www.supplychain-outlook.com
AUSTRALIAN LOGISTICS
Connecting people and goods across the country and beyond, Kuehne+Nagel Australia is internationally renowned for its supply chain optimisation
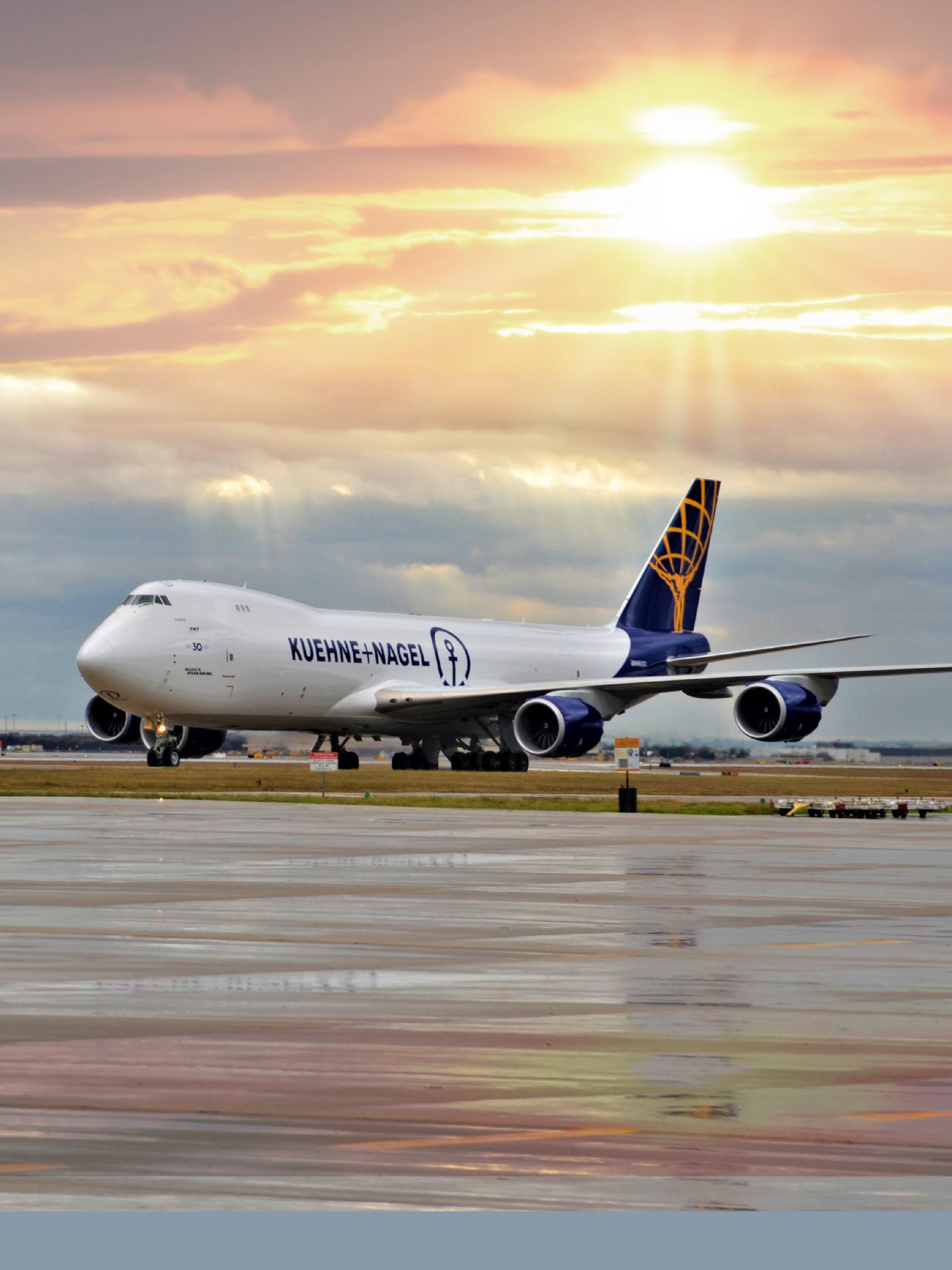

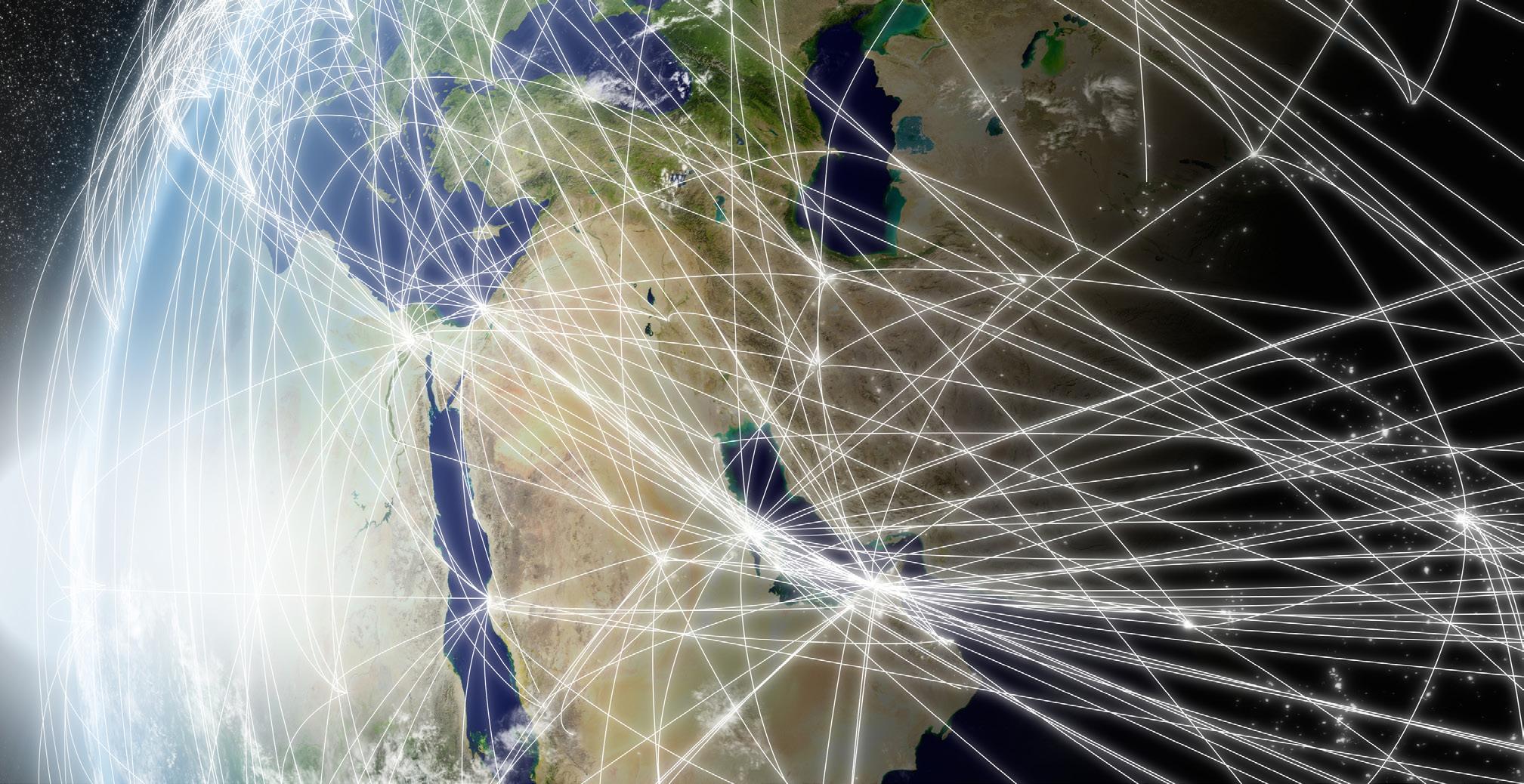
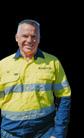
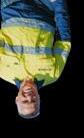
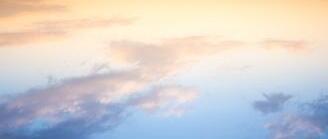
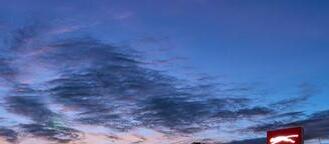
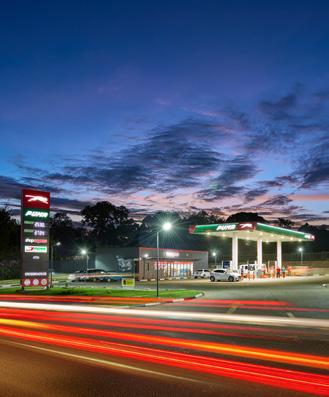
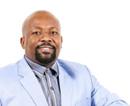
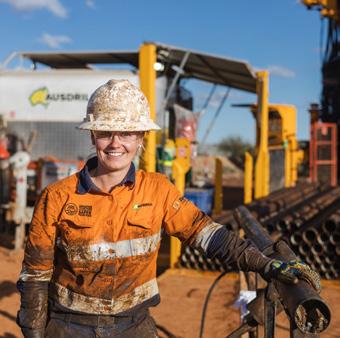
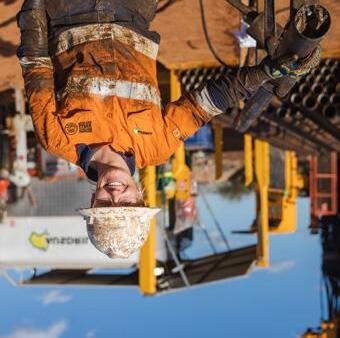




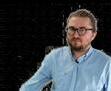
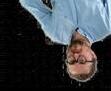
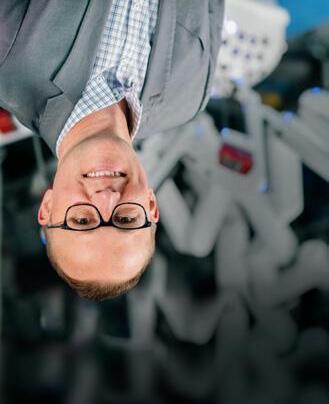
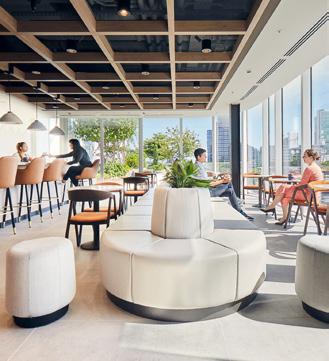
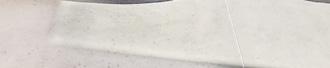
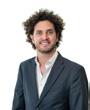



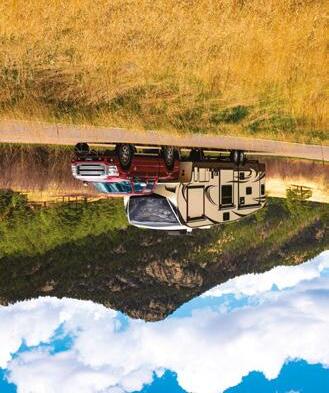
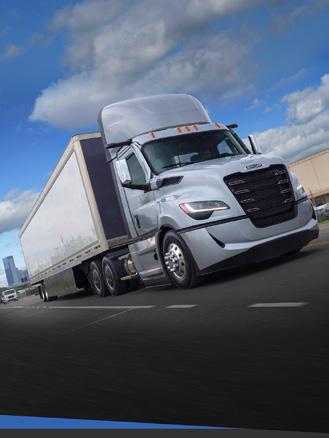
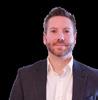




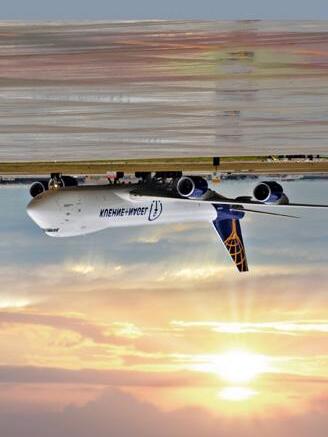


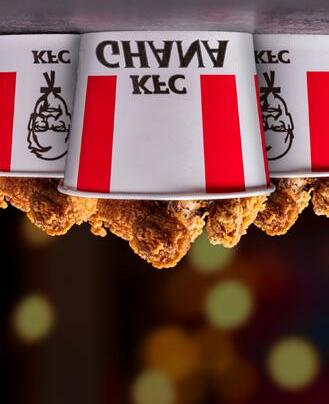
Africa Outlook, APAC Outlook, EME Outlook, North America Outlook, Mining Outlook, Healthcare Outlook, Manufacturing Outlook, Supply Chain Outlook, and Food & Beverage Outlook are digital publications aimed at boardroom and hands-on decision-makers, reaching an audience of more than 800,000 people around the world.
With original and exclusive content compiled by our experienced editorial team, we look to promote the latest in engaging news, industry trends and success stories from across the globe.
Your company can join the leading industry heavyweights enjoying the free exposure we provide across our platforms with a free marketing brochure, extensive social media saturation, enhanced B2B networking opportunities, and a readymade forum to attract new investment and to help you grow your business.
Visit www.outpb.com/work-with-us for details on how your company can feature for free in one of our upcoming editions.
EDITORIAL
Head of Editorial: Jack Salter jack.salter@outpb.com
Deputy Head of Editorial: Lucy Pilgrim lucy.pilgrim@outpb.com
Senior Editor: Lily Sawyer lily.sawyer@outpb.com
Editor: Ed Budds ed.budds@outpb.com
Editor: Lauren Kania lauren.kania@outpb.com
Editor: Rachel Carr rachel.carr@outpb.com
PRODUCTION
Art Director: Stephen Giles steve.giles@outpb.com
Senior Designer: Devon Collins devon.collins@outpb.com
Designer: Louisa Martin louisa.martin@outpb.com
Production Manager: Alex James alex.james@outpb.com
Digital Marketing Director: Fox Tucker fox.tucker@outpb.com
Website Content Manager: Oliver Shrouder oliver.shrouder@outpb.com
Social Media Executive: Jake Crickmore jake.crickmore@outpb.com
BUSINESS
CEO: Ben Weaver ben.weaver@outpb.com
Managing Director: James Mitchell james.mitchell@outpb.com
Chief Technology Officer: Nick Norris nick.norris@outpb.com
ADMINISTRATION
Finance Director: Suzanne Welsh suzanne.welsh@outpb.com
Finance Assistant: Suzie Kittle suzie.kittle@outpb.com
Finance Assistant: Victoria McAllister victoria.mcallister@outpb.com
CONTACT
Supply Chain Outlook
Norvic House, 29-33 Chapelfield Road
Norwich, NR2 1RP, United Kingdom
Sales: +44 (0) 1603 804 445
Editorial: +44 (0) 1603 804 431
SUBSCRIPTIONS
Tel: +44 (0) 1603 804 431
jack.salter@outpb.com
www.supplychain-outlook.com
Join us on Linkedin: linkedin.com/company/supplychainoutlook/ Follow us on X: @outlookpublish
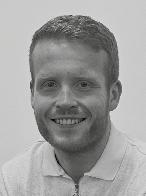
ECONOMIC CORNERSTONES
Welcome to our fourth edition of Supply Chain Outlook magazine.
Freight forwarding and logistics are mainstays of the economy in Australia, a vital nation for international trade.
At the head of the industry since 1971, as well as the front cover of this issue, Kuehne+Nagel Australia provides unparalleled freight forwarding and supply chain solutions.
The company’s operational expanse is unlocked by the international network of leading logistics provider, Kuehne+Nagel, encompassing 135 years of expertise.
“Our logistics experience and cross-industry know-how give us valuable insights into how to improve customers’ needs,” affirms Francis Murugan, Managing Director of Kuehne+Nagel Australia.
Mining is also a cornerstone of the Australian economy, driving innovation, exports, and sustainable resource development.
“Kuehne+Nagel ensures that mining and energy companies can maintain efficient, safe, and sustainable operations, even in challenging and remote environments,” shares François Sellin, Global Lead Mining.
In Guinea, meanwhile, a leading role in the national economy is played by the Port of Conakry as the West African country’s primary commercial port.
Indeed, 90 percent of foreign trade in Guinea is carried out at the port, whose services include handling, towing, mooring, and ship security.
“The vision of the Port of Conakry is to become a hub in the West African subregion, where the market is very competitive with the presence of several ports in the Gulf of Guinea,” outlines Biro Diallo, Managing Director of the port authority – the Autonomous Port of Conakry.
Ports are also a pillar of economic well-being in the Caribbean, where cruise ships represent an exciting area for growth and development.
“The Caribbean is where almost every cruise line in the world comes for five, six, or sometimes seven months in the year, which makes us a very critical space. If the Caribbean was not involved in providing cruise services, there would be a real problem in the world because it is a multi-billion-dollar industry,” notes Darwin Telemaque, Chairman of the Port Management Association of the Caribbean.
This issue also includes corporate stories from HMM America, Coach USA, Campbell Transport, and more as we showcase the companies that keep global economies and supply chains moving.
We hope that you enjoy your read.
Jack Salter Head of Editorial, Outlook Publishing
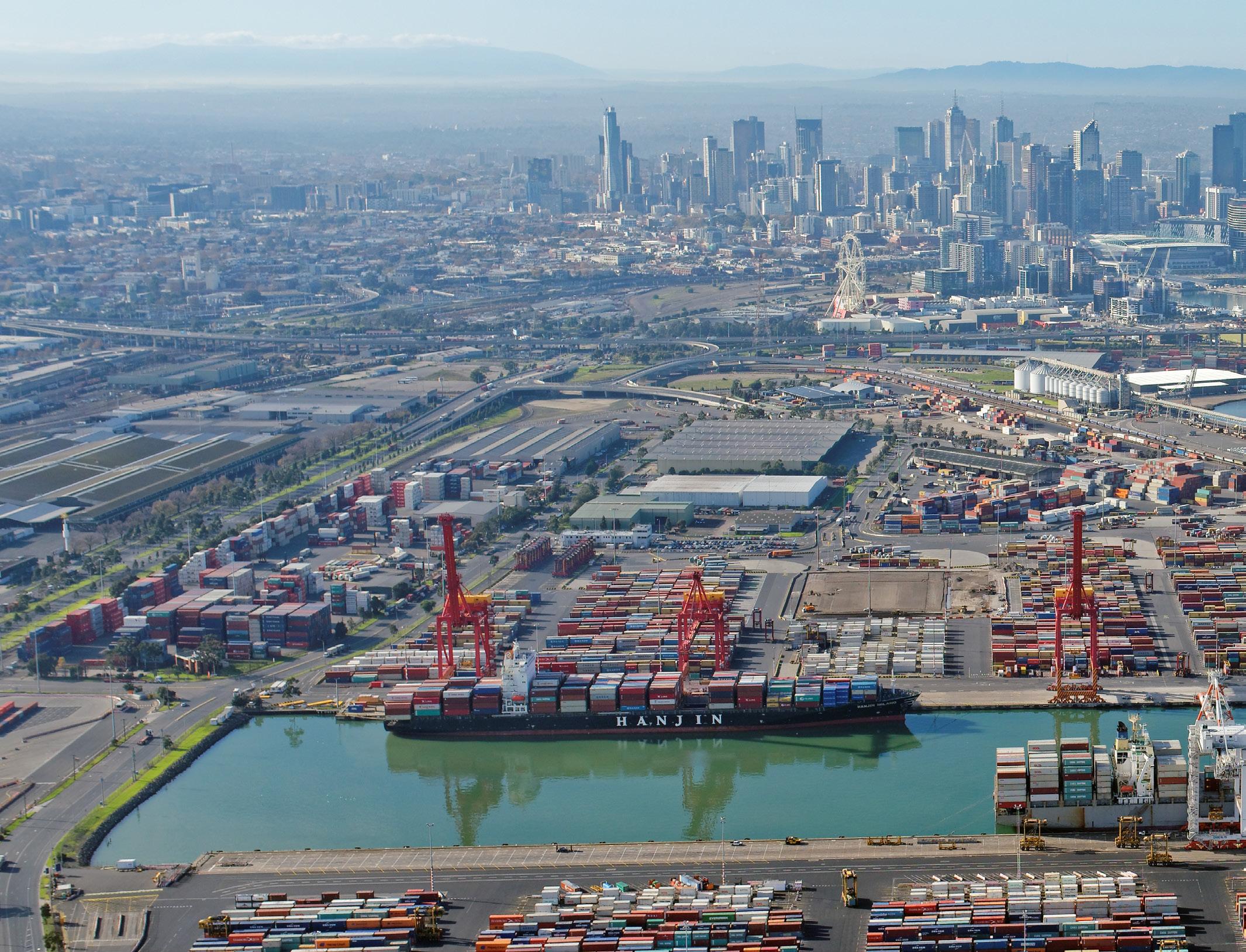



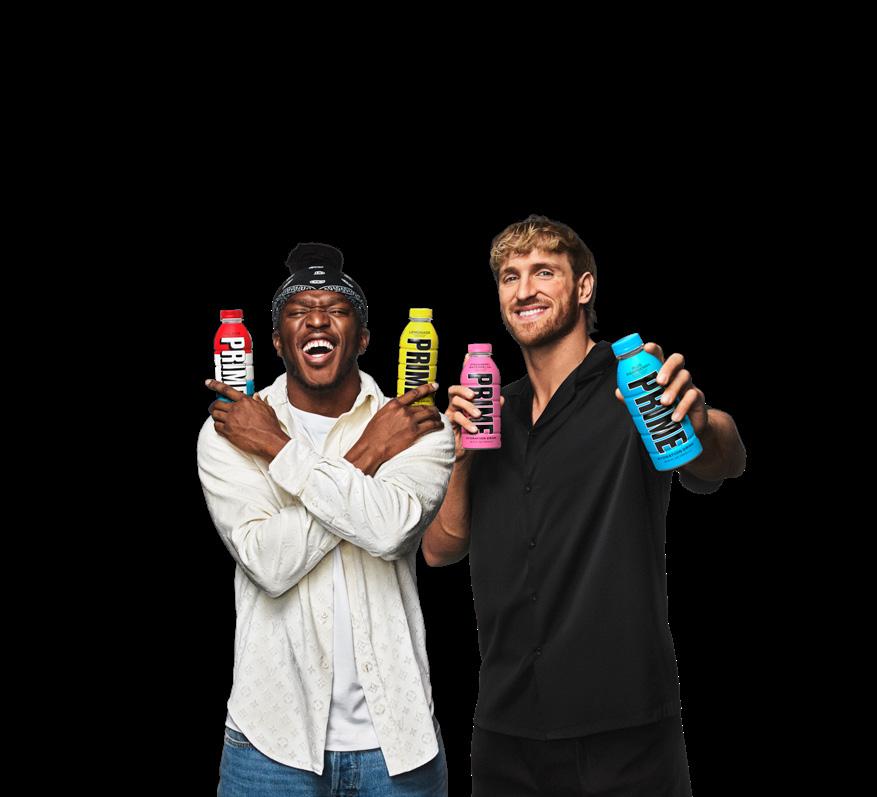
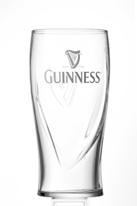
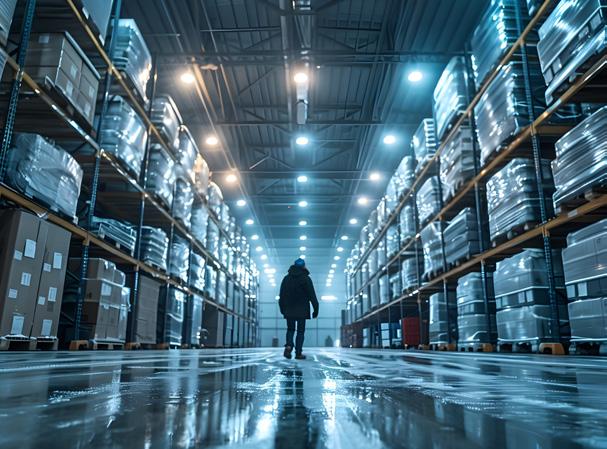
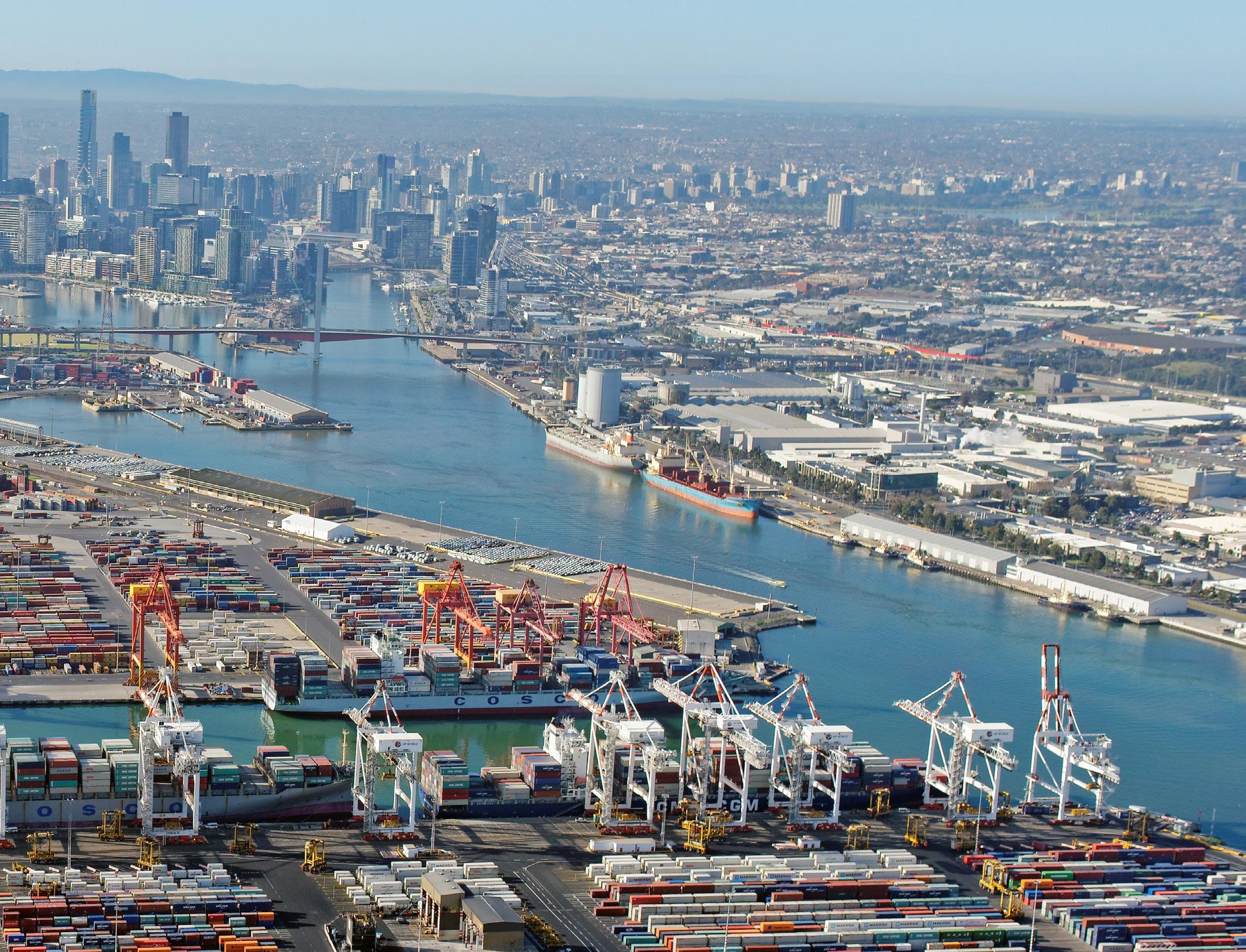
FEATURES
AFRICA
52 Autonomous Port of Conakry
Guinea’s Commercial Gateway
Overseeing activities at the Port of Conakry

NORTH AMERICA
62 HMM America
The Ocean Carrier of Choice
State-of-the-art ocean services
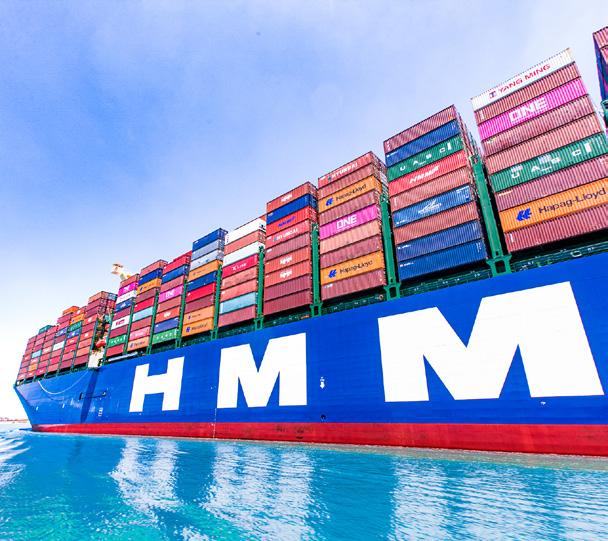
70 Coach USA
Driving Success Across the Nation
Connecting people, places, and opportunities
78 Ferromex
Full Steam Ahead
Mexico’s largest cargo operator
ASIA PACIFIC
86 Campbell Transport
The Go-To Logistics Provider
Serving multiple industries and guaranteeing truck driver safety
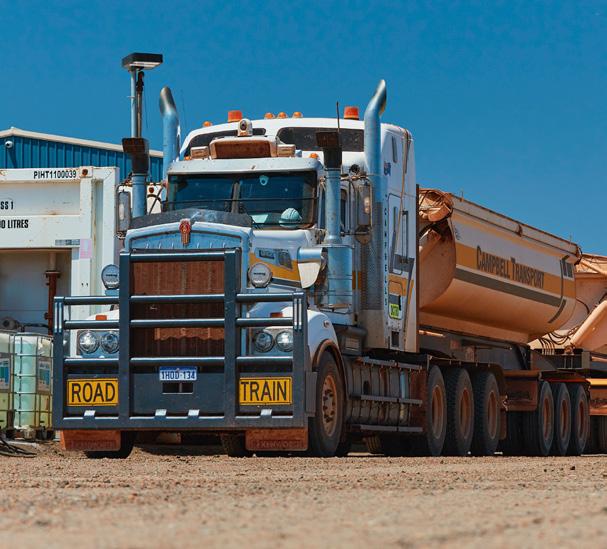
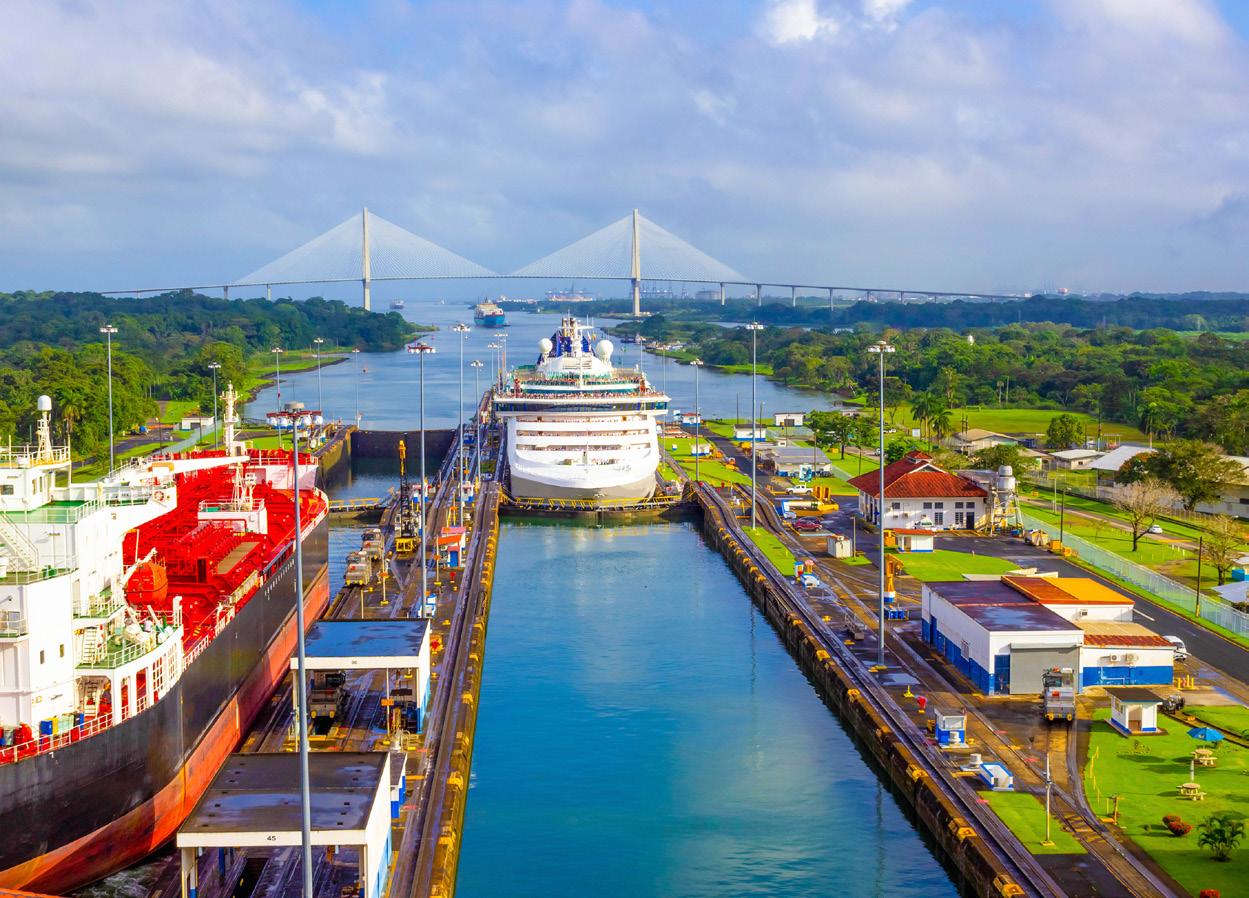
LEGISLATION WAGES WATERWAY WAR
LEGISLATION RECENTLY INTRODUCED by Congress means that US President, Donald Trump, could buy back the Panama Canal.
The Panama Canal Repurchase Act of 2025 would authorise the President, in coordination with the Secretary of State, Marco Rubio, to conduct negotiations to reacquire the 51-mile waterway, which was initially signed over to Panama by late President Jimmy Carter, in 1977.
At a recent press conference, Trump said he couldn’t guarantee he wouldn’t use military or economic coercion to gain control of the canal. However, Panama’s Foreign Minister, Javier Martínez-Acha, remains resolute that it will stay in Panamanian hands.
DRIVING GLOBAL GROWTH
SOUTH KOREAN AUTOMAKER
Hyundai Motor Group (Hyundai) has unveiled an ambitious plan to invest a record USD$16.6 billion to strengthen its position in the global automotive supply chain.
Amidst uncertain international economic and political landscapes, the company is increasing electric vehicles (EVs), hydrogen-powered products, and cutting-edge
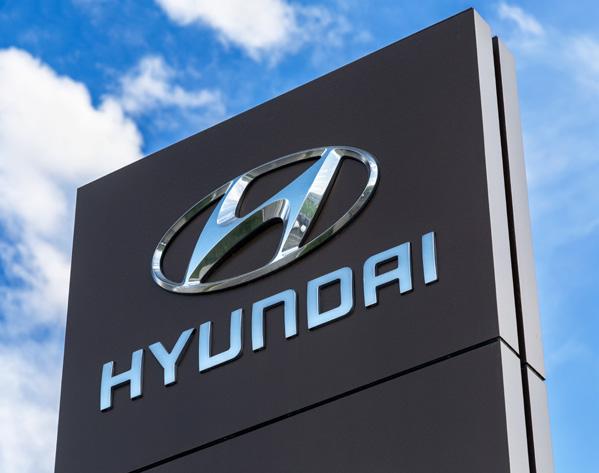
EUROPE & MIDDLE EAST
THIS IS NOT JUST A LOGISTICS FLEET
MAJOR RETAILER MARKS
& Spencer (M&S) has added 85 zero or lower-emission vehicles to its supply chain fleet in the UK in a bid to become net zero by 2040. 80 of the new vehicles are powered by compressed natural gas (CNG), making it the first retailer in the country to do so.
The new vehicles also include five zero-emission battery electric heavy goods vehicles (HGVs), which will operate between M&S’ clothing and home distribution centre in Welham Green, Hertfordshire and 30 stores across London and the Southeast.
The 42-tonne battery electric Renault trucks will directly replace diesel HGVs. Once the 85 vehicles are operational, almost 10 percent of the company’s logistics transport will be powered by zero or lower-emission solutions.
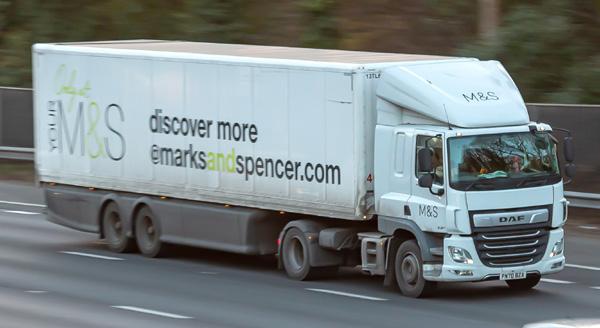
technology. Hyundai is currently the world’s third-largest automaker, and its new strategy, alongside initiatives such as selling cars through Amazon, will position it to compete with emerging low-cost rivals.
However, President Trump has threatened to introduce a universal tariff on products imported to the US, which could subsequently disrupt the company’s supply chain and exports.
EXPANDING AFRICAN AIR LOGISTICS
AFRICA EFIS MAROC, AN ECS Group subsidiary, has partnered with China Eastern Airlines, further solidifying its leadership in African cargo logistics.
The agreement, which began on the 19th January, will introduce three weekly flights between Casablanca and Shanghai via Marseille, France, and is to be carried out with Boeing 787-900 aircraft featuring an 18-tonne cargo capacity. The tailored cargo management solution will therefore enhance both operational efficiency and customer satisfaction.
NORTH AMERICA
SMOOTH SYSTEM OPERATORS
US SUPPLY CHAIN management company Blue Yonder has unveiled essential updates to its artificial intelligence (AI)-powered platform. The move will enable organisations to streamline operations, expand globally, and achieve objectives.
The new approach involves leveraging machine learning (ML) as

Additionally, the new collaboration reinforces Morocco’s role as a gateway to Africa and reaffirms its commitment to expanding its presence across the continent.
well as AI to enhance omnichannel commerce, logistics, and the user experience, which will empower organisations to respond to dynamic market shifts and increase profitability.
The updates result from two years of innovation, involving more than 8,000 integrated workstreams across supply, demand, and business planning, solidifying Blue Yonder’s leadership in supply chain modification.

