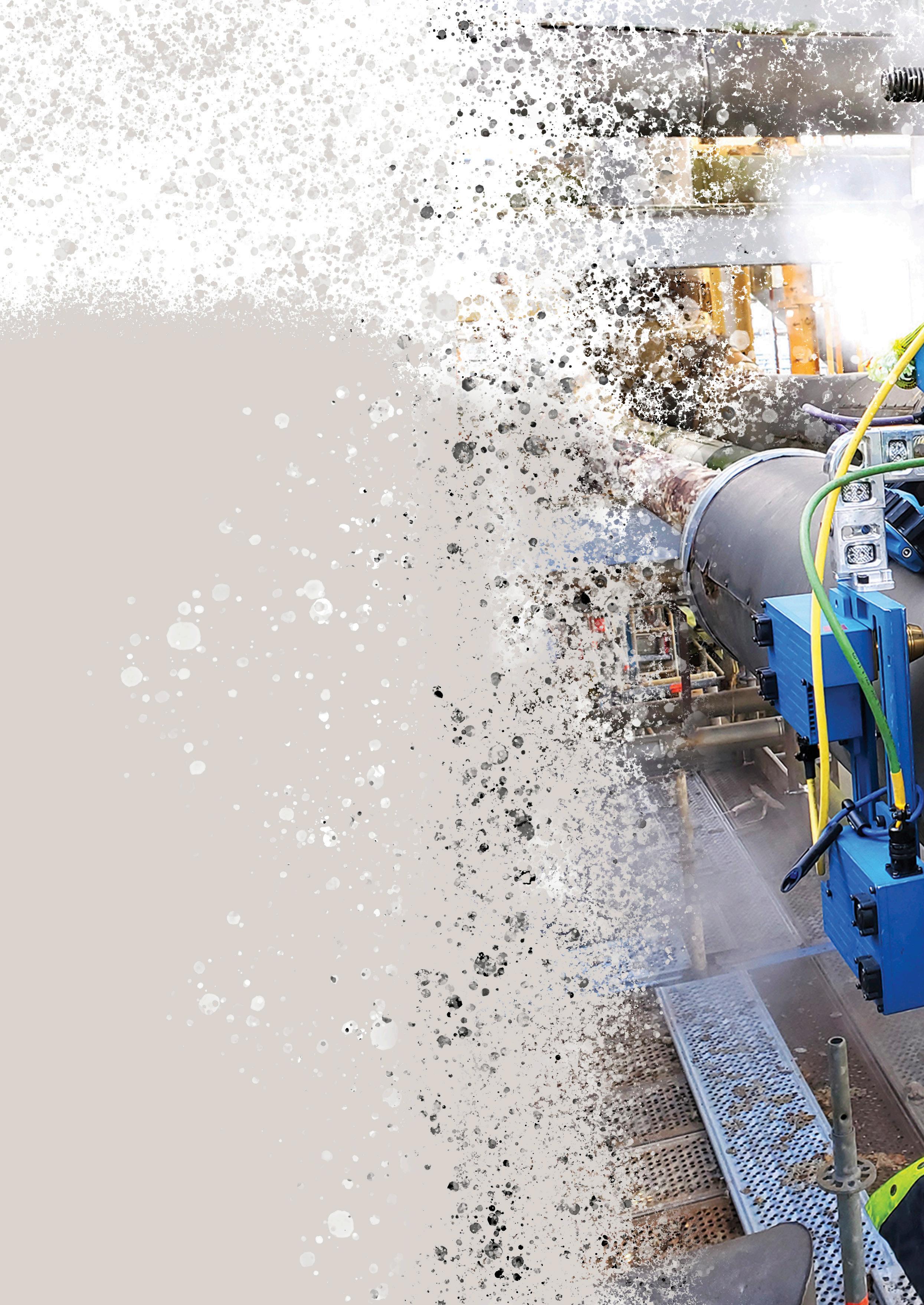
17 minute read
The ‘ART’ of pipeline inspection
John Musgrave and Ian Moreau, MISTRAS Group, USA, outline the benefits of using proven, innovative automated radiographic testing (ART) technology for pipeline and piping integrity screening.
valuating pipeline and piping integrity, particularly on insulated lines, can be a challenging endeavour. Despite the many traditional and advanced techniques and technologies available to integrity and inspection managers, each method typically comes with a downside in the form of high costs, extended time requirements, operational impacts, requirements to strip insulation, and more.
Inline inspection (ILI) is typically considered the gold standard for identifying corrosion, but this time, cost, and labour-intensive process comes with a major opportunity cost because it requires pipelines to shut down operations during the inspection, in addition to oftentimes rigorous maintenance requirements to prepare the line for the ILI tool run.
