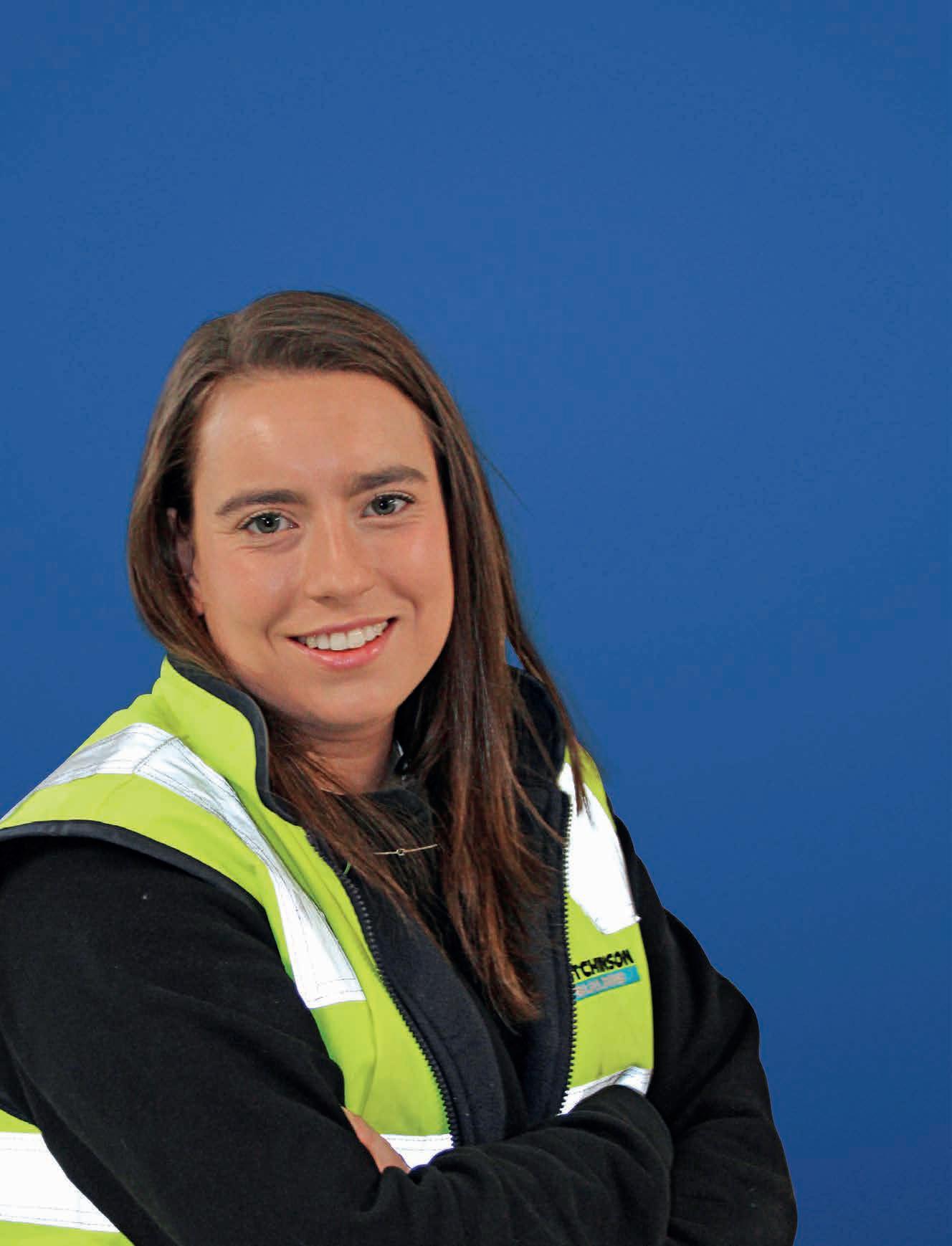
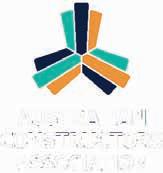
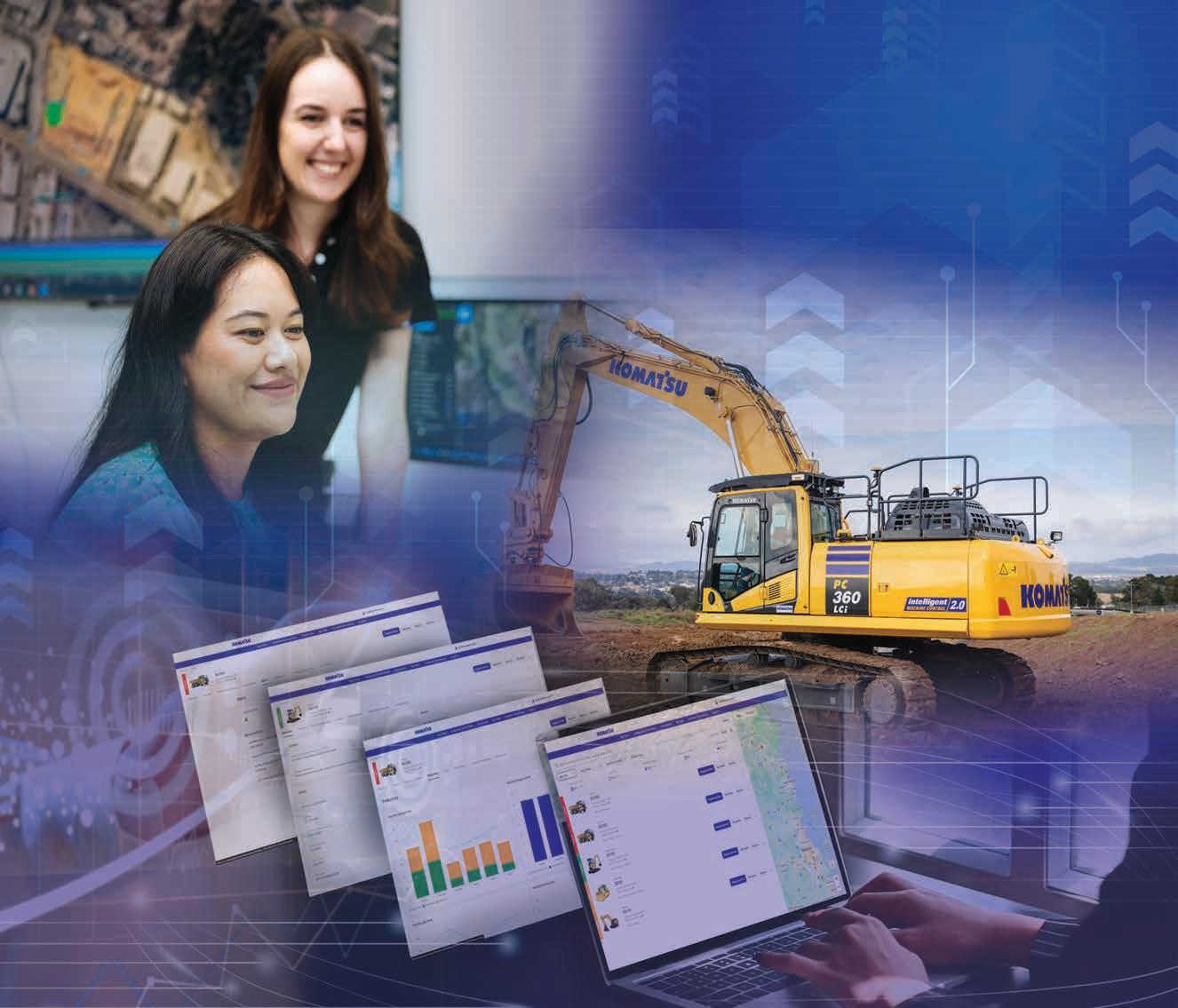
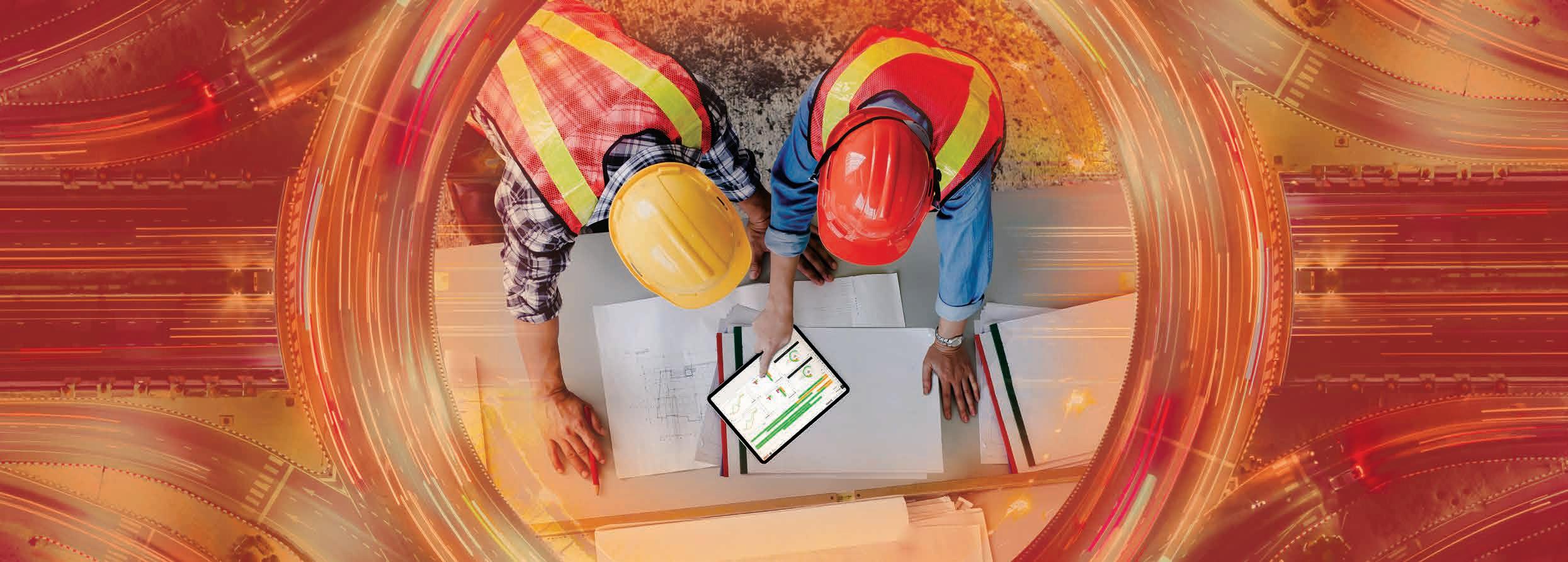
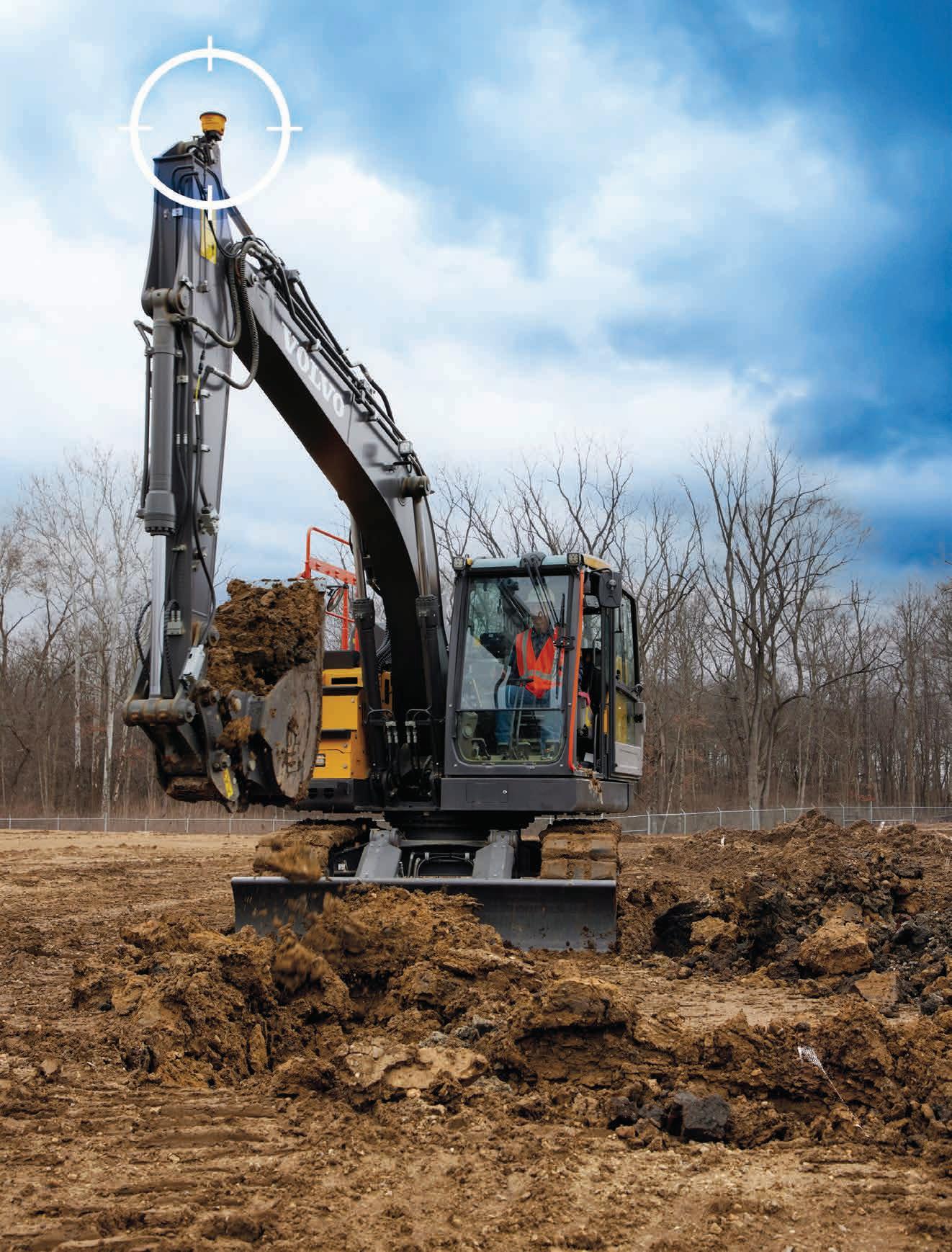
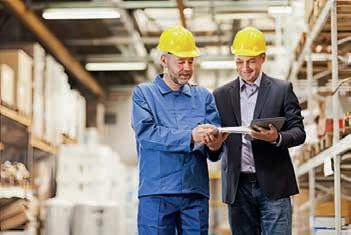
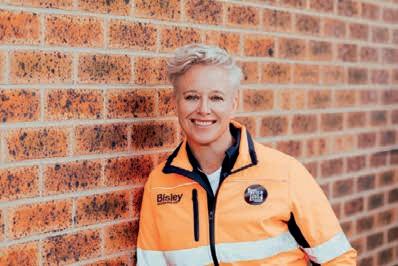
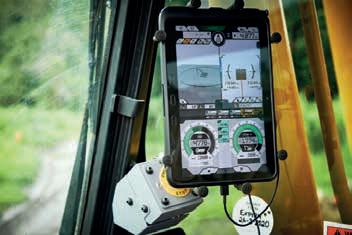
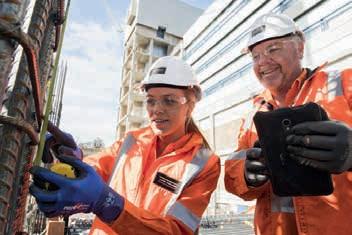
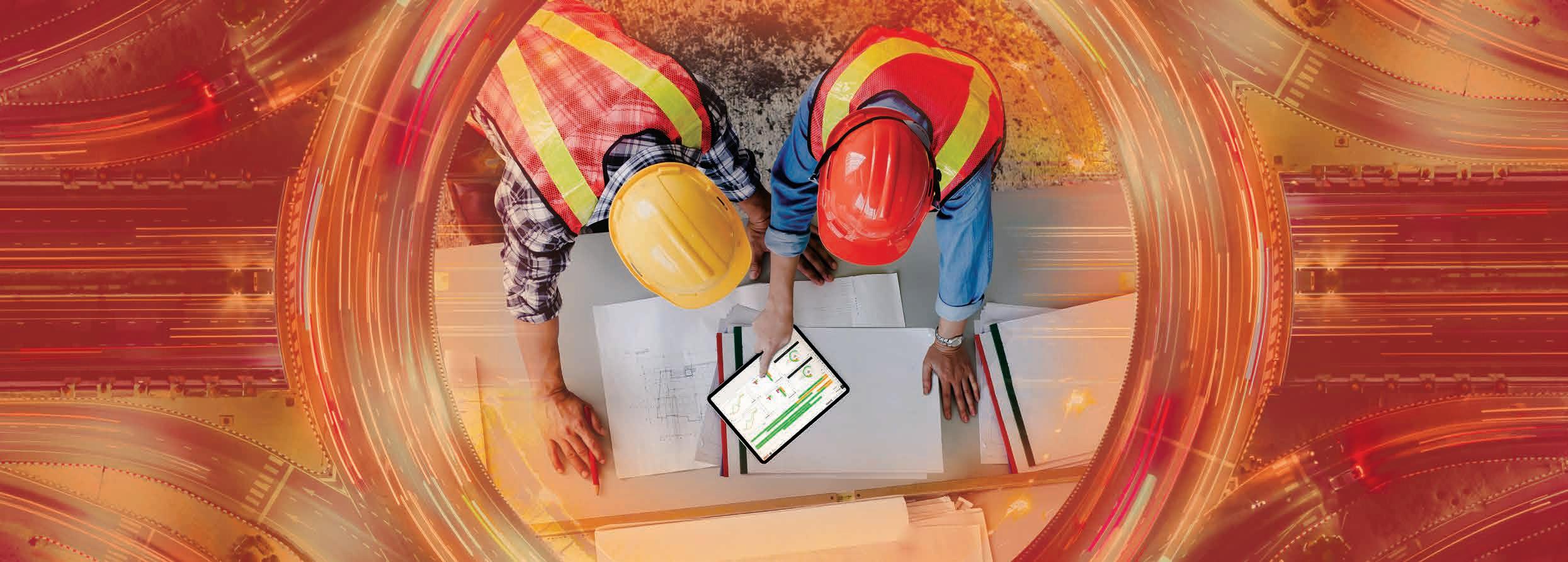
Along with our standard array of features tailored for the construction industry, this month’s edition includes the official Inside Construction Expo 2023 Showguide.
Inside Construction Expo is almost here, so we’re sharing everything the premier industry event has to offer.
The official Inside Construction Expo 2023 Showguide covers everything you need to know about the two-day event to be held on 20 to 21 September 2023 at the Melbourne Convention and Exhibition Centre, including the conference program and speakers, expo exhibitors and Foundation Awards finalists
What’s more, the August edition of Inside Construction comprises our regular line-up of features showcasing the latest in industry news, products and innovations.
This month, we put a spotlight on the companies that are delivering impressive technologies – from plant and asset management platforms and accounting and project management software to procurement technology and transformation solutions that drive efficiency, productivity, resilience and sustainability for project stakeholders – for the construction industry market.
BG&E civil design drafter Laura Miranda shares her inspiring journey as an international student and engineering professional, and Kane Constructions ACT general manager Jo Farrell reveals how she jumped hurdles and overcame criticism to prove that women are capable of building successful construction careers.
While the Australian construction industry continues to face one of the largest skilled labour shortages in its history – with an 80 per cent rise in specialised and skilled worker vacancies since late
2019, according to the 2022 Arcadis Construction Costs Index Report – this edition explores a number of solutions that can help attract, recruit and retain workers.
As always, the Australian Constructors Association, Formwork Industry Association, National Precast Concrete Association Australia, National Association of Women in Construction and Empowered Women in Trades put forward solutions to major industry challenges, covering topics such as safety training compliance, gender diversity and productivity.
We hope you enjoy this month’s edition, and be sure to get your tickets for Inside Construction Expo 2023 – Melbourne’s leading event for the major vertical construction and infrastructure sectors.
Chief Executive Officer John Murphy
Chief Operating Officer Christine Clancy
Group Managing Editor Andrew Hobbs andrew.hobbs@primecreative.com.au
Editor Ashley Grogan ashley.grogan@primecreative.com.au
Sales Director Brad Buchanan bradley.buchanan@primecreative.com.au
Art Director/Design Daz Woolley, Caterina Zappia
Head of Design Blake Storey blake.storey@primecreative.com.au
Design Production Manager Michelle Weston michelle.weston@primecreative.com.au
Business Development Manager William Jenkin william.jenkin@primecreative.com.au
p: +61 0478 820 221
Client Success Manager Glenn Delaney glenn.delaney@primecreative.com.au
Cover image credit Procore
Head Office Prime Creative Pty Ltd 379 Docklands Drive, Docklands, Victoria 3008 Australia p: +61 3 9690 8766 f: +61 3 9682 0044 enquiries@primecreative.com.au www.insideconstruction.com.au
Subscriptions +61 3 9690 8766 subscriptions@primecreative.com.au
Inside Construction is available by subscription from the publisher. The rights of refusal are reserved by the publisher
Articles
All articles submitted for publication become the property of the publisher. The Editor reserves the right to adjust any article to conform with the magazine format.
Copyright
Inside Construction is owned by Prime Creative Media and published by John Murphy. All material in Inside Construction is copyright and no part may be reproduced or copied in any form or by any means (graphic, electronic or mechanical including information and retrieval systems) without written permission of the publisher. The Editor welcomes contributions but reserves the right to accept or reject any material. While every effort has been made to ensure the accuracy of information, Prime Creative Media will not accept responsibility for errors or omissions or for any consequences arising from reliance on information published. The opinions expressed in Inside Construction are not necessarily the opinions of, or endorsed by the publisher unless otherwise stated.
We’re using Site Hive, the latest in hi-tech noise, dust and vibration monitoring. These units provide real time data to our team so we can mitigate the impact of our construction on the community.
Scan here to read about our sustainability targets
This month Inside Construction is launching Project Picks, putting a spotlight on the key major construction and infrastructure projects that are shaping Australia’s built environment.
Multiplex
$750 million
: Funded by the NSW Government, the project will deliver a waterfront promenade, a ferry wharf and more than 6,000 square metres of new public open space. The new building will include a variety of fishmongers, restaurants, cafes, bars and specialty food retailers in a market hall setting.
A highly anticipated feature is the visibly accessible auction area, providing onlookers with a deeper understanding of what’s said to be the Southern Hemisphere’s largest fish market, and its supply chain. The engineering is innovative and unique, from the hydrostatic basement to the glulam timber
Contractor: Mirvac
Details: Mirvac will deliver one of the country’s first true mixed-used precincts, including LIV Aston’s 474 build to rent apartments, set to launch in mid-2024; a new-era workplace at 7 Spencer Street; quality retail and new green, public spaces, all in Melbourne’s emerging new Northbank on the Yarra River.
Status: Topping out in October, LIV Aston is in the final structural stages of construction with the lift core at level 28 and the façade completed to level 19 of the building’s 32 levels. Once completed LIV Aston will feature 2,600 square metres of indoor and outdoor resident facilities including a 25-metre lap pool, infrared sauna, steam room, gym, yoga deck, rooftop lounge, private dining, outdoor dining and BBQ area, media rooms, co-working
roof structure, and modular canopy roof. Sustainable environmental features such as solar panels and a water recycling system will be incorporated into the design.
Status: Multiplex recently drained 100 million litres of water from the cofferdam within Blackwattle Bay, enabling work on the main structure to commence. Concrete pours for the hydrostatic, watertight basement have commenced and establishment of the precast promenade areas is underway.
Initiatives: Multiplex has made a global commitment to reduce its carbon footprint and support its clients and supply chain to do the same. The new Sydney Fish Market site is one of the first in Australia to use renewable HVO100 diesel to power its tower cranes.
club including 2,688 square metres of office space amenity, and green spaces, including pet park and pet washroom. Due for completion in 2025, 7 Spencer Street is in the early stages of construction, with Mirvac and capital partner, Daibiru, set to deliver 21 levels and approximately 46,000 square metres of state-of-the-art office floor space, featuring over 10 individual terraces. Well located on the corner of Flinders Street, in close proximity to Southern Cross Station and the tram line interchange, the combined project is delivering over 550 new construction jobs.
Initiatives: This entire precinct, including LIV Aston and 7 Spencer Street, will be fully electrified, while setting ambitious sustainability targets including a 5 Star Green Star rating.
Contractor: BESIX Watpac
$43 million
Details: Axis Alexandria is a complex industrial warehouse facility consisting of 10 units on a prime 1.69-hectare brownfield site in Sydney. It’s the first multi-storey facility of its kind for Australian industrial developer, Goodman.
Set for delivery later this year by BESIX Watpac, Axis Alexandria’s eye-catching architectural façade is taking shape and the last major concrete pour was completed this month. The current focus of works is infilling a breezeway spanning 25 metres to connect the two double-storey warehouses rising 18 metres above ground level.
Early in the design phase of Axis Alexandria’s development, the project team identified recycled steel as a key material that could be incorporated into the industrial facility’s construction. BESIX Watpac’s partnership with a trusted supplier played a pivotal role in the successful execution of this initiative. Together, the teams navigated the complexities of sourcing and repurposing recycled steel, ensuring it met stringent quality standards.
Initiatives: Throughout delivery, over 1,500 tonnes of 80 per cent recycled steel was incorporated into the main structure of the project. This created significant cost efficiencies and displayed BESIX Watpac’s dedication to closing the material loop to achieve a more circular construction model.
Contractor: Lendlease
Value: $1.2 billion
Details: Victoria Cross will be a vibrant transport hub and mixed-use precinct that includes a 42-storey commercial tower, four level boutique commercial building, three level hospitality venue and approximately 20 new retail shops located directly above Sydney Metro’s new Victoria Cross Station. There will also be a retail concourse offering high quality grab and go cuisine amongst some of Sydney’s cult foodie favourites and five new signature restaurants fronting new public green spaces.
The 56,000-square-metre commercial building, Victoria Cross Tower, will offer a hotel inspired lobby to accommodate up to 7,000 workers, in addition to community, third working and function spaces and a 200-square-metre community hub.
Status: Under construction. The first stage of the project, which includes the retail shops in the laneway and concourse, are expected to open alongside the new metro station in 2024, with the commercial tower, boutique office building, hospitality venue and signature restaurants to open in 2025.
Initiatives: Victoria Cross aims to redefine sustainability for commercial buildings in Australia. Victoria Cross Tower will be one of Australia’s first all-electric commercial buildings powered entirely by renewables. It will be net zero carbon in both construction and operation and is targeting a 6 Star Green Star rating (Design & As Built v1,2) and 5.5 NABERS rating, as well as a Platinum WELL rating. The project team is also part of the Girls in STEM program which seeks to promote and educate some of the circa 17,000 school students in North Sydney on careers in the property and construction industry.
(Quite possibly) the most helpful financial software on the planet. From supplier invoices and mobile purchase orders, to progress and expense claims, or even simplified client claims – we sort it all.
Lentune easily integrates into all major accounting and project management software.
Hutchinson Builders’ commitment to genuine diversity and inclusion starts with its culture – a culture that Kate Lucarelli says helps team
Kate Lucarelli is a shining example of a young woman thriving in the construction industry. Since joining Hutchinson Builders, affectionately known as Hutchies, the devoted construction professional has moved from strength to strength in her career, moving into a project management role after just 12 months with the business.
Her success stems from a passion for the construction industry and the opportunities it presents, but also from the inclusive and diverse workplace culture she’s part of at Hutchies.
“There are always going to be hurdles and barriers when breaking into a maledominated industry, but Hutchies has been supportive in the development of my career,” says Lucarelli. “Bring focus, resilience and passion to the table and then, with the support of the right employer, the challenges become surmountable – if you’re the right person, you’ll find the right job.”
Kate hopes other young women will learn from her example.
“You can’t be what you can’t see,” she says.
“I hope that as more women take up the tools and positions in management they will serve as role models; and that young women considering their career options will see the possibilities and think about the opportunities the construction industry has to offer.”
Lucarelli speaks highly of Hutchies’ approach to promoting diversity and inclusion in the workplace. The company readily recognises aptitude and attitude, with a strong focus on rewarding merit, regardless of background, she says.
“My construction journey started when I left school and completed a four-year Bachelor of Applied Science in Construction Management degree, with honours,” she says.
“In the years that followed, I worked for the likes of ABD Group as a project coordinator/ junior foreperson and then Kapitol Group as a site manager, where I gained experience delivering a range of builds.”
“In January 2021, I was offered a position as a project engineer at Hutchies and took the opportunity with both hands.
“Hutchies supports its company members to succeed and reach their full potential as well as to take on challenges.”
There are always going to be setbacks when taking on the norm but with determination, the right mindset and the right attitude, people can build a rewarding career, Lucarelli says.
Lucarelli took on her first build as a project manager at Hutchies in 2022, overseeing the delivery of the Rockbank Primary School in Victoria (now Thornhill Park Primary School). Currently, she is the project manager for the
new Binap Primary School in Brookfield – a Victorian School Building Authority (VSBA) project. Once complete, the new school will house up to 575 students, including approximately 50 places for young people with specialist needs. Lucarelli says she loves working on VSBA’s projects, because with them comes a level of fulfilment.
“At the end of these kinds of projects, you get to see the space that you’ve created actually getting used by local kids,” she says. “These schools play a major role in those kids’ lives, so it’s really fulfilling to be part of their delivery.”
As a project manager, Lucarelli is a direct conduit between the client and the site team, liaising with the project contract administrators and design and site team; driving program and direction; and facilitating communication with subcontractors. It’s a role that she continues to thrive in, something she says is in part due to Hutchies’ willingness to give everyone an opportunity to discover their strengths.
Lucarelli works in the company’s Melbourne team, led by team leader Bernie Nolan, who says Hutchies strives to provide the right opportunities and environment for all its employees to be successful.
“At Hutchies, we want to be reflective of the diversity that exists across the community,” says Nolan. “Currently, we still see some hesitation in young women wanting to do trades, but we want to at least give everyone the opportunity to explore working in construction.”
“We’ve got a wide range of people with a wide range of skills and a wide range of backgrounds, and everyone has their place – it’s about finding them and getting them into the right place so that they can thrive in our industry.”
Since joining Hutchies, Lucarelli has not only excelled in her role as project manager but has also attended events like the Department of Education’s Trades Fit Expo, where Hutchies partnered with Incolink and CFMEU to promote trades. Lucarelli, along with a number of Hutchies’ female leaders, attended the event to spread the message to young women and non-binary students about the vast opportunities within the construction industry.
“They also shared the various pathways into the sector – whether it be through an apprenticeship, a construction management degree or work experience – to help the
attendees understand that there are viable alternatives out there,” says Nolan. “Kate’s been to several schools to share these messages and is a great mentor for young women looking to start a career in construction.”
“Kate fits into our culture like a hand in a glove.”
It’s important for Hutchies to foster a diverse workforce, says Nolan, but it’s also important for the industry.
Nolan has worked in the construction industry for over 35 years and says he has seen the dynamic of the sector change considerably as more women and underrepresented groups have joined the workforce. “Our industry is a much better place than it was five years ago, 10 years ago, and certainly 25 years ago, thanks to the increasing diversity we’re seeing across the sector,” says Nolan.
“Hutchies is committed to inclusion, and one of the core pillars of inclusion is being aware of the opportunities that women can have within our industry – and it’s limitless.”
In Australia, women account for around only 15 per cent of the construction workforce, with less than five per cent in trade and labouring roles. Attracting women to the industry is an ongoing challenge for construction companies, but with the right culture, environment and opportunities, Nolan says the industry can make great inroads in improving diversity across the sector.
Currently, 23 per cent of Nolan’s direct team are women, including Lucarelli in a project management role, design managers, site supervisors, forepeople, project engineers, apprentices and cadets – well above the industry norm.
“Championing diversity on a wider industry level comes back to our focus on having the right culture in our organisation, which is a culture of respect for everyone,” says Nolan. “Our success is based on all of our people working respectfully and collaboratively with our clients, project teams, subcontractors, consultants and community.”
“If we’re bringing the right people into our organisation, then we don’t need to have specific policies, rules and regulations about how to be inclusive, as it happens naturally and evolves.
“There are always going to be hurdles and barriers when breaking into a male-dominated industry, but Hutchies has been supportive in the development of my career.”
“That’s what we find within our workforce at Hutchies – we have people from different backgrounds and experiences working together to create positive outcomes for our clients, people and the community; and it all comes back to culture.”
Hutchies is also a huge supporter of the Victorian Government’s Building Equality Policy (BEP), which aims to improve gender equality in the building, infrastructure and civil engineering sectors. The BEP applies to government projects around the state and mandates female representation in at least three per cent of each trade role, seven per cent of each non-trade position and 35 per cent of management, supervisor and specialist labour roles. Launched in January 2022, the BEP also mandates that four per cent of labour hours for apprentices and trainees will be required to be performed by women.
Victoria’s Minister for Industrial Relations
Tim Pallas said: “These targets are the first step in significantly increasing the number of women in construction.”
“It’s essential to cement the role of women in a modern construction industry and we’ve worked with employers, industry and unions to work towards these targets.”
The Victorian Government is fostering opportunities for people of the state, including disadvantaged Victorians through social and indigenous engagement, says Nolan.
“The state is pursuing improved diversity through its contracting and asking us, as a construction contractor, to make commitments to support delivering on those goals – and we’re on board,” he says. “There’s no escaping that in the short term the Building Equality targets are high.”
“We need to address, among other things, the lead time required to create a pipeline of talent coming through the education
“At Hutchies, we want to be reflective of the diversity that exists across the community.”
Traininggives
studentsthe
chance to learnon
live jobsites, working with the latest construction techniques, equipment and policies.
system through a grassroots approach. innovation and flexibility from all within the construction industry to attract and foster the right people to achieve gender equality.”
Hutchies has long been living the values of fostering workplace diversity and inclusion as advocated for in the BEP, thus it was a natural decision to support the state’s movement.
In 2012, Hutchies employed a dedicated Indigenous specialist with the aim of respectfully engaging and working with Aboriginal and Torres Strait Islander communities. “This has evolved to become the Statim Yaga (start work) program, which we started in partnership with the Federal Government’s Employment Parity Initiative (EPI),” says Nolan.
Launched in 2015, the Employment Parity Initiative set a target of placing an additional 20,000 First Australians into private sector jobs by 2020. In alignment with this initiative, the focus of Statim Yaga is on Indigenous training and employment while increasing the cultural capability of Hutchies, says Nolan. Under Statim Yaga, Hutchies set a target to train and place 550 Indigenous jobseekers into employment within the construction industry by the end of 2020.
