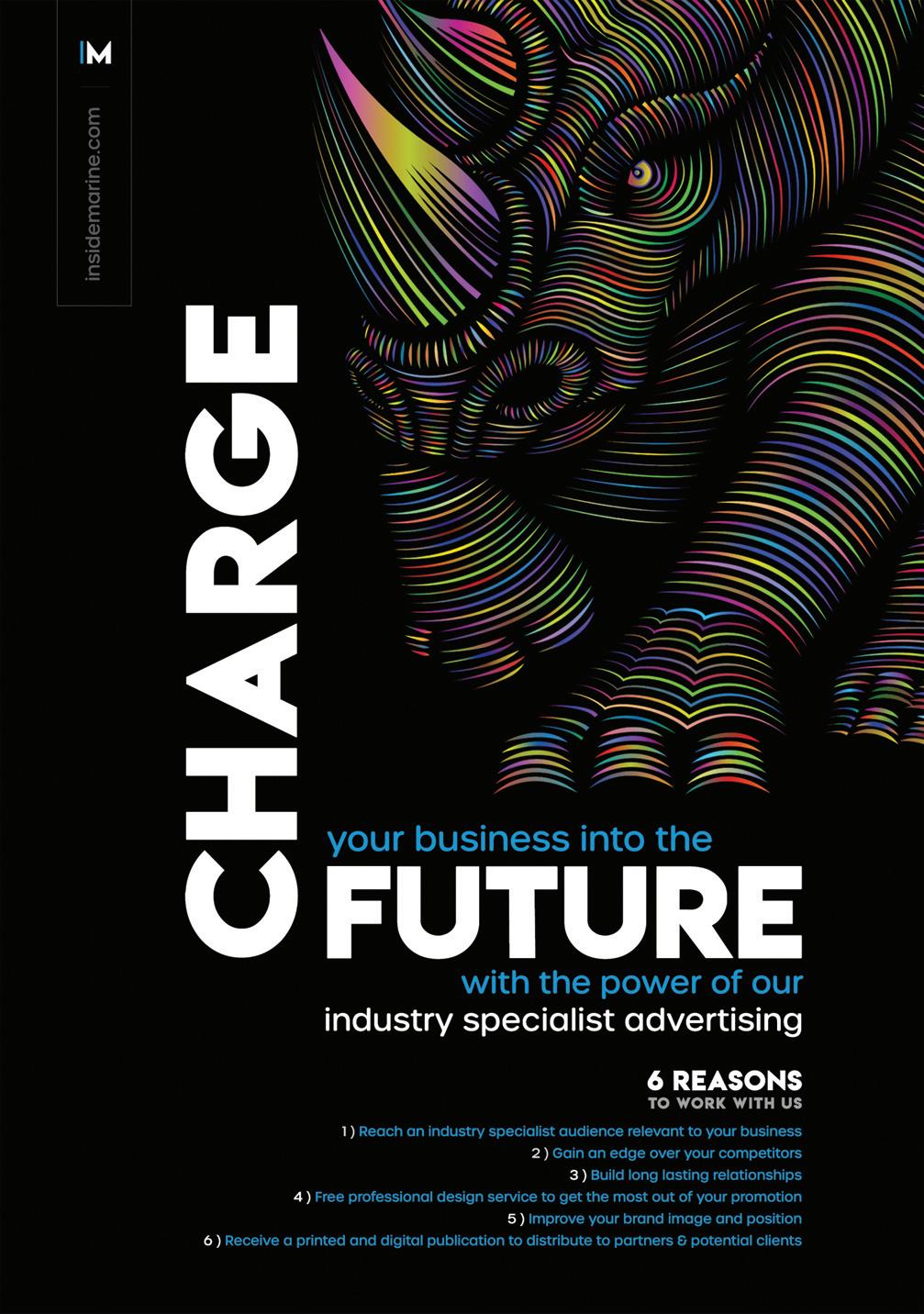
Inside Marine 95
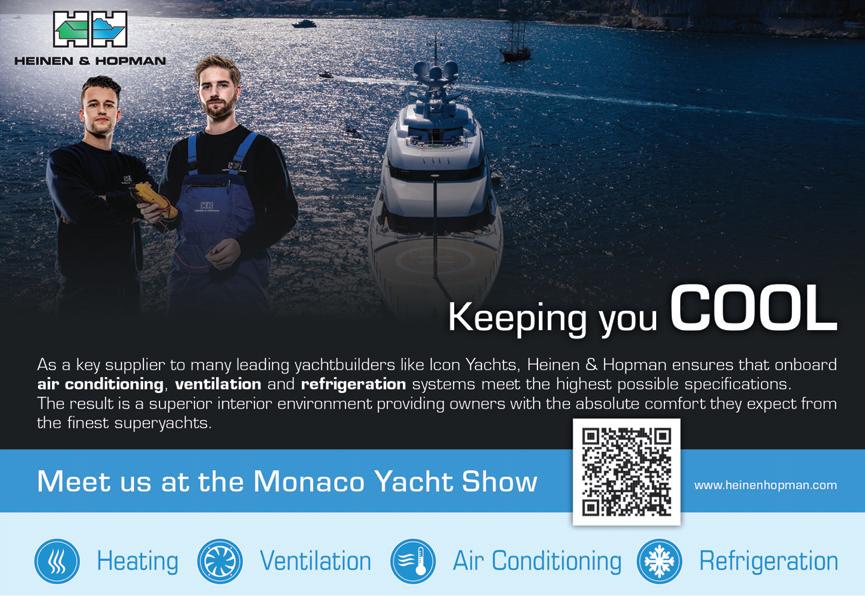
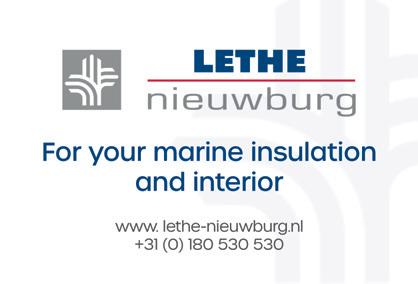

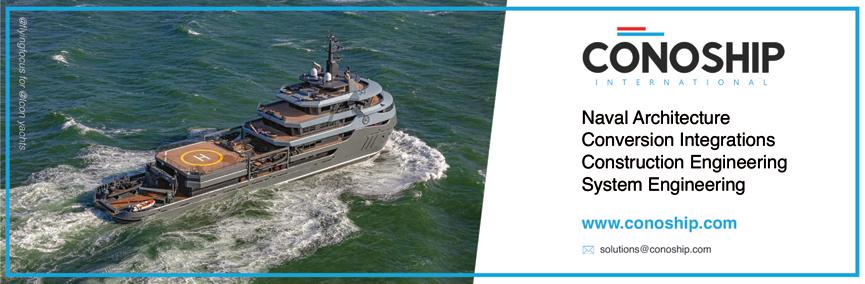
Proven concept Perhaps the best way to showcase the abilities of ICON Yachts is to take a look at the 2020-delivered Ragnar, and its ongoing work on Project Master. The 68.2m expedition yacht Ragnar, began her life at sea in 2012 the ice breaking multi-purpose support supply vessel Sanaborg, before she began her transformation into what we see today in July 2017. Designed by RWD in the UK, her unique style draws on a fusion of
ICON YACHTS I PROFILE 96 Inside Marine results. One area that ICON Yachts is gaining particular recognition is within the conversion market, with the shipyard’s conversions to date having a previous life as world-class commercial ocean-going vessels capable of withstanding the toughest conditions. Not only are you getting a proven vessel as a starting point, but you also save time when compared with a newbuild, which in turn saves the client costs. ICON Yachts ensures its clients get a quality investment by working through a highly thorough fea sibility process, ensuring all prospective vessels have already been built to an excep tionally high standard. ICON Yachts retains the vessel's capabilities while changing its function from ocean support and rescue to exploration yachting.
“Ideally, the platform vessel is relativel y new and already equipped with modern ship systems. ICON Yachts sets out, through a unique feasibility study, to ensure the selection of the most optimally suitable vessel, matching the requirements for the Expedition Yacht. Selecting the right plat form vessel is essential and ICON Yachts has the unique expertise network and resources to do so.”
Mr Hylkema said: “Conversion projects have a significantly smaller footprint com pared to full new build projects as large sections can be considered as upcycled. Especially in present times, with extended lead times, supply chain issues and soaring raw material prices, conversion projects yield undeniable large benefits.”
“Explorer yacht owners are typically very well aware of sustainability issues and during their expedition often observe first-hand retreating polar ice caps for instance,” said Mr Hylkema. “They often work closely together with research teams and experienced expedition specialists.”
“With conversions, a client will approach us with a dream, or vision, of what they want. We will then work with them to identify and shortlist a selection of suit able vessels on the market, and once the client has made their choice, we will liaise between parties on behalf of client advice and assist where necessary, whilst also conducting pre-engineering, inspection and survey work,” explained Mr Hylkema. “Once the purchase has been made by the client, we will then arrange everything else and get to work.”
This new kind of yacht building also has a positive impact in sustainability, he“Conversionsexplained. are more sustainable.
Stepping in at such an early stage requires ICON Yachts’ commercial and engineering staff to carry out an extremely thorough and extensive process, but as Mr Hylkema explained, this time is considered a wellspent investment as it ensures the best possible platform vessel for the project.
It is essentially a type of upcycling, you take an existing proven vessel and give it new life. There is an entirely different footprint in the area, lower than that of new builds. Use of the latest equipment and innovations also helps of course, with respect to minimising pollution.”
Sustainability is of growing impor tance when you take into account the trends pushed forward by a younger, new generation of yacht owners, who, it could be argued, have sustainability and envi ronmental concerns closer to their heart than your traditional superyacht owner of times gone by.
Friso Hylkema, Business Development Executive
“It’s really quite fun, actually, because before the vessel has been converted, the client can set foot on it and really get a feel for it. Even though it’s still a com mercial search and rescue vessel, you can walk around, you can walk into the bridge, interior spaces and engine room, you feel the dimensions and the robust ness and it’s a really impressive experi ence and totally different and much more stimulating than a blank piece of paper on the drawing board.

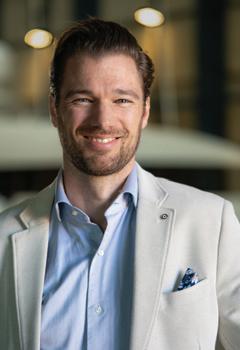
“All are very involved in each project, with an efficient, creative and flexible mentality,” said Mr Hylkema.
Moving forward, the company intends to further enhance its quality and capabili ties, revealed Mr Hylkema. “We’re growing and are constantly investing in our people in addition to investing in updating and upgrading our facilities.”
As is standard, the client approached ICON Yachts without already having a vessel and requested the company to aid in finding a suitable vessel for conversion. ICON Yachts worked with the experienced owner’s list of require ments for the vessel, which included it being a family orientated vessel capable of exploration and extended voyages and remote destinations around the world, for both personal use and suitable for charter.
Project Master A conversion currently underway at ICON Yachts is Project Master. Originally an off shore supply vessel, like Ragnar, Project Master will end up as a luxury explorer superyacht. Designed by yacht designer renowned Espen Oeino, large parts of the original support vessel can be recognised in the new design (including the impres sive bow and bridge), but the yacht will be significantly different with several decks added mid-aft.
Using the vast amount of experience acquired in the conversion market, ICON Yachts recommended using Ocean Ness, a 20-year-old 66m offshore supply vessel.
With enough space for 12 guests, a crew of 19 and luxury amenities such as a sauna, personal subs and a helicopter deck, Project Master is set to be completed in 2023. Personal investment ICON Yachts consists of passionate people comprising a mix of industry experts, yachting enthusiasts, skilled craftsmen, professionals and fresh talents.
The energy used by ICON Yachts is also 100% from green sources, while the company, as you’d expect, has all the necessary certi fications, including ISO 14001 compliance.
Inside Marine 97 inspirations including medieval war craftsmanship and British heritage.
Friso Hylkema said: “The approach that we have taken since Ragnar and now on our upcoming projects is to not just restore a classic, which is what many other yards do with conversions. But it is taking a modern, already proven and robust oceangoing support and rescue vessel; then using that as the ultimate platform for expedi tions. Then we take that into a yacht that is basically unrivalled in capabilities with regard to expeditions.”
With a number of additional contracts and projects being discussed but yet to be made public, ICON Yachts is extremely wellpositioned for the years ahead. n
“Ocean Ness had been in service for years, providing year-round missions in the harshest conditions,” said Mr Hylkema.
When emphasising ICON Yachts’ experi ence in the conversion market, Mr Hylkema said: “We are the only yard in the world conducting modern Conversion-Explorer projects in succession. We work closely with our clients to source the best possible ship for conversions, to cater to their needs, whatever they may be.”
“ Officially a FSRTS (Field Standby Rescue Tug Supply), vessel, she is highly capable in all conditions, boasts a North European build quality, was in excellent condition and meticulously maintained.”
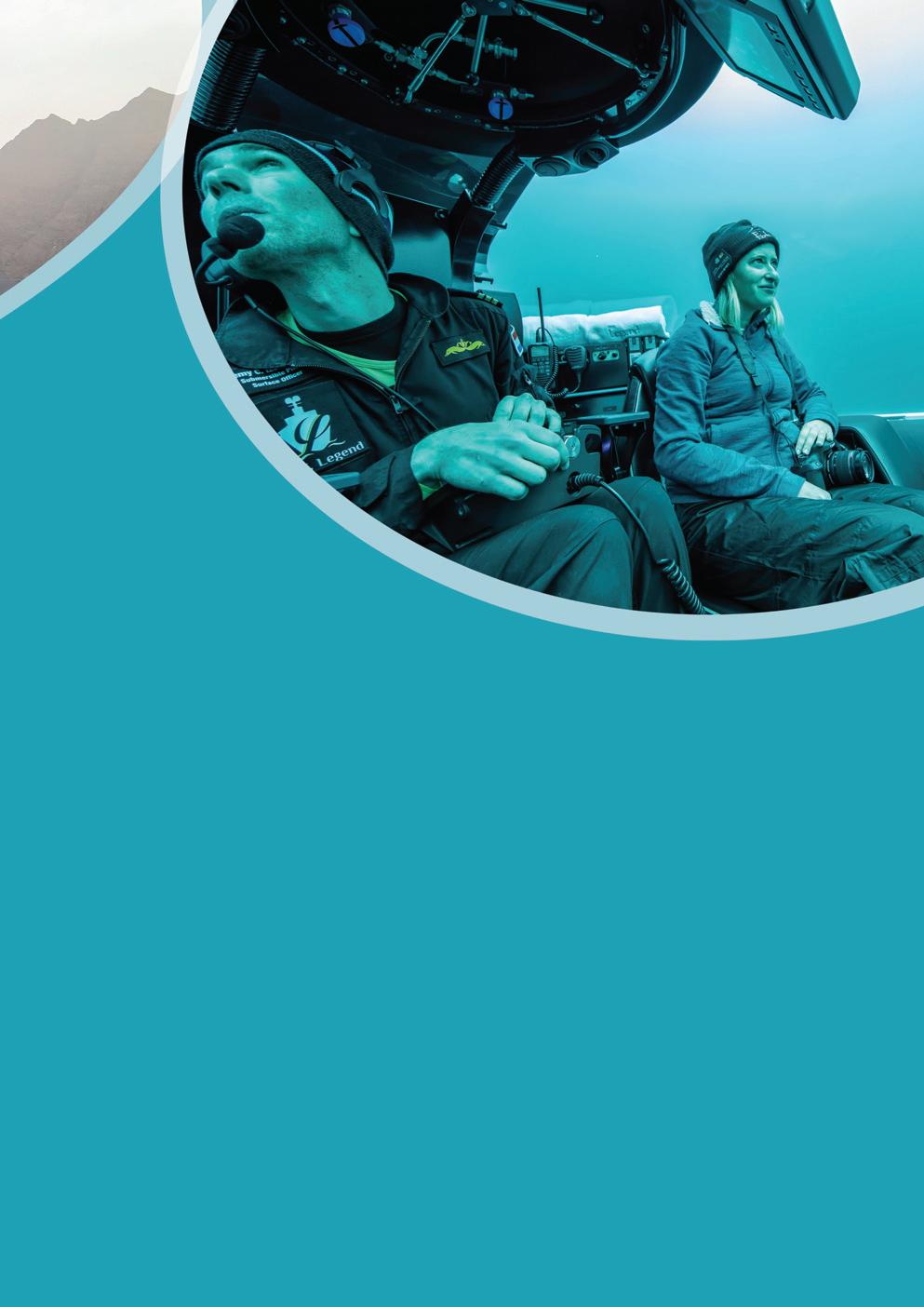
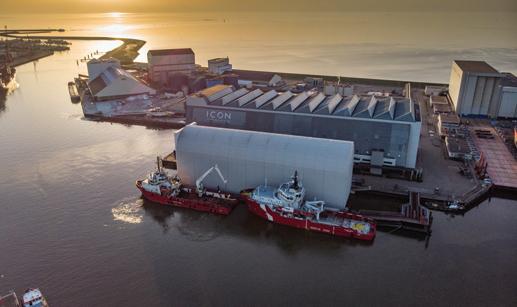
Blount Boats is a full-service shipyard a nd manufacturer of bespoke, commercial aluminium and steel long-lifespan vessels of the highest quality, up to 220ft.
pany’s human resources department, her nephew is an engineer in the company, and Ms Blount herself has a background in finances and accounting behind her name as ThePresident.company has a comprehensive inhouse design and engineering department that plays a key role in Blount Boats’ ability to build virtually any kind of vessel. In 74 years of operation an impressive variety of ships have left the yard, including fer ries (passenger and vehicle), harbour tugs, fishing boats, small cruise vessels, dining vessels, and even a small ice breaker.
The company has firm plans to increase its covered space and intends to build a whole new covered workshop, pending the necessary approvals from town and state agencies. A smelly pile of clam shells
The story of Blount Boats, in the picturesque town of Warren in Narragansett Bay, Rhode Island, has the most unlikely of beginnings that includes a hurricane and a great big pile of clam shells. Marcia Blount is the company’s President and also the daughter of its founder, Luther H Blount. She sat down with Richard Hagan to share the company’s epic history and highlights, and to discuss its latest exciting chapter.
The shipyard is located on six acres of waterfront land, containing two large workshops and an EPA-approved paint tent. In total, it boasts 50 highly skilled veteran staff members, ranging from engineers to the actual production staff. The company remains privately owned and in the control of the Blount family with all five of the orig inal Blount siblings still involved in the business: Ms Blount’s sister runs the com
BLOUNT
BOATS I PROFILE 98 Inside Marine
BUILDING A SHIPBUILDING
“We’re capable of building all sorts of types of vessels,” confirmed company President, Marcia Blount. “We’re only limited by the size of our yard and the depth of the water on the Warren River.”
Today, the Blount family has a reputation for building some of the finest, toughest and best-loved vessels in North America,
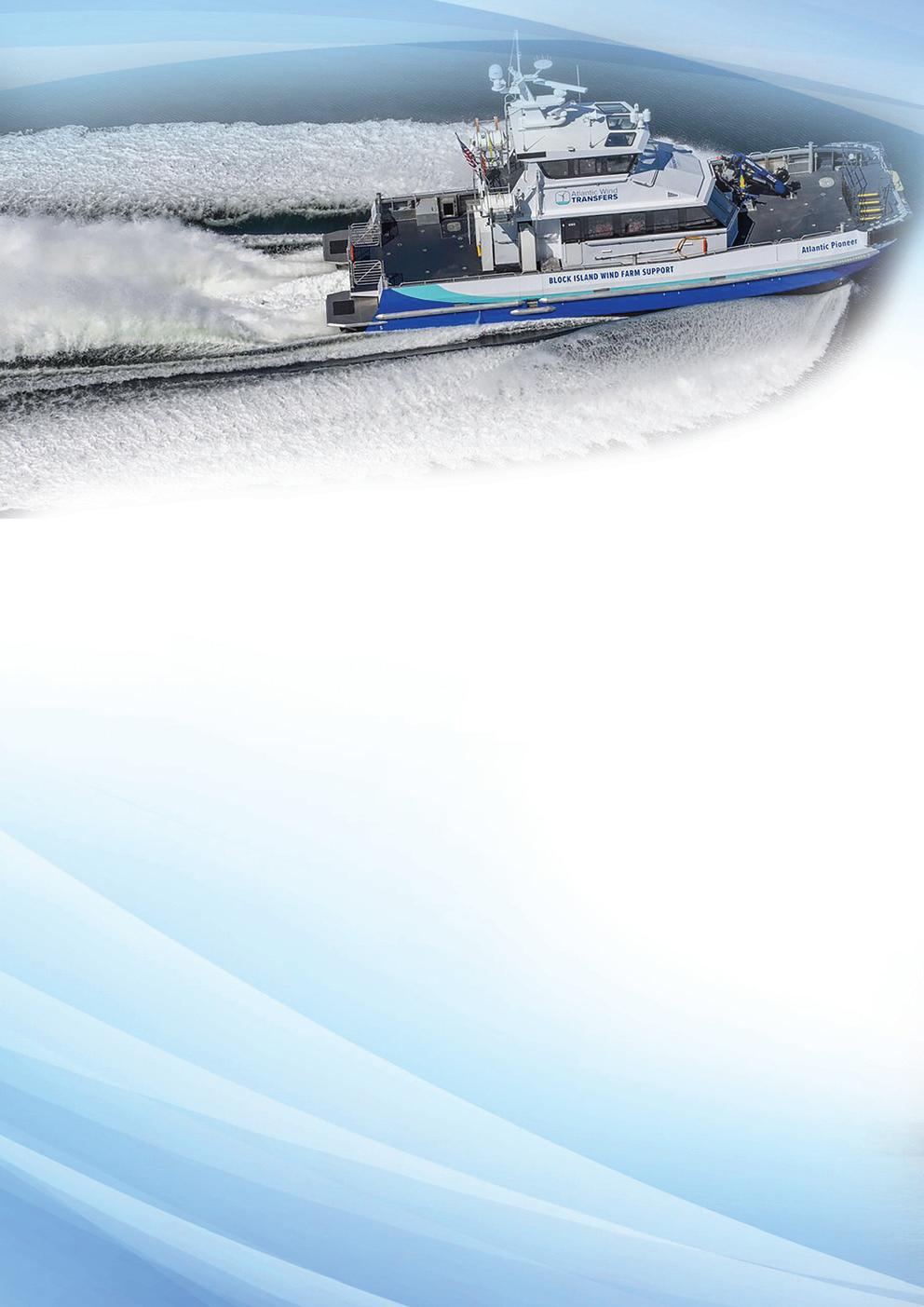
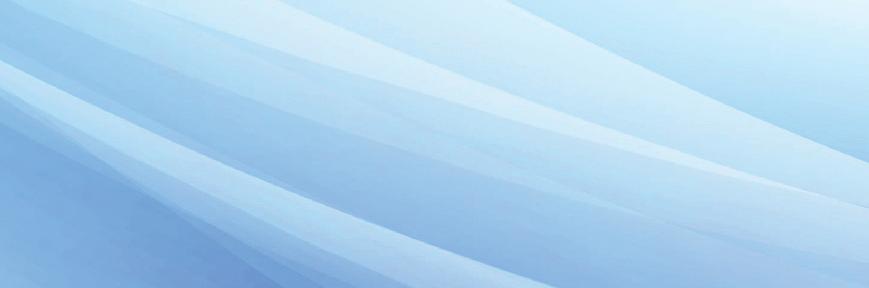
Ferrying in the end of the war
On the back of the success with the con struction of the hopper barge for the clam shells, Mr Blount Sr placed an advert for his boatbuilding services in a local maritime publication. His first order soon arrived, designing and building a lube oil tanker for a local customer. Further enquiries soon followed and the business of Blount Boats was born. The end of the war had brought a surge in demand for commercial vessels. “The ship yards had all been building naval vessels for the war and not much else, so there was a huge demand for a lot of vessels, especially ferries,” she noted.
World War II began shortly afterwards, during which Nelson Blount opened a business in the area, making clam chowder (soup) to feed the troops at the various army camps nearby.
The twenty-something-year-old Luther Blount leapt into action to help his brother : working on his grandmother’s land next to the river, he built a hopper barge from 55-gallon (220 litre) drums that he then used to transport and dispose of the shells further down the bay. “It worked! They got rid of all of the clam shells and everybody was happy,” said Ms Blount, adding, “And by the way, Nelson’s clam chowder business is now Blount Fine Foods – a major company!”
“When my father came back from the war, Nelson, his brother, was processing clams up the street and there were all these clam shells lying around,” she explained. “He’d built up a huge pile of clam shells and the fathers of the town told Nelson to do some thing about the smelly shells.”
But all of that changed when Narragansett Bay and the surrounding region were rav aged by the deadly 1938 New England Hurricane which to this day, remains one of the most destructive tropical cyclones to ever strike the area. “It caused a tsunami that ripped up the floor of the whole bay and destroyed the oyster population. It ruined the family business,” Ms Blount recalled.
“The land we’re on belonged to my great grandmother,” she explained. “Our family were oystermen on Narragansett Bay and lived and worked on this six acres of land.”
Blount Boats met this demand with a series of 65ft passenger and vehicle ferry builds, but Ms Blount highlighted, one in “Theparticular.mostfamous ferry boat we built was the Miss Liberty, delivered in 1953. She was built to take visitors to the Statue of Liberty in New York City, travelling from the Battery to the Statue. I went on its inaugural cruise when I was seven years old. She’s actually still running but under a new name, and
Inside Marine 99 but according to Ms Blount, the family has been earning a living at the shipyard site for over a hundred years.

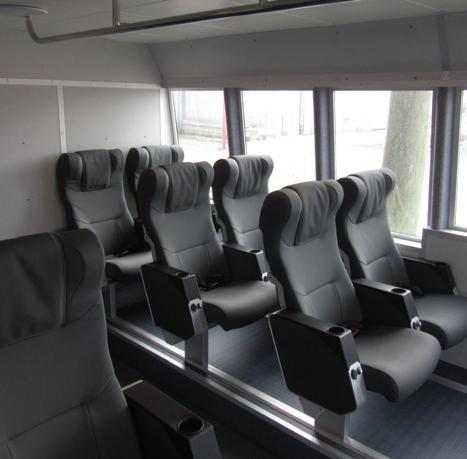
Meanwhile, in 2021, Blount Boats secured an order for four new G Class offshore crew transfer vessels (CTVs), from American Offshore Services (a joint venture between Sweden’s Northern Offshore Services and American stakeholders). The four vessels are a first in the US and are hybrid-ready, boasting a special hull compartment that will accommodate battery banks in future.
In 2016, Blount Boats delivered the first boat built under the South Boats license, for use at the first wind farm in the United States. “We were in the right place, at the right time, and we recog nised the opportunity. That vessel, Atlantic Pioneer, is still operating flawlessly,” Ms Blount commented.
Inside Marine
BLOUNT BOATS I PROFILE since her delivery, she’s taken about 60 million people to the statue!”
A second vessel built under license with Chartwell Marine Ltd was subsequently built for Siemens’ two turbines off the Virginia coast and named The Endeavour. It was delivered in 2021. The delivery of those two vessels would prove to be a major milestone for the com pany. It unequivocally demonstrated Bloun t Boats’ technical and manufacturing prowess to the demanding, fast-growing offshore wind industry and it cemented the yard’s ability to reliably deliver the kind of robust vessels required for offshore duty.
The arrival of wind energy Over the decades that followed, Blount Boats built an impressive variety of robust, sturdy and reliable vessels, but the major turning point for the company arrived in 2010 with the rise of the offshore wind industry and a visit from another shipyard. “South Boats from the Isle Of Wight came to see us in 2010,” Ms Blount explained. “They were the premier builder of crew transfer vessels in Europe and had devel oped various innovations, including a spe cial bow, for service on the wind farms off the UK. We signed a licensing agreement with them to build South Boats models.”
“There’s a lot of trust required to be successful in this business,” Ms Blount confided. “It takes several years for people to get to know you and your product. These are complex vessels and buyers want to ensure that they’re in the right place to build their boat. We’ve carefully managed our customer relationships and as a result , many have continued working with us for years. Once they build with us, they build repeatedly with us; they keep coming back.”
“We’ve obviously built many others like her,” she continued. “In fact, we built most of the fleet that goes from the Battery to the Statue, but she’s one of our most famous.”
Building a new era Ms Blount heralded the construction of those four new CTVs as being the start of a new era for the firm. “For us, it’s huge, and to have a backlog is a wonderful thing. We’re now in a time where there’s substantial demand for these CTVs. All sorts of vessels are needed for 100
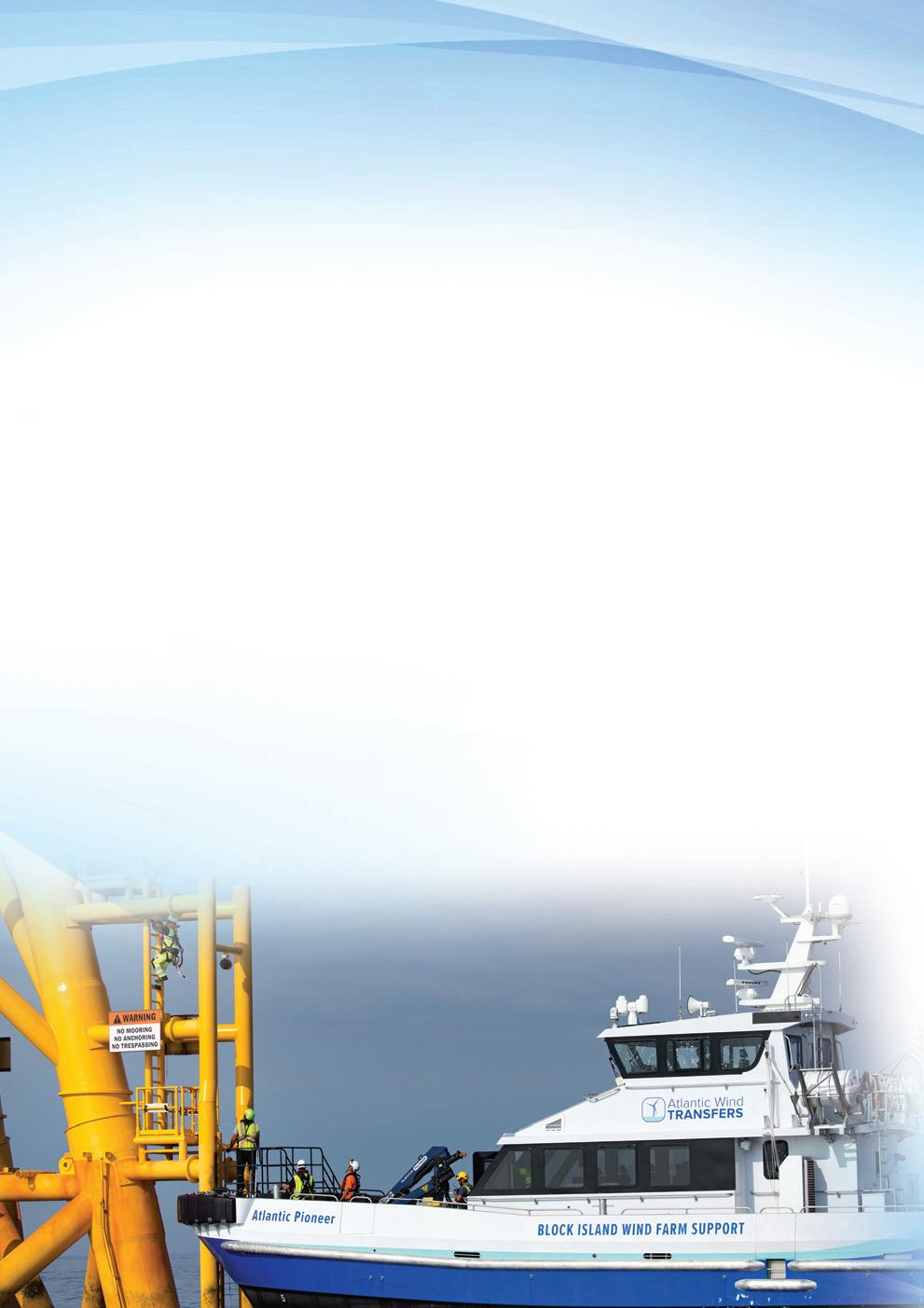
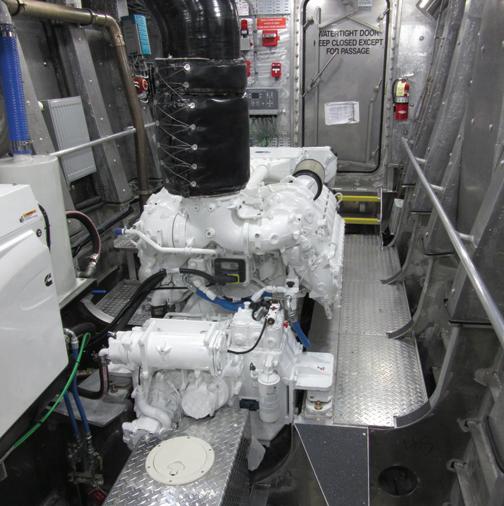
Inside Marine 101

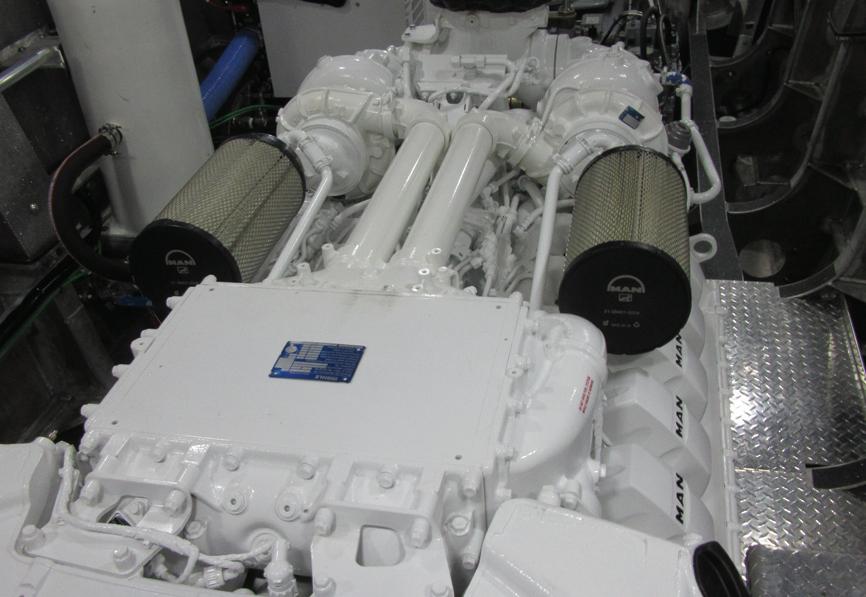
BLOUNT BOATS I PROFILE 102 Inside Marine
wind farms and many of them are much larger than what we’re able to build, but in the niche that we’re in, these CTVs of 100150ft is probably the category that we’ll be building and maintaining for the next five to ten years.”
“It’s a wonderful boat; it replaces a vessel that was built in 1942,” Ms Blount noted.
Ms Blount concluded with some insight into the company’s passion for the work it does.“When our employees go on vacations, they’re always tracking down the Blount boats that they’ve built. They consider the boats to be ‘their’ boats. There’s definitely something special about building a product with your own hands. “We build beautiful, useful products. It’s meaningful work.” n
“We told the customer that our boat’s going to last as long as that one!” she added, laughing.
In May 2022, the company also celebrated another first: the completion and delivery of a 90ft icebreaker buoy tender for the State of Maryland that had been under construc tion since early 2020.
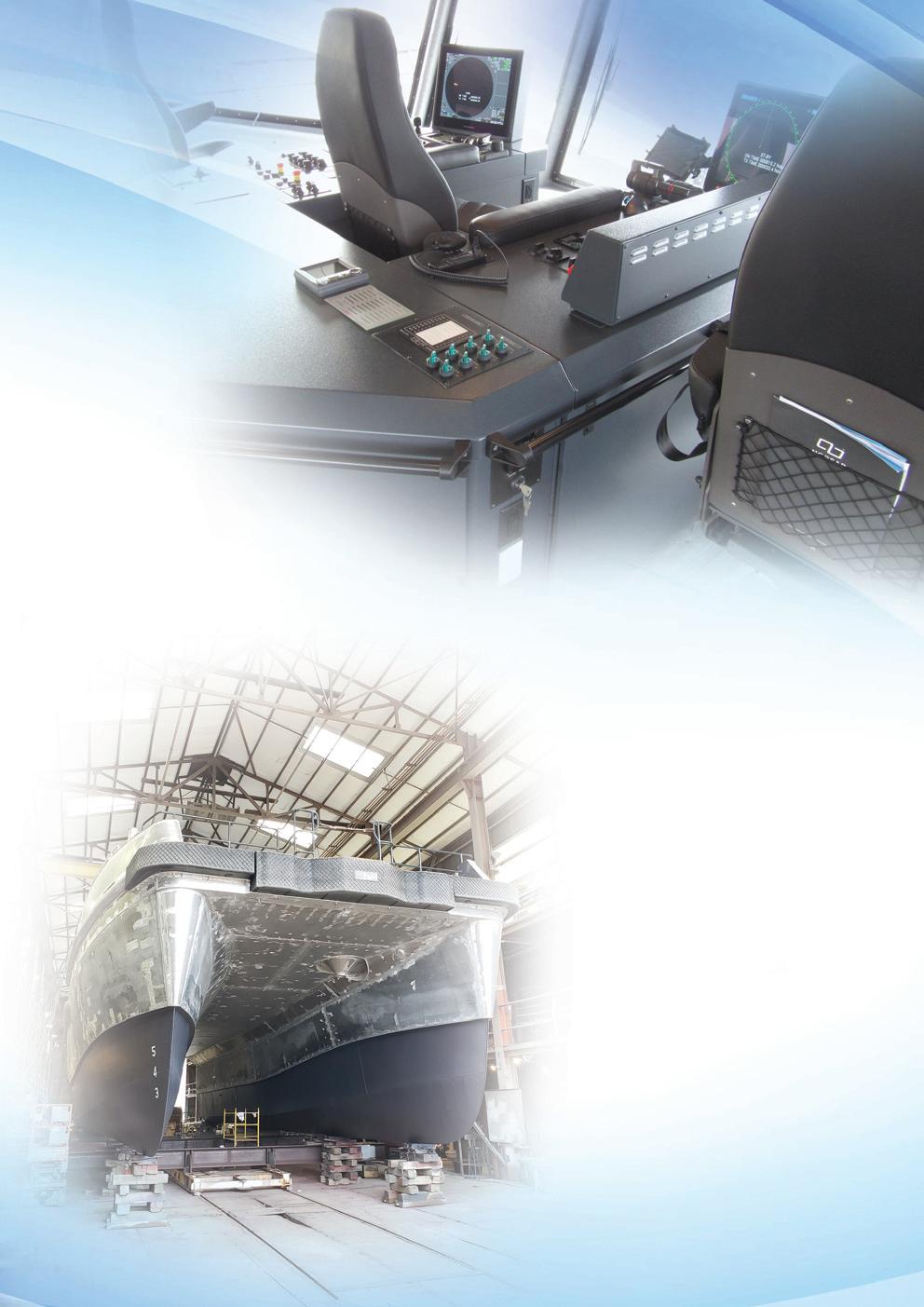

Since its founding over 23 years ago, Rhode Island based Senesco Marine has become a leading name in tug and barge building services and repair, having completed over 50 vessels. A highly specialised staff ensure all vessels are finished on time and to the highest standard.
SENESCO MARINE I PROFILE
Jordan Yallop spoke to Ted Williams, President of Senesco Marine to find out more.
Senesco Marine has quickly made a name for itself as the premier shipyard for new construction and vessel repair in the American
Since 1999 Senesco Marine has been building steel and alu minium vessels to various regulatory standards, basing its success on the quality of workmanship and a commitment to delivering a contracted vessel on time.
104 Inside Marine
Ted Williams, President of Senesco Marine said: “The company was formed by a group of local entrepreneurs looking to bring new jobs to the local area. They started building basic barges and got some good traction there. The company was then purchased by the current owner of the company in 2006, which was a key milestone where the company really started expanding. That owner then went on to build a lot of tugs and barges over the next two decades.”
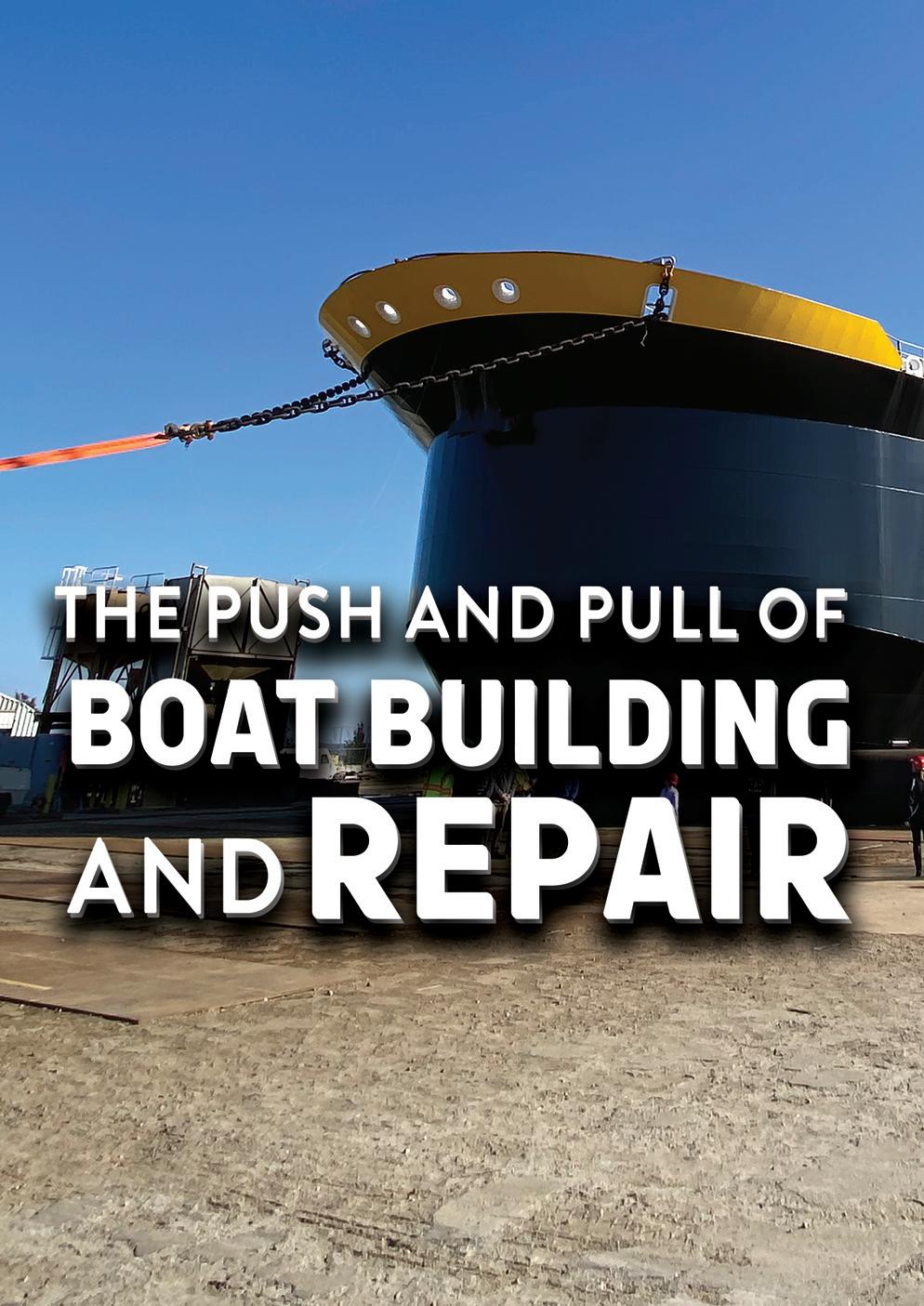
Inside Marine 105
The company started out by building small deck barges, devel oping relationships with customers, and fulfilling needs in the marine marketplace. Since then, the shipyard has built larger barges and entered the competitive tug building market. Senesco is very proud to announce its successes in this venture by deliv ering two of the world’s first aforementioned facet tugs. This has led Senesco Marine into the aluminium fabrication industry.
northeast. Consisting of 27 acres of Narragansett Bay waterfront property, Senesco Marine has created a highly efficient shipyard capable of producing a vast array of vessels for its customers’ needs.
Senesco Marine has successfully built and delivered on-time over a dozen 80,000 bbl and 100,000 bbl double-hulled fuel barges as well as numerous tugs. Senesco Marine is now heavily involved in the off shore wind industry,cur rently constructing three crew transfer vessels . Additionally, the shipyard is leading the way in green energy production for the maritime industry, currently building two hybrid ferries, which will become the first ever built and in service on the east coast of the US.
Mr Williams said: “As of today we have 250 employees, but we’re growing quickly. We anticipate having that number increase by about 100 before the end of 2022. It’s a good time for expansion rightThenow.”company’s facility has over 215,000 sqft of covered floor space and a three-acre repair yard featuring the Leslie G, a 4,500-long ton capacity dry dock with an 82 ft span between the wing walls, sta tioned at Senesco’s 1,200-ft pier with 30 ft water depth. On the south side of the pier, Senesco’s DD2, a dry dock with a capacity up to 2,300 tons, provides an inside beam of 57 ft and a length of 250 ft. With this available pier space area, customers can be provided with plenty of room for topside work or just daily wharfage. Senseco
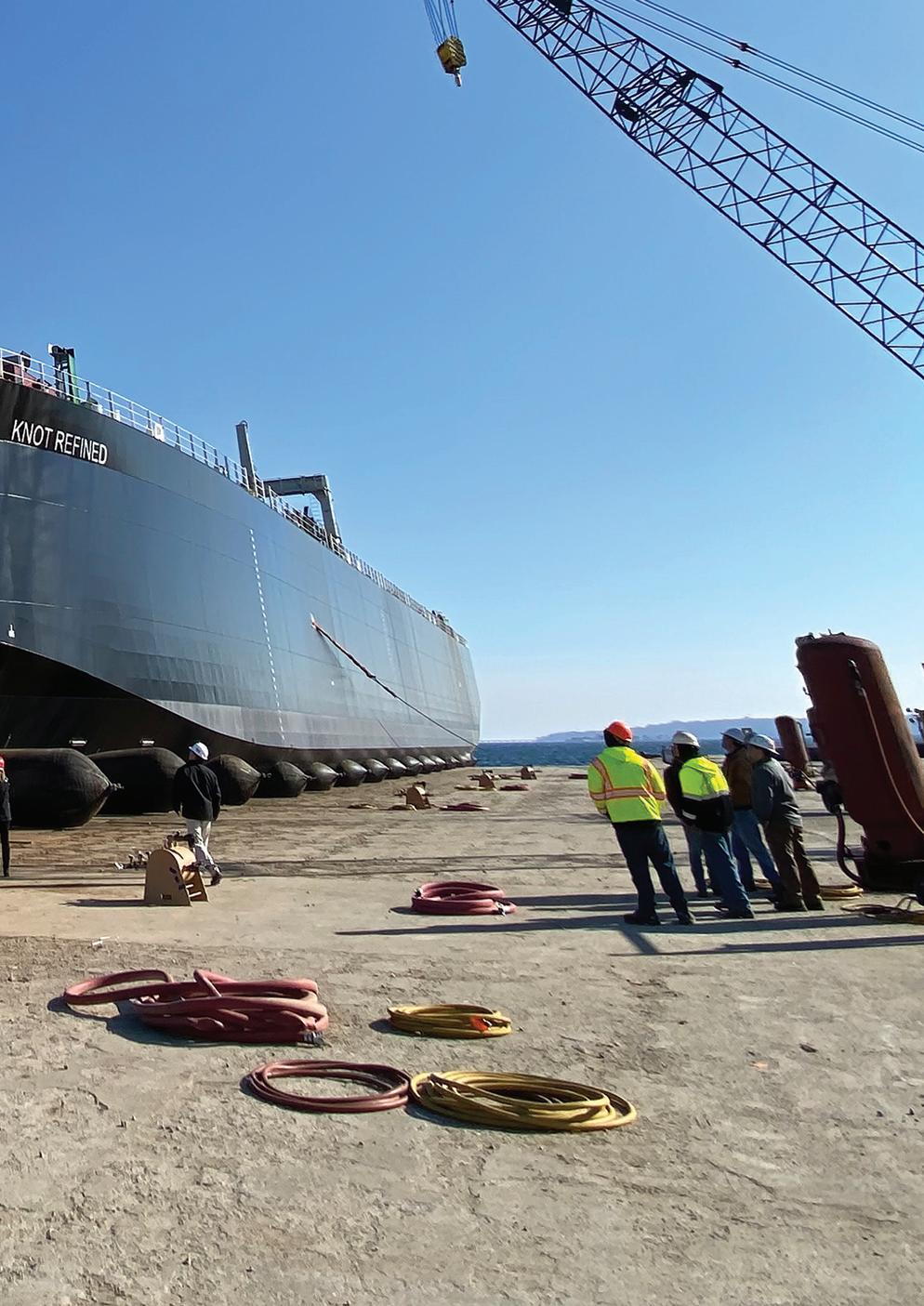
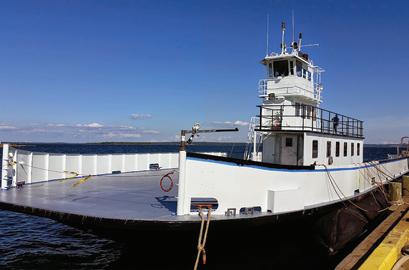
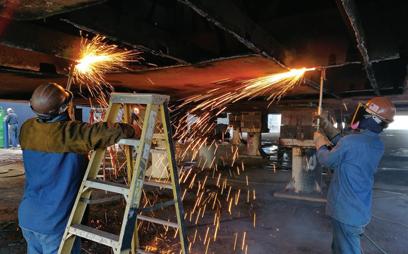
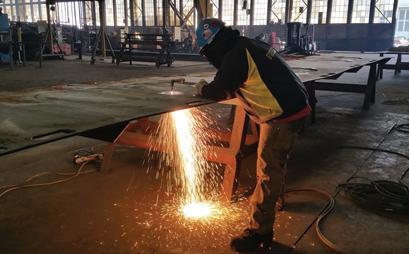
Mr Williams said: “We have a multi-pronged approach here, poised, and ready to continue building barges, we have a great asset. One of Senesco’s strongest assets is our size. We’re the largest commercial shipyard and repair facility in the north eastern United States. So, we have a lot of size, a lot of room, and large areas to launch vessels.
A multi-pronged approach
106 Inside Marine prides itself on the repair yard workforce being able to handle all of your in-the-water and out-of-water repairs, ranging from Regulatory Body Scheduled Inspections to full vessel retrofitting.
Senesco Marine proudly employs a hardworking force of managers, fitters, welders, outside machinists, engineers, quality control, and administrative personnel dedicated to maintaining the shipyard’s outstanding reputation for putting the highest quality vessels into the marine workplace. Whilst Senesco is best known as a builder of large steel vessels, the company has expanded new construction operations to include
A lighter approach
Senesco can work with a client’s current design and build through completion or take conceptual designs and work with its naval archi tects to develop a design that will meet your needs. Senesco is outfitted with programmable CNC plasma cutting machines, a full function panel line with a 110,000 sqft fabrication building and 110,000 sqft assembly building to start the construction process. The company can receive materials by rail, truck or barge. In-house transporta tion capabilities allow the company to pick up a 750-ton vessel or project and move it anywhere in the shipyard.
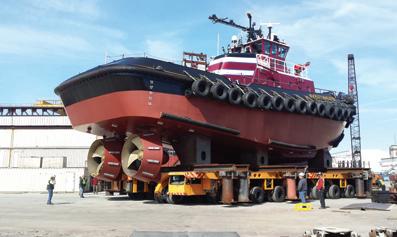

