€6.9542Issue EDITIONIRISH SUSTAINABLE BUILDING BIG inConcrete-freePICTURENZhomeshowcasednewpictorialfeatureINSULATION | AIRTIGHTNESS | BUILDING SCIENCE | VENTILATION | GREEN MATERIALS D6 deep retrofit Enerphit upgrade rejuvenates Rathgar redbrick Ed Begley Jr Hollywood star on 50 years of eco activism Roman past, passive future City of York shows visionary decarbonisationTHEplans OFPOWERONE Galway passive self-builder sparks low carbon block making
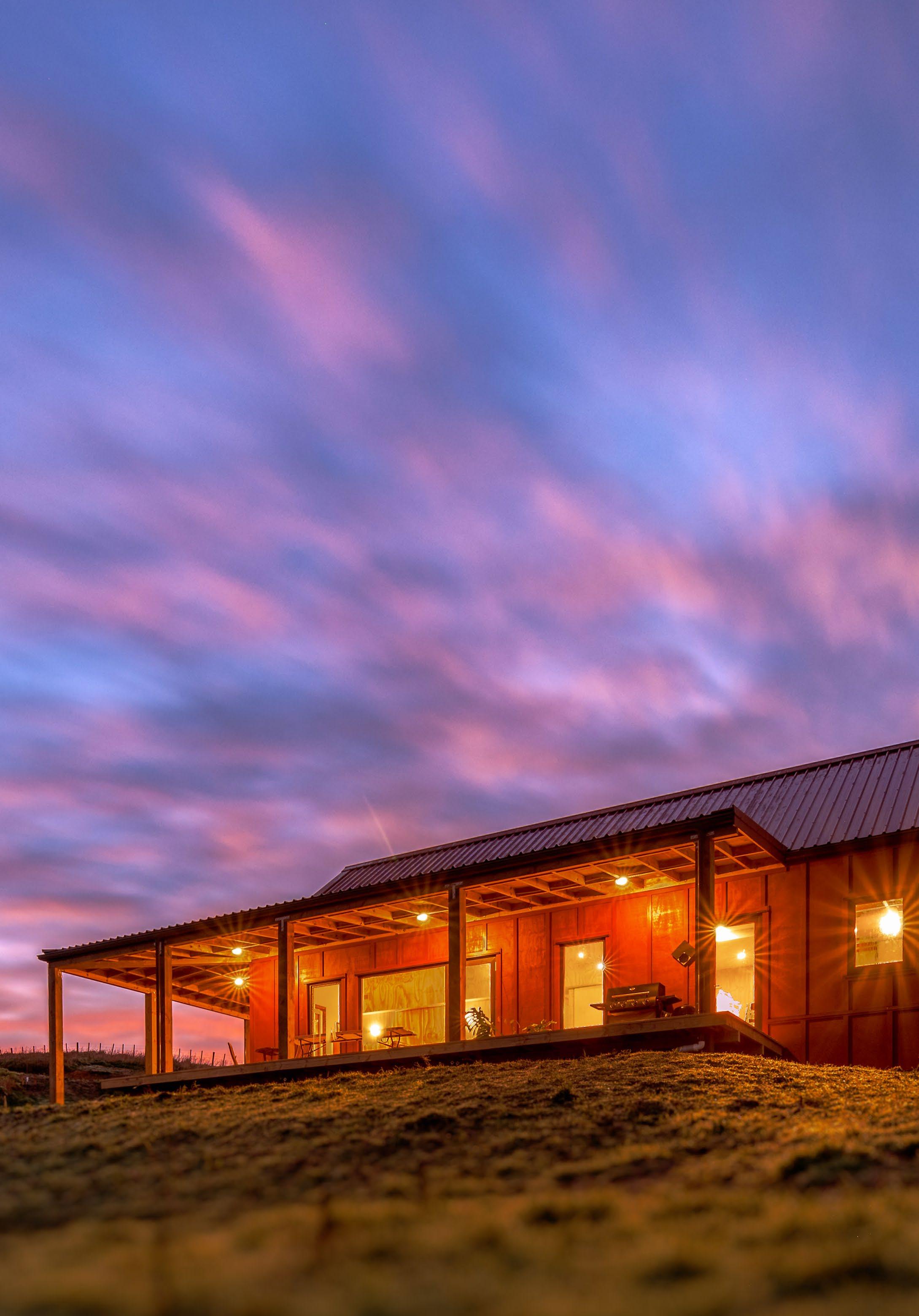
For more information on
service please visit: www.aereco.ie POWERED BY A NEW PARTNERSHIP FOR HEAT RECOVERY VENTILATION IN IRELAND
Combing Aereco's expertise in indoor air quality and its industry leading reputation for outcomes in the sector with class leading technology from Wolf. Aereco will be supplying Wolf's domestic range of Heat Recovery Ventilation Units and a select range of commercial products. the products and
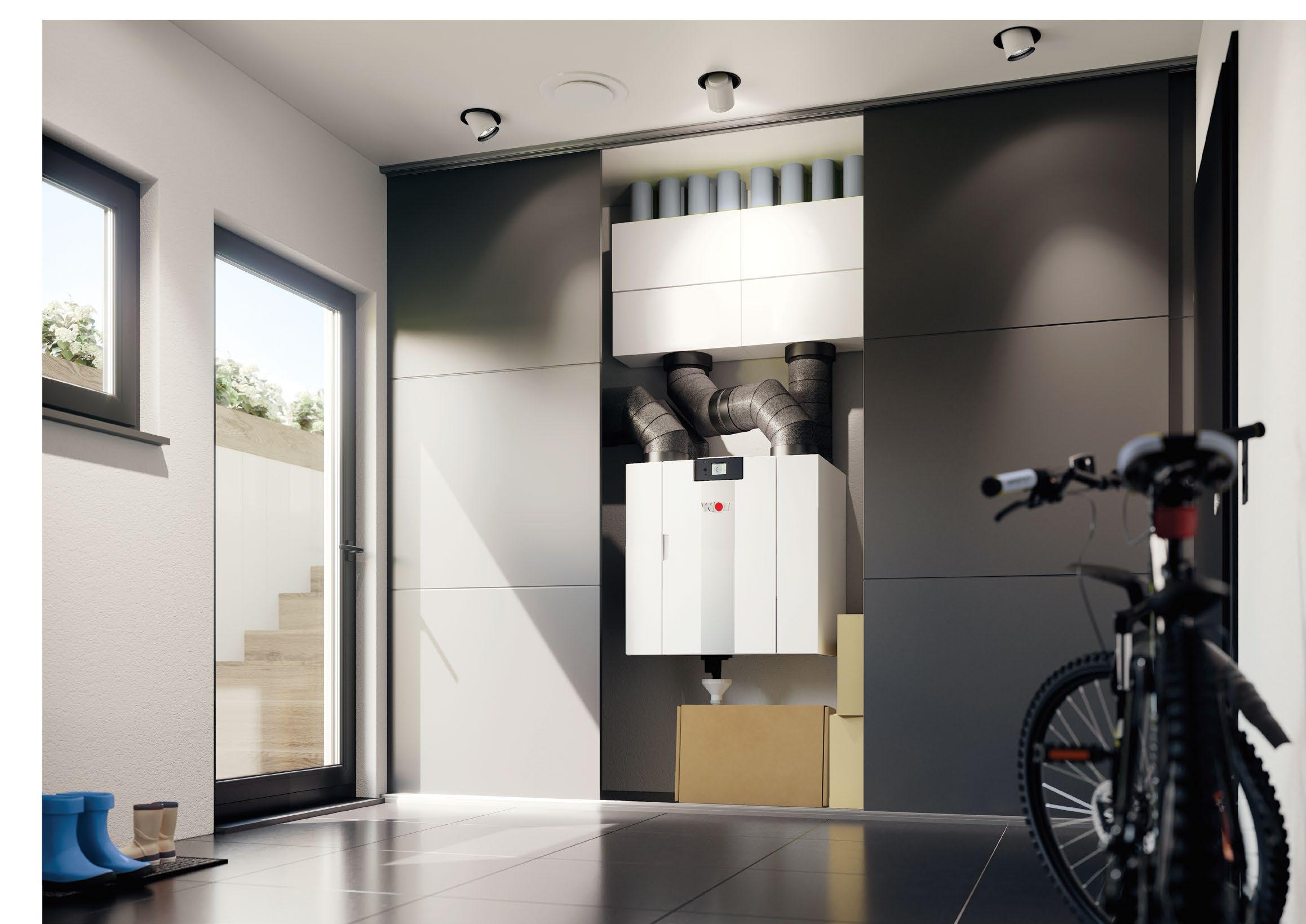
About Passive House Plus is an official partner magazine of the International Passive House Association. Passive House Plus (Irish edition) is an official magazine of the Passive House Association of Ireland.
TheRegards,editor editor’s letter ISSUE 42 Publishers Temple Media Ltd PO Box 9688, Blackrock, Co. Dublin, Ireland t +353 (0)1 210 7513 | t +353 (0)1 210 7512 e info@passivehouseplus.ie www.passivehouseplus.iePublisher’scirculationstatement: 7,000 copies of Passive House Plus (Irish edition) are printed and distributed to the leading figures involved in sustainable building in Ireland including architects; consulting; m&e and building services engineers; developers; builders; energy auditors; renewable energy companies; environmental consultants; county, city and town councillors; key local authority personnel; and to newsagents nationwide via Easons. Disclaimer: The opinions expressed in Passive House Plus are those of the authors and do not necessarily reflect the views of the publishers. Editor Jeff Colley jeff@passivehouseplus.ie Deputy Editor Lenny Antonelli lenny@passivehouseplus.ie Reporter John Hearne john@passivehouseplus.ie Reporter Kate de Selincourt kate@passivehouseplus.ie Reporter John Cradden cradden@passivehouseplus.ie Reader Response / IT Dudley Colley dudley@passivehouseplus.ie Accounts Oisin Hart oisin@passivehouseplus.ie Art Director Lauren Colley lauren@passivehouseplus.ie Design Aoife O’Hara aoife@evekudesign.com | evekudesign.com Cover Lower Saddle passive house, New Zealand Photo by Dan Scott Print GPS Colour Graphics www.gpscolour.co.uk | +44 (0) 28 9070 2020 Contributors Ed Begley Junior actor and environmental activist Toby Cambray Greengauge Building Energy Consultants Brian Crowley Irish Green Building Council John Fingleton Irish Green Building Council Joe Lyth Respond Architects Barry Mc Carron Passive House Association of Ireland Eoin Broin TD Sinn Féin’s spokesperson for housing Marc Riain doctor of architecture Sofie Pelsmakers architect Peter Rickaby energy & sustainability consultant David W Smith journalist
ph+ | editor’s letter | 3 PASSIVE HOUSE+ EDITOR’S LETTER
W e are living in extraordinary times. But the language we use to explain this moment in history is not fit for purpose. Climate change is far too insipid and neutral a term for what is happening to the world. Climate crisis is better, climate emergency is better still, but both terms suffers a fatal flaw, in that that our experience of crises and emergencies is that of temporary events, where decisive action can pull us back from the precipice. As James Vaccaro of the Climate Safe Lending Network put it in an article pitched at financial regula tors, we need to be talking in terms of climate collapse. The situation we face is not like the global financial crisis, from which the markets ultimately recovered, even if that recovery baked-in residual suffering for the many while pushing wealth into the hands of the few. Nor is it an emergency from which we can be saved through the ingenuity and bravery of medics and firefighters. It is a collapse. And what’s more the collapse is unavoidable, to some extent. The delay between belching emissions into the atmosphere and impact on climate means that even if the people of the world collectively downed tools today, ditched their cars, disconnected their heat and electricity supply and stopped eating, the world would still get hotter, and the weather would still become more extreme. Faced with the inevitability of further deterioration in climate, we must start to adapt in earnest. This is not to say that we should abandon our efforts to reduce emissions. Nothing could be further from the truth, and the thought of echoing the kinds of sequences of arguments peddled by fossil fuel shills makes me feel physically ill. It goes a little like this: The climate isn’t changing. Actually it might be changing, but it has always changed, and we’re not adding to it. Okay, maybe we’re adding to it, but it’s too expensive to do anything about it. It’s too late – let’s just focus on adapting. We must commit fully to adaptation, but we must also increase our resolve to dramatically cut emissions, reduce our voracious appetite for precious, finite resources and snap out of our indifference to the destruction of the ecosystems which support the existence of life on earth. The mind boggles as to what kind of response could address such a demanding ask, but mercifully, in the context of the built environment, we already know a lot of the answers. Avoid building if possible, and retrofit first. If we must build, don’t make it too big, make it adaptable, and try to put it where we can potter about on foot, bicycles or public transport. Build it out of the most environmentally benign materials possible, in a manner designed to withstand all kinds of craziness in terms of changes to weather and microclimate. And build it to proven high performance standards like passive house, to minimise energy use and reliance on energy infrastructure that may struggle to keep up. We also have adaptation of another kind to do at Passive House Plus – adapting to the departure of our deputy editor Lenny Antonelli, who has been a valued colleague and friend for the last 14 years. We had been going six years when Lenny joined us, immediately enriching the magazine with his rare ability to write in a scientifically literate yet extremely readable manner. I will greatly miss his counsel and our ruminations on the minutiae of sustain able building, but he has left an indelible impact on this magazine, and the rest of us at Passive House Plus will be watching his future success with pride.
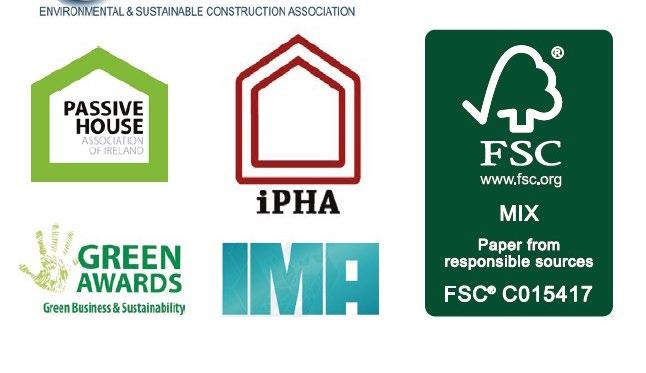
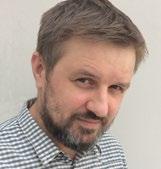
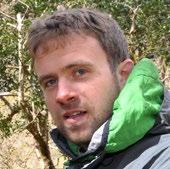

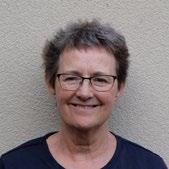
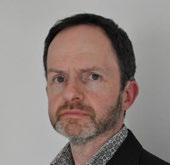
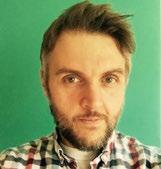
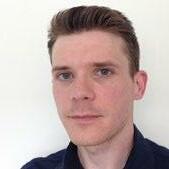
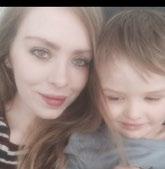
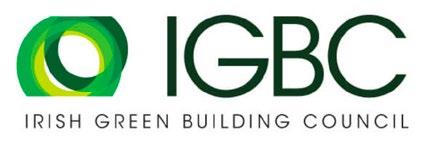
COMMENT In the latest missive in his series on the history of low energy design, Dr Marc Ó Riain looks to some wacky and wonderful experimentation in a project that aimed to transform public perception of Milton Keynes; Dr Peter Rickaby says that doing retrofit well and at scale remains an enormous technical and financial challenge; and co-authors of the new book Designing for the Climate Emergency - A Guide for Architecture Students shed some light on the thinking behind the new guide.
Breath of life Enerphit upgrade rejuvenates Rathgar redbrick The skilful deep retrofit of a red-brick semi on the south side of Dublin has brought an old property into the 21st century in terms of energy performance and living space, while carefully upgrading its century-old façade with breathable materials.
CASE STUDIES Block buster Galway passive house births low carbon concrete blocks With emphasis in sustainable building shifting towards reducing embodied carbon, an obvious question comes into focus: is this an existential threat to the concrete industry? One passive house in Claregalway shows that – with a little help from Passive House Plus – concrete product manufacturers can make meaningful moves in the right direction of urban design.
BIG PICTURE In the first installment of a brand new photo essay feature, in which we profile passive houses and other eco-buildings from around the world, architect Joe Lyth writes about how the aesthetic of simple backcountry cabins inspired the design of his rural home on New Zealand’s North Island. NEWS New digital hub launched for sustainable building upskilling, EU proposes gas demand reduction plan till spring, and world’s first passive house hospital completed in Frankfurt. 27
10 32 COVERSTORY 8 44
4 | passivehouseplus.ie | issue 42 CONTENTS PASSIVE HOUSE+
CONTENTS 10 20 32 20
FINAL SAY: REFLECTIONS ON LEAVING PASSIVE HOUSE PLUS After fourteen years working on Passive House Plus and its predecessor, our departing deputy editor Lenny Antonelli muses on how our understanding of sustainable building has changed over the years – and on what may come next.
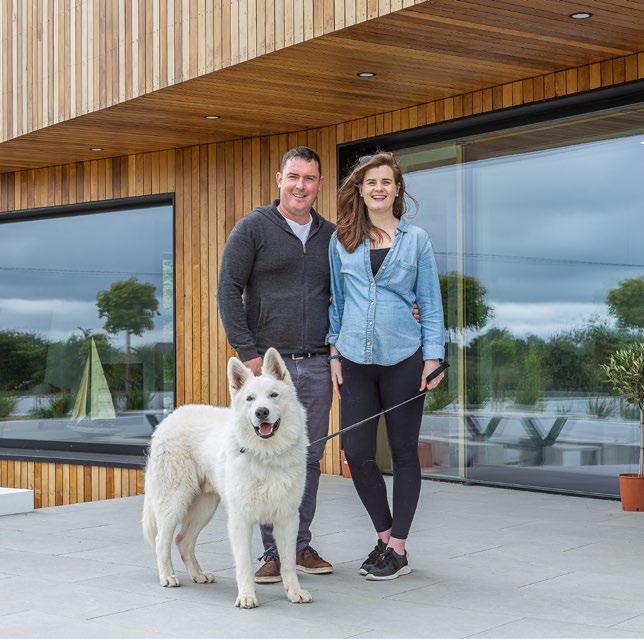
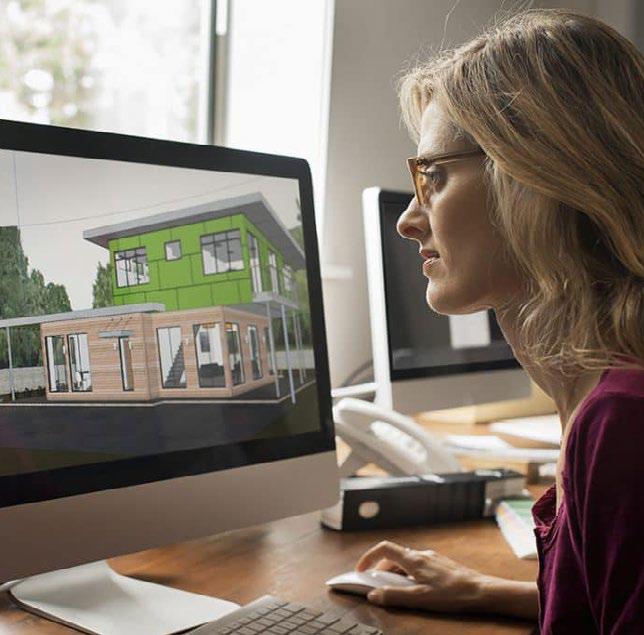

INSIGHT Hollywood star on 50 years of eco activism Actor Ed Begley Junior is one of America’s bestknown and longest-standing environmental activists. Fresh from lighting up our screens in the final season of Better Call Saul, Begley spoke to Passive House Plus about the roots of his activism, and what drives him on in the face of such adversity.
The historic Roman city of York is embarking on an ambitious programme to redefine council housing for the 21st century, building 450 mixed-tenure passive houses across eight sites in the city, and unashamedly prioritising walking and cycling, and shared outdoor green spaces, over cars. It may seem too good to be true, but a cityscape whose architecture still so manifestly displays its extraordinary history is now pointing to the future of urban design.
MARKETPLACE Keep up with the latest developments from some of the leading companies in sustainable building, including new product innovations, project updates and more. Is it okay to retrofit heat pumps before building fabric? How flexible can heat pumps be to handle what may be inexactly defined heating demands, asks Toby Cambray?
8290
Going swimmingly Devon complex is set to be UK’s first passive certified leisure centre The environmental journalist George Monbiot has written about how we need an era of ‘public luxury’ and ‘private sufficiency’ — as opposed to private luxury for the few — to mitigate overconsumption and climate breakdown. And it’s hard to think of a better example of public luxury than this superb new leisure centre in Exeter, which consumes just a fraction of the energy of typical facilities, and is set to be certified to a bespoke version of the passive house standard.
From Nero to zero Local authority housing takes a giant leap forward in York
ph+ | contents | 5 PASSIVE HOUSE+ CONTENTS ph+ | contents | 5 44 56 66 56 76 66
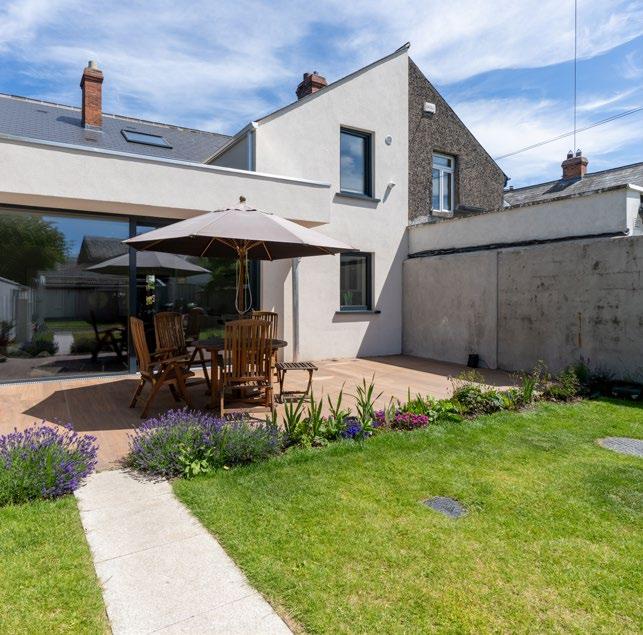
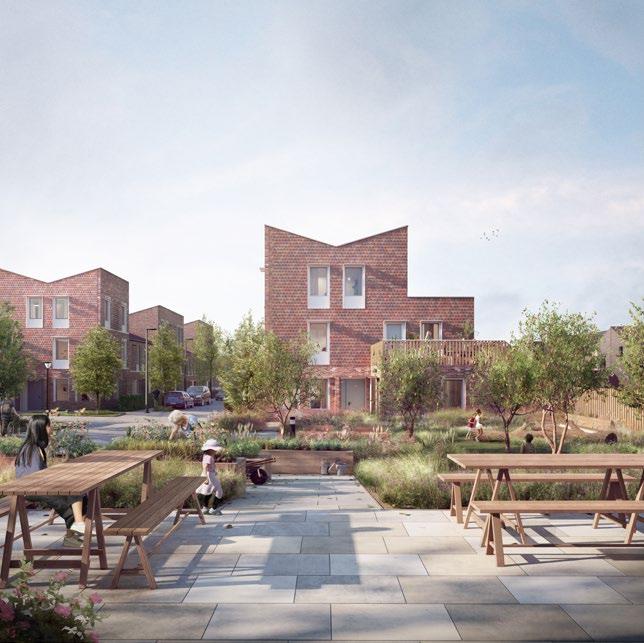
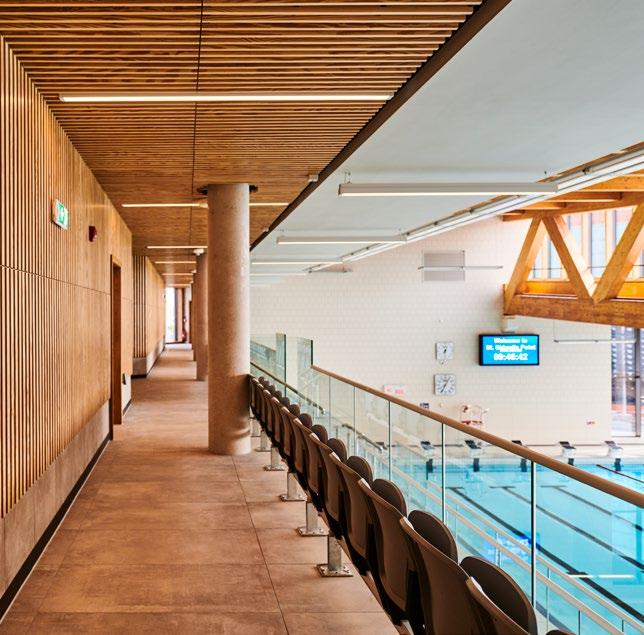
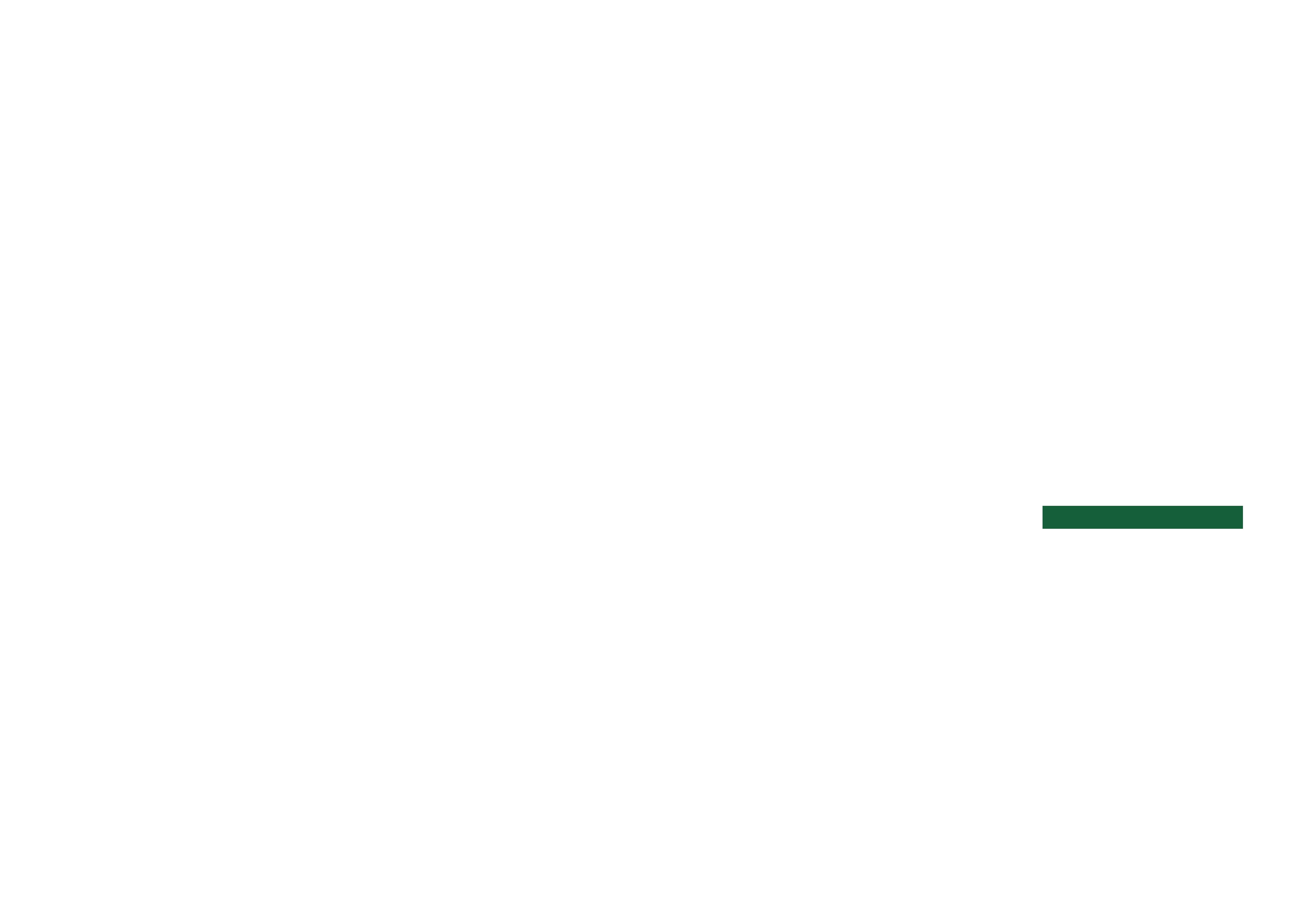
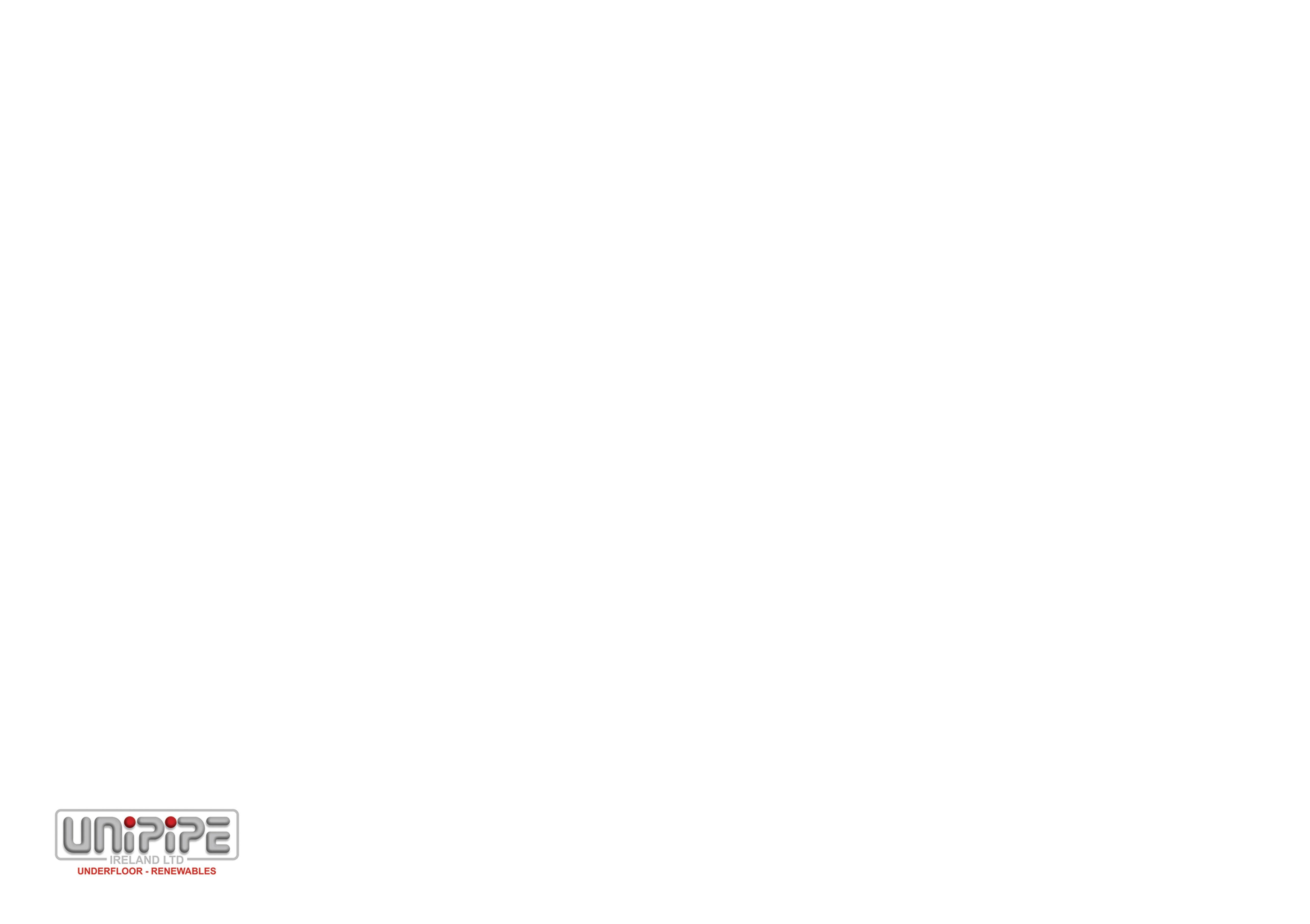
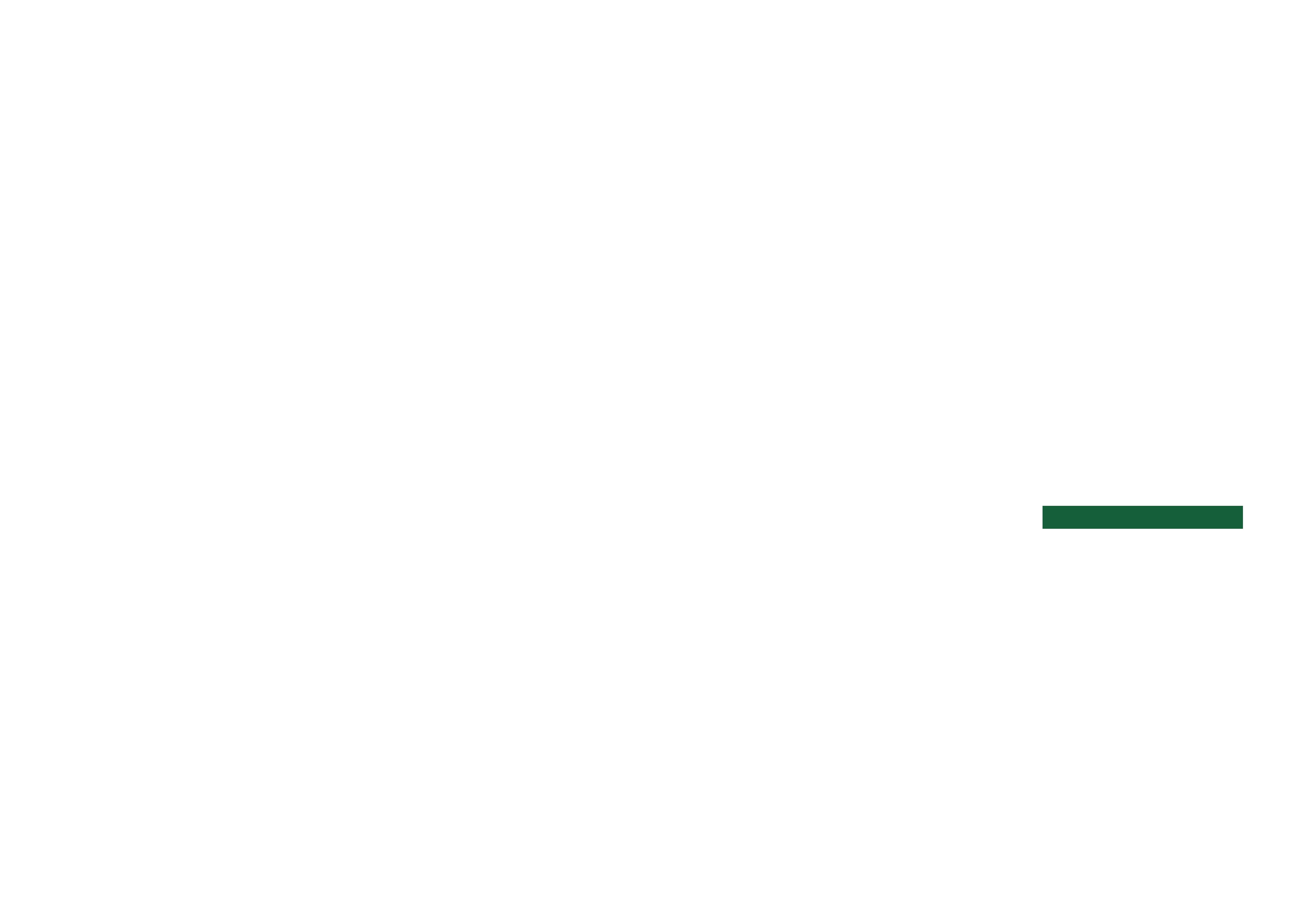
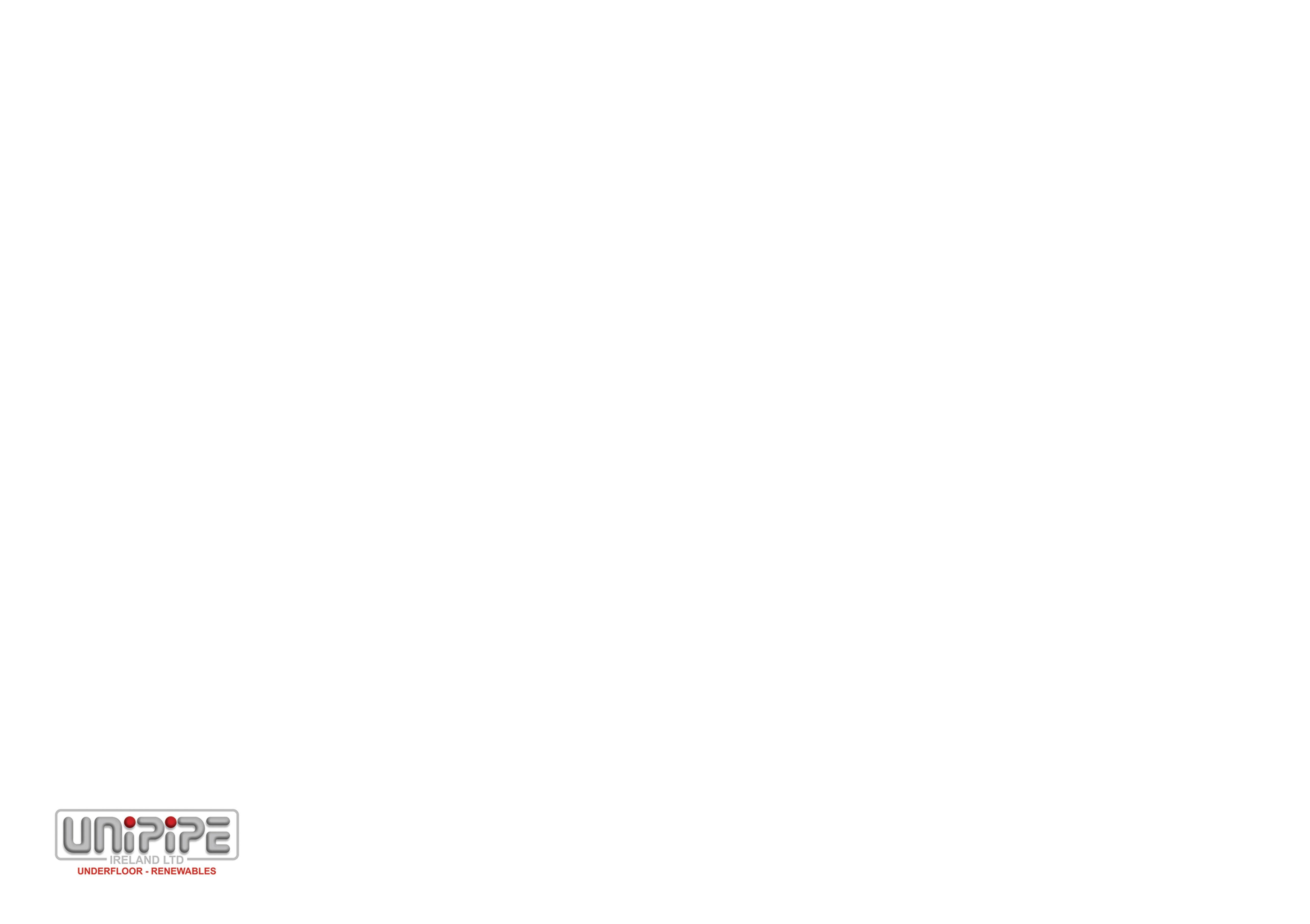
airtightness, the elimina tion of thermal bridging, and mechanical ven tilation are increasingly accepted as integral to good building, even when it’s not a passive house being built. The regulations inch closer to embracing these concepts too, albeit faster in Ireland than the UK. Developers might argue that passive house is too difficult or ex pensive, but it’s rare to hear anyone say that it isn’tOverbetter.the last few years, the leading edge of green building has turned its attention to measuring embodied carbon, a much more subjective task than measuring heat loss or airtightness. But embodied carbon is now, thankfully, creeping its way towards the reg ulatory agenda too. Of course, all of this is happening far too slowly given the dangerous warming of the planet, and I don’t mean to make this progress sound inevitable: it is only down to the hard work of those who push for better building standards each day. But it does make me wonder what the next vanguard will be. In a recent issue of this maga zine, Peter Rickaby argued that retrofit should not just be about energy and carbon, but that it must also create beautiful places to live. And I wonder if we need to make more space on the cutting edge of sustainable building not just for left-brained concepts like building physics and heat loss, but right-brained ones like beauty, community, and equality. Obviously, these are not new design con cepts, but it sometimes feels that the mathsbased world of passive house and the woollier realm of architectural ‘placemaking’ exist in different galaxies. It’s heartening to see proj ects like the passive house schemes in York that are profiled in this issue, which is also my last as deputy editor of the magazine. The York schemes aim to dramatically cut energy and carbon, but also to foster community, and create beautiful places to live. Last year, my fiancée and I moved from Galway City to Cloughjordan Ecovillage, an intentional community adjacent to a small town in the Irish midlands. The houses in the ecovillage, which are all of natural materials, were built between 2008 and 2013. Heat is provided by wood-chip district heating, walk ing and cycling is prioritised over cars, food is grown on the community farm and allot ments, and there is ample space for nature in the woodlands, orchards and grassland. But more than that, it has been a revelation to live in a place where social encounters and gatherings and neighbourliness are designed into the fabric of the community. And where people have literally built their own homes, often with little previous experience. It is also obvious to me that a community with its own farm and heating network, and its pool of skills and resources, will be more resilient as climate breakdown begins to dis rupt our lives more and more. It’s measurably better for the planet too: a 2015 study found that a resident of Cloughjordan Ecovillage has an ecological footprint of 2.03 global hectares, far lower than the Irish average of 5.3 (but still above the 1.6 that the Global Footprint Net work says is available to everyone). There’s also something powerful in a com munity taking charge of providing for its own housing needs. Earlier in the summer, the Cloughjordan Cohousing group hosted an event called ‘Housing Ourselves’, which heard from different Irish groups trying to get com munity-led housing projects off the ground, such as Nimble Spaces in Kilkenny and Com mon Ground in Wicklow. It was inspiring to hear from those seeking to sidestep the failure of the state and take the provision of affordable housing into their own hands. But it was also frustrating to see how these groups have sometimes struggled within a system geared more towards developers than communities.Iattended not just as a journalist, but also as someone who, at 36, does not own his own home and now wishes to put down roots in a community without taking on an absurd level of debt. Affordability is an overlooked aspect of sustainability: it is hard to live sus tainably and modestly, to choose the bicycle over the car, to buy directly from local farm ers, and to share skills and resources, when we are wracked with debt and overworked. New ownership models like cohousing can help us to move beyond the false dichotomy of massive debt (a mortgage) or insecure tenure (renting), but they need support (see Self Or ganised Architecture’s roadmap for communi ty-led housing in Ireland at www.soa.ie). Over my years with the magazine, editor Jeff Colley and I often joked about the irony of writing about beautiful, architect-designed passive houses while having little prospect of living in one, with our journalists’ salaries. That prospect seems further away than ever given Ireland’s housing crisis, but I am hope ful that the failure of our top-down housing model can spur the growth of a more equi table one that blossoms from the bottom up.
After fourteen years working on Passive House Plus and its predecessor, our departing deputy editor Lenny Antonelli muses on how our understanding of sustainable building has changed over the years – and on what may come next.
LENNY ANTONELLI COLUMN
8 | passivehouseplus.ie | issue 42
New ownership models like cohousing can help us move beyond the false dichotomy of massive debt or insecure tenure, but they need support.
O ne of my earliest assignments for Construct Ireland magazine, the predecessor to Passive House Plus, was to visit two certified passive houses in ru ral County Carlow. This was back in 2008, when the magazine’s understanding of what ‘sustainable building’ meant was still evolving. The two houses had little aesthetic merit, but they were only the second and third cer tified passive houses in Ireland. Back then the German standard seemed strange and exotic, and while the houses were plain looking, they also felt like the future. Four years later the magazine felt confident that yes, this was the future, and we rebranded as Passive House Plus and launched a UK edi tion. At the time, there was plenty of debate in eco-building circles over the merits of passive house — about whether it was too onerous, too architecturally stifling, too airtight and too reliant on mechanical ventilation. But in hindsight it certainly feels like passive house won the Super-insulation,day.
Final say: Reflections on leaving Passive House Plus
A fully referenced version of this article is online at www.passivehouseplus.ie
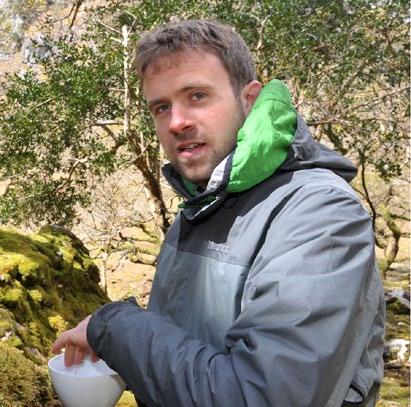
UNPARALLELED CHOICE OF PASSIVE CERTIFIED PRODUCTS – OUTWARD OPENING, INWARD OPENING, UPVC, ALUMINIUM, ALUCLAD T. 064 7751151 E. www.munsterjoinery.ieinfo@munsterjoinery.ie SHOWROOMS: CORK, DUBLIN, GALWAY & BELFAST GROUND BREAKING U-VALUES FROM AS LOW AS 0.47W/M2K WINDOWS & DOORS
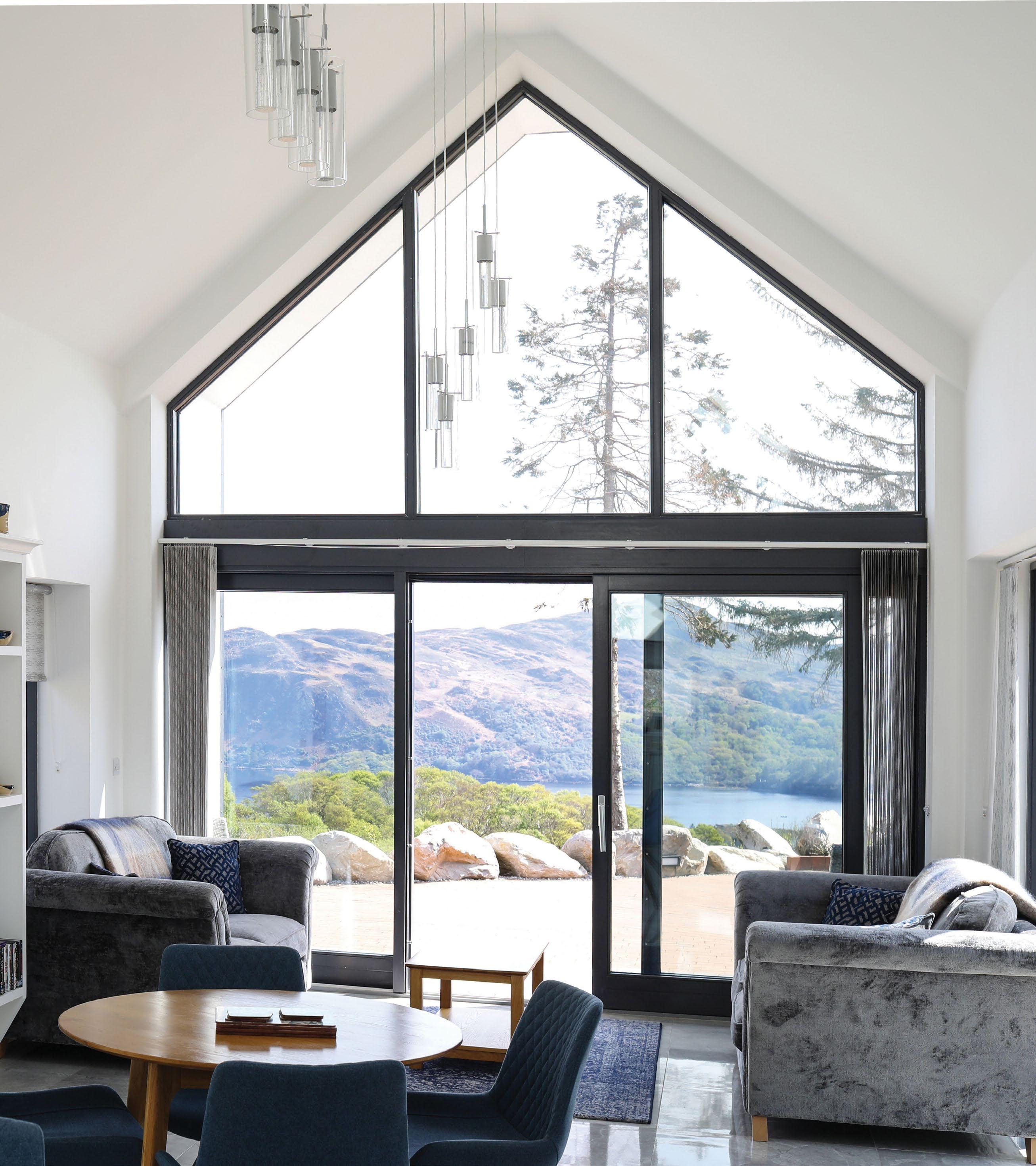

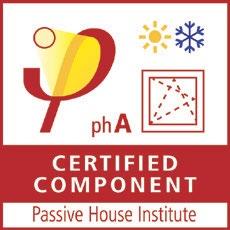
10
PASSIVE & ECO BUILDS FROM AROUND THE WORLD
BIG PICTURE In the first installment of a brand new photo essay feature, in which we profile passive houses and other eco-buildings from around the world, architect Joe Lyth writes about how the aesthetic of simple backcountry cabins inspired the design of his rural home on New Zealand’s North Island.
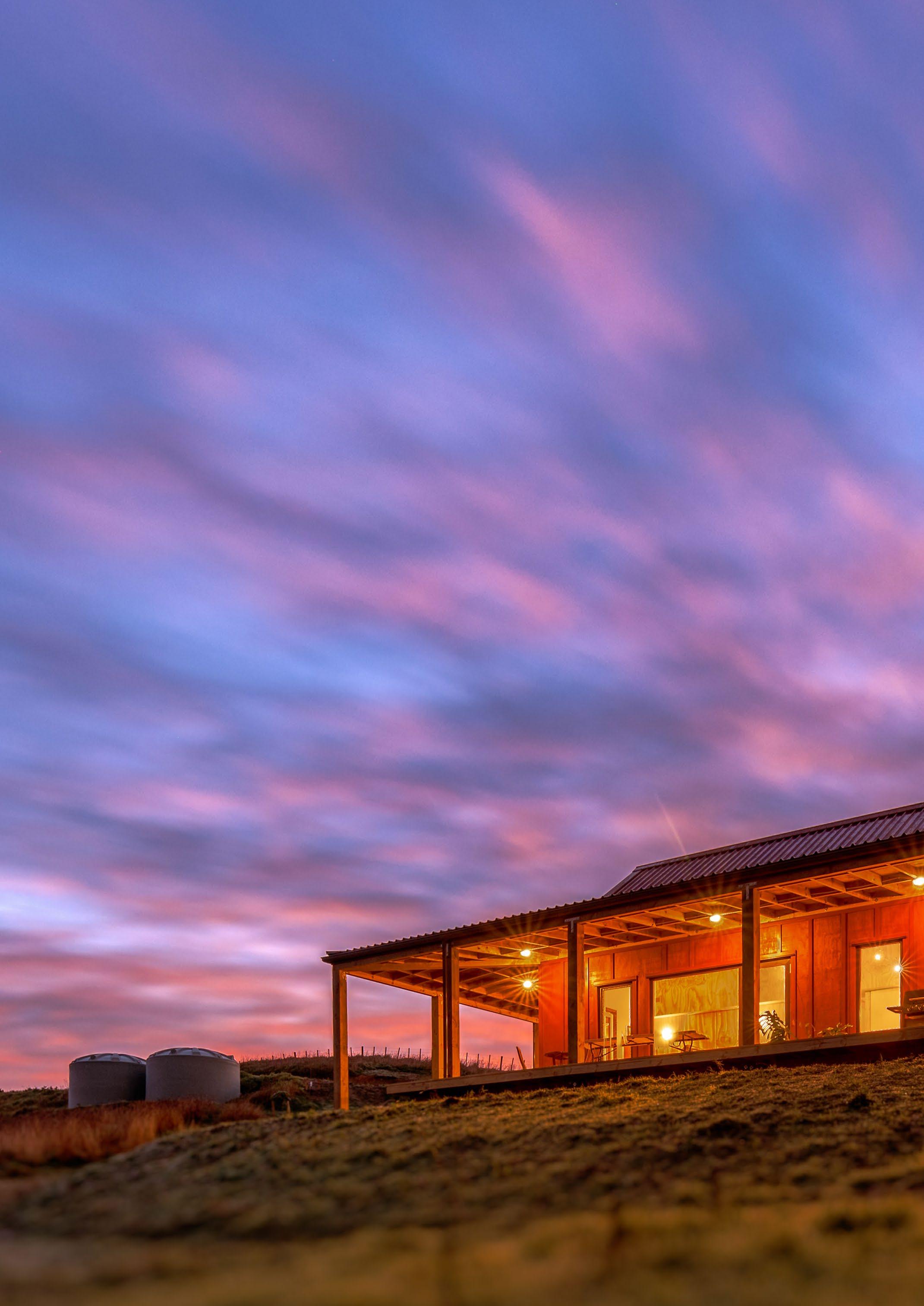
ph+ | new zealand big picture | 11 BIG PICTURE NEW ZEALAND
The project came about as a result of our kids getting sick in our standard, too-cold-or-too-hot, mouldy New Zealand house, and my wife Sarah and I being unable to watch any longer. We decided to put our (minimal) money where our mouths were, to prove that high per forming, healthy homes can be achieved at standard budgets, while still being beautiful places to live. Cost was the key constraint. As first-time buyers with a small deposit, prioritising and compromising were essential. An envelope-first strategy was decided on to prioritise performance: site specific insulation, good air tightness, great windows and doors, no thermal bridg ing. We would develop the interior as a family once we moved in. What resulted is an unpretentious, passive house certified home that blends into its rural context, while keeping its inhabitants warm, dry and healthy year-round.Theinitial design was a single-storey home that could be extended into the roof space later. But to get funding from the bank, however, we ended up having to build the first-floor bedroom and bathroom to increase the value of the house to match the build cost, but without running up the construction cost – a challenging exercise and negotiation with the contractor!
1. Envelope first
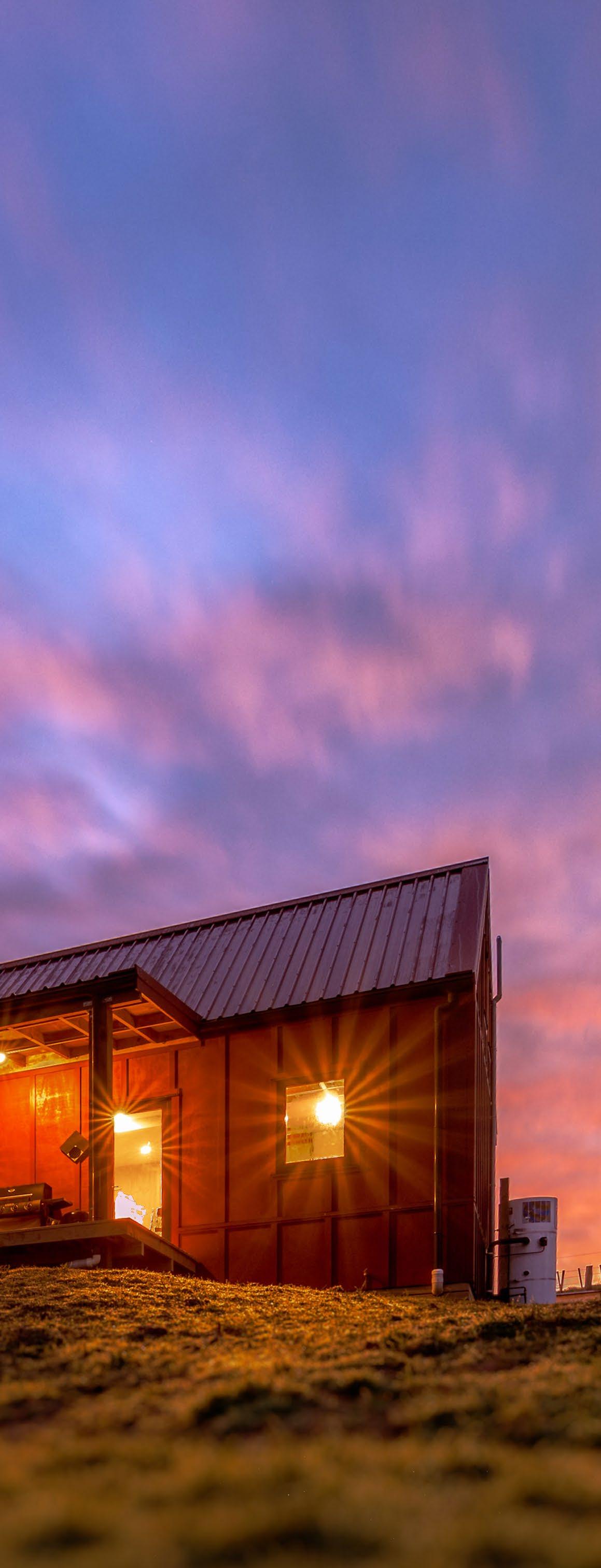
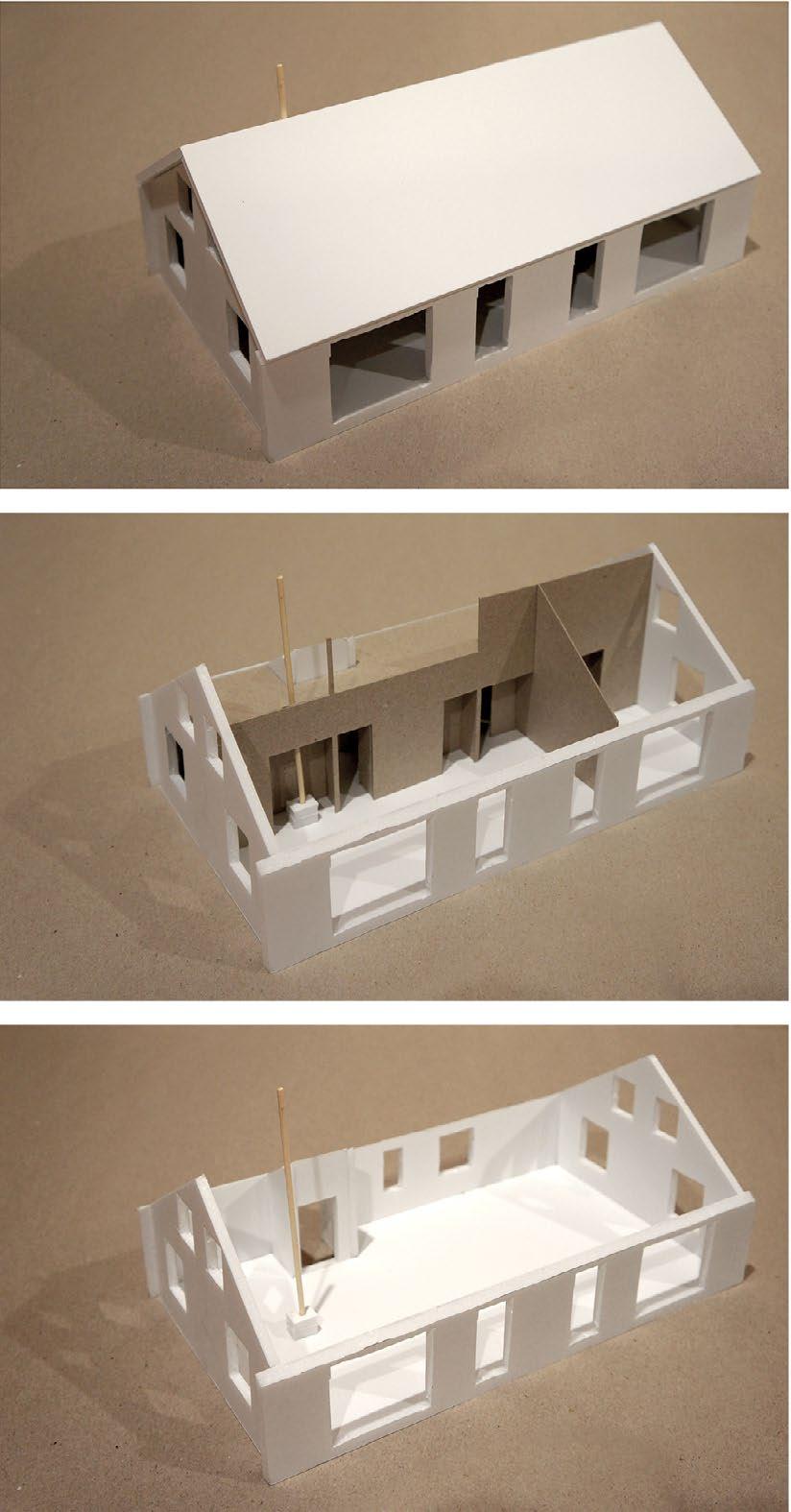
3. High performance Lego
NEW ZEALAND BIG PICTURE 12 | passivehouseplus.ie | issue 42
The panels were cut to shape in the factory from the building information model (BIM). They arrived on site all numbered, and went together like a Lego set. The walls took a couple of days to install, then the mid floor and gables, before the roof went on in a day and a half. The project achieved a final blower door test result of 0.375 air changes per hour, so the passive house airtightness target (0.6) was more than achieved.
Our search for a plot of land took us about 45 minutes north of Auckland, where we found a site barely within our budget. The northwest facing saddle here has expansive views of the Makarau River valley, and the surrounding area consists of weathered rural infrastructure, traditional villas, and a grow ing number of new homes, all embedded into a mixture of pasture, pine wood and native bush. The exposed site is both baked by the sun and battered by rain and winds, so the proposal had to respond to a range of environmental factors to ensure durability, performance, andThehabitability.designdeveloped with the location and took prece dence from both its rural context, and our love of the simple robustness of backcountry huts. Lower Saddle sits comfort ably into its surroundings like it was always there – belying the high-performance nature of the project. The response included careful orientation to the view, the sun and the pre vailing wind, with thoughtful positioning of openings, north and western overhangs, and exterior shading. Cost and performance were our priorities, and to minimise thermal bridging and embodied carbon, steel and concrete were out. Due to the sloping site a suspended timber floor on piles with sheep’s wool insulation was chosen over a carbon-hungry concrete slab, and structural insulated panels (SIPs) were select ed for their thermal and airtight qualities, with prefabrication reducing waste and construction time.
2. Of its place

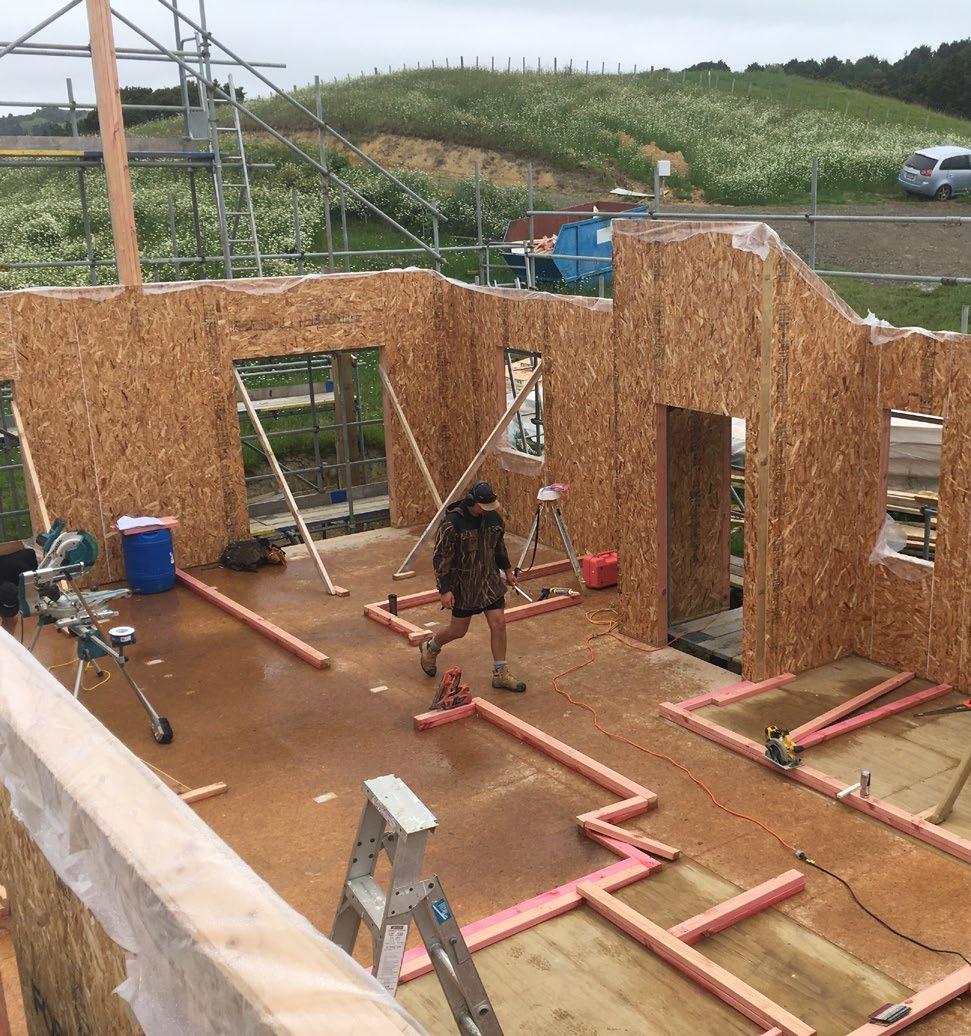
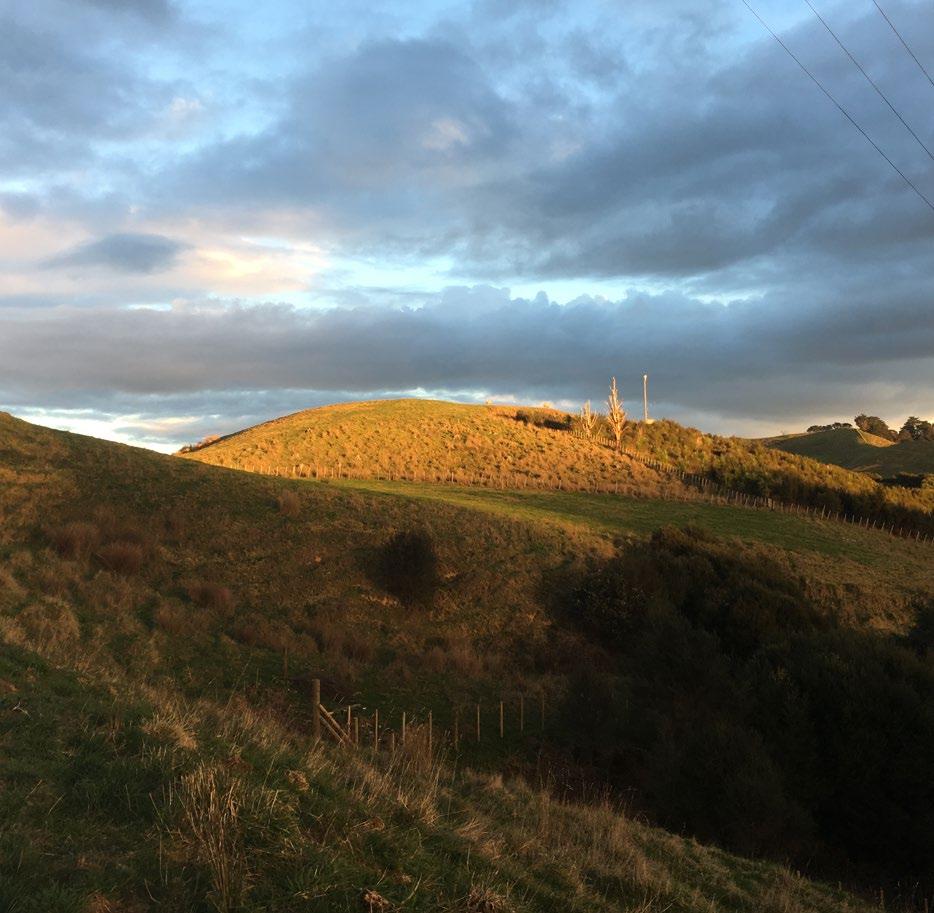
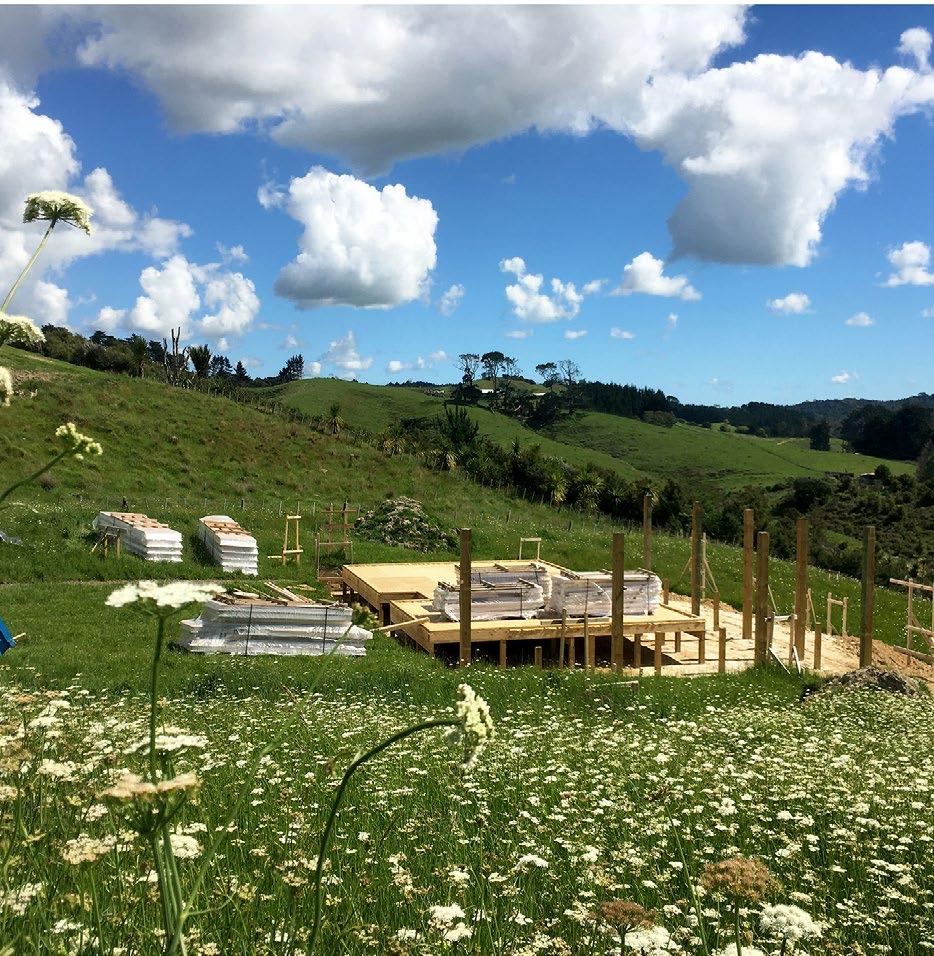
Finished photos: Dan Scott Construction photos: Joe Lyth
4. Wider environment
As well as being energy efficient, we aimed to minimise the project’s impact on other resources. Large rainwater tanks and efficient sanitaryware ensure ongoing water resilience, and all sewage and sanitary waste is treated on site, in turn watering and fertilizing a growing orchard. A solar hook-up is included, and we plan to install PV in the medium term when we have the budget. The site was open pasture when we purchased it, and is slowly being developed based on perma culture principles, with some areas being replant ed with native trees, some left to re-wild, and the rest being developed into food production and a food forest to feed us, and hopefully eventually, the wider community.
5. Interior environment
All buildings need adequate ventilation to ensure good indoor air quality, but opening windows, which is relied on in NZ, only works some of the time. Mechanical ventilation works all the time, with openable windows for additional user comfort and control. We installed a ducted mechanical ventilation system with heat recovery from Stiebel Eltron in the good-sized laundry. In the full height mezzanine I designed in a bulkhead down the spine of the building to accommodate the ducting, and to make it easier and more cost effective to install. We have been monitoring the interior with Tether environment sensors and the system has performed perfect ly, with the interior almost always between 18-24C with no active heating or cooling, constant levels of humidity, and very low CO2 readings.
|
ph+ | new zealand big picture | 13


NEW ZEALAND BIG PICTURE 14 | passivehouseplus.ie | issue 42 Standard window frames in NZ are solid alu minium, and double glazing is a relatively new thing, so anything of reasonable performance has a cost premium. We ended up working with a company to import our windows from Poland for a 40 per cent cost saving includ ing shipping and import, with triple glazing for thermal performance and sound, timber frames for look and performance, and alumin ium facings externally for durability. Due to shipping issues and Covid they were a month late, and the process had some valuable lessons for me going forward, but they fit, the glazing performs perfectly, and the timber looks great. To keep costs in check the design utilises a simple, compact form and efficient design of spaces to reduce the building footprint, simplify the construction, and mitigate the volume of materials. Every inch of space inside works hard, and the covered decks to the north and west provide further living space outside. Visual connections between the rooms create a feeling of space with a double height living space and over looking mezzanine, and high-level windows and ‘arrow slot’ openings into the upstairs rooms - they re mind me of medieval castles, where a little window high in the wall of a banqueting hall would often be the most intriguing part. 6. Windows, windows, windows 7. Space and form
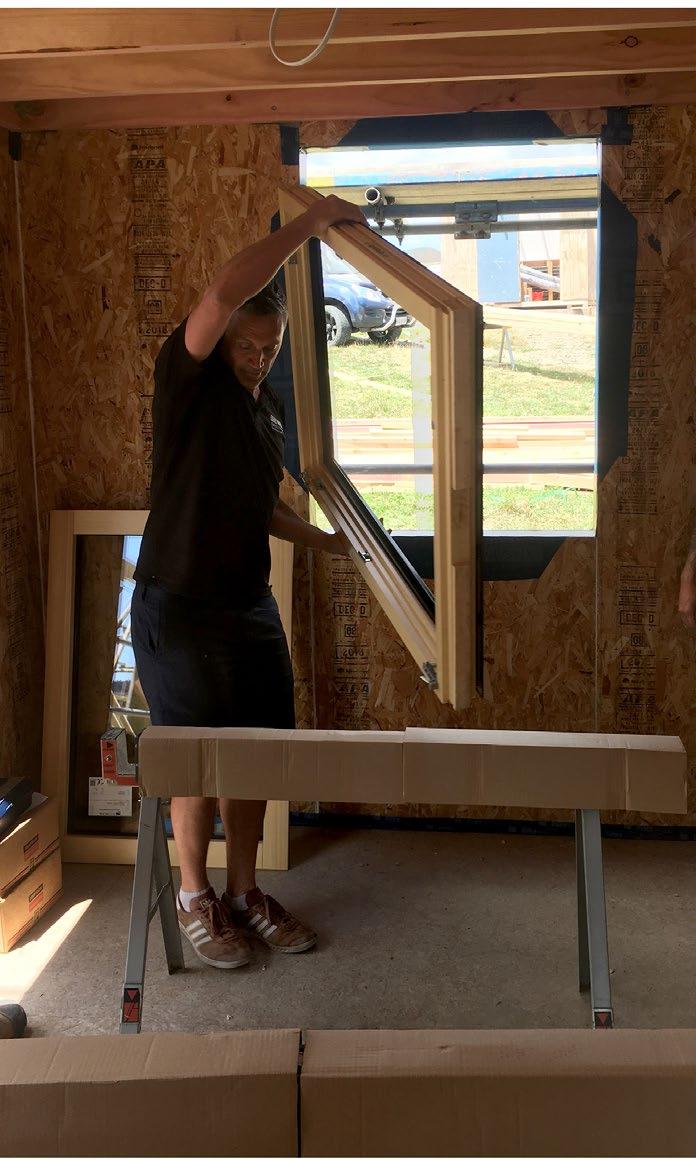
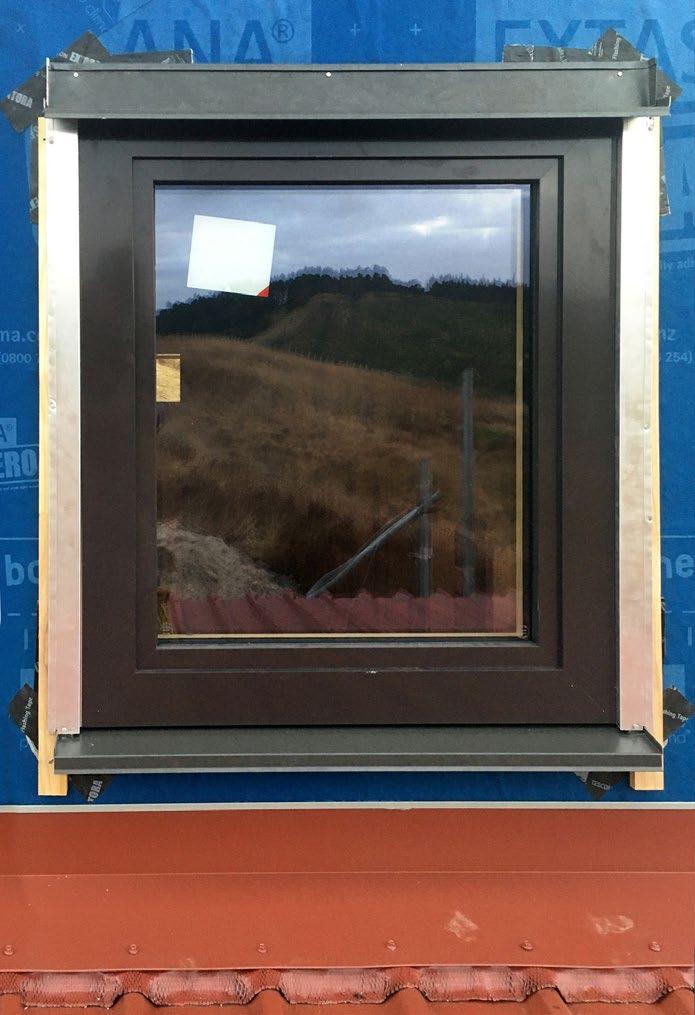

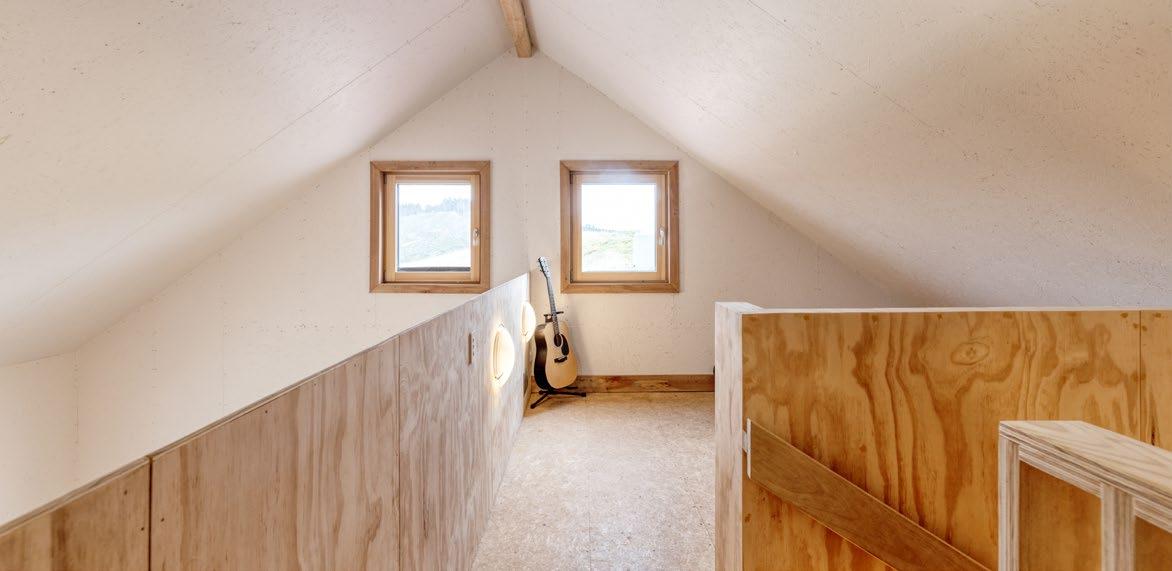
heatpump@grantengineering.ie Trust Grant on the journey to warmth and comfort by sending house plans to withwarmthBuildGrant Our complete integrated heating packages provide everything needed to build a highly efficient, warm and comfortable home. Tailored to suit the homeowners’ requirements, each Grant heating package is correctly sized and specified, free of charge, to achieve compliance, maximise efficiencies and provide long-term savings. Packages feature the Grant Aerona3 air to water, air source heat pump, Grant hot water cylinders, Grant Afinia aluminium radiators and the Grant Uflex underfloor heating system. Smart controls are also available.

