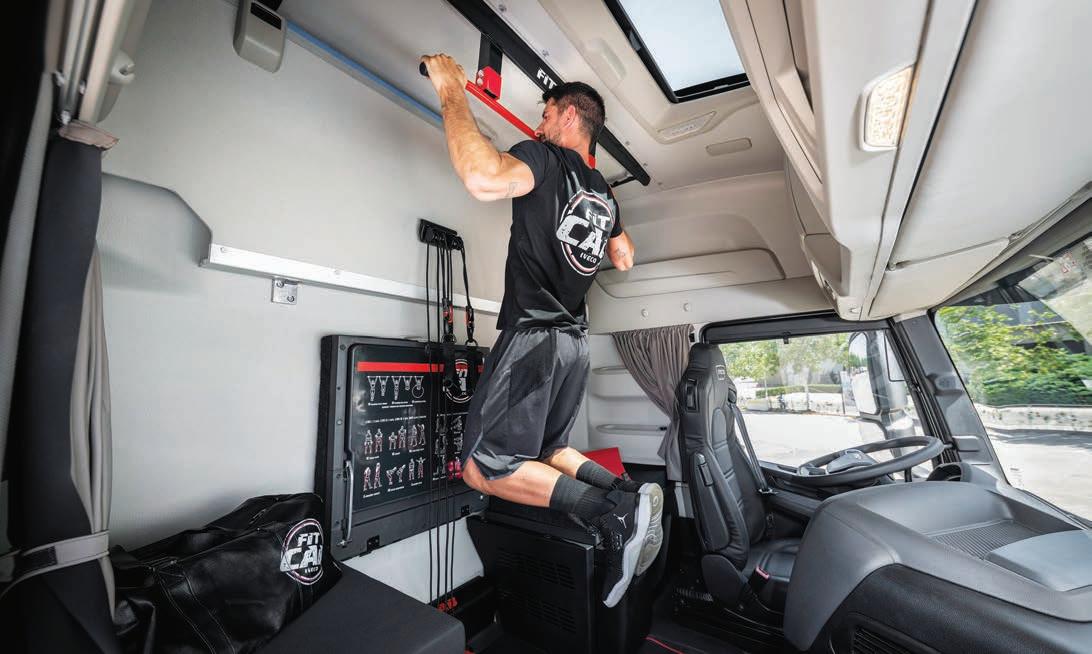
23 minute read
Cabin Fever
THE INTERFACE BETWEEN HUMAN AND MACHINE IN MODERN TRUCKS HAS NEVER BEEN MORE ADVANCED. BUT WHAT’S IT LIKE ON LONG HAUL DUTY WHEN THE VEHICLE IS NOT IN OPERATION WHILE THE DRIVER RESTS? MANUFACTURERS HAVE TURNED THEIR COLLECTIVE ATTENTION TO THE ACCOMMODATION FACTOR AND DRIVERS ARE THE BENEFICIARIES.
IVECO’s FitCab concept cabin.
There has been strong competition among the world’s truck manufacturers to provide the most technically advanced vehicles with high tech engines and transmissions and an ever-expanding array of electronics-based systems such as adaptive cruise control, lane departure warning and electronic stability control which come under the banner of ‘driver support’ systems. Despite the hype, high level autonomous vehicles, whether fully autonomous or in part, are still many years into the future, meaning the human factor will remain necessary to the fundamental
operating system for long haul trucks. Just as the electronics contribute to the efficiency and safety of the vehicle, the driver remains a key part of the overall package and the environment in which they work and rest has to be suitable for purpose and flexible in its application. There has been significant evolution in the design and function of truck cabs from the perspective of being both work places and living spaces. If you ask most professional drivers bigger is not necessarily better, but it certainly helps. Fridge/freezers, microwave ovens and televisions were once considered gimmicks but these types of options are now expected, as is climate controlled air-conditioning, USB power outlets and some form of desk or table surface to make completing entries in log books easier than balancing on the knees or the steering wheel. The health and wellbeing of long distance truck drivers has become a topical issue due to the negative effects of the sedentary lifestyle of spending 12-14 hours a day sitting behind the wheel and the scarcity of appropriate rest area facilities. Australian vehicle dimension regulations work against extra-large size sleepers favoured so much by operators in North
CABIN FEVER
America and the competitive nature of the road transport industry and the constant drive to maximise efficiency means that no long distance operator is going to compromise on load capacity by sacrificing freight volume for a longer cab if they don’t have to. The Kenworth K200 with its optional 1090mm wide King single bunk has ruled the cab-over sleeper stakes for many years and lately a number of challengers are emerging. It’s not just the big cab-over from Kenworth that offers comfort and space for a resting driver as following on from the introduction of the 2.1 metre wide cab T610 bonneted models in early 2017, Kenworth has progressively released a number of applicationengineered T610 cab configurations, including a day cab, 860mm aero, 760mm mid-roof, and most recently the 600mm aero sleeper which took up the mathematical challenge by providing room for both a good sized sleeper behind and a bullbar up front in combination with fulllength 34 pallet trailer sets and still staying within the 26m B-double envelope. Earlier this year a 1400mm (55 inches in old money) Australian designed and engineered aero roof sleeper option was added to the Kenworth T610 option sheet. It will suit a variety of applications from single trailers to roadtrains. Offering enhanced driver comfort, space and flexibility in its factory fit-out, the most spacious sleeper in the Kenworth range comes with even more interior space and in-cab standing room than its 50 inch predecessor. The 1400mm sleeper comes with a 790mm wide innerspring mattress, and the option of a king single, which is 300mm wider again than the standard at 1090mm. The additional upper bunk option is 100mm wider than in the 50 inch (1270mm) sleeper. Both the single and dual bunk configurations feature separate clean and wet storage areas under the lower bunk, provision for a stand up fridge and a shelf cavity for appliances such as a microwave. The Aero roof allows freedom of movement with full height standing room between the seats and contributes to the overall aerodynamics to maximise fuel efficiency. Volvo has become a real contender in the big cab market by developing the latest XXL version of the FH16. The extended cab revealed at the 2019 Brisbane Truck Show has been created