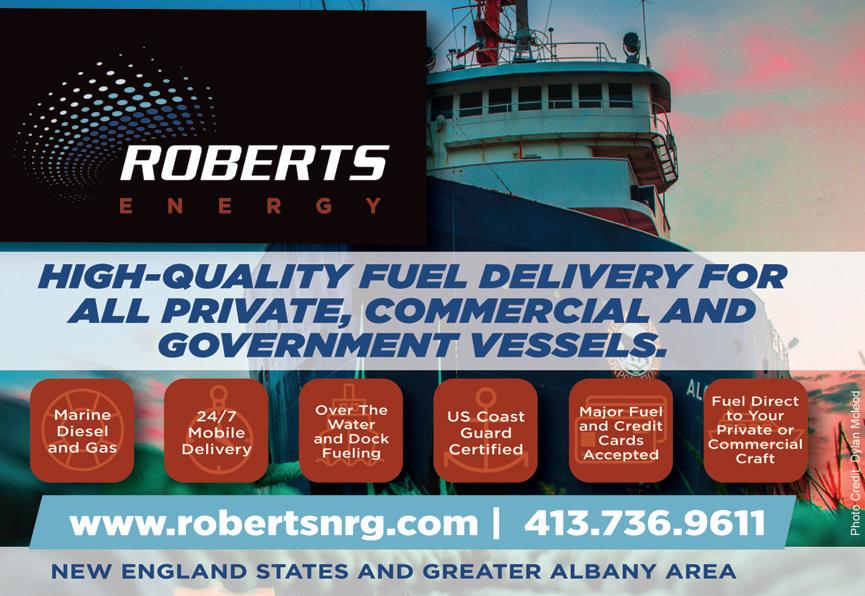
Senesco’s impressive 27-acre facility on Narragansett Bay, together with its quality workmanship and overall management processes have enabled the shipyard to operate as a fully certified shipyard by the American Bureau of Shipping (ABS) and DNV-GL. With the expan sion of aluminium production, Senesco has also continued to improve steel vessel production with the acquisition of new state-of-the-art equipment and a consistent, highly skilled work force.
One area that is seeing growth within the United States is off shore wind.
Inside Marine 107 aluminium vessel fabrication. A new, full service indoor aluminium production area has been segregated within Senesco’s eastern assembly building to accommodate all clean aluminium construc tion work. The new aluminium shop is set up with two overhead cranes, press brakes, shear, and various new aluminium welding and cutting machines.
The large production area enables the yard to build multiple aluminium vessels at the same time to increase efficiencies and economies of scale for production. In addition to the physical facility, Senesco’s work force and in-house engineering team enable the yard to handle all aspects of the construction process and make key decisions to ensure projects remain on budget and on time.
Serving offshore wind
“It is important to highlight that Senesco is in a great position, both literally and figuratively, to be involved with the burgeoning offshore wind industry,” said Mr Williams. “In the US we are cur rently building three CTVs aluminium double hulled catamarans that will carry personnel and cargo; out to the growing windfarms. We fully expect that this area of business will increase exponentially over the next few years.
When asked about the future Mr Williams said: “Senesco is now one of the established leaders in new construction as well as repair capability for offshore wind in the Northeast.”
n
“The support vessels that the wind industry will need is just one of the great opportunities available to us. We have also recently launched a 6,000 ton, double hulled, steel dry bulk barge, which is a testament to the great skill of our team.”
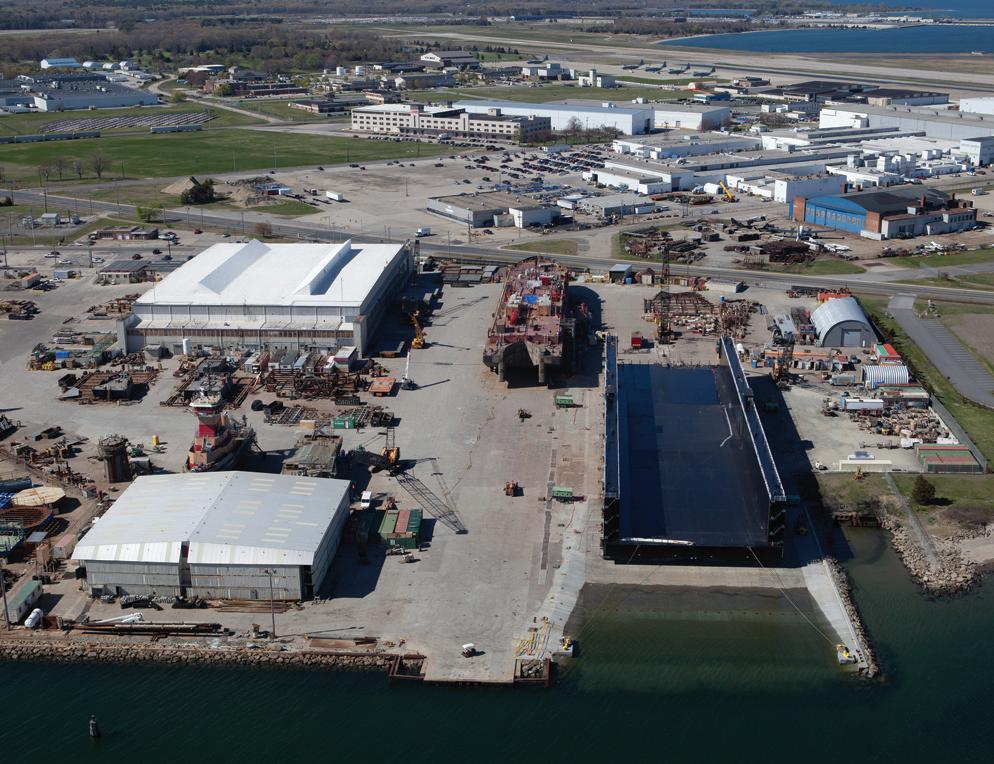
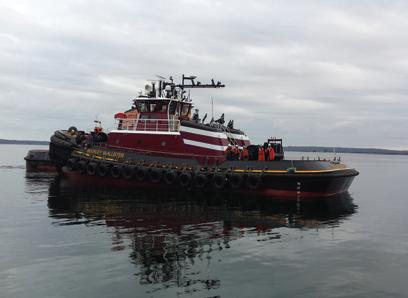
Hat-San Shipyard eyes the market with confidence, having recently heavily invested in expanding its operations, by more than doubling its workspace capacity. The Turkish shipyard’s global reputation for quality remains key to fuelling its future order stream, whether for conversion, new builds or ship repair projects.
HAT-SAN SHIPYARD I PROFILE 108 Inside Marine
Andy Probert spoke to Özgün Oruç, Repairs Division, Marketing Manager. TO SHIPYARD’S
ADDS

Inside Marine 109
H at-San Shipyard’s motto ‘Cooperating Friendly’ is a tes tament to the positive culture that thrives throughout the workforce and as an acknowledgement of its com mitment to clients’ projects on a friend-first, business-second approach. It is a philosophy that acts a foundation upon which the shipyard has flourished. Parent company Pekar Group began its association with ship ping when it bought the current 50,000 sqm shipyard from its previous owners in 2007, one of the later ones to be trading from Yalova, a city in north-western Turkey, near the eastern coast of the Sea of Marmara.
“The infrastructure enables Hat-San to respond to its three pillars of business: ship repairs, conversions and new builds simultaneously,” confirmed Özgün Oruç, Repairs Division, Marketing Manager. A 406m pier has been created within the new yard area, increasing the total pier length to 2,500m. Other investments include additional cranes, new high-tech workshops, service buildings and a new 250m long Panamax-size floating dock in April 2022 to help improve docking capacity. The yard added a 20,000 sqm enclosed work shop for steel cutting, fabrication and related activities.
Backed by investment Within a year, Pekar Group has invested in a 180m x 52m slipway with a lifting capacity of 300 tons and 6,000 sqm closed spaces featuring five gantry cranes and state-of-the-art steel cutting and block production facilities. In 2014, the second phase heralded a 180m x 30m floating dock, a second slipway of 170m x 24m, and two piers of 215m and 150m in length. Closed block production areas were extended and outfitted with new cranes. Within the last three years, Pekar Group has doubled the operational workspace of Hat-San, having acquired 60,000 sqm of land next to the facility.
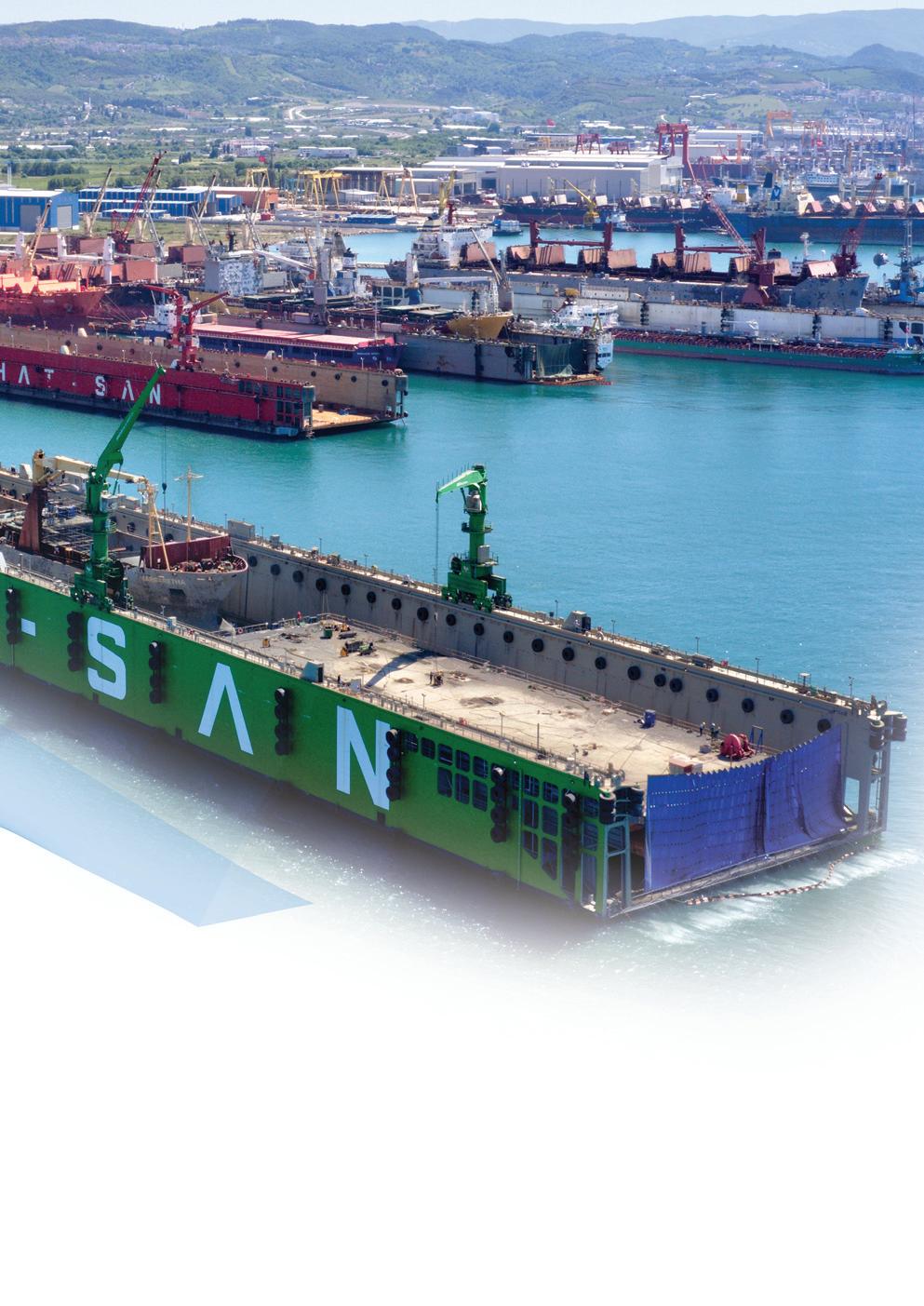
The yard, which presently employs 250 people directly and 1,500 sub-contractors, has also experienced a high level of activity on its ship repair side, thanks largely to the addition of the new floating dock.
In totality, Hat-San now boasts five slipways, two floating docks, four piers and one quay, which Mr Oruç acknowledged “strengthens our hand in our ability to respond to clients’ projects.”
Mr Oruç commented: “Hat-San has also converted two offshore support vessels and two floating barges for the Karadeniz Group to become highly mobile power ships.”
Mr Oruç said: “Since acquiring the new yard space, our employee numbers have also increased by 25%, and business growth has spiked by 50%. On the repair side, we are very busy. Work is ongoing for a large international clientele, prominent among them are Greek ship owners.
Recently Hat-San completed a conversion project for a Britishİ talian joint venture. This was a barge conversion project intended for use in launching new naval builds. On the conversion side, the shipyard has installed dozens of bal last water treatment systems and scrubber conversions to Tier III requirements, and remains one of its busiest areas of business.
The shipyard has enjoyed a long and successful association with Karadeniz Energy Group since 2014. Hat-San has com pleted seven conversion projects leading to the creation of power ships, including the world’s biggest, which has a capacity of 500 MW and was deployed to serve in Ghana, Africa.
Diversity of work Hat-San’s first job under the new ownership was a new build bunker tanker for a Turkish owner. But it has since made a mark in the ship repairs and floating deck space, with prior projects including Handysize vessel conversions, refitting a live fish carrier for a Norwegian owner, and an oil product tanker. The shipyard has also built four purse seiner/trawler hulls for Norwegian owners in cooperation with a shipyard in Norway.
Hat-San created a floating dock for the Turkish Navy, operational since 2020, and another one, a 180m x 30m unit, with a 10,000-ton lifting capacity, for Denmark’s Orskov Shipyard. This increased dock capacity and is utilised to service large fishing vessels, offshore supply vessels, and short sea vessels.
HAT-SAN SHIPYARD I PROFILE 110 Inside Marine

Inside Marine 111
“Our motto is “Cooperating Friendly”, which essentially means our customers directly experience this,” he said. “In business relations, customers benefit from a friendly and positive approach We readily adapt or react to any problems quickly, and feedback suggests that clients like our transparent approach and are more inclined to work with us in the future.”
The shipyard is also hoping to reel in new clients and estab lished customers, having exhibited at the recent Posidonia exhi bition and with intentions to be present at SMM in Hamburg, Germany, in September.
Having navigated the pandemic’s restrictions, Hat-San has incurred minimum delays on shipping projects and is now focused on con tinuing to plot a cautious route through the challenges of the prevailing global economy and external impacts, such as the Ukraine conflict and high inflation.
“It has meant becoming more flexible and adaptable to these difficult times, so there are still opportunities out there that we seek to grasp,” he added. “In the next three years, we will con sider creating another Panamax floating dock to increase our potential for more new builds and ship repairs.”
“We are also in dialogue with several owners for new builds, and hopefully, these will come good despite industry challenges.”
Mr Oruç emphasised that the yard’s and the parent company’s culture of harmonious working had helped foster good relations among the staff.
The company’s mission is to maintain international standards, ensure client satisfaction, protect their staff’s health and safety, while implementing technological developments in the marine industry.
He concluded: “Having doubled our workspace, increaseddocking capacities and enhanced facilities in general, we are confident in building on Hat-San’s renown for quality in every project and will further enhance our global reputation.” n Özgün Oruç, Repairs Division, Marketing Manager
Seeking new opportunities
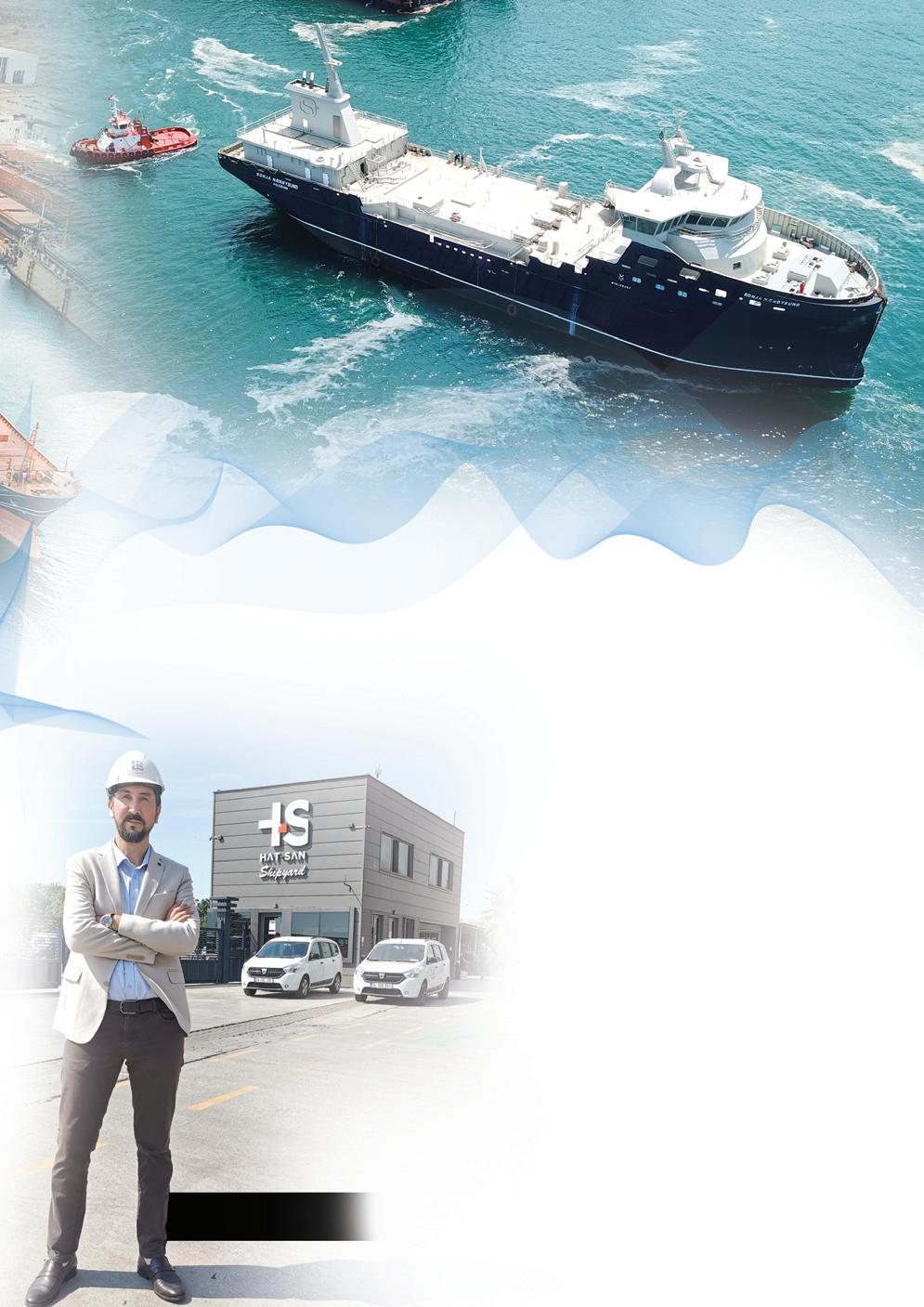
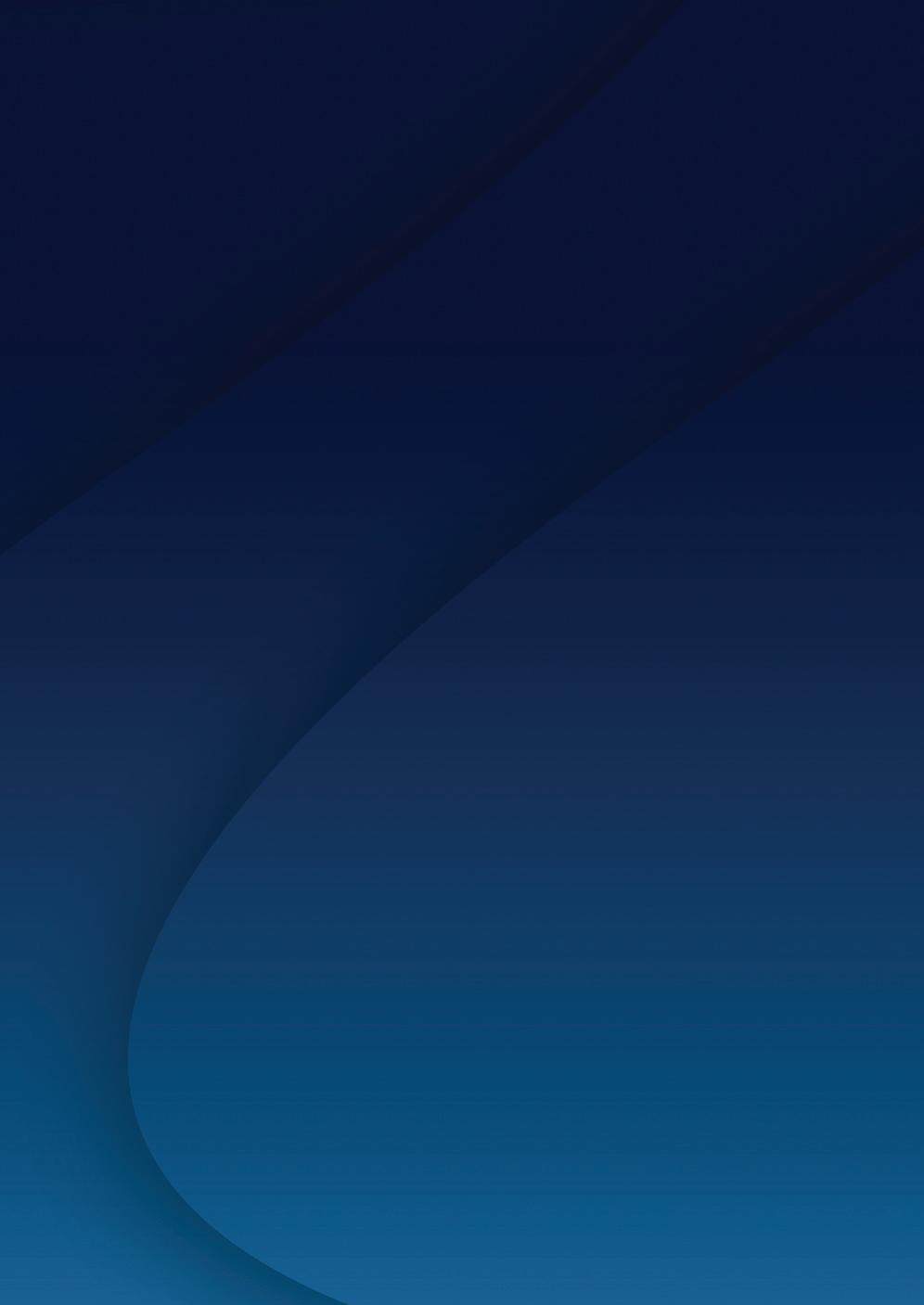
PORTS seven seas, five oceans, one voice port of portland port authority of trinidad and tobago port of long beach i M

100miles upriver from the Pacific Ocean, on the Columbia River, lies the Port of Portland. It shares the same North American coastline as the Port of Long Beach and the Port of Los Angeles, both of which have made news headlines for several years due to major container shipping bottlenecks that have continued to affect both ports, with no end in sight. Consequently, shippers with cargo destined for the US West Coast have increasingly sought alternatives to the long delays at these two ports and since 2021, the Port of Portland has emerged as a favourite option.
The Port of Portland is surely the embodiment of that sentiment. In the midst of the container shipping crisis, the Port of Portland has found great opportunity.
“We have a very seasoned and skilled marine department,” he revealed. “They have strong backgrounds including EPC procure ment, freight forwarding, shipping line administration and even former Coast Guard personnel.
“We work hard together,” he added. “We’ve put the effort in and we’ve developed a team focus in which we celebrate the wins together. We’re recognising the fruits of our labour now.”
Building success through teamwork
THE DARLING OF WEST SHIPPINGCONTAINERCOAST
PORT OF PORTLAND I PROFILE 114 Inside Marine
According to Bulk & breakbulk Manager Michael Richards, one of the reasons that the Port of Portland has successfully capitalised on this opportunity is the excellence of the staff in the port’s marine department.
Albert Einstein is quoted as having once said: “In the midst of every crisis, lies great opportunity.”
Bulk & Breakbulk Manager Michael Richards, fresh from signing on two major new inter national shipping lines, spoke to Richard Hagan about the surge of new business that the port is enjoying.
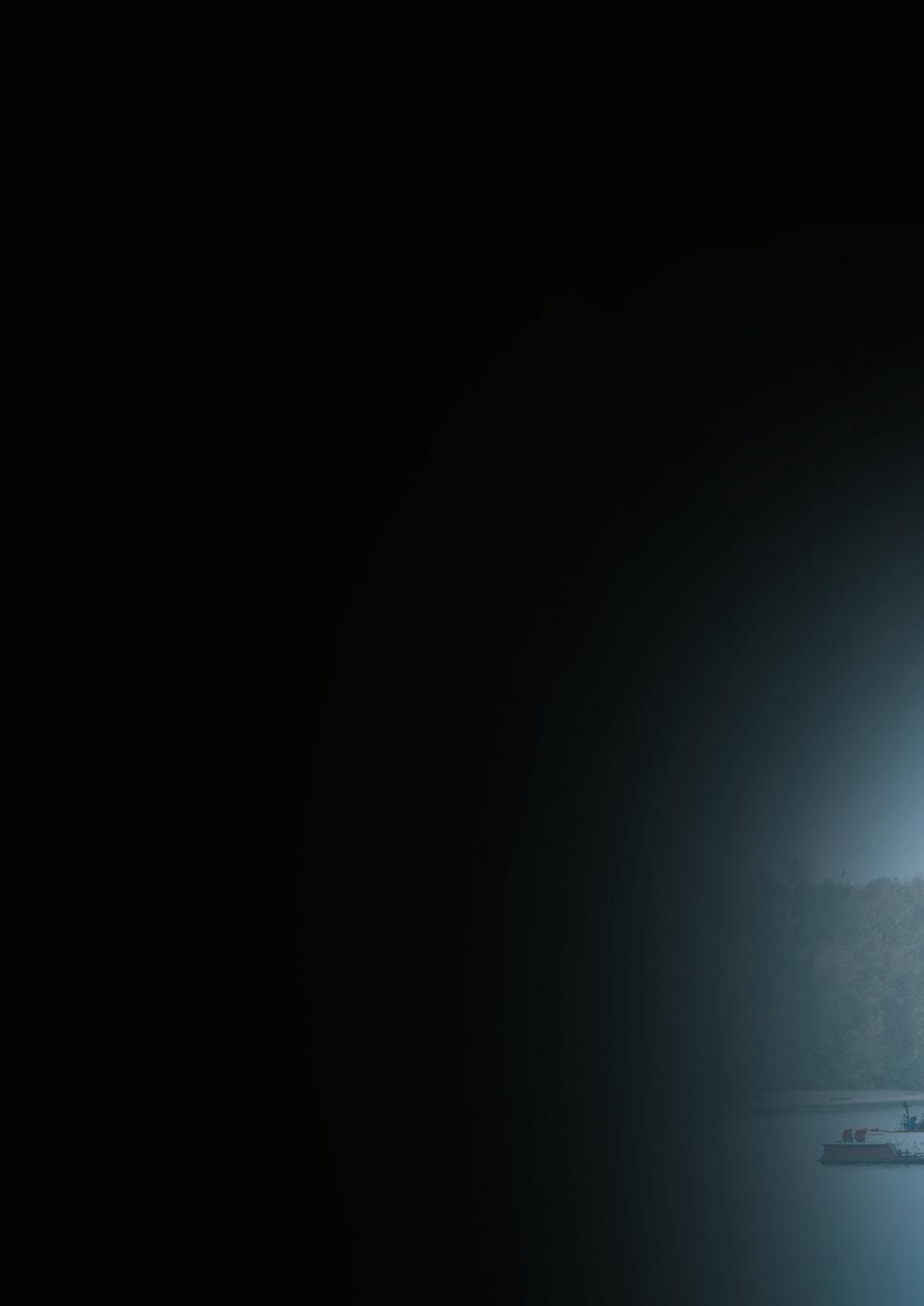
“The labour issues we’ve had in the past have been completely resolved and they are such an asset now. You can sense the excite ment from the labour force on the dock when new cargo comes in; you can feel it in the air.”
“This was the largest vessel to ever come up the river,” Mr Richards said proudly. “It’s the biggest container vessel that can sail up the river based on the 43ft draught limitation. That was big news for us.”
The return of the big box ships Due to its location, the Port of Portland faces inescapable chal lenges in attracting container cargo customers. Chief amongst these is that the Columbia River is maintained at a depth of 43ft, which is not deep enough to accommodate the latest generation of fully loaded cargo vessels. Also, reaching the port requires a 100 mile piloted journey upriver. As a result of these and other chal lenges, the port’s container terminal, Terminal 6, lost its last remaining regularly scheduled container service in 2016. But then everything changed. Following concerted efforts behind the scenes by the Port of Portland’s marine department, and helped along by the container shipping bottlenecks that con tinue to afflict the US West Coast, Terminal 6 has made a tri umphant comeback.
The first milestone in its recovery was the return of South Korean national carrier SM Line which relaunched a weekly ser vice to Portland in January 2020. Then in September 2021, SM Line added two more vessels per month to its rotation. Simultaneously, the port announced that shipping conglomerate MSC would bring a weekly service to the Port of Portland as well. MSC’s first vessel to arrive was the Panamax class MSC Ela, with a capacity of 4,900 TEU. Weeks later, the much larger MSC Navios Unite, with a capacity of 8,200 TEU, sailed its way up the river and arrived at the port to great fanfare.
MSC and SM Line are not the only ships choosing the Port of Portland, however. In addition to the liner services, the port is also experiencing an increase in ad-hoc liners, Mr Richards revealed.
Mr Richards also highlighted the port’s skilled and highly moti vated unionised labour force on the dock as being another reason for the port’s success.
Inside Marine 115
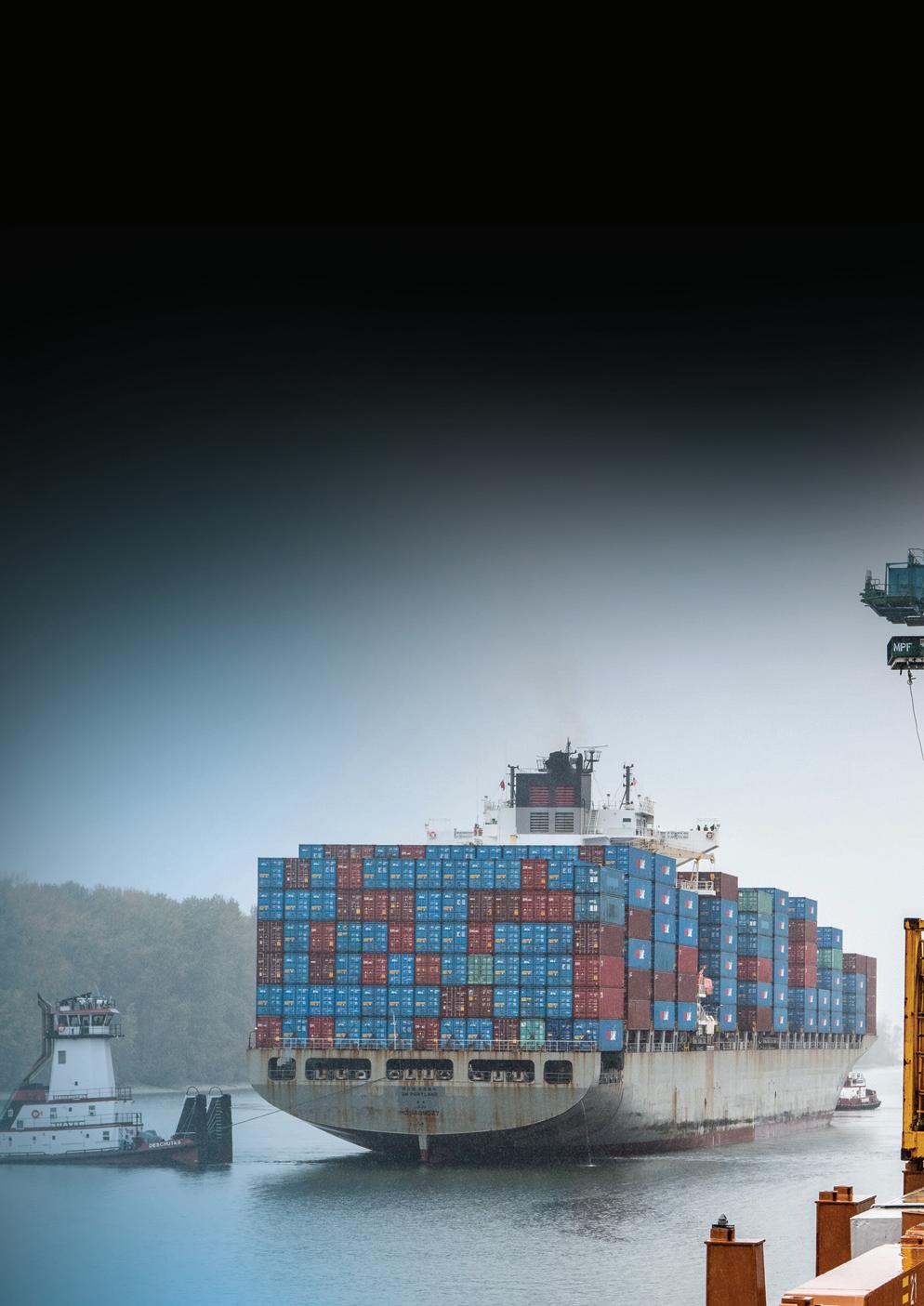
“We’ve recently started moving large lithium-ion batteries for wind, solar and battery farms,” confirmed Mr Richards.
With the surging container activity at Terminal 6 requiring everincreasing storage space, space management has become one of the port’s biggest challenges.
Breaking into breakbulk With a number of renewable energy projects in various stages of approval and construction around the United States, the Port of Portland is handling large amounts of breakbulk cargo in support of a number of these projects.
Cars, containers, and the art of juggling
Undeterred, the Port of Portland’s maritime department is laser-focused on further developing its container and breakbulk cargo services, both of which are its biggest growth areas.
PORT OF PORTLAND I PROFILE 116 Inside Marine
“Our success is due to a lack of congestion at our facility, and our ability to get ships in and out,” he said. “There are no ships waiting around to be unloaded. That lack of congestion is a big benefit that we can offer customers and it’s made us something of the darling of the West Coast in the container business.”
“We recently brought in our first shipment of batteries that are roughly the size of a 20-foot container each. We expect multiple more shiploads of those batteries. They’re handled very much like containers but with some additional precautions since they’re so heavy. They’re definitely handled a little more gingerly!”
These battery units arrive at the Port of Portland as breakbulk cargo, a category in which the port is enjoying surging interest from“We’vecustomers.seenMSC bringing in breakbulk on their container vessels. It’s cargo like gearboxes and components for wind energy, as well as heavy machinery and heavy vehicles,” Mr Richards detailed. “We’ve also seen the transformers for those projects coming in for the first time in over five years. Some transformers are 100 tonnes, some 250 tonnes. They’re all coming and going on these ships. Altogether, we’ve experi enced a big uptick in our breakbulk business.”
“With the introduction of MSC and SM Line and all of the ad-hoc ships, and the space required for our auto business – bringing in Toyota and Hyundai – the biggest challenge is trying to juggle all of these things,” Mr Richards conceded.
“It requires constant work,” said Mr Richards. “For example, the 53ft containers require a special spreader beam for the cranes. Those beams are becoming harder to procure. We just purchased
“We now have a weekly liner service that is exclusively importing 53ft containers as well as the 53ft containers we’re seeing on the ad-hoc liners. That’s an opportunity that simply didn’t exist prior. Having a weekly liner service of 53ft containers and sending them out by rail and truck, has been a big and very exciting surprise for us.” Mr Richards was proud of the Port of Portland’s strong position in the US West Coast logistics chain.

“We’ve brought in smaller items like gearboxes but the big com ponents haven’t come our way yet,” Mr Richards remarked. “A lot of it is owing to the lack of space due to the significant growth of our container operation.”
Inside Marine 117 two new spreader beams in addition to the ones we already had, so we’re investing in the infrastructure needed for this side of the business. All of that while juggling the space and maintaining and acquiring new equipment.”
Wrapping up our conversation, and in the context of the port’s redevelopment efforts to accommodate its surging growth, Mr Richards highlighted a project that is particularly close to his own heart: the redevelopment of a space that previously housed an old grain“Weelevator.havethree conceptual project options for the redevelop ment of the space,” he announced. “We’re currently subject to NDAs, but I can reveal that the plans are at an advanced stage and we expect to make an announcement on it in 2023. This project is the dearest to my heart as I’ve been working on it for the past six years so it’s something I’ve put a lot of time into. “All I can reveal for now is that it will be a new commodity that hasn’t been handled by the Port of Portland in the past. Watch this space!” n
To help ensure the continued smooth operation of its fastgrowing container operations, the port plans to repave some of its space to handle additional containers whilst also reviewing the use of some neighbouring industrial property that it owns. The port’s research indicates that the availability of sufficient space will lead to it receiving a greater share of breakbulk cargo for offshore wind farm projects.
Accommodating surging growth

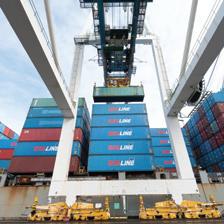
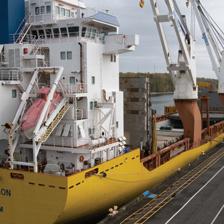
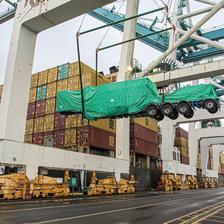
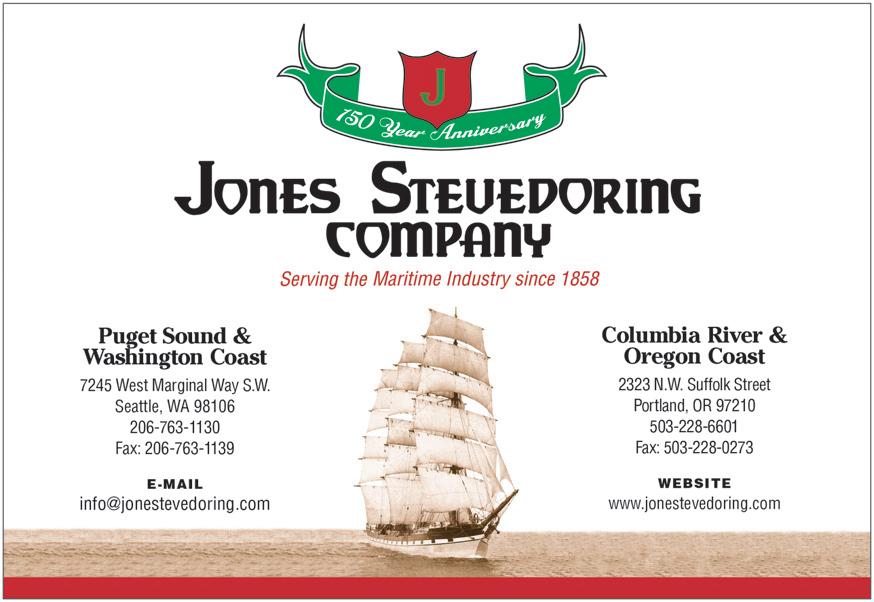
118 Inside Marine
T
he Port Authority of Trinidad and Tobago has witnessed a decline in volumes over the past five years –however, the trend prior to this saw sig nificant increases topping a maximum volume of 400,000 TEUS in 2009. Given the decline in volumes and the port’s lack of investment in any major infrastruc tural upgrades and equipment acquisition, a new page could yet turn on its 70-year history, with the national Government considering privatising port operations.
Rising increasingdemand,investments
At every stage in its history, stretching back to 1962 when it came into being, the Port Authority of Trinidad and Tobago has made significant steps to operate to global industry standards, while delivering vital services at local and regional levels. The authority manages the Trinidad ports of the Port of Port of Spain (PPOS) and the Scarborough port, primarily overseeing domestic, tourism and commercial ship ping across the two islands.
PORT AUTHORITY OF TRINIDAD AND TOBAGO I PROFILE
The Port Authority of Trinidad and Tobago has been the gateway to the capital of the Twin Islands of the Republic of Trinidad and Tobago for more than 70 years, Inside Marine reports on the port’s latest developments.
As a prime location for trade along the east coast of the USA, Latin America and South America, the islands of Trinidad and Tobago operate as an important dual import and export hub.
PPOS, sitting on 63.5 hectares of land, is one of the most technologically advanced in the Caribbean. It serves as the country’s largest containerised port, with a significant market share, and handles all major dry car goes, general cargo, breakbulk, and domestic passenger traffic. The authority employs over 1,500 people, and oversees real estate including berths, and manages fully equipped gantries, reach stackers, cranes, trucks and other shipping aspects.
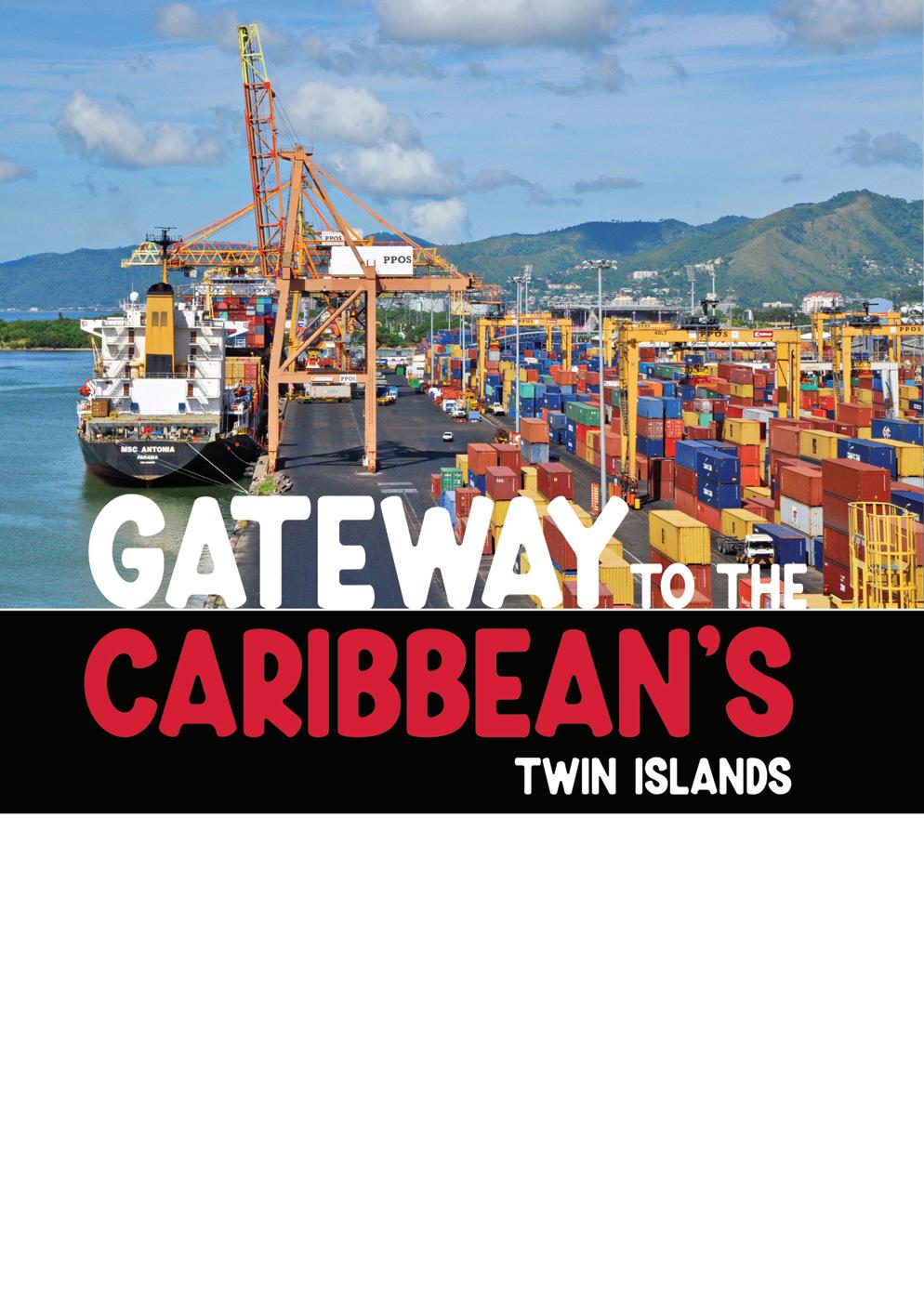
Inside Marine 119
“PPOS was deemed an essential service and a vital entity towards the sustenance of our nation’s economy. So, the port has main
“At this time, a committee has been appointed to consider the relevant arrange ments and options. As we are in the early stages of this undertaking, PPOS is awaiting the Government’s directive on this matter,” acknowledged Ms Elbourne. Until there is further clarity, the authority is currently dealing with a more pressing matter – the impact of Covid-19.
Privatisation possibility At this critical juncture in the authority’s history, the Government of the Republic of Trinidad and Tobago has announced a pro posal to engage a private operator for PPOS.
Marcia Charles-Elbourne, Deputy General Manager of the Port Authority has advised that recent investments included the purchase of two empty container han dlers, 15 trailers and container scanners. A new Panamax crane began operation mid-2021, with tenders for new empty con tainer handlers and a reach stacker to be issued soon after. In 2002, the authority saw a throughput of 120,000 TEUs, rising to 400,000 TEUs in 2009. Today, the average combined throughput at the Port of Port of Spain and its competitor port, the Port of Point Lisas, is now around 450,000 TEUs. The average p roportion of domestic to transhipment business in Trinidad is 60-40. Ms Elbourne reflected: “Covid-19 created significant disruption to PPOS achieving its targeted volumes in 2020. There has been a 14% decline in container volumes and almost 50% in RoRo volumes compared to 2019.” Yet, one of the high lights of 2020 was the arrival of PPOS’ largest containerised vessel, handling approximately 1,500 TEUs. The authority has also been responsible for managing and operating the inter-island Fast Ferry service, where vessels are capable of holding vehicles and up to 800 passengers, make a crossing between Trinidad and Tobago in approximately two and a half hours, com pared to the previous six-hour journey.
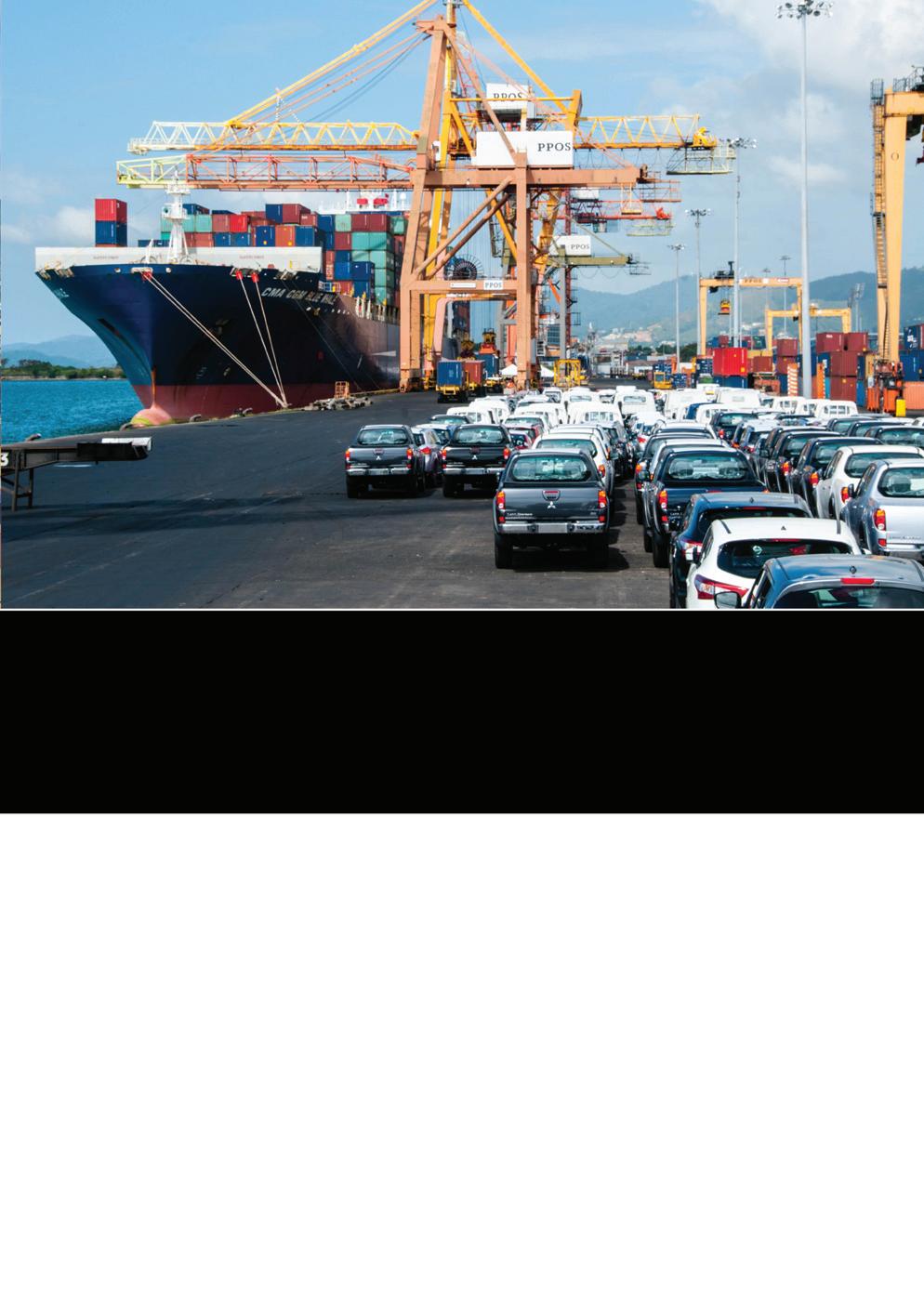
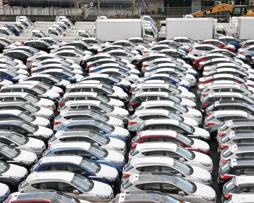
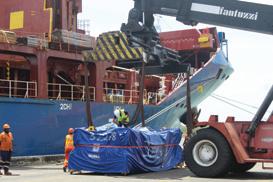
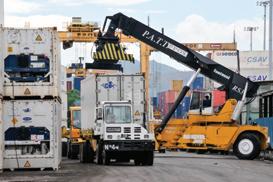
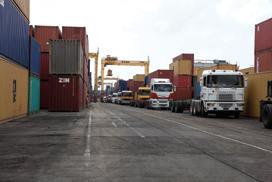
“PPOS has successfully navigated busi ness productivity and Covid prevention by adopting several health and safety proto cols with the guidance of the Ministry of Health and the Chief Medical Officer.” Prevention measures have included the enforcement of social distancing, wearing of masks, frequent handwashing, temperature checks, and regular sanitization of offices, workspaces and terminal equipment.
TRINIDAD
AUTHORITY
PORT OF AND TOBAGO
Enhancing efficiencies and overcoming challenges
These ranged, she said, from outdated laws and regulations that act as deterrents to efficient trade facilitation and ease of doing business to support agencies being paper-based, thus incurring lengthy docu ment processing times and redundancies.
Shipping stakeholders are currently out of sync in enhancing trade facilitation, such as the hours of business at the port versus
tained regular operational business hours, even during the peak of the pandemic,” Ms Elbourne commented.
Sensitisation sessions were held with employees, as well as installation of signage as reminders to the HSE protocols, new utility sinks and sanitization stations, and the pro vision of masks, gloves, sanitizers and PPE to all PPOSstaff.has also continued to enhance efficiencies across its operations to remain viable and competitive, keeping its supply chains open, and providing a continuous flow of Whiletrade.thepandemic was indeed a con cern for the authority, she spoke further about the day-to-day challenges which con tinue to beset its operational capabilities.
I PROFILE 120 Inside Marine
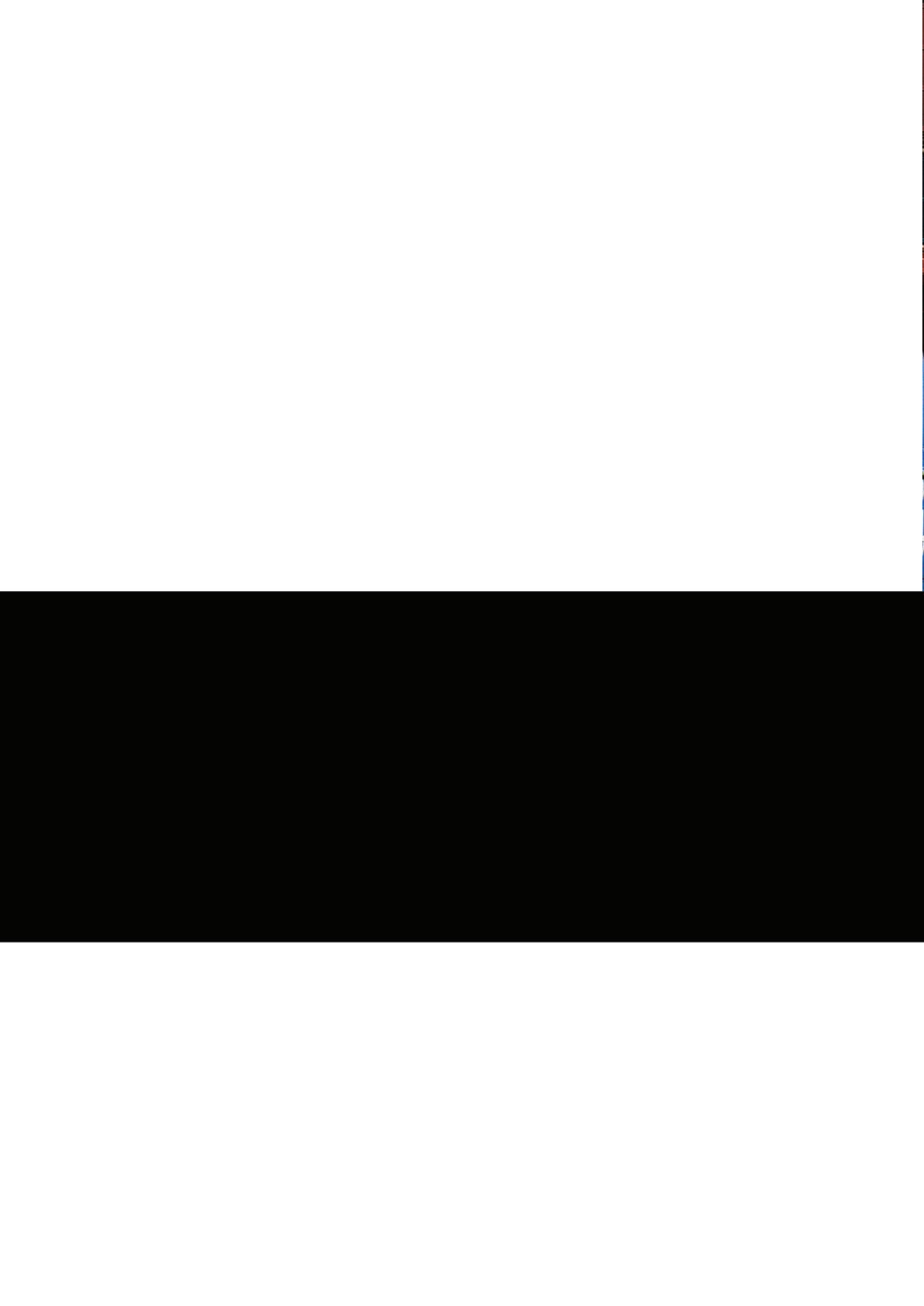
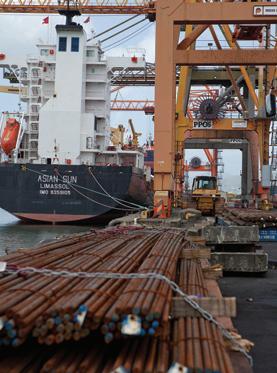
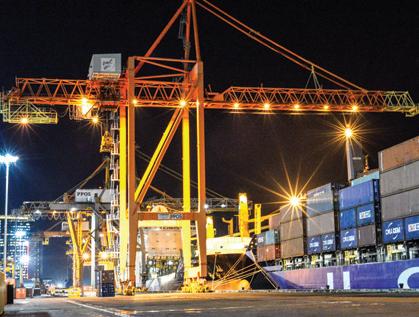
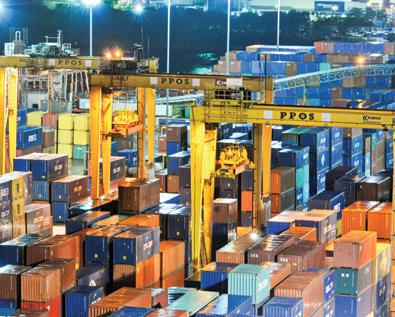

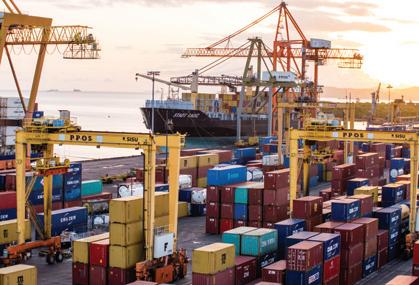
As Trinidad and Tobago lies beneath the Caribbean hurricane belt, there is a far reduced risk of disruption to business.
External factors which create further inef ficiencies within the PPOS’ operations range from delays in getting approvals at various agencies (increasing the dwell time of cargo at the port) to a lack of interoperability with the port’s TOS which creates additional pro cessing time and delays for customers.
“We benefit from a safe and sheltered harbour and a strategic location,” said Ms“WeElbourne.alsohave a stable environment that is not prone to political unrest, and labour
“Indeed, the most important factor is good customer service that connects and builds relations with port clients. We are always promoting a positive, safe and friendly envi ronment, to ensure clients leave satisfied and are willing to return.”
Inside Marine 121 unrest is infrequent. Our tariff rates are low when compared to competitor ports and we have a multipurpose, technologically advanced facility that seeks to reduce the processing time of customers.
Towards a new normal Timely and clear communications through notices, social media and the Authority’s website continue to forge a unique connec tion with port clients. Ms Elbourne added: “The fast-tracking of digitalisation has shown encouraging ways of enhancing processes which con t ribute to the ease of doing business. Many stakeholders have been forced to implement the use of technology, and digital transfor mations have significantly improved the logistics supply chain.” She concluded: “While Covid-19 has pre sented many unique challenges to our port, we have demonstrated an ability to adapt to change, to think ‘outside the box’ of usual norms to service customers in a new dynamic way, and adjust to a new normal.” n hauliers, importers/exporters, and agen cies which are required to provide approvals, she added.
Paper-based agencies which require customers to take unnecessary steps in document processing have been largely eliminated by the introduction of the SEW, but not all major agencies are currently on-board. “There is also an absence at the facility for online payments at some agen cies,” she went on.

