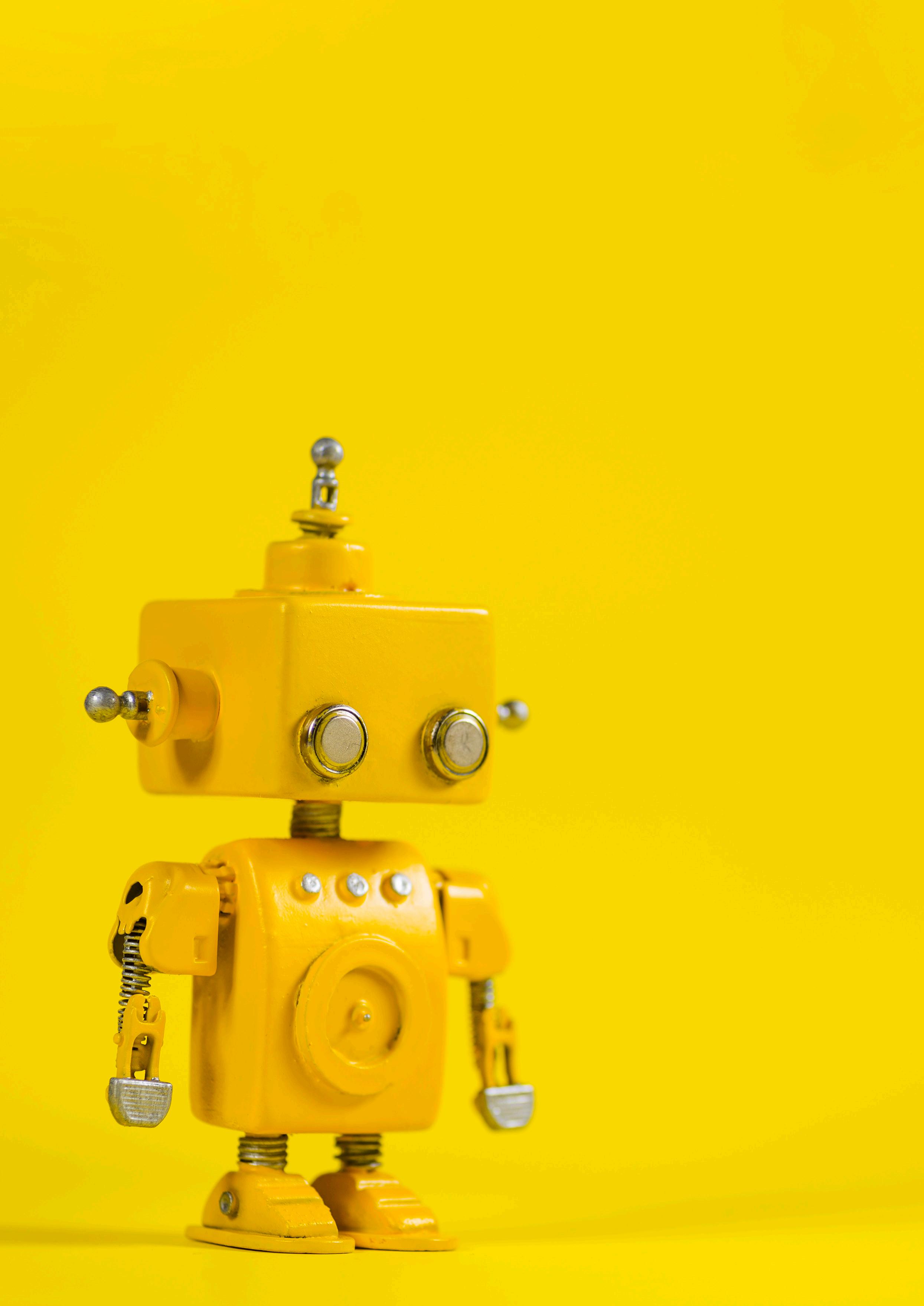
7 minute read
Making delivery robotic
Liam Hanna, NDT Robotics and Scanners at Eddyfi Technologies, UK, outlines the critical factors in an efficient inspection programme for LNG tank maintenance, focusing on deployment and delivery.
Being able to do more with less is especially applicable when it comes to better LNG tank maintenance programmes. The modern-day smartphone is an excellent example of this, with its ability to enable so much more than simple verbal communication functionality. In the non-destructive testing (NDT) world, the same concept of getting the most out of the inspection technology has seen product advancements that have pushed the boundaries of what is truly possible today. This is not unique to process plants, as any industrial manufacturer understands the need to reduce downtime for maximum productivity. The LNG industry has witnessed the shift towards risk-based inspection (RBI) to minimise shutdowns and take advantage of available resources during planned outages. Of course, using the right NDT method is imperative to increase efficiency, but delivery and deployment are a key factor for success.
