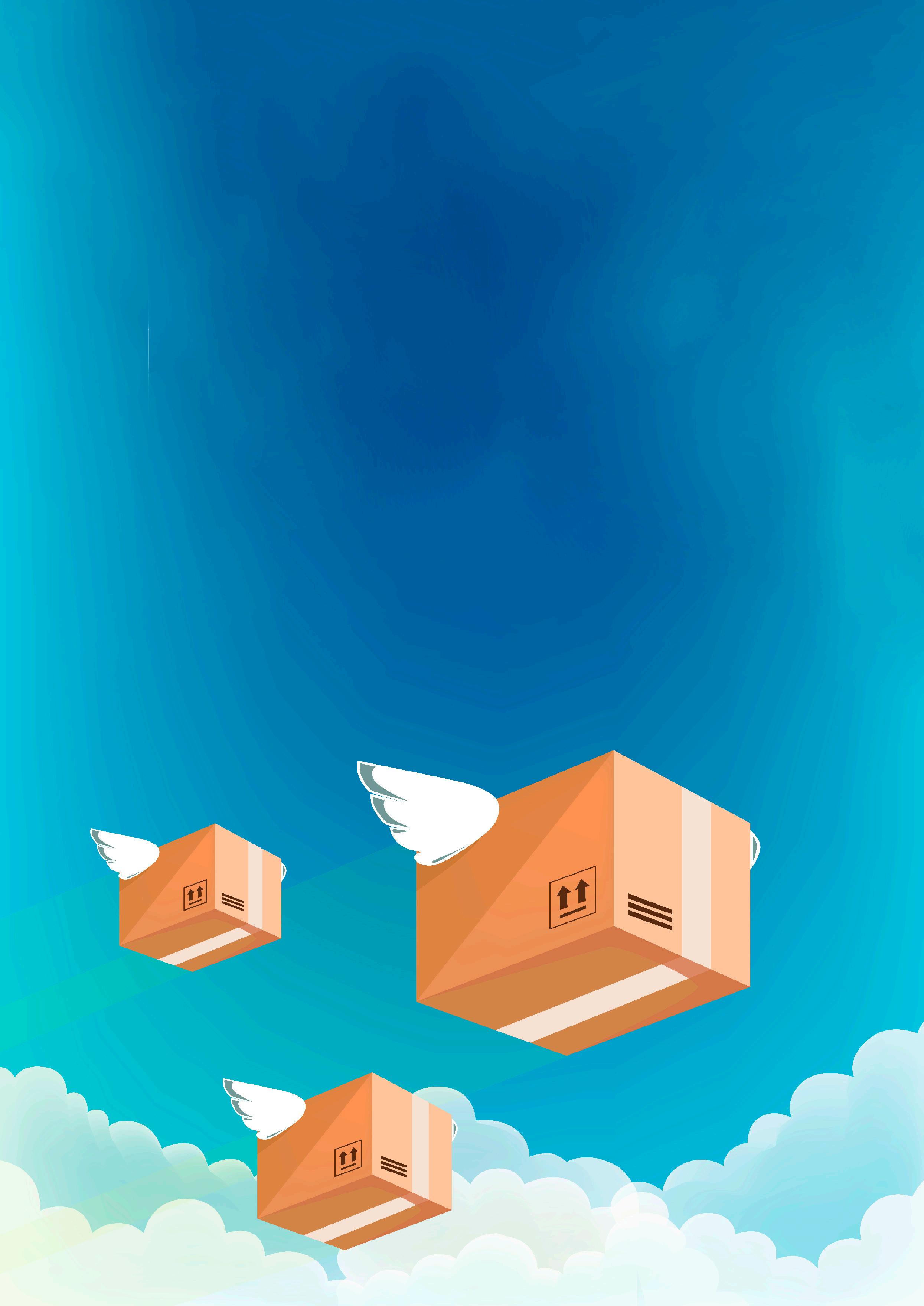
20 minute read
Delivering decarbonisation
Sven Lumber, Head of EcoTow, Group Operations, Svitzer, UK, outlines how the towage sector can improve safety and sustainability at LNG terminals, as well as highlighting the focus on decarbonising the industry.
ince the shipping industry first engaged with the LNG sector, the two have worked closely together to mutual benefit. Early LNG tankers used boil-off to power their vessels, making use of what may otherwise have been inefficient waste. As both industries focus on the challenge of decarbonisation, they stand to benefit once again from shared innovation. Organisations and governments around the world are now taking air pollution and climate change seriously. Shipping’s contribution to these pressing global challenges
is increasingly coming into question, as the maritime industry is responsible for emitting approximately 1076 million tpy of CO2e, which totals approximately 2.89% of total global greenhouse gas (GHG) emissions.1 Shipping faces the difficult task of decarbonising while remaining profitable and powering the world’s economy. Understandably, entire conferences are now dedicated to these efforts, as maritime companies, ship owners, and regulators pledge to act and ensure the industry reduces emissions and meets its climate targets – all while working out how to stay financially viable. The International Maritime Organisation (IMO), the UN body that regulates the shipping industry, has set a target to reduce the carbon intensity of all ships by 40% by 2030 when compared to the baseline of 2008 levels, with the eventual aim of eliminating them altogether. In Europe, even more ambitious decarbonisation goals are being set.2 The EU is targeting a reduction of GHG emissions by at least 55% by 2030 and aims to become climate neutral by 2050, which will require a 90% reduction in all transport emissions – including maritime. In early March, the UK government also announced a new unit at the Department of Transport, which was specifically created to tackle shipping emissions and advance the UK towards a more sustainable maritime future.3 Companies now find themselves complying with varying regulations depending on where they are in

Figure 1. Svitzer’s fleet at work at an LNG terminal in Australia.
