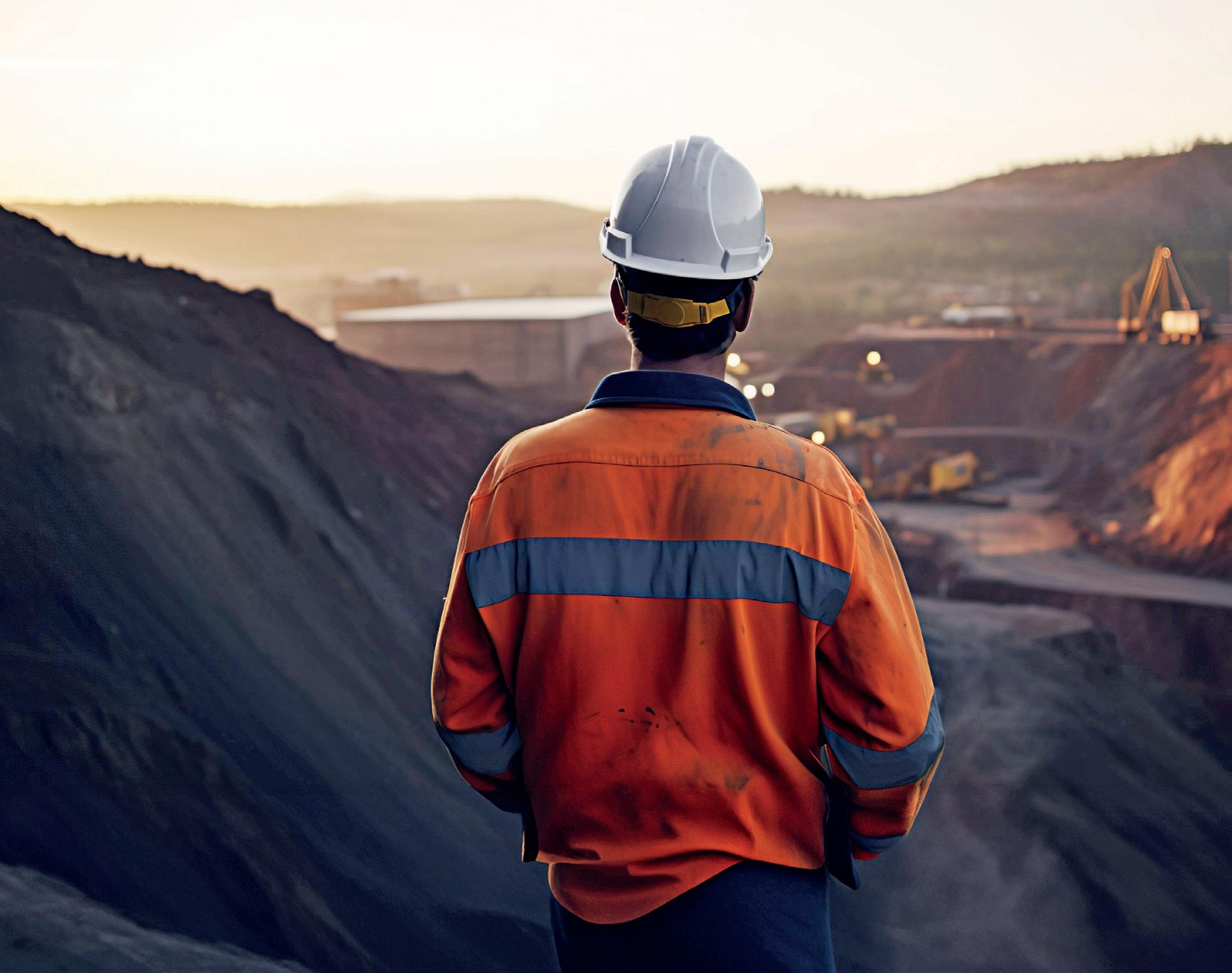
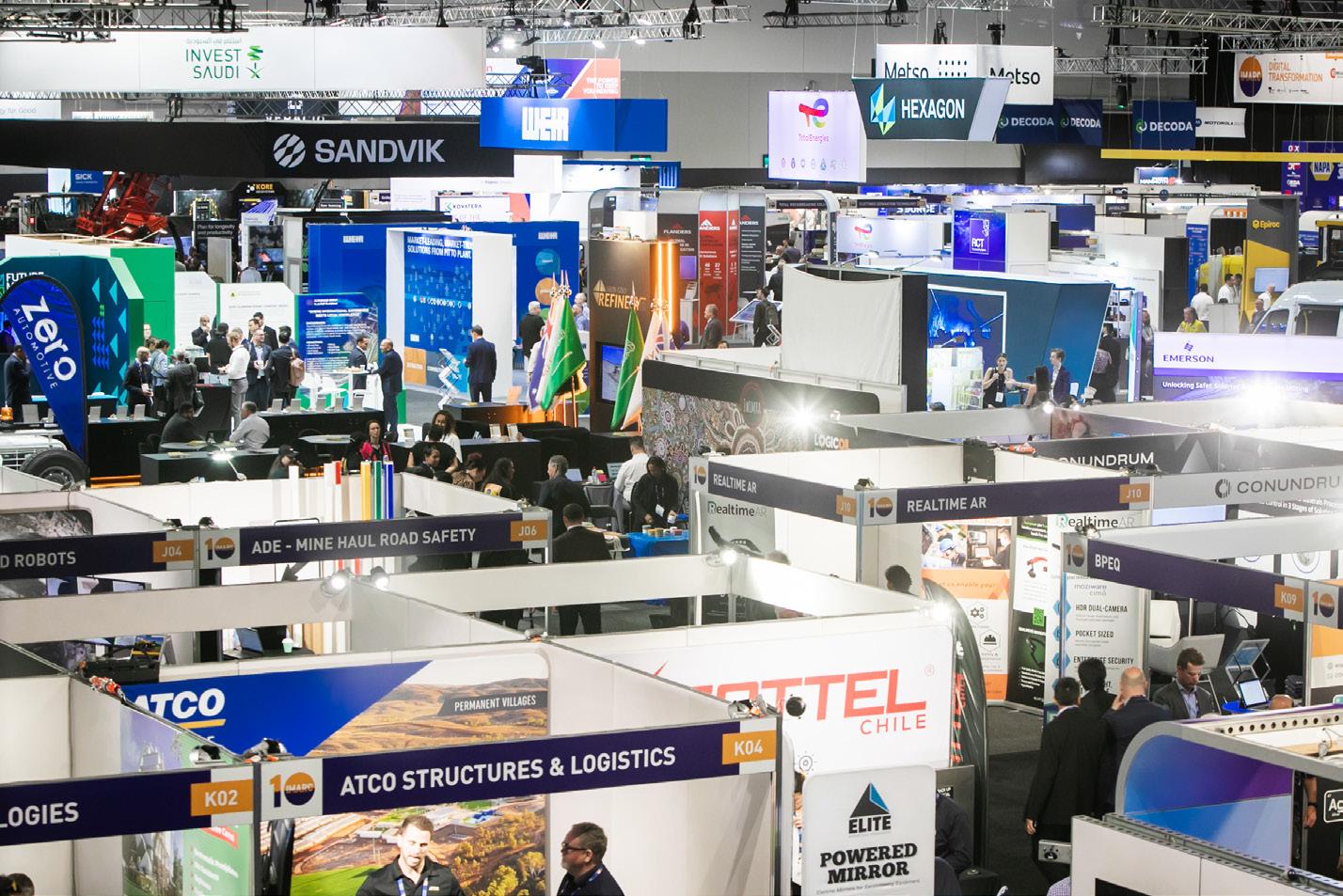

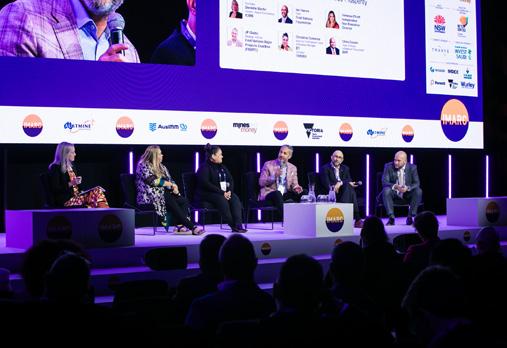
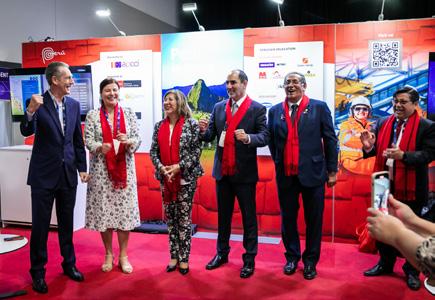
Scan to subscribe to Mining Magazine’s weekly newsletter – delivered to your inbox every Wednesday afternoon.
Scan to subscribe to Mining Magazine’s weekly newsletter – delivered to your inbox every Wednesday afternoon.
Prime Creative Media
ABN: 51 127 239 212 379 Docklands Drive Melbourne VIC 3008 Australia
P: (03) 9690 8766 www.primecreativemedia.com.au enquiries@primecreative.com.au
Editor Rebecca Todesco
Assistant Editor Sarah MacNamara
Journalist Kody Cook
Art Director
Alejandro Molano
Designers
Danielle Harris
Jacqueline Buckmaster
Business Development Manager
Ryan Sheehan
Marketing Manager
Radhika Sud
Marketing Associate Bella Predika
Digital Marketing Assistant Emily Gray
Publisher Sarah Baker
Managing Editor Laura Harvey
ISSN: 2653-634X
Avery warm welcome to the Winter 2024 edition of Mining – our second magazine of the year and the first with our new publisher, Prime Creative Media.
Despite the mercury dropping and the winter chill on the horizon, Australia’s resources industry is showing no signs of cooling down. In the last few months, the industry has seen gold, lithium and other critical minerals projects progress, as well as a welcome boost in funding for minerals exploration.
Keeping our finger on the pulse of the industry, Mining Winter covers the hot button issues across the sector, including adopting circular economy practices in the mining industry, the copper industry’s progress towards net zero and the new global standards for sustainability and climate reporting.
Adding to this un-brr-lievable edition is a contribution from the Chamber of Commerce and Industry WA that dives into the implications of Western Australia’s uranium mining ban, estimating that the ban could be costing the Australian economy more than $1 billion a year.
This issue also sees the return of one of our most popular features – and one of my personal favourites – Women in Mining. This edition, it is an honour to bring you the stories of some of
the wonderful individuals that are championing diversity and forging pathways for women to make a difference in the industry.
With additional features on environmental management, the trending commodities and investment in the mining industry, Mining Winter explores the key topics that are rocking the mining industry.
As always, if there’s a topic, project, technology or challenge you’d like to read in future editions, please feel free to flick me an email – I’d love to hear from you. In the meantime, stay safe and stay warm.
Rebecca Todesco Editor
While securing high levels of safety has always been a top priority in the mining industry, recent years have seen a spotlight shone on the state of mental health, as well as bullying and sexual harassment.
Countries around the globe are hungry for uranium to fuel their transition to net zero, and Western Australia has some of the biggest reserves in the world. However, a ban on uranium mining in the state has meant that much of the resource remains in the ground.
Navigating a career in the traditionally male-dominated mining sector is not for the faint of heart and requires strength and resilience. From her beginnings as an underground miner to her current role as President and Chair of the Australasian Institute of Mining and Metallurgy (AusIMM), Nicole Brook shares how she overcame obstacles to establish a successful career in the industry.
Although Melbourne is likely not at the top of the list of Australian mining jurisdictions that come to mind, for more than two decades the Melbourne Mining Club has been working to promote the resources sector and o er networking opportunities for senior leaders in global mining and mining service companies.
Isolation – both geographical and personal – is common in the resources sector. Sabina Shugg AM, founder of Women in Mining and Resources Western Australia (WIMWA), overcame her feelings of isolation and now uses her experiences to empower women, while promoting diversity and inclusion in the industry.
THE
Australia is a mineral-rich country, with each state having plenty to o er, but recent data has shown that Western Australia is once again the powerhouse of Australia’s mining and resources industries.
The term ‘circular economy’ can look vastly di erent across industries.
Graphene Manufacturing Group (GMG) announced that it signed a Queensland Critical Minerals and Battery Technology Fund Agreement with the Queensland Government.
As part of the agreement, the company would receive $2 million in grant funding from the Queensland Government for its proposed automated battery pilot plant for the manufacture of its graphene aluminium ion battery.
The Queensland Government established the Queensland Critical Minerals and Battery Technology Fund to support Australian business to compete globally by enhancing the extraction and processing of critical minerals in Queensland, accelerating the development of battery technologies and production of precursor or advanced materials in Queensland and supporting Queensland jobs and economic growth.
The grant is for the payment of 50 per cent of the capital cost of GMG’s proposed automated battery pilot plant, up to a maximum of $2 million, for the manufacture of GMG’s graphene aluminium ion battery. The pilot plant is to be constructed at GMG Richland’s existing manufacturing facility and the grant is conditional on various preconditions including GMG taking a final investment decision in the battery pilot plant project.
GMG’s CEO, Craig Nicol, said, “We want to thank the Queensland Government and acknowledge its commitment to supporting the critical mineral and battery manufacturing industry in the state. This is great recognition for GMG and
GMG’s next generation graphene aluminium ion battery and further shows the progress of the battery’s development. We are very excited about this next phase of its maturation.”
GMG’s Chairman and Non-Executive Director, Jack Perkowski, said, “This represents further progress for the company and I congratulate GMG on its success in securing this grant. I also would like to thank the Queensland Government for recognising and supporting GMG in this phase of its battery’s development.”
Queensland Government Deputy Premier, Treasurer and Minister for Trade and Investment, Cameron Dick, said, “The Miles Labor Government is propelling Queensland through an energy transformation that will create jobs.
“I am so pleased that this new plant will create 12 good quality jobs. Projects like this are helping set the path in creating thousands of secure jobs for Queenslanders while providing the clean, reliable and affordable energy every household and business needs.”
Mr Dick said that the $100 million Queensland Critical Minerals and Battery Technology Fund is playing its part by supporting businesses across the supply chain like Redflow, Revolver Resources and now GMG.
“GMG’s innovative use of graphene, in partnership with UQ, is another example of our homegrown ingenuity that we will continue fostering here in Queensland.
“Their graphene aluminium-ion batteries could prove to be a real gamechanger on the world market and elevate Queensland’s local battery industry to the next level.”
True North Copper (TNC) announced that it will begin mining ore at its Wallace North mine site in Queensland in early Q4 FY24 as part of its Cloncurry Copper Project.
The company said that mining preparation at Wallace North progressed in March as access and mine areas dried after monsoonal rainfall events in February and early March 2024, including:
♦ Mobilisation of mining equipment and support infrastructure to the Wallace North project site
♦ Preparation of existing access and haulage roads for upcoming mining activities
♦ Completion of short-term mine scheduling by technical service teams
♦ Onboarding of skilled mining fleet operators
The mining ramp-up will initially build ore stockpiles, with haulage beginning in mid-May 2024. Oxide ore will be transported by road train to the Cloncurry Operations Hub’s heap leach.
Sulphide ore will be transported to a nearby concentrator for toll treatment under TNC’s toll-milling agreement with Glencore.
The Cloncurry Copper Project currently incorporates the Great Australia Mine Reserve and the Wallace North Reserve, totalling 4.7Mt grading 0.80 percent copper (Cu) and 0.13g/t gold (Au) containing 37.5kt of copper and 20.0koz of gold at a strip ratio of 4.22.
TNC said that the Cloncurry Copper Project restart plan confirms positive project economics including mine revenue of $367 million with free cash flow of $111 million and a pre-tax NPV10 of $88M over a 4.6 year mine life, at USD$8,500/t Cu price and USD$1,850/oz Au price (0.7 A$:USD exchange rate).
The Federal Government announced that it will be supporting the development of Australia’s first combined rare earths mine and refinery in the Northern Territory with an investment of up to $840 million.
The refinery is expected to create more than 300 new jobs across the Northern Territory while also diversifying its critical minerals supply chain. A first of its kind in Australia, the project is a step forward for Australia’s rare earths and critical minerals industry.
The investment is set to position Australia as a global leader in ethical and sustainable manufacturing of these minerals.
The rare earths mine and refinery will be operated by Australian mineral exploration company Arafura and will be located 125km north of Alice Springs.
During construction it will create more than 200 jobs, with over 125 full time jobs ongoing, including the company’s stated ambition of securing 20 per cent local Indigenous employment.
Rare earths are used to make magnets and are an important component in renewable energy and defence technologies. Electric vehicle motors, wind turbines, robotics and mobile phones are examples of the kinds of technologies that utilise rare earths.
The government’s contribution is expected to unlock further investment from international financiers and commercial banks, highlighting the value placed on the investment.
Prime Minister, Anthony Albanese, said that the government is focussed on a future made in Australia, and that this project is an important part of that plan.
“This will create local jobs and economic opportunities, helping Australian and Territory companies and workers capture more value from the game-changing critical minerals deposits we have here.
“This project is a major vote of confidence in the Northern Territory, which continues to punch above its weight in global trade.”
Northern Territory Chief Minister, Eva Lawler, said that creating more work opportunities for Territorians now and into the future is the priority of the Territory Government.
“Arafura’s project is an example of how the government is attracting investment into our critical minerals sector that will significantly contribute to the Territory’s role in energy transition and reducing greenhouse gas emissions.
