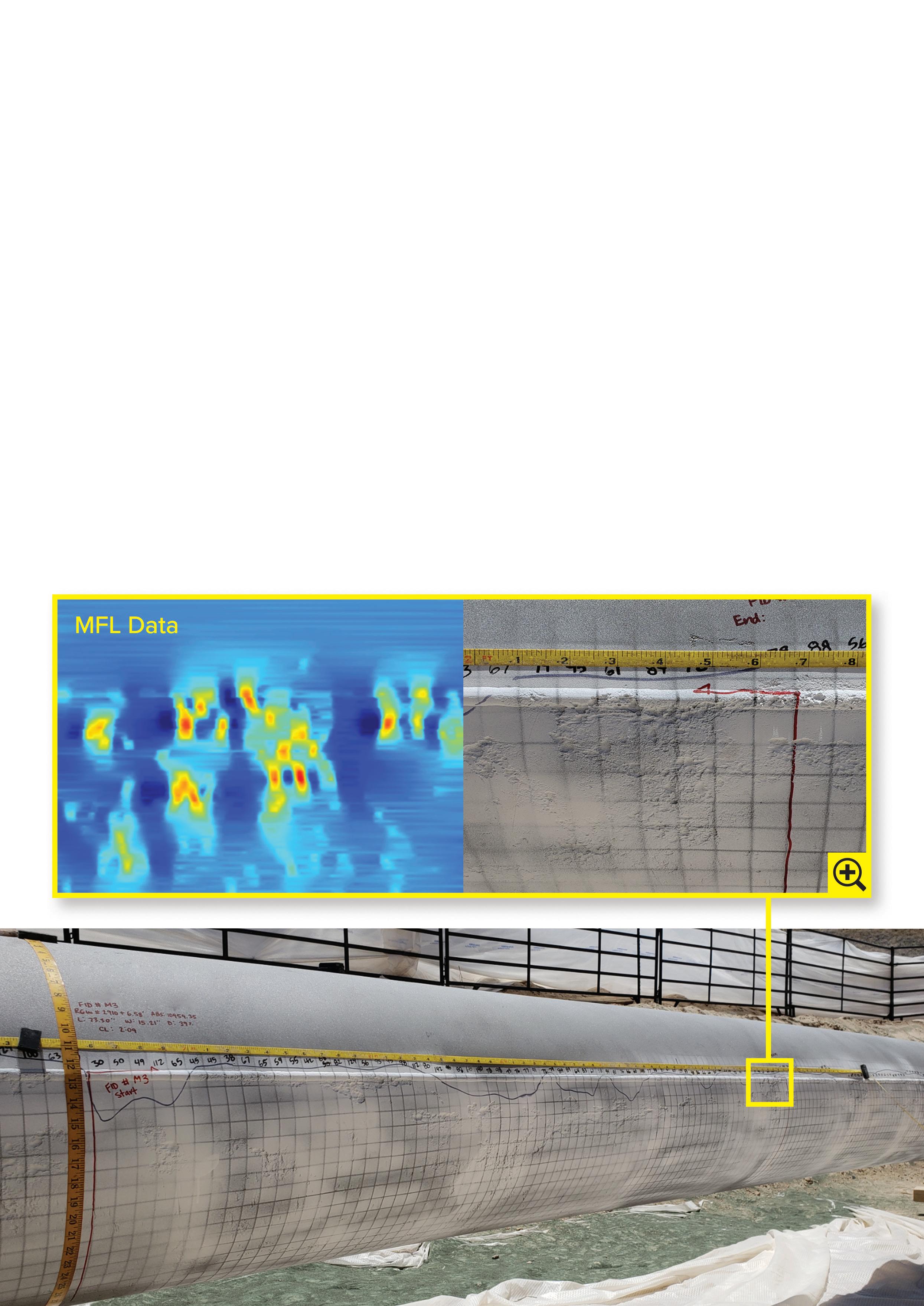
9 minute read
Embracing ultra-high-resolution
James Lavender, North America Business Development Manager, ENTEGRA, USA, discusses ultra-high-resolution ILI and the detection, identification and sizing of seam-weld corrosion.
As new technological frontiers have expanded, so has the technology within the pipeline industry. The phone you hold in your hand is more powerful than most computers of the early 2000s. The same is true for the technologies behind axial magnetic flux leakage (MFL) inline inspection (ILI) technology. Many misperceptions still exist about the ability of MFL to deliver – particularly with regard to seam detection as well as POD, POI and sizing of seam-weld corrosion – but in truth, the capabilities of MFL, and the ability to extract nuanced data from it, have grown exponentially beyond what was previously thought possible. This includes the all-important area of seam-weld assessment.
Driving this rapid improvement? The advent of ultrahigh-resolution (UHR) technologies backed by human-based insight, vision and analysis which are able to extract more
knowledge from the data itself. The ability of operators to see more and know more about their pipelines allows them to address these anomalies accordingly and keep their assets running safely.
