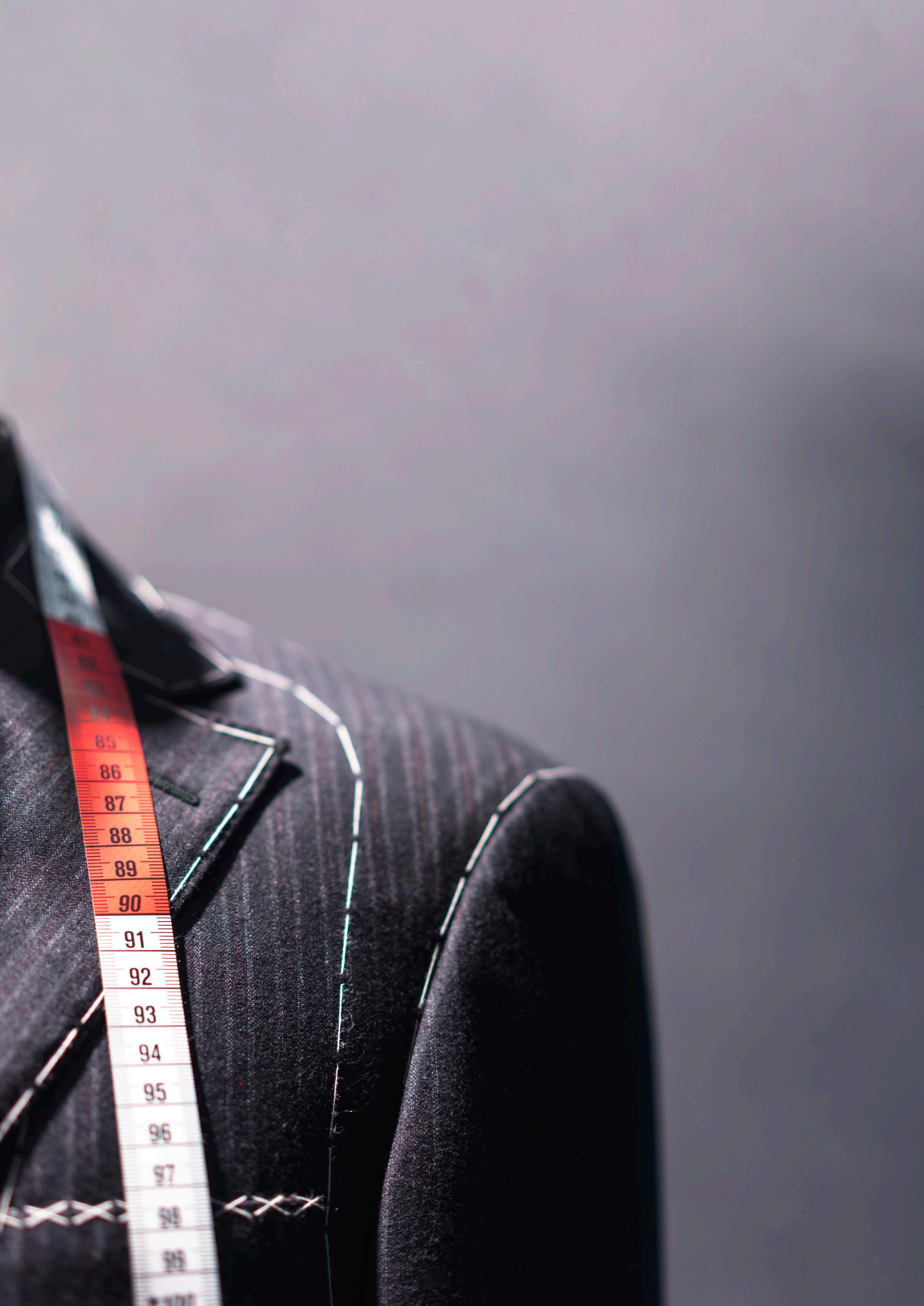
13 minute read
Finding the right fit
Thomas Hess, Burckhardt Compression, Switzerland, considers the range of compression technologies on offer for the handling of boil-off gas in LNG storage and shipping, and provides guidance on selecting the most suitable technology for different requirements.
ompressors are the main actors for gas handling in LNG facilities – both onshore and on ships. Handling of LNG boil-off gas (BOG) is complex, not least due to the very low gas temperatures. As the gas can be processed in multiple ways, each application has its own specific requirements. But why is gas handling required in LNG facilities at all? And what are the typical application ranges and compressor technologies available? This article provides a brief insight into the application range and the advantages of the LNG BOG compressor portfolio offered by Burckhardt Compression.
