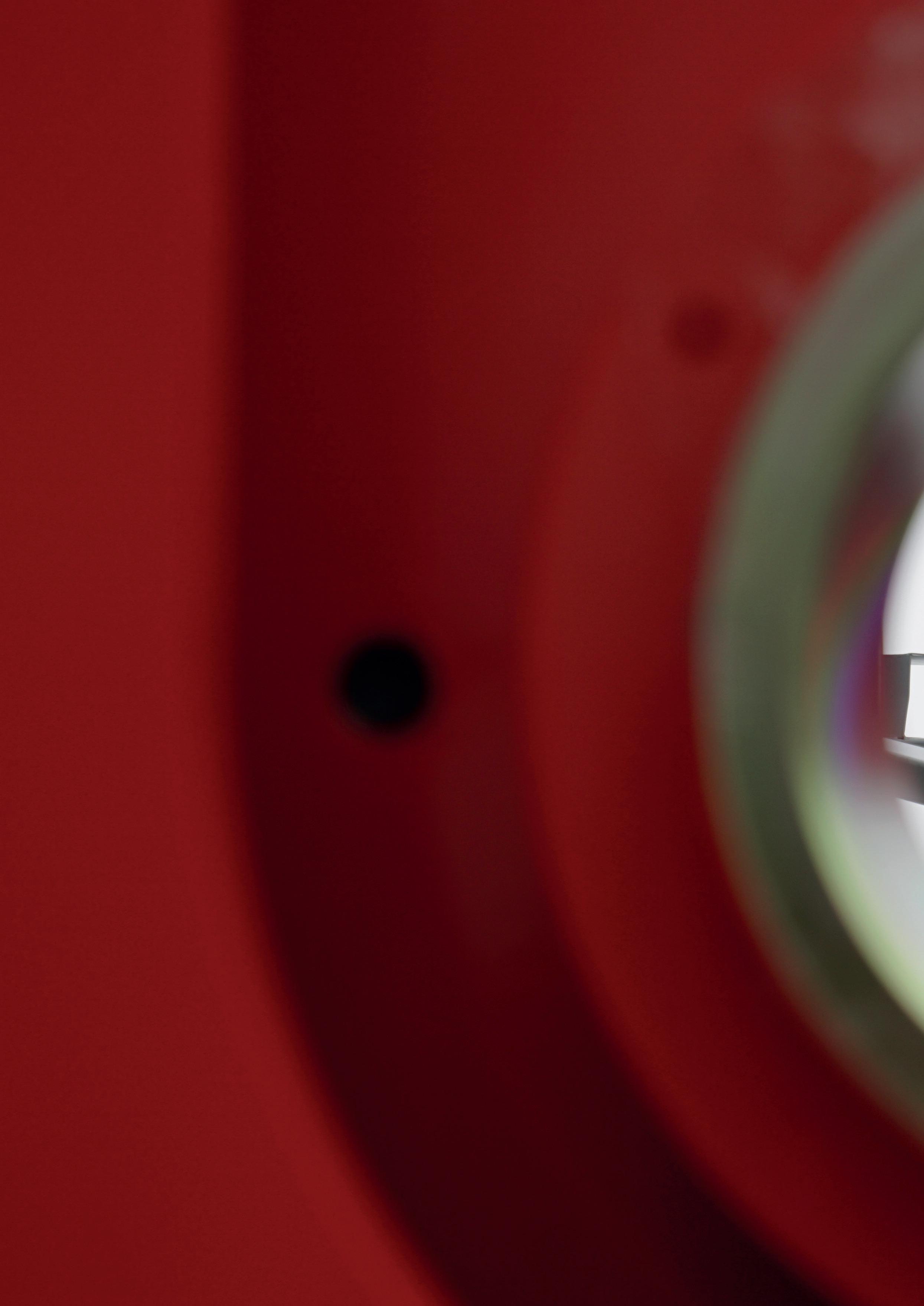
7 minute read
A Multi-Purpose Drill Rig
Ceren Şatırlar Balcı and Müzeyyen Çakır, Barkom Group
Drilling Rigs and Equipment, Turkey, review the functions and uses of a new multi-purpose drill rig and its role in the ever-changing mining industry.
