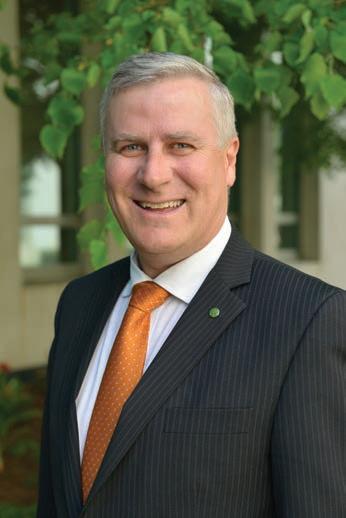
38 minute read
Prime Mover News
> Government forms joint committee to cripple road trauma
A new multi-party committee has been formed as the Australian Government ramps up resources on reporting the effectiveness of current road safety programs. The Joint Select Committee on Road Safety will comprise of nine parliamentary members and be chaired by Llew O’Brien, Federal Member for Wide Bay, as it provides recommendations for the newly established Office of Road Safety. Deputy Prime Minister and Minister for Infrastructure, Transport and Regional Development Michael McCormack said the committee will examine the effectiveness of existing road safety support services and programs. These will include opportunities to integrate Safe System principles into health, education, industry and transport policy. “The committee will also look at the importance of achieving zero deaths and serious injuries across Australia, but especially in remote and regional areas. It will also consider recommendations for the role of the newly established Office of Road Safety,” said McCormack. “I thank Committee Chair Llew O’Brien for taking on a critical leadership role within the new committee.” Assistant Minister for Road Safety and Freight Transport Scott Buchholz said the Joint Select Committee on Road Safety was brought about to evaluate current actions and to accelerate progress towards fewer deaths and serious injuries on Australian roads. “There is great opportunity for road safety and the Safe System approach to be better integrated into related policy areas. The committee will also carefully evaluate the possible establishment of a future parliamentary Standing Committee on Road Safety and what its functions may be,” he said. Committee Chair Llew O’Brien said he would be taking a strong interest in enhanced coordination between different levels of government, including infrastructure investment priorities. “As a former police officer, I know too well the horrific impact road accidents have on families right across the country,” he said. The Committee is expected to report on the impact of road trauma on the nation, including the importance of achieving zero deaths and serious injuries in remote and regional areas. It will review the effectiveness of existing road safety support services and programs, including opportunities to integrate Safe System principles into health, education, industry and transport policy. Among other inquiries it will look at measures to ensure state, territory and local government road infrastructure investment incorporates the Safe System principles road trauma and incident data collection and coordination across Australia and undertakings initiated to support the Australian Parliament’s
Michael McCormack.
ongoing resolve to reduce incidents on our roads. “The new committee will be looking into measures to ensure state, territory and local government road infrastructure investment incorporates the Safe System principles road trauma and incident data collection and coordination across Australia,” said O’Brien. “We will also consider any other measures to support the Australian Parliament’s ongoing resolve to reduce incidents on our roads.” The committee will present an interim report by 30 March 2020 and its final report by 31 July 2020.
> WA opposition proposes Roe 8 highway extension truck levy
A commercial vehicle levy for the Roe 8 highway extension in Perth has been proposed by state opposition in Western Australian despite it denying claims such plans would also encompass passenger vehicles. Abandoned in 2017 when the Government came to power the project would see, under a Liberal Government, a levy introduced for the heavy haulage industry who would be one of the major beneficiaries in productivity gains should extensions go ahead on Roe 8 and Roe 9. Opposition leader Liz Harvey distanced herself from a commuter toll. “74,000 cars and 7000 trucks a year would be removed from local roads and significantly improve road safety and congestion if this project goes ahead,” she said. Harvey said the project would create 10,000 jobs as the federal government was still willing to allocate funds of $1.2 billion for the highway extension. WA Premier Mark McGowan, however, opposed tolls, which at present do not exist in Western Australia. “Once you put it in place on a truck, an easy revenue raising measure is to put it in place on cars and that’s exactly what would happen,” he said. “If you go and Google the definition, a toll is the same as a levy ... so they’re going to open the floodgates to tolls in WA.”
Goodyear’s new flaGship hiGhway drive tyre KMAX G667+
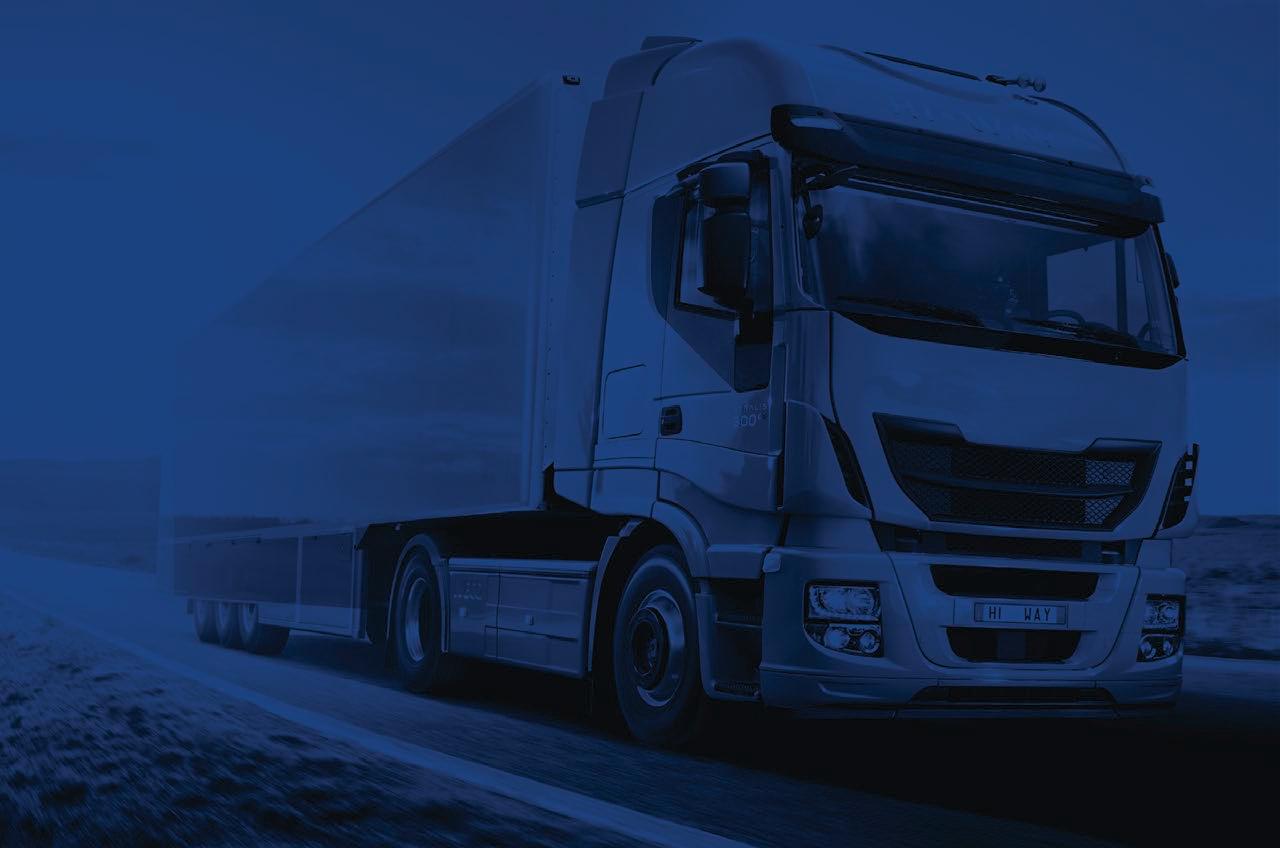
KMAX G667+
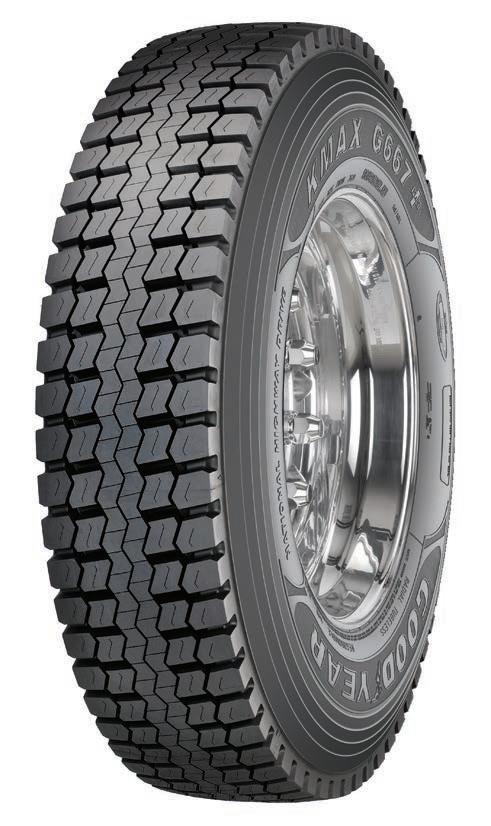
Developed for Australian road conditions with improved resistance to chipping and stone drilling while the deeper tread gives improved highway mileage.