The problem: seam-weld assessment As operators know, metal loss that interacts with a pipe’s long seam can pose imminent integrity threats. Especially considering that this is one of the most consequential areas of a pipe while remaining among the most difficult to accurately assess.
Differentiating metal loss as coincidental or preferential to the seam allows the pipeline operator to more efficiently prioritise their dig programme. Unfortunately, there is a myriad of variables such as different seam types, the age of the pipe, manufacturing methods, construction and welding processes, and other factors impacting an accurate assessment of this area.
With so many factors impacting an accurate, efficient MFL inspection of seam-welded pipe, it is easy to see why misperceptions of MFL performance remain, even to this day. Prior to UHR technology, axial MFL was limited to detection of volumetric anomalies with widths 10 mm or greater and, therefore, axial narrow irregularities required a much larger width for detection. The traditional train of thought was that the axial magnetic field had reached its technical limit of performance. It was once believed that sensor density and overall performance could not overcome the perceived shortcomings of axial MFL. Today’s axial UHR MFL has advanced well beyond the limitations encountered by past technologies. UHR is not only capable of detecting the seam, but goes beyond, identifying different types of seam welds. It also can detect, identify, and size anomalies on those welds to allow operators to address them accordingly and keep their assets running safely, smoothly and cost effectively. The solution: ultra-high-resolution There is not an industry standard for what constitutes UHR which has led to the term being overused and, in some applications, mis-used.
To begin with, true UHR MFL tools contain a higher number – and concentration – of primary axial sensors. True UHR technology also boasts a larger number of secondary sensors like ID/OD. Finally, the UHR MFL/Cal combo tool includes an array of caliper sensors so dense and sensitive, it can map the surface of the ID wall (Figure 1). This gives the UHR platform an incredible POD and POI on all aspects of anomalies detectable by MFL technologies – and some previously considered virtually impossible to detect.
State-of-the-art electronics are also distinguishing factors in determining whether or not a platform in question is truly UHR. True UHR collects data in a manner never before seen, delivering extremely high sampling rates and allowing for the collection of two to three times the amount of sampling data vs traditional Axial MFL.
Innovation in design and engineering is also a key differentiator. It’s not all sensors and electronics, but also the mechanics of the tools themselves. New-generation UHR tools not only have more dense sensor arrays and higher-speed data sampling, but are also shorter, lighter and more collapsible. Their design and fabrication physically reduce chattering in the line, which in return reduces the vibration and noise on the sensors, allowing for a smooth, comprehensive – and accurate – collection of UHR data.
Knowledge vs wisdom There is an old adage: “knowledge is knowing that a tomato is a fruit, but wisdom is knowing not to put tomato in a fruit salad.” So, too, with trying to understand the difference true UHR technology backed by human-experience based analysis can make to an ILI.
