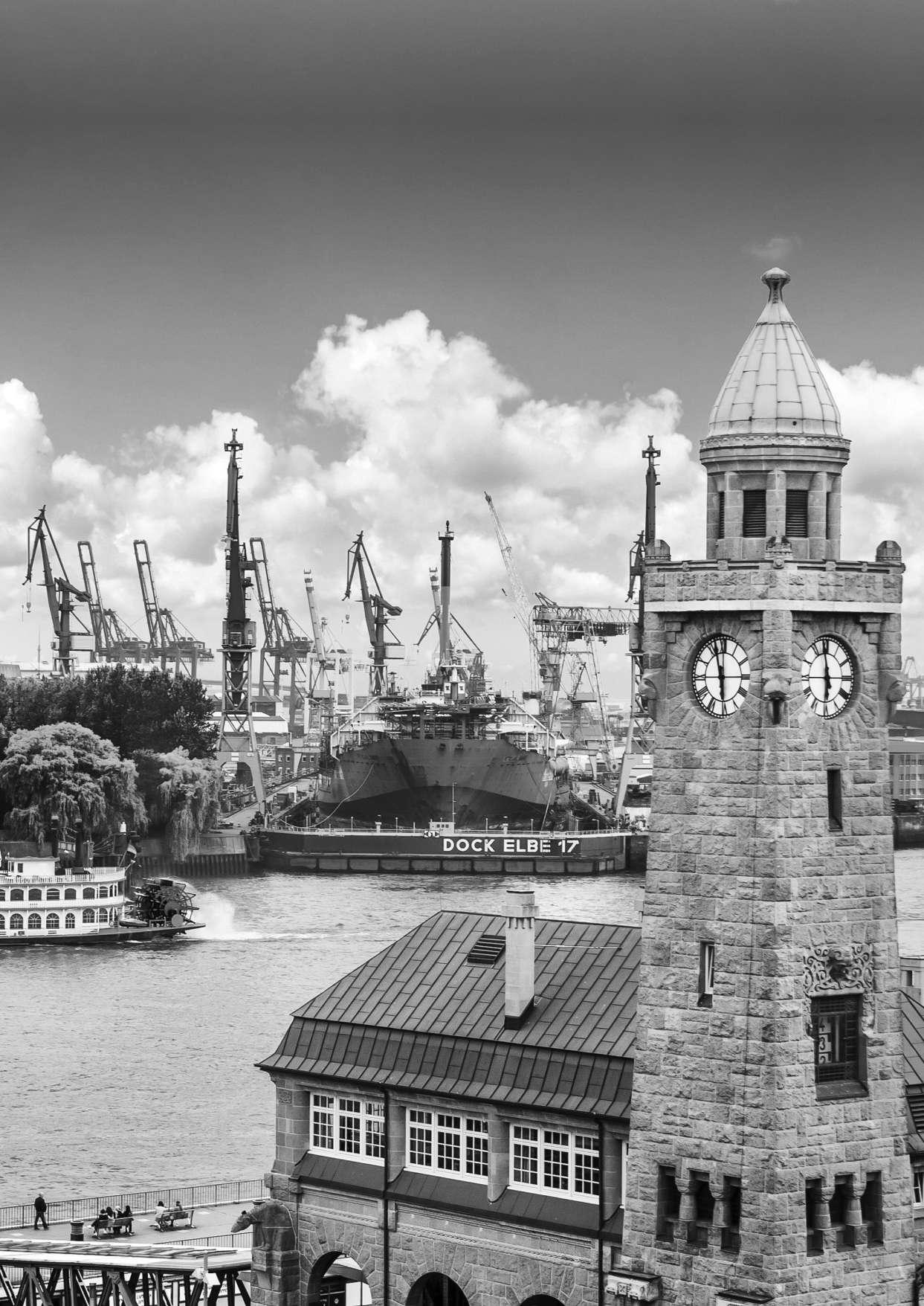
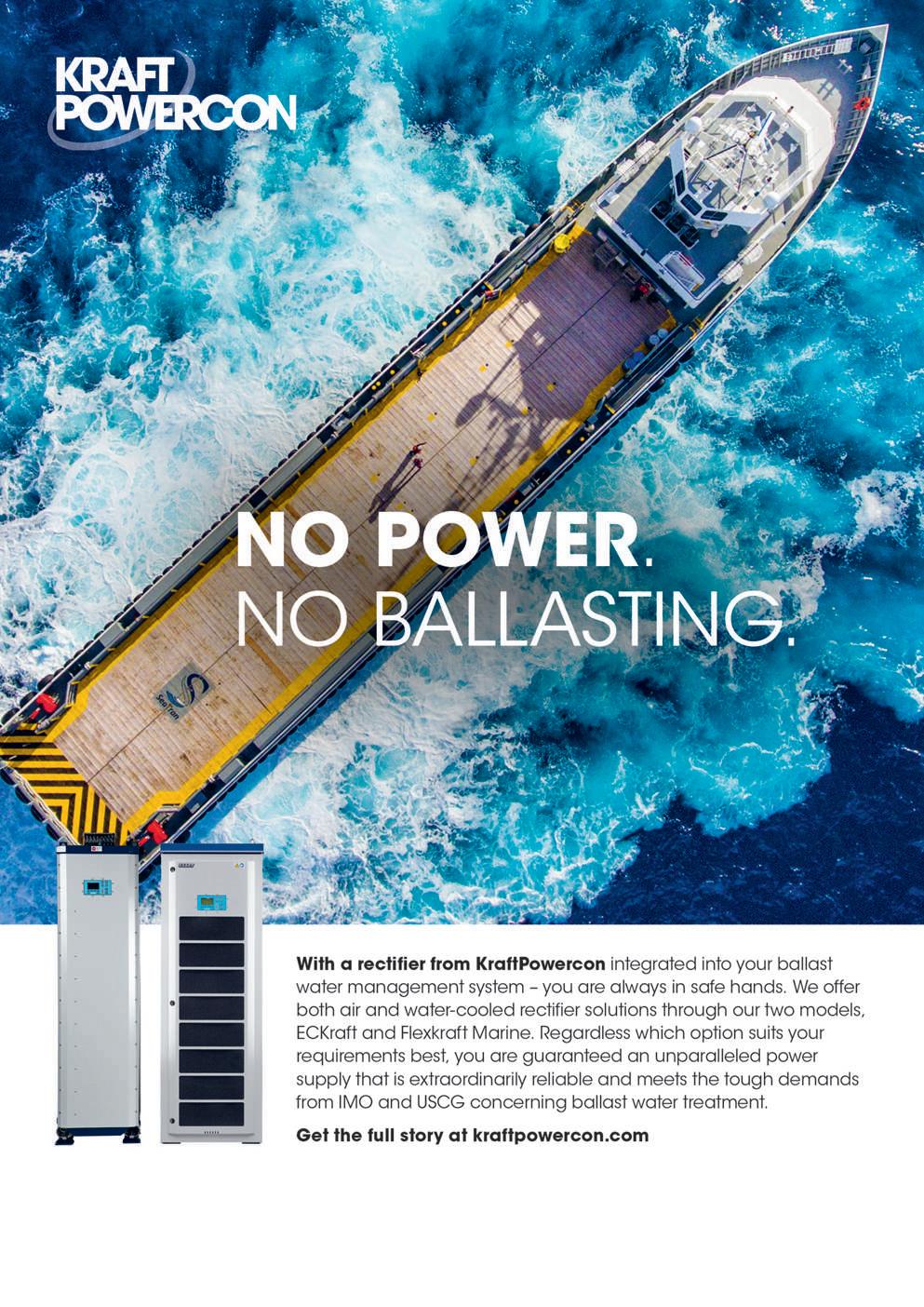
John White Managing Director
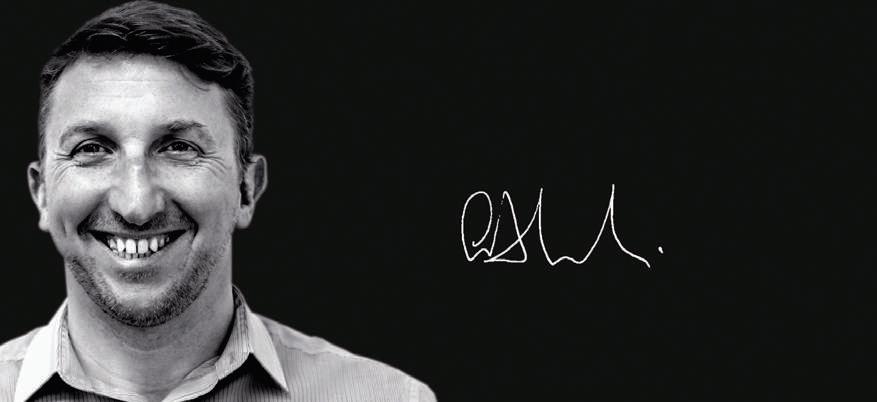
John White Managing Director
Managing Director John White welcomes events back onto our calendars.
Welcome dear reader to your latest edition of Inside Marine. There is a certain buzz and energy in the office – there is always of course because clearly my team all love their job and their boss – however I mean a little more of a buzz than normal.
One of the more popular editions for my team to work on is what we refer to as our SMM edition. An edition that is, as always, full of all sorts of company profiles, advertisements, news and views, however, a special edition that focuses on the upcoming SMM event in Hamburg.
We have been an official media partner to this prestigious event for a decade now and the only one we have missed in that time is the one that we all missed due to Covid-19 lockdowns. Therefore, I must give some of the credit for my increased staff energy to the fact that international shows, fairs, events and exhibitions seem to be firmly back on our calendars.
As many of our regular readers already know, we do enjoy being partners with some major events within the maritime industry and after the forced sabbatical due to Covid-19, I am sure that you are as happy as we are to be able to exhibit, visit or even simply read about events again.
Our editorial, sales and marketing teams are certainly glad to be in contact with the event planners, and likewise, the events teams seem overjoyed to be able to discuss media partnerships with us once more.
As an international media company specialising in business-to-business publications, we naturally must conduct much of our work over the telephone and by email,
however, the chance to meet many of you face-to-face is always a pleasure. Events of course allow us all to not only promote our products and services but also network on a more personal level. I know that the teams I often send out to these events enjoy the experience… I suspect in part due to some of the post-event restaurants and bars that some of you ‘force’ them to frequent with you!
We have been working closely with the SMM event organisers to help promote this popular event and with many of the exhibitors to help drive some traffic toward their stands. Therefore, be sure to spend some time browsing that section of the magazine if you are planning to attend this year.
Unfortunately, I cannot send a team out this year as there is simply too much to do back at headquarters with our new look websites, online company profiles, social media activity and general digital marketing plans, however, if you are lucky enough to be going, please send Hamburg our regards and we shall have to be content with the fact that at least we are there in spirit with our magazine available in the press booth there as usual. I shall sign off now and let you enjoy this edition. If you would like to take advantage of the talents of my various teams to help you promote you company or event, then I would suggest that now is as good a time as any, especially whilst they are all so excited and energised! n
Return of the living trade fair
News
36 Marine news in brief
Latest news from the marine industry
Matter of fact
42 Did you know?
Interesting and unusual marine facts from around the world
What’s new in the marine industry?
44 From simple ideas to engineering feats
The latest innovations, ideas and product launches
Special
50 Revitalising a historic legacy Alabama Shipyard
Shipyards
Inside
Maersk Supply Service launces new venture company, Stillstrom, to deliver offshore vessel charging
64 50 years a Chilean legend ASENAV
74 Fixing big ships in the northeast North Atlantic Ship Repair
82 Heading in the right direction
Couach Shipyard
88 Turkey’s largest ship exporter ARES Shipyard
92 Spanish experience and added value Aresa Shipyard
Owners, operators & managers
98 Global ship management that cares Columbia Shipmanagement
106 Crossing the sea of opportunity Baja Ferries
112 Forging ahead on all fronts BREB
118 Boutique solutions to modern shipping problems
Norstar Ship Management
124 Modern vessel operator making waves from Mexico E-NAV Offshore
130 Fuelling ambitions and industry for 50 years
Naftomar Shipping & Trading
136 Service, crystallised Crystal Pool
Equipment & services
144 The buzz for marine services
Epsco (Cyprus) Ltd
152 Deep dive into revolutionary subsea ROV tech Bisonte
158 The catalyst for green energy Permascand
166 Saving energy and fuel with smart valve control Eltorque
170 Power on sea Amco Veba Marine
174 Engineering excellence across the seven seas Hydrus Engineering
180 Combatting corrosion
Mahnke
184 Doorways to Dutch precision
Newthex
188 In search of perfection
Hydrasearch
192 Braking news
DELLNER BUBENZER
196 Taking marine’s carbon capture technology to the next level
VDL AEC Maritime
200 Keeping the maritime industry fuelled up
SEKAVIN
204 Adding value to waste management
Sepor
Water treatment
210 First every time in global water protection
ERMA FIRST
220 A solution to water scarcity
SLCE Watermakers
Ports, harbours & terminals
228 Award-winning excellence in port sustainability
Peel Ports
234 Mexican port set for new highs
Altamira Terminal Portuaria
Engines, motors & propulsion
242 Propelling waterjet solutions to the next level
HamiltonJet
248 Generating growth in electronic propulsion
OSWALD Elektromotoren
252 Casting a spell on diesel machinery
Merlin Diesel Systems
Foundries & forging
258 Always one step ahead Friulforgia
266 Foundry group remains reliable performer
CMW Foundries
Electronics
272 Moving forward in marine servicing
Tefin Marine
Electronics Service Network
276 The beating electronic heart of maritime
Böning Automationstechnologie
Valves, bearings & piston rings
282 A change of bearing
Mikasa Corporation
286 The technology within Precision Products (UK) ltd
290 Dutch maritime heritage meets European quality
Wouter Witzel EuroValve
Digital transformation, as well as climate change and the maritime energy transition all take centre stage at the 30th SMM. With an expanded spectrum of key areas and additional presentation formats, the leading international trade fair for the maritime industry accompanies the change at close quarters. Maritime industry professionals from all parts of the world will get the complete overview of innovations from all sectors, and of course they will finally enjoy again the opportunity for live encounters on the exhibition ground as well as in the high-profile trade conferences. www.smm-hamburg.com
The show features everything the leisure marine industry has to offer. Ranging from paddleboards to superyachts, and all the products and services you need to enjoy life in, on or around the water – you’ll find it at the show. Show favourites, new exhibitors and exciting attractions make sure there’s a lot to see and do: From kayaks to catamarans, SUPs to superyachts, there’s a boat for everyone.
www.southamptonboatshow.com
Breakbulk Americas is the event for all those involved in the project cargo and breakbulk industry. Focused on companies and projects from Canada down to the tip of Argentina and the Caribbean, this is the place to expand your operations in one of the most promising regions of the world. In addition to meeting more than 200 exhibitors, you’ll find a full conference agenda featuring industry leaders, including shippers, global project forwarders, leading carriers, and more. You will hear perspectives and lessons learned from major project participants, information that you won’t find anywhere else. www.americas.breakbulk.com
The Monaco Yacht Show is world-renowned for the exceptional quality of its superyachts and their impressive length: among the +100 units on display, +40 new models are unveiled as world premieres each year. The fleet has an average length of 50m and mega yachts exceeding 100m. The show has become an emblematic event for private visitors who come to discover an outstanding concentration of superyachts available for purchase or charter and to meet the industry experts in the festive and glamorous atmosphere of the Principality of Monaco. www.monacoyachtshow.com
The METSTRADE Show is the world’s largest trade exhibition of marine equipment, materials and systems. Labelled as the only truly international B2B exhibition for the marine leisure industry, METSTRADE has served as a platform for innovation, market developments and networking since launching in 1988. In addition to the overall leisure marine industry, METSTRADE caters for three specialist sectors, namely superyachts, marinas and yards and construction materials through three specialised pavilions, each offering a smaller self-contained show within the larger METSTRADE Show context. www.metstrade.com
After two years of industry change, port technology advancement and digital acceleration, TOC Asia will connect the port and container supply chain community across the APAC region. Hear from change-makers within the global container supply chain and discover the latest innovations within terminal operations. Alongside a first-class conference, visitors will also benefit from a global port technology exhibition and the return of TOC’s famous social programme. TOC Asia will enable you to identify and leverage the key market opportunities that are waiting for you. Visit TOC Asia for solutions, powerful learning and the long overdue networking that only face-to-face events can bring. www.tocevents-asia.com
CF Industries becomes the latest big name to sign up to the centre, set up in 2020 to identify, demonstrate and mature viable operational zero carbon solutions and their transition pathways.
The Copenhagen-based Mærsk McKinney Møller Center for Zero Carbon Shipping has announced that CF Industries will become its latest Strategic Partner, committing to a long-term strategic collaboration and contribution to the development of zero carbon technologies and solutions for the maritime industry.
As one of the world’s leading ammonia producers, CF Industries brings decades of experience in safe production, storage, transport, and trade of ammonia and is supporting global decarbonisation by producing nearly 2 million tons of low-carbon ammonia production capacity by 2024. This includes installing a 20MW electrolyzer to enable the production of green ammonia at its Donaldsonville Complex in Louisiana. All are critical aspects when looking to unlock ammonia as a fuel pathway, enabling the transition of the maritime industry.
In welcoming CF Industries to the Center, CEO Bo Cerup-Simonsen said: “As a US based producer, CF Industries brings additionality to the centre’s established partner portfolio from both a geographical and a value chain perspective. This will significantly compliment and strengthen our ability to work, collaborate, and create impact on enabling robust low-emission ammonia fuel pathways, addressing safety topics on handling and operation of ammonia, and creating robust engagement on regulatory topics.
“CF Industries has a strong sustainability agenda and will play a prominent role in transforming the ammonia industry. The company is well positioned to pave the way forward for low emission fuel production.”
With 100,000 ships consuming around 300 million tons of fuel annually, global shipping accounts for around 3% of global carbon emissions, a share that is likely to increase as other industries tackle climate emissions in the coming decades.
Achieving the long-term target of decarbonisation requires new fuel types and a systemic change within the industry. Shipping is a globally regulated industry, which provides an opportunity to secure broad-based industry adoption of new technology and fuels.
To accelerate the development of viable technologies, a coordinated effort within applied research is needed across the entire supply chain. Industry leaders play a critical role in ensuring that laboratory research is successfully matured to scalable solutions matching the needs of industry. At the same time, new legislation will be required to enable the transition towards decarbonization.
The Mærsk Mc-Kinney Møller Center for Zero Carbon Shipping is a not-for-profit, independent research and development centre working across the energy and shipping sectors with industry, academia, and authorities. With its partners, the objectives of the centre include exploring viable decarbonisation pathways, facilitating the development and implementation of new energy technologies; building confidence in new concepts and their supply chains; and accelerating the transition by defining and maturing viable strategic pathways to the required systemic change.
The centre, based in Copenhagen but works with partners globally, was founded in 2020 with a start-up donation of DKK 400 million (approximately €54 million) from the A.P. Moller Foundation.
CF Industries joins a list of Corporate Partners at the centre that already includes Alfa Laval, American Bureau of Shipping, A.P. Moller - Maersk, bp, Cargill, CF Industries, DP World, Hapag-Lloyd, MAN Energy Solutions, Mitsubishi Heavy Industries, Mitsui, NORDEN, NYK Line, Seaspan Corporation, Siemens Energy, Stolt Tankers, Sumitomo Corporation, Swire Group, Topsoe, TotalEnergies and V.Group.
CF Industries is on a path to decarbonise its ammonia production network – the world’s largest – to enable green and blue hydrogen and nitrogen products for energy, fertilizer, emissions abatement and other industrial activities. The company has nine manufacturing complexes in the United States, Canada, and the United Kingdom, an unparalleled storage, transportation and distribution network in North America, and global logistics capabilities.
Tony Will, President and CEO of CF Industries said: “As the world transitions to low carbon alternative energy sources in order to realise net zero carbon emissions, collaboration across industries is critical to accelerate the development of achievable solutions.
“We believe ammonia has an important role to play in the world’s transition to clean energy and is a particularly promising approach for the maritime industry.”
French ferry operator Brittany Ferries has signed a long-term agreement with Titan LNG for the supply of LNG and Liquified Bio Methane (LBM) to two new LNG-fuelled hybrid Ro-Pax vessels that Brittany Ferries will operate between England and France from 2025.
Brittany Ferries’ two 194.7m, 1,400passenger LNG-hybrid ships will join the fleet in 2024 and 2025, replacing two of the longest-serving vessels, Bretagne (1989) and Normandie (1992). They will follow two new LNGfuelled ships, Salamanca, which entered service in March this year, and Santoña which will arrive on fleet in 2023.
The new ferries will serve established routes connecting Portsmouth with St Malo, and Portsmouth with Ouistreham. Titan aims to supply fuel to both vessels during usual cargo operations alongside (SIMOPS) to avoid delays to sailing schedules.
The hybrid vessels will have a large battery hybrid power system of 10 MWh for propulsion and manoeuvring in port and an 8 MW electric shore connection that will allow charging in port, when infrastructure allows. As well as significantly cutting emissions, hybrid propulsion promises less noise and a smoother ride for passengers.
“Ships like Salamanca, Santoña and our forthcoming hybrid ships are cleaner today
and greener tomorrow,” added Frederic Pouget, Operations and Ports Director Brittany Ferries.
“Thanks to LNG, they promise an immediate and significant reduction in air quality emissions and a small reduction in GHG emissions. They are greener tomorrow because they are capable of running on fuels like LBM first and later future fuels like Hydrogen Derived Liquid Methane. These have the potential to slash well-to-wake GHG emissions. Our new vessels will therefore automatically become greener when these fuels arrive and there is great potential for expanding the development of the LBM value chain with Titan LNG.”
As a leading independent supplier of LNG, Titan LNG is the frontrunner in economic and clean (bio)LNG supply to the marine and industrial sector in Europe.
Titan LNG believes LNG is the best transport fuel and essential in the energy transition during the coming decades.
In creating the infrastructure for further decarbonisation via (bio)LNG and synthetic LNG, carbon-neutral solutions can be achieved.
With headquarters in the AmsterdamRotterdam-Antwerp area, Titan LNG and its partners believe LNG should be easily
accessible to all. Through building a global supply network, Titan LNG offers complete natural gas solutions: LNG bunkering, LNG transport and supply, LNG storage tank and vaporizer rental, including maintenance and service.
LNG distinguishes itself from oil-based fuels, as a cleaner, economical and safe fuel. It is abundantly available and has been used for over 50 years. With LNG becoming the fuel of choice for travel to Mars, Titan LNG believes the fuel will also enable clean transport on earth.
Régine Portocarero, Titan LNG’s Business Development Manager, said: “We look forward to our journey forward with Brittany Ferries and these innovative ships. We believe strong partnerships are essential for the maritime industry to successfully decarbonise. Furthermore, thanks to the unique farmer-shareholder ownership structure that underpins Brittany Ferries, we see great potential in available stocks for local LBM production.”
This partnership marks the significant expansion of Titan’s operations in the English Channel which will enhance the availability of LNG, LBM, and in the longer run hydrogen-derived LNG in the region. Titan will bring additional barge capacity to meet this demand. There are plans for a Krios series vessel to serve Brittany Ferries and to regularly transit between relevant ports. n
The 117,000 sqft manufacturing addition will house the latest state-of-the-art computerised and robotic steel processing equipment to handle all of the current and future demands of the US Navy and the US Coast Guard.
American shipbuilder Austal USA has celebrated the opening of the company’s state-of-the-art steel facility. The addition of steel shipbuilding capability compliments the company’s well-established aluminium shipbuilding expertise.
This $100 million investment is expected to create jobs and spur economic growth throughout the region.
“We are so excited to see our plans to add steel to our capabilities come to fruition,” said Austal USA President Rusty Murdaugh. “The addition of steel capability is a game changer as it opens up our capability to support the US Navy, US Coast Guard and other customers with high-quality ships. We appreciate the confidence the Department of Defense and the Department of the Navy have shown in us with the award of the DPA grant to get this project started and look forward to repaying that confidence with our future performance delivering high-quality steel ships.”
The 117,000 sqft manufacturing addition will house the latest state-of-the-art computerised and robotic steel processing equipment to handle all of the
current and future demands of the U.S. Navy and the US Coast Guard. A 60,000 square foot stock yard will be utilised for handling the raw steel and a 19,500sqft paint facility will provide the ability to paint and blast simultaneously in two separate cells, or both cells can be combined providing the ability to paint super-modules.
“Austal USA will operate our steel production line using the same lean manufacturing principles that we’ve refined over the last 15 years building LCS and EPFs for the Navy,” continued Mr Murdaugh. “That process has resulted in Austal’s reputation for delivering quality ships on time and on budget ship after ship. We will bring that same reliable production capability to steel ship construction.”
tain, protect, and expand critical domestic shipbuilding and maintenance capacity. Austal USA matched these funds and invested an additional $50 million into the completion of the steel facility.
The opening of the new steel facility follows the recent news that Austal USA was awarded a $230.5 million contract for the detail design and construction of EPF 16, the Navy’s newest EPF ship.
EPFs have demonstrated their operational capability to conduct a variety of missions to include humanitarian assistance, disaster relief, maritime security, surveillance, command and control, and counter narcotic missions around the globe.
“ “
Our reputation for delivering quality is a direct reflection of the commitment and dedication of our talented shipbuilders and suppliers
Austal has delivered 15 Littoral Combat Ships (LCS) and 12 Expeditionary Fast Transports (EPF) to the Navy while another seven total aluminium Navy ships are under construction. The company is also under contract to build two Navajo-class Towing, Salvage, and Rescue Ships (T-ATS); these will be the first steel ships constructed in the new facility.
Financing for the new steel production line was provided in part by a Defense Production Act (DPA) Title III Agreement between the US Department of Defense, in support of the US Navy shipbuilding industrial base, and Austal USA. The agreement, valued at $50 million, was announced in June 2020 and was part of the national response to Covid-19 to main -
“Like the previously delivered EPFs, EPF 16 will benefit from the serial production of this program, resulting not only in a worldclass ship but also providing assurance to the US Navy that capability will be delivered on budget and on schedule,” said Mr Murdaugh. “Our reputation for delivering quality is a direct reflection of the commitment and dedication of our talented shipbuilders and suppliers.”
EPF 16 will be the third ship constructed in the Flight II configuration. Flight II ships will enhance the original capabilities of the Spearhead class through incorporation of reconfigurable spaces for operating rooms and postsurgical recovery efforts.
Construction efforts on EPF 16 are expected to commence later this year with delivery projected for 2025. n
The new Carnival Grand Bahama cruise port destination, expected to open in late 2024, is being developed on the south side of the island and will continue to serve as a gateway to Grand Bahama while also offering guests a uniquely Bahamian experience with many exciting features and amenities, along with business opportunities for the residents of Grand Bahama.
With a strong showing of validation of the cruise industry’s return and optimism, and reflecting a long-standing partnership between Carnival Cruise Line and The Bahamas, Carnival, in cooperation with the Grand Bahama Port Authority and the Government of The Bahamas, recently held a groundbreaking ceremony for its new cruise port destination on Grand Bahama Island.
“As we celebrate our 50-year partnership with The Bahamas, today’s groundbreaking on our incredible new Grand Bahama destination represents an opportunity to collaborate with the government and people of Grand Bahama – to contribute to the local economy through job and business opportunities, meaningfully engage with local communities, and further expand our experience offerings for our guests who will have a breathtaking new port of call to enjoy,” said Carnival Cruise Line President Christine Duffy.
“Our sincere thanks to the government of The Bahamas and The Grand Bahama Port Authority for their continued support as we begin construction. Our guests already love The Bahamas, and we are certain this new project will give them even more reason to want to visit.”
The Grand Bahama Port Authority Acting Chairman, Sarah St George, commented: “The new Carnival cruise port destination will have a monumental impact on our
island’s economy, including a panoply of new business opportunities, a huge surge in tourist visitors, as well as increased activities for established businesses. It is transformational in the true sense of the word.
“We are immensely grateful to Carnival for choosing Freeport and Grand Bahama for this flagship project. Today, we mark this incredible achievement made possible by the efforts of Carnival with The Grand Bahama Port Authority, Port Group Limited, the Grand Bahama Development Company and Freeport Harbour Company, and the Government of The Bahamas. A project of this magnitude is only possible through genuine collaboration. Grand Bahamians have withstood life-changing challenges, particularly in recent years. Despite these, Carnival never wavered in their commitment to building their next cruise port in Freeport. We are very proud to have played our part to the best of our ability towards making this a reality.”
The cruise port development includes a pier able to accommodate up to two Excelclass ships simultaneously welcoming guests to a stunning white-sand beach The Bahamas are known for. Guests will be able to explore and enjoy Grand Bahama by way of sea, via a dedicated shore excursion dock, or by land, via the dedicated ground transportation hub. The cruise port itself will also feature an area designated as a nature reserve and an interior pool feature, along with many Bahamianoperated retail, food and beverage options for guests to enjoy.
“This development signals opportunities for creatives, vendors, and small and medium sized businesses, and represents our commitment to collaboration with local and international partners for the betterment of our island,” said The Honourable Ginger Moxey, Minister for Grand Bahama.
The cruise pier will allow Grand Bahama to welcome guests from Carnival’s larger ships, such as the 5,282-passenger Mardi Gras, which debuted in 2021 as the line’s largest and most innovative ship and North America’s first cruise ship powered by Liquefied Natural Gas (LNG), and Carnival Celebration, sister ship to Mardi Gras, which will begin sailing from Miami later this year.
Deputy Prime Minister and Minister for Tourism, Investment and Aviation, The Honourable I. Chester Cooper, added: “The cruise port is an integral part of our plan to restore Grand Bahama to economic viability. Carnival will play a critical role in stimulating our economy and shining a light on Grand Bahama as a rejuvenated and premier destination in our country and the region. We believe the excitement of what is happening on Grand Bahama will be contagious.”
Additional details on the design, features and the name of the cruise port destination will be revealed over the coming months. n
Inside Marine takes a look at a number of
Owner: Havila Voyages
Builder: Tersan Shipyard, Turkey
Vessel Type: Passenger (cruise) ship
Length: 124m
Info: Havila Capella is a plug-in hybrid ship with the world’s largest battery packs designed for passenger ships. The battery pack weighs 86 tonnes and has a capacity of 6.1 megawatt hours. The batteries on board the modern ship allows her to sail for four hours without noise and emissions, meaning she can sail quietly and sustainably through world heritage fjords and pristine surroundings along the Norwegian coastline. The ship is built to run on biogas, but is also prepared to run on hydrogen or ammonia and is therefore a ship built for the future.
Owner: Celebrity Cruises
Builder: Chantiers de l’Atlantique
Vessel Type: Cruise ship
Length: 327m
Info: Designed to give guests endless opportunities to disconnect from the world – while simultaneously reconnecting with the world that surrounds them – Celebrity Beyond goes further than imagined possible for a cruise ship, creating a new world of wonder and approachable luxury. With forward-thinking design by the world’s leading architects and interior designers, culinary excellence from Michelin starred chefs, world renowned wellbeing partners, exquisite art, luxury brand retailers and Celebrity’s uniquely intuitive service, Celebrity Beyond shatters every preconceived notion of the cruising experience. A floating boutique hotel, Celebrity Beyond exemplifies newluxury travel and its future at sea.
Owner: DEME Group
Builder: CSBC Corporation, Taiwan
Vessel Type: Offshore installation vessel
Length: 216.5m
Info: This revolutionary offshore installation vessel is designed to handle the next generation of multimegawatt turbines, jackets and components. It has an unrivalled combination of load capacity, impressive lifting heights and green technology. Owned by CDWE, a joint venture between CSBC, the largest shipbuilder in Taiwan, and DEME Offshore, Green Jade is the first floating, DP3 offshore installation vessel to be built in Taiwan. With a 4,000-tonne crane capacity, this pioneering vessel will enable CDWE and its customers to transport multiple jackets and foundation components for the new giant wind turbines in a single shipment, making it extremely cost effective.
Owner: Terntank Rederi AS
Builder: China Merchants Jinling Shipyard, Yangzhou
Vessel Type: Tanker
Length: 147m
Info: TERN FORS is a 15,000 DWT vessel with a cargo capacity of 16,500 cbm in 14 epoxy coated tanks. The pioneering new vessel design is derived from the product carriers of Ternsund-type. Together with the design partner Kongsberg Maritime, Terntank has taken a step further, combining LBG/LNG-powered engines with the Hybrid Solution® – a combination between battery pack, shore power connection and a DC-Link system. By combining the optimised hull and rudder design with dual fuel capability, TERN FORS will reduce fuel and energy consumption resulting in extensively low CO2, sulphur oxide, nitrogen oxide and particle emissions.
Owner: Royal Caribbean Group
Builder: Chantiers de l’Atlantique
Vessel Type: Cruise ship
Length: 362m
Info: Wonder of the Seas was completed in 2022 in the Chantiers de l'Atlantique shipyard in SaintNazaire, France, the fifth in Royal Caribbean’s Oasis class of cruise ships. Across Wonder’s eight unique neighbourhoods – a Royal Caribbean first – variety and innovation come to life in a line-up of unparalleled thrills, more than 20 restaurants, bars and lounges, and show-stopping entertainment. Wonder of the Seas has a gross tonnage of 236,857 across 18 decks. This ship accommodates 5,734 passengers at double occupancy up to a maximum capacity of 6,988 passengers, as well as a 2,300 crew.
Owner: East by West Ferries
Builder: Wellington Electric Boat Building Company
Vessel Type: Electric ferry Length: 19m
Info: The southern hemisphere’s first fully electric, carbon fibre commuter ferry has successfully completed its inaugural round trip. Ika Rere, Mãori for flying fish, has joined the East by West fleet operating the New Zealand ferry company’s Wellington to Eastbourne route. The 19m long, 135 passengercarrying fast cat is also the first vessel delivered by the Wellington Electric Boat Building Company, a joint venture between the ferry operator and established boatbuilder Fraser Foote. The ferry is very quiet at 19 knots and silent at 10 knots. It is faster and uses less energy than was first anticipated.
Offshore vessel-charging venture Stillstrom launched to support the decarbonisation of the maritime industry
launches new venture company, Stillstrom, to deliver
Maersk Supply Service, a part of AP Moller-Maersk, is launching its offshore vessel-charging venture, Stillstrom, to support the decarbonisation of the maritime industry by eliminating idle emissions. Together with Ørsted, Stillstrom will demonstrate the world’s first full-scale offshore charging station for vessels at an offshore wind farm, scheduled for installation later this year.
Maersk Supply Service’s pioneering new company will deliver offshore electric charging solutions to vessels at ports, hubs and offshore energy operations. “Stillstrom”, meaning “quiet power” in Danish, is an early-stage technology spin-out, whose full-scale product launch will be the first-to-market in offshore charging, enabling idle vessels to power from clean electricity.
Offshore charging for idle vessels is critical to facilitating the decarbonisation of the maritime industry, since it allows
vessel owners to replace fossil fuels with electricity while being safely moored to the charging buoy.
The first full-scale charging buoy will, as previously announced, will be demonstrated with offshore leader Ørsted in Q3 2022. The power buoy will supply overnight power to one of Ørsted’s Service Operations Vessels (SOV), thereby supporting Ørsted’s target of climate-neutral operations in 2025. Ørsted will be responsible for the grid integration of the charging buoy.
Making intellectual property publicly available Ørsted intends to make publicly available any intellectual property generated during the design of the buoy’s integration into the offshore wind asset, to maximise the potential uptake of this carbon-reducing innovation across the offshore wind sector.
The charging buoy itself is large enough to charge an SOV-sized battery- or hybridelectric vessel. The same solution will be scaled and adapted to supply power to larger vessels, enabling vessels of all sizes
to turn off their engines when lying idle. By substituting fossil-based fuels with green electricity, virtually all emissions and noise pollution are eliminated while the buoy is in use.
“Stillstrom is part of our commitment to solving the energy challenges of tomorrow,” said Steen Karstensen, CEO of Maersk Supply Service. “By investing in this ocean cleantech space at an early stage, we can help lead the green transition of the maritime industry. Stillstrom has been developed within Maersk Supply Service and the timing is right to create a venture that will be focused on delivering offshore charging solutions.”
Sebastian Klasterer Toft, Venture Programme Manager at Maersk Supply Service, added: “Our vision at Stillstrom is to enable maritime decarbonisation, by providing the infrastructure that will allow vessels to charge from clean energy when idle offshore. The mission is to remove 5.5 million tonnes of CO2 within five years of commercial rollout, additionally eliminating partic ulate matter, NOx, and Sox.”
Stillstrom is fully owned by Maersk Supply Service and has received funding support from the Danish Maritime Fund and EUDP.
Maersk Supply Service is a leading provider of marine services and project solutions for offshore energy sectors.
With a large fleet of anchor handling and subsea support vessels, the company specialises in towing, mooring, and installing floating units, and is expanding into renewable industries such as floating wind and ocean cleaning.
Maersk Supply Service, as a subsidiary of AP Møller-Mærsk, employs around 1,100 offshore and 220 onshore staff. Headquartered in Lyngby, Denmark, the company has a global presence in Angola, Australia, Brazil, Canada, Equatorial Guinea, Ghana, Mexico, Norway, the Philippines, and the UK. n
Excitement builds as September’s return of SMM is just over the horizon
6-9 Sept 2022 - Hamburg
TUR N of the living trade fair
SMM Hamburg returns in 2022 from 6th to the 9th of September. Business Unit Director Maritime and Technology Fairs & Exhibitions at Hamburg Messe und Congress, Claus Ulrich Selbach, chatted with Phil Nicholls about the forthcoming fair.
Digital transformation within the marine industry will be a big focus of this year’s event. What were the factors behind choosing this as a key area? How do you ensure that your topics reflect the current demand of the industry?
As the leading maritime trade fair, we have an extensive and multi-faceted industry network across the globe which allows us to follow the market dynamics closely. We constantly talk to our partners, exhibitors, and visitors about their needs, interests, and expectations for SMM.
One key issue is the digital transformation in the maritime industry. This is nothing new and has been a fixed component of SMM for years now. This year, we will take a closer look at all the digital innovations and solutions which can help the shipping industry become greener in the next couple of years.
SMM 2022 promises to drive the maritime energy transition. Can you share how the event’s Transition Stages will facilitate this process?
Our new Transition Stages will be the perfect meeting places for all the industry experts who want to drive the transition of the maritime industry.
In addition to our conferences, and in parallel on three stages at the exhibition area, stage partners and exhibitors will present innovative concepts and solutions on central topics of SMM 2022.
The Green Transition Stage in Hall A4 presents alternative propulsion and environmental technologies to reduce emissions, The Digital Transition Stage in Hall B6 features digitalisation in the maritime industry, and The Marine Interiors Stage in Hall B5 focuses on interior design, equipment, and technology for passenger ships.
Excitement builds as September’s return of SMM is just over the horizon
6-9 Sept 2022 - Hamburg
Another new feature for 2022 is the Start-up Route. What can you tell us about this aspect of the event? How popular is this area in terms of number of exhibitors booked and sectors represented?
As the name itself says, the Start-up Route guides visitors to entrepreneurs in the maritime industry which present their smart and innovative concepts at one of the Start-ups@SMM joint stand areas. There will be a special icon identifying the Start-up Route as well as the participating companies in the online exhibitor directory, the visitor guide, and the app.
So far, the feedback to the new Start-up Route has been great. Whilst I can’t give you exact details yet, you can be sure that there will be lots of interesting start-ups to discover.
2022 marks the 30th SMM. How are you celebrating this milestone?
We will celebrate the 30th edition of SMM together with our international friends and partners in various online and offline events. Let us surprise you!
What visitor and exhibitor numbers are you targeting this year? Is there any room to grow, especially in terms of number of exhibitors?
We are expecting 2,000 exhibitors and 40,000 visitors from more than 100 nations. Due to the pandemic, there is no room to grow this year. But I’m sure there will be in 2024.
Honestly speaking, we are quite happy with what we have got already – especially in times of the pandemic where it won’t be
possible to welcome all markets, such as from China. But we are hoping to increase the number of industry players from across the maritime supply chain that can make it to Hamburg this year.
With so many global exhibitions available to companies, why do you feel that SMM is so successful in attracting the world’s biggest companies? What benefits do these companies get from exhibiting at SMM?
There is just nothing that compares to SMM. Here you can meet all your business partners, customers, and friends from all over the world at one place within a short time span of four days. It saves so many trips and phone or video calls. It is the personal interaction that exhibitors and visitors are longing for most these days. SMM will be the first opportunity in 2022 to meet again in a very international atmosphere.
We will reflect the whole supply chain of the maritime industry –in both the 11 exhibition halls and our highly-ranked conference programme. In addition, there will be many possibilities to chat in a relaxed atmosphere or to even take a break in our beautiful park directly next to our halls or in our daily ‘wine o’clock’ social events.
Besides the fact that we will offer all of the industries’ solutions, innovations and inspiration, it is important to us that our exhibitors and visitors will have a good time at SMM. There will be several networking events so that each and every one can make the most of their participation. Especially in times like these where everything seems to be in constant change, where there are so many conflicts and crises in the world, we would like to make a small contribution by focusing not only on business but also on interpersonal exchange.
Excitement
as September’s return of SMM is just over the
Please can you tell me more about your conference programme – who do you have lined up to speak and what topics are high on the agenda?
There are so many great speakers and topics that I can’t sum it up in just a few words. All the details can be found on our website. To put it in a nutshell, all five conferences cover topics that are high on the industry agenda.
The Maritime Future Summit (5 September) focuses on the ‘Next Phase of the Digital Transformation’, especially on smart alliances and evolving multidisciplinary solutions. Gmec – the global maritime environmental congress (7 September) - addresses the shipping industry’s part in tackling the growing climate crisis. MS &D, the international conference on maritime security and defence (8-9 September), will discuss the industry‘s and navies’ security transition – from future military and non-military threats to artificial intel ligence for global as well as regional maritime security.
MS&D’s title this year is: Secure your position: Protecting the seven seas. Experts will discuss how navies and the maritime industry can prepare for security issues such as future military and non-military threats or technological developments of manned and unmanned platforms as parts of the Fourth Industrial Revolution (4IR).
The Offshore Dialogue (8 September) will discuss innovative maritime technologies for monitoring climate change processes in the oceans as well as opportunities offered by digitalisation to achieve our climate targets. Finally, the motto of the TradeWinds Shipowners Forum (6 September) is “Phoenix rise – Rebound prospects for containers and shipyards.”
What do you consider to be the main industry challenges for 2022 and the upcoming years? How far do events such as SMM go in helping companies overcome such difficulties?
Of course, I do not have as much expertise as all the stakeholders who will present at SMM, but it’s clear that it will take many innovations, discussions, and negotiations to fulfil the industry's own set goal to achieve net-zero emissions by 2050. All sectors agree on the fact that everything must be done to make shipping greener, to slow down climate change, with alternative energy sources or propulsion solutions.