“Backed by record levels of investment into exploration, the mining and processing of critical minerals is a priority opportunity for the Territory to create more work opportunities for Territorians.”
Federal Minister for Resources and Northern Australia, Madeleine King, said that Australia’s critical minerals will be crucial to the new low-emissions technologies that will help lower emissions and support Australia’s trading partners to meet their climate goals.
“The combined funding from the Critical Minerals Facility and the Northern Australia Infrastructure Facility will help Australia build downstream industries and support our goal to become a renewable energy superpower by 2030.
“To meet our net zero targets, we will need more mining, not less, to build the solar panels, batteries and wind farms we need to reduce emissions.”
new 32m over-road-rail-bridge has opened at the Nelson Point main line level crossing in Port Hedland. Delivery of the new bridge marked the completion of the Hedland Road Rail Safety Improvement Program, a $113 million package of work jointly funded by the Federal and Western Australian Governments and BHP, who contributed $44.74m over the two stages of the program. The program is aimed at improving road safety in the Pilbara and providing a better experience for roughly 6,000 vehicles per day.
The program also included:
♦ The realignment of 4.75km of Great Northern Highway, north of the airport, providing a grade-separated crossing over the dual rail lines to BHP’s Nelson Point facilities
♦ Construction of two roundabouts either side of the BHP rail line on Powell Road, at Dalton Road and Hamilton Road
♦ Construction of a 34m road-over-rail bridge over BHP’s rail line at Buttweld Road and realignment of 3km of Great Northern Highway – completed in November 2022.
BHP’s Rail Manager Operational Readiness, Sarah Dearman, said, “It’s fantastic to see the finished works and to know that daily road users are travelling safer as a result.
“We’re pleased that our contribution and collaboration with the State and Commonwealth Governments has made a real difference to the project.”
We produce Linear Motion Screens (HLS) and Circular Motion Screen (HKS) with a maximum length of 10,000mm and a maximum width of 4,000mm. We also deliver Banana Screens, Dewatering Screens and Hot Screens for material up to 1,000 °C. With a working moment of up to 15,000kgcm, our drive system exciters are also compatible with other brands.
The shift to renewable and clean energy sources requires innovative engineering solutions that ensure reliability, cost-effectiveness and sustainability.
On 22 August 2024, Engineers Australia will deliver the Climate Smart Engineering Conference (CSE24), an engaging, one-day conference program focused on a significant climate challenge – the clean energy transition.
Engineers Australia’s CEO, Romilly Madew AO, said this conference is an opportunity to hear from a wide range of experts in climate smart engineering, learn from successful technical solutions and strategies and connect with peers.
“CSE24 brings you the latest insights and engineering innovations – examining everything from the role of digital technology and AI to the challenges of decarbonising transport and upskilling in renewable energy.”
Navigating regulatory and policy frameworks and taking a system-of-systems approach to planning future energy systems will also be key themes.
Now in its fourth year, CSE24 is dedicated to addressing climate change from the engineering perspective.
With engineers and industry poised to play a major role in Australia’s clean energy transition, this is an opportunity to network, connect and collaborate to build a better and more sustainable world.
To view the program and register, visit engineersaustralia.org.au/cse
Climate Smart Engineering Conference
Thursday 22 August 2024 | Brisbane
driverless train operated by Rio Tinto derailed in Western Australia’s Pilbara region, with an investigation into the crash launched.
In a statement to the ABC, a Rio Tinto spokesperson said that the autonomous train hit a set of stationary wagons roughly 80km outside Karratha just after midnight on Monday 13 May.
The spokesperson told ABC that 22 wagons and three locomotives were impacted.
“There were no people within the vicinity of the incident and no injuries.
“We have notified the appropriate regulators and commenced an investigation.
“Work will soon begin to clear the rail line.”
The train was reportedly carrying iron ore and heading for port when it crashed. The scope of the cleanup and the time it will take to clear the track and resume operations remains unclear.
The Office of the National Rail Safety Regulator (ONRSR) told ABC in a statement that it received a report about a collision between a loaded ore train and a recovery train.
Image: Adwo/shutterstock.com
An ONRSR spokesperson, “The recovery train is reported to have collided with the ore train it was sent to recover after it was disabled by a mechanical failure.
“ONRSR is investigating the incident and will be making a series of enquiries.
“At this stage these are focused on the operation of and adherence to signalling systems in the area.”
This event marks the second Rio Tinto derailment in the Pilbara in 2024, after an empty autonomous train derailed 120km from Dampier in February 2024.
The Queensland Government has introduced new legislation to strengthen the coexistence framework of the state’s agriculture, resources and renewable energy industries.
The legislation is set to create a framework that assesses and manages the impact of coal seam gas-induced subsidence on agricultural land and provides a pathway for landholders to be compensated if required.
Other coexistence reforms include:
♦ Expanding the remit of the Office of Groundwater Impact Assessment (OGIA) to provide independent
scientific advice, assessment and development of tools to help manage the impacts of coal seam gas-induced subsidence on agricultural land
♦ Expanding the role of the Land Access Ombudsman (LAO) to provide support to stakeholders on a broader range of land access disputes through an alternative dispute resolution pathway
♦ The GasFields Commission Queensland (GFCQ) will be given a wider remit and become known as Coexistence Queensland. Its role will be to provide enhanced information, engagement and education services
to the community and industry on land access and coexistence issues across the resources and renewable energy sectors
The reforms are expected to build stronger relationships between resources, agriculture and other land uses and align with key focus areas outlined in the Queensland Resources Industry Development Plan.
In addition to the coexistence reforms, the legislation aims to improve processes for assessing and administering resource authorities and reduce the state’s financial risk from resource companies failing to comply with their environmental or rehabilitation obligations.
CSI Mining Services (CSI) has signed its very first joint venture partnership with Western Australian-based contracting company, PMW Industries (PMWI).
PMWI is a Traditional Owner Banjima business, with more than a decade’s experience delivering rail and civil services. Banjima Country is in the central Pilbara region of Western Australia and covers more than one million hectares of land.
CSI and PMWI have an established subcontracting relationship, delivering crushing, screening and rehabilitation services to Tier One mining companies. The new joint venture partnership is aimed at strengthening the existing relationship, with a focus on establishing a mining services contract portfolio.
The joint venture partnership ownership comprises PMWI at 51 per cent and CSI 49 per cent.
CSI’s Chief Executive, Mike Grey, said it was fantastic to continue to build on the business’ strong working partnership with PMWI.
“CSI and PMWI have been working together since 2022, including establishing an accredited Indigenous trainee program for crushing and equipment operators.
“We already have some great wins on the board, including upskilling 27 Indigenous trainees and achieving record tonnes crushed for a mining client.
“CSI is committed to building strong relationships with Traditional Owners and local Indigenous groups to advance economic outcomes and is thrilled to team up with a Pilbarabased Indigenous company.”
PMWI’s Managing Director and Banjima Traditional Owner, Paula White, said that the partnership would further empower and grow the business.
“We currently have more than 50 employees across Western Australia, with 55 per cent Indigenous – this is a great opportunity to grow our business and expand our capabilities.”
The Kelair-Blivet is a stand-alone packaged sewage treatment plant, designed to accept raw (unsettled) sewage and produce a high quality final effluent without the need for ancillary tankage or equipment.
Compact, flexible, modular system suitable for:
- Environmentally sensitive sites
- Townships and villages
- Construction and remote sites
- Areas not connected to mains
We know the importance of choosing the right equipment to match your process. With our extensive range of pumps, first class customer service and ongoing comprehensive support, Kelair Pumps are second to none when it comes to your pumping requirements.
AusProof has been committed to providing the industry with high quality cable coupler solutions that are safe and reliable since 1994. In 2024, AusProof celebrates its 30th anniversary of high quality design, innovative development and customer support.
Drawing on 20 years of experience in South Africa, Founding Director Philip Marks established AusProof with wife and Founding Director Wendy Marks with a commitment of refusing to give up in tough times, rising to meet each challenge and seeing each failure as a chance to improve.
Though AusProof has grown since its humble beginnings, no matter how much it may continue to grow, both Founding Directors believe in remaining humble.
“We remember where we came from – I think that’s pretty important. I think we’re pretty approachable,” Mrs Marks said.
Mr Marks also placed great importance on learning and understanding the needs of the industry.
“You don’t want to lose that,” Mr Marks said. “You’ve got to listen to them; feel their pain.”
Committed to looking ahead
A part of AusProof that will never change is its drive to find that next innovation to assist the industry however it can – whether it be in meeting operational needs or minimising costs.
Managing Director, Aston Marks, said “We want to make a difference in the usability of our product and help customers save time and money in the long run.
“Hopefully the industry feels honoured that our little company is just in their backyard. We're proud of it and hopefully they can be proud of it too.”
Visit AusProof’s website for more information on its available products and to get in touch with your local state sales representative at www.ausproof.com.au
Liontown has awarded the Kathleen Valley Village Services contract.
Sirrom Corporation has been awarded the contract following a rigorous tender process, during which the company showcased its experience and distinctive service offerings that Liontown believes will play a crucial role in the Kathleen Valley operation and life onsite.
Under the contract, Sirrom Corporation is responsible for the management of the Kathleen Valley Dragonfly Village, including the dining offerings, site-wide cleaning services and running of the onsite café, retail shop, tavern and gym.
Sirrom Corporation has committed to sustainably delivering a high-quality of dining options and engaging social spaces at the project, ensuring the team has an enjoyable home away from home to unwind and relax whilst minimising Liontown’s impacts on the environment.
Sirrom Corporation has also committed to working closely with the Tjiwarl Traditional Owners to support Liontown in creating social and economic value for the local communities.
Awarding the contract is another milestone for the Kathleen Valley Lithium Project as Liontown prepares for first production and steady-state operations, on track to commence mid-2024.
Your industry personnel roundup – here we cover who’s moved where, which boardrooms have been shakenup and the new leaders making big decisions in organisations across the industry.
In March, Evolution Mining appointed a new Chief Technical Officer, responsible for the various technical functions of the company’s operations, including long-term planning and operating of projects, studies and other technical services. Nancy Guay was appointed and is due to commence in the role on 1 June 2024.
In April the retirement of BHP NonExecutive Director, Ian Cockerill, was announced. Mr Cockerill was replaced by Don Lindsay, who commenced in his new role on 1 May 2024.
Rio Tinto has seen several changes to its Board and executive team in recent months. In April, Bold Baatar was appointed to the position of Chief Commercial Officer (CCO), effective from 1 September 2024.
Mr Baatar, who is the current Chief Executive Copper, will relocate to Singapore to take over the role from
current CCO, Alf Barrios. Mr Barrios will assume the position of Executive Committee Member and Chair for China, Japan and Korea until his retirement at the end of 2024 to ensure a smooth transition.
Furthermore, Rio Tinto Non-Executive Director, Simon McKeon, stepped down from his position on 2 May 2024 after the company’s annual general meeting.
Surefire Resources announced in May that it had appointed Jan De Jager to the role of CEO, effective immediately. Mr De Jager has more than 25 years’ experience in the sector and will assist the company in advancing its key vanadium projects.
In May, Perth-based resources company Hastings Technology announced an organisational restructure as part of its ongoing efforts to manage costs to fit with the company’s current needs. The material reduction in workforce numbers included CEO, Paul Brown, who is expected to leave the business on 31 May 2024.
Hasting Technology’s current Executive General Manager – Mining Services, Tim Gilbert, who joined the company in January 2023, will step into the role of Chief Operating Officer, reporting directly to Executive Chairman, Charles Lew.
True North Copper also saw changes to its Board in May, with the company announcing that Managing Director, Marty
Costello, would step down but remain on the Board as Executive Director Business Development.
The company also announced that it is actively seeking to recruit a new Managing Director, with an appointment expected by June 2024.
True North Copper Non-Executive Chairman, Ian McAleese, will temporarily assume the role of Executive Chairman until a Managing Director is appointed, at which point he will revert to his former role of Non-Executive Chairman.
Recent leadership changes have not been exclusive to mining companies, with some key industry associations also undergoing leadership reshuffles.
The Chamber of Minerals and Energy Western Australia welcomed several changes to its Board at the organisation’s 123rd annual general meeting in April, including the appointment of Simon Trott as President. Bill Beament was also re-elected to the Vice President role and Sanjiv Manchanda was newly appointed as Vice President.
Finally, in May, the Queensland Government announced that Critical Minerals Queensland – the dedicated office to identify opportunities in the industry and foster discussions with proponents, investors, community members and researchers – would be run by new project leader, Paul Holden.
Australian Power Equipment has paid a visit to its esteemed supplier, Bambang Djaja (B&D) Transformers, at its headquarters in Surabaya, Indonesia, and another of its manufacturing facilities just a short distance away.
Despite representing B&D exclusively in Australia for several years, this journey marked Australian Power Equipment’s first visit to East Java and the team was thoroughly impressed by what they encountered.
Representing core values
Australian Power Equipment’s core values constitute its dedication to delivering top-tier equipment to its clients, fostering genuine relationships within its supply chain and prioritising sustainable practices within the business itself.
These values resonated deeply with the ethos of B&D, a family-owned enterprise. Established in Surabaya in 1985, B&D Transformers has emerged as the premier Power, Distribution and Instrument Transformer manufacturer in Indonesia.
Throughout the years, the company has continued to elevate its standards, leveraging cutting-edge technology, state-of-the-art machinery and a team of highly skilled professionals.
The Australian Power Equipment team’s discussions with two of the company’s directors – Teddy Suwignjo and Henky Suwignjo – proved invaluable as avenues for innovation, with optimised shipping processes explored and the two teams aligned on sustainability objectives.
Australian Power Equipment Director, Andrew Cockbain, said, "The manufacturing facilities were truly impressive.
“I have full confidence in B&D’s operational prowess as a supplier, not only for their proven equipment, which we have provided to numerous clients across Australia, but also for their engineers’ collaborative approach, ensuring that new designs were embraced from the outset."
Strengthening global relationships
Fostering global partnerships is paramount for sustained success, with face-to-face interactions facilitating seamless information exchange.
Spending time not only with the heads of business but their families fosters a strong sense of connection, building an environment of transparency, trust and shared vision for the future.
Australian Power Equipment Director, Abby Crawford, said, "I was struck by their genuine commitment to sustainability.
leaders.
It’s evident that B&D prioritises both the environment and its people."
Whilst many countries throughout the globe have intensified their lens on sustainability reporting, including Australia, other countries have not yet prioritised this type of governance.
Nevertheless, it became apparent to the Australian Power Equipment team that B&D was already making significant strides in sustainability and by sharing resources and exchanging ideas, formalising these practices was well within reach.
With ongoing support and collaborative efforts, including open dialogue and information sharing, the Australian Power Equipment team believes B&D has the potential to lead the charge in advancing sustainability practices within Indonesia’s manufacturing sector.
As Ms Crawford said, “People like working with people they like.
“With mutual respect, strong work ethics, and a shared vision, the partnership between Australian Power Equipment and B&D Transformers presents a promising opportunity for ongoing collaboration.”
The future of Power Transformers in Australia appears promising as Australian Power Equipment and B&D Transformers continue to collaborate closely.
For more information, contact info@australianpowerequipment.com.au or visit the website www.australianpowerequipment.com.au
Australian Power Equipment is a leading provider of low, medium and high-voltage power equipment across the Power Generation, Infrastructure, Renewable Energy and Resources sectors.
As the agents for Üntel cables, B&D transformers, Leistung Energie switchgear, CAB cable systems and WE Walter substations, they can supply new equipment to specification.
With a strong commitment to sustainability, the company also provides repurposed and refurbished equipment including substations, transformers and switchrooms.
They can provide immediate solutions to unplanned outages with their in-stock equipment or their critical sourcing solutions.
Australian Power Equipment is dedicated to delivering exceptional customer service and electrical engineering support, ensuring businesses can make best-practice decisions for their operations.
AGENTS FOR
While securing high levels of safety has always been a top priority in the mining industry, recent years have seen a spotlight been shone on the state of mental health, as well as bullying and sexual harassment.
Increased attention on working in the Western Australian mining industry over the last few years has uncovered a number of concerning issues involving mental health, safety issues and workplace culture. This led to a response from the Western Australian Government and a commitment to improving the well-being of resources sector workers.
The Mental Awareness, Respect and Safety (MARS) Program Landmark Study was commissioned by the Western Australian Government in December 2021 to design and implement a project assessing the mining industry, regarding three focus areas:
♦ Creating mentally healthy workplaces – managing psychosocial hazards and promoting positive practices at work that support mental health and well- being
♦ Building a culture of safety and respect with safe, gender-equitable, respectful and inclusive workplaces
♦ Preparing for workplace safety in future mining – training the future mining workforce on work health and safety, including psychosocial hazards and controls and by addressing emerging risks and fostering innovation and research in mining health and safety
The Centre for Transformative Work Design, housed in Curtin University’s Future of Work Institute, was engaged as an independent research team to investigate these three focus areas.
This large-scale, multi-source, multimethod study in the Western Australian mining industry is the first of its kind.
As part of the overall MARS Program Landmark Study, previous reports have reviewed and gathered multiple sources of data. Three prior reports have been published as part of the Landmark Study and formed the foundation of the research discussed here:
♦ A desktop search of annual reports and other publicly available reports by ASX200 companies to understand the local landscape
♦ A literature review of existing academic studies investigating these topics of interest
♦ A survey of Human Resources and Work Health and Safety managers and professionals on the policies and practices within their companies
Understanding workers’ perspectives and experiences
In mid-2023, through consultation with industry and academic expert advisors, the Centre for Transformative Work Design launched a survey that was open to all workers in the Western Australian mining industry – including employees, contractors and labour hire workers. The three prior reports helped to build a strong foundation for the worker survey and interviews discussed below.
