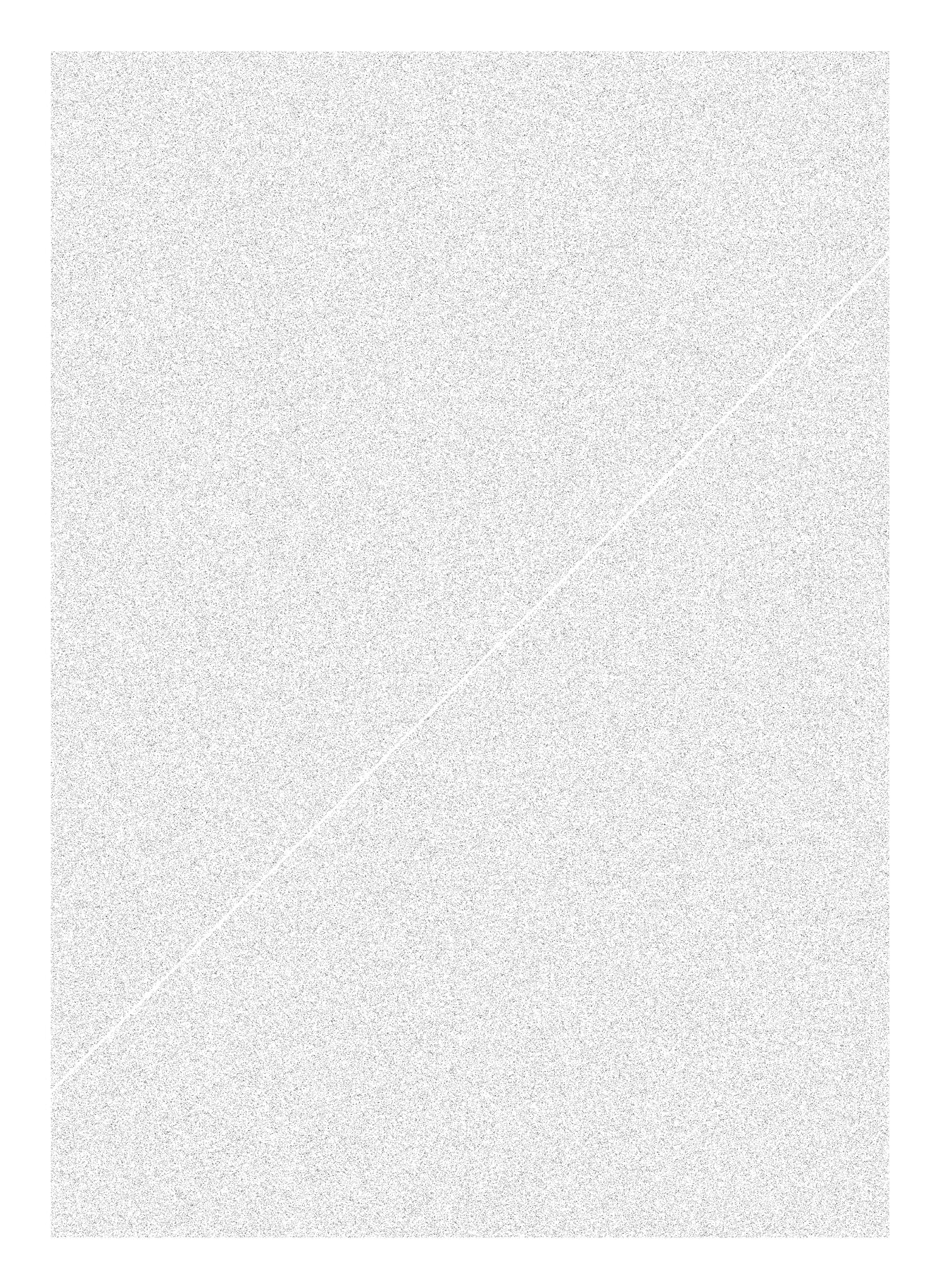
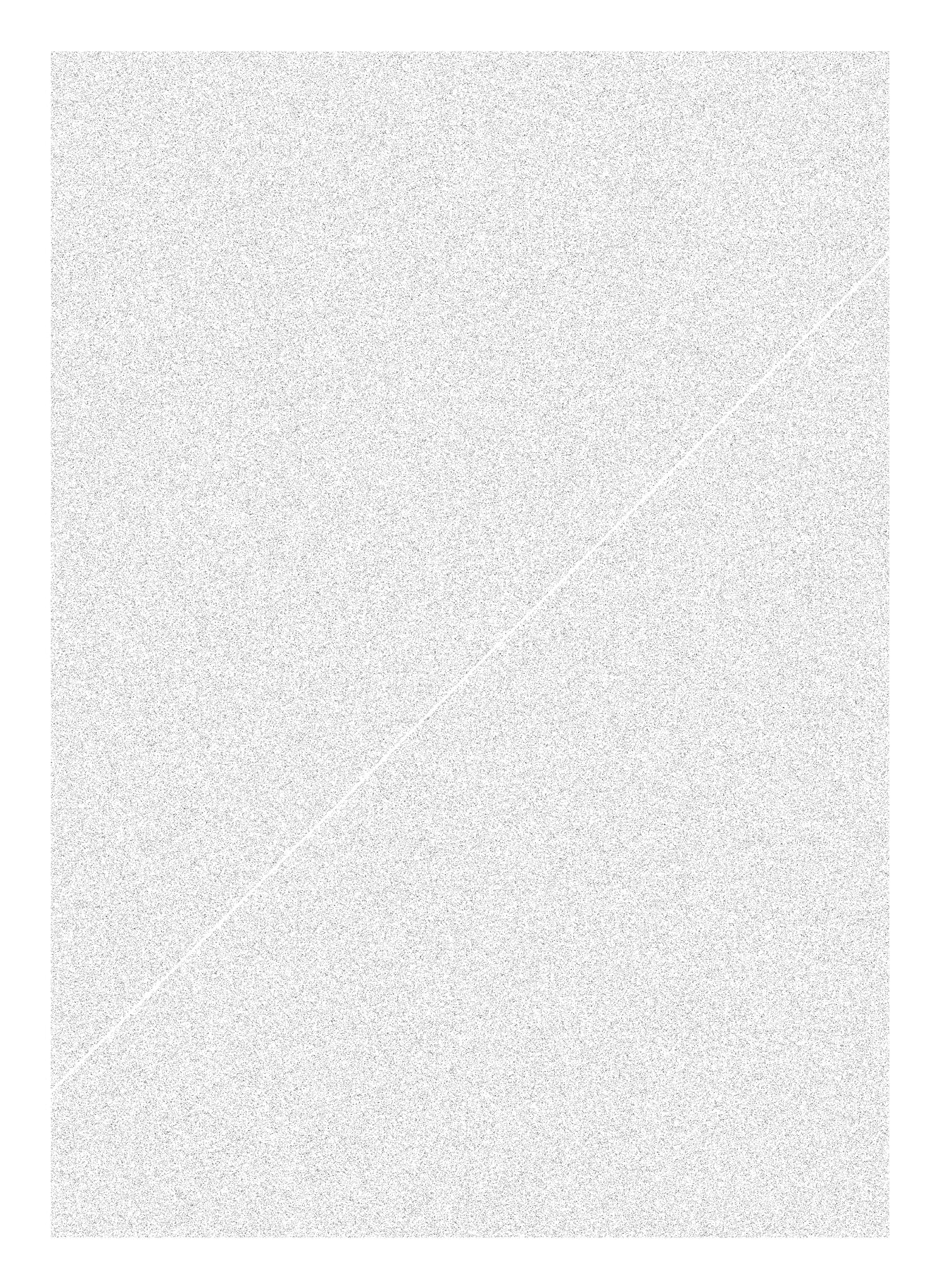
ISSUE 29
COMING UP
4 THE CRITICAL ROLE OF SEALING GASKETS IN ELECTROLYSERS
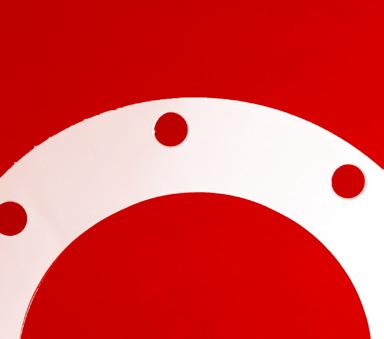
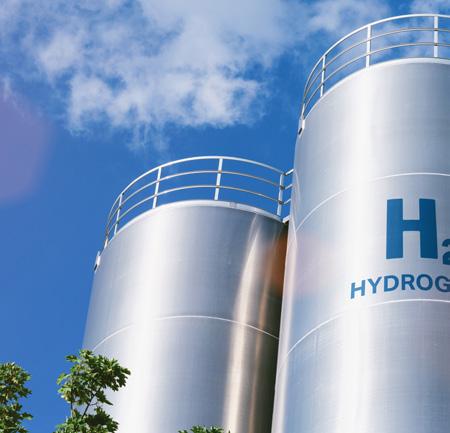
8
ADVANCING THE SAFETY LANDSCAPE THAT UNDERPINS THE HYDROGEN ECONOMY
16 BRIDGING THE GAP BETWEEN INNOVATION AND COMMERCIALISATION

20 THE EXECUTIVE SUMMARY
DECARBONISING ONE OF WORLD’S MOST POLLUTING SECTORS WITH ELEMENT 1
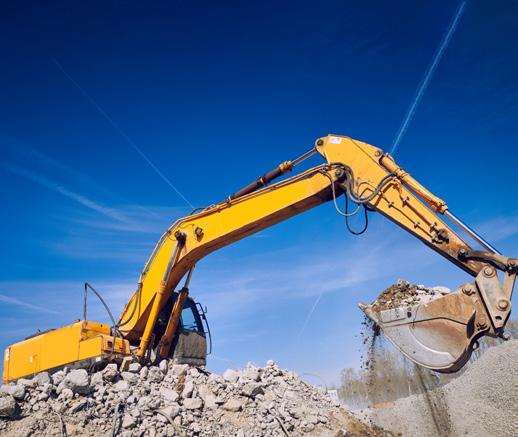
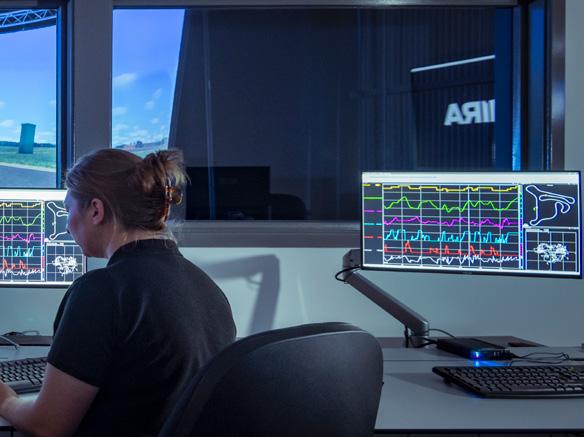
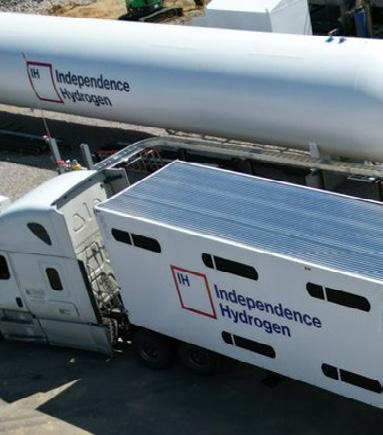
FOREWORD
“Bridging the gap between innovation and commercialisation is a continued and growing conversation”
Welcome to the latest edition of Hydrogen Industry Leaders, a magazine dedicated to the pioneers and visionaries shaping the future of the hydrogen economy. In this issue, we explore the innovations, challenges, and triumphs of an industry that stands at the forefront of the global energy transition.
In this edition, we delve into the latest technological advancements from hydrogen safety, to storage and distribution innovations. We also examine the policy frameworks and market dynamics driving investment and growth in hydrogen infrastructure worldwide.
Our featured articles highlight successful projects and collaborations that are setting benchmarks for the industry. We hear from leaders who are navigating the complexities of scaling up production and ensuring the sustainability of the hydrogen value chain. These stories of determination and ingenuity underscore the pivotal role of industry leaders in steering us toward a greener future.