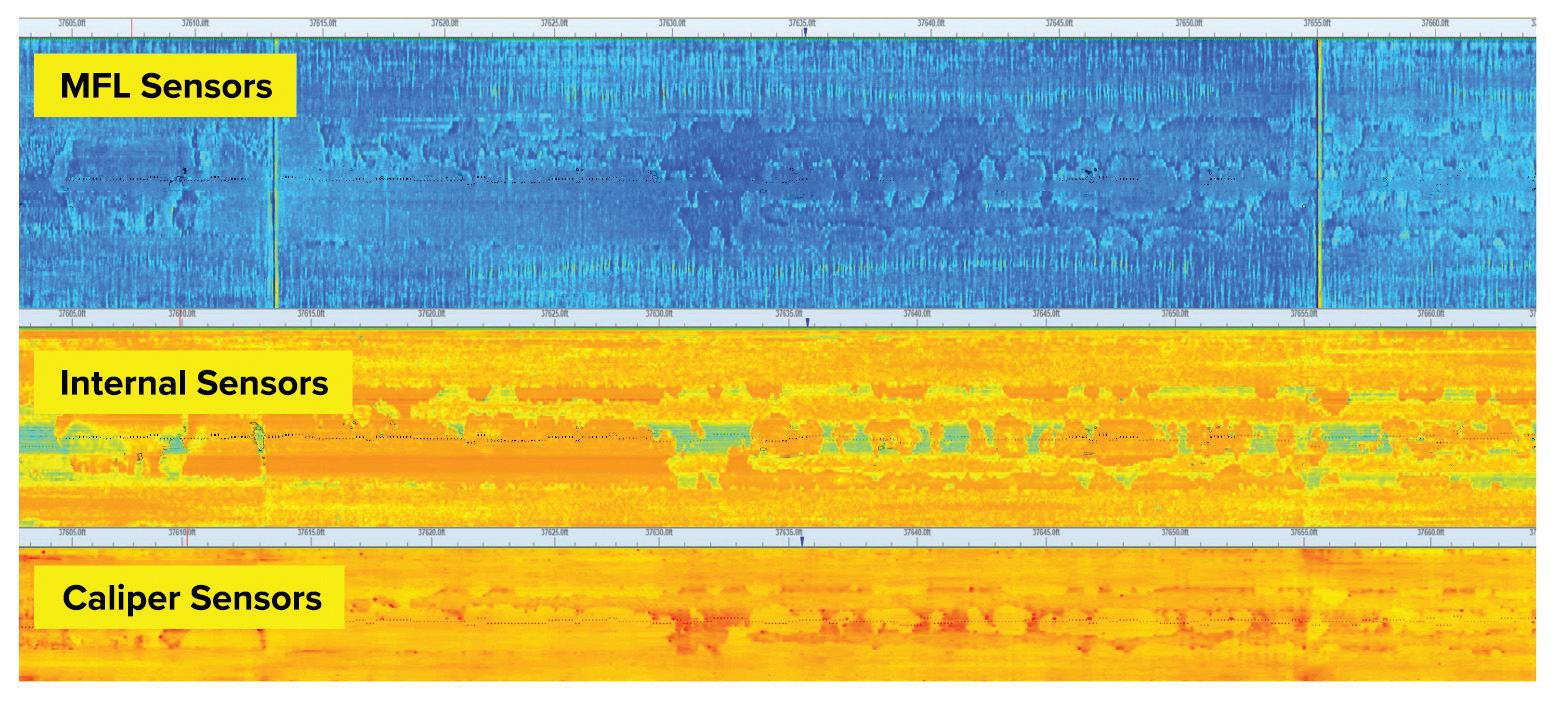
Figure 1. Correlating features across multiple datasets: note on this image how the primary and secondary sensors map the presence of scale in the line. You can clearly see how the UHR caliper sensors do a great job supporting and adding data to map the scale in the line.
An innovative, true UHR AMFL system delivers the knowledge, but that is just the beginning. A unique DA system is a must have. It provides nuanced assessments and recommendations – wisdom – based on that knowledge. That is why automation alone and black box DA assessment cannot replace human experience-based insight and deduction.
The proof is in performance The journey to seam assessment begins with the seam type. For most, seam assessment means to look for anomalies on or around the seam, but it is more than that. It’s not just about anomalies, but also about defining the type of seams in question. Knowing if you have an ERW, flash welded, DSAW and any other type of seam can provide valuable information about a pipeline operator’s assets. For example, seam types are often used in materials identification and records matching.
Another important aspect of seam assessment is the clock position within the pipe. A key part of construction, this must be offset to provide another layer of defence for the pipeline integrity, and it is also a common tool used to confirm location on dig verifications.
As shown in Figure 2, true axial UHR technology can easily detect both seam and clock position. Also, it can recognise the manufacturing differences between ERW and DSAW, where DSAW has enough nuance to be classified as such.
The UHR advantage Many MFL technologies have a much wider sensor spacing and struggle not only with seam detection but also with correctly identifying the location of ML on the seam and/or adjacent to it. A more-dense, UHR sensor array allows for a clear detection and distinction of the seam location and the anomalies that surround, cross or otherwise interact with the seam.
Combining this UHR technology with a human-experience based DA process, as mentioned, allows for the classification of these anomalies according to their true interaction – or lack thereof – with the seam. Similar to what an AI process or algorithm would do in this case, the first distinction would be ‘if’ yes/no and if yes, ‘how’.
Once the distinction has been made ‘if’ the anomaly indeed interacts with the seam or not, the next step is to define the ‘how’. For this step, the analyst must truly define and distinguish if these anomalies are metal loss crossing or interacting closely with the seam, or if it is traveling axially on the seam, and indeed preferential/selective metal loss.
While these classifications might not create a big change on the repair approach, they are a key factor for the future integrity programme of the pipeline and one that must be considered. This process requires a nuanced application of analysis
Figure 2. Detecting the seam across pipe types: while the difference between ERW, flash welded and DSAW can be subtle, UHR and expert data analysis can help to identify differences on seams such as those shown. Lap welded is a notable exception because of lack of volume in this manufacturing method.
