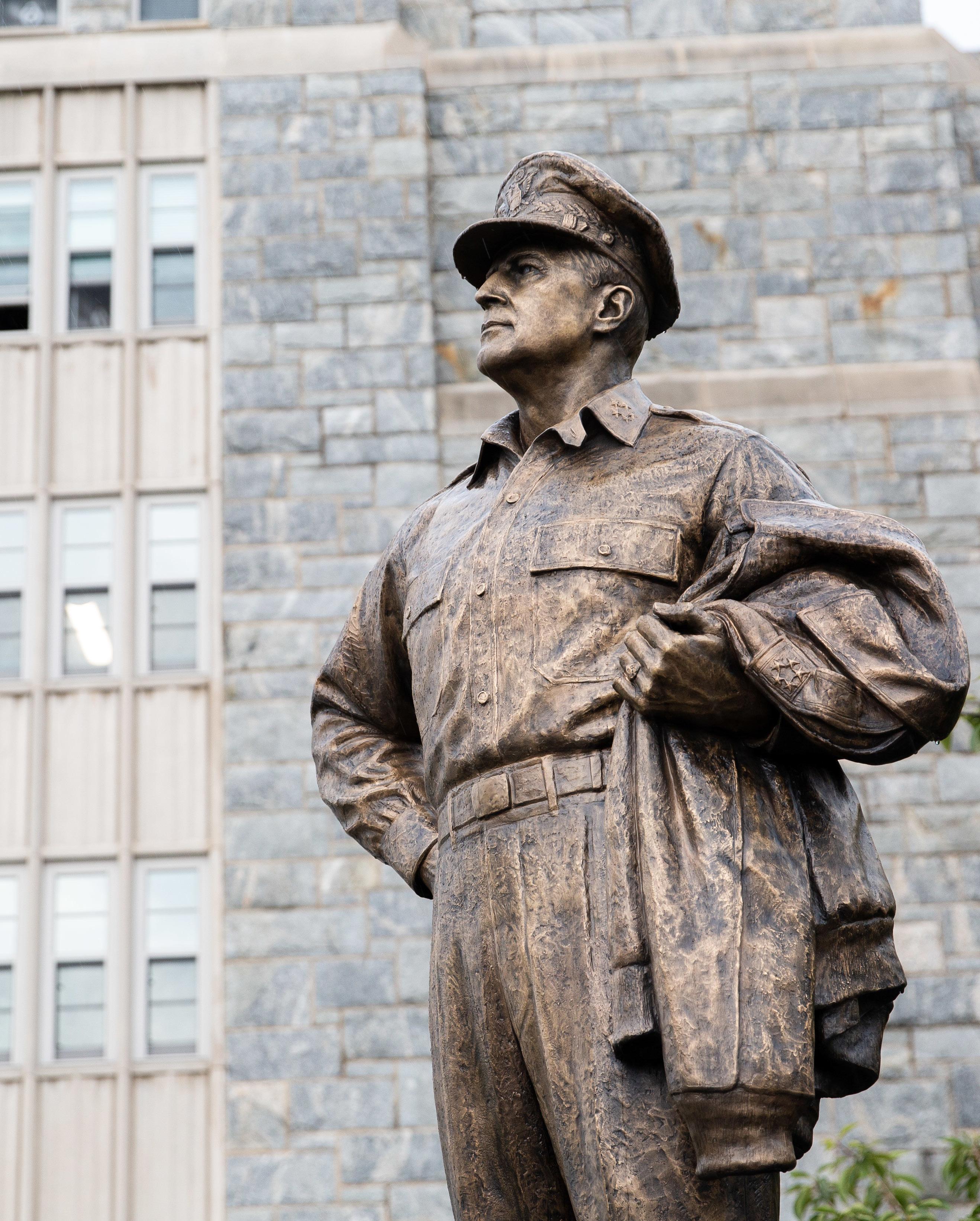

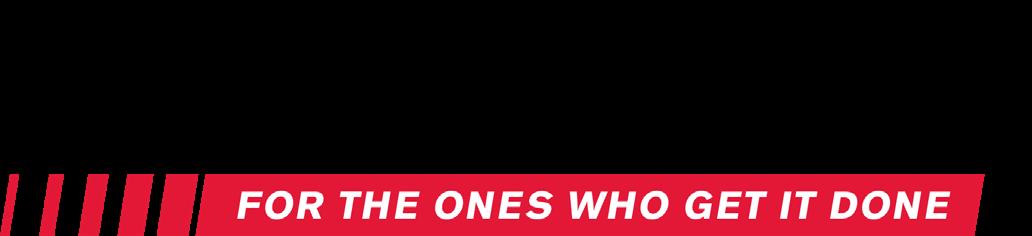
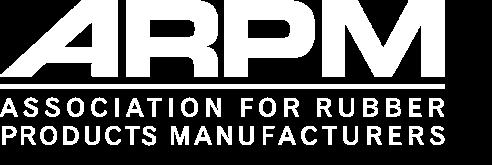
Life is somewhat ironic. As we grow up, it seems through our educational experience that we are always preparing for “the final exam.” Whether it be in high school, college or a special training experience, first we are taught, then we study and then we take the exam. We then measure our results by whether we pass or fail the final exam and not by the lessons we learn along the way. But in life, and most certainly in business, it’s so often reversed! The final exam usually happens before the lesson! In fact, it was once said that “the trouble with using experience as a guide is that the final exam often comes first and then the lesson.”
I reveal this concept because of my belief; my belief that all trade associations must work on behalf of their members to provide “lessons” before the final exams take place. This may sound a little unorthodox, but if you begin to examine the activities and menu of benefits that ARPM offers to its members, one can see a hint of the strategic thinking that was used to form the foundation of the organization. It was the goal and vision of ARPM’s founding fathers to collectively unite the experiences and lessons learned of the professionals leading each member company. As exhibited on ARPM’s website, there is a special location for individuals to identify their strengths (their experiences; their accumulation of lessons learned) so that others may tap into the knowledge base before the real world throws them a real exam or final test.
ARPM is unveiling its newly created ARPM Training Academy. The foundation for the ARPM Training Academy lies within ARPM’s industry-leading best practice documents, ARPM technical guidance documents and ARPM’s The Rubber Handbook. Our instructors are veteran experts in their fields, boasting over 140 years of combined experience in the rubber manufacturing industry so that we may successfully provide our members with the “lessons” before the final exam.
The ARPM Training Academy is a dynamic technical training resource that teaches fundamentals and advanced topics for the rubber industry. The ARPM Training Academy provides training for the entire workforce, and improves the
knowledge base from the entry-level machine operator to the highly-skilled engineering professional. Our newly created in-person training provides in-depth principles of design not available anywhere else in the rubber industry or academia. This in-person training is tailored to Design, Quality, Sales, Product and Process Engineers.
Seals Product Design and Manufacturing – June 5-9, 2023, in Columbus, Ohio
● One-week intensive course provides comprehensive and consistent training in rubber science, product seal design (for static and dynamic sealings) and producibility.
Belts Product Design and Manufacturing – Coming Soon
Hose Product Design and Manufacturing – Coming Soon
In essence, those professionals selecting to invest the time to attend ARPM’s Training Academy are ensuring they are prepared long before their final exams are placed in front of them!
I look forward to seeing you in Columbus, Ohio in June for the inaugural in-person class of the training academy –Seals Product Design and Manufacturing. Register today at www.arpminc.com! n
6 Success Leaders Drive Success by Asking the Right Questions
By Jim
LeGacy,vice president of sales and marketing, Titus Precision
12 Leadership
ARPM Leaders Reflect on the Bigger
Picture: The Building Leaders of Character Program
By Lindsey
Munson,editor, Inside Rubber
16 Technical Standards Machine Lead and the Failure
of Radial Lip Seals
By Greg Vassmer, technical coordinator,20 Operations
Weighing the ROI of Machinery
Capital Expenditures
By Liz Stevens, writer, Insider Rubber 24
By Erick Sharp, CEO and founder, ACE Laboratories
ARPM
ARPM Team
Executive Director Troy Nix – tnix@arpminc.org
Managing Director Letha Keslar – lkeslar@arpminc.org
Marketing Director Marcella Kates – mkates@arpminc.org
Analytics Tony Robinson – trobinson@arpminc.org
Director of Publications Susan Denzio – sdenzio@arpminc.org
Membership & Events Director Kaitlyn Krol – kkrol@arpminc.org
By Susan Denzio, directorARPM Officers and Board of Directors
President
Travis Turek, Bruckman Rubber Corporation
Vice President
James Wideman, MBL (USA) Corporation
Treasurer
By Jake Mazulewicz, Ph.D.Marel Riley-Ryman, Southern Michigan Rubber
Secretary
Joe Keglewitsch, Ice Miller LLP
ARPM Board of Directors
Rich Balka, Home Rubber Company
Bill Bernardo, Ebco, Inc.
Kirk Bowman, The Timken Company
Russ Burgert, Maplan Rubber Machinery
Aaron Clark, Danfoss
Joe Colletti, Marsh Bellofram
Randy Dobbs, Sperry & Rice
Ryan Fleming, Freudenberg-Nok Sealing Technologies
Doug Gilg, Continental ContiTech
Diya Garware Ibanez, Fulflex, Inc.
