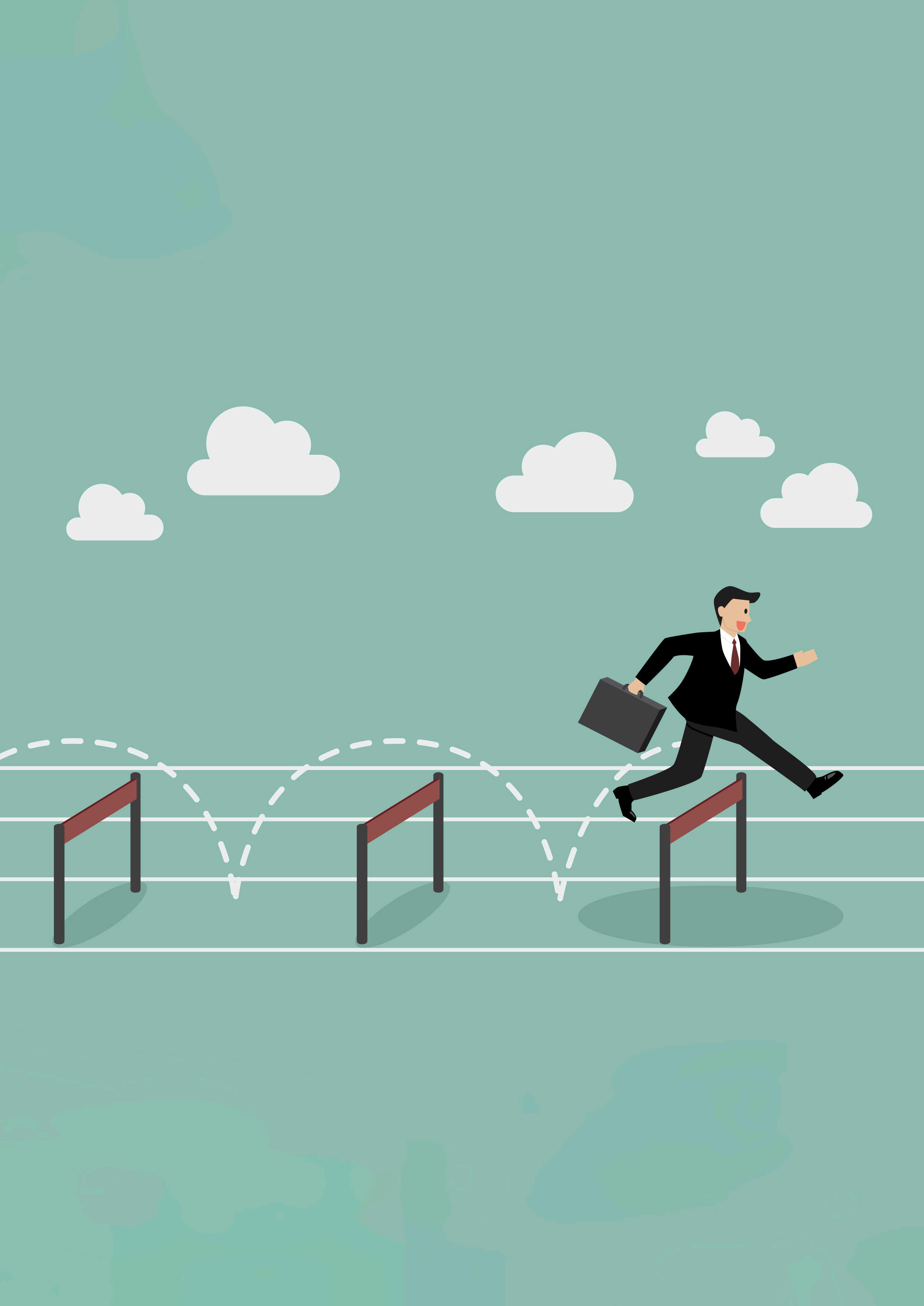
10 minute read
Overcoming challenges for the LNG carrier fleet
Rene Laursen, ABS Global Sustainability, Denmark, identifies how new baseline standards and a gradual tightening of permitted carbon emissions pose challenges for the LNG carrier fleet.
The impact of the International Maritime Organization’s Energy Efficiency Existing Ship Index (EEXI) is already being felt across the industry, and is posing significant challenges to both ship owners and operators.
In simple terms, the EEXI represents the application of the Energy Efficiency Design Index (EEDI) to existing ships, rather than newbuildings. Most existing ships do not have an EEDI value, so the EEXI needs to be calculated. This should ideally be below a certain limit.
EEXI calculation is challenging since it must be based on the available data for each vessel. This data is only partly available for older vessels; guidelines are still under development in order to address this lack of data, and ensure a level playing field and common interpretations.
To achieve EEXI compliance, adjustments to a vessel’s power rating will be the first choice for most vessels, while investment in energy efficiency technologies (EETs) – for which the power savings need to be quantified and verified – seems the preferred alternative.
However, compliance with EEXI is a technical measure requiring one-time certification. More challenging is the Carbon Intensity Indicator (CII), which is an operational measure mandating y/y operational efficiency improvement.