Developing new technology
The LNG industry presents a multitude of challenges. When considering commercially available products, it is important to understand what engineers and product teams ask themselves in the development of the solution. Does it enhance safety? Improve environmental performance? Increase operational efficiency? Aid in cost reduction or even avoidance? From transportation, treatment, refrigeration, liquefaction, storage, loading, and back to transportation again, the LNG industry is a perfect example of how NDT solutions can increase safety and performance and protect the environment at every stage throughout the process.
Whether operating in oil and gas, power generation, energy, nuclear, maritime and shipping, defence, utilities, or another critical industry, key applications repeat themselves: pipeline inspection, surface inspection, and
vessel inspection. Given the capital infrastructure that makes up LNG plants and the closely integrated individual systems, for example a pipe or a vessel, these systems always remain as pipes or vessels. It is understood that the inspection requirements may change, as may the technology being deployed. Eddyfi Technologies can offer diverse inspection solutions spanning multiple technologies, from ultrasonics such as conventional ultrasonic testing (UT), phased array UT, total focusing method, time-of-flight-diffraction (TOFD), or electromagnetic techniques, including alternating current field measurement (ACFM®), eddy current, eddy current array, pulsed eddy current, and magnetic flux leakage. However, the glue that holds everything together and allows for a truly remote, unmanned inspection solution is the delivery and deployment method. Whether that is a simple NDT scanner to aid in repetitive or awkward placement of probes for specific LNG equipment inspections, more automated crawlers for weld and corrosion mapping, or robotic solutions for ad hoc, hard-to-reach assessments in areas where a human cannot or should not be sent. Within the LNG market, these solutions are available to solve problems, reduce downtime, and increase efficiency in multiple areas along the chain.
LNG inspection improvements
LYNCSTM is an advanced modular ultrasonic inspection scanner designed to provide phased array
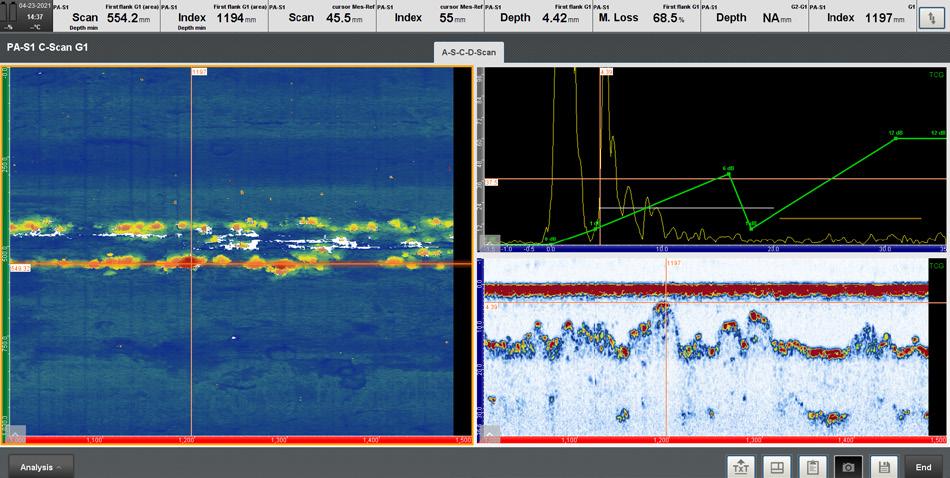
Figure 1. Phased array ultrasonic testing (PAUT) corrosion mapping data, showing reliable results delivered.
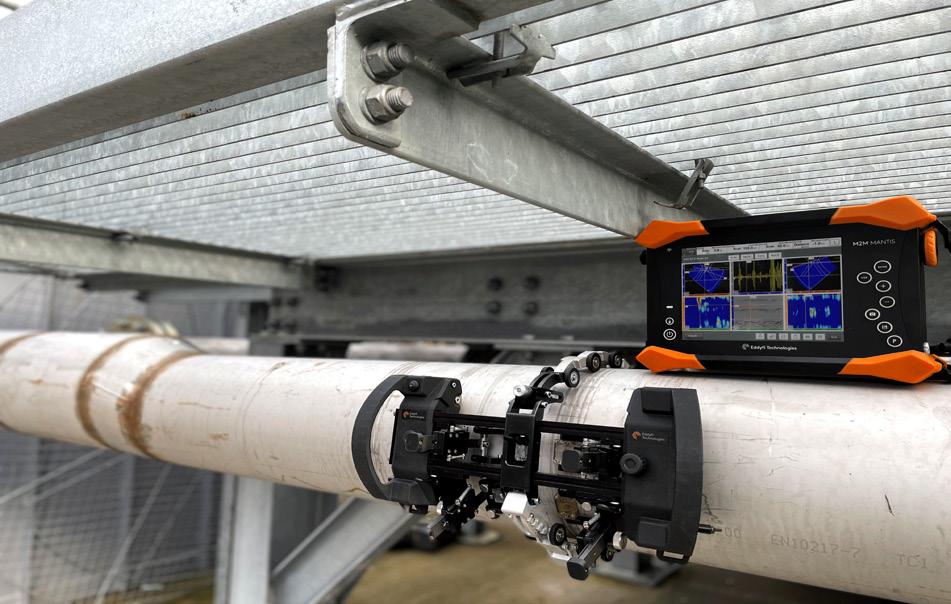
Figure 2. The multi-functional LYNCSTM scanner by Eddyfi Technologies addresses LNG PAUT inspections across multiple assets. ultrasonic testing (PAUT), corrosion mapping, and PAUT or TOFD weld integrity assessments. The versatile system allows users to interchange between weld inspection and advanced corrosion mapping in under one minute. Onboard scanner controls allow for one-man operation, with seamless integration to the portable Gekko® and MantisTM phased array instruments. When the device is in weld inspection mode, operators can start and stop a scan. When it is in corrosion mapping mode, operators can increment or stitch together data without touching the PAUT instrument. LYNCS, and other crawler and robotic solutions offered by Eddyfi Technologies, supplement decreased downtime and increased operational efficiency by: z Reducing the time an LNG plant is shut down for.
