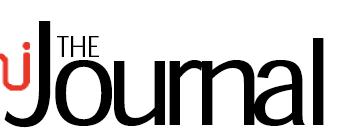
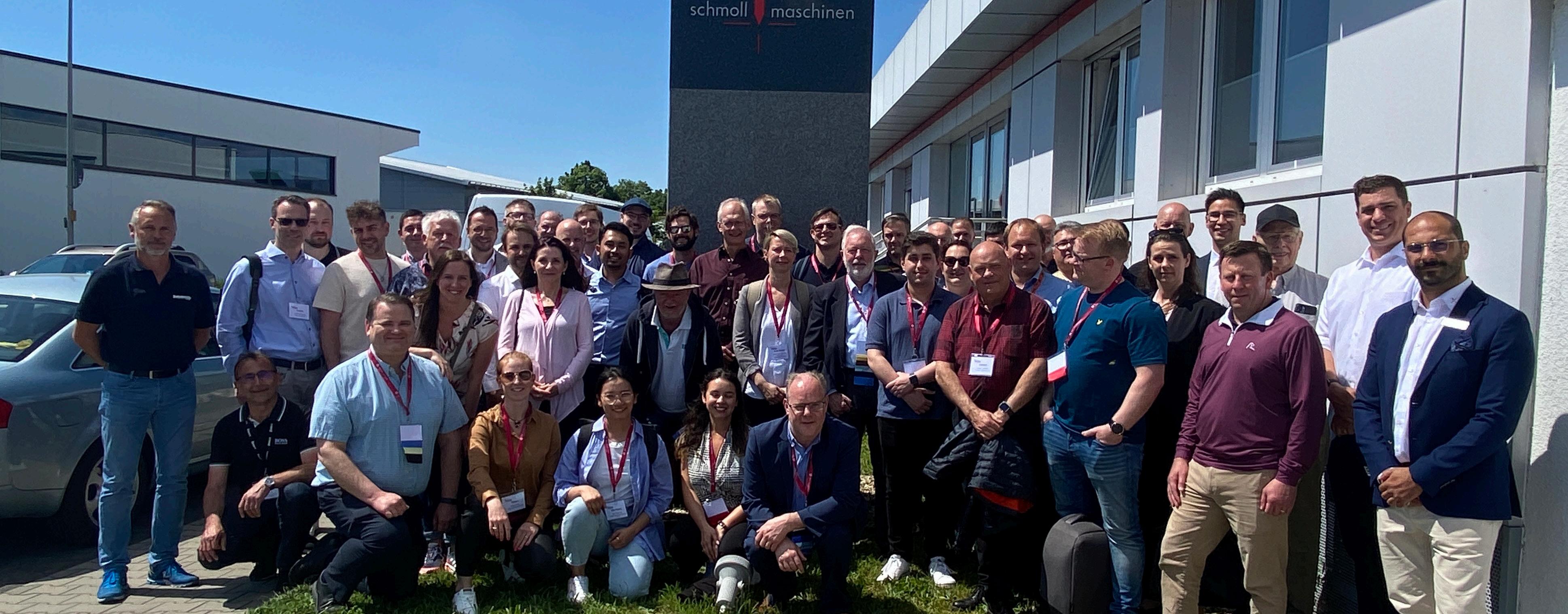
This Journal contains the technical papers and presentations from the PCMI Educational Webinar Series and Spring Technical Conference held in Frankfurt, Germany, from May 12 - 15, 2024.
Registration is now open for the PCMI Fall 2024 Technical Conference! Join us for an inspiring journey into cutting-edge innovations and unparalleled networking opportunities.
Programs In Development Include:
• Automation Part 1 - Robotics in Schmoll’s Direct Imaging Systems
• Automation Part 2 - Traceability with Serialization
• Back to Basics - Free Acid in Ferric Chloride Etching
• Building a Collaborative Relationship with Your Forming Supplier
• Chemistries and Applications
• Dry Resist for Chemical Milling
• Inkjet Printing
• Innovations in Manufacturing: Exploring the Potential of 3D Printing in a Photochemical Machining Manufacturing Facility
• Leveraging ChatGPT: Success Stories and Strategies from Industry Leaders
• Managing Change with New Technologies
• Methods for Implementing Economical Closed-Loop Water Recycling Systems in the Photo-Chemical Milling Industry
• New Product Showcase
• Point-of-Use Manufacture of Nitric Acid using just Air, Water, and Electricity
• Wet Chemistry Process Equipment and Inkjet Printing
Details:
Date: October 6-9, 2024
location: Rosen Shingle Creek Resort, Orlando, FLt
We’re thrilled to offer you an incredible opportunity to elevate your skills with our latest member benefit: exclusive access to the PCM Short Course by David Allen, Emeritus Professor of Microengineering at Cranfield University!
Introducing Our Updated Training Course: “Essentials of Photochemical Machining (PCM)”
This newly updated Short Course provides crucial insights and knowledge for both newcomers and experienced professionals in the PCM industry.
• Enhance Your Expertise: Stay at the forefront of the latest PCM techniques and practices
• Update Your Knowledge: Learn about essential advancements and industry trends.
• Flexible Learning: Access the course anytime, anywhere, and revisit the material as needed
Head over to our website and enter the code pcmicourse24 to unlock your free access to the course.
As a valued PCMI member, this training is absolutely free for you. Don’t miss this exclusive chance to advance your knowledge and stay ahead in the PCM industry!
The PCMI Journal is the official publication of the Photo Chemical Machining Institute. Its purpose is to serve the needs of the PCMI members: to keep them up-to-date on activities of the PCMI, and to provide technical information about the industry. To make the PCMI Journal as valuable as possible, we ask that members contribute technical articles and newsworthy items, including new material on state-of-theart photo chemical machining –equipment, techniques, etc.
We also accept articles that have appeared in other publications if they are relevant to our members. All material should be forwarded electronically in PDF format to: cflaherty@pcmi.org
Advertising is accepted for both the PCMI Journals and the annual PCMI Membership Directory.
For information concerning ad deadlines, formats, sizes and rates contact the PCMI Office:
11 Robert Toner Blvd., #234 North Attleboro, MA 02763 Phone: (508) 385-0085 cflaherty@pcmi.org www.pcmi.org
Officers, Directors and Active Past Presidents (As of January 1, 2024)
President Eric Kemperman, Etchform
Vice President Peter Engel, Newcut by Fathom
Treasurer
Blake Parkinson, Watlow
Secretary Neil Walker, Tecan Ltd.
Past President Peter Jefferies, PCMI Advice
Board of Directors
David Allen, Cranfield University
Glenn Dooley, NW Etch
Steffen Herz, Ätztechnik GmbH
Ana Lambert, Tech Etch, Inc.
Ken Marino, Orbel Corp.
