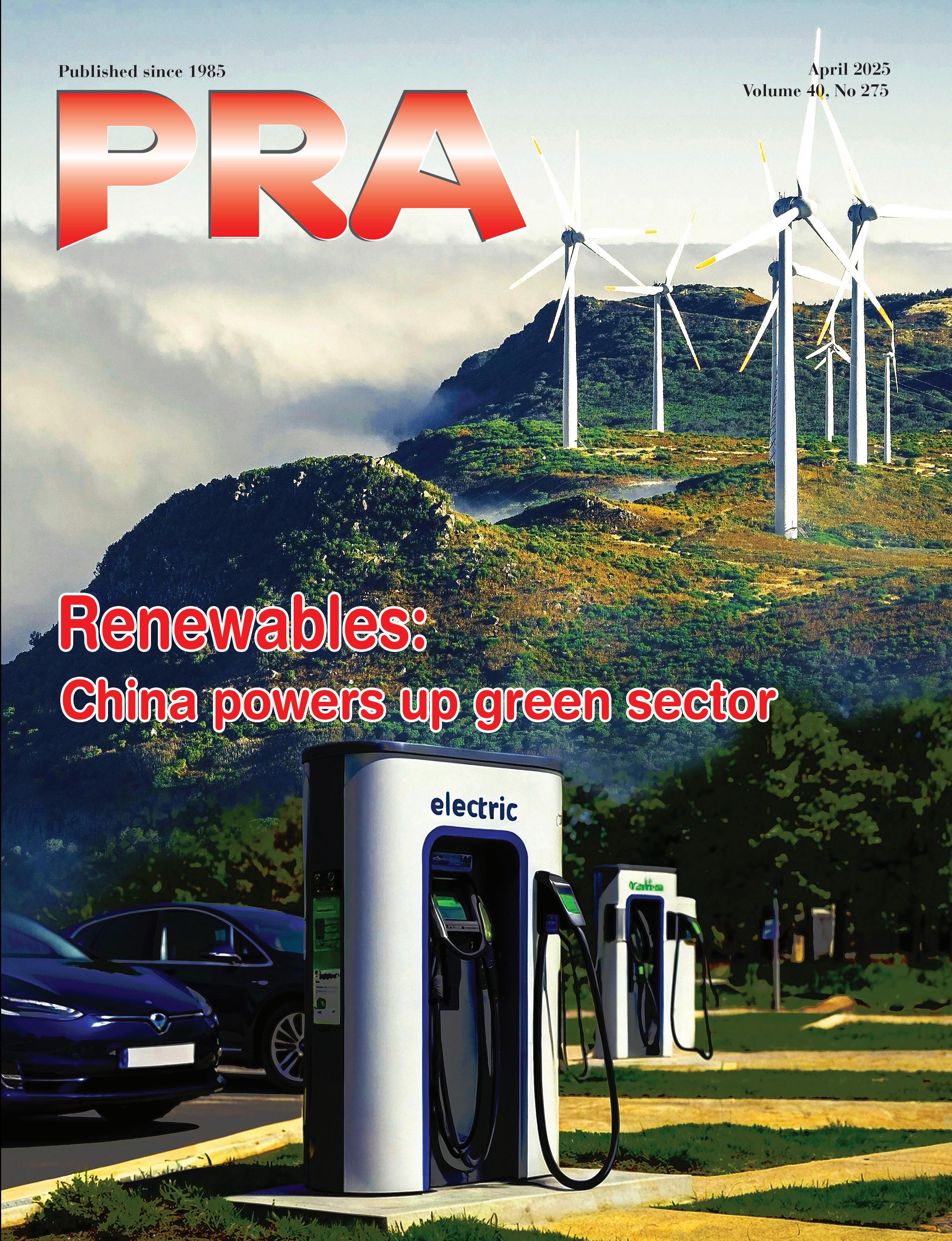
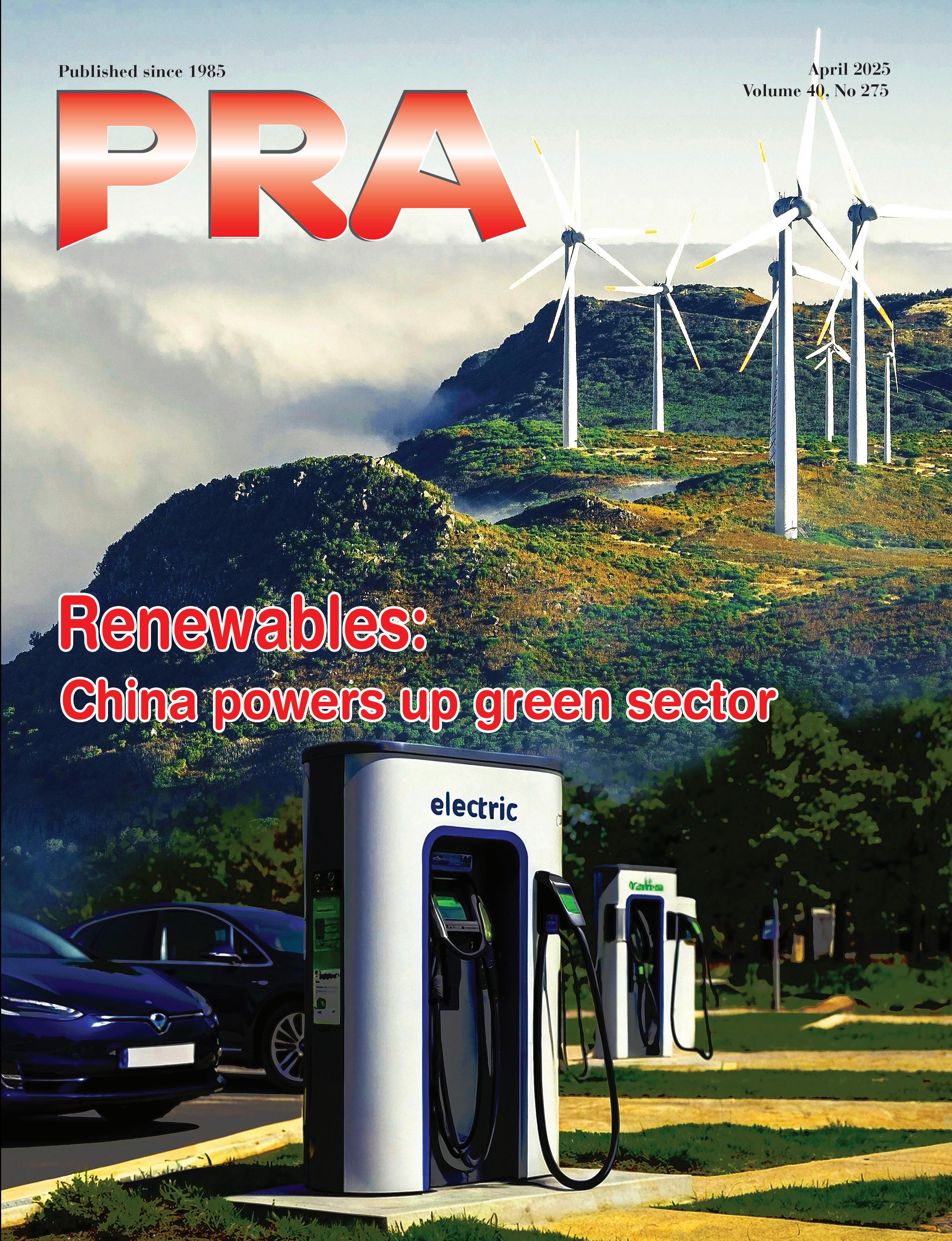
In this issue

Features
8 Country Focus: China – China is leveraging the country’s economic growth through its Made-in-China policy and investments in clean energy, electric vehicles and petrochemical products.
11 Additives – Mighty additives are packing a punch in materials for industries like construction, electrical, and packaging to meet rising demands for performance, durability, and sustainability.
13 Packaging – Against the backdrop of stringent regulations, ExxonMobil, India’s UFlex and Borealis are offering sustainable solutions. Meanwhile, open traceability is offered for materials with the Digital Product Passport (DPP) platform by R-Cycle, Korozo Group and Henkel
15 Thermoplastic Elastomers – From medical devices to sneakers, TPEs are redefining material innovation across industries, adds Angelica Buan in this report
17 Film/Sheet Industry – At the upcoming Chinaplas show in Shenzhen, machinery makers SML and W&H will showcase the latest; while Mexico’s Oben Group has commissioned a high-output BOPP line from German machine maker Brückner
Regulars
1 Industry News
5 Materials News supplements

Recycling: TAustrian machinery supplier Erema views opportunities for large-scale PET recycling systems in China
liquid silicone Rubber Moulding: Liquid silicone rubber (LSR) is making a clear impact in automotive and medical applications, says Angelica Buan in this report
chinaplas 2025: Industry innovations from exhibitors and a line-up of concurrent events will be presented at the show to be held at Shenzhen World Exhibition & Convention Centre, China, from 15-18 April 2025
Tyre: The recent higher than expected trade tariffs imposed by the US may shake up the Asian tyre sector that will require tyre makers to innovate and become more competitive in the global market
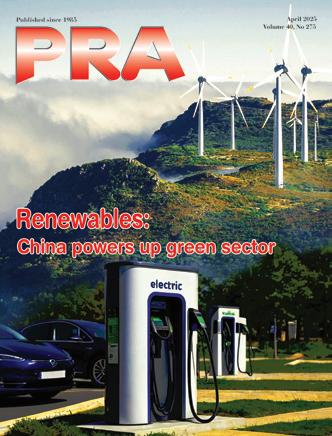
China is pushing ahead with its agenda on Made-in-China products and also scaling up renewable energy, with electric vehicles as one of the main drivers


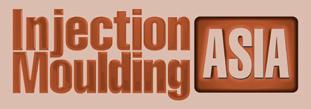
publisher/editor-in-chief
Arthur Schavemaker
Tel: +31 547 275005
Email: arthur@kenter.nl
Associate publisher/executive editor
Tej Fernandez
Tel: +6017 884 9102
Email: tej@plasticsandrubberasia.com
european correspondent
Jeanet Draaijer
E-mail: jeanet@kenter.nl
Asian correspondent
Angelica Buan
Email: gel@plasticsandrubberasia.com
circulation
Stephanie Yuen
Email: stephanie@taramedia.com.my
layout/design
Prestige Trading
Email: prestige9a@gmail.com
permits
ISSN 1360-1245
is published 4 (four) times a year in English by Kenter & Co Publishers’ Representatives BV.
Whilst every effort is made to ensure that the information contained in this publication is correct, the publisher makes no warranty, expressed or implied, as to the nature or accuracy of such material to the extent permitted by applicable law.
© 2025 Kenter & Co Publishers’ Representatives BV No part of this publication may be reproduced, stored or used in any form, or by any means, without specific prior permission from the publisher.
PRA is a digital publication that is circulated free to trade readers in the plastics and rubber industry. Please view this link to subscribe/renew your free subscription: http://plasticsandrubberasia.com/register.html
www.plasticsandrubberasia.com www.rubberjournalasia.com www.injectionmouldingasia.com www.eog-asia.com
Strong growth for bio-based polymers; Asia in the lead
The year 2024 was a “respectable” year for biobased polymers, with an overall expected CAGR of 13% to 2029, according to a new market and trend report “Bio based Building Blocks and Polymers – Global Capacities, Production and Trends 2024–2029”, written by Nova-Institute.
It adds that overall, bio-based biodegradable polymers have large installed capacities with an expected CAGR of 17% to 2029, but the current average capacity utilisation is moderate at 65%. In contrast, biobased non-biodegradable polymers have a much higher utilisation rate of 90%, but will only grow by 10% to 2029.
The share of aliphatic polycarbonates (APC; circular and linear), poly(butylene adipate-co-terephthalate) (PBAT), polyethylene (PE), polyethylene terephthalate (PET), polyhydroxyalkanoates (PHA) and starchcontaining polymer compounds (SCPC) was less than 5%.
Casein polymers (CP), ethylene propylene diene monomer rubber (EPDM), polybutylene succinate (PBS), polyethylene furanoate (PEF) and polypropylene (PP) accounted for less than 1% of the total bio-based polymer production volume and are not shown.
Additionally, the total production volume of bio based polymers has been 4.2 million tonnes in 2024, which is 1% of the total production volume of fossil based polymers, and the CAGR of bio-based polymers is, with 13%, significantly higher than the overall growth of polymers (2–3%). With these growth rates, the share of bio-based polymers will increase up to 2%.
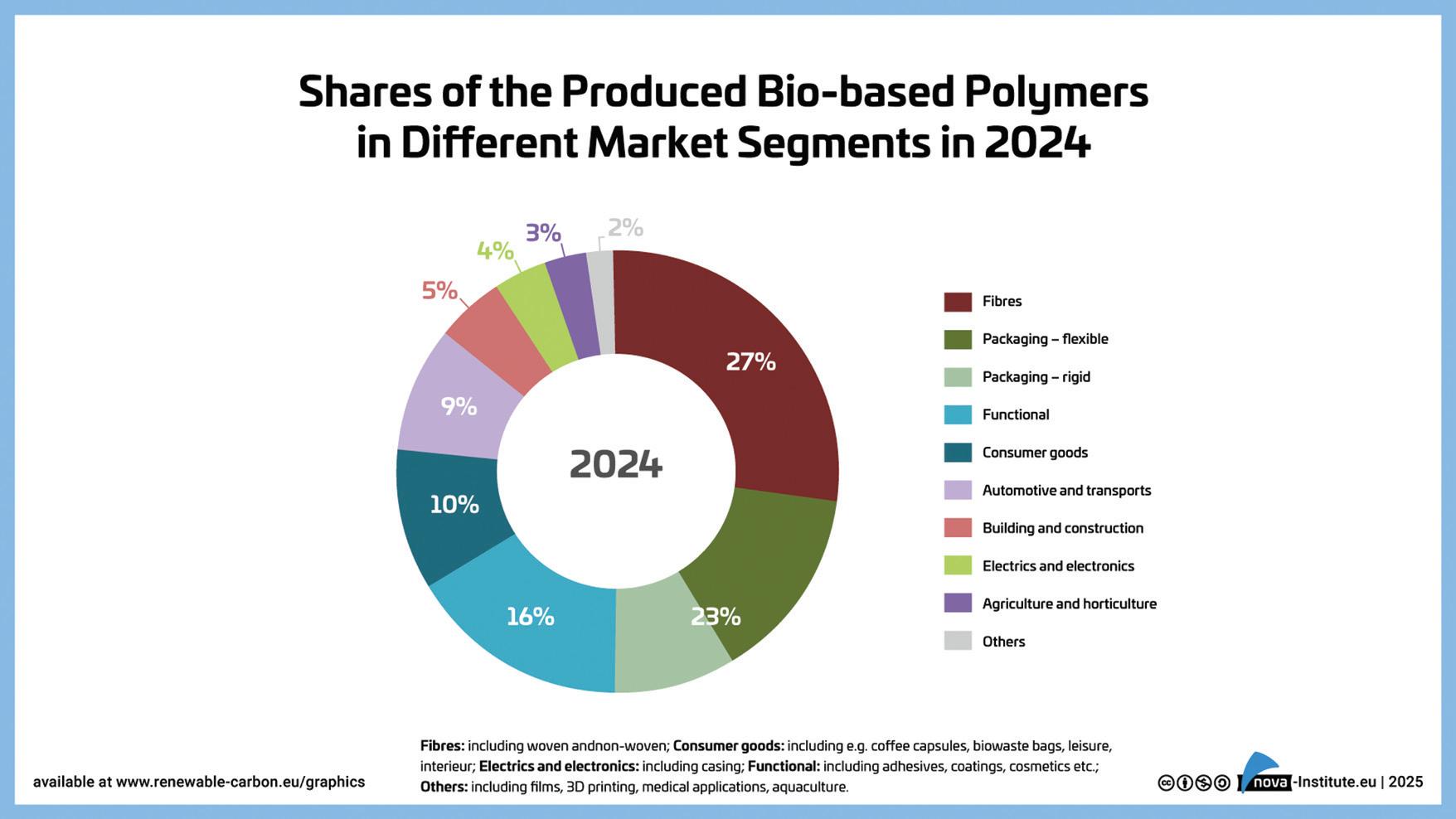
The report also highlights that while Asia and North America will continue to strengthen their global role in the supply of bio-based polymers, Europe's market share is expected to decline by 2029.
Types of resins
Of the total 4.2 million tonnes of bio-based polymers produced in 2024, cellulose acetate (CA), with a biobased content of 50%, and epoxy resins, with a biobased content of 45%, account for more than half of the bio-based production, 26% and 32%, respectively.
This is followed by 30% bio-based polyurethanes (PU) with 9%, 100% bio-based polylactic acid (PLA) with 8%, polyamides (PA) (60% bio-based content) with 7% and polytrimethylene terephthalate (PTT) (31% bio-based content) with 6%.
The increase in production capacity from 2023 to 2024 is mainly due to the expansion of PLA capacity and epoxy resin production in Asia, as well as a global increase in PU production.
Also, PP, PHA and PEF are particularly expected to grow continuously by 65% on average until 2029. While PHA capacities will increase mainly in Asia and PEF in Asia and in Europe, PP capacities will increase mainly in North America.
Demand for
bio-based
feedstock and land use
Considering the steadily increasing demand for bio based polymers, the need for biomass feedstocks should be considered as an important factor. This is particularly true for the recurring debate on the use of food crops for the production of bio based polymer.
The total demand for biomass was 13.6 billion tonnes for feed, bioenergy, food, material use, biofuels as well as bio based polymers.
While the majority of biomass (56%) is used for feed production, only 0.023% is required for the production of bio-based polymers, thus resulting in a biomass feedstock demand of 3.2 million tonnes for the production of bio-based polymers and reflects a land use share of only 0.013%.
This is due to the fact that the main feedstocks used in the production of bio-based polymers are sugars (25%) and starch (20%), which are obtained from highyield crops such as sugar cane and maize, resulting in a high area efficiency.
In addition, the protein content of these crops is used not only for polymer production but also for animal feed, so only the corresponding part is allocated to polymer production. Glycerol (31%), a biogenic by-product of biodiesel production, is a biomass with only an indirect, passive land use. This glycerol is mainly used in the production of epoxy resins via epichlorohydrin as an intermediate.
The biomass used also included 12% from non edible plant oils, such as castor oil, 9% from cellulose (mainly used for CA) and 3% from edible plant oil.
Of the bio based polymers produced (fully and partially bio based), 2.2 million tonnes were actual bio based components of the polymers (52%), meaning that almost 1.6 times more feedstock was required than was actually incorporated into the final product. The 1.4 million tonnes (36%) of feedstock that did not end up in the product is due to the high number of conversion steps and the associated losses of feedstock and intermediates, as well as the formation of by products.
Global shift to renewable carbon to overcome challenges
The key market drivers in 2024 were several global brands that have adapted their strategic agendas to
transition the polymers, plastics and chemicals industry to become sustainable, climate-friendly and part of the circular economy, thus offering their customers green solutions and alternatives to petrochemical products.
The only way to achieve this successful transition is to fully replace fossil carbon with renewable carbon from alternative sources: biomass, CO2 and recycling (www.renewable-carbon.eu).
By expanding their feedstock portfolio to include renewable carbon in addition to fossil-based carbon, these brands are leading the way from a market perspective. In particular, the use of biomass has increased and will continue to increase the supply of bio-based polymers.
Nevertheless, the market remains challenging, especially in Europe. While Asia and North America will continue to strengthen their global role in the supply of bio-based polymers, Europe's market share is expected to decline by 2029.
With new investments in several large-scale biobased polymer production capacities, Asia and North America will increase their market share by 4% and 5%, respectively, and together they will account for more than 80% of the global supply of bio-based polymers. Although some new large-scale plants are also planned in Europe, this will not be enough to prevent Europe's market share from falling from 13% today to 10% in 2029.
Although, the European policy landscape for biobased polymers is constantly evolving, it does so not yet provide a consistent policy framework that sufficiently incentivises the benefits, properties and applications of bio-based polymers – unlike other regions of the world.
Highlights of bio-based polymers
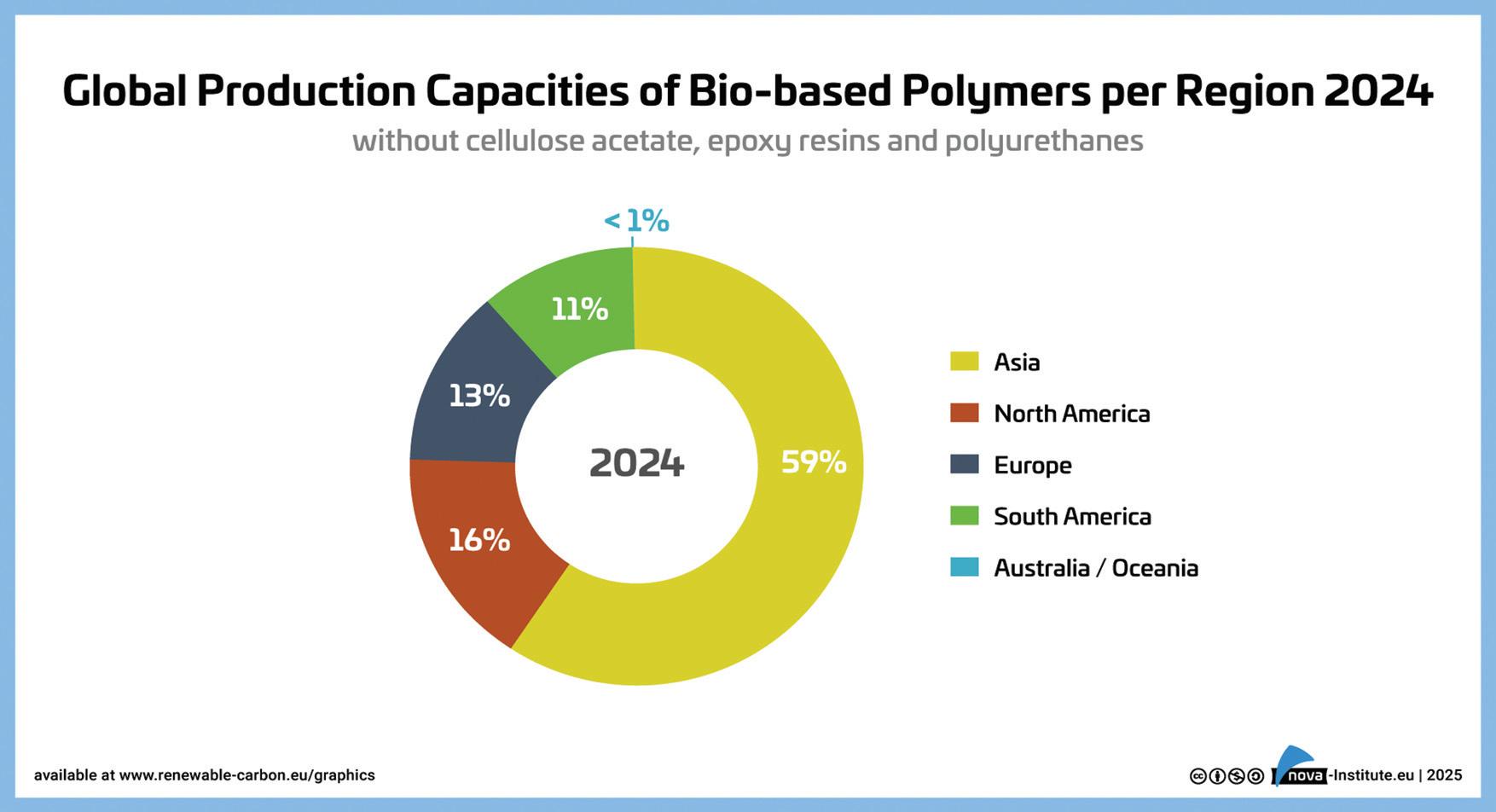
The global polymer market includes functional and structural polymers, rubber products as well as man made fibres. This report focuses on the bio based share of the structural polymers. Bio based structural polymers are composed of the polymers that will later form the structural mass of the finished plastic part, which is covered in detail in this report and the bio based linoleum part. Together, they total 4.3 million tonnes.

