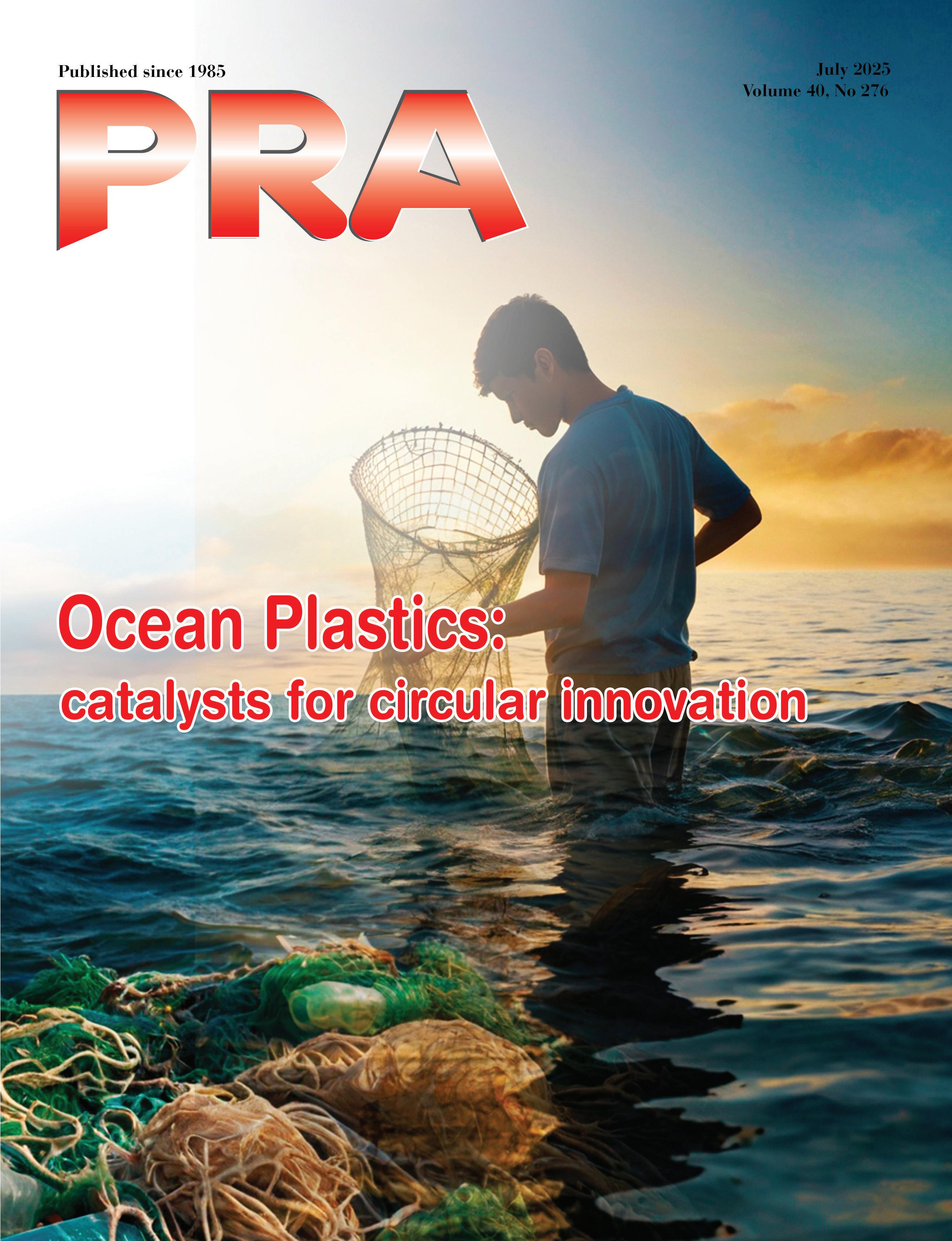
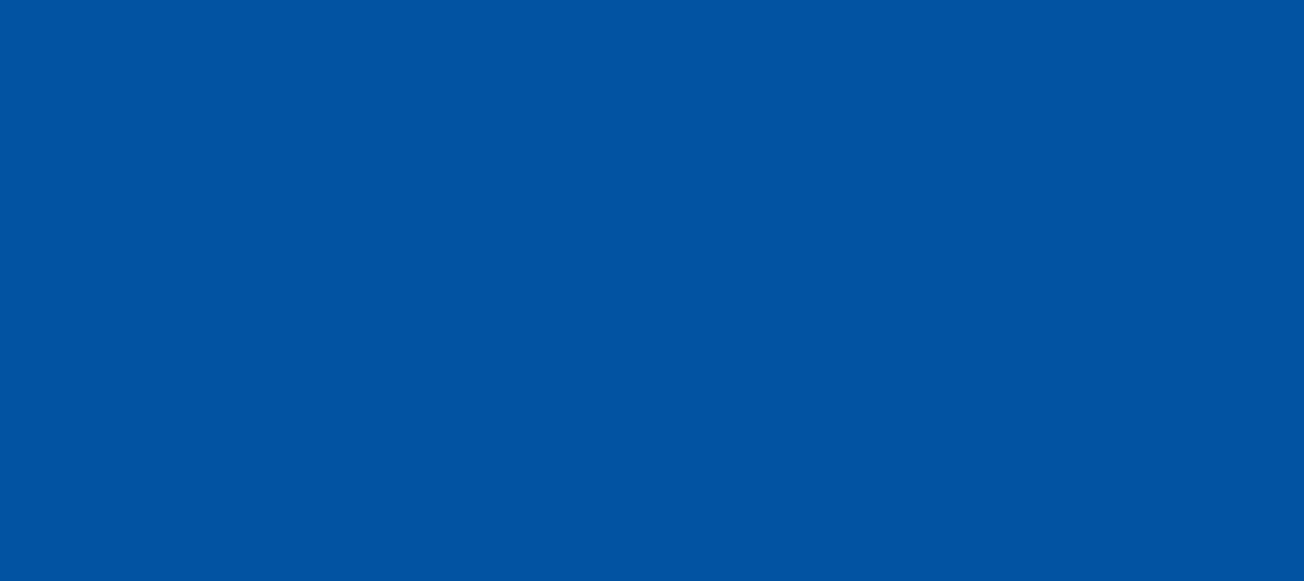
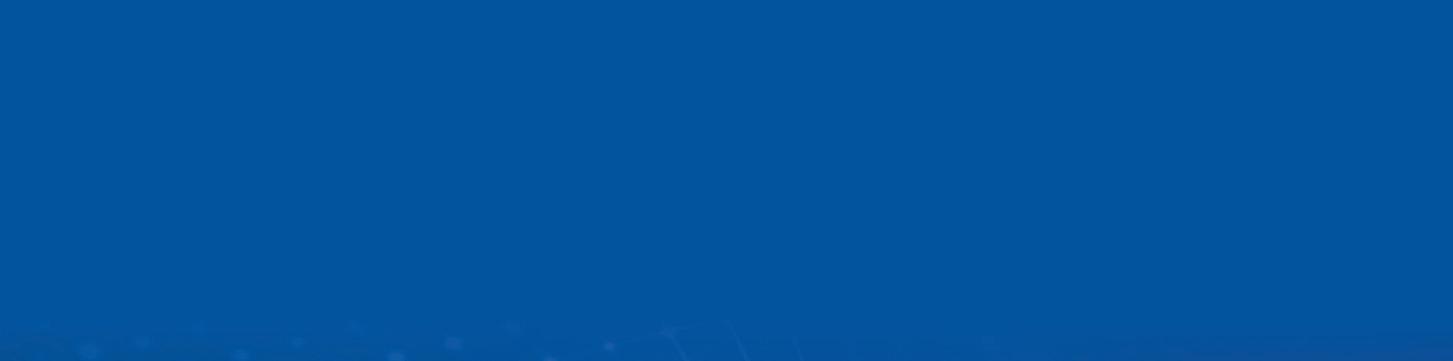
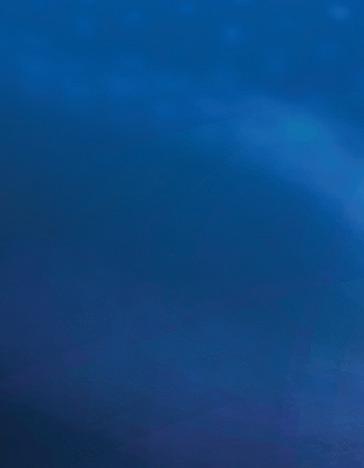
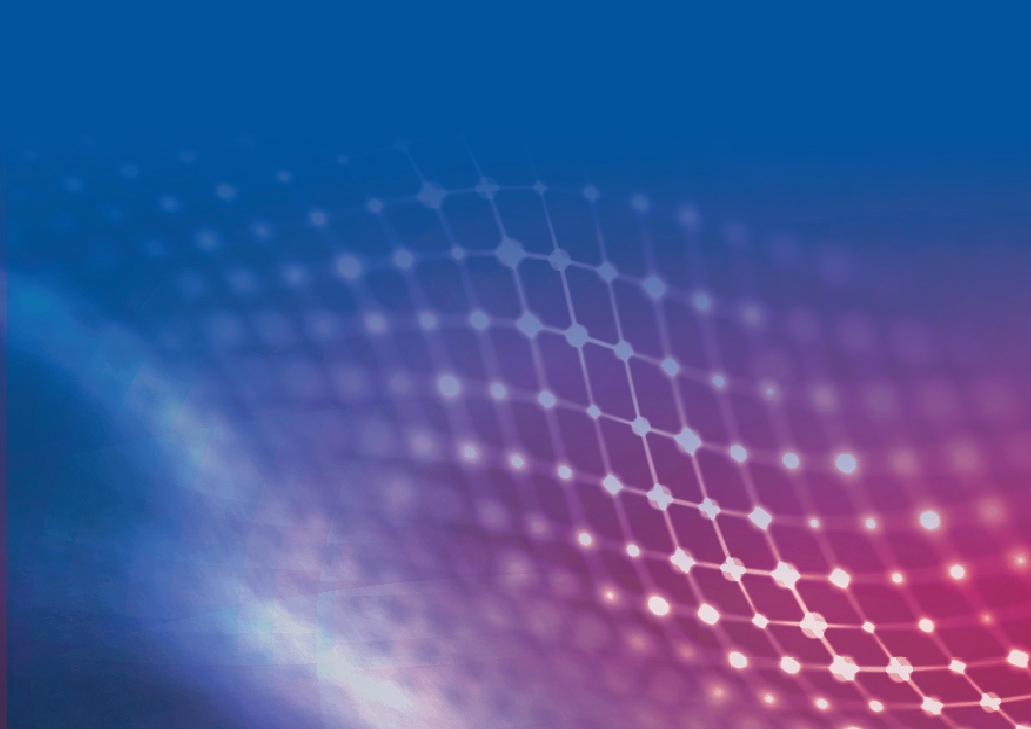
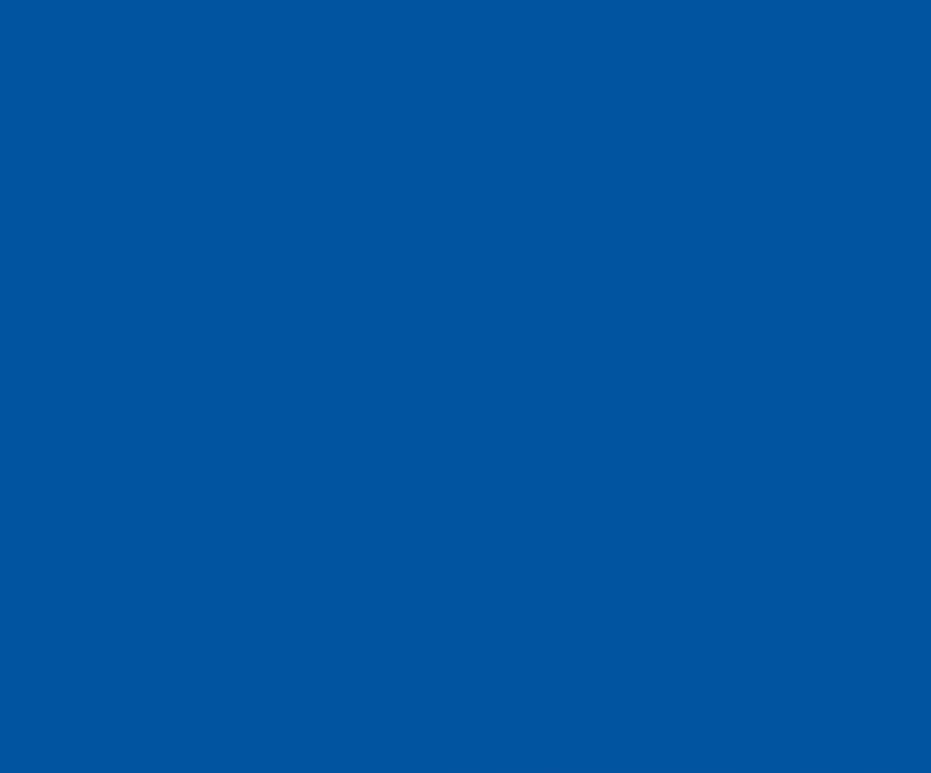
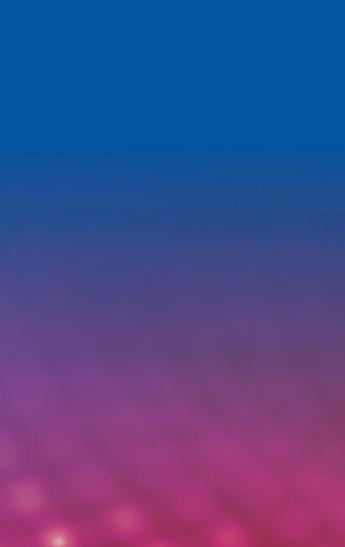
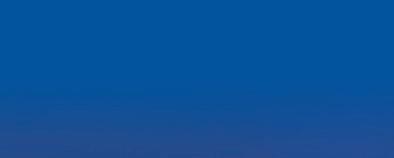
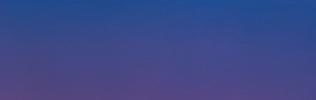
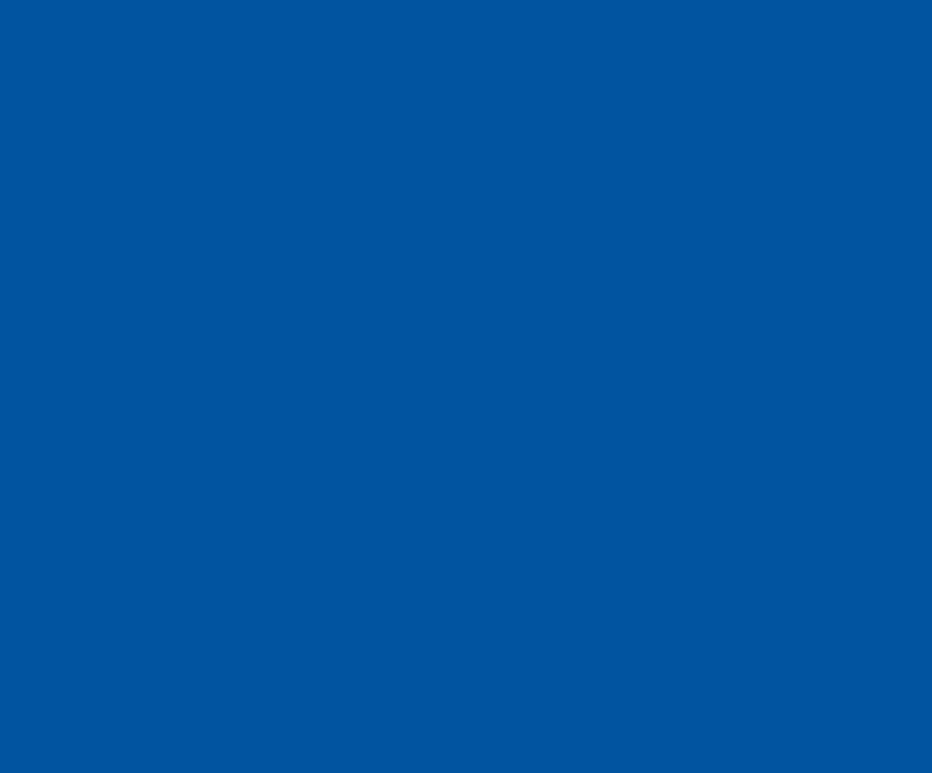

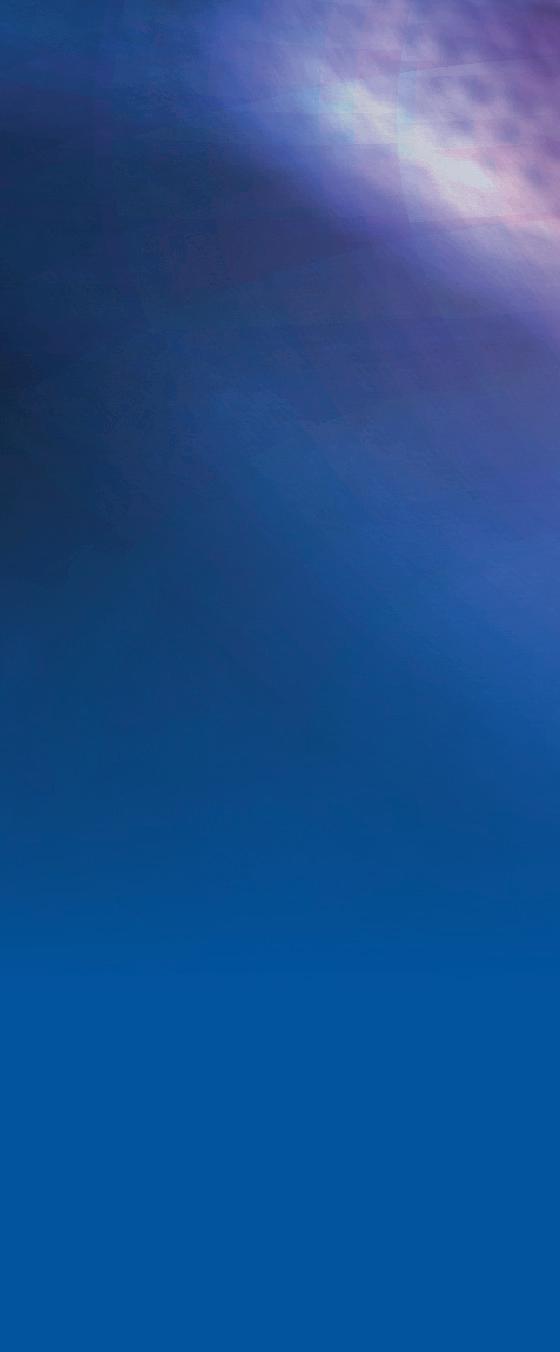
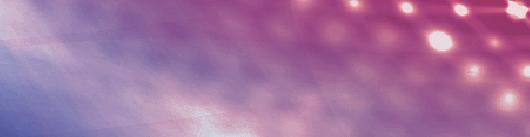
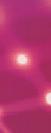
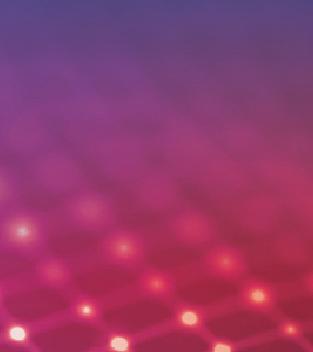
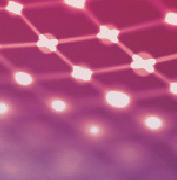
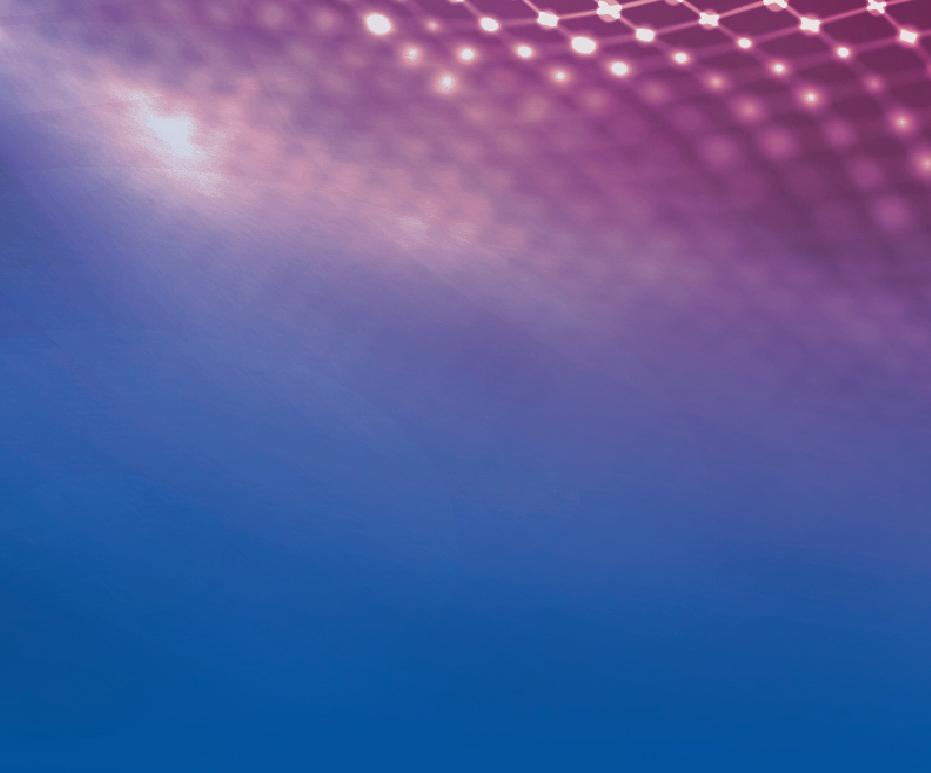

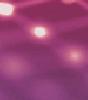
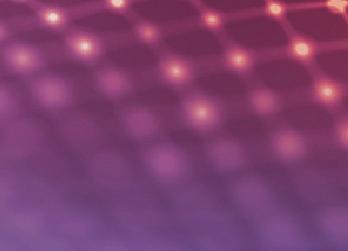
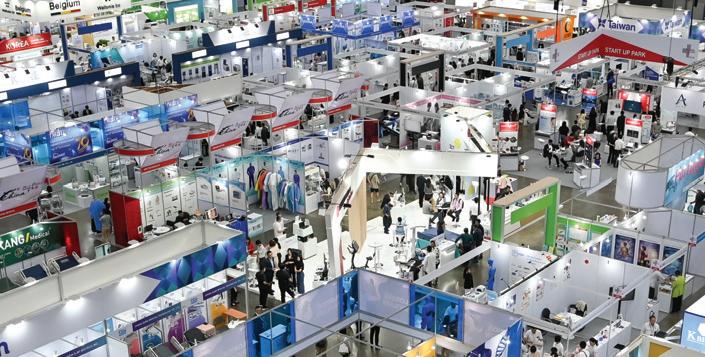

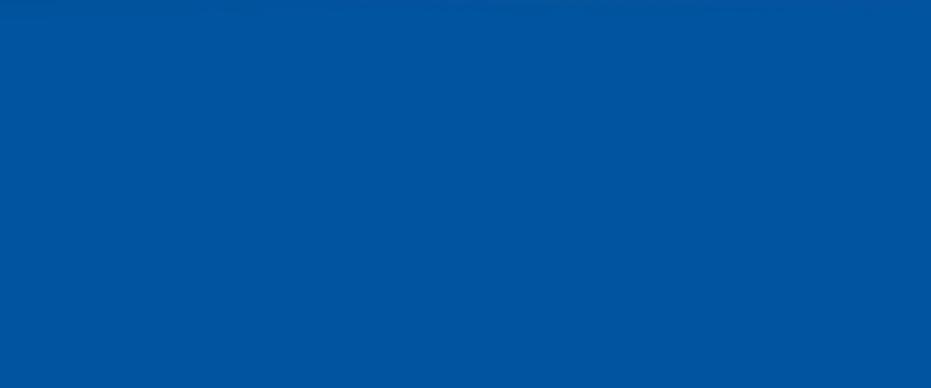
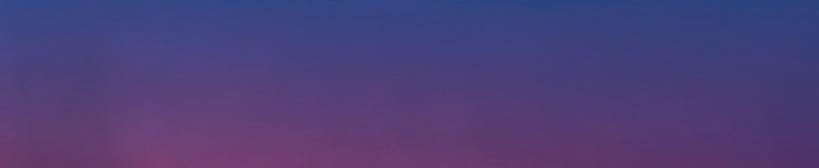
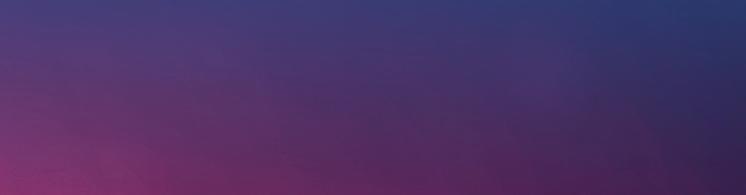
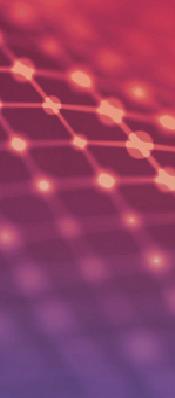
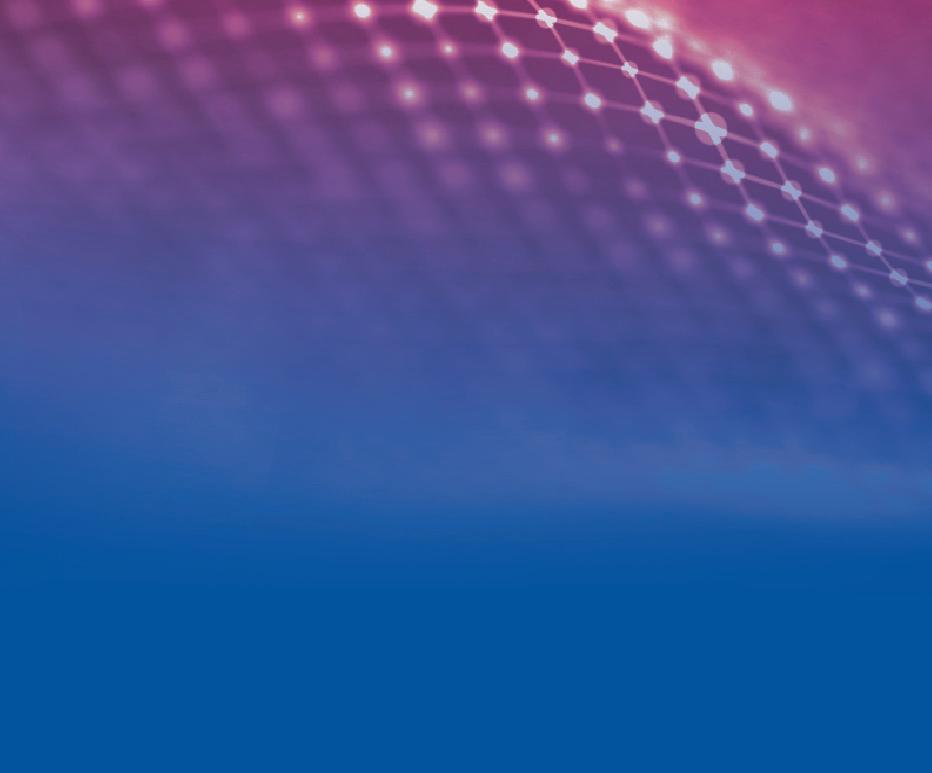
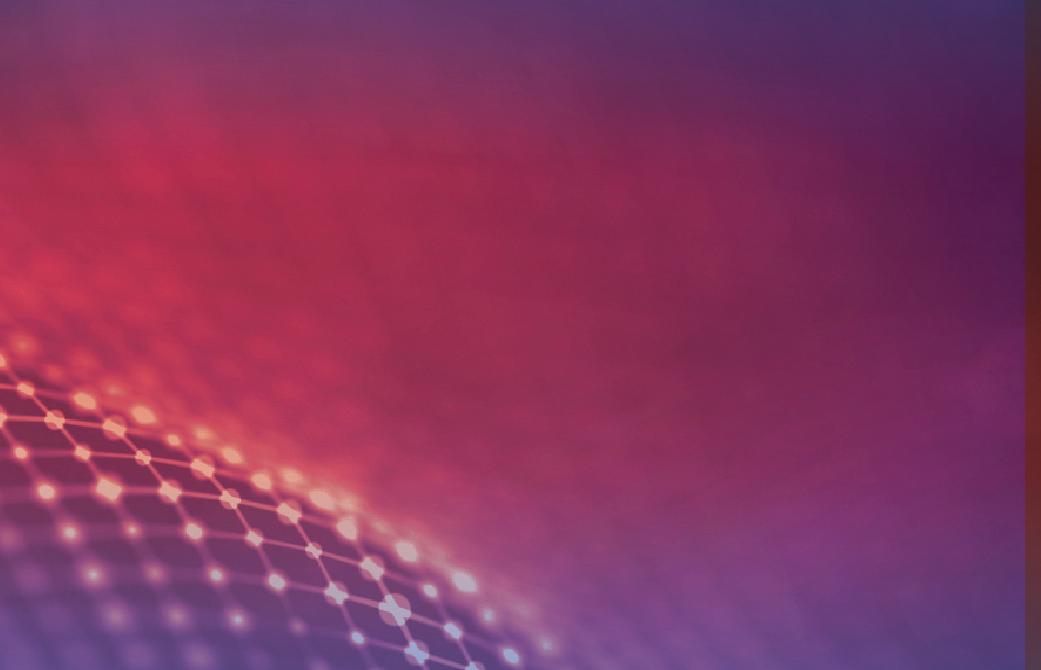

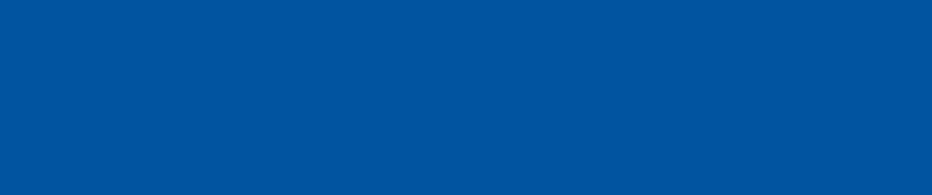
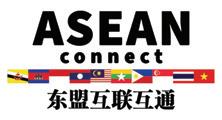
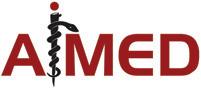


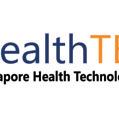
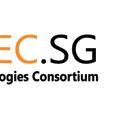
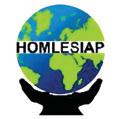
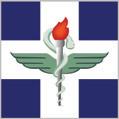
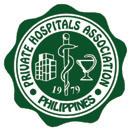
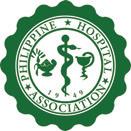
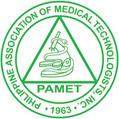
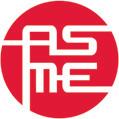
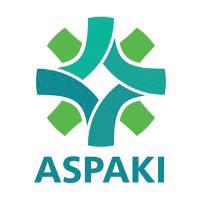
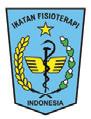
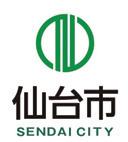
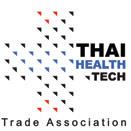


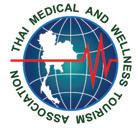
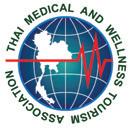
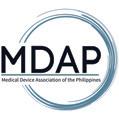
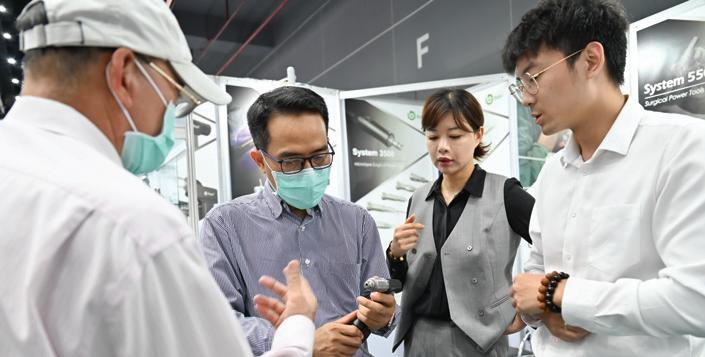
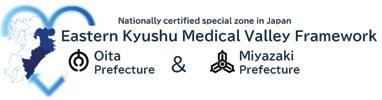
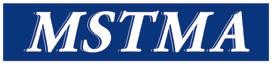
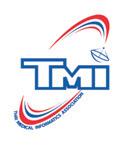
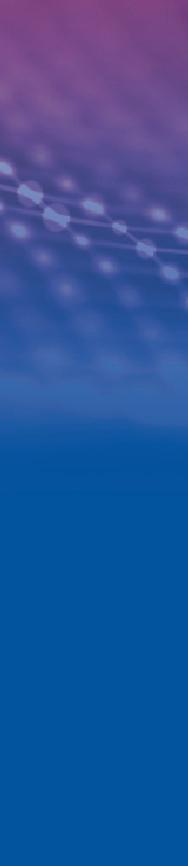
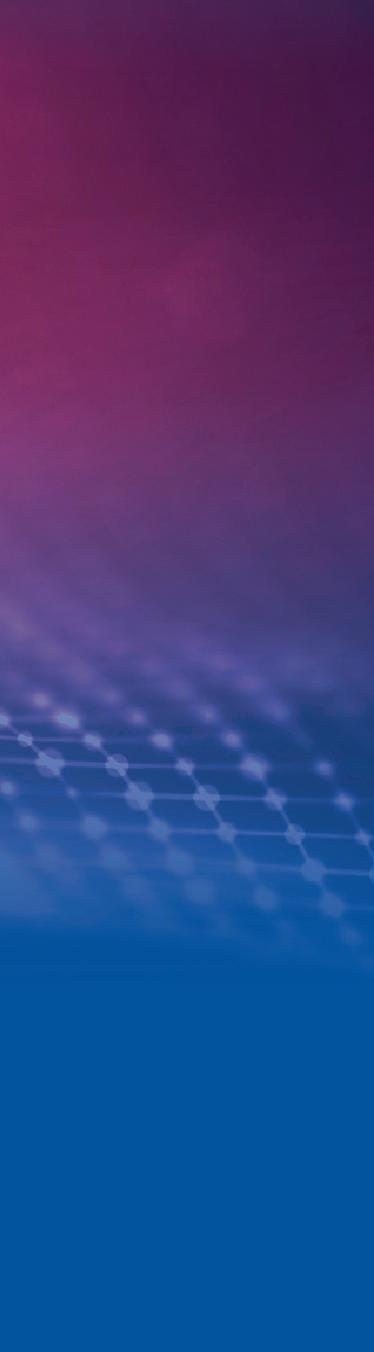
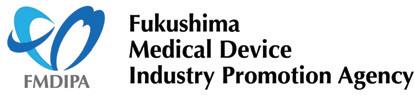
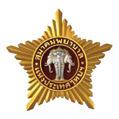

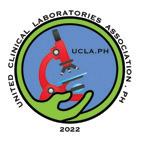


10 Country Focus: Taiwan – Taiwan is gaining tracks on the global innovation map, says Angelica Buan in this article, based on interviews with key exhibitors from the June-held Plastics, Rubber & Composite Material Fair Taiwan (PMT) exhibition
14 Building Industry – To push for recycling in the construction industry, Sulzer/Sika have tied up; meanwhile Canon/Repolytex are recycling electronics waste to construction boards; while Supersede offers rPP marine boards; and CRDC Global is promoting Resin8, a combination of concrete and plastics
16 Extrusion Machinery – Austrian extrusion machinery maker SML compares the different materials used for disposable coffee cups and lauds the advantages of PP-foam cups
17 Masterbatches – With the antimony trioxide market racking up high prices and China in the control reins of the supply chain, Swiss chemical firm Clariant says it may be time to switch to halogen-free flame retardants
publisher/editor-in-chief
Arthur Schavemaker
Tel: +31 547 275005
Email: arthur@kenter.nl
Associate publisher/executive editor
Tej Fernandez
Tel: +6017 884 9102
Email: tej@plasticsandrubberasia.com
european correspondent
Jeanet Draaijer
E-mail: jeanet@kenter.nl
Asian correspondent
Angelica Buan
Email: gel@plasticsandrubberasia.com
circulation
Stephanie Yuen
Email: stephanie@taramedia.com.my
layout/design
Prestige Trading
Email: prestige9a@gmail.com
permits
ISSN 1360-1245
Automotive: the sector is geared up for sustainability against the back of mandatory 20% recycled content in European vehicles; while Japan’s BlueRebirth Council has been set up to realise a circular economy in the country; Fiat becoming the first car manufacturer to incorporate recycled materials from Tetra Pak’s used beverage cartons; and Kraiburg TPE offering recycled content-TPEs for vehicles
