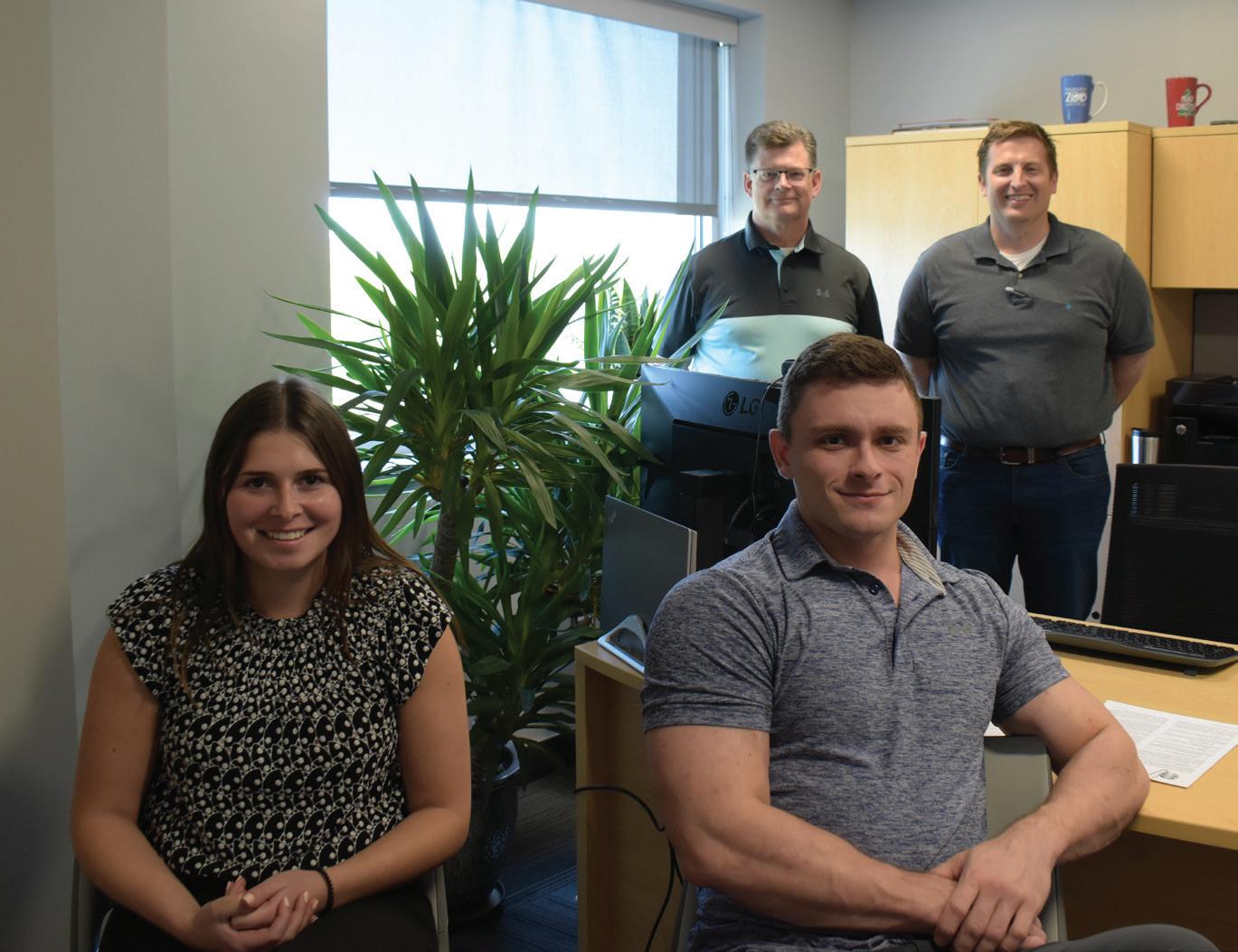
Planning for NextGen Succession
Energy Management Strategies
Expertise in Rubber Manufacturing
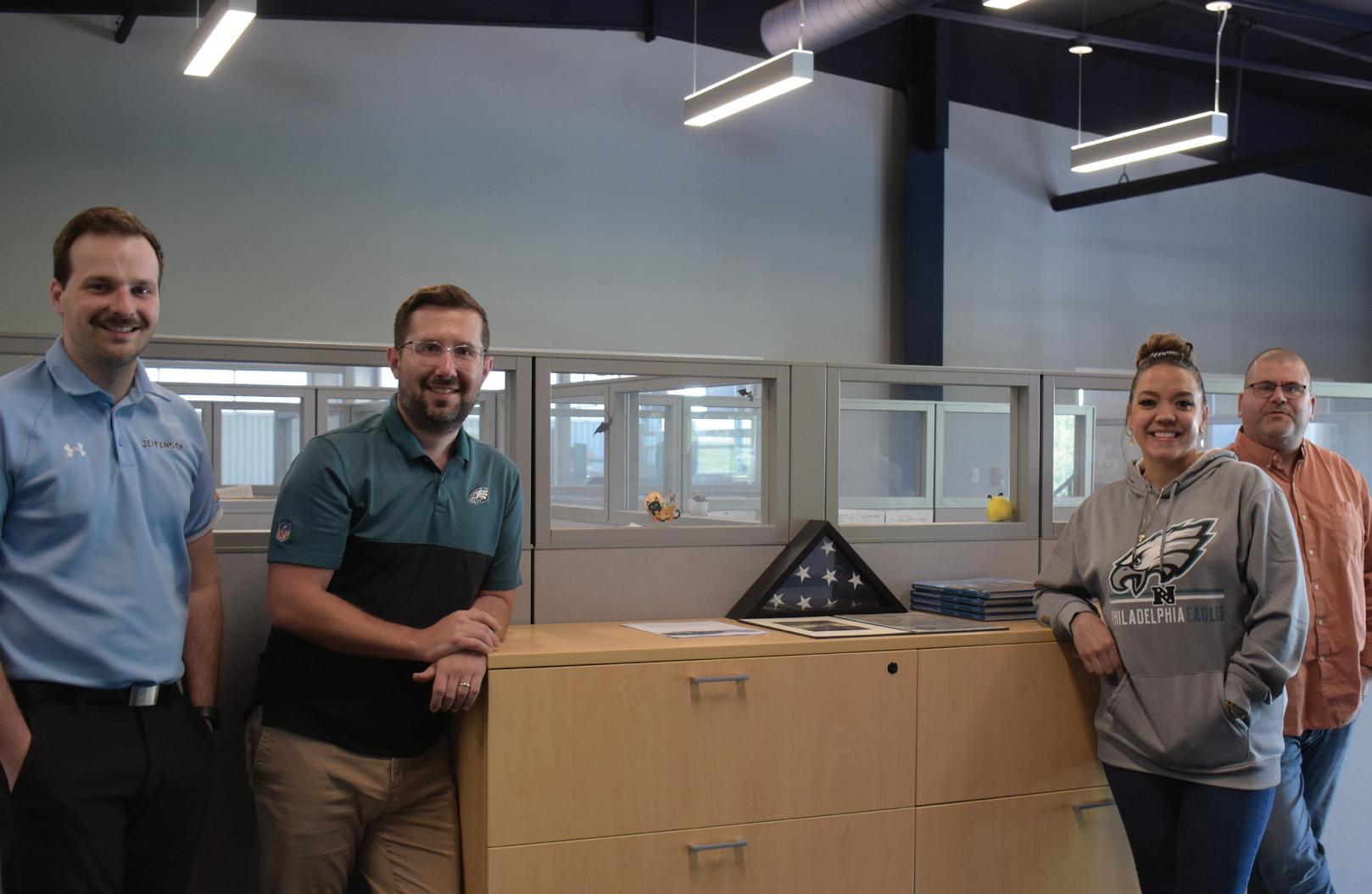
The Official Publication of the Association of Rubber Products Manufacturers Relationships are a Two-Way Street at Stockwell
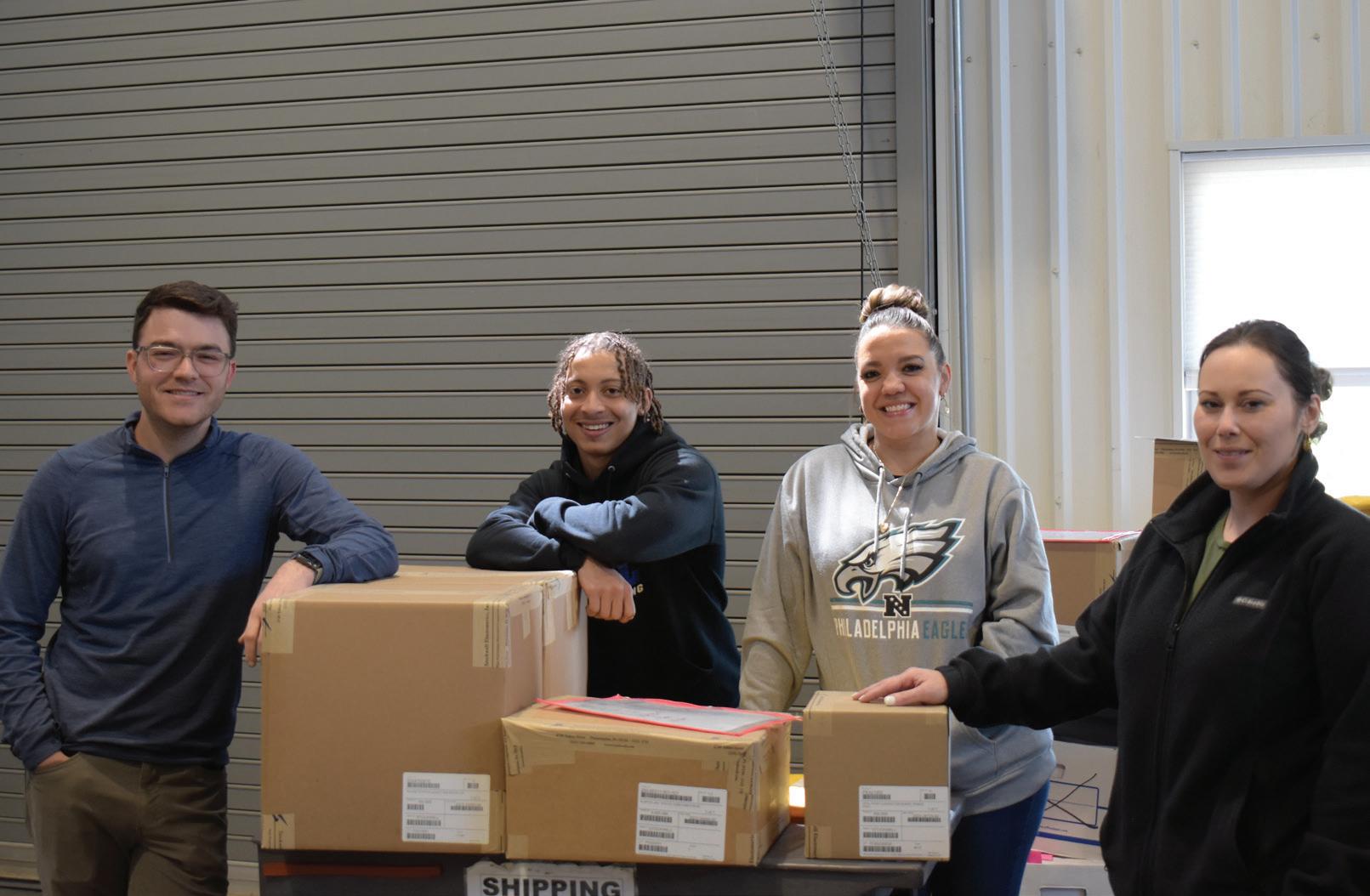
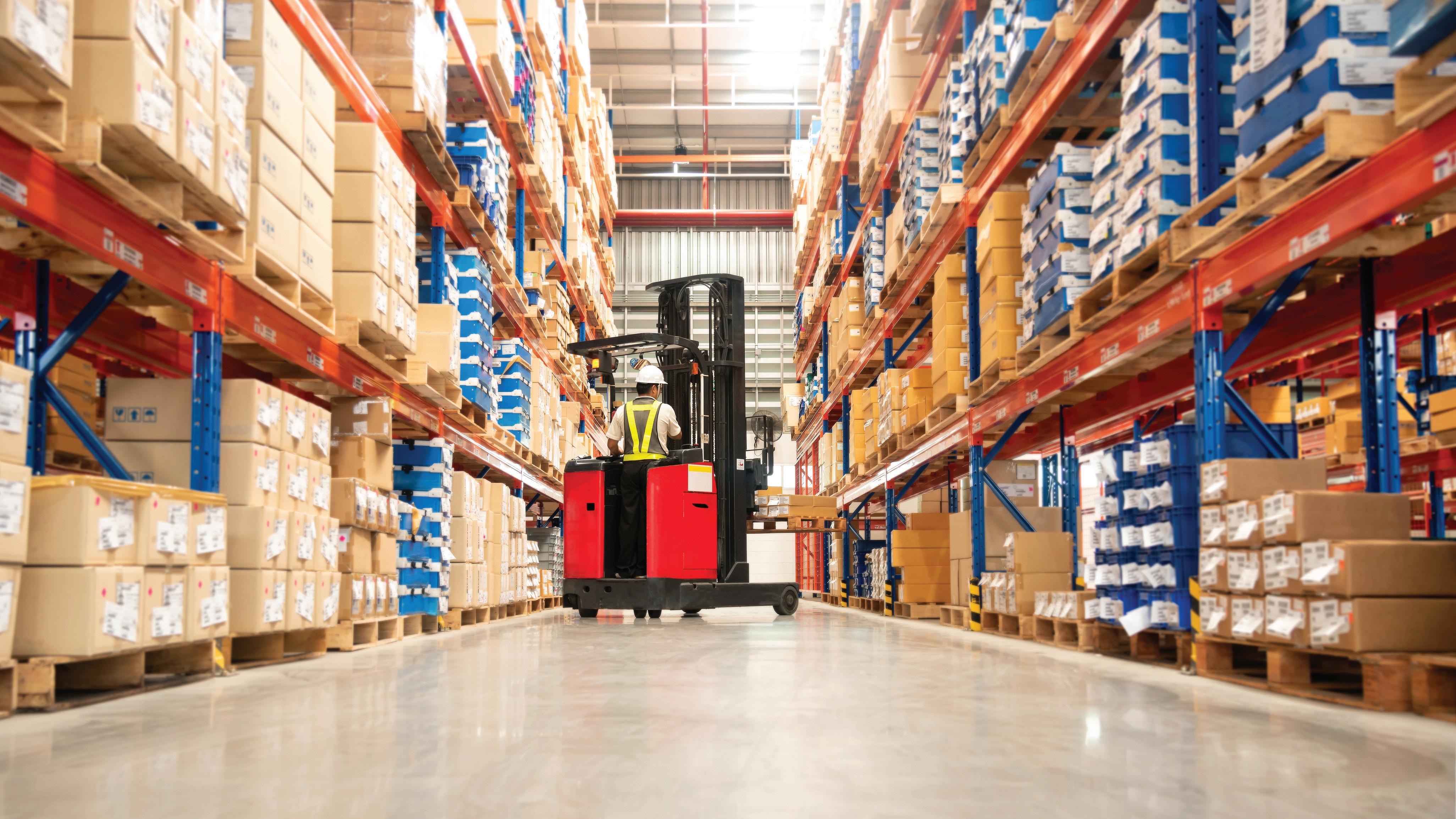
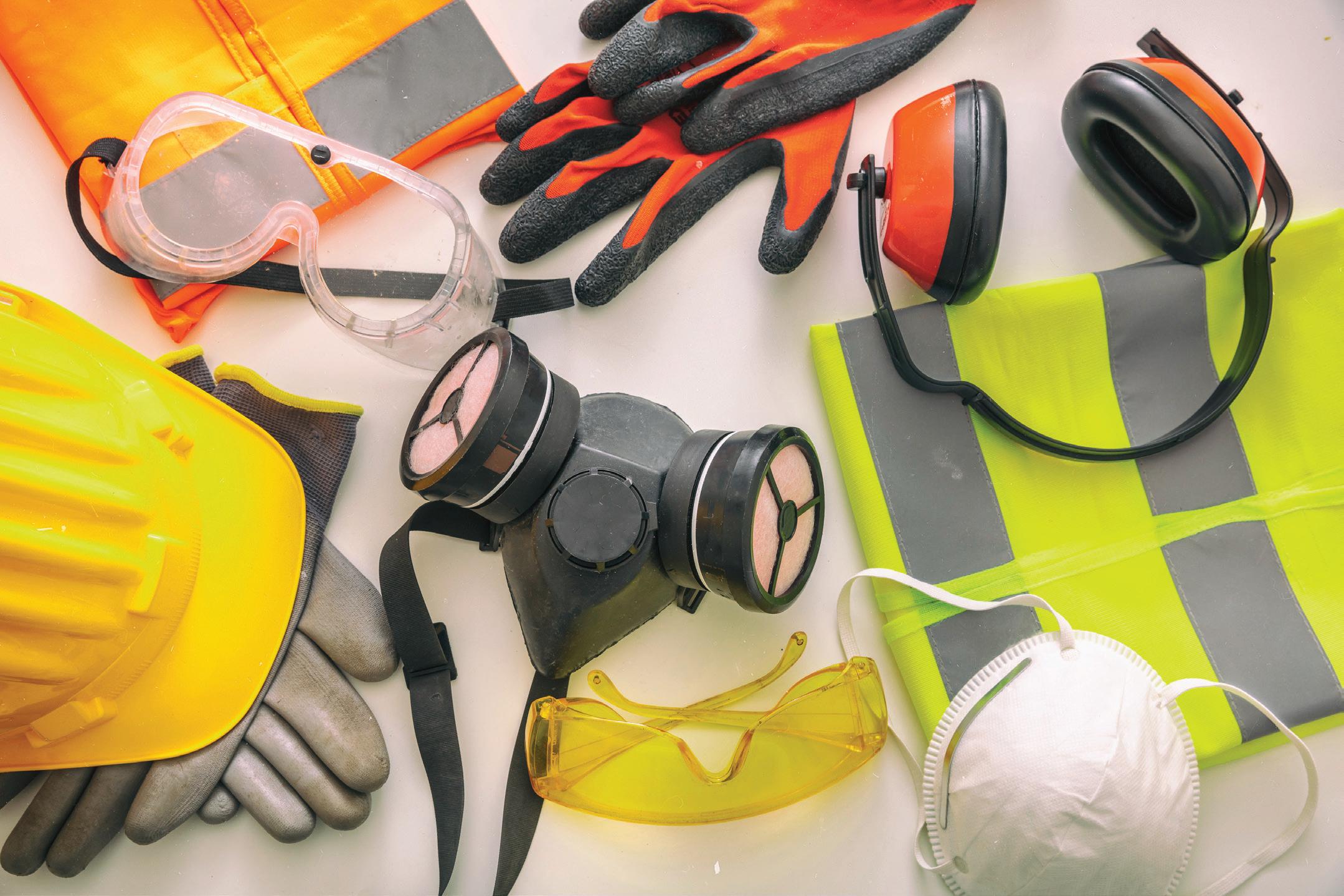
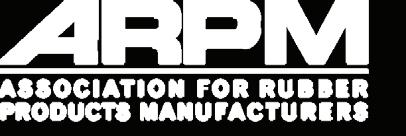