Floyd March Editor f.march@peloton-events.co.uk
Hannah Wintle Multi Media Journalist
Paul Rose Graphic Designer
THE CRITICAL ROLE OF SEALING GASKETS IN ELECTROLYSERS
BY ANGELICA PAJKOVIC, JOSMAR CRISTELLO, IGOR MEIRA, & JOHANNES MUELLER
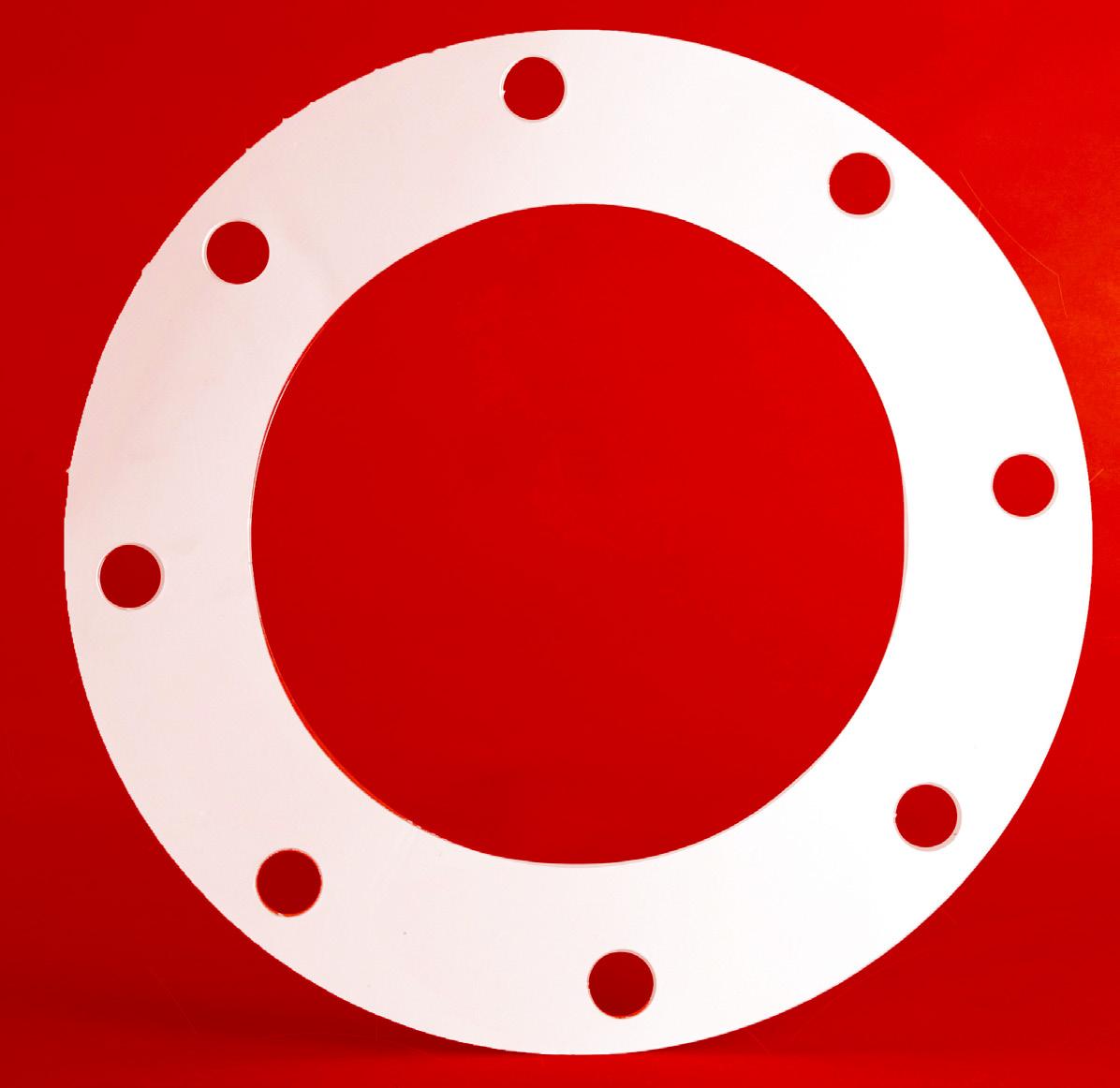
As the world pivots towards sustainable energy solutions, hydrogen production through electrolysis has emerged as a vital component in the global energy transition. Electrolysers, which split water into hydrogen and oxygen using electricity, are at the heart of this process. The efficiency and longevity of these systems are critically dependent on the integrity of their sealing gaskets, which play an essential role in ensuring the overall effectiveness and reliability of the process.
UNDERSTANDING ELECTROLYSER COMPONENTS
An electrolyser is a device that uses electricity to drive a chemical reaction, specifically the splitting of water (H₂O) into hydrogen (H₂) and oxygen (O₂). This process, known as electrolysis, is fundamental in producing green hydrogen, a clean energy source that comes from renewable energy sources like wind, solar, or hydropower and can be used in various industries, including transportation, power generation, and chemical manufacturing.
There are two primary types of electrolysers: Alkaline Electrolysers (AEL) and Proton Exchange Membrane (PEM) electrolysers.
Alkaline Electrolysers (AEL) have been used for decades and operate using a liquid electrolyte, usually potassium hydroxide (KOH), to conduct electricity. They are known for their durability and lower capital costs but are typically larger and less responsive to fluctuations in power supply.
Proton Exchange Membrane (PEM) use a solid polymer electrolyte, are more compact, can achieve higher current densities, and produce hydrogen at higher purities. They are often preferred for applications that require rapid start-up and integration with intermittent renewable energy sources. The primary drawback of PEMs is their higher cost due to the use of precious metals like platinum and iridium in their construction.
The efficiency of the electrolyser depends on how effectively this process occurs. High-efficiency electrolysers minimize energy losses and reduce the operational costs of hydrogen production
The efficiency of the electrolyser depends on how effectively this process occurs. High-efficiency electrolysers minimize energy losses and reduce the operational costs of hydrogen production, making the overall process more economically viable. Factors such as the quality of the electrodes, the effectiveness of the membrane, the purity of the input water, and the sealing gaskets all contribute to the electrolysers’ efficiency and, ultimately, the cost-effectiveness and sustainability of hydrogen production.
THE IMPORTANCE OF GASKETS
In an electrolyser, cell frames are used to separate the individual cells that house the unit’s anode and cathode. Positioned between each cell frame, gaskets prevent leaks, maintain system pressure, preserve the purity of the hydrogen produced, maintain electrical insulation, and ensure overall efficiency.
In addition to preventing leaks, a well-functioning gasket must withstand the compression forces exerted by the plates and frames, ensuring that they do not deform or intrude into the flow channels. Any such intrusion could block the flow of gases or liquids, reducing the electrolysers’ efficiency.
Understanding which gasket materials and fabrication methods result in the most reliable seal can help safeguard against unnecessary risks and ensure that the gasket is compatible with the electrolysers’ operational environment.
MATERIAL SELECTION
When it comes to gaskets, Polytetrafluoroethylene (PTFE) is renowned for its exceptional chemical resistance, thermal stability, and insulative and low friction properties. It is virtually inert to almost all chemicals, making it an ideal material for the harsh environments within electrolysers. However, not all PTFE gaskets are created equal. The performance characteristics of PTFE gaskets can vary significantly based on their manufacturing processes and the quality of the raw materials used. PTFE gaskets can be broadly categorized into three types:
f Skived PTFE
f Structured PTFE
f Expanded PTFE
SKIVED PTFE
Skived PTFE gaskets are produced by slicing thin layers from a solid PTFE billet in a process known as skiving. While skived PTFE retains the inherent chemical resistance of PTFE, it has a higher tendency for creep and cold flow under load due to its relatively low mechanical strength. Creep is the tendency of a solid material to slowly move or deform under mechanical stresses. In gasket applications, this means that over time, especially under sustained pressure and temperature, skived PTFE gaskets may flow, leading to a loss of sealing integrity.
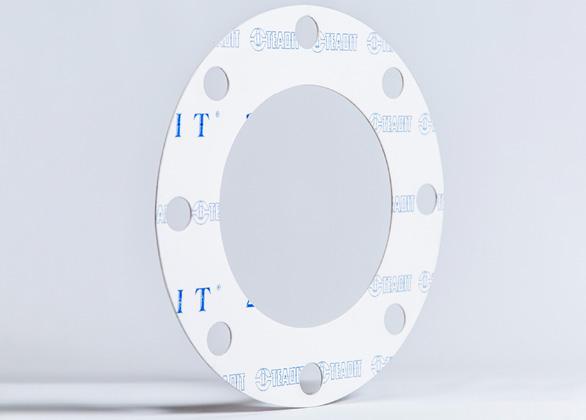
STRUCTURED PTFE
Structured PTFE gaskets are manufactured by introducing fillers—such as hollow glass microspheres, barium sulfate, or silica—into the PTFE matrix, followed by a calendering process. The combination of these two important steps not only enhances the mechanical properties of PTFE by reducing its tendency to creep but also orients the PTFE molecules, resulting in improved strength and stability. The fillers interlock with the PTFE molecules, creating a more robust structure and imparting different properties depending on the filler type used. Structured PTFE gaskets exhibit better load-bearing capabilities and reduced deformation under stress, making them reliable for long-term applications.
EXPANDED PTFE
Expanded PTFE (ePTFE) gaskets are produced through a specialized process that expands the PTFE material, creating a microporous structure with multidirectional strength. This expansion results in a gasket material that combines excellent chemical resistance with superior mechanical properties, including high compressibility and resilience. The multidirectional fibrillation of PTFE molecules enhances its strength and reduces creep. ePTFE gaskets, such as Teadit 24 SH, have a lower tendency for creep and can maintain a reliable seal over extended periods, even under fluctuating temperatures and pressures. Additionally, ePTFE gaskets are very soft and conform easily to flange surfaces, effectively sealing even surfaces with minor imperfections or irregularities.
CONNECTING MATERIAL CHOICE TO ELECTROLYSER PERFORMANCE
Selecting skived PTFE gaskets in electrolyser applications poses risks due to their propensity for creep, which can lead to seal failure over time. This is particularly detrimental in electrolysers, where maintaining a consistent seal is vital for efficiency and safety. The loss of seal integrity can result in gas leaks, cross-contamination of the gas flow channels, and decreased system performance.
In contrast, structured and expanded PTFE gaskets offer improved mechanical strength and reduced creep, making them more suitable for demanding environments within both PEM and alkaline electrolysers. Their enhanced properties ensure that the gaskets can withstand operational stresses over the long term, maintaining seal integrity and contributing to the overall efficiency and reliability of the hydrogen production process. Furthermore, PTFE fluoropolymers provide excellent electrical stability across various environmental conditions, setting them apart from other insulating materials. For reference, pure PTFE exhibits superior electrical properties, with a high dielectric strength of around 24 kV/mm.
In
PEM
electrolysers,
where gaskets must perform under limited bolt preload and very thin gasket thicknesses, structured PTFE gaskets like Tealon 1570 are particularly effective
For example, in PEM electrolysers, where gaskets must perform under limited bolt preload and very thin gasket thicknesses, structured PTFE gaskets like Tealon 1570 are particularly effective. The incorporation of fillers enables these gaskets to maintain a reliable seal even under the lower bolt loads typically found in PEM systems.
On the other hand, in alkaline electrolysers, expanded PTFE gaskets like Teadit 24 SH are widely used and can withstand harsh operating conditions without significant degradation. This resistance to chemical attack extends the service life of the gaskets, reducing the need for frequent maintenance and replacement.
Thanks to their chemical resistance, mechanical strength, and performance-enhancing fillers, both structured and expanded PTFE gaskets offer versatile solutions for different electrolyser types. While this article highlights a few examples, additional expanded and structured PTFE gaskets can also be specified or custom-selected to meet the unique requirements of each electrolyser. Even within PEM or alkaline electrolysers, variations in design, operating conditions, and performance requirements may necessitate different gasket solutions to ensure optimal sealing performance.
CHALLENGES AND INNOVATIONS
The development of gaskets for electrolysers is an ongoing process, with manufacturers continuously testing and refining their products to meet the specific needs of different electrolyser technologies. One of the key challenges in this field is ensuring that gaskets can withstand the operating temperatures and pressures typical of hydrogen production without losing their sealing capabilities.
For instance, some materials initially considered suitable for alkaline electrolysers have been found to have chemical incompatibility issues. In highly alkaline environments, certain gasket materials may degrade or react chemically, leading to premature failure and potential safety hazards. This highlights the importance of selecting materials specifically suited to the chemical environment within the electrolyser.
To achieve high sealability in electrolysers, it is essential to consider several factors
ACHIEVING OPTIMAL SEALABILITY
To achieve high sealability in electrolysers, it is essential to consider several factors:
1. Material Compatibility: Ensure the gasket material is chemically compatible with the electrolysers’ fluids, gases, and electrolytes.
2. Sealability Performance: Choose a gasket that can provide an effective seal with the available bolt preload, ensuring reliable sealing with the given mechanical constraints.
3. Mechanical Properties: The gasket must have the appropriate compression and stress resistance to maintain a seal without deforming or intruding into flow channels.
4. Temperature and Pressure Resistance: The gasket material should withstand the operating temperatures and pressures without losing its sealing properties.
