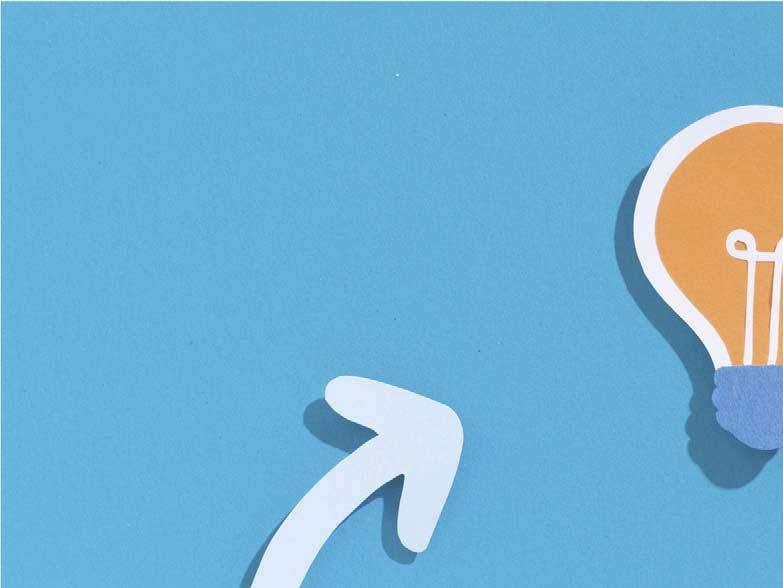
9 minute read
Responsive R&D
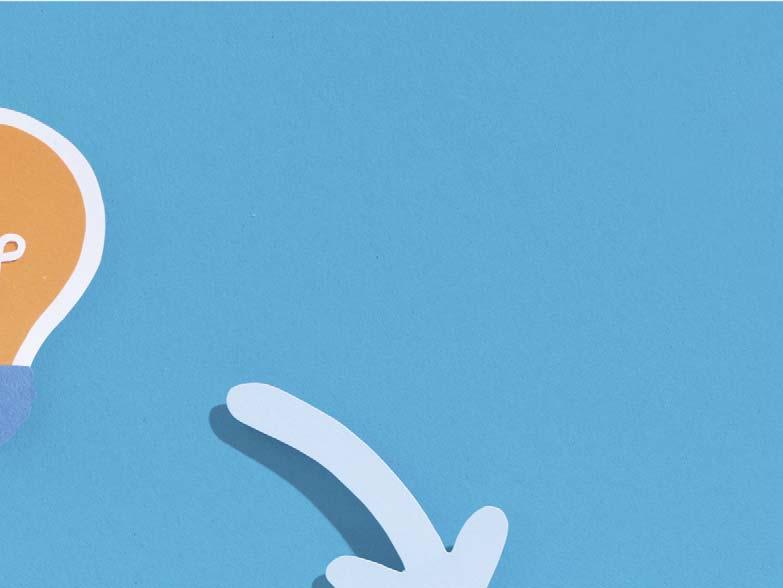
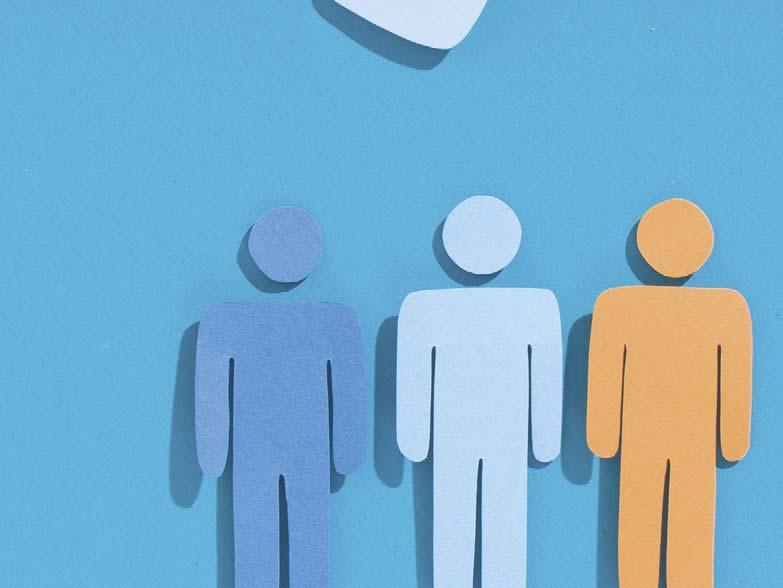
Scott Petrie, Adrilltech, UK, considers the development of continuous circulation systems and how the technology is being adapted in response to the pressures of the downturn.
