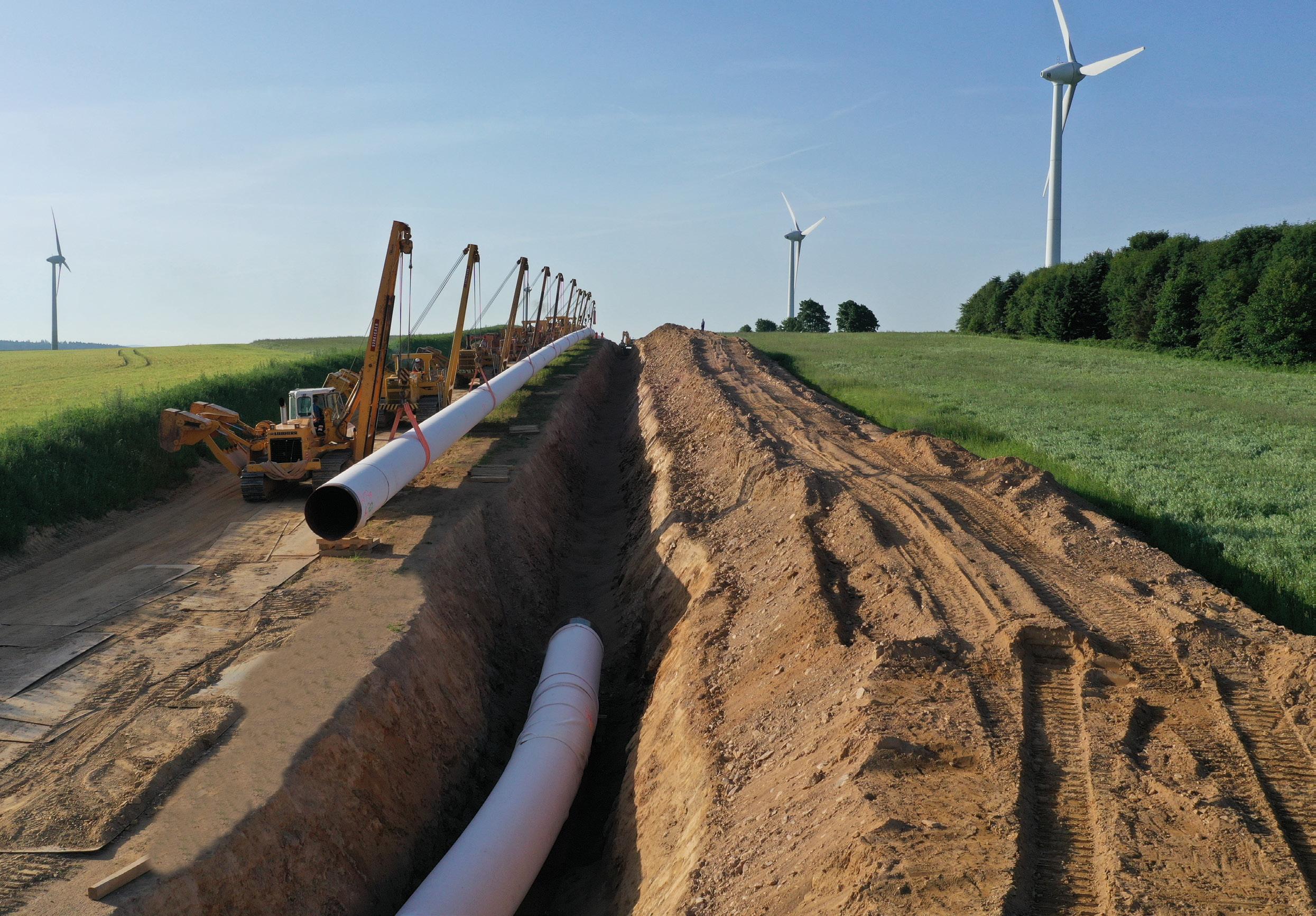
7 minute read
The future is electric
aerodynamics for optimum efficiency and extended operating time between scheduled overhauls. The gearless configuration provides several advantages including a smaller footprint, reduced lube oil requirements, and higher net efficiency. The high-speed VFD-powered motor significantly reduces CO2 and NOX emissions as compared to a gas turbine driver. The VFD addresses starting issues and allows for adjustable operation to match load/capacity requirements. The pipeline compressor’s single lift plug-and-play design includes auxiliaries such as lube oil, a buffer gas panel, and integrated, customised controls. Piping and wiring are included on the skid. The Elliott 140 TCH pipeline compressor is available from 10 000 - 42 000 hp to accommodate the full range of gas transport applications.
