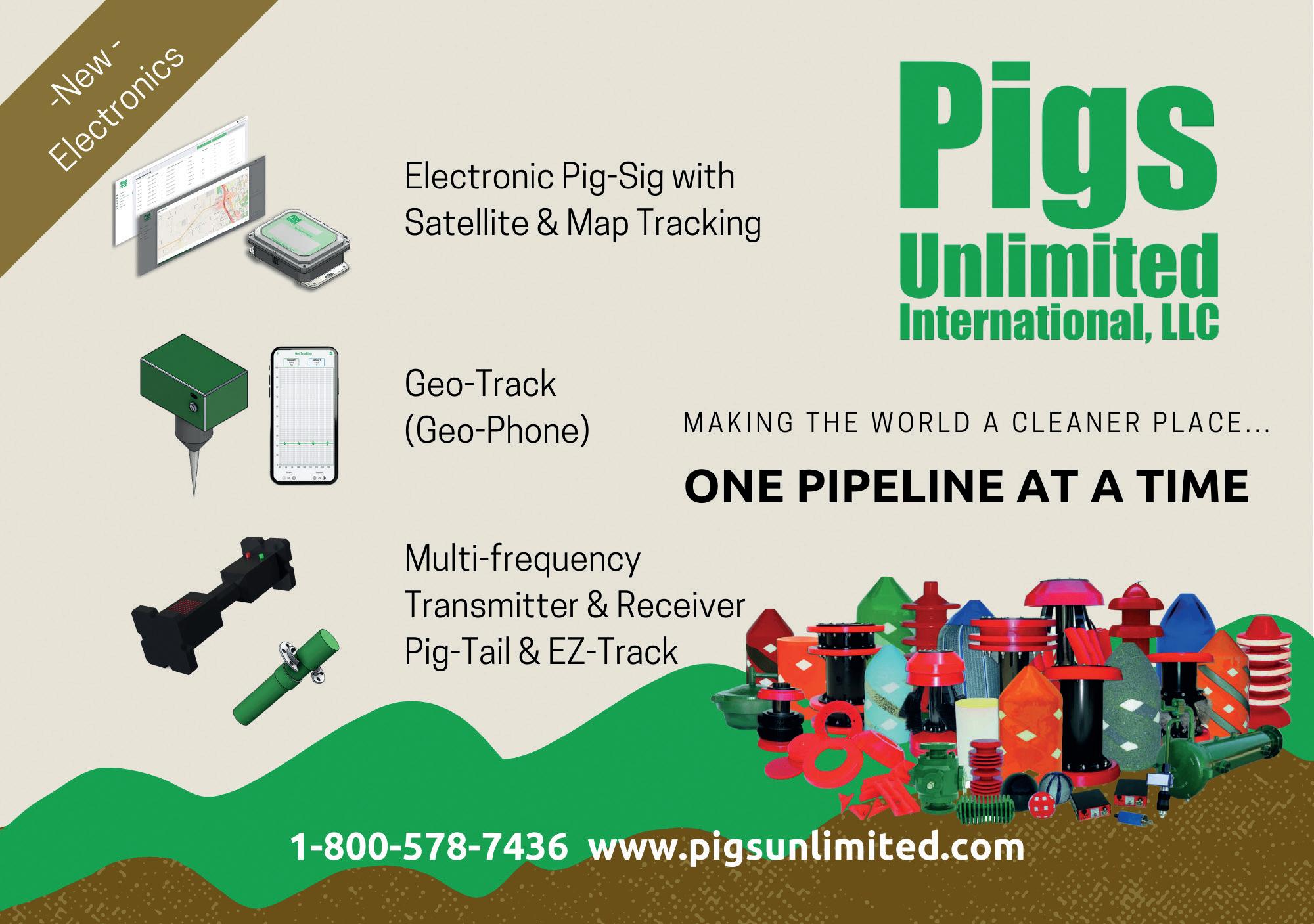
7 minute read
The vapour barrier solution
Table 1. Comparison of gas turbine and electric drive characteristics Compared feature Gas turbine
Efficiency
Investment cost
Maintenance
Reliability/availability
Mean time to repair
Pollution/emissions
Speed control range Speed control accuracy Low
High
High
Medium
A factor to consider
High
Limited
Medium
Design flexibility
Torque pulsation Low
Low Electric drive
Very high
Medium
Very low
High
Low - 4 hours
None
Wide and easily adjustable
High High
A factor to consider
Starting time
Noise level
Impact on power supply
Total life cycle cost (LCC) Medium - minutes Low - seconds
High Not applicable Medium
Requires investigation Depends on energy costs Depends on energy costs
and governance (ESG) demands added to the sector’s shift towards decarbonisation.
However, since gas turbines usually operate in remote areas, electricity supply was regarded as an initial hurdle, but with advanced technology, this is no longer the case. A good example is the Troll oilfield in Norway’s sector of the North Sea. The operator, Statoil, was looking to boost production on the giant Troll A platform by installing two compressors.
