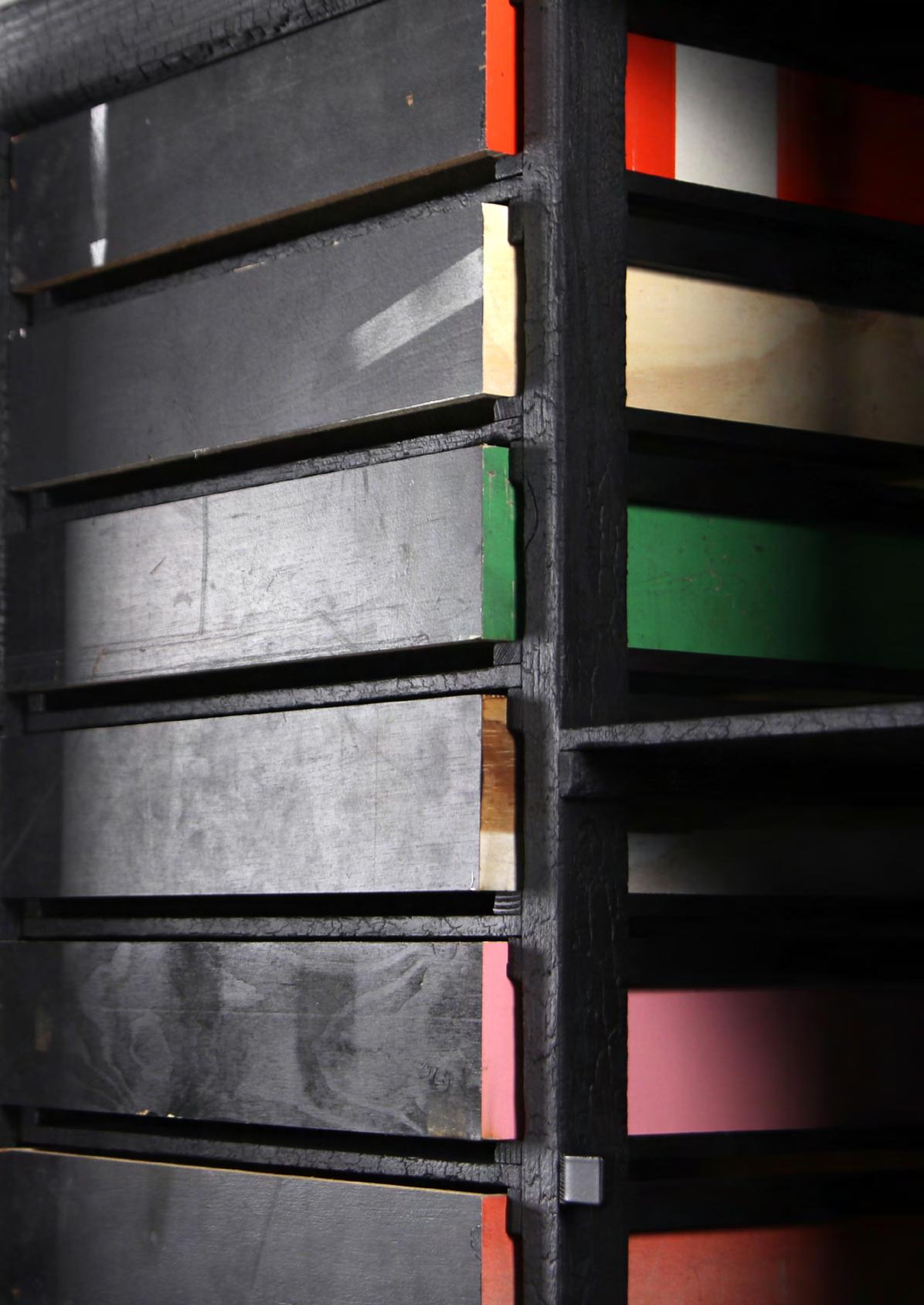
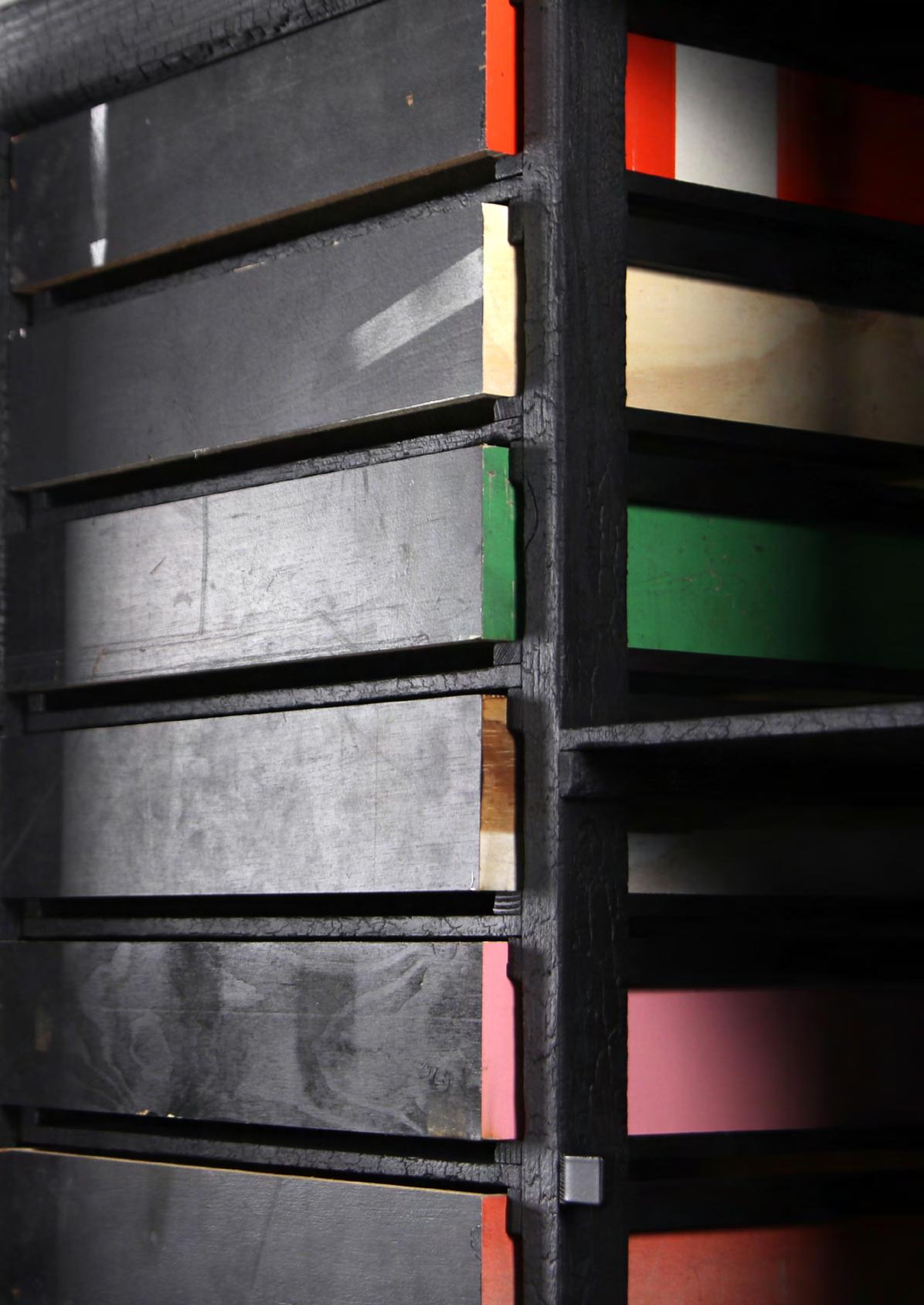
DDW2024
This year marks our 10th anniversary in the building, and it’s also the first year where, besides preparing for Dutch Design Week, we don’t have a construction deadline. It’s incredibly relaxed! This ties in with what might be the most important shift in my thinking up to now. I no longer want to operate on the edge all the time—borrowing hundreds of thousands of euros, spending even more, and expecting others to enjoy working day and night like I do, or worrying constantly whether we can pay salaries at the end of the month. About two years ago, I became aware of my need for financial peace.,
The main factor in this shift is the increasing role of uncertainty. The banking crisis, COVID, terrible wars—one event after another turns the world upside down. Yet, somehow, and thankfully, we haven’t been hit structurally by these events. Sales and production are going well, and we’re receiving interesting and enjoyable projects from great clients. The biggest uncertainty now is the government.
The wisdom from ancient Greece—”It is the government’s duty to ensure that citizens know today what will happen tomorrow”—is being constantly ignored. Last year, I seriously considered giving up altogether. But because what we create together is so incredibly enjoyable, that’s not really a fun consideration. So, I’ve decided not only to ensure that we can pay salaries at the end of the month but also to build reserves to handle the unexpected challenges that will inevitably arise.
We’ve stopped building and investing without financing, and it’s starting to pay off. This is the calmest lead-up to a DDW we’ve ever had. Thanks to the Environmental Agency, which enforces rules that, in our case, ironically harm the environment (as previously mentioned), we are presenting, alongside the Environmental Cabinet we showed in Milan, a new Environmental Sideboard. The pieces are stunning, and we should be grateful for setbacks that inspire such beautiful ideas!
Environmental Service Dresser
art nr year measurements
material
rrp
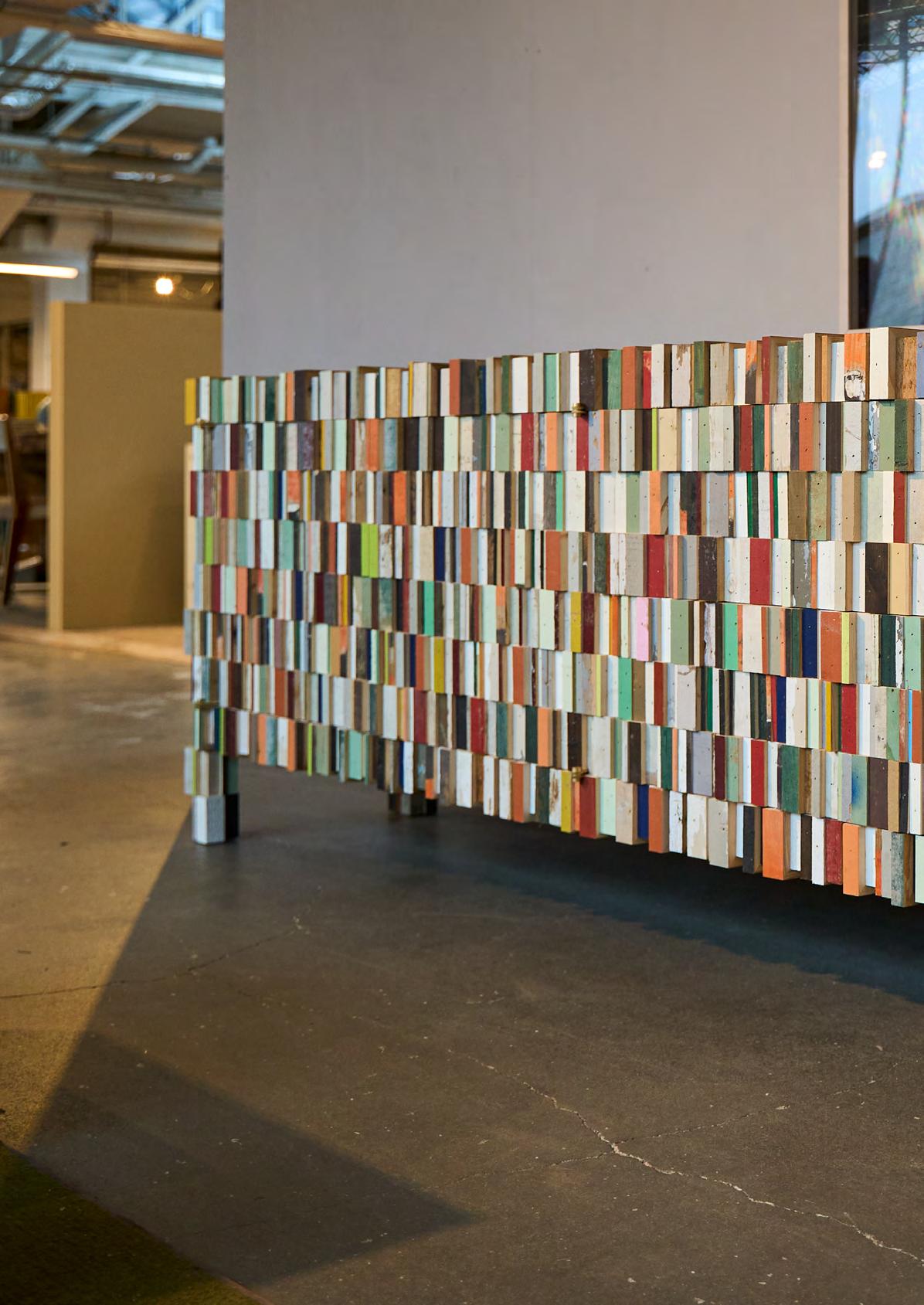
4204-4 2024
240 x 64 x 81 cm
scrapwood, plywood, brass
€ P.O.R.
