STRATEGIC PLAN
IN PROGRESS | DRAFT VERSION 1.1 | JULY 15, 2025
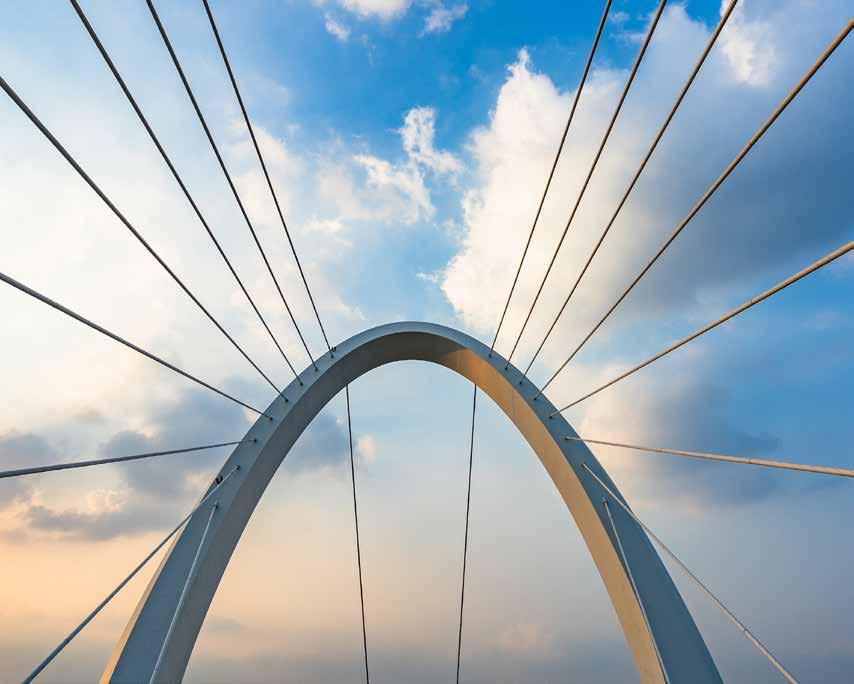
IN PROGRESS | DRAFT VERSION 1.1 | JULY 15, 2025
Founded in 2024, P+Ex is a non-profit center of excellence organization focused on preserving and extending the service life of concrete structures. Its mission is to drive global awareness, education, tools and actions to preserve and extend the service life of concrete structures to ensure a sustainable built environment.
Since its inception only a short time ago, P+Ex has conducted a series of workshops for concrete industry experts to develop a set of objectives and aspirational goals for the organization. The goals are:
GOAL 1: Highlight the societal benefits of enhanced service life for new and existing structures.
GOAL 2: Develop strategies to conserve resources and reduce environmental impact through proper concrete asset management.
GOAL 3: Raise awareness of the financial benefits of durability design and service life extension.
GOAL 4: Advocate for responsible stewardship of the built concrete environment.
GOAL 5: Serve as a knowledge hub for tools and techniques to extend service life.
GOAL 6: Publish periodic sustainability reports on the repair industry’s efforts and set future goals as needed.
Preserving and extending the life of concrete structures reduces carbon footprint, lowers resource consumption, and minimizes financial and social impact. P+Ex will provide a voice and a pathway for the concrete repair industry to aid owners to extend concrete structure service life through effective management of existing assets. Delivering the best way forward is essential for sustainability, and P+Ex is leading the conversation.
The ideas of Preservation and Service Life Extension have been in practice ever since modern concrete structures were first built. P+Ex, a 501c3 organization, created in 2024, is a non-profit center of excellence organization focused on preserving and extending the service life of concrete structures.
Its founding purpose is to begin a new way of thinking about concrete and its functional status in the built environment. Its goal is to work with existing industry and governmental organizations that are concerned with the sustainability of the built environment, e.g. including the American Concrete institute (ACI), the International Concrete Repair Institute (ICRI), American Society of Civil Engineers (ASCE), Global Cement and Concrete Association (GCCA), etc.