On the other hand, the total amount of bio based functional polymers consists of bio based functional polymers and paper starch, giving 13.7 million tonnes. In addition to these two groups, which account for 18 million tonnes of bio based functional and structural polymers, rubber products and man made fibres can also be bio based. In total, 15 million tonnes of rubber products and 7.8 million tonnes of man made fibres are made from bio based resources, 51% and 9%, respectively.
The different pathways of bio based “drop in”, “smart drop in” and “dedicated” inputs within the chemical production chain are also highlighted in the report. For each group, certain bio based polymers are presented as examples. In addition, biodegradable bio based polymers are highlighted with a green dot.
The different groups of bio based polymers are subject to different market dynamics. While drop ins have direct fossil based counterparts and can replace them, the dedicated ones have new properties and functionalities that are not available from petrochemicals. Both have their own advantages and disadvantages from a production and market perspective. While bio based drop in chemicals are bio based versions of existing petrochemicals that have established markets and are chemically identical to existing fossil based chemicals, smart drop in chemicals are a special sub group of drop in chemicals. Although they are chemically identical to existing chemicals based on fossil hydrocarbons, their bio based pathways offer significant process advantages over conventional pathways.
In addition, these bio based pathways can be based on completely new approaches, such as epichlorohydrin, where the fossil feedstock propylene is not replaced by bio based propylene but by glycerol from biodiesel production. Dedicated bio based chemicals are chemicals that are commercially produced via a dedicated pathway and do not have an identical fossil based counterpart.
Total installed capacity in 2024 was 5.2 million tonnes with an actual production of 4.2 million tonnes. Capacity is expected to increase to 9.5 million tonnes in 2029, indicating an average compound annual growth rate (CAGR) of around 13%. The following polymers
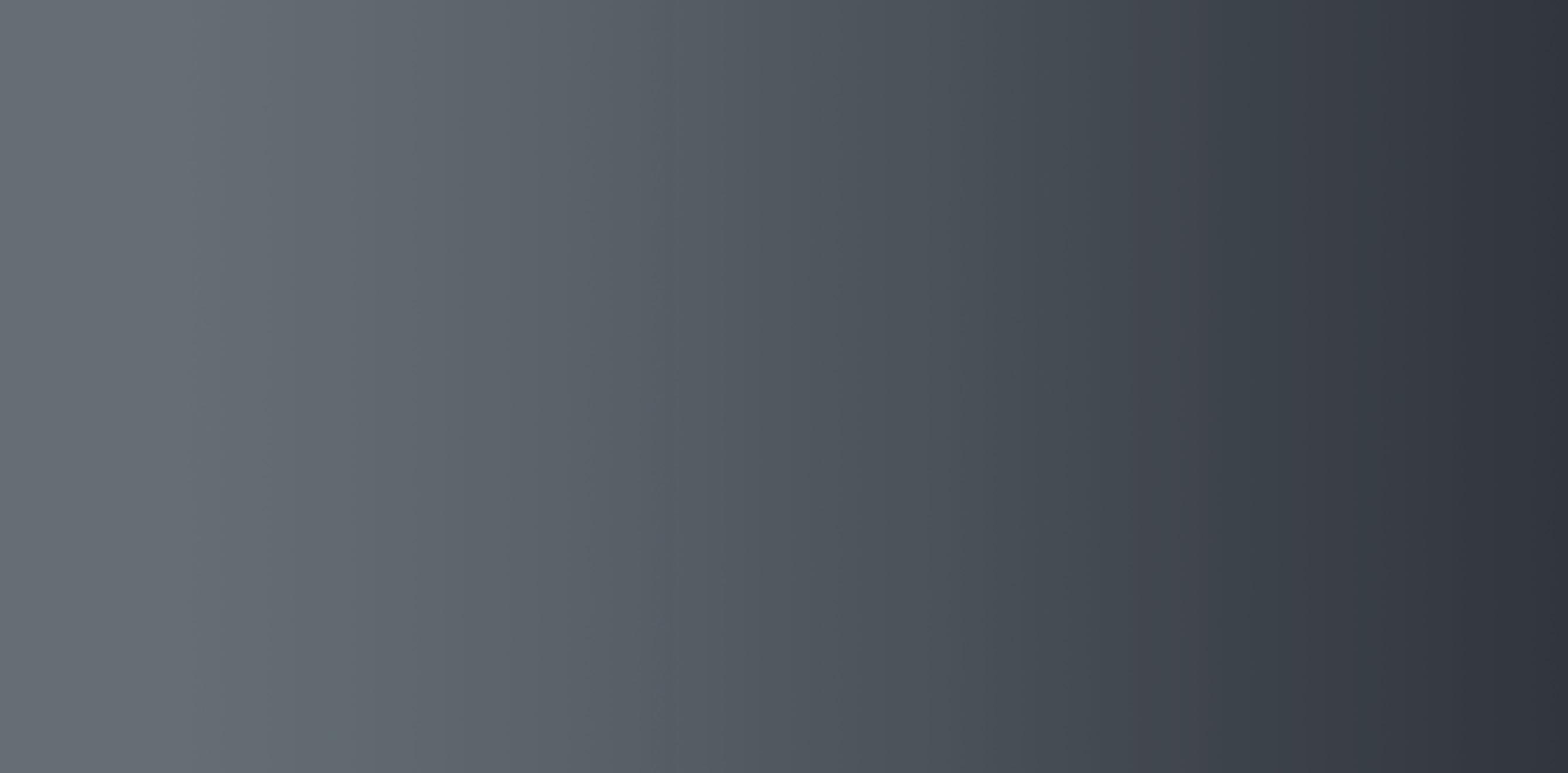
Full recyclability, excellent transparency and impressing mechanical properties: Ultra-thin MDO-PE and MDO-PP film produced on SML’s latest generation of cast film lines open new opportunities to manufacturers and form the technical basis for the mono-material packaging solutions of tomorrow.
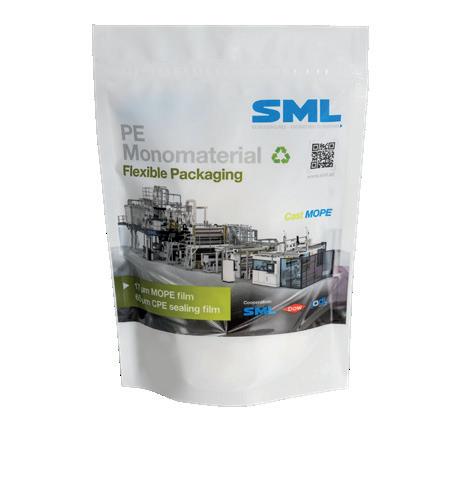

show an even higher increase, well above the average growth rate: PP, PHAs and PEF are expected to grow continuously by an average of 65 % until 2029.
Asia leading in the market
Asia as the leading region in 2024 has the largest installed bio based production capacities worldwide with 59%, with the largest capacities for PLA and PA. North America had 16%, with large installed capacities for PLA and PTT and Europe had 13%, mainly based on installed capacities for SCPC and PA.
South America had a share of 11% with major installations for PE and Australia/Oceania less than 1% of was based on SCPC.
With an expected CAGR of 25% between 2024 and 2029, North America has the highest growth in bio based polymer capacities compared to other regions of the world. This increase is mainly due to expanded and new production capacities for PHA and PP.
Market segments for bio-based polymers
Today, bio based polymers can be used in almost all market segments and applications, but the different applications per polymer can be very different.
In 2024 fibres including woven, non woven (mainly CA and PTT) had the highest share with 27%. Packaging, flexible and rigid, had a total share of 23%, followed by functional applications with 16 % (mainly epoxy resins and PU), consumer goods with 10% (mainly epoxy resins, PLA and PA) and automotive and transport with 9% (mainly PU, PA and epoxy resins).
Building and construction accounted for 5% (mainly epoxy resins and PU) and electrics and electronics for 4% (mainly epoxy resins and PA).
The market segments agri/horticulture and others had a market share of 3% and 2%, respectively.
Bio-based/non-biodegradable polymers and biodegradable polymers
Bio-based non-biodegradable polymers show a CAGR of 10% to 2029. The highest growth is expected for PP and PEF, followed by PE.
Despite a current moderate average utilisation rate of 65%, bio-based biodegradable polymers show a high growth of 16% to 2029. This is mainly due to high growth rates for PHA, PLA and casein polymers.
The biodegradability of polymers is completely independent of the resource from which the polymer is made, so being bio-based does not necessarily mean that certain polymers are biodegradable. PBS and copolymers such as poly(butylene succinateco-butylene adipate) (PBSA) are both industrial compostable, but only PBSA biodegrades also under home composting conditions and in soil, according to the conditions defined in the established standards and certification schemes.
The same applies to PBAT, which is industrial compostable and, for certain grades, also home compostable and biodegradable in soil. This biodegradability applies to both bio-based and fossilbased PBS and PBAT.
However, fossil-based PBS and PBAT production capacities, mainly in Asia, were at 3 million tonnes in 2024, with an assumed actual production of around 600,000 tonnes. Until 2029 fossil-based PBS and PBAT production capacities are not expected to increase significantly, with a CAGR of 1%.

Emerging innovations, sustainable solutions leading the industry
Latest plastic innovations with bioplastics, biodegradables, carbon capture and PCR/PIR are driving sustainable plastics forward, according to Angelica Buan in this report.
Production of plastics has come a long way in reducing environmental impact. Advancements cover the entire lifecycle of plastics, from how they're made to how they're disposed of, focusing on producing fewer emissions, enhancing recyclability, and using renewable materials. Still, scaling up sustainable plastics comes with challenges, including cost, efficiency, and technological limitations. Issues like production scalability, regulatory hurdles, cost reduction, and market acceptance remain key concerns.
Industry players are exploring new solutions to meet sustainability goals, while researchers continue developing technologies to make sustainable plastics a viable mainstream option.
Microorganisms reengineering biodegradable plastics
Biodegradable plastics break down through microbial activity, reducing waste and environmental impact. Derived from renewable resources, petrochemicals, or both, they offer a sustainable alternative to conventional plastics. Benefits include lower emissions, reduced landfill waste, and composting compatibility, making them useful in packaging, agriculture, and waste management.
Research continues to improve biodegradation efficiency and mechanical properties to rival traditional plastics, plus composting can also enhance soil health.
A study by the University of Connecticut (UConn) and bioplastics manufacturer Novamont found that Mater-Bi,

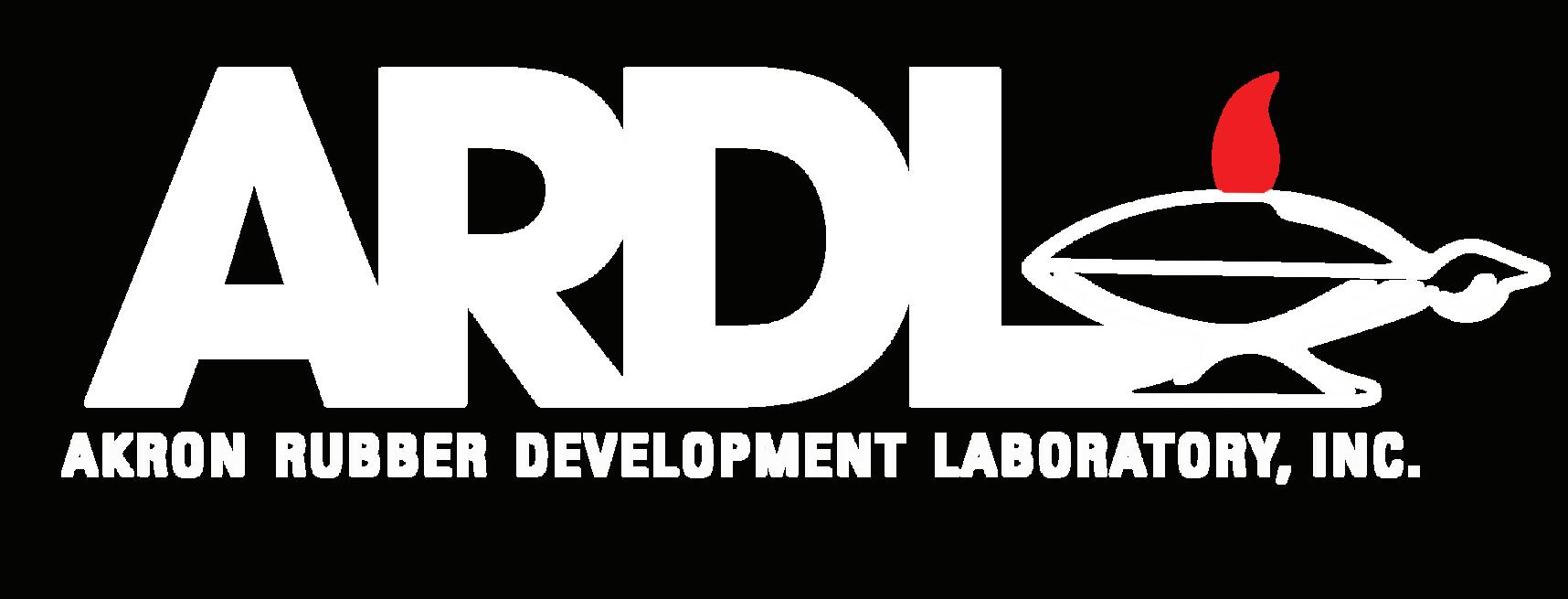
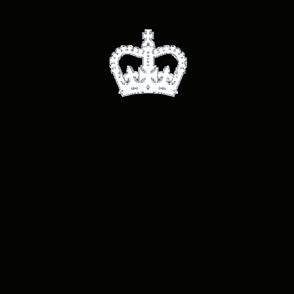
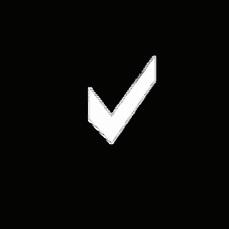
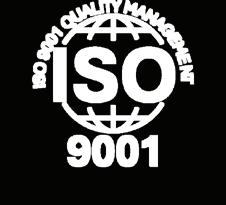
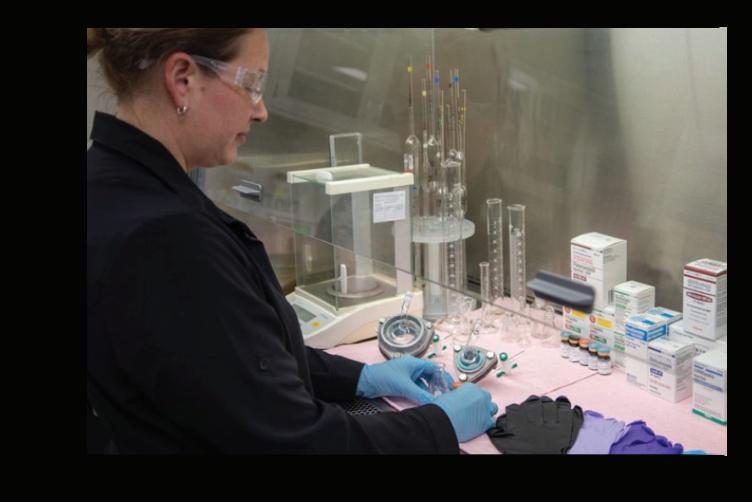

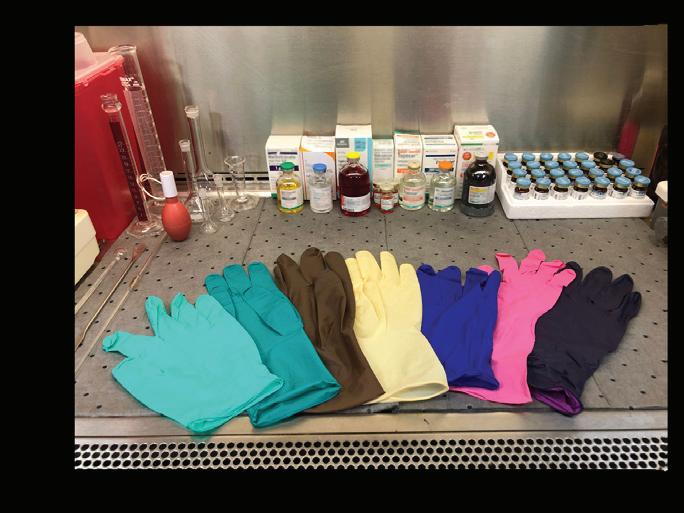
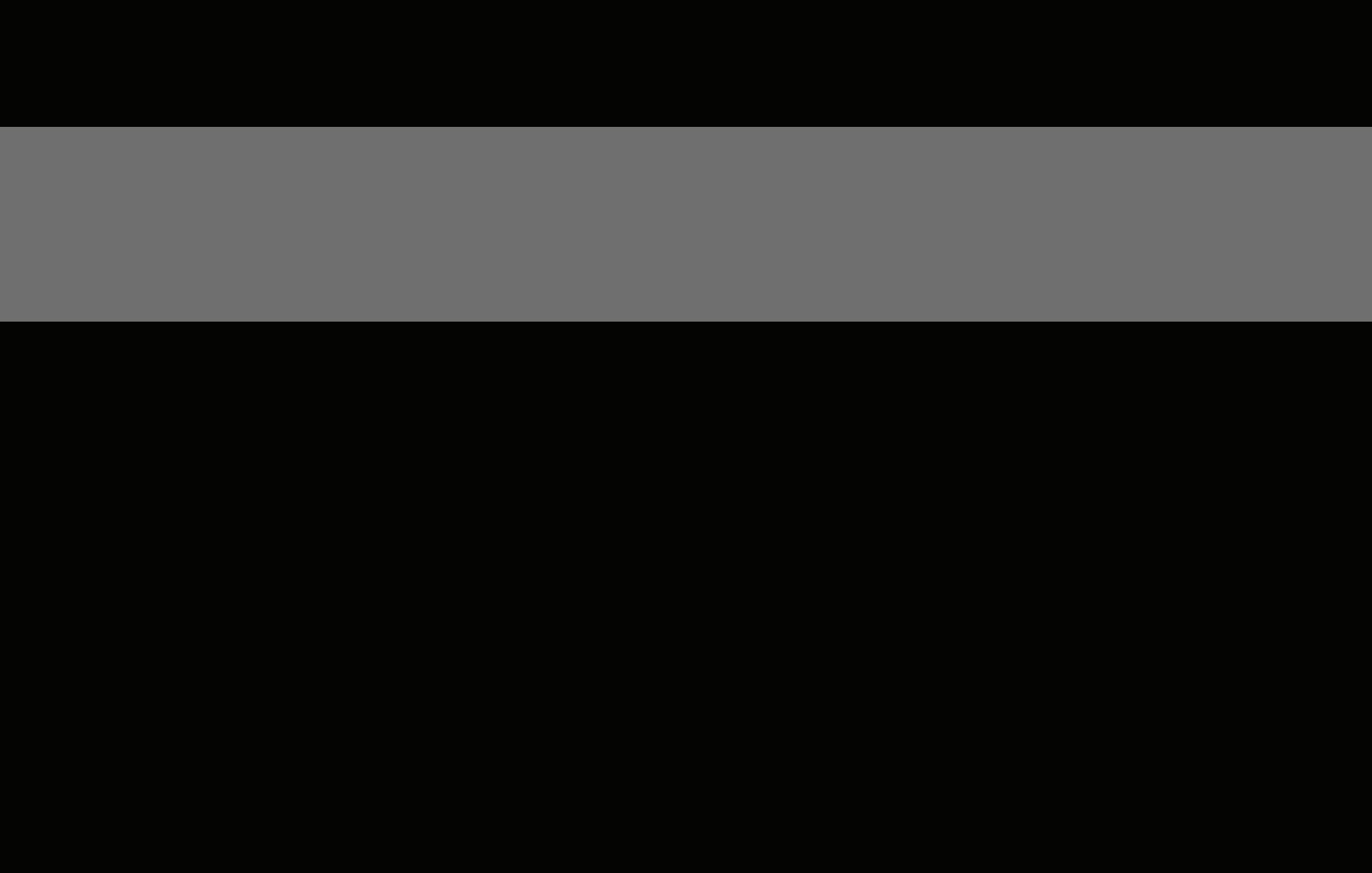
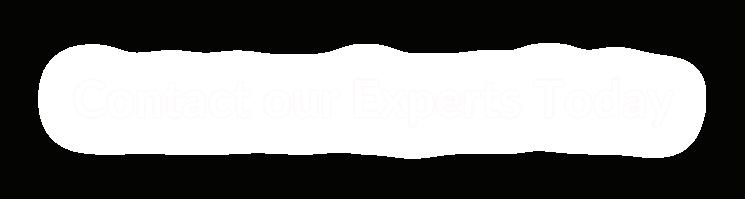
a starch-based polymer, degraded by nearly 50% over nine months in a marine setting, exceeding traditional plastics. Published in the Journal of Polymers and the Environment, the study tested Mater-Bi compostable bags in seawater, excluding larger organisms that could interfere with results. The material lost 25% to 47% of its mass or area, with warmer temperatures accelerating the process.
Led by researchers Hannah Collins, Larissa Tabb, and marine sciences professor Evan Ward, the study noted that biodegradable plastics like Mater-Bi could help reduce marine plastic pollution, particularly in aquaculture applications such as kelp farm lines and oyster grow-out bags.The collaboration with Novamont provided insights into real-world biodegradation beyond controlled lab settings, the researchers said.
Beyond biodegradation, researchers are also exploring new ways to develop bioplastics from renewable sources. Scientists at the Korea Advanced Institute of Science & Technology (KAIST) have created a method to produce polyester amide, a next-generation bioplastic, using microorganisms instead of fossil fuels. Headed by Professor Lee Sang-yeop of KAIST’s biochemical engineering department, this breakthrough, published in Nature Chemical Biology, signifies the first successful microbial production of polyester amide.
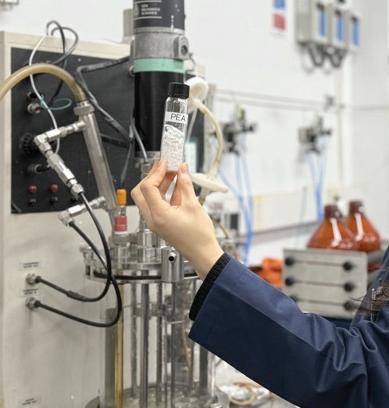
KAIST has successfully developed the first microbial production of polyester amide by engineering microbes to produce nine polyester amides from glucose via fermentation
Polyester amide, a durable plastic-nylon blend, is traditionally petroleum-based and polluting. The KAIST team engineered microbes to produce nine polyester amides from glucose, earth's most abundant biomass. Through an optimised fermentation process, they demonstrated the potential for large-scale production.
Testing by the Korea Chemical Research Institute confirmed that the resulting bioplastic has properties comparable to HDPE, making it a viable alternative to conventional plastics. Meanwhile, ongoing research is focusing on improving production efficiency for industrial uses.
Plastics from thin air: using carbon emissions as feedstock
Conventional petroleum-based plastics are making the industry a major contributor to greenhouse gas emissions. Currently, plastics account for about 8% of global oil consumption, a figure that could reach 20% by 2050 if current trends persist, according to the World Economic Forum
Using carbon dioxide (CO2) as a feedstock offers a way to reduce this environmental impact by decreasing reliance on fossil fuels and lowering emissions.
Capturing CO2 from industrial sources or directly from the atmosphere and converting it into polymers presents a sustainable alternative for plastic production. Emerging technologies in this field could reinvent how plastics are made and used, supporting a circular economy.
Among several companies that have made a leap into carbon capture is Finland-based energy company Fortum Recycling & Waste, which says it has developed the world’s first biodegradable plastic made entirely from CO2 emissions.
Fortum’s Inga polyhydroxyalkanoate (PHA) material caters to applications including food packaging, electronics, and cosmetics. It is biodegradable across all tested environments; recyclable, and said to offer excellent barrier properties. Last year, Fortum produced the first sample of Inga, according to Tony Rehn, Head of the Inga development team.
Similarly, start-up ReSource Chemical Corp is developing a cost-effective way to produce plastics using renewable feedstocks like CO2 and agricultural waste.
Having raised US$15 million in funding from investors including Chevron Technology Ventures, Mitsubishi Gas Chemical Company , and angel investors Adam Winkel and Matt Berger, ReSource's innovation is based on 2,5-furandicarboxylic acid (FDCA), a molecule that serves as a building block for PEF, an alternative to PET resin.
PEF is said to offer superior strength, durability, and thermal performance while requiring less material. It also provides better oxygen, carbon dioxide, and moisture barriers, significantly extending product shelf life. Despite these advantages, traditional methods for producing FDCA have been too expensive to make PEF a viable alternative.
ReSource has developed a streamlined process that eliminates two-thirds of the complexity in conventional FDCA production. This advancement reduces costs and enables scalable manufacturing. The technology is based on CO2 chemistry pioneered by ReSource’s founding team at Stanford University.
Sustainability aside, FDCA-based plastics offer a major safety advantage. FDCA is naturally produced in the human body, making it an ideal substitute for toxic additives currently used in plastics. PEF and other FDCA-derived plastics biodegrade more easily, breaking down into their original building blocks much faster than common plastics.
ReSource will use the funding to build an FDCA pilot plant and expand its specialty chemicals, aiming to mainstream FDCA-based materials.
Seeding innovation in renewable materials with non-food feedstock
Materials derived from renewable food-based feedstocks such as corn starch, sugarcane, and algae offer a feasible alternative to petroleum-based plastics, thereby reducing reliance on fossil fuels and greenhouse gas emissions.
However, Australia-based Ecopha Biotech Pty claims it has achieved a world-first breakthrough by successfully
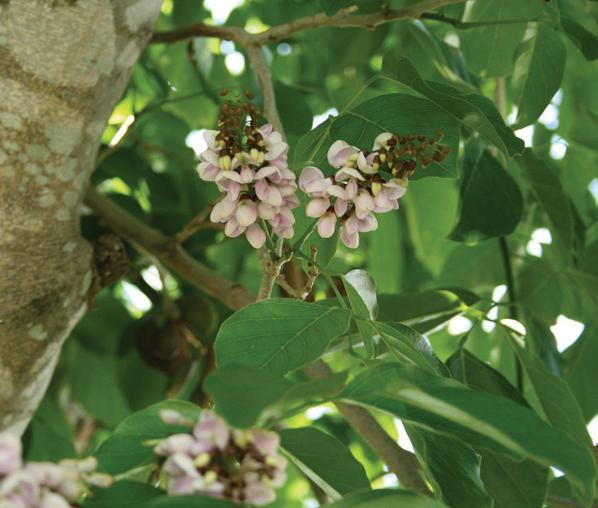
Ecopha has achieved a world-first by producing PHA from pongamia oil, a sustainable, nonedible resource derived from pongamia tree seeds
producing PHA from pongamia oil, which is a sustainable, non-edible resource extracted from the seeds of the pongamia tree that thrives in arid climates with minimal agricultural inputs.
Unlike biobased plastics made from corn or soy, using pongamia oil omits competition with food production while providing an efficient resource for sustainable plastic manufacturing, as pointed out by Dr Wilson Ling, CEO of Ecopha, adding the economic and environmental potential of this advancement.
The company’s patented process qualifies for carbon credits, further lowering production costs and positioning. Industries such as energy, mining, and manufacturing can benefit from this technology's carbon offsets.
Ecopha is commercialising its innovation through a partnership with Australian design studio Terra Sol, launching a range of certified compostable products including coffee cups, biodegradable lids, eco-friendly straws, and sustainable cutlery. With growing interest from various stakeholders, the company says it is ready to expand pongamia-based PHA applications.
Recycled content for plastic circularity
Plastics made with recycled content are gaining traction. By repurposing post-consumer and industrial waste,
manufacturers reduce reliance on virgin materials, which is an approach that extends the life cycle of plastic while promoting a more responsible and resource-efficient production process.
Building on this solution, Spanish energy and petrochemical company Repsol , and Tarragona-based ABS resins and derivatives Elix Polymers, have partnered to introduce ABS grades with 100% attributed chemically recycled content, further advancing circular solutions in plastics. Elix Polymers has expanded its E-Loop portfolio to include new grades combining both mechanically and chemically recycled materials.
In line with the collaboration, Repsol supplies styrene and butadiene derived from chemically recycled post-consumer waste and bio-circular raw materials, such as used cooking oil.The selection depends on the application and customer requirements. Repsol also ensures ISCC Plus certification for these grades through the mass balance model.The companies first established their supply agreement for chemically recycled materials in 2020.
In a similar vein, European producer of recycled PP Rialti has unveiled PP compound grades that incorporate both postconsumer recycled (PCR) and post-industrial recycled (PIR) content. These new grades incorporate 30-40% PCR and 20-40% PIR content, providing a sustainable alternative to virgin PP. The resins help meet End-of-Life Vehicle (ELV) regulations in mobility and offer solutions for construction and home use.
Since its 2023 acquisition by Austrian chemical firm Borealis, Rialti, which produces up to 50,000 tonnes/year of recycled PP compounds in Varese, Italy, has harmonised its portfolio with Borealis’ Borcycle M range.













