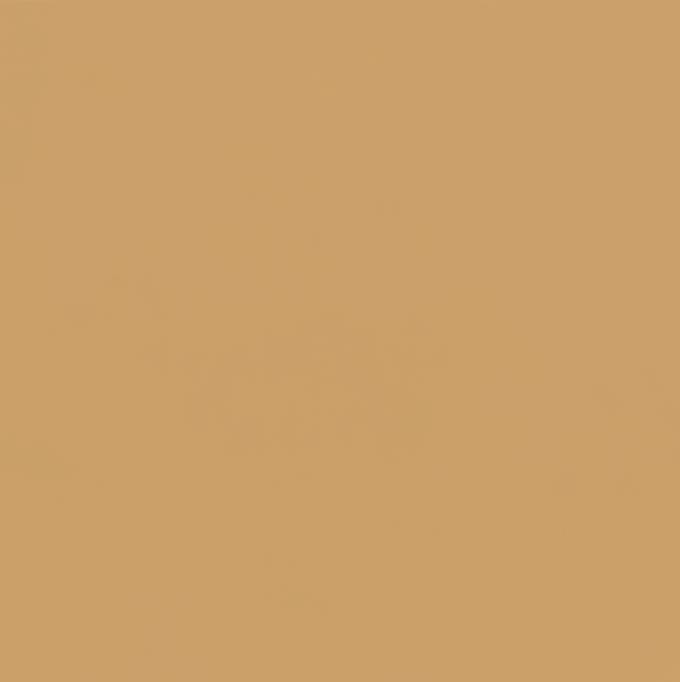
9 minute read
Unlocking stranded reserves
Geoffrey Thyne, Vladimir Ulyanov, Brandon Skinner and Salem Thyne, ESal, USA, describe how simple technology could double the recoverable reserves in many fields while reducing operating costs.
UNLOCKINGUNLOCKING UNLOCKING STRANDEDSTRANDED STRANDED RESERVESRESERVES RESERVES
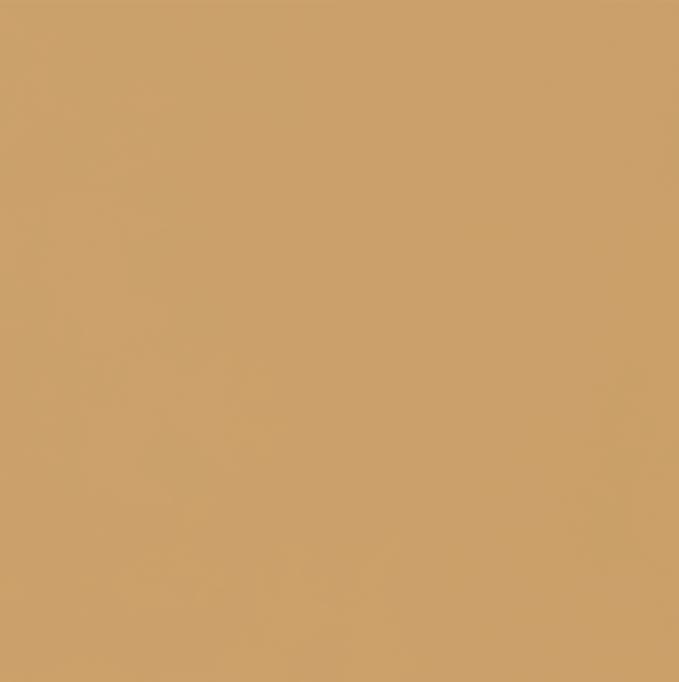
The oil and gas industry faces unprecedented pressure from demand changes, bans on drilling on federal lands in the US under a new White House administration and rising costs for drilling and production. New technologies in all phases of exploration, drilling and production have led to incremental production increases – but the average field still strands 65% of reserves aft er all available production techniques have been exhausted.
New discoveries regarding the connection between the chemistry of wettability and enhanced oil recovery (EOR) show promise for unlocking another 35% of reserves in approximately half of the world’s oilfields. As further data adds to understanding of the issue, there is hope that using salinity to improve wettability could boost production in up to 75% of fields.