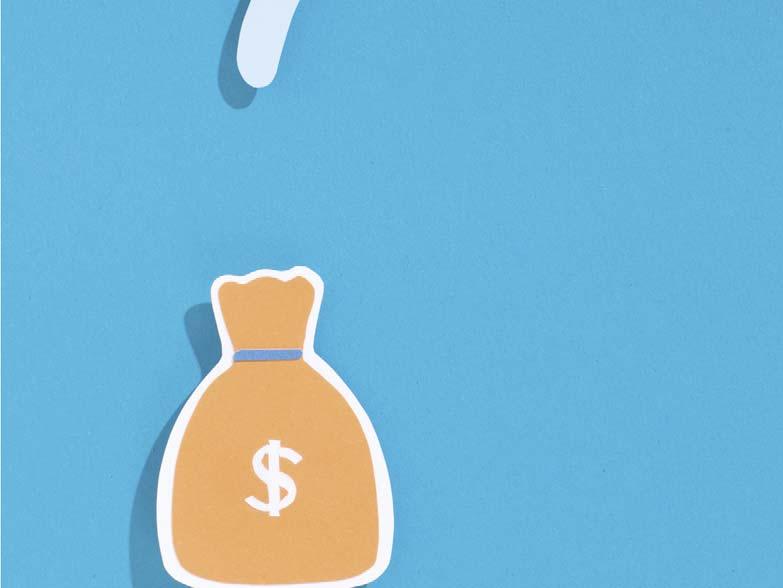
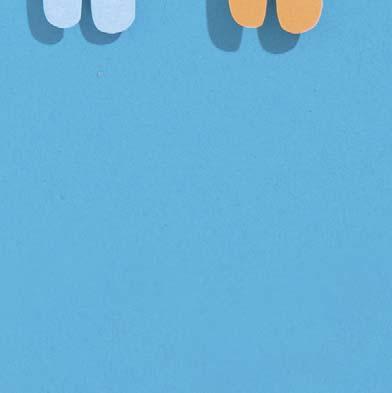
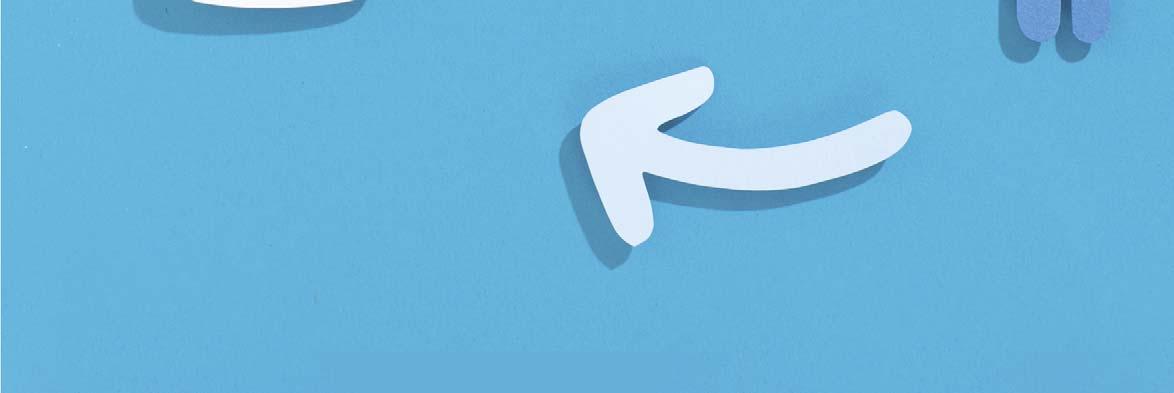
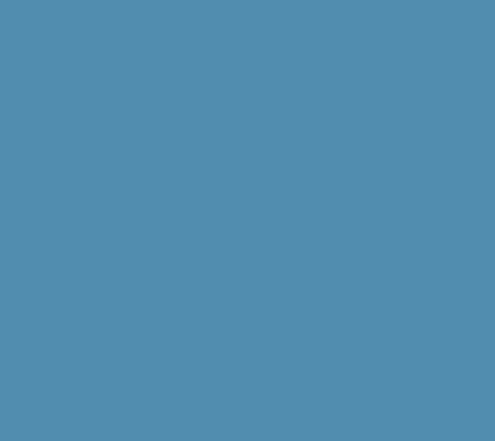
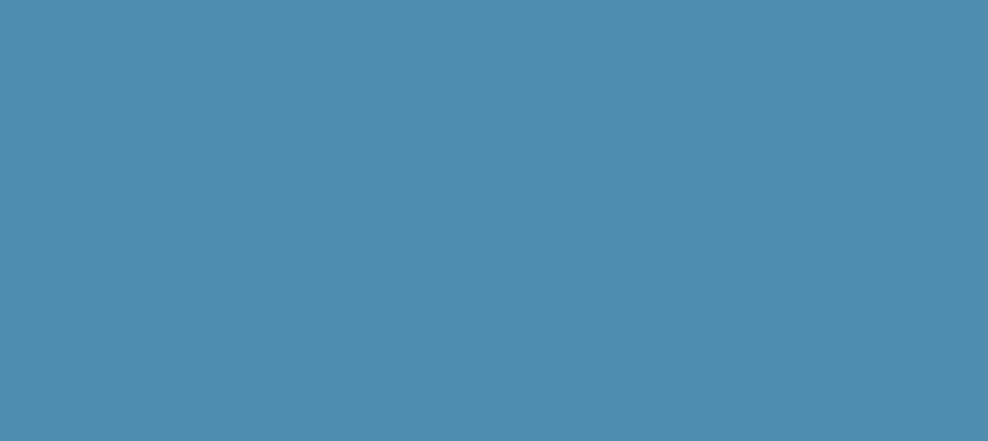

Managed pressure drilling (MPD) technology is now seen as a mature drilling technique, more of an accepted norm than the niche, novel technology it was 10 years ago. When MPD was developed, continuous circulation systems were perceived as a secondary, less capable off ering. However, 15 years on and, in areas where cost considerations are paramount, continuous circulation has firmly established itself as a high value, lighter footprint solution that is quickly deployable to drill depleted formations for gas storage, geothermal or enhanced oil recovery (EOR) applications.
By diverting flow from the standpipe via a dedicated port in the side of the drill string and therefore isolating the top drive from the inside of the drill pipe, the pipe can sit in slips while circulation continues through the pipe/annulus and back to the active pit. Once the top drive is isolated and bled down, the next stand can be picked up and connected to the stump without stopping circulation. Flow is then re-established through the top drive and the hose used to circulate while the connection is made, is bled down and disconnected. The string is then picked up out of slips and rotation restarted before going back to the bottom and drilling ahead.
System deployment is relatively simple, small and non-invasive, with much of the technology employed being standard oilfield equipment: hydraulically activated 10 000 psi gate valves, modified Kelly valve submersibles and conventional high-pressure and low-pressure pipework. Systems can be operated remotely and are non-electrical. The key, patented technology of the system consists of the non-return valve in the side of the Kelly valve submersible, which is rated to 15 000 psi.
Development of continuous circulation systems
Following Eni’s development of early continuous circulation systems for use in the Mediterranean, ExxonMobil pioneered use of the technology for drilling in remote locations where heavy losses were being experienced. Adrilltech has spent the last 11 years further developing the technology with lessons learned from over 100 operational deployments around the world; in multiple operating environments, including onshore, off shore, shallow water, deepwater and high-pressure, high-temperature (HPHT) – both alone or with MPD – the technology has delivered value.