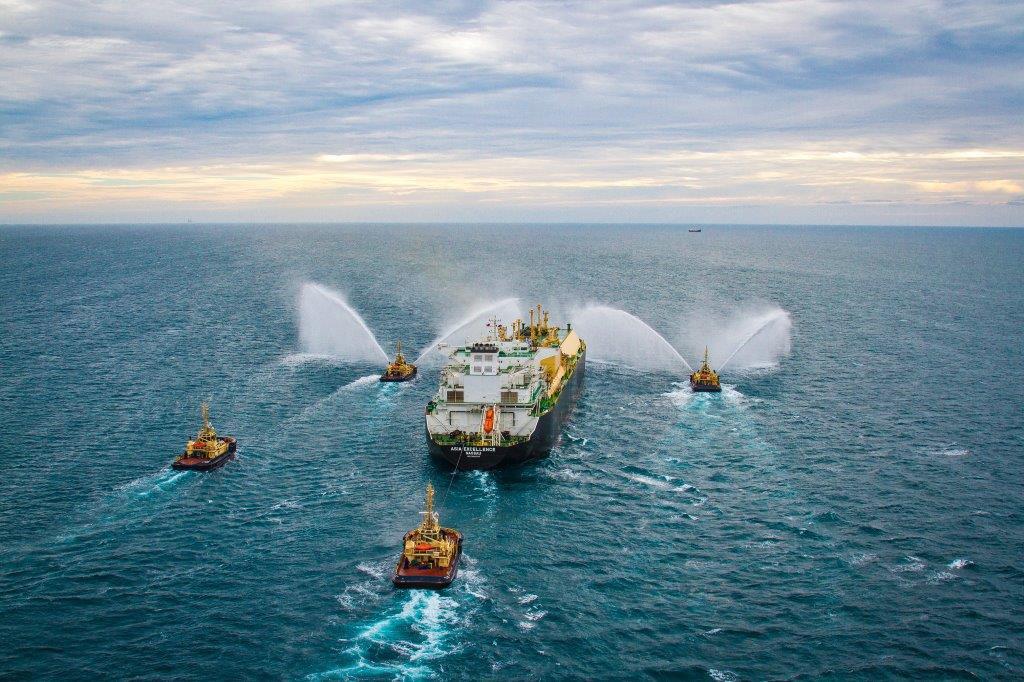
Figure 2. Svitzer’s fleet in action. the world. This multi-speed regulatory approach has led to a fragmented landscape, with no clear-cut set of rules by which organisations must abide, or action plan they must take. Other key barriers to decarbonisation in the shipping industry involve the sector’s reliance on fossil fuels, and the fact that assets last for decades. Decarbonisation must also be commercially viable for businesses, as most organisations simply do not have the capacity to completely and immediately replace their fleets based on speculative technologies. Equally for towage, there are not that many shipyards that can build tugs. This means change ends up being slow and hard to achieve in the timescale needed – especially as technologies that create alternative, zero-emissions fuels are still in development.
An immediate, intermediary solution
Despite these challenges, the journey to decarbonisation must begin now. Regulatory pressure has outlined a need for speed, which has led ship owners and operators to look to LNG as an immediate solution. LNG enables the shipping industry to begin decarbonisation faster, without spending exorbitant amounts on new infrastructure. Companies can begin working towards meeting regulatory targets today, as opposed to waiting for technologies to develop and a future perfect solution fuel to be created. As a result, LNG-fuelled vessels now amount to approximately 13% of the current new-build order book,4 with 2021 shown to be a record year for LNG-fuelled new-building orders.5 Promising alternatives such as LNG need infrastructure to support them, and expertise to ensure that the fuel is bunkered safely and optimally. This has spurred the development of LNG-dedicated terminals which accommodate the large carrier ships that load, carry, and unload LNG before it is regasified for uses across the residential, commercial, and industrial sectors. LNG terminals will continue to have a key role to play in facilitating decarbonisation across many industries, and towage is essential to ensuring carriers can make their deliveries, embark safely, and that the import and export of LNG is not interrupted.
As with any marine fuel infrastructure, safety is always paramount. However, LNG terminals have additional safety and environmental considerations when compared to traditional oil terminals. While natural gas is benign and will not explode or combust, when it is cooled it can be dangerous to handle, and requires skilled operators to handle it. Due to its extremely low temperature, there are cryogenic risks. LNG could injure people or damage equipment, for example, causing cold burns if it comes into contact with skin. LNG is also made up of 90% methane, which has high global warming potential, and so those handling it must be extra careful to avoid any spills or leakages. As the shipping industry continues to decarbonise, LNG terminals will continue to grow in number and scale. Towage is a key part of the supply chain that helps move LNG from vessels to ports and on to its next destination. As such, operators must be well-trained to ensure that the
regulations are met when handling the LNG, but also take the necessary steps to ensure crews remain safe and that accidents are kept to a minimum. It is due to LNG’s extra safety implications that the common practice at LNG terminals is to award towage contracts to a sole operator for an extended period of time – normally between five and 10 years. The tendering criteria for winning these contracts is how safely the operator can keep operations running. In the past 12 months, Svitzer has signed two 10-year contracts to service FGEN LNG Corporation’s LNG import terminal located in the Philippines,6 and Woodside’s LNG export operations in Western Australia.7 There are additional benefits for towage operators that do meet the higher threshold of safety requirements required and win long-term contracts to service LNG terminals. The stability of operating at these terminals gives towage operators the time, space, and opportunity to make positive commercial decisions that have a long-lasting effect on the safety, efficiency, and sustainability of the operations. In a normal port, the competitive atmosphere of towage can create situations that could be characterised as a race to the bottom. Innovation is stifled as operators must compete on price point and worry if there will even be jobs for them to carry out tomorrow. However, with contracts awarded to a single operator at LNG terminals, they have the time, freedom, and ability to plan and provide robust training and professional development programmes for members of the local workforce operating the tugs, as well as develop strategies that drive innovation contributing to wider sustainability aims.
While health and safety and costs are key considerations for towage operators delivering services at LNG terminals, decarbonisation is always part of the conversation. In its latest Gas Market Report, the International Energy Agency projects global LNG trade will increase by 5% this year.8 As towage steps up to support the growing LNG market, the sector also faces an increased responsibility to match the decarbonisation efforts of the wider shipping industry. Towage operators need to begin considering how to improve their carbon footprint while continuing to safely and efficiently deliver their service. There are great examples of operators delivering towage services that are championing decarbonisation and showing how it can also be possible for others. Svitzer has begun taking decisive action to use biofuels at the LNG terminals where the company operates. With the benefit of long-term contracts at these terminals, Svitzer has the ability to continue servicing the growing demand for LNG, while also finding new ways to decarbonise the supply chain. The company currently has five tugs serving the Isle of Grain LNG terminal in Medway, UK, which has been running entirely on hydrotreated vegetable oil biofuel since November 2021.9 Alongside the obvious environmental upsides of using biofuel in this way, the EcoTow project has also confirmed that it is operationally and commercially viable to use biofuels in the towage sector. Following this pilot, Svitzer made the decision to convert its whole fleet of 10 tugs in London, UK, and Medway; all are now powered by marine biofuel. In tackling decarbonisation, Svitzer benefits from being a global organisation. This has enabled the company to pilot different schemes out of different ports and see what works best. Through the company’s global network, Svitzer has also been able to offer customers the opportunity to use EcoTow to inset fossil-free towage even if they do not call at London or Medway.