8. Materials with character 9. Part of the family We moved in at the end of May 2021 before the exte rior was finished, and a couple of weeks before the hot water heat pump system was installed. (The house has no space heating system beyond a small panel heater, which we’ve turned on for an hour or two all year. We’re looking into electrical underfloor heating even tually, but we barely need it.) Since then, we’ve been developing, dressing and finishing the house together as we learn how it functions for us. Moving into a ‘shell’ has given us the chance to ex periment – I’m installing Woodtex panels between beams in the downstairs bedrooms for sound atten uation, and for texture. To keep costs down the fin ishing of the plywood was left to us, so we’re slowly filling, sanding and varnishing the interior walls. The house is truly growing with us.
Painted plywood cladding and metal roofing were se lected externally, with a scoria red finish reminiscent of tramping huts and embodying the local rural vernacu lar. Internally the SIPs were painted as opposed to lining them, reducing trades and cost. Plywood linings were selected for interior walls — lower carbon than plaster board, and easier for sanding off children’s drawings. We made the plywood kitchen, cast concrete sink and counter, and copper splashbacks ourselves, all ma terials that gradually gain a patina and character over time. Native Totara from a friend’s farm further north was milled into trims and skirtings. The plywood grain and textured SIPs that form the spaces are broken up by brightly painted doors, each a different colour to add splashes of joy.
NEW ZEALAND BIG PICTURE 16 | passivehouseplus.ie | issue 42
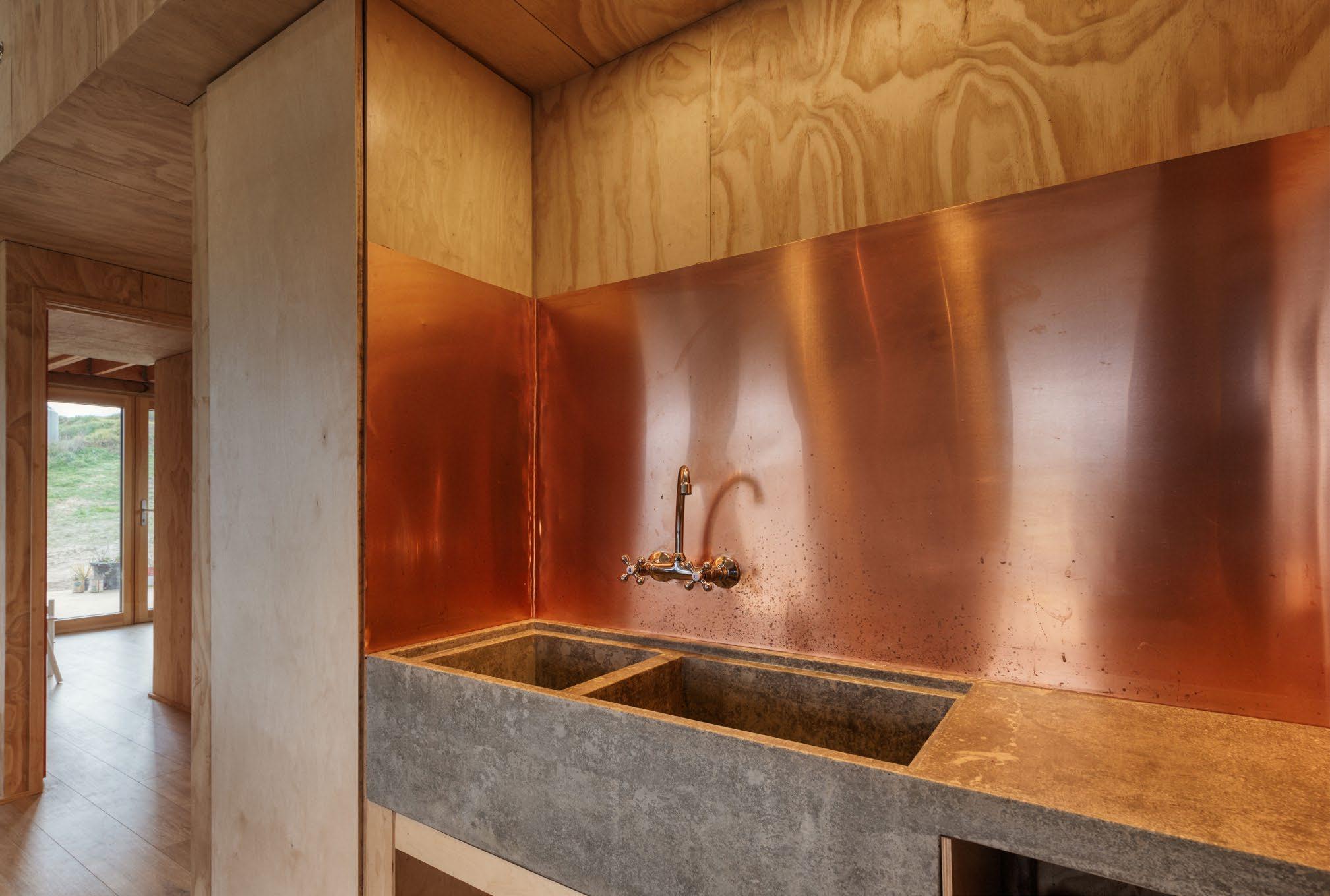
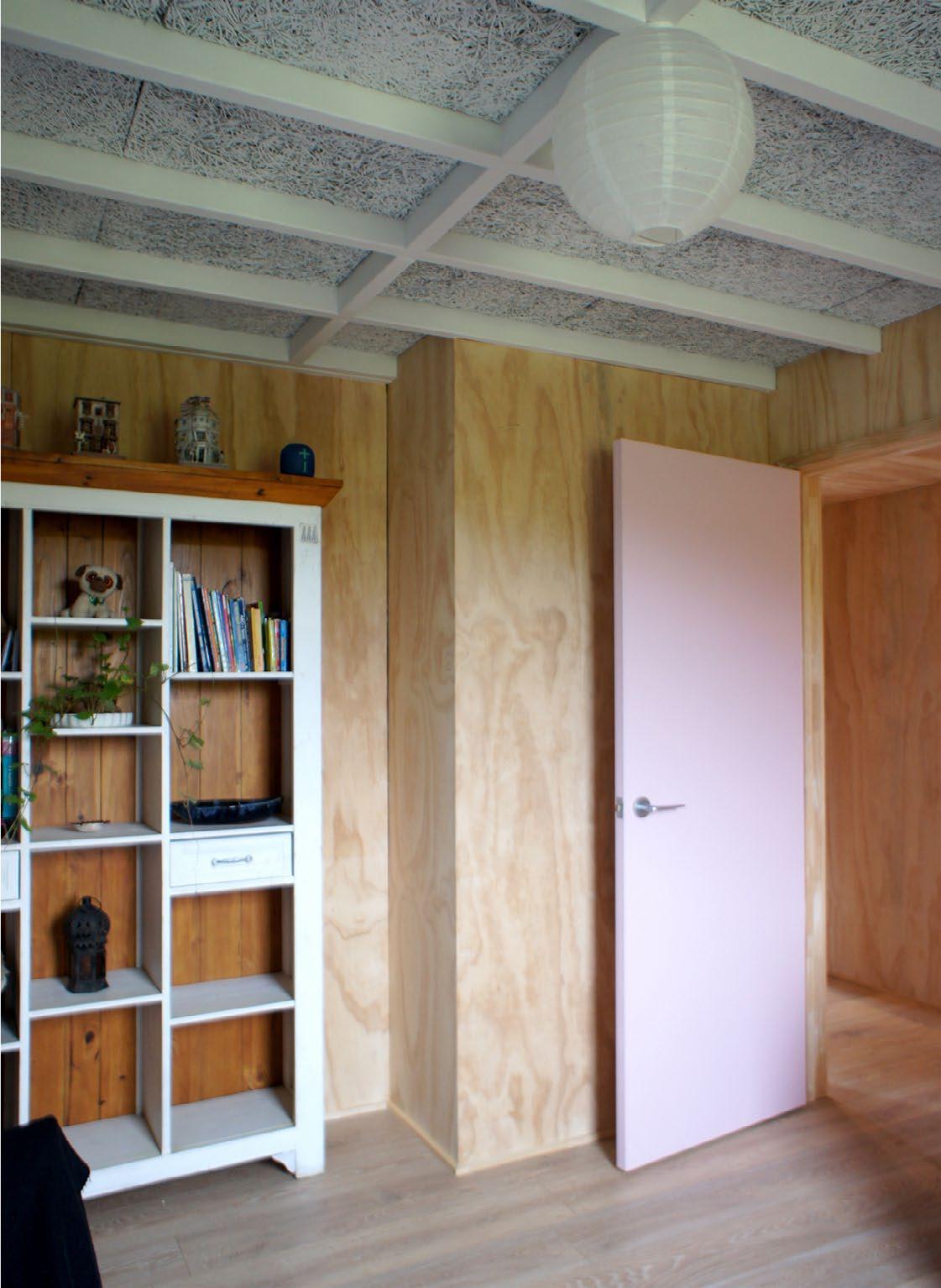
ph+ | new zealand big picture | 17 BIG PICTURE NEW ZEALAND
New Zealand has some of the lowest perform ing, unhealthiest, yet most expensive housing in the world. Lower Saddle shows that this doesn’t have to be the case — all Kiwis can have healthy, affordable homes with low op erating costs, and a light impact on the plan et. The project balanced priorities with what could be added or upgraded later – a kitchen is easier to upgrade than your windows and walls, for example. In following an envelope first approach, the high-performance home provides a healthy enclosure, with an interior that can be devel oped alongside our growing family, delivered on a budget lower than most minimum code homes. Materials and construction methodol ogy reduced the amount of embodied carbon and construction waste through prefabrica tion, setting out of materials to mitigate waste and minimise cost, and ongoing reuse of off cuts and materials in the project. Since we moved in the house has absolute ly ‘performed as designed’ with energy bills of $100-$130/month for everything (around 40 per cent lower than a standard NZ home, which would usually also include gas too), while maintaining comfortable temperatures year-round with no active heating or cooling, and the children’s respiratory issues have disappeared. 10. For the future 11. Performs as designed
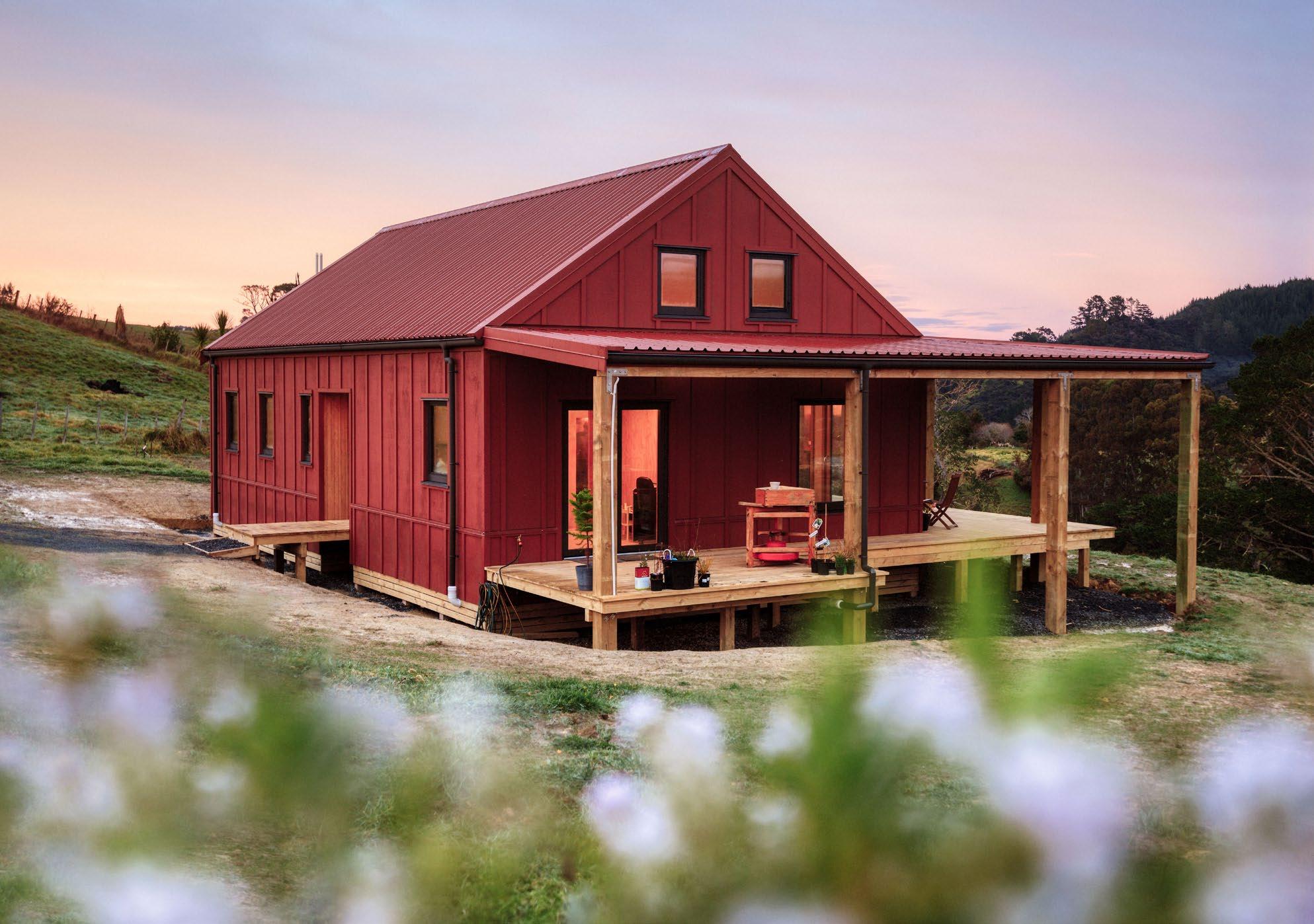
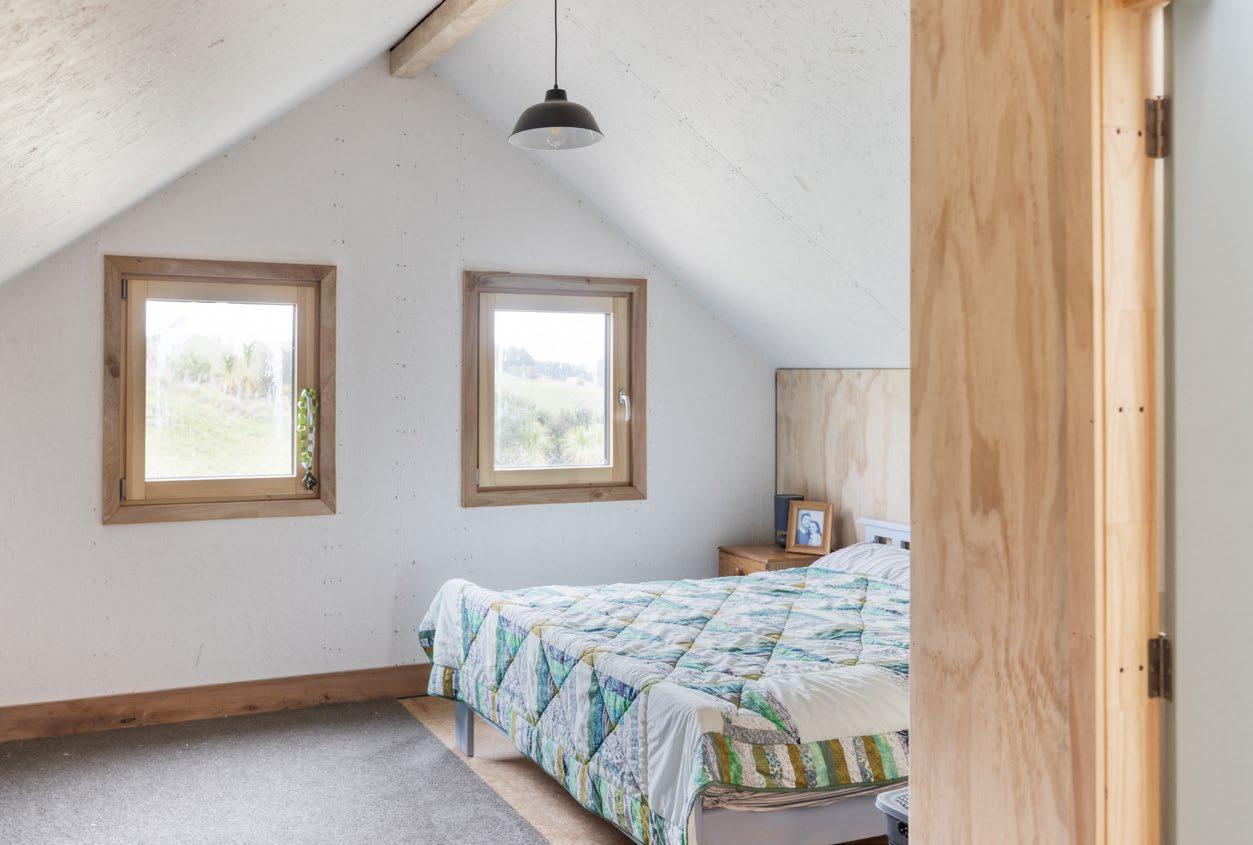
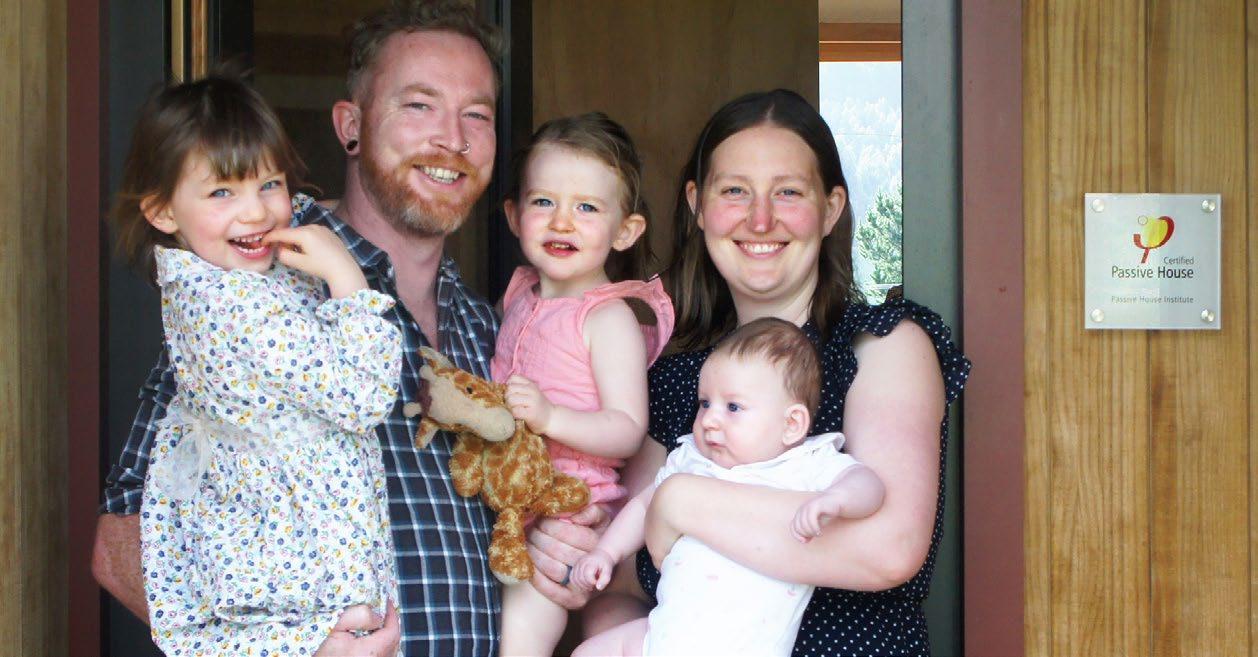
It’s time to spill beansthe ecologicalbuilding systems.com Discover our solutions online at A sustainable, safe, natural, and breathable thermal and acoustic insulation upcycled from used coffee bean bags combined with carbon negative hemp. Thermo Hemp Combi Jute is an easy to fit, natural way to insulate your home.
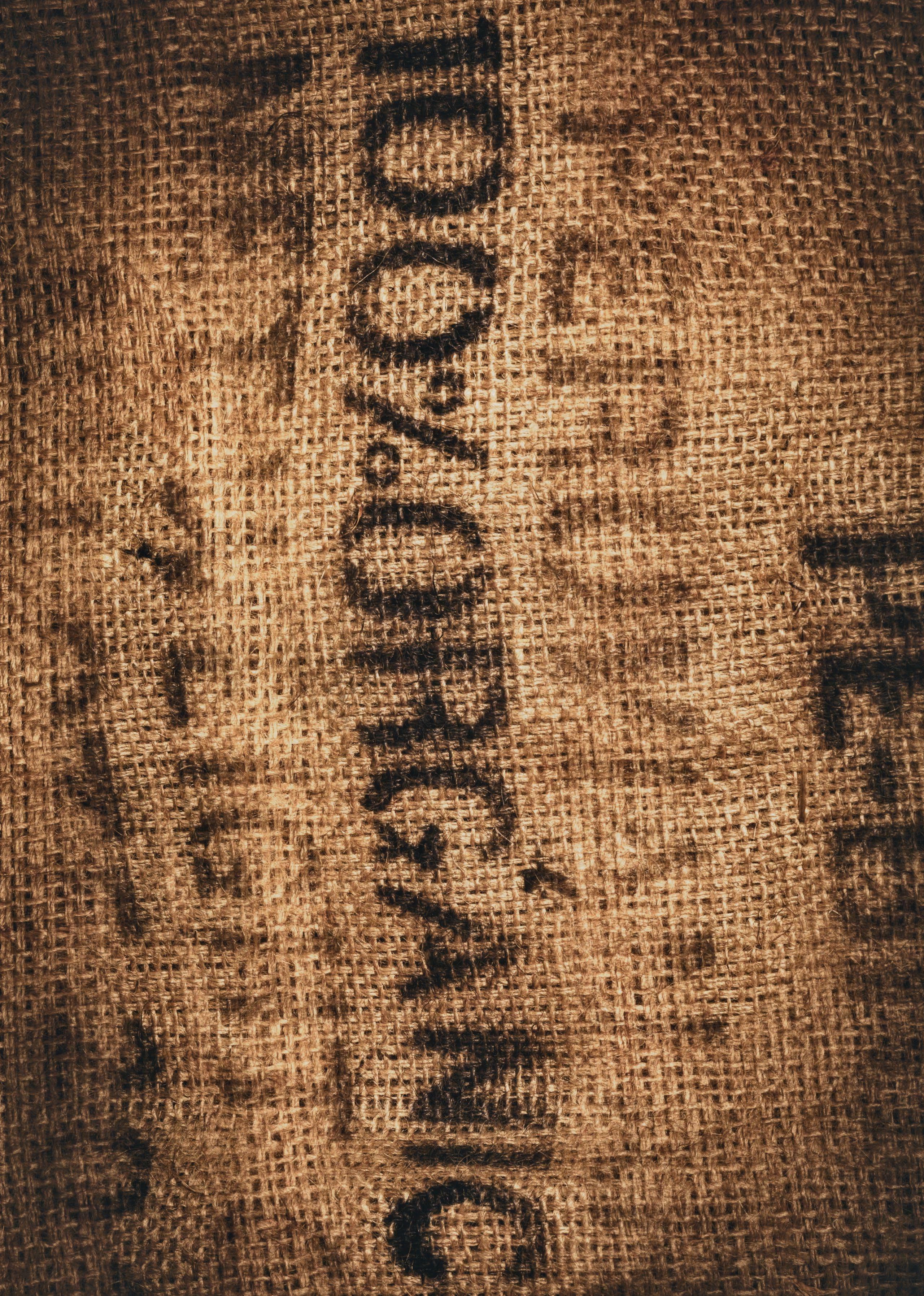
Embodied Carbon Excellence
Joe is a registered architect and certified passive house designer at Respond Architects in Takapuna. Originally from North Yorkshire in the UK, Joe studied and worked in London from early 2007 before making the move to New Zealand in 2016 with his wife Sarah, and has since welcomed three little Kiwis into the world. He is especially passionate about high performance and healthy buildings, and finished his own passive house certified home on a tight budget in May 2021, to show healthier, affordable buildings are possible for everyone in New Zealand.
.
ph+ | new zealand big picture | 19 BIG PICTURE NEW ZEALAND
12. A learning resource Since completion we have been able to grow into the home, but also use it to help educate others (thanks to Sarah’s incredible patience!). It’s been part of the international passive house open days, and the Superhome Movement tours, and will be again this year; I’ve used it as a vehicle to explain building performance in presentations to uni versities and product suppliers, and it’s fantastic to be able to invite clients up to show them what a passive house looks, feels and sounds like. As a model for other homes in NZ applied at scale, this would provide a warm, dry, healthy and affordable home for all New Zealanders, with minimal ongoing maintenance and operational costs; and as our home, we couldn’t be happier.
The project has achieved excellent em bodied carbon results, based on analysis by Elrond Burrell of Via Architecture, performed using PHribbon. It blitzed the RIBA 2030 Climate Challenge target for embodied carbon of 625 kg of CO2 equivalent per square metre, scoring a miniscule 120 kg CO2e/m 2 , and achieved an A+ for upfront carbon and A++ for embodied carbon on the LETI scale. The house is below the BRANZ detached house (embodied and operational) car bon budget for a 2C warming limit. How did the house achieve such low figures? A combination of factors con tributed, including the lack of concrete for foundations or superstructure, and the lack of rendered block or brick clad ding, and the lack of a heating system. One other key factor played a part: the timber used for the structure was covered by an Environmental Product Declara tion (EPD) from the Wood Processors and Manufacturers Association, which included New Zealand-specific figures for the end of life of timber. Because the timber was assumed to be landfilled upon the building’s eventual deconstruction and – unlike the RICS methodology in the UK – the majority of the timber is as sumed not to biodegrade as methane – a substantial amount of CO2 sequestered in the timber is assumed to remain seques tered. This hints at an inconvenient truth about life cycle assessment: if that timber had been assumed to be salvaged and re used in the future, the sequestered CO2 would have passed outside of the bound ary conditions of this building’s life cycle assessment and onto the next use – giving the same embodied CO2 result as if the timber had been incinerated. Had that been the case, the building would still have achieved a superlative score of 238 kg CO2e/m 2
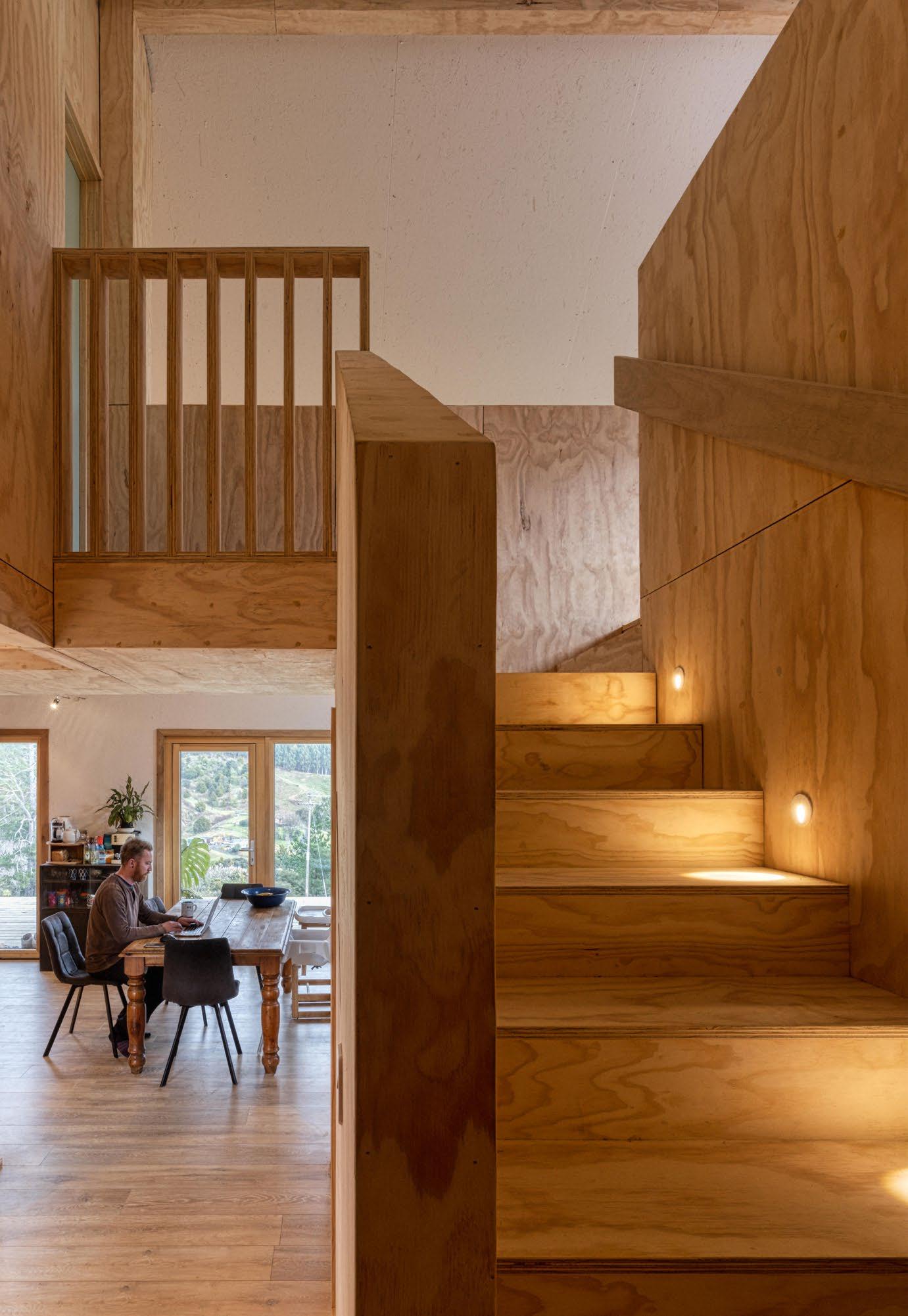
A s Russia weaponises gas exports, the European Commission has proposed a gas demand reduction plan, to cut use in Europe by 15 per cent until next spring. Almost half of EU member states are already affected by reduced deliveries.
Russian invasion of Ukraine, the commission adopted the REPowerEU Plan to end the EU's dependence on Russian fossil fuels as soon as possible. REPowerEU sets out measures on diversification of energy suppliers, energy savings and energy efficiency, and an accelerated roll-out of renewable energy. By progressively eliminating Europe’s dependence on fossil fuel sources and by reducing overall energy consumption through increased energy efficiency, the European Green Deal and Fit for 55 package have been designed to strengthen the EU's security of supply. REPowerEU aims to accelerate the instalment of renewable energy across the EU and the deployment of energy efficiency investments. Over 20 per cent of the EU's energy currently comes from renewables, and the commission has proposed to more than double this to at least 45 per cent by 2030. Since the beginning of the year an estimated additional 20 GW of renewable energy capacity have been added. This is the equivalent of more than 4 billion cubic metres of natural gas.
"This precisely is why the energy-efficient con cept is particularly worthwhile for hospitals,” said Passive House Institute joint managing director Dr Jürgen Schnieders. "This applies for efficiency measures for the building itself as well as for energy-efficient technical devices. ” The in stitute was closely involved in the planning and construction phases of the new building. The high energy efficiency of the building makes it possible to achieve the higher room temperatures required in patients’ rooms with less energy use. Fresh air is supplied by the ven tilation system, which saves energy via heat re covery. The baseline study showed that despite the higher room temperature and ventilation air change rate required, the space heating de mand could be limited to the passive house tar get of 15 kWh/m² using coordinated measures.
•
(above, l-r) Passive House Institute joint MD Dr Jürgen Schnieders, Hesse minister of economic affairs Tarek Al-Wazir and city councillor Rosemarie Heilig present the passive house certificate to management board chairman Martin Menger.
EU proposes gas demand reduction plan till spring
Thedeliveries.commission
The world’s first passive house hospital has been certified by the Passive House Institute – showing that the standard can be applied to even to the most demanding build ingThetypes.energy performance specifications for the new 700-bed hospital, Klinikum Frankfurt Höchst, were developed following a baseline study by the Passive House Institute commis sioned by the state government of Hesse. Due to their intensive 24-hour operation, hospitals are one of the most energy use in tensive building types, as a large number of technical devices are used in emergency rooms, operating theatres and intensive care units, as well as in the patients’ rooms. In a hospital, the electricity consumption is generally three to four times higher than in a residential building. The baseline study showed that the equipment can have a major influence on energy demand. Energy efficient devices were specified – not only because they use less energy, but because they reduce cooling demand too.
World’s first passive house hospital completed in Frankfurt
20 | passivehouseplus.ie | issue 42 NEWS PASSIVE HOUSE+ NEWS
The new hospital building provides more than 660 beds for patients and another 40 beds in an outpatient clinic, in addition to eleven operating theatres. Over 1,600 employees will be working in the new building. In order to assist with more hospital projects – including new builds and refurbishments – the Passive House Institute has made the baseline study on the implementation of the passive house standard in hospitals available free of charge.
“Taking action now can reduce both the risk and the costs for Europe in case of further or full disruption, strengthening European energy resilience,” the commission said. The EU is urging all consumers, public administrations, households, owners of public buildings, power suppliers and industry to take measures to save gas. The commission will also accelerate work on supply diversification, including joint purchasing of gas to strengthen the EU's possibility of sourcing alternative gas is proposing a new council regulation on coordinated demand reduction measures for gas, based on Article 122 of the Treaty. The new regulation would set a target for all member states to reduce gas demand by 15 per cent between 1 August 2022 and 31 March 2023.
The new regulation would also give the Commission the possibility to declare, after consulting Member States, a ‘Union Alert' on security of supply, imposing a mandatory gas demand reduction on all Member States. This can be triggered when there is a substantial risk of a severe gas shortage or an exceptionally high gas demand. To help Member States deliver the necessary demand reductions, the commis sion has also adopted a European gas demand reduction plan which sets out measures, principles and criteria for coordi nated demand reduction. The plan focuses on substitution of gas with other fuels, and overall energy savings in all sectors. It aims to safeguard supply to households and essential users like hospitals, but also industries that are decisive for the provision of essential products and services to the economy, and for EU supply chains and Followingcompetitiveness.the

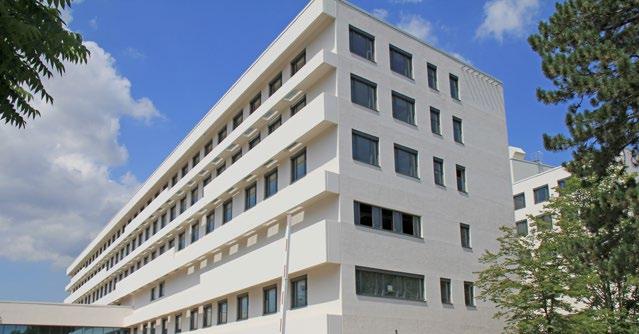
For more information on the Passivhaus Trust’s resources on embodied carbon and passive house visit: https://bit.ly/PHTEm bodiedCarbon
ph+ | news | 21 PASSIVE HOUSE+ NEWS New passive house & embodied carbon resources
T he Passivhaus Trust (PHT) has published resources exploring the role of passive house design in reducing whole life carbon emissions from buildings. The resources include a freely available position paper and primer, alongside an on-demand webinar, and draw on recent research that counters the argument that designing to decrease operational carbon emissions increases embodied carbon emissions due to additional materials. The paper outlines the relationship between passive house and embodied carbon, address ing common misconceptions. It says: “Pas sivhaus buildings are optimised for net zero, providing the best route to minimise whole life carbon. Outstanding levels of building performance minimise operational carbon, while the passivhaus design methodology encourages optimisation of embodied carbon through efficient use of materials and rad ically reducing the heat and cooling plant.”
Do thicker insulated walls, triple glazed windows, & MVHR ventilation systems tip the scales unfavourably for passive house when it comes to embodied carbon?
Comparing a house built to UK building regulations with the passive house standard, measured over 60 years, modelling shows that, even with additional building elements, the passive house has a lower initial embod ied carbon and less operational carbon over its lifetime, leading to a smaller whole life carbon footprint. By championing compact and rationalised design, improving the form factor of build ings and simplifying details, passive house buildings result in less material use, the mod elling concluded. Building to the passive house standard also avoids the need for a later retrofit to meet more demanding standards. Passive house quality assurance and use of higher quality materials contribute towards reducing embodied carbon through im proved resource efficiency. Quality passive house components can offer longer product lifespans and a reduced need for repair and maintenance.Therearealso substantial savings made in retrofitting existing buildings, compared with the high embodied energy costs of demolition and rebuilding. As an example, St. Sophia’s Primary School in East Ayrshire revealed that 40 per cent embodied carbon savings were made just by undertaking an Enerphit retrofit rather than rebuilding the school. The passive house community is in creasingly acknowledging and focusing on the issue of embodied carbon and material choices, demonstrated by the development of several carbon counting tools. The AECB PHribbon plug-in for PHPP makes whole life carbon calculations quick to perform using the material quantities already em bedded in a PHPP assessment. According to Passivhaus Trust policy and research director Sarah Lewis: “The rela tionship between embodied and operational carbon is rapidly changing. As buildings become more energy-efficient and heating is electrified, embodied carbon is a signifi cantly larger slice of a smaller whole life carbonLewispie.”added that efforts to tackle embod ied carbon must not come at the expense of energy efficiency. “Continuing to reduce en ergy demand is still important as it reduces peak loads and shrinking our collective winter energy demand will reduce the level of future zero carbon energy infrastructure and storage needed,” she said. “Reducing operational and embodied carbon is not an either/or choice. We must aim to tackle both simultaneously.”
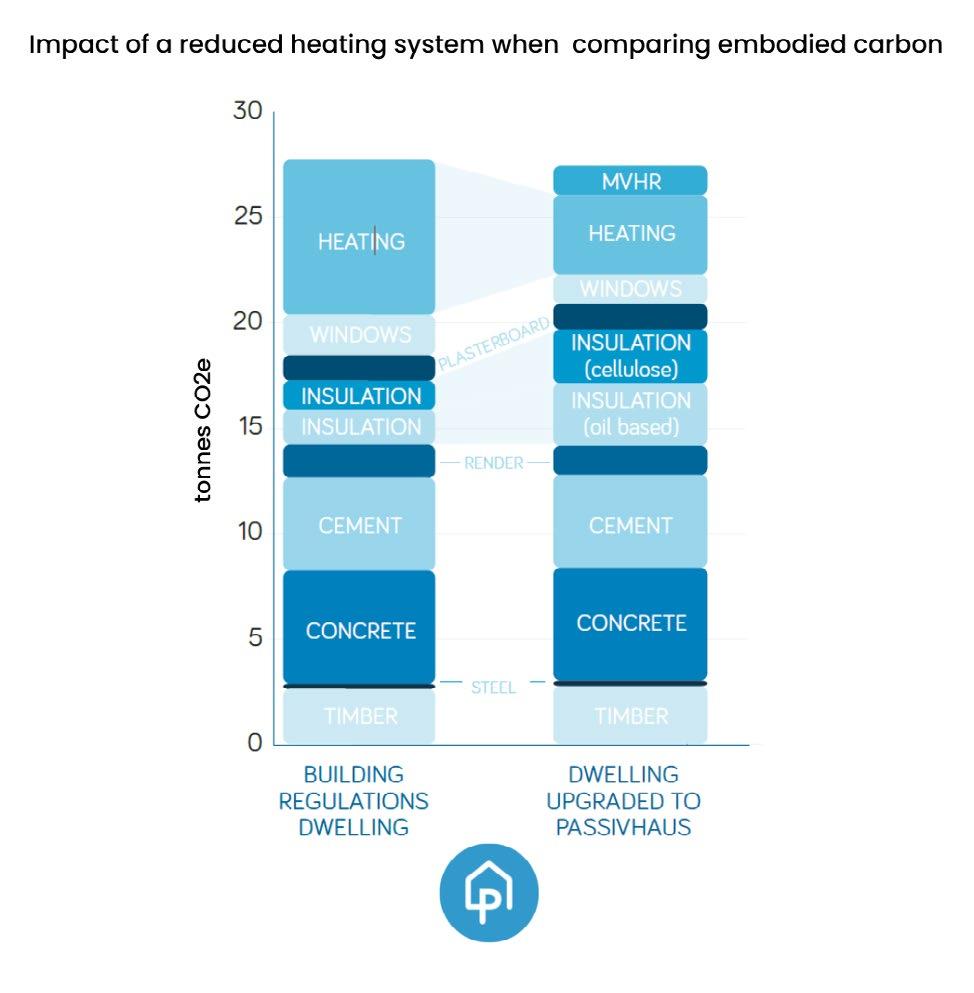
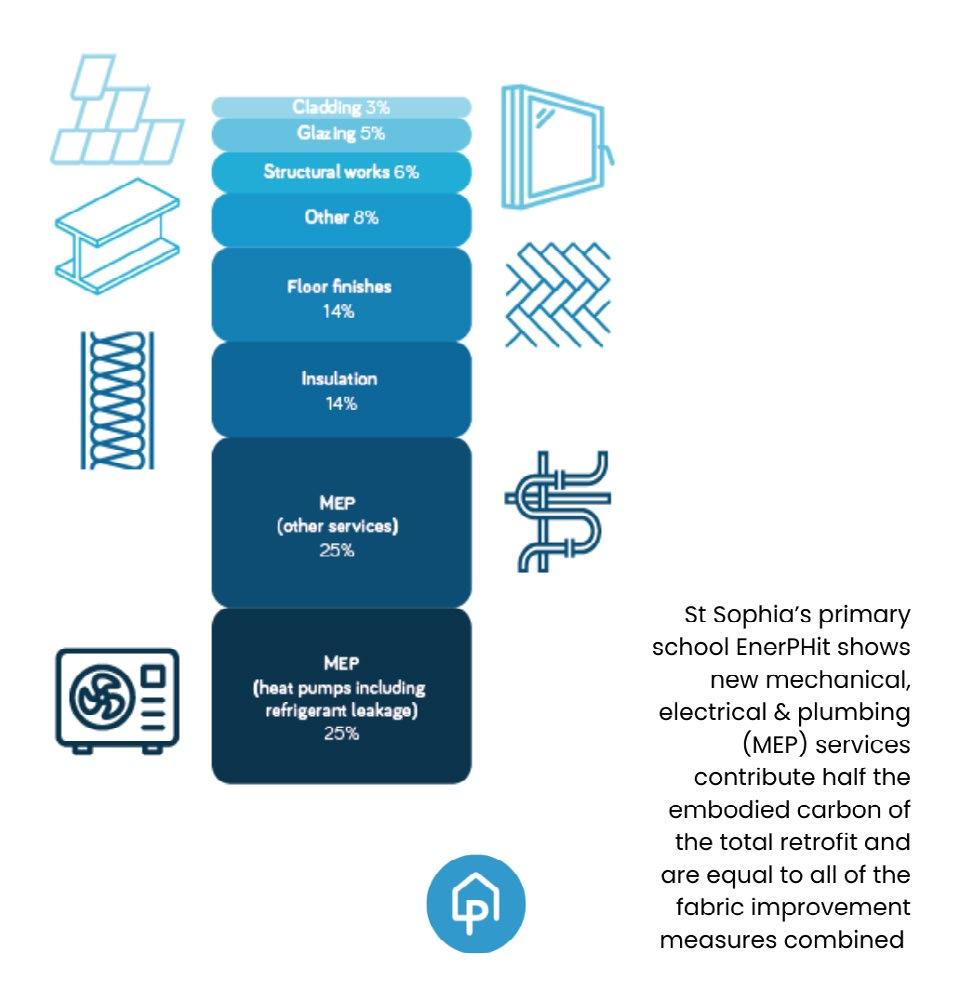
New courses listed on the hub include a postgraduate diploma in circular economy leadership for the built environment, and a certification in the energy renovation of traditional buildings, which is being run in conjunction with the Heritage Council.
DASBE is a partnership between two recently formed higher education institutes, the Technological University of the Shannon (TUS) and Atlantic Technological University (ATU), along with industry partners the Irish Green Building Council and Tipperary Energy Agency and is funded by the government’s Human Capital Initia tive Pillar 3. “It’s about a rapid response to train people in the skills needed to deliver on our climate targets, such as energy efficiency and retrofit skills,” said Alice Ryan of the Irish Green Building Council. “Right now, we are identifying the courses that are needed to develop the building industry in line with the Climate Action Plan.”
A new online hub aimed at upskilling the construction sector is now live. The Digital Academy for the Sustain able Built Environment, (www.dasbe.ie), will provide blended education in critical areas needed to upskill the construction and retrofit sectors in the coming years. It will focus on three core themes: energy efficiency, the circular economy, and digital skills for sustainable building.
New digital hub for sustainable building upskilling
While DASBE will initially serve as a central hub for relevant courses run by the participating institutes, it is also being developed to serve as an interactive online educational platform in its own right, specifically targeted at the construction industry, and it will make use of innovative modern technologies. Ryan said: “With retrofit for example TUS are developing a virtual reality experience, so you can virtually go into a building and learn about building defects in a hands-on way.”
(above) DASBE partner TUS is harnessing a range of digital tools for sustainable building learning including virtual reality and building information modelling.
The focus of DASBE will be on creating clear career pathways to fill roles that the industry needs to meet its climate targets. “The idea is to have a clear progression so that if someone has a level 5 certificate, it’s clear how they can progress from there to the next level,” said DASBE manager Elisabeth O’Brien of TUS. O’Brien said that the long-term goal is for all technological universities to work collaboratively by developing and delivering relevant programmes through the DASBE platform. She said that while previously higher education institutes would develop programmes on their own, the focus of DASBE is on close partner ship with industry, to better understand its needs, and with other education institutes. “We need to make sure we address what’s needed in the built environment right now, and what’s likely to be needed in future,” she added. The DASBE partners have completed a horizon scanning exercise seeking to identify skills needs and programme development opportunities in the short and medium term. This will include not just academic programmes, but training delivered in close conjunction with the further education sector such as the Educational Training Boards (ETBs), and industry training to support continuing professional develop ment (CPD) too.
22 | passivehouseplus.ie | issue 42 NEWS PASSIVE HOUSE+
A new level 8 programme in residen tial energy retrofit management will also start in September, run collaboratively between TUS and ATU. It will have three strands to choose from: building fabric, building systems, and retrofit manage ment. An increased role for qualified retrofit managers is seen as critical for safely delivering high quality deep retrofits that perform as they are designed to, without a performance gap. All courses will contain an element of online and flexible learning, to allow those currently working in the industry to upskill at their convenience. “The idea is to be as flexible as possible and take account of the amount of free time people have when they’re working,” said Ryan. “The ambition, over time, is to enable learners to access the modules that they need, when they need them.”
O’Brien also said that research and development is crucial to keep up to date with the fast changing industry, with TUS currently partnering on a number of European projects aimed at upskilling the building sector. These include Construc tion Blueprint, BIMzeED, BUSLeague and HumanTech. In Construction Blueprint (www.constructionblueprint.eu) TUS is sharing the NZEB skills course – developed in Ireland with WWETB – with 20 other countries. BIMzeED focuses on increasing building information modelling (BIM) skills to deliver NZEB buildings. BUSLeague aims to stimulate demand for sustainable energy skills in the construction sector, and is working to raise awareness of these skills at locations such as builders’ merchants. HumanTech will carry out technology-assisted training of advanced wearables, robotic devices and dynamic semantic digital twins in the form of virtual case studies, gamification, videos and on-site training. For more information see www.dasbe.ie •

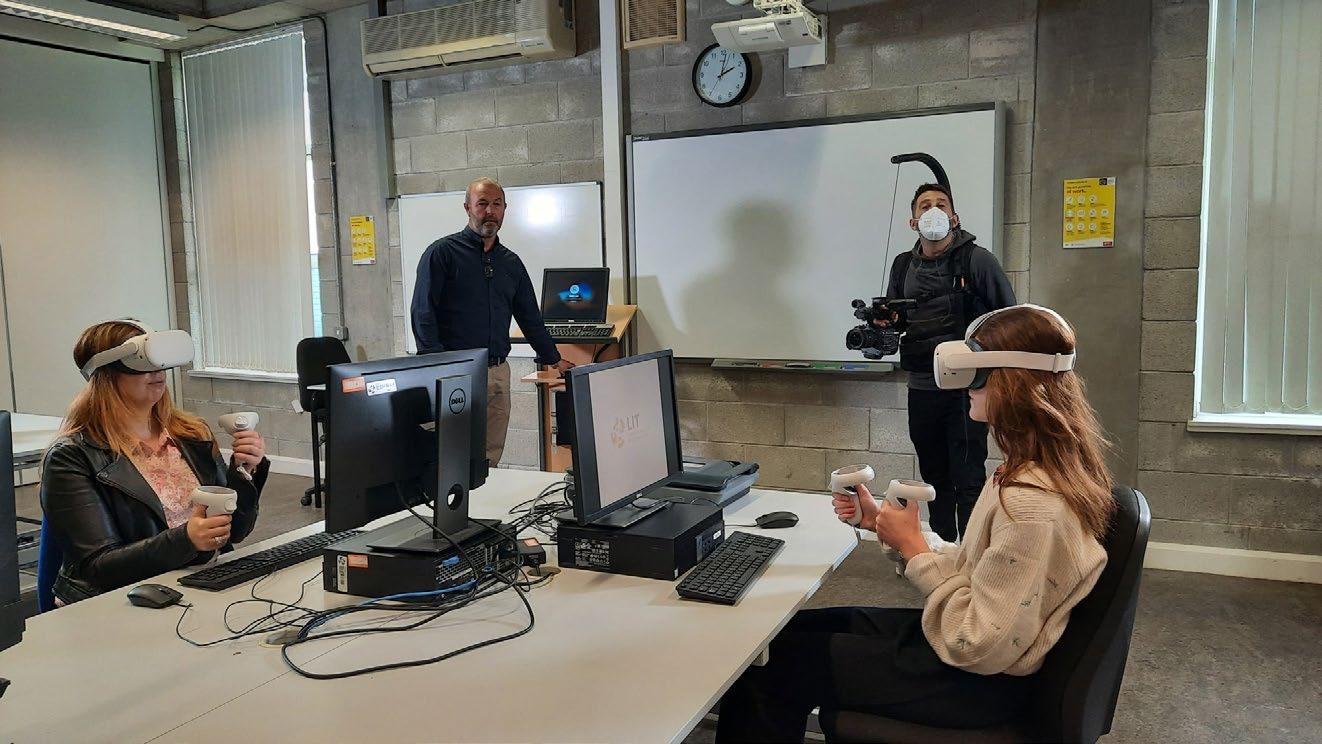
In the #BuildingLife Ambassador Spotlight Series, Passive House Plus is profiling leaders who have endorsed the Irish Green Building Council’s call to address the environmental impacts of buildings across their lifecycle. In this sixth interview of the series, Eoin Ó Broin TD, Sinn Féin’s spokesperson for housing, tell us why he is supporting the campaign. Why did you choose to become a #Build ingLife ambassador? Eoin Ó Broin: Through my work on hous ing and collaboration with the Irish Green Building Council, I became aware of the need to rethink our housing development. I believe that not only do we need more homes, but we can build these homes at a lower cost, while tackling climate change and affordability at the same time. Addressing embodied carbon is the way to do this. It allows us to tackle our carbon emissions, while delivering high qual ity homes. That’s why I am delighted to sup port the #BuildingLife campaign. What are you hoping to achieve with the #BuildingLife campaign? EoB: We have reached a turning point in the housing crisis and in how we develop our urban environment. We can preserve the status quo and continue to build as we have done for the last decades, but we know this is not good for our carbon emissions, affordability or liveability. Or we can intro duce real, long lasting political changes at local and national levels to support a com plete paradigm shift in what we build and how we build it. I passionately believe this is the only way to deliver low carbon, afford able homes, while improving people’s quality of life in our towns and cities. I support the #BuildingLife campaign to ensure the tens of thousands of new homes we need to build are good quality, affordable, zero carbon homes. Can you explain a few ways in which you and Sinn Féin are working towards a sus tainable built environment? EoB: We can’t decarbonise our built envi ronment without cross-party support. We all need to work together to lead that change. I recently asked a question to Minister Noonan on embodied carbon and I am bringing the findings of the #BuildingLife campaign to the Oireachtas Committee on Housing. A hear ing on carbon and energy within the construc tion industry was organised in early May. We have a real opportunity to shape government legislation and policy on this topic. We need to support modern methods of construction (MMC) and the development of biobased ma terials. The state can directly support this tran sition through public procurement and the strategic investment fund. Enterprise Ireland could also better support the development of these technologies in Ireland. So many things can be achieved and now is the time to do it.
- Elizabeth Assaf, owner, Urban Front
#BuildingLife: “Addressing embodied carbon is a no brainer” says Eoin Ó Broin TD
It is no doubt in my mind that this team are one of the best I have dealt with out of the many publications we use. They deliver and they deliver quality!
www.passivehouseplus.ie To enquire about advertising, contact Jeff Colley on +353 (0)1 2107513 , or jeff@passivehouseplus.ieemail Advertise with us.
#BuildingLife is a project led in Ireland by the Irish Green Building Council. The initia tive aims to achieve the mix of private sector action and public policy necessary to tackle the whole-life impact of buildings. Learn more at www.igbc.ie. •
It is always a pleasure to work with the Passive House Plus team. They provide a wealth of information, support and time to provide the best advert. Launching a new product is never easy, but in the space of only two months we’ve received over 150 enquiries through two issues of the magazine and all have been very fruitful. We have been quoting straight after the magazine is out. A lot of the customers enquiring have genuine current projects and this is reflected in how many respond to our follow ups.
High quality, mid-rise mixed developments are already being built with these technologies in other jurisdictions. Dalston Works in En gland is a good example of a 10-storey carbon negative timber frame building. Per square metre, it was also cheaper to build than a stan dard apartment block in Dublin 2. These are exciting developments that show we could address the housing crisis, while reducing embodied carbon emissions quickly. Tack ling our transport and agriculture emissions will be challenging, but addressing embodied carbon is a no brainer. It will contribute to a significant reduction in our carbon emissions, while allowing us to deliver cheaper, better quality homes faster. That’s why I believe we need to act on these emissions now and I am absolutely keen to work on this.
ph+ | news | 23 PASSIVE HOUSE+ NEWS
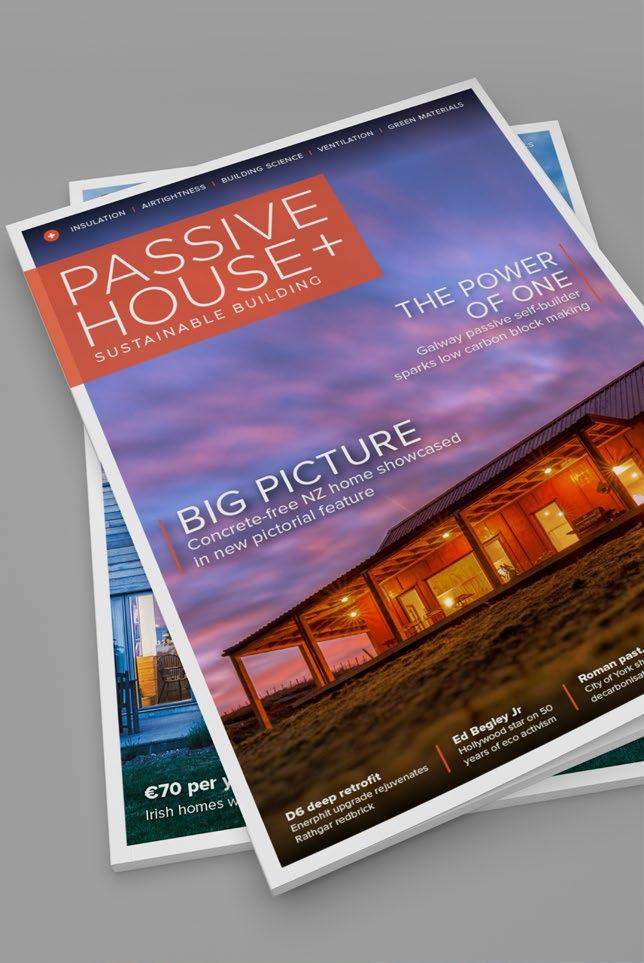
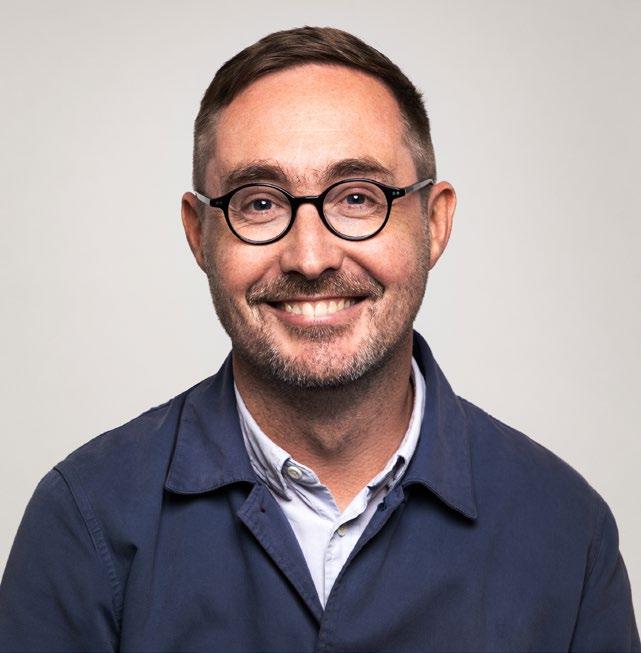
PHAI UPDATE PASSIVE HOUSE+ Certified Passive House Radon Monitoring Results 3Bq/mLevelRadon Certified Passive House Sample
The Environmental Protection Agency (EPA) recently published new updated radon risk maps for Ireland. With that also came the warning that the number of homes in danger is signifi cantly higher than previously thought –with as many as half a million people in 170,000 households possibly at risk. Radon, a naturally occurring radioac tive gas, is linked to 350 new cancer cases every year and the EPA has urged homeowners to test for it. Currently 95 per cent of Irish householders are living in homes that have not been tested for radon. Meanwhile, there is no require ment for those selling or renting their homes to test for radon levels. 170,000 homes are in high-radon areas – an increase of 45,000 on a survey from 2002. Radon levels in Irish homes vary widely from area to area and even from house to house. The only way of knowing the level in your home is to have a test carried out. Various factors such as geology, the construction type of the house and ventilation all influence the amount of the gas entering a building. The distribution of radon nation ally is largely determined by geology. Certain types of rock and deposits –including some granites, limestone, and shales – tend to be associated with high radon emissions. Part of the problem is that this radioactive gas is colourless, odourless, and tasteless. However, it's also easily detectible. Radon is measured in becquerels per cubic metre of air (Bq/ m3). A becquerel is a unit of radioac tivity and corresponds to one radioactive disintegration per second. According to the EPA, the average indoor radon level in Irish homes is 77 Bq/m3. The reference level for Irish homes above which it recommends measures to reduce radon is 200 Bq/m3 This sets the context for my own PhD research which was only completed a little over a year ago, investigating indoor radon concentrations in 97 certified passive house buildings here on the radon 97 passive houses in the study
levels from
Passive resistance to radon: Research shows promising results
24 | passivehouseplus.ie | issue 42 NEWS PASSIVE HOUSE+
When a standard works, it really works. New research indicates that the passive house standard doesn’t just stop at delivering real world ultra-low energy use, year-round comfort and a consistent supply of fresh filtered air. It may also reduce your risk of contracting lung cancer, as Passive House Association of Ireland (PHAI) chairperson Dr Barry Mc Carron explains.
(above) Monitored
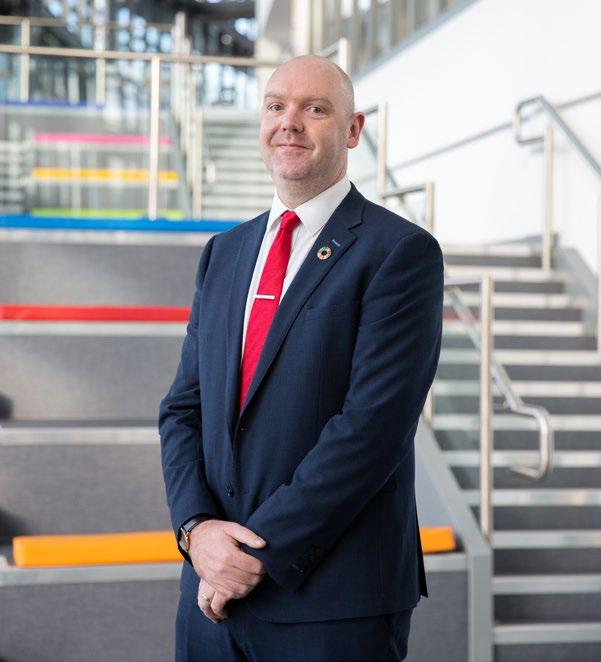
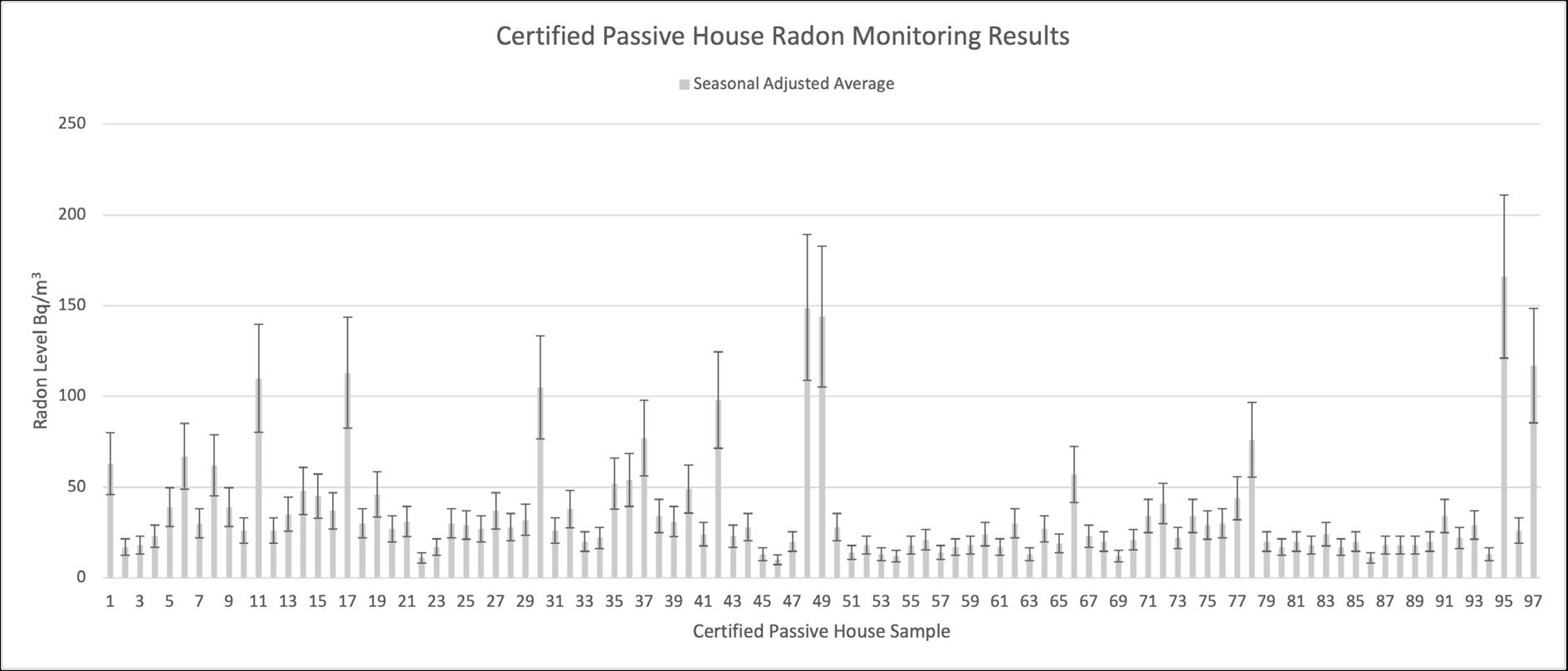
island of Ireland. Of the 97 certified passive houses studied, 92 were new build, and five were Enerphit retrofits. I also included a sample of comparison homes in the immediate vicinity of 25 of the passive homes monitored — these were of a similar size but of non-passive construction.
Radon monitoring showed the certified passive house dwellings had far lower indoor radon concentrations - both compared to the comparison dwellings and to Irish homes generally. The average level in passive homes was 36 Bq/m3, compared to an average of 88 Bq/m3 in the comparison homes. The national average level in Ireland is 77 Bq/m3 The Irish and UK governments have both set an ‘action level’ of radon gas concentration of 200 Bq/m3, above which remedial action to reduce indoor radon concentration should be taken. In the UK there is also a ‘reference level’ of 100 Bq/m3, which according to the public health authorities, all homes should aim to be below. None of the 97 certified passive homes (new build and Enerphit) exceeded the action level of 200 Bq/m3, while two of the 25 comparison homes (8 per cent) did so. All but 7 per cent of the passive homes were also below the lower ‘reference’ level of 100 Bq/m3, while 16 per cent of the comparison homes exceeded this. In Ireland as a whole, an estimated 25 per cent of homes are above 100 Bq/m3. The average in the five Enerphit homes was 72 Bq/m3 – not as low as the new build passive homes, but still lower than the national average, and below the 100 Bq/ m3 reference level. There were 10 matched pairs of homes located in designated high radon risk areas. Only one of the certified homes there (an Enerphit retrofit) exceeded 100 Bq/m3, with a recording of around 150 Bq/m3. However, the identical but non-retrofitted home next door had one of the highest radon levels measured in the survey, at over 400 Bq/m3 Although the numbers were too small to enable predictions about the radon performance of certified passive house retrofit more generally, these early results are encouraging signs on a potential benefit of the passive house approach. Overall, my PhD research studies indicate that combining effective balanced ventilation with a sealed floor (incorporating radon protection if in a high-risk area) reduces radon risk. Both features come as standard in a certified passive house or Enerphit. A complete airtight envelope, validated by testing, plus properly designed, installed, and commissioned balanced ventilation, are the cornerstones of low energy construction and healthy and comfortable living conditions. They are crucial elements in a radon mitigation strategy, too. There seems little reason not to build, and retrofit, everything to the quality assured passive house standard. This is even more pertinent If the statis tics are to be believed, as more than 7,000 people have died from radon related lung cancer over the past 20 years.
ph+ | news | 25 PASSIVE HOUSE+ NEWS
• 0 100 200 300 400 500 600 700 800 10987654321 Radon Level Bq/m3 StudiesCase 1 2 3 4 5 6 7 8 9 10 Passive House 18 43 23 26 72 37 20 67 166 37 Standard Homes 51 52 34 48 144 126 58 598 409 104 Direct Comparison Case Studies Passive House Standard Homes (above) Direct comparison of radon levels in individual passive houses versus standard homes in the immediate vicinity PASSIVE HOUSE+ PHAI UPDATE StudiesCase Radon Level Bq/m3 Direct Comparison - Case Studies ph+ | phai update

• A new climate risk indicator which replaces the flood risk one for a more comprehensive assessment of potential climate risks
• Minor changes to land use, construc tion team skills, and low volatile or ganic compounds (VOCs) HPI Version 3 will be launched in Sep tember 2022 and the changes ensure that this version is relevant for the present. Just like the EU taxonomy, the HPI is dynamic and will be updated as the EU taxonomy evolves, and more categories become regu lated. For more information on the changes to HPI Version 3, watch our webinar at www.tinyurl.com/hpiv3 and email brian@ igbc.ie if you’d like to give us feedback on the draft Version 3. For more information on the HPI, please visit https://homeperformanceindex.ie/.
These areas are further assessed across two different categories: “do no significant harm” and “substantial contribution”. To achieve EU Taxonomy compliance a proj ect must meet the requirements for all six areas as prescribed in the “do no significant harm” category and at least one area must meet its requirements for “substantial con tribution”. Currently the requirements for “do no significant harm” for all six areas have been released but for “substantial contribution” only two areas have had their requirements published. These areas are climate change mitigation and climate change adaptation. HPI Version 3 & the EU taxonomy Alignment with the EU Taxonomy in HPI Version 3 will be met by 11 of the revised 35 indicators. The most significant change is made for the energy in use indicator, with the “substantial contribution” for climate change mitigation of 10 per cent improvement on NZEB becoming a mini mum requirement. Other changes for min imum requirements in HPI and alignment of the EU taxonomy include:
The EU taxonomy and Ireland’s new homes
The EU taxonomy for sustainable activi ties is an EU wide classification of all economic activities considered environ mentally sustainable. For financial market operators to offer green products within the EU, they will need to show compliance with the taxonomy. Large companies will also have to disclose their activities in line with the Sustainable Finance Disclosure Regula tion [SFDR] and Corporate Sustainability Reporting Directive [CSRD], providing information about the ESG and sustain ability risks of their investments. In Ireland, international real estate investors look for developments with sustainable certification, as they need assurance that their long-term real estate investments are robust and tick more boxes than just energy efficiency. The Home Performance Index [HPI] is Ireland’s national sustainability certification for new homes. It is a readymade solution for finance providers seeking third-party assurance that eligibility criteria for new sustainable homes are met. The new HPI Version 3 will align with the EU Sustainable Finance Taxonomy and the EU framework for sustainable buildings, Level(s). Developed by the Irish Green Building Council, the Home Performance Index is independently assessed and awards certif icates for the standard of a home’s design, construction and environmental sustain ability. The demand for HPI certification surpassed 10,000 homes registered in April this year. The certification has 35 indicators across five categories: 1. Environment 2. Health and wellbeing 3. Economic 4. Quality assurance 5. Sustainable location HPI certification is similar to certification for commercial developments like LEED and BREEAM, except that it’s specifically designed for residential development and aligned with Irish building regulations, EU CEN standards and the international WELL community standard. The HPI is tailored to the Irish residential sector with international recognition by GRESB as a full points certification system. In the last year, in line with the SFDR and green financial products, two financial institutions, AIB and HBFI, created green financial products offering developers discounts on their development loans with HPI used as the qualifying mechanism. EU taxonomy overview The EU Taxonomy covers six environmen tal areas:
• Two new sub indicators: design for disassembly and design for adaptability
26 | passivehouseplus.ie | issue 42 NEWS PASSIVE HOUSE+
• Climate change mitigation • Climate change adaptation • Sustainable use and protection of water and marine resources
• Whole life carbon assessments for de velopments over 5,000 m2
• Introduction of a resource and waste management plan
The latest version of the Home Performance Index provides the perfect way of demonstrating that residential developments comply with the new EU Taxonomy on sustainability, write John Fingleton and Brian Crowley of the Irish Green Building Council.
• Pollution prevention and control
A carbon neutral Ireland and Europe by 2050 needs a great deal of investment. Public funds are not sufficient. A market transformation is needed so that private investment will flow into truly sustainable projects. How do we assess and evaluate if an investment is sustainable or not?
• Protection and restoration of biodiver sity and ecosystems
IGBC UPDATE PASSIVE HOUSE+
(above) HPI Version 3 is a readymade solution for finance providers seeking third party assurance that new homes meet the sustainability criteria of the new EU Taxonomy, write Brian Crowley (left) and John Fingleton (right) of the Irish Green Building Council.
• Transition to a circular economy
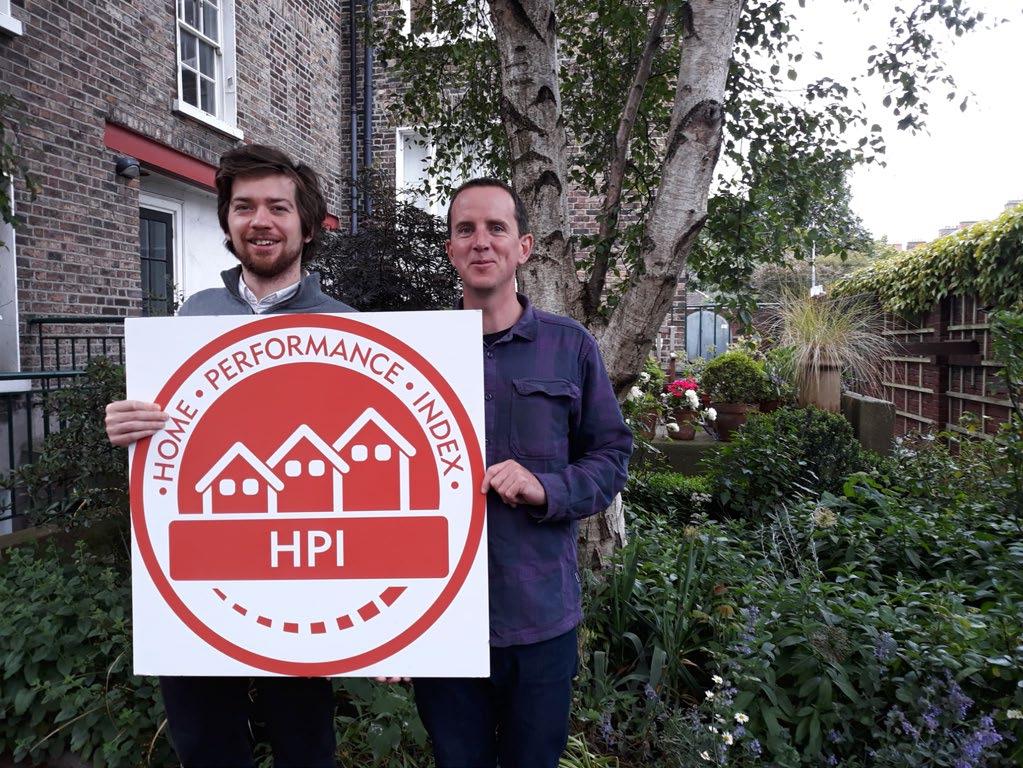
In the latest missive in his series on the history of low energy design, Dr Marc Ó'Riain looks to some wacky and wonderful experimentation in a project that aimed to transform public perception of Milton Keynes. Dr Marc Ó Riain is a lecturer in the Department of Architecture at Munster Technological University (MTU). He has a PhD in zero energy retrofit and has delivered both residential and commercial NZEB retrofits In Ireland. He is a director of RUA Architects and has a passion for the environment both built and natural.
A fully referenced version of this article is online at www.passivehouseplus.ie (above) Showcased in Homeworld ’81, Future Home 2000 included a number of experimental approaches including an adapted car engine to run an electric generator with heat recovery. Ó riain
The house is designed so that all major rooms face south and is very well insulated to about twice the current (1981) building regulation standards. It has double glazed windows with a special coating which lets in light but gives the equivalent thermal benefit of triple glaz ing, and is also draught sealed. Doors are foam filled to improve their insulation, and have special magnetic fridge type draught sealing. The conservatory also serves to sup port a small solar system for heating domestic hot water, made by Pilkington Solar Products. Unlike normal solar heaters, it needs no sepa rate store, pump or electronic controller, so is cheaper and maintenance free. The appliances in the house were chosen for their low energy use, for instance, the lights use only a quarter of the energy for the same amount of light as a normal bulb” (Fuller, S.; Doggart, J. and Ev erett, R. 1982). There were separate heating systems; coal and a specially adapted Fiat car engine that ran on gas driving an electric generator with heat recovery that made it 90 per cent effi cient. The whole house could be centrally controlled using a Honeywell digital meter. The overall efficiency of the building was 60 per cent better than a contemporary equiv alent. The house also featured a home office and an electric vehicle… 41 years ago! The HomeWorld exhibition was a thor ough success attracting 140,000 visitors in one month, attracting private developers to Milton Keynes, and reframing the town with a forward-looking development coun cil. However, the designers who had hoped that developers would grasp the innovations on show with new tech housing, were disap pointed by industry uptake. Moreover, as oil prices fell through to 1985, the projected pay back periods for energy saving measures rose. HomeWorld 1981 would be followed up in 1985 with Energy World which would go on to define a number of methods we use today like Building Energy Ratings. For anyone interested in this topic there is a good documentary, Homeworld ‘81: 40 years on, available at vimeo.com/540791219 n
HomeWorld 1981: car ideashousesengine-driven&lowenergythatstuck
column | 27 COLUMN DR MARC Ó RIAIN
One such project was ‘Future Home 2000’ designed by John Doggart and featured on BBC’s The Money Programme in 1981. The BBC referred to those who designed the houses as ‘energy conscious designers.’ The Future Home was essentially two super-insu lated houses set in an L-shape and connected by a glazed conservatory which utilised ther mal mass to bank solar gain. The house was fully prefabricated off site and brought to site in component form for assembly. It had a high degree of insulation in the timber frame walls (externally clad with brick), featured gold coated double glazing and solar water panels. It “has a large conservatory which faces south. This is heated by the sun, and small fans distribute the heat into the main house.
ph+ | dr marc
A s the UK labour government led by James Callaghan handed over to Margaret Thatcher’s Conservatives in May 1979, focus on public supplied housing would switch dramatically to private supply. Nowhere would this be more evident than in the last of the ‘new towns’ in the suburbs of London, Milton Keynes. As people tried to escape the congestion of London city, towns were being planned and formed around new ideas. Milton Keynes was founded on a bronze age site northwest of London which included the famed Bletchley Park, code breaker central during WW2 and the location of Alan Turing’s Enigma cracking machine. So new ideas and innovation were not novel to Milton Keynes. In the late 1970s the town was in danger of becoming a social housing ghetto, so the local council decided to try to attract private developers to build private housing. Inspired by precedents like Letchworth Garden City in 1905, a model town developed to entice city dwellers to the countryside, Milton Keynes Development Corporation decided to create a new exemplar zone to attract people to the town with energy efficient housing. They set up a private housing unit to build a series of exemplars from multiple developers, who were eager to establish a foothold in the de veloping town. The Milton Keynes Development Corpora tion decided that new energy efficient private housing would shift the public perception of the area and segue nicely to new Conserva tive policies of privatisation. It organised the construction of fifty-two houses for public exhibition, drawn from the best and most in novative designs from all over the world. The often wacky and innovative new forms were packed with modern technologies and new building methods that we take for granted today. The various designs featured heat recovery ventilation systems, heat pumps, heat exchangers, solar panels, south-oriented double glazing, passive solar gain, winter gar dens, thermal mass, super‐insulated timber frames, and kit houses from New Zealand for example (Byrne 2011). The buildings varied from very tradi tional Tudor style semi-Ds to, pyramids, mono-pitches, full A-Frames, prairie style bungalows, Saskatchewan inspired glass and brick houses, and treehouse inspired turreted houses. The variety was staggering, with thir ty-two variations in total, each developed by a different sponsor.
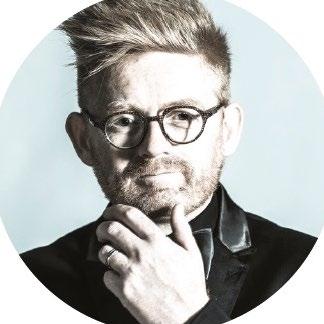
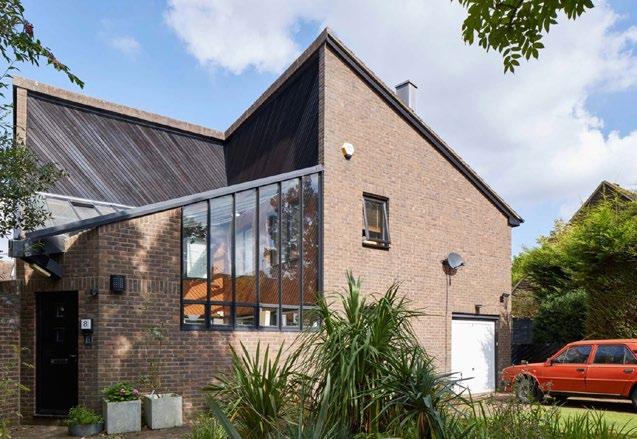
Dr Peter Rickaby is an energy and sustainability consultant working on retrofit projects with Savills social housing team. He also chairs the BSI Retrofit Standards Task Group, and is an Honorary Senior Research Fellow at UCL, where he helps to run the UK Centre for Moisture in Buildings (UKCMB). The views expressed here are his own, and do not necessarily reflect the views of Savills, BSI or the UKCMB.
The time hasanddemonstrationforpilotprojectspassed.
There are other examples, and we have workarounds, including hybrid insulation (EWI combined with IWI) and communal ground source heat pumps (GSHPs) serv ing streets and blocks, but they all add to the cost and complexity of the retrofit chal lenge. Some of them require integration with landlords’ asset management and investment strategies, so that retrofit is part of broader improvement plans and work can be prop erly programmed or proceed when properties are empty. Other options such as communal GSHPs require large capital investment, local disruption and serious engineering.
The second and equally important lesson is that the time for demonstration and pilot projects has passed. We have been piloting retrofit for twenty-five years. Now we have a climate emergency: to achieve zero carbon we have to deliver five retrofitted dwellings per minute, for the next twenty-eight years. We know how to do retrofit well, to man age risks and minimise unintended conse quences: that knowledge is coded into the Retrofit for the Future report, the Enerphit standard, the AECB retrofit standards, PAS 2035, the LETI Climate Emergency Retrofit Guide, the Construction Leadership Coun cil’s National Retrofit Strategy and other doc uments. With the exception of some largescale GSHP installations, we don’t need any more pilots — they are just an excuse for not rolling up our sleeves, getting our heads down and delivering domestic retrofit at scale. n But doing retrofit well and at scale remains an enormous technical and financial challenge, writes Dr Peter Rickaby
DR PETER RICKABY COLUMN 28 | passivehouseplus.ie | issue 42
Bad retrofit is worse than no retrofit
R ecently, I have been inspecting housing areas across the UK. Fre quently, I have visited them in person, walking the streets with landlords, going into homes and talking to residents. I have toured other areas using Google Street View and landlords’ databases. My aim has been to understand how we might retrofit homes and bring them to zero carbon. This exercise has been dispiriting: it has revealed how challenging it is to scale up retrofit, both technically and financially. The cost of improving the whole UK stock by 2050 is eye-watering – for social hous ing it is often tens or hundreds of millions of pounds beyond the resources at landlords’ disposal. And hanging over the problem is the current increase in fuel poverty, and the knowledge that fuel poor households are not interested in reducing emissions – they just want to be warm. My travels have reminded me of a lesson learned long ago, and have provided two new lessons. The reminder is of what we learned from the failure at Fishwick, in Preston: bad retrofit is worse than no retrofit. At Fishwick, nine years on from their bungled external wall insulation (EWI) programme, most residents are still living in damp, mouldy, unsaleable homes, waiting for remediation and redress. Similar cases have occurred in North Wales, South Wales, Hull and Middlesborough, and I suspect that there are more. These are cases that triggered the Each Home Counts review and drove the subsequent establishment of the BSI Retrofit Standards Framework and the development of the PAS 2035 specifica tion for whole-house retrofit. They emphasise that we cannot afford to let our retrofit tech nical standards and good practice processes slip or be eroded. On one large, city-centre estate in the north-east of England, about half of the early twentieth-century two-storey terraced houses were insulated with EWI ten years ago, by a previous and no doubt well-meaning land lord. The original houses are elegant, with bay windows, stone cills and lintels, and attractive brick details. The insulated houses are ugly and unpleasant – the elegant architecture has been covered up, poor detailing has resulted in water staining and mould on the render, and the interiors are damp and mouldy be cause of thermal bridging combined with under-heating and under-ventilation. There is even one street where the houses on one side have been insulated and exhibit all these problems, while the unimproved houses on the other side remain architecturally beautiful and dry, albeit cold. Residents must wonder why the EWI was installed, how it has come out so badly, and why we are even consider ing doing more of it. The first new lesson is that the usual ap proaches to retrofit — external wall insu lation, internal wall insulation (IWI), un derfloor insulation (UFI), air source heat pumps (ASHPs) etc., are often impractical or inappropriate, or difficult to implement. My colleagues and I have catalogued the circum stances that make EWI difficult or impossi ble: the dwelling is listed or in a conservation area, or subject to an Article 4 prohibition; or the architectural quality is high; or the front elevation abuts the public pavement, leaving no space for EWI; or there are side alleys or passageways that are too narrow to insulate; or there are no eaves overhangs to protect the top of the EWI; or the walls are festooned with services whose relocation will be too costly and take too long; or there are simply too many leasehold properties the omission of which would be unsightly and inappropri ate. Similarly, if we consider IWI, what do we do if the kitchens and bathrooms have just been replaced, or have ten years of remain ing life? Sometimes the rooms are too small (especially bathrooms, kitchens, hallways and stairways) and vapour-permeable IWI would be too thick. UFI is rarely affordable when the home is occupied, unless we opt for spray foam insulation applied by robot. Ser ried ranks of ASHPs on high-density terraced housing or medium-rise blocks are unlikely to be acceptable visually, or because of the noise they make; often there is nowhere that isn’t intrusive to put them.
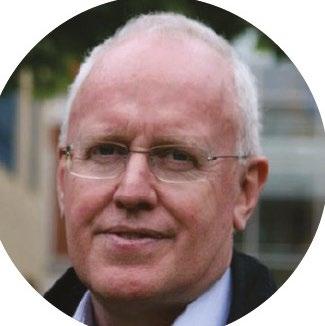
Passive House Institute Certified Mechanical Ventilation with Heat Recovery Systems Brink systems are also fully compatible with Ubbink’s Air Excellent air distribution systems. Air Excellent’s clever, push-together connection system combines unsurpassed ease of installation, with incredible levels of airtightness. Brink. Quiet, efficient and technologically advanced complete MVHR Systems. • Warm, freshly filtered air • Reduced asthma, hay fever and allergy triggers • Lower energy bills and emissions • Guaranteed, Dutch quality • Mould, mildew and condensation • Stale, foul, unpleasant, humid air • Musty and unpleasant odours • High humidity levels Say goodbye to: Say hello to: With Self Balancing technology for better energy e ciencies. Combine your MVHR system with an under oor heating package for even greater savings. Visit www.BrinkHRV.com/under oorheating to nd out more. Coming soon. Under oor heating packages. We only o er designs and systems that are fully NZEB and TGD Part F compliant. Learn more at www.BrinkHRV.com/newbuild Brink and Ubbink are distributed throughout Ireland by Kernohan Distribution. Web: www.iakonline.com or www.brinkhrv.com | Email: info@BrinkHRV.com or info@iakonline.com Intuitive under oor heating packages with high performance Valsir multilayer PEX pipe and smart self calibrating controls from Danfoss.