EUROPE & MIDDLE EAST
GUARANTEEING TRADE FLOW
THE UNITED ARAB Emirates (UAE) has recently signed a landmark trade deal with Malaysia, Kenya, and New Zealand. The inter-continental agreement is one of many trade and investment deals that the Middle Eastern country has made in recent years.
The agreement signed at the start of this month marks a turning point in UAE’s trade and logistics landscape, as according to the country’s Trade Minister, the three other nations are on an upward economic trajectory and are therefore key to continue supporting UAE’s global supply chain.
EUROPE & MIDDLE EAST
UPS INCREASES COLD CHAIN FOOTPRINT
GLOBAL DELIVERY AND supply chain titan UPS has increased its European cold chain footprint with two new acquisitions – Frigo-Trans and its sister company BPL - which provide healthcare logistics solutions. Both businesses are headquartered in Germany, with Frigo-Trans providing end-to-end warehouse and transportation solutions for pharmaceutical and BioTech customers and BPL offering shipping of time-critical and temperaturesensitive products.
UPS recognises the industry’s fastpaced innovation, creating demand for more integrated cold and frozen supply chains. Ultimately, the organisation hopes to provide more efficient and reliable services for the healthcare industry.
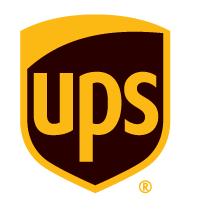
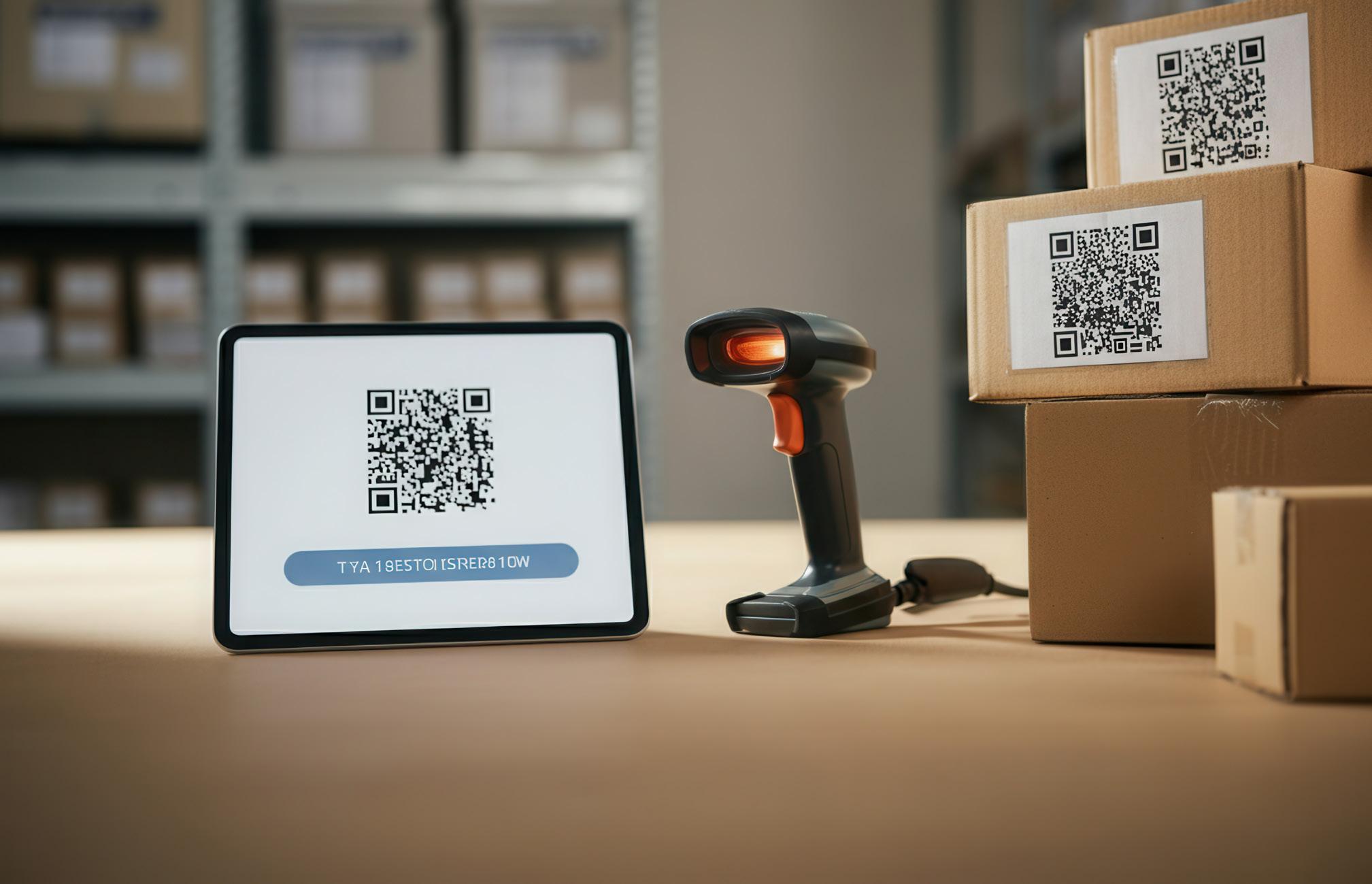
A NEW ERA OF SUPPLY CHAIN MANAGEMENT
The business world is transforming faster than ever, and the tools that shaped our past must evolve to meet the demands of the future. Few technologies have had the universal impact of the linear barcode which, alongside the shipping container, revolutionised global supply chains in the latter half of the 20th century. Today, the next generation of barcodes - QR codes powered by GS1 - are emerging as the next groundbreaking innovation that will define the supply chains of the digital age
Writer: Chris Tyas, OBE, Chair, GS1 UK
The traditional barcode gave businesses the ability to track products efficiently, streamlining logistics and operations on a global scale. Since first being adopted in 1973, they have revolutionised our day-to-day in ways most do not realise – keeping our shelves stocked with products and ingredients from around the world, helping us to find and buy products online, ensuring what we consume is genuine and safe,
and much more.
QR codes take this to a whole new level. With capacity to store up to 7,098 numeric or 4,269 alphanumeric characters, they carry significantly more data than their linear predecessors in a compact, easily scannable form.
This matters because consumers, businesses, and regulators are increasingly demanding greater transparency than ever before. Today,
it seems everyone wants to know where a product has come from, how it was made, and how to use or recycle it. This demand for information grows by the day, which presents a challenge for product-based businesses as physical space on packaging will always be finite.
QR codes powered by GS1 provide a simple, elegant solution, offering instant access to a wealth of information through one quick scan.
The consumer appetite for this kind of transparency is clear. A recent GS1 survey found that 79 percent of shoppers are more likely to purchase products with scannable codes offering deeper insights. With over 4.5 billion smartphone users worldwide, the QR code is the bridge that connects physical products to the accurate, trusted data that businesses, consumers, and governments care about most.
POWERING PROGRESS
The advantages of QR codes aren’t just theoretical; they’re already
transforming industries by offering enhanced traceability, streamlined inventory management, and new opportunities for customer engagement.
QR codes powered by GS1 are now being tested in 48 countries, representing 88 percent of the world’s GDP. Globally, GS1 aims to ensure a comprehensive rollout by 2027 and many leading household brands, including PepsiCo, Walmart, P&G, Loreal, and Amazon are already on board.
Take traceability, for example. By enabling real-time tracking of products through the supply chain, QR codes can improve safety by reducing counterfeiting and making recalls more efficient. In healthcare, QR codes are increasingly being used to ensure that medicines are tracked accurately, from production to patient use, reducing the risk of clinical errors whilst saving lives, time, and money.
For manufacturers and retailers, QR codes simplify inventory management by eliminating manual data entry, reducing errors, and improving visibility across supply chains. This leads to better decisionmaking, whether it’s maintaining stock levels, addressing disruptions, or reducing waste.
Already, QR codes are unlocking new ways to connect with consumers. By embedding product details, allergen information, or sustainability credentials, brands can offer the transparency that modern consumers expect. They can even link to exclusive content, promotions, or loyalty programmes, turning packaging into a powerful dynamic engagement tool.
A CALL FOR COLLABORATION
The success of the linear barcode wasn’t just about the technology – it was about
collaboration. Businesses, industries, and regulators came together to agree on the shared standards that have enabled supply chains and the interoperable data that powers them to cross borders, span continents, and stretch across the entire globe.
The transition to QR codes requires an even greater level of collaboration. These codes don’t just carry logistics data - they encompass environmental, health, and regulatory information as well. To succeed, industries must once again commit to common standards that will ensure consistency and reliability across diverse sectors and geographies.
This is where GS1 plays a critical role. As the global leader of interoperable data standards, GS1 provides the framework that will enables businesses to adopt QR codes efficiently, ensuring they deliver their full potential, especially in terms of transparency and traceability, at scale.
OVERCOMING CHALLENGES
Change is never easy, but always possible, and the global transition to QR codes will come with challenges. Many businesses, especially smaller ones, are faced with the cost of upgrading systems and training employees to use new technology. Legacy equipment and infrastructure may also struggle at first, creating short-term inefficiencies.
Consumers too face a learning curve. Whilst younger generations are comfortable scanning QR codes, older demographics may need more guidance to adapt. However, these challenges are surmountable, and the transformative benefits far outweigh the obstacles.
improving operational efficiency and meeting the growing demand for transparency.
THE FUTURE IS NOW
We’re standing at the cusp of a new era in supply chain management. Just as the linear barcode revolutionised the 20th century, QR codes powered by GS1 are set to transform the 21st. They offer businesses a powerful tool to navigate the complexities of modern supply chains by delivering transparency, efficiency, and trust.
The future is digital and datadriven, and QR codes are leading the way. By embracing this technology, businesses can build stronger connections with consumers, ensure compliance, and create a more sustainable, transparent supply chain for generations to come.
ABOUT THE EXPERT
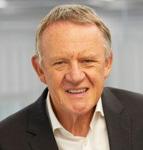
Chris Tyas, OBE, is the Chair of GS1 UK with a globally recognised pedigree in the consumer goods industry as a result of his careers at Mars and Nestlé. During his time at Nestlé, he held a wide range of executive supply chain roles, concluding his time there as Senior Vice President and Global Supply Chain Head.
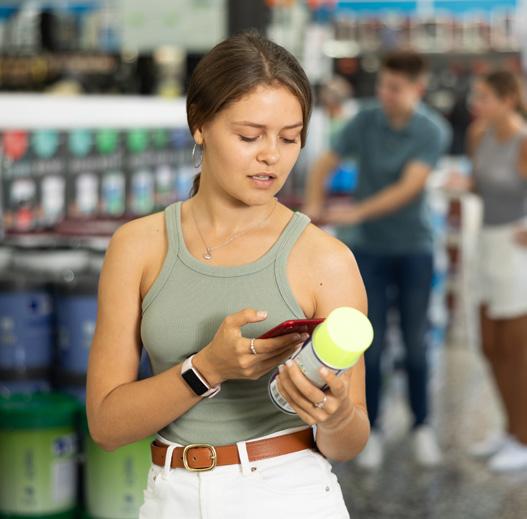
Businesses that invest early in QR codes will gain a competitive edge,
He is renowned for his ability to convene cross-industry groups to solve problems, such as his involvement in the UK government’s Food Data Transparency Partnership and co-chairing the Food Resilience Taskforce, for which he was awarded an OBE. He is also a non-executive board member of the Department for Environment, Food, and Rural Affairs (Defra).
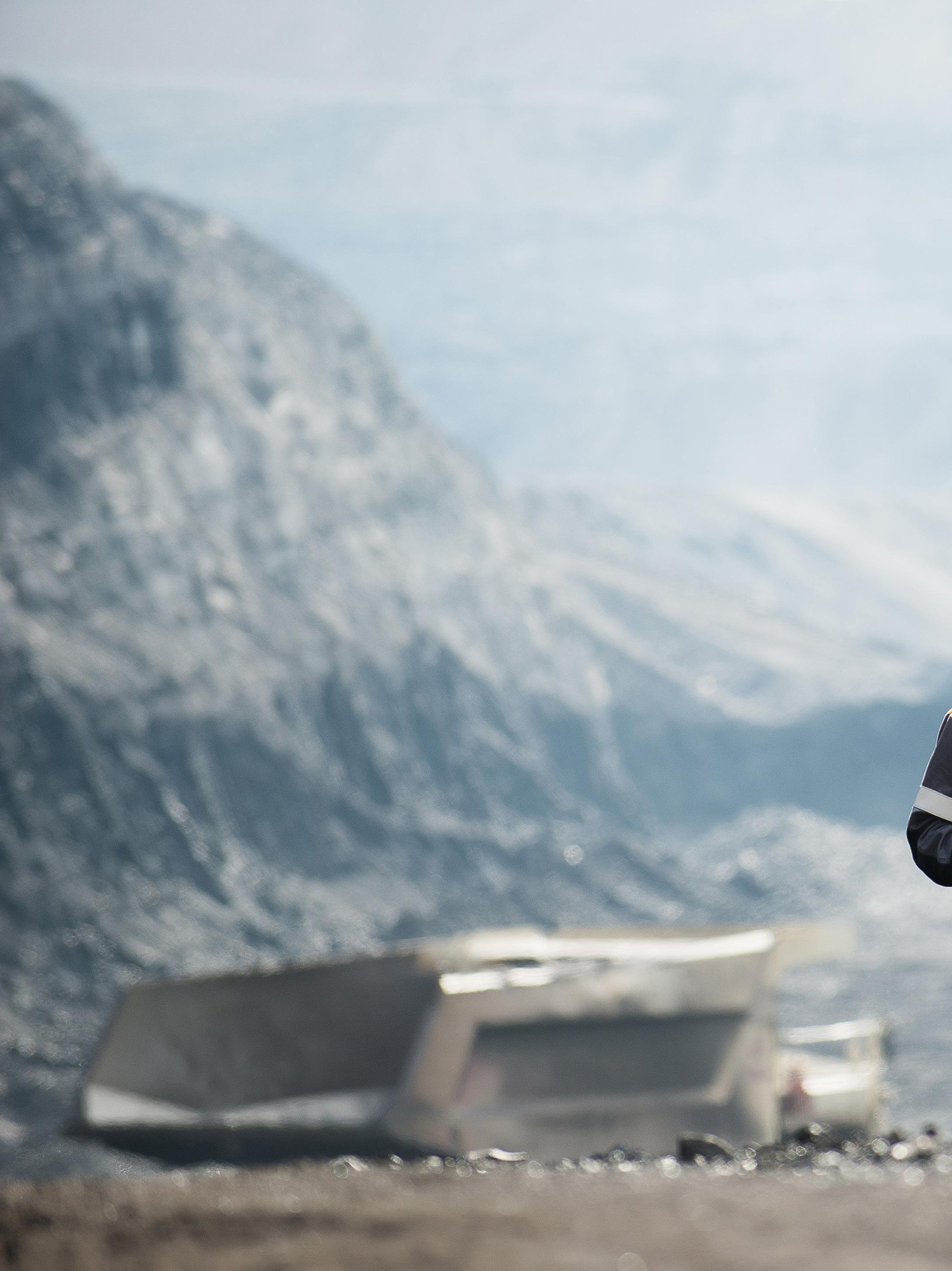
AUSTRALIAN LOGISTICS SHAPING
Connecting people and goods across the country and beyond, Kuehne+Nagel Australia is internationally renowned for its supply chain optimisation. Francis Murugan, Managing Director, and François Sellin, Global Lead Mining, delve into the company’s industry-leading logistics and mining solutions
Writer: Lucy Pilgrim
Having established itself as a vital nation for international trade, the Australian freight forwarding and logistics landscape is a mainstay of the country’s economy.
At the head of the industry since 1971, Kuehne+Nagel Australia provides unparalleled freight forwarding and supply chain solutions across the world.
Indeed, its operational expanse is unlocked by the international network of leading logistics provider, Kuehne+Nagel, encompassing 135 years of expertise.
Established by August Kuehne and Friedrich Nagel in 1890, the humble shipping business has evolved to
become a critical global logistics partner that offers highly specialised solutions for major industries worldwide.
Headquartered in Switzerland, Kuehne+Nagel ensures that urgent logistics needs are efficiently met.
“Our primary focus is to support the business needs of our valued customers by offering solutions to their challenges,” opens Francis Murugan, Managing Director of Kuehne+Nagel Australia.
The nation’s mining industry is a cornerstone of its economy, driving innovation, exports, and sustainable resource development. This leads to innovation by optimising supply

chains, prioritising health, safety, and environment (HSE) standards, and advancing towards a zero-carbon future.
“Kuehne+Nagel ensures that mining and energy companies can maintain efficient, safe, and sustainable operations, even in challenging and remote environments,” introduces François Sellin, Global Lead Mining at Kuehne+Nagel, who is responsible for mining business development worldwide.
Indeed, the organisation has successfully developed business in collaboration with a handful of the world’s major mining companies.
“No matter which industry you operate in, our team can assist. Our logistics experience and cross-industry knowhow give us valuable insights into how to improve customers’ needs”
– FRANCIS MURUGAN, MANAGING DIRECTOR, KUEHNE+NAGEL
AUSTRALIA
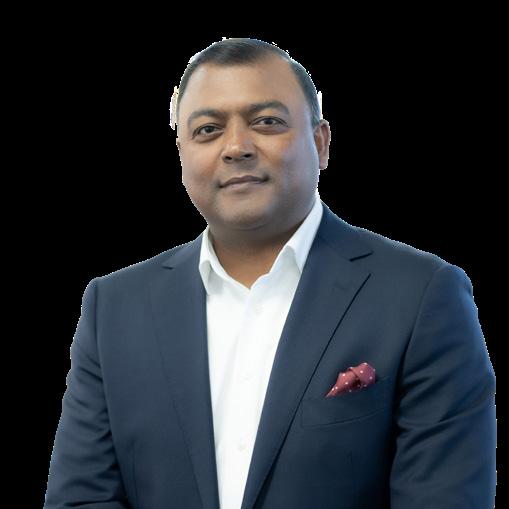
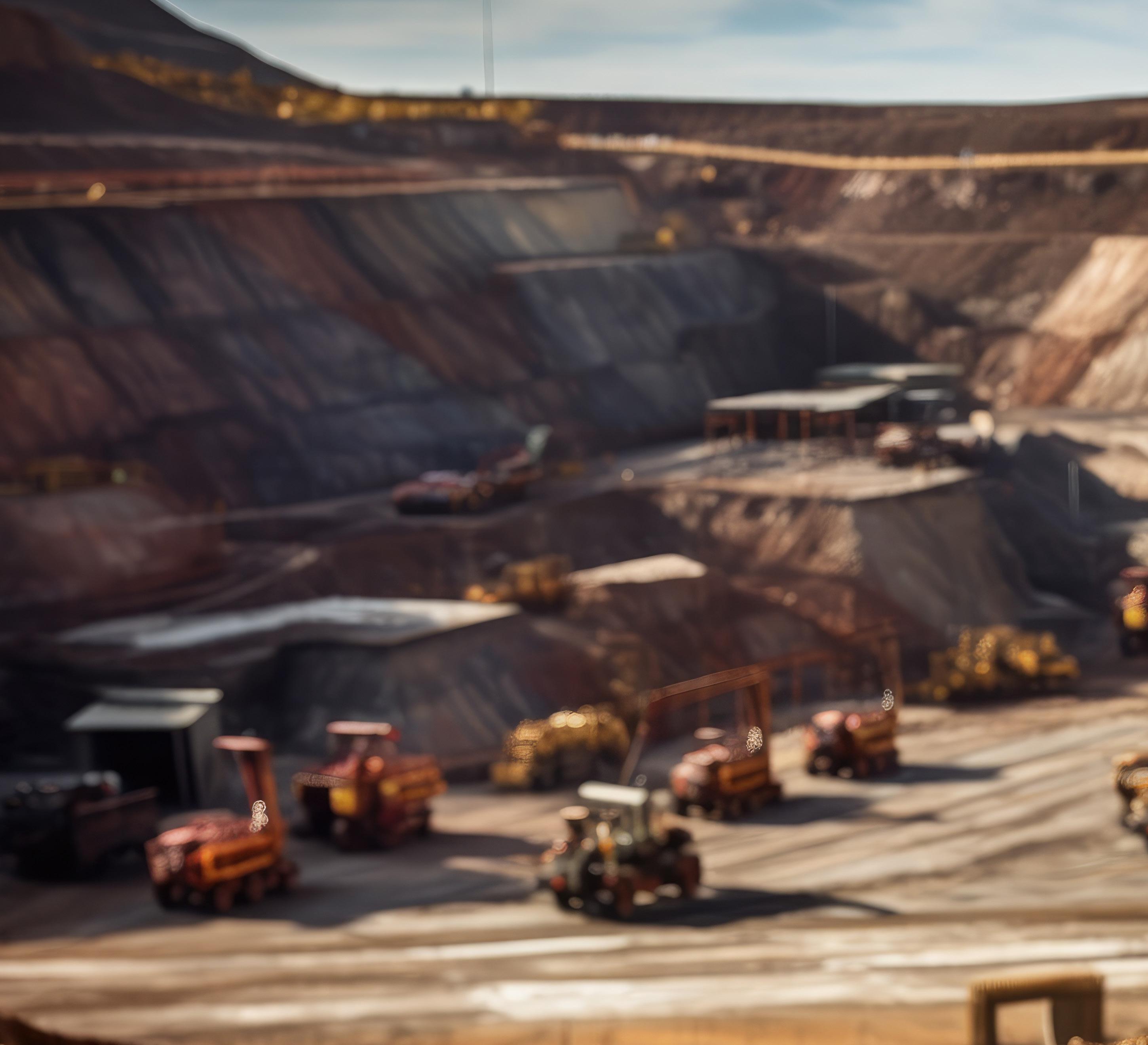
“Kuehne+Nagel supports all stages of the lifecycle of mines and provides customised solutions from exploration through to construction, operation, and closure,” he highlights.
SUPPLY CHAIN OPTIMISATION
Francis Murugan has amassed a vast pool of knowledge from his 30+ years in the industry, collating international experience in South Africa, Australia, and New Zealand.
He was exposed to logistics from a young age when he worked as an apprentice, providing a cross section
of the industry landscape.
As such, Francis Murugan is able to leverage his impressive background and experience to lead Kuehne+Nagel Australia’s strong market position in sea and air freight as well as contract and road logistics.
The company’s unmatched industry position is achieved by providing a highly comprehensive and impartial analysis of customers’ entire supply chains that efficiently identifies opportunities for optimisation.
“No matter which industry you operate in, our team can assist. Our
logistics experience and crossindustry know-how give us valuable insights into how to improve customers’ needs,” affirms Francis Murugan.
Indeed, Kuehne+Nagel Australia goes above and beyond to support businesses with both international and domestic supply chain optimisation projects.
From a mining and industrial perspective, Kuehne+Nagel addresses the demands of the mining and energy sectors by offering tailored solutions that emphasise
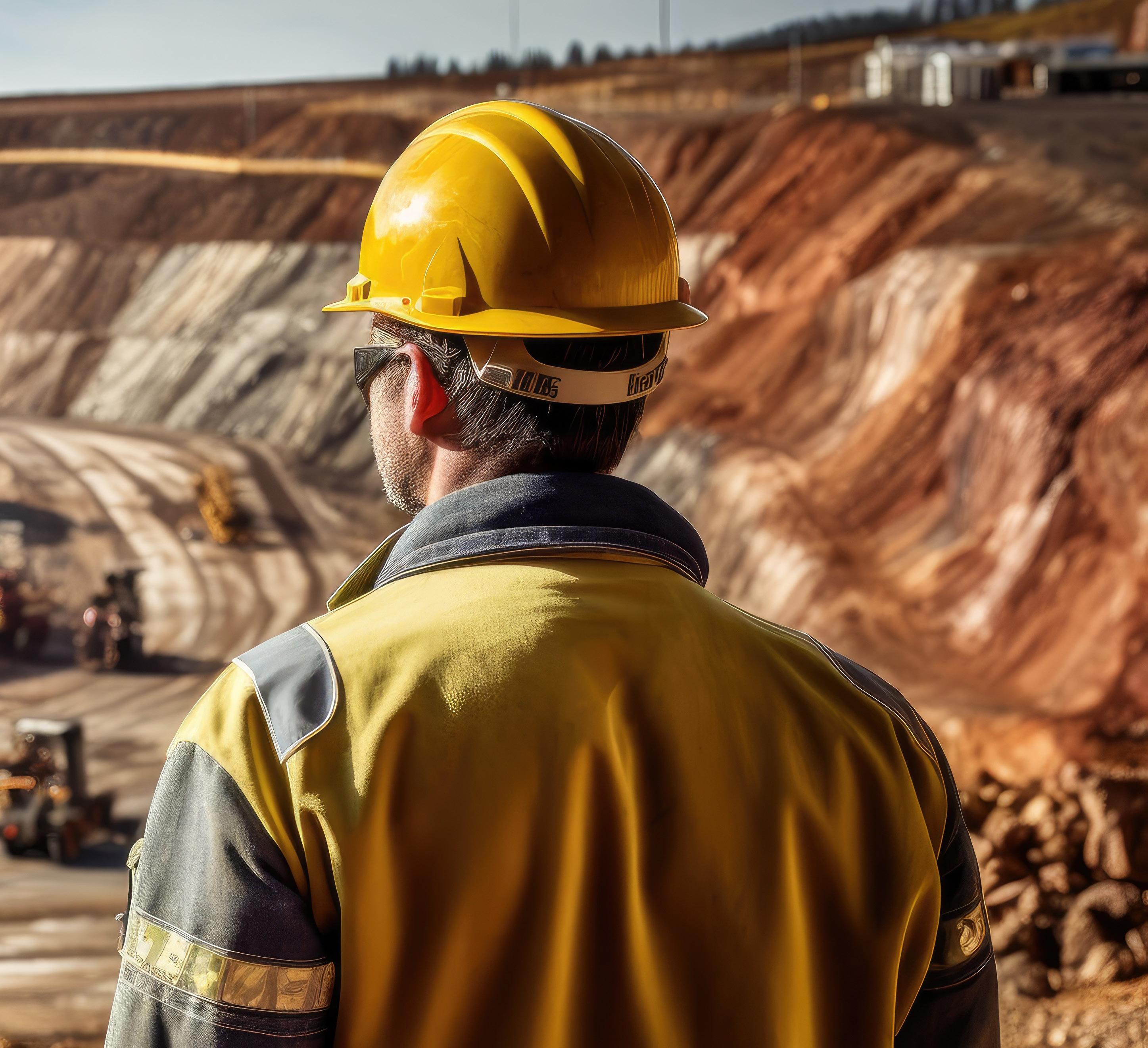
safety, efficiency, and sustainability.
The company’s integrated freight solutions, for instance, provide many multimodal transport options for customers’ supply chains, including break bulk, sea, and air charters that ensure the timely and secure delivery of equipment and materials to remote locations.
Moreover, Kuehne+Nagel’s engineering expertise offers a range of cutting-edge services including 3D model simulations, route surveys, and lifting plans to manage the complexities of transporting
oversized and heavy cargo.
The company additionally utilises digital platforms to provide real-time tracking and analytics, enhancing end-to-end operational visibility and aiding decision-making.
Furthermore, Kuehne+Nagel designs and operates supply chains that support clients’ sustainability goals, including reducing carbon footprints and promoting the use of renewable energy resources.
CONNECTING THE NATION
Comprising a workforce of over 650
KUEHNE+NAGEL –IN NUMBERS
• 400,000 customers trust the company to manage their logistics
• Almost 1,300 international locations ensure that Kuehne+Nagel remains close to its customers
• Close to 100 countries are connected by a strong network
• 80,000+ logistics and supply chain professionals
• Number 1 sea and air freight forwarder in the world
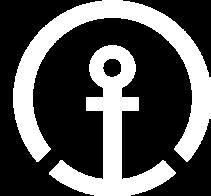
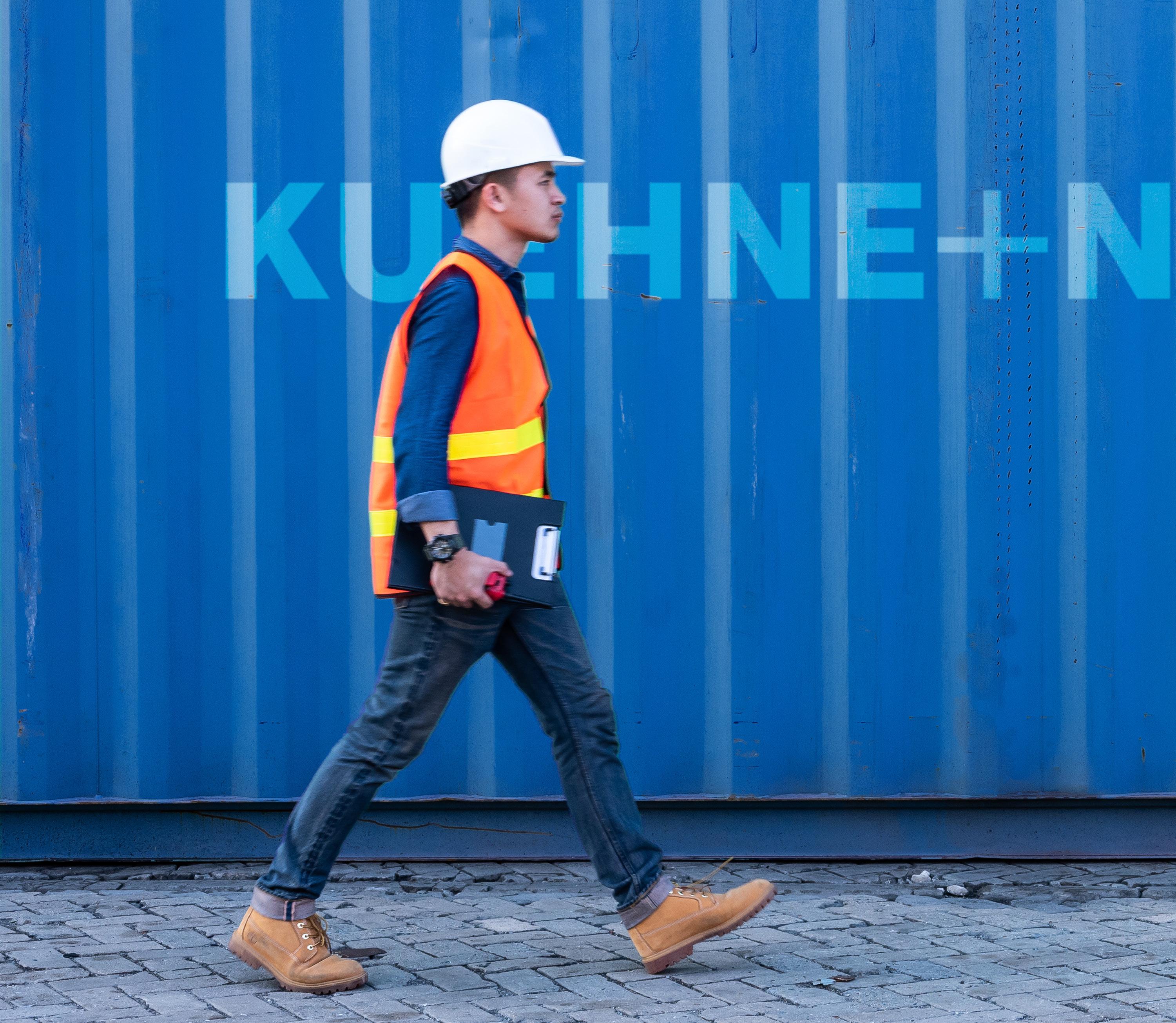
dedicated employees, Kuehne+Nagel Australia offers nationwide teams of experts that work with customers across a broad range of activities, including consumption optimisation, order enrichment processes, multicountry consolidation, value-adding services, and domestic inventory holding, alongside many other distribution solutions.
“We are investing in our network expansion across Australia, especially in regional areas, which allows us to support small and medium-sized enterprises (SMEs) and deliver against their market growth plans,” Francis Murugan shares.
Alongside helping smaller businesses with their growth aspirations, Kuehne+Nagel Australia is investing expertise in the project logistics space, particularly in the movement of large operations.
As a result, the company has continued to work closely with mining, oil and gas, and infrastructure customers to meet both domestic and global demands.
Kuehne+Nagel strives to become the leading logistics provider in the mining industry by continuously seeking innovative processes and services to optimise supply chains for its mining customers.
The idea is to build on its existing momentum with its industrial project services, with the company recently undertaking numerous initiatives to drive project capabilities on an industrial scale.
“These developments reflect Kuehne+Nagel’s commitment to expanding and innovating its industrial project services, focusing on advanced technology integration, strategic partnerships, and sustainable infrastructure to meet the evolving demands of the industry,” imparts François Sellin.
For example, the company has inaugurated a 55,000 square metre
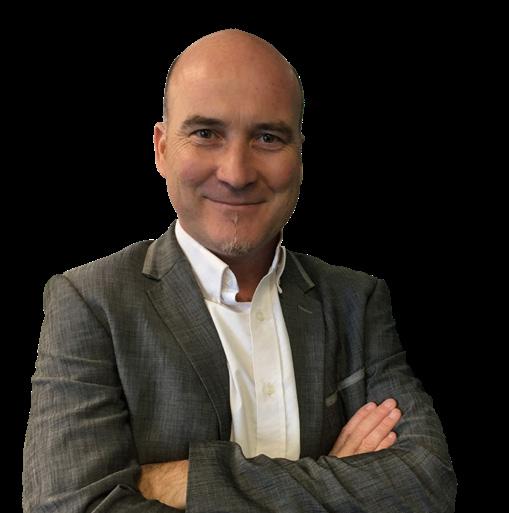
“Kuehne+Nagel ensures that mining and energy companies can maintain efficient, safe, and sustainable operations, even in challenging and remote environments”
- FRANÇOIS SELLIN, GLOBAL LEAD MINING, KUEHNE+NAGEL
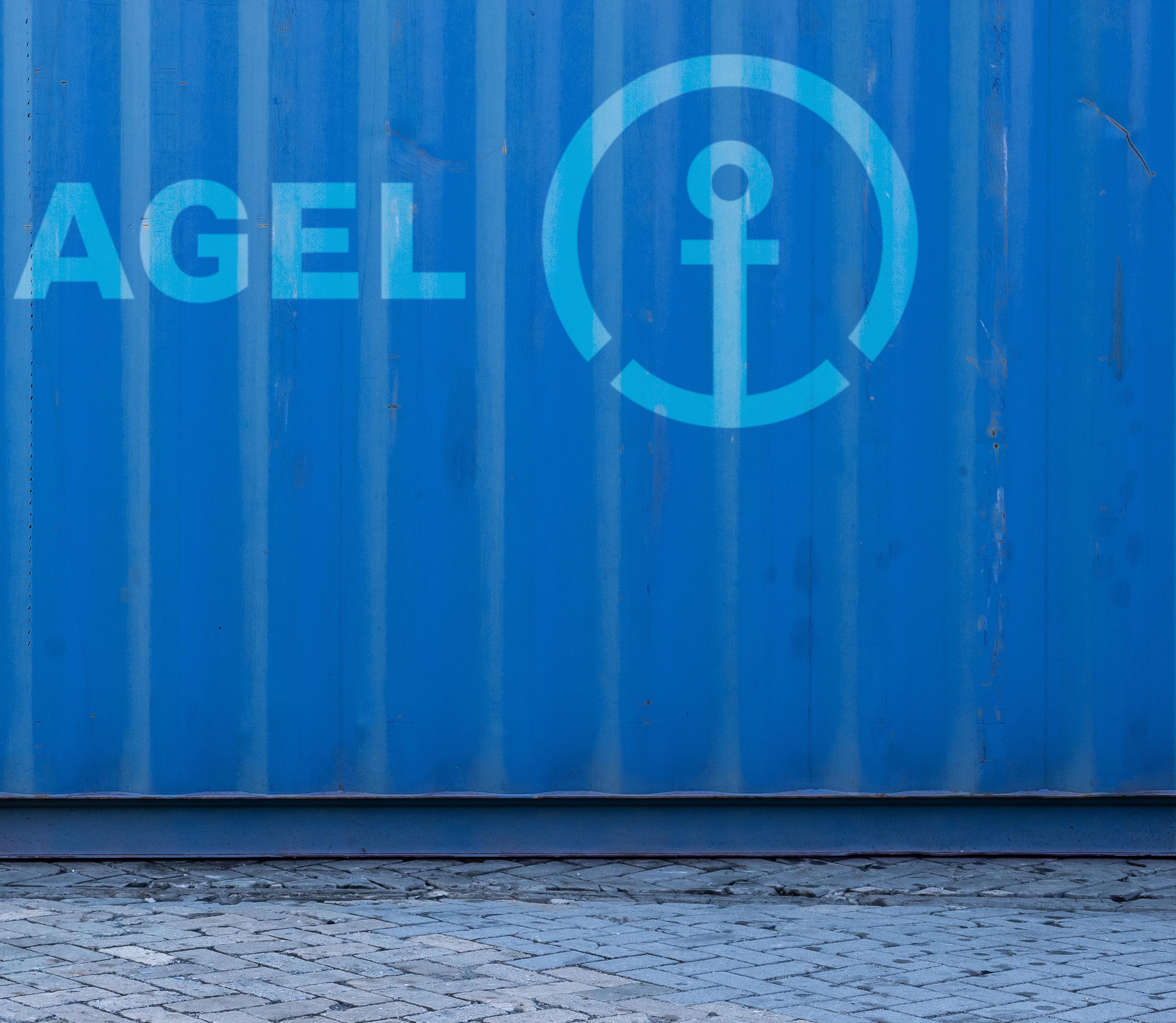
(sqm) contract logistics centre in the town of Mülheim-Kärlich in Germany.
“This facility is dedicated to the global spare parts supply for Wacker Neuson Group’s light and compact equipment. It employs advanced goods-to-person technology, utilising over 30 autonomous robots to optimise storage and retrieval processes,” he informs.
Elsewhere, Kuehne+Nagel announced plans last year to develop a 22,915 sqm logistics facility in EZDubai, an e-commerce hub in the most populated city of the United Arab Emirates (UAE).
Scheduled for completion
by Q2 2025, the facility aims to provide third-party logistics (3PL), e-commerce, and goods handling services.
“It is designed to achieve LEED Silver certification, incorporating innovative, energy-saving features to support sustainable operations,” Francois Sellin emphasises.
Additionally, the company entered into a strategic agreement with Capgemini in September 2023, working closely to deliver end-to-end supply chain capabilities.
This collaboration combines Kuehne+Nagel’s logistics management and execution expertise with
Capgemini’s Intelligent Supply Chain Optimisation (ISCO) capabilities. Moreover, the partnership aims to provide artificial intelligence (AI)-enabled, data-driven decisionmaking services, enhancing supply chain resilience, efficiency, and sustainability for clients across various industrial sectors.
ACHIEVING THE HIGHEST STANDARDS
As a world-class logistics provider, Kuehne+Nagel deeply understands the responsibility it has to mitigate the impacts of its vast supply chain and distribution activities.
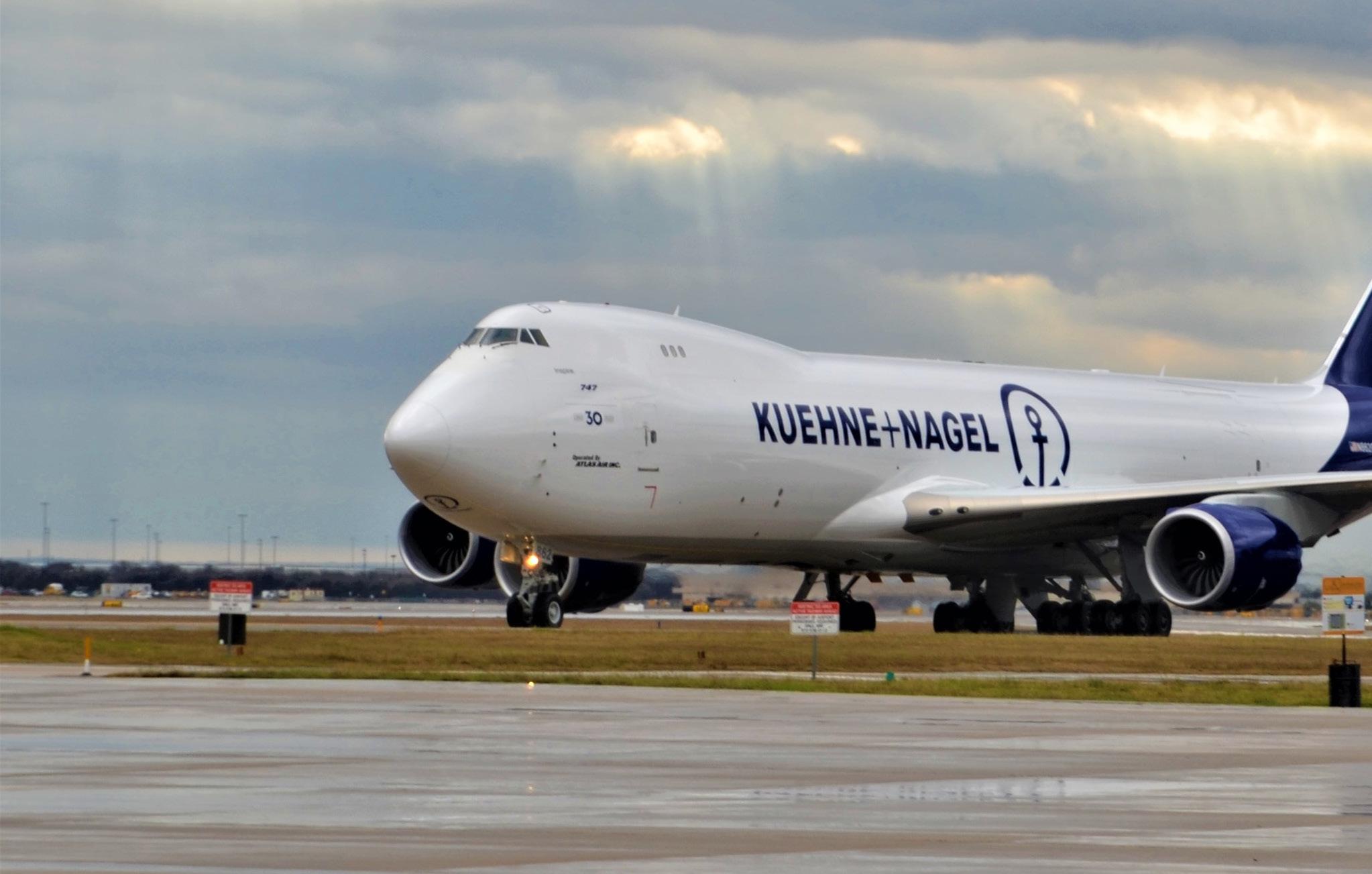
KUEHNE+NAGEL’S TECHNOLOGY
An integrated IT software platform is utilised to streamline and optimise supply chain operations across Kuehne+Nagel’s global network.
Key features include:
• End-to-end visibility – The system offers instantaneous tracking of inventory, shipments, and production schedules across multiple locations. This ultimately enables better decision-making and reduces inefficiencies caused by a lack of transparency.
• Data integration – Integrates data from various resources, such as enterprise resource planning (ERP) systems, warehouse management systems (WMS), and transportation management systems (TMS). The unified data environment ensures the consistent flow of information.
• Automation and standardisation – The system automates routine supply chain processes, such as order management, invoicing, and demand forecasting.
• Demand planning and forecasting – Advanced analytics and AI-driven tools help predict demand trends accurately, enabling companies to align production and inventory with market requirements.
• Supplier and vendor collaboration – The platform helps to facilitate seamless communication and collaboration with suppliers and vendors, improving procurement efficiency and reducing lead times.
• Cost optimisation – Optimises inventory levels, reducing transportation costs and improving operational efficiency.
“Companies can leverage Kuehne+Nagel’s systems to effectively synchronise their supply chain operations, drive efficiency, and remain competitive in a fast-paced, interconnected global market,” assures François Sellin.
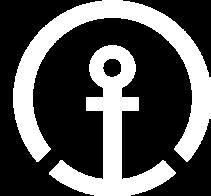
The company’s dedication is exemplified by its online health, safety, and environment (HSE) tool, a robust system designed to enhance safety, sustainability, and regulatory compliance across its global projects, thus maintaining the highest HSE standards whilst ensuring continued operational excellence.
The state-of-the-art tool includes comprehensive incident management that allows for the real-time reporting, investigation, and resolution of HSE incidents, ensuring prompt action and minimised risk.
The online HSE platform also includes modules for hazard identification and risk assessment, enabling proactive measures to prevent accidents and environmental harm.
Regarding the latter, the tool allows users to track key environmental metrics such as carbon emissions, waste generation, and energy consumption, therefore allowing them to support sustainability initiatives and comply with international