But the energy transition costs the industry a lot of money, and it takes a lot of expertise and concrete product solutions. Now, the demand in the industry, as in other industries, exceeds what the market can offer. So that might be one of the main challenges
in 2022 and the coming years. I’m sure your readers will find some of the many ideas and answers to this huge challenge at SMM in September.
For those who may be new to the event this year, and may be visiting Hamburg for the first time this September, what advice would you give? What can they expect from their trip to Hamburg and SMM?
Hamburg is always worth a trip. There is so much to discover in our beautiful city. The good thing is that SMM takes place in the heart of Hamburg – all the places worth visiting are just a few minutes away. I advise your readers to have a closer look at our homepage for more information: https: //www.smm-hamburg.com/en/infos/travel/hamburg.
Is there anything not covered by the above questions that you would like to share with our readers?
Thank you so much for all your questions, Phil. I think we spoke about everything that will be key at SMM. On a personal note, let me express how much I am looking forward to meeting all the friends of SMM in Hamburg from 6-9 September. Let’s cross our fingers that everything can take place as currently planned! n
APMTerminals Mobile has signed an agreement with the Alabama State Port Authority to add 32 acres to the current 134 acre container terminal yard to keep pace with future demand, creating one million TEU throughput capacity that is approved to handle 14,000 TEU ships. This represents the third expansion in the last six years as importers expand their volumes to meet regional consumer demand and tap into rail service to the Midwest US market.
The $104 million terminal expansion will begin later this year. The first 19 acres are expected to be completed in 2023 and the remaining 13 acres by early 2025. As part of the expansion, APM Terminals will purchase two, new super post-panamax ship-to-shore gantry cranes and related support equipment (such as trucks, landing chassis/container carriers) for crane operations which will complement the current four gantry cranes.
In 2020, the berth was expanded to allow two x 8,000 TEU vessels alongside. The US Army Corps of Engineers is currently dredging the Mobile Harbor channel to reach 50 feet by late 2024.
APM Terminals Mobile now ranks as the second largest US Gulf port of container imports. April 2022 container volumes through the port showed a 39.7% increase over April 2021 volumes. The port’s intermodal container transfer facility posted 112.6% growth during the same period. Refrigerated cargo also maintained its double-digit growth, posting a 57.9% gain over the same period.
“Supply chain leaders are looking to expand their routing options in 2022 to add more flexibility and fulfillment speed to serve consumer demand. We’re working with customers to deliver high port productivity, more port space and more inland logistics connectivity to address the market demand,” said Brian Harold, Managing Director of APM Terminals Mobile.
Sealand – A Maersk Company has added a new service called the Bonita Express with the inaugural call at APM Terminals Mobile on May 18th. The new, direct all-water service links Mobile to the key Central American ports of Puerto Cortes in Honduras and Santo Tomas de Castilla in Guatemala (with connectivity to multiple inland locations including to/from Nicaragua and El Salvador).
Turkish shipbuilder Cemre Shipyard will build the world’s first service operation vessel that can operate on green fuels for ESVAGT, the Danish provider of emergency rescue and response vessels.
The design of the vessel has been developed by the Norwegian design company HAV Design in cooperation with ESVAGT, and the vessel will be the third turnkey project Cemre has built for ESVAGT.
According to a statement by Cemre Shipyard, “This pioneering project will change the path of the offshore wind service and support the market to reach carbon neutral and environmentally friendly solutions.”
The SOV will be powered by batteries and dual fuel and pure methanol engines, capable of sailing on renewable e-methanol, produced from wind energy and biogenic carbon, which will lead to a yearly emission reduction of approximately 4,500 tonnes of CO2. These systems will provide carbon neutral power for the vessel’s propulsion, positioning, and main operations.
This 93m long vessel will provide accommodations for 124 persons and will be built according to DNV classification rules sailing under the Danish flag. The SOV will serve the world’s largest offshore wind farm, Hornsea 2 located off the UK’s Yorkshire coast in the North Sea.
This new state-of-the-art ESVAGT SOV is expected to provide high comfort standards to the crew and technicians on board in addition to space for recreational activities including fitness facilities, games rooms, cinemas, and individual accommodation.
The vessel will provide a highly efficient workspace together with safe transfer of the technicians at the wind farm via a motion-compensated gangway and transfer boats as well as a crane to lift heavy spare parts. The SOV will also be equipped with a helicopter deck for fast and easy access and transfer from shore.
“This success marks another milestone for Cemre, and having the confidence sourced from the former challenging ‘firsts’ we believe Cemre Shipyard will present this green-committed and futuristic vessel to the sector successfully when completed,” said Burak Mursalolu, Head of Business Development at Cemre Shipyard.
Satellite communications company Inmarsat has made its marketleading maritime broadband service, Fleet Xpress, available to shipyards. Installed during new building, Fleet Xpress for Shipyards eliminates time-consuming and costly installation works in port, offering owners a pre-fitted very small aperture terminal (VSAT) solution included in the initial cost of the vessel.
“Fleet Xpress for Shipyards is a game-changer for shipbuilders and owners alike, streamlining installation, providing remote connectivity from vessel launch and enabling optimal integration between integral onboard systems,” said Ben Palmer, President, Inmarsat Maritime.
“We are delighted to collaborate on the shipyard offering with JRC and Intellian, two of our value-added manufacturers and trusted partners.”
Inmarsat’s newly-launched service enables delivery of Fleet Xpress capability to the shipyard during vessel construction. All terminals, cables, and below deck units are installed as a Fleet Xpress line-fit service, allowing the yard to deliver a one-stop solution to the owner that improves safety and offers fast and reliable connectivity from the first voyage.
“Working with Inmarsat to deliver Fleet Xpress for Shipyards allows us to strengthen our relationship with yards as a technology partner for smart vessels,” said Eric Sung, CEO, Intellian. “As one
of the world’s top shipbuilders, we’re delighted that Hyundai Heavy Industries is among the first to recognise the value of this line-fit solution – we’re seeing significant interest from yards across all markets.”
For shipyards, Inmarsat said early installation of Fleet Xpress will enhance responsiveness to growing customer demand for highspeed communications and provide remote vessel monitoring and maintenance capabilities upon delivery. Furthermore, by using data to counter improper claims and ensure preventive operations, shipyards can minimise warranty costs.
With the vessel featuring state-of-the-art VSAT equipment at launch, owners and managers are assured that their bandwidth needs are fully integrated and sea-trialled at the point of handover, while the crew has access to fast, ultra-reliable connectivity as soon as they step onboard. In addition, Fleet Xpress allows the implementation of a range of digital services and automation onboard the vessel that further delivers advantages for ship performance and crew well-being.
“Fleet Xpress for Shipyards gives shipbuilders the competitive edge of being able to pre-install Inmarsat’s industry-leading Fleet Xpress service,” said Mr Palmer. “Early interest in the solution has been strong. With the first implementations executed, we already have several more projects in the pipeline.”
The world’s first autonomous commercial ship voyage in congested waters, powered by Orca AI, in partnership with the Designing the Future of Full Autonomous Ships (DFFAS) and The Nippon Foundation, has been successfully completed after 40 hours of navigation, with full autonomy being activated 99% of the journey’s time.
The trial was performed by cargo ship Suzaku, a 749 Gross ton vessel chosen for the project by the DFFAS consortium, comprising 30 Japanese companies and led by NYK group company – Japan Marine Science Inc (JMS) and MTI Co Ltd.
During the trial, the vessel automatically performed 107 collision avoidance manoeuvres on the outbound voyage alone, with the program director at the consortium suggesting that the system avoided a total of 400 to 500 ships. The voyage, which started from Tokyo Bay – one of the most congested routes in the world – sailed towards the port of Tsumatsusaka in the Ise Bay.
Powered by AI and deep learning technologies, Orca AI’s safety navigation system was set up on the vessel to act as a ‘human watchkeeper’ and provide real-time detection, tracking, classification and range estimation on 18 onboard cameras, totalling a 360° day and night.
Orca AI’s algorithms were trained on data collected over a year from Suzaku to identify targets in the complex Japanese shorelines environment. The information from the cameras reflected to the fleet operations centre in Tokyo – hundreds of kilometres away.
Yarden Gross, co-founder and CEO of Orca AI, said, “We are honoured to collaborate with the DFFAS consortium led by NYK group to drive automation and autonomous capabilities in commercial ships in some of the most congested waters in the world. The world’s first commercial autonomous voyage is a significant milestone in this journey and we expect to see big shipping companies implementing advanced AI and computer vision technologies to materialise the autonomous shipping vision.”
Dr Hideyuki ANDO from NYK group company – MTI.Co, Ltd added: “With the great majority of Japan’s international trade relying on shipping, it’s been imperative for us to find technological solutions that can make shipping safer.
“We thank Orca AI for helping us find the ultimate computer vision solution to enhance situational awareness on ships, despite the obstacles the global pandemic has presented. Their successful delivery of the entire project, thousands of kilometres away from Japan and with complex hardware and software being shipped and remotely updated regularly, is a prime example of the potential technology has to transform the industry.”
Headquartered in Israel and founded in 2018, Orca AI provides an intelligent safety platform for the shipping industry to increase safety, efficiency and sustainability. Founded by two experienced naval technology experts, Yarden Gross and Dor Raviv, Orca AI’s technology helps ships get an accurate, real-time view of the environment by combining new sensors with existing onboard systems to aid crews in making more informed navigation decisions, improving safety in crowded waterways.
SAAM
Towage continues to fortify its fleet. Its latest acquisition is a new tug, the SAAM James Point, that arrived in Vancouver, Canada after completing its loading operation onto the cargo ship BBC Moonstone in Halong Bay, Vietnam.
SAAM Towage Technical Manager Pablo Cáceres commented: “This state-of-the-art Damen tug has technology that reduces environmental impact and is highly manoeuvrable thanks to its size, innovative hull design, manoeuvre winch settings and installed capacity, making it a true contribution to our operations in Canada.”
The new Damen 2312 tug is named after respected Musqueam Point Family Patriarch, James Point. Born shortly after confederation, he was a fisherman, who worked the Fraser River, and up and down the coast. He was a well know lacrosse player in his youth.
“The Point Family feel that honouring great leaders/servants of the Musqueam people, such as James Point, is a very respectful way for SAAM Towage to recognise Musqueam, to acknowledge our historical presence in the waters of our territory, including the Lower Mainland/Southwest corner of British Columbia, and to celebrate our successful business relationship with SAAM Towage,” stated Director of Business Development of the Musqueam Capital Corp, Jay Mearns.
Featuring an innovative Damen ASD2312 design, this tug was acquired from the Dutch company Damen and built at its Song Cam shipyards in Vietnam. Measuring 23 meters long and 12 meters in beam, it boasts 70-bollard pull capacity, Kongsberg
azimuth thrusters and two CAT 3512C IMO Tier III main engines, which enable it to operate in emissions control areas (ECA).
“SAAM Towage is excited to add this innovative design to our Vancouver fleet. The characteristics of this tug design will complement the various berth configurations in Vancouver Harbour. We look forward to putting the tug to work with our local crews to enhance the marine safety system in Southern British Columbia,” said Vice President Operations and Indigenous Relations Officer of SAAM Towage, Mark Bingham.
venture headed by shipping giant Hapag-Lloyd is building a new terminal in the port of Damietta, Egypt.
“With the new terminal Hapag-Lloyd will significantly improve its transshipment operation in the East Mediterranean market as well as access to the local Egyptian trade,” said Rolf Habben Jansen, CEO of Hapag-Lloyd.
The joint venture, called Damietta Alliance Container Terminal SAE, consists of three core shareholders: Hapag-Lloyd Damietta GmbH (39%), Eurogate Damietta GmbH (29.5%) and Contship Damietta Srl (29.5%). Two other partners, Middle East Logistics & Consultants Group and Ship & CREW Egypt SAE, will each hold 1%.
The new Terminal 2 at the port of Damietta is expected to start operations by 2024. It will have a final total operational capacity of 3.3 million TEU and serve as Hapag-Lloyd’s dedicated strategic transshipment hub in the East Mediterranean.
Thomas H Eckelmann, Chairman of the EUROGATE Group Management Board, stated: “With the Terminal 2 being operational
in 2024, Hapag-Lloyd and its partners will be able to use a state-ofthe-art terminal with sufficient capacity, high productivity and a dense feeder network.”
Cecilia Eckelmann-Battistello, Chairman of the Board of Contship Italia, added: “We feel privileged and are extremely grateful for the support of the Egyptian government. The concession to operate the facility is granted to the joint venture for 30 years. This gives us and our respective customers a long-term perspective in the port of Damietta.”
The Egyptian Minister of Transport, Lieutenant-General Eng. Kamel Al-Wazir, commented: “This is a very encouraging, well planned partnership of international and Egyptian private sector in order to position Egypt as a global hub for logistics and trade. In this first phase we will establish the port of Damietta as an integrated logistics hub for containers, which will then be followed by the establishment of logistic corridors reaching to different manufacturing areas in Egypt by railway network.”
Kongsberg Maritime (KM) has signed a new technology contract of around €28 million with Chinese shipbuilder COSCO Shipping (Qidong) Offshore for an F-class, foundation installation vessel. The vessel will have greater lifting capacity than previous vessels and will be delivered to Danish service provider Cadeler in 2025.
The agreement will see KM supply a comprehensive technology package for the F-class jack-up which will be able to transport up to six XL monopiles (weighing 2,300-2,600mt each) per round-trip, substantially improving efficiency over current vessels.
The F-class vessel also features a unique convertible design, allowing a simple refit process to convert its role from a foundation installation vessel to a wind turbine installation vessel (WTIV).
This is the third contract KM has received for Cadeler installation vessels with KM’s Integrated Solution being crucial to the delivery and operation of all three vessels, which are destined to be among the largest of their type and capable of transporting and installing multiple sets of next- and future-generation wind turbines, and their foundations.
This well-proven suite of solutions combines KM’s optimised thruster package, electrical solution and dynamic positioning functionalities to maintain operability in all conditions and includes multiple digital tools to improve sustainability and reliability.
“Our vessels are designed to meet both the current and future needs of the offshore industry,” said Mikkel Gleerup, CEO at Cadeler. “So as the world needs more efficient offshore windfarms to help meet sustainability goals this requires larger turbines and larger, more efficient vessels to install them. Kongsberg’s innovative technology solutions are a key enabler in this.”
“This is a very smart vessel with a very bright future in the rapidly evolving offshore wind market,” added Egil Haugsdal, President, Kongsberg Maritime. “The bespoke solutions we have devised for the wind turbine installation vessels and this newly announced foundation installation vessel indicate how much thought and effort we devote to facilitating and encouraging sustainable marine operations.”
Cadeler is currently in discussions concerning a XL Monopile foundation installation contract in the North Sea, which will commence with this state-of-the-art F-class vessel.
The World Shipping Council (WSC) continues its work for a safe , secure and sustainable industry, and is excited to welcome a new member in Swire Shipping.
Headquartered in Singapore, Swire Shipping is a leading provider of specialist customer solutions for a wide range of cargo and aims to provide a full suite of land and ocean solutions. Swire Shipping celebrates its 150th anniversary in 2022, and for much of its modern history it has been actively involved in liner shipping in the Asia Pacific region.
“We are very pleased to welcome Swire Shipping to WSC. Expanding our membership broadens our perspective when repre -
senting the liner sector and we look forward to participation from Swire Shipping representatives in our councils and working groups,” said John Butler, President and CEO of the WSC.
Jeremy Sutton is Chief Operating Officer of Swire Shipping, and has been elected as a representative to the WSC Board, effective immediately.
“We are delighted to join the World Shipping Council and to share our knowledge and experience especially in the areas of safety, security and sustainability. We also look forward to learning from our peers and by so doing, contribute to building a vibrant, safe and sustainable industry for years to come,” said Mr Sutton.
On 17 March 1907, the White Star Line steamship SS Suevic ran aground on the Maenheere Reef off Lizard Point in Cornwall. Despite the fog and violent gale, five RNLI lifeboats sped to the rescue and subsequently set the record for most lives saved in a single operation – 456 passengers and crew over the course of 16 hours. After three weeks on the rocks, the wrecked SS Suevic was dynamited into two pieces. The reclaimed two-thirds of the stern was taken to Southampton, where a new bow was added. Suevic served in the First World War before being sold to a Norwegian whaling company and renamed Skytteren. The sea claimed her again in 1942 when escaping Sweden, she was scuttled to avoid capture by the German navy.
HMHS Britannic, Titanic’s younger sister, suffered a similar, short-lived life at sea. Entering service as a hospital ship in December 1915, less than a year later, on 21st November 1916, she struck a mine in the Aegean Sea and sank, becoming the largest single shipping loss of the First World War.
The first Transatlantic cable was built by Cyrus West Field from 1854 to 1858. It only functioned for three weeks before excessive voltage destroyed the cable.
The first true bell buoy was invented in 1852 by Lieutenant Brown of the US Treasury Lighthouse Establishment.
Every problem is a gift we would not grow without problems “ “ – Anthony Robbins –
The world water speed record was set by Australian Ken Warby in a jet-powered wooden speed boat, with an official speed of 275.97 knots (511.09 km/h, or 317.58 mph).
Construction of the 100ft superyacht HISTORY
SUPREME by Stuart Hughes required about 100,000kg of gold and platinum. The yacht features gold-plated hull and anchor, plus a meteoric stone wall accented with genuine T-Rex bone.
Europe’s mostimported fruit is the banana, 950,000 tonnes in 2018, while the USA’s first choice is the avocado, 1.2 million tonnes in 2021.
China’s Yangtze River is not only the longest river in Asia at 6,300 km, but it is also the world’s busiest river, carrying 2.93 billion tonnes of cargo in 2019.
About half the shipping containers imported into the UK will sail away empty. Thus, the UK’s largest export by volume is fresh air.
What’s new in the marine industry?
From simple ideas to engineering feats
Trelleborg’s marine and infrastructure operation launches SafePilot CAT PRO. The latest addition to its SafePilot range utilises state-of-the-art software and smart technology to help pilots and ports optimise safety, efficiency and sustainability in day-to-day operations. The completely independent portable pilot unit is designed for use in demanding applications requiring the highest positioning and speed accuracy. An extended battery life of 30 hours and ultra-fast wireless charging provides minimal loss of time between operations. SafePilot CAT PRO is configurable in four different operational modes to suit all types of vessel maneuvers with interchangeable units.
Armach Robotics, a spin-off company from marine software pioneer Greensea, has unveiled its first post-prototype Hull Service Robot (HSR). The HSR is a disruptive technology in hull cleaning, being man-portable at under 66lbs (30kgs) and around 34 inches (86cm) long. The HSR is a streamlined vehicle, capable of operating in fast water currents and on lower friction coatings, built around state-ofthe-art miniaturised navigation sensors providing rock-solid vehicle control. Armach’s ‘Robot-as-a-Service’ solution offers shipowners a constantly clean hull and following each cleaning operation provides an accurate georeferenced hull condition survey.
After successfully introducing real-time monitoring for its reefer container fleet in 2019 with the IoT product Hapag-Lloyd LIVE, the company will begin installing newly developed devices to all standard containers of its three million TEU fleet. Hapag-Lloyd LIVE will become available for its standard container customers during 2023. The devices will transmit real-time data from each container, making the supply chain more transparent by delivering GPS location data and monitor any sudden shocks to the container. The monitoring device integrates the latest energy-harvesting technology and low-power consumption techniques to ensure ultra-long lifetimes with high-frequency data sending.
Kalmar, part of Cargotec, has received an order for Kalmar SmartPort process automation solutions from Terminal Graneles del Norte SA (TGN) for their greenfield container terminal being built in Mejillones Bay at the heart of Chile’s mining region. TGN’s new port will feature an automated rail-mounted gantry crane system enhanced with Kalmar SmartPort solutions to improve the efficiency of the terminal. TGN will benefit from three Kalmar SmartPort packages to improve efficiency, security and productivity: SmartMap, SmartTrucks and SmartLane. The SmartPort products will be fully integrated with the gate operating system and Navis N4 terminal operating system.
Technology group Wärtsilä launches the 46TS-DF multi-fuel engine focused on efficiency, environmental performance, and fuel flexibility, signalling a new era of medium-speed marine engines. The Wärtsilä 46TS-DF has a two-stage turbocharging delivering high levels of efficiency and power density across a wide operational range for vessels. This level of efficiency reduces fuel consumption and lowers emissions, while being easily retrofittable for future carbon-neutral and carbon-free fuels as they become widely available. The dual-fuel Wärtsilä 46TSDF engine can run LNG, which dramatically reduces air pollutants as well as offering a viable platform for further decarbonisation using bio- or synthetic methane in the future.
Original
Naval architect firm C-Job has designed a brand-new liquid hydrogen tanker that it says will revolutionise the renewable energy market. The concept, developed in partnership with LH2 Europe, is a critical element in a sustainable liquid hydrogen supply chain. LH2 Europe will use the abundant renewable electricity in Scotland to produce green hydrogen, then market it in Germany. When completed, the 141m liquid hydrogen tanker will be powered by hydrogen fuel cells and carry three liquid hydrogen storage tanks with a total capacity of 37,500 cbm. The ship is expected to be commissioned six months before the first delivery of hydrogen in 2027.
Send us your innovation
We welcome all your latest innovations and product releases. If you wish for us to share these with our readers please send them to us today. Send your innovation
ABP cuts its carbon footprint further with two electric cranes at the Port of Ipswich
Associated British Ports (ABP), will further reduce carbon emissions, as two of the very first fully mains-electric powered hydraulic cranes arrive at the Port of Ipswich. These cranes are amongst the first of their kind in the UK and are the latest in a series of bold investments in sustainable measures from ABP, which have contributed to a 36% decrease in greenhouse gas emissions since 2014.
The cranes, Mantsinen model 95ER, have been configured around specific workings of the operations at the Port of Ipswich to optimise efficiencies and further reduce energy consumption. It is estimated that these two electric cranes will save up to 5,275 tonnes of CO2 over their lifetime.
ABP has partnered with provider, Cooper Specialised Handling in this pioneering agreement to invest in these multi-million-pound, state-of-the-art cranes that can be powered by the solar energy generated at the port itself. The two cranes will be able to manage a range of material received in the East Anglian port, which handles over 2 million tonnes of cargo each year and is the UK’s leading grain export port.
Paul Ager, Divisional Port Manager said: “ABP is really committed to reducing the greenhouse gas emissions arising from port activity. This £4 million investment at the port is the latest development in ABP’s carbon reduction goals tailored to its operations. The transition to electric machines will not only improve ABP’s cargo handling service to its customers but will also feed into ABP’s wider policy to reduce CO2 emissions all the way down to zero.”
For more information, visit: www.abports.co.uk
seven seas, five oceans, one voice
alabama shipyard i M
Storied US dockyard Alabama Shipyard has a proud history of shipbuilding and maintenance dating back over 100 years. Today, Alabama Shipyard continues to fulfil a critical – even strategic – role in the country’s naval fabrication and maintenance capabilities. The company’s management team updated Inside Marine about Alabama Shipyard’s plans, both current and imminent, to keep this veteran shipyard relevant for the coming decades. Report by Richard Hagan.
Just 18 miles inland from the Gulf of Mexico, in Mobile, Alabama, lies the aptly named Alabama Shipyard. Located on Pinto Island on a 45-foot deep channel, the yard has a proud history that dates back to 1916. During the Second World War, Alabama Shipyard made a formidable name for itself with its production of the famous Liberty Ships, at one stage launching them at an almost unbelievable rate of one new ship every week. B y the end of the war, Alabama Shipyard had been solely responsible for the production of 600 ships.
“The company has depths of history associated with it,” emphasised CEO Greg Wagner. “It has a history of helping not only the country but also the world. The Liberty Ships that were produced here, had a huge role in helping the allies win the war in the Atlantic.”
Of course, that was many, many decades ago; and in order to ensure the yard continues to thrive into the next several decades, Alabama Shipyard has assembled a dynamic management team that is laser-focused on updating and continuing the yard’s legacy in the coming decades and beyond.
In 2021, Alabama Shipyard completed the first phase of a multimillion dollar infrastructure renovation and upgrade project.
COO Lee Stokes described the work done on its largest pier: “The
project involved $8 million-worth of work revitalising and rebuilding the pier.
“In early 2022 we began CapEx work on the second of our large piers that hosts our drydock. We’re investing a lot of money back into the company here for the future and it’s all going very well,” he said. Mr Wagner echoed Mr Stokes’ comments: “We’re putting a lot of resources into the facility. It’s older and has been here for a long time. So we’re upgrading electrical cabling and installing compressors for each pier. Overall, all of the raw infrastructure is here, but we’re modernising the yard to have 21st century capabilities.”
“We’re also continuing to steady-up our plans to see what the best drydock solution for our vessels is,” added Mr Stokes. “It’ll remain an open item until we get that settled. We understand that we need more drydock capacity, but we’re being careful about establishing what size dock we need and where we’ll put it. We really want to make sure that we make the right decision.”
In the meantime, the company continues to rely on its gargantuan drydock, also named Alabama. Built in Japan and delivered to the US in the 1980s before being sold to Alabama Shipyard later that same decade, the drydock is one of the largest floating drydocks in the US. With an overall length of 240m and a width of around 50m,
“The project also ties us back to the Second World War, with this facility helping and supporting everything that was happening in the world. So it’s a huge point of pride for us having it here” is very important to us”
its 46,400 tonne capacity is able to comfortably accommodate up to Capesize vessels.
The Alabama’s heavy lifting is handled by its two 35 tonne wingwall cranes while the company’s highly skilled workforce of over 250 take care of all required work in the drydock.
Outside of the drydock facility, Alabama Shipyard has an 800 tonne US-flagged crane barge that is being integrated into its operations.
And finally, the company is actively pursuing ship recycling projects. This is an area that is seeing increasing growth as ship owners, under increasing public and regulatory pressure, eschew foreign shipbreakers in favour of local operations having all of the required safety and environmental measures.
In 2019, the US Navy initiated an environmental assessment to evaluate three new locations to include in its existing waste disposal sites; Alabama Shipyard is one of the three. Approval will allow the company to carry out dismantling of ex-nuclearpowered vessels for the US Navy.
“The yard is being studied by the relevant organisations and the decision is expected to be announced towards the end of 2022,” revealed Mr Wagner.
Meanwhile, Alabama Shipyard is participating in a very large, high-profile project to recycle a massive but unusual barge.
The US Navy’s Surface Ship Support Barge, or SSSB, is a 268foot long barge that the US Navy operated from 1964 to 2016. Its
role was to refuel nuclear vessels spent nuclear fuel pool. The project is valued at $129 million and has been underway at Alabama Shipyard since June 2021.
“Having the barge here is a big point for us,” said Mr Wagner “We’re proud that we’re undertaking the project safely and efficiently.”
In March 2022, Mobile celebrated the arrival of the US Navy’s iconic, world-renowned hospital ship USNS Comfort. Alabama Shipyard proudly won the historic $25 million drydocking and overhauling contract – the first of its kind won by the yard in 30 years. The contract is due for completion at the end of July 2022.
“It’s a big project with a big scope,” said Mr Wagner. “We’re proud to have it here, working on it and getting it ready for its next mission.
“Comfort is an important piece of equipment for the world as it supports humanitarian efforts globally,” he continued. “The project also ties us back to the Second World War with this facility helping and supporting everything that was happening in the world. So it’s a huge point of pride for us, and having it here is very important to us.”
Alabama Shipyard is particularly proud of the man agement team it has assembled to take the company forward into its bright new future.
Mr Wagner, of course, heads up the team and noted that he is proud to have returned to the yard after having left for other opportunities just after its purchase from former owner BAE Systems Southeast Shipyards.
“I was here in 2018 when we first purchased the yard, so rejoining the team as CEO in early 2022 has been a big milestone
in my career and I’m beyond excited to be back,” he admitted. “We then built up the team systematically, but a big highlight was the arrival of Lee and his team.”
“Greg recruited me to come over,” added Mr Stokes. “But he wouldn’t answer my call. I had to hunt him down!” interjected Mr Wagner. “I thought it was a prank call!,” said Mr Stokes, laughing. “But it all worked out great. Greg rounds out the executive team perfectly. His energy radiates daily.
Of course, executive management is only one part of the picture. Equally important is the company’s workforce carrying out the increasingly demanding and complex projects arriving at Alabama Shipyard.
“We started with eight staff in 2018 and we’re now at 250,” detailed Business Development Manager Nikole Lee. “That number excludes subcontractors as well as OEMs and technical teams. Depending on the workload, we can surge to upwards of 700 employees quickly.”
To keep its growing staff compl ement happy, Alabama Shipyard is adamant about maintaining a healthy and happy working environment.
“We work hard at being a company that values our staff,” said Ms Lee. “We ensure that they’re safe at work and getting home to their fam ilies every day. Folks want to feel valued and appreci ated, that they’re part of a family. We really try to drive that kind of environment.”
Mr Stokes agreed. “Here, you feel welcome. We try to invest in our people and even build a reputation within the community
that this is a great place to work; that you can have a long career here.”
In closing, Mr Wagner discussed his outlook for the future: “We’re very bullish for the next 12 months,” he stated emphatically. “Outside of current geopolitical tensions, we’ve got a globally strong economy. We’re situated on one of the deepest ports
in the world and there are no air height restrictions. Globally, that’s huge.
“In 2020/2021, we were very successful at keeping the yard full and we expect to maintain full utilisation (or as close to that as possible), through 2022 and into the future. So, we’re very optimistic over the next 12 to 18 months.” n
seven seas, five oceans, one voice
asenav north atlantic ship repair
couach shipyard ares shipyard aresa shipyard
Astilleros y Servicios Navales (ASENAV), regarded as one of South America’s long-standing and pioneering shipyards, has reached its 50th year landmark with sights firmly set on blazing a trail for the next half-acentury. With a diverse order book, including the biggest live fish carrier on the continent, ASENAV is also furthering research into emerging green technologies for vessel propulsion. Profile by Andy Probert.
Fusing heritage with modernity, the family-run shipyard is a beacon of great pride for Chile and South America, and one that burns bright globally as a pioneer in design and build innovation.
Approaching nearly 200 new-build projects since its founding in 1972, ASENAV is one of the leaders in wellboat constructions, a mainstay of the Chilean aquaculture, a recognised builder of expedition ships, and foremost in using new energyefficient technologies.
“ASENAV has achieved a lot in its 50 years and will continue to contribute to the local community and offer work standards comparable with more advanced nations,” asserted Germán Schacht, Business Development Manager.
That comes to the fore with a slew of various projects recently completed or presently under contract at the shipyard, located in Valdivia city, on the Calle-Calle River and 15km from the Pacific Coast.
In 2021, ASENAV delivered two vessels for the Chilean aquaculture industry. The Patagón X is a 2,000 cbm, 69.5m live fish carrier. The 1,985 tonne vessel, which has three wells for fish transport, marked a milestone as the tenth construction for its client Patagonia Wellboats, a leader of Chile’s live fish carrier segment.
This was followed by the Owurkan, a first-of-its-kind delousing vessel explicitly developed to treat different diseases that affect salmon, mainly focusing on the Caligus treatment through regulated therapeutic baths.
The vessel was built for Chile’s fish health management service provider owner SalmoClinic. Its CEO, Hans Kossmann, created the first wellboat for the Chilean salmon industry in 1998, and is also a Patagonia Wellboats’ director.
Due to operate in Southern Chile, the 62m vessel has a treatment capacity of 1,000 tonnes of fish per day. The vessel followed six years of research, while Owurkan means “Healer” in the southern Chilean Kawéskar dialect.
The vessel contains a tank with a large helix to provide a continuous swim-through bath treatment for salmon pumped aboard. The tank was manufactured by Norwegian company Stranda Prolog, which specialises in equipment for handling live fish and stress control.
Because the fish move through the treatment bath in a controlled manner, the amount of medicine needed is reduced and, therefore, the amount of process water to be handled.
A helix unit can treat 200,000 fish with an average weight of 3.5kg with only 700cbm of process water. That offers a 96% reduction compared to a comparable treatment in a cage and 90% compared to treatment in a wellboat. A novel pesticide degradation unit is also aboard the Owurkan.
As Mr Schacht explained: “One of the critical features of the vessel is reducing the use of pesticides or anti-parasites that today are used massively without adequate environmental control. This vessel takes care of the products used and does not impact the surroundings. This is the first vessel built worldwide for this specific purpose, and is expected to revolutionise the industry.”
ASENAV’s experienced engineering department designed the Patagón X and the Owurkan. Both have diesel-electric propulsion systems, reducing emissions and ensuring more efficient fuel consumption. The main generators operate in constant revolutions, and the integrated power management system distributes the electric power the vessel needs for different operation modes.
“This reflects the sustainable strategy the shipyard is pursuing, as the transportation industry generates emissions, and maritime transport is but an important fraction.”
Mr Schacht added the shipyard is also engaged in new projects, including building a 3,000 cbm live fish carrier – believed to be the biggest of its type to be built in the Americas.
The 79.8m vessel, being built for Patagonia Wellboats, will include the latest technology that reduces the environmental impact with the fit-out of diesel-electric propulsion with a total electric power of 3,000 kW.
“As all the main equipment are electric-powered, the ship will be prepared to incorporate in the near future different energy sources, such as green hydrogen, when these supply and distribution logistics exist,” he highlighted. The project will be delivered by May 2023 and be operational in the winter of that year.
Mr Schacht said: “This ship will have a greater transport capacity with only two holds instead of three and relates to the growth in the size of the farming cages. This facilitates trace -
ability and improves loading and unloading times.”
Additionally, a shelter deck has been incorporated to work in a covered area where the fish handling system equipment is located, giving crew and equipment greater protection from the weather. Spaces will be reserved for the future installation of an RSW system and a desalination plant to treat fish through freshwater baths. Cabin and common area space have also been increased, providing greater comfort to the crew.
Another vessel under construction is a speculative 25.6m ASD tugboat with 70 tonnes of bollard pull. Responding to market trends due to the post-pandemic economic reactivations, ASENAV saw an opportunity to provide a quick solution for clients in the short term.
Mr Schacht said this represents the 33rd tugboat to be built by the shipyard and the sixth vessel of a proven in-house design. The other five have been operational for more than five years, with exceptional performance results.
“Happily for us, we can confirm the ship was already sold prior to being ready for delivery, which confirms our initial analysis of the urgent need of the industry for this type of ships.”
Recently, one of ASENAV’s biggest achievements was being awarded a contract to build a 30.8m fishing and oceanographic research vessel for the Undersecretariat for Fisheries and Aquaculture - Chile.
This vessel, set to be delivered by the end of 2023, is a milestone for ASENAV, complying with strict vibration and noise standards for this type of ship.
“This shows the great confidence and trust national institutions have in our shipyard for the worldwide-renowned construction quality we maintain,” stated Mr Schacht. “It also allows us to enter a new market due to the high level of technology involved, which is one of the competitive advantages of our constructions.
“As ASENAV turns 50 in 2022, we will reflect on our tremendous history, our continued contribution to the local community and the drive to complete another 50 years of historic shipbuilding in southern Chile.”
Indeed, Mr Schacht is the third generation family member to enter the ASENAV business, which was founded by his grandfather, naval architect and mechanical engineer Eberhard Kossmann.
Eberhard Kossmann’s back story is a testament to his tenacity to survive the odds, just like his shipyard. Originally from Germany, he fled Eastern Germany by swimming a lake to the West before journeying to Peru to be with his brother. He then moved on, ending up in Chile’s most southerly region.
Settling in Valdivia, he was able to mix with the largely Germanic community and opened the shipyard in 1972. Today, the 130,000 sqm yard has three production plants, 30,000 sqm of building area, with capacities for 120m vessels, overhead cranes ranging from a 10 to 50 tonne lifting capacity, and maximum lifting of 120 tonnes.
ASENAV has docking piers of 188m and 82m long and drydocking of 1,300 tonnes. Its state-of-the-art equipment includes advanced robotic technology for welding, plasma cutting tables and associated works.
The shipyard is one of the most important employers in Valdivia, with between 600 to 1,000 employed workers – approximately 30% of them being subcontractors, depending on the type and size of the vessel being built.
The yard provides an important degree of sophistication in a regional economy dominated by the primary goods sector. In addition, ASENAV hires naval engineering graduates from Universidad Austral de Chile, a local university from Valdivia, one of the most prestigious universities in the country, and one of the few that teaches Naval Engineering.
As a pioneer in ferry building, ASENAV helped connect hundreds of islands in southern Chile. They introduced a simple, secure and lasting technique with a double-ended ferry solution and continue to make ferries for that same market today.
ASENAV remains critical to the connectivity of a country that is more than 4,000km long and has over 3,000 islands. In contributing to uniting Chileans nationwide, it expanded into the fishing vessel market as the industry boomed in Chile and was the first to introduce purse seine, trawler and combined technologies to the domestic market and exported similar vessels to Norway.
While the yard pioneered the design, construction and implementation of wellboats and fish handling systems to support Chile’s salmon farming industry – the second largest in the world – it also built vessels for clients in Fiji, the Bahamas, USA and Canada.
Mr Schacht said that with all this experience and technical knowhow, while actively supporting the local community, ASENAV’s focus is to deliver the current projects on time “as it is one of our key competitive advantages.”
“We hope to close a few more international newbuilding projects from Europe, and be able to enter that market. ASENAV today is focused on improving its efficiency in engineering and production to reduce costs and be more competitive.”
Norwegian company Stranda Prolog is a proud supplier of the HeliXir-tank system on board Owurkan (owned and operated by SalmoClinic and built by ASENAV). Stranda Prolog specialises in equipment for handling live fish and stress control in addition to advanced solutions for salmon harvest plants globally.
The large HeliXir tank provides a continuous swim-through bath treatment for salmon pumped aboard. This is a patented online precision bath process, environmentally friendly and provides good fish welfare. The system is flexible to use both fresh and sea water and elegantly operated by Stranda’s StraQS control software.
ASENAV’s engineering department, said Mr Schacht, is always looking to innovate and include state-of-the-art technologies.
“Our current focus is including propulsion systems using green fuels that will considerably reduce emissions – the industry’s primary concern today. This won’t happen until reliable supply and distribution logistics satisfy that demand, but when the time comes, we’ll be ready to adapt this technology in our constructions.”
The yard has been previously experienced in the expedition cruise vessel arena as the concept for a more personalised vessel in the tourism industry has grown. ASENAV designed a tailor-made 91m, 100-passenger capacity vessel to meet the Polar Code’s demanding requirements, enabling it to operate in the Antarctic and Arctic.
“The vessel, Magellan Explorer, built for cruise operator Antarctica 21 based in Southern Chile has the autonomy to operate for 60 days without touching port and is equipped with Tier III emission reduction technology,” said Mr Schacht.
The yard’s ability to deal with highly complex demands from customers was also met with the release of the Pelee Islander II Ro-Ro passenger ship for the Ministry of Transportation of Ontario, Canada. This is a standout project as all the building requirements had to be approved and meet the demands imposed by Transport Canada on all new vessels entering its territory.
ASENAV has also delivered six AHTSVs for Maersk Supply Service, which operates from Port of Saint John into the North Atlantic Ocean. These vessels were state-of-the-art constructions including Dynamic Positioning II System, which allows the vessel to stay automatically in the same place regardless of the weather conditions – a key requirement in vessels that support offshore platforms.
These vessels have between 80.20 and 90.15 metres of LOA, between 18.80 and 22.00 metres of BOA, gross tonnage between 4.323 and 6.490, 150 to 218 tonnes of Bollard Pull, around 6,500 sensors and more than 240km of cable in each unit.
The yard has adopted a 10-step plan to ensure workers’ safety from Covid-19 and worked closely with Universidad Austral de Chile to actively monitor any cases. This plan included more working shifts in smaller groups, constant temperature control, and PCR testing for all staff twice per month.
“For us, the most important was to keep the shipyard operating and keeping our workers and their families safe. To date, production has not stopped, and we have delivered three new building projects without delays,” he said.
Another challenge is the increasingly competitive landscape that has seen shipyards worldwide close and many more rescued by their governments or public institutions during the last decade.
New restrictions due to environmental issues favour ASENAV thanks to its drive for innovation.
“We are always ready to apply the most advanced technology available in our projects,” Mr Schacht said. “The first experimental vessels with hydrogen cells and propulsion based on auxiliary groups with LNG are a case in point.”
He emphasised: “Chile is a country with the largest free trade agreements globally, so ships built by ASENAV, in most cases, have advantages to be exported. We have the freedom to build with imported materials and equipment from around the world without restrictions.”
Mr Schacht also highlighted Chile’s solid institutional framework, atypical for a developing South American country, and the country’s deep-rooted international business culture.
“Having complete design capabilities for a project, we can work closely with clients and tailor a vessel to suit their needs. We guarantee high-quality international standards at a competitive price, and since the company was founded, we have maintained a policy of delivering vessels to agreed deadlines.”
ASENAV will continue to adopt more environmentally friendly technologies, Mr Schacht confirmed, focusing on green fuels and creating vessels that provide better performance, hydrodynamics, and operational results.
“While we are renowned for high-quality constructions and engineering concepts, reliability is also a very important requirement for our customers. They know that we’ll achieve the required project whatever it is. In addition, on-time delivery is key for us as clients plan their entire operation around a ship’s start and delivery date.”
The yard’s after-sales service ensures it accompanies the client throughout the entire operational life of the vessel and doing everything possible to solve any issues quickly. ASENAV can also
accommodate the design and construction of the vessel to solve a client’s requirements.
“All these qualities are fundamental to enjoying long-term relations with clients,” he said. “These also apply to our leading suppliers, whom we have been working with since the yard was founded.
“The relation between shipyard, supplier and client is completely symbiotic and ensures ASENAV remains involved in the vessel’s lifecycle.”
Mr Schacht added: “The marine industry faces an important challenge regarding environmental care and global warming.
I think this is the biggest issue that, as an industry, we need to figure out how to solve as soon as possible.
“We must work together with customers and governments to speed up the supply of new technologies and greener fuels. However, the assumption is that in the short term this will come with higher costs at the beginning, and the entire supply chain must assume this increase to reduce our eventual impact and have a better future for all. In the long run, this is clearly expected to have benefits for the operation besides from the reduction of the contamination of our environment.”
He concluded: “ASENAV has reached a significant milestone in 50 years of service to the community and the industry. We are firm in our desire to continue that trend for the next half-a-century.” n
With a commanding presence in America’s northeast and boasting 30 years of maritime industry heritage, North Atlantic Ship Repair has fought its way to the top in a limited but highly competitive and fierce market. Though the firm’s future was already bright, its recent acquisition by a passionate new owner has initiated exciting and considerable future plans which are already in motion. Edward Snyder, company President and CEO, filled Richard Hagan in on all the details.