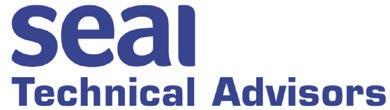
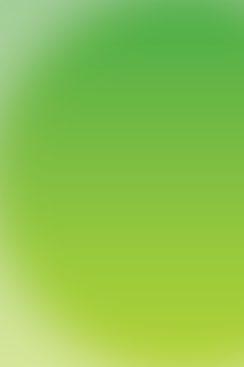
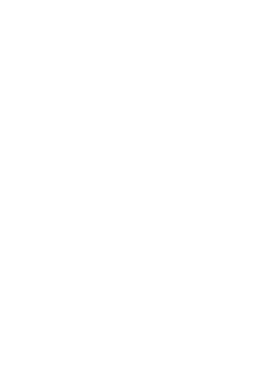

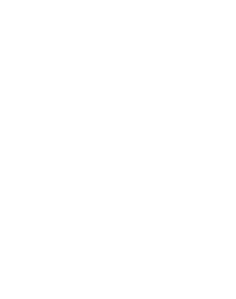
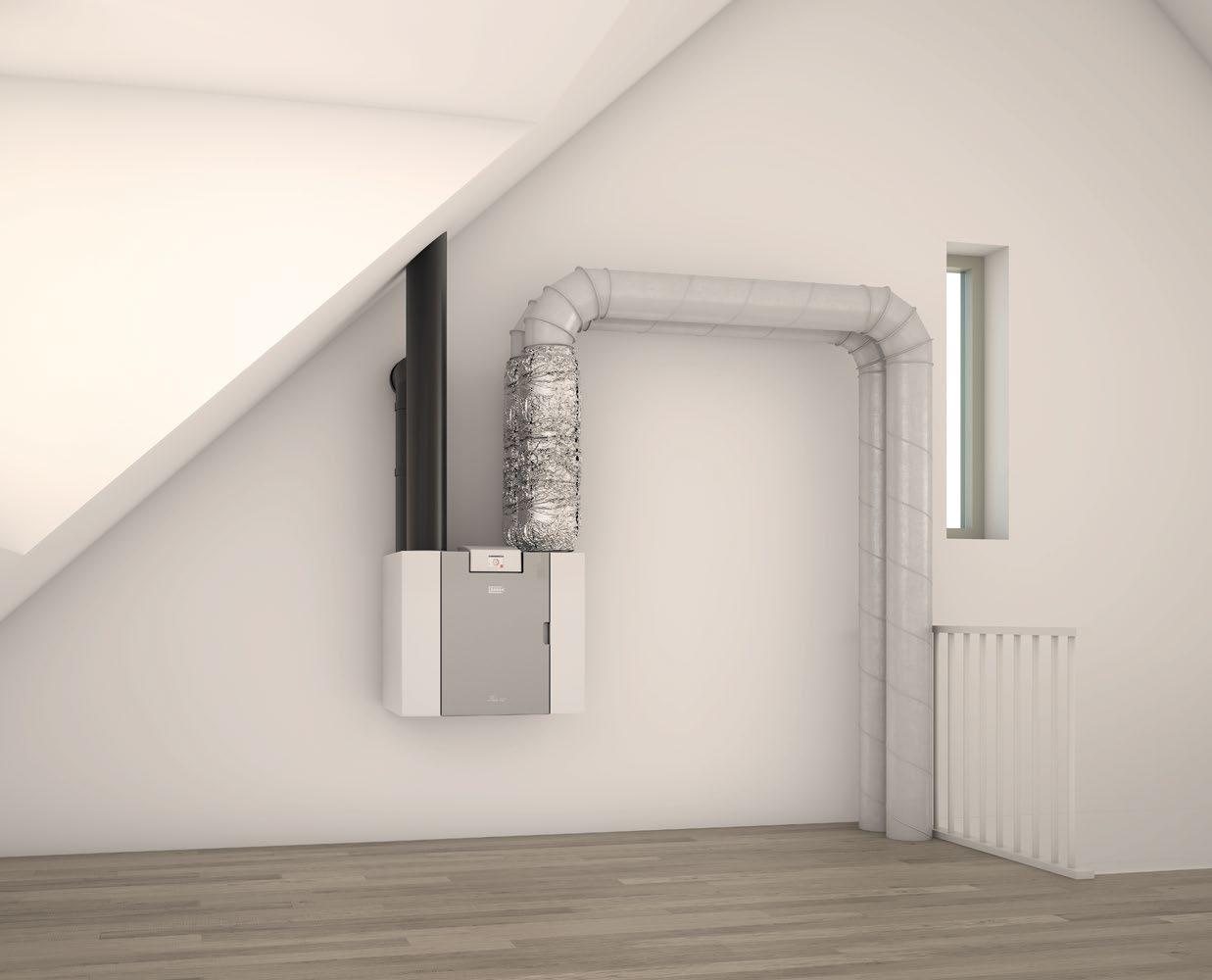
30 | passivehouseplus.ie | issue 42 CLIMATE EMERGENCY COLUMN
3. Creating positive and restorative designs (restoring prior damages inflicted), 4. Improving climate justice locally and globally (no longer exploiting others – human, non-humans and nature).
Almost every architecture project contributes to the climate crisis, embodied injustices and ecological breakdowns worldwide.
D esigning for the Climate Emergency took us over two years to write. In that time, we saw the pandemic hit each country and climate-related records broken in different parts of the world: the hottest temperatures recorded, the longest heatwaves, the worst wildfires, extreme droughts in some parts and floods in others. We heard the Intergovernmental Panel on Climate Change (IPCC) issue a Code Red: a severe warning that climate change is not distant. It is real, and it is already happening. We are in a climate emergency. The urgency and scale of the transforma tion that is needed is unprecedented. This is because globally, we have been burning fossil fuels such as coal, oil and natural gas at an incredible rate and scale. With every degree that global temperatures rise (it is already 1.1C globally, and we’re trying to limit that rise to 1.5C), we risk unhinging ecosystems further, leading to more extreme events and increased loss of lives, livelihoods, homes and cities, and devastation to the natural world. That is why each country is shifting towards a zero carbon or carbon neutral society. Because built environment processes are responsible for around 36 per cent of the CO2 emissions alone, carbon neutrality can only be achieved if we also stop using fossil fuels for the construction and operation of the buildings we design, and transform and start using the available resources we have responsibly on a global scale. And it is not just CO2 that matters: every minute of the day, we use resources that can never again be replenished and that create waste, destroy natural and human habitats, and pollute the air, water and soil we rely on, jeopardising human life and wellbeing, and other species. Design choices we make at our ‘drawing boards’ affect people and communi ties thousands of miles away. For example, we import cheaper materials from regions halfway across the world and ignore the environmental and human costs of doing so. Despite this awareness, almost every architecture project continues to contribute to the current climate crisis, embodied injustices and ecological breakdowns worldwide. Our architectural responses need to be drastically altered. Every single project needs to not only minimise but reverse these damaging processes immediately and create a positive and restorative impact – this is an essential part of a climate emergency design approach. To do this, we must make an urgent shift in the values we hold, and a shift in how and why we do things. This is what our new publication aims for. Our book, which is targeted at architec ture students (which arguably includes each of us as teachers and practitioners too), aims to tackle the quadruple challenges of the climate emergency: 9 781859 469644 ISBN 978-1-85946-964-4
26/01/22 12:27
Why we wrote Designing for the Climate Emergency
1. Ensuring climate change mitigation (ensuring our actions don’t exacer bate the crisis further), 2. Adapting to a changing climate (even if we stop burning fossil fuels today, we cannot escape the effects of a changing climate put in motion more than one hundred years ago),
Focussing on holistic design approaches through 10 key themes, it will help you integrate into your design projects consistently high values from all areas of sustainable architecture. Structured around the different stages of the design process through five illustrated chapters, it highlights what you need to consider when developing a project and when to think about it. Reflecting what is required by years of study, it outlines what a year 1 or year 3 student should be aiming for. This provides step-bystep guidance, preparing you for architecture practice. Unique features include: key recommendation checklists, measurements against the UN Sustainable Development Goals, readings, case studies, student examples, notes and an extensive glossary. Become inspired and more confident to build a sustainable tomorrow.
Over the last century architects have unwittingly played a key role in terms of climate collapse and a slew of linked catastrophic environmental and social harms. But as the new book 'Designing for the Climate Emergency - A Guide for Architecture Students' explains, architects can help humanity step back from the void by integrating evidence-based sustainability approaches throughout their work. Co-authors Sofie Pelsmakers, Elizabeth Donovan and Aidan Hoggard shed some light on the thinking behind the new guide.
Climate change is not distant. It is underway. We are in the midst of a climate emergency. Architects can – and must be – part of the radical change needed, and we must understand the impact of local decisions on the global scale. This book guides you as an architecture student to create truly sustainable designs, reflecting the urgent need for action. It tackles the quadruple challenges of the climate emergency: • Adapting to a changing climate • Climate change mitigation • Creating a positive and restorative design • Improving climate justice locally and globally.
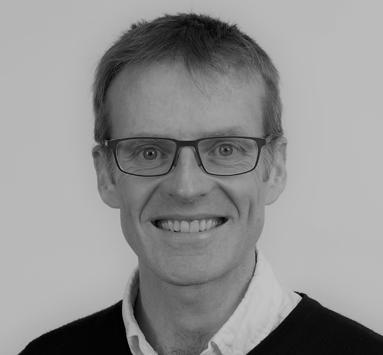
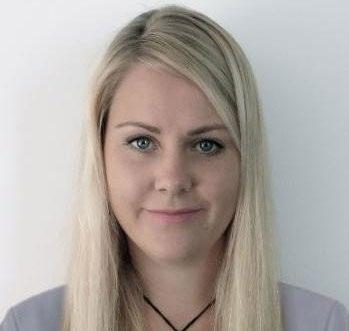
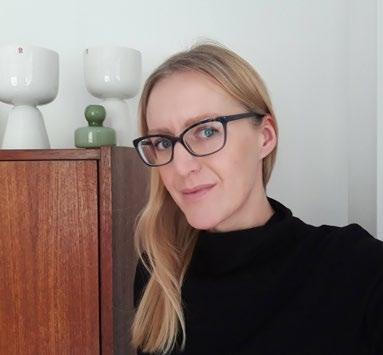
While the book provides a wealth of information, it does not focus on simply providing more knowledge and more information. Instead, it focuses on the right questions that students should be asking and when; what information they need, and the actions and decisions they need to take at these different stages of the design process. To help students do this, there are around thirty key recommendation checklists to use throughout the design process and related to different climate emergency themes; a selection of two hundred listed case studies; a glossary and key notes to further explain the text. There are also around two hundred images, half of which illustrate student approaches from the UK, Denmark and Finland. The book aims to instil sustainable values that go beyond the visible and calculable impacts of our own design decisions, and bring into focus the architects’ future and global responsibility. The future and global responsibility theme covers climate and social justice issues. The book also questions whether we should build at all, putting circular construction principles at its core (e.g., retrofit, adaptability, designing for disassembly) as well as future-proofing for a changing climate. In architectural education it is important to emphasise that designing sustainable architec ture and zero carbon buildings means little if this is only achieved on paper and if these standards are not met in reality, once the spaces are handed over to the users. As such, in the performance theme, we recommend that students create a ‘performance risk plan’ as part of their project to map out the project’s ‘risk areas’ (see Figure 2). By ‘performance’ we also do not simply refer to energy and CO2 (i.e., related to building and systems perfor mance) but also to users’ well-being, satisfac tion, and spatial and material performance. Our design decisions should be based on knowledge and the best available evidence, with foundations of how to achieve this provided in chapter one. However, we cannot claim our proposed designs are sustainable without evaluating if this is the case. While we cannot know for certain whether our designs work until they are built and used, we can do our best at the design stage to ‘test’ and ‘validate’ our designs. Validation means testing and checking if our project meets the sustainability goals we set in earlier design processes. In our book we focus on how students can set these goals early on, and a whole chapter is dedicated to valida tion and communication of these goals and approaches throughout the design process, illustrated with student examples. Other themes also aim to shift the role of the architect and the role of architec ture towards co-creating with others, and centring the needs of people and communi ties (including non-humans and nature, rather than centring ourselves or for recogni tion in outdated architecture awards. This is not to say that architectural contributions should not be delightful (delight is one of our ten core themes), but it is focused on the user and their experience. As architects, we are co-creators and custodians of the built environment. We can – and must – be part of the radical change needed, and we must understand the impact of local decisions on the global scale. There is no room for error. Instead of seeing this as alarmist or an attack on our creative pursuits, it requires determination, conviction and optimism to trust that we are part of the solution, not the problem. And it requires us to reframe what architecture is, with more, not less, creative thinking. Our book is both a call to action for students and teachers to urgently reframe our values and culture as well as a tool to help achieve it. n
ph+ | climate emergency column | 31 COLUMN CLIMATE EMERGENCY
identifiedPotentialrisk Implications How likely is it to occur? (likely, unlikely) Solution Implementedstrategy windunknownspeeds unclear if wind energy as proposed will be feasible likely; wind speeds in urban areas are often not high enough to make wind energy feasible try to haveduration;sitewindspeedmeasureonforashortproposealternativere-newableenergy;backupplan,andplanforboth alternativestrategyproposed
At the core of the book are ten climate emergency themes (see Figure 1), which are mapped against the UNSDGs and RIBA 2030 Sustainable Outcomes metrics, of which energy and CO2 is one theme. But our book goes beyond energy and CO2 solutions, ensuring that consistently high values in all areas of sustainable architecture are integrated into projects as part of a holistic approach to dealing with the climate emergency (see Figure 1). Often as architects we claim that our projects are sustainable, but they have rarely been holistically sustainable, tackling only certain aspects and neglecting others. By the end of studies, a student should be fluent in applying all themes in their design projects, as this is what is also necessary in practice.
(above) Figure 1. The ten climate emergen cy themes in which high standards must be achieved (left image): future and global responsibility, infrastructure, environment, passive resilience, energy and CO2, ma terials, health and wellbeing, people and community, delight, and performance. The middle diagram indicates that to achieve holistic sustainable architecture, certain sustainability aspects cannot be prioritised (large red petals), at the expense of reduced standards elsewhere (the red dotted lines with smaller red petals). Instead, all aspects must meet high standards, even when some themes are prioritise. Designing for the Climate Emergency - A Guide for Architecture Students, published by RIBA Publishing, is out now. Authors: Sofie Pelsmakers, Elizabeth Donovan, Aidan Hoggard & Urszula Kosminska (below) Figure 2. Example of a ‘performance risk plan,’ which can be used as a template for understanding and reflecting on the potential risks within a project.
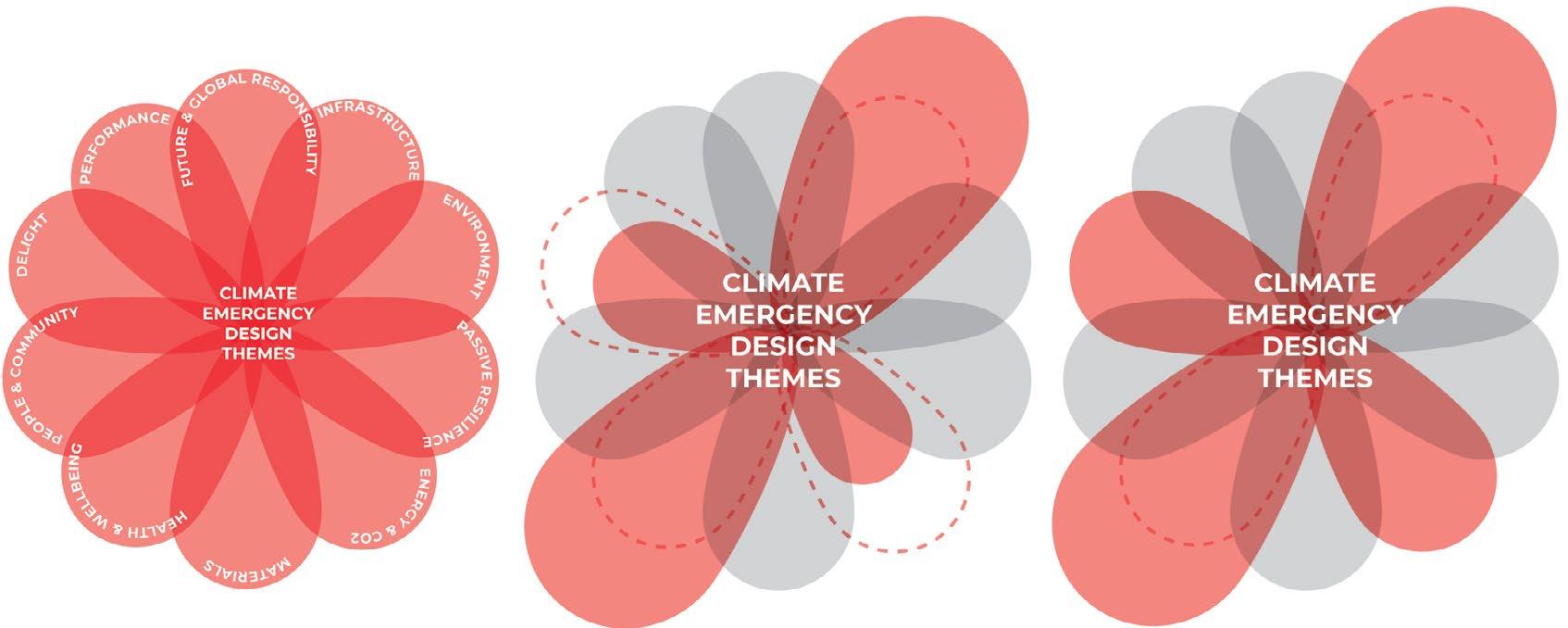
One passive house in Claregalway shows that – with a little help from Passive House Plus – concrete product manufacturers can make meaningful moves in the right direction.
With emphasis in sustainable building shifting towards reducing embodied carbon, an obvious question comes into focus: is this an existential threat to the concrete industry?
BLOCK BUSTER GALWAY PASSIVE HOUSE BIRTHS LOW CARBON CONCRETE BLOCKS
By John Cradden
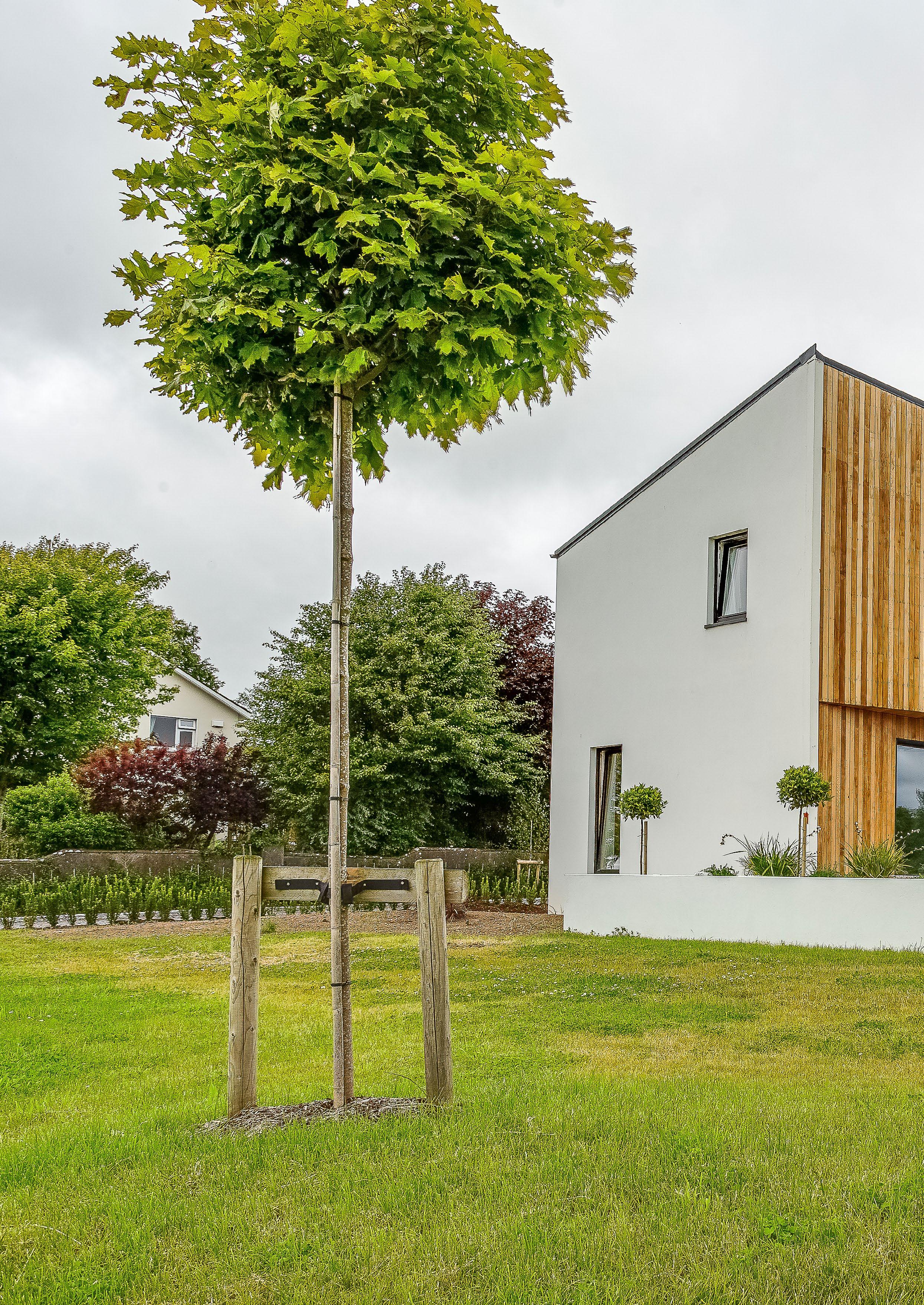
33 IN Building:BRIEFDetached 260 m2 cavity wall house Method: Cavity wall Standard: Passive house classic certified Energy bills: €79.50/month total energy costs including standing charges and VAT. See ‘in detail’ for more. €79.50 per month
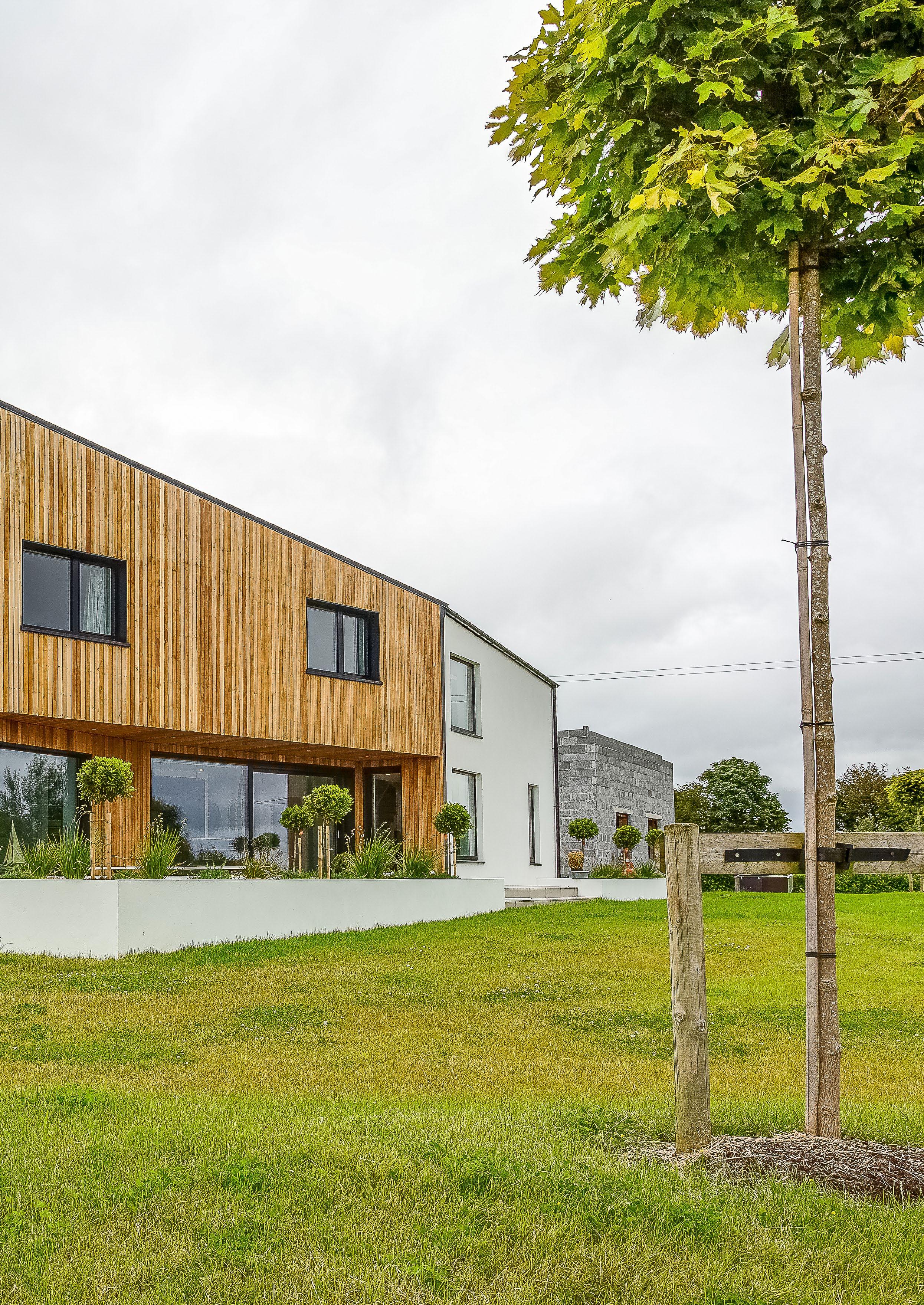
lack of work at the time pushed him into jobs as a BER consultant. He trained in a number of other areas, including airtight ness testing and, later on, passive house design, while setting up his own company Hession Energy. He had also worked with Robin Mandall Architects providing consultancy services, and had seen and loved Brendan Money’s work on a number of small residential proj ects. Despite having never worked on a pas sive house, Hession persuaded Money to take on the project and gave him practically a blank canvas to design a four-bedroom house with open-plan living areas — but not before briefing him on a few key prin ciples to make it work as a passive house.
34 | passivehouseplus.ie | issue 42 WAYNE HESSION CASE STUDY
I t’s sometimes thought that using tradi tional construction methods and largely standard details to build a new, passive house-certified home would be a (thermal) bridge too far for most Irish builders. Passive house designer and owner of this impressive new, four-bed, 260 m2 certified passive house in Galway, Wayne Hession, did consider using timber frame and other methods perhaps more suited to meeting the onerous build and detail standards re quired. But between himself and Brendan Money of Robin Mandall Architects, they chose to use traditional masonry cavity wall construction mainly for cost reasons and access to local skills. “Everyone that was involved working in the house was either a friend or cousin or someone I’ve worked with,” he said. Hession had spent some 20 years work ing in construction as an onsite engineer in England and Australia, before returning to Galway in 2014 with plans to build a new home on a site that’s been in his family for nearly 30 years. He planned to continue working in the sector on his return but the Hession managed to persuade Coshla Quarries to make blocks for him using GGBS
According to Money, these principles were to limiting north-facing openings, re ducing solar gain by shading to the south, keeping the form compact and stacking the service rooms i.e., bathrooms and util ity“Therooms.site was a relatively level field, so it made sense to position the house to the northwest to take advantage of solar gain,” says“TheMoney.form we developed respected the existing building line along the lane but we cranked the plan to orientate the form to the south more. The form is compact and deep on the northeast side, but the ridge line runs diagonally across the plan so that the roof begins and ends as a monopitch roof which reduces the impact of its Withvolume.”fewerwindows on the north side, the result is a building that opens up to wards the south and into the massive lawn, with the timber and overhanging areas con
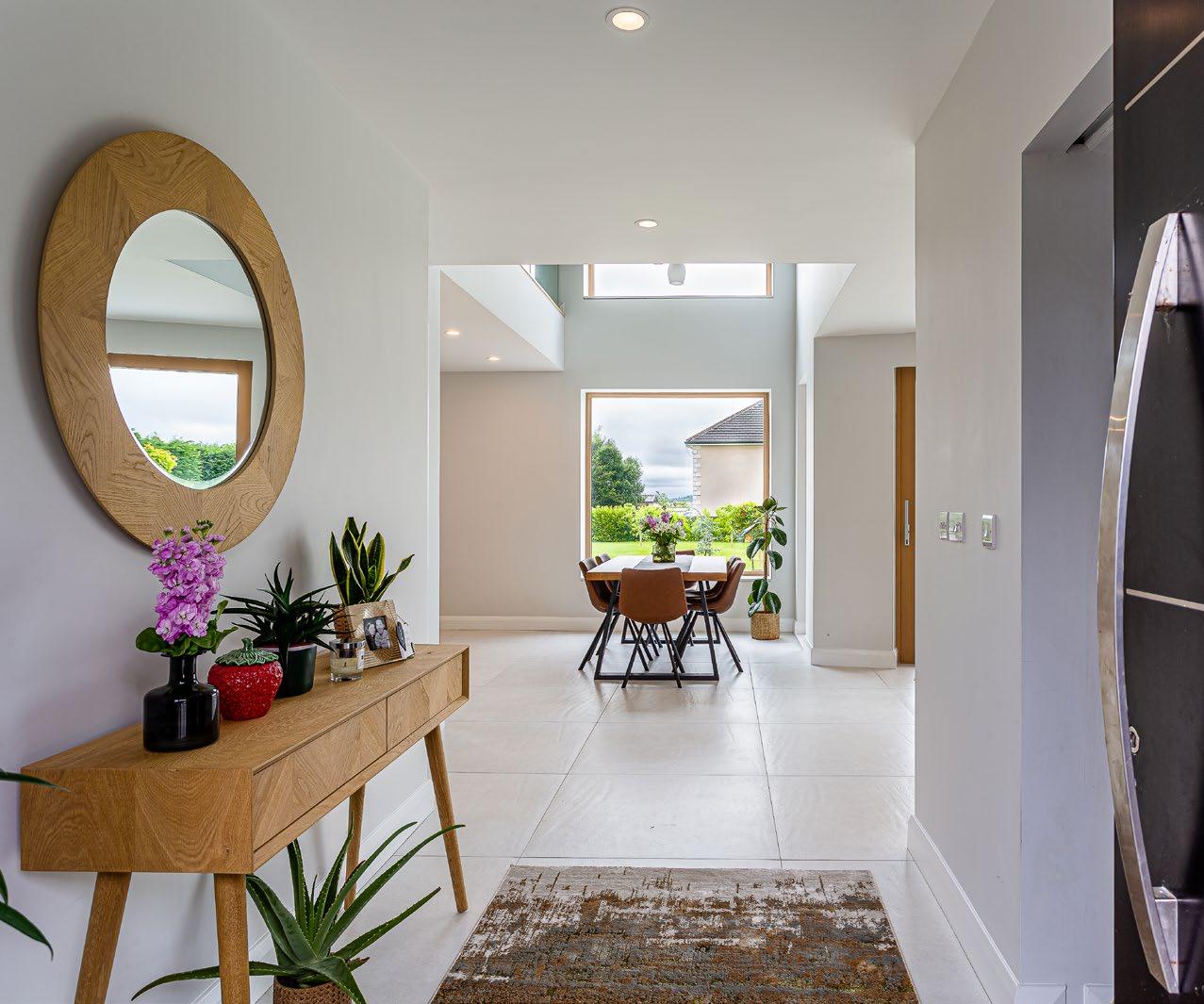
The digital version of this magazine includes access to exclusive galleries of architectural drawings. The digital magazine is available to subscribers on passivehouseplus.ie & passivehouseplus.co.uk
Another innovation found inside Hes sion’s home is a system which combines ventilation with air-based heating and cooling, from Galway-based ventilation manufacturer ProAir. The intention was to install ProAir’s standard heat recovery ven tilation system: the Passive House Institute certified PA 600LI unit. But the company’s CEO, David McHugh, asked Hession if he would consider a new product made in the Czech Republic called the Jablotron Futura, which integrates an air-to-air heat pump to the ventilation system to offer air-based space heating and cooling. Intriguingly, the system uses sensors in each room to offer demand control – for instance ramping up ventilation rates automatically in response to spikes in CO2 levels in particular rooms.
When the project was at design stage, Hession and Money met with Passive House Plus editor Jeff Colley, who suggested that a good way to reduce the carbon footprint of the build was to use concrete blocks made with 50 per cent of the cement substituted for Ecocem’s GGBS (ground granulated blast furnace slag), a steel industry by-prod uct that has independently verified embod ied carbon figures of up to 95 per cent lower than Portland cement. One obstacle that GGBS has always faced is the accusation that it can increase the curing time for con crete when added at higher percentages – an argument used to rule it out of use in block work manufacturing, where achieving early stage strength is key to enabling blocks to be lifted and batched, to avoid slowing down production. But Colley had learned that the architect Darragh Lynch specified blocks with 50 per cent GGBS on a phase of Bally mun Regeneration in 2012, with blockwork manufacturer Kilsaran using their curing chamber – a feature most blockwork man ufacturers don’t have – to make the blocks without a hitch. Hession got the bit between his teeth, and approached Martin Collins, general man ager of Coshla Quarries in Galway, to run the idea by him. Aided by Ecocem, who de veloped an accelerant to enable GGBS to be added at high percentages for typical open air blockwork curing facilities, Coshla man WANT TO KNOW MORE?
Hession says they have been using the sys means that we have all this beautiful space.”
ph+ | wayne hession case study | 35 The details are similar to how all masonry cavity wall houses are built necting to the inside. “We let the constraints become the driver,” says Money. Money’s first attempt at the design un doubtedly met with Hession’s early approval. “I didn’t give him examples. Didn’t give him briefs. Didn’t give him photographs. Pretty much what you see is what he designed first time around,” says Hession. Internally, there are a series of living spaces that link to a mezzanine room through a double height space over the dining table. “Through shifts in the geometry and chang ing, the rooms are interconnected and open but have their own distinct character and presence,” says Money. Hession is pleased that Money man aged to incorporate open-plan living areas but also that the house was situated as far north as possible to expand the extent of the south-facing garden, in contrast to many other houses where architects tend to plunk the house straight and centre. “It basically ufactured 50 per cent GGBS high density concrete blocks for Hession. Aiming for 13 newton strength, independent compression tests showed results of 17 to 22n. Given the continuing domination of concrete as the primary material in Irish construction, Hession believes more effort should be put into promoting the use of GGBS and other eco cements. “If the find ings are that you’re reducing roughly by 50 per cent the carbon footprint for a block build, that’s massive,” he said, adding that GGBS often doesn’t figure much in ICF (insulated concrete formwork) where large volumes of reinforced concrete are involved.
Photos: Stefan Hoare / Sheelin Photography
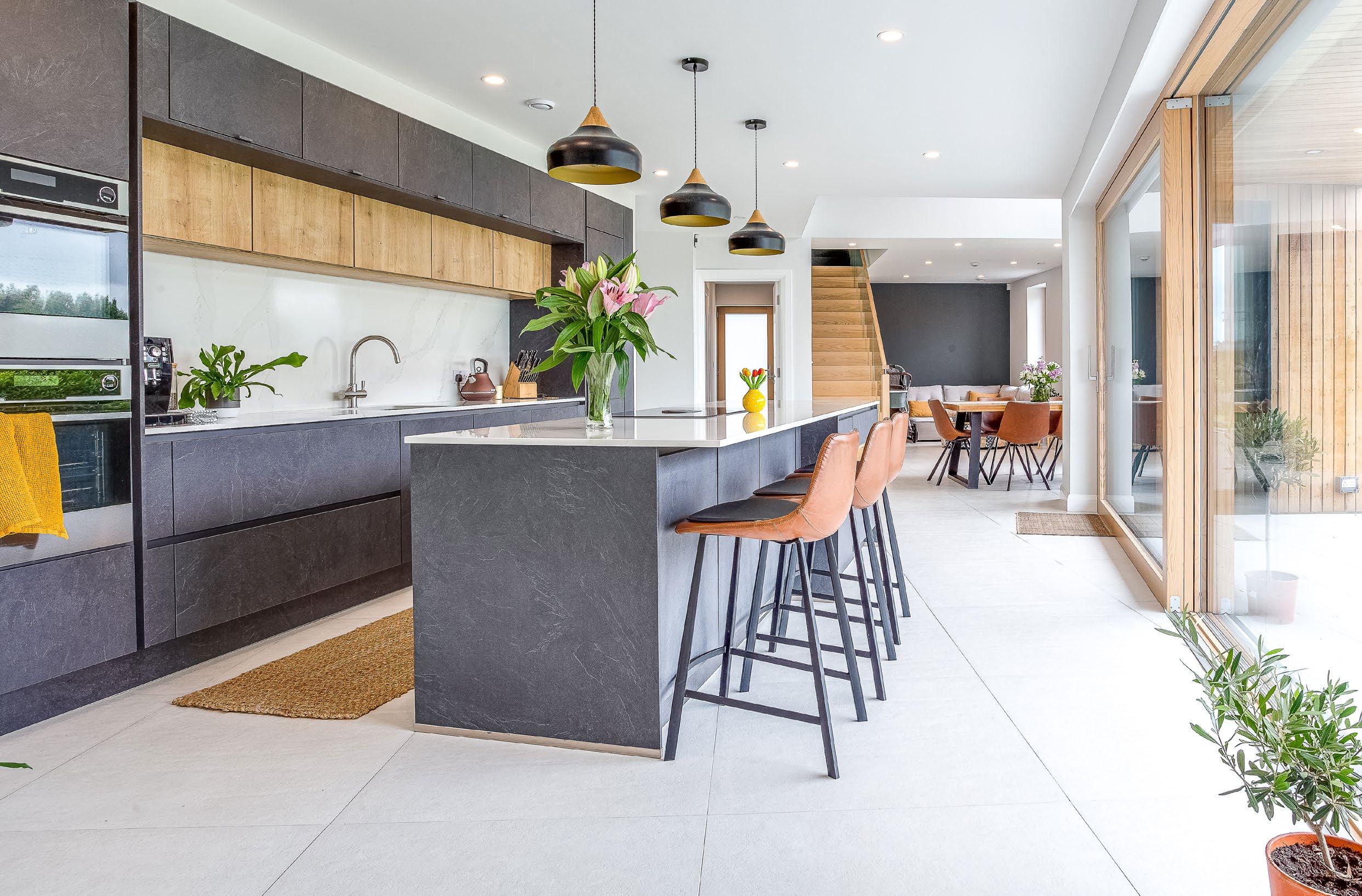

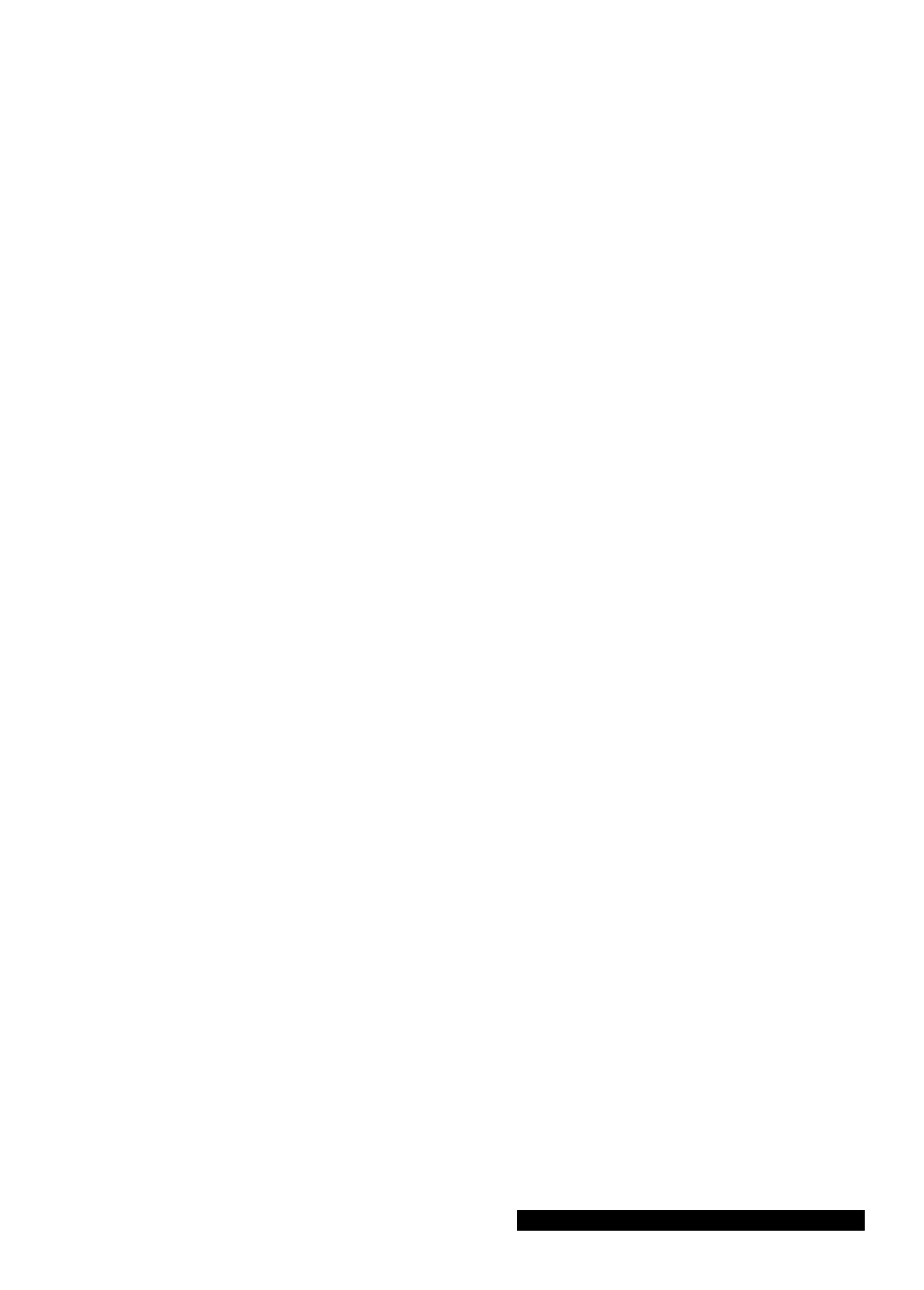
While Money’s involvement with the construction was limited, the geometry of the roof was a real challenge that required some refinements from him as the build pro gressed. “Easy to draw but hard to build,” Money says. “We provided a detailed set of drawings to set it out and the timber roof structure, with a lot of thinking, worked out. At the last moment, the plan to use an interlocking slate was abandoned as it was too complex to use. But to give Wayne his credit, he worked his way through the chal lenge we set.” The company supplying the interlocking slates said the pitch of the roof was right at the threshold for the warranty, so Hession decided to go with a Greencoat PLX colour-coated steel finish. When they eventually moved in, the dif ference in temperatures between his parent’s 1970s built bungalow and his new home took a bit of getting used to. “The average They haven’t ever turned on the heatingunderfloorupstairs
tem for active cooling recently because his wife Michelle is pregnant, and he describes it as very responsive. The house didn’t exceed 24C during the mid-July heatwave. Hession had already specified an air-towater heat pump system for heating, so the Futura is used only for cooling. One teething issue relating to filters led to the system hav ing to be switched off for a few weeks, but sensors installed as part of an NUI Galway air quality monitoring project in A-rated dwellings certainly illustrated how essential heat recovery systems are in airtight houses. “Basically because the filters were from the Czech Republic, during Covid we couldn’t get them so we had to turn off the HRV for about five or six weeks. About three or four weeks into it, James [McGrath] from NUIG got in contact and asked was everything all right? He could tell from the data that our CO2 and humidity levels were off the chart.”
ph+ | wayne hession case study | 37 CASE STUDY WAYNE HESSION
SELECTED PROJECT DETAILS
Clients: Michelle & Wayne Hession Project management: Wayne Hession Interior design/layout: Michelle Hession Architect: Robin Mandal Architects Ventilation: Partel Concrete blocks: Coshla Quarries GGBS: Ecocem Roof timber work: Long Life Structures Roof finish & cedar cladding: PJ Duggan Roofing Window and doors: J&N Windows Block laying and concreting: Dara Hession Block Laying Structural engineer: Charlotte Murphy Consulting Engineers Plumbing: Martin Duggan Plumbing Airtightness products: Siga Passive house certification & thermal bridge design: Earth Cycle Technologies Ground floor & cavity wall insulation: Xtratherm Heat pump: Firebird Ventilation & cooling: Jablotron, via ProAir Roof insulation: Dammstatt cellulose, via Ecological Building Systems Additional roof insulation: Isover Thermal breaks: Mannok, Puren Roof windows: Velux Landscaping: Mike Ryan Landscaping
The self-build took two years, which was just enough time to move in before Covid began in 2020. “I think when you take your time building, you have a lot of time to iron out a lot of issues,” he said. The hardest physical job was building the first floor, which involved installing Peri formwork, tying all the reinforcement and pouring the Ecocem GGBS concrete. “My self and my brother used to work in Western Australia on large concrete projects so that’s why we decided to do it ourselves.” In general, though, the build systems employed were fairly standard. Passive house U-values were achieved through using a cavity wall with 150 mm full fill insulation. Similarly the floor and roof use methods of construction that are common to masonry housing. Hession modelled all the junctions for thermal bridging and generally used Man nok thermal blocks to eliminate thermal bridges. The junction details did not differ that significantly from the acceptable con struction details (ACDs). There was initially a large thermal bridge between the soffit and the wall at the cantilevered section above the kitchen, but this junction was re-designed by Bob Ryan of Earth Cycle Technologies, and the thermal bridge eliminated. “I had imagined when we began that the passive house standard would mean elabo rate detailing using specialised products to overcome thermal bridging, but this was not the case and the details are similar to how all masonry cavity wall houses are built,” says Money. “It helped that Wayne ensured the workmanship was exceptionally good. Good airtightness is also remarkably easy to achieve with well-built masonry construction. “What I learned from this process with Wayne was that a passive house is not that much of a mystery. Using standard tech niques and details, and following the basic principles of passive design, it is readily achievable. I think there is a common per ception among architects that passive houses look the same way; small windows and a dull form dictated by minimising the building envelope. I’d like to think we have shown this is not the case and furthermore, stan dard materials and techniques can also be used to create a passive house.”


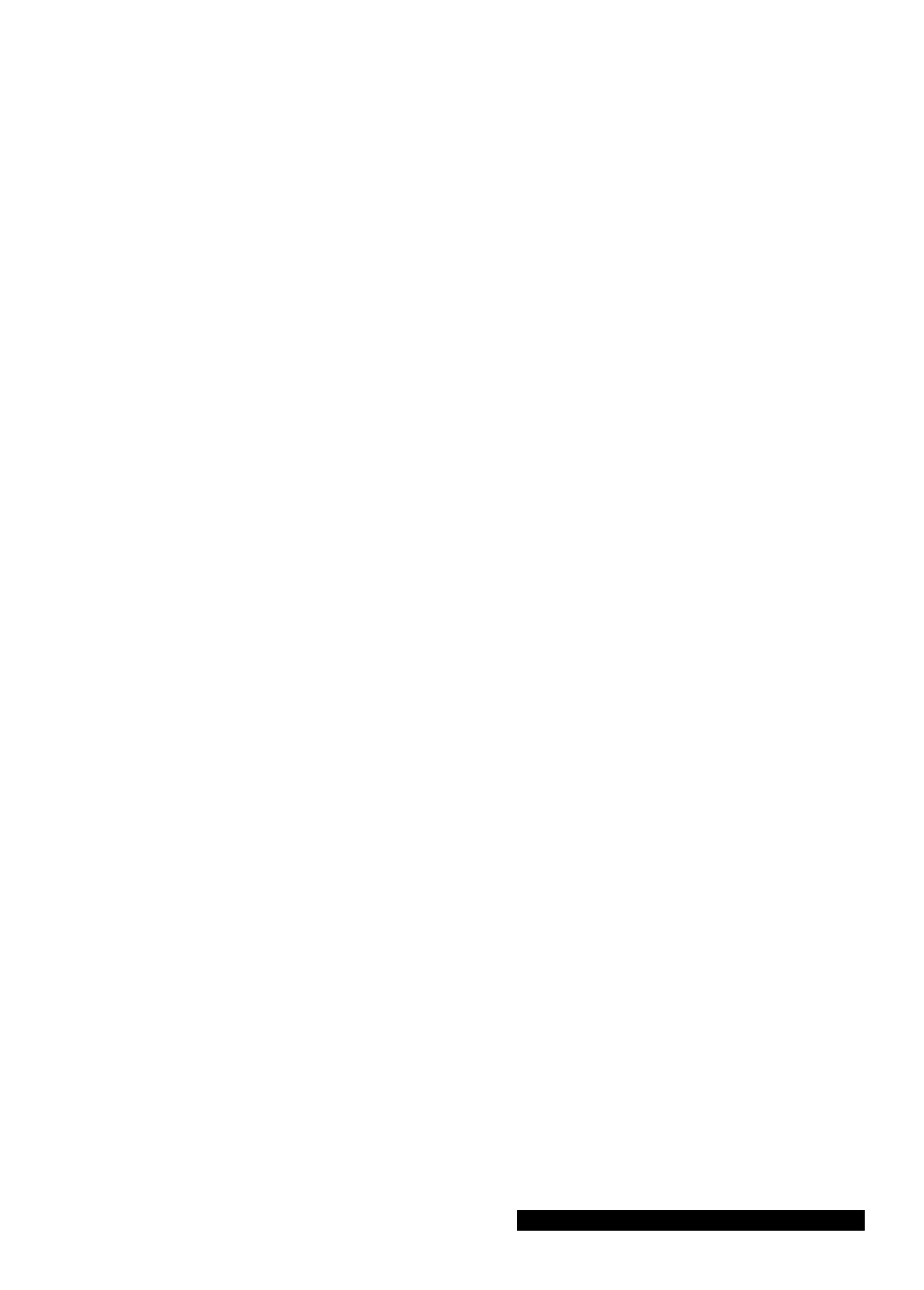
38 | passivehouseplus.ie | issue 42 38 North Point Business Park, New Mallow Rd, Cork City Bluebell Industrial estate, Bluebell, Dublin Sustainable Design, Energy Efficient, and Virtually Zero Maintenance 56b Briarhill Business Park, Briarhill, Galway WINDOWSNORDAN & DOORS With secured by design accreditation and weather performance far exceeding the standard, it’s clear that no one can like NorDan can. Visit our showrooms in Cork, Dublin or Galway to experience the NorDan difference first hand www.nordan.ie
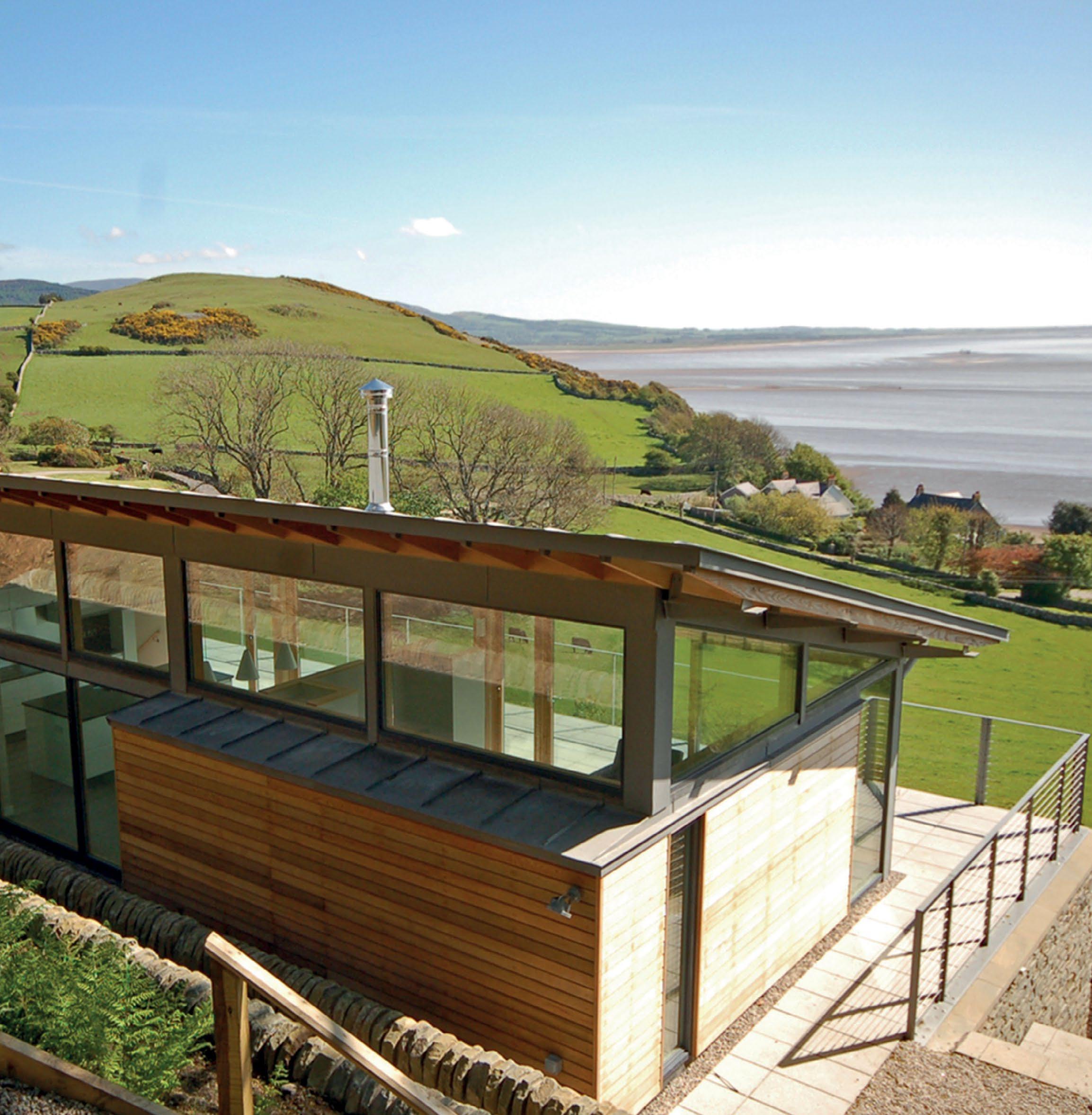
ph+ | wayne hession case study | 39 CASE STUDY WAYNE HESSION temperature [in his parents’ house] was around 18 or 19C and then all of a sudden we went into this house where even now, the temperature is always comfortable even with heating off for two or three months. But you do get used to it.” They haven’t ever turned on the underfloor heating upstairs, they just turn on the ground floor heating at night, every second or third night, during the cold est months of the year. Hession is still doing work on the land scape and building an adjoining garage, projects that will likely take another two or three years, and which include a long term plan to form berms and plant trees to pro vide shelter from the wind. For now, the house is already sheltered from the worst of the energy price rises to come. For the first 12 months, the all-elec tric energy bill came in at under €960 for the year, but they’ll surely only be paying not much over a grand in 2022. 7 8 9 1 23 4 5 6 1 Reinforced concrete raft foundation with 60 per cent Ecocem GGBS; 2 two courses of Mannok blocks at inner leaf; 3 150mm Xtratherm full fill cavity insulation; 4 Mannok blocks around window openings; 5 Purenit thermal breaks under sliding door; 6 Blowerproof airtight paint at the floor to external wall junction; 7 Xtratherm insulated floors and upstands; 8 Siga Majrex airtight membrane over 320 mm deep rafters at 600 mm centres; 9 rafters filled with cellulose and 100 mm metac insulation in the counter battens.
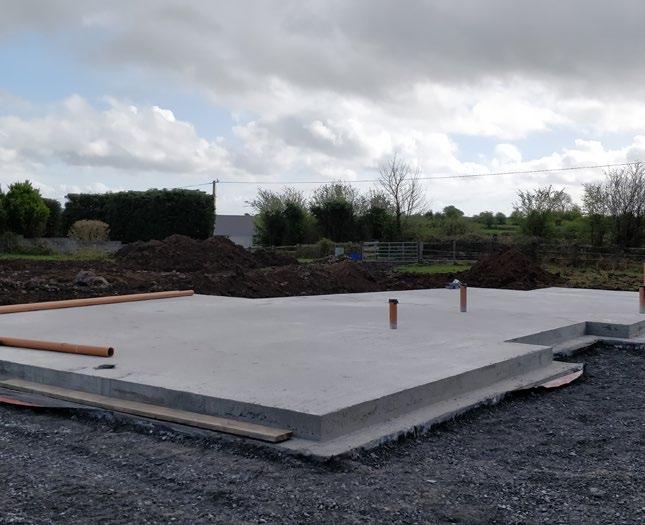
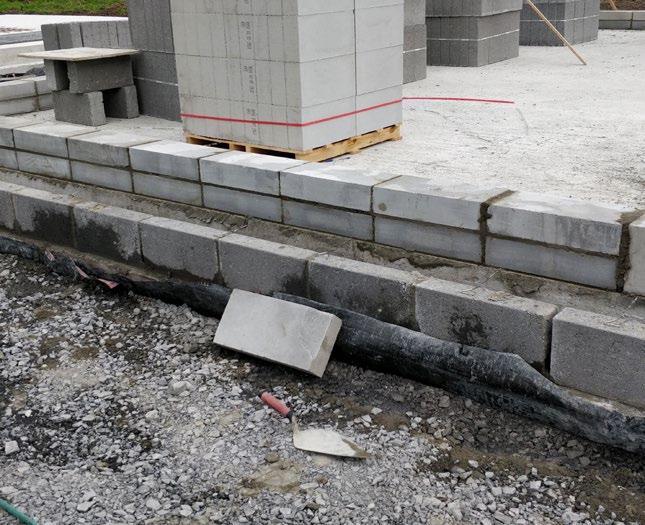
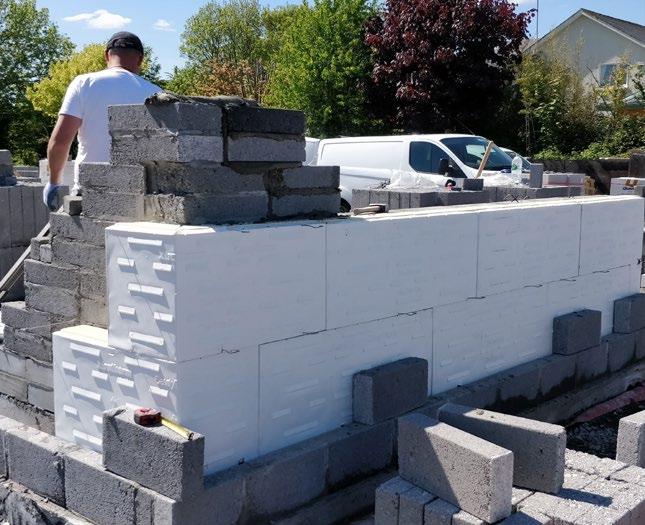
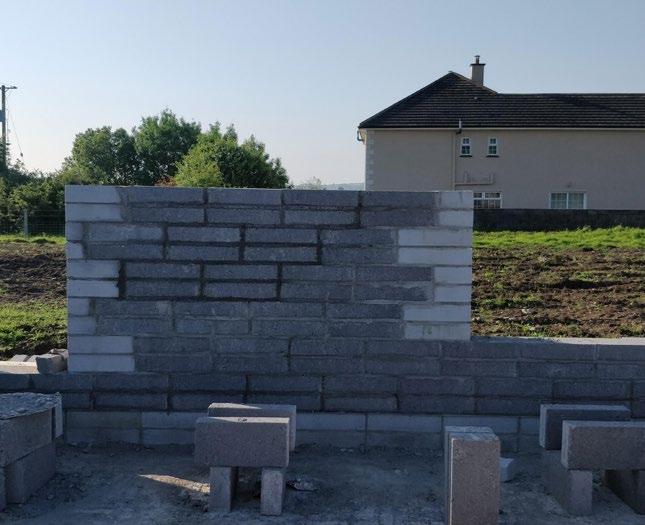
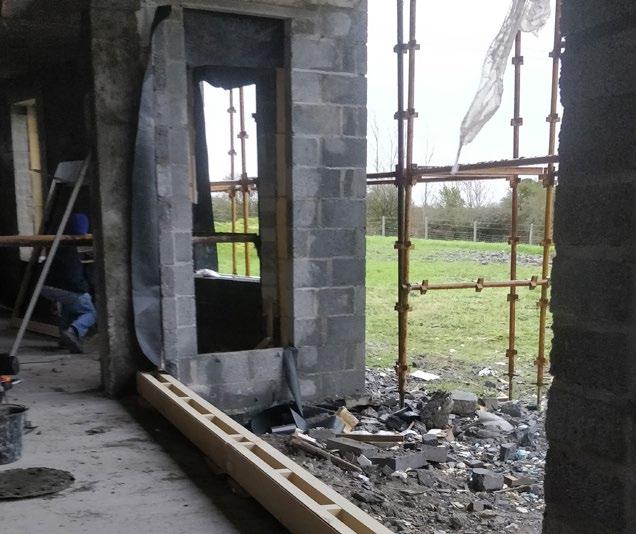
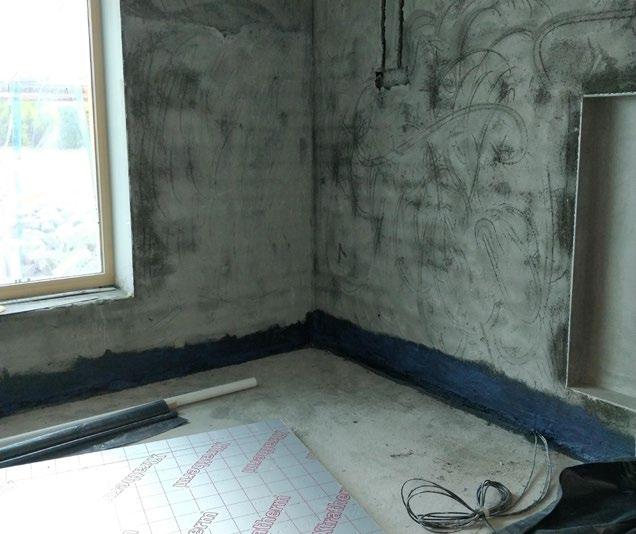
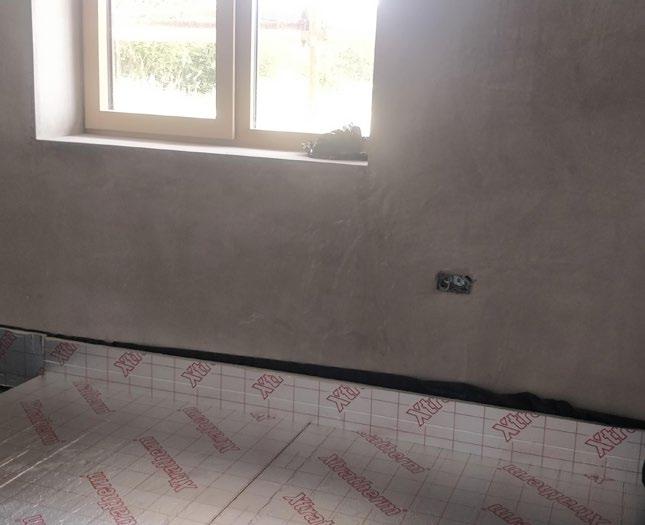
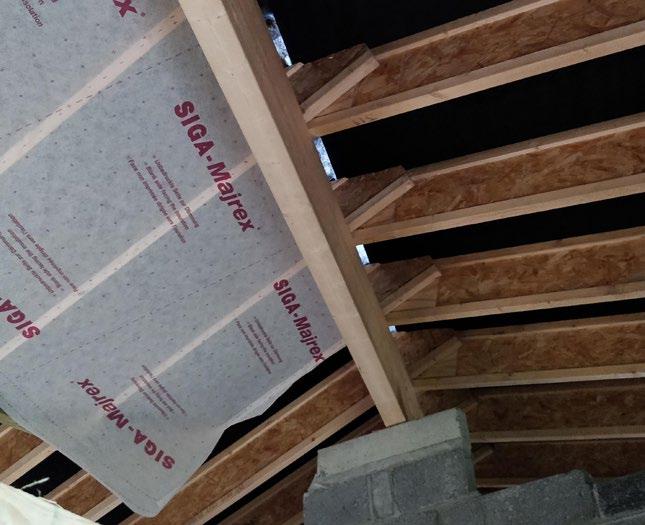
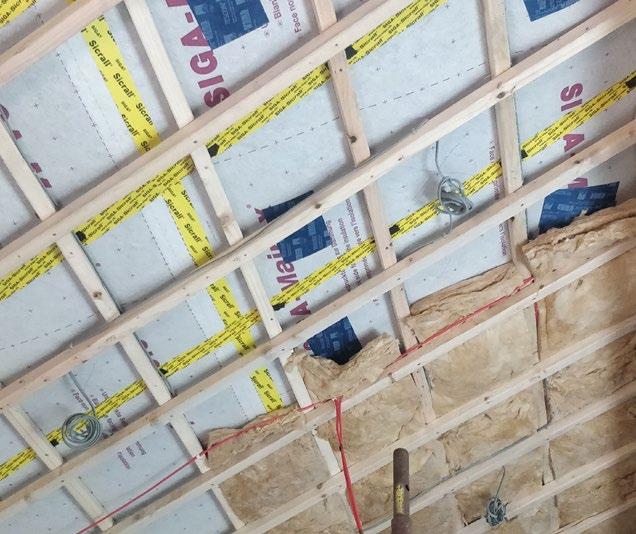

Climate Challenge Over 50% reduction in packaging materials* Halogen free formulation Reduction of onsite waste Improved thermal performance of 0.020
We are on a path of continual improvement in the sustainability of our products, working with our partners in design and construction to meet the most stringent targets for the construction sector such as the RIAI 2030 Climate Challenge. 2030 W/mK
40 | passivehouseplus.ie | issue 42 Visit xtratherm.ie to view the full ECO360 range Our best performing insulation to date is not only bio-enhanced, but is also designed to integrate with the most energy efficient building methods. *Investment in recycling technology will see Xtratherm reprocessing waste raw materials, resulting in up to 30% of recycled raw material input into new products, by 2026.
Bio-degradable packaging materials Download XCO2CarbonEmbodiedReport
Reset circularto Meets RIAI
Xtratherm is commited through our investment in R&D to be a leader for sustainability & circularity in our industry.
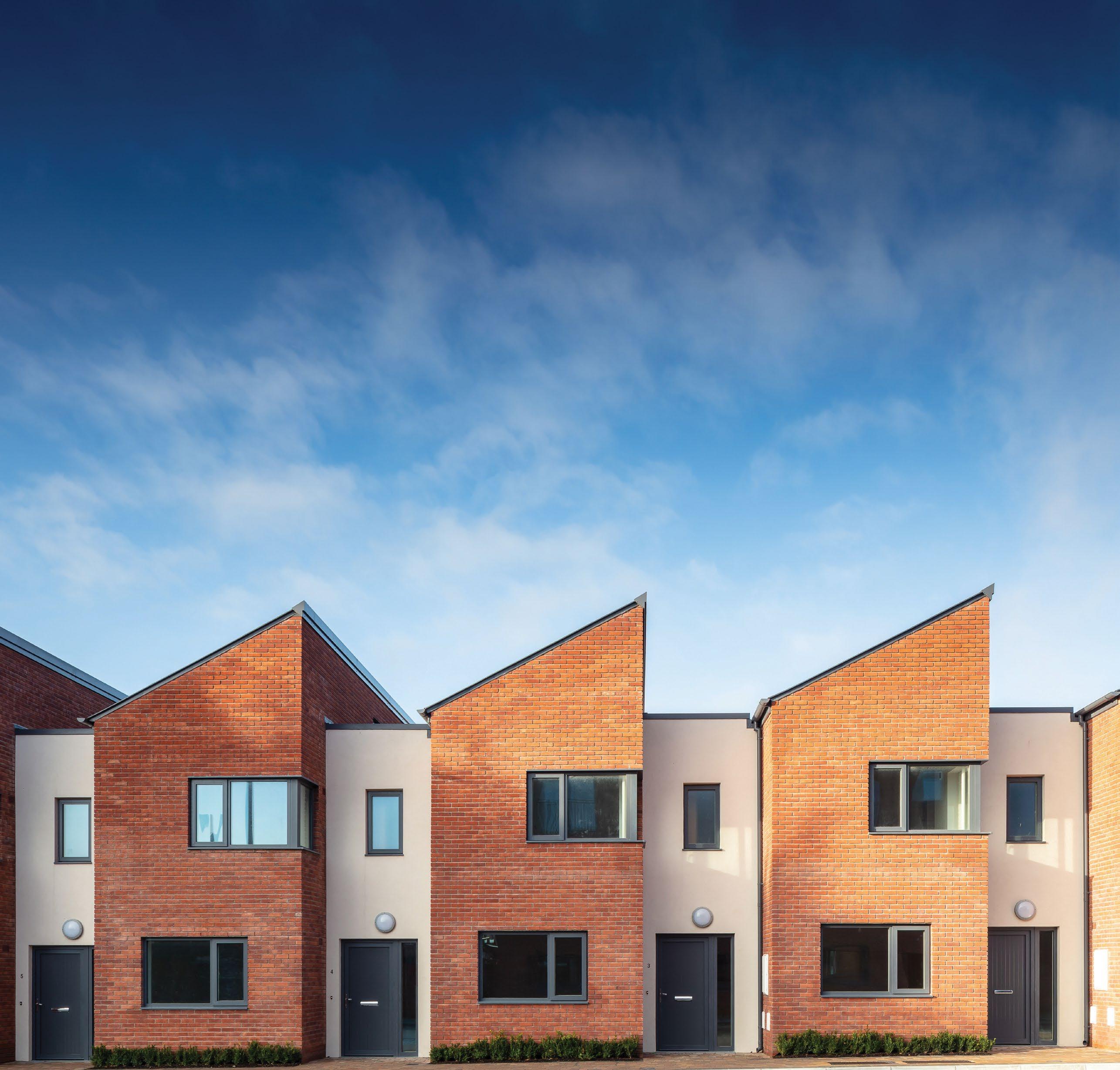

The net result: the building scores just under 97 tonnes of CO2e, or 373 kg CO2e/m2 GIA, indicating it’s likely to beat the RIAI 2030 target of 450 kg CO2e/m2 GIA for homes of over 133 m2. While decisions taken with the project regarding GGBS use greatly helped to reduce the embodied carbon, there’s no doubt that the house benefits from its comparatively large size, when considered against the RIAI’s target for homes above 133 m2 – a perhaps unfair advantage, given the house comes in at more than twice that size threshold.
EMBODIED CARBON By Jeff Colley
The Hessions plan to install a solar PV array of at least 6 kWp, and this was factored in. Assuming the low est embodied carbon result for a PV monocrystalline module – the Sun power Maxeon 3, the modules would add two tonnes to upfront emissions, a figure which would be assumed to double over the building’s full lifes pan, assuming the array is replaced once within that time. If a higher em bodied carbon module is used instead, the total for PV could quadruple, and increase the whole building embodied carbon total by over 10 per cent.
The staircase, balustrades and internal doors were omitted. Windows were in cluded – albeit relying on data from a similar product with an EPD - as was all insulation and thermal breaks, and approximations in case of the main building services items. In the absence of an EPD for either the Jablotron Fu tura unit or Enviroair air-to-water heat pump, data was taken from the closest available certificates – a Product Eco Passport (PEP) for a 4 kW compact unit, and an industry association ge neric PEP for air source heat pumps.
Spurred on by PHribbon creator Tim Martel, I took on the challenge of at tempting to calculate the embodied carbon of the Hessions’ house myself, using PHribbon. It proved an insight ful process made more challenging by the absence of robust, independently verified data for the project’s main em bodied carbon innovation: the low car bon blockwork. I felt some degree of personal respon sibility to establish the benefit of this specification given that I had suggested low carbon concrete blocks to Wayne in passing, without expecting him to find a blockwork manufacturer willing to make them. Irish EPD consultant Peter Seymour of Eco Review kindly assisted me by putting some indicative calculations together, looking at manu facturing stage emissions, based on the blockwork recipe used by Coshla. The results are striking. Had all cement in the blocks been CEM I Portland Ce ment, the total per m3 of blocks would have come to an estimate of over 145 kg CO2 per m3. But the 13 newton blocks used contained 50 per cent GGBS, and 50 per cent CEM II cement, virtually halving the estimated carbon footprint, with a score of 73.8 kg CO2 per m3 This decision alone resulted in a net saving of over 6 tonnes of CO2 for the house. 60 per cent GGBS was used in the ground floor slab, and 50 per cent GGBS in the first floor slab, resulting in an estimated reduction of circa 13 tonnes of CO2 compared to CEM I slabs. Almost three tonnes more were saved by opting for a 38 mm Cemfloor screed compared to a standard 75 mm sand and CEM I cement screed. The project was assessed against the RIAI 2030 Climate Challenge, includ ing an assumed 50-year life cycle, and lifespans of materials were kept in line with assumed values in default data or EPDs for products used. External works were omitted, as were enabling works and groundworks – the impact would have been insubstantial, as only three truckloads of soil were excavated, and transported for use on a farm 100 metres away. The scope of the assess ment is not complete, but covers all of the major items – including the sub structure, external and internal walls, the roof structure, and all internal and external finishes to walls, ceilings and floors with the exception of paintwork throughout and the bathroom tiles.
Ventilation supplier ProAir provided a detailed breakdown of the distribu tion system, including the weight of all plastic ductwork used, which enabled a calculation of the embodied carbon of this aspect based on generic PVC data. Underfloor heating and hot water pipe work was not included.
ph+ | wayne hession case study | 41 CASE STUDY WAYNE HESSION
Lifespans of the two units were assumed to be 17 years each, as per the PEPs, and default refrigerant data was re placed by data on the actual refrigerants used in both cases, with leakage rates in line with CIBSE’s TM65 methodology.
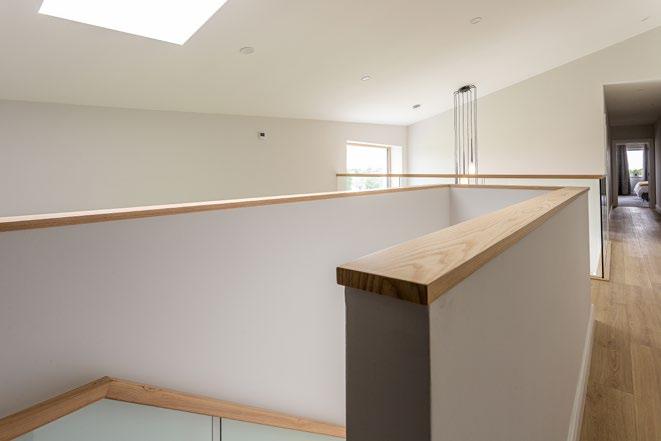
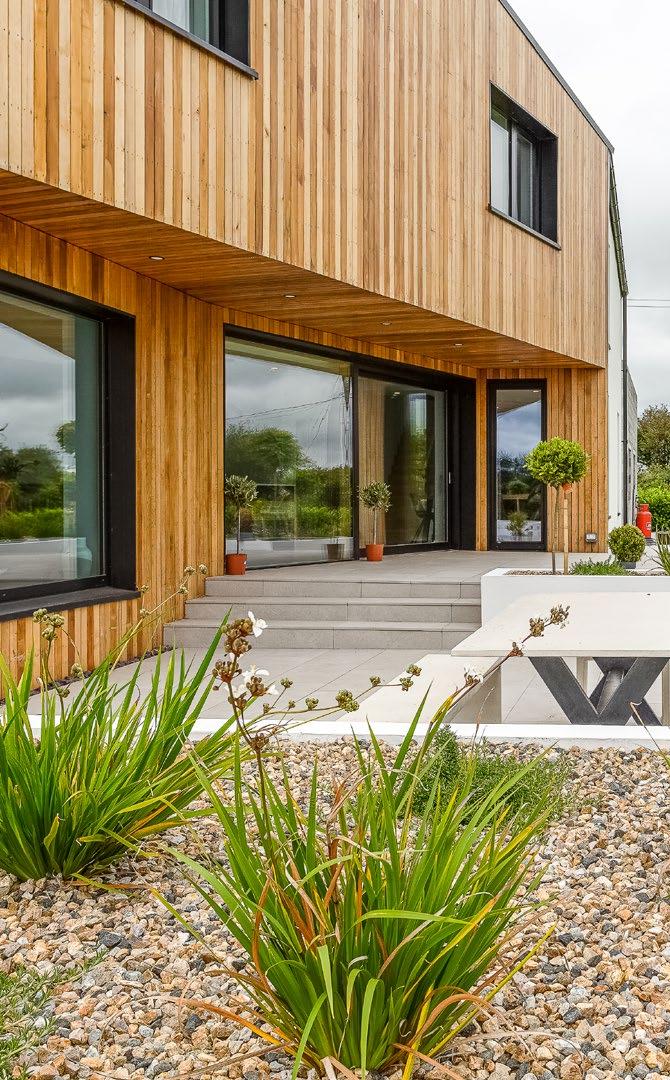
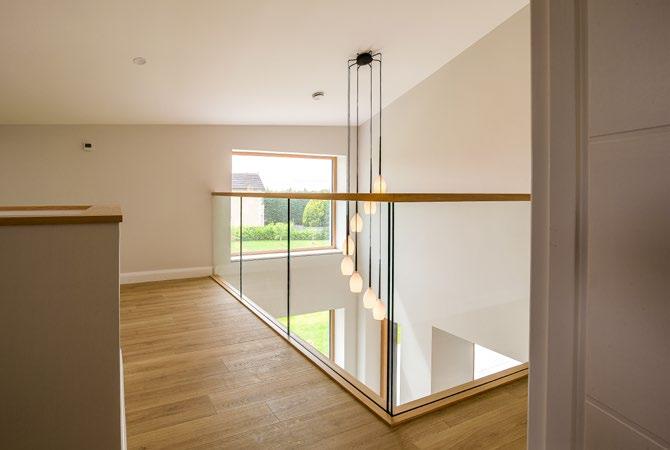
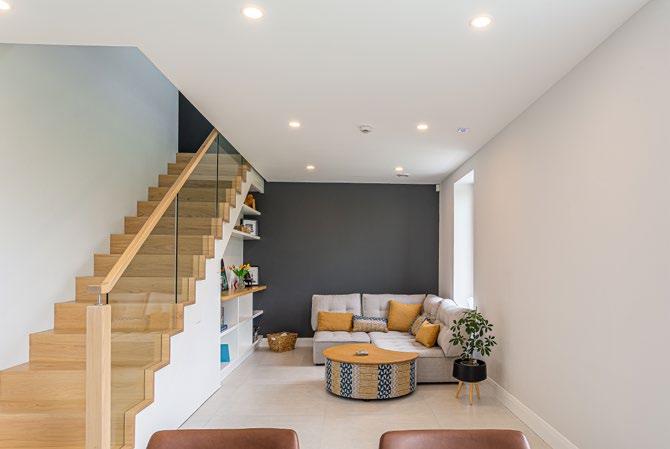
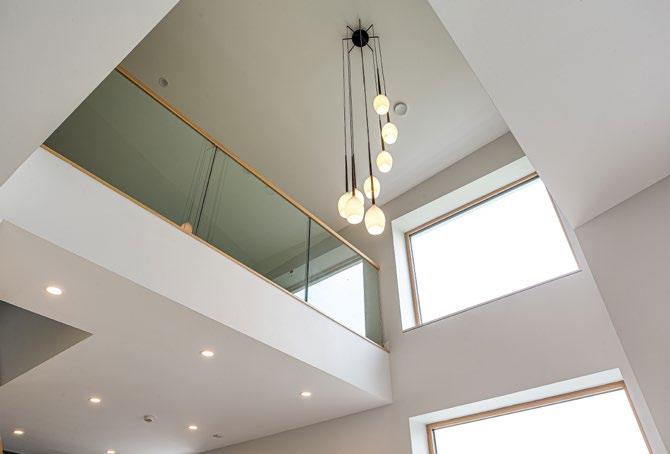
42 | passivehouseplus.ie | issue 42 WAYNE HESSION CASE STUDY WHY CHOOSE MVHR? Delivers warm, fresh & filtered clean air Eliminates condensation, mould & mildew Allows your air tight home to breathe Reduces your energy costs www.proair.ie sales@proair.ie With over 25 years experience, ProAir is Ireland’s only manufacturer and industr y leading specialist of Mechanical Ventilation with Heat Recover y (MVHR) Oursystems.nZEB qualified, professional team will provide an end-to-end ser vice to ensure your home will be healthy, comfortable and energy efficient whether you are building, renovating or extending. Galway Dublin Cork 091 739 442 01 503 4296 087 417 8109 Fully certified concrete, blocks & stone Coshla Quarries Ltd. Cashla, Athenr y, Co Galway
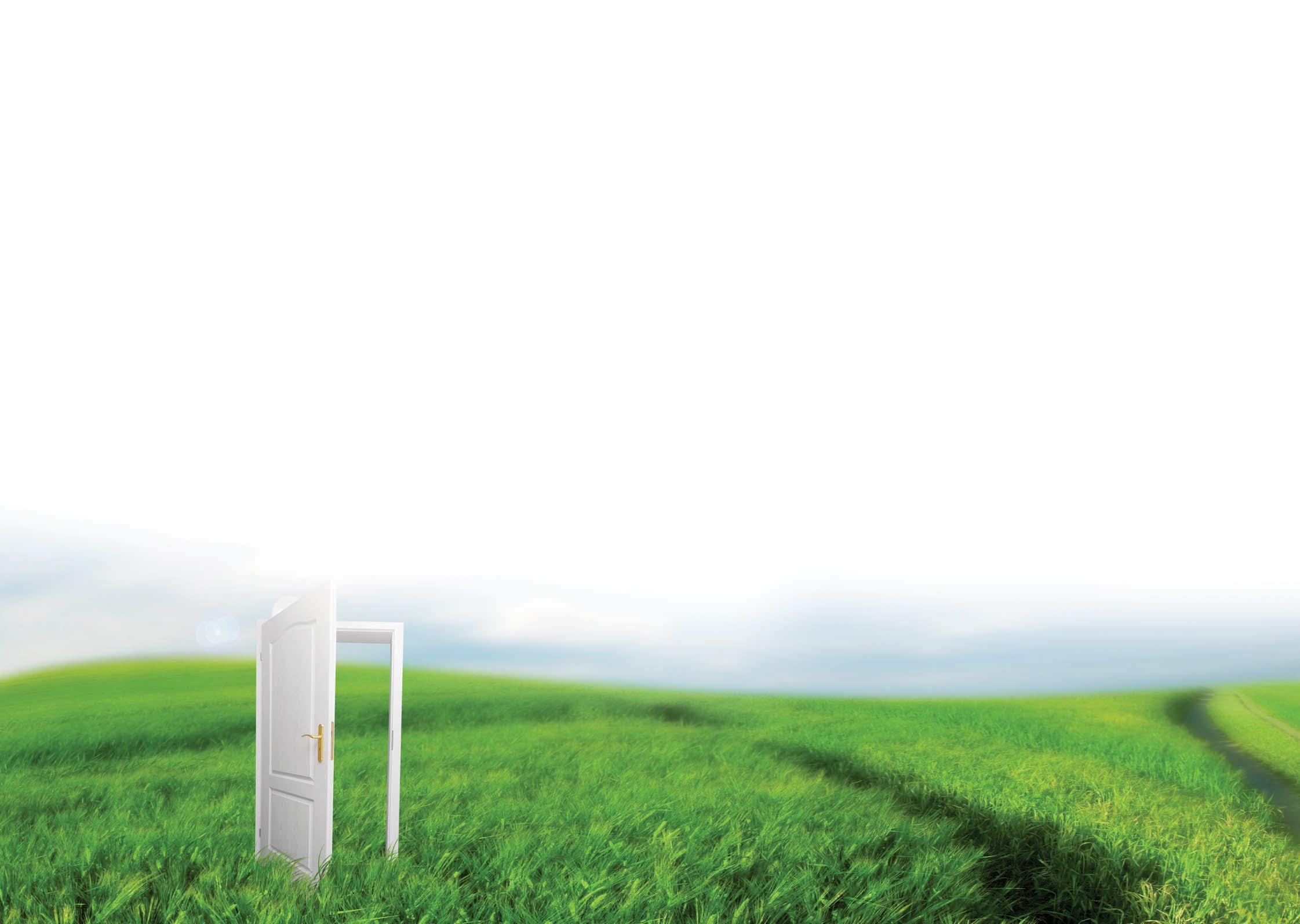
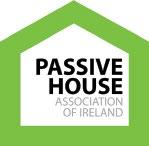