ABB’s solution brought together two ground-breaking technologies: the world’s first high-voltage DC power-fromshore connection to a platform and the first commercial installation of very high voltage synchronous motors, each with a power rating of 40 MW.
The solution takes 132 kV power from the mainland grid and turns it into DC at a converter station at Statoil’s gas processing plant. Two HVDC Light power cables, each with
a capacity of 40 MW, then transport the power at 60 kV to Troll A 70 km away. There, a compact, lightweight converter station turns the power back into AC, which then feeds to the two ABB motors that drive the compressors.
This method of supplying power to the compressors was better than the conventional solution of installing gas turbines on the platform because the capital, operating, and maintenance costs were significantly less. With no penalties to pay for exhaust and maintenance costs, payback for the total investment of US$270 - 280 million happened in less than three years. The solution also reduced the environmental cost of running the compressors by 230 000 t of carbon dioxide a year. The compressors are expected to extend the field’s productive life to 2063.
Replacing a gas turbine with an electrical drive With the push towards decarbonisation, most new compressor installations use electrical drives. While in some installations they might require a higher initial investment than gas turbine drives, their real benefit is seen over the operational life of the station. The reason is that electric drives have much lower operating expenses, leading to significant savings, especially when they’re factored in early in the plant’s design. With the right knowledge and assistance, it can also be relatively straightforward to replace an existing gas turbine with an electric system.
The main steps to assess feasibility are a torsional analysis, mechanical calculations, checking the turbine’s foundation to see if an electric motor will fit, and whether there’s a need for an intermediate frame. These steps are followed by harmonic studies, string analysis, control and power interconnection analysis, and piping.
Next in line is installing the electrification hardware, which includes the electrical house, switchgear, power and VSD transformer, MV and LV distribution, and the drive train with motor and drive. The final steps in the replacement process are process control and instrumentation integration, concluded by project commissioning.
Efficiency gains and TCO The energy conversion efficiency of a gas turbine is typically about 47% and this is only reached at peak performance. Conversely, a corresponding electric drive system achieves around 95% efficiency over quite a wide range.
In addition, the downtime of a gas turbine is costly, with multiweek shutdowns to repair mechanical wear and tear. The average maintenance interval for gas turbines could be six months or 4000 hours.
On the other hand, electric drives offer much more efficiency and less downtime. Even if they do go down, maintenance will require a few hours or half a day at most. The electric drive system typically has an availability higher than 99.9%.
With all these factors considered, using an electric-driven turbine could enable an operator to increase the uptime of their compressor station by approximately ten days a year. This results in significant savings by reducing lost productivity. Overall, electric drive trains (VSD and motor) can save significant operational costs, with a typical payback time of one to three years. This might even be reduced to a few months when the opportunity cost of selling the gas saved by electrification to the market, or using it in other processes, is included in the return on investment (ROI) calculation.
Recent successes: North America and globally Over the past decade, ABB has helped operators in North America to electrify their gas compression stations in order to increase reliability and flexibility by supplying electrical drive systems ranging from 4 to 29 MW. Although globally, ABB also has proven references and the capability to offer VSD packages above 30 MW. In a typical example, ABB was appointed to replace the existing equipment at a compressor station and upgrade it to higher horsepower while maintaining the existing maximum operating pressure. The objective was to utilise the existing infrastructure and enhance the pipeline’s output capacity.
ABB supplied an ACS5000 liquid-cooled medium voltage drive with a 36-pulse oil type isolation transformer and a fin-fan cooler to drive a high-speed compressor application (0 - 167 Hz). The ability to situate the converter transformer outside the electrical house, and the efficient liquidcooled design of the drive, has reduced the HVAC cooling to a minimum. This has resulted in significant capital and operational cost savings for the project and asset.
Later, ABB supplied another ACS5000 liquid-cooled medium voltage drive for another compressor station This project resulted in a considerable cost saving, as it was possible to reuse an existing transformer and fin-fan cooler.
A critical element in these projects has been the capability to work with different local compressor manufacturers to develop and engineer solutions tailored to suit the requirements of individual locations. This has enabled operators to receive a flexible solution, rather than having to take off-the-shelf equipment.
The critical nature of the compressor stations has also placed a major emphasis on service, especially in enabling on-time commissioning within very tight deadlines. This has been made possible by ABB’s network of service engineers located across North America. The aim is to ensure a rapid response onsite in the unlikely event that a drive should ever go down.
To take service to the next level, talks are ongoing with operators to discuss approaches for remote condition monitoring of compressor stations. This will enable proactive servicing to be scheduled before any issue develops into a fault.
The future is all-electric The simplicity of implementing an all-electric drive system for both new installations, or converting existing gas compressor stations, and the added safety and operational benefits, make it a highly compelling choice. The short payback time, reduced fuel consumption and GHG emissions lead to substantial savings in operating expenditure. In this context, the reduced environmental impact of electrification becomes a highly prized added benefit.