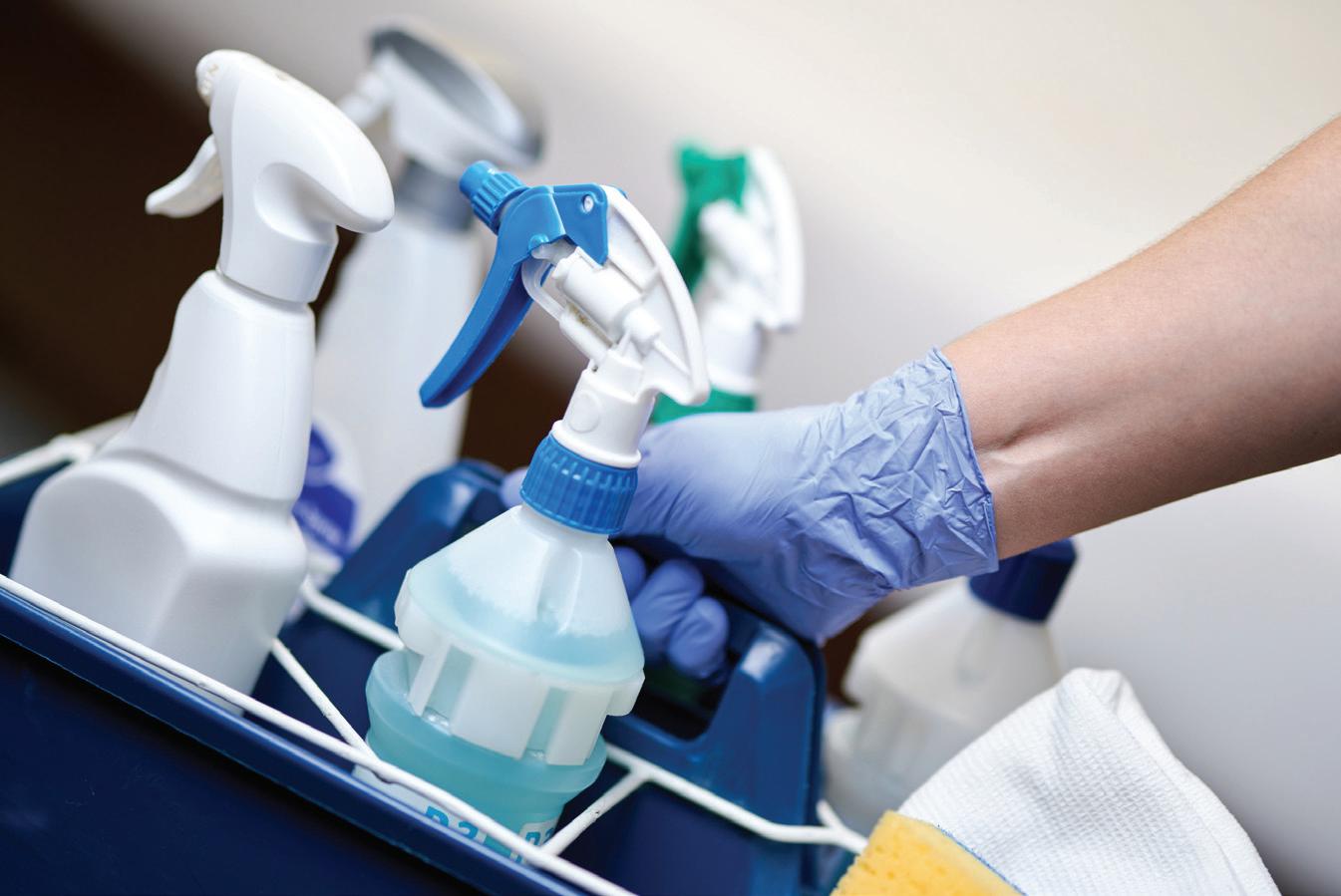


Planning for NextGen Succession
Energy Management Strategies
Expertise in Rubber Manufacturing
The Official Publication of the Association of Rubber Products Manufacturers Relationships are a Two-Way Street at Stockwell
As my family is preparing for spring break with a trip to “The Most Magical Place on Earth,” it dawned on me that your participation in ARPM is similar to the experience of visiting Walt Disney World.