Claudia Schemann, Metaq GmbH
Mike Soble, Chemcut Corporation
Jimmy Trost, Vaga Industries
Damian von Rickenbach, CMT Rickenbach
Active Past Presidents Bill Fox, Conard Corporation
Paolo Iellici, Lasertech Srl
Kirk Lauver, Chemcut Corporation
Chet Poplaski, Newcut (Retired)
Jerry Williams, United Western Enterprises, Inc.
Management
Executive Director Catherine Flaherty
Greetings, PCMI Members,
I hope you had a wonderful summer filled with rest, recreation, and business success.
As we move into fall, we’re gearing up for our technical conference in Orlando, Florida, from October 6–9. These sessions will provide new insights and help members stay ahead of new technologies. If you haven’t registered yet, I encourage you to do so. Our biannual conferences enhance both your professional network and PCM knowledge. You can register here
A big thank you to everyone who contributed to the recent conference in Frankfurt, Germany, especially Schmoll Maschinen our platinum sponsor and facility tour host, and gold sponsors Chemcut and Ätztechnik Herz GmbH. Special thanks also to Procter & Gamble Service GmbH for the historical tour they hosted.
I would also like to acknowledge the members I had the pleasure of working with on the Spring Conference Committee. They included:
• David Allen, Cranfield University
• Paul Campbell, Zapp Precision Metals GmbH
• Steffen Herz, Ätztechnik Herz GmbH
• Mercedes Runge, Procter & Gamble Service GmbH
• Claudia Schemann, Metaq GmbH
Providing key educational programs for PCMI members is a cornerstone of PCMI’s mission. The conference will surely meet all of your expectations concerning educational content, but so too will the newly redesigned Short Course.
This new modular educational program was launched this month, and we owe a debt of gratitude to Prof. David Allen for his work in remaking this important educational tool. The Short Course is a member benefit and free to all PCMI members, and we are confident that it will assist you with onboarding and training employees new to the PCM industry. You can learn more about the Short Course and download your free modules here.
I’m pleased to announce a multi-year agreement with MSP Management Solutions Plus, Inc. (MSP), a seasoned Association Management Company. MSP will provide expertise in strategic planning, membership growth, meeting planning, marketing, and social media. Read more about MSP here.
As we move forward with MSP, we acknowledge the distinguished tenure of our long-time executive director, Cathy Flaherty. Her dedication and leadership have been instrumental in shaping PCMI. We extend our deepest gratitude and wish her the best in her well-deserved retirement.
Sincerely
Eric Kemperman, PCMI President Research & QSHE Manager, Etchform BV
Hello PCMI Members,
I hope this message finds you well.
It is with mixed emotions that I write to you today. This will be my final letter as your PCMI Executive Director. After many fulfilling years in the association management business and serving as the PCMI Executive Director for the past 14 years, I have made the heartfelt decision to retire. I am looking forward to spending more time with my husband, family and friends, and on the golf course!
Reflecting on my time with PCMI, I am filled with immense gratitude for the wonderful memories and friendships I have made. The unwavering support and leadership from PCMI members have been invaluable, and the conferences held in so many beautiful cities around the world have been a true highlight of my career.
I will deeply miss the work, the camaraderie, and the shared experiences we have enjoyed. However, I am confident that I am leaving PCMI in very capable hands. I am pleased to introduce MSP Management Solutions Plus, Inc. (MSP) as your new management partner. With great confidence, I entrust the leadership of Shawn McLaughlin, MSP’s CEO, and Jennifer DiSanza, your new Executive Director. Along with the entire MSP team, the Institute will benefit from their extensive expertise in strategic planning, membership growth and retention, meeting planning, marketing, and social media.
MSP Management Solutions Plus, Inc. (MSP) is a seasoned and accredited Association Management Company (AMC) dedicated to supporting organizations in achieving their goals and long-term success. With nearly 30 years of experience and AMCI accreditation for two decades, MSP is exceptionally equipped to be our proactive and strategic management partner. MSP boasts a team of approximately 50 dedicated professionals who offer the perfect balance between the resources of a large AMC and the personalized attention of a small one. Known for their transparency, commitment, and client-focused approach, the MSP team encourages continuous learning, adaptability, and a strong emphasis on meeting client needs.
I am excited for PCMI’s future under MSP’s management. I am confident that they will not only continue to provide the excellent services and benefits our members currently enjoy, but also enhance them. MSP’s leadership will bring an elevated level of professionalism that will enable PCMI to experience exceptional growth, launch innovative programs, and offer our members additional insights on cutting-edge and relevant industry developments.
Thank you all for the memories, your support, and the warm relationships we have built over the years. It has been an honor to serve as your Executive Director. I wish you all the very best for the future.
Warmest wishes,
Catherine Flaherty PCMI Executive Director
The Photo Chemical Manufacturing Institute (PCMI) is pleased to announce the selection of Management Solutions Plus (MSP) as its new association management firm. MSP's expertise and dedication to excellence will provide PCMI with outstanding management services to drive the organization's mission forward.
MSP's commitment to excellence and innovative approach will provide PCMI with outstanding management services, ensuring the continued advancement of our mission. This partnership is poised to enhance our operational efficiency, member engagement, and overall impact within the photo chemical manufacturing industry.
We look forward to the positive changes and growth that MSP will bring to PCMI. Together, we will work towards achieving our strategic goals, supporting our members, and driving innovation in the industry.
Please join us in welcoming Management Solutions Plus to the PCMI family.
• Leadership and Governance: MSP will ensure effective leadership and governance practices, guiding PCMI toward its strategic objectives.
• Strategic Planning: MSP will assist PCMI in developing comprehensive strategies to enhance its operations, outreach, and impact within the industry.
• Conference and Webinar Organization: Leveraging MSP’s extensive experience, PCMI will deliver wellorganized and impactful conferences and webinars, facilitating knowledge exchange and networking among industry professionals.
• Marketing and Communications: MSP will enhance PCMI’s marketing and communica-tions efforts, increasing visibility and engagement with members and stakeholders.
• Membership Growth: MSP’s targeted approaches will help in attracting new members and retaining existing ones, ensuring a vibrant and engaged community.
• Committee and Board Management: Efficient management of committees and the board will be ensured, fostering effective governance and decision-making processes.
• Financial Services: MSP will provide robust financial management, ensuring transpar-ency and the sustainable growth of PCMI’s resources.
With MSP’s support, PCMI looks forward to achieving new milestones and continuing to serve its members with excellence.
1300 Piccard Dr LL-14
Rockville, MD 20850
301.258.9210
www.msp-amc.com
Based in Rockville, Maryland, the MSP team brings a wealth of experience and dedication to their roles:
Deryck White Director of Information Technology
John Ross Sponorship of Sales Senior Manager
Chemograf Ltd.
19 Hamarkeva Street Ind. Zone 58851 Holon +972 (3) 550 3717 Israel Amir Rozenfeld, CTO amir@chemograf.com www.chemograf.com
Equipment Technologies, Inc.