PORT OF LONG BEACH I PROFILE
122 Inside Marine
The Port of Long Beach has long been the premier US gateway for trans-Pacific trade and a trailblazer in innovative goods movement, safety, environmental steward ship and sustainability. Dr Noel Hacegaba, Deputy Executive Director, spoke to Andy Probert about the port’s ambitions, investments and determination to make Southern California a cleaner, healthier place to live and work.
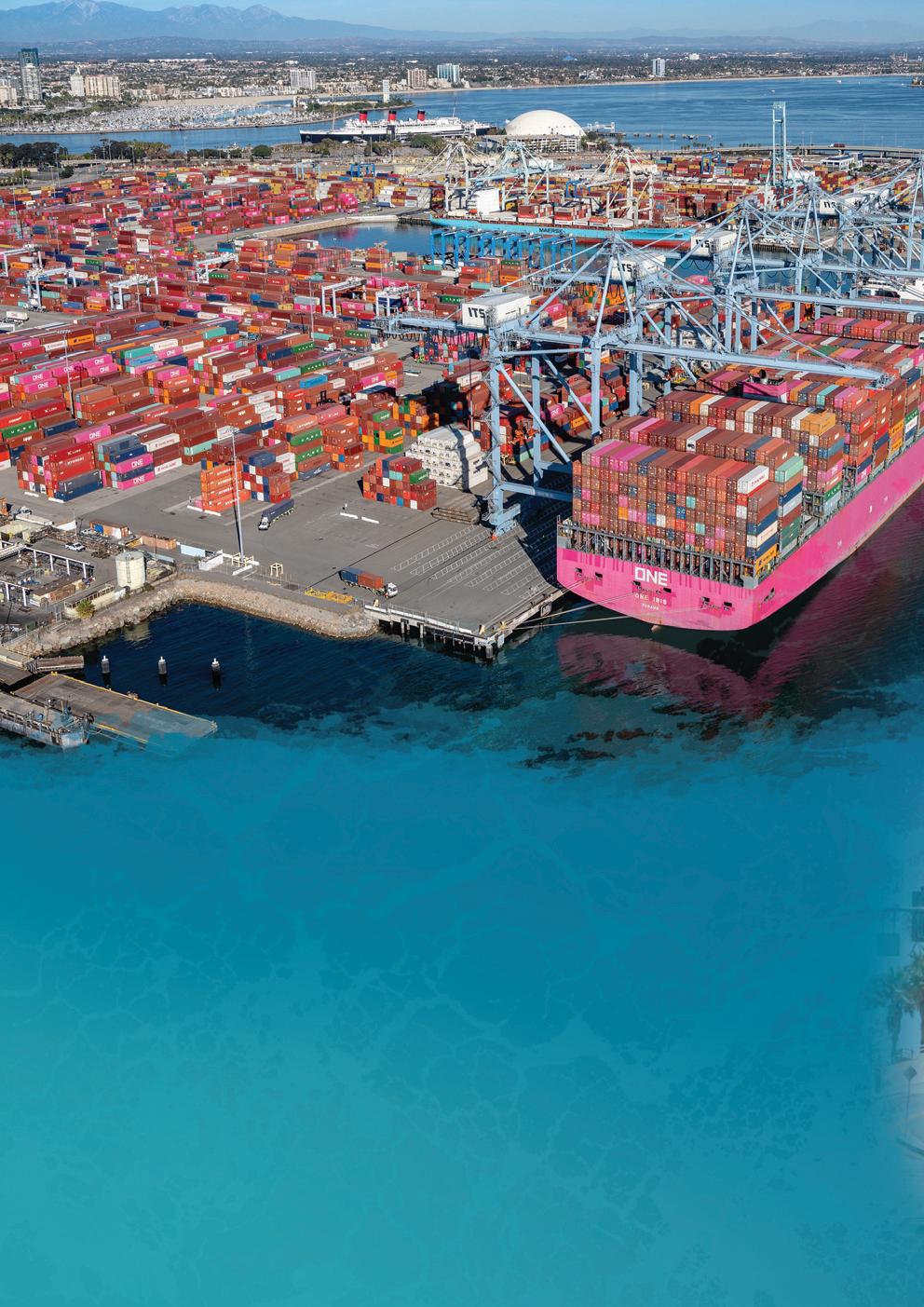
A digital infrastructure project –the Supply Chain Information Highway –is also being developed to help shippers t rack their cargo through the supply chain to maximise efficiency and visibility in cargo movement.
In 2021, the Port of Long Beach handled more than 9.38 million container units, marking its best year on record. And gross revenue grew 9% from 2020 to 2021.
Strategic investments In the 2010s, the port invested $4 billion in infrastructure, preparing to be ‘big ship ready’ and meet the challenges for the future. The investment covered terminals, dredging, roads and more.
In coming years, the port plans to spend $1.5 billion on on-dock rail projects to speed cargo movement through the harbour and allow terminals handling the biggest ships to move cargo faster. He added: “Our biggest investment this decade will be improvements to our rail system to make it possible for a greater share of the cargo moving through this port to go via on-dock rail.”
The centrepiece is the Pier B On-Dock Rail Support Facility, with the project scheduled to start construction in 2023. It will increase capacity and sustainability at the port, reduce truck trips, improve efficiency and lessen environmental impacts, even as they handle more cargo.
Led by a Board of Harbor Commissioners and Executive Director Mario Cordero, the port is on track for a green future, creating the world’s most modern, efficient and sustainable seaport.
A $1.5 billion new bridge replacing the old Gerald Desmond Bridge opened in October 2020, dramatically improving traffic flow around the port complex. Demolition of the old bridge, starting in 2022, will allow larger ships to transit the inner harbour more easily.
The third phase of Long Beach Container Terminal (LBCT), costing $1.5 billion, was completed in 2021, immediately adding 1 million TEU annual capacity. LBCT is now able to move 3.3 million TEUs annu ally – twice the cargo with less than half the air pollution of the two terminals it replaces.Aspartof an industry-leading $2.6 bil lion capital improvement program in the 2020s, the port is building some of the most modern, efficient and sustainable marine facilities in the world to accommo date bigger ships while generating thou sands of new jobs.
Deputy Executive Director Dr Noel Hacegaba, said: “These investments will enhance marine terminal productivity, deliver greater efficiency to our cus tomers and improve the sustainability of our operations.”
ASthe second busiest container seaport in the US, the Port of Long Beach handles trade valued at $170 billion annually and sup ports 2.6 million jobs across the nation, over 575,000 in Southern California, and more than 50,000 jobs – or one in five –in Long AdjoiningBeach.the Port of Los Angeles, it is one of the few US ports that can welcome today’s largest vessels, serving 175 ship ping lines with connections to 217 sea ports worldwide. Goods moving through the port originate in or are destined for every US congressional district.
Inside Marine 123
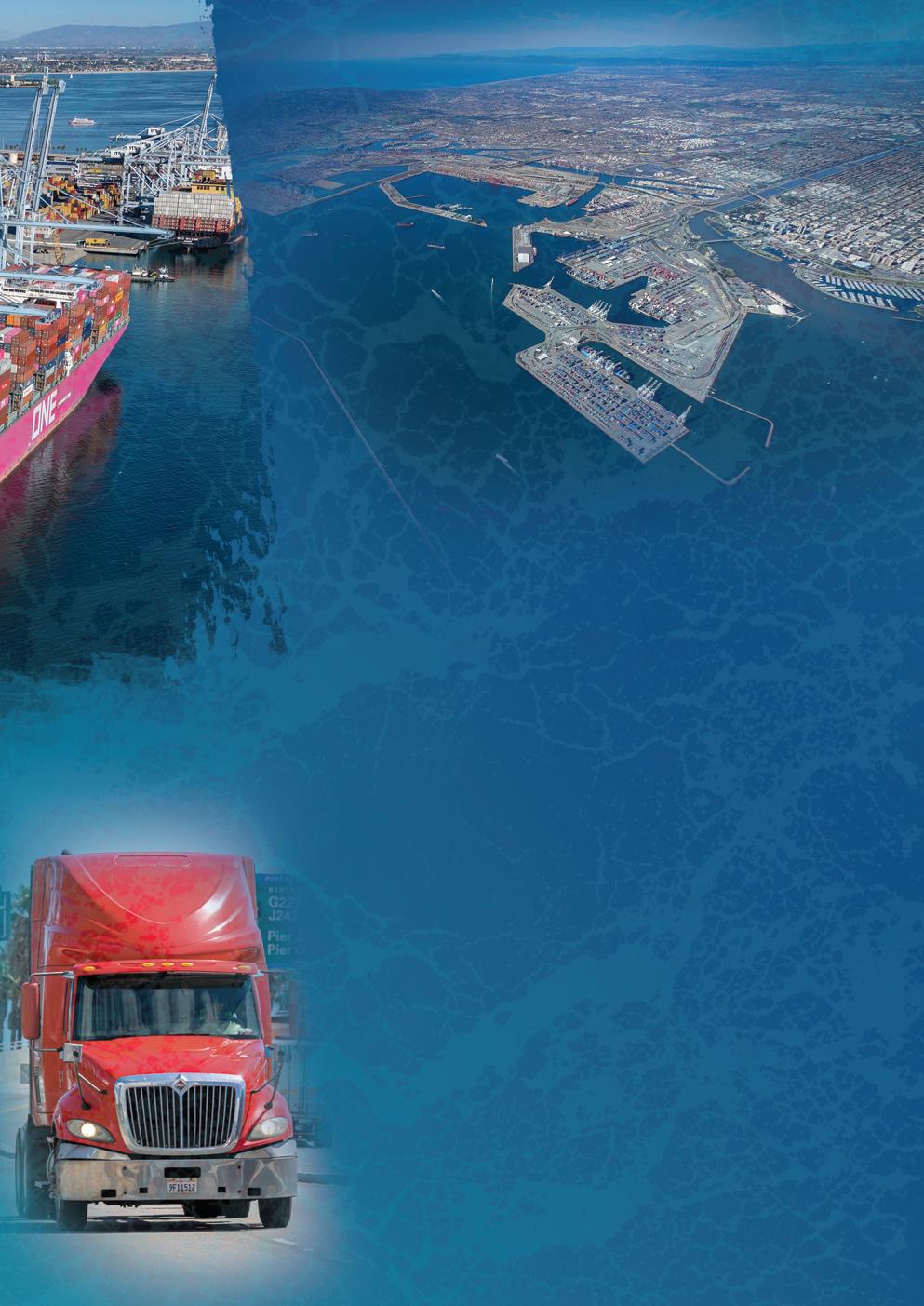
Sustainability landmarks After adopting its landmark Green Port Policy in 2005, the Port of Long Beach is more determined than ever to make Southern California a cleaner, healthier place to live, work and play.
“In an era of e-commerce and overnight delivery, consumers and shippers expect shipment visibility,” said Dr Hacegaba.
“Working closely with our industry part ners, the port met and exceeded its DPM reduction target in 2013 and its SOx reduc tion target in 2014,” said Dr Hacegaba.
It set ambitious goals for cutting the top three ground-level pollutants, and all three targets have been hit ahead of schedule.
I PROFILE 124 Inside
Laser-focused on cutting greenhouse gases, the port is moving forward with measures to transition off-road cargo han dling equipment to zero-emission vehicles by 2030 and the truck fleet to zero-emis sion vehicles by 2035.
As of 2021, smog-forming nitrogen oxides are down 62%. Under the Clean Air Action Plan, the port committed to reducing emissions of diesel particulate matter (DPM) by 77%, nitrogen oxides by 59% and sulphur oxides (SOx) by 93% by 2023.
Dr Hacegaba explained the money, paid by cargo owners, goes directly into the Clean Truck Fund, an incentive pro gramme to help companies switch to zeroemissions trucks. The fund is projected to raise up to $90 million in its first year.
PORT OF LONG BEACH Marine
The latest inventory shows the Port of Long Beach has maintained and built on its track record. DPM and SOx emissions are down a whopping 90% and 97%, respectively, since 2005. The port continues to use every available tool, including green lease provi sions and voluntary incentive programmes, to eliminate remaining emissions.
The port’s annual Air Emissions Inventory confirms its ongoing progress.
The port has partnered with leading tech firm, St Louis-based UNCOMN, to develop the Supply Chain Information Highway, who is collaborating with Amazon Web Services to provide secure cloud-hosting for the “Ultimately,data. our vision for the Supply Chain Information Highway is end-to-end visibility and coast-to-coast connectivity.
The Port of Oakland, Northwest Seaport Alliance, Utah Inland Port Authority, PortMiami and the South Carolina Ports Authority have agreed to join the effort, and we expect additional ports to join in the future,” Dr Hacegaba confirmed.
“We aim to enable stakeholders to make scheduling, planning and payment deci sions before cargo arrival and speed deliveries through the supply chain. ”
“This involves accelerating the develop ment, deployment and commercialisation of machines powered by clean energy,” said Dr SinceHacegaba.April2022, Long Beach and Los Angeles ports have been collecting $10 for every loaded twenty-foot container hauled by trucks in and out of their terminals.
The study, reviewed by regional, state and federal regulatory agencies before release, shows in its most recent update that, years ahead of schedule, the port reached and surpassed its third and final 2023 target for slashing ground-level air pollution from port-related operations.
In addition to air, water and land are equal priorities under the Port of Long Beach Green Port Policy. Ensuring cleaner soil and sediment is routine, and progress is continuously tracked. Released in 2021, the latest survey of water quality, aquatic habitat and biolog ical resources in San Pedro Bay shows the harbour’s ecosystem is thriving, with more than 1,000 species of plants, fish, birds, invertebrates and marine mammals.
The port’s air quality programmes tackle anything with an engine that enters the harbour district and moves cargo: ships, trains, trucks, small harbour craft, and offroad cargo handling equipment.

Inside Marine 125
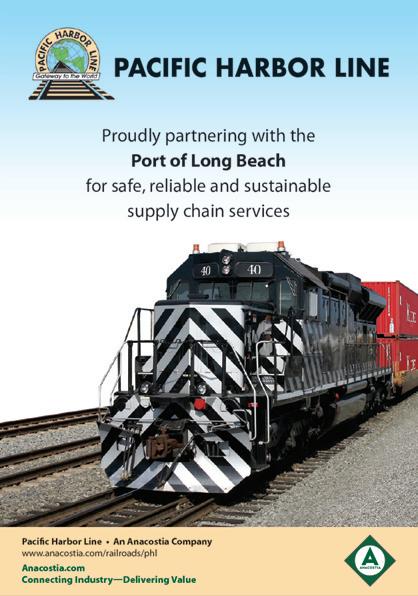
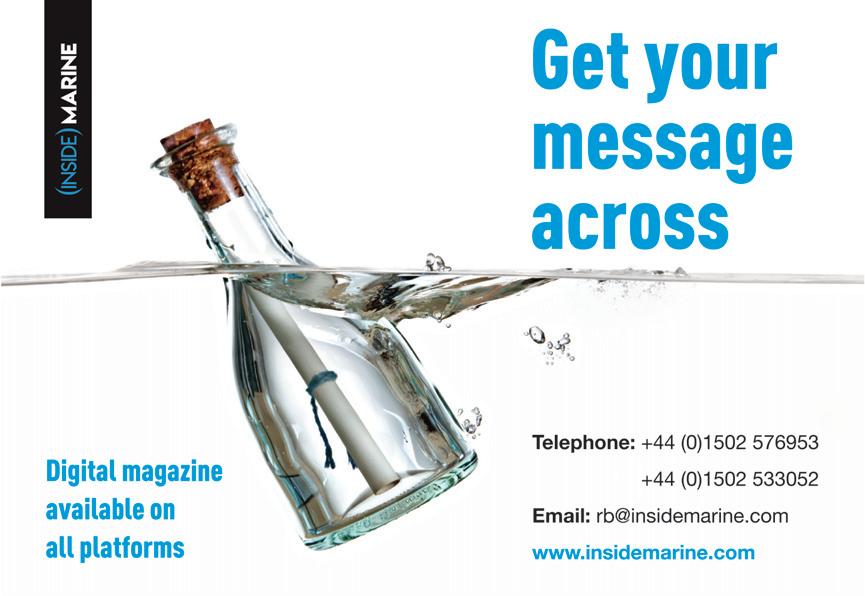

He added: “Our long-term dedication to remaining competitive and environmentally responsible has made the Port of Long Beach an industry leader that shares a common goal with the Biden Administration to enact policies related to climate change and reducing harmful emissions.
“Customers choose the port for the most dependable, cost-effective and fastest delivery of goods in the world, along with the strong relationships it maintains with industry, community, environmental advo cates and partner agencies.”
“Thetimes.state of the industry is one of trans formation and the Port of Long Beach is poised to lead that, given our commitment to operational excellence and environmental sustainability. We have an aggressive cap ital improvement programme focused on shifting cargo from truck to train, which is more efficient, faster and cleaner. And we are developing a digital infrastructure which could be a gamechanger for goods movement coast to coast.”
“The surge of cargo and high numbers of unscheduled vessel calls met a supply chain workforce impacted by Covid-19 and work place accommodations that limited capacity Still, our terminals and dockworkers are moving record amounts of cargo. The port moved a record-setting 9.38 million TEUs in 2021, and we expect another record for 2022,” he said.
Dr Hacegaba disclosed: “As the port of choice, Port of Long Beach has a single goal: superior customer service. For our business partners this means moving cargo more efficiently, at a competitive cost.
As for the port’s continued cooperation with suppliers and customers, he empha sized: “It’s all about communication. Our partners and stakeholders know exactly who they can contact and how to contact us because we are consistently making ourselves available.
Some of the port’s most significant challenges will be to maximise coopera tion to build a digital infrastructure to share data safely, continue receiving support from state and federal agencies to fund supply chain infrastructure projects, and build up the flow of US exports to help balance trade.
Dr Hacegaba concluded: “Change is the only thing you can count on. A successful supply chain requires cooperation throughout all the links in the chain, and that’s our primary goal. We work closely with our stakeholders to ensure close rela tionships and open lines of communication at all
“Our customers know we like to get their input before we launch new initia tives, such as the outreach we did before we launched the Supply Chain Information Highway.”
n THE PORT OF LONG BEACH I PROFILE 126 Inside Marine
Moving forward Dr Hacegaba emphasised the current supply chain surge with record amounts of cargo through the port essentially comes down to a single cause – the Covid-19 pandemic.
“The port has been successful with a two pronged objective of maintaining commer cial growth and environmental stewardship by demonstrating a commitment to opera tional excellence, preparation for future challenges and the strategic management of resources.”

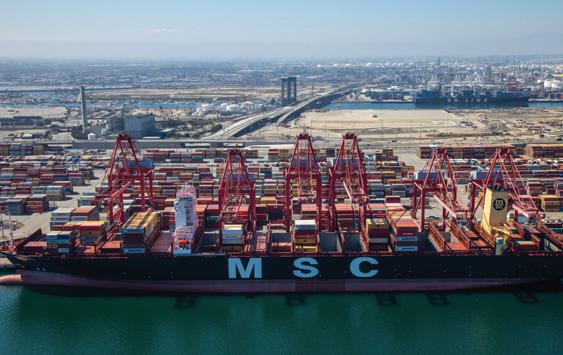

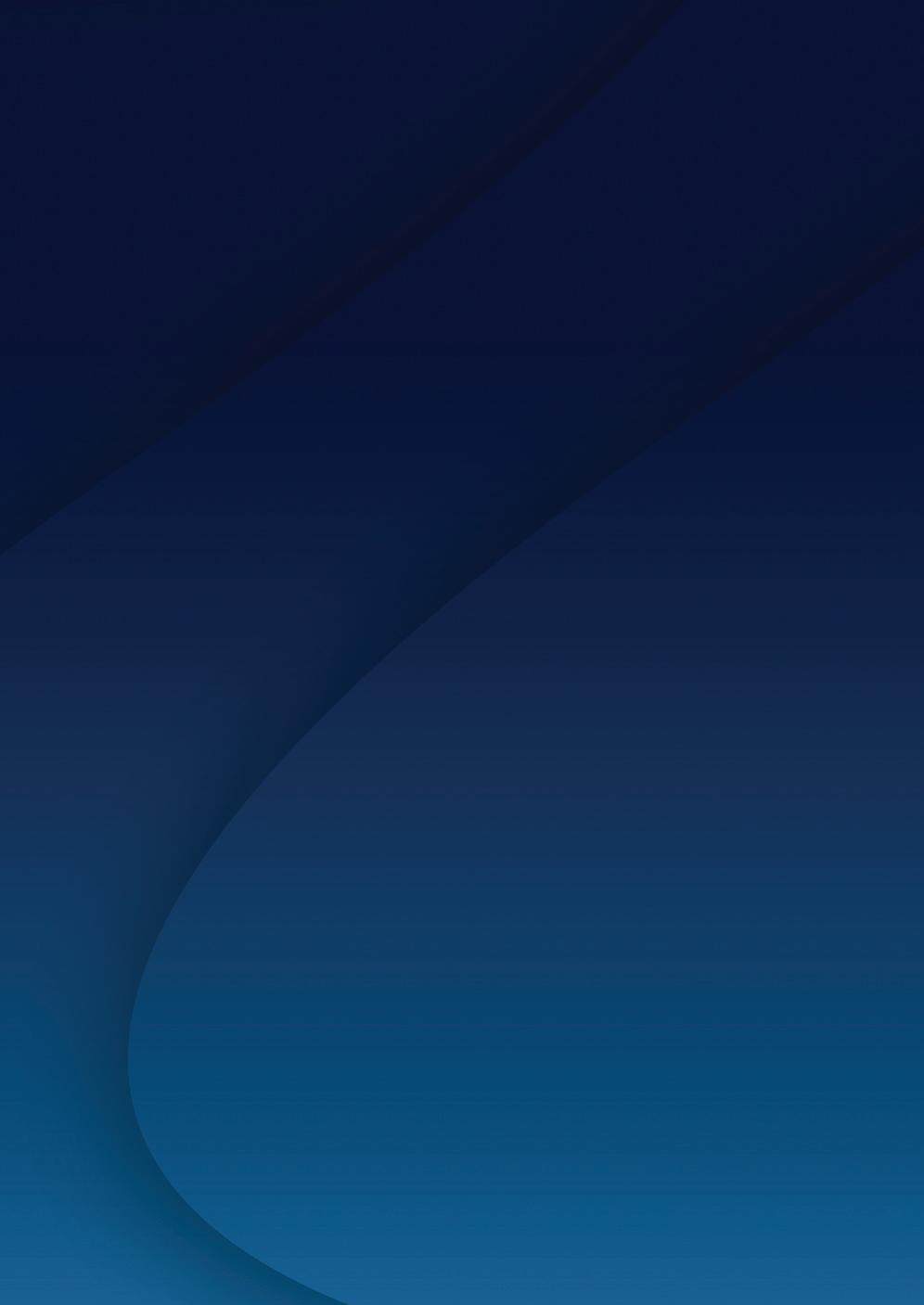
OWNERS,&MANAGERSAGENCIES seven seas, five oceans, one voice maritimex dockendale ship management eastern car liner americas ol shipping group variety cruises i M

MARITIMEX I PROFILE 130 Inside Marine
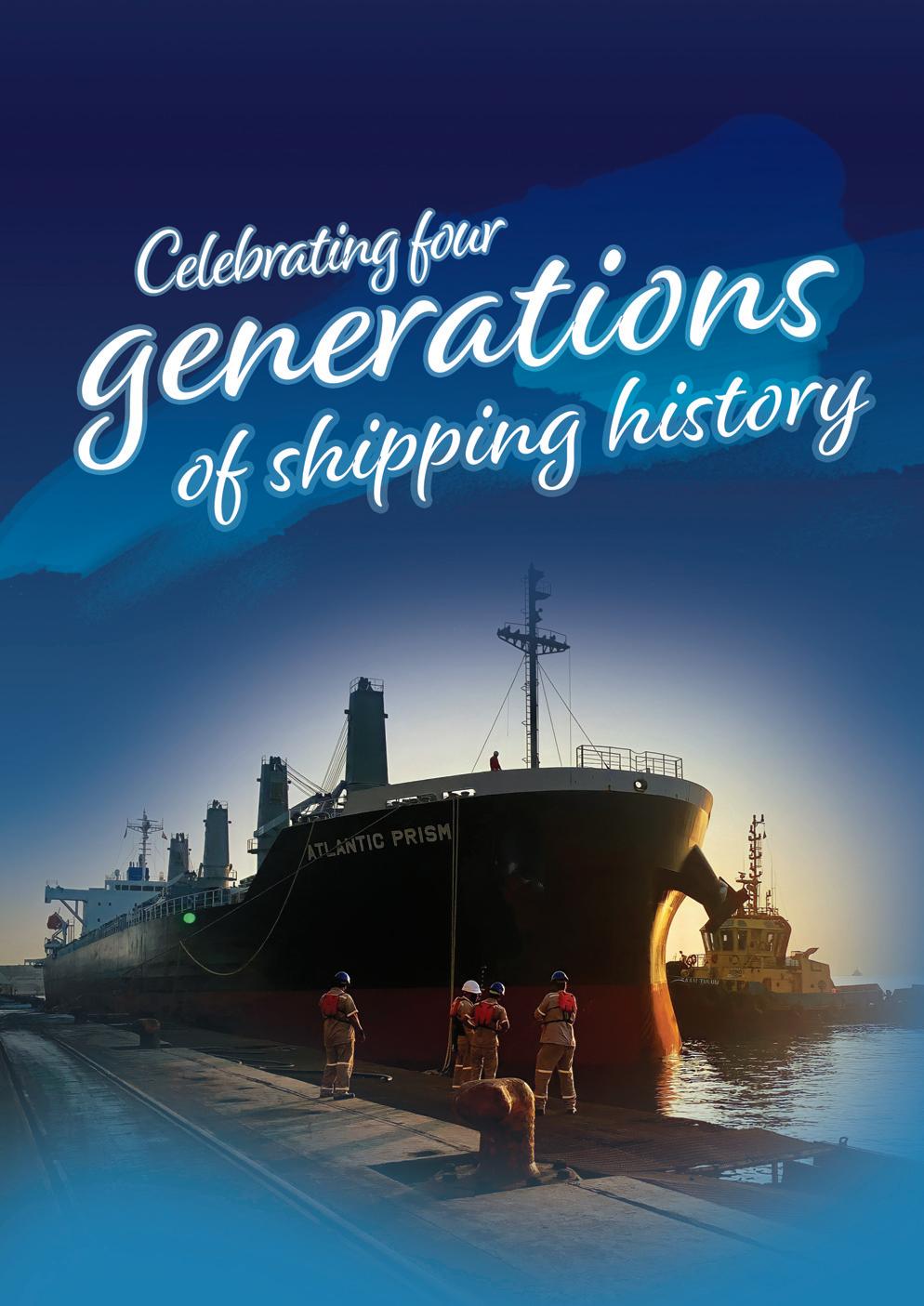
With a substantial footprint, a diverse service offering and almost 140 years of colourful history behind it, Maritimex, based in Mexico, is perfectly positioned to solve any client’s most difficult and demanding shipping challenges and requirements.
Maritimex is one of the most impor tant shipping agencies in Mexico, with more coverage than any of itsThecompetitors.company maintains offices in all of Mexico’s biggest ports, 16 of which are wholly operated by the company itself while the remainder are operated by sub-agents due to low or seasonal cargo movement.
A versatile vessel offering Maritimex operates four vessels: a Baby Capesize container ship, a Panamax and an 11,000-ton mini bulker make up its vet eran fleet. Those three were recently bol stered by the arrival of a new Handymax. Altogether, this fleet allows Maritimex to transport four million tons of cargo per year; nearly all of it on coastal traffic routes in Mexico, with occasional international trips across to the USA. All of Maritimex’s vessels are Mexican flagged and, by law, crewed by Mexicanborn nationals. In addition to its own fleet, the company also renders launch services via a pilot boat that it operates. Cargo on rails
Director Cristian Eversbusch spoke to Richard Hagan about how Maritimex contin ues its reputation for innovation, comprehensive service delivery, and flexibility.
An impressive head office located in Mexico City boasts six floors hosting all of the company’s most important functions, as well as acting as a sort of repository for the company’s fascinating historicalAltogether,memorabilia.over280staff fall under the Maritimex umbrella, including the shipping agency itself, as well as the company’s logis tics operations, land transportation and of course the administrative side.
The company offers all of the services one would expect of a large shipping agency, including sea transportation and agent consignee services. But it goes far beyond that, with a vast list of services on offer ranging from handling and dispatch of cruise ships, to towing, stevedoring, ship chartering, logistics and goods distribu tion services, storage, crew management and repatriation, terminal operation part nerships, fuel supply services, and project and heavy load handling services. Surprisingly, the company’s services are also diversified into the grain industry via a 100,000 metric ton grain silo in which Maritimex has a partnership that dates back to Maritimex2018. has a further partnership agreement for a large container yard in the bustling Manzanillo port where con tainers are stored, stripped and loaded. Clients’ road transport needs are also catered for with Maritimex’s inland trucking division that is specifically set up to move a huge variety of cargo by both truck and train.
One of Maritimex’s most innovative ser vice offerings is its unique, niche railway car shipping service. It’s exactly as fasci nating as it sounds. Via a subsidiary called CG Railway, the company owns and operates two highly bespoke, highly unusual transport vessels.
The vessels are each able to carry 60 rai l cars and both do about eight port calls per month, running between Quetzalcóatl, Mexico, and Mobile, Alabama in the US. The trip between ports takes about four days, and once in port, the vessels can be loaded or unloaded within an impressive eight hours.
Despite its successful history, the company isn’t sitting around on its haunches.
A robust service offering
Maritimex delivers an impressively diverse service offering. Foremostly, it is the oldest shipping agency in Mexico, where it delivers port and maritime transport services in the Mexican Republic.
Inside Marine 131
“It’s two vessels fitted with railway lines,” said Director Cristian Eversbusch. “They’re designed to carry rail cars. They are the only vessels of their kind and they only take rail cars. Both ships have been run ning since 2000, for 22 years now. It’s an extremely unique service.”
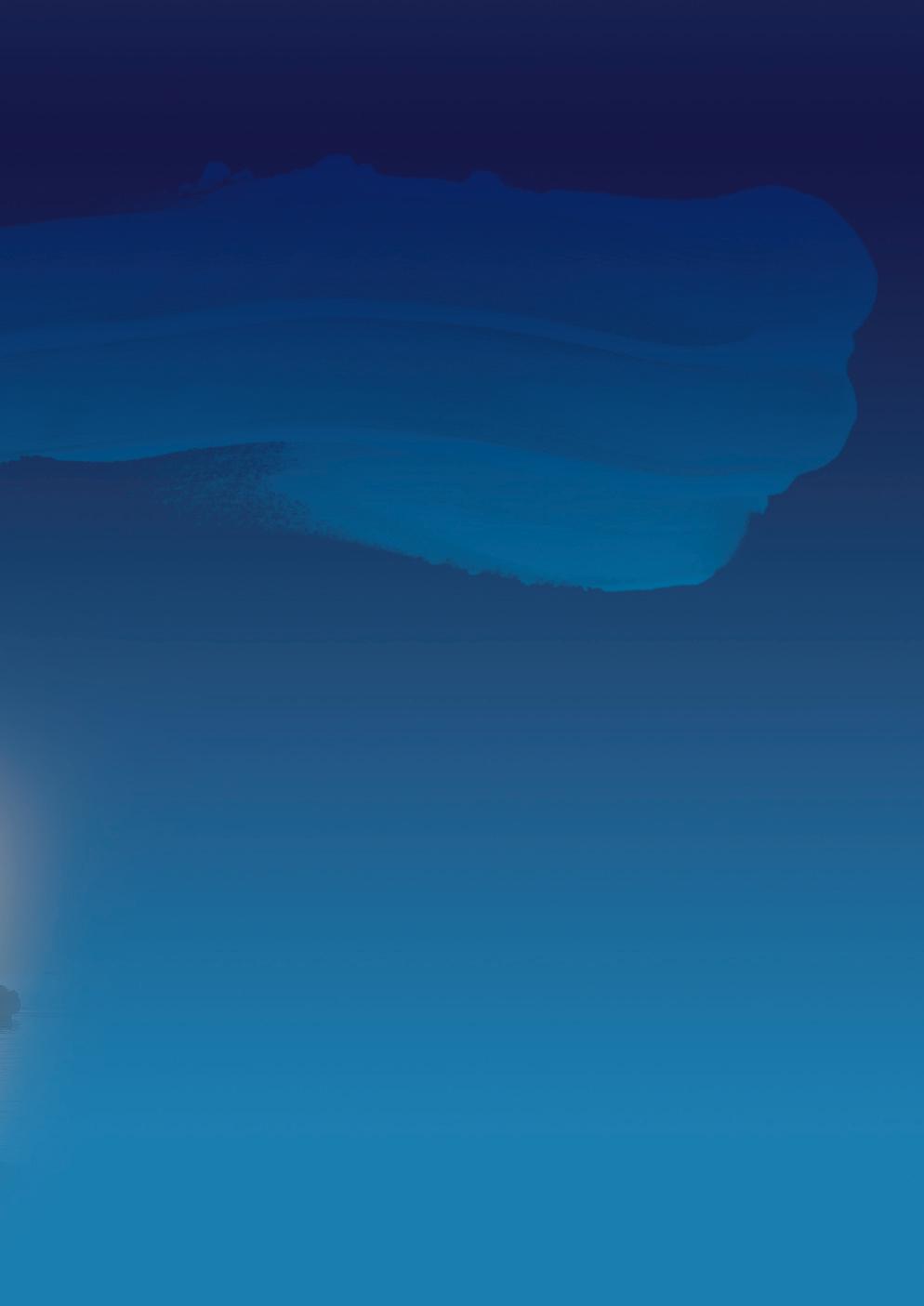
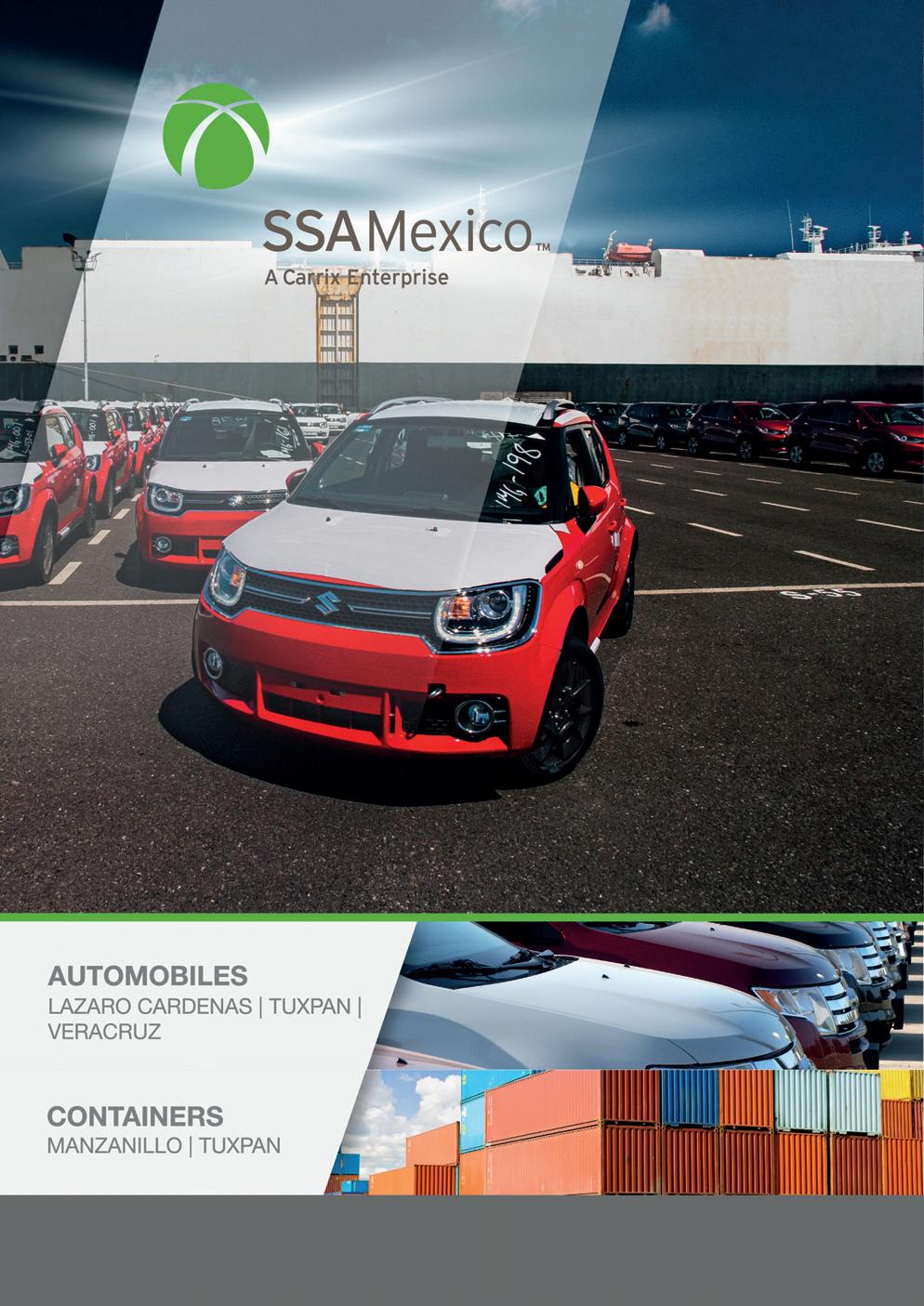
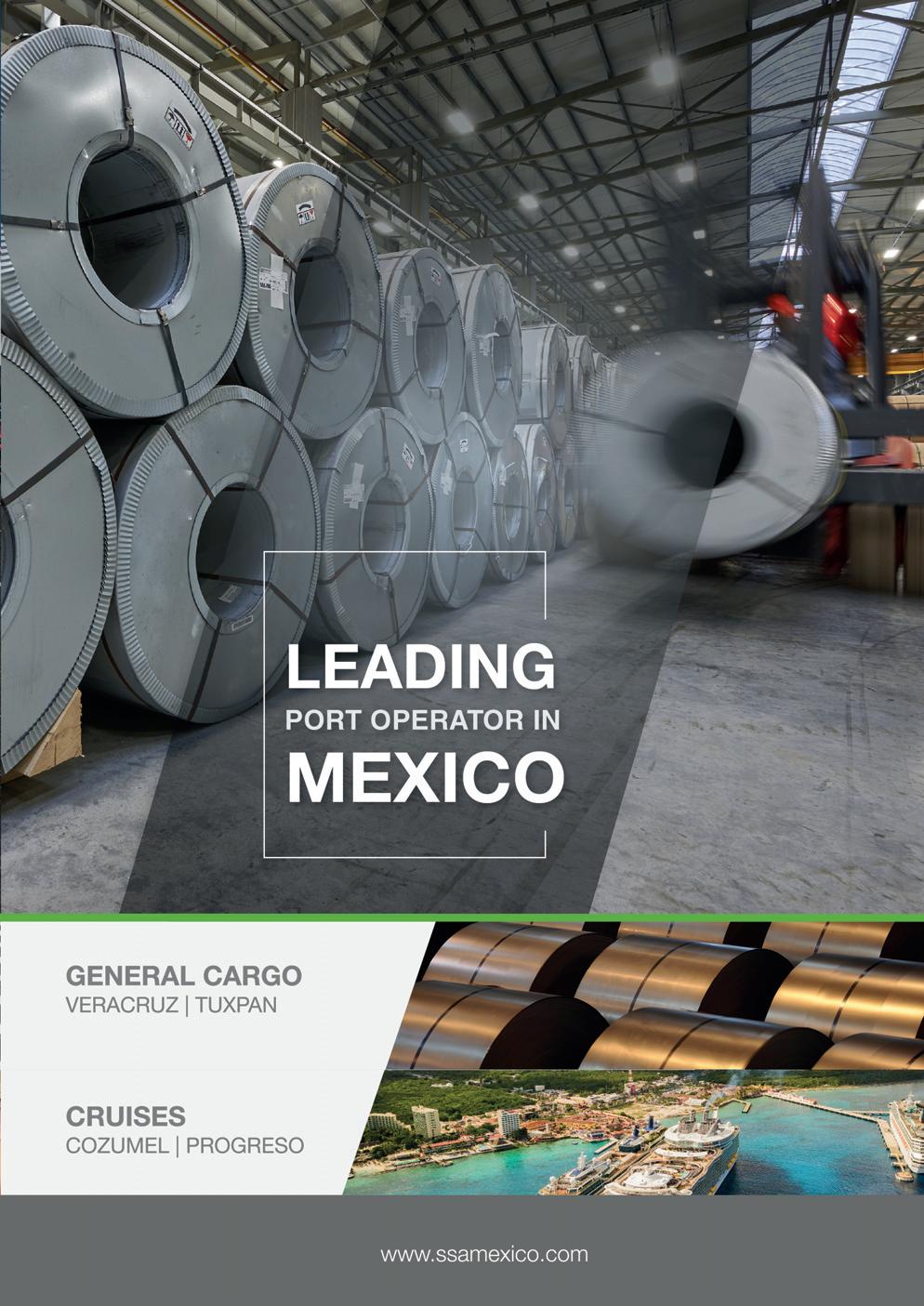
Perhaps the most interesting technical aspect of CG Railway’s operation is the way in which the ships are loaded. Each ship docks in a specially-equipped terminal. A sort of floating railway bridge is the inter face that then allows the railway lines on the ship to make a connection with the railway lines on the dock. Once everything is con nected, the rail cars are simply rolled onto the ship and eight hours later, the ship is on its way to its destination. After 22 years of successful operation, the company’s two existing rail transport ships are being replaced by two new ves sels, each boasting more than double the capacity. The new vessels ‘Maja’ and ‘Cherokee’ can each accommodate up to 140 rail cars across two decks, a substan tial expansion over the outgoing ships which each had a single deck and a 60 car capacity.
The key question then becomes: what is the reason that the company carries rail cars rather than just the containers or cargo that is on the cars, as per traditional methods? Mr Eversbusch had a clear answer: “The administration involved in transporting a load on the same rail car is simpler, the overall shipping time is reduced, and cargo damage is substantially decreased due to far less handling of the cargo.”
MARITIMEX I PROFILE 134 Inside Marine
A historic legacy Maritimex was established in 1885. The company began with a single, humble office in the port of Veracruz where it primarily acted as general and port agents for
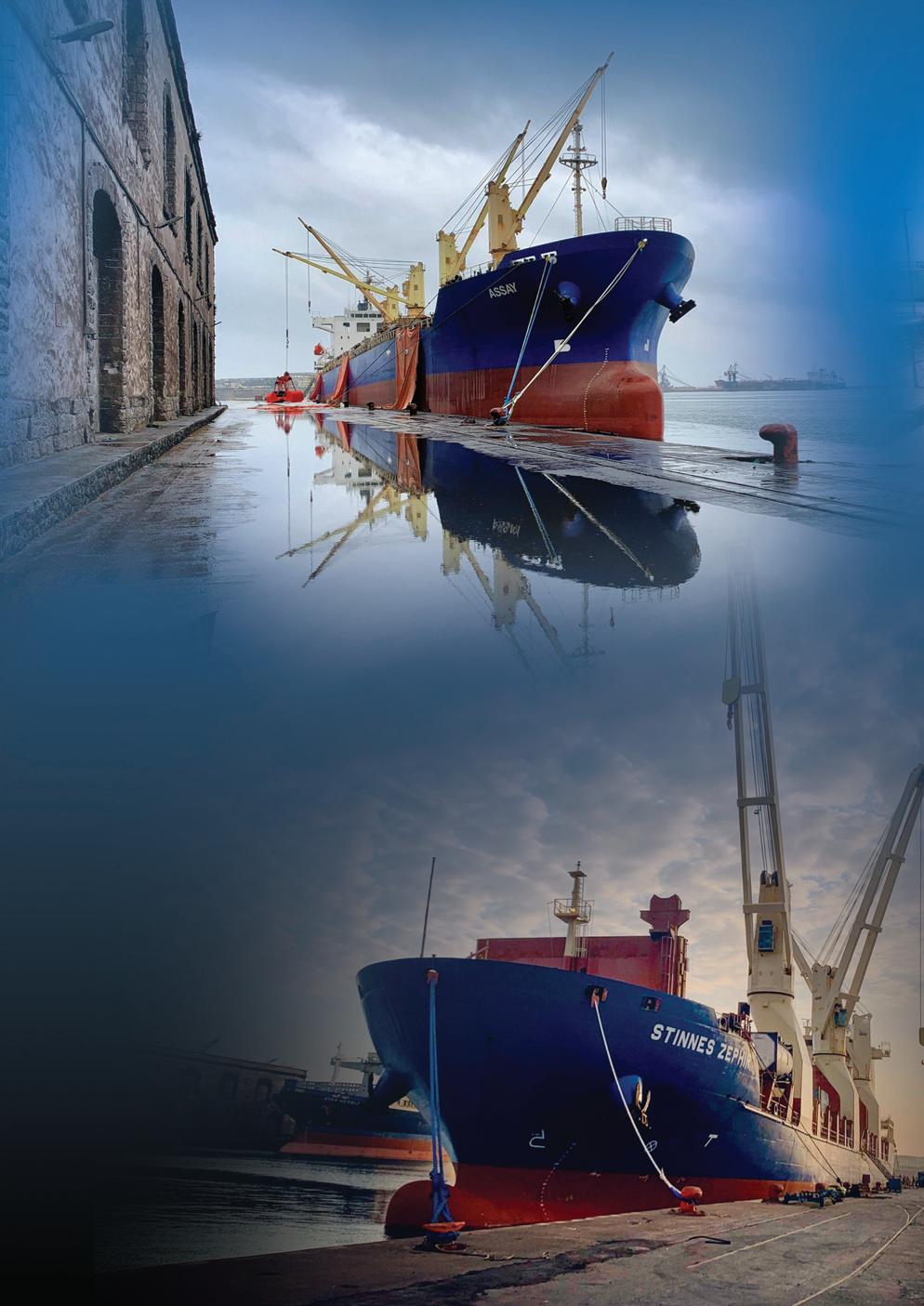
Maritimex is a family-run business that is now in its fourth generation of man agement. Today, Mr Eversbusch’s father, Ricardo Eversbusch, is the chairman of the board. The fifth generation, mean while, is being groomed to take over the business in future. The business was originally started by Mr Eversbusch’s grandfather who had come to Mexico from Germany in the late 19th century. Naturally, having survived two World Wars and a national revolution, the company has a colourful history. Mr Eversbusch was keen to share two particu larly interesting stories about his grandfa ther who once became an unexpected and unlikely political hero.
“In 1911, the Mexican Revolution was underway and things were getting really tough for everyone. President Porfirio Diaz had been pressured to resign and was forced into exile. My great grandfa ther found a passage for him on the lines we operated. He received the president in the Port of Veracruz and sent the presi dent on his way to France.”
“The company is looking to expand our coastal shipping services in Mexico as well as our warehousing, especially our grain capacity,” he continued. “We want to enlarge our intermodal container yard and in general, we want to serve more customers in Mexico.”
“We want the world to know that we’re in Mexico and we’ve been working here successfully for four generations. We are experts, with the footprint and the infras tructure to meet all of your shipping and logistics needs. We are here and we’re the perfect partner for you.” n
“When the revolutionary forces eventu ally approached Tampico, my great grand father negotiated with one of the revolutionary leaders to give the foreigners at the port (mainly engineers working at the large nearby international oil industry facili ties), time to evacuate. This was agreed to, and the foreigners left on various vessels. My grandfather was widely commended by the foreign embassies concerned, for his actions that saved so many lives.”
In closing, Mr Eversbusch drew on his family’s successful history as a message for potential future customers.
The second story took place in 1914 at the height of the Revolutionary period. “My great grandfather was living in Tampico at the time,” Mr Eversbusch recounted.
Future plans
With the company’s 140th anniversary now on the horizon, Mr Eversbusch com mented on the company’s plans for that milestone and the coming years: “We’ll definitely celebrate the 140 year anniver sary, but the one we’re really looking for ward to is reaching the 150 year mark. In the meantime, we’re working on intro ducing the fifth generation of the family to the business by ensuring that they get work experience in shipping companies outside of Mexico.”
Inside Marine 135 the Hamburg America Line. That line is also still around today, operating as Hapag-Lloyd.Thatparticular business relationship grew so strong that Maritimex retained it for 106 years. It eventually ended when HapagLloyd purchased Mexico’s TMM, effectively insourcing the services that Maritimex had been providing to date. Nonetheless, Mr Eversbusch was posi tive in his recollection of the relationship with Hapag-Lloyd and what it had meant for the company: “The relationship HapagLloyd enjoyed with us is the longest rep resentation relationship they’ve ever had anywhere,” he recalled. “We kept it in our family for 106 years; four generations of us were part of that relationship, actively working as agents for them.”