In order to reach a diverse group of mining workers, the research team liaised with industry peak bodies, employer associations, employee associations, unions and other relevant groups to recruit participants for the survey. The team also worked directly with companies who agreed to disseminate information via emails, posters and site briefings.
The confidential surveys were hosted online, with pen-and-paper surveys also made available to work sites and individual participants upon request.
In total, more than 2,500 people participated in the survey, representing the diverse range of the Western Australian mining population.
The research team also interviewed 60 mining workers to deeply explore their experiences at work.
In order to benchmark the mining sample against other industries, the team also surveyed a sample of workers in similar industries, including construction, agriculture, manufacturing, oil and gas and others.
that promotes workplace safety (safety participation). The levels of safety behaviours reported by the mining sample was significantly higher than the benchmark sample, suggesting that mining workers are highly engaged with safety behaviours.
While low, the data suggests that the underreporting of notifiable safety incidents and near misses continues to exist, with respondents suggesting that one in three near misses in the past 12 months were unreported.
The findings also indicated that although burnout is not necessarily unique to the Western Australian mining industry, one in three mining workers reported high levels of burnout. Across Australia and the world, levels of burnout have been on an upward trend, particularly in a post-COVID-19 environment.
Efforts to stem increasing burnout and improve mental well-being must involve everyone and should focus on the prevention of harm, such as by designing work with tolerable work loads and reasonable levels of job autonomy.
Finally, an insight that the results offered is that overall levels of bullying and sexual harassment are high in the Western Australian mining sector.
Looking firstly at bullying, 16 per cent of workers reported having experienced bullying, while 22 per cent reported having witnessed bullying at least two to three times per month in the past six months.
While it is undeniable that these numbers are too high, bullying appears to be less prevalent compared to a study of Western Australian FIFO workers conducted in 20181, suggesting that there has been a positive shift in the past five years. Despite this progress, more needs to be done to understand if this pattern is a true reflection of the shifting landscape in Western Australian mining.
"There’s a lot more acceptance and encouragement for people to support their mental well-being at work."
What the industry had to say
From the findings released in March 2024, safety emerged as a key strength of the industry.
Most Western Australian mining workers reported high levels of safety behaviours, including engaging in core safety tasks and following procedures (safety compliance), and other proactive behaviours that develop an environment
Secondly, turning to experiences of sexual harassment, covert forms of sexual harassment – such as behaviours that communicate denigrating, demeaning or hostile attitudes based on gender or sex – are common, especially for women. For example, the most common behaviour experienced by female mining workers was being put down or being condescended to (41 per cent),
followed by offensive sexist remarks (e.g., suggestions that people of their sex are not suited for the kind of work they do –34 per cent).
In contrast, the most common behaviour experienced by male mining workers was receiving crude and offensive sexual remarks, with 11 per cent of male mining workers reporting those experiences in the past year.
Regardless of gender, these covert forms of sexual harassment have been found to be more prevalent than the more overt forms of sexual harassment (which include behaviours such as unwanted touching, sexual assault, and being coerced into exchanging sexual favours for professional rewards or threats of professional harm).
While these covert forms of sexual harassment are sometimes brushed off as a ‘harmless bit of fun’, the data shows that the impact that these experiences has on peoples’ mental health is almost as detrimental as the more overt forms of sexual harassment.
The research identified that the main contributors to improving mental health and well-being and nurturing a culture of respect were factors at the organisational and job level.
Importantly, when workers have a shared belief that their companies and workplaces value and prioritise the mental health and well-being of all workers (what is known as psychosocial safety climate), this is linked to experiencing mental health and wellbeing at work, as well as lowered rates of bullying and sexual harassment. In other words, feeling that worker well-being is genuinely important to senior management has important and far-reaching positive impacts on creating healthier working cultures which, in turn, encourages people to treat each other with more empathy and to speak up if they need help, or notice that others may need support.
One interviewee said, “that’s been quite a big shift that I’ve noticed in recent years – there’s a lot more acceptance and encouragement for people to support their mental well-being at work”.
Leaders can demonstrate their commitment to mental health at work by creating a work environment that is free from stigma, promoting a culture that encourages people to speak up, and actively seeking questions and feedback.
The research further identified that the way that work is structured and organised (also known as work design) is another important contributor to
improving mental health and well-being and nurturing a culture of respect for one another. For example, a positive work design involves ensuring that workers have tolerable workloads, that they understand goals and processes, are empowered to make decisions around when and how they complete their work, and that they have rosters designed to support their mental health (such as shorter and even-time rosters).
Rather than addressing mental health and well-being reactively as issues arise, designing good work is a proactive way of preventing harm towards workers.
Effective work design reduces job stress, burnout, absenteeism, turnover and other negative mental health outcomes, whilst also boosting job satisfaction, thriving and other positive well-being indicators.
As part of the State Government’s investment in the MARS Program, several initiatives are being rolled out which potentially can help to address the results from these findings.
While not an exhaustive list, some example initiatives include:
This series guides senior leaders through the evidence-based Thrive at Work Framework to unpack how mining
workplaces can support all employees’ mental health and well-being, to get well, stay well and be the best they can be.
This initiative provides organisations with a set of tools, resources and supporting implementation guides to assist them to embed gender equality policies to benefit all employees.
This is a series of online and face-to-face training modules aiming to build more respectful workplace cultures and support for mental health and well-being.
This is a World Health Organisationrecognised best practice suicide prevention and mental health peer support program, with MATES in Mining focused on the unique needs of the mining industry. MATES focuses on site training and education to empower workers to manage mental health within the workforce.
This is a program tailored to the resources sector that trains people to become peer supporters and to support each other in the workplace.
Other mining companies are also implementing various initiatives, with the aim to continually build a safer and more respectful environment.
Physical safety has been a core focus of the safety critical Western Australian mining industry for many years. However, in more recent years – particularly in the past decade – the industry has shifted to a more holistic approach to safety and well-being for all workers, including a stronger focus on mental health and well-being.
Still more recently, this scope has expanded to include the eradication of disrespectful behaviours such as bullying and sexual harassment (which includes sexual assault). Aligned with the historical developments of the Western Australian mining industry’s focus on these aspects, the research findings reflect the varying stages of maturity of these three focus areas in the Western Australian mining industry.
There are clear strengths in the industry, most notably around workers embracing and integrating safety behaviours into their work lives. The research suggests that the sector has come some way. The industry has demonstrated that it is capable of significant positive change, but the proof will be in the pudding.
In 2025, The Centre for Transformative Work Design will rerun the survey and interviews to understand the impacts of efforts that have been made and report back on how things are tracking within the industry.
To stay up to date on this research, visit curtin.edu/mars-lms
Climax BB8100 Line Boring Machine, boring range 368.3mm2174.2mm. Image: FMT
Field Machine Tools (FMT) is Australia’s largest stockist of specialist onsite machining and portable maintenance equipment, o ering hire and sale of one of the most comprehensive ranges of portable equipment suitable for a large range of applications, materials and speci cations.
FMT is a dry hire only company – meaning it never competes against its customers for onsite service work – with conveniently located branches in Queensland, Victoria and Western Australia.
Removing equipment from a job site to a repair facility can delay project completion and put a dampener on profits. This is where Field Machine Tools can help.
FMT offers onsite repair and maintenance machines that will minimise maintenance times and keep equipment working for companies and their customers.
FMT’s wide range of portable equipment is available for rent or purchase Australia-wide from the company’s three branches. This includes equipment for machining applications such as Portable Milling Machines, Portable Lathes, Clamshell Pipe Lathes, Flange Facers (OD and ID Mount), Line Boring Machines, Vessel Grinding Machines and Pneumatic Based Drills.
For welding applications, FMT has Bore Welding and Cladding Machines and Induction Heat Treatment equipment. For valves, FMT has Valve Test equipment, Valve Repair equipment and Portable Valve Actuators. For heat exchanger, condenser and boiler manufacture, repair and maintenance FMT offers Tube Pulling Systems, Tube Cleaning Systems, Heat Exchanger Tools, Torque Controlled Rolling Motors and Australia’s largest range of Tube Expanders and consumables.
FMT is the Australian agent for major international brands, including:
♦ Climax Portable Machine Tools – an impressive range of highly-sought after industrial equipment designed by a market-leading manufacturer for the rugged challenges facing oil, gas, mining, chemical and power generation industries
♦ Modec Motors and Portable Valve Actuators have been used for 30 years as an alternative to traditional electrical motors in many demanding applications. The versatile range of Portable Valve Actuators facilitates preventative maintenance of valves, even in the most demanding of
environments, and incorporates a reaction device designed to reduce the risk of strain injury to the operator
♦ Krais Tube and Pipe Tools have been delivering top quality tube tools for more than 40 years. The range is comprehensive, with Condenser Tube Expanders, Boiler Tube Expanders, Tube Rolling Motors, Tube Installation Tools, Tube Cutting and Removal Tools, Tube Pulling Equipment and accessories
♦ Goodway Technologies is a US-based manufacturer of specialised industrial maintenance products for HVAC, energy, manufacturing, food and beverage production markets Established in 1995, Field Machine Tools is a privately-owned Australian company that provides engineering solutions for field applications to minimise downtime. The scope of operations is providing the most complete product lines available to OEM equipment manufacturers, maintenance providers, field service companies, power stations, petrochemical plants, the mining industry and other related industries.
The new Mining Sector Standard from the Global Reporting Initiative (GRI) creates a best practice ESG standard that captures key aspects of the mining value-chain. From junior explorers, to operational miners, to suppliers and contractors – it sets a new benchmark for ESG disclosures and Sustainability Reports.
The GRI standards are the dominant set of global sustainability reporting standards, with an average of 80 per cent of ASX50 companies and 77 per cent of ASX100 companies1 adopting the GRI standards framework2. GRI also offers the only reporting standards used by a majority of G250 companies in all regions (the Americas, Asia-Pacific and Europe, the Middle East and Africa) – meaning that many companies in the mining sector will have customers, investors and other stakeholders using the GRI standards.
What’s new about the GRI Mining Sector Standard?
ESG standards can help companies understand the information investors and other stakeholders are looking for and determine the sector-related metrics that may be relevant.
Currently there is no other reporting standard that covers minerals from the ‘impact’ perspective, with existing Sustainability Accounting Standards Board (SASB) reporting focusing only on the risks to financial capital providers. While European Union sustainability reporting standards will soon come into effect, there is, as of yet, no such sector standard for mining.
GRI 14: Mining Sector 2024 is a first for the industry, providing a navigational tool for the mining sector and setting out the most significant topics and impacts where expectations to see information reported exist. It addresses the need for consistent and complete reporting of the sector’s impacts on the economy, environment and people.
The GRI Mining Standard interfaces with GRI topic standards –including the GRI Climate Change topic standard exposure draft, which is due for finalisation during 2024. Efforts have been made for this to complement the Mandatory Climate related Financial Disclosure regime – which, in Australia, was tabled in the House of Representatives on 27 March 2024, in the form of the Treasury
Laws Amendment (Financial Market Infrastructure and Other Measures) Bill 2024 (Cth) (Bill). It is proposed to come into force on 1 January 2025.
Similarities include that both standards require physical and transition risk/opportunity plans and assessments, scenario analysis including for 1.5°C global warming, climate related targets and scope 3 GHG emissions reporting. The GRI Climate Change standard additionally requires:
♦ GHG emissions intensity disclosure
♦ Just Transition-related metrics (where relevant)
♦ Disclosure of ‘carbon removals’ in line with the Science Based Targets initiate (SBTi) Net Zero Standard Reporting companies need to begin planning for the Mandatory Climate related Financial Disclosures which, by July 2027, will capture most Australian companies with more than 100 staff, $25 million gross assets or $50 million revenue.
The Mining Standard applies to many organisations engaged in the mining and quarrying value chain, including:
♦ Exploration, extraction, quarrying and primary processing of minerals 3
♦ Support activities for core mining operations
♦ Supply of specialised products and services to mining organisations
Smaller companies can start using the Mining Standard as a guide, from informing the identification of material topics to setting out an ESG roadmap for action. These companies can then progress to sustainability reporting ‘with reference to’ the GRI standards (minimal effort to address three disclosure requirements) and thereafter report ‘in accordance’ with the GRI standards in subsequent years (requires addressing nine disclosure requirements).
All companies reporting ‘in accordance’ with the GRI standards must apply the relevant Sector Standard to determine whether topics within it are material.
Care was taken to build the GRI Mining Standard upon existing standards and protocols. Wherever impacts were identified that would not be covered by the GRI topic standards, the GRI Mining Sector Standard Working Group relied on existing responsible mining instruments and existing standards to align with what already exists and is considered best practice. An example would be how sector specific topics like mine closure and rehabilitation look at existing industry materials or International Finance Corporation (IFC) standards for resettlement.
The GRI Mining Standard was developed with a multistakeholder approach, addressing 25 topics that are potentially material. This is a significant expansion over the 12 topics covered in the SASB Metals and Mining standard. The topics include setting expectations for site-level transparency, climate change, emissions, biodiversity, water use, health and safety, human rights, land and resource rights, anti-corruption and community engagement.
It also introduces three topics not previously addressed by GRI that are of specific relevance to mining firms: tailings management, artisanal and small-scale mining and operating in conflict zones. It addresses the Just Transition from coal as a theme throughout the standard and it also lists decarbonisation and climate adaptation as the first and second topics ahead of the other 23 topics.
While waiting for the planned regulations for the Sustainabilityrelated Financial Disclosures in Australia, some mining companies report using the ISSB’s S1 General Requirements for Disclosure of Sustainability-related Financial Information This standard references the GRI standards and allows them to be applied in the absence of relevant IFRS standards being applicable to a sustainability-related risk or opportunity. For example, the 25 topics covered in the GRI Mining Sector Standard can be used to identify sustainability risks or opportunities not covered by the 12 topics of the SASB Metals and Mining Standard (SASB is now administered by the IFRS).
‘Site-level reporting’ is a focus of the Mining Standard, which reflects stakeholder requests for transparency of information. While site-level reporting is optional, its inclusion will likely raise stakeholder expectations and scrutiny over the level of information being reported.
Site-level data and reporting is usually kept behind the closed doors of teams onsite, head office and third-party assurers. Bringing such granular data into public visibility means that reporting organisations will need to be more comfortable with the data – which may increase the need for internal reporting and external assurance resources.
There has been considerable progress in the sustainability reporting landscape in 2023 through to the first quarter of 2024. Key milestones include a string of agreements on interoperability and future cooperation between European regulators, the GRI and ISSB.
Considering the GRI’s significance in the impact reporting sphere, the GRI standards can help global companies prepare for upcoming regulation in the EU – where double materiality is a focus. This has placed the GRI and International Sustainability Standards Board (ISSB) further in the spotlight, as the torch bearers of ‘Impact materiality’ and ‘Financial materiality’ respectively.
It is foreseeable that Europe’s regulation of double materiality reporting may eventually be adopted in Australia – after all, much of Australia’s sustainability and climate change policy has followed advancements in the UK and Europe. For example, in April 2022 the UK became the first G20 country to apply mandatory climate disclosures for the largest companies, ahead of an equivalent regime in Australia that is planned to commence on 1 January 2025.
Address the minimum regulatory requirements – e.g. the SR1 mandatory climate related financial disclosures, and the eventual sustainability related financial disclosures.
Set visionary goals and direction - e.g. alignment to Paris Agreement, Sustainable Development Goals (SDGS), etc. 1
Establish reporting standards to guide selection of material topics and disclosures –such as the GRI’s universal, sector and topics standards.
Select suitable industry performance standards – e.g. ISO standards, TSM, IRMA, etc.
5
Respond to and report against relevant ESG performance ratings – from MSCI, ISS, Sustainalytics, S&P, etc.
Globally aligned reporting standards
The GRI standards have proven useful to many companies to form a cornerstone of an ESG framework, roadmap and sustainability report. However, one of the biggest challenges with ESG reporting has been the lack of standardisation. Industry is finally seeing more initiatives to improve interoperability, such as between the GRI, European regulators and ISSB, and amongst mining industry associations that administer ESG performance standards. This can help to simplify the ESG reporting landscape.
Data collection and validation
Collecting and validating ESG data can be a challenge for companies. Unlike financial data, ESG data collection is less established, often less available and comes from multiple sources including those in the supply chain. Site-level data can involve different individuals, languages, currencies and other differences that can create sources of errors when reported up to head office. Additionally, validating the accuracy and completeness of such data can be difficult, time-consuming and resource intensive.
Opportunities to improve on data quality include:
♦ Determining data gaps and creating a roadmap for improvement, using the GRI standards and sustainability reporting regulations to determine relevant metrics
♦ Designing and documenting ESG reporting, processes and
internal controls. The rigour of reporting should be similar to financial statements reporting
♦ Implementing periodic data checks, rather than a single annual check when there is less time to deal with any errors
♦ Implementing IT systems to help data collection, monitoring and reporting to improve efficiency and accuracy as ESG reporting becomes more established
♦ Considering external verification or assurance. To help prepare for this, it is useful to keep in mind the reporting principles from the GRI, Taskforce for Climaterelated Financial Disclosures (TCFD) and ASAE/IAASB assurance standards
Integration with business strategy
ESG reporting should be aligned with a company’s goals, objectives and overall business strategy. However, many companies struggle with this integration, often due to ESG reporting being viewed as a separate initiative from core business strategy. It ultimately requires buy-in from senior management, which can be supported from various angles including through training, internal-audit scopes of work and integration of risk assessments into a business’ strategic plan.