Recycling: machinery firm Arburg has developed digital pilot functions to stabilise the moulding process for recycled material and bioplastics
lsR: Canada-based LSR specialist Silcotech and medical device maker Momtech partnered to bring a baby bottle nipple to market, to ease infants’ transition to bottle feeding
plastics are an eyesore and a nuisance to the environment, but positive efforts are being employed to counter
is published 4 (four) times a year in English by Kenter & Co Publishers’ Representatives BV.
Whilst every effort is made to ensure that the information contained in this publication is correct, the publisher makes no warranty, expressed or implied, as to the nature or accuracy of such material to the extent permitted by applicable law.
© 2025 Kenter & Co Publishers’ Representatives BV No part of this publication may be reproduced, stored or used in any form, or by any means, without specific prior permission from the publisher.
PRA is a digital publication that is circulated free to trade readers in the plastics and rubber industry. Please view this link to subscribe/renew your free subscription: http://plasticsandrubberasia.com/register.html
www.plasticsandrubberasia.com www.rubberjournalasia.com www.injectionmouldingasia.com www.eog-asia.com
The triennially-organised mega plastics show K2025, to be held from 8-15 October this year in Düsseldorf, Germany, has not lost its momentum as organiser Messe Düsseldorf said in a press preview recently, despite the uncertainty of global economic situations arising from trade tariffs and geopolitical events.
Speaking at the press event held in June, where around 80 journalists from 32 countries were joined by 15 exhibitor companies, Petra Cullmann, Executive Director of Messe Düsseldorf, said K2025 has been fully booked since May 2024. “The 18 halls, spanning over 177,000 sq m of space, will feature more than 3,200 exhibitors from 64 countries,” she said, adding that K2025 is like a “lighthouse that gives orientation to the industry”.
Cullmann also said the upturn in bookings contrasted to that of K2022, held against the back of countries coming out of the Covid pandemic, with travel restrictions still in place. Thus, K2022 featured 3,020 exhibitors from 59 countries and visitors from 167 countries.
While European and US exhibitors take up a sizeable space at the show, this year, the Asian region will make an “impressive” presence at K, with companies from China, India and Taiwan to take centre stage, and around 50 exhibitors from Southeast Asia. Malaysia is the most strongly represented country from Southeast Asia with 15 exhibitors, followed by Thailand and Singapore with 11 exhibitors each.
Other highlights at K2025 will be a forum to be presented by machinery and equipment manufacturers’ association VDMA . The focus will be on green: saving resources and reducing the carbon footprint through circularity; smart: digitalisation, automation and AI as well as on human resources.
Thorsten Kühmann, Managing Director VDMA, one of the sponsoring associations of K, stressed: “VDMA and its members will zero in on the motto of K2025 'The Power of Plastics!' with absolute conviction.” Companies participating in the outdoor forum include Arburg , Coperion , Erema , Lindner Recycling , Vecoplan , Wittmann Battenfeld and VDMA itself.
The Asian region will make an “impressive” presence at K, with a majority of exhibitors from China, India and Taiwan and around 50 from Southeast Asia
Plus a networking event specifically designed for women will debut at K2025. The organiser says “successful” women in the international plastics sector will take part in a panel discussion on their careers and experiences and will be available for questions from the audience. The aim is to promote exchange with one another, strengthen professional networks and enhance the visibility of female leaders in the sector.