by moving the rear wall back by 250mm to create 13 per cent more total interior volume than the previous XXL and yet it still manages a BBC (bumper to back of cab) length of 2475mm. The interior is cathedral-like with a maximum height of 2200mm. Volvo’s reputation for safety continues in this larger cab which meets the latest European Cab Strength regulations ECE R29-03. The bunk is 250mm wider and 130mm longer than provided in a regular Volvo FH. The custom innerspring mattress has a pillow on top of every spring unit which assists in adapting to the shape of the body and, from this correspondent’s own experience, provides a remarkable level of comfort. The angle of the mattress can be raised or lowered electrically to suit drivers who prefer to recline rather than lay flat. This adjustable bunk feature also corrects any levelling issues should the truck be parked in an off-camber area. It’s difficult to sleep if your feet are higher than your head. The Mack Anthem entered the North American market at the beginning of this year and five units are currently undergoing extensive testing in Australia prior to it becoming generally available here some time in 2020. The new Anthem cab provides Mack with the one feature that it has been missing with the likes of its Super-Liner and Titan: a high roof cab which provides easy walk through access to the bunk area. The driver need only tilt the steering wheel to be able to stand at
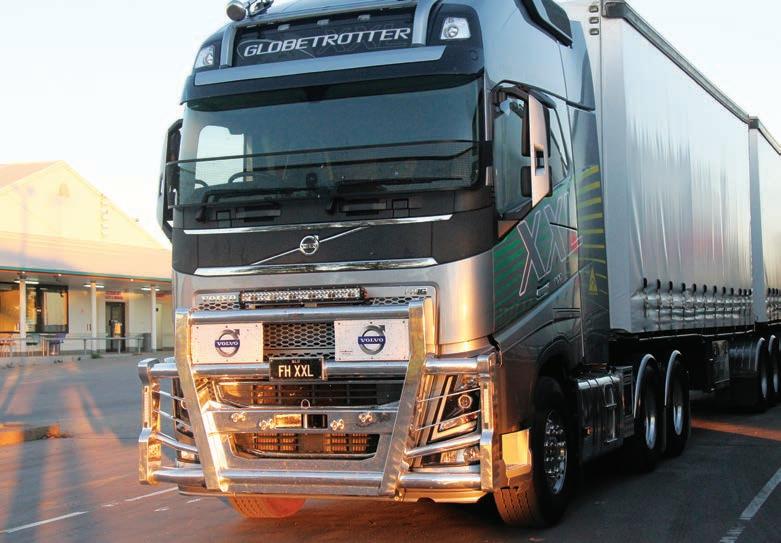
their full height and move around the cab without stooping to get to the bunk. The modular manufacturing process used by Mack will enable a variety of sleeper berth sizes to suit the local regulations. The impending disappearance of the Freightliner Argosy from the new truck market takes with it one of the true innovations of cab access – the fold out stair case. Kenworth did come up with a home grown version for the K200 but other than for a few show trucks the option doesn’t seem to have found much favour. As the Argosy is replaced by the bonneted Cascadia customers of Daimler trucks will soon only have the choice of a Mercedes-Benz Actros if they wish to stay with the cab over engine configuration. Mercedes-Benz presented its Actros ‘SoloStar’ Concept at this year’s Brisbane Truck Show which includes a bed with an 850mm wide symmetrical innerspring mattress and a lounge-style seat on the passenger side which transforms the cab interior to a flat floor bedsitter of generous proportions, allowing a resting driver the option of laying down in the bunk or stretching out on the recliner. Mercedes-Benz seem serious about taking this from concept to an available option if there is enough support indicated from the Australian market. MAN has introduced a high roof version of the TGX cab which is only available in conjunction with the D38 engine package and its floor to ceiling height of 2030mm makes it one of the larger European cabs. Launched in Australia this
Mack Anthem interior.
year it is identified by the additional fixed windows above the doors. Inside, new goose neck lights in the bunk area make reading while resting much easier. For a comprehensive insight into the big MAN see the August edition of Prime Mover. Scania’s New Generation Trucks (NGT) became available in Australia early in 2018 after a decade of development and around $3 billion AUD in investment. Moving the driving position closer to the windscreen and ‘A’ pillar has created more space for the bunk area as well as improving safety and vision from the driver’s seat. The range of adjustment of the driver’s seat has been increased so that drivers between 150cm and 200cm should be able to achieve a comfortable driving position and optional rotating driver and passenger seats are available to enhance the ‘up market office’ ambience of the cab. In addition to its perfectly
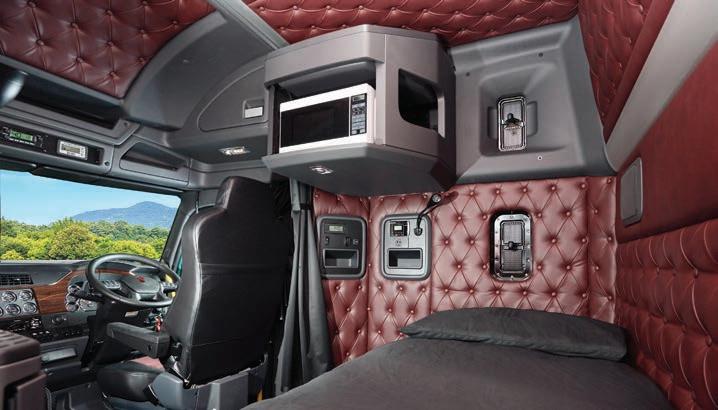
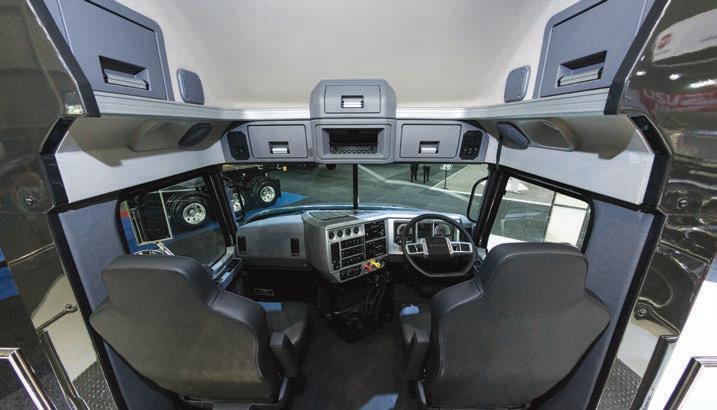
flat floor the new long haul, high roof ‘S’ cab can accommodate two 800mm bunks with the lower bunk extendable to 1000mm. Additional insulation has also been incorporated to assist in keeping the temperature steady and reducing noise transfer to contribute to better sleeping accommodation. This article isn’t meant to be a comprehensive matrix of cabin dimensions and accessories. The intent is to shed some light on the latest developme nts of truck drivers’ living quarters here and abroad.