Advancements in automated radiographic testing (ART) technology – developed by MISTRAS Group, a One Source provider of asset protection
Figure 1. MISTRAS’ ART crawler services offer single-view and multi-view radiographic scans, with the ability to simultaneously analyse the top, bottom, and sides of piping with a two-axis robotic arm to autonomously drive over supports without the need for multiple set-ups or systems.
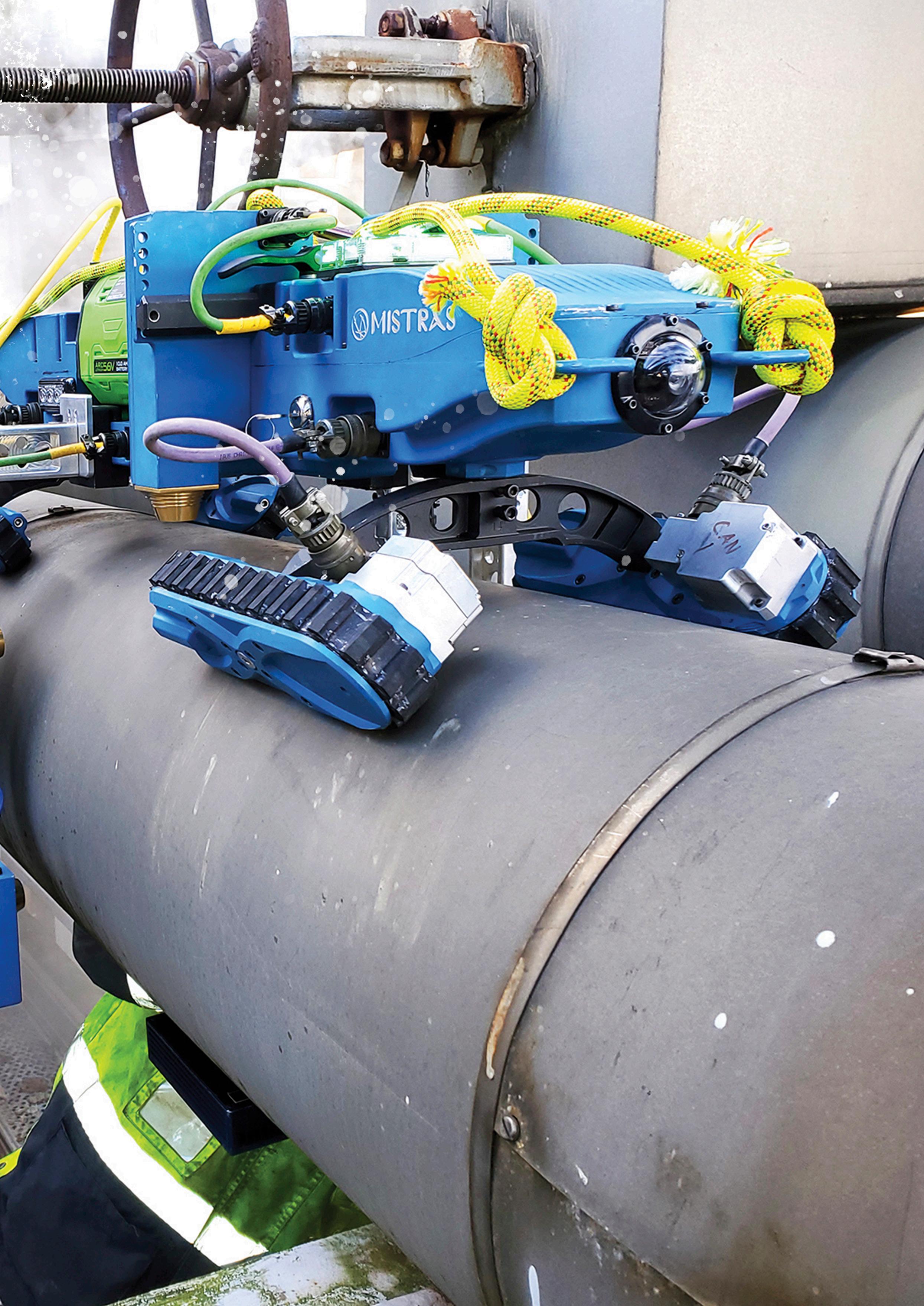
solutions – are creating a viable alternative to ILI that enables high-quality, rapid inspections with no need to strip insulation or take lines out of service.
This article looks at the variety of inspection options available to evaluate pipeline and piping integrity, and highlights ART’s accuracy, speed, and detection capabilities that make it a viable, effective alternative in lieu of ILI.
Common issues with ILI ILI tools require a handful of specific conditions to make a pipeline viable for pigging. Debris, rust, and other buildup can accumulate on the insides of a line, potentially blocking tools from moving through the line altogether or causing damage to the highly-expensive pigging technology, so lines must be properly cleaned and maintained prior to executing an ILI.