As with many new technologies, development of the Non Stop Driller (NSD) system was driven by necessity. While drilling top hole sections in the mountains of Papua New Guinea with fresh water, ExxonMobil was driven to seek an alternative approach as a result of experiencing total losses, lost bottomhole assemblies (BHAs) and an inability to reach section total depth (TD). By switching to foam drilling with a 3-phase separation system, some of the issues were alleviated. The change required rotating control devices (RCDs) to be installed, yet with 1600 psi of air pressure there still existed the issue of bleeding down and defoaming over each connection. This could result in connections taking an hour, bringing into question the viability of foam drilling these wells. By introducing the NSD system, which is capable of continuous flow throughout the connection process, the need to bleed down and defoam was removed and continuous circulation could be maintained while the next stand was picked up. Several days of rig time were saved per well, giving ExxonMobil the confidence to attempt directional work and drive section TD and casing setting deeper in the formations. Following the technology’s first successful campaign, further improvements were sought – the next stage of any work where underbalanced drilling (UBD) and air drilling are being used to simplify processes. At the time, MPD technology was becoming increasingly viable and therefore, following detailed FEED engineering, the value of combining MPD and the NSD system was established, with the combination of technologies enabling very narrow pore pressure/fracture gradient (PP/FG) window wells. MPD with NSD was applied to diff icult drilling environments in Malaysia, Egypt and the Netherlands on multi-well campaigns.
During the development of the technology much has been learned regarding the benefits of continually circulating the well. The process was seen to allow maintenance of stable equivalent circulating density (ECD) and continuous cleaning of the wellbore over connections, improve management of high specification mud systems and reduce weight-to-weight times during drilling and tripping operations. These improvements are seen whilst simultaneously reducing non-productive time (NPT) and assisting with the detection and management of well control events – oft en encountered during pump-off events and connections. Additionally, continuous circulation has been shown to enable the maintenance of the downhole tool temperature at safe, stable levels in HT applications.
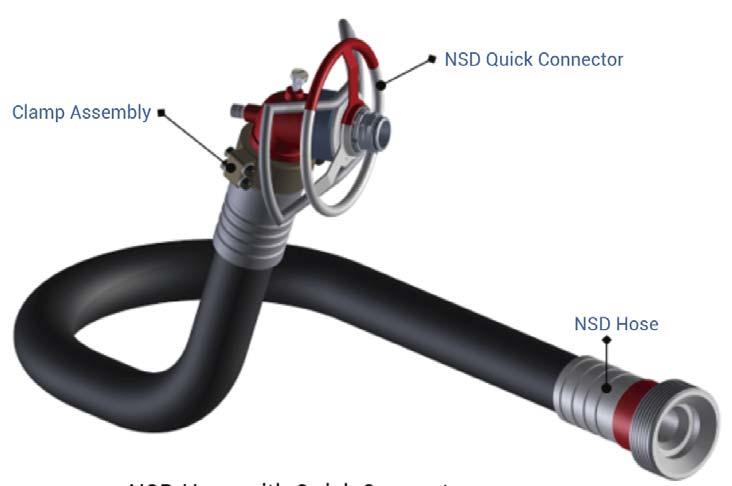
Figure 1. NSD hose with quick connector.
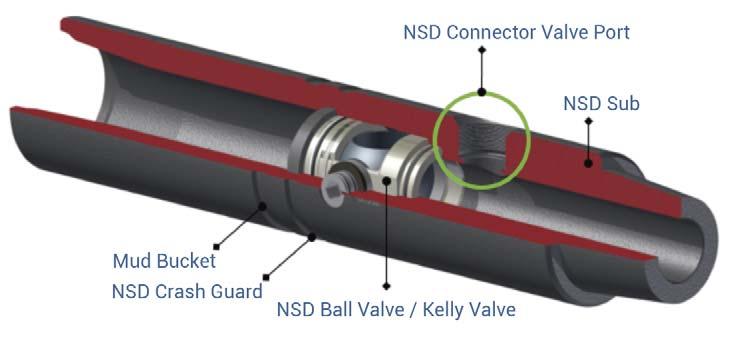
Figure 2. NSD sub with ball valve.