P+Ex has been founded as a global effort by the concrete industry. The founding board members include stakeholders from the United States, Canada,
the European Union, Japan, the Middle East, and Australia.
We seek the broad engagement and involvement of industry, academia, institutions, organizations, and independent individuals.
Instead of considering concrete structures as being built, used, ignored, demolished, and rebuilt, we should manage them throughout their use, prevent deterioration, repair and strengthen if necessary, and consider adaptive reuse if their original purpose becomes obsolete.
“Once a concrete structure is built, it can stay in service indefinitely, if it is well maintained, and the embodied energy from its original construction will serve generations.”
USA produces 400 MILLION cubic yards of NEW concrete per year (2.3% of global production)
cubic yards of concrete in service in USA (~2.4 billion ton CO2 footprint)
Preservation of the structure is preservation of its embodied energy. By understanding and managing concrete in a life cycle, circular manner, we will benefit from its enormous sustainability benefits while reducing negative impacts on our environment and our planet’s overall health and future viability.
Concrete, as we are often reminded, is the most commonly used building material in the world. The second reminder in that it’s almost always a greenhouse-gas-producing threat to our planet, due to cement production which is responsible for 8 percent of man-made carbon emission (Ref. 1) per year, every year.
We have another way to look at this. Once a concrete structure is built, it can stay in service indefinitely, if it is well maintained, and the embodied energy from its original construction will serve generations. From
Extending the service life of the existing concrete inventory by one day prevents 6.6 MILLION tons of CO2 emissions (net decarbonization).
this perspective, concrete can be seen, in fact, as an incredibly sustainable building material.
In the United States, 400 million cubic yards of new concrete is placed each year. The material production required for this contributes 80 million tons of Carbon Dioxide (CO2) to our atmosphere. The current inventory of existing concrete structures is estimated to be 12 billion cubic yards, which represents 2.4 billion tons of embodied CO2 captured in existing concrete.
Leaving this concrete in place and in use rather than tearing it up and building new – in other words, extending the service life of our existing inventory – saves 6.6 million tons of CO2 each day. To not follow the path of service life extension by properly maintaining and repairing our built environment would be illogical and wasteful. Hence, P+Ex has been created to facilitate this effort.
To understand why P+Ex was formed, we first need to understand the history of concrete.
Consider the concrete dome of the Pantheon in Rome, built from concrete using natural form of cements by the emperor-engineer Hadrian almost two thousand years ago and visited by millions of awed tourists each year. And it still keeps the rain out.
In the rest of the world, concrete is everywhere. You are probably reading this in a building supported by a concrete foundation and never give it a thought. Your municipality provides basic services through concrete pipes and tanks and roads and bridges, and all that functions year after year without much notice.
Concrete is strong under compression loading –pushing or pressure – but weak in tension – pulling or tugging. Because of that, for concrete structures to function, we add steel to them. The steel resists the tension loads and lets us build bigger structures with longer spans, greater capacities and leaner cross sections. Although reinforced concrete has transformed the modern-day built environment, we must contend with the drawbacks associated with steel embedded into concrete. Unfortunately, steel is made from metals that corrode in the presence of
THE HISTORY OF MODERN
CONCRETE:
moisture and oxygen. That corrosion expands the embedded steel which cracks the concrete, eventually creating spalls and delamination – and possible loss of integrity and need for repairs.
Steel corrosion is the most common reason for concrete deterioration – there are a bunch of other causes which we can get to at a later time. But it’s why you see rusty concrete when you drive under a hundred-year-old bridge, or trip over a what looks like a nick in a sidewalk. This deterioration can be prevented, but if it has already happened, the structure can be repaired and preserved. The concrete repair industry is a $40-50 billion a year endeavor in the US alone. Other than addressing safety and continuing serviceability, concrete repair preserves the energy that was used to build the structure in the first place.
Portland cement, the miracle substance that makes concrete possible, was patented in 1824 by bricklayer/mason Joseph Aspdin in Leeds, England. Mr. Aspdin had a kiln in his backyard and somehow serendipitously burned some clay and limestone together one day and came up with a bunch of rocks (called “clinker” today) that, when ground down into a powder, created a material (cement) that has much higher strength than the natural cements used in traditional masonry mortar. So just over 200 years ago, modern concrete was invented.
