Architect 2.0
The role of designers in a world where less is more
Modular marvel
Bio-based Offaly school arrives by truck Bay window Connemara scheme brings the Atlantic in
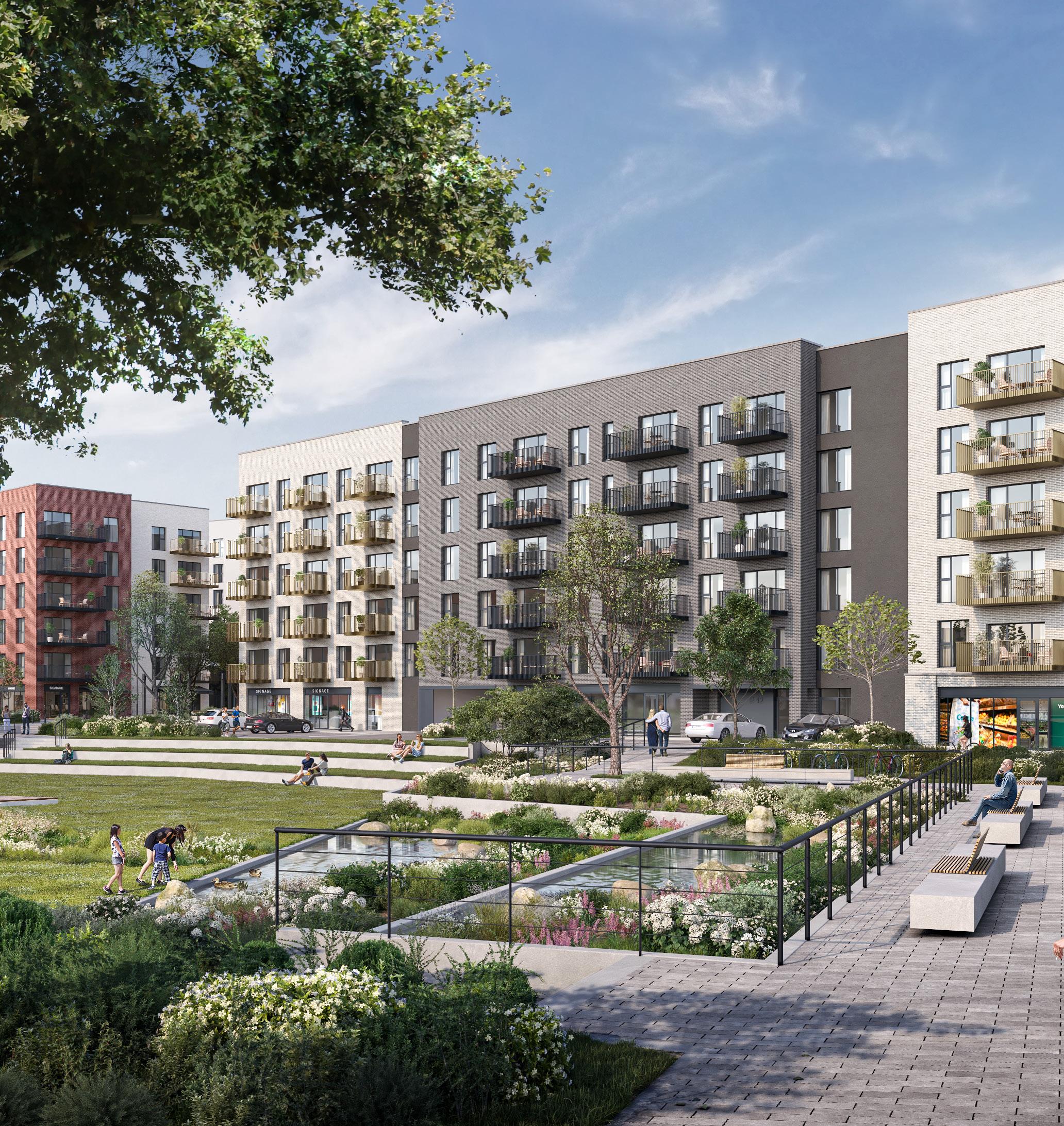
Architect 2.0
The role of designers in a world where less is more
Modular marvel
Bio-based Offaly school arrives by truck Bay window Connemara scheme brings the Atlantic in
Ireland’s largest developer goes passive at scale
Minimal Energy Usage. Maximum Living Comfort.
Read our position paper at cairnhomes.com/passive-house or scan the QR code.
Publishers
Temple Media Ltd
PO Box 9688, Blackrock, Co. Dublin, Ireland
t +353 (0)1 210 7513
e info@passivehouseplus.ie www.passivehouseplus.ie
Editor Jeff Colley jeff@passivehouseplus.ie
Reporter John Hearne john@passivehouseplus.ie
Reporter Kate de Selincourt kate@passivehouseplus.ie
Reporter John Cradden cradden@passivehouseplus.ie
Reader Response / IT Dudley Colley dudley@passivehouseplus.ie
Accounts Oisin Hart oisin@passivehouseplus.ie
Art Director Lauren Colley lauren@passivehouseplus.ie
Design Aoife O’Hara aoife@evekudesign.com | evekudesign.com
Contributors
Lenny Antonelli journalist
Caroline Ashe Brady KORE Insulation
Toby Cambray Greengauge Building Energy Consultants
Ellora Coupe Her Retrofit Space
Mhairi Grant Paper Igloo Architects
Kathryn Meghen RIAI
Marc Ó Riain doctor of architecture
Print GPS Colour Graphics www.gpscolour.co.uk | +44 (0) 28 9070 2020
Cover A rendering by 3D Design Bureau Ltd of Cooper’s Square, Seven Mills
Some of the most persistent myths about passive house, over the years, have been about its practicality and commercial viability. It’s all well and good for the committed enthusiast, the thinking goes, but once it interfaces with the real world of large scale property development, it won’t stack up.
When this magazine lobbied for a passive house planning requirement for all new buildings in Dún Laoghaire-Rathdown in 2015, both the then director general of the Construction Industry Federation and one of Ireland’s leading property journalists reached for the same metaphor in arguing against the plans: the luxury car. Sure, everyone might want to drive a Mercedes Benz, but most people can’t afford such a car.
I’ll do my best to avoid the rabbit hole of questioning the automotive metaphor –other than to say that it would be helpful in a climate emergency to move away from an oil age lexicon, where we no longer talk about concrete plans, steely determination, cementing relationships or putting the pedal to the metal. But I want to take issue with the substance of the argument: that passive house may be a nice thing to have for those who can afford it, but it’s not realistic for normal people. We built evidencebased arguments at the time that this was untrue, and that with expertise and care, passive house could be delivered at little extra construction cost and – if it became a condition on land – no net cost increase in terms of total development costs.
All the same, it is one thing to make an argument. It is quite another to see it become set in stone, to pick a less jarring metaphor. As this issue reveals, Ireland’s largest house builder, Cairn Homes, is currently on site with over 1,750 apartments
which are set to be certified to the passive house standard. Every one of these homes are social and affordable units, meaning that 1,750 households will not have to choose between heating or eating, and will not have to suffer the threats posed by damp, mould and poor indoor air quality.
And it gets better. Because they’re being delivered in sites aiming for biodiversity net gain, and with sustainable transport connections, and backed by the Irish Green Building Council’s rigorous Home Performance Index certification, they offer the real prospect of creating thriving communities which can show the way forward in terms of what property development in the 21st century must look like: places where people have the sanctuary and dignity of a quiet, comfortable home that is light on the pocket, with the delight of nature outside, and without the need to own a car to get around.
In so doing, projects like this show us the seemingly impossible: how to tackle the climate emergency, the biodiversity emergency, the energy crisis and housing crisis. The fact that Cairn have managed to do this without passing on any construction cost increases to their clients, is even more remarkable.
The cynic in me is still adjusting to praising a large-scale house builder. But I have no choice in this case. The leadership shown by Cairn Homes is game changing, and the entire construction industry in Ireland and the UK must sit up and take notice. If the largest house builder in Ireland can build at scale to the world’s leading low energy building standard, why can’t you?
Regards, The editor
If passive house is Everest, we’ve left base camp
The construction industry is moving in great numbers towards the passive house standard. In an adapted version of a speech at the Construction Industry Federation Conference in September, Passive House Association of Ireland chair Caroline Ashe Brady looks at the trek ahead.
Passive towers protect vulnerable Bronx seniors
How do you serve the needs of senior citizens who have fallen on hard times in the Big Apple? In Betances Residence, CookFox Architects have cooked up an extraordinary response, integrating the protective benefits of passive house with beautifully considered, user-tailored design.
Traditional homes retrofit grant pilot launched; £30m passive scheme launched in Down; and a pan-European consortium aims to kickstart the en masse greening and decarbonisation of Europe’s housing stock.
In the latest piece in his series on the development of low energy building, Dr Marc Ó Riain describes the evolution and Impact of EPCs in Ireland and the UK; and Ellora Coupe says our efforts to retrofit homes across the UK and Ireland will be severely hampered unless we engage meaningfully with and empower women homeowners and professionals.
Passive breakthrough
Ireland’s largest developer embraces passive house at scale
In September Cairn Homes lit the fuse on a passive house explosion, publishing a position paper on passive house and announcing the construction of nearly 1,800 apartments to the standard. But what’s behind the company’s bold move?
Bay window
Connemara passive scheme brings the Atlantic in Designing a passive house is one thing. Designing a scheme of passive houses to make the most of the views on an extraordinary coastal site is another. And designing that scheme to tie into the local supply chains and architectural vernacular – while ensuring the homes are set up for changing, potentially disengaged occupants – is the stuff of magic.
Offaly school uses volumetric modular timber build
Forgive the 80s hip hop house reference in the headline, but the volume of the walls in this volumetric modular school building in Birr was literally pumped up – with recycled newspaper insulation. Built to passive house principles, it’s a story of one Roscommon manufacturer reimagining the role that offsite methods can play in the delivery of highly sustainable permanent accommodation for schools – while delivering exceptionally low embodied carbon results.
Just what the doctor ordered
Stirling passive house blitzes RIBA 2030 targets What do you get when a clinician couple decide to build their dream family home? In the skilled hands of leading Scottish architects Paper Igloo, you get a forensically detailed, highly ecological, cosy home that wraps up low embodied carbon and passive house into a beautiful design.
The role of designers in a world where less is more
It’s a radical idea: that to negate the environmental damage of construction, we don’t just need to build sustainably, we need to build less. However, most architects and building designers earn a living by doing exactly the opposite: by building stuff. So how can the design practice be reinvented for a world in which we need to do more with much, much less?
Keep up with the latest developments from some of the leading companies in sustainable building, including new product innovations, project updates and more.
Passive house doesn’t care about materials
One stubborn trope in some corners of green building is that passive house is so focused on energy performance that its advocates ignoring materials. Not so, argues Toby Cambray.
The construction industry is moving in great numbers towards the passive house standard. In an adapted version of a speech at the Construction Industry Federation Conference in September, Passive House Association of Ireland chair Caroline Ashe Brady looks at the trek ahead.
At present, many players in the construction industry are quietly investigating the passive house standard. With approximately 3,000 passive units in the pipeline in Ireland, on site or heading for site and in tandem with Cairn Homes’ recent announcement that they are adopting the standard and will add over 1,700 units, this has become a mega trend. So why the move to passive?
The rise of green finance and lower interest rates linked to Environmental, Social and Governance (ESG) has been a major driver. This source of finance is especially important to the construction industry given the investment required to make projects happen. If you cannot prove through reporting that you are delivering on your ESG outcomes, not being able to access lower interest finance puts you at a competitive disadvantage.
The raft of legislation from Europe is another key driver. The Corporate Sustainability Reporting Directive (CSRD) comes into play in Ireland this year for twenty-six companies.
both the embodied and operational carbon of the built environment. We need to look at how we design and build, the systems we use, and to engage with the entire supply chain – it is the collective effort from all that will deliver a lower embodied carbon result. This is no easy task and there is an industry view emerging that it will take some time, and that operational carbon interventions may more quickly deliver reductions. Operational carbon is the in-use carbon produced from the finished building. A target to reduce is easier to achieve because it is the output of the design and build activity. What happens on site following appropriate design, reduces the performance gap and therefore operational carbon.
is just the recipe for passive is slightly different. To be bold, we have the solution for zero energy building. If passive house is the summit of Everest, then NZEB is a base camp on that journey.
But what will it cost?
A study in the UK by Atkins in 2019 found that passive projects in the UK cost approximately an extra 4 per cent but reduce to nominal levels if adopted at scale. The reality is every time we want to do something different it costs money. Whether you build ZEB buildings today or in 3 years, you will incur the cost of doing so. The beauty of passive is that once you nail the process the cost difference is marginal.
We already use the ingredients, it is just that the recipe for passive is slightly different.
A further 2,000 companies must report next year, including many in construction, and this information will be data mapped, allowing the finance and investment industry to easily compare one company to another.
The recast Energy Performance of Buildings Directive was enacted in Europe in May, calling for zero emission buildings. Over the next couple of years government will be deciding what this looks like in Ireland.
Consider the E in ESG. We need to reduce
Why does passive house solve these problems? In the 1980s, Professor Wolfgang Feist wanted to prove that it was possible to build without a traditional heating system even in colder climates. The first building, built 33 years ago, is still being monitored and has been an intensive research project from day one. Feist set up the Passive House Institute, a not-for-profit independent research institute, and currently it offers the only internationally recognised, performance-based energy standard in construction. There are now nineteen affiliates globally, including the Passive House Association of Ireland, and as of June 2024, 43,800 units have been certified. To say that this standard is tried and tested is an understatement. It has proven effective through post occupancy evaluation and the institute continue to review, learn and always improve the standard. A science-based approach, the standard also speaks to the G in ESG. It reduces operational carbon compared to NZEB with no green washing. Outcomes are explicit because the performance targets are absolute, with metrics defined through a transparent evidence-based process. The passive house planning package (PHPP) is a robust, accurate and practical tool that supports compliance and design, and produces energy forecasts with an elevated level of accuracy. The performance gap is now in the margin of error. Our industry is on a progressive journey to zero and how we have done things to now has served us well. As Stephen O’Shea from Cairn Homes recently said, we already use the ingredients, it
There are so many more benefits, for homeowners, councils and housing bodies – passive house protects the value of your assets. Maintenance costs are lower, the building fabric is protected, and the need to retrofit new buildings to meet 2050 targets will be obviated.
The social advantages speak to the S in ESG. Passive buildings offer greater comfort, healthier buildings, improving the quality of life for the occupants. And because the performance gap is closed, the monetary savings are real. What would you do with the money you normally spend on heating if you had it in your pocket today?
Everything has its time
Consider Steve Jobs of Apple. In the 1980s he said that he wanted everybody on the planet to carry a computer in their pocket. In the apocryphal words of Henry Ford, who revolutionised the production of motor cars, “If I had asked people what they wanted, they would have said faster horses.” In the 1980s Wolfgang Feist designed a building without heating. So, as you get in your car and look at the little computer in your pocket, ask yourself – is now the time for passive house? n
How do you serve the needs of senior citizens who have fallen on hard times in the Big Apple? In Betances Residence, CookFox Architects have cooked up an extraordinary response, integrating the protective benefits of passive house with beautifully considered, user-tailored design.
Words by John Cradden
Betances Residence is a passive house classic-certified residential development located in the Bronx, New York City that provides supported housing for vulnerable and homeless senior citizens in what is now a thriving majority Hispanic community. Comprising two eight-storey towers with 152 units and around 10,000 sq ft of community space and amenities, this development had to meet a very challenging brief, and the team behind it has not only ticked all the right boxes, but executed it in a way that has surpassed expectations for energy efficiency, comfort and air quality.
The brief
The commissioning of Betances is the result of a collaboration between the New York City’s Department of Housing Preservation and Development (HPD) and Breaking Ground, a non-profit organisation that builds high-quality permanent and transitional housing for
the homeless using both public and private funding. The RFP (request for proposals) for the development on what was an open parcel of land owned by the City of New York was awarded to CookFox Architects, a local firm that specialises in mainly large-scale projects, most notably St John’s Terminal, Google’s 1.2 million sq ft headquarters in the city, and the 55-storey Bank of America Tower. The firm had previously worked with Breaking Ground on another supported housing project, the Hegeman in Brooklyn back in 2010, but for both organisations, Betances was their first experience of building to certified passive house standard.
The case for passive house
Aside from the energy savings, CookFox’s director of communications, Jared Gilbert, points to two of the biggest benefits of passive house for the residents of Betances: better air quality and superior
acoustic insulation. Located close to some of the busiest state and interstate highways in the city, the South Bronx has one of the highest asthma rates in the United States. “I don't know if it's more noisy than other neighbourhoods, but we often think of quiet as kind of a luxury product in New York City,” said Gilbert. “One of the benefits of passive house is that because you have to create an envelope that's so tightly sealed, you get really good acoustic performance.” He added that while taking pictures of some of the residents, the woman sitting at the window said: “I love this building. It's so quiet in here.”
Gilbert says the challenges of achieving passive house certification were complex “given the constraints for economy, construction sequencing and ambitions for architectural experience for a multi-unit design”, but a closely aligned team led by consultancy Steven Winters Associates, Monadnock Construction, and a steadfast client enabled them to achieve it.
The architecture along 143rd Street in New York City is very varied, with early 20th century brick-built town homes and some
When someone has not had a home of their own for many years, that sense of protection and permanence is important.
later 1920s and 1930s apartment buildings next door, not to mention high-rise public housing nearby. A neat design touch that enhances the sense of permanence of Betances is the use of deep window recesses, creating stronger shadows that bring a feeling of solidity and heft that apes older buildings but without the need to build walls that are thick and heavy. Many later 20th century buildings tend to have very flat facades that may not age well. “Our expression of the depth of our exterior wall is meant to reinforce the idea that this building will be lasting and permanent,” said lead architect Darin Reynolds. “When someone has not had a home of their own for many years, that sense of protection and permanence is important.”
Aging gracefully
Above the ground floor level, Betances is clad in zinc, which aligns with the aim of using natural materials as much as possible as well as being relatively inexpensive. “The zinc we used on this project is pre-weathered, meaning that it come with patinated or oxidized surface, which causes its light, warm grey colour,” said Reynolds. “Over time, with additional weathering, the surface should darken slightly. This natural process allows the building facades to age gracefully and beautifully. It will look as good, or better in the future.”
Connection with nature
The use of zinc as a material that will age gracefully over time is but one example of the extensive application of biophilic design in Betances. Others – often done in conjunction with active design strategies to support health and wellbeing – include encouraging movement and activity by making the path through the building easy to navigate, lining it with plants and natural materials, and adding windows to the egress stairs to bring natural light and encourage the greater use of the stairs.
“As the building kind of took shape and began to be planted, we noticed that the neighbours started replanting the own backyards, with similar plants and things that we were using in these courtyards,” said Gilbert. “So, I love that idea that the building can make an impact on the neighbourhood in a positive way, and that there can be a relationship between not just the people, but the landscape in this building.”
The power of universal design
Given its central purpose as a building for senior citizens, it’s no surprise to see lots of examples of universal design, but they are all executed in a way that makes them feel
integral parts of the building, such as the discreet handrails along the ramp walkway. “The large entry ramp is a way to allow users with mobility issues to enter the building in the same way as someone without mobility issues,” said Reynolds. “The idea is that the experience is shared. By including natural materials and patterns, along with access to daylight and views, it actually elevates the experience of entering the building and makes it special for everyone.”
Gilbert adds that anytime he’s in the building for tours, most people tend to take the ramp rather than the stairs simply because they enjoy it more. “There's a slow descent towards that big glass where you're looking into the courtyard, so you just have this immediate connection to nature to the garden that's at the centre of the building and, as you sort of circle around that bend, you feel enveloped by the space.”
‘We got it right, here’
Brenda Rosen, president and CEO of Breaking Ground, says Betances meets a new standard for housing quality that everyone deserves, not just those who can afford it. “Whenever we begin a project, we approach it from the perspective of the tenants who
will call the building home. People experiencing homelessness deserve quality and sustainability in their housing, and we aim to ensure that people who are living with mental illness, long periods of homelessness, and other disabling conditions have everything they need to get and remain stable for the long term. And here we are also working with seniors, bringing another layer of complexity by ensuring that people can age-in-place in the community for as long as possible. One of my colleagues with deep experience opening our new projects said it best at the Betances ribbon-cutting: ‘We got it right here.’ I could not agree more.”
The digital version of this magazine includes access to exclusive galleries of architectural drawings.
The digital magazine is available to subscribers on passivehouseplus.ie & passivehouseplus.co.uk
Multi-award winning Belfast-based property developer, Fraser Millar, has launched Northern Ireland’s second large-scale residential passive house development – a 74-unit scheme of detached and semi-detached homes at a total project value of £30m.
Located on the Comber Road in Carryduff, Co Down, Beaufort Green follows the success of the company’s first passive house development, Lancaster Park, in south Belfast, which featured in issue 43 of Passive House Plus.
“The passive house standard has set a new benchmark for energy efficiency and sustainability in the housing market,” said Fraser Millar director John Carrigan, “The criteria for passive house certification significantly exceed Northern Ireland’s current building regulations – to the benefit of our homeowners”.
14 houses have initially been released with over three quarters booked. First completions are estimated for the first quarter of 2025.