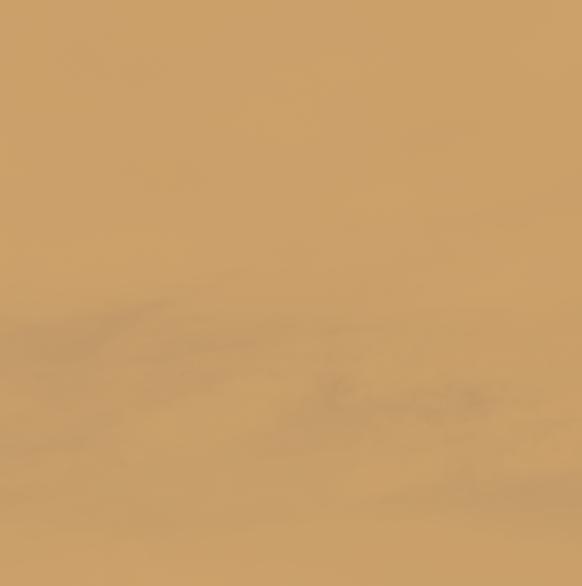
Background
ESal founder Geoff rey Thyne began this study of salinity and wettability almost by accident when assigned to prove the opposite of what was ultimately proven to be the case.
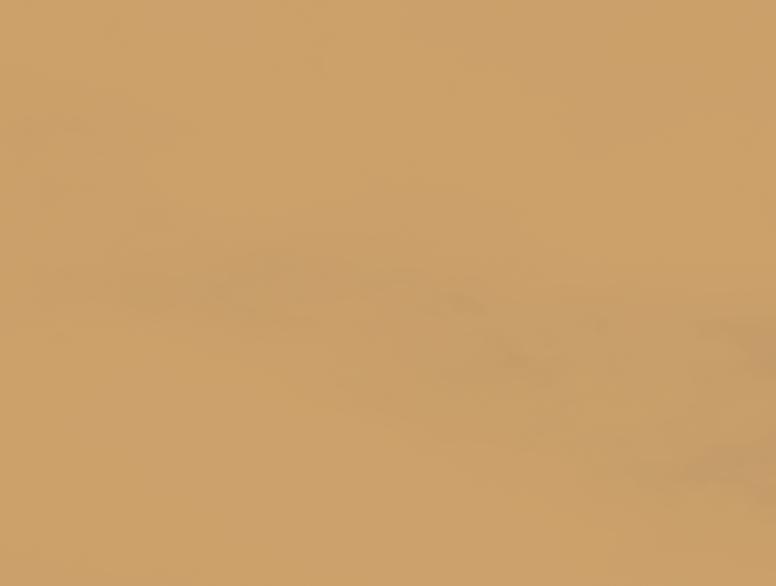

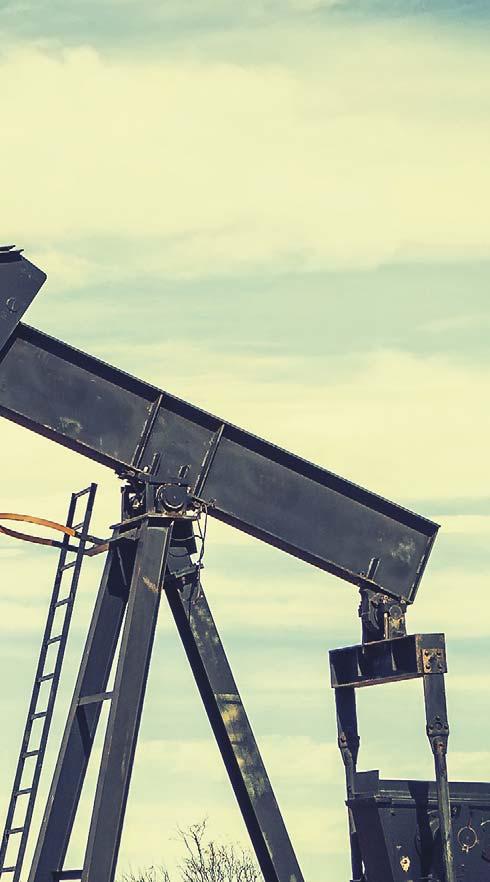
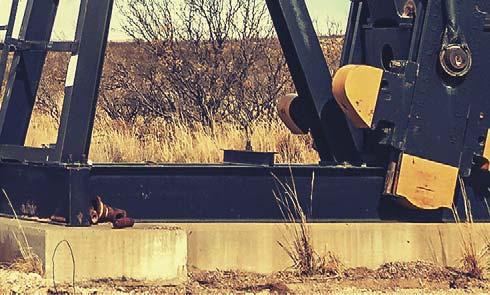
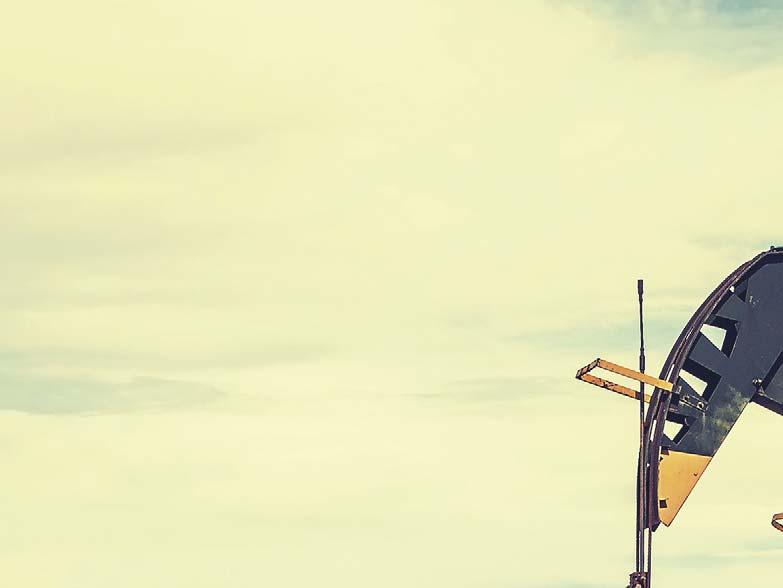
The task, assigned by a non-profit organisation dedicated to researching improvements in EOR, was to prove that using low salinity water (this from a coalbed methane project in the US state of Wyoming) would improve EOR rates. However, extensive laboratory and field testing showed that the low salinity water did not aff ect oil production at all.
In the process Thyne realised however that there were indeed some cases where saline water did boost production. He left the employ of the organisation and set out to use his training in chemistry and geology to determine the deciding factor.
The standard thinking was that a field should be water-wet to achieve maximum production, but there were indications as far back as 1959 that the best production came when oil and water move equally well, in what is known as neutral wettability: equally water-wet and oil-wet. This condition strikes the balance between adhesion (oil-wet) and water block (water-wet). This work was further validated by empirical data collected by Thyne over a period of several years.
Salinity and wettability had been studied for decades, but always from the engineer’s view of how liquids flow. This was understandable because the only known testing at that time involved contact angles, each study of which could require weeks – making in-depth study of the chemistry impractical.
