
16 minute read
Head to Head Hinos
HINOS HEAD TO HEAD
THERE HAS BEEN MUCH SAID AND WRITTEN ABOUT THE LATEST HINO 500 ‘STANDARD CAB’ MODEL. THE OFTEN HECTIC LAUNCH EVENTS AND INITIAL TEST DRIVES INVOLVE EXPERIENCING HALF A DOZEN OR MORE TRUCKS IN ONE DAY, SO PRIME MOVER AIMS FOR A MORE COMPREHENSIVE ASSESSMENT OVER TWO WEEKS IN THREE DIFFERENT MODELS. D ue to its multitude of updates and changes there is certainly plenty to say about the new Hino 500 ‘Standard’ cab range, so called in order to differentiate it from the ‘Wide’ cab range released in Australia in 2017. The Standard cab followed in November 2018 and is the fifth generation of the Hino 500. Virtually every aspect of the truck has been reviewed and refined with many of the changes drawing upon Hino’s parent company Toyota’s expertise from its extensive global research and development programs. The Standard cab line up has now grown from 33 models to 54 with more wheelbase options to allow for the fitment of bigger bodies. Hino has the only Japanese 14 tonne GVM crew cab on Australian market with the weight distribution ideal for tilt tray work. Hino has been achieving the dominant market share for this application with the additional benefit of a perceived brand endorsement by the high profile automobile associations which use them. The three Standard cab models in this exercise are an FC 1124 tray back with
The torque features help make the vehicles very driveable at low speeds in traffic.
an automatic transmission, an FD 1126 curtainsider again with an auto and a FE1426 curtainsider equipped with a seven speed manual gearbox. Each truck is loaded to around 80 per cent of their specific GVMs and over the period of two weeks we operate them in city, suburban and highway conditions. These latest models feature a full new interior with ‘earthy’ tones such as the coffee coloured upholstery which is complemented by some silver and faux carbon fibre trim pieces. This is a refreshing change from the dolphin skin grey we have become so familiar with in most Japanese trucks. Another difference is the implementation of a ‘smart’ steering wheel with integral controls for the multi-function display and the Adaptive Cruise Control. Much obvious thought has been given to the biometrics and the pedals have been relocated to contribute to additional leg room and the ISRI NTS2 suspended seat is easier to adjust than its predecessor and has an extra 48mm of adjustment and the redesigned mounting helps achieve almost 30mm of additional head room. With a rating of up to 150 kgs any driver will be able to operate these trucks in comfort. The floor around the lower steering column mount has been re-engineered with additional bracing and the steering box mount to the chassis has also been reinforced which contributes to a very positive road feel for the driver. The steering geometry incorporates extra wheel cut angles which result to excellent turning circles relative to the wheelbases. Pursuing the engineering mantra that ‘safety is not an option’ the Hino is equipped with the most comprehensive suite of safety systems currently available in a Japanese truck in the Australian market. These include Vehicle Stability Control, lane departure warning, a pre-collision system, Autonomous Emergency Braking, pedestrian detection and Hino’s Safety Eye system. These integrated functions are not just gimmicks; and while some may operate unobtrusively beneath the surface such
The Hino 500 is equipped with a new four cylinder Hino AO5 engine.