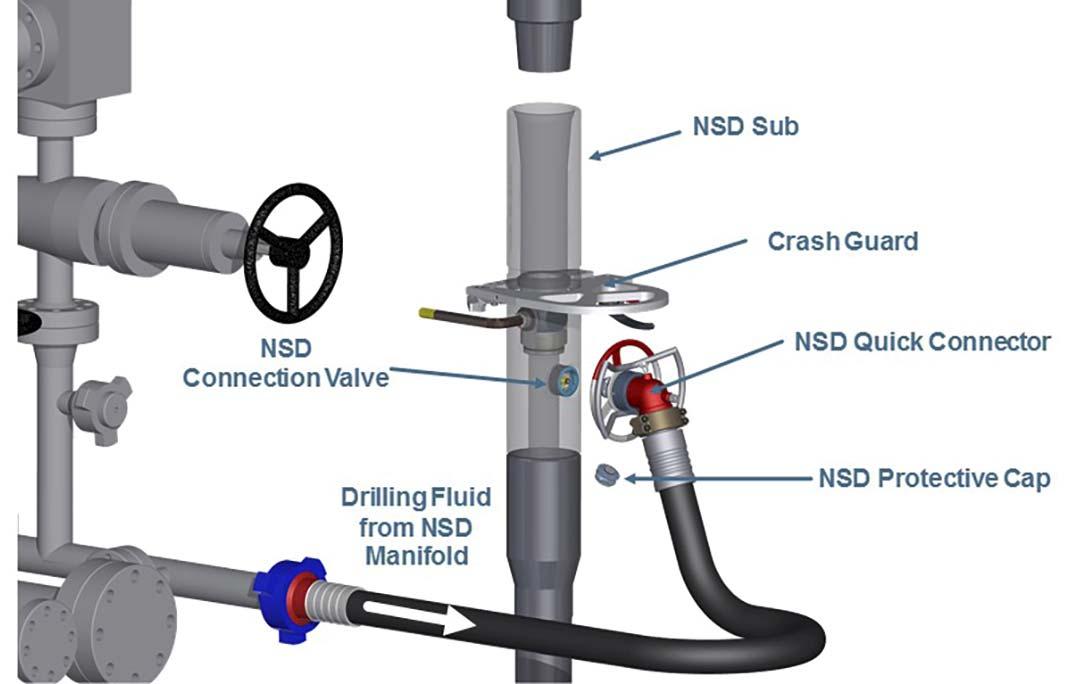
Figure 3. NSD rig floor arrangement.
Responding to the downturn
Despite these benefits, technology continuously evolves and during the recent downturn application of technology has been limited by many factors. Cost reduction, a lack of dedicated engineering resources to qualify new technologies, a switch in contracting philosophy to integrated services and changing regulatory approaches discouraging the use of new technologies are among the many issues faced when attempting to introduce innovative technologies. These constraints are driving developers to pivot into spaces where technology is most needed, applying R&D eff orts