11R22.5 SIZeS:

> Linfox launches first of its kind tri-axle tipper for Port Kembla
Lin-double tri-axle tipper with six-axle dog trailer at Port Kembla.
Logistics and commercial carrier, Linfox, has unveiled a new Lin-double configured tri-axle tipper coupled with a six-axle dog trailer for its coal run in Illawarra. The combination, pulled by a Volvo tri-drive prime mover, moves coal related products from the South32 facility on behalf of Illawarra Metallurgical Coal operations to Port Kembla for Bluscope Steel. Linfox, which has invested $20 million recently in a fleet of custom-designed trucks, engaged a team of Australian and international engineers on the
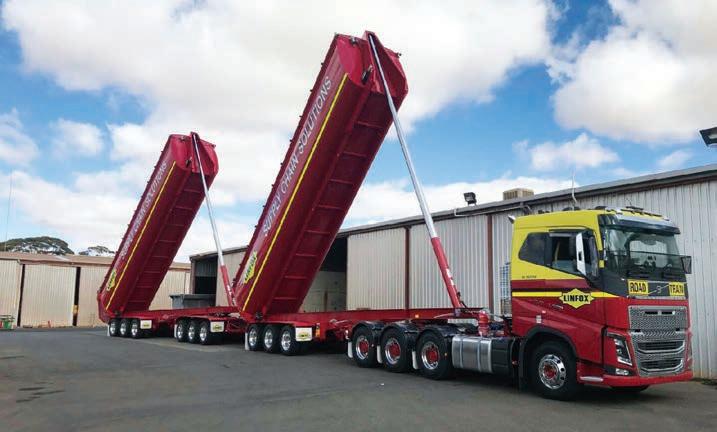
unique vehicle combination. “The vehicles were designed to address the particular challenges of hauling coal in the Illawarra, especially the steep descent down Mount Ousley,” said David Keane Linfox General Manager Business Development, Resources and Industrial. “We’ve essentially combined the most powerful Volvo prime mover available with additional braking and descent control technology and higher capacity trailing equipment,” he said. Illawarra currently outpaces Sydney in population growth and with the transit route between Westcliff and Appin Colliery involving steep grades down Mt Ousley and through heavy traffic, South32 required a supply chain partner with a transport solution that minimised its impact on the community and environment. In a company statement, Linfox said it was focused on the wellbeing and capability of its drivers as it planned to reduce the number of vehicle movements on local roads by 25 per cent. The vehicle, as the company strives to increase the tonnage of coal it moves on each trip while honouring its commitment to chain of responsibility, features radar adaptive cruise control and collision mitigation technology. Linfox also confirmed it had commenced construction on a new site in Port Kembla where South32 ships coal to international markets. The project will reportedly employ 130 local workers. This will include drivers, contract managers, operational supervisors, safety officers and administrators. Global demand is increasing right now for high quality coking coal which Illawarra has an abundance of for the production of steel.
> Arrow Transport acquires Sydney Sideloaders
Arrow Transport and Logistics, the fifth largest container transport operator by volume at the Port of Melbourne, has acquired Sydney Sideloaders, a top ten container transport operator at the Port of Sydney. The acquisition is part of Arrow’s ongoing strategy to grow its business by providing its clients with a greater range of services in a greater number of ports around Australia. Arrow anticipates the acquisition will help increase its footprint to operations in Sydney and enable it to extend the high level of service for which it is renowned in Melbourne into the important Sydney market. Sydney Sideloaders operates primarily from its site at the corner of McCauley Rd and Botany Rd, directly opposite the Port of Sydney terminals. Chris Divis, Director of Sydney Sideloaders, will stay on with Arrow after the acquisition as Port Logistics Manager NSW. Other members of the current operational team at SydneySideloaders will also join the Arrow team. In addition, Arrow will reportedly move some staff from Melbourne to Sydney to assist with the integration. “We are very pleased to have concluded this transaction with Arrow,” said Divis. “We look forward to being part of a larger, growing organisation that has the same focus on customer service that Sydney Sideloaders has always had.” Arrow Managing Director Craig Webster said he was extremely pleased to have had the opportunity to acquire Sydney Sideloaders. “The operation will complement our existing business extremely well and enable us to provide a greater level of service to new and existing clients in both Melbourne and Sydney,” he said. The acquisition is expected to be completed by 2 September 2019.
G500 punches above its weight
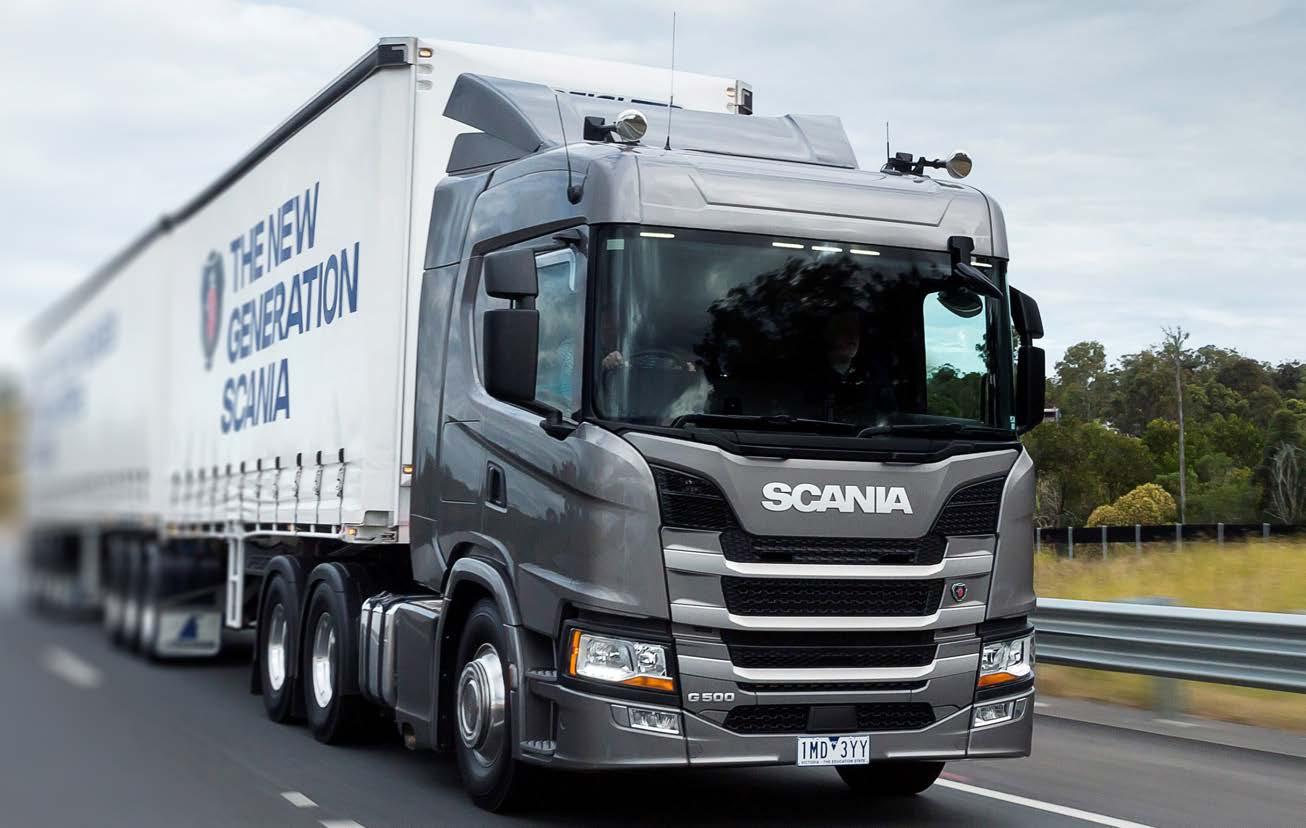
Scania’s New Truck Generation G500 6x4 prime mover is a real surprise packet.
• Brute pulling power. 500 hp and 2550 Nm of torque.
• Fuel efficiency. The new range has outstanding fuel consumption.
• Safety. Unique, world first side curtain roll over airbags as standard plus a host of other features make Scania’s New Truck Generation range the safest trucks in Australia
• Luxury Interior – excellent visibility, great cabin acoustics and customised digital dash.
And, with our included maintenance offer across the New Truck Generation range, you’ll have complete peace-of-mind for 5-years /500,000 km*.