The drilling industry requires constant improvements and innovations, both in terms of safety and productivity. Barkom Group has manufactured, and served, a wide variety of drill rigs and drilling equipment, following the needs of the market and updating their manufacturing stages to stay at the forefront of an ever-changing industry.
The company specialises in creating drilling equipment and rigs that deliver power and precision, while constantly improving on operator safety and productivity. Barkom’s vision is to create the most suitable drill rig for any given task, offering high levels of efficiency and operator comfort, while requiring minimal levels of service and maintenance. All equipment is designed to be highly productive, while keeping operating costs to a minimum.
Barkom Group’s new drill rig, which has recently been completed, aims to bring a new, innovative approach to exploration. The company’s research and development team, who set out to create a unique rig, have released the BD2000M: one rig that can drill using two different methods: diamond core drilling and reverse circulation (RC) drilling.
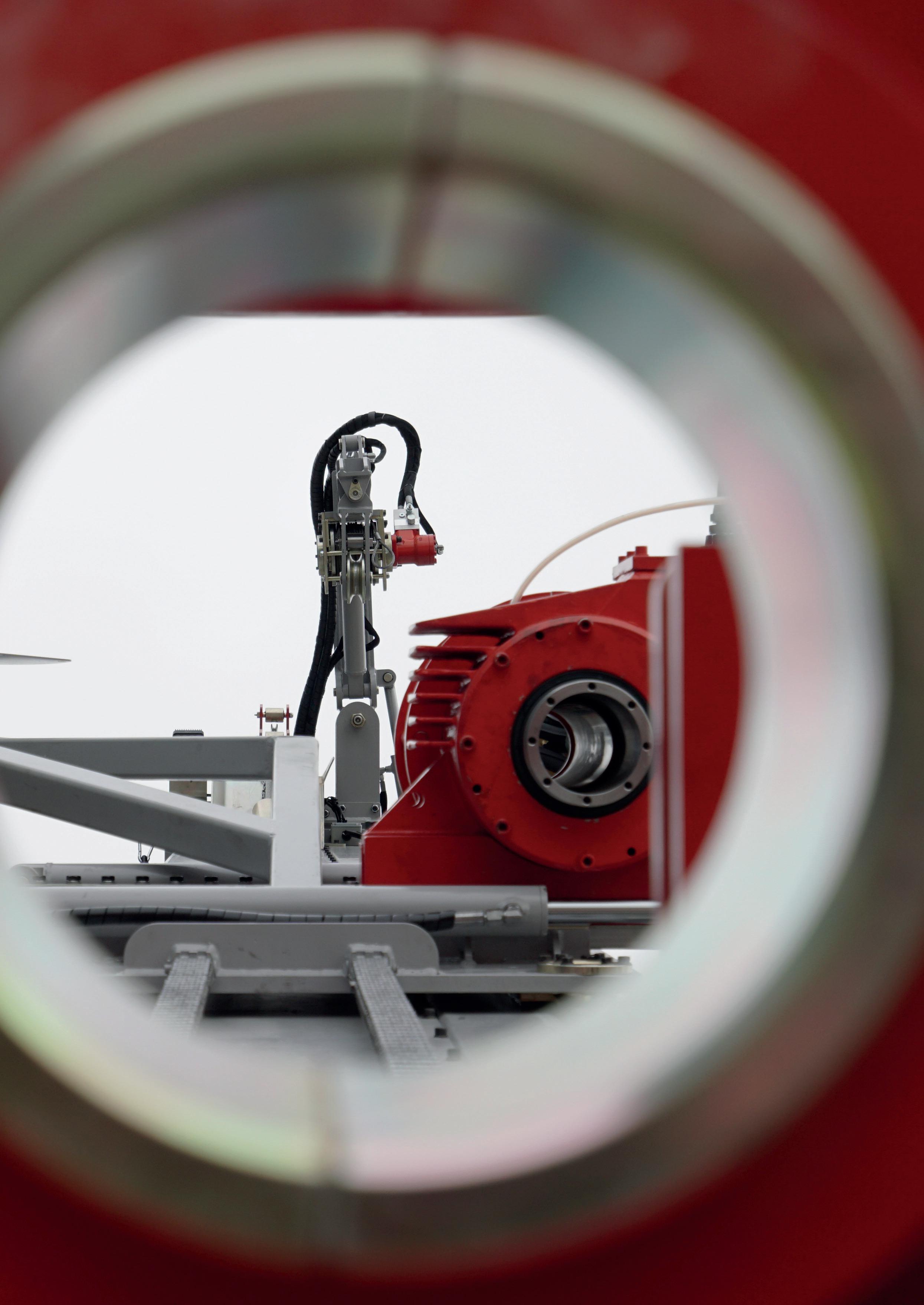
The two drilling methods
