H.E.L GROUP
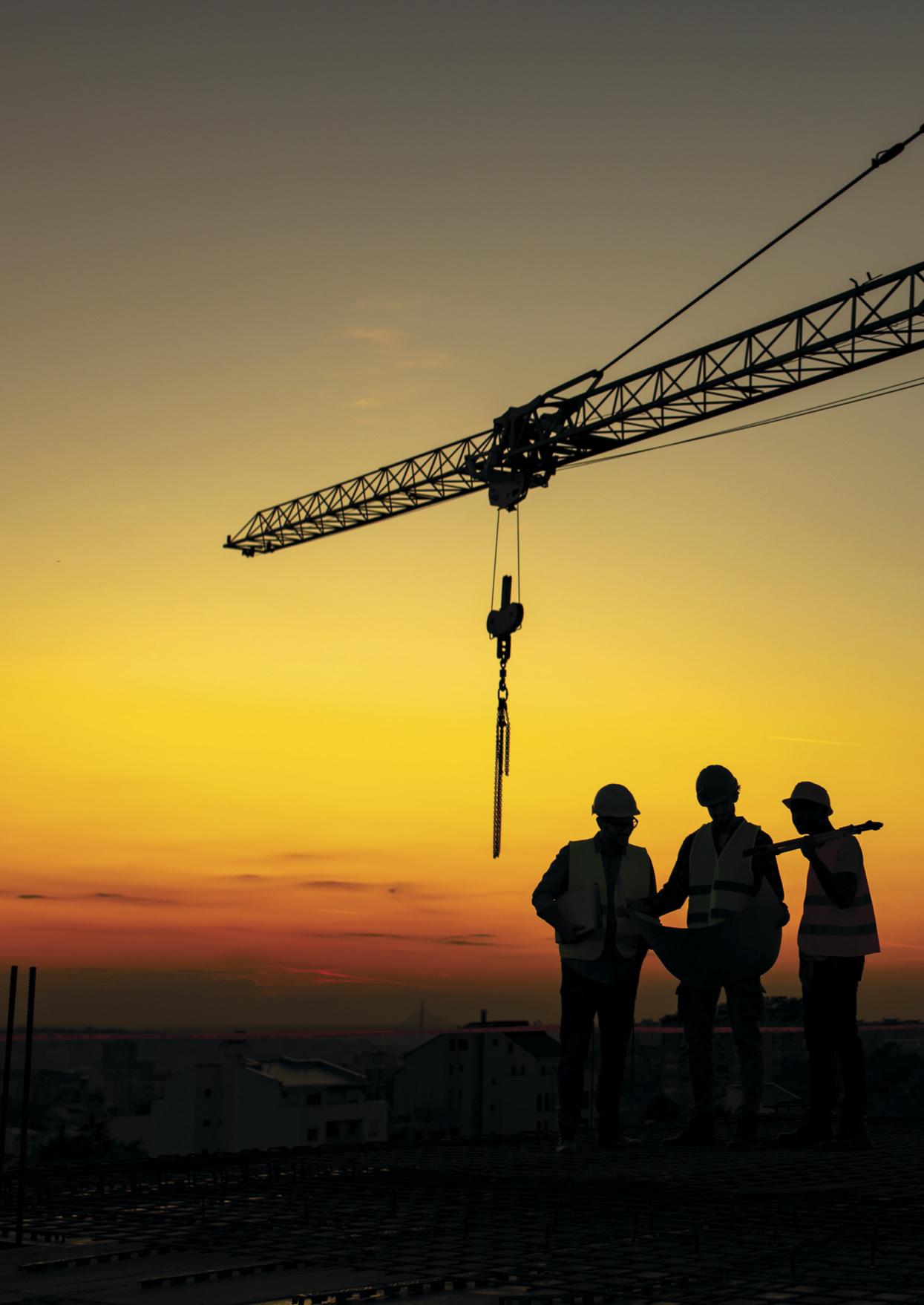

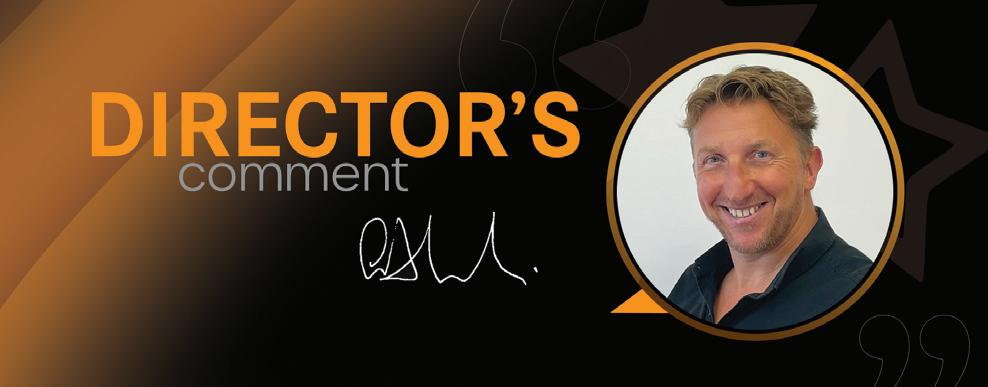
dear reader to you latest edition of Inside Industry, which we bring to you with mixed emo tions. For over thirteen years we have pro duced for you this very popular general industry publication. Our editions have circumnavigated the globe and brought the latest news, views, advertisements, company profiles and events details to hundreds of countries and almost as many different types of industry sectors.
We like to think that, as our slogan says, we have indeed helped to connect indus tries worldwide.
Why then the mixed emotions I hear you cry impatiently… or maybe you are patiently waiting for me to finish my ramblings so that you can indulge yourself in the far more interesting pages that follow. I will continue regardless. So, these mixed emotions are due to this being the last edition of Inside Industry. I know, I know, but before you take the day off to be alone with your tears and the grieving process, fear not, it is a rebranding of the name and a change in direction for some of the content. Therefore, wipe those tears away and bring out the bunting and champaign, for the next edition that you will receive, will be titled ‘Inside Sustainability’.
Inside Sustainability will continue to report on global industries and its purpose remains the same ‘connecting industries worldwide’, however, in addition to pro moting your products, services and future plans within your advertisements and arti cles, you will now have the opportunity to tell the world what you are doing to
reduce your carbon footprint and become more sustainable as a business. Sharing best practices and ideas will surely make the world a better place and we are therefore proud to be able to be a part of that journey.
This is nothing new of course, in fact many of you have been discussing sustain ability issues with us at Inside Industry for a long time and indeed your desire to do so during interviews we have conducted with you or content we have seen increasingly within your news and advertisements, has been a deciding factor in our rebranding decision. Other than the name change, many of you may not notice much difference within the magazine as we have, as touched on above, been transitioning the content for a while now. No former content that you have grown familiar with for over a decade will disappear, instead it is very much a case
of ‘in addition to’, rather than ‘instead of’. One thing you will notice is that Inside Sustainability will be a digital only maga zine. We will not be publishing a hard copy version of it for hopefully obvious reasons. Some more good news here is that because there is no hard copy, we have far greater flexibility with the digital version. I do not wish to spoil the fun of the first edition, so I am afraid you’ll just have to wait and see what is different in the first edition of Inside Sustainability. A little more teasing from me, there will be much more to come within the digital edition I can assure you.
I will sign off now by thanking you for your readership, comments, support, and wonderful content toward Inside Industry for well over a decade. Like a phoenix reborn, I am sure you will wish to stay around to see the new title take flight and again be directly involved in sustaining (sic) its flight. n
Managing Director John White and his tears… of joy.Managing
John White
Editorial
Barnes
Editorial Assistants
Phil Nicholls
Imogen Ward Hannah Barnett
Feature Writers
Filomena Nardi
Colin Chinery
Andy Probert
Romana Moares
Laura Watling Richard Hagan
Business Development Manager Darren Foiret
Senior Editorial Development Manager
Jasmine Lodge
Research Editors
Jeff Johnson Ginelle Lorenzo Clare Bishop Becky Scrivens Judi Wheaton-Mars Callum Smith
Sales & Marketing Director
Richard Brightmore
Sales Manager
Helen Leisi
Project Managers
Kym Hamilton Tony Ingrouille Chris Renicar
David Earl Connor Doddington Dane Coady Alexander Paterson Jamie McBride
Lisa Smith
Verity Manning
Spencer
White
Jones
Harris
O’Malley
White
Introduction
3 Director’s comment
Inside Industry goes shopping for a new outfit
Upcoming events in the industry
8 USA
America leads global campaign to fight climate change with landmark legislation
9 United Kingdom
High Value Manufacturing (HVM)
Catapult arrives in Manchester
10 China
Tate & Lyle expands its sustainable stevia programme in China
12 How is digitalization impacting manufacturing?
Michael Colarossi at Avery Dennison RBIS details how and why manufacturing companies need to embrace digitalization
News
16 Industry news in brief
The latest company and industryrelated developments from around the world
20 Did you know?
Interesting and unusual industry facts from around the world
For the executive
22 A passion for haute horology
F.P. Journe
28 The right fit
ESI Technologies
34 Driving the world’s energy transition Airem Energy
40 A renewable love for engineering
Brimmond
46 Building a reputation for innovation
King & Moffatt
51 Customised solutions for every storage need
STAMH
56 Laboratory equipment under the microscope H.E.L Group
62 Decades of collecting and preserving yeast strains
The National Collection of Yeast Cultures
66 How revolution sparked a reinvention Fontanafredda Cold Forging
70 Efficient thermal solutions for a greener planet
Provides Metalmeccanica
74 In pole postition to meet aviation MRO demands Pole Air Aviation
always open
PACK EXPO International offers a comprehensive selection of packaging and processing solu tions for industry, educational sessions and networking opportunities. Packaging and processing technolo gies and equipment on show will include: automation and robotics, printing and labelling, materials and containers, remote operation, processing equipment, supply chain, and track & trace technology. Held in Chicago, attendees come from the world’s biggest companies, as well as small start-ups looking to scale up production, and mid-sized companies that are launching products, growing their brands, expanding e-commerce, working on sustain ability and more . www.packexpointernational.com
The Government of the Arab Republic of Egypt will host the 27th Conference of the Parties of the UNFCCC (COP 27), with a view to building on previous successes and paving the way for the future ambition to effectively tackle the global challenge of climate change. The pro gramme unites government and non-Party stakeholders, fostering collaboration to deliver greenhouse gas emission reductions and ensure a just transition to a net-zero economy which alleviates poverty and he lps secure a sustainable future.
https://unfccc.int/cop27
FABTECH returns to Georgia World Congress Center November 8-10, 2022 and provides a convenient ‘one-stop shop’ venue where you can meet with world-class suppliers, see the latest industry products and developments, find the tools to improve productivity, and increase profits. Experience the power of in-person events to discover, educate, and moti vate the metal fabrication industry. www.fabtechexpo.com
For over four decades, Intermodal Europe has been the most targeted annual meeting point in Europe for companies associated with container shipping and intermodal transport across road, rail, and sea. The event facilitates the opportunity to meet and do business with 140+ leading global suppliers, discover the latest container innovations and technology, network with senior-level peers, and hear about the challenges and opportunities facing the container shipping market today from field experts.
www.intermodal-events.com
MEDICA is the world’s largest event for the medical sector. Seven main product categories will be included in the exhibition halls this year: electromedicine / medical technology, laboratory equipment, diagnostics, physiotherapy / orthopaedic technology, commodities and consumer goods, information and communication technology, medical service and publications. Each year, leading individuals from the fields of business, research, and politics grace this top-class event with their presence – naturally alongside tens of thousands of national and international experts and decision-makers from the sector.
www.medica-tradefair.com
Hosted at Olympia London, the UK’s biggest festival of construction features a jam-packed two days of incredible content across six conference stages with a 50% representation of female speakers, hundreds of exhibitors, live music, entertainment and networking events including Meet the Buyer sessions, Women in Construction and much more.
www.londonbuildexpo.com
Following a proposed $469 billion energy and climate spending currently going through congress, Ron MacDonald, President and CEO of Zinc8 Energy Solutions, outlines the benefits this could have nationwide if given the green light.
The$469 billion energy and climate spending agreement struck between Senate Majority Leader Charles Schumer and Joe Manchin, if successful in getting passed in Congress, will be the biggest legislative win for the clean energy movement since the Clean Air Act and represent the largest single largest federal clean energy investment in US history.
This energy and climate agreement details that a $27 billion ‘clean energy tech nology accelerator’ will be created to ensure America’s role as the leader in cutting-edge renewable technologies. US states and utili ties companies will receive $30 billion to ease the transition to zero-carbon, renew able electricity with millions of dollars in tax credits to support battery, wind, solar and other clean energy industries.
As a CEO of an energy storage company, which is developing and commercialising long-duration, low-cost zinc energy storage systems, and who recently received support from Charles Schumer for my company to establish a manufacturing facility in Ulster, (New York’s former TechCity site location), I can attest that my company, and the overall energy storage sector that I’m proud to be part of, is more readily embraced and supported by United States political leaders, its government and private and public enterprises, than any other country in the world.
“Zinc8’s interest in expanding hundreds of new jobs into the Hudson Valley at Ulster County’s former TechCity site, now called iPark87, would be a win-win-win,” said Senator Schumer in a recent press release. “A once-contaminated asbestos dumping ground can be revitalised and once again be the beating heart of Ulster County’s economy, all while powering a cleaner, brighter future, fighting climate change, and creating hundreds of goodpaying jobs.
“I made it clear to Zinc8 CEO, Ron MacDonald,” continued Senator Schumer, “that I stand ready to help their potential expansion in the Hudson Valley in any way, including fighting to secure the his toric federal battery research & develop ment incentives I passed in the Bipartisan Infrastructure & Jobs Law. Zinc8’s invest ment in the Hudson Valley would further power New York’s leadership as a global battery manufacturing hub.”
Energy storage is critical to America’s clean energy future. As renewable power sources like wind and solar provide a larger portion of America’s electricity, storage will allow clean energy to be available when and where it is most needed.
As America continues to invest and build its cleaner grid, energy storage will allow each state to better use existing resources
more efficiently and with fewer emissions. With storage, a state’s grid can reduce electricity from the dirtiest power plants during periods of peak demand, such as on hot summer days. As our world con tinues to fight climate change, the energy storage sector’s technology costs continue to lower with rising demand across nearly all industries.
Biden’s White House has set a goal to reach 100% carbon pollution-free electricity by 2035. This can only be achieved by investing in the companies that are actively producing the technology to produce mean ingful emissions reductions in this decade. The passage of this legislation will ensure the survival of these innovative cleantech companies who will lay the groundwork for a clean energy planet.