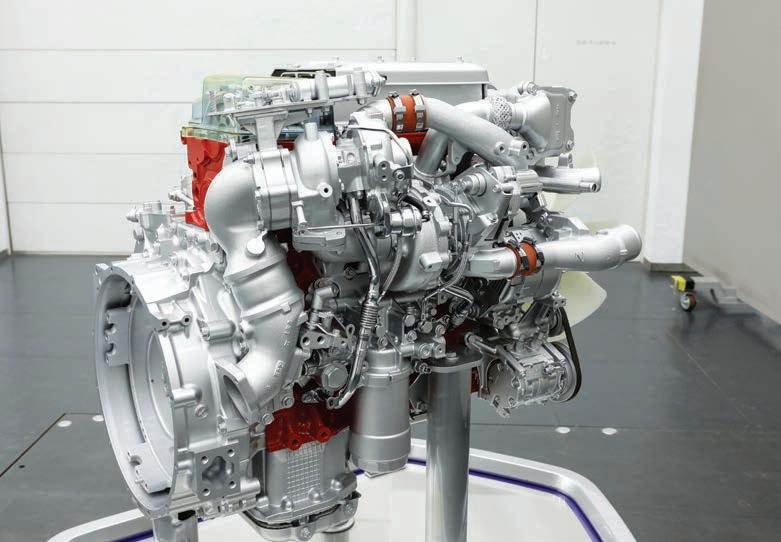
as VSC, systems such as the Adaptive Cruise Control make the driver’s task easier and contribute to reduced stress caused by other vehicles which switch into our lane and then inexplicably decrease their speed. The ACC simply maintains the gap between vehicles as pre-set by the driver. It’s comforting to know that the truck will automatically slow down if the driver’s attention is momentarily on the mirrors when some inconsiderate ignoramus decides that the right thing to do is slow down in front of a truck travelling on the open road. The big deal under the cab is the new four cylinder Hino AO5 engine which at its capacity of five litres is not exactly small. The engine is based on the architecture of Hino’s AO9 nine-litre sixcylinder which is fitted to the 700 series in Japan and the 500 Series Wide cabs in Australia. It’s got a big crankshaft with 90mm diameter crank pins and a short crank throw of 130mm that keeps the piston speeds down and, combined with the twin turbochargers (one wastegate type, the other a Variable Geometry Turbo), a maximum torque is delivered at relatively lower rpm. For the FC 1124 and the FD 1124 models the engine is rated at 240hp but the crucial peak torque of 794Nm is at 1,400 rpm. The FD 1126 and FE 1426 have the slightly higher power rating of 260hp at 2,300rpm and a maximum torque rating of 882Nm at 1,400rpm. A check of the engine graphs shows more than 750Nm of torque is still available at maximum power at 2,300rpm. When we drive the seven speed manual in the 14 tonne FE model for the first few kilometres it takes some concentration to shift up at 1,500 rpm or even lower rather than at 1,700 or 1,800. To assess the hill climbing abilities of each truck we pull into the Hawkesbury River rest stop on the M1 Motorway in order to begin the northbound ascent up over Joll’s Bridge from a standstill. All three models have no difficulty accelerating all the way to achieve the 100 k/hr speed limit before the summit. The same torque features also make the trucks extremely driveable at lower speeds in traffic. Models equipped with the Allison 2500 six speed are accounting for around 70 per cent of 500 Standard cab sales to date. The transmission selector is a T bar unit unique to Hino and is much more intuitive to use than the keypads often used to control Allison transmissions. The selector lever is fitted with a power/ economy switch that changes the shift parameters, and a lock out button to
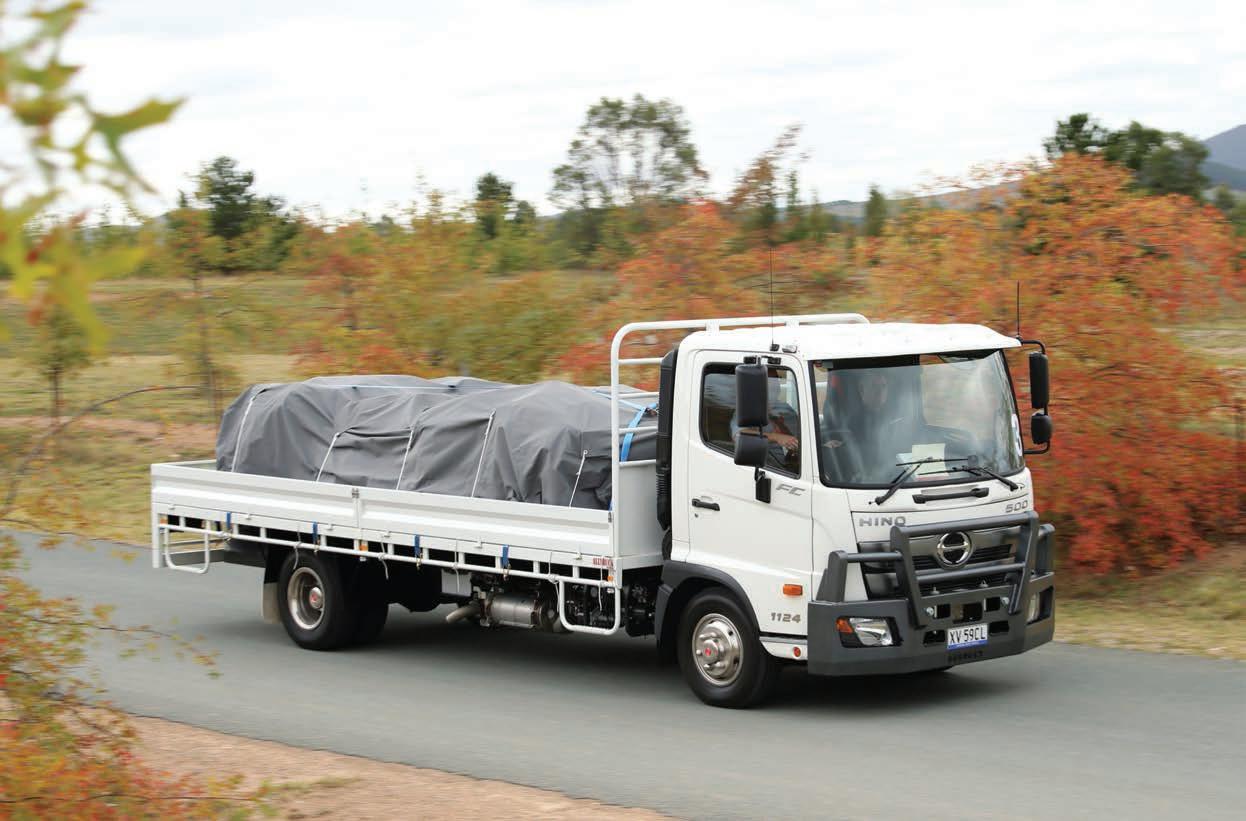