towards increasing value though improved rate of penetration (ROP) and reduced NPT alongside removal of personnel from the rig site via digitalisation and automation. NSD’s development has sought to meet these challenges head-on, developing the technology to reduce the cost of deployment, automate systems, train rig crews to use and service the equipment and off er the system for sale to drilling contractors. Specifically, driven by industry-wide ambitions
REGISTER HERE
ADIPEC 2021 VISITOR REGISTRATION IS NOW OPEN
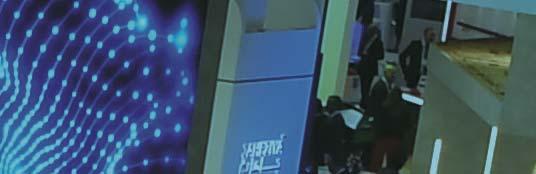
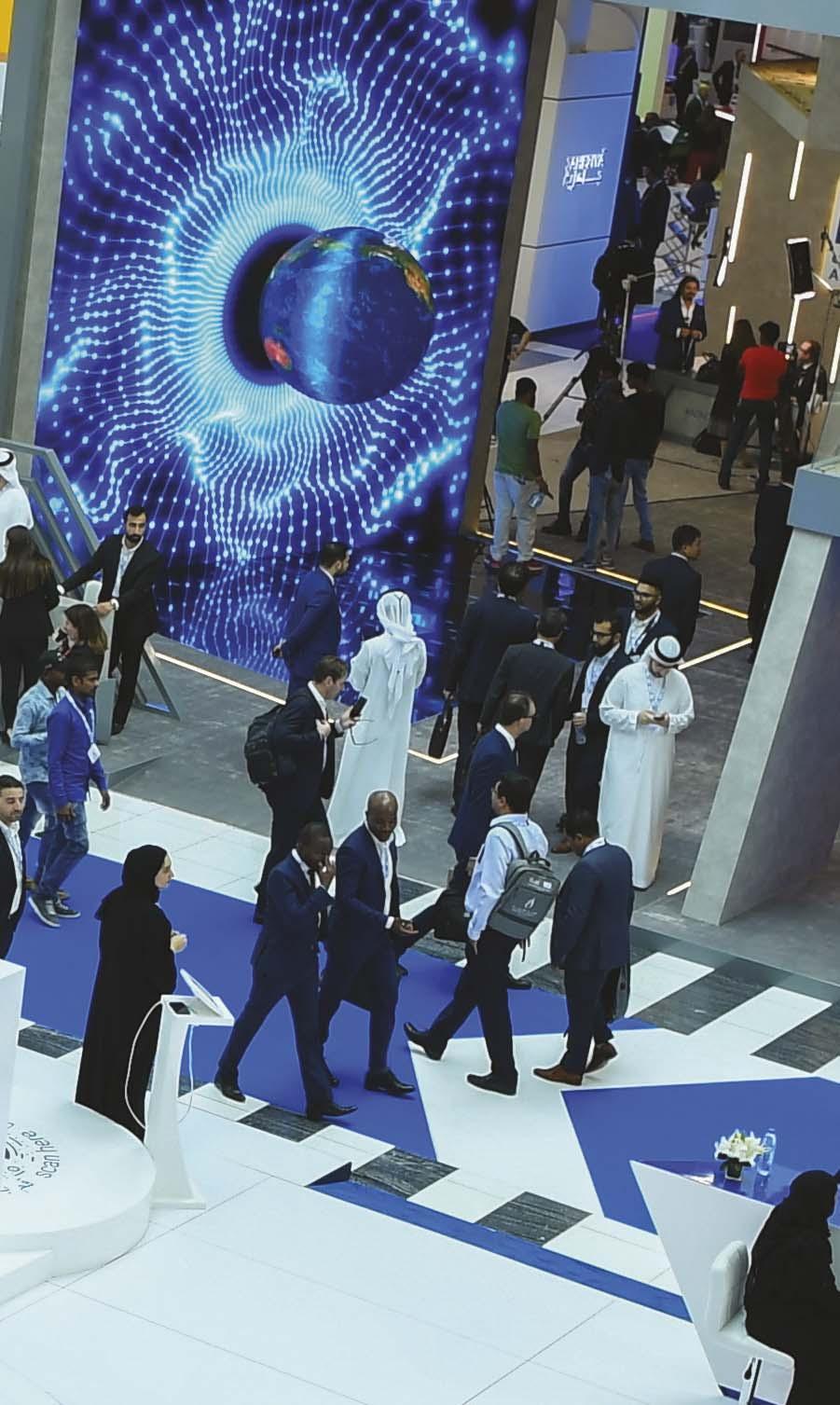
WHY VISITORS ATTEND ADIPEC:
GENERATE QUALIFIED LEADS.
80%
DO BUSINESS.
NETWORK.