While the construction industry has been slow to engage with monitoring the real world performance of buildings, Fraser Millar – who scooped Developer of the Year 2023 at the PropertyPal Awards – are proving to be an exception.
“We believe we are also the only property developers in Northern Ireland that collects monthly data to monitor the energy usage of our passive homes,” said Carrigan. “So far, we have received excellent feedback from our homeowners in Lancaster Park. Typical new homes, according to recent studies, are using nearly double the energy in their design projections. Whereas our passive homes are actually using slightly less than the calculated levels. This demonstrates that passive houses do what it says on the tin, which can result in considerably lower utility bills for the homeowner.”
Carrigan said Fraser Millar hoped to see sustainable building standards like passive house become more commonplace in Northern Ireland. “At Fraser Millar, we have cemented ourselves as the industry trailblazers, paving the way for a revolutionised way of living that is both better for the environment and for the health of occupants. The wider Northern Ireland housing industry is grappling with challenges and claims of low energy, but with passive house principles, the sector has the potential to be not only completely revolutionised but truly energy efficient.”
For more information visit www.frasermillar.co.uk •
The Sustainable Energy Authority of Ireland has launched a home energy upgrade for traditional homes pilot.
Owners of traditionally built homes can now apply for grant support through a number of SEAI’s registered one-stop-shop providers.
Typically, traditional homes differ significantly from homes built in the last century in one significant way: solid masonry external walls, built from traditional materials, with no continuous cavity. As few materials suitable for use in traditional buildings have been certified by bodies such as NSAI Agrément, the works in the pilot must involve homeowner-appointed traditional building professionals – including conservation-accredited architects, engineers or surveyors.
The move follows the Department of Housing publishing the guidance document, Improving Energy Efficiency in Traditional Buildings: Guidance for Specifiers and Installers.
The pilot, which will be open for 100 homes, seeks to gain a detailed understanding of the technical aspects, materials, products, and associated costs with the solutions required for traditional homes.
The announcement was welcomed by TU Dublin’s head of building performance and construction, Joseph Little, who called the news “the most significant government-led change in the energy efficiency of traditional buildings” since retrofit grants were introduced in 2008, adding that it would assert the importance of the role of conservation architects and other design professionals with expertise in ensuring the health of solid wall structures. “It’s going to reinvigorate the conversation about what is an appropriate specification and provide additional support for those seeking to move away from the narrow Agrément-approved approach.” Little said that once the pilot has concluded, the emphasis will be to move forward to a national scheme.
For more information, visit tinyurl.com/ tradpilot. •
Gas cooking is killing 40,000 European people a year in Europe, a major new study has revealed, with an average of almost two years taken off their life in the EU and United Kingdom due to exposure to nitrogen dioxide (NO2) emitted during gas cooking.The countries with the highest burden were Italy, Poland, Romania, France and the UK.
The European Climate Foundation-funded study, which was conducted by academics at Jaume I University, has calculated the first map of indoor NO2 concentrations in households according to cooking appliance for the European population. The annual concentrations inside the households of more than half of the countries exceeded the heath
guideline for NO2 proposed by WHO in 2021.
Gas cooking appliances are a significant source of household air pollutants, including NO2 , which is a harmful gas with known health effects. Gas hobs are present in 33 per cent of European Union households and in 54 per cent of households in the UK. Presence of gas cooking at home and exposures to NO2 have been associated with childhood asthma, premature mortality and other health outcomes in scientific studies.
Other pollutants emitted during cooking with gas appliances were not considered in the study. •
Europe’s burgeoning green homes market is a multi-trillion euros opportunity –but lenders must be wary of facilitating greenwashing, a pan-European consortium has warned.
According to Alexandra Hedesiu, managing partner at EnerSave Capital and spokesperson on the pan-European project Smarter Finance for EU: “The need to rapidly transition to a decarbonised, green European housing stock represents a multi-trillion euro opportunity –and it’s one that the finance community must embrace.”
With a range of drivers emerging to force the hand of finance to quantify and substantially improve the environmental and social performance of investments, Hedesiu warned against finance professionals seeking to do the bare minimum to meet the requirements for individual drivers in isolation.
“Investors who take a narrow interpretation of their obligations regarding any one green driver are heading for trouble,” said Hedesiu. “The EU taxonomy is one thing. But what about the Sustainable Financial Disclosure Regulations (SFDR), the Corporate Sustainability Reporting Directive (CSRD), or the recast Energy Performance of Buildings Directive? Property investments that barely meet the requirements of these drivers risk becoming stranded assets. The only prudent approach is to stop thinking about doing the bare minimum, and instead invest in property with credible green building certification.”
A European Union-funded consortium of
green building councils, energy agencies, NGOs and sectoral experts, Smarter Finance for EU is aiming to kickstart the en masse greening and decarbonisation of Europe’s housing stock by unlocking €100bn worth of EU taxonomy-aligned green homes – over €10bn of which has already been secured.
Green homes finance professional course launched
The consortium has developed a green homes-accredited finance professional training programme to upskill finance professionals on greening their portfolios, led by Hedesiu. “This comprehensive training initiative offers a robust curriculum,” said Hedesiu. “It encompasses key areas such as green homes certifications and EU taxonomy alignment, real estate loan portfolio assessment, reporting and governances, risk management, regulatory compliance and marketing strategies for residential green finance.”
Hedesiu said the training will play a key role in equipping finance professionals with specialized knowledge and skills in green financing, focusing on sustainable housing projects and green investment strategies.
Hedesiu announced the new training programme at the Smarter Finance for EU banking sector launch event, “Banking on green homes: exploring the world of sustainable finance”. Held in Brussels in May, the event focused on supporting the banking sector and the journey to “greenify” portfolios, and was attended by an audience of property financiers and investors.
The EU LIFE co-funded project, Smarter Fi-
nance for EU, is dedicated to driving the change Europe needs in the development of finance and credible green certification for homes.
Smarter has unlocked finance and green home certification for over 31,000 new homes across Europe, by taking a systemic, multidisciplinary approach to solving a systemic problem. The needs and motivations of all of the essential stakeholder groups that are critical to moving the green finance topic forward to promote greener homes for Europe’s are considered.
Co-ordinated by the Romania Green Building Council, the partners in Smarter Finance for EU include the Irish Green Building Council, Luxembourg-based sustainable finance facilitator EnerSave Capital, Passive House Plus publishers Temple Media Ltd, the association Energy Efficient Cities of Ukraine, Green Building Council España, Portuguese energy agency Adene, Habitat for Humanity International, and the European-Ukrainian Energy Agency. With energy poverty on the rise across Europe in the aftermath of Russia’s invasion of Ukraine, the consortium also includes a focus on developing hybrid green finance products to help lift vulnerable people out of energy poverty and provide healthy, comfortable homes with low exposure to energy price spikes.
A number of banking partners already offer finance products tied to green home certifications by partners in Smarter Finance for EU, and the EU Horizon 2020-funded programme which preceded it, Smarter Finance for Families. Tailored development finance discounts of 0.1 to 0.5 per cent are available in Ireland for housing schemes certified to the Irish Green Building Council’s Home Performance Index (HPI) certification by pillar bank AIB and Home Building Finance Ireland. A range of banks offer preferential green mortgages tied to Romania Green Building Council’s Green Homes certification, including Alpha Bank Romania, Banca Transilvania, BCR Erste Group, BRD Groupe Societe Generale, Garanti BBVA, Raiffeisen Bank Romania, Romanian Commercial Bank, Vista Bank and Libra Internet Bank, who also offer preferential development finance terms. Meanwhile, Smarter Finance for Families partner Polish Green Building Council has secured green mortgages on its Zielony Dom certified homes from BNP Paribas and BOS Bank.
For information on green home certification, finance for green homes visit www.smarter4. eu. For information on the courses offered by Smarter4EU partners including for green homes finance accredited professionals and a range of other courses, visit www.smarterfinance4.EU/ education •
New and tightening sustainability requirements are hitting the construction sector at an increasing pace. Irish Green Building Council membership engagement officer Lenny Antonelli goes through the main requirements – and offers clues on how to keep ahead.
How well do you know your CSRD from your SFDR from your CSDDD? Or even your EPBD from your EED? And do you know how these will impact your business? For those working in the built environment, it feels like there is an avalanche of new regulations and directives from Europe to get to grips with, each with its own confusing title.
The European Green Deal – the package of EU policy initiatives that aims to make the union climate neutral by 2050 – contains dozens of different laws, many of which will impact the building sector.
Some of the most important laws concern corporate finance and governance, rather than buildings explicitly. But their effect is quickly trickling down to the built environment. These are part of the EU’s Sustainable Finance Framework and could be grouped under the broad term ESG (Environmental, Social, and Governance). There is no strict legal definition of ESG, but the term is used to generally refer to corporate policy and regulation in these fields.
These new directives and regulations include:
› The Corporate Sustainability Reporting Directive (CSRD) requires companies to report on the impact of their activities on the environment and society. It applies to all publicly listed – as well as larger, non-listed – companies. It is expected to impact 50,000 businesses across Europe. The directive requires companies to collect more detailed and robust data on the environmental impact of their activities. For example, it is pushing companies in the building sector to measure the whole life carbon of their developments. Smaller companies not directly subject to the directive may also start to receive more requests for environmental information related to their clients’ CSRD reporting obligations. The CSRD was transposed into Irish law earlier this year, and the first Irish companies will begin reporting under the directive shortly.
› The EU Taxonomy Regulation (2020) is a classification system used to determine whether an economic activity is “environmentally sustainable”. It is designed
to prevent greenwashing. To meet the definition of sustainable, an activity must contribute substantially to at least one environmental objective, and do no significant harm to the other environmental objectives . Detailed sustainability criteria have been developed for buildings under the Taxonomy. Many investors, procurers, and developers are keen for their buildings to comply with the Taxonomy, as it will enable them to access ‘green’ finance at lower rates of interest.
› The Sustainable Finance Disclosures Regulation (SFDR) sets rules for how those who market and advise on financial products communicate sustainability information. In force since 2021, it requires these parties to evaluate any adverse sustainability impacts of their investment decisions or advice. The goal is to tackle greenwashing and make it easier to evaluate the sustainability of financial products. Real estate investors and other players in the property market may fall under the requirements of this directive.
› The Corporate Sustainability Due Diligence Directive (CSDDD or CS3D) was formally adopted by the EU earlier this year but has not yet been signed into Irish law. It applies to EU companies with more than 1,000 employees and net worldwide turnover of about 450 million, and to non-EU companies that generate the same amount of turnover within the EU. It requires these companies to carry out due diligence to identify actual or potential adverse impacts of their activities, and their chain of activities, on human rights and the environment. These companies will have to introduce a climate change transition plan to ensure their business strategy is aligned with EU climate targets under the Paris Agreement.
All of this legislation is starting to impact buildings here in Ireland. “We are seeing the impact of the new European legislation and regulations in various ways,” says Neil Menzies, director of sustainability at leading Irish real estate group Hibernia, which specialises in the Dublin office
market. Menzies says these new laws are making their way into the due diligence processes of institutional investors and lenders, who are increasingly asking to see things like energy and carbon performance data for buildings, decarbonisation strategies, and green building certificates. “Hibernia's sustainability strategy to build and operate the most sustainable buildings with the performance and credentials to support this ensures that we are able to respond to these queries”.
“We also see the impact through the growing requests from occupiers for more sustainable spaces and the performance of these spaces to help support their own requirements to comply with this legislation,” he adds, “especially legislation that requires them to report on their own ESG related performance and key performance indicators, such as the CSRD and CSDDD.”
Leading Irish homebuilder and developer Cairn Homes is reporting a similar impact. “Cairn will be reporting under CSRD from the financial year 2025, and as part of that will be reporting the percentage of our activities which are aligned with the EU Taxonomy,” says the company’s head of sustainable construction and reporting, Stephen O’Shea. “However, we are already seeing our institutional customers request evidence that buildings we are selling this year –which are likely to have been designed in 2019 and procured in 2021 – are so aligned.”
“Thankfully our early commitment to science-based decarbonisation targets has meant that we have whole life carbon calculations to hand, and our biodiversity net gain targets ensure that we have the surveys, designs, and data required to evidence our efforts in that regard.”
We see the impact through the growing requests from occupiers for more sustainable spaces to help support their own requirements to comply with this legislation.
Besides these ESG directives and regulations, other new laws under the European Green Deal relate more directly to buildings and energy. These are beginning to trickle down and impact project specifications too.
› The Energy Performance of Buildings Directive (EPBD) is the most critical European law for the built environment. Previous versions of the EPBD led to the introduction of BER certificates and nearly zero energy building (NZEB) standards in Ireland. The latest version was adopted by the EU earlier this year. It places a stronger focus on renovation and includes rules on embodied carbon for the first time. The directive requires that all new buildings be “zero emission” from 2028, and that the life cycle global warming potential (GWP) of all buildings be disclosed, and limited, from 2030. The EPBD also requires member states to improve the energy efficiency of their worst performing buildings. The latest version of the EPBD must be transposed into Irish law within two years. The IGBC is currently working on a project to support this transposition.
› The Construction Products Regulation (CPR) aims to ensure the quality and safety of construction products. The latest version (2024) lays down more harmonised standards to help construction products circulate freely within the single market. For the first time, the regulation considers both the lifecycle global warming potential of construction products and their wider environmental impact.
› The Energy Efficiency Directive (EED) (2023) sets overall energy efficiency targets for member states. It requires EU countries to achieve an 11.7 per cent reduction in final energy consumption by 2030, and with regards to buildings, puts a stronger focus on alleviating energy poverty, and on delivering energy efficiency improvements for vulnerable householders.
› The Renewable Energy Directive, last revised in 2023, sets a binding target that 42.5 per cent of the EU’s energy supply be delivered from renewable sources by 2030 (up from a 32 per cent target in the previous version).
These regulations are starting to have an impact too, especially the EPBD. Even though it will be a few years before its requirements come into force, many developers and procurers are keen to ensure buildings under design now are ‘future-proofed’ and compliant with the EPBD.
“The EPBD and EED impact us directly by setting stricter minimum requirements for how
we develop new buildings – for example more onsite renewables, increased energy efficiency, and ongoing monitoring of performance etc,” adds Neil Menzies of Hibernia. “We are moving from a world of voluntary sustainability action to one where sustainability action and performance is now a mandatory licence to operate."
There is a way through this confusion: focus on delivering high quality, healthy, sustainable buildings whose environmental performance is backed by solid data.
For anyone designing, procuring or developing buildings, the European policy landscape can seem daunting. But there is a way through this confusion: focus on delivering high quality, healthy, sustainable buildings whose environmental performance is backed by solid data. While it might technically be possible to, say, define and meet the requirements of the Taxonomy in quite a narrow fashion, the combined effect of all these initiatives will require a robust and holistic approach to sustainability.
The EPBD for example, will require us to start measuring the whole life cycle carbon of buildings and to pay more attention to indoor environmental quality; the CSRD is already putting pressure on developers to gather data on whole life carbon, biodiversity, and circularity; while the Taxonomy is encouraging developers to be more ambitious on carbon on circularity. The CPR, meanwhile, will normalise reporting on the environmental performance of construction products.
So, taking a holistic and rigorous approach to sustainability will be the only path forward.
The Irish Green Building Council’s Home Performance Index (HPI) can help for residential buildings. It takes a holistic approach to sustainability across more than 30 indicators, covering energy efficiency, indoor environmental quality, embodied carbon, water efficiency, daylighting, acoustics, biodiversity, and transport.
The next version of HPI, v3.1, will embed compliance with the Taxonomy as a minimum requirement for certification. HPI v3.1 will be launched in November at the IGBC’s Better Homes Conference. The development of this update to HPI was funded by the Smarter Finance for EU project (www.smarterfinance4.eu).
The IGBC provides Home Performance Index training for those wishing to advise clients on HPI and submit assessments, see www.homeperformanceindex.ie for more information. •
What is the difference between a law, a directive and a regulation?
At European level, a regulation applies to all member states and becomes part of national law. Regulations come into force immediately once adopted by the EU. A directive sets more general goals that member states must achieve, but they devise their own national laws for reaching these goals. Once directives are passed, member states have two years to transpose them into their national legislation. Laws and legislation are more general terms that cover both regulations and directives.
I
n the #BuildingLife Ambassador Spotlight Series, Passive House Plus is profiling leaders who have endorsed the Irish Green Building Council’s call to address the environmental impacts of buildings across their lifecycle.
In this interview, RIAI CEO Kathryn Meghen tells us more about why she is supporting the #BuildingLife campaign, and what the institute is doing to address sustainability in architecture.
Why did you choose to become a #BuildingLife ambassador?
Kathryn Meghen: A central focus of the RIAI’s work is to support architects and architectural technologists in the delivery of high-quality sustainable buildings and places. This is not only for the benefit of the building users but for the wider society as an important contribution to climate change action. Our
We need to create an environment to support the delivery of better-quality buildings, surrounded by community-focused infrastructure.
RIAI Strategy 2023-2027 also places a strong emphasis on sustainability, and we support our members through training, promotion and advocacy. For example, we will be launching a new environmental accreditation for our members this year, to support their skills and expertise in design for sustainability.
The climate change challenge is, however, complex and solutions can only be delivered through collaboration with our built environment colleagues. The #BuildingLife ambassador programme is a great avenue to work across all sectors of the industry to deliver this ambition.
What are you hoping to achieve with the #BuildingLife campaign?
KM: Architects have a leadership role in the built environment, and the RIAI has brought our knowledge and expertise in sustainable building design to our work on external bodies such as the steering group for the National Policy on Architecture and the Construction Sector Group. But I believe that we need to go further – as a #BuildingLife ambassador, my key ambition is to build new platforms for collaboration across the built environment
professions.
These new platforms and initiatives can drive new research into sustainable methods of construction, which are necessary to deliver the number of homes we need to create – as part of liveable urban developments – to accommodate our rising population. Together, we need to create an environment which supports the delivery of better-quality buildings, surrounded by a community-focused infrastructure.
The #BuildingLife campaign provides a platform for the collaborative effort needed to drive change. One of the important outcomes has been the IGBC’s ‘Building a Zero Carbon Ireland’ roadmap, published in 2022. The roadmap outlines the key actions the building industry must take to reduce its emissions by 51 per cent by 2030, in line with our national climate targets. It includes a useful separate roadmap for each of the key disciplines within the building industry – architects, contractors, engineers, planners, surveyors etc.
Can you explain a few ways in which the RIAI is working towards a sustainable built environment?
KM: We have a range of initiatives underway that are all linked to the RIAI Strategy, which seeks to inspire excellence in architecture to deliver a sustainable and resilient future. Key elements of this are the upcoming Environmental Accreditation system, which recognises our members’ ability, knowledge and skill in sustainable design. We have an extensive CPD programme of courses in sustainable design for performance and are currently working with the Irish Green Building Council on a joint programme of research, support tools, guidance and up-skilling of professionals to address the much-needed decarbonisation of our built environment. The programme, Design4Zero, is funded by the Sustainable Energy Authority of Ireland (SEAI) under its National Energy Research Development and Demonstration Programme. We are also creating awareness of exemplars of sustainable design through our annual RIAI Awards programme with a dedicated award for Sustainable Design. This year’s winner was the Department of the Environment, Climate and Communications Headquarters – an exemplary retrofit project by the Office of Public Works. We believe that valuable lessons from this retrofit project can be applied to our existing building stock. We are constantly reviewing our training and support for our members to ensure that they are best equipped for their important role in the design, delivery and management of a sustainable built environment.
#BuildingLife is a project led in Ireland by the Irish Green Building Council. The initiative aims to achieve the mix of private sector action and public policy necessary to tackle the whole-life impact of buildings. Learn more and endorse the Building a Zero Carbon Ireland Roadmap at www.igbc.ie/ building-a-zero-carbon-ireland/. •
Make the greener choice for your home, upgrade your existing central heating with an eco-friendly, low noise Midea Heat Pump. Air source heat pumps are the low-carbon future of home heating which integrates heating and domestic hot water into one system.
The future of heating, renewable energy is the greener, cleaner way to heat your home. Midea’s air source heat pumps are the costeffective way to lower your energy bills and switch to a low-carbon way of heating your home. Make yourself at home and start saving with Midea Heat Pumps.
OUR MIDEA MONOBLOC HEAT PUMP COMES WITH A MARKET LEADING 10 YEAR WARRANTY.
In the latest piece in his series on the development of low energy building, Dr Marc Ó Riain describes the evolution and Impact of EPCs in Ireland and the UK.
The introduction of energy performance certificates (EPCs) in 2007 represented a pivotal moment in enhancing consumer awareness of home energy efficiency in both Ireland and the UK. The concept of energy performance ratings dates back to Energy World’s initiatives in Milton Keynes in 1985 and the UK's National Energy Rating Scheme developed by the Building Research Establishment (BRE) in 1990. However, it was the global Kyoto Protocol of 1998 that spurred the EU to introduce its first Energy Performance of Buildings Directive (EPBD) in 2002. This directive laid the groundwork for integrating energy conservation targets into national regulations, prompting Ireland and the UK to revise their respective requirements for energy performance under building regulations, called Part L in both Ireland, and England and Wales.
In 2007, Ireland and the UK launched EPCs for residential buildings, extending to public buildings in 2008 with the introduction of Display Energy Certificates (DECs). Both rating systems evaluate and rate a building's energy efficiency on a scale from A to G.