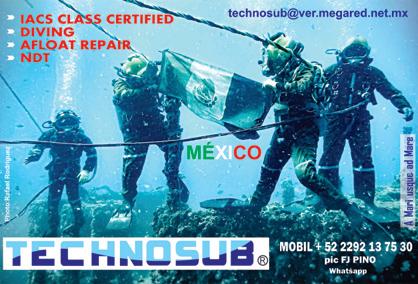
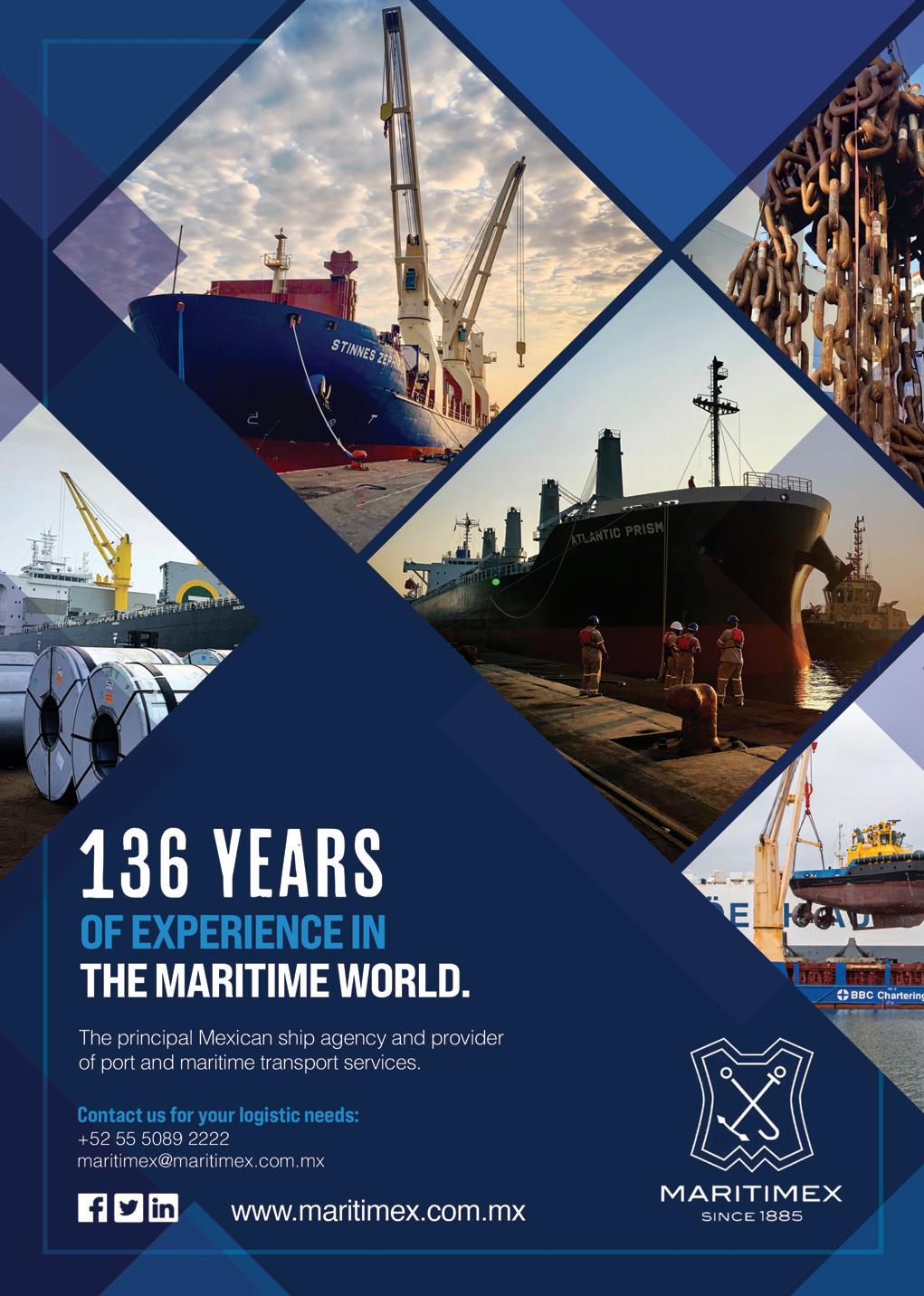
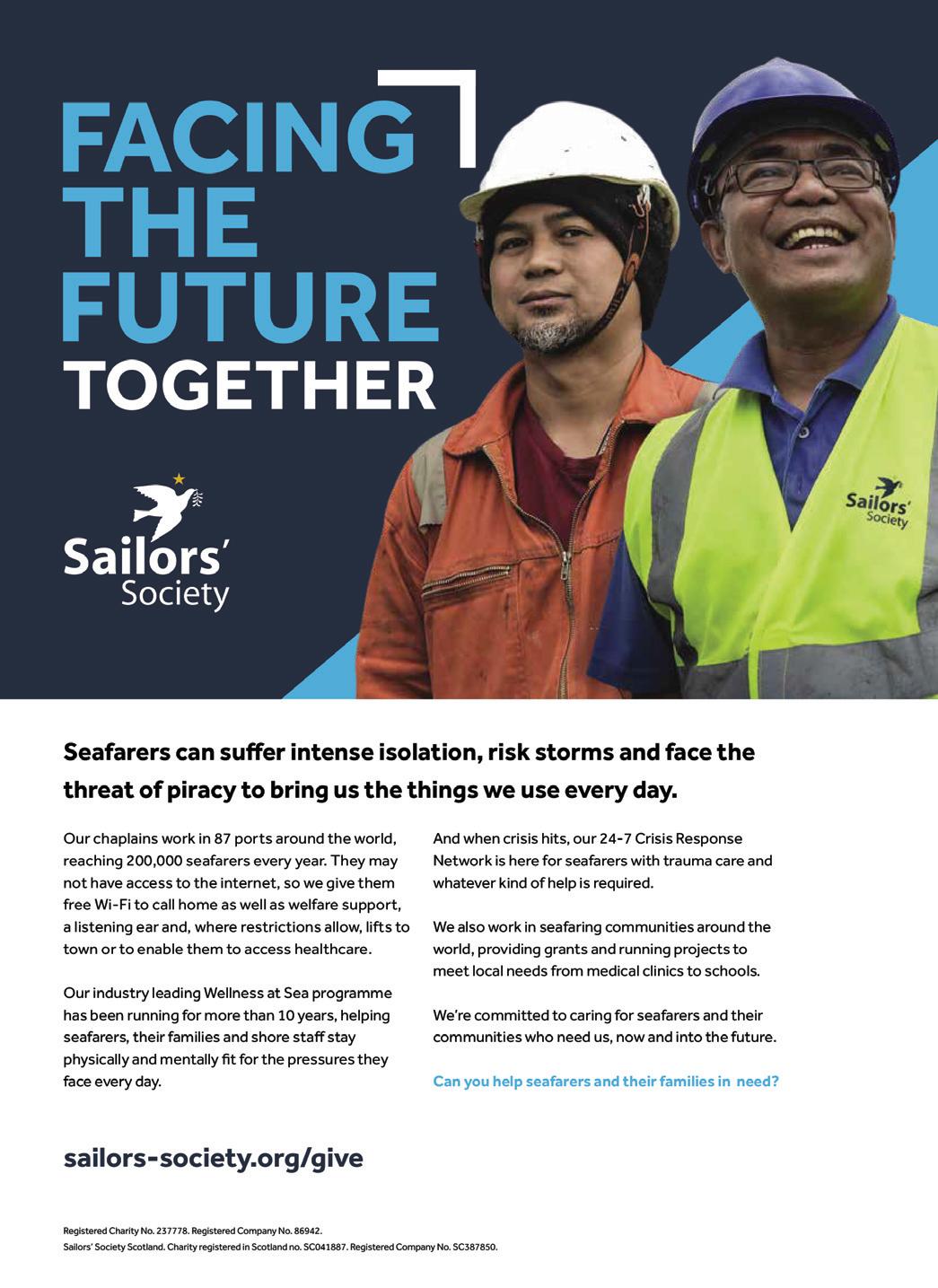
Having faced the challenges of Covid, Dubai headquartered Dockendale Ship Management has come out stronger and better, with no impact on the high-quality boutique customer service for which it is famous. Managing Director Satish Kumar revealed the company’s secrets to success and seafarer wellbeing to Richard Hagan.
DOCKENDALE SHIP MANAGEMENT I PROFILE 138 Inside Marine

According to Managing Director Satish Kumar, the company’s customer relationships are built on transparency and its ability to offer bespoke services.
“It’s something we maintain, and it makes us different from our competitors,” he said. “Our ability to offer customised ser vices is unique to us and it means that we’re constantly able to exceed customer expectations. Our ability to meet customers’ needs is appreciated via customer feedback forms. In that con text, we’ve maintained our generally high level of service and transparency throughout Covid, and today, the company is healthy and faring even better than before.”
He added that a properly trained crew could identify the issues on board and share the right information to the maker of the
Inside Marine 139
Training on topic A ship cannot sail without her crew, and therefore Dockendale Ship Management puts a huge amount of effort and resources into ensuring that its seafarers are well taken care of. Crew morale, in particular, is always a focus, and as Mr Kumar detailed, the com pany maintains it through its strong emphasis on ongoing crew training, especially in electronics.
“Traditionally, mechanical systems were taught in detail, but today the industry is trending towards electronic control systems for the main engines as well as for ballast water treatment and other systems. We want to ensure that we empower our seafarers to understand how these systems work so that they can operate them effectively at sea.”
INt he chaos and stress of Covid and its related uncer tainties and challenges, Dockendale Ship Management stayed the course and steadfastly con t inued to provide the customised customer service its clients love.
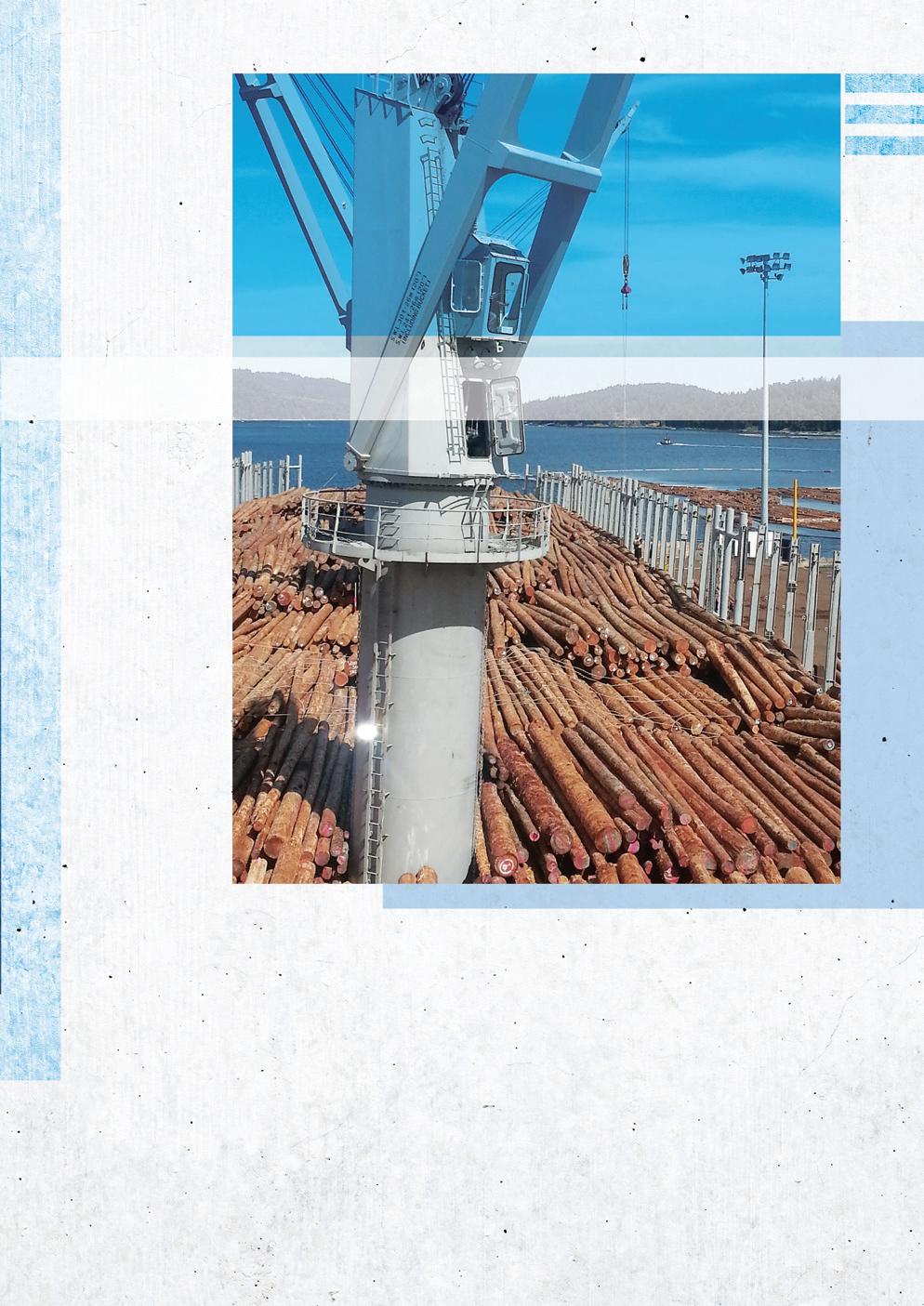
140 Inside Marine
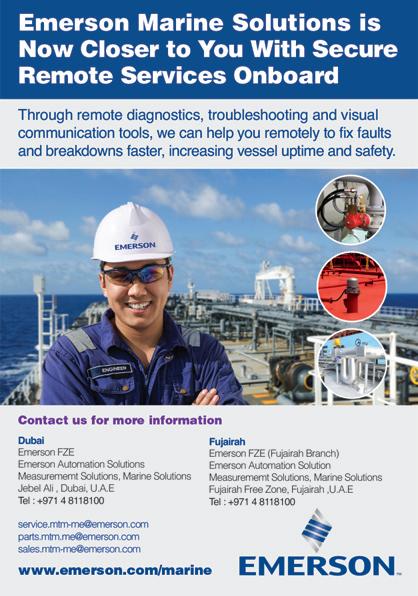
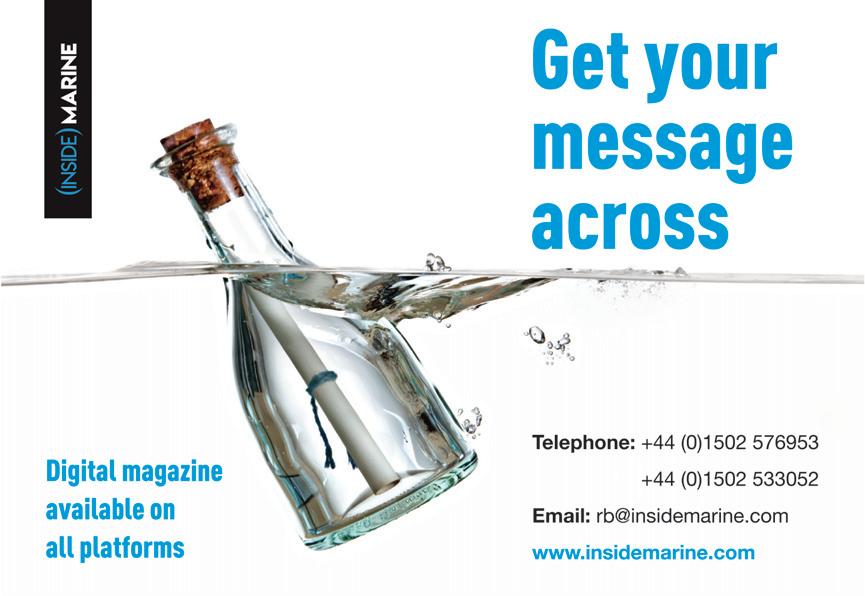


Inside Marine 141
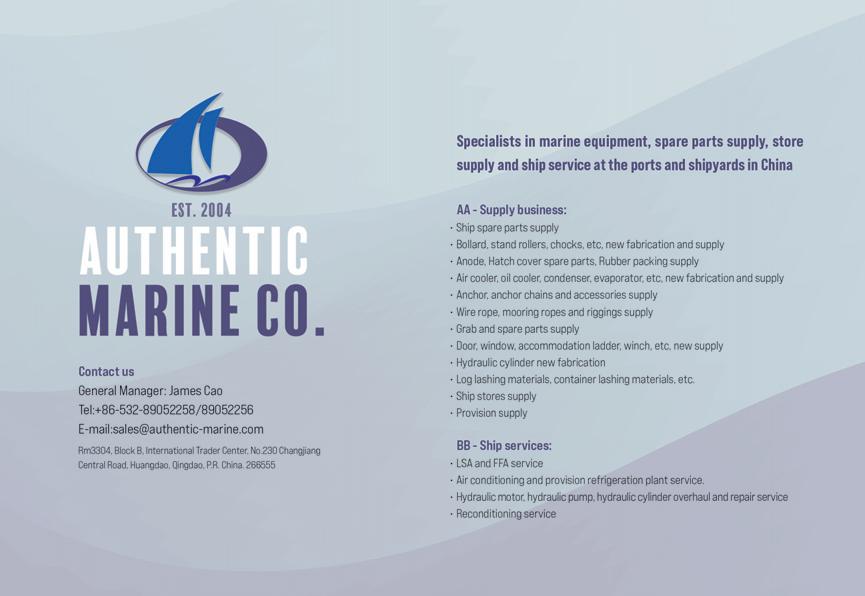
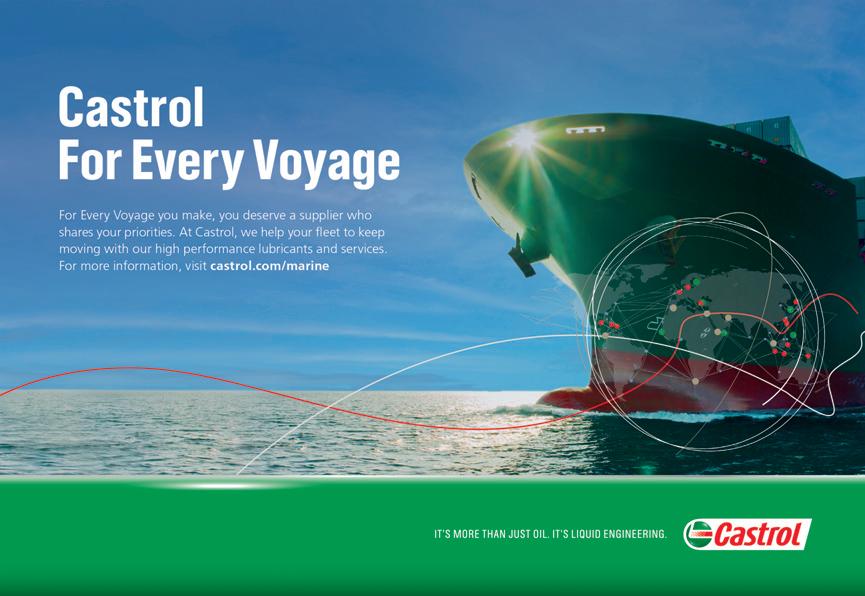
DOCKENDALE SHIP MANAGEMENT I PROFILE machinery or equipment. Dockendale Ship Management is cur rently rolling out VSAT installations to all of its ships to improve their bandwidth further and improve communication ability.
“The results of the programme have been great,” he con tinued. “The HR team constantly makes decisions about what we can improve based on those notes. These personal risk assessments have made a huge difference; accidents on board our ships have drastically reduced. We’re very proud of it,
Creating healthy workspaces Crew health is also vitally important to Dockendale Ship Management, and as we’ve seen during the Covid crew transfer crisis, mental health management is especially critical. Mr Kumar said the company’s staff visited vessels as and when possible and spoke to the crew and their families when their vessels docked in Indian ports. “We want to understand the crew’s mentality and mental health status,” Mr Kumar remarked. “We always say we want to know ‘the feeling behind the dealing’. How do the staff feel about our management approach? We don’t want to just assume that the staff are happy in their jobs and with the company’s decisions.”
The company additionally has a groundbreaking programme in place to continuously monitor and improve the safety of Dockendale Ship Management’s seafarers’ workplaces, and according to Mr Kumar, it all starts with handwritten notes. “Everyone on board is given a pen and a small notebook,” he said. “They record all of the risks they observe in their work every day, even in the smallest jobs. We encourage them to write everything down, even if it’s something as simple as a spanner that doesn’t quite fit its intended target. Those notes are seen in the office by our Manning Manager, who uses that information to improve the workplace safety of our seafarers.
142 Inside Marine
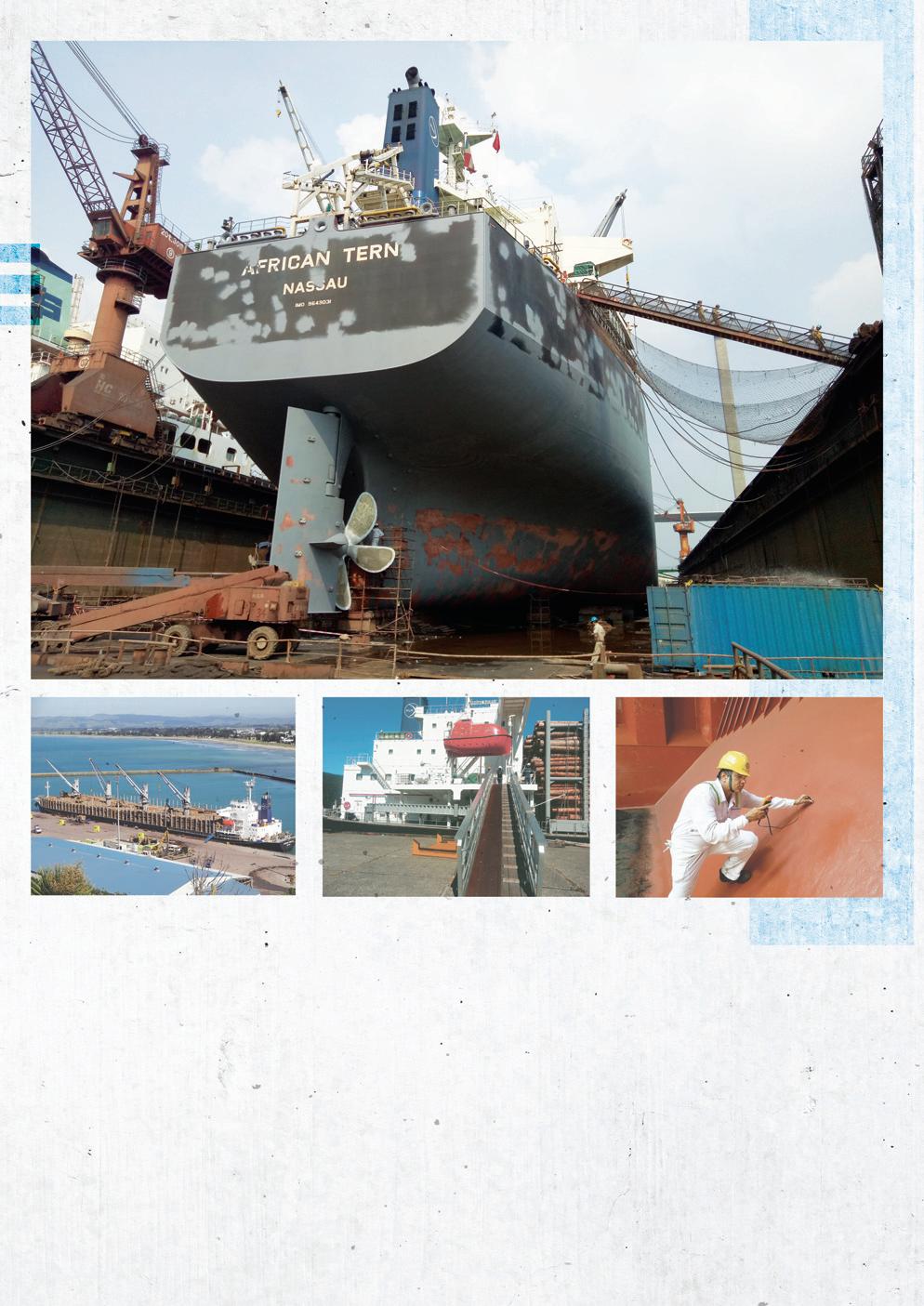
“Safety is obviously a concern with some of them, but we’re nonetheless at the initial stage of assessing the fuels market. As things progress, we’ll make a decision as to what the best choice of fuel is, but the availability of these fuels (and in the required quantities) is our biggest concern and the biggest challenge.
“It’s an industry-wide problem and, frankly, everyone is in the dark as to what the right future fuelling decision is,” Mr Kumar lamented. “Everyone is basically just waiting to see what is the best fuel going forward – considering economics and safety.”
“Of course, we’re studying all of the fuel options, including bio diesel, hydrogen, ammonia, LNG and others,” he continued.
Certified sustainability Dockendale Ship Management proudly boasts both an ISO 9001 and an ISO 14001 certification. The Managing Director expanded on the company’s continued efforts to meet these and other envi ronmental and sustainability commitments.
Mr Kumar confirmed that future fuels are an important debate at Dockendale Ship Management as well: “The whole world is struggling to choose the right fuel,” he said. “So in the meantime, we’re focused on being compliant with the IMO’s emissions regulations.
Fuelling the future Discussions around future fuels, as they’re known, continue to swirl throughout the shipping community. With so many potential fuels being offered as possible alternatives, ship owners and managers face critical decisions with potentially long-term repercussions.
Concluding, Mr Kumar offered some thoughts on Dockendale Ship Management’s future. “Optimism keeps people alive today, so we’re always opti mistic even though the global market isn’t looking great. Nonetheless, our plans are to get more ships onto our portfolio and to keep moving ahead toward our goals. I always say that we haven’t come all this way just to stay here. We have to move forward. We’re limitless.” n “Optimism keeps people alive today, so we’re always optimistic even though the global market isn’t looking great. Nonetheless, our plans are to get more ships onto our portfolio, and to keep moving ahead toward our goals. I always say that we haven’t come all this way just to stay here. We have to move forward. We’re limitless”
Inside Marine 143 especially because we don’t want anyone going back home with anWithinjury.”anaim to establish a framework for an effective system to c ontrol health and safety risks to crew, Dockendale is certified for ISO:45001.
“In 2021 we installed BWTS equipment on six vessels, and as of May 2022, we’ve done four, with two vessels still remaining to be fitted in 2022. It has all gone according to plan so far, thanks to good communication from our suppliers.”
“Our policy is to go green,” he remarked. “We adhere to the Japanese kaizen philosophy of continued small improvement steps. One of those is reducing our use of paper and increasing digitalisation throughout our offices. “We’re also getting rid of plastic bottles in the office,” he con tinued. “We encourage our staff to keep filling a glass or steel bottle and drinking from that instead. It’s just another small step we’re Meanwhile,taking.”thecompany is also fully committed to meeting international standards with regard to ballast water treatment Mr Kumar confirmed that while the company’s newer ships were delivered with such systems already fitted, Dockendale has been actively installing the systems on the rest of its fleet.
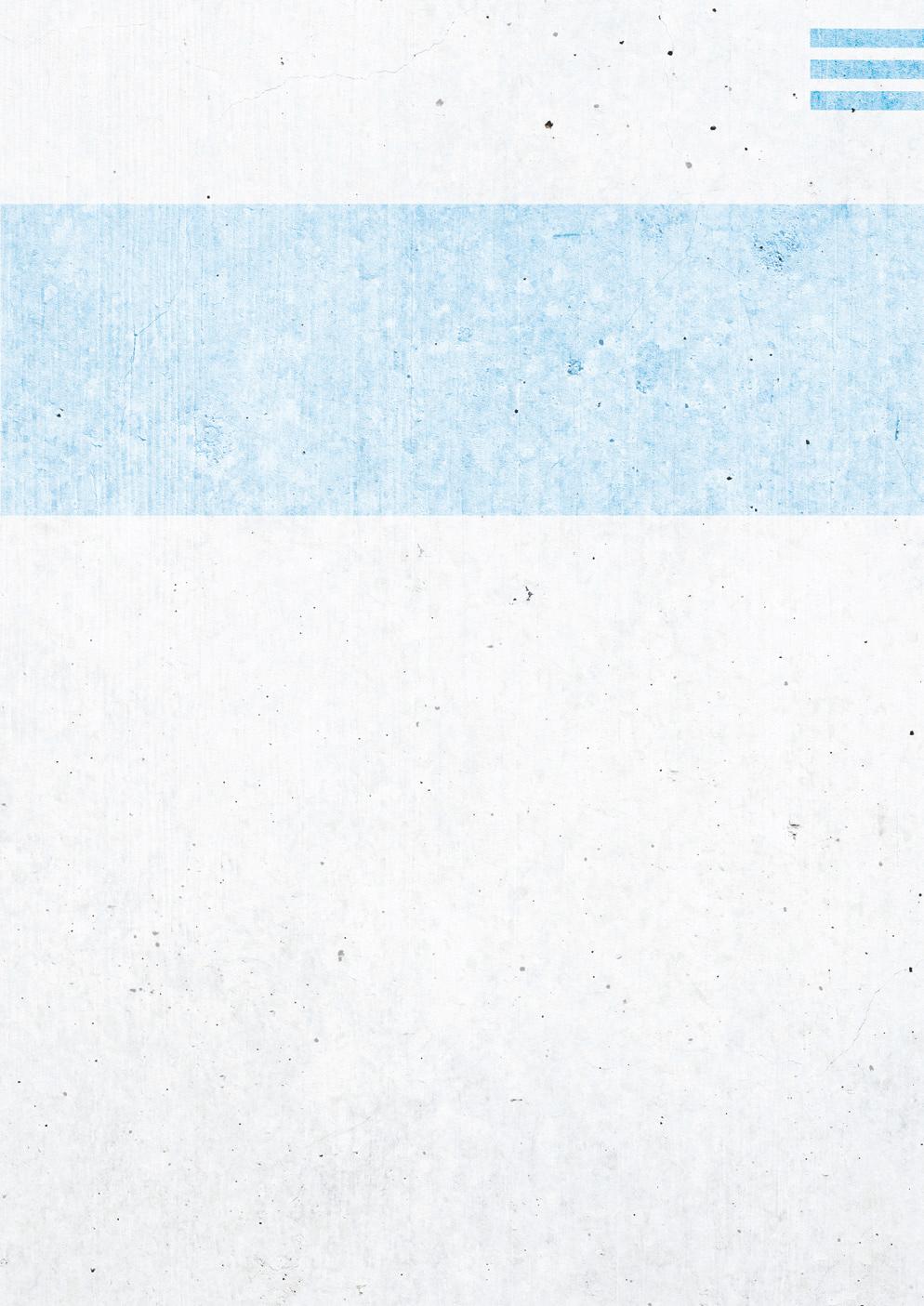

EASTERN CAR LINER AMERICAS I PROFILE 144 Inside Marine
Eastern Car Liner Americas (ECL Americas) is a subsidiary of Eastern Car Liner Ltd, a Japanese vessel operating ocean carrier based in Tokyo. The company’s fleet of Ro-Ro ships is the back bone of its service offering, but its fleet of multipurpose breakbulk ships has stolen the spotlight amidst the container shipping crisis. Bill Christ, Executive Vice President and COO of ECL Americas spoke to Richard Hagan about how the company is benefiting from the capacity difficulties afflicting container shipping across the Pacific.
CARGO theQUEUES with bulk
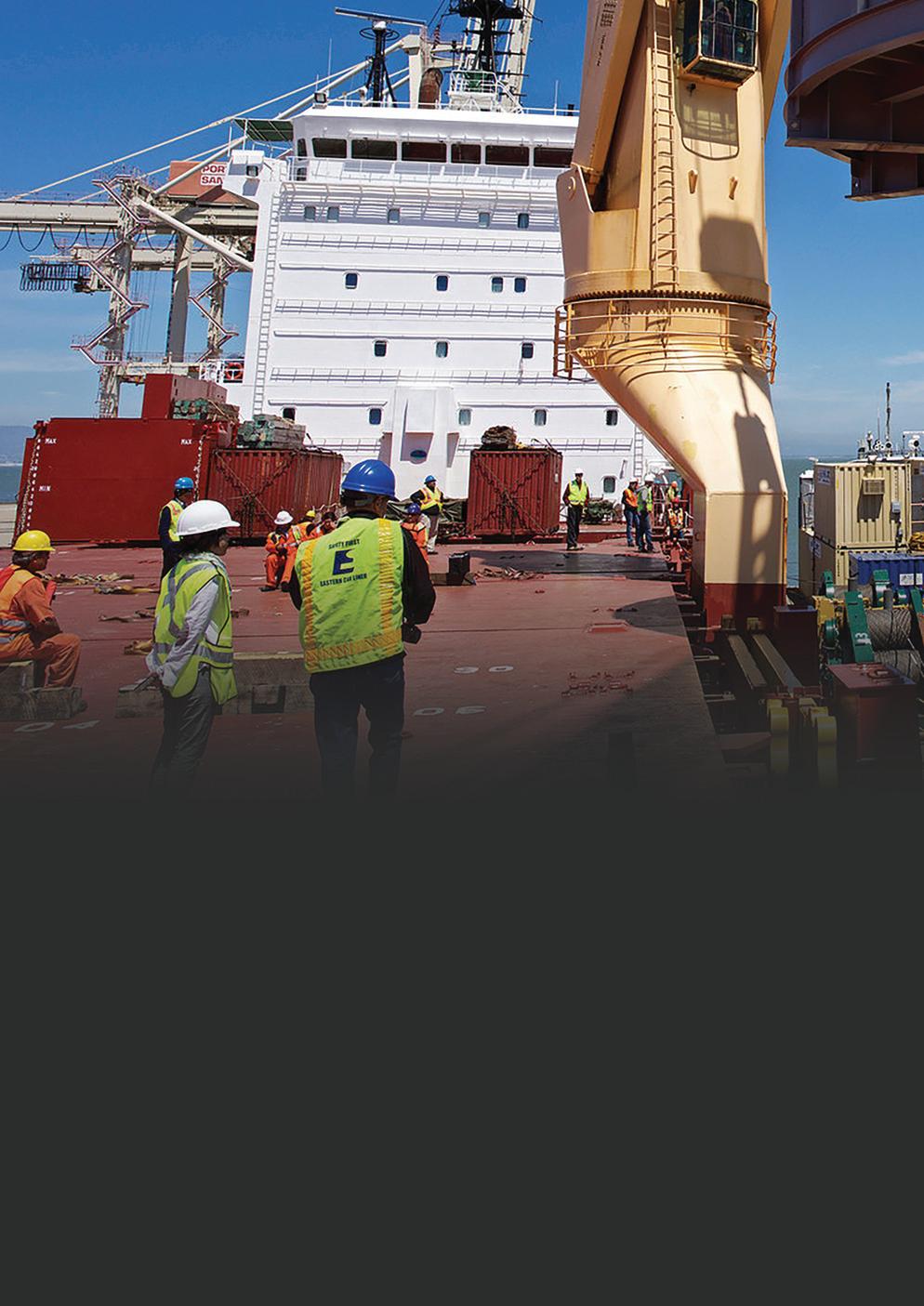
Shipping to North America
Inside Marine 145
“That turned out to be a much better way to ship these very large tyres,” said ECL Americas Executive Vice President and COO, Bill Christ. “Consequently, Eastern Car Liner Ltd established ECL Americas and since 1995, the base cargo of every ship of ours between Japan and North America has been those jumbo-sized off-road tyres.”
Eastern Car Liner Americas (ECL Americas) was born out of the fire and devastation of the 1995 Kobe Earthquake in Japan. With the ports and their container handling facilities knocked out of service, a major Japanese tyre manufacturer was in search of a new shipping solution for its jumbo-sized off-road tyres. These had previously been transported in open top containers to their destinations in North America. It was then that Eastern Car Liner Ltd stepped in and offered to transport the tyres via its breakbulk ships.
ECL Americas’ parent company, Eastern Car Liner Ltd, opened its doors in 1977. It operated – and continues to operate – a fleet of Ro-Ro and conventional breakbulk ships from Japan, to desti nations throughout the Far East and Southeast Asia, including Bay of Bengal, Persian Gulf and Australia. While its primary cargo is new and used cars, it also transports trucks and con struction equipment such as excavators. Bill Christ,Executive Vice President and COO
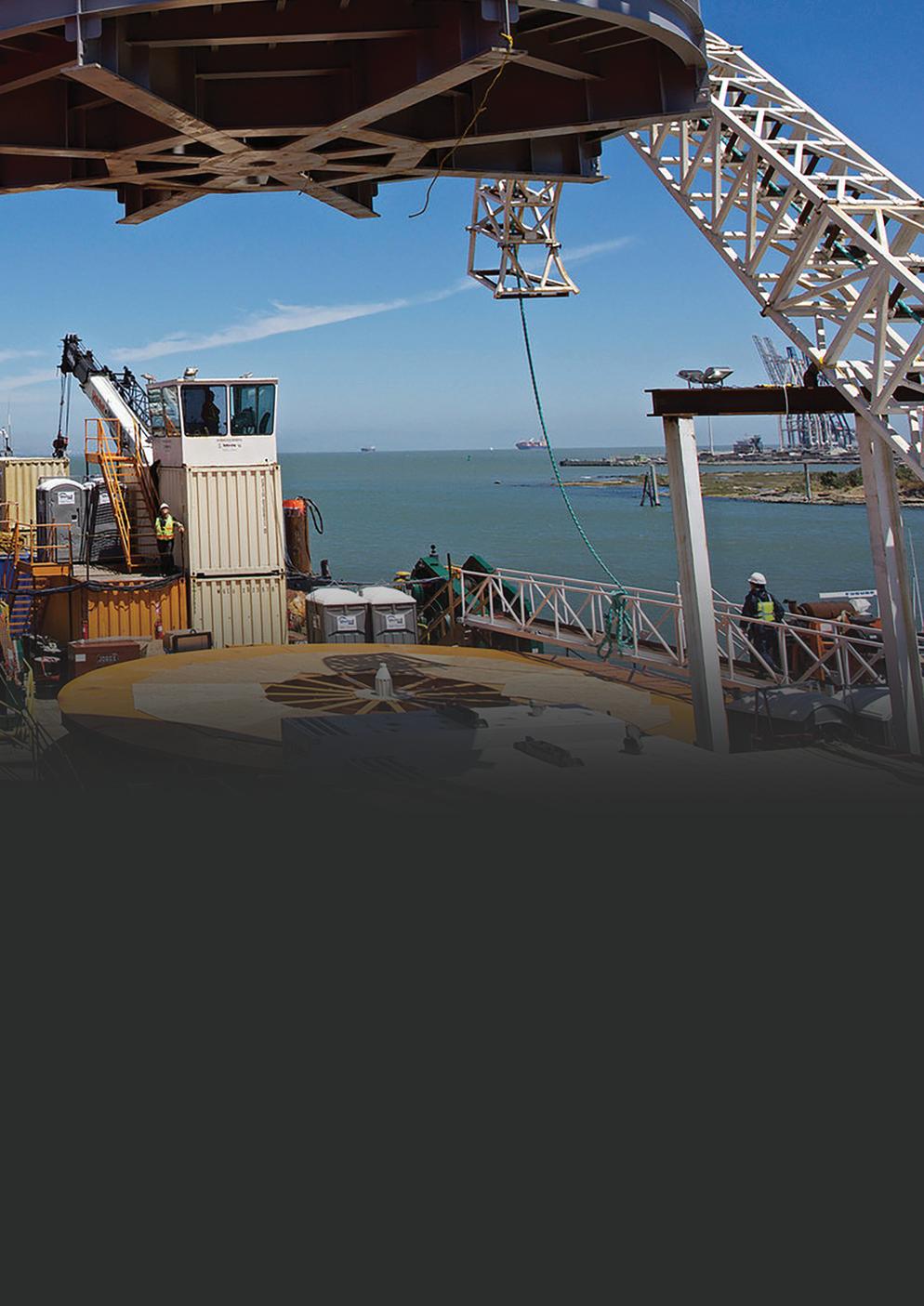

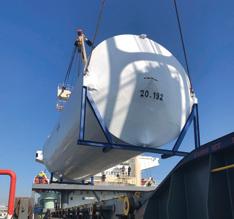
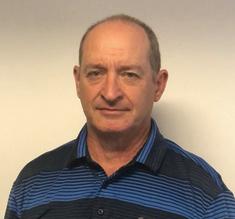
ECL Americas also carries a variety of other cargo, particu larly project cargo, machinery, construction equipment, and steel products like coiled steel, plate and wire rods. When its ships head back east, ECL Americas transports a great deal of US bulk commodities, primarily copper concentrates and var ious machinery consignments. In addition to its shipping business, Mr Christ revealed that ECL America has extended its services into the trucking industry as “ECLwell.
ECL Americas is the smallest of the subsidiaries and consists of three staff members, including Mr Christ, an assistant, and a sales executive based in Vancouver.
America is licensed and bonded as a truck broker. We spe cialise in cargos that are moving to and from our ships. In 2021 we became licensed and bonded as an NVOCC (non-vessel oper ating common carrier). This brings us additional opportunities in terms of scheduling, routing and capacity. Having this license gives us the opportunity to partner with other carriers to augment and fill out our own vessel operations.”
Eastern Car Liner Ltd is headquartered in Tokyo and employs 200 staff across its head office and its 18 overseas subsidiaries.
The company’s combined fleet consists of 15 Ro-Ro ships that operate primarily across Asia. Additionally, it operates 24 break bulk multipurpose ships, three of which are assigned to the company’s North America trans-Pacific rotation.
The trans-Pacific breakbulk fleet runs a semi-liner service, its regular route having stops at the Port of Long Beach, followed by Vancouver, Canada and then Everett, Washington.
146 Inside Marine
Opportunity amidst an unprecedented crisis As of June 2022, the container shipping industry continues to suffer from ongoing bottlenecks at major ports around the world. The problem is especially pronounced on the US west coast, with the bustling ports of Long Beach and Los Angeles forming the epicentre.
“We’re very much a niche carrier,” Mr Christ commented. “We don’t normally target container cargo, but the current situation within container shipping has created a lot of opportunities for us in addition to our usual non-containerised breakbulk commodities.”
EASTERN CAR LINER AMERICAS I PROFILE
The company was founded by a Japanese family but today, Eastern Car Liner Ltd’s ownership is shared between the family and several shareholding corporations.

Inside Marine 147
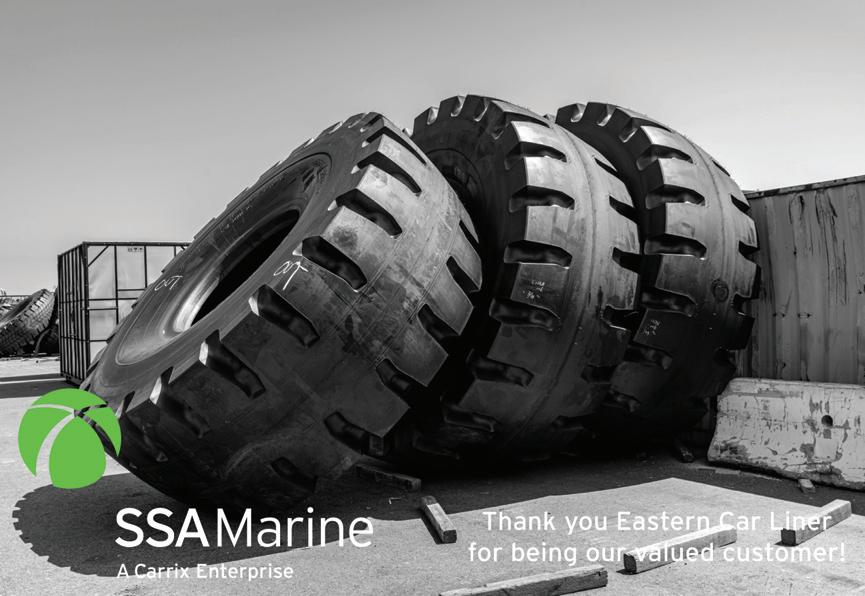
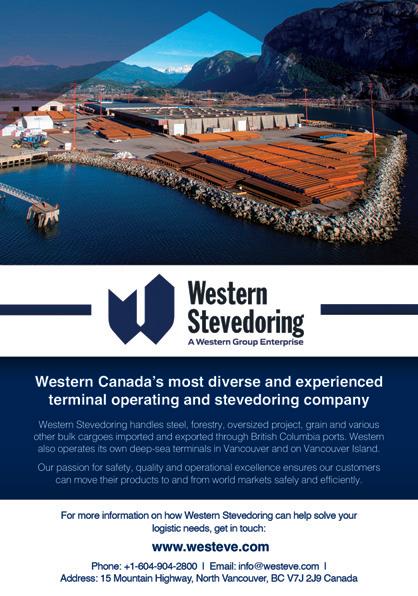
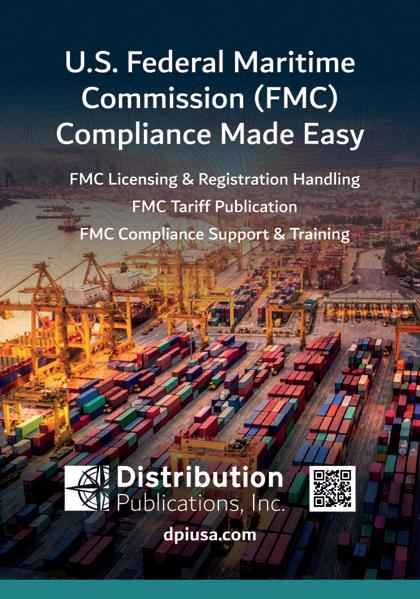
“Our ships don’t wait,” Mr Christ explained. “If anything, we might wait a day. Customers see that and ask if we’re able to get their cargo into our ships. It’s brought a lot of new opportunities forHeus.”went on to explain those requests in more detail. “A lot of cargo, mainly consumer goods, needs to ship in containers. Our ships are geared for oversize breakbulk, but people are nonethe less coming to us seeking alternatives because they simply can’t get their cargo onto the container ships.
“We don’t have our own containers as we’re not a container carrier, but people are bringing their containers to us and putting them on our ships. Some customers have been so desperate that we’ve been trying really hard to come up with some alternatives and different ideas for them. Cargo that should ship on containers is now moving to sources outside of the container pool. Even some
“The terminals there are just full,” he lamented. “They don’t have space to unload containers; there’s literally n owhere to put them. Every piece of available land has con tainers on it now. Ships sit at anchor or drifting, waiting to offload. People are waiting for one to two months for their“Peoplecargo.who traditionally rely on container ships have been put in a very difficult space,” he continued. “They’re not getting space on ships, access to equipment, or reliable schedules. Ships are waiting for extended periods.”
EASTERN CAR LINER AMERICAS I PROFILE 148 Inside Marine
According to Mr Christ, the problem is unprecedented in his career, but it’s also led to tremendous opportunities for ECL Americas. “I’ve been working in freight forwarding and ocean shipping for 35 years and there are activities going on right now that I’d never have imagined. The container crisis has really changed things quite a bit and a lot of cargo is now coming to us.”
ECL Americas’ big ace up its sleeve, amidst the crisis, is the fact that its vessels skip the queues at the container terminal, and visit the much less congested breakbulk terminals.
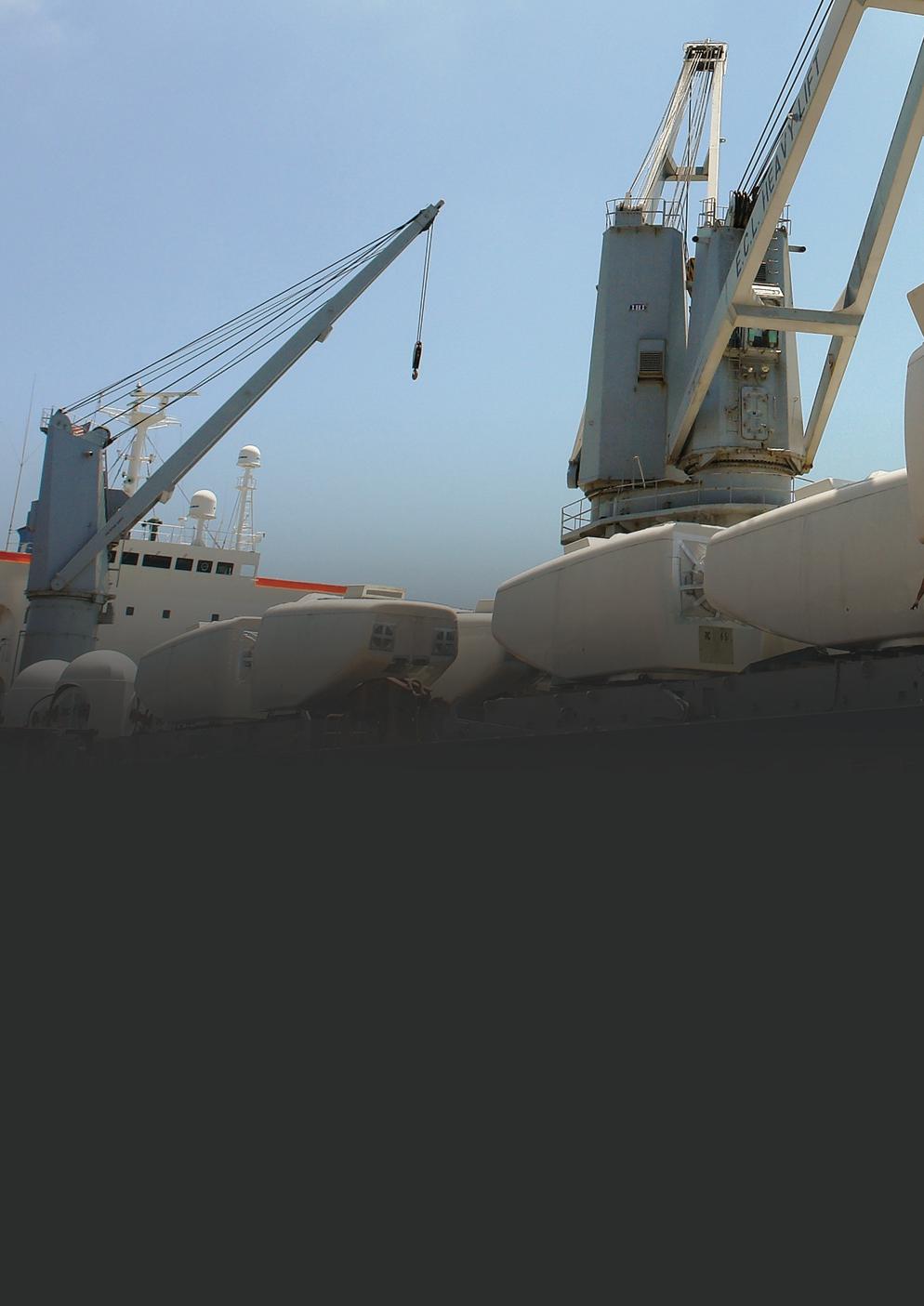
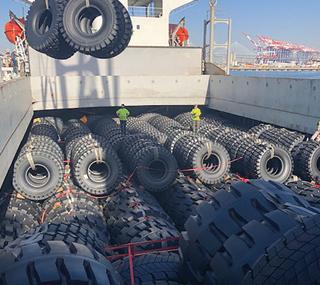
The company is now so busy that its primary challenge is capacity. “The North America group team at our Tokyo office doesn’t have enough capacity for the requests we’re getting. We’d really like to add more voyages in the trans-Pacific route but that would mean taking a ship from our intra-Asia network, and they need them there just as much as we do here. Meanwhile, in North America itself, our trucking business has been exceptionally busy. We’re very satisfied with it.”
Mr Christ’s link with Japan and his respect for its culture goes far deeper than his career though. In concluding, he pro vided some insight into how his Japanese links extend into his family and personal life as well: “I have a very long and deep connection with Japan, having spent my entire career working with and for Japanese customers. I’ve lived there twice and my wife is a Japanese national. My entire adult life has been con nected to Japan, so the culture and philosophy are close to my heart and a core part of who I am.” n
“Our decisions are based on long-term relationships and our priorities are with customers who have been with us the longest,” Mr Christ revealed. “Japanese business philosophy is all about sticking with customers and vendors for a long time. We’re small and attentive to their needs.” He added: “When you’re not dealing with cargo that fits in a box, you have to react to what they need, and we try to do that. Generally speaking, we’re doing everything we can to satisfy them and others as best as we can.”
The importance of long-term relationships As a subsidiary of a Japanese company, ECL Americas’ company culture is heavily influenced by its parent company’s own culture and business philosophy.
Inside Marine 149 of the big Ro-Ro ships that can handle static cargo as well are full. We’re sailing full, both east and west bound!”
He described the company’s tyre manufacturer client has been equally affected. “They still ship their smaller tyres – truck and car tyres – in containers, but they’ve not been able to get their supply chain moving on the container ships. So, they’ve come to us to book those smaller tyres with us. We’ve taken as many as we can, as best we can.”
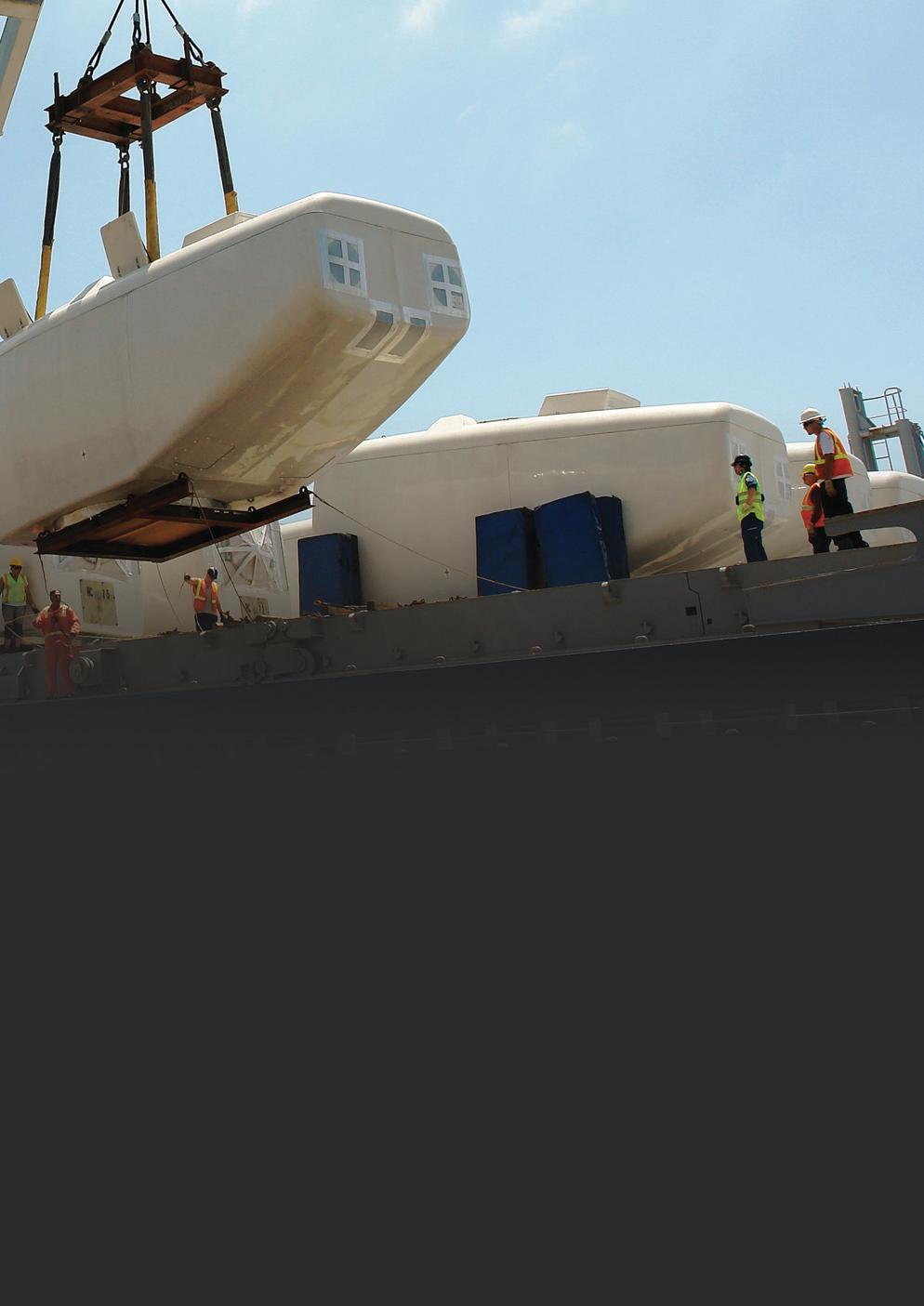
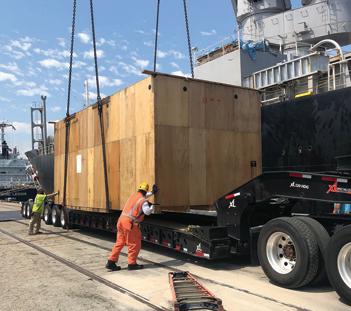
With more than 175 years of shipping history, the OL Shipping Group is a truly multinational company whose vessels are today ever primed for the ‘last mile’ of service in global ports. Enigmatic owner, Captain Eberhard Koch, sat down with Andy Probert and discussed how the company has continued to plot a cautious route as it navigates the demands and pressures of the 21st century.
MCP SALZBURG , Singapore, December 2018
OL SHIPPING GROUP I PROFILE 150 Inside Marine
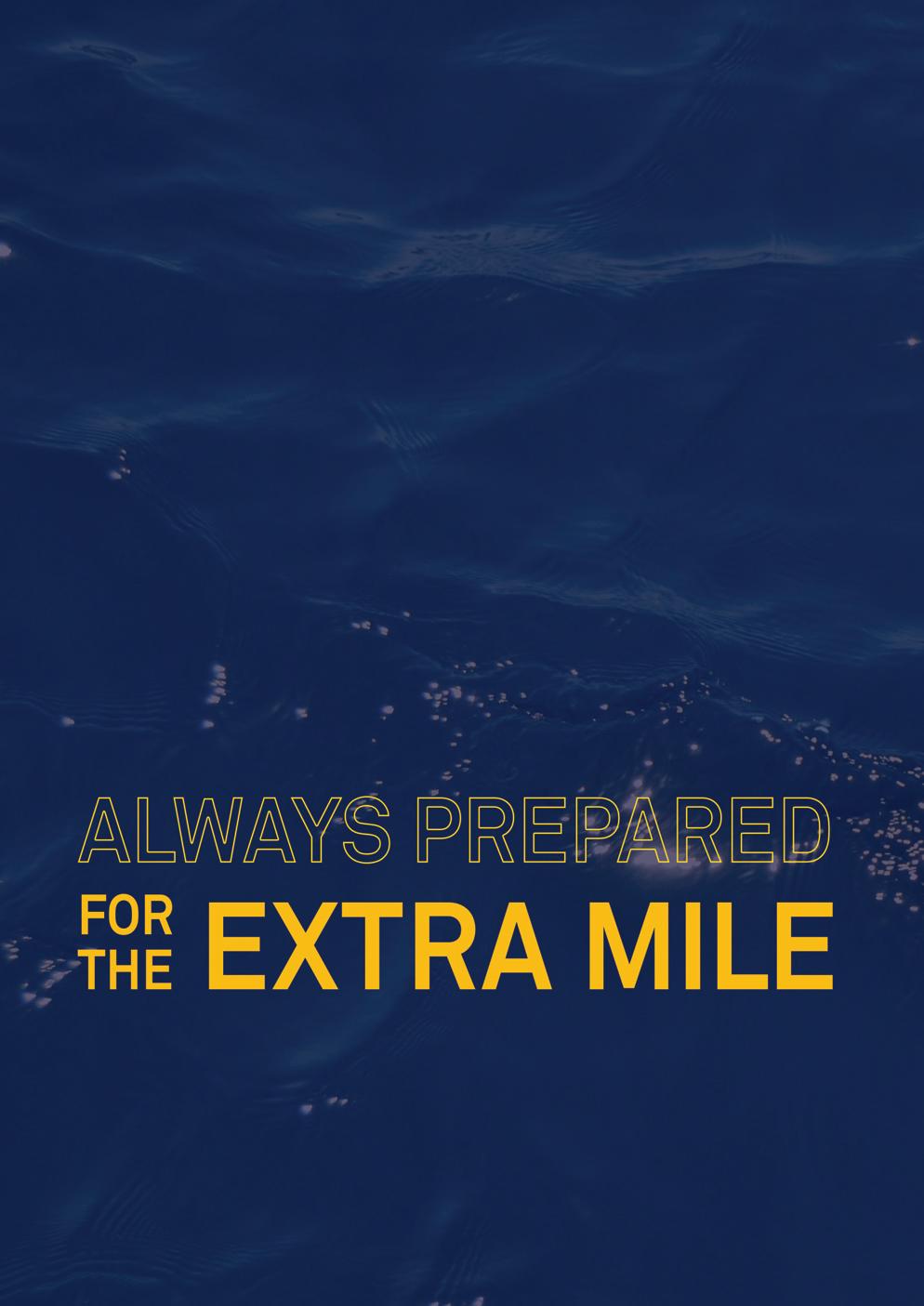