Today, through this program, the company has placed more than 750 First Australians into full time employment and in 2020, Hutchies won the Queensland Government’s Business Reconciliation Award for its genuine achievements through Statim Yaga. In 2019, the company also won the Queensland Community Foundation Philanthropist of the Year award for its support of several not-forprofit organisations including AEIOU, Bravehearts, National Association of Women in Construction and YoungCare.
Hutchies won the Large Employer of the Year in the Australian Training Awards in both 2011 and 2017 for the work of its
“We’re extremely proud of these accolades, which highlight our appreciation for good grassroots education, but I must point out that the construction industry needs to band together to continue improving learning pathways,” says Nolan.
“It’s not just about creating the right workplace culture, it’s also about getting more people into university, vocational education and training, and trades so that they can flow through to fill construction roles.”
“The huge pipeline of activity planned across Australia promises a bright future for anyone who wants to build a rewarding and fulfilling career in construction.”
Lucarelli agrees, saying that when she left school construction wasn’t on the cards. It wasn’t, and in many cases still isn’t, spoken about as a viable option for young girls at the end of their schooling.
“Making it easier for young women to enter the industry and showcasing the construction industry is a great career for men and women alike – that’s how we make true progress in getting a more diverse range of people in an industry that’s traditionally male dominated,” says Lucarelli.
Hutchies is not big on marketing its several accolades and achievements.
Instead, the company humbly and actively strives to set true change in motion to create a better future for its teams, communities and the construction industry.
Nolan says the company’s caring approach to diversity and inclusion and advocation for improved training and skills pathways will continue to evolve to create further opportunities for jobseekers, its employees and the wider industry.
“Hutchies is committed to inclusion, and one of the core pillars of inclusion is being aware of the opportunities that women can have within our industry – and it’s limitless.”Binap Primary School is one of the Victorian School Building Authority projects being undertaken by Hutchies.
Increase knowledge retention and confidence
Cut training time in half
Improves business productivity
Evidence in risk reduction and safety improvements
Uncovering and addressing ‘unknown known’
Impacting learner behaviour through highly personalised learning experience
Area9 RhapsodeTM adapts your content in real-time to optimise your personal journey to mastery.
Area9 Lyceum is committed to helping people reach their full potential. Our adaptive AI learning technology is grounded in scientific research and twenty-five years’ e xperience, serving over 30 million learners across multiple industries globally.
Global engineering and construction giant Laing O’Rourke is bringing change to the plant and equipment hire sector in Australia, supported by construction software platform COINS.
Laing O’Rourke is a $6 billion international operation with 70 years of involvement in the Australian construction and infrastructure industries, including nearly two decades under the Laing O’Rourke banner.
As part of an expansion project more than half-a-year in the making, Select Plant Australia, a business unit of Laing O’Rourke, is offering plant and equipment hire to the wider engineering and construction sectors.
Select Plant Australia innovation, systems and technology lead Omar Al-Khayat says the COINS plant and asset management platform allowed the organisation to consolidate software systems and easily transition the business model.
“We’re currently going through a transition from purely an asset management business model to plant and equipment hire that’s both internal and external to Laing O’Rourke,” says Al-Khayat. “With that comes a growth in our asset base, and a change in mindset and ethos of how we work and the way that we’re transacting.”
“We’re not just looking after and maintaining an asset; we’re also looking to transact on that asset.”
Al-Khayat says the change was about consolidating the multiple software systems that Select Plant Australia is using for asset maintenance, preventative maintenance and storing information.
“It’s really about bringing those three things together into one place and we realised COINS
Select Plant Australia has one of the largest fleet holdings in Australia, including reportedly Australia’s first two 250-tonne electric crawler cranes. Also pictured is a Matisa Tamper.
efficiencies in both time and revenue, he says.
“Our plant workshop has now been able to take the entire asset maintenance role on themselves, whereas previously it required the coordination of multiple teams to maintain an asset base,” explains Al-Khayat. “COINS allows us to not only consolidate software systems but simplify data and reporting too.”
Laing O’Rourke head of information technology Andrew Lankowski says the COINS platform is crucial for the organisation’s decision makers.
“COINS is our financial source of truth,” says Lankowski. “The ability to operate multiple financial entities within one operating company is a huge advantage for us.”
“There are a myriad of COINS reports and dashboards which feed information to decision makers – whether they’re project leaders or executives looking at forecasting or cash flow – and it’s essential they get accurate and up-to-date information.”
The collaborative working relationship Laing O’Rourke has with the COINS team is also part of the reason for the successful partnership between the two companies, Lankowski explains.
“It’s important to have reassurance we can grow within the product and having a local presence in Australia we can work with directly is vital from a support and partnering perspective,” says Lankowski.
“There’s a huge benefit to being able to pick up the phone and talk directly to Jim Farrer, the managing director of COINS in Australia, and we work well in that regard. This level of support and united way of working together is priceless.
“It’s also comforting to know that Jim and his team, who are now part of The Access
Group , can bring considerable additional capabilities offered by Access to the region.”
A global solution and lasting partnership COINS principal solutions architect Wayne Kemp says Laing O’Rourke uses the COINS platform globally to manage its complex scale and structure. “To have a product like COINS that has that capability and scalability to manage all those complexities of that organisational and business structure is important,” Kemp says.
“Laing O’Rourke has been using COINS for nearly 30 years in Australia, and as there have been major technology shifts and improvements in that time, COINS has been able to meet those core requirements of the organisation, and they’re still with us today.”
COINS places strong emphasis on building collaborative and supportive partnerships with all its clients, Kemp says, allowing the company to prove time and time again that it delivers customer implementations ontime and on-budget.
“Our average customer life span exceeds ten years,” he says. “That shows that successful construction companies not only choose COINS but are able to grow and scale their use of the COINS solutions over the longterm as their needs change.”
“COINS is able to integrate with Laing O’Rourke’s other systems. We’ve got open architecture and the technical prowess to support that integration.
“They can also tap into COINS’ own global support network, providing them with access to the technology and functional skill sets that COINS can provide.”
COINS integrates and supports, provides governance, industrial strength compliance and security access control, says Kemp, but also offers business improvement opportunities such as what Select Plant Australia has undertaken with plant asset control.
“The COINS Australia team looks forward to continuing its support of highly innovative businesses focussed on excellence, such as Laing O’Rourke and Select Plant Australia, whose transport infrastructure projects are vital to Australia,” Kemp says.
Omar Al-Khayat echoes Kemp’s emphasis on the importance of a collaborative business partnership to ensure success.
“COINS allows us to do it all – including preventative maintenance planning and scheduling, which is all then linked directly into its job card functionality so that we can raise a work order to do the job.”
“COINS is our financial source of truth. The ability to operate multiple financial entities within one operating company is a huge advantage for us.”
“Our business is in a state of change and the services and offerings we provide are changing and flexing as we find where we fit in the market,” says Al-Khayat.
“The implementation process we went through with COINS has really grounded the business in understanding what our system can do and how we should work.”
Al-Khayat says on a practical level, the support from COINS was excellent.
“The team was responsive and addressed issues quickly,” he says.
“We were able to get a good understanding of the functionality which helps us plan a roadmap of how we can leverage the technology in the future.”
In Australia, Laing O’Rourke focuses on delivering transport infrastructure projects, predominantly rail and road, defence infrastructure, and buildings at the transport interface, and COINS is specifically developed to handle the complexities of the Australian construction industry.
“Infrastructure investors are increasingly demanding businesses demonstrate lowrisk, governance-controlled operations before committing to a venture, and that is exactly what COINS empowers organisations to do,” Kemp says.
“Laing O’Rourke has used the COINS workflow capability in the product and has developed a lot of automated workflows for approval notification and compliance processes. COINS can deliver that type of capability to the construction and infrastructure market.”
COINS uses a straightforward configuration on a massive scale for Laing O’Rourke and can provide a huge range of complex security and access control.
“That’s a real strong suite of what COINS provides – that compliance and access control,” Kemp adds.
Laing O’Rourke’s highly trained and committed people understand the challenges of modern construction, the stakeholders involved, and how to work collaboratively to deliver its clients’ aims.
The company combines expertise with purposeful technology, deploying innovations like digital engineering and artificial
By leveraging the right technology, Laing O’Rourke aims to spark positive change for its clients, their projects, and the wider industry. Its 2025 mission is to be the construction sector’s recognised leader for innovation and excellence.
In 2020 and 2022, Laing O’Rourke was awarded the prestigious Workplace Gender Equality Agency’s (WGEA) Employer of Choice for Gender Equality (EOCGE) citation and in 2021 announced far-reaching new sustainability targets, including a commitment to decarbonise its own operations by 2030 and achieve equal numbers of men and women among its 5,500 global staff.
The COINS Australia team endeavours to simplify the way civil and engineering companies manage business.
From finance and operations, project delivery and time management, to controlling supply chain and services, all core functions of a construction company can be managed by COINS.
With constant change a mainstay of the construction industry of late, the right technology is essential to forecast, manage and operate a successful construction business.
• Integrated Project Control and Financial Management – accurate, timely and verifiable data available to all staff in the business.
• Business planning and forecasting focused on project performance review, opportunity pipeline and overhead management capability, streamlining end of month processing and forecasting to optimise margins and commercial outcome.
• Compliant Australian payroll, human resource and employee self service capability.
• Advanced procure-to-pay processing and commitment control.
• COINS Analytics – visualisation and business intelligence reporting of key metrics to better access key information to support business success.
• Fully integrated asset management and plant control.
• Industry compliance and governance functionality including project bank accounts, Security of Payments Act and taxable payment annual report.
“Laing O’Rourke has been using COINS for nearly 30 years in Australia, and as there has been major technology shifts and improvements in that time, COINS has been able to meet those core requirements of the organisation, and they’re still with us today.”Laing O’Rourke relies on COINS software to feed accurate information to decision makers across the company.
Lentune’s integration with Procore enhances interoperability and provides a seamless project cost management process for its customers.
Understanding collaboration is key to transformation, Lentune integrates with a number of the construction industry’s key accounting and project management software packages to deliver outstanding results for its customers.
It’s crucial that the industry band together to develop effective solutions to the labour and material shortages and supply chain challenges that are wreaking havoc on Australian construction costs.
While many businesses in the sector continue to work in silos, Lentune is harnessing collaboration to break down barriers in project cost management.
Spearheading Lentune’s relationships with the wider industry, CEO Jono Bonifant says Lentune can play a key role in facilitating the construction sector’s adoption of Procore Technologies’ Project Financials module.
Keeping customers at front of mind, Lentune is now helping construction businesses better manage their project costs by transferring invoices into Procore, without the need for data entry.
“Our integration with Procore enhances interoperability and provides a seamless project cost management process for our customers,” Bonifant says.
“Procore’s Project Financials is starting to grow and get a lot more traction in the market, and Lentune has really come into its own to be able to facilitate helping people adopt it easily.”
Productive partnership
Lentune’s integration with Procore eliminates data entry for construction project teams. Lentune automatically pulls supplier invoices and subcontractor claims directly from the business’s email and sends important data into the cloud. Then, if enabled, Lentune matches these invoices to the commitments in Procore. It can even check them for price discrepancies.
Next, the system automatically assigns the invoices to the correct project and cost code, and delegates them to the appropriate team member or department for approval. Finally, as soon as these documents are approved, Lentune sends the data to the business’s Procore project management software as a direct cost. The entire process is supported by automation to streamline workflows and provide complete visibility of project costs, saving Lentune’s customers up to 70 per cent of their invoice processing workload.
“This integration provides businesses the flexibility to be able to handle different workflows or requirements for different customers,” says Bonifant. “Understanding those nuances and being able to add value to the different ways people use a system is essential to a good integration like that of Lentune and Procore.”
The element of maturity that Lentune brings to a business’s financial information is only further bolstered by this integration.
Lentune creates an approval process with delegated authority and full visibility for project teams that facilitates the collection of data in a timely manner.
Ultimately, Lentune’s integration with Procore means that customers can get upto-date financial information quickly, giving everyone in the business an immediate understanding of project costs. By utilising Lentune with Procore’s Project Financials software, businesses get the best of both worlds – accounting teams get full visibility of project costs and the teams onsite get a system that eliminates the need for manual data entry.
Procore Partner Account Manager (APAC)
Jhon Camargo says it’s encouraging to see how Procore technology partners are successfully adopting ‘partnership-first’ go-to-market strategies. “These partners are leveraging knowledge, network and data to better serve their clients and empower digital transformation,” says Camargo.
New Zealand construction company iLine Construction is one customer loving Lentune’s integration with Procore. The company’s finance administrator Karen Bloxham says since adopting Lentune, iLine has seen a drastic reduction in data entry hours for its administration team.
“We’ve also seen a reduction in paper costs and waste thanks to the paperless integrated system, as well as fewer manual errors due to the reduction in data entry,” says Bloxham.
Through its integration with Procore, Bonifant says, Lentune has provided iLine Construction the ability to rapidly turn around quantity surveyor and financial reporting. “Transactions flow through Lentune and Procore almost instantly, enabling iLine Construction to approve invoices on a daily basis and sync them into Xero,” Bonifant adds.
Lentune’s motto is to “drive innovation and play well with others” – a mission that is clearly demonstrated by the company’s integration with Procore. But it doesn’t stop there. Bonifant says the company strives to integrate with the software its customers are already using, resulting in integrations with Xero, Jopbac, simPRO, CostCon and MYOB, as well as Procore. “The days of trying to do everything yourself are gone,” he says. “What we’re seeing in the technology space, especially with the rise of artificial intelligence, is that working together with the industry is the way forward.”
“Some businesses have platforms that are too vast, but we know that the greatest value comes from focusing on what we do best –eliminating tedious data entry by providing a robust, automated accounts payable workflow – while working well with other key software providers to move the sector forward.
“On the whole, we want to create a seamless, high-quality technology stack for our customers and our integration
with Procore enables us to do that.”
No integration is ever finished, explains Bonifant, and Lentune is always looking at how it can further its integration with Procore and other software.
“The Procore product range is continuing to excel and get better,” he says.
“We will continue to facilitate the syncing of data between Lentune and Procore to ensure together we create a solid platform that works well for our customers.”
By working together with other accounting and project management software in the market, Lentune is creating more clarity, control and insight for its customers so that they have more time to focus on higher value tasks.
“What we’re seeing in the technology space, especially with the rise of artificial intelligence, is that working together with the industry is the way forward.”By utilising Lentune with Procore’s Project Financials software, businesses get the best of both worlds.
With over half a million users in more than 100 countries, RIB Software is driving efficiency, resiliency, and sustainability for all stakeholders in the construction project lifecycle through its digital transformation solutions.
RIB Software’s Pacific managing director and vice president Chris Smith says the company is a major player in the Australian construction industry, and for good reason.
The construction industry is facing a number of challenges – from increased costs to sustainability concerns and inefficiencies –and RIB Software is providing digital solutions that can help alleviate these pressures.
“From data that we’ve compiled, as well as supported industry data, we’re seeing almost 95 per cent of construction businesses running out of budget, and experiencing severe delays and quality issues,” says Smith. “Ultimately, when you dig deeper into the root cause of these problems, the catalyst is poor collaboration across key stakeholders –what we call siloed point solutions.”
“When we talk about these siloes, we don’t just mean old technology solutions but also point solutions such as Excel and Word, as well as project processes managed through paper documentation.”
When you dig even deeper, says Smith, construction companies are struggling with cost overruns. Data collected by RIB Software shows that almost 80 per cent of construction companies experience budget overruns for a typical large, non-residential construction project, as well as an average of 20 months in delays to the original project schedule.
“We’re also seeing construction companies running on extremely low margins,” says Smith.“Further, large construction companies spend approximately $550 billion in rework globally – 52 per cent of which is due to poor data, miscommunication and lack of collaboration across projects.”
What’s more, buildings are currently responsible for 39 per cent of global energy related carbon emissions, according to the World Green Building Council.
The industry is also a very slow adopter of technology solutions, says Smith. “The statistics show that we’re only one place ahead of the agriculture sector in the technology adoption space,” he adds. “A concerning 170-million tonnes of construction materials go to waste each year.”
“We still see construction businesses using traditional paper methods – which again isn’t great for the environment – and siloed point solutions,
which result in low efficiency gains.”
It has also been reported to RIB Software that 35 per cent of professionals within the construction industry spend time on non-optimal tasks. “These are some of the standout challenges that the sector is currently facing,” says Smith.
To help the industry address these challenges, RIB Software provides digital transformation solutions that drive efficiency, productivity, resiliency and sustainability for all the different stakeholders throughout the project lifecycle.
“When you go into the core areas of our portfolio, they span the entire building lifecycle, from planning and design, pre-construction and construction, to operations and maintenance after the construction phase,” says Smith.
“Ultimately, these solutions reduce risk, waste and work, enabling construction builds that are more efficient and sustainable.”
RIB CostX is a 6D Building Information Modelling (BIM) solution which streamlines takeoff and project estimating during the pre-construction phase. The user can accurately estimate and build cost plans and bills of quantity (BOQ), compare subcontractors, automatically change and update quantities based on revised plans, and identify embodied carbon associated with the project’s construction.
The RIB Candy solution links the BOQ, project estimates and work program, allowing the user to confidently manage estimating, planning and project control during the construction phase. These comprehensive tracking capabilities allow the user to be confident in their data’s integrity and know what was calculated where.
Then, the RIB CX collaboration suite connects people, processes, documents and drawings – supporting every aspect of project operations. In RIB CX, the project team can create and manage tenders and contracts, capture field data such as labour hours, communicate with all stakeholders, and regulate quality standards, as well as manage BIM files. Then, after construction is completed, RIB CX collects all operational data and secures the digital as built for handover to the operations team. By utilising these solutions, project
“It’s been reported back to us that large construction companies spend approximately $550 billion in rework globally – 52 per cent of which is due to poor data, miscommunication and lack of collaboration across projects.”
Chris Smith, Pacific managing director and vice president, RIB Software.
teams have complete transparency of procurement, risk and estimated costs.
“We have also launched the RIB Carbon Quantifier, a free tool that allows measurement and analysis of the embodied carbon emitted throughout the lifecycle of a build,” says Smith. “The construction industry is a significant contributor to global carbon emissions, so we’re playing our part – by helping construction companies optimise their projects, as well as quantify and evaluate their embodied carbon emissions – to improve sustainability across the sector.”
RIB Software’s range of solutions produce huge efficiency gains for its customers, explains Smith. According to data reported to the company, those using RIB Software’s solutions typically see a 20 per cent increase in the winning of new business.
“It’s what we call work winning and revenue by standardisation and fast project analysis, eliminating risk and securing more margin,” says Smith. “We also see our customers increase supply chain optimisation by 20 per cent from using enterprise data that’s integrated to the different stakeholders across different projects and programs.”
On average, RIB Software’s customers have reported a 25 per cent reduction in costs and overheads, because they’re using the company’s fully integrated standard systems instead of point solutions and paper documentation. Customers have also reported an 80 per cent reduction in non-conformance reporting and changes, due to RIB Software’s solutions providing enhanced collaboration and transparency.
“Investing in our technology can have a
major impact on a construction company,” says Smith. “Our partnership with ACCIONA Geotech is a prime example.”
Engineering company ACCIONA Geotech recently won an international quality award on the back of utilising RIB CX to digitise governance, and project and business performance.
All-star team
RIB Software is part of Schneider Electric (SE), a global specialist for energy management and automation technology in the industrial and construction sectors. Specifically, SE has three business units encompassing the construction sector – design, build, and operate and maintain, and owns several companies in this space.
This includes the recently acquired AVEVA, an industrial software solution provider that spans engineering, operations, and maintenance, as well as Clipsal, who deliver residential and commercial electrical products and solutions.
However, RIB Software is the only business that sits under SE’s ‘Build’ portfolio.
“We’re the only company that SE has within construction management providing technical digital transformation solutions,” says Smith.
Ultimately, says Smith, RIB Software’s purpose is to empower engineering and construction professionals around the globe to build more efficiently and sustainably.
Inspired by this, and through combining local expertise in Australia and New Zealand with a global advantage, RIB will continue to drive digital transformation that makes a difference – today and in the future.
“When you go into the core areas of our portfolio, they span the entire building lifecycle, from planning and design, preconstruction and construction, to operations and maintenance after the construction phase.”RIB CostX powering the Christchurch Cathedral Reinstatement after devastating 2011 earthquakes in Christchurch, New Zealand. Source: Rawlinsons & Warren and Mahoney Architects.
From the foundations of Dincel’s engineering roots, combined with our commitment to constant innovation, Dincel has solved the universal building constraint of water leaking at the basement wall, including the wall/wall-footing joint.
We’ve even put our money where our mouth is by offering up to 50 years warranty on the basement walls.
For more information scan the QR Code above or contact Dincel on 1300 DINCEL.
Through its connected, intuitive platform ProcurePro is eliminating the common issues faced during the procurement process, allowing construction businesses to keep their projects on the move and on budget.
Procurement is mission critical to the success of construction projects. It’s one of the first processes head contractors carry out on a project and yet traditionally has been a disjointed, high-risk and time-consuming endeavour. Identifying the need for a better way, ProcurePro launched in 2020 and its solution is now cutting the time construction businesses spend procuring by up to 50 per cent.
Purpose-built for head contractors, ProcurePro is a powerful software solution that helps businesses procure trades quickly and efficiently, with complete visibility and control. Guided by the company’s founder and CEO Alastair Blenkin, and co-founder Tim Rogers (ex-Hutchinson Builders)
ProcurePro is creating massive efficiencies in the procurement process for the likes of Richard Crookes Constructions, Roberts Co, BESIX Watpac, Hutchinson Builders, Hansen Yuncken, Kapitol Group and Taylor Construction Group to name a few.
Generally, says Blenkin, the overall procurement process is a combination of 15 to 20 processes all tied into one and managed by legacy systems such as Microsoft Word and Excel, shared drive email and phone calls. “Consequently, contractors end up with a deluge of documents and spreadsheets which can lead to disconnected information, no visibility or traceability, missed lead times, poor data quality and gaps in scope of works,” he explains.
“This makes it difficult for contractors to gain visibility over their projects and make informed decisions.”
“Using this method, it can sometimes take a contractor over 40 hours to procure a single trade.
“ProcurePro solves all of these challenges –we’ve consolidated these 15 plus fragmented processes into a centralised piece of software.”
By delivering one centralised system for procurement, ProcurePro gives contractors complete visibility throughout the entire workflow, with all relevant data accessible in real-time, every single day
as procurement happens.
Further to the challenges associated with the traditional process of procurement, macroeconomic conditions affecting the Australian construction industry are making quality procurement systems even more crucial for head contractors. Supply chain disruptions, cost escalations and the ongoing after-effects of the height of the COVID-19 pandemic are putting contractors in an ‘innovate or perish’ position. Those sticking with outdated and inefficient processes run the risk of falling behind in an already extremely competitive industry.
“In procurement in particular, it’s really one of those ‘hair on fire’, top one, two or three business problems for builders, particularly through the lens of cost escalation,” says Blenkin. “In times gone by, contractors used to sign up a subcontractor and a couple of months later clean up the paperwork.”
“But that doesn’t fly in this market, particularly when costs have increased so dramatically, supply chains are disrupted, and labour shortages continue to burden the industry.”
In the current climate, subcontractors know they are in high-demand. If contractors don’t get a contract in place quickly to secure them, they run the risk of losing the subcontractor to a different job.
As a result, says Blenkin, ProcurePro is experiencing a huge demand from builders looking to level up how they procure trades.
“With ProcurePro the full process of tracking, issuing and chasing contracts is seamless,” Blenkin explains. “Everything is in one place, providing one source of truth for all parties.”
Moving away from fragmented and disconnected procurement, ProcurePro ensures the process is smooth and consistent with features such as a procurement schedule, a scope of works library, tender and price breakdowns, comparisons and recommendations, vendor management, contract creation, electronic signature and
“ProcurePro takes the commercial aspects of construction –tendering, letting, scopes and contracts – and wraps it up into a single piece of software which makes life a huge amount easier for our project teams.”ProcurePro founder and CEO Alastair Blenkin.
reporting and analytics.
ProcurePro enables contractors to view live updated procurement schedules all in one place as procurement is carried out, providing complete visibility every day of the month.
Contractors can rapidly create quality scope of works to prevent scope gaps, improve profitability, create consistency across projects and reduce revenue leakage. “The user can also view insights into vendors including vendor performance, workload and history to quickly identify supply chain risks and opportunities, providing complete supply chain oversight,” says Blenkin. “What’s more, tenders and addendums can be sent within seconds, and subcontractors can upload their quotes, transmittals and correspondence directly into ProcurePro.”
The platform also recommends and compares vendors based on historical information captured throughout the procurement process, including pricing and approval workflows.
Then ProcurePro automatically populates contract particulars ready for sending. Once sent, its electronic signature feature allows contracts to be signed fast with complete traceability.
“To top it all off, ProcurePro captures data and insights from the entire procurement process so that contractors can identify and mitigate risk, improve performance and reduce costs,” says Blenkin.
But what about the risks and costs associated with implementing a new technology?
Many contractors have war stories or scars from previous construction technology implementations gone wrong, causing them to be hesitant or disinclined to give it another shot. Construction companies also have a lot on their plate, from industry challenges to huge workloads, which can make it difficult for them to find the time or the resources to take on a new system.
ProcurePro is striving to change an industry mindset of technology implementation being a strenuous undertaking, instead showing it can be an extremely fruitful, simple and successful process.
“We’re trying to almost re-educate the market on how software implementations can and should be done,” says Blenkin. “Essentially, we’ve made ProcurePro easy to implement and fast to scale.”
“It’s also easy to use – we’re putting guardrails around people to make it simple for them to follow the procurement process and do their job.”
Blenkin says he’s had numerous customers come to him saying ProcurePro has enabled them to hire more junior or ‘greener’ staff because it’s such a user-friendly software. At a time when skill shortages are putting a strain on construction businesses, ProcurePro is creating opportunities to attract and recruit the next generation.
In just seven days ProcurePro can be set up for a business. By 14 days, ProcurePro can be live across a business with its teams trained and projects set up on the system. In 90 days, ProcurePro can be scaled company-wide across all projects.
“We’re all about giving the customer comfort throughout the change while also making it a fast and effective process,” says Blenkin.
“We pride ourselves on our less than 60 second response time in ProcurePro’s help centre, which has real people answering your calls and assisting you, in real-time.”
ProcurePro’s streamlined implementation process was powerfully demonstrated when Probuild collapsed, and Roberts Co took over a number of its projects in Victoria. ProcurePro was implemented on nine of these projects worth almost $1 billion in one morning.
“With ProcurePro the full process of tracking, issuing and chasing contracts is seamless.”
Fragmented and disconnected procurement causes inefficiencies, data leakage and frustration.
“In just a few weeks we had set up ProcurePro on all nine projects, given all team members a demonstration and training session, and the teams were off procuring on the system,” says Blenkin.
“This shows that implementation can be done quickly and efficiently for any size business, from the smaller builders to the larger scale contractors with multiple projects on the go.”
Having now experienced the power of ProcurePro herself, Roberts Co Executive Chair Alison Mirams says, “ProcurePro takes the commercial aspects of construction – tendering, letting, scopes and contracts –and wraps it up into a single piece of software which makes life a huge amount easier for our project teams.”
On average, says Blenkin, ProcurePro saves its customers 50 per cent of the time spent procuring by eliminating manual tasks, resulting in huge cost savings. “It might sound a little unbelievable,” says Blenkin. “But when you write down how many manual
tasks there are in the procurement process, including sending emails and updating Excel spreadsheets, it’s a lot.”
Some customers have reported even larger time savings, with Monarch Building Solutions estimating ProcurePro made its procurement process 60 to 70 per cent faster, resulting in an estimated cost savings of $750,000 in 12 months.
Similarly, Kapitol Group estimates ProcurePro has saved the company up to 15 hours in procurement per trade. Kapitol Group Director Andrew Deveson says ProcurePro has been a game changer. “From an owner’s point of view, the complete transparency is unbelievable – there’s no hiding or faking it,” he says. “It’s efficient, intuitive and has helped us attract and retain smart people, who spend more time on higher value work.”
While construction companies continue to be snowed under by a plethora of challenges, both on a macro and microeconomic level, software like ProcurePro can help take the pressure off. Why have a multitude of processes managed by different, outdated systems when one software can do it all?
“ProcurePro captures data and insights from the entire procurement process so that contractors can identify and mitigate risk, improve performance and reduce costs.”Connected procurement keeps fast-moving projects on program and on budget.
As part of its recently launched overall strategic plan – Horizon 2030 – McConnell Dowell Group (McConnell Dowell) has established a Carbon Reduction Plan to implement strategies across the business to reduce, or stamp out where possible, the company’s impact on the environment.
With the building and construction sector accounting for 39 per cent of global emissions, according to the Clean Energy Finance Corporation, McConnell Dowell is taking action to address the climate crisis.
Within the company’s Carbon Reduction Plan are three overall goals. Firstly, McConnell Dowell has set a target to be operationally net zero by 2030. The plan also includes a target to reduce the business’s direct carbon emissions, those that occur from sources controlled by the company, by 45 per cent. Thirdly, the company aims to implement an ethically sourced offset strategy. While these goals are certainly ambitious, McConnell Dowell environment and sustainability operations manager Tim Walker says everyone in the company, from executive management to those with boots on the ground, is on board.
“I’m very proud to work for a company that has senior management commitment around sustainability and high environmental, social, and governance (ESG) standards,” says Walker. “Our managing director and executive board have all reviewed and endorsed our Carbon Reduction Plan.”
Developed as a company roadmap, the plan is built on eight strategic focus areas – offices, system improvement, education, fuels, moving plant, light vehicles, stationary plant, materials and travel – and includes 44 carbon reduction initiatives to be rolled out across McConnell Dowell’s operations by 2030. The company has also formed an Environmental Sustainability Committee led by one of its regional general managers to help drive these initiatives. “Overall, we aim to achieve a 45 per cent reduction in Scope 1 and Scope 2 emissions, with the remaining to be offset, by 2030,” says Walker.
In achieving these goals, McConnell Dowell has placed a major focus on reducing its Scope 1 emissions, which are produced by its direct use of fuels.
“We are taking meaningful steps to ensure we can do everything we possibly can to reduce emissions with the current technology that is available,” says Walker. “For instance, we’re already in the process of transitioning our light vehicles to electric, with a goal of 100 per cent of our light vehicle fleet to be electric vehicles by 2030.”
“We currently have three fully electric vehicles and a number of hybrid vehicles within our fleet as well as an electric truck on the way; and are currently in negotiations with our leasing company to get another 40 electric vehicles added to our fleet in the next 12 months.”
Typically, in areas or remote locations where project teams are unable to connect tools and machinery to the mains power, they have to rely on another source of energy to power their equipment, like dieselpowered generators.
Construction is among the leading industries contributing the largest carbon footprint from the use of fossil fuels such as diesel.
That’s why McConnell Dowell, in partnership with Black Stump Technologies, has cocreated the ‘Solarator’ – a containerised power plant that combines solar panels, batteries and a small diesel-powered generator – which is capable of reducing diesel fuel consumption by up to 80 per cent for the company’s off-grid site facilities. McConnell Dowell estimates that over a 10-year period the units will save over 8,000 tonnes of carbon on its worksites.
“We have five of these power units that have been operating successfully across our business over the last six months,” says Walker. “We will continue to develop strategic partnerships with our supply chain to maximise sustainable outcomes.”
McConnell Dowell is also looking at a number of renewable fuel and biodiesel trials and is currently using biodiesel blends from five per cent up to 50 per cent blends on a number of its projects in Victoria.
“Additionally, we’re about to embark on a 100 per cent renewable fuel trial on a Western Program Alliance project we’re delivering,” says Walker.
Similarly, the company is driving down its Scope 2 emissions, which are produced indirectly from its consumption of purchased electricity.
Taking a whole-ofbusiness approach to tackle the climate challenge, McConnell Dowell Group has set itself ambitious but achievable targets to be operationally net zero and reduce its direct emissions by 45 per cent by 2030.
“I’m very proud to work for a company that has senior management commitment around sustainability and high environmental, social, and governance (ESG) standards.”
Where feasible, McConnell Dowell is connecting its satellite compounds that are built for infrastructure projects to the electricity grid to remove the need for dieselpowered generators onsite.
The company has also set a target to power its head and regional offices on 100 per cent GreenPower.
“By purchasing GreenPower from the grid we are essentially able to offset those carbon emissions that we would otherwise produce,” says Walker.
“Placing a focus on our electricity consumption by paying for offsets leads to cultural change through a focus on daily actions such as avoiding electricity consumption through the use of timers, sensor lights, LEDs and other efficient technology.”
Already championing a number of the sustainability initiatives outlined in its Carbon Reduction Plan, McConnell Dowell is pioneering the use of solar technology to power its construction site compounds.
Three years ago, the company capital purchased an 80-kilowatt mobile cantilevered
solar system, which was transported via shipping container to a high-profile State Government project, the Level Crossing Removal Project – Western Program Alliance. The grid-connected system was deployed at the site for a period of nine months. During that period, data shows the system:
• P roduced 54 megawatts of renewable energy.
• Sent 38 megawatts back to the grid, for the benefit of Victorian households.
• Saved 36 tonnes of CO2 emissions and at zero cost.
The power bill for the site was in credit, and the site achieved the notable milestone of being the first carbon-positive McConnell Dowell site facility during construction.
“We’ve also conducted a number of biodiesel trials and used more solar lights that rely on battery power rather than diesel power on these projects,” says Walker.
“We are learning from trials and gaining confidence in deploying new technology across more projects.”
In addition to McConnell Dowell’s 45 per cent reduction by 2030 and operational net zero
“We will continue to develop strategic partnerships with our supply chain to maximise sustainable outcomes.”Co-created with Black Stump Technologies, the Solarator is a compact containerised power plant for construction sites that combines solar panels, batteries and a small diesel generator.
(Scope 1 and 2) goals, the company targets a year-on-year carbon intensity reduction of at least 5 per cent until 2030.
Walker says this is measured across the business’s regions and business units, with carbon intensity calculated as carbon dioxide equivalent (CO2eq) tonnes/revenue.
“This allows us to compare carbon intensity per region and project to determine their carbon intensity profile and to double down on strategies to reduce emissions within those regions and projects,” he adds.
The company has also set its sights on tracking Scope 3 emissions through data capture technology and developing a plan specific to the reduction of Scope 3 emissions. These are the emissions the company is indirectly responsible for throughout its value chain, including from travel and the production of purchased materials. “We are also leveraging our digital engineering teams to refine a carbon model of materials early in the design phase, currently being trialled on various projects across Australia and New Zealand,” says Walker.