frameworks such as the United Nations Sustainability Development Goals (UN SDGs).
On top of this, the tool also facilitates regular HSE audits to facilitate ongoing compliance with internal policies and external standards. As a result, detailed reports are generated for regulatory bodies whilst also ensuring employees are trained and certified in HSE best practices.
The platform notably aligns with several internationally recognised standards, including but not limited to ISO 45001, 14001, and 50001, as well as the commitments of the Science Based Targets initiative (SBTi).
“By leveraging the online HSE tool, Kuehne+Nagel ensures a safe, sustainable, and compliant operational framework that aligns with both global standards and customer expectations,” François Sellin surmises.
A ZERO-CARBON FUTURE
As a world-class logistics provider, Kuehne+Nagel Australia deeply
understands the responsibility to limit the impacts of its vast supply chain and distribution activities.
“We are addressing carbon dioxide (CO2) reduction in all our transport and logistics services worldwide,” Francis Murugan states.
Kuehne+Nagel Australia works hard to balance environmental, social, and governance (ESG) commitments at both a local and global level.
Namely, it strives to maintain effective carbon management across all operations, provide environmentally-friendly solutions and offerings to its customers, and procure logistics services based on stringent sustainability criteria.
To achieve its ambitious environmental goals, Kuehne+Nagel Australia must meet two main targets. Firstly, the company strives to be fully carbon neutral in its direct sphere of influence, whilst also reducing its CO2 emissions by 33 percent by 2030.
“Our journey to a zero-carbon future also comes with a commitment to our customers by offering solutions
that reduce CO2 emissions in their supply chains.
“We do this by using big data and predictive analytics, as well as digital platforms to support the selection of more sustainable transport routes and modes,” Francis Murugan notes.
In line with its forward-thinking ESG commitments, Kuehne+Nagel Australia also has a strong partnership with Conservation Volunteers Australia (CVA).
“This allows us to work with local communities on programmes that are important to them. It lets our people give back to society in the communities that they live and work,” he explains.
CVA delivers numerous large-scale community events across the country, particularly revolving around the likes of World Environment Day, World Wetlands Day, and National Tree Day, in which the team gets involved in CVA’s critical environmental initiatives.
For instance, Kuehne+Nagel Australia last year provided support in CVA’s waterways and wetlands activities, which included removing substantial amounts of marine pollution from the beach, planting several wetland sites, removing 1,000 metres of invasive weeds, and helping the company plant 7,600 trees.
Alongside its ESG strategies, Kuehne+Nagel Australia continuously strives to go the extra mile for its customers, ensuring that its expert teams remain in close contact with them going forward.
As such, the company will continue to invest in its network expansion and find sustainable solutions for its global customers in 2025.
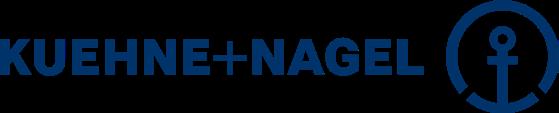
Tel: +6129 317 6000 yu.miguchi@kuehne-nagel.com au.kuehne-nagel.com/en/
IN PRIME POSITION
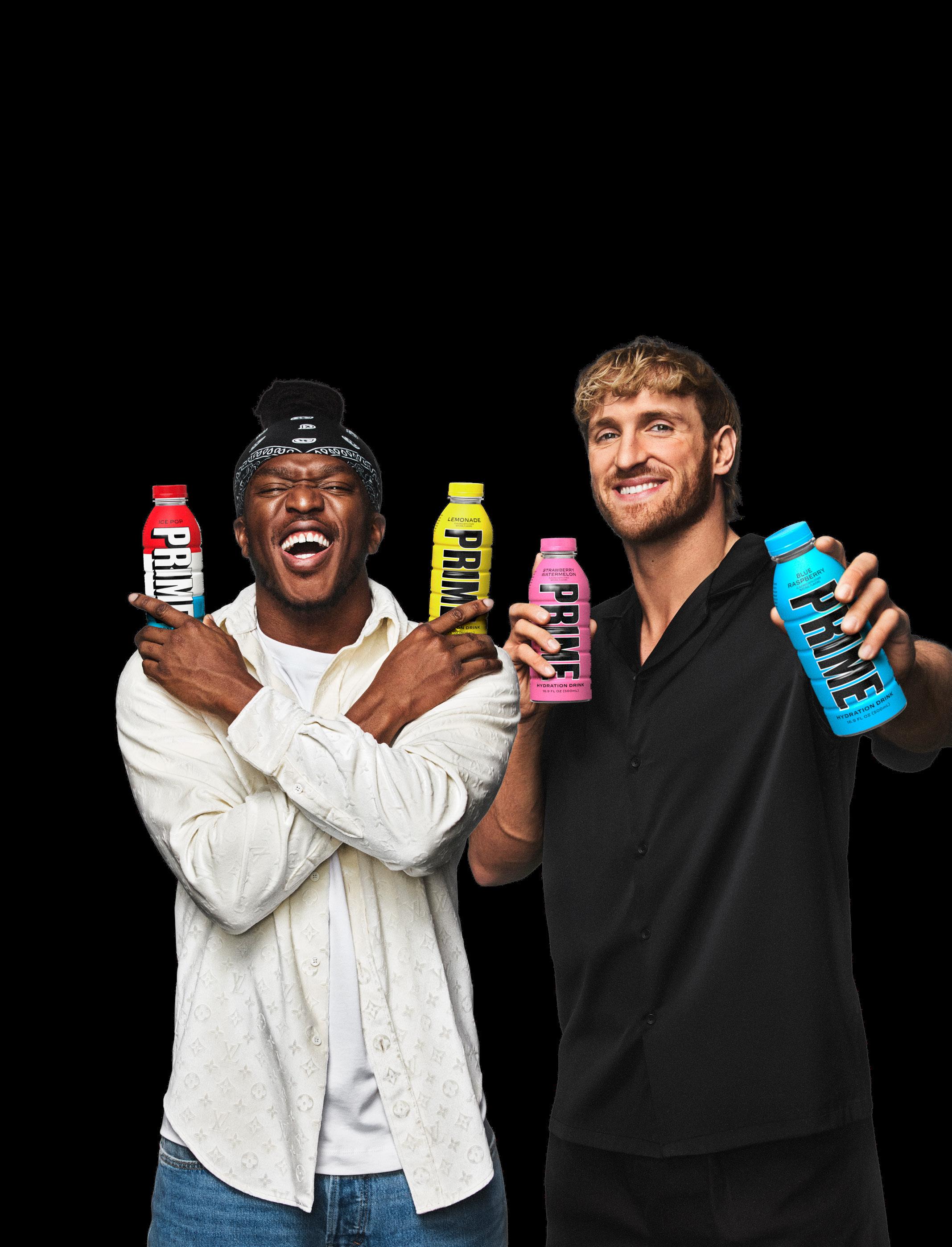
PRIME POSITION

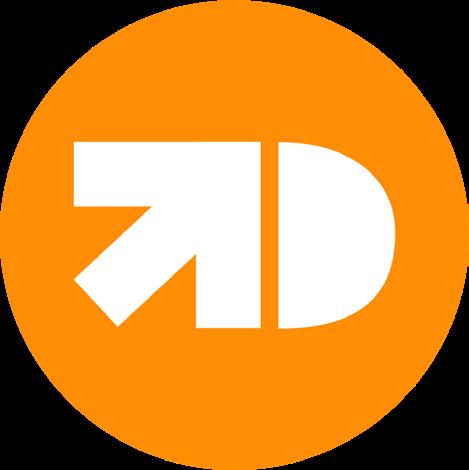
TradeDepot provides unmatched growth opportunities for some of the world’s most renowned brands. Onyekachi Izukanne, CEO and co-Founder, tells us how the leading e-commerce platform is going one step further to bring PRIME Hydration to the burgeoning African
There has been an undeniable buzz in the global energy drink market in recent years as more people choose the beverage as their go-to soft drink.
This is particularly the case across West Africa (WA), as the region’s energy drink consumption is expected to grow by 15.4 percent in the next five years, making it one of the fastest-growing drinks.
Taking the industry by storm is PRIME Hydration, the latest thirstquenching instalment from energy drink frontrunners, PRIME, which is being rolled out across WA.
Thanks to the collaboration with leading market and distribution platform, TradeDepot, and its unrivalled retail network, the flagship product will become a staple of WA fridges.
“We’re really excited about this partnership with PRIME Hydration. Together, we’re bringing a globally recognised product into vibrant and fast-growing markets like Nigeria and Ghana,” introduces Onyekachi Izukanne, CEO and co-Founder of TradeDepot.
“PRIME’s commitment to quality aligns perfectly with our mission of making premium goods accessible to communities everywhere.”
CONNECTING BRANDS TO CONSUMERS
Founded in 2015, TradeDepot is a leading global business-to-business (B2B) e-commerce platform that bridges the gap between major consumer goods brands and retailers worldwide.
Writer: Lucy Pilgrim
“With a mission to connect iconic brands with the next billion consumers, we leverage technology and strategic partnerships to provide access to markets, efficient logistics, and unmatched growth opportunities,” enlightens Izukanne.
Indeed, the company connects international brands to manufacturers,
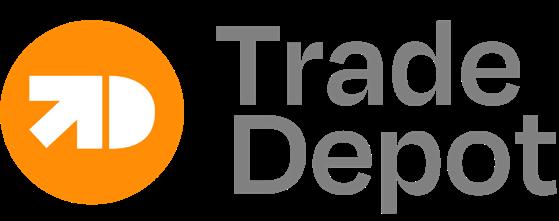
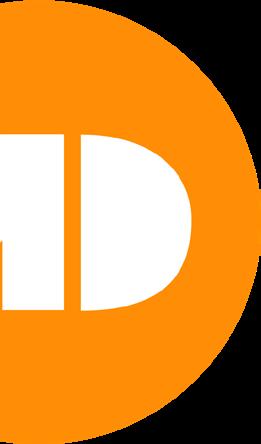
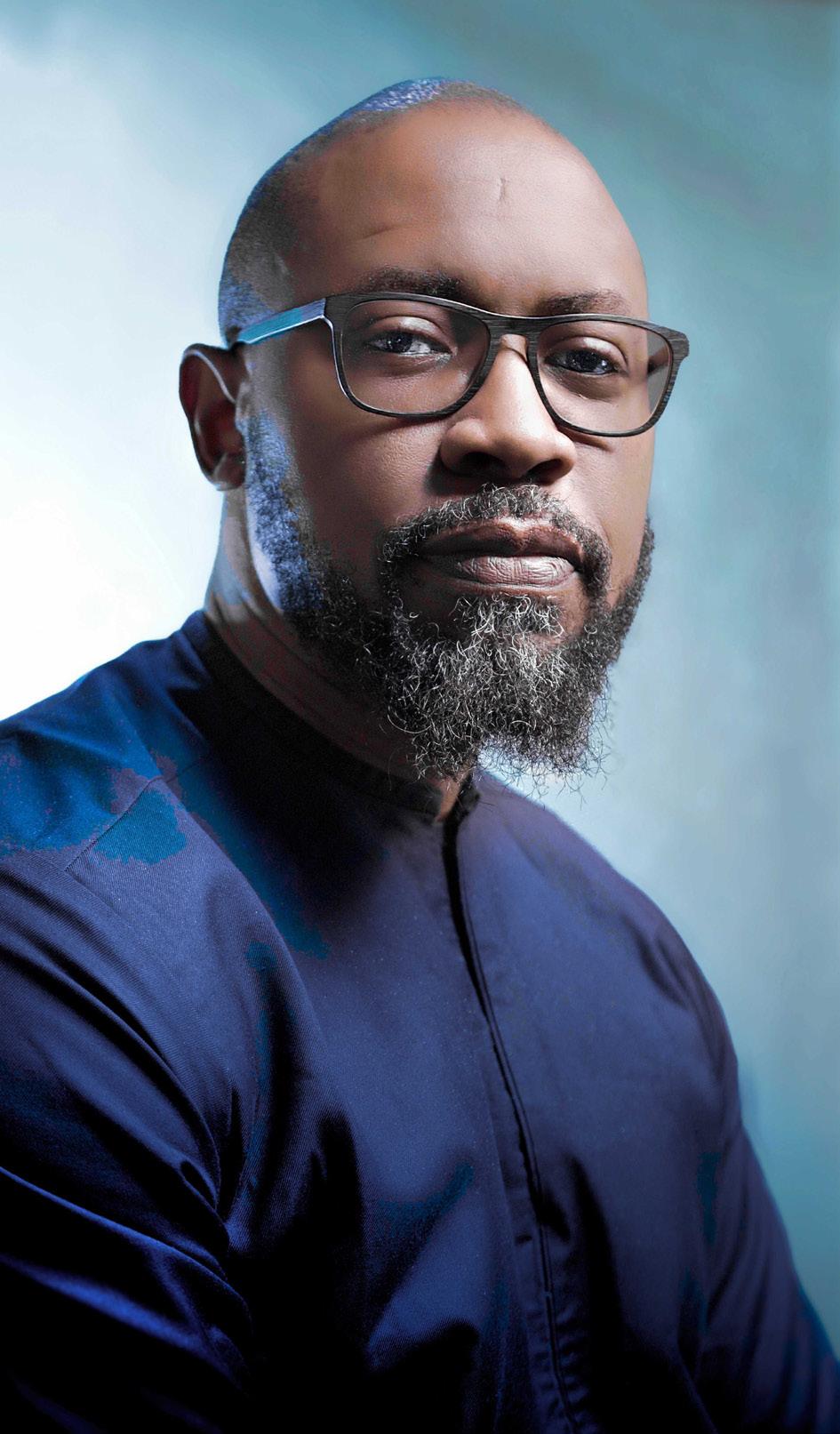
distributors, and retailers across Africa, Europe, North America, Asia Pacific, and the Middle East, making it a critical link in the global consumer goods supply chain.
TradeDepot collaborates with some of the world’s most iconic brands, including Unilever, Nestlé, Coca-Cola, PepsiCo, Akai, and more.

“PRIME’S COMMITMENT TO QUALITY ALIGNS PERFECTLY WITH TRADEDEPOT’S MISSION OF MAKING PREMIUM GOODS ACCESSIBLE TO COMMUNITIES EVERYWHERE”
– ONYEKACHI IZUKANNE, CEO AND CO-FOUNDER, TRADEDEPOT