To address this limitation and further evaluate this theory an associate of Thyne’s developed a direct testing method, combining samples of oil and rock in a field with water in a test tube, with varying degrees of salinity in each test. Small amounts of naphthenic acid were added. The test tube was then shaken and the contents allowed to settle out.
This test – repeated hundreds of times with similar results – yielded a major surprise. This flotation test could accurately measure wettability quickly and eff iciently across a wide spectrum of reservoir conditions. Oil-wet rocks would partition above water-wet rocks in the test tube and, through extensive modelling, would represent the accurate wettability state of the reservoir (Figure 1).
The key takeaway was that wettability is fundamentally a chemical reaction, not a property inherent to the reservoir.
Thyne realised that this method would allow ESal to quickly test for optimal wettability in multiple fields by putting rock and oil samples from a field into a test tube, and then over a series of tests manipulate the salinity of the water added to those samples to determine the best water for overall recovery.
Case study 1: the wrong wettability decreases production
In this case study, the field’s production had peaked at approximately 300 000 bbl/month, with a decline curve of 5.9%. The reservoir’s wettability was at 0.35 water-wet (Amott-Harvey). At the time the water sources were switched it was producing approximately 170 000 bbl/month.
The new water shift ed the reservoir wettability to much more water-wet conditions, at 0.9. Optimal wettability/production for this field is seen between 0.3 oil-wet and 0.3 water-wet.
As the new water spread throughout the reservoir, the decline rate almost doubled to 11.45%. These numbers were derived by observing individual well decline under close-to-optimal conditions prior to switching to the wrong water and the onset of reservoir damage (Figure 2).