The future of the sector
The environmental question dominates the agenda of the global industry discussion and is no longer something that can be left to a later date. The process of decarbonisation will not be easy for any part of the shipping industry. Difficult decisions will have to be made, timelines brought forward, and investments made in order to reach climate targets. Decarbonisation must also consider emissions from ports, as well as at sea. As in the rest of the shipping industry, what has now become abundantly clear is that tug owners and operators need to take action to reduce their carbon footprint.
While the towage sector certainly has unique challenges to overcome, there are steps that can be taken to not only decarbonise but ensure safety, especially in LNG terminals. LNG terminals will continue to play a key role as organisations across all industries begin to transition through fossil fuels to eventually use the net zero carbon alternatives currently in development. As a result, LNG terminal activity is set to continue growing. And so long as ships need to enter and leave ports across the globe, towage operators will always be part of the equation. Robust training programmes for tug crews that meet the additional safety requirements at LNG terminals are key, as are efforts to make these fleets more environmentally sustainable. The good news is that there are positive examples of success in the towage sector when it comes to using biofuels. This is largely thanks to the contract stability and focus on excellent safety standards at LNG terminals that help to create an environment in which operators can pursue wider innovation. However, it is critical that more of these initiatives are put in place to remove carbon from supply chains across the wider shipping industry in order to meet the 2050 carbon emissions target set out by the IMO.
References
1. International Maritime Organization, ‘Fourth Greenhouse
Gas Study 2020’, (2020). 2. European Commission, ‘Proposal for a regulation of the
European parliament and of the council on the use of renewable and low-carbon fuels in maritime transport and amending directive 2009/16/EC’, (2021). 3. Department for Transport, Courts MP, Robert, and Shapps
MP, the Rt Hon Grant, ‘DfT launches UK SHORE to take maritime ‘back to the future’ with green investment’, Gov.uk, (March 2022). 4. Sea-LNG, ‘2021 Outlook for LNG A View from the Bridge’, (January 2021). 5. Wold, Martin Christian, ‘2021 – what a year for #LNG contracting!’, LinkedIn, (January 2022). 6. Svitzer, ‘Svitzer Amea signs 10-year contract with FGEN LNG corporation’, (July 2021). 7. Svitzer, ‘Svitzer awarded Western Australia LNG terminal contract with Woodside’, (January 2022). 8. IEA, Gas Market Report, Q2-2022, (April 2022). 9. Svitzer, ‘Svitzer introduces carbon neutral towage services’, (November 2021).
Andy Foreman, Amarinth Ltd, UK, describes the challenges of designing cryogenic centrifugal pumps for LNG processing, as well as outlining how these pumps are developed to handle the industry’s unique demands.
The global demand for energy is growing again, and natural gas, the cleanest burning fossil fuel, is forecast to play a vital role in balancing economic growth and environmental responsibilities, with a projected growth in demand for LNG of 30% by 2040. Despite the short-term reduction in energy demand caused by the COVID-19 pandemic, the US Energy Information Administration (EIA) predicts that global energy demand will rebound to its pre-crisis level in early 2023 whilst also taking advantage of cleaner technologies than traditional coal and oil.
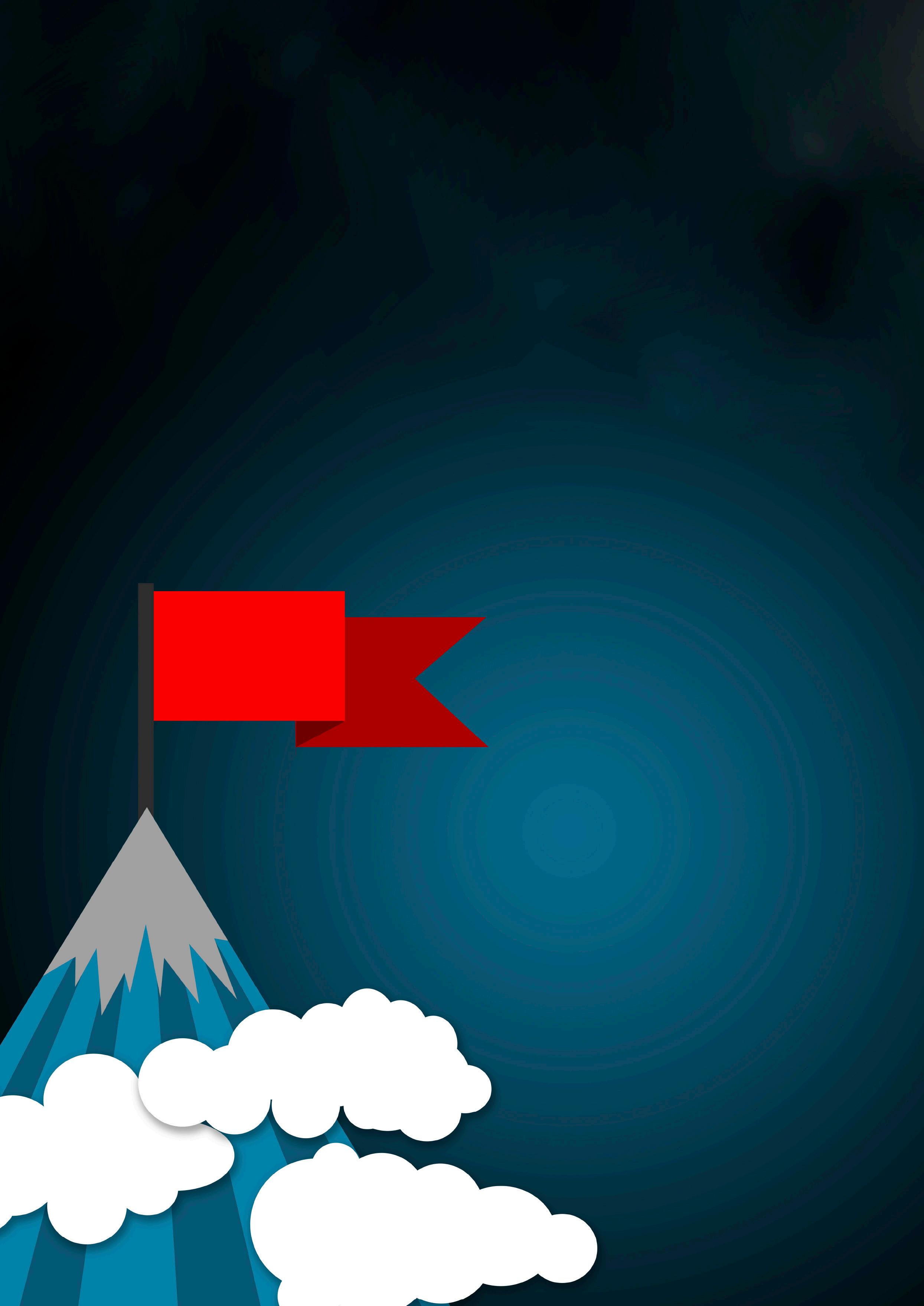
Cryogenic pumps
The production of LNG requires robust and reliable pumping solutions to move the gas through the necessary processes, often in challenging and hostile environments. At the front end, there is separation of gas and liquids, including mono ethylene glycol (MEG), from the raw gas feed. The separated gas then goes through steps to remove acid gases (such as CO2 and H2S), water (from the amine solvent used to remove the acid gases) before it is ready for liquification. Initial gradual cooling removes heavy liquids (such as benzene and other aromatics), and then the gas is finally liquified at atmospheric pressure by cooling down to -165˚C, which reduces it to approximately 1/600th of its original volume. From this point, any further processes and transfers including storing in tanks, bunkering, and loading and offloading onto vessels for transportation around the world, requires pumps that can operate dependably at this extremely low temperature. These pumps are termed
cryogenic pumps, as the cryogenic temperature range is defined as anything below -150˚C.