FAST FACT IVECO have taken the concept of driver health to a step beyond most with the IVECO FIT cab for the S-WAY model which became available in Europe at the beginning of this year. Dedicated hooks and anchor points are integrated into the exterior of the cab to host specifically designed exercise accessories. The interior of the cab is loaded with gym equipment, such as a wall-integrated multi-directional pulley, roof-integrated folding multigrip handles, and a package that includes resistance bands, sliders and weights. There is no indication yet if the IVECO S-WAY will eventually be available in Australia, with or without its gymnasium on wheels option.
Heavy Motor Accident Assist supports customers who operate vehicles over five tonnes.
DISTANCE GOING THE
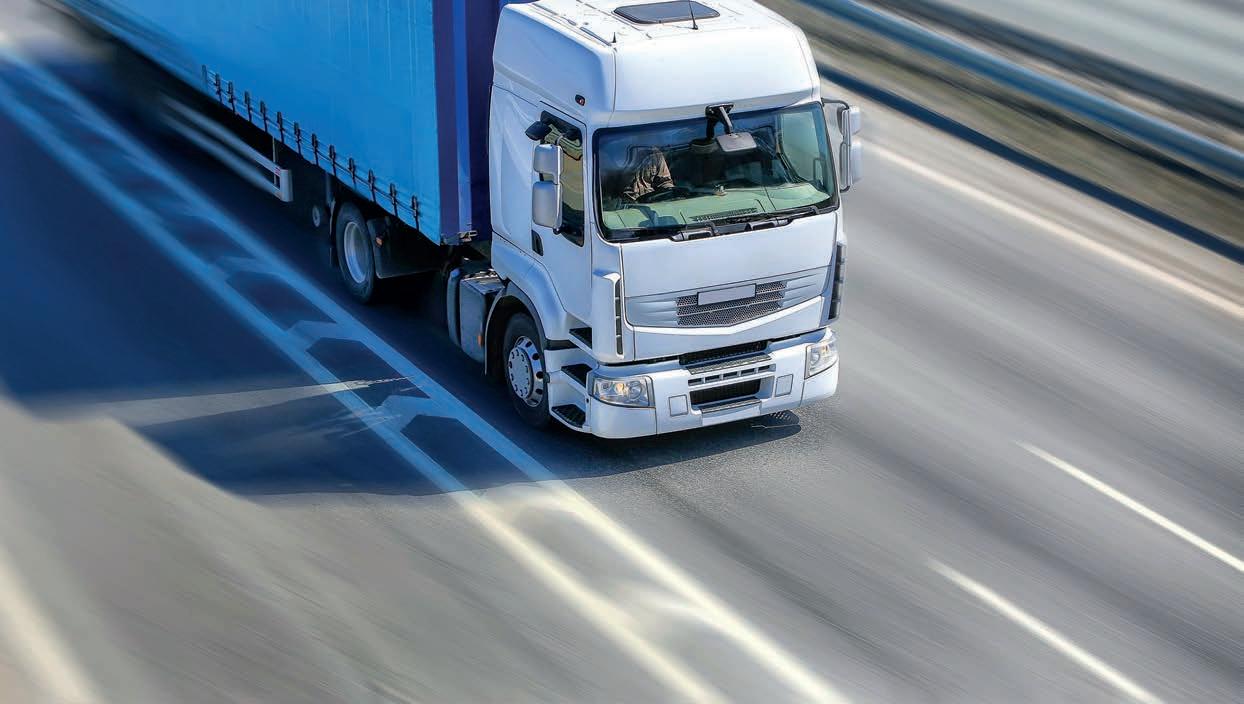
Duty of care for operators of commercial vehicles nowadays goes beyond the daily tasks of piloting trucks through traffic, uncoupling heavy trailers and delivering goods in a timely, safe manner. A healthy driver is usually happier and with their wellbeing improved, productivity, as has been proven in several recent studies, also increases. Accidents, however, do happen and driver well-being after an incident should be of paramount importance to their employers. While most fleet insurance primarily focuses on moving assets like trucks and trailers Zurich offers risk management for transport companies dedicated to the well-being of drivers so that they are provided aid before and after any incident. Zurich provides online solutions to assess and coach drivers on improving their driving style, as part of the service it offers which the company considers goes beyond that of a usual insurance claim. This is to help reduce their risk of being in an incident, injury and potentially experiencing temporary loss of income as a result says Mervyn Rea, Zurich Head of Risk Engineering. “Our Risk Engineering Assessments for Motor Fleets are strongly focused on the driver. We determine how an organisation recruits, manages and retains their drivers, comparing these with current best practice,” he says. “We can help our customers improve management controls, which ultimately proves beneficial to the drivers.” A mentor app, an optional product offered in the service, continually monitors key driving behaviour characteristics such as acceleration, braking, cornering, speed and mobile phone use, and offers coaching and safety tips to help improve driving style, and ultimately, it is anticipated, avoid a crash. Emergency responders are available to help drivers 24/7 says Craig Sandy, Zurich National Underwriting Manager, to secure assets, minimise time off the road and treat, if needed, injury. The Heavy Motor Accident Assist program supports customers who operate vehicles over five tonnes for an insurable incident. “Heavy Motor Assist ensures that the vehicle is recovered and dispatched to repairers promptly but also ensures that the driver is cared for, and repatriated to a place of safety,” he says. That might mean a hospital, work or home. “They will engage the necessary resources to attend the site of the accident, secure assets, deal with spills and clean up, arrange towing and emergency accommodation if necessary.” A dedicated Heavy Motor claims team, with 155 years’ experience in the category, was formed three years ago to accommodate the sometimes complex nature of transport claims. Zurich, according to Craig, recognised that a different skill set was required to manage heavy motor claims in contrast to light motor claims. “The team is uniquely placed to manage these types of claims so that customer expectations are met,” he says. “The time is also taken to understand our customers and their business. By applying this allocation method the required skills, technical capabilities and behaviours are aligned to those of our customers.” THE OPERATION OF HEAVY EQUIPMENT IS CONTINGENT ON PROTOCOLS AND SAFETY GUIDELINES BUT NOT ALL INSURANCE COVER IS ABOUT THE VEHICLE AND THIRD PARTIES. ZURICH OFFERS SERVICES TAILORED TO THE WELL-BEING OF THE DRIVER THAT COVERS MEDICAL AND RELATED EXPENSES, JOURNEY DISRUPTION AND EVEN PSYCHOLOGICAL COUNSELLING.