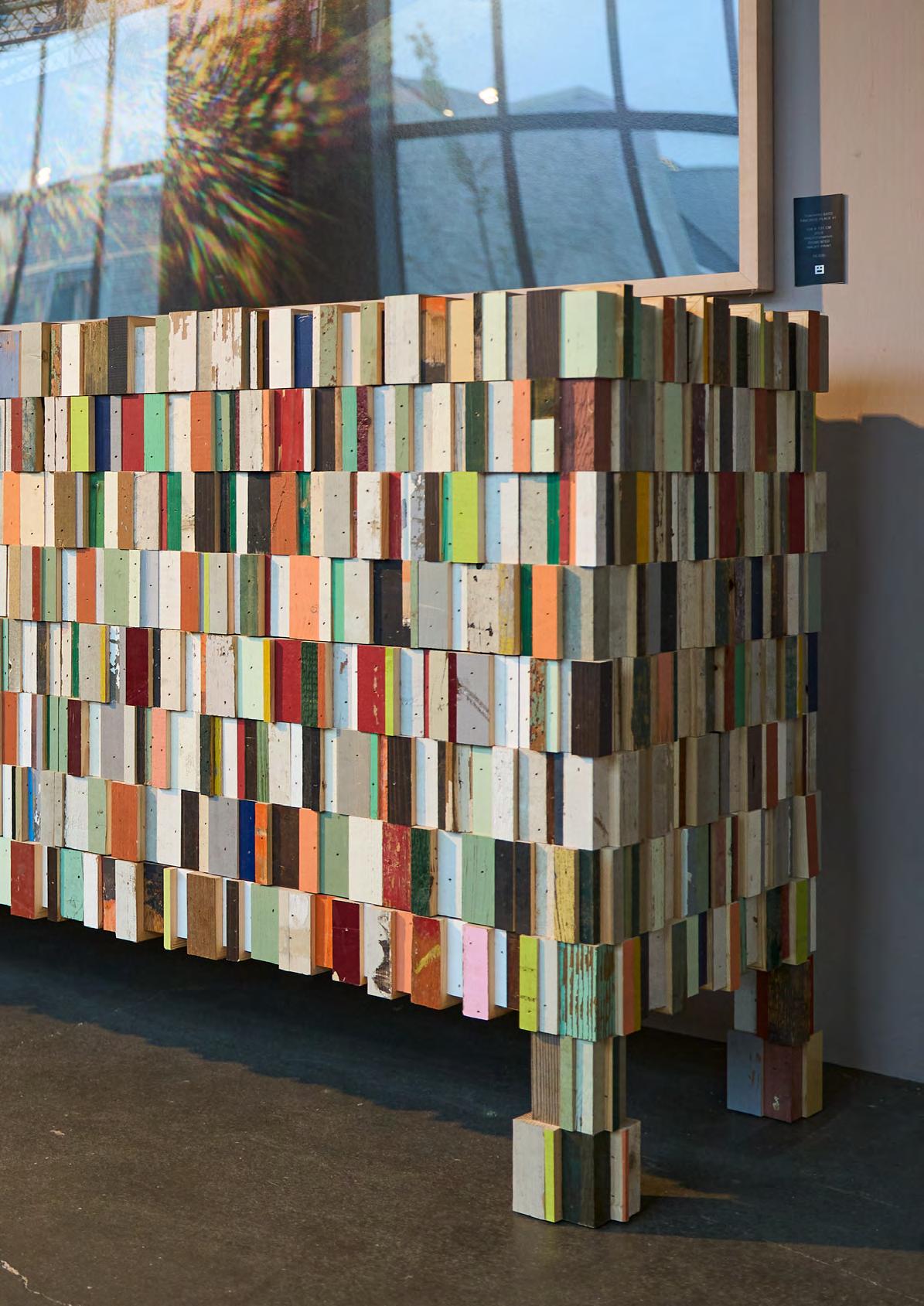
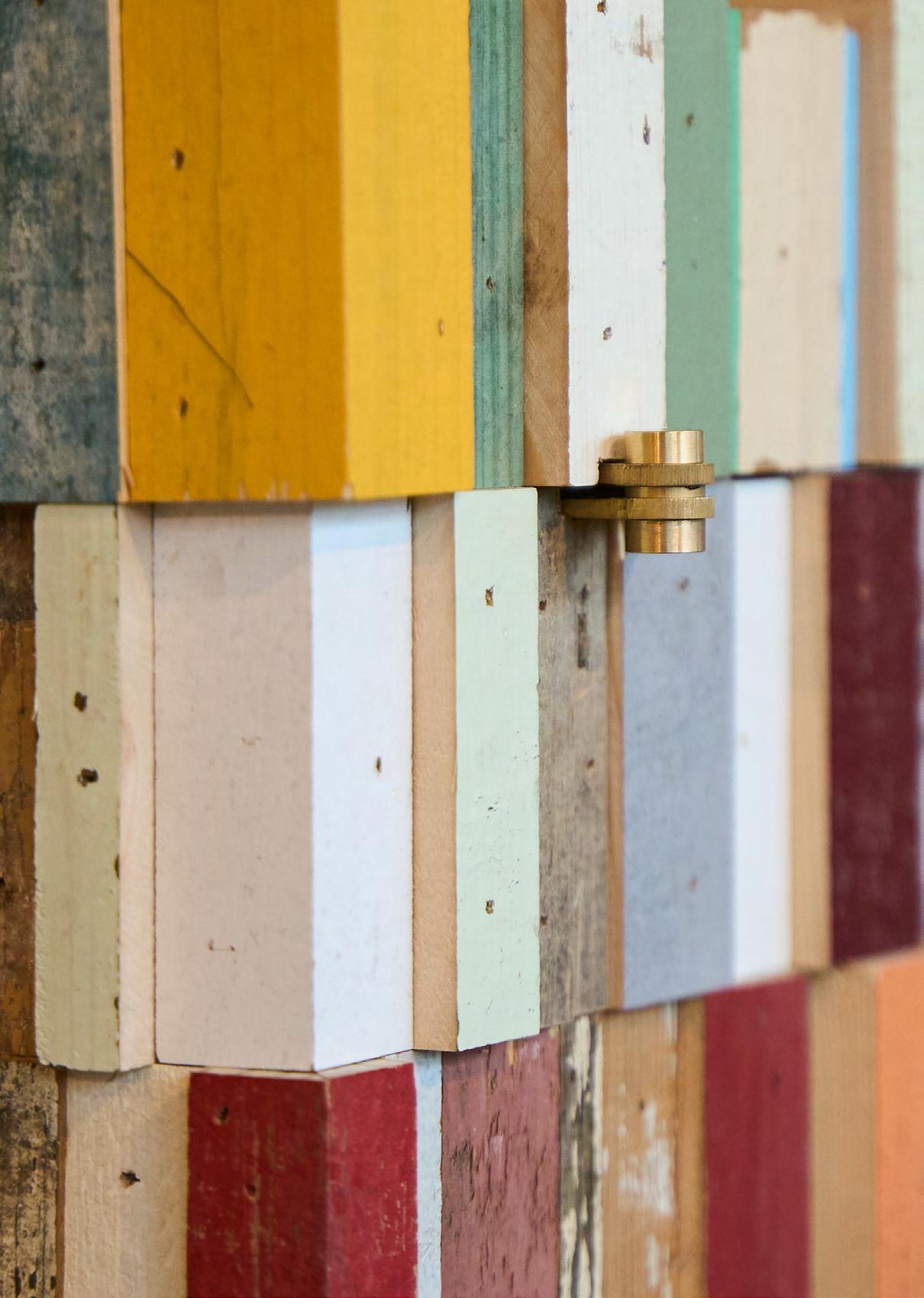


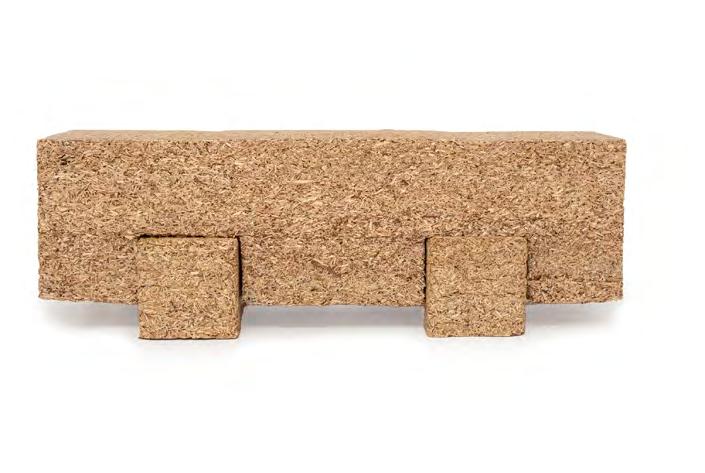
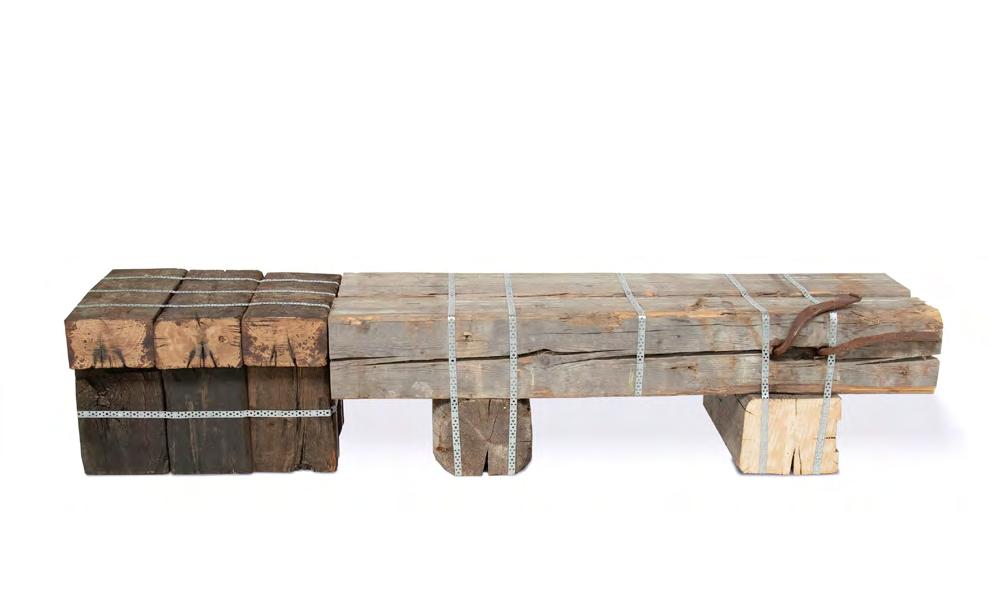
Wood Chip Objects
The troubles caused by the Environmental Service not only resulted in the Environmental Service Cabinet but also in the Wood Chip Objects. The wood that we can’t use in our wood gasifiers, we throw into the shredder. Instead of pressing it into briquettes and burning it, we capture the chips and turn them into objects. The essence is that we don’t press it because the volumes are too large, which would make it far too heavy and actually impossible to press. And since it’s an Environmental Service Cabinet, and we don’t use resins or other harmful substances, we searched for a bio-based binder. We haven’t found one yet, but a relatively harmless wood glue turned out to work.
The objects are now made with this glue. Previously, we created islands of waste for a Toon Laurense exhibition, where we also placed the two chipboard blocks. Now, we’ve added a stackable block staircase. It’s pretty useless, but monumental, especially when you consider the possibility of creating an enormous chipboard staircase in a space.
These seating objects were made for the same Toon Laurense exhibition. The beams were unusable for furniture or other objects, so they met the requirement of being waste materials. Using mounting tape, we created seating objects where texture, material, color, and especially size and proportion served as the main focus.
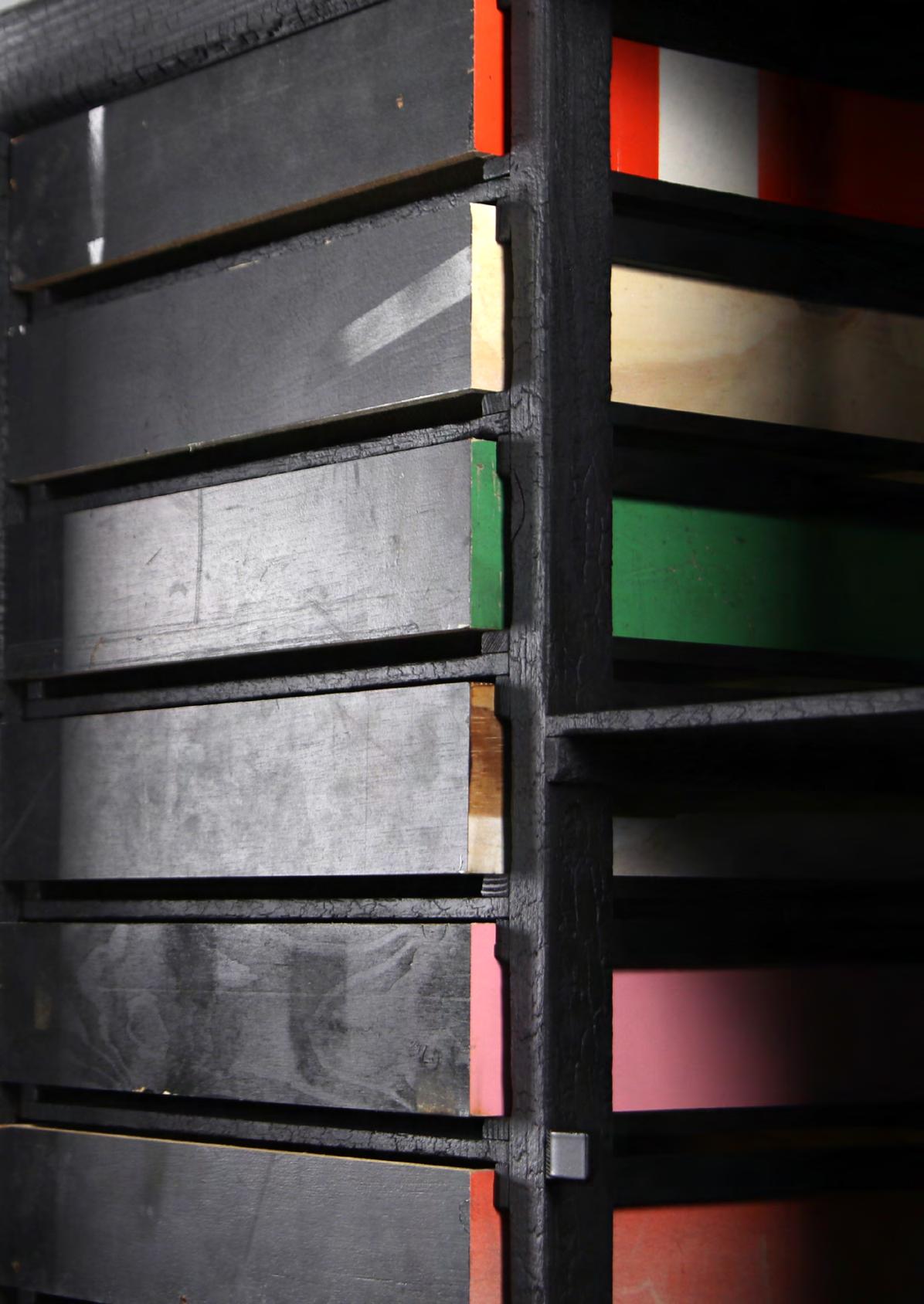
Baas & Eek
Maarten graduated from the Design Academy about 22 years ago. I did so about 10 years earlier. We’ve each built our careers in our own way, crossed paths along the way, and became friends. Just being together, eating, drinking, partying, going on holidays, cooking together, helping each other—real friends. Working together wasn’t necessary, but it’s fun, so we thought we could start by combining our graduation projects: Maarten burns my Classic Scrap Wood Cabinet.
The result is historic, a testament to friendship, a double classic, desirable, stunningly beautiful, but most of all, a lot of fun!
Classic Cabinet in Scrapwood - BAAS x EEK
100 x 50 x 215 cm
scrapwood, pine, burnt by Maarten Baas
€ P.O.R.