The 140 TCH is designed to handle most modern, mid-size and large pipeline compression applications. Its design is lean and simple, and focuses on making pipeline compression efficient, reliable, and cost-effective. The impeller aerodynamics are based on Elliott’s advanced and proven EDGE technology. With the axial inlet and flexible or customisable aerodynamic design, efficiencies of greater than 85% can be obtained. The direct drive compressor, with a variable speed electric motor, provides a wide operating range, including efficient turndown operation. With three standard frame sizes, 15MW, 25MW, and 35MW, the centrifugal compressor is designed for applications up to 7000 million ft3/d with a pressure ratio ranging from 1.15 - 1.8. The typical operating range for the 140 TCH is shown in Figure 3.
The machine design philosophy allows for simpler installation with a standardised package, an axial inlet, and selectable discharge for right or left piping configurations. The package includes an integral lube system for the compressor and motor, a simplified buffer or seal gas panel (the compressor only has one seal), an on-skid control system, and all compressor piping and wiring included on a single-lift skid for reduced footprint and weight. The compressor internals are contained in an inner-barrel design and can be removed from the driver side. This allows for easy maintenance and removal of the compressor internals without the need to move any piping. The removable barrel also allows for quick and easy, installable spare bundles or compressor restaging to change aero components, as needed (Figure 4).
The 140 TCH is designed to increase reliability by minimising component count. The compressor design allows for a direct drive electric motor, which does not require a gearbox, making the footprint small and light. The axial inlet and overhung design allow for a single seal. This results in a simpler, more reliable design with reduced emissions. The balance piston and balance piston line have been eliminated, further increasing reliability and reducing losses, which leads to increased efficiency.
With a clean and simple design and industry-proven components, the reliability, availability, and time between maintenance intervals has been increased. To meet modern pipeline compressor requirements for efficiency, reliability, and low emissions, Elliott has responded with a state-of-the-art pipeline compressor, incorporating years of experience and evolution into the design of the 140 TCH. This compressor is ideally suited to meet the increased capacity demands of modern pipelines efficiently with minimal GHG emissions.
IPLOCA - encouraging sustainable energy transitions in the pipeline industry
Anand Jha, Vice President of Global Sales for Chemical, Oil & Gas, ABB, USA, outlines a compelling alternative for pipeline gas compressors.
s natural gas moves from well sites to end users along a pipeline, friction, travel distance, and elevation changes slow gas movement and reduces its pressure along the entire line. Compressor stations are placed strategically along the pipeline to maintain the pressure and flow at an operable level. The stations are an integral part of the network, and the compressors must perform this critical task with high reliability and little maintenance requirements.
To gauge the importance of compressor stations for the gas industry, the US relies on a network of over 480 000 km of gas transmission pipelines. Typically, a compressor station is required at intervals of between 80 and 160 km, so many thousands are in operation across the country.