5. Durability: Long-term chemical and mechanical degradation resistance is crucial to reduce maintenance costs and ensure continuous operation.
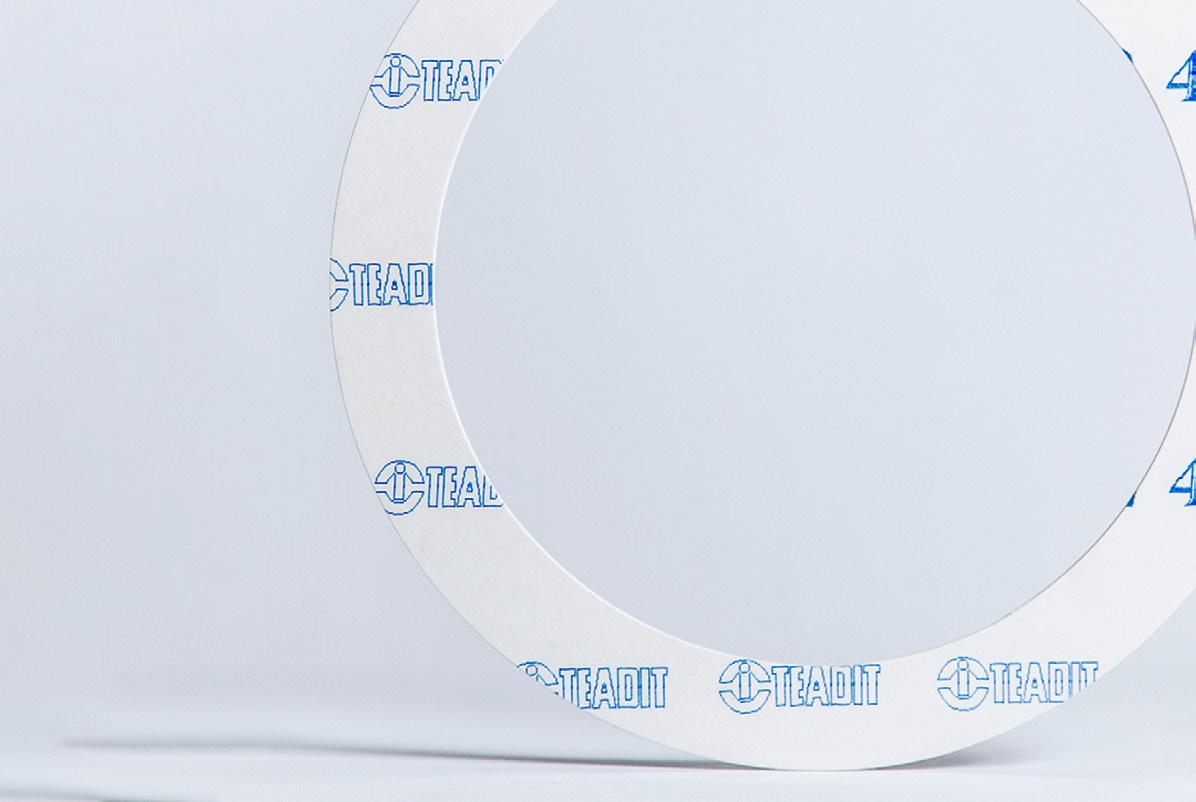
FINAL THOUGHTS
The role of gaskets in electrolysers cannot be overstated. As the demand for hydrogen production grows, the need for reliable, high-performance sealing solutions will only increase. By focusing on material compatibility, mechanical resilience, and durability, manufacturers can ensure that their gaskets contribute to the efficient and safe operation of electrolysers. As research and development in this field continues, one can expect even more advanced gasket solutions tailored to the specific needs of this critical technology.
ADVANCING THE SAFETY LANDSCAPE THAT UNDERPINS THE HYDROGEN ECONOMY
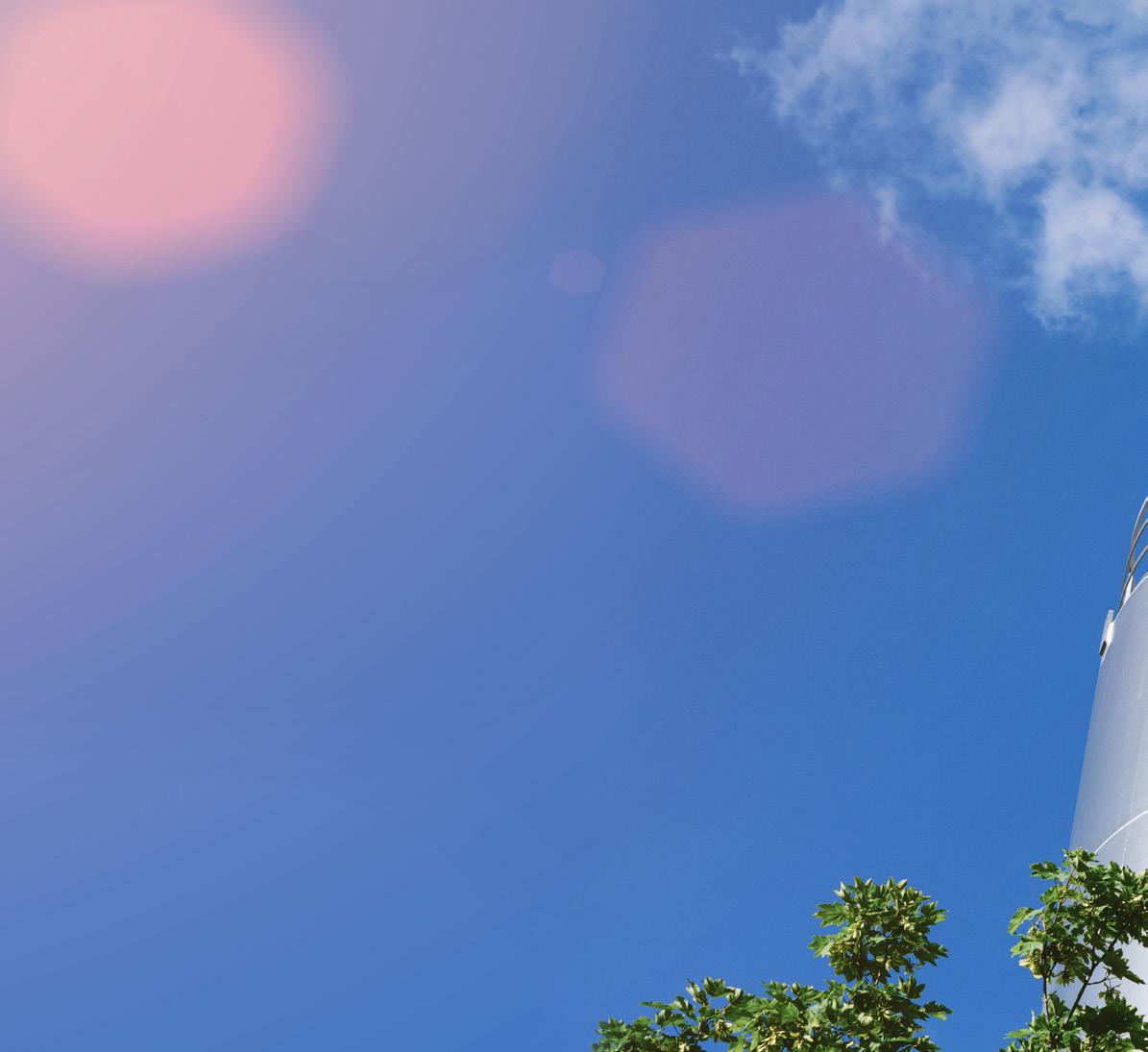
Growing the hydrogen economy and transitioning towards its use as an energy of the future is dependent on numerous factors, but arguably none so important as safety. Ensuring hydrogen is safe to use and work with forms the most base level of its uptake, instilling confidence in investors and triggering essential policy reform.
But as global climate deadlines draw closer, just how much work still needs to be done to ensure this crucial underpinning is in place? Hydrogen Industry Leaders spoke to Nick Smith, President of the International Association for Hydrogen Safety (HySafe), to understand the progress made to date and the work still to be done.
Everyone deserves to go home safely at the end of every day. In Maslow’s hierarchy of needs, aside from food and water, it’s the next biggest thing. It’s the most important thing.
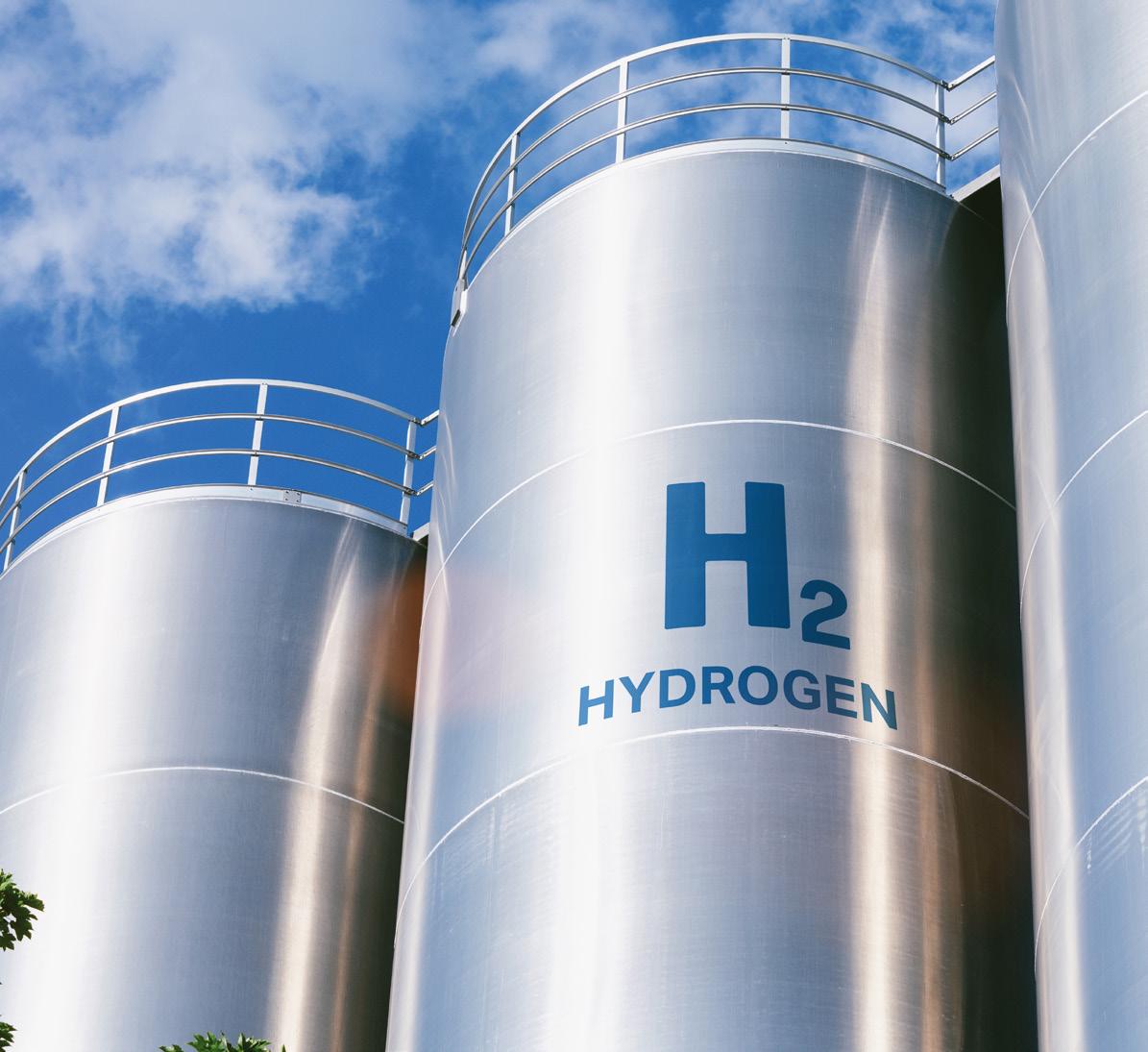
THE HYDROGEN SAFETY LANDSCAPE TODAY
The International Association for Hydrogen Safety has around 70 members worldwide, including universities, government organisations, and industry, and was initially created in 2005 out of the EU Centres of Excellence, before being formally established in 2009. “Its role is really to be a focal point for hydrogen safety, and the sharing of knowledge and research into hydrogen safety,” Nick said.
Today, safety considerations stem from the ambition to broaden hydrogen’s use across more industries than it has traditionally been utilised in. Nick explained: “Hydrogen’s not new. It’s been used by industry for close to 100 years. It’s well known in terms of its gaseous form and how it’s been utilised particularly by the refining industry and the ammonia industry.