During the tool run itself, production typically must be shut down to enable the tool to flow at its ideal speed to collect accurate, high-quality data. In addition, the construction features of a line can also prohibit the use of ILI tools. ILI tools require launchers and receivers to allow the tool to be inserted and removed from the line, and the size of the pig limits the bend radii that it can travel around. Lines without launching and receiving facilities, or those with sharp, small-radii bends can sometimes be modified, but this can come at a prohibitive cost that makes ILI an impractical option.
Alternatives to ILI Outside of ILI, there are a handful of accepted alternatives that come with their own sets of pros and cons, with some serving as more viable options than others for reasons related to costs, operational impacts, and more.
Insulation and/or coating removal A common, tried-and-tested method for determining CUI involves stripping insulation and/or removing coating and conducting visual, 3D laser mapping, and ultrasonic testing (UT). While this helps to ensure a high rate of accuracy and defect identification, it comes at great expense in terms of resources and opportunity costs. Additionally, in areas of above ground insulated pipelines, such activities can pose process safety issues with lines freezing when large sections of insulation are removed.
Since there is not a fool proof visual method to determine where CUI may be present, to get to 100% assurance this process must be executed throughout the full length of the line, which could mean stripping a cost-prohibitive amount of pipeline, even when the majority inevitably turns out to be corrosion-free. This lengthy process typically involves multiple contractors, often requiring different crews to assist with removing and reinstalling insulation and/or coating, conducting NDT inspections, and executing the necessary maintenance and repairs to remedy the discovered damages. If the piping network is at height, there are also the costs, time, and resources dedicated to constructing and deconstructing scaffolding. Lastly, removing and reinstalling insulation introduces the possibility of future moisture egress points, potentially creating the same problem that this method is designed to detect.
Manual radiographic techniques Another alternative is conducting manual radiographic testing (RT) – a reliable and proven technique able to identify flaws such as corrosion and cracking with high accuracy. However, while it’s effective for limited spot inspections at highlytargeted locations, traditional RT is too cumbersome a process for large-scale screening.
Compared to other NDT screening methods, manual RT requires relatively expensive equipment and a far slower inspection process. In addition, two-sided access to the test object is required, making it difficult to test some lines properly. Traditional RT also entails potential safety risks via radiation exposure, and thus should be used as sparingly as possible.
Overall, though RT is a proven technique that’s been used in the oil and gas industry for decades, advances in modern technology have moved beyond its analogue foundations toward higher-quality and more cost and time-effective automated solutions.
ART screening A more recent alternative to ILI is ART. Compared with other common inspection techniques, ART enables lines to stay in service during inspections, with the ability to gather highquality, DICONDE-compliant data with product still flowing through the lines, and with no need to strip insulation or remove coating. Various iterations of ART technology from MISTRAS Group can screen for CUI at four locations of the pipe (top, bottom, and sides), scan 360˚ for internal and external metal loss, and identify internal metal loss in the bottom quadrant of the pipe. All digital image scans are recorded and saved to provide a permanent record of the inspection data, and to facilitate future inspection comparisons or correlation with past ILI runs.
Benefits of ART compared to ILI A direct comparison of ART to ILI in a few key areas showcases ART’s efficacy as a corrosion screening tool.
Detectability and accuracy Regardless of the logistical benefits that ART offers as compared to ILI, they would be rendered moot if ART could not perform the actual inspection as effectively. However, ART proves to be a viable alternative in this area. Advanced ART systems can detect defects as small as 1 mm in dia. for internal corrosion. ART is on par with magnetic flux leakage (MFL) tool accuracy at +/- 10% for pit depth, and within +/- 1% for defect length and width accuracy.
ART is an effective screening tool in lieu of ILI for any aboveground piping when inspecting for corrosion under insulation, CO2 corrosion, and microbiologically-influenced corrosion (MIC). Particularly for CUI, ART should be considered the preferred method, as it is more sensitive to light external corrosion and can detect wet insulation even before corrosion forms.
Production impact Among the most critical benefits that ART offers compared to ILI is that ART can be utilised with product still flowing through piping and pipelines, enabling operations to continue as usual while inspections are being conducted. Whereas ILI oftentimes requires extensive internal cleaning before executing an ILI run, ART can be executed without dedicating time and cost resources to pre-inspection preparation. De-pressurising a line to prepare it for ILI also introduces process safety hazards, which should be avoided wherever possible. While the costs to an owner-operator to perform the actual ILI and ART inspections are relatively similar, the requirements to run an ILI tool to halt production, spend resources on preparatory measures, and potentially increase process safety risks make ART a far more cost-effective option.
Rapid deployment ILI runs are often planned months in advance because they are labour-intensive, have significant impacts on the other operating crews in the area, and require the ILI run to be the primary focus on large swaths of piping. Conversely, ART inspections can be mobilised in essentially the time it takes the service technicians to arrive onsite, making it an ideal option to confirm suspected leaks before they create more significant problems. In addition, because there is little-to-no asset preparation required and a minimal impact on simultaneous operations (SIMOPS), ART enables rapid field implementation from request to onsite execution.