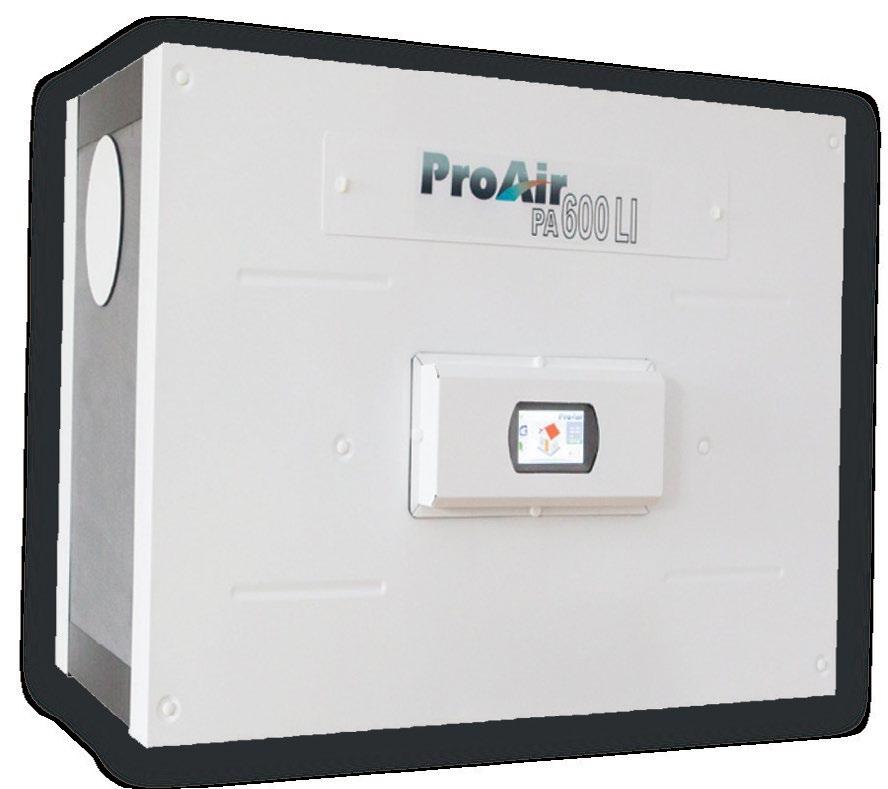

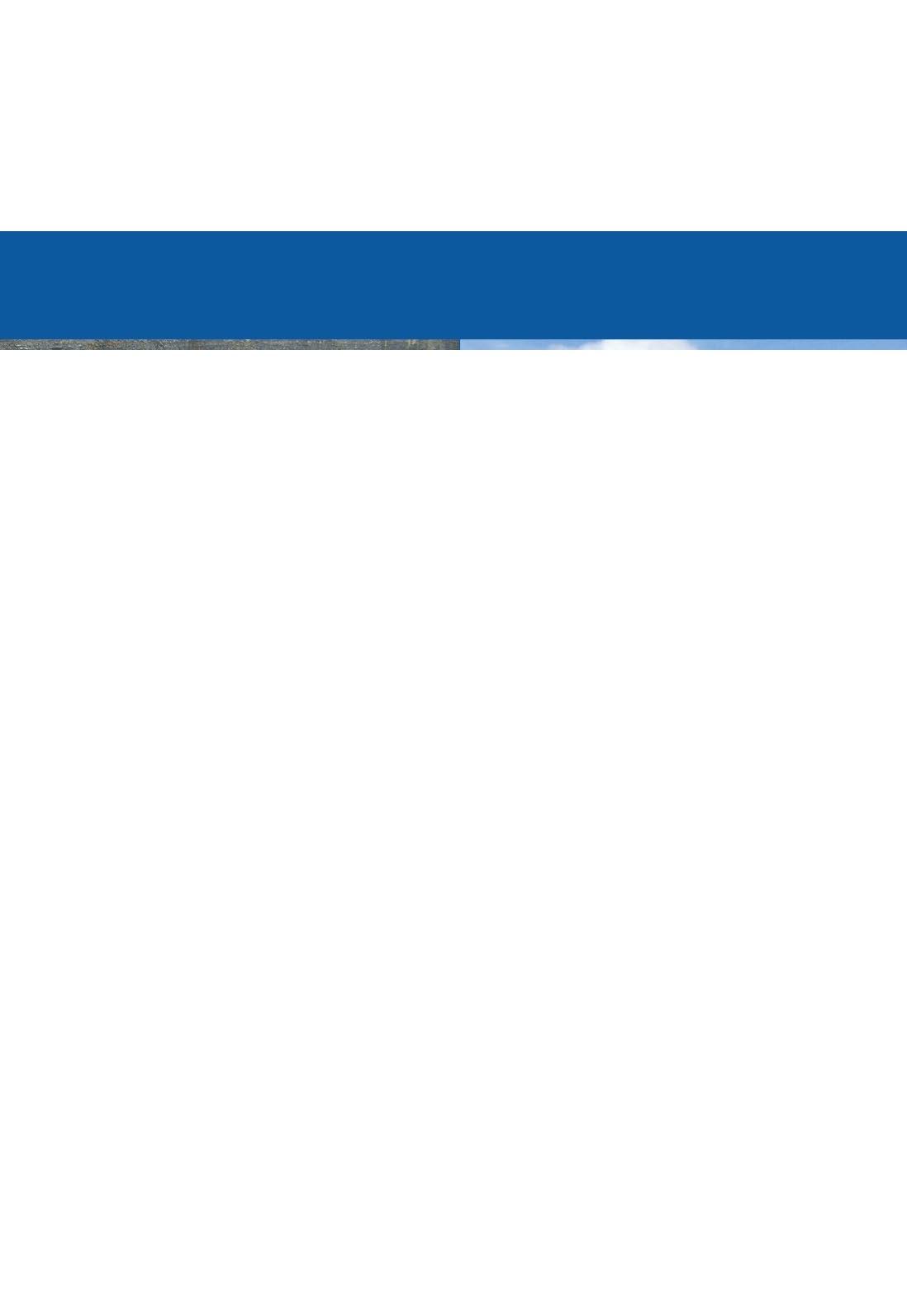
ph+ | wayne hession case study | 43 CASE STUDY WAYNE HESSION IN DETAIL Building type: Detached 260 m2 cavity wall house Site & location: Rural site, Claregalway, Galway Completion date: February 2020 Passive house certification: Passive house classic certified Space heating demand (PHPP): 14.15 kWh/m2/yr Heat load (PHPP): 9.74 W/m2 Primary energy renewable (PHPP): 38 kWh/m2/yr Overheating (PHPP): 0 per cent of hours above 25C Number of occupants: 2 (with a third expected imminently) BER: A2 (provisional) Energy bills: Electricity bill for the full year was €954 including VAT, standing charges and PSO levy (09/11/2020 to 09/11/2021). Estimated heating cost: €36 per month including VAT. Based on Bonkers.ie cheapest counter battens, plasterboard internally. U-value: 0.105 W/m2K Windows: Internorm KF410 uPVC/aluclad triple glazed windows. U-value of 0.74. Installed U-value (PHPP): 0.8 – 1.0 W/m2K Roof windows: Velux triple glazed Passive House Institute certified roof window. Overall U-value: 0.80 W/m2K (PH cert) Heating system: 7.5 kW Firebird EnviroAir air-to-water heat pump supplying underfloor heating throughout. Seasonal performance factor 370 per cent (Harp Database). Ventilation: Jablotron Futura combined ventilation, heating and cooling unit. Passive House Institute certified heat recovery rate 90 per cent. In this case the system does not provide heating – just ventilation and cooling. Electricity: 6 kWp solar PV system awaiting installation, with electric car on order too. Green materials: 50 per cent GGBS in the concrete blocks and raft, and first floor construction cellulose. rural tariff as of 4 August, including 23.23c day date and 12.62c night rate. Airtightness (at 50 Pascals pressure): 0.44 ACH or 0.593 m3/m2/hr Thermal bridging: Mannok blocks used around all the window and door junctions. Purenit under all the external doors and sliding door.
Ground floor: Reinforced concrete raft foundation with 60 per cent GGBS, 150 mm Xtratherm XT/UF, 38 mm Cemfloor screed. U-value: 0.14 W/m2K Walls: Render externally followed inside by concrete block (50 per cent GGBS), 150 mm Xtratherm Cavitytherm in a 155 mm cavity, with Mannok thermal block at window opes and first two courses, cement plaster airtight layer, gypsum plasterboard. U-value: 0.132 W/m2K Roof: Greencoat PLX colour coated steel, followed underneath by battening, breather membrane, OSB3, 350 mm Dammstatt cellulose between rafters, Siga Majrex airtight membrane, 100 mm Metac insulation between battens,
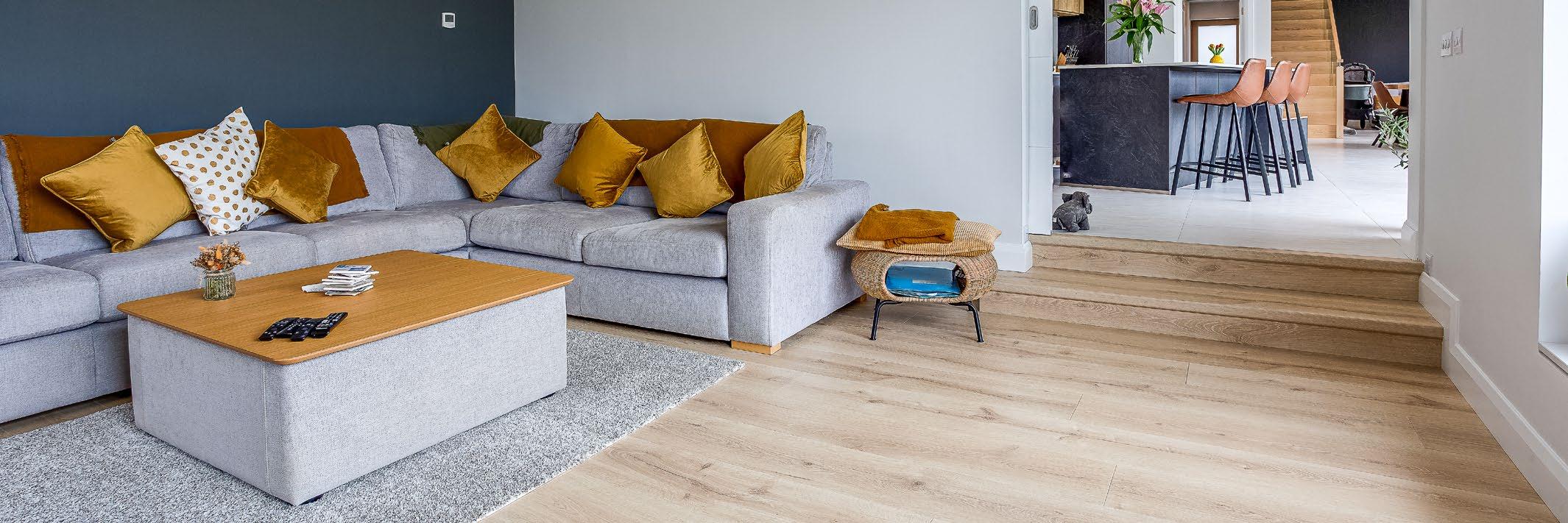
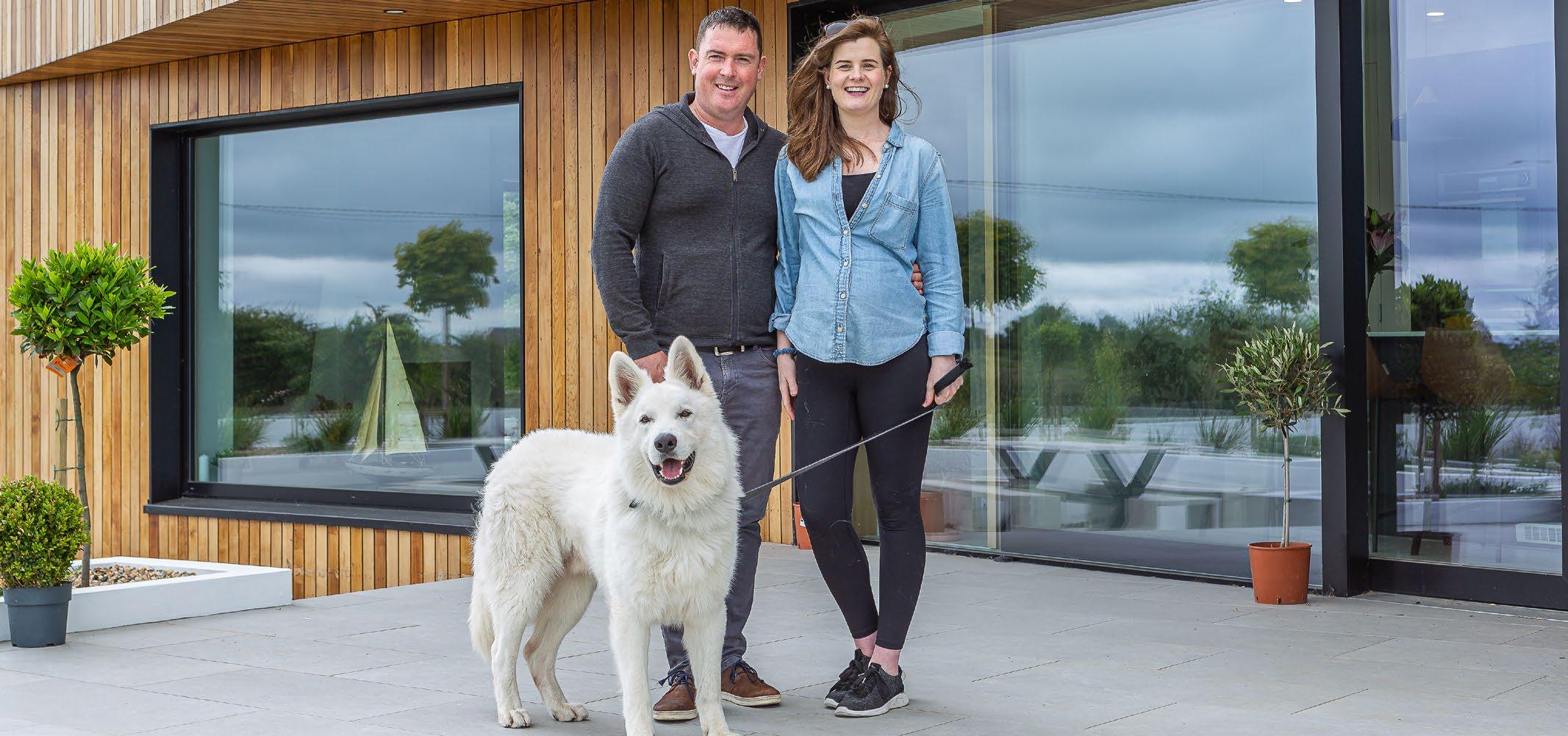
44 | passivehouseplus.ie | issue 42 NEVILLE ROAD CASE STUDY The skilful deep retrofit of a red-brick semi on the south side of Dublin has brought an old property into the 21st century in terms of energy performance and living space, while carefully upgrading its century-old façade with breathable materials. By John Hearne BREATH OF LIFE ENERPHIT UPGRADE REJUVENATES RATHGAR REDBRICK IN Building:BRIEFDeep retrofit & extension of 1920s semi-d Method: External insulation, breathable internal insulation, single leaf thermal block extension Location: Rathgar, Dublin Standard: Enerphit (certification pending) Heating cost: €24/month* *Space heating use only, modelled based on measured energy use. See ‘In detail’ panel for more information. €24 per month
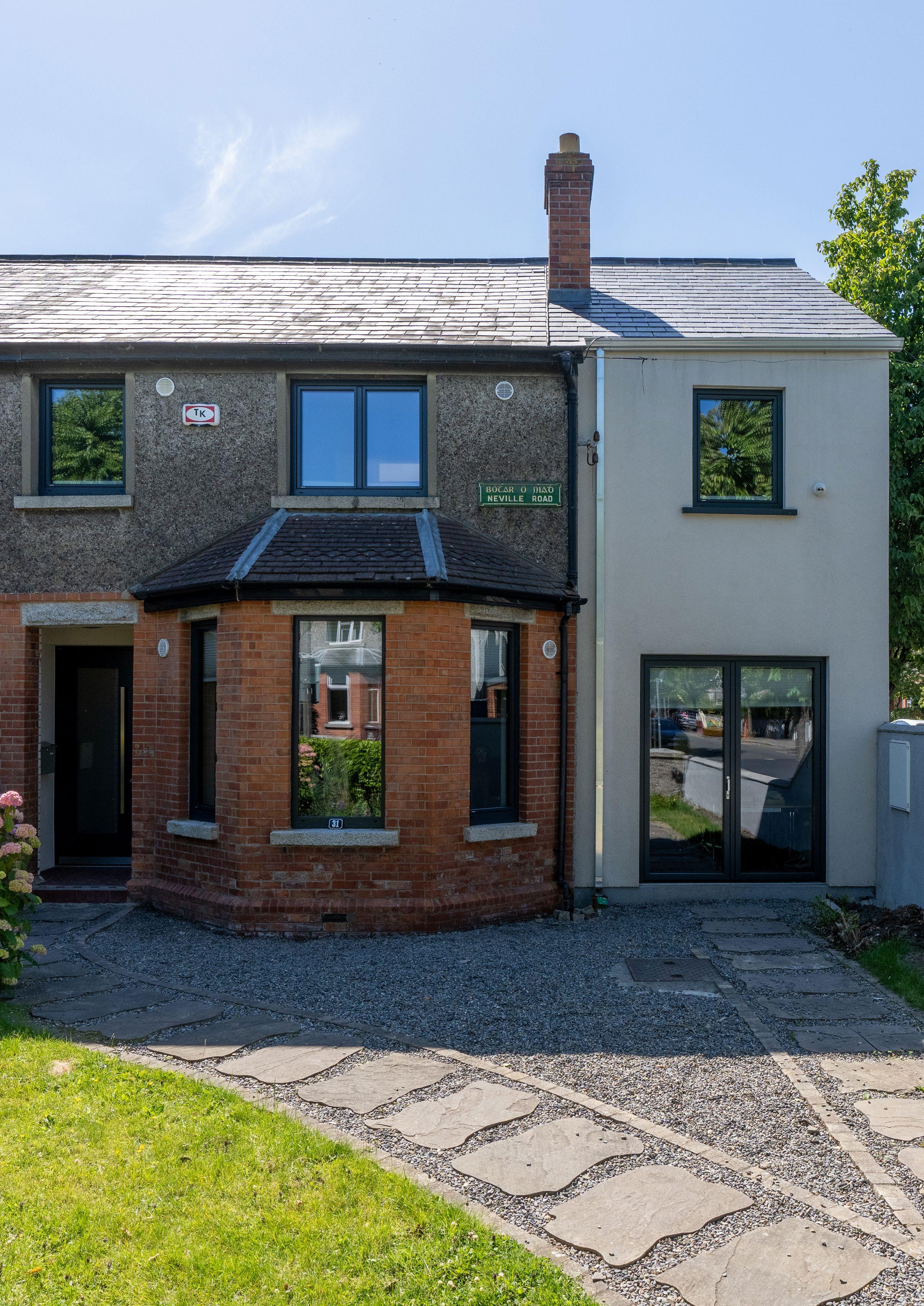
ph+ | neville road case study | 45 CASE STUDY NEVILLE ROAD
Downstairs, the open plan kitchen/living room connects directly to the garden via a large sliding door. “In going from the mas
Photos: Abdone.com
It’s a measure of just how well executed the project was that the blower-door test regis tered 0.9 air changes per hour – inside the Enerphit standard of 1.0 – on the first go. Neville Road in Rathgar is a 1920s devel opment of red-brick semi-detached homes, and this is the last house in the row. Brendan grew up in the house, and was now return ing to live there with his own family. Prior to the refurb, there had been a di lapidated single-storey lean-to extension to the side. This was set to be demolished and replaced with a single-storey rear extension and a two-storey side extension. Though it had been lived in continually, by the time the project began in 2020, the house felt a little unloved. Both wiring and plumbing needed extensive work, and the windows and doors were in need of replacement, while the layout of the rooms belonged to Brendan grew up in the house, and was now returning to live there with his own family. another time. “It was always going to be a deep retrofit,” says Reynolds. He notes too that the initial design specified a larger extension, but that before finalising the layout, he and the cli ents took a closer look at the family’s space requirements. “I’d recommend that anyone considering an extension, first look at the space that you use every day.” It can be a very revealing exercise because it invariably uncovers areas that are either being under used or not used at all. “A lot of us think, ‘I don’t have enough space, I need to extend the house,’ but hang on for a minute. Are you using all the space you’ve got well? Are there any spaces that you don’t use? Maximise what you have before looking atTheextending.”family wanted to retain as many of the old features of the house as possible, while at the same time creating spaces more attuned to how we live today: open plan living areas, additional bathrooms and bedrooms upstairs. The brief also included a self-contained studio apartment/office space, to cater for the needs of family mem bers as they change. “The extension is almost invisible from the outside,” says Reynolds, “the front façade is very low impact, very understated, but when you walk in the front door to the cen tral area, all of a sudden you have a double height, cathedral space with an overhead walkway linking with the master bedroom.”
A year after their house in South County Dublin had been retrofitted to the Enerphit standard, owners Brendan and Geraldine decided to apply for certification to the Passive House Institute. But to be certified as having met the Ener phit standard, new airtightness tests would have to be done. “Going back to do airtightness tests a year after completion isn’t ideal,” says architect and passive house designer, Mel Reynolds. “Normally you’d try and do your final test as close to when you complete as possible because buildings settle, doors warp, seals come loose... There was one sliding door that was in constant use. I was sure that there would be problems there.”
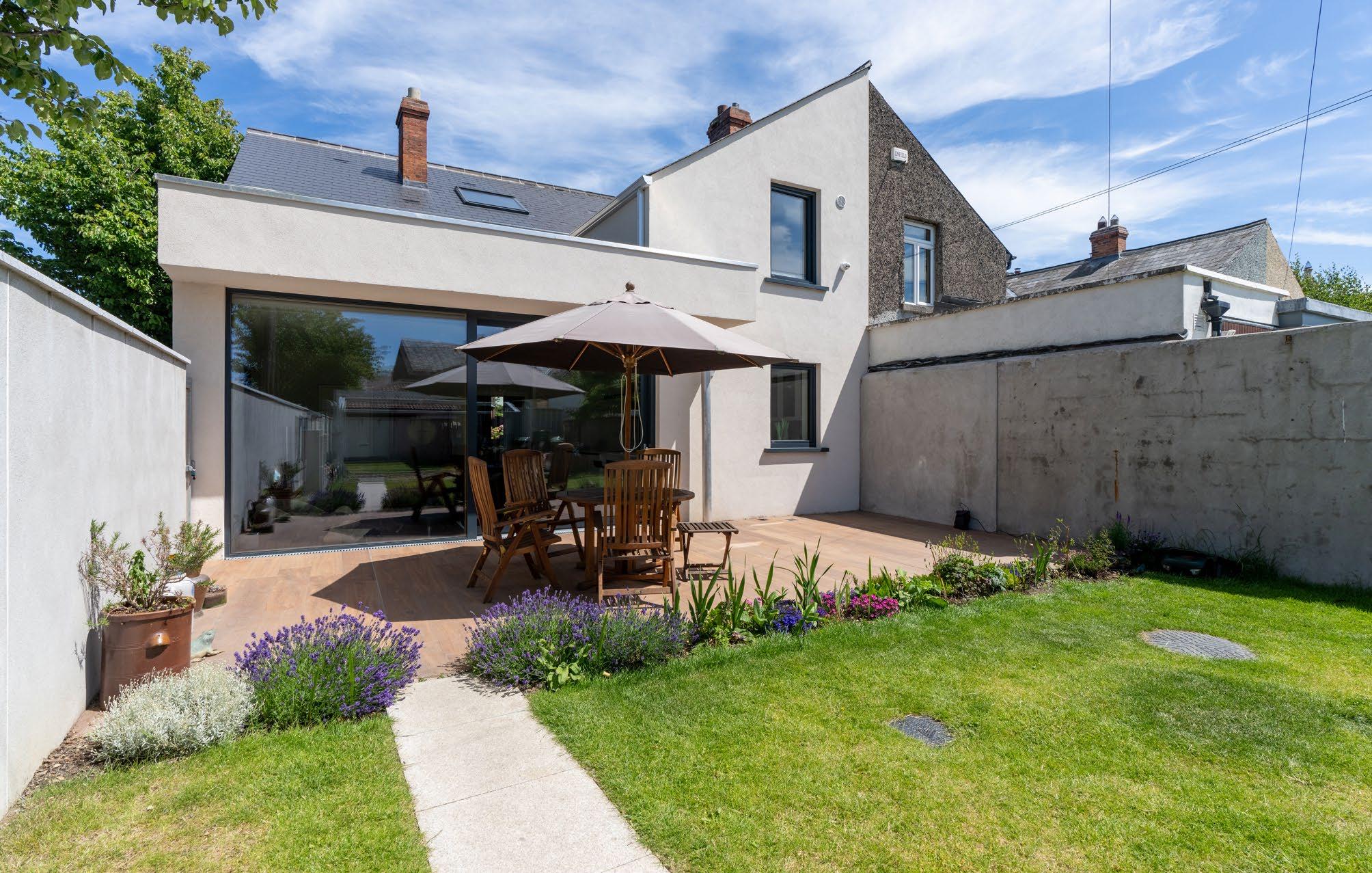
The original house relied on infiltration and opening windows for ventilation. The refurbished house uses Lunos decentralised heat recovery ventilation units from Partel, a technology which Reynolds came across be fore but hadn’t found the right opportunity to“Centraliseddeploy. mechanical heat recovery ventilation is great, you have ducts, you have a single unit and your efficiency is very high, but in existing buildings, fitting a centralised system is a real challenge because you don’t have the space for ducts, you don’t have the voids, plus you might have to retain ceiling details like cornicing.”
46 | passivehouseplus.ie | issue 42 NEVILLE ROAD CASE STUDY ter bedroom to the kitchen, you experience seventy per cent of your house; you’re not simply being threaded through it, while the double height brings the whole lot together.”
The story of the Neville Road deep retrofit really begins with an earlier Mel Reynolds project, the country’s first passive house ‘plus’ project, which was Reynolds’s own house at Cove Mews in Sandycove, a project featured in issue 35 of Passive House Plus. While working on this project, Reynolds was struck by how well several of the build ing solutions he implemented there would work on a Airtightnessrefurb.is always a challenge when you’re retrofitting, but two things served to make the process surprisingly smooth on Neville Road. The first was that the builder on Cove Mews – Sean Regan – also won the tender here, and so was equally familiar with the solutions deployed in the earlier proj ect. The second was one of those solutions: Blowerproof liquid airtight membrane. This is a BBA certified product with Class C fire rating which has been used in Europe for some time. It’s a paint-on product. In the new parts of the house, there was no need to batten out the walls or attach a screw-fixed plasterboard. Instead, the build team used dot and dab plasterboard, while in the older part of the house, the liquid membrane was simply applied to the exist ing“Itplasterwork.didn’ttake Sean any more than a week to get to a preliminary airtightness level of 0.9. Because he had done Cove Mews, air tightness here was a doddle. No need for all the tapes and things we used to use in junc tions and in floors, which were really labori ous. With this, you’re simply spraying it on. It’s perfect... The lesson for any contractor with these onerous, difficult-to-achieve stan dards is that when you’ve done it once, that’s it, it’s Whileeasy.”existing plasterwork was retained inside the house, the design team decided to replace the suspended timber floor with an insulated concrete slab featuring 50 per cent Ecocem GGBS. Walls are externally insulated where possible. The red-brick front façade was of course retained, and faced internally with a 60 mm Calsitherm board. Calsitherm is a breathable calcium silicate board, made from a mix of lime and sand, which is capable of regulating dampness in walls by absorbing it and then allowing it to evaporate and dry out. The design team conducted condensa tion risk analysis to determine the optimum thickness of the interior board. “When you have a protected façade or brick – as in this case – you insulate as much as you safely can and then compensate on other areas. That’s what we did here. In the end, our provisional rating was A1. Brendan mentioned that a scheme of very expensive new houses had just been launched not too far away from this one, and they were A2 rated. So, this 1920s build was delivering a better performance than those lavish new homes.”
By contrast, Reynolds says decentralised systems are ideal in retrofits. You install Maximise what you have before looking at extending.
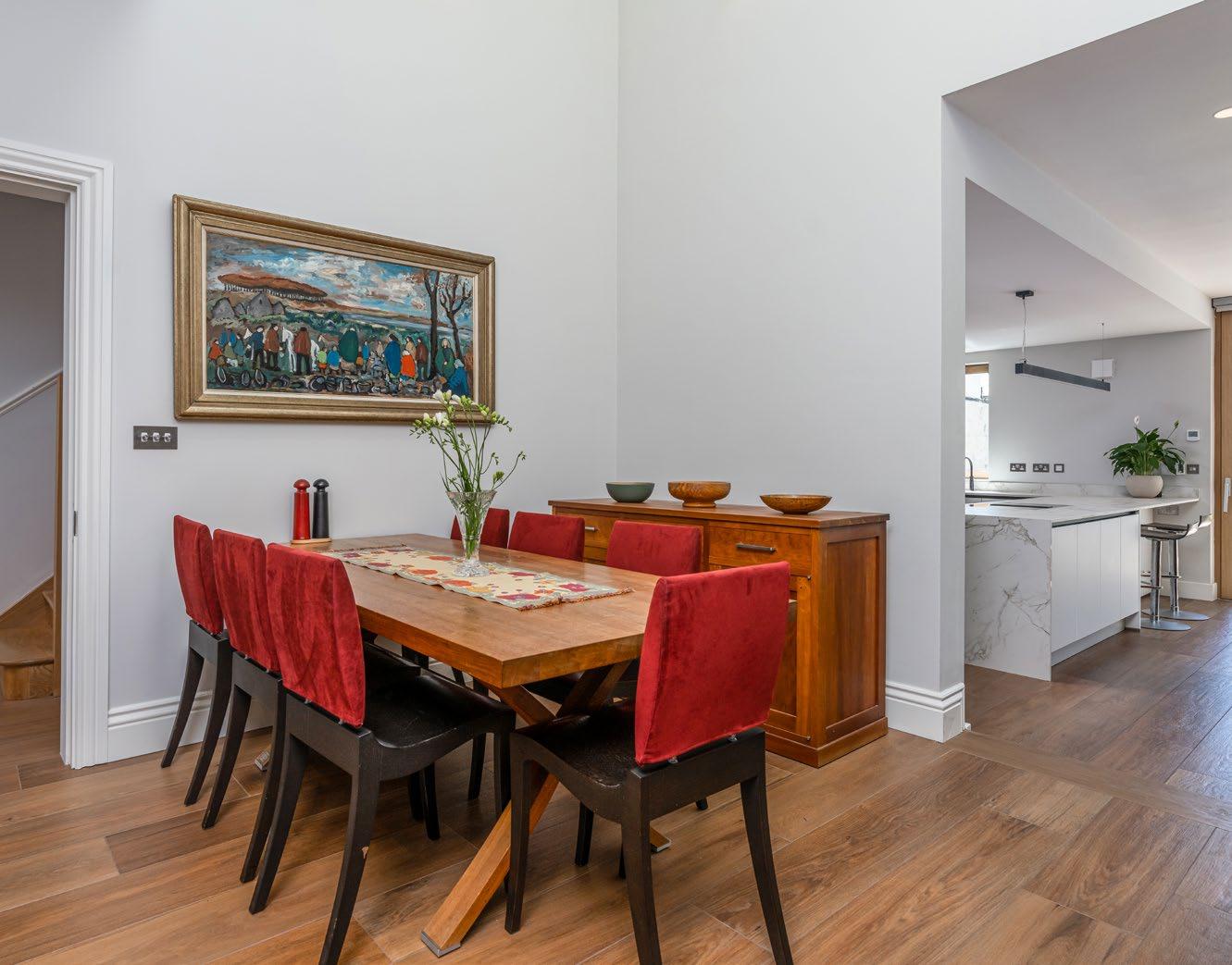

In the year up to the beginning of the project, the house had been occupied by two people – Brendan & Geraldine’s son and partner. When the retrofit was com pleted in late 2020, Brendan, Geraldine and their adult son Thomas moved in, with the occupancy doubling the following summer, when Brendan and Geraldine’s son John moved in with his partner and their baby. During the two-person occupancy pre-ret rofit, total energy used over a twelve-month period came in at 3,151 kWh of electricity and 11,103 kWh of gas. From May 2021 to May 2022 – a period including six occu pants from June to January – total energy use came to 8,551 kWh. But how would the house fare with half the number of oc cupants, as current? Cue energy modelling expert Tim Cooper, who devised a way to deduct the impact of increased occupancy, and account for the house drying out and the homeowners learning to use the new systems in the house – factors which sub stantially affected the building’s energy use.
CASE STUDY NEVILLE ROAD vents, bring power to them and each is com missioned individually.
“All they need is power, you don’t have any interruption to your ceilings or floors and the cost to run them comes to a total – across the whole house – of between €10 and €12 per year. It’s a brilliant concept for existing buildings, particularly when you want to get your airtightness down to passive levels.”
He continues: “The back elevation of the house has a unified, modern look, without fascia boards, so that internal roof insulation meets external wall insulation in one con tinuous layer, thereby eliminating thermal bridges. It’s a very elegant detail architec turally but it also has the added benefit of delivering high performance.”
Going back to do airtightness tests a year after completion isn’t ideal.
The net result: total energy use reduced from an unadjusted total of 8,551 to 6,290 kWh/yr. Of this, 1,452 kWh was attributed WANT TO KNOW MORE?
The digital version of this magazine includes access to exclusive galleries of architectural drawings. The digital magazine is available to subscribers on passivehouseplus.ie & passivehouseplus.co.uk
Cooper developed an energy performance model for the house, taking account of the extra demand placed on the house for show ering, space heating, cooking, refrigeration, washing and other appliance use – and tak ing account of the rated power use of the actual appliances in the house. The usage assumptions were corroborated by Brendan. Space heating increases were assumed from the house drying out and the occupants learning how to use the new heating system.
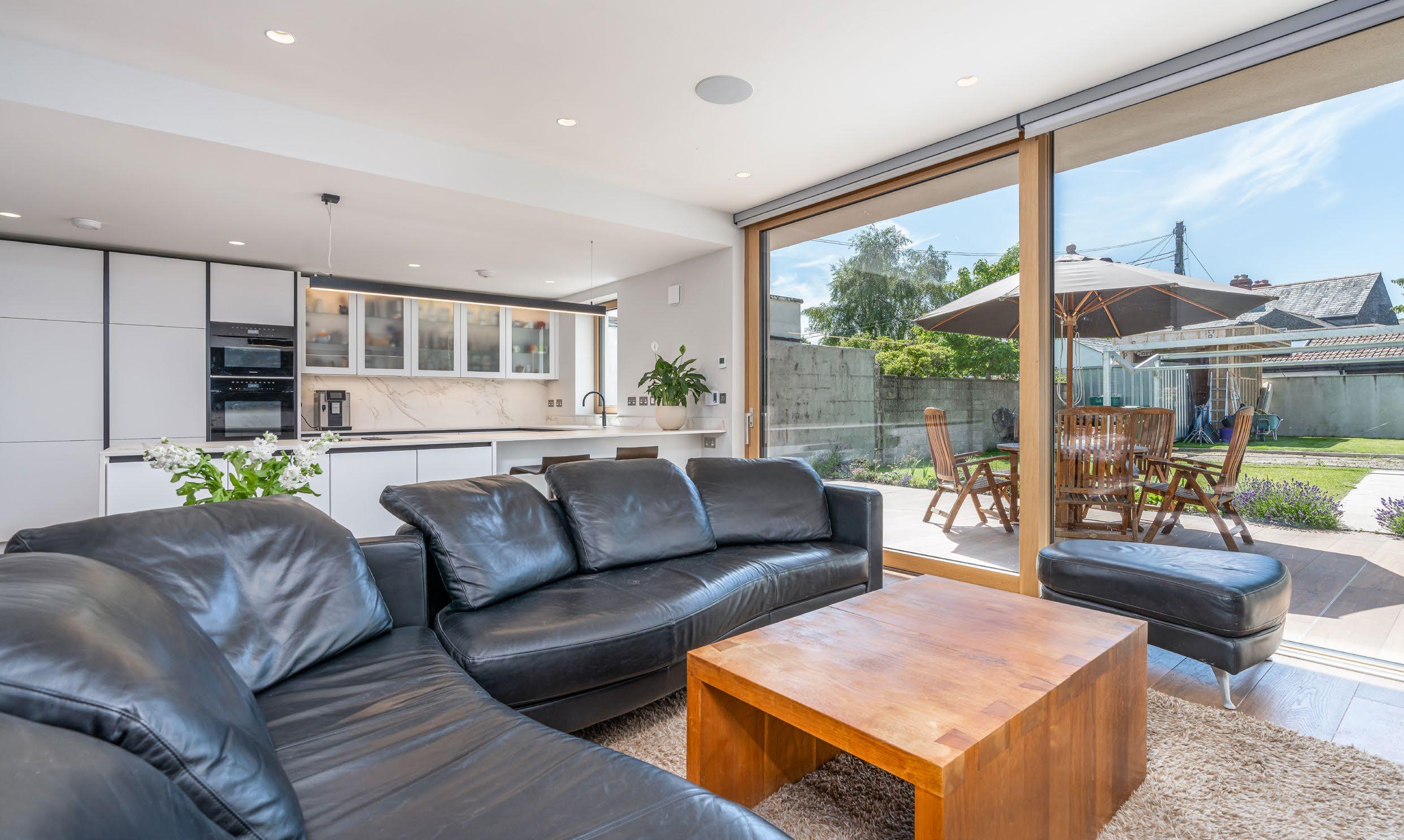
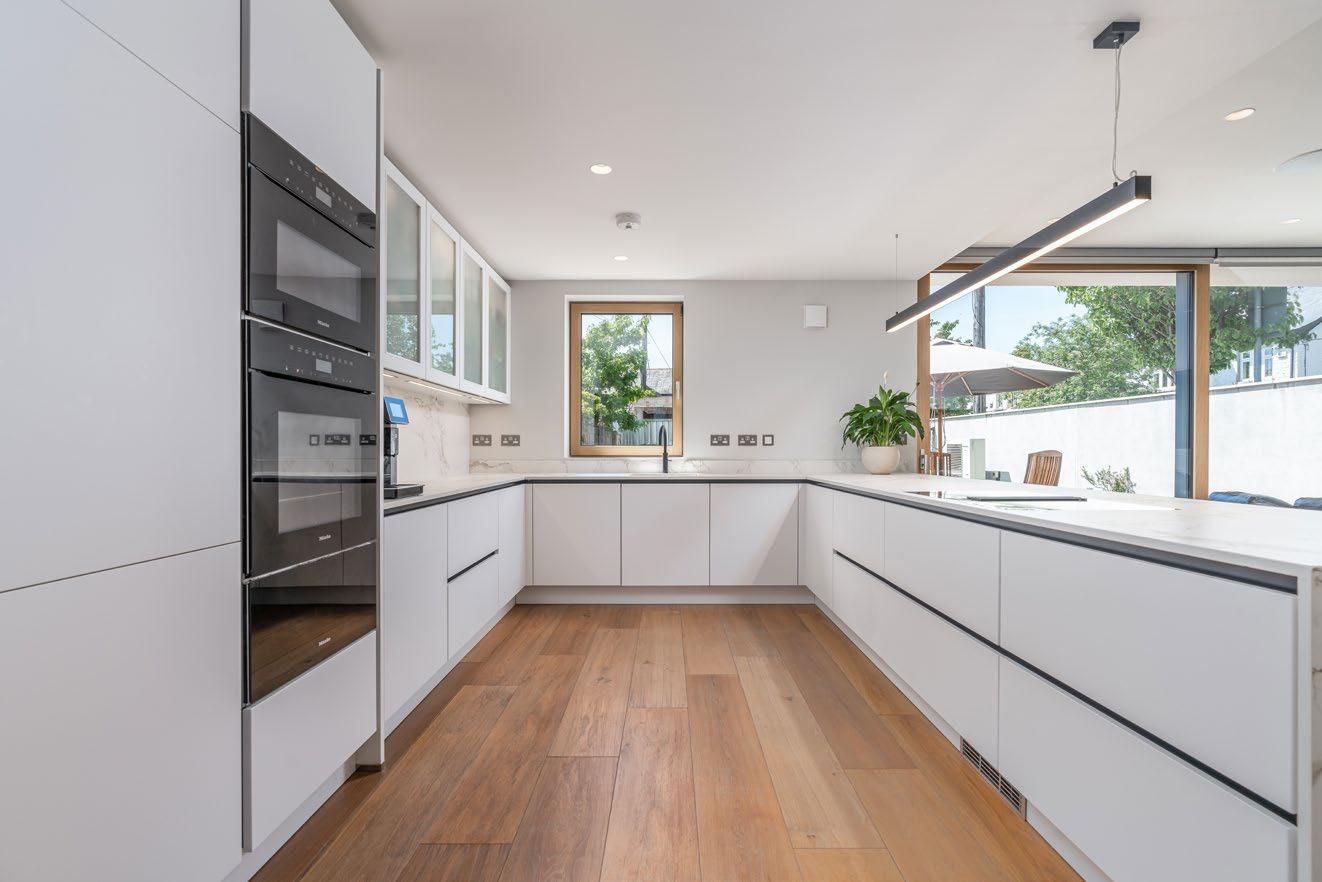
48 | passivehouseplus.ie | issue 42 NEVILLE ROAD CASE STUDY For a quality well-designed ventilation strategy for your building, ask Partel. technical@partel.com | www.partel.ie LUNOS Systems with Heat Recovery Save energy. Build smart. Controlled decentralised ventilation strategy for new-build AND energy retrofit planning › Low power consumption from 0,09 W/(m³/h) › Highly energy-efficient, heat provision level of 88% › Ceramic heat accumulator, heat provision level of 82% › Air supply and exhaust air with heat recovery at the same time To enquire about advertising, contact Jeff Colley on +353 (0)1 2107513, or email jeff@passivehouseplus.ieAdvertisewww.passivehouseplus.iewithus.
It is always a pleasure to work with the Passive House Plus team. They provide a wealth of information, support and time to provide the best advert.
- Elizabeth Assaf, owner, Urban Front
Launching a new product is never easy, but in the space of only two months we’ve received over 150 enquiries through two issues of the magazine and all have been very fruitful. We have been quoting straight after the magazine is out. A lot of the customers enquiring have genuine current projects and this is reflected in how many respond to our follow ups.
It is no doubt in my mind that this team are one of the best I have dealt with out of the many publications we use. They deliver and they deliver quality!

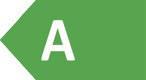
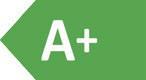
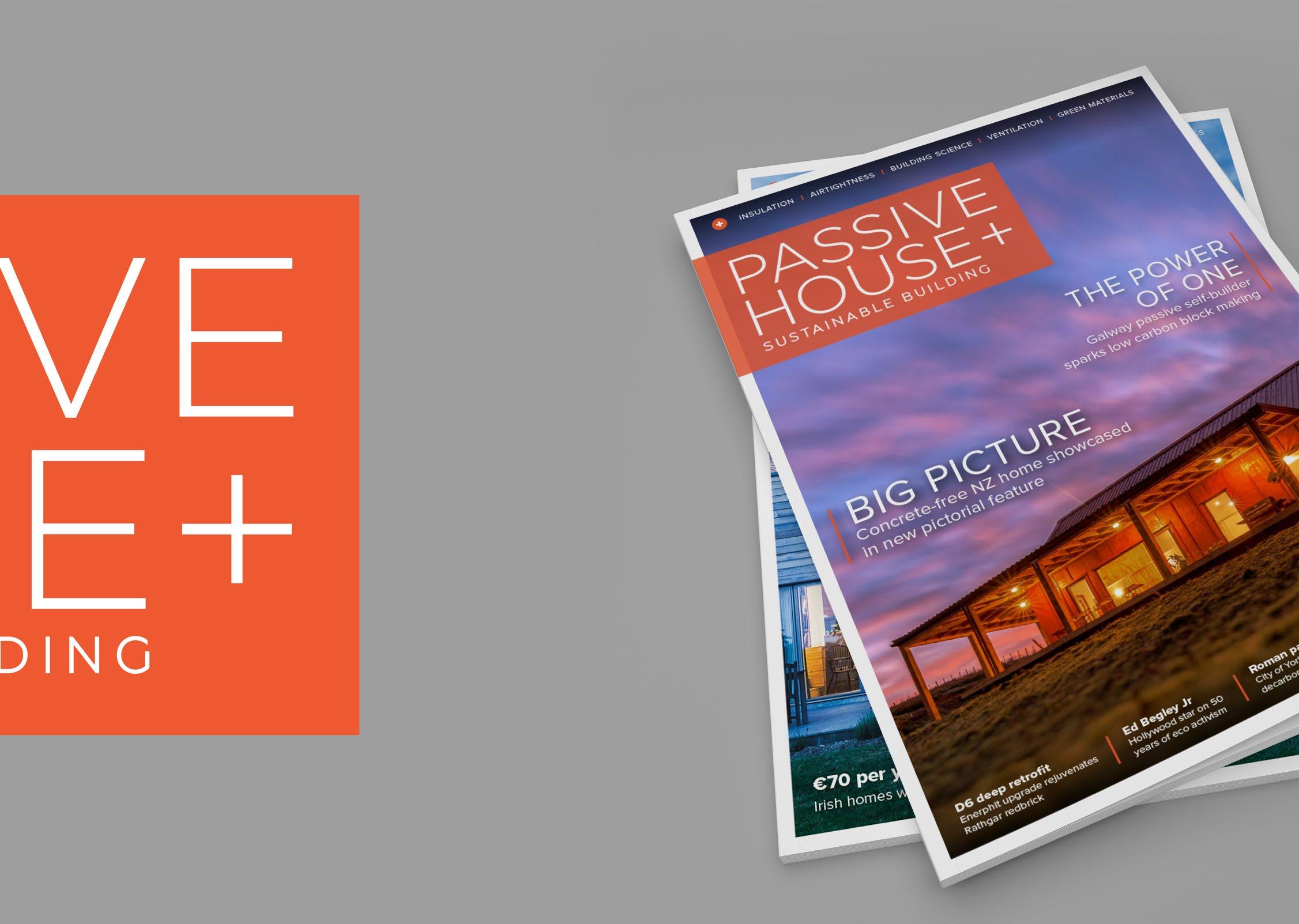
ph+ | neville road case study | 49 CASE STUDY NEVILLE ROAD to space heating demand, at a cost of less than €24 per month based on current elec tricityWithprices.therisk of rocketing electricity prices obscuring some of the energy savings ac cruing from the refurb, the clients decided to install PV panels after the project had been completed. Planning permission was granted for panels on the back of the house, but analysis by Tim Cooper - who is also arguably Ireland’s leading expert on PV – re vealed that chimney overshadowing would be an issue. So instead, the design team created a carport with a butterfly roof, and eight panels are due to be installed in the comingCooperweeks.predicts that once the PV array is in place - and using a dynamic model to project the output of the array on a gran ular level throughout the year, against his granular model of the building’s energy use – the array will reduce grid energy use to 4,181 kWh/yr. This is based on the planned installation of an eight panel (2.96 kWp) PV array. Cooper’s projections – based on the measured output of a similar array on a local project – to be 2,447 kWh/yr, includ ing 1,427 kWh of useful energy, and 1,021 kWh to be exported to the grid. Cooper projects that the useful energy generated by the array will knock over €330 off the house’s electricity bill. Like so many houses of its vintage, Neville Road was draughty and hard to heat, which is part of the reason why the clients specified underfloor heating throughout the refurb. When the team ran the design through the Passive House Planning Package (PHPP) software however, it suggested that under floor heating was surplus to requirements. It was retained – just in case – but two winters in, it’s hardly been used. Like many designers before him, Reynolds pays tribute to PHPP as a design tool. On a different project, the software suggested that the radiators that had been specified were unnecessary upstairs. “Again, just in case, we put in flow and re turn for the rads, but left the rads themselves out. That saved the clients about €3,000. If they wanted them later, they could put them in easily… And last year, we had supply chain problems, but if one insulation is un available, you can put the spec of a potential replacement into the software and it will tell you if it’s going to work or not.” Rainwater harvesting should be in all retrofits and new builds.

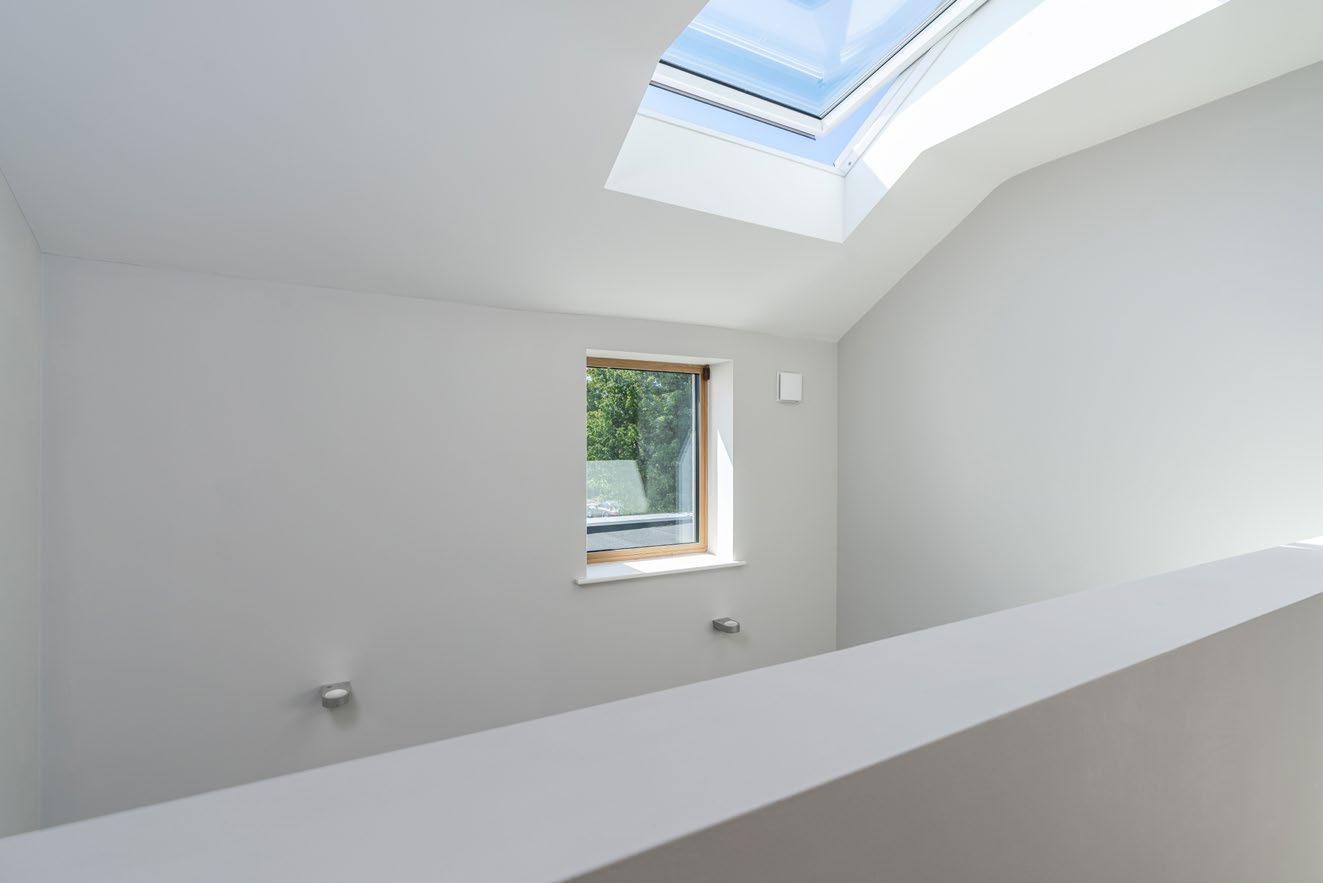
50 | passivehouseplus.ie | issue 42 NEVILLE ROAD CASE STUDY
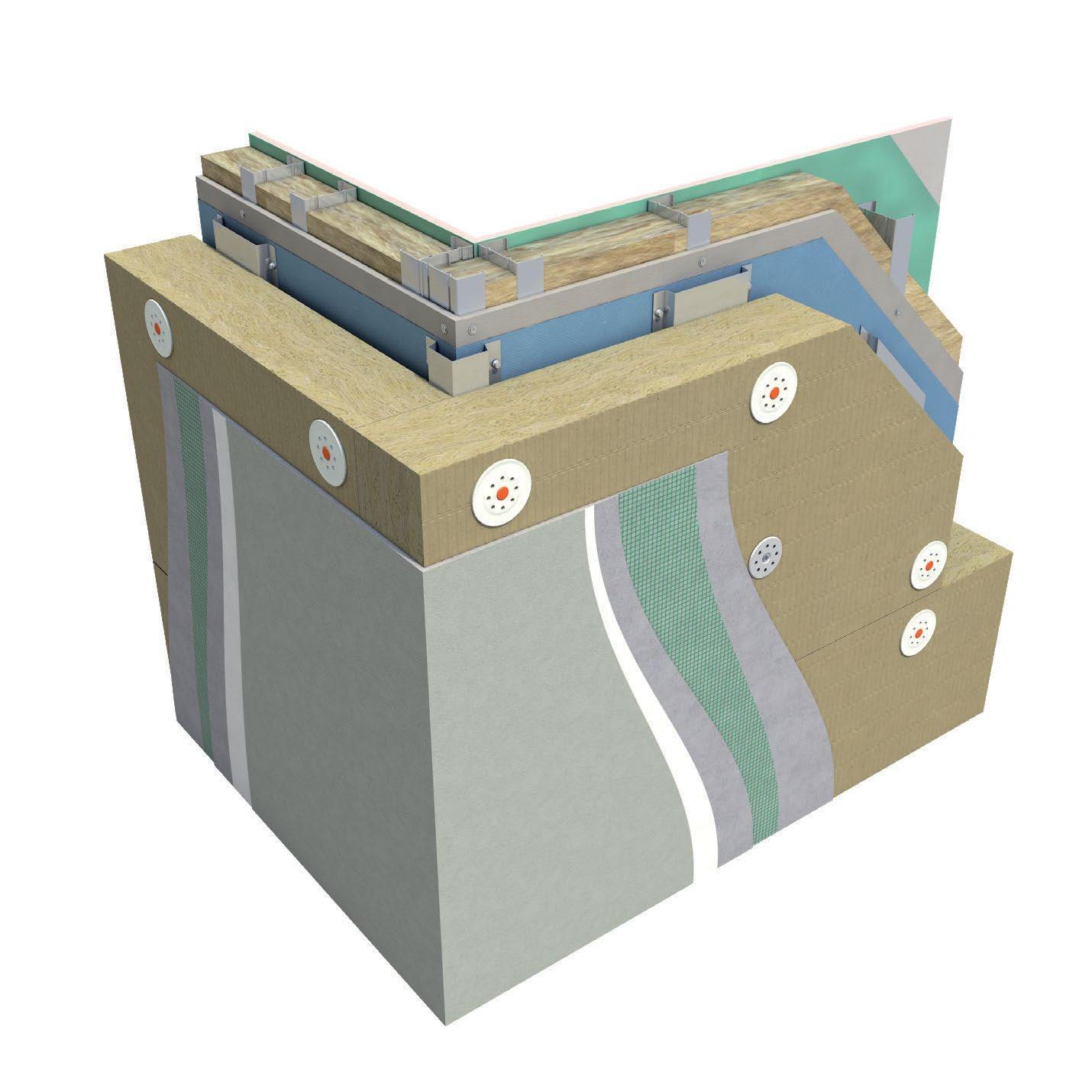
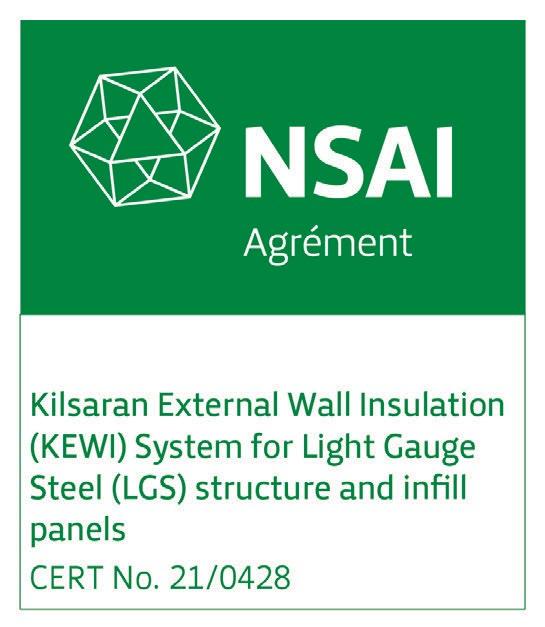
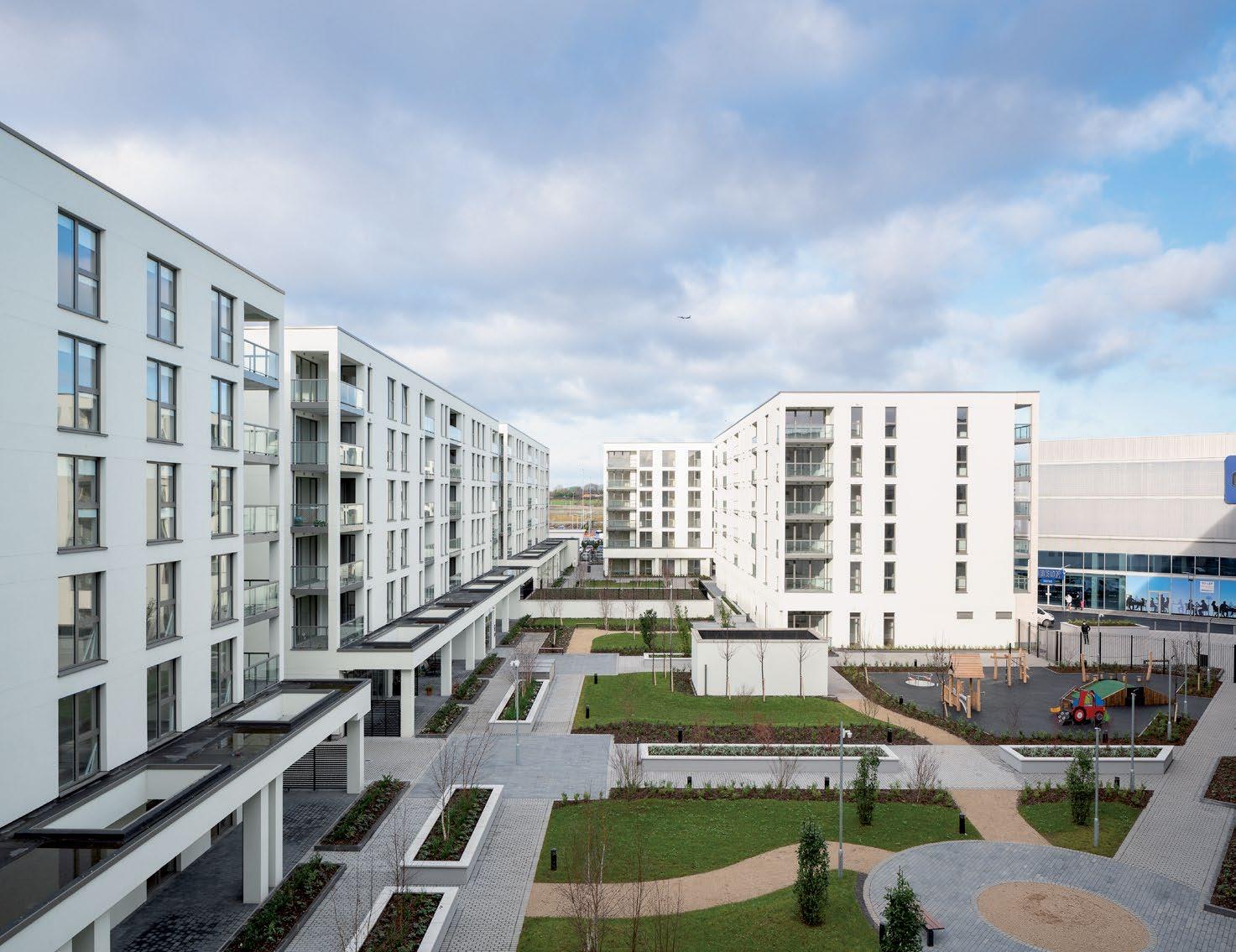
Hidden beneath the back garden of the Neville Road Enerphit, there’s a 5,000-litre rainwater harvesting tank which is plumbed to the WCs. This makes the house a lot more self-sufficient, and guards against the impact of water charges if and when they return. And as Reynolds points out, the cost of in stalling rainwater harvesting during refurb is far cheaper than doing so after the fact.
“I think rainwater harvesting is some thing that should be in all retrofits and all new builds, and should be incentivised. It just makes no sense to use potable water that we have already treated to flush toilets. So don’t buy an expensive sofa. Get one in Ikea and install a rainwater harvesting sys tem instead.”
1 Construction underway of the two-storey side extension constructed of Mannok Aircrete blocks; 2 delivery of the large glass patio door with pre-fitted brackets for the new rear extension; 3 Internorm triple glazed aluminium-clad oak units sitting proud of the blockwork to keep continuity with the external insulation layer; 4 carefully applied Siga airtight tape seals the joist ends and stud walls to the Mannok blocks; 5 wetroom tanking to wall of master bedroom ensuite at first floor level, pre tiling; 6 Blowerproof to inner surface of Mannok block walls with surface-mounted slimline boxes and conduits – no chasing required before dab and slab applied as internal finish; 7 60mm Calsitherm board applied to existing solid brick front bay wall with Blowerproof repairs behind (airtight layer on inner surface of existing wall) and Calsitherm applied to reveals; 8 Siga Majpall airtight membrane to double height ceiling.
ph+ | neville road case study | 51 CASE STUDY NEVILLE ROAD 1 2 3 4 5 6 7 8
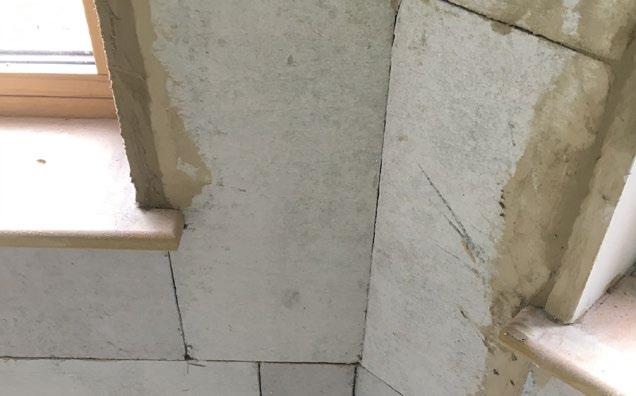

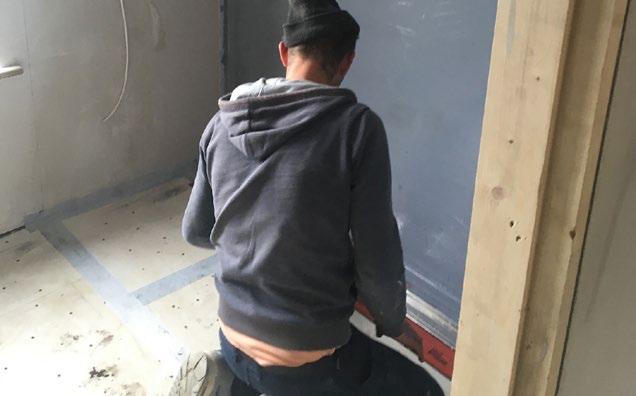
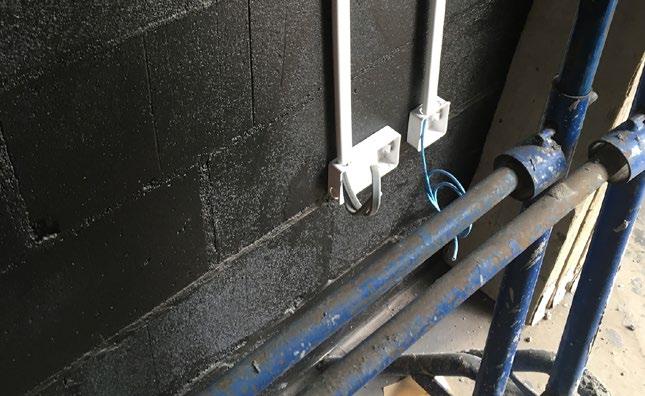

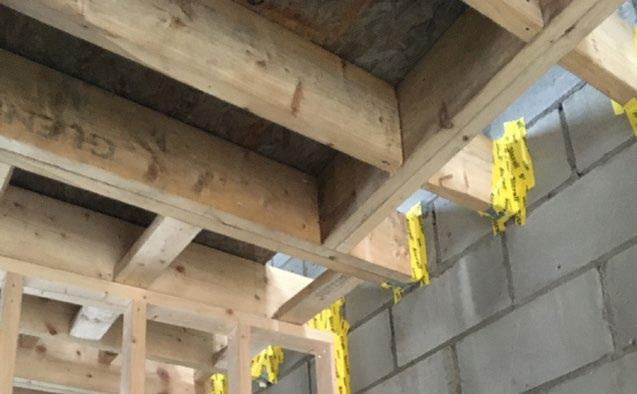
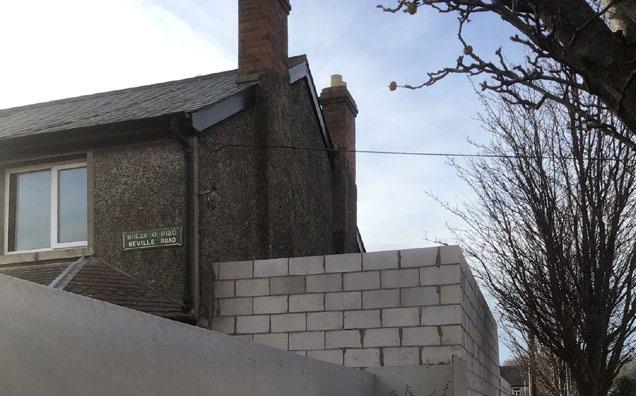
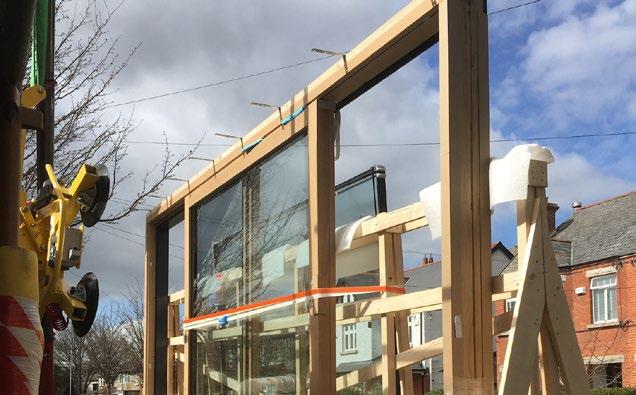
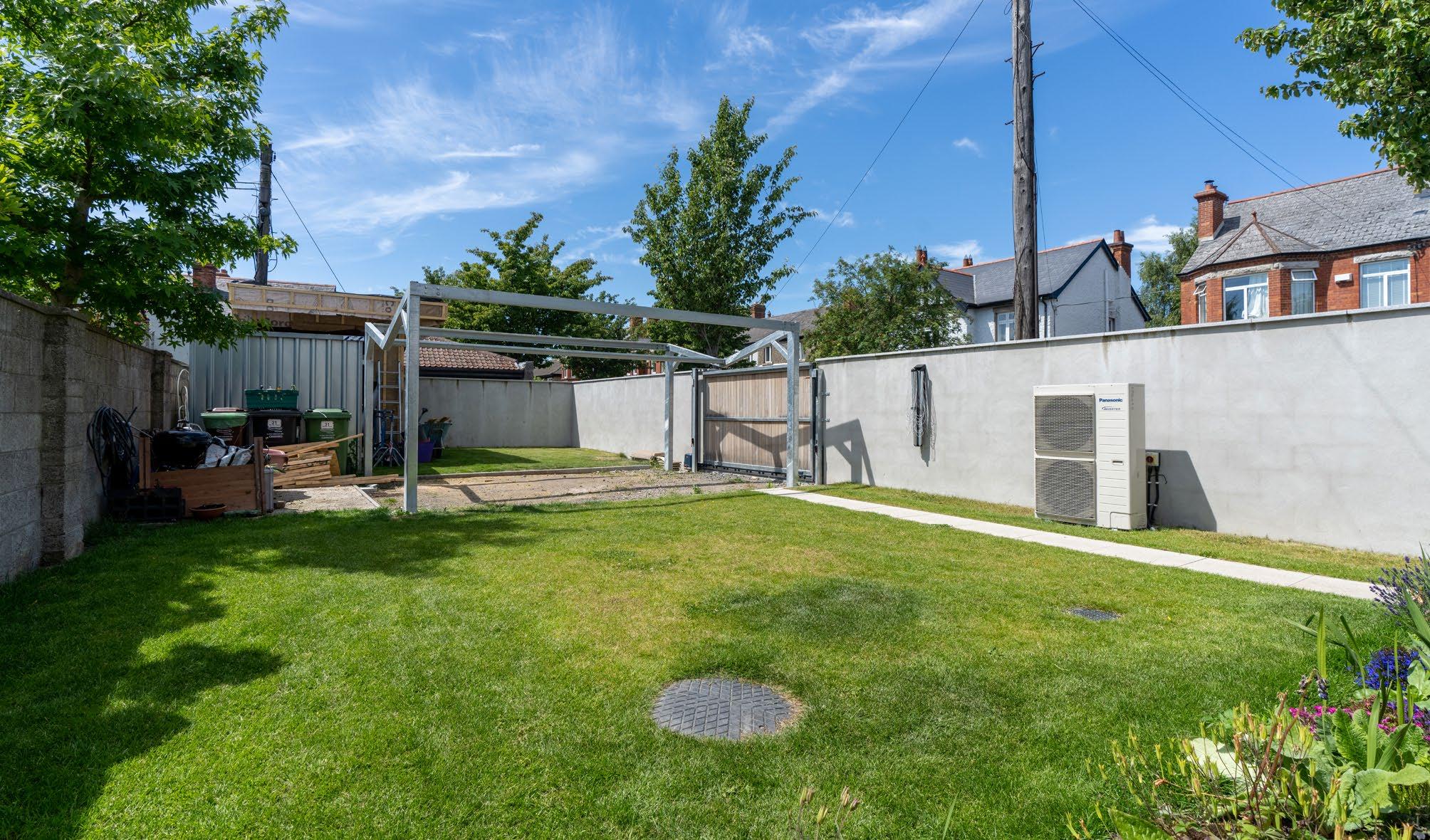
THE ISOVERNEW SOLUTIONS GUIDE Get the latest insulation, airtightness & dry lining solutions, as well as sustainability guidance, regulatory advice and case studies, from ISOVER. NAVAILABLEOW! GET YOUR FREE COPY HERE https:/www.isover.ie/solutions-guide
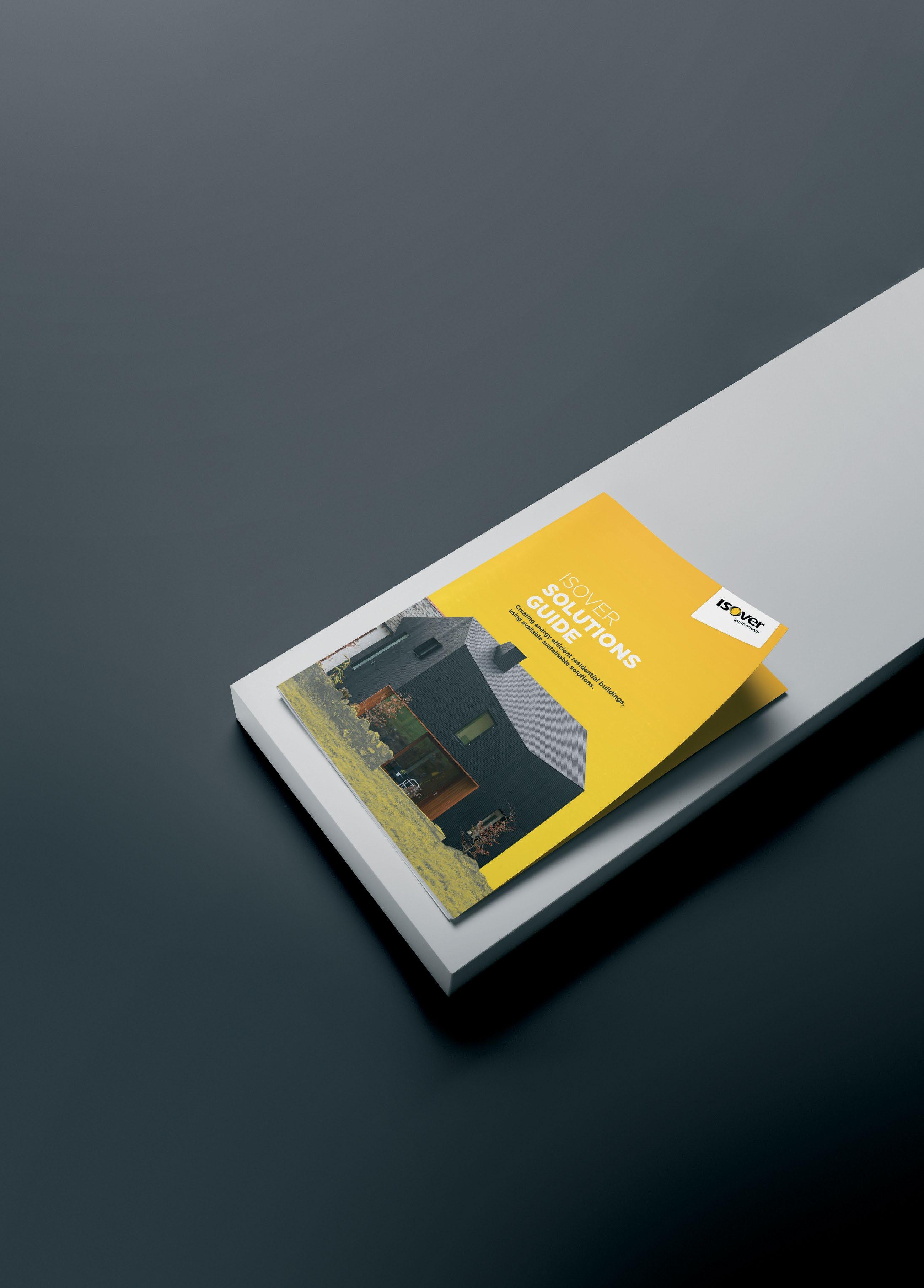
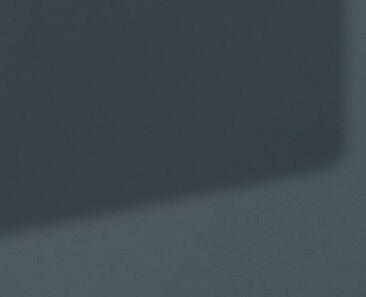
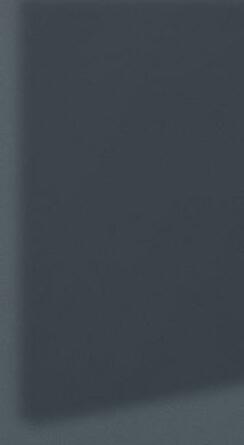
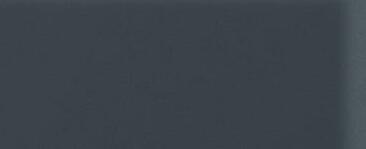
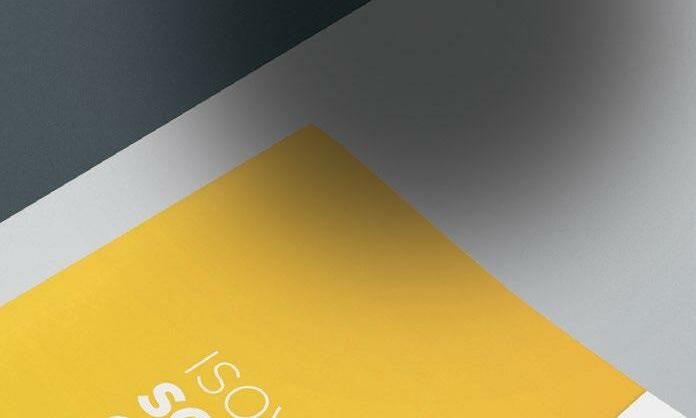