I think where the challenges in hydrogen safety come in when we’re now looking at novel uses of hydrogen.
Two key areas of consideration when it comes to safety must therefore be considered:
1. Firstly, the use of liquid hydrogen in particular, as opposed to gaseous hydrogen, is of increasing interest around the world, and understanding its behaviour is integral to determining how best to produce, store, and transport it safely.
2. Secondly, if hydrogen is likely to be used at scale in new industries, such as the steel and cement industries, the consequent education piece around using hydrogen and hydrogen equipment is vital.
Of course, the issue of hydrogen safety in its entirety stretches far beyond these two areas, and Nick pointed out that even in sectors that have experience in using hydrogen, new players entering these markets will also need to be able to ensure its safe use.
THE HYDROGEN ECONOMY IS BUILT UPON SAFETY
Despite vital safety considerations, the journey to adoption is seen by many as an essential road to travel, with hydrogen slated to play a considerably large role in the upcoming energy transition.
While certainly not a silver bullet, intrigue around its potential is growing worldwide. For instance, as of May 2024, the global hydrogen project pipeline has increased seven-fold since 2020, from 228 projects to 1572, according to the Hydrogen Insights 2024 report.
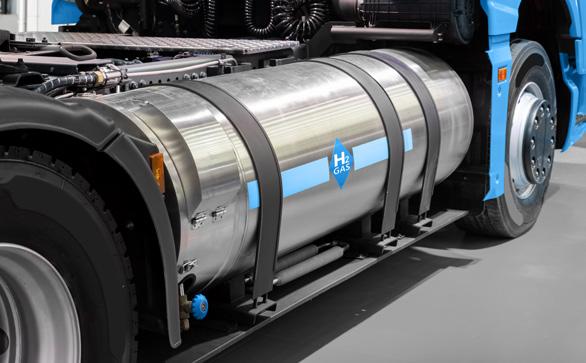
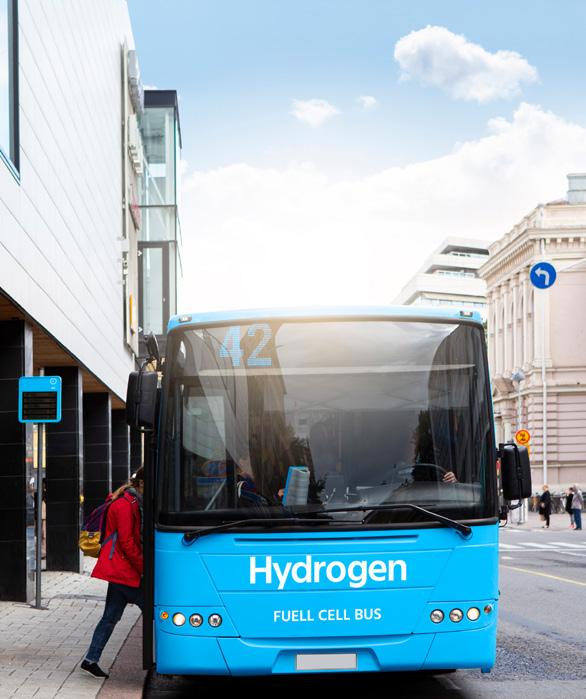
Furthermore, clean hydrogen projects that reached FID have also seen a seven-fold increase in committed investment, growing from approximately USD 10 billion across 102 projects in 2020 to USD 75 billion across 434 projects in 2024.
It is interesting to see how the economics have played out over the years, with trends suggesting that investor confidence is on the rise. As a key driver to maintain and increase confidence, ensuring hydrogen safety and continuing to develop safety procedures and education will ensure this momentum is maintained, and encourage further investment into the sector.
Nick added: “If you’re able to de-risk it and use it wisely, then you actually lower the cost of introducing hydrogen into the economy more broadly, and you build confidence and trust with consumers, industry, and regulators.
“Hydrogen safety is really important in terms of minimising cost to hydrogen adoption in the economy because it really plays a role in building that trust and certainty for regulators, consumers, communities more broadly and therefore industry and investors.”
SHARING BEST PRACTICE WITH
A GLOBAL NETWORK
HySafe built its global consortium with the view to share best practice globally, and support the burgeoning hydrogen sector by bringing together the research, education and commercial interests essential to its success.
Collaboration and knowledge sharing, therefore, plays a vital role as it enables global consistency and unlocks efficiencies. “From the association’s perspective, we’ve also had to look at where the demand is coming from for information and research,” Nick highlighted.
“We don’t have members in South America or Africa at the moment. We need to look at these areas where there’s potentially going to be significant hydrogen projects at scale, and uses of hydrogen.”
Ensuring the knowledge that already exists within the global hydrogen safety community is shared with these regions is crucial to ensuring that the work and research that has already been completed isn’t replicated, but rather added to and enriched.
Nick added: “[These regions] are able to use this education and knowledge of regulatory frameworks, codes, and standards to lower costs
and apply best-in-show information to enable their industry to thrive without incident, because as soon as you have a safety incident, consumer trust dissipates quite rapidly and it takes very long time to rebuild that.”
To facilitate this level of global knowledge sharing, HySafe holds its International Conference on Hydrogen Safety (ICHS) every other year, and publishes the resulting papers and reports.
Nick highlighted that the appetite for collaboration is only growing as the hydrogen economy expands, to the point that HySafe has just started their own journal - the International Journal on Hydrogen Safety - to continue publishing the best papers and research on a regular basis.
The
main reason for collaboration is
that you need to have that consistency of thinking around what is safe, what’s been tested, what’s been proven, and how you apply that to regulations, codes and standards.
HYSAFE IS FACILITATING PROGRESS IN SPITE OF ROADBLOCKS
As HySafe strives to support the hydrogen economy to achieve its full potential, it is important to identify the obstacles still in place.
The cost of electricity and equipment, the challenges brought on by the war on Ukraine, and supply chain impacts from COVID are all factors that are still being worked through, but Nick also emphasised that we have yet to achieve global regulatory harmony.
“The industry hasn’t had the chance to scale up properly yet,” he said. “We haven’t got regulations and codes and standards that are harmonised. We don’t have certification of origin of hydrogen to say which is green, blue, pink, or grey.”
HySafe has facilitated progress not only through their conferences, where industry presents their latest work for consideration and review, but also through the consortium’s members, such as research institutions that fund government work in
specific areas such as the safe use of hydrogen in residential areas.
Additionally, HySafe holds a Research Priorities Workshop every other year to prioritise and address areas where gaps have been identified, with a report published afterwards.
“We do tend to share that more broadly with targeted audiences to help with investment, funding, research and areas where we think there needs to be additional focus, because there’s still uncertainty in the hydrogen safety community.”
While there is still a way to go, the ongoing collaboration between government, industry, and research organisations, and the support facilitated by HySafe, is advancing understanding around hydrogen safety and facilitating progress in the sector, strengthening the foundation that the hydrogen economy is built upon.
DECARBONISING ONE OF WORLD’S MOST POLLUTING SECTORS WITH ELEMENT 1
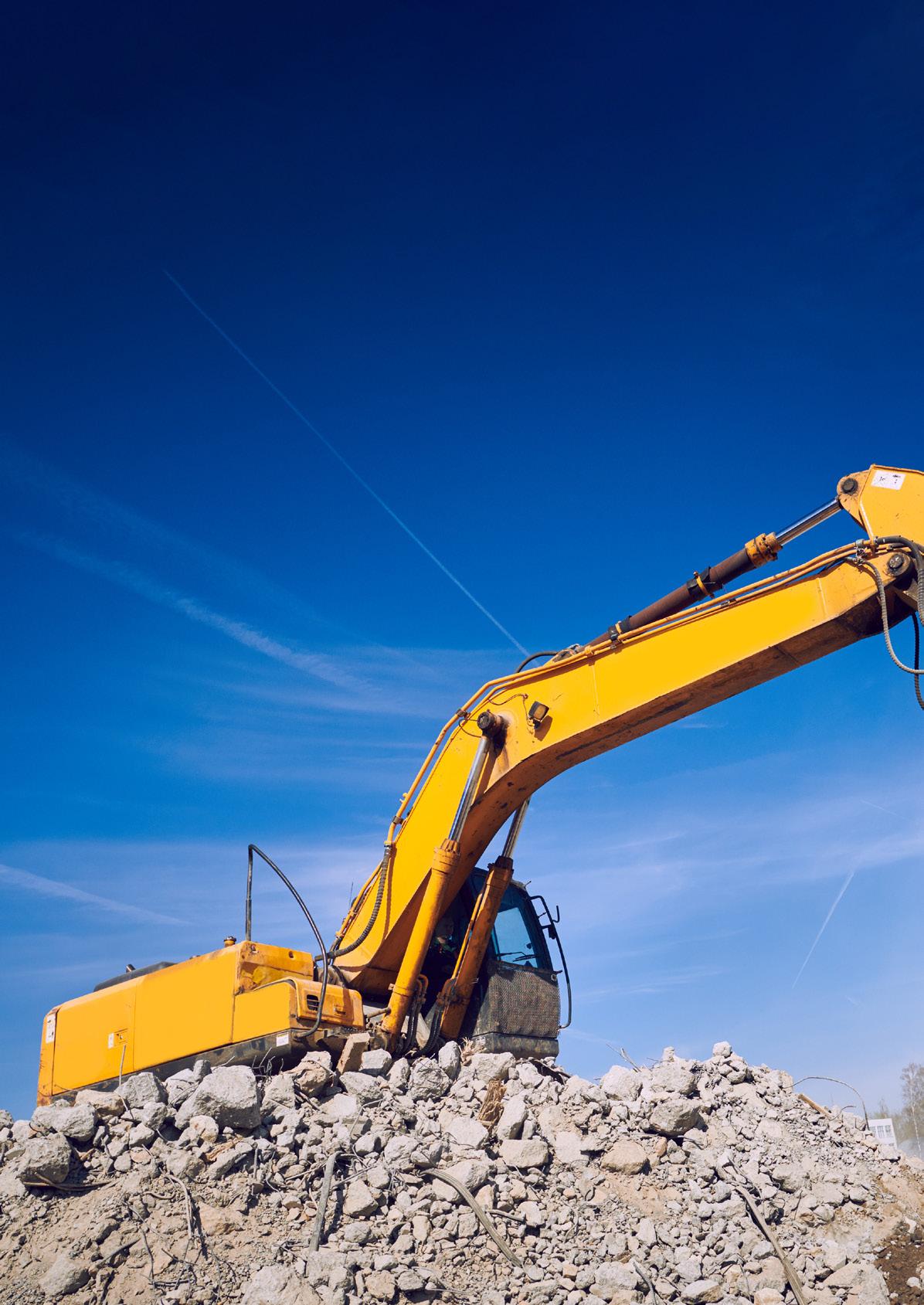
DECARBONISING WORLD’S POLLUTING WITH
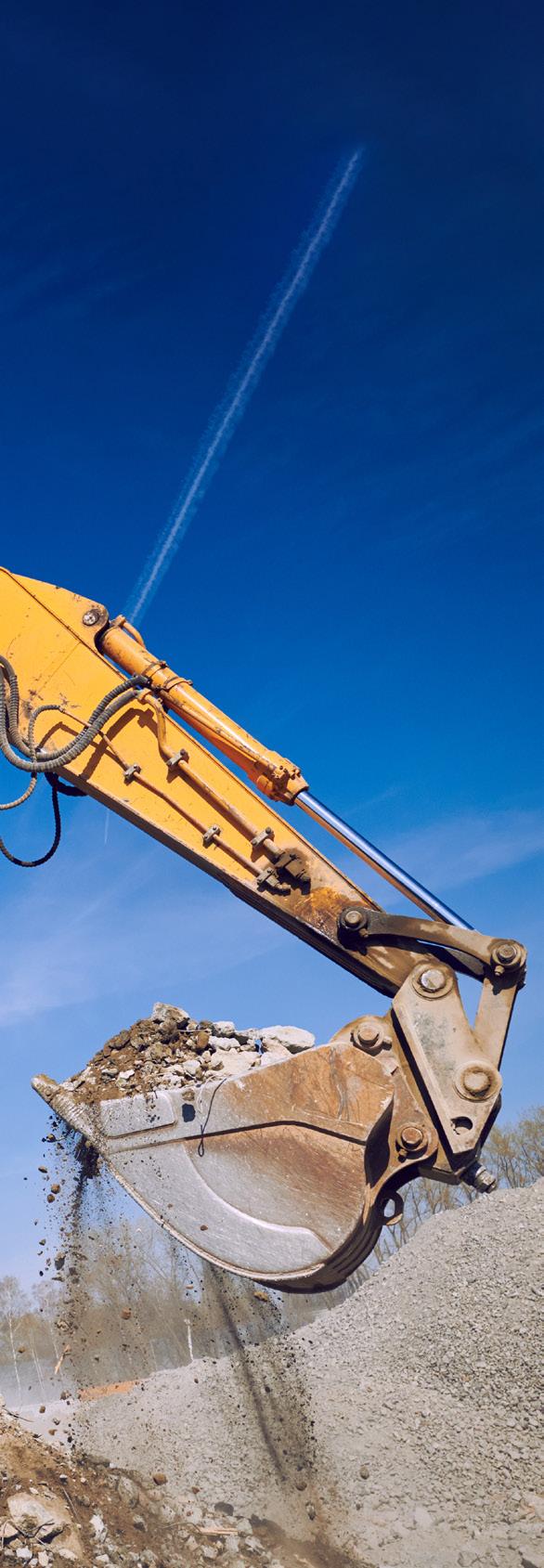
Responsible for a staggering 37% of global emissions, the buildings and construction sector is one of the largest emitters of greenhouse gases, thanks in part to the production and use of carbon intensive materials such as cement and steel.