Seth Johnson, Zochem LLC
Donovan Lonsway, BRP
Jon Meigan, Lake Erie Rubber & Manufacturing
Mike Rainey, HBD Industries Inc.
Mike Recchio, Zeon Chemicals L.P.
Brandon Robards, Ace Extrusion
Vice President, Editorial: Dianna Brodine
Editor: Lindsey Munson
Vice President, Design: Becky Arensdorf
Graphic Designer: Hailey Mann
Published by: 2150 SW Westport Dr., Suite 101 Topeka, KS 66614 Phone: 785.271.5801
As a commercial leader, I’ve been in a unique position, visiting hundreds of facilities and witnessing the companies that are doing everything correctly, and the companies that are not. In most cases, a lack of clear objectives and leader reinforcement is the downfall. This leads to lower productivity, low employee retention rates and departmental silos that keep cooperation at a minimum.
In my experience, when a company sets goals for its employees, the employees work hard to meet those goals. When these goals are met, the company can celebrate together and the employee feels invested in that achievement. Goal setting is an often forgotten and important retention tool. Employees are less likely to leave a company where they feel successful and celebrated. If goals are not set, reinforced, and measured, there’s nothing to recognize or celebrate.
There are key questions (talking points) that leaders can use to guide goal setting in each department throughout a company. The questions revolve around improving profitability; however, they also offer a way to measure progress and eventually success. There are tens of millions of dollars of productivity improvements available in US molding operations, but an organization must be hungry for change and have a plan. Organizational silos need to be eliminated. Nothing brings a team together like clear objectives and goals that can’t be achieved unless all departments work together.
In each department within a company, there are different styles of employees who are slowing organizational progress – or stopping it in its tracks. Who are these employees, and what questions can be asked to help them think differently?
The goals of a successful sourcing department are to manage (more so) in an inflationary economy, to drive down costs to ensure profitability and to make sure the plant never runs out of material. The purchasing team also is responsible for building supplier relationships. – Suppliers are an oftenunderutilized source of leads for new business growth. In many cases, the sourcing people who are the face of an organization aren’t building relationships with new suppliers. When this happens those leads are going to someone else –likely, a competitor.
Three types of employees who slow progress:
Mr. Favorite: He has his favorite suppliers, and he’s not interested in listening to others. He won’t return calls even if someone is offering shorter lead times or better pricing. What is he missing?
Ms. Surface Skimmer: She’s placing orders but lacks resin knowledge depth and doesn’t understand deep competitive advantages. She’s paying higher prices than necessary.
Mr. Comfortable: He doesn’t like change as it creates work. He’s losing money for the company because he won’t rock the boat.
Questions to ask:
● What is your cost-out goals for this quarter and next?
● What can the sourcing department teach others in the company about the players in the particular resin markets?
● How many parts rely on single-sourced materials?
● What is been done creatively to save the company money? Consignment, alternate supplier, negotiations?
Many people believe the human resources role is only focused on benefits administration, managing hourly wages and union negotiations. HR should be the conduit for bringing people together, framing and documenting the goals for the year, and creating a dashboard. When HR sets goals for employees and puts them in writing, it makes it easier to respond when John Q. employee comes in asking for a raise. For example, if a company wants to grow profits by 7%, all employees should know what their role is in that process –and their goals should be measured.
Three types of employees who slow progress: Mr. Ivory Tower: He thinks HR is a benefits administration position, not a job focused on people.
Ms. Politics: Enough said…
Ms. Plant-Focused: She spends 90% of her energy on the plant and needs more time with management staff to set clear individual and team goals.
Questions to ask:
● What is the succession plan for key roles?
● What is the company doing to hold onto top talent?
● What are the development goals for executive staff –both individually and as a team?
● What strategies will be used to attract top talent this quarter?
● What personality characteristics are being targeted during the recruiting process? Be specific.
The engineering group often sees every issue as black and white – engineers are responsible for design, but not costs. However, nothing new or innovative can be implemented without an engineer on the team. The challenge is to make them feel a part of the bigger picture. Conservative by nature, engineers may be tempted to ‘rubber stamp’ a design and push it through to the next stage of quoting. Instead of bidding exactly what’s on the drawing, where are the opportunities to submit a more creative proposal?
Three types of employees who slow progress:
Ms. Inflexible: She believes if it is on the print, no changes can be made.
Mr. All Over the Map: He’s full of energy but needs direction and clear goals.
Mr. Not Listening: He believes the engineering department rules the company. Don’t bother him with ideas – other departments don’t ‘understand’ the process.
Questions to ask:
● What is being done to eliminate the company’s singlesource problem this month?
● What is your cost-out goals for the quarter?
● Is the engineering team working with sourcing and manufacturing to make continuous improvements?
● What creative ideas were suggested during the last bid proposal? Did the company gain an edge?
● What currently is being done to enhance the skills of each engineer?
Department: Operations
Chartered with running the plant, the objectives for the operations team members are changing every day: saving money, faster changeovers, reducing scrap. It’s fire drill after fire drill. Setting annual goals and objectives helps the operations team prioritize and gives them some structure.
Three types of employees who slow progress:
Mr. Ride It Out: He’s not willing to change or take any risks because he’s seen it all before. Why change when it won’t work?
Ms. Penny Pincher: She’s focused on the micro details instead of the big picture.
Ms. High Level: She’s not engaged with the team on small productivity opportunities that could add up to big wins.
Questions to ask:
● When are the productivity project meetings scheduled?
● What is your cost-out goals for the quarter?
● What is being done to bring the key functions together?
● When will the next cross-functional team project be complete so the company can celebrate?
The sales team has the biggest diversity of styes and skillsets in the company – and it’s made up of a bunch of cowboys, by nature. Again, structured goals and objectives will make sales staff more efficient by giving everyone a road map – from the best salesperson to the ones who are struggling to meet objectives. It’s a good way to share successful sales tactics among all department members and create consistency in how the company and its capabilities are being portrayed.
Three types of employees who slow progress:
Mr. Same Update Every Month: He got a refusal reason from a prospect six months ago but doesn’t follow up … so he continues to use the same excuse, even though a new purchasing person is now in charge.
Ms. All About Price: She sells on price only and loses out on business when the competitors swoop in.
Mr. Time Management: He struggles with attention to detail, so he isn’t consistent with his sales efforts or customer contacts.
Questions to ask:
● What ‘elevator speech’ is used when selling the company to prospects or existing customers?
● Explain the sales plan for the quarter. Use specifics.
● What tools are being used to help the company win more business?
● What can each salesperson do to help the company sell more?
● What can the company do to help each salesperson sell more?
This can be an eye opener. If all team members are hitting their goals, the whole company can celebrate. However, leadership often sets the goals without defining how the leadership team will contribute to achieving them!
Three types of employees who slow progress: Ms. Unapproachable: Her door is closed to everyone except the executive team.
Mr. Critical: Spends too much time critiquing employees.
“THE QUESTIONS REVOLVE AROUND IMPROVING PROFITABILITY; HOWEVER, THEY ALSO OFFER A WAY TO MEASURE PROGRESS AND EVENTUALLY SUCCESS. THERE ARE TENS OF MILLIONS OF DOLLARS OF PRODUCTIVITY IMPROVEMENTS AVAILABLE IN US MOLDING
MUST
Ms. Too Busy for Outside Input: She’s ‘too busy’ to understand how suppliers can help achieve company goals or see the value of supplier partnerships.
Questions to ask:
● Are the right productivity metrics implemented? Are they reviewed frequently enough?
● Are the right sourcing goals in place for backups, market knowledge and partnerships?
● Are staff goals aligned with business and teamwork goals? Is HR a key part of the process?
● Has the engineering team been challenged to drive productivity and profit?
● What are the objectives for today?
● Is leadership empathetic enough with the challenges faced by the team?
By recognizing the types of employees who may be slowing progress in an organization, leaders can set clear goals and objectives that will help those employees see their roles differently. The goals should be challenging, but fair. Once the goals are set, company leaders need to consistently
ask questions about what progress has been made. The message must be repeated – employees may enter or leave the company or new programs may come in that temporarily interrupt the daily flow. Reinforcing the objectives helps keep the company on the path toward a profitable bottom line. n
Jim LeGacy is the vice president, sales, and marketing, for the Titus Group, a global hardware manufacturer with injection molding and zinc die casting capabilities in Columbia City, Indiana. LeGacy has considerable leadership experience in sales and marketing in the North American market, with recent roles with Ravago, Polymer Technology & Services and Sabic / GE Plastics. He is a Six Sigma Black Belt and has been awarded with seven commercial execution and leadership awards, including the “Breaking Glass Award for Imagination and Courage” at the GE Corporate Leadership Conference. For more information, email jim.legacy@titusplus.com
Led by Industry Expert Instructors with Over 140 Years of Experience
Seals Product Design and Manufacturing
If you are involved in the design, quality, sales, or manufacturing of rubber articles, and would like to know why it works not just when it works, this is for you!