Visit www.scania.com.au

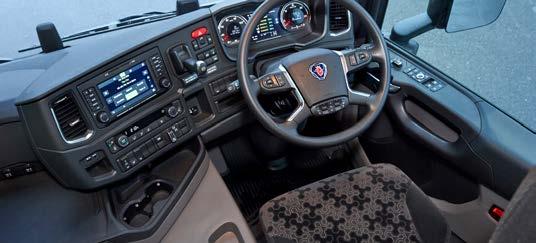
5 YEARS or
kilometRE
maintenance INCLUDED
> Hino advances 700 Series range with new additions
Commercial vehicle manufacturer Hino Australia has expanded its heavy-duty 700 Series range with the addition of a long-wheelbase variant of the FS 2848 6x4 model. The new long-wheelbase model is powered by Hino’s E13C 12.9 litre sixcylinder turbo-charged diesel engine, which produces 480hp (353kW) of power and 2157 Nm (1591lbft) of torque. Compliant with ADR80/03 (Euro 5) emissions standards, thanks to a combination of exhaust gas recirculation (EGR) and selective catalytic reduction (SCR) systems, the E13 C engine is matched to the latest generation ZF 16-speed automated manual transmission (AMT), the TraXon 2441TO. “We have developed this truck at the specific request of our customers – it is suitable for any number of applications from general farm duties or cattle trucks to a 14-pallet rigid freight truck or a flat tray with a rear-mounted crane,” said Hino Australia’s Manager of Product Strategy, Daniel Petrovski. “It features the overdrive version of the TraXon transmission and includes the standard fitment of the ZF Intarder, providing up to 3200Nm of auxiliary braking.”
Hino expands long-wheelbase variant to 700 FS 2848.
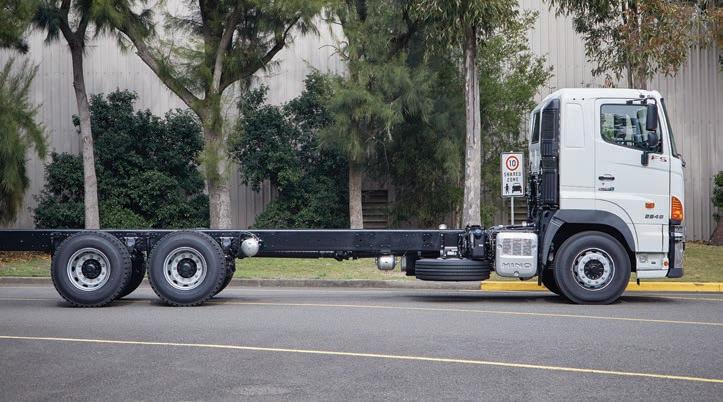
Named the FS 2848 AMT AIR 6267, the new variant rides on a combination of long taper-leaf suspension on the steer axle and Hendrickson HAS 460 air suspension on the drive axles. “The cab on the FS is mounted to the grid hole chassis via the Hino four-point cab air suspension with the driver seated in an ISRI 6860/870 air suspended seat with multiple air comfort adjustments and integrated seatbelt,” said Petrovski. “Adding to the truck’s appeal is the all-new Hino smart Multimedia System, which includes standard reversing camera, and an unprecedented level of vehicle connectivity and entertainment possibilities.” The Android-based 6.5’’ capacitive multi-touch digital screen features AM/FM/DAB+ digital radio, Wi-Fi connectivity, and the latest version of Bluetooth tethering which enables enhanced call handling, and improved speech to text functionality. Other features include a curated Hino application store and an optional truckspecific GPS navigation system.
> Iconic XXXX brewery receives 15-year extension
The logistics operation at the historic Milton Brewery in Brisbane where XXXX beer has been produced and shipped for over 140 years has been extended. Queensland Minister for Planning, Cameron Dick, confirmed the registration for the brewery would be extended 15 years giving certainty to the company so that it can continue to operate into the future within approved limits as the former commercial area faced increasing residential encroachment. “This enables Lion to continue operating from the same premises that has been home to XXXX for more than 140 years, by ensuring that existing uses on the site can continue, even as the area experiences growth intensification,” he said. “With a resurgence in inner city living it’s important to ensure that important existing uses, such as the XXXX brewery, can continue to operate.” The large brick building and prominent sign would be preserved along with existing 150 jobs on site. It brings to light the increasing challenges of dedicated logistics businesses having to co-exist in fast changing urban environments where residential space is in demand. Lion Group Supply Chain Director, Ian Roberts, who started working with Lion 28 years ago in the Milton factory, said the company had spent millions of dollars on improvements to the brewery to limit its environmental impact since 2009. “Just a few weeks ago we completed a $2 million solar project, which will reduce our annual carbon emissions by 1260 tonnes,” he said. “We have also significantly reduced our already low noise and light emissions, all of which are well within the limits allowed under our development consents, in order to continue being great neighbours. “20 years ago, Milton looked very different to how it does today. Previously it had been an industrial epicentre, but its proximity to the Brisbane CBD made it the perfect location for high-density residential developments.”
Unlock fuel tax rebates Automatically unlock the fuel tax rebates you’re entitled to on public and private roads.
EROAD’s Fuel Tax Credits (FTC) solution lets your company claim rebates on all the fuel tax you have paid, for vehicles or fuel-operated equipment, on or off-road. Maximise the rebate you are entitled to with EROAD FTC, even when fuel prices or fuel tax credit rates change. By automating the rebate process your fuel tax credits will be automatically calculated and reported for your business activity statements, reducing admin time and making the rebate process easier.
EROAD FTC enables you to: • Automate your FTC rebate claims • Claim up to 2.5x more off-road • Go back 4 years • Set simple boundaries • Claim for heavy and light vehicle • Maximise rebate claims
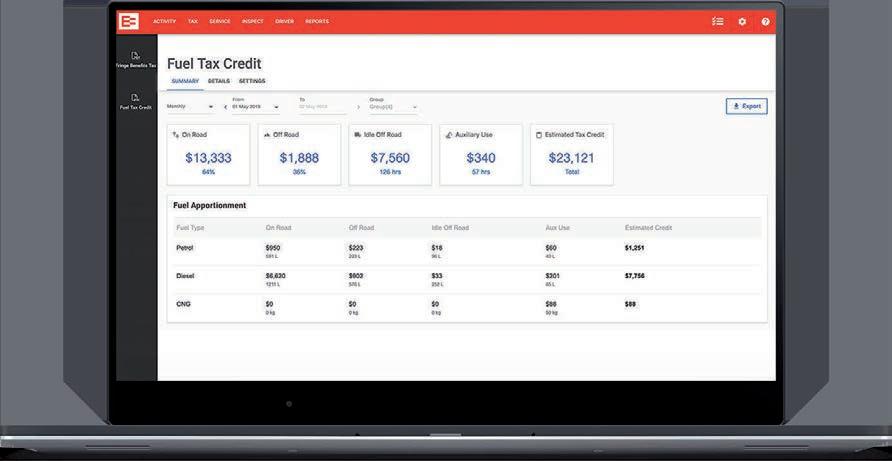
Contact us for details www.eroad.com.au • 1800 437 623 info@eroad.com.au
> Penske announces 2019 Master Technician award
The Penske Guild 2019 Master Technician has been awarded to a Penske Power Systems employee in Perth. Bryce Bell edged out five other finalists in the contest which involved technicians from Australia and New Zealand who competed in qualification rounds ahead of the grand final event. The annual skills and diagnostics contest includes general procedural tasks as well as advanced diagnostics scenarios, all done while racing the clock. “At Penske, we understand the importance of recognising and rewarding our very best technicians and the flow on benefits that come from a competition such as this,” said Russell Koch, Training Manager On-Highway and Development. “The competition is a great way to publicly display the technical excellence we are renowned for, both within our own organisation and the broader industry in general.” Having been with the organisation for almost a decade, Bell has worked across the full Penske Power Systems product portfolio including MTU, Detroit, Allison Transmission and, more recently, Western Star Trucks, MAN Truck & Bus and Dennis Eagle. “Since joining the organisation in 2010 as an apprentice, Bryce has displayed a great willingness to develop which
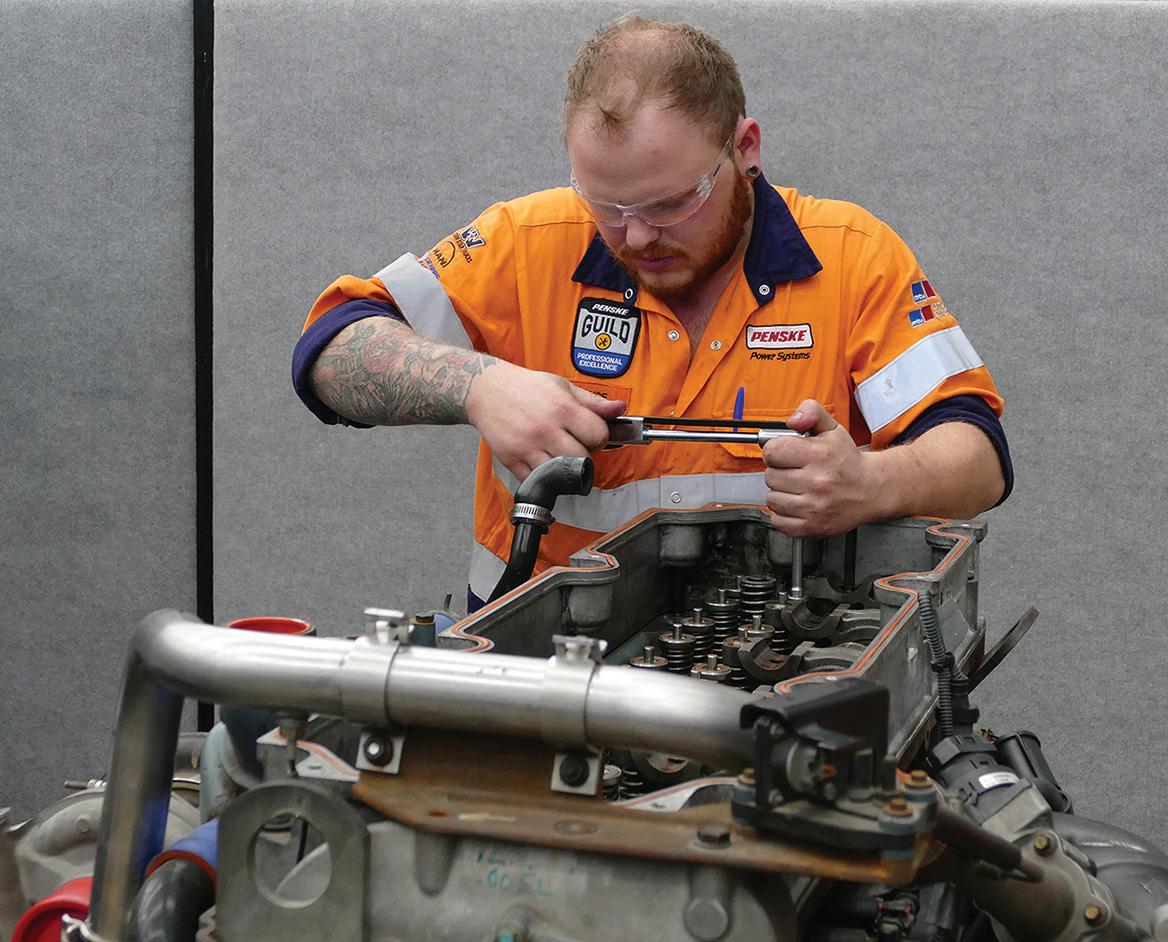
Bryce Bell, Penske Power Systems Perth.