For my (still somewhat young) family, a trip to Walt Disney World is a cherished family tradition. It’s a time when we immerse ourselves in the magic of fantasy and adventure, exploring new attractions, meeting beloved characters and creating unforgettable memories with loved ones. When we visit, we have a choice – we simply can admire the sights from a distance or we can fully engage in the experience of riding all the rides, watching the shows, tasting the “Dolewhip” and soaking in every moment of wonder and excitement.
Consider the Grainger program, for instance, as your FastPass to savings and efficiency. Just as you wouldn’t skip your favorite ride at Disney, taking advantage of this program can lead to significant cost savings and streamlined operations for your business. And much like eagerly awaiting Mickey’s autograph, ARPM offers access to invaluable resources such as free technical publications, ITR Economics insights and ARPM Training – each offering opportunities for growth, learning and professional development.
Just as I am 100% confident that my family will create lasting memories during our Disney vacation, a recent study by Harbour Results Inc. found that the more engaged a company is in a trade association, the higher its profit and throughput are. The data speaks for itself – active participation in an industry trade association can lead to tangible improvements on the bottom line.
So, as we navigate the year ahead, I encourage each and every one of you to approach your involvement in ARPM with the same enthusiasm and eagerness that you would bring to a day at Walt Disney World. Dive in, explore and make the most of every opportunity that comes your way. Together, we can create a journey filled with excitement, learning and camaraderie that rivals even the most magical moments at the “Happiest Place on Earth.”
Thank you for being an integral part of ARPM, and here’s to a year filled with adventure, discovery and endless possibilities! n
“TOGETHER, WE CAN CREATE A JOURNEY FILLED WITH EXCITEMENT, LEARNING AND CAMARADERIE THAT RIVALS EVEN THE MOST MAGICAL MOMENTS AT THE “HAPPIEST PLACE ON EARTH.”
A look at compound machinery and the design behind measuring the right quantities of materials to mixing the specific rubber formulation, including rubber and additives to create a rubber compound ready for processing at low cost and end-use performance.
By Sinead Ross, director ByARPM Team
Executive Director Letha Keslar – lkeslar@arpminc.org
Managing Director Kaitlyn Triplett – ktriplett@arpminc.org
Project Manager Paige Heck – pheck@arpminc.org
Marketing Director Marcella Kates – mkates@arpminc.org
Analytics Director Tony Robinson – trobinson@arpminc.org
Director of Publications Susan Denzio – sdenzio@arpminc.org
Analytics Lead Andrew Carlsgaard – acarlsgaard@arpminc.org
Strategic Advisor Troy Nix – tnix@arpminc.org
ARPM Officers and Board of Directors
President
James Wideman, MBL (USA) Corporation
Vice President
Ryan Fleming, Freudenberg-Nok Sealing Technologies
Treasurer
Donovan Lonsway, BRP
Secretary
Joe Keglewitsch, Ice Miller LLP
Past President
Travis Turek, Bruckman Rubber Corporation
ARPM Board of Directors
Rich Balka, Home Rubber Company
Bill Bernardo, Ebco, Inc.
Kirk Bowman, The Timken Company
Russ Burgert, Maplan Rubber Machinery
Aaron Clark, Danfoss Power Solutions
Joe Colletti, Marsh Bellofram
Randy Dobbs, Sperry & Rice LLC
Carl Flieler, Zochem LLC
Doug Gilg, Continental ContiTech
Cedric Glasper, Mechancial Rubber Products Corp.
Diya Garware Ibanez, Fulflex, Inc.
Jeff Leach, Passaic Rubber Co.
Jon Meigan, Lake Erie Rubber & Manufacturing
Mike Rainey, HBD Industries Inc.
Mike Recchio, Zeon Chemicals L.P.
Brandon Robards, Ace Extrusion
Caitlin Steele, Gates
John Stone, The Rubber Group
“If you can’t be replaced, you can’t be promoted,” are words that resonate with leaders.
This quote stands as a simple reminder and sound advice to those seeking a leadership role or being a “succession” –on-the-job training and sharing processes and procedures are critical components to reaching the next step on the ladder. When an employee makes a leader’s job easier and is disciplined in creating a cohesive environment of on-thejob training and sharing of job responsibilities throughout the team, these actions show that the employee is a continued asset to the leader and the company. In doing so, leadership and executives alike then can begin mapping a promotion or “succession” opportunity for that employee because they know there is a backfill of talent among the department team. Among the next generation of leaders, it is coaching them on mindset and critical thinking as well as sharing knowledge, teaching new skills, networking and training coworkers that opens the door to succession planning success for leaders and executives.
Effective leadership planning is essential to the long-term success of a company and recently, a presentation, “Preparing the Next Generation,” was given at the Association for Rubber Products Manufacturers (ARPM) March 2024 Human Resources Forum that gathered industry leaders who share a common goal – to learn about succession planning and how to engage and build the next generation of leaders. It was presented by Dr. Daniel Walker, director of continual improvement at PolyFlex, part of Nefab Group in Farmington Hills, Michigan, a partner for molded manufacturing automation, product protection and material shipping solutions.
With over 35 years in the industry and currently mapping his succession plan, Walker has the education and experience both personally and professionally to create and execute an effective leadership plan that sets a company up for future success. From a BS in plastics engineering technology and MS
in management strategy and leadership to a Ph.D. in business management, as well as his tenure as a teacher, change agent and Six Sigma black belt, these tools have given Walker a platform to guide and support companies through the next stage of their leadership planning.
According to Walker, executives and leadership should map their succession plans to include four key stages: culture and communication, leadership and learning, mentoring and succession transition.
Walker shared, “Starting the succession planning process is important because developing a successor– or depending on the position and job responsibilities, two or more successors –takes time, focus, effort and commitment as a leader and across the entire company.” The end goal of a succession plan for a leader and the company should be that the business continues long after the predecessor hits retirement or transitions into another role professionally. He continued, “It’s finding the right fit in succession to continue building and advancing the success of the company well before the leader’s departure.”
In addition to Walker’s presentation, he highlighted the strategies and structure of succession planning from the book, “Succession Transition” by Bill Hermann and Gordon Krater of Plante Moran, Detroit, Michigan. “Since I am in the beginning phases of my succession planning process, I rely on the guidance from the authors of ‘Succession Transition.’ The authors lay out a systematic process for engaging with, training and mentoring future leaders,” he said.
A company’s most important asset is its employees. Walker said, “It starts with recruiting and retaining the ‘right’ employees. Recruiting employees in the beginning who are selected to be a part of the team is an important and key step to ensure that, as a company, the culture is built from the ground
up. This presents leaders with the time needed to develop, train and lead the next generation of employees, aligning the company’s internal structure to its values and mission. It also sets clear and concise communication from top to bottom of the organization.”
In succession planning, two factors play a vital role in the overall process and should be nourished and developed within the company – culture and communication. When a company invests in its people, a foundation is built on positivity, recognition and accountability, which naturally creates open, transparent and honest communication. By fostering a strong culture, a company empowers its leadership and employees –and ultimately, gives insight as to whether a successor lies within the employee base or if the search needs to happen externally. A leader should be equipped to identify a person early on in the succession planning on the basis that the potential successor can step into the role with his/her unique skills, mindset and talent – resulting in augmenting the company before, during and after the “succession” has occurred. Once a successor has been selected, cultural alignment and communication throughout the company are important as the environment serves as a place where the future leader can thrive and grow in professional experiences.
Communication sets the tone within the company; employees thrive when they can freely have a voice, are in the know and feel a part of the company’s day-to-day decisions. Before succession planning and throughout the process, a company and its leadership team should have strong internal and external communication so that when the time comes to make the announcement about a new leader stepping into the predecessor’s position, no one is caught off guard and the map of that position is clearly defined and charted. It exudes a sign of respect and value in the relationship between the leader and successor with clients, customers, partners and employees –speaking to the company’s culture and end goal of long-term sustainability.
In Walker’s succession plan experience, he said, “Company culture has been a significant focus for the last five to 10 years at PolyFlex. We find that if the culture aligns with our values, training succession candidates is much easier. Identifying potential leaders is a process of conversation and observation. If you pay close attention to building up culture, maintaining clear communication lines and nourishing high performers, potential successors naturally emerge.”
“We need to have the courage to explore ourselves as leaders –whether in a leadership role, new employee or future successor. Knowledge is power!” said Walker.
First and foremost, a leader should fine-tune and enhance his/her own “leadership skills” alongside noted high-tier
“IN SUCCESSION PLANNING, TWO FACTORS PLAY A VITAL ROLE IN THE OVERALL PROCESS AND SHOULD BE NOURISHED AND DEVELOPED WITHIN THE COMPANY - CULTURE AND COMMUNICATION.”
employees to build a pipeline of future leaders. Professionally investing in self-discovery, reflection and/or external coaching is a component in anticipation of starting the succession planning process, placing the right skills in the right place. By reading books, conducting personality tests, attending seminars and workshops (like the ARPM Human Resources Forum) and possibly hiring an outside coach, these active opportunities are ways to develop as a leader but also to assist in better understanding oneself. Walker said, “It’s leading by example and setting the tone of a learning culture within the company.”
In succession planning, there should be an element of continuous learning and training for leadership, future successors and employees by:
y creating a learning culture and environment;
y demonstrating learning;
y encouraging formal (i.e., trade school, college, etc.) and informal learning (i.e., seminars, workshops, etc.); and
y creating a safe space to fail.
Key to the progression of learning is the opportunities that open a door to understanding his/her leadership style through self-discovery, including personality profiles (i.e., DISC, Strengthsfinder from Gallup), a personal study and professional counseling outside the company. It’s in asking the question, “Who are you?,” seeking honest feedback through one-on-one conversations, 360° reviews and focusing on introspection –that delivers the result of leadership influence. Walker said, “By conducting a personal study and understanding my leadership behaviors, I adequately can align my view of myself with how others see me, because, as a leader, effective influence is a leader’s top asset.”
To take it one step further, professionals (whether in a leadership role or not) can incorporate a six-month executive coaching series to bring light to unique skills, mindsets and talents, which otherwise would have gone untapped. There is strength in understanding “who you are” as a professional and utilizing new skills or enhancing current skills to work u
toward the overall goal personally in the job role but also for the company as a whole.
Walker said, “The most valuable lessons learned in life are from failures – and the more significant the failure, the more that is learned. It is a leader’s responsibility to create a space where employees feel safe to fail without negative repercussions to learn from that failure. Through these learned lessons an employee or a future successor is given growth and development opportunities that can’t be found in a textbook or words but an actionable, taught lesson.”
When there’s ownership of the “leadership transformation,” that’s when companies know a succession plan has the bones of a successful and seamless transition to the next generation of leaders. Walker said, “With the learnings from the personality profiles to the six-month coaching experience, I learned that surrounding myself with people who complement my strengths and compensate for my weaknesses transforms me as a stronger leader, giving me the tools to guide my future successor and overall creating a richer company culture.”
Polyflex reinforces the principles of leadership throughout its company and Walker has experienced this first-hand. He said, “As a leader, there is significant power in a company that backs the professional journey and lifelong pursuit of leadership development. For myself, my department and team, and the employees that fill various roles within PolyFlex, it is engrained to not give up on growth whether through formal education, books or learning from one another.” At PolyFlex, employees may join a formal leadership program (i.e., book club) that is based on a five-year trajectory, with many in the company sitting in various stages of learning – it’s in these types of employee investments that leaders rise and nextgeneration leaders are born.