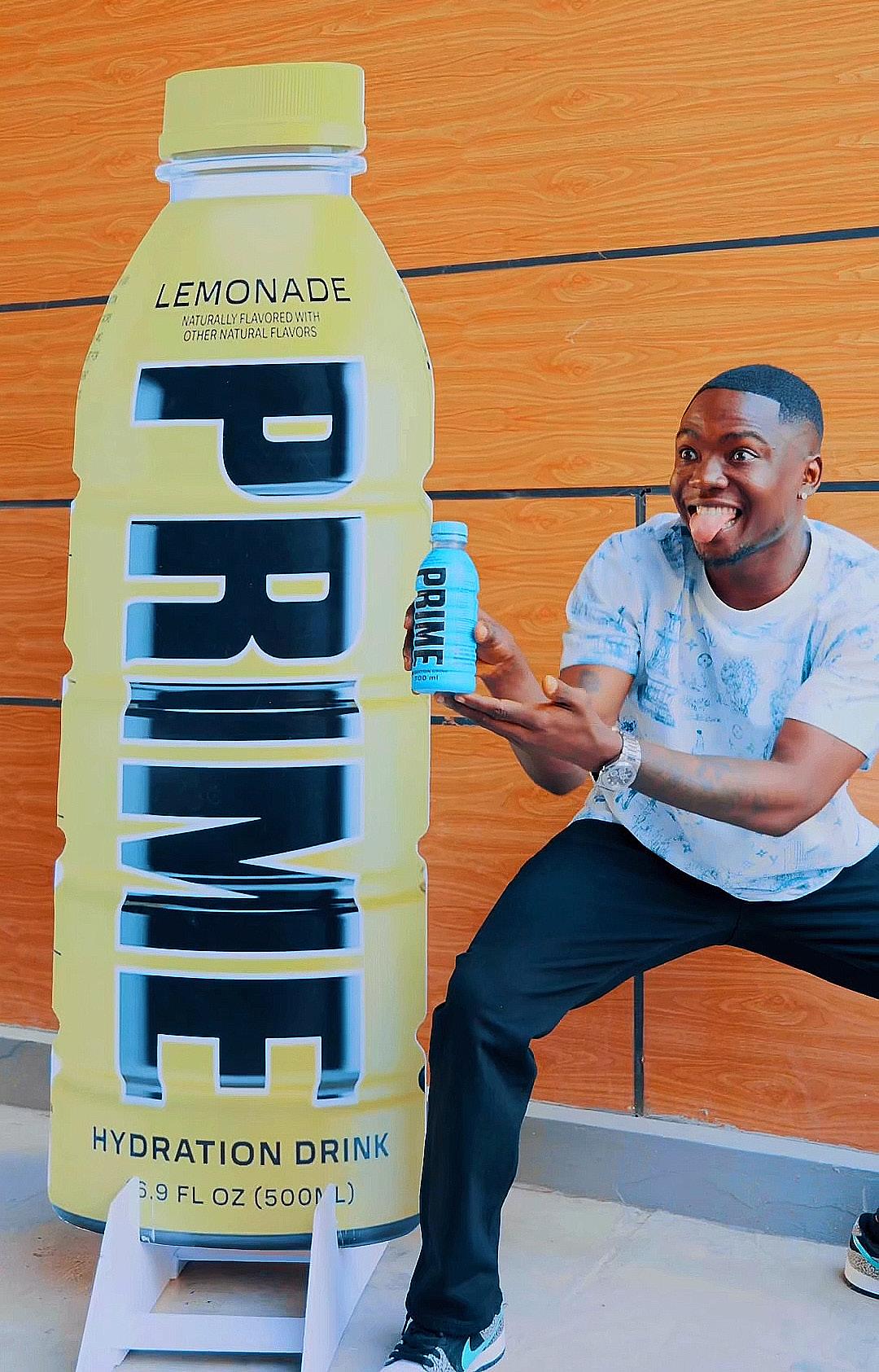
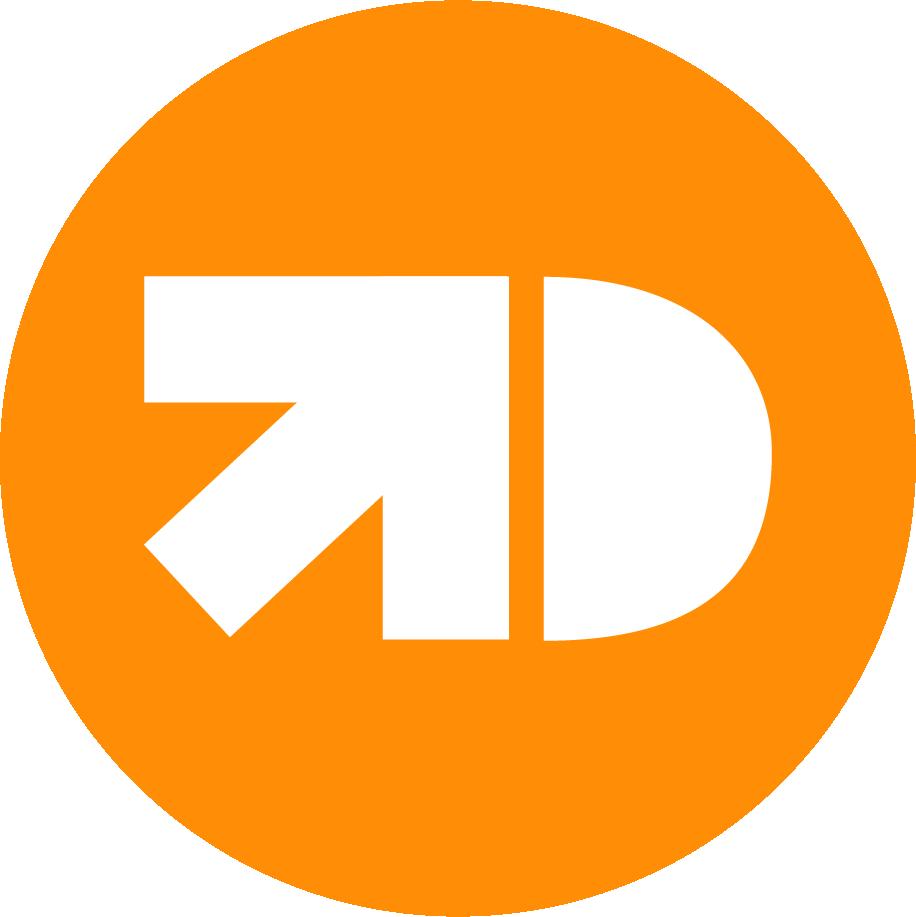
The company ensures that these brands reach new markets efficiently with an expert team of 1,000 people, encompassing both direct employees and an extensive secondary salesforce that supports distribution, retail engagement, and customer service across numerous regions.
This combined workforce enables TradeDepot to drive significant scale and impact in the markets it serves.
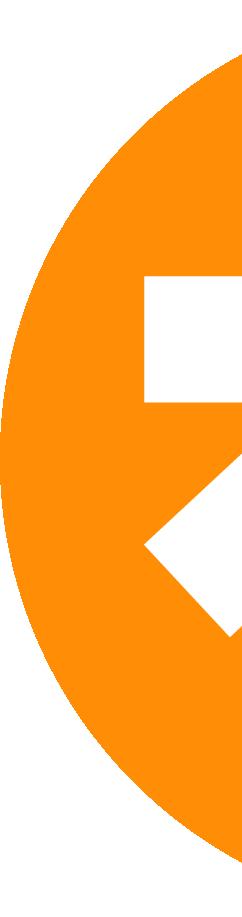
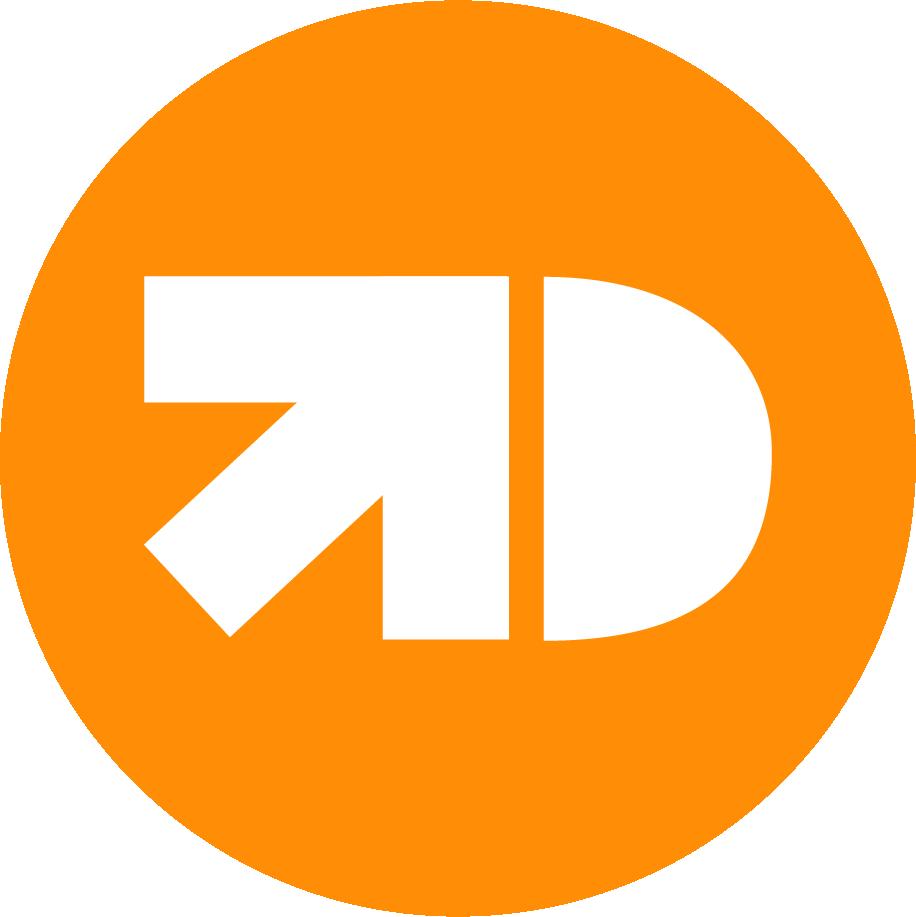
“Coupled with our deep understanding of market dynamics – from purchasing behaviours to seasonality trends – we help brands make smarter decisions,” he surmises.
BRIDGING LOCAL AND GLOBAL DEMAND
TradeDepot fastidiously helps brands expand into new areas by addressing the critical components of market entry, including regulatory compliance, demand insights, and efficient distribution.
The company’s platform simplifies bulk e-commerce, procurement, and inventory management, ensuring products reach the most in-demand markets.
“By investing in innovative tools and
efficient distribution networks, we ensure that products are accessible wherever there is demand, fostering growth for both businesses and the communities they serve,” highlights Izukanne.
This is fulfilled by providing companies with detailed insights to match the right products with the right markets, including understanding local preferences, competitive landscapes, and regulatory requirements, ensuring brands can navigate market-specific challenges seamlessly.
Such an approach underscores TradeDepot’s commitment to bridging the gap between global supply and local demand, enabling brands to thrive in new and existing markets.
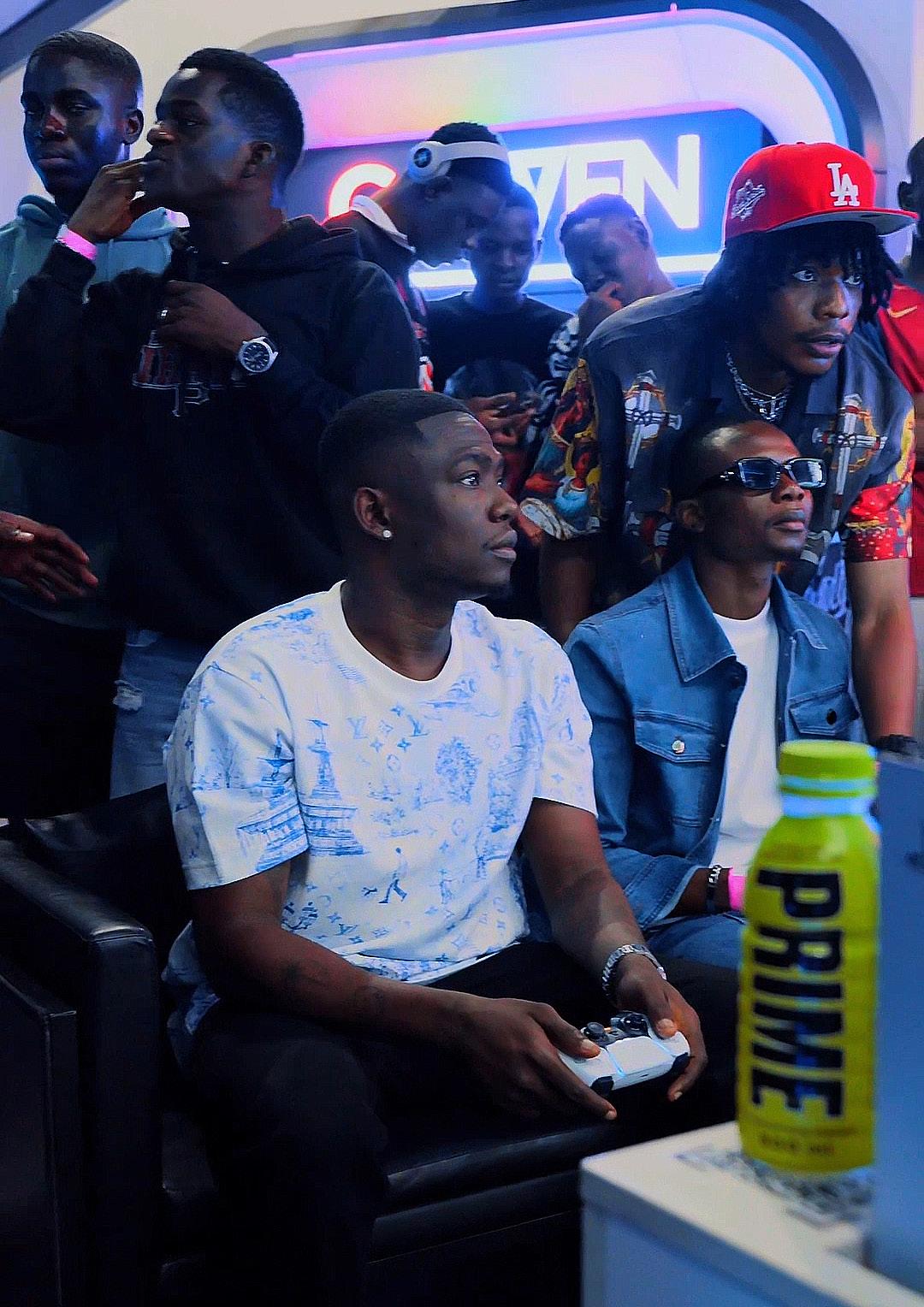

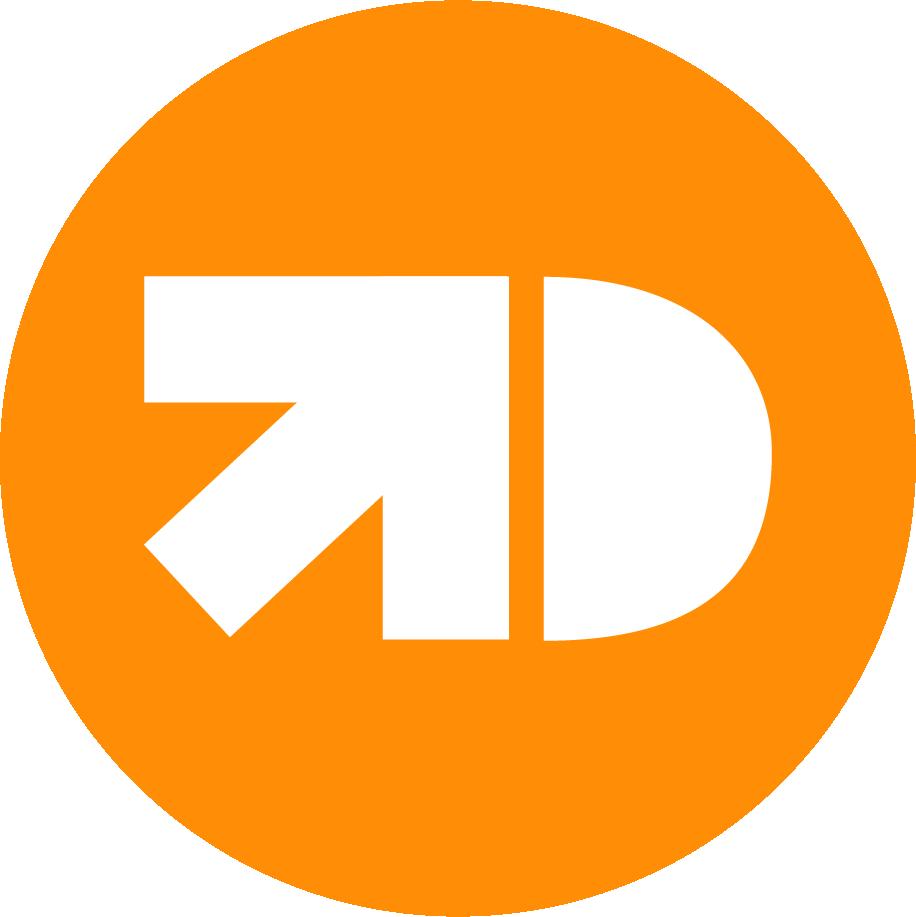

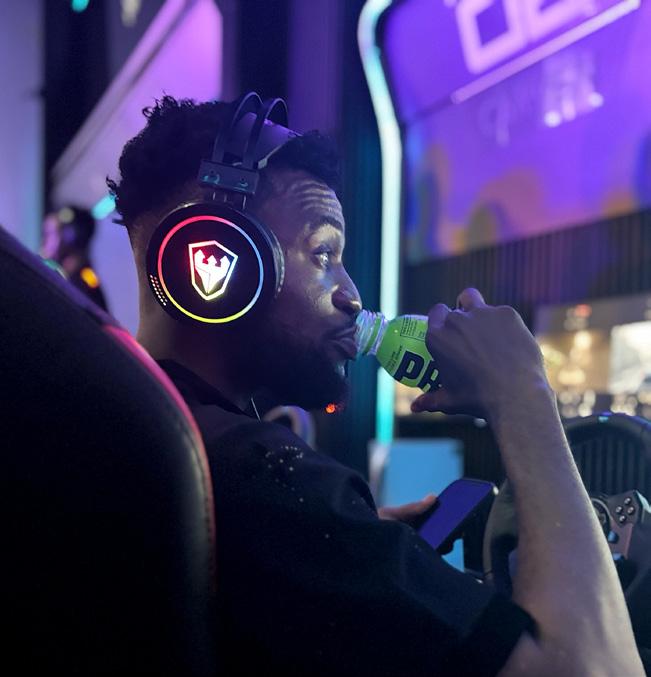

Throughout its portfolio of clients, the company also strives to help smaller businesses excel in the market.
“In markets like Africa, where small retailers dominate commerce, we help brands connect with these retailers efficiently,” he adds.
Thus, by leveraging real-time data and streamlining logistics, TradeDepot makes products accessible in both established and underserved communities, helping brands grow whilst empowering local businesses to thrive.
Meanwhile, the organisation’s cross-border capabilities simplify the complexities of global trading and guarantee seamless product flow and compliance with local regulations for smaller entities.
“Supporting small businesses is at the heart of everything we do. By providing them with credit, access to inventory, and reliable delivery, we empower them to grow, which in turn drives success,” impassions Izukanne.
THE PERFECT MATCH
Evidently, TradeDepot has a long history of delivering results across Africa, having built a reputation for helping brands grow by solving key distribution challenges and connecting them to the informal retail sector.
It is the company’s unparalleled expertise that will help elevate PRIME Hydration’s strong global reputation to the next level and skyrocket the product into the WA drinks market.
Such ambitious goals will be achieved by ensuring constant
availability and leveraging market insights to target the right audience, cementing PRIME Hydration as the go-to hydration brand in WA.
“Our commitment to efficiency, coupled with our understanding of local markets, makes us uniquely positioned to help PRIME Hydration succeed in these regions.
“We don’t just distribute products – we create ecosystems that ensure sustainable growth for our partners,” highlights Izukanne.
The partnership between PRIME and TradeDepot perfectly exemplifies the latter’s mission to connect local brands with consumers in a way that drives both accessibility and impact.
Therefore, the collaboration goes beyond simply delivering a product but rather creates opportunities for retailers to access high-demand global brands and empowers them to serve their customers better.
Energised and ready for 2025, TradeDepot’s priorities revolve around expanding its footprint across more geographies and broadening its brand portfolio to meet the evolving needs of customers.
Additionally, the company aims to connect even more markets with high-demand global brands, whilst ensuring seamless access for retailers and distributors through its technology-driven platform.
“For our partnership with PRIME Hydration, 2025 will be a pivotal year as we work to solidify its presence as a leading brand in WA.
“At the same time, we’ll remain committed to exploring new opportunities to expand PRIME Hydration’s presence into additional markets where it can deliver significant value,” Izukanne concludes.
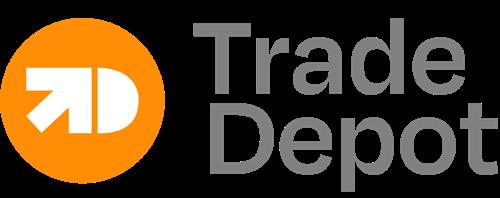


THE GREAT GUINNESS SHORTAGE
Following a recent spike in popularity and a crisis within its supply chain due to exceptional consumer demand, fans of the world-renowned stout, Guinness, have recently encountered a heartbreaking shortage of the famous beverage. We explore the reasons for this disaster and how to prevent similar challenges in the future
Writer: Ed Budds
Across the world, loyal fans and avid drinkers of Guinness, the iconic Irish stout beverage, have been left shocked and appalled as the historic brand has experienced unprecedented shortages across its global supply chains.
A disastrous start to the new year for the company has left many pubs, distributors, and most importantly customers reeling from the effects of what is being referred to as the ‘great Guinness shortage’.
A national shortage across the UK was first reported in December amid the unexpected skyrocketing popularity of the stout, with one in every 10 pints pulled in the capital a Guinness.
Whether this upsetting scarcity has been driven by the younger generation’s obsession with the recent viral internet trend of
‘splitting the G’, or is simply the result of production and distribution miscalculations during the peak Christmas period, one thing has become crystal clear – businesses everywhere must see this as a pertinent warning and rethink how they balance their supply and demand processes.
In the annals of beverage history, few have attained the iconic status, cultural influence, and global resonance of Guinness.
From its humble origins in Dublin’s St. James’s Gate Brewery to its historic place in literature and even royal visits, Guinness is more than just a tasty stout.
This majestic product weaves a tapestry of stories that have transcended time as it continues to be savoured worldwide, with every pint poured adding to its rich and frothy history.
DEPENDING ON DATA
Across a multitude of industries, supply chain disruptions such as the recent Guinness shortage are becoming more regular.
This can be attributed to many factors such as unpredictable consumer trends, global crises, or logistical challenges, meaning businesses must increasingly make special efforts to remain competitive and meet customer expectations whilst adopting smarter, more agile solutions.
Undoubtedly, the building blocks of any successful supply chain is the power of data, a tool which has reached the forefront of the working machinery of supply chains, allowing all forms of business to make informed decisions, maximise efficiency, and react swiftly to fluctuations in consumer needs.
Without such real-time data, companies are effectively rendered blind and therefore unable to adapt effectively to changing circumstances or anticipate problems before they arise.

FACTS ABOUT GUINNESS
• Whilst Guinness originated in Ireland, it’s now brewed in almost 50 countries around the world and sold in more than 120.
• The iconic logo of the harp, registered as a Guinness trademark in 1876, is also the national symbol of Ireland.
• The first overseas Guinness brewery outside of Ireland and the UK was officially opened in 1963 in Nigeria, which is now the second-largest market for the stout.
• Guinness’ exceptionally smooth taste can be attributed to the 300 million bubbles in every pint.
• Guinness is actually ruby red in colour – not black as people often assume. This is due to the roasting of the malted barley which happens at exactly 232 degrees Celsius.
• In 2017, Guinness confirmed that it had changed its filtration process, doing away with the use of isinglass, a by-product of fish. Without it, the beverage is now officially vegan-friendly.
• A third of all pints of beer sold in Ireland are Guinness.
• The perfect pint of Guinness takes exactly 119.5 seconds to pour.
• ’Splitting the G’ is a drinking game that sees players try to get the line between the foam and stout to sit in the middle of the letter G on the Guinness pint glass after their first sip.

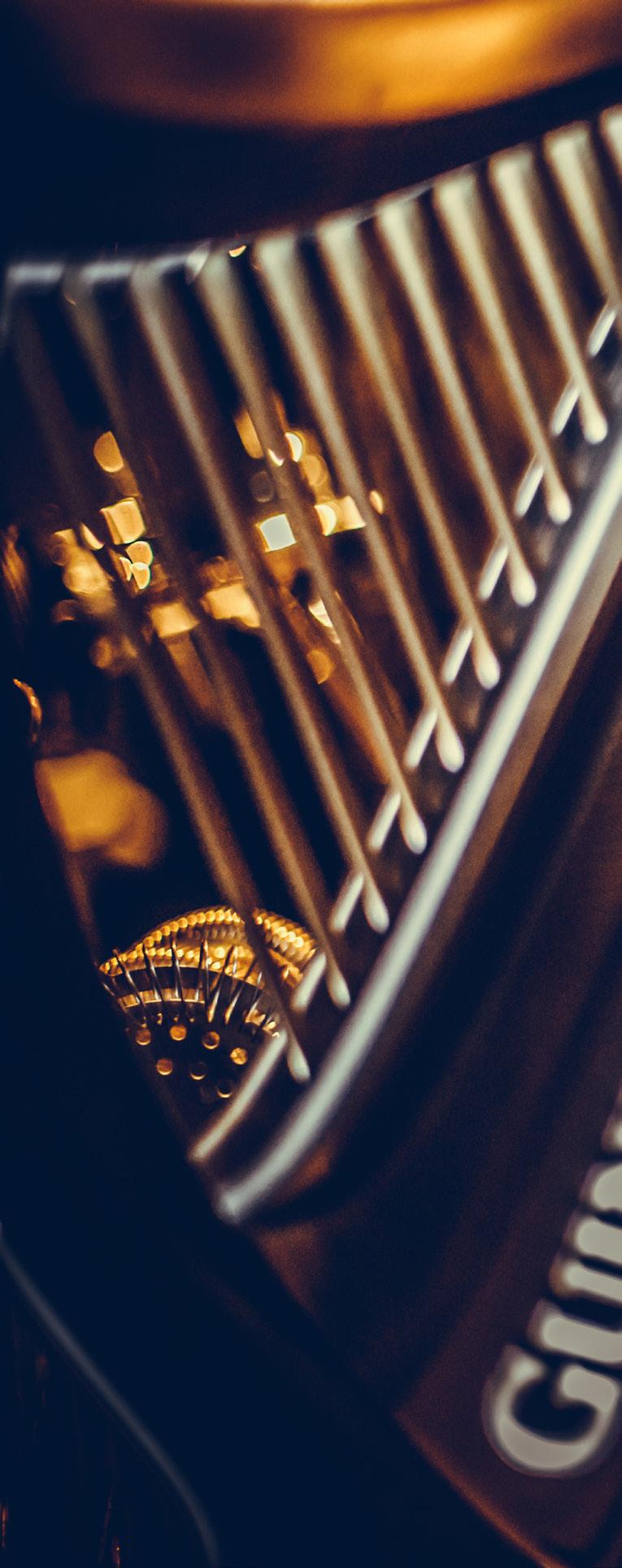
This is where the phenomenon of event-driven architecture (EDA) comes into play.
An innovative process that enables businesses to access, use, and act on data in real time, EDA ensures the correct information reaches the right applications at a specifically planned moment.
Unlike traditional batch processing systems which have previously relied on overnight data uploads, EDA leverages a continuous flow of insights, allowing businesses to respond to events immediately as
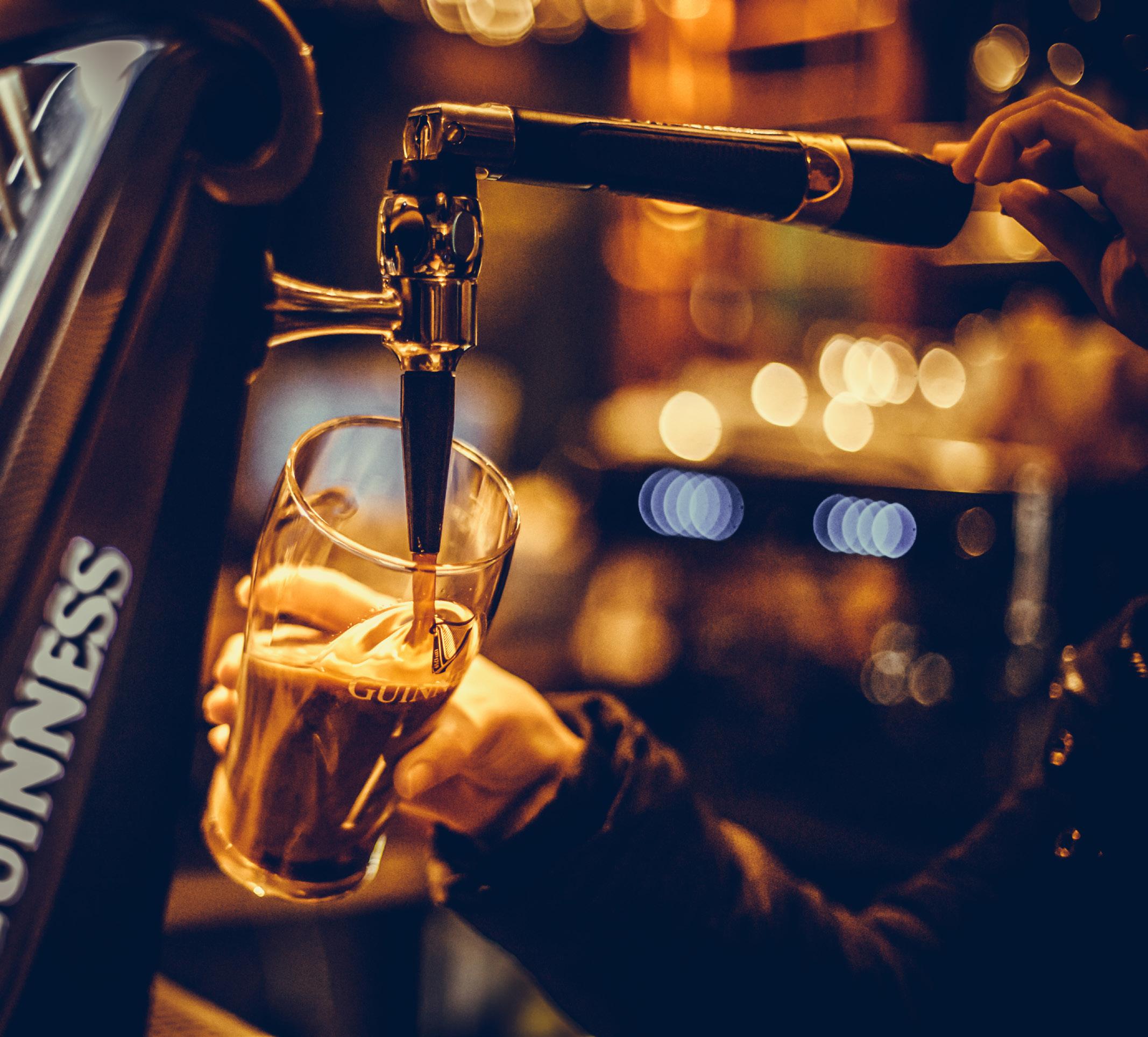
they happen.
This game-changing capability has become crucial in today’s fast-paced, ever-changing markets – with a real-time, event-driven supply chain, companies can monitor production, distribution, and sales data in all regions in real time, adjusting manufacturing and logistics in order to counteract any adversity encountered within the supply chain.
LEARNING FROM ADVERSITY
The Guinness shortage may seem
like just a drop in the ocean in terms of the vast global supply chain landscape, but it has been flagged as a reoccurring symptom of a much larger problem impacting organisations across all industries.
As consumer expectations continue to rise and the world becomes a more interconnected place, businesses that repeatedly fail to modernise their supply chains will risk losing a vital competitive edge.
By becoming more event-driven, companies now possess the ability to transform their supply chains
into agile, responsive, and efficient working systems.
The lessons from incidents such as the great Guinness shortage are clear – businesses must prioritise data-driven decision-making, invest in real-time capabilities, and ensure they are prepared for whatever challenges the future may hold.
Ultimately, for those who love a pint of the black stuff, the hope is these fresh changes and innovative solutions are introduced sooner rather than later.

CARIBBEAN PORTS SPOTLIGHT
A hub for maritime trade, many Caribbean countries depend on shipping to import and export goods that meet the needs of its people but are faced with a number of modern-day challenges
Writer: Jack Salter | Project Manager: Deane Anderton
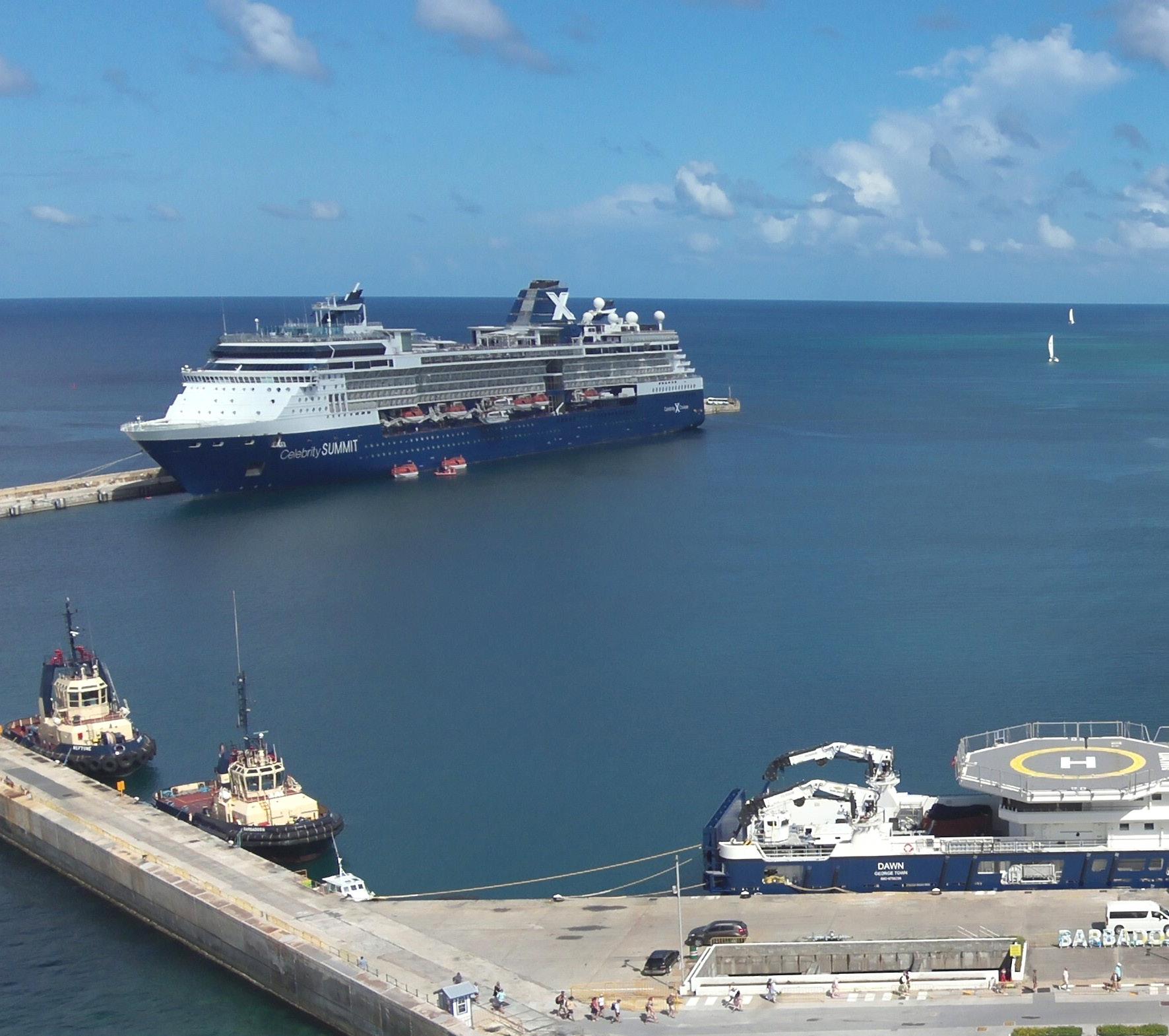
Caribbean ports are social entities that facilitate the very existence of people, enabling critical supplies such as food, clothing, and shelter to be received and transported across the region.
However, several challenges face the Caribbean when it comes to shipping, such as inadequate port infrastructure, environmental regulations, and high costs.
The former requires modernization, as several ports do not have the infrastructure to handle larger cargo volumes and ships, causing delays and increased costs for shippers who may opt to use other regional hubs as a result.
The limitations of this outdated infrastructure are exacerbated by environmental issues, as Caribbean ports are under strain from the demands of global regulations surrounding decarbonization.
Shipping costs, meanwhile, can be extremely high in
the Caribbean due to steep fuel prices, inefficient port operations, and limited competition among carriers.
These costs are substantially more than in other parts of the world, making it difficult for Caribbean businesses to complete on the global stage and increasing prices for consumers.
The impact of these various limitations is heightened even further in smaller Caribbean islands, where ports act as a gateway in and out of the country and are a pillar for their economic well-being.
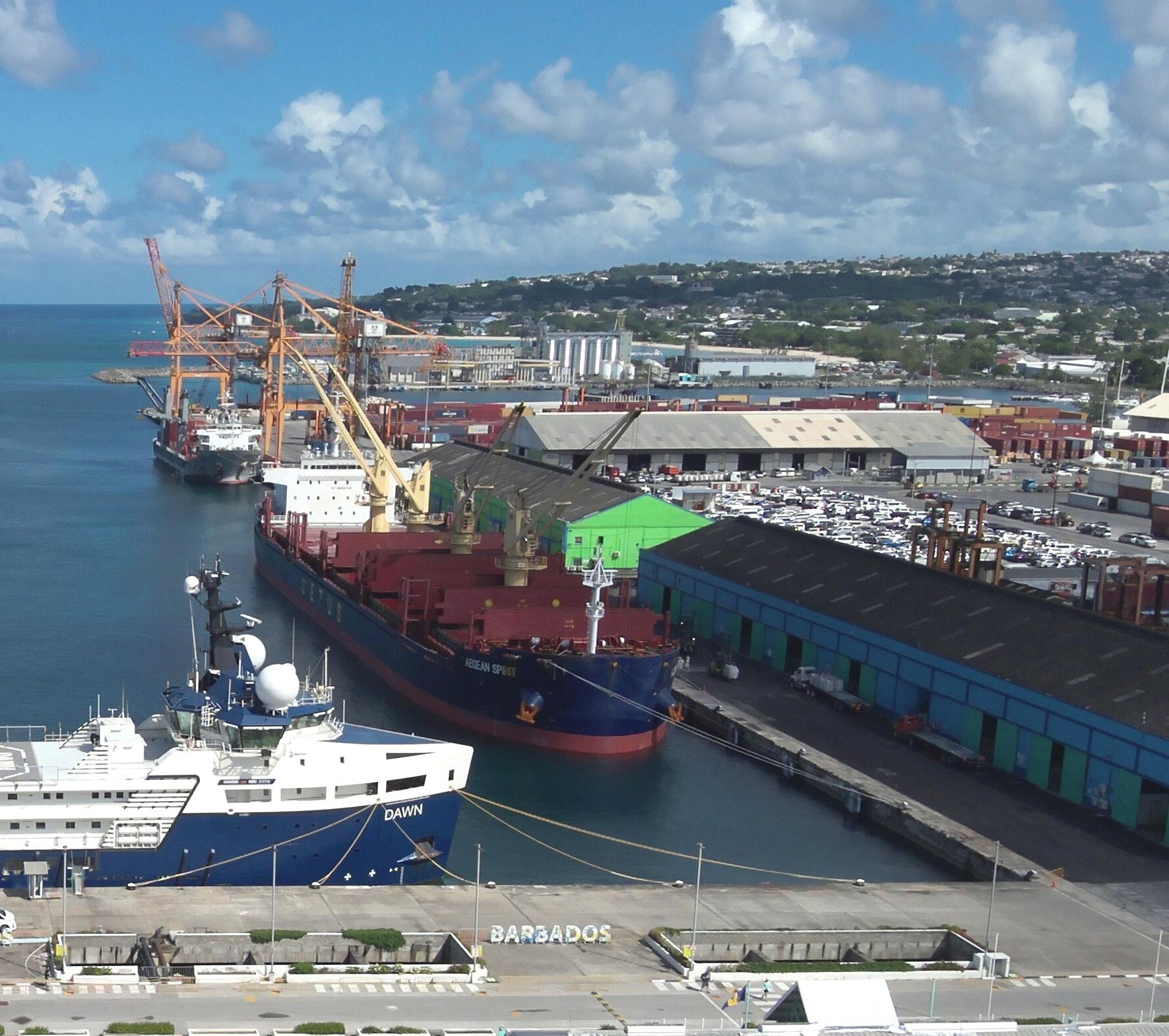
Despite these challenges, cruise ships represent an exciting area of growth and development for ports as they have become an important part of the Caribbean economy.
However, many smaller ports in the region do not currently have the infrastructure or capacity to simultaneously handle both cargo and cruise vessels.
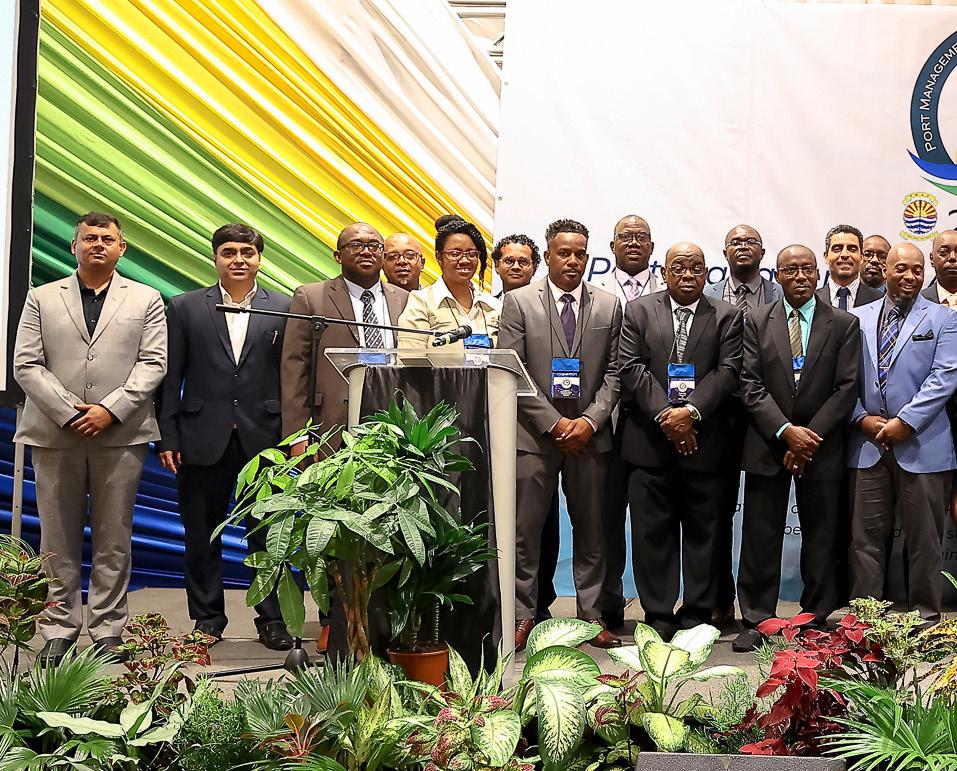
PORT MANAGEMENT ASSOCIATION OF THE CARIBBEAN INTERVIEW:
Darwin Telemaque, Chairman, discusses this integral role of the Port Management Association of the Caribbean as a node in the region’s ports network amid the modern challenges of digitalization and decarbonization
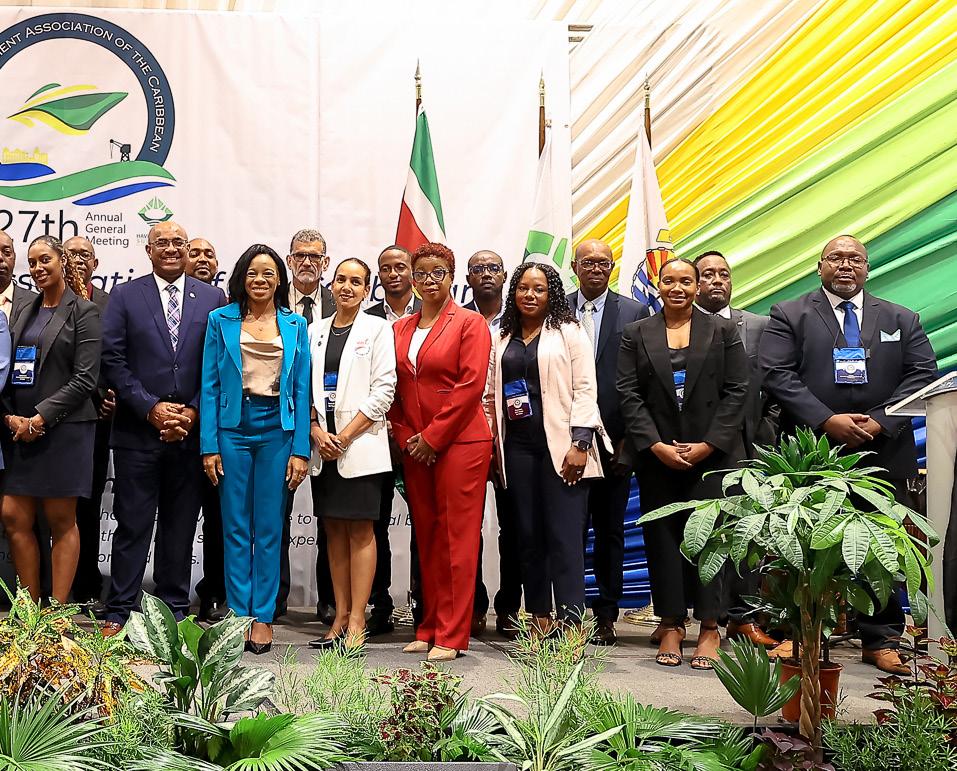
Supply Chain Outlook (SC): Firstly, could you introduce us to the Port Management Association of the Caribbean and outline your mission statement?