By bolstering domestic supply chains and manufacturing American-made, clean energy products to sell nationally and internationally, America will reach their goals of carbon neutrality and inspire other countries to do likewise.
Zinc8 Energy Solutions is a leader in Zinc-Air battery technology. The Zinc-Air Flow Battery from Zinc8 Energy Solutions is an energy storage solution designed to serve a wide range of long duration appli cations for microgrids and utilities. n
Mayorof Greater Manchester, Andy Burnham, said: “This is fantastic news for Greater Manchester and especially for our manufacturing sector. The HVM Catapult is there to help businesses innovate, which will spark further invest ment and support the creation of highquality jobs.
“Going back to the Industrial Revolution, our city-region has been at the centre of advances in science and technology. Innovation is just as important to our future.
Increased R&D spending and more produc tive businesses can power the growth of our economy and level up the North.”
The HVM Catapult and CPI unveiled analysis relating to the output gap to mark the opening of its Manchester offices in the heart of the city’s innovation district at Bruntwood SciTech’s Circle Square – a joint venture partnership between Bruntwood and Legal & General.
HVM Catapult Chief Executive, Katherine Bennett said: “Backing manufacturing through technology innovation in Manchester is an important part of the ‘level ling up’ agenda. Mancunians are extremely hard workers and there is so much opportu nity for growth in the region. Manufacturing not only brings direct benefits to the local economy, but every 100 manufacturing jobs creates in turn an additional 90 jobs in the wider economy.
“To expand its impact across the North, CPI’s new Manchester office,
alongside its office recently opened in Liverpool City Region at another of Bruntwood SciTech’s locations - Liverpool Science Park, will further connect the innovation ecosystem and boost pros perity across the North of England. HVM Catapult and CPI hope to pave the way for R&D in the region and deliver commercial and collaborative technology innovation projects that boost sustainability, health and economic prosperity.”
The first HVM Catapult presence in Manchester will support the region to deliver its technology and innovation plans, bolstering the local economy. HVM Catapult and CPI will encourage businesses to invest in innovation and support the creation of new products and processes, which could boost regional productivity annually by up to £500m.
Frank Millar, CEO of CPI, said: “CPI has worked collaboratively with busi nesses and institutions in Manchester over several years. With its industrial history, outstanding academic institutions, and thriving start-up, science and technology scene, opening an office in Manchester is delivering our strategy to enable placebased innovation. Through high-impact innovation partnerships, strategies and programmes, we’re excited to support businesses in Greater Manchester to become more competitive, delivering impact in the local economy, developing skills, and creating and protecting highvalue jobs.”
HVM Catapult works closely with important stakeholders including The University of Manchester. Professor Luke Georghiou, Deputy President and Deputy Vice-Chancellor at The University of Manchester, said: “The High Value Manufacturing Catapult will provide another key element in our rapidly devel oping regional innovation ecosystem; in Manchester, we have developed an approach which accelerates the flow of new knowl edge into applications.
“We do this through our world-class facilities in graphene and other advanced materials, biotechnology and health which together provides firms of all sizes the opportunity to work in partnership with leading experts, as well as giving access to our state-of-the-art equipment.
“A vital part of the Manchester offering is the highly qualified graduate workforce, which attracts knowledge-based firms into the city while also helping existing compa nies to grow their innovative activities.”
The HVM Catapult is the go-to place for manufacturing technology innovation in the UK. The seven centres across the country cover the full range of manufac turing technology capabilities, from materials and biologics to automation and virtual reality.
HVM Catapult works with businesses of all sizes and all sectors to turn ideas into commercial applications by addressing the gap in and accelerating the activity between technology concept and commercialisation.
A new office in Manchester for the High Value Manufacturing Catapult (HVM Catapult) and deep tech innovation organisation, CPI will bridge the region’s manufacturing output gap of £500m million according to new research cited by HVM Catapult.
Tate & Lyle entered the next phase of its sustainability programme for stevia, a plant-derived and in-demand low-calorie sweetener, by enrolling new farmers in China. The programme supports participating farmers to implement best practices identified in its 2019 stevia lifecycle-analysis and verified in its 2021 on-farm pilot.
leader in ingredient solutions for healthier food and beverages, Tate & Lyle partnered with environ mental charity Earthwatch Europe, working with Nanjing Agricultural University in East China, to develop the programme aimed at ensuring the stevia industry grows sustainably.
The expanded programme follows an on-farm pilot undertaken in Dongtai in 2021 that focused on improving the envi ronmental and social impacts of stevia production, based on the results of Tate & Lyle and Earthwatch’s life-cycle-analysis completed in 2019.
In 2022, an expanded cohort of farmers in Dongtai, Jiangsu Province, East China and additional stevia farmers in Linze, Gansu Province, West China will implement the agronomic practice changes piloted last year, and trial additional changes to further min imise their environmental footprint. With the stevia agricultural sector at a relatively early stage in its adoption of more sustain able practices, this science-led programme is helping to build the evidence base and demonstrate the positive environmental, social and economic impacts associated with these changes.
Participating growers will be supported to pursue sustainability-related verification for their stevia through the Sustainable Agriculture Initiative Platform’s Farm Sustainability Assessment, and have been encouraged to sign Tate & Lyle’s Stevia Supplier Sustainability Commitment a pledge to reduce the environmental impact
of stevia farming. Growers signing the Commitment will be helped to understand their environmental impact through sam pling, assessments, and participation in workshops with a clear goal of reducing environmental impact and improving pro ductivity and profitability.
“Supporting sustainable agriculture is front and centre of our plans to deliver on our commitment to be carbon net zero by 2050,” said Nick Hampton, Chief Executive of Tate & Lyle, “to help our cus tomers deliver on their carbon reduction commitments and to build a thriving farming community. Our stevia pro gramme in China epitomises our purpose in action and is laying the groundwork for the sustainable development of the stevia industry. We are excited to share our lessons and experiences to strengthen sustainability in the stevia supply chain and help farmers to unlock economic ben efits for their communities.”
Maria Pontes, Director of Programmes and Partnerships at Earthwatch Europe, commented: “This partnership, through its hands on approach to trialling change and sharing knowledge, has engaged farmers, encouraging them to improve the sustainability of their growing practices. We recognise the importance of supply chain resilience, so supporting
growers and building a strong supplier network, while making a real change to the environment, is a priority. We really look forward to continuing to work with Tate & Lyle to develop this programme.”
Professor Luo, project lead from Nanjing Agricultural University in East China, said: “It’s very important to involve farmers in the demonstration of stevia slow-release fertiliser application as it helps them to better understand and believe in the practical technology and its value, improving their trust that this approach will benefit them, which in turn will move the sustainability pro gramme forward. Participating farmers say that the optimised application of slow-release fertiliser technology, using this fertiliser once a whole growing season instead of multiple applications of different fertilisers, as they were pre vi ously, is making stevia farming easier.”
Tate & Lyle is a world leader in ingredient solutions for healthier food and bever ages. Supported by a 160-year history of ingredient innovation, Tate & Lyle partners with customers to provide con sumers with healthier and tastier choices when they eat and drink. Tate & Lyle expertly develops solutions which reduce sugar, calories and fat, add fibre, and provide texture and stability in categories including beverages, dairy, bakery, soups, sauces and dressings.
Digitalization
presents a steep learning curve, but manufac turing industry leaders today recognise the urgent need to invest in Manufacturing 4.0 technologies. With supply chain disruption and global economic and political upheavals impacting every sector, staying competitive is more challenging than ever, meaning the race to digitalize must go up a gear.
So how is a manufacturer like Avery Dennison approaching dig italization? As a starting point, we recognise the value of digitally connected operations bringing data to the forefront of decisionmaking. This is what’s driving the shift in how operations work across our global business.
Advances in technology and smart manufacturing are reshaping our business and delivering cost and efficiency savings. We are a company that manufactures an incredibly wide range of products including care labels for apparel, tags and packaging, and adhesives. We also have a large division that deals with supply chain intelli gence and data collection through RFID technology.
We operate hundreds of thousands of manufacturing platforms across a family of sector-specific divisions. So, leveraging data and smart manufacturing is critical to our success in delivering to our customers. Smart manufacturing is all about connecting processes
digitally with other networks, enabling machines to automate and produce independently and ultra-efficiently.
Our aim is to make tasks more efficient and we’re making tasks more effective, leveraging data to drive better decision-making. Whether that’s in the production of physical goods, quality checks, or communication with our downstream suppliers, it’s the connec tivity that counts.
We aren’t doing this alone, and it’s vital to be curious if you want to embrace the digital future. Early in our journey, we consulted other organisations that were further ahead on their journey to digi talize manufacturing, with the aim to learn from their experiences.
As an organisation, we’ve also embraced the concept of “min imum viable products”, allowing us to quickly test a concept, learn and improve. This iterative approach has been essential to our journey and will be foundational to how we continue to improve. Focus is equally critical, and we’ve embraced our digital journey while remaining focused on developing and expanding our core capabilities, to introduce new material innovations and solutions for our customers and end consumers.
For us, digitalization is affecting manufacturing in the following ways:
• Customer experience
This encompasses everything from how Avery Dennison engages with its brand customers, to how it designs its products, and how it tailors products to enhance the customer experience. For example, we’ve embraced digital sampling, partnering with external organisations to eliminate the lengthy and wasteful process of physical samples.
We’ve adopted 3D manufacturing in some cases, to produce proto type parts for clients to test in their manufacturing processes. While some of these enhancements remain in the testing stage, the ambi tion is to bring them to scale in an industrial manufacturing setting.
• Changing the solutions and products that are entering the market
Digitalising our solutions creates an opportunity for Avery Dennison to generate value that extends beyond a label. With the scan of a smartphone, our digital labelling technology can unlock direct-touser digital experiences.
Our intelligent labelling technology, including RFID, drives supply chain efficiency, improves transparency, and enhances
product authenticity. And some of our digital solutions, like digital care labels, can enable sustainability and circularity by providing product information that makes recycling, resale, and “take back” programs a reality.
• Manufacturing efficiency vs. effectiveness
Oftentimes, when organisations consider digitizing manufacturing, the core question is: how are we going to drive greater efficiency across our manufacturing platforms? At Avery Dennison, instead, we are asking, “how will digitalizing manufacturing help us be more effective in servicing our customers?” The focus on effectiveness and customers changes the conversation. Digitalising our platforms will enable far greater flexibility.
We’re also interested in using and leveraging data more effectively throughout the supply chain to plan better, source better, execute better, cut waste, and get faster. Focusing on effectiveness also changes the investment conversation focusing on technology to assist employees allows them to focus on the quality of the prod ucts that are produced.
Another key impact on manufacturing is AI (artificial intelligence) and Machine Learning which can help manufacturers monitor opera tions in real-time, spot inefficiencies as and when they occur, and forecast accurate delivery dates. We are also exploring how this tech nology can optimise quality and product development, using data to focus quality control on key failure points or improve how we design product experiments.
AI systems also enable predictive analytics, which can address operational challenges and disruptions to supply chains. McKinsey research suggests that AI can improve forecasting accuracy in manufacturing by 10-20%, which translates to a 5% reduction in inventory costs and a 2-3% increase in revenues. It’s no wonder AI is of such interest to the manufacturing sector.
We operate a very customized business. Everything we make is tai lored to our customers so digitization is very helpful in the customi sation process, speeding up what we can deliver. A lot of our output is for the fashion sector, which is highly time and demand-sensitive, so it makes sense for us to be able to make products in line with their essential just-in-time strategies. And in recent years we’ve developed software platforms and hardware that enables our customers to make their own products on demand, for instance, heat-transfer applications on t-shirts.
Special report: Michael Colarossi at Avery Dennison RBIS details how and why manufacturing companies need to embrace digitalization.I’m especially excited about innovations we’ve achieved in intelligent labels for the apparel sector. Avery Dennison’s Intelligent Labels are a suite of IOT-enabling technologies that authenticate product history, provide tracking and inventory solu tions and conjure richer consumer encounters. We’re operating today in a world of big data and massive amounts of information, so Intelligent Labels help create certainty, showing how a con nected world can be a better world, full of greater possibilities.
Avery Dennison is the new official supplier for names, numbers and sleeve badges for the Premier League. The agreement places emphasis on technology and sustainability and will see Avery Dennison use technology to increase efficiency and sustainability through reduced waste, using water-based inks, and creating
a “closed loop” configuration whereby plastics used in the applica tion of the product are collected and re-enter the supply chain.
These kinds of advances in understanding and learning from digital data allow manufacturers to move from being reactive to problems when they occur, to predicting and preventing failures before they happen. The gains being made from these learnings of behaviour from data are preventing operational delays and being replicated at scale across industries.
R&D, and getting value from any investment, remains impor tant. This is critical for projecting the ROI of the technology and meeting the needs of those hoping to benefit from it. n
The focus on effectiveness and customers changes the conversation. Digitalizing our platforms will enable far greater flexibility
Boeing announced in September that All Nippon Airways (ANA) will be the launch customer for Insight Accelerator (IA), a new cloud-based digital solution employing artificial intelligence to improve operational efficiency and avoid high impact service disruptions.
While the latest generation of commercial airplanes like the 787 generate a large amount of flight data, many operators lack the infrastructure to manage and leverage the information. IA uses out-of-the-box algorithms to sort and detect anomalies and create alerts to enable airlines to take proactive maintenance and repair action and prevent unscheduled delays.
“There are many products on the market for flight data analytics, but Insight Accelerator is the most effective tool for our aircraft oper ation,” explained Manubu Tono, All Nippon Airways manager of Planning & Administration, Engineering. “It’s very innovative and meets our primary goal of leveraging features in flight data that indicate a system failure before it happens.”
Based in Tokyo, ANA was the global launch operator of the 787 Dreamliner and is a launch customer for the 777X family. The car rier became the first airline in Japan to order the 737 MAX with
firm orders for 20 737-8s, and currently operates more than 170 Boeing jets. ANA operates the world's largest 787 fleet with 77 Dreamliners, including all three sub-models.
Boeing developed the IA platform based on decades of experi ence supporting the global fleet and developing rigorous methods while assisting ‘Airplane-on-Ground’ situations.
“IA’s built-in artificial intelligence, guided exploration and powerful visualisations allow airlines to investigate flight and maintenance data, identify trends and discover insights - all without specialized coding or programming skills,” said Duane Wehking, vice president of Digital Aviation Solutions at Boeing Global Services. “This is an easy-to-use solution that will provide value to airlines from day one.”