OBSERVE AND REPORT
AS FLEET MANAGERS TURN TO TELEMATICS TO BETTER SCHEDULE REPAIRS AND MAINTENANCE, EROAD OFFERS A PLATFORM THAT ELEVATES PREVENTATIVE MAINTENANCE SO THAT SMALL ISSUES, OVER TIME, DON’T BECOME BIG PROBLEMS.
Aproactive approach to fleet maintenance has myriad benefits for road transport companies whose obligations now span driver safety, uptime improvements and meeting chain of responsibility regulations. If the health of a company can be viewed through the condition of its commercial vehicles, running a safe and productive fleet requires a regular service and maintenance routine to ensure potential issues are detected and addressed to avoid costly emergency repairs and unplanned downtime. Tracking maintenance and fleet mobility are among the advantages offered by global telematics provider EROAD. Based in New Zealand, the company delivers automated service scheduling and a defect identification process which
“EROAD’s comprehensive data has allowed us to discuss speeding with our drivers and show them the specifics of when, where and how fast.” Kingsley Gordon IT Administrator
it says will reduce the risk of unexpected repair costs through full audit trails, resolution and certified repair. Predictive maintenance is created through usage based data that generates reports that capture the original inspection record and provide proof, according to EROAD, the fleet is safe and compliant. As a telematics platform, it provides data and analytics for a complete view of the fleet so that fleet managers can be up to the minute with scheduling repairs and maintenance, a must in an industry
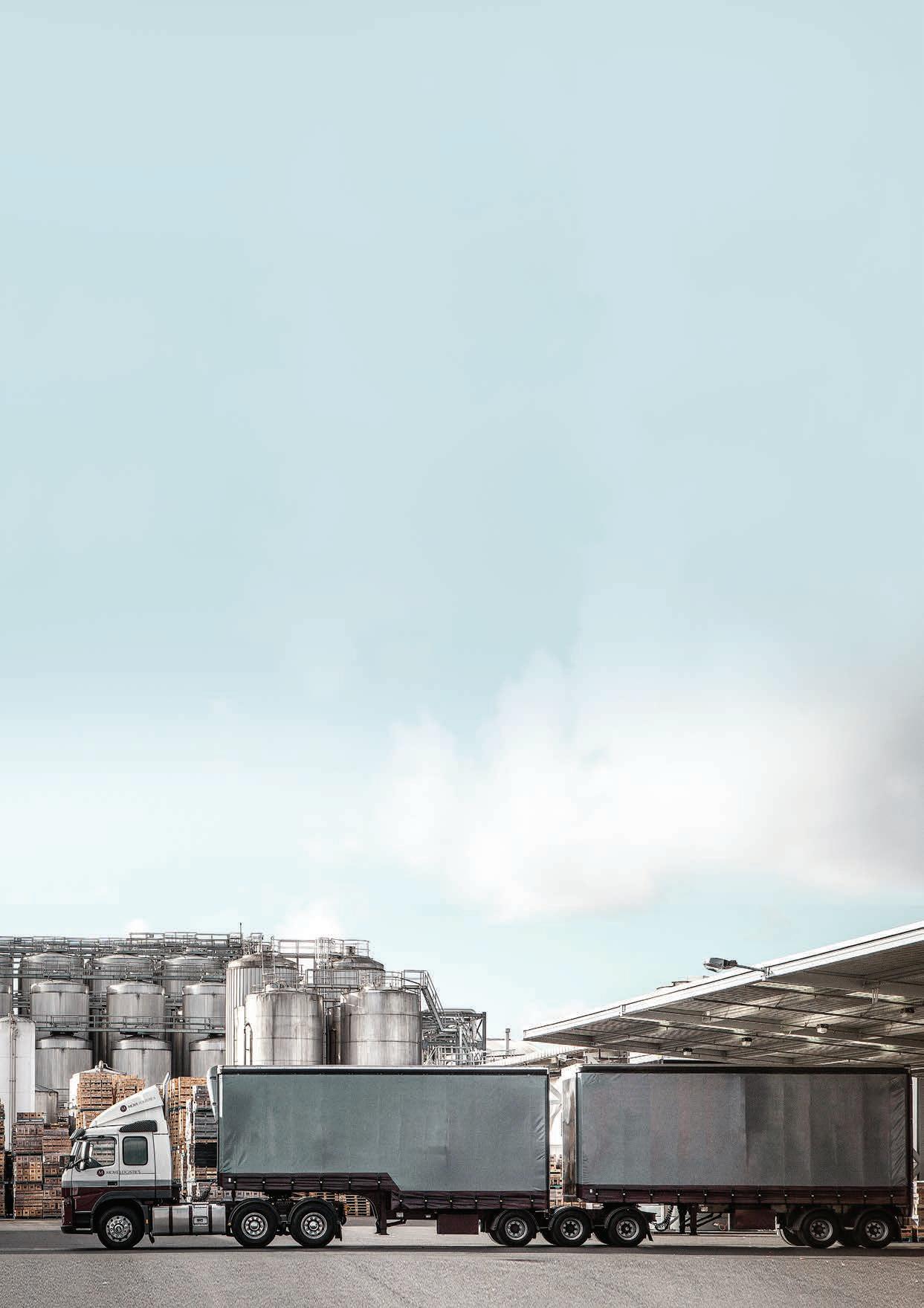
where commercial vehicles are subject to constant wear and tear. With safety of paramount importance in the supply chain, and productivity gains critical to driver engagement, EROAD helps monitor driver performance and identifies unsafe driving behaviours such as harsh braking, cornering or speeding so it can be addressed quickly to reduce the long-term impact on the vehicles. Key metrics such as mileage, fuel usage, time lapses and engine hours are all tracked to provide
EROAD helps to monitor critical driver performance.