Diamond core and RC are drilling techniques that utilise completely different systems. Diamond drilling has revolutionised the mining industry and directly resulted in the discovery of many minable orebodies that would otherwise have gone untapped. Before the introduction of mainstream diamond drilling, mining was still primarily dependent on finding outcrops of rock, with little information available about ore concentrations below the surface. Diamond drilling allows for the removal of solid cylinders of rock (core) from the depths of the earth. The term diamond core drilling comes from the ‘diamond bit’ used during this process. The diamond bit works with a system that is called the core barrel, which collects the core and is then attached to a drill rod, which measures approximately 3 m in length. More sections of the pipe can be attached to the top of the drill rod, allowing greater depths to be drilled as needed. Therefore, the number of rods attached to the top of the drill rod will determine the depth that can be drilled. Within the drill rod, a core tube is attached to a cable by a latching mechanism. The core tube is lifted to the surface using the cable, which is called wireline, to allow for the removal of the solid core.
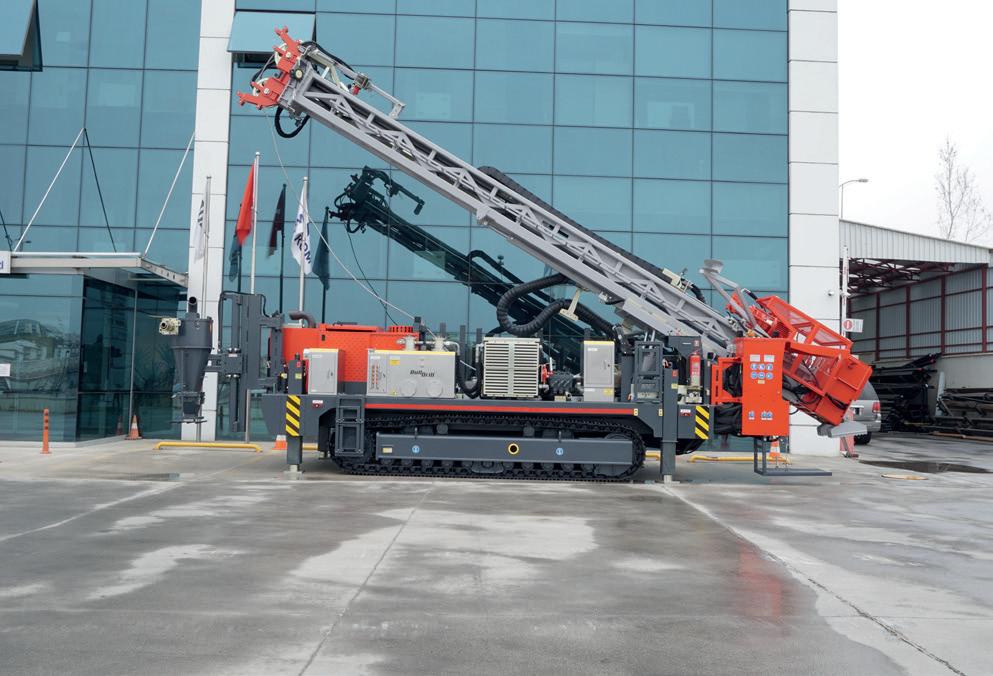
Figure 2. BD2000M general right side view.