Amarinth designs and manufactures centrifugal pumps for the oil and gas industry and can deliver the duties demanded by the LNG industry, including many of the world’s LNG plants and floating LNG (FLNG) vessels. In addition to oil and gas, Amarinth’s expertise extends to cryogenic pumps used by other industries working with liquified gases such as oxygen, hydrogen, carbon dioxide, and nitrogen, some of which require temperatures down to -190˚C, even colder than for LNG, and so the company brings a wealth of knowledge and expertise to the LNG industry in the design of cryogenic pumps. The cryogenic pumps for LNG are specialised and are specified for the unique demands of the industry, which includes submersion pumps in LNG at -160˚C, cooling down and warm-up procedures, low NPSH operation, condition and vibration monitoring, safety features, and specialised testing.
Specifications for LNG pumps
The design and manufacture of cryogenic pumps is tightly regulated, and so close attention must be given to published standards to ensure that the pumps operate reliably. The main specification for LNG centrifugal pumps, along with the rest of the oil and gas industry is: z API 610 – Centrifugal pumps for petroleum, petrochemical, and natural gas industries.
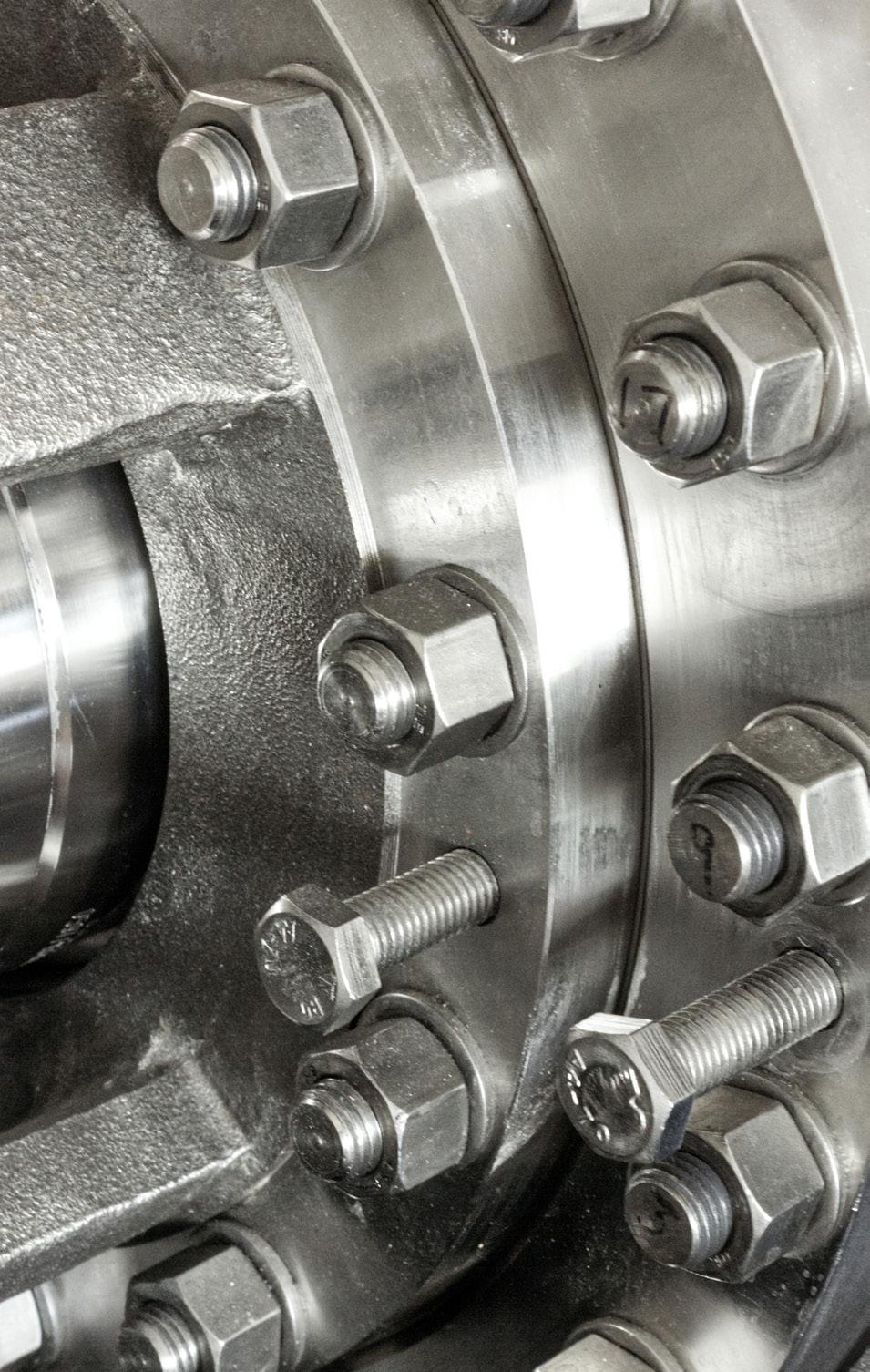
Figure 1. Pump materials must be carefully selected for cryogenic use. Reference is also made to several other directives due to the cryogenic operating temperatures, including: z NACE MR0103 – Petroleum, petrochemical, and natural gas industries – metallic materials resistant to sulfide stress cracking in corrosive petroleum refining environments.
z NACE MR0175 – Petroleum and natural gas industries – materials for use in H2S-containing environments in oil and gas production – part one: General principles for selection of cracking-resistant materials.