It took nearly 50 years, for Portland cement, patented by Joseph Aspdin in 1824 to become a common building material. By 1886, concrete was understood well enough for the Statue of Liberty to be placed on a colossal mass concrete foundation that still, unseen by the public, supports the monument today. In 1904, the American Concrete Institute (ACI) was founded, followed by the Portland Cement Association (PCA) in 1916 and Precast/Prestressed Concrete Institute (PCI) in 1954.
These organizations managed the concrete construction industry for decades, creating guidelines, standards and codes for the safe construction of concrete structures. (Additionally, more specialized groups have been created over the years, such as the Prestressed Concrete Institute, etc.) However, the industry lacked standards for maintenance and repair of concrete structures – there were no guidelines for how and when to intervene in a structure’s deterioration process and keep it in use in a safe manner.
563 562
“In reality, the most sustainable, low-carbon concrete structure is often the one already built.”
In 1988, at a World of Concrete seminar, people who specialized in concrete repair came together and shared their concerns about this lack of standards and guidelines for concrete repair. In response, the International Association of Concrete Repair Specialists was formed later that year. In 1993, the name was changed to the International Concrete Repair Institute (ICRI). About a decade later, in 2005, Vision 2020 (Ref. 2) was published, an allencompassing initiative to make the concrete repair business more effective, efficient, and sustainable, by the year 2020.
As these efforts have developed – ACI 562, a codewriting committee, published the first version of a building code in 2013, and ACI 563, a committee for repair specifications, published its first standard in 2018, and just published a revised and greatly expanded version in the spring of 2025. In a great achievement, ACI 562 has been adopted by the International Existing Building Code as of 2022. ICRI
established its Sustainability Committee 160 and published a white paper to address the intrinsic value of our existing concrete environment in 2016 (Ref. 3).
The circular economic approach to construction is a framework to prevent negative impacts of economic activity that can lead to the loss of valuable resources and damage to human health and our natural systems. Applying circular economic principles to transform the way concrete is designed, applied, used, and maintained in construction will offer significant opportunities to reduce Green House Gas (GHG) emissions as well and other environmental impact such as depletion of natural resources, pollution of air, land, and water, and the underutilization of assets such as buildings (Ref. 4, 5, 6).
Traditionally, concrete construction focuses on the creation phase – from cradle to gate. Recent developments in decarbonization strategies have been developed by the cement and concrete industry such as GCCA 2020 (Ref. 2, 7) to reduce GHG emissions and environmental impacts.
PHASE 3
Service Life Completion: Decommission and Rebuild
• After a long, useful life with several series of repairs and rehabilitation.
• Materials from demolition can potentially be reused/ recycled to create sustainable concrete or down-cycled for other efforts in new project.
PHASE 2B
Service Life Extension: Repair and Restore
• Rehabilitation: Addressing damage to extend usability.
• Could be a series of repairs and strengthening to keep asset functioning as intended or re-purposed.
Still, there are enormous potentials to be captured if the full life cycle of the structure is considered. In reality, the most sustainable, low-carbon concrete structure is often the one already built. Refurbishing and retrofitting existing structures to improve energy efficiency is usually the best option for avoiding and reducing carbon emissions from the built environment.
PHASE 1
New Construction: Build for Longevity
• Design and create to last and ensure strength and longevity from the start.
• Design for durability (e.g. inclusion of durability into ACI building code).
PHASE 2A
PHASE 2
Service life/use
Asset Management: Protect and Maintain
• Proactive care and maintenance to maximize service life.
• Surveillance & monitoring.
• Protective coatings and minor repairs executed on routine basis by asset managers/owners.
Fig. 1 illustrates the typical and enhanced life cycle of concrete structure beyond the “gate” into use, extension and completion phases.
Fig. 2 demonstrates the essential actions that support the transition towards a circular economy in concrete construction.
P+Ex is acting as a steward for the design of durable structures and long-term management of concrete structure.