has carried him through to achieving this accolade,” said Sean McLean, General Manager – On-Highway. “Whether in the workshop leading by example, or in the field managing one of our breakdown services for remote Western Australian customers, he demonstrates exemplary technical skills which were evident in the grand final,” he said. As the Penske Guild’s Master Technician, Bell will receive a trip to the United States to tour the worldclass manufacturing facilities of Detroit and Daimler Trucks North America. He will also tour the Team Penske motorsport facility in North Carolina.
> Dananni Haulage receives custom built Freightliners
Freightliner 6x2 CL112.
A pair of built-for-purpose Freightliner commercial vehicles have been delivered to a Perth speciality hotshot business. The 6x2 CL112s will be used to carry expedited freight on servicing high value industrial operations including mines in which critical parts and equipment are needed to mitigate productivity losses. With the sole objective to move the likes of engines for dump trucks as fast as possible, the application involves a 7.8 tray, a 48-inch sleeper cab and a retractable lazy rear axle. Owner Danni Kempton said reliability and driver comfort was crucial given the long distances her
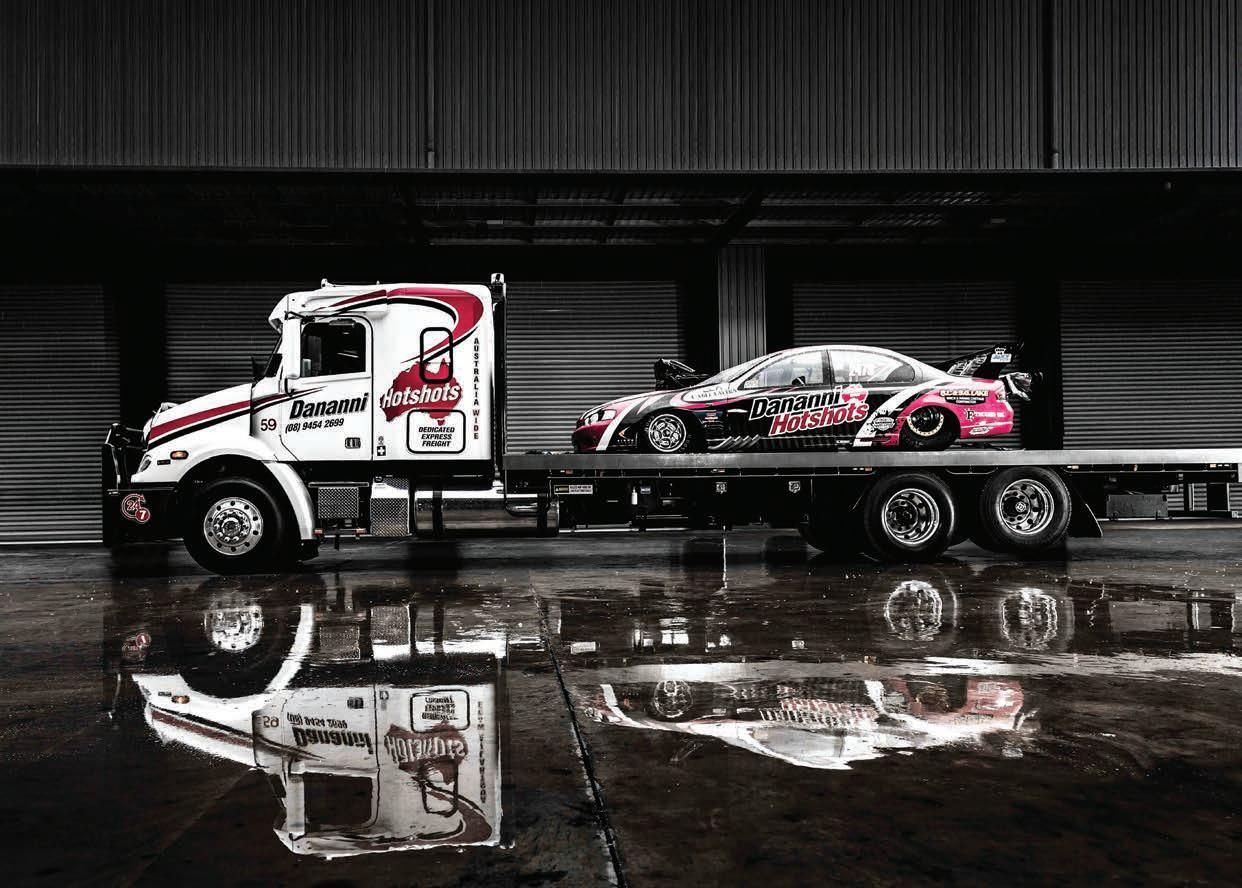
operators were undertaking. “We will go anywhere there is a road, so our drivers can be on the road six days straight,” she says. Although the 20-year old company is positioned to service mines in Western Australia, Dananni Haulage operates interstate going as far as North Queensland and Tasmania. Drivers run two-up, with one driving and the other resting. The Freightliners, according to Kempton who now has 23 trucks in her fleet, are the best trucks currently in operation despite receiving external skepticism in regard to the specification she chose for the vehicles. “There were people who thought I had no idea when I built up the Freightliners and were waiting for it to end up in a big mess,” she says. “But I had done my homework and I knew it would work. The proof is in the pudding and the Freightliners are the best two trucks we have.” At present she claims the Freightliners deliver fuel economy around 4.4km to 4.5km per litre when the lazy axle is off the ground. When deployed with a load the trucks are achieving between 4.2 to 4.1km per litre. Featured on the CL112 is an 8.9-litre Cummins ISLe5 six-cylinder engine set at 340hp and paired with an Eaton UltraShift AMT.
> Freight operators warned of Amazon and Uber disruption
Giant platform providers are expected to gain a foothold in Australia soon.