isolate top gear in circumstances where the transmission may be shuttling between fifth and sixth due to a combination of load and terrain. Transmission technology developments have brought about a significant change in the perception of what is required to contribute the best fuel economy in a medium duty truck. For decades it was generally accepted that a driver-controlled manual gearbox will deliver the best economy but today the expectation and reality are that the automatics provide the most fuel efficiency. The torque convertor ‘locks up’ from third gear and higher and the overdrive 0.6:1 top gear in conjunction with the various final drive ratios available exploit the torque of the engine in a beneficial way. The manual 14 pallet FE we drive has the Hino Stop-Start system which automatically stops the engine when the truck is stationary and restarts when the driver takes their foot off the brake. This feature is also fitted to Hino Standard Cabs equipped with the two pedal sixspeed automated manual transmission. Switching from model to model underscores the many similarities and highlights the differences. All use the same parking brake lever and on the full air braked FE1426 the lever operates an air valve which controls the maxi brakes, while in the lighter specified units it operates a cable connect to a parking brake assembly at the rear of the gearbox. The majority of media ‘drive’ events are scheduled during daytime hours to suit collective schedules and to enhance photo opportunities so it’s refreshing to spend some time in medium duty trucks during the night. The FD and FE models have LED headlights which provide a patch of crisp pure white light directly in front on low beam, and high beam delivers distant and broad illumination of the road ahead as well as the shoulders. Cornering and fog lamps complete the package. After a couple of weeks of driving three quite differently spec’d examples we can conclude that there is nothing ‘standard’ at all about this range and if anything, Hino has set a completely new standard for medium duty trucks which should appeal to the market and cause potential buyers to question their loyalty to other brands. The category-leading safety and
FC 1124 tray back with an automatic transmission.
driver support systems are important but in the final analysis the trucks have to perform their intended functions as well. There is no point in having the ‘safest’ truck if it’s not fit-for-purpose and the Hino Standard cab range is able to over-deliver on the practical operational criteria in addition to the safety and environmental considerations.
FAST FACT The Hino 500 Standard is the first medium Japanese truck below 15 tonnes GVM to have a proper engine brake integrated into its engine. The ‘Jake Brake’ has just one setting and combines with a traditional butterfly exhaust brake to provide classleading hill descent control. Similar to the larger prime mover engines more usually associated with this type of auxiliary brake, down shifting to increase the revs to over 2,000 rpm maximises the effectiveness and reduces reliance on service brakes to maintain safe downhill speeds.
HIGHER LEARNING
ADVERTISE IN OUR NOVEMBER 2019 PROMOTIONAL FEATURE.