Historically, compressors have utilised gas or steampowered turbines to maintain the natural gas pressure. Currently, some 90% still utilise this technology. However, these turbines produce high greenhouse gas (GHG) emissions, offer low efficiency, and are hard to maintain, especially in remote locations. Since a typical compressor station will require 10 MW or more, there is now a clear incentive to seek more energy-efficient alternatives. That is why there is now a growing trend to adopt electric drivetrains, both for newbuild projects and for upgrades of existing stations.
It is not only a question of saving costs through energy efficiency. Following the COP26 climate summit in late 2021, political leaders expressed a renewed focus on reducing
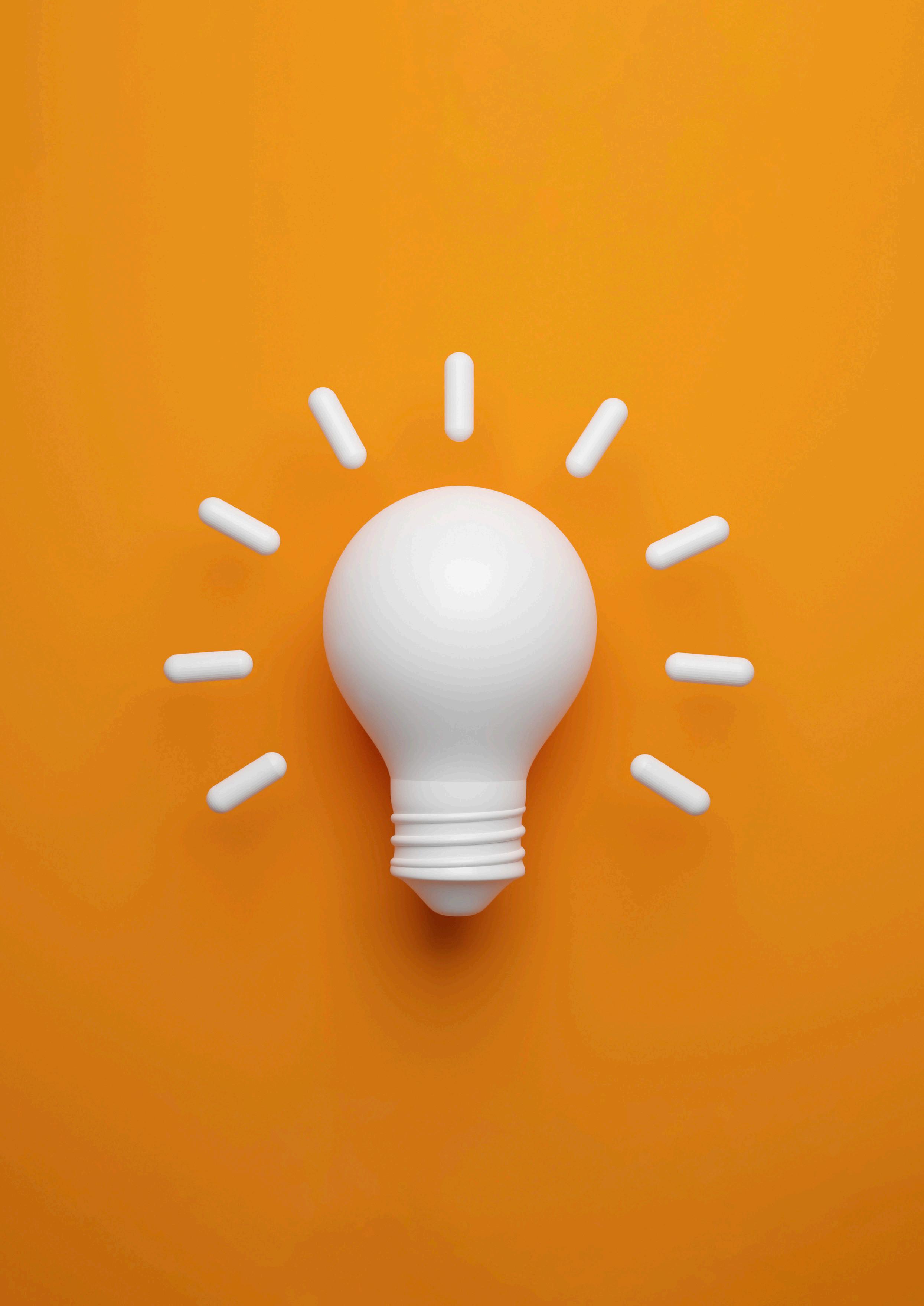
emissions and setting targets. As a result, most European countries and North America have set net-zero targets in their policy documents.
Whereas in the past, pipeline operators could have been tempted to stick with gas turbines since gas was the most accessible energy source, the political commitment to net-zero is compelling them to change tack. Since they now get penalised for GHG emissions, many of the world’s top oil and gas companies have set goals to eliminate such emissions from energy consumption and operations by 2050.
Electrical drive systems The traditional approach to gas pipeline compression is to use natural gas to fuel a large, stationary engine driving a turbine. An electrical drivetrain uses very much the same principle, but with the gas engines substituted by an electric motor operated by a variable speed drive (VSD).
One of the main reasons for using gas compression was that it uses a fuel readily available from the pipeline itself, while compression stations were often located in areas where there was no electrical infrastructure. That has changed in recent years with electrification becoming much more widespread, even in remote rural locations.
The primary function of VSDs is to control the speed and torque of the motor driving the compressors. VSDs are positioned between the electrical supply and the motor. Power from the electrical supply goes into the drive, and the drive then controls the power being fed to the motor.
Converting the incoming AC electrical power to DC power smooths out the electrical waveform and adjusts the frequency and voltage based on current process demands. This means operators can run an AC motor at the speed or
torque dictated by the demand, resulting in considerable savings.
Energy-efficient benefits of VSDs Running a compressor at full speed and controlling the flow rate and destination by manually opening and closing the valves makes the start-up process highly labourintensive. Starting up a gas compressor station can also be a time-consuming process – the labour costs add up when personnel have to travel long distances to remote sites, although this is an automated process in some facilities. But energy consumption is poor.
Running these applications with VSDs is a more cost and energy-efficient alternative, as it brings instant savings in energy consumption. The actual energy savings depend on the specific application: since the relationship between motor speed and energy consumption is non-linear, even a slight speed reduction can result in 25% or more energy savings. Startup is also usually only a matter of seconds.
VSDs also bring long-term competitive advantages like low maintenance costs, reduced waste and COX and NOX emissions, increased production hours, and even lower ambient noise emissions. These all play a vital part in meeting environmental goals.
