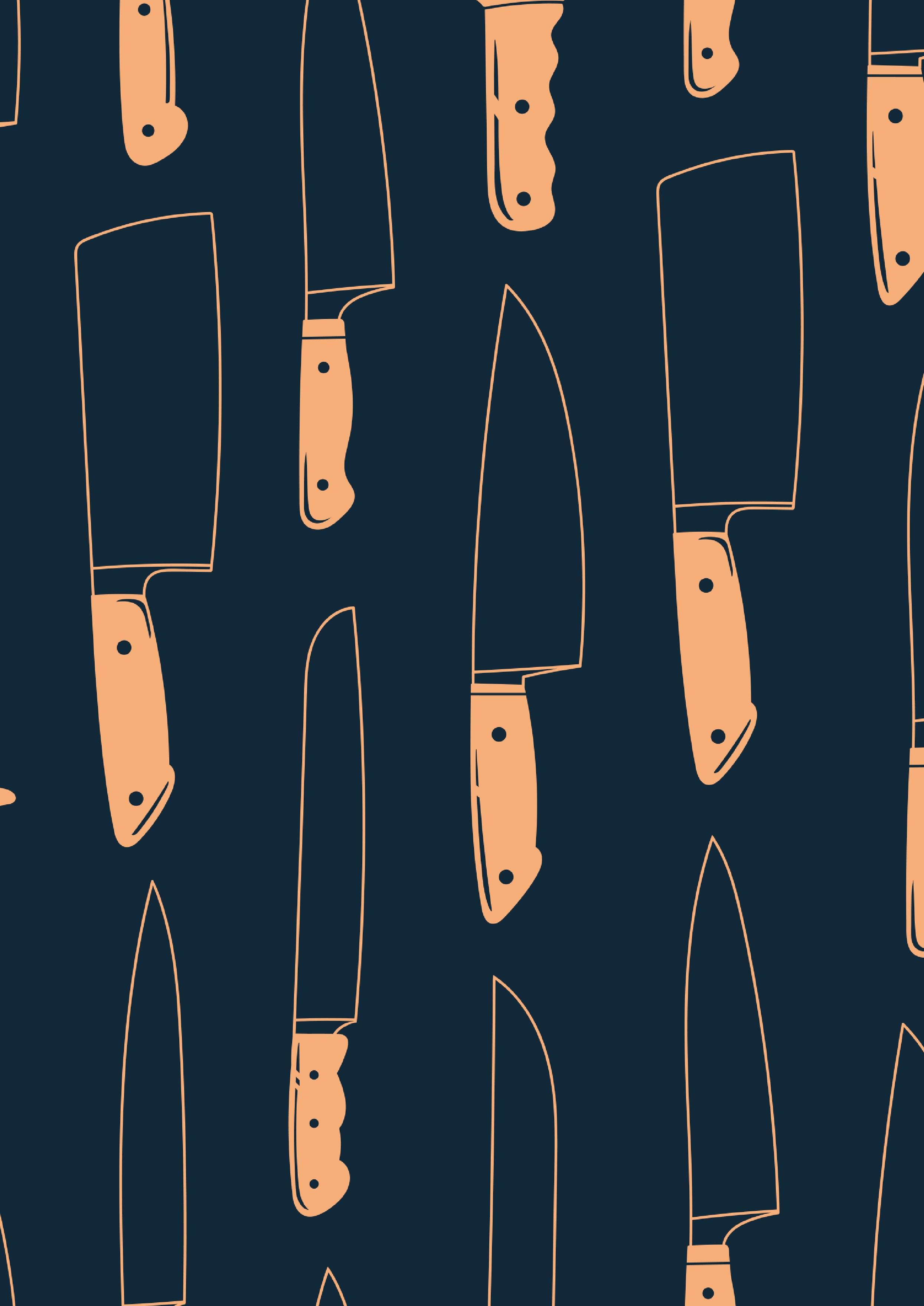
9 minute read
Cutting edge technology
EDGE TECHNOLOGY
Laura McShane, Decom Engineering, Northern Ireland, explains how the subsea cutting specialist completed a challenging decommissioning workscope offshore West Africa.
he Chinguetti and Banda fields lie in water depths which vary between 280 m and 830 m, about 90 km from the Mauritanian capital, Nouakchott. When the field was considered no longer economically viable, the decision was made to undertake abandonment and decommissioning of the 15 designated wells, consisting of three major phases.