According to Shanila Baseley, Borealis’ Vice President of Mobility and Advanced Products, Rialti’s new grades exemplify the push toward high-performance recycled solutions, making it easier for manufacturers to transition to more sustainable alternatives.







































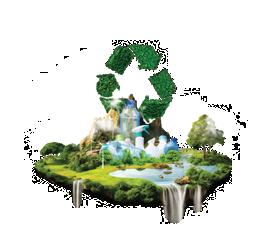

Clean energy and EVs boosting China’s economy
China is leveraging the country’s positive economic growth outlook through investments and conducive policies in clean energy and electric vehicles (EVs), says Angelica Buan in this report.
Accelerated growth from “Made in China” initiative China's economy continues to evolve in 2025, balancing steady expansion with emerging challenges. Industrial output reached US$5 trillion in 2024, according to the Ministry of Industry and Information Technology. The government’s 5% GDP growth target in 2025, will see a gradual slowdown due to US tariff hikes, with growth expected to reach 4.5%.
Meanwhile, a landmark policy is fuelling China’s growth. Made in China 2025 (MIC2025), is a state-led initiative designed to localise high-tech industries and establish the country as a global manufacturing powerhouse by 2049. It aims to reduce reliance on foreign technology, boost domestic innovation, and transition from a low-cost manufacturer to a direct value-added player in global hightech industries.
The plan focuses on increasing the local content of core components and materials, aiming for 40% by 2020 and 70% by 2025. State-sponsored investments and funding have been channeled into key sectors, including electric vehicles (EVs), next-generation IT, telecommunications, robotics, and artificial intelligence (AI).
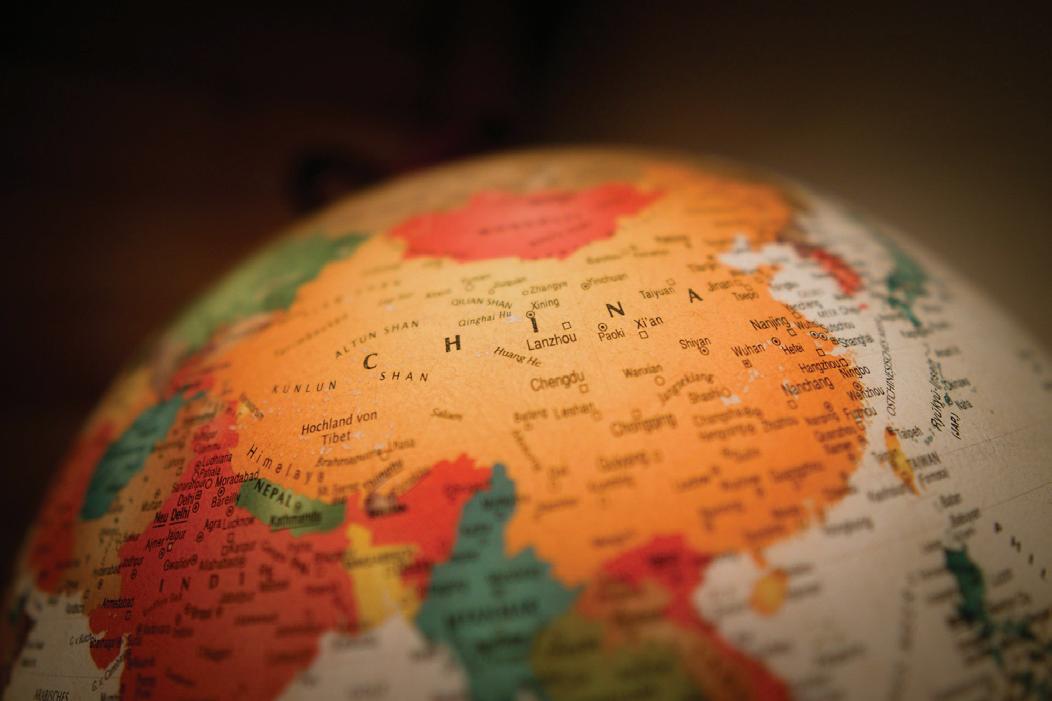
While the policy has accelerated China's technological growth, it has also faced reproach. Leading economies, including the US, Germany, and the European Union, have expressed concerns over intellectual property issues and alleged discriminatory practices against foreign companies.
Scaling renewable energy towards peak carbon emissions China remains the world’s largest producer and consumer of energy, and its policies heavily influence global markets and emissions trends. With nearly 90% of its greenhouse gas emissions coming from the energy sector, the country has set bold targets to move away from fossil fuels.
In 2020, President Xi Jinping announced a plan to peak carbon emissions before 2030 and achieve carbon neutrality by 2060. Achieving the 2030 emissions peak will depend on improved energy efficiency, an expansion of renewables, and a gradual reduction in coal use.
According to a study by Carbon Brief, China has made significant investments in clean energy, including solar, batteries and EVs, which have grown three times faster than the overall economy. New energy vehicle production has surged by 47%, while lithium-ion battery output increased by 37% year-on-year.
Renewable electricity consumption is set to rise to 33%, with half of new energy demand met by renewables. If achieved, the plan could cut up to 2.6 gigatonnes/year of carbon emissions.
In line with this strategy, China is expanding its renewable energy infrastructure with major projects, such as the construction of new energy bases in the Gobi desert. There are also plans to develop offshore wind farms, integrate renewable energy into local grids, and build transmission routes. Additionally, low-carbon upgrade trials would be launched for coal-fired power plants.
Some developments in the area of renewables that have come to fruition include China connecting one of its largest photovoltaic (PV) projects in Ruoqiang, in the Xinjiang Uygur region. The four-gigawatt facility is the country’s largest solar project in the desert.
Another massive project, the Motuo hydropower facility. project, is expected to generate three times the energy of the Three Gorges Dam, the world’s largest hydroelectric project, powering 70 to 80 million Chinese homes annually.
Fresh investments for clean energy/petchem projects
Elsewhere, Harbin Electric Corporation, one of the country’s three largest manufacturers of power plant equipment, has rolled out the first domestically developed 16-megawatt (MW) gas turbine, the HGT16.
Gas turbines are essential for energy, aerospace, industrial production, and offshore operations due to their high-power density, efficiency, and low emissions.
China's MIC2025 policy drives growth by localising high-tech industries to become a manufacturing leader by 2049
By transforming its manufacturing base, China intends to compete directly with advanced economies such as South Korea, Japan, and Germany.
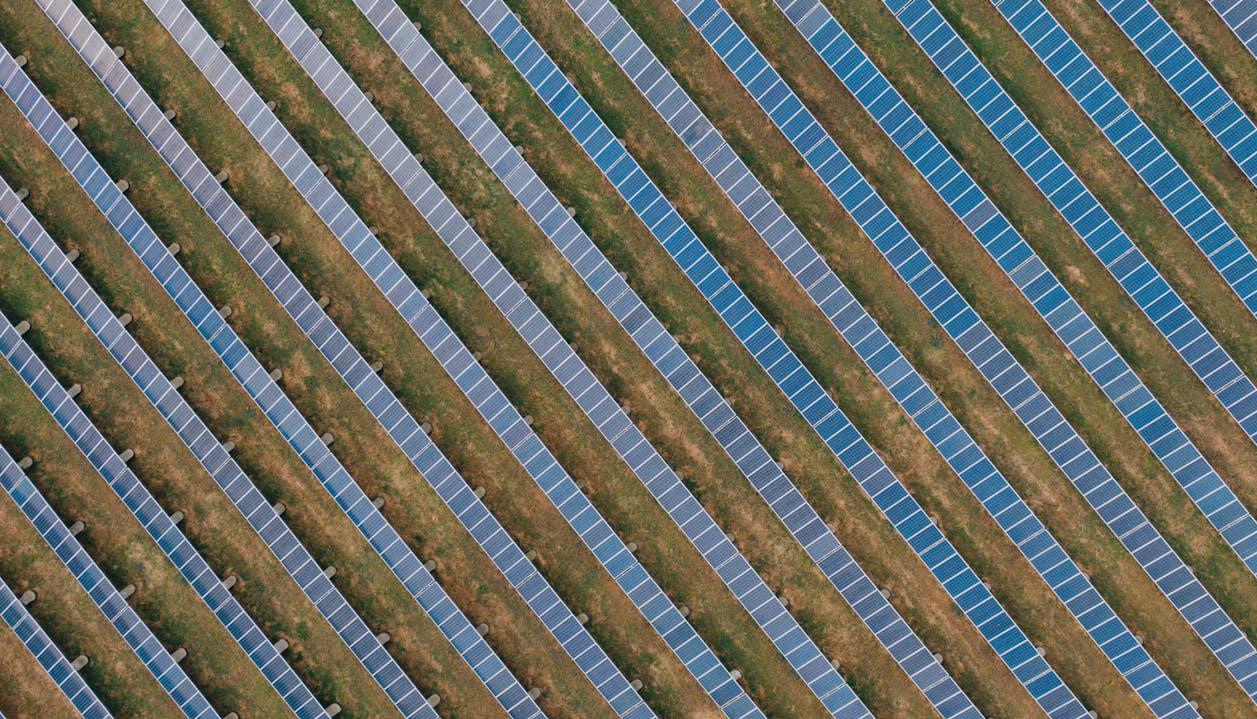
Jinneng Holding is building a $7 billion renewable project in Shanxi with 6 GW of wind and solar and 3.4 GWh of storage, set for grid connection by late 2025
This development strengthens China’s renewable power infrastructure. The HGT16 delivers at least 16 MW of power with thermal efficiency exceeding 36%.
As China continues expanding its clean energy initiatives, Jinneng Holding Group, a state-owned energy company, has also begun construction on a large-scale renewable energy project in Shanxi Province, northern China. The US$7 billion project will feature 6 GW of wind and solar capacity, along with 3.4 GWh of energy storage. It is scheduled to be connected to the Chinese grid by the end of 2025 and will supply power to the municipalities of Beijing and Tianjin, as well as Hebei Province.
Similarly, the petrochemical sector is advancing alongside these clean energy projects. Saudi Arabian Oil Company (Aramco), China Petroleum and Chemical Corp (Sinopec), and Fujian Petrochemical Company Limited have cooperated on an integrated refining and petrochemical complex in Fujian Province.
The facility will include a 16-million-tonne/year oil refining unit, a 1.5-million-tonne/year ethylene unit, a 2 million-tonne/year paraxylene capacity, and a 300,000tonne crude oil terminal. It is expected to be fully operational by 2030.
In a related development, US firm Apple Inc has announced a new investment in its China Clean Energy Fund to accelerate clean energy production in China. Launched in 2018, the second phase commits US$99 million to expanding renewable energy. The new fund aims to add 550,000 MWh of wind and solar capacity annually to China’s grid. With two-thirds of its China manufacturing already powered by renewables, Apple claims that this initiative helps its suppliers switch to cleaner energy.
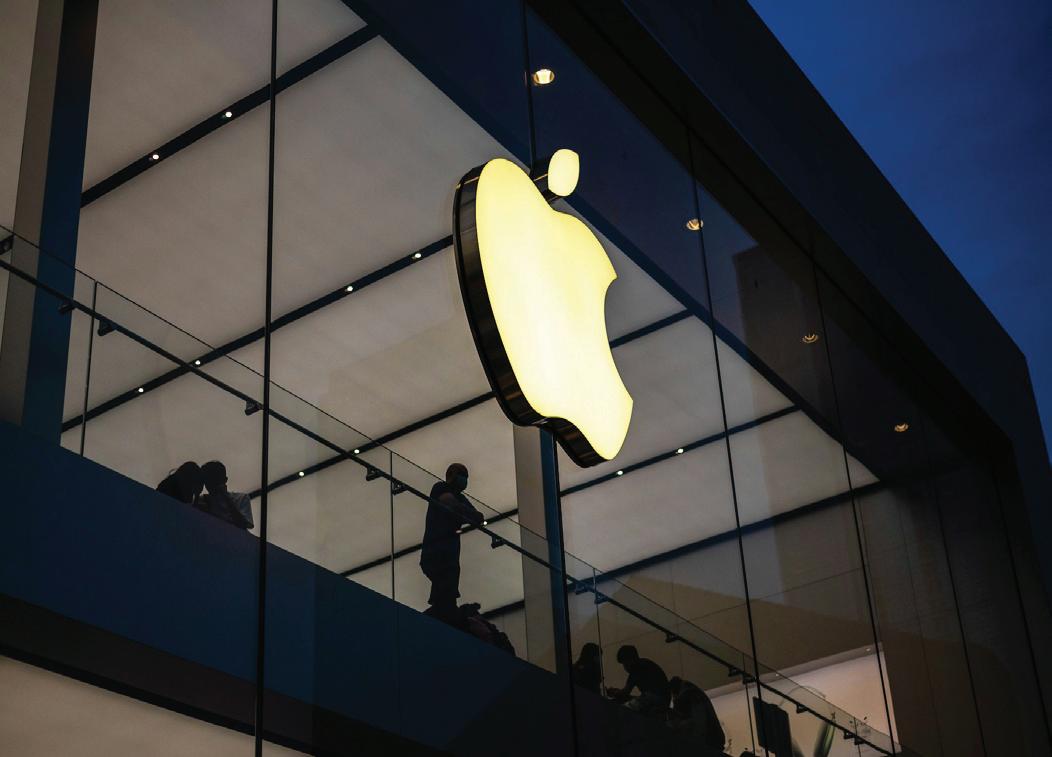
Apple is investing US$99 million in its China Clean Energy Fund to add 550,000 MWh of wind and solar power annually

Expanding hydrogen production
As the world's largest hydrogen producer, China generates about 33 million tonnes/year, primarily from fossil fuels used in refineries and chemical facilities. The China Hydrogen Alliance projects that hydrogen demand will reach 35 million tonnes by 2030, supplying at least 5% of the country's energy needs, and 60 million tonnes by 2050, covering 10%.
The National Development and Reform Commission and the National Energy Administration have launched a 15-year plan to expand the hydrogen industry and increase the share of renewable-based production, according to the International Centre for Science and Technology Innovation.
Companies across China, both private and state-owned, are entering the green hydrogen market by utilising local resources or developing industrial parks for solar- and wind-powered hydrogen production. Among them, Sinopec has launched four green hydrogen projects as part of its US$4.6 billion investment in the sector through 2025, aiming to increase its annual hydrogen production capacity to 500,000 tonnes.
State Power Investment Corp Ltd, one of the five major electricity generation companies in China and the only integrated energy group in the country that holds assets of nuclear power, thermal power, hydropower and new energies has also proposed projects, including a demonstration initiative in Tibet focused on using hydrogen to address the intermittency of renewable energy.
Private companies such as Shanghai-headquartered energy technology company Envision Group is partnering with Australian metal mining company Fortescue Metals Group to develop 10 million tonnes of green hydrogen by 2030.
EVs as engine of growth: weathering tariffs, strengthening domestic market
China’s automotive market is expected to continue growing, driven by government incentives and the affordability of locally manufactured EVs, according to an ING Think’s global car market report. EVs (battery electric vehicles or BEVs and plug-in hybrids or PHEVs) accounted for over 40% of total new car sales in 2024.
To accelerate EV adoption, the Chinese government has introduced various incentives, including purchase subsidies and tax breaks, to stimulate production and consumer demand while reducing emissions.
Meanwhile, China has firmed up its position in the global automotive industry, reaching 41% of the market by December 2024. Foreign brands such as Mercedes-Benz, Toyota, and Volkswagen are reportedly losing ground as markets evolve.
Rising exports of Chinese-built automobiles have led to increased tariffs and trade restrictions. In 2024, the US, under President Joe Biden’s administration, imposed a 100% tariff on Chinese EVs following a United States Trade Representative (USTR) review. Canada followed suit the same year, while the European Union imposed a five-year countervailing duty on Chinese BEVs in late October, citing unfair subsidisation.
Despite trade tensions, China remains focused on strengthening its domestic market. The government has extended tax incentives for new energy vehicles (NEVs), including EVs, PHEVs, and fuel cell vehicles (FCVs), to sustain industry growth. Since 2014, qualified NEVs have been exempt from the 10% purchase tax. Initially set to expire in 2020, the exemption was extended through 2022 and later until 2027.
China is on track to become the world’s largest automotive and NEV exporter. In 2024, NEVs made up 25% of China’s total vehicle exports, reflecting its dominance in global EV manufacturing, according to China Market Outlook 2025 by Mirae Asset
Brazil was the top destination for Chinese EVs in the first half of 2024, accounting for 16% of exports, followed by Belgium and the UK. This shift reflects growing demand in markets with favourable trade conditions. Southeast Asia and Latin America, still in the early stages of EV adoption, present strong growth potential for Chinese automakers. These regions have traditionally been led by Japanese and US brands, which have been slower to expand EV production.
China’s leading NEV manufacturer BYD is also expanding globally. The company is set to complete construction of its US$1 billion Indonesian facility by late 2025. Meanwhile, BYD’s revenue grew 29% year-on-year to US$107 billion, surpassing US automaker Tesla’s nearly US$97 billion for the first time.
In 2024, Tesla's revenue reached nearly US$97 billion, but BYD surpassed it for the first time with a 29% increase to US$107 billion
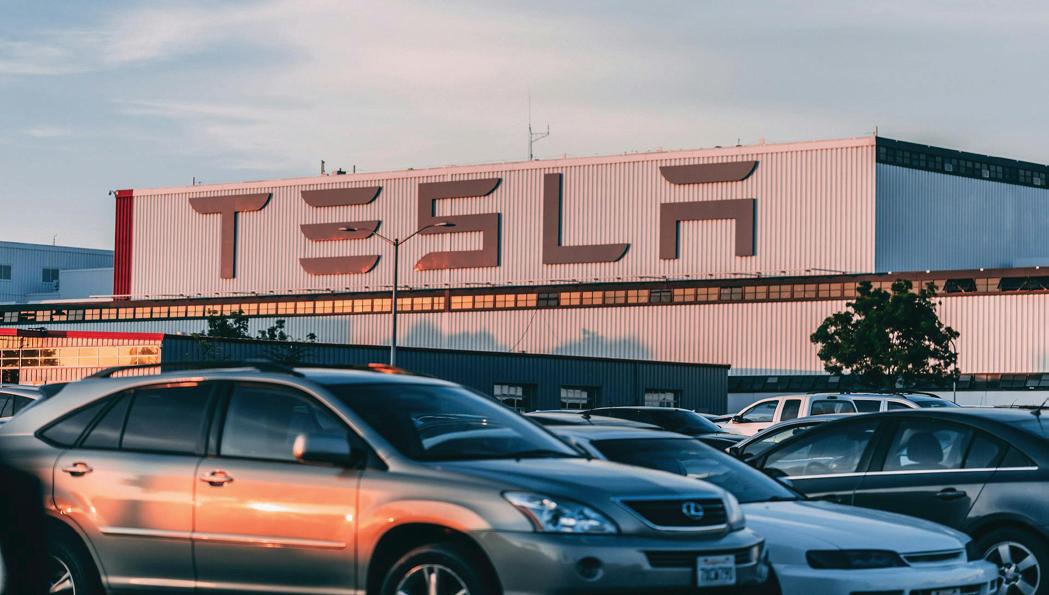
China’s NEV market reached nearly 12.9 million units in 2024, up 35% year-on-year, with BYD accounting for over 33% of total production, according to the China Association of Automobile Manufacturers.
Global automakers are increasingly forming technological partnerships with Chinese firms. Renault-Nissan, Volkswagen, BMW, Mercedes-Benz, Toyota, Stellantis, and Jaguar Land Rover have invested in joint ventures and collaborations.
Toyota’s first electric sedan, the bZ3, was developed with BYD’s assistance. In 2023, Volkswagen Group invested US$700 million in Guangzhou Xiaopeng Motors Technology Co acquiring a 4.99% stake to co-develop two VW-brand EVs for the Chinese market by 2026.
Looking ahead, China’s EV sector is expected to gather full steam in 2025 and beyond as strong demand and strategic market expansion sustain its global dominance in the automotive sector.
Additives
Additives extending the potential of materials
Innovative additives are helping industries like construction, electrical, and packaging meet rising demands for performance, durability, and sustainability by enhancing material properties like strength, heat resistance, and recyclability, adds Angelica Buan in this report.
Mightier materials with the right additives
The global plastic additives market is on the rise, with an estimated value of US$57.6 billion in 2025, forecast to reach US$69.9 billion by 2030, growing at a CAGR of 4.96%, according to Knowledge Sourcing Intelligence
Demand for additives such as bio-stabilisers, antioxidants, and flame retardants are increasing as industries seek materials with improved performance.The packaging, automotive, and construction sectors are among key drivers of this growth. To stay competitive, market players are focusing on R&D, introducing advanced additives that enhance plastic properties while meeting regulatory and environmental standards.
Packing a punch with recyclability
Offering brand owners and converters a cost-effective way to extend the shelf life and recyclability of PET bottles, US firm Avient Corporation has launched ColorMatrix Amosorb 4020L, an oxygen scavenging additive.
The material, which meets direct food contact regulatory requirements, enhances shelf-life performance for packaging applications such as condiments, sauces, juices, and beverages, including certain alcoholic drinks.This non nylon-based additive is compatible with recycled PET (rPET), making it an option for brands looking to incorporate higher levels of recycled material (up to 100%) in their packaging.
In a related effort, German specialty chemicals company Evonik’s Coating Additives business has launched a new co-binder,Tego Res 1100.This methacrylate copolymer enhances recyclate quality by making plastic film deinking processes faster and more efficient. It easily integrates into standard solvent borne ink formulations, offering broad solubility and compatibility with various binders and solvents, including alcohols and esters. Evonik says its testing shows that just 3-10% of the additive delivers deinking results, at temperatures as low as 40°C, with or without surfactants. Doubling down on sustainability while expanding its massbalanced additive portfolio, Evonik has also introducedTego