Other highlights include the Start-up Zone, which debuted at the last edition of K; Rubberstreet, which as its name suggests will showcase rubber products/services; and a project by the German plastics industry headed by PlasticsEurope Deutschland and Messe Düsseldorf. Themed “Plastics Shape the Future”, it will feature discussions on innovative technologies and materials, keynotes, a political panel, Career Day and Start-up Pitch.
Staying sustainable with reusable cups
With sustainability at the top of the agenda, the exhibition centre will walk the talk with reusable cups at all its restaurants and bars throughout K2025, made from Austrian polyolefins supplier Borealis ’s modified PP for foam, which is produced using chemically recycled feedstock based on Austrian firm OMV ’s ReOil technology.
This also marks the first time the venue will use a reusable cup system. The cups will be cleaned and used over the eight-day event, said the organiser, adding that this initiative represents a significant step towards reducing single-use packaging at global exhibitions, aligning with the objectives of the EU’s Packaging and Packaging Waste Regulation (PPWR).
To support reuse, Messe Düsseldorf will install special collection containers.
Besides, Borealis, the collaboration is supported by other partners: machinery maker Arburg and Bockatech with its EcoCore foaming technology, used for the cups, which reduces plastic
use by up to 50%, doubles the thermal insulation, cuts manufacturing time and provides 5x the strength while ensuring recyclability.
Meanwhile, MCC Global IML will produce the in-mould labels and packaging processor Miko Pac will produce the cups.
In this interview conducted by Germany-based VDMA Plastics and Rubber Machinery group with Manfred Hackl, CEO of Erema Group, in the run-up to the K2025 show in October. Hackl speaks about Erema’s participation at the K show, developments in the recycling sector, cost effectiveness of regranulate, with suggestions for the EU to initiate a CO2 incentive.
VDMA: Erema celebrated its 40th anniversary in 2023. How has recycling developed during that time?
Hackl: If you look back over these 40 years, you will realise that an incredible amount has been achieved in plastics recycling. Today it is technologically possible to do things that we could not have imagined 40 years ago, 20 years ago or even five years ago. Recycling technologies have developed rapidly. At this year's K, we will once again be presenting many new products, especially solutions that further improve recyclate quality.
We will also be running live recycling together with Lindner in the outdoor area. As the largest company in the Group, Erema will be at the centre of our trade fair presence, under the campaign title "Edvanced Recycling - Erema Prime Solutions for Advanced Recycling". The chosen spelling makes it clear that modern recycling is undoubtedly associated with Erema.
VDMA: Can you give a few examples of the developments?
Hackl: In 2016, the circular economy made its first big appearance at the K fair. A lot has happened since then. Nine years ago, for example, there was no rHDPE packaging for food contact, and no household bottles or body care bottles made from post-consumer material.
Supermarket film with recycled content was still quite a way off back then. All of these now exist, which shows how fast everything has developed.
The interaction of innovative solutions is still needed to drive plastic recycling forward: the right washing method with the right extrusion, with the right filtration to produce regranulate of the highest quality and odour neutrality.
We have the precise technology to ensure this through our group of companies; however, the circular economy will basically only progress if we develop together across the entire plastics value chain.
Manfred Hackl, CEO of Erema, says Erema and Lindner have jointly founded a holding company, Blueone Solutions, to develop a digitalised and industrialised process from waste to the finished pellet
VDMA: The current economic environment doesn’t look promising. What is the situation in your sector?