Phase 1 and Phase 2A, disconnected the FPSO mooring lines and recovered the risers, allowing for removal of the FPSO from the field, as well as plugging and abandoning the 15 wells. Norwegian subsea and offshore wind contractor, Havfram, was contracted to perform Phase 2B of the decommissioning work, which involved the removal and disposal, or rock dumping, of all remaining infield assets. Havfram commissioned subsea cutting specialist, Decom Engineering, to perform cutting operations on 15 termination heads (TH), six umbilicals, hydraulic flying leads, chains, and fibre ropes.
The THs are designed to terminate the flowlines to the subsea manifold. They provide an interface to the ROVCON tie-in connection tool which is a collet connector that provides the mechanical connection to the inboard hub. The production THs are insulated to prevent cool down of production flow during a production shut down. They are insulated in the annulus between carrier pipe and flowline with polibrid.
There are three off drill centre (DC) manifolds with TH connections. All DC Manifolds have similar configurations, except for DC-3 which has a pigging loop that would remain connected during manifold retrieval efforts. Cuts on DC-1 and DC-2 manifolds (six cuts each) needed to be as close as possible to the hub. For DC-3 manifold (three cuts), the cuts needed to be close to the flange side (i.e. at the connection to the flexible pipe to the termination head and away from the manifold and inboard hub) so that the weight of the TH protrusion would help balance the weight of the pigging loop module, which remained connected to the manifold during retrieval.
Decom Engineering were contracted by Havfram to supply equipment for both the subsea cutting of the previously mentioned products and the on-deck cutting of umbilicals. The C1-24 chop saw provided by Decom had a number of modifications custom-designed for the specific cuts to be made during the project. To achieve the cuts desired on the three manifolds, the clamping method was modified to allow the saw to be clamped onto the manifold securely during the cut, and remain securely clamped to the manifold once the cut had been executed. It was essential that once the cut was performed the saw would remain clamped in position to prevent possible damage to the ROV or the tool.
ROVCON cutting As previously mentioned, there were three manifolds to recover, the first of which was DC-3, requiring three off ROVCON cuts. A 2 t uplift buoyancy module was rigged to the saw, which would allow the saw to be clamped onto the ROVCON and disconnected from the crane.
The average cut time for a ROVCON was 35 mins. Once the cut was complete the blade was fully retracted. The upper clamp could then be opened – releasing the cut ROVCON whilst remaining securely clamped to the manifold. When the clamp was sufficiently open, the ROVCON dropped from the clamp arm onto the seabed. The slack was now taken up on the crane, the lower clamp was opened, and the saw released itself from the ROVCON.
Once the first ROVCON with a 10 in. internal flowline had been cut, the saw was repositioned on a centre ROVCON with a 6 in. internal flowline and the process repeated. If this was the second cut, the saw was unstabbed and recovered to deck
for a blade change. Once the three or six cuts were completed, the manifold could be recovered. The cut section revealed that the outer wall had a larger wall thickness than what was expected (35 - 40 mm).
A total of nine cuts were performed by the C1-24 chop saw to retrieve the chain from the northeast, south and northwest clusters. Initially, the saw was rigged without the buoyancy, however, after the first cut attempt it was decided to include the buoyancy module to help with the heave and reduce potential pinching. The first cut was performed using a used HMX blade, which had already cut two ROVCONs. Cut time for the chain was on average 25 - 30 min. The nine cuts were then successfully made with no further issues – three TCT blades were used with three cuts per blade.