June 5-9, 2023
Columbus, OH
Training includes:
comprehensive training in rubber science, product seal design, and reproducibility
one-week intensive course not available anywhere else copies of ARPM Product Standards and MO-1 The Rubber Handbook
Space is limited for this in-person class. Register today!
ARPM’s first-quarter plant tour will be a two-facility event, taking place at Chem-Trend and Freudenberg-NOK Sealing Technologies in the greater-Detroit area. During this all-day event, attendees will visit Freudenberg’s headquarters and R&D lab in Plymouth as well as Chem-Trend’s global laboratories and manufacturing facility in Howell. Both organizations are making strides to have more sustainable operations, and their progress and next steps will be the highlight of each tour. To learn more about this event and to register, visit www.arpminc.com/events.
ARPM’s Annual Environmental, Health and Safety Summit is being brought back in person in 2023! This event, May 2325, will highlight best practices in safety that you can take back and implement in your organization.
The most important element of the EHS Summit is the educational component contributed by industry experts. If you are an EHS professional and would like to share your professional experiences and program successes with our audience, we encourage you to respond to our Call for Presenters. All presentations must be non-proprietary and cannot mention specific goods or services
If you are interested in presenting at this event or have any questions, please contact Kaitlyn Krol at kkrol@arpminc.org
ARPM is excited to share that we will be offering oneweek intensive training courses through our new program, the ARPM Training Academy. The Seals Product Design and Manufacturing course is the first session and will be held June 5-9, 2023 in Columbus, Ohio. This one-week intensive course provides comprehensive and consistent training in rubber science, product seal design (for static and dynamic sealings) and producibility. This course of in-depth principles of design is not available anywhere else in the
industry or academia and is taught by industry professionals with over 140 years of combined experience. For more information or to register, please reach out to Letha Keslar at lkeslar@arpminc.org
ARPM is pleased to welcome four new Board Members in 2023. The new members bring a wealth of leadership experience and will be a great addition to the association’s Board of Directors.
Aaron Clark, chief chemist – Danfoss
Bill Bernardo, director – Ebco Inc.
Ryan Fleming, Americas MT Laboratory operations manager – Freudenberg-NOK
Rich Balka – president, Home Rubber Company
ARPM also would like to thank Charlie Braun of Custom Rubber Corp, Joe Walker of Freudenberg-NOK Sealing Technologies, Mike Smith of Basic Rubber and Plastics, and Dave Jentzch of Blair Rubber who are stepping down from the ARPM Board of Directors. Thank you for your service and all you have done to impact ARPM and the rubber industry.
Please join us in welcoming the following new ARPM members!
Sempertrans USA
Passaic Rubber Co
February 28, 2023 – Chem-Trend/Freudenberg-NOK Plant
Tour Event
March 1, 2023 – Safety Award Submissions Open
April 20-21, 2023 – Engineering and Quality Forum
May 23-25, 2023 – EHS Summit
You can register for these events, and see our full list of upcoming events at www.arpminc.com/events. n
Positioned on the west bank of the Hudson River, West Point is where the United States Military Academy and Thayer Leadership come together, combining the military elite with corporate America to experience the nation’s most prestigious leadership training program. Founded in 1802 by President Thomas Jefferson, West Point has seen many remarkable graduates, such as George A. Custer, Thomas “Stonewall” Jackson, Douglas MacArthur, Dwight D. Eisenhower, William Seawell and Buzz Aldrin, among other notables. In business, West Point graduates have served as chairman of the New York Stock Exchange, CEO of Johnson & Johnson, CFO of Twitter, CEO of Proctor & Gamble, among others.
According to the military academy’s website, “Colonel Sylvanus Thayer, the ‘Father of the Military Academy,’ served as Superintendent from 1817 to 1833. He upgraded academic standards, instilled military discipline and emphasized honorable conduct.” Thayer was the 33rd graduate of West Point and was noted for reforming the curriculum of an institution that lacked the structure it is famous for today.
Thayer Leadership at West Point is built on proven methods from the United States Army, blended with real experiential learning and academic instruction. The legacy and significance of the military leadership lessons and traditions have guided and empowered leaders to not just lead but to see the bigger picture, enacting change in their businesses from top to bottom, stimulating and cultivating productivity, and decisively responding with purpose and pride.
Nicki Hershberger, a senior technical advisor at Akron Rubber Development Laboratories, began her journey when she saw an ad for the program and instantly was intrigued. “As a manager, you always have to be looking for new ways to improve and motivate your employees,” she said. ARDL is an independent testing laboratory with around 100 employees and has both ISO and A2LA accreditations. Knowing her role in the company and being a key leader, Hershberger walked into the program with, “… feelings of excitement!”
Regan McHale, a second-generation president of Eagle Elastomer, a family-owned company that specializes in fluoroelastomer extruded products, entered the program by invitation from the Association for Rubber Products Manufacturers (ARPM).
Business leaders require stability and structure to successfully lead teams, and ARPM teamed up with Thayer Leadership’s Building Leaders of Character program to enhance the leadership abilities of rubber industry professionals. With years of research and Thayer Leadership’s belief that “Character is foundational to your ability to lead,” the two organizations unleashed a program built on engagement among industry peers, mentorship from top training experts and empowerment through the teachings and coursework.
ARPM’s managing director Letha Keslar was part of the development and construction of the leadership program. She shared, “Upon working with Thayer Leadership Development Group (TLDG), we knew that we found what our members were looking for... a customized leadership program that specifically was designed to positively impact and give usable leadership tools to manufacturing leaders of the ARPM network. The experience included such items as how leaders effectively and efficiently communicate to all levels of the organization; how teams accomplish missions in Volatile, Uncertain, Complex and Ambiguous (VUCA) environments; and how building and maintaining organizational culture is essential to not only winning battles, but wars – and how those lessons apply directly to the complex business world the industry operates in daily.”
According to Thayer Leadership at West Point, “True leaders – the ones who courageously enact change, master opposition, foster productivity and respond decisively –demonstrate leadership daily. It’s not enough to just know about leadership. At Thayer Leadership, we span the gap between knowing about leadership in theory and acting like a leader when it counts.”
The Building Leaders of Character Program Level 1.0 is a 14week program of 18 virtual sessions, ranging from 45 to 90
minutes, that immerses participants and drives interactions designed exclusively for ARPM industry professionals. As leaders, it is difficult, if not almost impossible, to step away from business demands for a few hours or even a day, so it is imperative to have the full support of the company behind those who enter the program. “I was lucky that my organization understands the value of continuing education,” Hershberger said.
Led by retired General Officers and faculty who pull in the leadership lessons they learned from West Point and the US Army, the program is an in-depth, intense experience. Sessions are comprised of applied academic classroom modules through online video, live interactive experiences, mentoring with expert faculty, networking among other rubber executives and participants, self-study and inspirational speakers.
Keslar joined the ranks of the program before the pandemic for the two-day training at WestPoint and participated in the online 18-week course. “During the opening on day one, Lieutenant General (Ret.) Ken Hunzeker said, ‘My only job beginning on the first day of any new command was to find and train my replacement,’ as succession planning is the number one priority in any military unit,” Keslar recalled. “I found this profound, to hear that a military commander’s focus was on the continuous development of leaders two echelons below his level, not the next level below, which is the common business standard.”
As a seasoned leader, McHale found several takeaways and key moments throughout the program, but his biggest takeaway was the lesson of the tactical pause. “I use it today, the concept of the tactical pause,” he explained. “It’s used by the military to ‘pause’ when an operation or plan is
“IS THE CURRENT PLAN ACHIEVABLE? DO WE NEED A NEW COURSE OF DIRECTION? SHOULD THE TEAM STOP ALTOGETHER? IT’S TRAINING I AND MY OTHER LEADERS ARE USING IN OUR FACILITY TODAY, AND I AM SO THANKFUL FOR THAT TEACHING.”
not going in the right direction. As a leader, it is our job to determine when and how we use the ‘tactical pause,’ where an assessment of the plan takes place. Is the current plan achievable? Do we need a new course of direction? Should the team stop altogether? It’s training that our leadership team is using in our facility today, and I am so thankful for
Additionally, McHale commented on moments of clarity throughout his coursework, sharing one example. “They have a mission, a plan and are in the fight,” he said. “The example that was given stuck with me – there could be a time when somebody’s got a specific responsibility to the mission and communications are lost or more combat is encountered than expected at that moment. A leader must make quick, sound decisions that have a lasting effect on the team. Those decisions have life consequences, and the ones making the decisions must remember what their role is in the bigger mission. It builds character for sure.
Even though, in business, we don’t have war situations, it resonated with me as a leader. As a leader, we must have a mission and a plan, along with the tools to make sound decisions. Even though sometimes our plan doesn’t go how we anticipated, we must problem-solve on the fly, create a new plan and make decisions. It’s how we adapt to the situation and the problem at that moment.”
McHale continued, “Communication and preparation were key actions that were takeaways for me as a leader. Whether it be talking through scenarios with the team leaders, creating a plan for the unknown and preparing for possible mishaps (like the military encountering heavier combat than expected), or cross-training employees so, if one department is down, we can allocate labor to assist or have back-up plans for production and the need to divert, if necessary. Those military leaders knew what they had to get done and could adjust because they planned and prepared for various scenarios, creating clear lines of communication within their teams.”