The production changes were dramatic. As a result of the switch, the company has: Missed 5 million bbl of production. Lost US$212 million in pre-tax profit. Trapped a total of 16 million bbl. Potentially lost US$363 million in pre-tax profit over the life of the field. Reduced field life by 23.5 years. Increased water handling, injection and disposal costs. Lost US$130 million in field value.
Many of these detrimental consequences can be reversed through optimal wettability alteration in the future by using the correct water.
Occurring naturally
One way to evaluate Thyne’s prior discovery would be to find where neutral wettability was already enhancing production in a field in which the oil, rock, water and temperature (also a factor) naturally aligned. Research found this condition in the massive East Texas oilfield, covering 140 000 acres across five counties.
The field is now approaching 80% recovery by simply reinjecting its own untreated produced water. That 80% figure is a much higher rate than the world average of 35%. This field is first in the US in terms of total volume of oil recovered since its discovery in 1930.
The true test, however, would come with changing the salinity in an existing field, then monitoring the results. Expectations were that optimal wettability would increase production by 35% in a field where that is a factor at all.
But the opposite is also true – changing the salinity improperly would lead to production loss and possibly damage the formation.
Case study 2: success with the right wettability
The second field is operated by the same company. Here, at the same time as the water switch in the previous field, they allowed ESal to evaluate the field and to adjust the water for improved production. The fields are geographically nearby, but diff erences in water, rock and oil combinations brought diff erent results in production. ESal tested field samples and accurately predicted the oil recovery improvements to be realised from appropriate water formulations. This field (Figure 3) peaked at approximately 230 000 bbl/month with a decline rate of 15.91%. Its original wettability was 0.6 water-wet. To test the benefits of updated wettability, a screening algorithm is used that evaluates a field based on temperature, depth, minerology, oil API and other factors. Samples come from rock, water oil core or cuttings. In this case the test took four weeks to arrive at formulations that predicted Figure 1. ESal’s flotation test measures the eff ect of salinity on wettability in a reservoir. improved production.