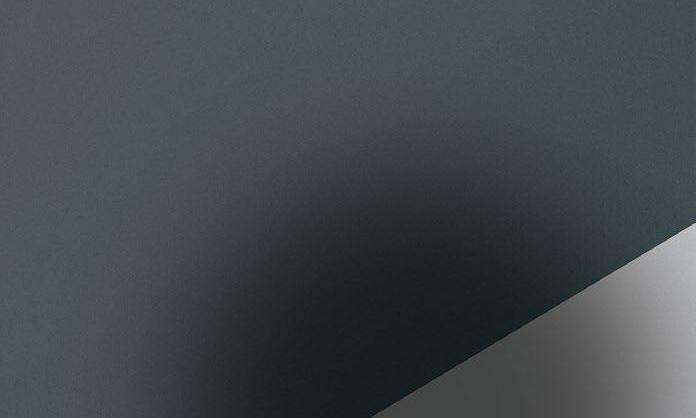


Calcium silicate board: Ecological Building Systems
Solar PV consultant: Tim Cooper Conservation Engineering Consultant Underfloor heating: Unipipe & doors: Internorm, via Eco Window Concepts
SELECTED PROJECT DETAILS
Architect & passive house design: Mel Reynolds Main contractor: Sean Regan Ltd Quantity surveyor: Damian Bowers & Associates Services engineer: Mike Kelly & Associates Structural engineer: Carraig Consultants
Windows
Flat roofing: Moy Materials
Decentralised MVHR: Partel Ironmongery: Ecco Architectural Hardware
Passive house certification & thermal bridge analysis: Earth Cycle Technologies
Electrical contractor: Thomas Kenny & Co Heat pump: Heat Merchants
Rooflights: Velux, via Tradecraft Blockwork: Mannok Rigid insulations: Kingspan Mineral wool: Isover
External render: Baumit Airtightness tapes/membranes: SIGA Liquid airtight membrane: Blowerproof Ireland
Sanitaryware: Bath House Kitchens: Timbercraft
Health & safety: Safety Solutions
Thermal breaks: Compacfoam, via Partel Concrete containing 50 per cent Ecocem GGBS: Kilsaran
ph+ | neville road case study | 53 CASE STUDY NEVILLE ROAD
FSC certified timber: Glennons BER: SC Airtightness & Ventilation Rainwater harvesting: Wastewater Solutions
Renewable energy consultant: Tim Cooper Conservation Engineering Consultant Roofing: KD Roofing Mechanical contractor: Mountain Lodge Mechanical Services
Metal fabrication: Dunfab Engineering
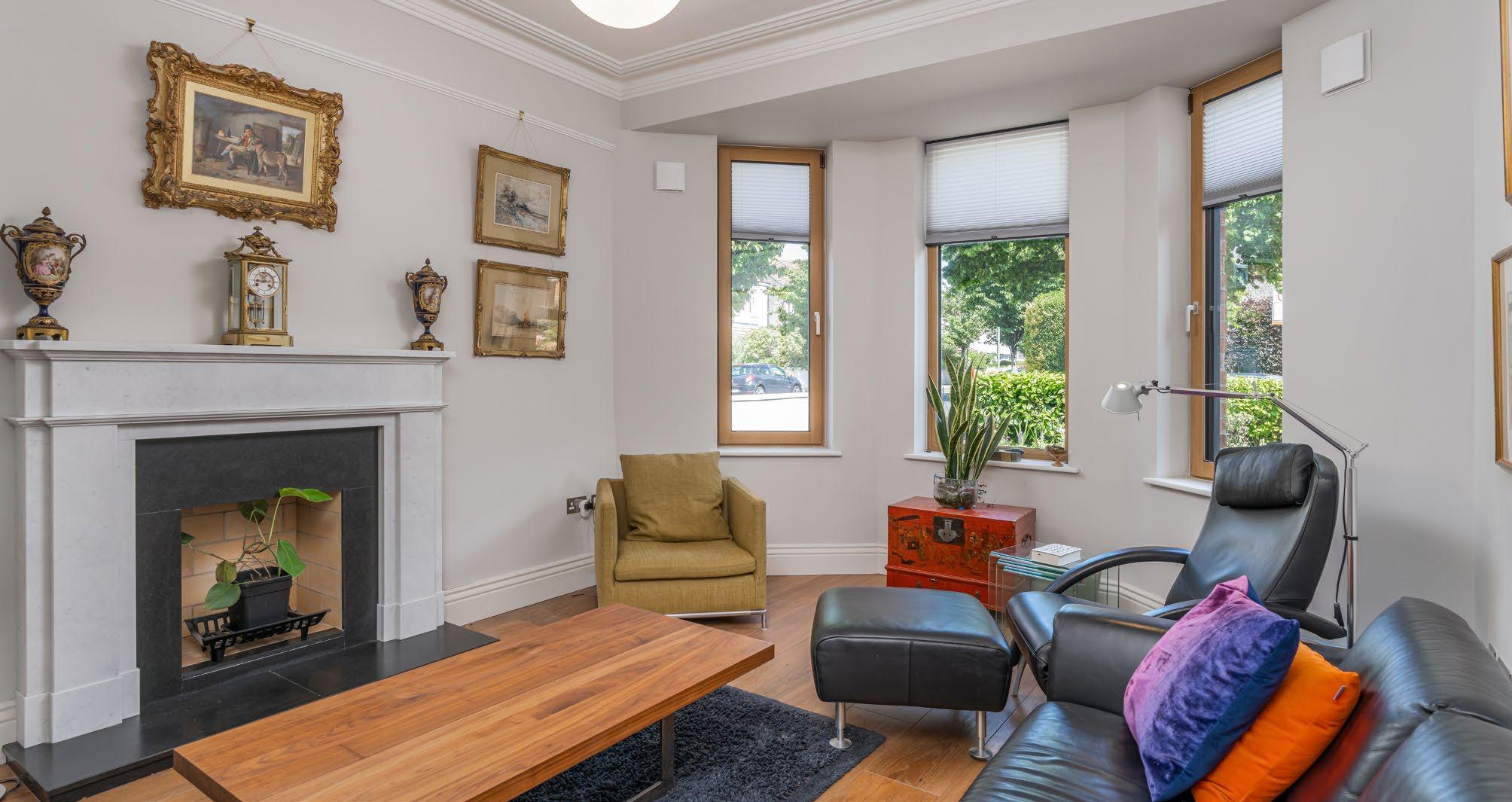
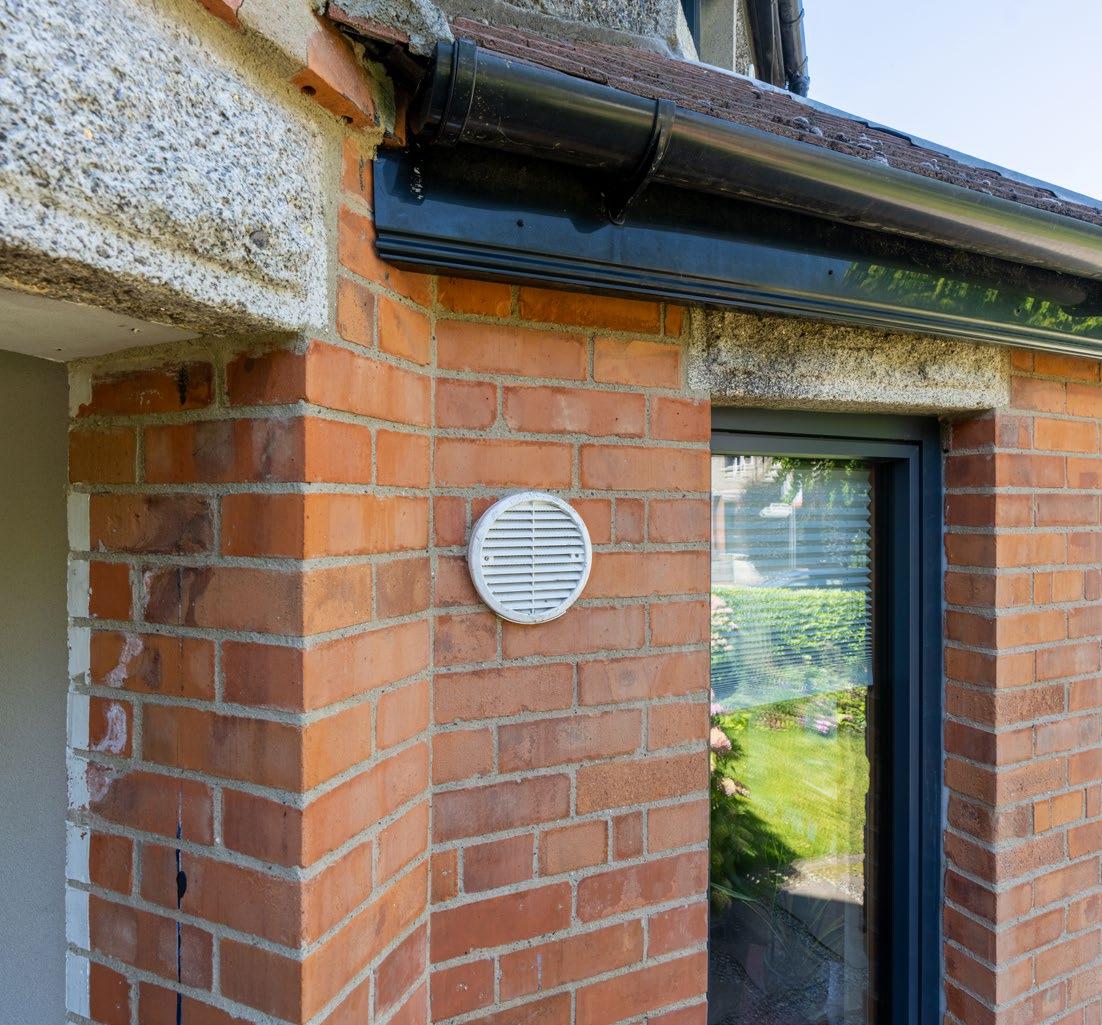
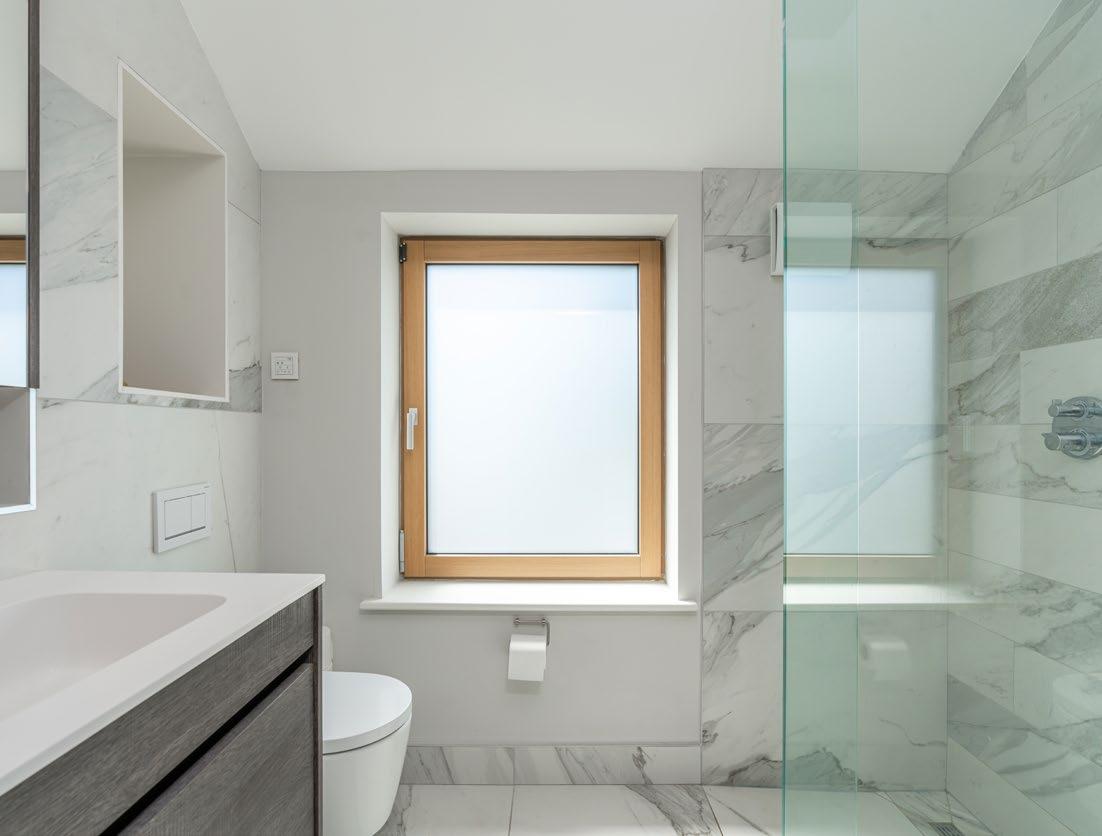
54 | passivehouseplus.ie | issue 42 Building remarkable Making life remarkable Our expert team drives an active programme of collaboration and innovation. We are building a network of the most forward-thinking partners and suppliers, to improve how we live through research, design and implementation. D/RES incorporates international best practice in Environmental Social Governance (ESG) and was awarded GRESB accreditation in 2021.Wewww.dres.iedesignand build homes with high levels of comfort and healthier living environments. Establishing sustainable communities is always at the forefront of our thinking. CMYCYMYCMYMCK V5 IRL Passive House - 93(W) x 135(H)mm.pdf 1 27/05/2022 15:00
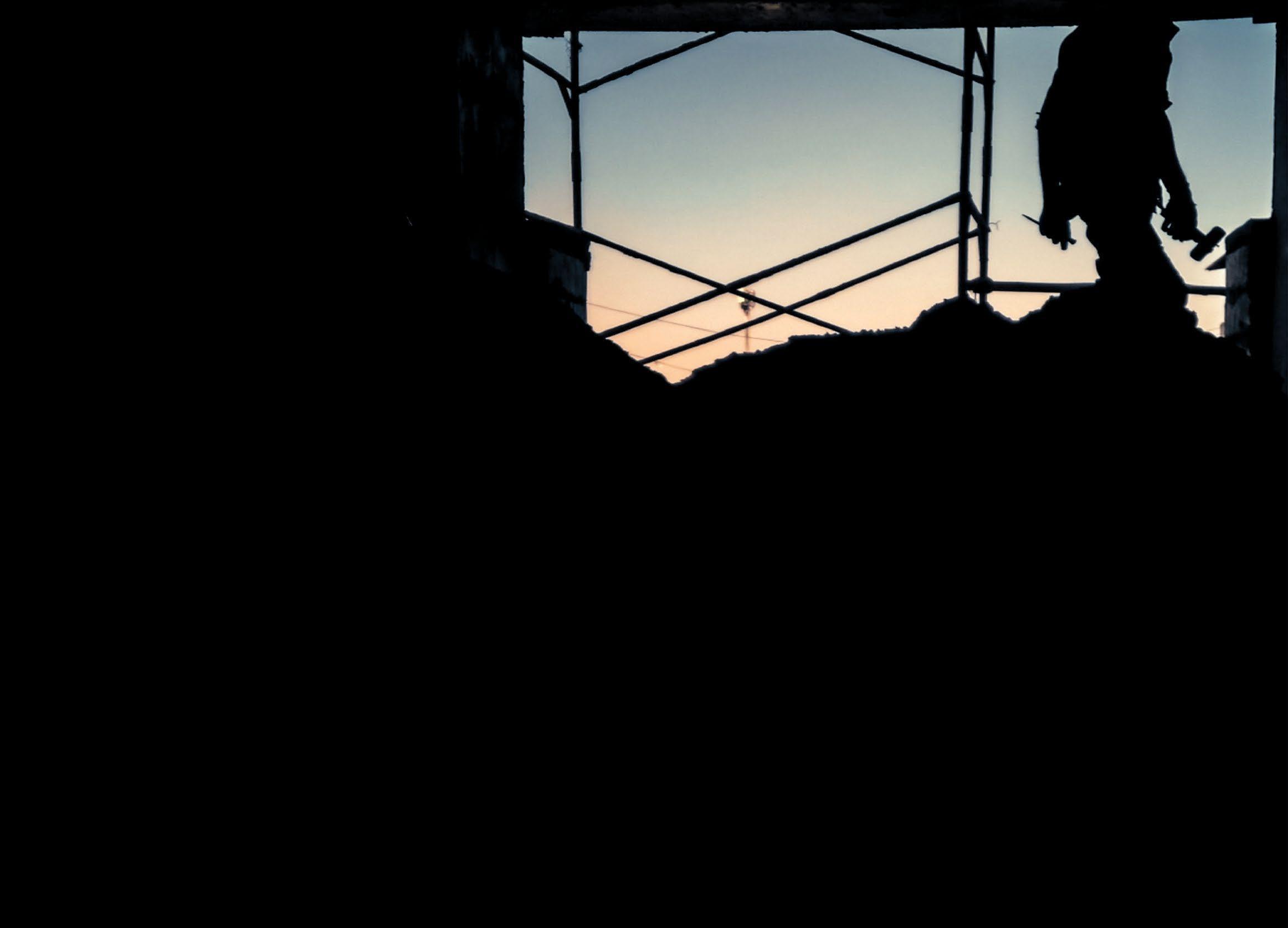
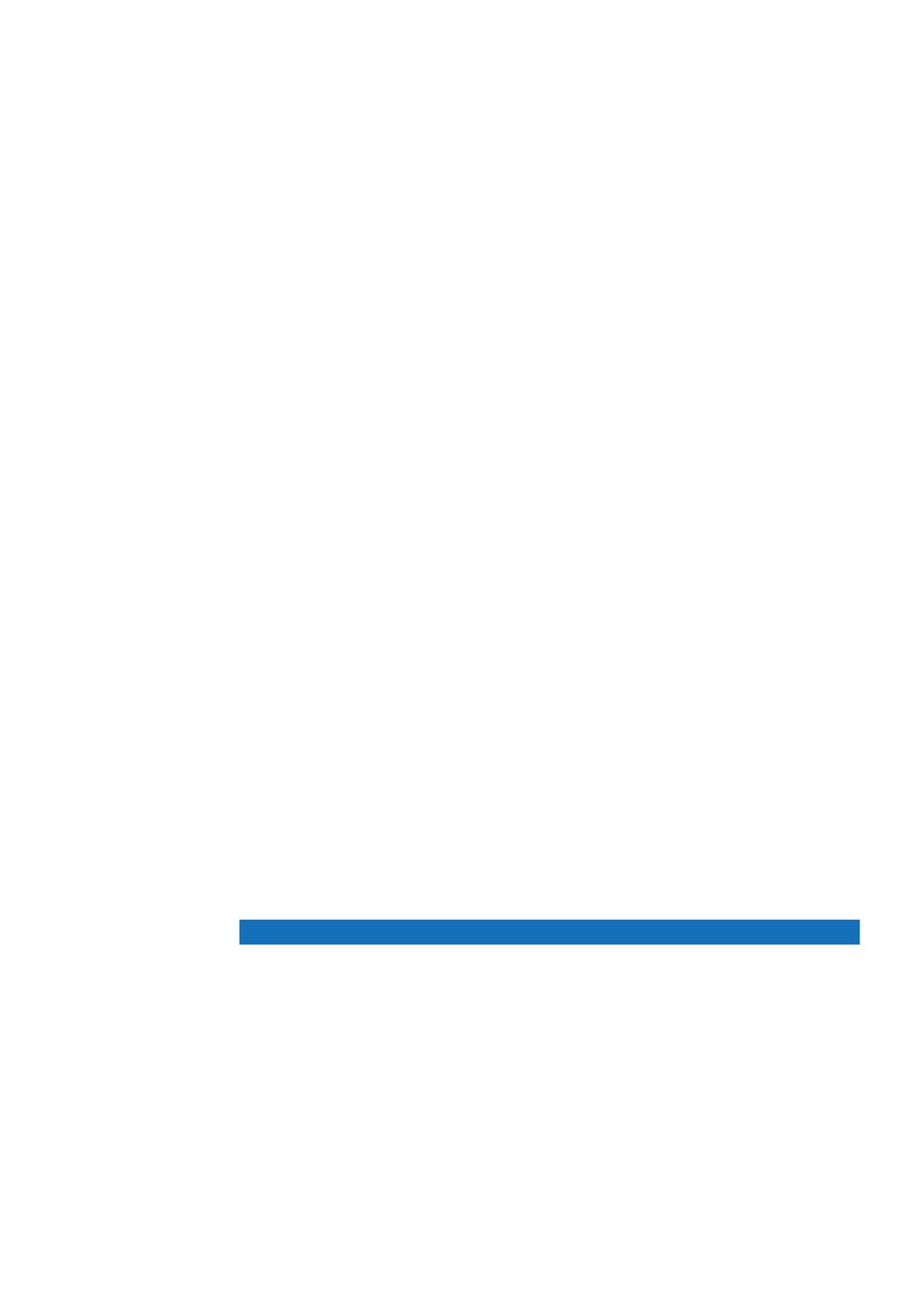
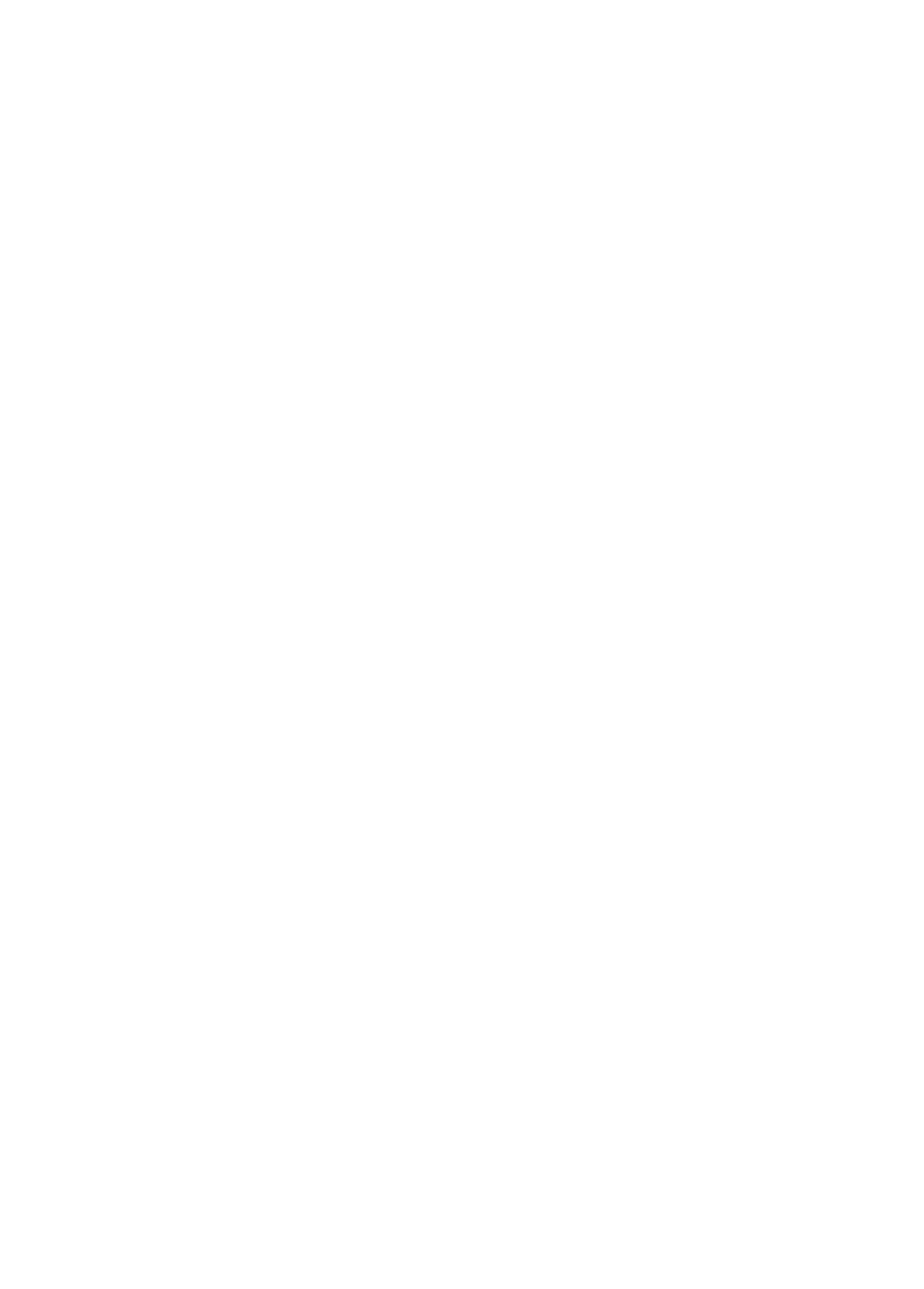
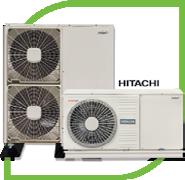

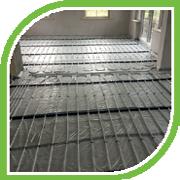
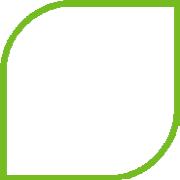

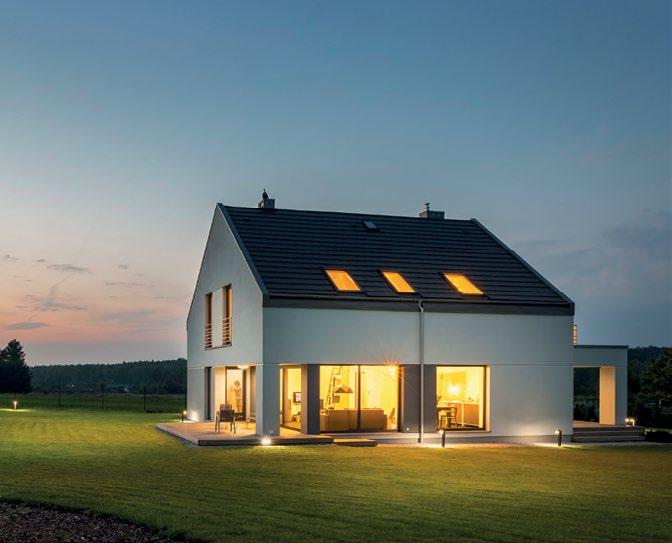
ph+ | neville road case study | 55 CASE STUDY NEVILLE ROAD Building type: 167.4 m2 semi-detached house from 1928. Works included 46.7 m2 part demolition of existing building and single-storey lean-to side garage, Enerphit refurbishment with new single-storey rear extension and two-storey side extension of 67.9 m2. Total completed net floor area 188.6 m2 Location: Rathgar, Dublin 6 Budget: N/A Completion date: October 2020 Enerphit certification: Pending BER (before): F BER (after): A1 (provisional) Heat load: 13 W/m2 Primary energy demand (PHPP): 45 kWh/m2/yr Primary energy renewable (PHPP): 25 kWh/m2/yr Heat loss form factor (PHPP): 2.79 Overheating (PHPP): 1 per cent (of hours above 25 C) Number of occupants: 3 Measured energy consumption Before: 3,151 kWh (electricity) and 11,103 kWh (gas) over 12 months pre-retrofit, with two occupants in the house. Total: 14,254 kWh After: (May 2021-May 2022) 8,551 kWh total consumption (all-electric) over one year post-retrofit, but with three occupants for four months, and six occupants for eight months. An energy model from Tim Cooper produced an adjusted figure for three occupants, allowing for the house drying out and homeowner learning to use the building, of 6,290 kWh/yr. This includes 1,452 kWh for space heating. Passive House Plus took the cheapest tariff available on Bonkers. ie as of 3 July 2022 of 19.69c (based on smart meter, urban connection, without night meter), meaning the portion of energy use for space heating comes in at €286/yr, or under €24 per month. Standing charges were excluded from this calculation, as they are incurred at the same rate merely by having an electricity connection. In fact, the decision to switch from gas to electricity for heating avoided incurring a second standing charge - ranging from €104 to €187/year, depending on the supplier. This reduction was not IN DETAIL factored into these calculations. Airtightness (at 50 Pascals): 0.9 air changes per hour. Before:Floor Uninsulated timber ventilated floor in main section of house with solid concrete uninsulated slab to original side garage. U-value: 1.85-3.48 W/m2K After: 150 mm thick 50 per cent GGBS RC slab insulated with 270 mm Kingspan K3 insulation. U-value: 0.073 W/m2K Before:Walls 300 mm solid masonry walls. U-value: 0.65-0.80 W/m2K After (generally): Acrylic external render on 140 mm Kingspan EWB insulation, on 300 mm existing masonry wall with 15 mm existing render, with Blowerproof airtightness paint (as required), with 12.5 mm plaster on 15 mm dabs internally. U-value: 0.12 W/m2K After (brickwork front elevation): Existing brick-faced 300 mm masonry wall with 15 mm existing render, with Blowerproof airtightness paint (as required), with 60 mm Calsitherm board skimmed internally. U-value: 0.585 W/m2K Before:Roof Sloped with mineral wool insulation. Roof slates to sloped areas and torch-on-felt to flat roof areas externally. 75 mm mineral wool insulation on the flat between roof joists and a combination of suspended ceiling tiles or plasterboard ceiling internally. U-value: 0.47 W/m2K After: Min 50 mm ventilated space retained between underside of existing slates and top of 100 mm Kingspan K7 Thermaroof insulation friction-fitted between rafters with counter-battens, and 100 mm Kingspan Thermaroof insulation to underside (200 mm total), with Siga vapour membrane and 13 mm plasterboard finish internally. U-value: 0.134 W/m2K Extension new walls: Acrylic external render to 140 mm Kingspan EWB insulation, to 215 mm Quinn Lite B5 blocks, Blowerproof liquid airtight membrane, 12.5 mm plaster on 15 mm dabs internally. U-value: 0.12 W/m2K Extension flat roof: Paralon NT4 2-ply roofing membrane on 120 mm Paratorch insulated board, on 18 mm OSB on timber joists, with 210 mm infill Kingspan K7 insulation and 15-90 mm Isover Metac insulation, on 15 mm OSB board underside, with 25 mm service cavity and 12.5 mm plasterboard internally. U-value: 0.10 W/m2K Windows & doors
Electricity: Yet to be installed. Plan is for 8 x 340 W peak PV modules, prioritised over heat pump for generating hot water.
Water: FLine Diver 5,000 litre rainwater harvesting tank supplying all irrigation and WCs. All sanitary fittings are low-flow 9 litres per min. Green materials: A 50 per cent GGBS cement used in all in situ-concrete, aerated blockwork throughout with FSC certified timber in all areas. All ground surfaces are permeable.
Before: Single glazed timber windows and doors. Overall approximate U-value: 3.50 W/m2K After: Internorm triple glazed aluminium-clad oak windows, with argon filling and an overall U-value of 0.73 W/m2K; G value 0.6 Roof windows: Velux triple glazed window No 68. Centre pivot, electrically operated pine finish internally. Overall U-value: 1.1 W/m2K Attic hatch: Wellhöfer Passive House Institute certified airtight hatch Heating system Before: 20-year old gas boiler & radiators throughout. After: Panasonic Aquarea air source heat pump with Harp database registered COP of 4.74, delivering to underfloor heating throughout, fitted with integral hot water cylinder. Before:Ventilation No ventilation system. Reliant on infiltration, chimney and opening of windows for air changes. After: Lunos decentralised E260 and Ego ventilation units. E260 has maximum efficiency of 96 per cent and 88 per cent to EN13141-8. PHI adjusted efficiency for this project is 75 per cent, with specific power consumption = 0.11 W/m3/h. E260 is the only decentralised fan with S1 wind class protection, and costs from €10 to €20 per annum to operate the system including filters.
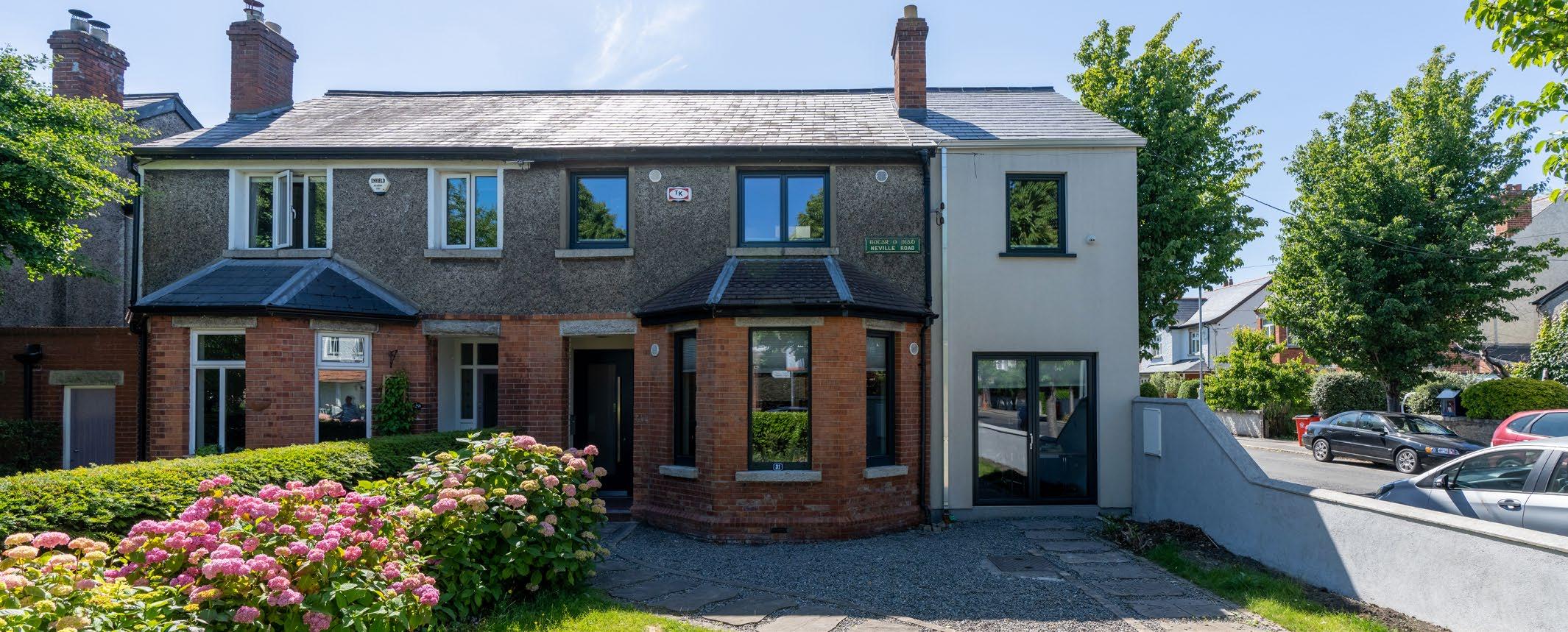
IN Scheme:BRIEF450 passive houses across eight sites in York; mixed tenure Method: Timber frame Location: York, England Standard: Passive house classic targeted
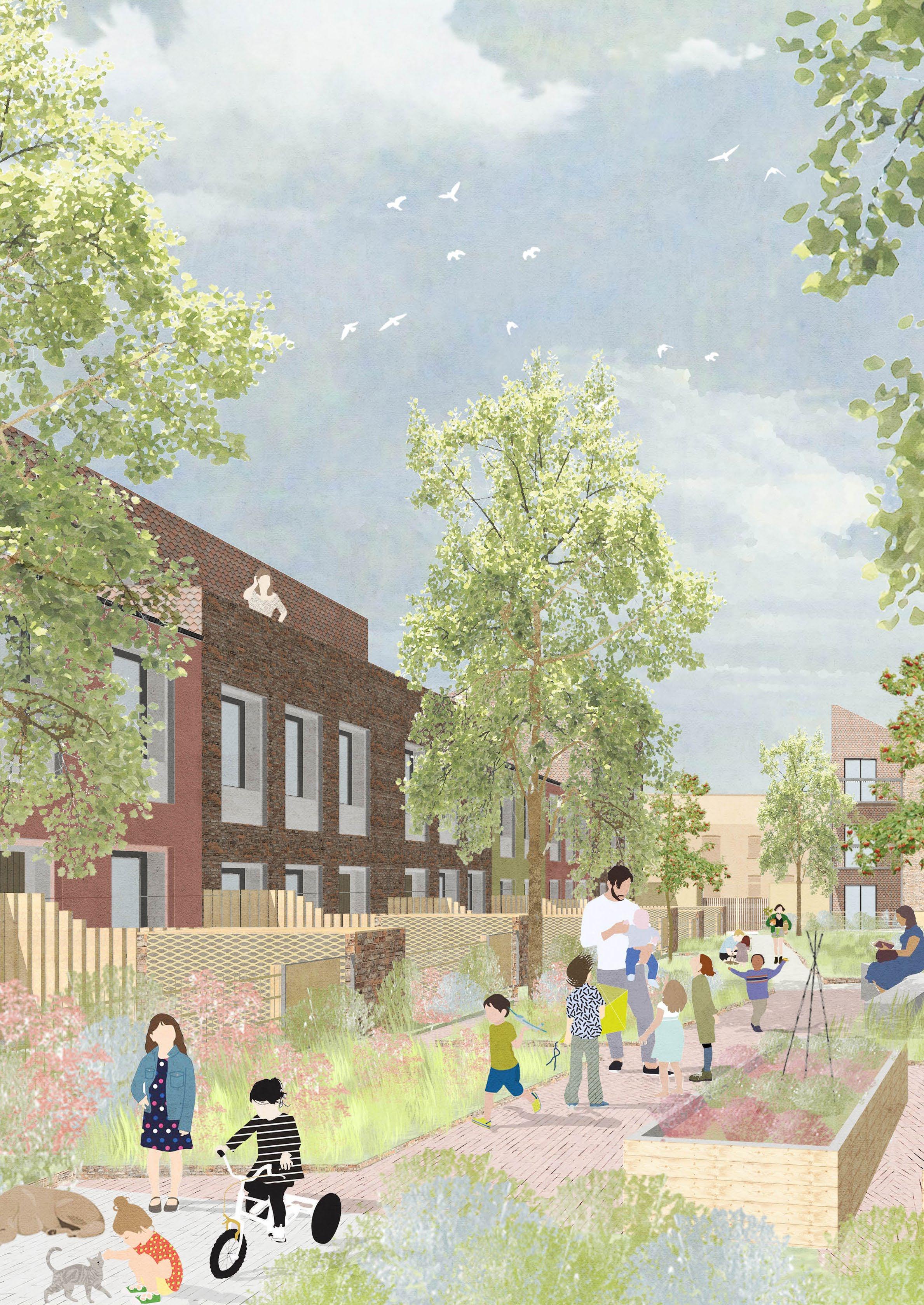
The historic Roman city of York is embarking on an ambitious programme to redefine council housing for the 21st century, building 450 mixed-tenure passive houses across eight sites in the city, and unashamedly prioritising walking and cycling, and shared outdoor green spaces, over cars. It may seem too good to be true, but a cityscape whose architecture still so manifestly displays its extraordinary history is now pointing to the future of urban design.
By David W Smith
FROM NERO TO ZERO LOCAL AUTHORITY HOUSING TAKES A GIANT LEAP FORWARD IN YORK 57
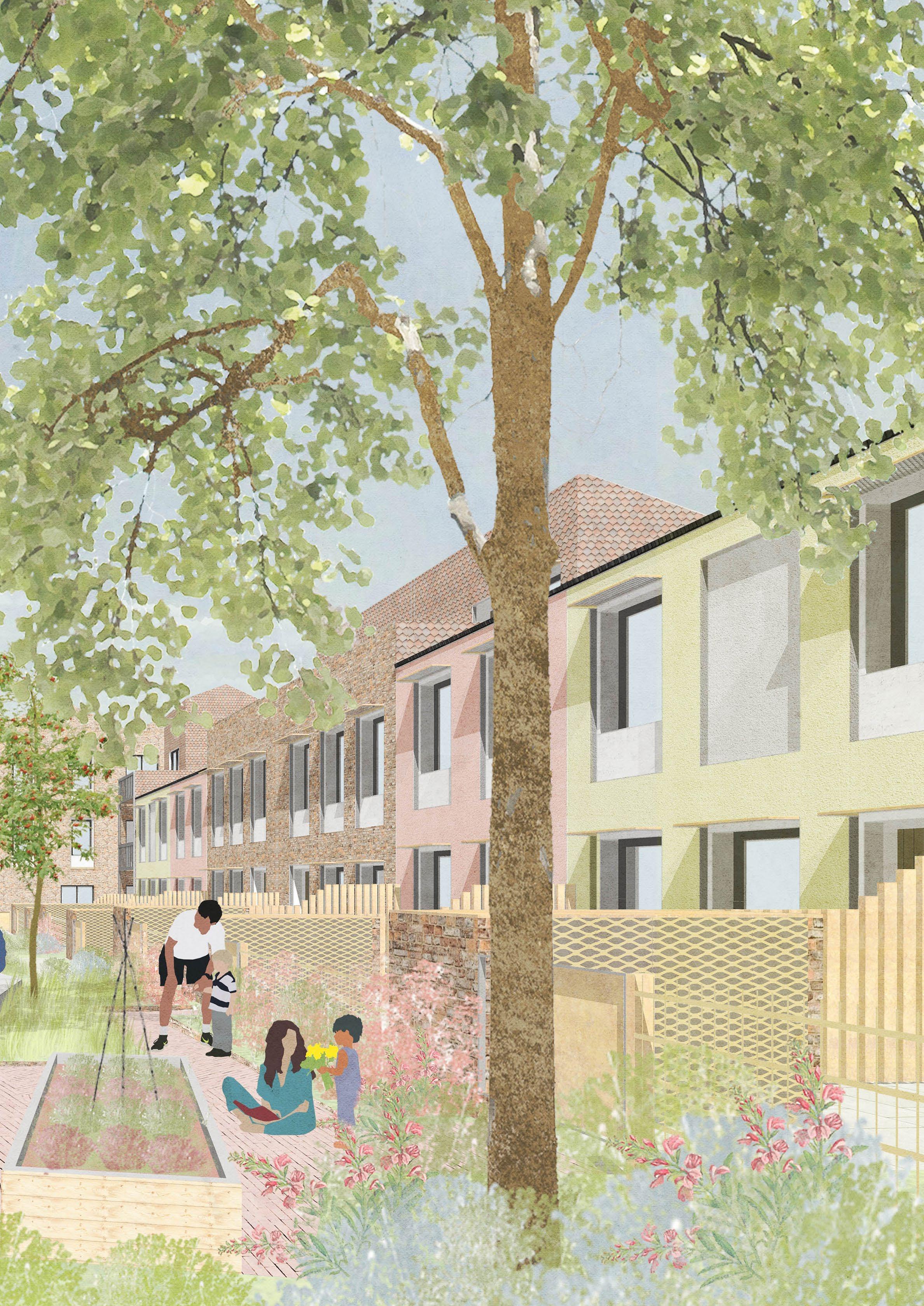
City of York Council began its 600-home project in 2017. At the time, the council owned several vacant sites and was facing an ongoing affordability crisis, with demand for housing outstripping supply. House prices are relatively high for the north of England. When adjusted for income, properties are similarly expensive to parts of the south east. The first 88 homes on the first site, a 165-home project at Lowfield Green, have already been occupied and the rest will be completed by late 2022. They were designed by BDP’s Sheffield office and are mixed ten ure, with 40 per cent social rent and shared ownership allocations, and 60 per cent pri vate housing sold under the Shape Homes York brand. But with the next stage of de velopment, York wanted to go much further on the outskirts of York at the start of the 20th century. In New Earswick, the arts and crafts houses lie along streets lined with grass verges. Two fruit trees have been planted in every garden and the homes are flooded with light. In an egalitarian manner, there are houses for both workers and managers. But whereas Rowntree was concerned with presenting an alternative to the city’s slums and deprivation, an effort has been made to adapt his ideas for the modern age, says Mi chael Jones, York’s head of housing delivery and asset “Josephmanagement.Rowntreewas a great inspiration. We directly borrowed from his ideas, such as planting trees for every home, designing homes so that they are filled with natural light and having front doors that open onto green spaces rather than roads. Like Rown tree, we have made the developments as in clusive as possible so people can live there regardless of job and income. Our goal is to tackle modern-day social ills, which are very different to what they were in 1902,” heOnesays. reason behind Jones’ desire to de velop passive houses for York was his expe rience in charge of an ambitious 500-home development for the Joseph Rowntree Trust in 2016-2017. Derwenthorpe was also a mixed-tenure scheme, with open spaces, self-sustaining communities and low car bon goals. But the homes were not passive houses and sometimes didn’t live up to their ambitions in terms of energy performance. “It too was very ambitious. We thought about health, wellbeing and communities that support each other, reducing reliance
We are passionate about mixedcommunitiescreatingwithdemographics.
58 | passivehouseplus.ie | issue 42
C ity of York Council has embarked on arguably the most ambitious passive house scheme so far con ceived by any local government in the UK. The council is building 600 energy efficient homes across about eight sites near the cen tre of the city, and 450 of them will not only be passive houses, but also net zero carbon for operational energy. What’s more, York have hired Stirling Prize winning architects Mikhail Riches to design the schemes. These radical developments are nothing less than a re-imagining of how society can best function in the 21st century. Everything has been done to make the mixed-tenure developments accessible to all social classes and age groups. Car use is discouraged; ev ery home has a bike shed and private open space; green communal areas run between the homes and around the sides. The schemes have taken inspiration from Joseph Rowntree, the York chocolatier who built the model village of New Earswick on the state and private car ownership. But there were performance gaps, some of the homes were not as warm as expected, or res idents felt draughts. What drew me to pas sive house is you get what you pay for. The testing and certification process provides a lot of confidence for the client team.”
But the council’s 600-home scheme, Jones is keen to emphasise, is not just about achieving the passive house mark. “I would never criticise anyone for doing pas sive houses. But you could live in a passive house with a large driveway and three cars. Our developments are about supporting a sustainable lifestyle in all of its facets — sustainable transport, being well connected and minimising the need to travel, as well as the houses being very energy efficient, and having the renewable technology to generate power on top of that.”
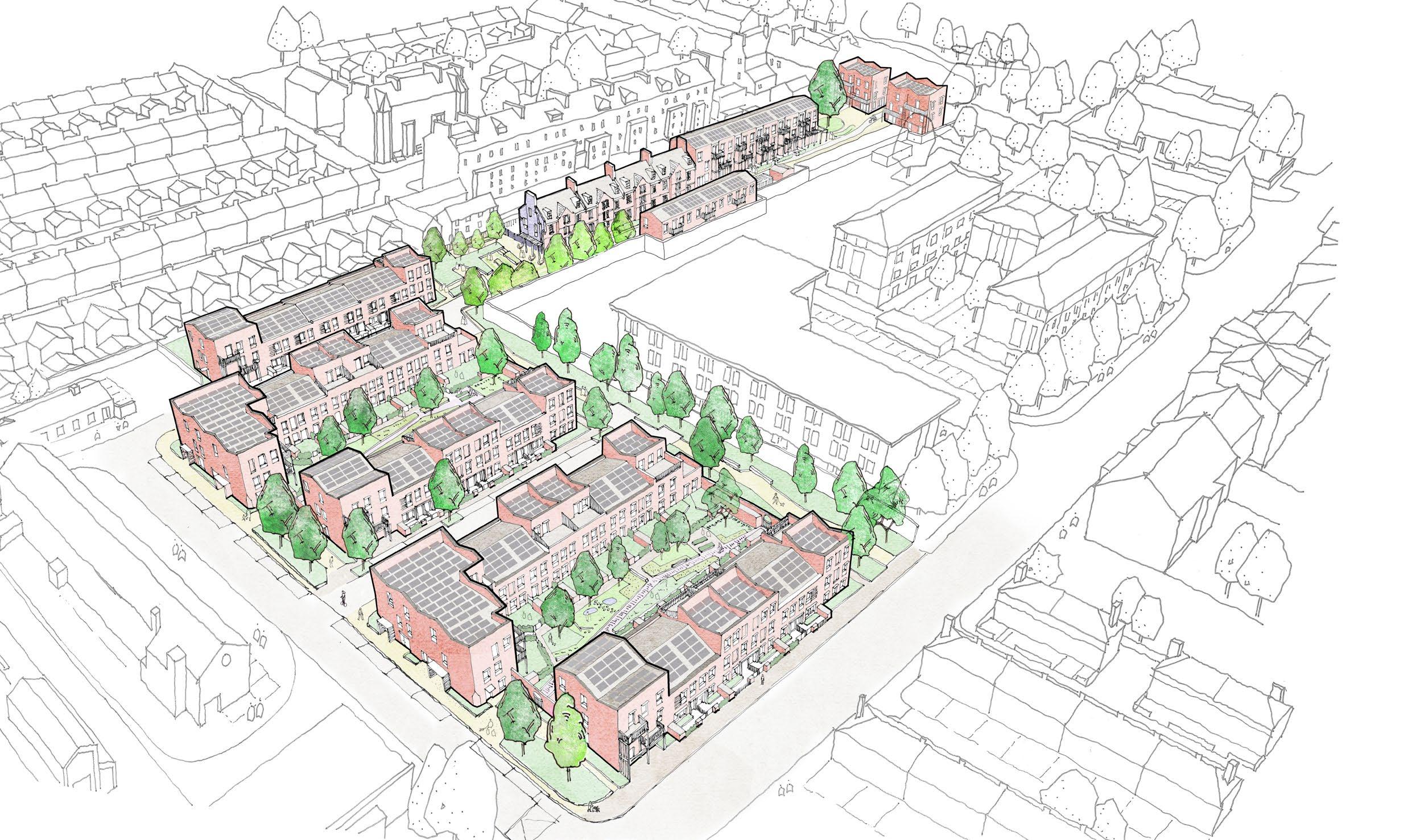
There has also been more local engage
ph+ | york case study | 59 CASE STUDY YORK Renders: Mikhail Riches / Darc Studio |
Drawings: Mikhail Riches
ment and consultation at York. The council hired Angela Koch, from planning consul tancy Imagine Places, to connect the design team and client with local stakeholders. The team met local businesspeople and residents to do demographic analysis of areas, then spatially map out facilities and services. They then held workshops with residents in local churches or community centres. “We used building blocks representing houses, or trees, or cars, and asked residents to move them around. The community became part of the design process detailing each project’s objec tives and working with the design team to build it. They had to make all kinds of tradeoffs and we found that residents pushed us towards having more trees, more green space and fewer car parking spaces. Given York is such a flat city, it’s a place you can live hap pily without a car, although we’re trying to put in car hire in every site. You can have a car for a few hours rather than one that sits on the driveway 90 per cent of the time.”
The schemes have taken inspiration from Joseph Rowntree, the York chocolatier who built the model village of New Earswick. and build zero carbon passive houses. Fifty architectural practices submitted bids and Mikhail Riches was appointed a week before winning the 2019 Stirling Prize for the ground-breaking Goldsmith Street, a certified passive social housing scheme in Norwich which featured in issue 32 of Passive House Plus. “I wasn’t familiar with the practice before their submission, but we visited Goldsmith Street and thought it was fantastic,” said Jones. “When they won the Stirling Prize, it gave us a lot of confidence we were right to take the next step on from Lowfield and build passive houses, incorpo rating PVs, air source heat pumps and re newables that take it to zero carbon.”
When David Mikhail, co-founder of Mikhail Riches, saw York’s advertisement in the Architects’ Journal he found the brief “really refreshing”. He says: “It was the first time I’ve seen a call for our services that suggested the client thought as we do and used the same language. It’s rare you get asked questions that – because you abso lutely know your stuff – you’re desperate to answer. Rather than the usual mind-numb ingly tedious brief, York were asking ques tions like ‘how would you go about making places suitable for pedestrians and cyclists rather than cars?’ and ‘how would you make a really great place to raise a family?’ It was aspirational design. So, they got it right from the beginning. And that was before the new councillors came into power a short
The first two zero carbon sites designed by Mikhail Riches are at Duncombe Barracks, on Burton Stone Lane in the Clifton ward, and Burnholme, in the Heworth ward. Both developments have planning permission and Jones has signed a contract with Caddick Construction to build them. Construction of Duncombe Barracks’ thirty-four homes, and one commercial unit, will begin this summer and is expected to take 18 months. Meanwhile, the construction of the eightytime later and became even more ambitious, targeting zero carbon. I don’t know another council targeting both zero carbon and de livering such high-quality homes.” The DNA of the York developments, Mikhail says, is similar to the Norwich pas sive houses. In Norwich, there are shared children’s play areas at the heart of the com munities and a similar idea is being devel oped for York on a bigger scale. Mikhail says: “But in Norwich they were just ginnels, slightly enhanced alleyways, whereas in York we’ve been more ambitious and generous. We’ve created raised beds for shared grow ing. At all stages, Michael and his team have an eye on creating first-rate places to live.”

60 | passivehouseplus.ie | issue 42 YORK CASE STUDY
(top left) York councillor & executive member for housing Denise Craghill visiting site with Caddick Construction director of housing Richard Greenwood. (bottom left) Pictured at Duncombe Barracks site, where public engagement boxes were placed are (l-r) Mikhail Riches senior architect Sophie Cole, ImaginePlaces founder Angela Koch, councillor Craghill and City of York’s head of housing delivery and asset management Michael Jones.
Another aspect of the scheme which may raise eyebrows among house builders and planners alike is density, with Burnholme, Duncombe Barracks and Ordnance Lane re
The projects aim to encourage sociabil ity to avoid the modern plague of social isolation, says Councillor Denise Craghill, York’s executive member for housing and safer neighbourhoods. “The shared spaces, including the raised beds and the ginnels, encourage socialising outdoors. It’s similar to something we’re seeing in existing Victo rian terraces in York which is the greening of spaces between houses. At the front of the houses we’re creating play streets where chil dren can scoot around and people can meet up,” she says. Craghill says it will be interest ing to observe how the major house builders react to the high quality of the homes, as well as their extra environmental credentials.
three Burnholme site homes will follow on a few months later. A third project on Ord nance Lane with eighty-three new homes has just won planning approval. More sites are under discussion and will follow. Each location has a mix of one-bedroom flats and houses of various sizes. Currently 40 per cent are affordable homes, which is roughly half council housing and half shared ownership. But Jones says the council wants to get grant funding to increase the number to around 60 per cent of the total. The coun cil has also introduced a priority scheme for key workers. “The vast majority of projects are now mixed tenure. If we did 100 per cent affordable housing schemes, we’d run out of funding quickly. This way the sales’ receipts help to cross-fund the development and it’s not exclusive in any way. It should al low us to keep doing this for years,” he says. An important element of the inclusivity, he says, is that some of the homes allow two generations of the same household to live independently within them. “Britain is the most age-segregated society in Europe and we’re passionate about creating communi ties with mixed demographics. With some of the homes, the ground floor is a self-con tained flat, so the property will have two separate kitchens. The living room will have a connecting door to the main house upstairs which will support the larger fam ily. This type of co-living could be suitable for grandparents, who might want their independence, but also need to be close to their family for support. It allows flexibil ity and you get the benefits of the physical strength of younger people with the wis dom of older people. “We feel that this could be a great alter native to a care environment for many fam ilies, which our residents tell us is the last resort, but one people often feel forced to take because of a lack of alternative options. This design might also work well for sons or daughters who have come home from university and can’t afford to buy their own home yet, or for other family members with care or support needs.”
We’ve created raised beds for shared growing.
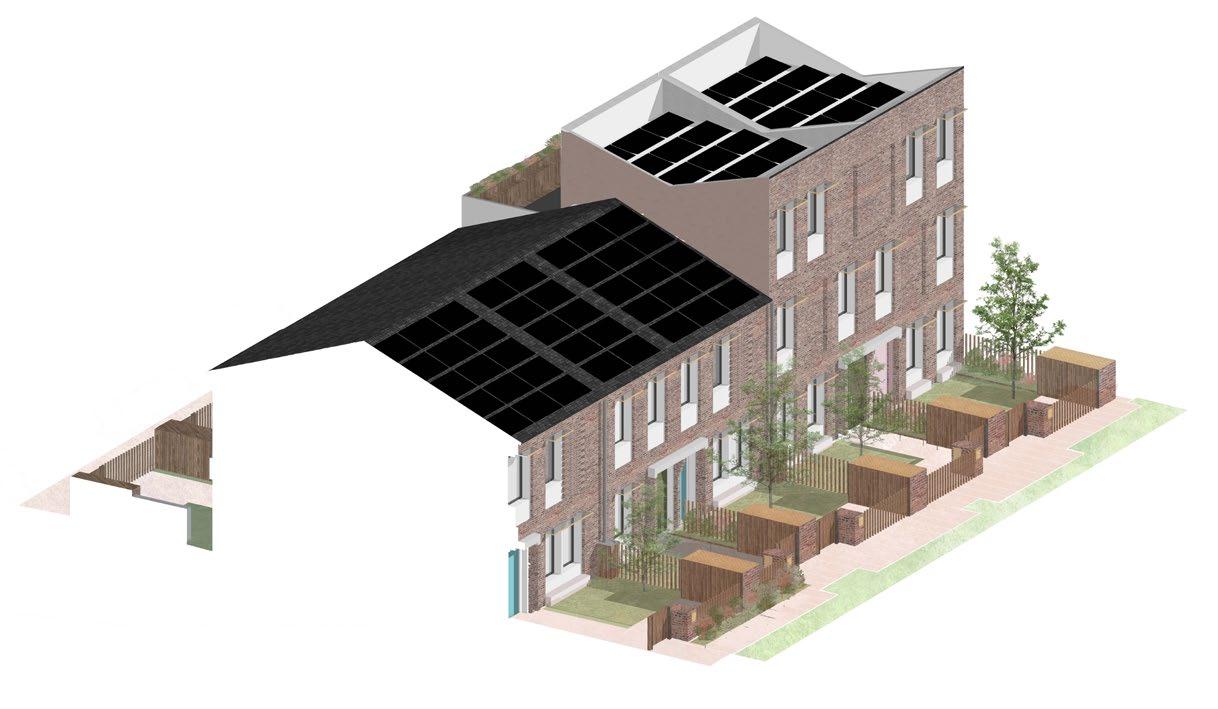
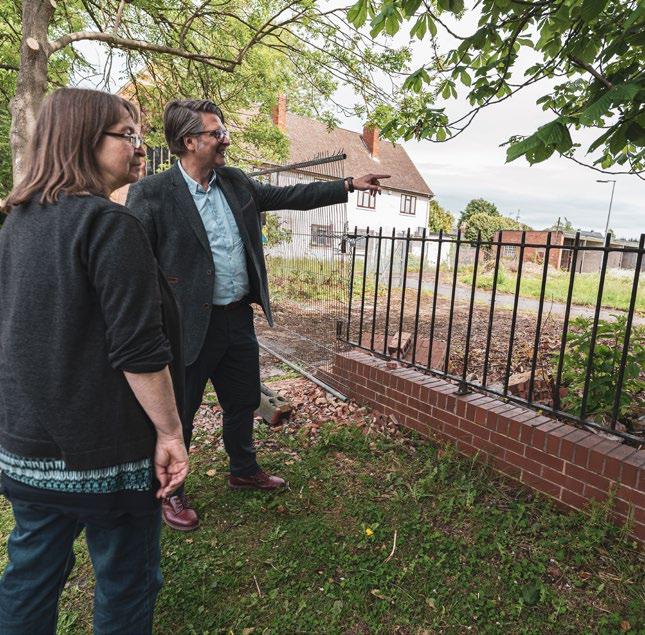

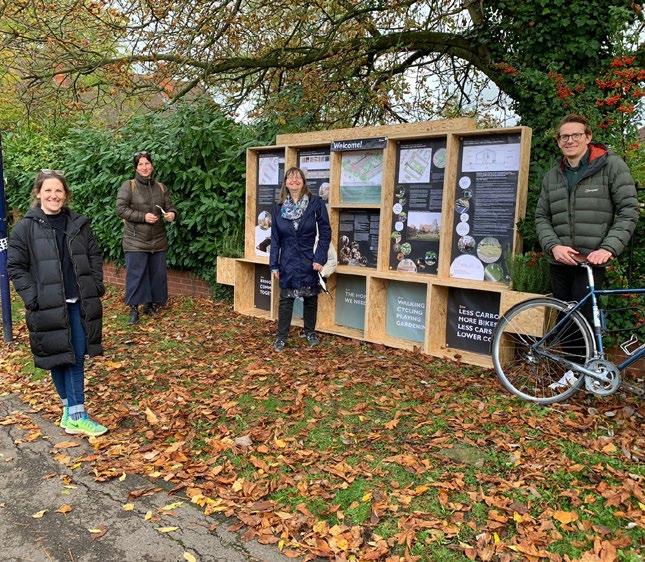
Product details reflect initial specification and are subject to change Developer: City of York Council Architect: Mikhail Riches M&E design: LEDA Civil & structural design: Civic Engineers Passive house consultant: WARM Project management: Turner & Townsend Main contractor: Caddick Construction Quantity surveyor: Turner & Townsend Timber frame supplier: Roe Ltd Airtightness products: ProPassiv, via Green Building Store; Tremco Illbruck, or equivalent Brise soleil: Cadisch MDA Air source heat pump: Valliant DHW cylinder: McDonald Water Storage Steel panel radiators: Stelrad MVHR: Zehnder Pitched roof PV: Viridian Flat roof PV: Bisol Blown cellulose: Warmcel, or equivalent External wall insulation: Permarock, or equivalent EPS insulation: Jablite, or equivalent Mineral wool slabs: Knauf, or equivalent Windows & doors: Idealcombi, or equivalent Clay facing brickwork: Crest BST, or equivalent Lime mortar: Limetec, or equivalent Oak flooring: Tarkett, or equivalent Car use is discouraged; every home has a bike shed.
WANT TO KNOW MORE?
ph+ | york case study | 61 spectively delivering 40, 52 and 62 dwellings per hectare, chiefly consisting of two-storey dwellings, along with some three-storey apartment buildings. (By comparison, the Irish government’s recently announced Croí Cónaithe scheme to support developing apartments for owner-occupiers requires a minimum density of 35 units per hectare –and a minimum of four storeys). “The dif ferences reflect the different context of the projects,” says Michael Jones. “Burnholme is a very suburban setting and Ordnance Lane is more urban, being a short walk or cycle from the Mikhailcity.”Riches had achieved a remark able 82 units per hectare for Goldsmith Street, but differing considerations allowed a relaxation in this case. “Part of this is around the client brief for the projects to be land scape-led and we are delivering more public open space than planning policy requires,” says Jones. “I was at a local plan hearing last week when developers were saying our proposed local plan density targets are un achievable. I think [these schemes] demon strate that you can achieve high density with national space standards and house sizes, at
As York is in the north of England, where daylight hours are shorter than in the south and the sun is at a lower angle, Mikhail Riches had to work out how to stop overshad owing from blocking the sunlight in win ter. This involved modelling the roofscapes so the sun penetrated the ground floor windows in the kitchens and dining rooms. “It was a lot harder to achieve than Norwich as the angle of the sun is different,” Mikhail says. In the short term, Michael Jones thinks some councils will be put off building pas sive houses, and zero carbon homes, be cause of the higher cost. But he expects it to become more mainstream. “Changes to building regulations will push all new builds to passive house. Costs are a bit of a barrier, but they will fall. A bigger issue is there are so few architects, or builders that have built passive houses. Early adopters like York will help to drive change by upskilling the mar ket and getting our region ready to deliver the standard,” he says.
The digital version of this magazine includes access to exclusive galleries of architectural drawings. The digital magazine is available to subscribers on passivehouseplus.ie & passivehouseplus.co.uk low heights, and create high quality public open spaces with biodiversity net gain.”
SELECTED PROJECT DETAILS
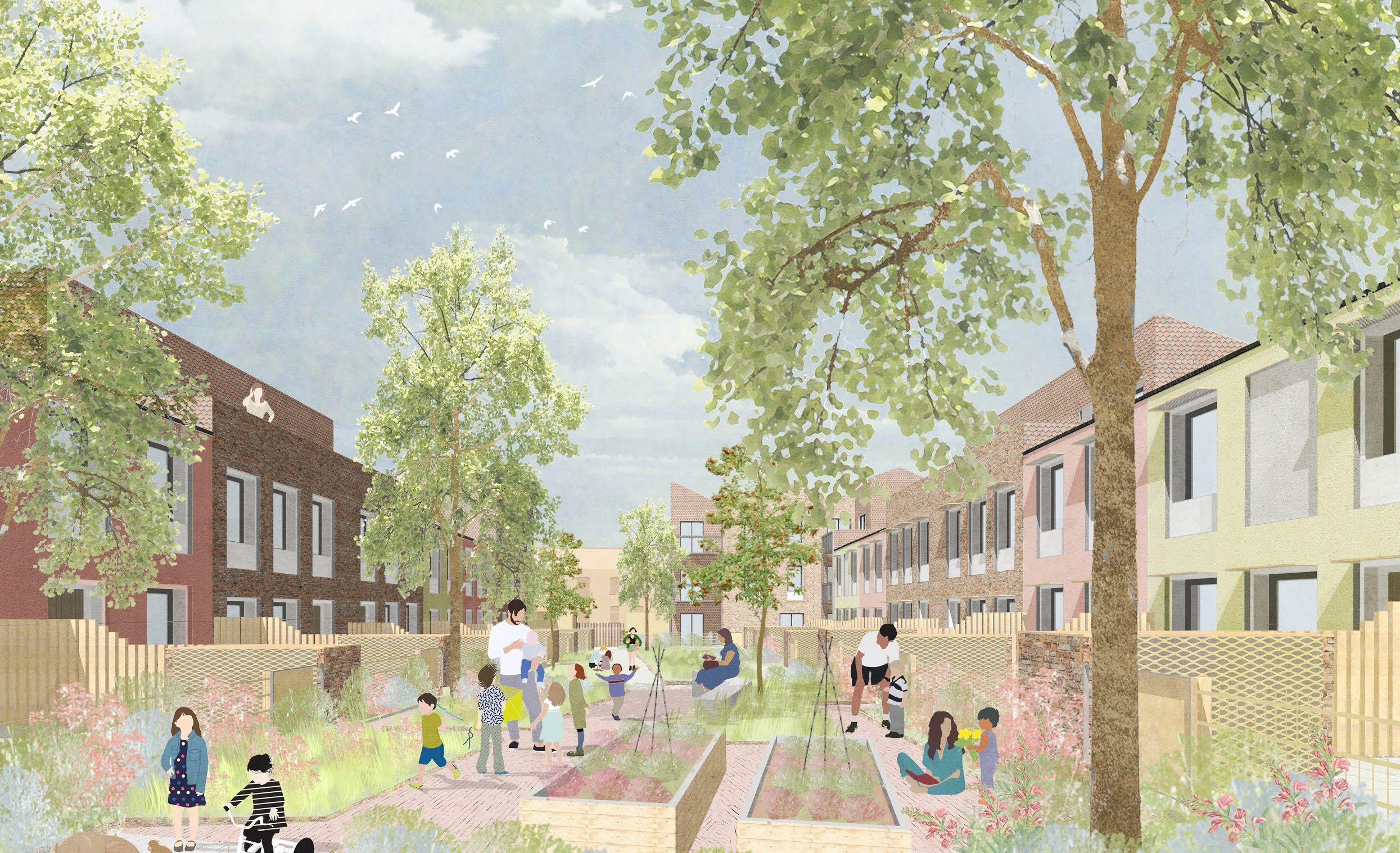
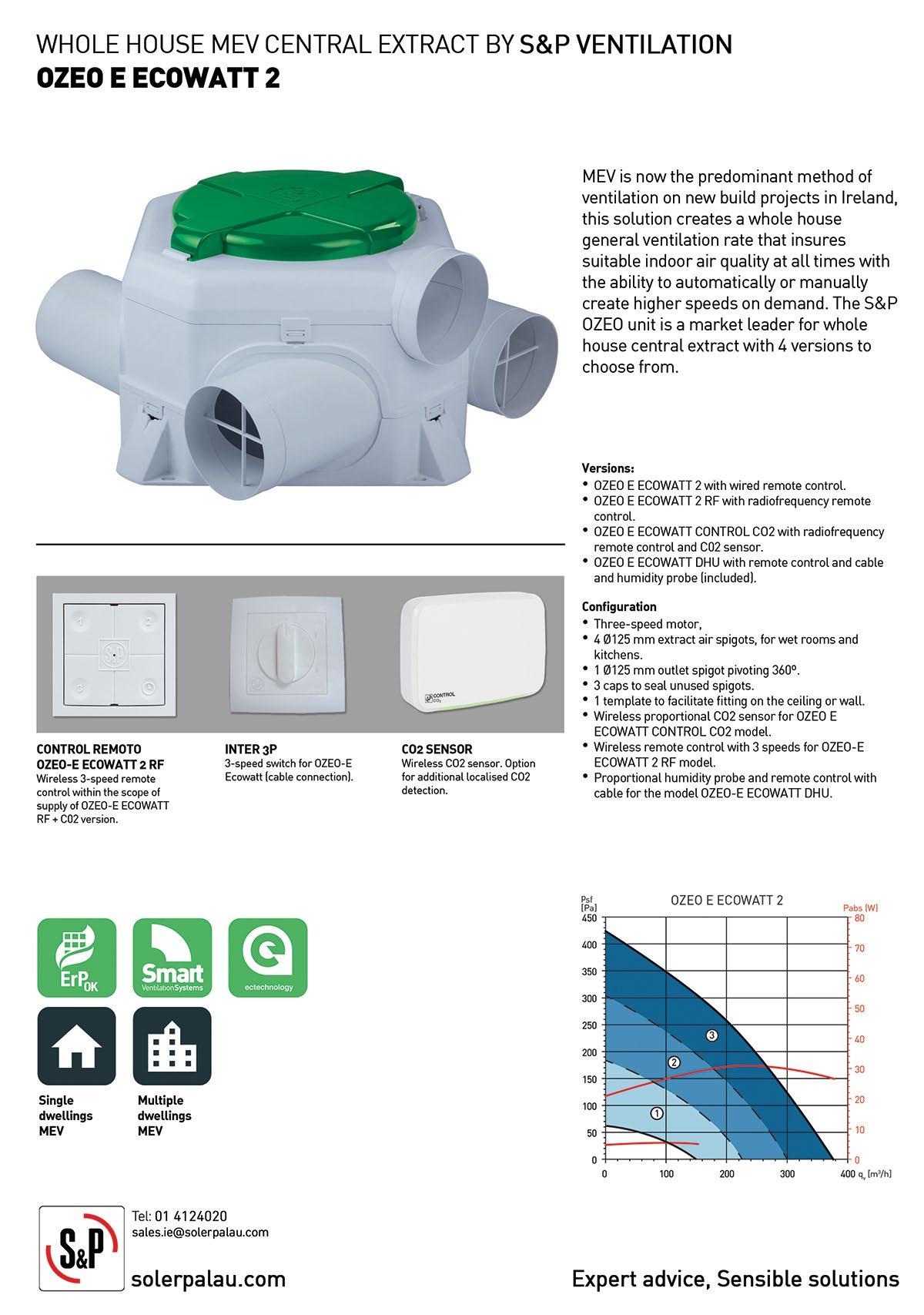
ph+ | york case study | 63 CASE STUDY YORK York wanted to reduce the embodied carbon of the construction by avoiding carbon-in tensive materials like concrete, while using timber frames. David Mikhail thought care fully about how to fulfil York’s request. “It’s incredibly difficult. Until we decarbonise the industry, we’re not getting low-carbon bricks. Since the Grenfell Tower disaster, it’s hard to get insurance companies to look at anything involving timber. And building control is also anxious about timber. As a result, it’s hard to get a mortgage for a building with, for example, timber cladding or timber decking on a balcony. It means we’re forced down the route of steel, glass and cement. But York has used timber frames for the superstructure and we’ve clad it in either brick, or clay tile. And we’ve used cellulose insulation, such as recy cled newspaper, or wood fibre blown-in insu lation, which gets the buildings into line with the RIBA 2030 Climate Challenge guide lines,” he says. In this regard, Passive House Plus played a hand, by introducing Mikhail to Tim Martel, creator of the AECB’s embod ied carbon calculation tool, PHribbon, who did some consultancy for Mikhail Riches before the project began. Caroline Martin of passive house consultants WARM then used PHribbon, with Martel helping define the scope, to calculate the scheme’s embodied carbon scores.
The scope of the assessment – which focused on three blocks of terraced homes and apart ments at Duncombe Barracks – is largely complete, including virtually all elements required for the RIBA 2030 Climate Chal lenge, albeit with incomplete information for building services (the MVHR system, heat pump, pipework and ductwork included), and fixed furnishings and equipment (WCs, basins and kitchen sinks were included). As per RIBA, external works were excluded. The results are indicative only – default data was used in many cases, or if EPDs weren’t avail able for a given product in the spec, default values or data from a comparable product was used. Blocks B and C meet the RIBA 2030 target of 625 kg CO2e/m2 GIA, with scores of 595 and 587 respectively while Block A scoresTaking642.Block A for instance, a large part of the reason for this score is down to what may be regarded pessimistic assumptions about the lifespan of components, and about their end of life. 397 kg of CO2e/m2 are estimated to be released by the point of practical com pletion (module A). By this point the build ing is also estimated to be sequestering 197 kg CO2e/m2 in the bio-based materials used such as timber and cellulose. The use phase (module B) adds a predicted 213 kg CO2e/m2 due to material repair and replacement assumptions. For instance, the PV arrays are assumed to need two replace ments within the 60-year reference life for the building, and the heat pump and MVHR system are assumed to need three replace ments. In well designed buildings such as these, taking account of what we know about the lifespan these kinds of technologies can achieve, may fewer replacements be more re alistic, subject to maintenance? And bearing in mind the strides some manufacturers are already making to radically reduce upfront emissions, is it really reasonable to assume that, say, a replacement heat pump installed 15 or 25 years from now will have similar embodied carbon to machines made today? The end of life phase (module C) adds a fur ther 230 kg CO2e/m2. Principally, this is be cause of the assumption that the CO2 seques tered in the timber and cellulose is released into the atmosphere – including the default assumption that the bulk of this material goes to landfill, and breaks down as methane. However as the article on Joe Lyth’s timber frame house in New Zealand demonstrates (see page 10), it is possible – at least based on New Zealand data – to assume the vast ma jority of sequestered CO2 in landfilled timber does not break down, and remains seques tered. Based on current rules, this would cre ate a curious state of affairs. If timber is reused or recycled at the building’s end of life, the se questered CO2 in that timber moves outside of the boundary conditions of the building, and passes on to the next use. However if the timber is landfilled, and if it’s assumed not to decompose in the landfill, then the seques tered CO2 needn’t be deducted – creating an incentive to dump rather than reuse timber.
EMBODIED CARBON
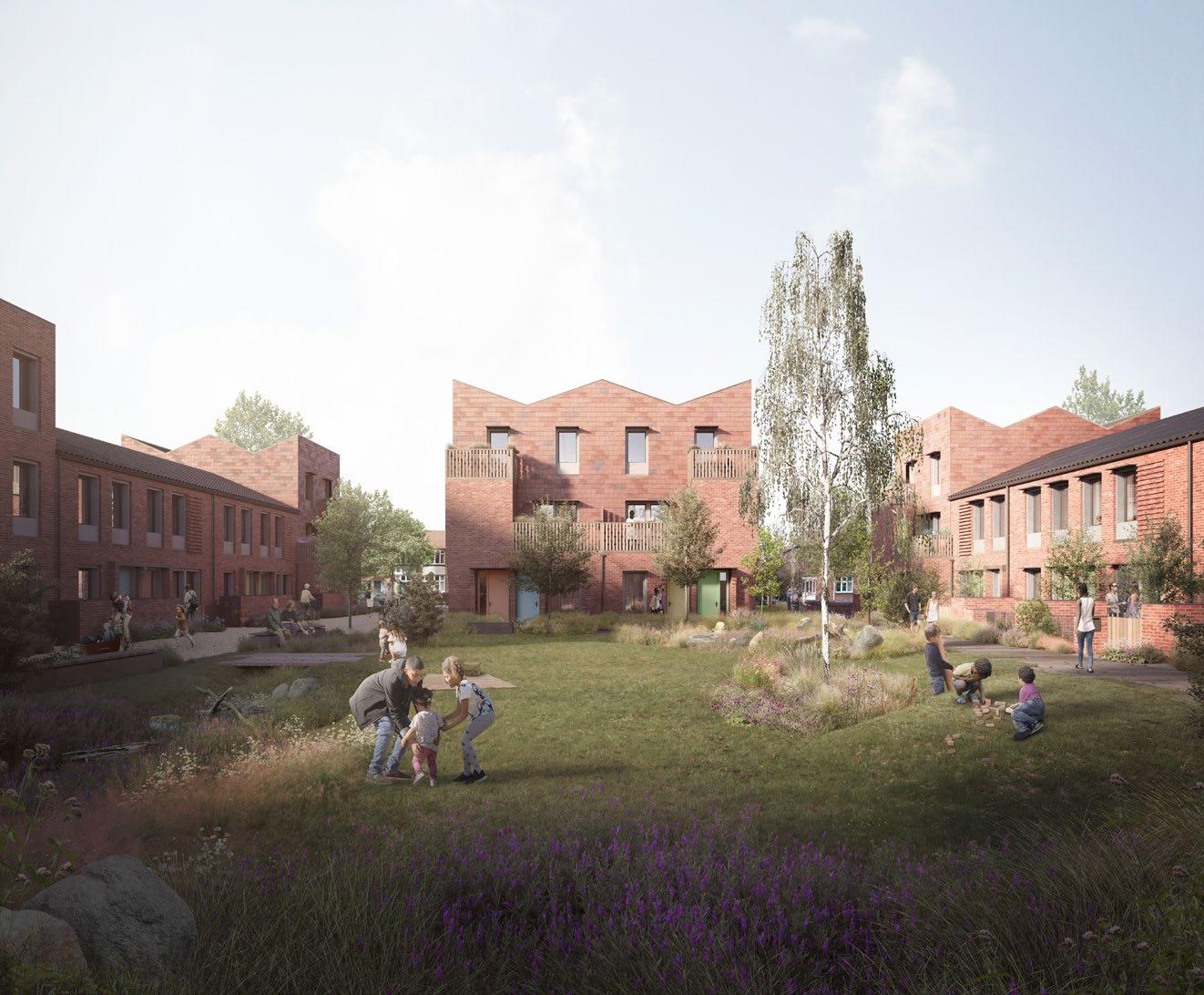
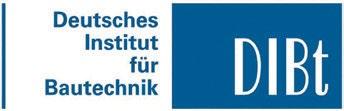