Although methodologies for calculating energy performance differ between the two countries, they both comply with the EU’s Energy Performance of Buildings Directive. In the UK, the Standard Assessment Procedure (SAP) is used to generate EPCs, while Ireland uses the Domestic Energy Assessment Procedure (DEAP) to produce Building Energy Ratings (BERs). Both procedures focus on fixed energy loads such as heating, cooling, hot water, and lighting. However, they exclude the impact of household appliances, such as refrigerators and washing machines, which are classified as "loose" or "plug" loads.
Unlike the DECs for public buildings, which are based on actual energy consumption, residential EPCs and BERs are based on theoretical models and fixed assumptions. This theoretical approach has led to a discrepancy between calculated and actual energy consumption. Studies, such as those conducted by O’Driscoll (2014), have highlighted the growing importance of plug loads in energy consumption, particularly in net zero-energy buildings.
Prior to 2005, compliance with Part L was relatively straightforward, based on standard U-values for building components. However, the introduction of BERs/EPCs necessitated signif-
icant revisions to Part L in the UK in 2006 and in Ireland in 2007. These updates incorporated new factors, including thermal bridging, airtightness, and – in the case of Ireland – contributions from renewable energy sources. While these changes aimed to improve energy efficiency and sustainability, they also added complexity to the design and compliance processes. As a result, energy consultants became crucial, using simulation tools to help architects achieve compliance through design modifications and the integration of renewable technologies such as solar pan-
renovations of existing buildings. In Ireland, a new coalition government in 2020 introduced a commitment to upgrade 500,000 homes to a B2 rating by 2030, with grants of up to 50 per cent available to improve eligible homes. The DEAP software was also updated and converted into a web tool, with periodic updates to primary energy factors for the electricity grid meaning that electrically heated homes achieved BER improvements even without fabric improvements – a shift which helped turbocharge the rise of the heat pump.
The surge in energy prices underscores the growing significance and awareness of energy performance certificates as a vital tool for assessing building energy efficiency, benefiting homeowners and investors alike.
els, heat pumps, and wood-burning stoves. The introduction of BERs, EPCs and DECs increased public awareness and influenced both individual behaviour and market dynamics. Reports from 2013 onwards revealed that properties with higher energy performance ratings commanded higher purchase prices, reflecting an energy efficiency premium. For example, the study by Duarte & Chen (2022) found that A-rated homes in Ireland saw a 9.5 per cent increase in value compared to D-rated homes, whereas F/G-rated properties experienced a 10.6 per cent decrease. In England, A-rated homes saw a 5 per cent premium, while F/G-rated homes saw similar levels of price reductions. Other countries, such as Norway and Denmark, reported even more pronounced premiums and reductions, highlighting the growing importance of energy efficiency in property valuation.
A 2010 recast to the EU Directive on the Energy Performance of Buildings introduced a new target for new buildings, the Nearly Zero Energy Building (NZEB), which member states had to define and implement by 2019. The directive also required member states to set minimum energy performance targets for major
The global energy crisis triggered by the war in Ukraine in February 2022 led to a dramatic rise in energy prices, with heating and electricity costs increasing by 70-80 per cent. This surge has driven a significant rise in building retrofits and solar panel installations. In Ireland, building retrofits increased by 53 per cent since the first quarter of 2023, and domestic rooftop solar production rose by 42.6 per cent over the same period. This surge underscores the growing significance and awareness of energy performance certificates as a vital tool for assessing building energy efficiency, benefiting homeowners and investors alike.
In the next article I will tackle the definition of Nearly Zero Energy Buildings a decade ago and whether these standards are still fit for purpose. n
Dr Marc Ó Riain is a lecturer in the Department of Architecture at Munster Technological University (MTU). He has a PhD in zero energy retrofit and has delivered both residential and commercial NZEB retrofits In Ireland. He is a director of RUA Architects and has a passion for the environment both built and natural.
At NorDan Vinduer, we firmly believe in the power of strength and resilience. Our roots are deeply embedded in Norway, where we engineer our doors and windows to withstand the harsh, unforgiving weather. This makes our products the ideal choice for Ireland’s diverse and challenging climate.
We have faced countless storms and emerged victorious, leading the way in sustainability, carbon reduction, and quality in every product we offer. Our dedication to excellence has established us as a leader in sustainable manufacturing of windows and doors.
Choosing the right windows and doors can be a challenging task, especially since it's not something we do frequently. This rarity makes the decision even more crucial. Our expert team are on-hand to guide you through key considerations to help you make informed choices.
Whether it’s a new build or refurbishment, each requirement is unique and the NorDan team are the perfect partners to help you find the ideal solutions for your project.
Our efforts to retrofit homes across the UK and Ireland will be severely hampered unless we engage meaningfully with and empower women homeowners and professionals, writes Ellora Coupe, founder of Her Retrofit Space.
Irecently sat down and felt compelled to ask ChatGPT to "name a process undertaken by women that has been made more efficient and stress-free through innovation and process changes." The results that came back were about washing machines, robotic hoovers, kitchen appliances, automatic dryers, laundry detergent, stain removers, and ironing. I had not mentioned anything in relation to cleaning or housework, but it still showed inherent biases and lacked the variety of skills involved in women’s lives today.
I asked the same question with "men" in place of "women," and the innovations listed were financial tracking, investing, online banking, and budgeting software.
My job is to constantly evaluate how to better support women homeowners in embracing retrofit projects. Women homeowners today require a multitude of skills including data analytics, financial tracking, procurement, cleaning, buying, designing, technological competence, scheduling, cooking, specification, and parenting, all while often managing another career.
Observing the pitfalls in the renovation or retrofit process through the lens of thousands of women in the community I run is disheartening. I spend every day listening to a multitude of stories from women around why and how things go wrong, how to try to mitigate risk and how to resolve disputes.
This experience has had two clear effects. It has only further inspired me to hone my focus on identifying the hidden opportunities to better support women. And it has made me conclude that the retrofit industry has an opportunity to create a better framework to improve the project journey for women homeowners. However, another dependency of this journey is whether the appetite to embrace retrofit exists amongst women homeowners.
So where do we look for solutions? With over 10 years working within the branding industry in the UK, there is still a misunderstanding that it is about selling products, ideas, and lifestyles to people that they do not need. If anyone thinks that pretty designs, well-written words, and compounding data are enough to convince a woman today to buy anything, then we have made the first significant mistake. In the retail
industry and consumer markets, they have to work exceptionally hard, invest significant time, and ensure they don’t underestimate women’s ability to grasp the truth about something and whether it actually benefits them profoundly.
We could revisit the stories about misogynistic tradespeople overlooking women to talk to the man, or the perception that women won’t understand construction, technology, or metrics, or that they get taken advantage of when it comes to costing, but I think it would do a disservice to the subtle, overlooked lesson: don’t underestimate women.
The real focus should be on highlighting the significant opportunities and misconceptions about women homeowners today that are blocking the pathway for women to embrace retrofit.
A recent report on retrofit by the Federation of Master Builders stated, "There is low consumer demand for work to reduce the carbon impact of existing homes, with consumers typically showing little or no interest in energy efficiency or low/zero carbon technologies."
I did think immediately that it hadn’t caveated that little to no public engagement had been made on any significant scale to enlighten, educate, and inspire consumers on the benefits and opportunities to retrofit their homes.
Are there lessons to be made from the growing number of significant sustainable decisions women make today? Did the dramatic rise in women buying more second-hand clothes come from a rise in living costs? Or was it a very clever platform called “Vinted” which improved the process, making buying and selling second hand clothes suddenly very easy?
Deloitte's 2023 report, The Boston Consulting Group (BCG), and McKinsey's findings highlight an exponential growth in sustainable purchasing behaviours among UK women, driven by environmental awareness, ethical considerations and a desire for durable, repairable products.
How can one presume a lack of appetite when the level of conversation with women homeowners around a retrofit approach or energy efficiency upgrades is at opposite ends of the scale compared to food, health, and beauty?
To address this, how should we engage better and capture the attention of women homeowners? Well, we can learn from the many
consumer-focused businesses that have made significant shifts in consumer behaviour, such as the non-alcoholic beverage industry or natural cleaning products industry.
Olio, the giving away instead of throw away app that lets you simply offer an item of very little value to anyone who can re-home it, has gone from 2.3 million users in November 2022 to 4.8 million in November 2023. Seventy percent of its users are women in the UK. There is absolutely no financial or social gain from giving away these items, but users understand that not throwing something away is better for our planet and are prepared to take up time in their day to offer items for free to someone in their local area. No one would know if they had thrown it away except them, so if the system is in place to do the right thing, people do.
It comes back to making assumptions, and this is also the case with the presumed adversity that women have to technology adoption. Women use technology for what it can do, not for the sake of it, and research shows that women can be early adopters of many systems and processes when they work really well. They have less tolerance for bad user interfaces; if it is hard to use, they will not use it, not because they cannot. Marketers and manufacturers have data to support that women do more research than men before making a purchase.
To truly enable women to adopt retrofit, the industry should focus on developing better project process-driven frameworks to improve the journey, design technology with intuitive interfaces, build robust support networks, and promote gender-inclusive policies and practices. We just may need to call on a different set of professions to enable women homeowners to lead the way, rather than perceive them as a barrier. n
more information visit www.herownspace.com
MVHR FOR RESIDENTAL APPLICATIONS
Elevate your indoor experience with InspirAIR Top MVHR system, a connected marvel of innovation designed to prioritise air quality, performance, comfort, and user interaction.
With Passiv Haus certification and recognition in the PCDB database, InspirAIR Top is your ultimate choice for top-tier indoor air quality, performance, and comfort.
Connec tivit y
VENTILATION FOR SCHOOLS AND COMMERICAL SETTINGS
DEX3000 - Decentralised Ventilation
A decentralised ventilation unit is a simple solution where one ventilation unit is placed in each room with separate connection through a wall or ceiling/roof.
The installation can be carried out classroom by classroom,
CX3000 - Ceiling units
The CX3000 is designed for integration into a suspended ceiling, or fitting into a ceiling or floor partition.
suitable for renovation or new build projects.
IRELAND’S
In September Cairn Homes lit the fuse on a passive house explosion, publishing a position paper on passive house and announcing the construction of nearly 1,800 apartments to the standard. But what’s behind the company’s bold move?
By Jeff Colley
In The Devil’s Dictionary, Ambrose Bierce defined the corporation as “An ingenious device for obtaining individual profit without individual responsibility.” Though Bierce’s masterwork dates back to 1906, these words could have been written yesterday. For more than a hundred years the perception has endured: Big Business Does Bad Things.
So what on earth, you might quite reasonably ask, is Ireland’s largest house builder, Cairn Homes PLC, doing building over 1,750 certified passive houses, with a further 1,250 in the pipeline for next year?
And it gets worse. It’s not just passive houses. It’s passive social and affordable housing, which is also aiming to integrate several other aspects of sustainability via using the Irish Green Building Council’s Home Performance Index (HPI), on sites which are aiming for biodiversity net gain, with sustainable transport options. It begs the question: who are we supposed to rail against, if house builders start acting like this?
Cairn’s passive house rollout is breathtaking in its speed and scale, with four large apartment schemes being built simultaneously around Dublin. The first two, Pipers Square in Charlestown, and Cooper Square in Seven Mills, are slated to have the first units ready to occupy (RTO) by the end of 2025, totalling 590 and 607 units each. Two smaller projects in Santry – 255 units at Whitehaven and 303 units at Niven Oaks – are due to have first units RTO by the end of 2025 and April 2026 respectively, with all four schemes set for final completion in the first half of 2026. This totals 1,755 units on site, all targeting passive house certification.
What’s more in the midst of implementing this change Cairn pulled together a position paper on passive house – which, full disclosure, I had the pleasure of co-authoring via my new communications consultancy, Zero Ambitions Partners – to explain why Cairn were throwing their considerable weight behind passive house, what benefits it would bring for everyone from residents to building owners to construction workers, and in the process reassure their clients that they hadn’t lost the run of themselves.
The anatomy of a transition How did Cairn’s decision to go passive come to pass? The answer, in part, starts with a positive-sense single-stranded RNA virus: SARS-CoV-2.
Cairn’s passive journey began during Covid lockdown in 2020. And though it is hard for me to process, Passive House Plus had a part to play in it. Cairn’s senior creative manager, Donal Thornton, rang me up out of the blue in October 2020, asking about the passive house standard, and evidently keen to learn what the
Source: MosArt
company could do to improve the sustainability of its projects. I remember being startled –pleasantly – that such a big housebuilder was asking these kinds of questions, and having a characteristically long and sprawling conversation on passive house and some quick wins Cairn could implement to specify low carbon building materials. Donal contributed to a presentation on the benefits that passive house could bring at Cairn’s Innovation Forum, and the seeds were sown. And then it went quiet.
In January 2022 Stephen O’Shea, an architect with twenty five years of private practice under his belt, joined Cairn – first as design manager, before becoming the head of sustainable construction and reporting in 2023.
By his own admission O’Shea had been “quite sceptical” about passive house for many years, before the opportunity to probe the standard arose when he sat the post graduate course in building performance (energy efficiency in design) at TU Dublin. “I came to respect its rigour, but it seemed very far removed from the cut and thrust of ‘normal’ building projects,” he says. “Then when I came to Cairn and learned about their attitude towards efficiency in their operations, their methods, processes and products, their passion for sustainability, and their focus on the customer journey I realised that there was the potential for a meeting of minds."
O’Shea commissioned feasibility studies on passive house for low density and high density schemes from seasoned passive house experts MosArt, drawing on the Wicklow company’s 20 years of experience in passive house consultancy, certification and training throughout Ireland, the UK and North America on projects of all shapes and sizes.
“We’re not new to big projects,” says MosArt MD Tomás O’Leary. The firm’s high density passive track record includes the likes of a 26-storey skyscraper for Cornell Tech in New York in 2016, and a current project that’s set to dwarf it not once, not twice, but three times: Urbanest’s 2 Trafalgar Way in London’s Canary Wharf, with three towers coming in at 28, 36 and 46 storeys each.
If there’s one thing passive house enthusiasts love it’s a graph, and a graph of Irish residential passive house projects involving MosArt outlines the Irish passive house story in stark terms, ironically evoking the infamous hockey stick graphs showing the rapid growth in recent and projected future warming arising from climate change. From 2004 to 2020, the line was pancake flat, except for a couple of bumps in 2008 with UCD’s Roebuck Castle student halls and in 2017 with Durkan Residential’s 59-unit Silken Park housing scheme. The figures started to tick up from 2021-2023, with projects like Fraser Millar’s 219 homes at Lancaster Park in Belfast and Durkan Residential’s 47-unit Egremont scheme in Killiney, before a near vertical rise in 2024, with almost 2,500 units on site this year.
Stephen O’Shea says Cairn took great com-
fort in MosArt’s long track record in passive house. “Having someone with Tomás’s breadth and depth of experience was absolutely key,” he says. “Knowing that he had been a member of the team that delivered the tallest passive house building in the world really gave us comfort that he had been there, done that, and he was very open to embracing a developer mindset. He knew that was key to making any largescale.
More reassuring still was the fact that MosArt were working on Shanganagh Castle, a social and affordable homes currently approaching completion which includes 546 passive apartments. Developed by Dún Laoghaire-Rathdown County Council and the Land Development Agency, the project will be the enduring legacy of the passive house clause in Dún Laoghaire Rathdown’s 2016 County Development Plan, which this magazine helped to push through.
“Shanganagh was a huge influence for us,” says Stephen O’Shea. “It answered the ‘Can this be done at scale in Ireland with Irish supply chains?’ question, and now we just had to decide how it could best be done for Cairn. We wanted to use our own methodology, which is very different from the precast solution being used there.
Stressing Cairn’s “openness to innovation and a trust in data”, O’Shea paints a picture of a company culture which encourages new ideas to be sought out, aired, discussed and fleshed out. “Through our Innovation Forum we were able to give the idea time and space to be considered and thoroughly researched,” he says. “What we found is that the benefits were considerable, and the difficulties were not insurmountable. Passive house had struggled with the image of being too difficult, too bespoke. But when we really examined the changes that would be required to our standard methodology, we found that they weren’t seismic.”
By happenstance or design, feasibility studies showed that Cairn’s quality assurance focus and approach to meeting the nearly zero energy building (NZEB) standard required under Irish building regulations made passive house surprisingly attainable. The apartment buildings needed no extra insulation, though Cairn’s house types needed extra floor and roof insulation, and all buildings would require triple glazing. The company was already using mechanical ventilation with heat recovery (MVHR) on some and the lower heating demand enabled a switch to a simpler, lower capital cost heating package: direct electric heaters and individual hot water heat pumps.
Following all of this early engagement and the formation by MosArt’s Stephen Donoghue of a study group of developers working on or considering passive house projects, Cairn bit the bullet and took the decision to commit to passive house on the Pipers Square site.
“We acquired Pipers Square with planning permission and started straight into pre-construction,” says Stephen O’Shea. “It was never designed with passive in mind. But the decision was made when we started on pre-construction.
In July 2023, just before Cairn had agreed to push the button on this project, I met O’Shea at an IGBC event in our roles as BuildingLife ambassadors under the World Green Building Council’s BuildingLife Campaign. At this stage there was – quite reasonably – uncertainty from some in the company about stepping into the unknown. O’Shea invited me to come in and give a corporate version of my TEDx talk to Cairn’s senior leadership team (SLT), to help tackle any nagging concerns. I had recently launched a sustainable building comms/strategy business, Zero Ambitions Partners, with my magazine co-founder and podcast co-host Dan Hyde, who used his corporate communications background to help me piece a presentation together. According to Stephen, it made
Passive house has the image of being too difficult. But the changes required to our standard methodology weren’t seismic.
a decisive impact.
“The change process has been a long one, so even though the strategic decision had been made to go passive for Pipers Square, bringing the SLT and other senior figures together in an open forum was critical,” he says. “We all know the myths around passive house, and we have all felt the fear of trying something new. So having that group addressed by a real subject matter expert who tackled those myths head on was a real turning point.”
My enduring memory of that day was the high level of technical questions coming from Cairn staff in the questions and answers session after my talk – and a clear focus on the customer which went right up to the top of the company, and CEO Michael Stanley.
While the company is implementing a number of decarbonisation strategies, the prospect of better outcomes for customers made passive house stand apart. “Michael Stanley very quickly saw the tangible benefits and added value that it would bring to our customers, and that made a big difference,” says O’Shea. “Other decarbonisation initiatives such as switching to HVOs for site machinery or using GGBS in concrete mixes don’t have such benefits and can feel somewhat academic as a result,
but passive delivers day-after-day, year-afteryear in ways that make real positive differences to people’s lives.”
Virtuous though Cairn’s efforts are, they’re not happening in a vacuum. The business community is coming under exponentially increasing pressure to engage with environmental, social and governance (ESG) investment principles and report on the positive and negative impacts of their activities, including reporting on emissions upstream and downstream of their operations. In the case of a developer, “upstream” means embodied carbon, and “downstream” means sixty years of projected emissions from operational energy use after the buildings are handed over – but all counted in year one in Cairn’s figures. “We measured our carbon footprint in accordance with GHG Protocol and realised how great a proportion of our total – over 50 per cent – comes from the use of the homes we sell.
But while large companies like Cairn are in the first wave of companies subject to the rigours of sustainability reporting obligations under the Corporate Sustainability Reporting Directive (CSRD), O’Shea stresses that the company’s actions are driven by its values, rather than carbon accountancy. “We strive to do the right thing, and then we report on those actions,” he says. “We try to actively avoid letting reporting dictate what we do – it can never be the driving force.”
He does concede, though, that passive house offered an advantage for their reporting. “We were aware that passive house could improve the accuracy of our reporting. We currently apply a substantial ‘penalty’ to our BER data when reporting on our emissions to allow for the performance gap, but if the data was coming from PHPP and the homes were being certified to the passive house standard then we could all but eliminate that safety factor.”
Grand plans are one thing, but putting in place a strategy to actually deliver are quite another. According to Tomás O’Leary, Cairn aren’t taking any chances.
“Cairn are throwing resources at upskilling and educating their staff at various levels,” he says. “They have set quite a few of their senior technical team to do the passive house designer course. We’re currently working on a tailored course for site supervisors.”
With all four sites progressing at a rate of knots, O’Leary is impressed by what he’s seeing. “We’re dealing with their site staff and site supervisors,” he says. “Our experience is that they’re really up for it. You don’t normally get total buy in, but they’ve bought in 100 per cent. They’re all in. Jamie Lacey, a technical manager. The intensity in his eyes – he’s hanging on every word, and he wants to deliver not just passive house but the best passive house in the world. It’s just such a joy to work with people like that.”
While the prospect of meeting passive house is in sight, O’Shea isn’t counting his chickens just yet. “We are now live on four projects, so every day brings new challenges. But our technical teams and consultants are working through them. We’re far from thinking ‘We have this licked’, but very confident that we’ll get there.”
The company has absorbed the extra construction costs for going passive on these projects, rather than pass them on to its clients. According to O’Shea, the costs are reasonably low, but a final construction cost hasn’t yet been reached. “Our commercial team are still working through the procurement of all the various packages so we’re not yet at a final figure. And that figure is of course likely to vary from project to project.”