Create the goals and objectives.
It has been established in 2024 as a non-profit center of excellence organization focused on preserving and extending the service life of concrete structures. Its mission is to drive global awareness, education, tools and actions to preserve and extend the service life of concrete structures to ensure a sustainable built environment.
Preserving and extending the life of concrete structures reduces their carbon footprint, lowers resource consumption, and minimizes social impact. P+Ex provides a voice and a pathway for the concrete repair industry to aid owners to achieve financial, environment, and social goals through effective management of existing assets. Delivering the best way forward is essential for sustainability, and P+Ex is leading the conversation.
Moving forward we have followed three phases to progress:
• Create the goals and objectives in a strategic plan (e.g. Road mapping workshops 2024)establish the structure based on this strategic plan, seek for endorsement from executives of various industry organizations (e.g. ACI, ICRI, ASCE, etc.)
Assemble the teams.
Manage the execution of the plan.
• Assemble the teams to develop the action items, organize workshops for each goal to further develop action items, and get buy-in
• Manage the execution of the plan - expand the participating companies, individuals, and contributors through the workshops
Since the inception of P+Ex in 2024, a series of road mapping workshops attended by industry experts have been conducted to get the effort under way. This integration of professionals representing the myriads of skills, knowledge, judgment and ethics of the concrete repair industry will be key to success of P+Ex.
Over 80 industry experts (see Appendix), including concrete repair contractors, general contractors, officials from government agencies, precast industry representatives, engineering designers, petrographers, concrete admixture suppliers, cement producers, material scientists, and concrete sustainability experts, helped to map out the goals and objectives.
Concrete structures can be designed and built for long service lives. They are resilient to natural disasters (wind, storm, earthquake, wildfire, etc.) and can provide protection to human lives. And even though design is usually made to a designated service life, concrete structures often remain in use for long after that intended service life is reached.
Design for durability is a key feature for new construction, service life extension, and preservation phases. Using the similar amount of resources to construct buildings with enhanced service life gives people a sense of safety and provides stability for generations to come.
However, lack of having durability requirements in the regulated building codes and/or lack of timely maintenance and repair programs can cause tragedy.
On June 24, 2021, at 1:22 AM, Champlain Condominium Towers South in Surfside, Florida, partially collapsed. The building, which was completed in 1981, was known to have deteriorated conditions and engineering reports had recommended extensive repairs – which had not been implemented.
Since then, increased scrutiny has been focused on the structural conditions of ocean-front reinforced concrete high-rise structures, and more stringent laws have been enacted in many jurisdictions. Since the collapse of the building, the National Institute of Standards and Technology (NIST) has been investigating the collapse and identifying causes of the failure. In February 2025, NIST submitted to Congress an update on its investigation. The report noted that the team has completed all experimental work on the physical evidence from the building’s structural
elements and should reach conclusions on the causes of the collapse within another year.
The goal of the NIST investigation is to uncover factors that contributed to the collapse of the building and make recommendations to improve public safety and preventative measures for recurrence of failures cause loss of lives (https://www.nist.gov/news-events/ news/2025/02/nist-report-congress-provides-updatechamplain-towers-south-investigation).
Through proper maintenance and care programs for concrete structures, their integrity can be confirmed and minimum disruption of daily life (e.g. shutdown facilities for use, productivity downtime, traffic interruption, noise, dust) can be achieved. By avoiding irreversible deterioration and damage, less construction materials/resources need to be wasted and be deployed for new constructions. This leads to the reduction of health hazards to both occupants and construction workers, such as fine particulates in the air, vibration, and acoustic pollutions (https:// build-construct.com/building/health-impactsbuilding-materials/). The savings in financial resources can be redistributed to other personal or societal needs. Historic preservation to maintain the character of communities and even national pride was demonstrated by the recent re-opening of Notre Dame Cathedral in Paris. Magnificently resurrected by a massive 5 year restoration project following a devastating fire in 2019, Notre Dame Cathedral stands proudly once again, having regained its world-famous opulent splendor (https://premierconstructionnews. com/2025/03/06/notre-dame/).