The company is already making great inroads in implementing recycled and low
carbon products – including low carbon concrete mix designs, and the use of recycled plastic products in rail sleepers, asphalt, noise walls and aggregates – across its infrastructure portfolio to reduce its Scope 3 emissions.
The other key part of McConnell Dowell’s Carbon Reduction Plan is in regard to its supply chain – its suppliers and subcontractor workforce. Around 70 per cent of the company’s Scope 1 emission profile is made up of diesel, which is primarily sourced from subcontractors using heavy machinery, excavators, trucks, dozers and the like. “The infrastructure that we build heavily relies on subcontractors,” says Walker.
“That’s why in our procurement of those subcontractors, our request for quote templates outline our commitments around sustainability aspirations, carbon reduction and where we as an industry are heading.”
“Without them changing along with us, the industry as a whole won’t change, so we’re building strategic partnerships with our supply chains to lay the foundations for a more sustainable future.”
“Overall, we aim to achieve a 45 per cent reduction in Scope 1 and Scope 2 emissions, with the remaining to be offset, by 2030.”
Further, the company’s sustainability and ESG strategies are embedded in its tender processes, requiring tender teams to address climate change risk and carbon reduction strategies.
Time is critical, says Walker, and the time to act is now, but construction companies can’t make true progress in addressing the sustainability problem in isolation. “Sustainability is about sharing knowledge and coming together to solve the issue that we have in front of us,” says Walker.
“We’re smart enough, and we have many solutions on hand, so as an industry it’s time to crack the whip and work together towards a green future.”
McConnell Dowell’s forward-thinking Carbon Reduction Plan shows how a large and
diversified construction company can go the extra mile to tackle the climate challenge. With carbon reduction, renewable energy and sustainable building practices set to be a focus for the industry and wider economy in the coming years, McConnell Dowell is blazing a trail for sustainability in construction.
McConnell Dowell is well on the way to replacing its light vehicle fleet with electric and hybrid vehicles; and have its first electric truck on the way.Why do people make errors? How do humans perform under pressure? These are just some of the questions that led to the establishment of cloud-based adaptive-learning software provider Area9 Lyceum.
Area9 Lyceum’s origin story is fascinating to say the least. Starting as a venture of Ulrik Juul Christensen in the field of medicine, today the company delivers improved educational and training outcomes, backed by a scientific approach, for various industries in Australia and around the world.
As a physician by training, Christensen has long had an interest in human factors.
In 1997 he launched his first company Sophus Medical, building simulators for the medicine field with a goal of discovering what leads to human errors in live operating environments. “I spent the first years of my career trying to dig into what leads to human errors, and in this case, what leads to life saving performance or the human errors that lead to death and disability in other parts of healthcare,” explains Christensen.
“What’s striking is we ended up on a long journey moving from training in very complex team-based situations to realising there were a lot of things that needed to be done on an individual level.
“We found that we were using expensive training environments to train in areas that could be learned in more accessible environments, like on a construction site.”
Eventually Laerdal Medical acquired Sophus Medical, but that didn’t stop Christensen from delving further into the research of cognitive workloads. In 2006 he founded Area9 and began building the first versions of adaptive learning systems.
By 2008, Area9 had partnered with McGrawHill Education to deploy its adaptive learning technology. “We built our first adaptive learning prototype for a focus group to gather their feedback and managed to strike a deal with the then president of McGrawHill Education who bought a part of the company,” says Christensen.
Quickly, Area9’s technology started to be used widely in colleges across the United States, processing approximately 1,100 student interactions per second.
This success gave Christensen the appetite to get back to his roots – to build systems that would allow humans to learn more complex things – and thus amicably parted ways with McGraw-Hill Education.
“In 2018 we launched the current company, Area9 Lyceum, where we assembled all of our software, internet protocol (IP) and educational IP to build the fourth-generation platforms with a goal of being able to harbour more dimensions of learning, not just knowledge,” says Christensen.
The McGraw-Hill Education partnership proved that the technology could handle extremely diverse learner groups – the exact same product was used for students with learning difficulties such as dyslexia, slow learners, fast learners and top performers. They didn’t have the same learning path but were using the exact same product.
This breakthrough, and the departure from McGraw-Hill Education, saw Christensen and his team shift their focus to diverse adult populations of learners, leading them to the construction industry.
“We never built this with a specific purpose for the construction industry,” says Christensen. “But construction happens to be an area where you often have people with very different backgrounds in the same room.”
Launching its e-learning platform Area9 Rhapsode, Area9 Lyceum became dedicated to corporate learning.
One of the early proofs that Rhapsode could make great inroads in construction learning was in road safety. Area9 Lyceum partnered with VEJ-EU, an independent association formed by the Danish road sector in Denmark, to provide meaningful learning experiences for road workers and bring learning that mattered out of the classroom and back to the roads with Rhapsode.
The Rhapsode powerfully combines presentation style work with adaptive learning that prompts questions suited to the learner’s development needs.
“For each learner, the in-built artificial intelligence identifies their competence through the course and adjusts in real-time to support their development to achieve proficiency,” explains Christensen.
Built upon research of the effects of adaptive learning and simulation in medical training, Area9 Lyceum has evolved to now address some of the construction industry’s most pressing challenges.Ulrik Juul Christensen, co-founder Area9 Lyceum.
Essentially, the program will select the relevant learning material based on each learners’ experience and knowledge.
The road construction sector has been fighting the problem of effectively training a diverse workforce for decades, says Christensen.
“They had the civil engineer responsible for the entire bridge in the same room as the asphalt labourer, both with completely different skills and competencies,” he adds.
“It’s been proven time and time again that when it comes to learning, you need to slow down.
“If you give a diverse group of 30 learners 45 minutes to complete the same training, it’s not going to work practically.
“That’s the point of difference with Rhapsode – we’re not putting a time frame on the learner; the dependant variable is time and the independent variable, the thing that doesn’t change, is performance.”
This approach to learning is a leap forward for training in the construction industry given the sector’s complex nature and consequently complex challenges. The ongoing skills crisis has put pressure on construction companies to find new ways to attract, recruit and retain talent and also placed job seekers in a position of power, letting them be strategic about the roles they take on.
As the next generation of construction workers comes up through the ranks, many have an expectation that the companies they join will have state-of-the-art equipment, practices and systems in place, like Area9 Lyceum’s platform Rhapsode.
“The construction industry is characterised by ‘doers’; people who like to sit in behind the steering wheel on the joystick and actually operate real things,” says Christensen.
“But how do you methodically then make a learning progression?
“This combined platform can take multidimensional learning into account and allow you to practice in more than just the knowledge dimension.”Area9 Lyceum’s adaptive learning platform automatically adjusts to the needs of each learner.
“That’s what Rhapsode is capable of –this combined platform can take multidimensional learning into account and allow you to practice in more than just the knowledge dimension.”
This in turn shortens the time to proficiency, posing significant productivity benefits. If a contractor takes 1,000 workers and puts them through a traditional eight-hour course, explains Christensen, it will cost the company 8,000 labour hours. With Rhapsode, he says, the contractor only has to take them out of production for half of that time.
Rhapsode also provides a reliable measure of each worker’s competence, as it measures everything they’ve learned throughout the course. With Rhapsode, construction businesses can save labour hours, training costs and enjoy full confidence that their workforce has the skills, knowledge and proficiency to operate safely and effectively.
Top players in the Australian construction industry such as The Australian Rail Track Corporation and John Holland are already leveraging the benefits of Rhapsode with regards to lead and lag safety indicators.
With the support of Rhapsode, ARTC has seen an improvement in Total Reportable Injury Frequency Rates, a higher level of engagement and a general reduction in work health and safety incidents across all operations through its Contractor Safety Management Program. For John Holland, Rhapsode in addition to reducing safety issues has saved the company more than 12,000 hours in training time, with courses taking 20-30 minutes less to complete than previous approaches.
These results speak for themselves, but Christensen says it’s crucial that the construction industry, and all industries, become critical consumers of learning.
“The industry needs to challenge learning providers, even Area9 Lyceum, to ensure that what we’re bringing to the table is going to provide learning improvements,” he says.
With Christensen at the helm, Area9 Lyceum is well equipped to prove the value of Rhapsode in delivering top educational and training outcomes for the construction industry and beyond.
“For each learner, the inbuilt artificial intelligence identifies their competence through the course and adjusts in real-time to support their development to achieve proficiency.”The Rhapsode LEARNER Dashboard.
Komatsu’s powerful PC138US-11 hydraulic excavator is a mean machine for roadwork, underground utilities, earthmoving and demolition applications.
For decades, Komatsu’s PC138 hydraulic excavator has been a go-to for construction professionals looking for a machine that packs a punch on the jobsite. But the company’s latest model, the PC138US-11, has taken performance to a whole new level.
Komatsu national business manager –construction Scott Berry says the PC138US-11, along with all of the company’s products, is manufactured to the Komatsu Engineering Standard (KES) – an in-house standard, which in many cases exceeds the requirements of the relevant international (ISO), Japanese industrial (JIS) and European (DIN) standards.
“One of our strengths is that the whole machine is designed, sold and supported by Komatsu,” says Berry. “All of our machines have Komatsu DNA inside and out.”
“The PC138US-11 is no different – it’s designed to our high-quality standards and comes with Komatsu’s market best-practice customer service and parts support.”
On the safety front, the PC138US-11 has Komvision, a 270-degree camera system which assists safety in the working area, helping the operator to detect and mitigate collisions. “We really focus on the safety side of things at Komatsu, and that is demonstrated in the rigorous design of our machines,” says Berry. “Safety is embedded in the engineering
of the PC138US-11, with features including hydraulic safety valves on the boom and the arm, handrails to provide safe access to the upper structure, factory fitted provisions for fire extinguishers and emergency stop switches (e-stops).”
In addition, in line with Australian standard specifications, the machine features factoryfitted quick hitch and hammer piping, as well as a reinforced arm and link.
With a net horsepower of 72 kilowatt/97.2 horsepower at 2,050 revolutions per minute, an operating weight of 15,140 to 15,500 kilograms and a bucket capacity of between 0.21 and 0.53 cubic metres, the PC138US-11 boasts power and durability.
“The booms and arms of the machine are constructed with thick plates of high-tensile strength steel and are designed with heavy-duty guarding in the bucket end of the arm to ensure maximum rigidity and durability,” says Berry.
Cleaner and greener construction practices are at the forefront of industry news, discussions and strategies, so Komatsu has also placed a key focus on designing the PC138US-11 with a greatly reduced emissions output. It’s equipped with an EPA Tier 4 Final emissions certified Komatsu SAA4D95LE-7 engine that reduces fuel consumption, reducing particulate matter (PM) and
“We really focus on the safety side of things at Komatsu, and that is demonstrated in the rigorous design of our machines.”The PC138USLC-11 provides high breakout forces for operation in difficult digging conditions. Scott Berry, national business manager –construction, Komatsu.
nitrogen oxides (NOx) by more than nine per cent when compared to Tier 3 levels.
“When an engine burns fuel, it emits soot, which is the dirt and smoke that you can see coming out of an exhaust pipe,” explains Berry. “A lot of engines have what’s called a diesel particulate filter, whereas our engine has a Komatsu Diesel Oxidation Catalyst (KDOC), which will catch a lot of that soot and reburn it off, so it doesn’t go into the environment.”
“It also has what we call a Selective Catalytic Reduction (SCR) system that neutralises NOx with a solution called AdBlue, which breaks down to an ammonia solution and reduces most of the harmful NOx to a more environmentally friendly mix of nitrogen, water and carbon dioxide.”
Further reducing unnecessary fuel consumption and exhaust emissions, the Komatsu Auto Idle Shutdown will automatically shut down the engine after idling for a set period of time.
As governments and major project stakeholders continue to lift their demands for solutions that emit fewer emissions – compelling contractors to meet these requirements in order to get the job, Komatsu is ensuring its machinery – like the PC138US-11 – is up to the mark.
Operationally, the PC138US-11 is optimal for confined and space-limited applications. Compared to conventional excavators, it has a greater front swing clearance when space is limited – with a minimum front implement swing radius of 1,980 millimetres and a 1,480-millimetre short tail swing radius allowing it to work in more confined areas. On many confined sites where a conventional excavator won’t fit, Komatsu’s PC138US-11 will.
“This big utility machine is extremely broad in terms of the different applications it can provide exceptional value for,” says Berry. “If the machine alone can’t get the job done, we offer a range of attachments including rockbreakers and saws, hammers, tilt hitches and all sorts of buckets.”
Naturally, the PC138US-11 can be fitted with Komatsu’s payload monitoring and 3D machine guidance Retrofit Kit (RFK) technology to further bolster its capabilities.
“Having a quality pilot management system like our RFK, particularly in civil works road applications, can really enhance job delivery
freeways, as well as fines for the owner.
“By equipping your PC138US-11 hydraulic excavator with the RFK, the system will measure each bucket load to ensure that there is no chance of overloading the truck –minimising risk for all parties.”
As with any of its machines, Komatsu provides PC138US-11 owners in-house, multilayered support that goes all the way back up to the factory. “We offer four years or 8,000 hours machine warranty, which we believe is market leading,” says Berry.
“We also throw in 2,000 hours of servicing, which is Komplimentary with Komatsu.”
Providing exceptional performance while reducing fuel consumption and improving safety, Komatsu’s PC138US-11 hydraulic excavator combines intelligence and durability to improve efficiency in the toughest of applications.
and arms of the machine are constructed with thick plates of high-tensile strength steel and are designed with heavy-duty guarding in the bucket end of the arm to ensure maximum rigidity and durability.”The PC138US-11 Series provides the performance and productivity you expect from Komatsu equipment. Komatsu’s PC138US-11 Series hydraulic excavators have a short tail swing profile, designed specifically for work in confined areas.
While small contractors may think new technologies are only for the heavyweights of the industry, Trimble’s solutions are helping construction businesses level up regardless of their size.
The prospect of construction businesses continuing to work the same way they have for the last 30, 20 or even 10 years is unlikely and, given the relentless rise of challenges both on an industry and economic level, unfeasible. The ongoing labour shortage, the demand for improved productivity and the need to stay competitive are just a few of the difficulties currently sweeping across the construction industry. Technology is a proven force multiplier, though for small and specialty contractors this may seem more burdensome than beneficial when considering the potential cost, time and disruption of existing legacy workflows. Understanding this, Trimble is working hard to ensure contractors large and small can leverage technology to improve construction workflows.
Every contractor hears buzzwords like office-to-field connectivity, machine control and rovers – solutions that Trimble machine control product manager Jack Young says are designed to plug a hole in business workflows with the promise of productivity improvements.
“Many small contractors might hear these words and think they are just for the big firms, but the reality is that there are a range of solutions continuing to emerge specifically for small site contractors,” he says.
“Almost any type of technology deployment will require a workflow adjustment, but most contractors conclude that the productivity achieved is absolutely worth it.
“We hear customers report dramatic changes in their workflow, with technology enabling them to multi-task, leverage the tracked and stored data and run multiple jobs at a time with complete efficiency across the board.”
With these positive outcomes in mind, Trimble is making sure that any size business, from family-owned builders to global contracting firms, can benefit from investing in the right technology.
The 2D edge
Often, one of the first big adjustments for a small or specialty contractor is adopting 2D technology, though Young says
diving into 3D solutions may be a better option for some businesses in regard to simplicity and productivity.
“It’s really about understanding what 2D and 3D are and how they apply to the type of work that you are doing,” explains Young. “2D workflows are exceptional for flat work, and contractors have gotten proficient at setting grade with rod guidance, pulling stringlines and then following that guide with pretty good accuracy and quality.”
“A 2D workflow works just fine and delivers the capabilities from a productivity standpoint that are needed for that contractor.”
For instance, Trimble Earthworks GO! is a solution purpose built for 2D automatics on skid steers with box blades that are commonly used for flat work. The high precision, laserguided 2D grading system utilises an onboard computer and external inertial measurement
“Many small contractors might hear these words and think they are just for the big firms, but the reality is that there are a range of solutions continuing to emerge specifically for small site contractors.”
Today’s technology isn’t just for large contractors. A variety of versatile and easyto-use solutions are available to help small site contractors work with greater efficiency and accuracy.
unit, delivering the fully automatic capability of Trimble’s other advanced machine control options at a lower price point and with more simplicity.
“Operators can simply attach the Earthworks GO! box magnetic mount to the machine, connect the cables, mount their smartphone or device in the cab, turn on the laser and start working,” says Young. “Among other features, the software saves machine profiles, allowing the operator to easily switch between machine attachments with no extra setups.”
It can also be pulled off one machine and hooked up to another machine in minutes.
For small site contractors working on projects with more complex shapes, Young says they should be looking at 3D technology.
“2D methods do not translate well in these environments, leading to extra work,” he says. “Also, owners, architects and engineers are rapidly moving to 3D specifications, and those requirements flow down to the contractor.”
Moving to 3D can be confusing from both a hardware and workflow perspective and in some cases overwhelming – with terms like real-time kinematic, point-to-point protocol and correction services coming into play – for small contractors. But the industry is delivering affordable, highly accurate solutions that are easy to use, as well as comprehensive support to make sure the transition to technology is seamless.
For instance, with just one system – the Trimble Siteworks Machine Guidance Module – contractors can perform a range of common
activities including site surveys, 3D machine guidance, in-field design and reporting. Designed specifically for small site and utility contractors, it includes the Trimble SPS986 or Trimble R780 GNSS Smart Antenna, both familiar tools in the construction space.
“Contractors can then combine the receiver with any device or Trimble field tablet that supports Trimble Siteworks software to turn it into a multi-purpose field solution,” explains Young. “The global navigation satellite system (GNSS) smart antenna can be used on a pole for surveying, and that same system can be transferred to the excavator.”
“The antenna attaches to the excavator stick and the data collector moves from the rover pole to a mount in the cab of the excavator.”
The Trimble Siteworks Machine Guidance Module was recently launched at CONEXPOCON/AGG in March this year and Young says the response from small contractors was overwhelmingly positive.
Many said the module meant they no longer had to choose between a technology solution on a machine and a technology solution that can be carried out into the field on foot. Traditionally, those two would have been separated due to various reasons, says Young. One being the rigours that are required for a system to survive on a machine versus the weight at which a system is on a survey rod for a contractor.
“The goal was to leverage a receiver that is designed for the rigours of a machine to provide a two for one system that performs the functionality in the field and the cab,” he says.
“We hear customers report dramatic changes in their workflow, with technology enabling them to multi-task, leverage the tracked and stored data and run multiple jobs at a time with complete efficiency across the board.”
Technology that runs on Android or iOS smartphones decreases the learning curve for users just getting started with technology.
“This means the user no longer has to transfer files manually via USB sticks or emails back and forth – it’s all there on the display.
“That resonated a lot with contractors that have experimented with certain technologies that haven’t quite worked out for them as they can do it all with one investment.”
For businesses without a base station, there are many correction sources provided by government entities, or there are services such as the Trimble RTX family of real-time GNSS correction services. RTX is available via IP/cellular from the user’s cell phone hotspot or directly from a satellite.
With the combination of the Trimble Siteworks Machine Guidance Module and RTX, the user can simply attach the components, turn them on and get to work. There’s no base station setup or correction source confusion, and the data gathered during layout is automatically available in the cab.
“One of the other advantages of a product like Siteworks Machine Guidance is that it is designed as a stepping stone to future investments,” says Young. “It’s not something that will be abandoned as technology advances but can be built on and expanded as business needs grow.”
Another point to consider is the value of
today’s technology subscriptions. Trimble is always trying to figure out how technology can assist with resolving the pain points of customer workflows. The company has realised that it needs to be as customisable with the way it offers its products as it is with the way it builds its products. That’s why Trimble has introduced the ability for its customers to subscribe to its solutions.
The upfront cost of subscriptions is much less significant for new contractors entering the technology ecosystem. The customer will always have the most up to date systems that Trimble has to offer via those subscriptions, reducing the complexity of technology maintenance that comes with traditional perpetual offerings.
The continuous improvement of applications in the way of features and functionality is also a good reason to have a technology partner to support contractors’ adapting workflows, says Young.
A reliable dealer partner like SITECH, with a full-time staff dedicated to customer success, is essential in this technology enabled era. A dealer partner can onboard a business’s team with new technology investments and also answer questions about capabilities along the way.
“SITECH knows how to take our products and apply them to the specific markets that exist around the world,” explains Young. “Because with construction it’s not a one size fits all.”
For contractors, technology can increase productivity, help significantly reduce rework and better equip businesses to handle work despite labour challenges – all in a safer work environment. With machine guidance solutions, nobody needs to be on the ground near the machine or in a trench.
Further, because all of the data is digital, businesses have better information to develop more confident estimates.
“Technology changes the way work gets done,” says Young. “You’ll be more competitive on bids, more productive in the field and ultimately realise better margins, which drives profits.”
The technology is out there to fit all businesses customised workflows, contractors just need to find their technology enabled ecosystem of opportunity.
“SITECH knows how to take our products and apply them to the specific markets that exist around the world.”With the Trimble Siteworks Machine Guidance module, users can easily transfer the GNSS receiver between the pole and the machine to provide both site survey and machine guidance capabilities.
An industry expert has peer-reviewed Dincel’s Waterproof System Warranty, confirming Dincel Structural Walling has produced an effective way of waterproofing basement walls using its wall panels and accessories.
Conducted over six months, ACOR Consultants has reviewed in detail Dincel Structural Walling’s (Dincel) investigations and technical development of the Dincel Waterproof System and the associated warranty to determine the validity of the claims and the effectiveness of the system.
Inside Construction caught up with Steve Darwell, COO at Dincel and chairperson of the Permanent Formwork Industry Council to discuss the review’s findings and how the Waterproof System Warranty for basement walls can improve compliance and building outcomes in the construction industry.
One of the biggest issues impacting the built environment today, says Darwell, is building defects caused by the incorrect installation of materials.
In Australia, the costs associated with building defects is approximately $714 million per year for domestic buildings – according to the 2021 Building Confidence Report: A case for intervention prepared by The Centre for International Economics – while defects in commercial buildings account for a whopping $1.8 billion in costs per year. Defective installation of building materials is a major contributor to these figures.
“It can be difficult at times for product manufacturers to influence how things are being installed onsite, but we have stepped up to the challenge,” says Darwell. “We’ve trained over 800 installers through our academy in the last three years in order to make sure that we’ve got the right people, with the right skills, installing our product.”
Dincel has addressed a number of building aspects in order to improve the installed quality of its walling system. The company has introduced a range of products, such as its reinforcing steel spacers, to make sure that steel reinforcement for Dincel Structural Walling is placed in exactly the right position every time. Dincel has also instituted the use of self-compacting concrete (SCC) to ensure that there are no voids in the product when installed. The company is so sure of the fact that a Dincel Wall installed in accordance with its installation procedures and using SCC will have no voids, it offers a Void Free Warranty.
What’s more, the company has employed a number of after sale installation specialists to inspect Dincel Structural Walling as it is being
installed to ensure it’s being done correctly.
In terms of the Waterproof System Warranty, Dincel has approached build quality in a similar way. “Our waterproof warranty for basement walls requires that we actually take control of the build,” says Darwell.
“We oversee the installation of the system, and the panels can only be installed by one of our certified and duly qualified installation partners, ensuring that the build quality is exactly right.
“When installed correctly in basement walls, the Waterproof System Warranty prevents water penetration from the ground as well as dampness and deterioration of building elements – and prevents unhealthy or dangerous building conditions caused by mould or fungi.”
But Dincel didn’t want builders to simply take its word for it. As with all of its offerings, Dincel engaged an expert to peer-review its Waterproof System Warranty.
The results demonstrated that the Waterproof System Warranty, when installed in accordance with Dincel’s Construction Manual and with the requirements outlined in the warranty, meets the definitions of waterproof as specified by Dincel.
When it comes to introducing new building solutions, Darwell says peer-review is vital.
“Without an expert peer-review, we’re just marking our own homework,” he says. “A qualified expert in an area will have seen far more issues and have a far deeper understanding of that particular area than a product manufacturer.”
“What we found during ACOR Consultants’ peer-review of the Waterproof System was that throughout the process, as issues were brought up, we were able to address them and hence improve our offering to the marketplace.”
But what does this mean for the construction industry?
Backed by these peer-reviewed findings, the Waterproof System Warranty can be beneficial to any build that has a basement, including detached homes, multi-residential buildings and buildings for the aged care, healthcare, education and commercial sectors.
With many located under the water table, basements are prone to water ingress. Even for those not under the water
“We’ve trained over 800 installers through our academy in the last three years in order to make sure that we’ve got the right people, with the right skills, installing our product.”
the environment changing and the planet warming, Darwell says the water tables are rising, making any basement currently below or near below the water table critical areas that require solid waterproofing.
“By applying the Waterproof System Warranty, we’re able to make sure that throughout the life of a project, water won’t ingress into either areas that don’t want to have water such as car parks, or habitable areas where you can’t have any sort of water or moisture,” says Darwell.
Dincel, along with building product manufacturer AFS, has formed the Permanent Formwork Industry Council (PFIC) in an effort to work towards better building outcomes for the industry and consumers through the application of consistent standards and education throughout the industry.
Incorporated in 2022, PFIC is the peak body representing polyvinyl chloride (PVC) permanent formwork designers, installers, suppliers and manufacturers in Australia, focussed on ensuring that all involved in the industry, particularly regulators, understand the needs, requirements and capabilities of the PVC permanent formwork industry. The council is also about ensuring that there are standards within the industry to make sure that suppliers supply products that are fully compliant with the Building Code of Australia, and that they take responsibility for ensuring that the people that install their products are fully and appropriately qualified.
“Additionally, the PFIC was established to make sure that installers in the industry are also following the correct processes and
that we constantly improve the standard of installed products in the market place.
“It’s about education – to let everyone in the supply chain – regulators, designers, certifiers and builders – understand what the capability of the product is.”
Dincel is championing improved installation quality not only through its own business, but across the building industry.
The company believes and has proven with the recent peer-review of its Waterproof System Warranty, that installation quality is critical to the success of its own products, as well as every product in the market.
Whenit comes to introducing new building solutions, peer-review is vital.
“It can be difficult at times for product manufacturers to influence how things are being installed onsite, but we have stepped up to the challenge.”
CR Kennedy’s digital data driven solutions are raising the bar for the construction sector, and Fabcon is jumping in on the action to harness more control over its projects.
Since its inception, Fabcon’s operations have been driven by a passion for staying ahead of the curve. The architectural stair and structural steel fabricator consistently strives to set the benchmark for high-quality project delivery and with its recent adoption of Leica iCON technology from CR Kennedy, the company is seeing optimal results.
Fabcon was established in 2010, providing structural steel for fit-out projects in Melbourne’s CBD, which ranged anywhere from operating theatres to cantilevered entrance canopies. Specialising in complex projects, accurate data and measuring have been integral to the business’s success.
Moving forward, Fabcon now delivers an abundance of high-end architectural stair projects – and with it demands data of extremely high accuracy to ensure the best quality builds. Traditionally a lot of the company’s set-out work was done by hand by an experienced and skilled survey team. While it was effective, Fabcon’s director Hamish Christie sought new ways to further streamline the process.
“We originally looked at survey tools years ago and as soon as we started putting them through their paces, they fell over in about the first half an hour,” says Christie. “When we attended Sydney Build 2022, we stopped by the CR Kennedy stand and were quickly amazed by the team’s expertise and passion for the Leica iCON technology.”
“We’re coming into this field with a lot of knowledge, and we are not a company that can be bought over very easily, so we were asking very direct, very pertinent questions on the Leica iCON’s capabilities.
“We pushed them and to our surprise all of our questions were effortlessly answered. I think this was a lightbulb moment for me and my colleague – we realised we had found a machine that could do everything we wanted. It was perfect.”
Following Sydney Build in March of 2022, CR Kennedy provided a demonstration of the Leica iCON for Fabcon in May of that year. By February 2023, Fabcon had employed surveying specialist David Lewis to run the
technology full-time across its projects. As project surveyor and draftsman at Fabcon, Lewis works with the Leica iCON daily to conduct layout, as-built and verification tasks on projects. Previously, Lewis says, setting out would be done using points and lines from a computer-aided design (CAD) file. If any point of the design plans had to be checked during layout, the surveyor would need to go back to the computer, analyse the plans, select the relevant point in the model and upload and transfer the relevant data to the total station. The total station then had to receive that data for the surveyor to lay out that one point.
“With Leica iCON, you can basically analyse everything on the controller,” explains Lewis.
“I love that it allows us to visualise the model and compare around it; you can look at different angles, click onto different objects, and it will give you information.”
“We integrate Industry Foundation Classes (IFC) models into the Leica iCON, enabling us to visualise what we’re setting out as we’re doing it, and also to zoom in on the model on the tablet when needed.”
“With this visual, we are able to completely comprehend exactly what we’re setting out, what it should look like and positioning.”
Leica iCON can also be used to check for clashes, says Lewis, ensuring each of the building components coordinate with each other and that no services have been built where the project team is trying to install.
“I love that it allows us to visualise the model
and compare around it; you can look at different angles, click onto different objects, and it will give you information,” says Lewis.
“You can physically check in real-time, for example a plate with 10 bolts – you can check the spacing between each bolt, as well as their size and dimension.”
Currently Lewis is part of the Fabcon team delivering tiered seating as well as other works for a project at AAMI Park. The tiered seating is a complex model, he explains, with both floor and wall mounted steel plates and between 400 and 500 bolts to secure the different plate layouts. “Projects like this require a high level of detail and accuracy that without the Leica iCON would be difficult to achieve,” Lewis says. “Leica iCON has enabled us to seamlessly deliver the project, which is almost at its completion phase.”
With over seven years in the field, Lewis has experience with a range of surveying systems but says he hasn’t come across anything as user-friendly and efficient as the Leica iCON.
“When I joined Fabcon I attended a one-day training with CR Kennedy, and within that one day I was able to grasp the concept of the Leica iCON software,” says Lewis.
“I became a ‘pro’ at using the machine within a week.”
As the Director of Fabcon, Christie has similarly been involved with developing and working with a number of different surveying systems within the business.
“I think this was a lightbulb moment for me and my colleague – we realised we had found a machine that could do everything we wanted. It was perfect.”Auto stake to floor or ceiling with the Leica iCON is very quick and efficient. Leica iCON technology helped Fabcon successfully deliver works for the Bank Australia, Collingwood Melbourne project.
Another feature of the Leica iCON that gives Fabcon confidence, he says, is that it doesn’t allow the user to make big mistakes.
“Big mistakes in our industry can lead to cost blowouts, rework and unhappy clients,” says Christie. “At Fabcon, we pride ourselves on surpassing client expectations in quality and service.”
There’s nothing worse than jumping into an Excel document, pressing one button and losing vital project information. With Leica iCON, the Fabcon team can get on with delivering high-quality projects with the certainty that they’re getting it right the first time.
What’s more, both Christie and Lewis agree that the support they have received, and continue to receive, from CR Kennedy has been unfaultable. “The confidence we gained from meeting the CR Kennedy team at Sydney Build 2022, followed by meeting the company’s national manager of building construction Bernie Edmonds, was phenomenal,” says Christie. “What also can’t be understated is the support we’ve received from CR Kennedy’s building construction technical consultant Alex Richardson who has been unbelievable in supporting us, especially Lewis, in the adoption of Leica iCON.”
“I absolutely cannot fault in any way, shape or form, Alex’s passion for the industry and passion for the product – we’ve never found him falling short of anything in the
sense of answering our questions.
“If he doesn’t know the answer, he’ll find it and bring it back to us.”
For Lewis, who came into the role at Fabcon with no technical support inhouse, CR Kennedy’s support has been exceptionally valuable.
“I’ve sometimes called Alex at seven in the morning with a complex question and he’s straight on the ball,” explains Lewis. “If he can’t figure it out then and there, he’ll pull up his own simulation of the Leica iCON model and figure it out within minutes.”
With a multitude of new technologies hitting the Australian construction market daily, the quality of support that comes with a new software or system can be what sets it ahead of the field. As Christie puts it, at the end of the day a new technology is going to be nothing more than an extra weight in the tool bag if there’s no support to ensure the user understands it and can use its full capabilities. CR Kennedy understands the importance of supporting its surveying equipment and solutions and Fabcon is reaping the benefits.
CR Kennedy segment manager – building construction Bernie Edmonds says it’s companies like Fabcon – which are thinking ahead, adapting and adopting digital technologies such as the Leica iCON – that will continue to thrive in the everchanging landscape of construction.
“When we attended Sydney Build 2022, we stopped by the CR Kennedy stand and were amazed by the team’s expertise and passion for the Leica iCON technology.”
For nearly 40 years, Esker has been enhancing document business transaction processes through leading-edge technologies for industries around the globe. A pioneer in cloud solutions, the company is making waves in the Australian construction industry by putting an end to manual data entry in the procure-to-pay (P2P) and order-to-cash (O2C) processes (the cash conversion cycle).
Harnessing its global footprint and multiindustry experience, Esker delivers artificial intelligence (AI)-driven solutions to the construction and infrastructure sectors.
In the P2P space, otherwise known as source-to-pay, Esker automates supplier management, contract management, procurement, accounts payable and expense management processes. In the O2C space, the platform automates the processes of credit management, customer inquiry management, order management, invoice delivery, payment, cash application, claims and deductions, and collections management.
Esker ANZ managing director Christophe DuMonet and customer experience manager Dalene Simpson are both extremely passionate about Esker’s solutions and their ability to empower the people and improve the processes that grow construction businesses.
“On the supplier side (or P2P side) organisations are buying goods and services which require purchase orders, receiving goods and invoices from suppliers, managing supply and onboarding suppliers into their systems,” says DuMonet. “On the customer side (or O2C side), companies are receiving order contracts from customers, providing quotes, eventually providing services or products to those customers, invoicing them and collecting payments.”
“It’s a lot of interactions which are supported by processes, documents, people and communication.”
Esker’s role is to support and enable those processes to make them more effective and efficient and make people more productive. The company’s end-to-end solution is constantly evolving to reduce friction – from things like misplaced documents and errors in processing and shipping – as much as possible. Shipping construction materials, for example, is expensive and getting it wrong can create a chain of negative effects
for a construction business. Having to ship materials to different locations is not great for the environment either.
DuMonet says an enterprise resource planning (ERP) system, or sometimes multiple industry specific systems, is at the core of most construction businesses – but many don’t interact with each other.
“We don’t compete against these systems or ERP; we don’t overlap with them either,” he explains. “Esker supports these accounting systems to eliminate the pains of manual processing and data entry.”
For instance, when a business needs to process a supplier invoice, the delivery to the right location might take place in an ERP or construction specific system. When this invoice comes in as a PDF via email it needs to be processed and eventually paid. But without a solution like Esker that automates and digitises the processing of that invoice, manual data entry is required. By digitising the process, Esker makes the PDF digitally available for processing and for access by multiple stakeholders in the organisation.