As global efforts continue to focus on decarbonising these hard-to-abate industries, the mission to bring emissions down in the construction sector doesn’t end there, and the use of hydrogen to make further progress is increasingly being explored.
One such project doing just this is Element 1, a cross-industry consortium with the shared vision of a net zero construction sector. Specifically, their aim is to reduce and ultimately eliminate the use of diesel on construction sites, and are exploring the ways hydrogen can be utilised to meet this end.
Their
aim is to
reduce and ultimately eliminate the use of diesel on construction sites, and are exploring the ways hydrogen can be utilised to meet this end.
Led by BAM, who worked on Phase 1 of the Red Diesel Replacement Programme and are experienced in introducing additional capability from the hydrogen sector, the project brings together and leverages the expertise of various other players from the construction, hydrogen, and research sectors, including contractors and suppliers, and is funded by a £4.8 million UK Government grant.
With a goal to completely eliminate the use of diesel fuel on all UK construction sites by 2040, Element 1 is centring hydrogen as the alternative, and exploring how it can be utilised in such a way that is scalable, commercially viable, and globally applicable.
Element 1’s first demonstration took place at the end of October in Manchester, after hitting multiple milestones at the facility over the course of the year.
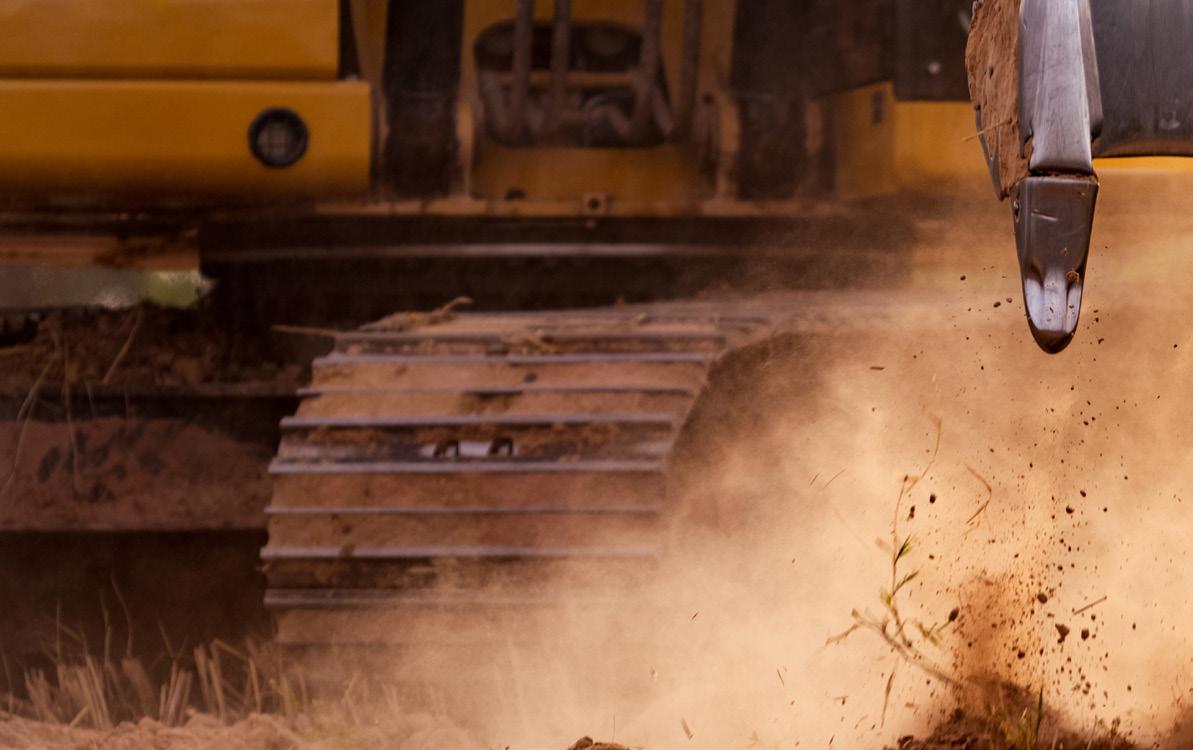
THE PROJECT SEEKS TO REDUCE EMISSIONS FROM
OFF-HIGHWAY CONSTRUCTION EQUIPMENT
Each year, more than one billion litres of diesel is used in the UK infrastructure construction sector, to power construction plant and generate electricity, lighting, and heating.
With up to 30,000 items of construction plant in use in the UK, emitting around 14Mtonnes of CO2 per annum, construction plant manufacturers are looking for routes to decarbonise. As such, smaller plant are turning to electrification as a method to decarbonise.
Element 1, on the other hand, seeks to address larger mobile construction plant, which are particularly difficult to convert to batteries due to the power required for operation, as well as the charging infrastructure needed.
As in any sector that recites the ‘no one silver bullet’ mantra, construction plant will likely utilise both types of power to facilitate the wide range of tasks they are needed for.
Funded by the Department for Energy Security and Net Zero, the project will introduce an endto-end hydrogen solution for construction sites, through their ambitions to accelerate hydrogen manufacturing and supply chain efficiency including off-site and on-site production, offgrid compression, and innovative storage and distribution solutions.
The project aims to create a system that replaces current diesel engines with ones able to use 3050% hydrogen. This not only reduces diesel usage and accelerates diesel replacement, it also enables existing plant use over its remaining life cycle to eliminate the carbon footprint of scrapping any machinery before the end of its lifespan.
The partners involved - BAM, Skanska, Flannery & Plantforce, ULEMCo, GeoPura, Reynolds Logistics, and BRE - are collaborating on the project over the course of its two year run, during which time its capabilities and practical solutions have been demonstrated before deployment is planned for Q4 2024.
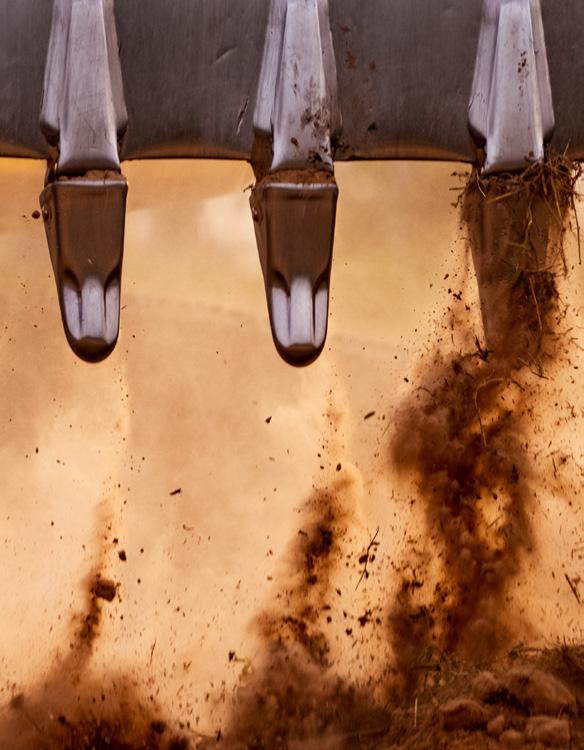
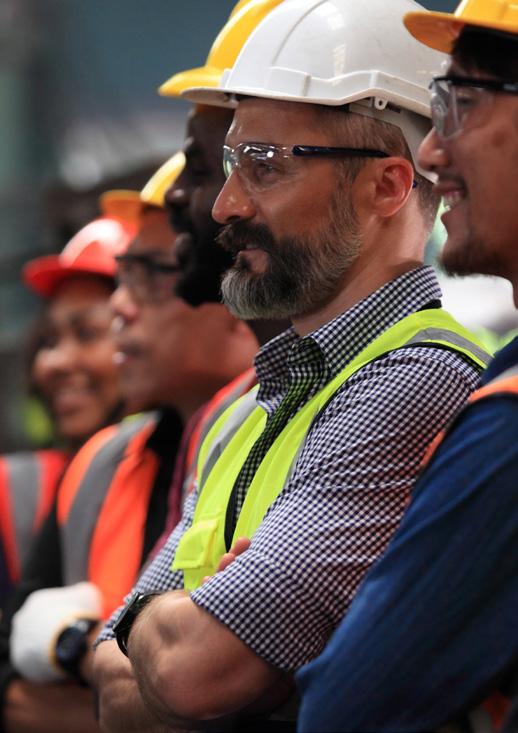
THE PROJECT’S SUCCESS TO DATE DEMONSTRATE SIGNIFICANT MILESTONES FOR
THE SECTOR
Element 1’s first demonstration took place at the end of October in Manchester, after hitting multiple milestones at the facility over the course of the year.
After completing tests on a Caterpillar 320 excavator to identify the percentage of diesel replacement, and designing an engine map to ascertain the optimum amount of hydrogen that can be introduced without impacting engine performance, the consortium successfully installed hydrogen tanks and control systems to two of the excavators in early August.
More recently, at the end of September, the project replicated this success by successfully installing hydrogen tanks and control systems to two Kobelco SK210 excavators, following similar testing.
The installation of these systems includes lifting the tank assembly onto each of the two excavators and attaching it to the body of the machine. The hydrogen fuel management system control unit is then attached and connected to the engine management system. The final part of the process is the installation of the Human Machine Interface (HMI) in the cab which displays key system information to the operator.
This latter milestone also signified the completion of the first full fleet of converted excavators ready for deployment, and marked a significant step in the project’s journey to eliminate diesel on construction sites.
Certainly, the progress made in Manchester highlights a significant step forward for this carbon intensive industry, and demonstrates the application of alternative fuels alongside electrification in the run-up to the energy transition.
As the wider construction sector continues to reduce its reliance on fossil fuels, whether through the materials produced or equipment used, Element 1’s mission to tackle construction plant demonstrates the potential that hydrogen specifically has to play in meeting net zero targets.
BRIDGING THE GAP BETWEEN INNOVATION AND COMMERCIALISATION
Since its formation as the Motor Industry Research Association in 1946, HORIBA MIRA has positioned itself at the forefront of automotive innovation. Today, as the world shifts towards a net zero future, MIRA Technology Park in Nuneaton, Warwickshire, is facilitating sustainable change as the transport sector strives to adopt greener technologies.