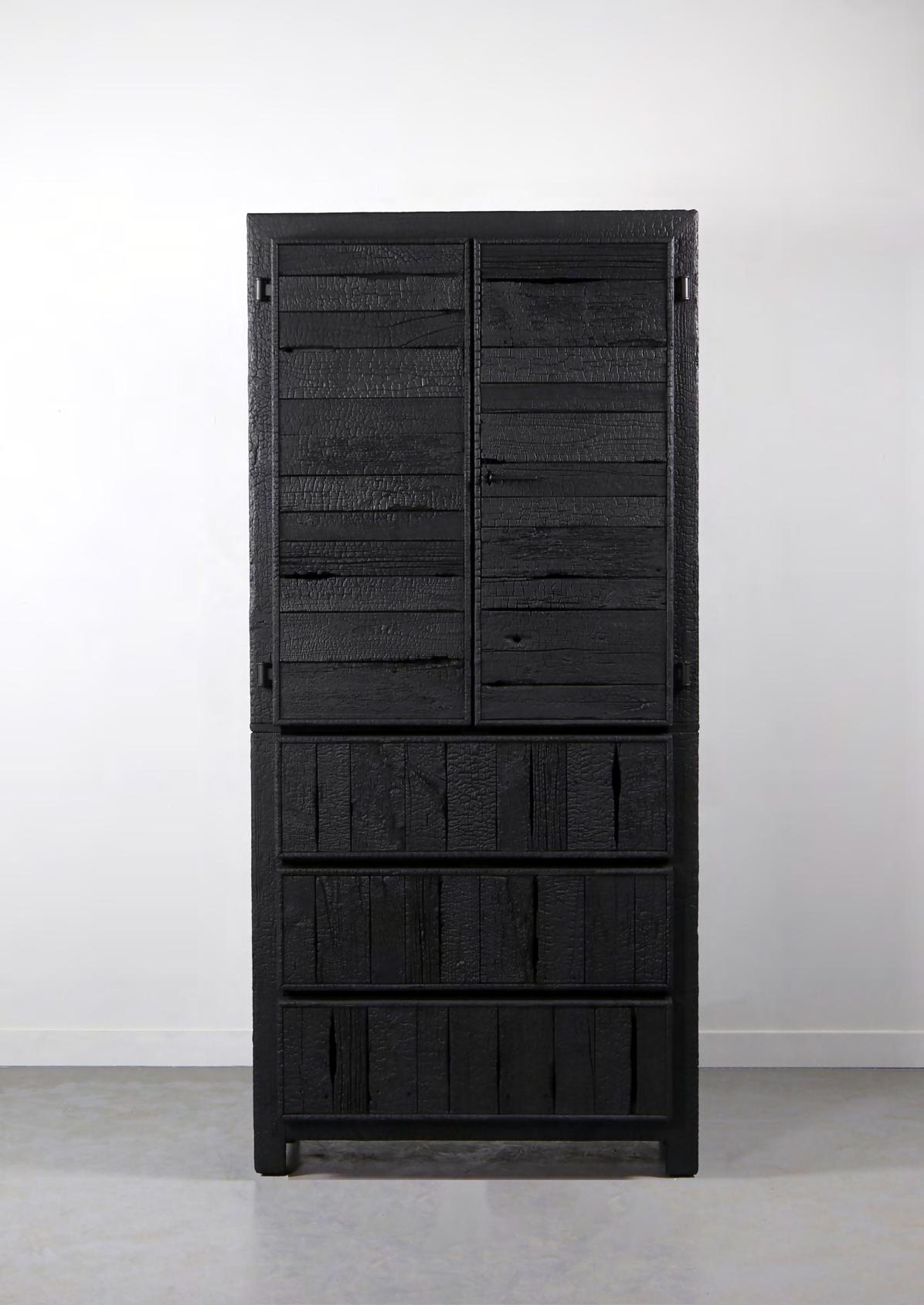
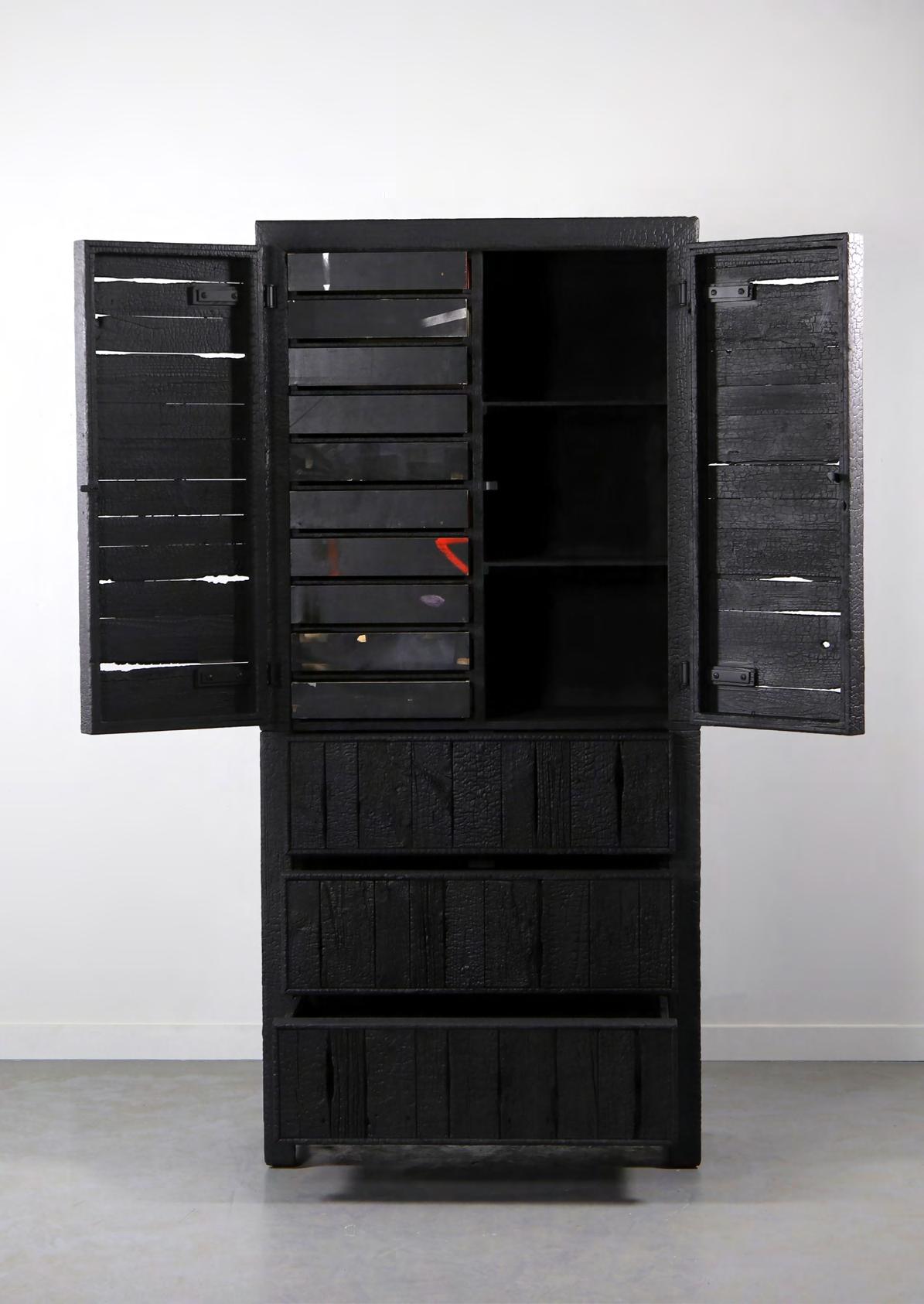
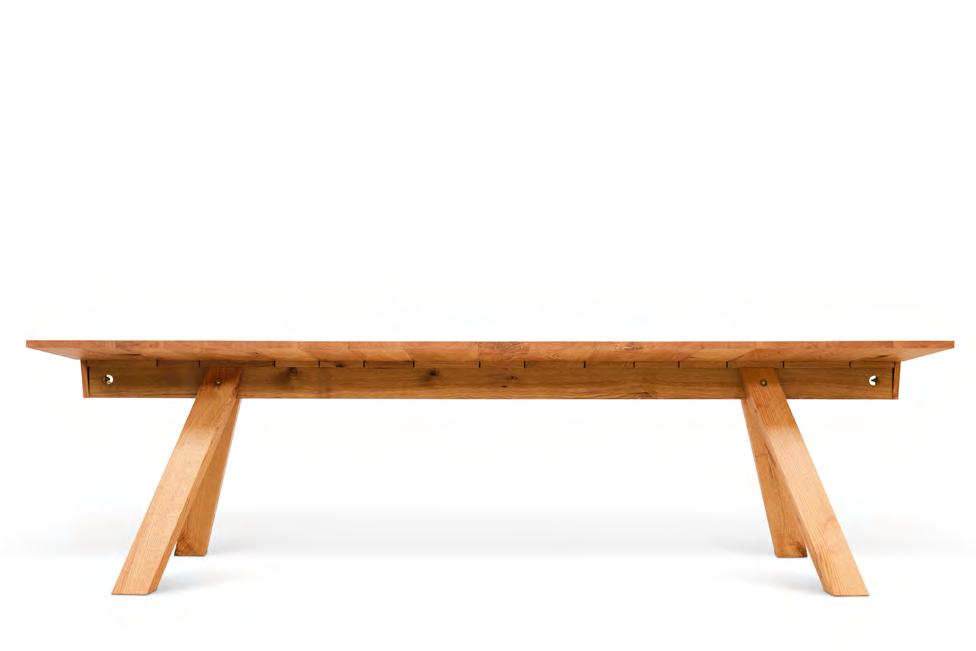

New Scrapwood Beam table, but in oak
The Scrap Wood Beam Table is actually inspired by problems we had with the Office Table. That one was made from oak. Now, we’ve created the Scrap Wood Beam Table in oak as well. The issue caused by the wood’s movement has been resolved, and the solution has made the table even more beautiful. The table is now made in standard sizes, making it easier to reproduce. Maybe that’s why the table looks even better in oak!
New Scrapwood Beam Table in oak
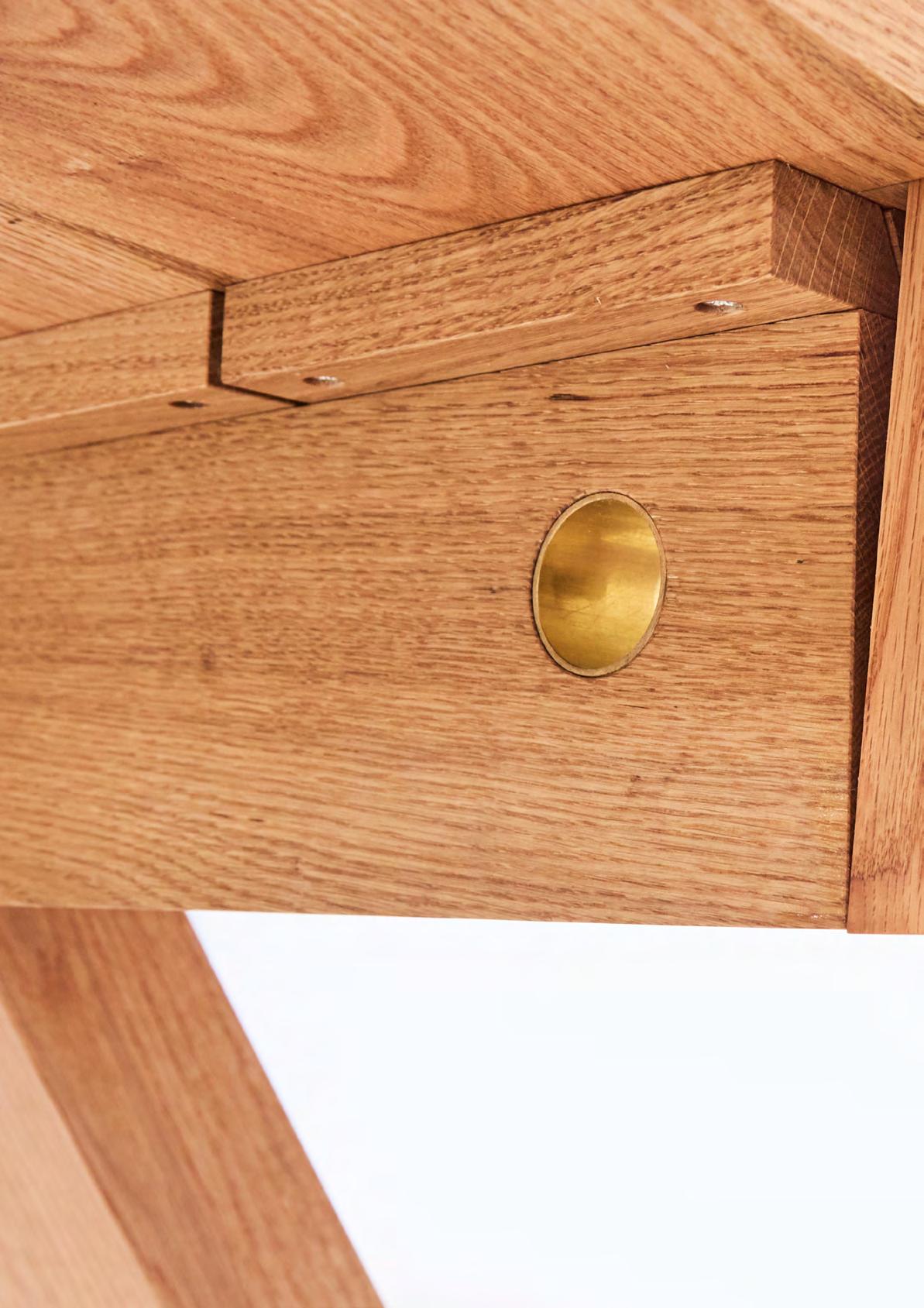
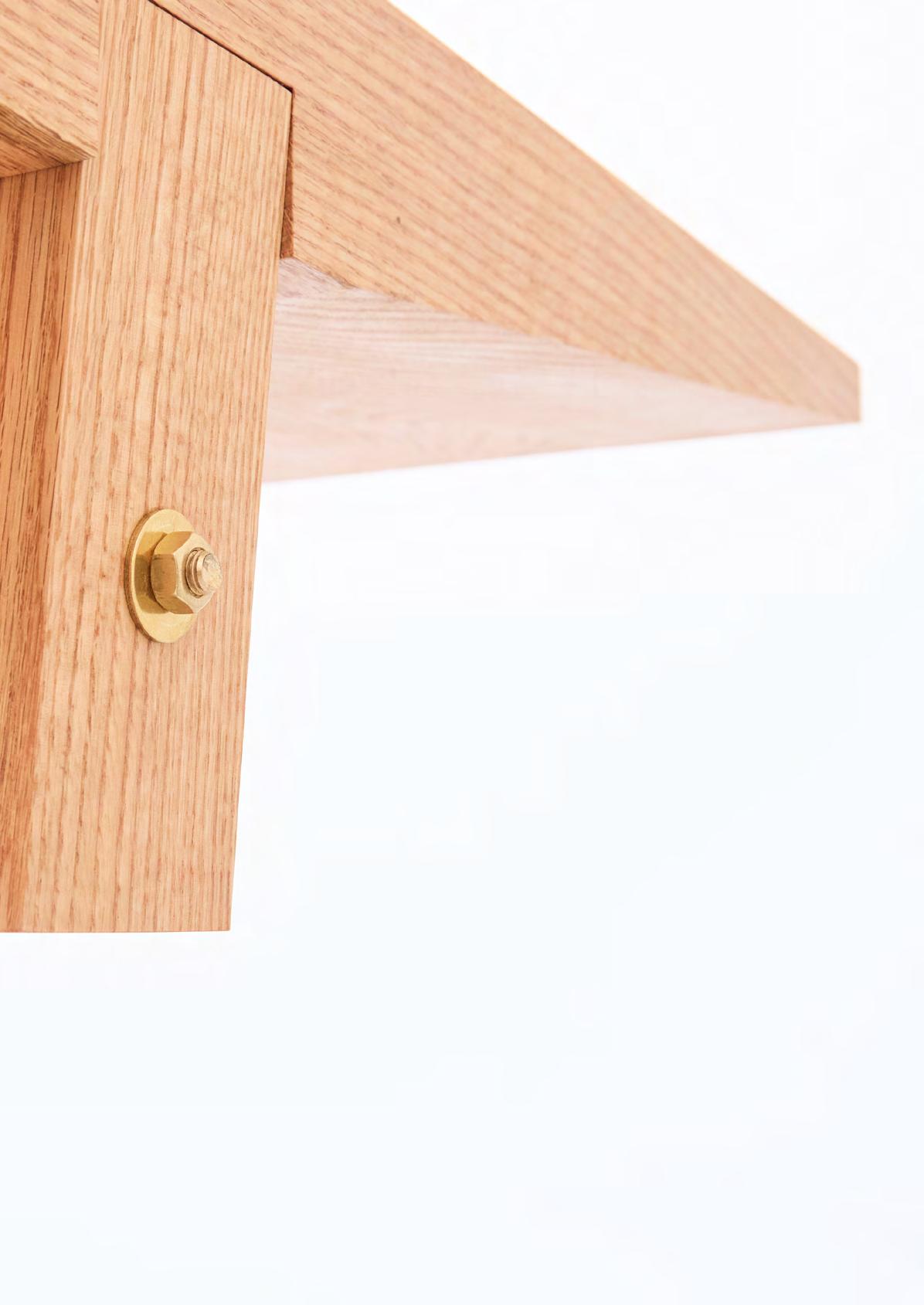
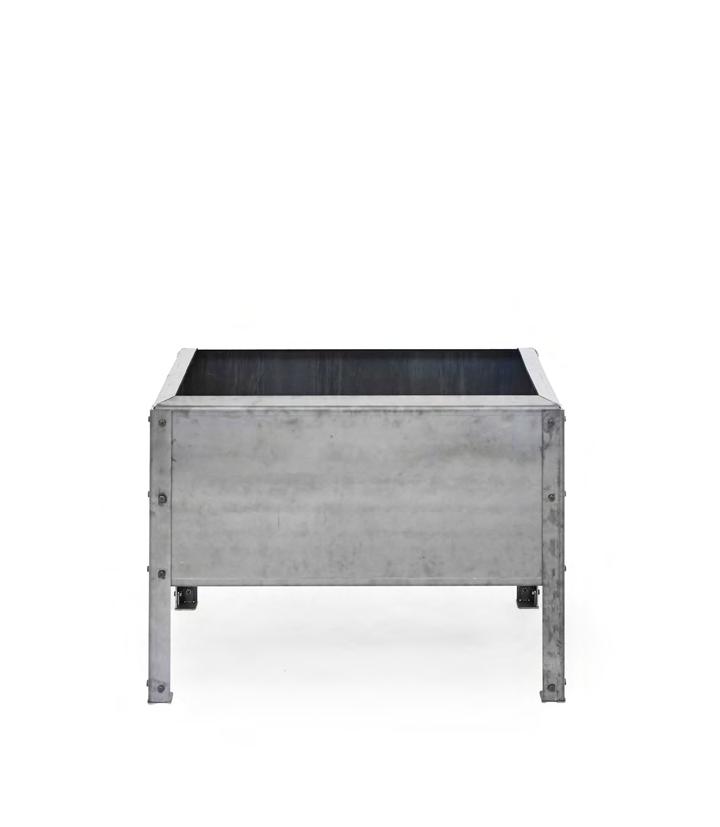
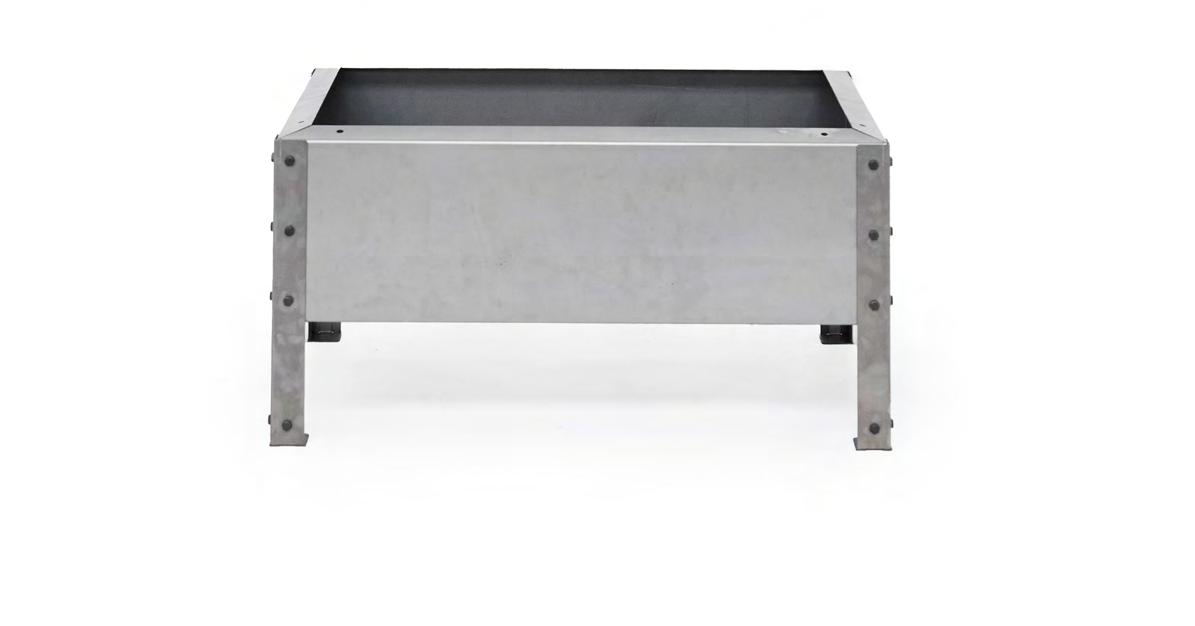
Planters
For years, we’ve been struggling with planters. Old industrial planters often turn out to be the nicest, while new ones are much less appealing. There are quite a few designer planters out there, but they’re often too “designed,” overpriced, and not really what we’re looking for. These planters come in a few sizes, materials, and colors, and they’re made from a single sheet, so almost nothing goes to waste, and they’re easy to produce. The fact that they’re not priced like something from Primark is because they’re made from real materials and crafted properly.