Hackl: We all hope that the K will have a positive effect on generating business for companies. I am encouraged by the fact that the EU's Clean Industrial Deal and the Green Deal are very much focused on
the circular economy. We are also noticing that the major brand manufacturers and consumers now want to keep materials within the plastics cycle.
VDMA: What is the logic behind the cooperation between Erema and Lindner?
Hackl: It is actually more than just a cooperation. We have jointly founded the Blueone Solutions holding company, in which Erema and Lindner each hold 50% of the shares.
Through the joint venture, we are creating a digitalised and industrialised process from waste to the finished pellet. At K, we will be presenting new solutions and demonstrating that we need to think holistically if we want to achieve the next level of recyclate quality.
VDMA: What needs to happen for recycling to be economical in the long term?
Hackl: The cost-effectiveness of recycling always depends on the price of virgin material. If the price is low, as is currently the case, recycling is more expensive. Comprehensive countermeasures are needed here so that long-term planning is possible.
How are you supposed to make a plant that has been depreciating over five or ten years economically viable if you have to purchase your input, your raw material, at monthly prices, as is the case today?
Instead of a plastics tax, a CO2 bonus for the regranulate would be desirable. If the positive CO2 contribution of recycled pellets – which is 25 to 30% depending on the application – is taken into account accordingly, this could contribute to the urgently needed price stability; both would be effective measures.
VDMA: Can this be implemented in practice?
Hackl: I am convinced that something has to be done if we want to promote the circular economy. The whole thing should be initiated by the EU. Then it is quite possible that others will follow suit.
Countries such as India, China, America and many others have already adapted their legislation in the area of the circular economy to comply with EU regulations.
In my view, the EU should once again take on a pioneering role and introduce models such as those just mentioned. We would then have a good chance of being a role model in Europe again.
Coastal and marine plastics pollution is both a growing environmental concern and a promising opportunity for circular innovation through recovery and reuse, says Angelica Buan in this report, taking a look at programmes being undertaken in Asia.
Although the terms Ocean-Bound Plastic (OBP) and Ocean Waste Plastic (OWP) are sometimes used interchangeably, they refer to different stages in the plastics pollution lifecycle. OBPs are discarded plastics found near coastlines in regions with inadequate waste management, while OWPs, by contrast, are plastics that have already reached marine environments and are later recovered from oceans or waterways. Whether intercepted before reaching the sea or retrieved after entering it, both types of waste can contribute to circular economy solutions through recovery and reuse.
Whatever the case, it all boils down to the fact that plastic pollution remains a serious environmental challenge. According to the United Nations Environment Programme (UNEP), the equivalent of 2,000 garbage trucks filled with plastic waste is dumped into oceans, rivers, and lakes daily.
A report by Our World in Data states that 70% to 80% of ocean plastics originate from land-based sources, primarily via rivers and coastal runoff. The remaining 20% to 30% comes from marine activities such as lost fishing gear and abandoned vessels.
Meanwhile, Asia is the largest contributor to ocean plastic, responsible for 81% of global inputs, with the Philippines alone accounting for more than one-third of the total.
Amid the global plastic pollution crisis, Asia has been reported as the largest contributor to ocean plastic, accounting for 81% of global inputs
Of the initiatives adopted to curb marine litter, the most widely espoused is the plastic bag ban, as a measure not only to stop pollution at source but also to reduce the production of materials that would later become a source of pollution at the end of their service life.
The notoriety of how plastic bag bans have been enforced, from tax levies to fines on establishments, is either lauded or decried by consumers, who have to cope with less durable paper bags, and by businesses that use and produce plastic bags, which have had to remodel their operations to comply.
The Philippines, found in studies to be a major plastic waste polluter, has significantly improved its standing, with a joint study reporting a recent decline in marine litter and total collected waste in the capital city's 12-km Manila Bay
A 2024 study by Ocean Conservancy , which identified plastic bags as leading among the top five ocean plastic polluters, reported a 29% drop in plastic bags found on beaches following plastic bag bans from 2022-2023. In the US alone, 100 billion/year plastic grocery bags were used, and on average, each bag was used for only 12 minutes before being discarded.
Similar findings were reported in a recent joint study by the EcoWaste Coalition and De La Salle University–Dasmariñas . The study, funded by the Korea International Cooperation Agency ( KOICA ) Philippines and the Korea Marine Environment Management Corporation through Our Sea of East Asia Network ( OSEAN ), recorded a decline in marine litter and total collected waste in Manila Bay, a 12-km natural harbour that serves the port of the country’s capital.
It recorded a 36% decrease in marine litter and a 42% reduction in total collected waste from 2023-2024 across more than ten project sites in two areas outside Manila – Cavite and Bataan, as well as in the National Capital Region.
However, the research also noted a 16% increase in litter during the wet season. Over 91% of the collected litter was still plastic waste, with hard/flexible packaging accounting for the majority.
While positive feedback on plastic waste initiatives is encouraging, it must not lead to complacency. At the global level, institutions are carving out strategies to mitigate the flow of plastic waste in marine environments. The third United Nations Ocean Conference (UNOC3), held in June in France, drew attention to the deteriorating state of the seas.
The global market for recycled ocean plastic packaging is on a positive trajectory, according to a report from Global Market Insights , titled Recycled Ocean Plastic Packaging Market 2025-2034. The market is expected to reach US$1.93 billion by 2034, up from US$647 million in 2024, driven by growing concern over marine plastic pollution, government regulations, and increased industry collaboration. Rising plastic waste in oceans and strong consumer demand for eco-friendly products are prompting companies, especially in the food, beverage, and cosmetics sectors, to use recycled packaging.
Certification systems such as OceanBound Plastic, the Global Recycled Standard (GRS), and Plastic Neutral add credibility and build consumer trust. Brands use these certifications to meet environmental standards and enhance product appeal in the retail space.
Polyethylene terephthalate (PET) remains the most widely used recycled material due to its durability and food-grade compatibility, followed by increased use of polystyrene (PS) and bag materials in retail and e-commerce.
With the deadline for Sustainable Development Goal (SDG) 14 fast approaching, delegates from more than 95 countries renewed calls for a Global Plastic Treaty after talks stalled last year. The call precedes the next treaty talks in Geneva this August.
Over 170 countries are negotiating the said treaty to create a common approach to stunt plastic pollution in oceans and coastal waters, including limiting virgin plastic production, phasing out harmful products like single-use plastics and microplastics, and encouraging a circular economy through better recycling, design, and reuse of plastics.
On another note, it also proposes strict regulation of hazardous chemicals in plastics to protect human health and the environment.
The food and beverage industry led adoption in 2024, while the e-commerce and retail sectors are expected to grow the fastest through 2034.
Regionally, the US, China, Germany, South Korea, and Japan are reportedly advancing the market through strict regulations, investment in recycling infrastructure, and promotion of circular economy practices. Technological innovations in sorting and processing are also improving the scalability and quality of ocean plastic packaging globally.
The recycled ocean plastic packaging industry spans multiple tiers such as packaging manufacturers, material suppliers, and recyclers, but nevertheless, still remains fragmented due to differing regulations, recycling technologies, and sustainability partnerships. Moreover, new products and industry alliances are helping oceanbased recycled plastics gain ground.
Safety concerns raised on OBPs in food packaging While the broader use of ocean-bound plastics (OBPs) across various industries is a desirable goal, British food safety authorities are urging caution when it comes to food packaging.
Recently, the UK’s Food Standards Agency (FSA) and Food Standards Scotland (FSS) concluded that there is currently insufficient evidence to ensure the safety of OBPs use in food contact materials. The assessment, led by the Joint Expert Group on Food Contact Materials (FCMJEG) and based on data collected from 2022-2024, focused specifically on potential health risks.
As a result, the agencies are advising businesses not to use OBPs in food packaging. This guidance does not affect recycled plastics from controlled sources like the UK’s kerbside collection systems, which remain compliant with existing safety standards.
The agencies recognised the environmental benefits of recovering at-risk plastic but stressed their duty to prioritise food safety. They noted that although abandoned environmental plastic represents only a small share of the recycled plastics market, current recycling practices for these materials do not meet the same safety benchmarks as kerbside recycling.
FSA also reiterated that food-grade plastic packaging should come from verified sources like kerbside collections to ensure it originally served a food-contact purpose.
Scaling solutions for at-risk plastic waste Plastics recovery initiatives are redefining how at-risk plastic waste, or plastic likely to leak into the environment due to inadequate waste management, can be reused at scale.
The ReSea Project runs clean-up operations in Jakarta, where its nearby sorting facility manually processes recovered plastics into bales for delivery to partners who repurpose the material
Companies such as recycled plastic supplier Bantam Materials UK, through its brand Prevented Ocean Plastic, ReSea Project , Alliance to End Plastic Waste ( The Alliance), and Asian Infrastructure Investment Bank (AIIB) demonstrate that building sustainable supply chains can generate a lasting impact.
Bantam’s Prevented Ocean Plastic Programme has set a new record in coastal recycling investment, channelling over US$1 million through its supply chain in a single week, its largest financial contribution to-date to recycling infrastructure and coastal communities at risk of ocean plastics pollution.
The company now invests over US$100,000/day in developing regions to support collectors and recyclers and since 2011, has provided US$250 million to these communities, providing steady income for waste collectors and fairer financing for factory owners who might otherwise resort to high-interest loans.
Prevented Ocean Plastic, a fully traceable and certified recycled material recovered from over 2.5 billion bottles since 2020, is used by major brands across food, beverage, personal care, pet, and cleaning products sectors.
In 2024, the programme opened its first large-scale plastic collection centre in Samarinda, East Kalimantan, Borneo, in partnership with Danone’s Aqua brand. Designed to process 500 tonnes/ month of plastics, the facility is the largest of its kind in the province, where plastics comprise nearly 20% of more than 791,000 tonnes of total waste, according to Indonesia’s 2022 national waste data.
The Samarinda centre is the ninth launched under the “25 by 2025” initiative, which aims to open 25 global coastal collection centres. Each facility is built in accordance to strict sourcing and labour standards informed by the Ethical Trading Initiative, ISEAL guidance, and Bantam’s own manufacturing protocols.
Also in Indonesia, the ReSea Project, a Danish company with clean-up operations based in Jakarta, is tackling ocean plastics pollution. Through its documented and third party-certified clean-up system, the company removes plastic waste that has already entered oceans and rivers.
ReSea’s sorting facility in Jakarta, located near key collection points, manually sorts the recovered plastics, compresses it into bales, and prepares it for delivery to partners who can repurpose the material for new uses.
Along the same vein, Singapore-based non-profit organisation The Alliance, together with Beijingheadquartered AIIB, has launched a co-financing initiative to support integrated solid waste management in over ten cities in Indonesia. Through this collaboration, The Alliance will contribute US$21 million in concessional funding into AIIB’s Solid Waste Management for Sustainable Urban Development Project through its Project-Specific Window (PSW), a mechanism that allows AIIB to manage and disburse grant co-financing on behalf of contributors.
AIIB will provide climate-aligned waste management services guided by circular economy principles, aiming to benefit more than 9 million people in Indonesia. The project will focus on building infrastructure, strengthening the capacity of local governments, encouraging behavioural change, and improving livelihoods for informal waste workers.
The US$21 million investment complements AIIB’s planned US$150 million financing over the next five years. This co-financing is further supported by a US$2 million project preparation grant from The Alliance, facilitated by AIIB, to help implement environmental, climate, and social best practices for circular and end-to-end waste solutions.
Circulate invests in Indonesian recyclers. Also related to Indonesia, circular economy investment firm Circulate Capital has made two new investments in the country: Pelita Mekar Semesta ( PMS ) and Polindo Utama (Polindo).
As demand for recycled content intensifies and policy momentum accelerates across Asia, Circulate Capital continues to invest in companies already operating on the front lines of the circular economy. These investments reflect the firm’s long-term commitment to the region and its belief that high-growth markets like Indonesia offer not just environmental and climate impact but a clear pathway to scale and returns.
PMS is a fully integrated plastic recycler with over 15 years of experience, operating in East Java. Serving both domestic and international markets, the company specialises in polyolefins. Circulate Capital’s investment will triple PMS’s blown film capacity, boost the production
of quality recycled pellets, and support the development of new collection and sorting infrastructure across multiple cities. PMS’s product range includes recycled pellets and finished goods such as garbage and agricultural bags.
Polindo, on the other hand, is a PET recycler with more than 20 years of experience and fully integrated operations across collection, washing, flake production, and pelletising.
Polindo’s operations focus on post-consumer plastic waste, ensuring materials are recovered directly from end users. Each year, the company collects and recycles over 2.8 billion plastic bottles, giving them a second life as high-quality recycled content. With Circulate Capital’s investment, Polindo will expand its PET recycling capacity and begin processing additional plastic types to meet growing corporate demand for traceable, recycled materials.
At scale, the two companies are projected to circulate 320,000 tonnes of plastic waste cumulatively by 2030, as well as add more than 30,000 tonnes of new recycling capacity, and improve the livelihoods of 10,000 workers across the value chain.
Indonesia generates an estimated 6.8 million tonnes/ year of plastic waste, over 70% of which is at risk of leaking into the environment. Yet, it also hosts one of the most dynamic ecosystems of local recyclers in the region, supported by a fast-growing wave of policy reforms and consumer demand that is accelerating the shift toward circularity..
Circulate Capital has now backed 23 companies across Asia and Latin America, channelling capital to scale solutions that reduce plastic pollution, drive climate impact, and build resilient, future-fit supply chains. Prior to these two new investments, the firm’s portfolio had already added 455,000 tonnes/year of new recycling capacity, avoided 627,000 tonnes of CO2 emissions, and improved the livelihoods of more than 6,600 workers across the value chain.
Taiwan is a polestar on the global innovation map with advanced materials and manufacturing solutions, says Angelica Buan in this article, based on interviews with key exhibitors from the June-held Plastics, Rubber & Composite Material Fair Taiwan (PMT) exhibition.
PMT: an arena for staging global competitiveness
At the recently concluded inaugural Plastics, Rubber & Composite Material Fair Taiwan (PMT), held from 4-6 June in Tainan, exhibitors showcased Taiwan’s technology prowess and its growing role in the global supply chain.
Organised by Venturap Conference & Exhibition Co and backed by the Bureau of Foreign Trade, PMT, which brought together 110 companies from seven countries, cast light on Taiwan’s supply chain capabilities: from raw materials and smart manufacturing to application-driven innovations.
Homegrown companies such as CSRC Group, Yong Shun Chemical Co Ltd, TENSO Machinery Ind Co Ltd, Sun Chiao Rubber Enterprise Co Ltd and PULROC (Rockey Composite Pultrusion Co Ltd) demonstrated Taiwan’s capabilities, reinforcing its position in the global materials and technology market.