The first four umbilicals were recovered to deck without a need for the chop saw subsea. These umbilicals were then sheared into 25 m lengths on deck using deck shears supplied by Hiretech. The lengths of umbilicals 1 - 4 were spooled onto the special handling drums during retrieval, they were then spooled out through the jaws for the shear cutter and into the carousel. Each cut took around 30 seconds.
Due to unforeseen circumstances, Umbilical 5 (UMB5) had to be cut into 30 m lengths subsea. This section of umbilical was a little over 2 km, meaning 68 cuts would be needed. After performing the first cut with the chop saw, it was immediately apparent that this would be a much quicker and consistent method (around 2 min. per cut) than the ROV super grinder (around 30 min. per cut). No need for a dredging process was an additional bonus.
The saw was slung directly to the ROV hook for this operation. The saw was brought down to depth, stabbed in, and function tested as with previous cutting operations. The saw was then positioned on top of UMB5 with collaboration between the crane driver and the ROV pilots. Once the clamps fully closed, the cut was started and took 2 min. The saw was feeding at maximum speed with blade pressures of under 80 bar. The clamps were then opened, the UMB dropped away from both sides, and a 30 m vessel move called. The cycle time from starting one cut to starting the next cut was around 10 min. One new TCT blade made the first 57 cuts before it was too dull to continue effectively. A new blade was fitted to make the remaining 11 cuts.
Additional work Due to the success and efficiency of the cutting operations on the ROVCONs, the client then requested that an additional water injection (WI) ROVCONs to be cut. Extra blades had been brought on the project in case of this event, so Decom was prepared with 10 blades to make the nine WI ROVCON cuts.
The WI ROVCONs were almost identical to the 10 in. flowline ROVCONs on manifolds DC1, 2 and 3. The only differences being that there was no polibrid insulation in the annulus between carrier pipe and flowline. The angle of the ROVCON to the seabed was greater at around 25 - 30°. Again, cut times of around 30 - 40 min. were achieved using the TCT blade, with the blade being changed each cut at the request of the client. This left one blade left over for the project.