Darwin Telemaque, Chairman (DT):
The Port Management Association of the Caribbean (PMAC) is a small but vital organization established for the purposes of coordinating issues surrounding ports in the Caribbean. Some of these concerns relate to legislative, financial, and operational modernization and, most importantly, the human capacity development of our people. As we participate in a sector that is mostly driven by large multilaterals and builds systems that focus on the needs of very large companies, whether it be mechanization, digital solutions, legislation, or regulation, decisions are sometimes made outside of our capacity to influence and direct.
We are left to grapple with the evolution of an industry in which our capacity to influence is very limited. However, the sector remains pivotal and critical to the existence of our island nations, many of which are single port states and don’t own any vessels.
As the industry evolves, we are forced to adapt to change. Sometimes it’s technology, other times it’s the size of the vessels, requiring expansion to both our channels and our docks.
Challenges continue to arise, and in a world where the small is insignificant, where do we find the capacity that can alleviate our concerns through a global space? PMAC has emerged as that facilitating entity.
Our mission statement is to foster operational and financial efficiency and enhance the level of service to the mutual benefit of Caribbean ports and stakeholders through the sharing of experience, training, information management, and ideas.
As a matter of fact, we have decided just this year that we are going to realign our vision and our mission.
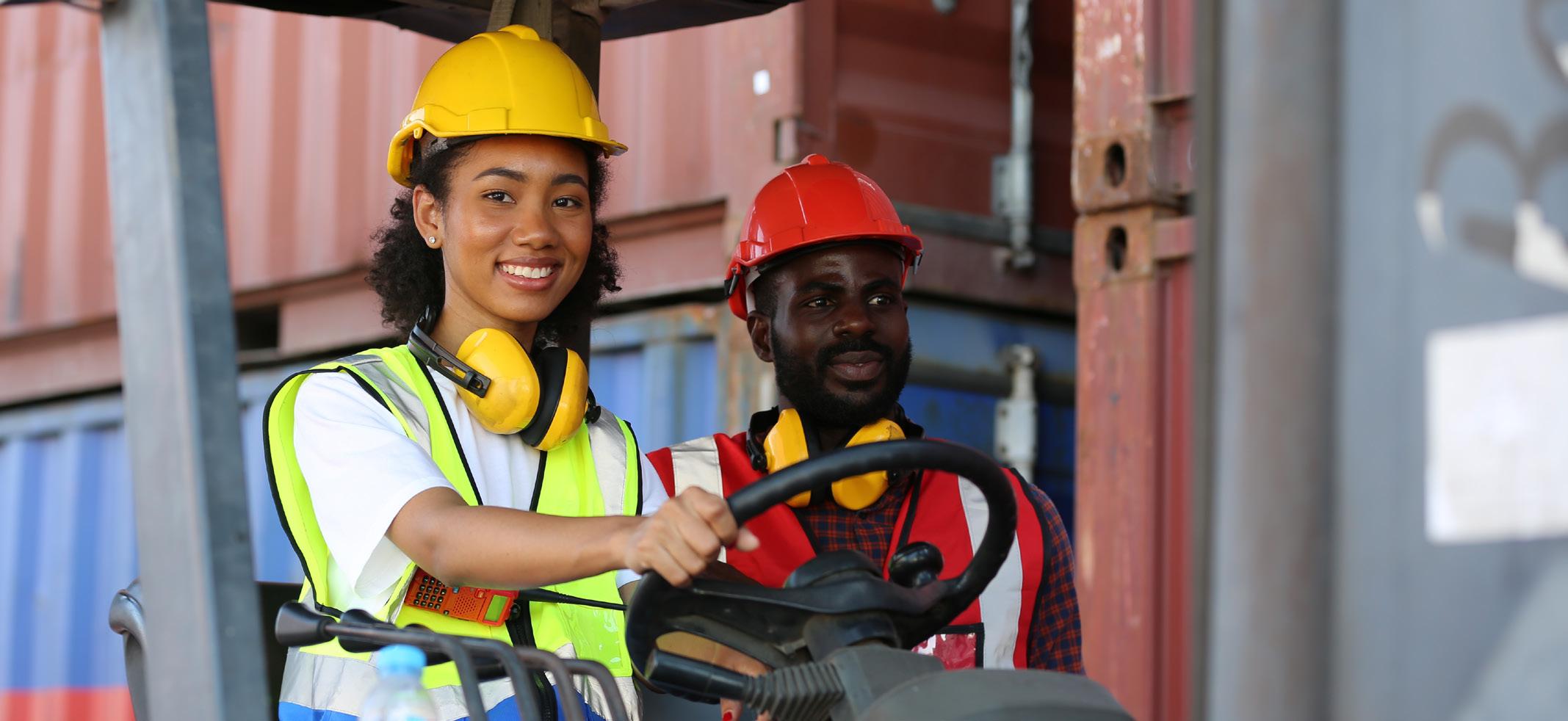
The Jamaica Special Economic Zone Authority has the perfect opportunity for you. Enjoy an array of fiscal and non-fiscal incentives aimed at taking your business to the next level, through increased production, reduced storage and production costs while increasing output.
Briefly introduce me to the Jamaica Special Economic Zone Authority (JSEZA), e.g. a short overview of your main products and services, locations, client base, number of employees, etc.
The Jamaica Special Economic Zone Authority (JSEZA) was established in 2016 under the Special Economic Zones (SEZ) Act, 2016.
The JSEZA main function is to facilitate developments within the SEZ regime in Jamaica. By offering a range of incentives, streamlined regulations, and excellent business facilitation to boost efficiency for business with SEZs. There are two main categories of incentives: fiscal and non-fiscal, that make it easy to hit the ground running. Some of these are:
SEZ Fiscal Incentives
• Corporate Income Tax (25 percent) reduced to 12.5 percent can be further reduced to 7.75 percent with the application of capital allowances, promotional tax credits and employment tax credits.
• Customs duty exemptions are available for goods imported and used in the SEZ.
• The SEZ Regime offers a 0 percent rate of General Consumption Tax (GCT) on locally purchased goods and services.
• Multi-Purpose Developers receive relief from income tax on rental income. *except for rentals where the landlord (whether the Developer or an Occupant) and tenant are connected persons within the meaning of the Income Tax Act.
SEZ Non-Fiscal Incentives
• Streamlined Business Facilitation: Dedicated support for SEZ entities, including business advocacy, development, and permit assistance.
• Modernized Customs Procedures:
Accelerated movement of goods and reduced administrative burdens.
• Robust Infrastructure Support: Improved transportation networks and utilities.
• Stable Regulatory Environment: Simplified licensing, permits, and regulatory requirements.
• Skilled Workforce Development: Access to training and skilled labor to meet specific business needs.
What steps do you take with local businesses to support the country’s economic landscape?
The Authority is committed to fostering a robust business environment and fostering the growth of local enterprises. To accomplish this, the Authority has implemented a range of strategic initiatives:
1. Strengthening Value Chains: The Authority promotes the development of connections between local businesses and SEZs, both backward and forward linkages, which in 2022 facilitated trade for over 100 entities with a total value of JMD $12,368,703,281.31.
2. Highlighting Investment Opportunities: The JSEZA team executes local conferences, serving as a leading platform for presenting and connecting Jamaica’s investment potential and players. These events aim to facilitate investors and foster connections between local businesses and global entities, promoting foreign direct investment and driving economic growth.
3. Knowledge Sharing and Capacity Building: JSEZA empowers businesses through workshops and training, equipping them for success in the global market and providing businesses with the essential knowledge and skills for successful operations.
4. Supporting MSMEs: JSEZA assists MSMEs
through facilitating access financing, training, and mentorship, empowering entrepreneurs and driving economic growth.
How do you promote Jamaica on the international stage for foreign direct investment (FDI)?
The JSEZA works towards building international partnerships which will help to facilitate more investment opportunities within our local Special Economic Zone Regime. We employ numerous strategies to promote the regime and activities of Jamaica, through online and social media platforms (such as Google Ad placement and Instagram) as well physical engagements. These strategies include but are not limited to: Trade Missions:
The JSEZA participates in and leads trade missions that will connect global suppliers and consumers all over the world. This has the potential to boost both our exports as well as investment in key sectors such as manufacturing, infrastructure, and logistics.
International SEZ Ambassadors.
We establish connections with investors through collaborations with SEZ ambassadors who seek to match potential investors with the development and projects based on their interests.
International conference and exhibition engagements:
The JSEZA also participates in conferences taking part in panel discussions and other activities with the aim of providing information on global stages about the value of investing in JSEZ regime and the benefits we offer.
Diaspora Integration Program:

This initiative enables Jamaicans residing abroad to serve as reliable sources of information for investors and corporations seeking to make investments in Jamaica, particularly in relation to the SEZ regime. Leveraging Local, Regional and international Partnerships:
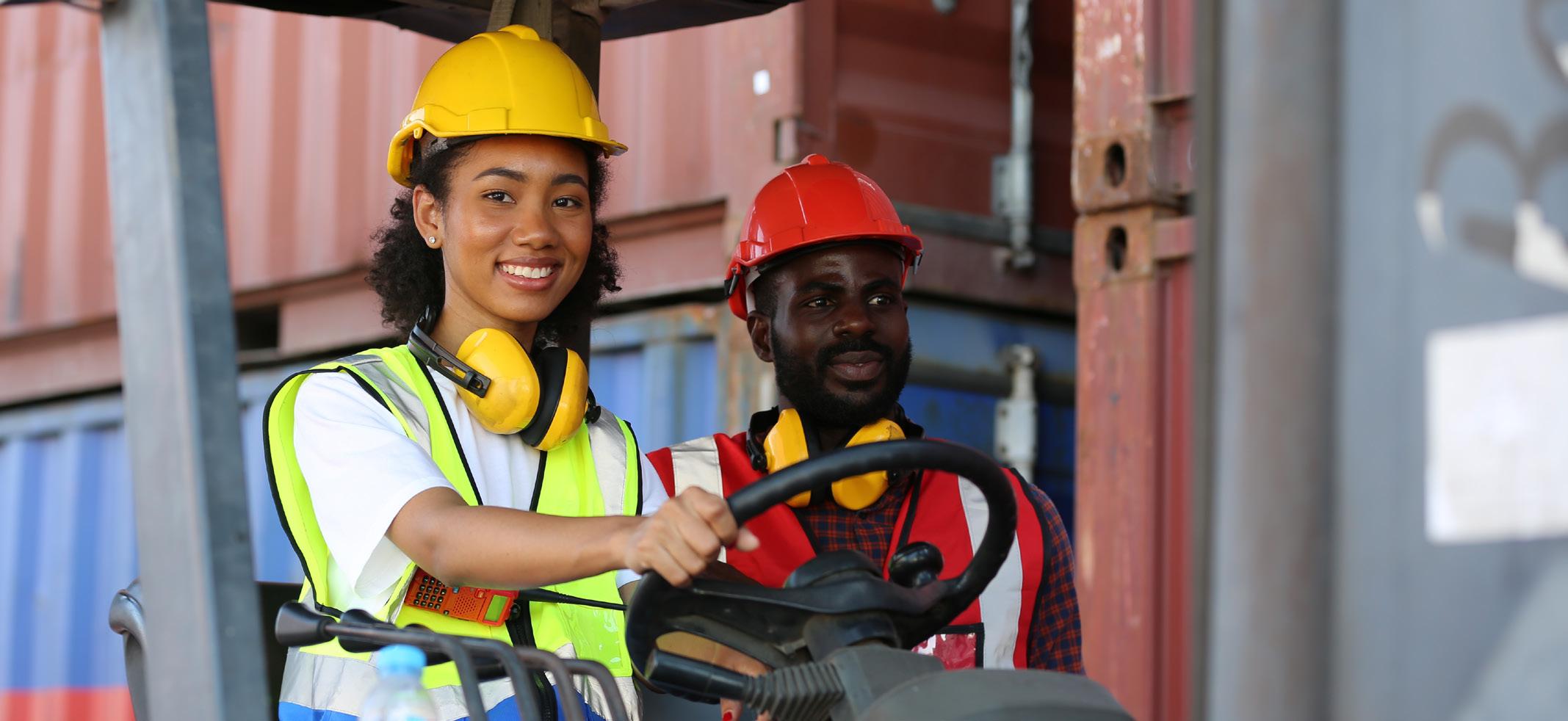
We aim to establish partnerships with local and international partners to exchange investment and marketing intelligence. This endeavor will assist in furthering JSEZA’s marketing efforts. By leveraging these relationships, the Authority has gained access to a larger database of investors in a shorter time, as well as increased promotional channels to expand the reach of our messages.
How might Jamaica’s Logistics Hub Initiative enhance global trade?
The JLHI based on Jamaica’s geographic location and modern infrastructure aims to position the country as a key point for shipping, warehousing and distribution in the region.
By becoming the central point for trading activities happening between the Americas, Europe and Asia, Jamaica can contribute to an enhancement in global trade. When successful this will result in reduced shipping costs and enhance business facilitation worldwide through increased access to goods.
The result will also include more investment and increase the creation of jobs locally while improving the efficiency of global trade.
Are there any recent projects that you would like to highlight?
We are really excited about the establishment of German Ship Repair Jamaica (GSRJ) Limited’s Special Economic Zone which is a groundbreaking 235-meter-long floating dry dock. The GSRJ can lift large vessels out of water for the purpose of conducting repairs. The company, in partnership with the Caribbean Maritime University and the Heart NSTA Trust, is also developing a model apprenticeship program for Jamaican youth. This program will provide individuals with the skills required to thrive in the marine industry, specifically in the area of ship repairs.
To learn more about this SEZ project, click the following link: German Ship Repair Jamaica Limited, 1st Dry Dock Ship Repair
The recently concluded development of UG’s Special Economic Zone in Westmoreland, Jamaica is also a major achievement. The successful completion of this development signifies the beginning of SEZ establishment in the parish which is set to stimulate economic activity within the outsourcing sector and result in job opportunities for approximately 700 young Jamaicans living in the area.
This acts as a method of diversification, given that the primary economic activities for the parish are agriculture and tourism. Similarly, are there any projects in the pipeline that you’re excited about?
The Authority is enthusiastic about the following four SEZ projects:
1. Olympus Sport City: We envision this SEZ as a world-class Green City Sports Hub that cultivates Jamaica’s future sporting champions.
2. Pandora Eco-Industrial Park: This SEZ is envisioned as a world-class manufacturing hub offering a ‘Start to Finish’ eco-system for local and global companies focusing on the pharmaceutical and nutraceutical sectors.
3. West 77° Technopolis (Silicon City): is envisioned as Jamaica’s internationally recognized epicenter for technology and innovation. This Special Economic Zone will provide a state-of-the-art facility that will unite leading innovators in industry, business, and education within a mixed-use, sustainable environment.
4. Xanadu Media City (Creative Hub): A Media City, envisaged as a world class hub for innovation and content creation A robust collaborative platform providing ‘Freedom, Flexibility, and Opportunity’ to creative professionals.
Projects aside, how do you facilitate job creation in local communities?
The JSEZ framework is crucial in fostering economic growth and generating employment opportunities in local communities. The creation of these designated areas promotes the growth of businesses and industries. Development within JSEZ’s require a labor force to execute activities. This generates employment opportunities for local residents across multiple sectors.
JSEZA promotes job creation by enhancing skill development through partnerships with local educational organizations and training institutions such as The HEART NSTA, The CMU, The UWI among others. Through these partnerships, we ensure that SEZs have access to a sustainable labor force.
The JSEZA also advocates for human development within the SEZ regime, and SEZs that embrace these values frequently cultivate a culture of training, creativity, and advancements in technology. Reports from within the zones indicate that substantial investments have been made in training and development programs to provide local workers with the necessary skills to fulfill their specialized needs of businesses. This in turn improves the employability of the local labor force.
How else do you support local communities across Jamaica?
The Authority’s pro-development stance should not negatively impact the livelihood of local
This could mean jobs for the construction phase of development, specialized labour in the form of consultants or professionals for the development of the corporate structure needed to support the development as well as the skilled and unskilled labour required for operations.
We also promote the development of “EcoIndustrial Zones.” It is therefore our intention to develop SEZs that consistently support and adhere to the ESG principles and thus reduce carbon emissions from energy used or consumed in the built environment.
Therefore, to ensure sustainable environmental, economic, and socio-cultural impacts during its operations, a SEZ that aligns with the framework should maintain green standards during its design, construction, and operational phases.
The SEZ ecosystem is designed to provide opportunities for companies known as zone users. While these companies may not meet the criteria for SEZ fiscal benefits, they can still operate within a zone and leverage the market created by the service demand generated by SEZs.
Looking ahead, what are JSEZA’s key priorities?
The SEZA’s key priorities include:
The Authority concentrates on boosting investments and exports, simultaneously cultivating a sustainable business community to guarantee the efficient operation of Special Economic Zones (SEZs). The organization seeks to achieve the following major objectives:
1. Enhance Economic Output: Facilitate profitability for SEZ stakeholders by providing a conducive business environment, streamlined regulations, and access to world-class infrastructure.
2. Revolutionize Global Trade: Advance Jamaica’s Logistics Hub Initiative to position the country as a leading regional logistics hub and promote sustainable trade practices and enhance regional connectivity.
3. Contribute to Sustainable Development: Align activities with the UN Sustainable Development Goals (SDGs) to ensure environmental sustainability, social responsibility, and economic growth.



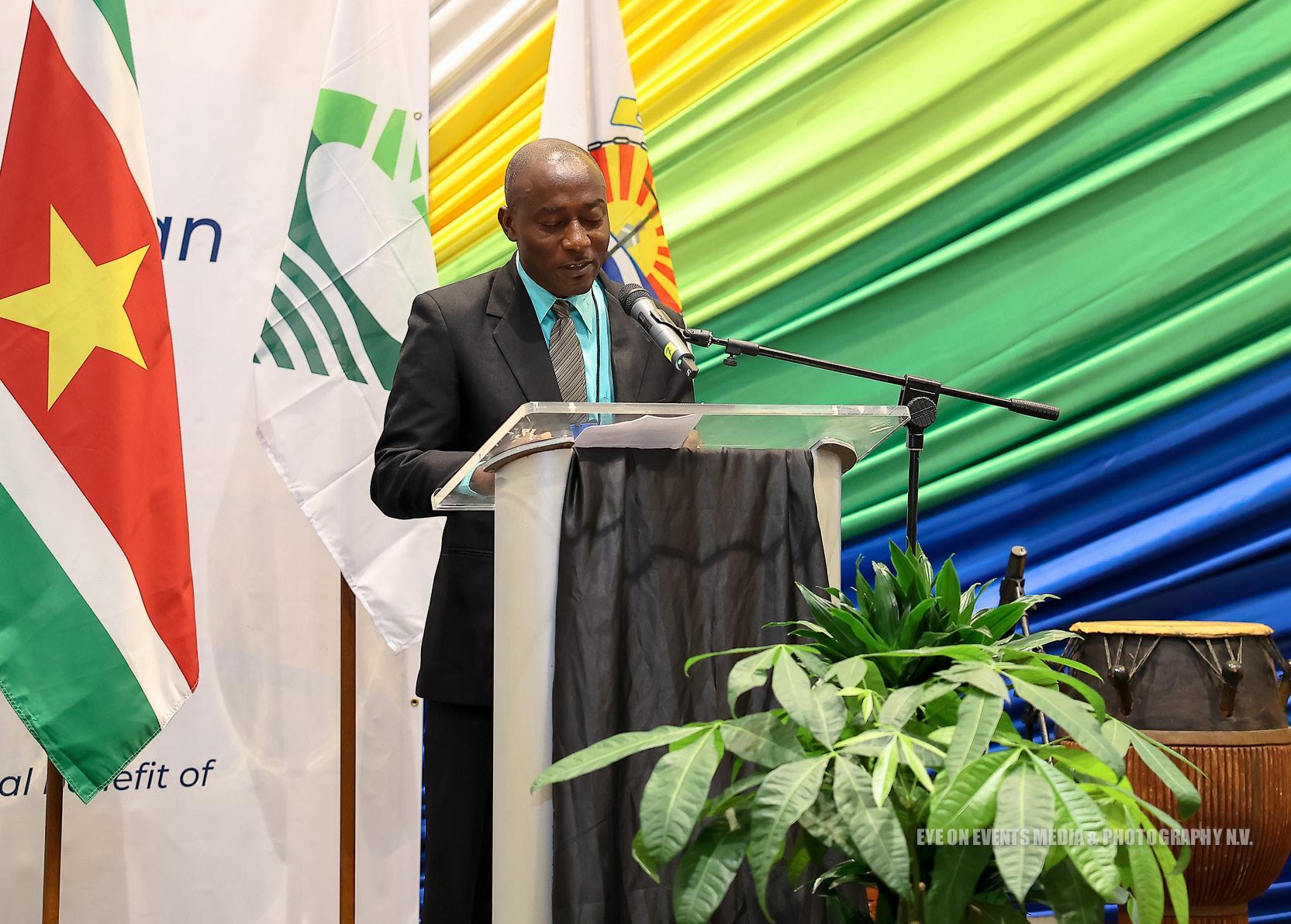
Therefore, in the not-too-distant future, we will be coming out with a new vision and mission statement.
We have sought to modernize PMAC’s approach in recent years; there have been so many changes to the industry that we feel our role must also change. The regulatory structures create challenges for many of us, and the need to be a lobbying voice for regional ports has emerged as a critical requirement for our members.
As these changes exist or emerge within a global environment, as the supply chain becomes broader and more integrated, we believe that the ability to at least be at the table as it relates to the development of regional ports must become a focus of PMAC. That too is part of the reason why we see the need to realign our vision and mission statement to meet the current needs of our membership and face industry demands.
SC: What is your current take on the Caribbean ports industry? Is it particularly exciting or challenging to work in?
DT: It is exciting because we serve our people and are not simply commercial ports that facilitate business. 98 percent of our food, clothing, and shelter are delivered in many cases through a single port. Therefore, our ports are not strictly a commercial space
where profits and losses are made; they are the basis for survival. The fact that we continue to be undaunted in finding solutions to meet those requirements is where our excitement originates.
Most businesses have a very strong economic basis for their excitement, whereas we are also excited because we take care of our people. Every single aspect of life on our islands depends on us, and if that doesn’t excite you then I don’t know what else does.
We are also the largest region in the world for cruise traffic. While we cannot accept the largest container ships, we play a very significant role in global marine traffic management. As such, our ports are sometimes required to accommodate cruise ships over cargo vessels to facilitate our economic development.
That sort of complexity may not exist in many large countries as you have separate cargo and cruise terminals, whereas a lot of our ports are faced with having to provide a dual service in a single space.
We want to make sure cruise passengers access the services provided by our people such as vendors, taxis, restaurants, tours, water sports, and more.
The reality of being in the region’s port sector is certainly a major responsibility. I tip my hat to all my colleagues who grapple with the reality of dealing with global issues every day, sometimes with very limited resources.

Over 30 years of experience in the industry, our team of seasoned professionals know the ins and outs of the cargo business. From break bulk cargo to containerized shipments, we've got you covered.
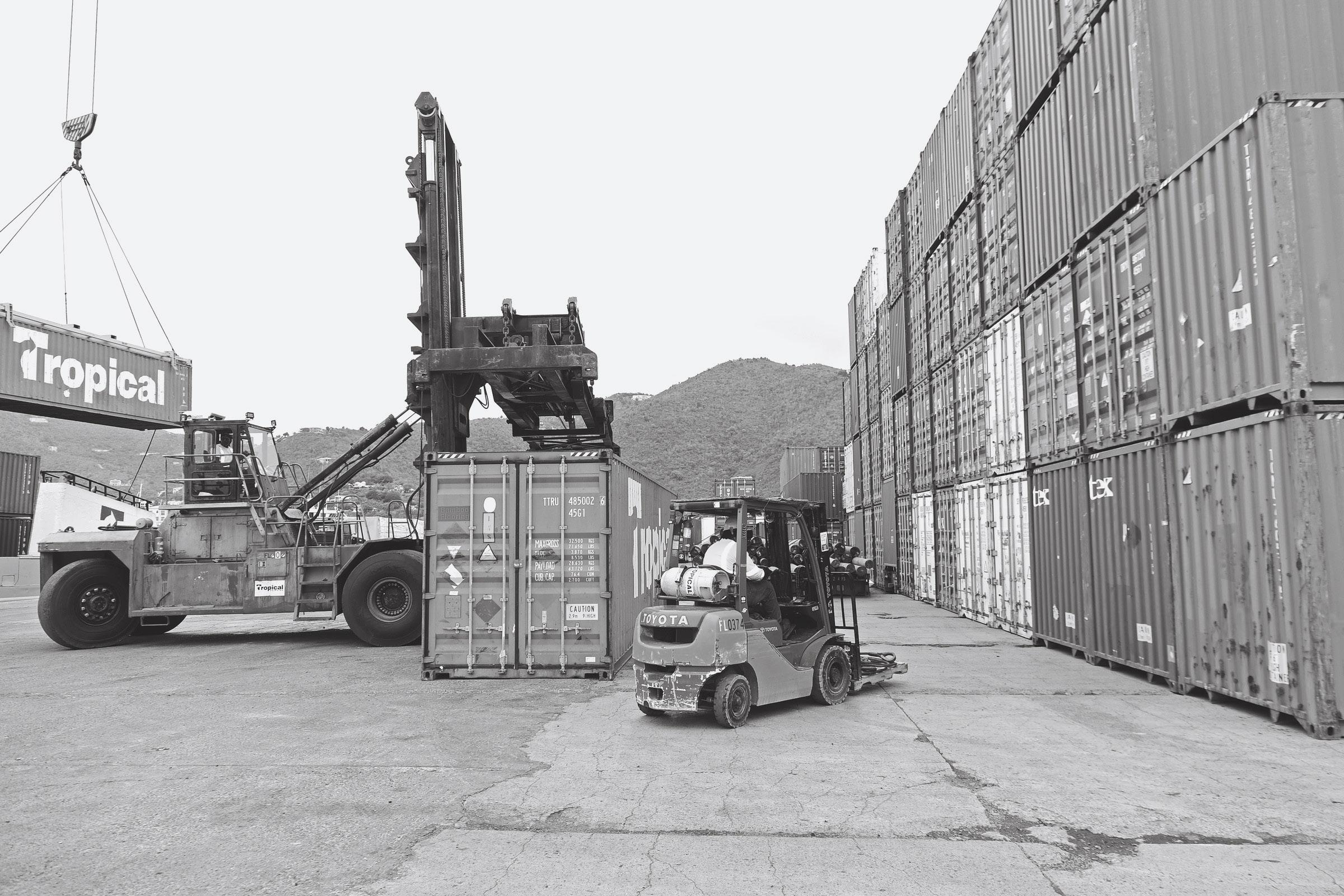
“WE HAVE SOUGHT TO MODERNIZE PMAC’S APPROACH IN RECENT YEARS; THERE HAVE BEEN SO MANY CHANGES TO THE INDUSTRY THAT WE FEEL OUR ROLE MUST ALSO CHANGE”
– DARWIN TELEMAQUE, CHAIRMAN, PORT MANAGEMENT ASSOCIATION OF THE CARIBBEAN
SC: What makes the Caribbean the gateway to the economy?
DT: The Caribbean is where almost every cruise line in the world comes for five, six, or sometimes seven months in the year, which makes us a very critical space. If the Caribbean was not involved in providing cruise services, there would be a real problem in the world because it is a multi-billiondollar industry.
I do not believe the Caribbean gets the respect that it deserves. Investments, partnerships, and outcomes should
flow with the recognition that this is a vital space.
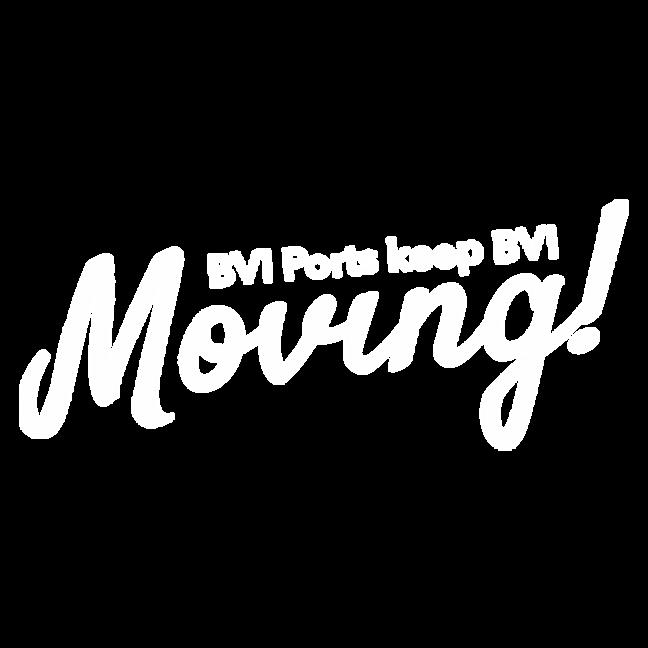
I believe the reason that happens is because the unified front that is required to be presented to the world does not exist in a region where you have so many flag states and independent states operating as a single region.
PMAC is attempting to be the face that presents the region as a single space with a common interest and afford the sort of presence that would lead to more global recognition.
SC: What integral role does PMAC perform as a node in the network of Caribbean ports, stakeholders, and strategic partners?
DT: That’s a very important question. We’ve been challenged by global regulations related to the transition from fossil fuels to clean, green ports. The International Maritime Organization (IMO) and the United Nations (UN) have come out with mid- and long-term measures regarding the zero emission standards that they wish to impose on shipping.
Since these ships come to our ports, it means the ports themselves have got to transition as well to meet the requirements of transport. How do we do that when basic challenges remain at port level and the development of our states has not yet surpassed the pre-industrial stage?
We are still not sufficiently industrialized, and the world has moved on to automation, digitalization, and decarbonization. We are being asked to follow along, but some of our ports are still at a very rudimentary level. Some were built in the 1960s and are still break-bulk ports not designed for containerization. We’ve not yet even designed container terminals, and we’ve been asked to decarbonize, so my role has certainly taken on a whole different perspective where I am challenged as the Chairman of PMAC to present the exact position of Caribbean ports so that regulators can take note of the impact they’re going to have in implementing these changes on our port sector.
Remember, our ports are not only commercial entities – we serve people, so these significant demands and changes mean that the impact is going to be felt directly by our citizens. We are trying our best to protect against that larger impact.
PMAC has taken on a global role where we are now lobbying the IMO, UN, and other global entities related to the fight against climate change. We support the efforts to improve the environment, and we are excited to play our part, but we have other development objectives that we need to meet before we can actually get to the required level. That has to be brought to the fore, and I’ve been
tasked with making that representation.
In addition, one of the things that we ought to be doing is to ensure that we modernize and have the appropriate automation within our ports so that we have the most efficient human capacity – I call that humanization.
As we modernize, automate, digitalize, and humanize, then decarbonization comes into place and the full circle gets wrapped up. That is where my mind is at and where our membership is looking for support, because to modernize means we need to find best practices and solutions that meets our needs.
We also need to obtain financing for our ports as our nations are heavily challenged with debt. Therefore, we want to find solutions for raising the necessary capital expenditure (CapEx).
Additionally, we are moving ahead with the implementation of a maritime single window within PMAC to meet IMO regulations. The IMO is supporting us on that, and PMAC is supporting its member ports as well as we attempt to meet regional and international regulatory requirements.
My role is to align PMAC to the best of our ability and be on course to meet the many demands that accompany these regulations.