• Support the inclusion of durability requirements in codes and standards, such as ACI 318 and ASCE 7. Follow international guidelines like ISO 2394, which specifies a 50-year service life for buildings. SHRP 2 and RILEM TC 230 PSC call for even longer service lives.
• Educate owners on the importance of regular maintenance of concrete structures to prevent deterioration and keep them safe. Emphasize common sense and education – teach owners the light duty tasks that can be done to prevent deterioration.
• Develop a guide for owners regarding inspection and maintenance of concrete facilities.
• Protect public safety by utilizing available technologies to enhance and protect concrete structures against aggressive environments.
Concrete is a long-lasting, energy-efficient, and versatile construction material. Much of the historical built environment still standing today was built using concrete and cementitious-based construction materials. Carbon dioxide embodied in concrete structures is generated during the production of the cementitious binder and associated reinforcing steel, the mining and transport of aggregates, and the transportation of the mixed concrete to the job site. As a result, concrete has a large carbon footprint compared to other standard construction materials like wood, steel, and masonry. While concrete structures are high in embodied carbon dioxide, they generally can use less energy to operate and, with frequent and timely maintenance, have the capability to last longer than structures built with other common materials. Concrete structures, if designed properly, can be repurposed. Repairs and repurposing contribute to a structure’s overall positive environmental impact and are much less impactful than a “demolish and rebuild” approach that is often required for structures that have been allowed to deteriorate.
• Assess and recommend methodologies and procedures to quantify the environmental impact and resource consumption for extended service life of concrete structures vs. replacement.
Stakeholders have varying awareness of their impact and obligations. Quantification tools offer approaches to address these challenges.
When developing methodologies and procedures, standardized scientific methods (e.g. ISO 14040 –Life Cycle Assessment, ISO 14067 (Greenhouse gases - Carbon footprint of products - Requirements and guidelines for quantification), EN 15804 (Sustainability of construction works -
Environmental product declarations - Core rules for the product category of construction products), ISO 14044 guidelines for life cycle assessment , must be followed for greater credibility.
For general customer needs, there are broad approaches, such as an online tool (Ref. 11) to estimate resource savings and greenhouse gas emission reductions for concrete repair projects.
• Assemble case studies using standardized LCA methods. For example, restoration and corrosion protection of a reinforced concrete building at Washington Airport prevented 1,688 tons of CO2 and 67 tons of acid rain constituents.
The Rainbow Bridge restoration followed ICRI procedures, avoiding 450 tons of CO2 and preserving 4,800 GJ of embedded energy (Ref. ICRI 160 Committee white paper). For new structures, approaches to protect against chloride ingress can significantly extend service life and reduce environmental impact (Ref. 12).
A concrete structure is an asset. It requires proper design, care and maintenance which can result in long lasting service life.
A little extra investment in the early aging of the structure will significantly reduce long-term expenses. When maintenance is neglected, repairs, when they become essential, will generally equal five times maintenance costs. If repairs are not carried out, rehabilitation costs will be five times repair costs.
To consider the financial impact of neglecting the need for maintenance and the benefits of periodical maintenance, we need to understand Wolter Reinhold de Sitter’s “Law of Fives.” Sitter, a part-time Professor in the design of structures in concrete at
the Eindhoven University of Technology, proposed a Law of Fives for structural concrete maintenance. The theory proposed that the life of a concrete structure, with respect to durability, can be divided into four phases (W.R. de Sitter, 1983, Ref. 8):
• Phase A: Design, construction and concrete curing
• Phase B: Corrosion initiation processes are under way, but propagation of damage has not yet begun
• Phase C: Propagating deterioration has just begun
• Phase D: Propagation of corrosion is advanced, with extensive damage manifesting ($1 spent at Phase A is equivalent to $5 at Phase B, $25 at Phase C, or $125 at Phase D)
• Conduct market research for Concrete Repair Industry (update Vision 2020 market survey). The annual cost for concrete structure repairs in the US was estimated at $18-21 billion (Ref. 2), with a 2006 survey on repair costs across market segments (Ref. 2, Appendix 4):
• Bridges and Roadways
• Piers and Wharfs
• Buildings
• Parking Structures
• Locks and Dams
• Residential
• Industrial Facilities
• Water Treatment and Pipelines
• Stadiums, Runways, Chimneys, Towers, etc.