100,000+ 135
PURCHASING POWER
$18.9 billion
ONE MEETING PLACE FOR ENERGY PROFESSIONALS.
51 26 2,000
#ADIPEC #ADIPEC2021
DOWNLOAD the dmg events AllSecure guide:
Country Partner Partners Platinum Sponsor Gold Sponsors
to reduce risk by removing personnel from the well centre, NSD has introduced a re-designed continuous circulation system that allows fully automated, hands-free operations to be performed, eliminating the need for personnel in the red zone and allowing rig crew to operate the system from the safety of the doghouse. It has additionally focused on developing engineering capabilities and FEED for specific projects, helping to clearly identify where value is added. Widespread acquisition of additional downhole information from pressure while drilling (PWD) has allowed more detailed studies into the technology to be carried out, demonstrating ROP advances and improved outcomes from circulating over connections while drilling and tripping, particularly in depleted or unstable formations.
Over the last two years, Adrilltech has identified several niche technologies which, when used either in combination with NSD or with each other, can bring added value with limited additional people at the rig site. An example is the combination of NSD with DrillClean, a cuttings volume management system. The combination allows accurate measurement of the volume of cuttings returned to the surface throughout the drilling of a section, even over connections, while pressure variations that may be related to cuttings loading can be measured and managed, avoiding hole cleaning issues and ensuring optimal ROP for drilling the well. The company has launched seven similar technologies that are eff ective both when used individually and when utilised in combination.
The successful application of new technologies cannot happen without eff ective management of change. Safety statistics when implementing new technologies are oft en highly favourable, as the first use of novel technology is usually closely scrutinised to ensure initial deployments are successful. A substantial part of the pre-planning phase is devoted to performing HAZID/HAZOP assessments, identifying all key interfaces and ensuring that adequate control measures are in place at every interface to significantly reduce the risks associated with any first-time deployment. Although adding value is a fundamental KPI for the first use of any technology, it is universally accepted that safety must be of primary concern; if additional time is required to ensure that everyone is trained, familiarised and working to the common goal of successful and safe implementation of the technique, then the process can be deemed successful. With new technologies, teams oft en begin with a healthy scepticism and there is a learning curve to follow. However, they quickly become enthused with new methods if they are seen to improve their work practices. Managing this change to get to this stage is crucial to the success and longevity of any project.
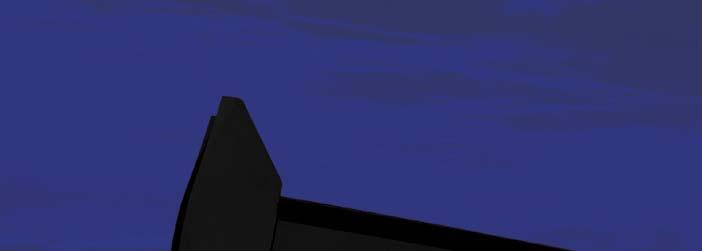
Stay informed
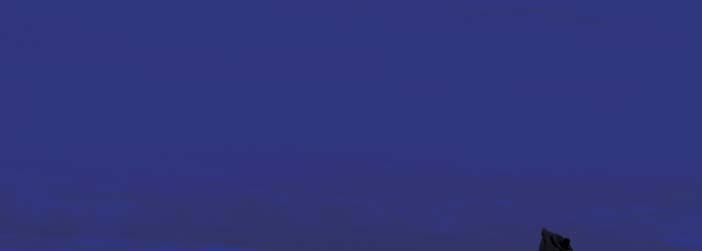
Conclusion
NSD continuous circulation has reduced overall section days in multiple wells and has a small and easily managed rig site footprint. Change is forever a feature of the drilling industry: the management of that change is vital to ensuring that new technologies add value with immediate eff ect. Adrilltech’s technologies aim to make the drilling process more eff icient, reducing the overall carbon footprint of well construction whilst helping operators to drill lower cost wells with the fewest people at the rig site. Throughout the technologies’ development many diff erent applications have been identified and realised by diff erent operators. Applying these advances to the nascent energy transition, the company have been active in the drilling of diff icult geothermal wells, such as improving hole stability during the drilling of ash and tuff deposits, while looking to minimise cost per foot drilled and maximising megawatt output per dollar input. The equipment helps drilling eff iciently to TD, protecting expensive BHAs from temperature and risk while drilling the lowest cost high-enthalpy geothermal wells.