Instead of spending 10 minutes per invoice, Esker ensures little to zero time is spent per invoice.
By automating manual inefficiencies and low-value tasks in procure-to-pay and order-to-cash processes, Esker is empowering construction businesses to make better decisions, focus on continuity and more importantly, focus on growth.Dalene Simpson, customer experience manager, Esker ANZ. Esker’s artificial intelligence-driven solutions allow construction companies to free themselves from lengthy processing times, high costs, errors and low visibility.
“If you look at each type of transaction, there is an interesting set of sub processes – which are normally manual activities that need to take place for that document to be processed,” explains DuMonet. “Esker is all about basically eliminating all this manual data entry and all the errors that come from data entry.”
“Also, newer generations don’t want to do data entry; I don’t think anyone ever has.”
A construction site is a stressful environment with moving parts, people and processes. Construction workers are often bombarded with activities they need to do to get the job done, including the task of processing transactions. Traditionally, people would need to go back to the office to access a paper transaction document. With Esker supporting transaction processes, such as purchase orders, procurement and accounts payable –supplier interactions – people have access to the information and data files onsite, on the road or in the office of a supplier, enabling them to make better decisions because they have everything they need at their fingertips.
Today, says DuMonet, people want access to information on almost any device, especially in the fast paced and constantly moving environments of the construction industry. “Being able to review, for example, invoices quickly and approve them or send them to the right person to address them is essential –that’s what we enable,” he says.
Surrounding its success in delivering great outcomes for its customers is Esker’s use of AI. Rife throughout the media are headlines about AI replacing jobs, although DuMonet
says at Esker they don’t believe this is the case. “Our vision in what we do today is to think more about how AI is supporting humans as opposed to replacing them,” he says. “We see AI as an opportunity to enhance the ability of a human to do certain activities more quickly and effectively and with less stress.”
“AI can be used to provide insight in terms of, for instance, gathering information about suppliers through credit management activities or processes.
“It can indicate to you that a supplier is becoming riskier by say, not delivering certain goods – in previous times, people would be in reactive mode because of this.” DuMonet says AI is not necessarily going to detect everything that can go wrong, but it can
Esker empowers users with easy access to information anytime, anywhere, enabling better decision-making.
Esker’s mobile application, Esker Anywhere, delivers faster invoice processing, improved efficiency, and onthe-road accessibility to review and approve spend requests or supplier invoices prior to payment.
“The use of AI is accelerating across the construction industry, and we’re making sure we’re ahead of the curve by delivering constantly evolving AI-driven solutions now and into the future.”
on many processes be much more proactive for people and businesses in providing them predictive analysis.
AI is embedded in almost all of Esker’s solutions. For example, Esker uses AI to do the pre-processing of cash payments from customers, meaning the system allocates cash that a business has received in its bank account, correctly. This provides businesses a better understanding of their cash flow position and forecast which, at a time of rising interest rates in Australia, is vital.
“Whether it’s about wanting to process documents much more effectively as opposed to the old-fashioned way, better understand a document or make better business decisions based on predictive analysis – these are the areas in which AI shines,” says DuMonet.
For systems to be effective, AI is really powerful in being able to figure out which data field means what on documents. AI can, for example, be used for very simple things like a triage of an email inbox. All sorts of business documents like purchase orders, claims and remittances are in
Esker, being an order management system, will pre-process each order so that they can go straight through to the right person or team without the need for manual intervention.
“For us, we’re focused on understanding the structure and content of documents so that we can rank these documents into the right place and into the right process, as opposed to someone sitting there and opening every email one-by-one and then forwarding them,” says DuMonet.
“So here, AI has this ability to be like a second brain that can analyse the content and do something with it.
“The use of AI is accelerating across the construction industry, and we’re making sure we’re ahead of the curve by delivering constantly evolving AI-driven solutions now and into the future.”
Fletcher Steel, Fletcher Building’s steel distribution division, is one company that found itself held back by inefficient, manual processes. Team members were swamped
“One big thing for endusers that’s really
importantto understand is our solutions allow people to go from a data capturing environment, which is quite a heavy lift for an individual, to a verification type of role.” Esker is a global artificial intelligence cloud platform built to empower the people and improve the source-to-pay and orderto-cash processes, which can help support and grow businesses.
in an accurate and time effective manner, which had an impact on team productivity, efficiency, and morale. Adding to this workload, missing remittances resulted in large amounts of unapplied payments, shifting the process from cash collection to cash allocation.
This motivated Fletcher Steel to reach out to Esker to find a way to simplify and speed up its labour-intensive cash allocation process, resulting in its adoption of Esker’s Cash Application solution.
“Esker automated every step of the cash allocation process, from remittance capture to the reconciliation of matched invoices into the ERP,” says DuMonet. “This optimised the allocation of the incoming cash and downstream processes such as collections.”
“Esker had an impact on reducing costs in Fletcher Steel’s cash allocation process and eliminated the need for manual processing, thus providing the team more time to enjoy their jobs and personal lives.”
Customer centric
Simpson says it’s customer success stories like that of Fletcher Steel’s that truly highlight the value of Esker’s solutions.
“One big thing for end users that’s really important to understand is our solutions allow people to go from a data capturing environment, which is quite a heavy lift for an individual, to a verification type of role,” explains Simpson. “The way of working certainly changes for our end users.”
“We know some people find change really challenging, so we’re all about supporting our customers to change the way they work while continuously highlighting the benefits of doing so.”
Further, Esker supports its customers throughout the ‘user acceptance stages’ to make sure end users are comfortable with the solution and functionality.
“A lot of our customers report back and say, suddenly, they’ve got this world of information opening up for them that they never had visibility into or access to before Esker,” says Simpson. “This allows them to then review business processes and policies, how they as a finance team can influence the rest of the business and start challenging and understanding the business’s roadblocks.”
With Esker doing the heavy lifting, Simpson says, it can also add intrinsic value to a person’s day-to-day life.
“Our customers can head home and cook dinner for the kids or go to the gym because the job is done quicker and more efficiently with Esker,” she adds. “It’s not just about those holistic advantages – work also becomes fun for our customers because they have a great solution that allows them to do things in the most efficient way.”
Having already fostered positive outcomes for hundreds of its customers, Esker continues to evolve to provide the best possible solutions that support the construction industry in its journey of transformation.
Already used widely in the United States, weathering steel has hit the Australian market and Hobson Engineering has stepped up to supply weathering steel bolts in metric measurements to meet local demand.
With the Australian construction industry only just starting to ramp up its use of weathering steel in recent months, Hobson Engineering is leading the charge to ensure the highstrength steel is utilised for the nation’s longterm infrastructure projects.
To help address Australia’s structural needs, Hobson Engineering is now supplying metric weathering steel structural assemblies.
Alex Sharp, senior engineer at Hobson Engineering, says the company has always championed the latest structural bolting standard, adding weathering steel structural bolts to its already extensive offering in an effort to push the construction industry forward. “Weathering steel is a steel with improved atmospheric corrosion resistance that, in the right environments, forms an
adherent rust patina protection that over time will solidify,” he says. “The Australian construction industry has now realised that we have the right climate for weathering steel, given its durable, low maintenance and cost-effective attributes.
“Hobson Engineering is steering the supply of weathering steel structural assemblies made specifically for the Australian market.” For over 50 years, weathering steel has been successfully used in infrastructure projects across America, Europe and Japan. Australia does use steels that are better at corrosion resistance than a standard steel, such as stainless steel which builds its own protective coating and doesn’t allow the base material to further corrode. However, these steels still
“We want to start building structures that are going to last 100 years plus.”
“Weathering steel is similar to stainless steel in that it builds up this layer that protects the underlying steel from further corrosion,” says Sharp. “So, although it looks like it’s rusty, it’s not continuously rusting.”
“Why this is useful is with most steels, or a basic steel, you need to put something on top of it to protect it – the most common method being to paint the steel.
Painted steel doesn’t rust, explains Sharp, because it’s not exposed to the environment. But it needs to be repainted regularly, otherwise the paint blisters and peels off, the steel gets exposed, it rusts and eventually will fail. Another option is to put a sacrificial coating on the steel, such as galvanise, but again, it will degrade over time.
“For most structures and big engineering projects, we don’t want something that’s only going to last 50 years,” says Sharp.
“We want to start building structures that are going to last 100 years plus.”
For instance, Sharp says, the Sydney Harbour Bridge requires constant yearly maintenance, costing millions of dollars. But with a material like weathering steel, maintenance is markedly reduced.
“Weathering steel creates a rusty patina that over time hardens,” says Sharp. “Essentially this means it requires no maintenance, which is what everyone is looking for.”
“Instead of looking at how much a structure costs to build, we need to start looking at the savings you can make over the whole life of the structure – this is where you start to see the real benefits of weathering steel.”
Until recently, all weathering steel fasteners imported into Australia had to be sourced from America and arrived in imperial units posing significant compliance challenges for construction project teams. Particularly for heavy industries like construction, compliance to Australian standards is vital to ensure the integrity of structures and the safety of the people using or occupying those structures. Hobson Engineering, understanding its responsibility as one of the leading suppliers of construction hardware in Australia, quickly identified the critical need for weathering steel structural assemblies in metric to guarantee compliance.
“When you try and slot in a product standard from another country or another system, a lot of the detail doesn’t quite match with how our standards are written,” says Sharp. “With our Australian structural bolts, only the first 10 or so pages really tell you how to make the bolt assembly, the rest of the standard, which is a 50-page standard, is all about quality systems.”
“The reason for that is Australia is an importing nation and as importers of construction materials we have the responsibility to know what we are importing because these materials are going into structures that, if they fail, could cause serious injury or loss of life.
“Realistically, you can say a lot of things to a factory, but businesses need to be checking that it’s actually happening.”
That’s why Hobson Engineering has put rigorous systems in place to ensure that the factory suppling its weathering steel structural bolts is manufacturing to the correct standards. To ensure these bolts are fit for purpose in Australia, Hobson Engineering
“Instead of looking at how much a structure costs to build, we need to start looking at the savings you can make over the whole life of the structure – this is where you start to see the real benefits of weathering steel.”
completes Rotational Capacity Testing of all its weathering steel structural assemblies.
In Australia ASTM A325M is the standard specified where structural bolts made from weathering steel are required. With this American product standard that the nation is using, there isn’t as much quality management embedded as is expected in local steel structure codes such as AS 4100 and bridge design code AS/NZS 5100.6. Without having it in the standard, companies importing directly from the United States are missing a lot of these quality checks that they would otherwise have with an Australian structural bolt.
Recent weathering steel projects in Australia have faced a number of challenges with imported imperial bolts. To tackle this issue, Hobson Engineering has integrated the quality systems from the Australian standard into the ASTM standard. “We now have the American weathering steel bolt in metric, with all of the quality systems required to meet compliance in Australia,” says Sharp.
“By supplying these assemblies in metric, we expect to see a more streamlined delivery of future projects in regard to compliance, quality and speed of procurement.”
With supply chain issues continuing to affect the industry and sustainable construction becoming a key requirement in project designs, it’s never been so important for contractors to consider the materials they are using.
Hobson Engineering’s business model is focused on having stock on hand. Fasteners are one of those things that project teams think about last minute, says Sharp, but should be looking at early in the design phase. “We see businesses design a complex project and
not question how they’re going to get the materials supplied,” says Sharp.
“They then go hunting around for it at the very last minute when they need bolts delivered within a week or two.
“Project teams historically were required to change designs to suit availability and experienced delays because delivery had to come from the United States, which took up to 14 weeks.”
By having metric weathering steel structural assemblies in stock for the Australian market, contractors can start designing projects without the worry of facing delays or compliance and rework difficulties later down the track.
As the Australian construction industry continues to move towards a reduced carbon footprint, weathering steel also poses great sustainability benefits. Weathering steel was designed to reduce maintenance, the use of paints and chemicals, and reduce the cleaning and safe working required to maintain steel structures.
“Once a weathering steel structure is constructed, no maintenance is required other than every now and then having to give it a spray down for graffiti,” says Sharp. “These benefits are key reasons why Hobson Engineering has stepped up to supply quality weathering steel structural assemblies, in metric and made for the Australian construction sector.”
As Australia accelerates its use of weathering steel to create the sustainable, safe and durable structures of the future, Hobson Engineering is ensuring it’s ahead of the game with its metric weathering steel structural assemblies in stock, ready for the next big project.
“We now have the American weathering steel bolt in metric, with all of the quality systems required to meet compliance in Australia.”Weathering steel patina colour over time.
In Australia an increasing number of construction and infrastructure project owners, including government, are setting tender requirements that encompass sustainable construction practices. To make the grade, contractors are being pushed to consider greener ways of constructing and JWA Oilfield Supplies’ (JWA) solutions are catching their attention.
JWA was established as a supplier of temporary roadway and platform matting solutions, primarily for the oil and gas sectors, in 2003. Twenty years on, the company is supporting major infrastructure and energy projects around Australia with its sustainable matting – including a large stack of Victoria’s Big Build projects.
What started with JWA providing product trials for a few of Victoria’s Big Build projects six years ago has quickly grown in scope. The company has now delivered matting for several Level Crossing Removal projects as well as the Metro Tunnel, West Gate Tunnel and North East Link projects – all under the state’s Big Build.
JWA operations manager optimisation Windsor Fick and Min Chua, IT development manager, have seen first-hand the significant impact the company’s composite mats have had on these Big Build projects by improving site efficiency, safety and sustainability.
When introducing its new FODS Rumble mat solution to the Australian market, JWA lent on its connections that it had developed from previous Big Build projects, where the company supplied its ground supporting matting.
“The first official Big Build project we supplied the FODS Rumble mats for was the South Yarra tunnel entrance, part of the Metro Tunnel, for the Rail Infrastructure Alliance,” says Fick. “The project team jumped in front of some other projects that were lining up to trial our FODS Trackout Control Mats, also known as FODS Rumble Mats, so that they could get in first – a clear sign that demand for our solutions was surging.”
Designed for sediment control, FODS Rumble Mats can be strategically placed at entry and exit points on construction sites to reduce the track-out of materials on the road, such as debris and sediment. This ensures little to no site sediment is tracked-out by machinery or vehicles onto public roads, protecting the environment and waterways.
The FODS Rumble Mats also protect the ground from machinery, reducing the need to remediate at project completion, and are made from 100 per cent recyclable polymer.
“From the South Yarra project, we received feedback that street sweeper runs were reduced by approximately 40 per cent
As the demand for green construction rises from both industry and government, JWA Oilfield Supplies is supporting sustainability from the ground up through its temporary roadway and platform matting solutions.JWA Oilfield Supplies supplied FODS Rumble mats for the South Yarra tunnel entrance, part of the Metro Tunnel project.
compared to previous track-out systems used onsite, and no digging of trenches for sediment traps was required,” says Fick. “The team also found the versatility and easy installation of the FODS Rumble Mats eliminated the need for them to dig a pit to install traditional rumble grids or a crushed rock pad.”
“Further, the FODS can be cleaned in situ – meaning they don’t have to be removed for cleaning and require little maintenance, allowing work to continue flowing.”
In November 2017, prior to introducing the FODS Rumble mats, JWA supplied matting for the teams working on the removal of the level crossing between Skye and Overton roads in Frankston, as part of the Level Crossing Removal project. The project teams identified JWA’s heavy-interlocking DuraBase bog mats as a solution to a number of challenges they were facing around road and asset protection, material and resource usage, site restrictions and remediation.
“Dura-Base matting provides stable surfaces for construction vehicles, protecting infrastructure and minimising damage,” says Fick. “It prevents soil erosion, offers consistent load-bearing platforms and improves operational efficiency and safety.”
JWA’s Dura-Base matting, constructed with high density polyethylene (HDPE) and a mix of ultraviolet (UV) stabilisers and static dissipaters, was used on the Skye and Overton roads project site to create temporary hard stand areas for piling and access tracks, forming a stable and seamless path for equipment and heavy machinery.
“The FODS Rumble Mats also protect the ground from machinery, reducingthe need to remediate at
project completion.”
“Our Dura-Base mats reduced the amount of crushed rock needed for the pad from 850-millimetres to 350-millimetres,” says Chua. “As a result, the time needed to shut down the road for works, as well as the number of trailers carrying crushed rock, was greatly reduced.”
Primarily, the Dura-Base matting was used on the project to protect the asphalt surface and buried services by spreading the load from piling activities so that it didn’t damage things like underground cables.
FODS Rumble Matting has also proven to be a popular solution for Level Crossing Removal projects since its first introduction to the Big Build on the Metro Tunnel, with over 10 of the projects already having used FODS and many more in the pipeline.
Another project where project teams reaped the benefits of JWA’s Dura-Base matting is the West Gate Tunnel. On this project, Dura-Base matting was used for power realignment on the West Gate Golf Course. Fick says JWA supplied the matting for use around the base of the tower to protect the asset of the stakeholder, in this case the golf green, and also to provide a smooth and stable service for the elevated-work-platforms and heavy plant needed to access the high voltage tower. “With Dura-Base matting, we’re not only providing a stable surface, but due to its almost Lego-like application it’s also very easy to install,” says Fick. “For example, if a project team has to have access over a grass field, they can put the mats down, use them to track heavy vehicles out like a 450-tonne crane, and at the end of the job they can simply pull them up.”
“Whereas if they put in a crushed rock road, that’s temporary – they have to bring
truckloads of it in, grade it and then at the end of the project the team has to dig it all out and try to bring the land back up to condition.
“Dura-Base matting, on the other hand, requires little to no surface remediation.
“This is especially important in problematic soils, such as acid sulfate soils, where ground disturbance and cross contamination can pose a significant environmental risk.”
Dura-Base mats are also weatherproof. Because it’s made of durable purposeengineered plastic, it doesn’t erode or get washed out by rain helping with project site access during inclement weather.
Six years on from JWA’s first Big Build project, Dura-Base and FODS Rumble Mats are still working across several Big Build sites in Victoria due in part to the company’s classic philosophy – reduce, reuse and recycle.
“We’re strongly focused on supporting a sustainable future for the construction industry,” says Fick. “First, with our matting solutions we reduce the use of resources onsite such as crushed rock and the amount of sediment from construction sites reaching public roads and waterways.”
“We also reuse in the way we distribute the mats on a rental basis and ensure that we service all mats up to condition as required when they return from a job.
“The average expected lifespan of our matting solutions is in excess of 15 years because every time they come back from a job, we wash them and inspect them.”
If there’s anything that needs to be serviced on a mat, even if it’s a minor gauge, the JWA team will service it and bring the mat back up to condition before sending it out to the next job. Then, when it gets to a point that the mats come back and are no longer serviceable, JWA will process the mats through its local recycling partners.
“Even for our washing facilities, we have been using tank water for many years and are constantly looking for new ways to upgrade,” says Fick.
As the focus on sustainable construction heightens across Australia, JWA is stepping up to the plate to ensure it has the solutions needed for the industry to build a greener future.
“FODS Rumble Matting has also proven to be a popular solution for Level Crossing Removal projects since its firstintroduction.”
In today’s digital age, it is widely acknowledged across the civil construction sector that machine control technology saves time, increases productivity, reduces material waste and rework and generally makes life easier on the jobsite.
Position Partners has been delivering Topcon positioning technology for heavy machinery for several decades, with a focus on userfriendly workflows that are easy to learn for operators and that enable project managers, site supervisors and surveyors to manage data seamlessly across all machine types and makes, survey rovers and more.
When customers and Position Partners’
“Topcon 3D Machine Control provides a flow of data that everyone, from designers and surveyors to supervisors and operators, can easily understand and utilise,” says Viljoen. “It really gives our business a competitive edge by enabling our team to deliver projects with improved productivity and greater accuracy.”
With around 45 Topcon-enabled machines, Batchelor Civil in Tasmania also chooses the brand for its ease of use and flexible platform. The company’s project manager Paul Mitchell says he can train a new user in minutes with the Topcon system.
During its delivery of an 80-house subdivision project, Batchelor Civil faced challenges associated with the use of global positioning systems (GPS) for driveways and kerbs due to tight tolerances and a busy, builtup site. By supplementing its GPS base and rovers with Topcon’s unique Millimetre GPS – which uses a high precision laser in addition to global navigation satellite system (GNSS) positioning – Batchelor Civil is now able to effortlessly meet the tolerances.
“We went from having plus/minus 30-millimetre accuracy with standard GPS, to between one and five-millimetre accuracy with the Topcon Millimetre GPS system,” says Mitchell. “It works really well on our rovers and we’re getting those one or three per cent falls spot on.”
Family-owned hire company Brooks Hire has met the increasing demand for machine control and on-board weighing systems for its customers with Topcon solutions from Position Partners.
Lenore Brooks, general manager, Brooks Hire says the company saw an increase in demand from its customers wanting more technology onsite, such as machine control, weighing systems and GPS solutions. “We wanted to fill this need and deliver our customers a more efficient service,” she says.
“We find that Position Partners is a great partner to deliver that technology to them.”
Topcon’s on-board weighing systems for loaders, excavators and other heavy plant machinery are designed to increase efficiency and productivity in construction, mining and industrial applications by delivering accurate weight information to the machine operator
via an easy-to-read control box mounted inside the cab. Loading accurately each time reduces return trips to the stockpile, resulting in fuel usage and machine wear savings.
Topcon weighing scales can enhance process efficiency, prevent loading errors and assist with live inventory control and material management.
Brooks Plant Manager WA/NT Gary Bushell says the company chose the technology because it is advanced and also because Topcon is constantly updating the system to ensure it is top of the line.
Topcon now offers advanced material management to complement the on-board scales, via Sitelink3D v2 office software and the Haul Truck application. The solution eliminates paper-based reporting with hands free, in-cab payload logging that is connected to the office for centralised reporting and tracking of material movement.
Increase productivity, reduce downtime
Another system providing great value for Position Partners’ customers is Tokara – a gateway for machines and assets. The service allows construction teams to send and receive files from most leading positioning technology brands and machine makes. Position Partners has tailored the Tokara service to deliver benefits for a wide range of stakeholders involved in civil construction projects, helping:
• P roject managers to proactively manage and ensure that all machines, sub-contractors and survey crews are working to the latest design file;
• Machine operators to work efficiently with design updates, support and training that is available in the cab;
• Surveyors to send design files to machines and supported survey devices remotely to ensure everyone’s working to the correct design;
• Foreperson, with an easy-to-read map that provides quick access to all machines and survey assets, site-wide; and
• Contractors to keep track of all equipment across multiple projects.
Brendan Lawrence, survey manager at Menai Civil uses Tokara to manage all the company’s machine control systems and survey rovers from a single interface, either using his laptop in the office or his field controller out onsite. He is the first point of contact for technical problems, which he usually solves using Tokara without having to physically visit the machine in person.
“I use Tokara every day to log in to machines and fix problems no matter where I am,” he says. “If I get a call from an operator or supervisor on another site, I can access the machine immediately and generally fix the problem they’re having or upload the files that they need.”
As the company regularly moves its Topcon systems between machines or swaps components, Lawrence can use Tokara to setup the machine remotely by uploading machine files and changing the radio frequency, network login and any other settings.
“Tokara is a big stand out because at the moment I don’t believe any other options out there have anything like it,” he says. “But also, the service Position Partners provides has always been great.”
Proximity and collision awareness technology has advanced considerably in recent years, with the latest systems incorporating artificial intelligence (AI) to automatically identify and alert operators to people. Blindsight is a new solution from Presien, distributed and supported throughout Australia by Position Partners, that can differentiate between humans and other objects even in challenging, dynamic environments.
Josh Allan, construction business manager at Position Partners says the great thing about Blindsight is that workers don’t need to wear a tag in order for the machine system to detect them, which helps to keep everyone onsite safe.
The solution can be fitted to all makes and models of machinery, with a combination of one or more sensors, and a small in-cab alert
“Topcon 3D Machine Control provides a flow of data that everyone, from designers and surveyors to supervisors and operators, can easily understand and utilise.”Tokara enables contractors and project managers to manage design files and support operators remotely.
gives the operator audible and visual alerts when a person or traffic cone is detected.
“Blindsight is configurable to every machine and every site’s unique requirements,” Allan added. “It alerts the operator without adding unnecessary clutter or another screen to the cab.”
The AI system differentiates between different assets (people, walls, safety cones around an object, etc) by determining their size and/or velocity. This essentially means any time a worker enters the vicinity of a machine, or it gets too close to an exclusion zone, the system will alert the operator immediately.
For managers and safety officers, comprehensive reporting on near misses –
including video recorded from the system’s cameras – can be used for training and process improvements to increase safety culture onsite. This data can then be digitally accessed by the site supervisor at any time.
“In addition to the day-to-day safety enhancements provided by systems like these for operators and workers, the data trends and reporting over time can give managers the big picture overview they need to identify ongoing hazards, training needs or process improvements,” Allan says. Position Partners will be showcasing all of these technology solutions and more at the upcoming Inside Construction Expo in Melbourne this September.
At Allcon, we love helping
find the right solution to your concrete problems. With over 35 years in the industry, we know that having the right gear at the right time, goes a long way to getting the best outcome.
“I use Tokara every day to log in to machines and fix problems no matter where I am.”
APS Industrial is taking a focused approach to supporting the construction industry’s electrical and power needs, backed by its partnership with key global technology providers, led by Siemens.
Established just over five years ago, APS Industrial (APS) is the construction industry’s new choice, but the industrial solutions supplier is already making waves in the construction and infrastructure sectors.
Providing a broad portfolio of industrial low and medium voltage electrical and automation products for the Australian market, APS is the key national distributor of Siemens, Weidmüller, Rittal, Belden, and Katko in Australia.
Joining the company two years ago, Electrical Products business manager Stephen Gough says APS’ rapid growth stems from its commitment to providing quality products, with a focused approach to servicing its customers.
“We make doing business easy,” says Gough. “We simplify the process by working closely with stakeholders at all stages in the pipeline of a project to make sure we’re covering all bases.”
Further strengthening APS’ role as the master national distributor of Siemens’ electrical and automation solutions for the local market, the company has recently opened a purpose-built Manufacturing
Centre featuring air circuit breaker (ACB) adaptation capability in Adelaide.
Through this facility, based at their existing site in Adelaide, APS’ experienced teams handle design, assembly, testing, research and development, and offer integrated estimating and design services locally to ensure excellent outcomes for its customers’ projects. “We know that speed to market is paramount in today’s market given the current and emerging challenges faced by the construction industry,” says Gough. “By having these capabilities and products locally, we are able to offer customised solutions with greatly reduced lead times.”
One of the biggest challenges to the growth of the construction industry over the last few years has been global supply chain issues, he says.
“The establishment of our new facility will reduce the reliance on global supply chains for a product that is critical to many applications and industries, and the construction sector is no exception,” explains Gough.
From a power distribution product perspective, APS recently launched Siemens’ Sentron 3WA Series ACBs, which the company
“We know that speed to market is paramount in today’s market given the current and emerging challenges faced by the construction industry.”APS Industrial’s distribution board manufacturing floor.
“Highly reliable in distributed energy systems, Siemens’ Sentron 3WA Series ACBs can handle voltage fluctuations of up to 10 per cent to protect infrastructure and buildings from damage caused by electrical faults, reducing downtime for our customers,” says Gough. “The 3WA Series also has in-built software that allows project teams to test and monitor them remotely and importantly, they can be integrated into automation environments.”
The digital compatibility, adaptability, high reliability in distributed energy systems and end-to-end digital lifecycle capabilities of Sentron 3WA Series ACBs ensure that demanding heavy-duty applications maintain supply.
“Siemens’ Sentron ACBs and the extended Sentron power distribution portfolio, which includes miniature circuit breakers and protection devices, forms an ideal solution for various sectors, such as infrastructure, commercial and residential construction,” says Gough.
At the forefront of Siemens’ Sentron range of products is connectivity and integration.
The ACBs, including the new 3WA Series, and circuit breakers talk to one another – resulting in seamless integration and application flexibility.
Further, they can all be programmed with an app through Bluetooth. “This means we can connect to the circuit breaker without having to open the switchboard or even go into the switch room,” says Gough. “By removing the need for a person to enter the switch room, we’re keeping them safe and clear of
The APS DB family comes in three models – the DB Ultimate, DB Eco and DB Essential –to suit all applications.
“If you want an off the shelf style distribution board for domestic, commercial and light duty industrial environments – the DB Eco is ideal, with an ingress protection (IP) rating of IP40,” says Gough. “This range is available from local wholesalers for pick-up and installation.”
The DB Essential is optimal for high-end commercial and medium-duty industrial environments such as office buildings, retail, hotels, education and warehouses. It has an IP55 rating, with a fully welded Katko enclosure. Already operating in data centres, airports and critical infrastructure across Australia, the DB Ultimate is an IP66 rated distribution board, which supports high-end industrial applications such as infrastructure, hospitals and power/energy.
“In January this year, we went back to TÜV Rheinland Australia and retested all of our distribution boards,” says Gough. “The DB Eco, Essential and Ultimate were all tested against the AS/NZS 61439 standard, and all passed extremely well.”
Like APS itself, the APS DB family of distribution boards represents a new choice for the local construction industry. Used on a large portfolio of industrial, infrastructure and building projects around the country, APS’ range is ever-evolving to meet the needs of its customers. Whether it’s a retail building, critical infrastructure or high-rise residential apartments, APS supplies the core components for power distribution in all applications.
“We make doing business easy. We simplify the process by working closely with stakeholders at all stages in the pipeline of a project to make sure we’re covering all bases.”APS Industrial’s Manufacturing Centre in Adelaide.
Having delivered solutions for a new data centre for a global technology company, local mining applications and a major Greenfield Pharmaceutical construction project, APS has received extremely positive feedback from local contractors and end users, says Gough.
“What makes these projects so important to APS’ service promise is that customers not only get their distribution board requirements
from us but also have access to the full power distribution portfolio, including Sentron ACBs and moulded case circuit breakers, plus Sivacon S8 low-voltage switchboards and motor control centres,” says Gough. Through its fully-stocked Manufacturing Centre in Adelaide, APS is ensuring its customers can access fast and reliable services, as well as fully certified, quality electrical and automation products, locally.
• Design of electrical systems using computer-aided design (CAD) software
• A ssembly of components into finished products, including both one-offs and multiples
• Research and development of new applications and technologies
• Testing, repair, and maintenance services for faulty products
• Testing and quality assurance to ensure optimal performance
• Expert advice on electrical control options, including programming support
• Specialised products including process control panels, water pump control panels, distribution boards, basic transfer switches and controllers.
“By having these capabilities and products locally, we are able to offer customised solutions with greatly reduced lead times.”Siemens’ new Sentron 3WA Series air circuit breakers, available at APS Industrial.
VEGA Australia, bolstered by its parent company’s global presence and innovations, is ensuring the local construction industry has reliable, next-generation measurement technology to optimise assets and boost operational efficiency.
Sensor and measuring instrument manufacturer VEGA has been developing the measurement solutions of the future, built upon a passion for innovation and transformation, for more than 60 years. In recent decades, the company’s local arm VEGA Australia has cemented partnerships with key players in the construction industry through its local supply of VEGA’s range of level, point level and pressure measurement instruments and technology.
Established in Brookfield NSW in 1987, and now situated at its state-of-the-art site in Caringbah NSW, VEGA Australia is key to supporting the improved productivity and processes of the local construction industry, including the building materials sector.
VEGA Australia managing director John Leadbetter has seen the company grow and develop in the local market throughout his 27 years with the business. He says the business’s success stems from the deep relationships and partnerships it has formed within the cement and concrete, quarry, brickworks, tunnelling and road construction sectors.
“We foster long term partnerships with the likes of Hanson, Holcim, Boral, Austral Bricks, James Hardie, CSR Gyprock and BHP Steel –many of which we’ve been working with for well over 20 years all around Australia,” says Leadbetter. “We are part of the international VEGA companies, and backed by that global experience, we’re able to deliver the highest quality, German-built level and pressure instrumentation locally in Australia.”
“As the latest technologies come out that could help improve our customers’ operations, we introduce those technologies to them and help them upgrade to those latest technologies.”
Providing the latest in measurement technology that offers productivity, reliability and safety gains is the cornerstone of VEGA Australia’s offering. At a time when a wealth of challenges continue to torment the construction industry, it has never been so important for the sector to harness solutions
to move the needle on productivity and efficiency. Improvements to the construction industry’s productivity performance could save Australia $47 billion annually, according to the Australian Constructors Association’s report Disrupt or die – Transforming Australia’s construction industry, 2020. Reliable measurement data can play a huge role in shifting these statistics, says Leadbetter. “In days gone by, level and pressure measurement tasks would be completed by a person that would physically have to go out and check the bins, dip tanks or silos and enter measurement records on spreadsheets about what material they had on a plant,” he says. “This resulted in extra work, safety risks from having that person around the equipment which may contain hazardous materials, and poor reliability due to the probability of human error.”
“Our instruments, on the other hand, provide a continuous, accurate output about the amount of level in a silo, saving time, improving efficiency and enabling maintainers to focus on other tasks.
“Our sensors can tell you where the sumps are and anything to do with information about what’s happening in the plant itself.”
As the construction industry enters an age of automation and information, VEGA Australia is delivering automated units that are developed to withstand and suit tough, dusty, noisy and mechanical industry environments. What the customer is looking for, says Leadbetter, is reliable and accurate information. They’re looking for automated solutions that they can integrate into their plant so that they require less manpower and more mechanical type power.
“That’s where VEGA Australia comes into it,” he says. “We don’t just offer goods for sale – we go out there and offer the sensor solution to the customer and assist them in identifying the best location for it, how to install it and most importantly, setting the instrument up.”
“By offering this comprehensive support and service, as well as our quality, technology-
“We are part of the international VEGA companies, and backed by that global experience, we’re able to deliver the highest quality, German-built level and pressure instrumentation locally in Australia.”
driven instruments, we provide the customer confidence that they have reliable equipment that’s dependable and that they will get years of service out of.”
The construction industry is also a huge generator of waste. During the 2020-21 financial year, building and demolition materials were responsible for approximately 25.2 million tonnes of Australia’s generated waste – according to the National Waste Report 2022 prepared for the Department of Climate Change, Energy, the Environment and Water by Blue Environment. Further to the environmental impacts associated with waste generation, it also costs businesses money. Having an accurate, repeatable system, like VEGA Australia’s sensor technology, can greatly reduce waste, says Leadbetter. For instance, the VEGAPULS level measurement radar can accurately track a tank’s capacity to protect against overflow, with no contact required by personnel.
Addressing the current skills shortage, VEGA Australia’s measurement instruments do the job of what previously would have required personnel to complete, resulting in a better use of resources. “Also, our sensors run on 24 volts direct current,” says Leadbetter. “They are low power devices that don’t require alternating current power or high power to run them.”