Ice Miller focuses on meeting the needs of our clients quickly, efficiently and cost-effectively. Ice Miller attorneys with rubber industry experience can assist with your greatest legal challenges. Contact Josef Keglewitsch at 614-462-2279 or josef.keglewitsch@icemiller.com for more information.
icemiller.com
Hershberger and McHale set their sights on grabbing every tactic for the toolbox and intaking every ounce of knowledge from the program.
Hershberger commented, “The goal was to learn better ways to communicate a vision and how to implement it. What intrigued me about learning from the military, was that the goals may be constantly changing as the situation evolves. In my experience, rarely has the initial vision in any organization stayed the same. The vision must adapt when moving from theory to reality and this is where most visions fail. However, failure is not an option in military situations, so managers have to learn to understand, change and adapt to new situations as they arise.”
Recently, McHale found himself in an unplanned position and it required him to pull from his leadership training. “It was Christmas, and the plant lost power due to cold temperatures,” he said. “The facility was empty as employees were enjoying their families, but the facility houses waterlines and a sprinkler system, so the first concern was keeping the pipes from freezing. The day after Christmas, I knew we had to prepare for the big potential problem of our facility flooding from pipes bursting. We couldn’t control getting the power turned back on, but we could control how we reacted. Taking swift action with other employees, we formed a plan and started taking the necessary steps – one of which was to contact the sprinkler company, which gave us a procedure to shut down the water. Then we looked to rent heaters from a local company. In the end, we avoided the worst possible outcome and, because of the training and lessons taken from the leadership program, it prepared me and others on the team with ‘the tactical pause’ to redirect, assess and create a plan.”
During the program, candidates are inspired, stretched and even pushed beyond their comfort zones. Hershberger found herself not only reevaluating and processing prior work-related scenarios, but also thinking of what she could do differently moving forward when speakers and faculty members shared real-life stories of their own. She said, “When speakers spoke about poor judgments they made or how they knowingly allowed actions that hurt the team and or the organization, these sections were eye-opening and left the group with a lot to think through. I liked the concept of ‘Red Teaming.’ This forces you to look at your organization through the lens of a competitor. I also liked the After Action Review (AAR), which allows you to sit down as a team after the fact, to say what went well and what we struggled with in a particular scenario.”
Following her experience, Hershberger said, “I feel the program made me a stronger leader.”
In McHale’s experience, “Life is about learning and, when given an opportunity to learn from the military, I took it. As a business leader, you’re focused on a company, with no real life or death threat, but then you see the impact of how the military develops leaders and impacts ‘life’ – I found that very interesting and eye-opening. The generals and their decisions, along with the pressures and expectations that they have on them, are enlightening. I found myself pulling from their experiences shared and adjusting my leadership tactics along the way. It’s not that I was nervous about the program upfront, it’s what happened during it – I was pushed to get uncomfortable and to be challenged in ways I never could have imagined. That’s what life is all about!”
ARPM business leaders, like Hershberger and McHale, who have completed the program through the years proudly use
the tools learned to exemplify the characteristics of positivity, trust and self-accountability – pulling teams together to meet company objectives, conquer communication challenges and improve organizational performance. And, the program is not just for the C-Suite executives. McHale sent two of his younger leaders through the program. “The program is an excellent opportunity for young leaders to build a good foundation and to gain important tools to assist them in their leadership growth,” he said.
The online course allows team members to participate in the program without travel costs or time away from the manufacturing facility, but those considering the Building Leaders of Character program should not worry that the online course is not on par with the in-person experience. “For my leadership journey, the online course was more impactful than being at West Point for the two-day training, as I was able to work at my pace on the course work, to reflect daily and fully discuss the lessons being covered,” Keslar said.
In reflection, Keslar said, “After years of research and attempts to create a competitive advantage for our members in developing the future leaders of their organizations, I am proud to say that we are ‘locked-and-loaded’ (a military term that means ‘we are ready to go’) in offering this Battle Tested Leadership program to all our member companies.”
ARPM’s next class of the “Building Leaders of Character” series will begin on March 27, 2023. Space is limited, so to save a seat(s), register on the ARPM website at www.arpminc. com. In addition, 2023 is a big year as The Building Leaders of Character Program Level 2.0 will launch. If readers have completed Level 1.0, they may be eligible to enroll in this program. For more information on ARPM and Thayer Leadership at West Point’s Building Leaders of Character Program, visit www.arpminc.com. n
This is part one in a two-part Tech Corner. In this issue, the column looks at shaft machine lead and its impact on radial lip seals. Next issue, new technologies will be discussed that are going to help robustly detect the problem.
So, what is machine lead and why do rubber processors care?
Machine lead or “twist” is a surface finish pattern inadvertently created on a shaft surface during manufacture that acts like a screw thread. This pattern can cause an oil seal to prematurely leak.
So how does this come about, and can it be detected before a product fails at the consumer level? First, look at how a shaft is made.
In the simplest case, a shaft is a steel cylinder with a tight tolerance outside diameter and a controlled surface roughness. The right size and finish are needed for the seal to properly fit on the shaft and to work and wear as expected while running. There is a lot going on in the tiny space near the seal.
To get the shaft to the correct size and roughness several machining steps are used. The best way to imagine it is that first, a single-point tool moves along the shaft, cutting to get the exact size. Then, using the preferred technique, a grinding wheel plunges straight into the surface, grinding to a desired finish. Either of these steps can leave behind a dreaded screwthread-like lead. In fact, any axial motion along the shaft axis cuts a helical pattern. There are other ways to finish a shaft, and unfortunately, most have the potential to cut a helical pattern.
Our good friend Archimedes in 234 BC discovered that if such a thread pattern is rotated it will act as a pump and transport material down the shaft – like a fence post auger digging a post hole.
Rubber processors do not want the shaft to act as a pump because …
A rubber radial lip seal works by acting as a small pump specifically designed to keep a sealed fluid on the correct side of the seal. This ability to pump can be demonstrated by putting a drop of oil on the air side of a seal in operation and watching it disappear as it gets pumped back where it belongs. Machine lead on a rotating shaft either will work with or against the radial lip seal depending on which way the shaft rotates. Either way shortens the seal’s life. In one direction the lead overcomes the seal pumping and allows oil to leak, while in the other direction, the enhanced pumping sucks air under the seal, burning the oil and wearing out the rubber seal.
It’s clear there is a need to measure this and it’s simple. Rubber processors need a speed-controlled motor, a length of quilting thread, a small weight and the shaft to inspect. Together these make up the oldest, unfortunately too variable, but still a very current method for checking machine lead.
ARPM OS 1-1 contains the specifics for this test which dates to at least the 1970s but is probably older. It is in use today thanks to its low-tech equipment, ease of use and fairly good correlation to finding root cause for actual seal failures.
The shaft to be tested is mounted on the motor and a loop of thread wrapped around the shaft and the weight hung from the thread. Using the motor, rotate the shaft. The thread either will stay where it is or move to the right or left. If set up correctly, any movement of the thread indicates the shaft has machine lead and the potential to cause seal failure. The speed of the thread movement is an indication of the severity of the lead problem.
All major seal manufacturers use this test to detect machine lead – but they don’t like it for good reason. Its results vary due to both the test equipment and technician attentiveness. But there are new techniques on the market with far fewer of these issues. In next quarter’s column, the new methods and a new project by the ARPM Seal Committee will be discussed to see how well they work. n
ACE Laboratories, Ravenna, Ohio, earned certification from the Miami-Dade Department of Regulatory and Economic Resources as an approved testing laboratory for a range of construction industry tests under its ISO/IEC 17025 scope of accreditation. ACE’s responsibilities include the approval of construction materials and products under the most common tests performed for Miami-Dade County that are to international standards ASTM D6083, ASTM D6694, ASTM D5147 and ASTM D5869. For more information, visit www.ace-laboratories.com.
AGC Chemicals Americas Inc. (AGCCA), Exton, Pennsylvania, a manufacturer of glass, electronic displays and chemical products, opened a new office in Cupertino, California, to support the advanced materials needed by semiconductor and electronics manufacturers on the northern West Coast. The Cupertino office promotes a wide variety of advanced materials of ETFE and PFA resins for tubes, hoses, gaskets and sheets; ETFE films for mold release film; and fluoroelastomers for components used in semiconductor plasma processes at elevated temperatures. For more information, visit www.agcchem.com.
The USDA awarded Bridgestone $35 million to grow its investment in desert shrub guayule to advance a climatesmart domestic rubber industry and offer a water-smart solution. The company also will work to educate growers on water utilization, soil health, nutrient delivery and the ecological benefits of guayule. The viability of guayule as a sustainable, domestically produced alternative to imported tropical rubber also has been explored by Ford and fellow tire maker Cooper, as well as Patagonia, for use in wetsuits. For more information, visit www.bridgestoneamericas.com.