BOG in LNG storage and transportation
For storage in liquefaction plants, receiving terminals, or onboard ships, LNG is kept at atmospheric pressure under cryogenic conditions of below -160˚C. This condition is ideal for efficient storage and transportation since the liquid occupies only 1/600 of the volume of the gas. The transportation of LNG from liquefaction plants to the receiving terminals is done by ship. Onboard modern LNG carriers, the cargo is stored in highly insulated membrane type containment systems. Since the trading of LNG is a global business, and voyages from loading terminals in the US to receiving hubs in Asia can take approximately 30 - 40 days, the handling of BOG becomes crucial in order to keep the cargo tank pressure under control. Bunker ships supply LNG to gas-fuelled ships. Although smaller in size if compared to LNG carriers, BOG management is required to manage the cargo temperature and tank pressure. Despite the highest level of thermal insulation on storage tanks and piping, heat ingress to the LNG is unpreventable.
The warming-up of the LNG leads to the formation of BOG, a problem which exists in the entire LNG production, storage, and transportation chain. Efficiently managing BOG in terminals and onboard ships represents a key issue. The amount of BOG generated is not constant and varies with the terminal or ship operation, tank filling level, gas composition, and ambient conditions, thus the volume of BOG to be managed is unsteady and fluctuates.
Whilst cryogenic pumps can efficiently handle the natural gas in its liquid state, compressors are required to treat the inevitable BOG. BOG management is required both onshore and on LNG ships. Accordingly, different operating conditions are specified for compressor systems depending on their application onshore or for maritime use.
Compressor selection
A wider selection of different compressor technologies is offered to the market for the handling of BOG. Proper selection of the type of compressor is dependent on the evaluation of many operating parameters and represents a challenge to the decision maker. Different compressor types have distinct advantages depending on the anticipated range of application. Burckhardt Compression provides a complete compressor portfolio for BOG applications, both traditional labyrinth sealing and labyrinth sealing in combination with ring sealing on higher stages. Burckhardt Compression can therefore advise where these different designs can be best applied.
Suction conditions
Whereas there is a wide range of discharge pressures specified for compressors installed in LNG terminals and LNG ships, the requirements on the suction side are rather identical. Since the gas is stored in non-pressurised tanks both at onshore terminals and on ships, a suction pressure level close to atmospheric conditions is specified (typically ranging
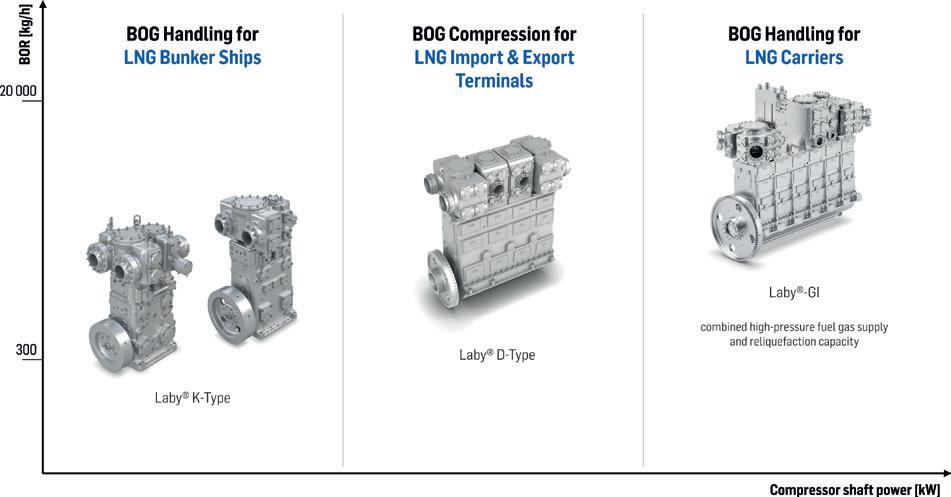