The ESG reporting landscape can be summarised into a system of tiers; a company at the start of its ESG disclosure
journey would usually start from the top and work down in building its approach and reporting on ESG topics.
The TCFD,4 GRI and SDGs are the most commonly used standards, used by more than 77 per cent of ASX100 companies. Combined, they provide a solid foundation for a company’s ESG framework and roadmap. Larger companies may report a mix of all of these standards in their sustainability reports.
For smaller companies, it is sensible to start simple. Developing an ESG framework and roadmap can often be prepared in under five pages. This will involve a materiality assessment and workshop to identify the most material topics to your organisation, and your stakeholders. Companies can then prepare a roadmap for action typically over a three year period or longer, which aims to gradually address the material topics and required and optional disclosures in the GRI standards, along with mandated climate and sustainability related disclosure standards/regulations.
Brendan Tapley is Managing Director of Decarbonate, a sustainability and climate change consultancy specialising in the mining and energy sectors. He is also one of four people in Australia to represent the Global Reporting Initiative (GRI) Mining Sector Standard Working Group.
Assess the current regulations, reporting landscape, and state of play and prepare a sustainability reporting framework and roadmap for action.
Understand ESG reporting ambitions and requirements
• Understand your company’s strategy and ambition with ESG reporting.
• Identify regulatory reporting requirements.
• Identify voluntary reporting standards that stakeholders would expect to see
• Benchmark peers’ approaches.
• Assess maturity/gaps.
Adopt ESG Framework consisting of core Standards
• Based on relevance and usefulness to the business & stakeholders.
• Start simple to keep it cost-effective, then ramp up over time.
• The most common standards include the GRI standards, SDGs, TCFD (and regulations e.g. the Australian Sustainability Reporting Standards). Identify relevant impacts, risks and opportunities guided by the ESG framework/standards. Perform an ESG materiality assessment considering perspectives of key stakeholders.
Prepare an ESG Roadmap over the next 3 years or beyond, including to address data gaps, with a 5-page ESG Framework and Roadmap for the company’s website.
Prepare initial sustainability report with reference to the chosen ESG framework and standards such as GRI standards. Addressing the regulatory requirements will be a priority.
An initial Sustainability Report will focus on a limited number of key metrics and information, including the following:
• The ESG Roadmap will contain actions aligned to the ESG framework (i.e. disclosure standards) starting with simple actions in year 1 to more progressive actions by year 3.
• Prepare a Climate Change section which addresses mandatory climate disclosure regulation.
• Consider suitable performance standards (ISO, TSM, IRMA etc).
• Consider the most relevant ESG rating agencies to respond to surveys.
• Preparing the Sustainability Report with reference to the GRI – which requires adding GRI content index, a statement of use, and to notify the GRI.
• A first -time Sustainability Report of < 30 pages is often all that is required, which should help to limit costs to <$35k if outsourced.
• Undertake a gap assessment to Plan for ramping up efforts to report in accordance with the GRI standards in subsequent years.
Prepare further sustainability reports accordance with the GRI standards. Implement sustainability reporting as a core part of the business and build a mechanism for continuous improvement.
Implementation of an ESG Roadmap and further sustainability reporting in accordance with the GRI standards can include to:
• Refine ESG governance structure.
• Align ESG key performance indicators (KPIs) to executive and Management incentives.
• Integrate ESG risks into the enterprise risk management framework.
• Incorporate opportunities into corporate strategy.
• Design and test ESG reporting processes and controls.
• Plan and deliver training curriculum to upskill and develop self-sufficiency.
• Report progress against the company’s wider ESG strategy, targets and regulatory requirements.
• Refine materiality assessments as stakeholder needs change.
• Aim for site -level reporting where relevant and useful, as per the GRI Mining Sector Standard.
• Refine reporting as regulation evolves and as GRI standards evolve e.g. around Transition Plans, Scope 3 GHG emissions, etc.
• Consider independent verification and assurance.
Countries around the globe are hungry for uranium to fuel their transition to net zero, and Western Australia has some of the biggest reserves in the world. However, a ban on uranium mining in the state has meant that much of the resource remains in the ground.
According to the Chamber of Commerce and Industry WA (CCIWA), the ban is a missed opportunity that could cost the Australian economy more than $1 billion a year.
CCIWA has been examining the potential of Western Australia’s uranium industry for the past 12 months. CCIWA’s inquiry involved a deep dive into the policy and regulatory framework around uranium in Western Australia and in-depth consultation with key stakeholders. It revealed a tantalising potential for the state, if it acts quickly to capitalise on current demand.
Spot prices for uranium more than doubled in 2023 and look set to continue on this trajectory as the market senses a shift in how the world’s biggest economies will keep the lights on.
Countries like the US, the UK, South Korea, Japan, India and France are all moving to dramatically expand their
use of nuclear power – considered to be a reliable and emissions-free energy source – as they work to decarbonise their economies.
For many Northern Hemisphere nations that are not as blessed with renewable resources as Australia, nuclear power plays a key role in helping reach their net zero ambitions.
Global commitments
CCIWA predicts that the commitment at the recent COP28 summit to triple nuclear production will drive a surge in demand for uranium.
At the same time, the supply of uranium is struggling to keep pace.
The current gap between supply and demand is being filled by inventories and reprocessed uranium, which will not last for long.
Adding to supply constraints is the fact that a large portion of uranium typically enters Eastern Europe through Russian ports. The ongoing war in Ukraine means
that the US Congress is now considering banning countries from sending uranium through Russia.
All of these factors have created a once-in-a-generation opportunity for jurisdictions with strong uranium industries.
Western Australia’s missed opportunity?
In Australia, South Australia has found itself in the box seat, with three active mines that are sending uranium overseas. These mines employ more than 1,400 people and are delivering multi-million-dollar royalty windfalls to the state.
The Northern Territory is not far behind – rapidly expanding exploration with the aim of riding the wave of demand for uranium globally. Both of these jurisdictions see great potential in uranium to create high-quality jobs for local workers and bring much-needed capital into their economies.
Western Australia is missing a trick. Uranium has long been a partisan
Labor first banned uranium mining
Government lifted the ban in 2008, which allowed for eventual approval of four new uranium mines in Western
When Labor government in 2017, the thenPremier, Mark McGowan,
Western Australia’s stringent and well-established regulations, paired with existing infrastructure and local technical know-how begs the obvious question: if South Australia and the Northern Territory can manage a uranium exploration and mining industry, why can’t Western Australia?
CCIWA’s inquiry found that Western Australia has around 226,000t of known uranium deposits, with potential to produce around 10,800t per year.
Due to a surge in uranium demand, supply is struggling to keep pace. Image: RHJPhtotos/shutterstock.com
At a ‘WA Breaking Ground’ forum hosted by the Association of Mining and Exploration Companies (AMEC) in March 2024, Western Australian Opposition Leader, Libby Mettam, pledged to overturn the government’s ban on uranium mining if elected next year.
“Embracing uranium mining in Western Australia is a strategic move that not only addresses our economic needs but also positions us as pioneers in the global transition towards sustainable energy,” Ms Mettam said.
Ms Mettam’s announcement was welcomed by many throughout the industry including AMEC, with the Minerals Council of Australia’s CEO, Tania Constable, saying that the policy change is a step in the right direction and could unlock the immense potential of Western Australia’s uranium resources.
As it stands, the rationale behind the uranium ban points to health, safety and environmental concerns. However, according to CCIWA, these concerns are not fundamentally different to those managed by any other mining operation. Western Australia is a mining state with a global reputation for safety and the world’s best practice.
Advanced extraction techniques and new technology have made it safer than ever to mine and transport uranium.
The mines in South Australia and exploration operations in the Territory operate transparently with local communities and Traditional Owners.
Companies that are allowed to export uranium do so under strict Commonwealth legislation which also ensures it is only used in electricity generation and does not fall into the wrong hands.
Australia is currently the world’s fourth largest producer of uranium. If Western Australia lifted its ban on uranium mining, Australia would be catapulted to second place behind Kazakhstan. If Australia were to be ranked higher, foreign investors looking to back uranium may potentially see Australia as a safer destination for their capital.
CCIWA believes there is a need for serious debate in Western Australia about the benefits of uranium mining, to balance prior views about the industry’s safety with the clear benefits to the national economy.
uranium mining from nuclear power
Public perception plays a big role in the debate around uranium mining in Australia.
Naturally, the issue of uranium mining is often tied to nuclear power, but it is important to stress that the two are, in fact, mutually exclusive – uranium can be exported without there being a domestic nuclear power industry in Australia.
CCIWA’s inquiry into uranium mining did not examine the issue of domestic nuclear power, but it is undeniable that no matter what Australia thinks of nuclear energy, other countries across the globe are embracing it.
If you switch on a light in London, Paris, Berlin, Dubai, Tokyo or New York, it’s likely that electricity has come from a nuclear reactor. While concerns around the safety of nuclear energy do exist in these places, it is clear that attitudes have changed over time, as better technology drives increased safeguards for people and the environment.
The shift towards nuclear energy in developed countries is a pragmatic one. Most younger people don’t remember the nuclear panic of the Cold War era and people in countries where nuclear power enjoys support are more
These countries will buy their uranium from somewhere, but –for now at least – it won’t be from Western Australia.
The nascent uranium boom comes at a crucial time for the Australian resources sector.
Increased volatility in the critical minerals market has highlighted just how important it is to have diverse mining interests.
Prices for battery minerals nickel and lithium have dropped to five-year lows and export earnings are forecast to be cut by almost half, fuelled by oversupply in China and Indonesia and slowing demand for electric vehicles.
As a result, investors who had seen great potential in critical minerals have begun to look more closely at uranium.
Western Australia is a mining state and its resources sector accounts for almost half of the state’s economic activity and underpins the relative stability of Australia’s national economy.
Demand for commodities is cyclical and the old adage ‘make hay while the sun shines’ can rightly be applied to Australia’s resources sector; timing is everything.
That being said, the uranium industry represents more than just turning a quick buck.
The countries who are embracing nuclear power are doing so with an eye to the future, given the significant expense and long time frames involved in commissioning a nuclear power plant.
They will be looking for a pipeline of safe and reliable sources of high-quality uranium to fuel their economies for decades to come.
If Western Australia wants a piece of the action, it needs to seize the opportunity or risk underplaying its hand, to the detriment of its future prosperity.
Challenge Accepted ; Our Pumps , Your Solution.
Challenge Accepted Our Pumps , Your Solution.
E mpowering your mine operations with Roto’s high pressure flexible shaft series pumps. Unleash the solution that challenges excess wate r, ensuring safe and efficient operations ; the Underground Maintena n ce Engineers’ Choice for ground water control.
Robust construction for prolonged life and reliable performance
• Robust construction for life and reliable performance
• Adaptable for challenging underground environments, available in fixed station configurations for single lift or staging along with portable packaged solutions
• Adaptable for underground fixed station configurations for single lift or along packaged solutions
• Forge a direct connection with the manufacturer, ensuring personalised support,
• Forge a direct connection the manufacturer, ensuring personalised support, Features:
Revolutions are exciting and invigorating but they can also be unpredictable.
Technological revolutions have become the norm in much of the world in recent decades, particularly in IT and communications.
Other technological changes move slower.
An example of this is energy generation, where the capital-intensive industry is linked to stable social structures that can take decades to adapt to changing circumstances and new technology.
Moving from playing music on a CD player to online streaming services is by nature a much quicker transition than closing coal mines and power stations.
The giant international steel industry is in a state of flux and, like any large international industry, change is a given. However, in recent times, the drive to decarbonise steel production is leading many to think that we are on the verge of a revolution.
Steel production contributes eight to ten per cent of the world’s human-made carbon dioxide, with most of the carbon
dioxide generated from the ironmaking step of the process.
This step is where iron ore is essentially converted into an impure iron using either coal or natural gas to fuel the furnaces and remove oxygen from the ore in ironmaking, before refining the material to steel in steelmaking. There is growing pressure in the developed world for heavy industries like steel to decarbonise.
The pressure on industry is most apparent in the EU, where there has been significant investment, often government and industry in partnership, in developing new low carbon routes to steel at an industrial scale.
In Sweden, an industry consortium is developing hydrogen-based ironmaking technology (in which hydrogen replaces hydrocarbons) and electric arc furnace (EAF) steelmaking powered by renewable energy on greenfield sites, with plans to build large-scale facilities capable of producing millions of tonnes per annum before the end of this decade.
In the UK, the process of closing existing blast furnace facilities – which involve coal-based ironmaking technology – and replacing steelmaking facilities with scrap fed EAFs connected to renewable energy is well underway.
Job losses in the thousands have been reported with this rapid change.
In Germany, thyssenkrupp – who operates blast furnaces – has been trialling replacing some of the carbon currently being used with hydrogen to find a way to gradually phase out the use of coal from its plants. Early analysis from thyssenkrupp suggests that the replacement of carbon with hydrogen can only lower the carbon dioxide generated from the existing technology by 20 per cent, which is much lower than the 90 per cent required to satisfy net zero scenarios by 2050. Many believe that the blast furnace will need to be phased out to achieve the 90 per cent reduction, with either the carbon in ironmaking to be replaced by hydrogen and/or the current furnace-based technology to be replaced by an electrolysis route.
Another example comes from Dutch steelmakers Tata Steel in the Netherlands, which has recently relined its blast furnaces, suggesting that it is expecting the technology to operate well beyond 2030. Simultaneously, the steelmaker has plans to install new hydrogen ironmaking facilities and an EAF for steelmaking on the same site as its blast furnace –essentially pursuing a hybrid strategy to decarbonisation.
There is growing evidence that there is some shift from the expected revolution towards a more gradual evolution.
Experts from Primetals, a major equipment provider to the industry, recently predicted that the blast furnace route will still dominate iron production well after 2040 and will still be producing around a third of the world’s steel by 2050.1
The pushback on rapid decarbonisation is strongly linked to concerns about the cost and scale of green hydrogen production.
Currently, green hydrogen is made from plants with MW power suppliers, but steel plants will need GW-powered plants to produce enough hydrogen to meet the requirements of typical steel plants around the world. Although there are plans for GW scale plants in several locations around the world, supply chain issues and concerns about costs have seen several large-scale plants delayed in their construction.
The cost of green hydrogen is also a concern, with current costs around the world varying between USD$4-10 per kilogram. Even at USD$4 per kilogram, the cost of steel is likely to increase more than 50 per cent, meaning the transition to hydrogen will either require tariff protection or subsidies if a steel company wants to survive the transition.
Of course, larger scale hydrogen production is likely to reduce these costs so stalling the construction of larger scale green hydrogen plants further undermines investment into hydrogen-based ironmaking technology. This has caused various experts to take a somewhat pessimistic view about achieving net zero for world steel production by 2050.2
In the midst of uncertainty about the transition to hydrogen-based ironmaking, Australian ore miners are evaluating how this revolution – or perhaps evolution –will affect the attractiveness of the giant Australian iron ore export industry. Australian iron ore – and particularly from the Pilbara – is high in gangue minerals which are easily removed in blast furnace technology.
In the case of the main hydrogen Direct Reduced Iron (DRI) technologies under development, removing the gangue minerals is not so easy and may require
the development of electric smelting furnace (ESF) technology. Utilising ESF technology would mean removing gangue minerals in the form of a slag, which can ideally be used as a feedstock into cement production.
The industry has been left with many questions, such as how Australian iron ore producers can adapt to the emerging green iron market and whether they will need to carry out more processing of iron ores before shipping.
Given the abundance of renewable energy to Australian iron ores, another factor under consideration is the feasibility of co-locating, including whether hydrogen plants should be made in close proximity to iron ore mines and if the iron ore can be converted to DRI close to the mines.
These questions and others are being considered by researchers at Melbourne’s Swinburne University of Technology and Australia’s national science agency, CSIRO, who formally joined forces after working together on similar projects and topics for many years.
The partnership between the two organisations is aiming to research and develop new green steel and mineral processing methods to drive the industry towards net zero, as well as guide future demonstrations and industry development.
In early April 2024, the CSIRO and Swinburne partnership secured funding from the Australian Renewable Energy Agency (ARENA) to assist with commercialising a new low carbon route to agglomerating iron ores for furnaces.
The project started as a PhD project at Swinburne before the two organisations joined forces with industry partners to develop the concept.
Initially, the new agglomeration process was designed to reduce the total carbon dioxide from iron production by over ten per cent, but the concept is being adapted to hydrogen-based ironmaking processes for either larger reduction. Promising laboratory results3 have formed the basis of patents and the new funding from ARENA will allow the project to move to commercial scale testing of the idea.
The driving force behind the development is Dr Suneeti Purohit, who came to Australia as a student with
1. Three phases to green steel, https://magazine.primetals.com/2023/06/12/three-phases-to-green-steel/. 2. Ibid.
Most of the carbon dioxide generated in steel production comes from the ironmaking step of the process.
Image: Kichigin/shutterstock.com
Professor Brooks at Swinburne and is now a scientist at CSIRO. Dr Purohit’s work has already attracted awards nationally, recognising a high level of innovation.4.
There are a multitude of other projects underway across the country, with ARENA’s April funding announcement resulting in $59.1 million being awarded across 21 research projects that are researching and developing commercialisation activities covering renewable hydrogen and low emissions iron and steel. The funding is being provided to research teams from some of Australia’s top universities, research organisations, start-ups and companies.
