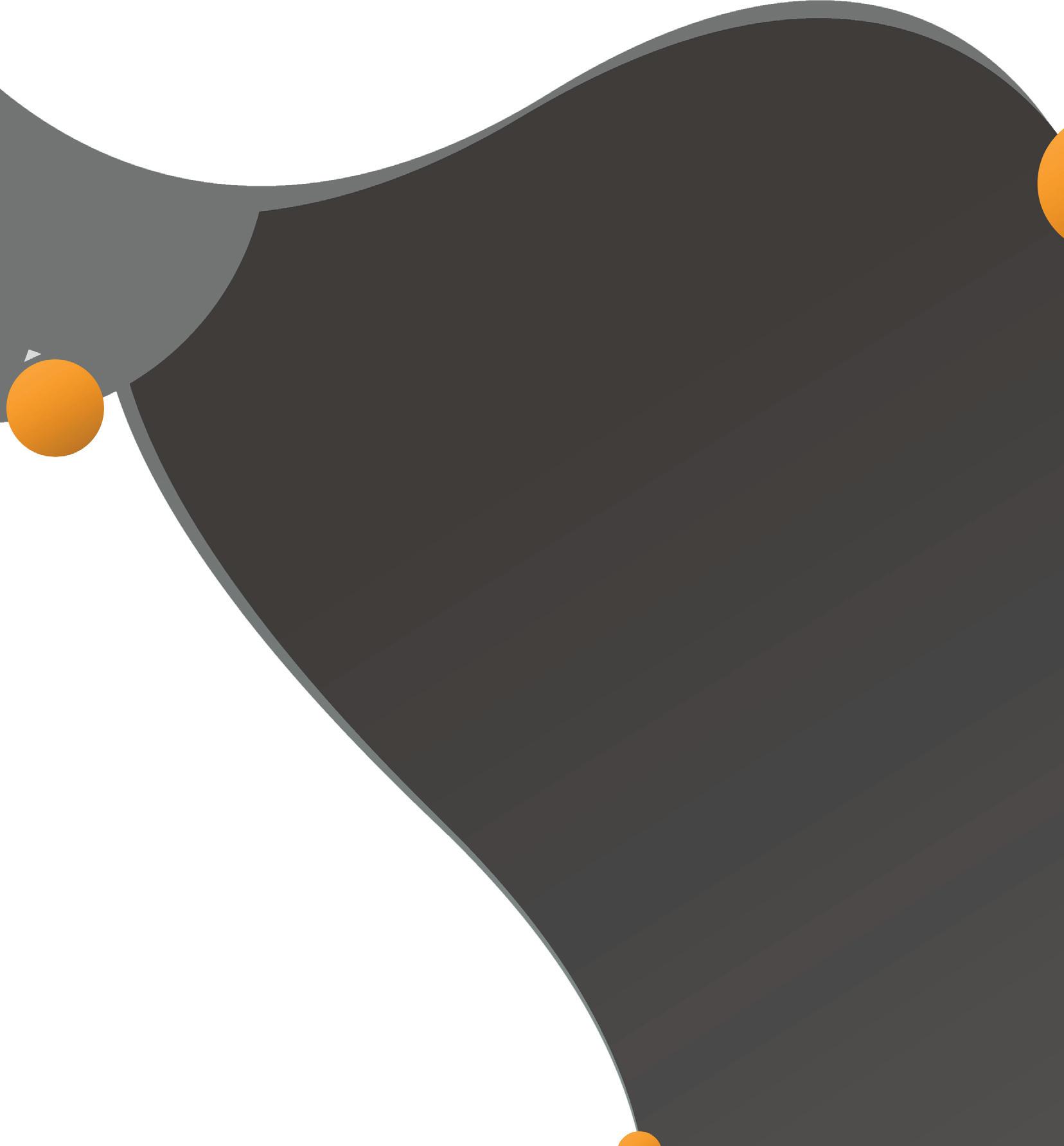
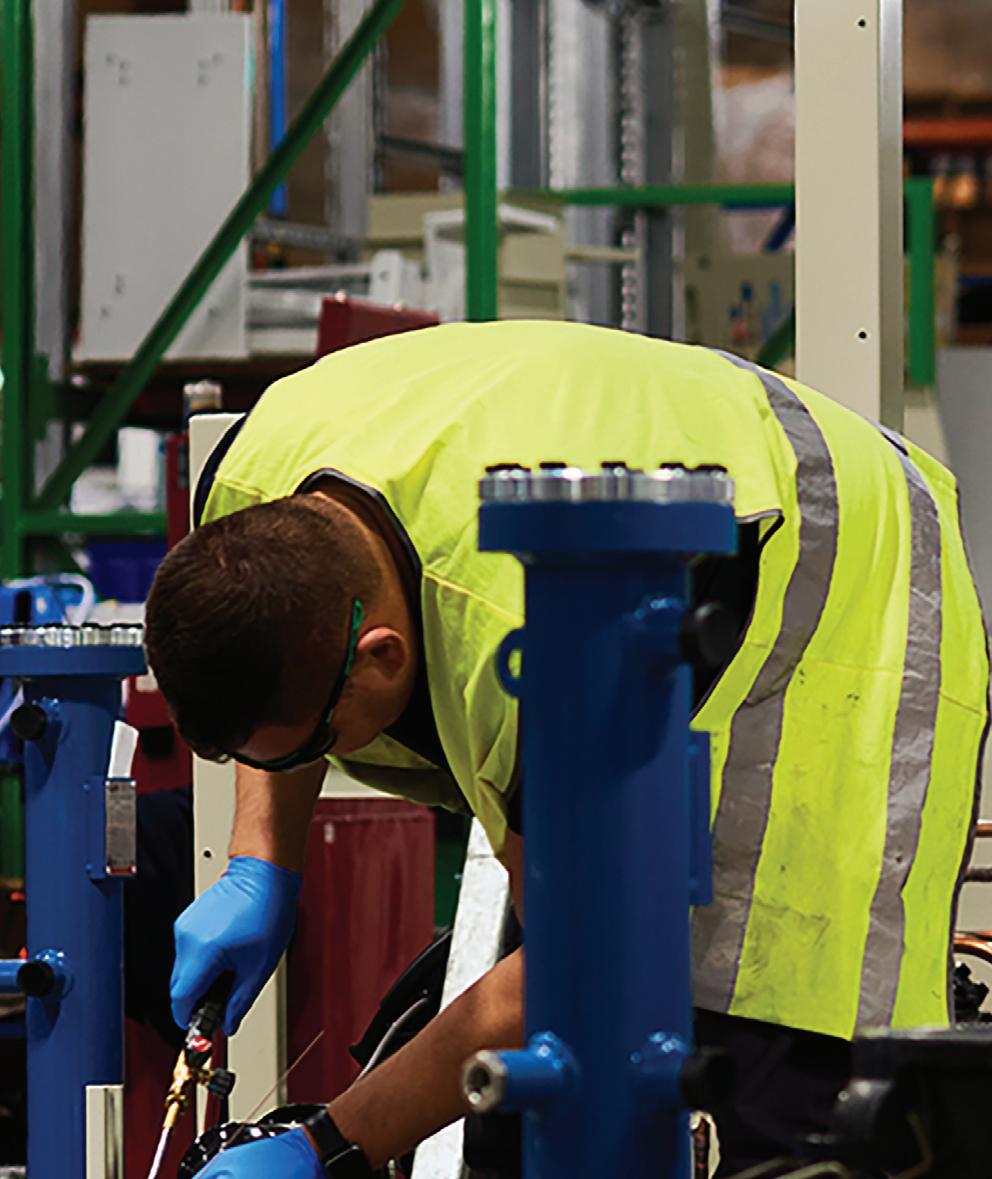
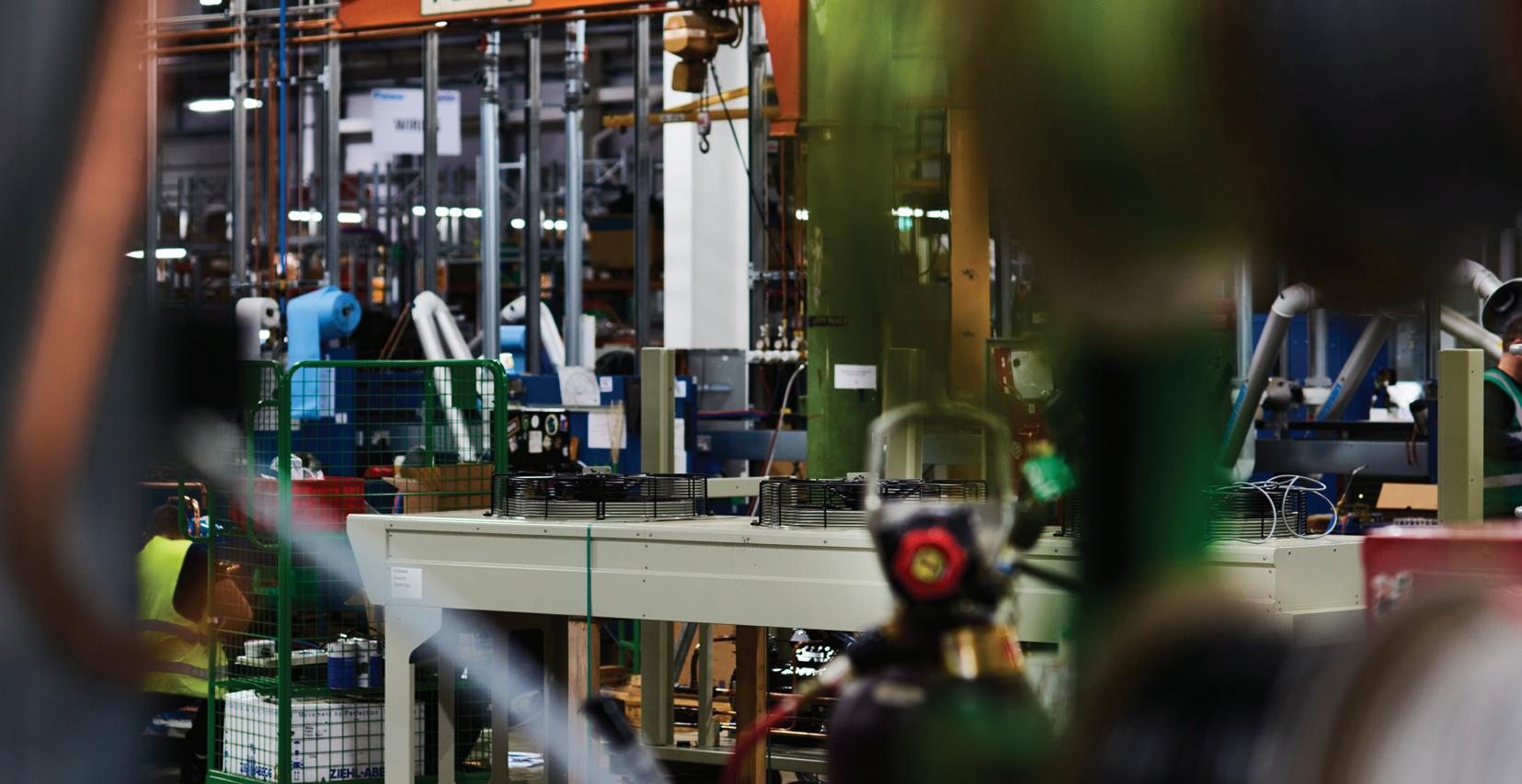

Hubbard Products has over 50 years’ experience designing, manufacturing and supplying the commercial and industrial sectors with cooling equipment. Having recently invested in a new facility, the company is working hard to expand its production capabilities. Sales Manager Alec Stilling and Head of Design and Engineering Ashwaq Mohammed spoke in-depth about the company’s current work scope and its amazing efforts towards improving its customer’s sustainability, in conversation with Imogen Ward.
Hubbard Products has developed highly efficient CO2 refrigeration units to reduce emissions within the industrial and commercial sectors. Using its first-class R&D department, and with the support of its parent company (Daikin), Hubbard Products developed innovative products targeted towards the carbon footprints of its clients.
“We build sustainable products,” Sales Manager Alec Stilling said, “examples include Hubbard Products’ CO2 Refrigeration Packs, A2L Packs and heat pumps.
Our customers have different expectations and aspirations – they’re at varying points in their sustainable journeys.
“Some customers are very far advanced and in tune with what they need to do by 2030, whereas others haven’t even begun to work out where they are headed. Our job is to help them get their foot on the ladder. Energy efficiency is in the DNA of Hubbard Products; it’s what we do best.”
Founded in 1968 by Geoff Hubbard, the company began developing small commercial refrigeration applications. In 1984, the company built its first commercial refrigeration multi-compressor pack for food retail; this project opened the doors to an entirely new market. From this point onwards, Hubbard Products manufactured an array of refrigeration and heat pump equipment, always
ensuring the highest quality for the best price.