Targeted approach Because of the high speed at which ART collects and processes data (often exceeding 1000 m/d in an upstream environment), an ART-focused scheme can screen 100% of a pipe in the time it typically takes to inspect 5 - 10% using manual methods. For this reason, ART is particularly impactful as a large-scale screening tool, helping integrity managers identify which pipe sections require further investigation. To fully inspect a line may far exceed the inspection and maintenance budget, and to select a sampling of the line may result in missed detection opportunities and eventual loss of containment. ART enables integrity and inspection personnel to pinpoint the areas of a line that require remediation while leaving insulation on noncorroded pipe sections intact.
Field-proven results supporting ART’s efficacy Below, a series of brief field studies demonstrate the efficacy of ART as a screening tool for piping and pipeline internal and external corrosion: ) An ART inspection was conducted with a focus on identifying external corrosion under insulation on a 34 km stretch of piping with a diameter ranging from 4 - 10 in.
The inspection targeted the bottom region of the piping.
In total, 103 m of CUI and 2.8 km of moisture saturation were detected. The ART screening determined that 31 km of the piping was free from CUI and moisture saturation.
) An ART inspection was conducted on 3615 m of 18 in. diameter emulsion piping. Corrosion calls included 37 at ≤20%, 12 at 21 - 30%, and 2 at 40%.
) An ART inspection was conducted with a focus on internal corrosion on an offline pipe to assess returning the pipe to service. 159 m of 8 in. diameter piping were scanned. 142 m of corrosion locations and two pipe ruptures were found for a corrosion find rate of 89%.
The operator terminated the remaining inspections due to the find rate and put the line in the replacement schedule.
) An ART inspection was conducted on 954 m of 20 in. diameter 3 phase piping. Corrosion calls included 120 at ≤20%, and 8 at 21 - 30%.
Final thoughts The robust detection and speed capabilities, and increased safety of ART make it preferable to other NDT technologies for conducting integrity surveys on insulated and non-insulated aboveground pipelines. Compared to methods such as ILI and insulation/ coating stripping, ART in most cases performs at least as accurately and with far fewer resources required for noninspection related tasks. Particularly useful as a large-scale screening tool to target piping/pipeline integrity and inspection programmes, ART is a viable, accurate, and cost-effective technology to help maximise asset uptime and integrity.
Figure 2. ART inspections services help detect internal corrosion, pitting, and corrosion under insulation (CUI) in upstream, midstream, and downstream aboveground piping and pipelines, even with product flowing through the lines.