Having reliability and optimal performance
24 hours day is another plus of VEGA Australia’s offering. All of its measurement units are self-assessing – they alert the maintainers to problems so that they can head out there and fix the problem or replace the damaged unit if required – meaning supervisors and managers don’t have to worry about things going wrong.
As the building materials sector continues to improve and develop its infrastructure, larger sites with several different pieces of equipment are required to achieve the higher throughput. Many sites are now being
fully automated, helping the production of materials for the construction industry to be delivered on time. Construction companies used to have delays purely due to the fact that the materials that were required for their projects were taking longer to get there, says Leadbetter. “If the materials are getting there on time, the construction companies are able to plan further ahead, reducing or eliminating the effect of delays,” he adds. “With our sensors doing the heavy lifting in the level and pressure measurement space, we’re supporting building materials companies in getting materials out to contractors at a quicker pace.”
Primarily delivering sensors for level and pressure measurement, VEGA Australia tailors its solutions to fit what the customer is looking for.
The company is at the forefront of radar level and guided radar developments, two product
“We don’t just offer goods for sale – we go out there and offer the sensor solution to the customer and assist them in identifying the best location for it, how to install it and most importantly, setting the instrument up.”
for the market, not the price point,” says Leadbetter. “We’re not all about the latest technology being the highest price.”
Many of VEGA Australia’s solutions will be on display at the 2023 Inside Construction Expo on 20-21 September. The company will be showcasing working models that aren’t just planted on a desk – they’ll be powered up and working.
“Attendees that visit our stand (D20) will get to speak to people who are dealing with their industry daily, and have industry knowledge and established industry relationships,” says Leadbetter. “They’ll get to meet our team and see the equipment in action and most importantly, see that we’re
at the event to help drive the construction industry forward.”
“We aim to play our part in helping develop and future-proof the industry, foster new and existing relationships, and hopefully show attendees something that they’ve never seen before.”
VEGA Australia, with the support and experience of the global group of VEGA companies, endeavours to be at the forefront of level and pressure measuring solutions for the local construction and building materials markets. Be sure to visit the company’s stand at Inside Construction Expo 2023 to discover the latest and emerging developments in sensor technology.
“With our sensors doing the heavy lifting in the level and pressure measurement space, we’re supporting building materials companies in getting materials out to contractors at a quicker pace.”
We’re experts in connected, supported solutions across mixed fleet.
• Topcon technology for every machine
• Tokara remote management for every asset
• Position Partners support for every project
If it’s got a cutting edge, we can measure it.
With the use of Deswik software, the McConnell Dowell John Holland Joint Venture has brought tangible benefits to the Kidston Pumped Storage Hydro Project, reportedly the first pumped storage hydro project in Australia for over 40 years.
Deswik is improving construction outcomes and site productivity through practical and cutting-edge digital workflows, as evidenced by its recent partnership for the Kidston Pumped Storage Hydro Project in Far North Queensland.
In early 2022, Deswik was engaged by the McConnell Dowell John Holland Joint Venture (MDJH JV) to visualise and review the existing P6 schedule for the project, said to be the first pumped storage hydro project developed by the private sector and the third largest electricity storage device in the country – and the results have been staggering.
John Holland deputy project director Peter Gaylard works directly with Deswik software on the Kidston Pumped Storage Hydro Project. His role is to oversee all design and construction activities associated with the powerhouse and the supporting infrastructure such as access tunnels, the upper reservoir and embankment dam.
McConnell Dowell project engineer –underground Jean-Luc Lejeune is also working directly with Deswik on the project, implementing the design in the underground phase, from the excavation of the powerhouse and the transformer hall to the construction of the access tunnels.
Both Gaylard and Lejeune concur that Deswik has been a crucial element to the project’s ongoing success.
“We engaged Deswik in early 2022 to visualise and review the project P6 schedule as on a site level we got to a stage where we didn’t have a firm grasp of our point in space in three-dimensions,” says Lejeune.
“Conceptually from design, we had our 2D drawings and alignment, but we didn’t have a robust system that provided a visual of where we were in the project versus where we were going.”
“Deswik brought the project to life in fourdimensions, the fourth dimension being time, and it was beneficial for the site team to see it play out in 3D.”
It helps the entire team visualise where the project is going, says Lejeune, and identify any efficiencies or excess resources being overdeployed in certain areas.
The outcome of this initial review was the project team found opportunities and risks and were able to optimise resources to
the project team to better explain what they’re doing. “It has enabled us to go to management and to both joint venture companies, as well as the client, with a 3D visualisation that they can comprehensively
company has had in the mining industry to the infrastructure and construction industries.
Rautenbach says the company’s partnership with the MDJH JV Kidston Pumped Storage Hydro Project is a great example of how
Deswik software can optimise the design and construction of infrastructure projects. “The software is being successfully adopted by project teams across roads, windfarms, tunnels, pumped hydro, rail and mass earthworks projects,” says Rautenbach. “For the MDJH JV, the use of Deswik has grown from initially being used as a review tool, to being used for design, scheduling, quantity calculations and in the survey process.”
“We started off providing the project team with the initial service of reviewing the project schedule, and now we’re seeing the team use Deswik daily to optimise design and resources to save costs associated with mobilisation and demobilisation times.”
Essentially, adds Banks, having an integrated digital model like Deswik that connects the 3D solids and the schedule in the same application – meaning project teams don’t have to rely on manual data transfer between packages – is a considerable project streamlining power.
The construction industry is a tough
the quantities, the engineers do the planning, and the scheduler completes the scheduling, and all use different tools and processes,” he says. “In Deswik we have integrated these processes, so it’s not just about the software but it’s also about the process.”
“When you’re generating a schedule in Deswik, you’re using the quantities from the CAD model directly, so you’re less likely to make mistakes and granular information such as quantities and material types by chainage is readily accessible.”
Deswik uses rules and technology to automate the generation of processes. On an infrastructure project for example, it could take weeks for a project team to develop a 20,000-line item schedule manually. Whereas in Deswik, Rautenbach explains, because the schedule is generated by Deswik software based on user inputs and sequencing rules, it can generate those schedules in minutes once set up.
Backed by the ongoing success of MDJH
Powerhouse mass excavation.“Deswik brought the project to life in fourdimensions, the fourth dimension being time, and it was beneficial for the site team to see it play out in 3D.”
Specialising in excavator and skid steer attachments, and complete boom and breaker systems for the construction, demolition, mining and recycling industries, Walkers Hammers is helping businesses break ground in project performance.
As part of the Australian dealer network for Rammer, Simex, ALLU, PneuVibe, GTS, TEFRA and Steelwrist equipment, Walkers Hammers is making sure construction professionals have the right attachment for the job.
With owner and sales manager Mike Coghlan at the helm, Walkers Hammers has been around in different capacities for almost 40 years. Today, the company focuses on supplying a premium range of equipment from well-respected industry brands, bolstered by its supreme support, maintenance and repair services.
Among its core products is the Rammer Rockbreaker in the Excellence and Performance Lines. Featuring an optimised piston design and a built-in pressure adjusting valve, which guarantees every blow is delivered with full power, Rammer Rockbreakers are ideal for virtually any construction, demolition or quarrying application. Awarded distribution rights for Rammer Rockbreakers in 1998, Coghlan says Rammer products are the Mercedes-Benz of hammers. “Rammer Rockbreakers are of the highest quality,” he says.
“They’re designed to last a lifetime if fully maintained.”
“We have a Rammer Rockbreaker for practically all applications, from customers with a little 1.6-tonne excavator looking to do small jobs to the larger contractors with multiple 30-tonne excavators delivering major
infrastructure, demolition or quarrying works.
“Our customers are pretty much anyone that’s into excavation, from those delivering civil works infrastructure – such as sewerage and trenching – to quarrying applications where customers use Rammer Rockbreakers to primary break or secondary break down large boulders into smaller sizes to fit the rock into a crushing plant for use in producing road construction materials.”
Technology also plays a huge role in Walkers Hammers’ Rammer offering.
All Rammer Rockbreakers are equipped with the RD3, a remote cloud-based monitoring system that collects data to provide customer insights into the attachment’s usage.
This data helps the customer and Walkers Hammers understand how the rockbreaker is being used and identifies any problems with the equipment as well as whether it’s being operated outside of its design parameters. It will alert the operator of planned services and suggested preventative maintenance and, through its GPS feature, monitor the rockbreaker’s location for increased security.
Maintenance is a crucial element in ensuring Rammer Rockbreakers live up to their ‘lifetime’ life expectancy, something Walkers Hammers places major importance on.
“By helping the operator identify incorrect use of the rockbreaker, it reduces the chance of failure and unscheduled downtime, improving the overall productivity of their
“Rammer Rockbreakers are of the highest quality. They’re designed to last a lifetime if fully maintained.”Grant Pierce, owner of Independent Earthworks, has his new Rammer 1655E ready for the next task.
assets,” says Coghlan.
Due to its ground engaging application, the Rammer Rockbreakers have what Walkers Hammers calls a duty cycle. The company recommends the rockbreakers be brought into its workshop in Laverton North, Victoria, for servicing, maintenance or a full overhaul once a year. Walkers Hammers will replace any worn parts, put the unit back together and give it back to the customer in prime condition.
Walkers Hammers has recently opened a branch in South Australia where it similarly provides purchase and hiring support and advice, and maintenance and repair services.
“It’s very important that we, as a company, listen to our clients and do what we can to meet their needs,” Coghlan says. “Many companies just want to sell you something – we want you to join our family because, as mentioned earlier, the Rammer equipment that we sell lasts a lifetime if you maintain it.”
“Our team members gain a deep insight of customers’ needs and applications through open and comprehensive communication prior to offering solutions.”
Walkers Hammers’ staff are passionate about fostering life-time relationships. So much so that they would rather explain the importance of maintenance at the point of sale and miss out on a sale than be dishonest about maintenance requirements. If the customer brings their rockbreaker in for a service and repairs every year, Coghlan says the rockbreaker will hold its value and provide reliable service up to its life expectancy.
Within Walkers Hammers is also its separate hire business, offering a great option for one-off projects and time-critical jobs. It also supports customers on the off chance that something goes wrong with their attachment.
If for instance something untoward happened and a new rockbreaker broke down (a situation Coghlan says is yet to happen), Walkers Hammers will provide the customer one of its hire breakers while the owned rockbreaker is being repaired.
“What sets us apart from other businesses is our exceptional service and I say that with a lot of confidence because we have the capability to back up our products if something goes wrong,” says Coghlan.
“We’re ready to step up to the plate and keep that client going.”
“If something breaks down, customers can’t work or make money until it’s fixed, so we back them up with our service without any delays.”
Commissioning and set up is also an integral part of the business. Walkers Hammers will go out to the customer’s site with the new rockbreaker, conduct a flow test and setting changes on the customer’s excavator, and test everything so that the excavator is set to meet the working parameters of the rockbreaker.
Further, choosing the right breaker tool for the job will increase the power and productivity of Rammer Rockbreakers. Rammer has a number of job specific tool models that allow customers to get the most out of their equipment. “Our technicians provide customers unparalleled technical advice and will always ensure they put forward the correct attachment and tools for the application,” says Coghlan.
By offering set up and installation, maintenance, onsite and repair services, as well as a quick turnaround and quality equipment, the company is ensuring it can provide exceptional solutions for generations to come.
“Our technicians provide customers unparalleled technical advice and will always ensure they put forward the correct attachment and tools for the application.”Walkers Hammers’ service technician advising operational and maintenance features of the Rammer 5011E with its customer – Indigenous Civil Group.
Evan Olver spent a majority of his career in the sign industry, completing sign manufacture, sign installation and everything in between. At the time, he relied on the Tec7 adhesive range to deliver quality signage, so when he found out it was no longer going to be stocked in Australia, he realised an opportunity that would ensure it would still be available for the local market – leading to the establishment of Olmurtech in 2014.
Today, Olmurtech is the official distributor of Tec7 products for the Oceania region and the Australian construction industry is reaping the rewards.
Led by founders Evan and Simone Olver, Olmurtech supplies a range of adhesive, sealant and cleaner solutions to the construction industry. Its product line provides the sector reliable bonding solutions with versatility and resistance to environmental conditions, specialised options and user-friendly application methods – all of which contribute to the efficiency and quality of construction projects.
Since its first container of just three Tec7 products, Olmurtech has continued to evolve and expand its range, introducing new products to the company’s portfolio year on year. “Olmurtech now has 14
different premium products from Belgian supplier Novatech International,” says Olver.
“The Tec7 range is arguably one of the highest quality commercialised MS polymers in the world, and we’re making sure the Australian construction industry can benefit from its local availability.”
The strength alone of the Tec7 range is mind blowing, Olver says. Made from an MS polymer, Tec7 products are a combination of two adhesive technologies, resulting in a solution that has many of the benefits and strengths of polyurethanes, yet the flexibility of silicones.
Trans Clear, a transparent sealing adhesive from the Tec7 range, has the capacity to hold approximately 22 kilograms of weight per square centimetre. Once cured, Trans Clear offers excellent adhesion, continues to be elastic, watertight and fungus resistant, and can be painted on immediately.
With even more strength, the all-in-one Tec7 sealant can bond, mount and seal and is capable of holding 32 kilograms per square centimetre, even under water.
Olmurtech also supplies the X-Tack, which has amazing capacity to hold weight while it’s wet. It’s ideal for applications such as wall and façade coverings, ceiling panels, window
When Evan Olver found out the Tec7 adhesive range was no longer going to be available in Australia, he knew he had to do something about it. As a result,
“The Tec7 range is arguably one of the highest quality commercialised MS polymers in the world, and we’re making sure the Australian construction industry benefits from its local availability.”Evan Olver, founder, Olmurtech. 12-millimetre hoop pine plywood installed with X-Tack at Jordan Springs Public School, NSW.
aluminium, metal and copper.
“One square metre of X-Tack will hold approximately 600 kilograms in sheer strength, while it’s wet,” says Olver. “Then, once that one square metre of product is cured, it will hold approximately 260 tonnes, or 26 kilograms per square centimetre.”
X-Tack also has great flexibility with 500 per cent elasticity, which allows dissimilar products to move, expand and contract at different rates. When a build requires the application of dissimilar materials, like an aluminium panel to a steel frame, both materials have different expansion and contraction rates, explains Olver. Any adhesive used needs to allow for those materials to move at their different rates, and because of X-Tack’s flexibility it will allow for that movement.
On top of its extreme adhering capacities, these products are impervious to most climatic conditions, able to withstand the tough environments that come with a construction site.
While the strength and durability of adhesives is vital to ensuring great project outcomes, so too is the construction industry’s move towards sustainability.
Construction projects being delivered by both the private and public sector are increasingly requiring greener building methods and solutions – and therefore designers and
WELL Building Standards in project design and delivery.
All project stakeholders can be confident that the Tec7 range is suitable for their next green project. Seen as an alternative to silicones or polyurethanes, the Tec7 range available through Olmurtech has been awarded a Global GreenTag PlatinumHEALTH HealthRATE outcome under the GreenTag Product Health Declaration (PHD) program and a Global GreenTag GreenRate Level B certification.
These certifications pose huge benefits for the tradespeople applying Tec7, as well as the end-users of the build. “It creates comfort and peace of mind for the end user of the project knowing that they’re not going to be 20 years down the track suffering from a condition because of the toxicity of an adhesive that’s been used,” says Olver.
The green certifications also create peace of mind for the tradespeople who are applying the products. Given they’re working closely with the products, tradespeople or installers are the most susceptible to problems associated with toxic construction materials.
“We’ve all dealt with, or seen over the last 50 years, the ramifications from asbestosis and now silicosis,” says Olver.
“As part of these green certifications we’ve achieved, Tec7 products underwent Global GreenTag’s stringent assessment for ethical manufacturing, health, safety and ecological
“It creates comfort and peace of mind for the end user of the project knowing that they’re not going to be 20 years down the track suffering from a condition because of the toxicity of an adhesive that’s been used.”18-millimetre birch plywood panels installed on a suspended ceiling with X-Tack at the University of the Sunshine Coast’s Petrie campus, QLD.
the space upon completion, can rest assured their health won’t be impacted.”
“It’s our responsibility as suppliers of the product to make sure that those people are safe.”
Olmurtech has supplied Tec7 products to construction sites across Australia, including for the new Jordan Springs Public School in NSW. In 2020, the company developed an X-Tack adhesive system for the project team to install 12-millimetre, prefinished hoop pine plywood external ceiling panels manufactured by Austral Plywoods. Installed above an area regularly occupied by school children, the strength and durability of X-Tack was vital to the project’s success.
“Using X-Tack in this application created a seamless finish as no visible mechanical fixings were required,” says Olver.
“For that particular project, we spent a lot of time working with the builders and designers and developing their confidence in our product.
“They were so happy with the quality and finish that they called on Olmurtech to supply X-Tack for stage two of the project, which again involved using it to hold up hoop pine plywood.”
X-Tack has also recently been used in a project at the University of the Sunshine Coast’s Petrie campus. The project involved the removal of panelling and the installation
above a regularly populated area.
“With that application, they didn’t want to see mechanical fixings, so the project team tracked us down and spoke to us,” says Olver. “I attended the site several times to install prototype panels for the tradespeople who would be using X-Tack to install the panels and showed them how and why the product was perfect for the job.”
“The engineers within that company decided it fitted the bill and went ahead with our X-Tack adhesive solution.”
With all of its products, Olmurtech provides “old-fashioned customer service”, something Olver says seems to be a lost art in many facets of the construction industry. The Olmurtech team gives as much attention, education and training to an individual who wants to buy a single tube of product to reseal a window as they do to someone who is purchasing pallets of product for a major project, he says.
“That’s our mantra and our culture – we know that customers hate being a number, so we ensure every customer feels equally respected, valued and well serviced,” Olver says.
With a commitment to delivering quality products, customer satisfaction and support, Olmurtech is simplifying building, construction, maintenance and repair for professionals industry-wide.
Hutchies is Australia’s largest privately owned builder. Over five generations, we’ve not only played a big part in building our country but also in nurturing communities. We believe in building schools that create community bonds and long-lasting legacies, fostering education and growth. Along the way, we’ve built a company with a debt-free balance sheet and the capacity to think big. We believe that by building places, including educational institutions, we build opportunities for the communities where we live, learn, and work. These projects aren’t just constructions; they are a symbol of our commitment to future generations. With over 100 years under our belt, Hutchies is just getting started. Because it’s not just about building. It’s about building legacies.
By providing the right gear at the right time, Allcon Group is helping construction professionals deliver fast, efficient, highquality concrete works for their major civil infrastructure projects.
For over 35 years Allcon Group has provided solutions to concrete problems, with a primary focus on making the traditionally laborious task of concreting easier. Established as a family business in 1987, the company was one of the first to introduce the plastic bar chair to the Australian market and today remains at the forefront of concrete tooling and equipment innovations.
From its humble beginnings supplying plastic bar chairs, primarily for the residential building industry, Allcon Group has diversified and expanded to service the major civil, commercial and industrial construction sectors with its range of hand-tools, equipment and consumables for concrete applications.
Sales manager Ben Weeks, whose grandfather started the business, has worked within Allcon Group since the moment he left school. Understanding the fast-paced and demanding nature of civil infrastructure projects, he says the company is committed to helping construction teams save time and get their projects finished to scope. “Our main point of difference is reliability,” says Weeks.
“Our customers can rely on our extensive industry experience, quality products and efficient delivery service to ensure they get
with an emphasis on quality and reliability.
“At the end of the day, our main aim is to enable construction professionals to do what is normally physically demanding work, more efficiently.”
Through its range and services, Allcon Group addresses a number of common concrete challenges seen in the civil construction industry, such as those caused by time constraints and unsuitable design specifications.
When it comes to concrete design, the Allcon Group team will provide a design sketch and project takeoff for its customer’s formwork requirements – including full dimensions – to provide them with an optimal, time-effective solution for their application. “Then, we ensure we deliver the solution on time,” says Weeks. “Often with major civil construction, project teams have tight delivery timeframes or time restraints associated with site access.”
On time delivery is also crucial to ensure goods – such as cardboard void formers, which are extremely sensitive to moisture – aren’t sitting around onsite getting damaged. Many concrete products have to be delivered and installed on the same day, or within a couple of days, to ensure that they aren’t damaged by being stored in
“Through our carrier network, in-house fleet of
“Our main point of difference is reliability.”manager, Allcon Group. Allcon Group supplied and delivered over 35,000 square metres of collapsible cardboard void former for the main terminal ground slab on the Western Sydney Airport Terminal project.
located warehouses in Victoria and NSW, we ensure quick and efficient delivery of all tools and equipment – helping our customers to keep their job moving,” says Weeks.
This on time service was essential for Multiplex and BKH Contractors’ delivery of the Western Sydney Airport Terminal project. Allcon Group supplied and delivered over 35,000 square metres of collapsible cardboard void former for the main terminal ground slab, during what was one of the wettest years on record.
“Despite these challenges, we were able to work with BKH Contractors and Multiplex to deliver semi loads of product to site with less than 48 hours of notice after the rain eased,” says Weeks.
Allcon Group similarly played a key role in BESIX Watpac and I&D Group’s delivery of Microsoft’s MEL 07 ‘hyperscale’ data centre –a multi-level facility near Melbourne Airport.
“Allcon Group supplied and delivered over 20,000 square metres of collapsible cardboard void former over a period of five months, which required careful planning and communication of site deliveries due to the tight delivery timeframes and the number of semi-loads required per month to ensure the project remained on schedule,” says Weeks.
Construction professionals also face challenges associated with project variations. The Superseal Group recently experienced such a challenge on the complex URBNSURF wave pool project at Sydney Olympic Park, where they found themselves having to shut down and drain the pool every three months for resurfacing and waterproofing maintenance.
“To minimise shutdown maintenance on the project, we put forward a tertiary waterstop solution that met the engineering requirements and critical demands of the unique application,” says Weeks. “The solution not only minimised shutdown maintenance works for the client, but also came with a 100-year product warranty.”
Another key product currently driving positive outcomes for Allcon Group’s customers is Geoplast, a plastic formwork system. Traditionally, formwork is installed using plywood which is custom cut to size by the formworker according to the job’s specifications. After being in contact with
fresh concrete, plywood starts to degrade, reducing the number of times it can be reused in subsequent projects. Geoplast, conversely, is a plastic, modular formwork system that can be reused over 100 times and requires no tools to install.
CPB Contractors recently used Geoplast from Allcon Group in its delivery of BHP’s Wind Fences Project in Port Hedland.
“By transitioning to the plastic formwork system, CPB Contractors was able to reduce waste and the use of chemicals onsite and found Geoplast to be approximately one and a half times more efficient than plywood,” says Weeks.
For spearheading the rollout of Geoplast as a replacement for plywood on the project, CPB Contractors’ Peter Ting was awarded Engineer of the Year at the 2023 Civil Construction Federation’s (CCF) Industry and Training Awards.
On top of its consumable and equipment ranges, Allcon Group supplies tools that can not only save time, but also improve health and safety for the user. Many workers in the concrete construction sector perform tasks that are highly repetitive, which can lead to repetitive strain injuries (RSI).
For instance, a common way to secure reinforcing bars in concrete construction is to use tie wire, which is generally installed by a professional steel fixer by hand. “It’s common for these professionals to end up with a RSI as a result of doing this task every day,” says Weeks. “Whereas the tie guns will tie the steel automatically – all the steel fixer has to do is pull the trigger.”
Additionally, concreters and builders have to rely on a dedicated steel fixer to come onsite and tie the steel, which they have to schedule. “If the steel fixer doesn’t show up, it delays the job,” says Weeks. “The tie gun allows the concreter to take control of that task themselves as it doesn’t require a professional qualification to be operated.”
“This allows them to be more flexible with timing and get the job done quicker.”
With a focus on its vision – to be the most reliable provider of concrete construction equipment and materials to contractors across Australia – Allcon Group’s range continues to grow to keep up with the ever-evolving needs of the construction industry.
“Our customers can rely on our extensive industry experience, quality products and efficient delivery service to ensure they get their concrete jobs done on time.”
Carmix is an innovative range of self-loading concrete mixers, dumpers and silos for onsite concrete production, and Pilecom Equipment has made it readily available for the Australian construction market.
National solution provider for solar farm construction Pilecom Equipment has recently launched an exciting new product range for the Australian construction and infrastructure sectors. In recent years, the company became the official Australian agent of Carmix mobile self-loading concrete batching units and products, which have since been changing the game for project teams working in rural, remote and difficult to access locations.
Pilecom Equipment is a local family-owned business led by director Boyd Cousins and his two sons, who all have a deep passion for the products and services they provide. Their excitement for the Carmix range is evident, and given the units’ unique capabilities, it’s not hard to see why.
Carmix is a range of off-road mobile concrete plants, ideal for construction projects in remote regions and with steep incline or narrow forest access, as well as for tunnelling works, mine sites and island constructions.
In contrast to conventional concrete trucks, Carmix plants are permanent four-wheel, hydraulic drive – designed for power in the toughest of project locations. Pairing the concrete batching units is Carmix’s dumpers, silos, pumps and baggers, which are also available at Pilecom Equipment.
“We currently have eight models of the Carmix self-loading concrete batching units available for the local industry, ranging from
the smallest machine with a one cubic metre mixer drum capacity, to the largest with a five and a half cubic metre capacity,” says Cousins. “These units are a dedicated batch plant that enable construction contractors to mix their own concrete onsite.”
“Being a permanent four-wheel drive machine, the Carmix off-road concrete plants are ideal in muddy conditions and can tackle a 30 per cent incline with ease.”
Commercial trucks often encounter the challenge of their load starting to tip off the back when they’re climbing a steep incline. Carmix units avoid this though their forwardfacing drum, meaning it won’t spill if it’s carrying a full load.
Remote projects come with unique problems. When it comes to concrete, many remote projects are a great distance from commercial concrete suppliers, resulting in exorbitant transport costs to have it delivered to site. There’s an increasing pressure on contractors to deliver commercial and government projects on time and on budget. By being able to mix their own concrete onsite with the Carmix, contractors can not only save on these costs but are also able to avoid project delays as a result of having to wait for supplied concrete to arrive.
For tunnelling construction, Pilecom Equipment offers two Carmix units, which can move with ease in environments with
“Being a permanent four-wheel drive machine, the Carmix offroad concrete plants are ideal in muddy conditions and can tackle a 30 per cent incline with ease.”Loading sequence of Carmix.
limited space – the Dumper D6 and the 45 FX. Both units can drive in and out without turning around thanks to their bi-directional steering system, which means the operator is always facing forward instead of having to turn their head to reverse out. “These units can also be retrofitted with roll over protective structures, falling object protective structures and cabin air control systems,” says Cousins.
Another huge advantage of Carmix units is that they’re easy to operate. Given the skilled labour shortage, says Cousins, equipment suppliers need to be supporting all levels of construction professionals.
“Those operating these machines don’t need a high-risk license, only a regular driver license or preferably a heavy-vehicle license,” says Cousins.
“Our team has extensive experience in operating these machines.
“With the purchase of any Carmix unit, we offer a full day of training either on the jobsite or in the contractor’s yard where we try to simulate project site conditions – we offer robust solutions and robust support.”
With the construction industry increasing its focus on environmental impacts and sustainability, Carmix can also mix green concrete. Carmix has the ability to mix green and recycled concrete where loading of nontraditional concrete materials is difficult.
“The Carmix is perfect for loading unusual aggregates,” says Cousins.
“We believe that our units can help increase the construction industry’s understanding of green concrete by enabling contractors to mix it themselves on their own sites.”
Productivity growth in the construction industry has majorly lagged other industries over the last 30 years – another challenge the sector continues to face. In 2020, the Australian Constructors Association commissioned a report by BIS Oxford Economics, which concluded the opportunity cost of poor productivity in the industry is likely valued at $35 billion for the 2019-2020 year alone. “Carmix’s self-loading feature improves productivity by taking the load off workers,” says Cousins.
“A single operator can shovel cement, sand and aggregates and mix the concrete onsite.”
Carmix silos – available from Pilecom Equipment in 16, 26, and 36 cubic metre models – are often used in conjunction with Carmix units to optimise site productivity and reduce cement wastage. “These systems are stationary horizontal cement silos fitted on telescopic stabilisers for easy loading and unloading from trucks,” says Cousins. “They don’t require assistance from lifting machines.”
“An electronic load cell weighing system can also be fitted to the Carmix silo systems, which manages cement discharge as well as quantity management of cement inside the silo.”
Contractors are searching for greener solutions, machinery that can withstand the harsh environment of the increasingly complex projects they’re working on, and equipment that can save them time and money to boost productivity and efficiency onsite – and Pilecom Equipment is offering solutions with Carmix.
Viva Energy, through its multi-faceted approach to sustainable energy solutions, is helping drive success in the construction sector’s journey towards decarbonisation.
Australian energy supplier Viva Energy is positioning itself to help support the construction industry’s transition to a more sustainable future through its range of low carbon products and zero emissions technologies.
Recognising the construction industry’s decarbonisation transformation is a complex and demanding endeavour, Viva Energy has established a Carbon Solutions team, headed up by carbon solutions manager Robert Cavicchiolo. The principal aim and mission of the team is to help the company’s customers on their decarbonisation journeys, supported by Viva Energy’s current and evolving mix of short, medium and long term products and solutions.
For decades the company has supplied a wide range of products and services to the sector, including fuels, lubricants, solvents, bitumen and technical advice. In alignment with the industry’s diverse needs, Cavicchiolo says delivering low and zero emission products for its customers is a tangible next step.
“As the construction industry continues its move towards more sustainable operations, Viva Energy’s low and zero emission solutions will play a more important role in the future,” says Cavicchiolo.
“We’ve been hearing feedback in the marketplace, for a number of years now, that our customers are starting to really focus on their emissions reduction, so we’re developing solutions to encourage and support these goals.
Viva Energy sees its approach to reducing carbon emissions in the industry as a stepping-stone approach, says Cavicchiolo.
“Our low carbon fuel products are part of that first step, enabling construction companies to choose sustainable energy solutions to power their equipment and assets,” he adds.
Viva Energy is striving to displace the construction industry’s existing diesel use with an alternative low carbon fuel such as biodiesel and renewable diesel (HVO). These options are drop-in solutions – they don’t require major upgrades to company equipment or assets. Typically, equipment may run on these drop-in fuels with only some restrictions or, in the case of renewable diesel, with minimal to no restrictions for the owner.
The carbon footprint associated with these fuels is typically a lot lower than conventional diesel from crude oil, says Cavicchiolo.
“There’s a net benefit in terms of the greenhouse gas emissions over the lifecycle of these low carbon fuels,” he adds.
“As the construction industry continues its move towards more sustainable practices and operations, Viva Energy’s low and zero emission solutions will play a more important role in the future.”Robert Cavicchiolo, carbon solutions manager, Viva Energy Australia.
“Effectively, this is enabling us and our customers to use lower carbon products, which then reduces the carbon footprint of the projects our customers are working on.”
Used as an alternative to conventional diesel, biofuels incorporate fatty acid methyl esters (FAME) which is typically produced from feedstocks such as tallow or used cooking oils. It’s a great short-to-medium-term solution for replacing conventional diesel in the operation of construction equipment and machinery.
“Biodiesel is a co-mingled product that has a bio sourced component, which is generally mixed at five (B5) or ten (B10) per cent in diesel,” says Cavicchiolo. “It’s a very mature product in the Australian marketplace, which has been manufactured for several years and is generally accepted by original equipment manufacturers (OEMs) at certain blend rates.”
Construction companies don’t need to change equipment or fuel sources, such as tanks, other than the addition of some labelling – it’s a drop-in solution.
“Viva Energy blends FAME-based biodiesels at our terminal gantries,” says Cavicchiolo. “Thus, from a quality assurance perspective, you know you’ve been delivered the right product that meet the recommended specifications.”
“We control the blending with wellestablished fuel management and quality systems that we have in place.”
Winslow Group is one company utilising Viva Energy’s FAME-based biodiesel in B5. Cavicchiolo says the civil construction firm saw it as a great option to start their journey around decarbonisation and also to address their own customers’ requirements.
For construction companies looking for an alternative lower carbon emissions
solution, Viva Energy intends to make available renewable diesel, also known as hydrotreated vegetable oils (HVO). These fuels are very similar in nature to conventional diesel. The great thing about HVO, says Cavicchiolo, is that there’s little to no incompatibility issues or blend limits for equipment owners (again, owners must always check with their OEMs). “Typically, OEMs are happy to use this as a drop-in fuel solution and at higher blend rates,” he says.
There’s some other side benefits of using HVO in place of diesel, such as a longer shelf life compared to conventional diesel, and it is less likely to experience microbial growth. Further, Viva Energy is planning to make HVO available in the local marketplace so that its customers can utilise it.
Viva Energy also offers its customers a range of Climate Active-certified opt-in carbon neutral products. It’s essentially a solution that’s available now, so that the customer can look at offsetting its emissions straight away, says Cavicchiolo.
With the use of opt-in products, a company doesn’t have to change its equipment, asset base, how it performs tasks in the field, or modify any of its existing practices, operations or maintenance regimes. The customer is using carbon credits which have been generated from approved carbon abatement projects to essentially cancel out or negate the emissions associated with the use of conventional diesel.
Viva Energy has certified opt-in carbon neutral products which meet the requirements of the Climate Active scheme’s Carbon Neutral Standard.
“It’s an easy solution for customers,” says Cavicchiolo. “But we do recognise that offsetting should be considered after
“There’s a wide range of short-to-medium-term options – including biodiesel, HVO and opt-in carbon neutral products – and we’re really keen to help our customers start that journey now, but also help them with the longer-term options.”Viva Energy is powering the construction industry with low carbon emission solutions.
“We also have a team called New Energies within Viva Energy, which is focused on medium and longer-term solutions around electrification, hydrogen and the adoption of zero-emission technologies.”
customers have explored physically avoiding, reducing or eliminating their emissions through other practices and solutions.”
“What we find, particularly in the field, is there’s not many options out there in terms of electrification and the infrastructure required to provide charging or hydrogen refuelling.
“This is when opt-in carbon neutral products may provide a viable option for customers.”
Viva Energy has placed importance on providing its customers optionality to address their emissions targets. The company can provide a solution for the customer no matter where they are on their decarbonisation journey, even those just starting out.
“There’s a wide range of short-to-mediumterm options – including biodiesel, HVO and opt-in carbon neutral products – and we’re really keen to help our customers start that journey now, but also help them with the longer-term options,” says Cavicchiolo.
“We also have a team called New Energies within Viva Energy, which is focused on medium and longer-term solutions around electrification, hydrogen and the adoption of zero-emission technologies.”