Table 1. POD and POI for seam types Probability of detection (POD) Probability of identification (POI) Pipe type Yes No Maybe Yes No Maybe
LF ERW • • HR ERW • • Flash welded • • DSAW • • Spiral • • SSAW • • Lap welded • •
Key: Yes: POD > 90%
Maybe: 50% ≤ POD ≤ 90%
No: POD < 50% Yes: POI > 90%
Maybe: 50% ≤ POI ≤ 90%
No: POI < 50%
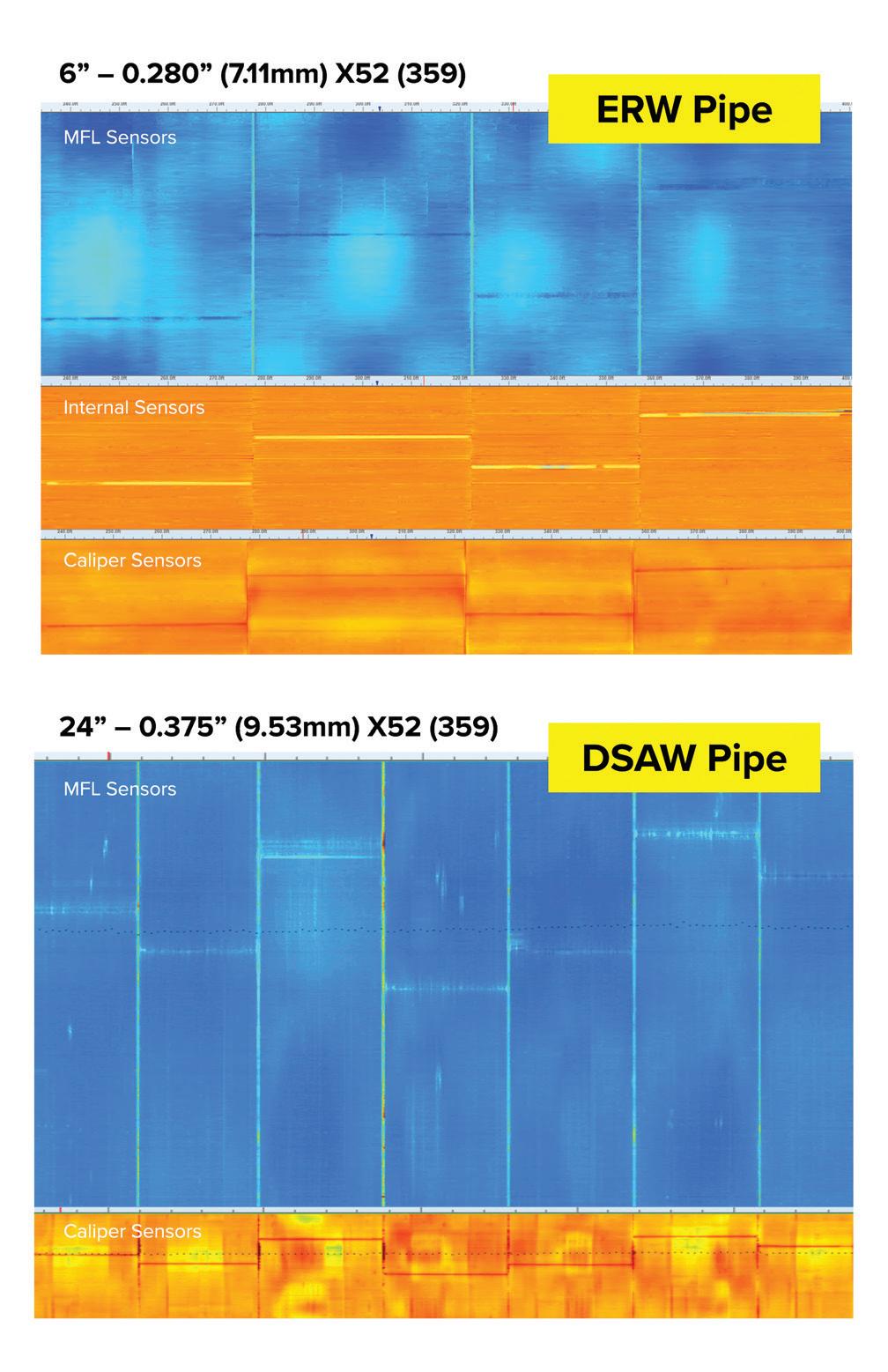
Table 2. POD and POI for anomalies on seam
Probability of detection (POD)
Feature type Yes POD > 90%
Corrosion
•
No POD < 50% Maybe
50% ≤ POD ≤ 90%
Metal loss
Corrosion cluster •
HIC
•
SCC
•
Arc burn
Grinding
Gouge/scratch
Axial crack
Circumferential crack Yes POI > 90% Probability of identification (POI)
No POI < 50% Maybe
50% ≤ POI ≤ 90%
Mill anomaly
Lamination
Void
Inclusion
Blister
Sliver
Lap
Spalling Manufacturing anomaly
Dent
•
Dent with metal loss •
Ovality
Buckle
Wrinkle
•
Ripple
•
Lack of fusion
Lack of penetration •
Seam weld crack
Slag (excess material) Spiral weld crack
Undercut Pipe deformations
Weld indication
that can only be achieved through humanexperience based DA. As shown in Figure 3, data confirms the characteristics that allow DA experts to classify metal loss on the seam as preferential where it is recognised as such.
As stated previously, the proof is in performance. Tables 1 and 2 show the current POD/POI for seam types and anomalies, which true UHR technology can detect and identify.