As a leading global aerospace company, Boeing develops, manu factures and services commercial airplanes, defense products and space systems for customers in more than 150 countries. As a top U.S. exporter, the company leverages the talents of a global supplier base to advance economic opportunity, sustainability and commu nity impact. Boeing's diverse team is committed to innovating for the future, leading with sustainability, and cultivating a culture based on the company's core values of safety, quality and integrity.
The latest company and industry related developments from around the world
Volta Trucks, the leading and disruptive fully electric commercial vehicle manufacturer and services provider, has confirmed that in September the first Volta Zero vehicle was completed at the com pany’s contract manufacturing facility in Steyr, Austria.
The landmark vehicle, the first of a series of second-generation ‘Production Verification’ prototypes, will form part of a Pilot Fleet of trucks. These will be loaned to customers for extended periods in late 2022 and early 2023 to allow fleet operators to understand how the first purpose-built, fully electric, medium duty commer cial vehicle will integrate into their operations. The start of series production of customer specification vehicles is on track to start in early 2023.
Volta Trucks’ contract manufacturing facility is run by Steyr Automotive, formerly MAN Truck and Bus Austria. Steyr Automotive was appointed in August 2021 following an extensive tender and based on their long experience of commercial vehicle manufac turing, existing infrastructure, and consequent speed to market. Steyr Automotive offers Volta Trucks more than 100 years of manu facturing experience building large commercial vehicles.
Steyr Automotive has reserved a capacity of 14,000 vehicles per year for Volta Trucks from their total available production. Over time, manufacturing the Volta Zero will create 510 jobs, plus 180 jobs in the building of the cargo boxes, in addition to an estimated 2,000 positions within the supply chain. The manufacturing con tract has a value of up to €1 billion over its lifetime.
Watching the first fully electric Volta Zero drive off the produc tion line in Steyr, co-Founder and Chief Manufacturing & Logistics Officer of Volta Trucks, Kjell Walöen, said; “This first vehicle rolling off the line at our manufacturing plant in Steyr is the latest significant milestone on the Volta Trucks journey towards the start of production of customers’ vehicles. To have achieved this significant landmark in just 12 months is a testament to the pace that we are working at to deliver the safest and most sustainable trucks to urban streets, and to the excellent collaboration we have with our partners at Steyr Automotive. Their team has used gener ations of premium truck-building experience to deliver the first Volta Zero off the production line on time, and to the highest quality standards.”
Falls continue to be a leading cause of preventable injury and death in the workplace, according to the Occupational Safety and Health Administration (OSHA). To help keep workers safe, MSA Safety, Inc, (the global leader in the development, manufac ture and supply of sophisticated safety solutions that help to protect people and facility infrastructures), is now offering a first-of-its-kind temporary horizontal lifeline that can help save time on the jobsite through its intuitive and toolless installation features.
MSA’s new Temporary Horizontal Lifeline allows for a 75% faster installation compared to traditional cable systems. The system’s inte grated locking and tensioning mechanism elim inates the need for nuts, bolts and wrenches, a key feature that makes the system significantly easier and faster to install because there is no need for tools.
“Our new Temporary Horizontal Lifeline was designed to address how long it took workers to install a traditional lifeline system by making this easier to use, but without sacrificing the level of safety for workers at height,” said Gustavo Lopez, MSA Safety’s General Manager of Industrial Products & Vice President of Connected Services. “This new system is lighter and easier to manoeuvre, and can be easily set up by one person, allowing the worker to spend more time on the job rather than setting up their systems.”
With locking and ten sioning mechanisms on the same side, workers no longer need to travel back and forth during set up. The new device also incorporates clear visual indicators to show when the system is properly installed. Designed to be adaptable to an ever-changing jobsite, the flexible, lightweight cable makes installation easier, plus MSA’s patented bypass shuttles allow two users to maintain 100 percent tie-off while passing one another on the same line.
“Most horizontal lifelines on the market today are heavy, time consuming to install, and require several tools,” Lopez said. “MSA’s new Temporary Horizontal Lifeline, however, is designed to be simple, intuitive and faster, to save companies time and money while helping to keep their workers safe.”
the
Send your latest news to: media@insideindustry.com
Scania announces far-reaching measures to decarbonise its supply chain by 2030. Together with its suppliers, Scania has outlined an ambitious industry-leading strategy to eliminate the largest carbon emissions sources from the most common produc tion materials and batteries.
“Once again Scania leads the way in ambitious climate action,” said Andreas Follér, Head of Sustainability at Scania. “We were the first in our industry to adopt science-based carbon reduction targets and we are now showing the way by decarbonising our supply chain.”
Through life-cycle analyses, Scania has identified four emission “hotspots” – batteries, steel, aluminium and cast iron – that together constitute approximately 80% of carbon emissions arising from produc tion materials. The supply chain decarbonisation strategy and targets initially comprise Scania’s production in Europe but will gradually be extended to its production in China and Latin America.
In electric vehicles, for example, batteries can account for half of sourcing emissions whereas in combustion engine vehicles, steel has the greatest carbon footprint. These four hotspots are therefore the focus of Scania’s supply chain decarbonisation strategy.’
The 2030 target is 100 percent green batteries, 100 percent green steel, 100 percent green aluminium and 100 percent green cast iron in its production. Scania’s definition of ‘green’ requires eliminating
the main sources of emissions by utilising new technologies, green electricity and /or recycled material. In batteries, for example, access to green energy in production is decisive. In the production of flat steel, replacing coal with green hydrogen is key.
“Scania has ambitious decarbonisation targets for all its activi ties, including our supply chain sourcing,” said John van Rossum, Head of Purchasing at Scania. “We’re pleased to note that several of our current and future suppliers are frontrunners in decarboni sation and will collaborate with us to reach the targets.”
Your input matters to us and we take all feedback on board to help our readers enjoy the magazine now and for years to come.
Send to: news@insideindustry.com
Interesting and unusual industry facts from around the world factmatterof
The largest solar farm in the world is the Bhadla Solar Park in the Indian desert state of Rajasthan. Bhadla has a capacity of 2,245 MW and is spread across 5,700 hectares (14,000 acres).
The largest wind turbine in the world is the 16.0-242, an offshore hybrid drive wind turbine from Chinese manufacturer MingYang Smart Energy. With 118m blades, the turbine has a 242m diameter and a 46,000 sqm swept area.
The Vista Moss Landing in Monterey, California, is currently the world’s largest grid battery. The site’s racks of Lithium-ion batteries can store 1,600 MWh.
The tallest crawler crane is the LR 13000 built by Leibherr in Germany. The crane has a maximum lift of 3,000 tonnes and a hoist height of 236m.
Every problem is a gift: we would not grow without problems “ “ Anthony Robbins
The smallest production car in the world is the Peel P50 from Peel Engineering. This three-wheeled vehicle is merely 137 cm long and 99 cm wide.
The longest train recorded is the BHP Iron Ore in Australia. In June 2001, the freight train travelled 275km; it consisted of 682 ore cars and eight diesel-electric motors, with a total length of over 7km.
The most expensive fabric in the world is woven from the wool of the vicuna, a relative of the alpaca. Vicunas live wild, high in the Andes, South America, so must be caught every two or three years to be shorn. Vicuna textile costs around $2,200 per metre.
Weiner Zeitung holds the record as the oldest daily newspaper in the world which is still in production. This official gazette of the Austrian government was first published in 1703.
The current holder of the title of largest combine harvester is the John Deere X9. Capable of harvesting 100 tonnes of wheat per hour, it also features a massage chair for the comfort of the operator.
François-Paul Journe has been inventing and making watches for over 40 years. He draws on his historical knowledge and expertise to face the most daring horological challenges, demonstrating a timeless consis tency in research and innovation with a single goal: make each mechanical timepiece as accurate as possible.
Excellence and precision are the essence of an F.P.Journe watch, as well as authenticity and chronometry. F.P.Journe produces all its movements in 18K Rose Gold, a first in the watch world and a unique feature of the brand. Signed with the label Invenit et Fecit (invented and made), each F.P.Journe exclusive movement guarantees a manu facture calibre, entirely invented, con structed, and assembled in the Geneva workshops. In the 18th century this inscrip tion used to be engraved on watches manufactured by prestigious French master-watchmakers upon their accep tance by the Royal Academy of Sciences.
At the crossroad between arts and haute horology, the independent F.P.Journe Manufacture is a world in itself, embodying excellence, know-how and innovation, in the respect of the haute horology tradition from which FrançoisPaul Journe is the proud guardian. It was founded with one principle in mind: inno vate and uphold, if not outrival the high standards of haute horology. Every effort was made to verticalize the production in order to produce inside its walls, almost all the components necessary for the making of F.P.Journe watches. It includes the cre ation and production of all its dials and watch cases which echo with the move ment in perfect harmony.
The modernity of machines and instru ments is essential to reach the expected level of perfection, but it is also paramount to maintain craft tradition, since many operations are still done manually, with an infinite precision, tirelessly repeated until flawlessness.
In his manufacture, François-Paul Journe is the master watchmaker and that differentiates the brand from other watch companies. With unmatched tech nical and watchmaker skills, he makes a point of honour to design and manufac ture mechanical watches one by one and in small series.
With a limited production of less than 900 mechanical timepieces per year, the sanc tuary of the F.P.Journe manufacturing process honours artisanal work. It prides itself in maintaining a genuine watch maker’s art. Each certified watchmaker is reacquainting with state-of-the-art haute horology, making a specific watch according to his technical sensitivity, and performing all production stages from beginning to end without anyone inter fering in the process, including the deli cate rating, casing-up and testing.
reserve, to the Astronomic Souveraine, an ultra-complicated watch with 18 functions and indications.
These exceptional creations have granted F.P.Journe the awarding of the most important international watch prizes throughout the world: seven distinctions at the GPHG in Geneva, from which three times it has received the ultimate dis tinc tion of the Golden Hand. And numerous times its creations have been awarded W atch of the Year accolades in Japan, China, United States, Switzerland and Mexico. François-Paul Journe has also been decorated with the title of Chevalier des Arts et des Lettres by the French Minister of Culture.
The exceptional F.P.Journe high horology creations have spanned over decades, showcasing an exceptional watch pedigree from the astounding Sonnerie Souveraine, the ultra slim Répétition Souveraine, the emblematic Chronomètre à Résonance, the Chronomètre Optimum, the amazing Octa automatic caliber with a 160 hours power
Because the exceptional F.P.Journe time pieces of watchmaking art deserve to be brought out to their true dimension, the brand opened a network of 10 boutiques in Geneva, Paris, Tokyo, Hong Kong, New York, Los Angeles, Miami, Beirut, Kiev and Dubai.
At each destination, visitors may dis cover the pieces of the Classique, lineSport and élégante by F.P.Journe collections in the brand’s exclusive universe, as well as special editions that are reserved solely for them such as the Black Label collection or the Boutique Anniversary Centigraphe. n
The Liberty flying car from Dutch company PAL-V International has passed the stringent European road admission tests and received an official license plate. This is after a rigorous and extensive drive test programme carried out on test tracks since February 2020. After highspeed ovals, brake and emission tests to noise pollution testing, the PAL-V is ready to take on the roads.
When I fired-up the PAL-V for the first time I really got goosebumps!” said Hans Joore, test-driver of the PAL-V. “Hearing the vehicle come to life was just magnifi cent and driving it was great. It is very smooth and responsive to the steering and with a weight of just 660kg it accelerates really well. The overall experience is like a sportscar. Liberty feels sensational.”
For more information, visit: www.pal-v.com
Photo credited to: PAL-V Internationalesi technologies airem energy brimmond king & moffatt stamh h.e.l group the national collection of yeast cultures fontanafredda cold forging provides metalmeccanica pole air aviation dalgakiran kompresör theuma
With over 100 years’ experience, ESI Technologies is a leading supplier of process equipment and engineering solutions for the biotech, pharmaceu tical, chemical, semi-conductor and the food and beverage industries in Ireland, UK and the Benelux. Sales Director UK, Rob Leadbeater, shared the details of an exciting product launch in conversation with Phil Nicholls.
line is available at ESI Technologies as part of its extensive portfolio of process equipment. This new line offers a high-performance, long-lasting solution specifi cally tailored for food & beverage and clean utility areas.
“ESI is the master distributor throughout Europe for T-Fit® products manufactured by Zotefoams,” Sales Director UK, Rob Leadbeater, explained. “We have been supplying T-Fit® Clean insulation into the biotech industry for approximately 12 years. Zotefoams recently launched a similar product called T-FIT® Hygiene which is ideal for the food and beverage industry with unrivalled performance.”
ESI was founded in 1919 as Southern Engineering, which grew to become one of the largest suppliers of process equipment in Ireland. The company steadily acquired agency agreements with a range of leading manufacturers, before emerging as ESI Technologies Ltd in 1997. ESI Process UK was formed in 2002, with ESI Ultrapure Division established in 2015 to focus on growth of the biopharma market.
ESI has been a part of the Indutrade Group of companies since 2013. Indutrade encourages organic growth through empow ering entrepreneurship and investing in people whilst using a decentralised model.
In 2019, ESI celebrated 100 years of business, following the expansion of its Cork headquarters with increased warehousing and office space. In addition to this, more recently the company added ISO Class 7 clean rooms dedicated to the manufacture of single use tubing assemblies to the life science sector. ESI Process UK, also with new offices and expanded warehousing, is based out of Cwmbran in Torfaen, South Wales to cater for nationwide support.
When a management buyout at ESI took control of the company in 2002, the group was much smaller with less than 20 staff. From that point, growth has been linear, with a CAGR of approxi mately 18%. This consistent growth has brought ESI to a much stronger position with a current turnover of around £70 million and a 100-strong team.
The diverse range of products at ESI has made the company the leading player in the Irish process equipment market, capturing approximately 25% share. ESI also designs and manufactures skids systems to perform a range of functions including contin uous batch process, heat exchange, fluid transfer, energy recovery and more. Products within ESI’s portfolio include valves, pumps, instrumentation, and safety equipment, all designed and manu factured to meet the unique requirements of the customer.
“We represent numerous product lines,” Mr Leadbeater said. “Many of which are sole supply, which means they are only available through ESI in the UK and Ireland.
“ESI has partnered with some of these suppliers for many years. Flowserve SIHI is our longest agency since 1962. Habonim, manufacturer of state-of-the-art industrial ball valves and actuators, has been working with us since 2000. Continental Disc Corporation is a leading rupture disc manufac ture who has worked with ESI since 2001. Other valued suppliers include Emerson, NovAseptic®, who is part of Merck Millipore, Amazon Filters, and Crane Saunders®.”