Capt. E. Koch supervising Drydock MCP GRAZ, Singapore, Sembcorp, December 2020
Empires come and go. But the delightfully named Österreichischer Lloyd Seereederei has prevailed in one form or another across three centuries. Its Germanic motto “Vorwärts”, or ‘Steaming Ahead’ in English, comes to mind as owner and CEO Captain Eberhard Koch, described the rise, fall and rise of this tenacious company.
As it is known today, the OL Shipping Group operates a fleet of four 618 TEU geared, multipurpose feeder containers presently on long-term charter to clients in East Africa and the Far East.
Recalling a rich history It is a far cry from 1833, when the first strands of its existence came into being during the time of Emperor Ferdinand I of Austria. Seven insurance companies of Trieste founded “Austrian Lloyd Trieste” along the same lines as Lloyd’s of London. By 1838, it had a 10-strong steamer fleet deployed as a postal sea service for the entire Austro-Hungarian Empire, including a fortnightly service between Alexandria to Limassol and Larnaca and from Constantinople to Cyprus and back.
MCP GRAZ drydock Singapore, Sembcorp
Capt. E. Koch, elected as the President of Cyprus Marine Club.
2018
Inside Marine 151
Growth continued apace, with the company expanding its fleet to 61 vessels and establishing its own shipyard. It took on an inter national dimension with three steamships operational at the opening of the Suez Canal in 1869. By 1886, it was one of the world’s biggest shipping companies, boasting 86 steamships deployed on 1526 round trips to global destinations. By the end of the 19th century, activities extended to Europe, Asia, Africa, and Australia. However, the fleet decreased significantly during World War 1, and by 1918 Austrian Lloyd was dissolved, mirroring the col lapse of the Austro-Hungarian Empire. After the war, some of the company’s operations continued from the port of Trieste under the name Lloyd Triestino. The Austrian company resumed in 1951, but it wasn’t until 1976 t hat it bought its first vessel, a multi-purpose, geared semi-container vessel, with the strong, backing of a German investor. With Capt Koch’s arrival as joint Managing Director in 1984, the company grew further, amassing 33 vessels from 3,000 to 120,000 DWT under the Austrian flag. In 1991, an in-house ship management company was established,
The vessels, each 7,700 DWT, are pressed into service for con tainer, bulk cargo and special projects, carrying everything from helicopters, steel coils, windmills, cement in big bags, tanks and heavy oil industry equipment. The two cranes are combinable to lift 80 mts.
“We have a well-earned reputation, born from a desire to execute our services with diligence, care, and transparency,” he said. “By providing reliable, high quality, sustainable, and cost-efficient transportation, we contribute to the success of our global clients by adding value and ensuring the shipping chain keeps moving.”
The ship owning companies and the in-house management com pany are headquartered in Limassol, Cyprus. A 10-strong on-shore team, including in-house crew managers, oversees the fleet’s global operations and its pool of 100-150 loyal seafarers. All vessels proudly fly the highly reputable quality flag of Cyprus.
December 2020
As Capt Koch asserted, OL Shipping Group’s primary role is to go the extra last mile, effectively carrying and discharging all manner of cargo into ports that larger container or multi-purpose ships cannot viably access or the infrastructure to load or discharge is not available.
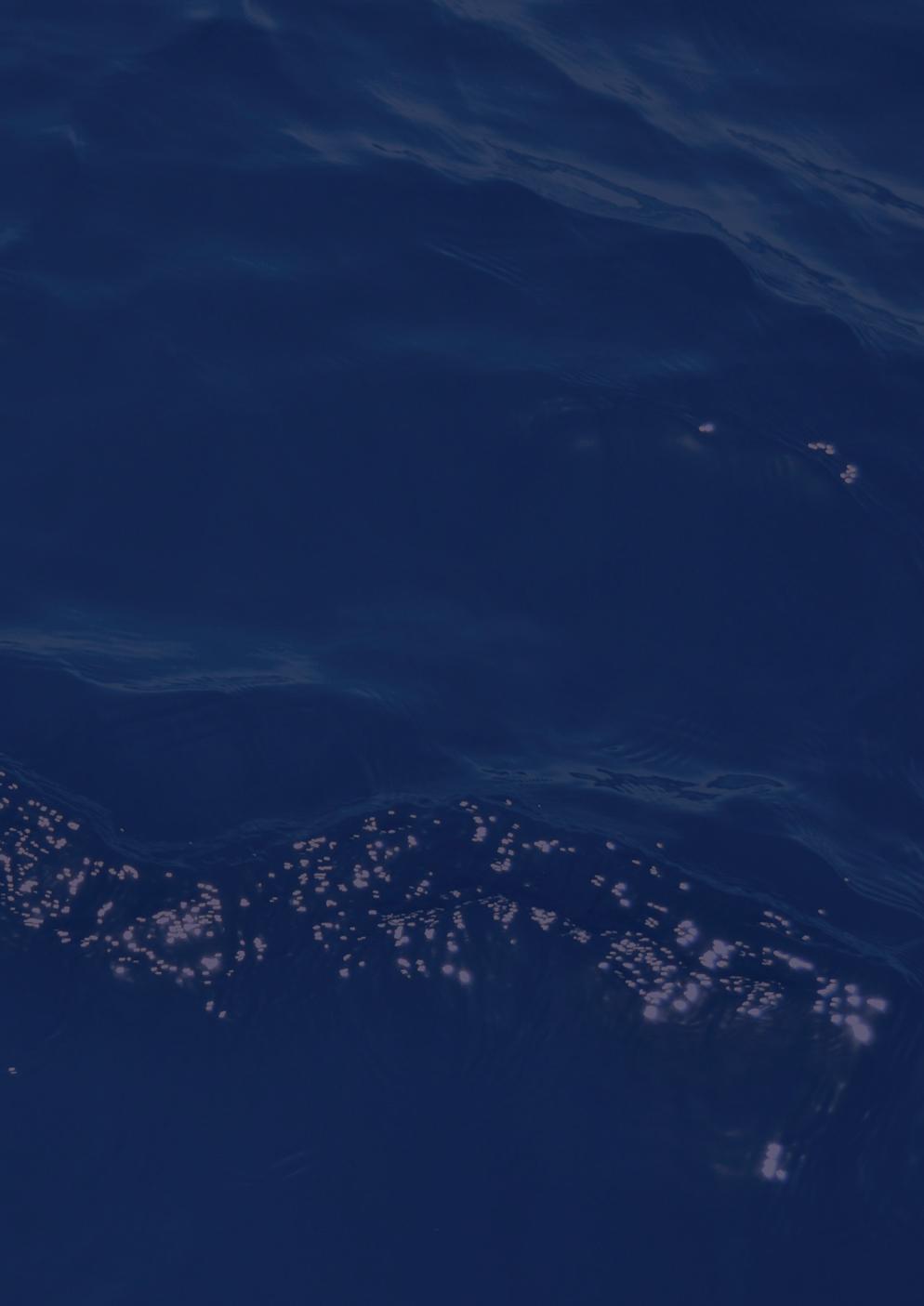
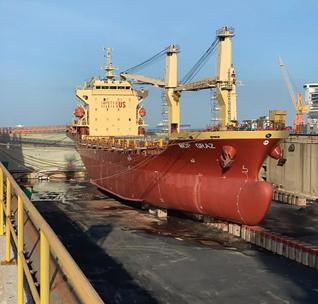
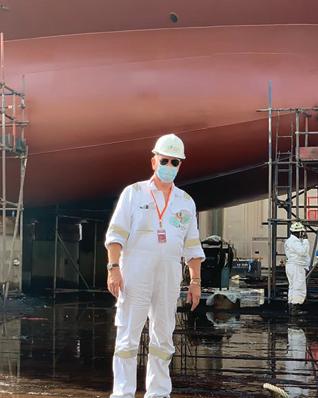
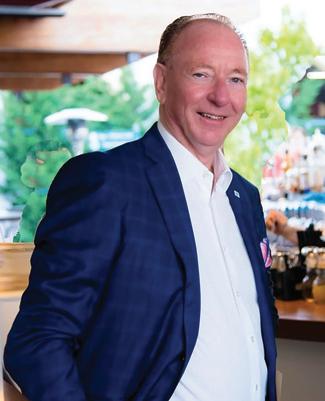
152 Inside Marine
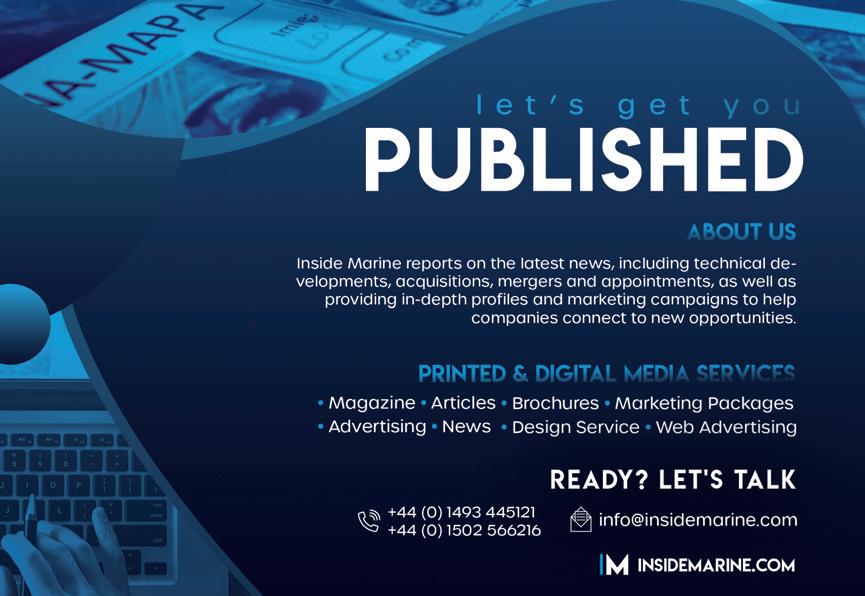
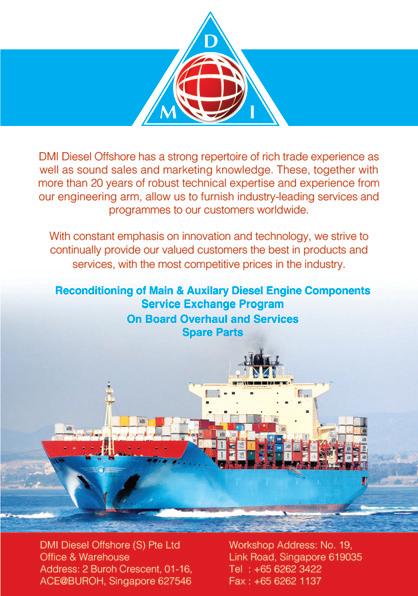

Inside Marine 153
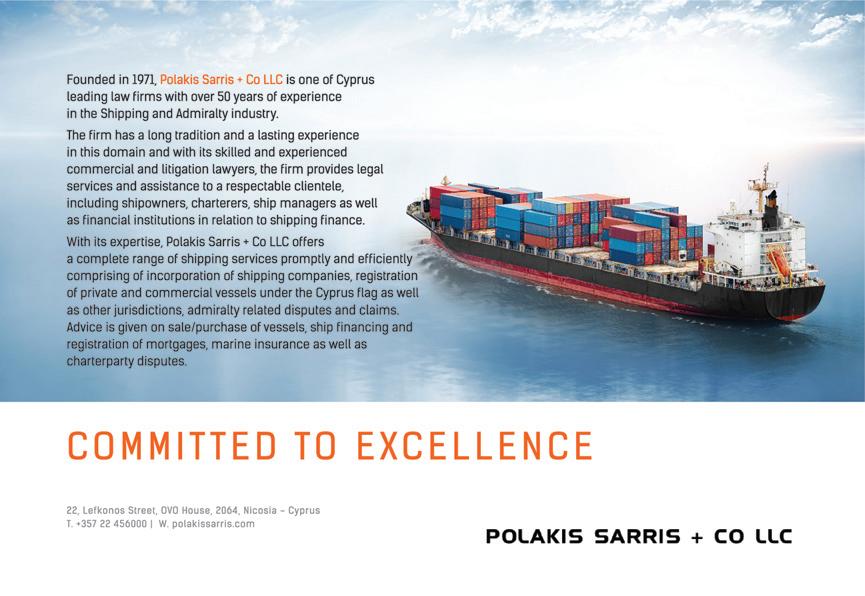

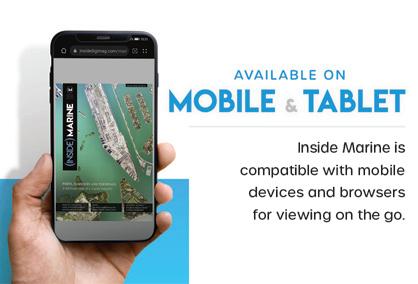
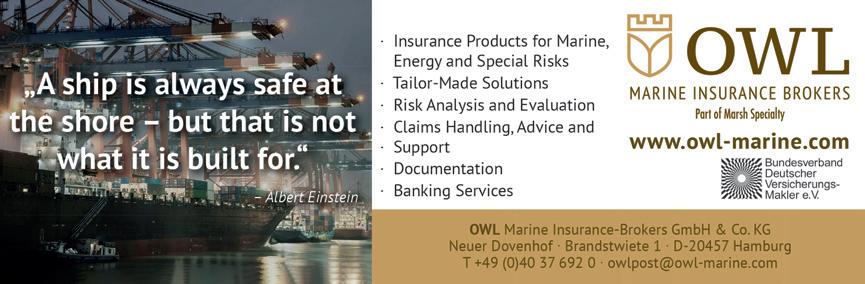
The OL Shipping Group is a member of the Cyprus Union of Shipowners, of which Capt Koch has been a board member since 2018.
OL Cadet/ Nautical apprentice
As group owner, Capt Koch cultivates strong family ethics and resilient commitment from management down to their “wonderful” multinational and multicultural teams.
Singapore 2020 Master MCP GRAZ, Yousif Girgis December 2020
Capt Koch re-affirmed the company is very much focused on achieving a safety-first, incident-free workplace. The bedrock of the group is based on six pillars: safety, performance, integrity, collaboration, sustainability and innovation.
He added: “Our people are at the heart of our business and the key to success. As our capabilities continue to evolve and expand, we remain focused on attracting the best talent to join our dynamic teams.
Moving forward in modern times
“By joining OELSM, employees become part of a global group of multinational experts. We are collaborative, curious, and always open to learning. Our international team bring different skills and ideas to inspire innovation.”
The family-run company has also been a long-time supporter of the ‘Adopt a Cadet’ campaign by the Cyprus Maritime Academy of which Capt Koch is Chairman of Governors.
“I am proud of being internationally recognised for our broad spectrum of close contacts and our excellent reputation with all stakeholders, he stated. “I believe this is a clear indication of our high-quality standards; delivering our services with confidence and adding value overall. Realising our values is the key to our longevity and success for long-term cooperation.”
As much as the group is responding to the industry’s main chal lenges, he said the pandemic had presented a unique set of issues, particularly with crew changes.
“There have been areas where crew changes were impossible. We could not take our seafarers home even after fulfilling their contracts; others were unable to join ships to replace stranded crews. This led to a significant loss of income, resulting in hard ship for seafarers and their families.
OL SHIPPING GROUP I PROFILE 154 Inside Marine overseeing 75 vessels at its peak, and the business switched to pure ownership again in 2006. Having previously relocated to Cyprus, the company rebranded and emerged re-energised.
“Crew change regulations are different from country to country, and in some places, like China, Covid-related policies vary signifi cantly from port to port.” He reflected: “This humanitarian crisis has resulted in significant mental strain, fatigue and, consequently, an increased risk of acci dents, imperilling the working conditions within shipping.” Capt. E. Koch with Head of Mechanical Workshop, Sembcorp,
“We believe training of new personnel is a necessary investment for the future of our fleet,” he said. “We employ young nautical offi cers who, together with the cadets, we train on board and who rep resent our future. We also have two highly motivated and inspired female cadets within our fleet.”
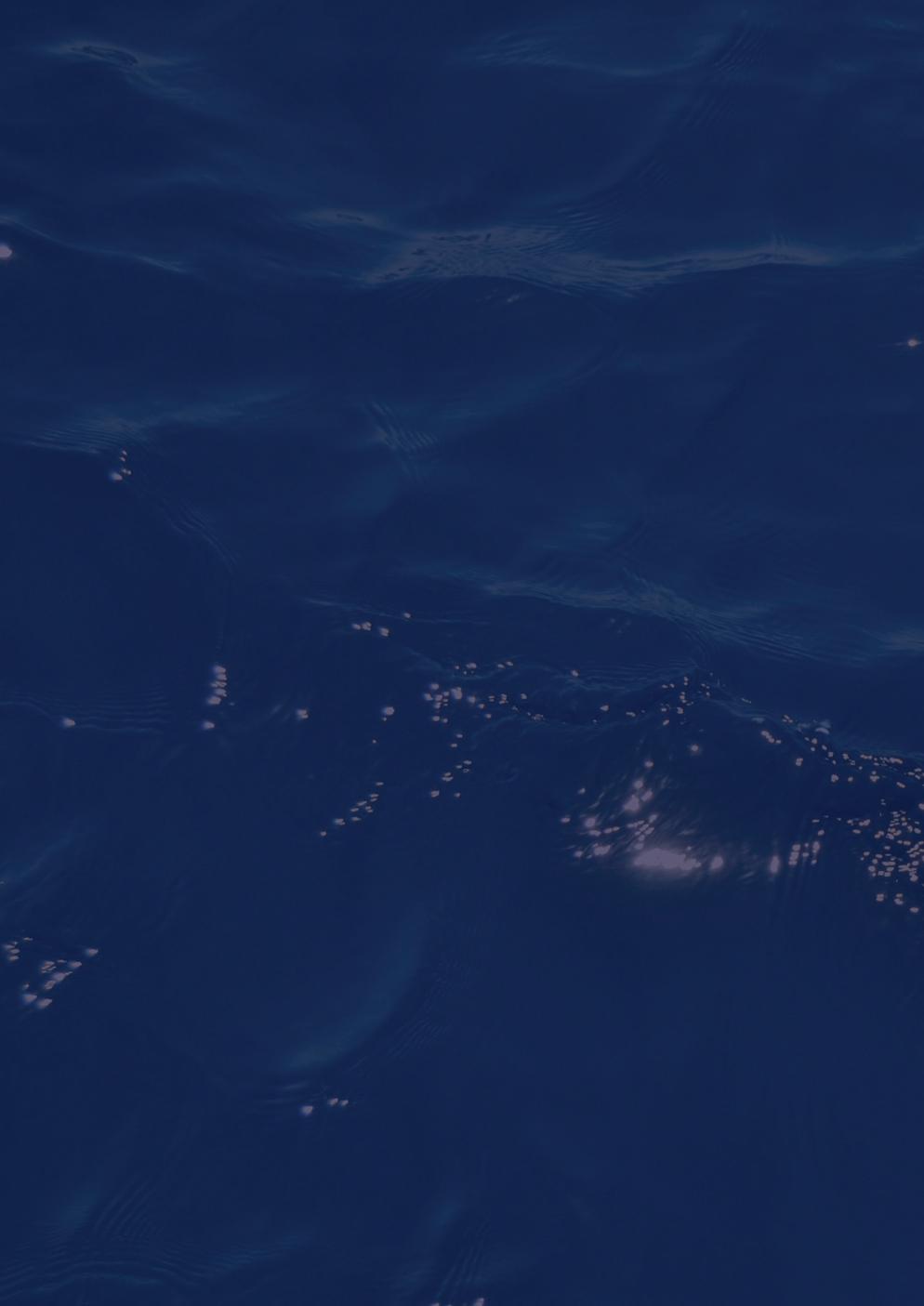
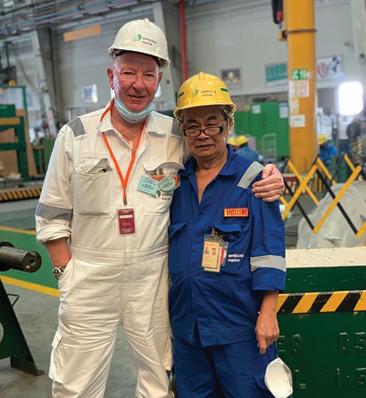
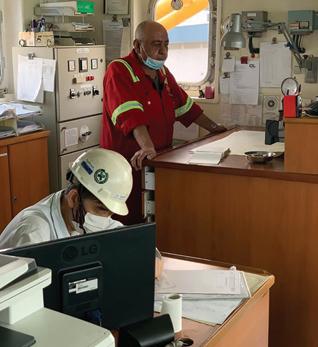
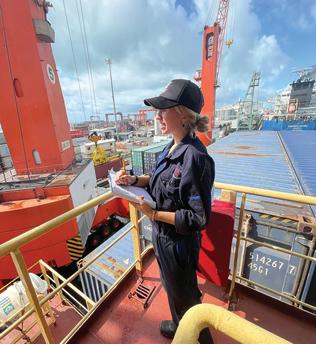
He concluded: “I believe our people in the OL Group are key players in this difficult global game and are already leaders providing solutions, cooperation, and excellent services to our customers and suppliers.”
He revealed the OL Shipping Group is fully committed to further greening of the maritime sector and is itself in the early stages of working on green shipping projects.
The Captain’s dream team
Acknowledging the impacts of the Ukraine conflict on the avail ability and working of Ukrainian crew members, he said: “We need to work together with all possible players in the shipping industry and in general.
“Some estimate more than $1 trillion in capital needs,” Capt Koch remarked. “Systemic changes in the way ships are designed, built, and financed may be necessary. Alternative financing and equity markets as alternatives to capital markets need to be explored.”
“We missed chances here and there. In 2006/2007 it was easy to finance the series of container ship newbuildings which still are part of our fleet today. Then, with the sudden downfall in markets, and the unwillingness of German banks to further finance, we were luckily supported by our shareholders: thus we managed to survive! What has also saved us through the decades was our belief in remaining conservative in this volatile business called shipping and not touching the German KG system.
“One thing that characterises our industry is the number and kind of challenges we deal with daily.” These, he pointed out, included being aware of the capital markets’ unwillingness to finance investments necessary to meet the extensive new envi ronmental regulations.
“Additionally,communities.onekeychallenge for the industry remains the Turkish embargo on Cyprus-flagged vessels entering its ports. There are hopes the ongoing political dialogue will lead to a set tlement, which would give renewed impetus to the sector.
“Having said that, we chose not to be the fastest in the expansion. Now, we have set aside enough funds to have the freedom to make analytical decisions. Our investment decisions in 2021/2022 have been very low. We have no newbuilding programme. If we invest, we will be buying second-hand vessels. There has been too much uncertainty to know which fuels to use in the future.”
Capt Koch asserted that to maintain recent positive trends, govern ments, and industry, along with international organisations, need to scale up their efforts to limit the effects of emerging variants of covid on crew changes while safeguarding the health and wellbeing of sea farers and global
“The next generation of shipping leaders will be focused on sus tainability, diversity, technological solutions, and environmental stewardship. They are sophisticated in finance and practical about operations, highly educated, from diverse backgrounds, love the industry, and understand its uniqueness.
“I consider myself an optimist. As with all difficult challenges with industry-wide innovation, there will be many opportunities, and we will embrace the future with a positive outlook.
“We have been in the business for a long time, and under our stable shareholding structure, we intend to stay in it for the longterm. Personally speaking, I’ve been in Cyprus for over 20 years now. I love living in Cyprus, and it really feels like home.” n
Inside Marine 155 MCP GRAZ, Anchorage , Singapore February 2021
Optimism before challenge Reflecting on investments the company has – or hasn’t – made in recent years, Capt Koch outlines OL Shipping’s pragmatic approach.
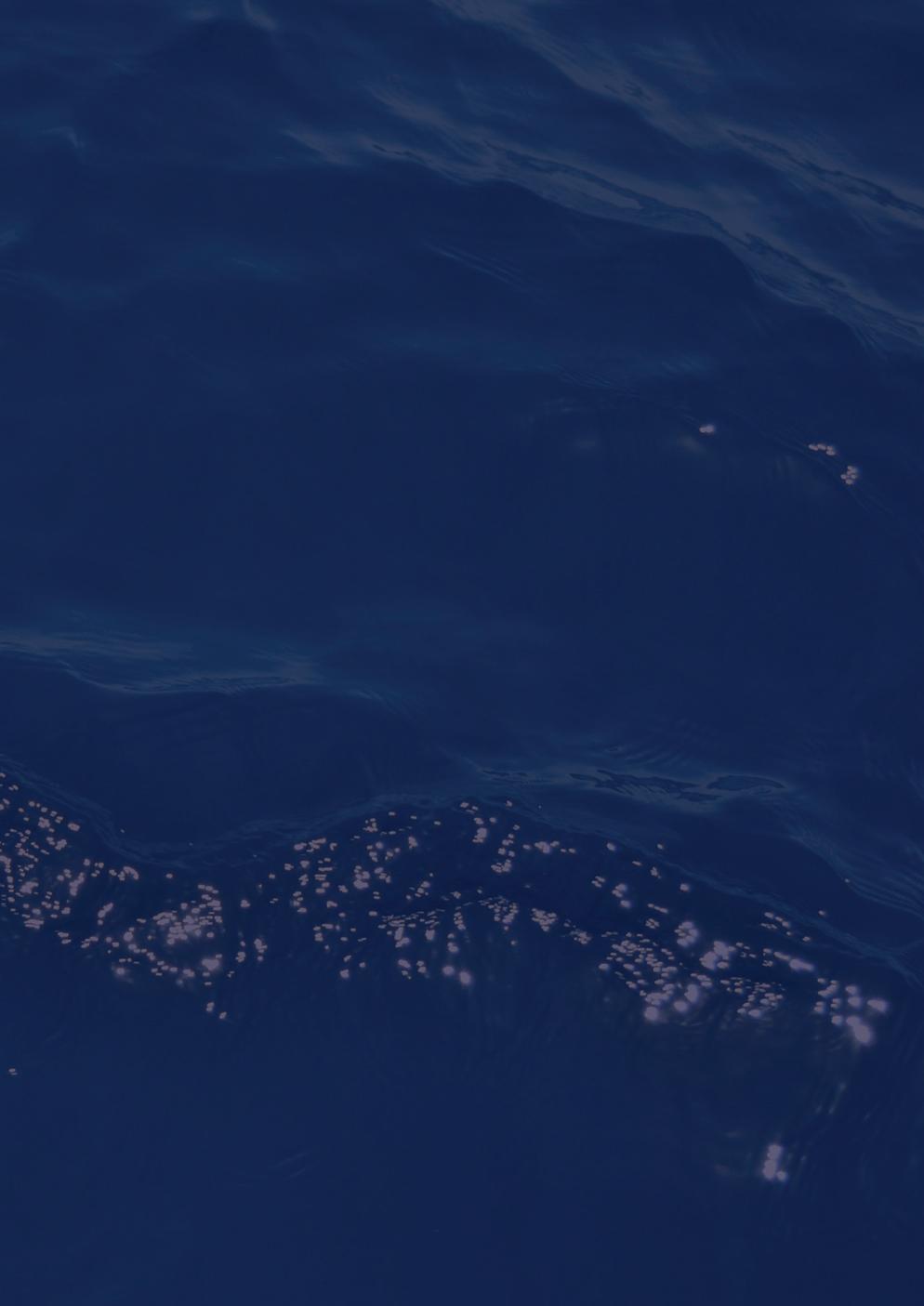
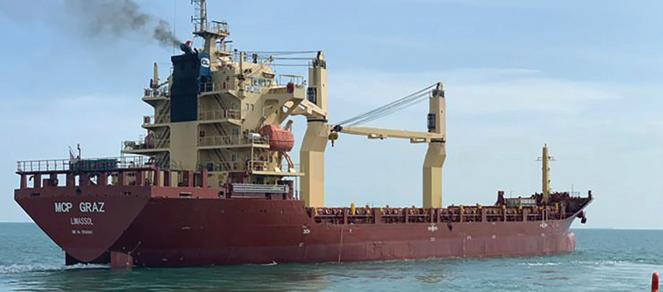
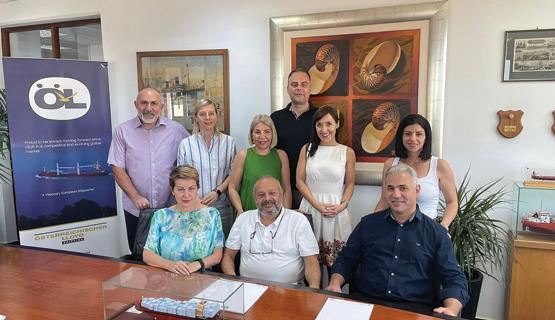
A
VARIETY CRUISES I PROFILE 156 Inside Marine
Variety Cruises is a Greek small cruise line offering immersive sevenday life-enriching adventures at sea. Filippos Venetopoulos, CEO, discussed his vision for the company with Phil Nicholls. T he Covid pandemic hit the cruise industry hard. Filippos Venetopoulos took over Variety Cruises as CEO in 2020 on the passing of his father and inherited a business with zero revenue. “I took over a 70-year-old start-up; that’s how I see our business,” said MrThisVenetopoulos. ‘start-up’began in 1949 when Diogenis Venetopoulos launched Zeus Tours Company. The company evolved into Variety Cruises in 2006 under the leader ship of Lakis Venetopoulos, in a merger with Hellas Yachts. Filippos Venetopoulos is now the third generation of the family at the helm of the business as it builds up again after the global pandemic. Variety Cruises operates a fleet of eight small cruise vessels. The fleet varies in size from 17 to 36 cabins, operated by a team of 250 employees. Variety offers 12 itineraries visiting 16 countries across four continents, operating 290 days a year and carrying, annually, around 15,000 passengers. As to be expected for a Greek company, the Variety portfolio features cruises around the Aegean and the eastern Mediterranean. Variety also provides a selection of cruises across the globe including ones exploring Tahiti, the Seychelles, West Africa and Costa Rica. The Limited Collection cruise packages from Variety feature itineraries devoted to themes such as Aegean wine, unexplored Greek Islands or a culinary cruise in the Seychelles.
The concept is providing seven-day life-enriching experiences at sea that allow the fleet’s guests to go deeper into the destinations. Deeper into the culture, deeper into the communities, deeper into the culture, so the limited collection allows returning guests to experience the same destinations by going deeper per the thematic.
Mr Venetopoulos is very clear about the USP of Variety Cruises: “It’s the overall cruise experience. It’s the size of the fleet, the Greek hospitality and the Greek twist that
The yacht cruise experience
bespokeodyssey
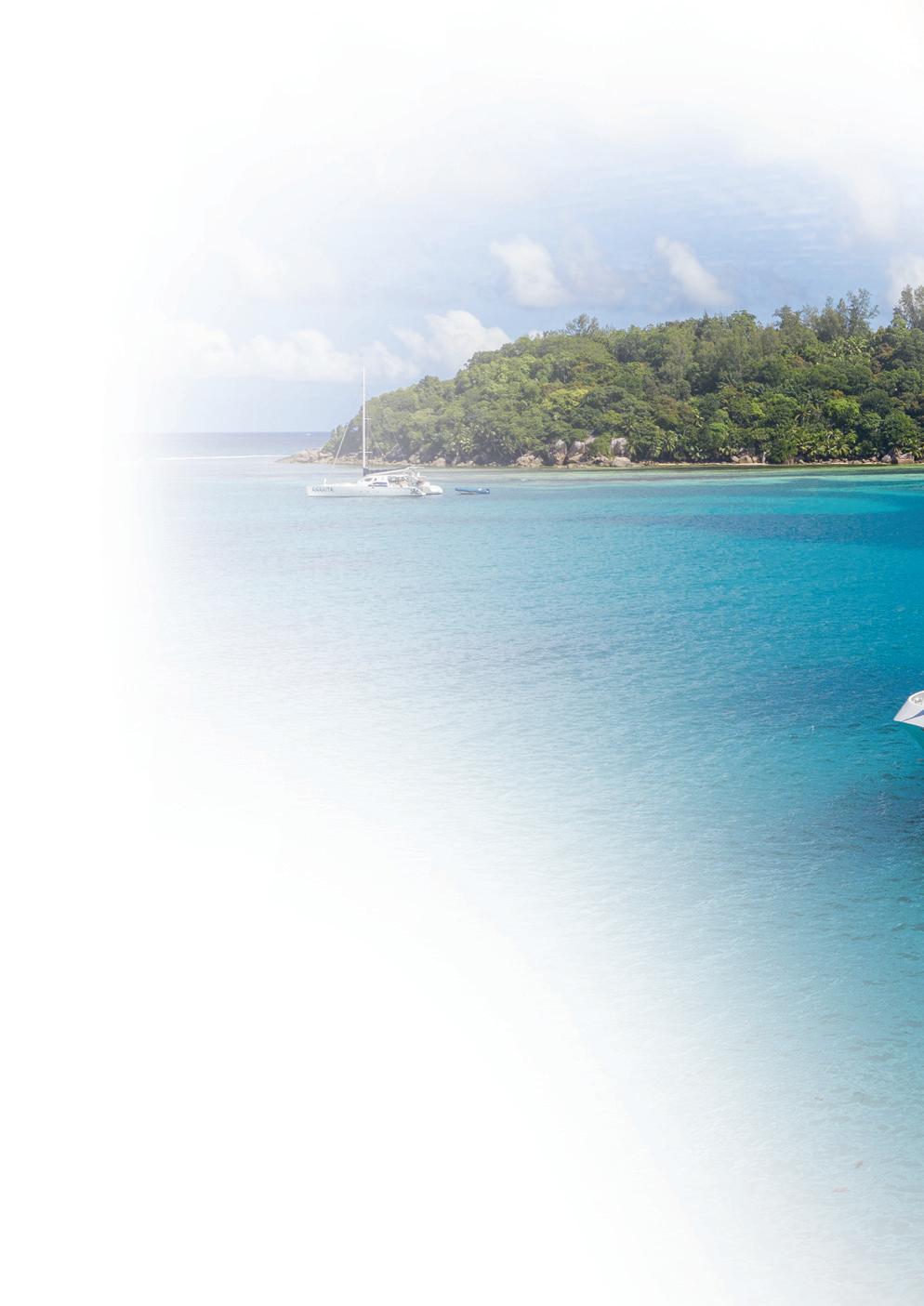
To be a ‘start-up’, even one with a 70-year history, is all about growth.
“Operating 60 small cruise yachts is an achievable target as part of a steady growth plan with the right distribution, the right branding and the right people supporting and creating our bespoke cruise experi ences,” he said. 2022 saw the first steps in this ambi tious growth plan. A cruise around Tahiti and French Polynesia was added to the Variety destination list. The themed Limited Collection Cruises option is another new addition to the portfolio.
we bring. We try and sell the destination while being on a very comfortable boutique yacht, with a soft adventure touch.
“There are many destinations that we’re not currently visiting,” he said, “Places in Asia like Indonesia, Thailand, Malaysia, Japan and the Philippines. Then there are other possibilities like the Maldives or the Caribbean islands; these are places where we could deploy a year-round operation.”
Inside Marine 157
Fleet expansion Alongside increasing the range of locations served by Variety Cruises, Mr Venetopoulos is exploring options to increase the number of vessels in the company’s fleet.
“A Variety cruise is about exploring the destination, it’s going into small beaches that only yachts can reach, it’s going into marinas instead of cruise terminals. It’s swimming off the back of the boat and having kayaks where you can paddle out to the beach and enjoy a barbecue. It’s alfresco dining, sleeping on the roof deck and watching the stars. It’s a very small boat yacht cruise experience.”
Mr Venetopoulos has ambitious plans for the future of Variety Cruises.
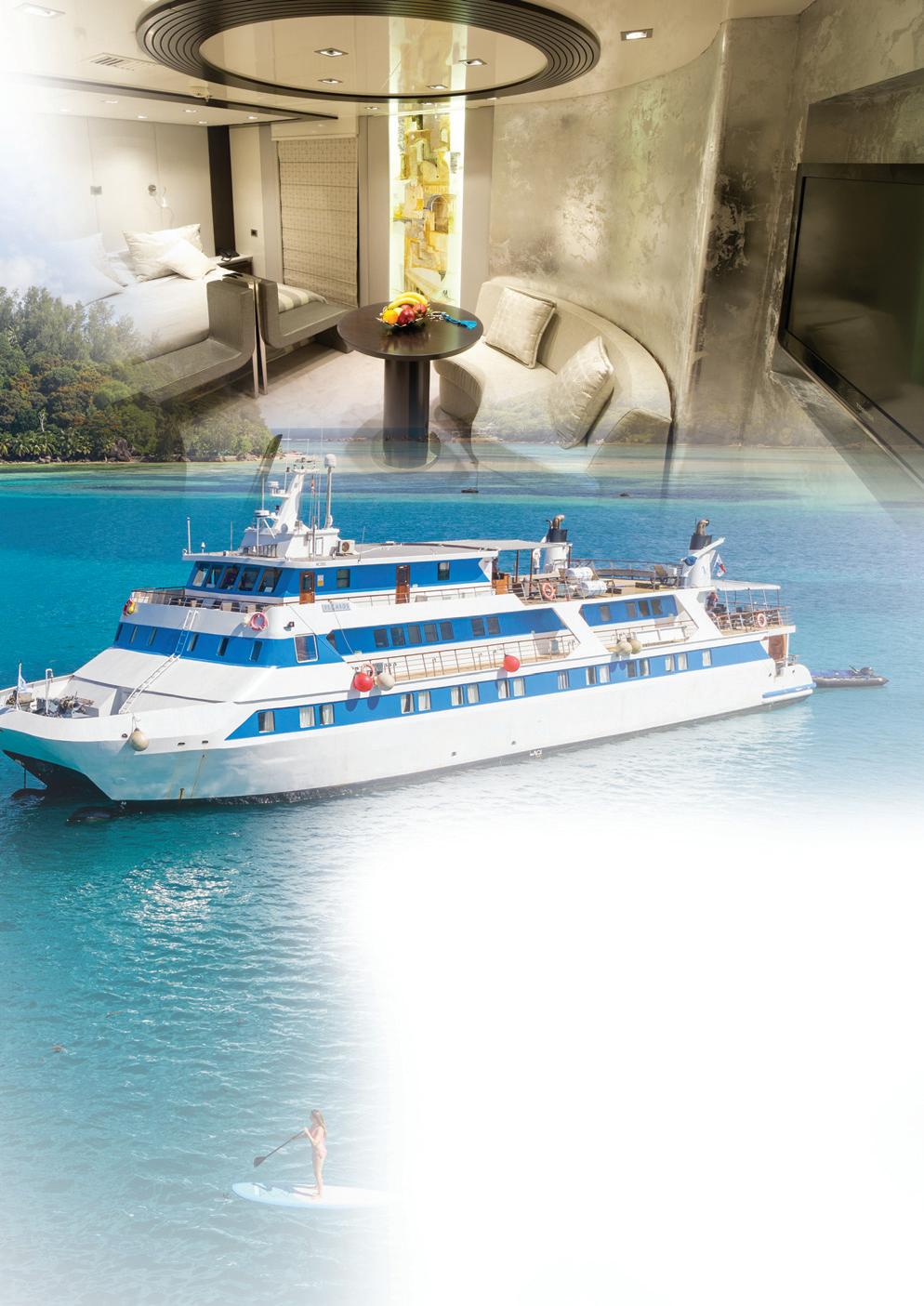
VARIETY CRUISES I PROFILE 158 Inside Marine
In 2019, Variety Cruises banned all single use plastic on its fleet and the refit pro gram reduces the ecological impact of each vessel. An example of the latter is the Callisto, launched in the 1960s, which is scheduled to be refitted with hydro-elec tric propulsion. Three foundational pillars
Variety Cruises is embarking on a fleet upgrade program over the next five-to-seven years. The schedule includes both a refit of the internal furnishings and improvements to the efficiency of the engines. These upgrades run in parallel with the boat building program at Variety Cruises.
“The latest ship we built was in 2012, which was the Variety Voyager, a 68m mega-yacht,” explained Mr Venetopoulos “One of the unique aspects of Variety Cruises is how we are a 360 degree, ver tically integrated business, which means we design, build, operate and distribute ourGrowthvessels.”inthe shipbuilding arm of Variety Cruises is another plank of Mr Venetopoulos’ plans. Each aspect of this plan is conducted with growing sustain ability goals.
“We are also engaged with our Variety Cruises Foundation, which focuses on three core pillars,” continued Mr Venetopoulos. “For us, corporate
“We seek to grow not only as a business in terms of numbers and size, but as a busi nes s with eco-evolution as our key goal, said Mr Venetopoulos. “We are committe d to having a plan of action over the next course of years to gradually lower our carbon emissions.”
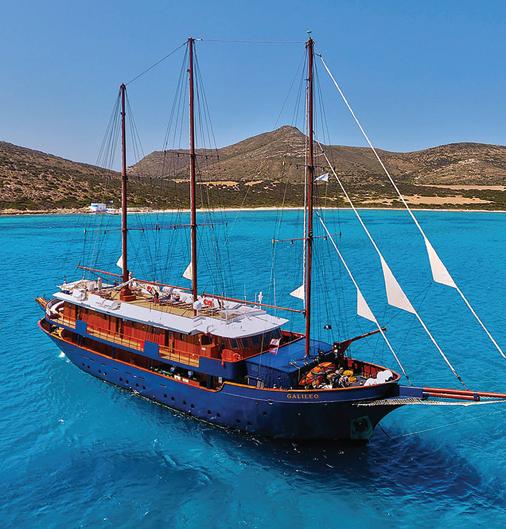
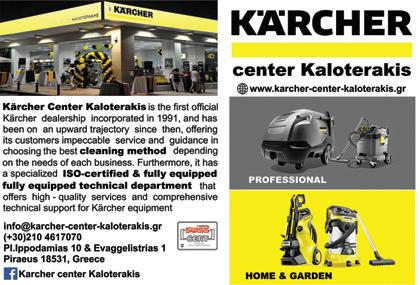
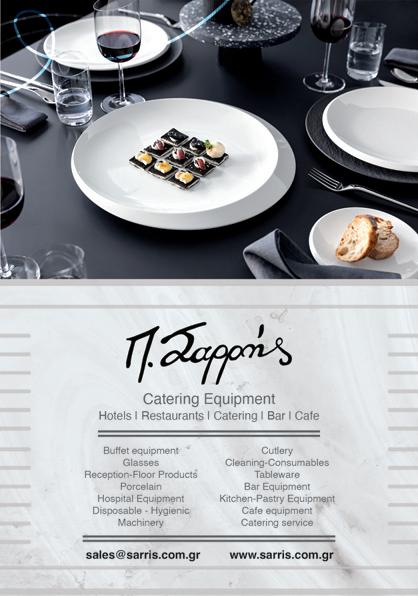
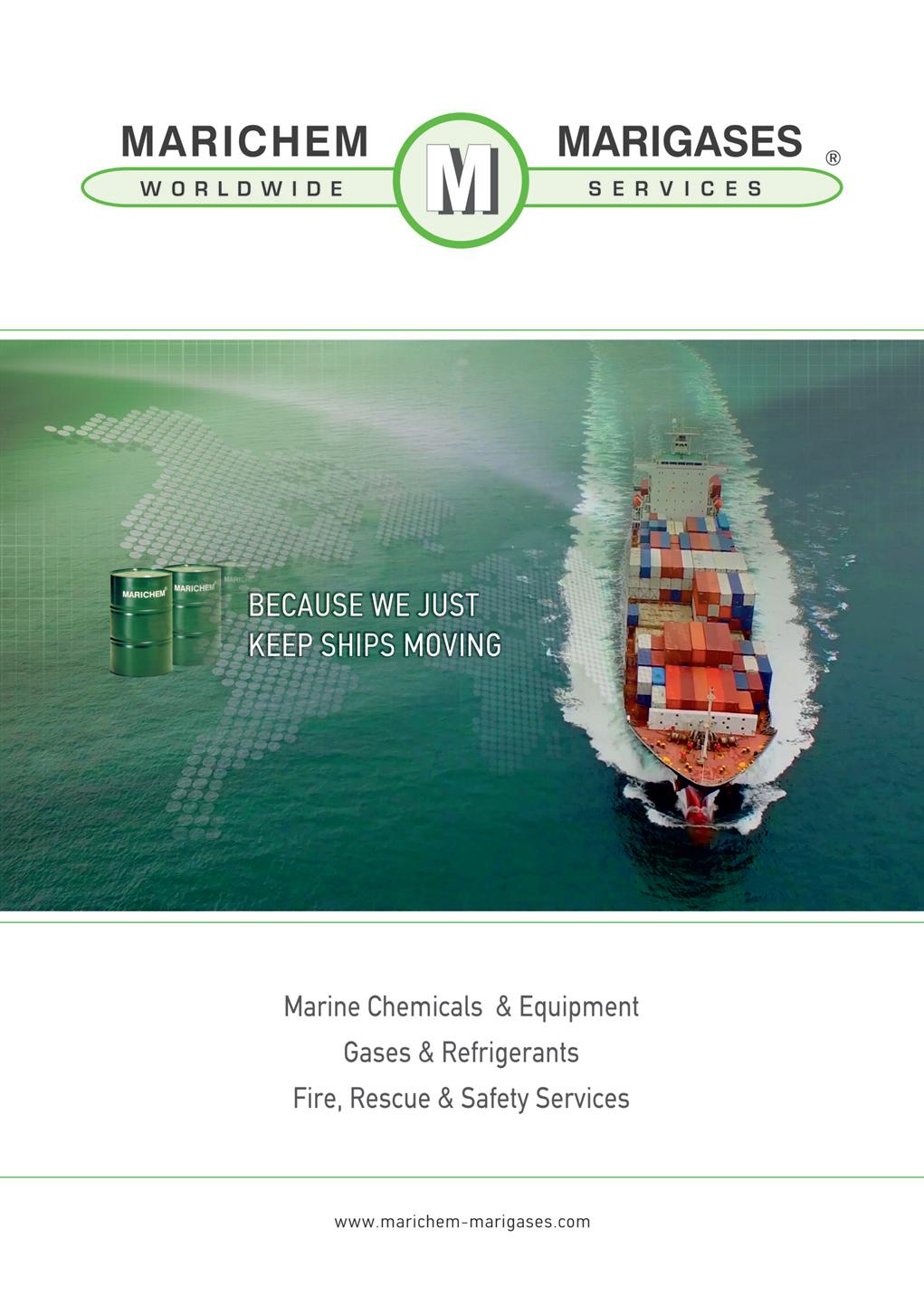
VARIETY CRUISES I PROFILE 160 Inside Marine
responsibility is not solely sustainability, which is a massive topic in the industry, but it’s about understanding our social impact as well.”
“Our inclusion goes further by sup porting the LGBTQIA+ communities which are facing a wide range of challenges in the geopolitical sphere, especially as we serve a number of different destinations with a different perspective on human rights,” stated Mr Venetopoulos. “Our close affiliations with the Trevor Project (the leading suicide prevention line for LGBTQIA+ youth), the IGLTA and other organisations are key to the continuing education of our team and communities, as well as that of safely catering for all guests regardless of background or gender identification.
The first core pillar of the Variety Cruises Foundation is diversity and inclusion exploring how to support female captains and staff to help them break any barriers they face. The cruise industry has a history of gender roles, which the foundation is seeking to banish.
“The second pillar is around education for all,” Mr Venetopoulos said. “My father built a school in West Africa with five class rooms.” With support from the foundation , this site has grown to include a well and a farm, building a new community in the area. Art plays a key role in our contribu tion in the education field as we seek to support education via the lesson most global of all; art. Examples include our collaboration with INSIDE OUT and French artist JR in The Gambia.”
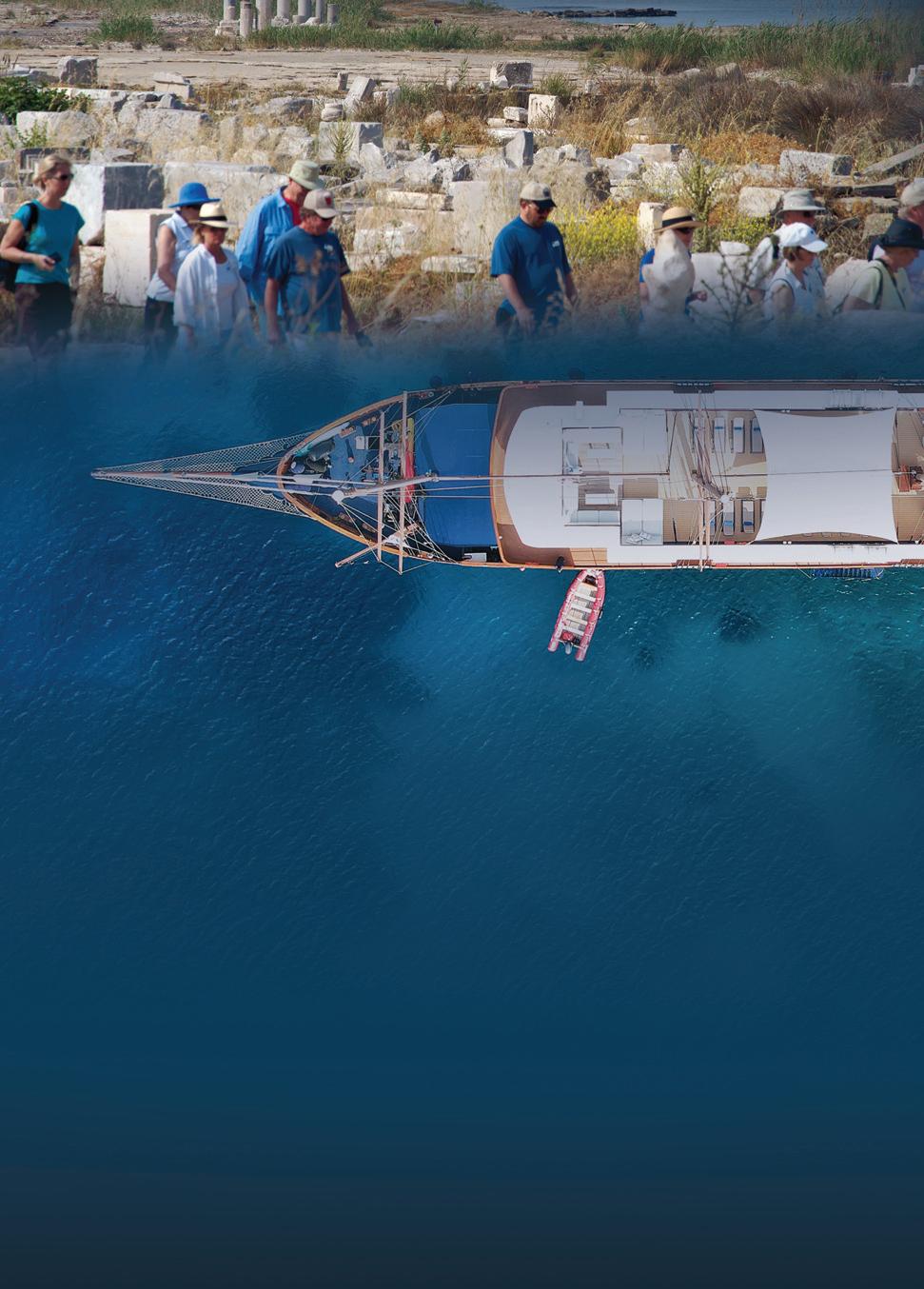
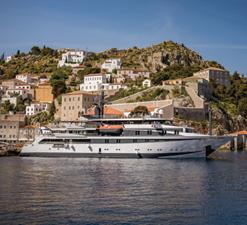
The Foundation’s third pillar is clean oceans for all, which deals squarely with sustainability, carbon emissions, plastic reduction and grey waters. This pillar is an objective for the whole cruise industry, but Mr Venetopoulos is clear on the value of taking positive action: “The more you are proactive instead of reacting, then the better you can deal with these issues.”
This vision is driven by Mr Venetopoulos’ personal enthusiasm for Variety Cruises: “What gets me excited is the heritage, the responsibility of the people we support and the impact we have in the destination Our vision is basically to create a better world at sea. We’re always open for part nerships and investments and support in delivering our vision.” n
Mr Venetopoulos has clear objectives for Variety Cruises : “We’ve been working on our 2050 vision of where we see the business. Our goal is to absorb 1% of the cruising market through building and operating an eco-friendly fleet of 60 small cruise boats around the world.”
Inside Marine 161
While addressing the above challenges, Variety Cruises is also facing the operating challenges of the business. Mr Venetopoulos acknowledged how fuel costs are affecting industries across the board. More specific to Variety Cruises is the difficulty of recruiting qualified staff when the industry stood idle for two years and people drifted away in search of employment. Recruitment remains a test, even though Variety Cruises needs only 18 staff for a ship, not the 2,000 or more of the larger liners.