The need for skilled people is essential in the modern road transport environment with shortages across industry for qualified and experienced workers an increasing issue as companies look to meet the growing freight task of a burgeoning consumer economy. With education and training fundamental to best practice, Prime Mover offers a special showcase on HR & Recruitment to explore new technologies, systems and businesses that aid Human Resources and those recruiters specialising in the all important Transport & Logistics sector.
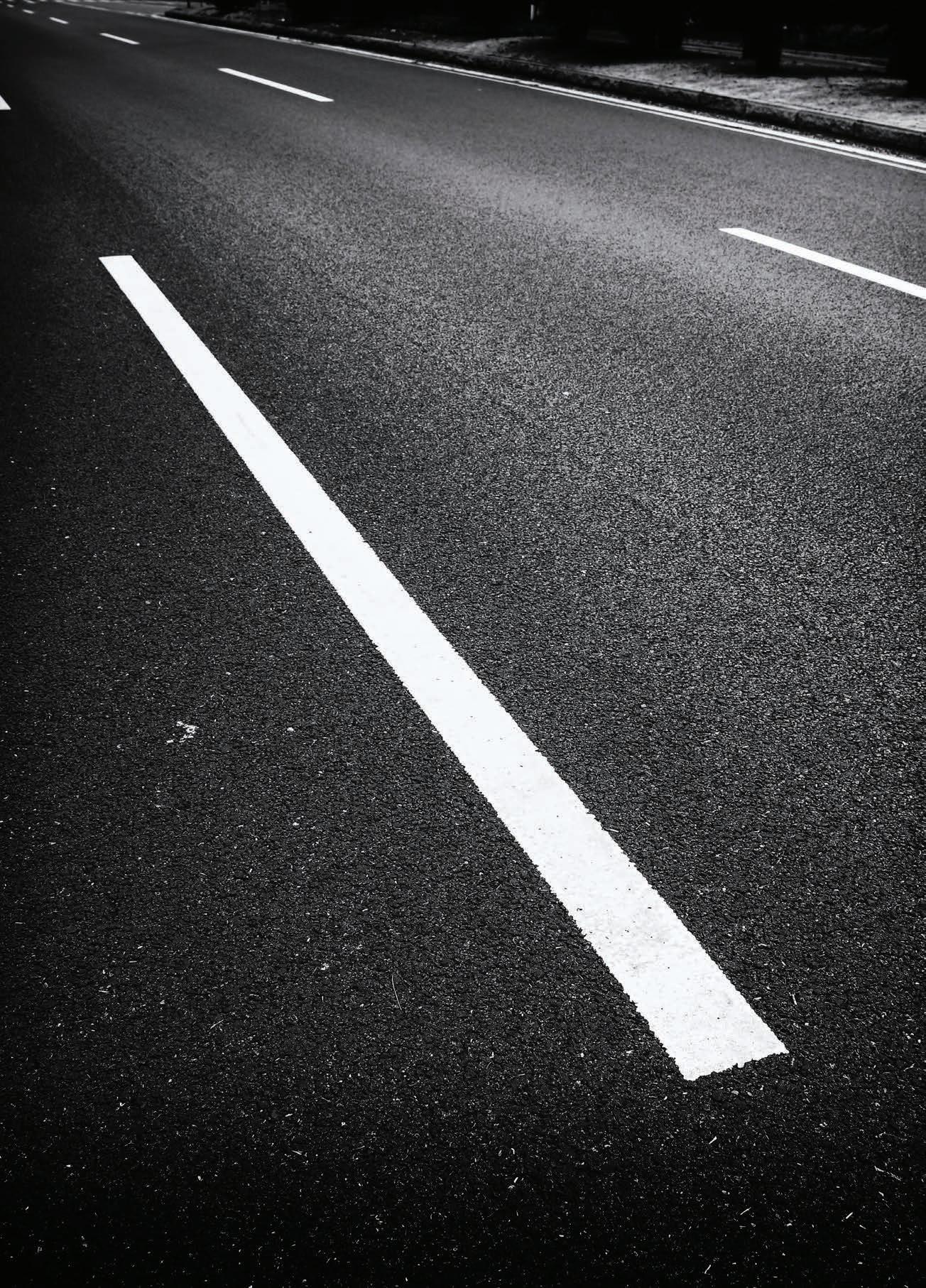
BOOKING DEADLINE 02 SEP 2019
September 2019
Qube Logistics New Frontiers
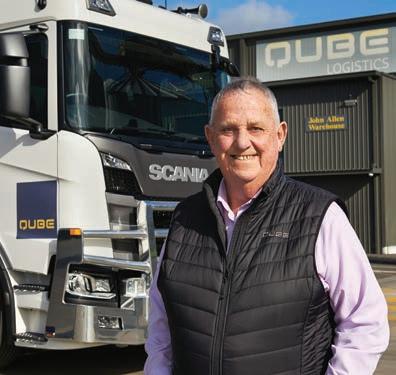
ISSN 1838-2320 11 SEPTEMBER 2019 $11.00
9 771838 232000
Industry Fleet: McMahon Services Feature: Cabin Fever Movers & Shakers: Jim Temple Personality: Hugh McMaster
Innovation Fleet: LogicHaul Test Drive: Hino 500 Sustainability: Michelin Automation: Goodyear
52 september 2017 THE PEOPLE & PRODUCTS THAT MAKE TRANSPORT MOVE
INNOV ATOR B Y NATURE
FROM AN EARLY AGE, JIM TEMPLE HAD A FONDNESS FOR TRUCKS AND TRANSPORT. AFTER COMMENCING TRUCK DRIVING AT 16, HE WENT ON TO FORM TEMPLE FREIGHTS IN PERTH IN 1959, SUBSEQUENTLY PIONEERING A NUMBER OF INNOVATIONS THAT SIGNIFICANTLY IMPROVEDTRANSPORT EFFICIENCIES IN THE WEST.
Raised in rural Western Australia, Jim Temple got his first taste of transport at the tender age of 14. He left school and started work as a plant operator with a company producing potash in the wheatbelt town of Chandler. He soon graduated to the position of offsider to a truck driver delivering the potash and, not surprisingly, it wasn’t long before the young Jim Temple was behind the wheel of an AEC truck. “I was a big strapping lad and we had to manually load the bags of potash, which were always red hot,” Jim recalls. “We drove to a railway siding at Weira and loaded them onto rail trucks bound for storage sheds in Fremantle. The driver was a very good operator and he taught me well, so after I turned 16 I was allowed to start driving on my own.” Operating a truck and dog trailer, which was an unusual combination at the time, Jim was charged with