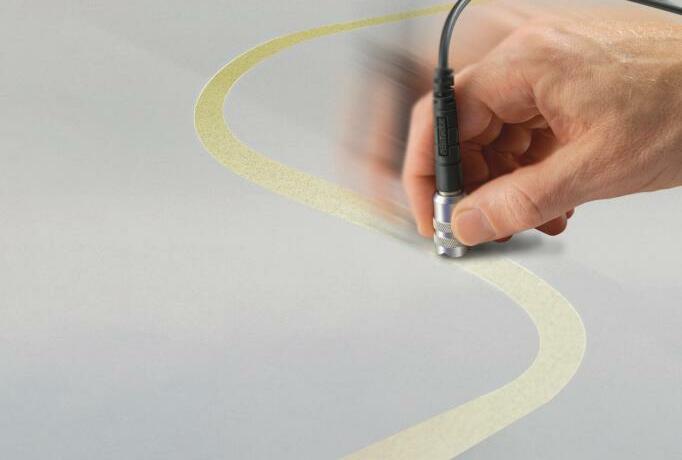

Conclusion UHR has paved the way for advancement in seam anomalies detection with the use of Axial MFL technology. What was once considered impossible – true pinhole detection, hard spots, material identification and more – is now all possible with a proven system combining the latest UHR technology with humanexperience based DA.
What started as a single channel technology with paper ribbons for data collection, evolved into multichannel and analogue data collection, the first combo tool, high-resolution MFL and now, into UHR MFL.