19 Park Avenue Hudson, NH 03051 United States (603) 881-5253
Jon Pelletier, President jon@equiptech.com www.equiptech.com
Schmoll-Maschinen GmbH
Odenwaldstraße 67 Rödermark, 63322 Germany +49 6074 8901 456
Dennis Pusch, Manager Sales and Business Development DI pusch@schmoll-maschinen.de www.schmoll-maschinen.de
Interested in shaping the future of PCMI? Join a PCMI Committee and get involved in conference planning, educational programs, membership initiatives, or technology services. As a committee volunteer, you’ll play a vital role in helping the Institute achieve its goals, advocate for your company’s interests, and expand your professional network.
The PCMI Conference Committee:
• Oversees the development of the program agenda, including determining the number and content of technical sessions and identifying potential speakers.
• Coordinates the planning of pre- and postconference programs, tours, and social activities
The PCMI Education Committee;
• Identifies the educational needs of the membership and develops programs to address those needs effectively.
• Plays a key role in shaping and contributing to the content of technical sessions at conferences.
The Membership Committee:
• Develops strategic plans for recruitment and retention.
• Actively recruits new members.
• Recommends strategies for developing technology projects that can benefit the membership;
The IT Committee;
• Reviews the website and social media to ensure they effectively enhance PCMI, facilitating networking, business promotion, industry learning, conference registration, and access to technical documents for members’ business development.
Click here for the Committee Nomination Form.
Special Thanks to PCMI’s Spring Conference Sponsors!
Platinum Sponsor Gold Sponsors
Special Thanks to PCMI’s Fall Conference Committee!
David Allen, Cranfield University
Paul Campbell, Zapp Precision Metals GmbH
Steffen Herz, Atztechnik Herz GmbH
Eric Kemperman, Etchform BV
Mercedes Runge, Procter & Gamble Service
Claudia Schemann, Metaq GmbH
Special Thanks to PCMI’s Fall Facility Tour Hosts!
Photochemical machining is a precise metal fabrication technique widely employed in the medical and aerospace industries. Utilizing controlled chemical processes and light exposure, this method ensures intricate, burr-free components for medical devices and aerospace applications, meeting stringent industry standards.
Chris Bonsell will discuss the controlled chemical processes involved in these photochemical machining processes. He will also:
• Explore specific applications of photochemical machining in the medical and aerospace fields;
• Discuss how PCM contributes to the fabrication of components for medical devices and aerospace technology.
• Highlight the advantage of burr-free and precise components in medical applications, and
• Discuss how PCM helps meet the stringent standards of aerospace applications.
. Christopher Bonsell is Process Engineer at Tecoment. Before moving to Tecoment, Chris worked as Chemical Process Engineer for Chemcut. He was the author of many of Chemcut’s technical blog posts and is a columnist for the industry magazine “PCB007”.
He graduated from The Pennsylvania State University with his Bachelor’s Degree in Chemical Engineering.
Chris is also serves on the PCMI IT and Education Committees.
Emeritus Professor David Allen, Cranfield University
David has published:
• Two PCM books:
Emeritus Professor David Allen started his career as a chemist (BSc, 1968) and moved into photochemistry research (PhD, 1972) while studying at Cardiff University. Following post-doctoral research at Warwick University and imaging technology development in industry, David joined Cranfield University in 1976. He was appointed a Technical Liaison Member to the Photo Chemical Machining Institute (PCMI) in 1981 and is currently on the Board of Directors of PCMI responsible for education. David became Professor of Microengineering at Cranfield University in 1998 and was elected as a Fellow of The International Academy for Production Engineering (CIRP) in 2006.
“The Principles and Practice of Photochemical Machining and Photoetching” (1986) and “Photochemical Machining and Photoelectroforming” (2015, reprinted 2016, 2017 and 2019)
• Five book chapters on non-conventional machining and contributed the chapter on ‘Etching’ to the online CIRP Encyclopedia of Production Engineering
• Seven confidential industrial PCM consortium reports
• 213 journal and conference papers and was awarded the higher doctoral degree of DSc from Cranfield University in 2013 for his thesis entitled “Contributions to Photochemical Machining and Photoelectroforming”.
David retired from academia in 2011 and he now carries out consultancy and staff training in PCM companies across the world. He has worked with 28 different companies over the past 13 years.
PCM of Difficult-to-Etch Metals and Alloys: Nickel- and Cobalt-Based Superalloys
Emeritus Professor David Allen, Cranfield University
PCM of difficult-to-etch metals and alloys: nickel- and cobalt-based superalloys
David M. Allen
Emeritus Professor of Microengineering, Cranfield University, UK (Presented at the PCMI Conference, Frankfurt, Germany on 13th and 15th May 2024)
Abstract
A superalloy is a metal specifically designed for applications requiring a high level of resistance to elevated temperatures, high tensile strength, and resistance to corrosion. Superalloys are therefore often used in chemical conversion plants, industrial and aerospace turbines, medical implants and devices containing precision springs and diaphragms.
These materials are extremely difficult to machine by conventional cutting methods as the materials work-harden when being machined. Fabrication by chemical machining is therefore a preferred technique. However, as these materials are also corrosion-resistant, they can also be difficult to etch.
This presentation reviews how a wide range of nickel - and cobalt-based superalloys can be etched by aggressive chemical etchants or, alternatively, by electrolytic photoetching techniques with reduced Health, Safety and Environmental (HSE) impacts.
Background
A superalloy is a metal specially designed for applications requiring a high level of resistance to elevated temperatures, high tensile strength, and resistance to corrosion [1,2]. These alloys are usually categorized under three possible types:
• a cobalt base (30-60% Co),
• a nickel base (≈50% Ni) and
• an iron-nickel base (15-60% Fe and 25-45% Ni) also known as a super stainless steel.
Over the past few years, I have received several enquiries concerning how to etch certain superalloys (a term first used in the mid-1940s), especially Inconel 625 which is rated as a “difficult-to-etch” material. Apparently, the interest is worldwide as I have received enquiries from UK, Continental Europe and USA .
PCM of Difficult-to-Etch Metals and Alloys: Nickel- and Cobalt-Based Superalloys
Emeritus Professor David Allen, Cranfield University
It is suggested that a difficult-to-etch material is one that cannot be easily etched in a “standard” etchant of ferric chloride, i.e. one that will etch carbon steel or copper. There is an historic (1980s) PCMI-generated, listing of metals and alloys (Table 1) that ranges from easy-to-etch materials (Good) to difficult-to-etch materials (Poor) [3]. The emboldened Inconel alloys and Hastelloy B are rated as ‘Good to Fair’, Udimet alloys as ‘Fair to Poor’ and Hastelloy C and René 41 as ‘Poor ’. The ratings are somewhat subjective but broadly reflect the Electromotive Force Series of Standard Oxidation-Reduction Potentials (ORPs) of the chemical elements.