The company is taking further initiatives to cut emissions within its own business
in addition to its customers. Viva Energy is building infrastructure which will enable its refinery at Geelong to co-process lower carbon feedstocks such as used cooking oil, animal fats and synthetic crude made from waste plastics; and developing one of the first commercial hydrogen refuelling stations in Australia – the New Energies Service Station.
“The New Energies Service Station will be a commercial hydrogen truck stop located in Geelong where our customers will be able to come in and refuel their trucks with green hydrogen,” says Cavicchiolo.
“As well as hydrogen, it will accommodate electric charging and also diesel refuelling to create a multi-energy hub.”
It’s not just the construction sector benefiting from Viva Energy’s solutions.
The company services a diverse range of industries, from aviation, marine, mining and agriculture to defence, manufacturing and road transport, to play its role in the wider nation’s shift towards a low carbon future.
As Viva Energy continues to expand on its range of carbon reduction pathways, new opportunities arise for the construction industry, and all industries, to harness its solutions for a greener and brighter tomorrow.
You have low VOC paint on the walls. The room is decked out with eco-friendly furniture, resting atop certified sustainable flooring. But what about the substance that literally holds everything together – adhesives?
Adhesives and sealants are typically used in large quantities for construction or interior design projects, and yet they can also be one of the most commonly overlooked materials in terms of their sustainability credentials.
Green Star® Credits, LEED® Credits and WELL™ Features can now be earnt when working with Green Building rating systems and Tec7 certified products.
For more information on TEC7 visit www.olmurtech.com.au
FAE is constantly developing and designing its product line to match the unique needs of the construction industry, ensuring its customers have the right machine attachment for road, highway, trail, quarry, mine and infrastructure construction applications.
Increased costs, poor project results and slow productivity growth are currently some of the most talked about topics in the Australian construction industry, but FAE is delivering solutions to help make these challenges a thing of the past. The company has created a product line of machine attachments specifically designed to maximise business and project performance.
FAE Australia Pacific managing director Alberto Rosso says the company has a product range dedicated to vehicles with hydraulic or mechanical power take-off. “A number of products within this range are designed for specific processes that require high-level results such as our multitask products, which amplify the versatility of both our attachments and of the driving machine already owned by the customer,” says Rosso.
“Depending on the customer’s needs, they can equip their machinery with our attachments and systems, such as our fixedrotor systems, variable geometry chambers, and high technology and precision water
systems, to further enhance performance.”
FAE’s product line features machine attachments that are capable of performing multiple jobs, from asphalt grinding and rock and concrete crushing to soil stabilisation, tunnelling and asphalt recycling.
“For instance, full-depth reclamation – a pavement rehabilitation technique – whether of the asphalt layer or the supporting substrate, is an innovative technique involving the milling and homogenisation of both layers with the simultaneous addition of water and structural binding agents, which normally consist of cement and/or lime, or other specific materials,” says Rosso. “This operating method entails the onsite recycling of all material, drastically reducing the need of machinery and, as a result, eliminating the costs of disposing of the surplus material.”
FAE’s specially designed heads are ideal for this type of application, enabling the operator to reach significant depths and work successfully in areas that are difficult to access and in confined spaces such as
“Depending on the customer’s needs, they can equip their machinery with our attachments and systems, such as our fixed-rotor systems, variable geometry chambers, and high technology and precision water systems, to further enhance performance.”FAE’s RPM/SSL Road Planer in action.
and moving about. This results in improved site logistics and therefore a reduction in costs, Rosso explains.
“FAE’s heads feature a variable geometry chamber,” says Rosso. “The rotor is attached to a moving frame that allows for extremely precise control over the working depth, without compromising structural strength.”
“To complete the line, water injection systems are also available to control the operating temperature of the rotor and teeth that come into contact with the asphalt, guaranteeing consistent productivity and giving the soil the right amount of moisture for top mixing results.”
FAE has a machine attachment for several structural and architectural applications, one being stone and rock crushing for road, commercial and large infrastructure construction projects. In these types of environments, large rocks and stones need to be reduced for total or partial burying or crushed to rubble to produce gravel.
The wide range of multitask crushers offered by FAE, says Rosso, means that every specific need associated with full-depth reclamation can be fulfilled with extremely high productivity and under all conditions.
Another application FAE’s attachments are used for is slab rock milling. FAE’s heads generate fewer vibrations and optimise the crushing process when used instead of conventional crushing equipment, in turn boosting productivity onsite.
“The wide range of specialty teeth patented by FAE offers a complete response to the most diverse operating needs,” says Rosso.
In asphalt treatment FAE can provide a range of solutions, inspired by its vast experience
offer speed and precision for improved operational reliability.
For instance, in situations where it is necessary to mill the top asphalt layer during road maintenance, FAE offers a series of models that are ideal for streamlining the job, Rosso says.
“Also, when it comes to processing asphalt and its subgrades, FAE offers a series of multitask heads that can perform crushing and mixing in a single pass,” he says. For soil strengthening applications, when soil stabilisation and mixing is required on construction sites to achieve the engineered load-bearing capacity, FAE delivers a wide range of products for incorporating various binding agents – such as lime, cement or special materials – into the substrate. FAE’s heads can be used to effectively build dirt and gravel roads, asphalt roads, railroads, airports, embankments and large parking lots as well as industrial, commercial or sports complexes and backfill or landfill.
Reaching large depths is not a problem for FAE’s heads, says Rosso. Again, the ability to use these heads in difficult to access and confined spaces creates significant savings on the initial investment.
FAE is showcasing a number of its products, specifically designed for the fast-paced, tough environments of the infrastructure and construction sectors, at this year’s Inside Construction Expo on 20 to 21 September at the Melbourne Convention and Exhibition Centre. For those looking to achieve highlevel results on their construction projects, visit FAE’s stand to discover the latest in its inventory of machine attachments, currently available at its Melbourne branch.
“The wide range of specialty teeth patented by FAE offers a complete response to the most diverse operating needs.”
We are now well in the second half of 2023, which means the beginning of The National Association of Women in Construction’s (NAWIC) awards season. In each NAWIC Chapter we invite members to nominate themselves or their colleagues across a wide range of categories of achievement in the construction industry.
As part of our You can be what you can see strategy, the NAWIC awards program aims to recognise, celebrate and promote the many significant achievements of women in construction and their allies. Our awards program is proudly supported by our corporate sponsors whose generosity provides a range of financial and in-kind prizes to our pool of worthy award winners. Importantly, our awards program is run by our passionate volunteers who give generously of their time to make this initiative happen, for the betterment of our industry. NAWIC extends its gratitude to both our sponsors and volunteers for their continued commitment to and support of women in construction.
Previous winners say the NAWIC awards program has created new career opportunities, enhanced their CVs and resulted in growth of their network.
Advocacy spotlight: shining a light on the pay gap
that values diversity and inclusivity. By raising awareness and driving action on gender equality, the WGEA Act plays a role in building a just and fair workforce, for all Australians. We take immense pride in our ongoing partnership with WGEA, united in our shared mission to achieve gender equality. Thank you WGEA for your commitment to advancing gender equality and supporting NAWIC’s mission. We would also like to take this opportunity to congratulate our Corporate Members who have achieved their WGEA Employer of Choice for Gender Equality citation. These organisations are to be applauded for their leadership and their commitment to workplace equity and equality.
NAWIC is grateful for the recent work of the Workplace Gender Equality Agency (WGEA) for taking the time to engage and educate NAWIC members and affiliates. WGEA hosted a free webinar for our members to learn about the important work done by the agency and how organisations can pledge their commitment to eliminating the gender pay gap. The insights and expertise provided on gender equality during the session were truly enlightening and had a profound impact on all attendees. During the webinar the WGEA Act was also explored. The WGEA Act is a law in Australia that aims to promote and ensure equal opportunities in the workplace. It mandates that private organisations with 100 or more employees must submit reports on their efforts toward gender equality. This requirement fosters transparency and accountability as it encourages businesses to address gender imbalances and create a work environment
The National Construction Industry Forum (NCIF) has taken a monumental step toward promoting an inclusive and diverse construction sector. Through its committee selection, NCIF has demonstrated a commitment to gender equality by achieving an impressive balance of women and men within their ranks. The NCIF consists of 50 per cent women and an equitable mix of industry, government and union representatives. The NCIF committee comprises a mix of industry leaders, professionals and advocates from various sectors within the construction industry. What truly stands out is the representation of both genders, which showcases a thinking approach to addressing gender disparities that have historically existed in this male-populated industry.
NAWIC wholeheartedly commends NCIF’s dedication to fostering a more equitable environment. As an organisation devoted to championing gender diversity and advocating for opportunities in the construction industry, NAWIC is excited about collaborating with NCIF on initiatives that promote gender balance, inclusivity and innovation. We look forward to supporting the initiatives and goals of the NCIF forum and hope to see a big push for changes to the culture of the industry and the experiences of women who choose to enter it.
The report published by the Australian Constructors Association – All risk, no
This month, The National Association of Women in Construction shares news of its Awards program and shines a light on the gender pay gap, equality and profit challenges in the construction industry.
“By raising awareness and driving action on gender equality, the WGEA Act plays a role in building a just and fair workforce, for all Australians.”
reward: Fixing the building industry’s profitless boom, July 2023 – provides insights and proposes practical measures to tackle the concerning financial state of the industry. It draws attention to the rate at which construction companies are entering administration, the decline in profit margins and the growing issues related to liquidity. The report raises concerns regarding the adversarial culture and shortterm focus within the sector and identifies the traditional reliance on fixed-price contracts as a key contributor to the sector’s instability.
In terms of addressing the market failure in the building industry, the report outlines the paradigm shift required: “Fundamentally, maximising the chances of a win-win outcome on a building project requires that contracting becomes far more relational than transactional.
Building is not a spot-marketing transaction; it is an ongoing process of interaction between parties throughout delivery; a relationship”.
Key principle reforms proposed for success include:
• I nvolving the contractor in the design process at the earliest opportunity.
• D o not set a formal cost at the start – commission a fee for service basis.
• I ncentivise collaborative out-performance – painshare/ gainshare models to drive commercially viable outcomes for all parties.
The report highlights the importance of government involvement in leading the way toward a more profitable construction industry. As an organisation deeply committed to sustainability, innovation and progress within the construction industry, NAWIC supports the proposals put forth in the report and welcomes further exploration on how these changes can be enacted.
The Formwork Industry Association’s Michael Sugg explores the difficulties faced by formworkers in meeting the training mandates set forth by the Work Health and Safety Act and proposes potential solutions to bridge the gap.
“The recently released Australian Work Health and Safety Strategy
2023-2033 states that construction companies need to make sure that, on their projects, there is ‘meaningful and relevant training for workers, delivered in a way they can understand’.”
Formworkers play a crucial role in the construction industry, being involved in shaping the foundations and structures of various projects. However, compliance with the safety training requirements outlined in the Work Health and Safety (WHS) Act can be a challenging aspect for these skilled workers.
Challenges faced by formworkers
1. Lack of accessible training programs
One of the primary hurdles faced by formworkers is the limited availability of accessible training programs that cater specifically to their needs. As their responsibilities and tasks may differ from other construction roles, formworkers often require specialised training, which is not always readily available.
2. Cost barriers
Completing training courses can be expensive, and this financial burden is a significant challenge for many formworkers, especially those working in smaller construction firms or as independent contractors. The cost of training, along with potential time off work, can create barriers to compliance.
3. Time constraints
Formworkers often work in demanding environments with tight project schedules. Finding time to attend training sessions can be problematic, and employers may face difficulties releasing workers for training without affecting project timelines.
4. Language and literacy barriers
For some formworkers, English may not be their first language, and they may encounter difficulties in understanding complex training materials, assessments, and instructions. This language barrier can hinder effective learning and comprehension.
5. Limited recognition of prior experience
The recently released Australian Work Health and Safety Strategy 2023-2033 states that construction companies need to make sure that, on their projects, there is ‘meaningful and relevant training for workers, delivered in a way they can understand’.
It supports the continuation and strong focus on compliance and enforcement by regulators, with a particular focus on systematic WHS management. If you don’t have meaningful and relevant training and cannot demonstrate robust WHS management, the risk is that the safety regulators will investigate the quality of your systems, including training and competency, to hold companies and individuals accountable.
WHS laws are risk based and don’t need an incident to occur for a business and its individuals to be liable. It is every employer’s responsibility to make sure their workers get the training, instruction and support they need to keep them safe at work.
The Formwork Industry Association (FIA), in conjunction with its members, has developed a new education and skills pathway to overcome the challenges faced by formworkers. Addressing compliance issues, the initial Safe Formworker Program has been designed to provide the following features to ensure construction, civil and formwork companies can comply with their obligations.
Tailored training programs
The Safe Formworker Program is a specialised WHS training program exclusively for formworkers that addresses their specific needs and challenges. The program covers essential safety protocols, techniques and technologies relevant to their roles. By addressing the unique needs of formworkers, this specialised training is more relevant and effective in enhancing competency and safety.
By FIA Chief Executive Officer Michael Sugg. michael@ formworkassociation.com.au M:0401 326 161
Experienced formworkers who have been in the industry for years may find it frustrating that their practical knowledge and skills are not adequately recognised for training compliance. Some training programs may not offer suitable avenues to assess and credit their existing expertise.
2. Government subsidies and support
To alleviate the financial burden, the FIA has secured funding from the NSW Government to provide 1,000 free places for formworkers’ training and access to the program and app.
3. Flexible training delivery
Offering flexible training options, the program is delivered via a modern mobile learning experience. It enables formworkers to complete their training without significant disruptions to their work schedules, by providing bite-sized mobile courses that can be completed in the shed during toolbox talks. The program also enables employers to support a learning culture that allows workers to upskill during quieter periods.
4. Multilingual training materials
The Safe Formworker Program has been translated into Arabic and can also be translated into other languages. This provides training materials in multiple languages to improve accessibility and understanding for non-native Englishspeaking formworkers. This approach will enhance the learning experience and overall training compliance.
5. Recognition of prior learning
Creating formal recognition of prior learning (RPL) processes will allow experienced formworkers to demonstrate their skills and
knowledge, gaining credit for their existing expertise toward training compliance. Our new education and skills pathway for formwork will enable these RPL programs to be successful and the app has certain features that allow workers to provide on the job video of their skills.
6. Industry endorsement
The Safe Formworker Program is endorsed by a growing number of construction companies that have specifically named the program as an essential compliance requirement in their tender process. Complying with the training requirements identified in the WHS Act is essential for the safety and wellbeing of formworkers and those working alongside them. By implementing the Safe Formworker Program, we can bridge the training compliance gap, ensuring that formworkers receive the necessary knowledge and skills to perform their duties safely and efficiently. Collaboration between governments, industry stakeholders and training providers will be key to fostering a safer and more compliant construction industry.
“The Safe Formworker Program is endorsed by a growing number of construction companies that have specifically named the program as an essential compliance requirement in their tender process.”
With demand for new developments in the nation’s capital at an all-time high, precast was specified as the material of choice for Renaissance Manuka, a premium apartment complex in Canberra’s inner south suburb of Griffith.
Located on the site of the old Stuart Flats, the predominantly precast Renaissance Manuka development covers three parcels of land located on Captain Cook Crescent, Stuart Street and Light Street, Griffith. It offers 414 one, two and three-bedroom apartments in five buildings of three to six stories across the three blocks, as well as a childcare centre, health facility and basement parking.
The buildings’ façades are a mixture of traditional brick – achieved by brick tiles cast into precast panels – mixed with white painted precast concrete walls and charcoal window framing, upper-level cladding and roofing.
Construction of the complex coincided with the height of the COVID-19 pandemic, creating a number of unforeseen challenges. Speed of construction and reducing site labour were the key drivers for the
of constructing a conventionally framed structure clad with brickwork.
The decision came at just the right time, when COVID-19 was severely impacting labour supply in the ACT and resulted in many months of time savings.
In all, 364 loadbearing and non-loadbearing precast elements were manufactured for Block 23 of the development, comprising wall panels, spandrels, columns, retaining panels and planter walls. Of the wall panels, 150 were manufactured using brick tiles that were cast into the faces, tops and edges of the panels, with the selected brick tiles matching the suburb’s traditional surrounding buildings. Precast elements were manufactured by National Precast Concrete Association Australia Master Precaster Advanced Precast at its Wetherill Park factory. Manufacturing the brick panels for the
Precast, Guida Moseley Brown Architects (GMB) and Northrop Consulting Engineers during the documentation phase was required to ensure a smooth build. Careful layout of bricks to accommodate differing panel sizes and differing tolerances of the various materials was essential during manufacture.
Rob McLachlan, Architect at GMB says: “The floor-to-floor height of the units has been worked out to exactly work with a brick dimension; where a normal floor-to-floor height is 3.1 metres, in our case it’s 3.188 metres and that’s a dimension that works perfectly with the brick rod.”
“It’s almost like the whole building has this brick rod overlay to it and we have sort of nudged it and organised it so that we’re not cutting bricks in half at the bottom in their horizontal axis – it’s really exciting when you get everything fitting just so.”
“It’s interesting because even though these bricks are brick tiles on precast, you still have the same set of problems; you still need to design the dimensions of the building to work to the bricks because they’re the visible thing that you see on the outside – that’s something we’re really proud of because when it’s done well there’s a peacefulness about the development.”
Renaissance Manuka has been marketed as “a quality build that has been meticulously
development of 30 units over four levels on Stuart Street, was completed in 2022. Stage 3, the largest of the stages – offering 276 units across five buildings fronting Captain Cook Crescent – is due for completion in 2023.
The design has been cleverly designed to maximise space, light and views towards Parliament House and across leafy parks and heritage homes. All of the apartments’ living areas connect to the existing landscape in some way.
“The church on the corner is a really key element in the landscape, so the building had to address the existing environment,” says McLachlan.
“There’s definitely a sleek modern theme but adding brick to it as an earthy element really gives that nice contrast.
“The brick is a brilliant relationship to the church and some of the houses on the southern side as well.”
Renaissance Manuka development.“Speed of construction and reducing site labour were the key drivers for the decision to use precast concrete while still achieving a brick finish.”
Empowered Women in Trades chief executive officer and founder Hacia Atherton shares her ideas on the best ways to promote a company culture that supports gender
Gender diversity in the workplace is a pressing issue that organisations need to tackle headon. According to a 2019 report from McKinsey & Company, gender-diverse companies are 25 per cent more likely to outperform those that are not gender-diverse. In this article, we will explore how promoting gender diversity can benefit an organisation and how to develop a culture of inclusion in the workplace.
Gender diversity refers to having a balanced representation of men and women in the workplace. It means creating an environment where people of all genders are valued and respected for their skills and talents. Promoting gender diversity is essential for creating a more equitable workplace where everyone has an equal opportunity to succeed.
1. Developing a culture of inclusion: To develop a culture of inclusion, companies need to implement inclusive policies and practices. This includes identifying and addressing any unconscious biases that may exist within the organisation. Creating a diverse and inclusive workforce is also crucial. Companies should strive to hire people from diverse backgrounds and encourage open communication and feedback.
2. Addressing bias and discrimination: Providing training on unconscious bias can help employees recognise and address negative attitudes and beliefs they may
have towards people of different genders. Implementing non-discrimination policies is also important. Companies should establish a zero-tolerance policy for harassment, including sexual harassment. These measures can help create a safer and more welcoming workplace for all employees.
3.Providing equal opportunities and benefits: Ensuring equal pay for equal work is a critical component of promoting gender diversity. Providing parental leave and flexible work arrangements can also help create a more inclusive work environment that supports employees at different stages of life. Organisations that prioritise creating a supportive and inclusive work environment are more likely to attract and retain top talent.
4. Measuring and monitoring progress: To gauge the success of their efforts to promote gender diversity, organisations should set goals and benchmarks. Regularly assessing progress and making adjustments as needed is vital. Celebrating successes and recognising areas for improvement can also help maintain momentum and drive further progress.
Promoting gender diversity in the workplace is not only the right thing to do, but it’s also good for business. By developing a culture of inclusion, addressing bias and discrimination, providing equal opportunities and benefits, and measuring and monitoring progress, companies can create a more equitable workplace that benefits everyone.
By valuing diversity and striving for inclusion, organisations can unlock the full potential of their workforce and create a brighter future for all.
“Promoting gender diversity in the workplace is not only the right thing to do, but it’s also good for business.”Empowered Women in Trades strives to encourage women and non-binary to pick up the tools, to help increase diversity and inclusion across the construction industry. Empowered Women in Trades’ Tool Skills Day and Site Immersion with Kapitol Group. founder, Empowered Women in Trades.
With Deswik’s design and algorithm-powered planning technology, you can rapidly create design alternatives, progress reports, and resource-loaded mass haul schedules to reduce risk and achieve cost-efficient outcomes.
Trusted by major mining companies, Deswik software is now employed by Tier 1 Contractors and Owners for infrastructure projects such as tunnels, roads, pumped hydro, and windfarms.
Request a demo:
E: infrastructure@deswik.com
Construction in Australia is facing a big problem. It is becoming less productive as other costs continue to increase. This should worry all of us because if we don’t fix this issue, we won’t be able to keep up with the demand for housing and infrastructure as our population grows.
Construction’s productivity problem reflects a broader problem in the economy. The Productivity Commission highlights that Australia is experiencing the worst productivity growth in 60 years. If we don’t change things, our living standards will drop, and we’ll have to work longer and earn less.
As one of the largest centres of value in the Australian economy, the construction industry plays a pivotal role in this story. Each year, construction firms directly add about $150 billion to the economy, and the construction supply chain generates an additional $300 billion. This results in employment for over a million fulltime equivalent workers.
If we want to improve the country’s overall productivity, we must focus on improving construction as well. While broad economic initiatives are essential, we must not overlook the potential productivity gains within specific industries like construction, which plays a pivotal role in driving productivity.
As we look ahead to the future of Australia’s built environment, our aspirations are enormous. In the coming decades, we intend to achieve a net zero transition, host major events like the Olympics and expand public infrastructure to accommodate the needs of a rapidly growing and ageing population. Our sights are set on these grand objectives but there’s a pressing concern that demands urgent attention – the productivity of the construction industry. The forward pipeline of committed works is already outstripping the rate of actual construction activity, further emphasising the crucial role of construction productivity. The good news is, there are plenty of solutions to boost
construction productivity. The real challenge is getting everyone to adopt and use these solutions in the construction industry. The fact is, the construction industry needs a new operating system; one that is more compatible with the wide range of solutions already available in the market to drive productivity growth. The industry’s current model drives all the wrong behaviours – a myopic focus on the shortterm with little bandwidth for innovation. The commercial environment of construction actively discourages the longer-term planning and decision-making needed to drive productivity growth.
The key to unlocking productivity lies in creating an environment for industry to innovate. Contractors and consultants must be incentivised to invest in and adopt innovative solutions, and clients should actively encourage and empower innovation in their projects. However, the true catalyst for this productivity transformation lies with the government. Only the government has the power and freedom to lead this charge. It already recognises its responsibility in leveraging public spending for broader societal goals, such as training, indigenous participation and diversity. Now, productivity should be placed at the forefront of these social performance objectives.
The Australian Constructors Association is proposing a concerted national approach to construction productivity reform – a National Construction Strategy. Our plan is a national and tripartite strategy accountable to the highest level of national policy oversight – National Cabinet – and underpinned by a shared responsibility between all levels of government, industry and the unions. Australia’s construction industry has been too inefficient for too long. Improving construction productivity is now a nation building priority requiring Commonwealth leadership to create a National Construction Strategy.
In an effort to boost productivity, the Australian Constructors Association is proposing a concerted national approach to construction productivity reform.
“The key to unlocking productivity lies in creating an environment for industry to innovate.”
Last month, while in the US for a Brinkman Construction Board meeting, I had the opportunity to introduce an Australian construction technology firm, Earlytrade, to several leaders in the US construction industry. Each industry leader was quite impressed with the Earlytrade model of automating early settlement discounts to facilitate the flow of working capital in the industry. But it was one statement that nearly every person made that made me cringe –“You know, we’re not really an ‘early adoption’ industry when it comes to technology.”
They are right. The 2022 Construction User Roundtable study I conducted involving 44 global construction leaders verified this idea.
Leaders such as the global head of construction for Microsoft, Black & Veatch, and Chevron rated technology adoption a 2.34 on a scale of 4.00 and made statements such as:
“Clients are asking for rigorous digital delivery ahead of its time. It’s making people crazy, costing dollars and we don’t get the benefit of the beginning of technology adoption.”
“Tech solutions are not end-to-end, they’re siloed.”
These are but a few of the statements made that reflect the challenges we face in adopting technology in the construction industry.
The “why”
So why are we “laggards” on the adoption curve? Here are some of my thoughts:
• Project schedule pressures – Schedule pressures on projects and programs leave little time for technology innovation. When we are all pushed to the limit and struggling to make project deadlines, is there really an incentive to try something new that in the beginning will slow us down? Probably not.
• Fear of failure – We all have it, that amygdala in our brain that tells us “I’ll never learn that technology” or “the young people will outpace me because they are better at technology”. It’s not just at the individual level. Organisations fear trying something that may not work.
• L ack of research and development (R&D) funding – According to McKinsey & Company, the construction industry spends less than 1 per cent on R&D, much lower than industries such as automotive that spend 3 per cent on R&D. Why? I believe it is because there is a lot riding on each project, and the risk of failure outweighs the incentive to try new things.
• Giving busy people more to do – Years ago we conducted a study for the Gas Technology Institute in the US on technology adoption in gas utilities. One key finding was we often ask busy people to lead technology adoption efforts without taking anything off their plate. When we underresource technology change, we really never know if the technology was the problem, or the lack of resources in adopting it.
• Technology selection challenges – Many, many years ago, when video first started (yes, I am that old) there was the VHS versus Beta debate. VHS won. We have similar problems in the construction industry, with different clients and contractors backing different technology solutions. It’s overwhelming to keep up with them all.
I think there are a few things we can do, as an industry, as organisations and as individuals, to accelerate the adoption of technology in the construction industry. A few ideas:
• Recognise we are laggards – The first step to solving a problem is to realise we have one. Decades ago, we realised there was a serious site safety problem across the industry, and we did something about it.
• Invest in R&D – Companies can deliberately set higher budgets for R&D, including technology. Budgets and the allocation of resources create priorities within organisations and teams.
• Reward people – Building technology adoption into people’s key performance indicators will create focus – we do what we are incentivised to do.
• Talk about it – People listen to what our leaders talk about. We spend a lot of time talking about safety. How could you
“Leaders such as the global head of construction for Microsoft, Black & Veatch, and Chevron rated technology adoption a 2.34 on a scale of 4.00.”Dr. Gretchen Gagel looks into the state of technology adoption in the Australian commercial construction industry.
replicate that for technology adoption and other important topics?
• Don’t just talk it about it – If your IT department, or chief technology officer, is the only person/team driving the adoption of technology, it’s not going to work. It is much like the 80’s when total quality management (TQM) became the fad of the decade. One approach with little success was to create quality departments; the other – making quality and TQM part of everyone’s job – was quite successful. Technology adoption must be seen as important to everyone in the organisation, not just the ‘techies’. This is a solvable problem, and I’m certain each of you have more ideas about how to accelerate technology adoption in our
industry. If this is a priority, what’s the next big step? How can you be a champion of technology adoption in your team and organisation? The results can pay big dividends.
Dr. Gretchen Gagel is Chair of Brinkman Construction (US), a member of the National Academy of Construction (US), a member of the Construction Industry Culture Taskforce (AUS), and an affiliate professor at the Australian National University and the University of Denver. As President/ Managing Director of Greatness Consulting she continues to advise organisations within the construction industry. You can hear more from Gretchen on her Spotify podcast, “Greatness”.
“Technology adoption must be seen as important to everyone in the organisation, not just the ‘techies’.”
From an early age, Jo Farrell was interested in the more hands-on activities. When it came to choosing a work experience field at school, she raised her hand to join the boys at the local steelworks, while her female peers went off into hairdressing and childcare – which the school counsellor openly discouraged. Already, at 16 years of age, Farrell started to realise that it was frowned upon for a female to enter a hands-on industry. But that, as well as several other barriers, hasn’t stopped her from achieving a successful construction career.
Today, with industry experience spanning Sydney, Canberra and even Lithuania, Farrell is the ACT general manager at large-scale commercial construction company Kane Constructions.
When she finished Year 12, Farrell knew she wanted a career in construction and started applying for jobs in her home town of Wollongong, NSW. There wasn’t any social media back then, she says, so Farrell typed out her CV and cover letter and started handing it out to local businesses.
“I probably applied for upwards of 150 building-related companies, big and small, and received rejection after rejection,” says Farrell. “I heard the typical lines – ‘girls aren’t strong enough’ and ‘we don’t employ girls’.”
“Then, finally I wore a builder down to give me a go, but he told me that I had to work for free for three months and would then decide whether he was going to give me a carpentry apprenticeship.”
“It wasn’t a guarantee, but I thought ‘if that’s my way in, that’s my way in’.”
Farrell worked onsite during the day and at a hardware store at night and weekends, while juggling jobs in hospitality as well. It was a battle of wills, she says. Every day Farrell turned up onsite and eventually the owner decided to sign her on, but with a classic “you’re not going to last in this industry” comment to boot. Now in her 27th year in the construction industry, she’s clearly proved him wrong.
Completing her first two years of her carpentry apprenticeship in Wollongong, Farrell then moved to Sydney to complete the remaining two with a façade company, delivering high-rise buildings in the commercial construction sector. After finishing her apprenticeship, Farrell made
her way through the ranks moving into a leading hand role, a supervisor role and securing a position as junior project manager, studying her certificate three and four in construction, and advanced diploma in construction along the way.
“I then completed my construction management certificate and found myself working as the operations manager of a large structural steel company in Sydney,” says Farrell. I was delivering huge projects like the Pitt Street Mall underpinning the Centrepoint Tower (now Sydney Tower Eye).”
“I worked non-stop since finishing school, really focused on my career and at 30 decided to travel overseas for a few months.”
A few months quickly turned into a few years. Farrell flew to London, trusting she would pick up casual work along her travels. After travelling for a while, and starting to run low in funds, she received a call from a recruiter offering her a job on a nuclear decommissioning project in Lithuania.
“Someone had sent him my CV and I legitimately thought it was a joke until he sent me these flight tickets to Lithuania to go for an interview,” says Farrell. “I thought, well you only live once – at worst it’s a free trip to Lithuania, at the best it’s a real job – so I jumped on a plane and off I went.”
It was a terrifying and humbling experience, she says, driving out of the capital with a Russian driver who couldn’t speak any English.
“I thought I had made a horrible mistake,” says Farrell. “Here I was driving along in the middle of nowhere, and lo and behold, there was an old nuclear plant located near the border of Latvia and Belarus with upwards of about 500 construction workers onsite.”
As soon as she arrived, the project manager asked Farrell to stay on for what was meant to be a six-month contract – she ended up staying there for three years. Not only was she the only woman onsite, but she also couldn’t speak any Russian, which was the main language spoken by the site team.
“The men onsite didn’t know what to make of me,” Farrell says. “They couldn’t work out why this woman was walking around onsite like a man.”
There was a language barrier, so she had to very quickly learn Russian to understand what her colleagues were saying and soon found
Jo Farrell hasn’t let anything hold her back from making her mark in the construction industry. She’s jumped hurdles, overcome criticism and proven time and time again that women are capable of building successful construction careers.
“I’m not going to overlook women that have the ability to step into these roles, just because the industry has traditionally gone straight for the male candidate.”
out there were some not-so-nice comments being made. One day, after hearing one particularly unpleasant remark, Farrell says she turned around and said in Russian “you know I can speak your language”, which shocked the onsite team to say the least.
Working on the project allowed Farrell to continue her travels, and in three years she had been to an impressive 45 countries, after which she decided it was time to head back home to Australia. Farrell sent all her belongings back home, bar a single backpack which she lived out of for a final 12 months of travel in South America and Africa.
Farrell didn’t want to go back to Sydney, so in 2013 she re-established herself in the next big city close to her home town – Canberra –where she gained her Class A Builder’s License and worked on the Canberra Light Rail Project.
From there, Farrell was offered her current role as the ACT general manager of Kane Constructions. “They interviewed about 22 people; I was the only female and they landed on me as the choice,” she says. “I’ve been in this role now for over three and a half years running the business alongside Kane Constructions operations manager, and my best mate, Philippa Seldon.”
One of the first things Farrell did was start employing women and giving them the opportunities that they’re in many cases overlooked for. When she first joined Kane Constructions, there was only one woman in the ACT arm of the business; today, Farrell leads 50 per cent female site teams.
“We did cop criticism, but it’s not about gender,” says Farrell. “I’m not going to overlook women that have the ability to step into these roles, just because the industry has traditionally gone straight for the male candidate.”
“We’ve worked really hard to differentiate ourselves in that way and are trying to change the language and mindset about women working in the construction industry.”
In tandem with Farrell stepping into her role as Kane Constructions ACT general manager, she started Build Like a Girl – a not-forprofit organisation that aims to encourage, recruit and retain women in the construction industry, which is now supported by industry associations, organisations and leaders.
Built upon Farrell’s own experiences working in the construction industry, Build Like a Girl
has helped 18 female apprentices get work in the industry since its establishment in 2020.
“Several tradespeople and I run Build Like a Girl in our spare time, trying to help women get a foothold in the industry in the same way we did,” says Farrell. “The construction industry is going through one of the single biggest skill shortages since World War Two, still feeling the impacts of COVID-19 and the dropout rates for first year apprentices in construction is 55 per cent for men and 74 per cent for women.”
“We need to be looking at long term investment, mentoring and coaching to actually keep women in the industry – we need a significant cultural shift – and that’s what Build Like a Girl focuses on.”
Farrell has continued to prove people wrong throughout her career and through her role at Kane Constructions and Build Like a Girl and is striving for industry change, hoping to make the barriers she faced in her career a thing of the past for women currently in, or looking to enter, the construction industry.
“Here I was driving along in the middle of nowhere, and lo and behold, there was an old nuclear plant located near the border of Latvia and Belarus with upwards of about 500 construction workers onsite.”Jo Farrell, ACT general manager, Kane Constructions.
Starting in the engineering profession at only 19 years old, Laura Miranda says you don’t need to fit a certain mould to have a successful career in the construction industry.
Born in Colombia, Laura Miranda moved to Australia with aspirations of creating infrastructure that shapes people’s lives and today – as a civil design drafter at BG&E – she’s doing just that.
Miranda has long had an interest in STEM careers, sparked by her father’s career in the engineering field and her love of math and science. “My dad was a process engineer in the pharmaceutical industry and would always explain to me how careers like engineering or biomedical engineering were going to improve the healthcare system,” says Miranda.