the task of venturing into the timber country to load and transport logs cut by mainly Italian and Slav timber cutters to fire the furnaces at the potash factory. “That’s where my initial knowledge of truck and dogs came into being,” Jim says. It would sow the seed that inevitably led him to introducing them into his own business years later. Jim’s move into truck driving later blossomed when the potash company engaged a Perth truck operator, Noel Sweeney and Co, to transport the product directly to Fremantle, rather than double handling it by rail. “Noel bought two Leylands – a Hippo and a Beaver – to do the job and I was one of a number of blokes hired to drive them. We drove the 360km through the night and it was quite a trip, especially the narrow winding bit through the hills of Northam,” Jim says. After doing this for a while the country boy decided it would be good to see a bit more of the city and took a job driving buses in Perth. Then at the age of 19 he got married and joined the police force, working his way into the transport department and later the heavy haulage department. But the allure of truck operating eventually saw Jim back behind the wheel, this time for Russell’s Transport hauling barley from the railhead. Jim says this gave him vital experience that was invaluable when he started his own business. “Russell’s Transport was contracted to the WA Barley Board and I learnt a lot about handling barley and how to sample the grain. It was my job to assess the quality of each load and the farmers were paid accordingly,” Jim explains. “Then when the transport contract came up for renewal
ATOR
I put in a tender and won, so off I went to Century Motors in Perth and bought my first truck.” It was a secondhand five-tonne International ASC 160 with 120,000 miles on the clock for which Jim paid 500 pounds, and not long after that he purchased his second truck, a fivetonne Fargo. The trucks were put to work carting the bagged barley, bound for storage and at a later date sent to the Fremantle port. This gave Jim a good understanding of the waterfront operations which stood him in good stead two decades later when he opened his own