Due to inflation, aging concrete structures, and growing repair needs, the US market for concrete repair could reach $50 billion, with further evaluations to follow.
• Assemble the best asset management practices for extended service life of concrete structures. Estimate the value of existing concrete structures to attract investment. Predict lifespan and plan for service life extension using guidelines like ACI 365.1R and ACI CODE 365. Real-world examples show that asset management, including maintenance, extends lifespan for safe use.
• Based on real-world applications in industrial and infrastructure sectors, tangible benefits of an integrated asset management can be demonstrated (Ref. 9). For example, through maintenance and rehabilitation interventions, the asset lifespan may be extended for safe and efficient use of infrastructure by 20-25%.
• Assemble case studies of financial benefits based on Sitter’s “Law of Fives.” Repair and rehabilitation are often more economical than replacement, with potential savings of three to ten times the cost (Ref. 10).
Concrete structure maintenance is not top of mind for developers and owners. There is lack of maintenance and repair of existing publicly used infrastructure (incl. roads, state dams, waterways, rail, bridges, public parks and recreation, rail, ports, etc.). The American Society of Civil Engineers (ASCE) 2025 Infrastructure Report Card gave the United States infrastructure a C Grade and said the investment gap in infrastructure maintenance and need was $3.7 trillion. A quote from the report summarizes the needs of US infrastructure: “For decades, investment at all levels of government and the private sector has failed to keep up with the increasing demands and
projects necessary to reach a state of good repair. By incentivizing innovation and maintaining—or in some cases adding—investment, America will sustain recent momentum on our infrastructure systems and ensure they are built for the needs of the 21st century”.
“Adding the big picture of sustainability –economic, social, and environmental –to professional engineering opportunities will help to change the culture and lift the image of the concrete repair industry as a noble, purposeful one.”
Current interest in choosing a career in concrete repair and protection industry is very low, mostly because of low information about the field. Very few schools have courses that introduce or prepare the student for the industry. Where courses and interested professors exist, students make their way into the industry with excitement and passion, but their education in concrete repair happens in practice rather than in school. Young engineers frequently get jobs where they are assigned to perform structural inspections of concrete bridges, buildings, or parking garages. They must be mentored on the job to learn that, in real life, concrete is exposed to service conditions that trigger
deterioration mechanisms, resulting in corroded rebar, delamination, and spalling that can create safety hazards and loss of load carrying capacity. Teaching our future engineers while they are in school about concrete’s behavior in service would prepare them better to enter their careers in practice. Adding the big picture of sustainability—economic, social, and environmental—to professional engineering opportunities will help to change the culture and lift the image of the concrete repair industry as a noble, purposeful one.
• Develop a concrete-specific asset management and life-cycle cost program.
• Introduce curriculum for college coursesUniversity Sustainability programs.
• Publish articles in trade publications.
• Engage in advocacy to improve design codes include durabilty requirements for aggressive environmental conditions.
• Communicate internally (within the concrete repair companies) and externally (all stakeholders and supporters) regarding the economic, environmental and societal benefits of preserving and extending concrete structures’ service life.
There are many different organizations involved with this industry. Technologies for durability design, strengthening and protection of concrete, forensic investigations, and repair have improved greatly in the last 30-40 years. Professional service companies, including architects and engineers, provide forensic evaluation of existing structures. Testing companies provide field and laboratory services to analyze materials. Structural engineers calculate load capacities and produce design details. Inspection companies ensure that installed systems comply with specifications. Material manufacturers are also an important part of the repair team providing not only specialized materials, but technical support to the specifier and installation contractor. Contractors integrate the design, specifications, materials, labor and equipment to complete the repair.