With such a diverse portfolio at ESI, a close relationship with suppliers is a key aspect of the business, and according to Mr Leadbeater: “We work closely with the manufacturers, and we have great relationships with them. Transparency between us, the manufacturers, and the end-user is something we pro mote, and this approach works very well for us.”
The recent launch from ESI is in partnership with supplier Zotefoams, a pioneer in cellular materials and the world’s largest manufacturer of lightweight crosslinked polyolefin block foams. Zotefoams’ T-FIT® closed-cell foam is the most cost-effective insulation solution for plant-wide fibre and dust-free installation in demanding, highly controlled production environments.
The T-FIT® Clean range is a modular cleanroom insulation system for pharmaceutical, biotechnology and semiconductor manu facturing. The sister T-FIT® Process line offers high-performance insulation for process areas demanding heat-tolerant insulation. However, the buzz at ESI is for the new T-FIT® Hygiene range from Zotefoams, which is tailored for aseptic areas in FMCG applications, especially food and beverage, dairy, and personal care.
“ESI is now promoting T-FIT® Hygiene toward the food and beverage sector,” explained Mr Leadbeater. “In food production there are lots of hot and cold lines. T-FIT® Hygiene protects operators against burns, including cold burns, plus preventing heat loss and condensation. It is constructed from a closed-cell foam, and it does not become wet or get bacterial growth on it.
Given its competition, T-FIT® Hygiene is the only thing that tr uly works now.”
The addition of T-FIT® Hygiene to the portfolio enhances ESI’s reputation as a one-stop shop for projects. While structured as a sales and distribution company, ESI maintains a strong engi neering bias displaying high levels of customer support. Much of this support is offered at the start of a client’s project, as ESI con sults early in the life of a project, offering its engineering exper tise to help the client select the right package of equipment.
One secret to the depth of knowledge at ESI is the high-level of staff retention, supported by dedicated investment in the team.
“People come to ESI, and they tend to stay at ESI,” Mr Leadbeater agreed. “Most of our heads of division have probably been with
the company somewhere between 20 and 30 years. “We take pride in having our product specialists factory trained, ensuring we understand emerging technologies that (coupled with their knowledge and experience), keeps our customers informed on what can best improve on site processes.”
The extensive package of equipment available at ESI, com bined with the knowledgeable staff, enables ESI to fulfil pro jects such as the one highlighted by Mr Leadbeater: “We are two-thirds of the way through a major pharma project located in the UK. ESI are supplying £2 million worth of equipment to the client, consisting of about 5,000 individual line items from 21 manufacturers.”
By operating in three different regions, ESI recognises market differences between Ireland, UK, and the Benelux. The Irish market has a focus on bio/pharma, while the Benelux office is busier with the life sciences. In contrast, business in the UK is more diverse, being a more balanced mix of industries for ESI, including power, nuclear, pharma, biotech, chemical, and food and drink.
With such a diverse portfolio, it was inevitable that ESI has been impacted by the disruptions in the global supply chain. Restrictions in the availability of raw materials and increases in freight costs are ongoing challenges for the company, however, strong relationships with suppliers have enabled ESI to handle these issues and keep the production line running.
Alongside these global issues, the com pany is also committed to environmental sustainability, according to Mr Leadbeater: “This is a target at ESI for the remainder of this year and going into the next. Education is a key criterion for us, where we focus on managing our own consump tion and the energy we use. ESI has employed a dedicated person to work with our Indutrade teams globally to ensure we hit firm commitmentsto get us to Net-Zero.”
As ESI pushes towards the goal of net zero, the company is also looking towards expanding its market share and main taining the trend of steady growth. To support these objectives, ESI searches for the right people to sustain this journey.
Working as part of the team is core to the ESI experience. “Ultimately, we’re a sales company,” concluded Mr Leadbeater. “People buy from people. I know technology is changing the way we buy, but whilst there is still a human aspect involved in the busi ness, then it makes life interesting, and every day is different.
“ESI is proud to support the industries that enable our daily lives: pharma, biotech, power, nuclear, food and beverage. We support these industries from a solutions point of view, promoting products that create a cleaner, safer, and more efficient produc tion site for our cus tomers.”
ESI Technologies celebrates 100 Years in businessWith an over-arching emphasis across industry on sustainable energy needs, Airem Energy is stepping forward as a leader in the energy transition, whether designing and producing a micro-grid, energy storage, or a combined heat & power (CHP) unit. With facilities world wide and backed by a host of top-tier partners, the company is well-positioned to provide some of the best fuel-flexi ble solutions, confirmed CEO Rob Marchitello. Profile by Andy Probert
The launch of Airem Energy began in AFG Holdings, a private equitybacked global oil and gas original equipment manufacturer. It soon became evident that an additional power offering was needed.
Rob Marchitello, who worked at AFG, proposed that package to AFG’s board, and Airem Energy was created as a busi ness division in 2019. This was to help meet the rising demand for distributed generation and sustainability.
Airem Energy’s first partner was OPRA Turbines of the Netherlands, a leading manu facturer of advanced gas turbine-based generator sets. OPRA Turbines utilised Airem Energy as a premier packager, service provider and project operator of ultra clean, highly reliable gas turbines in the Americas.
However, when the pandemic occurred, and the oil price slumped, AFG decided
to divest Airem Energy and it was acquired by Energas Technologies, who is also the owner of OPRA, in 2020.
In the process of rebranding the global company, Energas has been transformed into Airem Energy Holdings and thus OPRA became a fully integrated brand of Airem Energy Holdings and the opportunity was created to access an extended network to better meet customers’ needs.
Collaboration with experienced special ists in a broad range of applications allows Airem to accelerate and enlarge its field of global expertise and capacity to produce innovative solutions for a successful energy transition.
Mr Marchitello commented that the new organisation is committed to supporting its partners through the energy transi
tion with advanced, clean, climate-sus tainable and economically-viable power generation solutions.
He added: “Airem has a very different approach to the industry. We come looking to offer solutions, not just a product, whether that is through a combination of products or engineered solutions. We are a sus tainable energy solutions provider which is needed more than ever in today’s world Whether you believe in climate change or not is irrelevant; there are multiple sus tainable solutions to be provided to the market, and we look at it from that stand point rather than just trying to sell a turbine.
“These will perfectly match customers’ needs and achieve our mission: To Drive
the World’s Energy Transition,” he added, noting that Airem Energy Holdings now has operations across the US, the Netherlands and China.
Airem Energy’s OP16 turbine generator package is powered by the environmentally friendly, reliable and economical OP16 all-radial gas turbine. Designed and built in the Netherlands and packaged globally, the OP16 turbine packages bring the OP16 radial turbine to market, with local service and parts to support clients’ needs.
Uniquely in the 2MW power range, the OP16 turbine’s fuel flexibility enables power, oil, gas and industrial clients to use virtually any combustible gas or liquid to produce high-quality power and
heat on even the most remote site. This turbine can even use hydrogen as a fuel.
“Our ability to utilise waste fuels in gaseous and liquid form simultaneously, enables clients to use the world’s resources more effectively and reduce their carbon footprint,” Mr Marchitello explained.
Examples of these waste gases include flare gas and NGLs from oil extraction and refining, biogas, pyrolysis, syngas, land fill gas, and even VOCs from oil and LNG transportation or storage.
In more conventional CHP applications utilising natural gas, their high reliability and heat-to-power ratio provide an excel lent source of electricity and heat, often converted to steam. The simultaneous ISO
output of 1.8 MWe and 4.2 MW high-tem perature exhaust heat offers a perfect fit for clients.
Multiple units can be deployed in synchronous operation for a modular approach to larger electrical and heat loads, providing extremely high reliability and low impact to the facility during mainte nance events.
Airem Energy also offers the A400 turbine package, a highly-efficient, fuelflexible solution in a compact footprint. The unique 400kWe size provides an excel lent solution to energy projects in the 400kWe to 1,200kWe range. Combined with their fuel flexibility, from hydrogen to biogas, the A400 turbine offers a highly customisable solution to a wide range of challenging applications.
Mr Marchitello added: “If we can help our partners in whatever goal they have, whether it be electrically, reducing carbon footprint, power, steam, or a combination of both, the biggest thing we look at today is in providing a solution through the use
of a wide range of fuels that would other wise be flared. We can recapture pollutants and re-use them in our products.”
Drawing on the flare gas example, Mr Marchitello said Airem Energy could run this through their gas turbines.
“We are looking at other energy options , such as those drawn from plastics, to run through the turbine to create power and heat. We have also begun to partner with accretive technologies to offer more, whether as a different sized turbine, bat tery technology, or potentially solar. Not only is this from a socially sustainable footing, but it will help present a solution for both privately held or public-owned oil and gas companies, particularly those that will begin to be measured for ESG.
“We know we can provide tangible solu tions to them, with measurable results. We can go to a customer and discuss the effects of our solutions and what problems we can solve for them. Our intense engineering
effort on the solution side demonstrates the product’s potential. The reality is we sell that solution.”
Mr Marchitello said: “Having smaller, distributed solutions, such as a microgrid or a one-plant solution, is perfect for us and offers tangible opportunities for our clients.”
He cited an example of the turbines’ effectiveness. In Texas, a large midstream company, which had an unstable grid, has since had its turbines electrically integrated into the grid by Airem Energy.
“About two years ago, we had a huge winter storm, and everything froze. But one of the only plants in West Texas that had lights on was our client: being inte grated enabled them to seamlessly transfer to island mode.”
The company’s OP16 turbines can be utilised in many fields: oil and gas, hos pitals, general industry, universities, manufacturing plants, landfills, recy cling operations and even marine. “The markets are pretty much endless where our solution fits,” he said.
To strengthen its hand in the market, the company has formed a number of partnerships with accretive technologies worldwide. This includes one with Aurelia Turbines, a Finnish company that manu factures a 400KW solution turbine. It also has an agreement with UNIVASTUM, a company which provides patented gasifi cation technology as an economic and ecological solution for clean energy gen eration without harmful emissions in the waste-to-energy sector.
“We have channel partners in select areas as an extension of what Airem Energy is trying to achieve,” said Mr Marchitello. “We have one in Colombia that leads in Latin America (Symmetry Latinoamérica), and Kaltimex Energy to further strengthen growth in Asia-Pacific. Other partnerships allow for a global reach and provide for worldwide client support system.
Airem Energy recently signed an agreement with Econimo’s Silent-Power
AG from Switzerland which specialises in zero carbon CHP solutions using green methanol as fuel. While offering turnkey CHP solutions, the company also guaran tees a long-term supply of methanol to customers at agreed rates providing an alternative to fossil fuel and its increasing emission-related cost.
After successful combustion tests on methanol and studies on how to provide a methanol-powered OP16, both parties signed a distribution agreement making OP16 the exclusive core technology for Econimo’s small MW power range.
Airem is also part of the European-based Hydrogen Alliance that looks at driving future technology with hydrogen.
“We are very excited about the project potential for the future,” added Mr Marchitello. “The hydrogen revolution is coming and it is a big opportunity. We have already proven our turbine can run on 100% hydrogen and any mix thereof. Our aim is to stay ahead of the market, particularly with solutions.”
He emphasised that partnerships are Airem Energy’s main focus as “the oppor tunity to partner gets Airem quicker and shorter development cycles. Any partner ship must have an intrinsic value, so we go through a rigorous process choosing partners for the right reasons.”
Airem Energy’s management team is drawn from the renewables, fossil fuels and producer space, with more than 100 years’ experience. “The team is multinational, multi-layered and multi-cul tural, which is exceptionally important as diversity drives innovation.”
According to Mr Marchitello, the main objec tive for him is educating international organ isations on the need for a change in mindset “because human nature is to resist change. As we reflect what Airem can achieve, it resonates excitement. We are committed to what we can do in the ESG space.
“For me, this is the most exciting busi ness I have ever been involved with seeing the business grow and make a dif ference on a social level. At Airem Energy, we believe we can make an impact through driving the world’s energy transition. There is a lot of work to do on that front, which creates great opportunities.”
Mr Marchitello said: “We are trying to upscale in a controlled manner and create more opportunities and regional hubs on the service side. It is about servicing clients and making it easier for them to work with Airem Energy over the long-term.
“Decisions are made quickly and being that adaptable is a real advantage. We want partners to say they want to work with us again. Reputation can be hard-earned, but lost in the blink of an eye.”
He concluded: “As Airem Energy is the most fuel-flexible provider of heat and power technology globally and a solu tion provider that is second-to-none, we are completely energised and excited for the future.” n
Rob Marchitello CEOBrimmond has over 25 years’ experience delivering bespoke lifting, mechanical and hydraulic equipment and services across a wide range of sectors. Managing Director Tom Murdoch reviewed Brimmond’s achievements, the company’s recent rebranding and the robust plan for growth in conversation with Phil Nicholls.
has been steadily expanding since 1996, starting as part of a global hydraulic hose repair franchise, later moving into manufacturing. After steady growth, Brimmond Group embarked on a programme of consolidation with Pump Solutions being fully integrated into the group in 2018, followed by the absorption of Rigrun Europe in 2022.
Rebranding as Brimmond, the newly-simplified corporate struc ture allows the business to maintain its focus on quality engineering solutions while pursuing ambitious growth plans.
Managing Director Tom Murdoch joined the family business in 2016 after beginning his career as a graduate engineer with an Aberdeen-based subsea engineering company focusing on subsea tooling and projects offshore, West of Shetland. His many summers of work experience at Brimmond, followed by six years working in the business full-time, meant he was well prepared for what the future held.
Brimmond’s purpose-built facility opened in 2015. “We have a single site just outside of Aberdeen in Kintore, Scotland,” Mr Murdoch said, “It’s a 2.5-acre site with a 1,250 sqm workshop and two 20-tonne overhead cranes. Outside, we have our high-capacity testbed facility where we can test marine cranes, winches, and safely carry out ten sion spooling. Seven years later, it’s still a facility we are incredibly proud of.”
Despite global challenges, including the pandemic, Brimmond has continued to achieve and exceed projected business growth. Current turnover at Brimmond is £6 million, the third year in a row with record numbers. It continues to deliver the highest quality lifting, mechanical and hydraulic equipment and services to clients anywhere in the world through four main divisions: rental equipment; design and manufac ture; refurbishment and service; as well as marine cranes.
The range of services from Brimmond includes the design and manufacture of complete engineering solutions in collabora tion with various partners. Successful projects include power units, hydraulic control systems, pump units and so much more. Brimmond engineers also offer spooling services, and a suite of inspection, maintenance and refurbishment services on a broad selection of machines.