“It wasn’t until I came to Australia that I realised I was passionate and curious about finding out how things work.”
Upon arrival in Australia, Miranda says she found that the infrastructure was very different to that in Colombia. She would point out to her brother – who was living in Australia at the time – the different highway, bridge and drainage systems.
“I picked up on the difference in intersections and pedestrian facilities,” says Miranda. “I hoped one day I could be part of creating those infrastructures back home, because they can change and improve people’s quality of life.”
Starting her associate degree in civil engineering at TAFE Queensland in 2016, Miranda soon found herself having to complete professional experience as part of her studies. Juggling part time work in the hospitality industry and full-time study, and with the help of her then colleague who was a former recruiter, she began putting together her CV. As luck would have it, Miranda ran into a recruiter at a soccer game who happened to know of an international construction firm looking for a draftsperson.
“I had no idea what company it was for, but I sent through my CV hoping to find out,” she says. “One week later I received a call from Arup asking me to join the company.”
“I hadn’t finished my degree and didn’t know what the industry was going to be like, but I knew I had an eagerness to learn and collaborate with people, so I accepted the position and never looked back.”
Miranda joined Arup in 2017, as a civil engineering technician, gaining experience delivering major projects such as the Caloundra Road to Sunshine Motorway
project as part of the Bruce Highway Upgrade. In the context of this project, Miranda’s focus was instrumental in the creation of the construction drawings. This venture marked her initial collaboration since becoming part of the Arup team. Reflecting on those early days, she recollects the humorously memorable experience of saving 12d outputs in her C drive, a mishap that, while hilarious in hindsight, initially left her feeling quite disappointed. This anecdote underscores the valuable lessons she gained during her journey, ones that have since become sources of laughter and growth. Miranda also worked on the Cross River Rail project where she worked directly with the client Cross River Rail Delivery Authority. “My role was to create the environmental impact plans, which involved making sure that the impact of the alignment wasn’t going to be harsh on the local environment and heritage,” she says. “These projects not only taught me the positive impact engineering can have on local communities, but they also gave me the opportunity to work with brilliant minds.”
“Being able to collaborate with different people who all see things in a different light is one aspect of engineering that I love.
“That’s why I strongly advocate for diversity in the industry – we need diversity of thought to create solutions that can truly help shape the cities of tomorrow.”
Miranda’s aspiration was to transition into a civil design role, allowing her to delve deeper into engineering fundamentals and enhance her drafting skills through a solid foundation of knowledge. In March 2021, she took a significant step by joining GHD as a civil designer, engaging with diverse teams including tailings dams, water dams, tunnels and geotechnics. This experience exposed her to the intricacies of the resources industry and provided her with the chance to work within a team led by a female leader, which ignited her sense of inspiration. As the year progressed, Miranda’s professional journey took her to the Gold Coast. By the end of 2021, she had joined ADG Engineers, assuming the role of infrastructure designer. Within this capacity, she actively collaborated on significant infrastructure ventures, such as the Brisbane Metro Temporary Works project. Today, Miranda is a civil design drafter
“We’ve created a community and a space for people to share their stories, to inspire people, to create awareness – and that’s exactly what we were trying to achieve.”
at BG&E, where she creates construction drawing packages and designs roads for the transport infrastructure sector in accordance with government standards.
“I help engineers translate their ideas into a tangible solution,” says Miranda. “I was recently the lead designer for the Disaster Recovery Funding Arrangement (DRFA) program, which is a program aimed at restoring roads across Queensland that have been damaged by flooding and bushfire events.”
“We started by collecting information like photos of the current state of the road to then start proposing treatment, realignment or reconstruction solutions to enable people to drive safely on these roads again.
“It’s interesting to see the difference in the photos of the initial damaged road, to the photos once construction is complete and our designs have been brought to live – it’s a complete type of project where you get to appreciate everything that you’ve designed.”
As a member of the BG&E team, Miranda says she enjoys the culture and the people she gets to work with. Not only are they skilled technical engineers, but they also demonstrate a genuine concern for individuals, their personal passions and their professional aspirations, she explains.
Something Miranda has picked up on during her time in the construction industry is that it’s vital to have a voice.
“I was a little shy at the start of my career, but am naturally an extrovert, so it felt out of character,” she says. “I was missing out on opportunities because I wasn’t embracing my strengths as an assertive, open and collaborative person.”
“When you feel like you don’t have as much of a say because you’re young or just starting out, I think it’s really important to speak up because it helps you learn.”
Miranda is now helping other young women and engineering professionals find their voice through her You don’t look like an Engineer podcast. In partnership with her former colleague Sohan Roopra, Miranda launched You don’t look like an Engineer in 2022 on the back of being an interviewee for the TAFE Queensland Podcast where she shared her international student journey. “I saw the impact that the podcast platform had by simply sharing stories of real people,”
she says. “Apart from having the commonality of both being in the engineering profession, Sohan and I are both passionate about gender equality and are both women of colour.”
“We wanted to create a platform to share our experience because the power of storytelling is incredible and so You don’t look like an Engineer was born.”
The pair purchased a microphone and started sharing their stories, recording the first episode ‘Busting myths about women in STEM’ in May last year. It was incredibly well received, says Miranda, and just one week later a recruitment agency reached out wanting to sponsor the podcast. In following episodes, Miranda and Roopra started interviewing other professionals in the construction industry, providing a space for them to share how they overcame difficult moments in their career as well as in their personal life.
“We’ve created a community and a space for people to share their stories, to inspire people, to create awareness – and that’s exactly what we were trying to achieve,” says Miranda.
As someone who struggled with subconsciously wanting to fit in at the start of her career, Miranda is now letting her light shine and hopes to inspire others looking to enter the industry to do the same.
“Being able to collaborate with different people who all see things in a different light is one aspect of engineering that I love.”Laura Miranda, civil design drafter, BG&E and founder of You don’t look like an Engineer podcast.
The construction industry is a critical pillar of the Australian economy. It is the third largest industry, producing upwards of $437 billion in revenue and approximately 9 per cent of the nation’s Gross Domestic Product in 2022. The sector has a projected annual growth rate of 2.4 per cent over the next five years. With investments in new and existing infrastructure projects in every state and territory, the Australian Government’s national rolling 10-year infrastructure investment pipeline will increase from $110 billion to $120 billion, a new record, significantly boosting the sector.
The 2022-23 Victorian Budget continues the state’s investment in a major pipeline of projects, with $85.3 billion in general government spending on infrastructure over the next four years.
However, over the past two years, the construction industry has faced its share of challenges – many of which will likely continue to impact the sector for the foreseeable future. Skilled labour shortages and supply chain disruptions caused by COVID-19 have forced the sector to adapt and evolve to keep pace with a booming national infrastructure pipeline.
With that context in mind, what better time to discuss the future of the construction industry, and how we will collectively meet and overcome these challenges, than at Inside Construction Expo?
This event was designed to provide a forum to address these issues head on, and to discover the ways in which we can all work together to grow Australia’s major commercial construction and civil infrastructure industries.
At Prime Creative Media, we are dedicated to growing individuals, organisations and industries. And as everyone knows, you can only grow bigger, better and more resilient by
facing up to challenges, reflecting on them, and thinking creatively about how best to respond now and in the future. While disruptions like the pandemic and economic crises provide great challenges, they also provide great opportunities. Opportunities to improve health and safety requirements to ensure the wellbeing of our workers. Opportunities to streamline processes, maximise efficiencies and boost productivity.
Inside Construction Expo provides the perfect platform for our industry to come together, take stock, and engineer the future.
Designed specifically for the major commercial construction and civil infrastructure sectors, it will play a pivotal role in establishing face-to-face relationships, fostering connections between businesses and people, and showcasing the innovative ideas and solutions that will not only propel our industry forward – but the society that relies on it, too.
While there are too many fascinating topics to list them all here, you can rest assured that Inside Construction Expo will spotlight the latest in safety initiatives, digital modelling, sustainable design and materials, upskilling our current workforce and attracting others to the sector, big data –and much else besides.
I would also like to take this opportunity to thank our sponsors and partners – Würth Australia, Position Partners, Komatsu, Working at Heights Association Australia, National Association of Women in Construction, Institute of Quarrying Australia, Concrete Pumping Association of Australia, Crane Industry Council of Australia, Piling and Foundation Specialists Federation, Landscaping Victoria Master Landscapers and Formwork Industry Association – without whose support this event would not be possible.
DAY 1 – WEDNESDAY 20 SEPTEMBER, 2023 STAGE 1 – WORKPLACE WELLBEING & TEAM MANAGEMENT
10:00am – 11:00am Psychological Safety
11:00am – 12:00pm Leaders Driving Change
12:00pm – 1:00pm
Workplace Diversity & Inclusion
STAGE 2 – DIGITAL TRANSFORMATION
STAGE 3 – SUSTAINABILITY & ENVIRONMENT
The Use of BIM, VR & AI in Construction The Role of Circular Economy in Construction
The Benefits of Digital Twins Using Sustainable Materials
Innovative Construction Solutions – Komatsu
Carbon Reduction in the Built Environment
1:00pm – 2:00pmThe Future of Workplace Culture Building Smart Cities Concrete Sustainability
2:00pm – 3:00pm
Women in Construction
3:00pm – 4:00pmThe State of Mental Health in the Infrastructure Construction Industry
The Technology Behind Victoria’s Level Crossing Removal Project
Sustainable Heritage Listing Buildings – Living Future Institute of Australia
The Digital Transformation of Construction Designing for a Sustainable Future
4:00pm – 5:00pmEmpowering the Next Generation Connected Construction Through Technology Sustainability Leaders
7:00pm – 11:30pmInside Construction Foundation Awards Gala Dinner
DAY 2 – THURSDAY 21 SEPTEMBER, 2023 STAGE 1 – CONSTRUCTION PRODUCTIVITY
10:00am – 11:00am Supply Chain Distribution Challenges
11:00am – 12:00pm Productivity Onsite
12:00pm – 1:00pm Managing Offsite Construction Projects
STAGE 2 – THE SKILLS GAP: TRAINING, EDUCATION, RECRUITMENT & CAREERS
STAGE 3 – HEALTH & SAFETY
The Skills Gap Safe Working Environments
Addressing the Worker Shortage Risk Management
Improving Project Efficiency Height Safety
1:00pm – 2:00pmSocial Procurement in the Construction Sector Training & Employment Opportunities in Construction Fire Safety
2:00pm – 3:00pmUtilising Technology to Improve Productivity
3:00pm – 4:00pm Design for Manufacture, Assembly & Disassembly (DFMAD)
4:00pm – 5:00pmProcurement Transformation – Builders Leading the Way
Developing High Performance Teams The Use of Technology to Improve Safety
Specialist Training Employment Relations
Developing an Education and Skills Pathway – Safety Focus Onsite Safety Management
“We are excited about the Inside Construction Expo, where we will showcase how steel framing is the future of construction. Join us to discover one of the world’s most advanced end-to-end cold-formed steel building systems. The innovative FRAMECAD System is made up of equipment, design and engineering software, training and support. Experience first-hand how this system facilitates rapid construction, enhances building quality and promotes sustainability. No matter where you are on your steel framing journey, whether you deliver residential or commercial projects, visit our booth to see what’s new and learn where the industry is heading. The future of construction is cold-formed steel, so come discuss how to kick-start your steel framing journey.”
– Dan Spencer, Regional Manager Asia-Pacific, FRAMECAD.
“We can’t wait to see customers, both new and existing, at the Inside Construction Expo. The civil construction and infrastructure industries haven’t had a national tradeshow for some time, so we are pleased to support a new event for our sector. Position Partners has a lot of new solutions to demonstrate to attendees, including the next generation Topcon MC-X platform, Blindsight intelligent safety solution, wearable 3D scanning technology and wireless monitoring solutions to measure movement, dust and vibration. We will also be showcasing the latest developments to our Tokara platform, with the ability to manage everyone working to a design from a single interface.”
– Josh Allen, Civil Business Executive Manager, Position Partners.
“Industries across the spectrum, from utilities to transportation, are evolving to keep up with the pace of change driven by digital innovation. While some are being forced to change, others see the opportunity of embracing new technology to deliver efficiencies, cost savings or a better service. CR Kennedy is proud to be a Foundation Exhibitor and excited to be showcasing the latest building construction and machine control solutions from Leica Geosystems. This is your chance to see up close the iCON Total Stations and global navigation satellite system products along with the all-powerful iCON Build and iCON Site field software. Visit our stand and see how CR Kennedy is helping the construction industry solve complex challenges with accurate, easy-to-use instruments and intuitive software.”
– Nick Leith, National Machine Control Manager and Bernard Edmonds, National Building Construction Manager, CR Kennedy.
“Würth is renowned for its exceptional range of fixtures and fittings in the construction and engineering sector. Whether it’s fasteners, screws, bolts or anchors, our fixtures and fittings are engineered to provide high performance and reliable solutions. With a focus on quality, durability and precise functionality, our products meet the highest standards, ensuring secure and efficient installations. We are proud to feature our Würth 100-year designed anchor technology which is an example of engineering excellence, providing exceptional strength and durability, and reliable, high-quality solutions that stand the test of time. With our experts onsite showcasing our state-of-the-art production technology, we guarantee a reliable fastening solution for any project.”
“SAMI Bitumen Technologies, a pioneering manufacturer in the construction and infrastructure industries, has been at the forefront of producing diverse bitumenbased products since 1978. As one of the Founding Exhibitors at this year’s Inside Construction Expo, we are thrilled to have the opportunity to unveil the latest advancements in bitumen technology. Our extensive product range encompasses an array of solutions, ranging from standard grade road maintenance products to high-performance polymer modified alternatives, meticulously engineered for optimal performance in spray sealing, asphalt, and other road construction and maintenance applications. We cordially invite you to visit our booth where you can immerse yourself in our cutting-edge SAMI LC PMB range, as well as our sustainable Crumbflex and SAMIBioPrime products.”
– Sebastien Chatard, General Manager, SAMI Bitumen Technologies.
“I am thrilled to announce our participation as a Foundation Exhibitor of the Inside Construction Expo, where we will be showcasing our latest advancements in the construction industry. Our booth will feature our new prefabricated Ezibilt ramp, stair and deck solution, which perfectly complements our extensive core range of handrail and balustrade solutions. However, we don’t stop at just providing innovative products. At Moddex, we take pride in offering an end-to-end project management service. From design through to installation, our experienced team ensures a seamless and hassle-free experience. We are excited to connect with industry professionals at the expo, discussing how Moddex can add value to their projects and solve the complex design challenges they face. Find us at booth L22 and experience Moddex firsthand.”
– Joe Rowland, Sales Director, Moddex.“Across industries, Trimble solutions are transforming the way the world works. SITECH Construction Systems and BuildingPoint Australia are your exclusive Trimble partners for these solutions and services, selling, supporting and creating cuttingedge technology covering the entire construction cycle. At Inside Construction Expo we will be featuring construction robots and showcasing the future of construction with Spot the robotic dog. Attendees will be able to get hands on with our Trimble Earthworks excavator simulation, experience mixed reality, test the new X9 laser scanner, and discover how easy digital set-out has become with our Ri Total Station.”
– Connor Gallagher, Sales Manager for Victoria and Tasmania, Ultimate Positioning Group, SITECH Construction Systems and BuildingPoint.
“Inside Construction Expo comes at a crucial time for the construction industry in Australia. With its significant contribution to the economy, generating over $437 billion in revenue in 2022, the industry’s projected growth rate of 2.4 per cent over the next five years underscores its importance. The Australian Government’s increased investment in infrastructure further amplifies the sector’s potential. Nevertheless, the industry faces notable challenges that need to be addressed. The expo provides an essential platform to explore and tackle these issues head-on. Our booth will feature cutting-edge solutions, strategies and technologies, including iMC2.0, designed to address the challenges faced by the construction industry. Visit our booth and discover how Komatsu can revolutionise your construction projects.”
– Dean Geadtke, Executive General Manager, Construction & Utility, Komatsu.
INDUSTRY LEADER AWARD
Grant Fuller
Laing O’Rourke
Matthew Aitchison Building 4.0 CRC
Patrick Cran Crane Industry Council of Australia
Sarah Marshall Fulton Hogan
LOCAL GOVERNMENT PROJECT SUCCESS
Northern Rivers Rail TrailHazell Bros (QLD)
The Hills’ Local PoolThe Hills Shire Council
OPERATIONAL EXCELLENCE AWARD
Cross River Rail construction project
Manufacturing Automation
Mammoet Australia
Sunset Sleepers
CICA Articulated Mobile Crane Course Crane Industry Council of Australia
Asset Allocation Process Fulton Hogan
SAFETY PROGRAM AWARD
Contractor Safety Management Program ARTC
Construction Logistics and Community Safety National Road Safety Partnership Program
National Mental Health Steering Committee
SafeTest Dial Indicator (DI) Series
Proudly sponsored by
Fulton Hogan
SafeGauge
SUSTAINABILITY INITIATIVE OF THE YEAR
Material Processing Centre 2 (MPC 2) BINGO Industries
Fully Electric Fleet Alfasi Equipment Hire
Biodegradable Waffle Pods Waffle Foundations
TECHNOLOGY SOLUTION AWARD
ProcurePro ProcurePro
Autodesk Construction Cloud Autodesk
Site360 Teletrac Navman
Rhapsode by Area9
Lyceum
John Holland
ValueWise coaXion
WOMAN OF THE YEAR
Denise Fontein Alfasi Hire
Jessica Rippon Construction Legal
Nina McHardy Fulton Hogan
Christina Knorr
CJK Fire and Safety
Hacia Atherton Empowered Women in Trades
RISING STAR OF THE YEAR
Jessica Can Escamilla Gripfast Consulting
Miranda Swift Northrop Consulting Engineers
Marija Veljic
Sarah Frankson
Vanguard Wireless
Fulton Hogan
A subsidiary of the family-owned Alfasi Group, Alfasi Hire is one of the national leaders in equipment hire with over 3,000 machines, including EWPs, cranes, telehandlers and forklifts. Most recently, it has invested in Australia’s largest fleet of zero emissions, 100 per cent electric machines, helping its clients dramatically reduce their carbon footprint onsite. alfasihire.com.au
Allcon Group lives and breathes concrete – it loves providing solutions to concrete problems. From the moment it introduced the first plastic bar chair to the market in 1987, its whole focus has been to make concreting easier. The company knows that concrete waits for no-one. So, having the right gear, at the right time, goes a long way to ensuring contractors can provide the best outcome for their clients. allcongroup.com.au
Aussie Buckets is helping construction businesses get the most out of their heavy machinery. As a premier supplier specialising in custom-made, heavy-duty excavator attachments for major OEM brands like CAT, Komatsu, JCB and Kubota, it provides a comprehensive range of high-quality solutions. Additionally, its five year warranty accompanies every purchase.
aussiebuckets.com.au
Autodesk is changing how the world is designed and made. Its technology spans architecture, engineering, construction, manufacturing, media and entertainment, empowering innovators everywhere to solve challenges big and small. From greener buildings to smarter products, Autodesk software helps to design and make a better world for all.
construction.autodesk.com.au
Big Chief Hire delivers professional solutions for all earthmoving and truck hire needs, supplying state-of-the-art equipment that is regularly serviced and safety checked. Customers can hire from its extensive range of tippers, water carts, flat tops, excavators, graders, dozers, compaction rollers, generators, access equipment and much more. Anytime, anywhere – Big Chief Hire will be there. bigchiefhire.com.au
The Blundstone story started back in the 1800’s. Two English families, the Blundstones and the Cuthbertsons, arrived in Hobart and set up separate boot manufacturing businesses. Today the Cuthbertson family still owns Blundstone. Its safety styles are built to protect, with features that provide optimum protection against impact and penetration, plus resistance to cuts, chemicals, heat, electrical hazards, rolling forces and other foreign stimulus.
blundstone.com.au
The Brokk Group provides specialised and technically advanced demolition equipment and equipment for kiln maintenance, consisting of a number of high-profile product companies including: BROKK, AQUAJET SYSTEMS, BRICKING SOLUTIONS and DARDA. Brokk Australia is a subsidiary of Brokk AB and part of The Brokk Group of companies. It is the distributor for its products plus a range of partner products. Brokk is a wholly-owned subsidiary of the Lifco Group. brokk.com/au
Carmix Australia is a dedicated supplier of solutions for concrete challenges throughout Australia. The combination of simplicity and accuracy makes the Carmix units ideal for remote or difficult access regions, where time and/or delays waiting for concrete can cost big money. Its 45FX Evo is designed to enter tunnels and its silos/hoppers (3T to 45T) will manage your cement needs. carmix.com.au
Coast 2 Coast Attachments (C2CA) is the Australian east coast distributor for the complete range of Oilquick Automatic Quick Coupler Systems and Kemroc Cutters as well as the distributor for the complete range of Rotar demolition and recycling attachments in Australia and New Zealand. Based in Melbourne, C2CA also has service agents in both Sydney and Brisbane.
c2ca.com.au
CR Kennedy is a solutions provider for the surveying, construction, mining, mapping and wider geospatial industries that is able to source the latest in high tech spatial measuring equipment and related software solutions from partners around the world. The list includes land surveying equipment, unmanned aerial vehicles, high-definition 3D scanners and automated machine control. survey.crkennedy.com.au/ building-construction
CRM Strategy’s sole focus is to create and deliver technology strategies to deliver positive outcomes for construction and infrastructure businesses. For over 25 years, it has provided performance solutions in lead-management, pipeline development and project governance – empowering its customers with data so that they can make effective, informed decisions.
crmstrategy.com.au
Densley Earthmoving Repairs is a national sales, service and repair company. Its qualified staff carry out services and repairs on all mining and construction equipment, mobile and fixed plant. The company is the Victorian and Tasmanian distributor for the complete range of Montabert Rock Breakers and Drilling Equipment as well as the Australian distributor for H2Torqflo Hydrogen Injection on diesel engines.
densleyearthmovingrepairs.com.
Dynamic Rigging Hire is a lifting and rigging equipment rental specialist, based in Melbourne. It provides dry hire of rigging, lifting, load testing and height safety equipment to the construction, crane, and engineering sectors Australiawide. Its heavy lift gear includes spreader beams to 300t capacity with all the associated rigging, high-capacity air powered chain hoists and chain blocks, winches, load cells, test weights and height safety equipment.
dynamicrigginghire.com.au
With a long history in the earthmoving attachment design industry and over 100 years collective earthmoving attachment design experience, Elite Attachments Australia utilises this experience and know-how in the design and fabrication of its patented quick hitches for the excavator sector. Elite Attachments Australia has fostered a company-wide standard for high quality design, robust and practical fabrication and unwavering and comprehensive customer support.
eliteattachments.com
engcon’s global market position is based on a story that stretches back to the mid-1980’s, when the tiltrotator was a new invention, and Stig Engström was convinced that this would change the excavator industry. Since engcon was founded in 1990, the business has been centred around product development and end user focus – aspects that, among other things, resulted in several awards and continues to be important pillars for the company’s future development.
engcon.com/en_au
FAE is known for its design and production of heads for tractors, excavators, skid steers, special vehicles and tracked vehicles for forestry, agricultural, road and demining operations. With a range of over 90 products and 400 models, FAE is able to satisfy diverse customer needs. FAE’s range of heads includes forestry mulchers, cutters, stump cutters, stone crushers, stabilisers and multifunction heads.
fae-group.com/en_AU/faeaustralia-pacific-pty-ltd
Finer Hydraulics is a key supplier of earthmoving attachments. As authorised sales and service agents, Finer Hydraulics stocks a large range of Hydrapower skid steer attachments as well as Sima quality Italian-made bucket brooms and cement mixing buckets, ready for delivery Australia wide. Finer Hydraulics’ range of premier attachments for earthmoving machines can make work easier, faster and more profitable.
finerhydraulics.com.au
FleetCard frees its customers to get on with their business – one card is all it takes. FleetCard can streamline administration and provide its customers exclusive benefits. Accepted at over 90 per cent of Australia’s fuel sites, FleetCard is ideal for business vehicle expenses and provides visible savings and complete control for its customers.
fleetcard.com.au
FRAMECAD supports rapid construction, the smart way. The FRAMECAD end-toend design and manufacturing system helps contractors deliver large-scale Cold Formed Steel construction projects faster. FRAMECAD’s automated engineering and detailing software integrates with its factory control software and advanced roll-forming manufacturing equipment –giving its customers the technical tools to accelerate the construction process.
framecad.com
Construction company Galaxy City is committed to delivering exceptional results. With its expertise, it provides a tailored service to meet each client’s unique needs. It collaborates closely with its customers, ensuring a thorough understanding of the project’s objectives, timeline and budget. Safety is paramount, and Galaxy City adheres to strict protocols to protect its workforce and stakeholders.
galaxycity.com.au
Established in 1935, Hobson Engineering is a family owned and operated business that has grown to become one of Australia’s leading wholesale suppliers of quality fasteners, bolts, nuts, all thread rod, screws, and anchors to the mining, construction, oil and manufacturing industries. Hobson continues to build strong relationships with customers, suppliers and industry groups to promote the best installation practices and supply of the highest quality fasteners.
hobson.com.au
With a combined legacy of 200 years of safety innovation, Honeywell Personal Protective Equipment and Oliver Footwear provide comprehensive head-to-toe solutions for over 500 million workers globally. Their safety solutions offer optimal protection, high performance and durability, while enhancing comfort to increase productivity and efficiency.
sps.honeywell.com/au/en
JLG Industries is a designer, manufacturer and marketer of access equipment and telescopic material handlers. The company’s product portfolio includes brands such as JLG aerial work platforms, as well as an array of complementary services and accessories that increase the versatility and efficiency of these products. JLG is a subsidiary of Oshkosh Corporation. JLG Industries (Australia) also manufactures a range of Australian built mobile lighting towers and trailers.
jlg.com.au
JWA is a supplier of sustainable bog mats and temporary hardstands, ensuring compliance and safety for various applications, including roadways, crane pads, heritage protection covers and more. Its 100 per cent recyclable mats help minimise environmental impact. With its team of matting experts, it provides tailored solutions to meet various project requirements.
jwaoil.com
For over a century Komatsu has been providing essential equipment, technologies and services to the construction, mining, energy, government, waste and quarry industries. Its purpose is creating value through manufacturing and technology innovation to empower a sustainable future where people, businesses and the planet thrive together.
komatsu.com.au
Kommand Machine Control’s Unicontrol “Machine Control Made Simple” product range is made for dirt moving applications. Kommand Machine Control delivers solutions for machines such as excavators, dozers, wheel loaders and more, and coupled with site solutions such as rovers and base stations, the company makes moving dirt sound easy.
kommand.com.au
Machine Control Australia specialises in installation, support and training of any blade guidance system on the market. Machine Control Australia ensures it provides quality installs and takes no shortcuts. It gives its customers all the tools and information they need to get the job done in the most efficient manner.
machinecontrolaustralia.com
Mammoet Australia delivers solutions for any heavy lifting and transport challenge. With over 25 years of experience in Australia, Mammoet has established offices across the country, ensuring accessibility and rapid service. Equipped with state-ofthe-art technology and an extensive fleet, Mammoet brings its engineering expertise to tackle any challenge, from innovative and complex projects to straightforward lifts.
mammoet.com
Moddex is a supplier of low-risk, compliant modular barrier systems for large-scale infrastructure and construction projects. Its range of handrails, barriers, commercial balustrade, guardrail and walkway systems are pre-engineered in-house, meaning that all of its systems are ready to go and fully compliant to Australian and New Zealand Standards. Its innovative modular systems are fast to install and fit together seamlessly to suit any project without the need for welding or delays.
moddex.com
Porter Plant is a customer centric, relationship driven hire and asset performance management company. Its philosophy is to build trusted relationships and form partnerships to help its customers achieve their objectives and vision. It has strategically located branches and workshops across Australia, backed by a dedicated field service team and national supply agreements.
porterplant.com.au
As a provider of intelligent positioning solutions, Position Partners has more than 30 years’ experience supporting customers to deliver the most demanding infrastructure projects. Visit its stand for live demonstrations of Topcon’s new MC-X machine control platform and to discover the latest developments in Tokara. It will have a host of new solutions on display, including Blindsight intelligent safety for heavy industry, new Topcon material management for mass haul and more.
positionpartners.com.au
Through its 60-year industry experience and global footprint of over 550,000 users and 2,700 talents, RIB Software’s vision is to transform its business into a global powerhouse providing innovative software solutions to its core markets. Managing the entire project lifecycle from planning to construction and beyond, its portfolio of software solutions connects people, processes and data. RIB Software is a proud Schneider Electric company. itwocx.com
Royal Formwork Solutions Sales & Hire concrete formwork trade centres are a one stop formwork shop for concrete construction. The company provides expert formwork solutions for sale or hire with excellent service. It is a manufacturer, distributor and supplier of quality formwork systems, formwork accessories, falsework and general hardware. formworksolutions.com.au
The NON-DRILL Handrail System is a patented, innovative post and handrail system that eliminates the need to drill into structures. Developed in 2015 by Paul Breen, the NON-DRILL Handrail System has changed the way the building and construction industry provides edge protection for its workforce. NON-DRILL allows installers to pour concrete drains and pavements without any obstacles, while being resourceful by using the existing lifters to connect handrail posts. non-drill.com.au
Protective is an innovative, Australian technology company that designs, engineers, manufactures and supplies industries worldwide with globally patented engineered safety solutions for hazard identification and prevention of incidents associated with electrical shock and crushing. Protective is passionate about saving lives and designing innovative solutions to reduce the risk of incidents. protective.net.au
SAMI Bitumen Technologies is a pioneer in the Australian roads industry, meeting the market demand for advanced bitumen technology and consistently supplying the full range of high-quality bituminous products for the construction of critical infrastructure. It continues to provide advanced, green bitumen solutions that strengthen the infrastructure backbone of Australia. sami.com.au
VEGA has set itself a goal of developing innovative measurement technology that is easy to install and operate and offers maximum safety and reliability. VEGA’s headquarters is based in Schiltach in the Black Forest, where solutions to demanding measuring tasks are being turned into reality. As members of the Grieshaber Group, VEGA Grieshaber KG, Grieshaber GmbH & Co. KG and Supfina Grieshaber GmbH & Co. KG, VEGA Australia offers stability and reliability. vega.com
XCMG Melbourne has over 25 years of experience with earthmoving and construction equipment, and a reputation for value, excellence and reliability. XCMG is one of the world’s largest equipment companies and is dedicated to its core values: taking great responsibility, acting with great morals and making great achievements.
dnddiesel.com.au
Walkers Hammers specialises in excavator and skid steer attachments, boom systems and hydraulic power units for the construction, demolition, civil works, mining and recycling industries in Victoria, South Australia and Tasmania. Walkers Hammers is part of the Australian dealer network for Rammer, Simex, ALLU, PneuVibe, GTS, TEFRA and Steel Wrist equipment, allowing its customers to choose from a range of quality and reliable products.
walkershammers.com.au
Würth Australia is a vastly experienced specialist in assembly and fastening materials for the Australian construction industry, among others. From fasteners, fixing materials, assembly materials, hand tools, power tools, maintenance equipment and manufacturing equipment to personal protection equipment, technical chemicals and anchors, Würth delivers more than 20,000 high quality products.
wurth.com.au
Based in Sydney, Adam is the regional lead for Bryden Wood in Asia-Pacific. He has worked for Bryden Wood since 2006 developing innovative design solutions utilising BIM, digital technologies and Design for Manufacture and Assembly (DfMA).
Previously based in London, Adam established Bryden Wood’s Singapore office in 2014.
Benjamin Wade joined the Infrastructure Sustainability Council in 2020, bringing with him a practical and applied background in civil engineering.
The Council aims to drive infrastructure sustainability best practice across the quadruple bottom line using the IS Rating Scheme, as well as training courses, industry events and advocacy.
Digital Engineering Lead – VIC –Roads Aviation and Civil, WSP
Alex has worked on numerous Victorian road and rail projects over the last decade, improving connectivity and solving project delivery issues. These include the creation of data-rich 3D BIM models, model coordination and visualisation techniques, 4D construction sequencing, quantification (5D) and data extraction from BIM models, and the creation and maintenance of common data environments.
Team Leader – Melbourne, Hutchinson Builders
Bernie joined Hutchinson Builders in September 2015 and has over 35 years construction industry experience with companies including Leighton, Probuild, Lewis Constructions and Baulderstone. Bernie possesses skills in stakeholder and industrial relations management, business development and tender negotiation and understands what it takes to deliver both major and smaller projects.
Victoria-based Alexandra Nagy has worked in commercial construction for the last four years, delivering projects within the heritage Skycity Adelaide Casino, the Australian Space Discovery Centre, high-rise cladding works and BHP’s Melbourne office fit-out. Alex is an enthusiastic ambassador for more female participation onsite and works to draw awareness to the opportunities in construction for all.
Sales Executive Manager, Mammoet Australia
As managing director of Mammoet Norway for six years, Bjørn-Evert has experience in overseeing the execution of heavy lift and transportation projects. Today, he is the sales executive manager for Mammoet Australia and with his innovative thinking and previous experience, will be delving deeper into further diversifying the future of Mammoet Australia.
Brandon Hitch has served as CICA CEO since 2014. Previously a senior engineer with Cargotec Australia, today Brandon is one of CICA’s representatives for Australian Standards and Chair of the ME-005 Crane Committee. Brandon also represents Australia on ISO TC96 – Cranes and is chair of ISO TC96 SC9 – Bridge and Gantry Cranes.
For more than a decade, Chris has led initiatives to reduce suicide and poor mental health through workplace-based initiatives. Chris has led MATES in Construction through structured expansion and growth, including into New Zealand and now a pilot program for manufacturing.
Chris is also chair of non-government organisation Permanent Care and Adoptive Families.
Chartered engineer Christina Knorr is founder and managing director of fire engineering consultancy CJK Fire & Safety (CJK). Knorr is a registered fire safety engineer accredited in Queensland and by the NSW Department of Fair Trading She is also on the National Engineering Register (NER), accredited to provide fire safety engineering services Australia-wide.
Christina joined NAWIC in 2011 soon after graduating as a civil engineer. She began her construction career working for a Tier 1 builder and today works for one of SouthEast Queensland’s major concrete supply, pump and place contractors, De Martin & Gasparini. She loves celebrating the amazing achievements of women and their allies in this challenging industry.
Clare works to unlock collaborative potential by bringing together research and industry specialists to solve real-world problems as CEO of SmartCrete CRC, a Commonwealth funded Cooperative Research Centre supporting concrete sustainability and viability in Australia. Clare has extensive experience in roles in government, university and industry including grants program management, research and CRC operational management.