Figure 1. The Burckhardt Compression LNG BOG compressor portfolio: small two-crank Laby® K-type compressors cover the area of smaller flowrates, typically installed on LNG bunker ships but also in small scale onshore LNG facilities. Two- and four-crank Laby® D-type compressors with a stroke of 250 to 375 mm can be found in many LNG terminals. Six-crank Laby®-GI compressors complete the portfolio, being able to handle large flows of up to 20 tph and compressing gas to 300 bar. Laby-GI compressors are designed for maritime use but are also installed onshore. from 1.0 to 1.3 bar abs). Although the pressure range on the suction side is rather small, huge variations on the suction side temperatures need to be considered. Even though during normal operating conditions the compressor might be handling cold gas with typical temperatures of -120˚C to -90˚C, start-up conditions or the use of a partial reliquefaction system onboard an LNG carrier can bring the suction temperature up to 40˚C. Ideally, the BOG compressor is able to handle the incoming gas at both cold and warm conditions, without the need for extra equipment for gas temperature conditioning.
Flowrates
Specified flowrates for the compressor system vary with the storage capacity of the terminal resp., the size of the LNG carrier, or bunker ship. Moreover, the quality of the storage tank insulation finally defines the volume of BOG gas which needs to be compressed during normal operation. Burckhardt Compression offers a wide range of Laby®, Laby® K-type, and Laby®-GI compressor systems, suitable to cover the required flow capacities of the LNG industry – both onshore and at sea. Since the flow of BOG fluctuates greatly, capacity control becomes necessary. Compressor valve unloading is an efficient way to adjust the capacity of a reciprocating compressor by deactivating individual compression rooms. This makes reciprocating compressors in general more energy-efficient and power saving as competing screw or centrifugal type compressors.
Discharge pressure range
For onshore LNG terminals, the boil-off handling usually foresees the compression of the gas for the supply into a reliquefaction unit. Typically, a discharge pressure level of approximately 10 bar is therefore specified. With the same pressure, the natural gas can also be supplied into a power plant – if applicable.
Some terminals also consider the compression and supply of gas into the connected pipeline system. Depending on the local gas network characteristics, compressors must be able to deliver the gas at pressure levels of 30 bar up to 110 bar. Such conditions might as well be specified for so-called minimum send out (MSO) compressors installed on FSRUs. Onboard LNG carriers, BOG is used as fuel for the main propulsion system and auxiliary engines. Modern slow-speed, two-stroke, dual-fuel engines are nowadays the technology of choice for the propulsion system of new-build LNG carriers. As there are two competing engine technologies available on the market, two different discharge pressures apply:
z High-efficient and low-emission electronically controlled high-pressure gas injection engines (ME-GI, diesel combustion cycle) require gas supply pressures ranging from 270 bar to 310 bar.
z Low-pressure gas admission engine technology (ME-GA and X-DF, Otto combustion cycle) are supplied on lower pressure ranges from typically 13 bar to 17 bar.
Summing-up the above, LNG BOG compression is characterised by almost identical suction pressure conditions but a larger variety of discharge pressure requirements. Especially onboard LNG carriers and in receiving terminals, the gas compositions change with the quality of the LNG received.
With the expertise of more than 50 years in the handling of cold gases – both onshore and on ships – Burckhardt Compression is offering a complete range of efficient and reliable compressor solutions for the entire spectrum of compressor selection parameters.