Table 1. Etchability ratings of some metals and alloys [4]
Good Good to Fair Fair to Poor Poor
Copper (rolled) AISI 215 Stainless steel Molybdenum Tungsten
Copper (electrolytic) AISI 301 Stainless steel Nichrome Hastelloy C
Beryllium copper AISI 302 Stainless steel Udimet alloys Titanium
Brass AISI 304 Stainless steel Vanadium René 41
OFHC copper AISI 305 Stainless steel Chromium Niobium (Columbium)
Phosphor bronze AISI 316 Stainless steel Gold Tantalum
90-10 copper/nickel AISI 321 Stainless steel Lead
Zinc AISI 347 Stainless steel Manganese
Carbon steel PH 15-7 Stainless steel Rhenium
Kovar PH 17-7 Stainless steel Zirconium
Nickel AISI 410 Stainless steel
Monel AISI 420 Stainless steel
Nickel silver AISI 430 Stainless steel
Magnesium Inconel alloys
Aluminium Hastelloy B
Anodised aluminium
As Visser has shown, to etch a material it is necessary to increase the etchant concentration and/or increase temperature above its “retarding threshold” [5]. Thus, higher concentrations and temperatures are required to etch more difficult-to-etch materials. In a ferric chloride etchant, the ratio of Fe3+/ Fe2+ must be kept high to increase ORP. ORP is also increased when the operational temperature is raised.
It can be confusing that Inconel 625 is also known as Alloy 625, Altemp 625, CarTech 625, Chronin 625, Haynes 625 alloy, HPM 625, Incoloy 625, Nickel 625, Nickelvac 625, Nicrofer 6020, Pyromet Alloy 625, Udimet 625 and VLX 625. However, all the above are designated as Universal Number Specification (UNS) N06625 (Table 2) and Werkstoff Number 2.4856 confirming the specific chemical
PCM of Difficult-to-Etch Metals and Alloys: Nickel- and Cobalt-Based Superalloys
Emeritus Professor David Allen, Cranfield University
compositions of the alloys to be within a certain specification range ( even if not identical).
Table 2. Universal Number Specification Designations
UNS Designation General description
N00001-N99999
R00001-R99999
R3XXXX
Nickel and nickel alloys
Refractory metals and alloys
Cobalt alloys
After a short early career as a teacher, Elwood Haynes worked in the oil and gas industry. It was during this time that he developed his ideas for a “horseless carriage.” Haynes moved to Kokomo, IN in December 1892 and found time to work on his horseless carriage. His first automobile, “Pioneer” was successfully tested on July 4, 1894. While there is some dispute as to whom the honour of the first automobile in the United States should go, the succe ss of Pioneer led Haynes to form a company, which produced high -end automobiles through the mid-1920s.
Haynes was in search of a material that would resist tarnishing and be suitable for cutlery. After several years of unsuccessful experiments, he developed viable alloys in 1907 and was awarded two patents: one for a nickel -chromium alloy and one for a cobalt-chromium alloy, both to be used as cutting tools for automotive engine components. Then in September 1912, the United States Patent Office informed Haynes that he would also be granted two patents for new cobalt-chromium-tungsten-molybdenum alloys. It was this event that resulted in the formation of the Haynes Stellite Works in Kokomo. In the early 1920s, Haynes’ company was bought by Union Carbide.
At Union Carbide’s R&D facilities at Niagara Falls, NY, research was also being conducted into nickel-molybdenum alloys for corrosion resistance. This marked the origins of the nickel-base superalloy industry. A patent was obtained for a nickel-molybdenum alloy composition range in 1921, which eventually led to the invention of Hastelloy A alloy and, two years later, Hastelloy B alloy. The unique composition of Hastelloy B is still being manufactured today. In 1926, Hastelloy C alloy was invented. The fifth generation of this alloy, Hastelloy C-2000 alloy, is still being supplied to the chemical process industry today.
PCM of Difficult-to-Etch Metals and Alloys: Nickel- and Cobalt-Based Superalloys
Emeritus Professor David Allen, Cranfield University
Hastelloy D alloy, a nickel-silicon-copper material, was also invented during the 1920s. The latest version of this alloy, Hastelloy D-205 alloy, is used today in chemical plants that use hot, highly-concentrated, sulfuric acid.
The 1950s also marked the beginning of significant change for the company. New high-temperature wrought alloys were also being added. Multimet alloy, a nickel-cobalt-chromium-molybdenum-tungsten material, appeared in 1949, and in 1950, the cobalt alloy L-605, now also known as Haynes Alloy 25 or Alloy 25, was first manufactured.
A very wide range of nickel-based superalloy families have been developed as shown in Table 3.
Table 3. Some nickel-based superalloy groupings.
Superalloy UNS Werkstoff #
Hastelloy B N10001 2.4800
Hastelloy C-276 N10276 2.4819
General description
First generation Ni-Mo superalloy
Ni-Mo-Cr-Fe-W-Co-V
Hastelloy R-235 N06235 - Vacuum-melted Ni-Cr-Fe-Mo-Ti-Al
Hastelloy X N06002 2.4665
Inconel 600 N06600 2.4816
Inconel 601 N06601 2.4851
Inconel 617 N06617 2.4663a
Inconel 625 N06625 2.4856
Inconel 718 N07718 2.4668
Inconel X-750 N07750 2.4669
René 41 (General Electric) N07041 2.4973
Udimet 500 N07500 2.4983
Udimet 700 N07700 2.4636
Waspaloy (Pratt & Whitney) N07001 2.4654
Ni-Cr-Fe-Mo
Ni-Cr-Fe hardened only by cold work
Utility Ni-Cr-Fe alloy resists heat and corrosion
Ni-Cr-Co-Mo high strength at over 1800°F
High-strength, corrosion- resistant Ni-Cr alloy, service temperatures up to 1800°F
Age-hardenable, high-strength, corrosionresistant Ni-Cr alloy used up to 1300°F
Age-hardenable Ni-Cr alloy
Vacuum-melted age-hardenable Ni-CrCo-Mo-Fe-Ti-Al high temperature superalloy
Ni-Cr-Co
Ni-Co-Cr-Mo-Ti-Al-Fe
Age-hardenable Ni-Cr-Co-Mo-Ti-Al-Fe superalloy
Presentations on difficult-to-etch metals and alloys have been given previously at PCMI conferences and webinars [6-8] and a Cranfield University – PCM Companies Consortium report (restricted to consortium members until 2006) has also been written [9]. It concentrated on determining suitable etchants for difficult-to-etch materials, especially electrolytic etchants, with reduced “Health, Safety and Environment” (HSE) impacts.
PCM of Difficult-to-Etch Metals and Alloys: Nickel- and Cobalt-Based Superalloys
Emeritus Professor David Allen, Cranfield University
Allen et al reported the PCM of Ni-Span-C Alloy 902 (UNS N09902) - an extremely strong, precipitation-hardenable iron-nickel superalloy (42.5% Ni, 49% Fe%, 5.3% Cr, 2.4% Ti) with a thermoelastic coefficient that can be controlled by the amount of cold work and heat treatment temperature. The product, a small transducer body for in vivo blood pressure measurement (100 μm thick and approx.2.3 x 0.7 mm) , sits within a vein or artery and is placed in situ by means of a hypodermic syringe. It was etched successfully, using a two-stage process, in 3.4M (42°Bé) ferric chloride solution at 30°C [10].