Plantenbakken
year measurements material rrp
2024 various various € P.O.R.
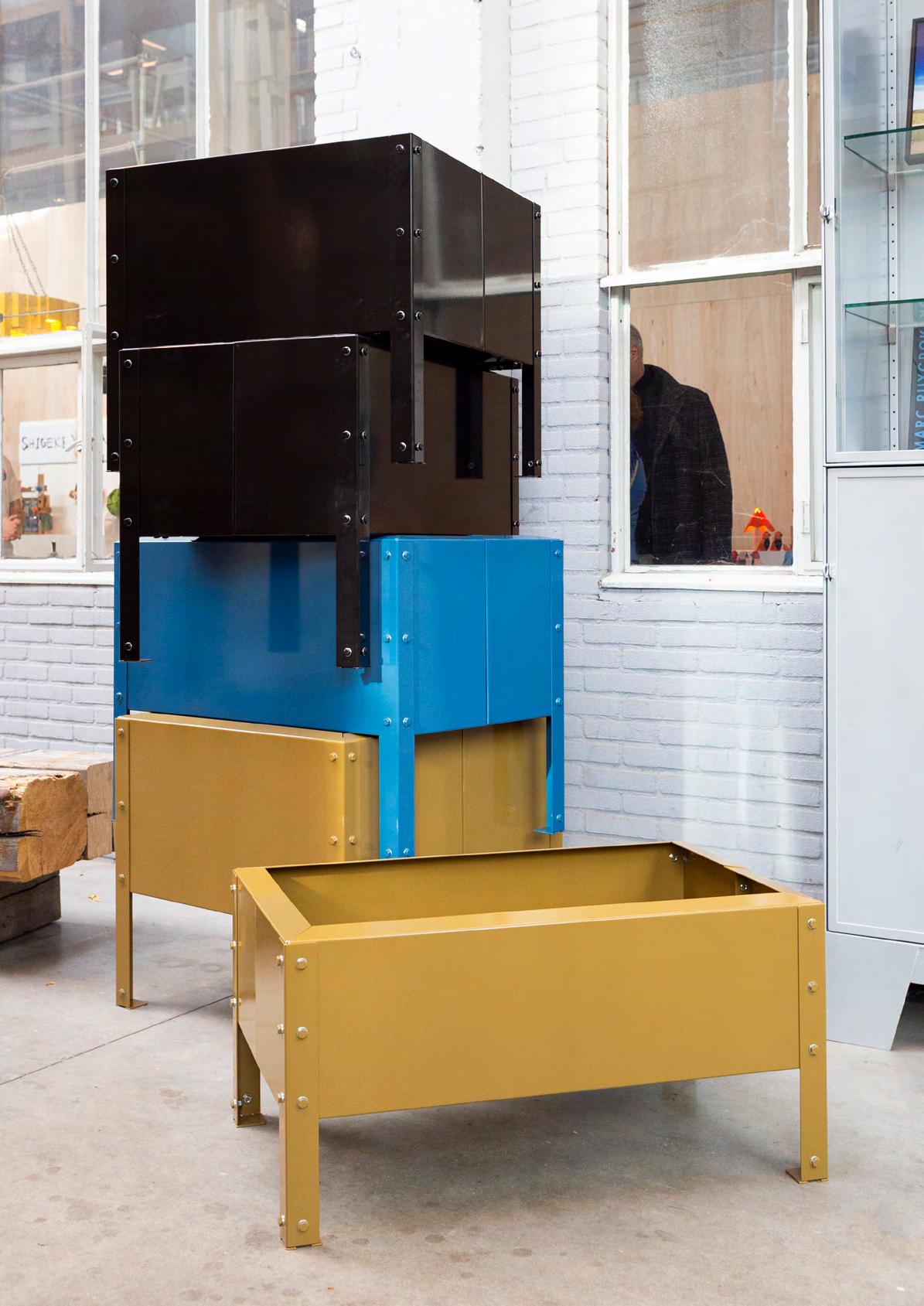
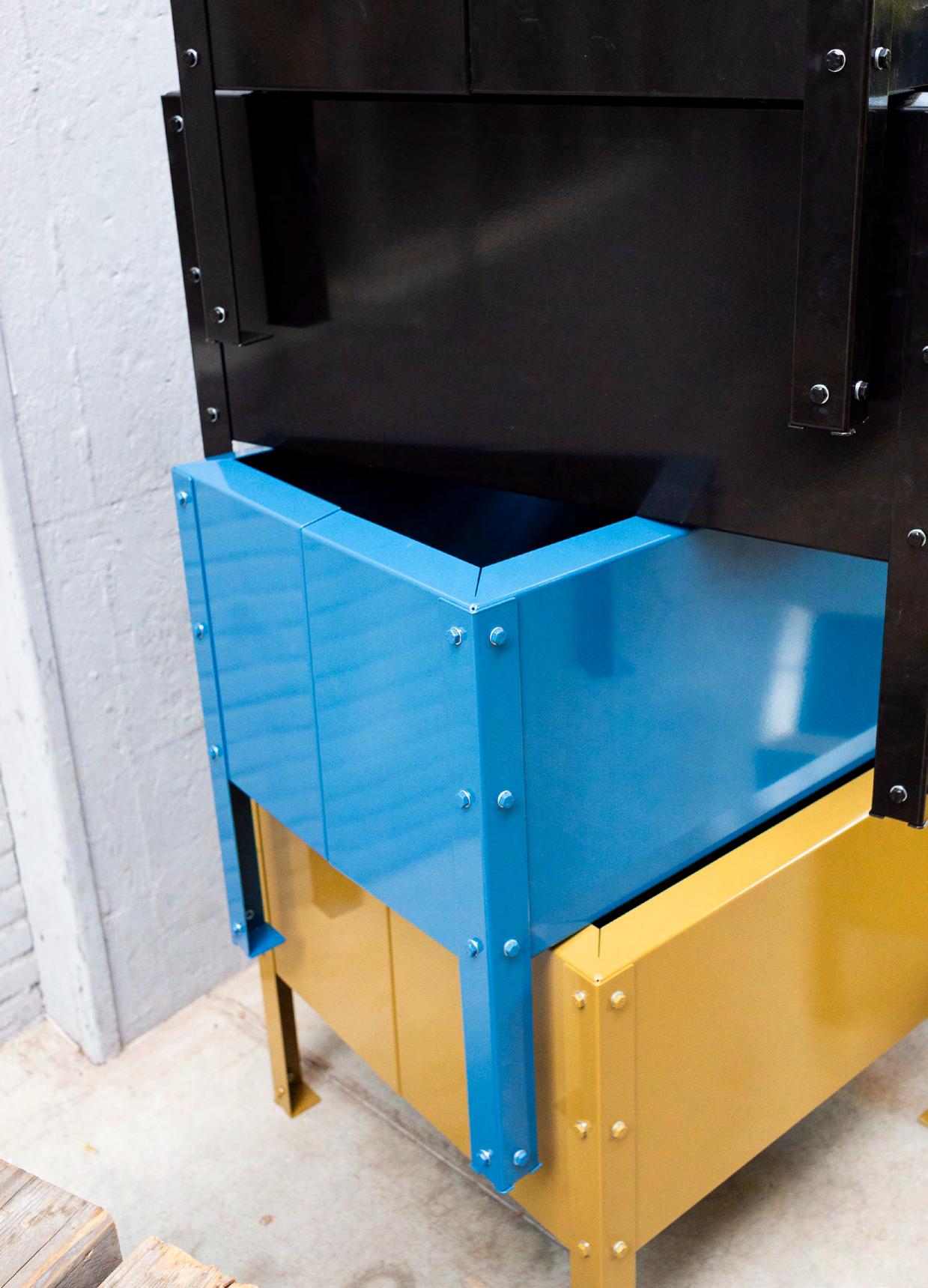
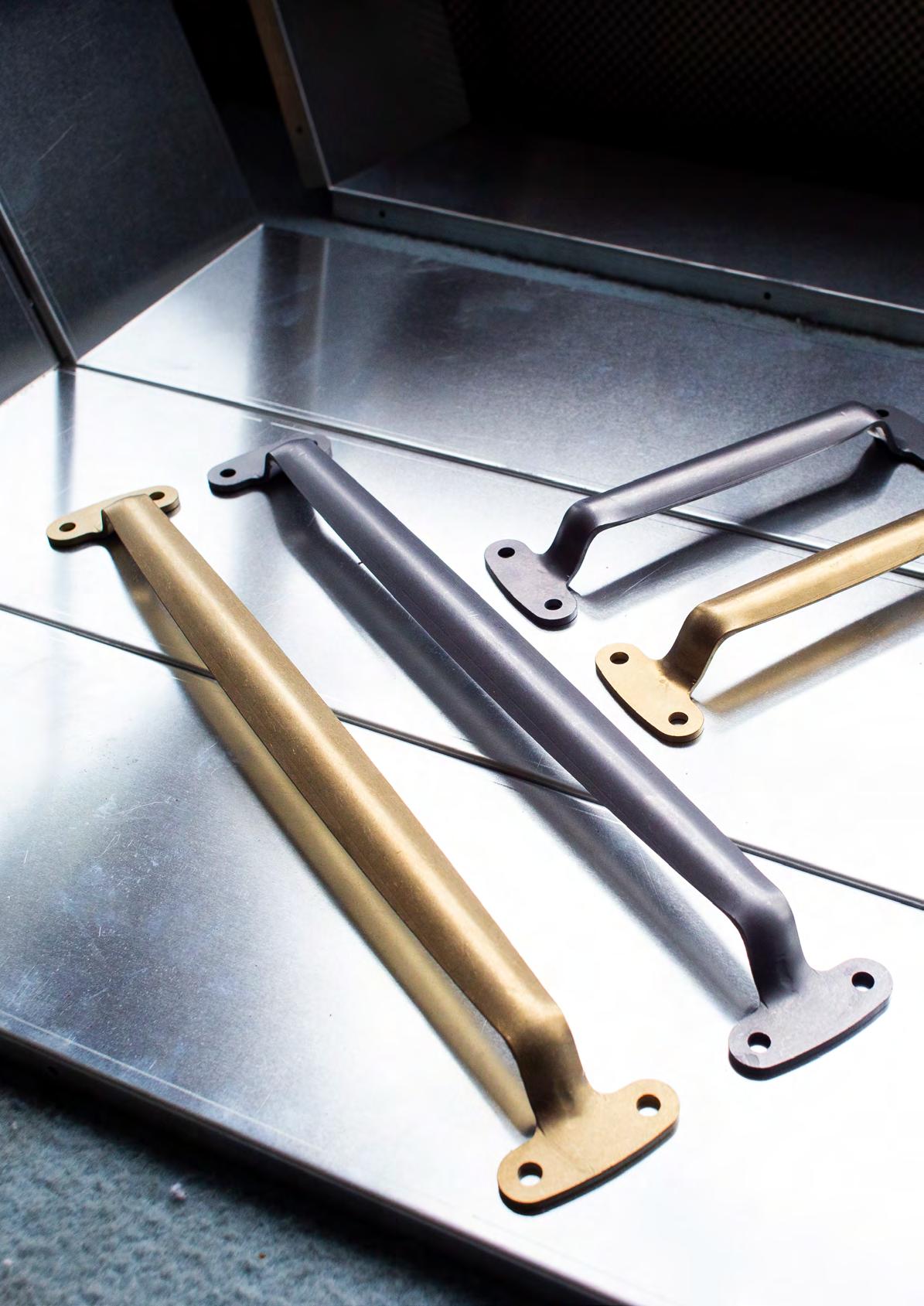

Handle
Our most insignificant introduction to date. Like mustard after a meal, it’s an addition to the hotel accessories collection: a metal handle. It’s not really a design because it looks like something that already exists or existed. But that turned out not to be the case, so I sketched the handle I felt should exist.