Today, we, as an industry, are busting paradigms on axial MFL technologies with true UHR and the systems it empowers. The only way to know the limit is to push to the limit. That’s what UHR is allowing operators to accomplish.
Applying the latest technology and human-based insight, vision and analysis to solve realworld-problems; putting that knowledge to work; rinsing and repeating: that is the ENTEGRA approach to UHR ILI and seam-weld assessment. It is something that has evolved – from a technical perspective, an engineering perspective, and a people perspective – since before ENTEGRA’s founding in 2016 by the same team of engineers, operators, analysts, and field professionals who first commercialised the MFL/Combo tool more than two decades ago.
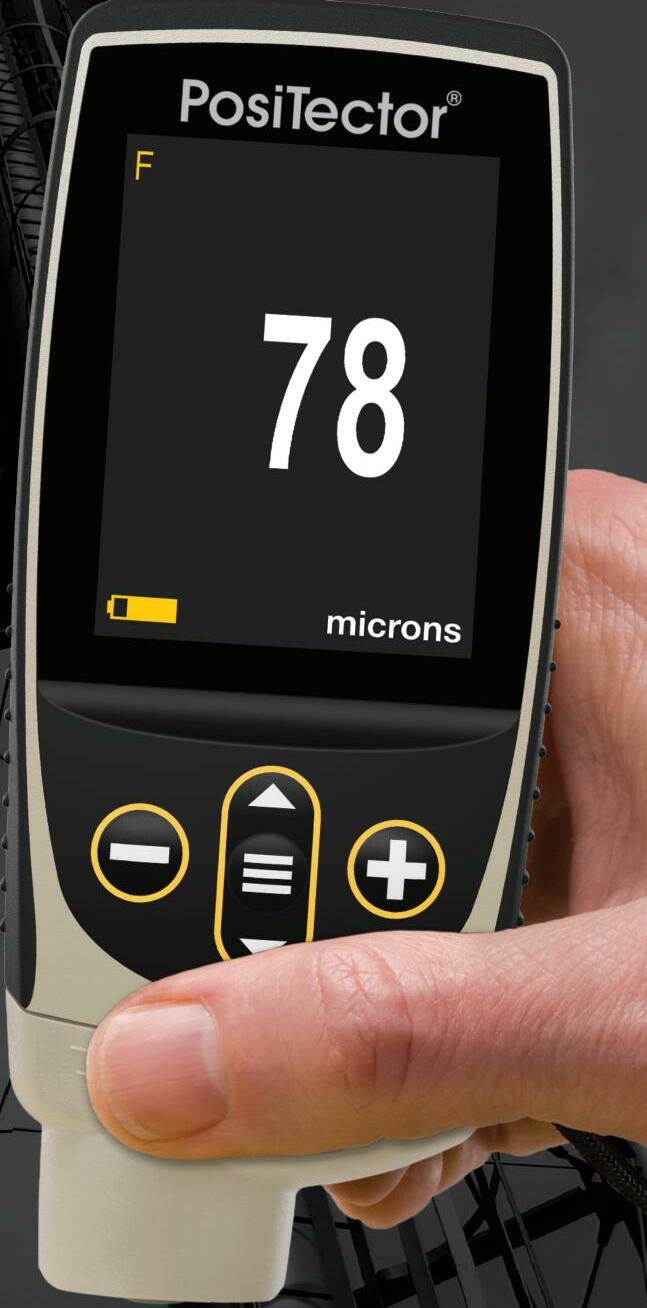
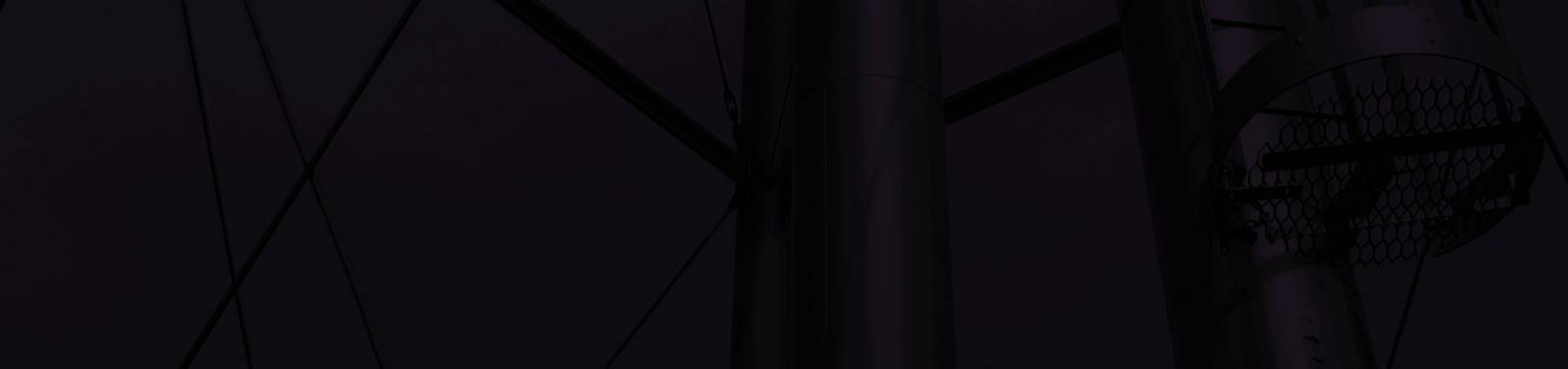
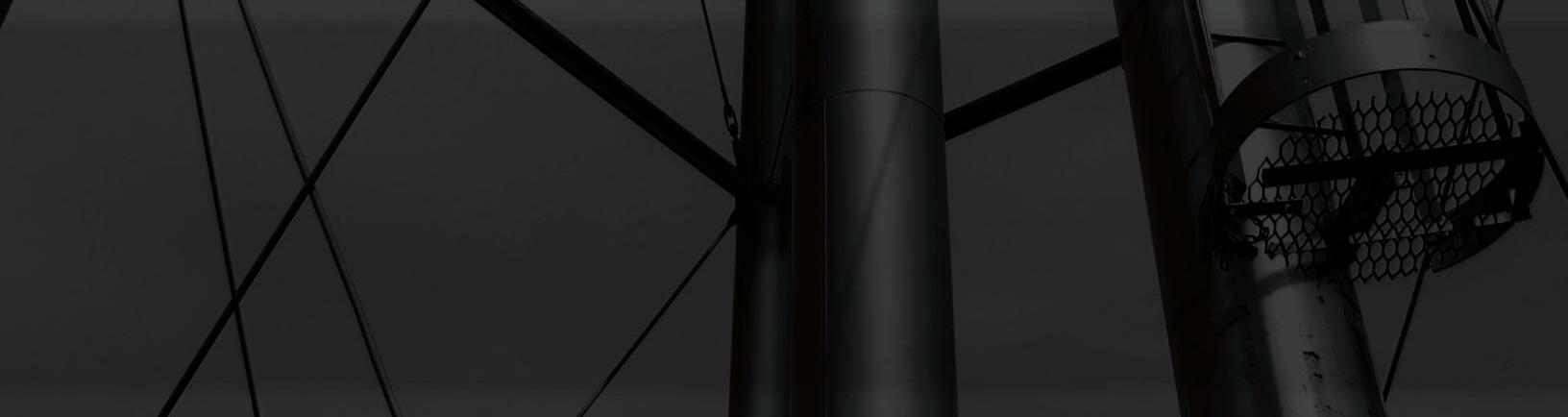
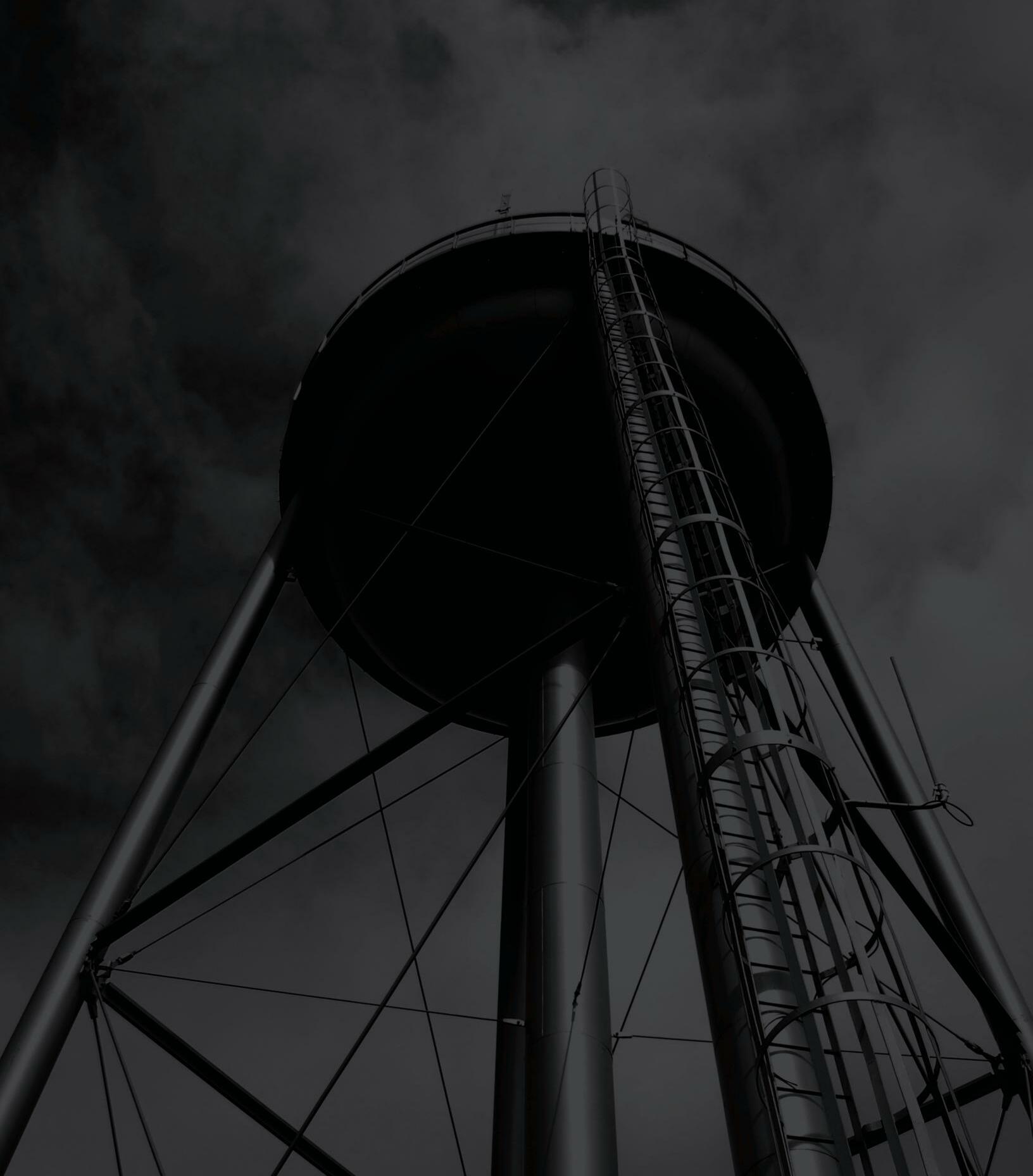
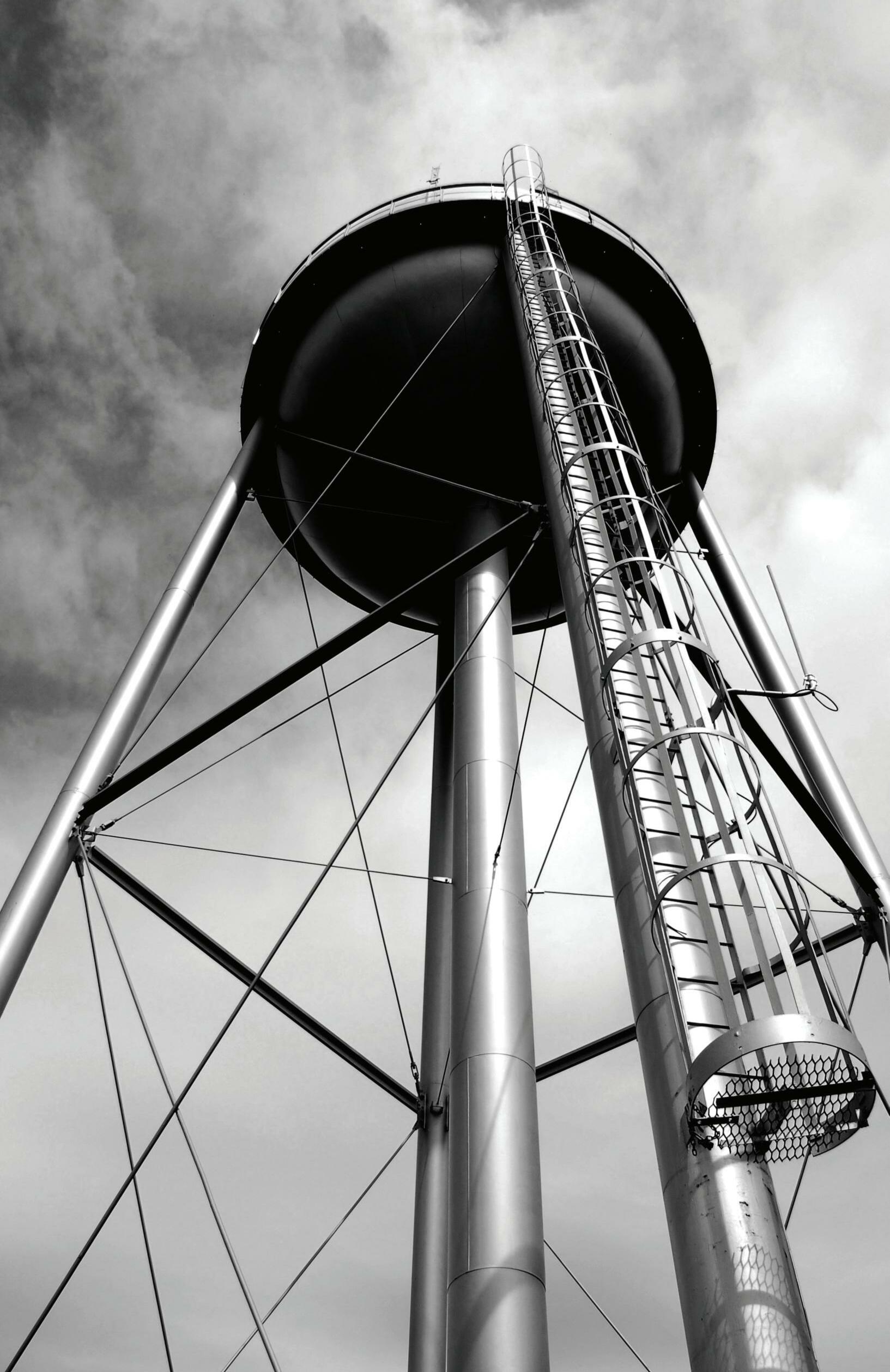
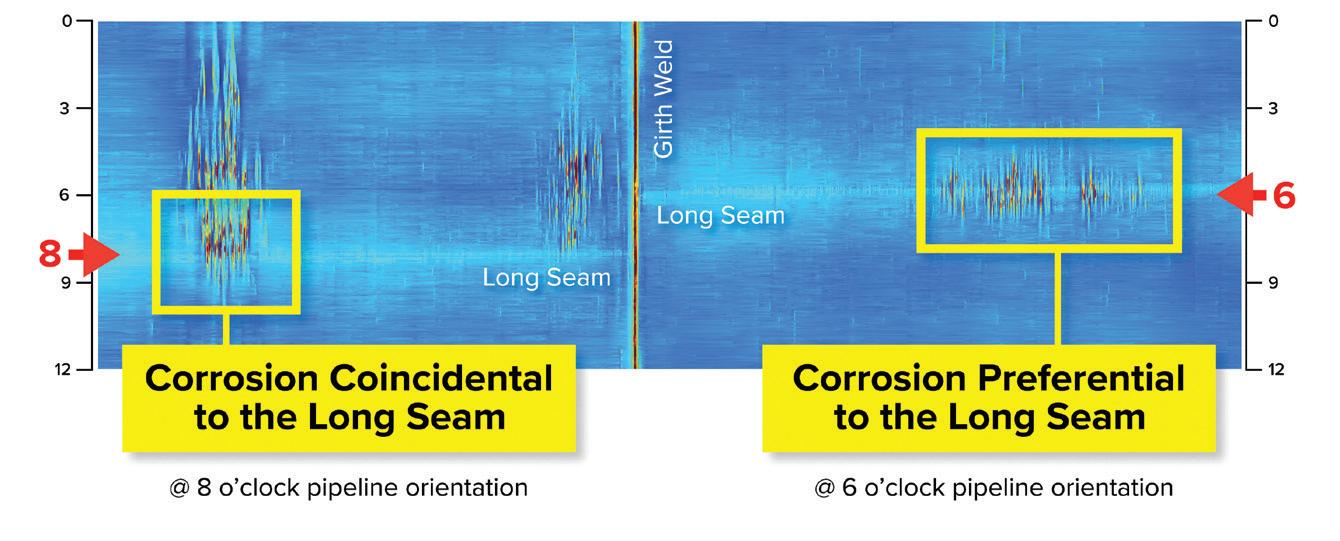
Figure 3. Classifying the orientation of metal loss on the long seam.
Coating Thickness Gauges
Fast and accurate measurement of paint and coating thickness over all metal substrates
n Ready to measure—no adjustment required for most applications n Fast measurement speed—60+ readings per minute n Memory mode—Store measurement data, view live statistics, and analyze live graphs n Included PosiSoft software—easily create professional inspection reports
PosiTector 6000 FS3
180+ readings per minute
Advanced models feature 3 Scan modes to increase measurement speed to 180+ readings per minute
PosiTector 6000 F1
Award Winning Interchangeability!
PosiTector gauge body accepts ALL coating thickness, surface profile, environmental, soluble salt, gloss, hardness, and ultrasonic wall thickness probes manufactured since 2012.