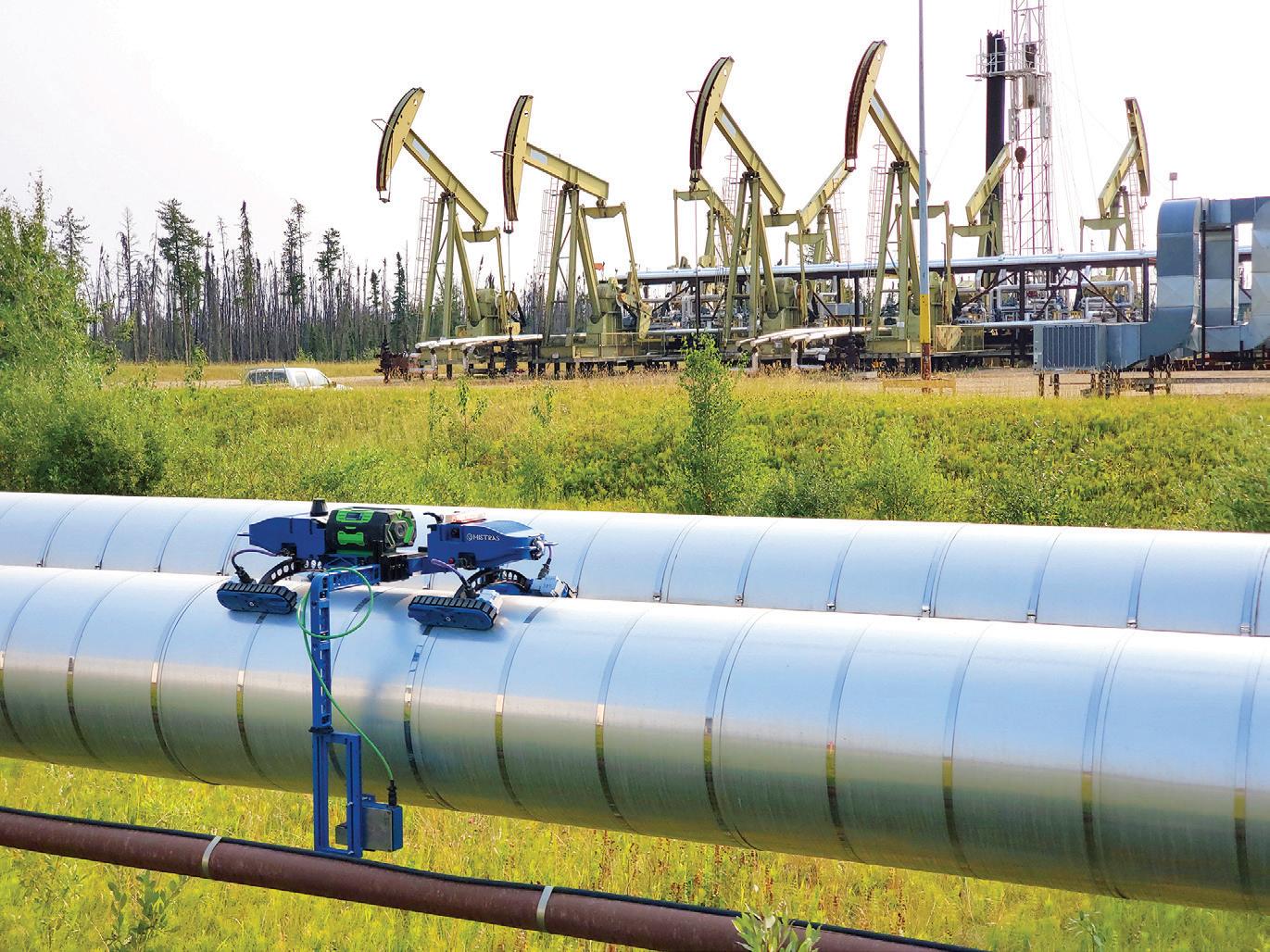
World Pipelines asks four ROSEN experts about pipeline pigging. PIGGING
ABCO ENTERS, Sales Manager, Netherlands
After studying at the University of Technology in Delft, Netherlands (Physics) Abco Enters has been in technical sales since 1990 for service companies in Non Destructive Testing, both for technologies and solutions. Contributing to prevent pollution to the (sea) environment from storage tanks, pipelines, wells and other physical assets. He has held varying roles over the years in different organisations in R&D, operations, sales, business development, general management and board of director level. Since 2021, he has been a Sales Manager for ROSEN Europe BV in the Challenging Pipeline Division.
After studying at the University of Hannover, Germany, Ulrich Schneider has spent over 40 years in operation and inspection of oil, gas and pipelines. At ROSEN, his focus is on business development and marketing for the dedicated Challenging Pipeline Division, specifically tethered inspection solutions. He has presented many papers at conferences worldwide in the last 30 years.
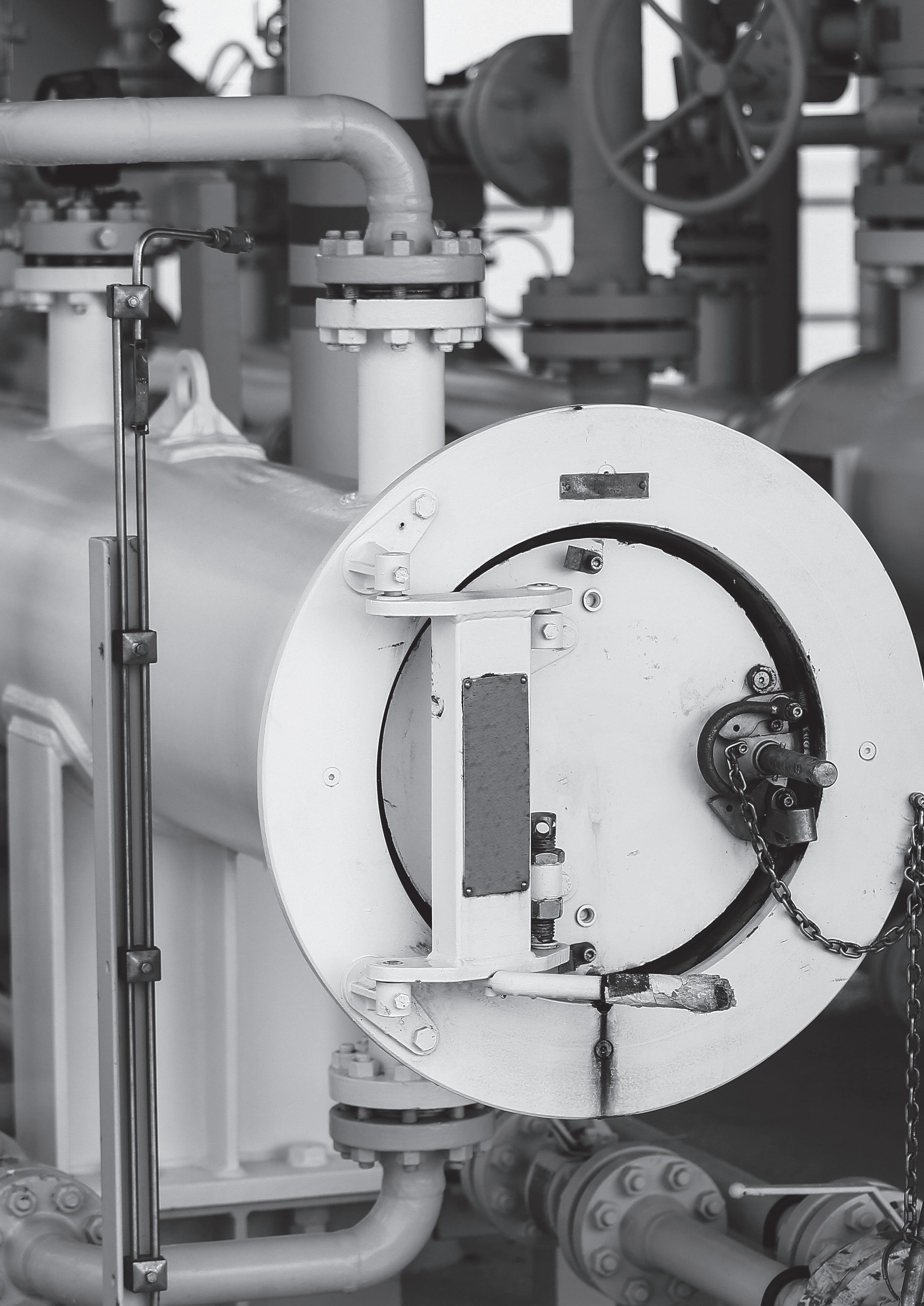
Chris Holliday holds the position of Technical Lead for Integrity Services at ROSEN Canada. Chris is a registered Professional Engineer in both Alberta and Saskatchewan. He moved to Calgary from the UK, where he is a Chartered Engineer with the Institute of Mechanical Engineers. Chris graduated with 1st class honors in Mechanical Engineering from Northumbria University followed by a Post Graduate Certificate in Pipeline Engineering from Newcastle University. Chris has spent the start of his career working for ROSEN as a pipeline integrity engineer in Newcastle, conducting engineering assessments, corrosion growth, dent strain & fatigue and crack assessments. During that time, Chris has presented a number of technical papers with an emphasis on the assessment of pipeline deformations reported by ILI and pipeline structural analysis in landslide areas. Chris is a sessional instructor at the University of Calgary on the Pipeline Engineer Graduate Certificate Program and he volunteers on the Young Pipeliners Association of Canada Central Executive Committee.
Corey Richards holds the role of Business Line Manager for ROSEN’s Field Project and Services and Challenging Pipeline Diagnostics Divisions for the Canadian region. Since 2014, his area of focus has been creating solutions for unpiggable pipelines in the Canadian, Oceania and Asia Pacific regions. He is located in Calgary after having spent five years in Lingen, Germany where he was based at ROSEN’s Technology and Research Centre. In his 13+ years with ROSEN, Corey has expanded his knowledge through various roles including: time in field operations and technical sales, before transitioning into his current position.