In addition, reference is made to the following industry, international standards, and directives: z European directives – ATEX, EIGA/IGC/CGA guidelines.
z Marine class certifications – ABS, DNV, BV, LR.
z International electrical standards – IEC 60034, 60079.
However, manufacturers must also make sure that their pumps meet operators’ hydraulic requirements, which may include duties such as low NPSH operation, and that they operate cost-effectively and are easily maintainable over their lifetime to minimise costs, and this is where the knowledge, skills, and ingenuity of a pump manufacturer successfully delivering pumping solutions to the broader oil and gas industry are very relevant.
Hydraulic specifications
Cryogenic pumps, like any other pump, must be well matched to the hydraulic requirements of the application to deliver reliable, long-term, cost-effective service. Design considerations include the required flow rates, suction pressure, and NPSH available and required (which will determine, for example, the usable and non-usable volume of a storage tank). In some applications, such as where headroom is restricted, cryogenic pumps may operate at low NPSH and so special consideration will then need to be given to low NPSH pump design and high-efficiency impellers to prevent impeller cavitation occurring, which could have disastrous consequences.
Materials
The pumps are in direct contact with the LNG (usually submerged in the LNG) and so are operating at cryogenic temperatures. The pump, and associated equipment such as valves, must be therefore manufactured in suitable materials for these conditions.
For most pump applications in the oil and gas industry, the materials are selected for corrosion resistance, and certain compromises must be made. However, within LNG applications there is not the same issue with corrosion (as LNG is non-corrosive), and it is therefore possible to manufacture in a range of materials more based on their suitability for the specific functions of the cryogenic pump service. The duplex stainless steels frequently used for oil and gas pumps become brittle as the temperature is reduced and so the primary selection for cryogenic services is stainless steel 316. This is an austenitic stainless steel and does not exhibit an impact ductile/brittle transition but a progressive reduction in Charpy impact values as the temperature is lowered and so it is much more suitable for cryogenic temperatures. Alternative materials such as
aluminium can also be used due to its stability, excellent thermal conductivity, ductility at low temperatures, and smaller variance in size with large temperature variations. Wear rings and bushings are often manufactured in bronze (and sometimes graphite) for their thermal characteristics in the required temperatures.
However, it is of the utmost importance that any materials selected can be cooled from ambient to temperatures between -150˚C and -190˚C and then warmed back to ambient temperatures without detriment to the build and integrity of the pump equipment. Within the LNG industry, material traceability is also crucial to product integrity. API 610 sets out traceability requirements, and so pumps for cryogenic application in the LNG industry will often be 3.2 certified, or as a minimum of 3.1 certified.
Equipment
The greatest challenge is to maintain optimum temperatures of each element of the equipment so that it runs efficiently over the long-term to reduce lifetime costs for the operator.
Motors
The induction motors in cryogenic pumps are integral to the pump equipment, and so many of the usual challenges of matching motor shaft bearing loads to the pump is eradicated and the whole motor is optimised for the required pump application. Although fixed speed pumps have their place, to vary performance the pump is mechanically throttled utilising discharge control valves, severely impacting pump efficiency (reduction). The efficiency and range of operation for pumps in cryogenic service can be significantly improved using variable speed controls. Adjustment of the speed allows for accurate control of the operating characteristics of the pump over a greater range with better overall efficiency. The efficiency of pump operation at flow points that are off design can be improved by varying the pump speed to a point on the pump hydraulic curve which matches the best efficiency point (BEP, the point at which the pump operates at peak efficiency) for the desired flow. This provides reduced operating costs, a higher level of control of the loading/offloading processes, and allows the pump to always operate at its optimum.
Seals
In LNG applications using submerged cryogenic pumps, LNG is allowed to enter the motor. This eliminates the need for seals, and in addition is used to cool the motor. Static seals would therefore only be required for the electrical and instrumentation elements. For cryogenic applications in general, there are a range of shaft sealing solutions should these be required for any reason. These include gas face technology single mechanical seals with purging outboard of the seal to ensure liquified gases do not escape into the atmosphere (due to their flammable state). Alternative solutions can utilise labyrinth seals with alternative containment measures.
Instrumentation
Careful consideration must be given to the instrumentation. These are best mounted within environmental heated enclosures, for example within heated cabinets.