According to Mr Murdoch, one of Brimmond’s USPs is the com pany’s culture of high standards at every level: “It’s the quality from the initial design through to the manufacture. If we aren’t proud of it, then it doesn’t leave the workshop. After all, our reputation is built on the quality of our machinery, not on our year-end results.”
With such a diverse portfolio of equipment and services, Mr Murdoch found it difficult to highlight just a single project to represent Brimmond’s capabilities.
“We have a 175-tonne meter crane in our rental fleet,” he said, “It recently returned from an 18-month contract assisting with the decommissioning of a North Sea platform. Within 10 days, our workshop technicians serviced and load tested the crane and it was back out on hire again, assisting with a concrete mattress decommissioning project.
“Another exciting project was the testing of a 110kW electric hydraulic power unit. This will be permanently installed on a windfarm installation vessel. The unit powers a device used for upending the monopile from the horizontal stack on the offshore vessel into the vertical position, in preparation for installation.”
In early 2022, Brimmond was one of just 20 companies chosen for the Fit for Offshore Renewables Programme (F4OR) from the Offshore Renewable Energy Catapult. Funded by the Energy Transition Zone
and delivered in partnership with the Nuclear AMRC and Opergy, F4OR will help develop Brimmond as a provider of equipment and services to the renewable marketplace.
“We have just completed our first F4OR audit which turned out to be a rather intensive programme,” explained Mr Murdoch. “This involved a business excellence audit and a company knowl edge audit, all designed to increase Brimmond’s knowledge within renewables.”
Brimmond’s participation in the F4OR programme is readying the company for the growth of the renewables sector.
“From a personal and business perspective, we understand that renewables are absolutely critical to our future,” Mr Murdoch explained. “Aberdeen already has a very strong reputation as a hub for offshore, particularly offshore wind, so we believe we are ideally suited to pursue this opportunity.”
Alongside the rebranding of Brimmond and the accompanying reorganisation, Mr Murdoch was appointed as the new Managing Director earlier this year. Preparing the company for the growth of renewables was just one part of Mr Murdoch’s vision for Brimmond.
“Firstly, I plan to continue to build on the reputation we have established over the past 25 years for building high quality, reli able and safe equipment,” he said.
“Secondly, I plan to lead our new business strategy. Up until now, the business has grown organically. Looking forward, our strategy is to grow our market share in the oil and gas industry and use our transferrable skills and experience to develop business in complementary sectors – marine, defence, aquaculture, and off shore renewables.”
As part of this business strategy, Brimmond works in close partner ship with its local network of suppliers. “The north east of Scotland has one of the most impressive supply chains anywhere in the world,” Mr Murdoch explained. “The manufacturing capability and capacity in the region is incredible. We try to source the majority of our products from those around us – both to support our local economy but also to minimise unnecessary carbon miles.”
By relying upon local suppliers, Brimmond enjoys the benefits of a short supply chain. This has cushioned the company from the worst effects of ongoing global issues. While delivery of imported goods has been delayed, Brimmond remains in a good place to ride out this particular storm.
Global supply is just one of the macro challenges facing the energy industry: another area which impacts every business in the sector is fluctuating government policies for the oil and gas industry, compounded by an uncertain political landscape. Current interest rates suggest a looming recession, but Mr Murdoch is optimistic.
“Brimmond is in a stable position because right now, with the growing focus on a safe, reliable and secure supply of energy, we have seen a number of contract wins within our core sector but have also already seen strong return on our diversification into adjacent sectors. Both areas of the business are doing well and it has refocused our attention on the importance of diversification.”
Brimmond’s unwavering focus on high quality engineering is reflected in the make-up of its employees, with a combined 75% of the team ‘on the tools’, either in the workshop or the engi neering department.
Mr Murdoch reflected: “I’m an engineer at heart and love every part of the business. From concept design through to Factory
Acceptance Testing, I find the whole process hugely interesting. There is no better feeling than going offshore and successfully installing a brand-new piece of equipment that you have person ally designed. It’s such a rewarding experience.”
This passion at the helm of Brimmond stands the business in good stead for an exciting future. n
King & Moffatt Building Services has over 40 years’ experience as mechanical and electrical contractors throughout Ireland, the UK and Europe. UK Managing Director Jonathon Pugh and Business Development Manager Stephen Kiely outlined the range of company projects in discussion with Phil Nicholls.
When Birmingham City Council wanted to rede velop the Alexander
Stadium ahead of hosting another round of interna tional events, the council worked with King & Moffatt, the go-to contractors for complex engineering projects across Europe. This latest flagship development was com pleted earlier this year and King & Moffatt continues its involve ment at the international athletics stadium with the ongoing maintenance contract throughout and after the Commonwealth Games have been hosted here in 2022. Both are involved in the legacy development, returning the stadium to the council after the Commonwealth Games.
“The stadium has been a real standout project for the com pany,” explained Business Development Manager Stephen Kiely. “This high-profile project in the UK involved the design and installation for renovation and a new stand. The work on the sta dium for Birmingham City Council was primarily to prepare the venue for athletics, but the site is already being shared as a repur posed venue for other sporting events and activities.”
King & Moffatt Building Services was founded in 1978 by Pat King and John Moffatt in Carrick-on-Shannon, Ireland. The com pany began as an electrical contractor, working for several major food production companies in Ireland. When these food compa nies expanded in the United Kingdom during the 1990s, King & Moffatt accompanied them to deliver new facilities. Business con tinued growing in the UK, and King & Moffatt UK was established in 2008.
The Carrick-on-Shannon headquarters now totals 40,000 sqft, including a training facility, and is specially fitted-out for mechan ical and electrical prefabrication. The UK division has offices in Birmingham, Stoke, Edinburgh and Wolverhampton. The group has 400 directly employed personnel, 160 of which are in the UK. Over the past 12 months, the UK division has generated £80 mil
lion turnover, up from £65 mil lion last year, operating within the annual group turnover of £135 million.
“What sets King & Moffatt apart from competitors,” said Managing Director UK Jonathon Pugh, “is our ability to design and build internally. We’ve got in-house design engineers, we’ve got our own BIM modellers and managers, as well as preconstruc tion teams.” By providing a complete package of services to clients, King & Moffatt also has an offsite pre-fabrication facility, a full FM with asset management taken into account using the BIM tech nology in early design, and an aftersales energy team for an offering that stands out from the competition.
“We are an innovative company,” Mr Kiely agreed, “and have embraced many new technologies such as BIM, VR and AR in recent years. King & Moffatt is now bringing that same energy on the path to digital transformation.
“Digitalisation is essential to staying competitive within our industry, where we see greater volumes of data than ever before. We have many different software systems bringing together data from all areas of our work. King & Moffatt has digital capabilities such as Scanto-BIM, which help distinguish us from our competitors.”
Embracing technology at King & Moffatt is a response to the evolving requirements of the market and enables the company to work closely with clients, according to Mr Pugh: “Things like the preconstruction, the coordination through BIM, IT and using on-screen technology means we can do things very reactively and at speed.”
Recent growth for King & Moffatt has come from a range of busi ness segments including logistics, airport hangars and film stu dios. However, the depth and range of the company’s capabilities are best illustrated by examining a handful of its latest projects.
The £72 million redevelopment of the 41-acre Alexander Stadium complex in Birmingham created a world-class, dynamic venue and supports the long-term regeneration of the city.
Yet, King & Moffatt’s innovative constructions include more than this one project. Another highlight was the world-class food production facility for DO & CO at London Heathrow Airport. This brand new 250,000 sqft production and distribu tion site provides gourmet catering for airlines such as British Airways. The facility consists of commercial kitchens, storage and processing areas, along with extensive office, meeting and presentation spaces. This development earned King & Moffatt a nomination in the international category of the Irish Construction Excellence Awards 2022.
An even larger King & Moffatt construction was the £300 mil lion SmartParc food production campus at Derby. This state-ofthe-art campus-style food manufacturing hub develops sustainable food production for the future. The 1.8 million sqft collaborative site is specifically designed to address the chal lenges facing the food industry, featuring cutting-edge manu facturing facilities, central distribution, start-up incubation units and a potential location for a Food Manufacturing Technology Centre of Excellence.
The parent King & Moffatt group has expanded rapidly in mainland Europe over the past couple of years, and is a key part of its overall future strategy. The group has subsidiaries estab lished in Germany and the Netherlands, with the majority of European work in the chosen key sectors of food, logistics, life
sciences, manufacturing and data centres. Recent work includes a major distribution centre in Munich for a global logistics company and a pharmaceutical project in Amsterdam.
King & Moffatt’s business model has evolved in recent years, but one constant has been how it remains first and foremost a clientcentric business. King & Moffatt views clients as partners and considers it a success when clients in turn view the company as partners.
“Communication with partners is key,” explained Mr Kiely. “We are open as a company and work with clients as a team. We see our selves as partners to our key clients and to our suppliers and sub contractors. We have a high percentage of repeat business because we work closely with our clients: this is at the heart of the King & Moffatt business model.”
“We are understanding with our supply chain partners,” said Mr Pugh, “to the point that if one of our suppliers has a slack period, then we support them and move them to a site where maybe they’re not actually required, just to keep them in our supply chain This works really well both ways, because they then support us when we’re working under pressure on a particular project or site.”
Sustainability is also part of King & Moffatt’s business model with paperless offices and robust environmental reporting on carbon reduction. Operations in the UK benefit from the central King & Moffatt offsite manufacturing facility, as Mr Pugh noted: “The
“We are open as a company and work with clients as a team. We see our selves as partners to our key clients and to our suppliers and subcontractors. We have a high percentage of repeat business because we work closely with our clients: this is at the heart of the King & Moffatt business model”
central off-site is fundamental because there’s less wastage, as we can use the materials on two or three different projects.
“Having a single location for materials coming in reduces not just the carbon footprint, but also the packaging, because we buy in bulk which reduces the amount of packaging and waste.”
King & Moffatt also engages in impressive sustainable building projects. A recent example of this is the McCormick Foods manufacturing facility near Peterborough in central England. The project applied the UK Green Building Council Net Zero Carbon Buildings Framework to help deliver net zero carbon in both construction and operations, the highest level of commitment in the framework. The factory will operate with renewable energy, reduced water consumption, state-of-the-art refrigeration and energy-efficient steam generators.
In the present economic climate, King & Moffatt is juggling the chal lenges of inflation, skills shortages and supply chain disruptions.
“One of the key ways we approach this is by educating our apprentices and trainees, who we believe are the best in the
industry,” explained Mr Kiely. “One way we retain people is by investing heavily in technology, giving our team the best tools possible to do their jobs. King & Moffatt wants to ensure that our people get a sense of achievement and satisfaction from car rying out their jobs, and one way we do that is through software and automation.”
“The fortunate part about how we work with our client base,” Mr Pugh concluded, “is our shorter delivery programme com pared to a lot of our competitors. So, a lot of our projects evolve very quickly, moving onto site very quickly and then quickly delivered. King & Moffatt doesn’t have two-year lead times hit by delayed deliveries and price increases. We are quite fortu nate in that respect, but there are still challenges.
“When we start with a customer we service them incredibly well, fixing ourselves onto the client and becoming an adopted arm of their company, of their business. This sets King & Moffatt apart from the competition because the customer has trust in us as we have faith in them.”
KING MOFFATTSTAMH is an engineering company providing consultancy, design, engineering, delivery, and implementation of complex automated warehouse equipment, including warehouse management software. Established in 2000, the Austrian headquartered company operates in Bulgaria, Greece, North Macedonia, Romania, Serbia, Kosovo, Bosnia and Herzegovina, Croatia, and other countries around the globe.
Nadia Blagoeva, Technical Director of STAMH shares that: “The whole idea of the company was to develop a team of engineers, specialised in complex intralogistics processes. We started from Bulgaria as a first branch, and throughout the years we have progressively developed our engineering teams and sales efforts in all Balkan countries.”
Article by Jordan Yallop.
STAMH I PROFILEAS an international company providing design, consul tancy and engineering of advanced automation and mechanised warehouses, the capabilities of STAMH also extend to the management software required to keep these systems running.
Nadia Blagoeva, Technical Director of STAMH said: “Our philosophy is to start with listening. This is a behaviour that society seems to be missing more and more in our current lives. The idea behind this approach is to understand the needs of our clients, to analyse, and based on our engi neering knowledge, to start developing a concept that is directly connected with the main factors of input from the clients’ side.”
In the last 20 years, the company hasn’t stopped developing intralogistics projects in many countries in South-Eastern Europe as well as in Asia and Africa.
Ms Blagoeva added: “Our engineering approach shapes us as a different company on the market. There are companies that are doing consultancy, others are doing building concepts, another would produce racking structures or technologies. But we are everything in one place.”
For the fourth year in a row, STAMH took part in one of the largest intralogistics exhi bitions in Europe - LogiMAT in Stuttgart and for the first time at Logismed in Morocco.
“One of the nice surprises we encountered at these events,” noted Ms Blagoeva, “was the
industry’s readiness to invest in semi-auto mated and robotic systems. This could be based on new demands after the pandemic, and the intention to develop their production bases and logistics hubs, based on better long-term planning.”
STAMH Group is focused on different types of Automated Storage Systems for boxes and pallets, Vertical Automated Storage and Retrieval Solutions, dynamic Gravity Systems for pallets and boxes, Conveyers and Automated Sorting Systems, Mobile Racking Systems for pallets, and long mate rial industrial palletizers and robocars.
The company has its own software depart ment, providing comprehensive technology, covering even the most sophisticated int-
ralogistics requirements. STAMH delivers deeply customised Warehouse Management Software (WMS), and designs and develops Custom Automation Software on-demand.
STAMH’s total staff number across its offices currently sits at more than 150 people. Up to date, the company has successfully completed more than 11,500 projects across more than 20 countries, worldwide.
When talking about the most popular prepandemic products, Ms Blagoeva unveiled: “Before Covid the most profitable projects were our Automated Solutions, with fully integrated equipment that substitutes rou tine manual activities and on the other hand, optimises the space in all dimensions. But today, the inflation from 2022 gave us another view of the markets. For example, semi-automated solutions such as the Mobile
Racking Systems save space and are consid ered a good base for profitable investments.”
STAMH is currently working on three fully automated projects, centred around heavy pallets organisation and warehouse processing. Pallets will be elevated, stored, a nd retrieved with stacker cranes. The com pany also has contracts with fulfilment centres that hope to improve their ability to cope with the new market demands and the increased number of orders they need to process simultaneously.