The team at Swinburne is also actively working with Calix P/L, an Australian based furnace technology company with a background in developing new lowcarbon technology, in their development of a fully hydrogen-based ironmaking process called ZESTY.
The novel process is designed to reduce the carbon footprint of ironmaking to close to zero by using electrically heated kiln technology to provide heat into the process and minimise the use of costly hydrogen in the process. Strong progress has been made at their pilot plant facility in Bacchus Marsh, with a range of ores being successfully converted into DRI at close to commercial grade.5
The joint program for Sustainable Mineral Processing and Green Steel is attracting investment from the partners, industry and funding agencies to evaluate both the scientific and economic issues around the green steel transition, whether it be a revolution or an evolution.
Significant innovation and technical excellence will be required to decarbonise the world’s steel industry and Australian researchers are likely to play a significant role.
3. Alternative route for magnetite processing for lower carbon footprint iron-making through lime-magnetite pellets containing CaFe3O5, https://www.tandfonline.com/doi/10.1080/03019233.2019.1569811.
4. Suneeti Purohit is helping reduce emissions from steelmaking, https://www.csiro.au/en/news/All/Articles/2023/June/Suneeti-Purohit.
5. Calix Zero Emission Steel Technology engineering study finds economical green iron solution, https://calix.global/sustainable-processing/zesty-study-economical-green-iron-solution/.
Engineering and delivering tailored air compressor systems, power generation solutions and now nitrogen generation sets, CAPS provides industry leading solutions in partnership with global equipment manufacturers.
Engineering and delivering tailored air compressor systems, power generation solutions and now nitrogen generation sets, CAPS provides industry leading solutions in partnership with global equipment manufacturers.
CAPS has been supplying and supporting the mining, agricultural and food manufacturing sectors since 1980.
CAPS has been supplying and supporting the mining, agricultural and food manufacturing sectors since 1980.
As many within the Australian mining sector know, the mining industry is exposed to various fire hazards that present across multiple sites. These include in and around process plants, underground conveyors, static and mobile plants, draglines, workshops, substations, monitored control rooms and switch rooms.
Generally, there are several types of fire suppression systems used to protect mining sites from fires. One of the more common methods is the use of water-based systems – such as sprinklers and deluge systems – which can quickly douse flames and prevent the spread of fire.
Another method utilises foam-based systems, which create a blanket of foam that suffocates the fire by cutting off its oxygen supply. Additionally, some mining sites utilise dry
chemical systems, which release a fine powder that chemically interrupts the combustion process.
These diverse fire suppression methods are crucial for safeguarding mining sites and ensuring the safety of workers and valuable equipment in the event of a fire emergency.
Beyond these measures, the use of scheduled gases plays an important role within the fire protection space and is a feature of some fire suppression systems. To safeguard workers’ safety and the environment, the use of these agents requires appropriate training and licence to handle.
When it comes to adhering to applicable fire safety laws and regulations, it can sometimes be difficult to know how to best secure safety onsite and how to locate appropriate resources
When it comes to adhering to applicable fire safety laws and regulations, it can sometimes be difficult to know how to best secure safety onsite. Image: A_stockphoto/shutterstock.com
to ensure applicable fire safety laws and regulations are being adhered to.
One such source of information is the Fire Protection Industry Board (FPIB). Acting on behalf of the Federal Government’s Department of Climate Change, Energy, Environment and Water (DCCEEW), the FPIB plays a key role in setting guidelines and outlining recommendations to ensure that the mining industry adheres to the highest standards of fire safety.
A co-regulator with DCCEEW, the FPIB has been implementing the Ozone Protection and Synthetic Greenhouse Gas (OPSGG) Permit Scheme since 2005, and supports the fire protection industry to ensure safe management of harmful controlled gases that damage the climate, the atmosphere and human health.
The FPIB facilitates important industry engagement and education programs, working with technicians and businesses to meet licence conditions and the permit scheme objectives. Additionally, the FPIB works with DCCEEW to reduce non-compliance and reports extinguishing agent discharges so that it can target communications and work to improve extinguishing agent handling practices and the regulations that inform them.
As a direct action of the Federal Government’s Montreal Protocol obligations and in line with global environmental initiatives, the FPIB also administers the fire protection division of the Ozone Protection and Synthetic Greenhouse Gas Regulations 1995 (the Regulations) on behalf of the Federal Government.
This includes managing the permit and licensing systems of individuals, workers and businesses who handle scheduled extinguishing agents for fire protection. The federal regulations dictate which scheduled extinguishing agents require a licence to handle, as well as controlling the manufacture, export, import, use and disposal of ozone-depleting substances and synthetic greenhouse gases.
As the primary regulatory framework, the Regulations determine which permit is required for what work and how they can be used.
The Montreal Protocol and Australian mining Adopted in 1987 by all governments across the world, the Montreal Protocol and its principal intention – to protect the ozone layer – is the primary reason behind the regulatory framework surrounding the use of scheduled gases in Australia.
The Protocol aims to protect the ozone layer by phasing out the production and consumption of ozone-depleting substances. While the initial focus has been on substances like chlorofluorocarbons (CFCs) and halons, recent attention has also moved towards synthetic greenhouse gases (SGGs) due to their impact on climate change.
Scheduled gases are a key focus area of the Montreal Protocol because the compounds that are used within these extinguishing agents are damaging to the earth’s ozone layer when exposed to intense UV light. Stopping the release of these gases into the atmosphere and preventing the creation of holes in the earth’s ozone layer is crucial in helping avert environmental disaster through the release of extreme levels of ultraviolet light.
Understanding ozone-depleting potential and Global Warming Potential (GWP) is important when using gaseous suppression systems and extinguishing substances. Ozonedepleting potential (ODP) is a substance’s ability to destroy ozone molecules in the Earth's stratosphere. Substances
that have the potential to cause ozone depletion are often referred to as ozone-depleting substances (ODS). These substances include; chlorofluorocarbons (CFCs), halons, carbon tetrachloride, methyl chloroform, hydrochlorofluorocarbons (HCFCs) and bromine-containing compounds like methyl bromide.
Similarly, GWP is a measure of how much heat a greenhouse gas traps in the atmosphere over a specific time period, relative to carbon dioxide (CO2).
The concept of GWP helps both scientists and policymakers understand the relative contributions of different greenhouse gases to warming temperatures and climate change. While CO2 is the most prevalent greenhouse gas emitted by human activities, other gases such as methane (CH4), nitrous oxide (N2O), hydrofluorocarbons (HFCs), perfluorocarbons (PFCs), and sulphur hexafluoride (SF6) also contribute to global warming. GWP considers factors such as the gas' ability to absorb infrared radiation, its atmospheric lifetime and its concentration in the atmosphere to quantify its warming potential.
With these environmental considerations in mind, the FPIB developed comprehensive guidelines for fire suppression systems used within the mining sector, as well as working to ensure all fire suppression agents adhere to regulations set by the Federal Government.
Gaseous fire suppression systems and equipment are found in both open-cut and underground mines, and it is quite common for sites to have a combination of scheduled and non-scheduled gaseous fire suppression systems, depending on the unique risks associated within the mine.
Primarily the most commonly used scheduled extinguishing agents within the mining sector are: FM-200®, FE-227™, NAF-P-III and NAF S-III because of their ability to efficiently
extinguish fires, whilst acting as the leading alternatives to the now-banned agent halon.
Outside of aviation and some marine environments, halon is now prohibited across Australian industries due to its extreme ozone-depleting and global warming potential upon entering the atmosphere.
Agents that are permitted for use under the Regulations must be obtained from companies who hold an EATA (Extinguishing Agent Trading Authorisation), a permit which is issued by the FPIB. These substances are used regularly on mining sites because they are non-conductors of electricity, cause minimal damage to equipment and have favourable environmental properties, whilst being clean and leaving no residue.
When using scheduled extinguishing agents, the FPIB recommends that builders, operators and owners of sites with gaseous fire suppression systems containing scheduled extinguishing agents ensure that the installation and maintenance of these systems is done by licensed technicians. Regular maintenance and service of gaseous fire suppressions should be conducted to ensure full functionality in the event of a fire and all technicians working with scheduled extinguishing agents must hold the appropriate licence, authorisation, or permit.
The value and effectiveness of gaseous fire suppression systems requires that they be properly designed, installed, commissioned and maintained. Put simply, if operators don’t get these elements right, a fire protection system is more likely to fail when needed.
In addition to this, although there is no requirement to replace systems, owners should consider changing these to environmentally friendlier alternatives where possible.
There are also a number of extinguishing agents that are not regulated under the government. For example, CO2, watermist and nitrogen or argon inert gases are non-scheduled substances that do not fall under the act.
Ultimately, environmental responsibility and care using fire suppression systems and extinguishing agents in the mining sector goes beyond regulatory compliance. It is a moral imperative and the mining industry – a significant contributor to domestic and global trade – must also bear the responsibility of minimising its environmental footprint.
Not only is following the recommendations outlined by the FPIB an important way of keeping sites and crew members safe, but staying compliant with the relevant regulations is critical in helping Australia uphold its international duty and obligations in reducing ODS and Synthetic SGG use under the Montreal Protocol.
Adopting fire suppression systems that don’t rely on ODS or SGG use where possible or preventing the required use of an extinguishing agent entirely can assist Australia’s mining industry in demonstrating a commitment to both safety and sustainable practices.
Through the integration of both safety and sustainability measures, the acquisition of appropriate licenses, training and maintenance, the resources sector can correctly and effectively protect against fires, but can do so while causing less damage to the environment.
The copper industry plays a key role in driving the push to net zero, but alongside assisting other industries to reach their targets, the copper industry must also take steps to decrease its own carbon footprint and reduce greenhouse gas emissions.
In late 2023, market analysts CRU predicted that copper demand will grow by 39 per cent to 42.5 million metric tonnes by 2050, but not everyone in the industry agreed. The United Nations said that demand would double and although S&P Global agreed, it said demand would hit 50 million metric tonnes a bit earlier in 2035.
The point is that copper speculation is now rampant as markets, traders and analysts attempt to get an accurate fix on demand, supply and, ultimately, prices.
Does it matter? If the world is to have any hope of achieving its climate goals it most certainly matters given the crucial role copper is playing in global decarbonisation and electrification.
Already a number of authorities like the US Government, the European Union, the International Monetary Fund, the World Bank and the International Energy Agency – and of course the Federal Government – are starting to question how to boost supply at a time when new deposits are hard to find and existing mines are increasingly producing lower grade ore.
Next generation copper
Finding and processing more copper ore is also an urgent quandary for copper companies who are under pressure to lower their own climate footprint.
This pressure comes as the copper industry is said to produce 0.2 per cent of the world’s carbon footprint each year across Scopes 1, 2 and 3, and as the copper industry aims to hit ambitious net zero benchmarks of its own.
A series of sustainable mining roadmaps have been developed and released by the International Copper Association Australia (ICAA) and other
stakeholders over the last few years in a bid to help the copper industry lower its carbon footprint.
The latest in the series of roadmaps, Ventilation and Emissions Reporting, was released in March 2024 and offers deep dive technological insights into how copper mines can tackle essential operational and processing issues like water management, material movement and mineral processing as sustainably as possible going forward.
Apart from a broad exploration of current, near and future technologies, systems and processes, the roadmaps plot how companies can benchmark their performance, improve reporting, understand regulatory frameworks and embed innovation both internally as well as collaboratively by tapping networking opportunities, funding resources and utilising new technologies and industry expertise.
Ventilation and Emissions Reporting serves as another critical element in that picture.
Ventilation is a crucial part of the upstream copper production process – particularly for underground mining – where efficient ventilation impacts the energy intensity and operating costs of a mine while contributing to a site’s emission profile and operational viability. It also impacts employee safety, environmental stewardship and assurance.
The importance of adequate ventilation is now well-recognised, with design specifications and regulatory imperatives constantly evolving to meet the demands of modern mining operations.
Each mining operation is different, and advanced ventilation systems are designed to address unique site-specific requirements and challenges.
Ventilation and Emissions Reporting outlines how companies can explore and progress a range of new models that could optimise energy efficiency for existing ventilation systems while exploring novel approaches to ventilation in the future. It begins with optimising planning and design methods coupled with exploring and adopting advanced technologies to support alternate models of airflow and thermal management and air quality control. Specific technology examples could include:
♦ The use of Digital Twin technology for optimised design
♦ ‘Ventilation on demand’ methods to drive positional efficiency and to optimise site energy consumption
♦ The application of advanced sensor technologies to drive interoperability between processes and capture data via Machine Learning and Artificial intelligence
♦ Wearable technology to support thermal management
Understanding emission reporting
Emission reporting is also highly complex as requirements to meet international standards – as well as country-specific and emerging frameworks – present significant challenges for copper producers.
Developments, including Scope 3 emissions accounting, natural capital accounting, mechanisms like Australia’s Safeguard Mechanism and ESG reporting are redefining the settings for environmental accountability.
Ventilation and Emissions Reporting
outlines a comparative analysis across a range of producers, key frameworks and mining regions, including Chile, Peru, the Democratic Republic of the Congo, North America and Australia, revealing the nuanced landscape of emission reporting in mining and the need for harmonised practices. The analysis involved benchmarking select industry advancements, examining the connection with emerging codes of practice and auditing the methodologies utilised for calculating greenhouse gas (GHG) emissions.
This effort highlights variations or deficiencies among companies and the need for more comprehensive baselines. Benchmarking paves the way for an in-depth evaluation of the sector’s total emissions and is an important tool to spotlight areas of focus towards reducing emissions in the future.
Collaboration and innovation
Ventilation and Emissions Reporting is, like the other four previous reports,
a unique collaboration between the resources sector, government, universities and the mining technology industry. Its core message is that innovation will be fundamental to getting the copper industry to net zero and that can only be properly harnessed through partnerships, shared knowledge, cross industry experimentation, facilitation of new ideas and methods and new company-wide approaches.
One real world example that has now grown out of the suite of net zero reports is a digital platform called CopperConnect, which is designed to aggregate knowledge, share insights, document new technologies and accelerate innovation. ICAA is now developing the new platform that will be open to the whole industry – a completely new, accessible and comprehensive way to understand the current state of the industry as it transitions to far more sustainable mining.
Ventilation and Emission Reporting was supported by ICAA and a collection of mining companies, and the ICAA’s
Roadmap to Zero Project is supported by the New South Wales Government.
Sector-wide initiatives for sustainable mining, institutional efforts exemplified by the International Council on Mining and Metals, The Copper Mark, and specific regional initiatives like Australia’s mining standards, set a range of frameworks to support sustainable mining practices. These collective endeavours are instrumental in shaping a more responsible mining sector.
Innovation is critical and the new report identifies systemic barriers in the industry, challenges traditional methodologies and fosters a culture of collaboration and knowledge exchange to foster real change. Every copper producer and each copper operation will face its own pathway to decarbonisation, but Ventilation and Emission Reporting suggests what can be done together.
The full report can be read at www.copper.com.au
Advanced ventilation systems are designed to address unique site-specific requirements and challenges. Image: Michael Evans/stock.adobe.com
Navigating a career in the traditionally male-dominated mining sector is not for the faint of heart and requires strength and resilience. From her beginnings as an underground miner to her current role as President and Chair of the Australasian Institute of Mining and Metallurgy (AusIMM), Nicole Brook shares how she overcame obstacles to establish a successful career in the industry.
Despite building an impressive career and passion for the industry, Nicole Brook didn’t always dream of working in the mining and resources sector.
Like many others, Ms Brook didn’t know what she wanted to do when she finished Year 12. Electing to take a general engineering degree at the University of Tasmania, Ms Brook first found out about mining engineering from a friend. Her immense love of learning is what initially drew her to the discipline.
“At the very core of my being is that I love to learn – it’s what I live for. It’s my favourite thing to do.”
Ms Brook said that the appeal of studying mining engineering was that it offered her the chance to learn about not just one engineering discipline, but all of them.
“You learn about geology, surveying, environmental science – it’s such a broad field of study. The breadth of things I could learn about was what attracted me to mining engineering.”
Once she had immersed herself in the world of mining engineering through her university studies, Ms Brook’s first vocational work experience at the Renison tin mine on the West Coast of Tasmania solidified her
interest in pursuing a career in the resources industry.
“I loved the application of what I’d been learning at university into what I was doing on the mine site. But even more so, I loved the camaraderie of the people I worked with in underground mines. You’re in that situation where you absolutely need to rely on each other and that’s very inherent in my nature – it really suits the way I like to work.
“I fell in love with it, and decided this is the place for me. Lots of things to do, lots of things to learn and great people to learn them with.”
After graduating, Ms Brook’s first few industry roles involved working in underground mines in New South Wales and Queensland. During this time, Ms Brook faced two significant experiences that impacted her deeply on both a personal and professional level, acting as the driving force behind the types of roles she sought out throughout her career.
Tragically, there was a fatality at the underground mine Ms Brook worked at within her first year of work in the sector, which makes her emotional to this day.
Since that time, Ms Brook has worked in a wide variety of roles, ranging from technically challenging positions in remote locations in which she learnt how to best manage the mines, to corporate business development roles in capital cities where she learnt about the business side of mining. Ms Brook has also worked in consultancy roles, which she said are a combination of both.
“It was all of those experiences that I sought, driven by those two early experiences, that developed my skill set and then led me to the roles where I feel I can make the most impact.”