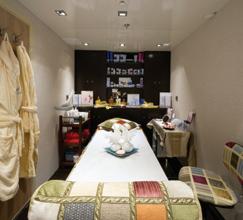
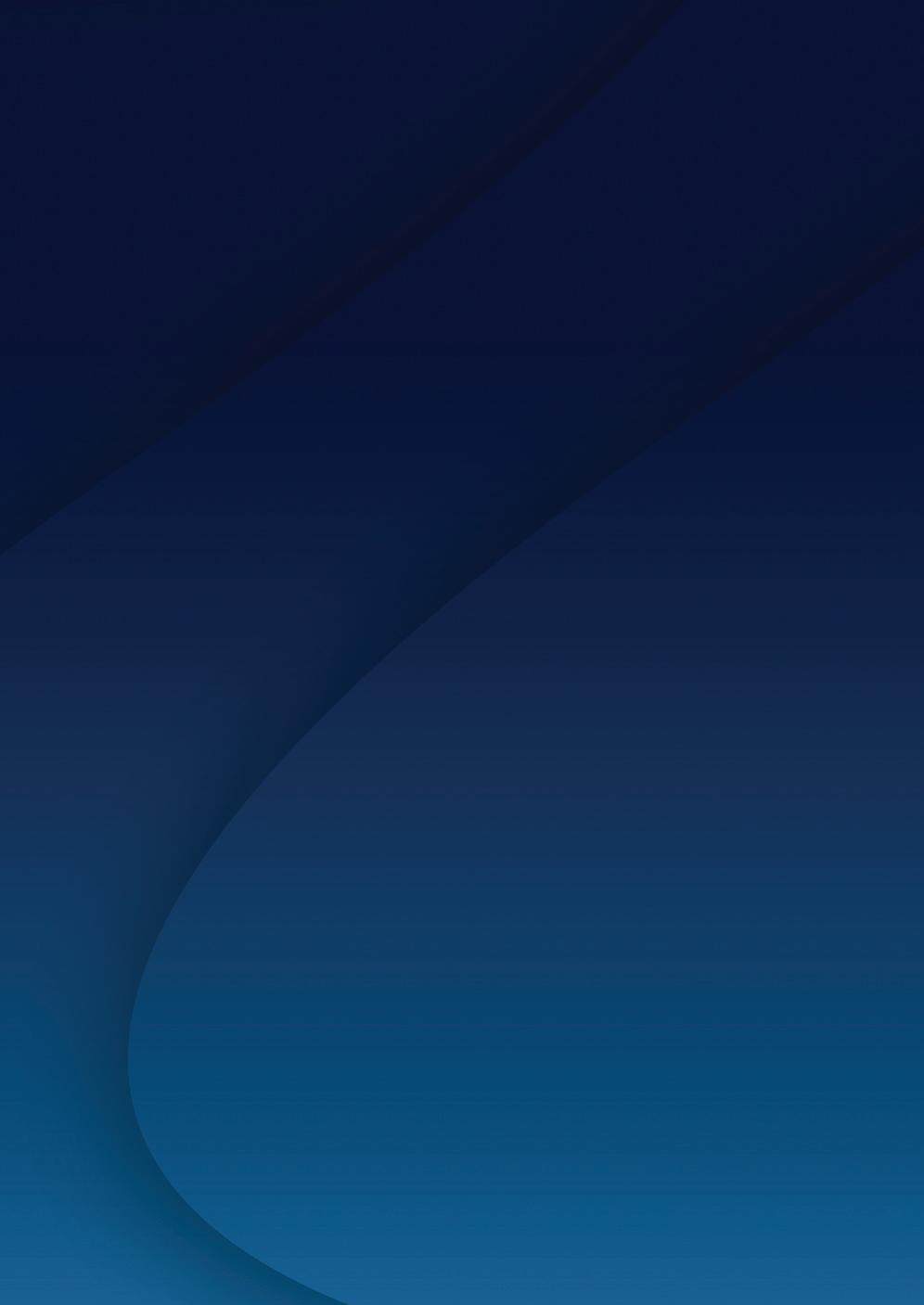
DESIGN & ENGINEERING seven seas, five oceans, one voice deltamarin weihe i M

Deltamarin has been providing ship design, offshore engineering, and construction support services for marine and offshore indus tries worldwide for over 30 years. Mia Elg, the Head of Research and Development at Deltamarin, spoke to Jordan Yallop about the company, industry, and the future of decarbonisation.
DELTAMARIN I PROFILE 164 Inside Marine
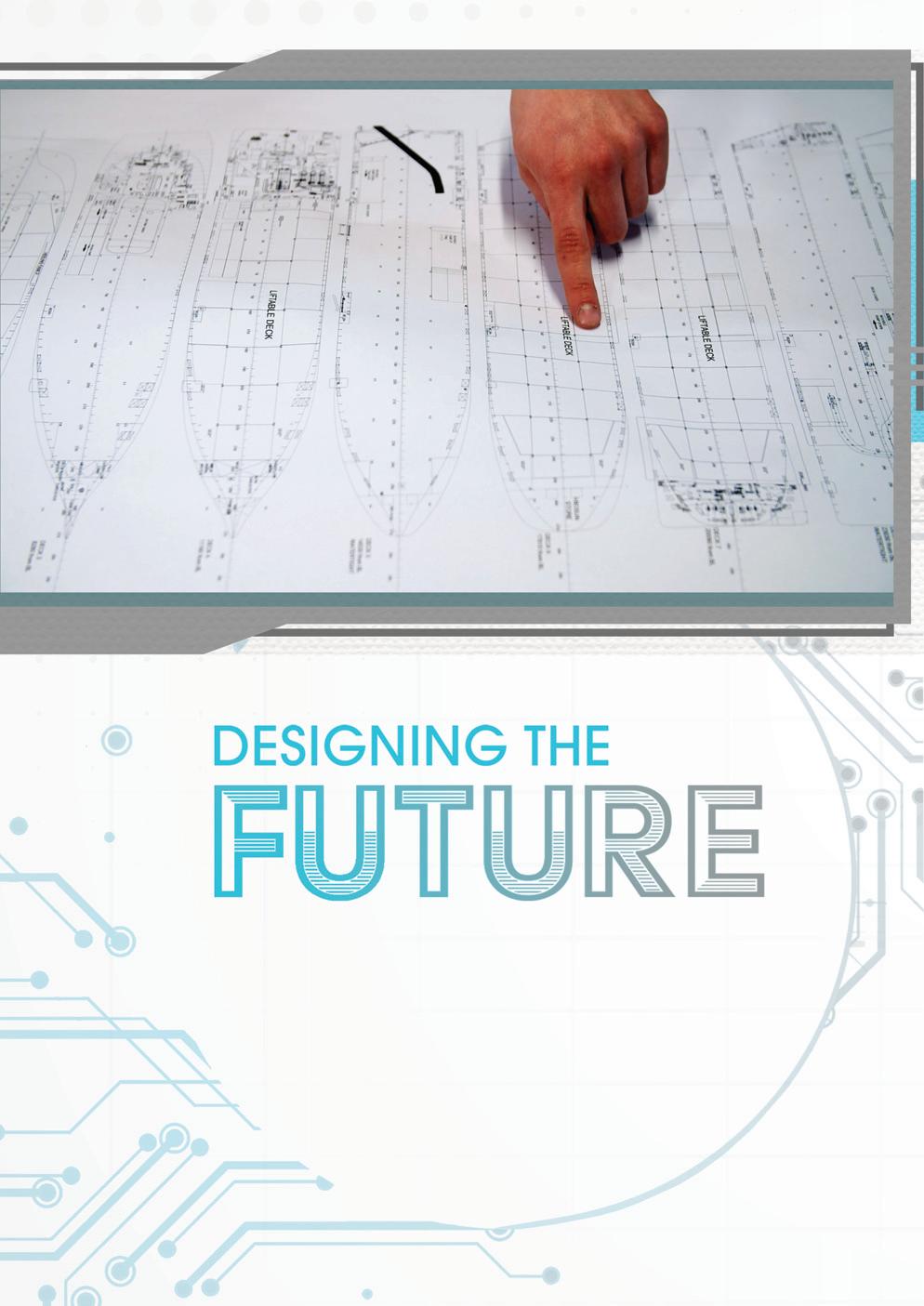
Inside Marine 165
Mia Elg, the Head of Research and Development said: “We pro vide solutions for the entire lifecycle of the ship; unlike compa nies that may focus more strongly on conceptual design or retrofit services. At Deltamarin, we support the customer from an idea generation all the way to design, supervising, construction, and operational support. And of course, also perform retrofits amongst other services.”
With over 5,000 references from complex marine and offshore projects, it is easy to see how Deltamarin has built up such trust in the sector. Thousands of concepts have been developed by the company’s experts and hundreds of vessels designed by Deltamarin are currently sailing around the world. Within Finland the company has three offices with a total of 250 employees – its headquarters in Turku in addition to offices in Helsinki and Rauma. Deltamarin has also offices in Poland, China and Croatia that together employ around 150 people.
Maritime, the next generation
The company consists of industry experts and forward thinkers and provides fit-for-purpose designs in all ship types and off shore vessels.
As a passionate ship design and engineering company, Deltamarin focuses on strengthening the businesses of its clients by innovating high-end vessels and supporting their construction with more effi cient and fit-for-purpose solutions.
Founded in Finland in 1990, Deltamarin provides ship design, offshore engineering, and construction support services for the marine and offshore industries worldwide.
Ms Elg said that Deltamarin has recently been working with sev eral development projects, but also with many commercial projects, which are aiming for zero or very low carbon intensity operation in future years. “It’s exciting to be an engineer today,” she smiled.
As a world-renowned ship designer, Deltamarin has extensive experience in all areas of the industry. One aspect that has seen huge growth in recent years is the transition to greener fuels. Ms Elg said: “We work with all kinds of marine structures, from offshore vessels to traditional cargo and passenger ships. Already from the beginning, we have had international customers and pro jects and have strived to be innovative – it is what we have been doing all along.”
“Indeed, all those years working for energy saving and emis sion reductions in a small team and finding ways to include the necessary analysis in its commercial products because it is the right thing to do… well, now all those analysis methods are being
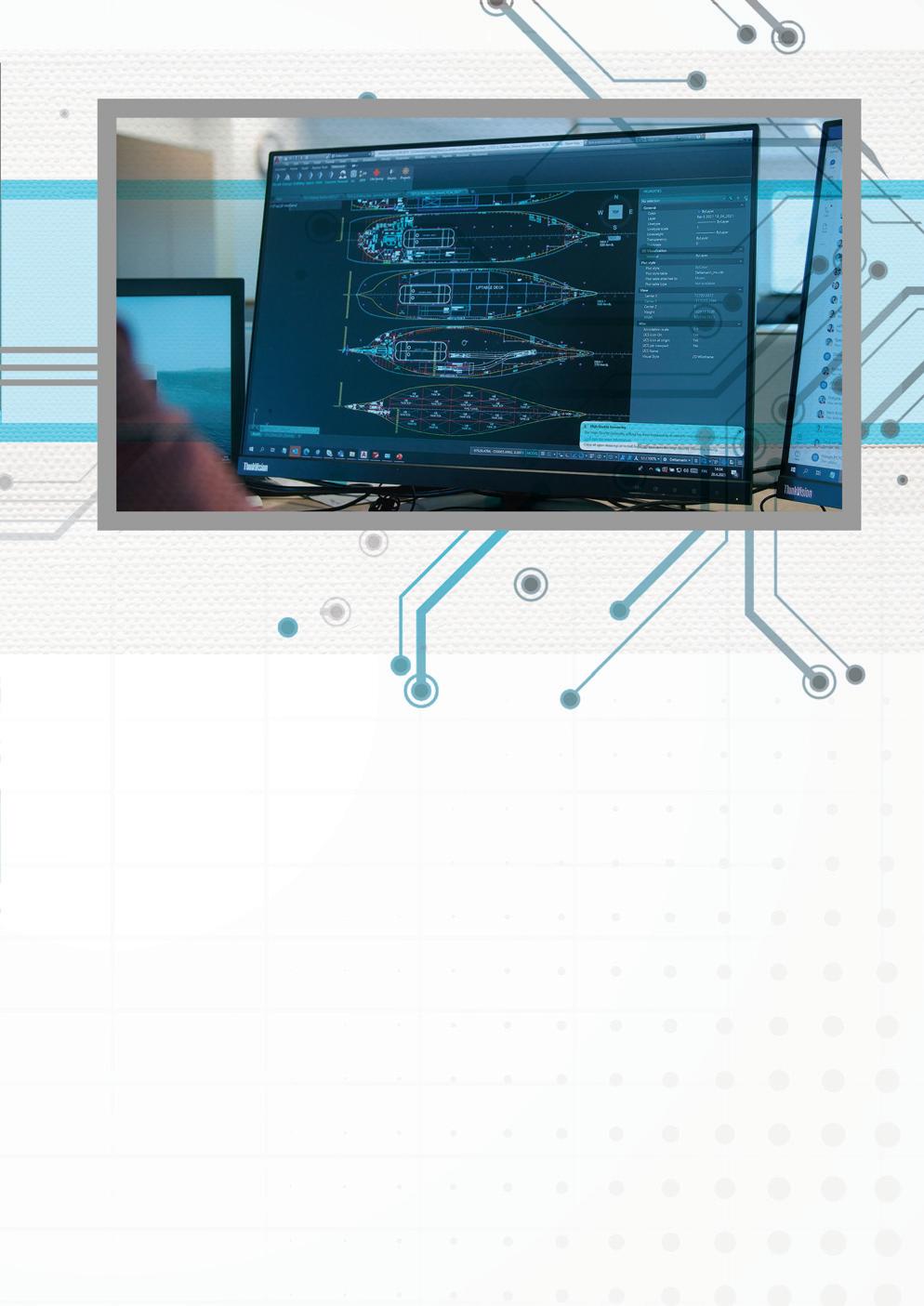
put to work in all of the company’s projects. And those technologies that could not make it to projects due to demand for pay-back time in two to three years suddenly become feasible if we expect that the cost of carbon-neutral or low-carbon shipping will be high.”
She further explained that decarbonisation within the shipping sector is a huge challenge, and one which requires ship operators to have a strategic process in place that combines awareness of current and potential upcoming legislation, market situation and fleet technical performance. A ship designer can help in getting the most out of the current fleet and upgrading it cost-efficiently to the level of sustainability required. Getting this done requires a deep understanding of the customer’s business, after which the designer can focus on finding the right technical solutions and this is where Deltamarin steps up.
“We must analyse how the ship is going to handle that kind of transition,” she said. “Typically, in addition to these designs and technology alternatives, there is always some estimation of which fuels will be fuel alternatives for the future.”
A good example of low carbon shipping designs are LNGfuelled ships which are being built to accommodate ammonia as a fuel in the future. According to Ms Elg, these types of topics are discussed in almost every project.
Digitalisation and digital twins
As a technology driven company, Deltamarin is always using the latest design innovations to increase productivity and push bound aries. One such technology is the use of a digital twin – a system that is being utilised with increased frequency in the maritime sector, par ticularly in projects related to decarbonisation.
DELTAMARIN I PROFILE 166 Inside Marine
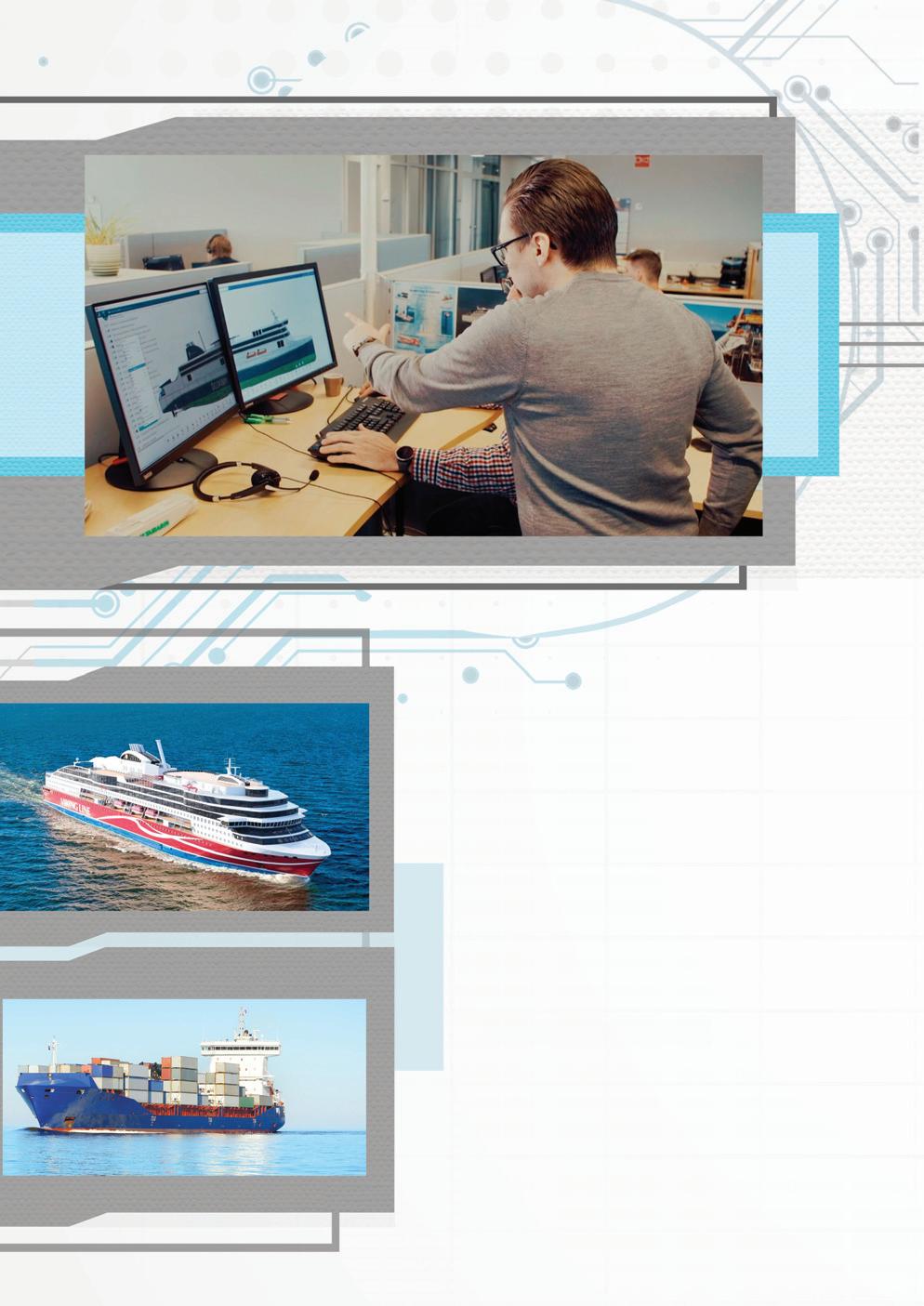
Ms Elg is confident that the future of ship design is in the data-driven design process, where you can form a digital thread between the early demands and targets for the project and the real operating ship. Even though a ship and her systems are dimensioned to certain design conditions such as “extreme” climate and seaway conditions and to a certain maximum speed, the system optimisation should be done for the most common conditions. She concluded: “At the moment we have been developing conceptual designs for zero emission ships and I think that we will be building them very soon. I strongly believe that the whole shipping industry is going to transition to these cleaner fuels soon.” And when that transition finally arrives, expect Deltamarin to be front and centre of the new, ship design era. n
Ms Elg explained that for the past five years, her development team at Deltamarin has focused on solving these challenges. What they have found is that an efficient process does not consist of one single program or tool, but a series of layers. The digital model of the ship that can ultimately evolve into its dig ital twin that consists of the early design phases of the most relevant areas of ship design. Deltamarin has been focusing on three main topics during concept design: energy and environmental performance simulations, the ship’s volume and structural model, and the data layer where wind, wave, and other measured data combine to esti mate its lifetime propulsion power profile.
Inside Marine 167
“At the moment we have been developing conceptual designs for zero emission ships and I think that we will be building them very soon. I strongly believe that the whole shipping industry is going to transition to these cleaner fuels soon”
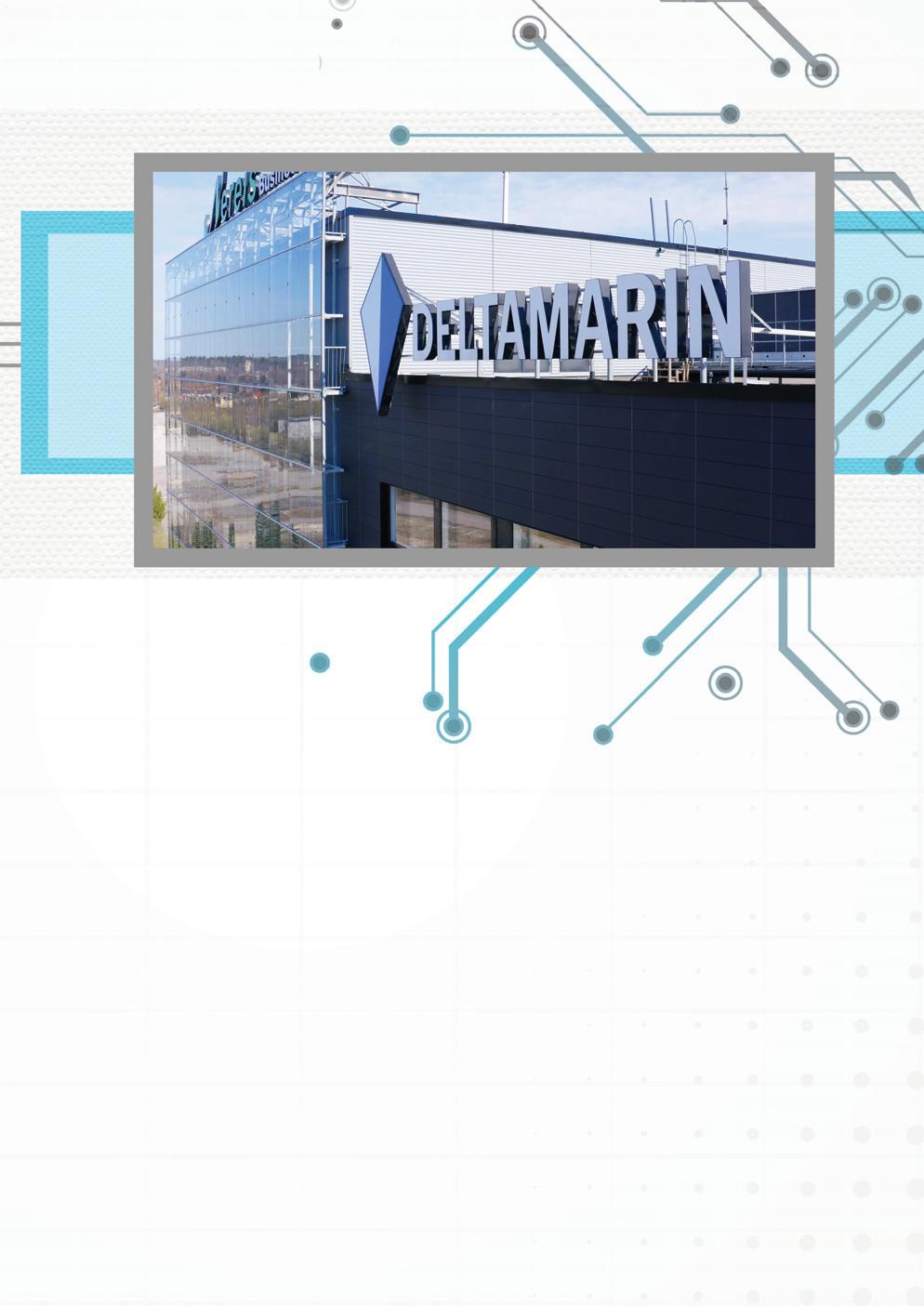

PLASMA-GREEN
Klaus Weihe founded the Weihe GmbH engineering company in 1987 selling exhaust silencers and related prod ucts. The company steadily expanded as customers demanded clamps and pipes with the exhausts, even asking Weihe for custom welding procedures. Klaus Weihe therefore opened a manufacturing opera tion alongside the sales division. In 2000, Weihe moved to its current site in Altenholz, near Kiel in northern Germany. The facility expanded by 1,000 sqm in 2006, then Axel Weihe took over the family busi ness in 2011. Over the years, Weihe steadily expanded its penetration further into the maritime, industry, power, rail and oil & gas.
WEIHE I PROFILE 168 Inside Marine
Weihe GmbH is a specialist German engineering company for plant construction and engine peripherals. Gorden Flucke, Head of Technical Sales, spoke with Phil Nicholls. for a clean future
Gorden Flucke, Head of Technical Sales, explained how Weihe is more than just a sales office. The team’s engineering exper tise mean Weihe “delivers complete system solutions to our customers.”

“The remaining 75% is split between the remaining sectors ,” Mr Flucke said. “Around 60% of our turnover is from the manufac turing side of the business, while the other 40% is from our trading products.
“I’d estimate around 80% of this turnover comes from loyal Weihe customers that we have had almost since the beginning.”
Mr Flucke is certain that this incredible level of repeat customer loyalty is due to Weihe’s reputation for a product portfolio characterised by high-quality, tailormade system solutions.
Weihe currently employs about 50 employees consolidated at the single site in Altenholz with a 2021 turnover between €5-6milion, with approximately 25% of the business in the maritime sector.
Inside Marine 169
Complete solutions Weihe supplies components and solutions for a range of areas, but the company’s core competency is for engine peripherals including exhaust aftertreatments such as particulate filters and catalytic converters , as well as exhaust silencers for all engine sizes. Weihe products are built to high quality and reliability standards, a vital feature for the maritime sector. The com pany is certified to the highest standard in many areas such as Pressure
Another successful Weihe partnership is with the American engineering company RW Fernstrum. Weihe stocks the Gridcooler keel coolers from Fernstrum, offering clients easy installation and cost savings against alternate cooling methods. Through close cooperation with the shipyards and the engine manufacturers, Weihe supplies this optimally designed cooling system. Weihe also stocks box coolers, flat coolers and heat exchangers. These com pact coolers are particularly suitable for commercial shipping as they allow spaces aving installation. The Weihe range is sup plemented by tube bundle heat exchangers for oil and water.
Expansion at Weihe continued with a new 500sqm hall built at Altenholz as an assembling workspace in 2021. Mr Flucke explained: “We started having more and more projects where it’s neces sary to not just produce the parts, but also to assemble the product and put it into frames or containers. So, we added our new hall.” Weihe also works closely with select partners. One such partner is Orcan Energy AG, the Munich based developer of pro duction-ready efficiency PACKs. Orcan’s patented efficiency PACKs generate zerocarbon electricity from heat – from engines , industrial- or cooling processes.
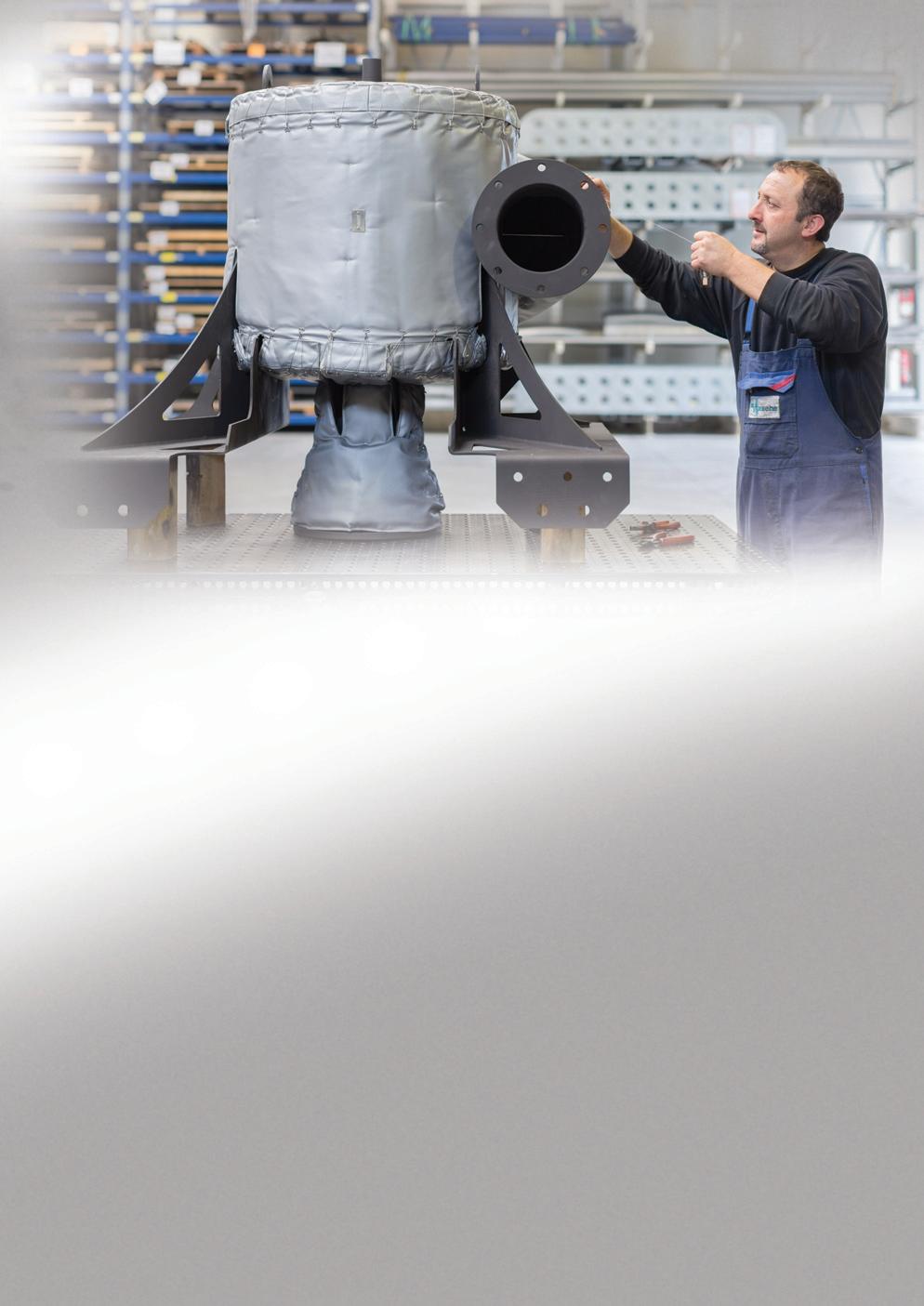
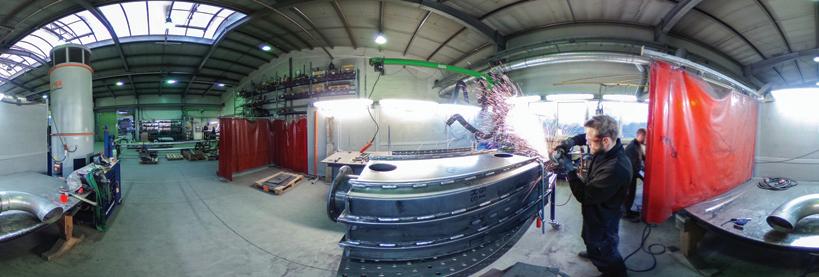
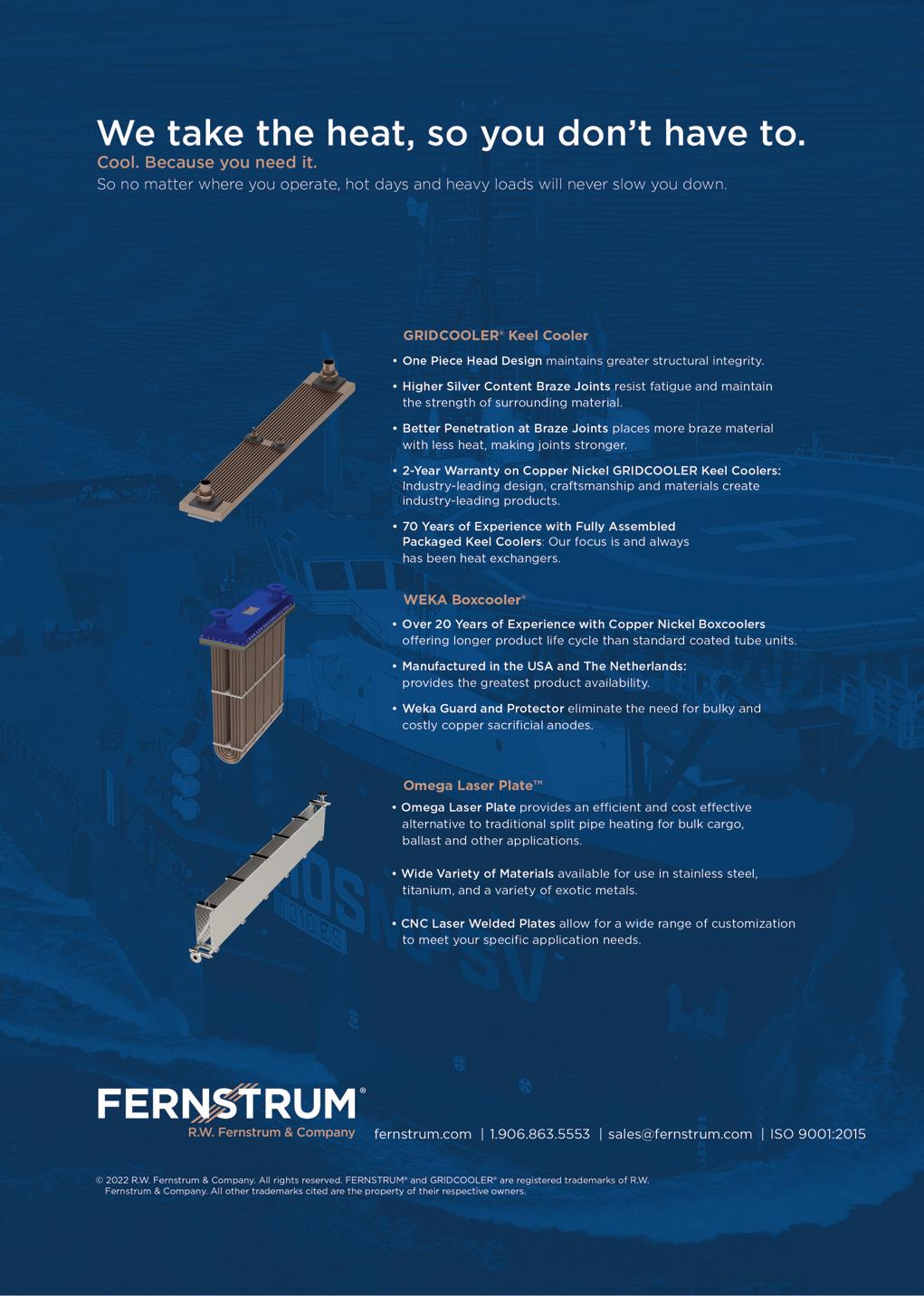
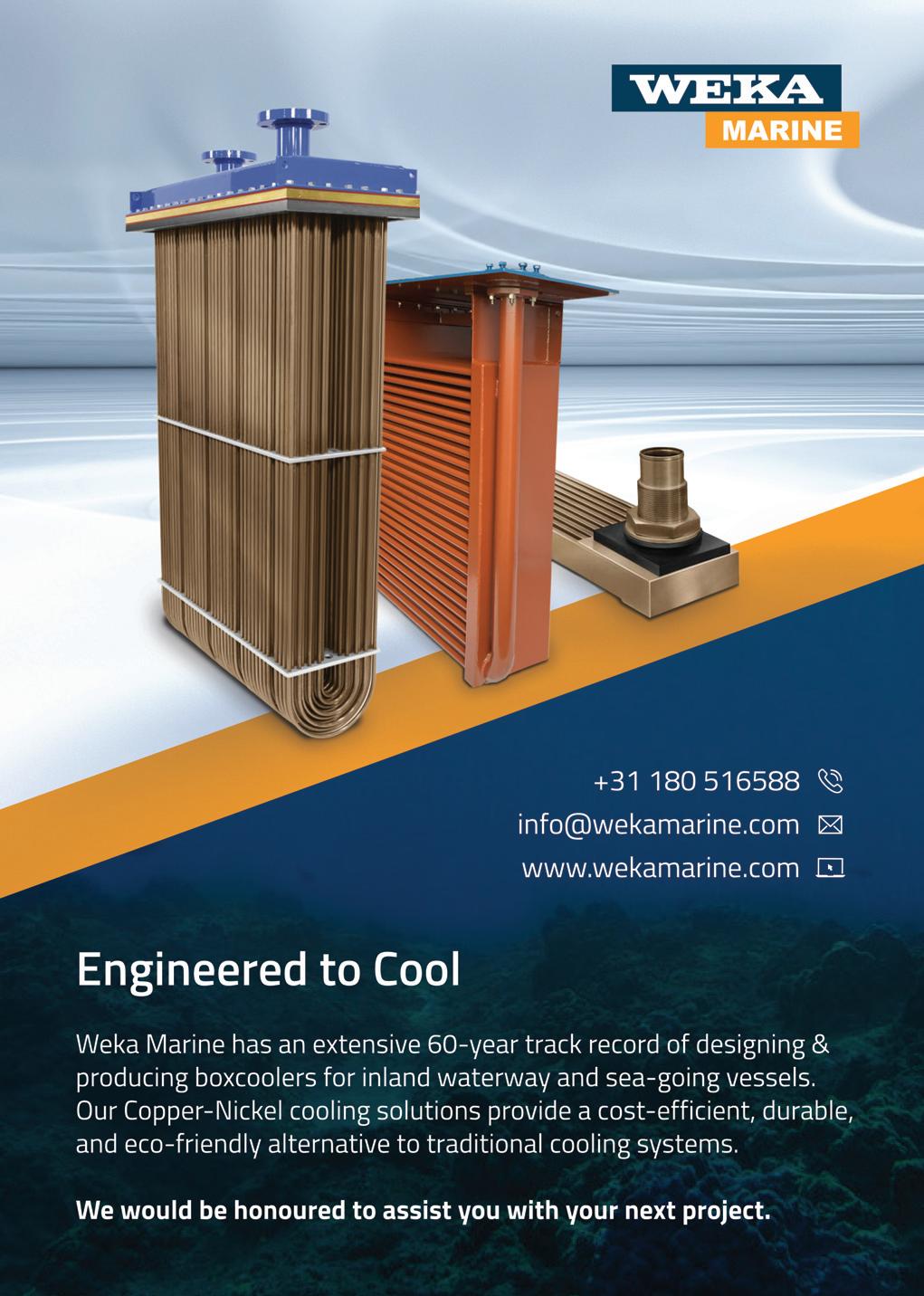
The launch of Plasma Green will be the centrepiece of Weihe’s program at SMM 2022 this September. Mr Flucke said he is looking forward to the return of the Hamburg event: “It’s the world’s leading trade fair in the maritime sector. So, I think anyone who’s working in this sector can’t afford to miss it.
Despite current market obstacles such as the Covid pandemic and the disruptions to supply chains, Weihe has exciting plans to upgrade its factory with an investment to increase the company’s manufacturing capacities. Following challenges finding qualified welding personnel, Weihe is going to install automated welding robots In addition, Weihe plans to add another 1,000sqm assembling space in 2023.
The core line of the technically mature ORC system is mobile modules from Orcan Energy AG, supplied by Weihe in different sizes.
WEIHE I PROFILE 172 Inside Marine Equipment Directive, DNV, military, rail and many more.
Turnover at Weihe has remained broadly stable for the past few years. Mr Flucke was only appointed to the role of Head of Technical Sales in October 2021. Trained as a mechanical engineer with a focus on renewable energy, he also has extensive sales experience across northern Europe and Scandinavia. He therefore enjoys the per fect combination of skills to drive Weihe forward towards growth.
Gorden Flucke Head of Technical Sales
The Weihe booth at SMM is shared with Fernstrum and profiles this partnership for keel coolers. Weihe also plans to use the fair to promote the new ORC system, designed to increase energy efficiency.
“When a client comes to us,” Mr Flucke said, “they know we will supply the com plete solution, not just a part from a cata logue which the client needs to change every two years.” Weihe works with a broad range of mar itime customers, beyond virtually every shipyard in Germany. Weihe fitted exhaust aftertreatments to police vessels and pro ject research vessels. Other samples include exhaust systems for luxury yachts, engine room heat insulation for the cruise liner Quantum Of The Seas and U-type box coolers on river cruise liners.
“The main benefit is to meet all our cus tomers, partners, and suppliers in person again, after all these years. It will be won derful just to meet people again and talk in person about our projects from the last few years, rather than on Zoom or Teams.”
Technical expertise With regards to the broader maritime market, Mr Flucke conceded that the market is highly competitive. Yet, he was confident in Weihe’s future: “What really makes us competitive is our technical sales department; we can go deep into the technical side of the client’s needs. We can help the client and give them detailed advice: we provide solu tions , not just products.”
Plasma Green and people Mr Flucke also highlighted a new product Weihe will unveil at SMM 2022: “We are working on a new category of diesel par ticulate filter called Plasma Green. It’s like a standard particle filter, just without the filter. The system uses cold plasma in an electric field, so the molecules are broken down into harmless elements.” Plasma Green filters are compact and suitable forTheretrofitting.PlasmaGreen project has taken many years to develop, with Weihe working in collaboration with the Technical University of Clausthal in Lower Saxony. Mr Flucke continued: “The goal of Plasma Green is to clean the exhaust from engines with a much smaller, more cost-effective product one with almost no maintenance.”
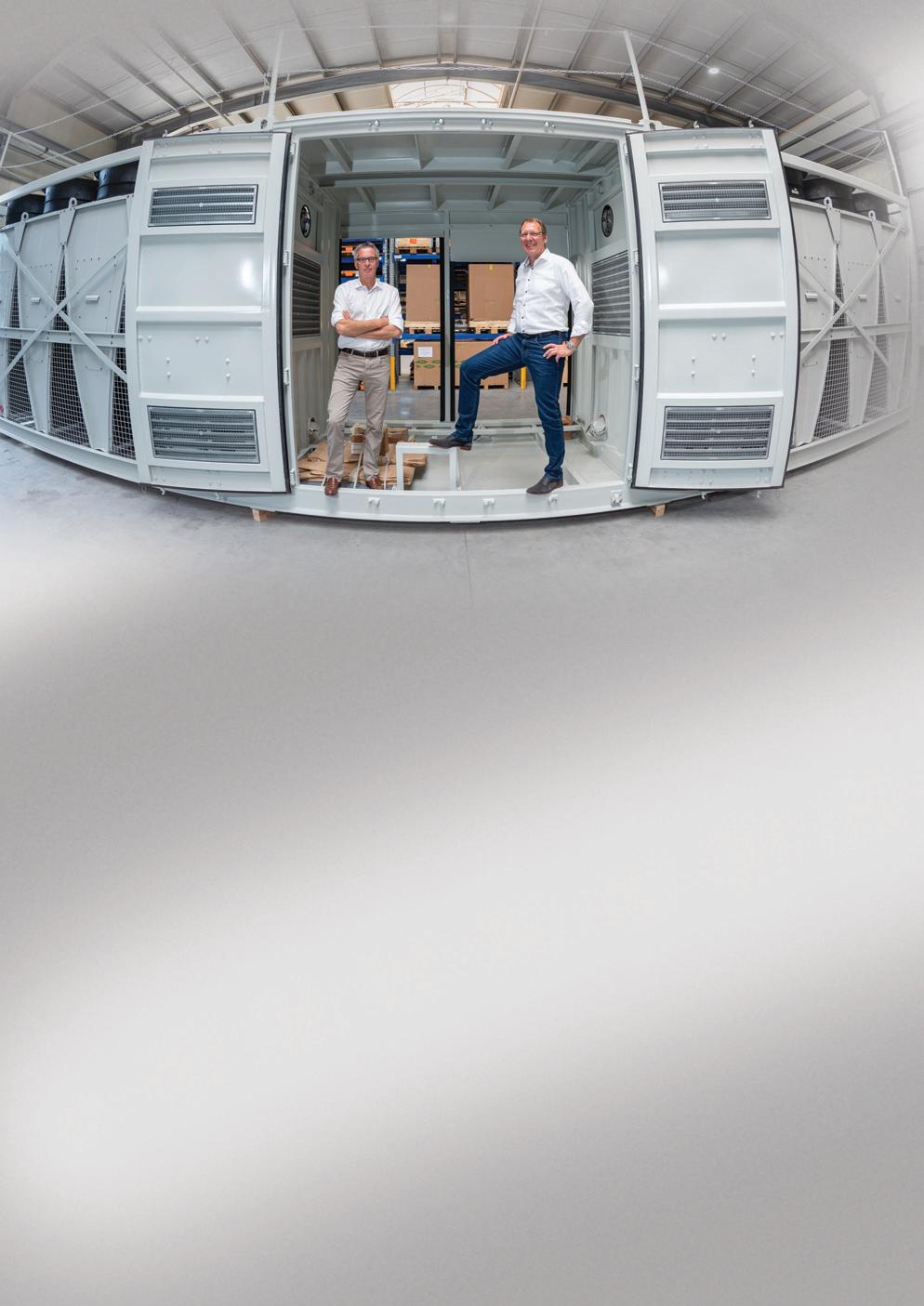
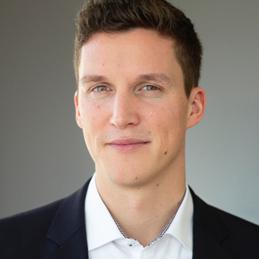
Weihe has a dedicated Defect Removal and Sustainability Team at its facility to improve its environmental impact. Alongside solar panels on the roof meeting around half of its electricity requirements, the manufac turing operation has transferred completely to LED lighting. The Weihe office operates entirely paper-free and the company relies upon recycled paper for packaging materials.
Inside Marine 173
Mr Flucke acknowledged a global trend away from fossil fuels and combustion engines: “We are selling fewer exhaust silencers and pipes, but on the other hand, the market for renewable energy is Theincreasing.”futureis green, so Weihe is posi tioned to grow as the market reacts to the global increase in energy prices thanks to its partnership with Orcan Energy, who is ramping up production of lines such as the efficiency PACKs that generate zerocarbon electricity from the surplus heat produced by combustion engines. Mr Flucke also predicted an up-tick in sales of Weihe particle filters with tightening regulations about maritime emissions.
In concluding, Mr Flucke has a clear vision for Weihe: “Our plan for the future is to continue to delight our customers, find new customers, be successful with our products, and contribute our share to c utting emissions whether they are audible, particulate or heat.”
n
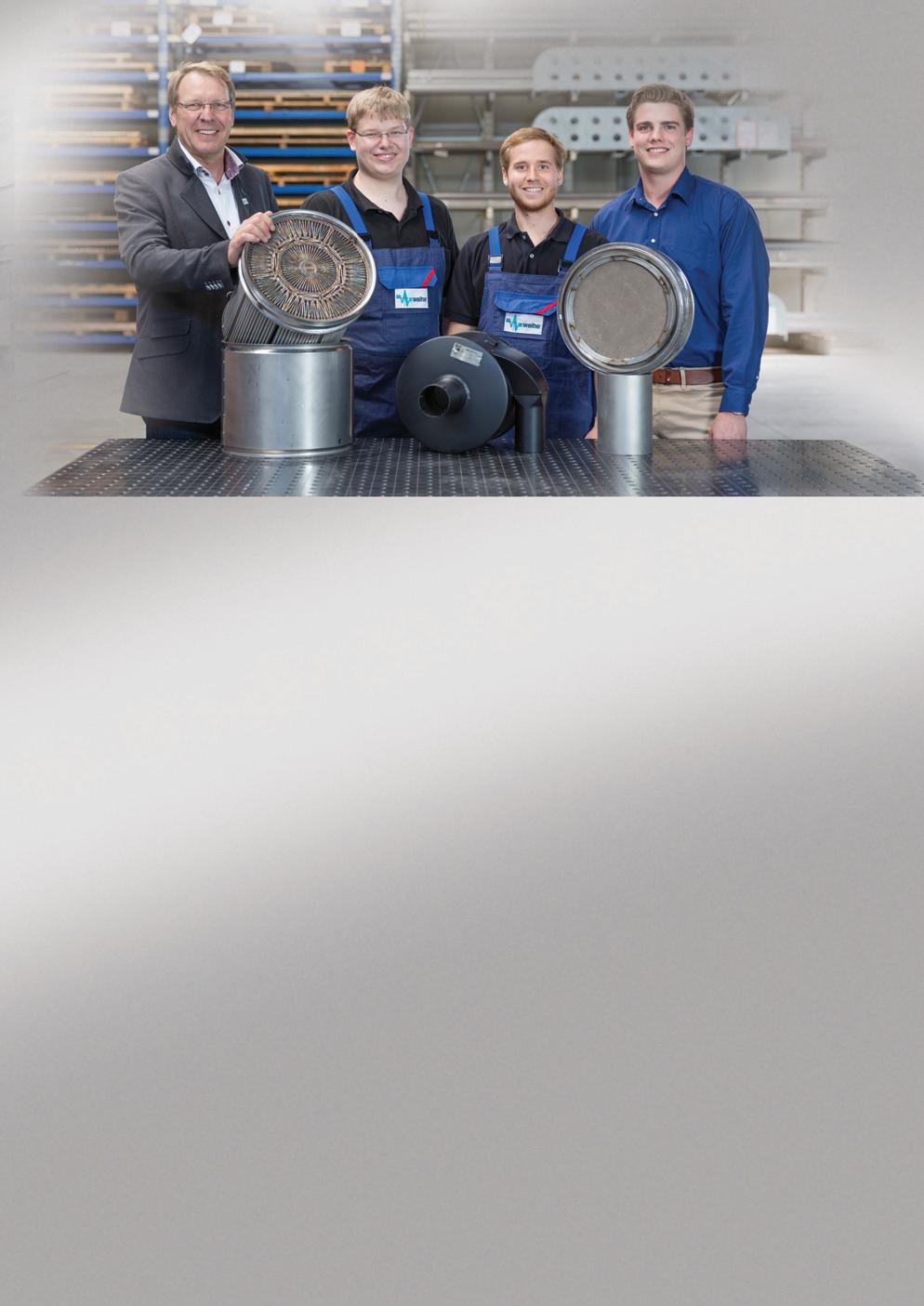
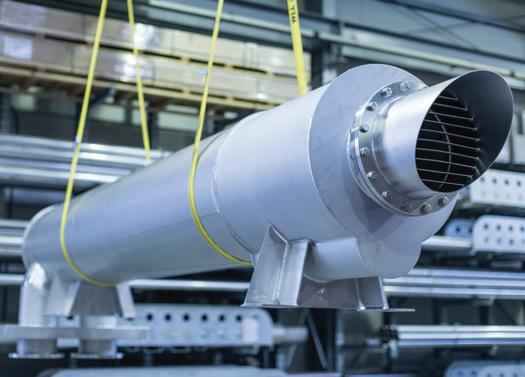
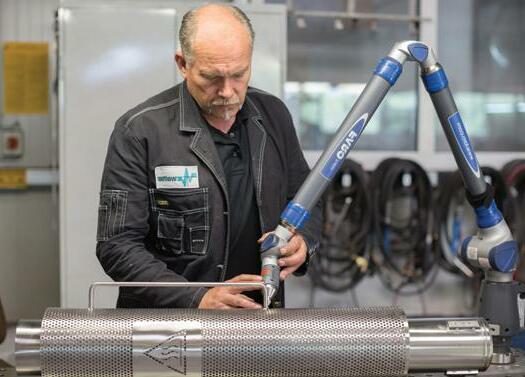
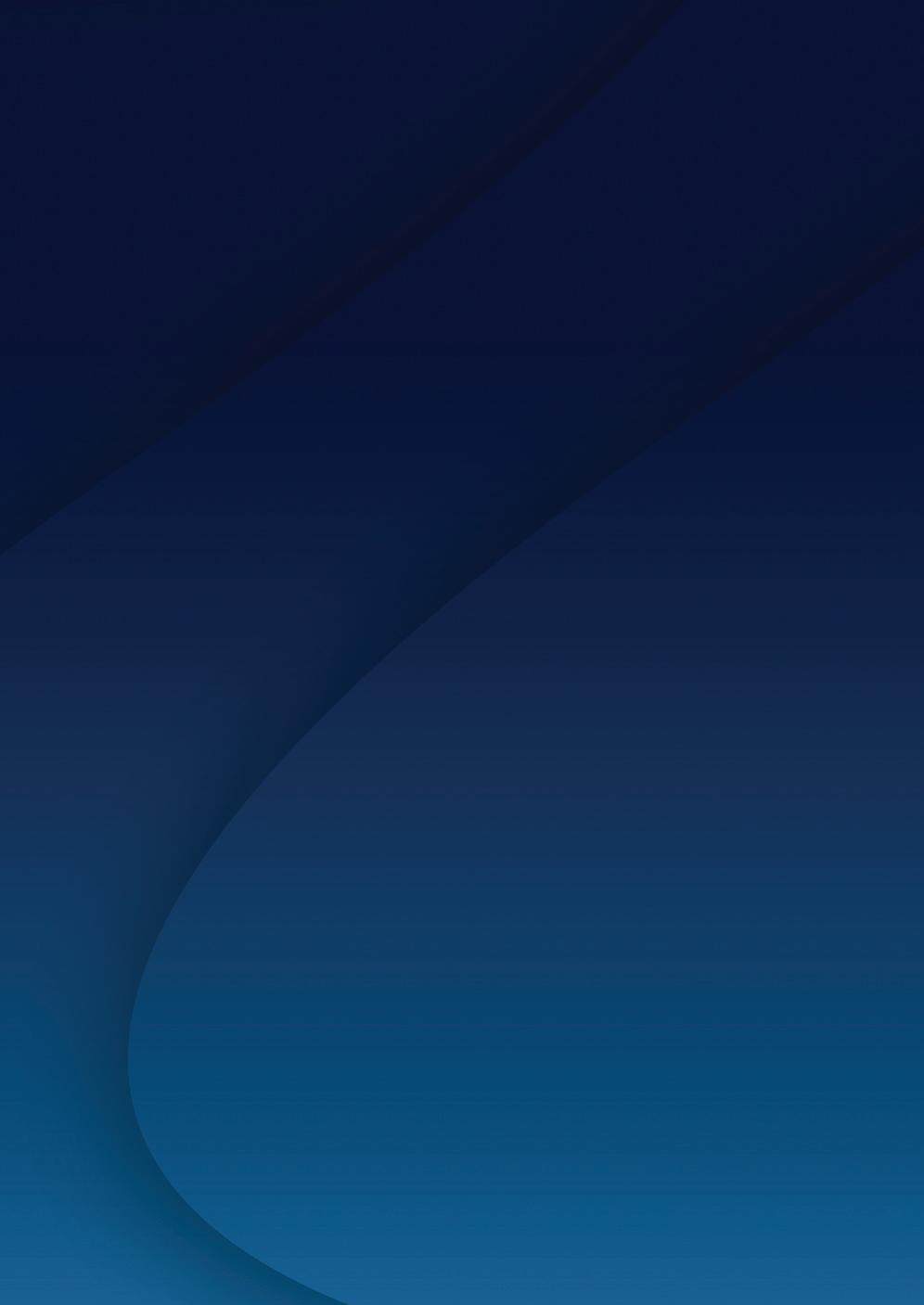
EQUIPMENT&SERVICES seven seas, five oceans, one voice oswald elektromotoren merlin diesel systems t-iss ocean craft marine precision products (uk) ltd i M