This paper concentrates on the capability of PCM to produce etched parts from a wide range of nickel- and cobalt-based superalloys, a topic never previously discussed at a PCMI Conference.
Useful information on PCM of various Inconel alloys has been found in some recent research publications from India [11-13].
An Internet and e-mail review of the capability of PCM companies to etch various Inconel alloys, classified by geographical location, is shown in Table 4. If a company has the capability of etching thin material only, the capability was reduced to 0.5*.
Table 4. PCM company capabilities to etch various Inconel alloys.
PCM companies and their locations
The compositions of some Inconel alloys that affect their etchability are shown in Table 5. The easiest elements to etch are highlighted in green, more difficult to etch in yellow and the most difficult to etch in red.
It is therefore anticipated that Inconels 600, 601 and X-750 will be the easiest materials to etch followed by Inconels 617 and 718 with Inconel 625 be ing the most difficult material to etch. This appears to be borne out in practice as appeals to PCM companies for examples of etched Inconel parts produced three components etched from Inconel X-750, two from Inconel 600 and one from Inconel 718.
Table 6 shows the results published on the etching of Inconels in ferric chloride.
PCM of Difficult-to-Etch Metals and Alloys: Nickel- and Cobalt-Based
Emeritus Professor David Allen, Cranfield University
Table 5. Chemical compositions of various Inconel alloys.
Table 6. Practical results of etching Inconel alloys in ferric chloride solutions
Inconel alloy Results of etching in ferric chloride (s= spray, i = immersion)
Perhaps surprisingly, considering its 8-10% molybdenum content, Inconel 617 can be spray-etched in 3.39M (43° Bé) ferric chloride at 50°C but care needs to be taken when etching large volumes. As the alloy is dissolved, [Fe3+] drops below the 50°C retarding threshold required for the alloy. The alloy surface therefore becomes passive (Figure 1). Because there is very little iron in the alloy (<3%), [Fe 3+] cannot be boosted significantly, even via chlorine gas regeneration, as there is so little [Fe2+] byproduct available for regeneration. Feed and bleed of fresh ferric chloride is therefore required. This can be an expensive procedure and may not be cost-effective.
PCM of Difficult-to-Etch Metals and Alloys: Nickel- and Cobalt-Based Superalloys
Emeritus Professor David Allen, Cranfield University
Figure 1. Etched Inconel 617 showing (left) passive surface and (right) active surface after etching for the same time (Photographs courtesy of Heatric Division of Parker).
Alternatively, Inconel 617 should be etched in higher Bé, concentrated ferric chloride solutions and at higher temperatures if possible.
Etchability ratings of Inconel alloys according to analysis of the published data are therefore as follows: Inconel X-750 (easiest to etch with an equivalent etchability to AISI 316 stainless steel for example), followed by Inconels 600, 601, 617, 718 and 625 (the most difficult to etch). It is therefore desirable to formulate suitable etchants with higher oxidising power to etch Inconel 625
Such etchants may be found in the chemical milling industry applied to manufacturing of aerospace parts from a wide range of nickel-based superalloys (Table 7). These etchant formulations can include aqua regia, an aggressive etchant that can etch gold and platinum, and the extremely dangerous hydrofluoric acid (HF) with its associated Health, Safety and Environment impacts [15].
General Motors, USA [16] patented an etchant comprising “…an aqueous bath…consisting essentially of 14% to 18% of ≈42° Baumé ferric chloride solution, ≈42% to 52% concentrated hydrochloric acid, ≈0.5% to 4% concentrated nitric acid, all proportions by volume, and antimony trichloride to at least substantially maintain surface smoothness.” This etchant was used to etch Hastelloy C-276, Waspaloy, René 41 and Inconel X-750.
North American Aviation, USA [17] patented use of a ferric chloride aqua regia type etchant comprising nitric acid, hydrochloric acid, ferric chloride, chromic chloride and a surface-active wetting agent. This etchant was used to etch
Hastelloy R-235, Hastelloy X, Waspaloy, René 41, Udimet 500, Udimet 700 and Inconel 700.
Emeritus Professor David Allen, Cranfield University
Table 7. Nominal compositions of some nickel-based superalloys.
Llewelyn Stearns, CA, USA [18] used a double-coating technique to improve the adhesion of the maskant onto the superalloy surface. He coated the surface with an epoxy resin, cured it and then dip-coated a photoresist on top of the epoxy. After exposure and development of the resist, he then removed the epoxy through the resist apertures with concentrated sulphuric acid. Using this technique, an etchant comprising 32% hydrochloric acid (9 US gallons), 40°Bé nitric acid (1 US gallon), 70% hydrofluoric acid (0.2 US gallon) and anhydrous ferric chloride to obtain a specific gravity of 1.26, he was able to etch Hastelloy B, Waspaloy, René 41, Inconel 617, Inconel 625 and the cobalt-based superalloy Alloy 25 at rates of 6-13 μm / minute.
It should be noted that Stearns’ patent of 1981 has been superseded by the invention of an epoxy photoresist that was not available at that time. SU-8 was first patented by IBM in 1989. By using an epoxy photoresist, only one coating of the metal is required. Examples of liquid and dry film epoxy photoresists that can be purchased now include SU-8, the original liquid resist that can be applied by dip-coating; SUEX, a Thick Dry Film Sheet (TDFS), 100 μm to over 1 mm thick and
PCM of Difficult-to-Etch Metals and Alloys: Nickel- and Cobalt-Based Superalloys
Emeritus Professor David Allen, Cranfield University
ADEX, a TDFS, 5-75 μm thick, applied by hot lamination; TOK TMMF S2000 DFR and DuPont PerMX DFR.
Spraying the same etchant onto the metal at 50°C using an “all -plastic” etching machine resistant to HF will give a fast etch rate comparable to that achieved in chemical milling by immersion at 60-71°C. The epoxy photoresist can be stripped as recommended by the manufacturer.
Cobalt-based superalloys
In developing and producing the turbocharger early in World War II, a discovery of major significance to the cobalt industry was made. The investment-cast, cobalt-base dental alloy, known as Vitallium, was observed to possess mechanical properties and microstructural stability that made it suitable for supercharger buckets operating at temperatures > 1000°F. Shortly thereafter, a modification of Vitallium, designated Haynes Stellite 21, was developed specifically for such high-performance, high-temperature applications. The use of this alloy expanded to buckets and guide vanes for aircraft turbojet en gines operating at temperatures as high as 1500°F, a performance considered remarkable at the time – hence the term “superalloy” was coined [19].