Technology for oil-free operation
Whenever cold gases must be compressed, Burckhardt Compression relies on Laby Compressor technology. Invented in the early 1930s, the Laby labyrinth piston technology has a proven track record in the gas compression industry for almost 100 years. If compared with other competing technologies, the labyrinth piston principle convinces with its robustness, simplicity, flexibility, and longevity. The simple three-piece design of the labyrinth piston reduces the amount of required parts to a minimum. The contactless sealing allows a wide range of operating temperatures and reduces wear in the cylinder section due to the absence of sealing elements. Frequent start/stop operations do not cause additional wear. The key feature of Laby Compressors for its success in the LNG industry is the fact that the compressor can be oil-free and
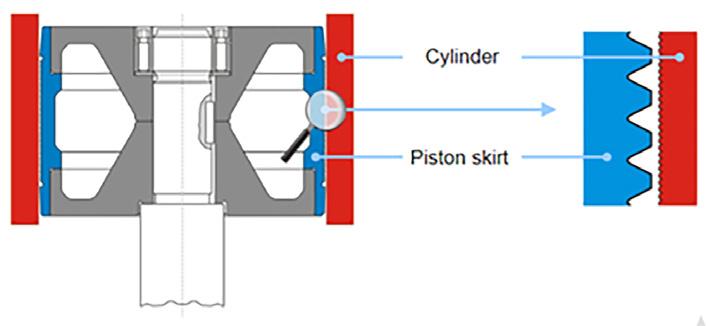
Figure 2. Labyrinth sealing between piston (skirt) and cylinder wall: the sealing effect is created by numerous tiny throttling points. Precise alignment of the parts allows contactless sealing. Wear on the piston skirt is very limited and lifetime of the parts very long. During operation, there is no permanent friction and only slight touching of parts. There are cases reported where piston skirts reached a lifetime of more than 100 000 operating hours.
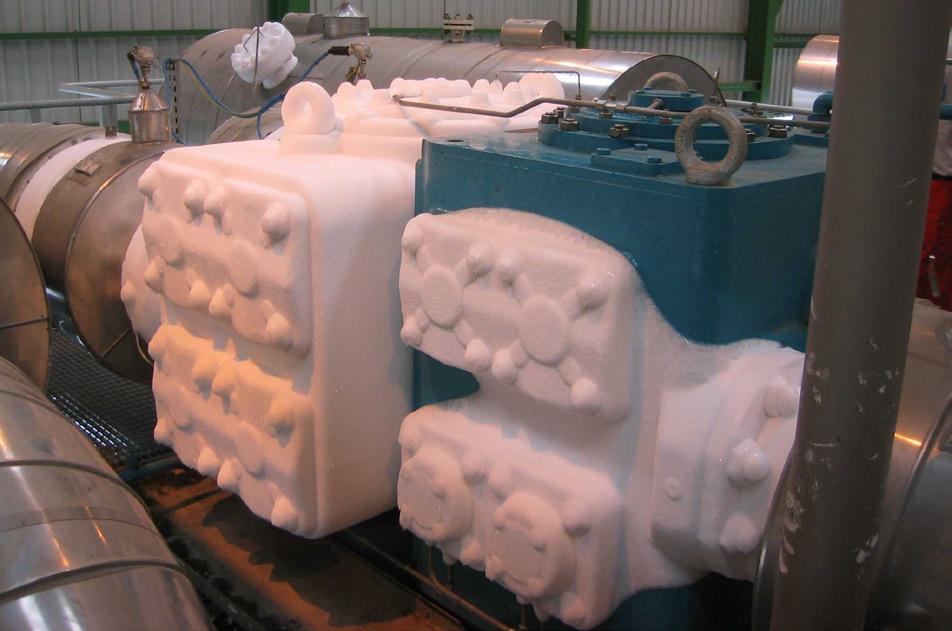
Figure 3. A two-crank, two-stage Laby D-type compressor installed in an LNG receiving terminal. Due to the low suction gas temperature, the first stage cylinder block is entirely covered by ice. Despite the compression of the gas, the suction temperature of the second stage is still below 0˚C. Ice is also covering the compressor inlet nozzle and the suction valve covers. flexibly operated at both very cold and warm suction temperatures. The compressor is able to directly take in BOG with the lowest possible temperatures – thus there is no need to pre-heat and condition the gas before compression. The use of special materials with the lowest thermal expansion co-efficients allows the operation of the compressor at suction temperature levels down to -160˚C. At the same time, the compressor might be operated with discharge temperatures up to 200˚C when handling warm temperatures at the inlet. The Laby Compressors provide flexibility and allow gas compression without the need for pre-heating.