Evonik Coating
Additives introduces its first massbalanced products, TEGO Wet 270 eCO and TEGO Foamex 812 eCO, cutting carbon footprint without compromising performance
Wet 270 eCO, a substrate wetting agent with over 40% biocarbon, andTego Foamex 812 eCO, a defoamer with over 60% bio-carbon.
Element of strength in construction materials
Construction materials need to be tough, durable, and built to last and that's where additives make a difference, while renewablecontent additives offer an extra advantage by enhancing sustainability.
Additives supplier Baerlocher provides Baerophob hydrophobic agents, designed to improve the durability of building materials exposed to harsh weather conditions.These are mainly used in cementitious systems especially dry plasters, pasty plasters/paints, paving stones, and more. Plus, the products are compatible with building materials such as lime, cement, gypsum, and wood.
The Baerophob range is based on renewable raw materials; are silicone and paraffin-free and provide hydrophobic effects due to their dispersion in building materials.They also help decrease the frequency of renovations and associated costs, requiring only a low dosage for cost-efficient use, says the firm.
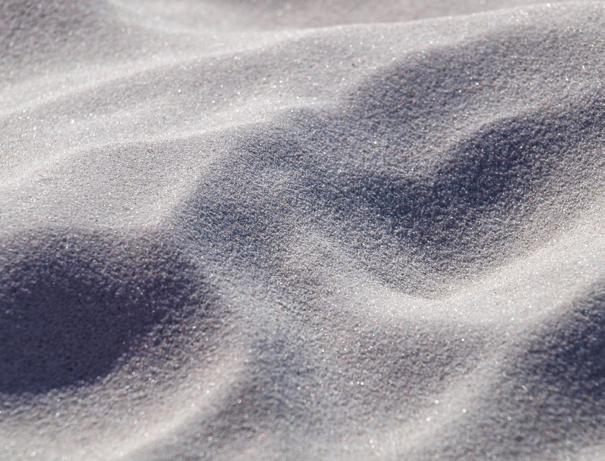
Baerlocher's Baerophob hydrophobic agents are used in cementitious systems like dry plasters, pasty plasters, paints, and paving stones
In line with sustainability, German chemicals company BASF and Swiss specialty chemicals company Sika have jointly developed a new amine building block for curing epoxy resins, now commercially available under BASF’s Baxxodur EC 151 brand. It is said to be ideal for flooring applications, such as in production plants, storage and assembly halls, and parking decks.
Baxxodur EC 151 provides epoxy resin flooring with low viscosity and optimal flow properties, making the coatings easy to apply and spread evenly. It requires significantly less thinner than conventional hardeners and reduces volatile organic compounds (VOCs) by up to 90%, plus allows for greater use of mineral fillers, lowering costs and contributing to sustainability, say the firms. Further, curing time is reduced by up to two-thirds, allowing for quick use after application.
As part of the research cooperation, Sika is applying the amine in Sikafloor coatings while BASF developed a suitable
Additives
manufacturing process and scaled it up from the laboratory to production level.
Additives beating the heat for electrical applications
Additives for high-temperature applications, such as those in the electrical and electronics segments, enhance the performance and durability of materials and are designed not only to meet the rigorous demands of high-heat environments but also to prioritise environmental safety by reducing harmful emissions.
Masterbatch firm Ampacet has introduced low-halogen and halogen-free flame retardant masterbatches that comply with IEC 61249-2-21 and EN 50642 standards.These additives provide flame resistance for electrical equipment in the building/ construction sector, helping ensure safety in the event of a fire.
Ampacet’s Halolite 527 (low halogen) and Halofree 533 (halogen-free) additives are designed for PP electrical equipment and other PP plastics. Both meet UL94 V2 and high Glow Wire Flammability Index (GWFI) standards. Available in natural colour, they can be coloured with separate masterbatches, or precoloured versions can be developed upon request.
Specialising in masterbatch solutions for high-temperature applications that require heat stability, Tosaf has developed white masterbatches designed specifically for extrusion coating. These are said to offer improved heat stability, reducing smoke and odour during processing, a common challenge in extrusion coating. With a low-emission profile, they improve workplace safety and meet tightening global environmental regulations.
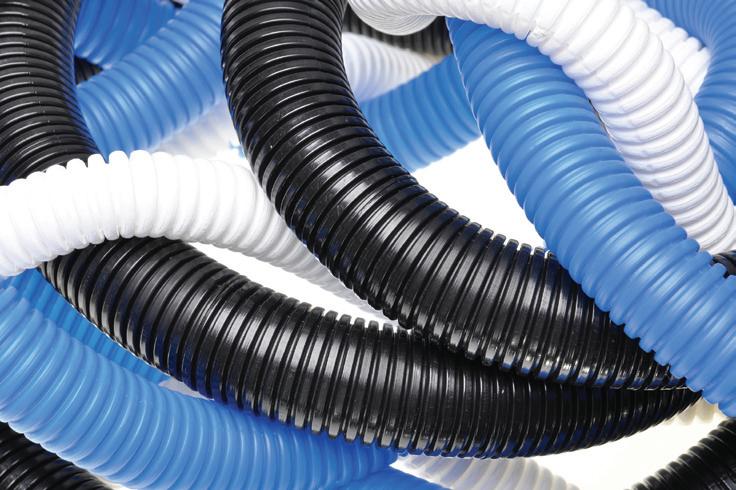
Tosaf's lowemission white masterbatches are specifically designed for extrusion coating, offering improved heat stability and reducing smoke and odor during processing
In addition,Tosaf says its extrusion coating white masterbatches enhance production efficiency by providing better process control, cutting downtime, and reducing waste.They are designed to address critical extrusion coating challenges, including necking, poor dispersion, gel formation, and die buildup.The heat resistance ensures high dispersion quality even under extreme conditions, resulting in smoother, more consistent production and fewer filter changes.
Plus, the high opacity masterbatches allow manufacturers to achieve the same visual effect with lower addition levels, even in thin layers, thus boosting production speeds, reducing material costs, and enhancing profitability.Tosaf offers PE-based ME800047, outdoor protective PP film option MP800502, and a combi white MB with UV stabiliser VE800497 for HDPE and PP tarpaulin production.
Meanwhile, materials firm Syensqo has launched a new range ofTecnoflon FFKM perfluoroelastomers using its proprietary non-fluorosurfactant (NFS) technology.These products expand Syensqo's FFKM line for semiconductor seals and O-rings and are said to be the first commercial FFKM materials made
entirely without surfactants, addressing the growing demand for sustainability.This launch is part of the company's plan to phase out fluorinated surfactants across all its products.
Syensqo is also introducing mass-balanceTecnoflon FFKMs with certified circular content, aligning with the EU’s Critical Raw Materials Act.
The initial launch includesTecnoflon PFR 6055B for semiconductor dry applications and high-temperature industrial uses, andTecnoflon PFR 6265B for direct plasma applications. Manufactured in Spinetta, Italy, these products will be available in April 2025, with more grades for wet processes and very hightemperature applications to follow.
Medical devices level up to sustainability standards
In the medical device and healthcare sectors, additives enhance the performance and functionality of medical devices, helping meet stringent industry standards.
Medical marking, like laser marking, is a vital process in the medical industries, enhancing the safety and reliability of products while supporting supply chain management.These markings ensure proper usage, quality, integrity, and sterility, as well as compliance with stringent regulations.
Ampacet has introduced ProVital+ LaserMark, a portfolio of masterbatches designed for laser marking on medical devices, in-vitro diagnostic equipment, and packaging systems. Its portfolio includes 1001513-EM, a high-definition laser marking solution designed for dark markings on transparent, translucent, white, or light-coloured PE or PP parts; and 1001514EM, an antimony-free environmentallyfriendly technology that is suitable for dark markings on white and light-coloured PE or PP parts.
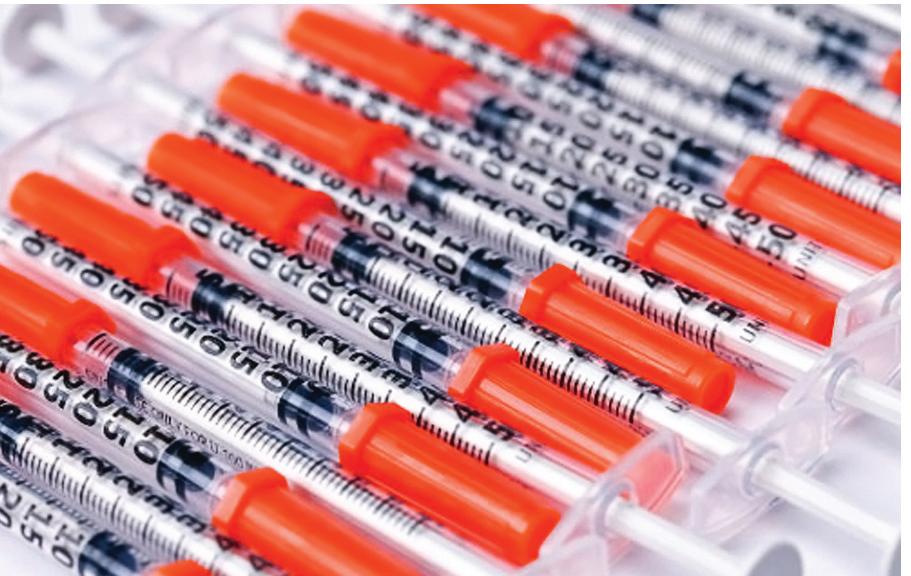
The ProVital+ LaserMark portfolio of masterbatches designed for laser marking on medical devices, in-vitro diagnostic equipment, and packaging systems
Ampacet adds the masterbatches are formulated with raw materials pre-evaluated for biocompatibility, in line with ISO 10993 for cytotoxicity, skin sensitisation, and irritation.
Similarly, US compatriot Americhem has launched the EcoLube MD line of PFA-free internally lubricated compounds for medical devices. EcoLube MD compounds and alloys help manufacturers reduce friction and wear in plastic parts, lower noise, and decrease the coefficient of friction in plastic-on-plastic and plastic-on-metal applications, without PFAs. Applications include minimally invasive surgical devices, syringe pumps, prosthetics, and surgical robots.
Offered in a variety of base resins, EcoLube integrates functional additives directly into materials, providing long-lasting internal lubrication. Low-friction, non-migratory additives are also designed to replace PTFE in thermoplastic applications.
Biocompatibility testing and medical certifications, backed by Americhem's Process Change Management and locked formulation promise, are said to make EcoLube MD an ideal choice for medical applications.
Smart, recyclable solutions for the packaging sector
The packaging industry is facing challenges, with consumers demanding sustainable solutions, while increasingly stringent regulations are being imposed. Thus, companies like ExxonMobil and Borealis are offering value-added solutions, to drive innovation in sustainable packaging solutions while addressing market needs.
UFlex and Borealis offer recycled materials for packaging UFlex Ltd, India’s largest multinational flexible packaging company, says it the first Indian company to receive approval from the United States Food and Drug Administration (USFDA) for its recycling process. This approval allows UFlex to use recycled polyethylene (rPE) in food packaging, marking a major step in reducing plastic waste and supporting global brands in meeting their sustainability goals.
UFlex says its recycling process is categorised as super-clean recycling, with the ability to de-ink postconsumer recycled (PCR) materials by more than 95%, Furthermore, to further strengthen its recycling infrastructure, UFlex is adds it is investing US$38 million in advanced recycling technologies. This includes the establishment of two new recycling plants at its Noida facility in India, with a combined capacity to process 39,600 tonnes/year of plastic waste. These plants will significantly boost the production of rPET and rPE materials for use in food packaging.
Additionally, the company has applied for US FDA certification to recycle polypropylene (PP).
At present, there are no specific guidelines for the use of rPE content in food packaging. However, there is a mandatory requirement under the Extended Producer Responsibility (EPR) regulations to incorporate recycled content in packaging. UFlex, in collaboration with industry players, adds it is actively engaging with
government bodies such as FSSAI and BIS to help develop the necessary guidelines for the safe and sustainable use of rPE content in food packaging in India.
Currently, UFlex has recycling plants in India, Poland, Egypt, and Mexico, processing post-consumer multi-layered mixed plastic (MLP), multi-layer aseptic packaging (MLAP), and PET waste.
Meanwhile, Austrian materials firm Borealis has introduced Borcycle M CWT120CL, a recycled linear low density polyethylene grade (rLLDPE) for non-food flexible packaging. Produced with 85% PCR and 15% LLDPE booster, the flexible packaging grade is based on Borcycle M, Borealis’s mechanical recycling technology.
The new grade is tailored for blown film applications across primary, secondary, and tertiary packaging. Key applications include stretch film and stretch hood, and films for agricultural, industrial, and protective uses.
The new grade was developed together with Ecoplast, a member of the Borealis Group, in a project that began in late 2022. Its launch in January 2025 marks the culmination of more than two years of work to overcome the complexities of incorporating a high proportion of recycled content.
It adds that the result is a material with exceptional stretchability, achieved through low gel content, as well as an excellent toughness-stiffness balance. These properties make it an ideal solution for packaging manufacturers seeking to meet or exceed the requirements of the EU Packaging and Packaging Waste Regulation (PPWR) without compromising performance.
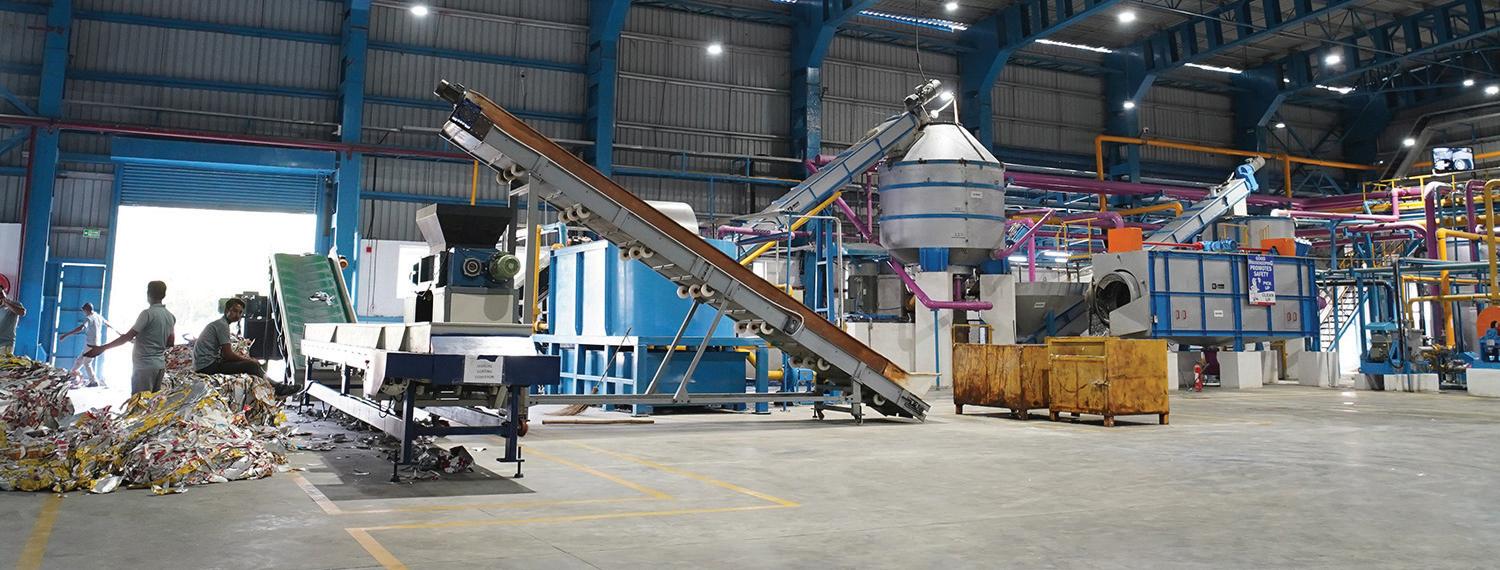
ExxonMobil, Kuraray, and Alico partner for PET and PVDC-free shrink bags for meat packaging In a collaboration with materials manufacturer Kuraray, ExxonMobil Signature Polymers and Colombian packaging manufacturer Alico recently partnered to create a solution for local meat producers.
To further strengthen its recycling infrastructure, UFlex is investing in advanced recycling technology

The firms developed Termoflex +B barrier shrink bags, utilising Exceed Tough+ m 0512, a Signature Polymers product, coupled with Kuraray’s EVAL's ethylene vinyl alcohol copolymer (EVOH) grades. The shrink bags were designed to address three key requirements: effective oxygen barrier properties, high shrinkage range, and optimal balance between mechanical and optical properties.
Manufactured in Colombia and now being implemented by local meat producers, the developed shrink bags are said to meet or exceed the performance of imported solutions, and eliminate the need for PET and PVdC while maintaining optimal barrier properties.
Furthermore, the bags achieve improved oxygen transmission rate at high humidity, compared to incumbent solutions.
The companies add that field trials prove the shrink bags’ ability to ensure comparable shelf life for fresh meats.
Traceability along the entire value chain
Meanwhile, in a joint project with open traceability and the Digital Product Passport (DPP) platform R-Cycle and flexible packaging converter Korozo Group, adhesives supplier Henkel has demonstrated the benefits that can be achieved through DPP.
With a key trend in the packaging industry being the shift toward a circular economy, materials need to be recyclable and raw materials used need to be derived from sustainable sources wherever possible. In addition, there need to be clear rules for disposal. Digital solutions are becoming increasingly important in the efforts to satisfy these requirements.
Against this backdrop, focus is turning to the Digital Product Passport (DPP), which is a key instrument in creating a digital record of the necessary information about the composition, life cycle and sustainability aspects of a
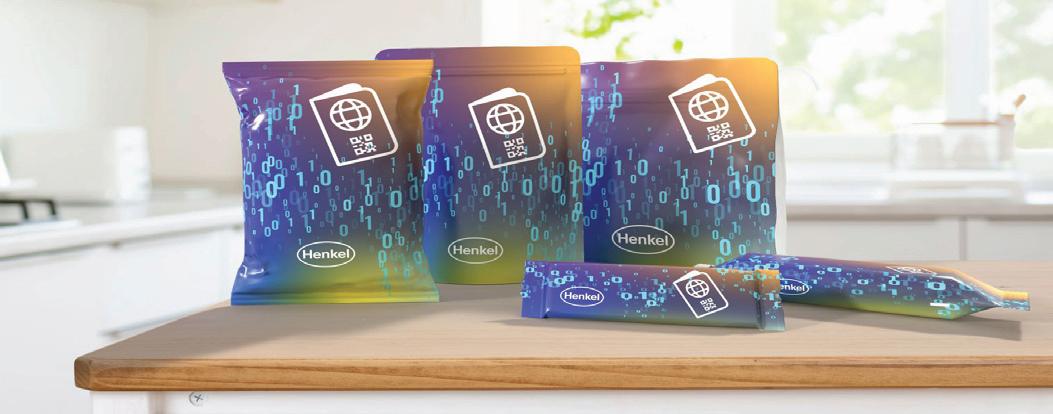
product and making this information accessible. Driven by regulatory requirements such as the European Union’s Ecodesign for Sustainable Products Regulation (ESPR), the DPP will become mandatory in many industries from 2027.
The digital data set contains information such as the material composition, technical specifications and recyclability of a product. Each product is allocated a unique identifier, accessible via a suitable marking, such as a QR code or RFID tag, to facilitate its traceability along the value chain. The quality of the assigned data recorded is crucial here. Companies along the value chain need to provide the relevant information, which is prepared in a standardised format and made accessible to all stakeholders.
In the packaging industry especially, the DPP not only satisfies regulatory requirements but also significantly improves the sustainability of packaging.
A functioning circular economy requires recyclable and ideally a high proportion of recycled raw materials to be already integrated into the procurement phase; these are then transferred to a design which takes into account various end-of-life scenarios. The goal is to recover materials for use in place of virgin material. Detailed material data simplify sorting and recycling, helping to preserve resources and increase the recycling rate.
In the joint project with Korozo and R-Cycle, Henkel decided to actively test and implement the DPP as part of its continuing commitment to make every package sustainable. The Loctite Liofol solvent-free adhesive developed by Henkel is used to laminate stand-up pouches.
This example, trialed in a Henkel consumer brands finished good, shows what the DPP looks like in practice. Each package produced with Loctite Liofol is given a QR code that is linked with the R-Cycle DPP. This ensures that technical data, safety information and environmental aspects can be accessed directly. Henkel is working with R-Cycle to extend this traceability, thus optimising the disposal and recyclability of the product as well.
In addition, Henkel records the carbon emissions generated in the manufacture and use of the lamination adhesive in the DPP. This information is critical to complying with the ESPR requirements and to assessing the product’s carbon footprint throughout its entire life cycle.
The information recorded in the DPP enable end-of-life companies to properly manage the disposed packaging when it arrives to the sorting and recycling center, positively contributing to circular economy and recycling ratio.
The product carbon footprint (PCF) of individual components and of the product overall has a particularly crucial role to play here. In this connection, Henkel has established extensive capacities to identify savings potential and provide reliable data for DPPs and reporting requirements. These data are especially relevant to the recyclability of packaging and the obligation to use recycled raw materials.
In the years ahead, it is envisaged that DPP will play a central role in the packaging industry as a key lever for driving innovation and increasing competitiveness.
In a partnership with Kuraray, ExxonMobil Signature Polymers developed barrier shrink bags for meat packaging, utilising Exceed Tough+ m 0512, coupled with Kuraray’s EVOH grades
As part of a joint project with R-Cycle, Henkel tested and implemented the Digital Product Passport with a pilot project using Loctite Liofol solvent-free adhesive to laminate stand-up pouches
ThermoplasTic
elasTomers
Growing footprint of TPEs in key industries
From medical devices to sneakers, TPEs are redefining material innovation across industries, adds Angelica Buan in this report.
If there is one advanced material that stands out for versatility, thermoplastic elastomers (TPEs) are hard to beat. Their ability to serve a wide range of industries makes them highly sought after, not to mention their role as a “canvas” for material innovation.
In the medical device industry, TPEs are valued for their flexibility, purity, and ability to replace latex and PVC. They’re also widely used in consumer goods for their soft-touch feel and colourability. Moreover, TPEs are found in athletic wear, sneaker soles, and shoe inserts, offering support and comfort. And with the growing focus on sustainability, TPEs tick that box, too.
Sustainable TPE with recycled content
Recent developments highlight new solutions that incorporate recycled rubber and medical materials, reducing waste while maintaining durability and quality.
US clean technology company Prism Worldwide and Canadian thermoplastics extruder Sherwood Industries have partnered to integrate Prism’s sustainable TPEs into extruded rubber sheets, providing a high-performance, eco-friendly alternative for industries such as automotive, household products, and sporting goods.
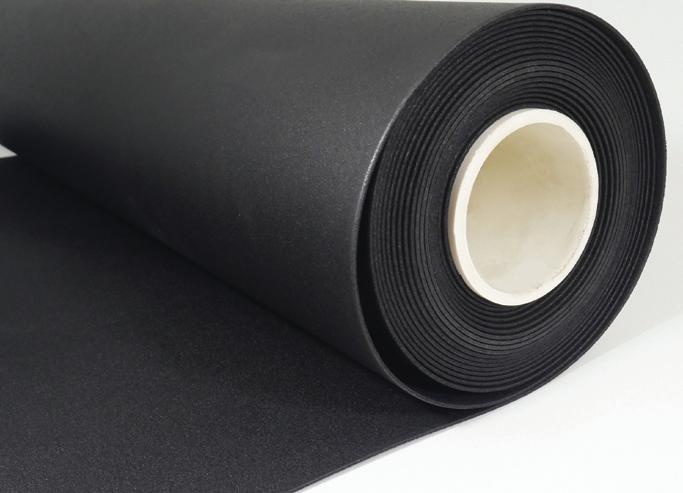
Prism Worldwide and Sherwood Industries teamed up to integrate Prism’s sustainable TPEs into extruded rubber sheets, offering a high-performance, eco-friendly solution for automotive, household, and sporting goods industries
Prism’s patented technology converts 100% of crumb rubber from end-of-life tyres (ELTs) into fully reusable thermoplastic rubber while retaining valuable polymers, additives, and carbon black.
Since April 2024, Sherwood has incorporated Prism’s ELT-based Ancora polymer into its production. Following successful test runs and positive customer feedback, Sherwood is moving forward with commercialisation and has invested in a new extruder for the ISO 9001:2015-certified sheets. Meanwhile, Prism’s recent US$40 million funding will further its efforts in sustainable materials development.
In the same manner, Taiwanese synthetic rubber materials manufacturer TSRC has developed Taipol recycled TPE (rTPE), a product line that blends performance with sustainability. Made from recycled medical materials,TSRC says it is able to transform reclaimed inputs into high-value, high-performance compounds.The product line includes variants containing 30% and 70% post-consumer recycled (PCR) resins, addressing the increasing demand for sustainable solutions across industries.
Compared to traditional materials like polyolefin elastomers (POEs), Taipol rTPE is said to offer improved impact resistance while using less material, resulting in cost savings and lower carbon emissions. Its pliable, flexible properties make it well-suited for soft compound formulations across a variety of applications. Additionally, it complements styrene ethylene butylene styrene (SEBS) by providing a more sustainable option with higher PCR content and reduced environmental impact.
Taipol rTPE is targeted at automotive components, consumer goods, and industrial products, including bumpers, electronics casings, wires, cables, and packaging materials. Certified under the Global Recycled Standard (GRS), it ensures full traceability throughout production and sales.
Safer and more efficient TPEs for medical uses
TPEs offer safer and more efficient alternatives to conventional materials in medical and healthcare applications. As leaders in this space, TSRC and Kraiburg TPE, a global manufacturer of TPE compounds, have introduced advanced TPE solutions designed to improve product performance, safety, and sustainability.
TSRC’s Vector medical solutions offer a range of TPEs tailored for the medical industry, featuring high, medium, and low molecular weights, along with high flowability and vinyl content. Rigorously tested for safety and reliability, Vector meets the ISO 10993-5 cytotoxicity standard.