By making a move like this, Cairn is sending
a signal far beyond its own team, towards the broader construction industry, that world-class low energy building is viable, attainable and good for business. But how has Cairn’s own supply chain responded so far? “I think it’s fair to say it took some of them by surprise,” says O’Shea. “Some consultants have been quick to embrace the new challenges while others have been less so. But generally speaking, people understand the positives and are willing to do their bit to ensure it happens.”
The passive house standard does place more exacting demands on everyone from designers, to consultants, to site managers, to tradespeople, to product suppliers, and Cairn are not underestimating what that means, and are putting supports in place to ease the transition. “Everyone is going to be challenged by the change,” says O’Shea. “Some people are enthused by that type of challenge while others may be more fearful, but we are designing bespoke training programmes so that each function and person is taught what they will need to know to deliver successfully. The learning curve will be very steep at the start as we have thrown ourselves in at the deep end, but we’re already seeing the
learnings from one project being brought to the next so it shouldn’t take us long to get more comfortable and confident.”
But what about the client? The prospect of low carbon, comfortable, low running cost homes has been “very well received” by the clients for these schemes. “Similar to ourselves, they have sustainability ambitions and targets and the best interests of their residents at heart,” says O’Shea, noting that while these clients hadn’t been asking for such exemplary performance, the existence of high density passive schemes like Cairn’s quartet and Shanganagh Castle may start to redefine client expectations.
“Once word got out that we could offer this level of specification and performance, others
wanted in. The LDA are already on site with a passive project, and we know that many clients have ambitious energy efficiency targets, so I think they would have gotten there sooner rather than later. But it is better for all parties that it be approached in a spirit of partnership and with a focus on the benefits it will bring to the residents.”
With any building, the proof in the pudding is in the eating. The passive house standard has existed for over a third of a century, with monitoring studies conducted on thousands of buildings to demonstrate the veracity of its seemingly outlandishly low energy use claims. This gives it an advantage over any Johnny-Come-Lately energy standards such
Once word got out
that we could offer this level of specification and
performance, other clients wanted in.
At MosArt, we believe in creating homes that are not only energy-efficient but also foster well-being and sustainability. Our integrated approach combines design, consultancy, and certification to deliver Passive House projects that nurture both people and the planet.
Collaborating with Cairn Homes, we're shaping communities with homes that are healthy, safe, and allow occupants to thrive. With over 30 years of experience, Our expertise in Passive House design, consultancy, education and certification ensures that Cairn’s developments meet the highest standards of sustainability and performance, offering long-term benefits for residents and the environment.
Discover how our integrated services are transforming Irish housing at:
Introducing the ProAir PA700LI 'Best in class' for Indoor Air Quality and Energy Efficiency, with CO₂ , Humidity & Temperature monitoring as standard.
With over 25 years experience, ProAir is Ireland's only manufacturer and industry leading specialist of Mechanical Ventilation with Heat Recovery (MVHR) systems.
Our professional team provide an end-to-end service to ensure your home will be healthy, comfortable and energy efficient.
Commissioning and Certification
Compliance with Building Regulations (Part F)
Warranty, Service and Support
as NZEB or the still-gestating Zero Emissions Building (ZEB) standard. But Cairn aren’t resting on their laurels. “We previously partnered with the LDA and University of Galway to carry out a two-year post occupancy evaluation study at an NZEB apartment development we developed in Greystones,” says O’Shea, “with a view to gaining a greater understanding of the performance gap and how occupant behaviour can influence it. We hope to enter a similar partnership with one of the customers for one (or more) of our passive house schemes so we can compare the performance and customer journey.”
Beyond these projects, the company has one eye on the able to pay market. “We would like to pilot a low-density passive house development and see what appetite there might be among private home buyers,” he says, “and then look forward to completing our current projects and following our customers experi-
ences in their world-class homes.”
So there you have it. I can still scarcely believe it, but Ireland’s largest home builder has done the unthinkable. Up till now, passive house has too often been the preserve of the enthusiast – the right thing to do, in a sea of people doing wrong or at least questionable things. I’m sure I speak for many people who advocate for passive house when I say that the scale of what Cairn are doing is startling. To mutilate and mutate the words of Oscar Wilde: there is only
one thing in life worse than not being listened to, and that is being listened to.
But we must remember the stakes: the world is on fire, the passive house standard is a tried, tested and trustworthy tool to help stop that fire from getting too much hotter while delivering benefits in the here and now for ordinary people, and Cairn’s leadership, without getting too hyperbolic, is the kind of example that proves, just maybe, that unicorns do exist: Big Business Can Do Good Things.
download Cairn’s passive house position paper visit cairnhomes.com/passive-house
CONNEMARA PASSIVE SCHEME BRINGS THE ATLANTIC IN
Designing a passive house is one thing. Designing a scheme of passive houses to make the most of the views on an extraordinary coastal site is another. And designing that scheme to tie into the local supply chains and architectural vernacular – while ensuring the homes are set up for changing, potentially disengaged occupants –is the stuff of magic.
By John Hearne
Development type: Cluster of four detached homes
Method: Full-fill cavity wall, strip foundations, air-to-water heat pump
Location: Brownfield site in Furbo, Co. Galway
Standard: Passive house classic and A1 BER
Heating cost: €19-21 per month space heating cost. See 'In detail' panel for more information.
€19-21 per month
You’ll travel a long way to find a more beautiful site than Radharc na Chaoláire in Furbo, Co. Galway. The four certified passive houses, designed by Helena McElmeel Architects, have uninterrupted views over Galway Bay, with the Burren and the hills of Clare in the distance. ‘Radharc’ means view in Irish, but Chaoláire would not be as easily understood beyond Connemara. It translates as ‘narrowing of the bay’ and is how generations of seafarers living in the Gaeltacht referred to the stretch of water which the houses overlook. Choosing a name like this is not just a sop to tradition. These houses were designed with reference to the built heritage of the area and constructed using local materials and local skills.
Architect and passive house designer Owen Morgan of Helena McElmeel Architects worked closely with Helena on the project.
“It was great,” he says, “to have a local team from the Connemara Gaeltacht delivering passive houses in the middle of Furbo. The other great thing about it is that passive is becoming normal. This is becoming the best way of doing things.”
Since establishing her practice in Galway just over ten years ago, McElmeel has been at the forefront of sustainable building in the west. She has witnessed the growing awareness of and appetite for passive house in both the industry and among the wider public.
“It's been much easier over the last few years than it was at the beginning,” she says, “when it was much more niche. It’s far easier to take clients with us on the passive journey now. Many want to go passive right from the start.”
Most of the projects underway at the practice are passive or EnerPHit, and many of those
Relying on wet plaster for airtightness isn't foolproof. Depending how the scratch coat is done, the plaster might look fine but could still be leaking.
McElmeel, who adds that there are plans to develop another portion of the site, which she hopes will contribute more fully to the streetscape and the community in general.
In designing the houses, the architects set out to reflect what can already be seen in the area. “You’re asking, where are the forms that we can play with? You're looking at the lean-to sheds which you’ll find up and down the side roads perpendicular to the sea all along the coast here. You’re also looking at the stone walls that enclose those structures, their monopitch roofs and render finishes. You have remnants of that left, but there's an awful lot of clutter in the way now, which makes it hard to see the vernacular.”
have either been certified or are scheduled for certification. “The more we build and the more evidence we collect about how they're performing, the more confident we can be in saying, ‘This works. These houses perform like they say on the tin.’” In Furbo, the client – Nikolai Burkhart, a Germany-based developer – bought into the idea of passive almost as soon as it was suggested. “The client was keen to build to the best possible standard – A1-rated, passive house, with a high standard of interior fit out,” says McElmeel.
The site may have wonderful views, but that is not to say that it was without challenges. Any Connemara builder will tell you: when you work out here, you have to negotiate with a large quantity of rock. It takes a great deal of patience, and a lot of work with heavy plant to prepare the site ahead of construction. In addition, there had been an ‘underutilised’ commercial building to the front. “This was in need of some TLC, to say the least,” says
She notes too that the detailing of these structures tends to be neat and clipped, with an absence of over-hangs. And no brick. There’s very little brick in Galway generally, which tends to constrain the palette of materials.
At treated floor areas of between 242 m2 and 245 m2, the houses are large and feature complex junctions. Yet a form factor of three reveals a relatively compact design, a factor which McElmeel explains, helps reduce embodied carbon by reducing material quantities used.
The central design challenge, McElmeel explains, comes back once again to those views. The developer wanted to maximise window sizes on the southern elevation to make the most of what is a unique selling proposition. The architect, on the other hand, was focused on performance and comfort, and that meant optimising the glazing for thermal integrity and overheating prevention.
This meant that window placement and size was the subject of what McElmeel calls “in-
tense debate”. Getting the mix right involved finding the sweet spot between these competing objectives. Low G glass played a role in reducing heat transference but couldn’t be relied upon exclusively, says Owen Morgan. PHPP modelling was used to explore the possibilities.
Using the data to demonstrate unambiguously that overglazing would be a problem did a lot of the hard work in the argument. The design team was also able to show how framing views using smaller windows can be just as effective as installing vast expanses of glass.
In the end, developer and architect went through window size and placement room by room. This approach worked, delivering a passive standard thermal envelope with minimal overheating risk: 2.3 per cent of the year above 25C on house one, 2 per cent on house 4 and 1 per cent on houses 2 and 3.
McElmeel points out that when it comes to overheating, you cannot rely on mitigation, and you can’t rely on occupant behaviour.
“All of the houses are occupied now. There’s been a handover, but they’re rented. You could have different occupants next year, and there’s no guarantee that documents will be read. People shouldn’t need information to live there comfortably.”
With an owner-occupier who’s just built their forever home, you can talk about shading and mitigation strategies, but for developer-led projects, that isn’t going to work. Moreover, as McElmeel points out, you won’t find overhangs or elaborate facia or soffit detailing in this part of the country. If you want your building to sit well amid existing structures, you’re going to have to leave those out.
While most of the practice’s projects at present are timber frame, all four houses at Radharc na Chaoláire are masonry-built. The developer’s construction partner – Noel Mannion and his team, NCP Togail Teo – specialised in block-built houses. Though the company had long experience in traditional building, this would be their first passive house.
“It was a significant step up for the construction team,” says McElmeel. “They were using materials, techniques and detailing that they hadn’t come across before.”
This meant that the architect spent a lot of time onsite working with the build team. In addition, the contractor undertook training as part of their commitment to deliver. Owen Morgan pays tribute to foremen Mick Conneely and Ciarán Ó Conaire, who fully bought in to the passive process and worked hard to deliver the spec. “Everyone knew what they had signed up to do,” says Morgan, “and they wanted to make it happen. Yes, there were times when it was challenging, but they stuck to the task and delivered on every target.”
Building during COVID and the outbreak of war in Ukraine caused both supply and scheduling challenges, as they did on every site, but the biggest challenge that the build team faced was airtightness. The views might be stunning, but achieving a passive standard building envelope on a site exposed to the Atlantic winter is no picnic, particularly with block construction. Morgan also pays tribute to veteran passive house specialist Roman Szypura of Clioma House, who went above and beyond in teaching and training the build team.
“Relying on the wet plaster as your airtight-
ness on blockwork isn't as foolproof as it might seem,” says Owen Morgan. “Depending how the scratch coat is done, the plaster might look fine but could still be leaking.”
The builder ended up acquiring a fan in order to run tests and address each leakage as it arose. That skill set improved as the project matured; the magic 0.6 ACH was secured far more quickly on house 4 than house 1.
McElmeel says that the single-mindedness of the contractor was crucial to the success of the airtightness strategy. “It just wasn't going to beat them... but that's not a given.”
Designed as rentals, the homes require little user engagement. People shouldn’t need to read documents to live there comfortably.
The design team also made efforts to reduce the embodied carbon of concrete used onsite. Fifty per cent GGBS from Ecocem was used in poured concrete from Coshla Quarries, including the raft foundation, though GGBS was not integrated into the blockwork. In addition, engineer John Britton and his team worked hard to make the concrete that was used work as hard as possible, by keeping structures lean and well-detailed.
As has been pointed out, these are big houses, aimed at the very top of the market. The interiors, which Owen Morgan describes as ‘a project within a project’ are beautifully finished. With this high-end passive scheme on the west coast, and a number of high density passive social housing projects announced by Cairn Homes on1 the east coast, there are clear signs of passive house breaking through at both ends of the market. But would such a high-density scheme have been possible in Furbo?
Helena McElmeel points out that higher density housing isn’t possible in the area due to the absence of local authority sewage and wastewater treatment infrastructure – and nor are there any plans to provide these essential services. Each of these houses had minimum site sizes and maximum density restrictions due to the need to have individual treatment systems. Shared treatment systems are discouraged in private developments by the local authority, following some bad experiences related to maintenance and upkeep during the Celtic Tiger era.
The real success of this project lies in the way in which it managed to keep so much within the parish. As well as making use of the stone excavated in boundary walls, the design incorporated a range of locally-sourced materials, including the distinctive stone – granite externally and green Connemara marble internally. It’s that combination of local skills and local materials that really makes this project such a passive house exemplar.
Redstone Calsitherm are high-performing calcium silicate insulation boards used internally on solid masonry walls. With their high capillary action ensuring humidity regulation, they provide unparalleled protection against condensation and mould risk in older buildings. The Redstone Calsitherm system has ETA and EPD approval, and is certified with an A1 fire-rating.
Diasen Diathonite Insulating Plaster Cork and lime-based levelling coat for Climate Boards
Adhesive Mortar
For bonding Climate Boards to internal walls
Redstone Calsitherm Climate Board
A1 fire-rated thermal insulation
Luno Finishing Plaster
Smooth finishing plaster embedded with mesh
Auro Natural Paint
Breathable natural paint
For use on internal walls only.
Exclusively available from
1 Armatherm thermal breaks prevent thermal bridging where a steel column meets the floor; 2 Alma Vert thermal break at thresholds; 3 thermally-broken Internorm HF310 timber/ alu clad windows; 4 thermally broken stainless steel Ancon brackets; 5 insulated roof upstand; 6 underfloor heating; 7 Pro Clima Aerosana Visconn wall chases; 8 plastering ahead of services being installed; 9 Ubbink ductwork install on-going; 10 Intello airtightness & vapour control layer under a Speedline metal furring ceiling channel.
Client: OceanView4U
Architect: Helena McElmeel Architects
Structural engineer:
Britton Consulting Engineers
Civil engineer: Profe Engineering
Energy consultant: 2Eva
Project management: Helena McElmeel Architects
Main contractor: NCP Togail Teo
Quantity surveyors:
Atlantic Quantity Surveyors
Mechanical contractor: Sheeran Heating & Plumbing
Electrical contractor:
Eamon Lynch Electrical
Airtightness consultant: 2Eva
Passive house certifier:
Earthcycle Technologies
Bonded bead insulation: Envirobead
Cavity wall installer: OCI insulation services
Thermal breaks at thresholds: Partel
Thermal blocks: Mannok
Thermally broken brackets: Ancon, via Leviat
Thermal break pads: Armatherm
Roof insulation: Isover
Additional roof insulation:
ALM HM Ireland
Above deck roof insulation: Unilin
Airtightness products:
Ecological Building Systems
Airtightness consultant:
Clioma House Ltd
Windows and doors:
Internorm, via Interlux
Internal electric blinds: Apollo Blinds
Heat recovery ventilation: Brink, via Kernohan Distribution
HRV installer: HRV West
Air-to-water heat pump:
Samsung, via Joule
Screeds: Cemflor
Concrete products: Coshla Quarries
GGBS: Ecocem, via Coshla Quarries
Engineered oak flooring: Trunk Flooring
Zink and flat roofs: Vertex Roofing
Landscaping: Colin Cooney Designs / Bill Madden Nurseries Ltd
Lighting: Hicken Lighting
Water conserving fittings: Waterloo Bathrooms Dublin
Wastewater treatment system: Biocell Water
Fit-out: Barry Hanley Carpentry
Fitted furniture/kitchens: AMC Kitchens
Loose furniture: Nordic elements
WANT TO KNOW MORE?
The digital version of this magazine includes access to exclusive galleries of architectural drawings. The digital magazine is available to subscribers on passivehouseplus.ie & passivehouseplus.co.uk
•Passive House certi ed components
•Highest energy e ciency in several size classes*
•Suitable for homes up to 360m2
•Bene t from in-built sound dampeners**
•Built-in pre-heater
•Full Summer Bypass as standard
•Wide range of lter choices
Brink systems are also fully compatible with Ubbink’s Air Excellent air distribution systems. Air Excellent’s clever, push-together connection system combines unsurpassed ease of installation, with incredible levels of airtightness.
*Certi ed Passive House Components Certi cate as of 01/02/2023 **Flair 600 model
Brink and Ubbink are distributed throughout Ireland by Kernohan Distribution: Fir Trees, Greenway Industrial Estate, Conlig, Co. Down, Northern Ireland, BT23 7SU E: info@iakonline.com | W: www.iakonline.com or www.brinkhrv.com
Building type: A cluster of four detached, two-storey passive certified houses located in Furbo, Connemara, Co, Galway. The detached houses come in two types; however, each one has a distinctive interior design, colour palette & furnishings.
Size: 260 – 270 m2 gross floor area, 242 – 245 m2 treated floor area.
Site type & location: Brownfield site in Furbo village centre, Connemara, Co. Galway.
Completion date: Phased completions April 2023 – August 2023.
Budget: Not disclosed.
Passive house certification: Passive house classic certified
Space heating demand: 12.6 – 13.9 kWh/m2/yr
Heat load: 12.5 – 13 W/m2
Primary energy non-renewable: 48 – 49 kWh/m2/yr
Primary energy renewable: House 1, 2, 3 & 4-27
kWh/m2/yr
Heat loss form factor: 3-3.03
Overheating: 1-2.3 per cent of year above 25C
Number of occupants: 3.1 occupants (all houses)
Energy performance coefficient (EPC): 0.135 – 0.137
Carbon performance coefficient (CPC): 0.084 – 0.085
BER: A1 (17.45 – 18.41 kWh/m2/yr)
Environmental assessment method: Not applicable
Embodied carbon: Analysis on-going
Measured energy consumption: Bills / POE not available currently on this project.
Energy costs: In the absence of monitored data, Passive House Plus calculated the space heating costs for the homes. Based on the PHPP-calculated space heating demand and a relatively conservative assumed coefficient of performance (COP) of 3 to 1 – far below the stated seasonal COP, the annual electricity demand per home for space heating ranged from 1,016 – 1,135 kWh/yr. A price comparison on Bonkers.ie for a rural home on a smart meter found the best rates for this electricity use at €227- €253/ yr per house, based on Energia’s Smart Data 30 per cent tariff. This figure includes VAT at 9 per cent and is based on 55 per cent of heat pump running time
at day rate, 34 per cent at night rate and 11 per cent at peak rate. As ever with electrical heating analysis in Passive House Plus, standing charges are omitted for a simple reason: the standing charges apply irrespective of electrical heating use, for any property connected to the grid.
Airtightness: 0.59 to 0.64 ACH at 50 Pa
Thermal bridging: For passive house certification the thermal bridges and associated heat losses were calculated for all construction details for each house type and inputted into each PHPP. MOLD software was used for these calculations.
Key measures taken to reduce thermal bridging included the use of Mannok Aircrete 7 blockwork courses at raft level and at parapets, Ancon thermally broken stainless steel support connections to outer leaf blockwork, Partel Alma Vert thermal breaks to all door thresholds and window cill connections, Armatherm pads under any steel columns brought down to raft level.
Ground floor: 75 mm Cemfloor screed, followed underneath by 160 mm PIR insulation (0.022 W/mK), 150 mm reinforced concrete raft (50 per cent GGBS), on Monarflex RMB400 radon barrier on T3 blinding. U-value: 0.132 W/m2K.
Walls: External sand / cement render, followed inside by 100 mm blockwork, 200 mm cavity pumped with EnviroBead Plus EPS Bead insulation (0.033 W/mK), 100 mm blockwork, internal plaster finish (airtight layer). U-value: 0.155 W/m2K (thermal bridges and from wall ties were calculated and included in the U-Value calculation).
Sloped roof (all houses): Mono-pitch zinc roof with VM Plus Zinc, followed underneath by 118 mm Warmdex (18 mm plywood with 100 mm PIR Insulation (0.020 W/mK), on plywood deck, on 220 mm joists with full fill Metac (0.034 W/mK). U-value: 0.093 W/m2K.
First flat roof type (all houses): Alkorplan PVC membrane on 120 mm Xtratherm (now Unilin) FR/ALU (0.022 W/mK), on plywood deck, on 180 mm joists with full fill Metac (0.034 W/mK), Ceiling zone with 50 mm Metac (0.034 W/mK). U-value: 0.086 W/m2K. Second flat roof type (houses 1 and 2): Alkorplan PVC membrane on 120 mm Xtratherm (now Unilin)
FR/ALU (0.022 W/mK), on plywood deck, on 150 mm joists with full fill Metac (0.034 W/mK), Ceiling zone with 50 mm Metac (0.034 W/mK).
U-value: 0.092 W/m2K.
Windows & external doors: Internorm HF310 timber/ alu thermally-broken triple glazed windows. Low G value glass to south façade. U-value: 0.69 W/m²K. Internorm HT400 timber/alu entrance door. U-value: 0.7 W/m²K. Internorm HS330 timber/alu lift-sliding door. Low G to south façade. U-value: 0.72 W/m²K.