One of the latest STAMH Group projects for fully automated-storage system for pallets was in Greece, for one of the leading dairy producers. It underlines the company’s inge nuity when it comes to space optimisation and process organisation.
The Self-Supporting Automated System is the first of its kind, given the seismic activity in this area. It was executed in compliance with the agreed terms for installation and in compliance with all international require ments for health and safety at work. The building has specific air-tightness levels needed for the installation of an innovative fire prevention system. It is based on the gen eration and filling of the space with nitrogen.
“The new equipment provides our client with the possibility to store, organise and process a larger number of products (in terms of inventory and volume), within the same area, in an extremely secure and cost-effective way,” stated STAMH Group’s Technical Director.
Ms Blagoeva notes that STAMH has felt a freeze in investment intentions regarding fully automated warehouses due to the cur rent situation and prices rise. Meanwhile, there has been a noted boom in the robotics segment. This is due to the lower initial investment levels of these solutions, when compared to fully automated warehouses, and the easily upgradable nature of the robotic solutions, implemented by STAMH.
STAMH’s offerings on the robotics front include robotic systems for boxes or stacks palletizing, industrial robots, and sorting and picking robotic systems. Industrial robots have a wide variety of applications in dif ferent intralogistics operations. Smaller and more manoeuvrable robots are used for packaging, sorting, order picking,
assembly, and disassembly. Large robots with higher capacity are preferred for heavy products palletizing.
With more than 20 years of experience in mobile bases production and the constant implementation of Mobile Racking Systems around the globe, STAMH is constantly upgrading its production facilities, while simultaneously enlarging the team who take care of the PLC programming and electrical designs modelling.
“This will give the company an advantage, because it will lead to the faster implementa tion of these systems within just 10 to 12 weeks,” stated Ms Blagoeva.
As with any successful business, there is a need for a clear and unobstructed supply chain. This has become more and more dif ficult in recent times due to many outside factors affecting different swaths of the industry. One of the key elements that can mitigate these factors is reliable suppliers and partnerships.
Ms Blagoeva said: “Without our partners we wouldn’t be in position to do our business at all. They are part of our success story. All our suppliers are our long-term partners, and this is important for trust generation,
going both ways. One of the main ideas for such partnerships is to have clear accounts and a similar vision for future innovations.”
STAMH’s overarching mission is to provide customised solutions for every storage need. It’s the reason why STAMH’s enthusiastic, professional, and motivated teams start the day with a smile, creating tailor-made, easy to implement, and working solutions.
Other important business principles are professionalism, dedication, respon sibility, respect, and last but not least –social responsibility.
“The responsibility of the company and its clients is as important to STAMH as the responsibility to the society,” concluded Ms Blagoeva. “Our company ethics, the con stant effort towards improving the working conditions and safety of our people, as well as our participation in numerous social and donation projects, are only some of the ways STAMH works for a better tomorrow.” n
This year H.E.L Group (H.E.L) expanded its operations in India with the establishment of a whollyowned subsidiary, H.E.L India, progressing from a long-standing distributor model. To support India’s growing biotechnology, process safety and the pharmaceutical industry, the new operation delivers dedi cated in-country support directly to H.E.L customers. Shortly after this announcement, Rajeev Kumria was appointed as General Manager of H.E.L India to oversee the cre ation and commercial effectiveness of the new business.
“We primarily provide direct sales and marketing, service, and support opera ti ons to customers in India,” explained Chief Commercial Officer Paul Orange. “India is an attractive market for us, where battery safety is huge. The other attraction is on the bioreactor side of the business, with massive potential there for us to make a difference. These opportunities both really tie-in to our broader mission –making a healthier, more sustainable and safer world.”
H.E.L has been solving complex chal lenges for customers since its foundation in
1987. The past few years at H.E.L have been busy whilst the business extends its reach into rapidly developing Asian markets including China, where the company’s instruments, software and automated solu tions are playing a pivotal role in improving the safety of chemical and industrial research, development and manufacuring.
The new operation in India follows a similar model to H.E.L’s move to a direct sales organisation in China, and was accompanied with the appointment of a Distribution Manager for the rest of th e Asian market. H.E.L also bolstered its team in
The UK-based H.E.L Group has 35 years’ experience developing and manufacturing innova tive scientific instruments and software designed to optimise key processes in chemistry and biology applications. CEO Louise Madden and Chief Commercial Officer Paul Orange highlighted the company’s growth and new equipment in conversation with Phil Nicholls.
the United States in line with the company’s heightened visibility around the world.
CEO Louise Madden acknowledged a selection of recent milestones for H.E.L: “We already had ISO 9001, but we’ve extended that to ISO 14001. We’ve now got three members of staff in our dedicated quality team, which was a key strategi c move. Operationally, we have made a huge investment into the company by intro ducing the SAP Business One ERP system in June 2020.”
H.E.L is based at a dedicated facility in Borehamwood in Hertfordshire, north of London. Expansion of the headquarters and upgrading of existing manufacturing capability here is planned to accommo
date H.E.L’s projected growth in output.
The facility is currently home to 65 of H.E.L’s 90 employees, but this number will increase in line with the ongoing trajec tory of the company which is experiencing a period of exceptional growth in demand.
The range of H.E.L products consists of world-class, innovative scientific instru ments to make any laboratory safer and more efficient. The portfolio includes biore actors, adiabatic and isothermal calorime ters, parallel reactors, and battery testing systems. All these instruments are offered with a broad menu of options to meet many research requirements, allowing customers
to select the precise configuration that matches their specific research goals.
The H.E.L range is growing further with the recent launch of the iso-BTC+ calorimeter for isothermal battery performance testing. The market trend is for ever-more powerful batteries, as Dr Orange explained: “The new i so-BTC+ allows performance testing on physically larger batteries, but more impor tantly, it allows testing of higher power bat teries than previously – it’s really about the power of the battery. For everything from e-bikes all the way to Tesla’s new car, the market wants more power.
“It’s easy to think about batteries in isolation, but a battery operates within a product. Our new testing equipment
enables researchers and developers to look at the battery as a component of a device because that’s how people interact with it.”
H.E.L’s equipment operates with labCONSOL®, the company’s own laboratory automation software. labCONSOL is fully cus tomisable to support laboratory operation, controlling both H.E.L systems and associ ated third-party hardware. The software implements safety controls and enables
equipment automation, and also records and controls experimental variables.
“Our USP really comes from our soft ware capability,” said Dr Orange. “There’s 35 years of knowledge and programming skills in our software, it’s an inherently highly flexible platform that is essentially device agnostic. We’ve invested recently to make the software even more intuitive with a truly user-friendly interface, which is getting a lot of good traction.”
The combination of flexible software and the bespoke capabilities of H.E.L’s prod ucts are demonstrated by a recent project highlighted by Dr Orange.
“A major national lab in the US came to us, because we have a certain skill set in the bioreactor area,” he said. “Our speciality is benchtop parallel bioreactors with the ability to work at high pressure, which is a really dif ficult space to work in. This lab essentially does contract work, so giving them a system that’s flexible enough to deal with the dif ferent rigours of their contract work is our sweet spot.”
As well as the recent growth of the com mercial organisation, H.E.L is investing in key leadership positions. “We have a new Director of Product Development,” said Ms Madden, “who joined us from a scientific instrumentation business where he’s run product development departments. Another new arrival is our Global Director of Service who will focus on making sure that our customers are happy.”
These new appointments highlight the importance of product development and customer service to the growth strategy at H.E.L. The company is focused on maintaining a steady release schedule of innovative products into the global market. A key pillar of supporting the company’s growth profile includes an internal training regime to bring the company’s new hires up to the knowledge levels of the experienced staff, further enhancing the levels of service offered to clients by H.E.L.
Healthy, sustainable and safe H.E.L is also invested in the future of the planet.
“This is part of our mission statement,” Ms Madden explained, “to help create a healthier, more sustainable, and safer world for everyone. We took the decision last year to achieve ISO 14001 accredita tion which focuses on enhancing our environmental performance, and each year we want to perform better than the last. I definitely do not want the company to be an ‘average Joe’; I want H.E.L to be the best in class for the size of our company.”
A close relationship with suppliers is part of making H.E.L best in class. “It is clear that the electronics industry has been hit hard by the global supply chain crisis,” said Ms Madden. “We have good
relationships with our suppliers, working with some of them for decades; but as a small company, our purchasing power is relatively low compared to the global giants.
“So, we agreed with our suppliers to place a two-year buying commitment with them. In turn, this gives them the purchasing power to work with their suppliers. This strategy has moved our suppliers further up the chain in their sector.”
H.E.L’s purchasing strategy has miti gated some of the effects of the global supply disruptions, yet, this issue remains the largest challenge facing the company. Sup ply fluctuations for electrical components, circuit boards, and even packing materials have all
had an impact, but the dedicated team at H.E.L keep the orders rolling out of the doors.
It is the quality of this H.E.L team which makes the company a great place to work, according to Dr Orange: “What delights me is seeing our staff demon strate how they’ve learned a new skill or stepped-up which then manifests in an improvement that aligns with the company’s goals. We work with machines all the time, but machines don’t get things done; people get things done.”
“H.E.L has a clear roadmap for scaling up,” concluded Ms Madden. “Our invest ment in the future is all about the three ‘P’s: People, Products and Processes. We know we’re a small company, but we want to do great things.”
The National Collection of Yeast Cultures (NCYC) provides a commercial service to identify, store and supply yeast cultures, storing over 600 brewing strains alone. Carmen Nueno-Palop, Business Development Manager at NCYC detailed the company’s ongoing responsibilities to Jordan Yallop.
in 1948, the National Collection of Yeast Cultures (NCYC) originated because British brewers realised the value of their yeast cultures and putting them in safe deposit to keep them secure. The NCYC maintains a collection of over 4,400 strains and also provides commercial services such as the secure storage of proprietary yeast strains for customers on a confidential basis, strain identification, yeast propagation and supply of yeast cultures.
For more than 70 years NCYC has collected and characterised yeasts of importance to the food and brewing industries.
Carmen Nueno-Palop, Business Development Manager said: “We don’t just sell yeast. We discuss customers’ needs and work together with them to achieve their goals.”
Currently located at the Quadram Institute (former Institute of Food Research) in Norwich, England, NCYC today offers a range of services to industry.
Ms Nueno-Palop said: “We supply yeast worldwide from Europe to Africa, Australia, or America. Our production capacity has duplicated over the past years, and we plan to extend it as demands increase. Sales by country in our website last year were UK 33%, USA 28%, Republic of Korea 4%, Switzerland 4%, Japan 3%, Brazil 2%, with other countries around the World accounting for the rest.
“The ratio for yeast supplied to academic versus commercial cus tomers is approximately 40% to 60%.”
The NCYC initially evolved into a broader collection when it moved to Institute of Food Research in 1981, collecting food spoilage yeast
which was able to evade the conventional food preservatives. In 1999 the collection became a part of The United Kingdom National Culture Collection (UKNCC), which was established to co-ordinate the activi ties of Britain’s national collections of microbial organisms – there are other equivalent collections for other organism as bacteria, algae, virus, cell lines.
Three years ago, the collection moved to its new facility in Quadram Institute Biosciences in the Norwich Research Park where it is currently based. At present the collection holds over 4,400 strains collected over the last 70 years. All strains in the open collection can be accessed and purchased directly from the NCYC website (www.ncyc.co.uk)
NCYC trades under QIB Extra Ltd, a company that provides bespoke research and market-leading services for the food, health and allied industries.
The NCYC’s new lab and state-of-the-art facilities are housed within the Quadram Biosciences Institute. Being part of a bigger institute sees NCYC reap the benefits of being at the heart of the research park, notably the interactions with the research community and the infrastructure the institute has to offer.
An example is the liquid nitrogen storage, the home of NCYC’s master stock’s cultures. The Cryo-suite at QIB enables NCYC to guarantee long term storage at -196°C.
One of the main services the NCYC provides is the confidential safe deposit or yeast banking service. The NCYC maintains propri etary yeast strains for customers on a confidential basis. The cul tures can be retrieved and available exclusively on the instruc tions of the depositor.
NCYC will use deposits to verify the authenticity of strains used in food and beverage manufacturing.
Ms Nueno-Palop said: “This service is valuable for important production strains and should be considered by anyone who wishes to take advantage of the NCYC’s facilities and expertise in culture maintenance.”
The yeast cultures are preserved under optimal conditions for the maintenance of their properties, under secure and confiden tial safeguard and yet be available on demand.
“This service is used by small, medium, and multinational companies,” Ms Nueno-Palop said. “The aim of each company is slightly different, but the goal is always to protect and insure
the production strain. If you insure your buildings and contents, why would you not protect the strain responsible for your final product?”
While the most popular service provided by NCYC is the confidential yeast bank, the company also offers a number of other services including a yeast identification service, offering a precision char acterisation of yeasts direct to customers worldwide. Molecular methods have revolutionised the speed and accuracy of yeast identification. In recent years, these methods have been applied to solve numerous practical problems such as the presence o f spoilage yeasts.
“We can closely work with many different companies to help identify either native strains that they want to exploit or even to identify any strain isolated by the company,” said Ms Nueno-Palop. “In this area we are currently offering a new service to isolate native yeast strains from vineyards.
“Why use a generic commercial wine yeast when you can use your own local native strains? This could make the wine even more special, and it is also a powerful marketing tool.”
THE NATIONAL COLLECTION OF YEAST CULTURES I PROFILECustomised yeast propagation for brewers is also a popular ser vice, mainly used by smaller or medium sized companies that may not have their own labs or propagation plants. As such, the yeast propagation service is important to these businesses as the NCYC can guarantee a pure yeast slurry than can be used for direct pitch in their fermentation tanks.
NCYC supplies strains via its website www.ncyc.co.uk to a large range of customers from academic to industry, from very small compa nies to multinational. Ms Nueno-Palop admitted Brexit has created new barriers as samples have to pass new controls in customs, how ever NCYC is still reaching customers worldwide.
Being able to revive strains deposited more than 50 years ago, highlights the importance of the work and role played by NCYC employee’s predecessors, collecting, and storing the strains for generations to come.
“You feel a sense of responsibility when opening strains that have been dormant for so many years, some even before we were born,” said Ms Nueno-Palop.
She concluded: “As a company we would like to carry on helping distributing yeast worldwide and increase our global network. An important long-term objective will be genome sequencing all the strains in the collection.” n
As the automotive industry continues to transition away from the combustion engine and focuses on everything electric, Fontanafredda Cold Forging (FCF) has been among the first companies to face the inevitable challenges of change.