a complete picture of the monitored vehicle performance, assisting fleet managers reduce idling and enhance fuel efficiency. Knowing the Australian environment is unique, EROAD has fine tuned its mobile application for local conditions to meet the needs of Conroy Removals, a trans-Tasman removalist company with branches in Brisbane, Townsville, Sydney, Melbourne and Perth. It deploys up to 50 vehicles daily. Drivers have been made aware of harsh braking and excessive speeds through the incab features of the EROAD system, enabling drivers to self-correct or receive additional coaching. Speed infringements have markedly decreased since Conroy Removals installed EROAD says IT Administrator Kingsley Gordon. “EROAD’s comprehensive data has allowed us to discuss speeding with our drivers and show them the specifics of when, where and how fast,” he says. Generating reports which capture the
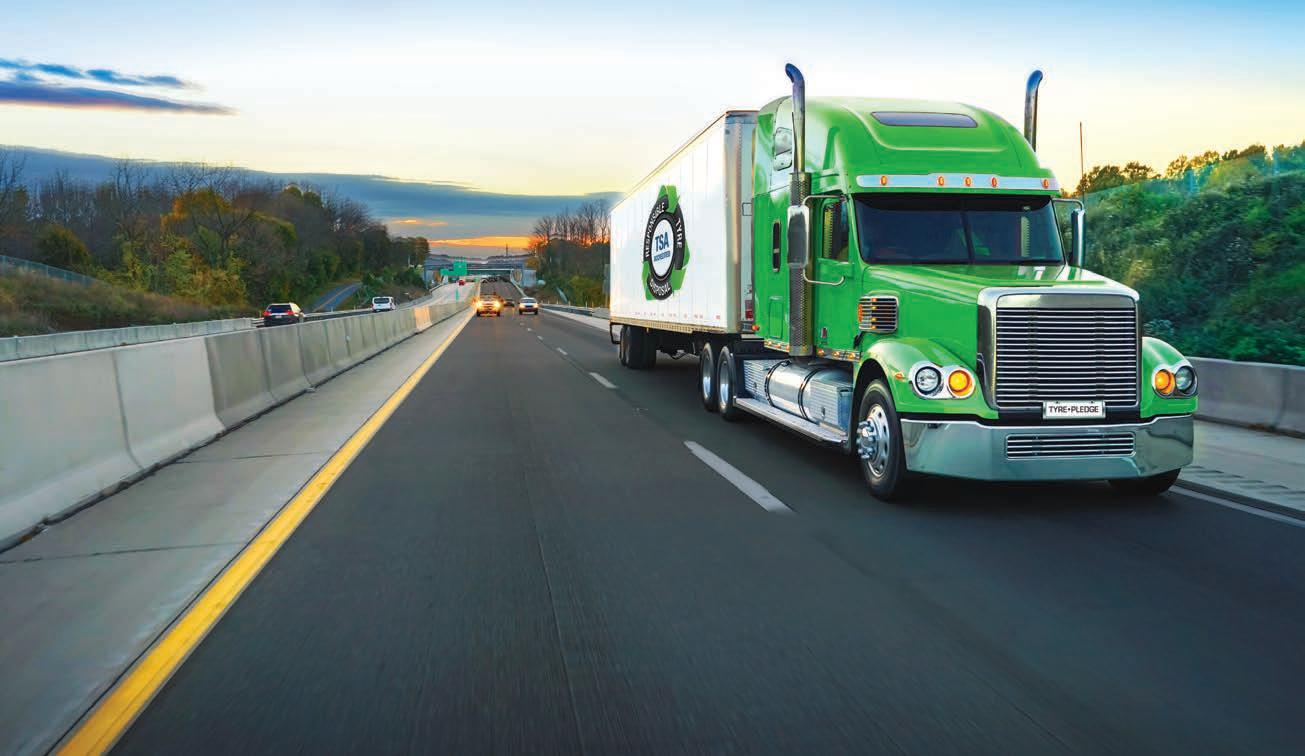
original inspection record, along with its resolution and who it was that actioned each item keep each vehicle road worthy and expedites the planning of budgets, asset utilisation and staffing. For Kingsley having the vehicles in good working order for longer periods of time also
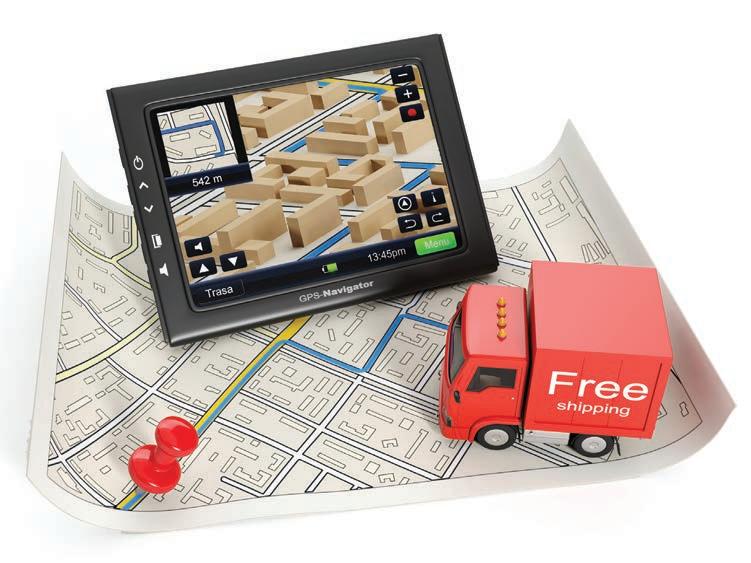
helps boost the likelihood of a return on investment. “It’s definitely made us more proactive in keeping the trucks safe. Because maintenance is simpler to manage, we’re able to keep on top of things a lot more easily,” he says.