The CII creates a downward trajectory for a ship’s carbon intensity, which is the value of carbon emissions generated by a unit of transport work, equivalent to one nominal tonne of cargo carried over a nautical mile. The CII assigns an ‘energy efficiency’ rating to all ships (from A to E).
Vessels in the D and E categories will have to demonstrate improvement annually, moving progressively towards category C. Ships that spend three consecutive years in category D, or one year in category E, will be subject to a mandatory review of the Ship Energy Efficiency Management Plan (SEEMP), and a plan of corrective actions must be made to achieve the Required Annual Operational CII.

Figure 1. The CII prediction shows that 100% of steam turbine vessels will have a hard time complying with the CII and will sit in category D and E in 2030.
Figure 2. Some 40% of DFDE LNG carriers will be in category D and E by 2030.
Figure 3. Some 25% of LNG carriers equipped with two-stroke engines will be in category D and E in 2030.
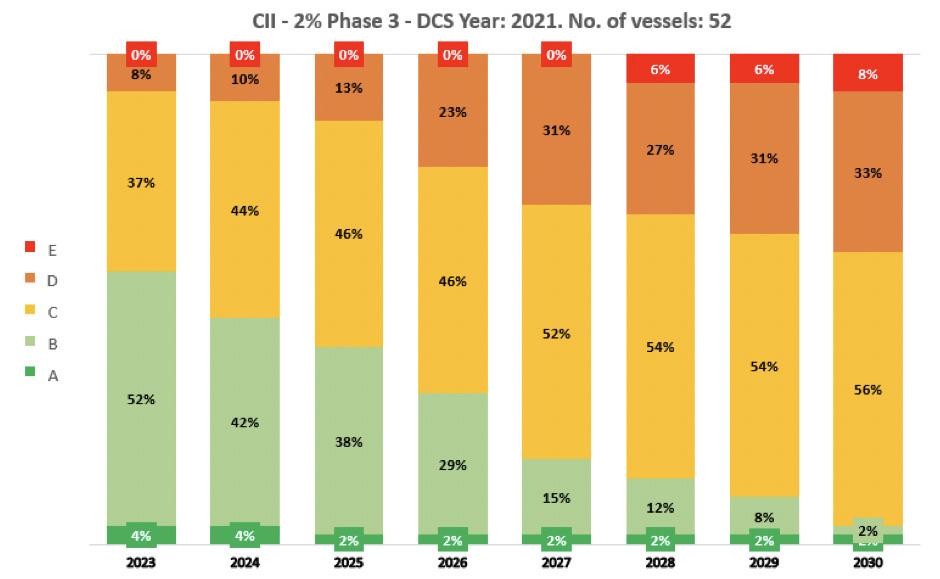

Higher performance
What is unclear at present is the sanction mechanism for vessels that fail to satisfy the regulation – how a sanction will be imposed and then lifted, as well as the exact calculation method, since potential exclusions and correction factors are still being discussed.
With these regulations due to come into force from January 2023, owners and charterers will need to demonstrate that the vessels they buy and operate are high performers, and that less efficient ships are subject to performance improvements.
Operators will face challenges, since even relatively young vessels will have to compete with newer vessels that are able to operate more efficiently at higher speeds.
Being forced to significantly reduce operating speeds across a fleet can also mean lower utilisation, which could result in less income for the operator. At the same time, the operators need to be satisfied that they can reduce the available propulsive power without compromising the safety margins of the vessel. With a vessel operating at lower power levels for prolonged periods due to propulsion power limitation, there is a potential increase in machinery maintenance costs per voyage.
Flexible designs
Today’s LNG carrier designs need to be flexible enough to take the impact of the EEXI and CII into account. Large ‘unknowns’ remain, but the aim is carbon neutrality at some point; whether that is 2050 or 2070 in a best or worst case scenario depends on an individual viewpoint. The reality remains that ship designers and owners need to design and operate ships that could meet such requirements.
LNG carriers have undergone a tremendous change in design over the last two decades, including several different propulsion solutions and tank arrangements. The required power to propel an LNG carrier has dropped by more than 30% over recent decades, while engine efficiencies have also improved in the same period. The gains have been achieved by implementing two-stroke engines in LNG carriers, combining this with improvements to the hull and propeller, developing more compact ship designs with more efficient reliquefaction and gas handling systems and by reducing boil-off gas (BOG).
The industry should not expect to see a similar reduction in power in the future, but there is the option to incorporate systems such as air lubrication system or wind assisted propulsion. Such systems will result in a reduction of fuel consumption, improving both the EEDI and the CII, but may result in a reduction in installed power.
New LNG carriers are designed for 25 – 30 years of operation, meaning that ships ordered now will probably need to fulfil the carbon requirements of 2045 – 2050. But before then, there will be well-to-wake accounting of greenhouse gas emissions implemented in the regulation, so these ships will most likely need to use carbon neutral or carbon-free fuel.