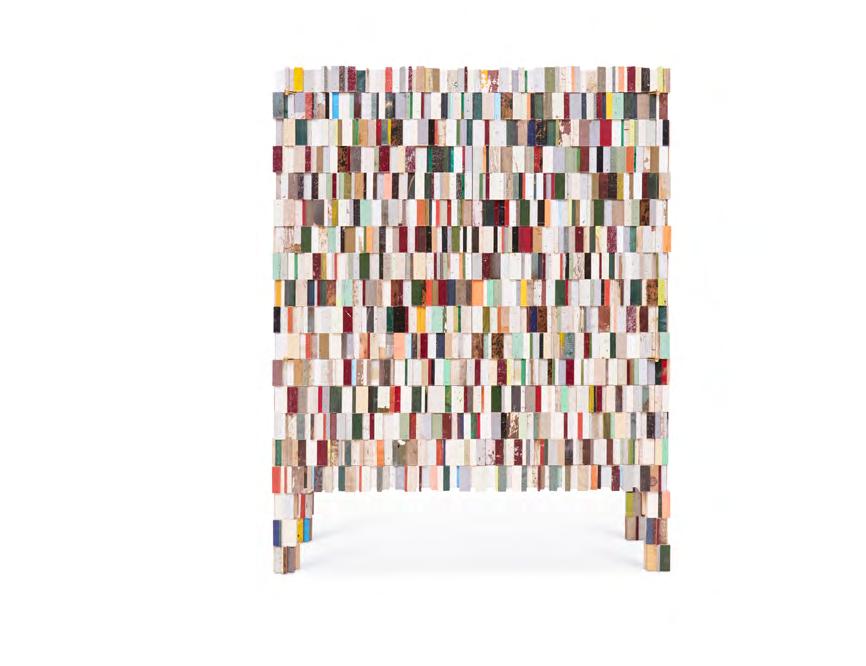
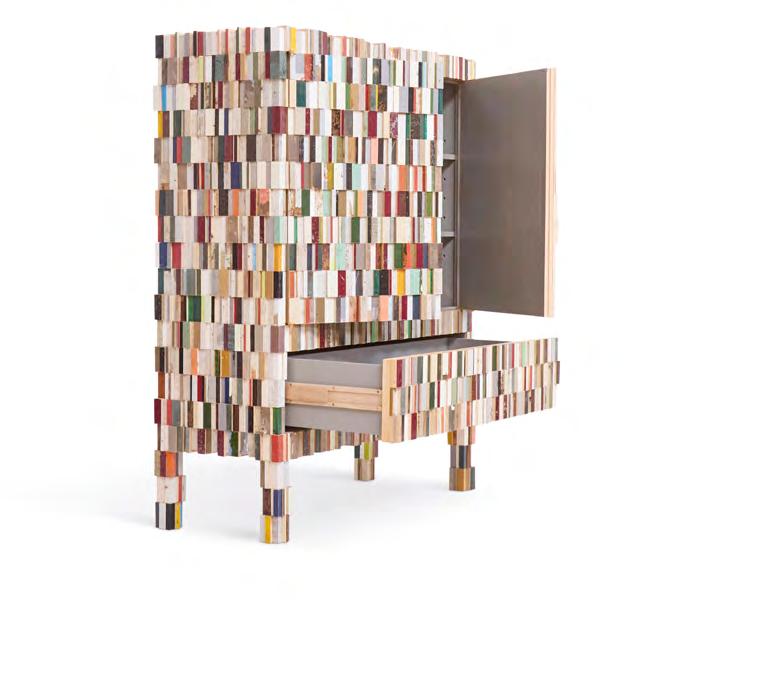
Environmental Service Cabinet
art nr year measurements
material
rrp
4204-3
2024
120 x 49 x 152 cm
scrapwood, plywood, brass
€ P.O.R.
Environmental Service Cabinet
In recent years, we’ve been increasingly plagued by agencies and governments imposing the most bizarre mandatory inspections, reports, and requirements. At one point, I thought that if one more “inspector” showed up uninvited and left behind a mandatory report (which usually means we have to invest tens of thousands or write things off), I was ready to throw in the towel.
No sooner had I thought that than the Environmental Service made its appearance. According to them, we’re no longer allowed to use (scrap) wood in our recently subsidized wood gasifiers, which we use to heat the building. Sorting is still allowed, but not sawing anymore, which is going to be a problem. I was, and still am, utterly frustrated by it. For us, the paint on the wood is precisely what we use in our products, so we don’t generate much waste. To make the best of a bad situation, I came up with the Environmental Service Cabinet. We saw all the wood into random widths of 10 to 35 mm and lengths of 80 mm, and we turn it into objects.
With the little waste that remains, we’re experimenting with making products from self-produced wood chips. We’ll showcase these products in October during DDW. The container we had to rent on orders from the Environmental Service, to have our wood waste officially