Closely coordinating with diverse organizations’ activities will eliminate duplication of efforts, improve sharing of resources, coordinate projects to eliminate conflicting recommendations, and improve the education of industry members. P+Ex should take up the responsibility to lead and act as the knowledge center and collaborate among experts.
OBJECTIVES:
• Identify organizations worldwide and individuals that could be a part of the P+Ex community and contribute to the body of knowledge and collaborate with them.
• Identify available resources that can be implemented or used as models for education pursuits.
• Explore partnerships with organizations such as LEED, BREEAM, Envision, HQE (France) and GREEN STAR (Australia) on developing mechanisms for CO2 credits rating/plaque.
• Update existing technologies for surface repair, protection, waterproofing, strengthening, repair materials, and field installation, equipment (update vision 2020’s collection of knowledge).
• Build up database hosting case studies of comparative LCAs, remaining service life estimation, improved ESG scores through repair and reuse of existing structures, etc.
PUBLISH PERIODIC SUSTAINABILITY REPORTS ON THE REPAIR INDUSTRY’S EFFORTS AND SET FUTURE GOALS AS NEEDED
Similar to a company’s sustainability report, P+Ex can prepare periodic reports to track the progress that the concrete repair industry has been making. First, report the base line. Set target improvement and track the achievement. It can also include benefits of service life extension and case studies. Make the document available for the whole industry.
OBJECTIVES:
• Engage professionals and start collecting data and set the baseline.
• Get industry buy-in and provide transparency.
Next steps include continuing the series of workshops and increasing the knowledge and understanding of the goals of P+Ex and how absolutely beneficial
the extension of structural service life will be for the environment. Outreach to industry organizations is under way. ICRI supports the P+Ex initiative, and meetings with ACI leadership are planned shortly to secure the support of the organization.
P+Ex was created to promote and lead preservation and extension of service life initiatives to contribute to sustainable solutions for society. We plan that this initiative will become a global effort and result in a great reduction in GHG emissions and a deacceleration of global warming.
And, in symbolic support of these efforts, the Statue of Liberty will still be standing on its giant hidden mass of concrete foundation, and the Pantheon will still be keeping out the rain.
REFERENCE LIST:
REF. 1 https://gccassociation.org/key-facts/
REF. 2 Vision 2020 – A Vision for the Concrete Repair, Protection and Strengthening Industry, ACI-SDC, 2006
REF. 3 Sustainability for Repairing and Maintaining Concrete and Masonry Buildings, ICRI Committee 160, Sustainability, 2016
REF. 4 https://www.theconcreteinitiative.eu/images/ The Concrete Europe- Position Paper - Green Deal Circular economy - 2020-04-21.pdf
REF. 5 Completing the picture: How the circular economy tackles climate change EMA FoundationMaterial Economics, 2019
REF. 6 Circular Economy strategies for concrete: implementation and integration, A.T.M. Marsh, A.P.M. Velenturf, S.A. Bernal, J. Cleaner Production 362 (2022)
REF. 7 GCCA Climate Ambition Statement-Towards Carbon Neutral Concrete G Cement - Global Cement and Concrete Association, 2020
REF. 8 Costs for Service Life optimization the “Law of Fives”, W.R. de Sitter, 1983. Durability of Concrete Structures - N° 152. CEB-RILEM International Workshop - Final Report
REF. 9 ESG and Asset Management, Alex Brisson, P+Ex Workshop, September 18, 2024
REF. 10 A Very Brief History of Time: From Ancient Cementitious Materials to the Marvels of Modern Concrete, Jeremy Begley, ICRI Concrete Repair Bulletin, March/April 2025, p. 9-15.