Speaking to Andy Probert, Managing Director Zeno Rigato recounts the decisions and why the ambitious Italian manufacturer is firmly looking up.
For Italy’s Fontanafredda Cold Forging (FCF), it must have been a moment similar to when steam was replaced by electricity in the 1900s.
In 2016, the automotive sector was coming to grips with a new revolution – with the combustion engine transitioning to fully electric and hybrid. For FCF, it signalled a third significant and telling turning point in its 40-year history.
Founded in 1981, FCF specialised in the cold forging of metal components for spark plugs before this was delocalised at the end of the 1990s to cheaper economies in Asia and Africa.
Cold forging is a displacement metal shaping and manufacturing process in which a metal – typically steel, aluminium, copper or titanium – is shaped. Starting from wire coils of diameter between 15 and 38mm, material is forced between a matrix and a punch to produce parts with a defined geometric form. These technologies enable high production of finished parts with better mechanical properties and negligible swarf.
Given the company’s excellent know-how in cold forming, FCF shifted its emphasis on producing highly complex components, such as advanced form parts, and developed its own niche in the European automotive industry.
While this business flourished, the electric revolution was rapidly moving into the industry’s rear mirror. FCF again shifted its business dynamics in anticipation of the industry’s exit from combustion engines.
“Only five years ago, 80% of our products were related to com bustion engines,” reflected Managing Director Zeno Rigato. “Today, only 20% of our turnover is linked to this product family and will drop to below 10% in the next five years.”
FCF has completely changed its product mix, focusing now on components related to steering, the braking system and chassis without having to reduce its 90-strong personnel.
It has also invested €2.6 million in new tools and €4 million in new machinery at its headquarters in Fontanafredda, an hour from Venice, to expand its offering and create opportunities to access markets and customers.
Innovation in the automotive sector has also led to the increasing use of aluminium alloys for various car parts to help reduce its overall weight.
With its gained metallurgical knowledge and in responding to multiple manufacturers’ requests, FCF has further invested in R&D to test and verify the best choices of aluminium alloys. This will help in terms of effectiveness for lightening requirements, corrosion resistance, mechanical characteristics, and improve deformability, enabling greater use of cold forging.
“In addition to recyclability, these activities will help guarantee a lower consumption of natural resources and make its use eco nomically sustainable,” Mr Rigato emphasised.
In 2021, FCF began serial production of three highly complex components for the steering in aluminium, having accepted the challenge of achieving the levels posed by one of its key clients, a leading Japanese company.
Mr Rigato commented: “By 2024, 10% of our turnover will be for aluminium products, and we are continuing to study new impor tant projects to increase this share further.”
To achieve these objectives, FCF is implementing a corporate digitalisation program with the installation of a Manufacturing Execution System (MES), which will primarily manage and control the company’s production process from start to finish.
This will help extract valuable information to integrate into the production execution and improve performance in terms of qualit y and cost. The project will be completed by the end of 2022. FCF is also looking to expand its range of cold-forged products following the acquisition of a new, larger press to produce components up to 1.2kg in weight.
Mr Rigato said the company plans to match these investments, by increasing its workforce from 90 to 100 in the next three years to aid the mass production of products it has developed in the last two years;
“After falling from €17 million turnover in 2019 to €13.6 million in 2020 due to the pandemic, we have begun to rise again. We hope to achieve €17.5 million in 2022 and, with contracts already acquired, reach €23 million by 2025,” he reassured.
The entire process of study, design and development of FCF’s molds continues to be carried out internally thanks to an R&D unit of designers, mold specialists and operational technicians Mr Rigato described as “the flagship of our company”.
With years of experience in cold forging, its R&D unit can inter vene in co-design with a customer from the earliest stages of designing a new product, with immediate advantages.
“This methodology allows us to reduce study times, increase product quality, and reduce development and production times by exploiting the advantages of plastic deformation technology.”
The R&D team uses two simulation softwares – Simufact and Coldform – to develop the plastic deformation process to verify the product’s feasibility and optimise its configuration.
Mr Rigato confirmed that FCF has a business plan in place, starting from 2022, to invest an additional €3.5 million in creating a new fin ishing department for the production of steering shafts. This will be ready in 2023 and help FCF reach turnover potential of €23 million.
When considering the many challenges FCF faces, Mr Rigato offered a surprising answer. “Undoubtedly, people are central to a company’s success. At FCF, people can find passion, wellness, trust, growth, evolution and fun. Because it is people who make the difference and only with them, especially in critical moments, is it possible to achieve extraordinary results.”
He added: “We want to become ambassadors of our technology, cold forging, and the significant benefits it can bring in carbon footprint reduction compared to hot forging or machining.
“Just think – a finished part with a weight of 1kg obtained by cold forming instead of bar turning can reduce processing waste by up to 70%. To obtain these results, we offer customers our collabo ration, and in the product conception phase so that it is adaptable to our technology.”
Mr Rigato added: “At a time when market spaces are shrinking due to technological evolution towards electric, we aim to stay one step ahead of the competition. We set ourselves apart by creating what may seem impossible today.”
FCF is keenly adopting socially responsible behaviour, moni toring and responding to all stakeholders’ economic, environmental and social expectations, and operating in compliance with inter nationally accepted guidelines.
Underpinning this, the company launched a training program for all its managers to promote ESG issues. FCF plans to produce its first sustainability report within the next three years.
Expanding on its relations with suppliers and clients, he said: “We believe that creating a climate of trust is the most authentic engine of any long-term relationship. When we trust each other, it is easier to solve problems.
“To create this climate, transparency in relationships is important; opening up and allowing projects to be monitored and con stantly communicating what we are doing.”
Mr Rigato concluded: “FCF continues to be optimistic. The automotive world and beyond is profoundly changing, under mining all the certainties we were used to in past years. But we are equally convinced FCF has, among its women and men, the creativity and passion needed to ride the wave.” n
Boasting a unique history spanning three continents, and business activities ranging from furniture to heat exchangers, Provides Metalmeccanica has evolved into one of the world’s leading manufacturers of heat exchangers. General Manager Franco Provenziani spoke to Richard Hagan about the company’s family ties, how the business has grown into a global powerhouse, with installations in some of the most recognisable landmarks around the world, and its recent acquisition by multinational manufacturing firm Wieland Werke AG Group.
Provides Metalmeccanica (renamed Wieland Provides Srl ) is a leading name in the design, manufacture and installation of bespoke heat exchanger systems. The company’s journey to the top of its market has been hard-won and fought across three continents and spanned several company evolutions.
Provides began life in 1968 as a specialist producer of metallic office furniture before moving into the construction of racks, alu minium telephone booths and step ladders and, finally, towards the production of pres surised gas tanks for both LPG automotive and domestic use.
In 1991, the business started working in the air conditioning sector for the very first time and, in 1996, it designed and manufac tured its first series of heat exchangers. And the rest, as they say, is history.
“In the 1990’s we were looking for a new core business,” recalled General Manager
Franco Provenziani. “Manufacturing LPG cylinders required a degree of expertise, but it’s relatively simple technology and we felt that we needed a more technologi cally advanced product. We found it in heat exchangers.”
An enquiry from whom was to become the company’s first customer in the 1980s k ickstarted the company’s decision to tackle the heat exchanger market, according to Mr Provenziani: “We began building one unit for this customer, per week. The busi ness evolved and grew and now, we produce 40 per day, and that’s just in Italy. Globally, the business is producing up to 70 per day.”
That impressive output is partly thanks to the company’s 240 highly skilled staff worldwide, spread across three factories. Its main facility in Italy is also its research and development headquarters. Furthermore,
it has a factory in the Sichuan Province in China, founded in 2005, and a third in the US state of Virginia, which opened its doors in 2014.
Its product range spans three categories: dry expansion evaporators, flooded evapo rators, and water cooled condensers. The quality of all its products is guaranteed partly by the company’s ISO 9001 certifi cation which has been in place since 1996, as well as a raft of other certifications. These include ISO 45001:2018 for occupational safety, and ASME, PED, AS 1210, GB, UKCA and CRN certifications, in addition to numerous marine certifications all relating to legal compliance and risk elimination.
Provides credits much of its market strength to its expert engineers and its deep techno logical capabilities in its R&D department in Italy.
“We have a very strong team of engineers who aren’t afraid of failure,” Mr Provenziani explained. “When we get an idea and we think it can work, we will try it. If it works, we go ahead with production. If not, we turn the page and try something else. It’s our strongest characteristic as a business.”
The company pursued constant invest ments in its R&D capacity, which has yielded a number of exciting develop ments over the years.
“We’ve introduced at least four different types of heat exchangers into the market, and all of our competitors worldwide have followed suit with those ideas,” said Mr Provenziani. “We’re market leaders in that kind of product development.
“For example, we’ve really focused on improving the environmental impact of our products. We introduced an extremely efficient heat exchanger that utilised 70% less refrigerant than a standard unit. Refrigerants cost a fortune, and the big industrial units we make literally have tonnes inside them. So, a 70% saving in refrigerant require ments marks a huge reduction not only in environmental impact but also in the cost of the unit. ”
That kind of operational efficiency is an intentional product of the company’s ethos:
“Our core business and our strength at the moment is our high-efficiency machines,” Mr Provenziani emphasised. “When we first entered the heat exchanger market over 30 years ago, we decided to differentiate our selves via our efficiency, so we’ve worked heavily on that aspect since day one, always
pushing efficiency, rather than price into the market.
“After all of these years in the market, we continue to create machines that are more and more efficient,” he added. “Together with our reduced refrigerant designs and our data centre work, that’s really put us on the map.”
Mr Provenziani continued: “Supplying the data centre market with units to make the chillers, we decided to go in deeper and now, after four years of research, we are able to cool the CPUs and GPUs inside the servers themselves with cutting edge two-phase tech nology that very few can master when dealing with such small heat exchangers, or cold plates as they are known in the industry. Provides hopes to become a leader in that field as well, and seems to have all the right cards in place to do just that.”
In February 2022, Provides was acquired by the multinational manufacturing firm Wieland Werke AG.
While the two companies have been col laborating on projects for over 20 years, Mr Provenziani, whose father was one of the three founders of the business all those years ago, confirmed the acquisition is expected to really enhance the synergies between the two firms.
“The acquisition is a huge step for us. Wieland is an enormous €5.5 billion com pany and a technological leader in its field. They’re copper manufacturers and make all the technical tubes for heat exchangers as well as many other products. They’re all excellent products and Wieland is also very strong in research and development. The
merger gives Provides an enormously strong position in the market moving forward.”
Provides anticipates that the acquisition will vastly strengthen its current push into the data centre market as well.
“The players are huge in that market. Wieland is a very active player using dif ferent technologies to Provides thus offering different leading edge technologies in that market. It’s a perfect synergy!
Mr Provenziani noted the demand for the company’s heat exchangers has grown exponentially in the last two or three years.
“Many of the companies we serve are supplying cooling systems for data centre cooling, and it’s become our best seller and a great growth driver for us. Now we can cool the data centre rooms and the servers directly as well – another first!”
Together with Wieland, Provides will be able to offer comprehensive, fullyinte grated, complete systems for its cus tomers and soon will deal with recycling the replaced chillers as opposed to only s upplying the heat exchangers, for example. “This for us, gives the word sustainability a whole new meaning for us and our market sector!” stated Mr Provenziani.
Thanks to its global manufacturing and sales footprint, Provides has completed projects in various locations and in general, its systems are present in some of the most iconic build ings around the world.
An especially high-profile project was its supply of cooling equipment to Dubai’s famous super-luxury hotel, the Jumeirah
Al Naseem. Another particularly recognis able one was its contribution of systems t o five out of the seven Freedom Towers in New York, in which 90% of the heat exchangers were supplied by all three of Provides’ factories.
“The football stadiums in Qatar are another highlight for us,” Mr Provenziani remarked. “For the upcoming FIFA World Cup Qatar 2022, we were contracted to manufacture all of the heat exchangers that will be used to cool the stadiums. They’re open-air arenas and they’ve guaranteed that they’ll keep their spectators at 26°C despite tempera tures outside the stadiums likely to greatly exceed that heat. We’ve built a huge number of those enormous machines for them.”
Following its acquisition by long-term col laboration partner Wieland, Provides is optimistic about its future. In general, the company plans to continue pushing for greater efficiency within its products, while also investing to increase the size of its footprint.
In conclusion, however, Mr Provenziani was clear that no matter how much it might grow, the company will never lose its passion for constantly pushing the boundaries.
“I refuse to let our people use the words ‘Never’ or ‘It’s impossible’. That’s a big nono here,” he explained. “We are famous for our perseverance in attempting to do some thing if we genuinely believe that it can be done. When the market or a customer have told us that “it can’t be done”, we’ve often asked, “Are you sure? Or has it just not been approached the correct way?”. A number of installations were possible as a result of us winning that bet. We’ve done it before and we’ll do it again! That’s a major strong point for us.”
Celebrating its 50th year of operation, Pole Air Aviation continues pushing ahead as an MRO specialist with a reputation for getting a job done. Peter Papadatos, Executive Vice President, Commercial and Strategy, offers Andy Probert an insight into the company’s global ambitions to continue flying high in a competitive sector.
Pole Air Aviation has evolved into a globally-recognised name in the repair and overhaul of aircraft com ponents and aircraft maintenance.
Beginning with the small-scale comple tion of instrument-type components for Canada’s utility aircraft fleets, today Pole Air Aviation specialises in components and instruments that span over 10,000 individual items. These cover military, commercial, and regional transport, pri vate and corporate aircraft.
In 2018, Pole Air created its aircraft maintenance division, with teams deployed worldwide, providing heavy maintenance, major repair and modifications.
“We have gradually increased our remit from instruments and component work to expand into more diverse services in the international market,” confirmed Peter Papadatos, Executive Vice President, Commercial and Strategy.
Pole Air’s customers include OEMs, airlines, maintenance providers and
international flight hours’ service providers primarily in North America, Europe and Africa.
“We enjoy a mix that ranges from com ponent work shipped into us. Mobile repair teams perform checks or aircraft recoveries all over the world. And as there’s also a significant amount of mili tary sector work, there’s a lot of distribu tion work involved.”
Most work is focused in the military sector for C130s / C27s / CL415s / 215s, while on the commercial side, they are experienced across many different types of aircraft.
The Montreal-based company is not only a fast and reliable source for engine mount isolator assemblies from the earlier Dash-8 and Q400 to ATR and EMBRAER aircraft, but also provides DC starter generator repair and overhauls.