PMT showcased 110 companies from seven countries
Tenso: precision in action with robots
According to Business Market Insights, the global robotic injection moulding machinery market was valued at US$2 billion in 2024 and is projected to reach US$3 billion by 2033, growing at a CAGR of 2.6% from 2025 to 2033. Against this backdrop, automation specialist Tenso turned heads at PMT with its display of robots. The company says it has spent 40 years advancing humanmachine integrated technologies and its robots are equipped with self-diagnosis features, designed to meet the company’s commitment to “zero defect” performance.
While primarily developed for retrieving finished products from machinery, Tenso robots can also manage more complex operations, including product sorting, insert moulding, and in-mould labelling, offering manufacturers increased flexibility in their automation processes.
To further improve operational efficiency, Tenso employs TTS, a proprietary rack and pinion transmission system that enhances motion accuracy and reliability, while integrating two other core technological features: TSPA, an all-aluminum, adaptable robot body and ETSS, an E-type safety structure.
Providing an insight into the operations, Ivan Chen, Marketing Manager at Tenso, shared that the company’s automation systems are compatible with machines ranging from 50-5,000 tonnes and are able to interface with global machine brands.
“Unlike other robot makers in Japan and Taiwan that typically design robots for machines from 1,500 to 5,000 tonnes, Tenso is able to offer systems for larger capacities. We also offer a more premium design with the rack and pinion system for transmission,” he said.
He also noted, “European robot makers use the same rack and pinion technology because they too prioritise safety and reliability in production lines. But here in Asia, the focus is generally more on saving cost.”
While Tenso continues to concentrate on the Taiwanese and Japanese markets, it has made inroads internationally, especially in the US, and recently appointed a new agent in Germany. Additionally, the company has expanded its presence in Southeast Asia, including Thailand, Indonesia, Vietnam, Malaysia, as well as in India, serving a range of industries. In Australia, Tenso caters to the packaging sector, particularly for yoghurt and coffee cups.
Attuned to the global sustainability agenda, Tenso has also adopted the use of energy-saving servo systems to replace traditional cylinders.
As well, according to Chen, a new high-speed, high-efficiency robot system is also currently under development.
CSRC: carbon blacks for sustainability and conductivity
Established in mid-1973, Taipei-headquartered carbon black manufacturer CSRC operates under the brand name Continental Carbon and is the only carbon black manufacturer in Taiwan as well as the sixth largest in the world.
CSRC showcased its Satin Black JE6900, a conductive carbon black for the wire and cable industry, along with Continex CC503X from its circular carbon series, at PMT
At PMT, CSRC showcased two products: Satin Black JE6900, a conductive carbon black known for its stable conductivity and dispersibility for the wire and cable industry; and Continex CC503X from the circular carbon series, which features sustainable material content and offers strong reinforcement and consistent quality.
In the past, Chinese manufacturers sourced conductive carbon blacks mainly from the US and Europe and CSRC has responded by meeting the increased demand within the region, according to John Hsu, Asia Pacific Regional Business Manager.
Another growing application is in the semiconductor sector, where components continue to shrink in size, increasing the need for precise and reliable conductive materials. “CSRC works closely with customers to develop carbon black suited for electrostatic discharge (ESD) protection,” said Hsu.
He went on to say, “China remains the primary market for CSRC’s conductive carbon black, particularly as demand expands beyond low-voltage uses to medium and highvoltage systems, driven by the growth of electric vehicles and charging infrastructure. For applications such as integrated circuits and printed circuit boards, interest is also rising in Southeast Asian markets including Vietnam, Thailand, and Malaysia, with a wider regional demand for high-performance conductive materials.”
In East Asia, Continental Carbon operates three key sites: Linyuan Advanced Materials Technology, CSRC China (Maanshan), and CSRC China (Anshan). In India, it runs Continental Carbon India Private Ltd and Continental Carbon Eco Technology Ltd
“We launched the second facility in India just last year. The next planned expansion is a new carbon black production site in Türkiye. This location was chosen partly because our parent company already has a joint venture there. The country also offers strategic access to both European and African markets, with the latter presenting strong demand growth due to its rising population.”
Hsu said construction of the Turkish facility is in progress and expected to be completed by the end of 2026. Phase I of the project will have a production capacity of 100,000 tonnes of carbon black. There are also discussions around a potential Phase II or a separate project.
“In parallel, through our joint venture with Eco Infinic, we are developing a recycled carbon black (rCB) facility in the US,” said Hsu.
Hsu also added that despite growing competition, demand in Asia remains strong, especially in the tyre industry, where ample rubber supply continues to support regional growth. “As long as we maintain our competitive edge, there is still potential to grow ahead of other players. For speciality carbon blacks, such as conductive grades, we have secured an edge, as many competitors remain focused on tyre-grade products. With supply chains increasingly moving from Europe and the US to Asia, the growth prospects for speciality grades appear stronger than those for conventional applications."
Hsu also said the company is actively developing sustainable carbon black with a joint venture partner and will focus on the end products of rCB and tyre pyrolysis oil (TPO).
“We are already working with major customers, including tyre maker Maxxis that has adopted our sustainable offerings.”
“Additionally, this year, we have developed a singlewall carbon nanotube (CNT) designed for use in lithium battery applications, particularly within the electric vehicles sector. Acknowledging the market potential, we began investing in single-wall CNT development several years ago. As the product is still in its early stages, we are working closely with customers in Taiwan and China to fine-tune its performance. While not yet launched at scale, the product has potential for broader rollout depending on its success in initial applications,” he furthered.
Hsu also explained further on the launch, “With our experience in conductive carbon black and existing customer relationships in the lead battery segment, we see this as a way to strengthen our product portfolio as well as concentrate our resources on a product that offers higher value and long-term potential.”
Pulroc: Pultrusion materials to break with convention
Also exhibiting at PMT was Pulroc, a fibre-reinforced plastics (FRP) manufacturer established in 1979 and based in the Central Taiwan Science Park. The company specialises in pultrusion technology and has participated in several government-funded FRP research projects.
At PMT, Pulroc highlighted the use of its profile products in home construction applications, such as balconies. “In Taiwan, the weather is mostly humid, so traditional materials tend to corrode easily. Using our products can reduce maintenance costs and improve the ESG (environmental, social, governance) aspect. We also produce a lower carbon footprint compared to aluminium, metal, or wood, since there’s less need for painting or anti-corrosion treatment,” according to James Ho, President at Pulroc, and who has taken over the company that was previously helmed by his father.
Pulroc highlighted the use of its profile products in home construction applications at the PMT; it is also exploring drone application for its composites
Ho added the company’s major clients include mass rapid transit (MRT) contractors in Taiwan, South Korea, Singapore, Dubai, and Brazil, as well as seaport construction and maintenance firms, architects, and designers involved in ecological and landscaping projects.
In addition, he mentioned that other major projects include protective covers for electrified rail systems in Taipei, Kaohsiung, Singapore, South Korea, and Dubai, as well as anti-corrosion liners for steel piles used in coastal port and dock engineering.
“We have another project involving steel piping at the Taipei port, which is a highly corrosive and electrolytic environment. We designed an FRP cover to protect the pipe.”
Meanwhile, Pulroc continues to explore new applications for its composite materials. “As for expanding into other sector applications, we can look into drones, where our products have benefits because they are lightweight, strong, and not affected by changes in weather. I think designing with our pultrusion products can also lower costs, because right now, carbon fibre is very expensive and not cost-effective. In the future, we can tap into the growing demand for drones.”
The company is also in the process of applying for certification under the Taiwan Green Material Labelling System.
When asked about the company’s situation over the next three to five years, Ho commented: “It’s very hard to predict, considering the global situation right now. At the moment, the domestic market is stable and if we decide to expand internationally, the potential markets will be Thailand or the Philippines, as both countries have growing economies and improving living standards.”
Sun Chiao Rubber: Advanced silicone for niche applications
Sun Chiao Rubber another PMT exhibitor, showcased its mettle in advanced rubber products and silicone applications. Established 30 years ago, the OEM producer has focused on ongoing material development.
At the show, it promoted automotive rubber components such as O-rings and demonstrated its growth as an innovator, evolving from traditional rubber to silicone. The company also presented an upgraded silicone material that is biocompatible, making it suitable for medical applications.
“Our rubber products for the automotive industry remain a steady market for us. While this product line continues, we are also promoting silicone materials for baby products such as pacifiers, breast pump parts, nasal aspirators, and other infant care accessories. Our offerings include biocompatible and food-grade silicone. In addition, we have developed a platinum-cured silicone material using a proprietary formula and specialised processing technology,” explained Arashi Chen, R&D Manager.
Platinum-cured silicone, also known as addition-cure silicone, is a high-purity, biocompatible material used in medical devices, implants, and tubing. It is non-toxic, resistant to contamination, and offers thermal stability and durability. It is also more flexible and longer-lasting than traditional silicone.
However, this material is generally more expensive to produce and more difficult to process due to the extremely high temperatures required for curing.
Chen intoned that Sun Chiao Rubber saw an opportunity with platinum-cured silicone being used for baby, hygiene and medical applications, something that has not been extensively done in the market.
“We discovered this through customer inquiries about using platinum-cured silicone for certain applications, which led us to begin R&D to explore its potential,” he said.
Meanwhile, for hygiene applications using silicone, the company already serves customers in the domestic market. For international expansion, it is targeting the US market, which is known for its strict regulations on medical products. The company believes that by meeting these high standards will make it easier for it to enter other international markets. It also views this as a priority because customers place a strong emphasis on product quality and performance.
The company is also collaborating with partners to explore ways to reclaim waste and convert it back into usable rubber materials. This includes collaborating with furniture makers and other manufacturers to repurpose rubber into new products, supporting circular use across industries.
When asked about expanding into other markets, Chen said the company plans to focus its growth on more familiar territory. “At this stage, we are focused on serving the automotive industry,” Chen explained, adding that the company is willing to work with customers from the design stage to develop new solutions for various industries.
Yong Shun Chemical: safe resin solutions for versatile applications
Yong Shun Chemical, which started in 1967, has built its growth on polyester polyol (PU) and unsaturated polyester resins (UPR).
According to Andy Tsai, Sales Representative, demand for these two products is high, with a total average monthly production capacity of 3,000 tonnes for both domestic and global markets.
Implying the versatility of the products, he said that the company caters to applications in the shipbuilding, construction and the creative art industry, the latter for artifacts and art structures for both indoors and outdoors.
Tsai also spoke about a new product offering, flameretardant vinyl ester resin (VER), noting that the company is the first in Taiwan to have the flame retardancy certification. In addition, the product is also non-halogen and phosphorus-free, making it an eco-friendly material.
Nevertheless, polyester polyol resins remain the company’s top-selling products, according to Tsai.
Yong Shun Chemical presented its polyester polyol and unsaturated polyester resins at PMT. It also said it offers biodegradable UPR solutions upon customer request
“Within our company’s main sales, the UPR material for shipping, construction, and artifacts covers 30% of our revenue, while polyester polyol accounts for 70% of sales. We have been very successful in polyol because we supply major glue manufacturers in Taiwan, such as those producing shoe gel, as well as overseas manufacturers for similar applications.”
He also furthered that the company had developed a new biobased polyol. “The goal is to create a product that is food-safe for use, for example, as a coating material for food or water cups. Our food-safe grade polyol can also be 100% biodegradable. This opens up opportunities in markets like the EU, where there is growing demand for food-safe and sustainable products.”
For export markets in Asia, the company supplies its full product range to Indonesia, the Philippines, Vietnam, and Thailand. “Demand for polyester polyol is especially strong in Vietnam and Indonesia, while UPR sees higher sales in Thailand and the Philippines. In Northeast Asia, Japan, Korea, and China remain our most stable markets,” Tsai said.
In terms of safety, Yong Shun Chemical is taking further steps. “Polyols are safe materials for shipping, whereas UPR contains styrene monomer (SM), a volatile, flammable liquid that can be toxic over prolonged exposure. Because of this, it is classified as a restricted material by the government when transported,” Tsai explained.
“It is for this reason that at present, we are focusing on product development rather than expansion. For example, we are exploring alternatives to SM. One approach involves using UV light to solidify the material, making it non-toxic. We are already conducting small-batch production trials and expect it to reach the market soon,” he said,
The company is also developing a UPR-based alternative for hydrogen tank applications by combining it with carbon fibre to reduce weight.
“Currently, epoxy resin is used with carbon fibre in this application, but the cost of epoxy resin is three times higher than UPR. We see an opportunity to replace it with a more cost-effective UPR solution,” Tsai concluded.
With around 2 million tonnes of plastic waste generated in the European construction industry each year, recycling these complex materials is highly fragmented, technically demanding, and often inefficient. As a result, the majority of construction plastics are disposed by the end of their lifecycle, since existing mechanical recycling methods produce low-quality materials that are not suitable for reuse.
Thus, engineering company Sulzer and chemicals firm Sika have signed an MoU to establish a joint venture to advance plastics recycling in the construction industry. The aim is to combine the strengths of both companies: Sika's extensive expertise in polymer applications and high-performance building materials and Sulzer's process knowledge in chemical recycling.
Shown here are joint venture initiators
Michael Schüepp, Head of Ventures at Sulzer, and Ivo Schädler, Head of Construction at Sika. Both companies are looking forward to jointly advancing the transformation of the construction industry towards sustainability
The joint venture, based in Zurich, Switzerland, will be founded as an independent company, with each partner holding a 50% stake. Operational activities will commence in the second half of 2025 with pilot projects in Germany, Austria and Switzerland.
With this joint venture, Sika and Sulzer are developing a system for the collection, processing and reuse of construction plastics using mechanical and chemical processes.
The joint venture between Sika and Sulzer will close gaps in the value chain of the construction industry, and will be complemented by local partners, such as logistics and recycling companies, which will be integrated into specific process steps. Recycled materials will thus be reincorporated into the manufacturing process.
Creating construction boards from electronic waste
In the US, digital imaging firm Canon and recycler Repolytex have a unique solution that skips the costly and complex process of sorting mixed plastics from electronics.
Instead, Repolytex separates the metals and processes the mixed plastics into a powder, creating a hybrid material to manufacture durable sheeting. The resulting boards are weather-resistant, dimensionally stable, and suitable for construction and marine applications.
Founded by industry veterans with decades of experience in metal sorting, Repolytex says it recognised the growing challenge of plastic waste from electronic devices, which led it to develop the process.
Prior to the development of the technology, recycled electronics plastic was predominantly shipped overseas, contributing to environmental concerns and economic inefficiencies.