In 2016, Hubbard Products made the decision to introduce CO2 Refrigeration Packs to the market. These products were aimed towards commercial companies, including big-brand names Asda and Marks and Spencer, to help them reduce their carbon footprint. These products have extremely low GWP refrigerant levels – the CO2 Rotary Condensing Unit which uses natural refrigerant, has a highly efficient GWP level of one. This refrigerant figure is impressively marginal compared to the legal requirements of refrigeration units in commercial settings. In 2017, Daikin purchased the company, considerably expanding Hubbard Products’ global reach.
“When I started 15 years ago,” Head of Design and Engineering Ashwaq
Mohammed said, “we used to build units with GWP levels of around 4,000. In 2016, we significantly reduced that amount to 2,000 GWP. We then turned to synthetic refrigerants which remain between 150239 GWP. We still use this type of refrigerant now. We also build systems using natural refrigerant. For these products we incorporate CO2 which is gas that is naturally available.”
T he company also produces a range of heat pumps. This product has seen a surge in demand from companies looking to further offset their carbon emissions. Included in this range is the Hubbard Heat Pump, this pump captures waste heat from conditioning compressors and condensers and converts it into a viable
source of hot water. This process effectively reduces the users’ heating costs through its recycling system – making it both efficient for the environment and extremely cost effective.
The most popular applications of all the Hubbard Products’ range are the Blast Chiller and Blast Freezer. These products can be adapted to fit different size specifications and use R448A/R449 A refrigerant. The company also offers
a heat pump module alongside its blast freezers, that utilises the product’s waste gas as a viable source of heat.
As business boomed, new ventures appeared on Hubbard Products’ radar. During the Pandemic, the company offered highly efficient solutions for the safe transportation of pharmaceuticals and medicines. The R&D department at Hubbard Products researched heavily into cold room solutions for monotherap y
and vaccine storage, resulting in three refrigeration units that are GDP compliant These options include the Invisible unit, SFZ2009 (installed beneath the chassis to preserve vehicle height and reduce bodywork); and the SFZ238 nose-mounted unit (designed with energy efficiency in mind).
“We are helping our customers and providing them with a portfolio of solutions that fit their specifications and engineering designs,” Mr Stilling said. “We can provide our customers with multiple options to find the most efficient product for the job. We are also highly flexible when it comes to customer requirements and will engineer a specific solution, putting us ahead of our competitors who have a more standardised range of products.”
The exploration into the pharmaceutical sector enabled Hubbard Products to strengthen its presence as a market leader in sustainable refrigeration units and cre ated potential for future expansion into other areas of the market. The company intends to double its turnover – using its increased production capabilities as a springboard towards success.
Committing to a five-year plan for growth (named Fusion 25), the company’s strategy merges with the goals of parent company, Daikin: contributing to a more sustainable society and achieving growth, Daikin has committed to nine themed strategies. Daikin wants its subsidiaries (including Hubbard Products) to achieve carbon neutrality, improve customer relations, and continue strengthening their technology development capabilities.
Hubbard Products is on target for 2025. Having moved to its new facility in 2021, the company took advantage of the larger space – successfully doubling its factory capacity. To meet its goals of carbon neutrality, the company ensured its state-of-the-art facility in Ipswich was highly efficient.
With a brand-new R&D lab under commission, Hubbard Products is also strengthening its R&D capabilities. “The commissioning of a new R&D lab means that we will have control of our own environment,” Mr Stilling said. “It will enable us to further develop our products and push the boundaries of what we can achieve. We have also recently taken on an R&D manager who will help meet our Fusion25 targets. On top of that, she also has her own plans for improving the business.”
Products has already had a positive impact on the company, having developed and manufactured most of its product components in-house. This integration meant that Hubbard Products avoided the brunt of the global supply issues. The company is, however, reliant on its suppliers for several key components. To avoid delays in production over the past few years, Hubbard Products has adapted its business model. The company is constantly assessing its supply chain to ensure operation is optimised, which has resulted in an ever-evolving supply chain.
“ We have concrete suppliers across all line items,” Mr Stilling concluded. “We had to adapt during Covid and now depend on multiple suppliers for everything. We always do background checks, making sure our suppliers are ethical and align with our sustainable ethos. It is important to us that we can continue to provide the best quality products to our clients, for the best value.”