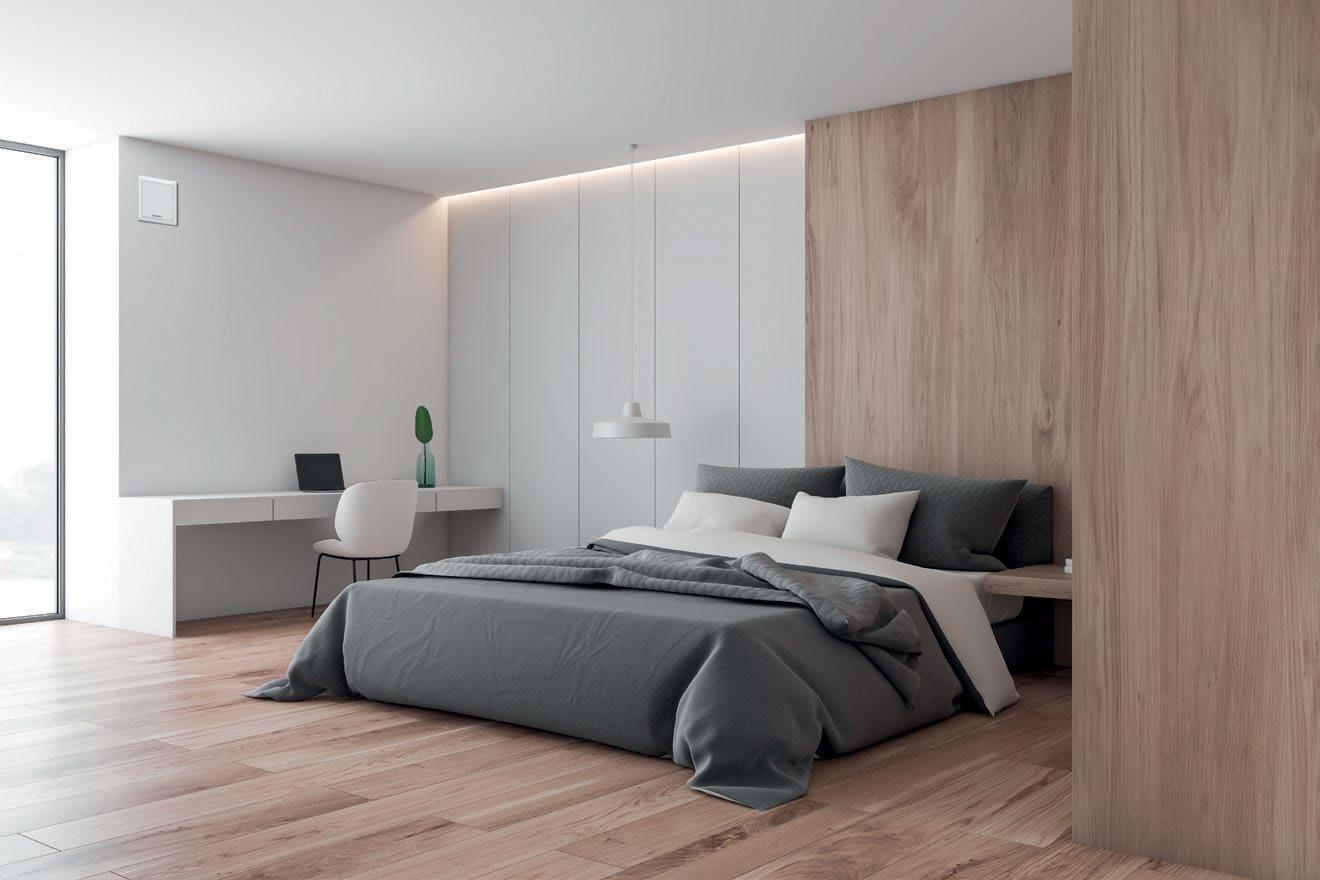
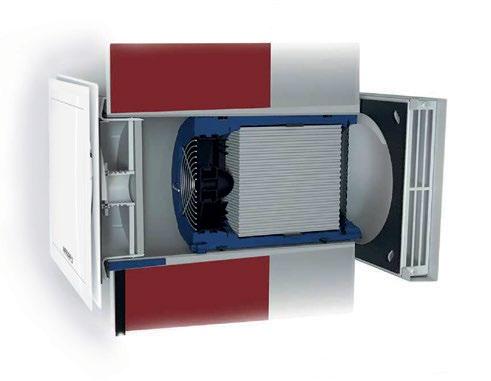

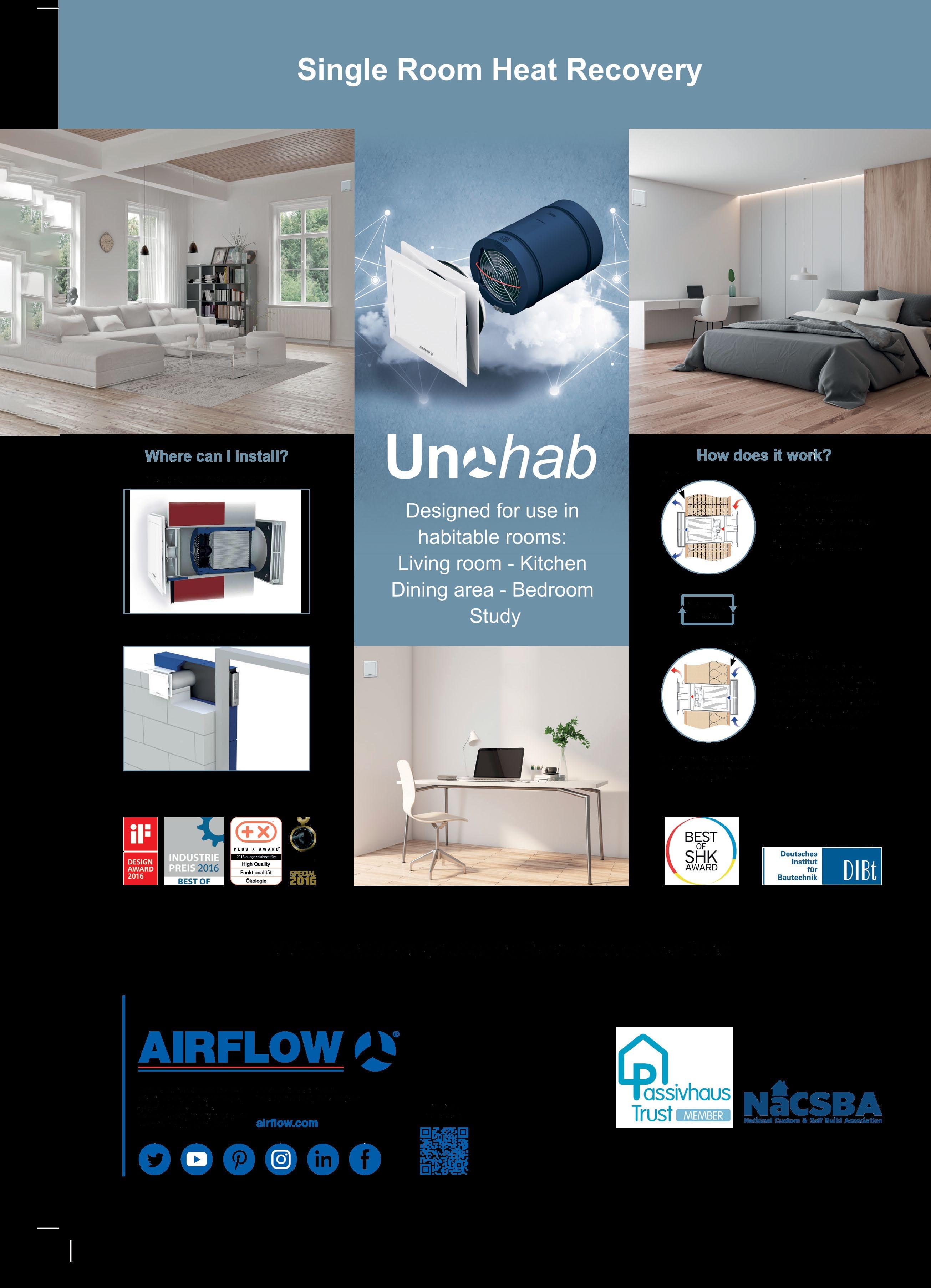
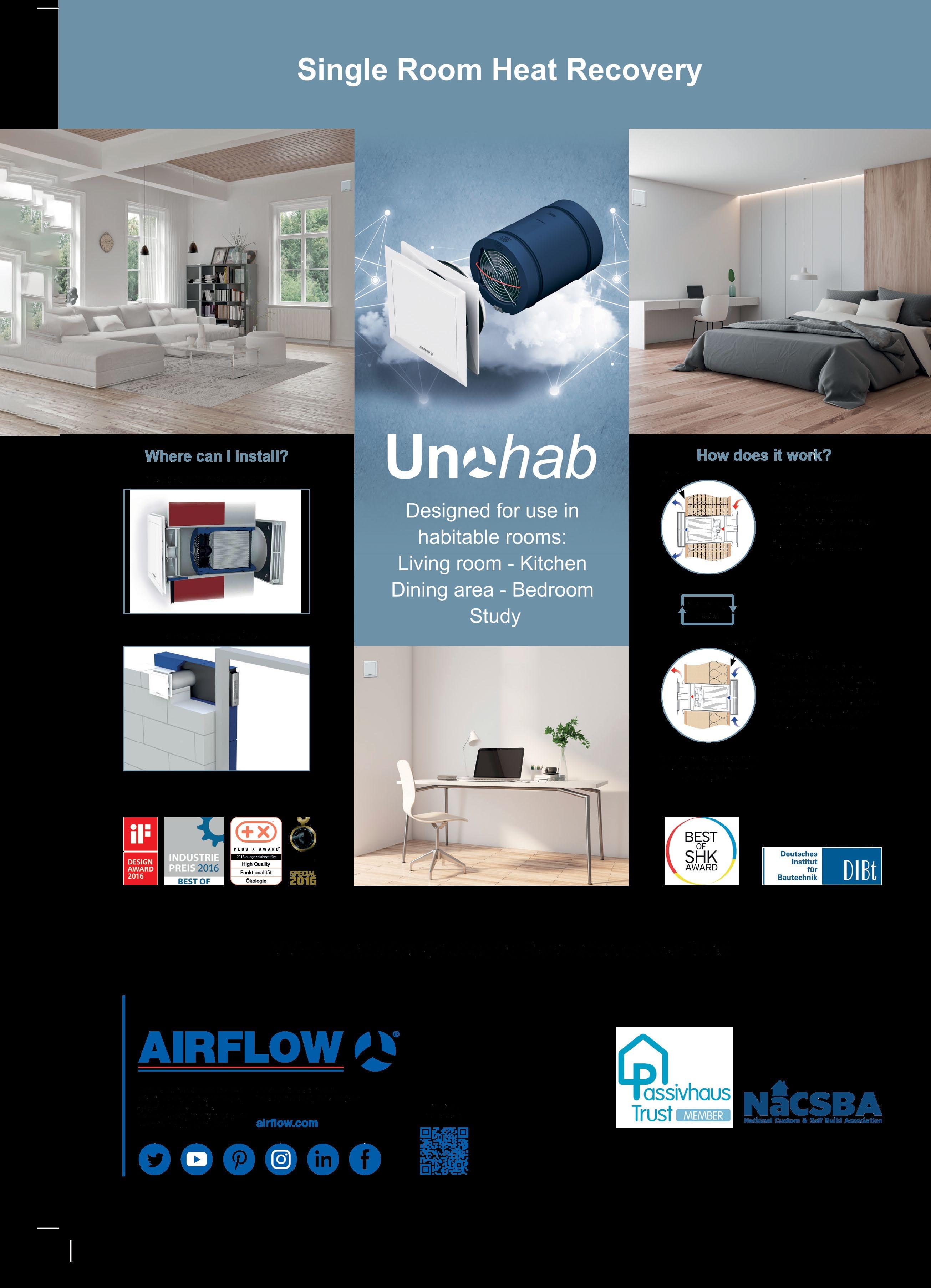
Ventilation: Zehnder heat recovery ventilation systems. Water: Rainwater harvesting via water butts. Low flow fittings on all plumbing fixtures. Electricity: 22 m2 Clearline Fusion PV system with average annual output of 5 kW per dwelling. No on-site storage, excess electricity will be exported to the grid. Green materials: Cellulose insulation, timber frame construction. Transport: Low number of car parking spaces, car clubs, free-to-hire e-cargo bikes, generous bike storage.
Predicated energy consumption: 35 kWh/m2/yr Pitched Roof: Clay Pan Tile, followed underneath by battens & counter-battens, breather membrane (Pro Clima Solitex Plus), 400 mm timber frame insulated with 380 mm Warmcel insulation, 13 mm Propassiv Board used as airtight layer, 45 mm cavity insulated with Knauf Earthwool, 15 mm plasterboard & skim. U-value: 0.097w/m2K Flat roof: IKO Spectratex polyester protection fleece, followed underneath by 200 mm / 300 mm IKO Enertherm tapered PIR roofboard, IKO Systems metal-Lined bituminous VCL, 25 mm plywood (WBP) & OSB3, 150 mm Knauf Earthwool, 400 mm timber frame with 380 mm Warmcel insulation, 13 mm Propassiv Board used as airtight layer, 45 mm cavity insulated with Knauf Earthwool, 2 x layers 15 mm plasterboard, skim. U-value: 0.0106 & 0.072 W/m2K (depending on PIR insulation depth). Windows & external doors: Ideal Combi Futura+ triple glazed aluclad windows and doors.
Heating system: Vaillant AroTherm Plus 3.5 kW air source heat pump with seasonal efficiency of 365 per cent supplying low temperature radiator heating system and a super insulated 180 litre domestic hot water cylinder.
Thermal bridging: Thermal bridge values have been assumed for step backs, balcony structures, internal walls to floor and party wall to floor junctions. These are currently based on details from previous projects and will be calculated at the next stage if necessary. All other thermal bridging has been designed out. Preliminary calculations have been undertaken for window installation values; these will be further refined at the next stage if required.
ph+ | york case study | 65 CASE STUDY YORK designed to the passive house standard. This development will have a range of sizes and types including eleven one-bed flats, eight two-bed terraced houses; nine three-bed terraced houses, and six four-bed terraced houses. Energy performance metrics are targets rather than measured figures. Product details reflect the initial specification and are subject to change. Building type: A typical 110.71 m2 terraced two-storey, three-bedroom house
Ground floor: 75 mm reinforced concrete topping, followed underneath by Visqueen vapour barrier, 225 mm Celotex foil-faced PIR board (thermal conductivity 0.022 W/mK), Visqueen EcoMembrane loose-laid polyethylene DPM, 225 mm Jetfloor insulated beam and block floor system (Infill blocks: 150 mm EPS grey insulation blocks; thermal conductivity 0.030 W/ mK), 250 mm void, 750 x 900 reinforced concrete footings. U-value: 0.083 W/m2K Walls: 102.5 mm brick on 50 mm cavity; or 7 mm PermaRock silicone render on 140 mm PermaRock mineral fibre insulation; followed inside by breather membrane (Pro Clima Solitex Plus), 400 mm timber frame construction with 380 mm Warmcel insulation, 13 mm Smartply Propassiv board as airtight layer, 45 mm cavity insulated with Knauf Earthwool, 15 mm plasterboard and skim. U-value: 0.097 (brick cladding build-up) and 0.80 (silicone render) W/m2K
Energy bills (estimated): As low as £300 per year based on domestic energy costs from 2021.
Based on PHPP estimates, City of York Council estimates that this example property could have a total electricity bill of £300. This includes standing charges but also savings/feed-in-tarriff from the solar PV array. The council says that this should be considered, “a very estimate as it is impossible to predict occupier behaviour. It could be considered an ambitious target that can be achieved with the right education and support.”
Location: Duncombe Barracks, Burton Stone Lane, York Completion date: December 2023 Budget: £13.69 m including land, works and on-costs for the whole development including thirty-four homes, one commercial unit, and high-quality public realm that comprises a central green space and a small civic square. Passive house certification: Aiming for PH classic standard Space heating demand (PHPP): 15 kWh/m2 Heat load (PHPP): 10 W/m2 Primary Energy Renewable (PHPP): Aiming to be below the PER limit of 60 kWh/m2 Heat loss form factor (PHPP): 2.24 for the whole terrace (comprising houses & flats) Overheating (PHPP): Designed for 0 per cent Number of occupants: 5-person household in this example; 141 at Duncombe Barracks in total. Environmental assessment method: Aiming to achieve carbon net zero in operation in line with the LETI framework. Airtightness (at 50 Pascals): 0.6 air changes per hour

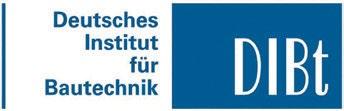
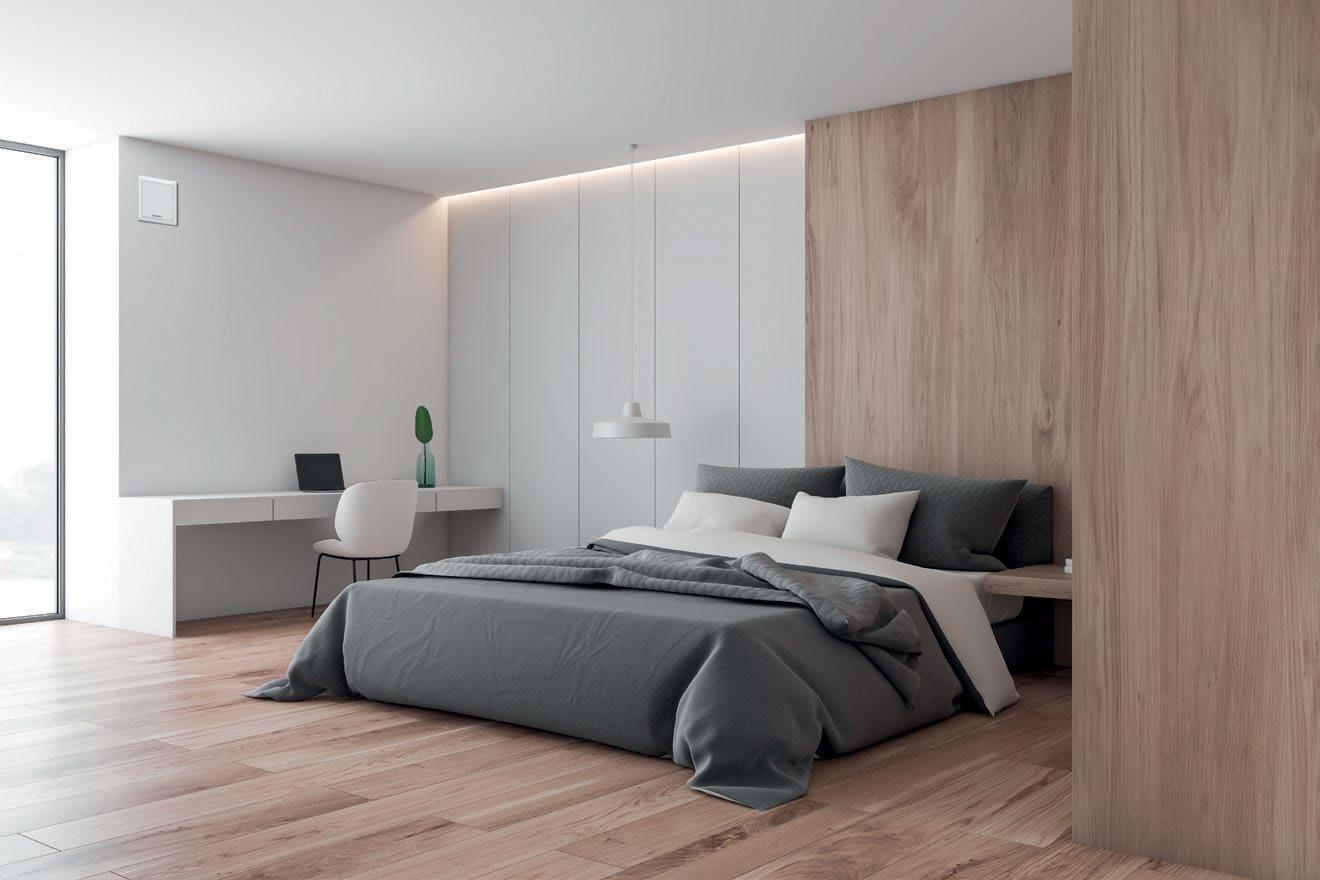
The environmental journalist George Monbiot has written about how we need an era of ‘public luxury’ and ‘private sufficiency’ — as opposed to private luxury for the few — to mitigate overconsumption and climate breakdown. And it’s hard to think of a better example of public luxury than this superb new leisure centre in Exeter, which consumes just a fraction of the energy of typical facilities, and is set to be certified to a bespoke version of the passive house standard.
SWIMMINGLYGOING DEVON
PASSIVE-CERTIFIED
By Peter Rickaby COMPLEX IS SET TO BE UK’S FIRST LEISURE CENTRE

67 IN Building:BRIEF6,700 m2 leisure centre Method: Mix of reinforced concrete, concrete blockwork, cross-laminated timber and lightweight steel frame. Location: Exeter, Devon Standard: Passive house certification pending Utility bills: £20/m2 per year (vs £57/m2 per year for a conventionally built leisure centre, see ‘In detail’ for more) prior to recent price spikes. Predicted net cost of £230/year post price spikes. £ 20 /m2 per year

St Sidwell’s Point Leisure Centre is set to be the UK’s first passive house certified leisure centre. It is also the product of Ex eter City Council’s commitment to sus tainability and the passive house standard, delivered by Gale & Snowden Architects and Space & Place Architects, working with Arup and the main contractor Kier.
The 6,700 m2 building (4,850 m2 TFA) provides two swimming pools (25 m and 20 m long, with moveable floors to provide variable depths), a toddlers’ confidence pool, a 100-seat spectator area, a 150-sta tion gym, a spin studio, a fitness/dance stu dio, a health spa with a hydrotherapy pool, changing facilities, a soft play area, a café and administrative offices. Space & Place were the lead archi tects, responsible for the interiors. Gale & Snowden Architects were the passive house designers and were responsible for the building envelope design, including airtightness and thermal bridge free con struction. Gale & Snowden also provided passive house consultancy for the services design, dynamic simulation modelling of M any of us have childhood mem ories of swimming lessons at lo cal pools or leisure centres that were chilly, draughty, noisy and pungent with the aroma of chlorine. My later, pro fessional memories of leisure centres are of twentieth-century gas guzzlers, usually the most energy intensive buildings in local authorities’ stocks, typically using 1,573 kWh/m2/yr – comprising 237 kWh/m2/yr for electricity, and 1,336 kWh/m2/yr for heating – according to CIBSE. Exeter City Council’s new leisure centre at St Sidwell’s Point is different. The ex pected 500,000 visitors per year will enter a typically passive house environment – calm, quiet, comfortably warm and brightly day lit. There is no smell of chlorine – the water in the pools at St Sidwell’s Point contains less chlorine than tap water. The building will use less than 375 kWh/m2/yr (the pas sive house target for this building, which the project team expects to beat) – a 76 per cent saving compared with typical leisure
68 | passivehouseplus.ie | issue 42 centres, and a 49 per cent saving compared with recent good practice. It also delivers a 50 per cent saving in water use, while providing exceptional internal air and wa ter quality. The building is resilient against predicted climate change until 2080 and conforms to Building Biology IBN best practice in healthy building design.


The two large pool spaces are located on the highly glazed south and west sides of the building, where they benefit from free solar heat gains; they are in separate zones with slightly different orientations, heat losses
by contrast, the gym, the spin studio and the fitness/dance studio are sources of heat, which often require cooling. This led to an energy efficiency strategy based on several zones, with different requirements, located in different parts of the building –and carefully separated. No zones are open plan to each other.
The water in the pools contains less chlorine than tap water. thermal performance, daylighting, over heating risk and resilience against climate change, as well as building biology consul tancy covering healthy building principles and the selection of materials. Arup were structural and services consultants. The main contractor Kier, and the sub-contrac tor T Clarke, who designed and installed the services, were integral parts of the team that delivered the building. For most passive houses, the energy strategy involves consideration of a sin gle zone, modelled using PHPP. The St Sidwell’s Point project is more complex because the building inevitably contains several zones with different environmental requirements and energy characteristics. For example, pool areas require heating (including the water), and must cope with evaporation of pool water into the space; and heat gains, and they are separated by glass partitions with well-sealed doors. The gym and studios produce heat gains from equipment and energetic people; they are located on the north and east sides of the building. To cool the gym and studios without throwing energy away, a heat pump removes heat and uses it to heat the pool water and other parts of the building. Zones with intermediate environmental requirements are located in the centre of the plan where they function as thermal buffers. Several plant rooms, large and
ph+ | st sidwell’s point case study | 69 CASE STUDY ST SIDWELL’S POINT
Photos: Tom Hargreaves
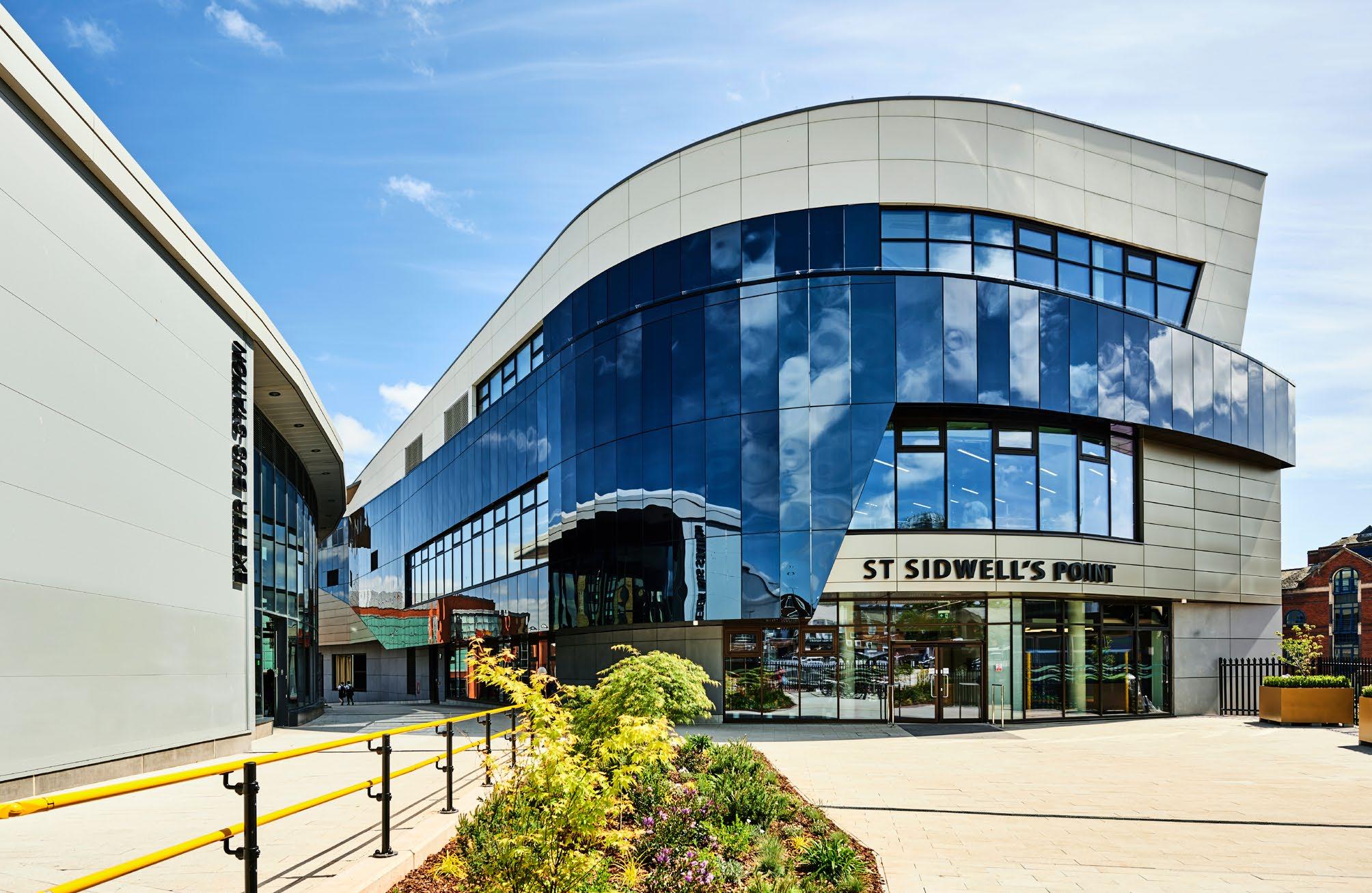
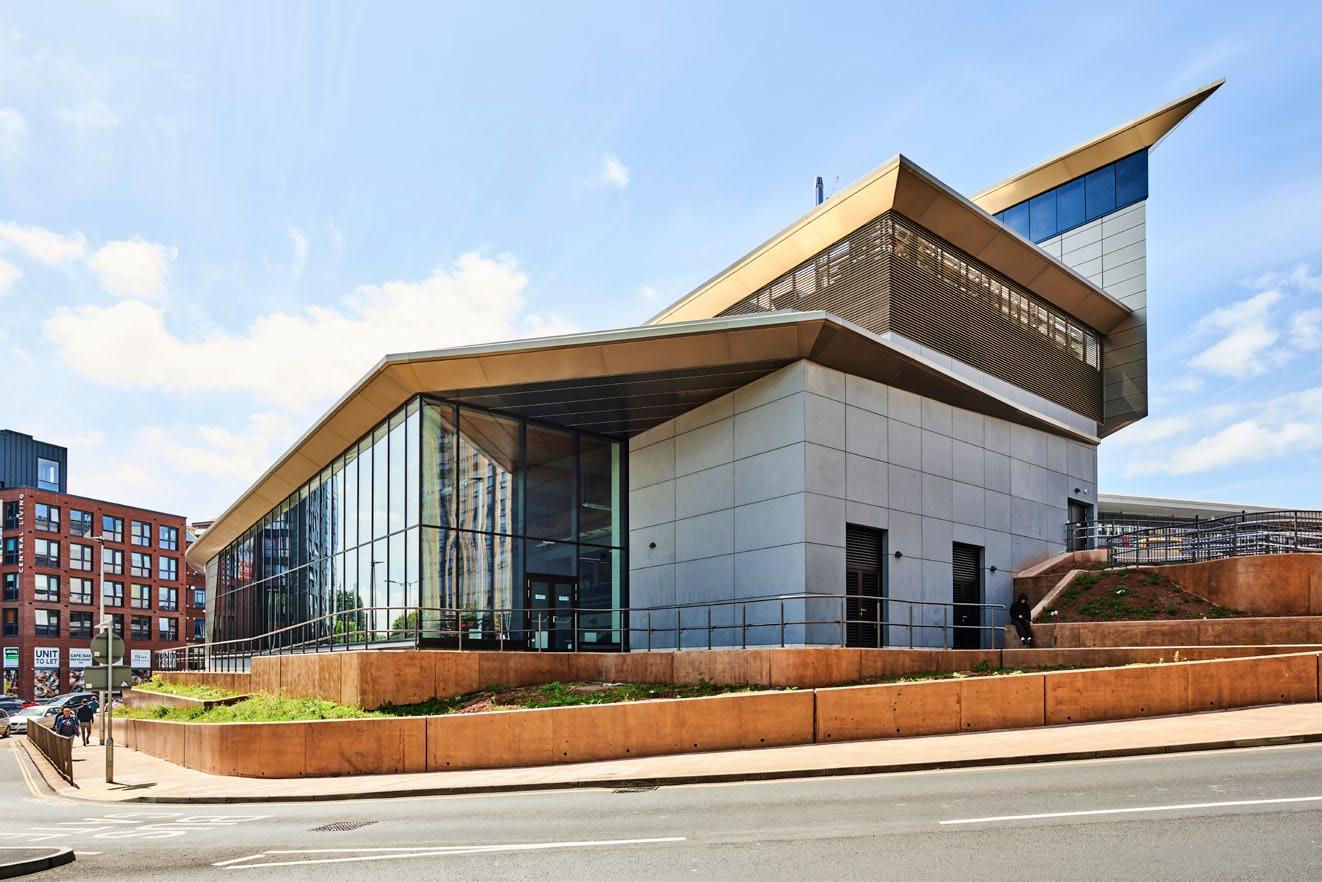
The form of the building reflects the energy efficiency and zoning strategy. The site in the centre of Exeter slopes downhill to a large traffic roundabout, to which the building presents a cascading series of curved forms incorporating the highly glazed south and west elevations of the pool halls. These ele vations are stepped back over two storeys to split the triple glazed facades into two, the lower sections being equipped with louvres to stop glare on the pool surface interfering with spectators’ views. The stepped roofs over the pool halls are supported by two huge, laminated timber trusses, spanning dramatically above the centrelines of the pools. Seen from the south and the west, the building is a curvy, shiny and layered composition of glass, smooth cladding and deep overhangs. The The building uses 70 per cent less energy than a more conventional leisure centre.
70 | passivehouseplus.ie | issue 42 ST SIDWELL’S POINT CASE STUDY small, are distributed around the building, to serve adjacent zones with different en vironmental requirements and to minimise the lengths of pipes and ducts. The energy efficiency of the pool spaces is optimised by keeping them warm (31C for the main pool) and humid (64 per cent relative humidity) to minimise evap oration of pool water – thus reducing the latent heat of evaporation, which is a sig nificant heat loss that has to be made up by the pool plant. The two smaller pools are also drained at night to reduce evaporation losses. With reduced evaporation, ventila tion rates could also be reduced to less than half that of an ordinary pool, as less dry air is Poolneeded.water filtration is a significant energy demand, typically accounting for approxi mately one-third of the electricity used in a pool building, and it is not covered by building regulations, so there is often little incentive to reduce it. At St Sidwell’s Point, a microfiltration system combined with ul tra-violet sterilisation was adopted, provid ing more efficient filtration and minimising chlorination, with less backwashing. The Passive House Institute set a challeng ing energy target of 40 kWh/m2/year for pool water circulation and filtration. This required careful planning and co-ordination of the pipework systems in order to reduce pressure drops to meet the target. In addi tion, the pipework had to sit within a ther mal envelope adjacent to the pool tanks in order to limit heat loss. In typical schemes it is buried in the ground uninsulated. The early stage dynamic modelling iden tified that there was a significant energy load in the gym and spin studios that could be used to heat the pool water and other parts of the building. One hundred and fifty gym users working out on a daily ba sis, plus the spin studios, produce elevated levels of heat gain. This drove the use of hybrid air source heat pumps which can de liver heat and cooling simultaneously. All of the waste heat from these spaces can be used for the majority of the water and space heating, resulting in a heat pump total effi ciency ratio (TER) of seven. In addition, a water source heat pump is used to recycle waste heat from the fil tration backwash to top up the water heat ing. The backwash water is then recycled for flushing toilets. Overall, this system contributes to the 50 per cent water use re duction the scheme has realised, as well as reducing the pool water heating load. The building also has passive house cer tified high efficiency heat recovery air han dling units with variable volume carbon dioxide, temperature and relative humid ity control, inverter-driven variable speed pumps and LED lighting throughout (less than 3 W/m2).
Form balancing efficiency & zoning
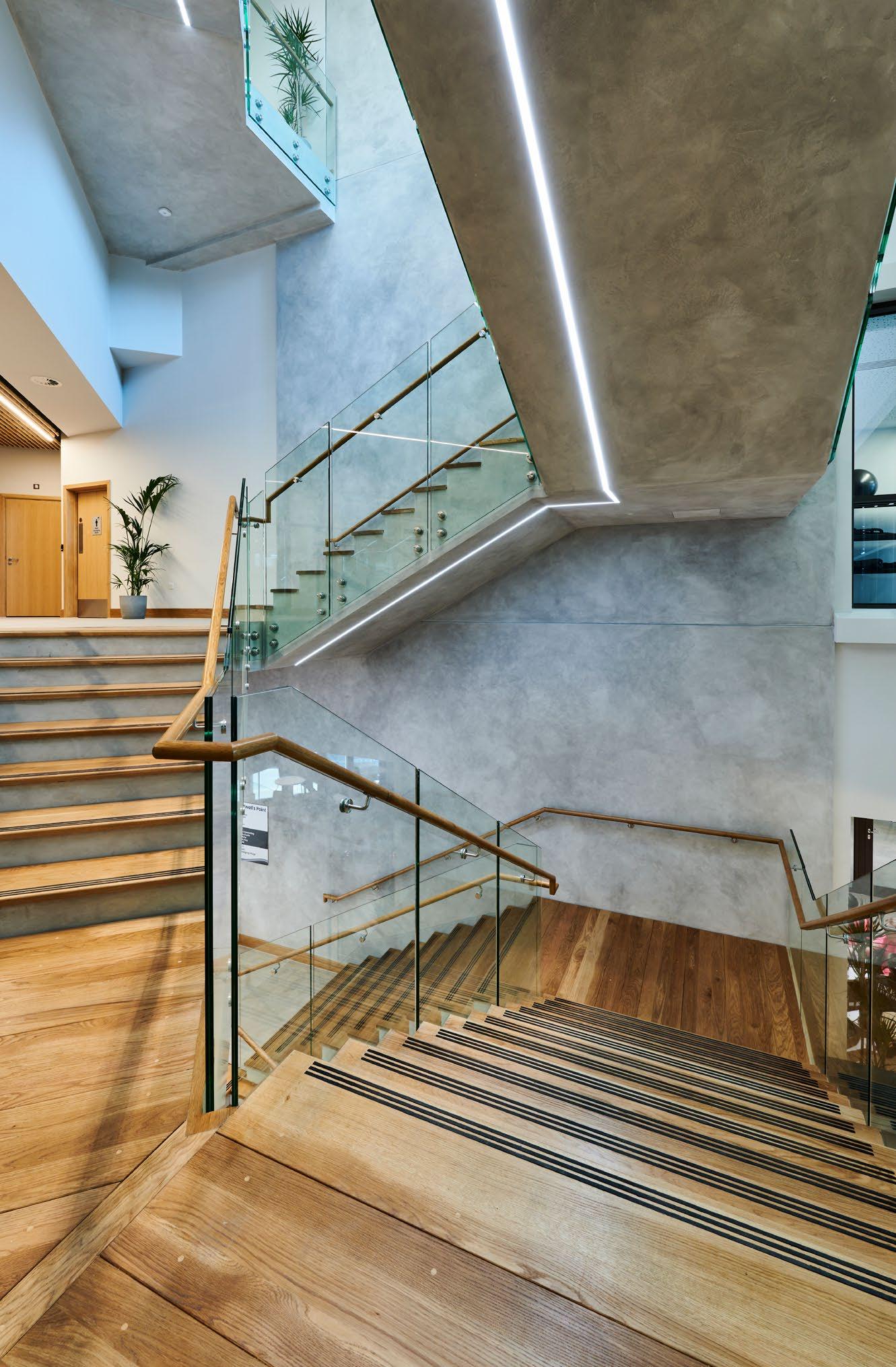
1 Primary trussed glue-laminated beam being installed over the main pool hall; 2 curved facade with Wraptite airtight membrane and thermally-isolated secondary steelwork and stainless steel helping hand brackets with a thermal spacer; 3 stick pins retain a heavy breather membrane without penetrating the composite airtightness layer; 4 areas of backing wall exposed showing the layers of construction behind; 5 an internal wall at basement level forming the external envelope of the building; 6 mineral wool installed around curtain wall openings to reduce the thermal bridge at jambs, cills and heads; 7 taping of the window units to the airtightness layer at reveals; 8 the building’s Swegon Gold RX units, the first air handling units for commercial buildings to be certified components by the Passive House Institute.
ph+ | st sidwell’s point case study | 71 CASE STUDY ST SIDWELL’S POINT other two elevations are similar but sim pler and less dramatic, because there is less need for solar control and they are more intimately associated with the adjacent city centre buildings. The structure and construction of the building are complicated, combining re inforced concrete, concrete blockwork, cross-laminated timber and lightweight steel frames with sheathing boards. Given the complex geometry of the building, achieving a highly insulated, thermal bridge free and airtight passive house en velope was described by the project team as the biggest challenge of the job. Atten tion to detail and numerous checks were required. Much effort was made to engage and train site operatives, including regular workshops to explain what was required and seek feedback. More than two thou sand individuals went through this process, each receiving a ‘passive house passport’ in recognition of their acquired learning and skills. Mock-ups of key construction details were made for testing, training and for building confidence that they would work on site. Kier’s senior project man ager, Joe O’Connell, remarked: “We were amazed at the buy-in we got from the sup ply chain and how proud those people are of the work they do. If you take them on the journey and take the trouble to explain what you are doing – and why you are do ing it and the benefit and what that means to them – most of the people on this site were coming up with ideas themselves and proud of what they were doing. It’s almost unheard of in my experience.” Care and diligence were rewarded when the building envelope achieved an air permeability of 0.3 m3/m2/hr at 50 Pas cals (equivalent to 0.1 air changes per hour), well within the passive house certification requirement. The interior layout of the building is complicated, reflecting both the shape and slope of the site and the zoning strategy. A central feature is the fiendishly compli cated, twisting central stairway, which pro vides access to multiple levels. All spaces except the changing areas are day-lit, and those on the highly glazed south side are The building is resilient changepredictedagainstclimateuntil2080. 7 8 1 3 2 4 5 6
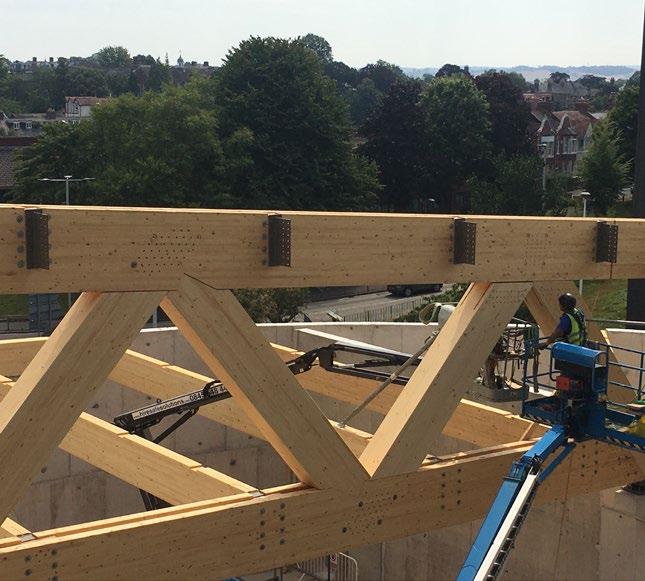
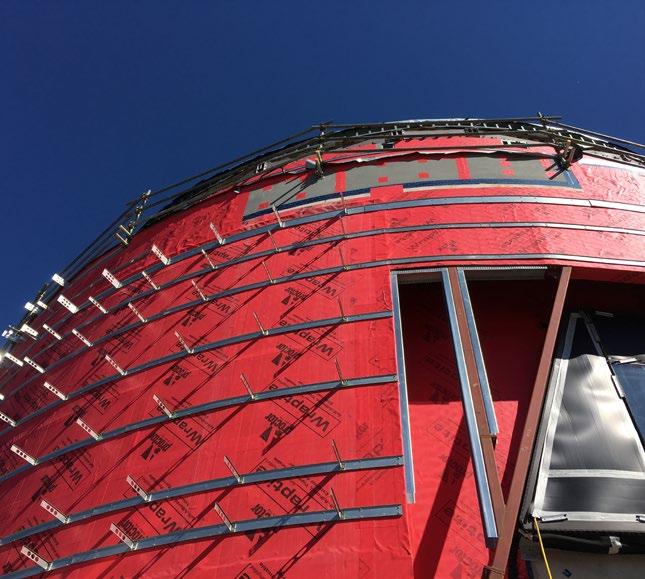

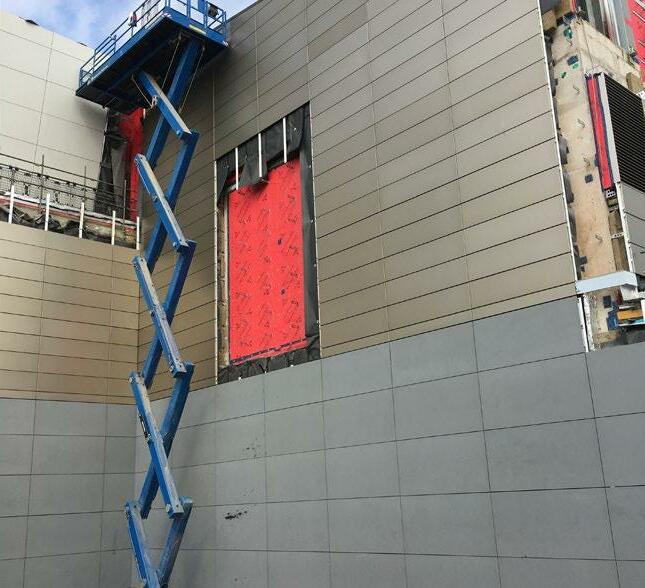
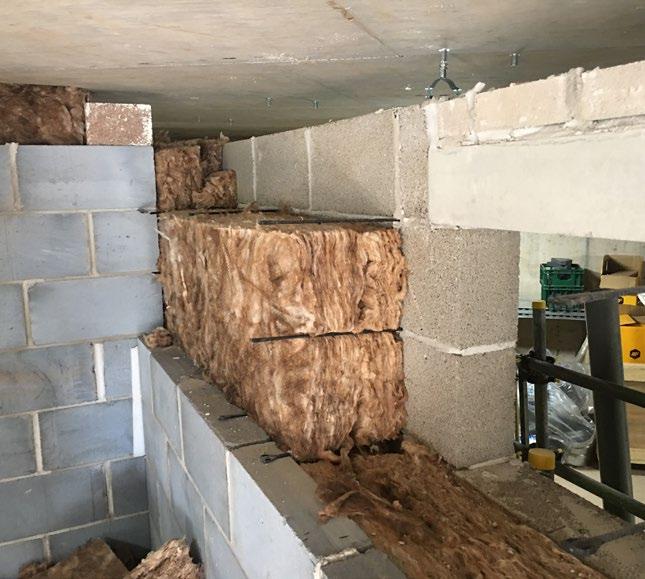
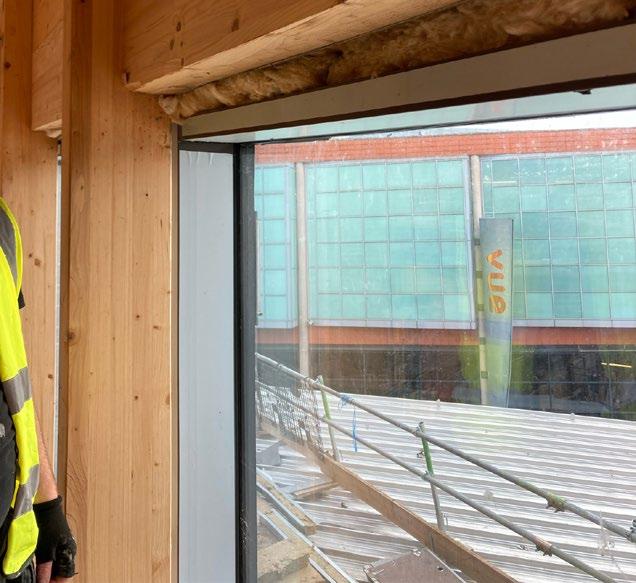
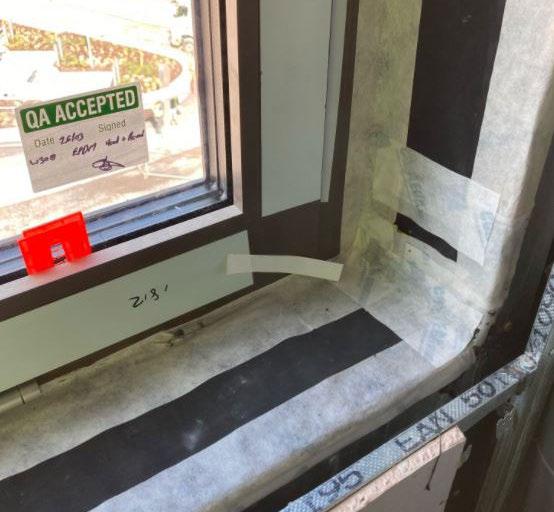
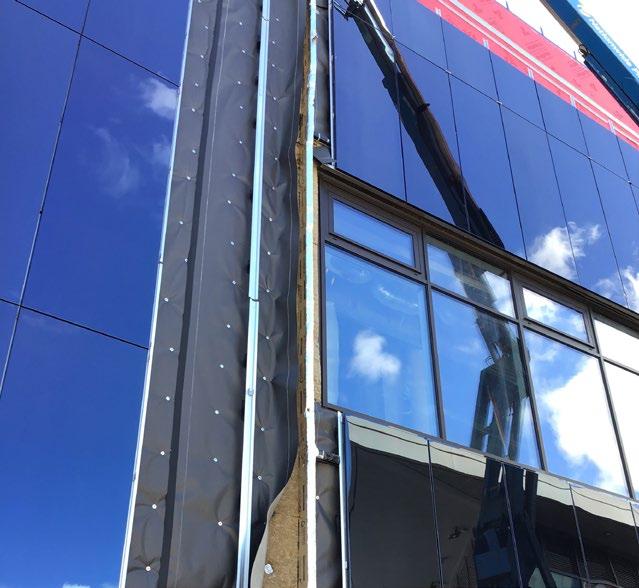
72 | passivehouseplus.ie | issue 42 bright and dramatic. The spaces on the north side of the building have smaller windows that provide a variety of intimate views of the surrounding town. The mate rials are natural, and mostly light in colour. Stair treads are wood, balustrades are lam inated glass topped with timber handrails, and the pools and gyms have slatted timber ceilings. Walls and floors in the pool spaces and changing areas are finished with ce ramic tiles. Overall, the interiors are mod ern, healthy, sustainable, reserved in style and neatly detailed, despite the challenges imposed by surfaces coming together at manyPassiveangles.house certification of the building presented unique challenges. The Passive House Institute had previously certified two swimming pool buildings in Germany, but St Sidwell’s Point Leisure Centre is much larger and more complex. At an early stage, Gale & Snowden de veloped a detailed dynamic thermal model which informed key passive house criteria in the context of the changing climate, us ing weather files from Exeter University’s Prometheus project. This model included fabric elements and services, and helped optimise orientation, glazing ratios, ther mal zoning and the key ventilation and comfort strategies. This exercise provided understanding of key energy loads for each thermal zone and of the balance between heat and ‘coolth’ between the zones, and helped to inform the heating and cooling services strategy. The standard PHPP tool is only suitable for single-zone simple building designs and the Passive House Institute had to develop a bespoke PHPP model for the scheme. Once this came together, the certification criteria were set for the key elements (see ‘In detail’ for the full list of bespoke certifi cation targets).
St Sidwell’s Point Leisure Centre is a £44 million building that has to pay for itself from revenue – neither building costs nor
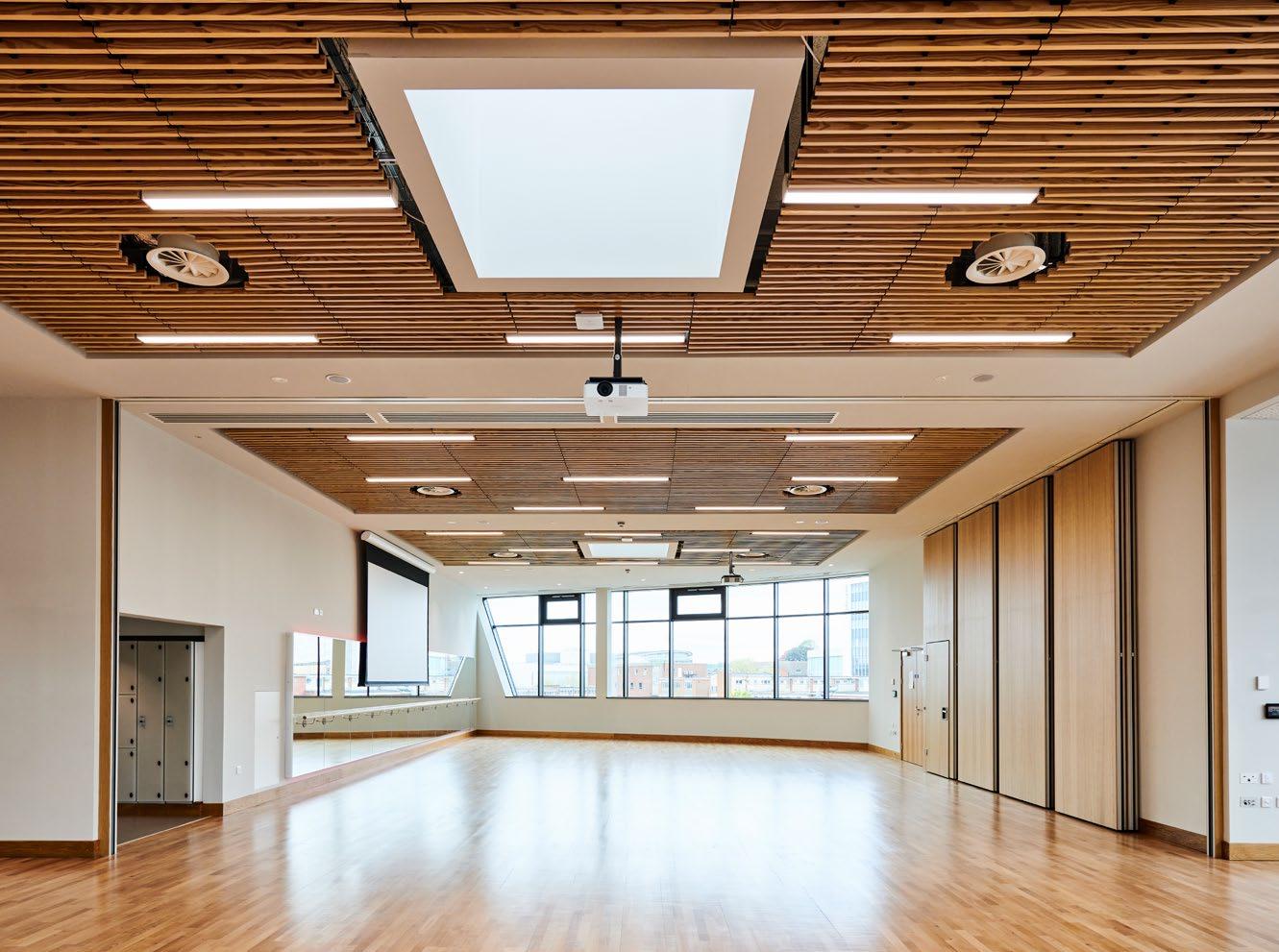
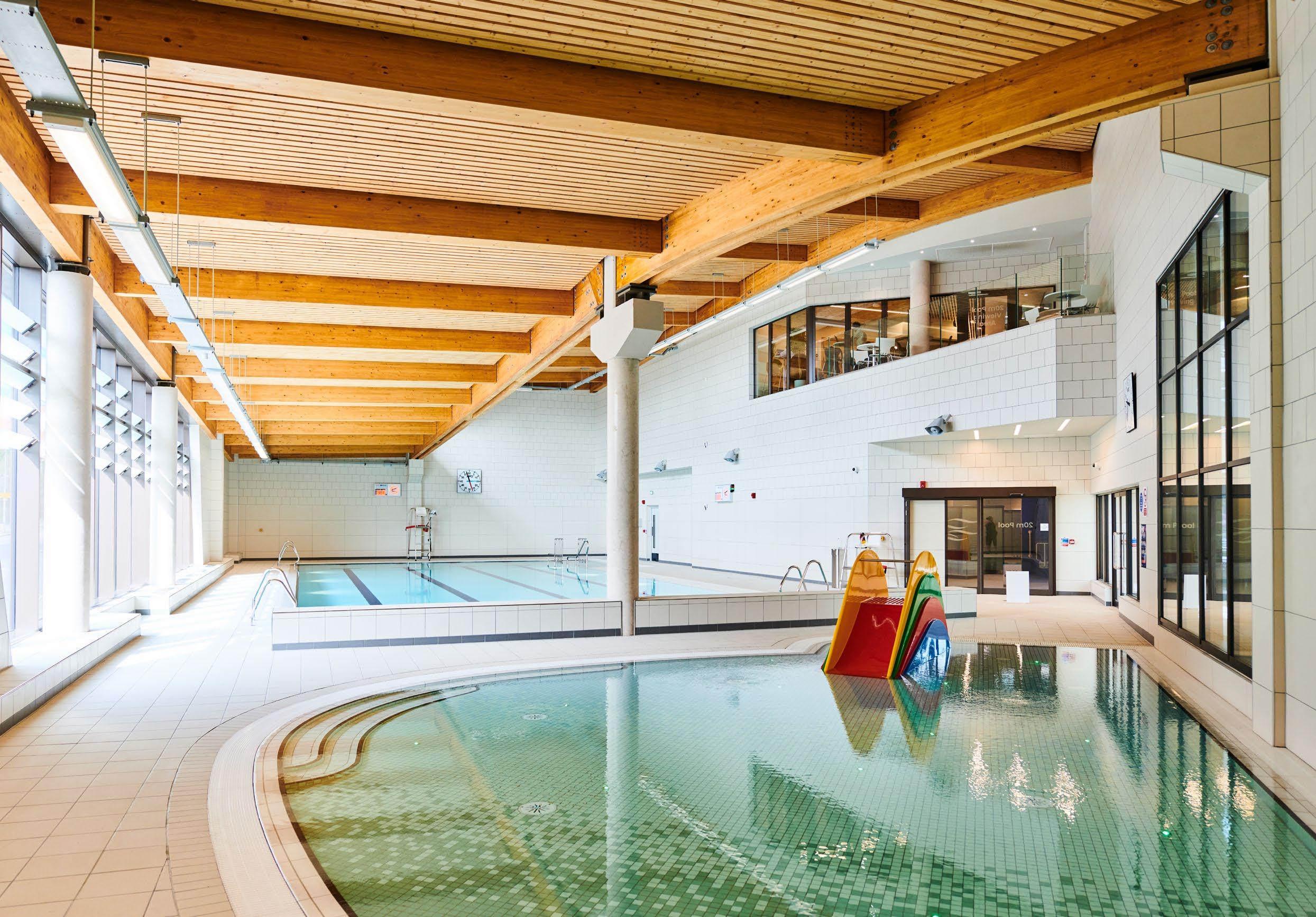
ph+ | st sidwell’s point case study | 73 CASE STUDY ST SIDWELL’S POINT
There are other large and complex pas sive standard buildings – for example The House at Cornell Tech, on Roosevelt Is land in New York, by Handel Architects and Buro Happold, a 26-storey student residence that includes a laundry, a gym and a spin room. But St Sidwell’s Point, with its four pools and multiple zones, its healthy building biology and its resilience against climate change to 2080, shows how even the most challenging brief can result in a landmark building that combines cer tified passive house performance with a benchmark for sustainability. We can ex pect to see more passive house leisure cen tres in the future.
SELECTED PROJECT DETAILS
Client: Exeter City Council Lead architect: Space & Place Architects Passive house designer & building envelope architect: Gale & Snowden Architects Future climate resilience consultant: Gale & Snowden Architects Main contractor: Kier Structural & MEP engineer: Arup Cost consultant & employer’s agent: Randall Simmonds Pool filtration specialist: FT Leisure Mechanical & electrical contractor & services design: T Clarke Building biology consultant: Gale & Snowden Architects Passive house certifier: Passive House Institute
Airtightness consultant & testing: WARM / Paul Jennings Airtightness membranes: A Proctor Group Cladding: AKV Roof system: Euroclad Plasterboard: British Gypsum Roof membrane: Triflex Passive house doors: Raynaers Windows, doors, curtain walling: Kawneer Glazing systems: AB Glass Ducted heat exchanger: Hoval Miscellaneous fans: Nuaire Air source heat pump: Mitsubishi Water-to-water heat pump: Menerga Pumps: Grundfos Engineered timber: Hess Timber Lifts: Kone Moisture resistant doors: Lami Doors
Waterproofing: Walker Waterproofing Access flooring: Carrino Access Flooring Joinery: Blake Joinery Air handling units: Menerga / Swegon Structural framed steelwork: Metsec Secondary steelwork: AnyWeld / Tata Steel / Hewas Water Cladding sub-contractors: Massey Cladding Solutions / Dales Groundworks and primary concrete framing: Stephenson WANT TO KNOW MORE? The digital version of this magazine includes access to exclusive galleries of architectural drawings. The digital magazine is available to subscribers on passivehouseplus.ie & passivehouseplus.co.uk
running costs are funded by council tax. The building has been designed for an eighty-year life, with 70 per cent less en ergy use than a more conventional leisure centre, and with a payback period of less than ten years. St Sidwell’s Point has brought leisure centre design into the twenty-first century. Building physics, the passive house stan dard and skilled architects and engineers have come together to create a striking piece of architecture that combines up lifting and healthy spaces with energy ef ficiency, all with attractive economics. As David Gale of Gale & Snowden puts it: “The building breaks new ground for the passive house standard and shows that it makes both financial and environmen tal sense when applied to complex build ings that traditionally use large amounts of energy – there is now no excuse not to adopt the passive house standard even for complex buildings.”
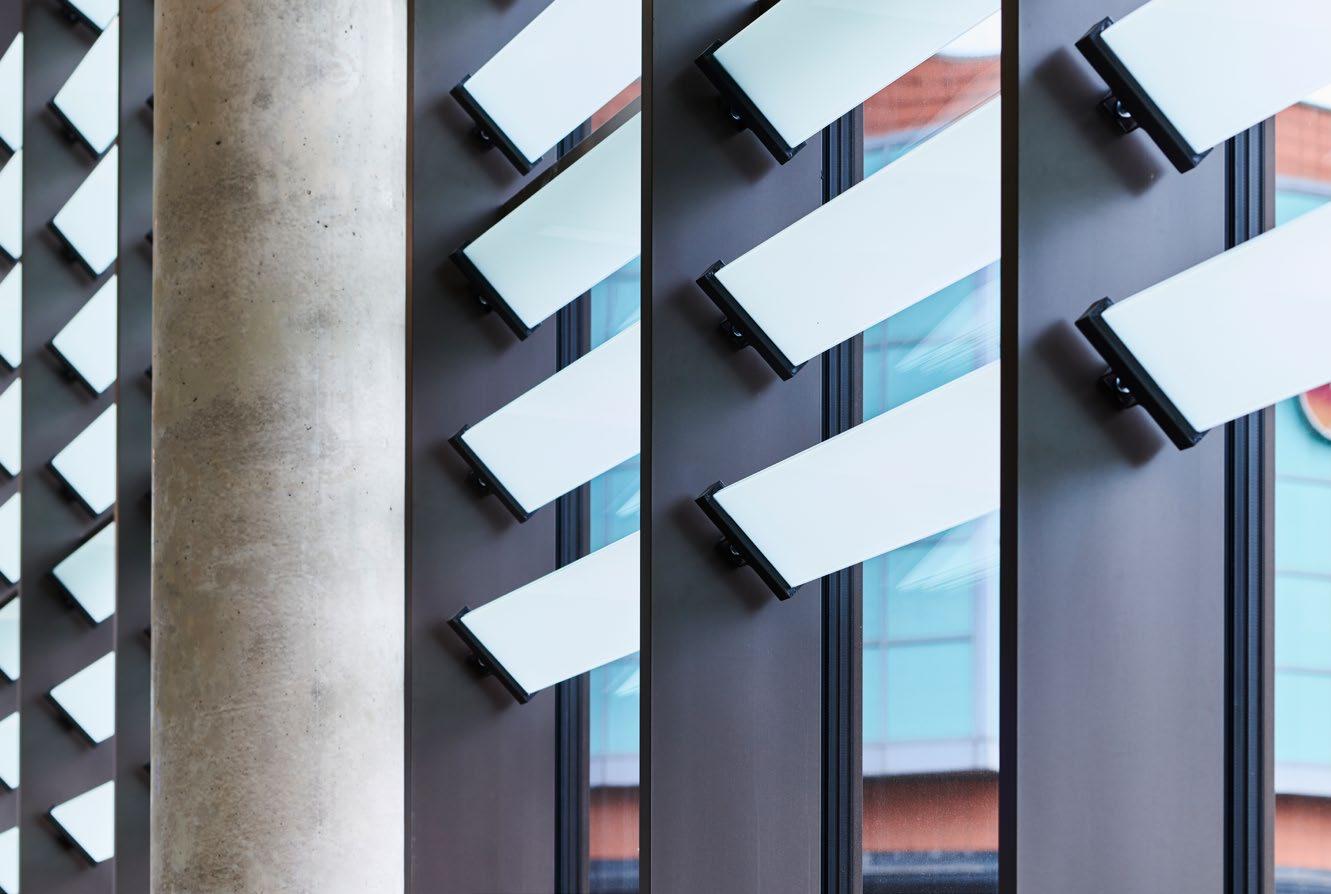
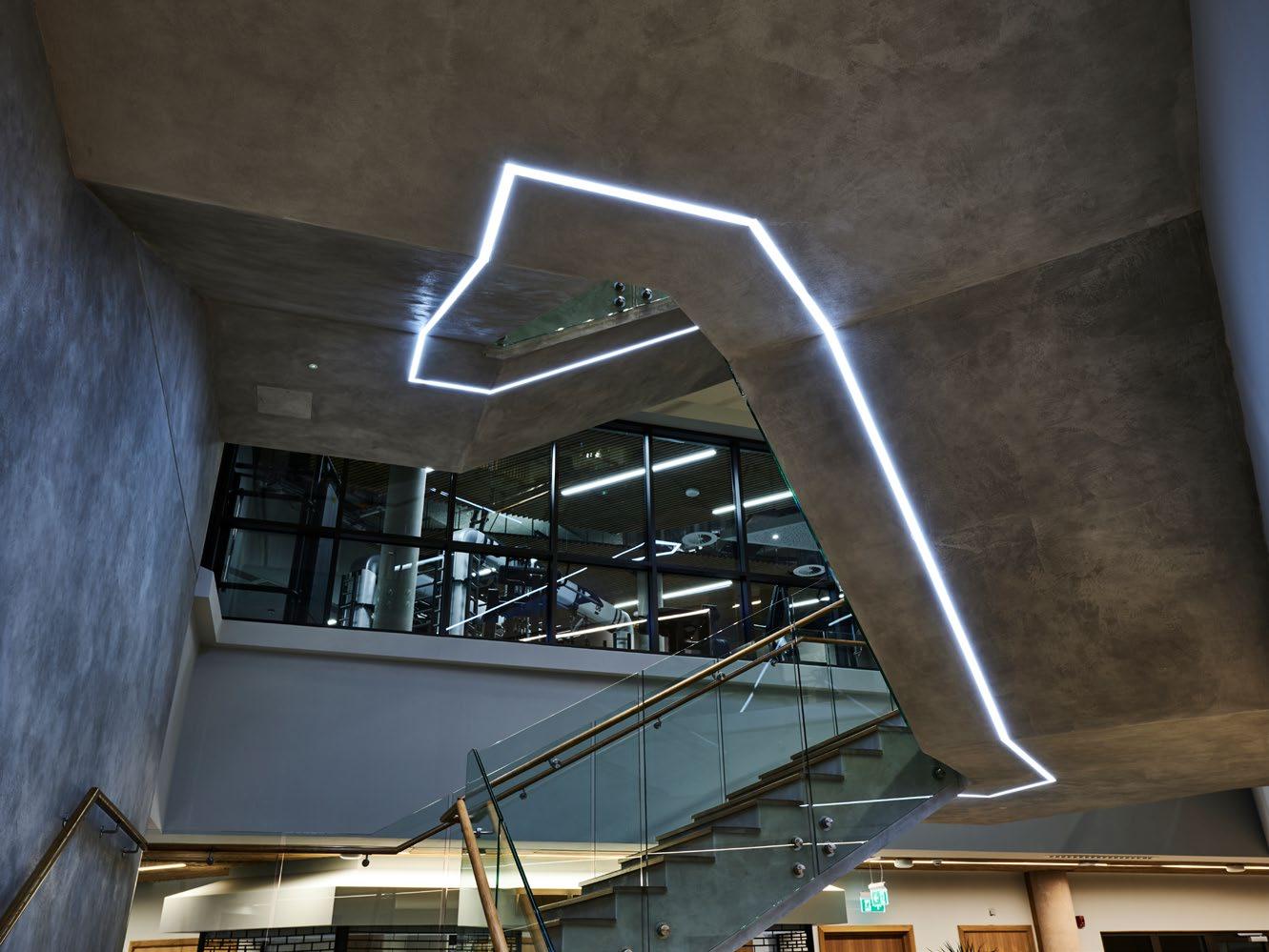
74 | passivehouseplus.ie | issue 42 ST SIDWELL’S POINT CASE STUDY WRAPTITE® THE SELF-ADHERING AIRTIGHT AND VAPOUR PERMEABLE MEMBRANE 0:03 3:29 NOW PLAYING www.proctorgroup.com 01250 872 contact@proctorgroup.com261 @proctorgroup
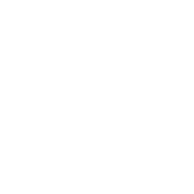
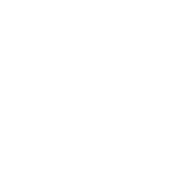
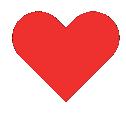
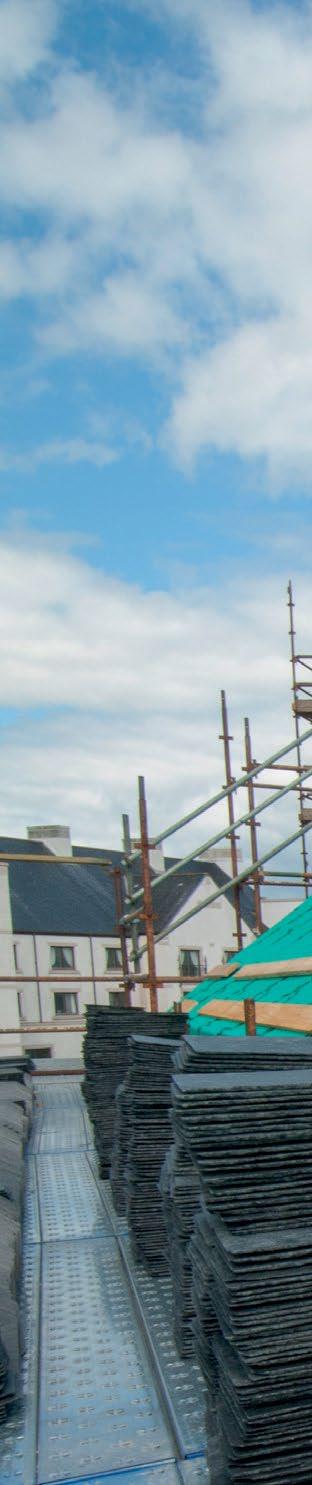
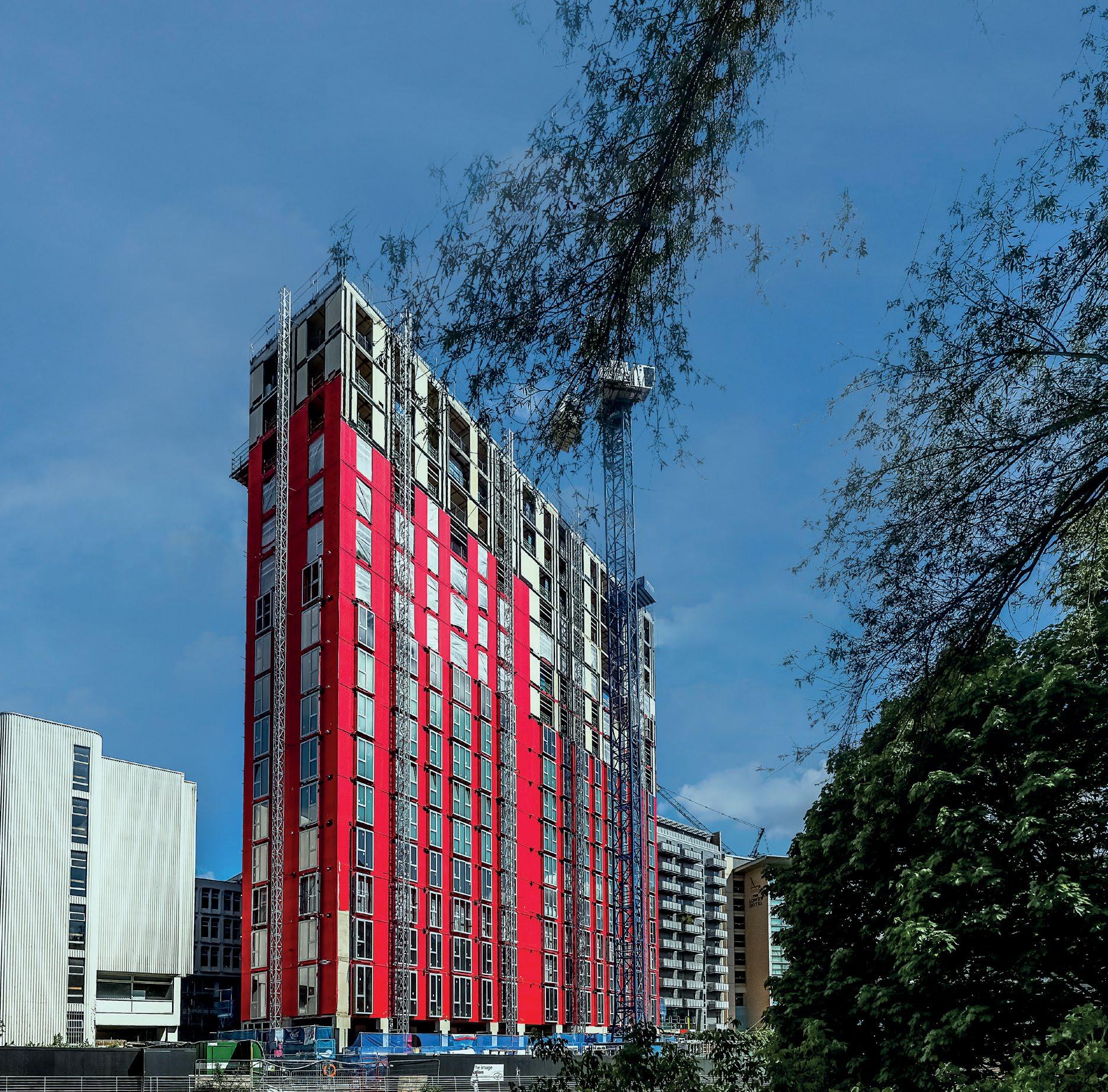

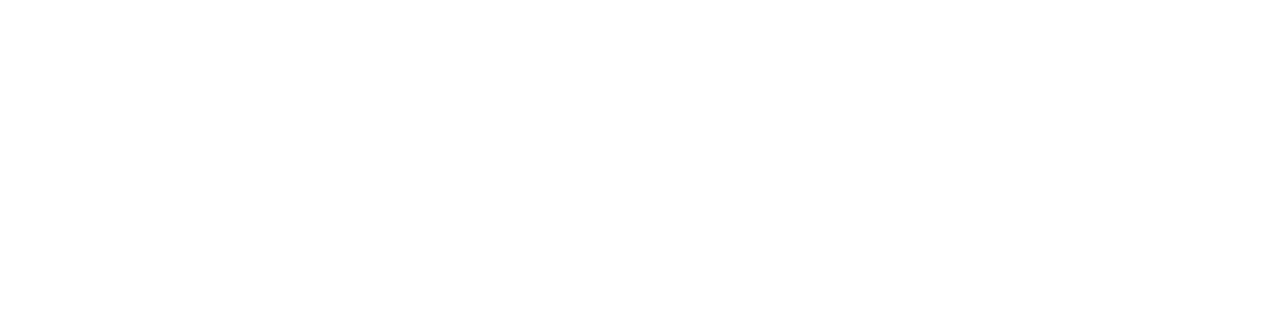

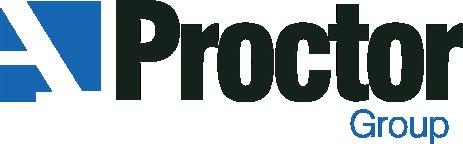
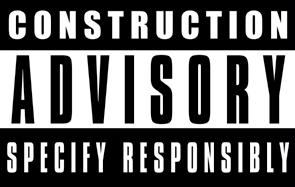
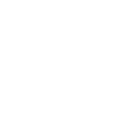