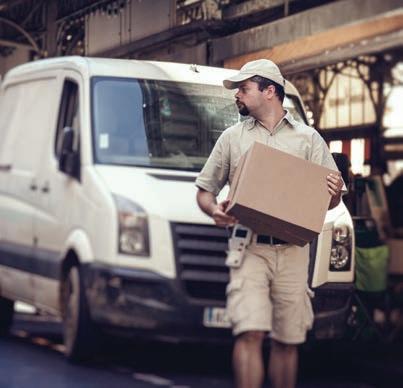
Platform providers such as Amazon and Uber Freight will threaten significant disruption in road freight markets attendees recently heard at the Australian Road Transport Industrial Organisation NSW Branch Annual Conference and Dinner. Those in attendance of the inaugural event were warned by delegates that platform providers were expected to take a ground zero approach to local industries as they looked to exert greater influence in the future. Speaking at the event, newly appointed NSW Shadow Minister for the Gig Economy, Daniel Mookhey, raised concerns about the current and emerging role of these providers in the industry. Calling for a level playing field, Mookhey said competitive neutrality was required to reduce the dominance of these businesses in the markets with which they operate. He noted urgent reform to arrangements related to the engagement of gig workers would ensure they were adequately protected under law. Uber Freight last month announced it was expanding its operations to Europe. ARTIO NSW Secretary/Treasurer Hugh McMaster said multinational companies in a rapidly changing world were setting out to further disrupt established commercial and operational arrangements in the industry. “These companies are further raising consumer expectations that the goods they order will arrive almost instantaneously,” he said. “They expect an already stretched industry to meet those expectations. “It is 40 years since Razorback and, in that time, industry has not shown the will to do the necessary work to develop an enduring policy framework which addresses its economic challenges,” said McMaster. “We need to ensure all road freight businesses have a level of regulatory support which ensures failures in the operation of Australian freight markets are addressed so that well-run business can aspire to making a reasonable return over the medium to long run while at the same time allowing for poorly run businesses to fail.” Attendees were told that a “tsunami” was coming as these giant platform providers were prepared to loss lead in order to gain a foothold in global freight markets. Shadow Assistant Minister for Road Safety, Glenn Sterle, spoke of the importance of industry engagement to address the industry’s long established and emerging challenges. McMaster agreed. “Perhaps with Amazon and Uber Freight rapidly expanding their global tentacles, and threatening more widespread and more significant disruption on the operation of freight markets, industry leaders will realise the increasingly important need to work together in anticipation of their arrival,” he said.
> Action needed for National Freight and Supply Chain Strategy: ALC
The National Freight and Supply Chain Strategy has been released as the country prepares for the next 20 years in a rising consumer economy. Developed by all Australian governments with extensive industry input, the Strategy and its associated National Action Plan will integrate the different transport modes for the first time according to Deputy Prime Minister and Minister for Infrastructure, Transport and Regional Development Michael McCormack. “Australian freight supply chains get petrol to our service stations, fresh food to our supermarket shelves, waste to the tip, construction materials to building sites and essential pharmaceuticals to our hospitals – delivering about 163 tonnes of freight per person around the country each year,” he said. “With our freight volumes expected to grow by more than a third by 2040 and online shopping growth at over 20 per cent a year, we need to increase the productivity of our freight system. At the same time, we have to plan for and manage the introduction of new technologies and risks from increasing natural disasters, such as the devastating floods in Queensland last year.” The Strategy will only succeed, however, if implementation plans due to be presented in November commit to meaningful actions, backed by new investment and real deadlines for delivery said ALC CEO Kirk Conningham. “ALC welcomes the fact that as a result of the Strategy agreed to today, Australia now has a clear set of actions for improving supply chain efficiency which all governments nation-wide have committed to pursue,” he said in a statement. “We now need those same governments to follow through with concrete plans for implementation, so that the Strategy can start to deliver tangible benefits for our economy, for consumers and for communities.” A single implementation plan would hold governments to account for delivering on the Strategy said the ALC.


Mark Tobin Managing Director Followmont Transport
Now available in 11-litre and NEW 8-litre From 360hp to 460hp
> Scania high productivity fleet safest in Australian waste transport: Brisbane City Council
Cleanaway Waste Management has endorsed the 18 new Scania commercial vehicles it took delivery of following 12 months of intense application pulling bespoke bulk tippers and rear ejector loaders. The order of 12 R 560 V8s and 6 G 480 six-cylinder diesel powered prime movers was part of a new contract to transport non-recoverable general waste from resource recovery stations to landfill sites for the Brisbane City Council. Key criteria for the trucks involved the flexible undertaking of a wide variety of tasks in anticipation of payload increases as the demand for waste services rises. A recent performance review of the vehicles afforded Shannon Gorman at Cleanaway Landfill and Logistics Manager Brisbane City Council Resource Recovery & Innovation Alliance – Solid Waste Services, the opportunity to reflect on the many accomplishments seen over the last 12 months. “At Cleanaway we had initially undertaken a comprehensive review of the Brisbane haulage task as a com ponent of the tender and mobilisation, identifying potentially significant opportunities for productivity gains through modelling and asset configuration,” he said. “I am proud to say that these gains have been realised. The bespoke Scania high productivity multicombination bulk waste transport vehicles have had a profound influence on the productivity, efficiency, safety and ultimate success of the essential waste services delivered to the city of Brisbane,” said Gorman. The high-volume complex spoke and hub reverse logistics chain of Brisbane’s massive waste transport task requires an equally complex operating rhythm. According to Gorman the scale of the task involved safely transporting 500 kilotonnes of waste over 1.2 million km through traffic of a major metropolis in one year. “We believe that this bespoke high productivity fleet is the safest waste transport fleet in Australia,” he said. “Operating at Higher Mass Limits (HML) the fleet moves more waste in fewer trips, equating to less congestion, reduced emissions and overall lower impact on Brisbane’s road network.” A new driver team was formed specifically for the job. Despite many of them not being familiar with European trucks the ergonomic features of the Scania found immediate appeal. “After outlining the extensive array of innovative active, passive and in cab support safety features of the trucks, the team was reassured that Cleanaway’s commitmen t and investment in safety was real,” said Gorman. As part of its ongoing service commitment, Scania provided driver training and Cleanaway observed immediate decreases in fuel consumption coupled with improved truck scoring. This scoring was used as an incentivised contract maintenance metric. “In the first month of operation the data rich output we were receiving was confronting, for the first time ever we had absolute visibility of how our trucks were being driven on the road and to be honest it highlighted some inefficiencies,” Gorman said. The connected service ecosystem provides intelligent dashboard views, fault identification, remote diagnostics, vehicle tracking, driver and vehicle performance as well as customisable detailed reporting tools. Having granular visibility to the exact correlation between driving behaviours like anticipation, coasting, gear shifting, acceleration, braking and running costs, according to Gorman crystallised the true value of the driver. “Recognising the need for a partnership with our drivers, we developed a rewards program to promote good driving behaviour and thank our improving and top performing drivers,” he said. “We have seen our average score increase greater than 25 per cent over the year, equating to significant financial savings as well as improving safety and environmental outcomes.”