disposed of, won’t fill up very quickly. More than ever, we’re selling our own waste. You’d think they’d be happy about that! When you think about it: we make products from scrap wood that would otherwise mostly go straight to the incinerators. The wood is almost fully used and ends up in valuable products, and the leftover wood goes (or used to go) into our high-quality stoves that meet the strictest standards.
Now, large amounts of scrap wood have to be disposed of due to a possible, very minimal contamination, and it will still end up being burned. Meanwhile, we have to find another fuel source to heat the building. It doesn’t take a university degree to realize that enforcing the rules in this case completely misses the point. But rules are rules, and figuring out a process that requires even more attention than our 40×40 products, where we can use almost all the remaining material, is actually quite fun.
I just wish I had thought of it sooner!
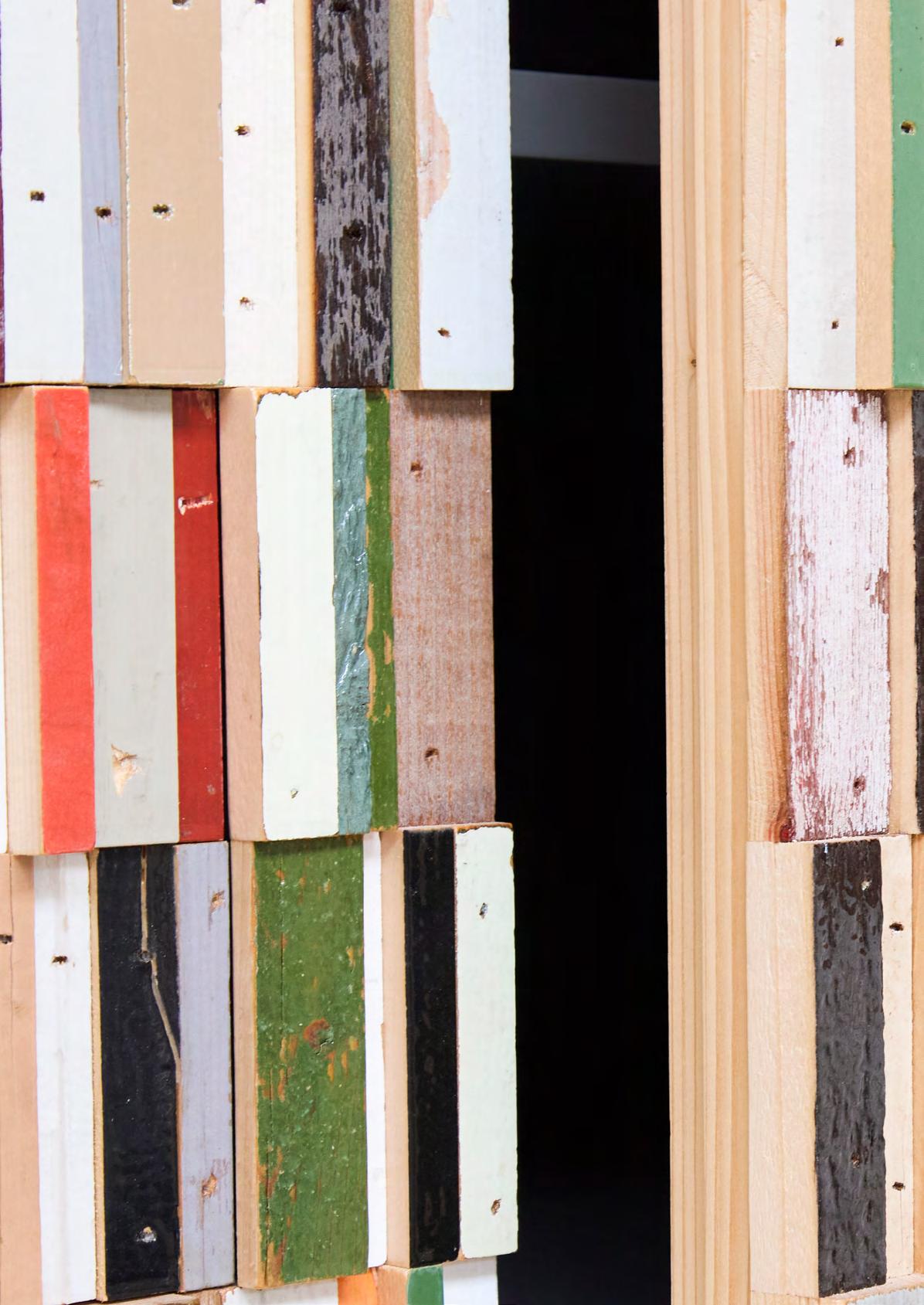
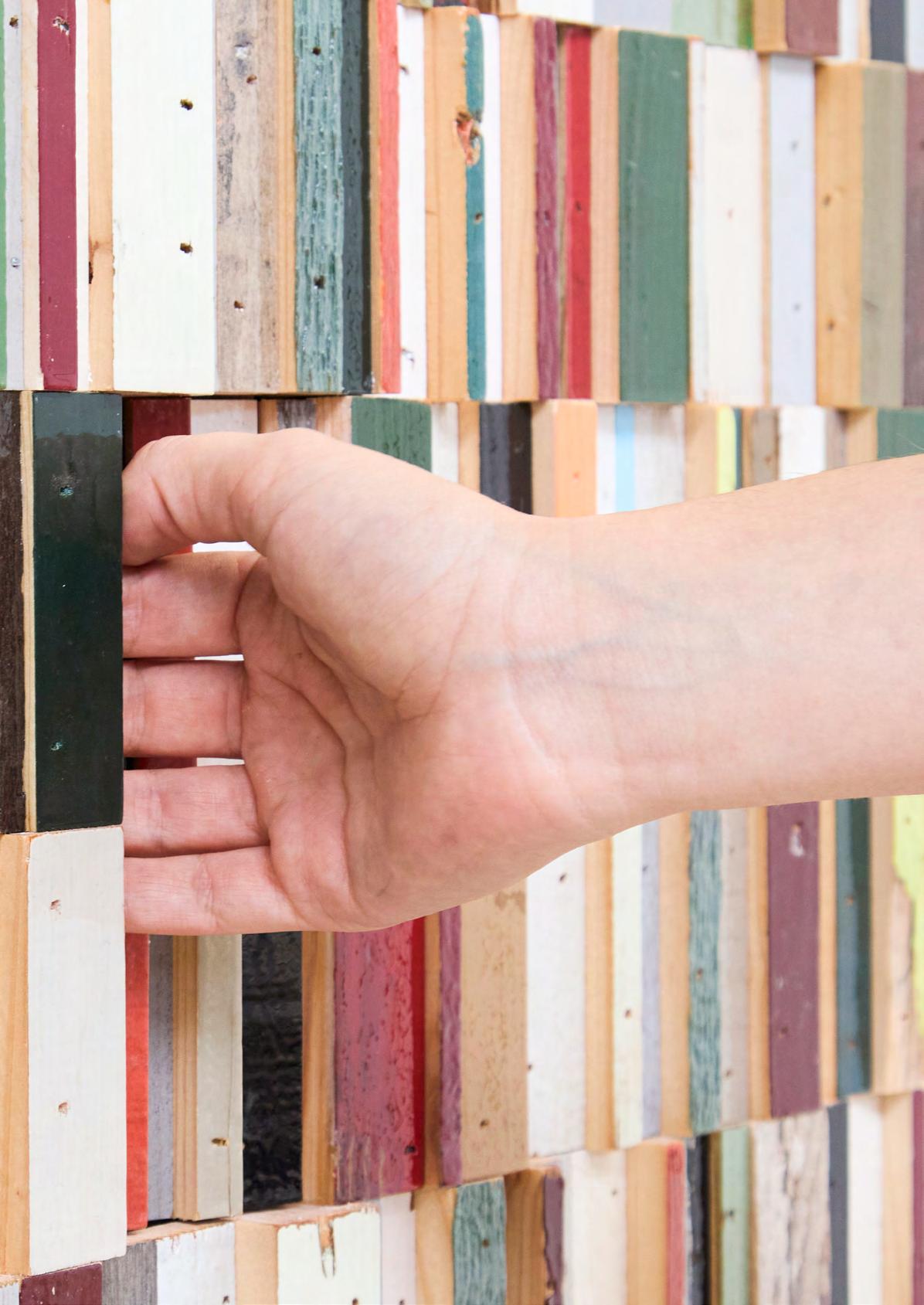
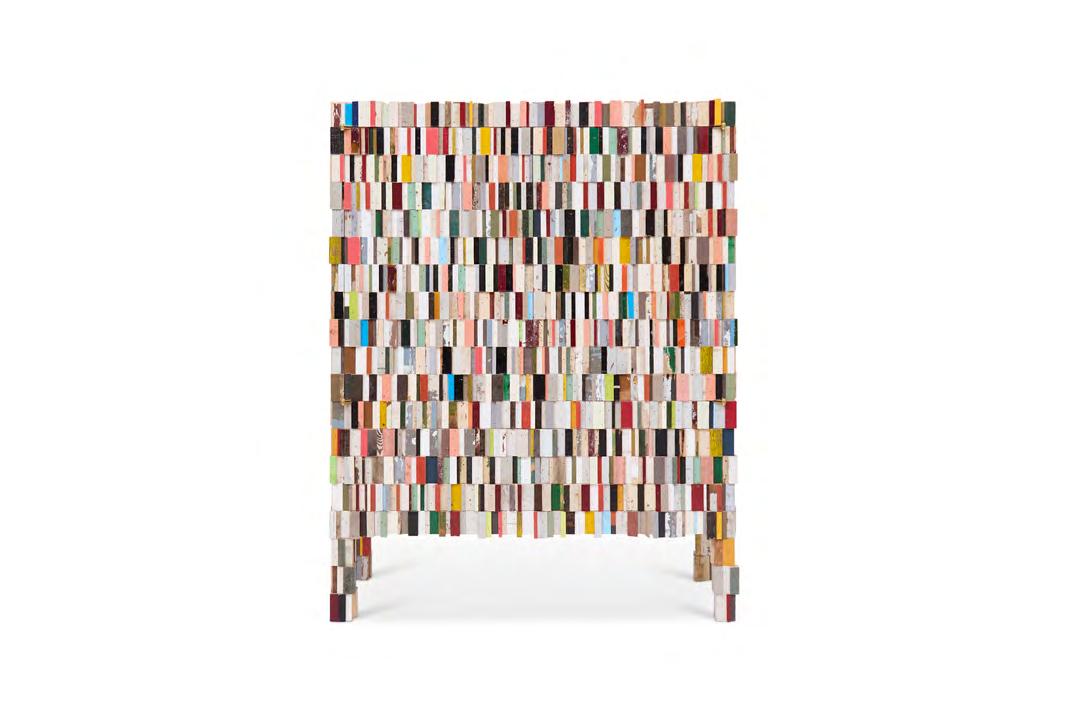
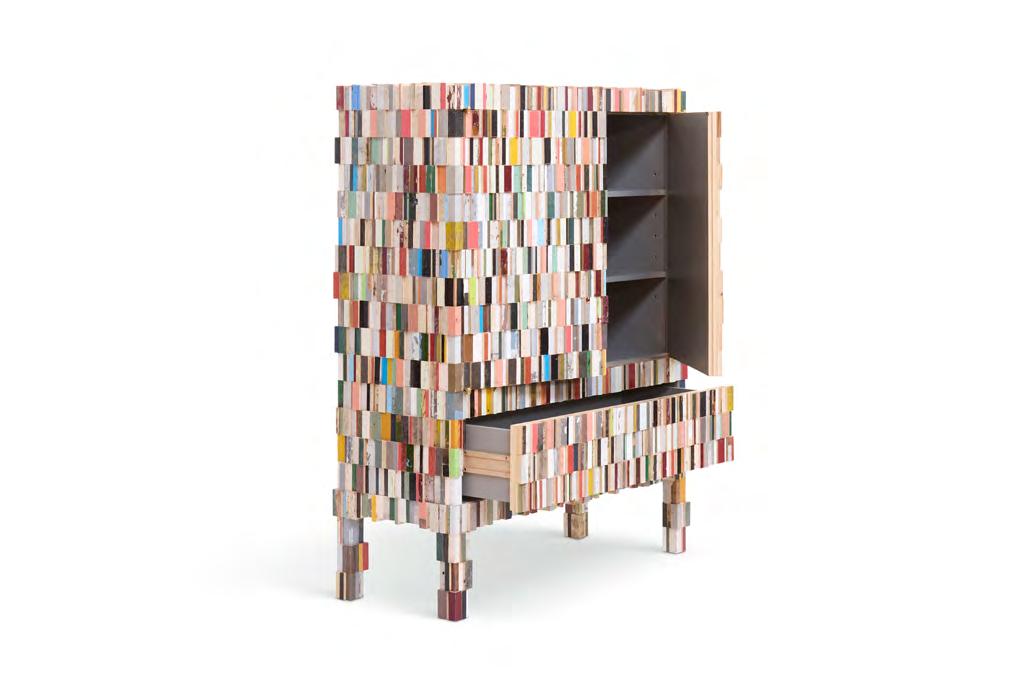

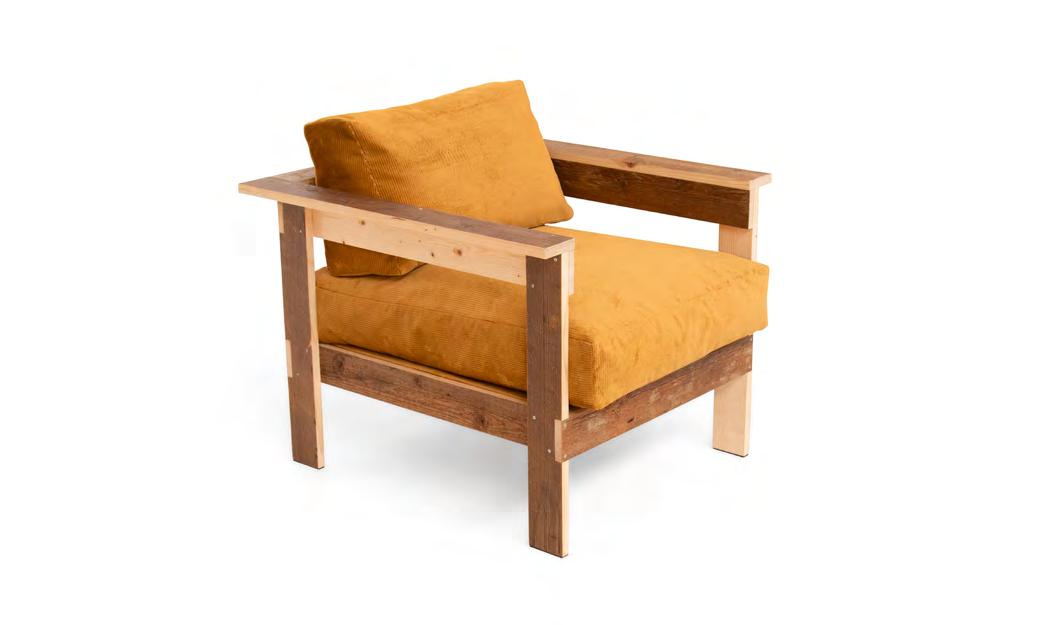
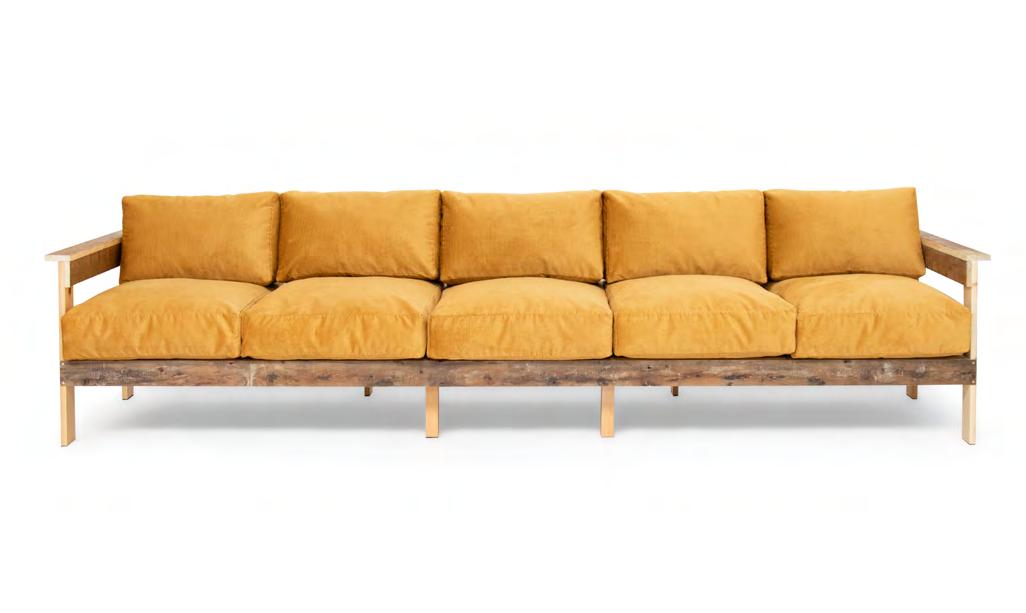
Couch and Armchair with Corduroy
Thirty years ago, I came up with a whole range of scrap wood benches and armchairs. It wasn’t a success. However, a reasonably well-selling Scrapwood Bucket Chair came out of it, and the Crisis Cushion Bench resembled its scrapwood predecessor. We could actually use a (scrapwood) bench, so I started sketching to fill this gap in the collection. The construction of the As-Thick-As-Wide scrapwood planks couldn’t be simpler.