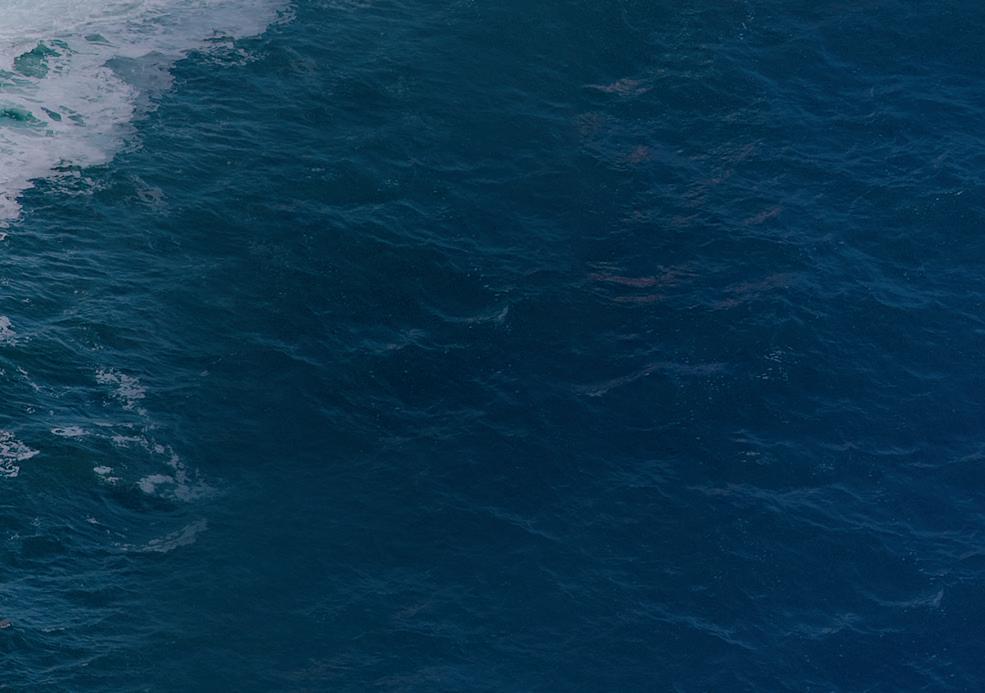
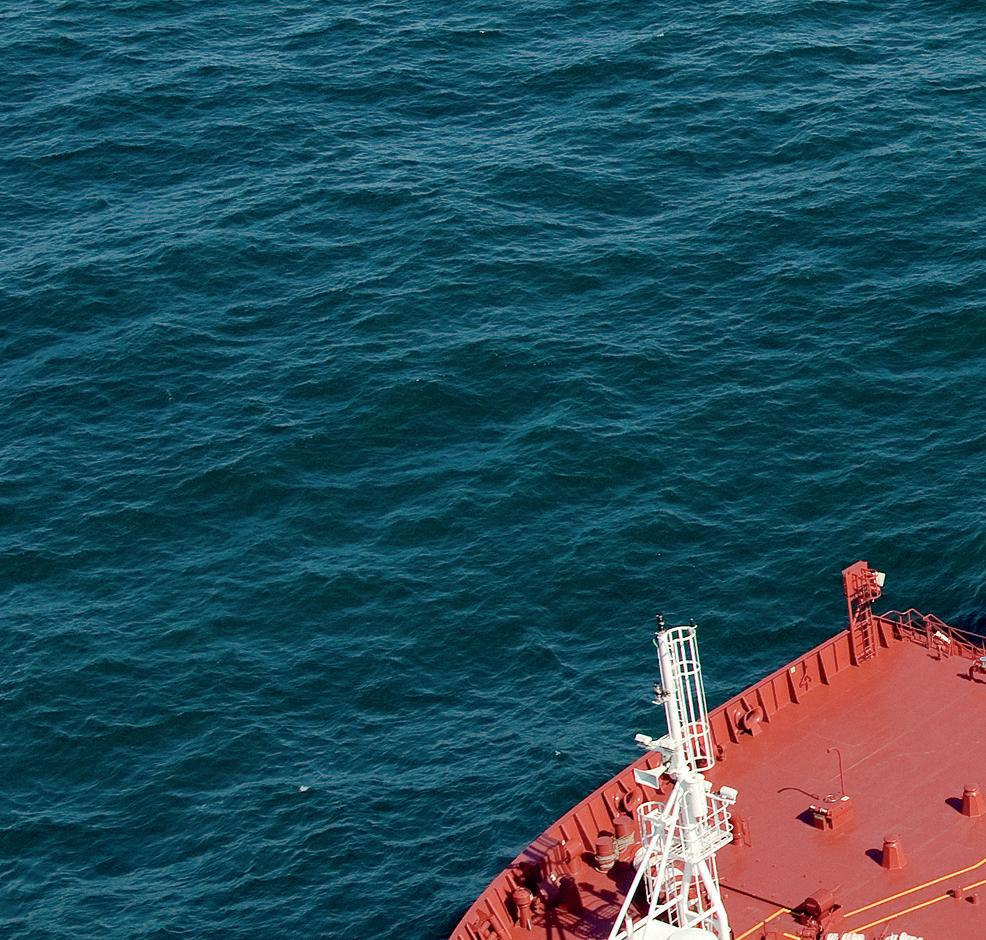
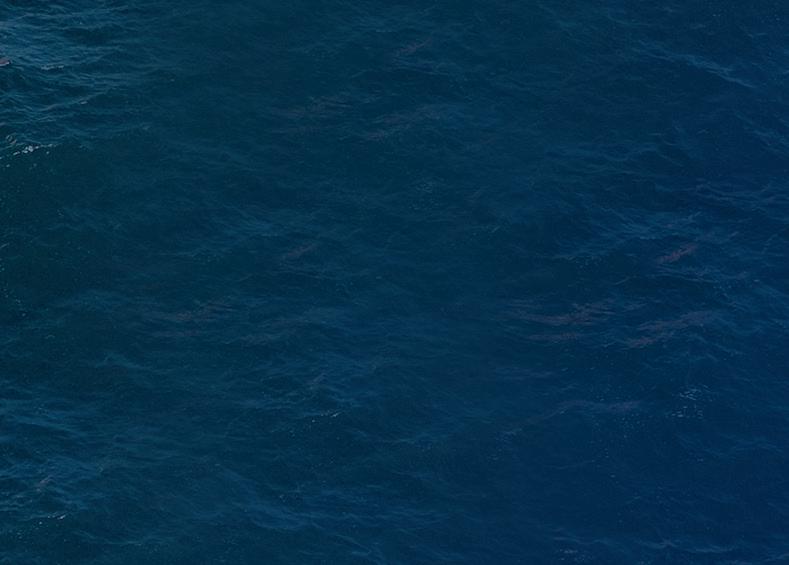
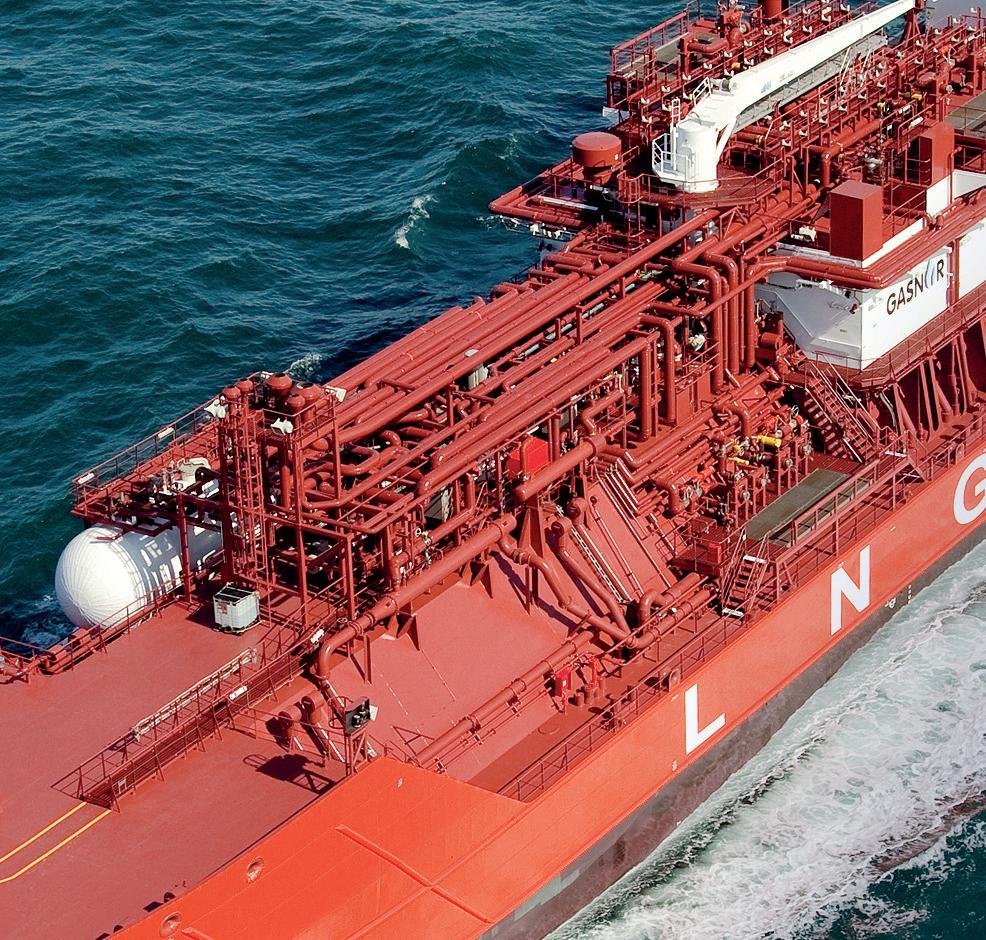
The Gas Experts
Innovations for Greener Shipping Greener Shipping
www.tge-marine.com
Engineering state-of-the-art Gas Systems for the Maritime Industry
TGE Marine Gas Engineering is the leading liquifi ed gas systems‘ provider specialising in cargo handling systems for gas carriers (LPG, LEG, NH3, Ethane, CO2 & LNG), FSRUs and bunker vessels, including tanks.
Furthermore, TGE Marine is a pioneer in fuel gas systems for LNG, NH3 and other alternative fuels. The company has been contracted for more than 250 gas handling, fuel gas and storage systems globally.
Fuel Gas Systems