North Atlantic Ship Repair, headquartered in Boston, Massachusetts on America’s northeast coast, is a ship repair service provider, specialising in the overhauling of primarily large vessels for both government and commercial clients.
The company owns two facilities; one in Boston, and one in Philadelphia. Both yards have similar capabilities, with each boasting its own dedicated production team and a drydock capable of accommodating ships of up to 1,100ft x 105ft, with over 60,000 tonnes displacement capability.
The Philadelphia facility has the added benefit of a 1,000ft pier, significantly improving its overall efficiency.
Between the two locations, the company has three large mobile harbour cranes, with two based in Boston and one in Philadelphia, and a 65 tonne mobile crane also located in Philadelphia.
Altogether, the company employs roughly 200 workers. Full production
teams are located in both facilities. Administrative services are all located in the Boston facility.
Having joined the company as a partner in the 1990s soon after its establishment (originally named Boston Ship Repair), Edward Snyder is a veteran of the company’s journey and his current title of President and CEO has been well-earned.
The company enjoyed early success as a standalone operation in Boston but was limited, with only a single drydock and no pier space. When the opportunity arose to acquire the Philadelphia shipyard location, it was a perfect means for expansion. Adding a second shipyard with a pier more than doubled the capabilities of North Atlantic Ship Repair.
In 2020, a local Bostonian acquired North Atlantic Ship Repair (formerly Northeast Ship Repair). Its new ownership
is deeply passionate about the shipyard and ensuring the sustainability of its operations, and the critical local blue-collar jobs it provides. There is a serious commitment to make critical investments into the shipyards to ensure North Atlantic Ship Repair continues to move in the modern era of ship repair. The new ownership has entrusted this vitally important task to the capable, veteran hands of Mr Snyder and his team.
“Our new owner has entrusted my staff and I to run the company and continue expansion into the next generation,” said Mr Snyder. “We are thankful for that backing!”
For decades, North Atlantic Ship Repair was owned by private-equity firms, which did not have a long-term investment timeline for the shipyards. Now, having the company’s ownership in the hands of a local businessman with significant roots to the City of Boston has proved to be a win/win, according to Mr Snyder. “Our owner has a great reputation with the City. He is a people’s person and has a love for the city and the area we’re in.”
One of North Atlantic Ship Repair’s highestprofile government customers is Military Sealift Command (MSC). The company has done (and continues to do) plenty of work with this department, but a particular highlight has been its maintenance work on the USNS Comfort.
The USNS Comfort is a very big, very white hospital ship owned by the United States Navy. Since her launch in 1976, she’s seen ongoing use around the world in major relief efforts, providing high-tech, advanced hospital and medical care facili -
ties to both warzones and natural disasterhit communities, amongst others. But at her age, and with her length of 894 ft, when she needs maintenance, she needs a drydock the size of the ones owned by North Atlantic Ship Repair.
USNS Comfort has been a regular visitor to North Atlantic Ship Repair in the past, which has carried out maintenance work on her at least three times since 2012 alone. And while she has always been a relatively well-known ship amongst the public, her deployment to New York during the height of the Covid lockdowns and her specific mentions in the media by the US government raised her profile significantly. And with that, North Atlantic Ship Repair’s profile was raised as well.
“We’ve received commendations from the government for our work on her,” Mr Snyder revealed. “It is very satisfying and we’re very proud of our contribution to this awesome vessel.”
While North Atlantic Ship Repair’s biggest client is the US government, the cruise industry also visits the facilities from time to time. Mr Snyder was keen to elaborate on the differences between these government and private client projects.
“Government jobs are longer in duration, while cruise ships need to be done within seven to ten days. When you’re working on a cruise ship, it’s non-stop work for 24 hours a day, seven days a week, and it’s changes on-the-go at all times. Therefore your production team needs to be able to adapt and make critical decisions to be successful. Our ability to provide a fully dedicated production team
to a cruise ship project is something that truly sets up apart from any of our competing shipyards.
“When a cruise ship is in, all hands are in and working many hours a day to get it done,” he continued. “Government work is more defined, with longer overhaul periods. But it requires higher certification levels and ongoing inspections throughout the process. The inspections are very specific and abundant in all aspects of the project. Basically, what we can do on a cruise ship in seven days takes us over a month on government contracts.”
In one particular cruise ship project highlight, the company achieved a remarkably fast turnaround between two massive cruise ships that both required drydock work, one right after the other.
“We had one cruise ship arrive and tie up just outside our drydock, and the other inside the drydock finishing up. As soon as the ship in the drydock was complete, we had to take it out and swap places with the other cruise ship. We managed to complete that operation within the same day due to similar docking plans. It was a real highlight for us and one which emphasises our efficiency, dedication and the speed at which we are able to make decisions.”
North Atlantic Ship Repair has exciting future plans that are already in motion.
“Our hope is that in the near future we can work with the City of Boston to re-construct the deteriorated South Jetty pier just outside our drydock,” revealed Mr Snyder. “This new pier will be a tremendous asset to the City of Boston and our shipyard in the future.”
He added: “We don’t have a pier there and one is greatly needed. There are
existing piers but age and deterioration has taken place and re-construction is needed.”
An ongoing planning effort is in progress at the Port of Boston to support an increase in marine traffic, specifically as it relates to larger vessels. To maintain its competitiveness, in 2014, the Massachusetts Port Authority commenced the Conley Terminal Modernization Program, an $800 million investment into the infrastructure of the Port of Boston.
This program included partnering with the US Army Corps of Engineers on the dredging and deepening of the Boston Harbor, rehabilitation of two existing berths at Conley Terminal, construction of a new deep-water berth and expansion of Conley Terminal yard.
“We believe the reconstruction of the South Jetty pier is the final piece of a very large effort to make the Port of Boston a full-service port for large vessels,” said Mr Snyder. “Our Boston facility will be able to service all the needs of the vessels transiting the area and layberthing at the South Jetty pier, potentially even allowing us to simultaneously work on two vessels at the same time.”
Meanwhile, Mr Snyder further revealed that the company has plans to significantly upgrade its workshop facilities in the near future.
“Everything in terms of the facilities goes back to the 1940s when they were originally constructed; like many shipyards our facilities are old. Therefore, we’re planning to substantially upgrade our facilities and the workshops within them.”
In conjunction with those large CapEx projects, the company has begun an apprenticeship training program partnering with the local communities.
“The program is an outreach to the underserved, minority communities of Boston, to attract them into these highpaying blue collar jobs. It’ll be a win-win for both us and the communities in an environment in which recruitment has become a major challenge.”
According to Mr Snyder, one of North Atlantic Ship Repair’s major hallmarks amongst its clients is its size – because of what that means for the kind of
service the company is able to deliver to customers.
“We’re focused on the individual project,” he explained. “Whether it’s a government or commercial customer, they have our full attention, whereas in bigger yards, the relationship and service may not be the same. We’ve always had a great reputation with our customers for our efficiency and dedication.”
Concluding, Mr Snyder offered his vision for the company’s future: “I want to help the business continue into the next generation. I’m one of the original owners, going back over 25 years, so our focus now is on building sustainability into the business. We want to grow it with our younger generation who are coming into the business right now and continue to create blue-collar jobs in the northeast for years to come.
“I’d like to know that when I leave, I have left it in the best possible hands and created the best opportunities for all involved.” n
Couach Shipyard remains ever buoyant with a strong order book and a recently revamped shipyard promoting better organisational flow. Alexis Philandrianos, Sales and Strategy Director, sits down with Andy Probert for a recap of the last 18 months for the French boat builder, and the story behind developing a technological and ecological evolution –a ‘green’ hull.
The engineers, naval architects and technicians of Couach Shipyard are noted for pushing back technological barriers. The luxury vessel, military and rescue boat builder in Arcachon Bay, close to Bordeaux, confirmed this position with the world’s first unit equipped with a 26m hull entirely molded in bio-sourced ‘green’ resin composite.
In partnership with Sicomin, one of its long-standing partners, the company has concluded four years of research with the realisation of a select bio-sourced epoxy resin to meet the main requirement: a first step towards the use, then the generalisation of this technology to green ships.
This resin comprises about 38% of products from renewable and vegetable resources, replacing synthetic products from petrochemicals, said Alexis Philandrianos, Couach’s Sales and Strategy Director.
In maintaining its reputation for hulls that offer a formidable passage at sea and unparalleled sailing comfort, its engineers
have built the bio-sourced epoxy resin hull on a new Fly 86/2600 model.
“The consequences of this development, namely weight saving, resistance, consumption and durability, make this yacht a real technological and ecological evolution,” attested Mr Philandrianos.
While striking a balance between comfort, safety, and performance, this addition follows the refined and dynamic design that is the hallmark of a long line of Couachbuilt yachts.
With two guest cabins and two crew cabins, the 86/2600 can accommodate up to nine guests and three crew. Along with top-of-the-line luxury and ergonomic lines, the yacht is the only one in its category equipped with a garage that accommodates a 395 dinghy, a jet ski, bicycles, surfboards, SEABOB and an area for diving equipment.
The vessel was handed over to a private European owner in early 2022, and feedback has been “very positive,” reported Mr Philandrianos. It again underscores the company’s portfolio of fleet options that evolve in delivering highly sophisticated vessels of exceptional technological performance while being lighter, smaller and faster.
He added: “This hull helps to reduce our carbon footprint. It was very challenging for us as we had to change the way of doing things and re-learn processes, but the result was a fantastic looking vessel. The bio-sourced epoxy resin has better mechanical characteristics than traditional resin and is more durable.”
Mr Philandrianos reflected: “While we are handling an order intake of over €200 million, we needed to reorganise our facilities and processes in 2021, and this is what we achieved. When handling large numbers of vessels – 22 on one contract and 12 on another – it is essential to be efficient.
“All the work we did in our industrialisation processes has improved workflows immeasurably. Now we are in full delivery mode.”
The period reflects one of the most productive eras in the company’s 125-year history. On the naval front, Couach Shipyard is concluding a five-year maintenance contract following the 2016-2018 delivery of 79 17m interceptor boats for Saudi Arabia’s coastal protection authority.
The interceptors were built with composites based on Couach’s 1650 FIC design. With inboard diesel propulsion with waterjets or surface propellers, they can exceed 60 knots and exceed 250 miles at cruising speed.
Couach is presently building a further twelve 22m patrol boats for Saudi Arabia. This momentum will be carried on with a three-year maintenance contract for these boats from 2022 to 2025 via a local company established in the Kingdom.
The company is also mid-way through a contract for Oman to deliver 22, 14m interceptors, with a view to completing the fleet order by 2023. “Patrol boats and interceptors offer enormous business opportunities for Couach, and we’re delighted
to continue working alongside clients to bring these contracts to fruition,” said Mr Philandrianos.
Its 10-year programme to replace 140 rescue vessels for Société Nationale de Sauvetage en Mer (SNSM), the French sea rescue organisation, is also gaining traction.
The shipyard landed the contract to help define the range structure of SNSM’s future nautical resources. Partly financed by the French Government, the phased schedule will cover vessels in five subcategories, ranging from 6m to 17m, and replace several 1980s built all-weather canoes.
“This is a very challenging programme as SNSM has a lot of stations and different needs. Vessel requirements in the Mediterranean will not be the same on the Atlantic Coast,” said Mr Philandrianos.
Couach, allied with architects Frédéric Neuman and Christophe Barreau and with SNSM, co-developed a boat that could meet all these diverse demands and needs.
“We built one boat that was perfect for everybody, but adapted to the mission of saving lives.”
The company is now testing the first boat, a 17m vessel, which is expected to be deployed to a rescue station in 2022. The schedule foresees at least 70 boats, with a view to more in the future, while the contract’s minimum value is estimated to be around €50 million.
The new 17m vessel has provoked interest from other voluntary lifesaving societies across Europe. One Danish organisation
has ordered a similar vessel, which is now under construction.
Couach remains busy on the R&D front, continually optimising and improving its fleet, such as the interceptor range being compacted to 12-14m, and a 17m option, with more systems and defence solutions.
Mr Philandrianos said the company was in discussions with potential clients to use some of their existing platforms, such as 22m or 28m, incorporate more systems and enhance them beyond being a patrol boat.
“We are looking at taking a small platform and integrating many sensors in CMS and making a very smart transition. We are promoting this idea, and clients have been largely receptive to that.”
He said: “We are also looking at the mine warfare sector, by taking a simple platform, integrating several solutions, and enabling a compact vessel to undertake such missions We continue to upscale the vessel and dare to do what our peers don’t.”
The company’s commercial options primarily sit between 23-42m, with hybrid propulsion, optimised hulls, lower fuel consumption and smarter systems. Couach can also build yachts up to 50m for specific clients.
Its 42m Lounge series hybrid superyacht comes with low energy consumption and a conversion system that generates electricity from the vessel’s movement. It is expected to become increasingly popular as more environmental-conscious customers enter the market.
Performance prediction modelling, hull performance, and hybrid propulsion and
defence solutions are also being created as the company continues to transition in an ever-evolving market.
“Environmental concerns are always a key priority,” said Mr Philandrianos.
“Hybrid power, a mix of diesel and electric, and even hydrogen are under consideration. We will focus even more on R&D and continue to develop new solutions. For example, the bio-sourced resin will change how we work and help us minimise our carbon footprint.”
Plans for the next one to three years are to promote new vessels offering multiple systems, continue with its localisation of services, and to raise the Couach brand image further by adding to its established list of international clients.
“We have also developed a 12m boat that can be easily transferred for production to other nations,” added Mr Philandrianos. “We have signed Memorandums of Understanding with two nations in Asia and the Middle East to do this, which will enable us to continue with our customer development.”
Mr Philandrianos added that Couach’s development has also led to the business taking on more skilled people, thanks to agreements with schools and universities for operators to engineers. It has also
developed and adapted its own academy to integrate more workers into production lines and offers greater flexibility as part of its continued expansion.
While challenges remain in maintaining quality, meeting orders on time, and remaining committed to contracts, Mr Philandrianos added: “We have to continue to find new ideas that make customers want us more than the competition. That’s why we are investing heavily in more R&D to make things smarter and smoother.”
He added: “The fact that we are doing both military and yachts is very interesting. On the military side, we focus on large num bers, while on the other, it is always a one-off vessel design.
“We have to maintain production flexibility and adapt to customers’ needs. This is what interests the clients. We can do exactly what they want us to do. A military customer knows we can design and build many units they require to their specifications. Having teams in the locality is priceless for them in the long-run. When we sell a boat, we sell our support and service capabilities.”
He concluded: “These last 10 to 15 years have seen a lot of changes at Couach, but now we are heading in the same direction. The future is bright. All the planets are aligning quite nicely, and we want to achieve more.”n
ARES Shipyard is one of Turkey’s fastest growing companies, having increased its sales revenue by an astonishing 4,473% in just five years. As the country’s largest ship exporter, it is no surprise that ARES has been awarded various accolades in the 16 years since the company’s founding. Based in the Antalya Free Zone, ARES has built more than 100 vessels for sectors including mili tary, commercial and pleasure craft. Jordan Yallop reports.
Recognised by the Union of Chambers and Commodity Exchanges of Turkey as one of the country’s fastest growing companies, ARES Shipyard also holds the title of Turkey’s largest exporter of marine vessels, having increased its sales revenue by a staggering 4,473% in just five years.
Ozgun Utku Alanc, CEO of ARES Shipyard said: “These numbers, not surprisingly, brought us the largest ship exporter title of Turkey with an annual export sales figure of almost $200 million.”
ARES Shipyard and its five production facilities are located within the boundary of the Antalya Free Zone.
Founded in 2006 by the Kalafato ˘ g lu family, ARES initially cut its teeth by successfully constructing and delivering small pleasure craft, small fishing vessels and leisure boats for the public market. Mr Alanc cited one of the company’s first critical milestones as “gaining experience in the fields of aluminium, steel and composite production”.
ARES really set sail for greatness in 2007 when the company made the strategic decision to specialise in the production of military and para-military craft.
Mr Alanc explained the context behind this decision: “The shipyard has aimed to become an international defence industry company by investing in human resources, organisation management, integrated logistics support, quality management and advanced production technologies.
“These investments, in a short period of time, resulted in a substantial number of sales of boats to various naval forces, coast guard commands, maritime police, port security and customs enforcement directorates, most of which were export programs.”
Gaining excellent traction in export markets, ARES has built and delivered vessels for clients in Oman, Qatar, Bahrain, Nigeria, Georgia, Tanzania, Cyprus and Turkmenistan. To date, ARES has built over 100 vessels with a market sector split of 85% military and paramilitary, with the remaining 15% covering the company’s commercial and pleasure craft activities.
“Within these percentages, the major military and paramilitary segment consists of mainly patrol vessels with the commercial
and pleasure craft segment consist of passenger craft, work boats and yachts in approximately same proportions,” clarified Mr Alanc.
ARES had been awarded ISO 9001, ISO 14001 and ISO 45001 quality management systems, as well as the Ministry of Defense Production License accompanied with NATO Security Clearance Certificate along with supporting Naval Forces and Coast Guard Organizations in military programs.
As mentioned, ARES has five production facilities within the Antalya Free Zone including, a harbour launch, metal, composite and carpenter workshops, paint ovens, training classrooms and modern office areas.
Mr Alanc spoke about the specifications of the company’s newest, fifth production facility: “It has been designed for steel and aluminium ship building. With this facility, ARES increased its total enclosed production area to 40,000 sqm and shipbuilding capacity has been increased to 90m vessels with 2,500 tonnes displacement.”
ARES is not just limited to its shipbuilding facilities; the company also has a separate marine furniture factory under the same corporate and commercial structure. This segment not only manufactures furniture for its own vessels but also produces luxury furniture for megayacht programs of other shipyards and companies.
ARES currently has around 400 employees, however, in line with the company’s growth and upcoming programs, this is projected to increase to around 450 employees by the end of the year.
When discussing the current and future trend for the shipbuilding industry Mr Alanc mentioned that smaller is the new big, elaborating: “If you can design and build vessels smaller in size, they are more seaworthy, more capable in performance and manoeuvrability.
“This also means they can be operated with less crew. As a result, not only do the lifecycle costs of the end users decrease but also the efficiency of the institutions increases, while keeping the operations going and providing non-stop security.”
Aside from the trend of decreasing vessel size, the trend that Mr Alanc projects to grow in the coming years is that of unmanned vessels. He did clarify that the aim is not the act of replacing manned vehicles with unmanned ones and eliminating the human factor – far from it.
“It is about complementing each other with their superiorities and utilising these advantages against nature for instance,
or ergonomic restrictions and most importantly decreasing the probability of losing human lives. That’s exactly why we have been investing in R&D especially in unmanned surface and underwater vehicles for the last five years,” said Mr Alanc.
ARES is an incredibly technology-centric company that invests heavily in R&D and is always striving to be at the leading edge of advancement. So it should come as no surprise to learn that the shipyard is at the forefront of the newest innovations around the unmanned vessel revolution.
ARES has partnered with Meteksan Defence, a Turkish defence technology company which specialises in radar systems, perimeter surveillance systems, laser and electro-optic systems and communication systems.
This partnership has borne Turkey’s first armed Unmanned Surface Vehicle (AUSV). A prototype was launched in December 2020, becoming the first of the ARES ULAQ unmanned line. The capabilities of this new breed of vessel are extensive and include full day/night vision, encrypted communications infrastructure, and can be operated from mobile vehicles or sea platforms, such as aircraft carriers or frigates.
Mr Alanc stated: “We are proudly aiming to develop the world’s best unmanned surface vehicles and establish ourselves as a pioneer in this field, bringing ARES and Meteksan into a leading position in the world, creating trends in the field of USVs.”
While this is the culmination of ARES and Meteksan’s future vision, ARES still has one foot planted firmly in the present as it also builds various vessels. At the beginning of 2017, the shipyard was awarded “The World’s Best Patrol Boat Builder” by an international maritime institution and the company’s ARES 110 HURCULES Fast Patrol Boat was elected as the best in class simultaneously.
ARES has an ongoing program for the Turkish Coastguard, where 122 ARES 35 FPB Fast Patrol Boats have been delivered already, making the program the largest serial production in the company’s history.
“The project is planned to last for five years and on the other hand, the contract allows for additional vessels. We are delivering six boats every two months based on our production program. Thus, one boat is being made ready to launch in only one week… this is something only ARES can achieve!” declared Mr Alanc.
We are a proud partner and supplier of ARES Shipyard and we wish them continued success and growth.
Our team has been designing and manufacturing in the UK, since 1901, the most innovative and high-performing lighting products in the market. We offer an extensive range of searchlights in all sizes, configurations and light sources, suitable for any vessel, application, or customer.
Our extensive range of high-power LED searchlights is widely regarded as the most powerful available worldwide.
editorial mention
ARES is certainly a company with a vision and as such had meticulously planned out its future. This took the form of a 10-year investment plan of five phases. As of 2022, ARES is in the eighth year of its plan and has already completed the first four phases. The first of these phases was to create the largest man/machine hybrid system composite production facility; the second phase was the block production facility for larger steel and aluminium vessels. The third phase was the state-of-the-art marine furniture production facility, while the fourth was to create the largest building and outfitting facility in Antalya Free Zone with a capacity of 90m vessels with 2,500 tonnes displacement.
“Our last phase includes a 170m, unlimited displacement, enclosed dry dock in Antalya Free Zone which is going to be the largest and most capable docking, building and refit facility of the Eastern Mediterranean. This investment is in progress and is scheduled to be commissioned by the end of 2024,” concluded Mr Alanc. n
Having recently celebrated its extraordinary 60th birthday, Aresa Shipyard, in Spain, is stronger, faster, and better than ever before. With a colourful and storied history spanning leisure, commercial and naval vessels, the company is harnessing all of its skills, experience and infrastructure as it consistently delivers on the demanding needs of modern clients. Aresa Shipyard’s CEO, Oriol López, spoke to Richard Hagan about the company’s impressive line-up of high speed, high quality naval and commercial vessels.
Aresa Shipyard’s history can be traced back to 1961 when it was established by Oscar López.
By all accounts, the company got off to a strong start. During the 1970s and 1980s, it established a manufacturing relationship with a major Italian shipyard. In terms of this agreement, Aresa built the yard’s models in Spain. The experience gained from that relationship provided the impetus for Aresa to subsequently design and begin producing its own range of leisure yachts. At that point in time, Aresa was a pioneer, being the only yard building yachts up to 24m in length.
The company’s next major turning point arrived in the late 1980s when it concluded a contract with the Spanish navy to supply two different coastal patrol vessels to the state, with 23 units delivered in total . The contract was an unmitigated success, but the Spanish navy ultimately shifted its procurement strategy towards much larger vessels from government shipbuilder Navantia. Nonetheless, its successful execution of that contract had solidified Aresa’s presence in the naval market. Later on, it would prove to be key to the company’s ongoing success today. Aresa began production for the commercial shipping sector in the early 1990s, before finally focusing on government projects in defence, fishing and transport from 2002 onwards for states around the world.
Today, Aresa is a leading manufacturer of modern, highly capable vessels for the defence, commercial and fishing industries. Its beating heart is its headquarters and production facility located a short drive north of Barcelona. The impressive 25,000 sqm factory floor supports its 100m long mooring berth and three 60m long hangers. At any given time, the company employs
approximately 150 staff including permanent staff and temporary contractors.
Aresa’s production strategy is built around manufacturing models that are adapted to suit its customers’ specific needs, and then supporting those models for the long term through the provision of after-sales and servicing support.
Modern naval doctrine is increasingly concerned by the threat posed by small, fast boats to naval vessels operating in shallower waters, especially along coastlines. In response, coastal governments have shown extensive interest in procuring their own small, light, fast attack and interceptor craft to meet and counter this threat.
Building very fast but capable boats sounds deceptively easy, but the truth is that it’s a real challenge requiring special expertise.
“High-speed vessels, at the lengths we specialise in, are the most difficult types to build,” Mr López added. “They must be secure but also robust enough for heavyduty use.”
Aresa has strategically positioned itself as a specialist builder within that niche. Its ability to build fast, safe, light and highly capable vessels for the world’s navies has seen it becoming the manufacturer of choice for navies in the region.
“We are really focused on small and medium-sized vessel construction. That’s what’s been coming to us in the last three projects we’ve executed,” explained Mr López.”
“This trend began emerging several years ago and it has led to a massive increase in demand from our customers for fast coastal patrol boats. Customers are looking for smaller, faster vessels with lower maintenance costs and shorter maintenance windows. Navies want faster vessels they can
operate easily and get out of the harbour within minutes. We’re now focusing on delivering these very fast boats.
“For example, our last order from the Saudi Navy was for ten vessels of 17m in length capable of reaching 60 knots. Following that, we delivered four 18m vessels capable of 40 knots to the Nigerian Navy.”
Any colour as long as it’s black Naval special forces are a particularly enthusiastic customer for Aresa’s boats. Naturally, its two latest product launches are aimed directly at this important market. The first of these is the Aresa 1500 Black Falcon HighSpeed Interceptor – a fast interceptor craft designed specifically for navy seal and other special forces requirements.
The crew and passengers are safely and comfortably catered for with shock-absorbing seats by world-renowned specialist manufacturer Ullman Dynamics. Meanwhile, the boat is powered by three Yamaha 425 XTO outboards - a first for the Spanish boatbuilding industry and the first military craft in the world to receive this power package as well.
The Royal Saudi Navy has already taken delivery of ten Aresa 1500 Black Falcons
and, based on the positive feedback from the Saudi teams, more are expected to follow for other navies in the region, according to Mr López.
“The model’s manoeuvrability, stability and control at high speed really impressed the Saudi Special Forces. It’s travelling at more than 60 knots, which is impressive compared to similar models from France and the UK. This project will go down as a record for our company because of the customer’s acceptance of the project and the way the navy is promoting it in the region.”
The other new product is the Aresa 5000-4000 Peacestorm offshore patrol vessel. This substantial yet nimble craft
is designed to operate effortlessly in shallower coastal waters. With an overall length of between 40m and 50m (depending on customer specifications), and a 10m beam, there’s plenty of space onboard for naval operations of various kinds. Peacestorm will be powered by 7,500hp waterjets or propellers and, thanks to its lightweight construction, is expected to reach a top speed of between 20 and 30 knots.
“We are already in negotiation with three defence customers who are interested in this model,” Mr López revealed.
Two Narwhal Rigid Inflatable Boats are carried on the aft deck for high-speed interception missions while the bridge, armoured to NIJ Level III+ is combat-ready
and designed to stay in the fight.
Mr López also wished to highlight a new boat the company has sold to the Nigerian Navy: The Aresa 1800 Fighter II is an aluminium patrol vessel featuring an armoured bridge. Able to reach speeds of 40 knots, the Fighter II is an evolution of the company’s Fighter I coastal patrol vessel.
“We designed it to be easy to maintain and operate, whilst still including the latest technology like airband communications for communication with aircraft, and a vertical launching platform for the auxiliary vessel on board,” he explained. “It features two engines of 1,250hp.
The Aresa 1800 Fighter II proved to be such a hit with the Nigerian Navy that Aresa expects additional contracts for these boats from both Nigeria and other countries.
From 2004 to 2009, Aresa completed a major project for the Angolan government, manufacturing a massive fleet of 210 fishing vessels for a combined value of €84 million.
“We supplied seven different fishing vessel models and some coastal patrol vessels to protect the fishing fleet on the water. The project was a major highlight for us because it was one of the biggest of its kind ever signed in Spain,” Mr López commented.
Another project highlight came in 20132017, when the company delivered 17 military vessels to the Cameroon government. It included technical support and a logistics program spanning five years for a combined value of €36 million.
In just the last three years from 2019 to 2022, Aresa has delivered €30 million worth of projects to its clients. “We show the market what we can do using the facts
of our delivered work, not just through our words,” Mr López stated emphatically.
Looking ahead, he concluded with some thoughts on the company’s future goals:
“We want to consolidate our progress in the 30m to 60m professional and defence vessel size categories.
Meanwhile, we’ll continue increasing our manufacturing capabilities and capacity, through increasing the height of our main hangers and adding more powerful rolling cranes.
“Our 60 year history of success in such a challenging market is proof that we can overcome any challenges through effort, hard work and passion.”
seven seas, five oceans, one voice
columbia shipmanagement baja ferries breb norstar ship management e-nav offshore naftomar shipping crystal pool
Columbia Shipmanagement is a worldclass maritime service provider offering a global portfolio of management options. Phil Nicholls reports.
Cyprus-based Columbia Shipmana-gement (CSM) continues its programme of steady expansion into 2022. Established by Heinrich Schoeller in 1978, CSM’s portfolio of ship and management services grew rapidly. The company reached 50 ships under management in 1981, 100 in 1986 and currently has over 400 vessels under management, alongside more than 1,000 vessels on procurement contracts and 290 new building supervisions.
CSM has developed from its Limassol headquarters in Cyprus to running 13 management offices globally, overseeing 15 crewing agencies and over 15,000 employees worldwide. The extensive range of personnel and services allows CSM to offer a one-stopshop solution for ship management. CSM provides flexible packages of modular management services, fully customisable and tailor-made for each client. The company’s turnkey solutions guarantee cost-optimised operations and deliver the benefits obtained from economies of scale.
The highly experienced CSM personnel, both ashore and offshore, ensure 24/7 communication and efficient operation of the fleet in
GLINAR™ is honoured to have a long-standing relationship with Columbia Ship Management. GLINAR™ supplied CSM with various spare parts, main diesel engines, compressors, turbochargers, etc. GLINAR™ is grateful to CSM for their confidence in our services and we hope our relationship only grows stronger in the future.
GLINAR™ Global Spare Parts Network is a union of spare part suppliers, established as a joint venture in 2006. GLINAR™ supplies genuine and OEM high quality spare parts worldwide, providing fast deliveries and competitive prices directly from manufacturers. All deliveries undergo strict QC before shipment and we provide warranties for delivered goods.
Glinar Turbo & Diesel is represented all over the world, servicing all manufacturers, both for spare parts and services. Glinar Turbo provides 24/7 services for overhauling and turbocharger repairs.
GLINAR™ GSPN is managed by ISO 9001:2009 and is proud to be your choice! We look forward to meeting you during SMM 2022 (Hall A4 stand A4.306)!
optimum conditions. The client’s business performance is CSM’s top priority. Ships under the company’s management are maintained to the highest standards, with condition and performance monitored through frequent inspections, sailing visits onboard as well as the implementation of enhanced reporting and quality management systems.
The CSM motto is ‘I care’, recognising the imperative of growing a strong company culture that its crews and clients can readily and willingly identify with and adopt. The corporate motto stands for: Commitment, Appreciation, Responsibility and Evidence.
These core values are the cornerstone of CSM’s company culture that each employee needs to understand, acknowledge and live by. A company which cares is a better company, better for its employees, better for its crews and better for its clients.
An example of CSM caring for staff was the recent partnership with Mental Health Support Solutions to deploy a team of 320 Ukrainian psychologists to offer counselling to refugees in the CSM ‘sanctuaries’ in Poland and Romania. The company raised $1.3 million and runs a Romanian hotel and two large Polish hostels as safe havens for families of seafarers as well as providing money for essentials and helping refugees navigate the asylum system.
Ship management does not stand idle. In March of this year, CSM Greece moved to new offices in Voula, a suburb of Athens close to the port of Piraeus. Lead by General Manager Gregory Spourdalakis, the new location will allow staff to promptly service CSM managed vessels in the area, as well as any clients and partners requiring support. The new Greek premises offer cost-effective and fully optimised support services expertly tailored to each client’s needs, delivering premium modular maritime solutions.
Mark O’Neil, CSM President and CEO welcomed the opening of a new office close to Piraeus, one of the most important ship owning locations. CSM anticipates working with existing and new clients to support their businesses and fleets.
2022 has also seen CSM sign a joint venture with Monaco-based Sea World Management (SWM) to expand CSM Group’s operations
in the French, Italian and Monégasque markets. The resulting company is Columbia Seaworld Management, or CSM Monaco, blending SWM’s management experience with CSM’s integrated maritime services. CSM Monaco is posed to care for tankers, bulkers, containers, cruise vessels, super yachts, private jets and the asset management sector.
The CSM Group already has extensive experience in the leisure sector through the Columbia Blue arm, which united the super yacht and cruise sectors.
Columbia Blue offers a diverse portfolio of services within the leisure, lifestyle, cruise, super yacht, aviation and hospitality sectors. The company provides asset management, concierge, events and aircraft management services, providing clients with a 360° turnkey service solution of the highest quality.
Another strand of CSM Group’s extensive portfolio is procurement services. To expand this business, CSM signed an agreement ear lier this year with International Maritime Industries (IMI), the Middle East’s largest shipyard. Mr O’ Neil signed a memorandum of understanding with Dr Abdullah Al Ahmari, IMI CEO and Ahmed Al Saadi, IMI Chairman and Saudi Aramco Senior Vice President – Technical Services.
IMI is the largest integrated, full-service maritime yard in the MENA region, located at the King Salman International Complex for Maritime Industries and Services in Ras Al-Khair on the east coast of Saud Arabia. The shipyard offers competitive, safe, high quality and on-time solutions to ship and rig customers from around the globe.
Under the terms of the memorandum of understanding, CSM is confirmed as an official consultant for the shipyard in the fields of ‘sensorisation technology’ for vessel performance optimisation, engineering solutions, vessel design, and newbuild planning and supervision. CSM will actively promote IMI’s set-up and technical capabilities to the group’s existing clients.
Mr O’Neil emphasised that the agreement with IMI reaffirmed CSM’s commitment to the Middle East and Saudi Arabian markets.
The IMI shipyard is scheduled to become operational in 2022, with a focus on newbuilds and maintenance work for VLCCs, chemical tankers, bulkers and offshore support vessels.
Maintaining the security of CSM vessels is another way the group shows that it cares. Pursuant to the safety of vessels, CSM signed an anti-piracy security protocol with the MICA Centre operated by the French navy. The Voluntary Naval Cooperation Protocol bolsters the security of vessels sailing through the South China Sea, the Strait of Singapore Malacca, the Persian Gulf and the Gulf of Aden. The agreement also relates to ships calling on West African ports, along with those passing through the Gulf of Guinea or the Mediterranean.
The French Maritime Information Cooperation and Awareness Centre is dedicated to global maritime security, based in Brest. MICA operates 24/7 to identify and analyse situations affecting maritime navigation throughout the world. The centre also provides ships and their owners with tailor-made security information about maritime risk, alerts in case of an incident, security assessments and specific briefings. It also provides direct support to the crews and shipowners in the event of a piracy alert by maintaining a direct link with the assaulted vessel, warning of ships in the vicinity and assisting to coordinate an intervention.
Demetris Chrysostomou, Managing Director of CSM for the Asia region and Group Business Development Director said signing the protocol enhanced the long-term safety of CSM ships and crews.
The sustainability credentials of CSM were recognised in the Reuters’ ‘Top 100 Innovators of Global Energy Transition’ list. The report recognised CSM’s joint efforts with TotalEnergies to develop a lube oil monitoring, optimisation and supply platform using the POCR system, while also investigating alternative propulsion and marine fuel systems.
Reuters noted that “the wholesale move to carbon-neutral energy systems, in less than three decades, is a task that demands almost undreamt-of levels of industrial creativity.”
As CSM continues its upward trajectory, it is clearly also a company that cares about the environment. n
Guarding the entrance to Mexico’s great blue Sea of Cortez are the rocky Baja California Peninsula in the west, and the Mexican mainland on the eastern side. Baja Ferries forms the crucial sea link that connects the Peninsula city of La Paz, to the mainland. But that’s only one part of the company’s relationship with the region. CEO Ariel Pozo joined Richard Hagan to discuss the company’s rich connections with La Paz and the crucial work his company is doing to uplift, empower and promote the community.
Baja Ferries is nestled in the port city of La Paz on the Baja California Peninsula in Mexico. Its large, modern ferries transport over two million linear metres and 300,000 passengers (plus their cars and cargo) per year, on the breathtaking passage across the Sea of Cortez.
As the main ferry service provider in the region, Baja Ferries plays a critical role in the lives of the surrounding communities who rely on its service to complete so many aspects of their daily lives, including staying connected to family, friends, social services, and work and business opportunities.
In recognition of the importance of its position in the local economy, the ferry operator has been laser-focused on constant reinvestment, diversification and growth to ensure that it is always comprehensively meeting the needs of not only its
passengers but also the local community. And as a ferry company, meeting its customers’ needs starts with its vessels.
Baja Ferries began life in 2003 running a vessel named California Star. With a capacity of 950 passengers and 2,000 linear metres of storage available, it was – at the time – considered too big by many observers. However, the vessel enjoyed a successful career dutifully running the Topolobampo to La Paz route. And in the end, its replacement was to be even bigger. Eventually, it was time to upgrade the capacity on that route and California Star was replaced by the even bigger Mexico Star. At a cost of €27 million, it is also now the largest ferry in Latin America, boasting 2,715 linear metres of space and capacity for more than 900 passengers.
Meanwhile, the company added more routes including Mazatlán to La Paz and Guaymas to La Paz, as well as a feeder operation between Manzanillo, Mazatlán and Guaymas.
Today, the company owns an impressive fleet of four vessels – Mexico Star, Baja Star, Oaxaca Star and Chiapas Star. In 2021, the fleet sailed over 180,000 miles combined. Or put another way, equivalent to seven laps around the equator.
The ships operate across three terminals, namely Pichilinque, Mazatlán and Topolobampo, and are served by six sales offices. All of this is coordinated by its headquarters in La Paz. Altogether, the company employs over 450 staff.
Beyond its ferry operation, Baja Ferries offers its customers a complete logistics solution, including domestic (cabotage feeding), multimodal logistics, intermodal and Inter-Pacific corridor, contract logistics, project cargoes, national and international freight forwarding, bulk and breakbulk shipping operations, and shipping agency services.
Of these, its most in-demand service is the cargo and passenger ferry service provided by its Ro-Pax ferries through the
Sea of Cortez, running the roughly nine hour, 500km trip between the Peninsula and the mainland.
In October 2021, its intermodal services were recognised when Baja Ferries won the AMTI 2021 Silver Container award. This award recognises companies that strengthen, develop and evolve intermodal services.
“This award is proof of our constant evolution to offer better services, and it’s a reminder that we must remain at the forefront of the sector to continue being a fundamental part of the economic and social development of the country,” emphasised CEO Ariel Pozo.
Contract logistics services offered by the company are especially comprehensive: they include the use of Baja Ferries’ transfer facility, cross-dock services, refrigerated cargo, storage and distribution and, most recently, first and last-mile transport services.
The crucial last mile
With so much cargo crossing the sea every day, the company soon identified an opportunity to diversify into the logistics business. The majority of the goods required
on the Peninsula must be carried across the Sea of Cortez, a task comfortably managed by the ships. But having arrived at La Paz, the next challenge faced by local businesses was how to get those goods from the port to their final destination.
In logistics, this is known as the ‘last mile’ and it is a perennial source of headaches, heartache and also evolution, for operators the world over. It was time for Baja Ferries to step in and solve the problem.
“We developed a logistics solution to solve the last mile challenge for our customers,” said Mr Pozo. “We developed relationships with all of the partners in the Peninsula, coordinating with all of the truck drivers. Together with our ships , we’re able to take the goods from the warehouse on the mainland, across the sea and to the final point of sale in the Peninsula. It’s a door-to-door solution.”
This move comes as a direct response to its customers’ needs: “Our customers tell us their core business is sales, not shipping, and they’re increasingly seeking last-mile solutions. We’re happy to pro -
vide it because by consolidating first and last-mile services, we’re far ahead of the competition,” Mr Pozo remarked.
To support its delivery services, Baja Ferries is building warehousing on the Peninsula for some of its regular logistics customers’ goods.
“We’re working together with these clients to offer not only last-mile logistics but also warehousing,” confirmed Mr Pozo, who said the company’s combined activities make it a significant player in the Peninsula.
“95% of all consumer goods and raw materials enter the Baja Peninsula by sea, of which we hold 72% of the market share. Our combined operations contribute 1.4% of the state’s GDP, which makes us key players in the economic and social development of Baja California Sur.
“ Our local warehousing and last-mile operations are a true point of difference versus our competitors,” he added.
Clearly, Baja Ferries is a company that is deeply invested in the needs of the communities within which it operates. And so it should be, as Mr Pozo pointed out.
“We have to keep thinking ahead, both in terms of changing vessels and adding infrastructure. The moment we stop investing in new, bigger vessels, we are losing the company’s edge in the Peninsula. We’re thinking of the area’s needs for the next five to ten years.”
While the company grows, so does its passion for reinvestment in and stimulation of the communities surrounding it.
With the onset of Covid, the people in La Paz and its surrounds including Sinaloa suffered greatly from the lack of tourism and general difficulties associated with the pandemic. Here, as Mr Pozo detailed, the company developed a range of measures to try and support the communities around it.
“Covid was a huge disaster here, many companies closed. As part of our efforts to protect smaller companies in the area, the moment Covid was declared, we acted. One of our first steps was to pay our local service providers in advance of service delivery. We wanted them to be able to focus on delivering their services and not on economic difficulties. After all, we had
the capacity to support them and we wanted them to feel like we were a partner rather than just a customer.”
Additionally, an internal memo was circulated amongst Baja Ferries staff containing a list of the small local businesses owned by family members of staff, with information about what each business offers. This initiative successfully created awareness amongst the staff about how they could best spend their money to support each other’s families.
“Small decisions like those add up and have a huge impact,” said Mr Pozo. “We are very proud of all of our efforts to support small companies.”
In closing, Mr Pozo drew attention to the company’s values, ethics and perspectives on business.
“Baja Ferries is a company that distinguishes itself for doing things the right way, for always having the best processes, for being an ally for the logistics sector, with society, and with the authorities, and for being the best option in maritime transportation.”
As a highly diversified, fully integrated shipping company, Cuxhaven-based BREB is at the centre of helping to connect countries and continents on many different levels. Managing Director Arne Ehlers spoke to Andy Probert on how BREB has evolved into a leading venture that offers some of the best logistics solutions globally.
Founded in 1951 in Bremen as Bremer Reederei Eilemann & Bischoff, the main activity at the since restructured BREB GmbH & Co KG was initially to operate a liner service from Germany to Scandinavia, and to run the only joint liner service into the Soviet Union together with a Russian and Lithuanian shipping company.
Today, BREB has expanded and is now a unique company straddling the maritime sector, not only as a shipping company with its own vessels but as a liner service provider, charterer, forwarder, port agency and even a terminal operator.
Headquartered in Cuxhaven, at the heart of the German Offshore Industry Centre, BREB also has offices in Bremen and Mukran in Germany, in addition to international sites in Lisbon and Zeebrugge.