ROVCON lessons learned The saw clamps were more than capable of supporting the 5 t load of the cut ROVCON, despite previous concerns of potential movement of the cut piece towards the end of the cut. This meant that the crane did not have to be rigged to the flowline, and saved a large amount of time during cutting operations. The pressure feedback shown at the Remote Control Unit and the valve pack would not have provided the required accuracy to perform any cut – the pressure gauges on the saw are essential for ROV operations.
The HMX blade was capable of cutting at least a 10 in. Flowline ROVCON and a 6 in.
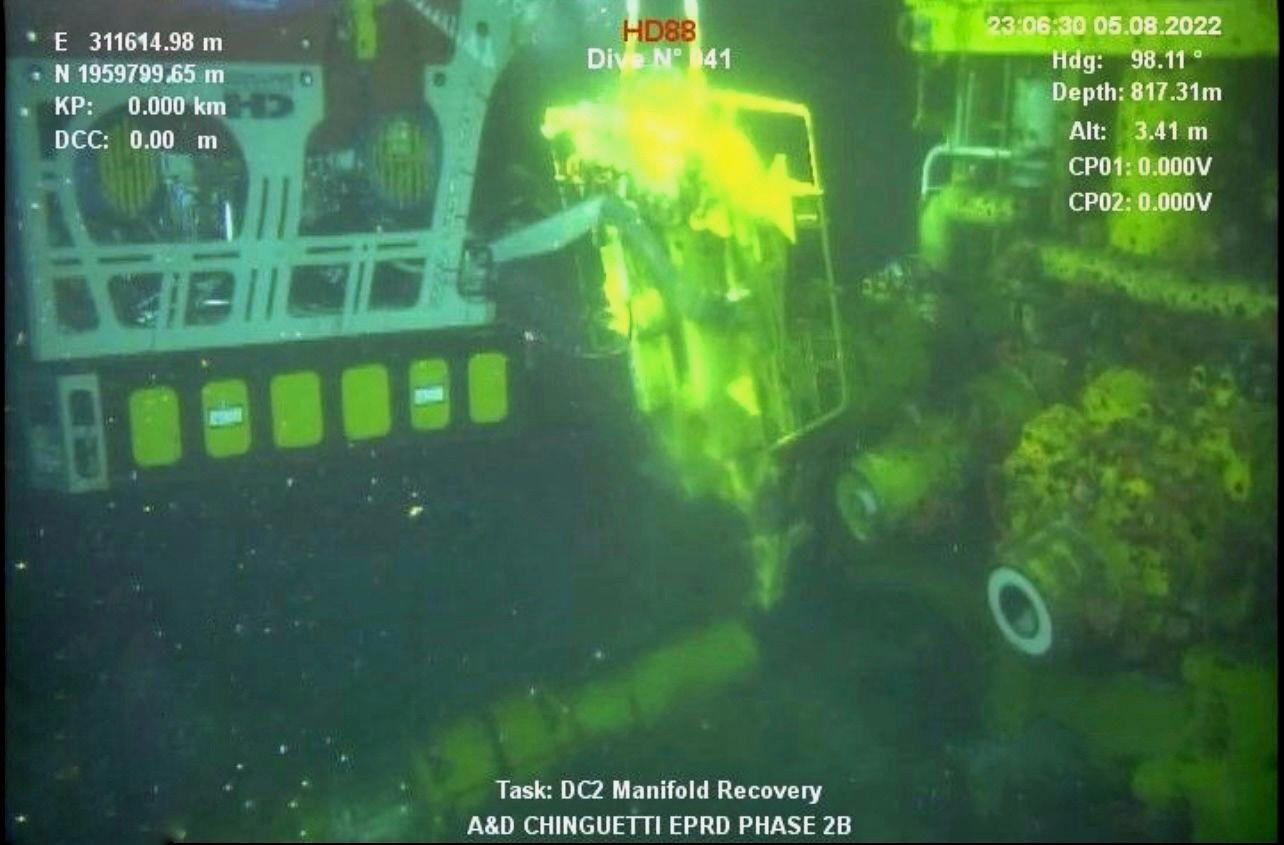
Figure 1. DC-3 manifold recovered to deck.
Figure 2. DC-2 manifold recovery, Chinguetti field – chop saw clamped on ROVCON.
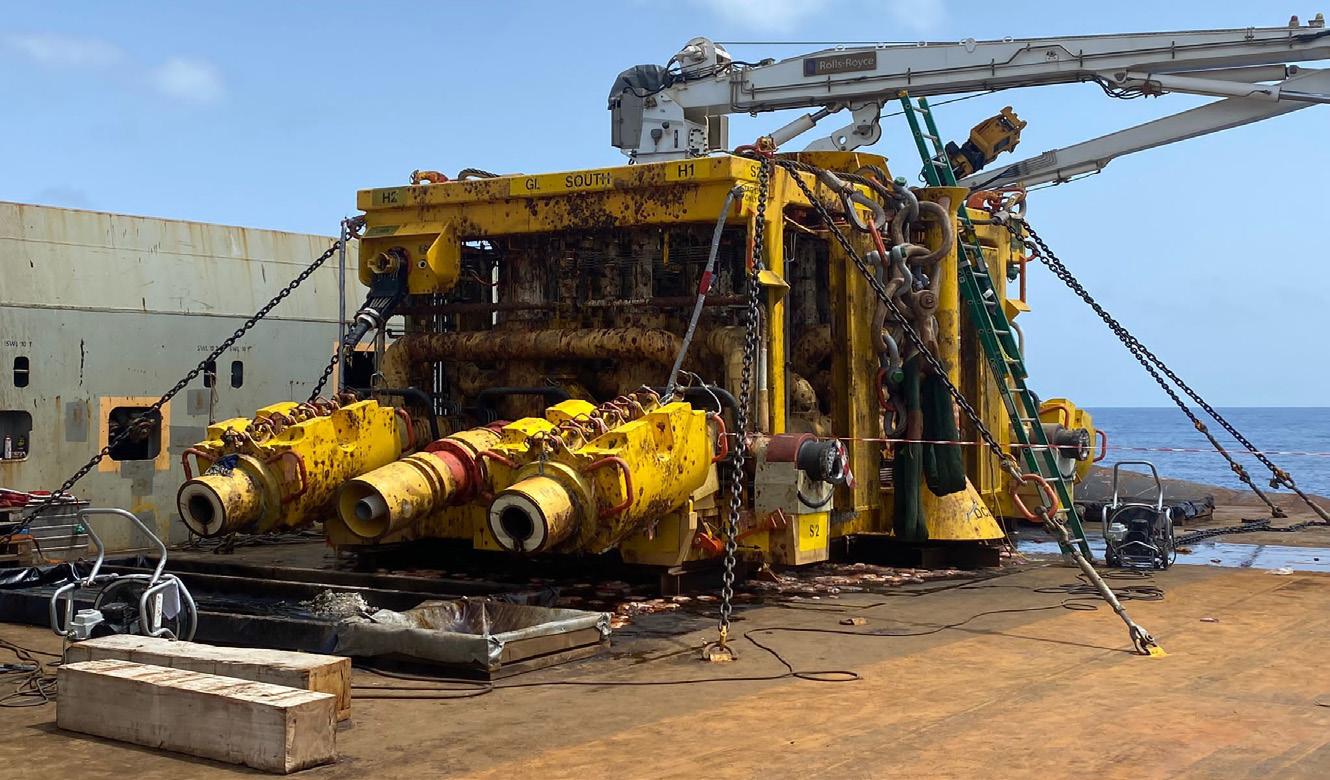
Flowline ROVCON. The TCT blade only ever attempted one 10 in. ROVCON, however, it is believed, based on the motor pressures observed towards the end of the cuts, that this blade would have been capable of at least another cut.
Mooring chain cutting The chain cutting operation was quick and efficient on the whole, however, could have been aided by the following: a dull blade will still struggle to cut even the softer products – such as chain. A new blade should always be fitted for the first cut of new products so that variables that affect the performance of the cut can be kept to a minimum.
It is difficult to land the saw exactly where is most desirable on the chain, and it is especially difficult to grab the chain in the vertical orientation. A V-block and jaws combination that allows the best clamp possible in the horizontal position is preferable. The 500 mm jaws on the upper and lower clamps are not suitable for clamping the chain.