REF. 11 https://www.vector-construction.com/ environmental-impact-calculator
REF. 12 Reduced CO2 in Durable Systems: using LCA and EPD to Avoid Greenwashing in the EU, Mikaela Decio, P+Ex Workshop, September 18, 2024
LIST:
• Sponsors workshop, Lyndhurst, NJ (April 2024)
• 1st Road mapping Workshop, BWI, MD (Sept. 2024)
• 2nd Road mapping Workshop, ICRI Denver CO (Oct. 2024)
BWI - BALTIMORE, MD (SEPT. 2024)
GROUP ROLE NAME EMAIL
James Bacarro james.bacarro@gmail.com
1 facilitator Rick Montani montani.rick@us.sika.com
1 facilitator Jeff Ellis jellis@strongtie.com
1 Environ Brittany Storm BStorm@mapei.com
1 DOT Reggie Holt reggie.holt@dot.gov
1 DOT Simon Tseggai stseggai1@mdta.state.md.us
1 Association William Nickas wnickas@pci.org
1 Corrosion Sivaraman Venugopalan siva@sivacorrosion.com
1 Material Lesley Ko lko@structuraltec.com
1 Eng Mike Drerup mike@drerupllc.com
1 Material Edward Brennan ebrennan@uscproducts.com
1 Association Matthew Carter matthewc@icri.org
2 facilitator David Whitmore davidw@vector-corrosion.com
2 facilitator EYAD ALHARIRI ealhariri@structuraltec.com
2 Enviorn Alex Brisson Alex.Brisson@norda.com
2 DOT Jonathan Moore jonathan.moore@delaware.gov
2 DOT Fawaz Saraf fawaz.saraf@dot.gov
2 Materia/sponsor Fabrizio De Rossi fderossi@mapei.com
2 Eng Matthew Mowrer mmowrer@o-n.com
2 Communication Mark Geraghty 2 Association Kevin Irving kirving@zinc.org 2 Material Sponsor Aamer Syed syed.aamer@us.sika.com 3 facilitator Edward Kluckowski ed.kluckowski@freyssinetusa.com
facilitator Jean-roch Lucas jean-roch.lucas@freyssinet.com
Mikaela Decio m.decio@mapei.it
Dipshikha Temburni dipshikha.temburni@dot.gov
Joseph Swann jcs@cromcorp.com
REF. 2, TABLE 1.3
A SURVEY ON COSTS OF REPAIR FOR DIFFERENT MARKET SEGMENTS
BRIDGES: $8B3
DECKS, SUPERSTRUCTURE COMPONENTS, SUBSTRUCTURE COMPONENTS
There are 235,000 conventionally reinforced concrete and 108,000 prestressed concrete bridges. Corrosion and other related deterioration mechanisms make 15% of these bridges structurally deficient. Seismic retrofit may also be required because of changes in code requirements. Repair methods include surface repair systems, removal and replacement, protective coatings, membranes, pile jacketing, cathodic protection systems, strengthening systems, and crack repair.
ROADWAYS: $4B+4 (Ref. 4 for remaining market segments)
SLAB ON GRADE, CURB AND GUTTER, SIDEWALKS
Freeze-thaw deterioration, alkali silica reaction attack, D-cracking, joint deterioration, buckling, and abrasion are some of the deterioration mechanisms. Repair methods include remove and replace, slab subsealing, doweling, partialdepth repairs, overlays, and use of joint and crack sealants.
PIERS AND WHARFS: $0.2B
PILES, BENTS, DECKS
Exposure to chlorides and vessel impact are primary distress mechanisms. Repairs include cathodic protection, surface repair systems, jacketing, and protective coatings.
BUILDINGS: $2B
FACADES, BALCONIES, PLAZA DECKS, EXPOSED CONCRETE
Airborne chlorides, freeze-thaw cycles, and carbonation are some of the distress mechanisms that may be related to design and construction errors. Waterproofing failures are also common, and seismic retrofits may be needed. Repair methods include foundation waterproofing, plaza deck waterproofing, and replacement or repair of balconies.
PARKING STRUCTURES: $0.5-1B (18,000 structures in the U.S.)
PRECAST, POST-TENSIONED, CAST IN PLACE, COMPOSITE
Water leakage through cracks and joints, chloride ingress, and freeze-thaw cycles are common mechanisms that cause reinforcement corrosion, spalling, and other distress. Repair methods include waterproofing membranes, joint sealants to control water intrusion, strengthening systems to correct design and construction errors, surface repair systems for spalling damage, and slab replacement.
www.pexcoe.org