The logical carbon neutral fuel choice for LNG carriers would be either bio-LNG or e-methane blended into conventional LNG. For the design of the LNG carrier, this will
require full separation between cargo handling of BOG and fuel for propulsion. This can be done by installing full reliquefaction on deck, including a dedicated LNG fuel tank where the bio-LNG/e-LNG used as fuel can be stored.
CII reporting
When specifically considering the requirement to report CII data by LNG carriers already in operation, reliance on gas will be even more important than it is today. Fall-back operation on fuel oil will give a carbon dioxide (CO2) penalty when CII data is reported.
A small number of LNG carriers feature newer two-stroke dual fuel engines and have implemented increased redundancy with gas use, though only one engine maker has introduced this to date. With a cylinder cut-out in gas fuel mode, the uptime on gas can be maintained, so such solutions will probably be implemented for other engine makers in the future.
Besides redundancy within the engine itself, there has been additional redundancy in the fuel supply system, especially LNG pumps, BOG compressors, gas sensors, and gas fuel filters, to secure an uninterrupted operation on gas. Over the last decades, this redundancy has seen full implementation in almost all new LNG carriers.
For the CII reporting, BOG burnt in the gas combustion unit will also need to be reported. If a failure happens in the gas system, the result will be that the engine system will fall back into fuel oil operation, resulting in higher volumes of BOG sent to the GCU and further increasing the CII carbon penalty.
For older LNG carriers which do not have the luxury of full redundancy, it will be a daily challenge to stay continuously in operation on gas. A well-trained crew with enough spare parts will be a must for keeping those ships within CII compliance.
Engine types
To help owners understand the impact of CII, ABS has created a compliance scenario based on the LNG carrier fleet equipped with steam turbines (Figure 1), equipped with dual fuel diesel electric (Figure 2), and equipped with two-stroke engines (Figure 3).
The CII prediction in Figure 1 shows that 100% of steam turbine vessels will have a hard time complying with the CII and will sit in category D and E in 2030. Steam LNG carriers – which represent one-third of the LNG fleet (27 m3 out of 86 m3 in total) are the least efficient of the ships operating in the gas fleet today. To become compliant with EEXI regulations, steam-powered LNG carriers will have to reduce their engine MCR by roughly 50% using a Shaft Power Limitation (SHaPoLi).
However, these ships already operate with approximately this power level. Therefore, applying SHaPoLi and reducing speed is not a practical solution, both due to the operational requirements of the LNG trade, but also due to the performance of the steam plant, which becomes very inefficient at reduced power/speed levels.
The EEXI regulations as proposed cannot be met as steam vessels do not operate the same way as the diesel vessels (for which the main concepts of EEXI have been developed) and there is no simple technical fix that can change them to make them compliant.
To do so would require major changes to those ships, requiring either: � Carbon capture: at present, there is no proven technology for marine applications available and no ports are equipped to receive CO2. There are carbon pre-capture technology options, that turns CO2 into solid carbon, which might be easier to handle in port. It will, however, require that hydrogen can be blended into gas and burned in the steam boiler. The expectation is that this is technically feasible, but it will require testing to verify it. � Installation of reliquefaction systems: this may help in managing BOG, but it will take energy to run and will not improve the overall fuel efficiency of the steam plant or reduce emissions. But this solution could be combined with the use of either ammonia or hydrogen blended into the gas going to the boilers. � Re-engine to convert to a dual fuel diesel vessel: this would, however, cost double digit millions and is not foreseen as an economic solution. Adding a single two-stroke dual fuel engine seems to be the cheapest of the options, but it is a bigger conversion, and it is not without financial and technical risk to complete such a project.
Some 40% of dual-fuel diesel electric LNG carriers (Figure 2) will be in category D and E by 2030. These ships constitute a little less than one-third of the LNG carrier fleet, and what is evident from the reporting is that many operate on fuel oil during the ballast voyage leg.
Achieving a better CII rating will require the amount of gas used to be maximised. If this does not have enough effect, DFDE carriers will also need to reduce speed during the ballast leg to save fuel. Reducing speed during the laden leg is not practical as DFDE carriers already operate solely on BOG and a reliquefaction system is typically not installed on those ships.
If they reduce speed further, the BOG will instead have to be burned in the GCU, so lowering the speed will have the opposite effect, in that more carbon will be emitted.
Four-stroke engines burn natural gas using the Otto cycle, and they have relative high methane slip levels that most likely will be penalised in the CII. Methane oxidation catalysts designed to reduce methane slip from the exhaust gases are under development from several manufacturers, and it is possible that such a system will be available and possible to retrofit.
Some 25% of LNG carriers equipped with two-stroke engines (Figure 3) will be in category D and E in 2030. These LNG carriers are the latest standard, and while they are the most efficient of the three segments, they constitute a little more than one-third of the fleet – though this share is growing rapidly.
Many of those ships are equipped with full reliquefaction, which means it is possible for them to reduce speed without burning additional BOG in the GCU. Many of them are operating on fuel oil instead of gas, so improving the CII rating becomes easy as most are dual fuel, so they can simply just switch to natural gas. Many of the two-stroke engines burn natural gas using the Otto cycle so also suffer from relatively high methane slip levels that most likely will be penalised by the CII.