Armchair in Scrapwood with Corduroy
art nr year
measurements
material
rrp
2024
89 x 88,5 x 68,5 cm
scrapwood, plywood, upholstered with corduroy
€ P.O.R.
Couch in Scrapwood with Corduroy
art nr
year
measurements
material
rrp
2024
300 x 88,5 x 68,5 cm
scrapwood, plywood, upholstered with corduroy
€ P.O.R.
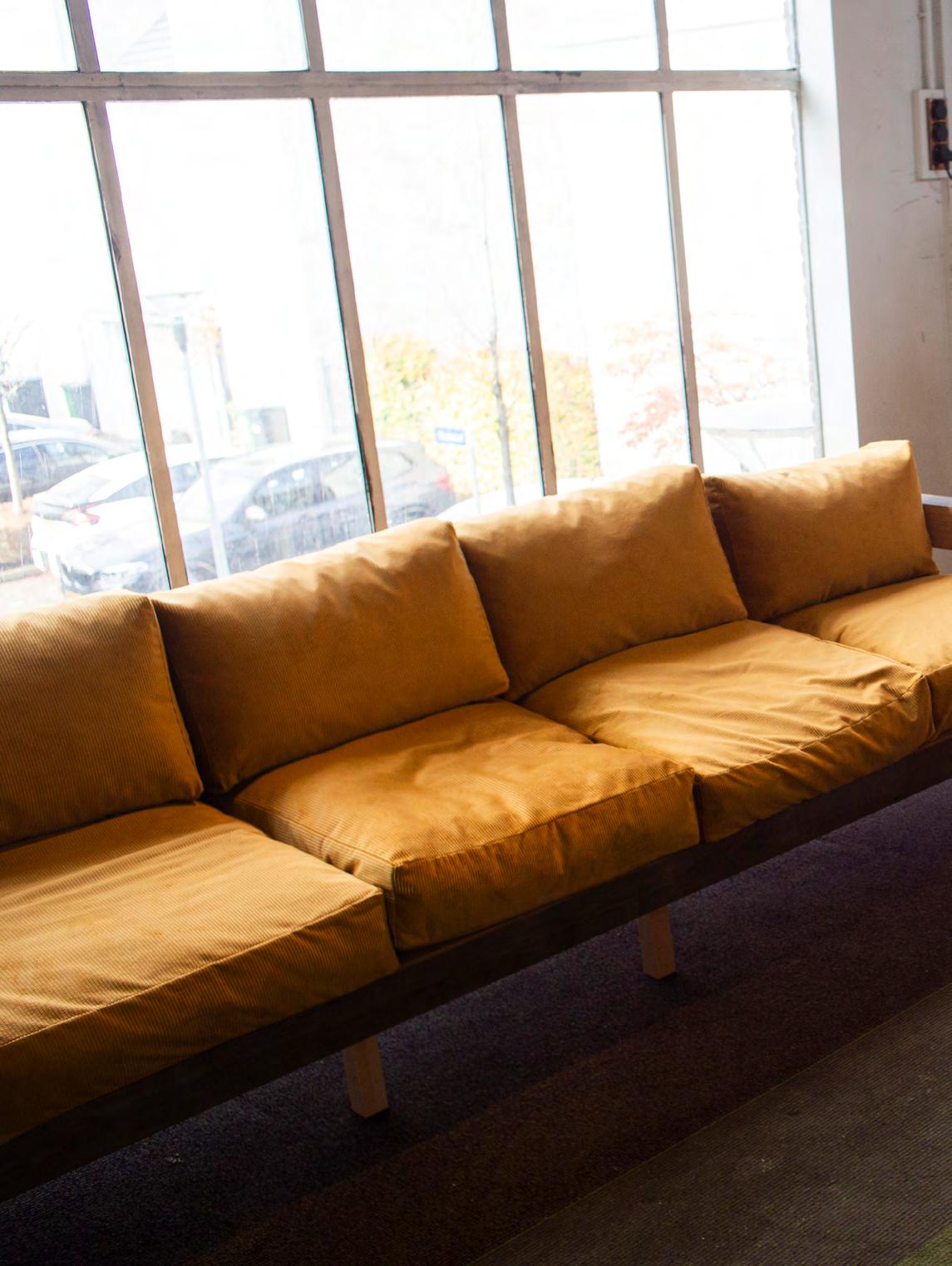

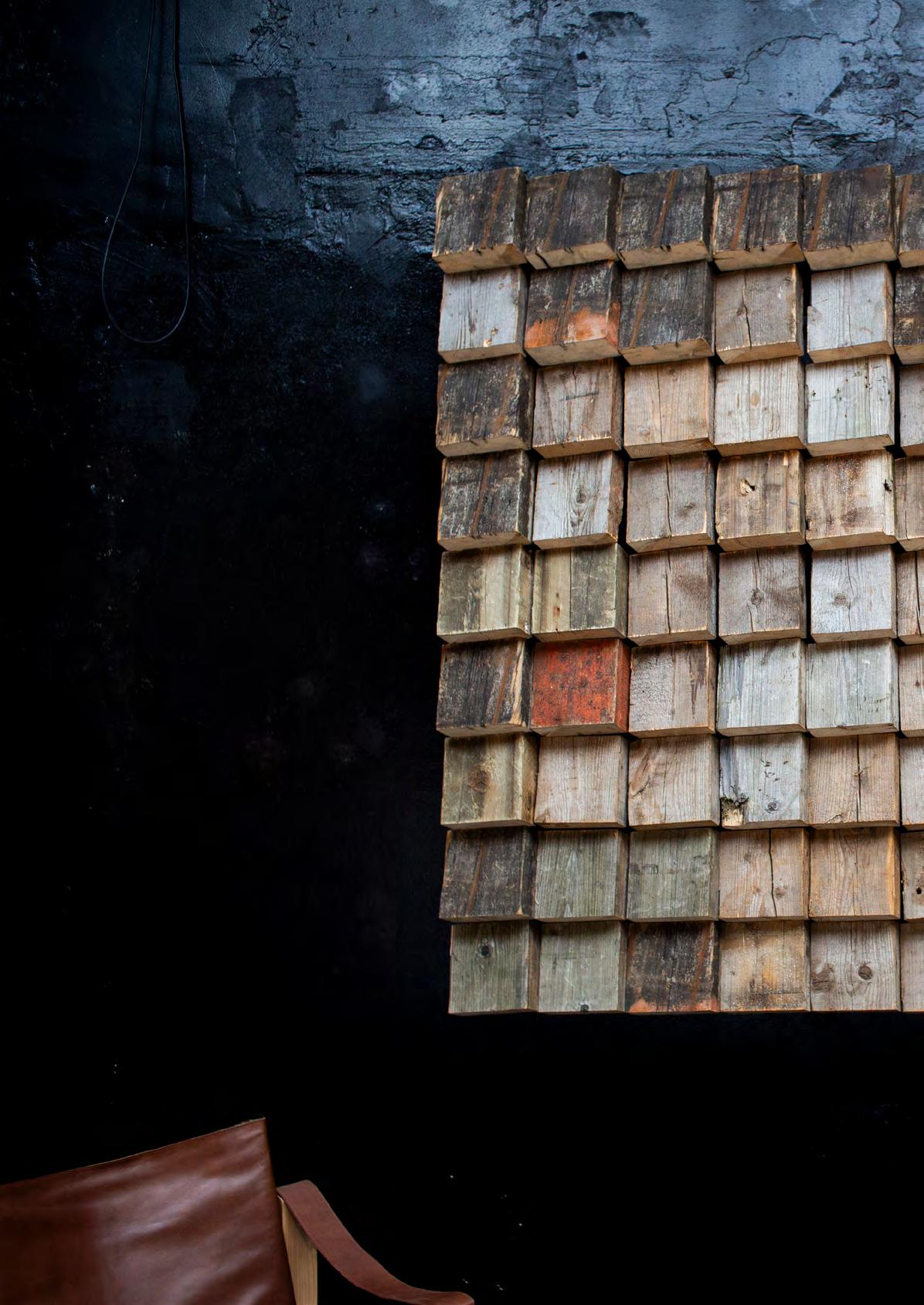
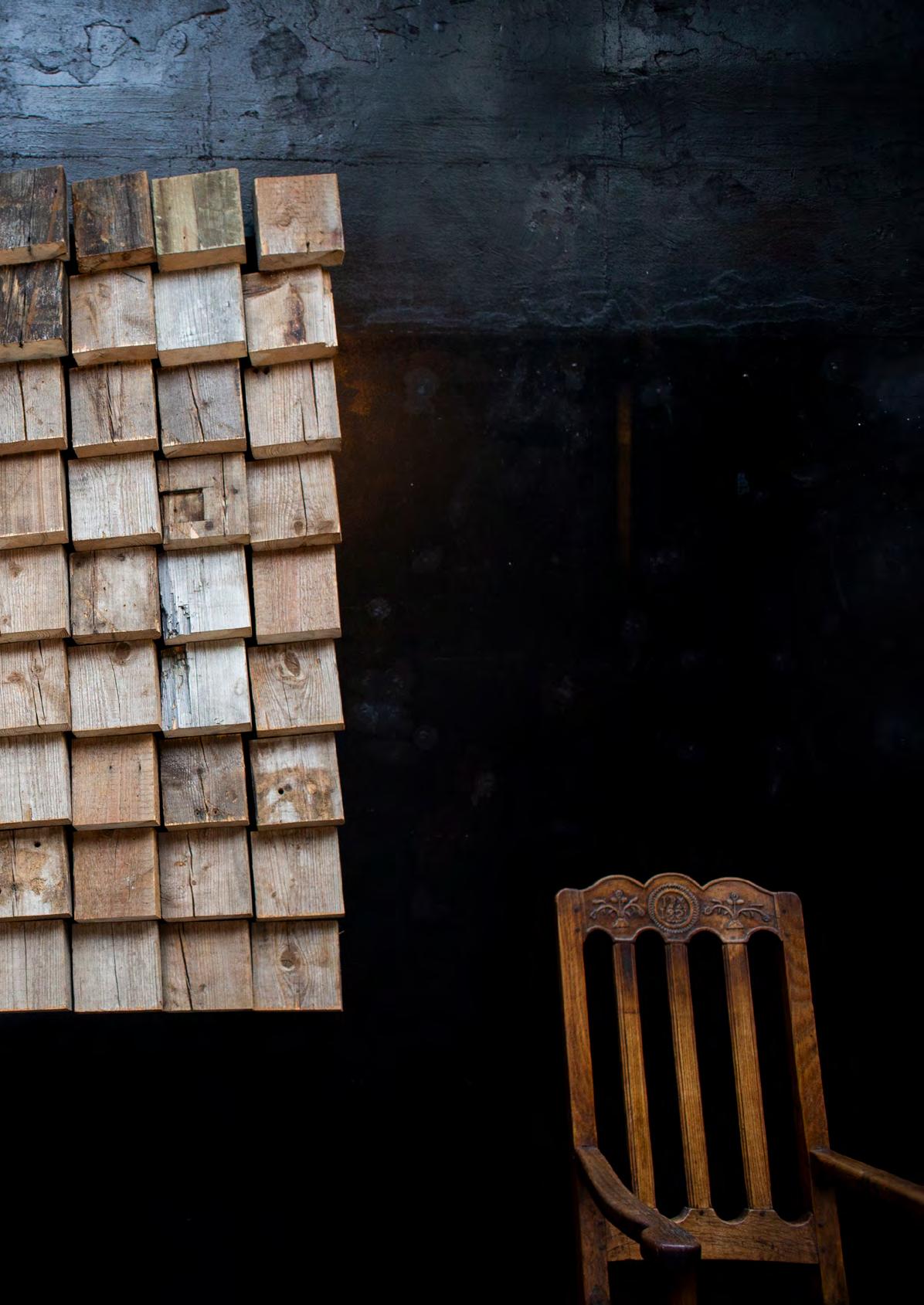
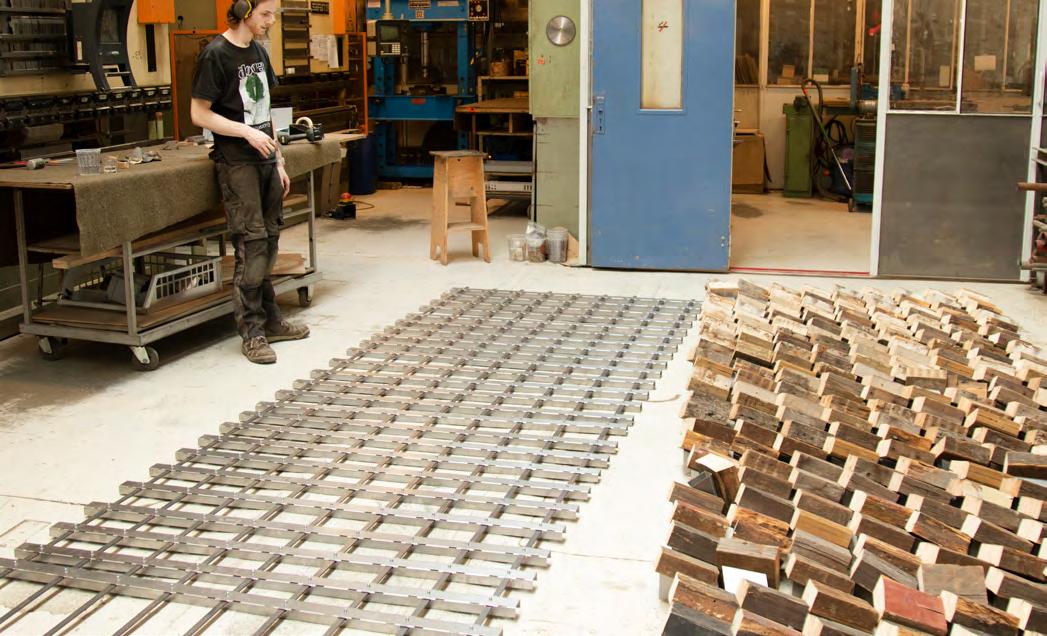
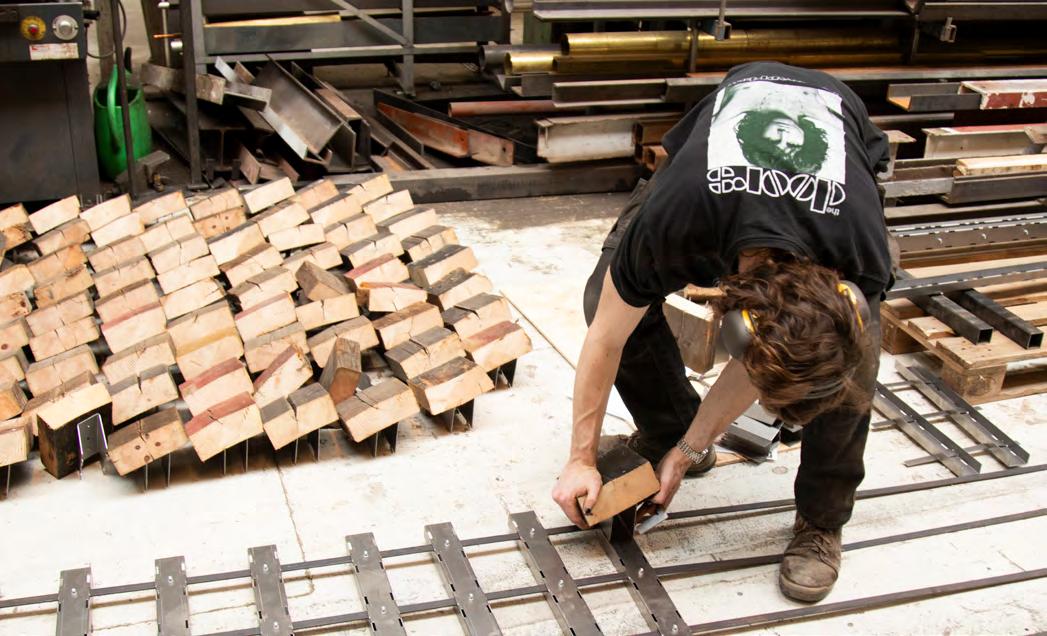
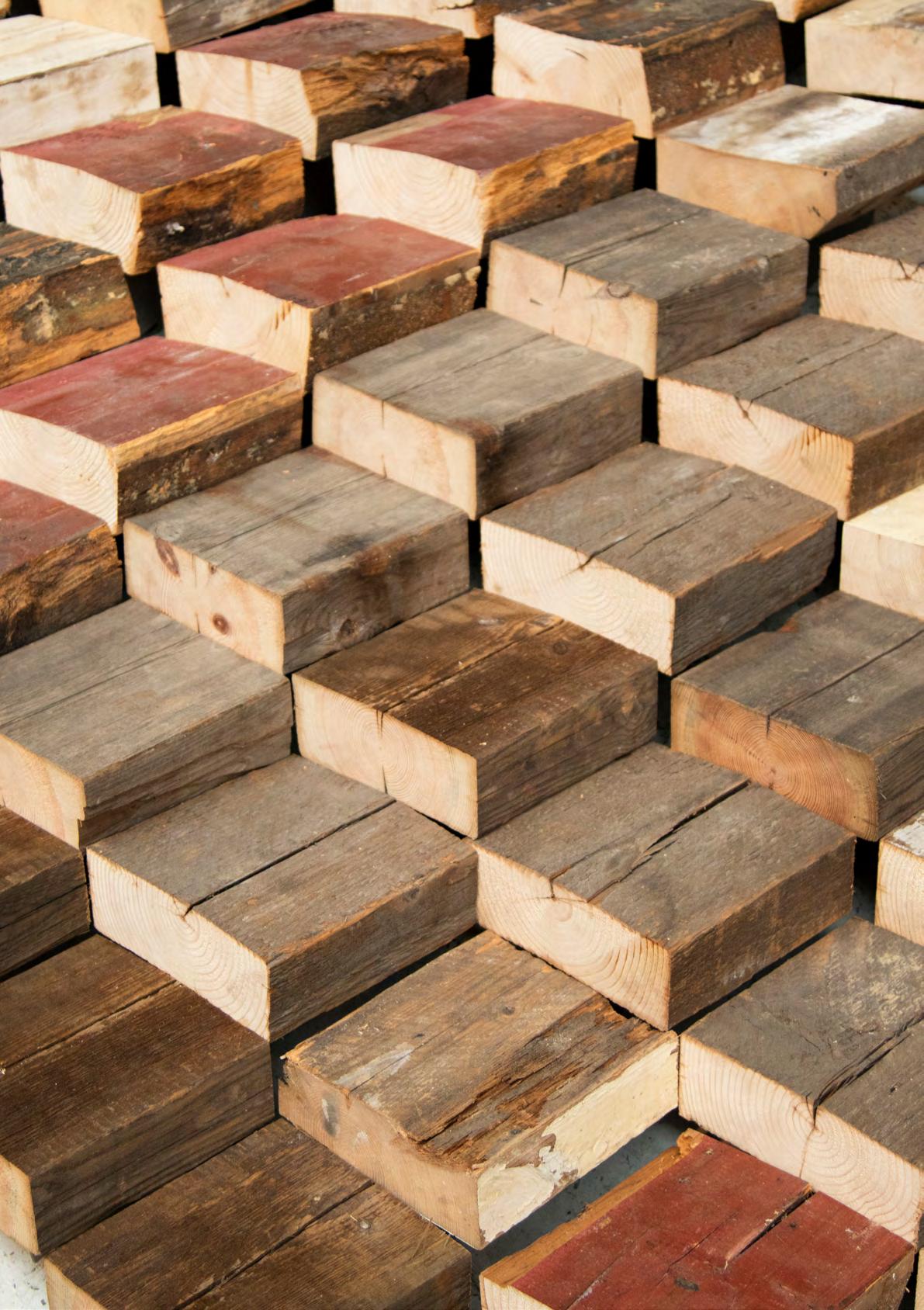

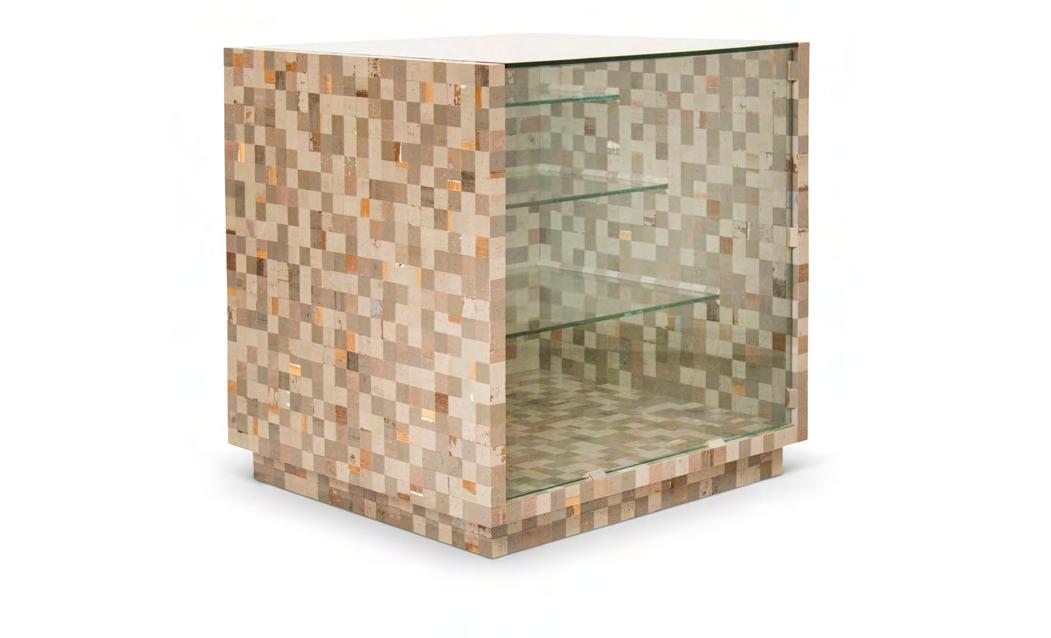
40x40 Collector’s Display Cabinets
Ten years ago, we presented glasses and other small items, creating a sort of panel material display case specifically for that occasion. It was essentially a type of non-design, purely intended for showcasing products. For the next eight years, we used the increasingly worn display cases to sell our small items. This year, we’re making “showcasing small items” our main goal once again.
We’ve created 40×40 Waste Collectors Display Cases. With the most ingenious 40×40 details, we’ve taken it a step further. Instead of being as cheap as possible and purely functional, they are now becoming works of art in their own right!
art nr year measurements material rrp
40X40
3890-141 - 144 2024
96 x 88 x 96 cm
scrapwood, plywood, brass, high-gloss lacquered € P.O.R.