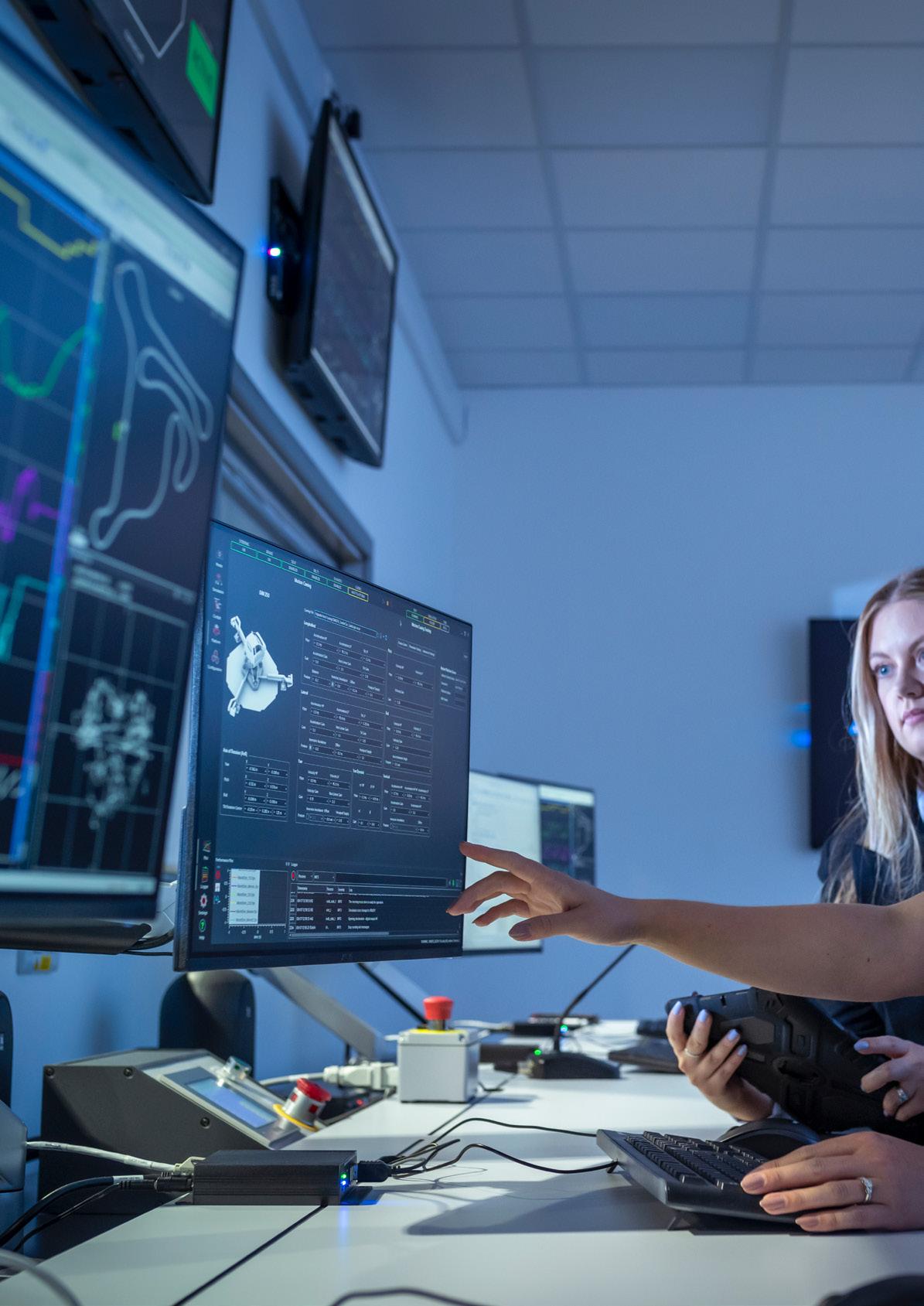
At the latest instalment of HIL 100 Breakfast Hub, Hydrogen Industry Leaders joined HORIBA MIRA at the Tech Park to hear how its facilities, technical expertise, and industry connections can help bridge the gap between R&D and the commercialisation of hydrogen technology.
AND COMMERCIALISATION
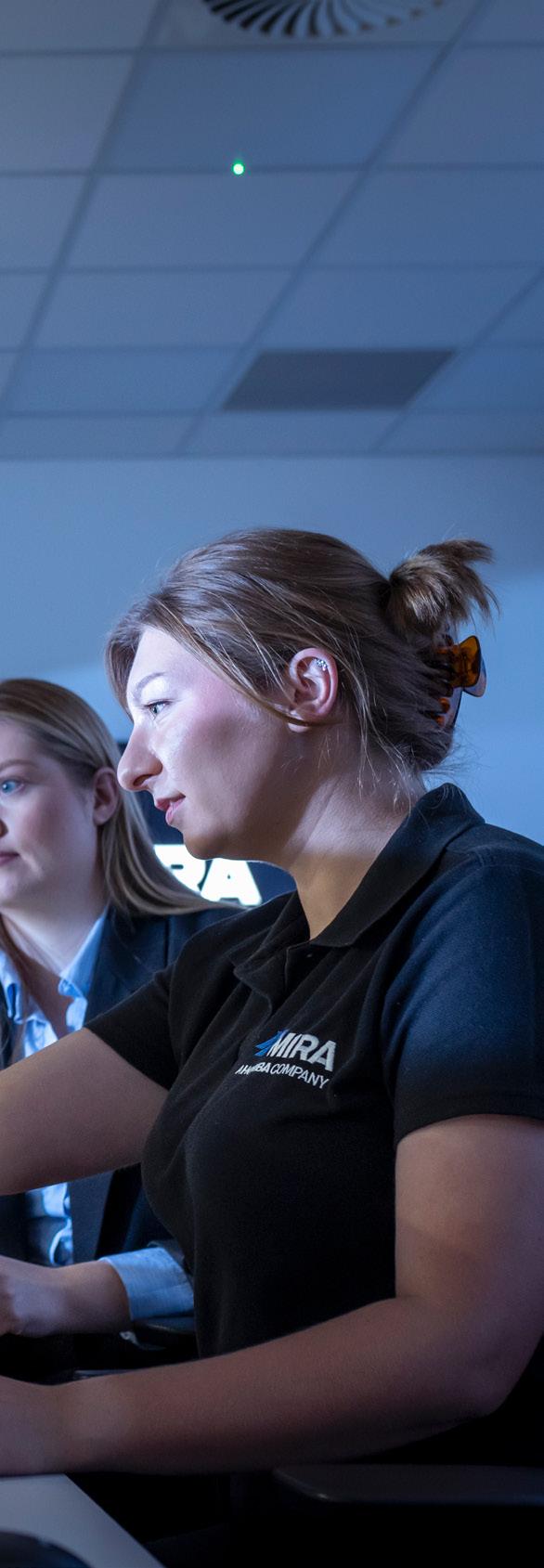
MIRA TECHNOLOGY PARK IS A CATALYST FOR DEVELOPMENT
As Europe’s leading mobility R&D location, MIRA Tech Park has more than 40 major test facilities and the UK’s most comprehensive proving ground, as well as being home to more than 35 global OEMs, Tier 1 suppliers, and specialist technology companies.
The purpose-designed campus creates a unique collaborative ecosystem, bringing together world-class facilities and skilled engineers to provide a location for innovation and technological development.
I think it’s really important to highlight that the success of the cluster has been around bringing that customer base and innovation together.
Sarah
Windrum, Future Mobility Cluster Lead, HORIBA MIRA
As the UK hydrogen economy grows, ensuring industry can develop hydrogen innovations on the site has become a priority for HORIBA MIRA.
Sarah Windrum, Future Mobility Cluster Lead at HORIBA MIRA, explained: “What’s been really important for us is that we remain technology agnostic. We want to work with all the companies and the new innovation that they’re developing.
“What we’ve done is made significant investment in our facilities in terms of making them hydrogen enabled and hydrogen ready so that you can develop a hydrogen vehicle here, just as you can develop a battery electric vehicle here.”
In a bid to promote sustainability, MIRA Tech Park is also currently building a solar PV array to facilitate the production of the site’s own green hydrogen supply, which will provide a sustainable supply of hydrogen to their customers.
Similarly under construction, Sarah drew attention to the Tech Park’s South Site, where outline planning has been approved for advanced manufacturing. She said: “What we’re looking to do is build on the tenants that we’ve got here on the park, on their R&D and their development, offering them a space where they can start to manufacture at scale.”
PROJECT ICEBREAKER
As MIRA Technology Park increasingly looks As MIRA Tech Park increasingly looks towards how it can uplift the hydrogen economy, Simon Dunnett, Technical Sales Manager - Net Zero & Vehicle Propulsion, emphasised the strides currently being made for heavy goods vehicles through Project ICEBreaker.
As an R&D proof of concept initiative, the project seeks to demonstrate hydrogen’s effectiveness in HGVs, and ascertain whether this can be made commercially viable for freight companies.
Funded through The Advanced Propulsion Centre, Project ICEBreaker is a collaborative venture between Viritech, HORIBA MIRA, and Intelligent Energy to develop a 44-ton hydrogen fuel cell truck that addresses the challenges industry faces in its attempt to decarbonise the 500,000 HGV’s in operation on UK roads.
The demonstrator vehicle, which debuted at Cenex in early September, exemplified how the sector can utilise hydrogen fuel cell powertrains for light and heavy-duty commercial vehicles, resulting in lighter and more efficient vehicles at a lower cost of ownership.
Two Intelligent Energy DRIVE HD100 fuel cells are the prime mover of the truck, delivering 200kW of primary motive power. These are supported by a small 16kWh battery with 400kW charge/discharge capacity and fuel cell optimised DC-DC converters.
Simon said: “Most other technologies are going into hydrogen fuel cells but with a bigger battery system. For ICEBreaker, we chose to work on hydrogen fuel cells with a small battery.”
In addition to Intelligent Energy’s fuel cells, the collaboration leveraged HORIBA MIRA’s expertise in vehicle engineering, systems and system integration, and digital twin technologies, as well as Viritech’s Tri-Volt Energy management system, which uses a DC-DC converter to link the drive system, battery, and the fuel cell together.
“For HORIBA MIRA,” Simon added, “the project aimed to demonstrate our vehicle engineering integration and test engineering prowess, as well as creating a test platform for further engineering development, so we can continue the development of hydrogen systems with real physical data.
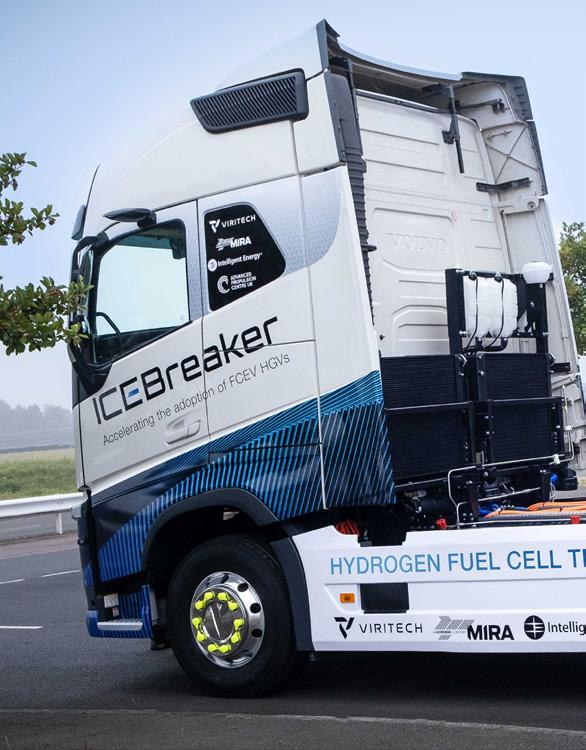
“We’ve also got vehicle control software that at the moment is set up for pure BEV, for internal combustion engine hybrids, and that now has been adapted for fuel cell applications. So it covers the three main core technologies.”
The Project also developed a correlated fuel cell powertrain digital twin. Simon explained: “Essentially, we’ve got digital twins of hybrid vehicles, battery electric vehicles, all the way down to individual cells and components.
“The digital twins are used for powertrain optimisation, making the vehicle as efficient as possible, and also total cost optimisation, looking at how to utilise these vehicles in fleets.”
The ongoing work on digital twins will unlock further efficiencies through machine learning enhanced powertrain optimisation to improve drivability, performance, and efficiency, as well as fleet planning and refuelling and recharging points.
Most other technologies are going into hydrogen fuel cells but with a bigger battery system. For ICEBreaker, we chose to work on hydrogen fuel cells with a small battery.
Simon Dunnett, Technical Sales Manager Net Zero & Vehicle Propulsion
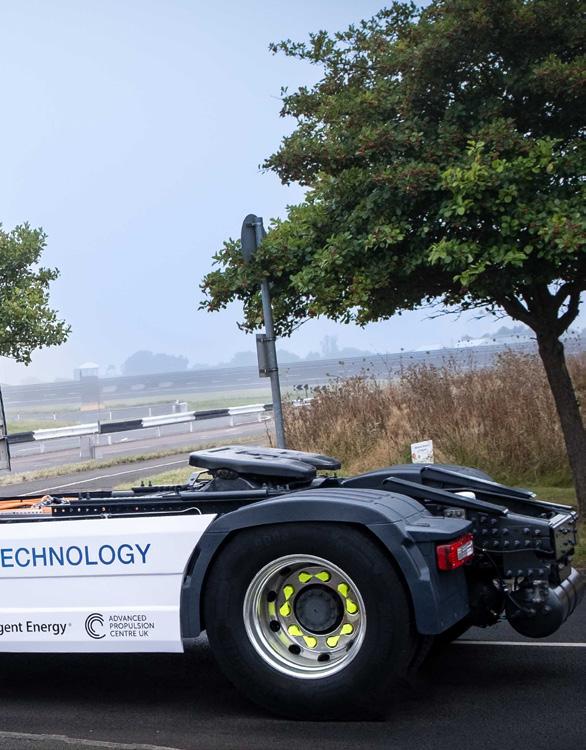
DEVELOPING THE SKILLS TO DRIVE INNOVATION
As well as providing the facilities and resources to develop cutting-edge innovations like Project ICEBreaker, MIRA Tech Park also prioritises skills, recognising that the commercialisation of these technologies is dependent on having the appropriate people in place.