Umbilical cutting The UMB5 cutting operation was completed in a fraction of the time allotted for it. There are still a number of lessons to be learned: the type of seabed has a big impact on visibility and ease of picking up the UMB. With the seabed being so soft, it enabled the saw to be lowered completely onto the UMB so that there was no chance of dropping the UMB when picking up.
The TCT blade made very quick work of the umbilical, with a cut time of around 2 min. However, this cannot be held indicative of all umbilical’s to be cut in the future. A careful inspection of the type of armour in the umbilical has to be made. UMB5 had large 6 mm solid strands of carbon steel which the blade did not snag on until the blade was dull. The same results could not be expected from a fine stranded stainless steel helical armoured UMB.
Havfram’s Project Technical Manager, Christopher Hawtone, said on completion of the project: “Havfram recently completed the second phase of a decommissioning project in a remote location using Decom Engineering’s C1-24 chop saw to perform subsea cutting of various assets, including 84 mm stud-less mooring chain, umbilicals up to 145 mm OD, and 20 in. OD Super Duplex flowline terminations.
“From the very start of Havfram’s interactions with Decom Engineering, the team were very professional and solutionoriented, ensuring that the challenging and unique cutting scope was approached with a collaborative problem-solving attitude.
“Decom Engineering delivered quality documentation and equipment on very short lead times, and provided both Havfram and our end client with confidence in the cutting system through full scale testing, both in a test basin and hyperbaric chamber. The technicians provided by Decom Engineering possessed extensive knowledge of the tooling and were well skilled, proactive, and excellent team players.
“During offshore execution, the Decom Engineering tooling was robust and performed efficiently, successfully executing over 100 cuts, a substantial growth in the intended number of cuts, in less than the scheduled time. Overall, Decom Engineering played a vital role in the success of the project, and we look forward to opportunities that allow us to work together again in the future.”
