
4 minute read
Engineering Precision in Microtunneling
by Pedemex BV
Laurini’s Casing Rollers and Spacers
Michelangelo Blasi, General Manager, Laurini
At the IPLOCA Novel Construction Spring Session 2025 in Palermo, Laurini Officine Meccaniche took centre stage with a presentation that demonstrated how innovative mechanical design can enable more sustainable and efficient pipeline construction.
At the event, I delivered a talk, placing the spotlight on one of Laurini’s most impactful areas of expertise: the engineering and supply of casing rollers and spacers for complex microtunneling projects. My presentation went beyond abstract concepts and sustainability buzzwords. At the heart of my message was the concept that sustainability goes beyond electric engines or eco-friendly machines — it’s about thinking better, reducing impact in every sense: time, cost, resources, and environmental footprint A key focus of the presentation was microtunneling, a trenchless technology used for pipeline installation. Through a guided boring system and a series of shafts, this method allows for minimal surface disruption.
Over the past years, Laurini has worked closely with contractors to co-design casing rollers and spacers that are not only mechanically robust, but also adaptable to the specific conditions of each tunnel. This includes projects where the pipeline must travel along a multi-shaft path, encountering vertical and horizontal curves, offset joints, and significant axial and lateral loads.
I presented a flagship case study: a 4,266-metre tunnel with a 2.0 m internal and 2.5 m external diameter, designed to house a 36” steel pipe. The pipeline would be pushed from shaft 5 downhill, traversing various sections before rising slightly between shaft 2 and shaft 1. The engineering complexity of this project required a precise and dependable support system.
The client's initial sketch suggested an 8-footed roller unit. However, Laurini’s engineering team proposed an optimised solution: a cantilever bogie system with 4 feet and 2 polyamide wheels per foot, significantly reducing both the contact points and the risks of misalignment or overloading — especially critical given the 12 mm offset between tunnel segments.
Laurini conducted detailed load simulations to cover all potential stress scenarios:
- Vertical loads when the pipe rests directly on the shoe
- Longitudinal loads as the pipe is pulled or pushed through steps or offsets
- Lateral loads during tunnel curvature or deflection
Using a certified hydraulic press, Laurini tested the rollers under extreme conditions, including load levels up to
40,993 kg per wheel at 200 bar. Every design was validated through finite element analysis (FEA) and destructive testing, ensuring that the final product met the project’s structural and safety demands. In addition to the mechanical core, Laurini integrated accessories such as grouting hose supports, essential for projects requiring tunnel filling postinsertion with cement or bentonite.
In tunnels where pipes are not aligned linearly, friction becomes a major risk. Laurini addressed this by developing spacers equipped with upper and lower wheels, allowing for 360° support across both vertical and horizontal curves. These spacers reduce resistance, preserve pipe integrity, and support long insertion paths without compromising the push force or safety of the operation. I emphasised that Laurini’s contribution extends well beyond the physical equipment.
The company delivered:
- Certified lifting beams for TBM positioning, compliant with DNV-ST-0378
- Manual installation tools that speed up assembly and improve safety
- Custom electric winches with rope guides and speed control
All components were delivered with full documentation and third-party certification, underlining Laurini’s commitment to both technical excellence and compliance.
Laurini’s work on casing rollers and spacers is not just about mechanics — it’s about making pipeline installation safer, faster, and less resource-intensive. Sustainability doesn’t mean doing everything — it means doing things better. Less time, less waste, fewer machines, same results.
By rethinking even the smallest mechanical components, Laurini is helping the construction industry build more responsibly — and more intelligently.
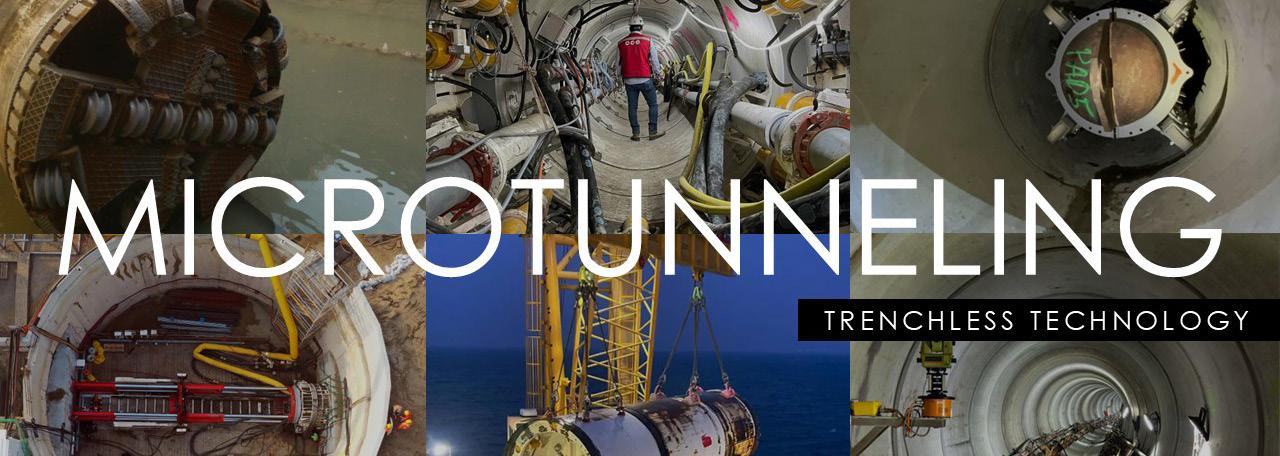