Kraiburg TPE launched the Thermolast H HC/ AD1/AP series in AsiaPacific for healthcare applications, ideal for smart skin diagnostic probe protectors. It ensures strong adhesion to PC, ABS, and PET, forming a durable, long-lasting seal
Thermoplas T ic e las T omers
As a plasticiser-free alternative to PVC, Vector TPE ensures environmental benefits as well as transparency in infusion bags, kink resistance in tubing, and resealing properties in medical stoppers, minimising fragmentation and contamination risks, it adds.
Meanwhile, Kraiburg TPE has introduced the Thermolast H HC/AD1/AP series for the Asia-Pacific market. Designed for healthcare and medical device applications, this TPE series is recommended for smart skin diagnostic device probe protectors, offering strong adhesion to substrates like PC, ABS, and PET while forming a durable seal that extends component longevity.
Fully colourable, it allows for customised designs that enhance user experience and brand recognition. Free from animal ingredients, it meets ethical standards, while its optimised mechanical properties ensure reduced maintenance needs. Its soft-touch surface improves control and precision during use, and its sterilisable nature allows for easy cleaning.
Compliant with GB/T 16886.5, ISO 10993-5, Regulation (EU) No. 10/2011, and US CFR 21 FDA (raw material conformity), Thermolast H HC/AD1/AP is ideal for flexible connectors in microneedling devices, films and seals for skin cleansing tools, handles for photon rejuvenation devices, and other medical and cosmetic applications.
Fire-safe materials for electronics and construction sector Adoption of flame-retardant materials enhances fire safety across industries, providing protection without compromising performance.
Kraiburg TPE offers more choices in fire safety materials with its halogen-free, flame-retardant TPE series, designed to minimise harmful emissions while meeting IEC 61249-221 standards. Tested for flammability and fire resistance, the material achieves a Glow Wire Ignition Temperature (GWIT) of 960°C on a 2 mm-thick sample. With slow ignition and low smoke emission, it offers self-extinguishing properties and temperature stability up to 85°C, helping prevent fire spread by inhibiting flaming droplets.
Contributing to sustainability with in-process recycling, the material adheres well to polyolefins like PP, enhancing manufacturing flexibility. These features make Kraiburg TPE’s flame-retardant compounds ideal for housing sensitive electronics, including internet hardware, where fire safety is critical. Further addressing fire safety needs, US polymer materials manufacturer Avient Corporation’s Eccoh XL 8054, a crosslinkable flame-retardant solution, is designed for lowsmoke, low-fume wire
and cable insulation. Compliant with stringent international safety regulations, including CEI EN 50363-0:2015 standards (G17 and G18) and the Construction Products Regulation (CPR), it offers manufacturers a cost-effective alternative to traditional elastomer compounds, according to Avient.
A key advantage of Eccoh XL 8054 is its processability. Unlike conventional materials that require continuous vulcanisation (CV) lines, it can be processed using standard single-screw extrusion equipment, simplifying production, reducing costs, and increasing line speeds. It also has high elongation at break, making it well-suited for shipbuilding, railways, construction, and solar cables.
In a related development, Avient has introduced Hammerhead FR composite panels for modular construction. This industry-first, patent-pending thermoplastic composite sandwich structure integrates flame retardance without additional sheets or coatings. Ideal for modular walls, flooring, and ceilings, the panels provide a lightweight, structural alternative to traditional materials such as gypsum, drywall, and framed assemblies.
Stepping up with footwear functionality
The footwear industry is seeing an innovation boost with new TPE solutions as US speciality chemicals supplier Huntsman Corporation is introducing its Avalon Gecko thermoplastic polyurethane (TPU) range designed for soling applications. Inspired by the natural grip of geckos, these materials offer rubber-like slip resistance in both wet and dry conditions while maintaining durability and recyclability. Ideal for running, hiking, and safety footwear, Avalon Gecko TPU balances softness with high abrasion resistance.
The series includes three specialised grades that are said to bond seamlessly with TPU midsoles without adhesives and can be mechanically recycled without performance loss.
Consistent with its sustainability commitment, Huntsman has secured ISCC+ certification for its TPU manufacturing sites in Jinshan, China, and Osnabrück, Germany. This globally recognised certification ensures traceability for recycled and bio-based products, enabling Huntsman to offer mass balance-certified materials. Its polyurethanes sites in Rotterdam and Wilton have held ISCC+ certification since 2023.
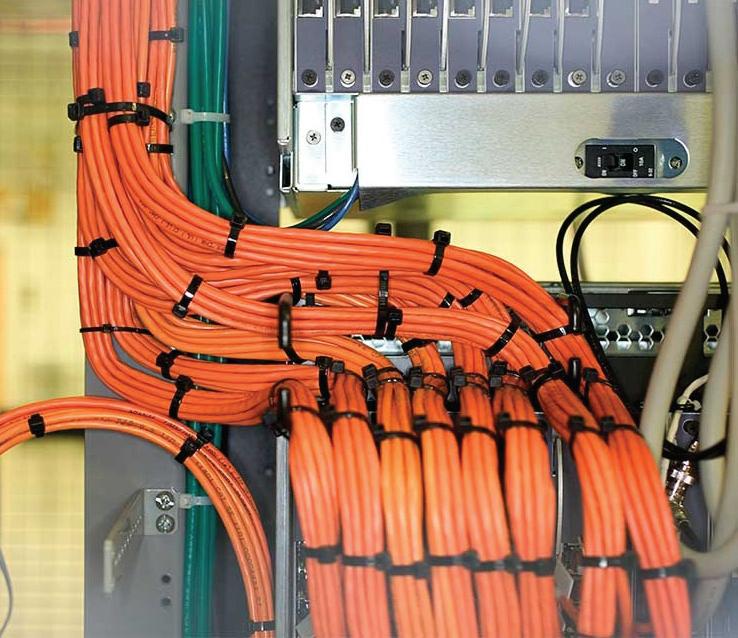
Meanwhile, US specialty materials company Celanese Corporation has launched Hytrel TPC RS40F2, a biobased thermoplastic polyester elastomer (TPC), which when foamed, is ideal for athletic footwear applications. The TPC incorporates a minimum of 20% segregated bio-content, verifiable via the C14 method. When foamed using a physical supercritical fluid (SCF) process, it is said to deliver energy return, rebound, and resilience, making it well-suited for midsole components.
Celanese partnered with processor Xingxun Enterprise to develop the processing of Hytrel TPC RS40F2 shoe soles using SCF foaming. The latter creates a unique cell structure that enhances material properties while eliminating harmful chemical foaming agents that produce volatile organic compounds (VOCs). This results in lower emissions, reduced odour, and improved mechanical integrity, says Celanese. Avient’s Eccoh XL 8054, a crosslinkable flame-retardant solution, is
Machinery on display by SML and W&H at Chinaplas 2025
In recent months, Austrian machinery maker SML's development efforts have focused on increasing capacity, productivity and efficiency as well as promoting recyclability in the sense of a circular economy.
Thus, at Chinaplas 2025, to be held from 15-18 April in Shenzhen, China, SML will focus on its new type of multifunctional cast film system for the efficient production of easy-to-recycle mono-material film and its advanced Triplex coating and laminating line for aseptic cardboard packaging.

SML will showcase its Triplex line for sustainable packaging
Besides standard products, such as CPP, CPE, Cast-PET and barrier films, SML's new cast film line fitted with a further-developed MDO unit is especially designed to process mono-oriented films for easy recycling. It features a wide functional range for standard food and non-food packaging to easy-to-recycle standup pouches in a thickness range of 15-60 µm; plus an advanced MDO unit with improved film properties and simple maintenance.
SML's Triplex coating and laminating lines represent a new approach in the manufacturing of liquid packaging board e.g. for dairy products or fruit juices. It is designed to process thin paper and rigid paperboard at an equally high quality. It features an optimised product change over with low waste; the best cost-performance ratio and comfortable operation and good accessibility. Meanwhile, Windmöller & Hölscher (W&H), a provider of machinery and
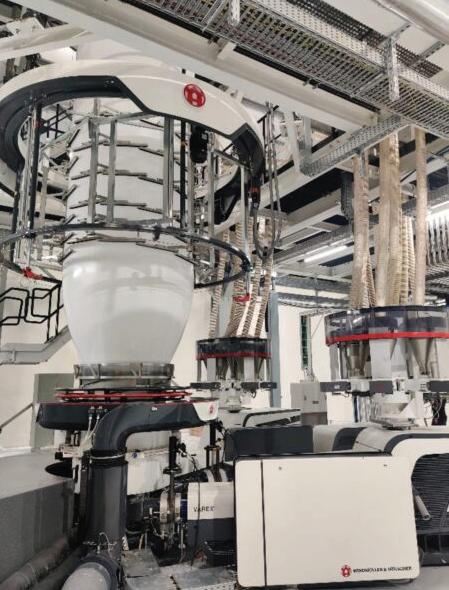
At Chinaplas, W&H will showcase a blown film line
Film/Sheet machinery
systems for the manufacturing and converting of flexible packaging, will present these solutions plus a focus on recyclability, at Chinaplas 2025. One will be the Varex's MDO-PE barrier solutions, accompanied by samples from various key industry partners.
Additionally, in collaboration with partner ExxonMobil, the family owned company will present Varex's blown film five-layer MDO PE, along with Optimex's blown film 100% PCR collation shrink. Filmex’s cast film PP and barrier structures, including MDO technology, will also be highlighted.
Other topics to be explored include paper bag solutions by Garant Maschinen, such as concepts for cross bottom bags or flat and satchel bags, which aim to offer paper alternatives, such as diaper overwraps and e-commerce mailer bags.
Oben to commission high output BOPP line
Mexican packaging film maker Oben Group continues to expand its footprint. Following the acquisition of KristaFilms in July 2023, the company is set to establish a new production facility in Monterrey, Mexico.
This facility will feature what is said to be the world's most advanced BOPP film production line from German machine maker Brückner.
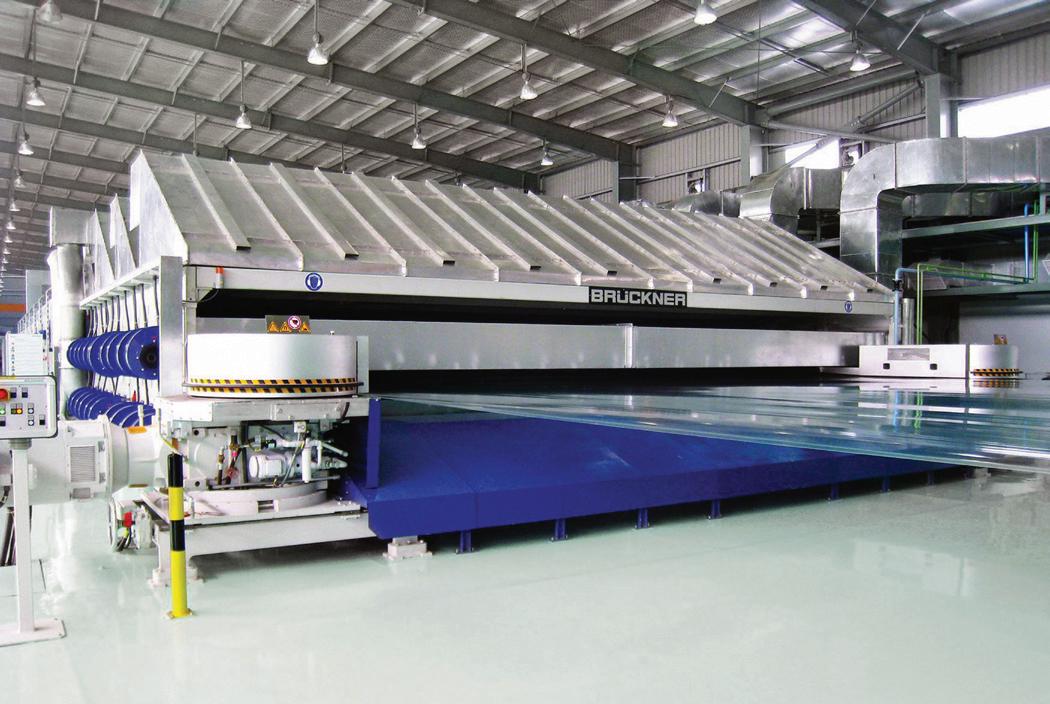
Brückner says Oben has ordered the first 12 m BOPP line with an output of 94,000 tonnes/year
The line will have a speed of 700 m/minute and a film width of 12 m, and an output of 94,000 tonnes/year, setting new industry benchmarks in output, speed, and winding diameter, according to the machine supplier. Oben Group has more than 17 manufacturing plants across the Americas and Europe, and is one of the world’s largest film producers with a diverse portfolio including BOPP, BOPE, BOPET, BOPA, PET-shrink, CPP, CPE, CPA, and cast; and films with added functionality by Al/AlOx metallisation and by single/double side water-based coating processes serving a wide range of industries. Additionally, Oben is a key producer of thermoformed products, PP construction boards, and PET straps, complementing its diverse and sustainable product portfolio.
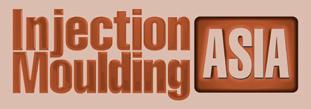
Injection Moulding Asia
Growing demand for large-scale PET recycling systems
Taiwan’s technological assets establish the country as a vital player in the region’s sustainability transition, says Angelica Buan in this report based on the recently concluded Taipeiplas show in Taiwan in September.
Demand for solutions for bottle-to-bottle recycling is increasing worldwide, even in countries like China. In view of this trend, the specifications for PET recycling machines to handle higher capacities are also growing.
With its Vacurema technology, machinery provider Erema says it offers a system that enables throughputs of up to 6 tonnes/hour.
“While the bottle-to-bottle market initially tended towards 3-tonne machines, over the past three years we have been seeing increasing demand for PET recycling solutions with throughputs in excess of three tonnes per hour,” says Christoph Wöss, Business Development Manager for the Bottle segment at Erema.
In total, a dozen Vacurema machines with throughput capacities of four to six tonnes have been installed and commissioned worldwide since 2020, according to the company.
“Together, these large recycling machines produce almost 350,000 tonnes of rPET per year, which is a clear sign that this order of magnitude is now commonplace in the industry,” adds Wöss.
Meanwhile, with its Vacurema technology, the Austrian machine maker says it offers a proven system for throughputs between 600 and 6,000 kg/hour. This technology is said to achieve efficient decontamination and gentle IV treatment and fulfils the strict requirements of the European and North American food safety authorities.
Even the basic version produces food-grade rPET, providing the basis for a wide range of end applications. Whether the pellets are then used with SSP for IV adjustment for bottle-to-bottle or high IV applications, an additional upstream vacuum treatment enables direct connection to preform production, or the material is processed inline into sheets or fibres.
“This versatility allows users to react flexibly to changes in the market and fluctuations in demand, an important advantage in a dynamic market environment,” adds Wöss.
The company also provides the advanced Vacunite technology that combines with the Vacurema system with integrated vacuum-assisted SSP in a nitrogen atmosphere. This combination further optimises the material properties and significantly reduces the yellowing of the pellets, which is an important quality factor in bottle-to-bottle recycling, says Erema.
What is more, the closed nitrogen cycle and optimised process control ensure even lower nitrogen consumption, and ultimately, a particularly efficient and environmentally friendly process.
Vacunite technology is available on machines for throughputs of up to 2,500 kg/hour that feature particularly low energy consumption and a compact design.
“In several markets, like Latin America, there is a clear trend towards larger PET recycling machines. We expect the market to develop this way in China too, to meet the increasing demand for high-quality rPET suitable for sensitive applications such as food packaging,” says Wöss.
Erema adds it has already installed more than 50 Vacurema and Vacunite systems in China, but only a few with throughputs in excess of 4 tonnes/hour.
Wöss sees opportunities here: “For Chinese recyclers, the bandwidth and flexibility of the systems offer great potential for a wide variety of applications.”
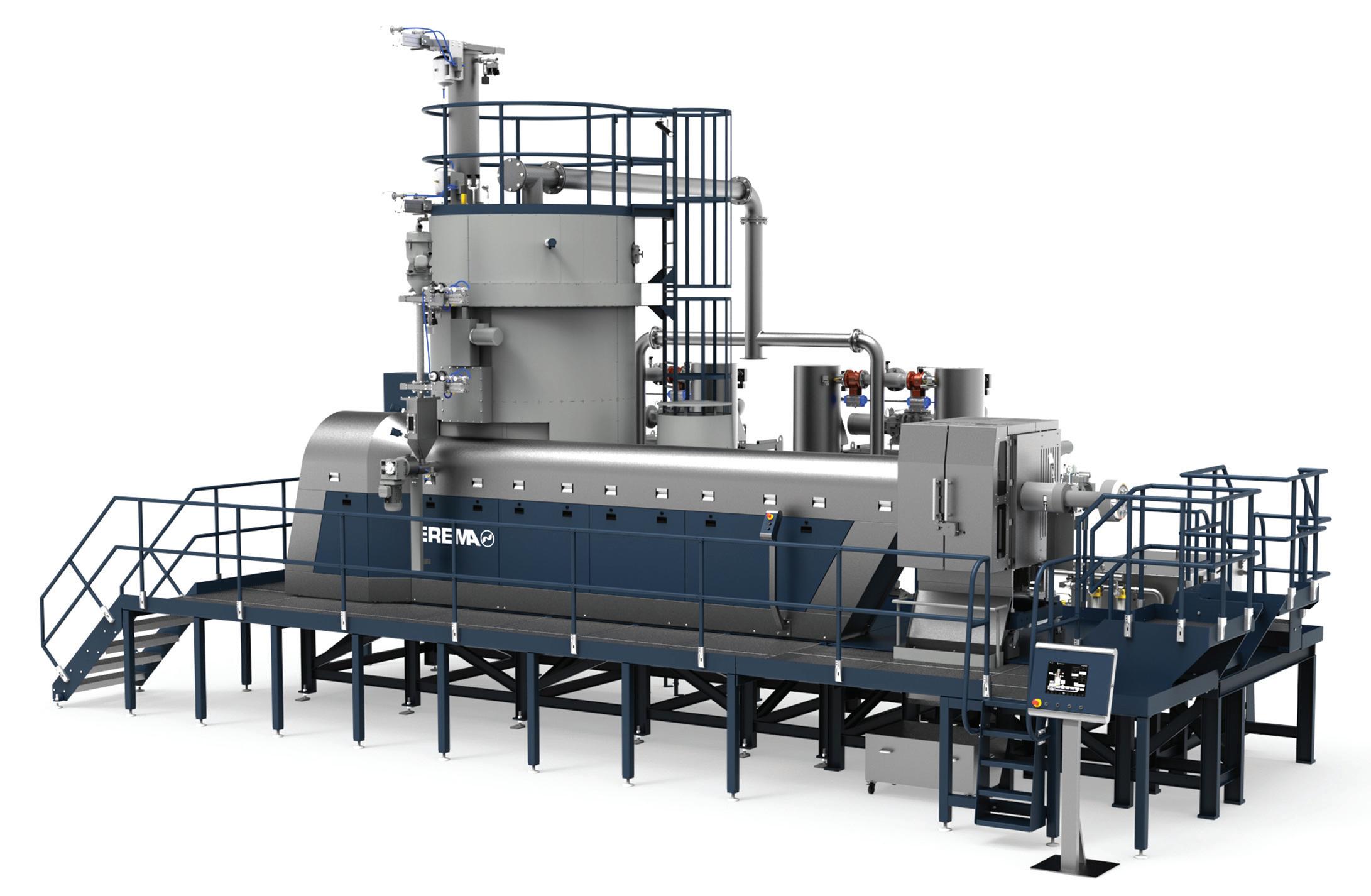
Though Erema has installed more than 50 Vacurema and Vacunite systems in China, but only a few with throughputs in excess of 4 tonnes/hour; it views the market as growing
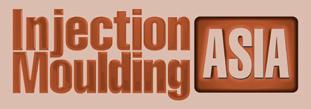
Injection Moulding Asia
LSR stretches to innovations in automotive and medical sectors
Liquid silicone rubber (LSR) is making a clear impact in automotive and medical applications, with the market responding favourably, says Angelica Buan in this report.
Global growth of LSR demand
Global demand for liquid silicone rubber (LSR) is reaching new heights as industries seek high-performance materials for medical devices, automotive components, consumer goods, and more.
According to a report by Persistence Market Research , the LSR market is projected to grow at CAGR of 8.4% through 2031. The automotive sector remains the largest end-user, driven by the need for durable, highperformance components, while the medical segment follows due to LSR’s biocompatibility, sterilisability, thermal stability, and flexibility, among other features.
To keep pace with rising demand, material solutions providers are scaling development and production, introducing advanced LSR formulations that enhance durability, flexibility, and precision. As innovation continues, new applications for this versatile material are emerging across industries.
LSR development spurs automotive market growth
Leading companies in the LSR sector are expanding production, developing new products, and adopting sustainable practices, especially for automotive applications.
German chemical company Wacker Chemie has further strengthened its foothold in the Asian market with new specialty silicone production facilities in Japan and South Korea.
The plants, located in Tsukuba, Japan, and Jincheon, South Korea, will support growing demand, particularly in the automotive and construction industries and represent an investment in the double-digit million-euro range.
Wacker stated that the additional capacity will help meet increasing demand, particularly in Asia, which already accounts for over 40% of Wacker’s sales, with Japan and South Korea playing a key role.
The Tsukuba site is focused on supporting the automotive industry, especially electromobility. It includes a production line for silicone-based thermal interface materials (TIMs), elastomers modified with additives and fillers to enhance thermal conductivity. These materials serve as gap fillers in electronics, improving heat management for components such as electric vehicle (EV) batteries. By embedding batteries in silicone encapsulants, heat dissipation is controlled, preventing overheating and improving safety.
Japanese automotive suppliers are actively investing in electromobility, aiming to refine battery-powered vehicle designs. Silicones are utilised in hybrid cable systems, thermal management solutions, potting for power electronics, and battery safety enhancements. The new production line in Japan will allow Wacker to meet regional demand for these advanced materials.
At the same time, Wacker has expanded capacity at its Jincheon site in South Korea. The company has been producing silicone sealants for construction there since 2010, later adding specialty silicones, LSR, and silicone elastomers for automotive and electrical applications in 2012.
Durable adhesion and coating solutions for mobility sector
In line with industry advancements, US chemical firm Dow ’s Silastic SA 994X LSR series, which it debuted in 2022, continues to support the development of technologies for the mobility and transportation sector, it adds.
The Silastic series consists of primerless, self-adhesive, general-purpose, and self-lubricating LSRs with a one-to-one mix ratio, designed for two-component injection moulding with thermoplastic substrates such as PBT and PA.
Furthermore, the series works for automotive uses like connector seals, battery vent gaskets, and radiator gasket seals in electric and hybrid vehicles, as well as environmental protection seals for lidar and radar housings in autonomous vehicles. It provides durable adhesion under heat and humidity, achieves full bond strength instantly, maintains a 12-month shelf life, and bonds strongly to various plastics and metals without additional heat treatment.
Critical material for reliable insulation
In another development, Japanese chemical company ShinEtsu Chemical Co has introduced ST-OR heat-shrinkable silicone rubber tubing, marking an industry first for busbar insulation.
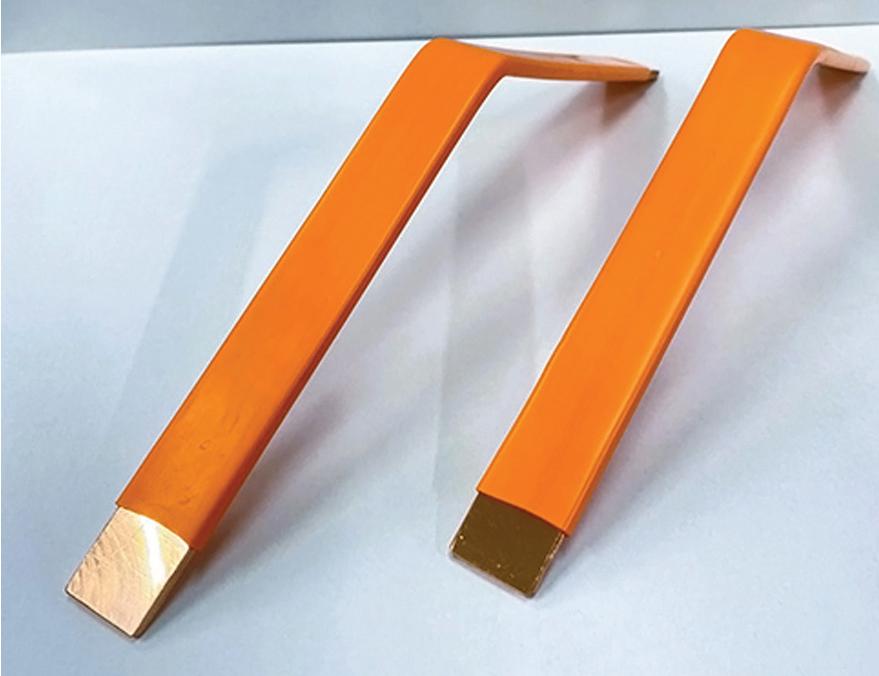
Shin-Etsu Chemical has introduced ST-OR heatshrinkable silicone rubber tubing for busbar insulation
Liquid Silicone Rubber Moulding
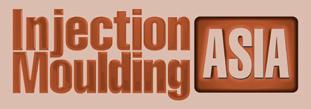
Injection Moulding Asia
Busbars, typically made of copper or aluminium and used in switchboards, control panels, and electric and hybrid vehicles, require reliable insulation due to the high voltages and currents involved.
The ST-OR tubing meets these demands with high electrical insulation properties, featuring a dielectric strength of 28 kV/mm. It remains stable in extreme temperatures ranging from −40°C to +200°C. The tubing’s bright orange outer surface also makes it a high-visibility alternative to high-voltage cables. Unlike other insulation materials, it retains the flexibility characteristic of silicone rubber, even after the heatshrinking process.
For applications requiring both electrical insulation and thermal conductivity, Shin-Etsu has developed the ST-TC-1, offering a thermal conductivity of 1.0 W/m·K. This version ensures efficient heat transfer while covering heating components.
A major advantage of this tubing is its ease of application. When heated, it shrinks around the busbar, creating a secure insulating layer without complex installation procedures. Moreover, this innovation enhances the reliability of power distribution systems while reducing time and labour costs.
Gecko-inspired material for patient safety Innovations in LSR are improving healthcare by enhancing medical devices, prosthetics, and patient safety solutions.
Researchers at the ACS Applied Materials & Interfaces , funded by the Foundation for Science and Technology in Portugal, have developed a geckoinspired slip-resistant material that could reduce injuries from slips and falls. The new polymer, made from LSR enhanced with zirconia nanoparticles, mimics the
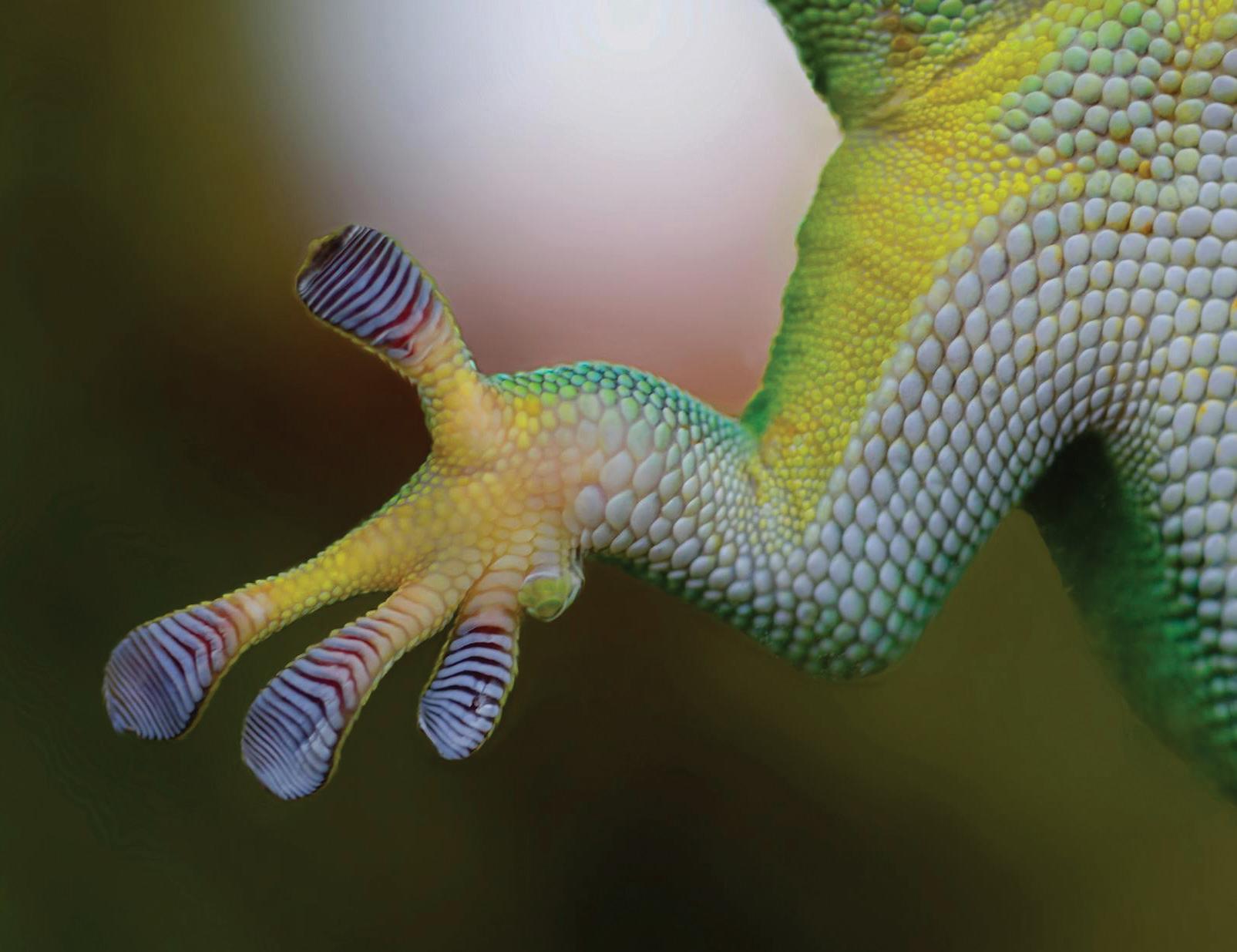
adhesive properties of gecko footpads and improves traction on slippery surfaces. Scientists believe it could be incorporated into shoe soles to enhance grip.
Many existing anti-slip soles, often made from natural rubber, struggle to maintain traction, specifically in wet conditions. Inspired by geckos, whose footpads use hydrophilic capillary-enhanced adhesion to grip slick surfaces, researchers sought to replicate this effect in a synthetic material.
The LSR/zirconia nanoparticles material, to attract water molecules, is rolled into a thin film, hardened with heat, and laser-etched with grooves to expose the hydrophilic particles. This structure allowed the polymer to create suction, similar to gecko footpads, making it highly slip-resistant.
Tests on different versions of the material, with zirconia concentrations ranging from 1% to 9%, showed that the 3% and 5% formulations provided the best grip. The researchers believe this technology could also have medical applications, such as in electronic and artificial skin, where polymers interact with fluid layers between surfaces.
Synthetic skin for medical research and infection prevention
In a related effort, researchers from Texas A&M University have developed skin-like replicas using Ecoflex LSR to study bacterial infections from intravenous catheters and test wearable sensors. The material mimics the texture, wettability, and elasticity of human skin, making it a promising platform for medical research.
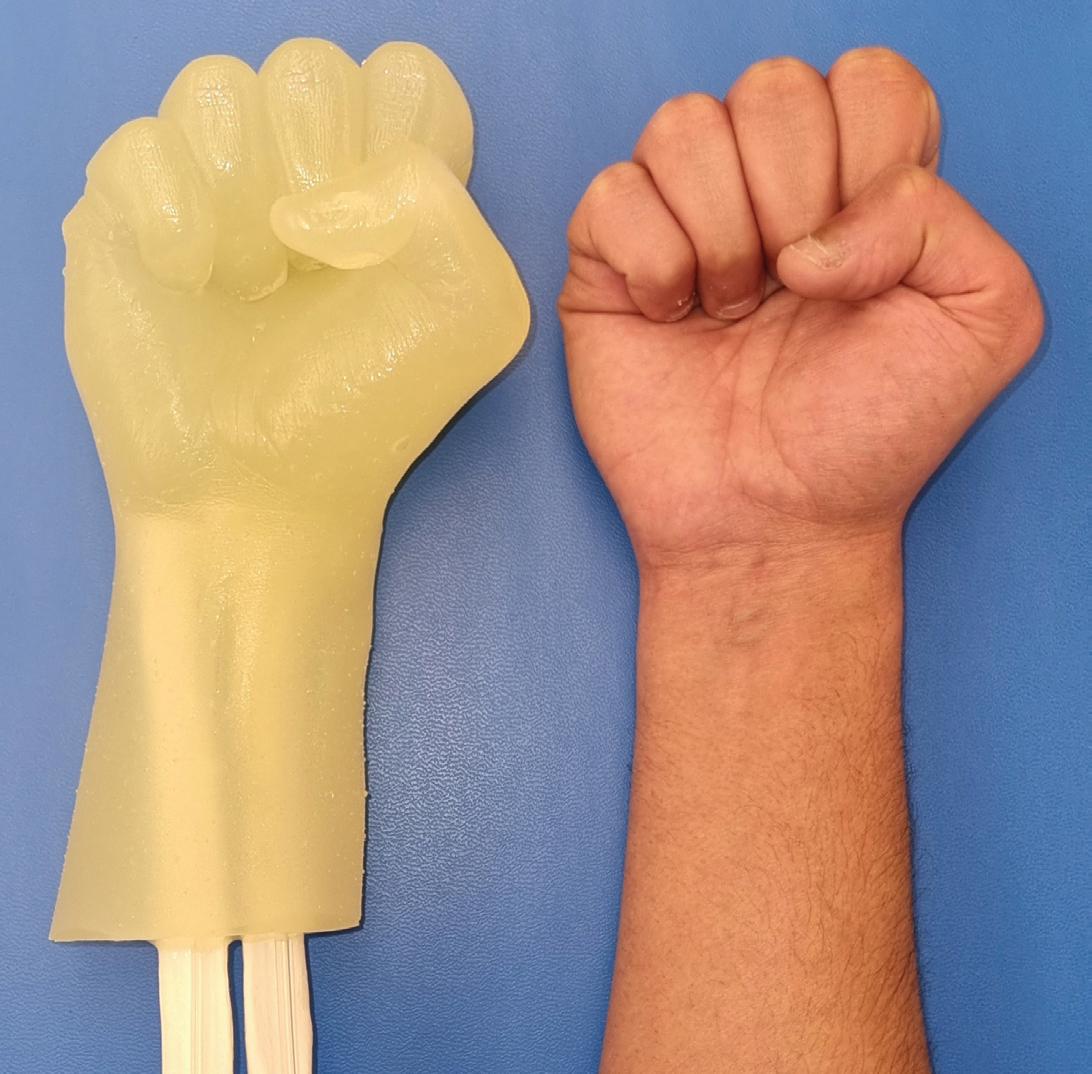
Liquid Silicone Rubber Moulding
ACS Applied Materials & Interfaces has developed a geckoinspired slip-resistant polymer made from LSR enhanced with zirconia nanoparticles that could reduce injuries from slips and falls
Texas A&M University has developed skin-like replicas using Ecoflex LSR that mimics the texture, wettability and elasticity of human skin, making it a promising platform for medical research
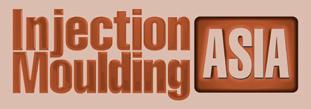
Injection Moulding Asia
The study, funded by the National Institute of General Medical Sciences , the Office of Naval Research , and the National Science Foundation ’s PATHS-UP Engineering Research Centre, was published in Scientific Reports. It highlights Ecoflex’s ability to replicate real skin conditions where bacteria grow and adhere.
Intravenous (IV) catheter-related bloodstream infections (CRBSIs) pose a major health risk. In the US alone, an estimated 80,000 cases occur in intensive care units each year.
A simulated catheter insertion successfully modeled bacterial growth, with plans to add body fluids for more accuracy.
Advancements in maternity and feminine hygiene products LSR technology is also advancing in the maternity and feminine hygiene market, improving comfort, durability, and safety.
According to Global Market Insights , the global maternity products market, valued at US$42.1 billion in 2023, is projected to grow at a CAGR of 6.8% from 2024 to 2032, driven by increased awareness of maternal well-being and the demand for specialised pregnancy and postpartum products.
Menstrual cups and breast pumps are emerging as key segments. The global breast pump market, valued at US$3.5 billion in 2025, is expected to reach close to US$7.4 billion by 2034, with a CAGR of 8.64%, according to Precedence Research
One company driving innovation in this sector is Switzerland-based Silcoplast AG , which specialises in high-precision components for maternity and feminine hygiene products. Using LSR and other materials, Silcoplast manufactures silicone injection-moulded products at scale while also offering customised plastic and silicone solutions.
In menstrual cup production, Silcoplast’s LSR injection moulding process is said to improve efficiency and sustainability by enabling the simultaneous filling of twomould cavities. The resulting menstrual cups are lightweight yet sturdy, featuring a specially developed matte surface for enhanced usability.