Repolytex/Canon are pioneering a groundbreaking solution to the plastic waste crisis, with a proprietary process that combines and repurposes various types of plastics found in electronic devices to construction boards
It adds that unlike other recycling methods that are limited by polymer compatibility, its proprietary process enables the company to effectively combine and repurpose various types of plastic. “This approach not only reduces plastic waste but also produces highperformance construction materials that are sustainable and cost-effective,” says the firm that operates from a flagship facility in Madison, North Carolina.
Countering trade tariffs with homegrown sustainable materials
Another US materials firm Supersede recently secured US$10 million in seed funding, consisting of US$5 million in convertible debt and US$5 million in senior secured equipment financing, to scale production of its Supersede Marine Board, a recyclable replacement for marine-grade plywood.
The investment includes participation from a major US building products distributor and circular economy firm Closed Loop Partners, as well as angel groups and individual investors.
Supersede has launched what it says is the world’s first marine-grade plywood replacement. The Supersede Marine Board, an engineered extruded sheet crafted from plastic waste, is 100% recyclable, waterproof, and rot-proof, and does not splinter or split. Beginning with the boat manufacturing industry, Supersede will also provide its innovative solution to manufacturers of modular homes, RVs, and trailers
As supply chain instability and material costs increase, particularly amid rising trade barriers, Supersede is positioned to disrupt the US market for structural wood panels, valued at over US$30 billion. The company’s solution arrives at a critical moment for sectors like boat, RV, and modular home manufacturing.
Marine-grade plywood has long been the standard for these sectors, but the material comes with drawbacks as it’s reliant on volatile resource extraction, prone to water damage, contains formaldehyde-based binders, and lacks an established end-of-life pathway, often ending up in landfills.
Launched last year, Supersede’s marine board offers a 100% waterproof, rot-proof, and recyclable alternative to plywood that integrates seamlessly into existing manufacturing workflows, according to the company. Using recycled polypropylene (rPP), the company's patented extrusion process creates high-strength structural panels that are said to outperform traditional plywood in water resistance, fastener retention, compressive strength and durability.
The panels are said to eliminate the use of toxic chemicals like formaldehyde and chromated copper arsenate, thus improving safety for workers and end users. The company says it plans to localise feedstock sourcing, thereby reducing transportation emissions and creating jobs locally as well.
Supersede says its solution eliminates multiple manufacturing steps, since the panels do not require sanding, sealing or drying, reducing labour costs.
The company also runs a buyback program to support closed-loop recycling: offcuts and end-of-life products can be reprocessed into new boards, helping manufacturers achieve zero-waste targets without compromising performance.
Sean Petterson, CEO/Co-Founder of Supersede said the funding will allow the company to scale up faster, including building a second manufacturing facility that will triple production capacity and add over 50 new jobs.
Meanwhile, CRDC Global , a green building materials and machinery technology company founded by the Centre for Regenerative Design & Collaboration ( CRDC ) in Costa Rica in 2018, is
promoting its latest Resin8 Core product, built on the success of the existing Resin8 solution that combines concrete and plastics.
To be commercially launched in 2026, Resin8 Core is created when Resin8’s recycled content reacts with cement-kiln emissions and captures CO2e before it can escape to the atmosphere. Captured gases get stored in a lightweight coating of mineralised limestone on each Resin8 particle, forming the Resin8 Core.
So what is Resin8? CRDC's patented low-carbon technology uses all types of shredded, mixed plastic waste that is mixed with minerals and processed through extrusion to create Resin8. This lightweight mineral polymer can be utilised in both structural and nonstructural concrete applications.
CRDC says independent bodies have tested its material and it has demonstrated an increase in compression strength, flexibility, fire/thermal resistance and acoustic properties. The company also claims that concrete applications using Resin8 exceed ASTM standards.
Resin8 is also considered as a viable component for 3D printed concrete, as highlighted in an article in Elsevier’s journal Construction and Building Materials. The research evaluated Resin8 mix with elements such as fly ash and sand. It noted an improved bond strength between the layers of the printed concrete with the addition of Resin8.
The company has commercial manufacturing operations in Costa Rica, South Africa, Australia, and the US.
The market share for disposable cups will more than double from US$13.45 billion in 2024 to US31.68 billion by 2037, according to consulting firm Research Nester. Good thermal properties, health safety and easy recyclability are essential properties for disposable coffee cups.
For several years now Austrian extrusion machinery firm SML has been developing processes to manufacture heat-resistant materials for applications such as coffee cups on its own sheet lines.
Meanwhile, thermoforming companies dispose of several different materials to manufacture cups in line with changes in market demands and in compliance with increasingly stringent environmental regulations, Rupert Becker, the Product Manager for sheet lines at SML explains.
But what might be the optimum material for the coffee cups of tomorrow, asks the company?
SML says weighing up the advantages and disadvantages of the individual materials, easy-to-recycle mono-material PP-foam is a top favourite pick for choice of coffee cups material
Cups from rigid PS
Conventionally, disposable coffee cups were mainly made of polystyrene (PS), which is relatively easy to thermoform. Polystyrene has, however, fallen from favour among several FMCG (Fast-Moving Consumer Goods) manufacturers due to potential health safety issues. Coffee cups made of PS can release odours and may affect the taste. The material can be recycled, but post recycling applications are limited.
PP-foam cups
To create a future-oriented and environmentally acceptable alternative to rigid PS products, SML has developed a new method to manufacture PP foamed materials.
PP-foam coffee cups are made from three-layer PP sheets. The central layer is physically foamed while the outer layers are rigid. The sheet is extruded using flat die co-extrusion technology in combination with a gas injection unit.
To create the specific cell structure of the foamed inner layer, a gas such as nitrogen is used. Coffee cups from foamed PP have excellent insulation properties and are heat-resistant up to 100°C.
Compared with cups from 100% rigid PP, PP-foam cups have a significantly lower density and lower weight. This means that less material is required to produce these. In addition, PP-foam sheet is very easy to thermoform. When it comes to recycling, a major advantage of PP-foam materials in comparison to other foamed plastics is that they can be sorted by the regular process in waste sorting plants.
PET-foam cups
The same thing that worked with PP also works with PET. As a next step, SML developed cups of mono-material PET-foam sheet. PET-foam sheet is not transparent, manufacturing processes and material properties are very similar to those of PP-foam sheet. PET foamed sheet can consist of up to 60% recycled PET, while still being in compliance with food safety standards. It cannot be sorted by gravity waste sorting plants due to its lighter weight compared to rigid PET.
C-PET light cups
C-PET light sheet is characterised by its suitability for transparent applications, high stiffness, and efficient production with a high output. The material is an economic and easy-to-recycle alternative to rigid PS and PP in thermoformed hot fill applications – such as coffee cups.
C-PET light withstands temperatures of up to 100°C. In thermoforming, shorter cycle times represent an economic advantage compared with conventional C-PET. Due to the similar density of virgin PET and its transparency, coffee cups from rigid C-PET light can be easily sorted and recycled in existing facilities.
And what about “paper” cups?
Practically, all of the coffee cups made from “paper” are of paper coated with polymers, either PE or bio-based PLA. The function of the polymer coating is mainly to provide moisture resistance.
So far, coffee cups from paper coated with plastics have become well established in the market. Their biggest disadvantage is the higher CO2 footprint of paper production and their limited recyclability since the polymer and the paper components of the cups have to be separated in a relatively complex process before recycling.
Today, polymer-coated “paper” coffee cups are generally categorised as single use plastics in accordance with EU directive 2019/904 regardless of whether the coating is made of PE or bio-based PLA.
“Our different extrusion lines are able to produce practically any material for coffee cups - from rigid and foamed mono-materials to polymer-coated paper. The question of ‘Which material is best’ naturally depends to a large extent on the specific requirements of the material manufacturers, the thermoforming companies and the end-customers. However, if we try to weigh up the advantages and disadvantages of the individual materials, easy-to-recycle mono-material PP-foam has a lot in its favour,” Becker concluded.
With the antimony trioxide market racking up high prices and China in the control reins of the supply chain, it may be time to switch to halogen-free flame retardants, says Swiss chemical firm Clariant in this article.
In today's interconnected manufacturing world, supply chain disruptions can have a devastating effect on entire industries. The current antimony trioxide market represents exactly such a scenario – creating both challenges and opportunities for innovation.
As manufacturers face rapidly increasing costs and uncertain availability of this flame retardant (FR) synergist, the search for alternatives has become increasingly urgent.
The antimony trioxide supply chain challenge
The numbers tell a worrying story. Antimony trioxide prices have increased 400% in the past year alone. According to Fastmarkets data from July 2024, the market experienced "the sharpest price rally ever recorded in the antimony market" since they began tracking prices in the early 1980s. More recent market
reports indicate prices reaching US$51,500 per tonne in early 2025, creating significant cost pressures for manufacturers relying on this material. What's driving this price volatility? The answer lies primarily in supply concentration. Approximately 75-80% of global antimony trioxide production is concentrated in China, creating a vulnerable supply chain. Environmental inspections in key antimony production regions like Hunan province have led to production suspensions. Simultaneously, depleting mine reserves and quality issues further constrain output.
Another issue are China’s export controls on various critical minerals, including germanium, gallium and antimony. Antimony is considered a strategic metal for its use in FRs, batteries, semiconductors, and defence applications, with increasing global demand.
The controls require exporters to apply for licenses before shipping antimony products abroad. The restrictions are part of a broader strategy to control critical minerals, citing national security concerns. These actions led to market impacts including price volatility and supply chain disruptions as countries seek alternative sources.
Wide reaching impact of antimony price increases
The effects of this supply chain disruption extend across many industries. The impact is significant for all manufacturers using brominated FRs formulated with antimony trioxide: a combination commonly employed in plastics for electronics, transportation components, and building materials.
First, there's the direct cost increase. Antimony trioxide typically constitutes between 2-4% of flameretarded plastic formulations when used as a synergist with brominated compounds. With prices quadrupling, this translates to considerable increases in production costs that either squeeze margins or force price increases downstream.
Second, is the uncertainty in material availability. Production planning becomes challenging when a critical input faces such volatility. Manufacturers must either secure larger inventories (tying up capital) or risk production interruptions.
These pressures are particularly noticeable in electronics manufacturing, automotive applications, and construction materials – sectors where flame retardancy requirements are non-negotiable for safety and regulatory compliance.
Phosphorus-based advantage
Phosphorus-based FRs offer an alternative path forward. For example, Exolit OP, invented and patented by Swiss chemical firm Clariant , represents a halogenfree solution that addresses both immediate supply chain concerns and offers specific additional benefits.
These FRs have found widespread use in engineering plastics like polyamides and polyesters as well as e.g. some expoy-based thermoset applications. They are available globally, through Clariant’s production sites in Germany and China.
"The current antimony trioxide market volatility presents manufacturers with both a challenge and an opportunity," says Adrian Beard, Marketing & Advocacy Flame Retardants, Additives. "Addressing immediate supply chain concerns will encourage companies to switch to phosphorus-based technologies that also offer improved environmental benefits alongside excellent flame retardant performance. This isn't just about solving today's problem it is about implementing a more resilient approach for the future."
Unlike traditional systems that rely on the brominated FR/antimony trioxide combination, Exolit OP works through a different flame retardancy mechanism. In addition to gas-phase action impeding the chemical reactions in the flame zone, the phosphorus-based chemistry creates a protective char layer during combustion, effectively isolating the underlying material from oxygen and heat. This approach has received validation through independent research.
The European Union's ENFIRO project (Life Cycle Assessment of Environmentally Compatible Flame Retardants), which involved 12 research partners examining 15 commercially available non-halogenated FRs, found that halogen-free options like Exolit OP “offer similar fire performance and technical application capabilities as BFRs [brominated flame retardants] while producing less smoke and less undesirable components in smoke."
Sustainability benefits
While immediate cost and availability concerns might drive initial interest in alternatives, the environmental profile of phosphorus-based FRs offers additional benefits.
A February 2024 life cycle assessment published by researchers at the Fraunhofer Institute for Environmental, Safety , and Energy Technology UMSICHT compared phosphinate-based FRs with brominated alternatives. The study, titled "Toward Sustainable Fire Safety: Life Cycle Assessment of Phosphinate-Based and Brominated Flame Retardants in E-Mobility and Electronic Devices," found measurable environmental advantages for the phosphorus-based approach.
This year, Clariant celebrates 50 years of its Exolit AP flame retardants that are based on advanced ammonium polyphosphate (APP) technology. Its FRs are used in a wide range of applications, including intumescent coatings, fire barrier sealing systems, thermoset composites for e-mobility battery housings and coatings, rigid polyisocyanurate (PIR) insulation foams and more
Being phosphorus-based and halogen-free, Exolit OP represents an environmentally improved option compared to legacy brominated FRs. This becomes increasingly relevant as industries face growing regulatory and consumer interest regarding chemical safety and environmental impact.
Testing has shown that phosphorus-based FRs produce less smoke during combustion compared to halogenated alternatives. This characteristic not only reduces the environmental impact of fire incidents but also enhances safety by improving visibility during evacuations.
For manufacturers concerned about long-term material performance, phosphorus-based FRs maintain their effectiveness through recycling processes. Exolit OP retains its flame retardant properties even after multiple mechanical recycling cycles – an increasingly important consideration as circular economy principles gain traction across industries.
Performance advantages
Beyond addressing supply chain vulnerabilities and specific environmental benefits, phosphorus-based FRs deliver performance advantages that make them an excellent choice regardless of antimony market conditions.
Exolit OP FRs typically require lower dosage levels compared to brominated systems with antimony trioxide. In addition, the density advantage is particularly noteworthy. Phosphorus-based
FRs have a lower specific gravity than bromine/ antimony-containing systems, contributing to lighter weight parts without sacrificing flame protection.
The current antimony trioxide market presents both immediate challenges and an opportunity to re-evaluate FR strategies. By considering phosphorus-based alternatives, manufacturers can address pressing cost and availability concerns with products that also offer environmental and performance improvements. This approach aligns with broader industry trends. Interest in FR solutions with improved environmental benefits continues to develop, influenced by industry trends such as miniaturisation in electronics and electrical applications, the ongoing focus on lightweight materials in automotive and changing mobility requirements.
For manufacturers considering a transition away from antimony-dependent FR systems, several practical considerations can help ensure a smooth implementation process.
First, it's important to recognise that while phosphorus-based FRs offer excellent performance, they are not direct drop-in replacements. Formulation adjustments are often necessary when implementing new FR systems.
This transition process requires careful evaluation and testing, and benefits significantly from expert technical support to address application-specific requirements.
Europe pushes for minimum 20% recycled plastics in new vehicles
The European Parliament recently adopted its proposals on new EU rules to cover the entire vehicle lifecycle, from design to final end-of-life treatment.