Among the cast alloys, X-40 soon displaced the original Stellite 21 because of its substantially greater elevated-temperature strength. Of the wrought alloys, S816 and L-605 (Haynes Alloy 25) were highly successful materials that emerged early in the history of wrought superalloy development. Haynes Alloy 188 and CM-7 are modifications of L-605. The strength of Haynes Alloy 188 is essentially the same as that of L-605, but it has much better oxidation resistance, making it a strong candidate for numerous applications where Hastelloy X is employed.
Some cobalt-based superalloys originated and were developed within the US watch industry, namely Elgiloy (Elgin National Watch Co., Elgin, IL , USA) and Havar (Hamilton Watch Co., Lancaster, PA , USA). This development was necessitated by the requirement to prevent corrosion of metal mainsprings when operating in saline and humid environments in wartime when accurate timekeeping is critical.
A selection of cobalt-based superalloys is shown in Table 8 and the various chemical compositions are shown in Table 9.
PCM of Difficult-to-Etch Metals and Alloys: Nickel- and Cobalt-Based Superalloys
Emeritus Professor David Allen, Cranfield University
Table 8. Some cobalt-based superalloys, designations and modern applications
Superalloy UNS Werkstoff # General applications
Alloy 188 (Haynes International)
Alloy 25 (L-605) (Haynes International)
Elgiloy (Alloy 3J21) (Elgiloy Specialty Metals)
R30188 2.4683 Seal rings & packing for gas turbines
R30605 2.4964 Jet engine parts, industrial furnaces, balloon stents, heart valves
R30003 2.4711 Springs, seals, orthodontics, implants, watch parts, satellite communications equipment and weapons systems
Phynox (Conichrome) R30003 R30008 2.4711
Havar (Hamilton Precision Metals)
MP35N (Carpenter Technology)
R30004 - Watch springs, diaphragms, implants
R30035 2.4999 Marine engineering, medical devices & dental products
Duratherm 600 (Vacuumschmelze) - 2.4781 Springs, corrosion-resistant membranes for pressure gauges
Table 9. Chemical compositions of cobalt-based superalloys
/ Phynox 3941
The etchability of cobalt-based superalloys from experimental investigations of spray etching in 38°Bé ferric chloride + 0.75% HCl solutions at 45°C is summarised in Table 10.
The etchability of cobalt-based L-605 (Alloy 25) from experimental investigations of surface microetching by immersion in methanol (80 ml), hydrochloric acid (20 ml) and ferric chloride (2 gm) solution is summarised in Table 11.
General Motors, USA [22] patented an etchant comprising “...an aqueous bath consisting essentially of ≈35% to 55% of a 42° Baumé ferric chloride solution, ≈26% to 40% concentrated hydrochloric acid, ≈8% to 14% concentrated nitric
PCM of Difficult-to-Etch Metals and Alloys: Nickel- and Cobalt-Based Superalloys
Emeritus Professor David Allen, Cranfield University
Table 10. Etchability of cobalt-based superalloys in ferric chloride
Cobalt superalloy
acid, all proportions by volume, and sufficient iodine to at least substantially maintain surface smoothness.” This etchant was used to etch Stellite 21 (R30021), S-816 (R30816), X-40 (R30031) and Alloy 25 (R30605).
Table 11. Surface microetching of L-605 (Alloy 25) in ferric chloride, hydrochloric acid and methanol
Electrolytic photoetching has been established as a viable option to PCM since the 1950s. In correspondence, Eastman Kodak suggested that etching of Elgiloy should be carried out electrolytically using aqua regia at room temperature using current densities less than 3 amp/in2 (0.47 amp/cm2) [23]
Using electrolytic photoetching as a method for fabricating small parts can produce a polished edge profile that gives electrolytic photoetching a significant advantage over laser cutting (Figure 2).
A miniature H-spring for a prototype medical device was required to be made from 41 μm thick Duratherm 600 (Figure 3) This is an age-hardenable, corrosionresistant Co-Ni-Cr superalloy developed by Vaccumschmelze GmbH & Co. KG, Germany. It is a material of choice for spring applications and has excellent ductility and formability in the soft temper state.
Conventional PCM could not be used to make this part. However, electrolytic photoetching in a methanol-sulphuric acid electrolyte produced the desired part [20]. In correspondence, the client company stated that it considered the edge definition of the manufactured parts to be “quite remarkable”. Table 12 shows
PCM of Difficult-to-Etch Metals and Alloys: Nickel- and Cobalt-Based Superalloys
Emeritus Professor David Allen, Cranfield University
some electrolytic photoetching systems with reduced HSE impacts that have been used to etch nickel- and cobalt-based superalloys successfully.
Figure 2. Polished edge profile fabricated by electrolytic photoetching of 100 μm thick nickel-titanium shape memory alloy in methanol-sulphuric acid [24].
3. Duratherm® 600 (41μm thick) miniature H-spring for a prototype medical device [20].
Emeritus Professor David Allen, Cranfield University
Table 12. Electrolytic photoetching of superalloys as an alternative, HSE-friendly manufacturing technique to spray-etching [9 and 25*]
Superalloy
• Inconel alloys have a wide range of etchabilities depending on their chemical compositions.
• Some nickel- and cobalt-based superalloys can be etched with standard ferric chloride solution.
• However, some superalloys require very aggressive etchants for PCM to be successful. These may be ferric chloride formulations with aqua regia and/or HF additions.
• Such etchants may require durable epoxy photoresists for imaging.
• The HSE-friendly technique of electrolytic photoetching can be used to manufacture small parts from nickel- and cobalt-based superalloys.
• Electrolytic photoetching reduces HSE impact of aggressive chemical machining and gives superior edge profiles in comparison to both PCM and laser cutting. However, tab width needs to be minimised for ease of separating the etched parts from the superalloy sheet.
• The range of superalloys is still expanding but corrosion resistance of superalloys makes production of parts by PCM an interesting technical challenge.
PCM of Difficult-to-Etch Metals and Alloys: Nickel- and Cobalt-Based Superalloys
Emeritus Professor David Allen, Cranfield University
Acknowledgements
I wish to thank the following for their various contributions to this paper:
• Chris Bonsell, Tecomet, Woburn, MA, USA
• Dr Paul Campbell, Zapp Precision Metals GmbH, Unna, Germany
• Glenn and Sean Dooley, Northwest Etch Technology, Tacoma, WA, USA
• Julien Duvillet and Damian von Rickenbach, CMT Rickenbach, La Chauxde-Fonds, Switzerland
• Peter Engel, Newcut by Fathom, Newark, NY, USA
• Phil Greiner, PEI, Milford, MA, USA
• Steffen Herz, Atztechnik Herz GmbH & Co., Epfendorf, Germany
• Fredrik Ingvarsson, Mikroponent, Värnamo, Sweden
• Dr Peter Jefferies, Heatric division of Parker, Birmingham, UK [PJ now PCM Advice, UK]
• Eric Kemperman, Etchform BV, Hilversum, The Netherlands
• Ana Lambert, Tech-Etch, Plymouth, MA, USA
• Kirk Lauver, Chemcut Corporation, State College, PA, USA
• Ken and Steven Marino, Orbel Corporation, Easton, PA, USA
• Aurelia Montoya, Elcon Precision, San Jose, CA, USA
• Paul Rea, Photofabrication Ltd., St Neots, UK
• Jimmy Trost, Vaga Industries, South El Monte, CA, USA and
• Dr Luke Watson, Tecan Ltd., Weymouth, UK.