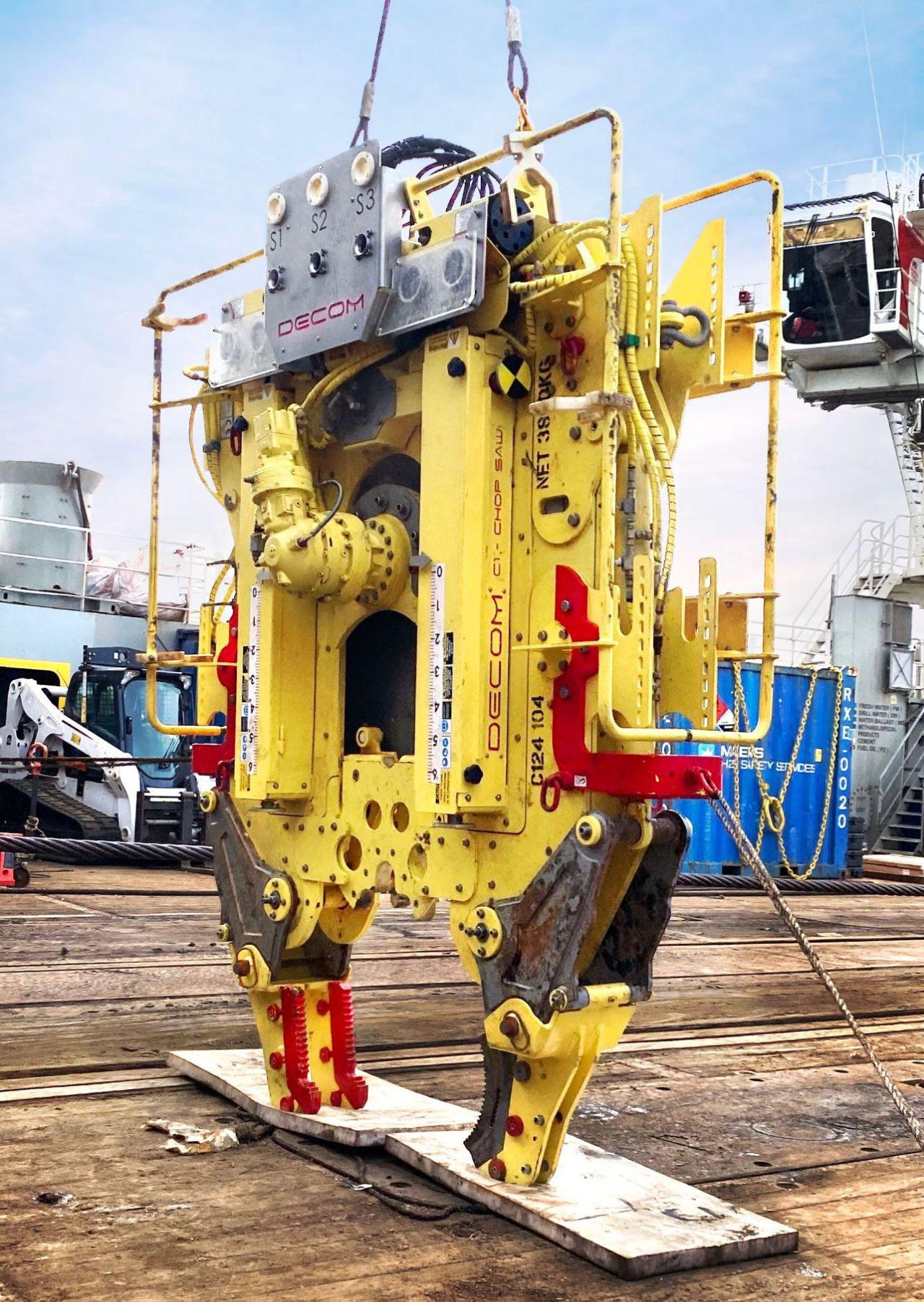
Figure 3. Decom Engineering’s C1-24 chop saw on deck.