Historically, OSWALD has derived the majority of its work for clients in fields requiring container handling, shredder machinery, automotive test stands, winch systems, plastics machinery and hydropower plants. But more recently, the business has seen signifi cant growth in the marine market for both electric propulsion units and marine generators.
“In the initial projects we supplied permanent magnet motors for a hybrid tugboat named Telstar, and a hybrid pusher boat
Its focus is on developing customised solutions and products that are best suited for each client’s particular application. As a manufacturer of customer-specific motors, OSWALD is able to produce individual quantities, but is particularly interested in series production, such as projects with 20 to 100 identical motors per year and even up to 500.
Motoring into marine
O SWALD Elektromotoren GmbH, based in Miltenberg, Germany, develops and produces customer-specific water and air-cooled electric motors ranging from 15kW to 2,500kW for a variety of industries and tasks. Its range includes high torque motors, synchronous motors, asyn chronous motors, generators, linear motors and magnetic field coils.
One reason for this surge in marine propulsion projects is OSWALD’s partnership with system integrator Hybrid Ship Propulsion BV in Rotterdam, which manufactures and delivers equipment for Concordia Damen shipbuilders in Werkendam, as well as for other shipyards in the Netherlands.
OSWALD ELEKTROMOTOREN I PROFILE 176 Inside Marine
With over 100 years of history, OSWALD Elektromotoren GmbH is a veteran manufac turer of electric motors and generators. Now in its fourth generation of family ownership, the company remains at the head of its industry through a relentless focus on innovation and its industry-leading custom fabrication service. Richard Hagan reports.
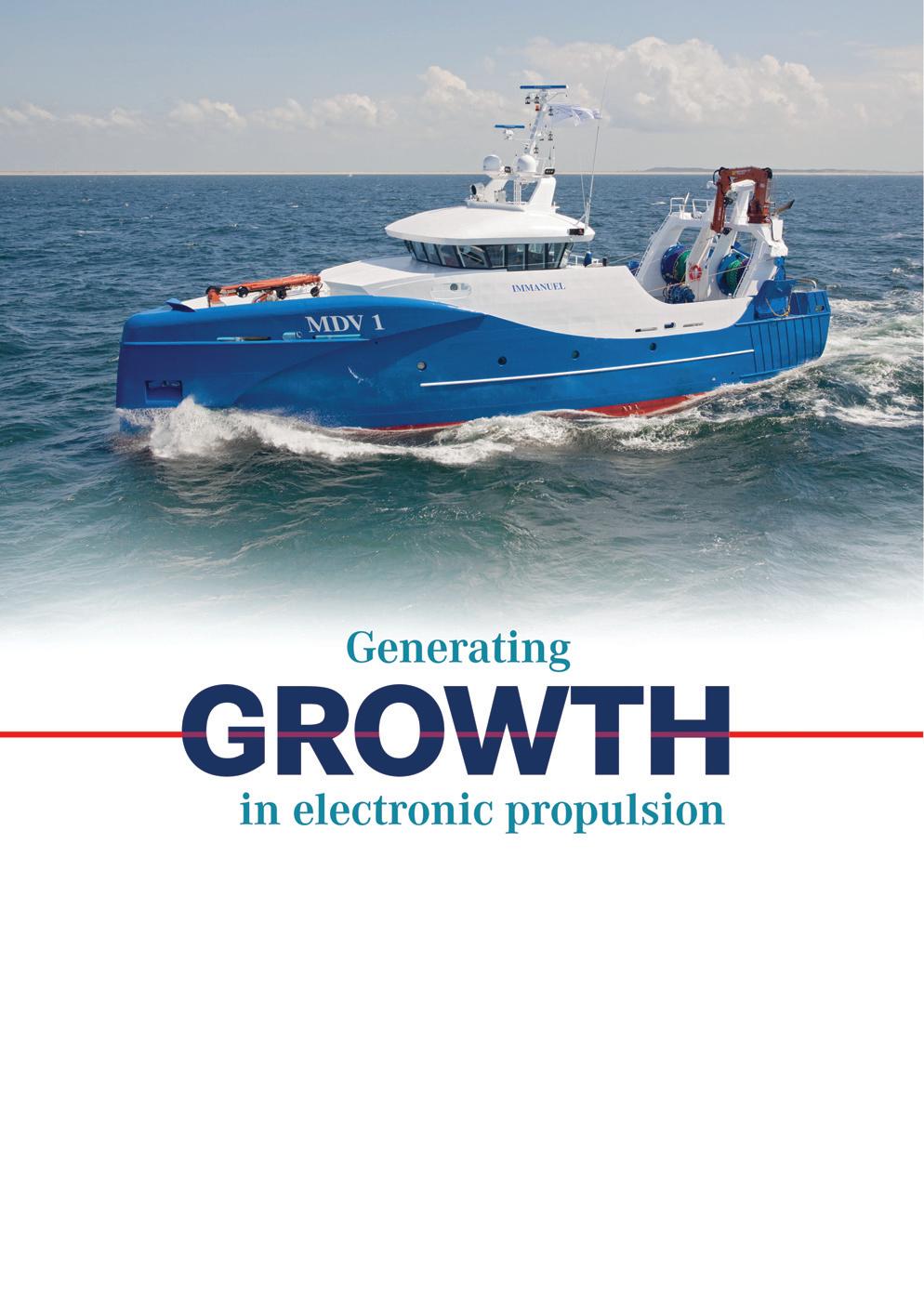
Fishing from the start
“The client knew us from previous work we’d done in other appli cations such as test rig motors,” said Mr Bachmann. “They wanted a hybrid system on the fishing vessel with a high-torque motor, which is something we were already doing for other sectors. The client knew us as a reliable partner in many other industry applica tions in which we’d worked together, and therefore appointed us for the fishing vessel project. Prior to the fishing vessel project, OSWALD had built only a few motors for marine applications, but the fishing vessel marked an unexpected turning point.
As part of the programme, all of the motors receive Lloyds approval for Inland Shipping and meet the project-related marine requirements.
“It wasn’t immediately obvious to most people that our motor was in there,” he added. “But it helped that this ship was using our tech nology because it became a great demonstration of our motor that proved that it works and that it’s reliable.
Inside Marine 177 named Cygnus,” explained Thomas Bachmann, Sales Engineer at ButOSWALD.that’s just the tip of OSWALD’s exciting, growing involve ment in the marine space. Mr Bachmann was keen to highlight another project it’s currently involved with.
OSWALD has designed and engineered these motors specifically for Project Parsifal; a fact that Mr Bachmann was especially proud of.
“This project was an opportunity to really redevelop and modify our existing motor design that we planned to use for the contract. We conducted a complete review of the motor, reviewing all of the components within it.
“Besides the technical optimisation, we wanted to ensure that in the end, the motor looks like something new, fancy and modern,” he continued. “That was part of the strategy for us. We specifically didn’t want to just take an existing design off the shelf and put a new box around it. Consequently, we invested several months into the development work for the new motor. The end result was quite amazing and the test bench results were perfect.”
An especially big milestone for OSWALD was its appointment in early 2021, via its relationship with Hybrid Ship Propulsion, to supply the main propulsion motors for Project Parsifal. This pro ject involves the construction of a series of 40 inland navigation tankers in the Netherlands. The vessels boast an environmentally friendly design and have been specifically engineered to be able to continue motoring even when water levels on the Rhine are low. Each ship built within Project Parsifal will be equipped with two PM 500kW motors, equating to a total order volume of 80 motors.
Mr Bachmann explained: “One of the impacts of this project was that everyone in the marine industry in the Netherlands knew about this fishing vessel because it was new technology and a complete new design by the shipyards involved. The market is closed and very small, the project was in the newspapers and in the media, plus the client marketed it very well.
OSWALD delivers up to four motors per month to the yard and, as of early 2022, OSWALD had delivered more than 20 motors in total.
Project Parsifal is the largest project that OSWALD has undertaken in the marine industry, but it’s perfectly within the company’s strategic vision as it involves manufacturing a large volume of iden tical motors. “It has significantly strengthened our position as one of t he leading manufacturers for this kind of special machinery,” Mr Bachmann confirmed.
OSWALD really began its foray into the maritime sector in about 2015 when it was approached by a long-standing client with a project in the Netherlands, to equip a fishing vessel with electric propulsion.

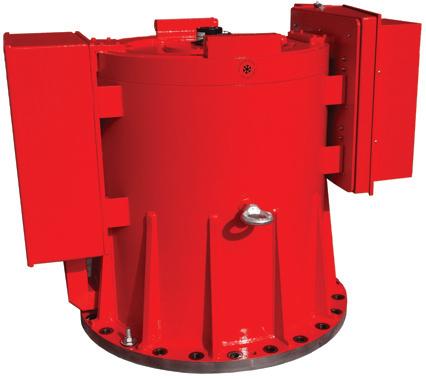
editorial mention
Thinking about strong and reliable PM machines? Think JLMag.
JLMAG RARE-EARTH CO. LTD.
BOMATEC
Snakeline magnets - higher performance at less cost. Snakeline magnets deliver eddy current reduction through a patented segmentation process. The serpentine pattern creates insulating lines in the part, providing higher frequency eddy current reduction. This efficient process results in time and material saved, which is especially required with expensive samarium cobalt magnetic material. With our proprietary epoxy filling technique already mature and deployed with our manufacturing partners, Bomatec has the capacity to quickly and efficiently deploy a Snakeline process across your design.
JLMag’s innovative magnet grades with high remanence and coercivity will help you design effective, compact and safe machines, while our newest 3D-GBD technology will help you reduce the rare earth contents and the overall cost of your PM design. JLMag also proposes high-end coating solu tions to protect your machines in aggressive saline environments.
178 Inside Marine
editorial mention
JLMag manufactures permanent NdFeB magnets and magnetic assemblies for the marine sector. We offer tailored solutions to each individual case, whether it is a propulsion motor, E-thruster or shaft generator.


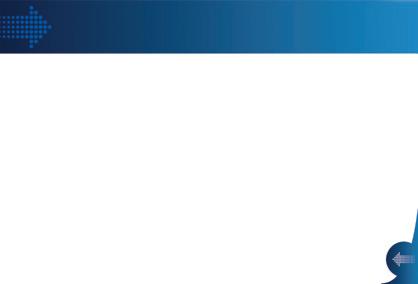
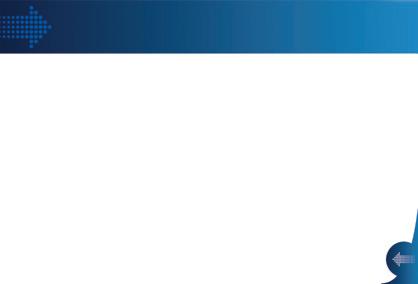
Inside Marine 179
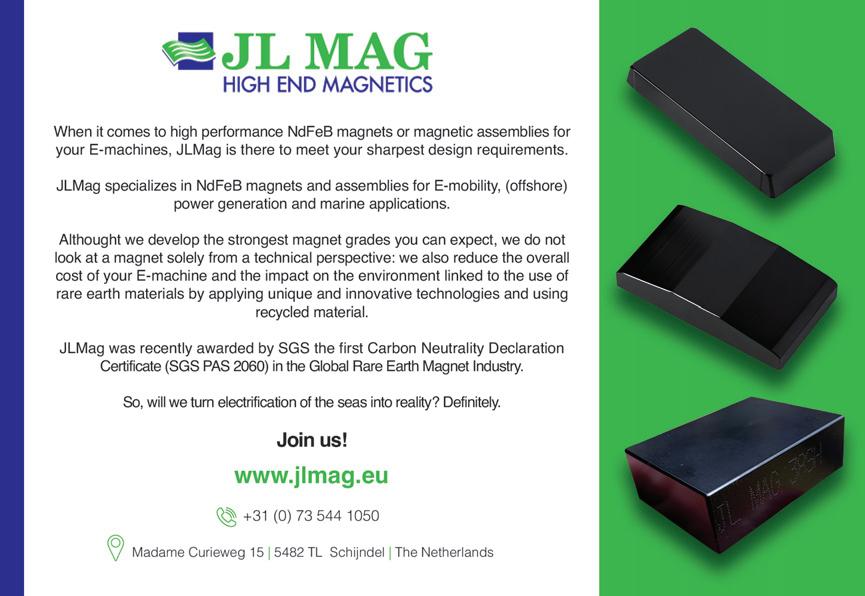

Our engineers have been tasked for the last three years with redesigning perma nent magnet systems for marine use. They are extremely efficient and reliable and it’s something that the superyacht shipyards are increasingly recognising “ “
To anyone in the industry, those end users he’s referring to will be completely unsurprising: they’re superyachts. And it makes sense, since permanent magnet generators are a more expen sive solution as opposed to conventional gensets. But as Mr Bachmann pointed out, their advantages justify the price.
“Our engineers have been tasked for the last three years with redesigning permanent magnet systems for marine use. They are extremely efficient and reliable and it’s something that the supery acht shipyards are increasingly recognising.”
OSWALD ELEKTROMOTOREN I PROFILE 180 Inside Marine
The company’s successful implementation of the fishing vessel pro ject led to additional, similar opportunities in which OSWALD was contracted to manufacture propulsion systems for other vessels. With a portfolio of vessels on the water proving that OSWALD’s equipment is robust and capable, new enquiries began pouring in.
A sea of opportunity
By 2022, OSWALD had delivered a dozen of these new systems to superyachts, and it has further PM generators on order.
“By this stage, the market was open to this new technology,” Mr Bachmann pointed out. “We could prove that we could build the machines that clients required, starting from the white paper all the way to the finished product. It was a very successful story for us in the OSWALD’send.”permanent magnet generators have become a second significant growth path for the company and it is one that the team was keen to discuss. For the last couple of years, OSWALD has been developing and building marine generator systems (gensets) for clients across Europe. These units typically have a power range of between 300 and 1500kW. “It’s a new area for us,” said Mr Bachmann. “End users are increas ingly demanding high-speed permanent magnet gensets instead of the conventional systems.”
“This growth is perhaps driven by the amount of capital in the superyacht industry,” Mr Bachmann noted. “They want all the new, fancy technologies but it’s good for us because it’s helping us to get into the market as well!”
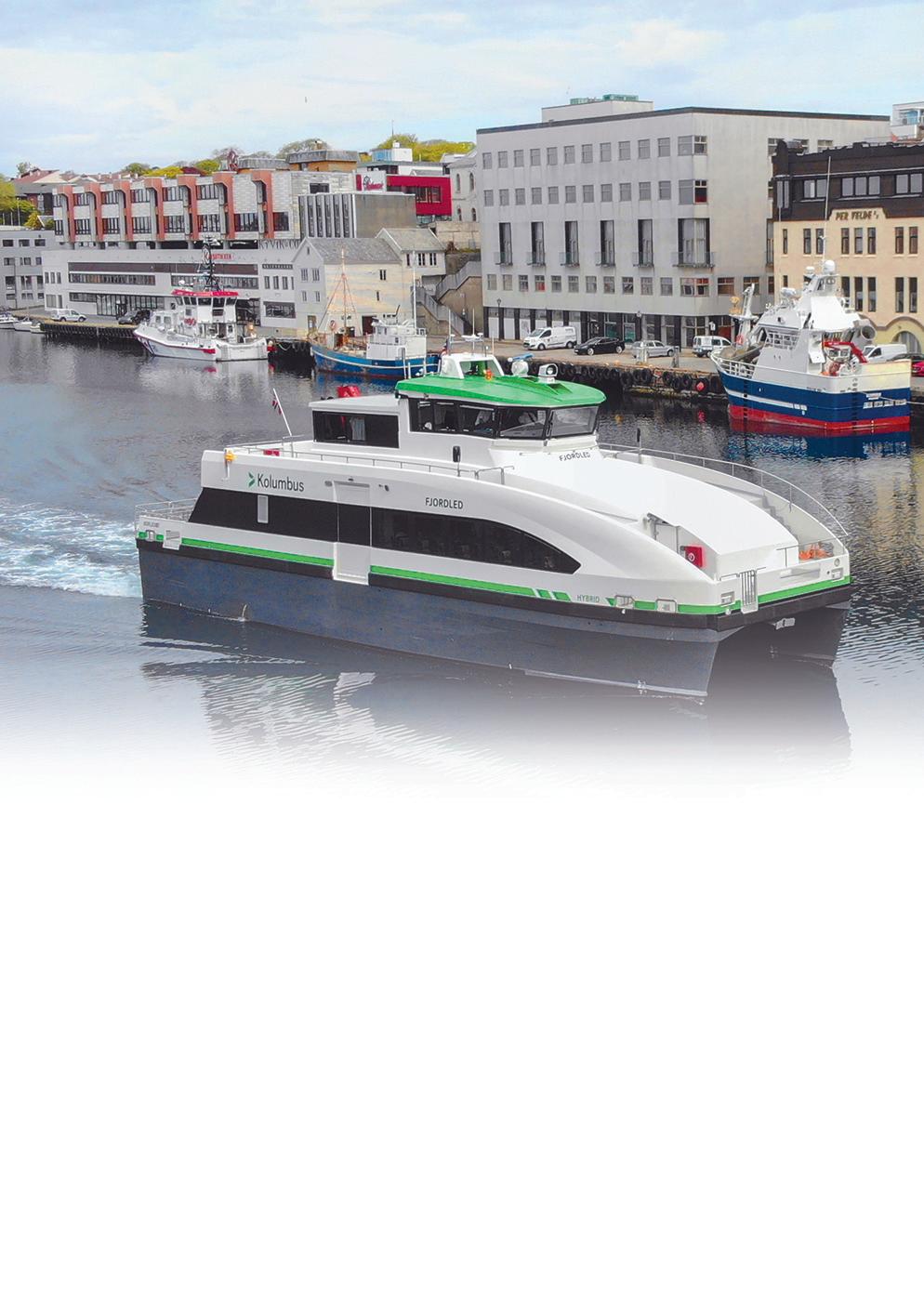
OSWALD’s headquarters is located in Miltenberg, Germany, in the north of Bavaria. It is the company’s only facility. It employs 200 people working in several buildings on the property.
Inside Marine 181
In 2020, the business invested in a new testbed building that doubled its testing capacity from 1MW to 2MW motors, with a voltage flexibility ranging from 400 to 690 volt systems.
Meanwhile, a new high-tech, fully automated stockroom building is under construction and when complete, is expected to significantly speed up the process required for staff to draw project parts and consumables. With only a single employee oper ating a terminal, the system will automatically pull stock at a high speed, significantly speeding up internal logistics.
In closing, Mr Bachmann emphasised the company’s adapt ability: “We are flexible, willing and able to deliver customised solutions. We’re not afraid of a challenge. We’re specialists in working with partners and customers to develop and success fully deliver solutions that are perfect for their applications.” n
Assets and investments
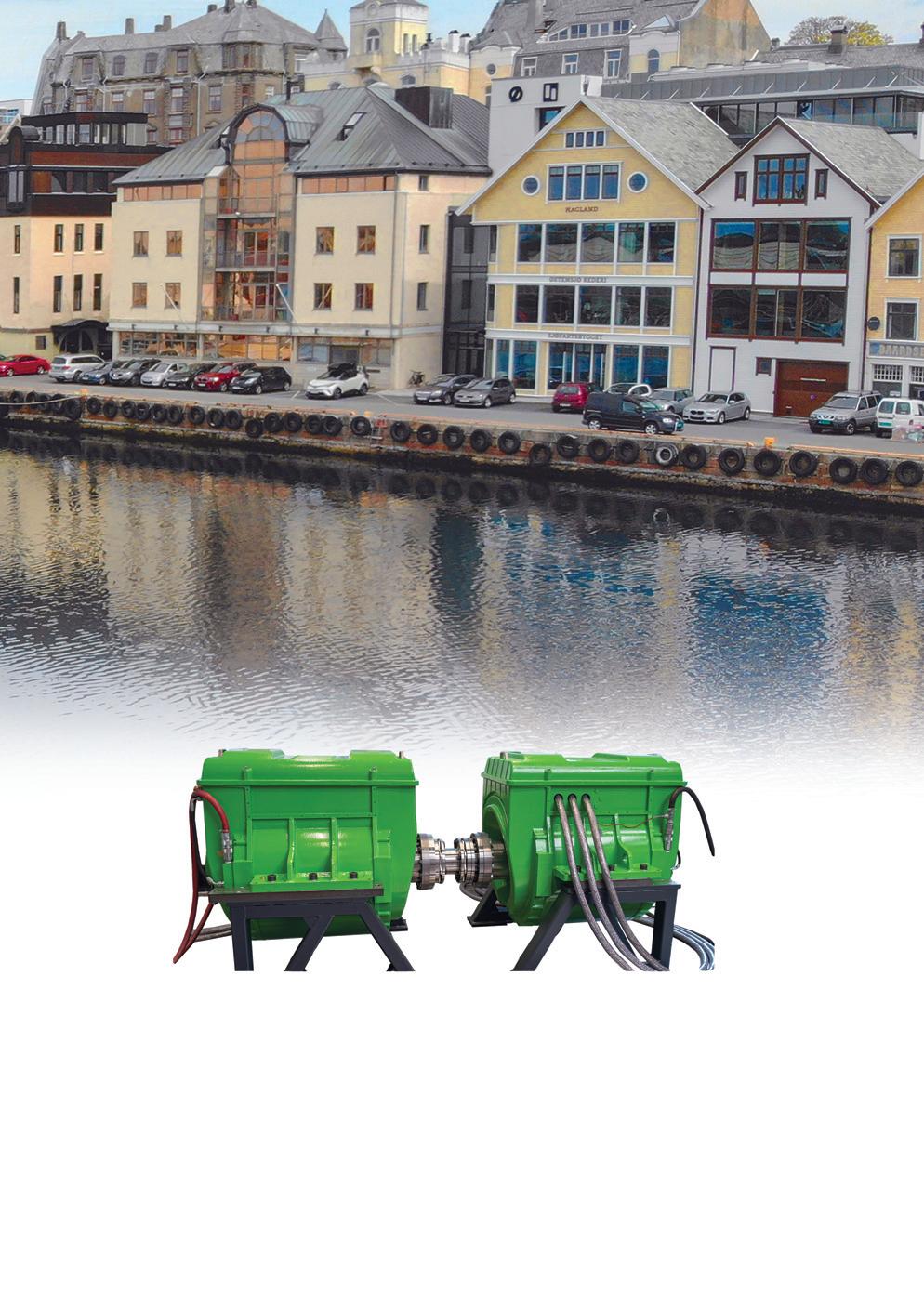
CASTING a spell ON
MERLIN DIESEL SYSTEMS I PROFILE 182 Inside Marine
With customers in over 100 countries, the UK’s Merlin Diesel Systems is a substantial and critical supplier of a variety of products and services in the worldwide diesel engine supplyHavingchain.firmly established its presence in the automotive market, the company has recently made a significant acquisition and stock investment that will substantially grow its share in the marine market. Merlin Diesel Systems’ management team spoke to Richard Hagan about this latest development and what it means for the company’s future. DIESEL MACHINERY
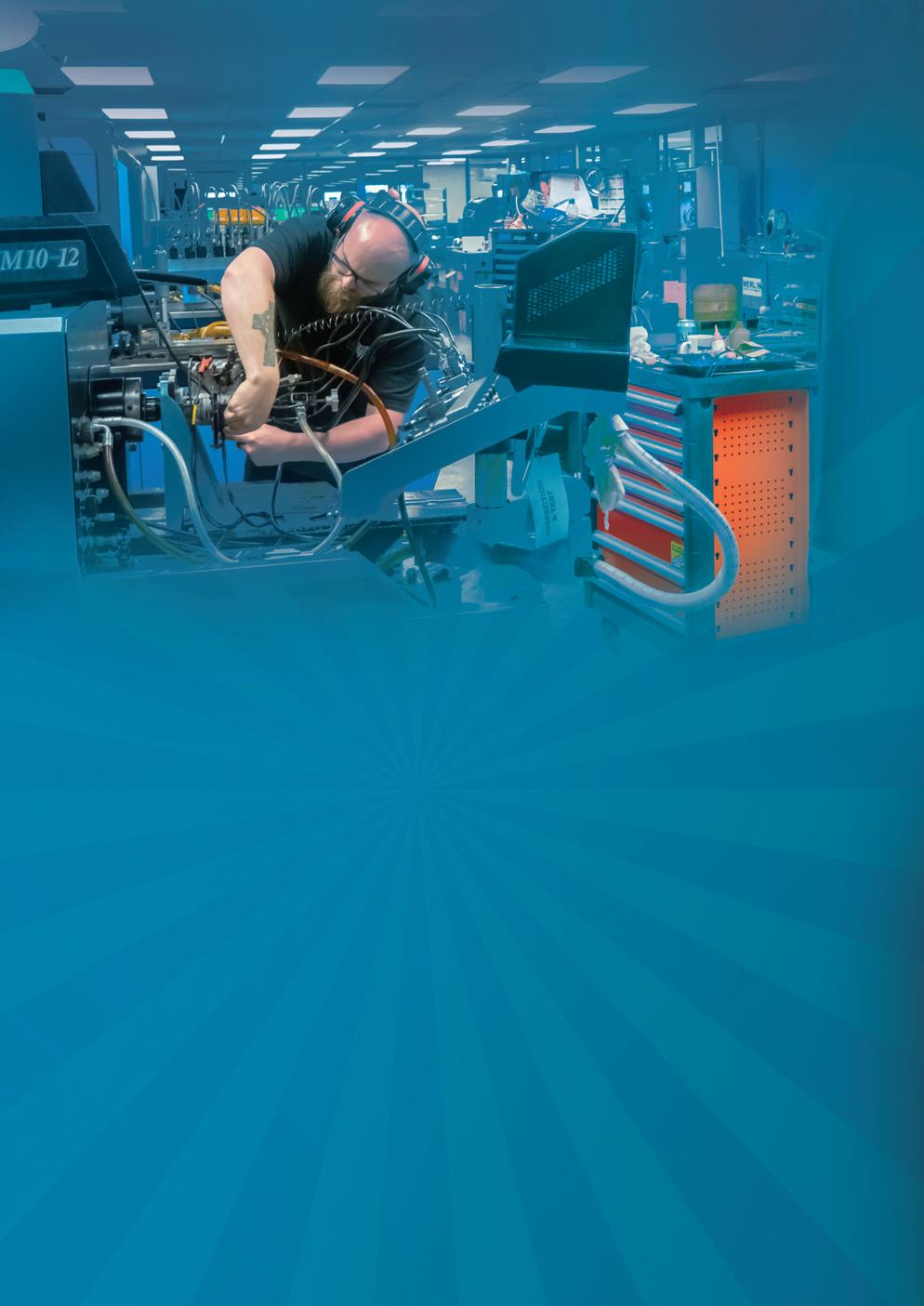
The history of Merlin Diesel Systems c an be traced all the way back to 1947 when the company was first estab lished in West Yorkshire by a certain Mr CT Rhodes of Halifax. Fast forward to today and it has grown into a veritable powerhouse within the diesel spares and servicing industry, both in the UK and abroad. From its headquar ters in Preston in Lancashire, Merlin Diesel supplies over 50,000 parts to customers in over 100 countries.
Merlin Diesel supplies a comprehensive range of products and services to the auto motive, heavy industry and maritime sec tors. The company’s very large production centre is said to boast one of the biggest and most sophisticated diesel workshops in the world. The company’s portfolio consists of two main categories: fuel injection spares, and test equipment solutions. Its spare parts product range spans diesel fuel injection parts from well-known, recog nisable manufacturers such as Bosch, Delphi Technologies, Yanmar, VDO, Perkins, Denso and many more.
Exporting in high gear Whilst the domestic market is an important part of Merlin Diesel’s business, export mar kets remain the company’s biggest source of revenue, according to Technical Director Scott Bramley: “Exporting spare parts is a major part of our business; we export about 65% of our products. Most of that is diesel fuel injection parts and complete units, with probably a 50/50 split between the“Wetwo.export parts like injectors, fuel pumps, pressure sensors and pressure control actuators,” he continued. “It could be for marine or heavy-duty automotive. Within the automotive sector, we are seeing real growth in areas like agriculture and highway, and now also marine as we start to widen our envelope.”
Inside Marine 183

Meanwhile, its test equipment range is sourced from similarly recognisable brands such as Bosch and Hartridge (a subsidiary of Delphi-BorgWarner), as well as manu facturing its own range of bespoke test equipment. Customers can choose from a variety of test benches for every conceiv able application, all supplied directly by Merlin Diesel. Stockholding cushions the blow
“At the moment, there’s limited repair solutions for certain fuel injection systems in large engine equipment,” he explained.
Maritime market expansion In 2021, Merlin Diesel concluded a sub stantial investment into sister company Tyne Electro Diesel. The transaction saw Merlin acquire a 52% share of Tyne Electro Diesel, a service provider focusing on the overhaul and repair of marine diesel sys tems. This acquisition is part of the com pany’s strategy for growing its market share in the maritime space.
“It’s crucial to our business moving for ward,” Mr Henry remarked, singling out opportunities in the repair of injection components in large engine equipment as a future driver of growth for the business.
Sales Director Derek Henry agreed: “Some of our main suppliers have had six price increases in the last 18 months, ” he lamented. “To try and manage that is veryNonetheless,difficult.” he highlighted the com pany’s robust stockholding as a major advantage at a time when stock short ages have become a chronic problem. “One of the strengths of our business model is that we have quite a sizeable amount of stock, and that’s really what drives a lot of our business and our success. Where most suppliers run out of particular parts, we still have stock. Today, we have £21 million in stockholding, and that tends to be a real strength for us.”
“With our investment in Tyne Electro Diesel, I think there’s a lot of opportunities.” Additionally, the company’s unique test bench services are on hand to continue
While the business continues to show strong growth, the team threw the spotlight on ongoing global parts shortages and supply chain price increases as a major source of headaches for its growth plans. “We’ve got some big challenges with shortages,” confirmed Mr Bramley. “It has cost us a lot of turnover, but so much of it is out of our hands. Some parts only have one supplier, so we can’t seek alternative sources for those. Additionally, we’re dealing with rising costs and there’s very little we can do to control that.”
MERLIN DIESEL SYSTEMS I PROFILE 184 Inside Marine
Regardless of supply chain challenges, the company registered a record sales month in March 2022. “Our customer base is growing,” said Mr Henry. “Globally, diesel continues to represent a huge opportunity for us.”
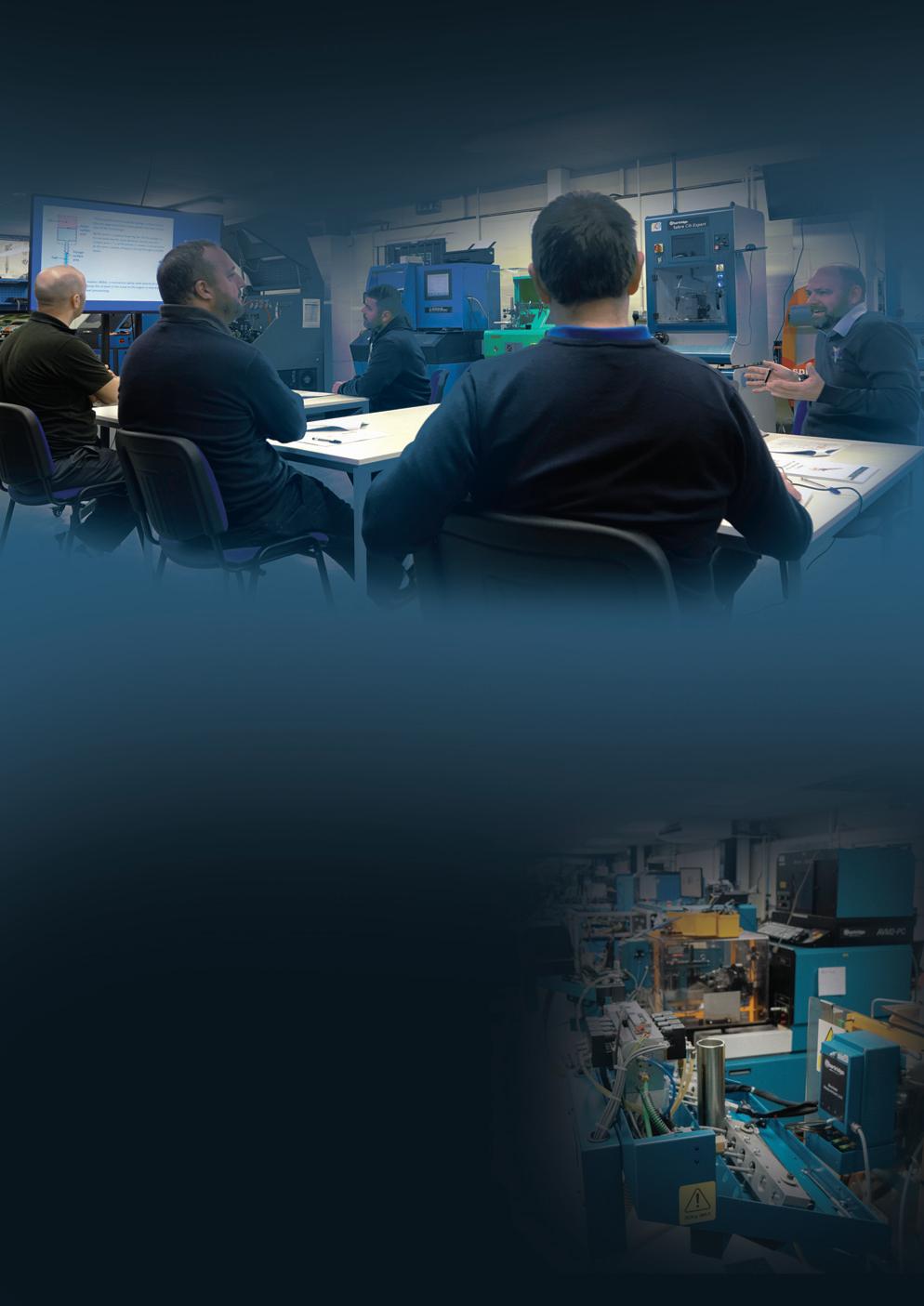
“We’re changing the whole workshop from the ground up,” said Mr Bramley. “We’re building a component assessment room as well as a cleanroom for product assembly. We’re also restructuring inter nally and adding an extension to the building to cope with our growth.”
Going forward, the team was optimistic about the future. “We still think there’s a lot of room for growth in the industry for us,” Mr Bramley asserted. “We want to look for new oppor tunities. We see a slight diversification from automotive, looking more towards the agricultural and industrial side of the business. And we want to look at contract business if we can find the right partners. The future looks bright.” Mr Henry’s focus was on a return to trade shows. “There are a number of shows we will be attending. Globally, we’ve histori cally been very proactive with visiting and exhibiting at shows. We’re about to attend Motortec in Madrid, Rematec in Amsterdam, SMM in Hamburg and Automechanika in Frankfurt. Towards the end of the year, we will also be in Paris, Dubai and Shanghai.”
Inside Marine 185 delivering substantial value to its efforts within the marine environment, where its Merlin DC-80 series test bench and Mark 6 common rail marine injector testing solutions are proving popular.
Factory expansion Merlin Diesel has enjoyed ongoing sales growth for the past two years, with a £5 million sales growth in 2021 alone. To accommodate the company’s current and future growth forecasts, it is in the midst of a major physical expansion of floor space and production capacity.
Mr Rawlinson concluded with a brief highlight of the company’s ethos. “It’s not just about winning the sale,” he said. “It’s about customer retention and welcoming feedback. We’ve got a great management team and fantastic staff, supported by excellent telesales staff both here in the UK and in our export team. They all go the extra mile.” n
To ensure that it retains its highly-skilled staff, Merlin Diesel has implemented a pay structure that is competitive, within a healthy and properly equipped workspace.
“Our test equipment division is also being expanded to give it more space because it’s really growing fast,” added Managing Director (Test Equipment Division) Mike Rawlinson. “Our diesel injector remanufac turing service has always shown strong growth, but the last two years in particular have highlighted the need to expand our capacity in order to be more efficient.”
With all of this new space comes the need for additional staff. The company has brought in a new management team to oversee its expanded operations. Under them, there’s a near-constant flow of new recruits joining the business, with a par ticular focus on apprentices. “We’re trying to bring in and train up as many young people as we can,” Mr Bramley explained. “It’s very difficult to bring in fully-trained diesel engineers simply because there’s just not that many of them around.”
“We like to promote people from within, and there’s a clear chance of progression to management roles,” Mr Henry noted. “We also pay an annual bonus and a generous pension. It’s about ensuring that we look after the staff as best we can.”
Once the £1.5 million expansion project is complete, Merlin Diesel will boast an extremely impressive 7,000 square metres of covered floor space. Injecting new people
Room for growth
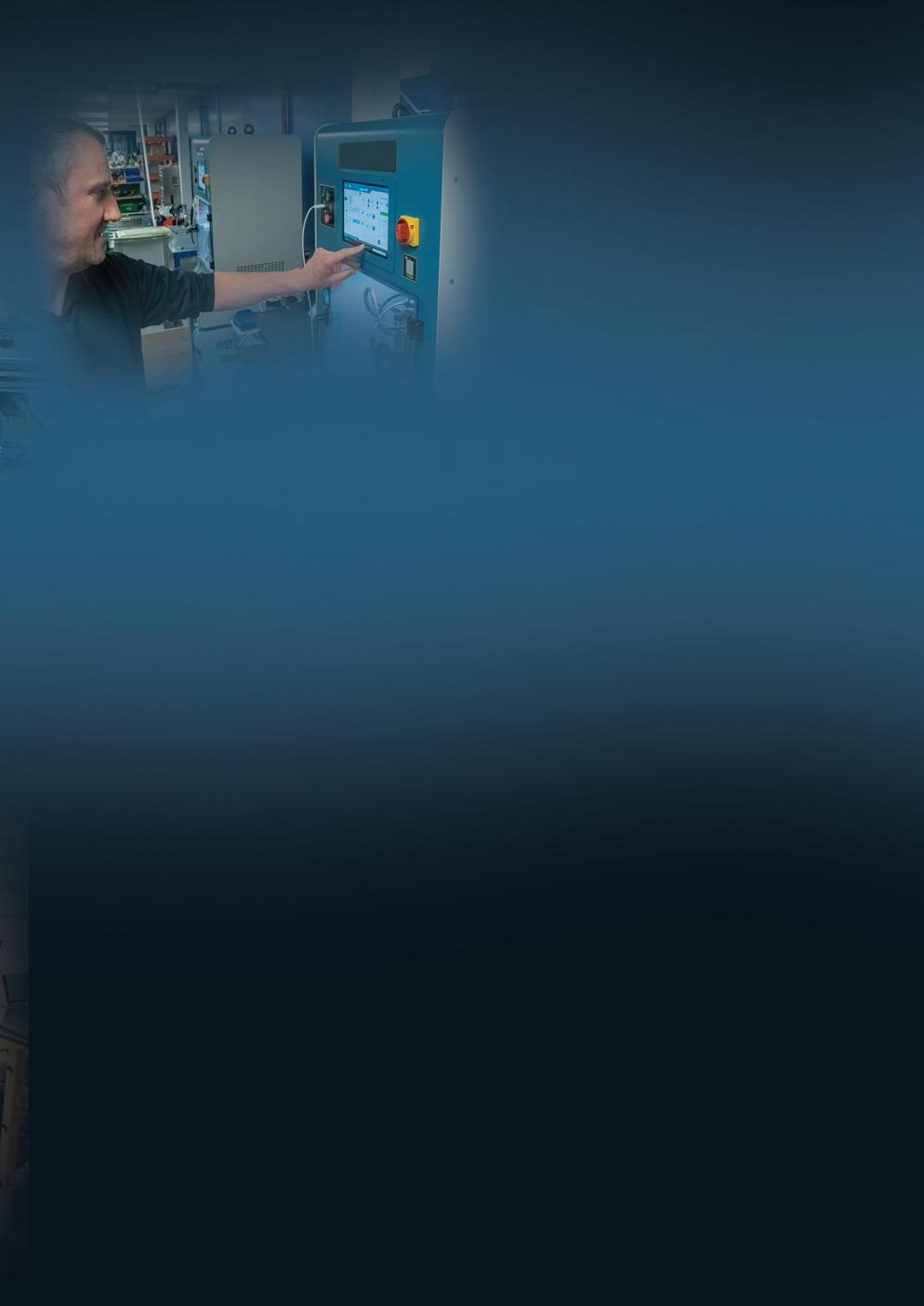
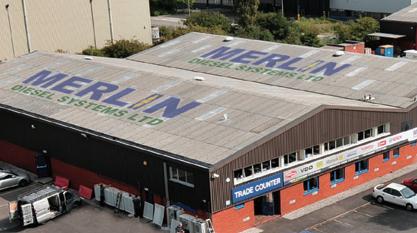
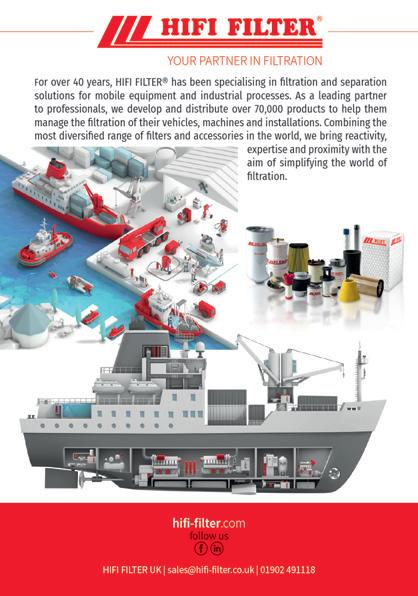
If disaster strikes at sea, quick and coordinated movement of passengers and crew to designated assembly stations can mean the difference between life and death. Dutch marine safety company T-ISS engineers and supplies the systems and products which ensure that everyone aboard can find their way to safety, even in the direst of circumstances.
T-ISS Director, Willem Heijboer, sat down with Richard Hagan to talk about the critical importance of safety signage on vessels.
T-ISS Director, Willem Heijboer
T-ISS I PROFILE 186 Inside Marine
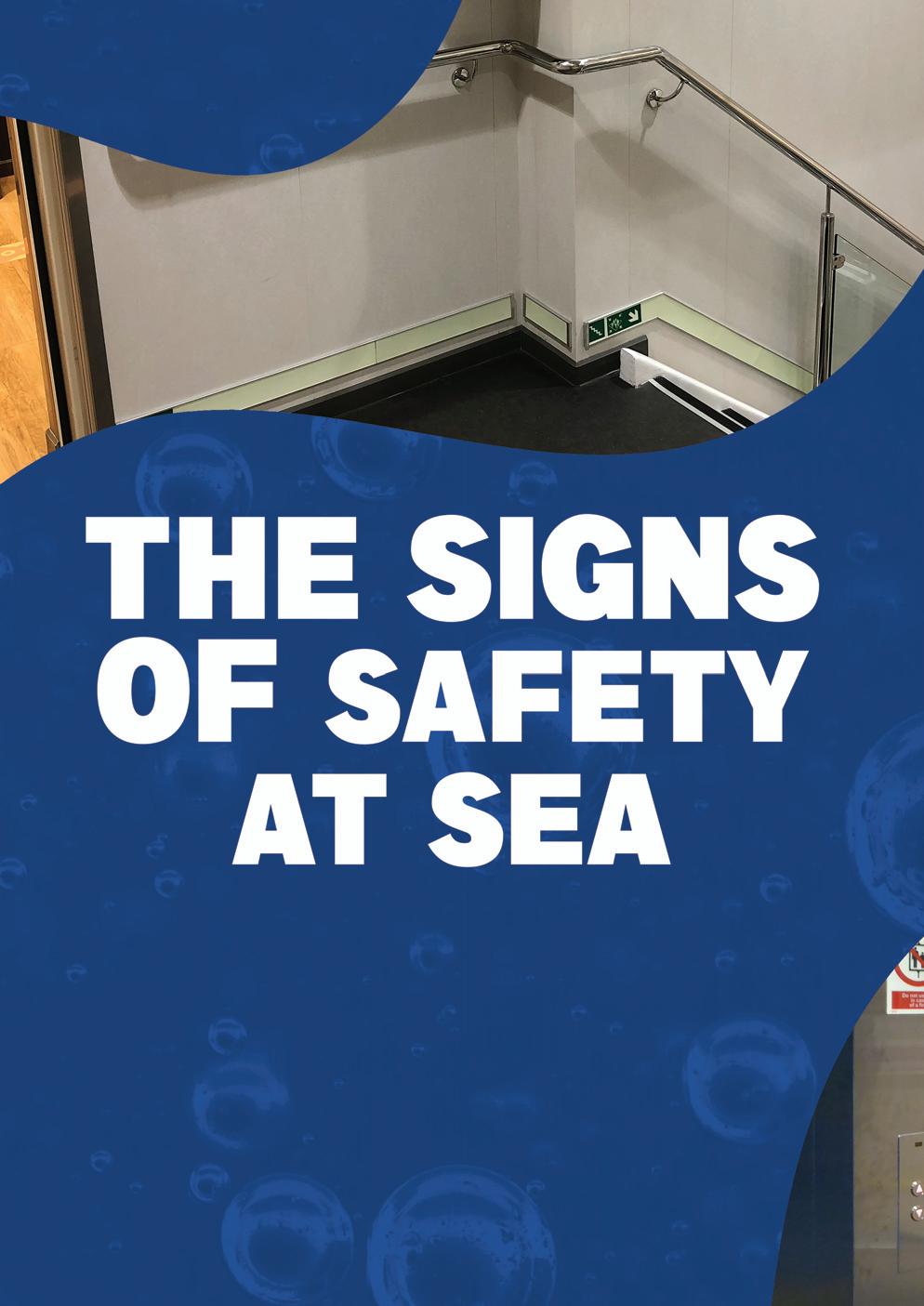
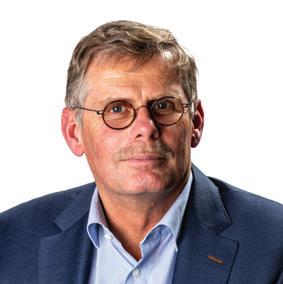
T-ISS, based in Dinxperlo in the Netherlands, supplies a range of certified maritime safety products. Its core business and speciality, however, is safety signage, both high and low loca tion lighting for maritime use. When the emergency alarm sounds on board a vessel, the ability of passengers, and even crew, to find their way to assembly and embarkation stations can very easily mean the difference between disaster and rescue.
Pointing the way to safety
Four decades of safety at sea Safety signage is a part of many of our daily lives that most of us largely either take for granted or ignore completely. But for Mr Heijboer, who has a background as a safety engineer, the
Inside Marine 187 issue of signage on vessels quickly took on a new meaning when he set up his maritime safety consultancy in the early 1980s.
“Safety signage is very important in preventing panic. SOLAS (Safety Of Life At Sea) regulations require also public address systems which use spoken words. But in practice, few people understand these instructions – they’re stressed or distracted, and have to find their way to the places of safety. Proper safety signage ensures that in an emergency, every passenger knows where to go and is able to find their assembly station.”
“We discovered that a lot of safety signage wasn’t correctly done,” he said. “In 1985 we completed our first safety sign project and in 1992 we did our first passenger vessel. The business has gone from strength to strength since then. We have since completed projects onboard many types of ships and offshore installations.”
In 2017, after working with T-ISS for years through his safety sign company, Mr Heijboer seized an opportunity to purchase T-ISS. It now has worldwide relationships for which it delivers projectbased safety sign solutions, starting with the engineering of a project, through to production, delivery and then installation. Each project is tailor-made for that particular client’s needs and typically includes installation, which can be handled by T-ISS as well.
According to T-ISS Director, Willem Heijboer, escape route signage is the keystone, ensuring that everyone on board a vessel is able to get to safety during such emergencies.
T-ISS specialises in providing safety signs as a system that enc-ompasses all of the components using the correct symbols required by SOLAS and IMO regulations and according to ISO standards. Altogether, the signage system T-ISS manufactures represents a set of visual instructions that anyone can under stand, regard less of their native language, and that anyone can actually see, regardless of whether there has been a power failure on board – as can happen in emergencies.
T-ISS boasts five sites, with three in Holland, one in Denmark and one in Germany, hosting a total staff complement of close to 100.
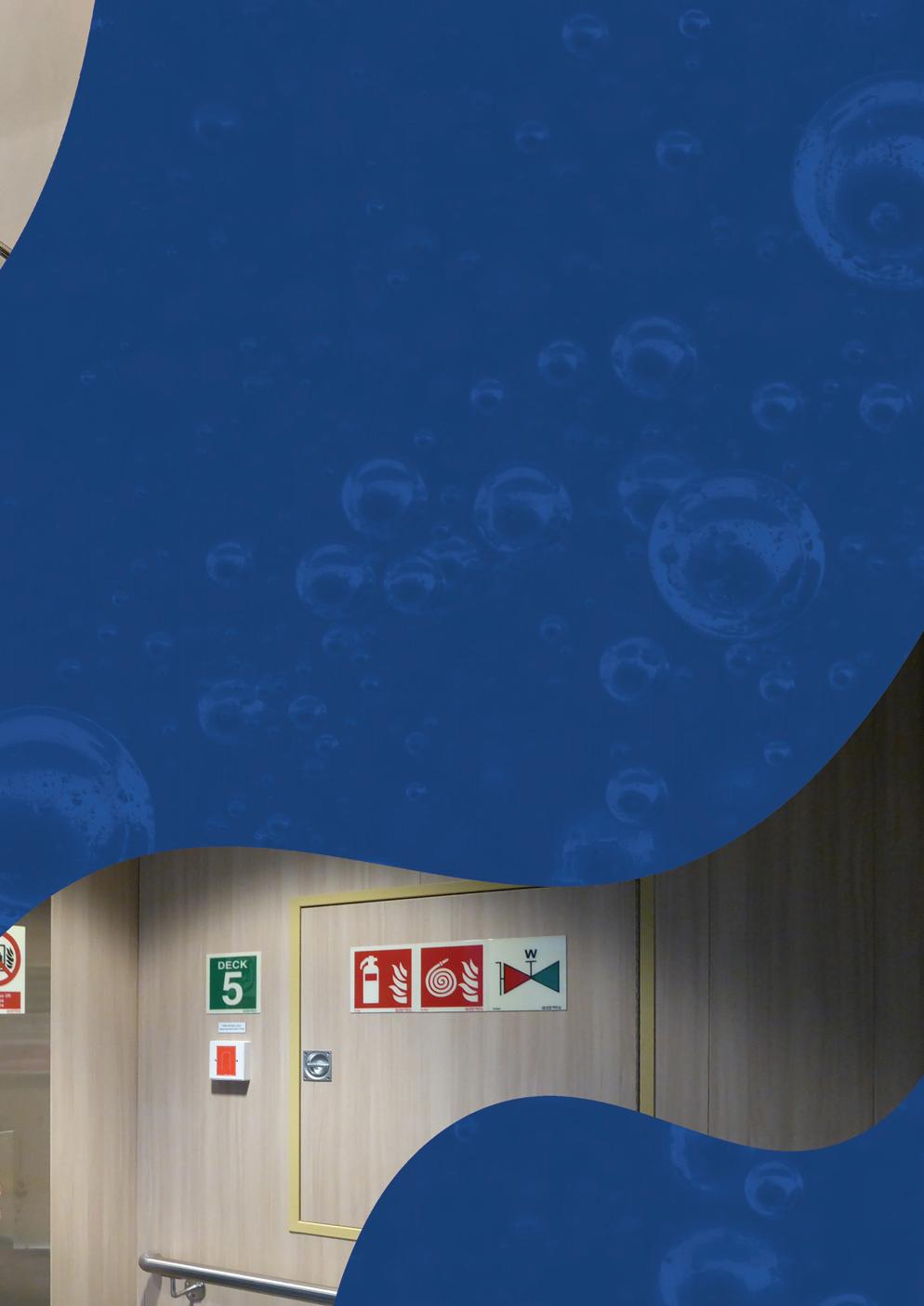