Under a phased approach, plastic used in each new vehicle type will have to contain a minimum of 20% recycled plastic, within six years of the rules’ entry into force, contrary to the earlier move for 25%.
However, to ensure the necessary long-term perspective for the industry and unlock investment, manufacturers have to meet a target of at least 25% within ten years, if enough recycled plastic is available at non-excessive prices. The Commission says it will introduce targets for recycled steel and aluminium and its alloys, following a feasibility study.
The regulation will apply to cars and vans one year after its entry into force (five years for buses, heavy-duty vehicles, trailers, motorcycles, quads, mopeds and minicars).
Manufacturers would also have extended producer responsibility, covering the cost of the collection and treatment of their vehicles that have reached the end-of-life stage. Specific requirements would apply for the removal of parts and components, of liquids, and of components containing gases, refrigerants, and hazardous substances before shredding.
As well, used vehicles should only be exported if they are not considered end-of-life vehicles, the text says.
Meanwhile, Brussels-based advocate for recycling in Europe EuRIC says that while progress has been made it warns that low targets, loopholes, and legal uncertainties risk holding back the investments and market confidence needed to scale Europe’s circular economy in practice.
“These low targets reward neither frontrunners who have already invested in circular solutions nor recyclers facing a 30% recycling obligation for ELV plastics without a guaranteed market,” said Maria Vera Duran, EuRIC’s Senior Technical Manager.
It also added that the lack of a mirror clause for imports under fair conditions further threatens European recyclers. Moreover, the review clause referencing “excessive prices” adds policy uncertainty, discouraging necessary investments, it furthered.
BlueRebirth to undertake vehicle recycling in Japan In other news, Japan’s Denso Corporation , Toray Industries , Nomura Research Institute , Honda Motor Co , Matec Inc and Rever Corporation have
are among dozens of firms that have set up the BlueRebirth Council to realise a circular economy in the automotive sector.
Its objective is to build a manufacturing/ recycling integrated value chain to realise car-to-car recycling, from automated precision dismantling to efficiently disassemble end-of-life vehicles (ELVs) for materials recycling.
According to the council, the automotive recycling industry faces challenges in promoting automation, digitalisation and in addressing worker shortages by improving workplace environments. By 2035, the council says it aims to change the automotive recycling industry into a “recycled materials manufacturing industry.”
BlueRebirth says it also will make recommendations to relevant companies and organisations and engage in discussions and research.
Fiat launches vehicle made from recycled beverage cartons
Meanwhile, beverage cartons have found new life in the latest model of Fiat Grande Panda. Launched by Italian car maker Fiat , it has become the first car manufacturer to incorporate recycled materials from used beverage cartons in a vehicle.
Switzerland-based Tetra Pak ’s polyAl material, a combination of polymers and aluminium components recovered during the recycling of beverage cartons, is used inside the plastics of the car’s interior, including the central console, dashboard, interior front and rear door panels.
The polyAl-based compound is called Lapolen Ecotek and produced by Italian compounder Lapo Compound that worked with Fiat to ensure this material was competitive in quality and price. The placement of the material in such visible parts of the interior, rather than in hidden areas, clearly demonstrates the material’s aesthetic potential. Fiat chose the material for its shimmering effect, created by the aluminium content of the recycled material, and because Lapo Compound was able to precisely match the specific shade of blue required.
Fiat’s use of the polyAl material in the Fiat Grande Panda showcases that this recycled material can now be utilised on a large scale by the automotive industry. The car is already on the market in most European countries, and will be available outside Europe by the end of the year.
In addition to its automotive applications, Lapo Compound is also conducting trials for other uses of the polyAl-based compound Lapolen Ecotek, including outdoor furniture and factory floors.
In line with the automotive industry’s move towards sustainability, German company Kraiburg TPE ’s Thermolast R RC/UV/AP series contains 15-40% recycled content and meets specific recycling standards.
While often seen as a secondary component, side steps in vehicles improve vehicle accessibility, enhance functionality, and contribute to a unified exterior design. Running boards improve access, safety, and comfort, especially for high-clearance vehicles like SUVs and trucks, as well as reduce seat wear by easing entry and exit in a vehicle.
Kraiburg adds that its latest recycledcontent TPE series delivers highperformance,, offers weather resistance, UV stability, and impact strength, making it ideal for enduring harsh outdoor conditions while maintaining long-term durability and surface quality.
The compounds also offer excellent adhesion to PP, low density for weight reduction, and temperature stability up to 90°C.
These features, along with proven performance in the two-year Florida weathering test with a GS rating of ≥ 4, make the series highly resilient under harsh outdoor conditions.
With a hardness range of 50 to 90 Shore A, it also covers various design needs, from flexible to more rigid structures.
Available in black colour, the series offers versatility and visual consistency, ensuring that car running boards maintain a sleek, modern appearance while meeting design requirements.
The series is also suitable for a wide range of exterior automotive parts, including cowl gaskets, underbody components, and window encapsulations.
Manufacturing moulded parts out of virgin material from shot to shot and batch to batch at a consistently high part quality is state of the art, but usually places high demands on the controller technology.
When it comes to processing content such as post-industrial recyclate (PIR), post-consumer recyclate (PCR) and bioplastics, the material and processing properties can vary considerably.
Control concepts that ensure constant mould filling and, ultimately, consistent quality of the end products are therefore required if recyclates are to be used efficiently.
Thus, German machinery maker Arburg has developed digital pilot functions for its machine controllers that keep the process stable during the injection and holding pressure phase.
“Black boxes” challenge
Arburg has developed digital pilot functions for its machine controllers for processing post-industrial recyclate (PIR), post-consumer recyclate (PCR) and bioplastics
Melting process as an influencing factor
A homogeneous and stable melting process is an important influencing factor in the production of good parts. It starts with the material being fed into the plasticising screw as evenly as possible.
If the material is in the form of granules, recycled plastic can generally be processed as well as virgin material without the need for additional hardware.
With flakes, size and shape can vary, while reground material, on the other hand, which is material from plastic parts that have only been shredded with a sprue grinder, consists of fragments of different sizes, ideally in grain sizes of 2-5 mm. These grains are usually accompanied by finer material, up to and including dustlike material. To ensure a stable melting process, any dust must be removed fromtheregroundmaterial.
Recyclate package for reground material and flakes
For the processing of reground materials and flakes, Arburg says it offers a retrofittable recyclate package that combines software and hardware features.
From the machine’s point of view, injection moulding involves two large “black boxes” that significantly influence process stability and part quality. This is because the machine itself has no knowledge of • which material is fed into the hopper, or • what happens between the two mould mounting platens.
These are two major challenges when it comes to reliably controlling process parameters such as the temperature progression of the moulding compound and the temperature progression and pressure profile in the mould.
The biggest difference between processing recyclates and virgin material is that the material properties and characteristics such as mechanical quality, colour and smell can vary within a delivery or an order over a wider range. Since no clear material specification can currently be assigned to the recycled granules in most recycling processes, no data sheet is available during machine setup, which makes processing significantly more difficult.
However, Arburg says its Gestica and Selogica controllers for Allrounder machines have pilot functions, for example, that counteract fluctuating viscosities in the melt: “aXw Control ReferencePilot” and “aXw Control RecyclatePilot” can detect and reliably even out irregularities and actively control the ongoing injection process in order to keep the mould filling as constant as possible and ensure consistent part quality despite major variations.
Among the software features are multi-stage start-up parameters and the digital “aXw Control ScrewPilot” assistance function, which ensures precise and stable mould filling. In terms of hardware equipment, a modified cylinder module enables uninterrupted feeding even of poorly flowing materials.
A plasticising screw with a modified, deeper highcompression (HC) geometry ensures homogeneous processing. Grooves in the feed zone help the material to be drawn in, despite its irregular shape, and conveyed forward in a stable manner. The screw also has a CrN coating to reduce the formation of deposits and wear caused by unexpected foreign bodies.
For processing regrind, Arburg offers a retrofittable recyclate package that combines software and hardware features
ScrewPilot: Control concept for the “fill mould” core process
Filling the mould cavity in a reproducible manner from cycle to cycle is the basis for consistent component quality. A successful control concept for this is the “aXw Control ScrewPilot” or “position-regulated screw” pilot function, where the filling process is adapted to the requirements of the flow path in several stages by a speed-regulated screw movement.
This concept can be compared to a driving assistant for cars: if the movement (in this case of the screw) deviates from the programmed speed due to disruptive influences
(here, for example, variations in the viscosity of the plastic melt), it is regulated in a way that ensures that the distance is still covered in the allotted time. The active acceleration and braking dynamically compensates for disruptive influences, so that a constant amount of melt is fed into the cavity.
These dynamics have proven to be particularly useful at high injection volume flows, especially when it comes to preventing pressure peaks and overfilling by targeted and rapid braking.
ReferencePilot: Control in the holding pressure phase
The holding pressure phase is also crucial for part quality. It is usually executed as a quasi-static, pressure-controlled process, with the optimum parameters previously determined by a machine setup technician.
No account is taken of short-term influences during ongoing production, such as viscosity variations in the melt (caused by recyclates, lubricants or colour additives), or long-term wear, e.g. on the nonreturn valve and other mechanical components. In the long term, this can lead to variations in the cavity pressure and hence to irregular part quality.
For this reason, as early as 1988, Arburg developed an injection process regulation function that is integrated in the controller and regulates the holding pressure curve in real time via a pressure sensor in the mould.
This software function has been continuously developed and is now known as “aXw Control ReferencePilot”.
The ReferencePilot uses the nominal value reference curve of a good part as the basis for active regulation in the holding pressure phase, where the current holding pressure is adjusted according to the internal pressure. A pressure sensor positioned as close as possible to the sprue in the mould is required as the associated hardware.
Mould cavity pressure as an influencing factor
So that it can quickly counteract disruptive influences and actively balance out pressure variations, the software receives signals regarding mould cavity pressure that are recorded in real time by the sensor. This enables ReferencePilot to regulate the internal pressure curve from the current actual value to the desired nominal value.
When ReferencePilot is used for control, the pressure conditions in the mould are precisely adjusted from shot to shot to match the reference, with the actual value being raised to the nominal value. This results in a constant shot weight and consistently high part quality, without the need for manual intervention during process parameterisation.
Calibrated pressure sensor required
To be able to use ReferencePilot, two conditions must be met: • The injection moulding machine must be equipped with “aXw ScrewPilot”, which is standard for electric and hybrid Allrounders.
• There must be enough space in the mould cavity to install a pressure sensor.
The sensor itself causes additional expense; in addition, expertise and time are required to recalibrate it for each setup process and to maintain it regularly. This is the only way to ensure that the internal pressure sensor measuring equipment is fully functional and delivers the correct signals.
If all requirements are met, the injection moulding process can be stabilised quickly and reliably through the interaction of the sensor and the pilot function. The number of start-up cycles can be greatly reduced and there is less scrap. The results are longer, trouble-free production times, fewer downstream testing processes and increased production efficiency. Depending on the case of application, investing in a sensor system can quickly pay off.
An alternative is the new “aXw Control RecyclatePilot” function, which controls the injection moulding process directly in the injection or mould filling phase based solely on data from the standard machine sensor system. Compared to ReferencePilot, which receives signals directly fromthecavity, theRecyclatePilot has a longer partial control circuit. Nevertheless, it offers a number of clear advantages:
• There is no need for additional sensors.
• The pilot function integrated into the controller can be activated simply by pressing a button.
• The function uses the proven sensor system inside the machine, which only needs to be calibrated every few years.
• This pilot function balances out short-term variations from shot to shot and also across cycles.
The operator initially optimises the process settings as usual so that the required quality of the good part is achieved. This reference is transferred to the pilot function via a control command. An additional command activates RecyclatePilot, which then analyses the injection behaviour, detects distinctive points and deviations in the injection process and ensures that the injected volume and therefore the mould filling remain constant.
This is done by comparing the event pattern in the same cycle with the reference entered during the injection phase and, if necessary, adjusting the switch-over point at short notice. In addition, correcting the dosage volume also makes the overall process more stable in the long term and across cycles.
Conclusion
The controller is the “brain” of an injection moulding machine and can provide operators with comprehensive and active support. With the help of digital pilot functions such as RecyclatePilot and ReferencePilot, process reliability can be significantly increased during the processing of recyclates by means of active control in the injection and holding pressure phases.
The injection profile and filling process of the moulded part remain stable and correspond to the specified reference.
In this case study, Canada-based LSR specialist Silcotech and medical device maker Momtech partnered to bring the mōmi baby bottle to market. The baby bottle nipple is said to ease infants’ transition to bottle feeding.
Anyone who has ever fed a baby can tell you it’s not necessarily easy, especially when the baby is transitioning from breastfeeding to bottle feeding.
In 2011, inventor Carr Lane Quackenbush set out to simplify the breast-to-bottle transition in partnership with serial entrepreneur Hal Eason, CEO/co-founder of Momtech , a company dedicated to providing new products for mothers and their babies.
The mōmi bottle has been engineered to facilitate an easy transition between breast, bottle and back, supporting natural infant oral mechanics
“We could never have gotten where we are without a true spirit of partnership with Michael (Silcotech President/co-founder Michael Maloney) and his team,” said Eason.
The mōmi journey began with Quackenbush, former President of a leading breast pump manufacturer, “retiring” to his personal workshop where he spent ten years designing and prototyping baby bottle nipples that could simulate the natural contours and function of a woman’s breast.
After six iterations of design and testing with small numbers of babies, Quackenbush approached Eason with a version he believed was market-ready.
Eason adds, “As simple as the product looked, it was the first of its kind in the market and presented a number of design challenges. It was not a slam dunk. In fact, Silcotech was the only company we found willing even to take it on.”
The mōmi nipple is rooted in the principle that nature is the gold standard of design and that current baby bottle technology is different from nature to a point where breastfed babies will either refuse to take a bottle or refuse to return to the breast should breastfeeding need to be interrupted.
“Every conventional nipple on the market is hollow, and that’s not natural,” Eason explained. “The fundamental differentiator of our product is that it has a solid soft silicone tip that resembles human tissue, enabling the baby to use the same oral mechanics whether being fed from the bottle or the breast.”
Silcotech was invaluable in navigating the various hurdles, starting with ensuring product safety.
Their efforts led to the 2023 arrival of mōmi baby nipples on the market and a much easier experience for babies making the breast-to-bottle transition.