LanzaTech NZ, Inc. (“LanzaTech”), Skokie, Illinois, is an innovative Carbon Capture and Transformation (“CCT”) company that transforms waste carbon into materials and
Sumitomo Riko Company Ltd., Nagoya-shi, Aichi, Japan, announced a joint-development agreement to reuse rubber, resin and urethane waste for the production of a chemical intermediate, isoprene. Isoprene is produced by plants and is the main component of natural rubber. For more information, visit www.lanzatech.com.
Momentive Performance Materials, Waterford, New York, released its new LSR and HCR-based NEVSil product family. Suitable for a wide range of sealing applications in vehicles powered by alternative energies, including e-mobility, hybrid concepts and fuel cell technology. In addition to a generally low compression set, the wide range of grades include hightemperature resistance, flame retardancy, self-lubricating, low viscosity, low stiffness, fast curing, increased crack and aging resistance, good colorability and thermal conductivity. For more information, visit www.momentive.com
Rahco Rubber, Inc., Des Plaines, Illinois, announced the hiring of Brian Mnichowicz to its engineering and technical team. Mnichowicz comes to Rahco with over five years of manufacturing engineering experience and extensive knowledge in process engineering, lean manufacturing, project management, automation systems, Six Sigma and mold design. For more information, visit www.rahco-rubber.com.
Minnesota Rubber & Plastics (MRP), a Minneapolis, Minnesota leader in material compound development and the manufacturing of custom elastomeric and thermoplastic components, has been acquired by Trelleborg, a worldwide provider for engineered polymer solutions that seal, damp and protect critical applications in demanding environments. Becoming part of Trelleborg Sealing Solutions unlocks new benefits for MRP customers, leveraging the strengths of both companies to become a one-stop-shop for customers requiring accelerated time to market, especially in the medical device market. For more information, visit www.mnrubber.com or www.trelleborg.com.n
When it comes to considering the capital purchase of a new injection molding machine or a significant upgrade, or a large financial outlay to stock up on related MRO items and safety gear, rubber injection molders have several decision-influencing factors to identify and weigh. The financial angle is always top of mind, and the return on investment for technology upgrades is paramount as well. Examining the labor efficiency improvements that might come from a purchase calls for also factoring in the additional training that might be needed with new machinery. Sometimes, taking a look at service and maintenance history for existing equipment is a key tipping point toward making a purchase, but this must be judged alongside the service and maintenance anticipated for a new system. And, finally, if the COVID-19 pandemic taught industry anything, it taught everyone that supply chain and freight time/cost really ought to be part of the decision tree for any crucial equipment and all of those “must have” supporting elements.
For insight and advice about running through these key factors, Inside Rubber talked with representatives from three large vendors for the rubber processing industry. DESMA USA, Inc., Hebron, Kentucky, is a complete systems provider that offers German-engineered rubber injection molding machines, domestically designed molds and custom automation solutions. Grainger, Inc., Lake Forest, Illinois, has more than 200 locations offering MRO and safety tools, supplies and gear. Maplan Rubber Machinery USA, South Elgin, Illinois, offers Austrian-made elastomer injection molding machines and automated system solutions.
In any industry, capital expenditure is the big kahuna; plant owners and management know better than anyone that there must be a dramatic and quantifiable return on such a large investment. DESMA USA’s Marc Vonderlage, North American director of sales, pointed to the quantifiable ROI that rubber processors can see following purchase of new injection molding equipment. “When properly specified, installed and operated, new equipment will impact rubber molding operations in several ways,” said Vonderlage. If the system is replacing an aging machine, reduced downtime, reduced maintenance costs and increased uptime are virtually guaranteed. “Another common benefit of installing new equipment,” said Vonderlage, “is a reduction in the number
of defects that may have been generated by older machinery. A new injection molding machine, operated properly and maintained as recommended, will deliver superior parts.”
In addition to increased uptime, improved throughput and reduced repair costs, a new system may facilitate faster production. “New equipment can offer improved production efficiency,” said Vonderlage, “This often is seen in reduced cycle times which are made possible by higher performance equipment. Production efficiency can also see a boost when workers are better motivated; in general, workers prefer to operate well running, clean, new machines.”
State-of-the-art equipment also can feature Industry 4.0 elements that dramatically improve a plant’s ability to track operational performance, and that which can be measured can be improved. “And, if automation is incorporated in a system,” Vonderlage said, “it can positively impact several areas, including increased throughput, reduced labor cost and improved product quality.”
Russ Burgert, director of after sales at Maplan, said that his company is seeing very strong sales overall and unusually strong sales for the start-of-year timeframe. “This level of sales is being driven by true need for the product,” said Burgert. “We are seeing enough industry come back after the recent slowdowns that plant owners have to buy new equipment to meet demand.”
Burgert pointed out a financial angle that can benefit any equipment purchaser who buys from a European manufacturer. “Financially, everybody needs to realize where the Euro is right now, compared to the US dollar. In the beginning of 2022, it cost about $1.14 to buy a Euro. In September, it was all the way down to $0.95.” That equates to a significant monetary advantage for American buyers. “The price of the Euro,” said Burgert, “is on the upswing, but it is not yet back to the high we saw at the start of 2022. We’ll see if it keeps climbing or if, hopefully, it turns around and drops again.” Burgert noted that Europe countries have seen a lot of volatility in the last year, making it difficult to predict how the value of the Euro might change. “The bottom line,” said Burgert, “is that people should really take a look at the exchange rate and take advantage of it while it is advantageous. It’s free money.”
The semiconductor has revolutionized life in the workplace. Plants are leaning in, more and more, toward automation for increased efficiency, higher quality, more dependability. Connectivity is proving its worth, allowing remote monitoring and adjustment of machinery. Big data is delivering astounding new insight into the nitty gritty of operations as well as raising flags about emerging patterns and trends that may signal problems cropping up on the production line.
Shelby Lasley, national accounts manager at Grainger, deals with manufacturing customers across the US. When asked if he has seen many customers implementing technology and adding automation, his answer was unequivocal. “Oh, 100 percent,” said Lasley. He cited the example of a packaging company that was continually challenged to keep the line running when workers, such as forklift drivers, didn’t show up for their shift. It was not uncommon for management to regularly pause their own work and take the place of a missing worker on the production line, in order to keep the operation from screeching to a very expensive, unnecessary halt. The owner of the company implemented robots and palletizers to minimize his dependence on undependable workers. “People are continuing to find new ways of doing business,” Lasley said, “and automation is definitely one of the major ways they are doing that. Automation because people don’t want to work, and automation just to be more efficient.”
For Burgert at Maplan, the most important technological advances lie in Industry 4.0’s connectivity; those advances are factors to keep in mind when deciding whether to invest in new equipment. “Industry 4.0 is a critical part of moving forward,” said Burgert. “It’s about connectivity to automation cells and allowing the machines to have more control.” Burgert stated that plant managers now can make changes to a production cell - as a whole system - from just one point, rather than having to individually adjust many controllers. Centralized machine-wide control also means that there are fewer specialized controllers to maintain, to repair or to replace. “With Industry 4.0,” said Burgert, “everybody can communicate very easily. It makes changing out molds easier because all of the settings are now stored in the mold recipe. It is seriously a gamechanger. And that isn’t even taking into consideration the ability to download data, and then doing what you want with the data.”
As for predicting the return on investment for technology upgrades or for a new machine purchase, DESMA’s Vonderlage offered good advice. “Judging the return on investment for a technology upgrade depends greatly on the starting point,” said Vonderlage. “If a company is starting with very basic, very old equipment, the advantages of a modern machine can be massive.” The impacts might include improved production efficiency, increased uptime, reduced part defects and reduced maintenance costs.
Regarding the ROI for a new machine, Vonderlage stressed that this must be considered on a case-by-case basis, with improved efficiency, improved product quality and increased uptime contributing significant benefits. ”It also is important to bear in mind the maintenance costs for old equipment. These days, there is a real potential for component obsolescence; that can create big risks for business interruption due to long down times for sourcing replacement components,” he said.
When weighing inputs and making decisions about new equipment purchases, it is crucial to consider the service and maintenance aspects. By looking at the service and maintenance history and trends for an existing machine, one can sometimes see the writing on the wall: the frequency and cost of repairs keeps increasing and there is no end
in sight. “That turns right back to financial impacts,” said Burgert. “Plant owners need to look at their annual spend on maintenance for each machine. And if that starts to turn lopsided then, yes, it is time to start looking at new machines.”
Vonderlage echoed that sentiment. “One of the key reasons companies consider a new equipment purchase is a realization of the excessive maintenance costs and downtime on the old equipment,” said Vonderlage. ”As machines wear or are damaged, costs to keep them operational increase and the amount of downtime increases as well.” Vonderlage pointed to the inevitable: eventually, almost all machines reach a point where it is no longer possible to repair them or no longer economical - in downtime and cost - to make continued repairs. ”And,” said Vonderlage, “even the best built machines will eventually fall victim to issues like component obsolescence.”