Passive house certification: Passive house classic certification pending Passive house certification criteria: Heating demand for pool halls: 40 kWh/m2/yr Heating demand for all other spaces: 20 kWh/m2/yr Total heating demand: 60 kWh/m2/yr Pool water heating: 73 kWh/m2/yr Domestic water heating demand: 0.7 kWh/m2/yr Cooling demand for gym spaces: 22 kWh/m2/yr Total energy use: 375 kWh/m2/yr Pool water circulation and treatment: 40 kWh/m2/yr Ventilation: 20 kWh/m2/yr Lighting|: 20 kWh/m2/yr Other appliances: 20 kWh/m2/yr Total electricity demand*: 120 kWh/m2/yr Airtightness (required Q50): < 0.4 m3/m2h Airtightness (recommended Q50): < 0.2 m3/m2h
Heating & cooling: Simultaneous heating and cooling plus domestic hot water services by 212 kW Climaventa air source heat pump. Menerga 37 kW combined heat recovery and water-towater heat pump system from backwash tank (combined COP 11.4). This tops up DHWS loads.
Water: Compared to traditional sand filtration systems, the microfiltration system for the pool requires less backwashing and up to 50 per cent water can be saved. With higher efficiency filtration coupled with UV sterilisation, chlorine levels are minimised to those better than drinking water. A water source heat pump is used to recycle the waste heat from the backwash water to top up water heating. Once the heat is removed, the backwash water is also recycled to flush WCs, contributing to the estimated 50 per cent water savings. Materials: Materials have been chosen to comply with building biology guidelines as much as possible. future weather without affecting the energy consumption of the building or compromising healthy building principles. Gale & Snowden Architects thermally modelled the building using Prometheus Project (Exeter University) weather files to 2030, 2050 and 2080 under an IPCC 50 percentile high emissions scenario (scenario a1fi).
Energy performance certificate (EPC): Pending Thermal bridging: Due to the complexity of a leisure centre design all thermal bridges were unique. Every junction is a bespoke design. Due to the scale of the building thermal bridges were numerous and there was a detailed exercise to design them out and calculate them. This involved working closely with the Passive House Institute who reviewed all calculations and approved them. Utility bills: The design team conducted a detailed exercise to assess the likely utility costs (electricity, gas and water) for a passive standard leisure centre versus a conventional build. This exercise found that the predicted utility costs for a conventionally built leisure centre would be £57/m2 per year, compared to £20/m2 per year for a passive standard leisure centre. Ground floor: In-situ concrete flight-augured pile foundations and pile caps, concrete blinding, followed above by 250 mm Jablite Jabfloor 150 XPS insulation, Sika Sikaproof A08 waterproofing membrane, 300 mm reinforced in-situ concrete slab. U-value: 0.14 W/m2K Typical wall construction: 3 mm solid aluminium cladding panels externally, followed inside by aluminium vertical support rails, Proctor Fireshield breather membrane, 250 mm Knauf Earthwool RainScreen slab insulation, Systea Edelstahlhalter thermally-isolated stainless steel façade brackets, Proctor Wraptite self-adhesive vapour permeable membrane, 12 mm Euroform A2 Versapanel, 150 mm Metsec steel framing system, 2 x layers British Gypsum plasterboard. U-value: 0.14 W/m2K
Primary roof (above pool hall): Trussed glue-laminated beams, cross-laminated timber roof panels, followed above by Euroclad vapour control layer, Euroclad galvanised steel top hat and 25 mm thick Rockslab rigid insulation, 50 mm Rockslab rigid insulation, Euroclad 150 mm
Roof 2: Mild steel primary structural frame internally, followed above by Tata D100 steel deck profile, 18 mm WBP plywood, vapour control layer, PIR insulation (250 mm to 783 mm depending on location), Triflex liquid-applied roof covering. U-value: Varies Windows & external doors: Kawneer RT82 HI+ PHI-certified inward-opening window system, U-value: 0.80 W/m2K; Kawneer AA100HI+ PHI-certified thermally broken curtain wall system, U-value: 0.72 W/m2K; Raynaers Masterline 8 PHI-certified door system, U-value: 1.25 W/m2K Roof windows: Lamilux CI FE rooflight, U-value 0.83 W/m2K; Lamilux CI FE manually operated access hatch, U-value 0.83 W/m2K.
Ventilation: There were 13 air handling units in total, all are passive house certified Menerga or Swegon units, with the exception of the pool halls as there are no certified models in this range. The pool AHUs were reviewed in detail and signed off by the Passive House Institute.
TR26 polyisocyanurate insulation, Euroclad Rocbar spacer profile, 80 mm Euroclad insulation quilt, 0.9 mm Euroclad aluminium standing seam roof sheets externally. U-value: 0.091 W/m2K
*All ventilation, lighting, appliances, pool water treatment and circulation Heat loss form factor (PHPP): 2.00 Overheating: The 25C overheating limit set in the passive house standard was not an appropriate metric to use (some zones are assigned to be 30C). The client briefing criteria regarding overheating was as follows: BS EN ISO 7730: Ergonomics of the thermal environment BS EN 15251: Indoor environmental input parameters for design and assessment of energy performance of buildings addressing indoor air quality, thermal environment, lighting and Summeracoustics.temperature criteria as follows, as defined in CIBSE Guide A: Offices 23 – 26C; swimming pool 30 – 34C; dry sports 14 –16C; hanging rooms 24 – 25C. The building was designed to be adaptable to meet predicted
ph+ | st sidwell’s point case study | 75 CASE STUDY ST SIDWELL’S POINT IN DETAIL Building type: 6,700 m2 leisure centre Location: Exeter City Centre Completion date: April 2022 Budget: Total construction costs for the building contract (i.e., not including professional fees, legal fees and all other client costs) was £34.5M.
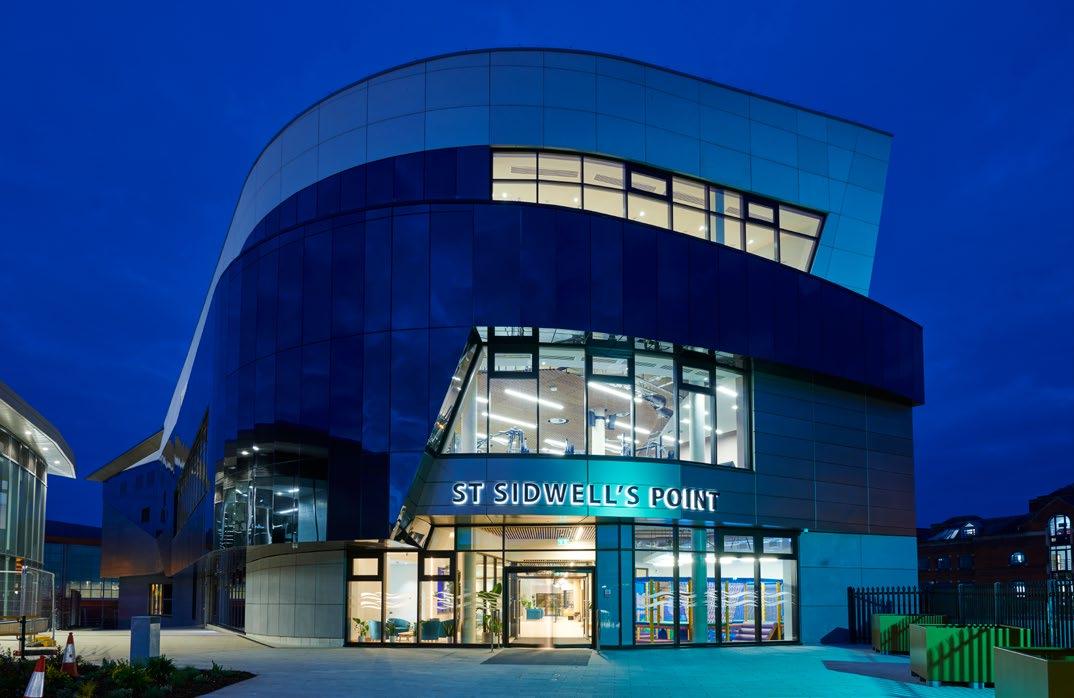
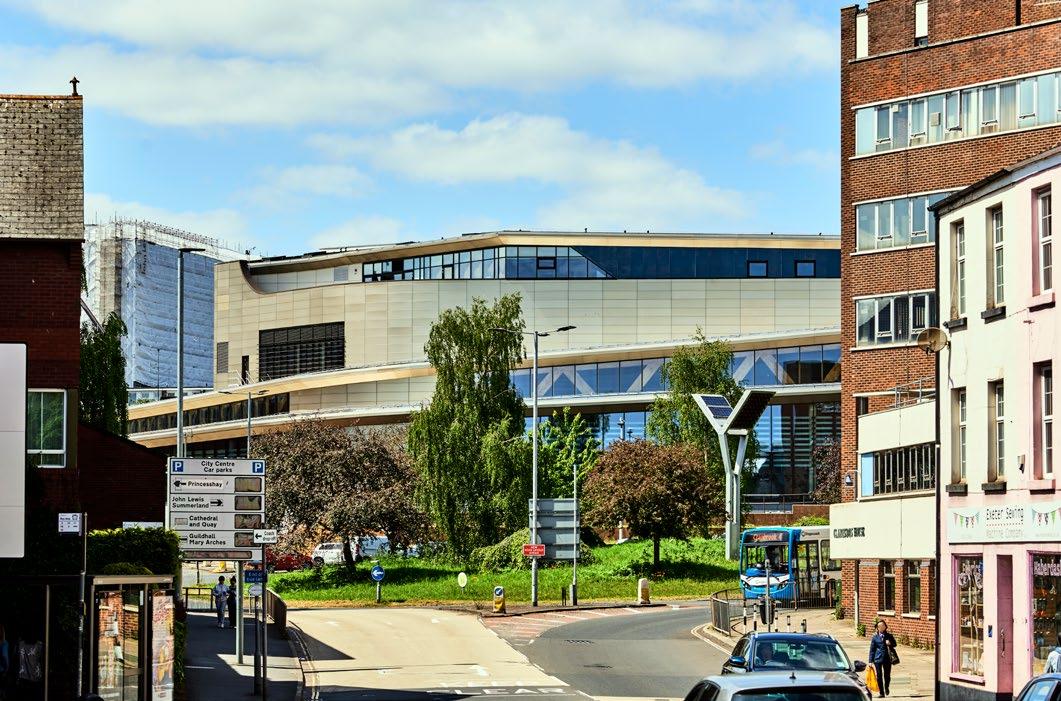
76 | passivehouseplus.ie | issue 42 ED BEGLEY JR INSIGHT
E d Begley Junior’s environmental roots are inextricably linked to his past –including his lived experience as a young man growing up in Los Angeles, and the inherited traits of his Irish forebears. LA at the time was choking so badly on smog from the city’s slavish devotion to the internal combustion engine that it earned the nickname Smell-A.
A longstanding vegan and animal rights activist, Begley’s Irish ancestors’ resource fulness and connection to the environment may have manifested itself more violently. “There's a book somebody sent me called Kerry man,” he says. “Apparently, there's some Kerry people related to me who were quite brave. They would swim into the chilly waters of the Atlantic with somebody in a boat nearby with a rope around them so they didn't drift away, and they would club a seal, and get some seal meat or seal oil for lamps.” Unperturbed by tales of the gregari ousness of his ancestors’ proto-environmen talism, Begley, who first visited Ireland with his father in 1966, has notions of returning. “I'd like to get back again while I'm still alive,” he says. I tell him it’s preferable to make the trip when you’re alive. “It’s much better, that I’m told,” he says. With a nascent environmental movement beginning to gestate in the 1960s, Begley was smack bang in the middle of an event that many people regard to be the birth of the green movement: the first Earth Day, in April 1970. Hearing talk of air and water pollution that chimed with his own experi ence, he had an environmental epiphany. But less than a week later, personal tragedy struck. Begley’s father suffered a heart attack and died suddenly and unexpect edly. Heartbroken though Begley must have been – he still talks fondly of his “wonderful dad” – Begley nonetheless threw himself into his budding environmentalism, in spite of his life being upended by the tragedy. With his limited funds, he even bought an early electric vehicle – a $950 Taylor-Dunn which Begley describes as a “golf cart with a windshield wiper and horn,” and a top speed of 32 km/h. He quickly retired it for a vehicle with more horsepower: a bicycle. “I wanted solar panels on my house and a nice electric car that had some range to it. And those things were very much unavail able to me. After my dad passed in 1970, I was a broke, struggling actor,” he says. “So, I got to do just what I could afford, you know – recycling, composting, vinegar and water instead of harsh cleansers, baking soda instead of [American household cleaning product] Comet. All the stuff that I could do that was very cheap, I did.” Years later, having saved money as a consequence of “picking the low hanging fruit”, Begley invested in making the first home he owned energy efficient. In 1982 Begley landed the role that made him famous, playing Dr Victor Ehrlich in ground-breaking medical drama St Elsewhere, for which he received six consecutive Emmy nominations and a Golden Globe nomination. With his Actor Ed Begley Junior is one of America’s best-known and longest-standing environmental activists. Fresh from lighting up our screens in the final season of Better Call Saul, Begley spoke to Passive House Plus about the roots of his activism, and what drives him on in the face of such adversity.
Ed Begley Junior: “A lot of people want to do something. You’ve got to give them choices that resonate with them.”
“I grew up in smoggy LA. And that pollution was horrible, it just seared my lungs every day,” he told Passive House Plus, speaking from his LEED Platinum certified eco house in LA’s Studio City district. For Begley, the palpable sense of wrongness in having to breathe in poisoned air struck a nerve. This outrage, combines with ways of living passed down from his Irish grandpar ents awoke something in the young actor. His grandfather and grandmother hailed from the Kerry towns of Killorglin and Killarney respectively, hardwired with the profound sense of frugality and resourceful ness that typified the generations who came up before the advent of cheap energy and the rise of throwaway consumerism. “It all came from my Irish grandparents, it really did,” Begley says. Having taken the boat to America in the late 1890s, the couple settled in Hartford, Connecticut, where his grandfather, a hod carrier, plied his trade. Begley’s father, Ed Begley Senior took a different path, rising to become a celebrated, Oscar-winning character actor, with film credits that include 12 Angry Men. But Begley Sr never lost his Irish parents’ thriftiness, and he passed it onto his son. “I always just revered that part of my past, that frugality,” he says. “My dad was a great influence on me, he was. We would save string and tin foil and turn off the lights and turn off the water. We were never wasteful. I got all that from my dad.”
Words by Jeff Colley In 1970 Begley bought an early electric vehicle which he describes as a “golf cart with a windshield wiper and horn.
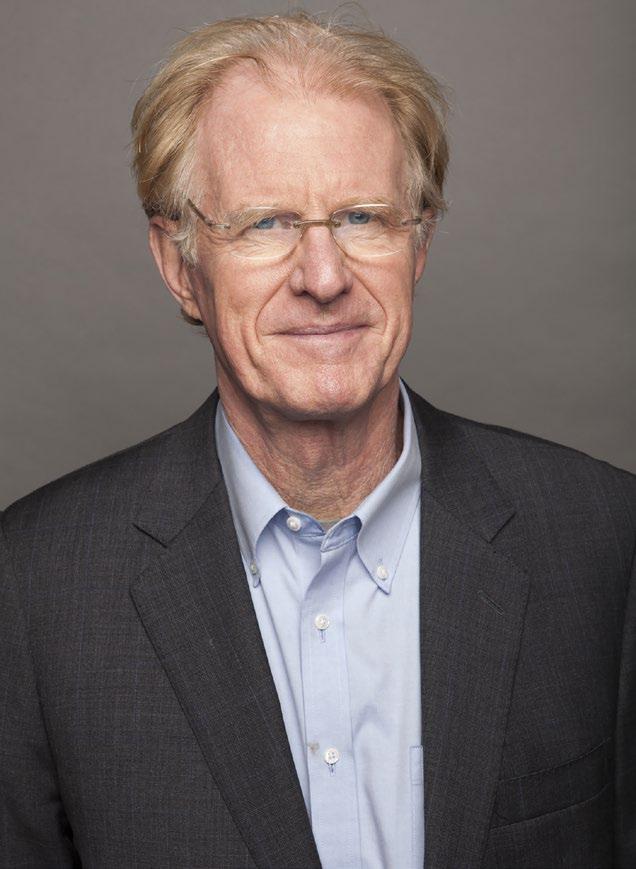
The passive solar designed house comes with twelve-inch-thick walls to maximise insulation, with a steel frame superstructure.
“I know there's a tremendous amount of energy used to make steel, I get that,” says Begley. “But most steel is post-consumer recycled, ” he says. “What used to be a car is now a frying pan, what used to be a frying pan is now a car – you know that metal is just too valuable to waste. That's why you
ph+ | ed begley jr insight | 77
Buoyed by the savings his decisions were delivering, Begley kept going, investing in a range of green measures in his 147 m2 home – a veritable micro house by American standards, let alone for someone in show business. This included tried-and-tested energy and water saving measures ranging from insulation, to solar to the – shall we say – experimental: a pedal-powered toaster. In 2000 Begley married Rachelle Carson, and the couple starred in a green living reality-TV show Living with Ed from 2007 to 2010, which pitted Ed’s efforts to minimise the family’s environmental impacts against Carson’s more regular folk-friendly views, in a case that was less good cop/bad cop, more eco-fundamen talist cop/bemused long suffering cop. Over time, with the success of the show and Begley continuing to land work in high profile, Hollywood fare – ranging from Christopher Guest’s mockumentaries to Six Feet Under, Arrested Development, Pineapple Express and countless others – Carson convinced Begley that a bigger house with more storage and more than one bathroom to share with their then teenage daughter was in order. “I always lived in smaller and very energy efficient houses and, and that's what I thought I was going to have the rest of my life,” he says. “But I had some success later in life with this reality show with my wife, and many other acting jobs. I went, let's go booyah. Let's go all the way and build not just you know, LEED silver or gold, but LEED Platinum, which is the highest MPG, if you will, for your home – the highest efficiency.”
“For so long we had it wrong here in the States, and I know, others got it wrong elsewhere. We would look at a building and ask: what's the cost of that building? We'd look at labour and materials, and it's highly inaccurate to look at it that way. What is the cost of running that building? That's another big cost over its long life. If you build it, right, as I have with my LEED Platinum home that I'm sitting in, right now, the cost of running it is very low. It's just simply the future. It's not just the future, it's today, what we must do, because otherwise you just keep trying to heat and cool these energy inefficient buildings and we'll go broke trying to do it.”
newfound success he bought a house and started investing more meaningfully in energy efficiency and renewables – which at the time came with a real cost premium. “15 years after I got involved in 1970, I could finally afford solar,” he says. “Not solar electric. That was still out of range for me pricewise and it was hard to get good solar electric panels, but I got solar hot water in ‘85. And I bought a wind turbine in ‘85 as part of a wind farm investment. And all that stuff worked and saved me money.”
As many Passive House Plus readers will be aware, LEED – short for Leadership in Energy and Environmental Design – is a voluntary rating system developed by the US Green Building Council to certify sustainable buildings and developments. Projects are assessed under a range of indicators, covering carbon dioxide, energy, water, waste, transportation, materials, health, and indoor environmental quality, with credits available for a wide range of measures. To achieve a platinum rating, projects must score at least 80 out of 100. “What I like about the LEED points system [is that] they look at everything. Are you getting marble from Italy? You know, how far is that stone coming from? Are you making a lot of trash when you build the job site building this home? Everything that you do big and small is factored into the point system. You get to say your home is green or not green. And I liked that, that they look at everything over the lifecycle of it.” One thing it is missing is an embodied carbon score, as these calculations were very rare at the time, in particular for dwellings. Given the progress now being made in this area Begley is open to the idea of appraising the building in these terms. For Begley, the choice between conven tional construction and a standard which strives to produce a healthy, low running cost, eco-friendly home should be a no-brainer – but it’s a no-brainer that many people still manage to miss.
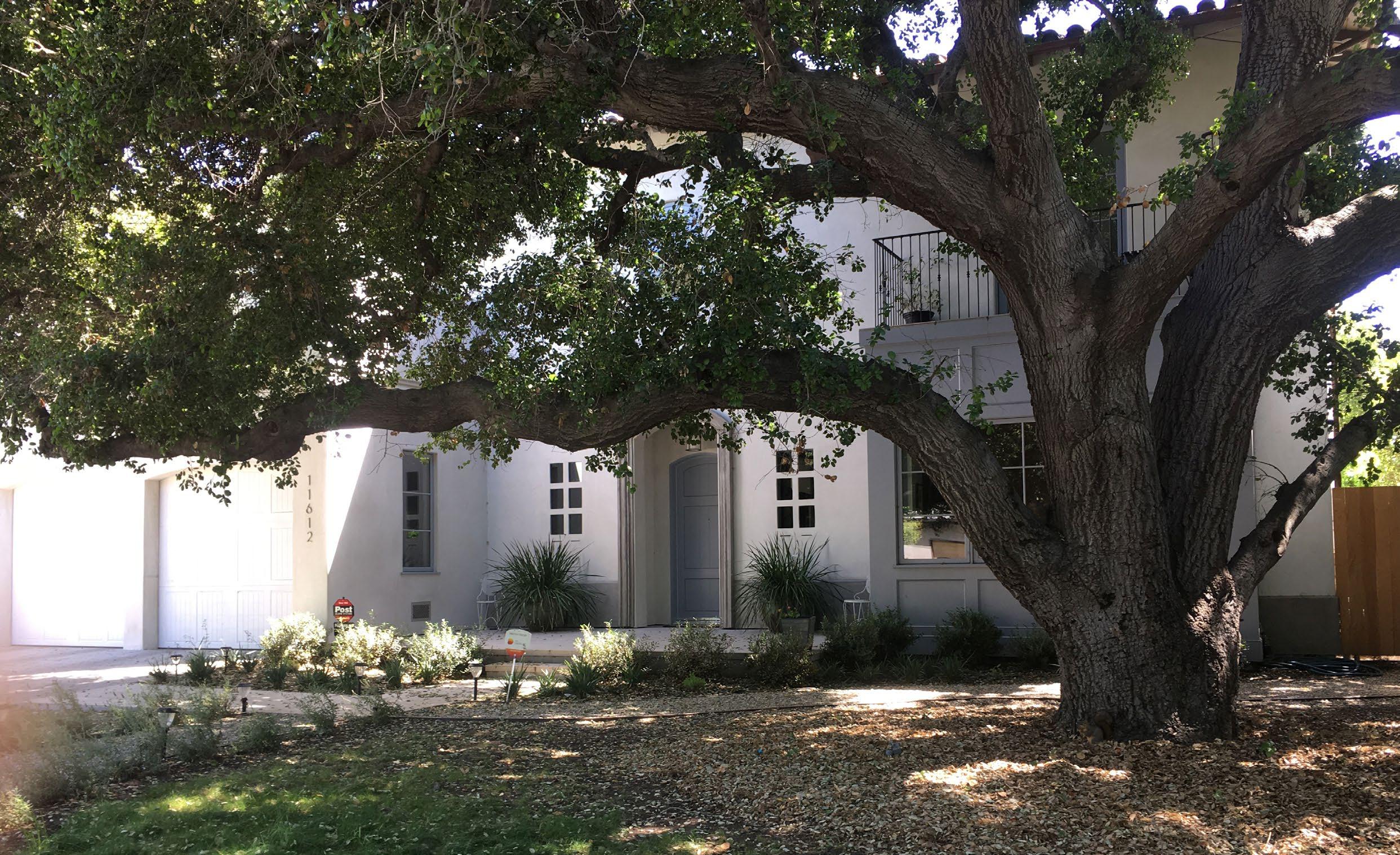
78 | passivehouseplus.ie | issue 42 ED BEGLEY JR INSIGHT
The changes present the biggest shake-up to the UK Part L regulation since the introduction of mandatory energy performance assessments in 2006. Combined with the new Part O Overheating document, the two codes will encourage design teams to pay greater scrutiny to operational energy demand and summertime overheating risks, and the interplay between the two dynamics.
Fabric First Approach Incentivised Under New UK Part L & O Regulations
The new electricity carbon factors will be based on monthly averages, rather than the old annualised average. The carbon factor is higher during the winter; a dynamic that better reflects the characteristics of the electricity grid. In so doing, a fabric first approach should be better incentivised under the new code, with reductions in wintertime energy demand having a greater impact on assessment outcomes than was previously the case. We can, therefore, expect to see thermal insulation, airtightness, and low psi-values playing a more prominent role in Part L outcomes than was previously the case. Inversely, the carbon savings available via a typical solar PV will be around 4.5 times lower than those occurring under the current UK Part L code, meaning that solar PV will no longer offer a ‘get-out-ofjail’ option for underperforming buildings. Indeed, the Part L ‘notional building’ will account for a PV array by default. Greater focus will therefore be placed on design teams to model Part L compliance risks right from the concept stage, with fewer options to rectify underperformance during the construction phase.
Headline changes to the UK Part L code include the introduction of a mandatory primary energy target and revisions to fuel carbon factors, particularly that of grid electricity. Grid electricity now enjoys a carbon factor some 2.6 times lower than the former Part L code, and lower than natural gas. As a consequence, electrical modes of space and water heating will be substantially incentivised under the new code.
IES’ expert level 5 assessors and VE software can help design teams investigate their architectural concepts in line with the new regulations. Contact details opposite. Helping you achieve your zero carbon goals with building performance modelling consulting@iesve.comwww.iesve.com/services
The hotly awaited changes to the UK Building Regulations Part L will come into effect from 15th June, alongside the newly introduced Part O, which covers overheating risk in residential buildings.
Part O, which accounts for overheating risks, will be introduced alongside Part L. Part O applies to dwellings, institutions, or any other building containing one or more rooms for residential purposes, other than a room in a hotel. The new code adopts the well-established CIBSE TM59 thermal comfort metric as one route to compliance.
ServicesConsulting

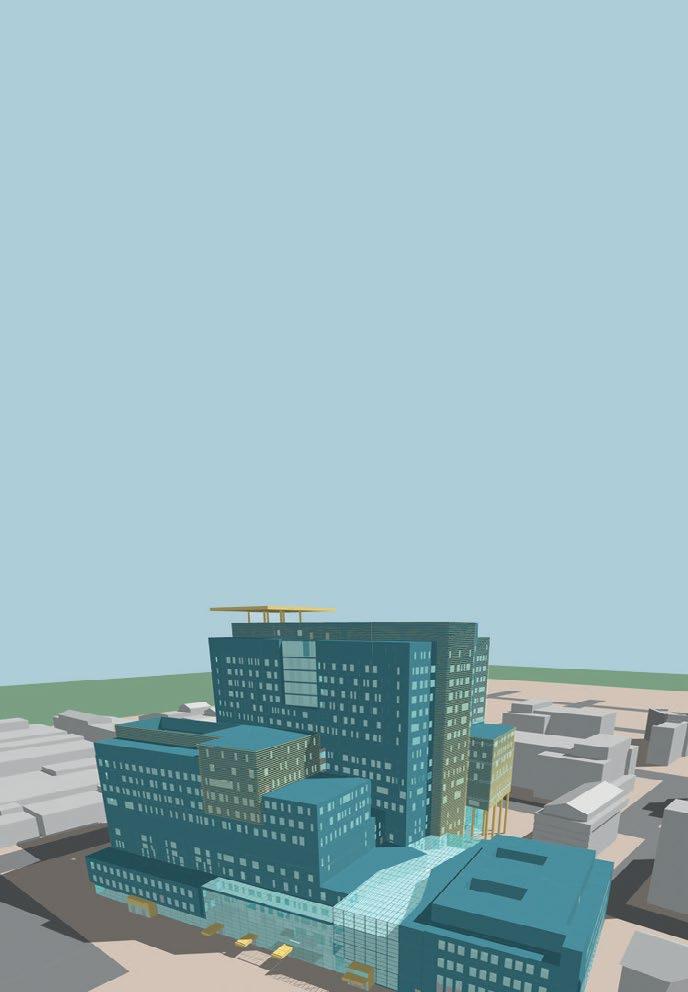
As one of America’s most high profile environmentalists for over half a century, Begley has been remarkably persistent in his efforts to win hearts and minds around to arguments that go against the national hegemony, and the largely unchallenged belief that bigger is better, that unmitigated growth is a good thing. Given how out of sync – how almost un-American – these ideas are, how has he managed to keep the fire lit, for want of a more climate-friendly analogy? “I was much better at making the argument years ago when I was single, and now I'm not sure I win the argument in my own home all the time,” he says. “This home is a perfect example. It's a fine home – LEED Platinum, very low energy use, nine kilowatts of solar, a 10,000-gallon rainwater tank, grey water system, heavy efficiencies, and every matter you could, you could think of, but you know, it's bigger than I wanted. My wife wanted some bigger spaces, closet space, or what have you. And if you're going to be married, you’ve got to make concessions and can't just do it my way the way I used to. People want a certain amount of comfort, and I've become more sensitive to that.” Begley points out that – though the new house comes in at almost 4,000 sq ft – over twice the size of his old house – the running costs are lower. “The electric bill is lower, the water bill is lower, the natural gas such as we use, it's pretty low. So, you know, you’ve got to balance and keep everybody happy. I've always been comfortable in a very small place, because that's what I grew up in. My dad raised me in a 1,700 sq ft house, which is huge by world standard: 1,700 sq ft for just three people? Oh my god, what are we gonna do with all that space? But for most people in America, that's a very small house. But I was very comfortable with that the first 67 years of my life and thought that's the way I was going to be carried out in a gurney.”
And Begley is not alone among his peers. One of Begley’s friends, Bryan Cranston – who appeared alongside Begley in the final series of Better Call Saul, reprising his Breaking Bad role – built a 2,500 sq ft LEED Platinum beach house in the nearby coastal town of Ventura, designed to passive house principles. “Very modest home, beautiful place,” says Begley. While Begley and Carson’s home is bigger, the activist in him has found other uses to justify the extra space. “One thing we do to mitigate that size, we're always having environmental board meetings here and different seminars and things,” he says. “We're using it not just as a home, but a space to gather and meet and plan, you know, for environmental groups that I'm part of. So, the space is used wisely in other ways besides us living here.”
ph+ | ed begley jr insight | 79 INSIGHT ED BEGLEY JR have those giant magnets, picking up cars in a junkyard and recycling that steel. It's less energy to mine it in the junkyard than it is to mine it in a mountain and make that ore into new steel.”
Curiously, Begley reckons that moving to a larger house may actually help encourage reduced house sizes for at least one demographic: his well-heeled friends. “We've got a lot of our high-profile friends to look at our place to go ‘Wow! I can live in a house as small as Ed’s.’ To them, my house is very small, at 4,000 sq ft. To them, that's like a shack. So, it's all in the eye of theAtbeholder.”timesthe tendency for many environ mentalists, horrified at the unfolding climate collapse, decimation of the natural world, and increasing disparity between the haves and have-nots, is to level righteous indignation at profligate public figures, and perhaps for a simple reason. Gallingly extravagant forms of recklessness like Kylie Jenner’s 17-minute private jet flights are a much easier target, than the rapacious corporate interests who have actively worked for decades to stymie regulation and create confusion. Begley’s show business friends may not quite meet such levels of disconnected decadence, but pontificating and pointing fingers isn’t his style. “I just refuse to judge my friends by their homes and their cars. I wouldn't have any friends. I encourage people. I do what I do. And you want to join me? Here's what I did. Give it a try. I try to be very inclusive. I think that's the best way to go. You get more people to join you if you're not always being divisive and trying to make people feel guilty. I think a lot of people want to do something, you’ve just got to give them some choices that resonate with them.”
If ever there was a need for such activism, it’s now. Passive House Plus interviewed Begley just after the US Supreme Court had made a number of rulings which threaten to take America back to the dark ages, be it with regard to healthcare, women’s reproductive rights, or the ability of the Environmental Protection Agency to live up to its name, by limiting its power to compel states to cut emissions, a decision which Begley describes as “shocking. I don’t know where we're headed in America but were on the wrong trajectory. And hopefully, we can get it back to magnetic north here. But we've gone mad in so many ways here recently. I'm not sure what's next.”
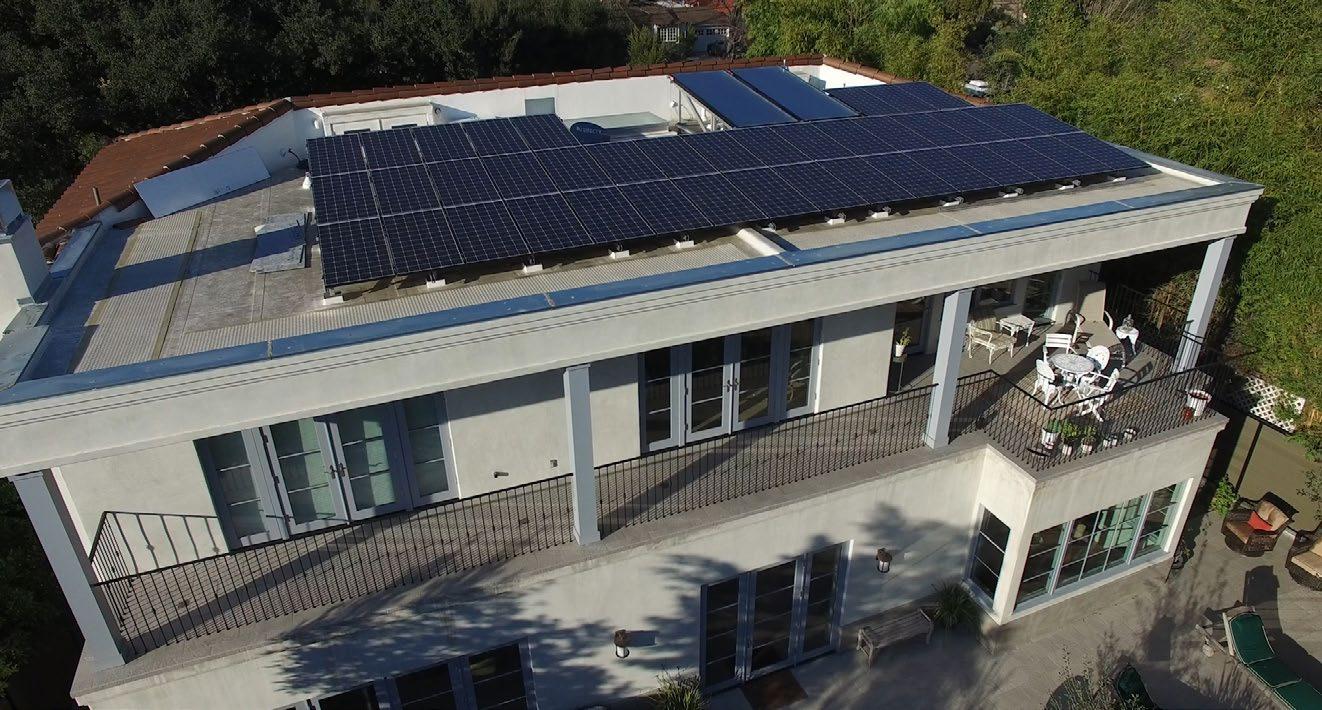

80 | passivehouseplus.ie | issue 42 ED BEGLEY JR INSIGHT DASBE is a hub for upskilling in the construction sector. • Starts Sept 22 • Level 8 • 30 weeks • CouncilTUS/Heritage • Blended • Course fee €800 Certificate in Energy Renovation ofBuildingsTraditional • Starts Sept 22 • Level 9 • 1 Year • ATU • Online • Course fee €600 • Springboard funded Post Graduate Diploma in Circular Economy Leadership for the Built Environment • Starts Sept 22 • Level 9 • 1 Year • ATU • Blended • Course fee €2250 MSc in EnvironmentBuiltRegulation • Starts Sept 22 • Level 8 • 1 Year • TUS/ATU • Blended • Course fee €3200 Higher Diploma in EnergyResidentialRetrofitManagement Visit dasbe.ie for a full list of courses in Energy Efficiency, Circular Economy and Digital Skills. Sustainable Air to Water Split & Monobloc Heat Pumps Better for You, Better for Nature sales@waterfordstanley.com051 302 300 Suitable for New Home & Home Heating Retrofits • LWT: up to 60ºC Variable Capacity 2kW to 12kW • Floor Area: Up to 275m2 Design Services • Monobloc or Split option • Heat Loss calculations • Underfloor Heating Design • On site commissioning Support Partners • Heat pump certification • Designer sign-off certification • SEAI Grant Support • Remote Diagnostic support waterfordstanley.com With a proven record in heating Irish homes, we are looking to the future with our Stanley Air to Water heat pumps. Why Choose a Stanley Heat Pump? WS22-_24-Heat-Pumps-Passive-House-Advert-93x135mm-270322.pdf 1 27/05/2022
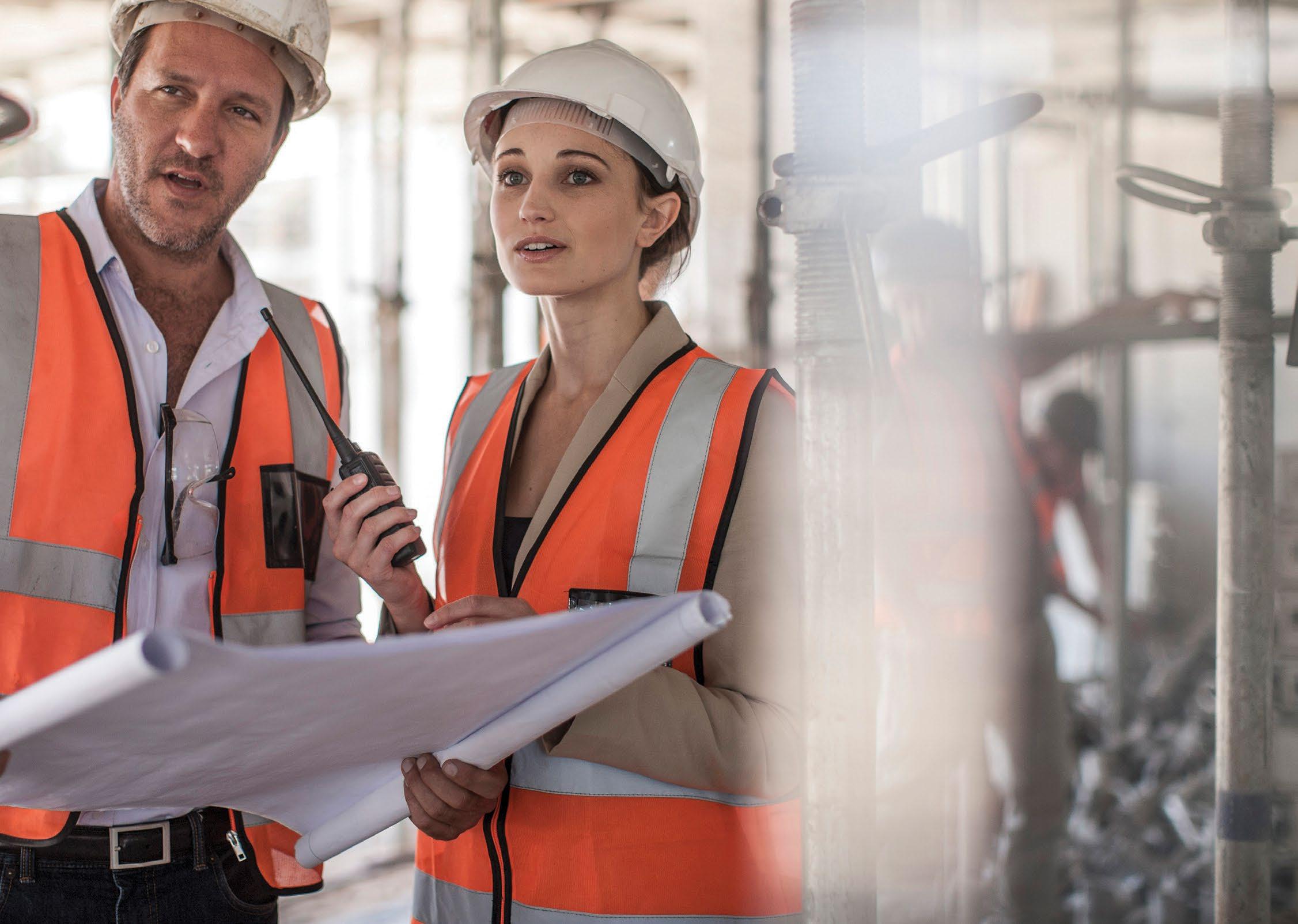

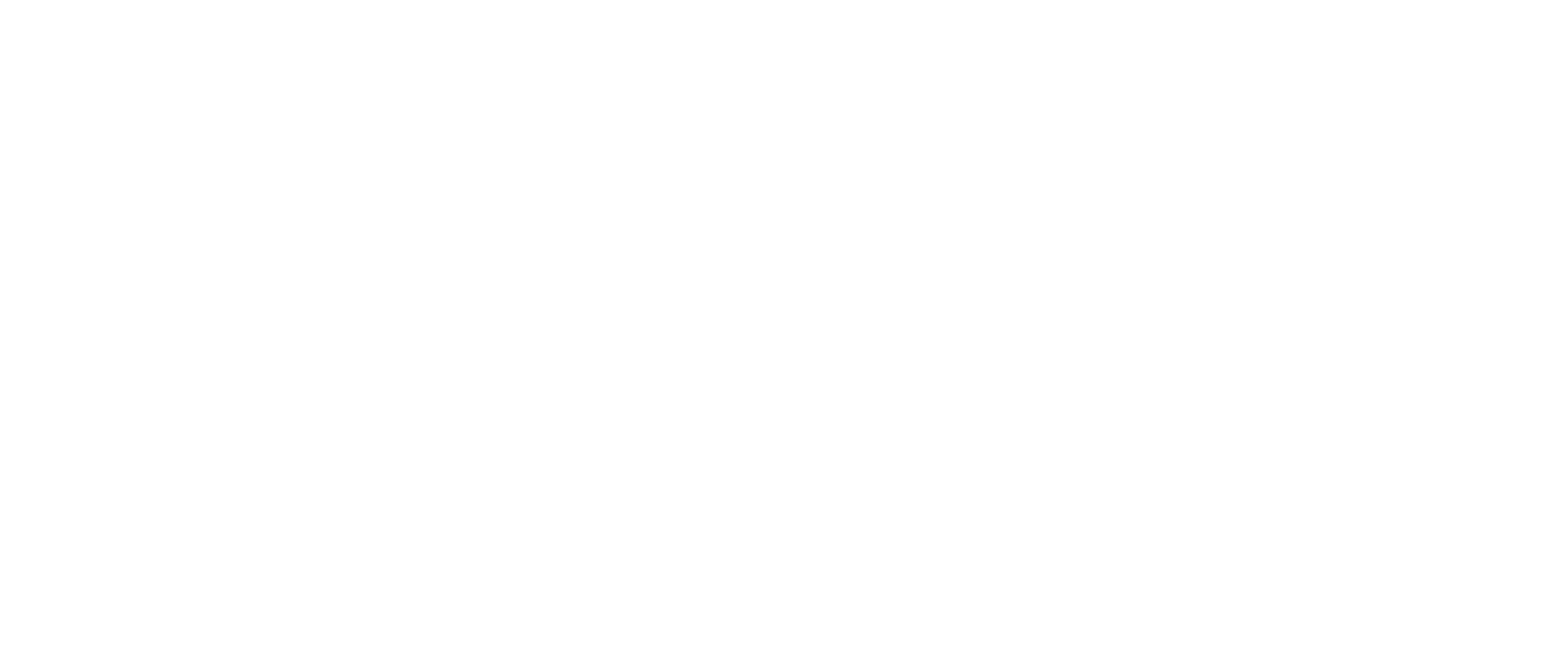
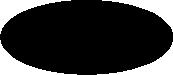
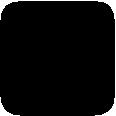


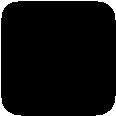
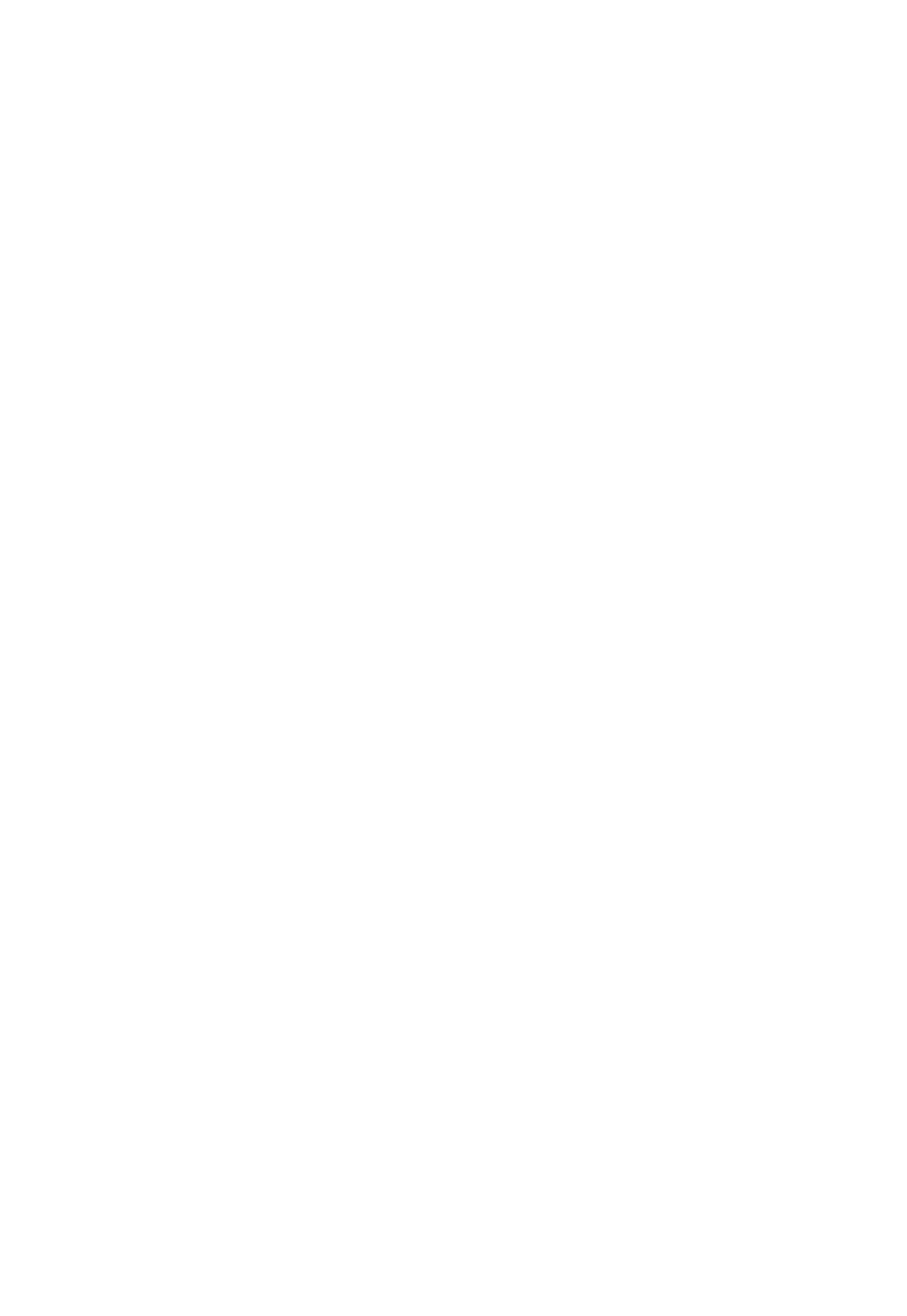
ph+ | ed begley jr insight | 81 INSIGHT ED BEGLEY JR
But Begley is at heart an optimist, albeit an optimist staring into the void. A momentary lapse in the face of such inexplicable malevolence aside, he quickly comes up with an antidote to this despair: a plan of action. Rejecting the trope that all we can do is take personal responsibility in an act of futility akin to attempting to bail out the Titanic with a thimble, Begley puts forward an approach for meaningful progress based on three pillars. “One is personal responsi bility. Doing all the stuff that I'm known for – electric cars, solar panels, all that. Wonderful. The other two are equally important and they must be similar strength and size. That is corporate responsibility. And good legislation [and] government.” Begley thinks back to his youth in the choked air of LA. “If you don't have all three we wouldn't have cleaner air in LA, which we do have now from the first earth day in 1970,” he says. “Because people did personal responsibility stuff like me. There were good laws. The Clean Air Act signed by an environmental radical by the name of Richard Nixon – he signed the damn thing. And then corporate responsibility, getting corporations to agree to these things and do things right. You have to have all three. It's not all on us the way some people were trying to frame it.” There’s a famous quote from Alfred Hitchcock. “I deny that I have ever said actors are cattle. What I said was: ‘Actors should be treated like cattle.’” We can only speculate what Hitchcock would have made of an actor like Begley, who is anything but bovine in how he uses the platform that his fame has given him. For Begley’s part, while he tries to tread carefully, the compulsion to move between acting and activism is too great. “A certain responsibility goes with this when you are given the megaphone or the microphone to talk about weighty matters,” he says. “You don't want to cry ‘fire’ in a crowded theatre. But if I’m supposed to go out and do a song and dance and the fire marshal, taps me on the shoulder and says ‘there’s a fire smouldering in the basement, make sure we evacuate row by row,’ am I supposed to just go and do a song and dance after hearing that? Absolutely not.” Begley has no time for the naysayers. “The people [who say] ‘We don’t want to hear about your environmental bullshit, leave me alone. You're an actor. Shut up and do your job.’ Not good enough. I've heard from the fire marshal. The fire marshal is the Union of Concerned Scientists, more than half the living Nobel laureates. All these great people with PhD after the name that have told us about climate change, and plastics in our ecosystem in the ocean, loss of coral reefs, amphibians dying off – all the stuff that we know about, we know about from the fire marshal. The people that know about such things that are scientists, so we have to promote that message and do it responsibly.”
Long may he continue to get the message out there. It’s one thing for a public figure to speak out on an important issue. It’s another thing entirely when they do so with such inexhaustible persistence, with such intelligence and knowledge, and with such humility. On the first occasion Begley appeared on The Simpsons, playing himself, at a deforestation protest rally, Marge asks him if he’s going to join her in the protest bus. “I prefer a vehicle that doesn’t hurt Mother Earth,” he says. “It’s a go-cart powered by my own sense of self-satisfac tion.” He puts on a helmet wired to the car, and whirs off over the horizon. You could be forgiven for thinking a magazine whose standard fare is the technical minutiae of sustainable building in Ireland and the UK has no business interviewing American celebrities. But then Ed Begley Jr is not your average celebrity. His unfuss iness, humility and willingness to really engage driven by a sense of purpose to help tackle crises of unprecedented scale and consequence, is inspiring. We live in a time of division, at an inflection point in our planet’s history. If we’re to have any chance of staving off disaster, it’ll be through following the examples of people like Ed Begley Junior. n An extended version of Jeff Colley’s interview with Ed Begley Jr has been turned into an episode of the Zero Ambitions Podcast, with co-host Dan Hyde, and is available on Apple Podcasts and Spotify.
I just refuse to judge my friends by their homes and their cars.
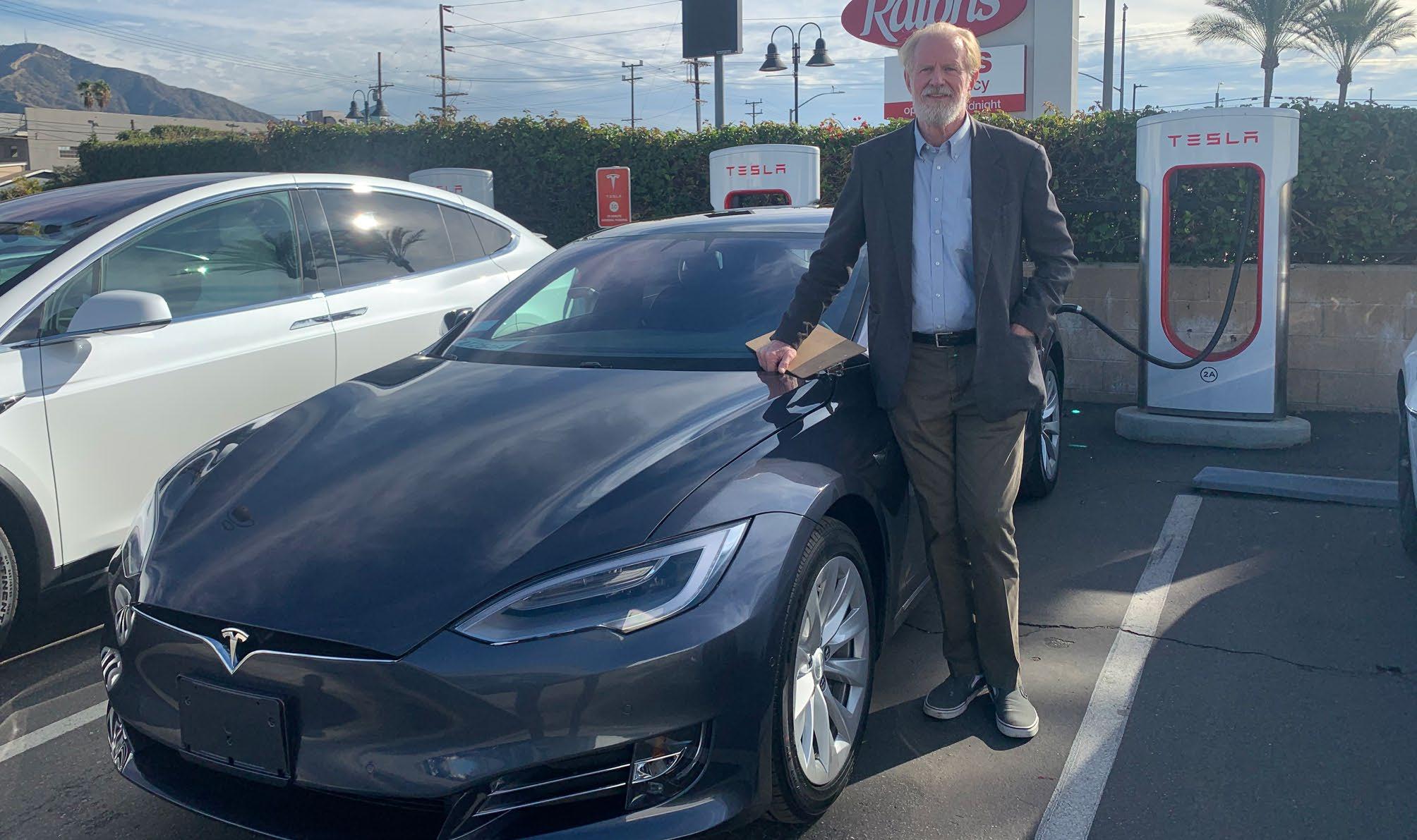
82 | passivehouseplus.ie | issue 42 MARKETPLACE PASSIVE HOUSE+ Marketplace News
Ecological launches Passive EcoWall to tackle carbonembodied‘blindspot’
In recognition of this challenge, Ecologi cal Building Systems has developed Passive EcoWall, a building concept that uses care fully selected materials with significantly lower carbon emissions to offer extremely high levels of thermal efficiency, up to and beyond that required for compliance with building regulations, attaining pas sive house levels of performance. Ecological’s Passive EcoWall provides a complete low energy, diffusion open building concept based on tried-and-tested passive house principles. It utilises Gutex woodfibre natural insulation, Finsa Su perPan VapourStop airtight and vapour control racking boards, and the Pro Clima airtightness and wind-tightness system. NZEB, certified passive houses and modular buildings have already been constructed in Ireland using this principle, delivering sig nificant reductions in energy use and high levels of comfort. The specification can also include Thermo Hemp Combi Jute, a com bination of hemp and upcycled jute fibres, or Thermafleece sheep’s wool insulation. “Our Passive EcoWall concept provides a truly breathable structure. It incorporates an innovative internal structural board, SuperPan VapourStop, which is pre-fitted with a vapour control and airtight layer. This in turn increases efficiency on site, re duces installation costs and provides a con tinuous internal airtight seal for buildings that reduces the risk of interstitial conden sation,” said Niall Crosson, group technical manager with Ecological Building Systems. “As modern structural elements are sealed more than ever to attain higher levels of air tightness, moisture management is essential, particularly in our damp climate. Un like many conventional wall systems, our Passive EcoWall also incorporates an ex ternal insulation layer of Gutex woodfibre boards,” said Crosson. “These provide high levels of thermal and acoustic insulation and are also extremely vapour diffusion open, allowing structural elements to dry out rapidly. In this way, condensation risk is dramatically reduced. “Passive EcoWall is a perfect example of how it is possible to combine low en ergy construction with more sustainable building materials that have significantly lower carbon emissions. Utilising build ing methods such as this will be key to not only reducing operational emissions, but the embodied emissions blind spot of the building industry in Ireland.” • (above) Internal and external views of the new Passive EcoWall concept from Eco logical Building Systems.
K ilsaran is the first company to be awarded NSAI Agrément certifi cation for external wall insulation to lightweight gauge steel (LGS) frame substrates. KEWI (Kilsaran External Wall Insulation) can be applied to LGS walls, for both infill and modular loadbearingKilsaranstructures.saidthat the innovative new system can be used for cost-effective offsite modular construction, which has many benefits including “reduced labour cost, less weather delays, better health and safety control, rapid con struction techniques and better quality”. Reinforced concrete frames in con junction with LGS for infill panels is a rapid build method that can be used in several situations with vari able finishes including render, brick, stone and other cladding solutions. KEWI is a mechanically fixed, ex ternal insulated render system, with a non-ventilated drained cavity. It is de signed for use with NSAI certified LGS systems that are certified for infill and structural LGS up to thirty metres in height. The renders used on the KEWI system are supplied by Henkel Polska. For more information, please visit www.kilsaran.ie/product/kewi/ •
Kilsaran gets NSAI cert for EWI to steel frame (above) Kilsaran External Wall In sulation was used at the six-storey Charlestown development in Finglas, Dublin; (below) cross-section image of a light-gauge steel frame wall insulated with KEWI.
E cological Building Systems welcomes the fact that embodied carbon has at last come into focus in Ireland. The recent report from the Irish Green Building Council, ‘Whole Life Carbon in Construction and the Built Environment in Ireland’, examines the current impact of construction on Ireland’s emissions and makes projections to 2030 based on the National Development Plan. A key initial finding in the report is that the carbon emissions associated with the construction and operation of buildings ac counts for more than one-third of Ireland’s emissions (37 per cent). More specifically, it found that heating, cooling and lighting our buildings accounted for 23 per cent of na tional emissions, while the remaining 14 per cent was comprised of embodied emissions. This 14 per cent can be categorised as the emissions ‘blind spot’ of the Irish construc tion industry. This is the first time embodied emissions have been measured in the Irish context, and indicates that the built envi ronment is one of Ireland’s largest emitters.
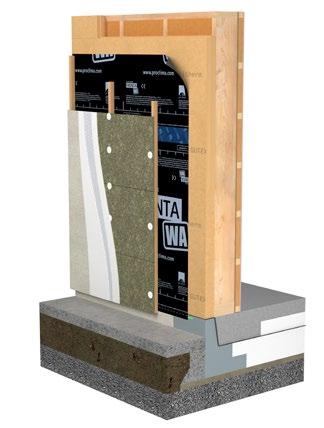
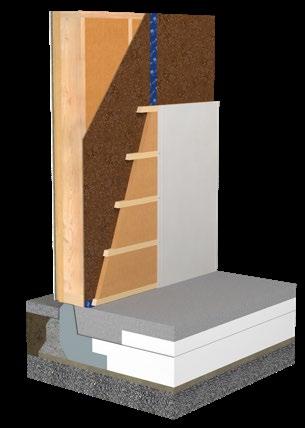
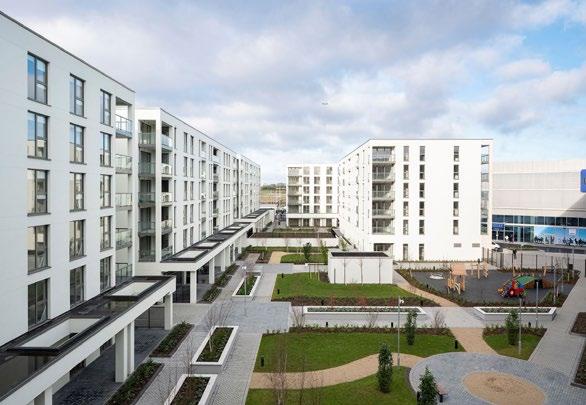
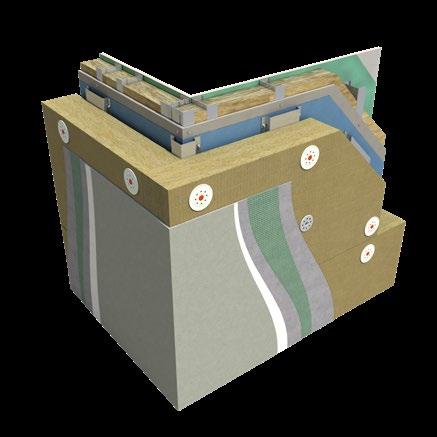
Both the heat recovery unit and the cooker hood are manufactured from metal and supplied with a grease filter, protecting the unit from cooking particles and oil build-up, and providing a fire-safe ventilation solution for kitchen installations. Airflow Developments said that the Adroit DV51CH recovers up to 84 per cent of the heat from the extracted air via a “highly efficient conduction process”. The DV51CH comes with a built-in humidity and CO2 sensor. The on-demand ventilation control feature means that air flow levels are adjusted automatically depending on indoor CO2Meanwhile,levels. the Adroit ‘Cloud’ function allows users to control ven tilation from their smartphone, tablet or PC. The front panel of the cooker hood also has four touch buttons to open and close the damper position, change the ventilation settings, adjust the brightness of the LED light, or turn it on and off. Airflow offers one of the largest ranges of passive house certified MVHR units (with fourteen units in total), comprising the Adroit range, the Duplexvent Flexi range and the Entro–H range. All of the company’s passive house certified MVHR units offer one hundred per cent summer bypass to isolate the heat recovery function during the hotter months and prevent overheating. They are also fitted with high-grade filters to provide a clean indoor environment, protecting the occupants from dust, pollen and any other airborne pollutants as well as protecting the unit itself from getting dirty. Airflow Developments is a member of the Passivhaus Trust. For more information see www.airflow.com • (top) 7 of the 14 MVHR units from Airflow’s Adroit range; (above) an illustration indicating how seamlessly the integrated cooker hood of the new Adroit DV51CH fits into kitchens.
Partel’s EPDs are registered on EPD Ireland, run by the Irish Green Building Council, and are registered at www.igbc.ie/ epd-search. In Europe, the digital data in cluded in EPDs will soon be available to use on ECO Portal, and via tools including One Click LCA and EC3 (Building LCA tools). The EPDs were carried out by Peter Sey mour, life cycle assessment consultant with EcoReview Ireland. “EPDs in the construction sector are the essential currency for communicating the environmental impacts of a product,” said Seymour. “The Partel EPDs present the environmental impacts from production, installation on site and the end-of-life sce nario for the products. They provide inde pendently verified environmental impact data essential for informed decision-mak ing in the climate crisis.” •
ph+ | marketplace | 83 PASSIVE HOUSE+ MARKETPLACE
Airflow launches MVHR cooker hood
The first Partel products to attain EPDs consist of five airtight and windtight solu tions widely specified in low energy build ings including the Exoperm Mono 150, Exoperm Mono SA 250 and Echofoil Exo breathable membranes, along with Vara Plus and Izoperm Plus vapour control layers. With the World Green Building Council setting targets that by 2030, all new build ings must be net-zero carbon in operation, and embodied carbon in building materials and equipment must be reduced by at least 40 per cent from today’s levels, Partel have set about playing their part to help deliver these targets – developing products to sup port the design of passive house standard projects, while quantifying and minimising embodied carbon in the process.
The company’s Adroit DV51CH won domestic product of the year at last year’s Heating & Ventilation Review awards and was highly commended at the Heating & Ventilation News awards.
P artel has become the first manufac turer of building envelope systems in Ireland to publish Environmental Product Declarations (EPDs) for airtight and windtight membranes. The Ireland-based company obtained EPDs as part of its commitment to provid ing evidence-based solutions for the delivery of quantifiably sustainable buildings – in terms of operational energy performance and whole life carbon dioxide emissions.
Partel founder and director Hugh Whiris key said achieving these targets would re quire “a sector-wide transformation that applies the principles of a circular econ omy,” a transformation that starts with product manufacturers obtaining EPDs to make the environmental impacts of their products transparent to building designers. “Accelerating carbon reduction through sustainable building components and en ergy efficiency are default parts of our busi ness practices,” said Whiriskey. “The EPDs allow us to demonstrate fully transparent, and reliable data to the construction market on our materials, and carbon footprint.”
A irflow Developments has launched a compact mechanical heat recovery (MVHR) unit with an integrated cooker hood, designed to combine ventilation and extraction of cooking odours.
Partel obtains EPDs for airtight membranes
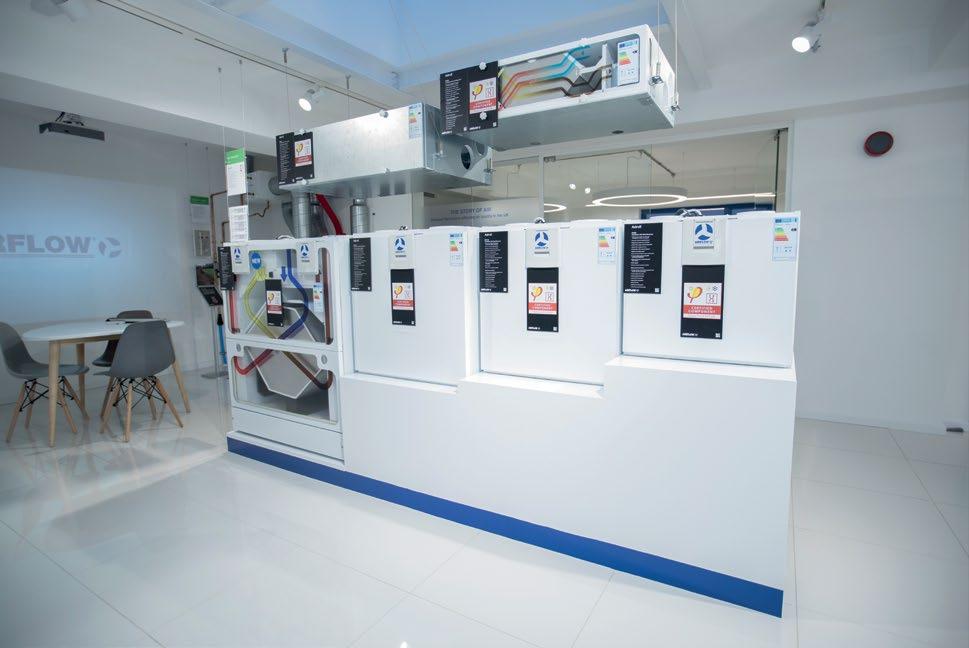
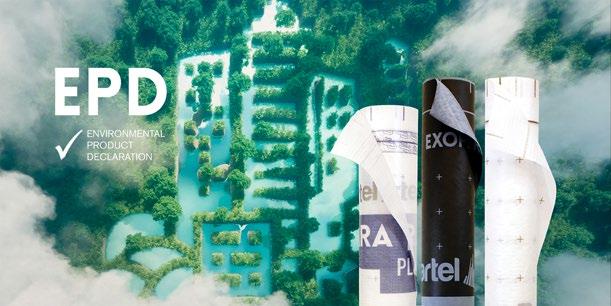
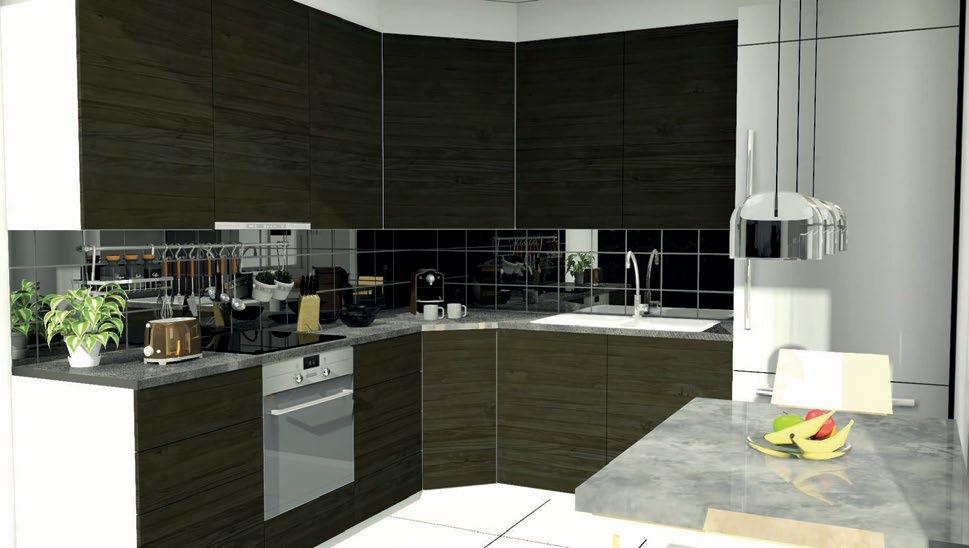
84 | passivehouseplus.ie | issue 42 MARKETPLACE PASSIVE HOUSE+
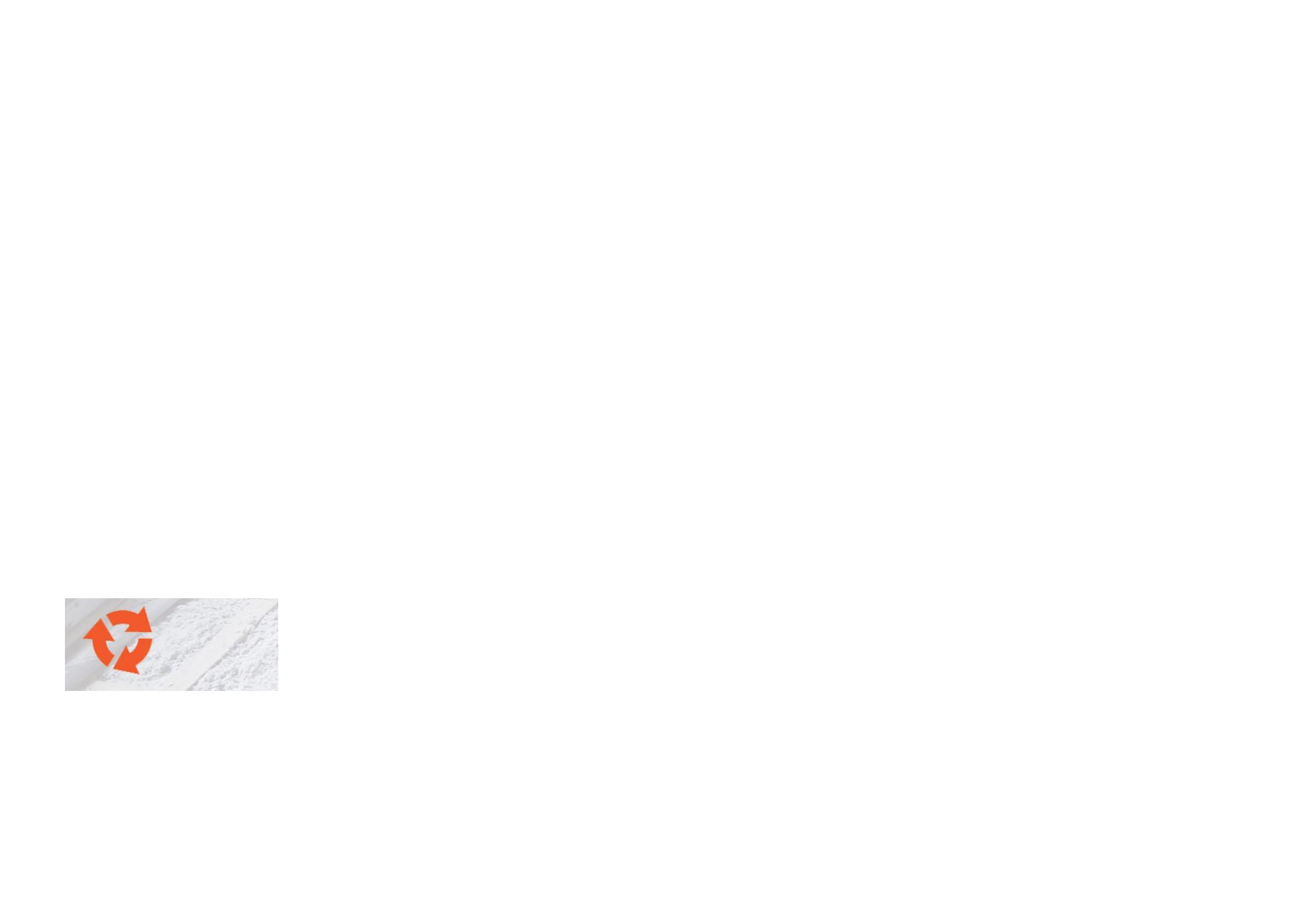

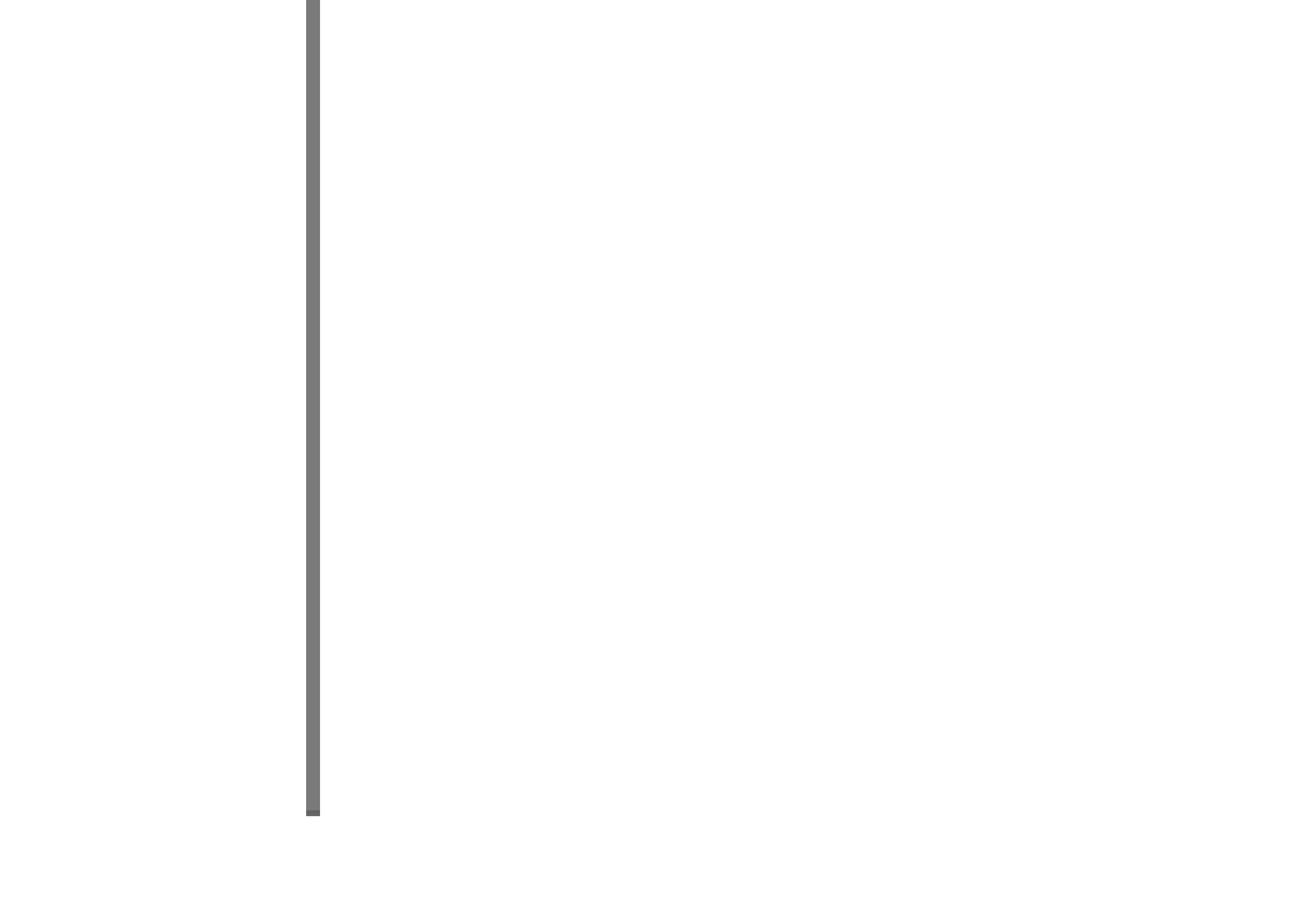
The Tramex Remote Environmental Monitoring System (TREMS) is a new cloud-based system designed, developed and built in Ireland by Tramex, for the most accurate and reliable monitoring and recording of a projects’ environmental temperature and humidity conditions.
For more information visit: https://tramexmeters.com/remote-envi ronmental-monitoring •
Firebird heatingrenewableofferdesign
ph+ | marketplace | 85 PASSIVE HOUSE+ MARKETPLACE
Forinsulation.moreinformation
With no monthly subscription fees, SIM included for 4G coverage, up to 15 years battery life, exceptional accuracy, and an easy-to-use and se cure cloud-based platform, the Tramex Cloud provides simple reporting, parameter adjustment, alert notifications and downloadable data.
Underfloor heating generally runs at 45C as opposed to 80C used in radiator systems, saving hugely on en ergy and running costs. Firebird’s Enviroair underfloor heating is a multilayer railing system. The multilayer pipe with an embedded aluminium layer is oxygen tight. De spite being highly flexible, this multilayer pipe is charac terised by high tenacity and fatigue strength. The fixing of the underfloor heating pipes takes place with the help of the self-adhesive fixing rails. A rail installation has the advantage that the heating circuits can be changed as desired without damaging the under lying visit www.firebird.ie or email newbuild@firebird.ie to avail of a free home heat ing consultation.
Tramex launches remote environmental monitoring system
Alert notifications can be sent to site agents for a quick resolution, or to an office for reference. Project information can be made accessible to all that require it.
World-renowned Irish moisture meter pioneer Tramex has launched a new cloud-based system for budding building pathologists – to enable users to remotely monitor buildings and detect potential indoor air quality, temperature and interstitial condensation issues.
A secure logging-in process into the Tramex Cloud allows required per sonnel access to the temperature and relative humidity data. All temperature and humidity readings are stored on the Cloud plat form and can be downloaded as CSV, Excel files or jpegs. Reports are generated for a quick glance view with colour-coordinated lines for even easier viewing. If the parameters on site are of a critical nature, TREMS can issue alert notifications if the sensor readings reach the set parameters.
Designed to provide an economical and low carbon alternative to traditional heating and hot water systems, the Enviroair air source heat pumps from Firebird are available in single phase outputs from 7.5 to 16 kW. Fea turing a single monobloc unit which is installed outside the property, the range is designed to provide a compact and space saving solution. Cheaper to install than a ground source heat pump, every kW of electricity used to power an Enviroair air source heat pump provides up to 5 kW of energy. Fire bird said that Enviroair heat pumps are ultra-quiet in operation and emit fewer decibels than a domestic fridge.
Stanley sheds light on how the system works: “Tramex Cloud sensors are placed in the required areas and send temperature and humidity read ings to the user’s Tramex Cloud station. The secure network then con nects to the Wi-Fi supplied by the Tramex station and sends all data to the Tramex Cloud platform. In your Tramex Cloud account all collected data can be viewed as files and in visual charts or graphs and compiled into reports. Why drive to a single site to take readings, when you can surf to the Tramex Cloud and monitor many projects all in one place with no subscription fee.”
The system enables users to monitor sensors from multiple buildings, floors or projects, or multiple rooms within a single building without having to set foot on site once the system is set up. “All of your projects’ environmental data can be monitored remotely, any time, any place, from anywhere,” said Tramex’s head of monitoring Ryan Stanley. “TREMS is your reliable partner for precise and accurate remote temperature and humidity monitoring.”
Firebird also offers underfloor heating in conjunction with its air source heat pumps. Firebird Enviroair under floor heating is suitable for a wide range of ground and upper floor constructions and can easily be combined with radiator systems for extensions and conservatories.
Leading heating expert Firebird is now offering full service design for renewable heating systems. The company’s technical team can calculate a dwelling’s exact needs with regards to radiators and/or underfloor heating, hot water and heat pump outputs — based on heat loss calculations and the heating requirements for each room — and advise an appropriate system to meet and surpass Part L of the building regulations.
• (above) A 7.5 kW Firebird Enviroair air-to-water heat pump was chosen for Wayne and Michelle Hession’s passive house in Claregalway, which features in a case study on page 32.
A family-owned Irish company founded in 1974, Tramex developed the world’s first non-destructive moisture meter, and their solutions –which also include interstitial probes – are used by experts and building professionals around the world to understand how buildings behave in terms of moisture and temperature.
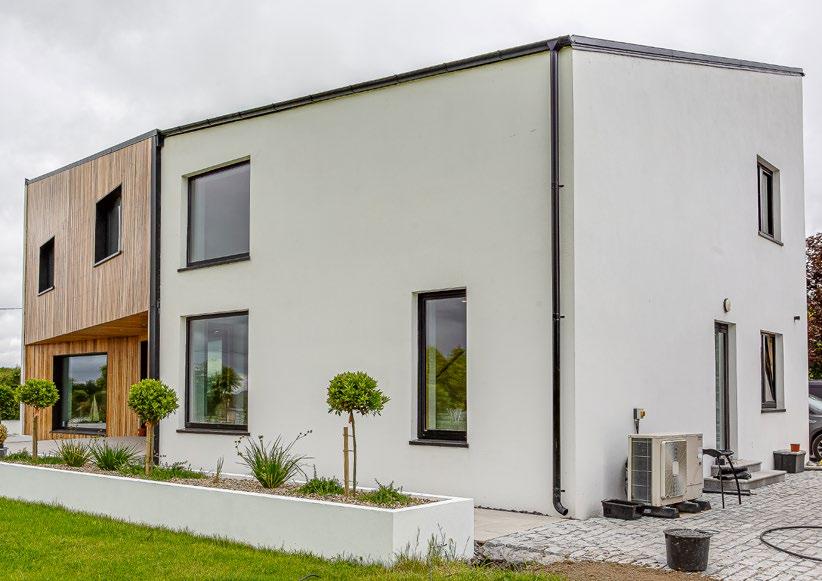
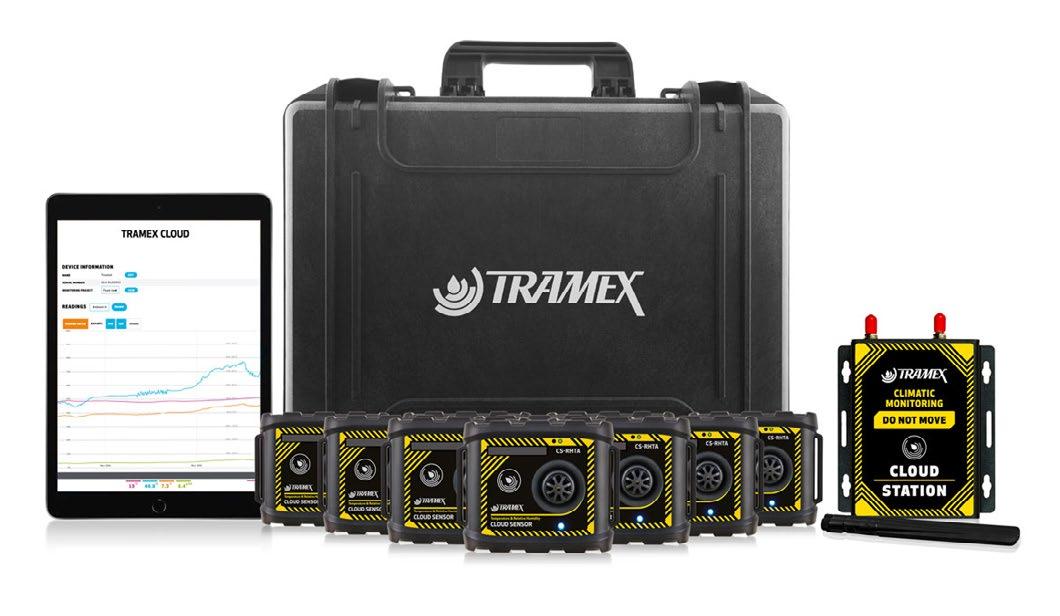
86 | passivehouseplus.ie | issue 42 MARKETPLACE PASSIVE HOUSE+
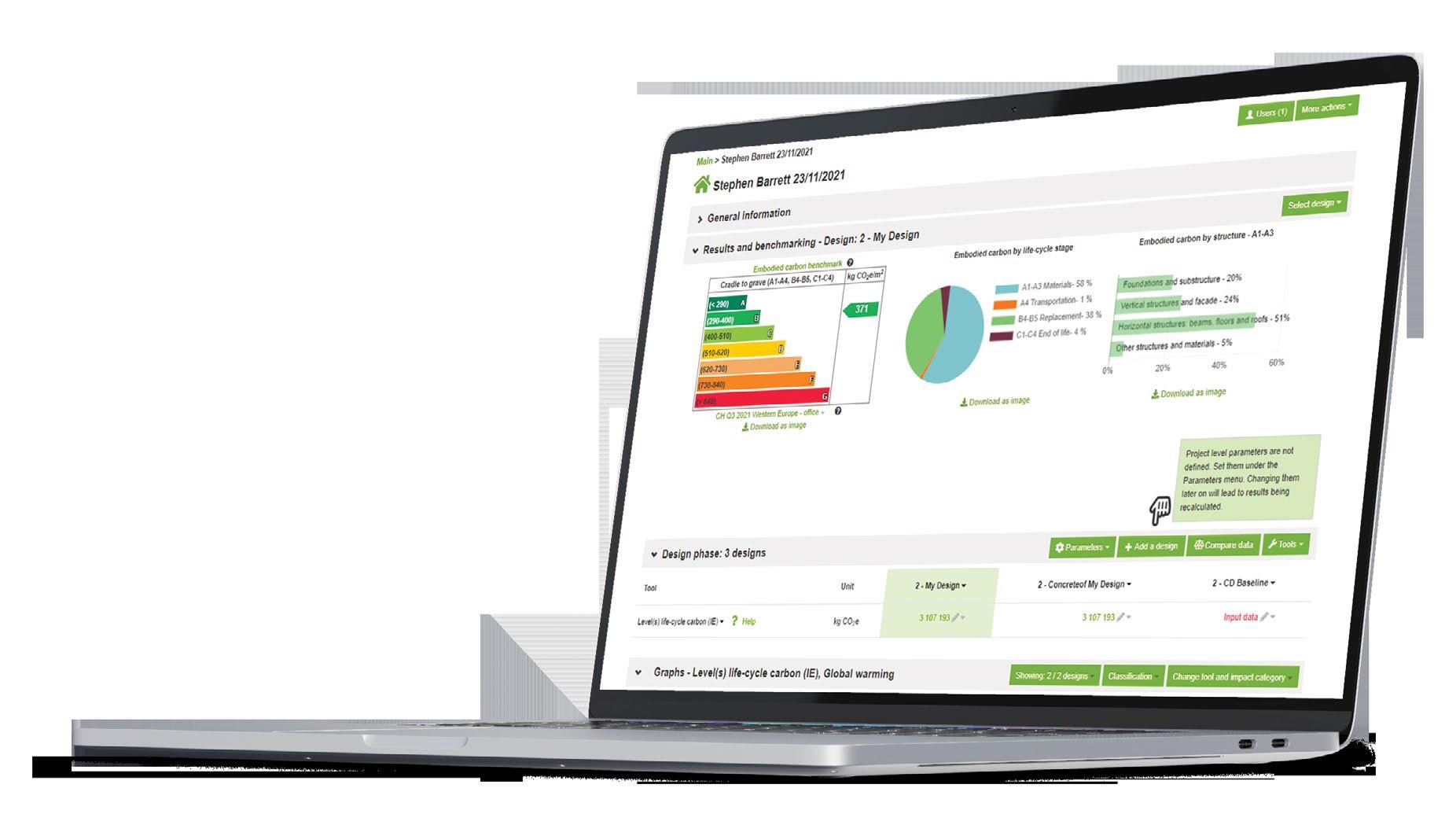