container yard, but more about that later. At the time he started his business the labour-intensive practice of hauling bagged grain was the norm, but Jim foresaw that bulk transport of grain and chicken feed was far superior and before long was able to put this into practice. In the early 1960s Diamond Ice (later to become Ingham’s Chicken) built a feed mill in the northern Perth suburb of Wanneroo. Jim succeeded in winning the haulage contract, using trucks fitted with revolutionary pneumatic discharge bulk bodies which blow the chicken feed directly into the farm silos. Jim says he was one of the first operators in WA to adopt this method of feed delivery. “I went to International and ordered four eight-ton trucks that were sent to J.B. Engineering in Victoria to have the bodies and pneumatic equipment fitted,” Jim says. “The trucks alone cost me 8,000 pounds each and I nearly fell off my chair when the bloke from J.B. told me each body would cost 8,400 pounds!” This style of feed delivery became the mainstay of the Temples operation and continues to this day, while the vehicles have increased dramatically in size to improve efficiencies and meet the needs of ever larger farms. The unloading is swift, taking just three minutes per tonne, Jim
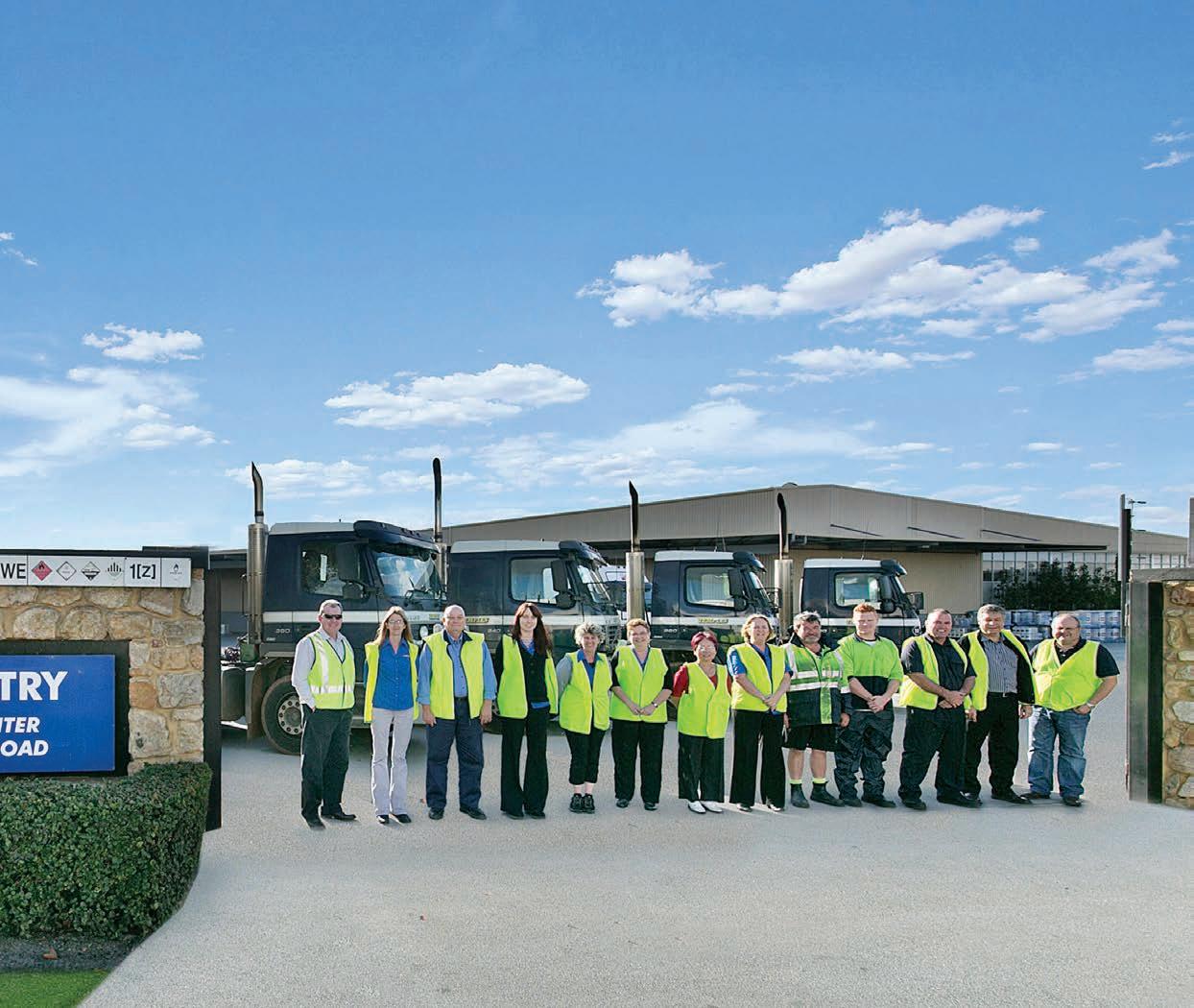
explains. This was a major improvement compared to unloading bagged grain into an auger. Today Jim’s daughter, Karen, is the load scheduler at Temples, ensuring the deliveries are conducted in a timely and efficient manner. “My aim has always been to foster new ideas and propose better ways to do things which improve efficiencies for our clients,” Jim says. “By doing these things I was able to win and keep many contracts over the years because I could do the work more cost effectively and still make a profit.” The method of delivery for live chickens, when Jim commenced carrying for Diamond Ice, was very different he recalls. “We bought 16 demountable bodies called Ackerman Trays and we had four rigid trucks which delivered them to the farms,” Jim explains. “After delivering an empty the truck driver would back under a full one and this saved a lot of time.”