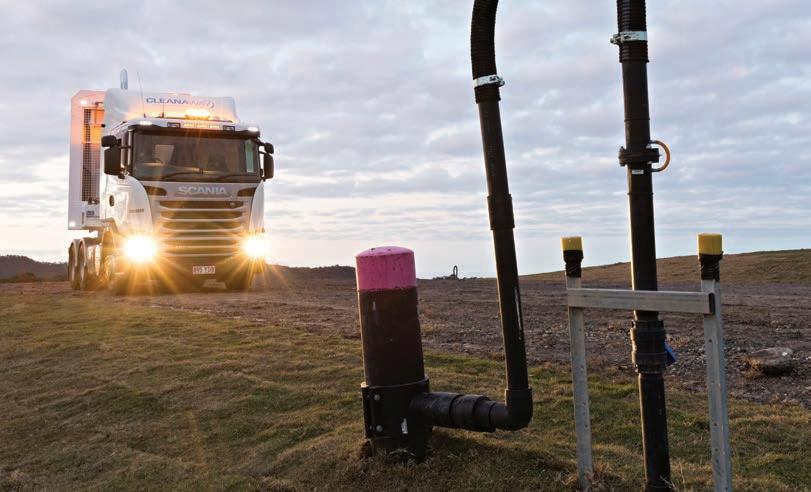
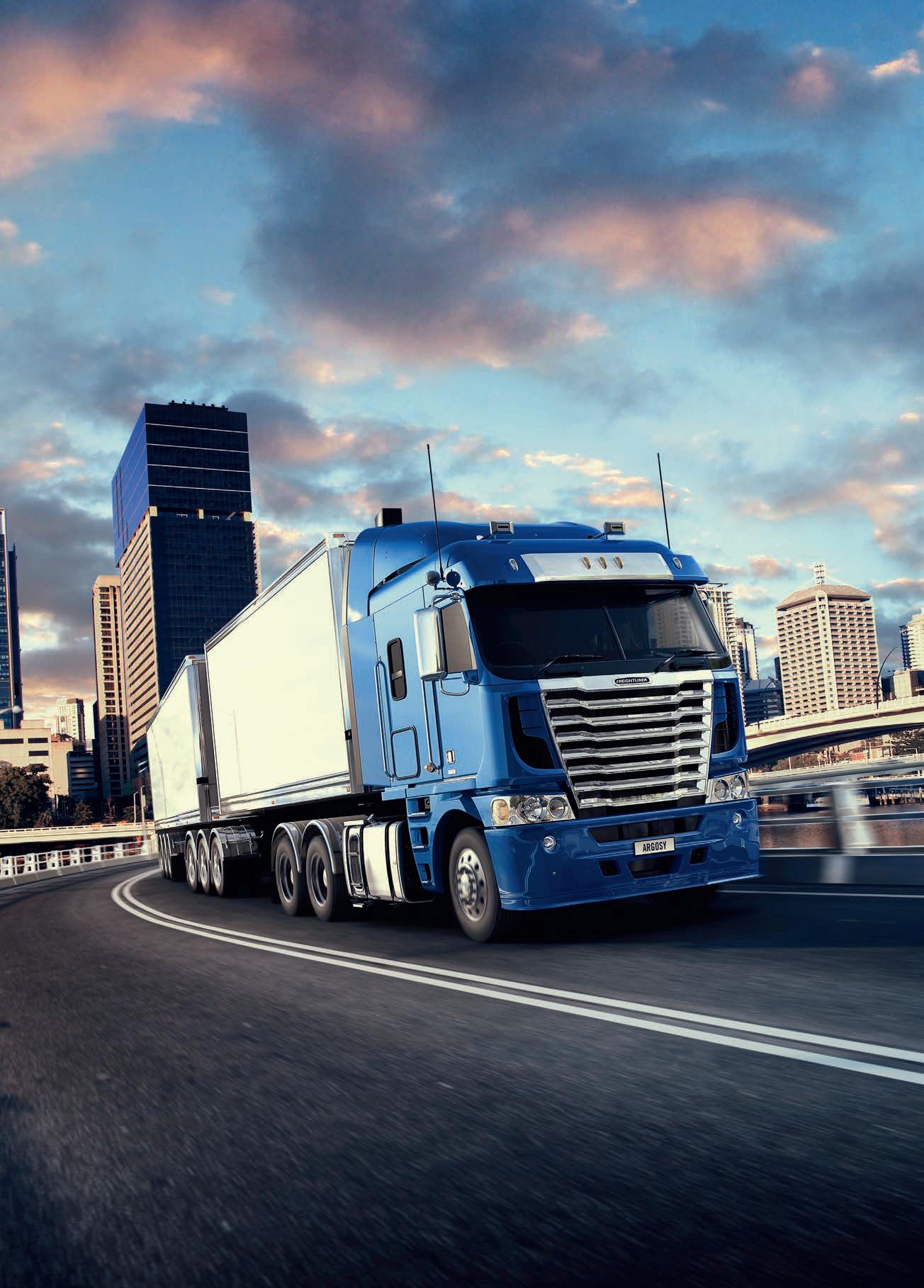
> Rail freight on life support as B-doubles dominate major interstate corridor
Annually the Hume sees 700,000 B-double equivalent return truck trips.
Road transport operators on the nation’s busiest freight corridor are having a major impact on rail carriers according to Australia’s biggest rail freight operator. Less than one per cent of 20 million tonnes of palletised and containerised freight is moved by trains between Sydney and Melbourne said Dean Dalla Valle Pacific National CEO in a statement. “Australia’s busiest freight corridor by volume has become a conveyor belt of 700,000 B-double equivalent return truck trips each year along the Hume Highway,” he said. A build up of red tape and excessive government charges applied to rail freight services was restricting the supply of goods on rail between Australia’s two biggest cities. “Bizarrely, at a time when Australians want safer roads, less traffic congestion during their daily commute, reduced vehicle emissions, and properly maintained roads, government policies are geared to
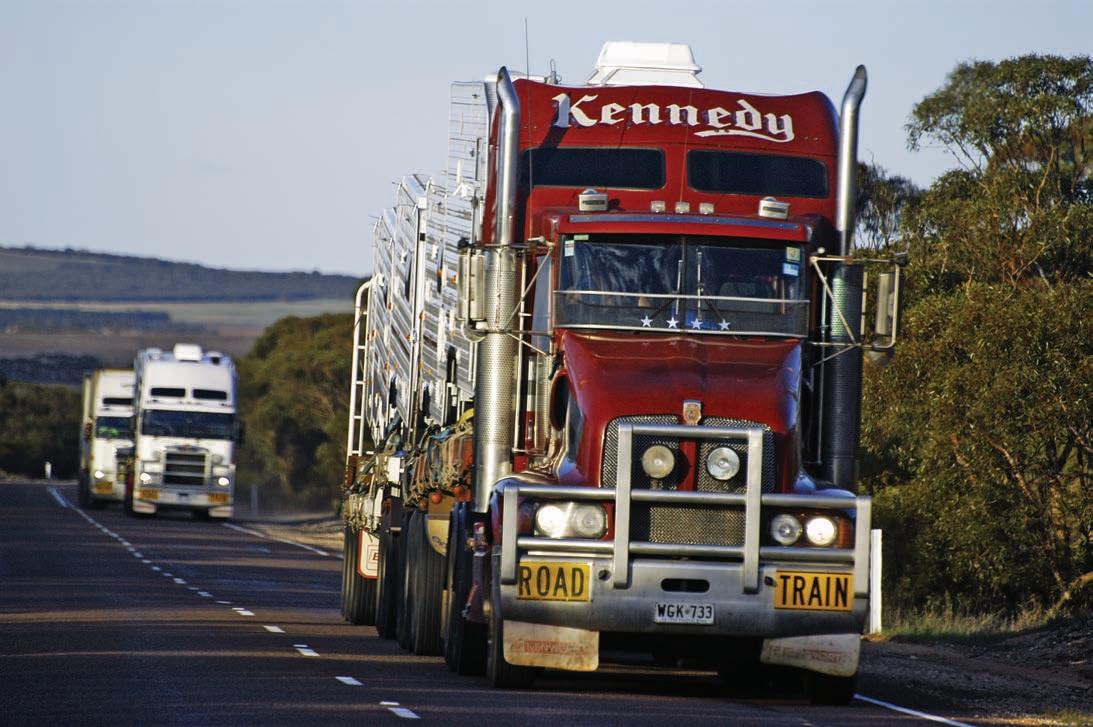
rolling out bigger and heavier trucks on more roads,” said Dalla Valle. Dalla Valle said trucks were not the root cause of most accidents, but the sheer size, weight and momentum of a truck crashing with a car often results in casualties or fatalities. With the duplication of the Hume Highway Dalla Valle suspected governments would permit even bigger commercial vehicles such as A-doubles and B-triples access on major arterials. Access costs for hauling a 20-foot container were skewed in favour of a B-double according to Dalla Valle. Pacific National claims a freight train is charged $94 per container compared to $55 for a B-double. “In terms of accessing the freight corridor between Melbourne and Sydney, that’s a massive 70 per cent cost penalty for rail – this rips the guts out of our industry,” he said. Dalle Valle viewed government funding for roads by road users as an offset for operational charges, something rail freight wasn’t at liberty to benefit from. “To achieve a minimum 50:50 freight volume share between rail and road, government access charges must be abolished on the rail corridor between the two cities,” he said. Pacific National estimates increasing the rail freight share between Melbourne and Sydney to 50 per cent would help save four lives and $300-million in road accident costs on the Hume Highway each year. Grain supplier, Viterra, as part of a cost-effective initiative to compete internationally, bucked the current trend of major logistics operations moving to trains over trucks to move freight in June when it announced it would supply grain entirely by road transport. Rail infrastructure conditions and the restrictions it imposes on operations made it less efficient the company said in a statement.
> IVECO launches new concept Fit Cab
At a global launch of its S-Way range truck cabins, IVECO has unveiled the Fit Cab concept designed to incorporate exercise and gym equipment under a healthier push to help long distance drivers, a group long associated with an ordained, sedentary lifestyle. Upcoming workshops for the concept were tested as part of a research project coinciding with the European Truck Racing Championship in Nurburgring, Germany. As the customer focused project enters its next phase of development, IVECO was assessing improvements to operator wellbeing, comfort and performance as it looked to mitigate the attritional nature of long haul driving through the cabin. “In developing our products we adopt a customer-and driver-centric approach: they participate in our field-testing activities, they give us guidance with their insights and feedback,” said Gerrit Marx, IVECO President Commercial and Specialty Vehicles. “With these concepts, we want to cocreate with drivers and owners these statement vehicles and, most importantly, we also want to engage them in a dialogue about their job to tailor the next trucks to closely match their needs and desires – trucks developed by the customers for the customers.” A five-year study conducted by Atlas Injury Prevention Solutions, based in Grand Haven, Michigan, recently found that 80 per cent of the more than 15,000 drivers
It’s a stretch: IVECO’s Fit Cab concept.