z Allowing solutions for in-service inspection.
z Performing inspections where multiple data sets and maintenance can be carried out in unison.
When faced with confined spaces, heights, and other hazardous areas, robotically deploying probes offers a better solution, such as using the ACFM electromagnetic testing technique. It offers distinct advantages for the inspection of the gas storage spheres, or Horton spheres, commonly found among LNG facilities. It requires minimal surface preparation, meaning that the protective layers found on support vessels, piping, etc. remain unscathed. Without the need for consumables to detect surface-breaking cracks in metals, which would normally be used in conventional methods, ACFM works through coatings and can be used as a screening tool ahead of significant surface cleaning to prevent unnecessarily preparing LNG assets without cracks. It provides depth sizing to establish thresholds for inconsequential cracking, which in turn prevents any unnecessary grinding. When compared to wet fluorescent magnetic particle testing (WFMT), ACFM has proven to be approximately 60% faster – and this was evaluated with the older, slower legacy ACFM technology. Three times faster than magnetic particle inspection (MPI), and even quicker when report writing is considered, a Petrobras gas storage sphere ACFM inspection found twice as many crack indications as MPI.1 Today’s SENSU®2 compliant array technology is NDT crawler adaptable and offers a wider coverage with spring-loaded sensors. Moreover, the technology allows scan speeds of 50 mm/sec. for data acquisition, regardless of remote-controlled operation. This is just one example of the importance of delivering the right NDT technique alongside the right deployment and delivery for higher productivity. Expanding on this, the MaggTM Enabled allows for a standardised approach for multi-sensor robotics, remotely deployable up to 100 m, and operable subsea up to 60 m (depending on supplementary NDT technique chosen), with tool-free probe mounting for ultrasonic testing, phased array UT, eddy current array, and ACFM. This configuration affords a modular, deployable solution that is easy to use, with training readily available remotely through the Eddyfi Academy. In general, the Magg is a proven and reliable remote inspection crawler designed to withstand the harsh conditions and industrial environments found in LNG production. The technology can quickly and easily navigate
critical restricted access areas, whether the surface is clean or close to unpractical. The unique combination of raw power, agility, and magnetic downforce allows the NDT robot to accomplish LNG inspections that most wheeled vehicles and crawlers simply cannot. Costs can be reduced or avoided by limiting or removing the expensive actions and operations associated with scaffolding, cleaning, taking the asset offline, and human entry to confined spaces. Cost drivers overlap with other drivers. For example, an inspection robot that is capable of carrying out multi-sensor NDT enables reduction in overall downtime, further reduced human entry, lower environmental impact through crawler mounted tooling operation, and improvement in safety as maintenance personnel no longer need to enter the LNG tank, vessel, or other confined spaces. So, while the NDT techniques may be tailored and vary for LNG tank maintenance, the delivery and deployment are a key factor in quite literally being able to do more with less. Whether performing corrosion mapping on the outer shell, assessing T-joint attachments, or checking out a tank roof, NDT scanners and robotics that provide multiple inspection technologies and applications are visibly making a difference in terms of increased productivity at LNG process plants worldwide.