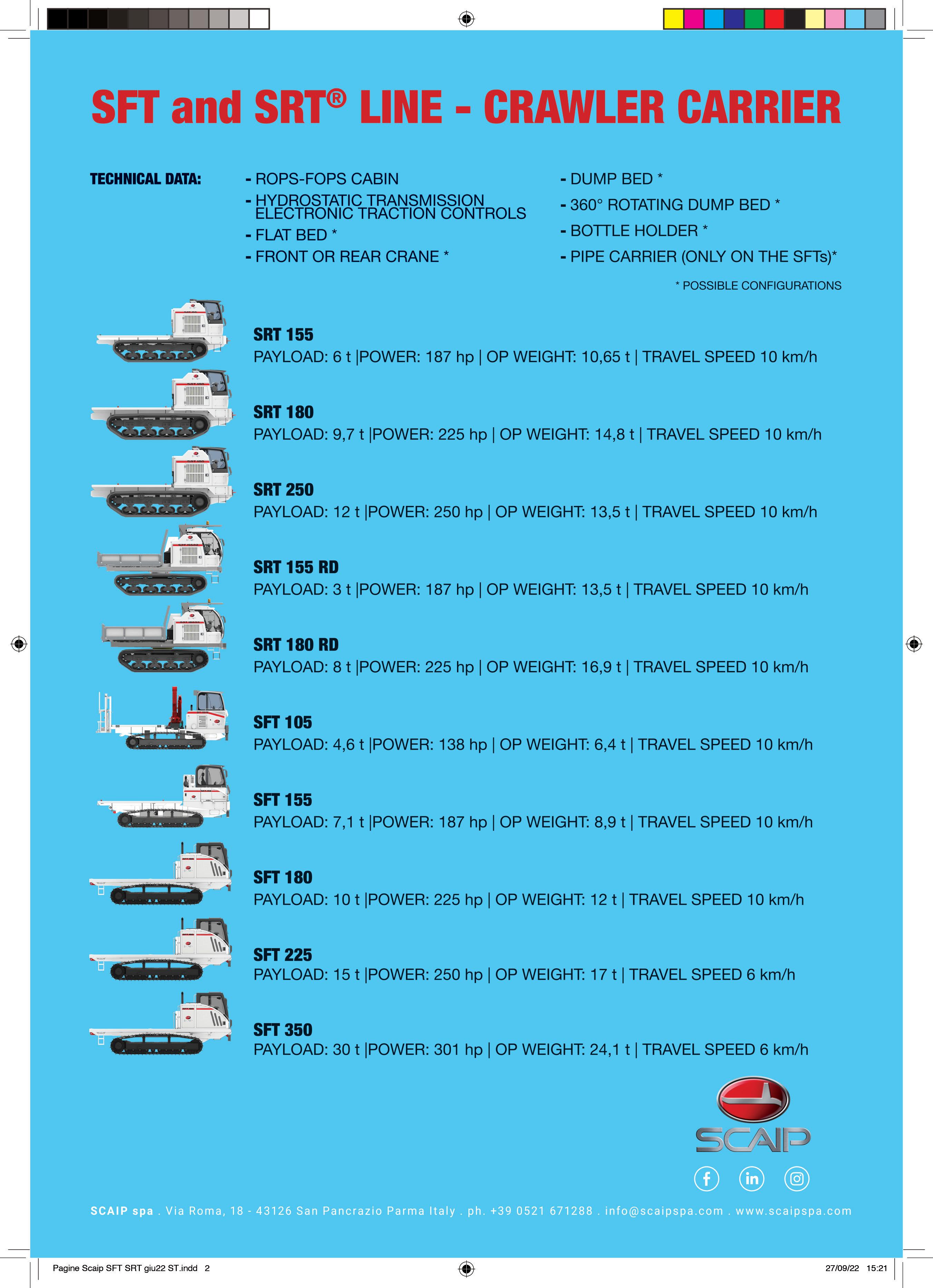
For ‘run of the mill’ and unique challenges, Ryan Ragsdale, Senior Product Manager, T.D. Williamson, USA, presents an isolation solution for gas distribution pipelines.
hen it comes to isolating gas distribution pipelines, there are routine challenges, and then there are extraordinary ones. And sometimes – perhaps surprisingly so – those problems have a similar root cause. And even the same solution.
One of the more common challenges is isolating a pipe that is out-of-round, or slightly oval. Although ovality is occasionally associated with third-party damage, more often it is traced back to the manufacturing process.
For decades, local distribution companies (LDC) have used a single, round, static seal to successfully isolate pipelines. In recent years, though, the concept of an ‘energised’, or expandable, seal that would be easier to insert into and retract from the pipeline became an attractive alternative. Combining a seal that could expand and adhere to the internal topography of the pipeline with the assurance of double block and bleed (DBB) would be a game changer. Especially for those pipelines with extreme ovality or that are not perfectly round.
That concept became a reality in 2020. That’s when global solutions provider T.D. Williamson (TDW) introduced ProStopp® DS isolation technology, the gas distribution market’s first and only low-pressure DBB isolation equipment with an energised seal.

Widely accepted technology Because of its DBB feature, ProStopp DS technology ensures total leak protection on