surveyed were likely to have three out of five conditions related to metabolic syndrome including a high obesity rate and are 130 per cent more chance to smoke than non-drivers. The Fit Cab, at this early stage, suggests a gym on wheels featuring devices for improving the driver’s mobility, stability, strength and overall fitness. Dedicated hooks and anchor points are integrated into the exterior to host specifically designed accessories. IVECO confirmed the retractable front step can double up as a training tool while a wallintegrated multi-directional pulley, a roof
> Volvo announces partnership with Samsung
Battery packs for Volvo Group’s electric trucks will be developed in partnership with global electronics tech leader Samsung SDI the commercial vehicle manufacturer announced this week. The collaboration with Samsung SDI is expected to help Volvo accelerate and strengthen its electromobility assets across all truck segments and markets. Battery packs, under the joint venture, will be developed specifically for Volvo Group’s truck applications. Samsung SDI intends to provide battery cells and modules to meet the demand for Volvo Group’s electric commercial vehicles with a view of utilising battery pack technology for assembly in Volvo Group’s manufacturing operations. As electromobility facilitates a cleaner and quieter way to meet increasing demands across transport it will open up new possibilities for Volvo customers according to Volvo Group President and CEO Martin Lundstedt. “The alliance with Samsung SDI is an
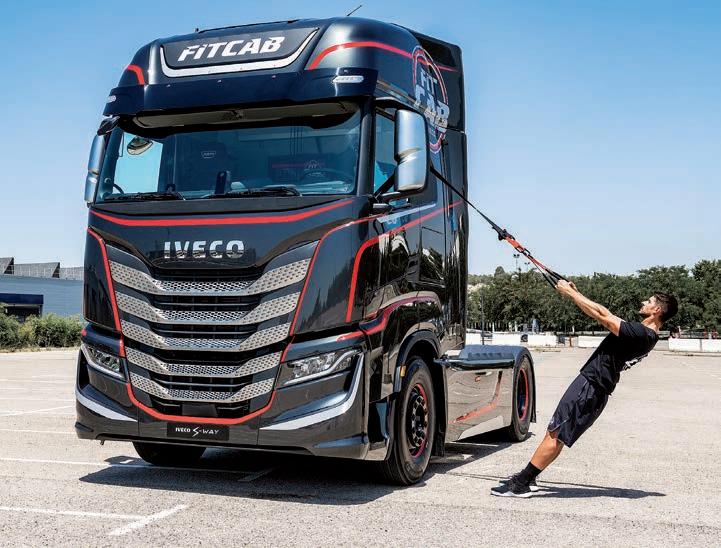
integrated folded multi-grip solution, and a functional package that includes resistance bands, sliders and weights distinguish the interior. The truck manufacturer also unveiled a new IVECO Magirus which incorporates multiple elements of the original brand through new technology and craftsmanship as it sets out to offer the ultimate in custom-made commercial vehicles. For European customers who obsess over the finer details the Magirus offers them an opportunity to customise their cabin with the best quality leather finishings, switches, inserts and metallic levers.
important next step on our journey towards offering the world’s most truly sustainable transport system with fossilfree alternatives for our commercial vehicles,” he said. The alliance according to Samsung SDI CEO Young-Hyun Jun will provide superior offerings in energy, safety and sustainability for the commercial vehicle industry. “We are confident that this alliance will secure the market leadership of the two companies in the long-term,” he said.
SAFETY NO SMALL AC
Held at the Knox Club in Melbourne, the wide-ranging safety presentation covered compliance issues facing road transport businesses and included a video presentation highlighting instances of negligence and failure of operators to comply with chain of responsibility (CoR) obligations. Fatigue management was given a particular focus during the hour long presentation which gathered together safety advisors, sales consultants, project management, warehouse managers, linehaul providers, fleet managers, supervisors, contractors, consultants and key accounts, drivertrainers, compliance co-ordinators, health & safety and contact managers employed or closely associated with freight carrier Cameron’s from across Australia. Company Director Glen Cameron says freight carriers needed to be aware of where failings can happen. That was sometimes a challenge itself and realising complete awareness was, in part, the reason behind inviting Inspector Brooks to speak to his staff. “Phil is pretty well skilled and has a great knowledge of what the police force have to go through,” he says. “We thought it would be a good idea to get him down here to tell it from their perspective.” Brooks, who has 32 years in the job and works closely with NSW Roads & Maritime Services and the National Heavy Vehicle Regulator (NHVR) on crash investigations reported that in his state there were 6.2 million vehicles currently registered and with population growth generating increasing retail, the freight movements from heavy vehicles were only going to escalate. Numbers had spiked since 2011. With an increase in high rise and congestion there were 240,000 registered motorbikes and scooters in NSW and that number was on the rise according to Brooks. During the presentation Brooks showed news footage of crashes involving trucks, highway fatalities and incidents of major compliance infringements made by transport companies that he had investigated. There was a recurring theme. “Fatigue is all the way from the steering wheel to the boardroom. That’s what’s costing lives on our roads,” he says. “The challenge is twofold. Trying to keep cyclists and pedestrians safe and to keep drivers upright.” The average age of a truck driver in NSW, according to Brooks, is 54. “It’s the age that sleep apnea, diabetes and epilepsy all starts to come online,” he says. Companies, such as the bigger logistics operators, were making inroads in fatigue management and the industry had come a long way from the days where drivers had nowhere to sleep, shower or eat. The latest technology in trucks is helping enormously according to Brooks. He cited the positive effects seeing eye technology, among others, was having for businesses willing to invest in it. “The Guardian technology is starting to make a difference,” he says. “It’s having an impact right across the industry.” Still, there was much to be done. AS PART OF ITS COMMITMENT TO PROMOTE AND INCREASE SAFETY BEST PRACTICE ACROSS ITS BUSINESS, GLEN CAMERON GROUP INVITED NSW POLICE CHIEF INSPECTOR PHIL BROOKS TO DELIVER A SAFETY PRESENTATION TO MANY OF ITS KEY DECISION MAKERS AT AN EVENT IN MELBOURNE.
Cameron Group invests in the latest safety technology in its truck fleet.

CIDENT
“Truck drivers are falling asleep and running off the road, so much so they are having same direction crashes,” Brooks explains. “Meaning they are going up the back of other gear that is going in the same direction. It’s about changing that culture across the board. It’s a critical issue for us and right across the industry.” Fatigue wasn’t always accrued on the job, working late nights or on linehaul assignments. Brooks recounts a driver who was not sleeping well. Other drivers knew about it, but he chose, at the time, not to say anything to his managers. The driver ended up crashing into the back of an empty low loader car carrier. For Brooks the issues can be addressed by looking first at drivers, the truck and the load being carried. “Certainly in the driver space it’s how we manage their fatigue upfront. We’ve got to make sure we have fatigue management protocols in place,” he says. Horrific accidents are often resultant from driver distraction, ‘which can include’ mobile phone use according to Brooks. He makes the point that all of them could have been avoided. The presentation offers a comprehensive overview of the many other safety issues road transport organisations had to be aware of. Drug use. Negligent road restraint. Speeding. Obsolete equipment. Mechanical fatigue. Poor repairs. Fatigue also applies to load restraint whereby freight was not being properly secured. There were too many cases on the highway in which freight was too high for the trailer gates. In heavy braking situations, freight was rolling onto the road and into passenger vehicles. Container boxes were contributing to roll-overs. In some dangerous goods carrying a lot
Chief Inspector Phil Brooks.
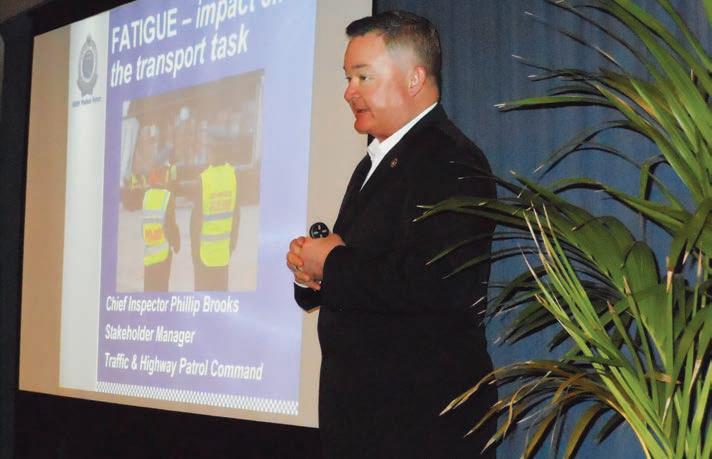
of the drivers still don’t have the right emergency gear. It’s the driver who gets hit with the fine, not the load master on the dock. Across a range of industry sectors’, Brooks has seen failures by businesses that hook up and leave the depot without proper tug tests. A truck that starts in Perth is pulled over in West Wyalong in NSW, carrying a mining truck radiator. All the straps on the load, Brooks recalls, had snapped. Container boxes that originate overseas, in which the contents go unrestrained, represent another challenge. In a growing consumer economy, Sydney has what Brooks refers to as a ‘box challenge.’ They have gone over causing rollovers and grief on roads which as a result come to a standstill for an entire day, disrupting commuters and industry while emergency responders clean it up. More recently Brooks said there has been an epidemic of truck fires across Sydney. Some brands are having to retrofit their own gear to try and prevent the high pressure lines from continuing to shake. Maintenance, on other occasions, is being bypassed – leading to incidents. Trailers are creating enough friction on the highway to light up the freight. “It’s a massive issue for the industry. I know the NHVR are looking into it but it’s something that we all need to have a very close look at in the truck and trailer,” explains Brooks. From a policing context, Brooks says there are three key areas that cause truck fires. These are fuel leaks from the engine; wheel bearings that haven’t been serviced or adjusted properly; and in trailer management with movement causing friction that in turn causes fires within the freight. “It’s those areas we’re looking at and it’s saying to industry that they need to reduce the risks in all of those areas,” he says. “Obligations and responsibilities are with the operators. It’s the most efficient way of ending risk on our roads.”