In line with leadership exploration and learning, a succession plan timeline of all the events – professional exploration, identifying a future leader, mentoring and training, transitioning, etc. – should be set early in the process, because this is when a leader is contemplating and exploring his/her retirement or professional transition. Walker shared, “I am planning on a five- to seven-year process for my successor(s). The timeframe is not so much tied to a calendar but rather the ability of the new leader/successor to learn and develop into the transitioning leadership role.”
No leader or company ever looked back on starting succession planning too early, so the sooner a future successor is identified for the transitioning position the more time is available for relationship building and mentorship. Professional exploration and learning as a leader are at the top of the list, but it is equally,
if not more important to mentor and train the successor that will sit in the same seat one day. Especially, if a leader is in a position that may require more than one successor to fill the role’s responsibilities.
To identify future leaders/successors of the company, leadership should take the following into account and actively engage key stakeholders:
y Inventory skills and unique contributions of employees.
y Conduct and review team personality profiles.
y Look at department teams with a critical eye.
y Seek potential candidates for advancement by looking at behavior, attitude, ambition and skill sets.
Walker said, “It’s in getting to know high-potential leaders in the company that leaders begin to start seeing succession.” Once a leader identifies a successor, it’s time to continue building a high-quality relationship through time, attention, consistency and openness. With that comes “windshield time,” which provides both the leader and successor with opportunities to share good and bad experiences, ask questions, experience real-time learning, issue feedback, etc. – it’s an investment and commitment to the growth of the successor building a present and future foundation for the company.
As a mentor, it is the lasting impact of walking through selfexploration, real-case scenario training, answering questions with patience and listening that will guide, support and ease a future leader. In mentoring a successor, there are various methods a leader can use as tools to form a connection and build a bond but also set him/her up for success in the position, including shadowing, training and coaching. Walker shared, “Once a leader identifies his or her successor, the time has come to begin the mentorship of giving the knowledge and experience by allowing him/her to shadow at business meetings, client visits and all the various activities that come with the role. A successor should take notes, observe the various daily situations and take in the decision-making process.”
He continued sharing, “Windshield time is a beautiful thing! As a leader, you should travel with your successor to get ‘windshield time’ where over two hours you do nothing other than share that time to talk, learn and listen. It’s time that allow the successor to ask questions, take notes to walk through scenarios, etc. Most importantly, this investment in time helps the successor not only understand what you do but also how it is done, and more importantly, the ‘why’ behind your actions as a leader.”
As a leader and future predecessor alongside the successor, the final piece to implement the succession plan is the transition of leadership. Throughout the succession planning process, a leader early on created and continued to monitor and adjust the
u
transition of the successor based on assessment and progress throughout the timeframe. The transition goal, if a leader is truly committed to the “succession plan” and work behind the process of building a successor, should be a seamless hand-off between leaders and the company with a deliberate focus on cultural engagement and clear communication.
In creating and executing the transition, the successor and leader work closely together throughout the succession timeline by frequently meeting to assess and monitor progress, challenging each other to stretch as leaders and holding each other accountable. “It’s having constant communication and conversations on progress and expressing where you both are in the succession plan. In doing so, it holds the successor accountable for executing the plan alongside the leader and vice versa,” said Walker.
When the day comes and the transition of the leadership role is official, it is the day that the predecessor must step aside knowing he/she is leaving a department and company ready for change. The leader has led and guided the successor through diligent training experiences, mentored and coached with the company and employees at the forefront and finally, created a transition plan that brings positive results to all involved. Walker said, “The predecessor now can step aside physically, emotionally and mentally from the company.”
Walker continued, “At the end of the day, we’re all human!”
As a tenured leader, there are years of hard work, relationships built and passion for the company – it’s never easy to say, “goodbye,” but it is a critical and necessary step to “exit left.” In doing so, this is a positive step forward, showing employees that the new leader is indeed ready to take on the day-to-day operations and responsibilities of the role.
On the contrary, in post-transition, Walker mentioned that succession plan success doesn’t mention to just leave and never look back. Rather, the predecessor should remain available to help ease the new leader into the position. Walker said, “If there’s a special holiday celebration, company picnic, etc., show up! Be present at the special events.”
In closing, whether an executive or in a leadership position, now is the time to begin developing a succession plan or finetuning it to meet the expected outcome of the role. The succession planning process takes years and must be met with intention and strategic direction. The next generation of leaders is looming front and center, ready to be trained, coached and mentored to ultimately one day lead the company into future endeavors of smashing goals and successfully meeting or exceeding the bottom line. n
“Discover Your CliftonStrengths – Strengthsfinder 2.0 from Gallup and Tom Rath” by Don Clifton
“Extreme Ownership: How U.S. Navy SEALs Lead and Win” by Jocko Willink and Leif Babin
“Inside” by Tasha Eurich
“Succession Transition –A Roadmap for Seamless Transitions in Leadership” by Bill Hermann and Gordon Krater
“The Speed of Trust” by Stephen M. R. Covey
“Unlocking Potential” by Michael K. Simpson
R U B B E R I N D U S T R Y P U B L I C A T I O N S
ARPM PROVIDES INDUSTRY TECHNICAL
STANDARDS FOR THE FOLLOWING CATEGORIES:
CONVEYOR BELT
HOSE
POWER TRANSMISSION
PROTECTIVE LINING
RAW MATERIALS
SEALING
HANDBOOKS AND GUIDES
ARPM Training Academy is pleased to announce the return of the Seals Product Design and Manufacturing training class. This training will take place July 15-19, 2024, in Indianapolis, Indiana.
This one-week intensive course provides comprehensive and consistent training in rubber science, product seal design (for static and dynamic sealings) and producibility. This course of in-depth principles of design is not available anywhere else in the industry or academia and is led by veteran rubber industry professionals with more than 140 years of combined experience. The foundation of this course lies within ARPM’s industry-leading best practice documents, ARPM technical guidance documents and ARPM’s The Rubber Handbook.
For more information and to register, visit www.arpminc.com/events.
In March, the ARPM Training Academy hosted the Advanced Rubber Product Manufacturing Technologies at Ice Miller in Chicago, Illinois. This three-day training course focused on the elimination of variation associated with the initial design of the rubber article and rubber compound through the control of the compound’s consistency and manufacturing process.
Each attendee learned about the advanced manufacturing technologies that extended from chemical weigh-up through compound production and followed into automated article manufacturing inspection.
Congratulations to the following companies for having employees complete the training course:
y BRP Manufacturing, Inc.
y Eagle Elastomer, Inc.
y MoldTech, Inc.
y Precision Associates, Inc.
y R.E. Darling Co., Inc.
June 12-13, 2024
Sales and Marketing Forum (Virtual)
July 15-19, 2024
Seals Product Design and Manufacturing Training (Indianapolis, Indiana)
The online portion of the ARPM Training Academy is available 24/7! The newly designed system now hosts 22 courses that provide learners with the introductory, core information that they need to understand the basics of each primary discipline in rubber manufacturing. These courses are free to members of ARPM.
For more information and to receive the online training access codes, email info@arpminc.org.
The Thayer Leadership Program reflects a thorough approach to developing leaders of character, grounded in the US Army’s timeless leadership principles of “Be, Know, Do.” This lifechanging leadership training is geared towards mid- to seniorlevel leadership who want proven, practical tools to be more effective leaders.
The Building Leaders of Character program begins September 10, 2024. For more information, visit www.arpminc.com/events/.
August 7-8, 2024
Environmental, Health and Safety Summit (Indianapolis, Indiana)
For the most up-to-date information and to register for events, visit www.arpminc.com/events
ARPM’s functional area forums are designed to help the association impact every job function in its members’ organizations. These events are packed with best practices, resources and relevant topics that promise to give attendees implementable tactics to improve operations.
y Sales and Marketing Forum (Virtual) – June 12-13, 2024
y Environmental, Health and Safety Summit – August 7-8, 2024, Indianapolis, Indiana
y Finance Forum (Virtual) – November 13-14, 2024
For more information and to register, visit www.arpminc.com/events.
MAPLAN is a manufacturer of rubber and silicone injection molding machines with an industry-best network of strategic partners. With 50 years of experience in a variety of application fields, its machines are known world-wide for accuracy, performance and efficiency.
MAPLAN offers the following to ARPM members, including:
y 24-month warranty on new press purchases
y Free MAP remote Module plus 24 months remote support
y 10% discount on spare parts packages with new press purchase
y 5% discount on spare parts and free oil filter set with PM contract
Please join ARPM in welcoming the following new members!
B&J Rubber Co. LLC
Chromatic 3D Materials
Colder Products Company
Yokohama – SAS Rubber Company n
Business gurus often talk about the view from 30,000 feet – the big picture that provides a look at overall operations. Perhaps, however, the focus should be on the view from 30 feet – a close-up of specific processes and procedures that make an impact now.
Long-term manufacturing careers in the US used to be the norm, in which employees gave a company their life’s work, knowing that their jobs were safe, and their contributions were appreciated. Companies invested in their workforce, providing loyalty, stability and more than just a gold watch at retirement. It seems that many American companies have jettisoned that corporate philosophy in favor of a stockholder-centric mindset in which the bottom line is all that matters and, therefore, employees are expendable. A 100-plus-year-old company in Pennsylvania, however, has held onto those earlier values, maintaining a thriving company in which employees are treated like family and where loyalty to the company is reciprocated by the company’s continued investment in employees’ health and well-being.
Stockwell Elastomerics, Philadelphia, Pennsylvania, provides custom gaskets for the technology equipment sector. This family business, founded in 1919, offers comprehensive product design and engineering, a wide inventory of highperformance materials, including silicone and other engineered materials, and full-service manufacturing for its customers. Stockwell Elastomerics, however, is as much an employeecentric company as it is a customer-centric operation. Just as the company has cultivated wide and deep industry knowledge and capabilities, Stockwell has implemented an array of programs for the benefit of its employees.
Inside Rubber talked with Tom Rimel, president, and Bill Stockwell, a fourth-generation Stockwell family member, former company president and current chairman, about the company’s commitment to its employees. Rimel described the workforce makeup of the company. “We are a technical manufacturing and assembly company,” he said. “We have grown significantly in the past three years and the headcount now stands at 108 employees. We have added a lot of new talent, and we have a great core of tenured, highly skilled associates, some of whom have 25 to 40 years of service.”
The employees at Stockwell support its operations in sales, engineering, facility maintenance and equipment setup, supply chain, manufacturing, quality control, customer service, IT, human resources, finance, accounting and management. In return, the employees can benefit from the company’s support for its workforce, including its employee stock ownership plan, support from Marketplace Chaplains, workforce development with the aid of Baker Industries and Stockwell Elastomerics’ continuous improvement culture.
“As the remaining family member of a fourth-generation business,” said Bill Stockwell, “I developed a yearning to see our business persist and remain independent. I watched other small- to mid-sized manufacturers sell to private equity or larger entities – which is their choice – but their secret sauce and their unique culture may have been lost.” Stockwell explained that, in the worst case, a business might be relocated, leaving many employees behind. “We are proud to provide exceptional service delivered by our committed team. Many of our tenured employees consider Philadelphia home, and we are proud to be an urban manufacturer, operating competitively in a northeast US city.” He noted that the company has 20-, 30- and 40-year employee owners who have invested time learning their jobs at the company and contributing to its success. “I wanted to provide an opportunity for their continued success growing this independent company beyond my time,” said Stockwell. “In 2014, I began considering an employee stock ownership plan (ESOP) as a vehicle for company independence in perpetuity. Although there are ESOP businesses being sold, we are developing governance and modeling a way to prevent a sale of the company from occurring.”