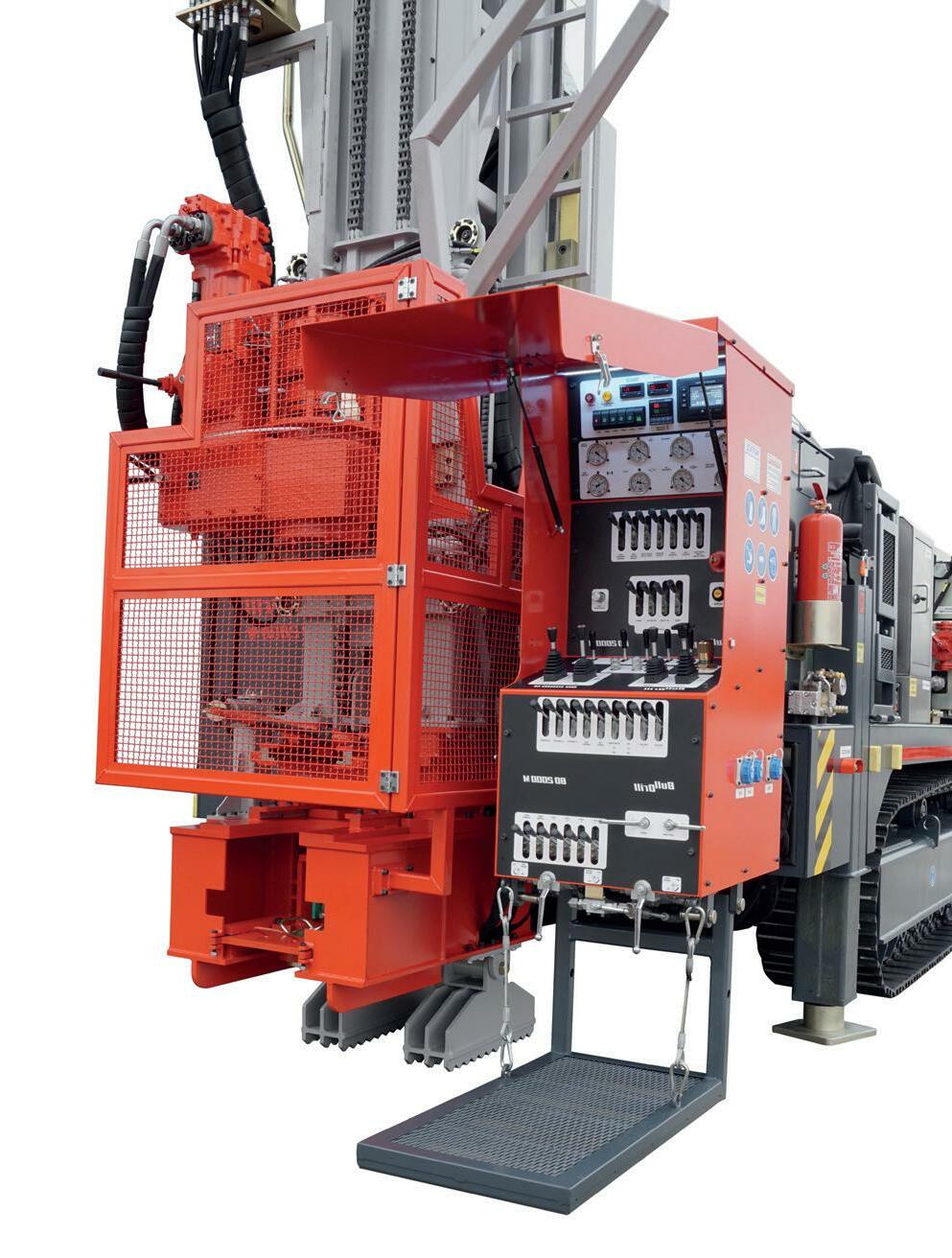
Figure 3. BD2000M control and rotation units.