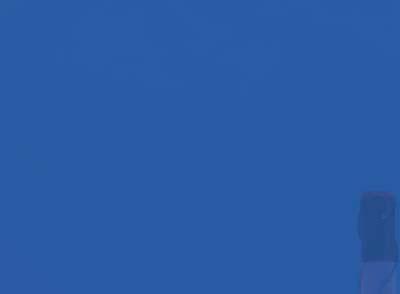
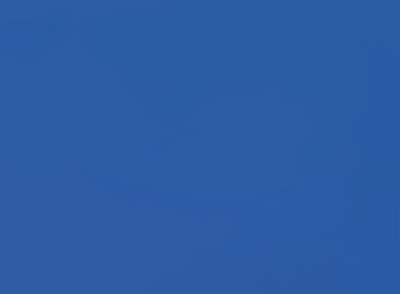

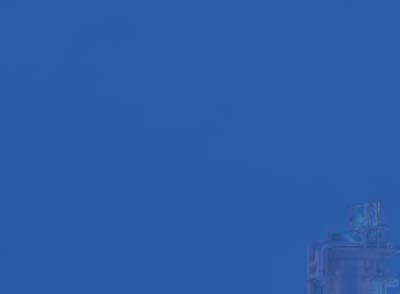
Global coverage of the downstream oil and gas sector
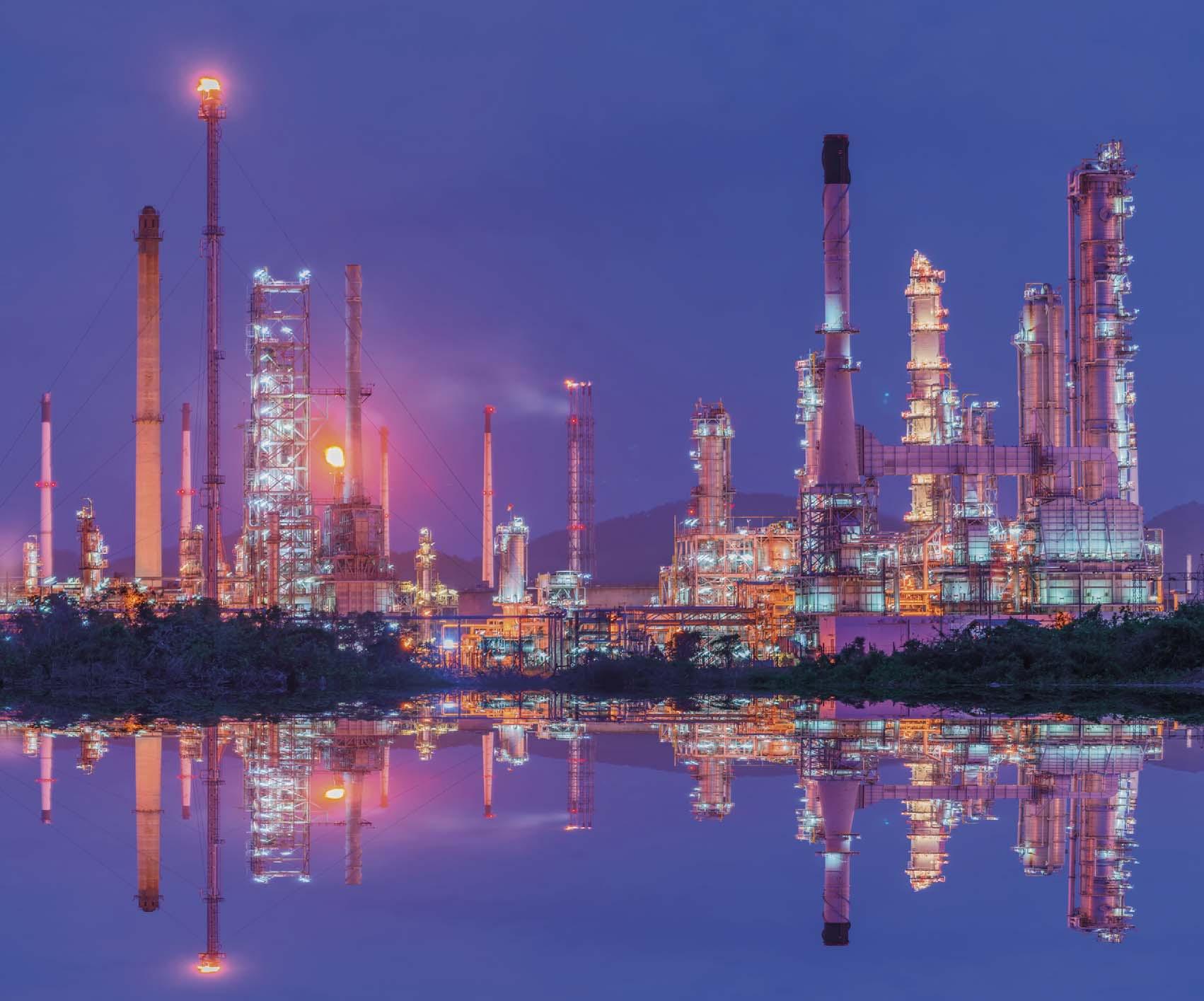
Changing the water to those formulations brought the wettability to 0.4 water-wet, approaching the optimal range. As the injection of the proper water mix continues, future wettability is expected to reach the 0.3 water-wet optimal range.
Within the first five months of the change in water injection the decline rate dropped from 15.91% to 10.22%.
Under these conditions the company has to date: Unlocked an additional 1.9 million bbl. Potentially unlocked an additional 4.9 million bbl over the life of the field. Gained an additional US$63 million in pre-tax profit. Boosted future expected pre-tax profit by US$92 million. Lengthened field life by 12.5 years. Increased field value by US$50 million. Stabilised what had been a growing water cut.
The cost for this procedure is approximately US$4.00 per incremental barrel produced.
Limitations

As stated, approximately 50% of fields tested show that there would be no production benefit to changing the water source. Pre-testing allows ESal to concentrate only on fields that would benefit from changes in salinity and wettability. The company is extensively testing samples from a wide variety of fields in order to expand their understanding of why some fields do not respond to these changes. The hope is that they can increase the number of fields that do benefit to around 75%.
Figure 2. Changing water source results in reservoir wettability damage, reducing estimated ultimate recovery (EUR) and field life.
Figure 3. Changing water source results in improving reservoir wettability while increasing EUR and field life.
The future
In addition to salinity, wettability can be optimised through surfactants or other chemical treatments. The company works with both chemical companies and water treatment companies to generate optimal wettability conditions in a reservoir.