The company instituted its ESOP in 2017, transitioning 30% of the company ownership into the Stockwell Elastomerics Perpetuity ESOP Trust. The nonprofit National Center for Employee Ownership describes an ESOP as “a type of
Stockwell Elastomerics’ Sales department
retirement plan, similar to a 401(k) plan, that invests primarily in company stock and holds its assets in a trust for employees. An ESOP may own 100% of a company’s stock, or it may own only a small percentage. ESOP participants (employees) accrue shares in the plan over time and are paid out by having their shares bought back, typically after they leave the company.” 1
Rimel explained how the Stockwell ESOP works. “Stock is granted to employees after one year of employment and then there is a five-year vesting period after the first grant,” he said. “Stock is given at no cost to the associates as shares become available for distribution. The shares are held for the benefit of the employees in a trust; shares never leave the trust. When employees retire or leave the company, the trust and the company repurchase their shares.” The company is on its journey from being privately held to being employee owned.
The ESOP makes Stockwell Elastomerics a better company, according to Rimel, in a variety of ways. “Everyone has a stake in our business,” he said. “We all benefit when the company grows and strengthens. Employee owners seek to understand the business better and understand their contribution.” For the most part, the individuals are more engaged in their jobs and their roles because of their stake in the company. “In general,” said Rimel, “the company can control its independence and its future to serve its customers and pursue its strategy – a stark contrast to what happens when a business is sold to an outside interest. The company enjoys lower turnover, higher loyalty and greater dedication to its customers. And it is a great recruiting tool. Our ESOP and 401(k) plan plus the employees’ own personal savings and investments combine for much stronger financial outcomes as they prepare for retirement.” In addition, Rimel said, an ESOP gives customers a sense of the stability of and future of the company.
company believes that making this independent, confidential group available to Stockwell employees, in combination with support from coworkers, provides opportunities to show care for the staff.
Rimel described the impetus. “Bill Stockwell wanted to give more support to employees,” he said. “We have standard employee assistance programs and support structures in the company – but we wanted to do more.” Stockwell elaborated on how the connection with Marketplace Chaplains developed.
Stockwell Elastomerics began working with Marketplace Chaplains (www.mchapusa.com) in 2011 to provide support for all employees and their families. Marketplace Chaplains provide support to workplace associates as they navigate the challenges as well as the joyful events in their lives. The
“I frequently spent time on the production floor – some days, as much time as in the office. Day and night. Business can be a battle, and some of our people experienced hardships outside of work that might have affected their ability to perform.” Stockwell said situations would arise where he counseled people in life and work situations but, in hindsight, he realized that he was not qualified as a counselor. “I became aware of Marketplace Chaplains through another Philadelphia manufacturer,” said Stockwell. “Although they are a faithbased organization matching my values, their approach is to meet people wherever they are in their walk of life. I am grateful for the chaplains attending to the needs of our people.”
Marketplace Chaplains provide either spiritual (Christian) or non-spiritual support to the company’s team depending on team member preference. They visit every week and attend most of the company’s social functions. “They are part of our family,” said Rimel. “All of us, from time to time, need additional support in our lives.” The chaplains provide personalized, brief, regularly scheduled workplace visits during strategic times, offering visibility, immediate access and relationship building without interfering with work. Chaplains also are available for off-site visits to respond to employees’ needs. “I will give a personal example,” said Rimel. “My father passed away earlier this year. Marketplace Chaplains sent a local team member
Stockwell Elastomerics’ Building C includes shipping, receiving, warehouse, company meeting room, sales and customer service offices.
to an out-of-state funeral to provide me and my family with support during a difficult time. This partnership is just another way to show that the company cares for its employees.”
“When employees are appreciated and cared for,” asserted Rimel, “they will take better care of our customers and each other. As a company, we are aware that many people have challenges in their lives that have nothing to do with their work life. Stockwell wants to support the whole person – including outside of normal work hours. Marketplace Chaplains has been a great partner here.”
The company strives to have a variety of benefits to care for its associates. “We want to support and care for the team, wherever they are in their lives,” Rimel explained. “Our medical plans
and employee assistance programs are lead mechanisms for mental health. The compensation, benefits and other things that we do for the team are in support of their overall health –physical, mental and emotional.”
“From 2016 through 2019,” said Bill Stockwell, “a few Philadelphia manufacturers formed an organization supporting each other’s growth, which we named PHLMFG. In 2017, our members reported a need for entry level production employees. That is when we were introduced to Baker Industries, whose mission is to develop entry level workers by hiring from the sidelines – including non-violent returning citizens (formerly incarcerated).” Baker’s model is to develop working skill sets in its program’s participants and guide these people to succeed by providing a range of supportive life skills. “I was hesitant before making our first hire,” Stockwell admitted. “But after quietly asking around, I learned that many of our own employees had a family member or a neighbor who had experienced incarceration. Our Baker Industries hires were met with open arms by our team, which was very gratifying for me.”
Baker Industries (www.bakerindustries.org), a nonprofit workforce development program, serves hard-to-employ adults in Philadelphia and the surrounding area by preparing them to be strong contributors to the technical manufacturing sector. Core strengths cultivated by Baker Industries that are of particular value to Stockwell Elastomerics include personal reliability and dependability, kindness, a sense of purpose and mission in one’s work, and individual importance.
Rimel says the relationship with Baker Industries makes Stockwell a better company. “We are a better member of the community,” he said. “This shows that we have a heart and that we stand for more than just making the world’s best highperformance gaskets and seals.” Rimel believes that Stockwell Elastomerics can have a positive influence on the lives of people who need a second chance. “We give our team an opportunity to help support someone’s return to society,” he explained. “By doing so, we create loyal team members who are grateful for the opportunity and perhaps they will want to give back to others. We cannot do it alone and have found that the special support, training and care from the Baker process is critical for long term success.”
Continuous improvement is a key focus at Stockwell Elastomerics, which always is looking to provide customers with better and faster service. And the company is no newcomer to continuous improvement. “I used to say, ‘Let’s get our money’s worth out of each economic recession,’” said Stockwell. “With each recession, we needed to double down by improving some aspect of our operation to compete and win business. Our rapid response capability is just one of many
results of a downturn.” The company intentionally maintains a strong balance sheet, including a healthy level of raw material inventory to enable rapid response for customers.
“In my view,” said Rimel, “Stockwell has been focused on continuous improvement since 1980 when the company was repositioning its place in the market. The company has been able to grow and prosper by doing things more efficiently, engaging the team and always adding to our ‘toolbox’ of solutions for our customers.” Stockwell has changed its core business to low-mid volume production of highly specialized products; this change has required it to be nimble and adapt its processes to support these new requirements.
“We are on a journey,” Rimel explained, “and we will never arrive at a state of perfection. Having recently hired many new associates, we have renewed our focus on continuous improvement as we train the next generation. We have a senior member of the team who is an accomplished continuous improvement/lean practitioner.” Rimel noted that the company’s best customers – known as HERO customers – also push Stockwell to be better in order to help them win in their markets.
Rimel cited several examples of safety improvements and hazard elimination that stemmed from continuous improvement. “We have added new equipment at the plant with enhanced safety automation and improved our PPE approach to focus on eye protection,” he said. Stockwell also has expanded its safety committee to two shifts and more committee members, and expanded its AED training and first aid training. It also has increased its chemical hygiene monitoring and modified its material cutting techniques.
Bill Stockwell commented on what the earlier leaders at Stockwell Elastomerics – his ancestors – might have found most interesting about today’s climate of continuous improvement and technological advances. “My father was an engineer,” said Stockwell. “He would find additive manufacturing such as 3D printing of fixtures and tooling to be incredible, especially since he spent many Saturdays in the shop figuring out how to build up a special bonded assembly for a custom job. And now, the technology is coming along for us to 3D print complex silicone rubber gaskets and special components for prototyping and low volume production. This,” said Stockwell, “is exciting!”
Hats off to Bill Stockwell and Stockwell Elastomerics for thriving in the long term, working hard to be as good to employees as it is to customers, and remaining engaged and continuously improving during an exciting time in the industry. n
More Information: www.stockwell.com.
References
1. “What Is Employee Ownership?” National Center for Employee Ownership. www.nceo.org/what-is-employee-ownership
The inception of the ARPM Training Academy emerged as a direct response to the industry’s discerned gap in accessible training resources concerning rubber products.
While existing avenues offered foundational knowledge, particularly in materials chemistry, there was a notable absence of specialized training focused on the intricate processes inherent in manufacturing rubber products. Given the extensive repository of technical guidance documents maintained by ARPM, it seemed natural that the inaugural in-person class would concentrate on one of the most comprehensive embodiments of these guidelines: oil seal products.
March 2024, Advanced Rubber Product Manufacturing Technology class at Ice Miller in Chicago, Illinois.
In the summer of 2023, the inaugural ARPM Training Academy class took place in Columbus, Ohio, hosted at the offices of the association’s legal counsel, Ice Miller. The spotlight of this event was on sealing products and technology, encompassing a comprehensive curriculum. From the material science underpinning sealing materials to the design intricacies of both static and dynamic sealing products, attendees were immersed in a wealth of knowledge. The expertise of industry stalwarts, serving as instructors, lent invaluable insights garnered over decades of experience.
Notably, the academy attracted a diverse array of participants, ranging from ARPM member companies to non-affiliated entities spanning various sectors, all united by their engagement with rubber products. The resounding success of the event, evidenced by its sold-out status, underscored the pressing demand for such specialized training initiatives.
Building upon the resounding success and feedback from inaugural attendees, a second academy class swiftly followed, pivoting towards advanced rubber product manufacturing technologies. This iteration provided participants with an exclusive opportunity to delve into cutting-edge concepts poised to revolutionize manufacturing processes. From
advanced formulations and virtual manufacturing simulations to futuristic rubber mixing techniques and in-line inspection protocols, the curriculum offered a glimpse into the industry’s future landscape. The overarching objective was to empower attendees with actionable insights, thereby bolstering their competitive edge and catalyzing operational enhancements. The overwhelming turnout at this academy reaffirmed the industry’s appetite for innovation and continuous improvement.
Joe Walker of Elastomer Technologies, and the architect of the in-person training courses, stated, “Collectively, these ARPM Training Academy classes serve as a testament to the industry’s commitment to fostering a highly skilled workforce. Amidst persistent concerns regarding talent shortages and the imperative for ongoing training, these initiatives offer a strategic avenue for organizational growth and talent development.
By transcending organizational boundaries and facilitating cross-industry benchmarking, the ARPM Training Academy not only elevates individual competencies but also contributes to the collective advancement of the industry. As businesses embrace these transformative learning opportunities, the dividends in terms of enhanced quality, reliability, and competitiveness are poised to be substantial. In addressing a longstanding void, ARPM Training Academy heralds a new era of excellence in rubber product manufacturing, promising to redefine industry standards and elevate bottom line performance.”
Moreover, ARPM’s commitment to advancing industry education extends beyond physical boundaries. The recent launch of the Virtual Training Academy further reinforces this dedication, offering a comprehensive resource of online modules crafted by industry experts. These modules provide learners with fundamental insights into the core disciplines of the rubber industry, revolutionizing training paradigms and eliminating barriers to education.
Greg Vassmer, an ARPM Training Academy committee member, emphasized – the transformative potential of this virtual platform, heralding it as the industry’s premier training resource. He said, “By democratizing access to specialized knowledge, the Virtual Training Academy ensures that every member can equip its workforce with the skills needed for success.”
The ARPM Training Academy, through its innovative programs and initiatives, not only addresses the educational voids within the industry but also propels it toward a future defined by knowledge, proficiency and unparalleled competitiveness. As industry professionals embrace these transformative learning opportunities, the promise of a brighter, more prosperous future for the rubber industry beckons. n
More information: www.arpminc.com/training-academy/
Ice Miller focuses on meeting the needs of our clients quickly, efficiently and cost-effectively. Ice Miller attorneys with rubber industry experience can assist with your greatest legal challenges. Contact Josef Keglewitsch at 614-462-2279 or josef.keglewitsch@icemiller.com for more information.