Predicting the lifespan of any particular machine or the future availability of one of its key components is a no easy task. “That’s a tricky one,” said Burgert. “Maplan currently is in a situation where the controller cards for our Gen 4 machines are obsolete. The controller manufacturer obsoleted the cards a few years ago; we had bought a large store of them but now those cards are running out.” Maplan builds its machine frames to last a lifetime, and Burgert said that by adding the company’s newest controller - the X6 - customers can protect their machine investment. “This comes in a new cabinet with state-of-the-art control, prewired. Customers can install the new cabinet and wire it up, and their machines are now good to go for another 12 to 15 years with those new controller cards.” But, noted Burgert, not all machines are cared for to a lifetime standard and therefore the working life determination often depends on how well the equipment has been maintained over the years.
Vonderlage raised the counterpoint to the argument of moving to new machinery due to high maintenance and repair expenses for existing equipment. “Workers and maintenance people learn their machines well over time,” said Vonderlage, “and often can quickly diagnose issues when they occur due to past experience.” Losing that familiarity and expertise can look like a factor against moving to new machinery, but is reliance on older equipment and an aging workforce to maintain it sustainable in the long run?
Vonderlage pointed out that new equipment generally has the advantage of being built around components with a long life span, and this is especially true of electronic components. “Furthermore,” said Vonderlage, “unlike older equipment, new equipment has been designed to minimize the wear and tear effect on mechanical components, and it therefore requires less maintenance.” The downside regarding maintenance on new, high-tech equipment, however, is that
workers and maintenance people frequently will need to have advanced training and higher qualifications to do the work.
Although the supply chain has recovered from its midpandemic crash, there still are pockets of continuing supply chain disruption. And although shipping and freight have recovered, for the most part, to their normal delivery times, the cost remains very high.
Lasley explained what he is seeing at Grainger, to give rubber processors a heads up on the future for buying tools, supplies and safety gear from this large distributor. “There are still supply chain issues in certain areas,” said Lasley. “We have items that we are not getting, just like everybody else. Like resin. Resin has been such an issue and it goes into so many things; there is just no way to get it during certain times. Everybody is having the same issue. But what Grainger is doing to address this is investing up front, buying in volume and increasing our on-hand inventories on all sorts of items.” Grainer also is expanding its product lines and finding alternate suppliers. “China is still shut down,” Lasley said, “and so we have gone to other countries. We are outsourcing from India a lot more and finding other avenues of suppliers.”
During the height of the pandemic, Lasley saw that many customers had to search far and wide for must-have items. In some companies, purchasing agents spent inordinate amounts of time searching for new sources. As necessary as it was at the time, it gobbled up a lot of man hours. “In some cases,” said Lasley, “people were spending hours or longer looking for an item, or shopping around to find a lower price. Sometimes it just wasn’t worth it. They spent hours trying to save money on an item, when they could have paid a little more and moved on to their next project for the day.”
Lasley said that some companies have not returned to their normal purchasing habits. “Some people stayed with that scattershot purchasing – they have all kinds of different places for getting things,” he said. “Some companies have 2,000 to 5,000 different vendors.” He pointed out that having 2,000 vendors also means cutting 2,000 purchase orders, processing 2,000 invoices and making 2,000 payments. To Lasley, keeping supply chain issues in mind is important for companies as they consider how and where to make tool and supply purchases. It may be more economical, timewise and dollarwise, to use a supplier like Grainger. This allows companies to consolidate their purchasing, and benefit from Grainger’s ability to buy in volume, from sources worldwide, and maintain a huge stock of inventory.
At Maplan, Burgert concurred that the state of supply chain and transportation issues should be part of the equation when considering a machine upgrade or a new equipment purchase.
“Yes, they absolutely need to consider those things,” said Burgert. “What normal is – I don’t know if we have a normal anymore. On the supply chain, we are really coming back. We don’t have those crazy swings of components being available and then unavailable.” He noted that sometimes lead time is still a bit longer on some of the chip-based components used in Maplan equipment, but that the situation is improving. “That, we believe, is well on its way to returning to its old normal.”
Not so, however, with freight and shipping. “Now, this transportation thing, that’s a whole different story,” said Burgert. “We are seeing transportation times close to what normal was and it is becoming steady, but the cost, the cost is not coming back down.”
Burgert offered some good advice for rubber processors mulling over machinery upgrades or new machine purchases. “For people considering procuring new equipment, I think they really need to take a long-term look to the future and try to get a feel for where the industry will be in ten years. I
know it’s hard to predict it, but we do see some trends moving forward, especially regarding labor. The rubber industry as a whole needs to be forward thinking, for example, about the future of process engineers.” Burgert already sees a shortfall in qualified process engineers, and notes that if that state doesn’t change, automation and new equipment with Industry 4.0 features will be even more important in the future than they are now.
Investment and ROI, workforce issues and possible automation solutions, the benefits of connectivity and big data, the history and future of service and maintenance expenses, the potential for supply chain disruption, and the realities of shipping times and costs. These are some of the factors that make up the whole “is it time to take the buying plunge “enchilada. There is no crystal ball to consult to see what the future will bring, and so rubber processors must weigh the factors that they can identify and then use their best judgment to position themselves now for the next phase in manufacturing. n
The rubber industry is a dynamic market sector that has grown and changed dramatically over the years through innovation and discovery. A number of rubber industry trends are impacting industrial and consumer product manufacturing worldwide. These trends include growing demand for synthetic rubber, the rising popularity of electric vehicles (EVs), ongoing supply chain disruptions, and consumer demand for sustainable rubber products and materials.
While the natural rubber market remains strong, synthetic rubber is growing in popularity.
A variety of factors are driving increased demand for synthetic rubber over natural rubber.
One advantage of synthetic rubber over natural rubber is the fact that it can be produced domestically on most continents. This is especially crucial when unpredictable factors make it difficult to source rubber materials or slow down procurement timelines. Rubber material supply may be affected by:
● War. In the beginning of World War II, the United States was cut off from the natural rubber supply in southeast Asia. The country was forced to scramble for alternatives, which led to a massive collaborative effort to produce synthetic rubbers for military and commercial use.
● Natural disaster. In recent decades, devastating fires have struck rubber plantations in Liberia, India, and Thailand, to name a few. Because rubber trees, or Hevea brasiliensis, take seven years to reach full maturity, fires and other disasters have lasting consequences for the global rubber supply. Recovery can be a years-long process.
● Supply chain disruptions. Virtually every industry was affected by the COVID-19 pandemic, and the rubber industry was no exception. Disruptions included labor shortages, raw material shortages, and production and distribution slowdowns, as well as major price fluctuations.
Ninety percent of the world’s rubber supply comes from Asia. Synthetic rubber, on the other hand, can be produced
domestically on most continents. With the lingering effects of the COVID-19 pandemic still affecting the entire rubber industry, synthetic rubber is a more accessible option in many situations.
Synthetic rubbers also are highly customizable and can be engineered to outperform natural rubber in specific areas. This might include abrasion, thermal resistance, chemical resistance, and processability. Not all synthetic rubbers exceed natural rubber in these areas, but for some applications, a customized synthetic rubber might be the superior choice.
Consumer demand for EVS is growing in the United States, Europe, and China. In the past few years, multiple countries, including China and the United States, have announced longterm goals to increase the percentage of EVs on the road. This shift toward electrification is already causing significant ripple effects in the rubber industry.
Internal combustion engine (ICE) vehicles generate heat and consume oil in operation. As a result, ICE vehicles have traditionally utilized a lot of nitrile rubber due to its excellent heat and oil resistance properties. Because EVs run without oil and produce heat very differently than ICE vehicles, these properties are less important.
When it comes to rubber materials in EVs, the greater focus is on thermal insulative values, electrical conductivity, and weatherability. Lightweight materials also are very important in EV production.
Due to the differences between ICE vehicles and EVs, there is a shift away from nitrile rubber and toward ethylene propylene diene terpolymer (EPDM), silicone, thermoplastic elastomers (TPE), and thermoplastic vulcanizates (TPV).
While the automotive industry is seeing worldwide demand for electric vehicles, the Asia-Pacific region - especially China - represents the largest share of EV sales. A significant portion of EV production and manufacturing is located in Asia as well. As a result, rubber demand in Asia is trending upwards.
Pricing, material shortages, and allocations remain major issues for the rubber industry. Many companies are struggling to get the materials they need, especially if their competitors or other industries are also attempting to source.
In some cases, companies are turning to alternative suppliers for materials. These materials need to be recertified by an independent, third-party testing laboratory to maintain compliance and ensure quality. Efficiency is critical to minimize any delays in production.
Limited supply and massive price fluctuations have forced some companies to switch to completely different materials. This often requires adjustments to compound formulations to ensure that the alternative material can match the performance attributes and quality of its predecessor. Many companies rely on independent rubber testing labs to mix and test multiple experimental formulations in a short time frame so they can choose a new one quickly and get back to full production.
A growing number of industries are striving to meet growing consumer demand for environmentally friendly products and practices. In the rubber industry, this applies to both rubber materials and the overall performance of rubber products.
Recycling rubber is an effective way to extend the life of rubber materials and is a priority for many key players in the rubber industry. Recycled rubber is a sustainable alternative to new materials, and many industries are finding creative ways to use it. Hospital flooring, playground and landscaping mulch, and rubberized asphalt are commonly made with
recycled rubber. Recycled rubber also is a popular choice for infill on synthetic turf, indoor tracks, and other athletic surfaces.