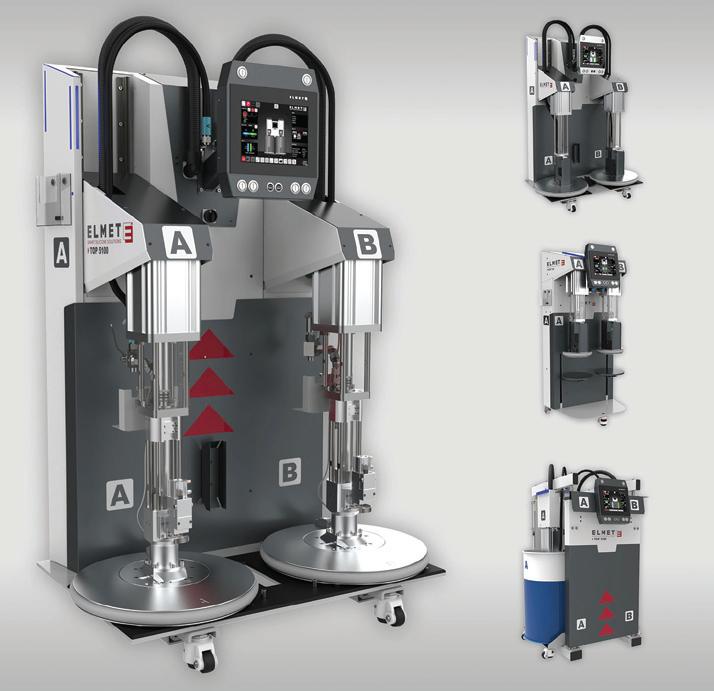
Austrian machine maker Elmet has launched its latest precision dosing system for LSR injection moulding, which is suitable for 20 and 200-l drums, replacing the previous Top 5000 version. Advances compared to its predecessor include amore compact design, optimised pump technology in terms of sealing technology for longer service life, higher resolution of the volume counters for more precision in production and the revised software. The dosing system can also be delivered FDA-compliant as an option, allowing for use in the food, healthcare and related industries. Plus, it is equipped with the M pump unit for an increased delivery pressure of 230 bar, so that all commercially available LSR materials can be processed in an extended viscosity range from 0.001 Pas to 3000 Pas. This includes carbon black or mineral-filled and self-adhesive materials, which tend to increase in viscosity, as well as abrasive materials, such as thermally conductive materials for the e-mobility sector
For breast pumps, Silcoplast produces medical-grade silicone components, including pump valves with a 60 Shore hardness to provide optimal flexibility and stability. The company also offers breast shield inserts in five sizes, ensuring a customised fit that improves milk flow and comfort. All materials used meet stringent hygiene and safety standards for medical applications.
Medical-grade silicone inks and device coatings
US-based tooling firm Avantor has introduced silicone inks through its subsidiary, NuSil Technology, for marking silicone components used in industries with strict performance requirements, including healthcare, optoelectronics, and electronics.
The only biocompatible inks for long-term implants, they resist corrosion and extreme temperatures, and are compatible with pad printing and silk screening on silicone devices such as extruded tubing, calendered sheeting, and moulded balloons. Available in various colours, they can also be customised for branding or identification.
In a related development, NuSil partnered with Silq Technologies Corp to expand the application of Silq’s patented zwitterionic surface treatment technology on medical devices made with NuSil silicone products. It helps prevent implant infections and complications without antibiotics and also reduces fibrosis, thrombosis, and encrustation while improving lubrication. However, manufacturing and cost challenges have slowed its commercial use.
Silq Technologies, a spin-out from the University of California, Los Angeles (UCLA), has created a scalable way to apply zwitterion surface treatments. Its ClearTract Foley catheter, using this technology, has FDA clearance and is being launched in the US. Early clinical trials show positive results and cost benefits, with final data expected soon.
Silcoplast produces medical-grade silicone injection moulded products at scale, such as breast pump and pump valve, for maternity and feminine hygiene sector
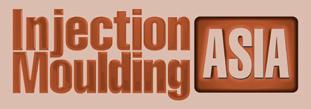
Injection Moulding Asia
Industry innovations at Chinaplas 2025
Amid rapid technological advancements and sustainable transformation, Chinaplas 2025 is set to deliver a line-up of concurrent events, highlighting the latest breakthroughs and emerging trends in the plastics and rubber industries. The show will be held at Shenzhen World Exhibition & Convention Centre China, from April 15-18, 2025.
From material innovations to smart manufacturing solutions, this year’s programme will spotlight industry pioneers, top scientists, and global brands. With “Transformation • Collaboration • Sustainability” at its theme, Chinaplas 2025’s concurrent events are expected to shape the future of the plastics and rubber industries.
As the official technologies release platform of Chinaplas, Tech Talk has witnessed the debut of over 300 innovative technologies since its inception.
There will be over 40 of the latest technological achievements at Chinaplas 2025 Tech Talk. Presented in an open forum format, Tech Talk offers buyers an opportunity to quickly gather technology trends in plastics and rubber industries.
Chinaplas 2025 Tech Talk will centre on six themes: Efficient Packaging Solutions, Green Low-carbon Solutions, Automotive Lightweighting Solutions, Rubber & TPE Technologies, 2025 New Materials, and 3D Printing.
A special " New Tech Display Zone" area will also be featured, providing a platform for interaction and collaboration between visitors and exhibitors.
Other highlights
Amongst the highlights at Chinaplas will be an interactive Product Innovation Gallery, a set of exhibition walls to be located in the Central Corridor on level 1. Themed “From Products to Technology”, the gallery will showcase hundreds of finished or semi-finished products, featuring industry giants like ExxonMobil , HRHB and Sabic
Meanwhile, the 3rd SciXplore Forum, to be held on April 16 (2nd show day), will bring together wellknown scientists and academicians in the industry to share the latest development trends and breakthrough achievements in the field of polymers and applications.
Keynote speeches will feature speakers such as academicians Zhengdi Cheng, Benzhong Tang, Seeram Ramakrishna, Liqun Zhang, Professor Kohzo Ito and Professor Ping Gao. They will delve into topics such as polymer physics, aggregation-induced luminescence, electrospinning technology and nanofibres, silica gel and elastomer, slip ring materials as well as ultra-high molecular weight polyethylene nanomemes.
Furthermore, a series of thematic forums will feature over 40 hot topics, such as recyclable medical packaging, cost reduction strategies and efficiency
improvements in electronic and electrical industries, and emerging trends in packaging as well as antibacterial technology for microbial odour control in plastic and rubber products.
With a total of six thematic seminars, this event provides invaluable insights into industry trends, technological advancements, and real-world applications.
To seize new market opportunities and foster valuable insights, Market Insights Hub will hold three thematic forums on Day 4 (Apr 18) to explore hot topics covering RCEP and overseas market exploring strategy, ESG and sustainable supply chain and insights report of new productive forces.
Lastly on Day 4 of the show, the organiser, in collaboration with Federation of Shenzhen Industry, will launch an Exclusive VIP Factory Tour for the first time. This tour offers a unique opportunity to visit exhibitors' factories and end-user sector facilities across industries such as electronics, packaging, medical, automotive, and building materials, providing a comprehensive view of the industrial chain from raw materials to end products.
Cutting edge innovations
Cutting edge innovations will be showcased by materials firms. For instance, German chemicals firm BASF will launch the Pro-Flex Terra foot prosthesis, co-created with prosthetic provider, Össur. Cellasto’s material solution, characterised by progressive stiffness and high impact strength, combines softness and flexibility with energy return, allowing the Pro-Flex Terra foot prosthesis to embody an intuitive response behaviour and replicate closely the human muscle-tendon motion.
The three-step Cellasto foam design addresses the limitations of traditional two-step designs. It adapts to a wide range of load conditions without mechanical or electrical adjustment, making it suitable for activities like slow walking, hiking, and high-impact sports in both extremely cold and hot environments. Additionally, it is ideal for use at the beach, pool, or in the shower. Users noted that they were rediscovering aspects of their mobility while using it.
BASF’s Cellasto and Össur have collaborated to enhance performance in foot prosthesis