300+ lawyers in Columbus and other offices
icemiller.com
TECHNICAL SERVICES
• Compound Development
• Failure Analysis
• Technical Training
• Prototyping
• Technical Consulting
MECHANICAL SERVICES
• Physical & Mechanical Testing
• Dynamic Testing
• Custom Test Design
• Engineering Consulting
• Rubber and Plastics Mixing
• Rubber and Plastics Molding
CHEMICAL SERVICES
• Chemical & Analytic Testing
• Formula Reconstruction/Reverse Engineering
• Microscopy
• PPE Testing
• Pharmaceutical & Microbiological Services
Seal s Product Desi gn and
Manufacturi ng Trai ni ng
JULY 1 5-1 9 | INDIANAPOLIS, IN
This one-week intensive course provides comprehensive and consistent training in rubber science, product seal design (for static and dynamic sealings) and producibility. This course of in-depth principles of design are not available anywhere else in the industry or academia.
The ARPM Training Academy is a dynamic technical training resource that teaches fundamentals and advanced topics for the rubber industry The ARPM Training Academy provides training for the entire workforce, from the entry level machine operator to the highly skilled engineering professional. Our powerful online training is accessible to everyone in an organization and will improve the knowledge base of the entire workforce. Our newly designed in-person training provides indepth principles of design not available anywhere else in the rubber industry or academia.
Who should attend this training course?
Design Engineers
Quality Engineers
Sales Engineers
Product Engineers
Process Engineers
More at arpminc.com/events.
In the dynamic realm of industrial innovation and advancement, staying ahead of the curve isn't just desirable – it's imperative. For professionals and original equipment manufacturers (OEMs) alike, access to cutting-edge insights and research isn't merely a luxury; it's a necessity. This is where ARPM Technical Publications emerge as indispensable tools, shaping the landscape of day-to-day business operations across various industries.
At the forefront of this transformative journey is ARPM, long revered as a paragon of excellence in rubber manufacturing and beyond. Central to its mission is the creation and dissemination of technical publications, that delve deep into the intricacies of rubber product manufacturing, materials science and related disciplines.
But what sets ARPM's technical publications apart from conventional white papers? The answer lies in their practical applicability and real-world impact. Unlike static documents that gather dust on shelves, ARPM's technical publications for belts, seals and hoses, are dynamic resources actively utilized by industry professionals and OEMs in their daily operations.
For professionals navigating the complex terrain of belt drive design and components, ARPM technical publications serve as indispensable references. From belt manufacturers to hardware suppliers, these standards ensure consistency and correctness within the power transmission industry. Notably, ARPM standards often offer greater detail and comprehensiveness compared to international standards set by the International Organization for Standardization (ISO), further solidifying their status as premier references.
Moreover, the influence of ARPM technical publications transcends national borders. International technical committees, including those under ISO, frequently reference ARPM standards alongside standards from other industrialized nations such as DIN, BIS and JIS. This harmonization ensures global consistency and facilitates seamless integration of best practices across diverse industrial landscapes.
In practical terms, the impact of ARPM technical publications is palpable across various sectors. Major automotive manufacturers like GM and Ford incorporate ARPM standards into their oil seal drawings, emphasizing the critical role these
“CENTRAL TO ITS MISSION IS THE CREATION AND DISSEMINATION OF TECHNICAL PUBLICATIONS, THAT DELVE DEEP INTO THE INTRICACIES OF RUBBER
publications play in ensuring product quality and reliability. Additionally, initiatives such as the Compound Consistency Guidelines, integrated into AIAG CQI 30, exemplify the crossindustry applicability and significance of ARPM standards.
For producers, equipment OEMs and end-users alike, ARPM technical publications serve as go-to resources, guiding product design, manufacturing and inspection processes. From meticulous inspection of incoming products to field operations and customer interactions, these standards form the bedrock of industry excellence and reliability.
In conclusion, ARPM's technical publications are much more than mere white papers – they are dynamic resources that actively shape the industry landscape and empower professionals to excel in their respective fields. From guiding production processes to fueling innovation and collaboration, these publications are indispensable assets for anyone striving for excellence in the world of rubber manufacturing and beyond.
As the industry continues to evolve, ARPM remains committed to providing the insights, resources and support needed to thrive in this ever-changing landscape. With ARPM's technical publications as their guide, professionals and OEMs can navigate the complexities of modern manufacturing with confidence and success. n
More information: www.arpminc.com
1 2
Anchor Investments, LLC, a private, Nashville-based real estate investment company with a strategic focus on acquiring, developing and managing income-producing commercial assets throughout the US, has acquired Southern Michigan Rubber, Inc. (SMR). Anchor Investments’ goal for the acquisition of SMR is to combine the years of experience, manufacturing capacity and capabilities to better support existing customers. SMR will continue to operate, service and support its current customers, vendors, from its existing location with minimal changes. The SMR team members will continue to run the operations in Three Rivers, Michigan. The previous owner and CEO, Marel Riley-Ryman will continue as a consultant for continuity, and Jordan Frye took on the role as president. Southern Michigan Rubber joins Elastotech and Titan BOP Rubber Products under the Anchor Investments elastomer division. Collectively, the elastomer division represents 90 years of manufacturing experience, over 70,000 sq. ft. of manufacturing and warehousing, and three ISO certified facilities. For more information, visit www.anchorinv.com.
Chem-Trend, a member of the Freudenberg Chemical Specialities Group and a developer of premium release agents, purging compounds, paper impregnation chemicals and other process chemical specialties and additives, has unveiled the next generation of tire molding solutions. Its extensive portfolio, encompassing a variety of products such as inside and outside paints, bladder coatings, mold coatings and tire uniformity rim lubes, serves as evidence of the company’s dedication to innovation and quality within the tire industry. Chem-Trend has evolved its product solutions to meet the complexities of modern tire design and vehicle electrification. Newer technologies developed through substantial market knowledge and collaboration, meet post-curing challenges such as laser cleaning and adherence of materials like foam for noise dampening. The latest product advancements address
3
4
the differentiated specifications of an electric vehicle tire, including design and shape, self-sealants in puncture-proof tires and incorporation of sensor technologies. Chem-Trend is a leader ahead of regulations, offering a comprehensive range of products formulated without per- and polyfluorinated alkyl compounds (PFAS) and sourcing safer silicones used in ongoing product development. Creating a healthier environment for all those who have a role within the manufacturing and use of the technology is a primary objective for global research and development teams. For more information, visit www.chemtrend.com.
DEGUMA, Buttlar, Thuringen, Germany, a machine manufacturer, has developed a new roller knife for more ergonomic work on mixing mills. Compared to conventional roller knives, this knife is made of walnut and has an optimized blade geometry that makes it lightweight and comfortable to hold. The radius ground blade is designed to easily cut rubber, compounds and silicone. The handcrafted knife is designed for daily use in the mixing room. The blades are made of highquality knife steel that resists rust and wear and cuts through compounds with ease and precision. For more information, visit www.deguma.com.
METTLER TOLEDO, Columbus, Ohio, a global manufacturer of precision instruments for laboratory, industrial and food retailing applications, has launched its new Advanced and Standard Balance portfolio including MX, MR, MA and LA lines. The new balances provide even greater resilience, measurement performance and a simpler user interface for a smooth, precise, sustainable weighing experience. Laboratories from large enterprises, medium-sized companies and startups worldwide now have a more comprehensive and wide selection of balances to ensure accurate weighing. The MX balances increase weighing performance, data management and user-friendliness. The MR balances deliver consistently accurate results even in the harshest weighing environments.
The MA balances are designed to focus on valuable and practical features to deliver quality without compromise. The LA balances offer simple functionality. For more information, visit www.mt.com/lab.
Orazen Extruded Polymers (OEP), Aurora, Ohio, a provider of high-quality polymer solutions for the commercial glazing and construction market, was honored with the RedHawk 50 Award from Miami University. This annual program, dedicated to identifying, recognizing and celebrating the 50 fastest-growing private companies worldwide founded or led by former Miami University students, has acknowledged OEP’s growth and success from a pool of 360 nominees. The RedHawk 50 Award is a testament to the dedication, innovation and entrepreneurial spirit of OEP and its founder, Mike Orazen, who is a proud 1991 alum of Miami University. For more information, visit www.orazen.com.
Rahco Rubber, Des Plaines, Illinois, a supplier of precision molded rubber parts, has announced the introduction of another rubber compound developed to pass NSF 61: Drinking Water System Components regulations with UL Certification. For use of non-leaching materials in potable water, this advanced Ethylene Propylene Diene Monomer (EPDM) compound is resistant to hot water chloramines and compliant to ASTM D 6284-98. While this new EPDM compound isn’t Rahco’s first and won’t be the last to adhere to regulatory and quality system standards, it serves as a reminder that custom rubber formulations matter. Here are three high-level elements to keep in mind: Drinking Water System Components; understand the benefits of EPDM; and understand Rahco’s quality commitment. For more information, visit www.rahco-rubber.com. n
You can always count on our team to conduct your testing programs with care and precision. Whether it’s validating new raw materials due to supply chain challenges, evaluating new product designs, or understanding current product shortcomings, our team of materials and product experts can be an extension of your internal teams. Contact us today to discuss your testing needs.
The Environmental, Health & Safety (EHS) Summit is designed to share best leadership and safety practices with industry professionals hoping to achieve world-class safety within their companies.
This one-of-a-kind learning and networking conference will focus on uniting manufacturing executives from across the United States. Attendees will focus on best practices in environment, health and safety along with becoming a better leader. This Summit promises to provide high-level safety professionals with implementable ideas they can take back to their facilities to improve their operations and achieve world-class safety.
Keynote Speaker
A full schedule will be available soon, but topics could include:
Environmental Regulations Injury Prevention OSHA Updates
Safety Culture SDS Sheets
Sustainability
With over 25 years in safety, operations and executive roles, Trinnie Cortez has been coaching leaders, developing teams and designing processes that have created highly motivated and effective teams in multiple industries ranging from construction to technology. Today, Cortez is putting his experience to work at Caterpillar Safety Services in Tucson, Arizona, helping companies understand themselves and improve their safety culture by changing mindsets, developing leaders and engaging employees.
“I look forward to the EHS Summit every year! The event is a place to reinforce things I am doing correctly, takeaway many best practices that directly apply to my business, get updates on what’s happening in the regulatory world and exchange ideas with others in the industry having similar business challenges.”
safety practices with industry professionals hoping to achieve world-class safety within their companies.
ARPM invites you to participate in the 2024 Safety Awards! The Safety Awards recognize companies in the manufacturing industry that have achieved excellent safety techniques that go beyond the average regulations. Visit www.arpminc.com/ehs to participate. Don’t Miss the Safety Awards Recognition!
provided me with new insights and ideas to what is happing in the industry, and the opportunity to meet and discuss with peers on similar topics. The resources and networking at the EHS Summit is one of the greatest assets."
Safety is not a oneperson job, it is a commitment from each person at your company. Therefore, the EHS Summit is open to everyone!
Safety should be a top priority at your organization, and continuously improving your safety program is essential to protect your employees.
, August 7-8, 2024
The Safety Achievement Awards are a way to recognize safety in the industry and facilities that have achieved a level of safety performance above the industry average. Awards are based on data reported on a company’s annual OSHA 300 Log of WorkRelated Injuries and Illnesses. A copy of the facility’s OSHA 300 and O300A forms are required to submit.
The Safety Best Practice Awards are a way to recognize the best practices that organizations have implemented to increase overall safety. Submissions should generally align with at least one of the following topics: employee safety training, safety committees, safety audits/walk-throughs, emergency training, behavior-based safety, tracking/displaying safety metrics, equipment and mold change safety, safety communication or other innovative safety best practices. Please include photos, videos, policies, checklists or any materials that help outline best practices.