Heating system: 8kW Samsung AE080RXYDEG EU air-to-water heat pump. SCOP 4.44. 230L stainless steel Duplex LDX 2101 Cyclone pre-insulated unvented pressurised hot water cylinder. Underfloor heating to ground and first floors.
Ventilation: Brink Flair 400 heat recovery ventilation system — Passive House Institute certified to have heat recovery rate of 89 per cent.
Potable water use: 118 l/p/day, calculated using the DEAP water efficiency calculator. Low flow aerators (5 lpm) to taps to reduce water consumption. Dual flush WCs. Almost half of the total relates to the 12l/ min overhead rain shower, offsetting the benefits of the low flow rate taps and lower flush volumes to WC cisterns – to be avoided on future projects.
Electricity: Currently no PV systems on site.
Appliances: Low energy use kitchen appliances were sourced – details of which were included in the PHPP energy models for the houses.
Sustainable materials: Metac insulation was used under the deck on all roofs, made from up to 75 per cent recycled glass. Partel Alma Vert (made from recycled PET bottles) thermal breaks were used to the custom designed thermal breaks to all thresholds and window cills. 50 per cent GGBS cement used in all poured concrete on site including raft foundations. Dry-jointing to the dry-stone walls, particularly to the rear, to support biodiversity insects and wildflowers. Stone used on houses was sourced in a nearby quarry. The decorative stone and Connemara marble were also sourced locally. Stone excavated on site was used for the boundary walls. Native wildflower planting to the southern area of the garden with all boundary walls dry stone construction.
This new system from Mitsubishi Electric is designed to provide heating and/or cooling as well as hot water for domestic and commercial projects.
Mitsubishi Electric’s Ecodan heat pump range is designed to satisfy a diverse range of project types and sizes. When the PUZ-SWM is used in combination with an E Generation cylinder, they deliver perfect heating, cooling and Domestic Hot Water (DHW) solutions. This superb duo combination of units provides industry leading efficiency and control, while boasting a list of exciting new features.
Other features also include; SD Card data recording, Auto- adaptive control and the ability to cascade up to 6 units which can provide 84kW of heating.
The new E Generation indoor unit range has 200lt and 300lt versions. These versatile units can be used for heating and cooling applications. The E generation range also includes a hydrobox option, which can be used in standalone heating-only applications, or where thirdparty cylinders are used. The new industry leading unit have been designed with the user in mind and features include:
Water piping is aligned at the rear side of the unit for easy connection and a neat finish, with all relevant parts located at the front of the unit for easy maintenance. In addition, nuts are fitted to improve ease of installation. To assist with commissioning, initial settings are narrowed down to the essential items and unnecessary settings are skipped automatically, reducing commissioning time significantly.
Mitsubishi Electric’s Ecodan heat pump range is designed to satisfy a diverse range of project types and sizes.
Mitsubishi Electric have designed a new solution to provide heating, cooling and hot water for domestic and commercial projects. By combining the new PUZ-SWM outdoor unit with the new E generation cylinders, they deliver perfect heating, cooling and Domestic Hot Water (DHW) solutions. This superb duo combination of units provides industry leading efficiency and control, while boasting a list of exciting new features. With an impressive heating efficiency rating of A++, a hot water efficiency rating of A+, this Ecodan solution sets a new standard for energy-efficient performance
• Heating and cooling: provides both heating and cooling for your projects.
• New colour touch screen controller: which offers even more intuitive control of space heating/ cooling. Utilising graphical images for features such as quiet mode and unit operation.
• Inbuilt magnetic strainer: ensures that no metallic debris can circulate through your system.
• Simplified piping: allows for easier installation
the quietest on the market. With an impressive heating efficiency rating of A++, a hot water efficiency rating of A+, the Ecodan PUZ- Split heat pump sets a new standard for energy-efficient performance. The unit also guarantees outstanding performance even at external temperatures as low as -25°C.
PUZ-SWM features
• Reversable unit providing heating, cooling and hot water;
• Available in 8kW to 14kW capacity (single and three phase versions);
• Max flow temperature of 68°C;
• Noise level of SPL 41dB-8kW;
• Pre-charged for 35m pipe run;
Mitsubishi Electrics Ecodan’s FTC7 controller makes it possible to control two different flow temperatures, thereby managing two different heating load requirements. Users can now add a new mixing control in Zone 1 as well as Zone 2, while controlling the flow temperature in both zones, providing more flexible heating. The new control system also allows for the monitoring of the temperature inside of a buffer tank and utilises this heat to avoid frequent on/off operation. This function allows better integration with smart grid or energy management systems.
Mitsubishi Electric Ireland Living Environmental Systems
@MitsubishiElectricIreland
@MEIrishBranch les.mitsubishielectric.ie
The Ecodan R32 PUZ-SWM outdoor units for heating, cooling and the production of domestic hot water are equipped with an ultra-quiet AA chassis. The units feature a new design which places the fan further away from the coil, a new refrigerant circuit layout, and rubber mounts for the compressor, which all contribute to this range of units being one of
Mitsubishi Electric’s Ecodan heat pump range is designed to satisfy a diverse range of project types and sizes.
Mitsubishi Electric have designed a new solution to provide heating, cooling and hot water for domestic and commercial projects. By combining the new PUZ-SWM
• Maximum pipe run 50m.
For more information visit:
les.mitsubishielectric.ie/ products/heating/domestic/ outdoor/puz-swm
or contact Mitsubishi Electric on:
t +353 1 419 8800
e sales.info@meir.mee.com w les.mitsubishielectric.ie
Mitsubishi Electric’s Ecodan heat pump range is designed to satisfy a diverse range of project types and sizes.
Mitsubishi Electric have designed a new solution to provide heating, cooling and hot water for domestic and commercial projects. By combining the new PUZ-SWM outdoor unit with the new E generation cylinders, they deliver perfect heating, cooling and Domestic Hot Water (DHW) solutions. This superb duo combination of units provides industry leading efficiency and control, while boasting a list of exciting new features. With an impressive heating efficiency rating of A++, a hot water efficiency rating of A+, this Ecodan solution sets a new standard for energy-efficient performance
Environmental Systems
@MitsubishiElectricIreland
@MEIrishBranch
OFFALY SCHOOL USES VOLUMETRIC MODULAR TIMBER BUILD
Forgive the 80s hip hop house reference in the headline, but the volume of the walls in this volumetric modular school building in Birr was literally pumped up – with recycled newspaper insulation. Built to passive house principles, it’s a story of one Roscommon manufacturer reimagining the role that offsite methods can play in the delivery of highly sustainable permanent accommodation for schools – while delivering exceptionally low embodied carbon results.
By Lenny Antonelli and Jeff Colley
Development type: 1,000 m2 class room building
Method: Timber frame volumetric modular building with bio-based insulation.
Location: Greenfield site, Birr, Co. Offaly.
Standard: Near passive, and ultra low embodied carbon (meets the RIAI 2030 Climate Challenge targets)
Heating cost: €91 per month estimated space heating cost – and set to fall once the PV array is installed. See 'In detail' panel for more information.
Gaelscoil na Laochra, in Birr, Co Offaly, was borne out of a desire by the Department of Education to build a high performance low embodied carbon school using modular construction to meet their permanent building standards. The original idea was driven by a senior architect in the department, Niall Lowther.
Reference to “prefabricated” schools probably conjures visions of cold, unsightly cabins in school yards, but these days the word “prefabricated” has largely been expelled from the construction lexicon, replaced by fresher terms like modular, offsite, and the zeitgeisty but nebulous MMC (modern methods of construc-
tion). And there is a new generation of offsite manufacturers delivering high quality, low carbon offsite structures that meet, or come close to, the passive house standard.
“We really have to figure out how to deliver low embodied carbon buildings, that was the primary driver for this," says Mick McDonnell, a senior architect at the Department of Education. “We were focused on embodied carbon as the main improvement over traditional building.”
Roscommon-based Lidan was awarded the contract. The innovative offsite builder who have become known for delivering ultra low embodied carbon, all-timber, turnkey build-
ings – and even for using ground screws on some projects as an alternative to conventional concrete foundations.
Lidan were appointed to deliver a new 1,000 m2 school building for Gaeilscoil na Laochra in Birr, Co Offaly – but the building posed challenges for a modular, offsite builder. The Department of Education's typical standard for new school buildings is a floor-to-ceiling height of 3.15 metres, which presents challenges of transporting modules taller than this by road.
However, Lidan set about aiming for the 3.15 m target, but it required delivering the 8 m x 4 m modules on low loaders, so as not to hit any overhead bridges on the road between
Roscommon and Birr. Lidan manufactured the modules in their Roscommon factory, but a bespoke approach was also required to build and deliver the school’s large open-plan rooms, such as the 70 square metre library, and the 100 square metre shared activity space.
“The ability to do the wide open-plan rooms meant that two walls needed to be omitted from some boxes, and in some cases three walls, prior to transportation," says Dan O'Brien of Lidan. "This in addition to the eight metre room spans required some specific structural engineering in terms of beams, and true to our sustainability strategy this was all done in timber.”
This added to the complexity on site. “The materials are more substantial, the modular units are much heavier, the transport and lifting is way more complex,” O’Brien says. At 1,000 square metres, it illustrates the increasing complexity of the challenges that skilled modular builders are willing to take on, and deliver, in Ireland.
The use of timber construction and a combination of cellulose and wood-fibre insulation also meant wider, thicker modules than if synthetic materials were used, but true to form, Lidan specified timber throughout – and took this philosophy to an obsessive level.
For a start, the entire structure is timber frame, with I-joists in the roof and floor, and glulam for structural beams. Lidan had won a national innovation award in 2020 on the use of glulams in structural widespan modular buildings. Recycled paper in the form of Isocell cellulose is the primary insulation, with Gutex woodfibre forming an additional external layer of insulation for the walls and flat roof. Most of the structural timber was of Irish origin (the glulam came from mainland Europe), and all of it was FSC-certified. The building was then clad externally with charred Siberian larch from MTS in Bray, with metal fixings from Rothoblass, and the larch was even fixed in place using a low carbon innovation: wooden nails. Lidan believe this may be the first time that wooden nails were used on a project of this scale in Ireland. With attention shifting to the circular economy, innovations like this may be destined to move from obscurity to centre stage for one very far-sighted reason: when the building reaches its eventual
end of life, timber nails will make it far simpler to reuse the timbers.
The modules were almost entirely finished in the factory. "You had an open-plan room, five or six boxes with two sides missing, going down the road fully finished – including all electrics, all plumbing - and skim finish plastered,” O’Brien says.
This obsessive focus on timber paid off in the building achieving an exemplary embodied carbon score: 488.2 kg CO2/m2, comfortably beating the RIAI 2030 Climate Challenge target of 540 kg CO2e/m2 for school buildings in spite of the heady duty concrete foundations, which were outside of Lidan’s remit.
Apart from Lidan’s core system there were
other neat sustainable touches in the finishes too: a standing seam metal roof, installed by hand, which is fully recyclable, and floors finished with Forbo Marmoleum, an all-natural alternative to linoleum, which is made from flaxseed oil, wood flour, pine resins and jute.
The building performs exceptionally well when it comes to energy performance. PHPP calculations at design stage showed that the building’s heat load was meeting the passive house target of 10 W/m2 – albeit factoring in a Passive House Institute-certified heat recovery ventilation system which wasn’t used in the end. The fabric standards are all in the region of typical passive house specs: U-values of 0.13 for the roof and floor, and 0.15 for the
walls, and thermally broken triple glazed windows with a glazing U-value of 0.53. An airtightness test by 2eva.ie revealed the finished school also hit the passive house airtightness target of 0.6, with all airtightness membranes pre-installed in the factory. Because airtight buildings can take longer to dry out, the Lidan team even used a waterless skim to reduce the amount of moisture internally.
The overall heating demand of the building is so low that Lidan opted to install direct electric radiators for space heating – which can be pre-fitted in the factory – rather than heat pumps, with a domestic hot water heat pump to meet the hot water requirement.
In an ordinary building the decision to opt for direct electric heating at a time of high electricity prices might be ill-advised – with each kilowatt of electricity generating only a kilowatt of heat, as opposed to a heat pump, which could deliver three to five times that return. But this building has a couple of things in its favour to mitigate the risks of high costs. There's the combination of excellent airtightness, high levels of insulation, triple glazing and heat recovery ventilation to dramatically reduce heat loss. There’s the fact that primary schools are only occupied during school days, and only for part of the day – with a boost of free “kiddiewatts” from metabolic heat loss starting each day when the children enter the building.
While no formal energy monitoring is taking place yet, school principal Niamh Ui Chléirigh says the radiators have seen little use. “We switched them off altogether in march,” she says. “One of the teacher's asked to switch them on last week [in October] because it was a chilly morning. There was no sun that day, and her room is at the back of the building where there's less sun. It was on for a maximum of two hours, because it got too hot.”
There are two heaters per classroom, Ui Chléirigh says, “but there's only ever one on. They're set to 20 to 21C, and they turn off when they reach temperature. They were used in February, when it was colder.”
The heat demand is reduced further by a heat recovery ventilation system, comprising 14 Daikin enthalpy recovery ventilation units.
Photos by Lidan
While these cross flow units don’t recover as much sensible heat as the counterflow heat recovery units that more commonly appear in these pages, they do recover latent heat, meaning some of the humidity from the extract air is passed to the supply air. “As a consequence,” says Tony O’Connor of consulting engineers TEM Engineering & Management, they “can provide a level of humidity control without sophisticated controls being required”.
The large ducts are exposed throughout the ceiling, and the system was designed to deliver up to 10 litres per occupant per second.
McDonnell says the department is also keeping an eye on the risk of overheating in schools. “It’s something we’ve always considered, and we need to ensure that the design teams who work with us fully understand and mitigate that risk.”
According to Niamh Ui Chléirigh, overheating has not been a problem here, bar some minor teething problems while the occupants figured out how to operate the new building. “Some of the classrooms got quite warm in May and June,” she says. “So we had to refigure out how to use the summer bypass on the ventilation systems, and that brought the temperatures down to acceptable levels.”
A 16kW solar photovoltaic array is set to be installed on the roof, to bring the building’s BER up from an A3 to A1 rating. An analysis for this article by solar PV expert Tim Cooper suggested a tailored solution to maximise solar contribution to meet the winter electrical load. “If the array was located along the top of the southeast facing wall, the winter output would be circa 40 per cent higher than on the roof – also meaning no tampering with the roof and no need for aluminium support frame. The modules can be mounted on a simple wooden frame fixed to the external wall. They would also reduce solar gain during the summer. Fixed in this way a 16kWp system will generate 1,760kWh from November to February,” says Cooper, “most of which will be used on site.”
The turnaround of the project was speedy. Work in the factory started in January 2023, work on the greenfield site began in July 2023, Lidan went to site in October during storm Ba-
Our
school is extremely comfortable and it makes for an exceptional learning and working environment.
bet and the building was complete in December of that year. The school community moved in during February 2024.
Dan O’Brien of Lidan says that, in terms of time, 80 per cent of the build was completed offsite, but in terms of the value of the project, 92 per cent of it was premanufactured value (PMV), finished in Lidan’s Roscommon factory.
McDonnell is eager to see the department carry out more pilot projects like this on innovative and sustainable methods of construction.
“The state has a duty to be a leader when it comes to sustainability,” he says. “I would be keen to see more post occupancy evaluations of these projects too.
But more than anything, he loves the look and feel of the building. “It’s got a burnt larch exterior, it looks lovely, it feels lovely. It’s nice to know that not only is the building delivering on all of its technical goals, but it’s a really nice environment for the kids. Just because it’s MMC doesn’t mean you have to give up on aesthetics and materials.”
Niamh Ui Chléirigh agrees. “Our new school building is amazing,” she says. “It is bright, colourful and cosy. The triple glazed, full length windows keep the school warm and allow an abundance of daylight into the classrooms. The technology in the heating and ventilation system allows us to regulate the temperature at the touch of a button or by using the app on our phones. The school is extremely comfortable and it makes for an exceptional learning and working environment. The school now has a wonderful home where pupils can learn and develop the skills they need for the 21st century in a beautiful state of the art building.”
A report by leading whole life carbon consultant John Butler assessed the building’s embodied carbon against the RIAI 2030 schools target of 540 kg CO2e/m2 of gross internal area (GIA) – covering the emissions from cradle to grave. The foundations and spoil removal alone add up to 184.7 kg CO2e/m2 – over a third of the RIAI target. Lidan’s challenge was to add a fully finished, high performance building – with highly insulated floors, walls and roofs, triple glazing, internal and external finishes including a standing seam aluminium roof, building services including MVHR, electric heaters, hot water heat pump, a large PV array and fitted furniture, and keep the score as low as possible. The overall score achieved was 488.2 kg CO2e/m2 GIA.
Cradle-to-grave building life cycle assessments divide a building up into modules covering three phases of its life, as follows:
Module A: the emissions released by the point the building is completed, through the manufacture of building materials, transporting them to site, and the construction process itself.
Module B: the emissions predicted to be released during the building’s use, due to maintenance, repair and replacement of components. Operational energy and water use comes into this phase too, but organisations like the RIAI, RIBA and LETI don’t include it in the cradle-to-grave totals – they’re reported separately instead
Module C: the emissions predicted to be released when the building reaches its end of life, through demolition and disposal of materials. This includes landfilling, incineration or recycling of materials.
There is also another phase – Module D, which we describe as the graverobber phase. It covers benefits from potential reuse of materials in other applications, and other benefits outside the boundary of the LCA calculation. To prevent potential future emissions reductions being netted off against emissions released within the building’s life, Module D figures are not counted in most embodied carbon targets, but can be reported separately.
What was the main cause of this result? To attempt to answer that, Butler modelled the effect of the same building being constructed conventionally, with cavity wall construction and PIR boards in the cavity and roof. For this article, we re-ran the calculation stripped back to only include the foundations and floor build up, external wall build-up, and roof systems. The external finish of the walls was included, but the floor finish and roof finish were also omitted, as were the windows and external doors. The figures were then worked out for three scenarios:
• The Lidan fabric, as built
• As built, without the concrete foundations
• A cavity wall build alternative
On a cradle-to-grave basis, the Lidan build system for this school – including piled concrete foundations – comes in 25.7 per cent lower than the cavity wall alternative. Take away the foundations from Lidan’s build, and it’s 68.5 per cent lower.
tions, the as-built school has almost as much CO2 stored in the Lidan building fabric as was released into the atmosphere by the point of practical completion. If we exclude the foundations, the stored CO2 is almost double that which was released by this stage, due to the high reliance on timber, cellulose, wood fibre and wood panel products in the build.
As Passive House Plus has previously reported, rules on building life cycle assessment mean that the CO2 emissions stored in certain building materials cannot be netted off against the emissions released into the atmosphere from building materials production, transport to site, the construction process, repair, replacement and maintenance, and end of life disposal. There is good reason for this. Plants provide an important function in absorbing CO2, and if those plants are harvested and the bulk of that CO2 remains stored in the resultant products which prevents the CO2 entering the atmosphere for 20, 50, or a hundred years or more, it buys us time in the climate fight. But netting those figures off against emissions
Of course, this is not to say that Lidan buildings don’t require foundations – except in cases where buildings are delivered to pre-existing foundations. But the company has experience of working with lower carbon alternatives to strip foundations – up to and including ground screws – and is exploring other foundation options to substantially reduce concrete use overall, and integrate low embodied carbon materials into the mix.
The sequestered CO2 emissions are noteworthy too. Even in spite of the concrete founda-
released from polluting products risks creating the impression that those emissions haven’t occurred, or are not an issue. For this reason, targets like net zero emissions are inherently problematic. It’s much better to count the emissions released, and separately count the emissions stored in materials.
While these “sequestered” emissions are calculated and accounted for – and considered as benefits for as long as they remain in the building – they’re effectively considered to be released into the atmosphere at the building’s
With increasingly accurate data emerging on emissions from current construction product manufacturing, transport and construction processes, the emissions released by the point of delivery can be proven with a high degree of confidence.
end of life. The rationale is that, even if materials containing stored CO2 are eventually reused in another building, the benefit of those stored emissions would pass out of the calculation for the original building, and into the calculation of the next use.
The treatment of end of life disposal has become a little more complicated since the advent of a new embodied carbon calculation standard, the RICS Whole Life Carbon Assessment for the Built Environment standard (WLCA), 2nd Edition, which came into force in July 2024. But the treatment of sequestered CO2 is essentially the same.
With Butler’s calculations on the whole building – including not just the Lidan fabric, but all elements – the sequestered total rises somewhat, due to stored CO2 in the internal doors, wood within the timber alu windows, internal partitions and some finishes. But this is dwarfed by an increase in emissions from a number of sources, including the standing seam roof, windows, finishes, electric radiators and ventilation systems, among others.
Building LCA involves a heady combination of logging what has been done, and trying to make informed predictions about what will happen decades into the future – over an assumed 50 year lifespan for buildings in the EU, and 60 years in the UK. These lifespans are sometimes described instead as reference study periods. To produce a cradle-to-grave figure, it’s necessary to set an estimate of building life. 50 or 60 years may seem pessimistically short for many building types, but using a set period does allow fair comparisons to be made between buildings.
With increasingly accurate data emerging on emissions from current construction product manufacturing, transport and construction processes, the emissions released by the point of delivery can be proven with a high degree of confidence. But the picture gets murkier after this, because looking forward involves making a number of assumptions. Two of the biggest such assumptions are around future manufacturing and waste disposal. The original RICS guidance on embodied carbon took a punitively precautionary approach in these regards, and assumed that if a component is replaced in,
say, 15 or 25 years, the replacement would have the same manufacturing emissions as the original component, and the old part would be disposed of in line with current waste disposal practice.