LNG, LPG, NH3 and other alternative fuels, including storage • LPG & Ethylene Gas Carriers & other Gas Carriers
Gas handling and storage systems for LPG, LEG & CO2 carriers • LNG / NH3 Shuttle Tankers & Bunker Vessels
Cargo handling and fuel supply systems as well as type C storage solutions • Floating Storage Units
FSOs & FPSOs, FSRUs LPG / LEG / CO2
LNG Tankers (Shuttle Tankers & Bunker Vessels)
Fuel Gas Systems
Floating Storage & Regasifi cation Units
Some pressure gauges can also be silicon oil filled, allowing them to operate at much lower temperatures than normal, but in general, instrumentation will need to be isolated from the extreme cold environment.
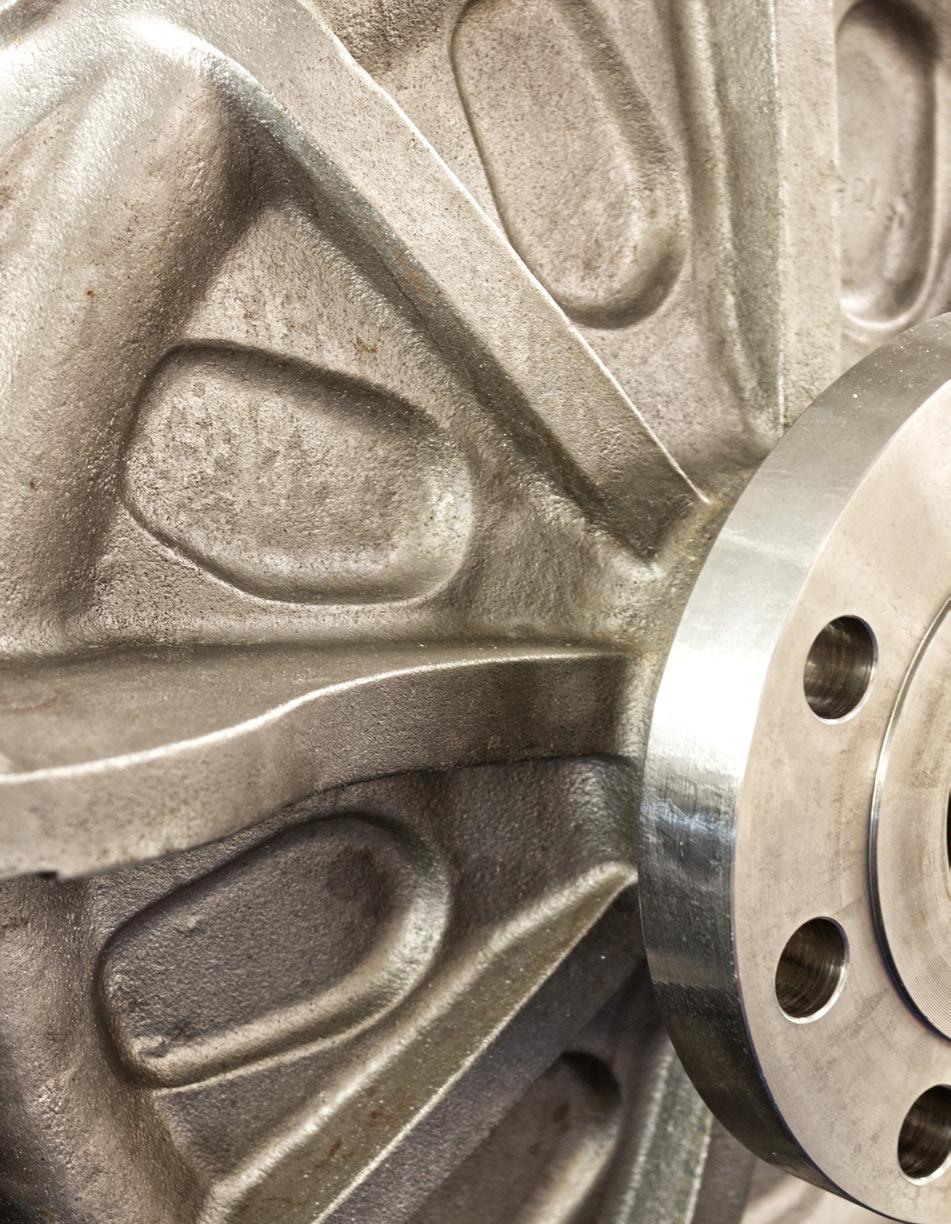
Figure 2. 316 stainless steel is frequently used for cryogenic pump casings.