Dry-running ring sealing technology
The use of labyrinth piston technology gets less efficient with higher discharge pressures due to the internal gas leakages across the piston skirt and the application of ring sealed pistons becomes attractive. Classic ring sealing systems require the need for lubrication. However, the presence of oil in the chain of LNG transportation is not always welcome. Originally widely applied in the area of hydrogen gas compression, dry-running ring sealing systems are nowadays successfully installed in natural gas high-pressure compressors. This technology became especially important for high-pressure fuel gas supply compressors installed on LNG carriers – the Laby-GIs.
High-pressure compressor systems
With the introduction of two-stroke, dual-fuel ME-GI engines for LNG carriers, high-pressure compression technology became required to provide the fuel gas at pressure levels of approximately 300 bar. Five stage Laby-GI compressors, combining labyrinth piston technique and sophisticated high-pressure ring sealing technology have been designed, to serve this specific application. As one of the advantages of these high-pressure systems, excess BOG, which is not consumed as fuel in the engines, can be efficiently and simply reliquefied in a partial reliquefaction process. This open-loop reliquefaction system works without the need of a refrigerant and additional rotating equipment.
Gas-tight compressor crankgear
All Laby, Laby K-type, and Laby-GI compressors applied in the LNG industry are of gastight and pressure-resistant design (from 2 bar up to 15 bar) and there is no need for a continuous purging with inert gas. As piston rod sealings for reciprocating compressors are not entirely avoiding gas leakages, typical compressors require these packing leakages to be sent to a vent or flare system. The leakage rates might be small for packings in new conditions but develop over time with the wear of the packing rings. Depending on the wear rate of the parts and adherence of the operator to the maintenance schedule, significant amounts of leak gas can accumulate over time. Since natural gas – despite all of its advantages – unfortunately is a great contributor to climate change, it must be addressed that the total of packing leakages of the compressors installed in the natural gas industry are representing a big environmental threat to the planet. However, the gas tightness of Burckhardt Compression compressors avoids leakages to the environment. All leak gas is internally recycled in the compressor system. Based on the large number of Laby and Laby-GI compressor units installed in LNG terminals and on LNG ships, several thousand of tonnes of methane emissions are saved y/y.
Maintenance aspects – benefits of reciprocating piston machinery
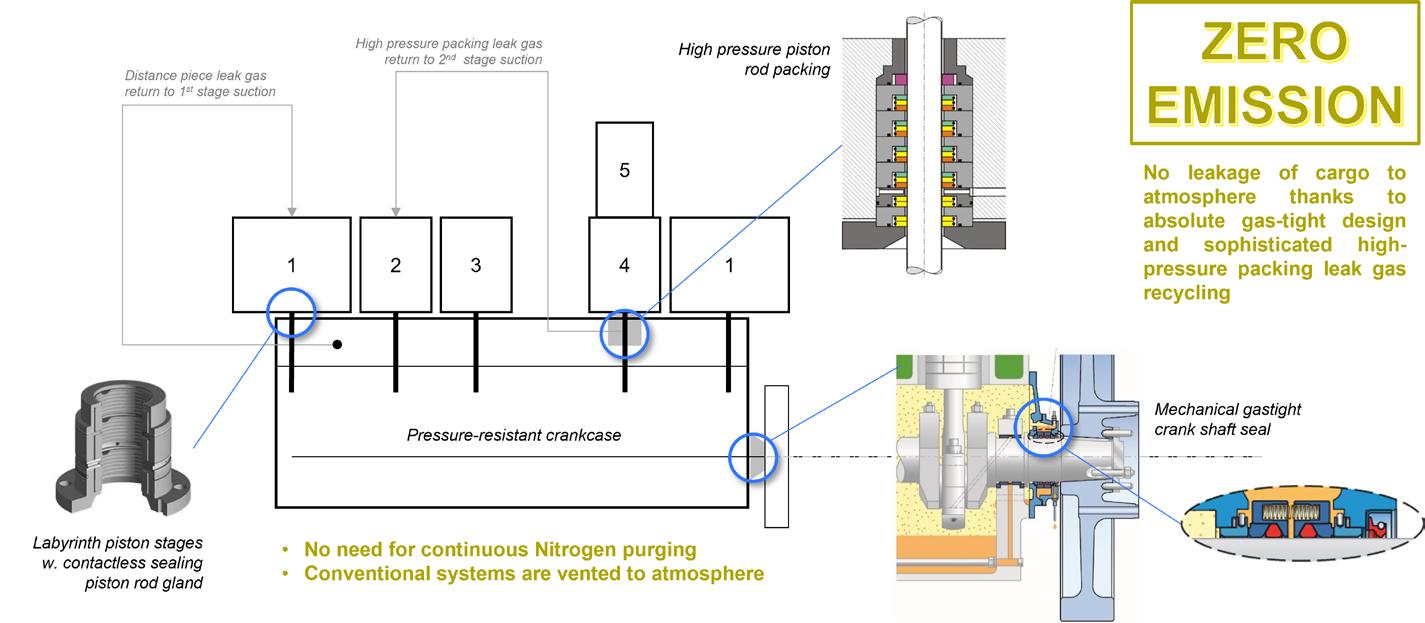
Vertical aligned reciprocating piston compressors are of very similar design as reciprocating combustion engines. This makes the compressor design welcome and preferred by maintenance personnel all over the world, since maintenance routines and handling of components are easy to get familiar with. This aspect becomes especially attractive for ship crews, being able to carry out onboard service activities on the compressor by themselves after a relatively short training by Burckhardt Compression service experts. Regular maintenance of labyrinth piston compressors is mainly limited to the compressor valves and piston rod gland rings. The absence of sealing elements on the cylinders limits the service tasks on the piston to a simple check of clearances and pretension values – no parts need to be replaced on a periodical base.