“No two days are ever the same. It’s never boring here,” commented Managing Director Arne Ehlers, who oversees all these different strands of the business.
BREB employs a fleet of modern geared multipurpose vessels from 4,000-9,000 DWT capacity in all European waters and North and West Africa, transporting breakbulk, bulk, special projects and containers. Its core business consists of building up shipping services by combining deliveries of semi-/finished products – for example, paper reels, wood pulp and sawn timber –with the supply of commodities for production, including sawlogs, pulpwood, woodchips and pellets, and China clay. For this purpose, BREB utilises different
contracts of affreightment for one or more clients and adds tramp shipping for maximum flexibility.
With a long history of carrying forest products of all kinds, today’s main commodity in both conventional liner services is sawn timber. Steel products, other breakbulk and general cargoes are shipped southbound.
Northbound, various kinds of dry bulk cargoes – sea salt, silica sand, biomass, fertiliser – are the predominant commodities. All different project cargoes are shipped as sole or part cargo to gain the best results for clients.
Mr Ehlers commented: “Our chartering department is experienced with many kinds of dry cargo, while BREB forwarding has developed new ways of hinterland logistics by rail, truck or barge.”
The original trading of forest products from Scandinavia to the continent and UK ended with the 2008 closure of a mill operated by one of the company’s main clients, leaving a fleet of modern-geared forest product carriers unemployed.
A year later, BREB began sending its first shipments of sawn timber to North Africa for Austrian Mayr Melnhof Timber Trading. And by 2011, more ships sailed this trade than they ever did in Scandinavia.
Today at the Slovenian Port of Koper, the main loading port of sawn timber in the Adriatic, BREB is listed as the number one liner service, carrying sawn timber to the Maghreb states of Algeria, Libya, Mauritania, Morocco and Tunisia. “This is the backbone of our liner service,” commented Mr Ehlers.
BREB’s Adriatic parcel service includes all major Adriatic ports and Koper as the liner hub. Up to six vessels are employed in this line offering the highest number of regular sailings of conventional tonnage to and from the Adriatic.
Operating since 2019, in cooperation with Scaldic Med Lines of Boeckmans, Belgium, the BREB continental line runs ten vessels ranging from 2,000-8,000 DWCC, both geared and gearless. This service calls at Scandinavian, German and ARAG-ports, UK and French ports en route, and the Iberian Peninsula.
In the Baltic Sea, BREB operates a container line between Sassnitz-Mukran, Germany and Baltiysk, Russia.
Meanwhile in the UK, Harwich based Brointermed Lines relies on BREB, together with Hugo Trumpy in Genoa to operate separate services from the continent to the Mediterranean. The companies agreed to combine forces with a vessel-sharing
agreement from July 2020 and now offer a monthly dedicated multipurpose service linking Bremen, Harwich, Antwerp and La Spezia to the main Algerian and Libyan ports.
The last two three years have seen an increasing number of vessels sailing under the BREB flag along the coast of West Africa.
“The whole African continent shows a significant economical growth with a remarkable number of infrastructure projects,” stated Mr Ehlers. “In line with this development, BREB ships a lot of material for such projects from bulk cargos like clinker to project cargos including huge concrete pipes.”
In 2017, Blue Water Shipping, Denmark, and BREB opened the Blue Water BREB Terminal in Cuxhaven. Within the first year of operation, they discharged 2,000 wind energy components. Today, this business operates on up to 200,000sqm of land, handling more than 3,000 onshore and offshore wind energy components per year.
“By the number of components, we are Germany’s largest wind terminal,” confirmed Mr Ehlers. “Cuxhaven is now
becoming even more attractive for international project shipping.”
Hence, BREB’s decision to invest €5 million in a new LHM 600 Liebherr mobile port crane lifting more than 200 tonnes.
“The investment makes sense from an economic point of view,” commented Mr Ehlers. “Both the numbers of wind energy components annually and the use of everlarger ship tonnage by customers, together with the positive development in the onand offshore energy sectors at Cuxhaven, were crucial in this decision.”
In 2020, BREB took another significant step forward when, with several partners, it launched trial shipments of Silkroad containers from Baltiysk to Mukran. Since July 2019, BREB GmbH has been a member Intergovernmental Organisation for International Carriage by Rail (OTIF) and was officially approved for the carriage of containers under a continuous rail waybill (CIM) from China to Europe.
BREB, with TE Bahnoperator, Mukran Port Terminals and EGP Eisenbahngesellschaft , founded the Baltic Sea Bridge, moving one block train every day from Monday to Sunday from Xi’an to Baltiysk.
From here, three BREB vessels – BREB MUKRAN, BREB BALTIYSK and from July 2021, BREB XIAN – take these containers
on board. Not only is Mukran linked to this service, but also Sweden via Karlshamn and Immingham. The first call of BREB BALTIYSK arrived in early July 2021.
Baltic Sea Bridge GmbH is also taking care of a full service from Wuhan in China to the final destination in Germany and Sweden. From container booking, via rail service through Kazakhstan and Russia, sea transportation between Baltiysk and Mukran until delivery to the final destination, the whole service is offered out of one hand.
Up to 14 block trains are handled every week in this 24/7 service with up to four sailings per week in each direction between Baltiysk and Mukran. The aim is to ship a minimum of 40,000 TEUs.
BREB also offers port agency services in all German ports and the Antwerp-Zeebrugge range to shipping lines, charterers and owners, and offshore projects.
“Being a shipowner, BREB has a good understanding of what a vessel and owner need. Running our own liner services, we also understand the demands of a shipping line and charterer,” added Mr Ehlers.
At Cuxhaven, BREB acts as liner agents for UECC and Flota Suardiaz. From 2011 to 2014, BREB acted as general agents for E.ON in Cuxhaven on installations at the Amrumbank West windfarm. Furthermore, freight forwarding firm Deugro’s rapid pipeline service for Siemens Gamesa is served by BREB Belgium in Oostende and by BREB in Cuxhaven and Mukran-Sassnitz Appointed by charterers and owners, BREB also provides services to conventional vessels for loading and discharging operations of project cargoes, generals, breakbulk and bulk.
Mr Ehlers acknowledged that while all activities had continued steadily during the pandemic, there was a 15% shrinkage in cargo volume for the first half of 2020 but
had rebounded by year end, with a 10-20% increase compared to 2019’s annual volume.
“We like to think that what defines and what makes us very different from the competition is that we operate a mediumsized company with a global view,” he said.
“We are internationally cross-linked, offer fast response times and being horizontally diversified, we gain a lot of information from different branches of the industry. We disseminate this to our departments and colleagues, and that enables us to combine any chain link in shipping to the benefit of the customer.”
Since 2019, BREB has been working on a new vessel design and hopes to move forward with a good number of ships in the 8,000 DWT class. Mr Ehlers explained that the vessel design seeks to combine all the different types of cargo the company moves without making it too overcomplicated.
“We are well-experienced in the 8,000tonne class, and the new vessel we envisage will be able to carry the sawn timber and also be contained fitted, with equipment with a twin-deck and optimised for deck cargo, such as for wind farm cargo.”
Mr Ehlers said the DNA of every activity performed under the BREB hub is to treat “suppliers and clients like you want to be treated. Respect, understanding and support are number one, and ensure you pay your bills properly. Never forget shipping is a person’s business. It’s more than just business. It’s like a big family, where you celebrate together, and sometimes you may have to fight.”
He added: “After 12 years of shipping crisis, the number of vessels, owners and operators has remarkably diminished. Since the beginning of 2021, we have experienced an ‘owners market’ and intensifying month by month.
“Bearing in mind the great number of postponed maintenance due to lack of liq -
uidity, a massive installation of ballast water treatment systems, the number of ships in service will be further reduced by necessary shipyard stays in the next two years.”
Many of the traditional financing institutes i n Europe have decreased or completely stopped their engagement in shipping. At the same time, free space at most shipyards are rare to find, especially for the multipurpose tonnage.
“This is the major challenge which needs to be overcome as European ship owners need to modernise their fleets,” remarked Mr Ehlers. “Having said this, we should keep in mind that shipping is firmly determined to change to climate-neutral propulsion.
“Here, ship owners are not in the lead but depend on the energy majors to develop and define tomorrow’s fuel. Everybody agrees LNG is only an intermediate solution, and we need a liquid fuel like green methanol or ammoniac produced via green hydrogen. But we need a final decision so manufacturers of main engines know what they have to develop, and we can go ahead.”
He added that new fuel technology, together with unique ship designs, will have the greatest impact on shipping in the next few years. “However, it seems the worldwide container-business-model has passed its peak. Only mega-carriers and mega-container hubs can keep the system running at reasonable prices.
“It is these huge dimensions and, consequently, inflexibility that makes the worldwide container trade so vulnerable. Just look at Ever Given getting stuck in the Suez Channel or the lockdown of Yantian, the fourth-biggest container port.”
Yet he views BREB’s own journey in the short-to-medium term with positivity, concluding: “We see a lot of signs that suggest a stable and robust market for many years to come.”
Singapore-based Norstar Ship Management Pte Ltd has delivered bespoke ship management solutions since 2009. The company’s mission statement is to deliver safe, efficient, and reliable transportation and logistics services that enable its partners to perform their operations at the highest standards. With an emphasis on seafarer welfare, the company’s vision is to operate in a better and more sustainable world through innovative and collaborative partnerships. Article by Jordan Yallop.
Norstar Ship Management Pte Ltd was founded in 2009 as the ship management arm of the Norstar Group. The larger Norstar Group was established in 1998 by Chris Bonehill, originally as a ship brokerage company based in London specialising in sales, purchasing, and newbuilds.
In 2005, brothers Chris and Tom Bonehill joined forces to expand their global operations with Chris being based in the west and Tom in the east. Since then, Norstar has expanded its operations in Singapore, Westport, Yangon, Tokyo, and soon the Middle East.
Since 2020, Norstar Ship Management has been helmed by Managing Director Dr Lars Gruenitz, who started his career in the construction of naval submarines. Dr Gruenitz moved on to various senior leadership positions, across a variety of different companies within the marine sector before taking up his role at the company.
As investors in ships themselves, the people behind Norstar have a deep understanding of their clients’ needs around the complex nature of ship management. Norstar Ship Management’s experts help clients reduce costs, improve efficiency, and either scale up or down.
The owners of Norstar have invested in ships themselves in the early 2000s and they were disappointed with the poor services that they received from some of the bigger third-party ship managers. The brothers were faced with instances where there was a lack of quality in the service or a lack of transparency in the practices. Dr Gruenitz said: “So they decided it was time to be in charge of their own quality.”
The owner’s approach to ship management means Norstar treats every vessel under their care as if they are the owners. Dr Gruenitz said: “We own tankers ourselves, so we understand and empathise with the owners. Whether those are our ships or our clients’ ships, we look after them well and maximise the owners’ earnings.”
When it comes to performance, Dr Gruenitz said: “Integrity is one of our values, which means if we commit to a budget, then we’re able to deliver."
Norstar Ship Management currently has 24 vessels under its management. Self-described as a boutique manager, the company has a smaller fleet so that extra care and attention can be paid to each and every need that the customer may have.
Dr Gruenitz explained: “Our fleet numbers dropped a little bit during Covid because some of the shipping companies had to sell off their ships. The ships that we have added last year are mainly bulk carriers as we believe bulk carriers need the same highquality standard as tankers moving forward.
“Traditionally, Norstar Ship Management is seen as a specialist in product and chemical tankers; that’s our bread and butter. I want to diversify that, so we have taken in bulk carriers and gas carriers, predominantly for crew management in the last few months.”
When talking about the difference between a boutique-style manager and a larger concern, Dr Gruenitz said: “If you work with a big manager, then if there is any problem on the ship you might be able to talk with the fleet manager and he may or may not have an answer for you. With us, our customers have really close interaction with both the commercial team and the operations team. To continue the personalised management style, we typically have a conference call once a month, where I’m also actively involved.”
Since his tenure as Norstar Ship Management Managing Director began in 2020, Dr Gruenitz has made significant developments, starting with restructuring. Digitalisation has been a main focus area of the developments implemented, whereby the company uses data to get real time visibility on its operations. This enables the company to make corrective actions with greater speed and effectivity.
Dr Gruenitz said: “When you talk about ESG there’s also a people component. What we have focused on is leadership development for the full team, running extensive leadership training
for the organisation. Since the first year and in the second year, we have really concentrated on the mental and physical wellbeing of the crew.”
At Norstar Ship Management, the wellbeing of its people is a top priority; the company has the belief that ensuring a healthier and happier workforce is essential for productivity and safe operations.
Dr Gruenitz said: “We all heard and read about seafarers being stuck onboard ships for months and months during the pandemic. It was then we thought it’s time to invest in mental resilience, and also medical support. So, at Norstar, we did two things.
“First, we worked with the biggest company when it comes to remote medical services, International SOS. We have engaged Med Sea, which is basically the maritime service part of International SOS, which means any medical issue onboard our ships will be taken care of remotely, quickly and professionally. This really helped during Covid because our sailors had not been allowed to go to a doctor.
“Secondly, we have also begun working with a company called WellAtSea, a Danish company dedicated to physical and mental wellbeing. Combined, the services added by these two companies has positively impacted in keeping our crew happy and healthy.”
With Dr Gruenitz in the driver’s seat, Norstar is embarking on a new chapter towards green shipping.
“We are also getting ready to be part of making a big green change in shipping,” he said. “We’re working closely with engine manufacturers to see what new ships must look like, because I believe it will be bigger than changing from steam engines to diesel engines. There’s lots of new technology coming up, which is super interesting.”
We are also getting ready to be part of making a big green change in shipping
Norstar’s crew pool is predominantly made up of Myanmar crew. The company has a dedicated crewing office in Yangon, Myanmar, with training facilities. Over the years, Norstar has successfully cultivated a strong team of seafarers managed by competent shore support staff made up of ex-captains. This allows them to provide a pool of well-trained and competent crew suited for every vessel’s needs.
Dr Gruenitz said: “There are a lot of misconceptions about Myanmar as a country. Many people think ‘Oh, there are strict protocols in place,’ or ‘Cannot do much.’ But the truth is even during Covid-19, and given its political situation, the seafarers can still move freely around the world.”
The recent steep increase in Chinese crew costs makes Myanmar crew even more desirable now. Dr Gruenitz added: “The good thing is Myanmar is a seafaring nation. When it comes to quality factor, the performance of Myanmar’s crew is top-notch.”
Norstar Ship Management has made investments recently in areas such as digitalisation and ESG (Environmental, Social, and Governance).
“Digitalisation was one of the investments that we will continue in, so we’ve invested in data analytics, and we invested heavily in cybersecurity. We also updated our systems for new emission monitoring systems,” said Dr Gruenitz.
The other major investment the company has completed is a new office location. At the end of last year, the company moved to a new office in Singapore that has been designed with the wellbeing of the workforce in mind.
Dr Gruenitz explained: “We designed this office to make our staff comfortable after Covid. For instance, we invested into ergonomic tables; they’re all height adjustable. We have a much more collaborative workspace, and a much greener office. I think it really improves happiness and productivity.”
Talking about the future of the marine industry with regards to emissions, Dr Gruenitz expressed his view that ammonia will win the race for new cleaner burning fuel. Ahead of this future, the company is actively getting ready for the change and is preparing to provide training in this new area. Working with international organisations, Dr Gruenitz is already planning for new training programmes centred around the use of ammonia fuel.
When it comes to the future of Norstar Ship Management as a company, Dr Gruenitz explained it best :
“My vision is not to reach the 500-ship mark – that would completely change the soul of what we do. The management style must stay the same whether it’s our own ships or our customers’ ships. We look after them really well and we always maximise the benefits of our customer,” he concluded. n
In only three years, offshore support vessel and owner E-NAV Offshore has risen to become the largest OSV owner in Mexico and one of the top 15 largest in the world. Having been established in the midst of Covid chaos and restrictions, the company has endured the worst and come out strong. E-NAV’s Partner, Vice President and CCO Diego Alonso Aguilar spoke to Richard Hagan about the company’s rapid rise to the top.
From its headquarters in Mexico City, E-NAV Offshore operates what it says is the most modern fleet of offshore vessels in the world.
Its fleet consists of 33 offshore support vessels of diverse capabilities, including construction, maintenance and subsea services. This diversity enables the company to participate in a wide range of segments in the offshore industry.
The modernity of its fleet is a point of pride for the company and a crucial selling point, said Diego Alonso Aguilar, Partner, VP and CCO.
“The worldwide OSV fleet is ageing, whilst the average age of our fleet is seven years old and some are really high-tech, too, meaning we are very modern in comparison. More than 80% of our vessels are diesel-electric, which produces reduced emissions and fuel consumption. In fact, we’re one of the few fleet owners with such a high average. Having such a young, modern fleet puts the company at an advantage.”
Following a 15 year history of working in the industry, Mr Aguilar’s business instincts for the offshore market proved vital in the creation of E-NAV Offshore and the subsequent acquisition of its new fleet.
“The market had been down since 2015 and based on that and my experience, I knew that there would soon be acquisition opportunities at great prices,” he explained. “That was the reason we entered the market during such a tough period, in the midst of
Covid and in a downturn in the industry. The timing has worked in our favour.”
Mr Aguilar conceptualised and founded E-NAV Offshore in partnership with a private equity group and two other business partners in 2019. This well-resourced partnership moved quickly and acquired its first vessels in 2019 and 2020.
“We were born in the middle of a pandemic, which was a very tough time to start a new business, but we’ve been very successful so far,” he commented.
“Then at the end of February 2022, we bought a large fleet of vessels that will operate in several countries.”
The fleet was acquired from Pacific Radiance amidst a restructuring process.
“We now have anchor handlers and large support vessels that weren’t
originally on our acquisition map,” Mr Aguilar revealed. “It made it a very exciting move for us. It has simultaneously made us the largest ship owner in Mexico and one of the top 15 mobile players in the world.”
E-NAV Offshore’s operations currently centre around three main markets: the Middle East, South-East Asia, and the Americas (including Mexico and the Caribbean). But according to Mr Aguilar, the company plans to invert its current market commitments.
“Today our biggest market is South-East Asia, followed by the Middle East and then the Americas. In the next 12 to 18 months we plan to reconfigure those. The Americas will become our strongest, the Middle East will take the middle spot, and South-East Asia the third.
“In our assessment, the market in the Americas is much better for us, whereas South-East Asia is a tough, highly competitive market,” he continued. “The local firms are very strong there. For those reasons, we’re planning to deploy our fleet into markets better suited for our operations.”
A particular highlight of the company’s global operations is its pioneering deployment of one of its vessels into Guyana. It’s a relatively untapped market that represents a real milestone for E-NAV Offshore, Mr Aguilar revealed.
“We were one of the first offshore vessel companies to work in Guyana, which is a market with huge potential. One of our vessels is still working there. That’s an important highlight for the company because there are only three or four other operators working there.”
Colombia is expected to be next: “We plan to start working in Colombia shortly, which is a fast-growing market for offshore business, with big projects from the likes of Total and ExxonMobil,” Mr Aguilar confirmed. “They’ve found a lot of oil there.”
Meanwhile, E-NAV Offshore also expects to see some projects flowing from the surging US renewable energy market.
“There aren’t enough vessels in the US to handle the work required in the offshore renewable energy market,” Mr Aguilar commented. “We anticipate that there will be plenty of opportunities in 2023 for us, especially for offshore
accommodation. We will be bringing one or two of our accommodation vessels in to support the industry and to take advantage of opportunities there.”
In an industry facing widespread uncertainty, E-NAV Offshore’s strong ownership structure and healthy resources are set to deliver a future that looks bright, said Mr Aguilar, who also drew attention to the company’s advantageous reach across several geographic markets.
“One of the most important differentiators for us is our financial situation. We have a green balance sheet and don’t have debt issues like so many others in this industry. The diversity of the regions we operate in is also key to our success. Normally, OSV operators are very regional, which makes it difficult for them to capture opportunities further away.”
The company intends to maintain its momentum through the careful management of its fleet profile. Mr Aguilar explained this means cutting the fat off its
recently acquired fleet in order to focus on its core competencies.
“We plan to sell off non-strategic vessels so that our fleet isn’t as complex or diversified. Going forward, we’ll focus on three or four segments and, based on those needs, we’ll look at further asset acquisitions. Our fleet size will probably stay around 30 to 40 vessels.”
Like any other fleet owner, E-NAV Offshore is prioritising emissions-reduction measures. According to Mr Aguilar, several solutions are either already in use or under investigation. One solution the company is actively exploring is the installation of cutting-edge carbon capture systems.
“Sustainability and emissions reduction are very important to us,” he confirmed.
“We’re working on a couple of hybrid solutions and analysing various incoming technologies. We’re testing carbon capture equipment on a select few vessels. We’re testing it to see how it works, how much carbon it captures and how we can measure it.
“Carbon capture is the second step in our sustainability program,” he continued.
“The first was bringing diesel-electric vessels into our fleet. The target is to have 100% of our fleet being diesel-electric. We’re already at 80% so we’ve made good progress on that.”
Beyond those measures, E-NAV Offshore is in close, active communication
with the companies that are at the forefront of developing emissions-reduction technologies. It is actively investigating any breakthroughs and investigating the same for economic viability.
In closing, Mr Aguilar remarked on the positive state of the market.
“The market has been great in 2022 so far. Offshore activity has grown a lot, with many acquisitions. We’ve seen more acquisitions in the last two years than we’ve seen in the past seven, so the market is really moving. We’re obviously concerned about the geopolitical climate and rising crude oil prices, but we’re excited to see that today the market is finally in our favour after seven years of difficulties.” n
For half a century, the name of Naftomar Shipping & Trading Co has been a constant in the changing world of liquid petroleum gas (LPG) but is still synonymous with reliability and a can-do attitude. As LPG has gone global, so Naftomar has risen to the challenge to ensure safe transportation by committing to continuous investment in its people and vessels. Profile by Andy Probert.
Apioneer of the LPG sector of the 1970s, Naftomar Shipping & Trading has remained ever-present down the decades and is now one of the most influential players in its field.
50 years later, Naftomar refuses to age gracefully, as it continues to adapt to modern technologies, advancing investment in people, rising to customers’ needs and industry pressures, while, significantly, retaining its reputation for reliability.
Having managed to retain full capacity for its 19-strong fleet of tankers even through the pandemic, Naftomar is stronger and more united than ever and ready to press on, according to Fleet and Technical Director, George-Paul Perantzakis.
Established in Beirut, Lebanon, in 1972 as a trading house focused on the distribution of petroleum products in the Mediterranean region, Naftomar took advantage of the vast potential of the LPG market and opened a chartering and ship management office in Greece.
A representative office was also opened in Paris under Chemigaz’s name, aligning the family-owned company to establish
and develop partnerships with oil majors, brokers, and the LPG market.
In 1991, Naftomar transferred its entire business operations to Voula, Athens. By that time, the company had, for 15 years, been operating its own dedicated fleet of LPG tankers, starting with the 4,000 cbm Gaz Unity in 1977, that paved the way for expansion into dedicated LPG transportation.
Today, the company’s expertise in shipto-ship cargo transfer operations is unrivalled. Since the 1990s, more than 4,000 ship operations have been safely concluded,
with more than 10 million tonnes of product trans-shipped.
The scope of Naftomar’s business extended further afield to embrace the trading of petrochemical gases, including ethylene, propylene and crude C4. This move further strengthened Naftomar’s relations with a number of specialised industries.
During the 1990s, it took the lead in developing Very Large Gas Carriers (VLGC) activities in the Far East and has since been recognised as one of the largest
independent ship operators in the region. In addition to pioneering imports into Pakistan and Syria, the company was instrumental in encouraging LPG imports into China by operating floating storage facilities, accounting for a significant proportion of all LPG imports. Imports rose from zero to 7 million tonnes.
Fast forward to 2022: Naftomar now operates a 45,000 cbm state-of-the-art German-made storage installation on land in Lebanon, as well as a floating storage facility in the Mediterranean.
The company now has an 19-strong fleet, including ten tankers built from new in 2010-11 to support its global LPG trading activities. These include fully refrigerated, semi-pressurised/fully refrigerated and fully pressurised gas carriers ranging in capacity from 7,200 to 84,000 cbm.
Mr Perantzakis stated: “Our flexibility means that our fleet is independent of our trading obligations. They can be chartered by Naftomar Trading for their own activities and cargoes, but can also be chartered by others, such as oil majors.
“We are one of most well-known players i n the market for LPG and ammonia, and our expertise in that space is second to none. We are pioneers of practices that are now common place, but we also remain a key innovator in the business.”
Naftomar’s tankers primarily focus on trading in the Med, but also operate worldwide, calling in at locations such as the USA, Far East, and Northern Europe.
He said: “Our diversified fleet means we have different sized tankers that can cater to all the demands of clients. We are highly adaptable to all circumstances.”
Naftomar is also heavily involved with the London-based Society of Gas Tanker and Terminal Operators, which drives guidelines, compliance and advice in the market.
The company now employs 120 staff at its Athens headquarters and has a pool of 900 seafarers drawn from the Philippines, and West and Eastern Europe.
“From day one, we have been committed to investing in people,” Mr Perantzakis emphasised. “To be successful in shipping operations, it is important to have the right people in the right place.”
The company has a comprehensive cadetship programme that helps it to select individuals of proven quality. That strategy has proven immensely important during the pandemic to help staff provide a service to clients at the highest level.
“This strategy gives us the opportunity and possibility to have a suitably educated and motivated workforce to assist in meeting
cl ients’ requests, keeping them happy, and enabling the business to grow. The human element is essential to us,” Mr Perantzakis underlined.
“Our approach is to build recruits from the ground up with the right training and education, and in this way, we have the company mentality incorporated in their mindset from the beginning of their careers.
“We believe that by unlocking the potential of our employees, we are safeguarding the long-term interests of our clients. It is a policy that continues to pay handsome dividends. Our approach has produced a highly motivated workforce that co-operates together to meet clients’ needs while leading the way in the international LPG sector.”
The biggest challenge for the next few years, he confirmed, will be the environmental compliance and transition to cleaner fuels and new technologies, and the overall goal of carbon emission reduction.
“It is a difficult task, involving many different aspects, such as operational improvement, new equipment coming into the industry, new fuels, and many different other things. So the challenge will be how to manage all these tools to reduce emissions.”
Mr Perantzakis said that due to this g lobal “shakeup” to the world’s fleet, the company was actively engaged with sup -
pliers and shipyards to understand what is available and what vessels can be manufactured that can improve things.
“We are in the active process of searching for the optimum solution to any new vessels. This research is still in its infancy, and we continue to evaluate our options and possibilities to make a sound financial and operational decision on any new vessel that will comply with all future industry needs.”
Mr Perantzakis said the pandemic proved an opportunity to increase the speed of digitisation across the company and make everything more efficient. “We also focused on the workforce by providing a safe environment to work in and perform to their best.”
“We were also determined to enable crews work safely, and were changed in good time. We even deviated ships to have crew changed, so allowing them to get back home despite the restrictions. We never spared
any effort in keeping their safety and wellbeing top priorities.”
He emphasised: “These are uncertain times. We are responding to the challenges of the environmental aspects, the market being affected by the conflict in Ukraine, and trying to retain high-grade staff. All these are challenges facing Naftomar and the industry today.”
But the company continues to reap the benefits of strong engagement with clients through its expertise and experience, with him adding: “Being reliable, sharing the same values and being transparent has enabled us to maintain long-term relations.
“The commercial market is very volatile and it is hard to keep a steady course. We have to adapt on multiple levels, support our clients, and promote a positive stance without any negative cost impact.”
Mr Perantzakis concluded: “Naftomar will focus on all these aspects, while ensuring the service we have provided for the last 50 years continues consistently.”
The northern most point of the Ligurian Sea plays host to the Gulf of Genoa, upon which sits the coastal city of Genoa. Historically speaking, this city has been one of the most important ports on the Mediterranean Sea. Even by today’s standards, Genoa is still the busiest port in Italy and the Mediterranean, and this is precisely where ship management business Crystal Pool is headquartered.
The company began operations in 2009 when it took up the management of chemical tankers and bulkers owned by the Rimorchiatori Riuniti Group. Since the company’s creation, it has managed various vessels for different flag states, and due to its exemplary performance, has even retained this management after part of the fleet changed owners.
Crystal Pool takes on all responsibility for the safe and efficient operations of a client’s vessels that are placed under the company’s management; including duties imposed by the ISM code.
Crystal Pool is also part of Rimorchiatori Riuniti Group, a leading maritime transportation company founded in 1922, operating tugboats in the harbour of Genoa. Since its cre ation, the group has continued to expand the scope of its activities both domestically and internationally.
Filippo Gavarone, Director of Crystal Pool said: “This company was started by my father Alberto back in 2009, who has a long history in ship management. Amongst those first vessels, some of them were owned by our group and our family. Back then this was a small key management company created essentially to take care of our own ships, but the fleet increased with the introduction of containers and anchor handlers.”
The Italian city of Genoa is home to Crystal Pool, a ship management company that is both dedicated and highly qualified: the company prides itself on its ability to manage sophisticated vessels across the globe. Holding the highest standards and an ethos of continuous improvement, the company delivers a bespoke, professional service to its clients. With a vision of wanting his company to be recognised as an industry leader, Filippo Gavarone spoke to Inside Marine reporter Jordan Yallop.
Today, the company offers technical ship management services, crew management services, health, safety, environmental, and quality management services in addition to ship’s financial management services. Crystal Pool’s fleet under management is today comprised of bulk carriers, container ships and offshore vessels.
Crystal Pool has approximately 15 highly trained and motivated fulltime staff, while also managing on average 10 ships at any one time.
Mr Gavarone said: “We want to put ourselves in the shipowner’s shoes, to try and understand what an owner truly requires; we want to be seen as an owner’s management office rather than a contracted party. Whatever discount we get from suppliers is passed to owners, and in terms of management fees, we always try to keep it simple and transparent.
“With regards to this we like to be flexible and open with the client. We want to build the relationship with them rather than just providing a service.”
One of the core services the company provides is technical management, which Crystal Pool describes as the core service of the business. This is geared towards the efficient operation of a wide array of asset types. This service also includes maintenance and refit support, which will be carried out to the highest standard. The company also has experience with new build supervisions, which includes a number of associated responsibilities such as evaluation of shipyards, negotiations and construction supervision.
Another core tenet of Crystal Pool’s services is crew management, with the company’s agency in Genoa ensuring a pool of highly qualified crew. Further to this, the company prides itself on its ability to cope with the dynamic world of international laws and regulations, as
well as being prepared for evolving demands. The pool of competent crew and officers is also certified as required, possessing the necessary qualifications for the vessel and its trade. The company also arranges crew to join the office for limited periods of time, to spend time with office personnel and understand the dynamics of working from shore.
Further points of contact handled by Crystal Pool include rota tion plans for crew recruitment and related procedures. This ensures crew retention and crew training in accordance with international regulations.
A large part of Crystal Pool’s involvement is ensuring proper health, safety, environmental and quality management systems are in place. While the company describes its mission as “providing our customers with competent, safe, environmentally sound and costeffective services”, it’s safe to say that it is committed to continually developing its skills and systems to provide the best for customers. This includes (but is not limited to) the continued assessment of all onshore and sea staff, who are trained to industry standards to allow them to excel at health, safety, environmental and quality awareness.
To promote continued excellence, the company actively encourages feedback from both employees and customers to improve services.
Ship’s financial management services also come into Crystal Pool’s remit. To this end, the company is transparent in all operations and ensures close working ties with both the captain and owners’ accountants so that systems are always kept accurate. The company also ensures budget preparation, expenses monitoring, invoice payment and financial reports.
“There are many different situations happening on board on a daily basis, which require a good amount of knowledge and expertise,” commented Mr Gavarone. “You must make sure you have the
right policies and procedures in place to always make the right decision; to that end, we are highly qualified to do so. We really can run any type of vessel.”
In light of the challenges associated with these modern times, Crystal Pool has dedicated itself to meeting the evolving requirements that many clients present.
“We not only offer technical, but also commercial and some consultancy services,” noted Mr Gavarone. “We aim to be a one-stopshop, able to provide a combination of services. Potential clients need that kind of service and so this flexibility is something we have developed in the past year. Clients can change; they are not always the traditional kind of shipowner.”
Mr Gavarone highlighted the difficulty the industry has faced over the last few years as a result of the Covid-19 pandemic; navigating the differing restrictions and regulations of countries was a new challenge that needed to be overcome. Likewise, the inability to visit the ships and crews in person – as well as the resulting challenges with crew changes and quarantines – were previously unheard of logistical hurdles.
Mr Gavarone said: “The management aspect is usually better, because we have a good retention rate where we
know our crew, we know our people’s capabilities. We always try to have plans to ensure sure that we know the right person is on the right ship.”
When speaking about the future, he said Crystal Pool will continue to provide a premium bespoke service to its clients and he is actively looking to increase the company’s tonnage.
“We really try to adapt the business based on the requirement of the clients, and being shipowners ourselves is a fundamental part of this aspect,” Mr Gavarone concluded. n
seven seas, five oceans, one voice
epsco (cyprus) ltd bisonte permascand eltorque amco veba marine hydrus engineering mahnke newthex hydrasearch dellner bubenzer vdl aec maritime sekavin
Epsco (Cyprus) Ltd offers a broad range of safety and support services to the maritime industry worldwide. Andreas Ioannou, Chairman, highlighted the passion and dedication within the company to Phil Nicholls.
Epsco (Cyprus) Ltd was founded by Andreas Ioannou in 1995 with just a fax machine and a personal computer.
“Even 27 years later, I still get a buzz out of getting things done,” Mr Ioannou said. “We are in a 24/7/365 business and often get requests that seem impossible at very short notice in places very far away, so the challenge and the joy comes from ensuring that those requests are fulfilled quickly and efficiently. That’s what continues to excite and motivate me.”
From Epsco’s humble beginnings in 1995, the company has steadily expanded. In 2007, Epsco was one of the first companies to develop the concept of managed safety service fleet agreements. “We have since been copied by much larger companies,” Mr Ioannou explained, “But none are as proactive or customer oriented as we are.”
In 2008, Epsco opened a sales office in Hamburg, with a second expansion the following year in Singapore. The company remains headquartered in Limassol, Cyprus, with approximately 40 employees in total. Several of these employees reach 20 years’ service this year, something else giving Mr Ioannou a buzz.
“We have always prided ourselves on being a good place to work, with a happy atmosphere and treating our employees as family,” he said.
INSPECTION & TESTING OF
• FIREEXTINGUISHERS
• SCBASETS
• EEBD'S
• MEDICALOXYGENEQUIPMENT
• FIXEDSUPPRESSIONSYSTEMS
• FIXEDDETECTIONSYSTEMS
• GASDETECTORS
APPtOVEO SERVICE SUPPLIERS FOR
ANNUAL & 5 YEARLY TESTING OF
• LIFEBOATS
• RESCUEBOATS
• LAUNCHINGAPPLIANCES
• RELEASEGEAR
• GANGWAYS&ACCOMODATION LADDERS
• LOADTESTINGOFCRANES
INSPECTION & TESTING OF
• LIFEAAFTS
•IIMMERSIONSUITS
• CHEMICALSUITS
• LIFEJACKETS
• HYDROSTATICRELEASEUNITS
HYDROSTATIC TESTING OF
• FIREEXTINGUISHERS
• SCBACYLINDERS
• EEBDCYLINDERS
• MEDICAL.OXYGENCYLINDERS
• CO2CYLINDEERS
• NOVEC,FM200,WATERMIST CYLINDERS
• L.IFERAFTCYLINDERS
Epsco offers a broad range of services to the maritime industry, facilitating clients’ compliance with IMO Ship Safety Equipment and SOLAS demands, with direct online follow-up of onboard safety aspects. These services directly contribute to removing hazards from contemporary seafaring life. The Epsco Group is proud to service over 3,000 vessels annually at all major ports around the world, along with 800 vessels under full safety contract.
The company’s safety service network contains in excess of 350 class and manufacturer approved service stations, enabling the provision of services to virtually any port worldwide. Epsco also has a network of over 200 dive stations, all class-approved, covering the main global ports. These outlets provide a range of services from underwater surveys and propeller polishing to in-water repairs.
These diving services are only the tip of the extensive range Epsco offers to clients. Ballast water management systems, ship repairs, drydockings and the provision of spare parts are all within the Epsco portfolio. Demand from long-standing clients lead to Epsco entering into a joint venture partnership with US Security experts RA Security, forming EPSCO-RA, to provide cyber security solutions to the maritime community.
“Whilst we offer a full range of marine services – from spare parts, ship repair and diving services – we are known primarily for safety, and especially for our fleet safety servicing agree -
ments which give a fixed cost for annual / bi-annual services,” Mr Ioannou said. “Our customers can thus plan their annual safety budgets and have peace of mind that we are looking after their vessels’ safety systems.
“We provide full back-up and reminders of any services due using our own in-house certificate management system to which our customers have their own secure access, so there is full transparency on what we are doing for them.”
The reason for Epsco’s success is clear to Mr Ioannou: “The fact that we now have over 800 vessels under fleet agreement with a growing clientele from all over the world. We are constantly improving our products to offer the best service possible. Many of our customers come to us through word of mouth or as individuals move from company to company and contact us if they go to a company that is not currently a customer.”
Late in 2021, Epsco established a sales office and service station at Rotterdam. This is hoped to be the model for additional stations around the world.
“Competition is definitely increasing,” admitted Mr Ioannou, “but we are still growing our customer base. What sets us apart is that we have purposely remained a small, proactive and agile outfit. We are not playing a numbers game: our customers’ needs are far more important to us than simply ‘selling services’.”
As an established company, Epsco values its partners. Their role in the business is clear to Mr Ioannou: “Our suppliers and partners all over the world are vital to our success. Having been in the market now for well over 27 years, we have formed many close, long-term relationships.
“We much prefer long-term relationships based of course on their standard of service, with companies that we trust rather than looking at their pricing. We do not abandon those relationships just because other suppliers approach us offering lower pricing. We trust them and they trust us.”
A view to a sustainable future
Epsco is a member of CYMEPA (Cyprus Marine Environmental Protection Association) and supports all of the company’s locally based activities. CYMEPA is an autonomous, not-for-profit organisation funded solely by its members, with the aim of encouraging
and actively assisting efforts to prevent all forms of pollution of the sea.
Sustainability plays a strong role in the operation of Epsco. The company is working towards a paperless office and recycles as much paper and waste as possible.
“We insist that all our suppliers use environmentally friendly materials in their packaging,” Mr Ioannou said. “In part, these actions are due to the onset of the pandemic as we have limited our travelling, but have decided to continue that as much as possible by holding online meetings rather than getting on a plane except where absolutely necessary.”
According to Mr Ioannou, Epsco has weathered the current global issues: “We have not been too impacted by global supply issues. We had the occasional issue obtaining supplies for customers, but we have always been able to find alternative solutions.”
Steady expansion continues at Epsco, with the recent investment in Rotterdam proving an effective model for future growth of its customer base. Mr Ioannou concluded by summarising the ethos of Epsco as the company continues to find joy in the challenges of the business.
“For us, the safety systems on board a vessel are one of the most critical aspects of shipping. So, we feel that we are being entrusted with a huge responsibility by our customers that we take very, very seriously and we will always.” n
As drone technology continues to develop at a startling pace, a team of scientists, engineers and inventors from Poland have commercially developed the ground-breaking Bisonte NIX 300 – the lightest ROV for the hardest underwater jobs. It suddenly enables seaport infrastructure operators to conduct an enhanced inspection without the need to risk divers’ lives. Profile by Andy Probert.
INthe marine industry, de-risking usually reads as minimising as much as possible. But eliminating risk to human life? Now that’s a whole new ball game altogether.
But Polish entity Bisonte has developed a complete solution to put robotics where divers have always swum and, in some cases, where they are unable to reach.
A crack team of engineers, inventors, and scientists have seamlessly combined cutting-edge technologies and hands-on experience to deliver the Bisonte NIX 300, an underwater drone that could potentially revolutionise the subsea and offshore industries.
“Bisonte was founded to provide the world with revolutionary robotic solutions and enable mankind to reach higher, farther and deeper without risking human life,” commented Lukasz Sadowski, Bisonte’s Chief Technical Officer. “The NIX 300 delivers that.”
Eight years in the making, the NIX 300 is a complete game-changer. Labelled t he smallest drone with the biggest capabilities, it is an ROV that goes beyond ROV capabilities.
Significantly, a pilot project was undertaken in December 2019 at Gdansk Port, one of the Baltic Sea’s largest seaports, and helped define the best-suited ROV solution for ports.
With its unique variable hull geometry, t he ROV can stabilise itself and reach even
the most difficult areas with unique precision. The drone does not require complicated and expensive infrastructure and can be deployed in water with reduced equipment.
With its 102-megapixel camera, customisable sensors and additional optional t ools, the drone provides high-definition video and images of inspected installations and infrastructure. Additionally, the drone does not require any external power sources as its internal battery can run for up to eight hours. Mr Sadowski emphasised the NIX 300 has been designed to create the most cost-effective solution beyond inspection.
“The ROV enables seaport infrastructure operators to conduct an enhanced inspection without engaging divers in dangerous activities,” Mr Sadowski outlined. “It also helps drive efficiency in tasks such as repairs and inspections, and increases employee safety.
The genesis of the idea was first broached among students in 2013 at the AGH University of Science and Technology in Krakow. AGH UST is a public university in Krakow, Poland, that focuses on creating innovative technologies.
Mr Sadowski, who was among those students, said: “We were presented with a problem of an inspection and maintenance of water dams. At that time, there were no solutions that could replace divers, and we were also free of any technology constraints and bias.
“So we approached the problem in an unorthodox way. And that’s when the idea of a variable buoyancy ROV was borne. We realised we had a breakthrough solution on our hands, and a decision was made to commercialise it.”
The first pre-prototype was successfully tested in a laboratory environment, achieving a staggering payload-to-ownweight ratio over 1.2:1.
2017 proved a breakthrough year for Bisonte as its technology was recognised at The International Exhibition of Inventions in Geneva, the world’s most important annual event devoted to inventions presented by universities and private companies.
That same year, the technology received a gold medal during IWIS – the largest in Poland and one of the biggest in Europe international events related to innovation and inventiveness.
Bisonte gained its first variable-geometry-based patent from the US patent office and received a grant of $1 million from Poland’s National Centre for Research and Development to develop the most versatile solution in the ROV market worldwide.
In 2019, Bisonte emerged with the NIX 300 underwater drone prototype, which was successfully tested in a natural environment and confirmed the technology’s superiority over every other ROV on the market.
Following the Gdansk Port success, Bisonte was backed with a Є 250,000 investment from LT Capital to help accelerate R&D and provide additional business support.