Neil Gallon is a Principal Materials and Welding Engineer working for the ROSEN Integrity Services division in Newcastle upon Tyne, UK. He holds a Masters degree from the University of Cambridge and is a Chartered Engineer, a professional member of the Institute of Materials, Minerals and Mining and an International/European Welding Engineer. He has over 20 years of experience in manufacturing and consultancy, including working for companies such as Tata Steel and GE. His current interests include the impact of gaseous hydrogen on materials and welds.
Discuss a recently carried out pipeline pigging/inspection project.
ABCO ENTERS, Sales Manager ULRICH SCHNEIDER, Business
Development Manager As we all know, not every pipeline is meant to be ‘pigged’; pipelines are frequently classified as ‘unpiggable’ due to their operating conditions, geometry, accessibility or a combination of these. For ‘unpiggable’ pipelines, ROSEN has often created tailored solutions to allow for inline inspection, as was the case for the inspection of a 10 in. offshore oil riser recently inspected by ROSEN Norway. For this project, the inspection unit – launched and received from a single point – had to navigate a total accumulated bend angle of 1188° (17 bends) while successfully inspecting the pipeline for wall thickness and cracks. ROSEN chose a tethered self-propelled bidirectional ultrasonic tool able to perform geometry, wall thickness and crack inspections in a single run. The tool was to be launched and received from a trap installed on the platform. After extensive testing and development, the necessary equipment (including a winch with a 1.2 km tether, with a breaking load of 2000 kg and a normal pulling force of 1000 kg) was brought to the site. Two electrical crawlers were run in a tandem configuration to ensure the tool could negotiate difficult installations, such as slippery valves, Ts, etc. An ultrasonic sensor carrier with 160 UT probes was used alongside two odometers measuring the distance travelled and the tool velocity. The second tool was a purpose-made scanner equipped with TOFD probes. Straight-beam pulse echo (PE) probes were installed to position the scanner correctly against girth welds to be assessed. When deploying TOFD sensors at corroded features in parent material, the tethered ultrasonic measurement tool position is used to determine the correct positioning of the TOFD tool. After presenting a site report, the equipment and the team were demobilised, and the detailed analysis was started from home. The data evaluation team now had four data sets for wall thickness (two forward and two return runs) and two data sets from the TOFD crack analysis. The full length and circumference of the targeted pipe section was successfully inspected, and the collected data was of very good quality, meeting the required specifications.