A look at compound machinery and the design behind measuring the right quantities of materials to mixing the specific rubber formulation, including rubber and additives to create a rubber compound ready for processing at low cost and end-use performance.
989.757.1300
www.bplittleford.com
B&P Littleford, Saginaw, Michigan, designs and builds a wide spectrum of mixing, drying, compounding, reacting, extracting an centrifugal separation equipment for many different manufacturing applications. Its TriVolution® Compounder offers dispersive and distributive mixing without damaging critical ingredients. The Compounder reciprocates the process screw three times for every one revolution. The flights interact with pins in the barrel much in the same way a continuous kneader does. Its controlled shear with enhanced material exposure also is well adapted for devolatilization and reactive processing.
203.502.8822
www.colmecusa.com
COLMEC USA, Inc., Trumbull, Connecticut, a global provider of design and construction of hightech rubber and silicone extrusion and mixing lines, has developed and patented a rubber mixing system for compounding rooms, consisting of a Conical Twin Mixer (CTM™), Conical Twin Extruder (CTE) and Gear Pump (GP). CTM™ is a counter-rotating conical screw mixer that has the peculiarity of having a blind flange at the material outlet that remains closed during the homogenization and mixing phase and automatically opens for the discharge phase. The hot compound coming out of the CTM™ is filtered directly in line by the CTE and GP system. In the CTE, the compound is kept smoothly moving and with low transport pressure. In the GP, the compound is pushed against the filter pack, but the high transport efficiency of the GP prevents the thermal rise of the mixture, keeping the batch at a low temperature (80°-90° C) and thus avoiding pre-vulcanization.
630.933.9100 www.busscorp.com
BUSS, Carol Stream, Illinois, is a global manufacturer of compounding solutions for demanding applications. A continuous process in rubber compounding offers numerous advantages. It avoids fluctuations between individual batches, and the need for personnel is reduced by automating production. At the same time, minimizing scrap leads to lower material costs. A closed system ensures greater safety and allows for the extraction of gases and toxic fumes. Material handling also is simplified by automatic feeding systems. The COMPEO kneader by BUSS with its precise temperature control, the ability to mix high proportions of filler in an excellent yet gentle way, handling of sticky materials and the ability to inject liquid ingredients directly into the process zone, supports all these advantages of a continuous system.
330.798.4925 www.hexpol.com
HEXPOL Compounding, Barberton, Ohio, is a technological leader in the development and production of highquality rubber compounds, provides equipment that is standardized and universal but also request-specific from companies. HEXPOL’s in-house engineering team has developed and provided key units for its production lines. Besides optimization and customization of core equipment such as mixer, mill and extruder-gear pumps, HEXPOL’s core competence lies in conveying systems, ingredient preparation and handling and finally accurate dosing in the shortest time. The wide range of different bulk materials and polymers requires robust and universal equipment to optimize the needed footprint and corresponding cost. This is reflected by short change-over times with minimized left-over material and even the opportunity for integrated recycling. n
In the United States, industrial buildings contribute to onethird of total energy consumption, yet a majority lack an implemented energy management strategy. The primary source of energy consumption in industrial buildings is production-related, with costs determined by regional and local utility companies passing on rising power generation costs to industrial ratepayers. The growing industrial energy use strains an already faltering grid system, and utilities and building operators need to work together to find savings in energy demand and costs. Successful building operators navigate market shifts by focusing on long-term energy cost control and leveraging available utility programs to reduce onsite energy needs.
Implementing a well-crafted energy management strategy results in lowered costs and operational efficiencies for industrial building operators. This article delves into specific actions that can be taken to establish an energy management strategy, featuring client stories. Titan Energy, a contributor to this article, is an energy management consultant specializing in helping clients manage both the supply side (procurement of energy) and the demand side (working to reduce energy consumption).
When devising an energy procurement strategy, industrial facilities often find tracking energy commodities opportunities increasingly challenging. Over the past three years, natural gas and electricity prices have been extremely volatile, with prices hitting record lows and highs with no sign of normalizing. This type of energy market is prompting industrial managers to seek ways to mitigate risks. In deregulated commodity markets, manufacturers can access products to lock in natural gas and electricity costs for the long term, ensuring immediate savings and long-term budgetary certainty.
The 2022 Inflation Reduction Act (IRA) extended the Investment Tax Credit (ITC) for on-site generation projects enabling industrial facilities to install solar, battery storage, cogeneration and fuel cell plants. These projects can be owned by the facility or third-party owned with lowered fixed costs for 20-30 years and no upfront cost.
Local and regional utilities offer rebates and incentives promoting the purchase of energy-efficient appliances, equipment and fixtures. These incentives can cover up to 100% of project costs and may be financed at a fixed 0% rate for eligible ratepayers. The goal of these programs is to lower demand on the grid while improvements are made for the future.
Utilities invite large power users to participate in grid demand programs in return for revenue. Industrial facilities can take advantage of lower capacity demand during peak hours in the summer, shifting work hours to accommodate peak demand without affecting productivity. Incorporating on-site emergency backup, such as a battery storage unit, makes manufacturers integral to local grid operations, enhancing grid resiliency by reducing the likelihood of brownouts and blackouts.
Administrators can effectively manage and visualize energy usage and spending by implementing an energy data platform integrated with their utility invoicing system. Low-cost, automated subscription services collect utility bills across
“THE GROWING INDUSTRIAL ENERGY USE STRAINS AN ALREADY FALTERING GRID SYSTEM, AND UTILITIES AND BUILDING OPERATORS NEED TO WORK TOGETHER TO FIND SAVINGS IN ENERGY DEMAND AND COSTS.”
electricity, natural gas, water and recycling, conducting audits on invoices and benchmarking energy use, sustainability, and emissions data. This capability allows for data-driven decisions regarding production by sorting and filtering based on location, business unit and cost center.
Titan Energy recently worked with two companies facing energy challenges.
Titan Energy was called in by a label manufacturer to analyze, audit and capture utility lighting incentives for a location in the Northeast. The mercury vapor lamps in the press used in the curing process were old and inefficient and needed to be replaced with new high-efficiency LED lamps.
Utilizing an audit comparing the old UV curing technology and new UV LED fixtures, the label manufacturer was able to obtain utility incentive funds for a non-routine, hybrid LED processing application by demonstrating a significant reduction in energy use during the printing process.
These incentives covered 45% of project costs and instantly increased the net return on investment. With the new UV LED lighting fixtures, the label manufacturer was able to reduce maintenance downtime and increase label production by 33%, as the fixture increased processing from 600 units/ minute to 800 units/minute, while simultaneously reducing energy use.
Custom electricity pricing also was secured to better reflect the facility’s low demand usage, allowing them to take advantage of rate savings. Furthermore, all building lighting was upgraded to LED throughout the facility, reducing operational costs for years to come. These changes result in a savings of $162,841 annually and a reduction of more than 11.08 million kilowatthours over a 10-year period.
An international manufacturer needed to pay closer attention to each of its production sites to meet cost-saving targets, mitigate risk and help enhance a centralized energy procurement approach. Previously, the manufacturer’s energy accounts were contracted on a one-size-fits-all energy procurement approach, but a comprehensive utility bill audit helped establish a solid baseline understanding of the benefits and risks of each energy market and led to an expansion of its network of top energy suppliers across diverse deregulated energy markets.
A request for proposal was issued on the customer’s behalf, negotiating the most competitive rates, simplifying the legal review process and onboarding the client onto a data management platform to track costs and savings. A fixed-rate product was locked in until 2024, offering both immediate savings and protection against any future market pricing shifts.
This paid off for its Texas location when February 2021’s polar vortex brought record-cold temperatures to a significant part of the Midwest and Texas. The additional heating demand and transportation issues created scarcity in the natural gas market, skyrocketing natural gas and electricity prices. During this polar vortex, the manufacturer was protected from any market exposure because of the fixed-rate product. Instead of paying an escalating $12.50/kWh (a >300% increase), the client kept paying $0.04/kWh and avoided a $5,000,000 February bill. n
Sinead Ross is the director of marketing at Titan Energy. In operation since 2001, Titan Energy is an independent energy management consulting firm that creates comprehensive energy management strategies backed by data to control and reduce energy costs. For more information, call 860.967.1611, email sross@titanenergyne.com or visit www.titanenergyne.com.
Reprinted with permission from Plastics Decorating (www.plasticsdecorating.com).
When processors and manufacturers think about conserving valuable resources, they are not only considering energy; they’re also looking at raw materials, time and people. The following are three real-world examples of how companies are using their manufacturing enterprise resource (ERP) systems to reduce waste while maximizing efficiency.
Comar is a manufacturer of plastic packaging products and components for medical, pharmaceutical, healthcare and other markets. With facilities across the United States and Ireland, the company relies on real-time monitoring in its DELMIAWorks manufacturing ERP software to gain insights into how every machine in each of its production centers is operating. By monitoring production variances, defects can be adjusted out to increase yield while decreasing waste.
In addition to cutting scrap and driving efficiency, Comar is leading innovations in sustainable packaging. For example, the firm has collaborated with equipment vendors to improve process control on creating a new injection stretch blow molded bottle for gummy vitamins, and it has been able to reduce the amount of resin needed per bottle by up to 20% depending on the bottle size.
“‛Sustainability and Reduce, Reuse, Recycle’ are core to many of our customers’ value propositions,” said Comar Executive Vice President of Sales and Marketing Scott Conklin. “We are using insights from our DELMIAWorks system to help introduce new products that support their initiatives.”
Gamsee Industries (Victoria) Pty. Ltd. is a supplier of highquality plastic products throughout its customer base across Australia, which has continually reinvested in all-electric molding technology for its energy efficiency, precision, speed and cleanliness.
Gamsee also relies on real-time production monitoring in its DELMIAWorks manufacturing ERP system to immediately red-flag injection-molding jobs that are running outside of the cycle-time specifications for that particular job, so the team can make adjustments. “For example, when a press is running in the green on the real-time monitoring screen, that’s good because it’s running right on time,” explains Gamsee General Manager
Kris Juzva. “But, when the press shows red on the screen, that’s a problem and a fire that needs to be put out.”
Juzva adds, “With the ability to forecast, track and monitor injection-molding production, we minimize waste – both material and human resources – enabling us to maximize resource utilization.”
PAC Strapping Products, Inc., is a full-service master distributor and manufacturer of plastic and steel strapping, systems, tools and accessories, which relies on the DELMIAWorks manufacturing ERP system to increase office employees’ productivity.
One area is maintaining individualized pricing for each customer. Previously, a PAC employee working 40 hours per week took two and a half to three weeks to manually update pricing for each customer. Now, the inventory module, which also handles pricing, automates most of the work and the process takes about two hours.
“I can’t tell you how much the inventory module in DELMIAWorks has helped us to maintain our margins by quickly updating prices for our customers to align with the new costs,” notes PAC Vice President and General Manager Marc Albero. Similarly, billing used to be a four-hour manual exercise. Now, using the ERP invoicing module, a PAC employee can verify the packing slip, inventory and whether the order has shipped – cutting the billing process to just 15 minutes.
These are three examples of how processors and manufacturers are automating their shop floor and business processes to reduce waste while protecting the resources, which are key to growth and profitability. Armed with data-driven insights, the potential to optimize operations further is nearly limitless. n
Steve Bieszczat is responsible for DELMIAWorks brand management, demand generation and product marketing. Bieszczat’s focus is on positioning DELMIAWorks with the strategic direction and requirements of the brand’s manufacturing customers and prospects.