“The drone is the first underwater vehicle to achieve a 1:1 payload-to-own-weight ratio without vertical thrusters,” attested Mr Sadowski. “In comparison to other ROVs, ours has a variable geometry giving positive buoyancy to maintain its depth. The huge payload to work ratio is a major differentiator, as well as its precision.
“It allows us to mount ROV workload on the system and it can lift around 100kg of equipment – which doesn’t exist on the
market today. We have cre ated a new class of ROV that can operate up to 300m in depth and can now start to replace divers that operate in dangerous environments.”
He said the ROV is highly adaptable to operate different equipment: “we have a platform that provides more visibility
for the operator with top of the line sensors and thrusters powerful to fight high currents. It is small enough, ready to be deployed for different activities, such as inspection of hulls, and we can offer a flexible solution to meet any clients’ needs. We can offer an ROV platform to a wide customer base.”
Mr Sadowski said the NIX 300 would be the beginning of the NIX family, due to the technology’s scalability.
“We developed the NIX 300 because 300 metres of freighting is the biggest market in terms of quantity of customers and problems we can solve. But we can go deeper and make the ROV bigger, so it opens up many exciting opportunities.
“If we get an order, we can make our system operationally ready within two months. We base our business on trusting our technology, because we are providing solutions, not half-measures.”
Bisonte is now finalising the commercialisation of the NIX 300 and contacting potential clients.
Mr Sadowski concluded: “Replacing humans with robotics and having a system with speed, we hope Bisonte will become an important player in the market for the long run, with the NIX ready to shape the industry.
“We are driven by the need for change and to grow in an eco-friendly, responsible and sustainable manner. We believe we have breakthrough technology, and industry agrees we have something big to offer. We are developing technology of the future right now.” n
Having recently celebrated its 50th birthday, Permascand continues to innovate and grow, with new developments in its production capabilities and exciting inroads into hydrogen production. CEO Peter Lundström, CTO Fredrik Herlitz and Viktoria Lindstrand, Permascand’s CCO, sat down with Richard Hagan.
Permascand, based in Sweden, is a global independent provider of electrochemical solutions. It’s one of the top producers of catalytic coatings in the world, and it also produces a variety of electrodes and electrochemical cells and solutions utilised in a variety of industries across the planet.
Its manufacturing infrastructure has always been an important priority and it continues to be so, according to company CEO Peter Lundström.
“In the last few years, we’ve invested a lot in the company, both in terms of our soft and hard values,” he said. “But now we’ve really focused on increasing the automation and robotisation of our production line. It’s taken lots of time and money, but it’s all now up and running.”
The company’s recent public listing has given it the headroom to forge ahead with investments into a technology centre that is expected to significantly improve its research and development capabilities.
“The phase we’re in now is building up the R&D of our products and our manufacturing solutions,” confirmed CTO Fredrik Herlitz. “We’re investing heavily into the concept. Inside, we’re installing the next generation of equipment for catalytic coating materials of the future. We believe that the innovations there will reduce both raw material consumption and the overall environmental impact.”
The equipment Fredrik Herlitz referred to is a testbed measuring 15m x 3m in size : small in comparison to the final, industrial-scale equipment that it emulates, but perfect for its mission. The company envisions that mission as being not only an R&D facility but also as a marketing vehicle of sorts.
“While it’s a demonstration of something that will be beneficial to us as a company, it’s also beneficial for our customers and for the environment,” said CCO Viktoria Lindstrand. “We want to use the work we’ll be doing here to ensure that our customers
are kept happy with our solutions. And it’ll show the industry that we’re delivering great products and investing into the future with renewables, including green hydrogen and power transmission.”
The company expects green hydrogen to be a huge opportunity for both it, and the industry, for the foreseeable future. “This is going to be a major growth driver in the next five to ten years,” Peter Lundström noted. “There’s a lot of electrochemical equipment that needs to be produced. In the long term, this is the biggest growth segment in the market not only for Permascand but for the whole industry. ”
It soon became clear from the team’s comments, however, that that growth path won’t be easy and there are many challenges that will have to be overcome. The sheer volume of product that has to be manufactured to meet the world’s needs for hydrogen is the first challenge.
“The issue relates to electrochemical technology and the industry’s production capacity for that technology,” Viktoria L indstrand explained. “Hydrogen factories will be on a very large scale, requiring many square metres of catalytic materials as well as a lot of electrodes and electrochemical cells.
“As a manufacturer, we know that manufacturing large-scale electrochemical cells with good performance and a long lifespan is not that simple,” she continued. “It’s really difficult, no matter how you design it. And we’re concerned that nobody is really talking about this problem and what needs to happen in order to solve it.”
Company CTO, Fredrik Herlitz, highlighted raw material needs as a particular concern: “Raw material supply and sustainability of the usage of those materials is a key factor,” he revealed. “To build the
big hydrogen plants that will be required in 20 to 30 years to come will require a huge change in society. You need good catalyst materials in competition with everything else in society.”
Here, Fredrik Herlitz is referring to the industry’s growing need for precious metals, in direct competition with the increasing need for those same metals in other industries, including automotive –for electric vehicles – and consumer electronics, for things like mobile phones and computers.
“There’s a worry around iridium,” Peter Lundström added. “A recent report in the market made it clear that industry, in general, has to be more efficient and use less iridium going forward. Today, demand for iridium is manageable but in future, we expect to see very high prices and insufficient supply.”
“Reducing the level of iridium in the manufacturing process whilst also keeping electricity consumption down is a huge
challenge that needs to be solved,” he continued. “They’re talking about having to lower iridium consumption by 90%. It’s going to be very tough.”
A major strategic goal at Permascand is improving its operational efficiencies to constantly improve its sustainability. Its efforts are directed at three main areas; energy consumption, waste management and social responsibility.
“Every decision we make is tempered around minimising our impact on the environment,” Peter explained. “Internally, thanks to a number of upgrades and other investments, we’re now using less energy whilst producing twice as much as before.”
“We’re also recycling and cycling back everything. Any material that goes into the waste is recycled,” he added. “But we’re actively trying to reduce our waste through improving our sourcing. And finally, we’re constantly improving our products so that we use fewer materials in their construction.”
Social responsibility is an important theme at Permascand and it is actively involved in supporting and caring for the surrounding community, as Peter Lundström highlighted: “We are the biggest employer in the community, so one of our first priorities is ensuring that Permascand remains profitable and stays in business to support our employees.”
“We’re cautious about how we award sponsorships,” Viktoria Lindstrand continued. “We support local schools and there are a couple of small programs that we’re involved with, but it’s always local, including when giving to sports teams.
Its sponsorship efforts extend beyond school activities and into the community itself: “We recently sponsored a fishing contest in the village. We do it because we love the community and because we can.”
School pupils are invited to participate in the company’s apprenticeship and training programs as well. These activities promote the career opportunities at Permascand and
inform the students of the various roles that they can look forward to should they choose to pursue employment there. Scholarships are also made available to the school, and are awarded to the best students in its industrial program.
Permascand has a clear, confident strategy and vision for its future. “We never see challenges, only opportunities,” Peter Lundström remarked. “We want to be an independent, global leader in the supply of electro-chemical solutions. We have to overcome every obstacle.”
Concluding, he said: “We’ve been through the pandemic and for two years we’ve dealt with high material prices, longer lead times and crazy transportation issues. We’re a stronger company today than two years ago. There will always be challenges. We manage our hurdles and get over them. That’s the culture we’re building.” n
Norwegian Eltorque AS develops and manufactures electric actuators and flow-control systems for the international shipbuilding and onshore industries. Herman Klungsøyr, EVP Strategic Sales, related the story to Phil Nicholls.
Eltorque AS was founded in 1996 to develop and manufacture actuators from a unique electric patented motor concept into electronic remote actuation of valves. After breaking into the high-end fishing vessel market in 2000, Eltorque developed a complete remote control valve system with a wide range of actuators for the ship building industry.
From high-end fishing vessels and a new generation of actuators for the offshore market to commercial vessels, the company is the market leader in Northern Europe with over 1,000 projects supplying 120,000 highquality actuators.
According to Herman Klungsøyr, EVP Strategic Sales, it has taken Eltorque many years to convince the conservative shipbuilding industry to leave traditional old-school actuation and move to modern electronic actuation and valve control.
“The huge benefit and the revolution to the industry is the automatic shut off of power to the electric
motor when the valve has reached its designated position,” he said. “A patented selflock technology – unique to Eltorque actuators – holds the valve in the designated position without using power. This is a massive power and fuel saver compared to all other actuators on the market.”
Along with the most compact actuator design in the market, featuring the most advanced self-calibrating algorithms, remote torque, speed and temperature control with a self-diagnostic software to monitor the “health” of the valve, Eltorque actuators and remote valve control systems can be left alone
for decades without any issues. It will live silent within the operation of the vessel doing its job without any demand for attention.
“This is a true, innovative ship equipment revolution compared to the traditional systems that are still used even on new vessels,” Mr Klungsøyr declared.
Eltorque actuators and remote valve-control systems can be used for all systems on board, meaning the operator on the bridge can easily monitor and control the ballast water system, the fuel system, and the loading and unloading of fluid, cargoes, tank gauging, measure pressure and flow valve throttling, ballast water cleaning systems, exhaust cleaning, A/C systems and VA systems in general.
The Eltorque motor technology is matched with built-in encoders to produce highly intelligent units with no need for maintenance, no limit-switches, and a low energy demand. If anything needs to be changed or
modified on the control unit, the motor unit can be left untouched.
“This makes it super easy to do maintenance, if ever,” said Mr Klungsøyr. “In addition, the Eltorque technology enables all information connected to the system to be transferred to shore-based computers. Subsequently, all updates and system improvements can also be done from shore.”
Eltorque is the market leader within the mid- and high-end vessel market built in Europe, with a turnover in 2021 of €15 million. The company consistently embarks on 50-70 new projects every year, selling an average of 10,000 precision actuators annually.
Eltorque holds such a strong market position by expanding into more segments. Its actuators can be found in cruise ships, RoPax and car ferries, tankers and bulk carriers amongst others. Alongside this growth across market segments, Eltorque has seen substantial expansion internationally.
Electronic, maintenance-free actuators offer a strong product portfolio, with sales across Asia, USA and South America. The company has focused on joining the suppliers list for those European companies operating shipyards in China.
“We expect strong growth in this region over coming years,” said Mr Klungsøyr.
The international reach of Eltorque can be seen in the worldwide spread of offices. The company is headquartered in Trondheim in central Norway. There is a warehouse and production facility in Vanvikan across the Trondheim fjord, along with a sales and service operation in the shipbuilding town on Ulsteinvik in western Norway. Eltorque has sales offices in Leesburg in central Florida, Singapore and Bremen, Germany.
The range and flexibility of Eltorque actuators is represented by the diversity of the companies Mr Klungsøyr highlighted as
satisfied clients. Within Norway, Eltorque supplies the VARD shipyard in Ålesund who build high-quality specialised vessels for the energy, seafood, adventure and security markets. Another Norwegian client is Aas Mek Verksted AS in Vestnes, who used Eltorque actuators in a line of wellboats transporting live fish.
European customers include Lürssen in Bremen, Germany, builders of luxury yachts. Further afield is Cantiere Navale Visentini in Donada, near Venice, who build combined Ro-Ro and passenger ferries. Global projects include the Tersan Shipyard Inc in Yalova in north-west Turkey, on the eastern shore of the Sea of Marmara. Eltorque also supplies VARD’s shipyard in Vung Tau in southern Vietnam.
A recent project which demonstrates the value of Eltorque components is the Prospero tanker built by the Wuhu Shipyard Co Ltd, the largest shipyard in Anhui Province in eastern China. This award-winning vessel design was constructed for the Swedish company Rederi AB Donsötank from the Southern Göteborg Archipelago. The Prospero features Eltorque cargo-valve actuators and ballastwater valves as part of a build philosophy aimed at future-proofing the vessel using electrical valve control over hydraulic.
Mr Klungsøyr conceded that competition in the market is “increasing every year, mostly based on price.” The response of Eltorque is to focus on quality and customer satisfaction. The company works
continuously to provide product and service improvement, with the results proudly displayed on its website. Client satisfaction with delivery and technical service stands at 90%, while the total satisfaction for products and ordering are an impressive 96%. As Mr Klungsøyr said: “the customer means everything.”
Ethics and green shift
Eltorque’s focus on customer satisfaction is scaffolded by the company’s robust ethics policy. This requires directors and employees to maintain a high standard of business and personal ethics in the conduct of their duties and responsibilities. The company seeks to conduct business with reputable customers, consultants, and business partners involved
in lawful business activities and whose funds are derived from legitimate sources.
A demonstration of these ethical trading principles is found in the Eltorque dedication to sustainability. Its actuators are one of the most energy-saving products found in the market.
Mr Klungsøyr said the company’s ambition is “always to be in the lead developing sustainable products.” The company focuses on the green shift, emphasising four benefits to customers from Eltorque actuators which are sustainable, maintenance free, energyefficient and compact, with reduced weight and volume.
The travel restrictions imposed by the coronavirus pandemic brought changes in the daily routines at Eltorque. Primarily, response times via email and telephone intensified, while Microsoft Teams joined the toolbox. Yet, according to Mr Klungsøyr, these challenges also brought the company team closer together, finding the value in each employee.
Eltorque was also in the fortunate position of having built long-standing relationships with clients. The good reputation which had brought customers to Eltorque sustained these partnerships through the
travel restrictions and other necessary measures. Production continued on-schedule and no contracts were cancelled. Eltorque employees showed themselves adaptable and the company remains in a strong position after two years without travelling.
As business slowly moves into a post-pandemic world, such travel restrictions are gradually lifting. Mr Klungsøyr is eager to return to face-to-face business at trade shows like SMM.
“SMM is one of the biggest and most important exhibitions for Eltorque,” he said. This trade show includes most of the maritime industry segments Eltorque supplies.
Mr Klungsøyr is looking forward to networking with colleagues, partners and customers old and new. The SMM trade show will be the opportunity to present new prod ucts and solutions to the market. There is also the chance to be informed about new products on the market and any new companies in the field.
The future is electric Looking ahead, Mr Klungsøyr is confident in the future for Eltorque.
“We live in a world where everything that can be electrified will be electrified,” he said. “It’s just a matter of when.” Eltorque pioneered the electrical
actuator, giving the company an advantage when the global trend is or electrification.
Mr Klungsøyr sees great growth potential in the maritime market with Eltorque pursuing a vision to be globally recognised as the “best in class” supplier of valve control systems for the maritime and offshore industries. Eltorque has secured a strong position in Europe and is now looking to expand into China and establish a sales network in the United States.
The unique and innovative valve control solutions manufactured by Eltorque can replace any conventional system. The company is a trusted partner for shipyards and shipowners seeking to achieve their climate-friendly goals when retrofitting or shipbuilding.
Mr Klungsøyr concluded: “With our key locations around the globe, loyal partners and an efficient sales force, we would be able to take on all the projects that come along. We believe the future will be highly automated with remote operated systems – even the ship itself. Automated enabled vessels will be the future for two reasons; fuel efficiency and safety. Eltorque is well positioned for this future which is right around the corner!” n
Amco Veba Marine cranes reflect the technical expertise and extensive experience of a company that has recently enhanced its offering to meet the individual needs of its customers even better than ever before. Romana Moares reports.
Located in Italy, Amco Veba Marine is the dedicated marine crane brand of Hyva Group, one of the global leaders in its sector. The company designs, manufactures and supports an extensive range of folded telescopic and articulated cranes to suit the marine environment and designed for onshore, shipboard and offshore installations.
Amco Veba Marine cranes are designed for various applications, from general cargo handling to ship-to-ship operations. They can be used onboard many different vessel types for various on-board and off-board lifting operations, but also used on offshore platforms and production units.
All Amco Veba Marine cranes come with the double-rack solution as standard to guarantee smooth and safe rotation for the limited rotation angle version, and with the slew bearing for those with the continuous rotation angle.
The cranes are equipped with different safety systems designed for easy use, and designed for minimum weight while providing rigidity for maximum lifting and handling. They are of compact design, so as not to interfere with small vessel stability and space availability.
The cranes are designed in line with European standards, and the company also offers a wide range of products designed to meet major international specific norms and the main marine classification society regulations.
Amco Veba Marine has been part of the Hyva Group since 2007 drawing on the synergies of a strong, multi-national corporation.
“Hyva is headquartered in the Netherlands, with more than 3,500 employees , operating across a variety of sectors with 12 plants and over 30 fully-owned subsidiaries around the world,” explained Massimo Magli, Business Development and Sales Director, pointing out that under the Hyva Group, Amco Veba Marine has reinforced its position as a well-known and respected brand around the world.
He revealed that the company has recently defined a strategic plan backed up by considerable investment to further develop the marine business by enhancing the product range and adding new, larger crane versions as well as developing a fully dedicate sales and service network worldwide. A new logo has also been created to improve brand awareness.
“There is now a much stronger focus and commitment on promoting Amco Veba Marine as a brand specifically dedicated to cranes designed and developed for marine applications,” said Mr Magli. “The fact that we are part of a financially strong multinational group clearly is an advantage, helping to strengthen the brand worldwide.
“ The idea of the five year investment programme is to offer a complete range of marine cranes (including the bigger version) within a few years. To this end we have made some internal changes to further improve our engineering capability.”
Mr Magli emphasised that environmental considerations and personnel safety continue to be a priority for the company. New modifications include bio oil replacing conventional oil to prevent environmental damage to seas in case of any leakages.
Under its new strategy, both products and services have been enhanced. The company has recently introduced a Multi-Level Protection (MLP) programme, to allow customers to choose dif ferent crane protection levels for the environment in which
a crane is expected to operate – from softer ambient conditions to the most severe and harsh humid salt environments. As such, under this new strategy, the customer will get the best value-added solution for their specific needs.
The MLP programme is an integrated and structured plan of solutions with care for all crane parts; from complete surface treatment up to the hi-durability of hydraulic cylinder rods, pin protection, hydraulic fittings, rigid pipes, rubber flexible hoses, screws, bolts, junction boxes and all electrical components.
“There are different protection levels, starting with the basic one, most suited for inland applications, all the way to the heavyduty protection level, which will be chosen by those seeking solutions for severe marine applications on offshore vessels, boats and offshore platforms,” Mr Magli detailed.
On the product level, the company now has five new crane models available: the VR24, VR34, VR40, VR60 and VR62 – fully foldable and with endless rotation. The models are equipped with a radio remote control system, and specific fibreglass plastic protection covers to grant a perfect resistance to the environment, protect the important main crane components and give the crane aesthetic appeal.
And unsurprisingly, considering the never-ending nature of R&D endeavours at Amco Veba Marine, more new models are in the pipeline, Mr Magli confirmed.
While product development and engineering is done in-house, cooperation with clients is key. Mr Magli explained that the company first prepares a prototype which is then tested by the client. Potential modifications are then implemented to come up with a perfect product.
He further acknowledged that the company has not been hit hard by the global pandemic and revenues have increased by 10% during both pandemic years. This was the result of excellent internal forecasting systems capable of handling material shortages, as well as general business expanding into new markets. The company is now improving its penetration in all European countries and also focusing on the southern region of the Far East.
“Hyva has solid relationships in its supplier network and the financial resources to buy stock even before the orders are confirmed, so, anticipating supply chain disruptions and lack of availability of materials, we were able to handle the biggest current challenge well. In fact, this has given us a competitive advantage, as we are able to provide shorter lead times than our competitors.
“Given the focus the group has now put on the marine crane business, and capitalising on our reputation, proven track recor d and the increasing number of satisfied clients, Amco Veba Marine will continue on its journey to becoming a major player in this sector,” Mr Magli concluded.
As decarbonisation becomes the latest buzzword to echo around the marine industry, the team at Hydrus Engineering provides both mid and long-term, high-end solutions to the global fleet. Business Development Director and Company Partner George Ntroulias talks ammonia, the company’s ambitions and drawing up plans for electric ferries. By Andy Probert.
Big challenges and bigger ideas are the fuels that fire the furnace deep within the innovative minds of Hydrus Engineering. Since 2009, those same minds have helped redesign the fate of many vessels the world over, but it appears they have only just begun.
As a global engineering firm consistently delivering the latest technologies, Hydrus Engineering’s aim, by default, is to leave a lasting impression on ship owners and shipyards. Given its blistering performance in 2021, the Athens-based company is confi dently striding ahead in delivering on the decarbonisation agenda.
Trying to distil the very DNA of Hydrus, Business Development Director and Company Partner George Ntroulias replied candidly: “We care for our clients. We want excellent results by any means. We want them happy! And that has nothing to do with profit. For us, it’s a matter of attitude.”
With that in mind, the company has put itself on the front foot in demonstrating an alternative view for the shipping industry as calls to reduce carbon footprints continue to ring out.
“It is a strategic goal for Hydrus to have a major engineering role in the decarbonisation era of shipping,” he said. “Within this scope, certainly in the last two years, we have tried to be in the vanguard of alternative fuels development while investigating several available fuels and technologies.”
The company’s successes remain based on four foundation pillars: people, practices, client satisfaction and corporate sustainability. Established back in 2009, the engineering service provider set out to manage new shipbuilding projects before expanding into repair, retrofit, field attendances and energy management services.
Ambitions to build the next eco-friendly era of shipping have also been matched by Hydrus riding high in business. It completed a highly successful 2021, which translated into a 35% growth compared to 2020.
Ballast water treatment retrofit studies and installations continued to be a substantial profit centre.
“We completed over 200 retrofit studies and more than 100 installations in 2021, surpassing 800 green retrofit projects in total,” reported Mr Ntroulias. “We also supervised more than 120 dry docks in the last year and our new-building division committed on 12 new projects relating to LNG, LPG, tankers and containers.”
The company has also invested in specialised engineers, software and training that will allow its teams to perform advanced analysis involving computational fluid dynamic principles.
Following the organisational restructuring of 2018, which led to the creation of three main divisions and three supporting departments, in 2021, Hydrus transformed into Société Anonyme to strengthen its financial foundations and promote its competitive advantages more efficiently at a global level.
Recognising the market’s needs not only for engineering solutions but also for technological ones, since January 2022 Hydrus’ energy and innovation department has been partnering with experts from the IT sector to operate a separate legal entity called EniSolv.
EniSolv aims to be a technology company providing turn-key solutions for ships’ performance monitoring and optimisation, through a wide range of products and services. These include IMO DCS and EU/UK MRV compliance tools, GHG emissions’ KPIs and analysis, fuel management systems, hull condition monitoring, trim optimisation and tailor-made solutions for shipping companies and charterers.
These approaches to making shipping smarter also back up Hydrus’ deep commitment to playing a major engineering role in the industry’s decarbonisation era.
In December 2021, Hydrus’ proposal for ammonia storage on a large scale on commercial ships, up to 900 cbm, was accepted in principle for Horizon Europe funding. Horizon Europe is the successor
programme of H2020, the European Union’s flagship research and innovation programme, and will have a budget of more than €90 billion over seven years.
Mr Ntroulias commented: “The project’s overall goal is to develop a next-generation, sustainable, commercially attractive and safe technology for long-term storage and transportation of NH3-fuel on ships.
“Teaming up with our partners in the project, we will develop new design solutions that will also offer the feasibility of storing 900 cbm of liquid ammonia and demonstrating it on a 31,000 DWT multi-purpose vessel by 2025.”
Additionally, five different types of vessels and related fuelstorage tank concepts will be studied and documented for the best optimisation of the development process.
Hydrus also remains highly focused on the decarbonisation challenges presented by clients for the short and long term.
“For the next few years we will be working to achieve turnkey solutions for Greenhouse Gas (GHG) retrofits with a focus on short-sea and coastal shipping. Through these services, we aim to assist our clients in extending the lifecycle of their vessels by achieving considerably lower CO2 emissions to comply with the upcoming limits.”
The company’s strategy and vision also include the development of in-house eco-designs such as electric ferries and hybrid Ro-Pax ships. Hydrus has already completed the concept and basic design of two electric ferries of 50m and 100m in length.
“For the 100m concept, we have also investigated the option of hydrogen fuel cells in combination with a battery management system,” Mr Ntroulias revealed. “For us, in Hydrus, shipping needs massive R&D work to meet the upcoming challenges.
“Unfortunately, the maturity of the available technologies is quite low, especially when we talk about ocean-going ships,” he reflected.
Mr Ntroulias said that having developed comprehensive know-how in engineering and project management in the last four years, Hydrus was now taking its first steps beyond shipping. “Our aim is to provide solutions to the energy sector by focusing on sustainability.”
These focus on green recycling with upgraded recycling procedures and infrastructure, floating wind farms in Greek seas in cooperation with major EPC contractors, and the energy upgrade of core and comprehensive EU ports.
While Covid-19 has placed companies on notice to prepare for alternative business models and develop smart ways of engagement, decarbonisation, predicts Mr Ntroulias, will certainly change the way the shipping industry works.
“Considering the upcoming regulations for the emission control and reduction, most clients face an asset management problem. Ships built less than ten years ago need major modifications and
considerable speed reduction to comply with the IMO’s new CO2 emission limits,” he reflected.
“In the next few years, we‘ll see major changes in global trade which must be followed by fleet renewal. But honestly speaking, I don’t see major developments in the shipbuilding industry. That’s a bottleneck we cannot avoid.”
With the volatility in the energy markets, he foresees the industry having to react quicker with efficient solutions, especially for the LNG fleet, where a substantial number of ships cannot meet the IMO’s CO2 emission limits due to the high trading speed.
He added: “As far as our clients are concerned, we listen to their needs and cover them in the most efficient way. As a service provider, we support our strategy in two main pillars: our employees and clientele. Both have been developed with hard work and honesty.
“For our suppliers, I believe it’s matter of trust and respect. We are investing in long-term co-operations, building a robust network of reliable suppliers, many of whom have remained with us since our first year of business.”
He concluded: “From day one, our motto has been ‘Engineering Excellence’. It remains unchanged because that’s where we are at. Not only delivering engineering excellence to clients now, but investing in future eco-solutions for all.” n
The name Mahnke has been ever-present in the world of vulcanisation (the processes for hardening rubbers) since 1921. Today, the company’s varied products can be found in a wide variety of industries. As Jordan Yallop discovered, one of the most recent markets Mahnke has ventured into is the maritime sector, where the company’s many specialist corrosion resistant coatings are proving essential in this industry.
Peter Mahnke GmbH, based in Kalübbe, Germany, enjoys a stellar reputation within the vulcanisation industry. The company was founded by Peter Mahnke together with his sister Evelin Mahnke-Vock in 1970 with the aim of fully focusing on the vulcanisation techniques for the industrial sector. Previous to this, the name Mahnke was primarily focused on the repair of car tyres and despite the difficulties presented by the socioeconomic factors of the time, the business built by Friedrich Mahnke thrived and became a well-known company.
The 1950’s saw a shift in production, whereby the company’s previous specialisation in tyres was being replaced due to more demand for industrial applications. These two areas of production originally took place simultaneously, but as time pro -
gressed, the industrial applications sector was growing. The subsequent decades were characterised by continued growth of the company and by economic success, and two years later, Peter Mahnke GmbH was founded.
Today, the company’s customers include various businesses ranging from chemical, energy, heavy industry and shipyards.
Janosch Mahnke, Managing Director, talked about why the company has delved into the maritime sector: “We started in a new business field in 1990 called surface protection, which provides rubber linings that protect against corrosion.
“This new business avenue opened up our company to the maritime sector, and today we supply the rubber lining of the cooling systems on board vessels.
The rubber lining serves as this corrosion protection inside the whole cooling systems pipeline.”
The mission to protect Mahnke currently has three facilities –in Hamburg, Rostock and Kalübbe – with the latter being the company’s main manufacturing facility where the production of the products destined for the maritime sector are also handled. The 79 employeestrong business has a manufacturing area of around 3,000 sqm which constructs the various products that range from conveyer belts, corrosion protection coating and cargo hatch cover seals.
The company’s workshop, which employs modern technology such as blasting plants, autoclaves and Unimog systems, underwent expansion in 2019.
“We expanded our main location in Kalübbe by adding another manufac -
turing hall in order to be able to meet the increasing demand for products utilised in the offshore industry,” said Janosch Mahnke.
Mahnke produces a number of modern conveyer belt technologies and this area of manufacture accounts for a large portion of the company’s output. The other main area is its surface protection; the reliability of these corrosion resistant solutions comes from Mahnke’s many years of experience and extensive laboratory testing. The company prides itself on using an individual analysis method when supplying its products. The type of surface that needs to be protected is examined so Mahnke can advise customers on precisely what type of protection is most suitable for their needs.
This process ensures that the protection medium that is chosen is the most efficient one available. The company offers various
types which include soft rubber lining, hard rubber lining, Coroflake, PU surface protection and Flexthane.
Due to rubber linings having excellent chemical and corrosion resistance, this type of surface protection sees widespread use in the maritime industry. To this end, Mahnke has developed Remaclave 60 ISO/803, a product specially engineered with a two-layer lining of 2mm hard and 3mm soft rubber. This product’s high resistance to chlorinated and oily seawater makes it ideal for use in shipbuilding as a protection for seawater carrying pipes and is used by many renowned shipping companies. To date, Mahnke estimates it has lined over 25,000m of pipe on 50 separate vessels with Remaclave.
“Remaclave is our best-selling product for rubber lining due to its use in seawater carrying pipelines in cruise ships. This product gives us a combination of the
advantages of hard rubber lining and the advantages of soft rubber lining,” said Janosch Mahnke.
As with all the company’s products, a strict quality assurance system is in place to ensure that all products and solutions are installed with a consistent high quality. Mahnke is the sole supplier of rubber lined pipes to all major German shipyards and there are currently over 300 ships worldwide with rubber lined pipes installed by Mahnke. These solutions are not just limited to maritime functionality; they also have applications in power stations, waste incineration, chemical and offshore settings.
Mahnke’s marine portfolio also includes hatch seals for sea-going vessels. These seals are offered at both an excellent quality and a great price point.
Another area that Mahnke operates in is wear protection. This area adds lifespan to items that can endure wear and tear as part of their daily operation or transportation. Mahnke tailors this service individually to each application, and as such, the solutions can solve a range of problems form noise to caking.
Mr Mahnke was keen to highlight the company’s global, 24/7 customer service ethic approach.
“We are doing on site repairs and such jobs all over the world,” he said. “So if a client calls us, we will send our supervisor or maybe a whole team in order to do the repair on site and this can be in Asia, America or Europe.”
Thanks in part to Mahnke’s age and experience, the company enjoys long-term relationships with its suppliers. One of these is Rema Tip Top, a supplier of materials needed for the coatings and rubber linings which Mahnke produces. After being in business together for over 50 years, the two companies work closely together when such opportunities arise.
Mr Mahnke said: “We have the opportunity to use Rema Tip Top’s laboratory to analyse materials for chemical resistance on the rubber linings, or we are able to choose some tailored products; we can also choose the right lining for the plant or for the vessel.
“In addition, there is a long-standing and trusting cooperation with producers in the Asian region. The company San Run International Trade Co Ltd has established itself within the last 20 years as a trustworthy partner and supplier for the production of special rubber components in order to complete the
product portfolio. These cooperations are important to secure a firm position in the market.”
He added: “As a family business, we have maintained long-term customer relationships and because of this close contact to our customers and their plans, we can easily adapt our material and products to their current requirements. This is a point where we can stand out from other companies.”
In light of current supply chain issues and a degree of uncertainty in the markets, Mr Mahnke expressed his optimism for the m arket due to the nature of the products –
they are always in demand. To emphasise this, he pointed out the company is seeing an increase in demand for products destined for both the offshore and renewable energy sectors – with the company making 2,000 rubber lined parts for clients in offshore wind power alone in 2021 – an increase of nearly 100%.
“We need to adapt to the new industries, such as green energy. Whatever problems will come to the industry we will find a way to deliver our corrosion protection, because corrosion will always be an issue that needs companies such as ours to resolve,” he concluded. n
With clients spanning both the superyacht and naval industries, Netherlandsbased Newthex enjoys a uniquely comprehensive level of participation within the sector. Managing Director Jeroen Mulder spoke to Richard Hagan about the company’s unique product and service offerings.
Newthex is a specialist in the design and production of weather and watertight doors, hatches and lifting systems for the superyacht and naval industries.
Having originally been founded in the early 2000s, the company initially specialised in the design, fabrication and installation o f watertight hinged-door systems. Over time, it has evolved into designing and manufacturing large hull doors and watertight hatches and today it also offers a number of other interesting solutions to the naval and yachting sectors.
When it comes to large hull doors in the superyacht market specifically, design attention has increasingly fallen on an area which has become known as the ‘beach club’, located at the very stern of the yacht. This is a space that is at the waterline and which can take an almost infinite number of forms, but in principle, it’s like an open-plan living space that flows from the inside of the yacht, to the outside and allows guests to have direct access to the water.
Beach clubs have evolved to include amenities such as large social areas, cocktail bars, spas and gyms.
Since beach clubs encompass both interior and exterior spaces, and since they’re located at the yacht’s waterline, they cannot exist without large, watertight hull doors. These are the same hull doors that Newthex specialises in designing, manufacturing, assembling and installing.
The rise in popularity of beach clubs has meant that equipment such as tenders – normally stored at the stern – now have to be stored in other areas of the yacht, such as in dedicated garages in the bow. This requires another set of large watertight hull doors to allow access for the tenders and their launch equipment.
With the large number of doors required on large, modern superyachts, and all of the moving parts involved, ensuring faultless mechanical performance is critical.
“Everything that you make foldable becomes an opportunity for a breakdown,” highlighted the company’s Managing Director, Jeroen Mulder. “For that reason, we use as few parts as possible. The fewer parts you use in the manufacturing of these things, the less opportunity there is for failures or breakdowns.”
This is especially important given the increasing size of superyachts. “We’ve definitely seen a trend that these components are getting bigger,” he continued. “With bigger doors and hatches comes the need for bigger drives, bigger axles and more hydraulics.”
Newthex resolves this challenge by standardising the design of its systems. “Whether it’s a six-metre or twelve-metre long platform, you still have a drive system with a number of locking
cylinders. Whether it’s a tender garage door or a beach club door, or a hull door on a naval vessel, the systems we use and the design principles are very similar,” said Mr Mulder.
The Newthex team is relatively compact and consists of 25 professionals, all specialising in particular disciplines.
The company’s beating heart is its engineering department.
“It’s our biggest and most important department; it’s where the concepts are developed,” Mr Mulder remarked.
Meanwhile, its growing project management department is the interface between the company’s engineering department and its customers, as Mr Mulder confirmed: “We’ve recently further developed our project management department through adding more project managers to allow us to better serve our clients. It gives us more of a focused client service approach.”
In terms of production, Newthex maintains close relationships with a network of specialist manufacturing partners who are entrusted with the heavy manufacturing of all of its projects. Every completed project is delivered to the Newthex premises where it is assembled and tested by the company’s expert team of specialists who ensure every product carrying the Newthex stamp meets the company’s exacting standards.
The testing process followed by Newthex is precise and measurable. Known by the acronym ‘FAT’, short for Factory Acceptance Test. The process is carried out in the presence of client and ship owner representatives. Each door is attached to the Newthex test rig and assembled in such a way that it is an accurate working setup of all the actual hydraulic parts and other components required for that specific door.
The door itself is then evaluated for correct movement, speed and hydraulic pressure as well as for water tightness. By performing all of these tests at the factory, the shipyard saves assembly time, which is a significant benefit for the yard.
Products that successfully make it through the FAT are then proudly shipped off to customer shipyards all over the world including Holland, France, Spain, Germany, Italy, Turkey, UK, US, China and India.
Mr Mulder highlighted Newthex’s brand new helicopter hangar lift solution as indicative of the company’s unique engineering depth and creativity.
“It’s a platform that lowers a helicopter into the hangar, and we then close the hatch on top of that. It’s a big project. The whole platform is operated by one large hydraulic cylinder which pushes itself up and down along the four cables mounted to the frame and the platform.”
With superyachts steadily becoming bigger, the demand for helicopter lifts is an emerging demand, noted Mr Mulder: “It’s an interesting trend that we’ve started seeing in superyachts. We’re definitely getting interest for more of them and in fact, we’ve just signed a contract for another one.”
In the meantime, Newthex’s engineers are also developing a solution for a hull dock door that will allow a superyacht’s tender to drive straight into the stern of the vessel. It’s all in a day’s work when you’re an engineer at the cutting edge of bespoke hull door engineering!
Newthex is uniquely positioned to serve both naval and superyacht category clients , with a market share that is roughly equally spread between both. But as Mr Mulder pointed out, while the company is grateful for the diversity in its market, naval contracts have their own challenges.
“We’ve always enjoyed a balance between yachting and naval projects, but we’re definitely seeing an increasing number of enquiries for naval vessels,” he remarked. “The challenge is the lead times involved between the enquiry and the awarding of the contract; and then the contract itself is typically very long in duration, so you need to be very patient.
“We are currently working on a large project for a foreign navy,” he continued. “The period of negotiation – from enquiry to signing
Managing Director
– took three to four years, and the contract duration now is for five years. And that scenario is the same whether it’s in Holland or elsewhere in Europe.”
On the other hand, he added, naval projects tend to be somewhat less complex than yachting projects. “Naval vessels are less complicated but the projects are of long duration because they’re for more than one vessel. Yachting, in contrast, is all oneoff . The systems we deliver for them are not very complicated but the detailing for them makes it so.”
In closing, Mr Mulder drew attention to the company’s diverse client base as being a major reason why he feels optimistic about the future.
“Our combination of naval and superyacht industry projects puts us in an interesting niche. We’re even slowly getting interest from the cruise ship industry too.
“Some of our competitors deliver thousands of watertight doors per year, and they’re very good at that. We don’t do that kind of volume and standard items; our organisation is not setup for that. But if clients want a special door with a slightly different size, layout or weight, or anything else special, Newthex is ready to take their call.” n
Supplying the world’s navies with mission-critical equipment is no easy task. But with over 60 years of design and manufacturing experience, Hydrasearch has developed the specialised knowledge and an extensive product portfo lio that has made it a trusted partner for the supply of various precision naval components to the US Navy and many others. But the navy isn’t its only customer. Hydrasearch also has a dominant presence in leisure boating and commercial maritime, and now, the company is exploring a brand new segment. Patrick Garrett, Vice President of Sales at Hydrasearch, dropped the gangway for Richard Hagan.
Hydrasearch, based in Stevensville, Maryland in the US, manufactures a substantial catalogue of highly specialised componentry for a variety of maritime markets.
In order to comprehensively cater for the specific markets in which it operates, the company is divided into three main divisions: Hydrasearch Defence, Hydrasearch Recreational, and Hydrasearch Commercial.
Hydrasearch Defence represents the company’s signature operational activity. Components produced within this division can be found on all major US Navy ship platforms, including submarines and nuclear combatants, as well as many other naval ships worldwide. The product offerings from Hydrasearch Defence include Replenishment at Sea and Underway Replenishment hardware, high-pressure hoses and fittings, critical systems hoses and fittings, and aerospace fittings.
Hydrasearch’s Refuelling at Sea (RAS) equipment is a particular highlight. It is one of only three companies in the world that produces a full line of RAS products. As such, these products are used by navies around the world.
Hydrasearch Recreational is organised around its venerable Buck Algonquin b rand. Via Buck Algonquin and the brand’s 65-year history, Hydrasearch has successful, long-standing supply partnerships with many major boat builders. It manufactures a wide variety of equipment for this market, including deck hardware, drivetrain parts, exhaust fittings, valves, steering hardware, strainers, hoses and clamps, plumbing and related fittings, thru-hull fittings, and coupling and shafting accessories.
Hydrasearch Commercial, meanwhile, is the company’s newest division and is targeted at the commercial marine industry from workboats, offshore support vessels, oil rigs and tugs to ferries,
cargo ships, barges and defence vessels. Its product portfolio includes vent check valves, raw water strainers, deck drains, 100R5 hydraulic fittings, sounding tubes, full cast stainless steel rudders, air pipe heads, international shore connections and a variety of valves and brass pipe caps.
Hydrasearch opened its doors in Annapolis, in 1962 as a think tank to support hydraulic research and design for the defence industry. At the time, it specialised in the manufac ture of hydraulic valves and components.
Remarkably, only months later it was acquired by DVCC, Inc (today called the Dixon Group). DVCC, Inc would include other companies, such as Dixon Valve & Coupling, LLC and Buck Company, LLC.
Years later, during the 1970s, designing and manufacturing solutions to allow naval ships to refuel at sea. Refuelling at sea systems would go on to become a major part of its portfolio, and today it supplies the equipment worldwide to South America, the UK, Australia, Italy and Spain and to storied customers such as Rolls-Royce.
Emboldened by its growing success with those systems, Hydrasearch decided to further its relationship with the defence industry in 1989 by pursuing Qualified Product Listing (QPL) status for its components. Hydrasearch successfully gained QPL status for a number of fittings over the decades that followed and today, they are a large portion of the company’s revenue, as Patrick Garrett, Vice President of Sales, confirmed:
“QPL fittings are our biggest seller by dollar value. We’re on 12 different QPLs right now and we’re looking to add five more by the end of 2022.”
In addition to its QPL achievements within defence procurement, in 2021 Hydrasearch became a single-source hose provider to the US Navy, including its submarine fleet, for large-bore critical hose and hose assemblies for hose sizes ranging from five to twelve inches.
Hydrasearch’s entire operation is housed at one site, spanning 63,000 sqft at its cutting-edge headquarters in Stevensville, Maryland.
“It’s a complete machine shop,” said Mr Garrett. “We’re a manufacturer but we pride ourselves on turning metal. We have 12 CNC machines and a variety of manual machines. We fabricate the entire process starting from raw materials like bronze, steel, aluminium, nickel, hastelloy and titanium, through to complete, finished goods.”
Quality control is centred on Hydrasearch’s high-tech testing capabilities and quality lab. It has the ability to test hoses and everything else in scenarios including underwater tests, liquid field testing, hot oil tests and various others. Two portable 3D scanners are able to quickly check dimensions whilst a high-tech optical comparator obtains optical measurements at high speed.
Speaking of a horizontal mill that was recently added to the shop floor, Mr Garrett commented: “It increased our envelope
size from around the 12 inch range to a 20-by-20 inch envelope. Its design reduces new project setup and run times as well.”
Another highlight for 2022 was the addition of three welding bays to the shop floor, effectively insourcing a process that was previously outsourced. The welding operation is currently being geared towards meeting Tech Pub 248 & 278 Navy Welding Certifications to allow it to contribute meaningfully towards demanding naval projects.
Hydrasearch employs over 60 staff at its headquarters, which is impressive, but it’s a drop in the ocean of the 1,400 employees working underneath the Dixon Group. Mr Garrett revealed Hydrasearch directly benefits from the significant pool of manufacturing and financial resources available within this large industrial group.