Conclusion
NDT is at the heart of monitoring LNG tanks and other critical assets for their structural integrity to help ensure the prevention of any potentially catastrophic failure resulting in environmental contamination and loss. A strong risk management programme will go beyond meeting relevant regulations to further optimise the inspection and maintenance activities designed to improve reliable performance and profitability of terminals. This is achievable, in part, through RBI methods and the implementation of inspection robots and scanners for in-service remaining life asset integrity assessments. These in-service assessments are necessary to identify potential areas requiring an update, repairs, or routine maintenance for current and future needs during planned shutdowns. It is imperative that the NDT device performing non-intrusive inspection and/or remote internal inspection collect repeatable, actionable, meaningful, and preventative inspection results; moreover, it should be capable of collecting multiple datasets in real-time to provide a complete picture of current conditions. This enables better forecasting and better decision making, due to a code compliant and permanent record of inspection. In an industry that cannot afford for things to go wrong, innovative technology takes the guesswork out of choosing the right technique at the right time and delivery by the right deployment method.
References
1. TREMBLAY, C., ‘More Productive Process Plant
Inspections with ACFM®,’ https://blog.eddyfi.com/en/ more-productive-process-plant-inspections-with-acfm
The premier source of technical and analytical information for the renewable energy industry, covering solar, wind, bioenergy and storage.
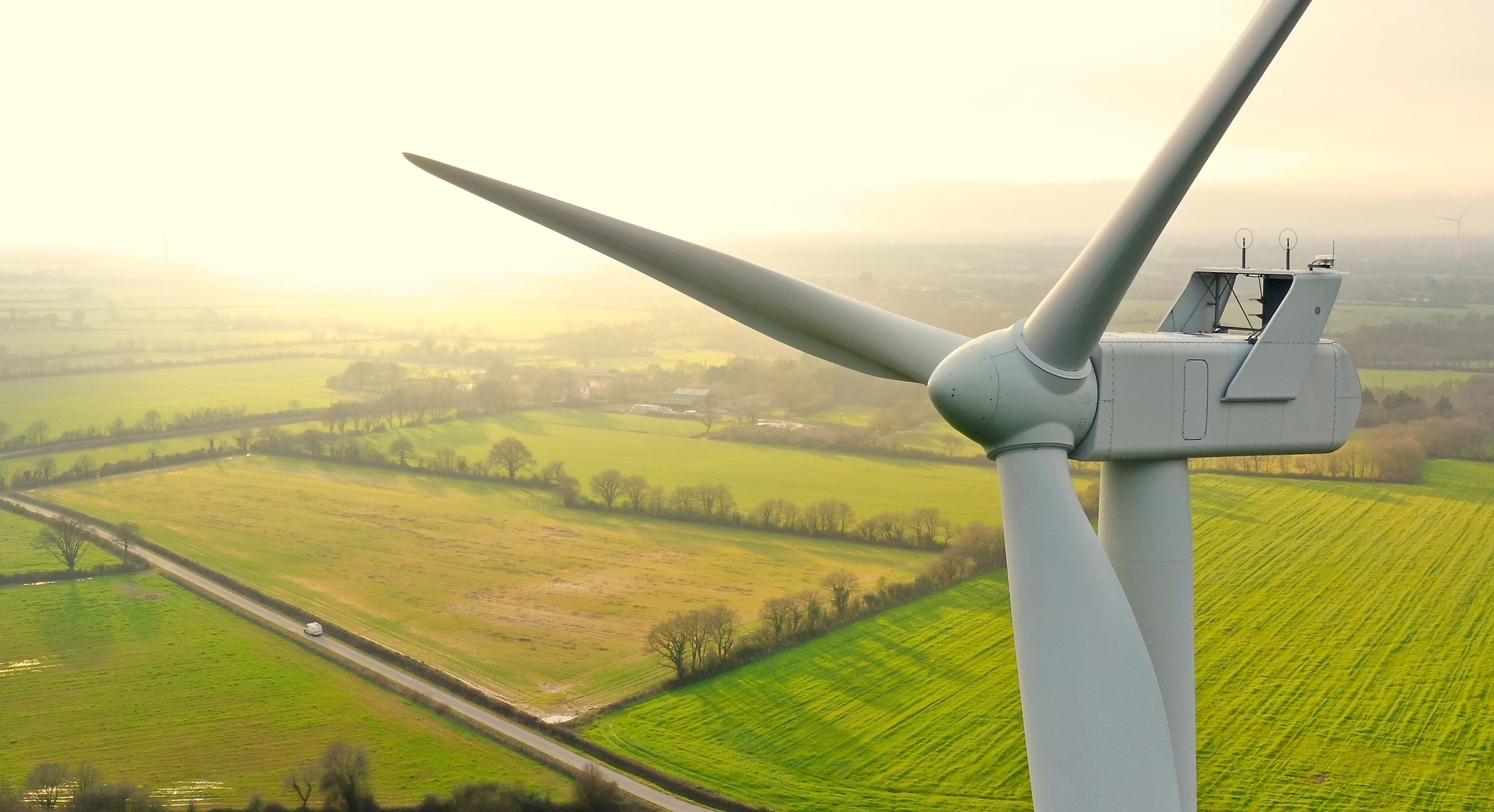