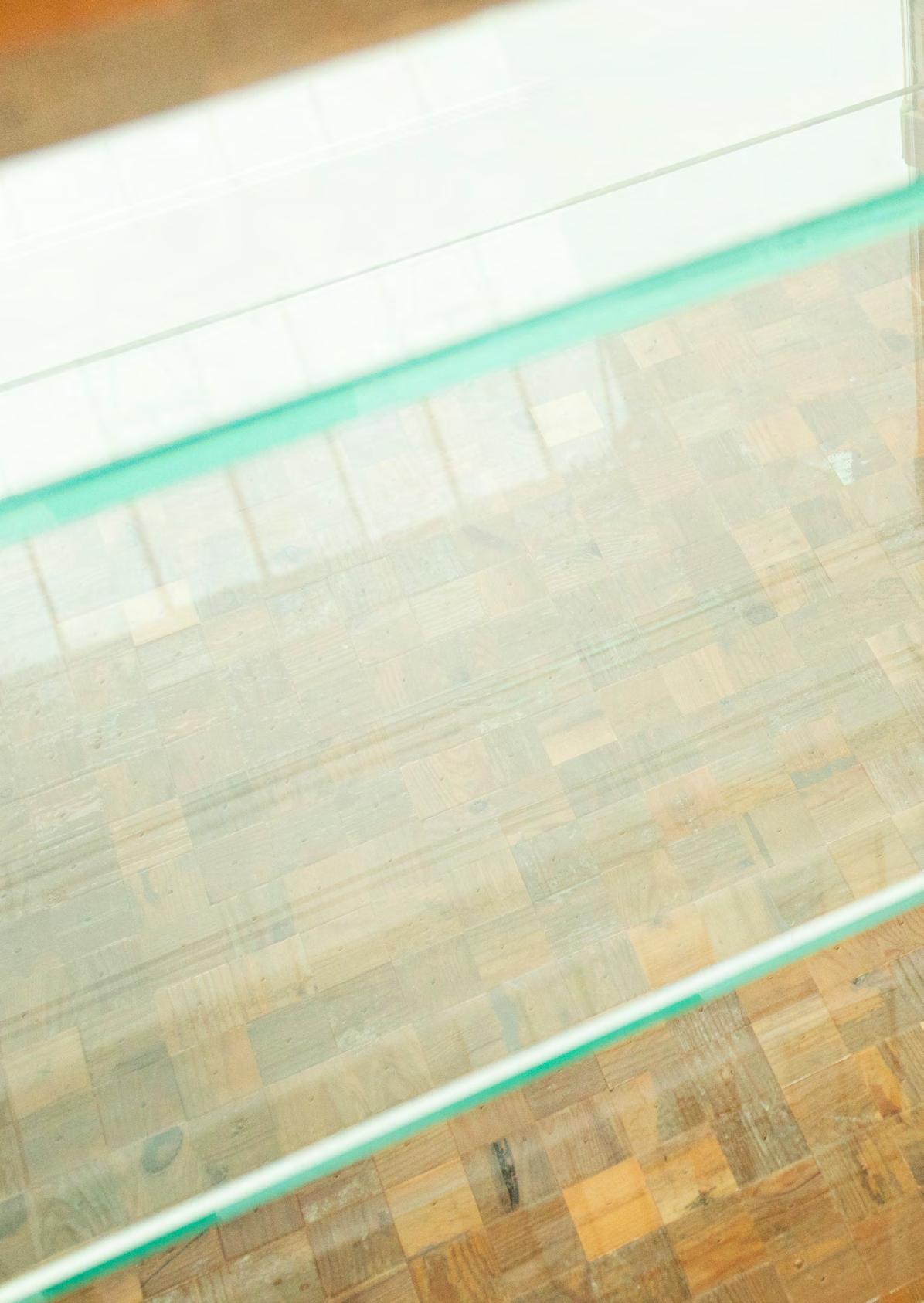
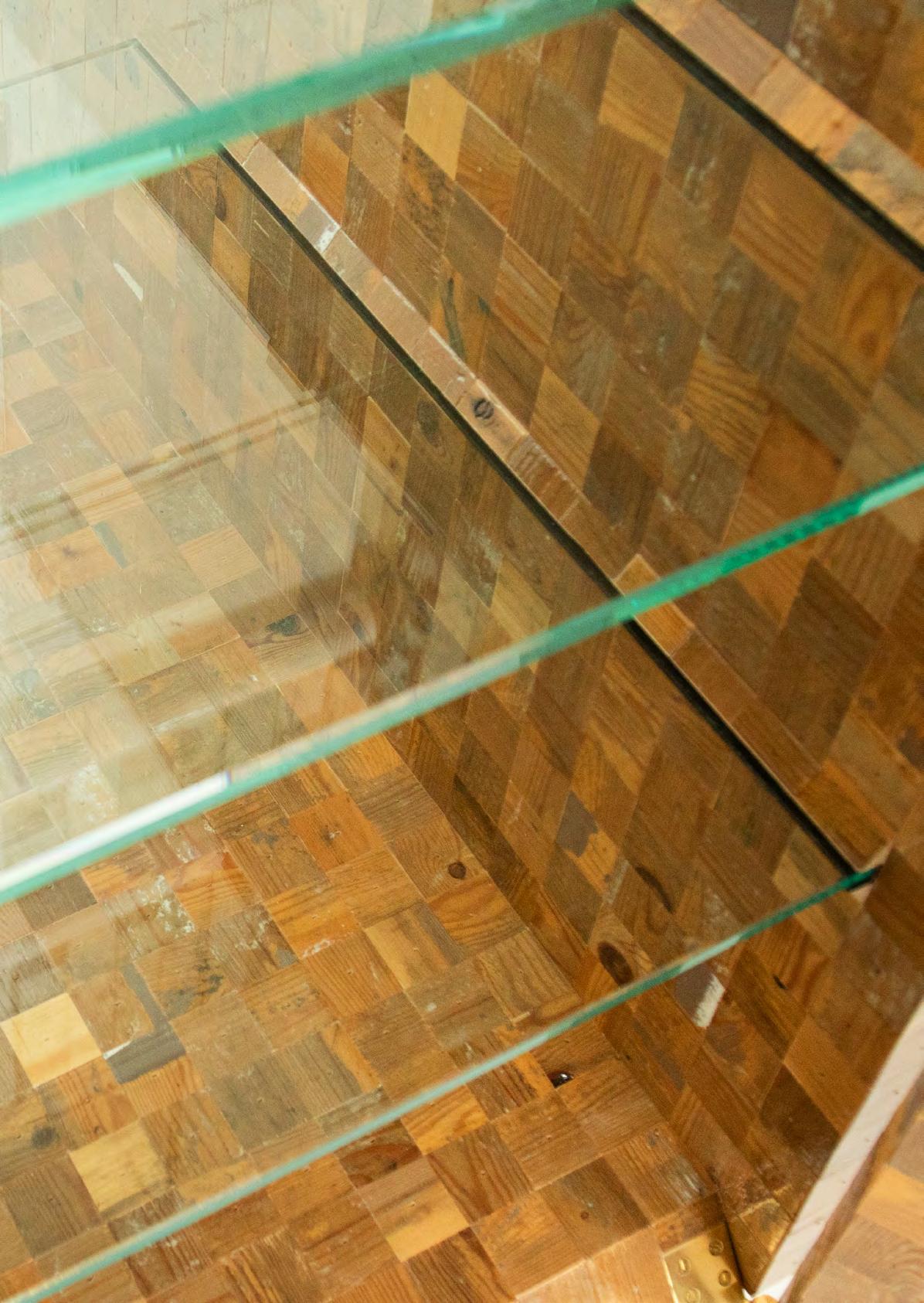
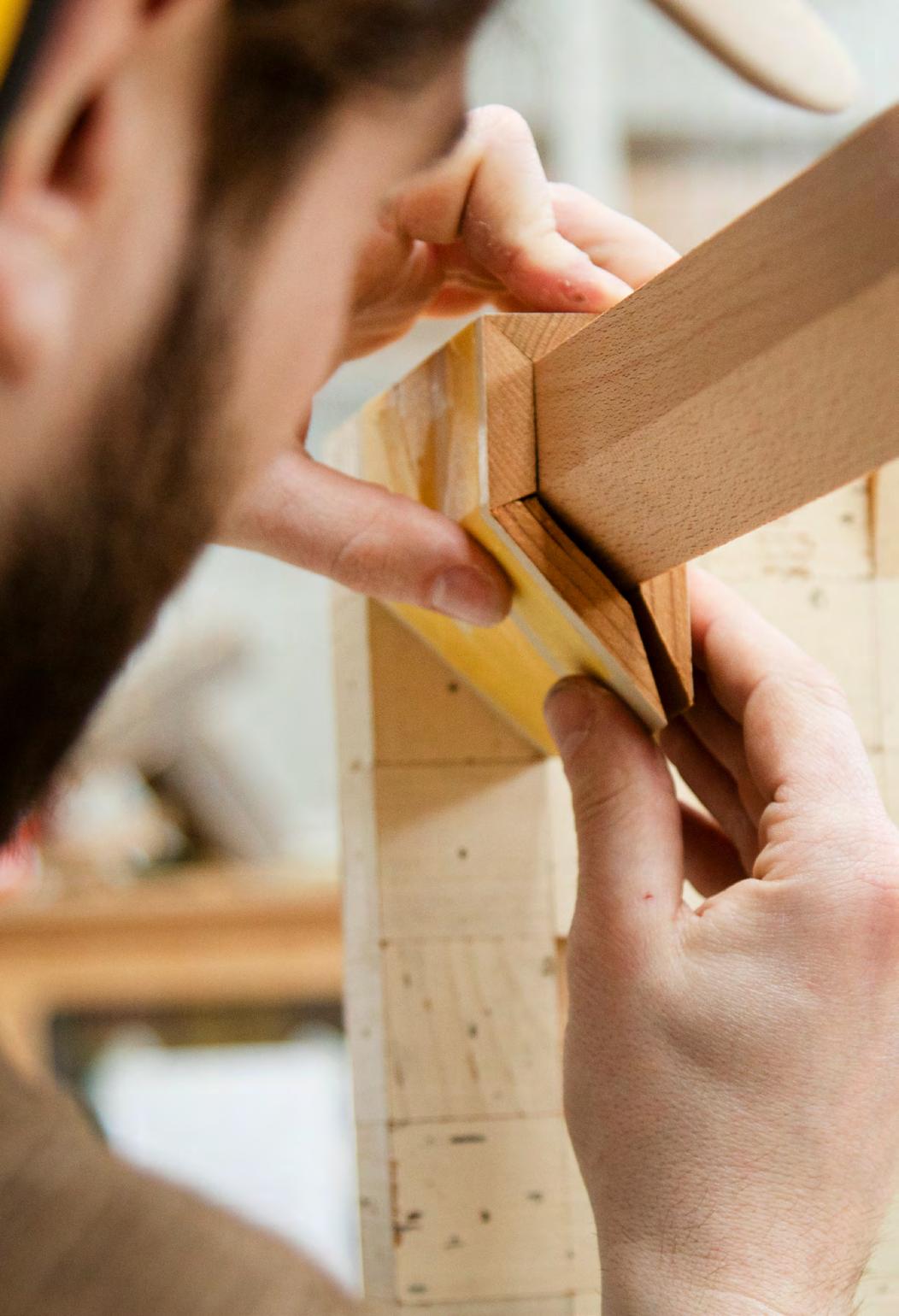
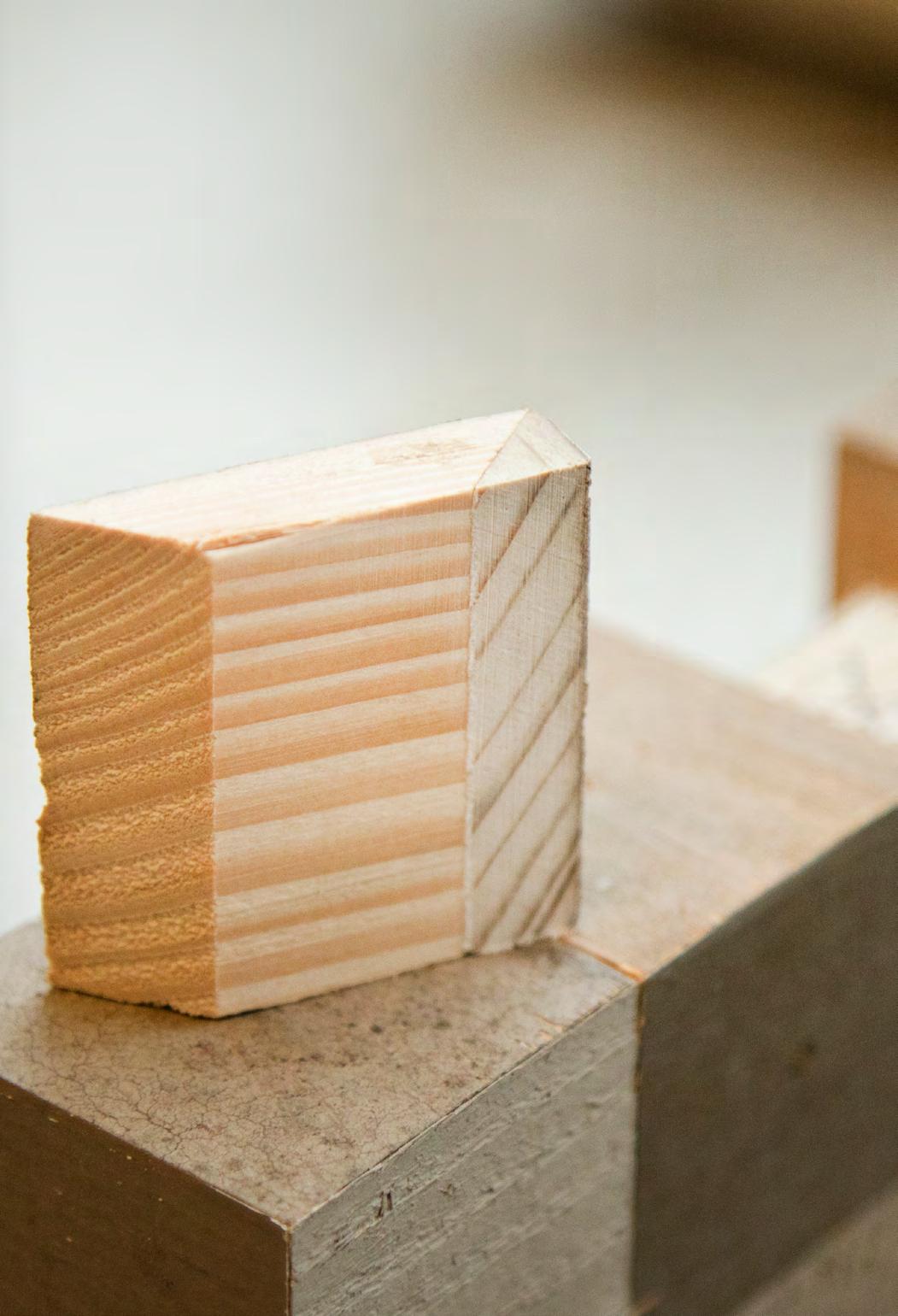
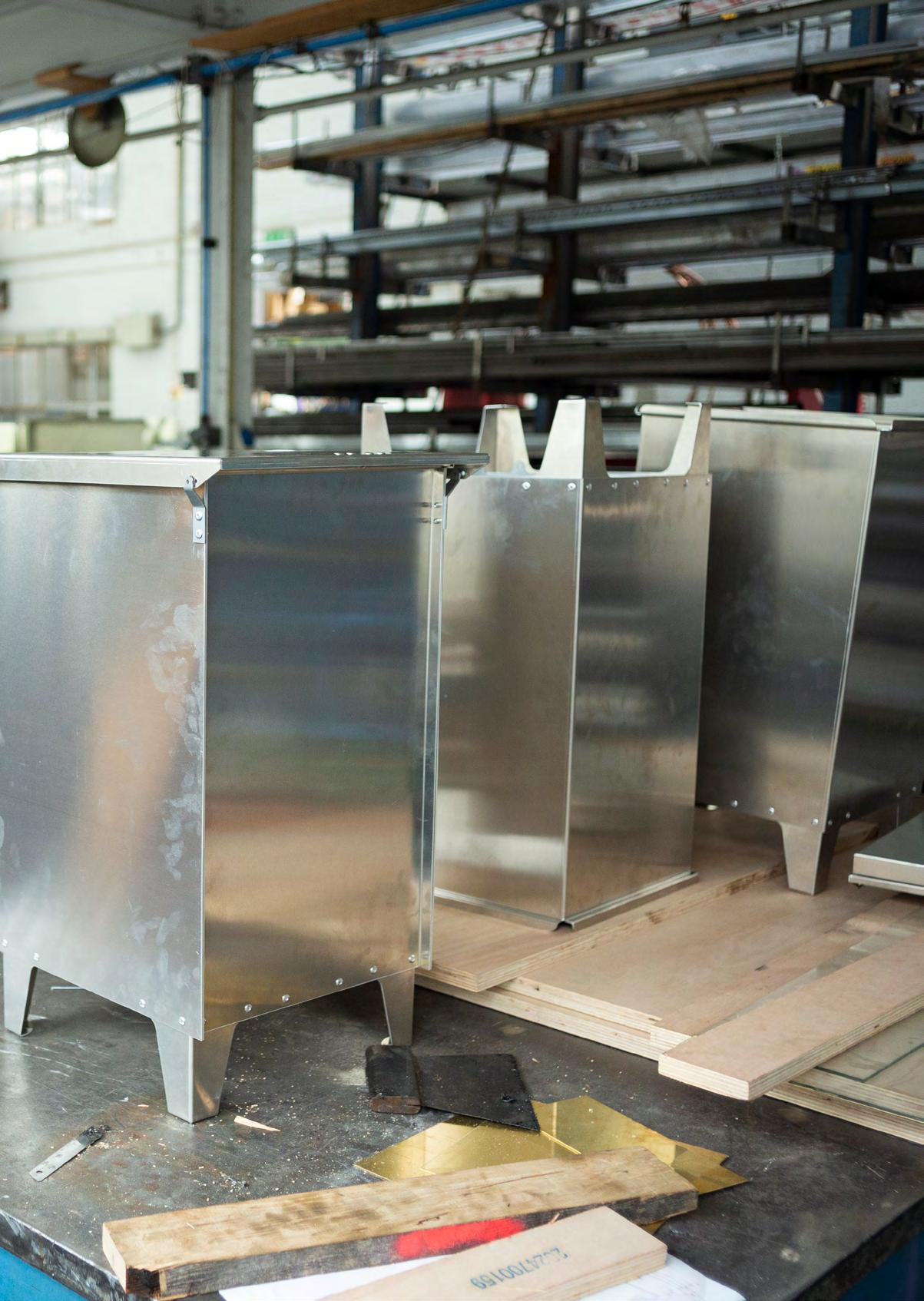
“The
Trash Bin”
There are some pretty nice trash bins out there, so this design is actually somewhat redundant. Still, in the past, we’ve frequently created custom bins. Since we don’t have a trash bin in our collection yet, I thought we should invest some time in “The Trash Bin.” As always, the design is largely influenced by the fact that we produce in small quantities in the Netherlands. We did everything we could to create a trash bin that’s as affordable as possible. It’s a hopeless battle, as it still ends up being an expensive bin. When we had to choose materials, we went with aluminum and copper. Aluminum is relatively affordable, doesn’t rust, and thus doesn’t require finishing, making it the most cost-effective option in this case. Fortunately, aluminum is actually more expensive for most manufacturers than steel alternatives with finishing. So, our cheapest bin is quite stylish. Copper also doesn’t rust and is ridiculously expensive, but we figured there are enough people for whom budget isn’t a concern and who just want something special. Plus, it’s simply a beautiful trash bin that fits a 40-liter bag perfectly and makes it easy to insert and remove.