“The Dixon Group has three North American-based foundries, which we will use as often as we can; however, we will work with as many as 12 other foundries outside of our core group to manage any supply chain issues we may encounter.
“Our group gives us access to extensive 3D printing facilities that give us the capa bility to rapidly prototype tools and patterns, which has dramatically sped up prototyping times, from months down to weeks or even days. The Dixon Group also has ten other manufacturing facilities in the US, plus worldwide distribution.”
Today, Hydrasearch continues its reputation for innovation, evolution and diversification that has defined its journey for over 60 years.
Its latest growth plans are boldly taking the company into the aerospace market. As part of these efforts, the company is working towards meeting and completing AS9100D manufacturing requirements. AS9100 is a widely adopted and standardised quality management system for the aerospace industry and according to Mr Garrett, it’s expected to be a real evolution for Hydrasearch’s manufacturing processes.
“Entering the aerospace industry will make us and our processes better and more efficient,” he noted. “The quality requirements in aerospace will be impactful for us not only in that market but in maritime as well. It’ll see us working more with unmanned vehicle programs and external engineering groups.”
Meanwhile, Mr Garrett revealed that the company’s Buck Algonquin brand is reaping the fruits of a surging leisure boating market, particularly in the US.
“We’ve seen a great increase in new business. Our recreational and commercial lines enjoyed a 45% increase in revenue in 2021 and it’s not showing signs of letting up in the near future.”
The company’s ongoing commitment to its relationship with the US defence industry was recently rewarded in the form of a special government grant.
“We were selected as one of the candidates for the Advance Procurement Funds for the Surface Combatant Industrial base within the FY20 Appropriations Act,” Mr Garrett revealed. “We were awarded a six figure grant to help the Navy shipbuilders and our industry partners continue to provide products on schedule and at an affordable cost to the US Navy, in support of enhancing domestic industrial capabilities.”
In concluding, Mr Garrett highlighted the importance of the company’s relationships with both its customers and its suppliers for its success.
“Our customers are just as important as our suppliers,” he remarked. “We couldn’t have one without the other. There are so many barriers to entry in this market, that we really need one another. Our vendors hold us to our promises just as we keep our promises to our customers.” n
DELLNER BUBENZER, formerly Dellner Brakes, is a global leader in the manufacture and design of braking systems, suppling diverse and multi-faceted sectors of industry. The rebrand came into effect in June 2021, combining the names of Pintsch Bubenzer and Dellner Brakes, which has cemented both into a new era for the Dellner Bubenzer Group. As an industry leading supplier of marine braking solutions, DELLNER BUBENZER will be exhibiting at SMM Hamburg this September. Jordan Yallop reports.
Uniting the knowledge and experience of Pintsch Bubenzer, Dellner Brakes JHS, Dellner Industrial, Dellner Brakes and Rima, DELLNER BUBENZER joins an eminent line up of specialist industrial companies that make up the Dellner Bubenzer Group.
Friederike Imhaeuser, Head of Marketing at DELLNER BUBENZER said: “Since our rebrand in June 2021, who we are or how we produce, develop, or serve has not changed in any way. We have simply come together stronger and united under one name; our roots are always the same. Our business partners and customer will recognise the familiar faces from the past, because we are one big family, under one umbrella and one name.”
DELLNER BUBENZER creates bespoke braking solutions for a diverse range of industries including marine, offshore, oil and gas, wind energy and industrial. Attention to detail, commitment to service and innovation makes DELLNER BUBENZER a front runner in its field. This stems from decades of accumulated experience in the sector, merged with the highest standards in quality, innovation, and safety.
Within the marine segment, DELLNER BUBENZER is an industry-leading manufacturer of innovative turning, stopping and locking (STL) systems for marine propulsion shafts – integral t o a vessels innerworkings. The STL solution provided by DELLNER BUBENZER enables maximum manoeuvrability by
enabling swift directional changes, lower fuel consumption, loading reduction on propulsion systems and allows faster routine maintenance without sacrificing safety.
The company also offers a range of high-quality pneumatic drum clutches and brakes for use on reverse reduction gears, propulsion shafts and hydraulic pump drives, monitoring and control systems, hydraulic power packs, and a range of components and accessories, including full wave and half wave rectifiers.
We are not an island
Today DELLNER BUBENZER’s global reach extends to two production facilities in Germany and further sites in Sweden, Italy, China, India, Poland, Denmark, and the Czech Republic. The company also has sales and service representatives in the Netherlands, USA, Brazil, Dubai, Malaysia, and Singapore.
“When it comes to the modular STL concept, we can supply a standalone stopping (brake) system, a combination stopping (brake) and locking system or a combination stopping (brake), turning and locking system. Within various kinds of vessels, this modular based system has great value, and we have for decades also supplied to the naval sector which currently is a rising star”
“We currently have around 900 employees, over 25 locations over the whole world on all different areas, over 45 representative and agents around the world and the global service team of over 50 trained technicians,” listed Ms Imhaeuser.
A part of our vision is to be as close to the customer as a worldwide oriented company. And of course, this is one of the main topics with our global service network.”
Peter Mikaelsson, Vice President and Head of Marine Braking Systems added: “One of the key areas that we can offer right now i s supporting the local marketplace with a greater portfolio of product and services.”
DELLNER BUBENZER prides itself on its team, to which it calls its family, stating that they are ‘anchored by integrity and committed to sustaining our best-in-class brand’.
Peter Mikaelsson said: “The Dellner name is a family name here in Sweden, with a long heritage within the industrial sector. The team spirit is considered a core value within our operation.
“It was very important for us to become as one with this rebrand. By sorting the whole operation into the one name was really important to get our people together and unite. We are a strong team instead of, how do you say, random islands in the big sea!”
Braking history
DELLNER BUBENZER provides solutions in engineering, braking system design and climate testing. The company offers engineerin g solutions including, engineering and 3D construction of components,
assemblies, tools, and special parts. The company also optimises existing solutions, technical documentation, customised testing, and the development of prototypes.
The company also provides superior braking system designs for static and dynamic applications, and climate testing of customers’ brake systems to ensure they can stand up to the toughest weather. 24/7 preventative services, reactive services, and life cycle management for all its customers, are all par for the course.
Focusing on DELLNER BUBENZER’s activities in the marine sector, Mr Mikaelsson said: “From the Swedish operation we are focusing on the STL, which is our multifunctional single interface unit, and we are experiencing big growth in this area. This first quarter has been fantastic for us to be honest.
“ When it comes to the modular STL concept, we can supply a stan dalone stopping (brake) system, a combination stopping (brake) and locking system or a combination stopping (brake), turning and locking system. Within various kinds of vessels, this modular based system has great value, and we have for decades also supplied to the naval sector which currently is a rising star.”
When it comes to new products, the SB 28.5 was launched this year. The culmination of decades of innovation, SB 28.5 incorporates elements of sustainability into its design without compromising effectiveness or efficiency.
Raphael Woelck, Product Manager, Motor Mounted Brakes said: “There is quite a long history with that series, it was one of our very first brakes. It has been a constant process of devel op -
ment and improvement, based on the feedback we get from the market. It nicely represents the journey and the closeness we have to the customer. With these brakes, we try to always focus on the customer’s needs.”
One of DELLNER BUBENZER’s many strengths is its versatility in providing solutions for the customer. One such case study reaffirming this point was highlighted by Peter Mikaelsson: “The Swedish operation this year, will break delivery of 100 unique designs of the STL system. These are no off-the-shelf products that you can come and buy; we have made 100 unique design solutions and we will make delivery of this amount by the end of this year.”
The global supply chain issues plaguing aspects of every industry has seen companies adapt in ways they may not have needed to before. For this to work, close ties and trust among partners is invaluable.
Mr Mikaelsson said: “Good relationships with suppliers are essential at the very least. We always follow the philosophy of setting up a real partnership not just a working relationship. We are in close in contact with our customers with our suppliers and that gets the best results in all aspects of business.”
Considering these issues, the overarching theme at DELLNER BUBENZER, is one of unity and teamwork, all geared up to serve the market even better than before. With a strong base of experience and technology, the company aims to get closer to every marketplace.
Mr Woelck said: “The first step we made towards this was the rebranding, which has allowed all the companies we have now in the group to synergise like never before. It was like a big puzzle and now it is completed; it gives a nice picture.” n
Nearly a decade on from installing its first maritime scrubber, VDL AEC Maritime is again taking a leap into the future and seizing the initiative with the development of carbon capture technology. While the industry and the IMO continue to debate a clear path forward on the issue, the Dutch-based company is bravely going where few fear to tread on the transitional journey for greener shipping. By Andy Probert.
Maritime scrubbing system specialist VDL AEC Maritime has never been afraid of pushing back the technological boundaries to protect the environment. As climate change resonates throughout the industry, the company has embarked on new developments to deliver dynamic carbon capture solutions for the marine industry.
Its track record of onshore emission and odour-reduction scrubbing systems evolved in 1994, but when the IMO in 2010 declared its 2020 low sulphur fuel emission resolutions, AEC Maritime was borne.
With its first maritime scrubber system installed by 2013, AEC Maritime then launched a joint venture with VDL Groep, and since 2018, its scrubber technology has continued to flourish. It is now installed on many vessels globally.
Today, the Eindhoven-based company, now branded as VDL AEC Maritime, is part of the VDL Groep and is among the industry’s top 10 s crubber suppliers. This positioning has been complemented by its continual development of sulphur oxide scrubbers, and now, carbon capture solutions.
Sales Director Joost Wijdeveld explained the marine industry currently faces three options in tackling greenhouse gas emissions: use less fuel, switch to non-carbon fuels, or embrace carbon capture.
While the first is potentially impractical with less fuel meaning slower transportation and bringing the industry to a veritable halt, switching to e-fuels, such as ammonia, methanol or hydrogen, is still in its infancy, and renewable energy sources may be insufficient to produce enough e-fuels in the medium to long term.
“The most certain strategy for reducing CO 2 emissions is to capture the carbon released from the exhaust gases during combustion,” said René Veldman, Product Manager, VDL AEC Maritime.
An envisioned carbon capture system requires hardly any modifications to the current engine system and is already compliant with IMO 2030 and IMO 2050. The system can be integrated into new build vessels and retrofitted to existing vessels.
CO 2 could be used to make methanol based on green energy. This methanol
has a low carbon intensity and can be used again on board as ship fuel, creating a carbon-neutral cycle. Eventually, it also contributes to a more gradual transition to synthetic fuels.
Mr Veldman explained that captured CO2 could be stored on the vessel in a tank. The CO 2 would be transferred from the vessel to an onshore storage facility in port and then moved to a plant to produce synthetic fuel. Hydrogen from green energy (sun or wind) is combined with the captured CO 2 into new synthetic fuel, which could be used in any application, for example, in the maritime, aviation or transport industries.
“In this way, carbon emitted by the vessel is either re-used for new fuels, or stored long-term which is labelled as carbon neutral. Either way, it has a positive contribution to decarbonisation,” he added.
Mr Wijdeveld said VDL AEC Maritime was advancing carbon capture technologies for marine environments as part of two partnerships – EverLoNG and the LNG-ZERO Projects – to help achieve shipping decarbonisation goals.
“Both are subsidised Dutch consortia working to marinised carbon capture technology – effectively making established land-based technology applicable to the marine sector.”
EverLoNG is a project consortium that features 16 project partners from Germany, the Netherlands, Norway, the UK and the USA. These include exploring different low-carbon technologies, including shipbased carbon capture (SBCC), which could provide a low-cost solution compared to zero-emission fuels.
The project aims to encourage the uptake of SBCC by demonstrating its use onboard LNG-fuelled ships and moving it closer to market readiness. Their research will optimise the technology and consider how best to integrate it into an existing vessel and port infrastructure.
EverLoNG’s interlinking studies would support the development of full-chain carbon capture, utilisation and storage networks – connecting SBCC with CO2 transport links,
geological CO 2 storage and markets for CO2 use. They include Life Cycle Assessment and Techno-Economic Analysis. It is also contributing to the development of regulatory frameworks for the safe and effective use of SBCC.
LNG-ZERO is an ambitious research project that aims to develop the technology and strategy needed to reduce exhaust emissions to contribute to sustainable shipping.
A threefold strategy will achieve this: capture the carbon dioxide, significant reduction of methane slip (CH4) / N-emissions, bring the captured carbon to shore for new applications (such as a base material for the production of synthetic fuel) or directly offshore for permanent geological storage, and achieve a massive reduction of GHG in the complete chain. Any residual emissions are offset by the use of bio-LNG.
The project, which TNO initially introduced, includes the efforts of energy and infrastructure developers (Shell, Carbon Collectors, end-users (Heerema, Anthony Veder) and important suppliers and system integrators, including VDL AEC Maritime.
TNO and the technical universities of Twente and Delft are the research partners working on the eco-topics. Safety and performance standards are being developed in conjunction with Lloyd’s Register.
The companies working on this project have created a €6.1 million budget, of which the Dutch government has granted a subsidy of €4.4 million.
Mr Veldman asserted: “LNG-ZERO is to aim for a high impact and be ahead of future IMO regulation. In this project, we’re developing technology to ensure the maritime industry’s total decarbonisation – and fight the global climate crisis challenge.”
In parallel to these projects, VDL AEC Maritime is developing an in-house project, with its carbon capture partners, for Heavy Fuel Oil (HFO) vessels, which face an even bigger challenge in the decarbonising arena.
“We are actively looking to launch for clients or projects. Next to developing carbon capture technology, with our back-
ground in SOX scrubbing we prove that we can do such big projects on vessels in a safe way,” said Mr Veldman.
He explained: “We are heading for an increase in maritime greenhouse gas emissions of 20% by 2050 despite current industry-wide efforts. Growing trade volumes, technological developments and existing CO 2 reduction initiatives across the sector will not give shipping enough traction to deliver what is needed to meet the current IMO targets. Shipping needs to step up.”
While the IMO has taken measures to tackle climate change and reduce carbon emissions, it is expected national and local legislation will seek stricter targets. It may only be a matter of time before carbon taxes begin to bear down on global shipping.
“It is important for ship owners to prepare themselves thoroughly and sustainably for the future, in which everstricter requirements will be imposed on the emission of greenhouse gases,” said Mr Veldman.
Both gentlemen re-iterated the company offers complete and tailor-made design,
engineering and in-house manufacturing of clean air technology systems for industrial and marine organisations.
A VDL AEC Maritime scrubber is always tailor-made, assured Mr Wijdeveld.
“The size depends on the maximum capacity of the engine, keeping the lowest energy consumption in mind. If space is limited, we can adjust the scrubber size. We can outfit the ship with closed-loop, open-loop or hybrid scrubber solutions.”
Apart from continuing to use HFO while complying with IMO regulations as all scrubbers do, it offers specific cost-saving advantages.
“The biggest is that, through patented design, our scrubber uses a relatively low amount of water, which minimises the size of pumps and piping,” outlined Mr Wijdeveld. “This results in a low amount of energy consumption for the water flow.”
He added: “‘Strength through cooperation’ is the VDL Groep motto. We work globally and build relationships with clients and suppliers looking for longterm partnerships, and quality for the current business case with scrubber systems, and potential future projects.”
Mr Wijdeveld asserted that VDL AEC Maritime, whose slogan is ‘Scrubbing made simple’, always strives to supply systems that are easy to install and simple to maintain without compromising quality.
With all these attributes, the company recently secured orders to retrofit two SOx scrubber systems for Seatrade Groningen BV. These will be delivered before the end of 2022.
Mr Wijdeveld said: “This deal is very important for us. We are very excited and looking forward to great cooperation with Seatrade Groningen.”
Both agreed the biggest industry challenge was the carbon capture conundrum, with Mr Wijdeveld adding: “The maritime world is not yet ready for carbon capture, and the IMO does not have real incentives to introduce such technology, and the class rules are not even ready yet.”
Meantime, VDL AEC Maritime enjoys the backing of its Dutch family owned parent, VDL Groep, which focuses on long-term relations and goals with suppliers and clients.
VDL Groep employs over 16,000 people and consists of 105 different companies, spread across 20 countries, each having their own strengths and capabilities and
all working closely together, which can be utilised across different sectors.
“One main focus for the VDL Groep is the global energy transition in all forms and sectors,” said Mr Wijdeveld. “This enables VDL AEC Maritime to focus on the hard-to-abate shipping industry with SBCC and other aspects for the future, which may include the VDL Groep’s electrification technology with batteries and fuel cells.”
He concluded: “We at VDL AEC Maritime believe SBCC will be a major game-changer. SBCC development is aimed at sustainability, and we require sustainability from our supply chain to minimise the carbon footprint. The whole world is screaming for action on decarbonising the maritime industry. We agree, we all need to act now.” n
SEKAVIN is a Greek family-owned, global energy provider, committed to reliable and efficient bunkering services. The company is a physical supplier in Piraeus and Syros, where SEKAVIN owns a strategically located fuel bunkering station in the Central Aegean. SEKAVIN also services a wide range of customers through its global bunker and lubricant trading desk. With more than 40 years of experience, its team is highly regarded for ensuring efficient and high-quality services to a host of clients. Profile by Andy Probert.
Established in 1979, SEKAVIN has become a specialised, leading supplier of fuel oils, distillates and lubricants to the broader region around Piraeus Port, Agioi Theodoroi and Syros Island.
The company’s physical supply desk is complemented by a back-to-back bunker trading division that serves clients worldwide, a physical operations unit for vessels coming to Greek ports and an agency mainly serving clients in Greek ports.
The $200 million company, which employs 120 people, registered an average 15% growth in volumes in 2021 and has predicted similar growth in 2022.
“The combination of these three units brings added value to our customers, serving them across the entire value chain surrounding t heir bunkering operations,” commented Sifis Vardinoyannis, Director to the Company Board, and day-to-day Operations Manager.
“SEKAVIN has been one of the main suppliers in Greece since its founding and has maintained good market share in the bunkering market. Our philosophy entails catering to clients’ priorities and providing competitively priced, effective services.”
SEKAVIN’s ownership and operation of a bunkering station south of Syros Island, in the Central Aegean, is logistically placed to serve vessels on various routes: from the West Mediterranean and Adriatic to North Greece, the Bosporus Straits, Black Sea, Asia Minor Levant and Suez Canal.
The station has five tanks; three for fuel oil with tank capacities ranging from 2,800 cbm to 18,000 cbm, and two storage units for gas oil, ranging from 800 cbm to 2,000 cbm. Supplies from the 30,000 cbm hub take place ex-wharf for vessels up to 20,000mt or by barge at anchorage off Syros Island for vessels above 20,000mt. Mr Vardinoyannis emphasised the deviation costs that would have been incurred on vessels calling for bunkers to nearby ports are eliminated.
The company operates the bunkering station 24/7 in accordance with ISO specifications, with continuous supervision and fast turnarounds with pumping rates up to 500MTS per hour, while providing a full range of fuel oil grades from 30CST up to 380CST.
“We have experienced and well-trained personnel who spare no effort in making the most difficult request possible for a customer’s total satisfaction.”
SEKAVIN also pays attention to the ecological aspects of bunkering activity, strictly following existing rules around petroleum transshipping operations and preventing leakage of oil products.
“We strive to minimise the risk of environmental incidents at all times and are ready to respond rapidly and effectively should a problem arise.”
The Syros facility also provides a revised oil spill response facility contingency plan. It is equipped with antipollution equip -
ment and modern technology to prevent oil spills and detect leakage of oil products. The company’s antipollution team is highly trained and the company invests to ensure the health and security of its personnel at all times.
The Piraeus-headquartered company also utilises four barges for fuel deliveries from the Motor Oil Refinery and the Hellenic Petroleum Refinery on charter to clients’ vessels to all Greek ports.
Mr Vardinoyannis said SEKAVIN operates four vessels ranging between 900 and 5,000 DWT. They include a long-term bareboat charter of a vessel in Syros and the time charter of a vessel to a sister bunkering company in Greece. The company owns two 3,500 DWT oil tankers, the Kalikratis and Zakros, and expects a new vessel in mid-2022.
“Our clientele buys from traders and charterers to direct owners,” he informed. The type of vessels they serve is around 70% bulkers, 20% tankers, and the other 10% is a mix of vessels from cruise ships to ferries.”
SEKAVIN also supplies MFO380cst, MFO180cst, MGO and lubricants to all types of vessels and ensures operational excellence across the supply chain from the refinery to vessel.
Boosted by an excellent performance in 2021, the company is now looking to expand operations into other ports and increase market share in Greece.
It is an
interesting time in the industry, as energy transition and scrutiny of shipping places bunkering firmly at the centre of these overlapping circles.
It remains a very competitive landscape “ ”
“This may well include an expansion of our barge fleet, but we are also looking at renewables and anything to do with carbon offsets,” commented Mr Vardinoyannis.
“Our driving force at the moment is the back-to-back trading unit, and the goal is to expand our capabilities to include physical operations in various locations. If we reach a critical volume that makes sense for us to create a physical operation, then we will do it.”
During the pandemic, the company sold off some of its old vessels and managed to time-charter its vessels for short periods, which helped pay off running costs.
“Performance in Q1 2020 was very strong, but it was more of a transitional year,” stated Mr Vardinoyannis. “2021 overall was a strong year, both in terms of volumes and margin, with increased demand driven by our trading unit which commenced operations in May.”
He added: “Challenges do remain, with commodity price volatility exacerbated by major geopolitical events in the Ukraine, the evolving compliance and regulations framework, while competition in the bunkering market heightens as new players come into the industry. Nonetheless, our business is always committed to serving our customers first, leveraging our decades-long experience and in-depth knowledge of the shipping and bunker markets.”
Mr Vardinoyannis said that being transparent, honest and accountable gives SEKAVIN’s suppliers and clients confidence, and “we always deliver what we promise”.
He concluded: “It is an interesting time in the industry, as energy transition and scrutiny of shipping places bunkering firmly at the centre of these overlapping circles. It remains a very competitive landscape, and I believe our company is strong and optimally positioned. We therefore look forward to the future with optimism.”
n
Sepor is one of Italy’s leaders, delivering multi-level solutions in waste treatment, pollution prevention and tank cleaning. The jewel in its crown is a recently opened multi-purpose, sustainable solid and liquid waste hub in the port of La Spezia. Andy Probert discovered more from Business Development Director Mattia Mori.
ITis probably unusual to find a solid and liquid waste treatment plant located at the heart of a major trading port – let alone a few steps from a cruise terminal and less than 500m from a city centre.
But therein lies the ingenuity of the ambitious Mori family that stands behind Sepor, a 70-year-old, family-owned business, and owners of their April 2021 opened commercial treatment plant at the head of Molo Garibaldi in La Spezia port.
La Spezia, the second-largest city in the Liguria region, is located on the Ligurian Sea and one of the main Italian military and commercial harbours.
Sepor’s waste treatment plant, or port reception facility – is a realisation of everything the Mori’s stand for in their life-long understanding and knowledge of waste treatment solutions.
The company, founded by Cesare Mori in 1952, specialised in supplying port services to commercial ships in transit through La Spezia. However, over the years, Sepor’s services have subtly turned more towards the ecological sector for the port and the industrial sector.
These services extended to tank cleaning and industrial and naval high-pressure washing for refineries, depots and the oil and gas industry in general. Sepor built its first port reception facility
for wastewater treatment in La Spezia in 1988, later enhancing that with the construction of a waste sterilization plant.
Today the business is considered an industry leader in industrial and naval decontamination, tank cleaning, waste recovery and treatment, pollution prevention, and land and marine oil spill response.
The new facility is a batch and biological chemical-physical plant with ultrafiltration, authorised to treat 75,000 tonnes of liquid waste annually. The plant is powered most of the year by an impressive photovoltaic system built on its roof.
“The plant’s uniqueness is that it operates totally in vacuum conditions to avoid any odours escaping to the outside environment,” commented Business Development Director Mattia Mori, grandson of Cesare.
Plant management is fully automated: a single operator from a control room can manage every single process. It can treat up to six types of contaminated liquids simultaneously, each with different treatment processes, plus two other processes for the management of oil treatment lines.
He added: “It is the result of our 40-year experience in the port reception facility sector. It represents excellence in technology, sustainability and environmental protection compared to similar plants at ports in Italy and across Europe.”
The plant is authorised to carry out operations and treat liquid waste produced onboard ships, and is also equipped with a sterilization system to eliminate any pathogenic microorganisms, viruses and bacteria from the solid waste delivered by ships before being sent to landfill.
Sepor currently operates four divisions, the biggest being the port and non-port related waste disposal services which accounts for 48% of turnover. It has a reclamation division of tanks and naval units (25%), a port services division (20%) and land and maritime environmental emergency services (7%).
Turnover in 2020 surpassed €11 million following five years of constant growth.
“We believe our results are among the best for Italian companies that operate in the management of port reception facilities and in the environmental sector,” Mr Mori asserted. “Our company is not in debt, and we use almost exclusively equity capital for our investments.”
He added: “We believe the greatest growth opportunity in the next few years will come from the waste disposal sector. Thanks to the new port reception facility, we hope to triple the amount of waste managed annually.
“Waste comes from the port and largely from various production plants located throughout Italy. We are also receiving significant waste streams from Southern Italy.”
Customers range from public bodies, such as port authorities and the Military Arsenal of La Spezia, to maritime terminals, shipping companies, oil and gas multinationals in Italy, multi-utility companies and customers in the manufacturing industry.
“Our strength is that we have managed to establish ourselves widely across Italy and have large numbers of satisfied customers. In 2020, we counted 352 customers.”
Sepor also operates eight vacuum trucks and other trucks/cranes mostly to Euro 6 emission standards. Also on the company’s books are ten barges of various sizes; seven recently built with double hulls to ensure greater safety against the risk of spills, and with a company-invented system of easily removable crates to allow faster reclamation operations.
It also has two tugs, two vessels for collecting garbage from ships, and the Optimist and Acqua Azzurra dedicated to oil spill responses.
The 2003-built Optimist is a versatile catamaran for a marine environmental emergency, such as the recovery of accidentally spilt petroleum products and small-sized floating solid waste from the sea surface. It can be disassembled, transported and re-assembled in an emergency location within hours: making it suitable for quick transportation across lakes or rivers in case of need.
The Acqua Azzurra is Sepor’s best performing catamaran for emergency responses. National and international clients have chosen the vessel to manage environmental emergencies in very delicate situations. The first time it was used was after the sinking of Costa Concordia at Isola del Giglio and is still considered the best catamaran of its type offered by Italian suppliers.
Mr Mori added that Sepor, in 2005, innovated its tank cleaning division with the acquisition of the company’s first “No Man Entry”, a device for the automatic fluidisation of the storage tank sludge and the enhancement of the petroleum product content.
This followed with the “Lombrico” robot (Earthworm) for the extraction of sludge from containers and tanks, and a “Spider” robot for vertical washing of tank shells.
“We also have machines to perform hydro-cuts in environments at risk of explosion and mobile machinery to minimise sludge and for water treatment,” he emphasised.
“The ultimate goal is to minimise disposal and use of water, recovering and enhancing petroleum products during reclamation works. These are becoming complementary operations to our tank cleaning procedures that oil companies really appreciate.”
Mr Mori acknowledged that Sepor, whose CEO is his father, Giorgio, cannot stand still in investment and innovation.
“All our innovations of the last few years result from careful technical and economic research. This has been carried out by our internal management, of which both my brother Jacopo and I are part, and which includes people of different age groups and diverse technical-cultural backgrounds.
“Our equipment is always at the forefront: we cannot run the risk of being left behind in a constantly evolving market that increasingly rewards sustainability and innovation.”
Testament to that is the recent commissioning of Sepor’s first fully electric-powered vessel to collect garbage from ships.
Designed with a fibreglass hull, the 18m vessel will be delivered in early 2022 to replace an existing diesel-powered vessel.
“This new unit will be used to sort garbage into different bins and transport these bins to the berth,” detailed Mr Mori.
“To recharge the electric engines, which will occur at night, we have equipped our berth at La Spezia with a charging column. We anticipate it will be the first port in Italy to adopt such a solution.”
He added: “Our goal by 2026 is to replace all our diesel-fuelled ships with electric or mixed propulsion vessels. We also plan to replace our land fleet with more modern Euro 6 emission standards and, where possible, with suitable hybrid electric vehicles.”
In recent years, Sepor has made improvements in the field of self-produced energy from renewable sources. It has installed photovoltaic plants for a total of 110kw and seeks to increase this in coming years. The company is planning an annual sustainability report and considering applying for a B Corp Certification which measures a company’s entire social and environmental performance.
Sepor’s ambitions are to operate beyond Italian borders in time. Occasionally it performs work in the tank cleaning oil field in Croatia, Israel and previously Libya.
“We would like to expand abroad in the port and waste treatment sectors, but these activities are highly capital intensive and require
the right partners,” Mr Mori remarked. “At present, we concentrate on our national market as it still gives us great satisfaction.”
Mr Mori acknowledged “the world is changing faster than ever before and we are experiencing an epochal moment of transition as our stakeholders are increasingly attentive to the environment and sustainability.”
He concluded: “Sepor will continue to focus on environmental and sustainability solutions. What makes us proud and certifies our success are our financial results. They are our guarantee that the market rewards and appreciates us. But what makes us unique is our spirit of innovation: we are always in constant search for excellence and improvement.”
seven seas, five oceans, one voice
erma first slce watermakers
ERMA FIRST, a leading Greek maritime-focused engineering group, has continued to evolve at pace during the pandemic by successfully transitioning to become a multiplatform solutions provider with the concerted aim to protect the environment. Having made two key acquisitions, including oneTANK, the world’s smallest ballast water treatment system, the company is now poised to launch BLUE CONNECT, an alternative management power system for vessels. By Andy Probert.
Greek maritime engineering company ERMA FIRST has gained an excellent reputation as an expert manufacturer and installer of ballast water treatment systems in the last decade. Having more than 3,000 units aboard vessels, it has been at the forefront of a fast-maturing niche market given the imposition of IMO and USCG rules on environmental protection.
While the company enjoyed a 20% uplift in BWT business in 2021, ERMA FIRST has also demonstrated its adaptability in a relatively fast-moving market.
“We completed two acquisitions, launched a new product and have other plans in the pipeline reflecting a strategy and desire to become a multi-product, multi-market player,” confirmed Managing Director and co-founder Konstantinos Stampedakis. “We are not afraid of change. We embrace it.”
Piraeus-headquartered ERMA FIRST was established in 2009 with its first generation BWTS certified in 2012 and onboarded to 50 vessels. Its second-generation FIT system was launched and installed on 2,100 ships, ranging from luxury yachts to crude oil tankers.
The company expects to see BWTS installations hit a peak of 1,000 vessel installations in 2022, compared to 800 units in 2021 and 420 installations on 320 ships in 2018.
The system was the first full flow electrolysis BWTS vendor worldwide to be granted United States Coast Guard (USCG) approval. A second USCG citation followed in 2020 for its third filter alternative by adding HYDAC filters to its range of options.
Tested in three water salinities, the FIT system offers a reliable, simple and effective solution for all types and sizes of vessels. Covering an extensive capacity range from 50 to 3,600m3/hr, FIT’s primary components are a high-end backwash filter and an electrolytic cell.
A self-cleaning automatic screen filter has a nominal filtration rate of 40 microns. It offers enormous zooplankton, phytoplankton and sediment removal, minimum pressure and uninterrupted, long-lasting operation on a small footprint element.
ERMA FIRST introduced several advancements to FIT in 2021 to aid efficient installation on larger vessels and tankers. It also launched a remote monitoring system operation for the system, with embedded artificial intelligence for data analysis collection.
While the company, which employs 200 people across Piraeus and offices in Korea and China, has continued to keep pace with BWTS demand from international clients, it also consolidated its business standing with expansion and acquisition in 2021.
Its first acquisition was Bremen, Germany-based marine water specialist RWO GmbH. RWO provides water and wastewater treatment systems for ships, ports and offshore installations and is a market leader in bilge water separation systems.
RWO’s product portfolio includes the treatment of drinking and process water, bilge oil water, ballast, wastewater, and a comprehensive range of after-sales spare parts and services. Over 16,000 ships have been equipped with RWO’s oil water separators since 1975.
Mr Stampedakis commented: “In RWO, we acquired a world leader in water treatment systems for the shipping industry with a solid customer base and a reputation for excellence and reliability. Such acquisition makes ERMA FIRST one of the biggest marine equipment suppliers when it comes to the installed basis which is in the range of 20,000 vessels.
“We have a track record of innovation with our ballast water technologies and are well known for our high-quality engineering and customer-first ethos. We are committed to building on RWO’s experience and to help take the company, its products and people to the next level of international success.”
ERMA FIRST then followed this with the acquisition of oneTANK, the world’s smallest and easiest to install ballast water treatment system. US-based oneTANK was a subsidiary of naval architecture and marine engineering firm Glosten and had developed a small scale innovative, low-cost, IMO Revised G8 Code and USCG approved compliant system.
The system can be installed in larger vessels’ aft peak tanks based on a patented mixing technology developed by the US Geological Survey. It is also suitable for workboats, tugboats, semi-submersibles, fishing vessels and superyachts.
The technology is already being adopted on ships in aft peak tanks within Overseas Shipholding Group’s tanker fleet and the dredger MV Charlock in the Netherlands.
“This is a game-changing ballast water treatment technology,” declared Mr Stampedakis. “oneTANK is compact, simple to use, and fully automated. It delivers a quick to install additional solution for after peak tanks on big ships and a stand-alone solution for small vessels.
“To win the battle against invasive marine species and effectively protect our vulnerable marine eco-systems, ballast water from internationally trading smaller vessels also needs treating in a way which is practical and economically viable. We believe we have this solution in the form of oneTANK.”
The system treats ballast water within the vessel’s ballast tank and has no filters, ultra-violet lamps or electrolytic chlorine generators. Its footprint is only 600mm x 600mm, half the size of its nearest competitor, and power consumption is similar to that of a household washing machine.
oneTANK provides a ballast water management solution that works in all water qualities and salinities. The system uses an 8.25% or 12.5% sodium hypochlorite (bleach) and 30% sodium thiosulfate solution – readily available chemicals from suppliers worldwide.
Application is practical for smaller vessels as a 20-litre container of 12.5% bleach will treat approximately 288 cbm of ballast water. For larger vessels, oneTANK can treat tanks as large as 4,000 cbm.
ERMA FIRST has since announced it would be supplying oneTANK to Damen Green Solutions, the Netherlands-based shipbuilding and engineering expert. Damen has a broad selection of BWT systems in its range, and the addition of the ERMA FIRST oneTANK will provide its clients with a solution that is small and modular.
He explained: “oneTANK is small enough to be housed in a 20ft container. This means installation is quite straightforward and, more importantly, at the end of the vessel’s operational life, it can be removed and installed on another vessel.
“The system is a game-changer for the target vessels with space limitations, struggling to comply with stringent ballast water regulations. For ERMA FIRST, it opens a completely new and exciting avenue of business opportunity and potential in the BWTS niche.”
The recent acquisitions complement the 2019 takeover by ERMA FIRST of METIS Cyberspace Technology, previously owned by Olympia Group.
METIS specialises in electronic engineering, IoT, cloud computing and artificial intelligence, offering a platform that enables shipping companies to acquire and analyse data to improve performance over a wide range of operational aspects.
The innovative METIS platform uses cloud-based virtual personal assistants that work ceaselessly to provide in-time information, diagnosis and prediction to company personnel through a conversational user interface focused on the requirements of shipping companies.
METIS’s expertise is complementary, offering an extensive added value to ERMA FIRST’s. With technology playing an increasingly critical role in every aspect of the industry, both companies recognise the need to accelerate the development of green digital solutions to ensure they remain competitive.
Mr Stampedakis revealed the company has also launched ERMA FIRST BLUE CONNECT, an alternative management power system. It is a containerised solution installed on the vessel and can be connected to shoreside electricity sources when in port, helping them reduce environmental impact.
He explained: “There are many localised regulations in ports worldwide that do not allow a vessel to burn any fossil fuels while it is in berth. Instead, the port offers a shore power connection. But to connect with an alternative power source, a vessel requires something like BLUE CONNECT that allows this connection.”
The concept of cold ironing, another definition of the alternative management power system, is not new and has been helping ships reduce their direct carbon emissions and comply with local air quality regulations. However, the increasing amount of renewably generated electricity now available on port electrical grids means that plugging into shore power really can be carbon neutral.
Every ship operator is facing the challenge of reducing their carbon footprint and increasing energy efficiency. Cold ironing offers a way of achieving this. Plugging into shore power and switching off engines also means less noise and less local particulate pollution for local port communities.
BLUE CONNECT was officially launched in November 2021 at a conference in Greece after extensive R&D trials were completed. It will initially be offered to the container, RoRo, cruise and tanker sectors.
BLUE CONNECT will provide Onshore Power Supply (OPS) systems suitable for retrofit and new-build vessels. It will be available within a container or as a stand-alone system with components installed at a convenient onboard location.
“We have received many enquiries for BLUE CONNECT, and we are hopeful that we will sign a couple of projects that will act as a pilot so the unit can perform, it can be reviewed and any design changes handled before mass production,” said Mr Stampedakis.
ERMA FIRST has also initiated R&D projects for three new products, including one for carbon capture and storage, which Mr Stampedakis described as the next big challenge facing the shipping industry.
“Challenges, such as the global supply chain issues around electrical and electronic products, and spiralling raw material cost, are being faced. But due to good planning and stocking equipment, and support of loyal suppliers, we are managing. If this situation does not resolve itself by the end of 2022, we will plan accordingly to continue to meet the high demand of the market.”
Mr Stampedakis said: “Given our financial sustainability, bringing on board two new companies and their products, and with BLUE CONNECT, we believe we will remain strong in the market.
“As for green sustainability, we are trying to measure the carbon footprints of our products in their lifecycles, trying to find ways of reducing the transportation mileage of the products, and we are also initiating a procedure of improving our packaging, either through wood or recycled materials.”
Never a company to stand still, ERMA FIRST, said Mr Stampedakis, is always looking to improve its products, making them more efficient – both cost-wise and performance-wise.
“We are committed to clients; we still manage each project uniquely with a dedicated project manager and team,” he said.
“We are not afraid of investing in new products or investing in products for the marine environment. It makes ERMA FIRST a one-stop solution for many ship owners for wastewater or water treatment onboard the vessel.
“What defines us is our can-do attitude, dedication and open relationships with clients. We will do all we can to deliver, meet their needs and find a solution to any challenges they have.”
He concluded: “We do believe when it comes to ballast water and oneTANK we can provide for every type and size of vessel. By investing in RWO, we have more than 20,000 vessels equipped with our products.
“ERMA FIRST is shifting its profile from a single-product, singlemarket company to a group of companies, with multiple products. We consider ERMA FIRST is now one of the strongest on the market, with a consistent focus on quality marine protection.”
How can a family business survive against competitors several times its size? SLCE Watermakers, a designer and manufacturer of reverse osmosis (RO) equipment for over 30 years, offers us some hints. The French-based company was established in 1989 by two engineers: Patrick Riot, the current Managing Director, and Gilles Gury, President. Ever since its creation, the business has experienced steady growth and today has 46 staff, a turnover approaching €10 million, and has delivered more than 600 machines in 2021.
Afew years prior to its official establishment in 1989, the seeds of reverse osmosis (RO) specialist SLCE Watermakers had already been sown. In 1984, Patrick Riot and Gilles Gury were working together on water treatment for another company which delved into RO development when it wanted to diversify its activities.
“A few years later, the new owner decided to focus back on the core business of this firm and decided to stop RO development,” said Mr Riot. “We agreed to leave the company with the RO prototype and one customer because we believed RO equipment to be a promising business.”
The pair’s instinct was right. Over 30 years later, Mr Riot and Mr Gury are heading a €10 million business which successfully continues to purify water through the reverse osmosis process.
“Compact and reliable equipment for the yachting market is where we started,” said Mr Riot. “Once the reliability of the equipment was proven, we quickly added the fishing market to our portfolio. Once again, the products proved to be reliable enough for very heavy duty use in harsh environments. Addressing the fishing market was also an opportunity to test our ability to provide efficient technical support and quick delivery of spares worldwide.”
Full of confidence, the company then decided to address the Navy sector. However, Mr Riot admitted this market proved to be more difficult to penetrate than initially expected.
“Indeed, the players tended to stick to the evaporator technology and above all to companies with a proven logistic support,” he said.
The breakthrough came when the French Navy, having some issues with the evaporators of a ship in operation, approached SLCE Watermakers for a solution. The company supplied a preseries equipment it had just qualified, and after a couple of weeks in operation, the Navy was convinced of the efficiency, flexibility and reliability of our RO solution, including the logistic support provided by SLCE Watermakers.
“From that day, the French Navy replaced most of its evaporators with RO systems and decided to integrate them into their new programs as well,” said Mr Riot. “This gave us higher visibility in the Naval world and an opportunity to export our solutions worldwide.
The Navies of Singapore, New Zealand, Morocco, Belgium, Argentina, Saudi Arabia and UAE, to name a few, have since been supplied by SLCE Watermakers.
“With this new market, we showed our ability to offer high-class logistic support and traceability with very complete documentation,” Mr Riot said.
In the early 2000s, SLCE Watermakers launched a new range of equipment integrating an energy recovery solution which reduces power consumption by more than half compared to classic systems. At that time, SLCE Watermakers was the only company offering such a solution for capacities between 100 and 500 cbm per day.
“To give an idea of the impact,” said Mr Riot, “The island of Ile de Sein in Brittany used to consume 25 litres of petrol to produce 1 cbm of freshwater with their evaporator. When the municipality switched to a classic RO system, they dropped petrol consumption to 2.5 litres per cbm of freshwater. Eventually, with the energy recovery solution we offered, they reached 1cbm of freshwater for 1 litre of petrol.”
With such impressive results, SLCE Watermakers began taking enquiries from the cruise ship sector for this range of products. Starting with a medium size cruise ship, the company then had the opportunity to provide equipment on a larger cruise ship which was producing 1,250 cbm per day.
“Once again, we proved to be successful,” Mr Riot said with pride. “At the end of our first project with Meyer Werft on their build of Saga’s newest boutique ocean cruise ships, Spirit of Adventure and Spirit of Discovery, we were delighted to receive incredibly positive feedback on the quality of our products.
“Above all, the shipyard congratulated us on the fact that, for the first time ever, they had accepted reverse osmosis plants after the first sea acceptance test. For us, it was as we’d planned it.”
Today, SLCE Watermakers’ range offers solutions with capacities between 1 and 1,500 cbm per day of fresh, industrial or nuclearquality water from sea, borehole or tap water.
Speaking about the transition from manufacturing a couple of yacht units to solutions for cruise ships, Mr Riot said the evolution did not happen overnight.
“In terms of organisation, we now have two philosophies cohabiting: one for standard products and one for special projects,” he explained.