Temples pioneered the use of B-doubles on a twin-steer Volvo prime mover in the ‘80s.
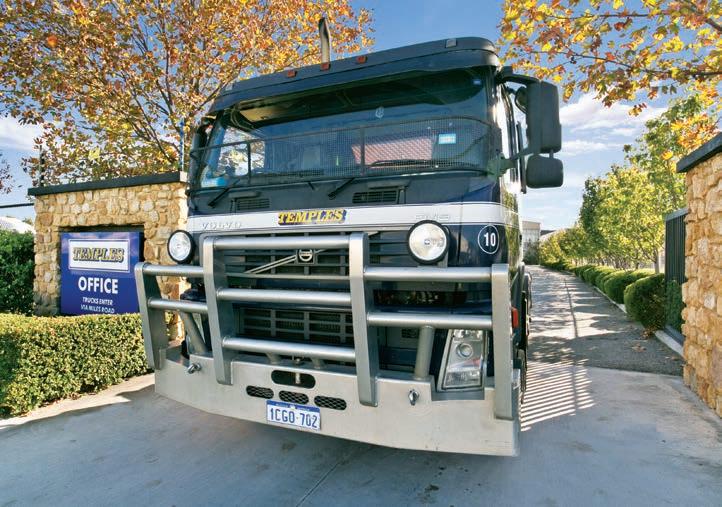
Another groundbreaking move came in the late 1970s when Jim opened his own container park, with a capacity of 4,000 containers, at Spearwood, about 12km from the Port of Fremantle. He explains that this was a particularly volatile era on the WA waterfront with many strikes causing major delays in receiving and delivering containers. “We acquired a large Clark forklift capable of lifting full containers and we installed about 60 power points,” Jim elaborates. “At the time ours was the only yard equipped to plug in refrigerated containers.” With considerable foresight, Jim was prepared to run the terminal 24/7 when necessary and it wasn’t long before he was receiving containers from a range of operators and subsequently delivering them at the most expedient times. “We had operators hauling containers from the southwest and other outlying areas to our yard and when the port was ready we would deliver them, which gave us additional work,” he says. “I had a very good relationship with Seatainer Terminals, the main waterfront operator, and we would often deliver containers between midnight and 4am when things were quiet and we’d have a turnaround time of half an hour, compared with two to three hours if you went in willy-nilly.” During his time operating the container park Jim was also appointed as a Commissioner with the Fremantle Port Authority for a period of four years. Towards the end of the ‘80s, Jim says Temples was the first company in Australia to introduce a B-double trailer combination, pulled by a twinsteer Volvo prime mover. He recalls stating at the time that the B-double would go on to become a major force in improving efficiencies in the transport industry. “I needed to simultaneously carry two 20-tonne containers for a new contract I’d won,” Jim says. “Howard Porter built the trailers and I was granted a permit to transport the containers from a Western Mining site on a specific route into the port.” Jim Temple plans to write a book detailing the events and aspects of his life revolving around the transport industry in Western Australia. Suffice it to say, his various enterprises have made a significant contribution to the industry as a whole – in multiple things that move and shake.