DANIEL PETROVSKI
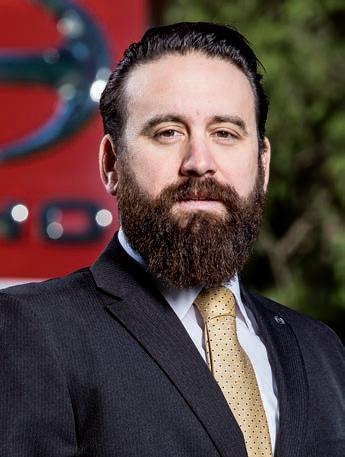
Daniel Petrovski is the Manager of Product Strategy for Hino Australia. His role incorporates the critical business functions of product planning and future product strategies for all Hino vehicles in Australia. Petrovski leads a team of engineering, product development and vehicle homologation personnel, and ensures the Hino products for the Australian market meet ever-changing market requirements and developing trends.
WHY SAFETY IS NOT AN OPTION
AEB, VSC, PCS, ACC – the list of acronyms for safety features on Hino trucks has become quite extensive and continues to grow. Until recently, these crucial safety features were not even available in Australian passenger cars – their fitment as standard equipment has been fast-tracked due to their ability to minimise crashes and potentially save lives. According to the Queensland Department of Transport and Main Roads calculations, every road crash fatality costs the community an estimated $2.7 million, and every hospitalisation costs $239,000. You can immediately see the massive cost of accidents to the broader Australian community. With increased responsibilities and obligations under Occupational Health & Safety and Chain of Responsibility legislations, we know safety is at the forefront of our customers’ minds. This is why for the allnew Hino 500 Series Standard Cab, we have selected, as standard equipment, the most comprehensive active safety package ever offered by a Japanese manufacturer in the Australian medium duty truck market. Headlining the substantial leap forward is the Pre-Collision System (PCS) which includes Autonomous Emergency Braking (AEB), Pedestrian Detection (PD) and Safety Eye (SE). These innovative safety systems can save lives and hundreds of thousands of dollars, but what are they, how do they work and why are they important?
PCS – Pre-Collision Safety In the all-new Hino 500 Series Standard Cab, PCS includes Safety Eye (SE), Autonomous Emergency Braking (AEB) and Pedestrian Detection (PD). PCS uses both camera and radar technology to detect potential collisions with another vehicle, a pedestrian and/or other objects. PCS continuously scans the road in front of the truck and assists the driver to actively minimise the type of accidents that regularly occur through poor vision, driver distraction or poor judgement. In this case, PCS detects the vehicle ahead via Safety Eye, and warns the driver both audibly and visually on the Multi Information Display.
AEB – Autonomous Emergency Braking If the driver fails to react to the imminent danger, PCS can, as a last resort, engage Autonomous Emergency Braking to apply the brakes to minimise the vehicle’s speed and subsequent damage to the vehicle in the event of an accident, or in some circumstances, assist the driver to avoid the collision altogether.
ACC – Adaptive Cruise Control ACC takes the basic principle of cruise control a step further – while maintaining the speed set by the driver, it also continuously scans the road in front of the truck. If a slower vehicle is detected in front, the ACC will reduce the engine acceleration and even engage the engine brake to adapt the truck’s speed to that of the other vehicle.
The ACC system will then continue to ensure the truck maintains a safe following distance from the vehicle in front. This intelligent speed adaption means that cruise control can be used more often – it is particularly valuable on Australia’s many regional and extra urban single lane roads.
LDWS – Lane Departure Warning As the name suggests Lane Departure Warning System alerts the driver both visually on the Multi Information Display and audibly through the speakers if the vehicle deviates from its lane without the indicators being triggered by the driver.
SW – Staggering Warning Erratic driving due to fatigue or a medical condition triggers the truck’s Staggering Warning which alerts the driver via audibly and visually. It also pre-charges or prepares the PCS system to get ready for a potential incident.
VSC – Vehicle Stability Control Working in conjunction with the brake and engine control systems, VSC helps to stabilise the vehicle when turning on a curve. This may prevent the truck from potentially rolling over when entering a corner too fast. VSC operates by monitoring the steering angle, wheel rotation speed, yaw rate and lateral G forces. VSC can then autonomously take the appropriate action required such as reducing engine power and/ or applying individual brakes with the intention of keeping the vehicle upright and safely negotiating the corner. According to the US National Highway Traffic Administration (NHTSA), such intervention could prevent up to 56 per cent of rollover crashes and 14 per cent of loss-of-control crashes. This is why Hino led the market when it introduced VSC as standard equipment to our entire 300 Series range in 2011. This critical lifesaving feature was extended to the 500 Series Wide Cab and 300 Series 4x4 in 2017, and, most recently, the allnew 500 Series Standard Cab models. Hino is the first and only Japanese truck
A reverse camera will be a standard feature on all Hino trucks by the end of 2019.
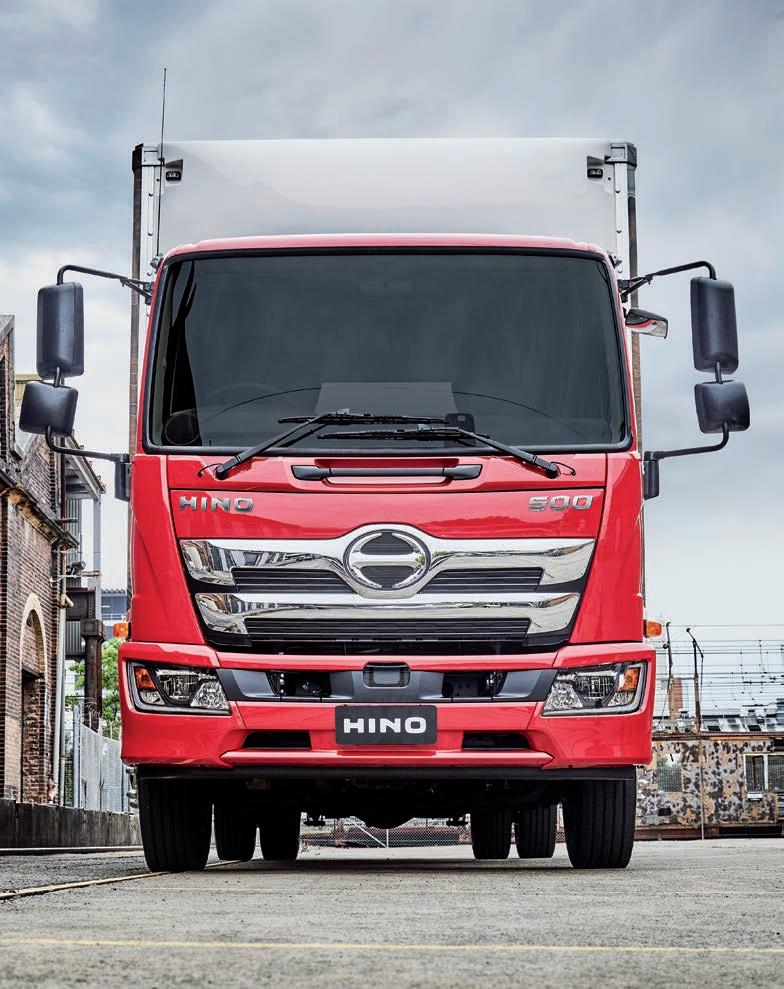
manufacturer to offer Vehicle Stability Control (VSC) as standard equipment on every model from the 300 Series car licence through to the 500 Series 6x4 350 horsepower FM models.
TC – Traction Control Traction Control is another safety feature introduced first in Australia by Hino. It is especially useful in slippery conditions, and, of course, works in conjunction with the broader VSC system.
Reverse Camera A reverse camera eliminates the blind spot at the rear of the vehicle and optimises visibility around the truck – it will be a standard feature on all Hino trucks by the end of 2019, and is equipped with night vision capability plus a microphone and is linked to the truck’s audio visual unit.
A long-term safety leader At Hino, safety is not an option – the benefits speak for themselves. We are passionate about offering a range of commercial vehicles that include the highest levels of safety available, and with drivelines engineered for an ideal balance between the best driving performance and the best operational efficiency.