A Chartered engineer and leader of Cundall’s Brisbane office, David combines effective communication with detailed building simulation to tackle complex engineering solutions, including: energy, comfort, embodied impacts, local climate and indoor environment quality. As an accredited sustainability assessor and member of the NABERS Independent Design Review Panel, David has helped create better outcomes in the industrial, retail and aged care sectors.
With over 15 years of Commonwealth public sector experience in industrial relations, economic policy and managing employment programs. David has represented the Attorney-General’s Department (AGD) in engagement with Australian Industry on industrial relations issues. He also represented the Australian Government at the United Nations’ International Labour Organization.
David has over 20 years of experience in engineering and construction, working in leadership roles encompassing both technical and non-technical aspects of large multidisciplined infrastructure projects. At LXRP, David leads ‘the Hive’, LXRP’s Research and Innovation function, which has delivered more than 40 initiatives with significant tangible and intangible benefits to the $18 Billion program.
Dean Riha currently heads up the Metropolitan Roads Program Alliance and brings more than 26 years of experience in delivering civil infrastructure, the last sixteen of those with Fulton Hogan. Dean stepped up into the alliance general manager role at the beginning of 2020, just in time to navigate the challenges of COVID-19 whilst managing the expanding scope of MRPA.
Deepak is a multiple award-winning international speaker and top-selling author based in Sydney.
His books on construction technologies, such as Autodesk Navisworks and Autodesk Advance Steel, are top sellers in their categories and are used by dozens of universities worldwide. Currently, Deepak works as the principal business consultant with Autodesk, helping customers optimise their technology use.
Emily Trevaskis’ current focus is the Suburban Rail Loop Project. With 14 years’ experience in human resources on numerous major construction projects within Victoria, she understands the mental health impacts experienced by people working within the construction projects. She has a drive to make changes within the industry to support the retention and growth that’s needed to support major infrastructure investments.
Frank Khoweiss has spent the best part of the last 20 years working in recruitment–as an operational consultant, business development manager, account manager and senior sales manager.
As IPA’s Government & Construction sector lead, Frank works with some of IPA’s largest gov-ernment and construction clients and with IPA’s delivery teams nationally.
Frank Scerri is business development manager at Employsure and the founder of Workplace Compliant, a provider of workplace compliance including employment relations and work health and safety best practices in Australia. Frank has helped numerous businesses across various industries navigate complex legal and regulatory frameworks to achieve compliance and best practice.
HSE Advisor, Brisbane Airport Corporation (BAC) Giselle Phillips’ successful initiatives have elevated safety standards and improved wellbeing. Her dedication and achievements have earned her prestigious accolades, such as the Women in Industry 2023 Woman of the Year Award and the Safety Advocacy Award.
Giselle is passionate about driving positive change, fostering a supportive and inclusive industry culture, and empowering others.
Regional Health & Safety ManagerVictoria / Tasmania, McConnell Dowell
Grant is co-founder of McConnell Dowell
Construction’s Wellness in Infrastructure Initiative and associated Steering Committee, established in 2018 with a commitment to sustainably improve the wellness of white-collar professionals in the construction industry. He has also recently joined the Department of Premier and Cabinet’s (VIC) Mentally Healthy Workplaces Consultive Committee to provide advice, input and feedback.
A member of the National Academy of Construction, Gretchen advises large corporations and government agencies to support the cost-effective planning, design and construction of capital assets.
Gretchen is chair of Brinkman Construction (US), past chair of Bridges to Prosperity (Global), director Conversant (AUS), and director (membership) of the International Women’s Forum (AUS).
Chief Executive Officer, Empowered Women In Trades
As CEO and founding director of social enterprise and charity Empowered Women in Trades, Hacia works tirelessly to attract, support and retain women in skilled trades. Her unwavering commitment to this cause is transforming the industry, making it accessible and inviting for aspiring women and ensuring their long-term success.
Technical Services Manager, Sami Bitumen Technologies
Hamidreza is the technical services manager of SAMI Bitumen Technologies with more than 12 years of experience in different technical roles in the pavement industry. He has a PhD in pavement engineering from the University of Tehran with first rank. He has more than 25 papers published in international journals or presented at prestigious conferences.
Harman brings 20 plus years of experience with tech-related businesses in USA, Dubai, India and Australia to his role, developing innovative solutions for smart cities and buildings. He serves on Standards Australia’s committee for Smart City Systems and is part of the innovation team at a major transport infrastructure project in Victoria, focused on smart parking, construction technology and connected working initiatives.
At Senversa, Jacob serves as the head of technology and innovation, where he leads digital strategy, manages IT operations, and directs the team responsible for digital products and services. His career journey includes founding and leading social enterprises like Code for Australia, as well as undertaking diverse roles at Aurecon, the last being the position of global director of digital products.
James has over 27 years’ experience in the construction industry working for Tier 1 contractors in Australia and Asia.
A qualified civil engineer, James melds his background with his people-centred leadership style to lead safety and environment functions at a business unit level to create safer and more sustainable workplaces.
Janitha is a Chartered project management professional and civil engineer. Starting his career as a site engineer and later with the National Water Supply and Drainage Board in Sri Lanka, Janitha moved to Australia and joined John Holland for the Goulburn Murray Water Connections Project as a separable portion manager. He is also chair of Young Engineers Australia’s Tasmanian Chapter.
Jason has worked with firms like BlueScope Steel, Wesfarmers, Caterpillar, and has experience across supply chains, manufacturing and services. Most recently he led the international scale up and commercialisation of the world’s only zero-cement concrete. He is now with TSA Management, bringing carbon into focus across their project management and advisory solutions.
Jeremy is a director of JTA Health, Safety and Noise, a broad based OHS consulting company operating throughout Australia and New Zealand. He is a fellow of the Australian Institute of Occupational Hygienists (AIOH) and currently its president elect. He is a certified industrial hygienist (USA), a certified occupational hygienist (AUS), a Chartered generalist OHS professional and Chartered fellow of the Safety Institute of Australia.
Jessamie has spent the past decade growing her knowledge of sustainability and regenerative design across many fields, from community, organising, political campaigning, climate campaigning, residential development, building design, landscape design and environmental advocacy to public transport. She weaves ancient and contemporary systems-thinking frameworks with technical tools and industry benchmarks to help teams see new potential in their work.
Joe Smith is CEO of the National Fire Industry Association, Australia (NFIA), having joined the association in 2020. Joe has experience at several peak industry bodies in Australia including the Australian Dental Association and the Law Society of NSW, as well as significant national and international political experience from his time in the UK and EU.
John is a principal and transport lead at Woods Bagot with 23 years’ experience practicing architecture and urban design. He has experience leading major civic projects across multiple sectors, including Sydney’s Wynyard Walk, Sydney Metro Central Station, Crows Nest Station and Metro West.
John has a background in high performance roles in professional sport, including seven AFL clubs, and culture development roles in two A League clubs. He has also coached an Olympic gold medallist.
He is a published author and has lectured in PE and Medicine across several universities, as well as serving for 5 years on RMIT University’s School of Health Sciences Program Advisory Committee.
Jono Bonifant is the director and CEO of construction software company Lentune. Lentune’s recent selection for the prestigious Culture 50 - Emerging Companies award reflects Jono’s dedication to creating a positive work culture, driven by core values. He is passionate about empowering others to embrace innovation and make a lasting impact.
Karli Sutherland is the co-owner and business manager of Quicklift Crane & Access Hire, which has been providing lifting solutions to the Goulburn Valley and surrounding areas for the past 24 years.
As CICA Board director and chair of CICA Diversity Networking Committee, she is passionate about supporting women into non-traditional roles in male dominated industries.
Katie is the accelerating net zero buildings lead at NABERS, helping develop an embodied emissions rating tool that will be the national standard for measuring, verifying and comparing embodied emissions in new buildings and major refurbishments.
With a background in service design and digital strategy, Katie says industry collaboration is a core aspect of this work.
Ken McBryde is Gensler’s head of architecture in Australia and New Zealand and a thought-leader in design for manufacture, assembly and disassembly, modern methods of construction, sustainable design and mass timber. He is a multi-award-winning architect and the recipient of five Good Design Awards and has been closely involved in two Sir John Sulman award-winning projects.
Kenny is a Chartered engineer with over 18 years of experience in concept and detailed design of bridges, prestressed concrete structures, earth retaining structures and other civil structures.
Kenny has led the bridges and civil structures teams on many road and rail projects, including the M4 Smart Motorway, M1 Smart Motorway and the Western Road Upgrades –Initial Rehabilitation Works.
Kieran completed a Bachelor Engineering and Bachelor Commerce followed by a PhD in Engineering, at the University of Sydney. Kieran joined Laing O’Rourke’s R&D team to deliver innovation on bids and projects and commercialise new products. In 2020, Kieran raised venture capital to spin off Laing O’Rourke’s artificial intelligence vision technology into a separate company, Presien.
Laura has two decades of industry experience working in environmental sustainability and social justice in Australia and South Africa.
She is currently the CEO of the Living Future Institute of Australia (LFIA). LFIA harnesses the built environment as a powerful vehicle to create a world that is socially just, culturally rich and ecologically restorative.
In addition to the above, Dr Luke Downey an adjunct research fellow at the Institute for Breathing and Sleep at the Austin Hospital. In 2018 he authored the Swinburne University report ‘Measuring the Psychological Impact and Work-Related Stress and Related Occupational Factors in the Australian Infrastructure Construction Industry’; resulting in the establishment of the Wellness in Infrastructure Initiative.
Maddie began her career at SHAPE in August 2021 as a building cadet, being promoted to project coordinator after just six months. She has worked alongside her team on multiple large-scale marquee refurbishment projects as part of national adjustments, bringing communication skills and technical knowledge together to drive the team towards mutual project goals.
Martin has worked in workplace health, safety and environment for over 30 years – including executive and senior executive roles on both the client and contracting side. Having previously worked for AGL Energy, CPB Contractors, Tenix, Downer, UGL and Sydney Motorway Corporation, he is a passionate advocate for mental health in the construction industry.
Switching from civil engineering into the software world, Matt has become an expert in construction technology.
Most of his time is spent with builders, subcontractors and software designers to brainstorm better ways to manage construction sites. But when he’s not he’ll be finding his way to the coast for a surf.
With more than 15 years working in education and employment sector roles, Mel is experienced in designing and delivering programs to support career development in federal and state government initiatives. She is passionate about supporting people to make informed career choices and encouraging them to step outside their comfort zones, and watch the magic happen.
Michael was appointed COO of UGL in 2020, after joining six years prior as a UGL group general manager and with over 40 years in construction contracting and infrastructure.
Michael is also chair of Australian Terminal Operations (a joint venture between BP Australia and UGL), as well as the director of the Australian Contractors Association.
Pricipal, Kilgariff Advisory – former Chief Executive Officer, Roads Australia
Michael Kilgariff is a former CEO of Roads Australia and former managing director of the Australian Logistics Council.
Michael understands major economic, social and government policy drivers and the key issues impacting on industry – leading to his recognition as Michael won the Transport and Logistics Executive of the Year in the CEO Magazine 2014 Executive of the Year Awards.
As CEO of the Formwork Industry Association (FIA), Michael Sugg, along with the FIA Board, set up the first such group in Australia to continuously improve competence and safety across the industry.
Alongside members, the FIA has advocated for skills and educational change to improve safety and address the current and future skills shortages.
At just 21, Miranda has become a national advocate for change within construction. She co-created a unique mentoring program called ‘Hustle’ and launched it across NSW with Engineers Australia. She is currently working as a cadet engineer with Northrop Consulting Engineers while studying a Bachelor and Master of Civil Engineering.
Nick helps stakeholders engage with Green Building Council Australia (GBCA) services and membership offerings to drive sustainable outcomes.
Nick is also the GBCA’s national lead on sustainable precincts, planning and infrastructure – integrating them into rating tools, technical support, education and thought leadership.
Oliver has worked for Fulton Hogan for almost seven years, moving into construction at the start of 2022.
He has worked on Fulton Hogan’s Level Crossing Removal Project (LXRP) alliance and across Melbourne in its civil department. He is an advocate for better mental health within the industry and creating workplace environments that are sustainable for all involved.
Paul King leads Bentley Systems’ global Construction Solution Engineering team, helping project delivery organisations create strategies focused on business value and integrating them into everyday operations.
He supported major projects such as the London 2012 Olympics, Masdar City in Abu Dhabi and Crossrail in the UK.
He sat on the UK’s Avanti program, which led to BS1192 and ISO19650.
Having been CEO of one of Australia’s biggest transport companies, Peter now leads the industry as CEO of the Victorian Transport Association (VTA).
As VTA CEO, Peter is the voice of the transport and logistics industry in Victoria. With a focus on leadership and advocacy, Peter is committed to enhancing the productivity, safety, workforce development and sustainability of the industry.
Phil has over 40 years’ experience of engineering consultancy and 20 years’ experience as managing director of Irwinconsult.
He is a committee member of the Victorian Property Council and the Australian Board of the Council on Tall Buildings and Urban Habitat, and his input has been sought for heritage structures in Melbourne and for a developing tall building industry in Darwin.
As the sustainability director on North East Link Tunnels Package: Spark D&C, Rachael is leading the charge on one of Australia’s largest infrastructure projects, bringing her more than 15 years of experience in project delivery.
Rachael believes the engineers and specialists working on Victoria’s Big Build are at the forefront of delivering sustainable infrastructure solutions.
Rachel’s innovative strategies and passion for working towards equality and equity for First Nations people, women and others from priority backgrounds, has resulted in long-term employment, training and social procurement outcomes.
Rachel knows that small industry changes lead to larger social change and is committed to sharing ideas and learning from others to make this happen.
Renny is the Australian Water Association’s NSW Mentor of the Year and was a finalist for the Women in Industry Mentor of the Year Award.
With experience in research, planning, treatment, operations and circular economy, she sits on the Advisory Board for the University of Newcastle’s Chemical Engineering Department and teaches engineering complexity to students in Newcastle and Singapore.
Dr Ross Digby provides strategic leadership for all electrotechnology, engineering fabrication, civil construction, tunnelling, industrial skills and workplace safety courses delivered at Holmesglen Institute.
Ross is responsible for the strategic leadership of the Victorian Tunnelling Centre and plays a key role at Holmesglen in the provision of leadership for applied research in the construction sector.
Ryan is a sustainability expert and the founder of everfocus, a boutique advisory dedicated to helping organisations take focused action for maximum impact and long-term sustainability.
An Engineer with an MBA and 25 years of leadership experience in diverse corporate operations, Ryan has implemented enduring solutions to improve the sustainability of businesses and their communities.
A national leader in circular economy (CE), Dr Sarah King invented ‘ASPIRE’, a CE matchmaking marketplace, and has delivered a national CE roadmap. She has delivered research on advanced recycling of plastics, battery recycling opportunities and supply chain options for remote recycling of problematic waste streams. Sarah is also an adjunct associate professor with Swinburne University of Technology.
Sarah has spent a career spearheading change in the infrastructure industry, including driving sustainability, increasing Indigenous engagement and procurement, workforce employment, skilling and training and driving improvements in diversity.
Leading health and safety, people and culture, industrial relations and environment, community and sustainability for Fulton Hogan, she is a highly respected leader.
Sarfraz is a certified quantity surveyor and a professional member of the Australian Institute of Quantity Surveyors (AIQS), with more than 18 years professional experience.
Currently working on Victorian and SA projects for the Australian Rail Track Corporation (ARTC), his experience extends to clients, Tier 1 contractors and consulting firms –in multimillion dollar projects within multiple industries.
Scott is a professional marketer, copywriter and safety specialist with over 20 years’ experience designing, driving and facilitating communication and education as fundamental engagement tools. Specialising in safety and rescue, both operationally and as a consultant, he uses his experience across multiple industries to deliver solutions targeting specific stakeholders using communication as the critical driver for change.
Sebastien started as a technical manager with Colas in Thailand in 2006, before being transferred to Western Australia as a technical support manager in 2008.
He was moved to operations in 2010 as state manager WA and bitumen procurement manager.
He was then transferred to NSW at the SAMI HO in 2015 as operations and commercial manager, before becoming general manager of SAMI in May 2017.
Shane Hodgkins is co-founder and CEO of Matrak – a global materials tracking network connecting construction supply-chains that aims to reduce risk and overheads.
Matrak has completed almost 300 projects for most of the Tier 1 and 2 builders in Australia, alongside customers in China, South-East Asia, UK, Canada and US. The company’s goal is to help its customers become preferred players in the industry.
Steve is responsible for establishing and maintaining client relationships for Civillo, a unique, geospatial SaaS solution built specifically for the civil construction industry. Civillo uses a blend of CAD and GIS to improve communication efficiency among all stakeholders, to ensure everyone has access to the latest spatial information throughout major project implementation.
Sylvia is a professional engineer with a 15-year background in leading engineering teams and functions. She has been involved in diverse projects, including train build and delivery, compliance, independent assurance, operation support, asset management and configuration, as well as design engineering.
She is currently the engineering manager at TLS NSW and Rolling Stock Services.
Teagan has over 15 years’ experience in the heavy industries, having delivered 1,200 plus hours of one-on-one coaching and worked with more than 500 leaders through workshops, coaching and consulting services.
Teagan is the author of Rules of the Game: Women in the Masculine Industries and is co-founder of the not-for-profit Diversity Practitioners Association in Australia.
With over 18 years’ experience in the commercial and residential construction sectors, Tom has proven industry expertise in the fields of estimating, building and construction consulting. A visionary leader and big picture thinker, Tom ensures consistent delivery of quality outcomes for partners, teams and communities.
Tom is passionate about staff wellbeing, enhancing company culture, enriching communities and building relationships.
Tom is the founder and executive director of Australia and New Zealand staffing and workforce management business PeopleIN. With 26 companies as part of the group, PeopleIN services industrial, health and professional verticals. The company has focused on both local and international staffing solutions in the construction, mining and infrastructure sectors since establishing over 25 years ago.
After more than two decades of industry experience in the built environment and as founder and consulting director of Trimoda Digital, Will continues to assist organisations in developing digital built capability. Will has led key strategies and capability uplift programs for digital twin and digital engineering capability internationally to improve clients’ business and project outcomes.
To be displayed at this year’s Inside Construction Expo, Komatsu’s Retrofitkit from its Smart Construction range is bringing conventional hydraulic excavators into the digital age.
Komatsu’s Smart Construction range has taken the industry by storm, enhancing the management of jobsites around the world through technology. A Foundation Exhibitor of the 2023 Inside Construction Expo, Komatsu will be displaying the latest in its smart range, including the Retrofitkit for hydraulic excavators.
The Retrofitkit solution from Komatsu is a 3D global positioning system (GPS) that includes payload – a function that measures bucket capacity – and increases the effectiveness and productivity of hydraulic excavators. Once a hydraulic excavator is equipped with the Retrofitkit, it enables the machine to perform digital construction.
A well-established construction professional, Tony Clear joined Komatsu in November of 2022. Throughout his career he has gained a wealth of experience in machine control – including a notable role heading up sales for machine control construction for Leica Geosystems in Europe, the Middle East and Africa. Clear says machine control and guidance is one of the fastest growing solutions of the Komatsu business. “A major part of growth in any machine, from dozers to excavators, in the last 10 years is technology,” he says. “Our Retrofitkit is fitted with 3D machine guidance, Payload Meter and enables the operator to acquire 3D construction data which can be visualised on the Smart Construction Dashboard – all functions that truly change the landscape of a construction site.”
Machine control has traditionally only been utilised by larger companies for highend and complex functions, but Komatsu is changing the game.
“We’ve ensured the price point of our Retrofitkit system is advantageous to any size business, from the small family-owned builders and farmers using it for drainage and dam rectification to the top tier building contractors,” says Clear.
The true value of the Retrofitkit comes to the fore with its 3D machine guidance function. It not only improves efficiency and productivity but also dramatically improves safety onsite. A global navigation satellite system (GNSS) 3D machine guidance defines the machine location and inside the cab
a tablet device provides a visual depiction of the difference between the design data of the construction area and location of the excavator bucket.
In the case of delivering foundation works, for instance, the 3D machine guidance function replaces the need for surveyors to set grades with a laser level, providing instant cost savings in surveying works and improving safety by reducing the amount of people needed in the machine work area.
“Using 3D machine guidance, the operator receives real-time feedback for their bucket position against the surface, vastly reducing the possibility of over-digging, digging into boundaries or hitting services below the surface,” says Clear. “It enables the operator to visually dig to the exact digital plans in-built into the cab tablet screen.”
This in turn optimises labour productivity, as the operator doesn’t have to leave the cab to check the digging is accurate or wait for the surveying team to re-set lines. The operator can simply look at the screen and see exactly what they’re doing.
Further improving safety, efficiency and productivity, the Payload Meter function enables the operator to see the weight of the material in the hydraulic excavator bucket. This proves particularly useful when loading a truck, as trucks have to be under a certain load limit as stipulated in state and national guidelines.
Without the Payload Meter function, says Clear, operators generally fill the truck underneath its load limit using an educated guess based on the bucket’s capacity. “The Payload Meter on the other hand allows the operator to load to the target bucket weight getting the job done quicker, reducing material and haulage costs and increasing the effectiveness of the machine, ultimately resulting in less fuel consumption and emissions,” explains Clear.
Adding to its capabilities, the Retrofitkit collects data from the machine to generate a history of payload reporting as well as 3D as-built data for processing. “With the addition of Komatsu’s Smart Construction Dashboard, this data can be visualised, allowing automatic updating of design surfaces,” says Clear.
“For the construction businesses wanting to take their operations to an even higher level, a
number of other Smart Construction solutions can also be integrated with the Retrofitkit.”
Support of its solutions is equally high on the agenda for Komatsu. Clear says while outsourcing support seems to be rife throughout the industry, Komatsu provides all of its support in-house.
“We’re leaning into support,” says Clear. “Our first level of support that we have is our dedicated phone number for Smart Construction users that’s on a sticker inside the machine cab.”
“A person picks up at the end, not some automated message, and we’re able to resolve issues raised in the call for around 80 per cent of our customers over the phone.”
The second layer is Komatsu’s dedicated team of Smart Construction Technical Advisors which are available to head out to the
customer and rectify any challenge or query onsite. On top of that, Komatsu’s Customer Technology Advisors (CTA) can be hired by the customer to work on the customer’s site. These experts can deliver a range of works including setting up base stations and recalibrating machines.
“We can also do a drone flight every month and, for example, compare those drone flights so that the customer can see the exact amount of material that’s been moved onsite,” says Clear.
Combined with the company’s multilayered customer support, Komatsu’s Smart Construction range is offering active solutions to construction industry challenges. The Retrofitkit is just one of Komatsu’s Smart Construction offerings that is a must see at Inside Construction Expo 2023.
“Using 3D machine guidance, the operator receives real-time feedback for their bucket position against the surface, vastly reducing the possibility of overdigging, digging into boundaries or hitting services below the surface.”The Retrofitkit enables the operator to visually dig to the exact digital plans in-built into the cab tablet screen.
Specialising in the construction of largescale, architecturallyinspired buildings, Haddarco is embracing Leica iCON technology from CR Kennedy to take its unique digital designs, no matter how complex, to the field.
Haddarco has long been known for thinking outside of the box to create beautiful, unique buildings. Delivering complex structures is no simple task but with tools and technology on hand like the Leica iCON, Haddarco is ensuring every project is delivered to the highest standards.
Haddarco has been delivering buildings for a range of sectors including commercial, education, community, medical and aged care since 1965. The company’s director Mohammed Haddara says that due to the increasing complexity of its projects’ architectural and engineering designs in recent years, Haddarco found that it was relying heavily on surveyors to conduct setout and positioning tasks.
“Surveying can be straightforward if it’s a square or rectangular building, but when the structure is curved or an odd shape, things get more challenging,” says Mohammed. “We had to get surveyors in for various elements of each project, costing us money and time having to wait for them to arrive.”
In 2021, Haddarco delivered a particularly challenging design at the Islamic College of Melbourne (ICOM) in Tarneit, Victoria.
The building was curved and although successfully delivered, the company had to spend big bucks on surveyors. When Haddarco won the second stage of the curved ICOM project at the start of 2022, Mohammed turned to CR Kennedy for a solution and discovered the Leica iCON surveying system.
After adopting the system, Mohammed says the company’s project teams saw almost immediate results. Using the technology,
Haddarco’s teams are now able to take their own digital designs to the field and have complete control over how and when crucial elements of a project’s design are set-out onsite, irrespective of the complexities.
This proved especially useful in Haddarco’s delivery of the second stage of the ICOM project, which included the set-out of 970 pieces of structural steel, weighing a total of 130 tonnes. On the ground floor, the design required the concrete columns to be located in the right spot to transfer the loads to the first floor. The first floor had 150 steel plates that had to be passed into the slab in the right location so that the columns could be welded to cast in plates.
“These plates only have a 20-millimetre margin, so we had to get them right,” says Mohammed. “The Leica iCON was a big investment but looking back, especially for this project, it was worth every cent.”
“It saved us so much time and was extremely accurate – we input all the drawings into the system; our fabricator then made up his own 3D model, which was checked against the drawings and then confirmed.
“All 150 plates were in AutoCAD form in the model – we then imported this model into the total station, and it gave us every centre of every single plate straightaway.”
Haddarco now uses Leica iCON for setout across all of its projects. The company’s project teams used to spend days measuring and setting out grid lines, but now, with the Leica iCON, all set-out information is in the total station. This not only eliminates the time required to conduct set-out using traditional
“One of the biggest positives we’ve experienced since adopting the system is in regard to its ability to combine all the drawings – architectural, structural and civil – to check if they align.”Haddarco is using the Leica iCON to deliver the second stage of the Islamic College of Melbourne (ICOM) project in Tarneit, Victoria.
Haddarco increased confidence in delivering architecturally challenging designs, explains Mohammed.
“One of the biggest positives we’ve experienced since adopting the system is in regard to its ability to combine all the drawings – architectural, structural and civil – to check if they align,” he says. “That then allows us to, when we get the instrument out onsite, actually locate every element of each of those drawings, giving us a lot more confidence that everything is working together.”
Before the Leica iCON, Haddarco had to bring in a surveyor, who would only provide grid lines based off architectural drawings. Haddarco’s project teams would then have to head back to the office or manually view structural and civil drawings to ensure everything aligned. With the Leica iCON, the project teams can input all drawings into their total station, allowing them to do ongoing checks and overlays at the press of a finger.
It’s not just the Leica iCON’s features that have Mohammed impressed. He says the support from CR Kennedy has been fantastic.
“CR Kennedy brought the system to our site for a demonstration and even allowed us to keep it for a few weeks as a trial,” he says.
“We started using it and loved it, so leased the unit for another month and received awesome technical advice along the way
us over the line to purchase the Leica iCON.”
The hardest part of adopting any technology, he says, is actually getting people to use it to make life easier.
“CR Kennedy gave us the unit to trial and showed us how to use it; there was support there before we even purchased the Leica iCON; when we purchased the system, they supported us even more; and then we were completely convinced that investing in the Leica iCON from CR Kennedy was the right move,” explains Mohammed.
The Leica iCON has given Haddarco more control over the whole life cycle of its projects – from initial design to onsite construction, through to completion and proof of construction reports and data –which Mohammed says continues to save the business time, costs, and improve onsite accuracy and efficiency.
The company initially bought the Leica iCON to set-out buildings, but the application has quickly grown in scope. Haddarco’s project teams are utilising it for external elements, landscaping and civil works and continue to use it across all areas of building.
It just goes to show how, along with the comprehensive support provided by CR Kennedy, a large contractor can utilise the Leica iCON to produce great project outcomes.
“To be honest, the service was what truly got us over the line to purchase the Leica iCON.”The curved structure of the Islamic College of Melbourne (ICOM) project, delivered by Haddarco.
Similar to other sectors in the construction industry, building a road relies on nonrenewable materials that can have a detrimental impact on the environment due to the extraction process used. An innovator of pavement technology, SAMI Bitumen Technologies (SAMI) has partnered with the pavement industry to reduce the carbon footprint of road construction through several sustainable initiatives and products.
With over a decade of experience in the industry, SAMI general manager Sebastien Chatard, knows all too well that sustainability is an ongoing challenge in road construction. Starting his career in 2006, Chatard held a number of roles in road construction and maintenance company Colas before joining SAMI in 2015.
As general manager, he is helping drive the company’s sustainability objectives.
“The resource extraction process for road construction results in the release of greenhouse gases (GHG) and poses potential environmental impacts,” says Chatard. “To address these sustainability challenges the pavement industry is exploring alternative approaches to pavement construction.”
“One such approach involves the introduction of innovative products that have fewer environmental impacts, while maintaining or improving engineering performance.
“These products aim to strike a balance between sustainability and functionality.”
Another strategy the industry is striving to implement is the manufacturing of highperformance materials that can increase the lifespan of constructed roads and reduce maintenance cycles. These materials are specifically designed to withstand the stresses experienced by road surfaces, leading to longer-lasting pavements and reduced maintenance needs.
By adopting these alternative approaches, the pavement industry aims to achieve sustainable solutions that minimise environmental impacts without compromising the performance or safety of constructed roads.
To support these industry goals, SAMI manufactures and supplies sustainable products to reduce the carbon footprint in pavement construction. For instance, the SAMIGreen (low carbon polymer modified
bitumen) range, launched in recent months, incorporates biogenic materials and polymer modifiers, improving pavement performance and durability while reducing the carbon footprint of road construction by around 50 per cent.
The pavement industry is actively pursuing strategies for reducing, reusing and recycling materials. Reduction efforts aim to minimise the carbon footprint associated with these materials by developing bio-based alternatives, like the SAMIGreen range, that offer comparable performance for spray seal and asphalt.
“The SAMIGreen range consists of biogenic materials and bio-based additives to reduce carbon emissions of the final asphalt,” says Chatard. “These modified bitumen products enhance pavement performance, durability and resistance to deformation while minimising the need for frequent maintenance and repairs.”
“By utilising SAMIGreen, the industry can achieve sustainable pavements with reduced carbon footprints throughout their lifecycle.” SAMIBioPrime, a sustainable product that replaces petroleum-based primers used in pavement construction, is another solution inspiring industry improvement. SAMIBioPrime is a bio-based primer derived from vegetable derivative renewable resources that reduces dependence on fossil fuels and contributes to the overall carbon footprint reduction in pavement construction.
“We can decrease carbon dioxide equivalent (CO2e) emissions by around 200 tonnes per square kilometre of our roads by replacing conventional cutbacks in prime coats with SAMIBioPrime,” says Chatard. “Depending on the underlying calculation assumptions, SAMIBioPrime has the potential to be a carbon-neutral product.”
Across its product range and operations, SAMI continues to make great strides in the sustainability space. Furthering its commitment to the reduction of carbon emissions, the company is promoting the increased use of bitumen emulsion – an alternative to traditional cutbacks. Bitumen emulsion is produced and applied at lower temperatures, resulting in reduced energy consumption and lower greenhouse gas emissions. Using bitumen emulsion has several safety and environmental
Embracing a daring mindset that encourages innovation, forward-thinking and taking calculated risks, SAMI Bitumen Technologies is helping drive the movement towards sustainable and efficient road construction practices.
“These products aim to strike a balance between sustainability and functionality.”
is highly recyclable, with the potential for 100 per cent reuse. The industry can also incorporate a certain amount of waste materials from other industries into pavement construction processes. However, careful
materials satisfies compatibility with existing pavement products. “It is essential to avoid situations where the lifespan of the pavement decreases, necessitating the use of additional resources,” explains Chatard.
“Additionally, it is crucial to ensure that recycled or reused materials do not pose health risks to the community or cause permanent damage to the environment.
“Proper evaluation for toxicity and carcinogenicity must be conducted to ensure the safety of both humans and the environment before introducing any such materials for use.”
Therefore, the industry focuses on designing new products and formulations that facilitate the reuse strategy while maintaining the required functionality and performance of pavements.
Similarly passionate about the reuse of materials, SAMI promotes the use of its Crumbflex, a hybrid product that combines crumb rubber derived from end-of-life tyres with elastomeric polymers.
“By replacing a portion of the traditional asphalt binder with crumb rubber, the overall carbon footprint of the product is reduced by approximately 10 per cent,” says Chatard. “Crumbflex exhibits the same engineering properties as highly modified binder with virgin materials, but in a more sustainable way.”
In the main, this product enhances flexibility and durability, diverts waste from landfill and reduces the consumption of virgin materials.
Through these sustainable products and practices, SAMI is actively contributing to reducing the carbon footprint of the pavement industry by minimising resource consumption, promoting recycling and utilising eco-friendly alternatives.
As the demand for more sustainable and efficient road construction practices continues to grow, Chatard says SAMI finds itself at the forefront of this movement whenever it successfully persuades its customers to opt for emulsion over cutback products or hot binders in spray sealing.
“Additionally, when we encourage the use of emulsion prime instead of cutbacks as a prime coat, or advocate for the adoption of cold or warm mix technologies in lieu of hot mixes, we actively contribute to these advancements,” he says. “Each day we witness a remarkable increase in the number of projects that embrace these alternative approaches, underscoring the
importance of our efforts in promoting environmentally friendly and innovative solutions within the industry.”
SAMI – in alignment with its parent company Colas – has set a target to reduce its carbon footprint by 30 per cent by 2030 and achieve a 100 per cent reduction by 2050.
Australia possesses the world’s most extensive road network per capita, spanning an impressive length of over 874,000 kilometres, according to the Bureau of Infrastructure and Transport Research Economics, part of the Department of Infrastructure, Transport, Regional Development, Communications and the Arts.
“A considerable 40 per cent of this vast network is paved using diverse bituminous products – such as prime coats, initial seals, SAM seals, and SAMI seals – that serve essential purposes,” says Chatard.
“Regrettably, it is disheartening to note t hat Australia still relies heavily on cutback products for these applications.”
Cutback products are used in precoating aggregates, providing a penetrating coat to base courses and reducing the viscosity of bitumen or modified binders before spraying.
“Astoundingly, the Australian road industry consumes a staggering quantity of approximately 12,000 tonnes of kerosene and 15,000 tonnes of diesel each year during the production process, excluding the fuel itself,” says Chatard.
“However, this significant volume could be substantially diminished by substituting cutbacks with bitumen emulsions, leading to an annual reduction of approximately 12,300 tonnes of CO2e emissions based on calculations using the Australian Flexible Pavement Association LCA calculator – this is just by replacing cutback with bitumen emulsion.
“Also, our bio-based materials have a lower carbon footprint without compromising engineering properties.”
It’s clear SAMI is making its mark in sustainable road construction and maintenance built on a foundation of caring for its employees, stakeholders and the communities it operates in; sharing knowledge, resources, and expertise to drive sustainable development; and pioneering sustainable solutions.
“These modified bitumen products enhance pavement performance, durability and resistance to deformation while minimising the need for frequent maintenance and repairs.”