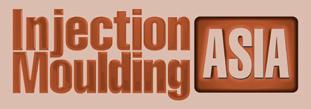
Injection Moulding Asia
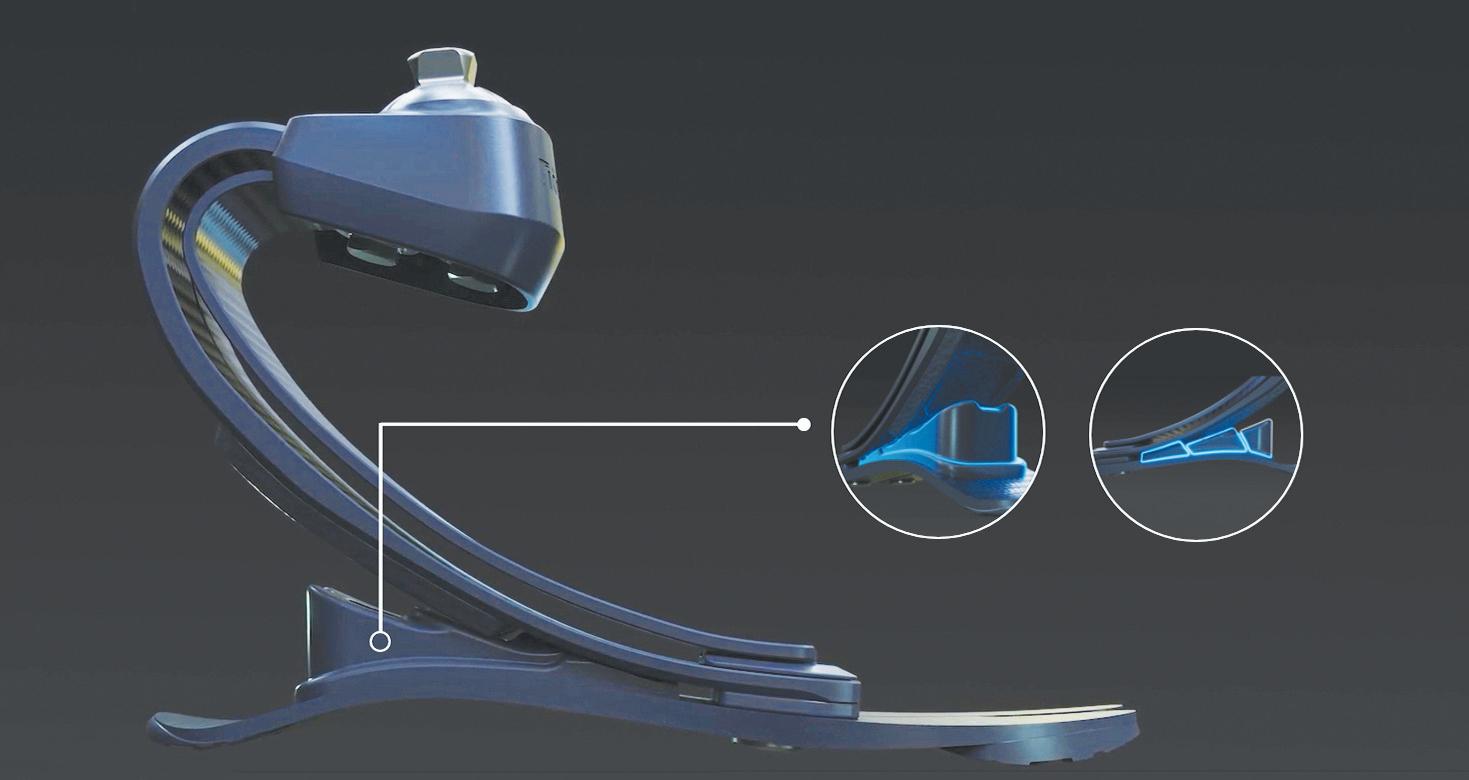
Össur foot prosthesis featuring Cellasto's advanced three-step foam design
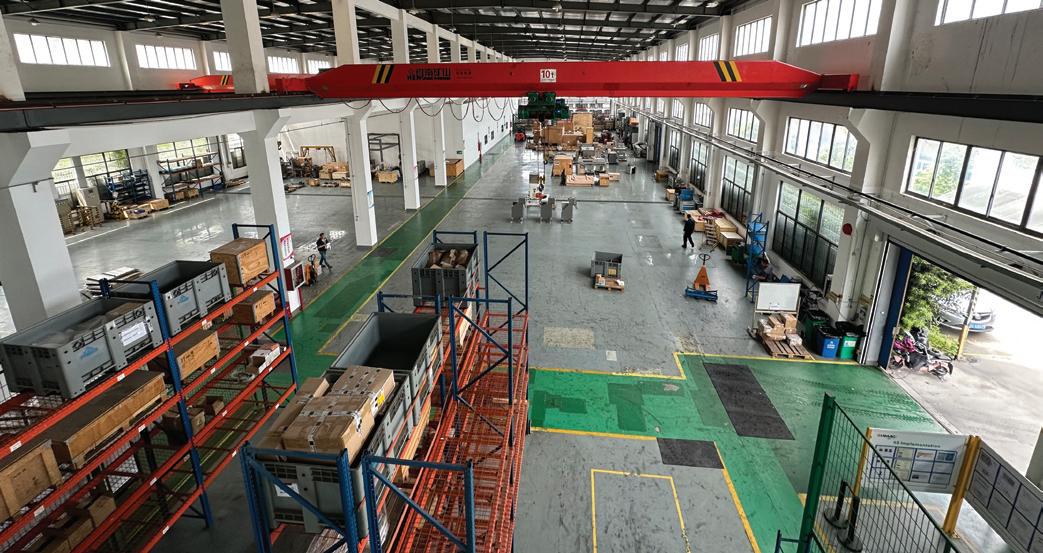
Companies pumping in investments in China
Switzerland-based Maag Group has been stepping up its localisation strategy in China. It has continuously increased its business activities and sales. Now, the company operates a 7,500 sq m-assembly shop in Jiading, Shanghai, which has recently been doubled in size.
Products engineered in Switzerland or Germany, adapted to the local needs in China and are manufactured and assembled at its Shanghai factory. Maag says it has been localising products for the Chinese market for more than 20 years starting from components to nowadays complex production systems.
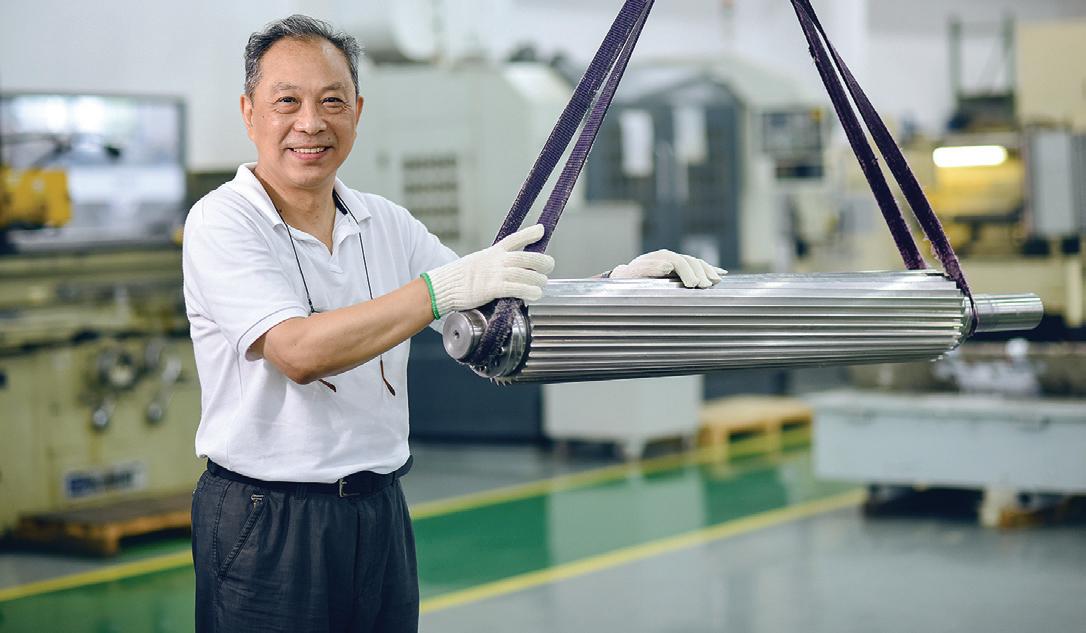
It has already been producing GA series extrusion pumps, Baoli strand pelletisers, and Zhuli underwater pelletisers in China. The C-USG, a similarly adapted version of the proven M-USG underwater strand pelletising system is expanding the market-specific portfolio. The original German design forms the basis for this new version. While some key components are supplied from Germany, the majority of parts come from local production. Furthermore, at its local grinding centres in Shanghai (East China) and Guangzhou (South China) it grinds cutting rotors, cutting blades and die plates.
Another company pumping up efforts in China is German injection moulding machine maker Arburg, which set the initial course for its "local-to-local" activities back in 2020, with the opening of the Arburg Technology Factory (ATF) in Pinghu. Initially, activities
focused on adapting Allrounder machines to customerspecific requirements and implementing turnkey systems in cooperation with local suppliers of moulds and peripheral equipment.
This was followed in 2023 by the Flexlift linear robotic system and 2024 the Allrounder Golden Electric Evo. Both product series are specifically tailored to the requirements of customers in Asia and are also exclusively available there. Assembly in the ATF ensures quick availability of the entrylevel electric machines.
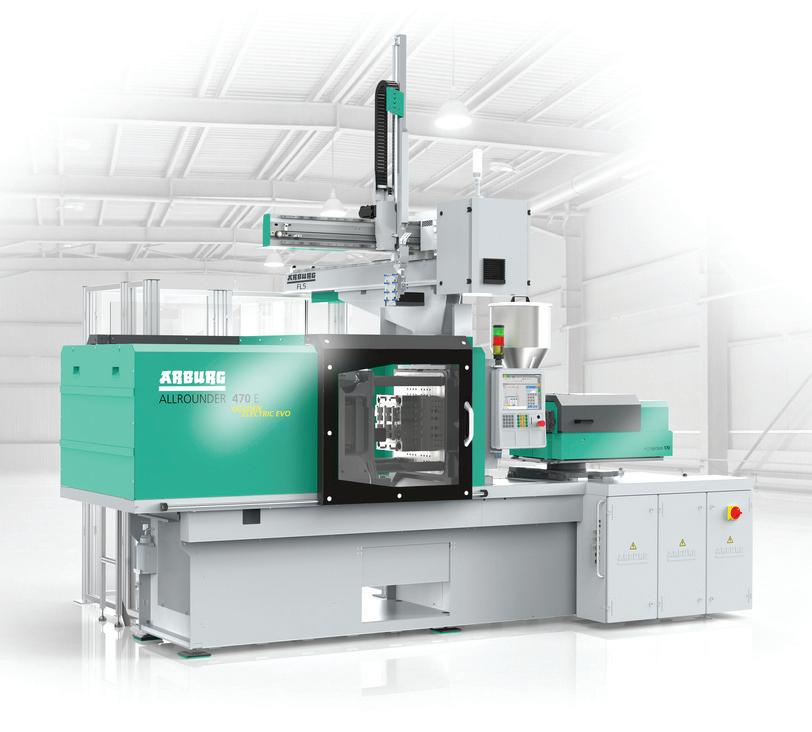
Arburg will present the Allrounder 470E Golden Electric Evo, which is an entry-level electric machine for the Asian market
The portfolio includes the sizes 370, 470, 520 and 570, which cover clamping forces ranging from 600 to 2,000 kN. The injection units range from size 100 to size 800, for shot weights of up to around 430 g of PS. The Golden Electric Evo series is also suitable for LSR applications and can be automated with a Flexlift linear robotic system, which is also specially designed for Asia.
The Allrounder Golden Electric Evo is extremely precise, thanks to its high-quality injection units. The servo-electric drives for "inject", "dose" and "open and close mould" deliver fast acceleration, high speeds, and simultaneous movements, all of which add up to short cycle times.
Compared to standard hydraulic machines, the dry cycle times are up to two seconds shorter. What's more, the energy requirement can be reduced by up to 50% with the toggle-type clamping unit, the high efficiency of the servo-electric drive and recovery of braking energy.
For more information or enquiries about the show, please visit www.ChinaplasOnline.com or contact Chinaplas.pr@adsale.com.hk
Maag says it has doubled the size of its production space in Shanghai
Maag’s production shop in Shanghai
Rubber Journal Asia
Tyre Sector
Asian tyre sector to amble along with US tariff imposition
The higher than expected trade tariffs imposed by the US may shake up a few industry sectors in Asia, including the tyre sector that will require Asian tyre makers to innovate and become more competitive in the global market, according to Angelica Buan in this report.
Market highs and lows
The global tyre industry is still a solid driver of growth— and the numbers back that up. In 2024, the market was valued at around US$137 billion, and it’s expected to grow at a CAGR of 4.2% from 2025 to 2032, reaching about US$191 billion.
In the global scene, the US tyre market is said to hold a 28% share and is projected to grow at 5.4% during the forecast period, according to Maximize Market Research’s tyres market 2025–2032 forecast.
The five leading exporters of new rubber tyres, namely, China, Thailand, Germany, Japan, and the US, accounted for 46% of global rubber tyre exports in 2023.
Meanwhile, the Asia-Pacific region already accounted for nearly half or 48% of the global tyre market in 2024, and it’s expected to grow at a CAGR of 5.3% from 2025 to 2032.
Asia is home to three of the world’s four largest tyre markets—China, India, and Japan. Together, they made up 70% of the region’s tyre market in 2020, which was estimated at 1.3 billion tyres valued at around US$97.4 billion, based on Smithers’ The Future of Tires in Asia 2025 report.
But over the past three years, the industry in Asia has had its fair share of challenges. These include shortages and unstable prices of raw materials, shipping and logistics issues, rising freight costs, and tighter environmental regulations. Geopolitical tensions have not helped either.
Raw material supply problems and price swings have been especially tough for the sector. Many of the top players have had to deal with serious supply chain disruptions. With raw material costs constantly changing, manufacturers are left with a lot of uncertainty, which can drive up production costs and eventually impact consumer prices, too.
Tyre makers in Southeast Asia are also facing growing pressure from stricter environmental regulations and higher sustainability standards. At the same time, many Asian governments are pouring more money into transport and infrastructure, which is pushing new rules aimed at cutting CO2 emissions and rolling out tyre labelling programmes.
In China, for example, there’s a strong push for low rolling resistance (LRR) tyres, largely because of government efforts to bring down emissions.
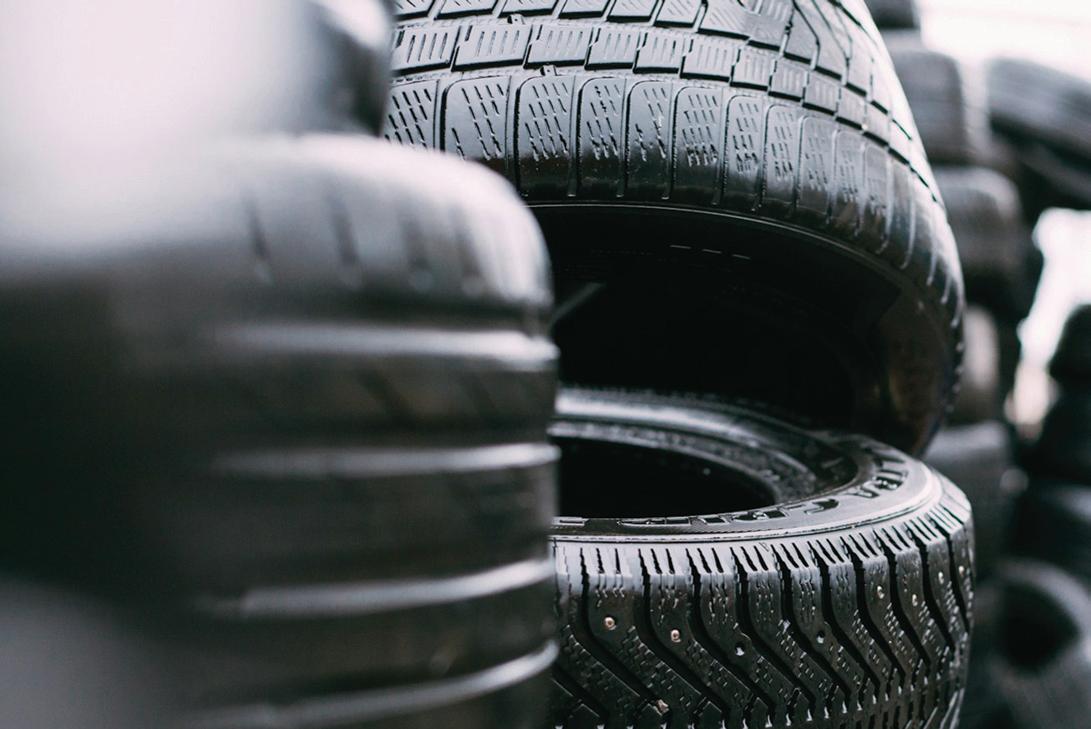
US tariffs add on to challenges
In a plot twist just when the industry seemed ready to bounce back it has taken a hit by the imposition of new tariffs that are expected to shake up the global supply chain once again—for better or worse.
US President Donald Trump’s new tariffs, which add on to the sweeping 10% duty on all US imports, will affect the tyre industry in Asia hard, especially major exporters to the US. These “reciprocal” tariffs target countries that the Trump administration says impose high duties on US imports or enforce non-tariff trade barriers.
According to S&P Global Mobility, the US has imposed a 25% tariff on all light-duty vehicles imported into the country, with collections starting in April 2025. For automotive parts, tariffs will kick in no later than May 2025. In 2024, the US imported the most number of vehicles from Mexico, followed by South Korea, Japan, and Canada, according to S&P Global Mobility estimates.
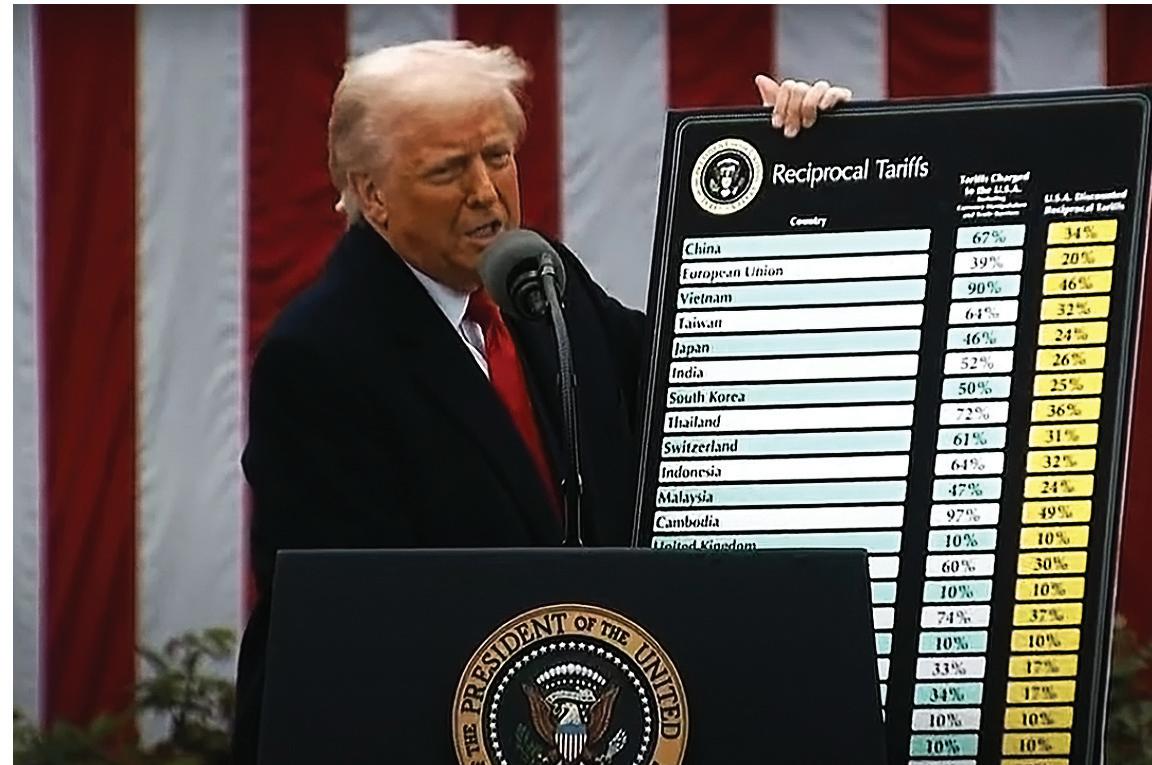
The Asia-Pacific region accounted for nearly half of the global tyre market in 2024 and is expected to grow further in the coming years
US President Donald Trump’s reciprocal tariffs are expected to impact Asian countries facing rates between 17% and 49%—except for places like Singapore, which face only the baseline 10%.
Rubber Journal Asia
The US administration has implied that tariffs on automotive and automotive parts, including tyres, are to remain in place indefinitely, with high, persistent rates and few exemptions.
The impact isn’t limited to imports. Rising costs will also affect the US automotive manufacturing sector, eventually leading to higher vehicle prices for consumers.
D-day for Asian tyre sector?
Asian countries will be hit hard by these changes, especially since out of the ten biggest exporters of passenger tyres to the US in 2024 – Thailand, Indonesia, Vietnam, South Korea, Japan, Cambodia and Malaysia – will be subject to reciprocal tariffs.
Thailand was the biggest exporter of passenger tyres to the US last year, shipping an estimated 35.3 million units, a yearover-year increase of 16.4%, according to Modern Tire Dealer’s statistics.
Specific countries and reciprocal rates affecting Asia are Thailand (37%), Indonesia (32%), Vietnam (46%), South Korea (26%), Japan (24%), Cambodia (49%) and Malaysia (24%). China, the world’s largest producer and consumer of tyres, will now face a reciprocal tariff rate of 34% in addition to the 20% tariffs already in place.
Looking ahead to 2025, US tyre imports are projected to come primarily from Thailand (US$312 million), Mexico (US$172 million), Canada (US$150 million), Vietnam (US$118 million), and Japan (US$109 million).
Perhaps the silver lining in this tariff turmoil is that, while these measures may increase costs for US consumers and decrease competitiveness for Asian exporters, they could also shift supply chains and alter market dynamics in the tyre sector. Already, many manufacturers are moving production away from China to other economies in South/Southeast Asia where tariffs are lower.
Ready for the roller coaster ride
Thailand, which has maintained its position as the top tyre supplier to the US, is bracing for the possible adverse impact of the new tariff hike. The country already dealt with a 25% tariff on steel and aluminium that took effect in March 2025, along with a 25% tariff on automobiles and components introduced shortly after.
Despite these challenges, Thailand is still set for growth, driven by strong domestic and international demand from downstream industries. Economic growth, rising investments, and a booming global tourism industry are expected to boost demand for automotive products and tyres, according to Kungsri Research’s rubber industry outlook.
While the US remains Thailand’s leading export destination, the country also ships tyres to over 69 nations worldwide. Vietnam and India are two other major markets for Thai tyres, capturing 19% and 12% of the market, respectively. Other key export destinations include Mexico, Russia, Philippines, Peru, Ecuador, and Indonesia, as indicated in Volza’s global trade report.
Meanwhile, Vietnam has been touted as the world’s largest exporter of tyres, with most of its shipments headed to the US,
South Korea, and Germany. The US is by far its biggest market with over 90% of Vietnam’s tyre production exported there. In 2023 alone, Vietnam exported US$3 billion worth of tyres, with 644 exporters involved in the trade, according to Tendata’s iTrader audit.
Several factors have fuelled Vietnam’s growing tyre exports to the US, including tariff advantages, rising demand, costeffective manufacturing, and trade agreements. For instance, Vietnam signed a Bilateral Trade Agreement (BTA) with the US in 2000, which took effect in 2001, giving it an edge in trade relations.
With the US imposing higher tariffs on Chinese goods, Vietnam has become a more attractive spot for manufacturing. On top of that, being the third-largest rubber producer in the world gives Vietnam a competitive edge in the tyre industry, according to China Research Intelligence.
Over in the Philippines, some sectors could see trade disruptions but compared to India and Thailand, the overall impact might be more limited due to lower trade volumes across most sectors, according to BVA Research.
Malaysia finds itself in a similar position. While there are moderate tariff differences with the US, the country’s overall exposure remains lower than India and Thailand’s, due to smaller tariff gaps and the structure of its trade. That said, Malaysia’s plastic and rubber sectors stand out as areas with some of the highest tariff differentials.
Innovations on a roll
With market volatility in the air, tyre manufacturers need to rethink their strategies, especially since political shifts and ongoing trade negotiations create uncertainty, making it harder for companies to plan long-term. For tyre makers, staying flexible is the name of the game with some exploring alternative sourcing options or looking into building up domestic production.
Others are moving their operations to countries with fewer trade hurdles, such as setting up factories in countries that will enable them to sidestep tariffs and get closer to the North American market.
Still, for most major tyre players, it is business as usual, for now, with innovation and collaboration remaining their strongest cards in this challenging time.
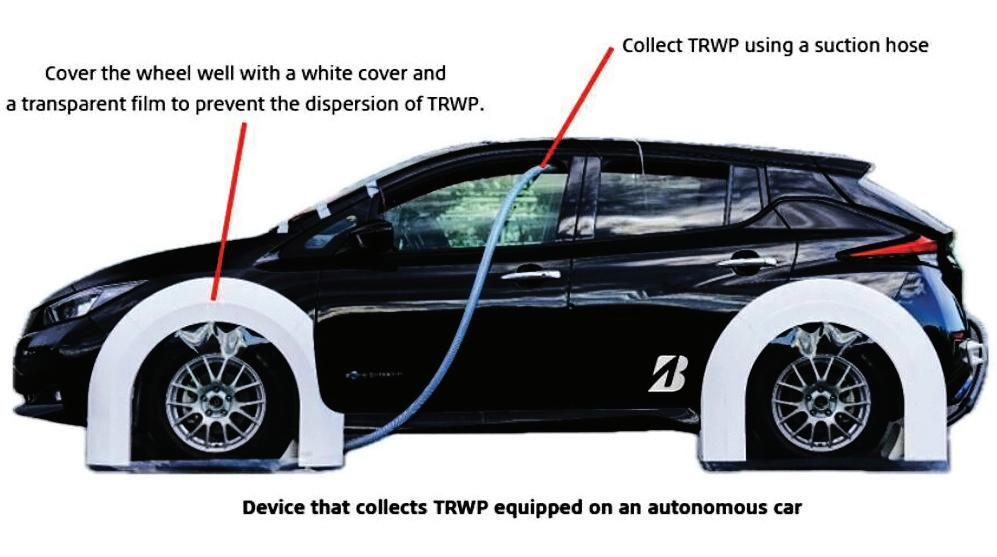
Bridgestone has developed a new method to collect Tire and Road Wear Particles (TRWP) as part of its sustainability efforts
Rubber Journal Asia
Tyre Sector
For instance, Japan-headquartered Bridgestone Corporation is taking steps toward sustainability with the development of a new tyre and road wear particles (TRWP) collection method. TRWP are tiny fragments generated by friction between tyres and the road, an inevitable part of driving that ensures safety and comfort. These particles are a mix of tyre tread and road surface materials.
To better understand the environmental impact of TRWP, Bridgestone is actively researching their size distribution, dispersion behaviour, and methods for efficient collection. The company’s efforts include visualising particle dispersion by combining high-speed cameras with laser light scattering. Building on these insights, Bridgestone has developed a specialised device that encloses the tyre and captures TRWP more effectively.
In addition, the company is testing this method using autonomous electric vehicles (EVs) with regenerative braking. This approach minimises the influence of exhaust emissions and brake dust, allowing cleaner data collection and more accurate environmental assessment. Bridgestone hopes these innovations will advance understanding and pave the way for practical solutions to mitigate TRWP’s environmental impact.
Indian tyre maker CEAT, a portfolio company of Mumbaibased RPG Enterprises, is shifting toward a more versatile product strategy. The company, which previously offered a dedicated EV tyre line, is now developing dual-compatible tyres designed to work seamlessly with both EVs and internal combustion engine (ICE) cars.
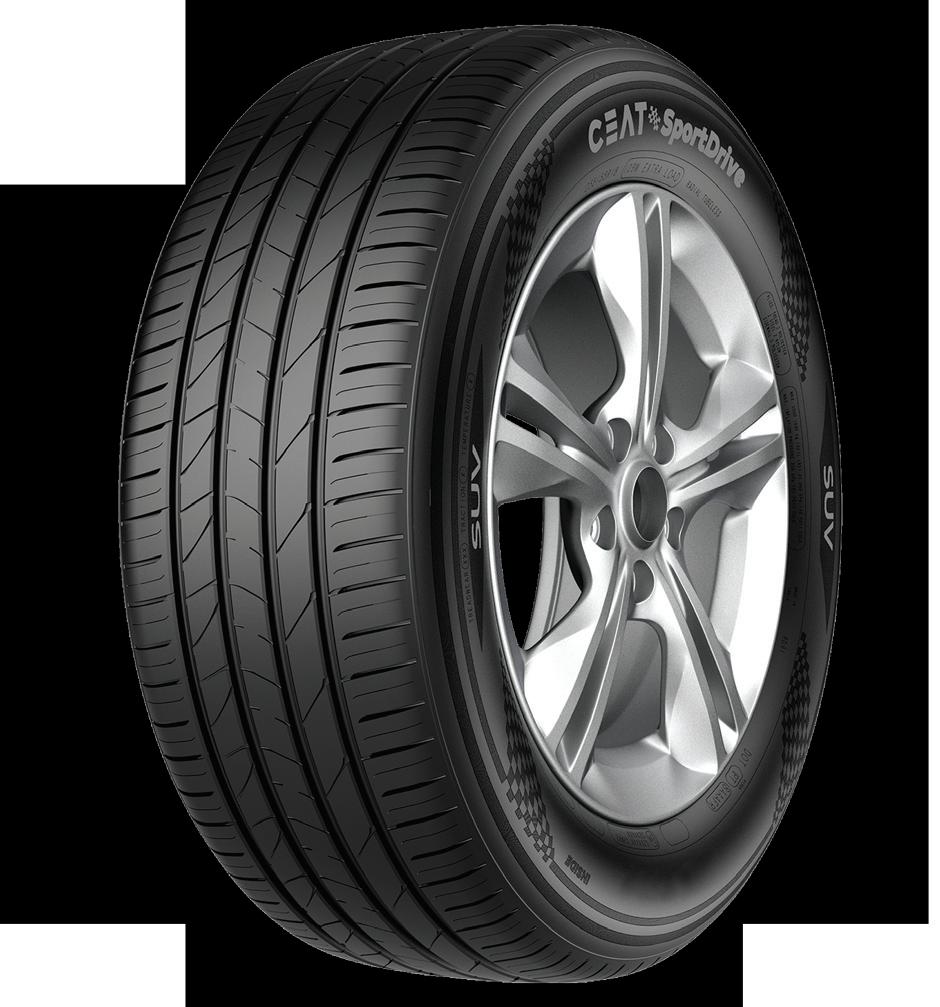
Acquisitions and expansions
CEAT’s SportDrive range targets the luxury sedan and highperformance SUV segments
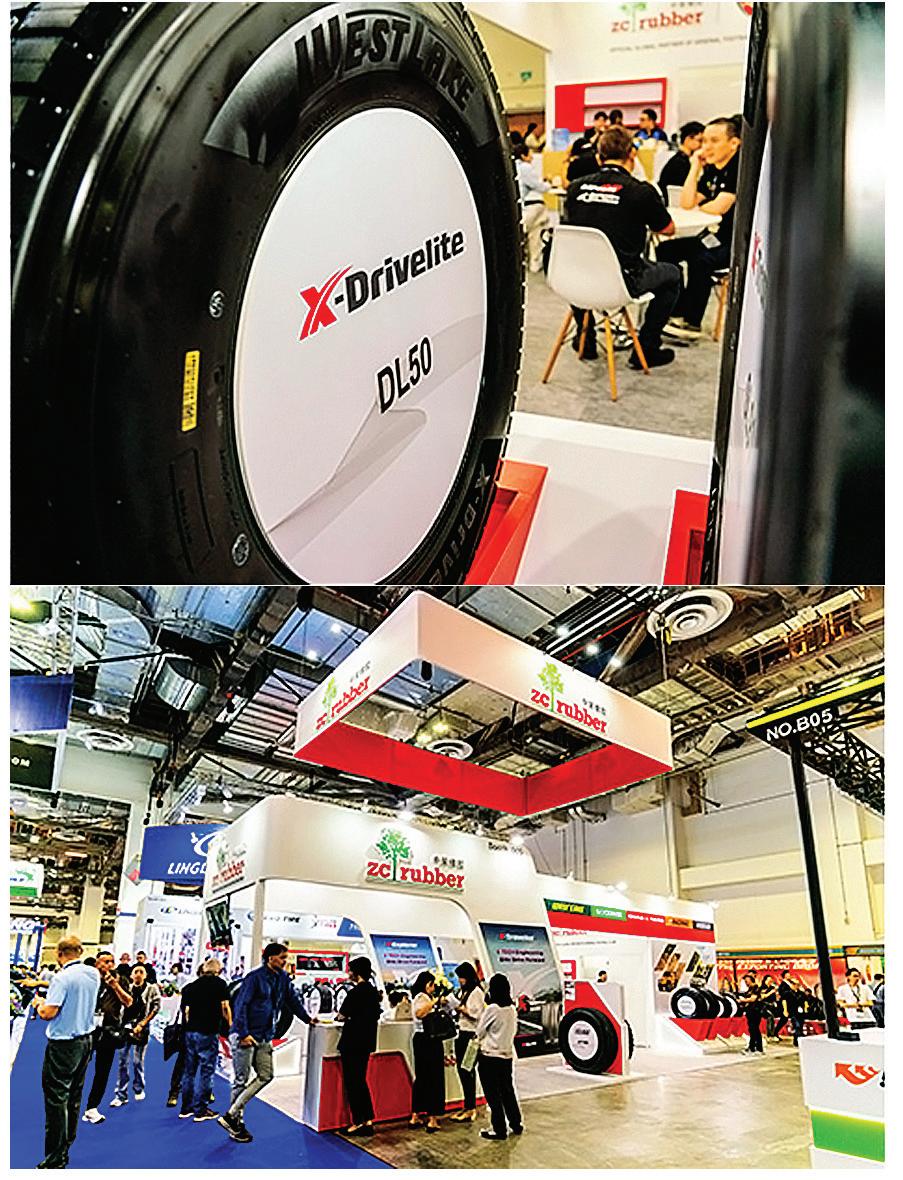
Elsewhere, China’s ZC Rubber, after 12 months of construction, began Phase I production at its new Indonesian plant, PT Matahari Tyre Indonesia (MTI), located in Kendal Industrial Park, Central Java. The 500,000 sq m facility, backed by a US$280 million investment, is ZC Rubber’s second overseas plant. It is equipped to produce a wide range of products, including truck and bus tyres, two-wheeler tyres, bias tyres, inner tubes, tracks, and carbon black. Once fully operational, MTI is projected to generate annual revenue of approximately US$720 million.
Meanwhile, despite the 25% tariffs on South Korean exports, Hankook Tire is pressing ahead with efforts to grow its presence in North America and plans to double its production of lead-acid batteries at its Tennessee plant to 3 million units/year.
Overall, more Asian tyre makers are moving forward with strategies to either avoid the impact of steep tariffs or adapt to them. In a sink-or-swim environment, Asian tyre manufacturers continue to show they’re more than capable of steering through adversity, and coming out ahead.
In a major move, CEAT is also acquiring the Camso brand’s off-the-road (OTR) tyre assets for US$225 million from French tyre maker Michelin. Originally based in Canada, Camso was acquired by Michelin in 2018 and supplies bias tyres and tracks for highway construction equipment. With this acquisition, CEAT gains global ownership of the Camso brand along with two manufacturing facilities.