Depending on the application and pressure range, labyrinth piston skirts can reach a long service lifetime. This, of course, is different for ring sealing systems, facing continuous wear due to friction with their counter parts. Burckhardt Compression develops and continuously improves the available polymer sealing materials both for lubricated and dry-running sealing systems. The latest generation of dry-running Laby-GI, high-pressure compressors is equipped with state-ofthe-art ring sealing technology, providing an expected lifetime of up to 24 000 operating hours. Conclusion All members of the reciprocating Laby product family (Laby, Laby K-type, Laby-GI) operate reliably both under cryogenic and warm suction conditions. On Laby-GI Compressors, for increased discharge pressures, dry-running ring sealing technology can be applied to higher compression stages. The gas-tight design protects the environment from natural gas emissions and saves operational costs by avoiding gas losses. The compressor systems are low in utility consumption, as there is no need for continuous purging of the crankgear or preheating of the suction gas. Maintenance routines are simple, and operators appreciate the uncomplicated handling of service activities. Maintenance intervals of 24 000 operating hours help to keep the lifecycle costs low and allow ships to operate continuously
Figure 4. Typical flow diagram of a five-stage Laby-GI high-pressure fuel gas compressor installed on an LNG carrier. The compressed gas can be supplied to the ship’s main and auxiliary engines but also to a partial reliquefaction system. For reliquefaction, the gas is compressed to 300 bar and cooled down to approximately -100˚C in a cold box. The low temperature of the LNG boil-off at the inlet of the compressor system is providing the cold energy. Due to the expansion of the gas from 300 bar to approximately 4 bar (Joule-Thomson effect), the temperature of the gas is further dropped and liquid can be separated in a knock-out drum. The liquefied portion of the gas is sent back into the LNG cargo tank whilst a smaller amount of so-called flash-gas is recycled to the compressor unit. These reliquefaction systems convince with their small footprint and simplicity, not requiring additional refrigerants or rotating process equipment, such as pumps and compressors. Accordingly, both CAPEX and OPEX for such a system are very low. Figure 5. Piston rod gland and piston rod packing leakages are recycled inside the compressor system. No gas can leave the compressor, since there is a mechanical crank shaft seal installed. Thus, all Burckhardt Compression LNG BOG compressors do not contribute to methane emissions. without the need for larger service interruptions before reaching the dry dock. Due to their flexibility and robustness, Laby compressors are the ideal solution for the efficient management of LNG BOG onshore and at sea. For approximately 40 years, Burckhardt Compression Laby Compressors have played a key role in LNG BOG handling. Over 100 LNG BOG compressor systems can be found in more than 30 LNG terminals all over the world. 91 high-pressure Laby-GI Compressor units are in operation onboard modern LNG carriers, managing BOG and supplying fuel gas to high-pressure, two-stroke, dual-fuel diesel engines. Smaller Laby K-type BOG compressor units handle boil-off onboard 22 LNG bunker ships in operation. With the growing use of LNG as a fuel in the ship industry, the Laby K-type compressor is as well applied on gas-fuelled merchant vessels, such as ultra-large container ships or oil tankers.