In addition to this “status quo” scenario, the 2nd edition of RICS includes a decarbonised scenario – meaning it is possible to assume that product manufacturing and disposal will have decarbonised to some extent over time.
By definition the projected decarbonisation scenarios do not apply to the construction phase, as we can instead use current data to provide more accurate figures here. They only apply to the use phase and end of life phases, and take into account projected decarbonisation in the manufacture of replacement materials, and cleaner construction waste disposal when the building reaches its end of life.
As it stands the “decarbonised” scenarios have not been added to the RIAI, RIBA and LETI targets, so when we talk about RIAI 2030 Climate Challenge targets above, the projected emissions for the use and end of life phase are likely to be punitively high.
Reflecting changes introduced in the new RICS standard, Butler carried out two versions of the calculation, based on a non-decarbonised and decarbonised scenario. The non-decarbonised scenario represents a very much worst-case situation, whereby national and global energy use and manufacturing does not decarbonise at all in the future. End of life demolition, removal of materials, and replacement of building elements across the lifespan are assumed to carry the same embodied carbon impact as they do today.
The decarbonised scenario assumes that energy use and manufacturing will continue to decarbonise over time. Under the decarbonised scenario, end of life demolition, removal of materials and replacement of building elements across the lifespan are assumed to have a lower carbon impact than they do now.
Client: The Department of Education
Main contractor/volumetric
modular builder: Lidan
Project architect: AXIS Architecture
Consulting engineer/energy consultant: TEM Engineering & Management DAC
Civil / structural engineer (foundation): Malachi Cullen Consulting Engineers
Civil / structural engineer: MMOS Engineers
Embodied carbon consultant: John Butler Sustainable Building Consultancy
Mechanical contractor: Frank Roche Air-Conditioning LTD
Electrical contractor: Lidan
Airtightness tester/consultant: 2Eva
Fasteners and connectors: Rothoblaas
Cellulose insulation, tapes and membranes: Isocell
Wood fibre insulation: Ecological Building Systems
Airtightness products: Isocell
Windows and doors: Rationel
Internal doors and glazing: Loughnanes Joinery
Cladding supplier: MTS
Fit-out: Lidan
Fitted classroom furniture, coathooks, wet areas: Western Postform
Flooring: Forbo, via MJ Flooring
Roofing: Lidan
Drainage, paving and landscaping:
Vision Contracting
Insurance: Gateway Insurances
Electrical radiators and lighting: Kellihers / CT Electric
Mechnical ventilation supplier: Daikin, via Frank Roche Air-Conditioning LTD
Access control doors: Colemans Electrics
Sanitaryware: Chadwicks
WANT TO KNOW MORE?
The digital version of this magazine includes access to exclusive galleries of architectural drawings. The digital magazine is available to subscribers on passivehouseplus.ie & passivehouseplus.co.uk
Join the Irish Green Building Council and accelerate your journey towards a sustainable built environment.
BECOME A MEMBER TODAY www.igbc.ie/membership
Discover our wide-range of online CPDs, Webinars and inhouse training.
Contribute to the development of new tools, processes and policy. Innovate Drive, develop and deploy innovation in construction.
Join IGBC now to access complimentary membership of the new National Research Centre for Construction Technology and Innovation, Construct Innovate.
Already an IGBC member? You can now opt in to become a member of Construct Innovate for FREE.
Building type: 1,000 m2 permanent school, built using a volumetric modular timber frame system.
Site type & location: Greenfield site, Birr. Co. Offaly
Completion date: January 2024
Budget: Not disclosed
Passive house status: Designed to passive house principles. Not certified.
Space heating demand: 22 kWh/m2/yr (provisional, calculated in PHPP)
Heat load: 10.4 W/m2 (provisional, calculated in PHPP)
Overheating: 0 per cent above 25C (provisional, calculated in PHPP)
Number of occupants: 4 Classrooms + 1 fully equipped special educational needs base. Maximum capacity c.100 pupils.
Energy performance coefficient (EPC): 0.33
Carbon performance coefficient (CPC): 0.26
Non domestic BER: Draft: A1, with a score of 0.16, and 11 kWh/m2/yr, pending the PV array installation.
Embodied carbon (Cradle to grave total): 488.2 kg CO2e/m2 GIA
Heating bills: Calculated at €1,095/yr (or €91/month) based on information from the school principal, including a Flogas 24 hour rate of 24.79C per kWh, assuming 16 radiators running for four hours per day from November to February. This figure may drop substantially when the 16 kWp PV array is installed, subject to a winter sun-oriented design, to reflect the potential for PV to assist a building with a use and load profile unusually well matched to winter sun.
Airtightness: 0.64 ACH at 50 Pa
Ground floor build up: (Inside to out) Forbo Marmoleum flooring; plywood; OSB; airtight membrane; I-joist insulated with Isocell cellulose insulation; Smartply OSB3; breather membrane; treated lath ground floor, Cemrock baseboard on precast concrete ground beams. U-value: 0.125 W/m2K Walls build up: (Inside to out) Plasterboard; service void; Finsa Vapourstop racking board; mm timber frame insulated with Isocell cellulose insulation; Smartply OSB3; Gutex Multitherm; breather membrane; ventilated cavity; charred Siberian larch cladding. U-value: 0.155 W/m2K
Flat roof build up: (Inside to out) Plasterboard; service void; Finsa Vapourstop racking board; I-joist insulated with Isocell cellulose insulation; OSB3 ; windtight breather membrane; a truss to create a fall and ventilated cavity; tongue and groove OSB; breather membrane; metal standing seam roof. U-value: 0.125 W/m2K
Windows and external doors: Rationel Auraplus timber aluclad windows and doors. Ug-value: 0.53 W/ m2K. Whole window U-value: 0.79 W/m2K
Heating System: WLS1000 iLifestyle WI-FI 1000 W6 digital oil electric radiators, and domestic hot water heat pump.
Ventilation: 14 X Daikin Vam-J enthalpy recovery ventilation units to cover classrooms, library and resource area, quiet space, multi-purpose room, multi activity area, shared activity space, special education teacher spaces and supporting teacher spaces. Electricity: 16Kw PV solar array to be installed. Sustainable materials: Isocell woodfibre external insulation; timber frame using C16, FSC timber.
STIRLING PASSIVE HOUSE BLITZES RIBA 2030 TARGETS
What do you get when a clinician couple decide to build their dream family home? In the skilled hands of leading Scottish architects Paper Igloo, you get a forensically detailed, highly ecological, cosy home that wraps up low embodied carbon and passive house into a beautiful design.
By Mhairi Grant, Paper Igloo Architects
Development type: 258.6 m2 detached home and home office
Method: Naturally insulated timber frame, insulated raft, infrared heating, PV
Location: Stirling
Standard: Passive house classic
Total energy costs: £147.90 per month total energy costs (all energy use – home, garage, and charging two EVs – inclusive of VAT and standing charges. EV charging using 48.5 per cent of annual energy consumption. See 'In detail' panel for more information.
£147.90 per month (all energy costs)
What does it take to build a low energy, low carbon house?
When we first met Sarah and Marcus in late 2019 their brief was quite loose. Having outgrown their current flat with the arrival of their second child, they wanted to move somewhere in the Forth Valley region close enough to their workplaces, and either renovate or build a new home, ideally to the passive house standard. That seemed straightforward enough.
Over a period of several months, we viewed a lot of interesting properties and sites together, but it felt like nothing was quite right for one reason or another. Just as the search was starting to take its toll and dampen spirits, a plot at Blair Drummond came on the market. Set in the open landscape in an attractive semi-rural location, yet only a few miles from the City of Stirling, it seemed like the perfect fit for their environmental ambitions and family needs.
In early 2020 – during the process of searching for the plot for this house – we decided as a company to commit to only design our new build projects to the passive house standard. Early discussions about this project were a key part of that decision. We had designed many low-energy or passive house buildings in the past. My journey into low-energy design began with a renovation of my parents’ existing 1868 family home in the Highlands when, some 20 years ago, I created my own SAP spreadsheet to better understand the calculations. In 2013 I became a passive house designer in order to design and build our own certified home and home-office in which we currently live. Despite the potential commercial risk to our company, the commitment seemed like both a natural evolution and an environmental necessity.
For any architect, establishing the initial story with a client is a multi-faceted creative process, yet inevitably it culminates in a deceptively simple list of spaces: an open-plan kitchen dining space, a set number of bedrooms to accommodate everyone who will live
Sub-contractors and suppliers can hold the key to lowering or raising embodied carbon without even realising it.
stand how they live their current life, and how they want to live their future life, you become an integral part of their story: a facilitator and curator, a support and a guide, a counterpoint to thoughts, discussions and decisions. That’s when the creative process can really flourish, and the outcome can be transformative.
there and regular visitors, spaces for the children to grow and be apart from their parents at certain times, and spaces for the whole family to come together in.
However, the joy and excitement in any architectural process goes beyond the prosaic. When you really get to know people and under-
For a client who is committed to passive house this journey has another layer of meaning: the desire to reduce energy demand and create a warm, comfortable, and future-proofed home can be used to push every member of the design team to think beyond the usual. Working as both the architect and passive house designer simultaneously, certain questions inevitably come to the fore in your mind whenever pen is put to paper. How can the layout be optimised, not just from a building physics perspective, but how can those
often dry, analytical processes be used as a creative tool? How can we turn discussions about compact plumbing arrangements and the location of the MVHR unit on their heads so as to infuse our creative spirit with energy, and drive us to create delightful, beautiful spaces?
Coupled with matching our clients’ low-energy ambition we brought the ideas of natural materials, vapour-open construction and designing for deconstruction to the table. We also recommended that one of the higher levels of sustainability in the Scottish Technical Standards be targeted due to the additional multifold benefits; in this case together we settled on the Silver Active level which includes enhanced acoustic separation between spaces, a dedicated day-lit home office space with wired internet (which reduces their car dependency), increased spatial requirements for bikes, prams
or wheelchairs, and water saving measures throughout. Similarly to passive house, we find that these ambitions and standards can guide, direct and enliven, rather than restrict or limit, the creative process.
In December 2020 we presented our initial designs to Sarah and Marcus; by March 2021, the planning was submitted. The layout had evolved from conversations around needs arising from changes to the life / work balance the clients sought. This included the need for dedicated space for parents who live at a distance to come to stay more often, in part to assist with childcare, in part to be able to meet frequently as an extended family. The need for spaces for the clients’ hobbies and pastimes also came to the fore. This generated a layout that simultaneously responded to the site and wider context.
The design evolution was interesting: due to the clients both working varying shift patterns, one of their key dream spaces was a home gym (but a space which could take on another use in the future) so that they could fit their chosen form of exercise around their work patterns, without being out of the house and away from their children. We initially proposed locating the gym in the garage building – a double use of an alternative space but one that did not involve using valuable thermal envelope to enclose it. After some discussion, it became clear that the gym needed to be within the passive house thermal envelope so that everyone in the house at any one time could be within shouting distance of one another!
The integration of the gym inevitably increased the house size. We looked at containing the gym in a single-storey volume at one end of the dwelling, but the form factor change and creation of additional junctions led to a further revision where the extra footprint was simply extended vertically. A secondary benefit was the addition of a new upstairs room which could form a hobby space for Sarah and her crafting activities, but also function as a guest bedroom when friends and siblings with their own families come to stay.
The overall layout of the house also responds to the wider context. The house sits above a small burn, and fronts a local loop road which connects the building cluster (of which Melamar is the final addition) to adjacent rural farmsteads. The design enhances not only the owners’ experience of the site, which is defined by long views over fields to the south and west, but has also transformed their quality of life. This connection to nature, both visual and physical, has given the clients some muchneeded relief from the stress of their day (and night) jobs. Working as doctors in an enclosed hospital environment, providing critical care for people often at their most vulnerable takes a toll on the human psyche – having a calm and peaceful space to retreat to at the end of a difficult and emotionally draining shift has had a significant impact on their well-being, with Sarah expressing to me recently the joy she now feels upon returning home every day. These feelings are subtly articulated in the
architecture: the striated Scottish Caithness stone walling with the recessed pale lime mortar on the east elevation defines the more ‘formal’ public realm by creating a robust and solid, yet highly textural mass when the house is viewed on approach or by passersby. This is complemented by the softer, naturally weathered, hand-nailed Siberian larch rainscreen cladding enveloping the remainder of the building, facing the private garden spaces, referencing the informality of the wider agricultural context, and echoing qualities of the nearby rows of mature deciduous trees that define the boundaries between adjacent fields.
Windows: views, light, seats and storage in one
Two unconventional bay windows to the rear serve to combat the less optimal but necessary north-south long axis of the building. Located in the primary, family-orientated spaces, the cladding on the west is peeled back to reveal two optimally orientated windows with integrated seats and storage below, which not only allow sunlight deep into the plan, but also direct longer views to the hills beyond, while giving privacy to both the occupants of this house
and the immediate neighbours.
The stairs are also carefully positioned. Separating the grandparents’ room from the remainder of the accommodation on the ground floor and coordinated with a roof-to-wall window over an amply lit void to the kitchen below, the landings become natural stopping points at which one can pause, absorb the view, and feel peace and calm through a visual connection with the natural world beyond.
The technical design phase had, inevitably, focussed primarily on marrying these architectural, spatial and perhaps slightly more esoteric aims with compliance. By August of 2021, the building warrant was submitted. There were no major bumps in the road during this phase, but it wasn’t until May 2022 that the warrant was granted. A contract was then signed, with a main contractor mobilised but on stand-by, and a timber frame manufacturer ready to deliver the kit only a few weeks later. The warrant approval was the last link in the chain to allow the works to formally commence on site.
With all of the key design decisions locked in place to ensure the road to both passive house certification (being undertaken with the team at Etude) and low-embodied carbon (although
with no formal metrics being sought), at this stage the road ahead looked clear and straight.
As a company, our journey into low embodied carbon design began with our own house Ostro, where we learnt that our key decisions around choosing a vapour-open timber frame, insulated with bio-based materials, minimising layers, and simplifying the form factor, had naturally led to a low embodied carbon design, even despite the use of an EPS insulated raft with a concrete slab foundation system. In both that building and Melamar, post-completion embodied carbon analysis has shown that these critical decisions for the super-structure can create buildings with around 400kg/ CO2e/m2.a with no great difficulty.
In this design as with others, the insulated raft foundation became the ground floor finish, eliminating the need for additional material and using the carbon-heavy slab for dual purpose. This type of foundation also typically requires less excavations than strip foundations, and in this case, as on all our projects of this type, there was no soil removed from site. No foundation
solution is perfect from a holistic environmental perspective, but this one does also have the value of adding a small, manageable amount of thermal mass to the building, which when coupled with the ceiling-mounted, thermostatically controlled, infra-red heating panels as the primary space heating source, offers a third comfort benefit.
When embodied carbon and supply chain collide
The concrete slab procurement brought about an interesting realisation on embodied carbon: sub-contractors and suppliers can hold the keys to lowering, or raising, the overall embodied carbon of a given design without even realising it. We had worked hard with the structural engineers, Narro Associates, to specify 70 per cent GGBS replacement to the slab. However, when the main contractor came to place the order the message coming back down the chain from the supplier to concrete sub-contractor to main contractor was loud and clear: “there is none available”. Unfortunately, in construction as
elsewhere in life, the aphorism ‘time is money’ rings true, and, with a timber frame already prefabricated and ready to be delivered just over the horizon, we had no financial choice but to sanction the main contractor to use a standard concrete mix. Interestingly when we came to undertake the retrospective embodied carbon analysis, the supplier was contacted and either couldn’t or wouldn’t confirm one way or another the mix they had provided, so in the whole life carbon calculations CEM I was assumed as a worst case.
It is easy to imagine that the only thing necessary to combat this effective control over outcomes is to include (as we did here) specification of a lower embodied carbon alternative in the tender documentation. However, when faced with the reality of cost increases for delays on site caused by the supply chain, many architects, clients and contractors feel the pressure to compromise to keep a project on track and delivered. There is an opportunity here for empowerment within the industry; with wider-spread education, knowledge and
Client: Sarah Barr & Marcus McMillan
Architect: Paper Igloo Ltd
Civil / structural engineer: Narro Associates
Energy consultant: Paper Igloo Ltd
Main contractor: SK Joiners Ltd
Electrical contractor: Knowire Installations Ltd
Airtightness tester / consultant:
Thermal Image UK Scotland
Passive house certifier: Etude
Life cycle assessment consultant: Paper Igloo Ltd
Build system supplier: Eden Insulation
Wall & roof insulation: Eden Insulation
Additional wall & roof insulation: Ultimate Insulation
Floor insulation: Build Homes Better
Mechanical ventilation supplier: Paul Heat Recovery Scotland
Airtightness products: Eden Insulation / Ecological Building Systems
Additional airtightness products: Ultimate Insulation
Windows and doors: ENERsign GmbH
Roof lights: Jewsons
Photovoltaic supplier: Ceiba Renewables
Shading devices / brise soleil: Clydeside Sheet Metal Ltd
Cladding supplier: Thornbridge
Sawmills / Norse Stone Ltd
Finance: Ecology Building Society
Structural concrete slab:
Tillicoultry Quarries / Central Rebar Ltd
Flooring: The Rubber Floor Company / The Wooden Floor Store
Roofing: Vertex Roofing & Cladding Ltd
WANT
The digital version of this magazine includes access to exclusive galleries of architectural drawings. The digital magazine is available to subscribers on passivehouseplus.ie & passivehouseplus.co.uk
7 airtightness detailing at window reveals; 8 insulation to reduce thermal bridging at window reveals; 9 airtight grommets were used to prevenet infiltration via penetrations for wires; 10 the building was finished in Caithness stone; 11 a suspended ceiling was created to house the ductwork and other building services; 12 MVHR ducts were insulated and sealed –and capped during construction, to prevent debris and dust entering the ductwork and MVHR unit during construction.
improved regulation perhaps there could come a more streamlined realisation of our collective environmental goals.
We chose the I-Joist kit manufactured and erected by Eden Insulation as it utilizes mechanical fixings and non-adhered layers, and in this case was insulated using blown cellulose, with an external wood fibre wrap factory fitted behind the breather membrane, which together with the vapour-open racking board, manages interstitial moisture movement. The selection
As on all of our projects of this type, there was no soil removed from site.
of these non-toxic materials will allow many of these elements to be safely composted at end of life if they cannot be reused or recycled.
To address excess waste from renewal and replacement cycles, and to avoid potential damage to the air and vapour control layer (AVCL) board, a service void is included throughout all external walls and pitched ceilings. To improve the wall U-values slightly (to compensate for heat loss from some view-oriented window orientation compromises) we filled these service cavities with friction-fitted wood fibre batt insulation, which can also easily be removed for recycling or composting at end of life.
We created an additional deep horizontal service void above many of the ‘wet’ rooms to contain MVHR ductwork, pipes and electrical
cabling, all below the fire-rated intermediate ceiling. This design move permits easier access to service installations over time, reducing disruption and consequential waste following any internal upgrades or services replacement cycles. It also preserves the acoustic and fire performance of the intermediate floor, and so represents a low-risk solution.
The wall and roof construction were erected in just a week, allowing the main contractor to
progress with the other elements of the build immediately. However, there was a significant delay to the programme thereafter due to the delivery of the windows – a hangover from the production and delivery delays caused by Covid the preceding year. Once these were installed in early 2023 the building was finally weather-tight.
IEQ: from shading to low VOC paints
Much of the necessary or desirable shading in this home comes from the deep reveals afforded by the selection of a naturally insulated frame. Bucking the thermally poor trend of placing the fenestration flush on the outer plane of the wall, here we followed the more optimal passive house approach: with the windows placed centrally in the thicker walls the lateral and reveal shading provided the right degree of protection from excessive solar gain. This strategy was complemented by the visually light and delicate brise soleil above the west facing windows. Their perforations track the sun’s path through the day, while still allowing a curated percentage of light to filter through, creating moving patterns on the internal walls and floor, which delight and add a little whimsy (which every home needs!)
Dedicated indoor air quality monitoring has not been undertaken in this dwelling, other than a CO2 monitor in the master bedroom, as required under Scotland’s building regulations, which has shown average CO2 levels of 533 PPM, and a maximum peak of 762.5 PPM, both well below the safe limit, thanks to the constantly running MVHR system and absence of any fuel-burning appliances for heating or cook-
ing. Meanwhile, all internal decorated surfaces are finished with low VOC water-based paints, or Osmo natural oil-based products, which not only creates less internal air pollution, but allows painted or finished timber-based materials to be safely re-purposed, or recycled, at end of life. Additionally, the fire-retardant treatment required for the timber cladding to the north gable wall due to distance to boundary was also water-based and so is less deleterious to the environment than alternatives.
Although passive house certified in August 2023, Spring 2024 saw the culmination of this journey with completion finally reached after the standard defects period; a journey which had started back in 2019 with Sarah and Marcus’s desire to change their lives for the better and a short email to an architect’s office.