Advantages of diamond core drilling
n Speed of operation: The speed of diamond core drilling is faster than the alternatives. This is due to the high amounts of pressure – generated via a hydraulic piston – that the diamond drill bit is able to exert onto the material that it is drilling through. n Safety: There are drill rig models that can give an option for a remote controlled traveling system. This means in unsafe areas the drill rig can travel without the operator. n Accuracy: The diamond drill bits can withstand tough forces, and the equipment that is used with diamond core drilling will help give the desired results. n Adaptability: diamond core drilling is not limited to one mine type, with this method, it is possible to drill through any type of ore.
The RC method
RC drilling is fundamentally different from diamond core drilling, both in terms of equipment and core sampling. One major difference is that RC drilling creates small rock chips instead of a solid core. Other differences are in the rate of penetration and cost (p/ft). RC drilling is faster than diamond core drilling, and can also be less expensive depending on the project. The technique focuses on core recovery, drilling in a very broken formation and trying to receive as much core as possible, all things better suited to RC drilling than diamond core drilling.
RC drilling requires much larger equipment, including a high capacity air compressor. The compressor forces air down the outer space of a double wall pipe. The air then circulates back up through the inner pipe carrying the rock chips (core), which are recovered at the surface. The chips travel at such high velocity that they must be slowed down first, using a cyclone. The return pipe directs the chips to the inside of the wall of the cyclone chamber, and then to spiral downwards to the bottom of the cyclone, losing velocity in the process. The chips are collected continuously as the drill advances into the ground. Drill pipes used for RC drilling range from 3.5 – 8 in. in diameter, and 20 ft in length. Each pipe is extremely heavy and requires the use of a winch to lift and position over the drill hole.
Since its foundation in the early 1970s in Australia, RC drilling has become a preferred method for initial exploration and grade control due to its many advantages. These include: n Extracts reliable samples that are free of contaminants. n Time and cost-efficient.
n Well-suited for difficult terrains. n High penetration rates. n Minimal environmental impact.
A multi-purpose drill rig
The Bulldrill BD2000M is a powerful, versatile drill, efficient in all forms of exploration drilling and boasting a range of standard features and options. It is possible to switch between different drilling methods without even leaving the hole. Barkom Group’s BD2000M drill rig is equally productive in all drilling methods, and is adaptable in mineral exploration, directional, and geotechnical drilling across the globe.
The BD2000M offers more depth capacity in both diamond and RC drilling, and has the highest capacity in terms of depth in Barkom Group’s range of exploration drill rigs.
Key technical features for the BD2000M
n The hollow spindle type rotation unit, with 2x4 gears, has the ability incorporate both methods of drilling – diamond core drilling and RC drilling – in one unit.
So, a single hollow spindle rotary head can achieve both methods of drilling. n A heavy-duty, top drive rotation unit, which includes a type second hydraulic motor, is also one of the options offered in RC drilling and diamond core drilling. n The system calculates the torque given to the rod threads, increasing drill rod productivity and life span. n The tray includes an onboard rod storage bin, which holds diamond core rods or reverse circulation rods. n Its strong chassis and travel system makes overcoming physicals obstacles and advancing forward simple. n It has an easy setting and stability capability in sloping and difficult terrains. n Due to the hollow spindle rotation unit, rodrunning does not waste any time. n It has a Volvo (315 hp) engine transferring power to the selected hydraulic components. n Has robust hydraulic jacks, truck or track mounted; 22 t pullback, 12 t pull down; inbuilt breakout system; manual breakout; wireless remote for tramming; 6 m drill pipe capacity; 1 m – 250 kg jib winch; hose covering; robust rod holder (hydraulic power opens/closes by gas spring); high capacity wireline drum (6 mm – 2300 m rope); risk assessment; and more.