Currently, Ms Brook is a Non Executive Director at Whitehaven Coal and the President and Chair at AusIMM. While the two roles seem quite different – one at an ASX 100 company and the other a not-for-profit association representing professionals in the resources industry – Ms Brook said the roles are really quite similar; both positions require her to harness the experience she’s gained throughout her career to influence outcomes in the resources industry.
“There’s more to be done. But it’s certainly nice to not be the only woman in the room anymore.”
“That event really instilled in me an absolute passion for understanding the environment in which we mined and making it safe for everyone. It drove my technical passion to really understand the geology, the geotechnical, the ventilation – all of the things that go into making a mining environment safe. I wanted to learn as much as I could about difficult technical environments.”
Within the same 12 month period, the mine that Ms Brook was working on went bankrupt.
“I saw the impact that had on not only the workforce, but also the management team, the community and the broader suppliers and mining services industry.”
The experience drove her to want to learn more about the business of mining so she could gain the knowledge required to generate opportunities for people and create sustainable mines.
“Both roles involve firstly developing a deep understanding of the business. You’re always scanning the horizon for trends that are coming, shaping strategy, making sure that the business has good and sustainable governance practices and helping management to achieve their goals.”
Despite some misconceptions about the mining industry, Ms Brook said it isn’t all about big machines working in remote places, but is instead about the people who are making a positive difference.
“Day to day, I get to interact with passionate, caring people which is absolutely awesome.
“My role is incredibly rewarding. I’m able to see the absolute depth of talent we have here in Australia.”
Reminiscing about her 28-year career in the industry, Ms Brook said that her biggest highlight was during her time at Glencore leading a professional
“Throw out what you think being a leader in the mining industry is.”
team that, in the space of a few years, transformed the business through mergers and acquisitions, whilst still strengthening and managing the existing business.
Ms Brook said her highlight is not necessarily related to the business outcome, but the way the team operated throughout the process.
“We had a culture of inclusion, respectful debate, collaboration –solving some really complex issues in an extremely stressful environment. I’m incredibly proud of how the team did that.”
Though Ms Brook’s career has been overwhelmingly positive, it has not been without its challenges. Ms Brook said that the biggest challenge she’s encountered is not linked to one event, but the situations throughout her career where her own insecurities got the better of her.
“Like many women, I’ve had imposter syndrome at certain times. If I have regrets, they would be learning afterwards that someone else felt the same way I did and that we might have achieved a better outcome if there’d been a broader discussion, or left a legacy for the next person.”
Industry improvements: slowly but surely
Ms Brook began working as an underground miner only four years after New South Wales had lifted its legislative ban on women working underground. As a result of this, many of the men that Ms Brook worked with had never worked with a woman underground before.
“That sounds as if it would throw up a whole heap of challenges – and it did – but actually, my lasting memories of that time are overwhelmingly good. And they’re good because of those men.”
Despite her largely positive experiences, Ms Brook acknowledged that there are barriers to overcome when working in a male-dominated industry like the mining and resources sector. For Ms Brook, a big hurdle has been the assumptions – both large and small – people made about her because of her gender.
An example of this that Ms Brook was able to pinpoint is her experiences being the only woman in the room and it being automatically assumed that she would be the one to take notes.
“It sounds like a tiny little thing, something that’s just nice to do as
part of the team. But actually, it means that you’re not participating in the conversation.”
Another clear example that sticks in Ms Brook’s mind is an occasion in which her team had worked really hard to acquire a particular mine, but when it came time to visit the mine and meet the team, it was assumed that she wouldn’t want to participate.
“The people who decided that I didn’t need to go were doing it out of a good
motivation as they knew I was very busy and so assumed that I couldn’t make the time.
“They wouldn’t assume that of a man.”
Overcoming barriers and opening doors
Since her days as an underground miner, Ms Brook said the overall level of functional infrastructure onsite has improved.
“When I started, there wasn’t a bathhouse for women. I had to use the manager’s personal shower, which was accessed through and adjacent to his office. Thankfully, things have changed in that respect.”
Ms Brook said that there is now a much greater awareness of and acceptance that a diverse workforce leads to better outcomes.
“There’s also many more role models for women, which I think is incredibly important and is something I touched on in my closing remarks at the AusIMM International Women’s Day Event.
“They’re all really positive advancements from where we’ve come.
“There’s more to be done. But it’s certainly nice to not be the only woman in the room anymore.”
Inspiring the next generation
In 2018, Ms Brook was named Exceptional Woman in New South Wales Mining and was also selected for the 100 Global Inspirational Women in Mining.
Ms Brook said this recognition was incredibly humbling and also goes out to all of her hidden support systems.
“It’s easy to think that you’re out there doing it yourself, but it’s just not the case.
“Without my husband, my mum, my friends – without my colleagues, who always managed to effectively manage me up – I couldn’t have done what I’ve done throughout my career,” Ms Brook said.
“It was an incredibly proud moment for me, but I was also really proud for them.”
When asked what kind of message she would like to pass on to other women in the industry or young women considering a career in the resources sector, Ms Brook said the first step is to “throw out what you think being a leader in the mining industry is”.
“If you think about the personal attributes you need to influence, it’s not about being the loudest, or the strongest, or the smartest, or anything like that. It’s about emotional intelligence. It’s about adaptability, self-awareness, active listening and intuition,” Ms Brook said.
“I would hate to think that any woman thought that she couldn’t be a part of or do a role in the mining industry just because she’d never seen anyone do it.”
“Those are not skills that are exclusive to men. Women are strong in a lot of those skills.
“Throw out what you think that model of a leader is, take your skills and then combine them with a bit of self confidence.
“You do that, and you’ll be that leader who takes us into the future.”
To advocate for women in the industry, Ms Brook emphasised that it is essential that women understand there are multiple models of success.
“I would hate to think that any woman thought that she couldn’t be a part of or do a role in the mining industry just because she’d never seen anyone do it.”
Ms Brook said it all comes back to the adage: you can’t be what you can’t see.
“We need people to share their stories. We need to share challenges and successes. The more diverse
storytelling we have that we can shine a light on, the more chance we have that it’s going to resonate with someone.”
To ensure women’s participation and confidence in the industry continues to increase, Ms Brook highlighted the importance of senior female leaders leading by example, demonstrating the type of leader that the industry needs.
“There is so much opportunity for women and their skills. We need to continue the good work we’ve done on providing infrastructure and support systems that enable women to participate.
“We’ve seen job sharing at the highest levels and women promoted during maternity leave,” Ms Brook said.
“It can be done. We just need to lean into it and highlight the examples of good practice.”
Industry awards are a great way to gather and celebrate the achievements of peers. The 2024 Chamber of Minerals and Energy’s (CME) People’s Choice Award winner and General Manager of Remote Operations at Roy Hill, Lily Meneghel, sat down with Mining to chat about her win and her plans to use her new platform to promote gender diversity.
Mining: You pursued a Political Science university degree before pivoting to a career in the mining and resources industry. What inspired you to make this change?
Lily Meneghel: Growing up in the ACT, I was initially attracted to a career in political science – politics being a strong interest of mine as a young person. I was drawn to the possibilities of making positive changes that this career offered.
However, after I finished school, a holiday to Western Australia broadened my perspective. The vastness and intrigue of the mining industry captured my imagination.
What was it about the mining and resources sector that made you want to enter it?
Mining and resources appealed to me for the following reasons:
Being part of something big
The sheer scale of operations in the Pilbara was fascinating to me. The logistical challenges of moving millions of tonnes of iron ore was something I became really interested in and my career has been centred around solving these challenges. Equally fascinating was the fact that iron ore is used in so many aspects of our daily lives.
Innovation
Having a passion for technology, I was attracted to the sector's investment in cutting-edge technology and continuous improvement practices. I wanted to be part of an industry that is not only economically significant but also at the forefront of innovation. At Roy Hill, I found a company that is led by Chairman, Gina Rinehart AO, who has pioneered a culture of innovation that has delivered not only safer and more efficient operations at Roy Hill, but right throughout the broader mining industry.
Professional growth
The diversity of roles within the sector offers vast opportunities for professional development. I was excited by the prospect of taking on new challenges
and growing my skill set in a dynamic environment.
Local and global impact
Understanding that the sector is fundamental to building and supporting modern societies, I was drawn to the opportunity to contribute to an industry that provides essential materials for everyday life and technological advancements.
Locally, mining acts as the catalyst for economic progress in Australia and has a positive downstream impact on other industries which supports all Australians. Upon entering the industry, you relocated to Port Hedland. What were the initial challenges you faced making the move?
In 2008, having just turned 22, I relocated more than 3,000km away to Port Hedland to start my first mining job with BHP. That is where my real journey began; where I embarked on a huge learning curve about the workings of the resources industry and the grand scale of the projects being undertaken in one of the most isolated places in the world.
The remote nature of living in Port Hedland was a significant change from living in Canberra. The transition required me to adapt to a smaller community and to find new ways to stay connected with loved ones. In facing these challenges, I focused on building strong relationships with my colleagues and the local community. This helped me to quickly feel at home in Port Hedland.
I embraced the learning opportunities presented by the new environment, which has been incredibly rewarding both personally and professionally. You started in computer programming before moving to operational roles. Can you talk us through the various roles you’ve had within the industry that have led you to where you are now?
My entry point into the industry was based on my self-taught computer programming skills, but quickly after joining I realised my passion was in
operations. Since then I have held a number of technical and leadership roles centred around optimising the movement of iron ore through the supply chain. These roles have provided the perfect mix of technical innovation and operational challenges.
My current role as General Manager Integrated Remote Operations at Roy Hill spans across the entire operations, optimising the movement and blend of iron ore from pit to port.
I’m really fortunate to lead a team of talented professionals who are committed to operational excellence.
What do you consider to be the biggest challenge you’ve encountered in your career to date? What has been the biggest highlight?
I commenced at Roy Hill as a Manager in Control Operations in April 2022. This role has proven to be the most challenging but also most rewarding of my career so far. The role involved me leading the successful transition of the Automated Haulage System (AHS) Control Operations to Roy Hill’s Perth Remote Operations Centre (ROC), making the decision to move the controlling equipment for this program 1,300km away in the Pilbara.
This was a complex and challenging project that required managing many layers of operations in a new organisation. The first move was organising a series of trials at the ROC to ensure it had the capability to work as expected and support all AHS and conventional functions required.
The second part of the transition was the human element; familiarising ROC personnel with the AHS system, terminology and processes, while ensuring sufficient training was provided to support full-scaled operations. The successful transition of the ROC has been valuable in terms of achieving significant organisational cost and time efficiencies and although challenging, a major personal highlight of my career to date.
Can you give some insight into your experience working in such a maledominated industry? What are some of the unique obstacles you have had to overcome?
I've encountered a few unique obstacles that have ultimately contributed to my professional growth. One of the most significant challenges has been overcoming preconceived notions about women's roles and capabilities in the workplace. To overcome these obstacles, I've focused on expanding my knowledge, skills and professional networks and taking all opportunities that become available to me.
You have been involved in mentoring programs and initiatives such as the Parental Return to Control Program and the Control Operations Traineeship Program to empower others, particularly women. What are some of your biggest takeaways from these initiatives?
A few key takeaways come to mind from initiatives aimed at empowering women and facilitating parental return to work, in particular into fields such as control operations.
Inclusivity boosts innovation: It’s simple; nurturing different perspectives can lead to more innovative solutions and better decision making.
Support systems are crucial: Programs that offer mentorship and support networks are vital for helping individuals navigate their careers, especially when returning from a break or starting in a new field.
Flexibility is key: Initiatives that offer flexible work arrangements for parents can be incredibly beneficial, making it easier for parents to balance work and family responsibilities.
Confidence building: Such programs often help participants build confidence in their skills and abilities, which is crucial for their growth and advancement in the workplace.
Skill development: Continuous learning and upskilling are important. Programs that focus on training and development help participants stay current with industry standards and technologies.
Barriers are being broken: These initiatives demonstrate that barriers to entry or re-entry into specialised fields can be overcome with targeted support and structured pathways.
Retention and satisfaction: Programs that support personal and family responsibilities as well as career development can lead to higher job satisfaction and retention rates among participants.
Role models matter: Seeing successful women in leadership and technical roles can inspire others and shows that career progression is possible.
Cultural change: Such initiatives contribute to cultural change within organisations, challenging stereotypes about who can succeed in certain roles.
Feedback and adaptation: Gathering feedback from participants helps to continuously improve these programs, ensuring they meet the needs of future cohorts effectively.
Why is it so important to you to mentor and empower others in the industry?
With fewer female role models in leadership positions, I've had to be proactive in seeking out mentors – both male and female. This has not only helped me grow but has also allowed me to mentor other women in the industry, fostering a more supportive environment for all.
For me, mentoring provides an essential tool in helping more differing perspectives find a home in mining engineering. Mentoring has been as much about my professional growth as it is to the people that I mentor.
You won the People’s Choice Award at the 2024 Chamber of Minerals and Energy’s Women in Resources Awards. What does winning the award mean to you? What message do you hope to convey to young women in the industry?
It was personally such amazing recognition to win the People’s Choice Award. I strive to provide a positive impact on the industry and this acknowledgement from my peers made the award even more valuable and appreciated. I hope the award serves as encouragement to other women in the industry that their contributions can be recognised and celebrated, inspiring them to strive for leadership in their own careers.
The award also highlights the importance of inclusion in the resources sector, sending a message that the industry values the perspectives and skills women bring to the table.
At Roy Hill, we are deliberate on both increasing representation of women in operational roles, as well as creating pathways for women into senior leadership roles. Through Mrs Rinehart’s leadership, we continue to implement initiatives that enable us to build a pipeline of talent for the future through higher numbers of women in our early careers programs which span across
our trainees, apprentices, vacation and graduate programs.
It’s a complex challenge faced not only by the mining and resources sector, but all industries and sections of the community. I’m proud to be working for a company that is genuinely committed to encouraging more women into the industry and these events highlight the message to young women that their contributions matter, to aim high, seek support and be persistent.
What advice would you give to young women who are interested in, or are in the early stages of their career in your industry?
Embarking on a career in mining can be an exciting and rewarding journey. My advice would be to invest in your education, understand the qualifications required for the roles that you are interested in and pursue the relevant courses, certifications or degrees.
Build a strong professional network, attend industry conferences and connect with peers and mentors who can provide guidance and support. Seek out mentors, both male and female, who have experience in the mining industry.
Gain hands-on experience. Taking opportunities to work onsite to grow your understanding of the day-to-day operations of a mine is crucial for career growth. Be your own advocate, speak up about your career goals and don’t be afraid to negotiate for what you deserve.
Stay informed – keep up with industry trends and technological advancements. The mining sector is evolving and staying informed will help you adapt and remain relevant.
Be prepared for challenges. The industry can be demanding and sometimes male-dominated, so resilience and determination are key. Take care of your health and well-being; mining careers can sometimes involve long hours or remote work and your health matters.
Share your knowledge and experiences to be a positive role model for others and remember to support other women in the industry as you progress.
The mining industry offers a wide range of career paths, from engineering and geology, to finance and human resources. There's a place for all skill sets and backgrounds and your unique perspective can contribute to the industry's growth and innovation.
Lead by example and use your success to help others.
For some, the path to the resources industry is clear cut, but for others it can be a case of taking the road less travelled. For Clarisse Orchard, it was her passion for creating things by hand that eventually led her to the position and industry she thrives in.
ollowing her high school graduation, Ms Orchard found herself at a crossroads, trying to determine the path she wanted to take.
“When faced with what I wanted to do with my life after graduating, I was guided down the path of university by my parents, but the only thing that stood out to me was how much I enjoyed welding in high school.”
For Ms Orchard, it was the appeal of developing hands-on skills that allowed her to create things from scratch that initially led her to pursue a welding career and, unknowingly, introduced her to a mining and resources position, which Ms Orchard said she is currently in and “loving”.
Ms Orchard began her career in the resources industry as a trade assistant.
“I worked in many hands-on roles within the business – from general workshop duties to maintenance and assisting in the busy store area with packaging, receivals and dispatch of finished goods.”
Even though these roles were not necessarily what Ms Orchard had initially pictured for herself, she tackled them with a cando attitude in the hopes that the business would recognise her potential.
“When they did, I was offered an apprenticeship as a heavy boilermaker which lasted for four years, during which I gained the hands-on and engineering skills that allowed me to excel further in my chosen career.”
A year after the completion of her apprenticeship and following many site visits for shut-downs, the company Ms Orchard was working at went through an organisational change. The change opened a vacancy for a Technical Process Specialist (TPS) who would work through all stages of projects, from front end assessment and quoting to job planning, management and close-out.
“I believe my perseverance and dedication early in my career set me up for the dynamic role as a TPS,” Ms Orchard said.
Tackling common challenges
Though her career path may be different from other women in the industry, Ms Orchard said that the biggest challenges she’s had to face are likely similar to those of her peers.
“We face clichéd stereotypes based around women in mining. The focus is put on women to ‘man up’ and prove themselves when compared to their male colleagues.
“From the beginning of my journey to where I am now, there has always been a battle of showing who I am and what I can do to ensure that my value is seen as the same as everyone else.”
Where other women may find the transition to a maledominated field confronting, through her years in the industry, Ms Orchard feels she has found her place despite the obstacles she’s faced.
“This was my first job coming out of high school, so this is all I know.
“Working with male colleagues has had its challenges – like having to prove my capabilities daily, changing my natural conflict responses to better suit my male coworkers, changing my physical attributes to suit the role’s demands and always comparing myself to a physical gender difference that is apparent in everything we do.