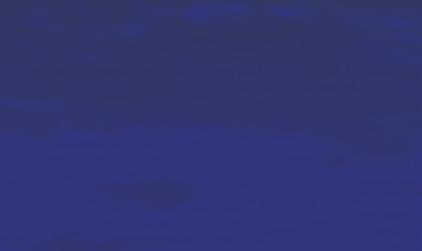
Keep up to date with us to hear the latest in upstream oil and gas news
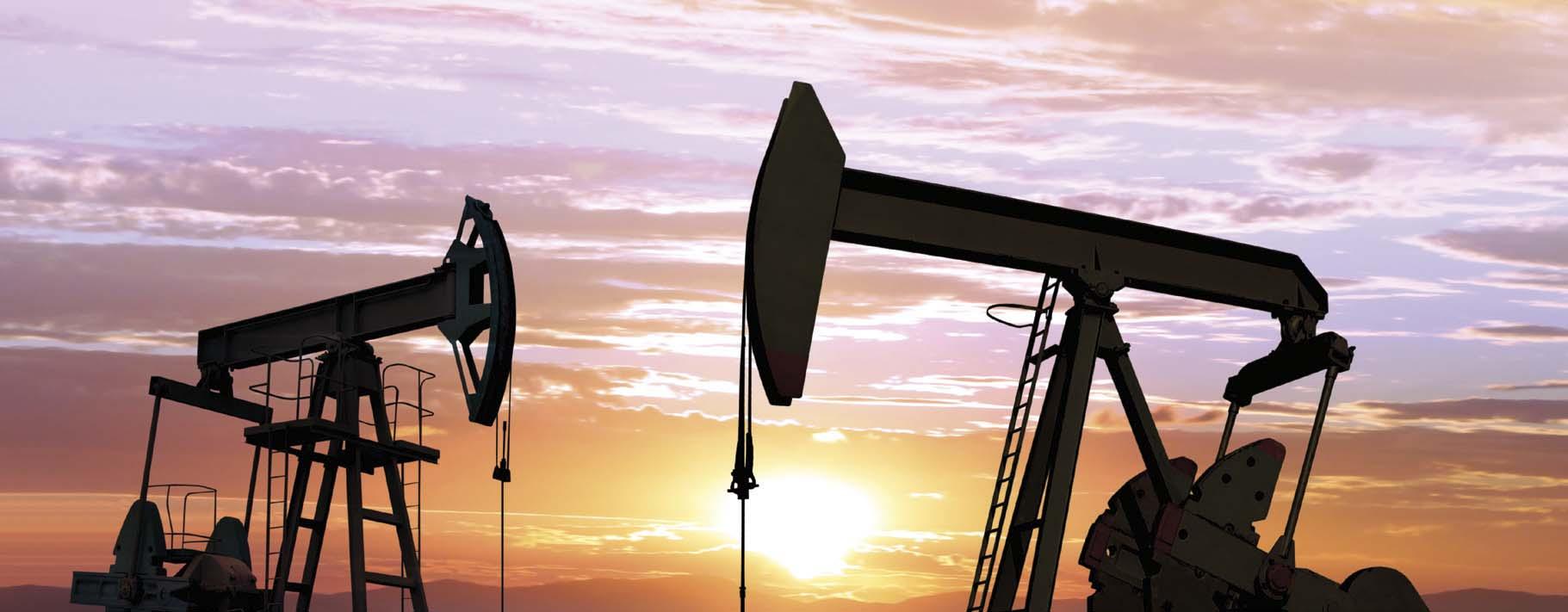
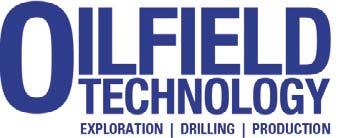