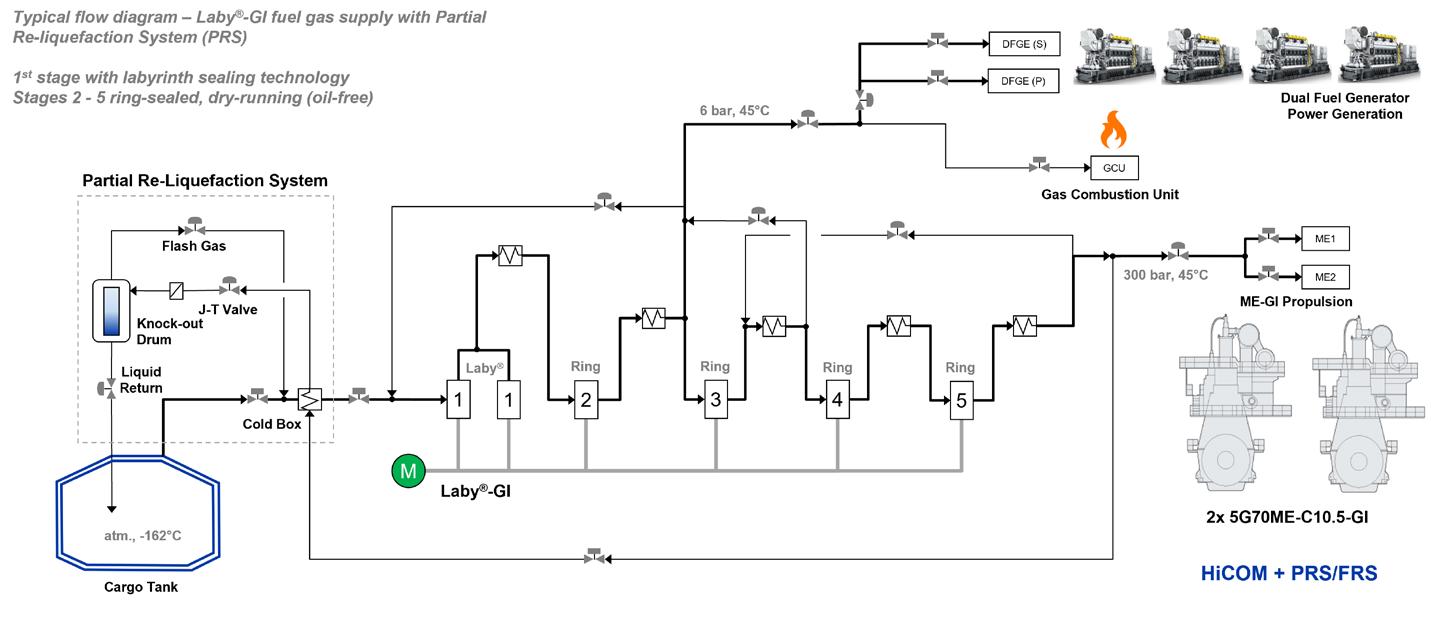