“At times, to overcome obstacles in the last decade, I have had to think like a man, act like a man and talk like a man. If I didn’t learn to adapt, I wouldn’t have been able to survive in this industry.”
Alongside the challenges she faced in her career are some tremendous highlights and the opportunity to lay the foundation for other women entering the industry. When asked to nominate a career highlight, for Ms Orchard, it was a cinch.
“The highlights of my career are successfully earning my boilermaker certification and being a finalist in the Women of Resources Awards for 2024.”
Ms Orchard said that being nominated in a category which celebrates her progression in her trade after all she’s been through was such an amazing feeling.
“The nomination took me by surprise because I never knew the journey that I had been on was such an inspiration to other women. It made me very proud of my achievements. The recognition this award created was terrific and it has positively impacted my career and self-esteem in many ways.”
Using the new platform the nomination awarded her, Ms Orchard hopes to encourage other young women wanting to start a trade in mining, but also enable them to have realistic expectations about their future working environment.
“You will be doubted. You will be judged. You will be assessed more than your male colleagues. But you will also find strength in the tough times; you will find pride in yourself as you progress.
“You will develop lifelong skills that you can carry in and out of work that you never thought you could achieve because you pushed past all of the roadblocks and made it to the other side.
“Through your pride and strength others will be proud of you, too – even the men.”
The knowledge that her achievements as a woman in her career are rare helps motivate Ms Orchard to persevere in the industry.
“To look back at what it has taken for me to get to this point serves as its own encouragement to keep going because every time I have failed or been rejected it has given me the opportunity to better myself.
“My colleagues at Callidus Welding Solutions have been a huge support to me throughout my trade and at times helped me find the drive to keep continuing on.”
Although being exposed to the trade industry as a young high schooler gave her some insight into what life would be like if she pursued a trade, Ms Orchard said she didn’t get the chance to witness the mining work culture for women and the expectations that came with getting a trade.
This kind of exposure, Ms Orchard said, would be helpful for the young female generation and she suggested establishing programs that bring industry leaders into high schools to speak to the young women about the industry.
“Educate them on the pros and cons, what they can expect and how they can overcome those challenges. We can encourage our female youth to go out there and get a job in mining without fear or doubt.”
Skills shortages continue to plague industries throughout Australia and the need to tap into and attract a more diverse workforce has generated a wide range of industry programs and initiatives.
Thiess’ Mt Arthur South operations is striving for a new era of inclusivity in the mining industry with its innovative Mt Arthur South Indigenous and Inclusiveness Trainee Employment (MASITE) Program.
Launched in March 2021, the MASITE Program offers comprehensive 12-month traineeships and aims to encourage Indigenous and female candidates from the local community to pursue careers in mining. Since its inception, the program has not only helped shift the culture at the Mt Arthur South site, but has also earned industry recognition for the results it has achieved.
A key aim of the MASITE Program is to attract fresh talent to mining by focusing on candidates who are new to the industry, with program trainees coming from various backgrounds, ages and life experiences, enriching the workplace with their unique perspectives.
During the 12-month traineeship, participants gain both theoretical knowledge and practical skills under the guidance of experienced mentors and trainers. The program aims to equip trainees with the expertise they’d need to thrive in mining operations while also fostering a sense of community and inclusivity.
The training hub also features traditional Indigenous artworks from the Polly Farmer Foundation and a yarning circle, offering a welcoming space where trainees can learn and connect with one another.
On successful completion, participants earn a Certificate III in Surface Extraction, CAT 793 rear dump truck skills, light vehicle competency and a first-aid certificate. This training ensures trainees enter the workforce well prepared for the demands of the mining industry.
One of the first female Indigenous program participants, who has progressed to the position of Dispatch Officer, Isabella Ford, said “It has been an amazing opportunity to grow a career with a supportive group of people. The MASITE program has allowed me to gain so many new skills and has set me on the right path for my career. I feel excited about the future.”
Since its launch, 122 individuals have participated in the MASITE program, including 73 women and 57 who identify as Aboriginal or Torres Strait Islander. The increased diversity has had a positive effect on the Mt Arthur South site’s culture, with female representation growing to 23.7 per cent and Aboriginal and Torres Strait Islander representation rising to 11.2 per cent.
The program has a high conversion rate of trainees to permanent roles at Thiess, with 92 per cent of MASITE trainees making the transition to permanent employment after completing the program.
Mt Arthur South Project Manager, John Hamson, said, "We created the MASITE program to bring new opportunities to underrepresented groups in the mining industry. Our goal was to encourage Indigenous and female candidates from the local community to pursue a career in mining. The success we’ve seen – both in terms of participant outcomes and industry recognition – is a testament to the dedication and hard work of our entire team.”
The high conversion rate from traineeship to permanent employment has led to the trainees becoming valued members of the team.
“For many participants, this program has been life-changing, providing a new pathway to rewarding careers and creating a brighter future for them and their families,” Mr Hamson said.
The MASITE Program’s impact has not gone unnoticed.
At the 2024 NSW Women in Mining Awards, the MASITE program won the ’Excellence in Company Programs and Performance’ award, further underscoring its positive impact on the mining industry.
Looking ahead, Thiess plans to continue onboarding between 48 and 72 new MASITE trainees in 2024, in a sustained commitment to expanding the program. Other Thiess operations on the east coast of Australia have expressed interest in adopting the program, with discussions underway to expand its reach. Although each site has unique challenges and requirements, the core principles of the MASITE Program – including its focus on inclusivity and comprehensive training – can guide broader implementation.
The MASITE Program’s success at Thiess’ Mount Arthur South site can serve as an example of how targeted programs can help drive positive change in the mining industry. By focusing on diversity and inclusion, the program has helped to improve the site’s culture while providing valuable training and employment opportunities for women and Indigenous Australians. With ongoing support and plans for expansion, the MASITE Program is expected to continue its positive impact, paving the way for a more inclusive future in mining.
Although Melbourne is likely not at the top of the list of Australian mining jurisdictions that come to mind, for more than two decades the Melbourne Mining Club has been working to promote the resources sector and o er networking opportunities for senior leaders in global mining and mining service companies.
Founded in 2001, the Melbourne Mining Club (MMC) is a not-for-profit joint venture (JV) between the Minerals Council of Australia and the Australasian Institute of Mining and Metallurgy (AusIMM). With a clear goal of providing a forum to discuss the key topics facing the global resources industry, the MMC’s volunteer-based Steering Committee organises six lunch events per year, inviting the chairs and chief executives from mining giants to come and speak.
At the MMC’s May 2024 lunch event, it was announced that, after a decade in the role, Richard Morrow would be retiring from his position as Chair of the Steering Committee and Orica’s Vice President – Global Business Services and Organisational Effectiveness, Sally Cox, would be stepping into the role as the first female Chair in the MMC’s history.
PR to resources: making the switch
A Bachelor of Arts followed by a graduate degree in Business and Public Relations led Ms Cox to a role in a PR firm specialising in financial and corporate communications. This eventually provided a pathway for communications roles in the mining and resources sector.
“After a number of years working for clients across the energy, FMCG and financial services sectors, I ultimately took an in-house role with mining company Zinifex Limited as a Communications Advisor.
“I was immediately enthralled by the industry and loved learning about the business, how mines and processing plants operated, its challenges and how the company managed them proactively with a focus on ESG.”
Ms Cox said she also recognised the career pathways on offer in the sector
and how, if people were willing to jump in and give something a go, they could be rewarded with new challenges and opportunities.
“This was how I started to move across different functional roles and branched out from communications to human resources, strategy and transformation.
“I have been supported by wonderful leaders in the industry who encouraged me to try new things, pursue further education, enabled me to manage the challenges of raising a family and the flexibility required to successfully manage work/life balance.”
Although Ms Cox said there have been plenty of challenges that she encountered throughout her career, she said that she always received the support of her leaders along the way.
Pinpointing one time that presented not only the biggest challenge but also a career highlight, Ms Cox spoke about
the time she spent living and working in China.
“I spent three years working in Hong Kong for BASF, one of the world’s largest chemical companies, through a period of great disruption including the 2019 protests in Hong Kong and the global COVID-19 pandemic.
“Being away from home, working across new jurisdictions in Asia, learning new cultural contexts and navigating a complex multinational organisation was personally challenging, but also very rewarding and definitely a career highlight, as I feel I really developed my leadership skills through the experience.”
Throughout her time in the resources sector, Ms Cox has made the effort to attend industry events to not only stay abreast of the challenges and innovations in the industry but also to network with her peers. Her efforts meant that she was acquainted with and attended events held by the MMC before she accepted her new role.
“I first joined the Steering Committee of the Melbourne Mining Club in 2018.
“For many years I had been a guest at the events and supported the CEOs of companies I had worked with to prepare keynote speeches for the lunches. The Club provides a unique networking opportunity and promotion of the industry and I felt after many years of
benefitting from it that it was time I also dug in and contributed.”
Speaking about stepping into the role, Ms Cox said it is an honour to chair the Steering Committee of the MMC as it enters its 23rd year.
“The Steering Committee is a passionate group of volunteers from across the industry, supported by our joint venture partners. I hope to continue to build on the platform and legacy the Club has created and ensure it delivers value to its members and guests into the future as our industry continues to evolve.”
As the first woman to hold the position, a key focus for Ms Cox is increasing diversity within the sector.
“I am very passionate about supporting Diversity, Equity and Inclusion (DEI) in the industry and am proud of the progress we have made to date. We have many wonderful female leaders in senior roles right across the industry and it’s important that the Mining Club also reflects and leads on this.
“I think the business case for gender diversity is now well accepted across all industries – we know that more diverse and inclusive organisations are more successful across financial, social and other performance metrics.
“Mining, like a number of other technical industries, has been traditionally male-dominated and, like other industries, will benefit from a greater balance of skills, experience and
viewpoints, particularly in leadership discussions.”
Reflecting on her own experiences throughout the nearly 20 years working in the traditionally male-dominated sector, Ms Cox said she can see how far the industry has come in the time since she first began her career.
“In my early years I remember being not only the only woman in the room, but also often the youngest person in the room. It felt intimidating and was challenging to feel confident to share my opinions.”
Stepping into the role as Chair of the Steering Committee, Ms Cox finds herself with a new platform where she can offer advice to young women who are interested in or are already in the early stages of their career in the mining industry.
“The mining and resources sector provides fantastic career opportunities across a very broad range of roles, technical disciplines and locations. DEI and employee engagement are in the core of corporate strategies and the opportunities for young people are very attractive as the industry seeks to build its future talent pipelines.
“The industry is constantly evolving and adapting to external challenges and today sits at the forefront of supporting the global energy transition – it’s an exciting place to be.”
Isolation – both geographical and personal – is common in the resources sector. Sabina Shugg AM, founder of Women in Mining and Resources Western Australia (WIMWA), overcame her feelings of isolation and now uses her experiences to empower women, while promoting diversity and inclusion in the industry.
Having had her father and an uncle study geology at the WA School of Mines, Ms Shugg had some knowledge of the Australian resources industry before she even began her own career in the sector.
Following in family footsteps, Ms Shugg would eventually graduate with a degree in Mining Engineering from the WA School of Mines in 1993.
Ms Shugg’s career in the industry, however, started before her tertiary education – working as an assay clerk at the Jubilee Mine in Kalgoorlie. This opened up a number of opportunities, including roles as pit tech supervisor, surveyor and eventually pit supervisor.
Career progression
After university, Ms Shugg began working underground and held a variety of roles from underground operator to underground manager, quarry manager and more.
Reminiscing on her early career, Ms Shugg said, “It was an interesting time and some days were more difficult than others. People are generally happy to give you a go if you come in with the right attitude, so all you can do is do the best you can.”
Having gained experience in both open pit and underground mining environments, Ms Shugg was able to secure her first-class mine managers ticket but wasn’t quite ready to use it right away.
“It was a matter of getting some experience as an engineer, doing things like ventilation, drill and blast, planning – really understanding what it is that makes the mine work.”
Ms Shugg said that kind of experience, as well as working in tandem with other parts of the mine – such as metallurgy, geology and maintenance – is the nuts and bolts of what goes on in a mining environment.
Careers in the mining industry can take on many forms, both on and offsite – something Ms Shugg can attest to. As well as working in mines, Ms Shugg’s career has involved a number of corporate roles, from technical and management consulting
roles and Board positions, to a position as Director at the WA School of Mines.
Ms Shugg said that the biggest highlight of her time working in the sector is the growth that she has witnessed for women in the industry.
“The mining industry has so many opportunities. So many people I know started as operators and ended up in roles such as managers and directors. There are some fantastic career options with wonderful financial outcomes for people, their families and their communities as well.
“Part of what I have tried to do along the way is support women, to make sure that those many opportunities are available for women and not just for the lucky few.
“If we can make workplaces welcoming for women, they’re welcoming for everyone.”
The power of shared experience
Ms Shugg said there were times throughout her career where she felt isolated – both professionally and geographically –and despite utilising existing resources, didn’t quite find the support she was looking for. As a result of this, it occurred to Ms Shugg that a group specifically for women in mining might be able to fill the gap.
Ms Shugg began to explore how women in the industry could get together to find a way forward and make a difference and in 2003 she founded pre-eminent Women in Mining and Resources Western Australia (WIMWA) to do just that.
“For our first event, we just all got together and everyone had a lot to say – 60 people turned up and we were all pretty excited to have this forum.”
Following a number of grassroots networking events, Ms Shugg’s peers were able to get contributions from their companies to host the events and provide speakers, allowing WIMWA to host eight to ten events per year.
With this support, WIMWA was able to highlight the conversation on diversity, which led to higher level and longerterm support from industry and helped get some of WIMWA’s initiatives off the ground.
Due to WIMWA’s early success, the organisation began to host a one-day seminar that grew into a two-day summit,
enabling more people to participate. Recent events have had up to 1,200 attendees each day and, unlike WIMWA’s early days, the audience at WIMWA events is now roughly 30 per cent men.
“It’s great for everyone to come along and see things differently. They can then go back and make real changes in their organisations.”
WIMWA also hosts a mentoring programme, in which mentees are matched outside their own organisation, which has helped close to 1,500 people over more than a decade and led to some excellent outcomes.
“People have had all sorts of changes in their careers and lives as part of the WIMWA mentoring program and they go out and share what they’ve learnt with their teams and their communities.”
Over time, WIMWA has shifted and led the conversation in Western Australia and further afield with its activities and by creating a forum for women (and men) in the mining and resources industry to talk about their lives, share their experiences and extend their professional networks.
According to Ms Shugg, things have changed a lot since she entered the mining and resources industry, especially for women.
“In the beginning of my career, there were really no senior women in the industry and across the huge range of jobs available, there were very few women. Progression in the industry was very much linear, which often precluded women from getting into particular roles.
“Now, there are women doing every kind of role right across the sector.”
Ms Shugg referred to diversity and inclusion statistics from the Chamber of Minerals and Energy of Western Australia, which indicate that women comprise 21.5 per cent of the resources industry in Western Australia1
“With women in more senior positions, things are being done in a way that wouldn’t have been considered in the past. A long time ago, people wouldn’t have even imagined women being in these roles.”
Speaking further on diversity in the workplace, Ms Shugg dismissed the idea that some women in the industry only get their job because of their gender.
“Most women get their jobs because they’ve got the right skills and the right values.”
In all of the changes the industry has experienced, Ms Shugg likes to think that her work with WIMWA has played a role in shifting the conversation. Though the industry has made strides in inclusion and diversity in recent years, there is still room for improvement.
“Women have plenty of attention on them as to whether or not they’re doing a good job.
“We need to focus on supporting everyone – women and men – in the workplace to get the best outcomes.”
For women in the early stages of their career in the resources industry, Ms Shugg’s first piece of advice is to stand tall and remember that they have earned their place in the industry.
“You’ve got the job, you’ve got the skills and training and you’ve got the values. Every time you walk into a room, you should remember that you deserve your place in that room.”
Ms Shugg also emphasised the importance of enlisting the help of a diverse group of allies to combat the isolation that can sometimes come with working in the industry.
“You need a group of people you can rely on to get the support you need, not just the support you want. In the same way that there is a need to have a mixture of thinking to get the right challenges in a team; for you as an individual you need to have allies that are on your side, but also those who think differently to you to challenge you to help you to grow.”
Ms Shugg said that ultimately, promoting women’s inclusion in the industry comes down to leadership.
“The way people role model their behaviour and display their values trickles down. When workplaces and spaces are welcoming for women, they’re welcoming for everyone.”
Ms Shugg said that people from diverse backgrounds who didn’t fit the previous model of how things were done in the industry – whether it be diversity through gender, sexual orientation, religious or cultural beliefs – have more of a presence in the industry than ever before.
“There are a lot of complex factors that go into creating a welcoming environment, from the recruitment process, to training, to the support provided for employees, but again, these structures rely on strong leadership.”
“Once those standards are set, the rest follows on.”
Australia is a mineral-rich country, with each state having plenty to o er, but recent data has shown that Western Australia is once again the powerhouse of the country’s mining and resources industries.
The Chamber of Minerals and Energy of Western Australia (CME) is a leading advocate for the mining and energy sectors in Western Australia –a significant responsibility given that the Western Australian resources industry supports three in ten jobs across the state and nine per cent of Australia’s gross domestic product (GDP).
CME is a member-based organisation, with early roots stretching back to 1895 in the Goldfields mining town of Coolgardie, that strives to advocate on behalf of its members. With advances in technology, safe mining operations and sustainable practices, the key issues facing the industry have changed a lot since CME’s official inception in 1901, but the organisation’s focus remains the same.