IN THE WHEELHOUSE
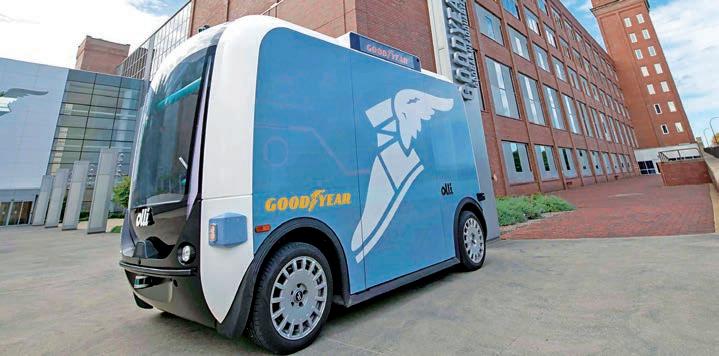
AS IT PREPARES FOR THE FUTURE, GOODYEAR, RECOGNISES AUTONOMOUS VEHICLES HAVE THE POTENTIAL TO DRAMATICALLY SHIFT THE REQUIREMENTS AND EXPECTATIONS OF THE TYRE. TO BUILD KNOWLEDGE AND DEVELOP SOLUTIONS FOR THIS TYPE OF APPLICATION GOODYEAR HAS PARTNERED WITH LOCAL MOTORS WHO ARE DEPLOYING AUTONOMOUS SHUTTLE BUSES CALLED ‘OLLI’. M oving humans safely through autonomous technology may not be a new enterprise. Most people are not concerned with the concept of getting into a driverless elevator even though the concept of an elevator needing a driver would be foreign to many. Elevators, when first introduced, were exclusively controlled by elevator drivers. The driver was not only responsible for moving the elevator up and down but also for positioning it within the destination floor. By the start of the 1900s, companies had developed systems to make elevators fully automatic. However, early adoption was slow going and these did not readily spread into service. The issue at the time was people did not trust that a machine could do the job as well as a driver. Nearly 40 years later, a widespread strike of the New York elevator operator’s union changed the situation leading to widespread introduction and acceptance of automatic elevators. Autonomous vehicles are far more complicated in comparison to an elevator. Similar principles do, however, apply to both. Change, according to Goodyear, can be difficult to introduce but once accepted it’s impossible to reverse. Driverless cars have more complexity, variables and stakeholders involved but at the same time there are greater benefits as well as more advanced technologies and resources available to solve the issues that lay ahead. In order to better understand these coming changes, Goodyear has partnered with Local Motors on an autonomous shuttle bus called Olli. The relatively small, by people carrier standards, eight-person autonomous electric vehicle has been designed with an urban environment in mind. Its application is suited to hospitals, campuses, stadiums, entertainment districts, large commercial areas and locations where people need to be moved from one place to another. At current, there are 300 running globally. In Australia the first is being seen at work in Adelaide. As it primarily operates off public roads at lower speeds, the Olli is easily deployed within varying regulations. According to Goodyear Chief Technology Officer Chris Helsel, this also provides an ideal platform to develop autonomous algorithms in which to learn about the best way to optimise tyre management without a driver. “Our work on autonomous vehicle projects, such as the Olli, is another mile marker on our journey to future mobility solutions,” he says. “We learn through pilot programs with leading start-ups, transferring advanced vehicle and ride-sharing data into truly usable and connected information to improve operating performance and benefit customers.” In this scenario, as feedback will no longer come from the driver, tyre conditions will have to be monitored via sensors. Insofar as tyre pressure and real-time temperature can be measured by sensors, in future other parameters are likely to be included such as tread depth and road condition. According to Goodyear, involvement in these embryonic stages of autonomous vehicles will help it as a company establish the best ways in which to connect this information to the systems that require it. Ultimately, it facilitates building a process to ensure tyres and vehicle perform as intended. “It is not yet clear how long it will take autonomous vehicles to become mainstream, but it is apparent it’s progressing and that the changes will need to be managed carefully by all stakeholders,” Goodyear said in a statement. “It’s not hard to imagine that in the future if someone was asked whether they are concerned about getting into a driverless vehicle, they will reply with ‘what other types are there’?” Olli is an eight person electric autonomous shuttle bus.