Around half of its teams are involved in safety sign projects while the others handle other projects such as directional and decorative signage and the supply of safety products and tapes.
“From my profession as a safety engineer, I saw a lax attitude towards signage standards (as well as so many errors in its applica tion), that I decided to become involved in standardisation activities for this signage. For the last 20 years, I’ve been directly involved with ISO, specifically with all maritime ISO safety sign related stan dards. That includes low location lighting, safety symbols and fire control plans. “As a member of TC145 and TC8, I helped develop many standards. Now I’m a project leader for the development of a stan dard of safety instructions and convenor of a working group for a pipe-marking standard.”
“SOLAS requires that you must be pointed to the assembly station and from there, to the embarkation station. Instead, escape routes often just end up on an open deck when the regulations state that you’re supposed to actually go to or be led to the assembly station.”
“ISO standards require that safety signage worldwide must be identical and must use symbols, because everybody can read sym bols, regardless of what language you speak,” he continued. “ISO provides all of the relevant symbols, and yet people don’t use them. You see so many vessels with only the word ‘EXIT’ on their signage and when you follow it, you sometimes end up back where you started, as it’s not clearly marked where the assembly station is located.
“An escape plan is required to assign both primary and secondary escape routes. On board vessels you often see ‘EXIT’ and ‘Emergency Exit’ but in fact, just the correct symbol is required for emergencies.”
T-ISS I PROFILE 188 Inside Marine
Signs of confusion
Having been repeatedly frustrated by just how common the problem is, Mr Heijboer embarked on a personal campaign to do something about it.
Safety signage as a system Regulations require that all passenger vessels must have low location lighting (LLL) on board. The LLL guides people to the assembly station, also in power failure conditions. Where LLL is installed, safety instructions are required, both in cabins and public spaces, displaying the calculated primary and secondary escape routes.
Mr Heijboer highlighted a specific but common mistake he sees within the industry, relating to escape signage: “It’s regulated in SOLAS that all escape routes must lead to assembly stations by using the standardised symbol, and then from assembly stations to embarkation stations. In practice, in many cases, you just see a sign with the word “EXIT”. But in my opinion, exiting a vessel is cold and wet,” he said, laughing. “It can work for some smaller spaces, but from larger spaces, corridors and staircases, the escape route to the assembly station must be indicated.
According to Mr Heijboer, there is a general lack of awareness throughout the maritime industry regarding the correct use and implementation of safety signage on board vessels. This point even extends, he says, to the very people charged with ensuring the sig nage is “Surveyorscorrect.from classification societies must have knowledge of so many fields that signage often falls short as a visualisation of the escape calculations plan,” he noted. “And while SOLAS and ISO both contain regulations with regards to safety signage, few companies apply them correctly.”
He explained that symbolism, instead of only text-based signage, is vitally important because of its ability to transcend language barriers.
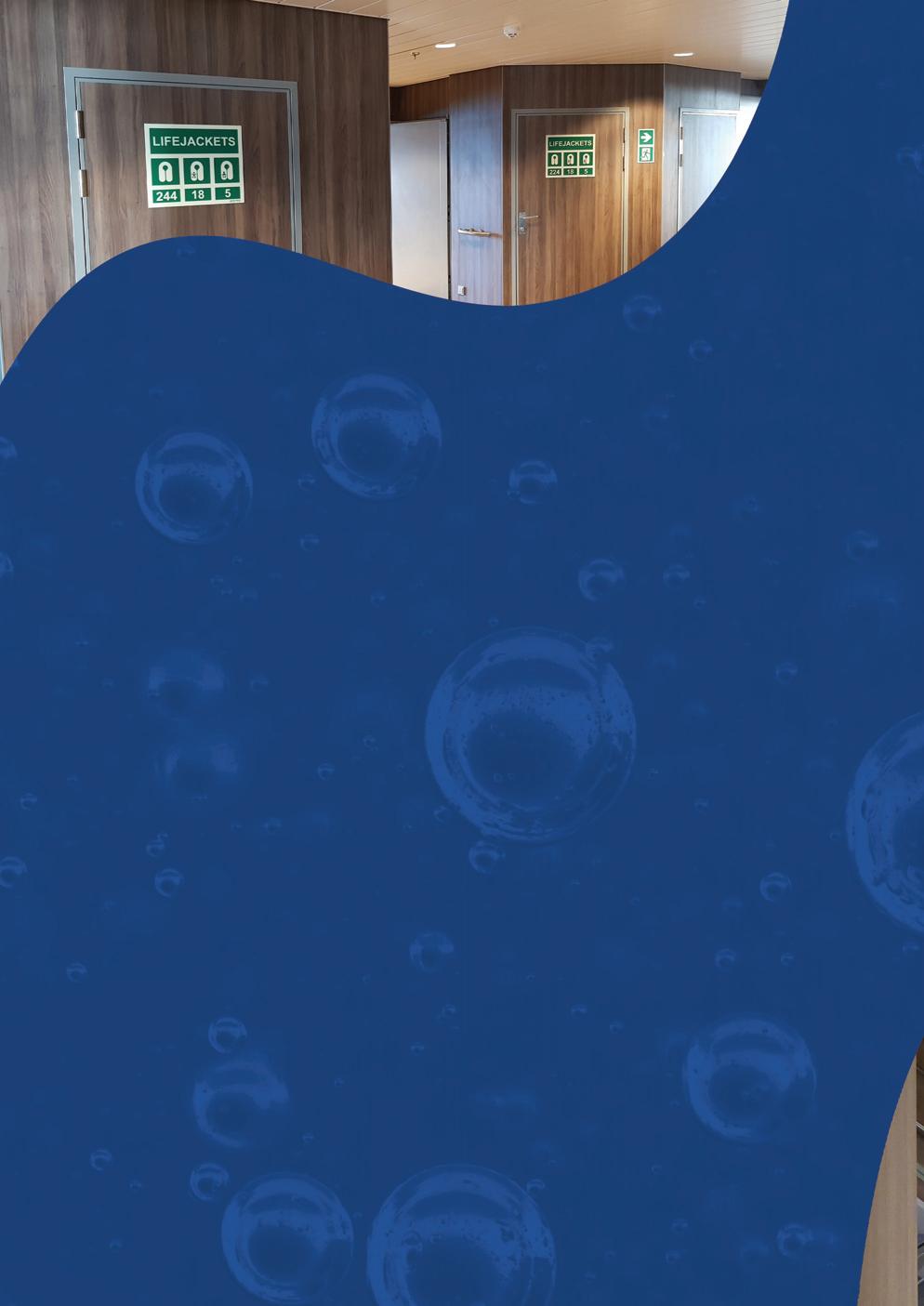


“Thanks to our particular combination of experience and knowl edge, we have an expert level of knowledge about safety signs, and we’re able to do all of the engineering. It’s a really specialised thing for us. But for me, it goes further than just doing business and earning money. It’s like a mission for worldwide safety that I’m on; a cam paign. I like that.” n
Inside Marine 189
“If the power to the ship is lost, the photoluminescence is activated and the sign remains readable and visible for over three hours. After those three hours, it’s still more readable than the minimum require ments in ISO and IMO regulations,” Mr Heijboer proudly remarked.
“Our adhesives are so strong that if you install our sign in the wrong location, you’re going to have a huge problem removing it!” he commented with a chuckle. The T-ISS signage range is also 100% non-PVC. “PVC gives off chloride gas in a fire, so it’s not allowed on vessels,” Mr Heijboer revealed. “A lot of our competitors deliver PVC signs but it’s something that nobody thinks about. Our signs won’t release any toxic gases in case of burning.”
“Every passenger vessel must have LLL on board and every five years it must be tested,” noted Mr Heijboer. “We’re certified for carrying out those tests and often we combine this with a safety signT-ISSsurvey.”manufactures all of its signage itself, so bespoke signs are no problem. All of its signage is fully UV and saltwater resistant and is applied using the highest-quality adhesives.
“Where most of our competitors are just selling signs, we are selling a complete system. We’re not working only towards the letter of the requirements and regulations, but we’re also engi neering towards the goal of the regulations.
T-ISS will design, manufacture and supply a complete safety sign system in line with the ship’s escape calculations plan. This will include both the high and low located signage (photoluminescent or electrical LED) and the safety instructions on board.
More recently, T-ISS has introduced LED escape signs that utilise both LEDs and photoluminescent material.
It goes without saying that escape route signs on the bulkheads, at the ceiling and on the LLL must comply with the safety instructions, and vice Essentially,versa.rather than just selling you an isolated handful of PVC signs (which in any event aren’t legal on ships for safety reasons),
The importance of specialised safety knowledge In closing, given the gravity of the subject, Mr Heijboer was emphatic about why it’s so important that vessel owners should work with spe cialists in this field when procuring safety signage
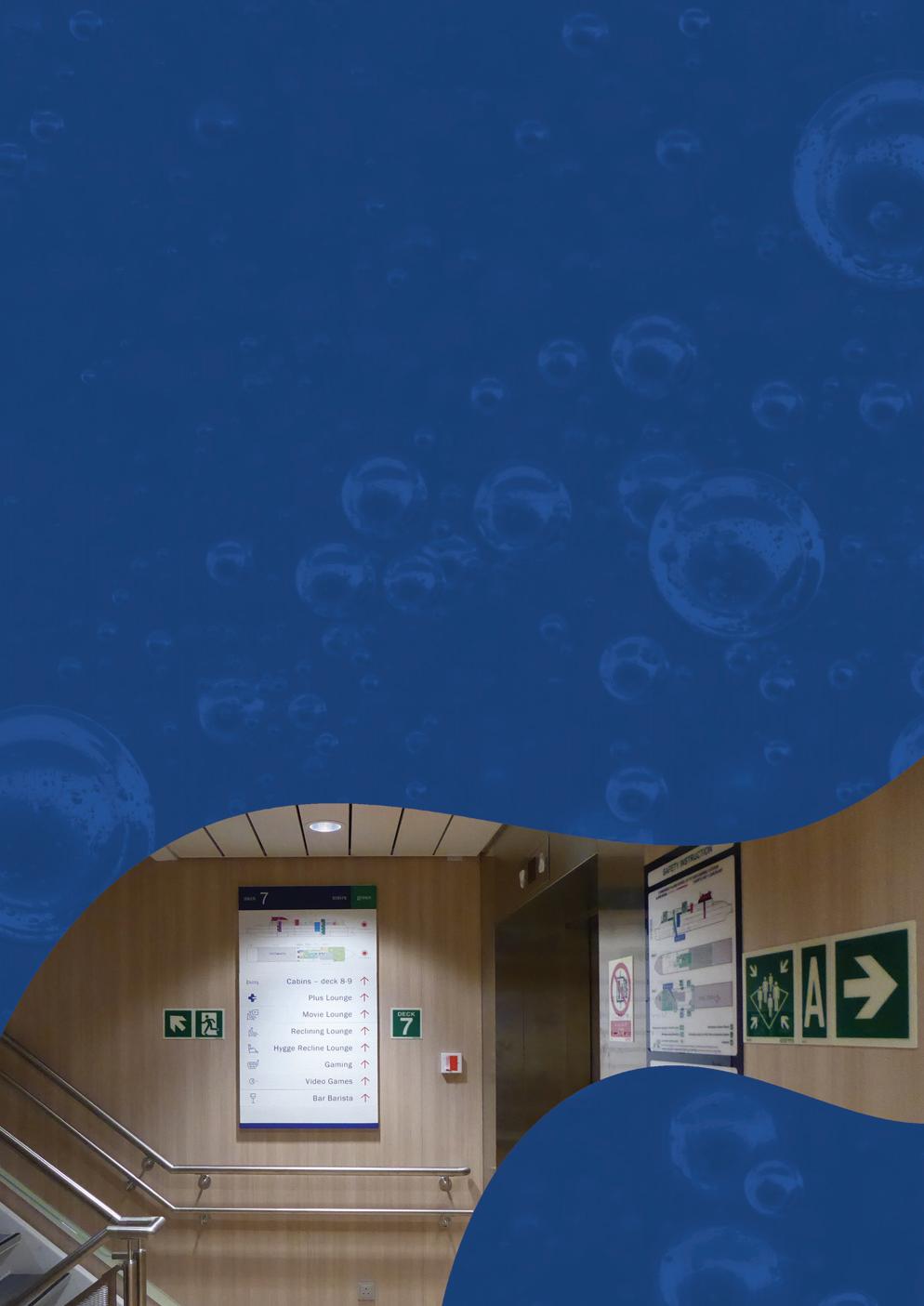
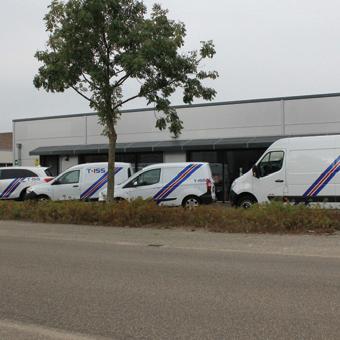
Ocean Craft Marine is a specialist manufacturer of rigid hull inflatable boats, customised for professional, military and leisure applications. The company recently launched a new initiative to revitalise the small boat industry. Roy Nouhra, CEO, founder and owner, and Jo Stapleton, Director of Sales and Marketing, Americas Region, explained the project to Phil Nicholls.
OCEAN CRAFT MARINE I PROFILE 190 Inside Marine
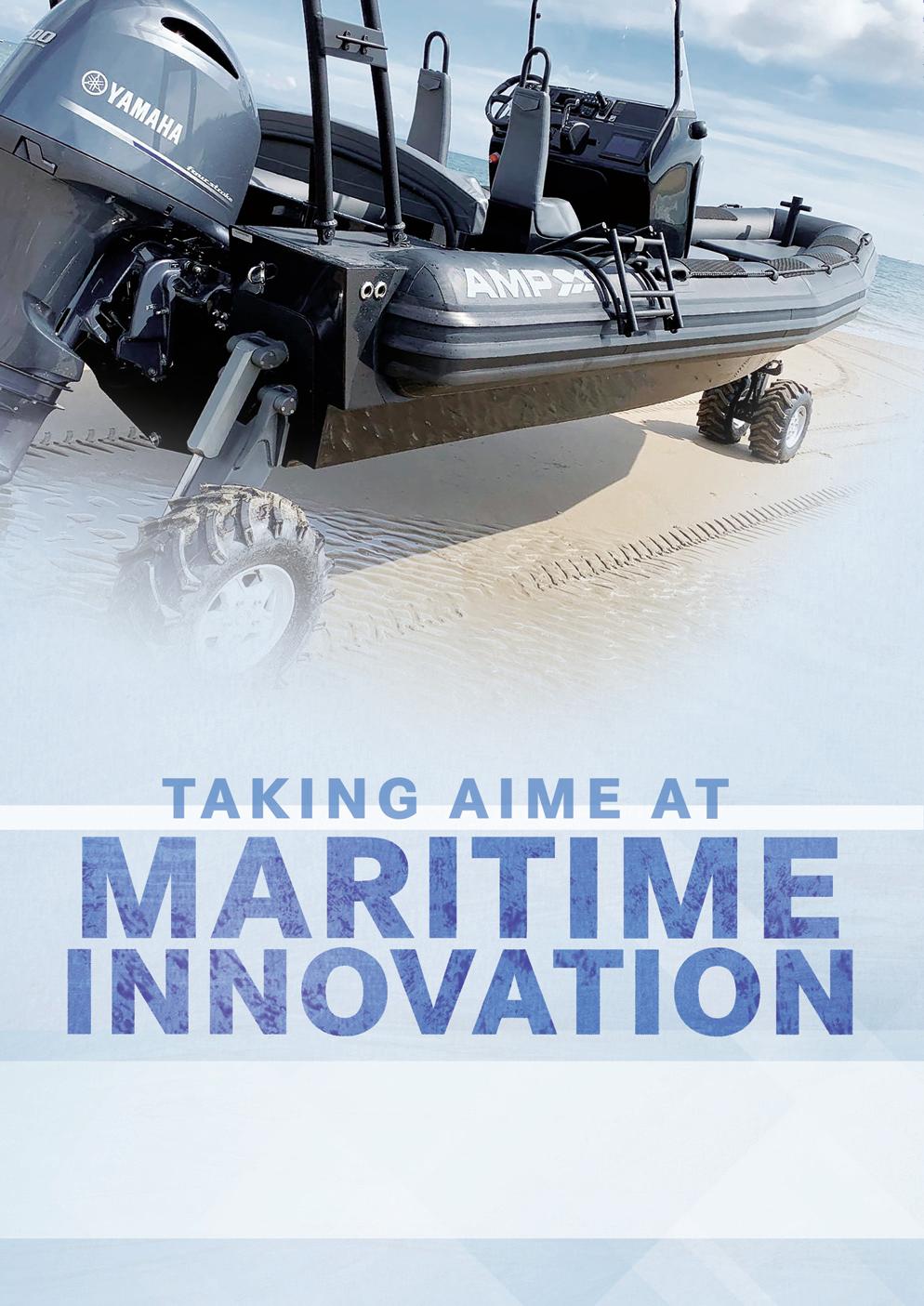
T he Ocean Craft Marine range mirrors ASIS Boats, offering rigid hulls in fibreglass or marine-grade aluminium and the hypalon sponsons can be fitted with either pneumatic or Hyb Foam® technology. Based in Maryland on the east coast of the United States, Ocean Craft Marine has a sales office in Annapolis and a factory on Kent Island, with a staff contingent of 160 employees between the two.
Mr Nouhra is taking the helm of AIME in the wake of his experience in the maritime industry. He began ASIS Boats in 2005, a world leader in manufacturing Rigid Hull Inflatable Boats (RHIBs) for the military, professional and leisure sectors, with boats sold in over 80 countries worldwide. Built in a 11,000 sqm facility in Jebel Ali, Dubai, ASIS rigid boats are offered with fibreglass or aluminium hulls, both available with amphibious options. Building on this success, Mr Nouhra began Ocean Craft Marine to focus on the North and South American markets.
A professional RHIB has a cargo capacity in excess of 1.5 ton s with the ability to operate continuously at speeds of 100km/h in 1m seas. The professional boats are used by many maritime end-users including fisheries, search & rescue, oil support, law enforcement, eco-tourism, science and research companies.
The unique hull design at Ocean Craft Marine is part of the USP of its boats, featuring a unique reverse chine design enhancing the on-water experience. When a hull is viewed in cross-sec tion, the sharp angles of the chines are evident. Reverse chines angle downwards, parting the water to the side of the boat as well as downwards as the boat powers through the water.
The core of the Ocean Craft Marine portfolio is the profes sional boats range with outstanding performance built for no-failure-zone applications where reliability and consistency are critical requirements.
AT the 9th Annual Maritime Security East & Response Boat Expo & Conference 2022 in Virginia Beach VA, Ocean Craft Marine announced the establishment of the Accelerator for Innovation in the Maritime Ecosystem (AIME).
Reverse chine design
“The reverse chine design started out as a way of making the boat faster,” Mr Nouhra explained. “And then we realised it wa s also making the ride drier because it was throwing the water downward. It was making the ride comfortable because it was creating an air cushion under the boat, reducing the shocks
Roy Nouhra, CEO, founder and owner, outlined the goal of the AIME project: “It’s a new approach to the industry, where we bring all the players together, to play in the sandbox, to develop and make the systems-talk together, so that we can give a solution to our customer that is technologically the most advanced one.”
Inside Marine 191
Alongside the professional range, Ocean Craft Marine also produces military-grade RHIBs built for the demanding require ments of mission survivability and mission success. The Ocean Craft Marine hull design enables remarkable high-speed tac tical turns and excels in the roughest of sea conditions. The mil i tary range of RHIBs are suitable for conducting coastal patrols, harbour defence, vessel boarding search & seizure (VBSS) oper a tions or shoal-draft riverine missions.

training supplied as part of the company’s after-sales package: “Most of the rescue organisations in the United States are volun teers, so the training has to be part of the package and focused on their specific operation. That’s why we do what we do; it all goes back to the safety of the crew and the safety of their mission.”
The discrepancy between Ocean Craft Marine’s business model in relation to competition is a source of frustration for Mr Nouhra: “Today the market is not driven by innovation or providing solutions or even understanding what the customer really needs. Today, it’s only about building what the customer has been using for the last 15 or 20 years. Then everyone moans that the technology is obsolete and the boat building industry is where it was in World War Two.”
This frustration was a driving force behind the creation of AIME. Ocean Craft Marine plans to invest over a quarter of a billion dollars through the next ten years to establish the industry’s first indepen dent maritime innovation laboratory.
Once the bespoke boat is delivered to the client, this is not the end of Ocean Craft Marine’s involvement. Jo Stapleton, Director of Sales & Marketing, Americas Region, emphasised the full cycle of
“Our approach is a little bit different from the competition,” said Mr Nouhra, “Because before we deliver a boat, we actually visit the customer and see their operational environment. We hear what they need, figure out their unmet needs and then find them the right solution.”
The capabilities of the Ocean Marine Craft boats are a clear driver of sales, according to Mr Nouhra: “We always say ‘butts in boats are what sells boats’, because the minute a client rides in our boat they understand the difference between a Porsche and a Ford.”
In addition to the unique features of its boats, Ocean Craft Marine also has an unusual sales process, delivering a complete package to the customer.
OCEAN CRAFT MARINE I PROFILE 192 Inside Marine for the operator, and it made the boat much more manoeuvrable at high speed.”
A new approach
“Most of the rescue organisations in the United States are volunteers, so the training has to be part of the package and focused on their specific operation. That’s why we do what we do; it all goes back to the safety of the crew and the safety of their mission”

Inside Marine 193
“We want to bring the industry – the ones who are willing to move forward in technology and adoption – together,” Mr Nouhra said. “And within the industry, they’re all jumping on board saying what we’re doing is pure genius. Because today, when you buy a car, all the systems talk together. When you buy a boat, none of these systems talk together, and it makes no sense.”
A testing future Ocean Craft Marine is positioned to benefit from its links with ASIS Boats to offer AIME the options of using the ASIS facility in Dubai as a testing ground for the project. The high heat, high humidity and high salinity found in Dubai make it a valuable test site. Likewise, ASIS’ links to New Zealand gives AIME another set of environmental features for trials.
Mr Stapleton offered an insight into the practical operation of AIME: “We’re working to advance communication and break down the barriers put in place. AIME is trying to find solutions to the end user’s problems as opposed to the spec writer’s problems.”
“As a company, our raison d’être is saving people’s lives,” Mr Nouhra concluded. “We are a company with a heart.” Ocean Craft Marine has a heart large enough to aim at saving the entire small boat industry. n
Just as AIME drives innovation in the wider industry, Ocean Craft Marine pushes forward its own sustainable development. Options on the boats include hybrid engines delivering a 20% reduction in fuel consumption, or even fully-electric power systems.
The future of Ocean Craft Marine is more than just the AIME project, Mr Stapleton said: “For the future, we are looking at the recreational dive market as a potential growth place, because nobody makes a boat just for diving.” Additional expansion is expected in the oil and gas exploration sector, along with patrol boats for security companies.
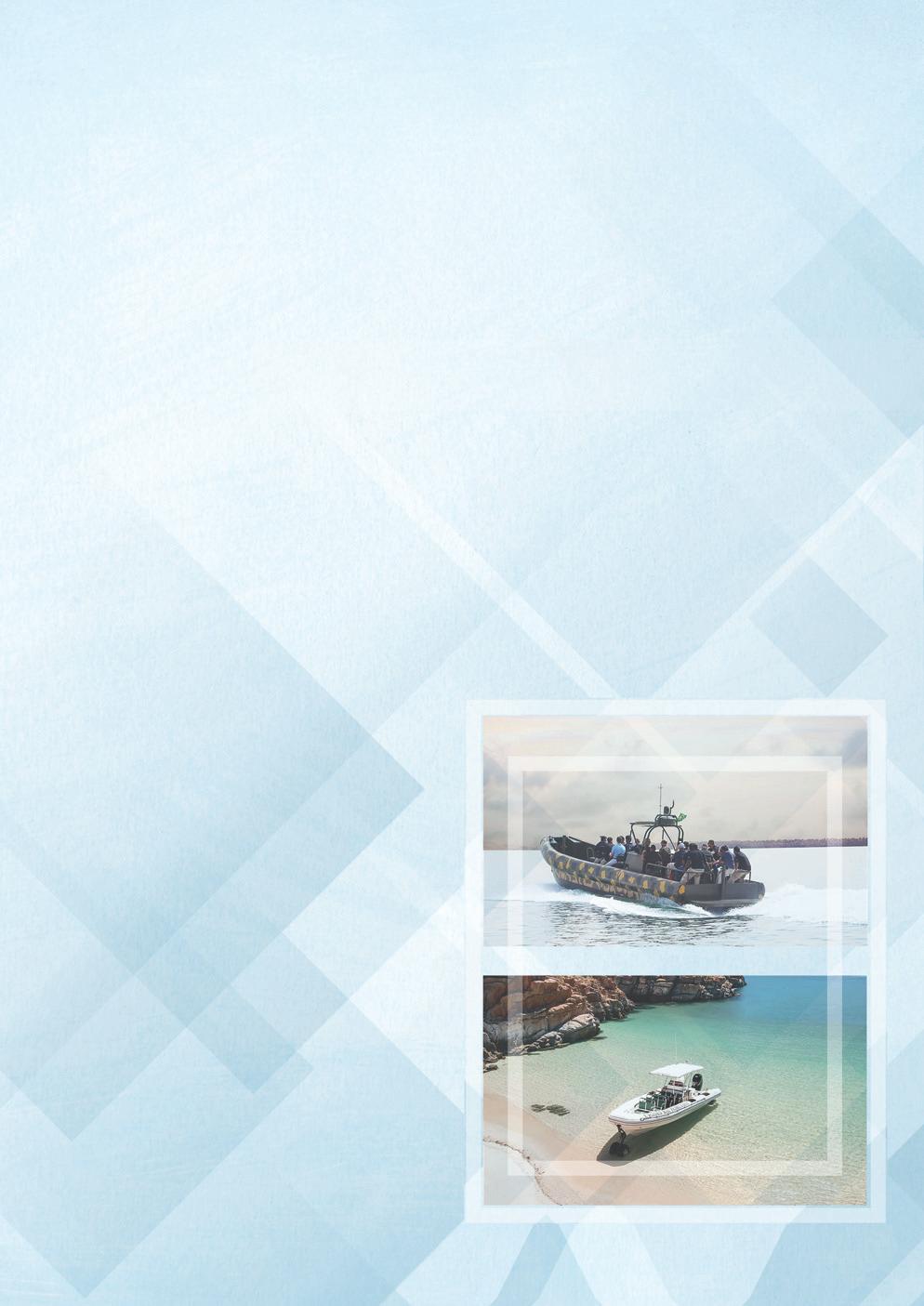

PRECISION PRODUCTS I PROFILE 194 Inside Marine Wherethereareengines,therearepistons,allofthemrequiringpistonrings.EnterPrecisionProducts(UK)Ltd:oneoftheworld’sleadingpistonring,metallicandnon-metallicsealingsolutionmanufacturers.Itstagline,‘Thetechnologywithin’,perfectlydescribesthecompany’sspe-cialityinengineeringsomeoftheworld’sbiggest,mostwidely-used,complexandtechnologicallyadvancedpistonringsandmetallic/non-metallicsealingsolutions.PrecisionProducts’SalesDirectorDominicRogers,andSalesManagerPaulBallin,satdownwithRichardHagantotalkaboutthebigbusinessofkeepingtheworld’sbiggesttwo-strokeenginesrunningsmoothly. technologywithin® the
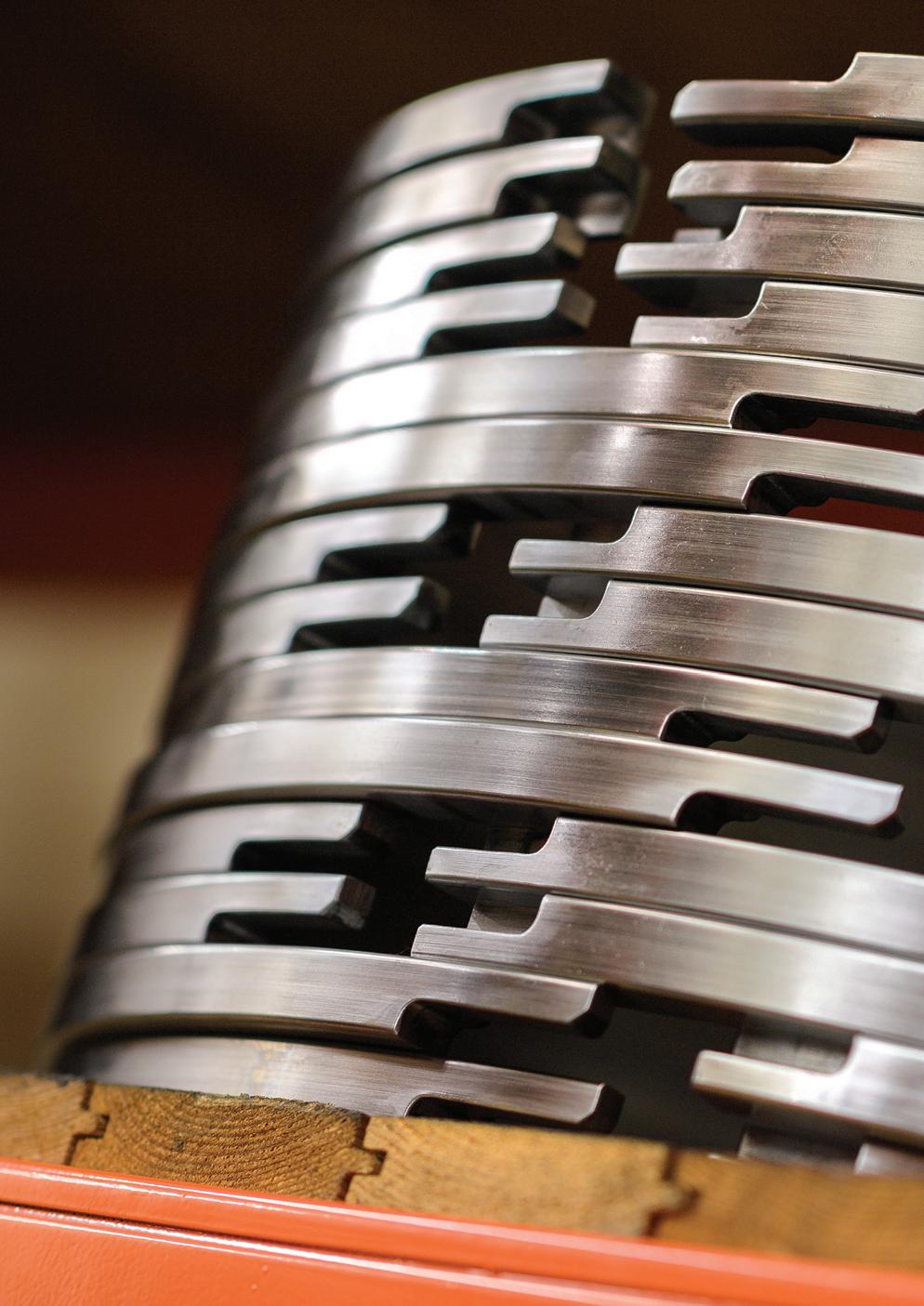
“We were recognised for our very struc tured strategic growth program, excellent sales growth, strong order book, and growing our market share despite challenging busi ness conditions,” explained Dominic Rogers, Head of Sales at PPUK. PPUK credits its recent growth with its technical agility in the market, industry diversification, and new product introduction.
P recision Products (UK) Ltd (PPUK), is a leading manufacturer and supplier of low speed two-stroke, medium speed four-stroke, industrially applied piston rings, and metallic and non metallic engineered sealing solutions.
PPUK was established in 1994. Just over a decade later, the company was acquired by the Indutrade AB group in 2008. With over 200 companies under its umbrella, Indutrade is an international industrial group that acquires and develops compa nies that are characterised by high-tech know-how and an ability to build enduring, close relationships with customers and suppliers. Indutrade’s business philosophy is based on entrepreneurship and decen tralised leadership, and PPUK fits perfectly.
Inside Marine 195
As of the end of 2021, PPUK had 92 employees, a number that grew even in the midst of Covid. It operates from a single, modern factory loaded with all of the technology and facilities required to make some of the world’s most advanced piston rings and valueadded engineering solutions. With the support of substantial invest ment from Indutrade, PPUK has developed its facility significantly in the last three years. This includes the addition of Arc, Plasma & HVOF thermal spray capability and expanded hard chrome and ceramic chrome capacity, supported by advance ments in CAM turning and grinding tech nologies through working closely with machine tool manufacturers to develop bespoke solutions to some of the indus tries, toughest challenges.
In 2021, PPUK was recognised by the cov eted MakeUK, North East Yorkshire and Humberside Manufacturing Award, for its contribution to the sector in terms of its strong business growth and strategy.
“We are able to manufacture engineered solutions for both the marine and indus trial market base of up to 2m in diameter,” said Dominic. Engineered to succeed The company embraces the difficulty of developing and engineering bespoke solutions for Traditionally,customers.PPUK’swork was dominated by the manufacture of solutions for OEMs including some of the world’s leading twostroke engine manufacturers. “We manufacture large-bore diameter piston rings for the two-stroke engine
From its advanced factory in Chesterfield, Derbyshire, the company manufactures and supplies products to companies around the world in both marine and industrial markets.
Award-winning growth
Aligned with several other capacity-based investments, this period of development has significantly underpinned PPUK’s growth strategies. The facility also had a complete overhaul to improve its sus tainability offerings in parallel with 50% growth of its manufacturing footprint.

Evolving with the market
PPUK has been highly active in is the wind turbine industry, which sees the company manufacturing large metallic rings of up to 2m diameter.
“We’ve been manufacturing them in various sizes, quantities and materials for over 25 years,” said Dominic. While PPUK will continue to support those long-standing customers and mar kets, it is actively pursuing opportunities in developing bespoke, custom-engineered solutions for new, diverse customers around the world. “We are evolving into an engineeringled organisation so we have recruited highly-skilled engineers to support our customer demand,” Dominic revealed. “We will develop, with our customers, technological solutions to meet their specific application requirements.
“The industry is ever-evolving,” stated Dominic. “This is especially true within the marine market. There are new fuels coming down the pipeline, so to speak, either with a reduced sulphur content or alternative, environmentally friendlier fuels. The piston ring has to be able to withstand these different kinds of fuels.
196 Inside Marine market,” noted Paul Ballin, Sales Manager for PPUK. “We have a number of approvals from two OEMs – the biggest in the world – and are dedicated to developing solutions withAnotherthem.”market
“We were a make to print organisation,” he continued. “Now we are growing the company’s capability. The engineers we have employed have the exact skill-set required, and we’re adding further value by having a full engineering suite avail able for customer projects. We want our customers to have faith in what we do and have it add value to the relationship between us and their designers. In general, we are an engineering-led organisation.”
“Raw material prices have become a chal lenge due to the global commodities market affecting us and our supply chain partners,” Dominic explained. “Energy price increases have also started to present additional challenges . We are therefore working hard across our networks, suppliers, and customer partners to manage this. It is certainly a tough balancing act!”
Rising costs, rising challenges Dominic and Paul both highlighted raw mate rial and energy price increases as a major challenge for everyone in the industry.
In dealing with rising prices, the com pany leans on its historically close rela tionships with its customers and suppliers, both of whom are regarded as partners withinDespitePPUK.the challenges inherent to Covid19, the company achieved impressive growth of 28% in 2021, all whilst navigating the restrictions and difficulties of the pan demic. In essence, PPUK has clearly made a material difference in the industry, both in supporting the global customer base and its employees in the local area.
PRECISION PRODUCTS I PROFILE
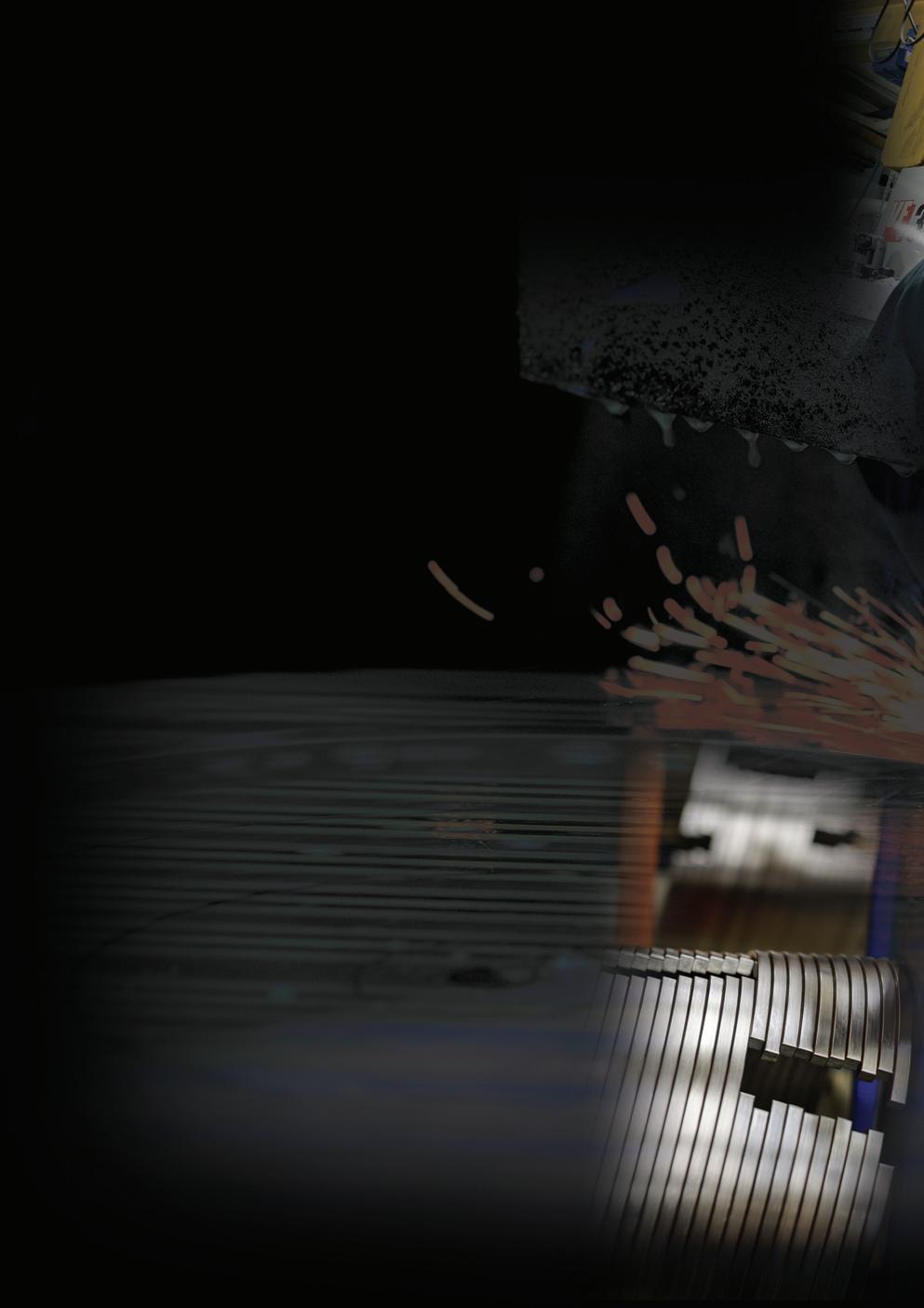

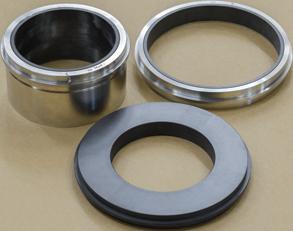
Inside Marine 197


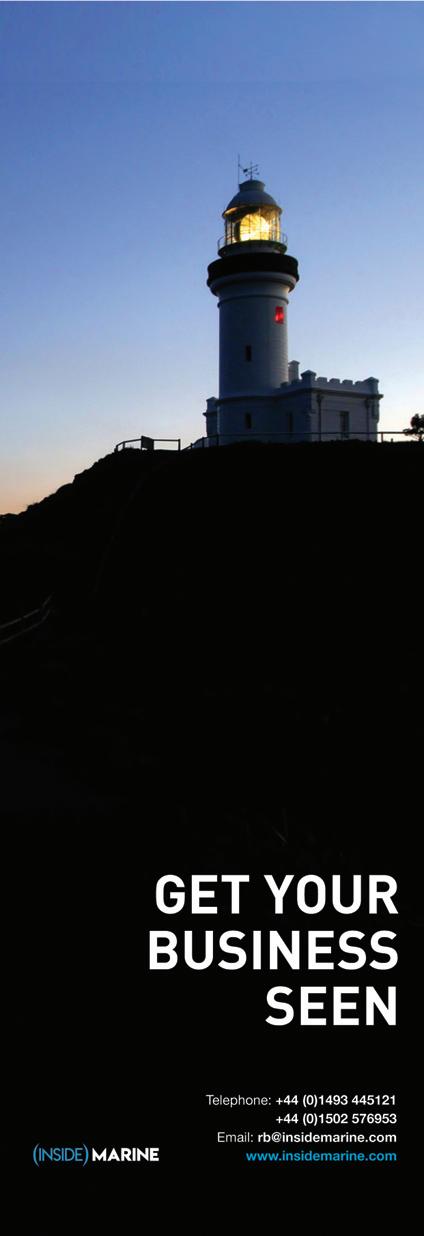
For more information, please email: contact@ppuk.com or visit www.ppuk.com
That’s all the more impressive when considering that as many as 30 operations are routinely required in the manufacture of a piston ring.
In concluding, Paul described PPUK as a very well-managed and ambitious com pany which always looks after its staff and“Ascustomers.welooktowards 2022 and beyond, our mission is always to show our customers the added value that we offer, whether it’s through customer service, engineering excellence or supporting them in chal lenging times. And we will balance all of that with robust relationships with our suppliers – they’re partners too. You have to work as a team; you’re only as strong as the team around you.” n
Constant evolution is especially impor tant given the surging global demand for the kinds of engineered solutions supplied by“OurPPUK.biggest challenge is meeting the volume that customers demand and need,” he added. “The demand is high: however, PPUK is able to meet its share of the market with attractive lead times as a result of our growth based investments.” “Fortunately, we’ve optimised our manufacturing capabilities and reduced our lead time to an optimum level below the industry standard. At this point, when a customer has a breakdown or needs a com ponent to support their customer, due to our determination to remain agile we can turn around and manufacture precisely what they need in a matter of weeks,” Dominic emphasised.
Dominic pointed out that OEM pump companies who want to maximise efficiencies and optimise electricity con sumption are potential customers that would particularly benefit from lightweight and durable solutions.
The industry is trying to optimise the best solution that fits these alternatives.
“Our customers will be looking for the optimum solution in the engine to support their customers’ expectations,” he con tinued. “We have to be able to adapt and provide solutions to meet those demands. And we have the know-how and agility to doTothat.”complement its existing product portfolio, the company has begun to offer turnkey, engineered composite solutions.
198 Inside Marine PRECISION PRODUCTS I PROFILE
DirectorSalesRogers,DominicPaulBallin,SalesManager
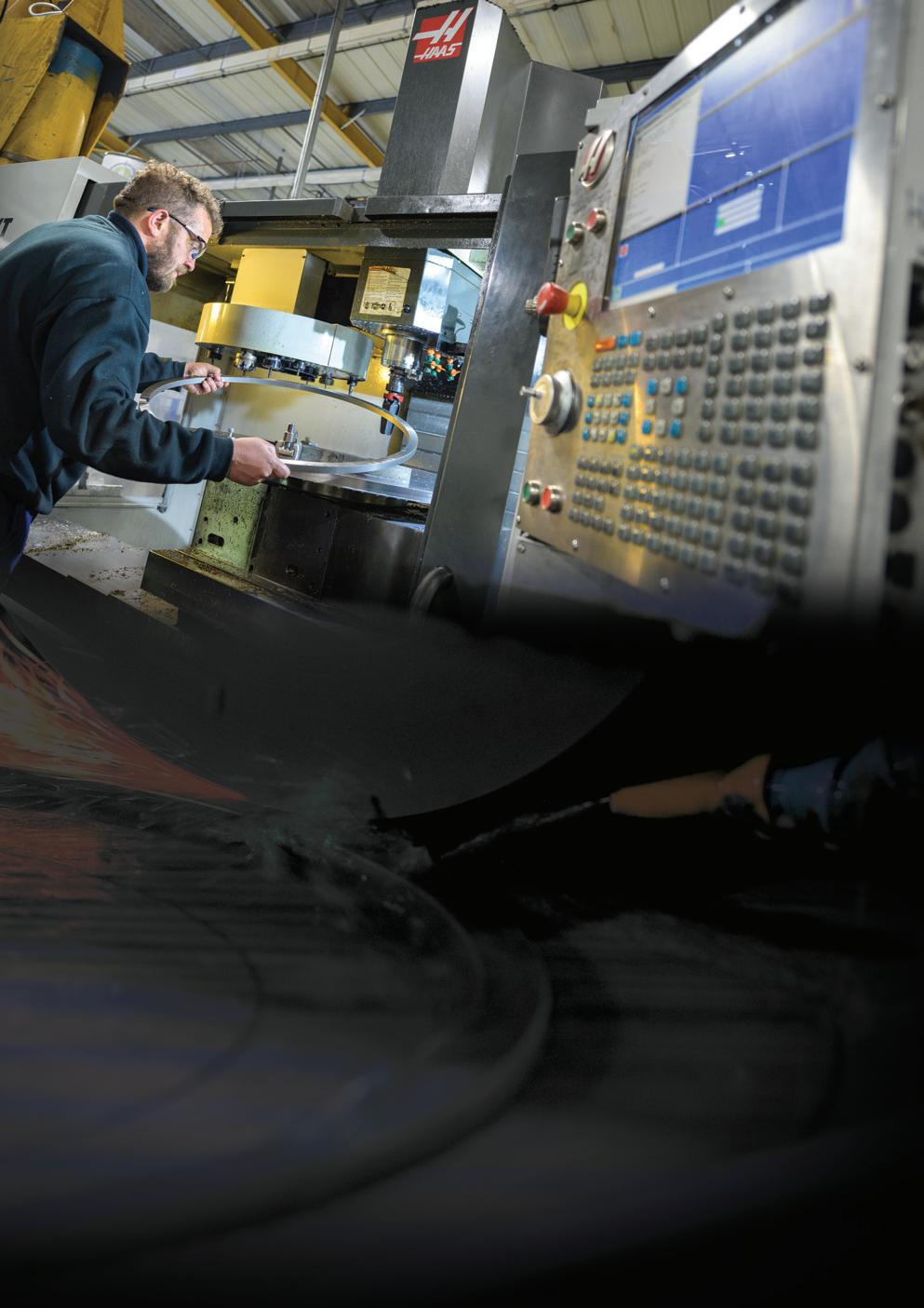
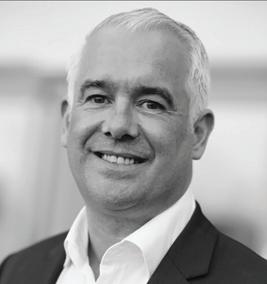
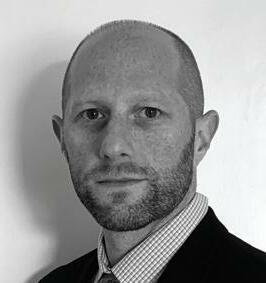
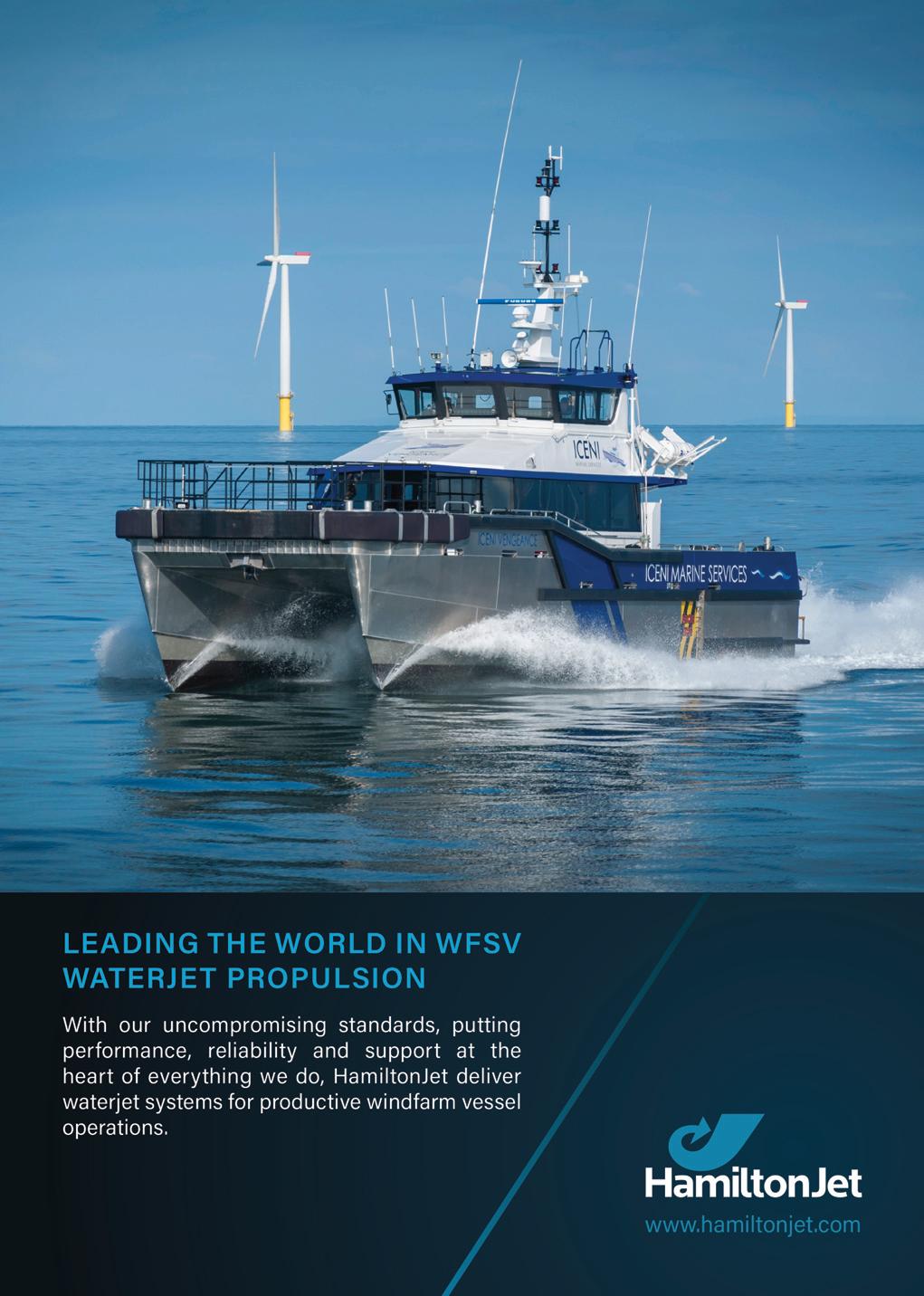
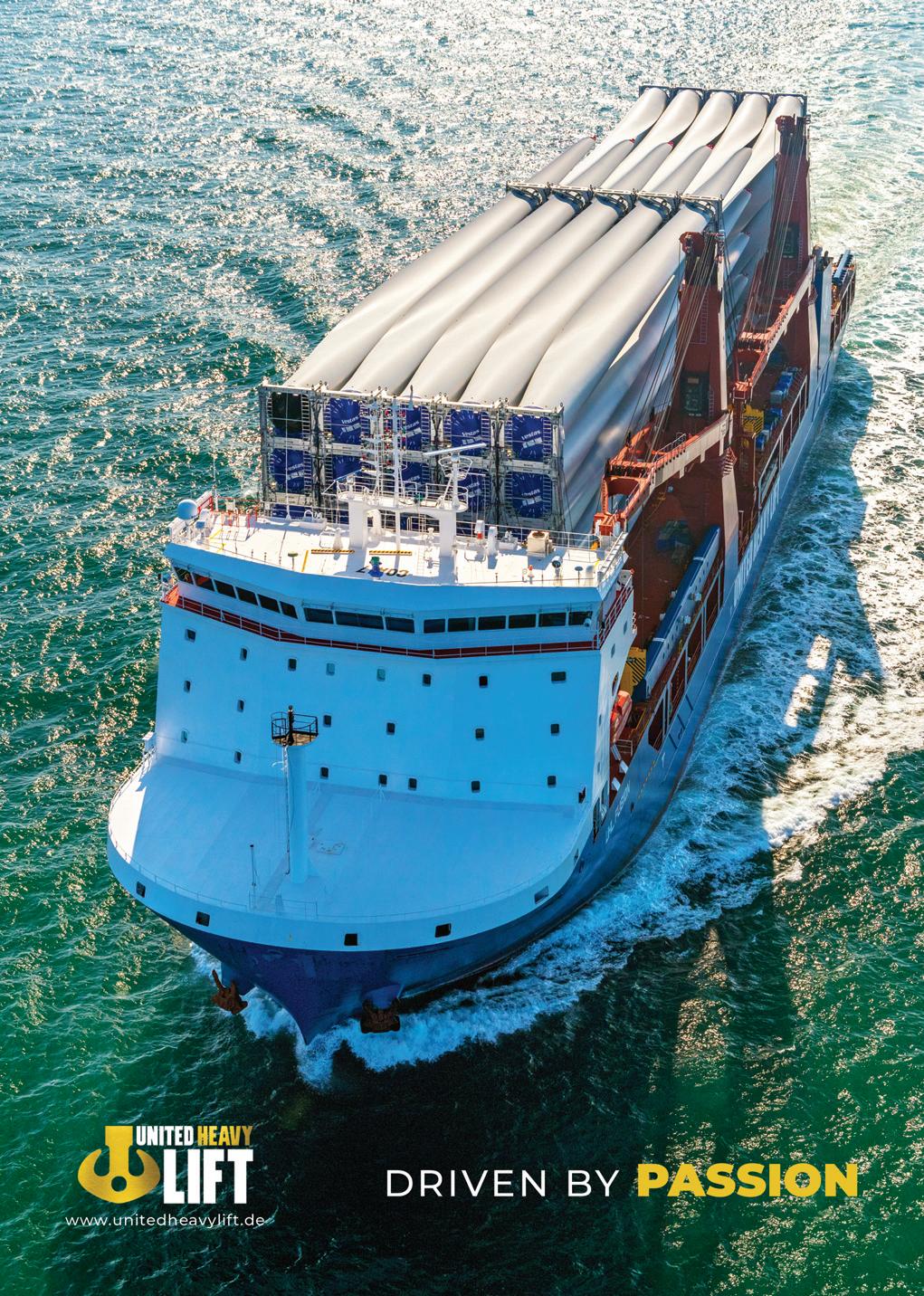