SC: Finally, how do you see Caribbean ports developing in the next five years?
DT: First of all, I can’t overemphasize the nature of our ports as the gateway to social and economic development in Caribbean countries.
However, most of our ports were built in the 1960s and ought to be upgraded, so there’s quite a bit of work to be done. In recent times, we have had two ports in Antigua and Barbuda and Saint Vincent and the Grenadines being completely rebuilt.
All the remaining ports are due for retrofitting or redevelopment, but they will determine for themselves what they wish to do. The need to modernize is now upon us because ports are built to last an average of 50 years, and that means if they were built in the 1960s, then most of the ports need to be redeveloped.
Not only that, but they’re also break-bulk ports built to handle boxes, pallets, and sacks. Now that containerization is the order of the day, we need to see many of our markets receive the full benefits of containerization, the efficiency that it brings, and see how those efficiencies can translate into better costs and impact the business that is done through our ports, ultimately improving the point of sale.

I try to never think globally about this subject, because with break-bulk ports, the first step is not to digitalize or decarbonize, but to modernize the facilities. We have ships that were recently built 1990s and 2000s coming into ports that were built in the 1960s, so we have to fix that alignment to have ports that match the developments made by ships in terms of infrastructure, digital connectivity, and automation that’s required to advance the operation of those vessels. If we can get there within the next five years, it would be a massive achievement and improve operations in the region.
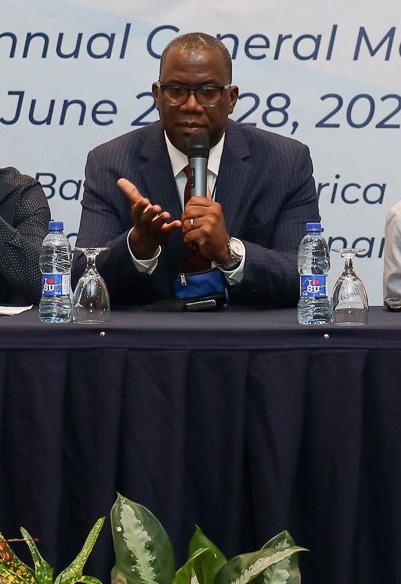
“OUR PORTS ARE NOT STRICTLY A COMMERCIAL SPACE WHERE PROFITS AND LOSSES ARE MADE; THEY ARE THE BASIS FOR SURVIVAL”
– DARWIN TELEMAQUE, CHAIRMAN, PORT MANAGEMENT ASSOCIATION OF THE CARIBBEAN
to have 20+ ships coming into our ports, but in recent times that number has gone down to five.
We’re not seeing new entrants coming into the marketplace, and I believe that is to do with the level of inefficiencies that exist at our ports, both because of their size and dual use for cruise and cargo ships. Those challenges have to be addressed so that we have the appropriate facilities to meet global demand for cruises as well as the needs of our people in a space that isn’t as large as other countries but can become more efficient and deliver a higher quality of service.
In five to 10 years, I expect to see significantly more modernized port facilities throughout the region, which means there is need for significant investment in the port sector.
We’re hoping that the right investors can come in and support modernization, and that it is done prudently with a very high focus on mitigating the heavy burden that can come with this sort of development, keeping in mind the role that we play.

The other challenge is that we have been losing shipping lines in the Caribbean over the last two decades. We used www.pmac-ports.com


AUSTRALIAN COLD CHAIN SPOTLIGHT
Essential for preserving integrity from point of origin to consumption, the cold chain plays a crucial role in maintaining the quality, safety, and freshness of perishable products throughout Australia
Writer: Jack Salter | Project Manager: Deane Anderton
The Australian cold chain is integral to ensuring that perishable goods are delivered in optimal condition to consumers, fulfilling demands for quality and safety while supporting economic and public health objectives.
A complex system that requires ongoing innovation, strict regulatory compliance, and effective management to
adapt to the challenges of a global market, the cold chain provides controlled temperature environments necessary for preserving these products.
By maintaining specific temperatures, the cold chain ensures that food items such as meat, dairy, fruits, and vegetables remain fresh, retaining their nutritional value and safety until they reach the consumer.
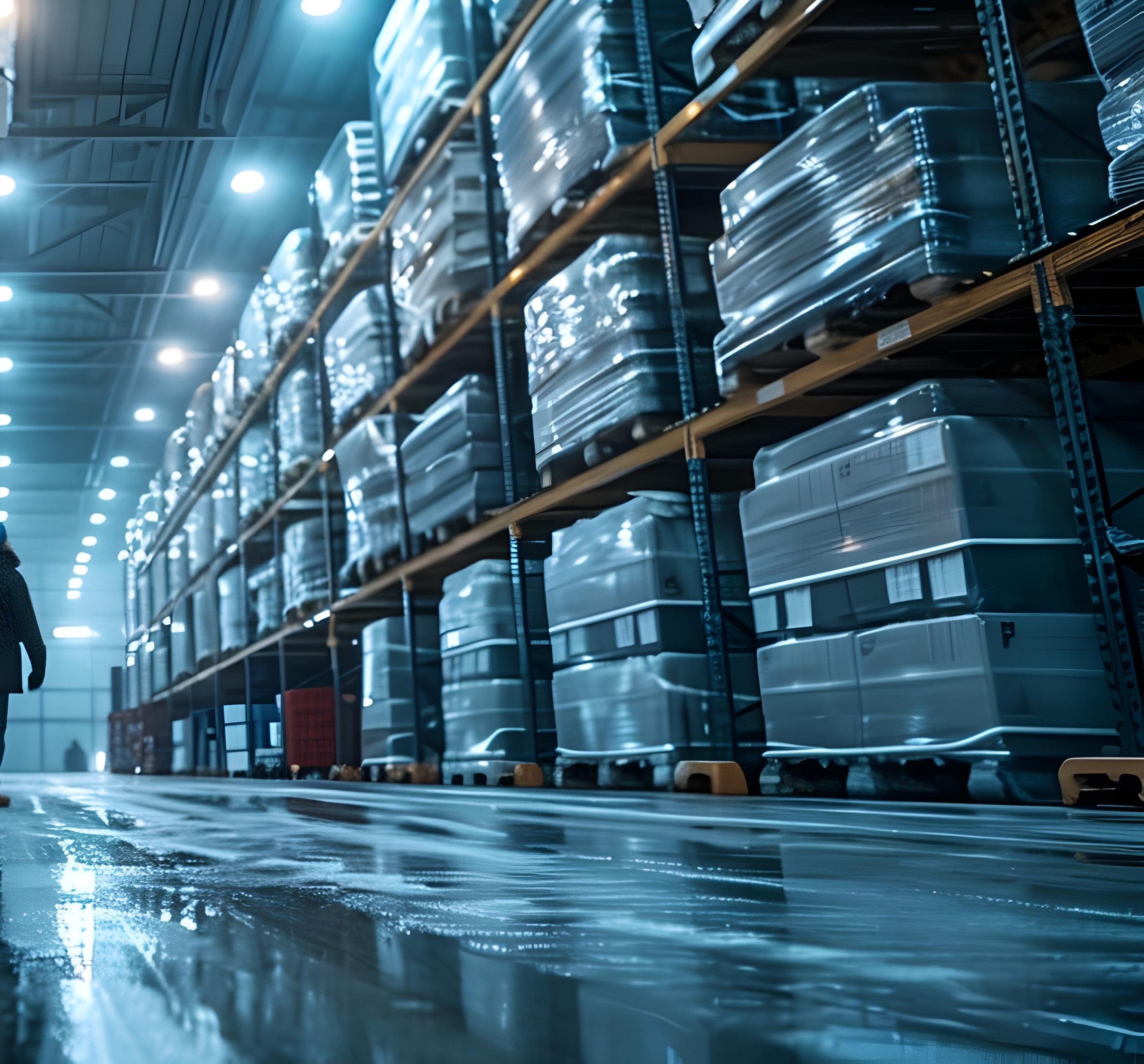
Effective cold chain management also significantly reduces the likelihood of spoilage by inhibiting the growth of pathogenic microbes and slowing the enzymatic breakdown of food products.
This not only helps in reducing food waste, but also ensures economic efficiency by minimising the loss of valuable goods.
By extending the life of perishable products, the cold chain enables producers to reach markets that may have previously been inaccessible due to distance or transit times, opening up new opportunities for growth and expansion for Australian businesses both domestically and internationally.
Products that are well-preserved and maintained through effective cold chain management also often command a higher market value, meaning consumers and businesses are willing to pay a premium for goods that guarantee freshness and safety.
Consistent and reliable cold chain management likewise leads to higher consumer satisfaction, as it ensures products maintain their desired state and quality from the
point of production to the point of sale.
To prevent foodborne illnesses, meanwhile, it is crucial that proper cold chain practices are maintained as many perishable foods can harbour bacteria and other pathogens if they are not stored and transported at correct temperatures.
The Australian cold chain helps to mitigate such risks, contributing to public health and safety in the country.
It equally ensures compliance with strict regulatory standards regarding the transportation and storage of perishable items, particularly food and pharmaceuticals, which are designed to protect consumers and ensure businesses operate within legal requirements.
To futureproof its critical role, the cold chain in Australia is continually evolving with technological advancements such as real-time temperature monitoring, Internet of Things (IoT)-based logistics, and improved refrigeration equipment.
These technologies further enhance the efficiency and reliability of the cold chain, reducing energy consumption and improving environmental sustainability.