Figure 1. Extensive testing is required for any custom ILI solution. ROSEN conducted testing for this solution at the Bergen Norway location.
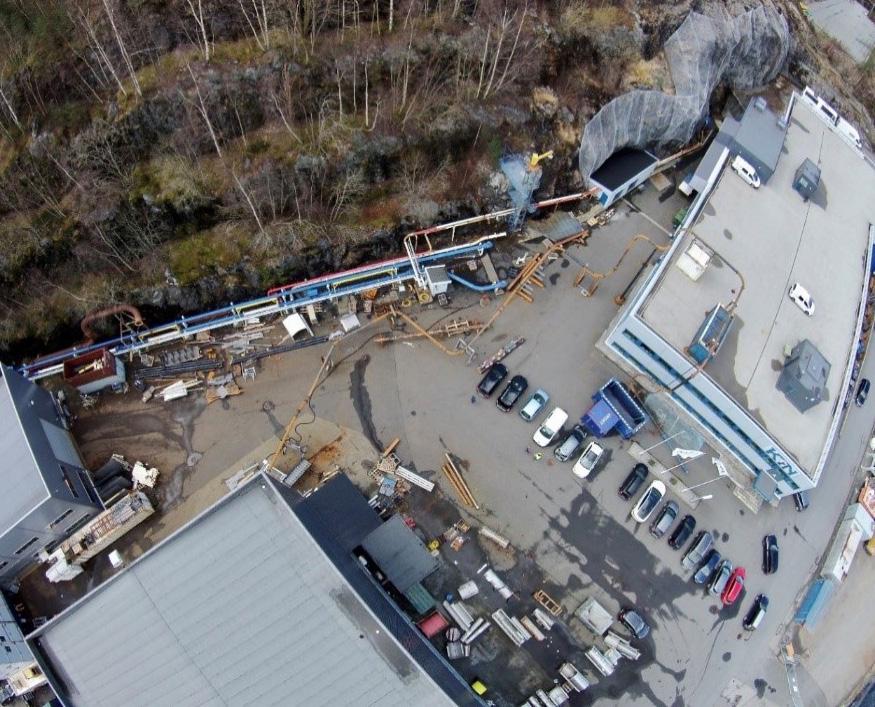
How do you predict, or assess, pipeline failure? How do your tools help manage risk?
CHRIS HOLLIDAY, Integrity Engineering Lead A variety of methods as well as technologies are available to predict, or assess, pipeline failure. Prior to inline inspection, risk assessments of entire pipeline networks are possible; these can be used to segment individual pipelines into low, medium or high risk. Various factors are considered when making this categorisation, including the variety of threat and the inspection history. Although this is a higher-level assessment, it can often lead to smarter decision-making for future integrity management efforts.
Oftentimes that next step includes data collection. ROSEN’s inline inspection (ILI) tools are equipped with a variety of sensor technologies, each able to gather highresolution data regarding the condition of the pipeline. Of course, once an ILI has been completed, the valuable data gained is translated into a variety of assessments, which cover risk management services, risk-based inspection planning, process safety management, safety and reliability services, and additional asset integrity services.
A more recent approach to predicting pipeline failure includes ROSEN’s Integrity Analytics Initiative. This method uses a large repository of historical ILI results (feature listings) along with corresponding pipeline information called the Integrity Data Warehouse (IDW). As of now, the IDW holds information about more than 12 000 pipelines worldwide, and it is growing rapidly. This data – paired with relevant geo-enriched, socioeconomic or operational metadata – provides a clear foundation for scalable AI solutions. The approach becomes particularly relevant for uninspected pipelines. By learning from the condition of similar

Figure 2. Geohazards can change the shape of a pipeline and may create local features, such as dents, buckles, ovalities and bending, all with potentially detrimental effects on the pipeline’s integrity.
Figure 3. A phased approach allows for a feasible hydrogen conversion strategy.
pipelines that have been inspected in the past, we can begin to understand the different variables that predict pipeline threats and develop models to predict the condition of uninspected pipelines. We can observe trends in inspected pipelines and apply what we have learned to uninspected pipelines. ROSEN has been advancing this initiative, and partnering with operators, to explore many applications of the IDW, such as corrosion prediction, external interference hit rate, crack prediction, condition metrics benchmarking and ranking, and corrosion growth rate prediction for uninspected pipelines. Future areas of interest include offshore asset condition, pipeline movement, bending strain and enhanced ILI anomaly classification.