Eason points out that this device was born out of game-changing liquid silicone rubber (LSR) processing brought to the table by the LSR experts at Canada’s Silcotech
Silcotech’s Maloney, adds, “It’s a highly regulated space, all focused on the ultimate effect on the baby. And then there are mechanical considerations, as well, such as the fact that babies eventually develop teeth. You have to make sure that when biting down on the nipple, the baby doesn’t break off a chunk that becomes a choking hazard.”
mōmi’s best-selling product is a two-bottle set of 4-oz lead-free glass bottles with signature purple collars and level 1 nipples
Healthcare professionals, buyers, and industry leaders from across the globe will gather in Bangkok from 10 to 12 September 2025 for MEDICAL FAIR THAILAND 2025, the region’s leading exhibition for medical and healthcare innovations. Organised by Messe Düsseldorf Asia, this 11th edition promises to be the largest yet, featuring over 1,000 exhibitors from more than 40 countries, presenting 10,000+ products and solutions across the healthcare value chain.
Held at BITEC, Bangkok, the three-day event provides a comprehensive platform for sourcing, networking, and learning in one of the world’s most dynamic healthcare markets. With 20 national pavilions and country groups represented, including Austria, Belgium and Germany, attendees can expect a world-class showcase of medical technologies, diagnostics, digital health solutions, and advanced MedTech manufacturing.
Why MEDICAL FAIR THAILAND Matters
Southeast Asia’s healthcare demands are rapidly growing, fuelled by demographic shifts such as an ageing population, rising chronic diseases, and increasing healthcare investments. MEDICAL FAIR THAILAND addresses these trends directly, offering a platform that connects global innovations with regional needs.
The exhibition spans 20,000 sq m and caters to hospital buyers, distributors, healthcare providers, and innovators seeking to explore next-generation technologies and forge cross-border partnerships. Attendees can compare solutions side-by-side, understand emerging trends, and discover innovations shaping the future of care delivery.
Spotlight on Key Zones
To ensure targeted engagement, the event features several specialised zones:
• LaunchPad Zone: Showcasing start-ups and emerging MedTech companies, this space highlights disruptive innovations and fresh ideas from first-time exhibitors.
• Community Care Zone: Focused on rehabilitation, homecare, and ageingin-place solutions, this area responds to Southeast Asia’s rising demand for patientcentric and value-based healthcare.
• Medical Manufacturing Zone: Dedicated to advanced production, automation, and supply chain solutions, reflecting Southeast Asia’s increasing role in global medical device manufacturing.
Among the event’s highlights is the WT | Wearable Technologies Conference Asia 2025, co-organised with MEDICAL FAIR THAILAND. This fullday conference will take place on 10 September 2025, from 10 am, at BITEC Bangkok.
From smartwatches detecting heart irregularities to wearable ECG patches enabling remote patient monitoring, wearable tech is reshaping healthcare. The conference will bring together global experts to discuss the latest developments in digital health, sports tech, remote monitoring, and telehealth.
Free for all registered visitors, the conference also offers exclusive networking opportunities with industry leaders, making it a prime platform for exploring collaborations and showcasing innovations to new audiences.
Beyond the exhibition floor, MEDICAL FAIR THAILAND offers a comprehensive programme of industryled seminars and forums. Topics include AI-driven diagnostics, rehabilitation medicine, eldercare, hospital management, and digital transformation.
For the first time in Bangkok, the event will also be co-located with GITEX DIGI_HEALTH 5.0 Thailand, part of GITEX GLOBAL’s digital health movement. This summit will spotlight future-ready tech solutions, adding another layer of engagement for attendees invested in the digital transformation of healthcare.
Secure Your Spot Visitor registration is now open at www.medicalfairthailand.com
The effort to meet all the challenges set before the team led to a product that mixed three different types of LSR, a mixing process at which Silcotech is an expert.
“Implementing multiple materials within a single device was the only path we saw at the time to get the part to meet both the functional expectation and the safety requirements in creating a nipple that emulated more natural breast behaviour – allowing a baby to control the flow of milk through the duct,” Maloney explained.
The first-generation mōmi nipple mixed three types of LSR, with the mixing done by Silcotech. The second generation now features one type of LSR. The nipple is currently offered in three flow rates to grow along with baby
Reaping the fruits of collaboration: the nipple
The three-material Gen 1 mōmi nipple proved a big success for the company, resulting in enthusiastic praise from users along with encouraging suggestions on how to make the product even better.
So is the continuing process of production and response, according to Maloney. “Product design is an iterative process. You need to develop a product to get out there in the market to see how they react, hear the feedback and then stay on your feet and move with whatever that feedback is. Our evolution went down that path and, as we learned, we were able to strip away some functionally that we thought we needed that we didn’t, and it was all based on true feedback from the field and genuine physical testing.”
“We found out that the geometry of the Gen 1 nipple, while getting its intended job done very well, led to suboptimal oral function for some babies,” said Eason. “In Gen 2, we were able to adjust the geometry while also reducing the number of LSRs used from three to one. We’re looking forward to even more improvement in Gen 3.”
While all of the adjustments made along the way seem matter-of-fact in hindsight, the road wasn’t uniformly smooth.
Echoing Thomas Edison’s sentiments about the importance of discovering what doesn’t work on the path to discovering what does, Maloney said, “The acceptance of failure and the ability to fail fast is critical, because the reality is that success requires iterations of failure. The more often you can fail the more likely you are to succeed. Don’t get bogged down by bumps in the road as you’re travelling to your path of success.”
Expounding on the benefits of a good personality mix, Eason added, “You have to have the right people in the boat. There are programmes that we’ve walked away from because of character and integrity issues.”
The Momtech/Silcotech collaboration has been a shining example of how to successfully manage multiple creative minds to bring a product to fruition after the invariable multiple rounds of design iterations.
As a result, mōmi baby nipples are helping many thousands of mothers and babies enjoy a stress-free transition between breastfeeding and bottle feeding.
Safe and sustainable materials take hold of the baby care market
Needless to say, the use of LSR in baby care products has gone past its teething stage: it is here to stay, as its application is expanding rapidly due to growing demand for safer, longer-lasting, and more hygienic options. LSR has become a preferred material for items like bottle nipples, pacifiers, and teething rings because it is non-toxic and free from harmful substances. Its biocompatibility, hypoallergenic properties, and resistance to heat and cleaning agents make it ideal for daily use and repeated sterilisation.
By 2030, the LSR market across various applications is projected to reach 386 kilotonnes, growing at a compound annual growth rate (CAGR) of 6.9% from 2025, when it is estimated to be 276 kilotonnes, according to Mordor Intelligence ’s LSR market share analysis.
Looking further ahead, the market is expected to expand from nearly US$3.6 billion in 2025 to US$11 billion by 2037, based on Research Nester ’s Liquid Silicone Rubber Market Size, Growth Report 2037
The baby care and healthcare industries are anticipated to capture a larger share of this market in the coming years. However, growth may be constrained by the relatively high cost of LSR as a material.
Moreover, the LSR market for baby care is expected to witness significant growth across several key regions, driven by rising demand in the healthcare and baby care sectors, ongoing technological advancements, and supportive government initiatives. One such initiative is China’s 2021–2025 action plan for improving child health, which is expected to further boost demand for LSR in the years ahead, according to Mordor Intelligence.
6 – 9 AUGUST
Cambodia Int’l Machinery Industry Fair (CIMIF)
Venue: Phnom Penh, Cambodia
Tel: + 886 2 26596000 Fax: +886 2 26597000
Email: akai@chanchao.com.tw
Website: www.chanchao.com.tw/CIMIF/ Website: www.chanchao.com.tw/hanoiPrintPack
21 – 23 AUGUST
Interfoam Southeast Asia
Venue: SECC, Vietnam
Tel: +86 10 5867 7299 Fax : +86 10 5867 7126
Email: ouyang@interfoam.cn Website: www.interfoamvietnam.com
3 – 5 SEPTEMBER
Propak India
Venue: India Expo Mart, Greater Noida, Delhi NCR, India
Tel: +91 98338 98098
Email: prachi.shah@informa.com Website: www.propakindia.com
3 – 5 SEPTEMBER
4th PHA World Congress - 2025
Venue: Düsseldorf, Germany
Tel: + 49 2161 -664864
Email: phaworldcongress@gopha.org
Website: www.pha-world-congress.com
3 – 5 SEPTEMBER
UTECH Asia | PU China
Venue: Poly World Trade Expo, Guangzhou, China
Tel: +44 0 7739 302081
Email: mabarber@crain.com Website: www.puchina.eu
10 – 12 SEPTEMBER
3P Pakistan
Venue: Karachi Expo Center, Pakistan
Tel: +92 21 35810637-39
Email: enquiry@plasprintpack.com Website: www.plasprintpack.com
10 – 13 SEPTEMBER
VietnamPrintPack
Venue: Ho Chi Minh City, Vietnam
Tel: +886 2 2659 6000
Email: exfdp@chanchao.com.tw Website: www.vietnamprintpack.chanchao.com.tw
17 – 20 SEPTEMBER
Pack Print International
Venue: BITEC, Bangkok, Thailand
Tel: +65 6332 9620 Fax: +65 6332 9655
Email: ppi@mda.com.sg Website: www.pack-print.de
17 – 20 SEPTEMBER
VietnamPlas
Venue: Saigon Exhibition & Convention Center, Ho Chi Minh City, Vietnam
Tel: +886 2 2659 6000
Email: exfdp@chanchao.com.tw Website: www.vietnamplas.chanchao.com.tw
18 – 20 SEPTEMBER
PackPrintPlas Philippines
Venue: SMX Convention Center Manila, Philippines
Tel: +63 917 706 8134
Email: info@packprintplasphilippines.com
Website: www.packprintplasphilippines.com
Check out the Advertisers' page on our website.
Information is categorised by the YEAR & DATE of publication for easy reference.
For further details, email us at: news@plasticsandrubberasia.com
1 – 3 OCTOBER
METALEX Vietnam
Venue: Ho Chi Minh City, Vietnam
Tel: +84 286 287 3355
Email: metalexvietnam@rxtradex.com
Website: www.metalexvietnam.com
7 – 8 OCTOBER
International Trade Fair for Composite Materials, Technologies and Products - Kompozyt Expo
Venue: Expo Kraków, Poland
Tel: +48 12 651 90 38
Email: pluciennik@targi.krakow.pl
Website: www.kompozyt-expo.pl
8 – 15 OCTOBER
K 2025
Venue: Düsseldorf, Germany
Tel: +49 211 4560 01
Email: info@messe-duesseldorf.de Website: www.k-online.com
15 – 17 OCTOBER
ASEAN Ceramics
Venue: Impact Exhibition & Convention Centre, Bangkok, Thailand
Tel: +65 6433 7046
Email: aseanceramics@mmiasia.com.sg
Website: www.aseanceramics.com/thailand
21 – 24 OCTOBER
AllPack Indonesia
Venue: JIExpo Kemayoran, Indonesia
Tel: +62 21 6345861
Email: info@kristamedia.com
Website: www.allpack-indonesia.com
28 – 30 OCTOBER
Film & Tape Expo
Venue: Shenzhen World Exhibition and Convention Center, China
Tel: +86 21 2231 7018
Email: edison.li@rxglobal.com
Website: www.film-expo.com
12 – 15 NOVEMBER
Vietnam International Industrial Fair (VIIF)
Venue: Hanoi, Vietnam
Tel: +84 24 3834 5655
Email: viif@vefac.vn Website: www.viif.vn
13 – 15 NOVEMBER
Plastics Recycling Show India (PRSI)
Venue: Bombay Exhibition Center, Mumbai, India
Tel: +44 0 7739 302081
Email: mabarber@crain.com
Website: www.prseventindia.com
19 – 22 NOVEMBER
Plastics & Rubber Indonesia
Venue: JIExpo, Kemayoran, Indonesia
Tel: +62 21 2525 320
Email: faradiba@pamerindo.com
Website: www.plasticsandrubberindonesia.com
Publishing Office / Scandinavia, Benelux & France
Postbus 130, 7470 AC Goor, The Netherlands
Tel: +31 547 275005 Fax: +31 547 271831
Email: arthur@kenter.nl
Contact: Arthur Schavemaker
European Correspondent: E-mail: jeanet@kenter.nl
Contact: Jeanet Draaijer
Regional Office
B6-11, Menara Indah, Jalan 9, Taman TAR 68000 Ampang, Selangor, Malaysia
Mobile: +6017-8849102
Email: tej@plasticsandrubberasia.com
Contact: Tej Fernandez
China & Hong Kong
Room 6B, Floor 6, Building HengLong, No. 50 Renming Zhong Road, Zhangjiagang, 215600 China
Tel: 0512-58919146
Fax: 0512-58919145
Mobile: +86-17751702720
Email: henry.xiao@matchexpo.com
Contact: Henry Xiao/Zhu Wei
Malaysia (Print, Web, Digital Advertising & Conferences)
Tara Media & Communications
Mobile: +6017 610 1270
E-mail: yokepeng@taramedia.com.my
Contact: Yoke Peng
Southeast Germany, Switzerland & Austria
Verlagsbüro G. Fahr e.K
Breitenbergstrasse 17
D-87629 Füssen, Germany
Tel: +49 8362 5054990
Fax: +49 8362 5054992
Email: info@verlagsbuero-fahr.de
Contact: Simon Fahr
North-West Germany
JRM Medien+Verlag Minkelsches Feld 39 D-46499 Hamminkeln, Germany
Tel: +49 2852 94180
Fax: +49 2852 94181
Email: info@jwmedien.de
Contact: Renate Wickenhöfer
Malaysia. India, Indonesia, Singapore, Thailand, Australia, New Zealand, Korea & Philippines
Tara Media & Communications
B6-11, Menara Indah, Jalan 9, Taman TAR 68000 Ampang, Selangor, Malaysia
Mobile: +6017-8849102
Email: tej@plasticsandrubberasia.com
Contact: Tej Fernandez
Italy, Spain & Portugal
MediaPoint & Communications Srl Corte Lambruschini, Corso Buenos Aires, 8, Vo Piano - Interno 9, 16129 Genova, Italy
Tel: +39 010 570 4948 Fax: +39 010 553 0088
Email: info@mediapointsrl.it
Contact: Fabio Potesta
Taiwan 宗久實業有限公司
Worldwide Services
11F-B, No.540 Sec.1, Wen Hsin Rd., Taichung, Taiwan
Tel: +886 4 23251784 Fax: +886 4 23252967
Email: global@acw.com.tw
Contact: Robert Yu 游宗敏
USA & Canada
Plastics Media International
P. O. Box 44, Greenlawn, New York 117430, USA
Tel/Fax: +1 631 673 0072
Email: mjm@4m-media.com
Contact: Michael J Mitchell
www.plasticsandrubberasia.com www.rubberjournalasia.com www.injectionmouldingasia.com
September 3-5
Poly World Trade Expo • Guangzhou
3-5 September 2025
Poly World Trade Expo, Guangzhou, China
The leading event for the Chinese Polyurethanes Industry.