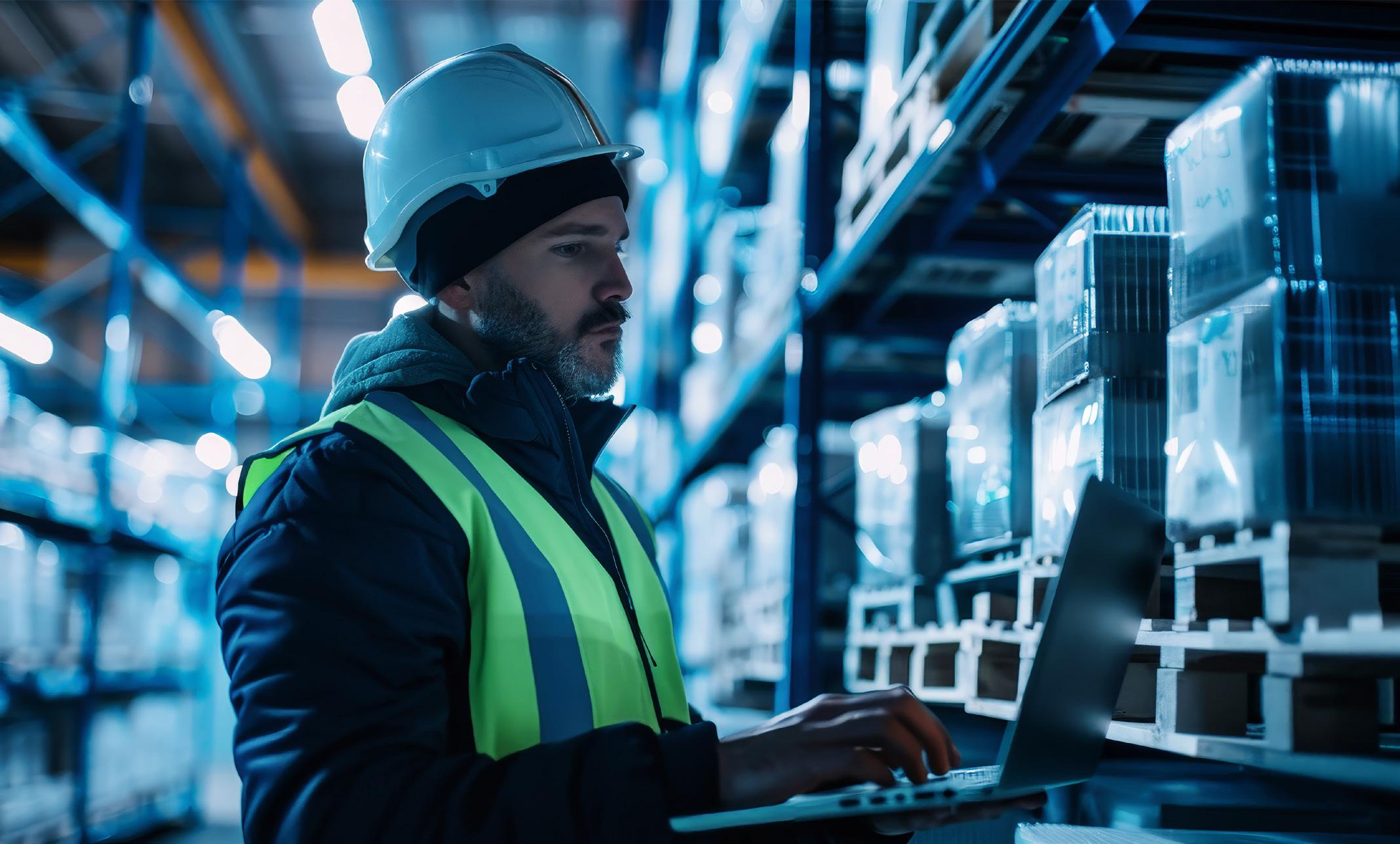

REFRIGERATED WAREHOUSE AND TRANSPORT ASSOCIATION OF AUSTRALIA INTERVIEW:
Marianne Kintzel, Executive Officer, outlines the vital role of the Refrigerated Warehouse and Transport Association of Australia (RWTA) amid the latest industry developments, such as setpoint temperature changes and booming demand for cold storage facilities
Our purpose is to strengthen and invigorate the Australian cold chain by providing insightful and ethical leadership for our members.
SC: What is your current take on the Australian cold chain? Is it particularly exciting or challenging to work in?
MK: It is a dynamic and exciting industry to be involved in, but not without its challenges. Where there are people, there needs to be effective cold chain processes in place.
Supply Chain Outlook (SC): Firstly, please could you introduce us to RWTA and explain your purpose?
Marianne Kintzel, Executive Officer (MK): RWTA represents the industry sectors involved in the Australian cold chain and looks to meet the increasing demands of Australia through the provision of temperature-controlled warehousing, refrigerated transport, and related essential services.
The cost of energy is forever increasing, sustainability processes need to be implemented, and a skilled labour force requires attention. For instance, Australia is tens of thousands short of skilled truck drivers, and with an average age of 58, it is set to get worse rather than better.
Throughout the COVID-19 pandemic years, the cold chain continued to ensure there was fresh and available food for all. During this time, there was considerable consolidation in the industry to create additional disruption to our sector.
Insurance costs are skyrocketing, so we are investigating
a Discretionary Mutual Fund (DMF) on behalf of the cold chain in Australia and New Zealand (ANZ). RWTA is working to explore if a DMF can reduce property insurance premiums for the cold chain in ANZ.
If adopted, will help to mitigate the problem of increasing premiums for Industrial Special Risk (ISR) policies, which provide cover for physical loss or damage to property and the financial losses incurred.
The cold chain in Australia has its own unique issues but continues to grow and develop, with automation and safety processes a constant focus.
SC: In what ways does RWTA represent both the warehousing and transport sectors involved in the Australian cold chain?
MK: RWTA plays a vital role in representing both the warehousing and transport sectors that are integral to the Australian cold chain.
• Advocacy and policy influence – RWTA acts as a powerful advocate for the interests of the cold storage and transport industries at various levels of government and industry. It engages in lobbying efforts to influence policy decisions that impact the cold chain sector, aiming to shape regulations that support the industry’s growth and operational efficiency.
• Standards and best practices – We promote high standards and best practices within the cold chain industry. It helps develop and disseminate guidelines and protocols that ensure safety, efficiency, and compliance across both the warehousing and transport segments. These standards are crucial for maintaining product integrity and consumer safety.
• Education and training – RWTA provides educational programmes and training resources to enhance the
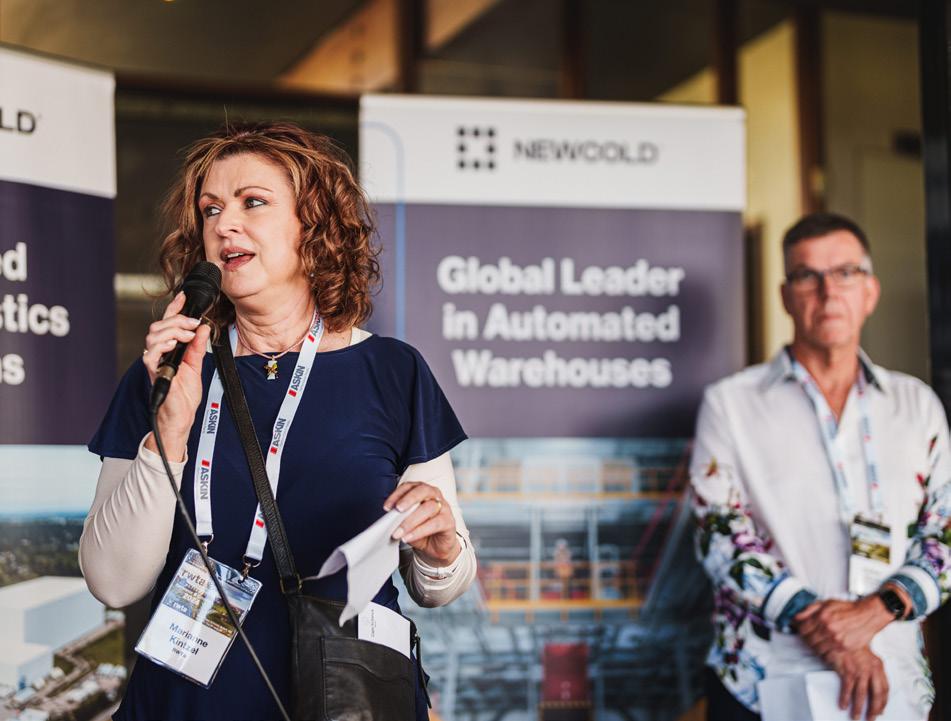
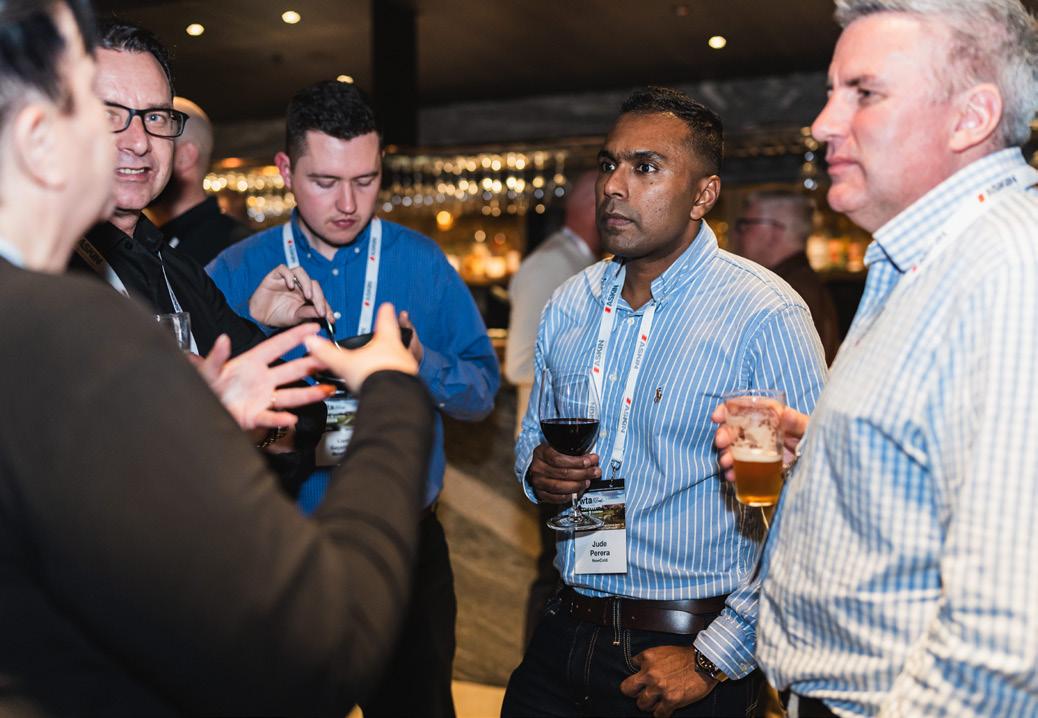
professional skills of those working within the cold storage and transport sectors. This includes workshops, seminars, and courses on the latest technologies, regulatory requirements, and operational best practices in cold chain management.
• Industry networking and events – The association holds an annual conference, multiple networking events, and a golf day in most states annually that bring together professionals from both the warehousing and transport sectors and provide opportunities to network and do business. These events facilitate knowledge sharing, networking, and collaboration among members, offering opportunities for business development and industry advancement. We’re very excited to be offering access to over 15 functions in 2025, including our annual RWTA Conference, which next year is being held at The Langham, Gold Coast.
• Information dissemination – RWTA plays a key role in gathering and distributing information relevant to the cold chain industry, including market trends, technologies, regulatory changes, and research findings. This information is crucial for businesses to stay competitive and compliant.
• Representation and membership services – RWTA represents a wide range of members, from small operators to large corporations within the cold storage and transport sectors. It offers various membership benefits, including access to industry insights, advocacy on behalf of members, and discounts for services and products.
• Crisis management and support – We provide support and guidance to members during crises that affect the cold chain, such as natural disasters, economic downturns, or regulatory changes. The association
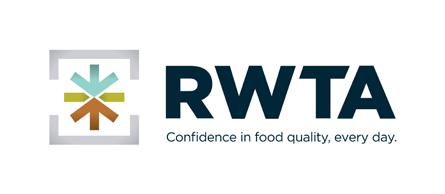
helps coordinate response efforts and communicates with governmental bodies to mitigate impacts on the industry.
• Public relations and awareness – By promoting the critical role of the cold chain in food safety and public health, RWTA helps to raise awareness amongst the public and stakeholders about the importance of refrigerated warehousing and transport. This enhances the sector’s profile and underscores its importance in the global supply chain.
• Innovation and technology adoption – RWTA encourages innovation and the adoption of new technologies to improve the efficiency and sustainability of the cold chain. It supports initiatives and partnerships that explore innovative solutions, such as automated systems, advanced refrigeration technologies, and energy-efficient practices.
Through these activities, RWTA ensures that the warehousing and transport sectors of the Australian cold chain are well supported, professionally managed, and adequately represented, enabling them to effectively meet the demands of a dynamic global market whilst maintaining the highest standards of quality and safety.
SC: Can you tell us more about the change in cold chain set-point temperature from -18°C to -15°C and how this is impacting energy efficiency?
MK: The move to -15°C is a global campaign to change the standard temperature for frozen food from -18°C to -15°C. The campaign aims to reduce greenhouse gas emissions, lower supply chain costs, and secure global food resources. The campaign was launched in 2023 and found that the change in temperature would:
• Save 17.7 million metric tonnes of carbon dioxide (CO2) per year.
• Create energy savings of around 25 terawatt hours (TWh).
• Cut costs in the supply chain by at least five percent and in some areas by up to 12 percent.
SC: What about the development of cold storage facilities and infrastructure across Australia?
MK: There is a booming demand and record rents for Australia’s cold storage facilities. Australia’s cold storage capacity per person is lagging behind the Netherlands, Canada, the UK, and the US, with at least 400,000 square metres (sqm) of new temperature-controlled space required by 2028.
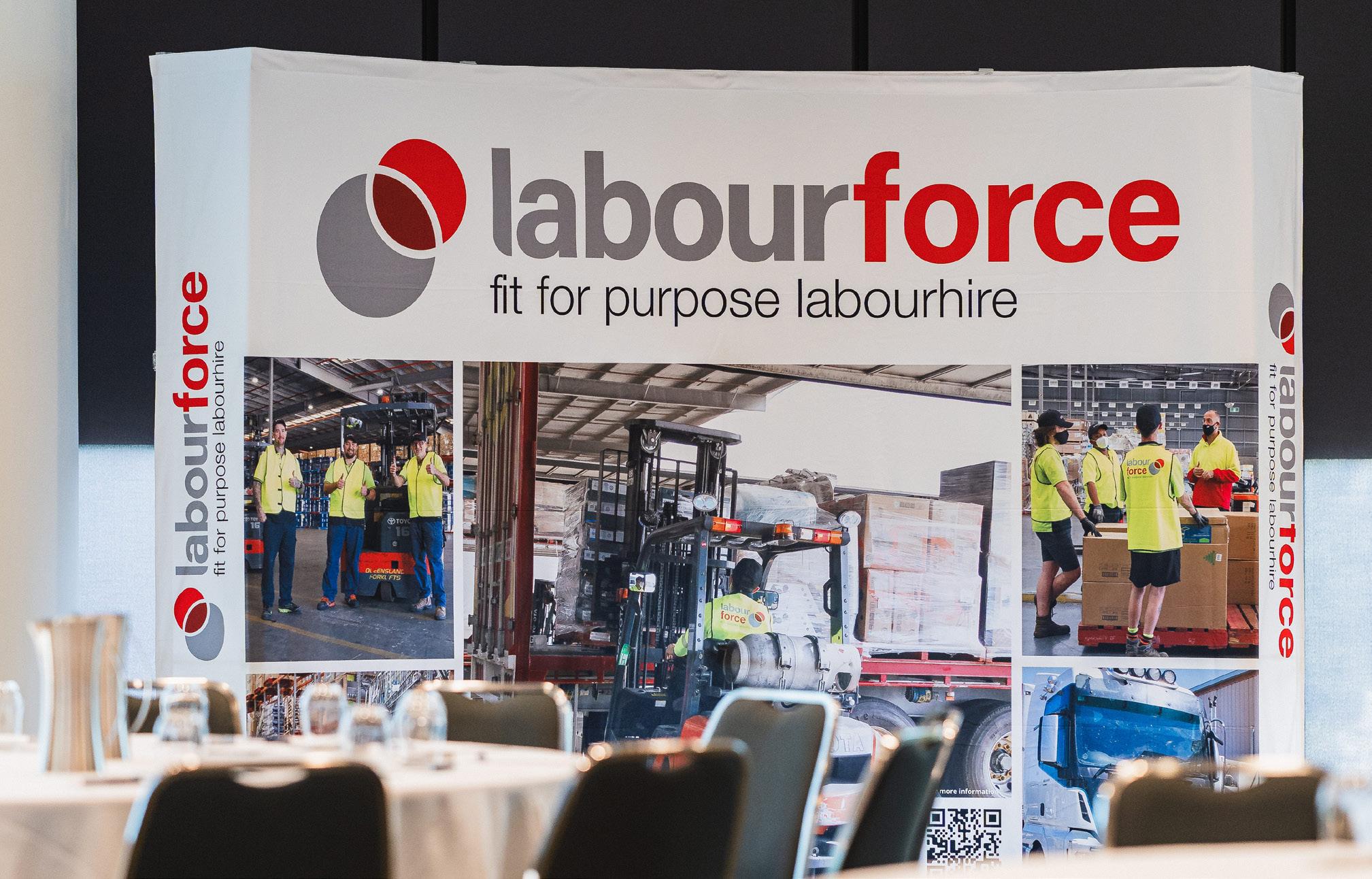
“RWTA PLAYS A VITAL ROLE IN REPRESENTING BOTH THE WAREHOUSING AND TRANSPORT SECTORS THAT ARE INTEGRAL TO THE AUSTRALIAN COLD CHAIN”
– MARIANNE KINTZEL, EXECUTIVE OFFICER, REFRIGERATED WAREHOUSE AND TRANSPORT ASSOCIATION OF AUSTRALIA
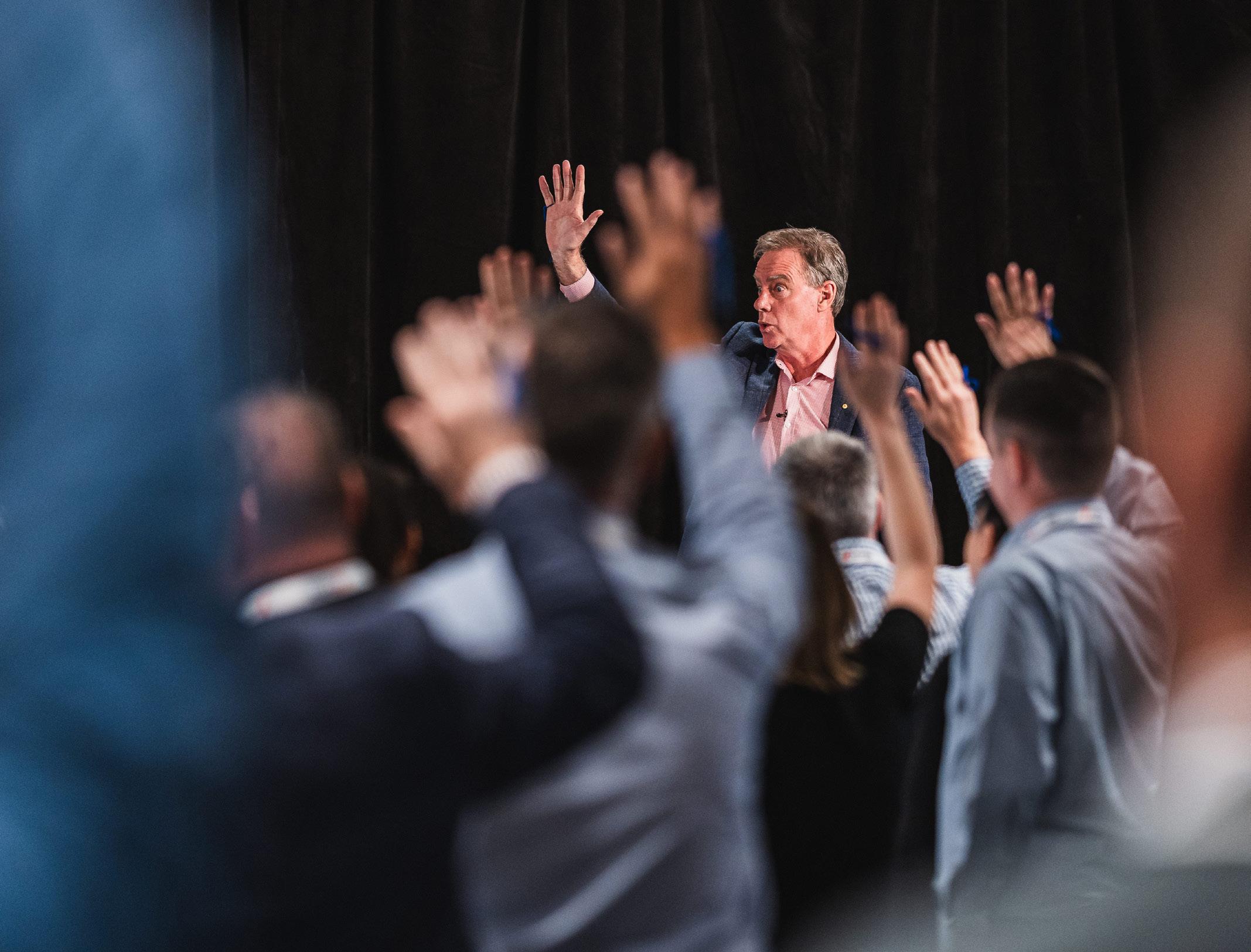
Australia currently has 0.4 cubic metres (cbm) of refrigerated warehouse capacity per urban resident, behind the US at 0.6 cbm and the Netherlands at 0.9 cbm.
To reach US levels would require approximately an additional 400,000 sqm of new warehouse space to be developed in Australia, stretching up to 1.3 million sqm to be in line with the Netherlands.
SC: What was the theme, focus, and aim of the 82nd RWTA Conference that took place in August?
MK: The theme of this year’s RWTA Conference was ‘On Thin Ice, Navigating Australia’s Cold Chain Viability’.
As we confront challenges such as geopolitical unrest, food insecurity and food wastage, environmental changes, regulatory updates, and technological innovations, this theme emphasised the importance of maintaining a robust, strong, and sustainable cold chain operations in our country.
Our aim is to foster dialogue amongst industry leaders, policymakers, and stakeholders to share insights and best
practices. The conference will focus on strategies to ensure we bolster overall supply chain sustainability.
We invited attendees to join us in identifying and addressing the key challenges facing our industry, with a focus on collaborative solutions and innovative approaches.
Together, we can strengthen Australia’s cold chain and ensure its long-term viability.
SC: How successful was the conference in strengthening the Australian cold chain and ensuring its long-term viability?
MK: There were multiple speakers, panels, and tech talks to debate what solutions we can integrate into companies to make the year ahead a success.
These include diversity and inclusion, energy consumption, sustainability, usage of land and space to extend the industry, changing the standard temperature for frozen food to -15°C to save on costs without risking quality and confidence in food quality, maximising labour where there are shortages, and much more!
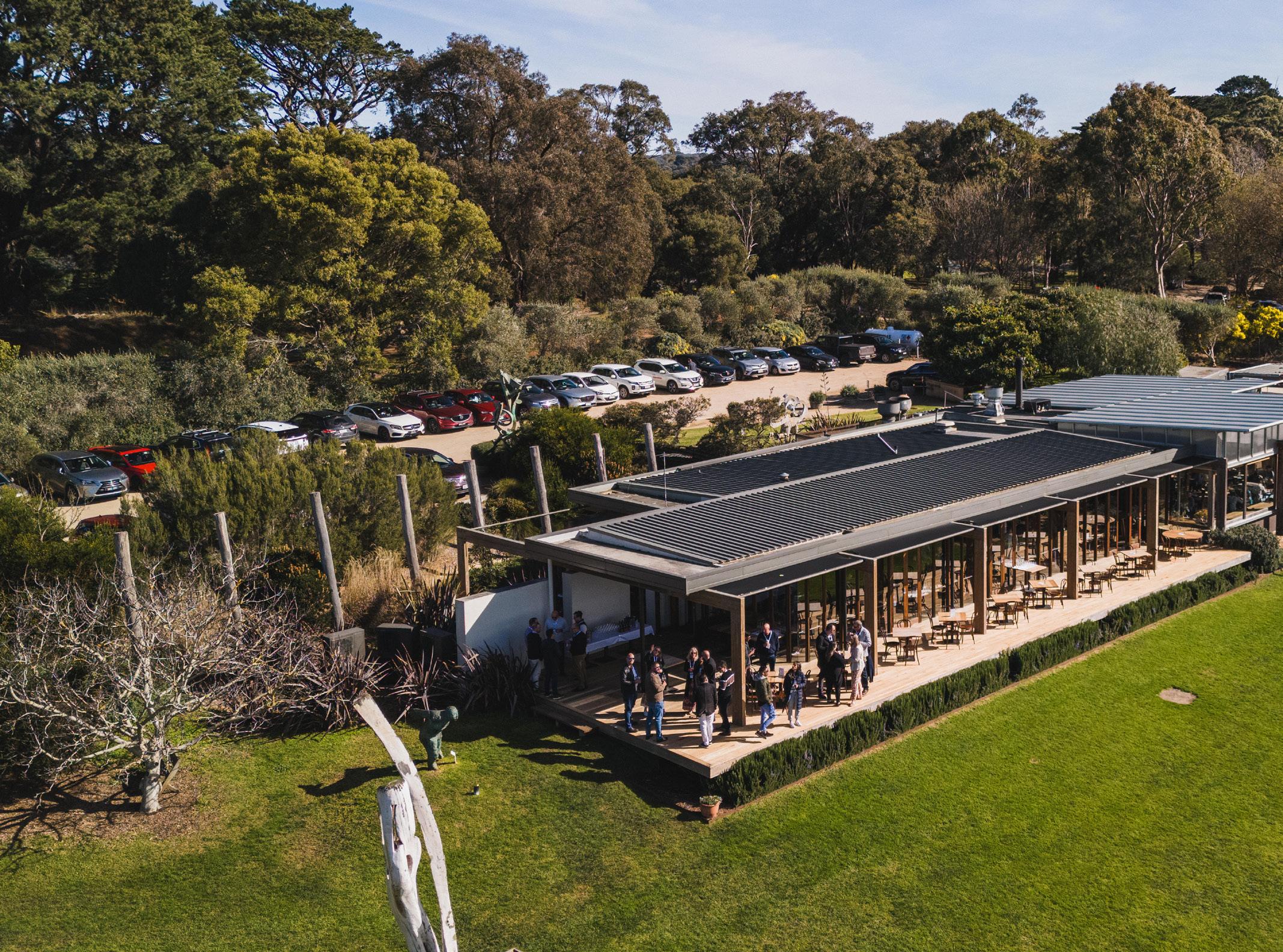
“WE AIM TO STRENGTHEN THE AUSTRALIAN COLD CHAIN INDUSTRY, ENSURING IT REMAINS ROBUST, COMPLIANT, AND COMPETITIVE IN A RAPIDLY EVOLVING GLOBAL MARKET”
– MARIANNE KINTZEL, EXECUTIVE OFFICER, REFRIGERATED
WAREHOUSE AND TRANSPORT ASSOCIATION
OF AUSTRALIA
SC: Finally, what are RWTA’s key priorities in order to continue representing the warehousing and transport sectors involved in the Australian cold chain?
MK: RWTA focuses on several key priorities to effectively represent and support the warehousing and transport sectors within the Australian cold chain.
These are designed to address the challenges and opportunities in the industry, ensuring sustainability, compliance, and growth. RWTA’s key priorities involve:
• ADVOCACY AND LEGISLATIVE INFLUENCE
Regulatory advocacy – RWTA actively engages with government bodies to influence policies and regulations that affect the cold chain industry. This includes lobbying for favourable legislative changes and ensuring that the industry’s needs are considered in policymaking.
~ Compliance support – Providing members with guidance and resources to navigate complex
regulatory landscapes, helping ensure that they remain compliant with current laws and regulations.
• INDUSTRY STANDARDS AND BEST PRACTICES
~ Promoting best practices – RWTA is dedicated to promoting and developing industry standards that ensure safety, efficiency, and sustainability in cold chain operations.
Quality assurance – Encouraging adherence to highquality standards helps maintain product integrity and consumer safety, which are critical for the reputation and reliability of the cold chain industry.
• EDUCATION AND TRAINING
Professional development – Providing ongoing education and training opportunities for industry professionals to help them stay updated with the latest technologies, practices, and regulatory changes.
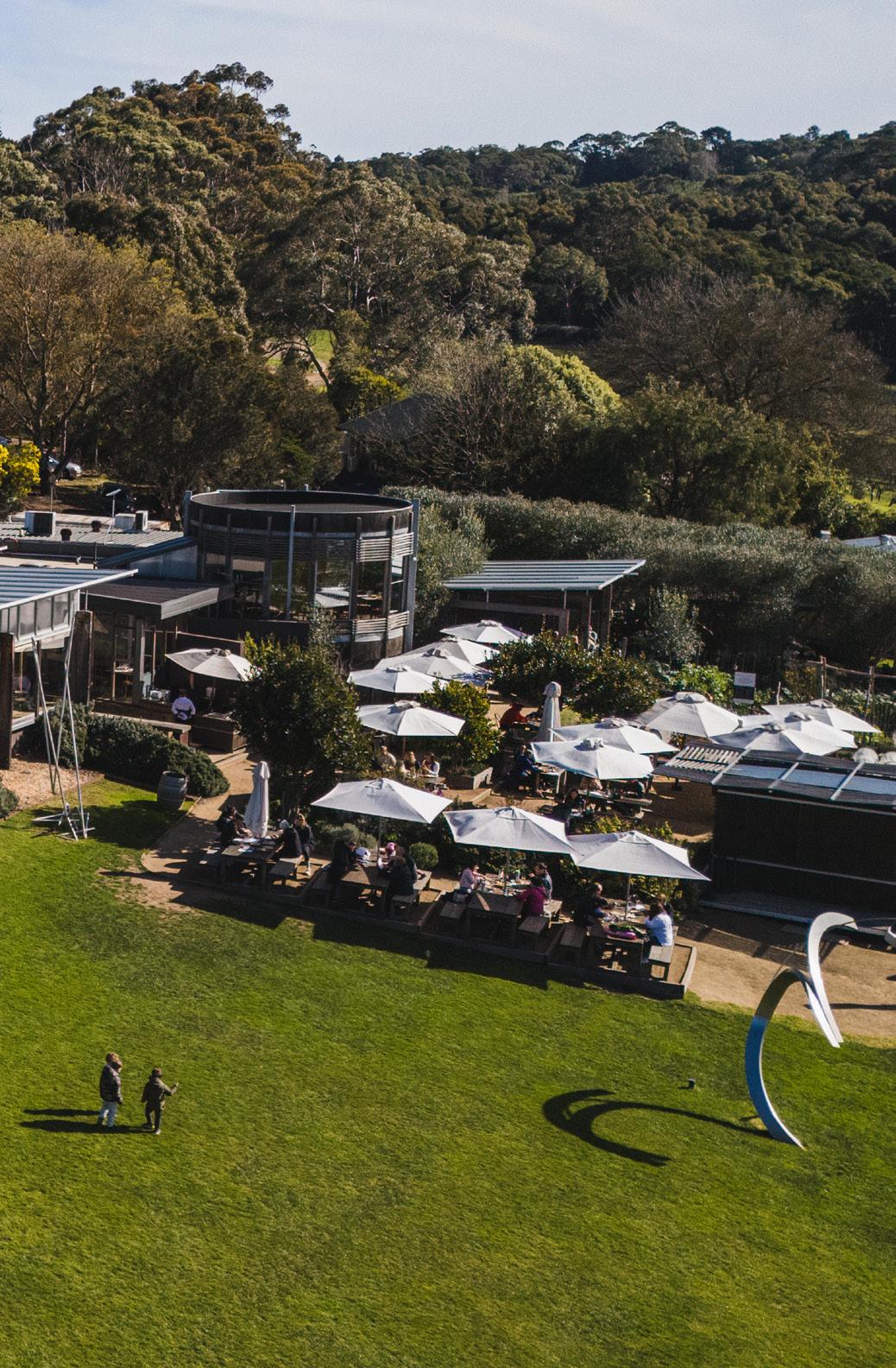
~ Workforce development – Initiatives to attract, develop, and retain skilled professionals in the cold chain industry, addressing potential skill shortages, and enhancing the workforce capability.
• TECHNOLOGICAL INNOVATION
~ Adoption of new technologies – Supporting the adoption of innovative technologies that improve the efficiency and sustainability of cold chain operations, such as IoT, artificial intelligence (AI), and automation.
R&D – Encouraging research into new methods and technologies that can solve existing challenges in the cold chain sector.
• SUSTAINABILITY AND ENVIRONMENTAL RESPONSIBILITY
Sustainable practices – Promoting environmental sustainability in warehousing and transport operations, including energy efficiency, waste reduction, and the use of eco-friendly materials and processes.
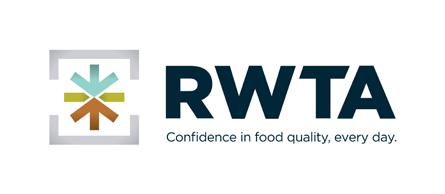
~ Advocacy for green policies – Engaging with policymakers to support the development of green logistics policies that align with global sustainability goals.
• MEMBER SERVICES AND SUPPORT
Network and community building – Facilitating networking opportunities for members to share knowledge, collaborate on common challenges, and foster business relationships.
~ Member benefits – Offering a range of services tailored to the needs of the cold chain industry, such as legal advice, insurance options, and financial services.
• CRISIS MANAGEMENT AND INDUSTRY SUPPORT
~ Emergency response – Developing and coordinating response strategies for industry-wide crises, such as pandemics or natural disasters.
Advocacy for industry support – Working to secure government and financial support for the industry during challenging times.
• PUBLIC AWARENESS AND INDUSTRY IMAGE
~ Promoting industry value – Enhancing public and stakeholder awareness of the vital role that the cold chain plays in the food supply and health sectors.
Positive industry representation – Actively working to improve the public image of the warehousing and transport sectors through outreach and education.
By focusing on these priorities, we aim to strengthen the Australian cold chain industry, ensuring it remains robust, compliant, and competitive in a rapidly evolving global market.
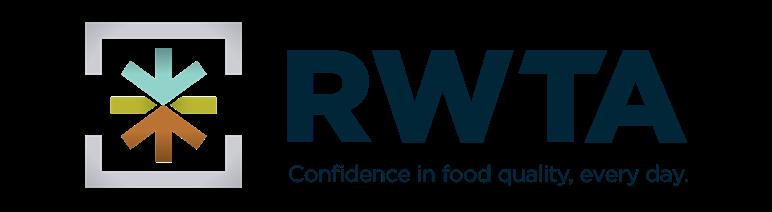
Tel: 0490 799 777 mariannek@rwta.com.au www.rwta.com.au
Building for the Future: How Today’s Warehouse Solutions Deliver Enduring Value for Tomorrow’s
Somerville Road, Tottenham - cornerstone of Melbourne’s industrial landscape
ABOUT ALIRO GROUP
Aliro Group, established in 2017, is a leading property development, investment, and funds management firm, delivering enduring value across a diverse range of real estate projects. In just a few years, the Group has grown its assets under management to over A$3.31 billion (A$4.41 billion on completion of developments), a clear testament to its capacity to identify and deliver quality, strategic developments. The Group’s impressive track record spans core, core-plus, value-add, and opportunistic strategies, demonstrating their ability to meet the complex needs of large-scale tenants, particularly in the industrial sector.
As businesses strive to adapt to an increasingly complex supply chain environment, the need for intelligent, sustainable, and flexible warehouse spaces has become a pressing issue. While demand for industrial real estate in Melbourne has traditionally been driven by location and capacity, the evolution of business needs calls for a more nuanced approach. Warehousing today is about more than just size and location—it’s about creating spaces that are future-ready, adaptable to technological advancements, and aligned with Occupiers’ sustainability goals.
Jason Blake, Development Director of Victoria at Aliro Group, notes that the key to creating spaces for tomorrow’s supply chains is the ability to anticipate future demands. “What we’re seeing now is a shift towards more flexible, high-tech warehouses that can evolve as businesses grow. It’s not just about providing space; it’s about enabling businesses to adapt quickly to change, whether it’s new technology, changing customer expectations, or evolving as market demand shifts.”
Aliro’s Somerville Road development in Melbourne’s Inner-West Tottenham area stands as an example of how these new demands are shaping the future of logistics, blending strategic location, cutting-edge design, and forwardthinking features.
A NEW VISION FOR WAREHOUSE DESIGN
The industrial real estate sector faces challenges in meeting modern logistics needs while maintaining efficiency, affordability, resilience and environmental concerns. . Traditional warehouse designs, built to meet the needs of a more conventional supply chain model, often struggle to keep pace with the speed of technological and environmental, social and governance changes. Today’s warehouses need to incorporate flexibility, sustainability, and connectivity. These factors must be considered from the ground up.
“Somerville Road is an embodiment of this shift, featuring a range of innovative and sustainable design principles that not only improve operational efficiency but also position the development as a key player in the future of industrial spaces. From advanced logistics facilities to green technologies, Somerville Road is pushing the envelope in modern warehousing,” added Blake.
REDEFINING OPERATIONAL EFFICIENCY
One of the key priorities at Somerville Road was integrating sustainable solutions that meet the operational needs today and anticipate future demands. With features like solar PV systems, electric vehicle (EV) charging stations, and rainwater harvesting systems, the development not only supports current operational requirements but also positions tenants to be at the forefront of eco-conscious logistics practices.
Blake explains, “Sustainability isn’t just a buzzword—it’s an essential aspect of how we need to think about the long-term viability of any development. At Somerville Road, we’ve prioritised green technologies and energy-
ESG is a cornerstone of Aliro’s vision Aliro’s ESG Strategy is to build resilient assets, create places where people can connect and thrive, and operate the business in a responsible and ethical manner. Aliro Group’s core plus industrial vehicle, AGIV (Aliro Group Industrial Vehicle) recently received a Sector Leadership prize and been ranked #1 in its peer group by the Global Real Estate Sustainability Benchmark (GRESB) for 2024. This achievement solidifies AGIV’s position as a leader in sustainable industrial real estate and reflects Aliro’s commitment to embedding ESG excellence in everything they do.
efficient solutions that help reduce environmental impact while improving the bottom line for businesses.”
This integration of eco-friendly features is not just about meeting the growing demand for environmentally responsible real estate but also about making these properties attractive to businesses that see sustainability as a key part of their long-term strategy.
STRATEGIC LOCATION MEETS FUTURE-READY LOGISTICS
Somerville Road’s location, strategically positioned within 10 kilometres from Melbourne’s Central Business District and a major transportation hub, the Port of Melbourne, highlights the growing importance of accessibility in industrial real estate development. The site also provides direct access to major thoroughfares such as the Princes Highway, West Gate Freeway, and Western Ring Road. This prime location makes it an ideal hub for logistics and distribution. In today’s fast-paced supply chains, proximity to key transportation links, infrastructure, and urban centres is crucial for ensuring smooth and efficient operations.
Beyond location, the design of Somerville Road caters to the evolving needs of logistics companies
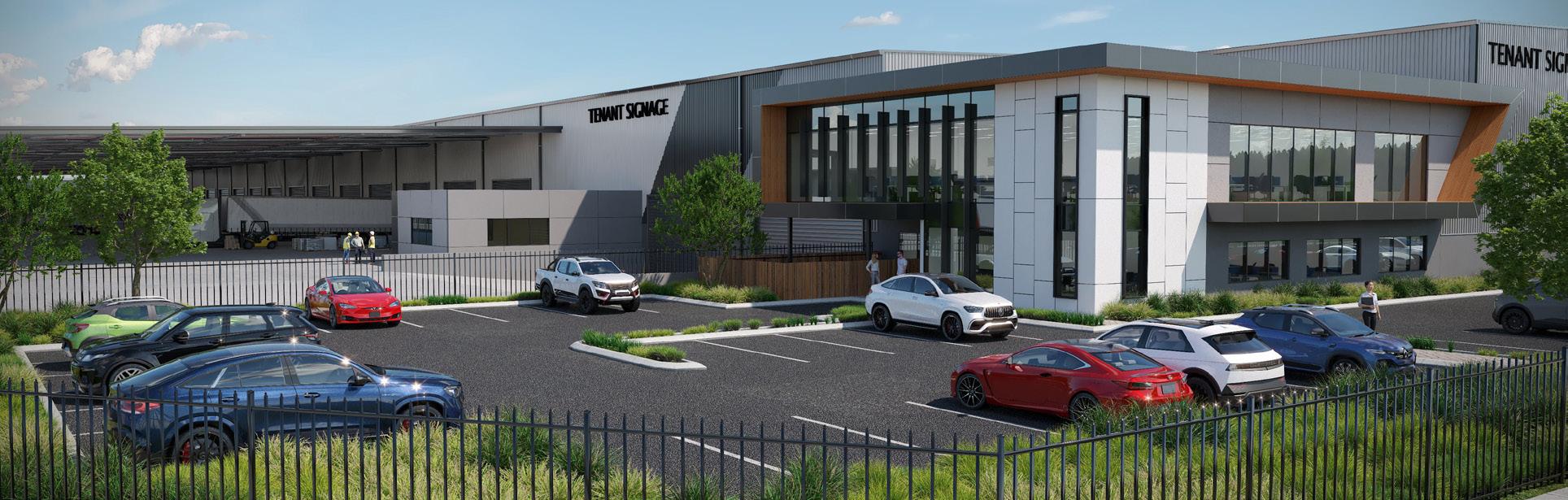
Tomorrow’s Supply Chains
by incorporating scalable spaces that can adjust to a range of business activities - from last-mile delivery hubs to large-scale distribution centres. THE ROLE OF SUSTAINABILITY IN FUTURE WAREHOUSING
Aliro’s commitment to sustainability is evident in its leadership in ESG practices. The Somerville Road facility exemplifies the company’s dedication to reducing emissions, implementing solar energy systems, and integrating rainwater harvesting. These technologies are becoming essential to future-proof industrial real estate, which is increasingly expected to meet strict sustainability standards.
The importance of sustainable real estate development is growing as businesses face increasing pressure from consumers, regulators, and investors to meet environmental goals.
According to a recent industry report, industrial real estate that incorporates green building certifications and sustainability measures has seen higher occupancy rates and greater tenant retention. As companies seek to meet their own environmental targets, spaces like Somerville Road, with its eco-friendly design and operational capabilities, will become even more valuable.
SHAPING THE FUTURE OF INDUSTRIAL WAREHOUSING: A NEW ERA OF LOGISTICS
As the logistics sector evolves, businesses need spaces that meet both current and future demands. Sustainability, adaptability, and innovation are no longer optional, as illustrated by the Somerville Road development in Melbourne. By integrating green technologies, scalable designs, and future-proof features, this project sets the standard for the future of industrial warehousing.
Daniel Wise, Managing Director & Chief Executive Officer of Aliro Group added, “As we move into 2025, our commitment to Environmental, Social, and Governance (ESG) principles will continue to drive everything we do at Aliro Group. We understand that to create lasting value for our clients and partners, we must go beyond simply meeting market demand. It’s about building sustainable,
Somerville Road Development: Key Facts
Location: 10km from Melbourne’s CBD and 9km to the of Melbourne
of Warehouse 2: 51,230 sqm of Warehouse 3: 22,141 sqm
Clearance: 14.6m ridge height in Warehouse 2
Floor Load: 8-tonne post load floors
Solar Power: 500kW solar system in Warehouse 3
Storage Temperature Range: -25°C to 4°C (Warehouse 3)
Pallet Capacity (Warehouse 3): Up to 30,000 pallets
Truck Access: B-Double access with heavy-duty hardstand
Canopies: 34.5m wide super canopies on Warehouse 2
Aliro Group’s Track Record of high-profile developments
Aliro Group has made significant strides in Australia’s real estate sector. Its progress and development expertise can be seen via the completion of a series of high-profile projects.
MOCO Food Services Facility
As the trusted development partner of ISPT, Aliro recently completed a state-of-the-art facility for MOCO Food Services at the Barracks in Metroplex Estate, Wacol, Queensland. This 18,000 sqm facility, pre-leased for 15 years, features 19 loading docks, a 5,000 sqm freezer, a 2,300 sqm chiller, 4,000 sqm of ambient space, and specialised refrigerated meat processing areas, showcasing Aliro’s ability to deliver tailored solutions for clients.
Elevations at Greystanes
In New South Wales, Aliro celebrated the official opening of Elevations at Greystanes on September 20, 2024. This project has provided over 80,000 sqm of premium industrial space across multiple warehouses since 2021, featuring state-of-the-art facilities, an onsite café, a professional-grade basketball court, and a BBQ area. The development of Warehouse 7, the final warehouse in the estate, is currently underway and is set for completion in March 2025.
Ellison
Estate
Aliro’s commitment to excellence was further seen with the practical completion of Stage One at Ellison Estate in Geebung, Queensland. This stage encompasses 23,600 sqm across six tenancies within two prime industrial facilities. With tenants like JS Hayes and Applied Medical already secured, Aliro is well-positioned to forge strong partnerships with future tenants. Stage Two, slated for completion in December 2024, will introduce 12 high-exposure showroom units spanning 11,200 sqm.
Chobani Australia Facility
The Chobani Australia facility at 8-22 Quality Drive, Dandenong South, has garnered external attention by being shortlisted for the Best Business or Industrial Park at the 2024 Innovation & Excellence People’s Choice Award. In partnership with Qanstruct, Aliro transformed a former vehicle parts warehouse into Chobani’s national head office, featuring a fully refurbished 10,986 sqm storage warehouse and a newly constructed 9,500 sqm temperature-controlled facility.
TripleTwoNine Project
The TripleTwoNine project in Caringbah, NSW, underscores Aliro’s ability to refurbish and reposition existing properties. The 27,000sqm warehouse, originally built in the 1980s, was transformed into a prime grade industrial facility with sustainability upgrades, including a 300KW solar array and comprehensive EV charging provisions. This project achieved a 5 Star Green Star Design & As-Built rating and secured major tenants like Australia Post and Woolworths, showcasing Aliro’s commitment to delivering high-quality, sustainable real estate solutions.
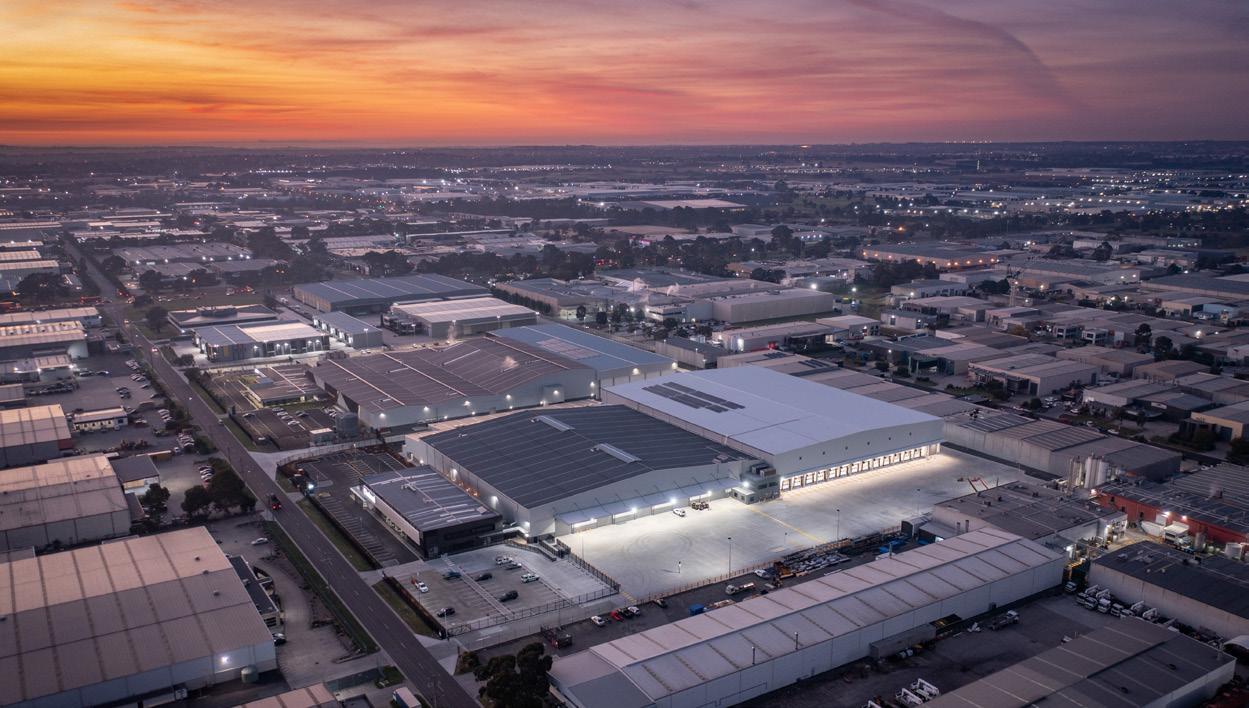
adaptable developments like Somerville Road, which not only deliver operational efficiency but also ensure long-term, responsible growth.”
The shift in industrial real estate extends beyond Somerville Road. As digitalisation and environmental goals reshape the sector, businesses must invest in spaces that evolve with these changes. The Somerville Road
development exemplifies Aliro’s expertise in meeting the evolving demands for flexible, highquality industrial spaces.
To explore how Aliro Group can help your business find future-ready spaces or to learn more about our innovative projects, contact us today. Together, we can shape the logistics solutions of tomorrow.
Industrial & Logistics | For Lease
Warehouse 2, 427-451 Somerville Road, Tottenham
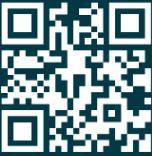
CBRE Asia Pacific, on behalf of Aliro, is excited to exclusively present for lease Warehouse 2, 427-451 Somerville Road, Tottenham. Available from Q2 2025.
Warehouse 2A
+ Total Building Area: 9,455sqm*
+ Warehouse Area: 9,015sqm*
+ Office Area: 440sqm*
+ 10,500* Pallet Capacity
Warehouse 2B
+ Total Building Area: 16,480sqm*
+ Warehouse Area: 15,940sqm*
+ Office Area: 540sqm*
+ 23,320* Pallet Capacity
Key Property Features Include:
+14.6m* high warehouse clearance
+34.5m* super canopies
+Multiple on-grade roller shutters and recessed docks
+8 tonne post load floors