Which types of pigging services are in increasing demand?
COREY RICHARDS, Business
Development Manager Depending on the market, many operators are now in second or third-round inspection intervals, meaning they have established integrity programmes to address their most critical threats. They therefore are able to focus on more than the standard assessments and address more exotic features, such as selective seam weld corrosion, coincident anomalies (such
as dents with gouge/metal loss), material properties and girth weld assessments. Additionally – and, driven by the PHMSA gas rule, particularly in the US – material verification assessments are becoming more prevalent. Pigging services around geohazards are in increasing demand due to awareness of associated failures. Our expertise when it comes to slope stability issues and the assessment of related data is getting more and more accurate, allowing for better risk mitigation strategies.
Can you talk about pigging other types of pipelines, such as hydrogen or mixed-product lines?

NEIL GALLON, Principal Materials and Welding Engineer Pipelines transporting hydrogen are still pipelines, so all the threats operators face with natural gas lines are still relevant. However, there are certain characteristics of hydrogen that may increase the risk of some threats more than others. In general terms, hydrogen has little effect on increasing the risk of metal loss, a large effect on cracking, a very large effect on fatigue, and an unknown effect on dents and gauges. In terms of cracking and fatigue, three factors to watch for are 1) a decrease in material toughness; 2) a decrease in ductility; and, therefore, the inevitable 3) increase in the fatigue crack growth rate.
ROSEN has successfully inspected in hydrogen and has a comprehensive approach to both the integrity management and the inspection of hydrogen and blended pipelines.
Additionally, ROSEN has developed a phased framework for safely converting existing infrastructure to hydrogen pipelines. The framework is based on a structured approach, which makes the process digestible and creates a step-by-step guide. Figure 3 shows what these phases include.
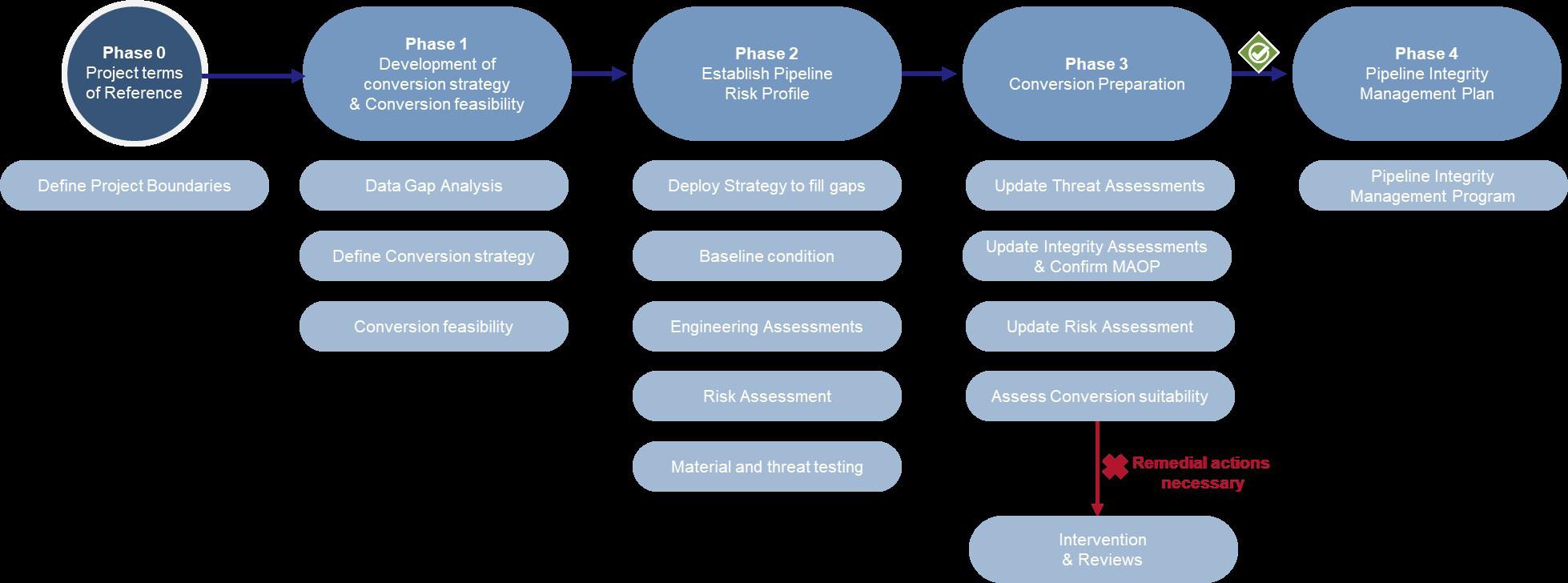