For almost 130 years, CME has represented its members to ensure that the resources sector’s priorities and benefits are understood across governments, businesses and the community. It now has more than 70 ordinary members and 100 associate members representing a diverse range of Western Australian resources projects across the minerals and energy sectors.
Every year, CME surveys its members to gain insight into the level of expenditure by the Western Australian resources sector on wages and salaries, business spend, contributions to the community and payments to the government at local, state and federal levels.
CME’s statistics for the 2022-23 financial year were released in March 2024 and show that the resources sector drives the Western Australian economy and accounts for approximately 30 per cent of the Western Australian Government’s revenue. Publicly available data from the Australian Bureau of Statistics
(ABS) and state agencies shows that in 2022-23, the Western Australian resources sector accounted for almost half of the state’s economic activity and 91 per cent of goods exports.
Survey results and statistics collected by the CME for its annual Economic Contribution Factsheets shows a record $132 billion in direct spending by the Western Australian resources sector in Australia in the 2022-23 financial year – a 32 per cent increase from the previous 12 months.
The CME data for that period showed that at a community level, more than 18,000 local businesses, nearly 1,400 community organisations and 78 local governments benefited directly from spending by industry in 2022-23.
The direct economic contribution of the sector in Western Australia also grew more than 30 per cent, surpassing $77 billion and representing the equivalent of nearly $27,000 for each person in the state.
In short, mining and resources accounted for approximately half of Western Australia’s economic activity and capital expenditure and close to 90 per cent of its goods exports.
In addition to surveying its members, CME commissions third party modelling to quantify the indirect spillovers of this spending throughout the economy and regions. This recognises the vast supply chain that supports and benefits from the industry’s activity.
In 2022-23, spending by the Western Australian resources sector supported more than 350,000 additional full-time equivalent jobs across the remainder of the state’s economy.
CME’s Chief Executive Officer, Rebecca Tomkinson, said the data indicates that the flow-on effects of Western Australian mining and resources operations are felt at all levels of communities right around the country.
“Given that our data represents a snapshot of the activities of only CME member companies, the full influence and benefits provided by our sector would be even greater than what is outlined in our Economic Contribution Factsheets,” Ms Tomkinson said.
“It’s enormously important for not only Western Australians but all Australians that these contributions are able to keep growing and that our industry can continue to deliver for communities.”
Ms Tomkinson said that the most recent economic contribution data was produced against a backdrop of substantial federal reform in industrial relations, emissions management and environmental protection.
Those reforms, Ms Tomkinson said, would hold major ramifications for the resources sector – and by default the state and national economies – if not managed properly.
“It’s critical for industry and, by extension, communities Australia-wide, that the process surrounding these reforms is transparent and consultative to ensure the end result is fit-for-purpose and has longevity.
“The Federal Government’s announcement of a staged approach to implementation of Nature Positive is an encouraging development that provides additional time to work through the details of complex reform.”
The global energy transition – and Western Australia’s role in it – has created a step-change for the state’s mining industry and it has had to respond quickly to take advantage of market demand.
With an abundance of key reserves in battery minerals and the resources needed to develop renewable technology, the state has emerged as integral to Australia’s decarbonisation ambitions.
For Ms Tomkinson, this represents an opportunity to evolve the business as the world advances towards greener energy.
A large part of Ms Tomkinson’s leadership role at CME is stakeholder relations and a formidable agenda of engagement across the state and nationally. Advocating for the industry and communicating its challenges and benefits, Ms Tomkinson said, requires a dedicated, bipartisan government relations approach supported by strategic communications and media engagement.
“At the very core, people are the reason for the industry’s success. Whether its highly skilled engineers or technicians, direct and indirect employees, businesses and the community, the resources industry contributes materially to the lives of all Western Australians. It’s part of our DNA,” Ms Tomkinson said.
“CME leads policy development on issues impacting the sector, promotes the value of the sector to the community and provides an avenue for members and stakeholders to collaborate.
“One of the ways we can articulate those benefits to the Western Australian community – and more broadly to the Australian economy – is via our annual economic contribution factsheets.”
CME believes that one of the Western Australian mining and resources sector’s biggest opportunities lies in the global energy transition and progress towards net zero.
The vast majority of minerals required to construct a solar panel, a wind turbine or a battery can be found with relative abundance in Western Australia. This includes lithium, bauxite, nickel, rare earths, silicon, cobalt, copper, graphite, vanadium and a long-time staple of the Western Australian and Australian economies – iron ore.
Liquefied natural gas from Western Australia also remains very much in demand in Asia and will have strong appeal for emerging nations in the region looking to fuel economic growth while reducing their reliance on coal.
Meanwhile, Western Australia has climatic conditions that are conducive to the implementation of solar and wind power, which are already being used to decarbonise mining and resources operations and will have a role to play in the production of low-carbon fuels of the future.
Hydrogen and ammonia are two such fuels in which Western Australia has an opportunity to be a global leader in clean production and the infrastructure – existing and proposed – to get these commodities to market.
Ms Tomkinson is confident the state also has great promise as a carbon capture and storage hub, for both domestic emissions and those of trading partners overseas. The passage of The Petroleum Legislation Amendment Bill 2023 through the Legislative Council, she said, provides a framework allowing carbon capture and storage (CCS) to be broadly utilised in Western Australia and adding CCS technology is seen as an important part of Australia’s decarbonisation pathway.
“CME continues to support investment in a broad range of affordable technologies including for energy efficiency, abatement and carbon sequestration, so the passage of this legislation is important to enable industry to include CCS in their decarbonisation pathways.”
Ms Tomkinson also referred to the Federal Government’s May announcement of $566 million to boost data collection and map resources deposits on land and under the seabed as part of the Resourcing Australia’s Prosperity initiative. Ms Tomkinson said the investment in Geoscience Australia under the Future Made in Australia policy was an intelligent way to leverage geoscientific data and ensure projects had greater clarity for investment and initiation.
“It means companies can understand where critical resources seams are located and how they interact with the needs of other important onshore and offshore projects.
“Having publicly available information is critical to ensuring there is common understanding of locations of resources so that future development can balance land interests and values across environmental protection, agriculture, electricity generation, transmission infrastructure, social needs and large-scale renewable energy projects.
“It’s counter-intuitive, for example, to place a wind or solar farm directly over an area that is needed for the critical minerals deposits required by renewable energy projects,”
Ms Tomkinson said.
“All roads to global net zero run through Australia and, more relevantly, Western Australia. This pathway becomes even clearer as operations in our state increasingly move along the value chain into downstream processing.
“In the long run, we feel our industry’s strong commitment to positive environmental outcomes and Australia’s stable political systems will be strong and enduring attractions for both customers and investors.
“Western Australia continues to produce almost half the nation’s goods exports and to generate almost $260 billion for the nation, so it’s also essential that government policy settings and support mechanisms allow our operations to be as competitive as possible on the world stage.”
As CME and its members work to shape the future of Western Australian mining and resources, the development, attraction and retention of a skilled workforce continues to be a key focus area.
Ms Tomkinson is optimistic that the stereotypical and one-dimensional notion of the industry as “dig it and ship it” is already shifting and hopes in decades to come that it disappears altogether.
Ms Tomkinson highlighted the complexity and sophistication of existing resource operations which she said will only increase as new technologies are integrated, including renewables, to power these processes and steps along commodity value chains.
“We need all kinds of people from diverse backgrounds and skills in our industry,” Ms Tomkinson said.
“Yes, we need drillers and mining engineers and truck drivers – jobs that people have associated with mining and resources for decades. But we also need renewable energy experts, environmental management and rehabilitation specialists, lawyers, human resources personnel and, increasingly, people who are highly proficient in data analysis and robotics.”
Ms Tomkinson said that the industry as a whole had embraced innovation and new technologies to help maximise safety and sustainability through research and development, AI, predictive maintenance and automation.
“There’s a significant focus on reducing greenhouse gas emissions, primarily through electrification of operations, including constructing new solar and wind renewable energy projects. Members are trialling electric train locomotives, haulage trucks and other equipment.”
Ms Tomkinson said the industry’s real-world innovations are leading-edge and being applied at a practical level to advance decarbonisation initiatives, but the industry’s skilled workforce needs to look to future needs as well.
“Recognising the need to develop a talent pipeline through STEM and other initiatives, CME and its member companies have introduced and expanded a first-of-its-kind Digital Technologies Program at schools around Western Australia.
“By giving students an early introduction to technology skills that a variety of industries need, we are opening up all kinds of careers for them.
“Some may eventually pursue a career in mining, others may elect to develop their interests in other fields. Either way, we’re confident the program will have a positive influence on the future prospects of young Western Australians.”
Ms Tomkinson said the Western Australian mining and resources sector was working hard to grow diversity and inclusion throughout its workplaces.
“The ultimate goal is that our workforce mirrors the demographics of society. We’re not there yet but we’re committed to doing everything we can to ensure it happens,”
Ms Tomkinson said.
“We want to see more women in our operations and we want them to feel safe and respected at all times.
“That’s why CME and its members have worked closely with the Western Australian Government’s Mental Awareness, Respect and Safety (MARS) Program Landmark Study to help understand what some of the current barriers are to participation of women and how we can make things better.
“We want to keep growing this representation and diversity in all forms by ensuring all our workspaces are welcoming and inclusive for everyone. Western Australian mining and resources is already a leading employer of Aboriginal people but again, we can do more.
“It’s very much a journey of continuous improvement, one in which CME and its staff are privileged to represent our members and the broader industry.”
The term ‘circular economy’ can look vastly di erent across industries.
There are some great initiatives already in place in the mining industry to achieve mine site optimisation and integrate circular principles, however the shift towards a truly circular economy in mining is still an emerging concept.
WSP’s Circular Economy Lead in Australia, Valentina Petrone, said that it is important to remember that a circular economy approach is defined by three key principles:
♦ Design out waste
♦ Keep materials in use
♦ Regenerate natural systems
“What often happens across businesses and industries is that, unfortunately, we forget about principle number one (design out waste), which is very critical because whenever we design anything – and it can be the phone we use, the car we drive, a big mining site or infrastructure – the design is the part where we set the project in the right direction during the construction phase and across the whole life-cycle of an asset.”
Ms Petrone said that the second principle (keep materials in use) involves how an asset is maintained in good operation with planned maintenance. It also involves how to easily replace materials that require frequent replacement and what happens to the materials that reach the end of their useful life.
The third principle (regenerate natural systems) is often the most challenging in mining as it aims to support natural processes and build natural capital instead of continuously degrading nature through extraction.
Turning attention to mining
Ms Petrone said there is room for the implementation of circular economy principles in mining in several areas.
The first is applied to the initial design of the mine site itself. From the early stages of design – starting from the site investigation and master mine planning – it’s crucial to keep circular economy principles in mind. From a circular economy perspective it is just as important to maximise the lifespan and usage of the mining operation to extract the highest possible value, as it is to include the responsible retirement of assets during mine closure.
In terms of construction, there are some circular design strategies that can be applied. Thinking in terms of design for flexibility and adaptability is a valuable exercise to undertake, because an asset of certain capacity and volume that may currently be considered as necessary could experience a change in the future if additional reserves are identified.
During construction, there is an opportunity to address efficiencies, especially if constructing a new mine site or new infrastructure. The construction of mine sites can be done in a way to
minimise wastage; buildings can be designed with water efficient fittings in mind, and they can integrate low carbon energy sources tied to the grid or as part of onsite hybrid power solutions.
Another place for circular economy implementation is the operations side, focusing on the recovery and reuse of byproducts and waste as much as possible. The most common application of this principle in mining involves reprocessing tailings materials to extract leftover minerals and construction materials. The responsible management of water resources is critical here too.
“At the end of the day, we want to try to keep materials in the loop as much as possible,” Ms Petrone said.
During the operational stage, mining companies should endeavour to progressively rehabilitate their footprint. This is not always possible and is dependent on the mining method, however, opportunities may exist to replace infrastructure which may present a reuse potential as part of its replacement.
At closure, plans for transitioning a mine to an agreed next use offer the largest opportunity to support natural systems, recreate new systems, or repurpose assets for alternative uses.
In keeping with the principles of a circular economy, mining clients need to go beyond ensuring they have the financial means to implement the conditions of environmental authorisations as part of closure planning
and concurrent contaminated land rehabilitation planning.
Instead they need to limit or reduce adverse effects on the receiving environment.
Opportunities include incorporating long-term considerations and potential liabilities into operational designs to avoid and/or mitigate closure liabilities altogether, rather than simply planning to manage them in the future. For mining clients to retire their assets responsibly, closures must be thoroughly planned in advance and sufficient financial provision made for the retirement of assets.
“In terms of transition and regeneration, there is a bit of a planning issue at the moment in Australia. Where a mine site is allowed from a planning perspective, in 30 years we might not be able to build and reuse this site for a different purpose.”
This barrier is something that is sometimes discovered at the end of a project when it has not been planned in advance.
Ms Petrone said that considering the post-mining transition from the very beginning is a key step in adopting circular economy principles.
“We need to think about the whole life-cycle as early as possible, not just as an afterthought, because the risk is that we miss opportunities. It's really about having a long-term mindset from the very beginning.
“It’s asking how we can design those assets thinking about the whole life cycle and what might happen in 50 years when the sites might come to a natural end, or if there’s another shift in the needs of the markets.”
When asked to pinpoint closed mine sites that successfully adopted circular economy principles, Ms Petrone referred to the Eden Project in the UK – where the land was used as much as possible before being converted into a place
with different biospheres that are open to the public and a fully sustainable community hub and example of biodiversity.
Another example highlighted by Ms Petrone was the Municipal Stadium of Braga in Portugal – a stadium that was built in a former mine site with architects utilising man-made parts of the landscape.
A successful example closer to home is the Kidston Gold Mine, a former open cut gold mine in northern Queensland that has been reused as a pumped hydro storage system to support and store energy from a 50MW solar farm.
All three sites are, according to Ms Petrone, “good examples that not only resolve the problem of a man-made change in the landscape but also provide job opportunities for the local communities”.
This kind of mine reuse is a popular topic in Australia because there are examples in New South Wales and in Western Australia where cities or big towns were built around job opportunities that will be gone upon mine closure.
Although the examples are all different from each other, a common characteristic they share is thinking outside the box and viewing these mined environments as an opportunity instead of just a hole in the ground.
“I think the main lesson learned is the shift from seeing it as a problem to seeing it as an opportunity to build something new, as applicable.”
Although circular economy principles in mining are still relatively new, a focus on responsible mine closure is not, and there have been instances where adoption has not been successful, for a number of reasons.
“It’s a matter of barriers and I would say that regulation, planning and costs, including remediation costs, might be the main ones,” Ms Petrone said.
“There might even be local communities that are not happy about the different site uses. Contaminated soil could also be a big barrier. If we need to remove all those contaminants, it might come with a very high cost so an option might be just to do a remediation and not give people access to that site.”
For companies embarking on their circular economy journey it can be a daunting process and a good way to start the process is through some mapping.
“The first step is to undertake an audit of the mining company – understanding what assets exist, how they're managed, at what stage they are within their life cycle – to map out what the next step
will be. If they are open to designing new sites, having a very early assessment of what the opportunities are and what will happen in the long term.”
Ms Petrone said that another critical step is assessing the company’s opportunities from an industrial symbiosis perspective – seeing how the waste of one industry or one asset can become an input for another one, assessing one or multiple sites and seeing if there are any other surrounding companies or organisations that could benefit.
A key element in increasing the adoption of circular economy principles in mining, according to Ms Petrone, is shifting industry thinking away from the idea that it requires extensive added effort and cost and towards viewing it as an opportunity instead.
“Circular economy is a novel approach in terms of how we are trying to manage waste differently to the point that, ideally, we won’t refer to it as waste anymore, but as resources.”
Ms Petrone stressed the importance to mining companies of carefully considering their options and doing some investigating to see how something that “might be an additional cost at the beginning, might even become cost neutral at the end of the process”.
Interested in working with Mining Magazine? Scan to download our media kit.
SPECIAL
MAJOR FEATURES Asset management Energy efficiency Mine rehabilitation
SPECIAL FOCUS Stakeholder engagement
EQUIPMENT & MACHINERY Instrumentation, control and monitoring
DISTRIBUTION TBC
DISTRIBUTION
MAJOR FEATURES Smart mining
and waste management Safety and training Survey and data Mapping, GIS & surveying
SPECIAL FOCUS Risk management
EQUIPMENT & MACHINERY Communications Pumps & Dewatering
DISTRIBUTION TBC
Deadline: TBC
MAJOR FEATURES Circular economy Environmental management Big data and IoT Women in mining
SPECIAL FOCUS Investment
EQUIPMENT & MACHINERY Materials handling
DISTRIBUTION TBC
Enabling you to deliver the most sustainable green hydrogen, Danfoss will provide you a grid friendly, approved solution with impressive energy efficiency. Low harmonics and a high power factor ensure that you have a competitive power supply for your electrolyser at hand. Long experience in power conversion combined with a leading position in the world, Danfoss is your ideal partner for your investment in the hydrogen market. Take advantage of our experience to ensure that your system is scalable and economically viable. Recognized world-wide as a reliable supplier, Danfoss adheres to the highest international standards in production and development quality.
Danfoss has solutions to get your business on target for a decarbonized economy.
Learn more at Get on target in Power-to-X on our website drives.danfoss.com