Other factors to consider in favour of electric drives are the capability to benefit from the high reliability and excellent control properties of the electronically adjustable AC drives and the need to avoid GHG emissions.
The advent of electric compressors The oil price collapse of 2014 forced changes upon the gas pipeline market, including capital cost reductions and downsized budgets. But even as energy costs increase, as is currently the case, the need to achieve a good return on investement (ROI) on infrastructure remains as valid as ever. The excessively high operational expenditure of gas turbines in terms of maintenance prompted operators to pay closer attention to the cost aspect. They started looking for an optimised solution focusing on the total cost of ownership (TCO) and not just the initial cost. This, together with stricter environmental regulations, saw electricdriven compressors entering the market in the early 2000s. Carbon tax and credits and investors’ environmental, social,
Figure 1. The Troll A platform features electric compressors driven by high-voltage 40 MW motors.
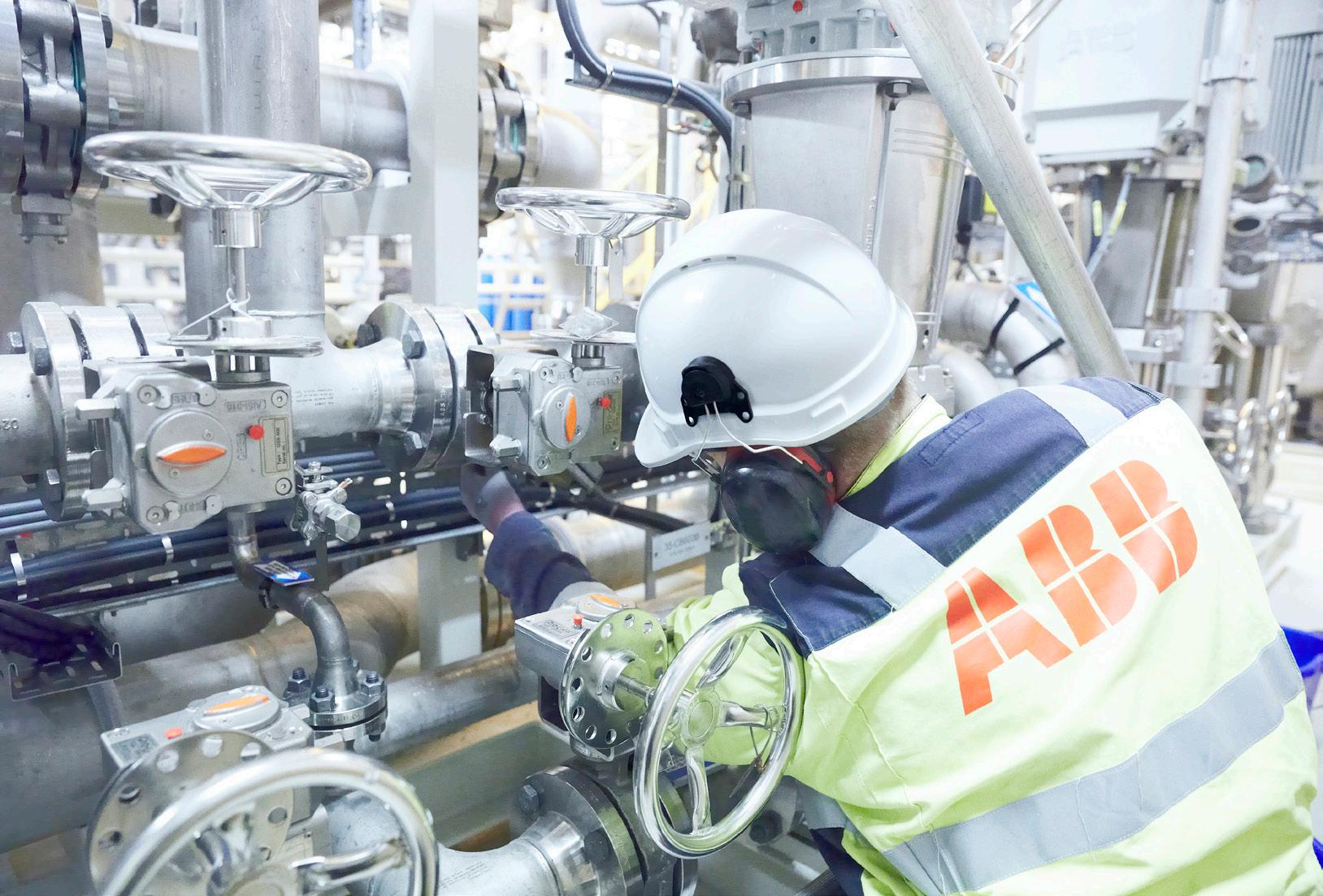