Besides providing cabin equipment, Pole Air’s teams are adept at servicing brakes and wheels and offer repair solu tions ranging from legacy analogue prod ucts to the latest electrical components. They also offer expertise in hydraulics, pneumatics and fuel systems, electrical equipment, such as static inverters, and interior and exterior lighting.
Mr Papadatos said the company’s 60strong team was due for expansion to meet increased demands from the com mercial jet world as the sector recovers
post-pandemic and exceeds 2019 perfor mance levels.
He added: “The military side of the busi ness never really stopped, but the real boom has been in the business jet sector. We are getting so many demands from business jet clients we are struggling to keep up.
“Supply chain issues and recruiting people are the biggest challenges as we ramp up. They are the only limiters as to what we can do.”
However, he cautioned: “That creates another potential challenge. When you recruit new people, you have to figure out how to bring them up to speed and impart the company’s acquired knowledge, exper tise and experience.”
The company moved into new facilities two years ago, having outgrown its pre vious premises. Mr Papadatos revealed Pole Air’s ambitions to move into Tier 1 supplier levels were ongoing.
“We have enjoyed success with some operators coming to us for their various
needs. We are going directly into world air forces, major airlines, and plan to further enhance our presence in the business jet sector.”
He confirmed: “Our highly trained staff continue to be devoted to providing cus tomers with top quality products that are quickly turned around to minimise unwanted downtime for aircraft operators.”
While diversity was a key element to success, he warned: “I think the industry’s layoffs and then mass hirings have put off a lot of people re-joining the industry.”
Mr Papadatos was keen to highlight the fact that Pole Air did not execute any layoffs during the pandemic.
“That decision has helped position ourselves in the industry,” he said. “Diversification has also served us well; we are looking to implement concrete actions around sustainability and be ready for the new technology phase.
“Sustainability is not just about what you are going to do to service an aircraft, but how you will industrialise internally to serve those markets. For example, what happens if an airline maker goes to direct hydrogen injection or introduces fuel cells in electrification.
“While we need be ready for these new technologies, we need to position Pole Air on how we can be sustainable in our different operations. We can do that now while keeping a long-term outlook on the technology front.”
Pole Air’s three-year business plan, noted Mr Papadatos, was constantly evolving. He intimated that ideally, the
company wants to anchor itself with crit ical partners in military, commercial and business jet markets.
“On the commercial side, we have won a significant contract with Jazz Aviation and that has spurred interest from other airlines and carriers. On the military side, we want to get in and start servicing sig nificant air forces.”
Recently Pole Air signed an agreement with Satair, a leading global provider of innovative aftermarket services and solutions in the civil aerospace industry. This onboarded Pole Air as an approved third-party seller to Satair’s marketplace for component distribution and MRO ser vices for aircraft worldwide.
The agreement brings Pole Air’s tech nical know-how in aircraft component Repair and Overhaul to Satair’s e-com merce platform providing global reach and offers customers a significant selec tion of parts and services.
“It is one of many steps we are taking within our new digital strategy to promote accessibility and facilitate communica tions with customers worldwide,” said Mr Papadatos, adding that Pole Air’s ambitions always align with its clients’ future successes.
“Our relations are close, open and transparent, and that honesty leads us both to finding innovative solutions to move forward.
“There are a lot of repairs you can poten tially look at and offer up. Most clients pick them, others decline, but it takes effort. After all, we are a repair shop, and they are willing to listen and look at dif ferent solutions. That brings added value to relationships.”
He concluded: “While we know sus tainability has to be addressed and new tech is coming forward, my concern is that the new generations coming through may not understand where avia tion has come from and may lose some of the know-how we have imparted in making it both safe and efficient. If this is lost, the industry could take a long time to recover.” n
The past few years have been busy ones for Dalgakiran Kompresör as it consolidates its position as the leading Turkish manufacturer of com pressors. The opening of a new factory in 2020, located in the town of Dilovası in Kocaeli Province, had a huge impact on Dalgakiran Kompresör’s capabilities and lays the foundations for future growth.
“We are now using the highest technolo gies in our new 50,000 sqm production facility,” Export Sales Manager Ercan Asmaz explained. “I am proud to say that it is one of the biggest industrial air com pressor factories in Europe. Thanks to our capacity increase, we are now serving our customers in a faster way.”
Dalgakiran Kompresör was established in 1965 and steadily expanded. In 2004, Hertz Kompressoren was founded in Germany with the aim of manufacturing air compressors with a high level of German engineering. Another successful partner ship for Dalgakiran Kompresör is with th e Japanese company IHI, a comprehensive heavy-industry manufacturer who enjoys an 80% market share in Japan’s turbo com pressors. This joint venture was begun in 2016 and means that today IHI-Dalgakiran has hundreds of turbo compressors run ning in Europe, the Middle East and Africa.
Another recent development at Dalgakiran Kompresör was the appointment of Steven
Young as the new CEO in 2021. Mr Young spent 25 successful years within Bosch Group, most recently as President of Bosch Turkey and Bosch Middle East.
Mr Young now supervises the operation of Dalgakiran Kompresör’s new advanced production facility with 500 employees. This site produces all of the company’s industrial air compressors, with the cen trifugal compressors manufactured in Dalgakiran Kompresör’s second factory operated in partnership with IHI.
“Currently, we export more than 70% of what we produce,” said Mr Asmaz, “and ship to more than 130 countries. With the opening of our new plant, Dalgakiran Kompresör now has the capacity to produce 20,000 screw compressors. That means a new screw compressor is coming off the production line every 10 minutes. To accommodate this productivity, we are constantly increasing the number of our distributors globally.”
The Dalgakiran Kompresör catalogue includes three types of compressors. The assorted screw type compressors include the Inversys series offering up to 35% energy-saving operation and the robust DVK series, a proven design with tens of thousands of units in the field. The com pany’s reciprocating compressors
are available with single-, double- and three-stage piston block options. Finally, Dalgakiran Kompresör offer a variety of turbo compressors, manufactured under the IHI-Dalgakiran badge.
Diversification of the Dalgakiran Kompresör product line comes from the supplemental equipment produced by the company. These items include a range of compressed air dryers, pressurized air filters and air receivers.
However, Mr Asmaz was eager to high light the latest additions to the Dalgakiran Kompresör range: “We have two new lines, one of them is the Class-0 oil-free scroll compressors. With this addition, Dalgakiran Kompresör now has four different series of oil-free compressors in our production range. These units are the IHI-Dalgakiran turbo compressor, the Eagle oil-free double stage screw compressors, the Pet Master 40 bar, oil-free reciprocating compressors for the PET industry and our scroll compressors.
“The other new line is our new Impetus series double stage, oil injected screw com pressors . When developing these units, we focused on achieving high-efficiency and low noise. These 90-315 kW compressors have the best-in-class efficiency, enabling our customers to find products with lowest total cost-of-ownership in the market.”
The recent launches from Dalgakiran Kompresör have been developed with an eye on the client’s energy savings and environmental sustainability.
“Energy efficiency is the most prioritised target in all of our recent series develop ments,” explained Mr Asmaz. “In order to reduce the carbon footprints of our customers, we work hard to decrease the specific energy consumption values on all of our compressors.”
Sustainable operation is not limited to only the new releases at Dalgakiran Kompresör, according to Mr Asmaz: “Our Technology and Innovation Department continues to make improvements on the current product lines and studies how to develop new high-efficiency series of compressors. Additionally, an 18-75 kW Impetus line is planned to be released in the beginning of next year.”
Dalgakiran Kompresör’s Technology and Innovation Department is the first compressor R&D centre in Turkey. This department drives the development of compressors and helps the company pro duce tailor-mode products according to the exact needs of its customers. To maintain high production levels, the company works closely with suppliers and partners.
“With the recent global supply chain crisis, everyone better understood the value of the suppliers,” Mr Asmaz said. “We need a perfect supply chain to meet the require ments of our customers in a short time.
At Dalgakiran Kompresör, we always work with yearly forecasts for our suppliers. By analysing and monitoring both sales and production, we can foresee demand and act quickly to prevent delays.”
The Covid-19 pandemic impacted the machinery industry in unexpected ways, but those companies that survived are stronger for the experience. The pandemic underlined the importance of investing in both new technologies and the workforce. Companies such as Dalgakiran Kompresör who hold substantial stocks of components have avoided the worst of the global supply chain crisis.
A nother result of the global pandemic was the cancellation of so many trade fairs. As restrictions relax around the
world, Dalgakiran Kompresör is excited to once more attend events and connect inperson with its international partners. The company’s 2022 schedule includes SMM and Automechanika in Germany, Gulfood Manufacturing in Dubai and Propack West in Nigeria, while attendance at Comvac is already booked for 2023.
Alongside these trade show plans, Dalgakiran Kompresör has a clear strategy for the future. The company is targeting $1 billion revenue and 5,000 employees by the year 2030.
“Having Dalgakiran and Hertz compres sors operating in more than 130 countries makes me very proud,” concluded Mr Asmaz. “It is truly a pleasure to see our machines being used by manufacturers operating in hundreds of different fields.
“Although the competition is getting harder, Dalgakiran Kompresör tries to stay ahead with our best quality-ratio products, different product series for every customer profile, plus our agility and flexibility in the field of customer relations.” n
When
it comes to doors and frames , there are probably few better on the market than Theuma With 60 years’ heritage in the trade, today, Theuma focuses on the production, sales and instal lation of ready-to-install and tailor-made door sets.
Whether it’s a one-off or mass production order, the company continues to assert itself as one of the most crucial door and frame manufacturing companies in the Benelux region. It is the market leader in Belgium and number two in the Netherlands for interior door systems and frames for utility and residential construction.
Every day, 300 dedicated employees at sites in Bekkevoort, Belgium, and Nijkerk, in the Netherlands, produce these interior doors and frames based on three core raw materials: wood, steel and aluminium.
Theuma, which realised around €70 mil lion turnover at an annual average growth
rate of 8-12%, sells to clients in Belgium, the Netherlands, France, the UK, and other smaller export markets.
In the UK, where director Ian Gooding heads up Theuma’s presence, the com pany concentrates as a volume player on the supply of doors for hotel chains and student accommodation markets.
Mr Gooding predicted the UK market within the first six months of 2023 would return to “where it was three or four years ago. Now the pandemic is over, Theuma is doing extremely well and, hopefully, the UK will be a part of that success over the next several years.”
Theuma Group CEO Peter Le Roy added: “Theuma wants to be renowned as a reli able partner for its customers wherever they are. We do this with excellent ser vice before, during and after delivery.”
This is all underpinned by an innova tive and high-quality product range,
a robust production system and exten sive investments in digitalisation. The company has also realised greater busi ness through B2B, B2C and e-commerce with the acquisition of Anyway Doors and PortaPivot in 2020.
Mr Le Roy said that corporate social respon sibility (CSR) is at the forefront of the com pany’s agenda. The company is intensifying the use of green energy, and installing solar panels at its facilities in Belgium and the Netherlands, further reducing its annual carbon footprint by 400 tons per year.
All sourced wood and all sourced wood components for their door production are Forest Stewardship Council (FSC) certi fied. Theuma has previously invested in a wood-dust and a scrap incinerator, which is used for heating and supplying energy to the presses.
As one of Europe’s leading door manufacturers, Theuma NV places sustain ability front and centre in all its production activities. CEO Peter Le Roy talked to Andy Probert about his company’s ambitions to reduce its carbon footprint to zero by 2035 while continuing to build on its reputation for quality products.
Unique to the company is the use of the greenest coating technology available on the market, both for doors and metal frames. In the production of lacquered doors, Theuma uses electro-beam curing technology, which is free from any ozone depletion emissions and excludes the use of photo-initiators and solvents.
Mr Le Roy said: “This results in the greenest lacquered doors on the market and makes the colour of the doors insensitive to UV light and much more scratch resistant.” Additionally, all metal frames are coated with electro-powder coating technology.
Theuma has also committed to obtaining silver Cradle to Cradle certification by the end of 2024. Cradle to Cradle Certified is the global standard for products that are safe, circular and responsibly made.
Leading brands, retailers, designers and manufacturers across the value chain rely on the Cradle to Cradle Certified Product Standard to ensure their products positively impact people and the planet. The platform assesses the safety, circularity and respon sibility of materials and products across five categories of sustainability performance.
Mr Le Roy said: “Theuma’s products and processes are now being thoroughly anal ysed, and these activities are all part of our ambition to reduce the company’s carbon footprint to zero by 2035.”
Odice, founded in 1983, is a specialist in passive fire protection. We are the leader in the development, transformation and produc tion of intumescent fire seals and thermal insulating materials. We share with our customers our knowledge about fire resistant materials, our standards and the different testing methods in order to move their projects forward. In parallel, we offer customers use of our furnaces for testing internal fire resistance.
Another game-changer for the company is the digitisation of its processes, both in the factory and the office. Significant effort is being realised with the installation of a new press and assembly line, which enables mass customisation on one pro duction line. Each door is foreseen with an RFID tag, which is used to steer all machines in the manufacturing process.
New tools are also being implemented in the office, with a new ERP system going live at the Netherlands base in 2023. A new CRM system, a new quotation tool and a new planning tool linking all internal and external installers to the same network are also underway.
Mr Le Roy said part of its €15 million expansion project includes investment in a new laser punch machine and associated robots to produce wall thickness adaptable metal frames.
He added: “The group is also investing in expanding its team of experts in IT, R&D and sales.” Specifically, R&D efforts are focusing on new fire-resistant, acoustic- resistant and burglary-resistant door sets . A new range of Ei1 fire-resistant door sets will launch in late 2022.
In design door sets, Theuma is preparing new product introductions for the coming years, with ultra-matt finger print-proof finishes and colours based on its EBC technology.
Despite Theuma offering the broadest range of ready-to-install door sets from entry to high-end designs, Mr Le Roy pinpointed some challenges the industry faced as it emerged from the pandemic years.
“The biggest challenges we are experi encing are the price rises in raw mate rials, labour market shortages and the energy crisis.”
However, Mr Le Roy said the group con tinues to offer great added-value service to clients with its focus of on-time deliv eries of quality and safe products. The company continually develops new prod ucts and designs, and carries out compre hen sive fire-testing of bigger and larger doors for the market.
He concluded: “The industry is changing daily, especially with fire safety. There are too many companies who know very little about fire doors, but you can do a week’s training course, and you are suddenly an expert.
“Theuma NV, as a long-established manufacturer, will never compromise on safety or reliability. We are building a business with quality people, products, and a great repeat customer base sup ported by loyal, longstanding relation ships with key suppliers.” n