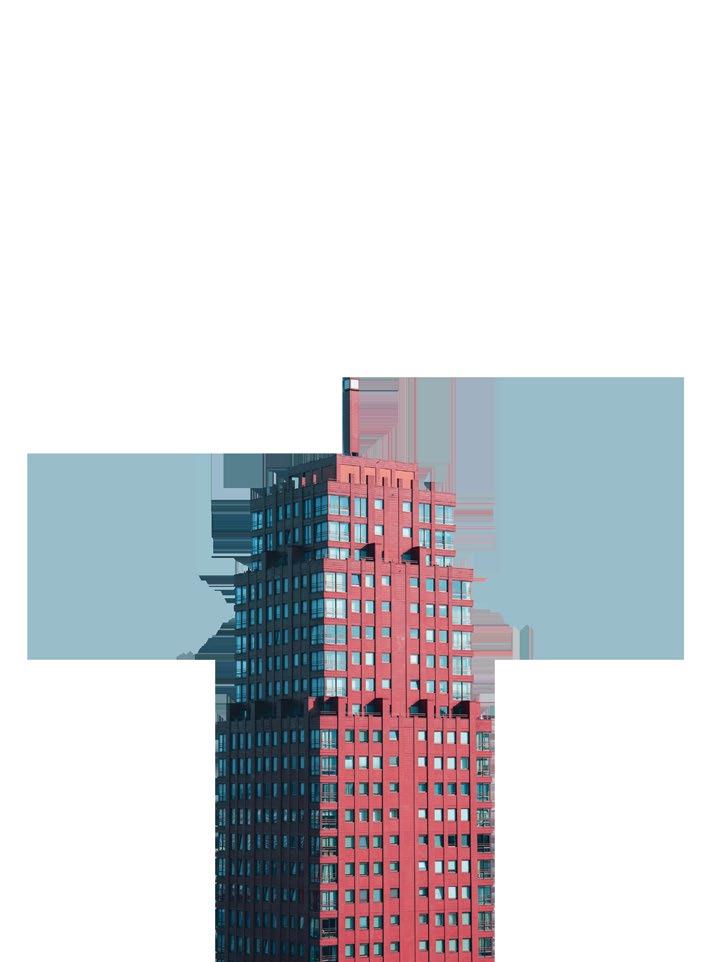
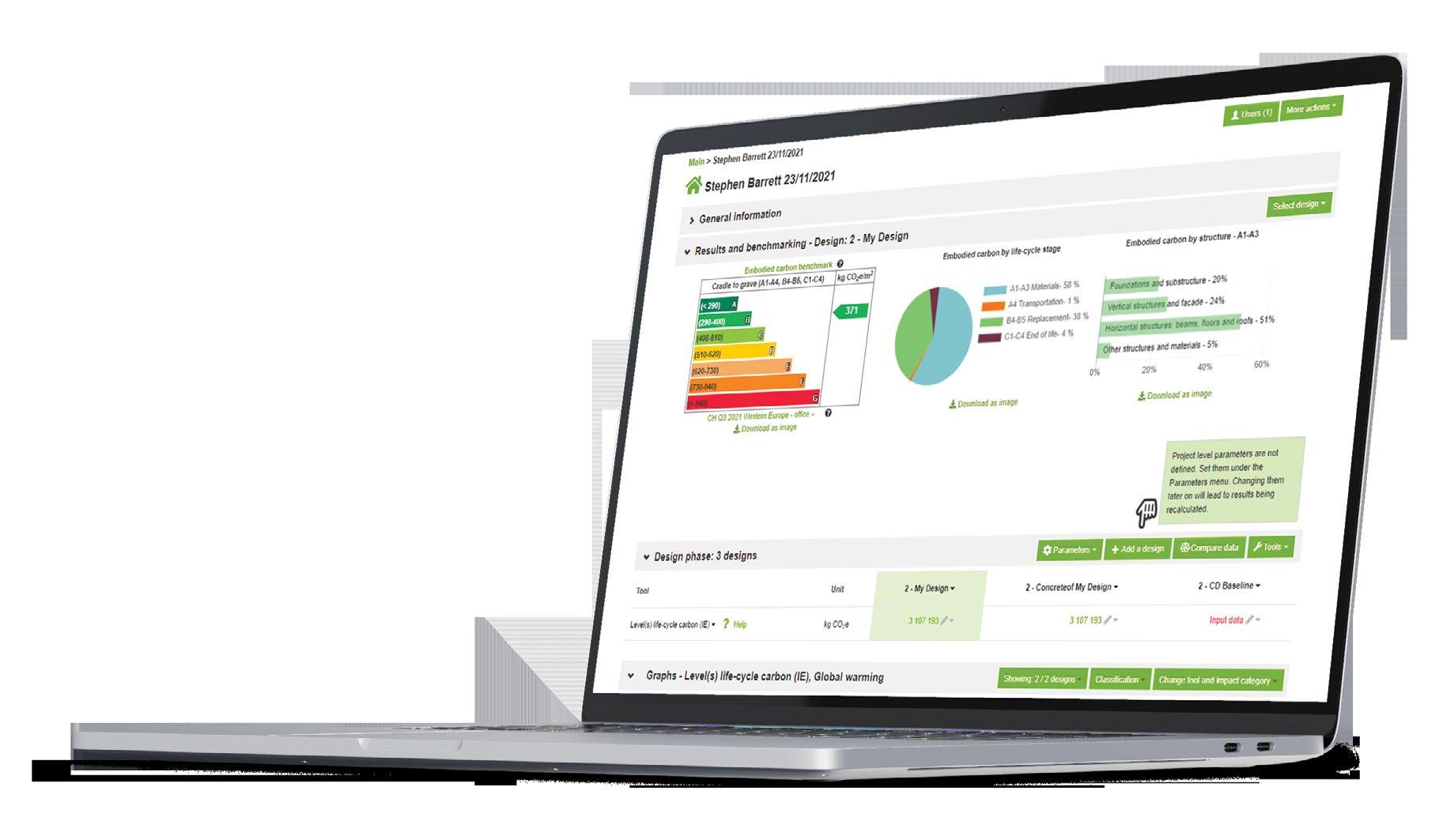
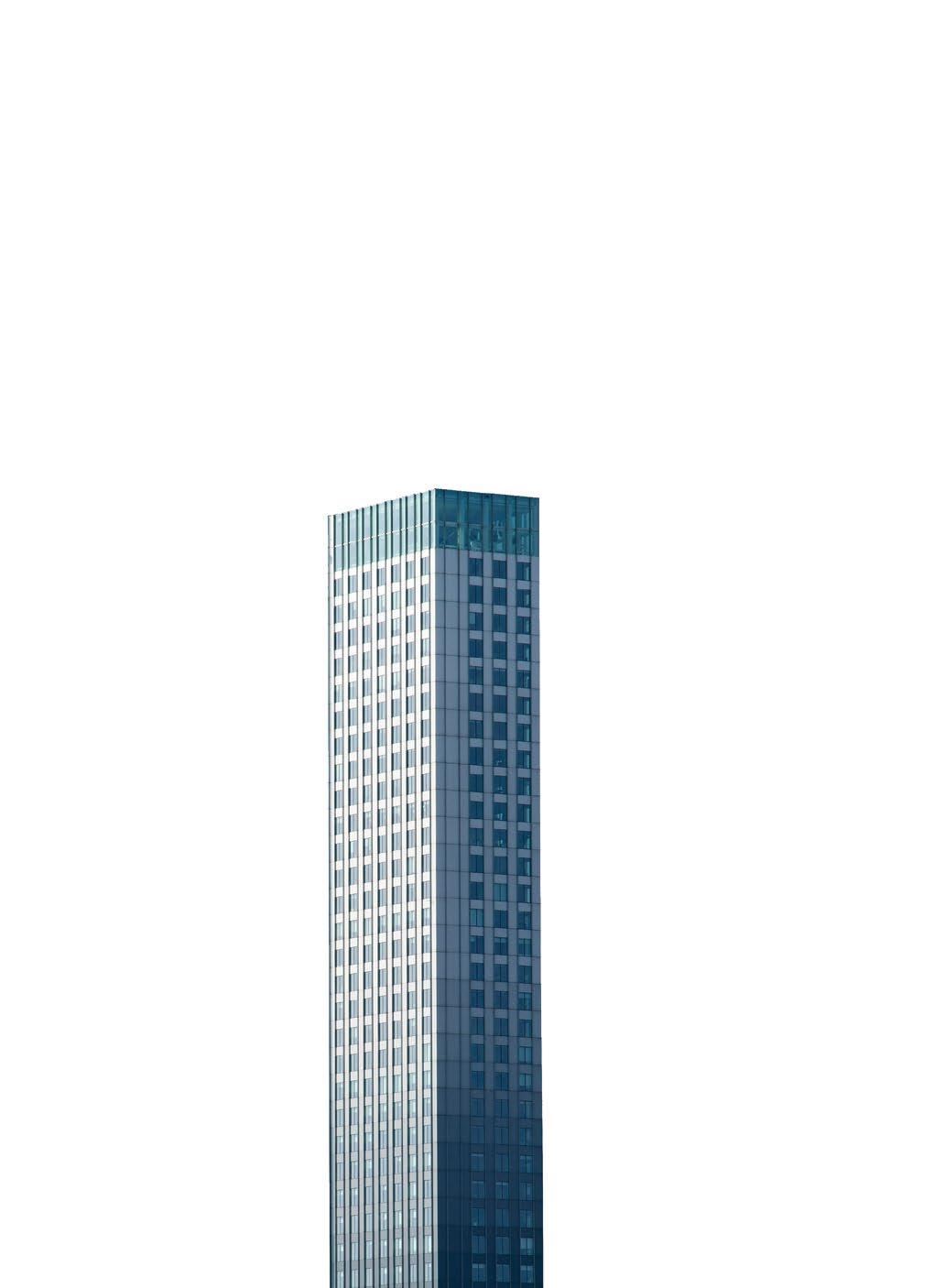

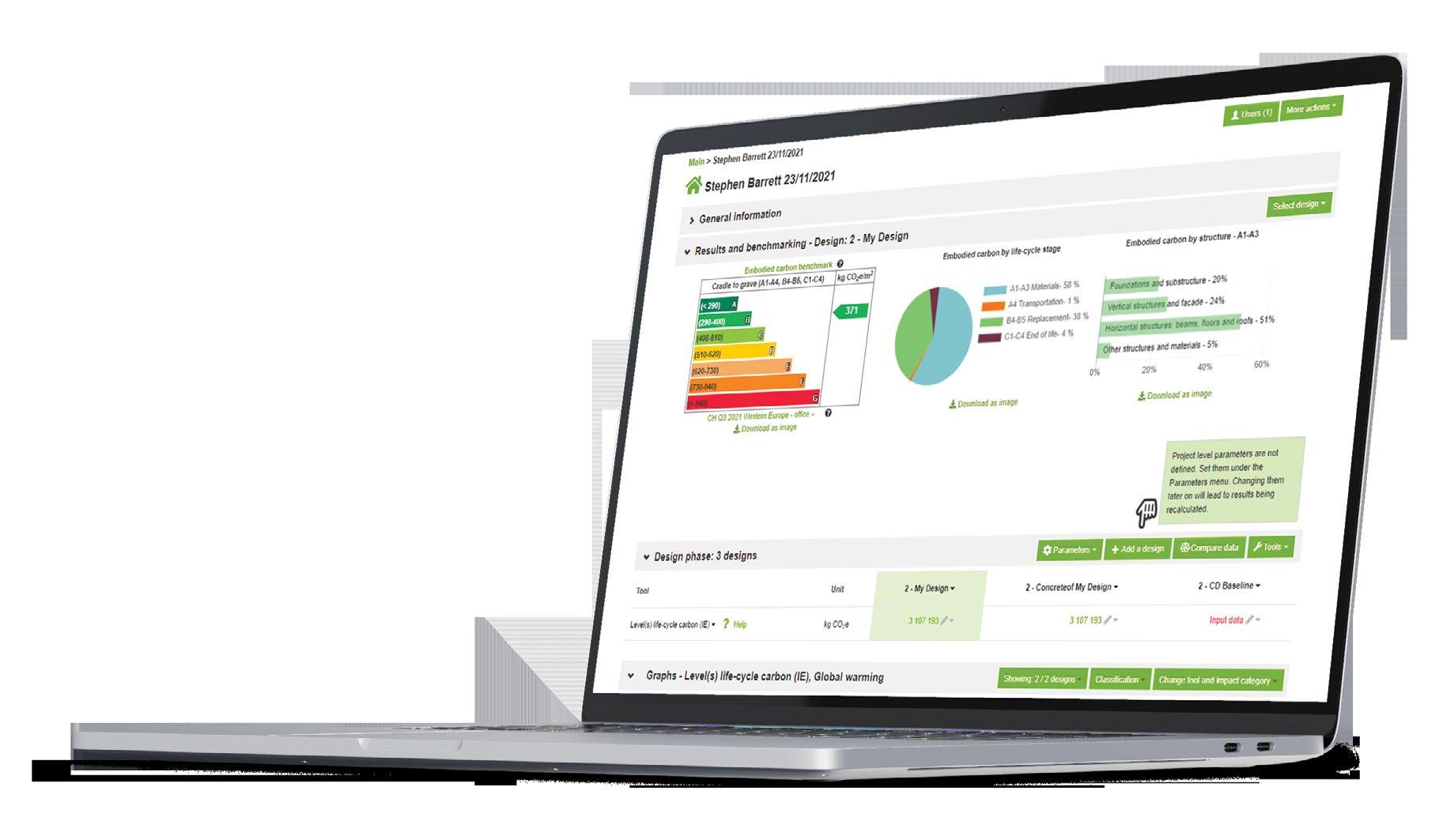
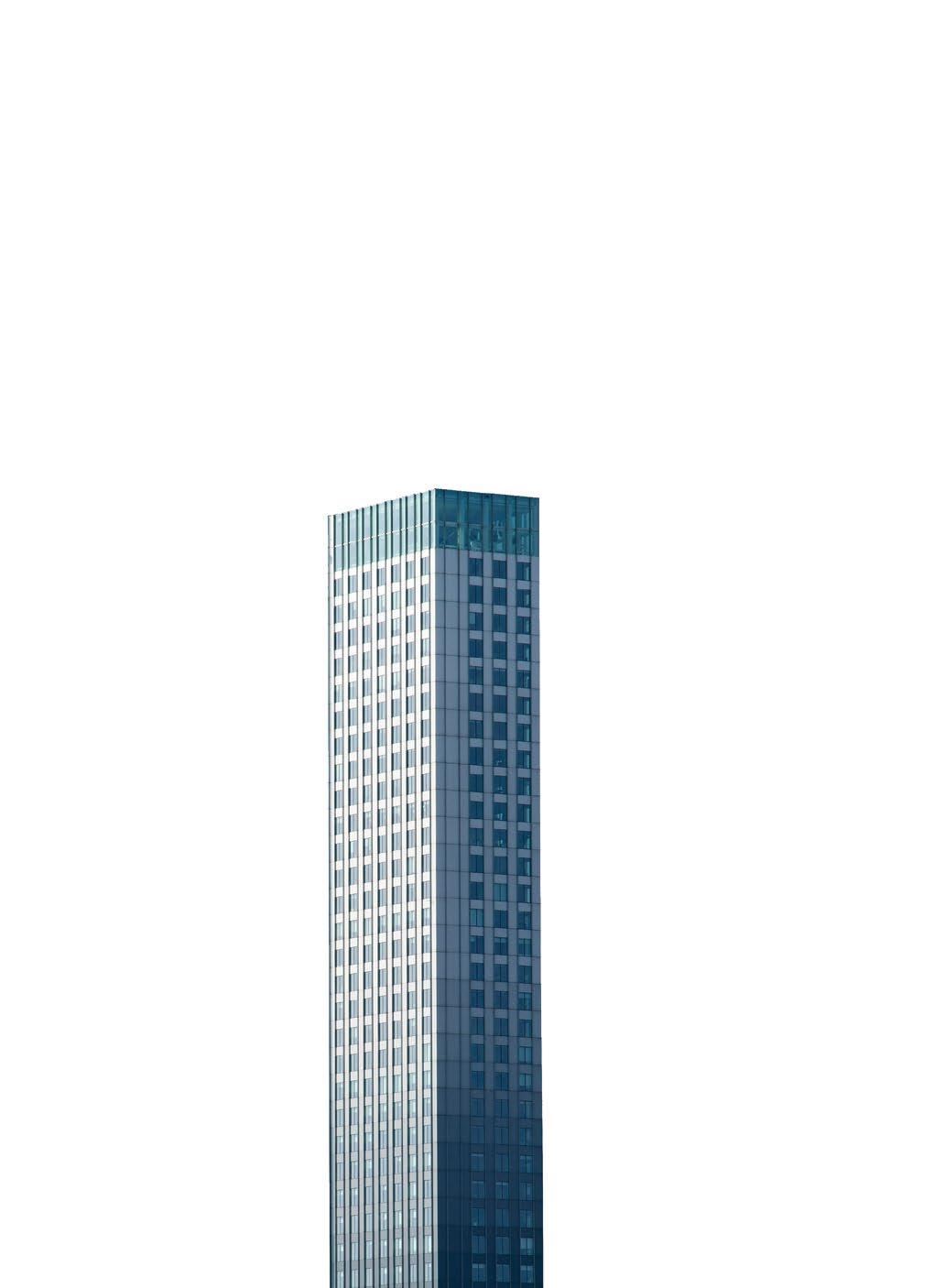

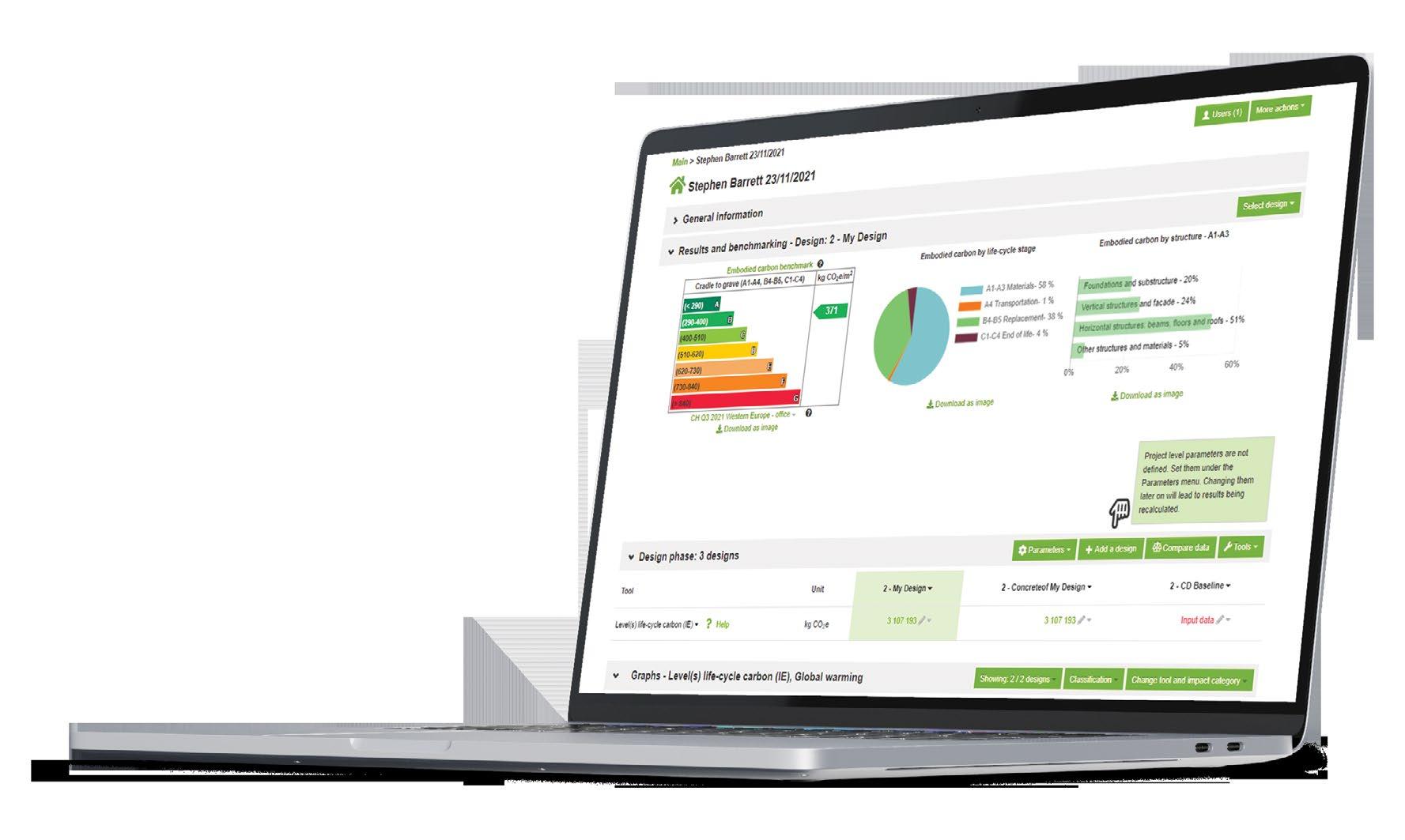
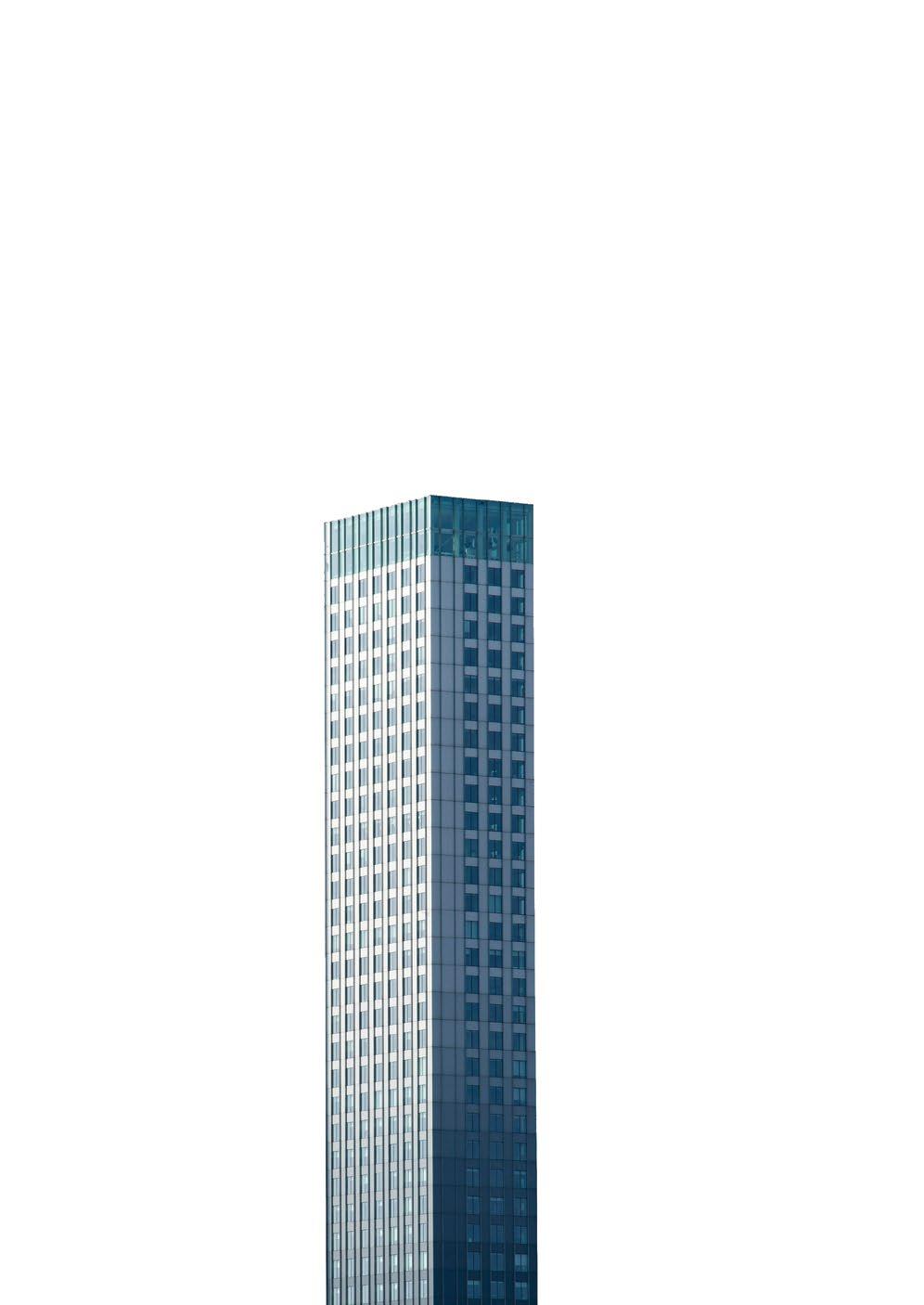
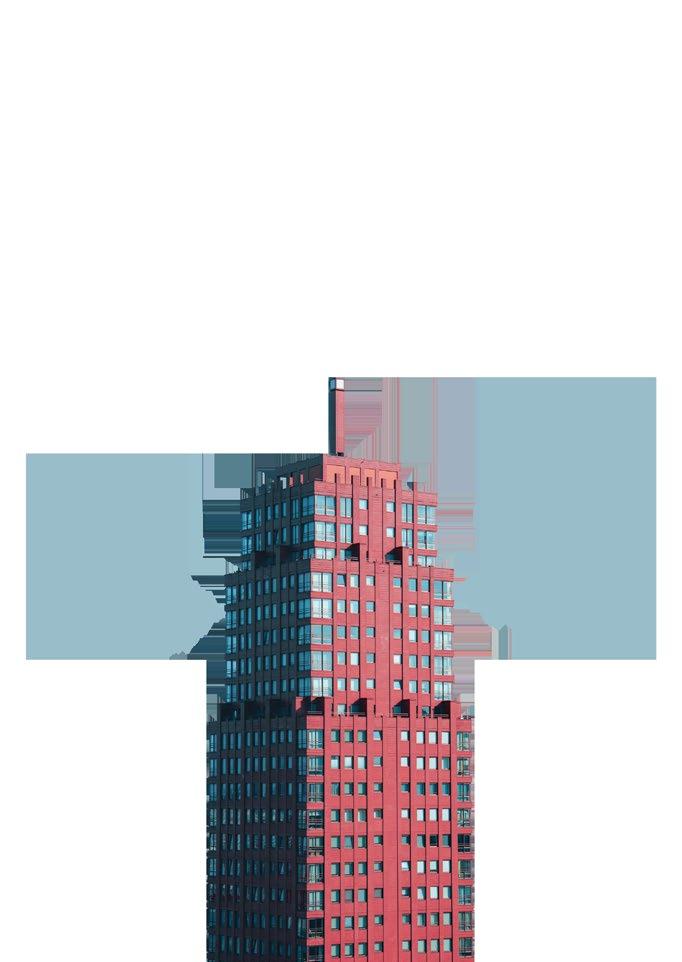
Stephen Grant, founder of Grant, said: “We are delighted to join such an estab lished and respected trade association as Octabuild. We have over four decades of knowledge, innovation and expertise in the heating industry, so joining the company of some of Ireland’s most trusted and inno vative manufacturers was a natural move. Collaborating with Octabuild will certainly enhance our relationship with the building trade so we are looking forward to the op portunity to celebrate the achievements of our top performing builders merchants in the 2022 Octabuild Awards for Excellence culminating in October.”
Grant joins Octabuild (above) Grant director Niall Fay and managing director Stephen Grant.
Launching initially with Kore Floor, Kore Fill Diamond, Kore Roof Insu lation, the Kore Insulated Foundation System, Kore External, Kore Void Formers and Kore Geofoam, this exclu sive offering is available in a variety of EPS grades this autumn. Kore was Ireland’s first expanded poly styrene manufacturer to hold an EPD for EPS, and is in the process of obtaining an updated EPD to integrate the Kore Low Carbon EPS product line. Commonly used in low energy buildings across Ire land and the UK, Kore’s EPD-verified products offer additional credits in build ing sustainability assessment schemes like the Home Performance Index, LEED (Leadership in Energy and Environmen tal Design) and BREEAM (Building Research Establishment Environmental Assessment Method). Kore estimates, based on information provided by BASF, that the company’s low carbon product range will save 2.223 kg CO2 equivalent for the pro duction of 1 kg of EPS versus standard Kore EPS. A typical home of two floors, 100 m2 will save 800 kg CO2 by choos ing Kore’s low carbon solutions. According to Kore’s operations di rector, Pauric Kavanagh: “With Kore Low Carbon EPS, our customers will receive identical quality and perfor mance of the product that they are used to, while making an effort to reduce cli mate change through utilising a more sustainable material.” •
L eading EPS insulation manufac turer Kore is set to launch Kore Low Carbon EPS onto the Irish market – unlocking dramatic reductions in embodied carbon without affectingManufacturedperformance.using BASF’s Neopor BMB (Biomass Balance) or Styropor BMB – the new insulation achieves substantial embodied carbon reduc tions by using renewable resources such as bio-naphtha or biomethane derived from organic waste, crops or vegetable oils as feedstock in the very first steps of chemical production. Based on data from Environmental Product Declarations (EPDs) obtained by BASF, Neopor BMB reduces em bodied CO2 emissions by at least 80 per cent compared to Neopor during the manufacture of the raw material. In sulation boards made of Neopor BMB have the same properties as their fossil equivalents. In addition to operational carbon savings delivered over the prod uct’s lifespan, Kore’s early stage analysis indicates that embodied carbon savings of at least 60 per cent may be achieved by the boards during production – fig ures which are subject to verification.
Visit www.grant.eu for more information on Grant’s range of innovative heat ing solutions. •
(above) Kore’s new low carbon EPS being cut on the production line.
Kore launches low carbon EPS
ph+ | marketplace | 87 PASSIVE HOUSE+ MARKETPLACE
G rant has announced its membership of Octabuild in a move that will see the company strengthen its relations in the building and construction industry and showcase its award-winning home heatingOctabuildtechnologies.wasestablished in 1984 with the objective of promoting the benefits of high quality, Irish manufactured products for the building, construction and DIY sectors. Ray Molyneaux, chairman of Oc tabuild said: “Octabuild companies are com mitted to excellence in providing an efficient and reliable service to builders merchants based on a core set of values, including innovation, leadership, sustainability and partnership. We are delighted to welcome Grant to join Dulux, Etex Ireland, Glennon Brothers, Gyproc, Irish Cement, Kingspan Insulation and Wavin Ireland in delivering on this mission into the future.”
Over the past 40 years Grant has expanded its product portfolio to include a wide range of renewable heating technologies including Grant Aerona3 R32 air-to-water, air source heat pumps, Grant Sahara solar thermal panels, Grant Uflex underfloor heating, Grant integrated units and pre-plumbed hot water cylinders, Grant Afinia aluminium ra diators, and Grant Spira condensing wood pelletTheboilers.company has also invested over €250,000 in R&D to ensure its Grant Vor tex and Euroflame ranges of condensing oil boilers are HVO biofuel compatible. Niall Fay, director at Grant added: “One of the key motivators for us becoming a member of Octabuild was the organisation’s com mitment to promoting sustainability in the building industry. We look forward to working together with them, to educate builders merchants and their customers on the benefits of clean energy heating solu tions that can deliver a fully decarbonised, resource efficient home heating with long term cost savings.”

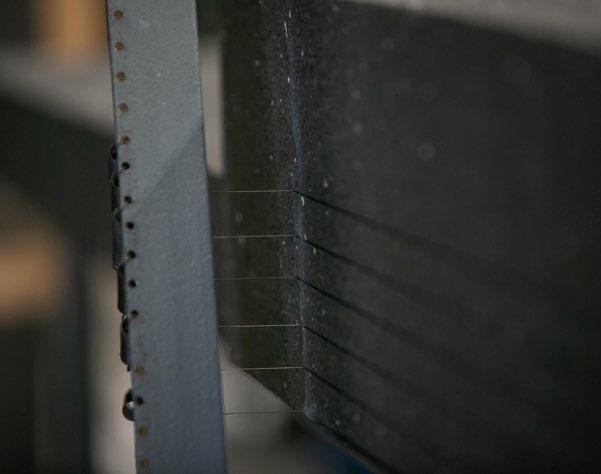

Low carbon, cement free carbon rooms being built in Cork
88 | passivehouseplus.ie | issue 42 MARKETPLACE PASSIVE HOUSE+
A garden room built by Cork-based Blue Mountain Garden Rooms has a significantly lower carbon footprint when compared to an equivalent log cabin with a concrete base, or to a block-built log cabin with a concrete base, a recent analysis has found. The EcoPOD from Blue Mountain Gar den Rooms has a gross embodied carbon of 1,660 kg CO2e (kilograms of CO2 equiva lent), compared to 2,230 kg CO2e for the log-built cabin with concrete base, and 3,710 kg CO2e for the block-built cabin. This is before carbon stored in the timber is subtracted, giving a net carbon footprint for the EcoPOD at the point of practical completion of -2,244 kg CO2e, compared to 14 kg CO2e for the log cabin, and 3,071 kg CO2e for the block-built structure. This analysis mainly used carbon factors from the ICE Database v 2.0, as well as some environmental product declarations (EPDs), and assessed materials from bills of quantities, so principally covered the ‘cradle to factory gate’ period of the building life cycle. The analysis was funded by Cork City Local En terprise Office under the Green for Micro scheme, and was conducted by sustainability consultancy Sustineo. “As Ireland is now delivering buildings with the highest possible energy ratings, focus must shift to the embodied carbon of construction materials,” said Sustineo MD Raoul Empey. “In terms of greenhouse gas emissions reduc tion, embodied carbon has generally become the most significant impact of a building’s whole life cycle carbon impact. Blue Mountain is a small sustainable tim ber frame fabrication company that erects and builds garden rooms and house extensions. “We focus on carbon neutral building materi als and low-impact building methodologies,” said the company’s Conor McManus. McManus said that the company has a strong focus on eliminating construction waste. “Our waste management strategy starts with the materials and methodologies we choose to build with, after that our prior ity is to keep waste to a minimum,” he said. “Our timber carcass can be disassembled at end of life and reused. Our cellulose in sulation is made locally here in Cork from recycled newspaper by Ecocel,” he added. The company’s garden rooms are all manu factured off site in Cork.
•
Blue Mountain Garden Rooms has also completely eliminated the use of cement and concrete from its builds, and installs its garden rooms on ground screws from Stop Digging Ireland. “Our pile system can be re moved and reused at the end of a building’s life, unlike a concrete base,” McManus said. He added that very little ground is broken with this practice with minimal disruption to soil and site. The company uses only FSC and PEFC certified timber, and specifies Irish timber as much as possible, though McManus says it can be difficult to guarantee Irish timber at the moment due to supply chain challenges. He added: “We believe longevity is crucial to sustainable building and therefore choose durable materials to build structures that will last. Our external cedar cladding has a life ex pectancy of forty years while our membranes and tapes have a life expectancy of one hun dred“Weyears.feel a key component of sustainability is simplicity and replicability, and to this end we feel that our model and building meth odology not only meets best practice criteria within the Irish construction sector, but is easily replicated with the materials and skills available.” The company has a close relation ship with Dublin-based garden room manu facturer Rooms Outside, with which it shares best practice methodologies for designing and building sustainable garden rooms. “Our goal for next year is to fit, as standard, environmentally friendly Marmoleum floor covering,” McManus added. “We would hope too, in the future, to change our inter nal finish which will completely remove the use of clean water out of the build process. We see this as our biggest, but not unsur mountable challenge. We have almost totally eliminated the wet-trades from the build and associated use of processed water. The only area now using clean water is the skim finish internally.”According to Raoul Empey, recent prog ress on embodied carbon calculation mean it should be a standard part of construction projects of all shapes and sizes. “With ad vances in software, such analyses have become simpler and are really available to all design teams,” he said. “It’s up to those developing the client brief to build in carbon efficient de sign at the outset, and it is wonderful to see that demonstration of environmental creden tials is not just reserved to large construction companies. Blue Mountain EcoPODs shows that it is also possible for smaller companies to build structures that align with our net zero goals in that more carbon is stored in the building materials used than was emitted in theirFormanufacture.”moreinformation, please visit www.bluemountaingardenrooms.ie/https://
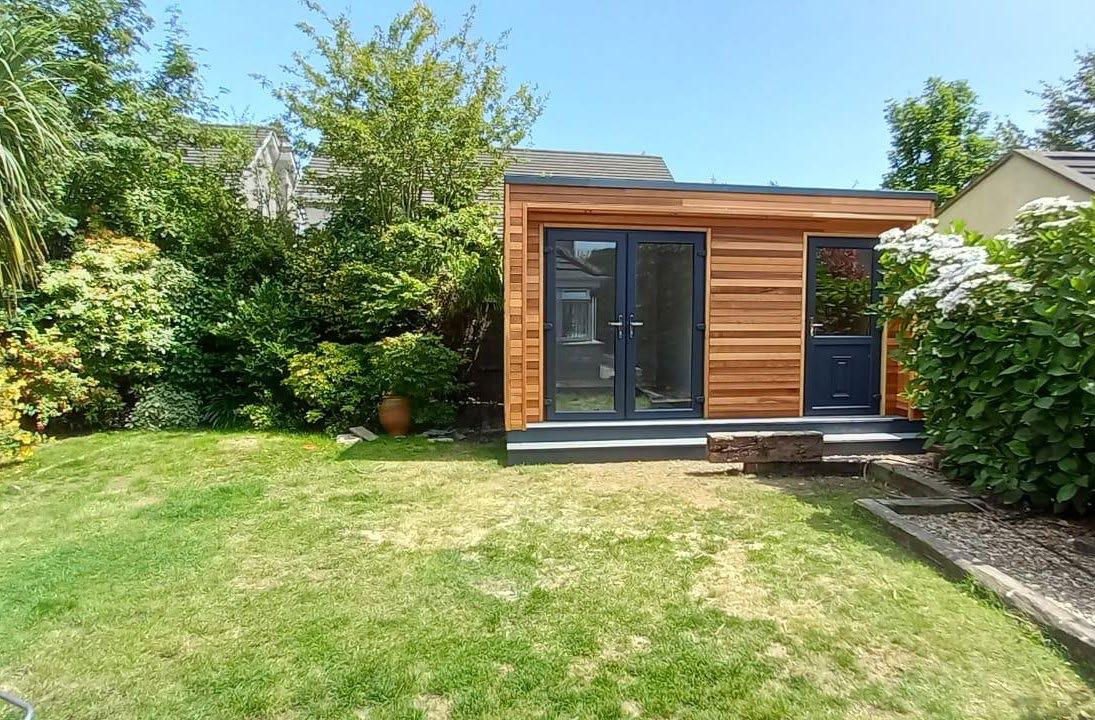
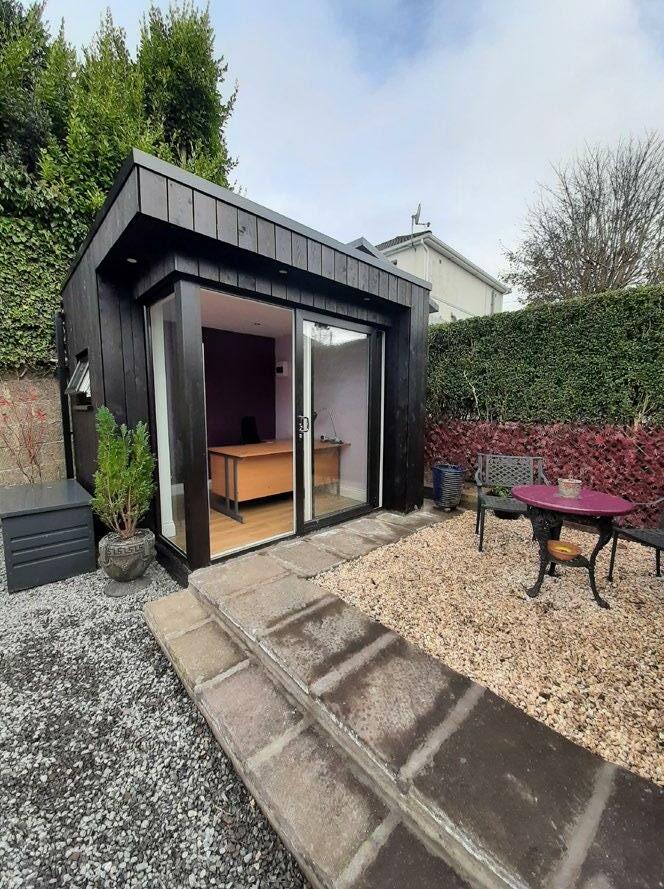
•
• (below) An Elensio 250H hot water heat pump, part of Hevac’s new Elensio range.
Origen, part of the Hevac Group, have introduced the Elensio as the latest part of the company’s heat pump range. Hevac’s product support & compliance manager Calin Tasnadi told Passive House Plus that the Elensio is earmarked for specific applications: apartments & a specific retrofit scenario. “The Elensio is ideal for apartments, sold in conjunction with smart radiators and heat recovery ventilation systems,” he said, referencing the fact that apartments built to the NZEB standard may have little or no space heating demand, particularly in the case of mid-block mid-floor units. “It’s also ideal for retrofits where someone has replaced the boiler recently, and wants something specific to reduce energy use for hot water.”
The Elensio comes in four variations – the 200 and 250, which work off external air only, and the 200H and 250H, which work off external air but can also be connected to solar panels or a boiler. All units include an immersion as back up. Each machine includes 0.15 kg of R290 in the refrigerant circuit. R290 has a 20-year global warming potential of just 0.072. Meaning the 0.15 kg in each Elensio is equiv alent to just 11 grams of CO2 – or to put it another way less than a third of an apple, or a five-minute mobile phone call.
Hevac launches hot water heat pump with green refrigerant
The government substantially increased the available grant for attic insulation earlier this year, and given the expected boost in attic upgrades this is likely to stimulate, John Egan of Cork-based cellulose insulation manufacturer Ecocel says that it’s critical homeowners consider factors such as moisture performance, as well as airtightness and carbon footprint when choosing their insulation material.
Grants from the Sustainable Energy Authority of Ireland will now cover ap proximately 80 per cent of the cost of attic insulation, with the grant for a typ ical semi-detached home increasing from €400 to €1,200 for example, as a re sponse to the current high cost of energy.
“Since the announcement of the in creased grants for attics it is import ant that we use sourcedEcocel.luloseIrish-manufacturedcircular-economy,low-carboncelfibreinsulation,”saidEganof“Ecocelismadefromlocallyrecyclednewspapers.”Egansaidthatcelluloseisahygroscopic,breathablematerial,whichmeansthatitcannaturallyabsorbmoisturethatmigratesfromadwellingintotheroofspace,andthenreleaseitintotheventilatedatticspace,withouttheneedfortheinstallationofaseparatevapourcontrolmembraneduringretrofitworks.Thispreventsdampnessandmouldandensurestheinsulationcontinuestoprovidethelevelofinsulationitwasdesignedto,headded.“Cellulosewilllastthelifespanofthebuildingwithoutavapourmembrane,providingconsumerswithlong-termpeaceofmindandvalueformoney,”Egansaid.RecentresearchfromtheUniversityofUlster[seeissue41ofPassiveHousePlus]alsofoundthatEcocelatticupgradesimprovedtheairtightnessofthreedwellingstested,byupto9percent.EganaddedthatBERsshouldrequireareal-worldassessmentofbuildingperformanceatcertainintervals(suchasone,fiveand10years)afterabuildingisoccupied,toverifythatthebuildingisperformingasitwasdesigned,andtocheckifinsulationisstillperforming.“BERsmeannothingunlessyou’retestingafterwards,”hesaid.
L eading sustainable heating systems provider Hevac Group has launched the De Deitrich Elensio hot water heat pump range onto the Irish market – using a refrig erant with a risibly low global warming potential (GWP). Manufactured by European heating behemoth BDR Thermea, the Elensio has been developed specifically to generate domestic hot water for dwellings – with the four units in the range achieving temperatures of 54-55C at impressive COPs of 3.09 to 3.54 when tested in line with the European standard for hot water heat pumps, EN 16147.
ph+ | marketplace | 89 PASSIVE HOUSE+ MARKETPLACE
Choose cellulose to againstprotectdamp in attics — Ecocel
With no outdoor unit, Tasnadi stressed that the Elensio’s air supply is ducted di rectly from outside air, with cooled air also ducted back outside. “It’s not designed to interface with the ventilation system at all, meaning you’re not over ventilating to make hot water,” said Tasnadi, who pointed out that Hevac also offer Nuaire MVHR systems to provide ventilation while maintaining thermal comfort. The air flow to the Elensio units goes up to 380 m3/hr – a limit set to keep noise levels low.
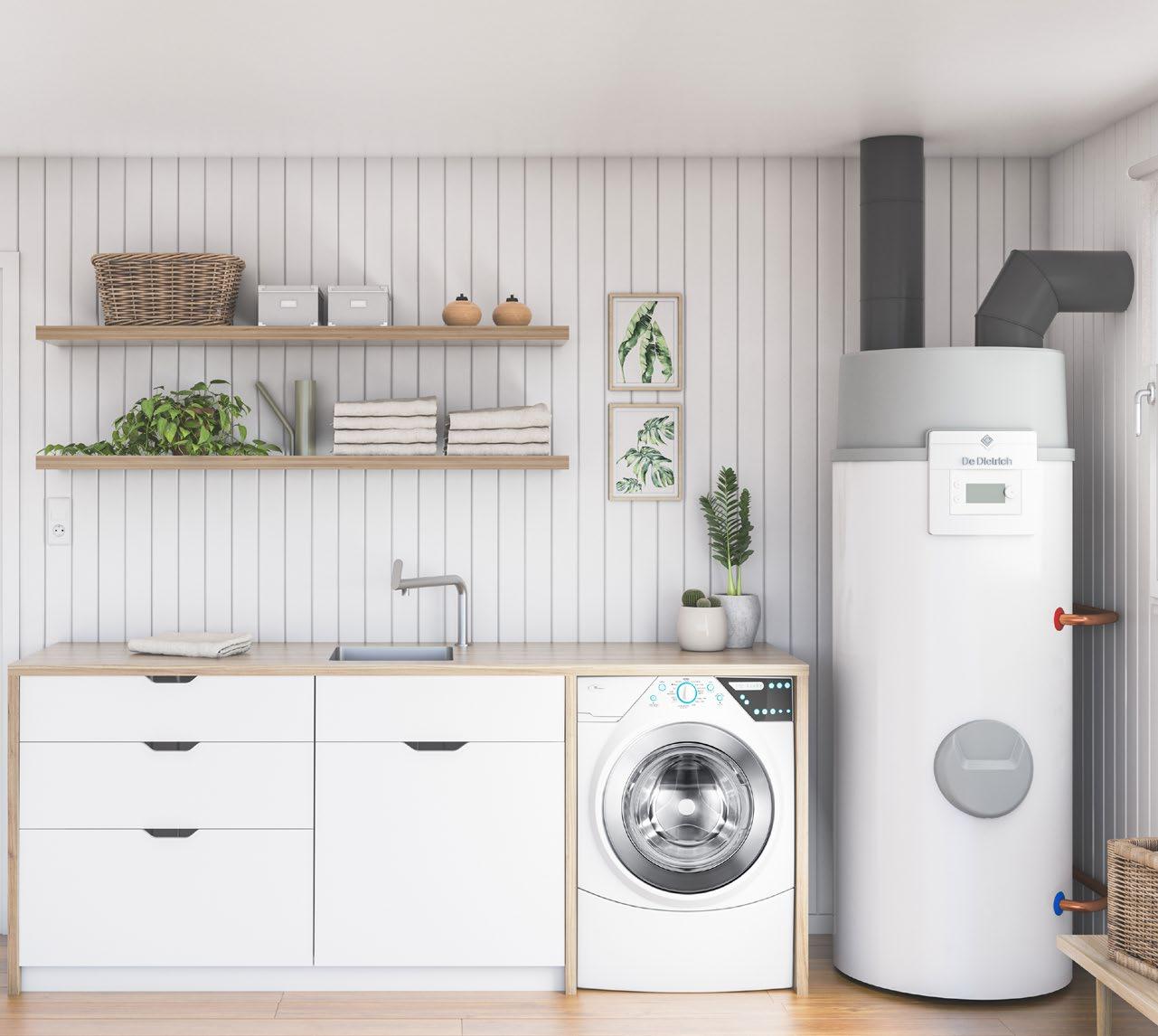
Toby Cambray is a founding director at GreenGauge and leads the building physics team. He is an engineer intrigued by how buildings work or fail, and uses a variety of methods to understand these processes. without (or at least, with less of) an efficiency penalty. There’s a lot more to unpack there, and I’ve probably upset a lot of heat pump engineers by oversimplifying. There are a cou ple of important caveats here – firstly that the hydronic design (i.e., pipe and radiator layout and sizing) is on-point, and secondly that the system is (re)commissioned to a high stan dard. Both of these are large rabbit warrens in their own right; many subtle parameters can (and should) be optimised on some modern units. This means that we perhaps shouldn’t be too worried about the fabric retrofit (if it does indeed happen, and to the standard assumed) undermining the performance of the heat pump. It would also not be beyond the bounds of possibility to swap it out for a smaller unit, passing the partially used one on to a larger home. An alternative approach is to put in an undersized heat pump before a fabric retro fit. This means that on the coldest days, the house might be a little chilly, or it is necessary to top-up with some direct electric heaters. While this has a running cost and carbon im plication (although average grid emissions are now very low, the periods of highest demand depend on higher emitting generation), and have an implication on the infrastructure, this would of course be mitigated on completion of the fabric retrofit. So, should we worry about accidentally oversizing heat pumps in a step-by step ret rofit? Perhaps less than we used to. All of this depends on some important assumptions of course: that the heating system is carefully de signed, with prior knowledge of the fabric ret rofit; that a good quality unit is used with an inverter drive and a comprehensive controller; that the heat pump system is commissioned to a high standard, and re-commissioned af ter a deep energy retrofit to suit the new load; and that ultimately, that fabric retrofit is com pleted to a good standard. n
On top of that, it’s not uncommon to add an arbitrary 10 or even 20 per cent to a heat loss even for heat pumps, sometimes disguised as a “warm up factor” but is basically a fudge or comfortReadersmargin.ofPassive House Plus will have some inkling of how inaccurate heat loss calcs might be (assuming they are done at all). I doubt that many (if any) installers on typical heat pump installations insist on an airtight ness test being done, or carefully document and account for all thermal bridges (I was de lighted to hear Nathan at the BetaTeach pod cast mention he’s used a co-heating type test to quantify this, but it currently seems unlikely this will be a mainstream service). How are the U-values arrived at? If we aggregate all these inaccuracies, do we tend to over or underes timate? But more importantly, how much does it matter? After all, looking at the range from one popular manufacturer, the domestic ASHPs come in 6, 8.5 and 11.2 kW. If your heat loss calcs come out at 7.25 kW, you have to choose to be 20 per cent oversize or 14 per centThereunder.are several more elephants in this room of uncertain heat loss. Firstly, there is the vast majority of the year when it’s nowhere near our worst-case scenario of zero or even -5C. A heat pump therefore spends most of its working life “oversized” compared to the ac tual demand, and we don’t worry about that. Another lurking proboscidean is hot wa ter; in order to re-heat a cylinder in a sensible period of time, we need a certain amount of power. A one hour re-heat of 200 L would re quire about 10 kW – significantly more than the peak heat loss from a well-insulated flat for example. There are alternatives to heat pump powered cylinders, but they are generally com promises and the subject for another column. It turns out that unlike the Irish border we can throw a bit of technology at this issue to make it go away, namely inverter driven compressors. Happily, with a few exceptions, many new heat pumps have this feature. The inverter is a like a dimmer switch to the light bulb’s toggle switch, allowing efficient oper ation at part load. This means that the heat pump’s thermal output can be turned down
How flexible can heat pumps be to handle what may be inexactly defined heating demands, asks Toby Cambray ?
DR TOBY CAMBRAY COLUMN 90 | passivehouseplus.ie | issue 42
A couple of issues back I discussed the idea that in order to decarbonise our housing stock as rapidly as possible, the dogma of fabric first should be ques tioned. This led to an interesting question from Lloyd Alter, of Treehugger.com: “If you install a heat pump first and do the fabric second, is the HP not then grossly oversized? I understood that’s a problem withWhilethem.”this is a valid question, it’s an area where the solutions have evolved with tech nology and the answer is different to what it would have been if it was five or ten years back. I’m primarily talking about air source heat pumps in this article, but some of the points apply to other types. The problem that Lloyd alludes to is to do with the risk of “short cycling.” This comes down to a straightforward way you can control a heating system which I like to call “IT Crowd” control; switching it off and on again. This is how conventional fossil boilers and thermostats work – they run, warm the building up, then switch off (fossil boilers can modulate but let’s keep it simple for now). The controller has a little hysteresis, which means it doesn’t immediately switch back on as the temperature drops, but permits maybe a degree of drop and therefore some period of time before the boiler kicks back in. Due to the mechanics of heat pumps, this leads to in efficiencies – it takes a bit of time and energy to build pressure and temperatures back up to operating conditions, which you don’t get back at the end of the cycle. It can also shorten the life of the compressor as a lot of the me chanical stresses occur on start up. But as with many things in sustainable en ergy, its more complicated than that. For a start, how do we size heating systems anyway? We *should* do a full set of heat loss calcu lations, and produce an “accurate” peak heat load – let’s say 10 kW for a typical-ish, not very well insulated house. If we’re a bit mean we might pick design conditions of 0C outside and 20C inside, giving 500 W/K. Assuming our heat loss factor is correct (spoiler alert, it’s probably not) if we went for a more conserva tive 24C inside and -6C outside, we’d need a 15 kW heat pump – the size is very sensitive to the conditions we pick as our worst case.
Is it okay to retrofit heat pumps before building fabric?
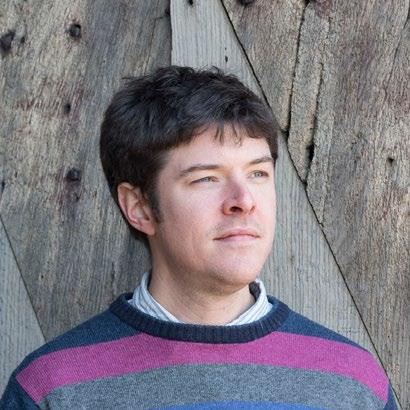
HIGH PERFORMANCE PROFILED INSULATION BOARD EPS 100 Silver & EPS 100, 200, 300 White Tapered FLAT ROOF Inverted FLAT ROOF Profiled FLAT ROOF Standard FLAT ROOF KORE INSULATION THE GREEN, KILNALECK CAVAN, IRELAND WWW.KORE-SYSTEM.COMINFO@KORESYSTEM.COM+353494336998 The ideal insulation solution for a variety of applications, including warm and cold roofs, inverted flat roofs, metal deck and tapered roofs Residential | Commercial | New Build | Retrofit SCAN TO LEARN MORE DESIGN GUIDE | CASE STUD IES | BENEFITS

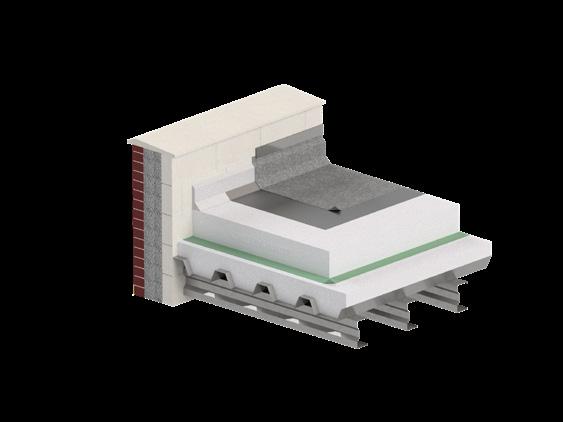
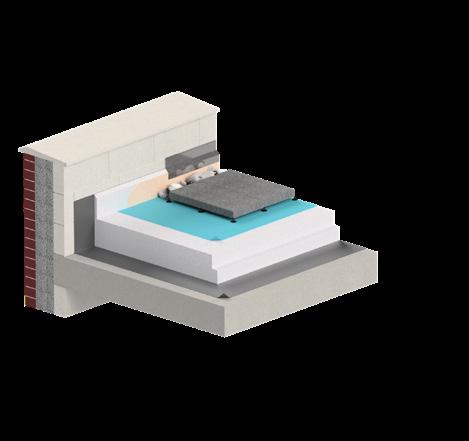
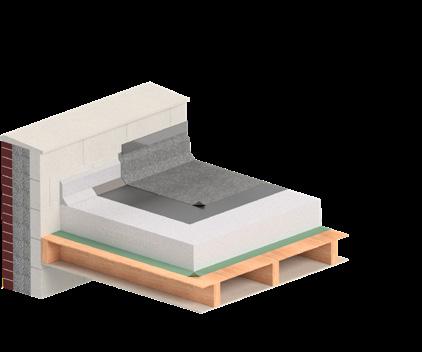
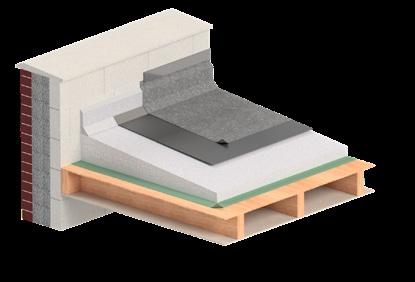
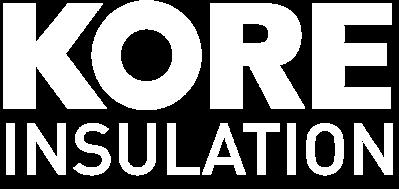
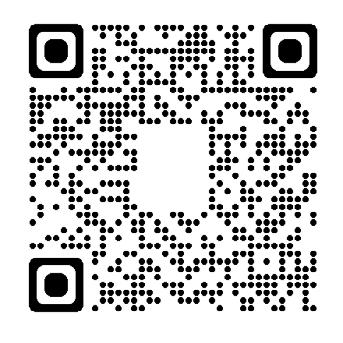


Established service partner network all around Ireland trained by Daikin R-32
Welcome renewable heat into your home
Daikin UpgradesEnergyHome about
Complete range of highly efficient R-32 heat pumps from 4 -16kW Market
Learn
Welcome renewable heat into your home
ph+ | oknoplast advertorial | 3 ADVERTORIAL OKNOPLAST
Complete range of highly efficient R-32 heat pumps from 4 -16kW Market
Daikin Altherma 3
DHWheatingleadingandefficiencies,providingCOPsupto5.1and3.3respectively Smart Control as allowingstandardcontrol of your system from your phone or smart speaker Assorted range of outdoor and indoors units to flawlesslyintegrateintoanyneworexistinghome
Established service partner network all around Ireland trained by Daikin R-32
For more information visit www.daikin.ie or email heating@daikin.ie for dedicated design support European market leader in heat pump technology
Both low and meetingoptionstemperaturehighavailableallheatingdemandrequirements
For more information visit www.daikin.ie or email heating@daikin.ie for dedicated design support European market leader in heat pump technology
Both low and meetingoptionstemperaturehighavailableallheatingdemandrequirements
Daikin Altherma 3
Daikin UpgradesEnergyHome Learn about
DHWheatingleadingandefficiencies,providingCOPsupto5.1and3.3respectively Smart Control as allowingstandardcontrol of your system from your phone or smart speaker Assorted range of outdoor and indoors units to flawlesslyintegrateintoanyneworexistinghome
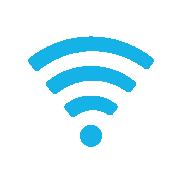

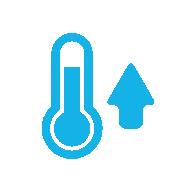
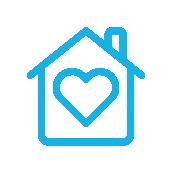
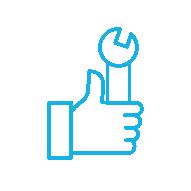
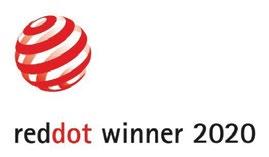
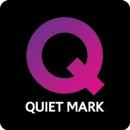
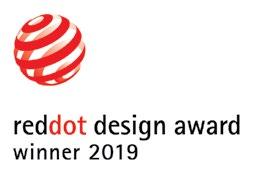
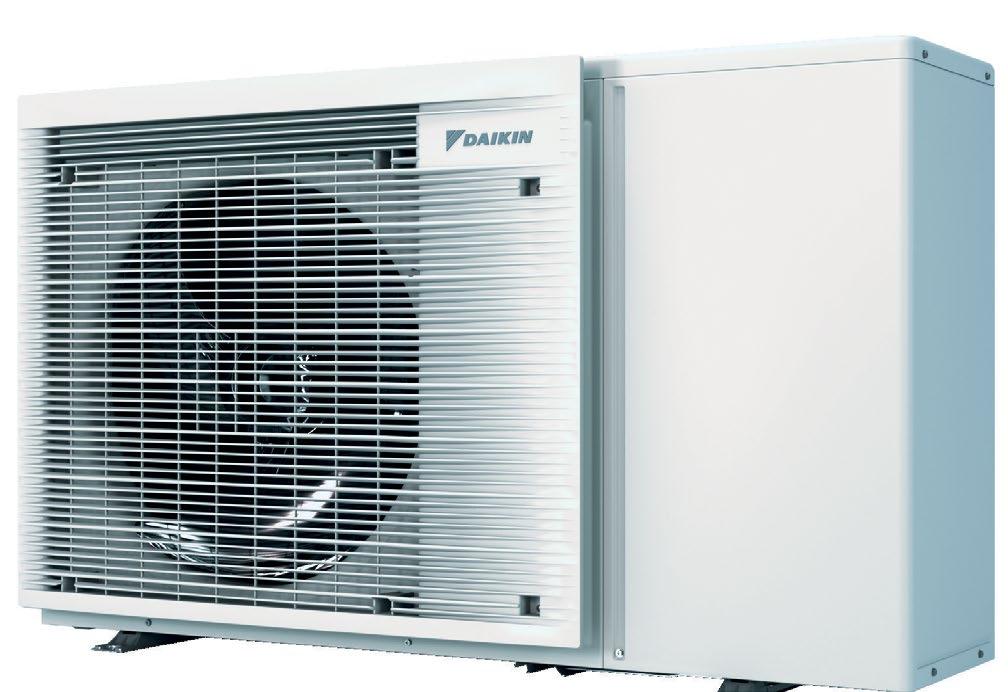
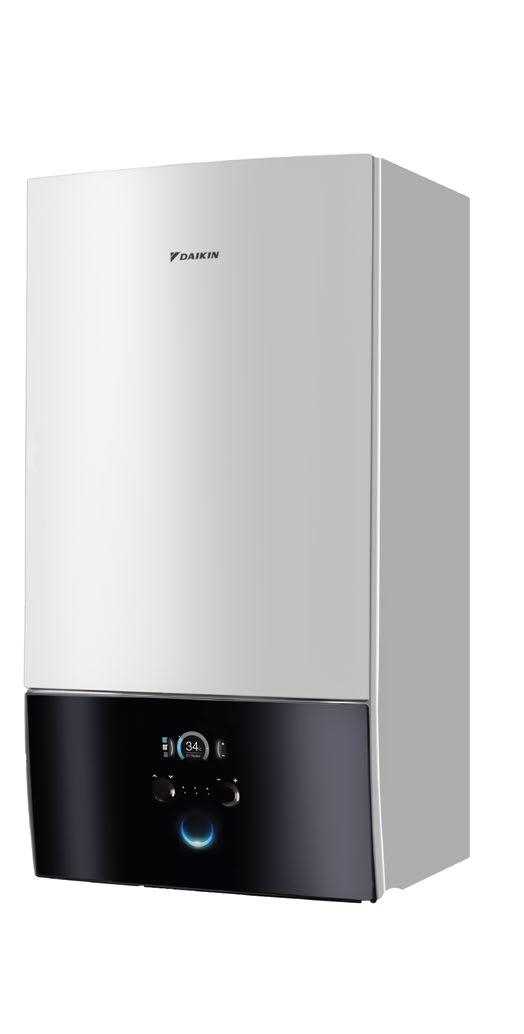
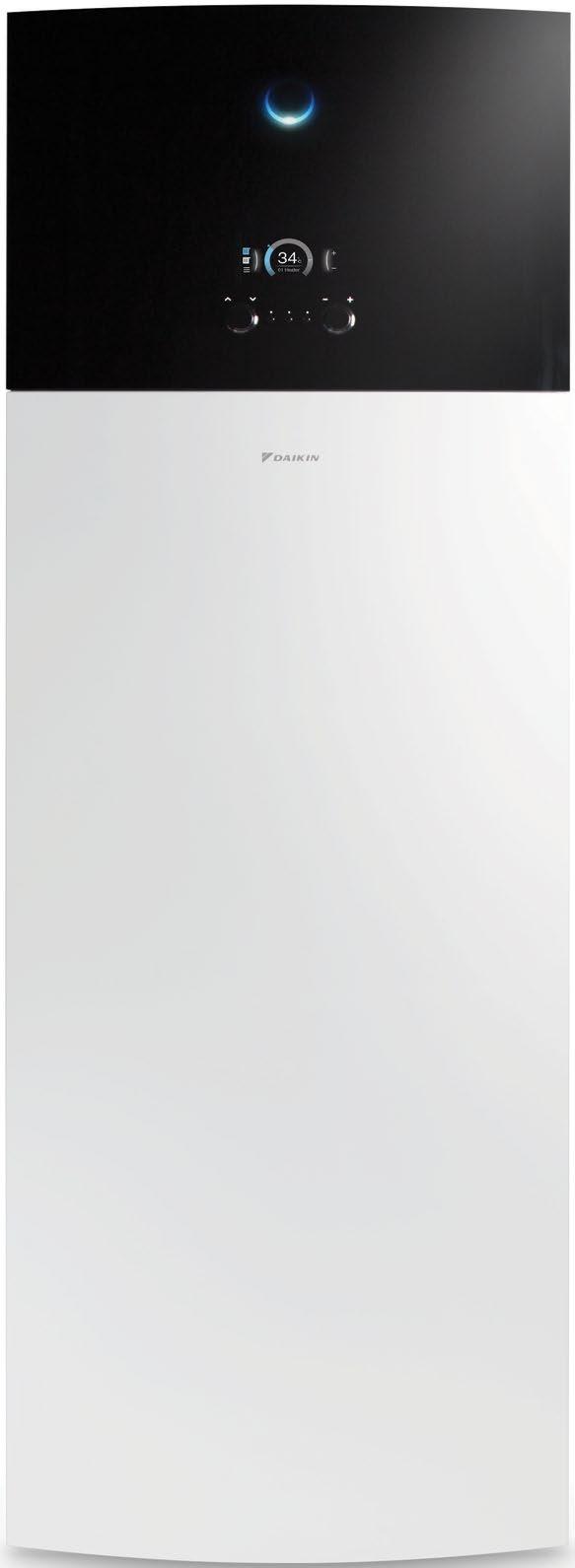
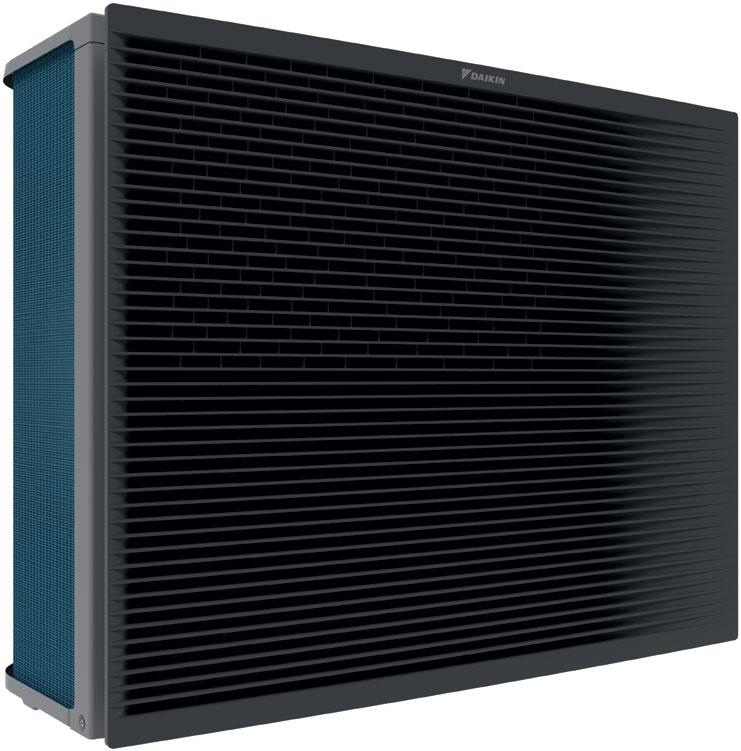
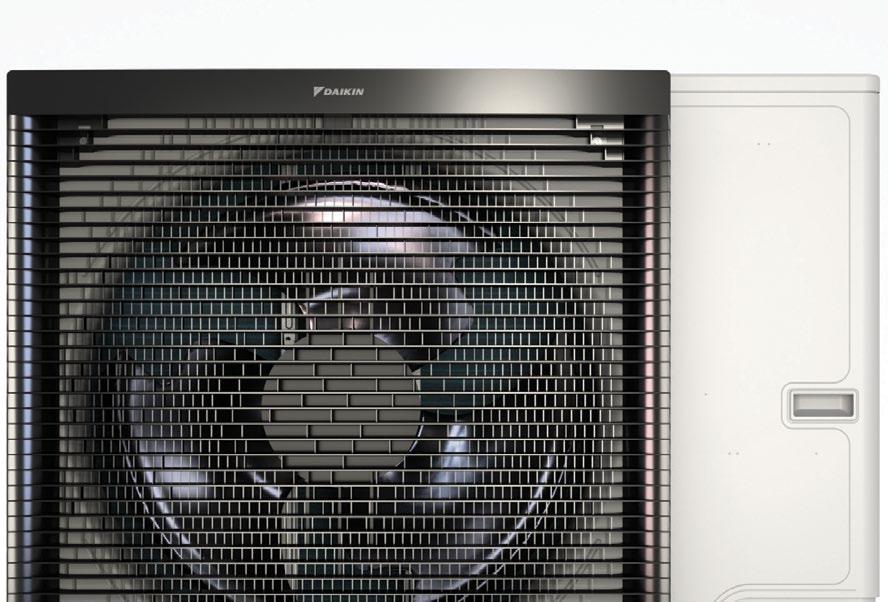

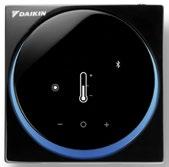
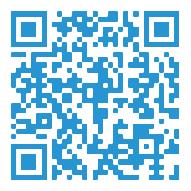
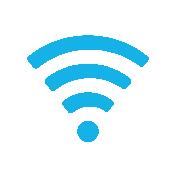
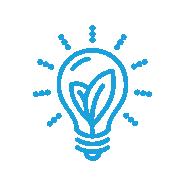
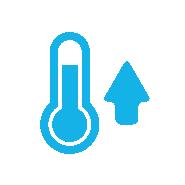
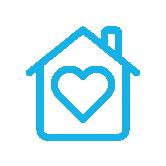
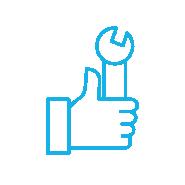
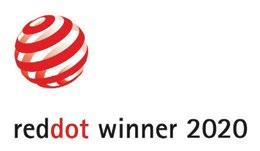
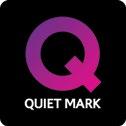
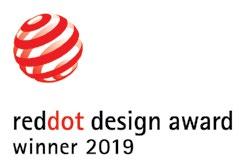
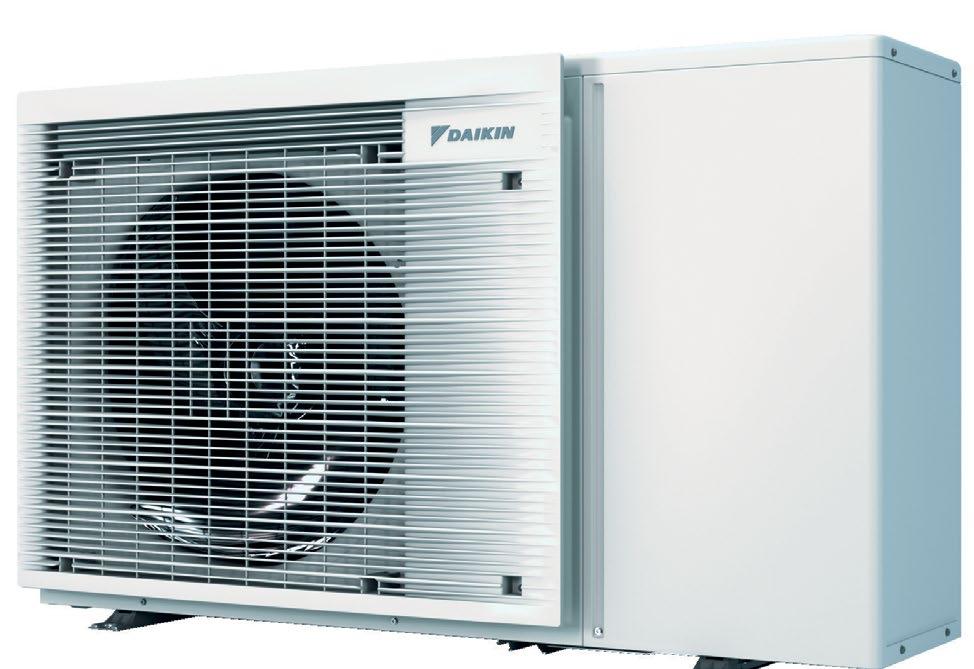
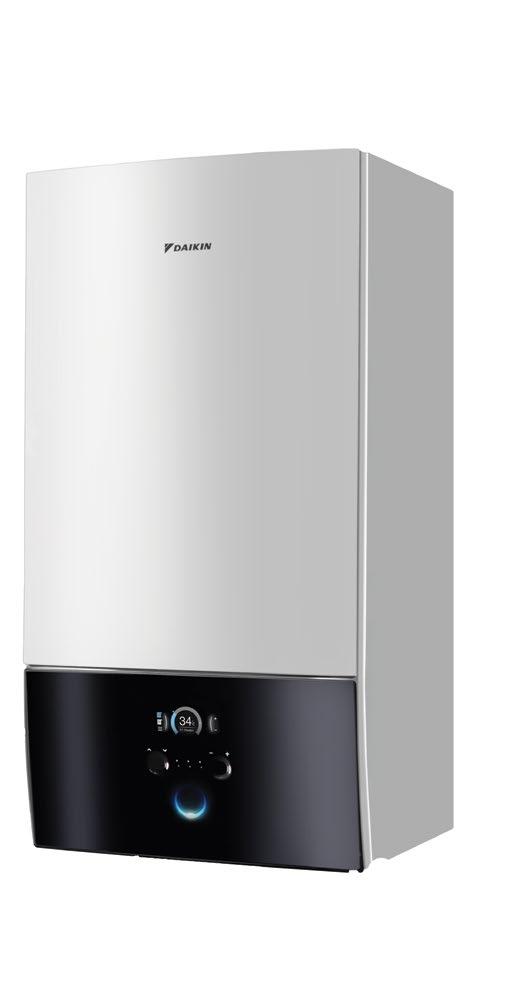
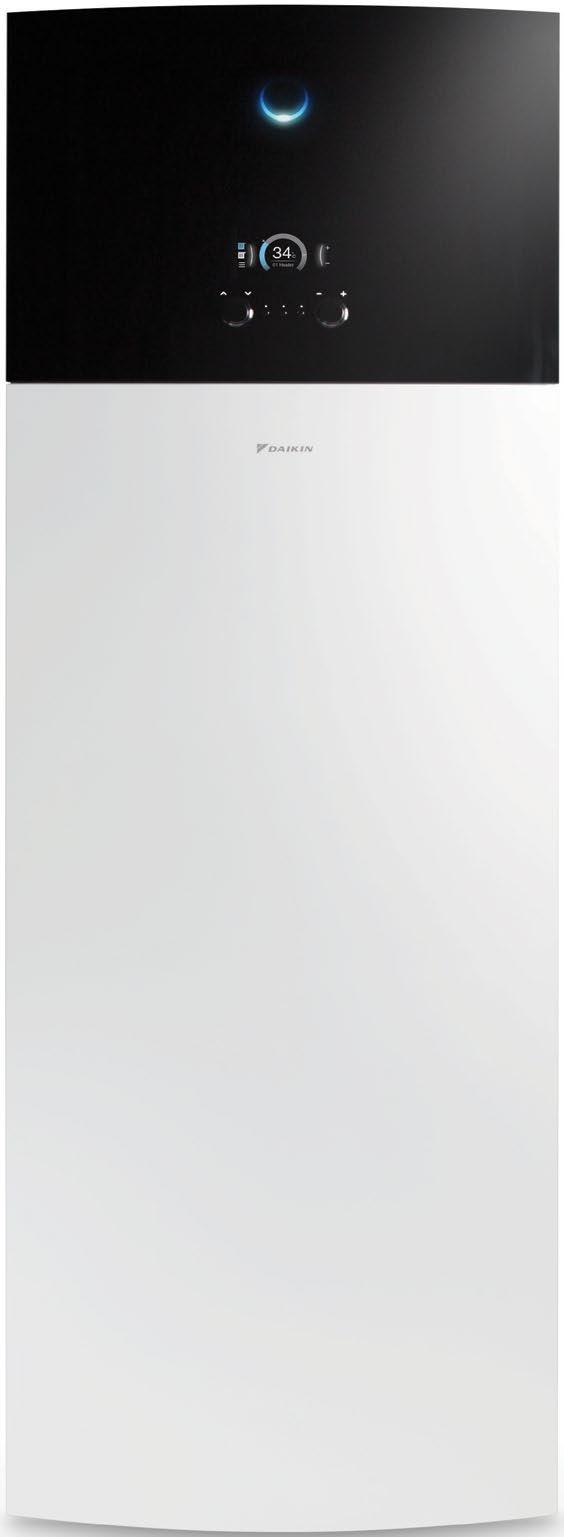
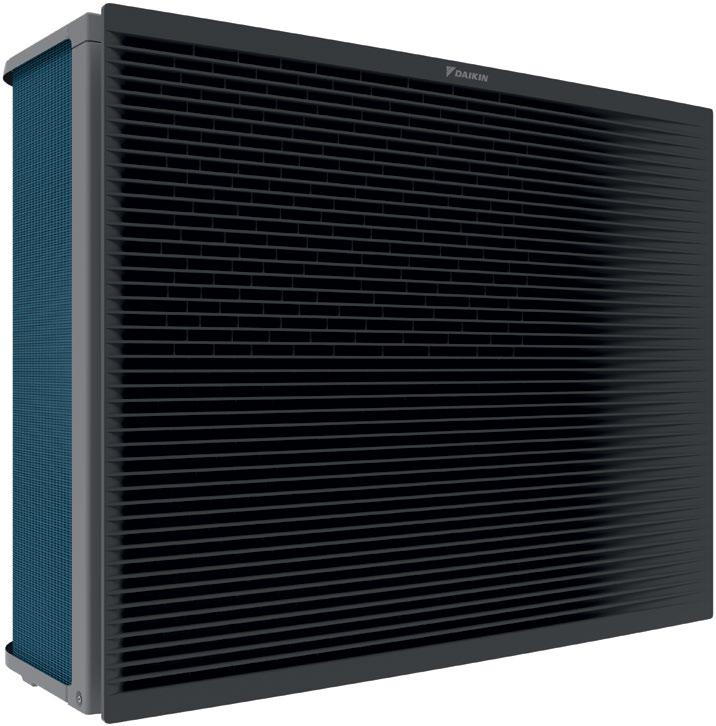
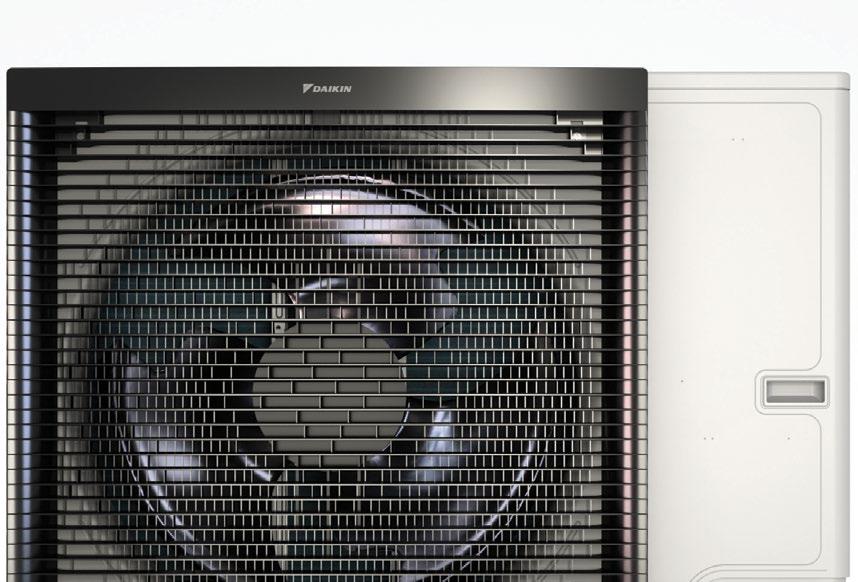


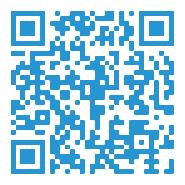