ZC Rubber has introduced its X-Elite Series to the Southeast Asian market, developed under the company’s proprietary X-Tech System
Hankook’s Ventus evo offers better braking, cornering stability, and fuel efficiency, while maintaining high-speed performance
Events
15 – 18 April
Chinaplas
Venue: National Exhibition and Convention Center (Shanghai), China
Tel: +852 2516 3316
Email: Chinaplas.pr@adsale.com.hk.
Website: www.chinaplasonline.com
9 – 12 May
Plastasia
Venue: Bangalore International Exhibition Centre, India
Tel: +91-98450 89641
Email: info@plastasia.in Website: www.plastasia.in
14 – 17 May
Metaltech & Automex
Venue: MITEC, Malaysia
Tel: +603 9771 2688 Fax: +603 9771 2799
Email: boonwye.yap@informa.com
Website: www.metaltech.com.my
14 – 17 May
Plastic & Rubber Thailand
Venue: BITEC Bangkok, Thailand
Tel: +66 (0) 2036 0500
Email:plasticrubber-th@informa.com
Website: www.intermachshow.com
14 – 17 May
Intermach and MTA Asia
Venue: BITEC Bangkok, Thailand
Tel: +66 (0) 2036 0500 Ext.216
Email:Intermach-th@informa.com
Website: www.intermachshow.com
27 – 30 May
Greenplast
Venue: Fiera Milano, Italy
Tel: +39 02 8228371 Fax: +39 02 57512490
Email:info@greenplast.org Website: www.greenplast.orgI
29 – 30 MAY
4th ASEAN Circular Plastics Summit
Venue: Ho Chi Minh City, Vietnam
Tel: +86 512 6538 9108 ext. 808
Email: james.chen@apexevents.cn
Website: www. plastics.apexevents.cn
4 – 6 JUNE
Thailand International Exhibition for Personal Protective Equipment (CIOSH Thailand)
Venue: BITEC, Bangkok, Thailand
Tel: +66 2 559 0856-8
Email: info@exposis.co.th Website: www.ciosh-thailand.com
4 – 7 JUNE
HanoiPlas
Venue: Hanoi, Vietnam
Tel: +886-2-2659-6000 Fax: +886-2-2659-7000
Email: exfdp@chanchao.com.tw Website: www.hanoiplas.chanchao.com.tw
Check out the Advertisers' page on our website.
Information is categorised by the YEAR & DATE of publication for easy reference.
For further details, email us at: news@plasticsandrubberasia.com
11 – 14 JUNE
ProPak Asia
Venue: BITEC, Bangkok, Thailand
Tel: +66 (0) 2 036 0500 Ext. 246
Email: watcharee.w@informa.com
Website: www.propakasia.com
17 – 19 JUNE
Rosmould
Venue: Crocus Expo IEC, Moscow, Russia
Tel: +7 (495) 649-8775
Email: marketing@rosmould.ru
Website: www.en.rosmould.ru
18 – 21 JUNE
InterPlas Thailand
Venue: BITEC, Bangkok, Thailand
Tel: +66 2686 7222 Fax: +66 2686 7266
Email: interplas@rxtradex.com
Website: www.interplasthailand.com
18 – 21 JUNE
Manufacturing Expo
Venue: BITEC, Bangkok, Thailand
Tel: +66 2686 7222
Email: manufacturing-expo@rxtradex.com
Website: www.manufacturing-expo.com
24 – 26 JUNE
ProPak China
Venue: Shanghai, China
Tel: +86-21-33392119
Email: amy.wang@imsinoexpo.com
Website: www.propakchina.com
18 – 21 JUNE
Plastech Vietnam
Venue: Saigon Exhibition and Convention Center, Vietnam
Tel: +84 28 3848 8561
Email: info@veas.com.vn
Website: www.plastech-expo.com
2 – 4 JULY
Interfoam China
Venue: SNIEC, China
Tel: +86 21 63232733
Email: katelyn.xue@interfoam.cn
Website: www.interfoam.cn
2 – 5 JULY
MTA Vietnam
Venue: Ho Chi Minh city, Vietnam
Tel: +84 28 3622 2588
Email: mtavietnam@informa.com Website: www.mtavietnam.com
2 – 5 JULY
HanoiPrintPack
Venue: Hanoi, Vietnam
Tel: +886-2-2659-6000 Fax: +886-2-2659-7000
Email: CustomerService@chanchao.com.tw Website: www.chanchao.com.tw/hanoiPrintPack
ADVERTISERS’ ENQUIRIES
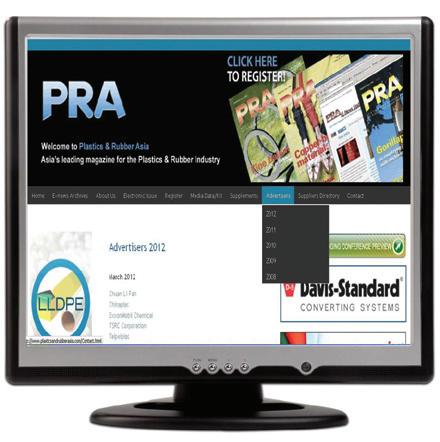
Publishing Office / Scandinavia, Benelux & France
Postbus 130, 7470 AC Goor, The Netherlands
Tel: +31 547 275005 Fax: +31 547 271831
Email: arthur@kenter.nl
Contact: Arthur Schavemaker
European Correspondent: E-mail: jeanet@kenter.nl
Contact: Jeanet Draaijer
Regional Office
B6-11, Menara Indah, Jalan 9, Taman TAR 68000 Ampang, Selangor, Malaysia
Mobile: +6017-8849102
Email: tej@plasticsandrubberasia.com
Contact: Tej Fernandez
China & Hong Kong
Room 6B, Floor 6, Building HengLong, No. 50 Renming Zhong Road, Zhangjiagang, 215600 China
Tel: 0512-58919146
Fax: 0512-58919145
Mobile: +86-17751702720
Email: henry.xiao@matchexpo.com
Contact: Henry Xiao/Zhu Wei
Malaysia (Print, Web, Digital Advertising & Conferences)
Tara Media & Communications
Mobile: +6017 610 1270
E-mail: yokepeng@taramedia.com.my
Contact: Yoke Peng
Southeast Germany, Switzerland & Austria
Verlagsbüro G. Fahr e.K
Breitenbergstrasse 17
D-87629 Füssen, Germany
Tel: +49 8362 5054990
Fax: +49 8362 5054992
Email: info@verlagsbuero-fahr.de
Contact: Simon Fahr
North-West Germany
JRM Medien+Verlag
Minkelsches Feld 39
D-46499 Hamminkeln, Germany
Tel: +49 2852 94180
Fax: +49 2852 94181
Email: info@jwmedien.de
Contact: Renate Wickenhöfer
Malaysia. India, Indonesia, Singapore, Thailand, Australia, New Zealand, Korea & Philippines
Tara Media & Communications
B6-11, Menara Indah, Jalan 9, Taman TAR 68000 Ampang, Selangor, Malaysia
Mobile: +6017-8849102
Email: tej@plasticsandrubberasia.com
Contact: Tej Fernandez
Italy, Spain & Portugal
MediaPoint & Communications Srl
Corte Lambruschini, Corso Buenos Aires, 8, Vo Piano - Interno 9, 16129 Genova, Italy
Tel: +39 010 570 4948 Fax: +39 010 553 0088
Email: info@mediapointsrl.it
Contact: Fabio Potesta Taiwan 宗久實業有限公司
Worldwide Services
11F-B, No.540 Sec.1, Wen Hsin Rd., Taichung, Taiwan
Tel: +886 4 23251784 Fax: +886 4 23252967
Email: global@acw.com.tw
Contact: Robert Yu 游宗敏
USA & Canada
Plastics Media International
P. O. Box 44, Greenlawn, New York 117430, USA
Tel/Fax: +1 631 673 0072
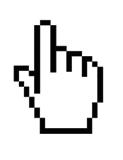
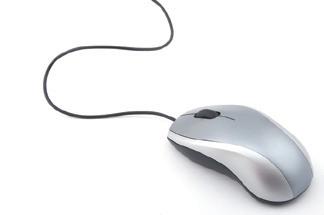
Email: mjm@4m-media.com
Contact: Michael J Mitchell
www.plasticsandrubberasia.com
3-5 September 2025
Poly World Trade Expo, Guangzhou, China
September 3-5
Poly World Trade Expo • Guangzhou
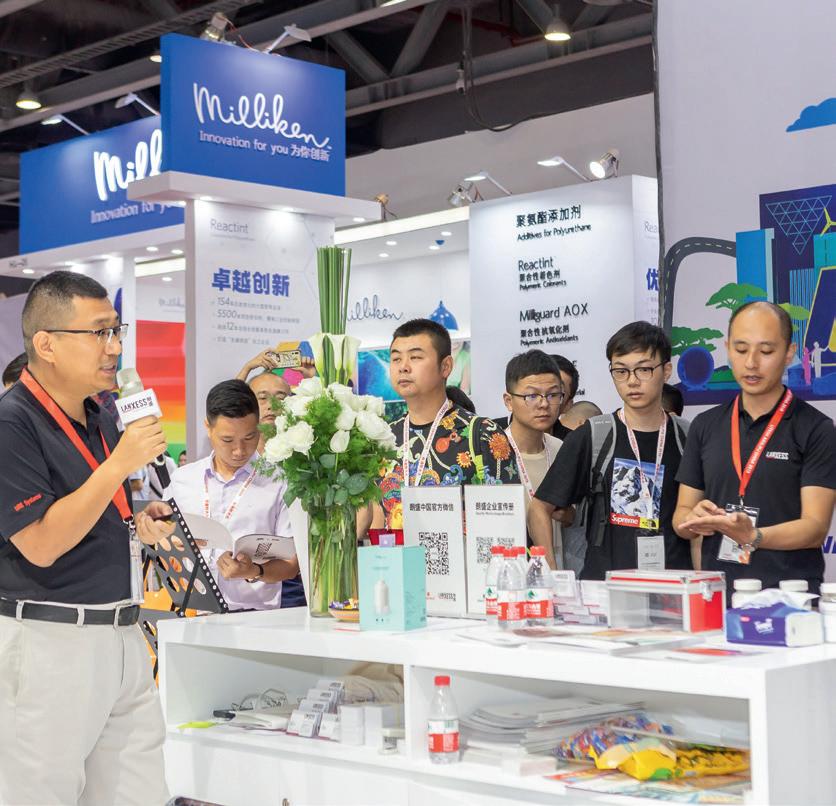
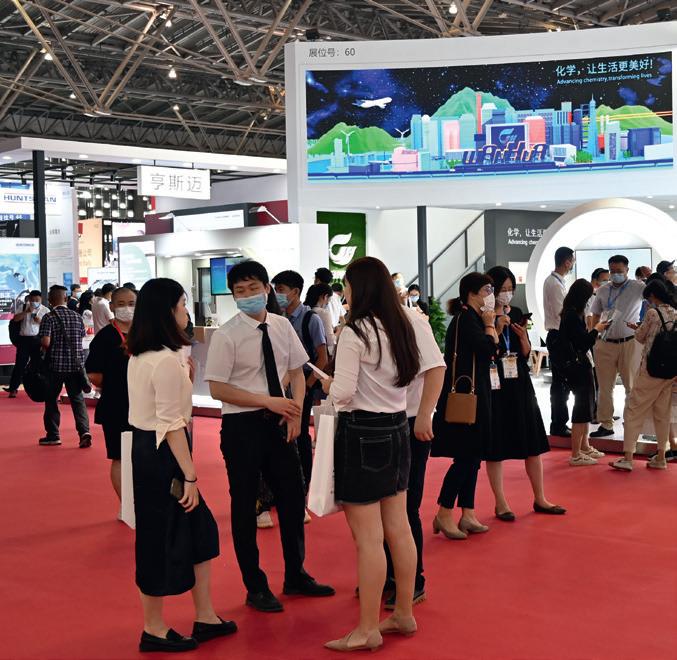
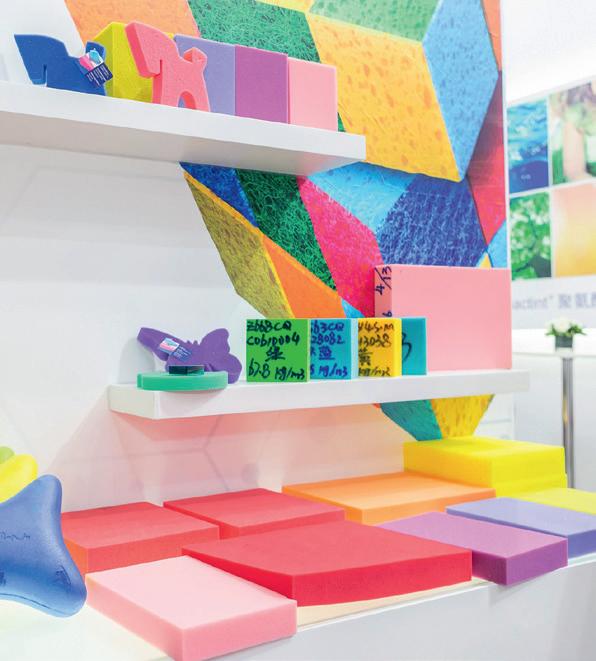
The leading event for the Chinese Polyurethanes Industry. Organised by
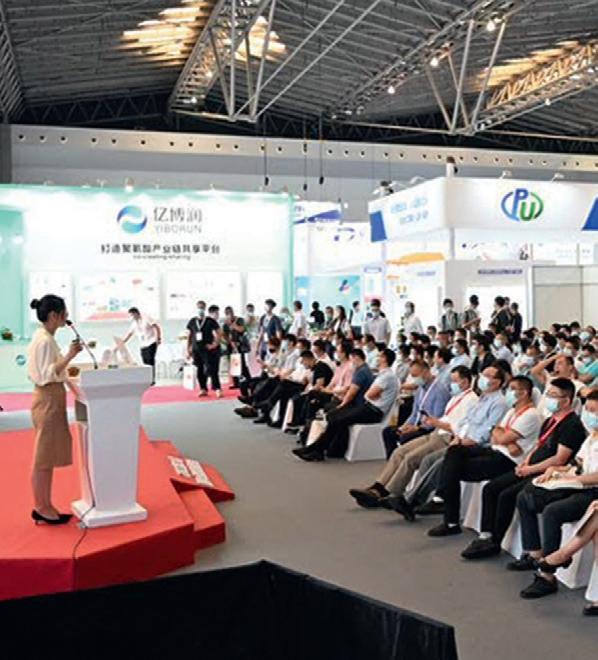
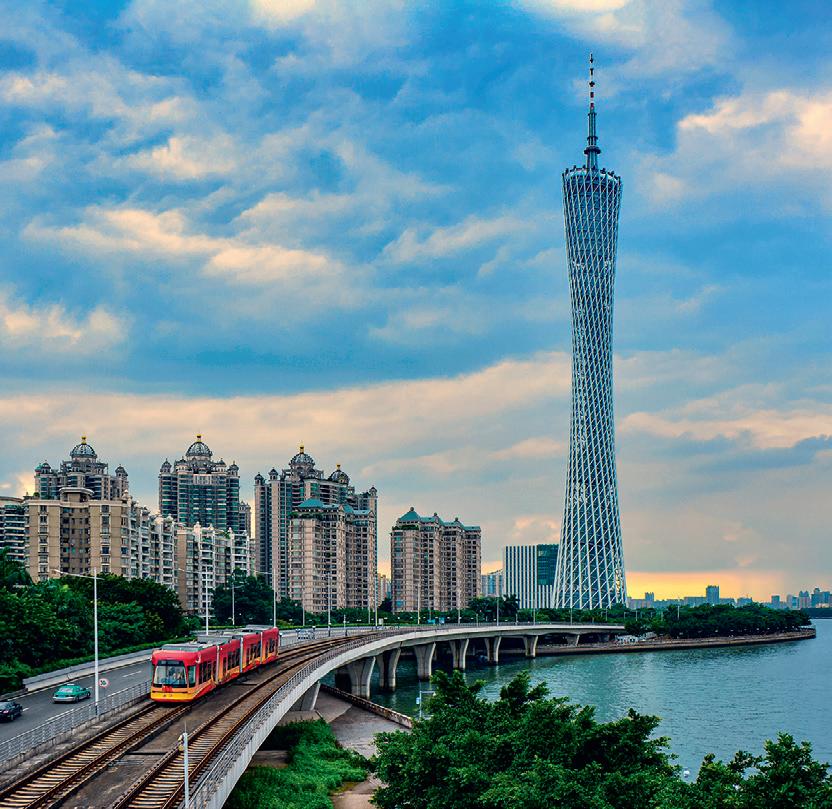
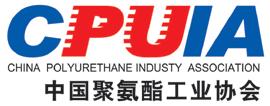