In tandem with our clients (who are also self-confessed lovers of spreadsheets) we have been monitoring the environmental perfor-
mance of the house in a few different ways. Temperature and humidity sensors in the west-facing home office room and the open-plan dining area below have shown the usual patterns for low-energy dwellings emerge. When all windows and doors are closed while the occupants are out during the day the indoor temperature rises slightly due to solar gains, particularly as the long elevation faces west. The house is then cooled overnight by following a routine of purge ventilation via the rooflights on the western roof slope coupled with some ground floor windows on tilt. Overheating frequency has been assessed in these spaces during the first 9 months of occupation at circa 2.86 per cent and 5.36 per cent respectively, which is largely in line with the averaged PHPP estimation of 3 per cent. This should improve over time as the owners become more familiar with a routine of window opening overnight.
Additionally, the renewables systems installed in this direct electric building, which comprise a 6.84kWp PV array fixed over the west facing Greencoat roof covering, connected to a 13.5kW Tesla Powerwall battery, a well-insulated HWC with a divertor from the PV system, and the two EV charging points, all provide detailed .csv export files from which the graphs of energy consumption shown here are derived.
Moreover, the building uses a notable 65 per cent less energy for space heating than a baseline equivalent home of the same design when benchmarked against the 2021 Scottish Technical Standards, which was the year it was consented.
Since the project has concluded the clients have been busy not only assisting me in my favourite pastime of creating graphs of their energy consumption, but also embedding their new home into their first garden. They have planted a mixed species hedge along the eastern boundary to improve the habitat for wildlife, sown a wildflower area including spring bulbs to the front garden, and are gradually implementing their plans for additional permeable landscaping and pollinator-friendly planting in the rear garden.
The flexibility of the spaces, the accessibility and potential for future changes have created
a home that not only suits our clients now but will allow for adaptability to suit both them and future occupants without the need for invasive retrofitting works: a home for life. Our clients chose the house name Melamar as an ode to their feelings about the culmination of this once in a lifetime adventure – loosely meaning one’s true or emotional home, this is a place in which they feel rooted and content.
If I had to distil the answer to the question I first asked myself when starting to write this article - what does it take to build a low energy, low carbon house? – I would say above all else it takes tenacity.
THE CLIENT’S VIEW
We love living in our new home. We wanted to reduce our carbon footprint and aiming for the passive house standard seemed the obvious way to do that. It's obviously a huge privilege to be able to live somewhere specifically designed for our needs, and we may be biased, but our home is perfect for us. Even after a year, it continues to bring joy when we come home.
Having experienced all the seasons now, the house has been very comfortable winter and summer and performs extremely efficiently. We had 10 adults and 7 children in the house for Christmas and didn't need any heating on. We were a bit worried that maintaining two electric cars would make it a bit more challenging, especially with work commutes. However, the setup we have with the solar panels, home battery and a favourable tariff with Octopus has made it quite straightforward. Running costs have been incredibly low, and although Mhairi did tell us that would be the case, it has still been a very pleasant surprise.
The whole process of self-building has been hugely rewarding, though we can take very little credit. The whole team have done an amazing job, and we have come out the other side with an incredible family home which will hopefully allow us to live sustainably for the future.
Building type: Detached 1.5 storey timber frame house with thermally separate but conjoined double garage.
Size: 258.6 m2 treated floor area (305.5 m2 gross internal area) for the house only. 334.9 m2 used in the embodied carbon analysis, to include the garage and the ‘footprint’ of the pergola structure.
Site type & location: Semi-rural site adjacent to small building group in Countryside Policy area, Blair Drummond, Stirling.
Completion date: Building Standards Completion 11 December 2023
Budget: c. £785,200 excluding site purchase, all professional and statutory fees and client supplied items, but including some landscaping (hard surfaces, decking & fencing).
Number of occupants: 2 adults & 2 children, with extended family staying often.
Environmental assessment method: Section 7 in Scottish Technical Standard - Silver Active achieved.
Passive house certification: Passive house
classic. Certified August 2023.
Energy performance calculation tool: PHPP. (SAP was also undertaken for building regulation compliance but all figures relate to PHPP)
Space heating demand (PHPP): 13 kWh/m2/yr Heat load (PHPP): 9 W/m2
Primary energy non-renewable: 93 kWh/m2/yr
Primary energy renewable: 39 kWh/m2/yr
Airtightness rating: 0.1 ACH AT 50 pa
Heat loss form factor: 2.79
Calculated overheating risk: 3 per cent of year above 25C (calculated using PHPP)
Air quality index: Fair (an annual average score of 23, based on Blair Drummond Safari Park, using the Plume Air Quality Index)
Air quality context: Site is next to agricultural fields to the west, so some degree of protection may be required when farmers are spreading fertilisers on fields.
Indoor environmental quality monitoring overview: 2 Tempo Disc Bluetooth sensors placed in the dwelling since 2023 to monitor temperature and humidity. One was placed in the home office, one in the open-plan kitchen/ dining space (which has only recorded since 7 May 2024 due to a set up issue). Data is gathered hourly and recorded in a .csv file.
Open-plan kitchen/dining room: Context: Typically open to living space (west & south facing) Monitoring period: 7 May – 5 August 2024 (initial results. Average temperature: 23/24C. Percent of period above 25C: 5.16 per cent
Note that this is 5.16 per cent of a three-month summer period, indicating that the whole year figure is likely to be substantially lower. Monitoring shows a consistent pattern of temperatures rising when occupants are out at work all day and have left all windows closed for security. Relative humidity: Average of 53.77 per cent (minimum 37.9 per cent, maximum 64.7 per cent).
Home office: Context: Typically door closed for privacy, single-aspect (west facing). Monitoring period: 13 Dec-21 May 2024. Average temperature: 18.8C. Percent of period above 25C: 2.86 per cent. Relative humidity: Average of 46.0 per cent (minimum 27.5 per cent, maximum 65 per cent).
Master bedroom: Context: CO2 monitor required under Scottish Technical Standards. Data has been gathered on two occasions (30.04.24 & 21.05.24) and averaged.
Average CO2 levels: 533 PPM. Prior 8-hour average CO2 levels (at time of data collection): 647 PPM. Prior 24-hour average CO2 levels (at time of data collection): 552.5 PPM. Prior 24-hour peak CO2 levels (at time of data collection): 762.5 PPM. Percent of period above 1500 PPM: 0 per cent
Radon: Not monitored, however according to the UK Radon Risk Map the site is not within any radon potential area (less than 1 per cent maximum radon potential).
Thermal bridging: Measures taken included thermal bridge-free insulated raft foundation system in combination with thermal bridge-free timber frame, thermally broken window frames and insulated reveals, including modelling of key junctions including ground floor perimeter, thresholds, dormer header meeting pitched roof, ridge, rooflights cill details, to verify performance. See online panel for more detail.
Ground floor: 250 mm reinforced C35 concrete slab (CEM I) with power-floated finish (final floor finish), Visqueen Ecomembrane recycled polyethylene DPM, Isoquick insulated raft foundation system, 50 mm grit layer, min. 150 mm compacted Type 1 sub-base. U-value: 0.122 W/m2K.
Walls: 20 mm thick x 80 mm wide untreated Siberian larch rainscreen cladding OR 100-125 mm Caithness stone wall finish with lime mortar and raked joints, 50x45 mm treated timber cladding battens, Pro Clima Fronta Quattro UV stable breather membrane (behind timber rainscreen finish) OR Fronta WA (behind stone wall finish), 22 mm Gutex Multiplex Top rigid wood fibre board, 300 x 45 mm blown cellulose filled timber I-Joist frame, 12 mm Finsa SuperPan VapourStop AVCL board with joints taped with Pro Clima Tescon Vans airtight tape, 45 mm service cavity insulated with 40 mm Steicoflex 036 flexible wood fibre insulation, 12.5 or 15 mm plasterboard or Fireline board (depending on location). U-value: 0.13 W/m2K.
Roof: Standing seam Greencoat (zinc coated steel) roof finish, 18 mm external grade plywood, 45 x 50 mm treated timber battens, Pro Clima Solitex Plus vapour open roofing membrane, 22 mm Gutex Multiplex Top rigid wood fibre board, 300 x 45 mm blown cellulose filled timber I-Joist frame, 12 mm Finsa SuperPan VapourStop AVCL board with joints taped with Pro Clima Tescon Vans airtight tape, 45 mm service cavity insulated with 40 mm Steicoflex 036 flexible wood fibre insulation, 12.5 mm plasterboard. U-value: 0.11 W/m2K
Windows & external doors: Passivhaus Institute certified Enersign triple glazed alu-clad timber frame windows (with thermal break), with argon fill. Averaged installed U-value = 0.72 W/m2K (from PHPP).
Roof windows: Passivhaus Institute certified Fakro FTT
U8 quadruple glazed roof windows with thermal flashing kit. 8 x Alu-clad timber frame rooflights with argon fill. Averaged installed U-value = 0.95 W/m2K (from PHPP).
Acoustic test results: Under Section 7 Silver requirements all internal partitions and intermediate floor have been constructed in accordance with lab tested systems by British Gypsum (partitions) and Knauf Brio (floor) which achieve the following: Airborne sound: 44dB. Measured energy consumption: From Octopus energy bills between 12.08.23 - 11.08.24: 12,139.5kWh. Note: this differs to the total consumption from the MyEnergi devices of 14,856kWh because the bills only include export from 17.02.24 – 11.08.24. Based on larger GIA (due to lighting / power in garage and lighting to pergola) and total measured consumption excluding exported energy and EV charging, this would equate to: 29.63 kWh/m2 GIA for 25.08.23 - 25.08.24
Energy bills (measured or estimated): Energy bills between 12.08.23 - 11.08.24: Octopus bills with 3 different tariffs over time accounted for. Most recent tariff is Octopus Intelligent Go, with current rates of 7.14 p/kWh for 11:30pm - 5:30am & 26.29 p/kWh for remainder of day/night. Current Standing Charge = 56.22 p/day. All figures excl. 5 per cent VAT. Total bill for this time period (12 months): £1,690.33 excl. VAT or £1,774.85 incl. 5 per cent VAT. This includes total energy usage for house and garage plus standing charges – space heating, hot water, regulated & unregulated energy use and the charging of 2 EVs. It does not account for exported energy back to the grid. Cost for total energy usage as noted above but excluding standing charges was £1,483.48. Note: The total energy costs above include the EV charging: it was not until the new Intelligent Octopus Go tariff was utilised on 02.11.23 that the EV charging times were optimised to either be overnight with battery charging taking place on a sunny day, or more often in winter, to charge the battery over-night at the lower rate and then top-up charge the car(s) from the battery during the day.
Upfront total (A1-A5, excluding sequestered CO2): 284.8 kgCO2 e/m2 GIA, (LETI band A rated).
Upfront sequestered CO2 (A1-A5): -149.7 kgCO2 e/ m2 GIA.
Cradle to grave total (A-C): 393 kgCO2 e/m2 GIA (meets RIBA 2030 Climate Challenge target). Calculated using PHribbon v5.23, which follows the RICS 1st edition methodology very closely. Instead of the ‘uncertainty matrix’ in the methodology of the RICS 2nd edition, as much as detail as possible was included in the calculation, including all built elements on the site (garage and pergola) even though these are out-with the thermal envelope.
Building elements included:
Substructure; superstructure (structural elements, building envelope, internal elements; finishes (excluding paint / decorations, however all wall / ceiling paint was low / zero VOC by Tikkurila, and all exposed wood was finished with OSMO); fittings (all sanitary fittings included; all built in joinery included except for kitchen units by IKEA & worktops which were Corian on the back wall and porcelain on the island; services (Exclusions: electrical / wiring works & plumbing waste pipework & Tesla Powerwall battery. Inclusions: copper feed DHW pipe work, MVHR unit, PV panels and all heating emitters.). EPDs used included actual products from suppliers including Gyproc, Knauf, Steico, Gutex, Greencoat, Firestone, Aquapanel, Fakro, Sunpower, and Zehnder, with industry association EPDs, EPDs for similar products and default data used in other cases. A full list is available at www. passivehouseplus.co.uk/Melamar
Energy bills (measured or estimated): Direct electric with PV array, divertor, battery storage and EV charging points. PV panels: 37.1m2 array of 18 x Sunpower 380 panels, with 13.5 kW Tesla Powerwall battery, Myenergi Eddie divertor from PV to unvented. 300L Heatrae Sadia Megaflop Eco Plus hot water cylinder with back up 3kW immersion. Space heating emitters: 3 x electric towel rails (1 per wet room) plus 7kW of infrared panels distributed throughout the ground floor, all individually thermostatically controlled. 2 x Myenergi Zappi EV charging points on the garage. Excess electricity exported to the grid. Electricity import rates: 7.14p/kWh for 11:30pm - 05:30am & 26.29p/kWh for remainder of day/night. Electricity export rate: 15p/kWh (fixed rate). Estimated annual electricity yield from PV after the inverter (absolute) from PHPP: 4,164 kWh.
Ventilation: Zehnder ComfoAir Q350 MVHR system; PHI certified to have heat recovery of 86 per cent; efficiency in PHPP Ventilation worksheet = 88.5 per cent. No additional cooking fumes extract ventilation, only MVHR extract in kitchen.
Water conservation measures: Recoup ‘PIPE+HEX’ wastewater heat recovery unit installed below master en-suite shower. Dual flush toilets, aerated shower heads & taps. To comply with Scotland’s sustainability target Silver Active, flow rates are 4.5L (WC average flush volume); <6L per min taps serving wash hand basins & sinks, and <8L per min shower heads. 255L water butt in garden collecting rainwater for garden use. Calculated water usage: 94.3 litres per person per day, calculated using the ‘Water Efficiency Calculator for new dwellings’ online tool. Meets 2025 target in RIBA 2030 Climate Challenge.
Sustainable materials: Timber frame using FSC certified timber. Cellulose & wood fibre insulation throughout walls and pitched roof. All timber from FSC sources. Scottish stone. Untreated timber cladding. No adhered layers within substructure of superstructure to permit deconstruction at end of life. (SEDA Guide for Deconstruction followed for main aspects of superstructure.).
It’s a radical idea: that to negate the environmental damage of construction, we don’t just need to build sustainably, we need to build less. However, most architects and building designers earn a living by doing exactly the opposite: by building stuff. So how can the design practice be reinvented for a world in which we need to do more with much, much less? By Lenny
Antonelli
New York architect Clare Miflin likes to tell a story about an engineer she knows. The engineer was consulting for a leading university, who were keen to build a new, green ‘net zero’ building on campus. The engineer told the university that if they just made some timetable tweaks, they wouldn’t need the new building at all — they could fit all their lectures into existing classrooms. But the university had a donor, and the donor was keen to see their name on this new green building. So, the building went ahead.
In this climate constrained world, Miflin
says, there must be a better way. “We have to start rewarding different things, rewarding things that add value,” she says. “We want jobs, but we don’t want to use physical resources. Could architects be paid in a different way?”
Emerging thinking says that the climate and ecological crises are so profound that ‘sustainable building’ is no longer sufficient — instead, we should question the merit of new buildings, make better use of existing space, prioritise retrofit. ‘New’ should be our last resort. This is reflected in new initiatives
from the likes of ARUP and the World Green Building Council, and more recently, articles in leading magazines.
Last year, UK housing secretary Michael Gove refused Marks & Spencer permission to demolish their flagship Oxford Street Store in London, partly because demolition would, he wrote, “fail to support the transition to a low carbon future, and… fail to encourage the reuse of existing resources” (this decision was later overturned by the High Court).
For those working in building design, the idea of building less raises critical questions:
if we traditionally make money by building more, how can we make money by building less? What architect ever earned a buck by convincing a client not to build something?
This problem was neatly surmised in an image posted to Instagram by Australian architect Jennifer Crawford in 2022 (hat tip to Lloyd Alter who first wrote about Crawford’s work).
Crawford previously worked in residential development, but in 2020 she started her own design firm — with a twist. Our Home Coach helps clients to meet their needs not just by building homes and extensions, but by applying good design to do more with less. Most of Crawford’s clients are homeowners looking to renovate.
“I talk people out of doing a lot of stuff,” she says, “because I know how hard it is, how long it takes, how much money it takes.” She says that in Australia, many clients are keen to scale down their renovation plans because the price of construction has skyrocketed.
“The solution is not always a building solution,” she says. “Sometimes it’s a landscaping solution, sometimes it’s a furniture solution. Sometimes you can rearrange furniture in a room and turn one space into two.”
In researching this article, we spoke to a number of architects and other built environment professionals about how architecture might change in a world where we need to build less, and the phrase that kept coming up was ‘adding value’. Can designers add value to their clients’ lives and buildings, without adding floor area?
Crawford offers a practical example: a client had a disused garage they wanted to con-
vert into a guest suite and office. The roof was very low, and the client, who is tall, found the space cramped. Their plan was to add a second floor, creating two separate spaces. But Crawford proposed a smaller, cheaper solution: raise the roof slightly, install skylights, a drop-down wall bed, and a drop-down wall desk. The building was thermally retrofitted too. Now the same room can serve as an office, bedroom, or sitting area, depending on which furniture is in use. “The footprint stayed the same, and now they’ve got three rooms in the space of one. In my mind that’s adding value.”
Another example: the French architectural practice Lacaton + Vassal, who won the Pritzker prize in 2021 and whose motto is “never de-
molish”, were asked to redesign a small square in Bordeaux. After observing the square closely and speaking to locals, they recommended that the city do almost nothing to the space — it was already close to perfect. “Embellishment has no place here,” they wrote. “Quality, charm, life exist. The square is already beautiful.” They recommended basic maintenance work: replace the gravel, clean the square more often, adjust traffic management slightly.
“We don’t add value if we skimp on the dishwasher and then truck disposable plates to landfills 350 miles away,” Clare Miflin writes of designing a cafe. “We do if we realise the building doesn’t need its own auditorium because there is one next door that the client could share.”
This philosophy creates a whole new set of questions for designers to ask: How can we reduce the waste flows from this building? How can we get more from the existing space? Do we really need to extend? Could we make the design smaller, even ask our neighbours to share some facilities?
This might not be the design work that architects are accustomed to, but it is design. “I think there is so much of a role for architects because they can think systematically, and design solutions in a systematic way,” Miflin says. Having previously worked for conventional design practices, she established her consultancy Think Woven in 2018, and the non-profit Centre for Zero Waste Design, in 2019. The focus of both is to design circular flows for materials through buildings. Neither is a conventional architectural practice, but Miflin prefers to hire architects because of their ability to think systematically and solve problems with good design.
She says that ideally, architects would be engaged much earlier in projects — even before site selection — to find ways to reduce the use of resources from the outset. And they would stay involved long after occupation, to fine tune the building and oversee post-occupancy evaluation. “Right now, architects
get no feedback from projects to help them design better,” she says. (In Scotland, John Gilbert Architects set up an office dedicated to building performance evaluation as part of their response to climate breakdown, and now build this service into all of their projects).
Marianne Heaslip. “Some of the joy in that is helping people to figure out what they want, working out the context of an existing building, making it a good place to be — but also making it function from a thermal point of view. I think some of the best designers and
Getting to net zero would have been easier if we increased our footprint, limited occupancy, and outsourced as many impacts as we could. But would that have made the project more sustainable?
As we confront the planetary crisis, could the focus of design shift from creating new buildings to designing communities and systems that regenerate the living world? How can communities organise themselves to provide for food, shelter and transport in a carbon-constrained world? This requires good design. (The work of the Australian permaculturist David Holmgren to reimagine the suburbs of Australia touches on this).
“I’ve done a lot of community engagement and community design work,” says architect
architects, that’s what they’re about.”
In 2009, after she was laid off from her role with a conventional design practice, Heaslip used her redundancy to pay for a masters in retrofit at the Centre for Alternative Technology in Wales. She’s now technical director at People Powered Retrofit, a not-for-profit community benefit society that works with householders, contractors, and housing providers to facilitate high quality retrofit.
“We do early-stage surveys and options studies for domestic retrofit using our Home
Retrofit Planner tool,” she says. “By providing the comparison and contextual information, we have been able to convince a client on a few occasions to forgo the extension they had planned and instead go further with the retrofit elements of the work, so they had a more comfortable and functional home, or could more affordably run a heat pump. It's not always possible to make that case, but it's getting more common that sufficiency is seen as important as efficiency. And when it comes to work for an architect, there can be as much to do in a considered whole house retrofit as a standard extension”.
Heaslip says that shifting focus from new build to retrofit will change the nature of architecture somewhat. “A lot of people see architecture more like an art-based discipline, rather than a maths one or an engineering one. But I think a lot of the skills called for in low carbon sustainable building or retrofit are a little more science based.” Budding architects and design professionals will need to understand building physics, heat, moisture, and embodied carbon.
“Architects will get more creative and more specialist in existing building types and moisture management,” say Retrofit Action for Tomorrow (RAFT), a new London-based design practice with a focus on decarbonisation and climate resilience for schools. “Existing buildings need thoughtful specialist design,
Perhaps one of the most forward-thinking pieces of design ever published in these pages: The Beehive, originally published in issue 24 of Passive House Plus. This derelict newsagents was reimagined by C&O Architects as an ecologically-insulated 45 m2 home in Shrewsbury, squeezing every ounce of utility out of a small space. While not Enerphit certified, revised PHPP calculations by passive house consultant Nick Grant for the case study in light of a methodological update to take account of higher internal gains in smaller homes meant the building likely comfortably met the standard.
finding low intervention spatial solutions that work with and enhance [them].” But to facilitate this, architectural education needs to change and focus more on retrofit, they say.