Conclusion
Barkom Group will continue to sign joint projects with leading universities in the field of R&D and make significant scientific contributions to a rapidly developing industry. By continuing to work on new projects in strength, power, hydraulic design, mechanical design and prototype manufacturing of rigs, the company will move forward by offering the latest high value-added products to its customers.
FLOTATION 360™
Complete your circuit with the chemical, service and predictive capabilities of FLOTATION 360:
Advanced Chemistry Superior, customized frothers and collectors
Global network of technical consultants and labs ensuring continuous service and support
Optimize performance to increase recovery Reduce potential impacts of future ore changes Enhance reagent dosing and consumption Peace of mind for an efficient, productive, and optimized flotation operation
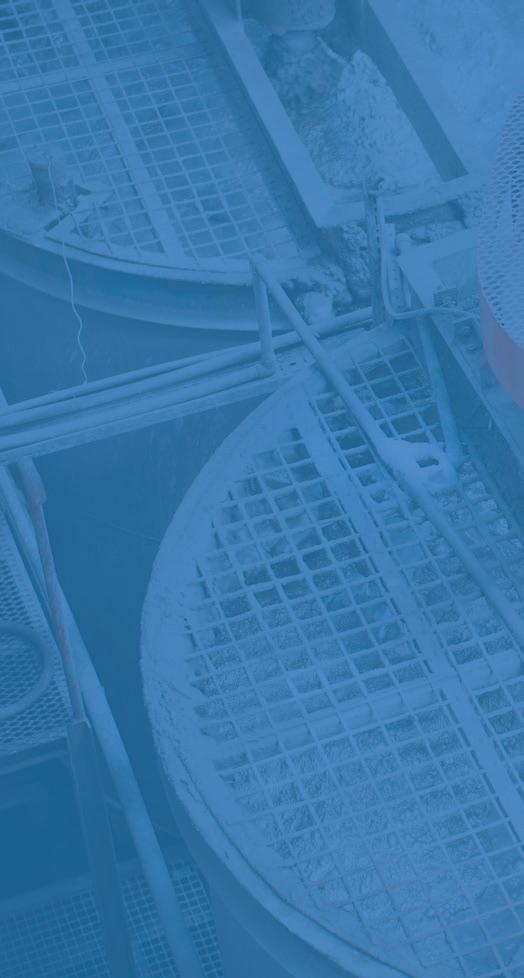
Expert Service
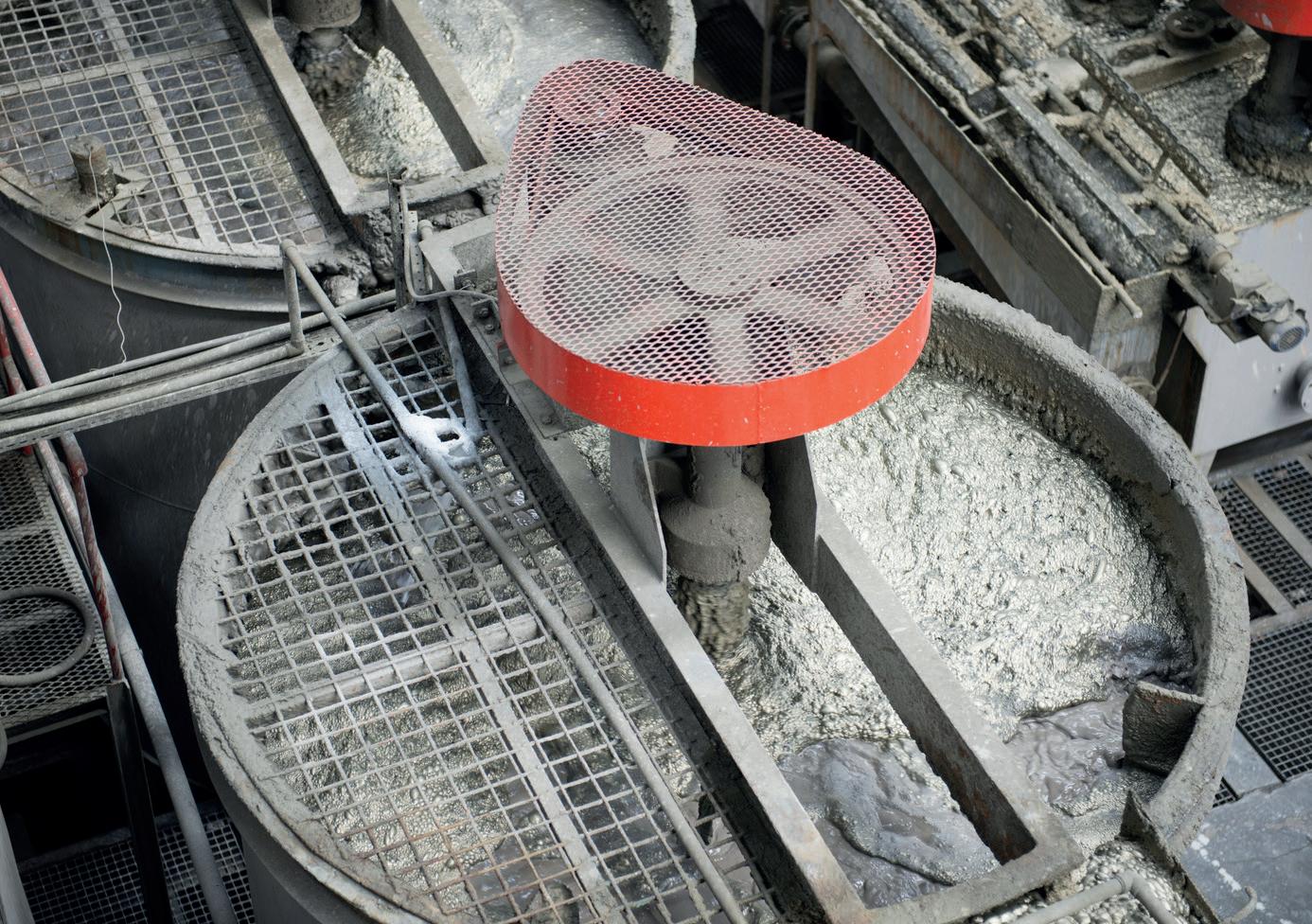
Digital Solution
COMPLETE, END-TO-END FLOTATION OPTIMIZATION
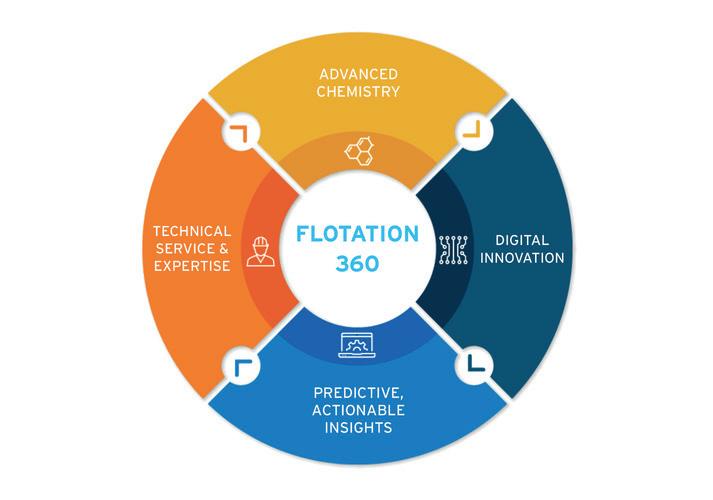
To learn more about how Nalco Water can help maximize your flotation performance, visit https://www.ecolab.com/nalco-water/offerings/flotation-360