References
1. A Kracke, Superalloys, the most successful alloy system of modern timespast, present and future, 7th International Symposium on Superalloy 718 and Derivatives, The Minerals, Metals and Materials Society, 2010.
2. Introduction to Aerospace Materials, Ed. AP Mouritz, Woodhead Publishing Ltd., 2012. ISBN 978-1-85573-946-8.
3. DM Allen, The Principles and Practice of Photochemical Machining and Photoetching, pp. 38-9, 1986. ISBN 0-85274-443-9.
4. PCMI data published in DM Allen, Photochemical Machining and Photoelectroforming, p. 104, 2015. ISBN 978-1-5262-0188-1.
5. A Visser and D Weissinger, Spray Etching of Stainless Steel, PCMI #4000, 1993.
6. DM Allen and PJ Gillbanks, The photochemical machining of some difficult-to-etch metals, Proceedings of Technical Program of National
PCM of Difficult-to-Etch Metals and Alloys: Nickel- and Cobalt-Based Superalloys
Emeritus Professor David Allen, Cranfield University
Electronic Packaging and Production Conference, Vol. 1, 487 -494, 25th-27th February, 1986.
7. DM Allen and P Jefferies, Exploring the different etchants used in the PCM Industry, PCMI Journal, 139, 10-29, 2022.
8. C Bonsell, Photochemical machining medical and aerospace industry metals, PCMI Journal, (in the press).
9. HJA Almond and DM Allen, “Difficult-to-etch” metals and alloys, PCM Research Consortium #3, February 2003.
10. DM Allen, JO Elortegi and L Defourny, Some applications of photochemical machining in biomedical engineering, Processing of Advanced Materials, 3,125-129, 1993.
11. DV Wagh, D Dolas and MD Dhagate, Experimental investigation of photochemical machining on Inconel 600 using ferric chloride, International Journal of Engineering Research and Technology, 4, 289-293, 2015.
12. Nitin D Misal and Mudigonda Sadaiah , Investigation on surface roughness of Inconel 718 in photochemical machining, Volume 2017, Article ID 3247873. https://doi.org/10.1155/2017/3247873
13. Nitin D Misal and Mudigonda Sadaiah , Multi-objective optimization of photochemical machining of Inconel 601 using Grey Relational Analysis, Materials Today: Proceedings 5, 5591–5600, 2018.
14. DM Allen, unpublished, 2015.
15. DM Allen, HF etchants and safety considerations, PCMI Journal, 91, 31-34, 2003
16. US Patent 3,057,765: Composition and method for milling stainless steel and nickel base alloys, General Motors Corporation, Detroit, MI, USA, 9th October 1962
17. US Patent 3,232,802: Process of etching and etching bath for nickel base alloys, North American Aviation, CA, USA , 1st February 1966
18. US Patent 4,284,486: Patterned chemical etching of high temperature resistant metals, Llewelyn Stearns, CA, USA, 18th August 1981.
19. Morral, F. R., "Cobalt-Base Alloys In Aerospace" (1970). The Space Congress Proceedings. 3. https://commons.erau.edu/space-congress-proceedings/ proceedings-1970-7th/session-1/3
20. DM Allen, Electrolytic photoetching: an ECM/PCM hybrid, Proceedings of the 3rd National Electrical Machining Symposium, 54-59, May 1988.
21. S Thorat, V Lonkar, D Patil and M Sadaiah, Some investigations on photochemical machining of cobalt-chromium L605 alloy, Proceedings of AIMTDR-2016 Conference, 1418-21, 2016.
PCM of Difficult-to-Etch Metals and Alloys: Nickel- and Cobalt-Based Superalloys
Emeritus Professor David Allen, Cranfield University
22. US Patent 3,057,764: Treatment of metal surfaces, General Motors Corporation, Detroit, MI, USA, 9th October 1962.
23. Letter from LM McDowell (Eastman Kodak Co., Rochester, NY) to FA Christensen (Elgiloy Co., Elgin, IL), 3rd August 1970.
24. DM Allen et al, The chemical machining of Ni -Ti foils, wires and sputterdeposited films for the manufacture of shape memory alloy microactuators, Proc. International Conference on Precision Engineering ‘95, 549 -562, Singapore, 1995.
25. Y Arruti, Controlled etching of Inconel 617 alloy, MSc thesis, Cranfield University, 2005.
Inkjet Printing Strategies and (Future) Applications
Hans Fritz, Owner and Milena Fritz, CEO, SAT Electronic GmbH
Inkjet printing – an additive process with a revolutionary impact on sustainable and cost-efficient production processes.
Starting with the basics about: How does an inkjet printer work? What is the mechanism behind? What parameters need to be considered?
Continuing with applications and the future development combined with the potential this process brings:
There are already a lot of applications for inkjet systems with a wide range of different inks and suppliers; what else is possible and where will we use inkjet in the future? We will provide an overview but also outlook for PCMI. Direct Imaging – Key Technical Points for Chemical Etching Application
After completing an apprenticeship as a radio and television engineer, Hans Fritz gained experience as a field service engineer with Gerber Scientific. He later transitioned to the PCB industry and worked as a field service engineer before becoming the managing director at Hakuto Europe.
In 1993, he founded his own company, SAT, and has since been leading the family business with approximately 30 employees, specializing in providing machines for production, such as lamination, exposure, handling, and drilling, as well as offering expertise and maintenance services.
Hans focuses on innovative and new processes, such as Ink Jet Printing, to support customers and drive success in the industry.
Since January 2023, Milina Fritz has been leading SAT Electronic GmbH, a midsized family business in the PCB industry. She focuses on assisting customers in planning, implementing, and finding flexible solutions using modern and efficient technologies, as well as providing top-notch maintenance service.
Before this role, from September 2018 to December 2022, she served as a Strategic Business Partner and Key Account Manager in Human Resources for Divisions Chief Operating Office at UniCredit Bank AG.
In her educational journey, she is pursuing an MBA in General Management at Munich Business School in addition to completing a Double Degree Master’s in Psychology & Management and Management International School of Management in 2018.
She also earned a Bachelor of Science in Psychology from Otto-von-Guericke University of Magdeburg in 2016. Furthermore, she has been actively involved in social engagement since 2014, volunteering as a paramedic with the Bavarian Red Cross.