Recycled rubber often comes from a variety of sources. It is critical to test each batch of recycled rubber for hazardous materials, such as mercury or lead, to ensure that the material is safe for commercial use. A rubber testing laboratory can utilize sophisticated techniques to identify and quantify any impurities to determine whether recycled rubber meets safety standards.
Another key sustainability trend in the rubber industry relates specifically to the performance of rubber products. The most obvious example is tires. A key performance attribute of a car tire is rolling resistance, which refers to the energy needs to keep the tire rolling consistently. The rolling resistance of the tire can have a significant impact on its overall fuel economy. Rolling resistance is meaningfully impacted by the rubber compound utilized in the tire tread. The tire and rubber industries have invested ample resources into research and development in search of an optimized tire tread compound that reduces rolling resistance - and thus improves fuel economy - without sacrificing other key performance attributes. If adopted on a global scale, an optimized tread compound could make a meaningful difference in worldwide fuel consumption. This industry-wide pursuit of a greener tire has had ripple effects throughout the rubber industry. n
Reprinted with permission from ACE Laboratories, www. ace-laboratories.com.
Erick Sharp is the founder of ACE, establishing it in December of 2014. He has over 20 years of experience in the rubber industry. During that time, he has held technical and operational roles within international companies. Sharp has a degree in industrial engineering.
Following the supply chain and shipping/freight meltdowns early in the COVID pandemic, manufacturers have been taking steps to prevent similar snags in the future and to mitigate the impact of disruptions that might otherwise hobble industry and commerce. The steps toward re-shoring production, locking in alternative sourcing and lining up more options for shipping now are being combined with trends toward sustainability, natural resource protection and creating a circular economy.
The rubber industry is fully on board. With natural latex rubber an off-shore and unpredictable material source and petroleum-based synthetic elastomers falling out of favor with consumers, industry leaders and high-profile partners increasingly are exploring innovative new sources for rubber compounding materials.
“We are less than 10 years away from demand [for natural rubber] exceeding supply,” stated Angela Campo, research chemist at AFRL’s Materials and Manufacturing Directorate and deputy program manager for BioMADE.
“The Air Force needs a secure supply chain of natural rubber. As we saw during COVID, many shutdowns occurred where many countries were no longer shipping items. Eventually, that picked back up, but we don’t ever want to be in that position of not having a consistent supply of critical materials,” Campo said.[1]
The US Air Force Research Laboratory, in collaboration with the Goodyear Tire & Rubber Co., BioIndustrial Manufacturing and Design Ecosystem (BioMADE) and Farmed Materials, is mounting a multimillion-dollar project to explore using a dandelion species as a domestic source of natural rubber for use in aircraft tire production.
Kok-saghyz, referred to as TK, TKS, Kazakh dandelion, rubber root or Russian dandelion, is an Eastern European native that yields high quality rubber when its roots are crushed. The objective of the US-based team is to cultivate and harvest the species here during a multiyear program, strengthening the domestic stockpile of natural rubber. BioMADE has subcontracted Farmed Materials for its TK crops, which will be used by Goodyear to manufacture aircraft tires to meet Air Force specs, lessening the nation’s dependence on imported natural rubber.
Dandelions are not the only emerging agricultural source for natural rubber. A desert shrub called guayule, which can yield an alternative to natural rubber, has caught the attention of the US Department of Agriculture. The USDA has recruited Bridgestone Americas for a project to cultivate and scale up guayule farming in the arid US southwest to some 25,000 acres of farmland for planting and harvesting. Guayule is a perennial woody shrub native to the US/Mexico Chihuahuan Desert.
Per “Bridgestone Wins $35M USDA Climate-Smart Grant to Further Advance Guayule Natural Rubber Production,” published by Sustainable Brands, “Bridgestone Americas was awarded a $35 million climate-smart grant by the US Department of Agriculture (USDA) to further cultivate and scale the use of desert shrub guayule as a sustainable way to expand natural rubber production in the US.”
“Part of the USDA Partnerships for Climate-Smart Commodities initiative, the $35 million investment in guayule will allow Bridgestone to expand natural rubber production in the Southwestern US with lowered greenhouse gas emissions and water use for growers amid the ongoing regional water
crisis – and creating jobs in the region for local farmers and Native American tribes to build a rubber bioeconomy based on climate-smart and sustainable practices.”
“The viability of guayule as a sustainable, domestically produced alternative to imported tropical rubber – an industry rife with deforestation, carbon emissions and human rights abuses also has been explored by Ford and fellow tire maker Cooper; as well as companies including Patagonia, for use in wetsuits.”[2]
Southeast Asia’s Goodyear Malaysia has engineered unique concept tires in partnership with French car maker Citroen for its electric and sustainably-manufactured concept car, the EV. Goodyear’s tire, the Eagle GO, is made by combining natural rubber with sunflower oils, rice husk ash silica and pine tree resins, among other ingredients.
According to Citroen, the Eagle GO concept tire can be renewed twice during its lifetime and can achieve a lifespan up to 310,000 miles.[3] Since the US has plenty of pine trees, sunflower crops and rice cultivation, the Goodyear-Citroen innovation in sustainable, agricultural-sourced tire material may gain traction in this country, too.
The participation of industry leaders in these initiatives reflects a commitment to expanding the domestic production of natural rubber as well as industry support for sustainable manufacturing. n
References:
1. Bennet, Jamie. “AFRL, Partners Eye Dandelion Species as Natural Rubber Source for Producing Aircraft Tires,” executivegov.com. November 29, 2022. https://executivegov. com/2022/11/afrl-eyes-dandelion-species-as-source-ofrubber-for-producing-aircraft-tires/
2. “Bridgestone Wins $35M USDA Climate-Smart Grant to Further Advance Guayule Natural Rubber Production,” Sustainable Brands. November 18, 2022. https:// sustainablebrands.com/read/chemistry-materials-packaging/ bridgestone-wins-35m-usda-climate-smart-grant-to-furtheradvance-guayule-natural-rubber-production
3. “Goodyear, BASF help Citroen take sustainability ‘to next level,” European Rubber Journal. October 4, 2022. https:// www.european-rubber-journal.com/article/2092154/ goodyear-basf-help-citroen-take-sustainability-to-next-level
The Environmental, Health & Safety (EHS) Summit is designed to share best leadership and safety practices with industry professionals hoping to achieve world-class safety within their companies.
This one-of-a-kind learning and networking conference will focus on uniting manufacturing executives from across the United States. Attendees will focus on best practices in environment, health and safety along with becoming a better leader. This Summit promises to provide high-level safety professionals with implementable ideas they can take back to their facilities to improve their operations and achieve world-class safety.
A full schedule will be available soon, but topics could include:
"This was my first safety summit. Expectations were unknown, but from the opening greeting, the Summit made me look at myself for my 'why' and the ways I lead safety at my organization. It provided me with new insights and ideas to what is happing in the industry, and the opportunity to meet and discuss with peers on similar topics. The resources and networking at the EHS Summit is one of the greatest assets."
T h e E n v i r o n m e n t a l , H e a l t h & S a f e t y ( E H S ) S u m m i t i s d e s i g n e d t o s h a r e b e s t l e a d e r s h i p a n d s a f e t y p r a c t i c e s w i t h i n d u s t r y p r o f e s s i o n a l s h o p i n g t o a c h i e v e w o r l d - c l a s s s a f e t y w i t h i n t h e i r c o m p a n i e s .
" T h i s w a s m y f i r s t s a f e t y s u m m i t E x p e c t a t i o n s w e r e u n k n o w n , b u t f r o m t h e o p e n i n g g r e e t i n g , t h e S u m m i t m a d e m e l o o k a t m y s e l f f o r m y ' w h y ' a n d t h e w a y s I l e a d s a f e t y a t m y o r g a n i z a t i o n . I t p r o v i d e d m e w i t h n e w i n s i g h t s a n d i d e a s t o w h a t i s h a p p i n g i n t h e i n d u s t r y , a n d t h e o p p o r t u n i t y t o m e e t a n d d i s c u s s w i t h p e e r s o n s i m i l a r t o p i c s T h e r e s o u r c e s a n d n e t w o r k i n g a t t h e E H S S u m m i t i s o n e o f t h e g r e a t e s t a s s e t s "
W H Y E H S ?
S a f e t y i s n o t a o n ep e r s o n j o b , i t i s a c o m m i t m e n t f r o m e a c h p e r s o n a t y o u r c o m p a n y . T h e r e f o r e , t h e E H S S u m m i t i s o p e n t o e v e r y o n e !
S a f e t y s h o u l d b e a t o p p r i o r i t y a t y o u r o r g a n i z a t i o n , a n d c o n t i n u o u s l y i m p r o v i n g y o u r s a f e t y p r o g r a m i s e s s e n t i a l t o p r o t e c t y o u r e m p l o y e e s .
Bruce Whitney is the program director for Integrated Community Solutions to Active Violence Events, an Arizonabased charitable foundation dedicated to traumatic event prevention and preparedness training. As one of the founding members of Arizona’s Disaster Medical Assistance Team (AZ DMAT-1), he also presently serves as its deputy team commander. A passionate educator, Whitney has been actively teaching public safety to healthcare professionals, military personnel and the community for over twenty-five years.