“Standard products are built on dedicated assembly lines organised according to the Lean Manufacturing method. It enables us to produce a couple of hundred machines compared to a couple of machines in the early days. These assembly lines are followed by a test bench where every single unit is fully tested before shipment.”
Special projects benefit from the company’s new 1,000 sqm building extension which was finalised in early-2022.
“With new 20-tonne and 10-tonne bridge cranes, a 450 sqm test bench and a 24,000 litre seawater tank, we are ready to handle more special projects than before and in better conditions for our team,” said Mr Riot.
He added: “It goes without saying that we would be nothing without our team. We are constantly doing our best to offer good and safe working conditions to our workforce. We also make sure they gain competencies and responsibilities with their experience. As a result, we have a very stable team; some of them have been with us for more than 25 years. The result is a high level of service to our partners.”
According to Mr Riot, there are two philosophies that companies in SLCE Watermakers’ market could follow.
“The first one is to target a market price and the level of quality will be a consequence of that,” he said. “The second way is to target a level of quality and the price will be a consequence of it.”
He explained: “In the middle of the sea, crew can’t have spares delivered, or a technician coming on-board. Therefore, we believe quality is critical. That is why we stick to the second philosophy. The whole team then focuses on one target: making the level of quality required at a price as close as possible to the market price by looking for and eliminating any waste.
“Our design team will optimise the integration of the components, and our quality team will check the supplied components to avoid any issue after assembly. Eventually, if we cannot match the market price, we prefer not to take a project rather than have an unhappy customer. In the long-term, we have found this to be a winning strategy.
Exports currently account for 70% of the company’s turnover. To achieve such global coverage, SLCE Watermakers has developed an international network of distributors. When partnering with these distributors, Mr Riot strongly believes that stability ultimately offers customers a better service.
“We have been working with many of our distributors for more than 15 years,” he said. “We work with Vanson in India, Aquanautic in Singapore, Oceanpower in China, and Sin Tung Hin (formerly known as SOPOM) in French Polynesia. The experience of our partners combined with complete training in our premises, means our network is built to offer high-class technical support.”
Speaking of the company’s long-term plans, Mr Riot said one of the first steps will be the transition of the company to the second generation of ownership, which is earmarked for 2023.
“Next year, Benjamin Gury and Charles-Henri Gury will take charge of SLCE Watermakers. This is a long`-organised transition as Benjamin started with us almost 15 years ago in the design office. After evolving as a Sales Engineer, he will become the next Managing Director; his brother being in charge of the supply chain.”
Outlining the plans in greater depth, Benjamin Gury added: “There will be no revolution as the company has steadily been evolving to match its economic and technical environment; we will remain attentive to the changes and keep being proactive.
We will maintain our focus on stability. In a fast-changing environment, stability is an everyday struggle. However, we believe it is a key
ingredient for long-term relationships with our workforce, suppliers, distributors and customers leading to cost efficient and high quality solutions. Remaining a family business will help in this regard.”
Increasing the sustainability of the company’s activity – from the design to the recycling of its system, without forgetting the fabrication and the operation of the equipment – will also be key topics for the years ahead.
“With a French partner, we offer equipment powered by the sun without the use of batteries which is the Achilles’ heel of solar power systems – they are expensive and have a rather low life span,” revealed Benjamin Gury. “The idea is to regulate the water production based on the solar power available instantly. For instance, when a cloud passes by, the unit slows down. The idea is to store freshwater instead of electricity. This solution has been implemented several times already.
“We also recently equipped a pilot-factory producing greenhydrogen. The equipment produces 20 cbm of pure water every day. This water is then electrolysed to release the hydrogen. Before this project, we equipped the Energy Observer, a research vessel which uses a fuel cell requiring hydrogen directly produced on board. We are one of the first bricks of the emerging green-hydrogen industry!”
Benjamin Gury concluded: “These are examples of what can be done regarding sustainability when several companies combine their expertise. Four other projects related to sustainability are currently on our agenda for the coming years and I hope we will be able to present the results of two of them at SMM 2024.” n
seven seas, five oceans, one voice
peel ports altamira terminal portuaria i M
Peel Ports, one of the UK’s largest port operators, is on a mission to minimise carbon emissions, investing in a range of green technologies throughout its operations. Lewis McIntyre, Managing Director for Port Services at Peel Ports, explained how ports can play a pivotal role in reducing global supply chain emissions.
SAone of the UK’s leading port groups, the operator owns and manages some of the UK and Irelands, most important ports and terminals. From Dublin, to the West Coast of Scotland, down to the South East of England, Peel Ports provides critical infrastructure for vital supplies.
Each year Peel Ports safely handles over 65 million tonnes of cargo from across the globe, representing a 14.2% share of the UK market. The port operator has a strategic focus on sustainability and aims to ensure that its strong port operation facilitates regional economic growth.
This year, the company has been recognised by Maritime UK with a prestigious award for seizing the opportunities presented within the UK Government’s Maritime 2050 strategy for the sector.
It is the third award Peel Ports has won in the last 12 months after receiving Greenfleet’s Private Sector Commercial Fleet of the Year award for its conversion to electric vehicles, as well as winning UK Ports Directory’s Port Operator of the year in 2021.
According to Lewis McIntyre, Managing Director for Port Services at Peel Ports, what really sets the company apart from its competitors is its willingness to invest.
“In the last five years, we’ve invested over £750 million into our facilities,” he
remarked. “The £400 million investment into Liverpool2 has been a game-changer for The Port of Liverpool and has firmly positioned viable alternatives to congested ports in the South East of England.
“We invest where it matters and where we can make a difference,” he added. “We’ve even spent £100 million on a biomass facility at one location because that’s what we needed to do for one of our customers.”
Peel Ports operates across five geographical areas, including the West Coast of Scotland, North West England, South East England, Norfolk and Ireland. Across these areas, it has 18 terminals, including container, Ro-Ro, car, steel and metals terminals. In total, its facilities occupy 3,500 acres across the UK and Ireland, of which its warehousing and distribution centres alone span a massive 9 million square feet. The business is manned by a staff complement of around 2,000 people.
Sustainability is a major strategic priority for Peel Ports and it informs much of the company’s decision-making, explained Mr McIntyre: “For the company, sustainability is about investing in the business so it can grow and prosper long into the future, whilst still being a good neighbour and employer, minimising our
environmental footprint and creating career opportunities for local people through well-paid quality jobs.
“In addition to our 2,000 employees, we probably have 2,000 businesses in Liverpool alones which directly benefit from our operations . For example, we might create more warehousing space and that create jobs for third parties and, in turn, this supports the wider economy.”
In October 2021, Peel Ports announced its commitment to become a carbon neutral operator by 2040.
“We’re doing a huge amount of work to reduce our carbon footprint and that’s beginning to be acknowledged,” Mr McIntyre remarked. “In December 2021 we won an industry award from Greenfleet which recognised our strategy to convert all our vehicles to electric by the end of 2022, and we are already 50% of the way there.
“The fact that it takes probably eight or nine months to procure an electric vehicle indicates the amount of planning that went into that achievement; we’re working to stay ahead and make a difference now in order to achieve our future goals.”
By December 2022, Mr McIntyre confirmed all Peel Ports’ vehicles will be powered by electric or biofuels.
In addition to changes to its fleet, the company has made other investments in its infrastructure to reduce or eliminate emissions altogether. In 2012, whilst upgrading its L2 facility in Liverpool, the company opted for energyefficient electric cranes that are capable of generating surplus electricity and exporting it back to the network. The company also utilises custom software to minimise container movements at its ports for maximum efficiency.
In 2021, Peel Ports built 300,000 sqft of warehousing. To make operations as sustainable as possible, the latest intelligent lighting was installed; and on the rooftops, rainwater is used to top up water levels in the docks, reducing costs and emissions when compared to the more traditional method of pumping the water in.
Peel Ports is planning to reduce emissions through shore power systems through cold ironing – meaning vessels, when idle in port, can turn off their diesel engines and plug into a port’s electricity supply instead.
With the cost of diesel at record levels in the UK, combined with red diesel subsidies being removed by the UK government as of April 1st 2022, addressing fuel emissions throughout the supply chain is another critical aspect of the logistics industry’s shift towards decarbonisation. To this end, Peel Ports
has also begun using Green D+ HVO (hydrotreated vegetable oil) instead of diesel oil. Biodegradable and made from 100% renewable raw materials, D+ HVO is seeing CO2 levels reducing by up to 90% and other particulate matter, including NOx, is cut down significantly too.
Peel Ports’ Liverpool2 or ‘L2’ facility is a highlight of its asset portfolio. Featuring eight 92metre high ‘megamax’ quayside cranes, the port makes a major visual statement but it is also making an intrinsic impact locally and
nationally. By repositioning Liverpool as a true deep-sea port with comprehensive facilities, the company has hugely reduced the impact of HGVs on UK roads.
“Liverpool continues to drive market share because we’re seeing that supply chains want more resilience,” said Mr McIntyre. “We’ve calculated that a huge proportion of the cargo arriving in the south – London and Southampton – goes to Birmingham – and further – by road. By offloading that northbound cargo in Liverpool instead, 30 million road miles were eliminated in 2021 alone. It also means that logistics companies become
more profitable because cargo arriving in Liverpool can be delivered to its destination the same day, instead of sitting in Southampton waiting for a haulier to drive it up.”
L2 recently celebrated its fifth birthday with the completion of phase two of its development. This involved the addition of ten cantilever rail-mounted gantry cranes (CRMGs), taking the terminal’s total to 22. The cranes were built by Chinese manufacturer Zhenhua Heavy Industries Co and will allow the company to accommodate the growing volumes of cargo welcomed at the port.
Peel Ports’ teams are extremely focused on being good neighbours and supporting local communities.
“We want to push on and do the best that we can – we want to ensure our local communities thrive and benefit from the growth of the business by enabling local opportunities for skills and employment, whilst showcasing our sustainable agenda.” Mr McIntyre remarked. “Most of our staff live near to the ports and we want them to be proud of where they work.
“Our teams are local ambassadors for what we do. They will look at opportunities to support local causes and projects and they often visit schools or provide tours to
educate on the crucial role and impact ports have in our everyday lives.”
A major benefit for local communities is in the careers and quality jobs opportunities available in ports, maritime and the wider supply chain. Mr McIntyre and his team will be launching a new programme to showcase these areas across the group.
“Port careers are not what you might assume – people think that working at a port means driving a forklift truck or a crane, but it’s so much more than that,” he stated. “We have graphic designers, specialist engineering roles in IT and automation, careers in finance… the list goes on. So our efforts within the commu -
nities are about opening up about what goes on beyond the gates .
“For example, if you want a career in IT, you can come and develop a career at the port. Our cranes, for instance, require a huge amount of automation and in general, there’s a large amount of technology in this business. We’re often at the cuttingedge of technology as innovation supports our sustainable growth aspirations.
Mr McIntyre concluded: “Peel Ports is a key facilitator of goods moving into the British Isles. In addition to reducing emissions at our ports, we are also working alongside shipping lines and supply chain partners so they can become greener. It is a journey and there is a lot more to be done.”
A combination of infrastructure improvements, effi ciency drives and rising container traffic volumes has fuelled Altamira Terminal Portuaria’s rise to become Mexico’s fourth busiest port. With a new multi-million dollar berth extension set to boost capacity further, Terminal Director Captain Adonay Navarro Saad firmly believes the only way is up. Report by Andy Probert.
Thas been Altamira Terminal Portuaria (ATP). Tucked up in the northeast state of Tamaulipas, the country’s fourth busiest port has big plans to enable it to remain shining bright for years to come.
Handling less than 75,000 TEUs a quarter of a century ago, the terminal annually handles above 500,000 TEUs. “We manage 6.5 times more container traffic now than when we first started, but we are confident that figure could well reach 650,000 TEUs in years to come,” asserted Captain Adonay Navarro Saad, Terminal Director.
That punchy number is derived from the terminal’s plans to build a third berth at the cost of $25 million and, by sheer desire, to become the most efficient and competitive port operator in the Gulf of Mexico.
This latest commitment also reflects the port’s continued and timely improvements with infrastructure, yard and dock equipment, and high-tech solutions to deliver an efficient ecosystem. This allows cargo to be loaded /off-loaded in quick time, to be either trucked across Mexico or shipped globally.
The bigger vision to make ATP a top three national port is being backed by its parent company, Grupo Mexgal, a 100% Mexicanowned corporation. Mexgal is an independent group with long experience in international transportation and port activities.
“The total approach to customer service has driven us to constantly increase productivity rates, but never lose sight of our commitment to providing quality services,” said Capt Navarro.
In October 1995, due to the Mexican government’s privatisation of the port infrastructure, ATP obtained a concession to run the multi-purpose Terminal One at the Port of Altamira and further develop container handling, dry and breakbulk cargoes. The terminal had a 300m berth, but ATP was approved to extend it by another 300m in 2007 - 08.
“That helped us offer two berths to accommodate bigger cargo volumes and arriving vessels. Doubling capacity and being able to handle vessels simultaneously was a big step for us,” he said.
In 2012, Mexican law changed again, allowing terminals to apply for an extra 350m berthing space. ATP, which operates the original 600m berth and an additional 117m berth to accommodate small ships, was granted that new extension in 2018.
Works are to begin shortly on extending the original berth by 60m to an overall 660m in continual length.
“There will also be a deviation from the original line by 20 degrees, allowing us to build an additional 290m berth,” Capt Navarro revealed. “This is due to the port configuration: an unbroken 950m linear line would otherwise extend into the turning basin.”
He added: “That will allow us to have three berthing positions to efficiently attend different kinds of ships and comfortably accommodate the extra capacity in future years.”
ATP handles cargo throughput from vessels calling from northern Europe, the Mediterranean, South America and the east coast of the USA. Shipping line clients include some of the world’s most prominent, including MSC, Maersk and ZIM.
Given the steep growth experienced in the last 20 years, the terminal has also seen its workforce rise from around 100 to 1,200 employees in 2021. The terminal, which operates on a 24/7 basis, has a berth occupancy of 45%.
ATP has achieved intense productivity levels thanks to its four ship-to-shore cranes plus Panamax, and three mobile
cranes, (two of which have a capacity of up to 100 tonnes each), which, in tandem, allow the handling of parts with a load of up to 200 tonnes.
With three cranes, vessel productivity is in the order of 1,500 to 2,000 movements per call, equating to 85 to 90 container moves per hour, although that figure regularly tops 100 moves an hour.
Underpinning this, ATP uses the latest version of the Navis N4 terminal system, furthering its position as a go-ahead port operator. The N4 3.7 version was launched in mid-2019.
“N4’s features enable us to optimise operations and respond swiftly to changing business requirements, keeping us one step ahead of the curve and helping us satisfy customers,” Capt Navarro remarked.
In parallel with other systems, the port also handles container cargo disbursement to trucks. In Mexico, the more common way is for a trucker to arrive with their vehicle and platform for container delivery.
“On average, we do 700 to 800 container dispersals to trucks,” added Capt Navarro. “The average turnaround time for a truck is about 25 minutes. That efficiency is achieved by ATP’s fleet of 14
rubber-tyre gantries (RTG) cranes. For cargo disbursement to trucks, we have expanded our lanes from two to nine as volume levels have risen.”
Whilst being a multi-purpose terminal, ATP’s container traffic consumes more than 93% of business activity compared to general cargo and automotive. “In the last two years, we have been more aggressive with our general cargo and believe we will be handling close to 150,000 tonnes of general cargo once 2021’s figures are finalised. Among them, we serve a monthly service of STINNES LINE break bulk and steel cargoes”, revealed Capt Navarro.
ATP is the only terminal at the port of Altamira to handle automobile shipments for import and export. This peaked at over 300,000 automobiles in 2021, with exports mainly to the US east coast, Europe, South America and Middle Eastern markets.
Capt Navarro added: “Because Altamira is in the industrial corridor, with many exporting petrochemical and plastics manufac turers located here, we have, in the past, exported more than imported, with a 60-40 split. But today, that is closer to 50-50. That means we are handling very few empty containers, or about 10% of total volume.”
ATP’s import volumes, including components for the automotive and other industrial sectors, are predominantly distributed across Monterrey and the north-eastern parts of Mexico.
The terminal’s main competitors are others across Mexico and the Port of Houston, which lies about the same distance from Monterrey, (the region’s main industrial hub), as does Altamira.
“Altamira has become very competitive, but the biggest transportation option in and out of the terminal is still by truck rather than railroad. This is based on cost, logistics and delivery time,” he highlighted.
The construction of the new berth in 2022, an additional $5 million spend on three new RTGs, and plans to add a fifth Ship-toShore Super post-Panamax crane to serve in the next three years will help consolidate the terminal’s performance.
“These will all combine to be able to handle more significant terminal volumes,” Capt Navarro stated. “When the additional berth becomes operational, our volumes could well be above 600,000 TEUs in the next two to three years. This is also set against an average business growth rate of 7% annually.
“Everyone anticipated 2021 to be a weak year given the pandemic, but that was not the case. Freight volumes returned to
what we were handling in 2019, and we expect to top that by 5%.
The recovery was abnormal and not expected.
“Our goal is to ensure that we continue to offer a quality seamless service with the best equipment and people available, and not to impact a client’s own operations adversely.”
He concluded: “Whether it’s clients, importers, exporters, or with suppliers of our equipment and software infrastructure, we have always maintained long-term business relations through efficient, timely and open communication.
“We want customers to identify with our terminal and for ATP to be their best, preferred choice for all their cargo handling solutions. We are always striving to improve for them, and for the good of the terminal.” n
seven seas, five oceans, one voice
hamiltonjet oswald elektromotoren merlin diesel systems
As the leading designer and manufacturer of waterjet propulsion systems and with more than 80 years of experience, HamiltonJet offers unmatched quality in the global supply of waterjets and controls systems. Innovation remains at the core of the company, and in recent years it has advanced further, developing integrated waterjet solutions and controls for autonomous and unmanned vessels. Profile by Andy Probert.
Waterjet technology is the DNA that continues to flow through the veins of HamiltonJet, from the very day that Sir William Hamilton pioneered the first commercial system in the 1950s.
Fast forward to 2022: the New Zealand company is the confirmed market leader of waterjets and vessel controls thanks to its trusted expertise and innovation in delivering robust and high-performance propulsion technology.
A preferred supplier to boat builders, naval architects and marine operators, HamiltonJet’s influence runs deep and wide across the marine industry. An estimated 60,000 waterjets have been installed on vessels in various segments, such as offshore, pilot, rescue, fire, military, patrol , windfarm, fast ferry, fishing, aquaculture and recreational applications.
Its current portfolio features 21 different jet models, from the mechanically controlled HJ212 absorbing 70kW all the way through to the electronically controlled HT1000, capable of absorbing 7,500kW, for vessels from 5-100m in length.
The products, designed and built to world-leading industry standards, are
manufactured in-house at HamiltonJet’s Christchurch factory, with foundries for casting stainless steel and aluminium, cutting-edge machining facilities, extensive testing and inspection procedures.
To deliver a global service at a local level and be closer to clients, the company employs 470 people worldwide, with a global network of strategic offices in the UK, Seattle and Singapore, underpinned by over 50 distributor partners and a host of service agents.
HamiltonJet’s eventual journey into waterjet technology came from its forerunner, CWF Hamilton & Co, formed in 1939, through its specialism in engineering for earth-moving equipment capital projects, such as hydroelectric dams.
In the early 1950s, Sir William began to experiment with waterjet propulsion to enable his family to enjoy the shallow and fast flowing rivers in New Zealand. The first waterjet was launched in 1956 and quickly superseded a year later by the first axial flow system, the Chinook, which is the genesis of every waterjet that exists on the market today.
Hamilton set the pace in the market, professionally and personally, in the waterjet space. The family’s vessel was the firstever recorded to cover the entire length of the Colorado River, it also accompanied Sir Edmund Hilary in a voyage along the River Ganges to its source in the Himalayas.
Tom Pannell, HamiltonJet’s Global Distributor Manager, said the company had , up to the early 1980s, continued waterjet technology as a side line, accounting for 10% of business. However, it decided on a complete redirection; to focus on its waterjet technology following significant economic change in New Zealand.
“Today, HamiltonJet produces more waterjets per year than all its competitors. We have total control over production, with quality and innovation key strengths.”
Antony Tomkins, HamiltonJet’s Global Business Development Manager, said: “Over the last 15 years, we have been very market-specific in our approach, and with 11 different market segments, we have built our strategies and approaches structured around how those vessels are used.”
The biggest markets for HamiltonJet include windfarm support vessels, ferries, patrols and military.
“When we select a jet to a project, we ensure it’s the right jet for that application, not just the installed power,” outlined Mr Tomkins. “For example, jet sizing is different for a windfarm vessel compared to the same size and power for a ferry. The results can be significant and directly impacts the way a vessel performs.”
Kevin Robertson, General Manager of HamiltonJet’s EMEA office, added: “We have introduced new jet models frequently so that we can replace existing waterjets with more efficient designs and operating envelopes.
“The idea was to introduce two new jets a year until we have replaced the fleet, and we are on track with that. The efficiency savings have been quite considerable. We have increased speed up to 7% and increased bollard pull up to 20% on average.”
Sea trials for a waterjet are just about to be completed in the Middle East with one client, and Mr Robertson said the performance had “been up to 60 knots”, which is likely to lead to new orders.
He said the success of HamiltonJet’s involvement in some of the UK’s search and rescue services is being actively utilised as a template for other sea-bound search and rescue organisations across Europe.
Mr Robertson added: “We have been fortunate to have maintained long-term
relations with distributors and partners for in excess of 35 years, through the good and the bad. These are long trading relationships that are not just about selling a product; we are with them every step of the way.”
HamiltonJet recently launched JETsense, in collaboration with Sea Machines. The system utilises autonomous navigation, multi-sensor fusion and computer vision to move waterjet vessels to the forefront of 21st century navigation and utility.
JETsense employs AI and advanced autonomy to perceive the domain and maintain precise steering and speed control during a voyage and re-route to avoid traffic and obstacles. It also provides a new level of streaming data to improve on-water operations.
The product, which features Sea Machines’ technology at its core, offers a helm-based system to advise, safeguard or assume active control of open water vessel transits.
At its official launch, HamiltonJet’s Managing Director, Ben Reed, emphasised: “JETsense is the first product on the market to incorporate Sea Machines’ advanced vision package. It pairs onboard autonomy with enhanced situational awareness in a highly desirable way in many manned applications. Throughout development,
we prioritised helm integration and the ease-of-use for mariners.”
In 2019, Sea Machines and HamiltonJet successfully commissioned an SM300 autonomous control system aboard a HamiltonJet-powered 17m workboat in New Zealand. HamiltonJet continues to trial this marine technology and provides on-demand customer demonstrations in the Southern Hemisphere.
Continuing at the forefront of propulsion technology, mixing innovation and evolution, the company is now developing new jet control applications to ensure HamiltonJet’s brand remains firmly on an upward trajectory.
Mr Tomkins said: “On the evolution of hybrid and electric vessels, there is a general industry push towards low or zero emissions, and that is a particular challenge as the technology isn’t readily available for the high speed maritime sector – yet.
“But two years ago, HamiltonJet launched EHX, a hybrid interface where we can supply the entire driveline, and crucially the cont rol system integrates all that complex hybrid control. And it is the same control system as all other control systems.
“From an operator’s point of view, it makes the control of the hybrid model and the mode selection very easy and intuitive, and removes the need for different screens and controls. EHX is a neat and clean solution, and we are seeing interest from
different segments, such as windfarm and passenger vessels.”
He added the company has flexibility across the offering to deliver the best solutions for our clients. “When we talk to clients about hybrid and electrification, we can talk from personal experience because we have trialled these systems on our workboat . So we understand the challenges, we know what to think about, and we can be proactive in supplying trusted and tested equipment.”
HamiltonJet has been equally active in developing several options concerning autonomous systems for the past 13 years.
“13 years ago, it was considered crazy thinking, but as the years have gone by, the autonomous and unmanned space has grown and grown,” Mr Tomkins remarked. “Our experience integrating systems, such as JetLink, has seen significant growth, and we are continuing to build on that.”
HamiltonJet has also launched the HJX29 – the first model in its new HJX waterjet series. This range sits just below the HTX jets in size and will gradually replace the globally popular HJ jet range. Mr Reed said HJX packs a real punch, adding: “HJX jets will deliver 4-6% more thrust at higher speeds than the previous HJ Series waterjets.
“ Despite their compact dimensions, the HJX range will be capable of achieving speeds over 50 knots when matched with suitable engines and hull design. Compared
to the HJ series, HJX also achieves 15-20% more bollard pull and greater sway thrust than the previous HJ series.”
Looking ahead, the company is currently investing in a new facility on the existing production plant in Christchurch.
While logistics and shipping, in general, were proving challenging, the flexibility and robustness of its distributor network remained a major strength.“I have 22 distributors in the EMEA, and there are significant jets on order for he next few years, which highlight the confidence in our products,” commented Mr Robertson.
Mr Pannell said: “Reliability, consistency, core competence, and passion are our key differentiators. We only focus on waterjets and that places us differently
from most other competitors. As a fourthgeneration family-owned company, it is uniquely focused on that challenge and reflected in the products we design and manufacture.
“Clients are regarded as partners, and they frequently comment HamiltonJet is always there. It is a company not driven by the bottom-line; our passion permeates throughout the business from top to bottom.”
Mr Robertson concluded: “HamiltonJet is committed to investing in infrastructure , technology and product development across the board, as well as investing in people. We are well poised for the future because we continue talking to all elements of the industry.” n
With over 100 years of history, OSWALD Elektromotoren GmbH is a veteran manufacturer of electric motors and generators. Now in its fourth generation of family ownership, the company remains at the head of its industry through a relentless focus on innovation and its industry-leading custom fabrication service. Richard Hagan reports.
OSWALD Elektromotoren GmbH, based in Miltenberg, Germany, develops and produces customer-specific water and air-cooled electric motors ranging from 15kW to 2,500kW for a variety of industries and tasks.
Its range includes high torque motors, synchronous motors, asynchronous motors, generators, linear motors and magnetic field coils. Its focus is on developing customised solutions and products that are best suited for each client’s particular application. As a manufacturer of customer-specific motors, OSWALD is able to produce individual quantities, but is particularly interested in series production, such as projects with 20 to 100 identical motors per year and even up to 500.
Historically, OSWALD has derived the majority of its work for clients in fields requiring container handling, shredder machinery,
automotive test stands, winch systems, plastics machinery and hydropower plants. But more recently, the business has seen significant growth in the marine market for both electric propulsion units and marine generators.
One reason for this surge in marine propulsion projects is OSWALD’s partnership with system integrator Hybrid Ship Propulsion BV in Rotterdam, which manufactures and delivers equipment for Concordia Damen shipbuilders in Werkendam, as well as for other shipyards in the Netherlands.
“In the initial projects we supplied permanent magnet motors for a hybrid tugboat named Telstar, and a hybrid pusher boat
named Cygnus,” explained Thomas Bachmann, Sales Engineer at OSWALD.
But that’s just the tip of OSWALD’s exciting, growing involvement in the marine space. Mr Bachmann was keen to highlight another project it’s currently involved with.
An especially big milestone for OSWALD was its appointment in early 2021, via its relationship with Hybrid Ship Propulsion, to supply the main propulsion motors for Project Parsifal. This project involves the construction of a series of 40 inland navigation tankers in the Netherlands. The vessels boast an environmentally friendly design and have been specifically engineered to be able to continue motoring even when water levels on the Rhine are low.
Each ship built within Project Parsifal will be equipped with two PM 500kW motors, equating to a total order volume of 80 motors. OSWALD delivers up to four motors per month to the yard and, as of early 2022, OSWALD had delivered more than 20 motors in total.
OSWALD has designed and engineered these motors specifically for Project Parsifal; a fact that Mr Bachmann was especially proud of.
“This project was an opportunity to really redevelop and modify our existing motor design that we planned to use for the contract. We conducted a complete review of the motor, reviewing all of the components within it.
“Besides the technical optimisation, we wanted to ensure that in the end, the motor looks like something new, fancy and modern,” he continued. “That was part of the strategy for us. We specifically didn’t want to just take an existing design off the shelf and put a new box around it. Consequently, we invested several months into the development work for the new motor. The end result was quite amazing and the test bench results were perfect.”
Project Parsifal is the largest project that OSWALD has undertaken in the marine industry, but it’s perfectly within the company’s strategic vision as it involves manufacturing a large volume of identical motors. “It has significantly strengthened our position as one of t he leading manufacturers for this kind of special machinery,” Mr Bachmann confirmed.
As part of the program, all of the motors receive Lloyds approval for Inland Shipping and meet the project-related marine requirements.
OSWALD really began its foray into the maritime sector in about 2015 when it was approached by a long-standing client with a project in the Netherlands, to equip a fishing vessel with electric propulsion.
“The client knew us from previous work we’d done in other applications such as test rig motors,” said Mr Bachmann. “They wanted a hybrid system on the fishing vessel with a high-torque motor, which is something we were already doing for other sectors. The client knew us as a reliable partner in many other industry applications in which we’d worked together, and therefore appointed us for the fishing vessel project.
Prior to the fishing vessel project, OSWALD had built only a few motors for marine applications, but the fishing vessel marked an unexpected turning point.
Mr Bachmann explained: “One of the impacts of this project was that everyone in the marine industry in the Netherlands knew about this fishing vessel because it was new technology and a complete new design by the shipyards involved. The market is closed and very small, the project was in the newspapers and in the media, plus the client marketed it very well.
“It wasn’t immediately obvious to most people that our motor was in there,” he added. “But it helped that this ship was using our technology because it became a great demonstration of our motor that proved that it works and that it’s reliable.
The company’s successful implementation of the fishing vessel project led to additional, similar opportunities in which OSWALD was contracted to manufacture propulsion systems for other vessels. With a portfolio of vessels on the water proving that OSWALD’s equipment is robust and capable, new enquiries began pouring in.
“By this stage, the market was open to this new technology,” Mr Bachmann pointed out. “We could prove that we could build the machines that clients required, starting from the white paper all the way to the finished product. It was a very successful story for us in the end.”
OSWALD’s permanent magnet generators have become a second significant growth path for the company and it is one that the team was keen to discuss. For the last couple of years, OSWALD has been developing and building marine generator systems (gensets) for clients across Europe. These units typically have a power range of between 300 and 1500kW.
“It’s a new area for us,” said Mr Bachmann. “End users are increasingly demanding high-speed permanent magnet gensets instead of the conventional systems.”
To anyone in the industry, those end users he’s referring to will be completely unsurprising: they’re superyachts. And it makes sense, since permanent magnet generators are a more expensive solution versus conventional gensets. But as Mr Bachmann pointed out, their advantages justify the price.
“Our engineers have been tasked for the last three years with redesigning permanent magnet systems for marine use. They are extremely efficient and reliable and it’s something that the superyacht shipyards are increasingly recognising.”
By 2022, OSWALD had delivered a dozen of these new systems to superyachts, and it has further PM generators on order.
“This growth is perhaps driven by the amount of capital in the superyacht industry,” Mr Bachmann noted. “They want all the new, fancy technologies but it’s good for us because it’s helping us to get into the market as well!”
OSWALD’s headquarters is located in Miltenberg, Germany, in the north of Bavaria. It is the company’s only facility. It employs 200 people working in several buildings on the property.
In 2020, the business invested in a new testbed building that doubled its testing capacity from 1MW to 2MW motors, with a voltage flexibility ranging from 400 to 690 volt systems.
Meanwhile, a new high-tech, fully automated stockroom building is under construction and when complete, is expected
to significantly speed up the process required for staff to draw project parts and consumables. With only a single employee operating a terminal, the system will automatically pull stock at a high speed, significantly speeding up internal logistics.
In closing, Mr Bachmann emphasised the company’s adaptability: “We are flexible, willing and able to deliver customised solutions. We’re not afraid of a challenge. We’re specialists in working with partners and customers to develop and successfully deliver solutions that are perfect for their applications.” n
With customers in over 100 countries, the UK’s Merlin Diesel Systems is a substantial and critical supplier of a variety of products and services in the worldwide diesel engine supply chain. Having firmly established its presence in the automotive market, the company has recently made a significant acquisition and stock investment that will substantially grow its share in the marine market. Merlin Diesel Systems’ management team spoke to Richard Hagan about this latest development and what it means for the company’s future.
The history of Merlin Diesel Systems c an be traced all the way back to 1947 when the company was first established in West Yorkshire by a certain Mr CT Rhodes of Halifax.
Fast forward to today and it has grown into a veritable powerhouse within the diesel spares and servicing industry both in the UK and abroad. From its headquarters in Preston in Lancashire, Merlin Diesel supplies over 50,000 parts to customers in over 100 countries.
Whilst the domestic market is an important part of Merlin Diesel’s business, export markets remain the company’s biggest source of revenue, according to Technical Director Scott Bramley: “Exporting spare parts is a major part of our business; we export about 65% of our products. Most of that is diesel fuel injection parts and complete units, with probably a 50/50 split between the two.
“We export parts like injectors, fuel pumps, pressure sensors and pressure control actuators,” he continued. “It could be for marine or heavy-duty automotive. Within the automotive sector, we are seeing real growth in areas like agriculture and highway, and now also marine as we start to widen our envelope.”
Merlin Diesel supplies a comprehensive range of products and services to the automotive, heavy industry and maritime sectors. The company’s very large production centre is said to boast one of the biggest and most sophisticated diesel workshops in the world.
The company’s portfolio consists of two main categories: fuel injection spares, and test equipment solutions.
Its spare parts product range spans diesel fuel injection parts from well-known, recognisable manufacturers such as Bosch, Delphi Technologies, Yanmar, VDO, Perkins, Denso and many more.
Meanwhile, its test equipment range is sourced from similarly recognisable brands such as Bosch and Hartridge (a subsidiary of Delphi-BorgWarner), as well as manufacturing its own range of bespoke test equipment. Customers can choose from a variety of test benches for every conceivable application, all supplied directly by Merlin Diesel.
While the business continues to show strong growth, the team threw the spotlight on ongoing global parts shortages and supply chain price increases as a major source of headaches for its growth plans.
“We’ve got some big challenges with shortages,” confirmed Mr Bramley. “It has cost us a lot of turnover, but so much of it is out of our hands. Some parts only have one supplier, so we can’t seek alternative sources for those. Additionally, we’re dealing with rising costs and there’s very little we can do to control that.”
Sales Director Derek Henry agreed: “Some of our main suppliers have had six price increases in the last 18 months, ” he lamented. “To try and manage that is very difficult.”
Nonetheless, he highlighted the company’s robust stockholding as a major advantage at a time when stock shortages have become a chronic problem.
“One of the strengths of our business model is that we have quite a sizeable
amount of stock, and that’s really what drives a lot of our business and our success. Where most suppliers run out of particular parts, we still have stock. Today, we have £21 million in stockholding, and that tends to be a real strength for us.”
Regardless of supply chain challenges, the company registered a record sales month in March 2022. “Our customer base is growing,” said Mr Henry. “Globally, diesel continues to represent a huge opportunity for us.”
In 2021, Merlin Diesel concluded a substantial investment into sister company Tyne Electro Diesel. The transaction saw Merlin acquire a 52% share of Tyne Electro Diesel, a service provider focusing on the overhaul and repair of marine diesel systems. This acquisition is part of the company’s strategy for growing its market share in the maritime space.
“It’s crucial to our business moving forward,” Mr Henry remarked, singling out opportunities in the repair of injection components in large engine equipment as a future driver of growth for the business.
“At the moment, there’s limited repair solutions for certain fuel injection systems in large engine equipment,” he explained. “With our investment in Tyne Electro Diesel, I think there’s a lot of opportunities.”
Additionally, the company’s unique test bench services are on hand to continue
delivering substantial value to its efforts within the marine environment, where its Merlin DC-80 series test bench and Mark 6 common rail marine injector testing solutions are proving popular.
Merlin Diesel has enjoyed ongoing sales growth for the past two years, with a £5 million sales growth in 2021 alone. To accommodate the company’s current and future growth forecasts, it is in the midst of a major physical expansion of floor space and production capacity.
“We’re changing the whole workshop from the ground up,” said Mr Bramley. “We’re building a component assessment room as well as a cleanroom for product assembly. We’re also restructuring internally and adding an extension to the building to cope with our growth.”
“Our test equipment division is also being expanded to give it more space because it’s really growing fast,” added Managing Director (Test Equipment Division) Mike Rawlinson. “Our diesel injector remanufacturing service has always shown strong growth, but the last two years in particular have highlighted the need to expand our capacity in order to be more efficient.”
Once the £1.5 million expansion project is complete, Merlin Diesel will boast an extremely impressive 7,000 square metres of covered floor space.
With all of this new space comes the need for additional staff. The company has brought in a new management team to oversee its expanded operations. Under
them, there’s a near-constant flow of new recruits joining the business, with a particular focus on apprentices.
“We’re trying to bring in and train up as many young people as we can,” Mr Bramley explained. “It’s very difficult to bring in fully-trained diesel engineers simply because there’s just not that many of them around.”
To ensure that it retains its highly-skilled staff, Merlin Diesel has implemented a pay structure that is competitive, within a healthy and properly equipped workspace.
“We like to promote people from within, and there’s a clear chance of progression to management roles,” Mr Henry noted. “We also pay an annual bonus and a generous pension. It’s about ensuring that we look after the staff as best we can.”
Going forward, the team was optimistic about the future.
“We still think there’s a lot of room for growth in the industry for us,” Mr Bramley
asserted. “We want to look for new opportunities. We see a slight diversification from automotive, looking more towards the agricultural and industrial side of the business. And we want to look at contract business if we can find the right partners. The future looks bright.”
Mr Henry’s focus was on a return to trade shows. “There are a number of shows we will be attending. Globally, we’ve historically been very proactive with visiting and exhibiting at shows. We’re about to attend Motortec in Madrid, Rematec in Amsterdam, SMM in Hamburg and Automechanika in Frankfurt. Towards the end of the year, we will also be in Paris, Dubai and Shanghai.”
Mr Rawlinson concluded with a brief highlight of the company’s ethos. “It’s not just about winning the sale,” he said. “It’s about customer retention and welcoming feedback. We’ve got a great management team and fantastic staff, supported by excellent telesales staff both here in the UK and in our export team. They all go the extra mile.” n
seven seas, five oceans, one voice
friulforgia cmw foundries i M
The latest round of investment at Friulforgia Srl, the Italian forging company, expanded the scope of its marine products. Mosè Molaro, Sales Manager, outlined these new opportunities to Phil Nicholls and Daniel Barnes.
Friulforgia is part of the TTN Group f ounded by Ernesto Pirovano in 1978, providing thermochemical surface heat treatments to the Italian forging industry. TTN Group steadily expanded, serving a growing number of forges with a range of speciality treatment services. A regular expansion of equipment allowed TTN Group to handle progressively larger projects, such as deep bore drilling equipment up to 16m.
In 2008, Mr Pirovano decided it was tim e to become a vertically integrated production company and founded his own forging shop. This project became Friulforgia, built from scratch at a facility outside Sedegliano in the Province of Udine in the northeast of Italy, opening in February 2009. Friulforgia began with just 12 members of staff but has now grown to 70 employees carrying out a range of heat treatments, rough machining, and final machining.
Friulforgia remains part of TTN Group’s seven companies spread across three countries: Italy, Spain, and the USA. The group employs 500 people and has an overall turnover of €70 million – €20 million of which is attributed to the success of Friulforgia.
The throughput of Friulforgia guarantees a capacity of 800 tonnes per month. To sustain this growth, the company has kept a continued program of investment in both equipment and personnel. A new
press in 2018 increased Friulforgia’s capacity from 25 MN to 38 MN. The machining workshop was doubled in size in 2019, with Friulforgia installing additional mills and lathes for final machining during 2020 and 2021.
The key investment for 2021 was a new multi-tasking turning machine. The latest addition allows Friulforgia to produce machined shafts up to 20m long, via turning, boring, milling and grinding.
“This major investment was specifically planned in order to provide an even more complete service to our customers in the marine industry, where propeller and intermediate shafts can be very long and challenging,” explained Friulforgia’s Sales Manager, Mosè Molaro.
Friulforgia’s new lathe can work in conjunction with the assorted bore drilling machines operated by TTN Group. This combination enables the group to drill and hone holes up to 20m long. Friulforgia now has the capability to deliver to clients fully machined forgings, ready to mount on ships.
Friulforgia is equipped to produce a diverse range of products in a broad range of markets including offshore, subsea and hydro power. Friulforgia also supplies clients in the marine, metallurgy, power generation and power transmission industries.
Tacchi Giacomo e Figli SpA is a leading company in the production of lathes and large deep hole drilling machines used in the processing of propeller shafts for the naval industry amongst other applications.
We have recently supplied and installed a drilling machine capable of machining a boring depth of up to 22m and an internal diameter of 800mm.
As for external machining, we have recently supplied and installed machines for turning, milling and grinding of shafts with external diameters up to 2,100mm and length of 22m.
In addition, for applications in other sectors of the heavy precision mechanical industry, we have supplied machines to produce workpieces with larger diameters and lengths weighing up to 320 tons, for both lathes and drilling machines.
Our organisation, for both sales and service and spare parts, covers the whole world, from Europe to North and South America, India, the Far East and Australia.
For more information, visit our website www.tacchi.it.
editorial mention
“We are well-known in several different markets thanks to the diversity our product range, as we can forge any shape with our open-die presses, and we can do it with any kind of steel grade,” said Mr Molaro.
“We forge long products such as shafts, rods, pinions, pipes, as well as massive cylinders, bushings, wheels, valves, clamps, sockets and many other shapes.”
Friulforgia has been active in the marine industry since the beginning of the company. Initially, the company delivered premachined propeller and intermediate shafts to one of the major European manufacturers of marine thrusters. The customer quickly accepted supply of additional Friulforgia final machined items. This relationship steadily expanded into the provision of a range of steering and propulsion components every year.
Friulforgia has since expanded its client base to several other thruster and rudder manufacturers. Marine products include shafts, crank pin discs, hubs, flanged pipes, and other propulsion-related components for any kind of thruster. All these items are certified by third-party accredited registers directly in Friulforgia.
Mr Molaro acknowledged that competition within the forging industry is tough, especially in Italy. However, Friulforgia benefits from being part of the wider TTN Group as it can work with metallurgists and machining specialists within the organisation. The client benefits from this simplified procurement structure where a single point of contact provides access to so many specialised processes.
“There is no other company in Italy that can provide such a wide range of services altogether, and by investing in our 20 metre-long multitasking lathe, Friulforgia is now ahead in the marine competition.”
Friulforgia enjoys a close relationship with suppliers too.