Changing how we evaluate buildings can swing the pendulum too. “We celebrate excessively large passivhaus projects when they use as much energy as a moderately performing three-bed house,” say RAFT. “We extend so much when we retrofit that we wipe out the carbon savings gained by retrofitting.” Instead, they say, we need a celebration of spaces that work hard for their size, of sensible retrofits, of normal looking projects that prioritise comfort and function over aesthetic and luxury.
Building metrics need to evolve too, Clare Miflin says. Energy consumption and embodied carbon are typically measured per square metre of floor area, meaning a building can be far larger than needed and still meet benchmarks like the passive house stan-
dard or the RIBA 2030 Climate Challenge. Miflin writes of an environmental centre she designed: “We had to fit the café’s energy use within the energy budget provided by the
The question remains: can architects and designers make a good living in this new world of building less?
solar roof. Getting to net zero energy would have been easier if we increased our footprint and roof area, limited the occupancy of the building, and outsourced as many impacts as
we could. But would that really have made the project more sustainable?”
Instead, if we also measured energy use or embodied carbon per occupant, it would be harder to certify a 300 square metre house occupied by just two people. Miflin mentions a project she’s consulting on where the design is based around ensuring each occupant can live within a fair ecological footprint. “They had to drop the 140 m2 hotel rooms from the plan because they couldn’t make them fit within that metric,” she says.
We also need to think hard about the public value of buildings, she says. “Should you get positive metrics for designing a building for a hedge fund, for example? I have designed greenhouses for schools that are hard to make energy efficient, given the constraints of greenhouse forms and technologies, but when you see how excited the kids are in those spaces — learning about plants, food, and ecology — you know the
greenhouse has almost certainly had a net positive environmental impact.”
But still, the question remains: can architects and designers make a good living in this new world of building less?
Jennifer Crawford admits this has been the “tension” for her practice since she established Our Home Coach. Because she talks her clients out of doing big projects, she needs more clients to make a living. “How
do I make money? This is still my challenge,” she says. “My intention is, I don’t want to build more if more does no good, but I will build more if more makes sense.”
RAFT are optimistic about the future.
“Architects’ jobs… will always be in demand, if we collectively organise toward a profession focused on retrofitting cities that are socially and climate justice focused,” they say. “We cannot solely rely on the mar-
ket and interventions within the market to provide this for the architect. The possibilities for retrofitting cities — on a physical and social level, toward climate, disability, economic, and social justice — are incredibly exciting, as the architect positions themselves within a wider community of engineers, teachers, social workers, artists and health professionals. Our issues are all interconnected.”
S
isk, in collaboration with a consortium of leading low carbon industry experts, has announced that it has been successful in securing £500,000 from Innovate UK funding as part of the Contracts for Innovation: Decarbonising concrete competition, to invest in a pioneering scalable low carbon demonstrator, marking a world first new low carbon concrete technology.
The low carbon demonstrator project features a consortium including, Sisk, Ecocem, Ramboll, Loughborough University, Creagh Concrete, Capital Concrete and BRE Group.
The innovation aims to revolutionise the commercial viability of low carbon cement within the construction sector.
The project will pioneer the use of Ecocem’s advanced cement technology (ACT), in a demonstrator which will be the first structure of its kind.
A breakthrough cement technology, ACT combines a range of technical innovations with the use of widely available low carbon materials to decarbonise the production of cement by as much as 70 per cent, while enhancing the strength and durability of the concrete it is used to manufacture.
The project will conduct technical and testing verification, as well as environmental assessment and validation of the concrete product, both in a laboratory and at a concrete production and live construction site.
The low carbon demonstrator will be based at NE02/NE03, Wembley Park, where Sisk has been working on the redevelopment of Wembley Park for its long-term client, Quintain for the past 20 years.
Sisk’s innovation and design director SarahJane Pisciotti said: “Carving a route to net zero through innovation is key to our sustainability strategy at Sisk and we are delighted to get this ambitious demonstrator to decarbonise cement off the ground.”
Ecocem’s director of concrete technology deployment John Reddy said: “Since embodied CO2 in construction is 11 per cent of all global emissions, and clinker, the critical ingredient in cement, generates 65 per cent of these, finding ways to reduce emissions from cement and concrete is critical. We have assembled a great delivery team of experts under the leadership of Sisk and our consortium will demonstrate that rapid decarbonisation of the cement and concrete industry is possible now, using ACT technology which brings new thinking to existing proven materials and processes. This funding from Innovate UK is a very welcome investment in delivering a low carbon future for construction and a great example of how governments can take the lead in scaling innovation and enabling decarbonisation.”
KORE Retrofit, a leading provider of sustainable retrofit solutions in Ireland, is pleased to announce the appointment of Dr Barry Mc Carron as its new managing director. Mc Carron brings extensive experience in sustainable development, building energy performance, and project management to this pivotal role.
Before joining KORE Retrofit, Mc Carron served as head of business and industry support at South West College. He holds a PhD focused on monitoring indoor radon levels in certified passive house buildings, an honours degree in architectural technology and management from Ulster University, and an MSc in sustainable development from Queen’s University Belfast. Mc Carron also recently chaired the Passive House Association of Ireland (PHAI), further establishing his credentials in the field of energy efficient construction.
KORE Retrofit is an SEAI-registered one-stop-shop, a fully managed solution designed for homeowners carrying out multiple energy upgrades. This service guides homeowners from the initial energy assessment to contractor quotes, with KORE Retrofit overseeing quality and project management throughout.
Mc Carron recently completed an award-winning passive house-certified bungalow retrofit in Monaghan, demonstrating how traditional Irish bungalows can be transformed to meet
modern environmental standards.
Throughout his career, Mc Carron has been recognised with numerous accolades, including the Belfast Builder’s Association Outstanding Achievement Award and the Gibson Institute Scholarship. A committed advocate for climate action, he has contributed to several United Nations climate change conferences (COP17, COP26, and COP27) on issues related to climate finance and mitigation.
Mc Carron is also a respected researcher, and sits on the Ministerial Advisory Group for Architecture in Northern Ireland and the RSUA Climate Change Committee as well as the board of Grove housing association. Recently, he was also appointed as the technical chair for the Chartered Institute of Architectural Technologists in Ireland.
“We are thrilled to welcome Dr Barry Mc Carron as the new managing director of KORE Retrofit,” said Caroline Ashe Brady, commercial director at KORE Retrofit. “His leadership and deep commitment to sustainable development make him the ideal person to guide our company as we continue to deliver innovative retrofit solutions across Ireland.”
In his new role, Mc Carron will oversee all aspects of KORE Retrofit’s operations, driving the company’s mission to enhance energy efficiency and sustainability in homes across Ireland. For more information visit www.koreretrofit.com.
Ireland’s first 3D printed housing project has been delivered in Dundalk – integrating Firetite aerated clay cavity wall insulation.
The collaboration between Louth County Council, Louth & Meath Education & Training Board, and Harcourt Technologies utilised 3D construction printing technology to construct a three-unit terrace of three-bed homes at Grange Close, Dundalk.
Harcourt Technologies (HTL) were awarded the opportunity to provide Louth County council with Irelands first 3D printed home at Grange Close. The project is the first social housing scheme in the world to combine 3D construction printing (3DCP) and ready-mix concrete – with a low embodied carbon mix.
A 3DCP construction method uses large-scale 3D printers onsite to create three-dimensional structures layer by layer. Layers of 50 mm ready-mix concrete are deposited through a gantry based 3DCP machine according to a digital model, eliminating the need for traditional blocks.
HTL MD Justin Kinsella said that the company had made particular efforts to reduce the embodied carbon of the system, by adjusting the concrete recipe – using the largest proportion of aggregate in the mix possible, meaning less cement binder, and larger sized aggregates.
According to HTL director Jandré Oosthuizen: “The typical 3D printed building worldwide is currently constructed with a mortar material – concrete without large aggregates – which has a much higher cement content. The embodied carbon for the typical building would be roughly 450 kg CO2e/m3. I.e., we have roughly a 30 per cent saving,” and a cradle-to-factory gate total of 349 kg CO2e/m3
At Grange Close, Firetite clay foam cavity wall insulation was chosen to fill the 3DCP cavity walls. The world’s first three component mineral clay insulation, Firetite has a thermal conductivity of 0.034W/mK. This self-sealing material also has the added benefit of providing a Class A2-s1:d0 fire rating eliminating the need for fire cavity barriers in the cavity wall.
With the best EMICODE emissions classification of EC1plus and contributing 30 points to any BREEAM building, Grange Close also benefits from Firetite’s environmental credentials.
For more information on Firetite visit econbp.com/firetite/, and for Harcourt Technologies visit www.htl.tech.
Galway-based mechanical ventilation with heat recovery (MVHR) manufacturer ProAir has achieved best in class energy performance levels on a new MVHR system.
Designed for homes of up to 270 m², the PA700LI has achieved test results showing a thermal efficiency of up to 95 per cent.
ProAir founder and MD David McHugh said “The PA700LI is an exciting Irish innovation in indoor air management and has fulfilled my ambition to develop the highest possible efficiency unit on the market. We are confident there will be a lot of interest in this unit which, under test conditions at the Building Research Establishment in England, has demonstrated the highest efficiency in its class on the Irish market.”
McHugh said the company was “extremely proud” to develop and manufacture the product in Galway, where Ireland’s only manufacturer of MVHR has been at the cutting edge of research and development. The PA700LI was developed in-house, but the company also has an ongoing relationship with Atlantic Technical University where research into the next generation of MVHR is taking place. “When the two R&D departments fully coalesce,” said McHugh, “we can look forward to more firsts in terms of efficiency and highest technology levels”.
The unit includes sensors to monitor temperature, humidity and CO2 for enhanced indoor air quality, and uses this information to provide intelligent ventilation and the optimal indoor environment. Touch pads provide users with simple and straightforward control, and wireless boost switches offer the option to boost the system.
With a summer bypass as standard, the unit has a specific energy consumption (SEC) rating of A+, using humidity and CO2 sensors to automatically control both the summer bypass and boost function. The PA700LI operates continuously at low speeds to minimise electrical consumption.
ProAir has also introduced ProAirVENT Connect, a mobile app to enable homeowners to control the PA700LI system on Apple and Android smartphones “from the next room, or even the other side of the world”. With user consent, the ProAir technical support team can access the system, which allows remote updates and diagnostics for service and customer support.
An additional Bluetooth app, ProAirVENT Local Control, is used to commission the unit and allows users to change the settings locally.
McHugh emphasised that ProAir is committed to excellence from design, to installation, to commissioning. “As with all ProAir systems, the ProAir team will develop a ventilation strategy exclusively for you and a bespoke system is designed specifically for every project,” he said. “Our highly skilled technicians install in compliance with the most up to date building regulations, Part F 2019, and certification is provided upon completion.”
For the data sheet on the ProAir PA700LI visit tinyurl.com/ PA700LI
Since hosting their first women’s day event in 2022, Mitsubishi Electric Ireland have established themselves as leaders in creating a platform for women to come together, connect and bond.
As a company that believes in fostering an empowering environment for women in this industry to thrive, Mitsubishi Electric Ireland found it to be a perfect match when Adrienne Gorman, the head of the new chapter of Women in Building Services Engineering (WiBSE) in Northern Ireland, reached out and asked the Irish branch to sponsor and co-host an event to celebrate the launch of their newest chapter.
“It is vital for women to create an open community, uniting their experiences in building services,” said Gorman. “This fosters progress and inclusivity while inspiring younger girls to pursue STEM fields, demonstrating that with determination and passion, the possibilities are limitless.”
Part of the Chartered Institute of Building Services Engineering (CIBSE), WiBSE’s purpose is clear: to inspire the next generation of women in building services engineering and to create a robust support network.
“Hosting events like this helps to show case the limitless career advancement opportu-
nities, including advancing into senior roles, success stories and courses that are available to women in our industry,” said Mitsubishi Electric consultant sales engineer Margaret Rafter. “They also provide an opportunity for female engineers from diverse fields to connect, collaborate and explore cross-sector growth within the industry”.
The event featured an evening of ‘Paint & Sip’, providing attendees with a unique opportunity to engage in a creative activity while meeting new people and networking.
The event, held at The Waterman House in Belfast, marked a significant milestone in Mitsubishi Electric and WiBSE’s mission to inspire and support women in the industry. The establishment of the newest chapter in Northern Ireland highlights the importance of such platforms in empowering women and fostering a more inclusive and supportive industry environment.
“These events are crucial for individual development and for promoting broader gender equality in the professional world,” said Mitsubishi Electric Ireland’s Leinster region business development manager Siobhán Gilroy. “They help highlight and address challenges in our industry and promote discussions on equality and inclusion”.
A. Proctor Group has announced the promotion of Adam Salt to the position of head of global sales modular offsite, effective immediately.
The newly created role sees Salt promoted from his previous position as a business development manager within the group, and reporting directly to managing director Keira Proctor.
Salt is now responsible for overseeing the export division, growing and developing key accounts, researching potential new distributors, and building a significant customer presence internationally. This pivotal role will also see Adam spearheading the company’s modular strategy on a global scale, driving growth and innovation in this rapidly evolving sector.
“Adam has consistently gone above and beyond in his contributions to A. Proctor Group,” said Keira Proctor. “His passion for the industry, combined with his strategic thinking and ability to foster client relationships, makes him the perfect fit to lead our global sales with a focus in the modular offsite sector.
“Coupling Adam’s experience with our established export division, and solutions like our ground-breaking, self-adhered Wraptite® external air barrier, makes this the perfect time to expand our focus to global markets. We are excited to see how he will drive our growth in this key area.”
As part of his new responsibilities, Salt will maintain links with the UK and Ireland’s modular sectors. He said: “I am honoured to accept this position and lead our global sales efforts. A. Proctor Group is known for its commitment to quality and innovation, and I’m eager to work with our talented team to expand our reach and continue delivering exceptional value to our customers.
“Modular offsite is growing in other parts of the world, especially North America. Something that people often remark on is how they see the UK almost like pioneers of modular construction, so I’m delighted to have this chance to help the sector grow globally.”
For more information visit www.proctorgroup.com
Leading heating technology manufacturer
Grant has announced the launch of its next generation air source heat pump – the Grant Aerona 290, which is now available to order.
Designed in Ireland for the Irish and UK climate, Grant said the new machine is in another league in terms of innovation and efficiency and a significant addition to the Grant product portfolio.
Throughout the research and development phase, Grant heavily invested in design and testing the new range to ensure the technology is best suited for year-round climate conditions in Ireland and the UK. The Aerona 290 provides an environmentally friendly, low carbon heating solution as it uses the energy efficient and natural refrigerant R290, which has a global warming potential (GWP) of 3. In simple terms, one kg of R290 in the atmosphere is equivalent to 3 kg of CO2. Some heat pumps on the market still use refrigerants such as R410a, which has a GWP of 2,088 – meaning each kg of refrigerant is equivalent to 2,088 tonnes of CO2
Models within the range have an energy rating of A+++ (at 35C flow temperature) and their outputs have been rated at -5C air temperature and 55C water flow temperature. All models have been tested to
perform in extreme low and high temperatures with performance levels in terms of kW output consistent regardless of the climate and outside temperature, even at –3C. The Aerona 290 also features a built-in immersion and high capacity 9m head circulation pump.
Designed with aesthetics and acoustics in mind, the Grant Aerona 290 range features five models, with the 4kW, 6.5kW and 9kW units available first and the larger 12kW and 16kW coming in early 2025. Featuring a durable, powder coated black casing, the Aerona 290’s appearance has been developed following extensive analysis of customer feedback. The ultra-low noise levels of the units, which have achieved Quiet Mark accreditation, are the result of innovative sound-reducing features within the units including acoustic cotton sound insulation in the casing and anti-vibration feet.
Grant is also launching the Aerona Smart Controller, and QR Smart Pre-Plumbed AWave Integrated Cylinder. Models within the Aerona 290 range can be monitored and managed remotely, giving both installers and their customers full control of their heat pump system and providing offsite diagnostic support when required. Designed for use with the Aerona Smart Controller, Grant said the Aerona 290 can be operated
and managed with ease through straightforward set-up and commissioning, innovative control and support thereafter.
Grant founder Stephen Grant said: “The launch of the Aerona 290 heat pump marks a significant development in sustainable home heating and within our product portfolio. As our next generation heat pump, the Aerona 290 comes as Grant celebrates 15 years of being in the heat pump market and is testament to our commitment to design highly efficient, reliable heating technologies which can make a real sustainable difference. As more homes make the transition to lower carbon heating solutions, we look forward to continuing to support customers through the delivery of technologies, products and services that can help them make a real difference.”
Grant’s in-house renewable technical specialists will also continue to provide their free of charge heating system and design specification support to installers, merchants, and their customers to ensure correct sizing of the new Aerona 290 heat pump as part of an integrated heating system. All Aerona 290 heat pumps will also be commissioned onsite by Grant at no extra charge.
For further information, please visit www. grant.ie
One stubborn trope in some corners of green building is that passive house is so focused on energy performance that its advocates ignoring materials. Not so, argues Toby Cambray
Objections to passive house based on environmental impacts are nonsense, but they also hint at more systemic problems with the industry, which have been exposed by the Grenfell enquiry. A key observation of the enquiry is the complexity of the failure, including aspects from the technical, commercial, regulatory and cultural realms. In this piece I’m reflecting on just one element of this multi-faceted tragedy.
We often hear complaints from those sceptical of passive house that it fails to address up-front carbon and other issues that are not directly associated with operational energy. To anyone who understands the slightest thing
conductivity. With that, you can decide what thickness of material is required to achieve a U-value, and then you can go to the pub.
This is of course nonsense, because there are many other factors that are necessary for insulation to do its job. Perhaps even more important, the insulation must perform as part of a system that is not just well-insulated, but stands up, is airtight, resistant to fire, low moisture risk, quiet, incorporates services, is maintainable, and low in up-front carbon and other environmental impacts.
Arguably, this conductivity trap played a part in the Grenfell tragedy; the thinner build up that a lower theoretical conductivity al-
For passive house, it’s not just about U-values. The form, fenestration / orientation, infiltration and ventilation influence how good the U-values need to be.
one else has used it yet – the focal point of their designs. This approach is simultaneously at odds with, and symptomatic of, the shortcomings that Oliver Wainwright bemoans in the Guardian in September: “architectural education is a five-year training in visual representation and rhetorical obfuscation, with precious little time spent on learning how to actually make a building.” There are notable exceptions to this and some schools of architecture do furnish their students with a sound technical base, but my sense is that for many universities Wainwright is on the money.
The thing is that buildings are complicated; they need to do a lot of things, some of which are easy to count while others are intangible; many are essential, and some are purely whimsical. It is really hard to balance off all these things, but to do so successfully we must engage seriously with all of the constraints simultaneously – including beauty.
about passive house, this is an anathema. The implication is that passive house encourages us to use lots of concrete, plastic foam insulation and other things that are, or are at least perceived to be, bad with respect to environmental issues other than operational energy. This is not the case, and I’ve yet to meet a passive house proponent who doesn’t also care about all of these other impacts.
A lot of the hang-ups seem to be around insulation, because you often need a bit more than in a regulation standard building – but even this ceases to be true for very low form-factor buildings such as, say, a tower block of flats. Furthermore, insulation is not very dense, so the impact per unit volume is small.
We all know that there’s only one number you need to know about insulation: the
lows has advantages that are compelling on a superficial level, but a proper decision must be based on a much deeper analysis which it seems was lacking from the Grenfell design, and countless other schemes.
For passive house, it’s not just about U-values. The form, fenestration / orientation, infiltration and ventilation influence how good the U-values need to be. Get these things right and you need less stuff – not just insulation and super high-performance windows, but less structure and finishing material. Passive house incentivises fabric sufficiency through the medium of operational energy. This is probably not surprising to most of the readers of this magazine.
These critics often seem to be the materials fetishists, who make the latest hand knitted seagrass – or literally anything, as long as no-
The wilful misunderstanding of passive house and the incompetence demonstrated in the design of the Grenfell cladding, both belie a reluctance to address the manifold challenges that designing in the 21st century involves. Picking the insulation should be the easy bit. It’s harder to integrate it into a scheme that’s successful on all the other criteria. And even that pales in comparison with making a culture, an economy and a society where everyone is safe and happy while operating within planetary boundaries. But it is this which we must try to do. n
There are many good reasons why Irish homeowners are investing in heat pumps. They are one of the most energy-efficient ways of heating (or cooling) a house, using far less energy and costing less to run than traditional heating systems like oil or gas boilers.
Heat pumps provide reliable, consistent heat and hot water all year round – no turning the boiler on and off or the immersionwhile installing one will improve the energy rating, and therefore the value, of your home.
Daikin heat pumps, known for their stylish and state-of-the-art design, provide an additional layer of appeal. Beyond aesthetics, our heat pumps offer peace of mind by operating super efficiently even in extreme conditions down to -25 °C.
Perhaps most notably, the environmental appeal of heat pumps lies in their reliance on predominantly renewable energy sources, such as air. This eco-friendly attribute translates to reduced carbon emissions and fosters a more sustainable lifestyle.
And finally, when you factor in generous SEAI grants and a reduction in VAT on heat pump installation as part of Budget 2025, switching to renewable energy has never been more affordable.
www.youtube.com/@daikin_ireland www.facebook.com/DaikinIRE