Wettability testing during the completions phase can inform the salinity of water needed for hydraulic fracturing, which can optimise production from wells too young for EOR.
A production increase of even 15% in existing wells on a large scale could add 400 million bbl of oil to recoverable US reserves. Across the world, boosting production to 70% instead of today’s standard 35% could add more than a trillion barrels to reserves across the world.
Many fields across the world have never undergone EOR of any sort. Determining which areas could benefit from EOR and applying wettability principles there could boost production even more.
Conclusion
The cost of this treatment, at approximately US$4.00 per additional barrel of production, is much less than the cost of drilling and completing new wells.
With economic and environmental concerns mounting across the globe producers are seeking ways to improve costs and eff iciencies, as well as boost their environmental, social and governance (ESG) footprint. Making minor changes in produced water for use in EOR procedures that could double current production would seem to be a simple decision.
As the oil and gas industry adapts to rapid changes more companies are emerging from their hesitancy in adopting new technology. Whereas the old mantra was, ‘Someone else must try this before we will’, there is little time for that kind of waiting now in the face of research and field data showing how to boost production.
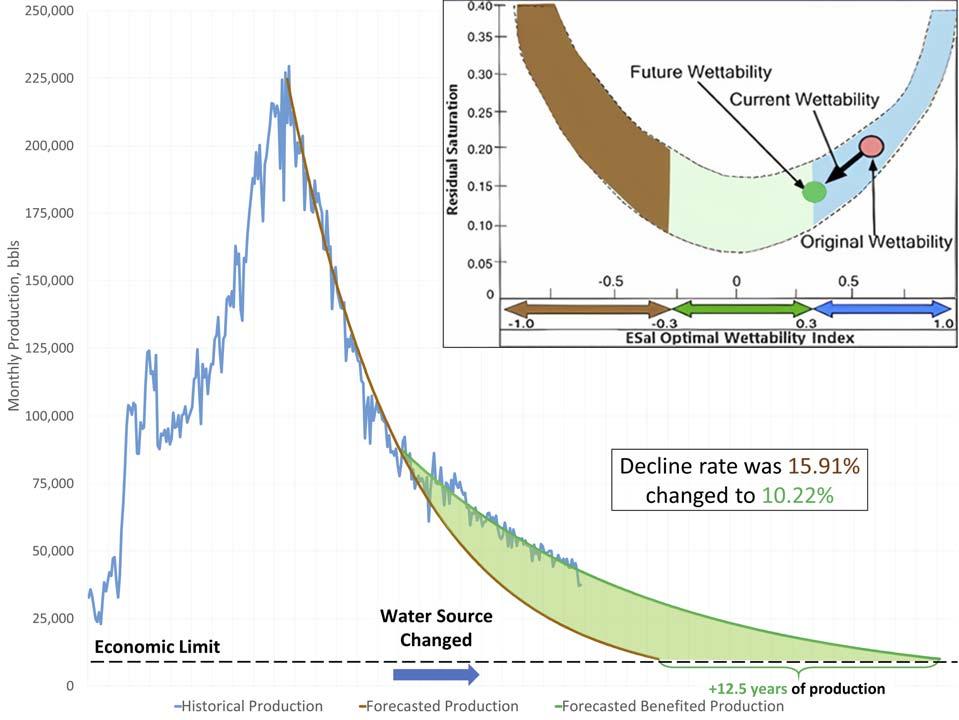
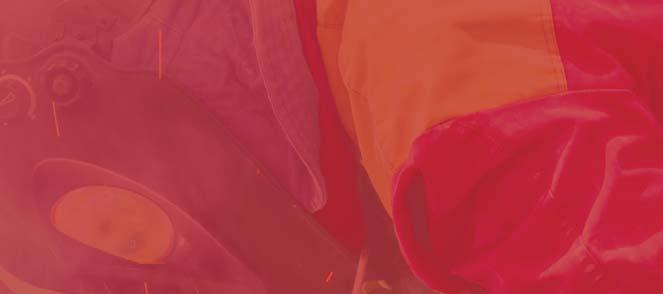
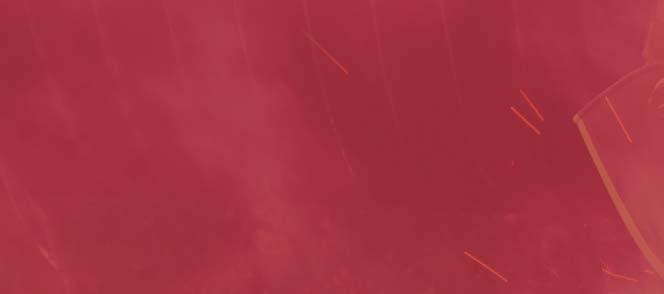

Keep up to date with us to hear the latest pipeline news
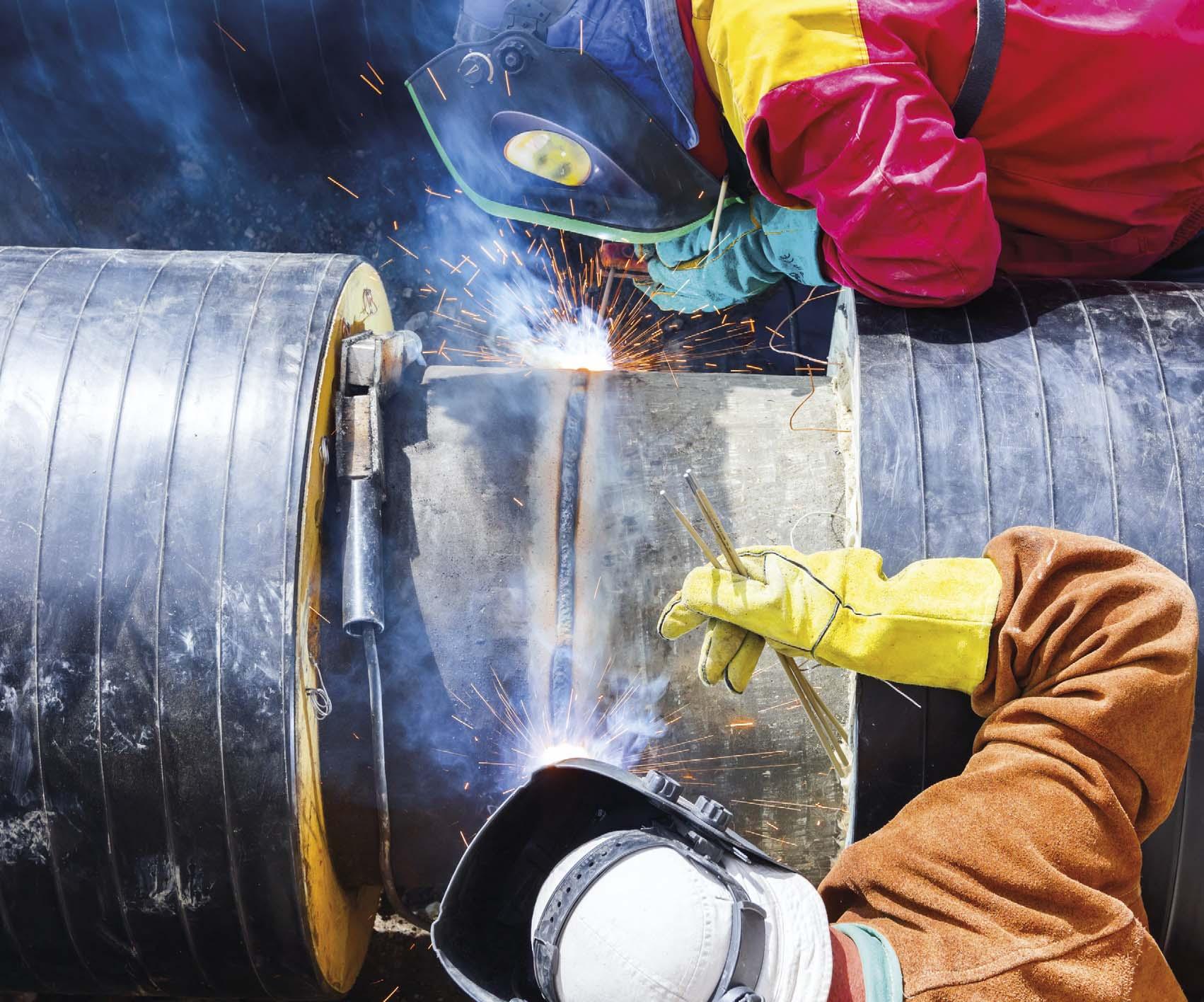