MIRA Technology Institute (MTI), a collaboration between North Warwickshire and South Leicestershire College, HORIBA MIRA, the University of Leicester, Loughborough University, and Coventry University, is a specialist facility based at MIRA Tech Park designed to train the next generation of transport and energy engineers.
With investment from the UK Government’s Growth Fund via the LLEP, MTI provides specialist skills training in various emerging technology areas including electrification and driverless cars, and seeks to ensure there is a robust and sustainable pipeline of future technical specialists and engineers.
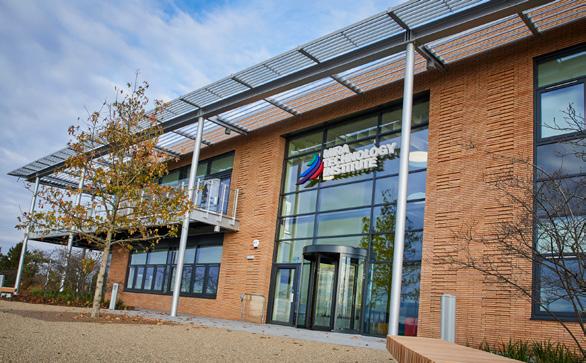
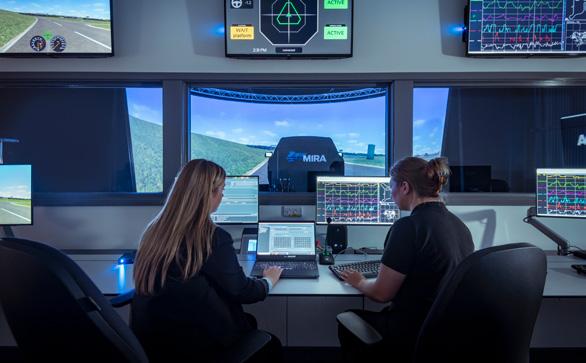
Lisa Bingley, MTI’s Operations Director, said: “We’ve got lots of emerging technology, and there is a skills gap. We all know that. We’re here to help us get to net zero.
“We’re providing automotive training and beyond because we’re going to pick up the energy side as well, and we’ll expand out into all of the relevant, emerging technologies.”
Where hydrogen is concerned, MTI is the first in the country to receive a Toyota MIRAI Rig for training purposes, and have also won £200,000 in funding to update its workshops to become hydrogen ready.
MTI is also the first of its kind in the UK that can offer training spanning from Level 1 to Level 8 qualifications, and by offering employer-led courses, the Institute ensures it is developing the skills the industry is calling for.
With cutting edge innovations like Project ICEBreaker and the next generation of skills gathered on one site, MIRA Tech Park is blazing a trail not only in the development of hydrogen technologies, but in facilitating routes to market to support the burgeoning hydrogen economy.
The EXECUTIVE SUMMARY
Welcome to The Executive Summary, a new addition to the HIL eMagazine format, where I will be scouring the internet for the biggest reports of the month, the most interesting international findings and an insight you might have missed.
I am looking for this to be community led too, so if you see a report that warrants coverage in the magazine, feel free to drop me an email or tag me on Linkedin and I’ll be sure to take a look at it.
Onto October then, and generally a LOT of news came out from the hydrogen sector, specifically the UK. Despite the limelight being shone on the UK, there have been some significant reports released such as the Global Hydrogen Review 2024 and the Hydrogen Industry Report 2024.
Additionally, you may have seen Hydrogen Europe release their Hydrogen Infrastructure report. One you may not have noticed was the OIES report on whether green hydrogen CfD can match the costsaving success of renewable electricity.
Floyd March, Editor Email me or tag me on LinkedIn
TOP LINE FROM KEY INDUSTRY REPORTS FROM OCTOBER
Breaking these down, the top line from the Global Hydrogen Review 2024 explained “Global hydrogen demand reached 97 Mt in 2023, an increase of 2.5% compared to 2022. Demand remains concentrated in refining and the chemical sector, and is principally covered by hydrogen produced from unabated fossil fuels.”
The Hydrogen Industry Report 2024 found the hydrogen industry has experienced a growth of 3.44%, with over 13,500 companies active, indicating the sector’s expanding presence in clean energy.
Additionally, they found that there was an increase of 704 000 jobs in the last year highlighting the industry’s role in job creation and the growing demand for hydrogen technology expertise.
On the continent, the infrastructure report from Hydrogen Europe focused on the fact that: “The lack of adequate hydrogen infrastructure is a critical challenge impairing the development of the hydrogen market across Europe.
“To unlock the potential of hydrogen and ensure European decarbonization targets are fulfilled, infrastructure will have to be developed throughout the continent to connect production to demand centres, enable imports of cheap hydrogen and provide a resilient system through storage capacities.”
The final report in the Executive Summary this month sees OIES explain CfDs, successful in the electricity sector, are now being applied to lowcarbon hydrogen production in the UK to reduce costs and increase capacity. However, green hydrogen CfDs may be less effective than electricity CfDs in driving cost reductions and managing risk.
Total hydrogen production capacity by location HAR1 Projects
Global Hydrogen Review 2024: TECHNOLOGY INNOVATION IS MAKING HEADWAY, WITH SIGNS POINTING TO ACCELERATED PROGRESS IN THE NEAR TERM
The outlook, however cautious, from the first report of the Executive Summary was positive. Some of the key findings included the fact that Government investment in hydrogen technology R&D has been growing since 2016, and this effort is starting to bear fruit.
To date: “Progress has occurred mostly on the supply side, and numerous technologies are either already commercially available or close to this point. Promising results are also being seen for end-use technologies, with several applications in industry and electricity generation reaching demonstration stage, as well as significant progress in transport applications, particularly in the shipping sector.”
In addition, the number of patent applications leapt up 47% in 2022, with most of the growth coming from technologies that are primarily motivated by climate change concerns.
LOW-EMISSIONS HYDROGEN WILL REMAIN EXPENSIVE IN THE SHORT TERM, BUT COSTS ARE EXPECTED TO FALL SIGNIFICANTLY
Despite the optimism sprouting from the depths of wider industry, there is sustained uncertainty about costs. The future cost evolution will depend on numerous factors, such as technology development, and particularly on the level and pace of deployment.
The report explained: “With the deployment seen in the IEA’s Net Zero Emissions by 2050 Scenario (NZE Scenario), the cost of low-emissions hydrogen production from renewable electricity falls to USD 2-9/kg H2 by 2030 – half of today’s value – with the cost gap with unabated fossil-based production shrinking from USD 1.5-8/kg H2 today to USD 1-3/kg H2 by 2030.
“This cost gap will remain an important challenge in the short term for project developers, but for final products for which hydrogen is an intermediate feedstock, the impact is likely to be manageable in many cases.”
Increased activity around patenting suggests that additional public funding for R&D and growing confidence in future market opportunities, backed by supportive policies, are stimulating more new ideas and product designs with commercial potential.
Increase in patent applications in 2022
the cost of low-emissions hydrogen production from renewable electricity falls to USD 2-9/kg H2 by 2030 ...half of today’s value
The Hydrogen Infrastructure Report 2024 by Hydrogen Europe
THE CRITICAL NEED FOR DEVELOPING HYDROGEN INFRASTRUCTURE
Coming as little surprise, the Hydrogen Infrastructure Report highlighted the holes and opportunities in the current landscape in Europe. While the report was extensive in the typical bombardment on lack of regulatory frameworks, current infrastructure not scaling at the right pace, and funding gaps that we’ve come to expect in these reports; there was also notable mentions of the need for more system integration readiness.
Offering recommendations to these issues and more, the reported stated: “The European Commission should, develop an EU wide storage strategy that translates into concrete legislative measures.
In addition there were strong calls for the EC to develop a Union strategy for imported and domestic hydrogen as mandated under RED3, a European hydrogen grid strategy based on the European hydrogen backbone initiative and develop an EU strategy on flexibility with a system integration approach across different timeframes.
EU Strategy for energy system
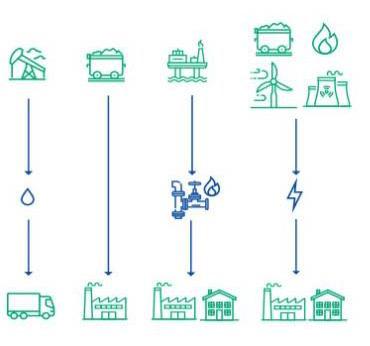
The energy system today: Linear and wasteful flows of energy, in one direction only

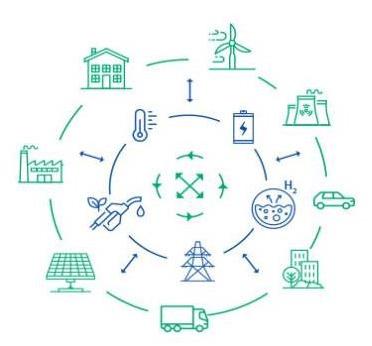
Future EU integrated energy system: Energy flows between uses and produces, reducing wasted resources and money
SECTOR GROWTH, EMPLOYMENT SURGE AND GLOBAL HUBS PAINT MORE POSITIVE PICTURES
Infrastructure issues, however vital, don’t paint the overall picture of the positivity surrounding the sector. With the scope of the Hydrogen Industry Report 2024 being so vast, it lended itself to a more positive outlook on the holistic side of the hydrogen sector.
On sector growth the report explored the fact that: “The hydrogen industry has experienced a growth of 3.44%, with over 13 500 companies active, indicating the sector’s expanding presence in clean energy.”
On further inspection this sector growth has had a huge impact on an employment surge of 704 000 according to research conducted by the author’s of the report.
Many of these jobs are offsetting job losses from traditional coal facilities closing down etc, which should help ease tensions around the perceived net zero agenda and shed some light on the positives and job opportunities net zero and low-carbon ventures bring to the workforce.
The innovation doesn’t end on technical and engineering levels, but the way in which we fund these projects have seen all kinds of innovative models, from CfDs coming from Japan, the IRA from the Biden Administration and various allocation rounds coming from the UK Government and a further commitment to CCS through recent announcements.
Through the reports findings, this positivity was ameliorated from other concerns industry leaders have. It stated: “Over 4 300 funding rounds closed shows a dynamic investment environment and strong financial interest in hydrogen technologies.
“More than 17 900 patents filed emphasizes the industry’s commitment to research, development, and securing intellectual property.
“The hydrogen industry is buoyed by significant investments from leading financial institutions. Top investors contribute more than USD 6.4 billion, highlighting the sector’s strategic importance and the confidence that investors place in its prospects.”
3.44% GROWTH within the hydrogen
industry
13,500 with over companies active
Some of those investors include:
f Warburg Pincus: Stands at the forefront with an investment of USD 1.2 billion across 5 companies, showcasing a strong commitment to driving innovation in the hydrogen space.
f EnCap Flatrock Midstream: Has invested USD 1.1 billion in 2 companies, signifying a targeted investment strategy in the infrastructure supporting hydrogen development.
f Oaktree Capital Management: Has allocated USD 890 million to 5 companies, reflecting their confidence in the hydrogen industry’s long-term value.
These investors are instrumental in propelling the hydrogen industry forward. They provide the capital necessary for technological advancements as well as the financial endorsement that underpins the sector’s future viability.
CAN UK GREEN HYDROGEN CONTRACT FOR DIFFERENCE (CFD) MATCH THE COST-SAVING SUCCESS OF RENEWABLE ELECTRICITY?
While these big industry reports shed light on various challenges and future predictions of market trends, the final report in The Executive Summary focuses on the current CfD model being used in the UK.
The Hydrogen Allocation Round (HAR) plays a pivotal role in the UK’s efforts to boost the production of low-carbon hydrogen, which is a key part of its strategy to reduce carbon emissions.
The purpose of HAR is to mitigate the challenges and risks faced by the emerging hydrogen production sector.
The HAR uses a competitive process to determine which hydrogen production projects receive government support. This system is designed to select projects that can deliver hydrogen at the lowest cost while meeting essential technical and commercial requirements.
Distribution of Hydrogen Project Sizes (MW)
In this process, projects submit bids that include their proposed strike prices and the volume of hydrogen they plan to produce. The government then evaluates these bids according to specific criteria to decide which projects will be awarded support.
The strike price is essentially the price per megawatt-hour (MWh) that a producer needs to cover the costs of low-carbon hydrogen production and earn a reasonable return on investment.
The subsidy model is designed such that it provides financial support to successful producers by covering the gap between the strike price and a reference price.
The reference price, in this context, is based on the market price at which the producer sells their hydrogen, with a minimum set at the natural gas price, which serves as the closest fossil fuel alternative.
The reference prices, expressed in pounds per MWh, are intended to reflect the market value received by the producer for hydrogen sold for specific qualifying purposes, such as power generation, transportation, or industrial use, but excluding exports or blending into the natural gas grid.