DOWN ON THE DUMPS
Truck drivers will be asked to help with the clean-up of illegally dumped waste tyres, by using smartphone app, Snap Send Solve. Tyre Stewardship Australia (TSA) has partnered with Snap Send Solve, a platform that allows anyone in Australia to report issues directly to relevant local authorities. The app now offers the ability to identify and resolve incidents of illegally dumped and stored tyre stockpiles. Over the years, Australia has been home to large stockpiles of illegally dumped tyres; the impact to the community, the State and the environment is devasting, often leaving behind large costs associated with the clean-up and reclamation of the land. TSA, with the help of Snap Send Solve is encouraging the transport industry and wider community to get behind this initiative and stamp out illegal dumping and storage of waste tyres. “Australians are fed up with tyre stockpiles. Snap Send Solve is an easy and direct method in which users can ‘snap’ a photo and a report, including the geolocation and any other relvevent details, all of which are automatically directed to the appropriate authorities,” says TSA CEO, Lina Goodman. “More importantly, the logistics industry knows all too well the dangers associated with waste tyres – whether this be a fire, traffic hazard or workplace obstruction – we are now asking drivers to become ‘snappers’ and alert any incident of tyre dumping to authorities, particularly as they are driving across borders and through regional and remote locations.” Transport and Logistics Industry research suggests around 75 per cent of freight is transported through major hubs, growing regional areas, rural and remote communities. These are the precise locations that harbor piles of waste tyres. A not for profit organisation, Tyre Stewardship Australia, was established five years ago and is funded by eight leading tyre importers, which include Bridgestone, Continental, Goodyear, Kumho, Michelin, Pirelli, Toyo and Yokohama. TSA’s objective is to ensure the environmentally sound management of end-of-life tyres and create new markets from tyrederived products. “The logistics industry plays a vital role in ensuring their waste tyres are disposed of in a sustainable manner with particular focus on specifying the brands that are contributing to best environmental outcomes,” Goodman says. TSA also encourages organisations within the logistics sector to show their support for sustainable tyre waste management by becoming an accredited participant. Joining TSA is free and operators need only to log on to the website at tyrestewardship. org.au to complete an application. “Becoming TSA accredited is the first step towards taking responsibility for the tyre waste produced by the logistics industry,” Goodman says. According to CEO and Founder Danny Gorog, Snap Send Solve is designed to assist people in identifying and solving local issues for the benefit of communities everywhere. “We are very proud to assist in the preservation of our environment and working with TSA is one of the ways we can help,” he says. Free to download from the App Store or Google Play, and available online, Snap Send Solve eliminates the complexity of knowing where and how to report incidents on the spot by enabling users to capture and send photos of issues that need attention – from abandoned trolleys to animals, dumped rubbish and graffiti, and damaged playground equipment or cracked pavements, among other things to the relevant Council or authority. Fleet Managers can learn more by contacting TSA on 03 9977 7820 or info@tyrestewardship.org.au. THE ILLEGAL DUMPING OF TYRES HAS SEEN TYRE STEWARDSHIP AUSTRALIA PARTNER ON A NEW INITIATIVE IN WHICH DRIVERS CAN SNAP AND SEND ILLEGAL TYRE DUMPING HOT SPOTS TO HELP SOLVE THE ISSUE AND BENEFIT LOCAL COMMUNITIES AFFECTED BY IT.
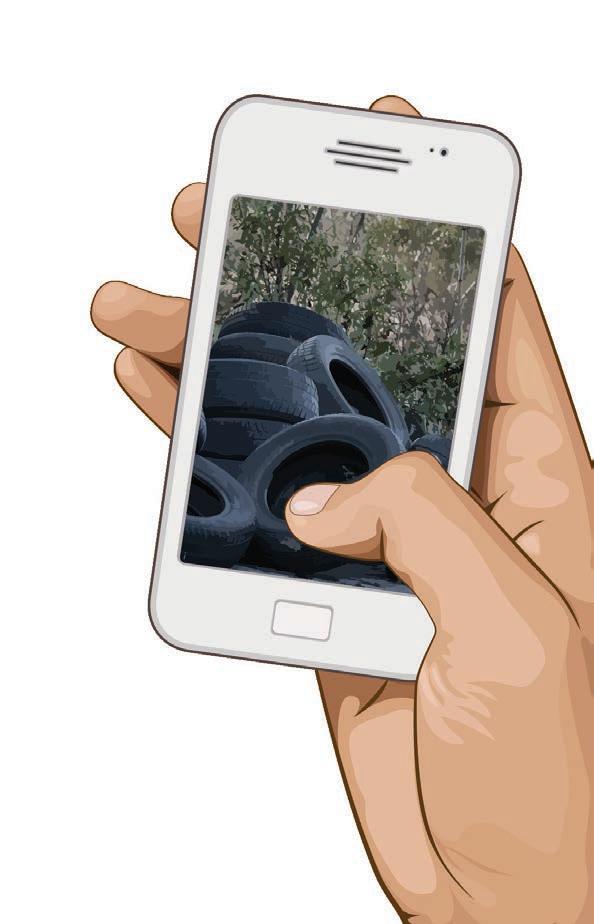
COVER VERSIONS
SG FLEET, A LEADING PROVIDER OF FLEET MANAGEMENT SERVICES, HELPS BUSINESSES RUNNING COMMERCIAL VEHICLES UNDERSTAND THEIR OBLIGATIONS ACROSS INSPECTIONS, MAINTENANCE STANDARDS AND DEFECT MANAGEMENT. WITH INSPECT365, A NEW PRODUCT DEVELOPED TO KEEP THOSE WHO NEED TO KNOW IN THE LOOP, THE COMPANY HAS DELIVERED A SOLUTION THAT ACTIONS EVERYONE ACROSS THE CHAIN OF RESPONSIBILITY IN REAL-TIME.
For businesses whose heavy vehicles are not part of the main revenue stream, like councils, department stores, garden suppliers and agricultural companies in which trucks and heavy equipment merely augment other parts of the operation, management, without the proper structure in place, can be vulnerable to failing Chain of Responsibility (CoR) compliance, and exposed to obligations that go all the way up the line. SG Fleet, according to its Managing Director Andy Mulcaster, is working closely with customers by recognising how the new laws pertain to them by recognising the gaps in their education. “With the changes that took place in October the market is a bit wider than many realise and a lot of the people on the fringes of transport may have missed that story,” he says. After looking at the market SG Fleet took a view that there was a need for a software tool to improve safety practices and mitigate risks for vulnerable fleets and it set about developing it. That tool
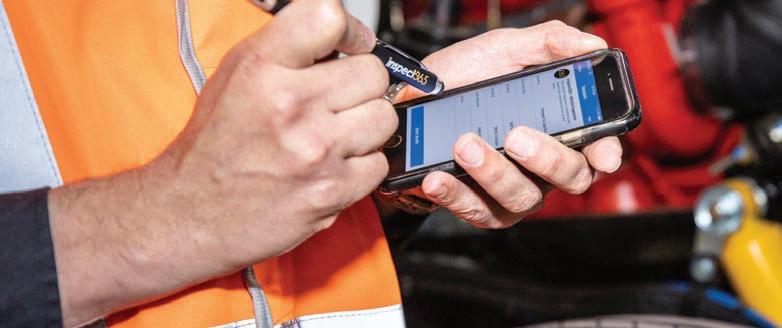
Inspect365 logs defects the moment they are recognised.