More information: www.solidworks.com/delmiaworksmanufacturing-erp
There always is something happening in the economy guaranteed to make a fool of economists. After all, the only function of economic forecasting is to make astrology look respectable.
For most of last year, the predictions were some versions of gloom and doom, and every quarter there was further evidence of growth (5.2% in Q3 and around 2.4% in Q4). Now there is debate over what to expect in 2024. There are those that are calling for a shallow recession in the first half of the year (-0.9% in Q1 and -0.7% in Q2). On the other hand, there are those that see decent growth in the first half of the year but a slower end to 2024. The Armada models seem to be favoring the latter interpretation.
There have been four drivers of growth over the last few quarters. These have been responsible for the performance in the third quarter and fourth quarter of last year and seem to be factors now as well. The fear is that two of the four already are showing signs of retreat and the other two will be facing some challenges. These also are significant drivers for the construction business.
The first is consumer spending, which has been performing well above the 20-year trend line despite the fact consumer debt is sitting at record levels ($7 trillion in credit card debt and $20 trillion in overall debt). The latest retail numbers were far better than expected with a reading of .63 compared to .15 in November. At the moment, the bottom third of income earners are living paycheck to paycheck and the middle third is starting to feel the pinch as well with 55% living paycheck to paycheck, but the upper third still is spending aggressively. The crucial factor for consumer spending is employment.
As long as people feel secure in their employment, they will continue to spend and access credit. With the jobless rate still at 3.7%, there is not a lot of employment angst.
The second driver has been non-residential construction. It has been growing for several years now, but the industry is starting to worry about the pipeline in 2024. Many of the large projects that drove growth have been completed and there have been few new ones undertaken. There is one major factor on the horizon, and it relates to the third driver for the economy – government spending. The money that flowed out of the government to cope with the pandemic has been dispersed but two years ago there was a surge in allocating money for infrastructure with the CHIPS Act, Inflation Reduction Act and others. This money now is starting to flow as the states and communities have been kicking in their share. This will be a major motivator for non-residential construction as long as these projects are linked to infrastructure.
There still is not much movement in office development or retail but medical development is making a comeback, and the logistics business remains strong. There also is significant growth in the manufacturing sector as there still is interest in reshoring with further investment in robotics and technology.
The third driver already mentioned – government money – was starting to be a factor at the end of 2023 and will make its presence known in 2024.
That leaves the fourth driver, which is the inventory build triggered by the challenges in the supply chain. The supply chain chaos of the last few years convinced many that the JIT
system was broken and that inventory hold was necessary. There has been a dramatic increase in inventory accumulation as businesses no longer trusted the ability to get products when they needed them. That inventory build drove third-quarter expansion. Now these inventories are fleshed out, and the reorder cycle is starting to reassert itself. That will slow some of the accumulation that had been taking place. On the other hand, the recent issues in maritime transportation have started to push the supply chain crisis back to the forefront.
The fact is that factors such as a reduction in interest rates by mid-summer can alter these assessments. There also can be negative factors playing a role – surge in joblessness, higher priced commodities, further trade tensions and maybe even a reaction to the political situation in the US.
All four of these drivers affect the industry in positive and negative ways. Fortunately, the good news has been outweighing the bad for the last few quarters, and there is some expectation this trend will continue. Every month there is an expectation that consumers suddenly will wake up and realize they are in debt to their eyebrows, but the data is not yet supporting this. There is, however, a clear division appearing between the upper third of income earners who have barely seen their spending patterns alter and the lower third where 85% are reporting they are living paycheck to paycheck.
The second driver has been showing more resilience than many expected as home starts are up – at both, the single- and multi-family levels. The key thing to recognize is that growth has been occurring in some parts of the country and often at the expense of others. The growth sectors have been seen in the southwest and southeast, while populations have been exiting the west coast and northeast. The prime motivation for this migration seems to have been the cost of living issues.
The bottom line is that 2024 is starting better than many had expected. The big question now is when will interest rates come down, and that depends on the inflation question. The rate of inflation has fallen to 2.5%, but that decline has been connected mostly to energy and food – notoriously volatile. As long as wages still are rising there is the continued risk of the wage/price spiral, and that worries the central banks.n
Chris Kuehl is managing director of Armada Corporate Intelligence. Armada executives function as trusted strategic advisers to business executives, merging fundamental roots in corporate intelligence gathering, economic forecasting and strategy development. Armada focuses on the market forces bearing down on organizations.
More information: www.armada-intel.com
Reprinted with permission from Plastics Business (www.plasticsbusinessmag.com).
“The only real mistake is the one from which we learn nothing,” said Henry Ford.
Trying, failing and succeeding are part of the business environment. No one succeeds without trying, and no one ever tries without failing at least occasionally. Here are tips for finding value in the inevitable failures experienced by those trying to succeed.
A new business and a growing business must go through trial and error to advance. A new business always is going out on a limb; will the limb hold or fail? A business wading into a new market can get nowhere without taking the first risky step. In all endeavors, there is potential achievement and the risk of failure. The odds often initially favor defeat, but they trend toward success with repeated enlightened attempts. This advice from the Forbes article, “11 Essential Next Steps for Business Leaders After a Setback,” 1 applies to established businesses and new businesses alike.
When starting a business, one is literally walking into the unknown with uncertainties haunting every business move. With that said, expect a lot of mistakes as the business evolves. Continual failure is necessary for learning and future success. Leaders must adapt, take notes, adjust to protect the business and put measures in place to mitigate these mistakes from reoccurring. – Tian Derose, EAMA, Inc. Failure Is Valuable
Every experience has value but sometimes it takes effort to identify it, especially when it comes to the value of failure. While not welcoming failure, successful businesspeople know that it will occur; they do not fear it or avoid reflecting on it. They know that failure can be a valuable and necessary aspect of learning, growing and improving.
In his article, “The Smart Way to Learn From Failure,” 2 author David Robson describes the “ostrich effect” that some people
employ to avoid facing bad news, disappointment or failure. “Devaluing the source of your disappointment is just one way your mind may avoid coping constructively with failure,” writes Robson. “Another coping mechanism is to hide your head in the sand, shifting your attention away from the upsetting situation so that you don’t have to process it.” To illustrate this, Robson recounts a study by university researchers to gauge people’s memory of positive and negative experiences.
The people were asked to choose one of two answers to identify objects, and then were told of their hits and misses – a chance to learn from success and failure. In a second round of identifying objects, the participants had learned from their hits but scored no better on their earlier misses. To delve deeper, the researchers conducted another study, asking new participants to review the earlier study participants’ hits and misses, and then to identify the same objects. These people consistently scored higher – they had learned from another person’s hits and from their misses. The takeaway: people often forget their own mistakes but are quite able to learn from someone else’s mistakes.
How, then, to help people recall failures rather than forgetting them? Choosing to view failure as a learning experience rather than as a loss is a good starting point. Approaching failure as an opportunity to learn why the failure occurred and to then apply those lessons moving forward can remove the stigma of defeat. The Forbes article1 offers a valuable suggestion:
Approach Failure Like an Experiment … how we handle failure sets the tone for our culture. We focus on the outcome, do our best to avoid shaming our colleagues and approach it almost empirically like a science experiment. Consider what variables you need to change to achieve a different result. – Brian Shore, elevēo
Successful business leaders know that failures will happen and that value can be derived from examining them; they openly own their failures and ask for honest feedback. Two things manifest by owning failures and welcoming reactions: leaders model a valuable trait for others to emulate, and leaders receive helpful input for addressing the cause of the failure.
In his TIME article, “Why Your Team Needs a Failure Philosophy,” 3 author Roi Ben-Yehuda notes that most organizations “are hyper-focused on end results, have a low tolerance for experimentation, and provide little time for reflection, all of which create an environment incompatible with learning.” One way to make the most out of failure is to have a business culture with a healthy failure philosophy. During interviews, ask about candidates’ attitudes toward failure. During onboarding, describe the company’s positive philosophy toward failure. In team meetings, acknowledge errors, then search for teachable moments.
Ben-Yehuda has another tip. “Creating rituals around your failure philosophy – a practice adopted by some of the world’s most innovative teams – also helps make failure feel less lonely and more instructive.” In a final point about leaders owning their failures, Ben-Yehuda quotes Navy Seal Team 6 Commander Dave Cooper: “The most important words a leader can say are, ‘I screwed that up.’” For leaders with the courage to freely admit screwups, writes Ben-Yehuda, “the question isn’t ‘Will we fail?’ but rather, ‘How will we learn from our failures?’”
Before the “do’s,” here’s an important “don’t” from Steven L. Blue’s Industry Week article, “6 Important Business Lessons I Learned from Failure.” 4
Don’t ever waste time on why something went right. Of course, always analyze how you might have done better, but that should not be the focus. Leaders should always do a deep dive on their failures for the lessons they hold.
To learn from failure, examine it closely with a post-failure audit, including analyzing the variables and their weaknesses as a scientist would do following an experiment. Here is how Christian Busch, director of the global economy program at New
York University’s Center for Global Affairs, described deriving value from failure in Suvarchala Narayanan’s Strategy+business article, “Connecting the dots in an uncertain world.” 5
Conduct Project Funerals
When a project – for example, a new technology that was brought to market – doesn’t work out, the respective project manager “lays it to rest” in front of colleagues from other divisions and reflects on why it did not work out and what can be learned from it. This is not about celebrating failure – it’s about celebrating the learning from failure. What often happens is that people in the audience “coincidentally” connect it to a project that they are working on, and elements of the project are then unexpectedly repurposed for another use.
Accept the inevitability of failure, own it, acknowledge its value, find its lessons. Then carry on. This Forbes article excerpt 1 wraps it up and puts a bow on turning failure into advantage:
Reflect but do not Wallow
After a failure in business, honest reflection is essential to unlock any valuable lessons that can be learned. Then, quickly move on. Do not wallow; instead, examine the situation with an honest eye, adapt and move forward. Leaders who strive to create an environment that normalizes openly discussing failure gain valuable insights and allow for greater opportunities for success the next time around. – Ronke Komolafe, Integrated Physical & Behavioral Health Alliance n
1. Forbes Business Council, “11 Essential Next Steps for Business Leaders After A Setback.” March 27, 2023. Forbes.com. https:// www.forbes.com/sites/forbesbusinesscouncil/2023/03/27/ 11-essential-next-steps-for-business-leaders-after-asetback/?sh=1708567362cf.
2. David Robson, “The Smart Way to Learn from Failure.” October 21, 2022. BBC.com. https://www.bbc.com/worklife/ article/20221019-the-smart-way-to-learn-from-failure.
3. Roi Ben-Yehuda, “Why Your Team Needs a Failure Philosophy.” August 8, 2022. TIME.com. https://time.com/charter/6204322/ failure-philosophy/.
4. Steven L. Blue, “6 Important Business Lessons I Learned from Failure.” April 20, 2023. Industry Week. https://www. industryweek.com/leadership/strategic-planning-execution/ article/21264377/failure-is-the-gift-that-keeps-on-giving.
5. Suvarchala Narayanan, “Connecting the Dots in an Uncertain World.” September 16, 2020. Strategy+business. https://www. strategy-business.com/article/Connecting-the-dots-in-anuncertain-world.
H E I N D U S T R Y N E E D S Y O U
J O I N T H E N E T W O R K
T O D A Y !
A S S O C I A T I O N F O R R U B B E R P R O D U C T S M A N U F A C T U R E R S
B e n c h m a r k i n g | I n d u s t r y S t a n d a r d s | T r a i n i n g | N e t w o r k i n g | a n d m o r e . . .
L i s t e d i n R u b b e r a n d P l a s t i c s N e w s " T o p 5 R u b b e r
I n d u s t r y A s s o c i a t i o n s Y o u S h o u l d K n o w . "
V i s i t a r p m i n c . c o m f o r m o r e .