Visit www.arpminc.com/ehs
T h e E H S S u m m i t w i l l b e i n - p e r s o n , M a y 2 3 - 2 5 , 2 0 2 3 .
C o l u
George Hupp is a retired criminal investigator, who currently volunteers for Integrated Community Solutions to Active Violence Events and runs a small life-safety consulting and tactical training company, Heloderm LLC. Hupp, an avid public speaker, shares his life experiences and knowledge on subjects as diverse as first aid, crime prevention, active shooter response and government ethics. He is an ASHI/HSI certified instructor, an NAEMT-certified Tactical Emergency Casualty Care and Tactical Combat Casualty Care instructor and a nationally registered EMT. Hupp has been teaching civilians, police and the military since the 1980s.
The 2023 Safety Awards recognize companies in the manufacturing industry that have achieved excellent safety techniques that go beyond the average regulations. The awards will be given out based on OSHA 300's Log of WorkRelated Injuries and Illness statistics and Safety Best Practices.
Mmmmm, pizza! When the order is placed, it typically is understood what options are available – size, toppings, additional side items, delivery and, of course, the total cost. Now, imagine if it were possible to create a healthcare delivery system that was as understandable to people as ordering a pizza. Believe it or not, a system does exist that is affordable and easy to use.
Ask any business leader about rising costs, and it is most likely that healthcare benefits escalation will be mentioned as one of the top three most important concerns. The issue, however, is that rarely are employees pleased with the insurance options and, in many situations, the benefit plans are under-utilized. Could this be a result of a lack of understanding, both in regard to what is available and how to gain access? The answer to this question is yes! Recent studies indicate that educating employees about their insurance benefits and how to use them at the critical “point of need” positively impacts outcomes and satisfaction levels.
Nearly every employer has experienced the pain of educating employees about benefit options. Communication efforts generally include flyers, mailers, posters and wall diagrams pinned in break rooms or cafeterias. Most employers use open enrollment meetings to deliver large amounts of benefit information, but in the end, employees are left with an abundance of questions. Even though support usually
is made available from most plans through the phone number included on the back of the insurance card, many employees will not engage with this customer service option. Rather, questions are pointed directly to human resource professionals when a point of critical escalation has been reached; these interchanges can become quite personal and involve confidential health, claims and billing issues. Since most human resource teams don’t have the wherewithal to access the appropriate level of data to understand what an individual might be undergoing, the interchanges often are unproductive and extremely frustrating, causing employees to look unfavorably at the benefit offering. At the end of the day, company executives must consider other options to ensure investments in insurance benefit plans yield the positive impact expected on both employees and their families.
Best-in-class company leaders now are using concierge service professionals to eliminate the frustration and close the benefit education gaps for their employees. These services have proven to reduce the workload of management teams and improve the employees’ viewpoints of the company benefits provided, resulting in decreased employee turnover.
Employee concierge services focus on simplifying the healthcare journey for employees, especially when the journey is full of unknowns that tend to accompany critical
life illnesses and injuries. With one simple call, employees have direct access to a concierge service (“pod”), or a dedicated team of medical technicians and specialists, to help them navigate the healthcare maze of delivery options. Embedded in the infrastructure of the overall solution and inserted into the confines of the administrator, the employee concierge’s dedicated team has access to the data, the member’s health records and the providers. Being better connected to the human element helps to resolve issues, clarify points of concern and provide the best direction for employees; these services have been proven to impact health outcomes.
From a finance and funding perspective, an actuarial study conducted over 15 years demonstrated that concierge services provided to employees and dependents actually reduced claims by 17.5%. The boutique concierge service platform eliminates the 1-800-number call-center feel and replaces it with a laser focused, high-performance team that does one thing – answer the questions and provide guidance for employees and their dependents – that’s it! Because the dedicated teams take a very focused, specialized approach to create a better experience, employees are able to navigate easily amidst the complex healthcare delivery system in such
a way that no one feels alone. Imagine an employee who has just been diagnosed with a critical illness, receiving a communication similar to this:
“Hello, Mr. Smith. We are here to help you, we completely understand your health plan and we will ensure you receive the best services in the most expeditious manner possible. Now, let’s get started.”
Concierge services systems are proven to provide employees with better support in making consumer-driven healthcare decisions, which increases plan utilization. Return on investment studies have shown that claims decrease when usage increases. When employees routinely seek a doctor’s care, conditions that have a chance of becoming severe often can be caught early and are more easily treated, lowering the total cost of care. n
CAPTIV8’s solutions fully integrate employee concierge services for its members. To learn more, contact Susan Denzio at sdenzio@firstresourceinc.com.
Many leaders argue that their teams are just too busy to spend time discussing why a successful project went well. They just wrap up fast, then dive into the next project. So, the unspoken insights and unwritten lessons learned from that project rarely ever get shared or discussed. Often, they just get forgotten in the frenzy of working project after project.
Would you hire an engineer to build you a bridge if all that engineer ever studied was how bridges collapse? Would you hire a recruiter to find you a job if all that recruiter ever studied was how people get fired?
The best leaders help their teams learn regularly from their successes, not just occasionally from their failures. But learning from success happens automatically… doesn’t it?
Soldiers perform complex, dynamic, often dangerous missions. And they want to learn as much as they can from each one. In the 1980s, leaders in the US Army realized that they needed a practical way to help soldiers share the unspoken insights and unwritten lessons they learned from their missions. They realized that sharing tribal knowledge and applying tacit skill were key to winning wars. And since it was the Army, they developed a process -- a non-punitive, semi-structured, post job team debrief called an After Action Review (AAR).
After Action Reviews have proven so wildly effective that every branch of the military now uses them. And for some units like flight crews and Special Operations Forces, AARs are almost a religion. They’ve been called, “one of the most successful organizational learning methods yet devised.”
The process of leading a basic AAR is simple. Soon after your team completes a project, gather them in a private space for about 30 minutes, and ask these four questions:
● What did we set out to do?
● What did we actually do?
● How did it turn out the way it did?
● What will we do differently next time?
Have you ever had a discussion degenerate into a fact-free “war of opinions”? That’s the fate you’ll suffer if you start a debrief by asking for opinions. True, questions 3 and 4 are subjective and do indeed ask for opinions. But notice that questions 1 and 2 are much more fact-based. It may seem silly to ask, “What did we intend to do in this job?” But different people have different goals for the same job. The accountant on your team may have intended to maximize revenue. The safety specialist on your team may have intended to reduce the risk of injuries. The team leader may have wanted to finish the job ahead of schedule and under budget. So always start your After Action Reviews by getting facts with questions 1 and 2 before getting opinions with questions 3 and 4.
“What went well, and what went badly?” This may seem like a great question for a debrief. After all, it cuts straight to the point, right? Here’s the problem. This question nudges us to discuss blame, not improvements. And blame stops learning in its tracks. Look at the four After Action Review questions. There’s no hint of fault, failure or blame in any of them. That’s intentional. After Action Reviews focus on learning, not blame. Make sure you keep that focus in every AAR you lead.
Soldiers are fond of sayings like, “No mission plan ever survives contact with reality” or “The planning is more valuable than the plan.” And in reality, the percentage of complex missions that go exactly according to plan is nearly 0%. Soldiers and other experts in complex, dynamic systems know that in any given job, there’s always a gap between what we plan to do and what we actually do. Notice how
“AFTER ACTION REVIEWS FOCUS ON LEARNING, NOT BLAME. MAKE SURE YOU KEEP THAT FOCUS IN EVERY AAR YOU LEAD.”
question 1 asks about the plan. Some call this “Work as Imagined.” Question 2 asks about the actual job. Some call this “Work as Done.” When you lead your After Action Reviews, use questions 1 and 2 to explore this critical gap, but not eliminate it.
Some leaders do AARs only for accidents or errors. If you do that, your team will quickly associate AARs with failure. And they’ll give short, vague answers to get it over with as fast as possible. So, lead about 80% or more of your AARs for successful projects. That way, your team will learn to trust the process and value the results.
Unspoken insights and lessons learned are the most valuable things a team can discuss in an After Action Review. Those unspoken ideas have a half-life of hours or less. So, if you wait a day or more to lead your AAR, much of the priceless, unspoken wisdom will already have been lost, perhaps forever. So, lead the AAR as soon as the project wraps.
Most leaders like to answer questions. Usually that’s a good thing. But not in an After Action Review. If you give in to the temptation to answer the questions, you’ll shut your team down until the only person talking is you. So, in an After Action Review, remember that the leader is the person who talks the least. Choose your AAR leaders accordingly.
If you want a low-cost, low-risk way to build trust and expertise on your team, you will likely never find a more practical method than leading After Action Reviews. If the US Army has used them for 40+ years, just imagine what kind of value they could create for your team. n
Jake Mazulewicz, Ph.D. shows leaders in high-hazard industries why errors are signals, not failures, and how to address the deeper problem, so that everyone can work more reliably and safely. He keynotes and advises globally. He has a decade of experience in Safety for electric utilities, and served as a firefighter, an EMT and a military paratrooper. To learn more, visit www.reliableorg.com.