became Inspect365. Working with Michael Crellen, who was at the National Heavy Vehicle Regulator at the time the product was under development, the team at SG Fleet sought direct input as to the type of solutions inspectors would expect from an operation that could confirm it not only had a process in place but that there was some rigour behind it. The next step was to approach a number of customers with commercial assets, who offered ideas as to what such a product that helped mitigate risks would look like. It paved the way to develop an end-to-end inspection process regardless of the environment, equipment or application it was used in. SG Fleet chose to deploy the Safety Culture inspection app and then integrate and manage the data within their own bespoke application, Fleetintelligence. “Whether they talk to us or someone else they need to have a solution,” Andy says. Under the CoR regulations having an audible process where a record is lodged and kept so it can be accessible later is a requirement. An operator or workshop manager using Inspect365 is able to log the defect from the moment it is recognised. Should a driver notice an issue with a vehicle they can immediately pull over and make an entry into the system. From that moment an electronic record identifies the issue and the workshop manager is then able to access the record from the time it was logged. It appears as an action for him. “From that point onwards there’s a documented outcome in terms of the vehicle going to a qualified repairer and the repairer determines what needs to be done and eventually a sign-off from that repairer to confirm the vehicle has been repaired appropriately to the required standard,” Andy says. “In that way you have closed the loop which is the requirement of the CoR vehicle standards.” The customer also receives access to the repairer’s invoice through the process. Effectively, Inspect365 creates a detailed breakdown of what is undertaken on the vehicle based on the problem that was first reported. “This is all about identifying drivers being asked to take equipment out that might not be safe so everyone understands their part in the process and where it is reported,” he says. “Inspect365 can formalise and provide a trail of reports so that a driver knows if a vehicle is not safe to take out or alert a workshop manager to a service that is required.” Inspect365 follows that process all the way through and customers can see it. “Non-compliances happen all the time,” says Andy. “As long as you’ve got a process to deal with non-compliance, noncompliance is not necessarily a bad thing. You’re managing it.”
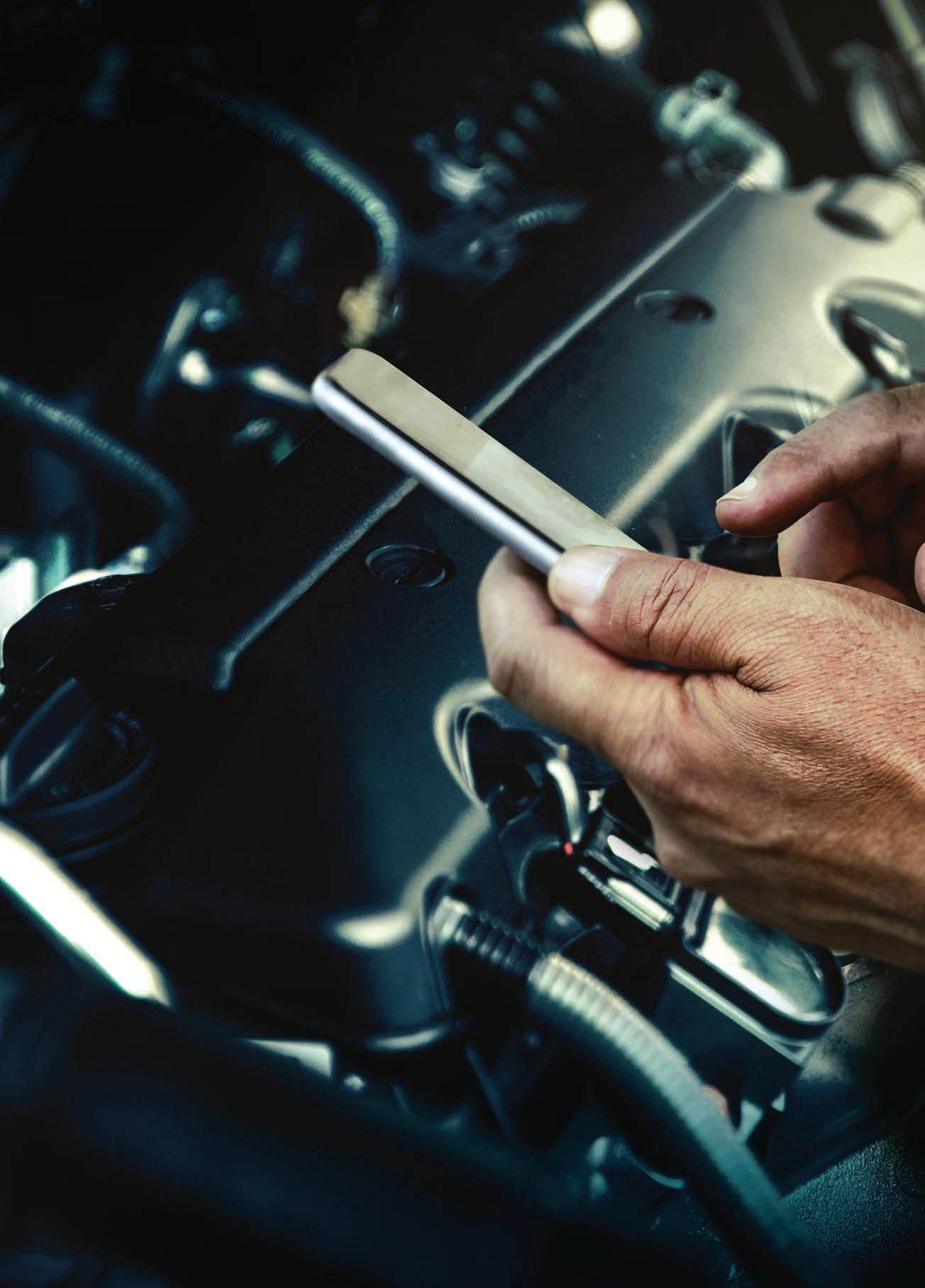