“We buy hundreds of ingots to be forged every year,” Mr Molaro said, “And there are no compromises on quality.” The company buys many varieties of steel – from carbon to stainless steel, including tool steels, Duplex, and super Duplex – choosing suppliers very carefully, following strict qualification and monitoring procedures. Most ingots are bought from Italian mills, but Friulforgia also sources from mills in Austria and Germany.
Friulforgia carefully matches the ingot to the product, as each supplier performs better on some steel grades than others. By knowing its suppliers so well, Friulforgia selects the best solution to maximise the final performance of its products to the benefit of its customers.
“In the past decade,” Mr Molaro explained, “We have witnessed a strong tendency of centralisation in the scope of components procurement, as our customers prefer to buy comprehensive solutions from the manufacturers instead of dividing the orders between different suppliers, where each performs a different activity.”
Friulforgia is perfectly positioned to capitalise on this trend. A continual program of investment in final machining and testing equipment maintains Friulforgia’s strategy of vertical integration.
Francesco Rizzani, Plant Manager at Friulforgia, outlined the importance of sustainability at the company. The company has ISO 14001 certification and strictly monitors its impact on the environment.
“We plan on achieving yearly improvements in energy consumption and waste
production,” Mr Rizzani said. “We are now evaluating the implementation of a photovoltaic installation on our roofs to cover more than 30% of our electricity needs.
“Our commitment to respect nature, environment and safety is sustained by major investments to contain furnace emissions and to have scrap material properly disposed of. We believe any business activity should promote the health of the local community; this is possible only if you respect who and what is around you.”
Addressing the wider industry, Mr Molaro considered the challenges facing Friulforgia: “With the energy crisis and the war in Ukraine obstructing the supply of primary elements for steel production, we can consider ourselves lucky as our Italian suppliers of ingots managed to absorb the blow and keep working, allowing us to produce continuously with no setbacks.”
The biggest challenge facing Friulforgi a is competing with the Asian market where manufacturing costs are lower. Some customers transferred into Asia, shifting their procurement to local suppliers. However, the outlook for Friulforgia remains buoyant due to its diverse market portfolio. The ongoing investment strategy means “a constant development and improvement of our customer base,” asserted Mr Molaro.
During the pandemic, the company explored innovative ways to connect with customers.
“We found alternative solutions to promote our activities,” Mr Molaro revealed. “This included renewing our website and
creating a virtual tour of our production premises. These choices were successful and greatly appreciated by both new clients and well-established customers.”
Moving forward, Mr Molaro is enthusiastic for the return of trade shows.
“This year we will finally be able to attend at least three separate shows: OTC in Houston as ForgeTTN; Euroguss in Nuremberg as TTN Group; and SMM in Hamburg as Friulforgia. In each of these shows we will have our own booth and w e are very optimistic about the outcome, as we think that after two years of restrictions the attendance will be very rewarding.”
This positive outlook also applies to the future of Friulforgia.
“The verticalisation of our activities has always been one of our priorities,” Mr Molaro said. “We will maintain this trend in the future, with further investments in final machining and the other activities directly related to it.”
The next planned investments at Friulforgia are related to the heat treatment capacity which will be doubled by 2023. The current growth in renewable energy will offer Friulforgia new opportunities within hydropower generation, offshore platforms and associated marine industries.
Friulforgia’s business model maintains complete control of the manufacturing process.
To this end, Mr Molaro concluded: “We believe the best way to serve our customers is to provide them with the most complete solutions possible in order to simplify their procurement activity, and to do it with no need of sub-suppliers.”
CMWFoundrieshasmaintainedacutting-edgeapproachto itsoperationsforoverfourdecades,supplyingcastingsto manyindustries,includingthemarineandoffshoresectors. Withpressuresmountingontheglobalfoundryindustrytodo morefortheenvironment,thePortuguesecompanyisproactivelyresponding.ProfilebyAndyProbert.
For over 40 years, CMW Foundries has focused and specialised in producing complex and technical sand castings for wear resistance applications either by the effect of abrasion, impact, high temperatures and/or corrosion.
A modern Portuguese foundry group founded in 1981, CMW Foundries was initially called Cruz Martins & Wahl. It has three production plants, two near Porto and one near Lisbon.
The group has become a key reference point for its castings in global markets, including shipbuilding, offshore, dredging, mining and quarrying, cement, valves, petrochemical, general engineering, power, and construction equipment.
Its optimum capacity allows the manufacture and delivery of finished castings in a range of alloys – high chrome white irons, stainless and heat resistant steels, duplex and super duplex, Inconel, carbon steel and austenitic manganese steel.
CMW produces high chrome, carbon/low alloy steel, austenitic manganese steel and heat resistant steel castings up to 8 tonnes, with stainless steel, super duplex, duplex and Inconel alloys up to 3.5 tonnes.
The plants have a total of ten electric induction melting furnaces with capacities ranging from 850kg up to 6,000kg, and one electric arc furnace with a melting capacity of 6,000kg.
The foundry features several moulding lines: two automatic systems, one George Fischer for green sand, an IMF for phenolic alkaline sand, two semi-automatic moulding systems for phenolic alkaline sand (for frames up to 4,000 x 2,000 mm) and two hand moulding lines without moulding size restrictions.
Metallurgical laboratories, a pattern shop with CNC equipment, a machining shop with lathes up to 3.4m turning diameter, a grinding shop, heat treatment ovens with capacities up to 20,000 kg and different means of air, water and polymer quenching are also on site.
Commercial Director Manuel Mendes said: “The group has been growing sustainably, investing in equipment, people and infrastructure to serve our markets and meet the demands for highquality standards.
“We keep engineering, pattern-making, production, quality control and machining all under one roof. This creates an efficient process and short communication lines, reflecting our full commitment to ensuring high-quality products and on-time delivery.”
Each plant has a pattern shop and quality control laboratories running. “We apply the most accurate methods to guarantee the quality of our castings, such as solidification simulation, fast pro totyping, laser scanning control and non-destructive testing.”
He added: “CMW has maintained a solid financial structure, allowing the company to preserve investments at levels that guarantee the good health of its production equipment and necessary upgrades to comply with environmental standards. All these have enabled us to be at the sector’s forefront, adopting the latest technology and best practices.”
The €16.3 million-turnover company, which employs 210 people, experienced growth of around 15% in 2021. Over 90% of turnover
is derived from export markets, such as Germany, France and the Netherlands. Mr Mendes detailed: “Between 15-20% of turnover is derived from the maritime and offshore industry.”
Castings manufactured by CMW Foundries are an integral part of equipment operating in high risk environments for example in energy, maritime, offshore, dredging, pump and valves sectors; industries where it is essential to meet the highest standards of quality and reliability.
To this end, CMW Foundries, in addition to its quality management system in accordance with ISO 9001:2015 and PED 20104/68/EU annex | 4.3 (parts for application to pressure and steam), has obtained special approvals for the maritime and shipbuilding sector of its manufacturing process for castings in cast steel and stainless steel by major entities such as Lloyds Register (LR), DNV-GL, American Bureau of Shipping (ABS) and Bureau Veritas (BV). These approvals guarantee the conformity of the production process and quality control with global standards and regulations.
Mr Mendes noted that in light of the lack of manpower and the difficulty of the finishing work on the castings, CMW began a cycle of investments in 2018 in automation and robotics.
“Huge steps continue to be taken in launching Industry 4.0 technology, which allows decision-makers to know up to the minute how production is evolving and keep track of KPIs and operational efficiency.”
In 2021, CMW invested €1 million to better protect the environment, and further improve health and safety, work conditions, Industry 4.0 upgrades, and storage capacity.
Reflecting on CMW’s business plans for the next few years, Mr Mendes said: “Given the instability we are living with, caused by the pandemic and the Ukraine-Russian conflict, (which has impacted the energy market in a completely unprecedented way), the short-medium term strategy is being adjusted.
“We are increasingly concerned with energy efficiency and environmental sustainability issues and investing in ways to become more autonomous to give more stability to our business and our customers.”
Despite the impact of Covid-19, the company responded proactively to guarantee employee safety and constantly adapted to the pandemic.
“We were even one step ahead of governmental strategies, such as the obligation for all staff to use masks two months ahead of the government’s decision,” said Mr Mendes. “This constant attention to detail allowed us to maintain operations without experiencing major turbulence.”
As much as the foundries are adapting to the demands of the industry and its clients, Mr Mendes said the three biggest challenges facing CMW today are the spiralling energy costs, raw material costs and lack of personnel.
He added: “The latter two were critical in 2021, but have been surpassed by rising energy costs this year. It’s a critical issue, and a fine line between survival and cessation.
“Many metallurgical companies are already considering reducing activity or limiting workdays to reduce losses. Now more than ever before, an urgent response is needed at European and local government level. It is time for the European Union to wake up and be more supportive and more creative in applying concerted policies to mitigate the impact of these challenging times, particularly in the areas of energy and raw materials to ensure supply, reasonableness in prices and equal access to each state member.”
Mr Mendes said CMW differentiates itself from industry peers through its high versatility and producing parts of various sizes and weights in a wide range of ferrous alloys – up to 8 tonnes depending on the alloy.
“We also conduct all necessary activities in-house, with no need to subcontract other than specific services that are not part of our daily activities, such as quality control by X-ray or surface treatment of pickling. We rely on a network of highly efficient partners located close to our facilities.”
He added: “The success of any business is defined by relationships. Each company stands in the middle of a chain of relationships composed of suppliers and customers, taking raw materials, products and services from one end and adding value to generate profit out the other. This is how CMW relates between all parties and is always focused on maintaining long-term relations.”
Mr Mendes said that “predicting the business future was not easy in the face of what we are experiencing. We hope the geopolitical and sanitary situations return to normal as soon as possible and we start to see a line of stability. However, our flexibility should allow us to go through these turbulent periods in better conditions when compared with other competitors in the same sector.”
He added: “Anyhow, a couple of trends will mark our path. Automation and robotics are a go in terms of investments as the foundry industry is not attractive to Millennials and GenZ-ers.
Increasing the technological component in the foundry will require more qualified staff, including young programmers and computer scientists.”
Another topic of concern is environmental and health and safety rules. He reflected: “The pressure from official entities can be asphyxiating because they do not seem to understand the timings necessary for an industry of this size to adjust procedures and equipment.
“Of course, CMW has worked in compliance with environmental and health and safety regulations since it was born. Production of castings within a sand foundry can create emissions, and environmental awareness is managed in our daily operations to minimise any impact on our surroundings.
“On top of this, to make our manufacturing process as lean as possible, we always seek the circular economy, reusing production consumables as much as possible and minimising waste. It is a metal recycling industry, metal scrap comes in, new castings come out ready to be used.”
Mr Mendes concluded: “Foundries will always be necessary to the industrial world, but we have witnessed in recent years a dangerous relocation of this industry to the East and Asia, with frequent shutdowns or bankruptcy of European foundries.
“Europe is not cherishing its foundries. Not supporting them in the necessary transition, and becoming more dependent on other regions exposes themselves to logistical crises. This is a major threat.” n
seven seas, five oceans, one voice
tefin marine electronics service network böning automationstechnologie
Tefin Marine Electronics Service Network prides itself as a provider offering solutions, not only products. As a market leader in the high profile marine electronics servicing industry, the company prides itself on its fast and direct customer care to the extent that it has become one of the company’s core values. Over 20 years of experience in the sector allows Tefin to provide assistance with quality, competence and reliability, offering total solutions and competitive pricing.
Tefin is a marine electronics service network bringing quality, professional and customised services and innovative solutions to the sector. The business is always researching and looking for new approaches and ways to keep up with the evolving requirements of the global market. The R&D “lights” are always on at Tefin for new challenges!
In addition to electrical and electronics services, the company also offers consultancy for projects, shipbuilding/drydock and mediation for clients: immediate global response to clients’ requests wherever and whatever. Tefin covers marine navigation, automation, connectivity, propulsion and digital services.
When speaking to the management about the start of the business, it was interesting to learn that the Tefin project started over 20 years ago summoning the ability to fulfil the market request for a dynamic, innovative and cutting-edge business and the determination for eco-friendly, safe and seamless navigation.
The company provides technical services and maintenance for any type of ship while meeting the changes of the market head-on
by virtue of its in-house culture of technological and environmental innovation. This ability is strengthened by the teamwork between industry experts and leading international partners.
But what was and is Tefin’s vision? Tefin is a family business born from the passion and inspiration of the Minieri family. The company’s founder, Luigi, works alongside his wife, Adele, and his sons, Angelo, Emanuele and Mattia. Adele is the company’s accounts manager, Angelo is responsible for the commercial division, Emanuele heads the technical aspects and Mattia oversees the international arena.
In the words of the founder, Luigi Minieri, Tefin is defined thus: “Energy and quality move us forward! We think the past is the basis for anticipating the future, while experience and innovation are the key elements driving us.”
There is indeed an emotional return in the daily running of a family business that stands out in the market. Members are all well connected to the company – its history, its products, its relationship to the community, its loyalty to employees and clients and these show in the care and variety of services offered by Tefin.
Tefin is headquartered in Naples and is also located in Genoa, Rome-Civitavecchia, Messina, Palermo, Amsterdam, Rotterdam, Antwerp and Tunis. Within Naples the company has two facilities, the 3,000 sqm headquarters and a 250 sqm satellite office within Naples’ port area.
Tefin’s workforce includes over 75 technicians who are highly trained on the various brands and products and are spread out and available in the different sectors. For important, special projects, Tefin may source additional technicians from within its consortium – up to 150 people, or as needed. Tefin has modern facilities and meeting rooms where clients can visit and meet to discuss projects. It operates workshops, dedicated to carrying out maintenance on small equipment, and warehouses to manage parts and products.
A spokesperson for Tefin’s management said: “Immediate availability of spare parts directly from our inventory results in a quick solution to any problem in a single service call. We have flexible and mobile service teams ready to go at all times of the day. The service focuses on instalment, maintenance, repairs on or replacement of and modification of equipment and systems.”
Tefin’s business includes three main sectors: service, shipbuilding/dry dock and R&D.
Refitting is Tefin’s most requested service; it requires both skilled personnel and extensive experience. Tefin has both. Refitting represents 40% of the company business.
“Presently we are dealing with a major rejuvenating activity, a sort of face lift for the Guilio Verne (Prysmian Group), a cable laying vessel built in 1983. A 40-year-old ‘lady’ we have known and supported many times, for which we are now providing successful total maintenance,” said the Head of Tefin’s Technical Division.
Within the automation segment, Tefin optimises equipment performance and improves the reliability of systems. The result of this is ships running to a greater degree of efficiency, providing more cost-effective naval operations. The dedicated automation teams are highly skilled in these tasks and are responsible for solving the complex problems inherent to these naval and industrial systems and the processes involved. The teams develop and suggest the best solutions, technologies and procedures to increase safety levels.
Research and development are also at the forefront of what Tefin is achieving. On this front, two major projects have come to fruition recently, including an innovative energy saving system.
The first one, ESS, is a smart Energy Saving System, an innovative onboard automation system, designed to optimise power consumption and reduce environmental pollution. It is applied to ventilation and Sea or Fresh Water-Cooling Systems. This intelligent system informs and communicates in real time how to correctly manage consumption, ventilation and sea/fresh water-cooling systems.
The second major R&D project is the R3S System. Developed in-house, it is a simple but innovative product application essential
for the prevention of fires on board Ro-Ro ships, thanks to the monitoring of the electrical sockets of the refrigerated trailers.
The R3S limits failures, protects cargo and integrates seamlessly with the tools to control fire systems that are currently on the market.
Tefin’s R&D team is currently working on shore-to-ship power or alternative maritime power, also known as cold ironing. This system has a positive impact on reducing emissions because this energy can be derived from a cleaner source than fuel burning engines.
Tefin is interested in and supportive of both the green economy and the blue economy as they are linked. Tefin is presenting a number of its products at SMM 2022, including: R3S, ESS, an intelligent battery charger for vehicles on board, a yachting smart automation system and an amplified fire system detector.
Tefin said it is fully aware of the strategic importance of intercultural differences when navigating markets.
Tefin’s International Division, Communication/Marketing stated: “Knowledge of foreign languages and the development of effective intercultural business skills are important issues. We believe that speaking a foreign language is not enough, as what are needed are the skills and the ability to communicate and mediate concepts, perspectives and projects in the most effective ways.
Knowledge of foreign languages and the development of effective intercultural business skills are important issues
“ “
“We at Tefin have been working on this aspect and we look at cultural differences as further business enrichment. We feel that intercultural skills in business are an asset and a priority to facilitate communication worldwide – and are a sign of respect for our partners.”
Speaking about the future, the company stated: “The Covid-19 pandemic has forced significant changes in the way companies perform worldwide. There will be a need to adopt new operational practices and changes soon. Changes are challenging the field with a re-evaluation of the supply chain management and logistics, raw material shortages, delivery times, terms and conditions and prices, just to mention a few.
“However, the incredible adaptation performance of the maritime field and the people working in it will shift focus on connectivity, digitalisation, collaboration, alternative fuels and robotisation. Some sectors such as yachting and offshore will possibly excel.
“Viva il Mare!” n
In the fast-moving world of superyachting and commercial marine electronics, Böning Automationstechnologie GmbH & Co KG has risen to the top of its market through its commitment to flexibility and innovation. Böning’s fully integrated bridge electronics solutions, which include everything from vessel control, navigation and communication systems to engine control and diagnostics, are uniquely bespoke to each installation.
Richard Hagan spoke to the company’s Head of Sales, Marinko Vukancic, to find out how the company adapts its services to each client’s particular needs.
ITwouldn’t be hyperbole to describe Germany’s Böning Automationstechnologie, based in Ganderkesee, on the outskirts of Bremen, as the beating heart of the superyachting and commercial shipping sectors.
With its systems now installed in over 15,000 commercial ships and superyachts, Böning’s software and hardware are essential to the operation of so many vessels and are a feature in the daily lives of many seafarers.
Established in 1977, Böning at first consisted of an engineering office which was later upscaled into a complete development and production facility.
The company initially focused its efforts on the commercial shipping market but by 1996, the business was producing solutions for the fast-growing superyacht industry as well. Simultaneously, Böning began working with a major German marine engine manu facturer to develop and produce engine diagnostic components.
“That was an important milestone for our global expansion,” said Marinko Vukancic, Böning’s Head of Sales. “It paved the way for us to become a well-known brand across the industry.”
Böning’s global ambitions were accelerated during the 2008 global financial crisis. Its efforts during the period that fol -
lowed resulted in the company’s substantial international footprint. Today, Böning branches are well-established in Brazil, Croatia, Italy, Spain and the US, as well as various independent representatives and distributors supporting operations in key global locations.
“Having such a large and established global network really allows us to comprehensively meet the service and delivery expectations of shipping companies and yacht owners,” Mr Vukancic noted.
Böning designs, develops and manufactures bespoke electronic devices and systems for ship automation. In simple terms, this refers to the systems – whose front-end often takes the form of a series of screens – that allow a crew to view various aspects of the ship’s performance, location, speed and general status.
Depending on the complexity of a particular installation, the screens will show engine diagnostics (temperatures, various statuses of different components), ship speed and location, radar and compass displays, GPS information, and the status of the different interior systems. These can include things like lights (internal and external), air conditioning, emergency sensors (smoke alarms, emergency water pumps etc), ballast tanks, stabilisers, audio systems and many, many more.
The challenge that Böning’s teams must address with every new order, is the integration of all of those systems and sensors onto a single set of screens, or other control panels, on the ship’s bridge and elsewhere. But it’s a challenge that Böning has developed a formidable reputation for successfully tackling.
The benefit of specifying our sophisticated infrastructure is that it allows us to use one or more multi-function displays for several systems that are all interfaced via our alarm, monitoring and control systems,” explained Mr Vukancic. “That reduces the number of different on-screen menus the user needs to learn, and it avoids mixing different hardware designs from different manufacturers.”
The company has become so good at building these cleanly integrated bridge systems that it has become a key selling point for its products and services.
“The glass touch screens common on leisure yachts are preferred because of their neat aesthetic,” said Mr Vukancic. “Our infrastructure allows us to combine all of those various other
systems into a single smart solution and it’s what enables this clean bridge concept. All the while providing a clear overview of the operation of the ship.”
Most of us are familiar with the speed at which consumer electronics are improving every year, so it should come as no surprise to hear that seafarers – and especially superyacht owners –expect to see similar levels of sophistication in the electronics and control systems installed on their vessels.
But in a market in which almost every yacht is a completely bespoke one-off model, shipyards have come to rely absolutely on Böning’s unique flexibility, and its ability to adapt each system to the specific needs of a particular vessel. This trademark flexibility is due in large part to Böning’s uniquely comprehensive inhouse design, development and manufacturing abilities.
“It allows us to react to customer requirements and demands faster and more independently,” Mr Vukancic noted. “It also allows us to provide a level of after-sales support that is unmatched in the industry. In 45 years of our company’s history, we’ve never had a case in which we couldn’t provide a certain spare part. Where devices are discontinued due to the unavailability of components, we either offer a redesign or we offer a compatible refit solution It’s very important to us to offer the best possible service and, most of all, that our customers feel well taken care of.”
The company boasts 120 staff members employed under its 4,000 sqm roof which boasts office space, production areas and storage space. Its development department is the company’s central nervous system and is the part of the business primarily responsible for bringing every Böning system to life.
“That department is very competent and handles the same number of tasks you’d expect from similar departments in much
bigger companies,” Mr Vukancic proudly explained. “It allows us to build every project from scratch and take it all the way to the completed product.”
With the onset of Covid and all of its associated lockdowns and travel restrictions, Böning adopted a novel approach to maintaining its business relationships.
“All of our regular trade shows were cancelled,” Mr Vukancic recalled. “But we felt that if you cannot go to the exhibition, we’ll bring the exhibition to you! And so, we started our own roadshow,” he added, smiling.
Böning promptly kitted out a large trailer with all of its latest technology and other innovations and began organising trips to countries across Europe, including Germany, the Netherlands, Italy, Croatia, Turkey and Poland.
“It was a huge success and what especially surprised us was the high quality of the conversations we had on site with our customers,” Mr Vukancic revealed. “It allowed us to meet the project managers and the engineers as well – the people who normally wouldn’t attend a trade fair. Nevertheless, now that Covid restrictions are more relaxed, we still look forward to meeting our customers again at upcoming trade fairs.”
An integrated approach
Böning’s customers have shown increased demand for the ability to design and program their own Böning systems. The company has fully embraced that demand as part of its global expansion efforts and has consequently launched the Böning System Integrator Network.
This initiative seeks to train its customers to a level at which they are able to design and program their own system using Böning technology.
“The integrator will be enabled, step-by-step, to manage their Böning projects independently of us. We’ll obviously support them wherever required, but the ability to handle these projects by themselves means that the integrator can generate his own added value. This is true not only during the new build phase but later, during after sales service too,” explained Mr Vukancic.
In closing, Mr Vukancic pointed to an interesting anecdote about Günther Böning, the company’s founder and CEO, who has a wellknown mantra within the company that describes his and his team’s commitment to customer service: “The sale opens the door but the service keeps it open.”
After nearly half a decade in business, Böning Automationstechnologie has built a reputation amongst its customers for providing the kind of service that exceeds the norm. Whether it’s replacing a 25-year old part with a brand new unit made to perfectly fit the original, or whether it’s jumping into a specially modified trailer on a cross-country tour to take its products to the customer when the customer couldn’t visit them, Böning Automationstechnologie continues to innovate not only in terms of the way it connects technology but also in how it connects people.
And with its focus on the future harnessed to its robust design, engineering and production facilities, Böning Automationstechnologie looks set to comfortably add another successful half century to its first. n
seven seas, five oceans, one voice
mikasa corporation precision products (uk) ltd wouter witzel eurovalve
Mikasa Corporation has been a major player in the rubber products manufacturing sector for well over a century. While originally catering to the consumer and sporting goods market, Mikasa has been producing rubber-based parts for the marine sector since the 1970s. Fast forward to today and Mikasa has the goal of using the extensive knowledge and experience the company has accumulated to expand further into the global maritime markets. Article co-written by Jordan Yallop and Daniel Barnes.
Since the company’s founding, Mikasa has always strived to create the best rubber products possible for its clients. Following an expansion into the manufacture of submerged bearings, pumps and rubber linings for propulsion shafts for the marine sector, Mikasa has enjoyed continued success. Such is this success, the company now aims to expand further into global maritime markets.
Mr Yoshihiko Onishi, Executive Officer of Mikasa Corporation, spoke of the company’s goal: “Based on the experience gained in the supplying our bearings into
the coastal vessel market in Japan, we are looking to break into the global coastal or inland vessel markets. At the same time, we will also develop the market for oceangoing vessels.”
Beginning as the Hiroshima Gomu Corporation in 1917, founded by Mr Masutaro Masuda, Mikasa originally manufactured and sold various rubber products such as rubber flip-flops (known as Zori in Japanese culture). Over the years the company has built a large positive reputation as a sporting goods manufacturer, with a primary focus on sports balls. These products have been used
in various world championships and Mikasa’s volleyballs have been officially used by the Volleyball World Championship for over half a century.
It was in the 1970s that Mikasa entered the burgeoning marine sector, with a catalogue that now includes rubber bearings, rubber linings for ship propulsion shafts and the company’s FF-Bearing.
Mr Yoshihiko Onishi said: “Utilising our rubber processing and manufacturing technology, we developed a water-lubricated bearing in 1975, and since then it has been widely used for ships and pumps. Developed
in 1981, the FF-Bearing has a self-lubricating polytetrafluoroethylene resin at the part that slides with the shaft to provide ultra-low friction and high durability.
“In 2018, we developed an upgraded ver sion of FF-Bearing Crescent Type to celebrate the company’s 100th anniversary.”
Mikasa’s industrial arm is located in Hiroshima along with the head office, where over 150 employees are based – 30 of which are specialist manufacturers. The company’s sporting goods production plant has over 400 employees and is located in Thailand.
Mikasa offers rubber linings for propeller shafts to support a maximum length of 20m in size, making it the only company in Japan capable of such a feat. Another noteworthy point is how all of Mikasa’s bearings are water lubricated and therefore have a diminished impact on the environment in contrast to oil lubricated bearings.
Such is the trust in the company’s home in Japan, Mikasa’s water lubricated bearings were used in the construction of the SHIRASE, the Japanese Ministry of Education, Culture, Sports, Science and Technology’s Antarctic exploration ship.
On the 24th of February 2022, the company also joined the Green Award incentive program. Mr Masahiko Izumi, Sales Manager of Mikasa Corporation explained this move was carried out in order to further contribute to the marine transportation industry and the conservation of a rich marine environment through the company’s products.
“We will sell our company products at a 5% discount to Green Award certified shipping companies, to shipyards that are contracted by a Green Award certified shipping company and have a Green Award interim certificate for the new build project,” he outlined.
To accommodate the company’s future expansion, plans are in motion to increase the size of the research and development facilities at Mikasa headquarters. This is to facilitate the plans to enter the oceangoing vessel market with the company’s water lubrication system.
“In both the domestic and global markets, our aim is to venture into the oceangoing ship sector in the near future, and the FF-Bearing Crescent Type can be adapted to the shaft weight of large ves -
sels. Currently, oil lubrication is the mainstream option in the ocean-going vessel market, but we would like to replace this with Mikasa’s water lubrication,” said Mr Masahiko Izumi.
Mikasa currently produces three specialised products for the marine segment: rubber linings for propulsion shafts, water lubricated bearings, and the FF version of the company’s water lubricated bearings.
Mikasa lines propulsion shafts with rubber to prevent corrosion associated with marine usage. The rubber lining must be exceptionally strong against contraction, expansion and torsion – due to temperature changes rotational torque and external shocks. These highly trusted products
eliminate the permeation of seawater by encapsulating the at-risk components in hardwearing ebonite.
Propulsion systems can be classified into two major types – water and oil lubricated systems. Mikasa started developing rubber water lubricated bearings in the early 1970s. These products are characterised by their low power loss, low wear, and the fact they cause no damage to the shaft and sleeve of the vessel.
Mikasa’s water lubricated FF-Bearings have the characteristics of rubber bearings with added polytetrafluoroethylene, meaning they have just one-eighth the frictional resistance of traditional rubber bearings. This reduction in friction also means that more energy is saved, further contributing to reduced CO2 emissions. These FF-Bearings are also self-lubricating, which eliminates some of the dis -
advantages of traditional rubber bearings – such as burning and noise issues under specific circumstances.
Mr Masahiko Izumi said: “At the time of its development, Mikasa’s FF-Bearings were sold only to the Ministry of Defense and coast guards, but since 2000, it has been expanded to the general merchant ship and pump market.
“It’s durability and abrasion resistance have been recognised by many customers as a proven track record, and in 2021 it was used in more than 50 newly built domestic vessels. The number of new domestic vessels built in Japan is about 70 per year, so you can see how large our FF-Bearing market share is.”
Due to the efficacy of the FF-Bearings, MSC Cruises selected Mikasa unique bearings for use on four luxury cruise ships, the first of which will be delivered
in May 2022. Green technology is a key concept on these new ships, which goes to show the utility of Mikasa’s bearings.
Charting a future course Mikasa strives to always meet industry trends. Most recently it has committed to providing products that contribute to its customers’ ESG management and SDG initiatives. Furthering the point that the company’s FF-Bearings reduce more friction than standard rubber bearings – Mikasa’s own research has found that switching to FF -Bearings can reduce a ship’s fuel consumption by as much as 5%.
Mr Yoshihiko Onishi stated the company’s goal of entering the ocean-going vessel market is also its biggest challenge.
“Many people in the ocean-going vessels market have never dealt with water lubrication systems, so we need to explain to them the benefits of it from scratch. There are many advantages to using seawater lubrication, any issues can be prevented with proper management, so we need to continue to provide accurate information to our customers.”
He concluded: “This move to the oceangoing vessel market will require a global support system, so we will continue to develop our bases, including through collaboration. We will also need to increase the size of our products to accommodate larger vessels, so we will be increasing the size of our production and testing facilities.”
Inside Marine has translated and edited parts of this article based on a manuscript by Kaiji Press Co Ltd. Permission to reprint has been obtained from Kaiji Press Co Ltd. n
theWherethereareengines,therearepistons,allofthem requiringpistonrings.EnterPrecisionProducts(UK)Ltd: oneoftheworld’sleadingpistonring,metallicandnonmetallicsealingsolutionmanufacturers.Itstagline,‘The technologywithin’,perfectlydescribesthecompany’sspecialityinengineeringsomeoftheworld’sbiggest,most widely-used,complexandtechnologicallyadvancedpiston ringsandmetallic/non-metallicsealingsolutions. PrecisionProducts’SalesDirectorDominicRogers, andSalesManagerPaulBallin,satdownwithRichard Hagantotalkaboutthebigbusinessofkeepingthe world’sbiggesttwo-strokeenginesrunningsmoothly.
Precision Products (UK) Ltd (PPUK), is a leading manufacturer and supplier of low speed two-stroke, medium speed four-stroke, industrially applied piston rings and metallic and nonmetallic engineered sealing solutions.
From its advanced factory in Chesterfield, Derbyshire, the company manufactures and supplies products to companies around the world in both marine and industrial markets.
PPUK was established in 1994. Just over a decade later, the company was acquired by the Indutrade AB group in 2008. With over 200 companies under its umbrella, Indutrade is an international industrial group that acquires and develops companies that are characterised by high-tech know-how and an ability to build enduring, close relationships with customers and suppliers. Indutrade’s business philosophy is based on entrepreneurship and decentralised leadership, and PPUK fits perfectly.
As of the end of 2021, PPUK had 92 employees, a number that grew even in the midst of Covid. It operates from a single, modern factory loaded with all of the technology and facilities required to make some of the world’s most advanced piston rings and valueadded engineering solutions.
With the support of substantial investment from Indutrade, PPUK has developed its facility significantly in the last three years. This includes the addition of Arc, Plasma & HVOF thermal spray capability and expanded hard chrome and ceramic chrome capacity, supported by advancements of CAM turning and grinding technologies through working closely with machine tool manufactures to develop
bespoke solutions to some of the industries toughest challenges.
Aligned with several other capacity-based investments, this period of development has significantly underpinned PPUK’s growth strategies. The facility also had a complete overhaul to improve its sustainability offerings in parallel with 50% growth of its manufacturing footprint.
In 2021, PPUK was recognised by the coveted MakeUK, North East Yorkshire and Humberside Manufacturing Award, for its contribution to the sector in terms of its strong business growth and strategy.
“We were recognised for our very structured strategic growth program, excellent sales growth, strong order book, and growing our market share despite challenging business conditions,” explained Dominic Rogers, Head of Sales at PPUK.
PPUK credits its recent growth with its technical agility in the market, industry diversification, and new product introduction.
“We are able to manufacture engineered solutions for both the marine and industrial market base of up to 2m in diameter,” said Dominic.
The company embraces the difficulty of developing and engineering bespoke solutions for customers.
Traditionally, PPUK’s work was dominated by the manufacture of solutions for OEMs including some of the world’s leading twostroke engine manufacturers.
“We manufacture large-bore diameter piston rings for the two-stroke engine
market,” noted Paul Ballin, Sales Manager for PPUK. “We have a number of approvals from two OEMs – the biggest in the world – and are dedicated to developing solutions with them.”
Another market PPUK has been highly active in is the wind turbine industry, which sees the company manufacturing large metallic rings of up to 2m diameter.
“We’ve been manufacturing them in various sizes, quantities and materials for over 25 years,” said Dominic.
While PPUK will continue to support those long-standing customers and markets, it is actively pursuing opportunities in developing bespoke, custom-engineered solutions for new, diverse customers around the world.
“We are evolving into an engineeringled organisation so we have recruited highly-skilled engineers to support our customer demand,” Dominic revealed. “We will develop, with our customers, technological solutions to meet their specific application requirements.
“We were a make to print organisation,” he continued. “Now we are growing the company’s capability. The engineers we have employed have the exact skill-set required, and we’re adding further value by having a full engineering suite available for customer projects. We want our customers to have faith in what we do and have it add value to the relationship between us and their designers. In general, we are an engineering-led organisation.”
Dominic and Paul both highlighted raw material and energy price increases as a major challenge for everyone in the industry.
“Raw material prices have become a challenge due to the global commodities market affecting us and our supply chain partners,” Dominic explained. “Energy price increases have also started to present additional challenges . We are therefore working hard across our networks, suppliers, and customer partners to manage this. It is certainly a tough balancing act!”
In dealing with rising prices, the company leans on its historically close relationships with its customers and suppliers, both of whom are regarded as partners within PPUK.
Despite the challenges inherent to Covid19, the company achieved impressive growth of 28% in 2021, all whilst navigating the restrictions and difficulties of the pandemic. In essence, PPUK has clearly made a material difference in the industry, both in supporting the global customer base and its employees in the local area.
“The industry is ever-evolving,” Dominic stated. “This is especially true within the marine market. There are new fuels coming down the pipeline, so to speak, either with a reduced sulphur content or alternative, environmentally friendlier fuels. The piston ring has to be able to withstand these different kinds of fuels. The industry is
trying to optimise the best solution that fits these alternatives.
“Our customers will be looking for the optimum solution in the engine to support their customers’ expectations,” he continued. “We have to be able to adapt and provide solutions to meet those demands. And we have the know-how and agility to do that.”
To complement its existing product portfolio, the company has begun to offer turnkey, engineered composite solutions. Dominic pointed out that OEM pump companies who want to maximise efficiencies and optimise electricity consumption are potential customers that would particularly benefit from lightweight and durable solutions.
Constant evolution is especially important given the surging global demand for the kinds of engineered solutions supplied by PPUK.
“Our biggest challenge is meeting the volume that customers demand and need,” he added. “The demand is high: however PPUK is able to meet its share of the market with attractive lead times as a result of our growth based investments.”
“Fortunately, we’ve optimised our manufacturing capabilities and reduced our lead time to an optimum level below the industry standard. At this point, when a customer has a breakdown or needs a component to support their customer, due to our determination to remain agile we can turn around and manufacture precisely what they need in a matter of weeks,” Dominic emphasised.
That’s all the more impressive when considering that as many as 30 operations are routinely required in the manufacture of a piston ring.
In concluding, Paul described PPUK as a very well-managed and ambitious company which always looks after its staff and customers.
“As we look towards 2022 and beyond, our mission is to always show our customers the added value that we offer, whether it’s through customer service, engineering excellence or supporting them in challenging times. And we will balance all of that with robust relationships with our suppliers – they’re partners too. You have to work as a team; you’re only as strong as the team around you.”
Reliability, availability and quality. Three hallmarks that, according to Dutch butterfly valve manufacturing specialist Wouter Witzel EuroValve, separate the company from the competition. And for its end users, which include commercial and naval vessels that cost tens of thousands of euros per hour to run, reliability is the key to the company’s competitiveness and operational integrity. Wouter Witzel EuroValve’s Sales Manager, Martijn van den Bergh, sat down with Richard Hagan to discuss the importance of high-quality, reliable butterfly valves in the maritime industry.
With over 50 years of production behind it, Wouter Witzel EuroValve has earned its place as a household name within the maritime industry.
The company specialises in the manufacture of butterfly valves for both commercial and naval vessels.
For the uninitiated, a butterfly valve is a special valve that is mounted insidea pipe and used to control the flow of liquids. It consists of a circular plate or a pair of hinged semicircular plates, attached to a spindle. The plate or plates are then opened or closed in order to allow or prevent the flow of liquids through that pipe.
Depending on the complexity of the ship and some other variables, any given vessel may require a package of between 100 and 2,000 different butterfly valves. With so many moving parts and, by extension, potential points of failure, it is in any ship owner’s best interests to buy valves that guarantee hassle-free operation, said Wouter Witzel Sales Manager, Martijn van den Bergh.
“Ships can cost hundreds of millions or even over a billion euros,” he explained. “Valves are one of many different components inside, and a package of valves can
cost between €100,000 and €400,000. On a ship that can cost €100,000 per hour to operate, do you really want to have trouble with your valves? No, you don’t. You want reliability, availability, security and quality, and this is what we deliver for our end users. ”
In fact, the company’s flagship product – its rubber-lined butterfly valves – have developed a reputation within the industry for their long lifespan.
“They often last for the lifespan of the ship,” Mr van den Bergh proclaimed. “Our products have a five-year standard warranty.”
Wouter Witzel has various competitors, many of which are based in the Far East and in China. Mr van den Bergh conceded that while his competition is cheaper, they cannot compete with Wouter Witzel’s hallmark quality and reliability.
“Regardless of the competition, our customers still demand our high-quality European-made product. When we can’t meet our quality standards anymore then we aren’t any better or worse than our competitors.”
In the midst of Covid and the global shipping crisis, Wouter Witzel has placed a major focus on its procurement
depart ment and practices to ensure uninterrupted workflows whilst also protecting its quality standards.
“The price of raw materials and transport has increased a lot,” he noted. “So while we already have multiple suppliers, the crisis has forced us to find more suppliers – sometimes as many as third or fourth suppliers for one particular item. We’re constantly searching around the globe for new suppliers who can fulfil our requirements, especially our high quality criteria. That makes purchasing much more difficult.”
The global shipping bottlenecks have, however, benefited Wouter Witzel in the form of increased new business.
“We’re seeing more enquiries, more orders and higher turnover now, much of it coming from businesses who are unable or unwilling to continue sourcing components from suppliers located outside of Europe,” Mr van den Bergh confirmed.
Building a better butterfly valve Wouter Witzel’s product range consists of products across four broad categories: rubber lined butterfly valves, high-
performance butterfly valves, check valves and finally operation, actuation and control products.
Of these, its rubber lined valves are its best-sellers and Mr van den Bergh was keen to highlight some of the reasons why those have been such a success for the company.
One reason, he noted, is the overall lower cost of automating its rubber lined valves. They require “the lowest torque in the world”, resulting in significant savings in the cost of the actuators required to automate Wouter Witzel valves.
“Actuators are very expensive,” he said. “While you pay more for our valves in comparison to our competitors, actuators for our competition’s valves tend to be larger and often cost more than the valves themselves. Our valves, with their low torque and high reliability, require smaller actuators, and when you can buy an actuator that is a size smaller, then you save an enormous amount of money.”
A second important reason is the durability of Wouter Witzel’s rubber lined valves , particularly in high-stress, high-velocity environments. Mr van den Bergh cited
off shore wind turbine installation vessels as being a particularly good example of a vessel requiring especially high durability from its butterfly valves.
Given their requirement to stay perfectly level in the water, ballast water is rapidly pumped between tanks, the flow of which is controlled by butterfly valves that must be able to deal with such a demanding environment.
“These ships are extremely big,” Mr van den Bergh commented. “Their ballast tanks are controlled by butterfly valves, which have to cope with high-velocity water flowing through the open valve. The disc is obviously an obstruction to the water, and due to that obstruction, you get an unstable water flow with turbulence, cavitation, noise, vibration and so on. The rubber lining on the disc and valve must be able to withstand those conditions.”
To ensure that its valves’ rubber linings stay on, Wouter Witzel vulcanises and then bonds the rubber to the disc. The end result is so durable that if one wanted to subsequently remove the rubber, it would have to be burned or machined off. “In comparison, the rubber linings of cheap
competitors tend to detach under those high-velocity conditions, making the valve unsuitable for the application. In our valves , detachment isn’t a problem at all,” Mr van den Bergh assured.
In November 2021, Wouter Witzel introduced its latest innovation: an aluminium butterfly valve.
The new product is said to be suitable for all applications and has been specifically developed with weight-saving and mobile installation needs in mind.
As per the rest of the Wouter Witzel range, the new aluminium valve features low operating torque and world-class durability. It can, the company says, also be installed without the use of external gaskets. The new valve boasts a five year warranty and is already available for purchase.
In mid-2022, Wouter Witzel finalised the installation of a large rooftop photovoltaic solar array at its facility. Through this and other measures, including a reduction in travel and increasing reliance on video calling software for meetings and other functions, the company expects to see a 49% reduction of its CO2 emissions by 2030.
Wouter Witzel also maintains a close relationship with its surrounding communities via a bouquet of social responsibility programs. One program involves setting aside 3,000 production hours per year in their facility, for functions that are filled
by people with various disabilities. This programme creates work that disabled people are specifically capable of doing, allowing them the dignity and satisfaction of participating in a professional workplace and earning a decent wage. Additionally, Wouter Witzel offers ten apprenticeship positions per year.
Outside of its factory, the company supports 20 poverty-stricken families with birthday presents each year for the children within these families, and it
sponsors several local football teams in terms of uniforms or other kit.
Mr van den Bergh concluded with some comments on the Dutch maritime industry: “I feel that it’s a pity that the EU doesn’t have great support for local producers. Thankfully, we benefit from our great maritime heritage and the strong Dutch maritime industry. All of the big names are part of the community here and we look forward to doing some great business together in the years to come.” n