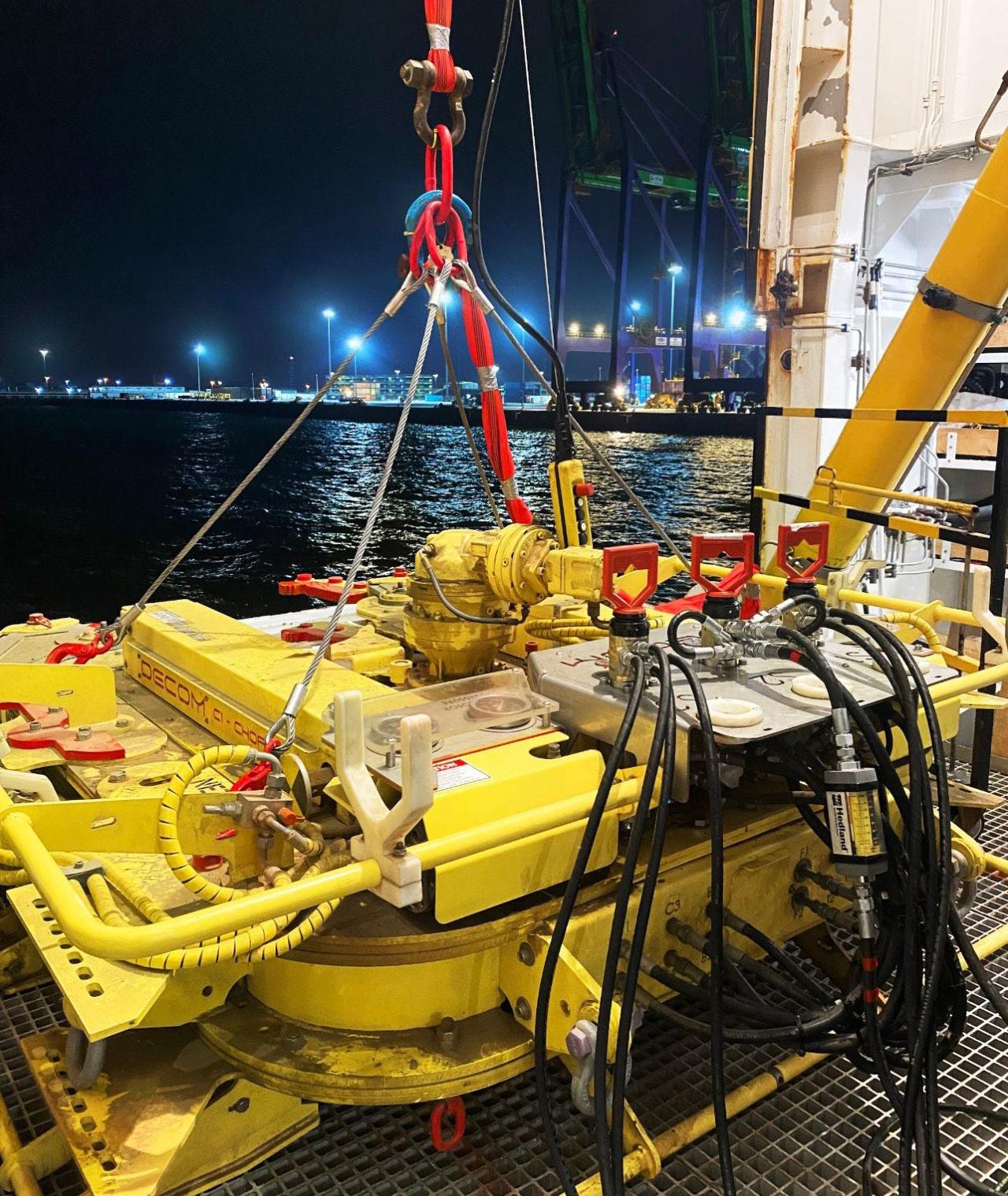
Figure 4. On-deck function testing of C1-24 chop saw.