Number of Projects
Total Capacity Share by Lead Developer
The floor price, which serves as a minimum benchmark for the reference price when calculating the difference amount, is set as the lower of the strike price or the gas reference price for the relevant billing period .
The floor price ensures that the reference price cannot fall below a certain level (the floor), even if the achieved sales price is very low. This prevents the government from having to pay excessively high subsidies in situations where market conditions cause the achieved sales price to drop significantly.
As the figure shows, early projects are mainly located in regions that are either historically industrial (e.g., Yorkshire, North West, and Wales) or have significant renewable energy potential (e.g., Scotland).
Also, while some projects are relatively large (e.g., Bradford Low Carbon Hydrogen with 24.5 MW), majority are much smaller which may indicate that at this stage industry is still not confident with undertaking high scale projects.
Furthermore, as seen from the pie chart in Figure 1, the list of successful projects includes a wide range of developers, from established energy giants like Scottish Power and EDF Renewables, to smaller or niche players such as HYRO and GeoPura.
The Hydrogen CfD model is more complex compared with traditional CfDs in the renewable electricity. This is because it is designed with the aim of addressing the unique challenges of a developing hydrogen market.
The report concluded: “The Hydrogen CfD model’s complexity is a direct response to the challenges inherent in a nascent and evolving market including the lack of market liquidity, the need to prioritise strategic applications, and the imperative to manage subsidy costs effectively.
“This is why hydrogen CfD framework incorporates multiple mechanisms to ensures that hydrogen production can progress steadily, even as the market is still non-existent.
“However, the extent to which it can achieve its primary objectives related to hydrogen scale up and cost reduction is highly affected by these challenges as well unique economic features of hydrogen production.
“Specifically, as we show later in the paper, in comparison with renewable electricity, the current hydrogen CfD framework provides insufficient levels of risk mitigation.”
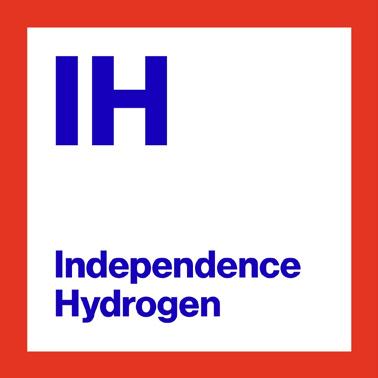
INDEPENDENCE HYDROGEN INC. ANNOUNCES FIRST OF ITS KIND, OPEN SEASON CLEAN HYDROGEN GAS SUPPLY
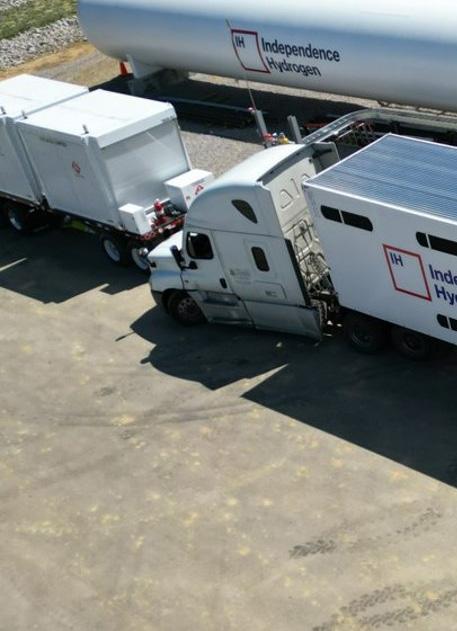
Independence Hydrogen, Inc (“IH”) is pleased to announce that it is holding an open season for 7 metric tons a day of clean, fuel cell grade, high-pressure gaseous hydrogen, available by a proposed in-service date of 01 October, 2026.
The hydrogen will have a carbon intensity score of approximately 1.1 kg CO2e/kg H2 and will be available at a production facility near Valdosta, Georgia, or delivered from such facility to customer locations in the Eastern United States (“Project”) (“Project Open Season”).
The Project Open Season will commence at 11:00 a.m. CST on October 28, 2024, and end at 5:00 p.m. CST on December 20, 2024 (the “Open Season Period”).
We are very excited about this open season. This second project to be built by IH is based on a proven and proprietary design that will meet the growing demand for clean hydrogen in the United States.
Dat Tran, CEO Independence Hydrogen.

PROJECT OPEN SEASON PROCEDURES
IH will provide a copy of a pro-forma precedent agreement for the Project Open Season upon request by any potential customer, provided that IH and such customer shall have first entered into a mutually agreed upon non-disclosure agreement. All requests for the non-disclosure agreement, proforma precedent agreement, or any inquiries should be directed to IH at openseason@ih2.us .
Any customer desiring hydrogen supply under the Project must execute and deliver a precedent agreement to IH on or before 5:00 p.m. CST on December 20, 2024. All submissions for this Project Open Season should be emailed to Ben Taylor at btaylor@ih2.us and Scott Brooks at sbrooks@ih2.us IH may at its sole discretion accept any precedent agreements received after the expiration of the Open Season Period.
If the total volumes requested in the Project Open Season exceed the planned scope of the Project, IH, in its sole discretion, may revise the scope of the Project to increase its size.
Independence Hydrogen regionally produces and distributes clean gaseous hydrogen in the United States. Our unique business model advances a standardised and scalable approach that offers speed to market, while lowering execution complexity and costs. More information about Independence Hydrogen can be found at www. independencehydrogen.com or https://ih2.us/.
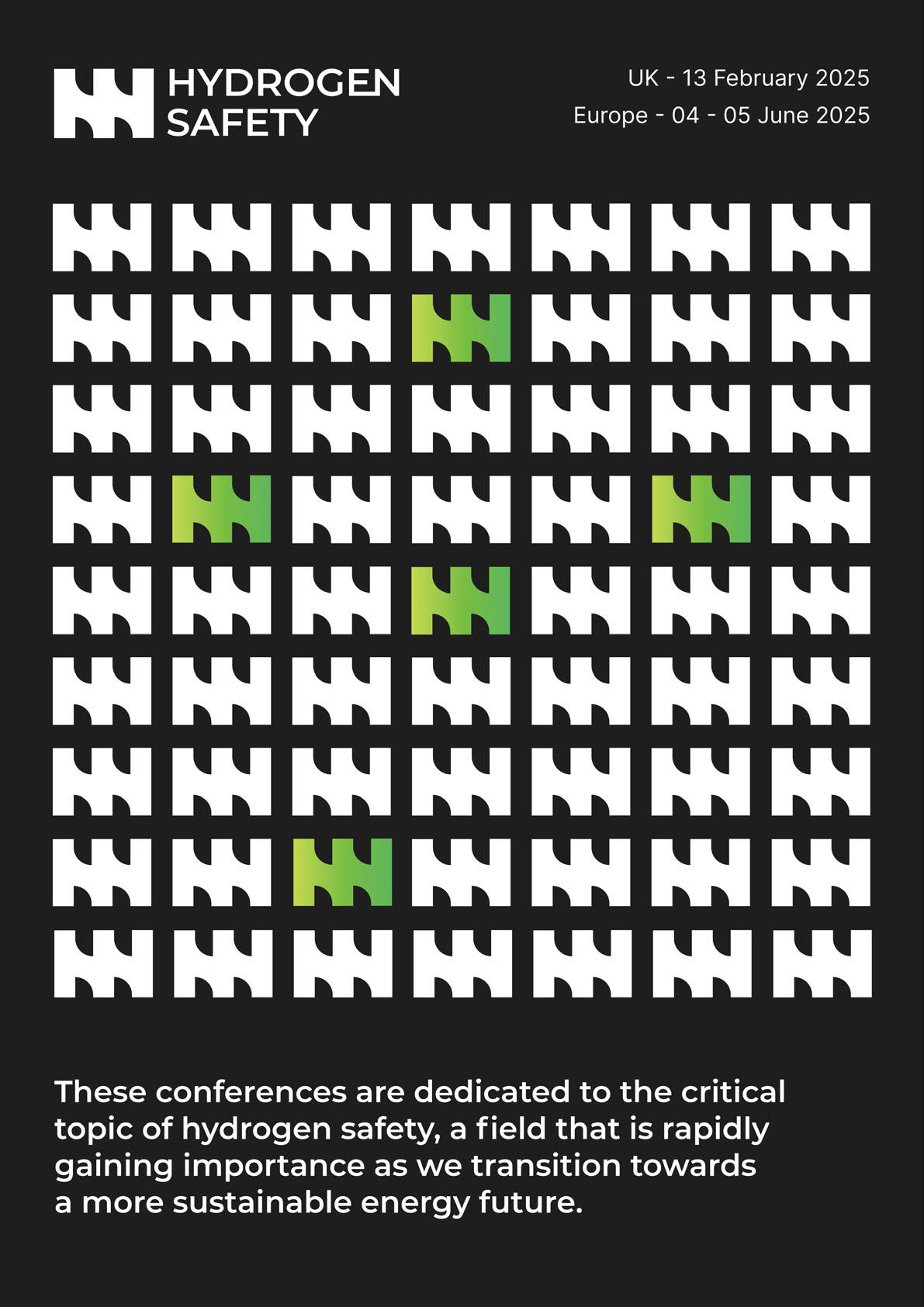

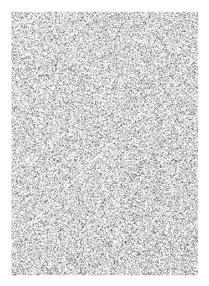
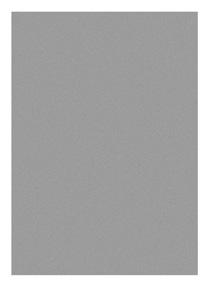
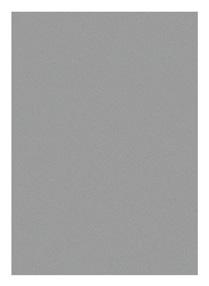





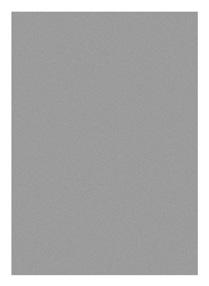
Hear from industry experts across aviation, rail, and the highway sectors.

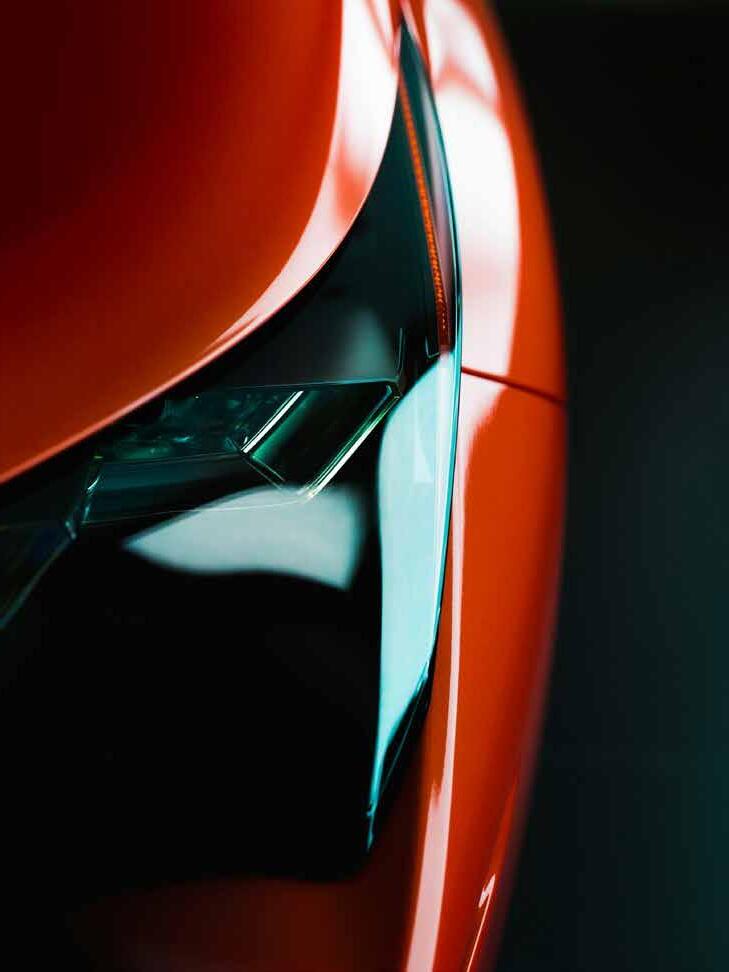
We will be hearing from industry experts across aviation, rail, and the highway sectors to find out about their vision to create a sustainable future and how hydrogen will fit into the energy mix.
The conference will allow organisations an opportunity to showcase products and solutions that the transport sector can take away and incorporate into their long-term vision.
This includes innovative new products, solutions and overall new ways of thinking which will help transform the UK into a truly resource-efficient nation.