Inkjet Printing Strategies and (Future) Applications
Hans Fritz, Owner and Milena Fritz, CEO, SAT Electronic GmbH
Inkjet Printing Strategies and (Future) Applications opportunities of on- demand Inkjet printing
In today’s economy, companies are balancing the goals of making a profit, producing the highest quality to serve customers' needs, being digital, and, by the way, being sustainable. Those demands have led to a rethink of some steps in production and machinery. Let me introduce one option to you that serves the above-named demands: additive manufacturing with selective Inkjet Printing.
By applying a unique printing strategy, which uses several printing stages to ensure clear printed lines with no bleedings and fully covered edges, we can print etch and plating resists, solder masks, direct metal ink, and legend in different colours on several materials. Applications can include metal milling, secondary masking, etching of punching or nameplates, applying plating resists, i.e., silver masking, and a lot more.
A big advantage is the possibility of printing selectively where you need the ink and spare areas that are unnecessary to cover in order to save ink and material. Also, the opportunity to print in areas with high topography of more than 400μ (ca. 15,7 mil), which allows a higher flexibility than using dry -film lamination
MicroCraft Inkjet printers can be built according to customer needs and are available in several configurations (2, 4, and 8 printheads of different types) and droplet sizes from 13pl down to less than 2.5pl. They have functions like an AOI that automatically checks every nozzle and, in addition, also the full printing to secure the highest quality, a head maintenance station that automatically cleans the printhead regularly, and an air-supported purge system to ensure free and unblocked nozzles.
Interested and you need more information? Let’s get in contact: sales@sat.eu; +49 8061 3506-0
A3 Thinking, a principle of Lean manufacturing, is a powerful tool for the problem-solving and decision-making processes. Utilizing concise problem statements, a thorough review of the current condition, data-driven analysis, and collaborative solution development, A3 Thinking can enable breakthrough solutions and help solve some of your most challenging problems.
This presentation will provide an overview of the basic concepts and share examples of success that have come from implementing A3 Thinking. Attendees will also enjoy an interactive activity that will help them prepare to use A3 Thinking to solve a current problem they are facing.
Blake Parkinson has over 15 years of experience in the semiconductor industry with experience with both dry and wet chemical etching, advanced process control, new product development, and manufacturing operations.
He has a Master of Business Administration from William Woods University and a Master of Science in Chemical Engineering from the University of Texas at Austin.
Blake has been published in IEEE and in four conference proceedings. In his work with Watlow, Blake manages a segment of the Semiconductor Business Unit, focusing on expanding customer adoption of products that use PCM manufacturing processes.
Blake currently serves as the Treasurer for the PCMI Board of Directors.
This presentation provides a comprehensive analysis of critical factors essential for Photo Chemical Etching manufacturers operating in Sheet to Sheet (StS) and Roll to Roll (RtR) applications.
It emphasizes the importance of advanced alignment facilitated by precise target detection techniques, considering material and surface preparation, to ensure quality photoresist exposure, productivity, and meticulous machine thermal requirements for consistent performance over time.
Additionally, it highlights the native automation capabilities provided for Sheet to Sheet machines and RtR processes. Ergonomic considerations such as automated software functions and user-friendly interfaces are also addressed to enhance workflow efficiency.
Alexis Guilbert graduated from Esigelec School with a Bachelor’s degree in Electrical Engineering.
He embarked on his career as a Method & Industrialization Engineer for distribution transformer systems at Alstom.
Limata´s laser and UV-LED exposure machines in the application field of “chemical milling”
Demonstration of practical use cases with the benefits of these direct imaging technologies for applications in the chemical milling area.
Going from miniature finest achievable patterning on div. metal materials to the largest direct imaging bed for military and aerospace applications.
I am a 40-year-old CTO of Limata, overseeing R&D, production, and service, leveraging my background in electrical engineering from Munich and previous experience at Rohde & Schwarz GmbH in RF amplifier R&D.
I founded Limata in 2010 and have accrued 14 years of expertise in the machinery business focused on direct imaging.
Pusch,
This presentation will highlight the advancements in direct imaging, coming a long way from its “standard” resolutions down to single-digit figures, focusing on the developments in the light source and imaging technology itself, but also the interdependencies between equipment capabilities and existing processes aimed to evolve towards generating finer structures and features.
Miniaturization as a determined goal does not only address higher resolution but also higher accuracy requirements.
The importance of highly accurate front-to-back alignment, especially for metal etching applications, along with increased complexity due to higher demand for automation and traceability functions, will be answered in this presentation showcasing intelligent solutions to today’s equipment and the approach of diverse challenges from an application’s / process perspective.
Dennis Pusch, M.Sc., is the Manager Sales and Business Development for Schmoll’s Direct Imaging product line.
He has supported the DI product since its early beginnings at Schmoll Maschinen and understands its technology,application, market and customer requirements well, counting several years of experience working in this field.
Supporting and working with global customers, Dennis has a good insight on current market trends and new requirements.
Metal 3D Printing: How to Successfully Utilize the Benefits of AM
Roland
Spiegelhalder, Product Manager Additive Manufacturing, RUMPF Laser- und Systemtechnik GmbH
Metal 3D printing, also known as additive manufacturing (AM), revolutionizes how we create metal components. In conclusion, strategic adoption of metal 3D printing unlocks innovation, efficiency, and competitive advantage. This presentation elaborates on the basic principle of the process and its limits as well as best practices shown by applications out of various industries.
Roland Spiegelhalder as a Product Manager Additive Manufacturing within the TRUMPF organization is responsible for AM technology containing the metal powder bed especially the TruPrint 3000 and TruPrint 5000. His background is in aerospace engineering and he has over eight years of experience in the field of powder bed fusion AM technology. As an R&D Engineer at TRUMPF, he has been awarded a patent for metal additive manufacturing scan strategies, with several other patents pending. Before his role at Trumpf headquarter he spend three years in the US as Project and Product Manager for AM.
John Wilson, Director of Technical Services, MIVA Technologies GmbH
My presentation outlines the evolution of direct imaging from CRT, LCD, and finally DLP.
This development path started with early attempts in the 1980s utilizing blue laser and has led to dedicated high-energy wavelength technologies required in today’s photo-lithography.
I will cover the next steps of DI technology, from maskless microelectronics applications to high-resolution high throughput printed electronics and chemical milling.
John Wilson is Director of Technical Services for MIVA Technologies GmbH.
He started work in PCB manufacturing in the UK before moving on to become general Manager at one of the UK´s leading manufacturers of precision photo masks.
As a communicative and creative end-user, he helped MIVA Technologies improve and adapt their machines to the needs of the high-resolution imaging market.
Having been around MIVA machines for 25 years, John brings in-depth experience to the MIVA team. He is active in helping to develop new products and supporting our machines in the field across a wide range of applications, from microelectronics, printed electronics, PCBs, chemical etching, etc.
•
• Producing an initial prototype
• Small pilot production runs
• Feasibility studies
• Producing scale-up data
• Operator training and education