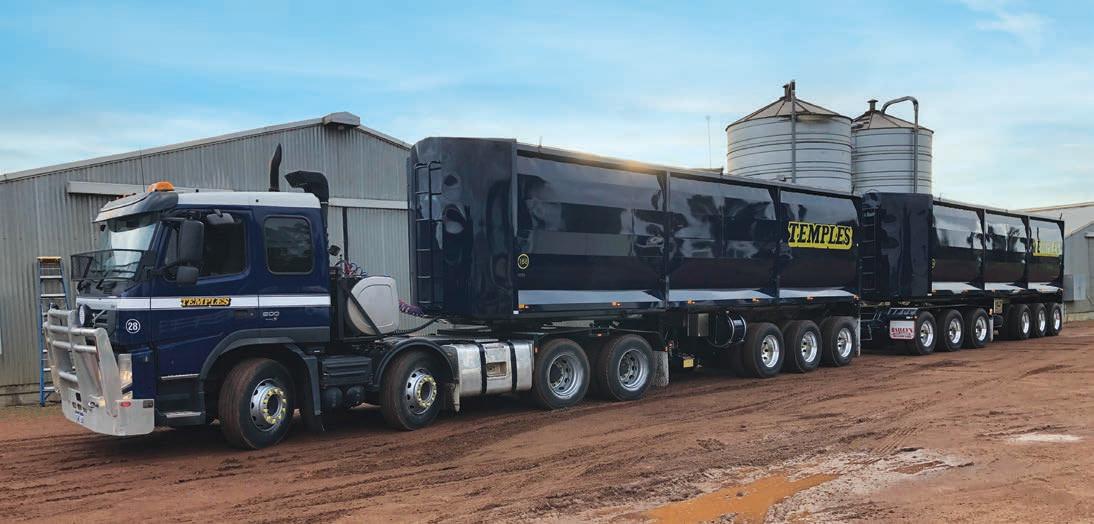
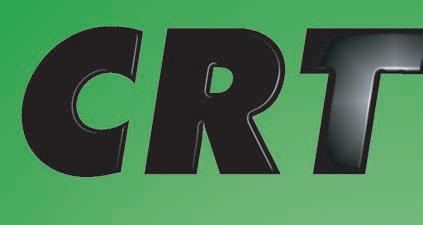
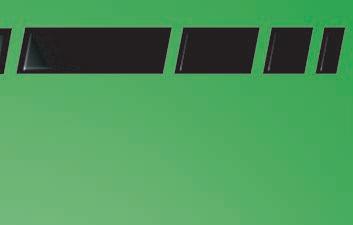
NOW ON TWITTER
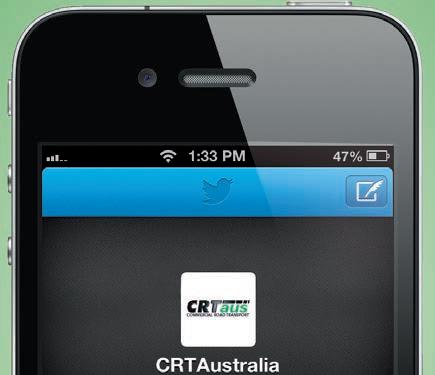
Follow us on

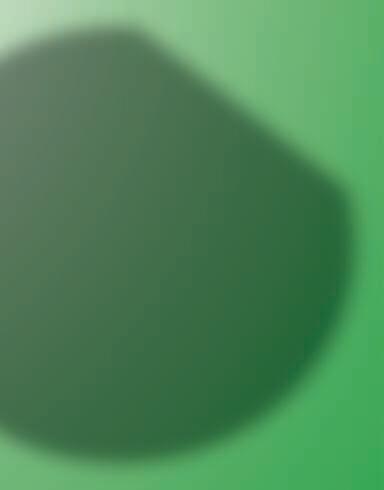
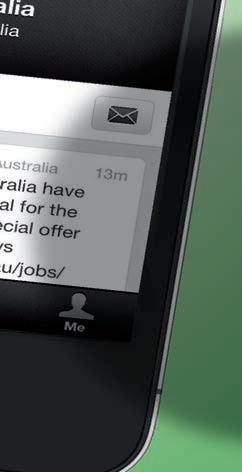
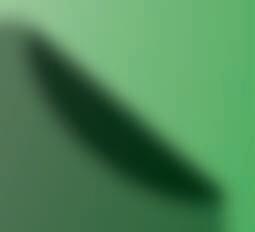