Figure 3. Comprehensive condition monitoring equipment ensures cryogenic pumps operate safely and reliably.
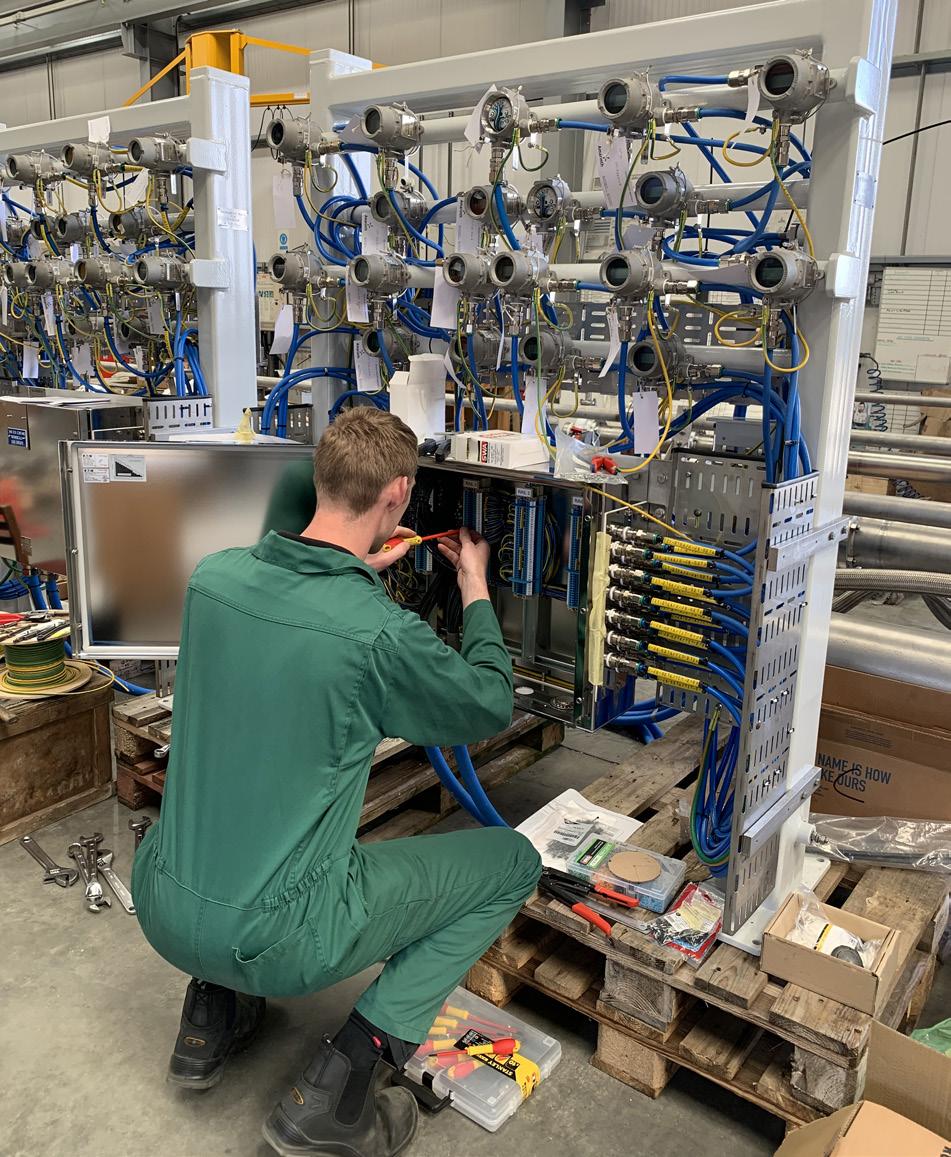
Condition monitoring
Cryogenic pumps usually function within what is defined as a hazardous area, and so it is of the utmost importance that these pumps maintain a high integrity. Therefore, the pump is closely monitored for mechanical vibration with the use of accelerometers within the pump housing and resistance temperature detectors (RTDs) to ensure no hotspots occur within the motor arrangement. These monitoring devices all need to be intrinsically safe (i.e. designated IS devices within the International Standards) to operate within the defined hazardous area.
As with any pumping scenario, parameters such as pressure, flow, and motor amps will be monitored as indicators to pump running performance compared against new parameters. These also provide early indicators of other potential failures, such as presence of vapour should LNG start converting to its gaseous state.
Cooldown and warm-up procedures
Before operating with LNG, pumps (along with pipelines, tanks, and other ancillary equipment) must be pre-cooled to prevent stress on their materials from overly rapid cooling, or the LNG converting to gaseous form. Similarly, warm-up procedures are also an important consideration, particularly when pumps and equipment are being prepared for inspection or maintenance. Cooldown and warm-up procedures therefore need to be carefully considered when specifying the pump so that the pump manufacturer can model the thermal expansion properties of the equipment to minimise stress and possible separation of components.
Testing
As a result of the unique design of cryogenic pumps and the very low operating temperatures required, they cannot be tested with water in the usual way. Cryogenic pumps for the LNG industry must be tested with LNG to verify their performance, in so far as possible, under the conditions of actual usage. This will verify, for example:
z Performance of the motor and its ability to start in the cryogenic environment. z Pump performance characteristics operating in the cryogenic fluid, which is also crucial for NPSH testing, particularly for when the pumps will be used in low NPSH environments.
z There is no internal leakage due to differential shrinkage and expansion when all the components are working at their actual operating conditions and temperature and during cooldown and warm-up.
Summary
The unique requirements of moving LNG at cryogenic temperatures mean that the pumps must be specifically designed for the required application, meeting an extremely high standard of durability and reliability. As a result, a broad range of skills and expertise are required in the specification, design, material selection, manufacturing, and testing of these pumps which needs to be drawn from the demands of the oil and gas industry as a whole and specialist cryogenic experience. This ensures that the pumps will meet the required duties and operate reliably and efficiently over their lifetime in extreme conditions.