Warehouse 2C
+ Total Building Area: 11,410sqm*
+ Warehouse Area: 10,870sqm*
+ Office Area: 540sqm*
+ 16,150* Pallet Capacity
Warehouse 2D
+ Total Building Area: 13,885sqm*
+ Warehouse Area: 13,345sqm*
+ Office Area: 540sqm*
+ 19,450* Pallet Capacity
+Targeting 5-star Green Star accreditation
+Significant solar array
+Heavy duty hardstand
+Flexibility to combine tenancies into larger sizes
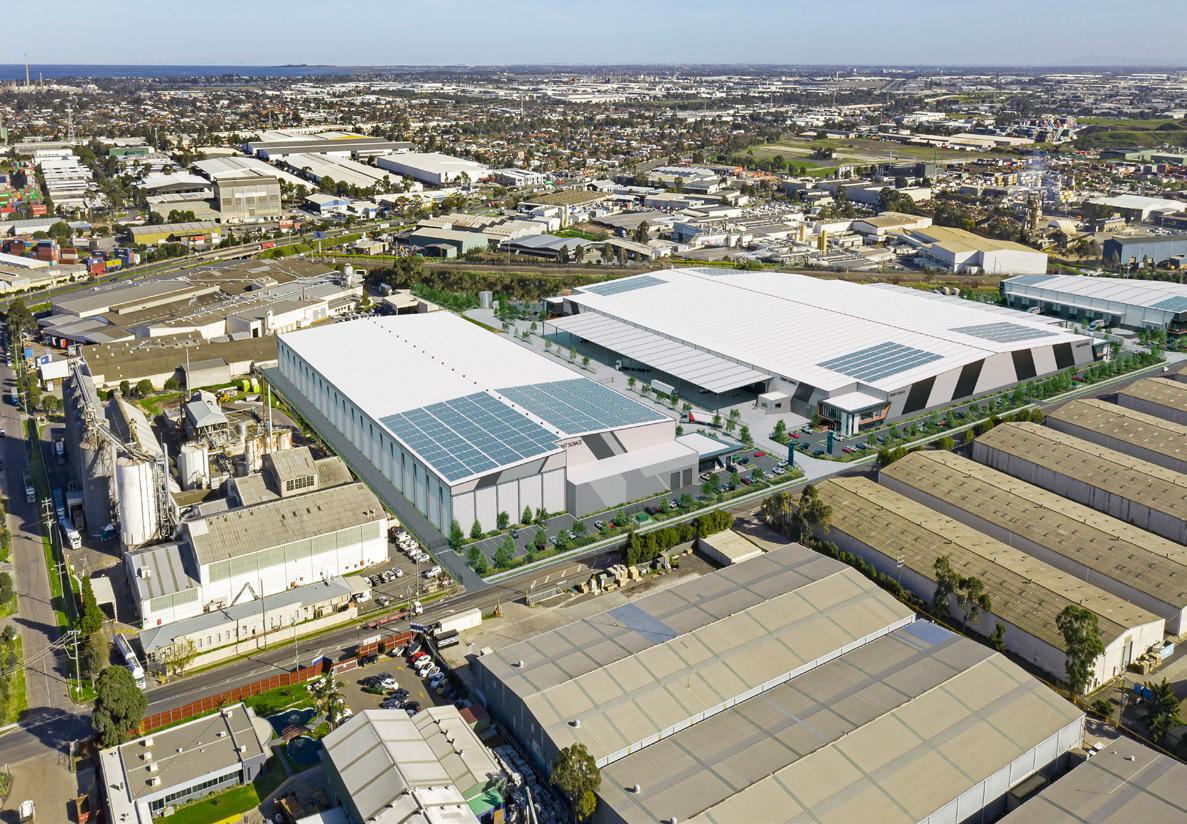
&
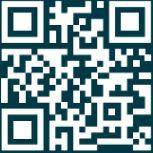
CBRE Asia Pacific, on behalf of Aliro, is excited to exclusively present for lease Cold Store, 427-451 Somerville Road, Tottenham. Available from Q4 2025.
Key Property Features Include:
+Total Building Area: 22,040sqm*
+Warehouse Area: 21,295sqm*
+Office & Staff Amenities Area: 745sqm*
+Cold Store Area: 20,315sqm*
+Four (4) cold storage chambers (-25°C to 4°C), each averaging 3,800sqm*
+12.3m* high clearance warehouse/office facility
+Flexibility to accommodate single or dual users
+Designated separate entry and exit points for cars and trucks
+Targeting 5-star Green Star accreditation
+500kw solar array
+30,000* pallet capacity
+10m* cantilever awning for all-weather loading
+40m* hardstand and 22 recessed docks
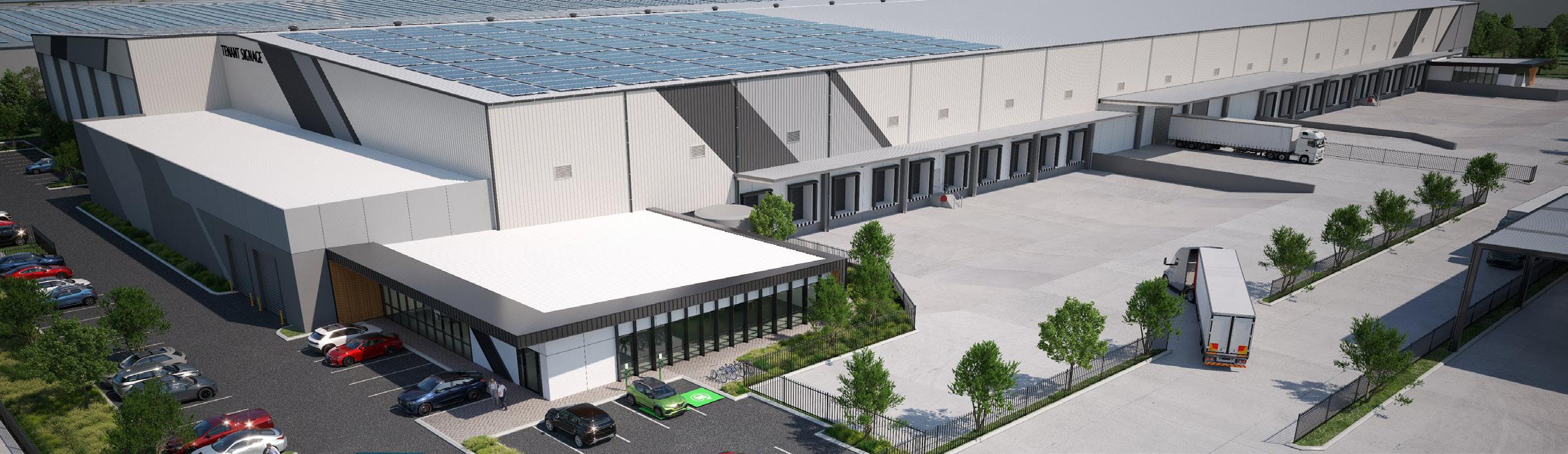
Tom Hayes
Industrial & Logistics
Senior Director
+61 413 997 703
tom.hayes@cbre.com.au
Harry Kalaitzis Industrial & Logistics Senior Director
+61 409 994 419
harry.kalaitzis@cbre.com.au
Tom Murphy
& Logistics State Director
+61 434 414 901
tom.murphy@cbre.com.au
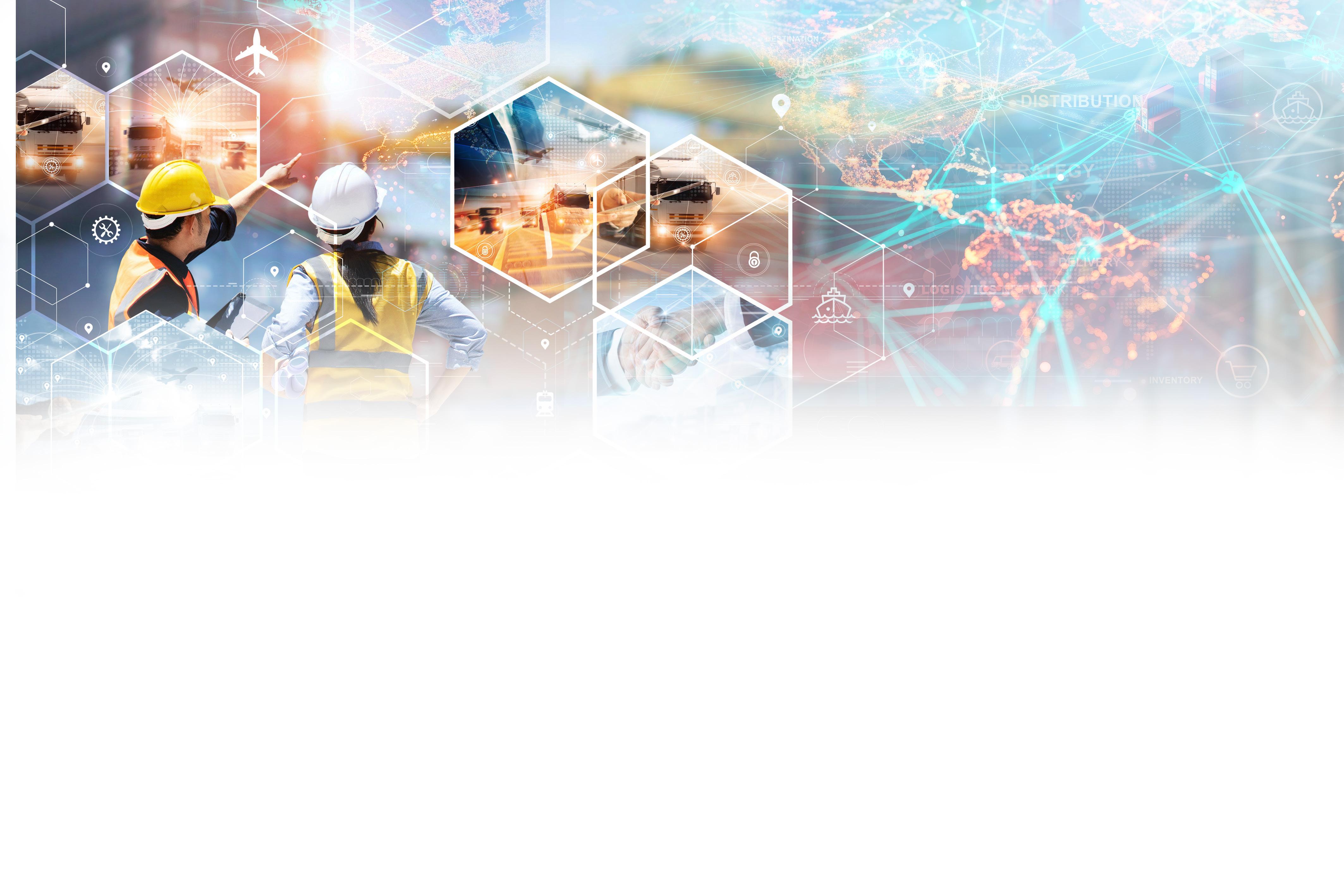
The global resource for supply chain professionals and organisations
Building on the global success of our regional titles – EME Outlook, Africa Outlook, APAC Outlook, and North America Outlook – Outlook Publishing is proud to introduce a digital magazine and web platform, dedicated to the supply chain sector.
As supply chain organisations worldwide confront unprecedented change, embracing technological innovations and incorporating critical environmental sustainability agendas, now more than ever is the time to showcase the strides being taken in this dynamic sector.
A multi-channel brand, Supply Chain Outlook brings you the positive developments driven by organisations across the global supply chain industry through its various platforms. Discover exclusive content distributed through its website, online magazine, social media channels, and dispatches delivered straight to your inbox with a bi-weekly newsletter.
Through this compelling new venture, we foreground the movers and shakers of the industry. To participate as a featured company and join us in this exciting endeavour, contact one of our Project Managers today.
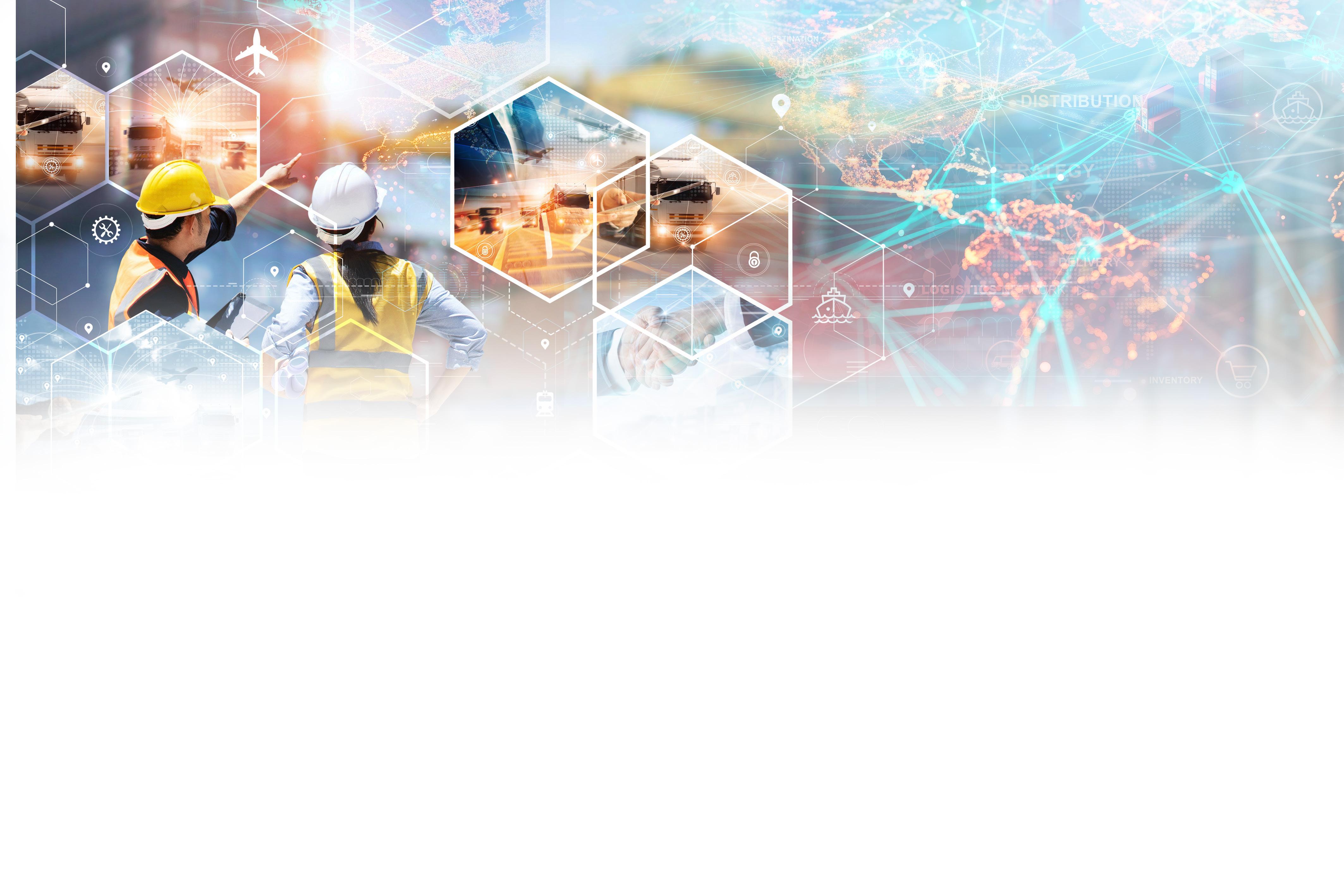
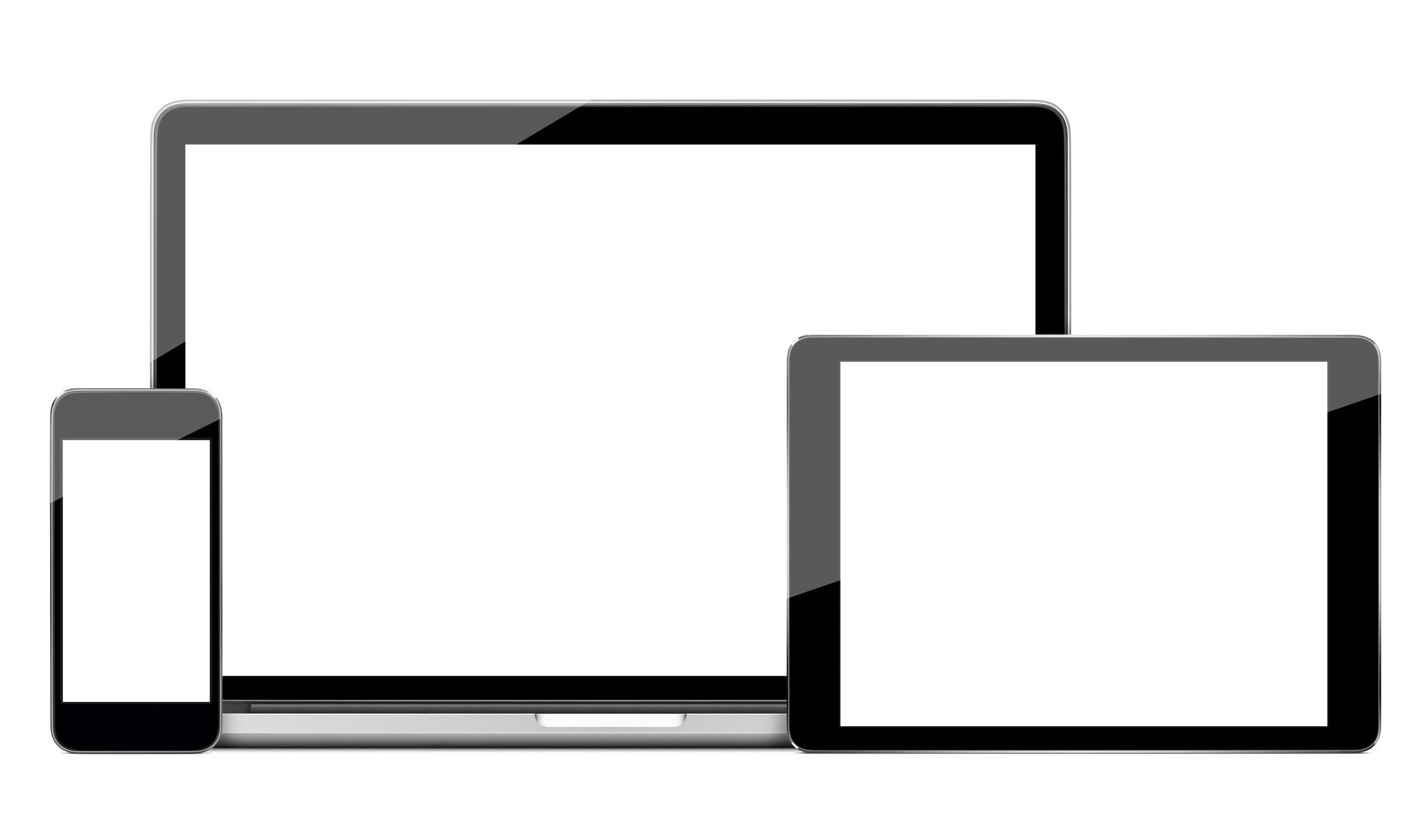
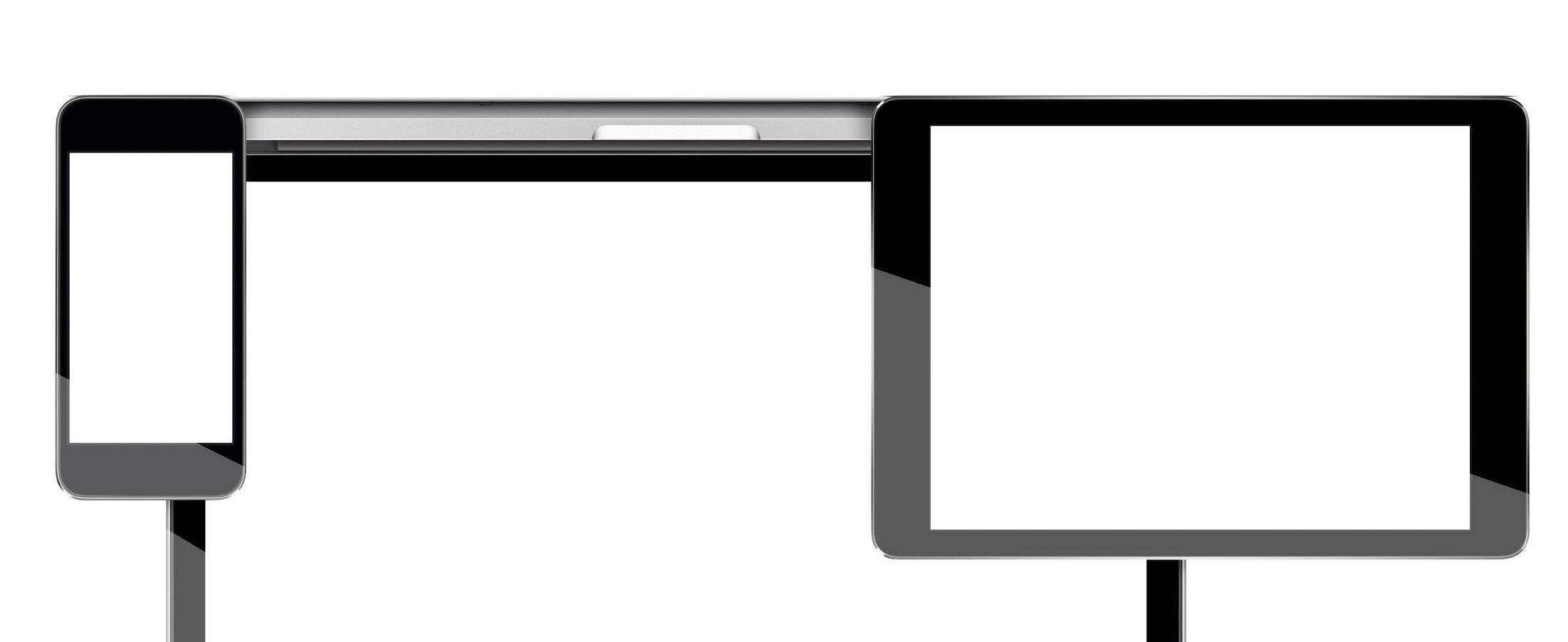
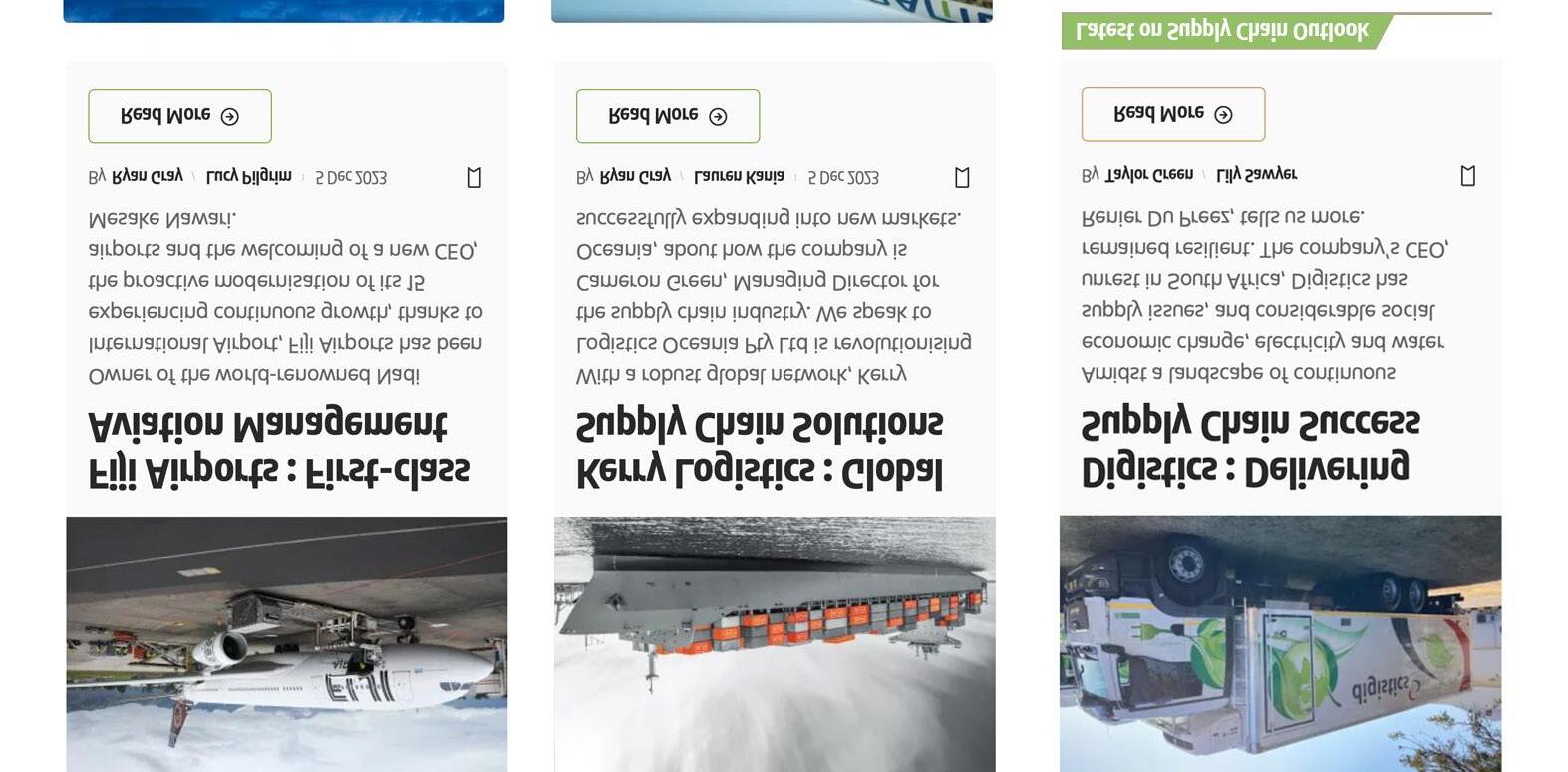

GUINEA’S COMMERCIAL GATEWAY
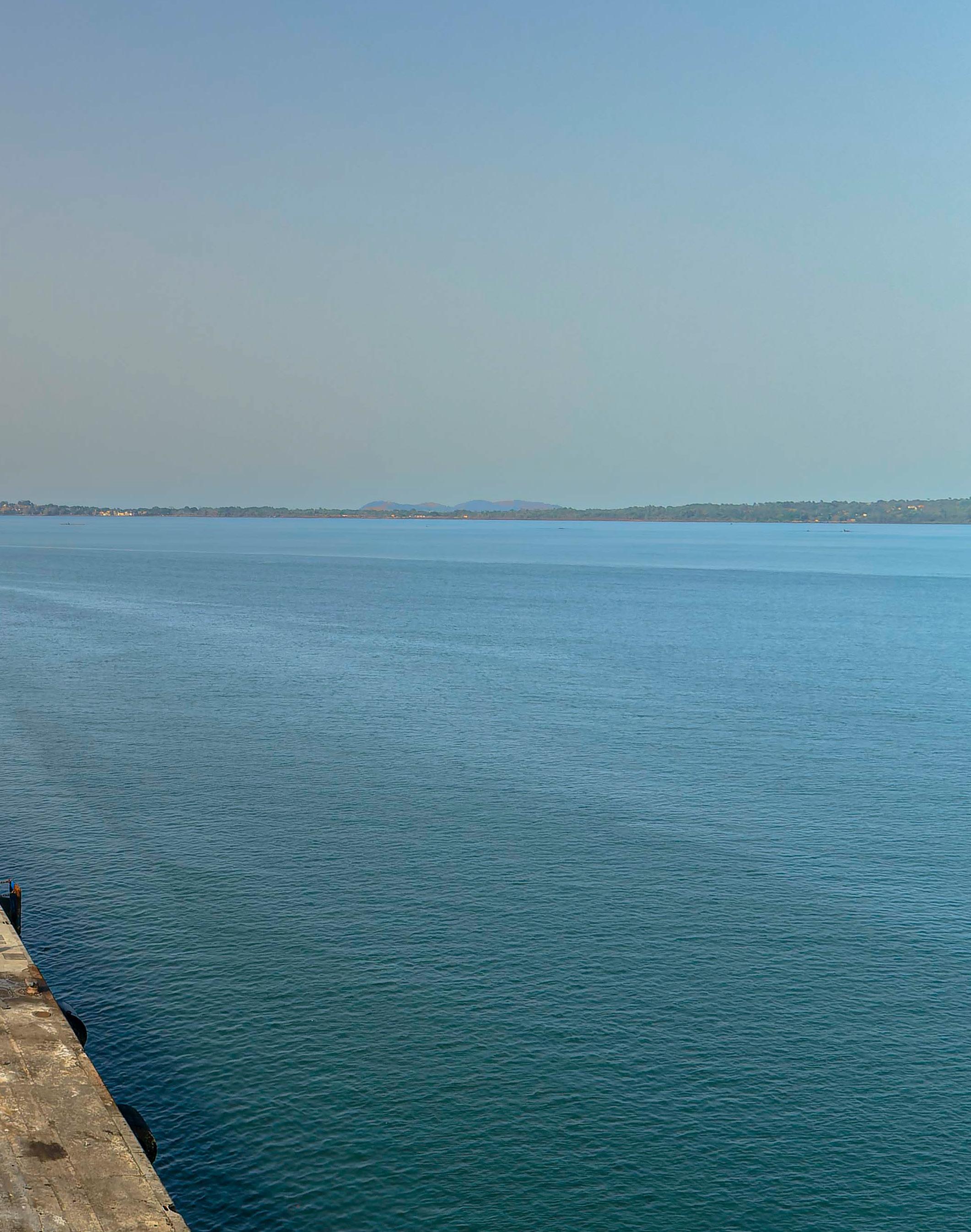
Activities at Guinea’s main commercial port are regulated, monitored, and controlled by the Autonomous Port of Conakry, whose Managing Director, Biro Diallo, discusses its strategic location and investments to improve performance
Writer: Jack Salter | Project Manager: Josh Whiteside
As the primary commercial port in Guinea, the Port of Conakry plays a leading role in the national economy.
90 percent of foreign trade in the West African country is carried out at the port, whose services include handling, towing, mooring, and ship security.
The Port of Conakry comprises four main terminals – container, conventional, hydrocarbon, and mining – in addition to an artisanal fishing port. These terminals are granted to private operators who are responsible for making necessary investments in the development of port infrastructure and equipment.
With 13 berths
ranging from depths of -9 to -13 metres (m) and a basin that can accommodate drafts of -10m at low tide, the port therefore has a diverse client base as it is capable of receiving all types of vessels, including container and roll-on/ roll-off (Ro-Ro) ships carrying goods such as rice, sugar, wheat, oil, cement, bauxite, and alumina.
“The vision of the Port of Conakry is to become a hub in the West African subregion, where the market is very competitive with the presence of several ports in the Gulf of Guinea,” outlines Biro Diallo, Managing Director of the port authority – the Autonomous Port of Conakry (APC).
“We are working to improve the quality of our offerings and infrastructure through major investment,” he adds.
ADVANTAGEOUS LOCATION
Located in the capital and largest city in Guinea, the Port of Conakry’s strategy lies in serving hinterland countries without maritime frontage.
Although competition from its West African neighbours is extensive, the port has a comparative advantage as Conakry is located 974 kilometres (km) from Bamako (Mali), 1,183km from Dakar (Senegal), and 1,747km from Abidjan (Ivory Coast).
“To capitalise on this strategic geographical position, we must carry out a commercial attack on the Malian market, which has enormous potential in terms of importing and exporting food, oil, and cotton products,” Diallo outlines, citing Mali as one of the world’s leading exporters of cotton with 300,000 tonnes (t) harvested every year.

“WE ARE WORKING TO IMPROVE THE QUALITY OF OUR OFFERINGS AND INFRASTRUCTURE THROUGH MAJOR INVESTMENT”
– BIRO DIALLO, MANAGING DIRECTOR, AUTONOMOUS PORT OF CONAKRY
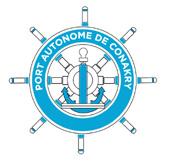
This strategy was materialised with the launch of the first Malian cotton convoy through a commercial protocol, allowing 115,000t of stretch cotton to pass through the Port of Conakry.
“On top of that, we need investments in port, road, and rail infrastructure to reduce administrative, security, and customs processes on the Conakry-Bamako corridor,” adds Diallo.
In terms of sustainable solutions, the Port of Conakry is also expanding
its storage capacity for goods to 500,000 20-foot equivalent units (TEUs) by the end of the decade, which will increase the port’s Malian market share.
INVESTING IN PERFORMANCE
Such investments are key to the success of the Port of Conakry, whose container terminal was also granted €500 million of funding in 2011 by French conglomerate, Bolloré.
This has allowed the port to
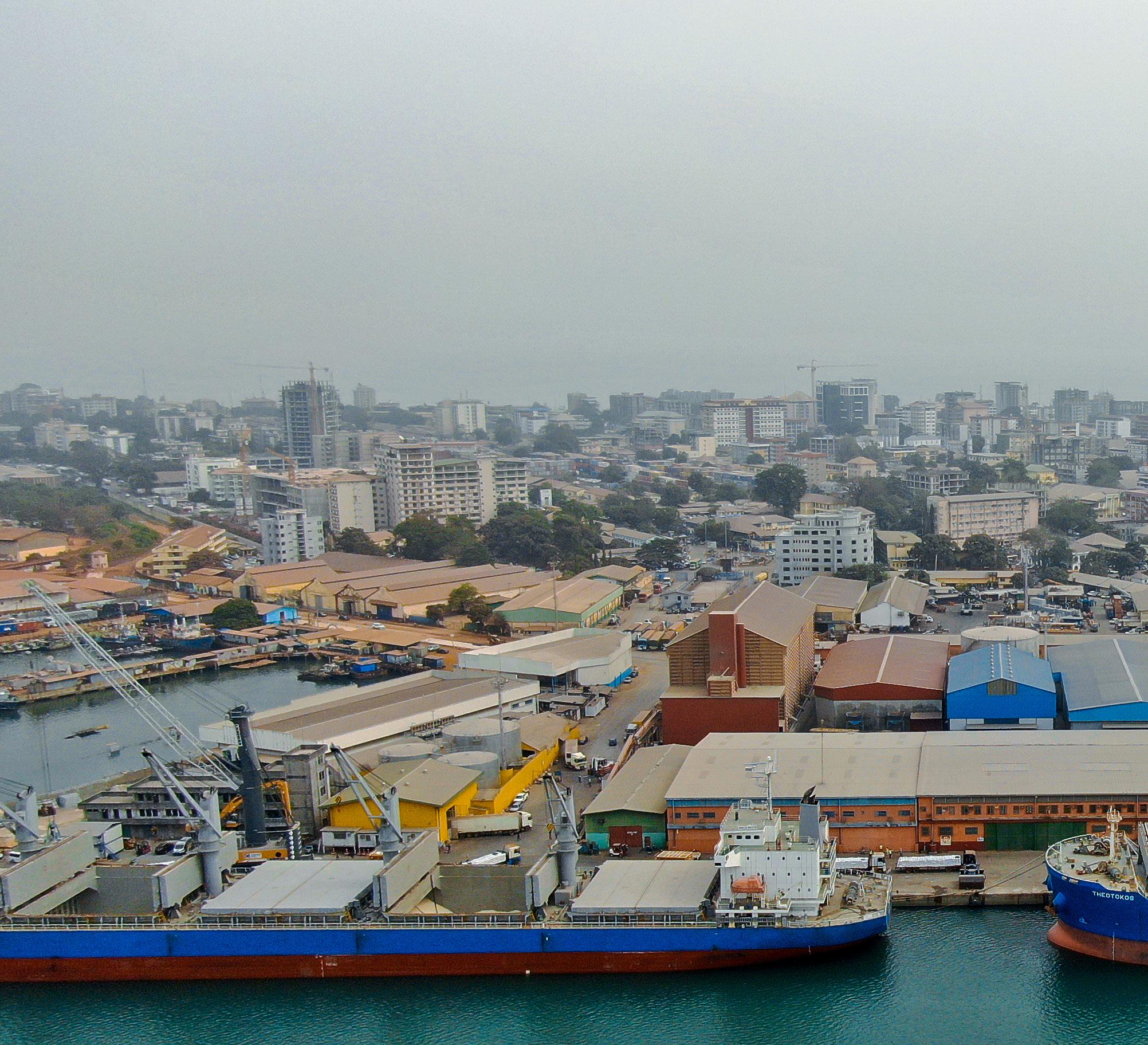
acquire 12 rubber-tyred gantries (RTGs) as well as two quay gantries on rails, increasing the capacity for handling goods to a rate of 60 containers per hour.
The investment has also been put towards rehabilitating a 270m quay, constructing a 340m linear quay built to depths of -13m, and developing 24,000 square metres (sqm) of land to increase the Port of Conakry’s storage capacity.
“These investments have improved the performance of the port in terms
of loading and unloading rates,” Diallo acclaims.
A six-hectare extension of the western zone of the Port of Conakry has also increased port traffic and congestion at the container terminal.
Elsewhere, structuring projects are underway at the conventional terminal, managed by Turkish multinational conglomerate, the Albayrak Group, who granted USD$500 million of investment into the Port of Conakry in 2018.
The works being carried out concern public lighting, the development and construction of quays and open land, acquisition of two cranes with a capacity of 120t, and construction of a 4.2km penetrating road and parking lot for 1,200 trucks and related services.
“These large-scale projects are likely to improve our attractiveness and service offering to port users in order to make the Port of Conakry a competitive port in the subregion,” states Diallo.
SUPPLY CHAIN OUTLOOK: WHY IS THE INDUSTRY BOOMING IN GUINEA?
Biro Diallo, Managing Director: “The industry in Guinea has been booming for a decade thanks to registered foreign direct investment (FDI). Labour is very affordable, security and justice conditions are met to reassure investors in order to provide capital, and investment and tax laws are competitive and responsive to investor needs.

“A favourable business climate is guaranteed by an investment code that reassures and secures investments. Thanks to all these efforts, Guinea earns points every year in the World Bank’s Ease of Doing Business rankings.
“The incentive reforms of the Guinean authorities are also likely to protect public assets through good governance and the fight against corruption.”
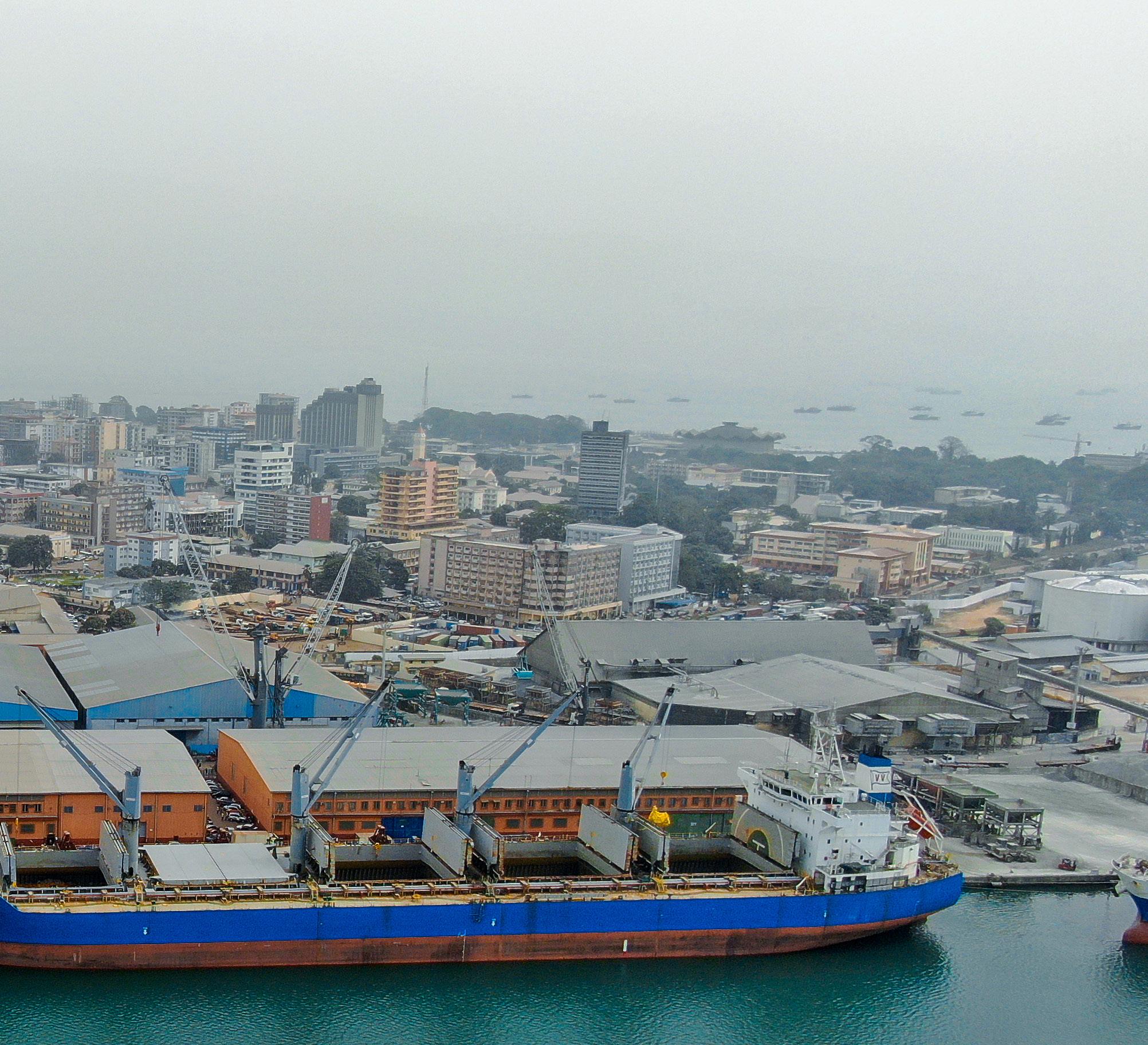
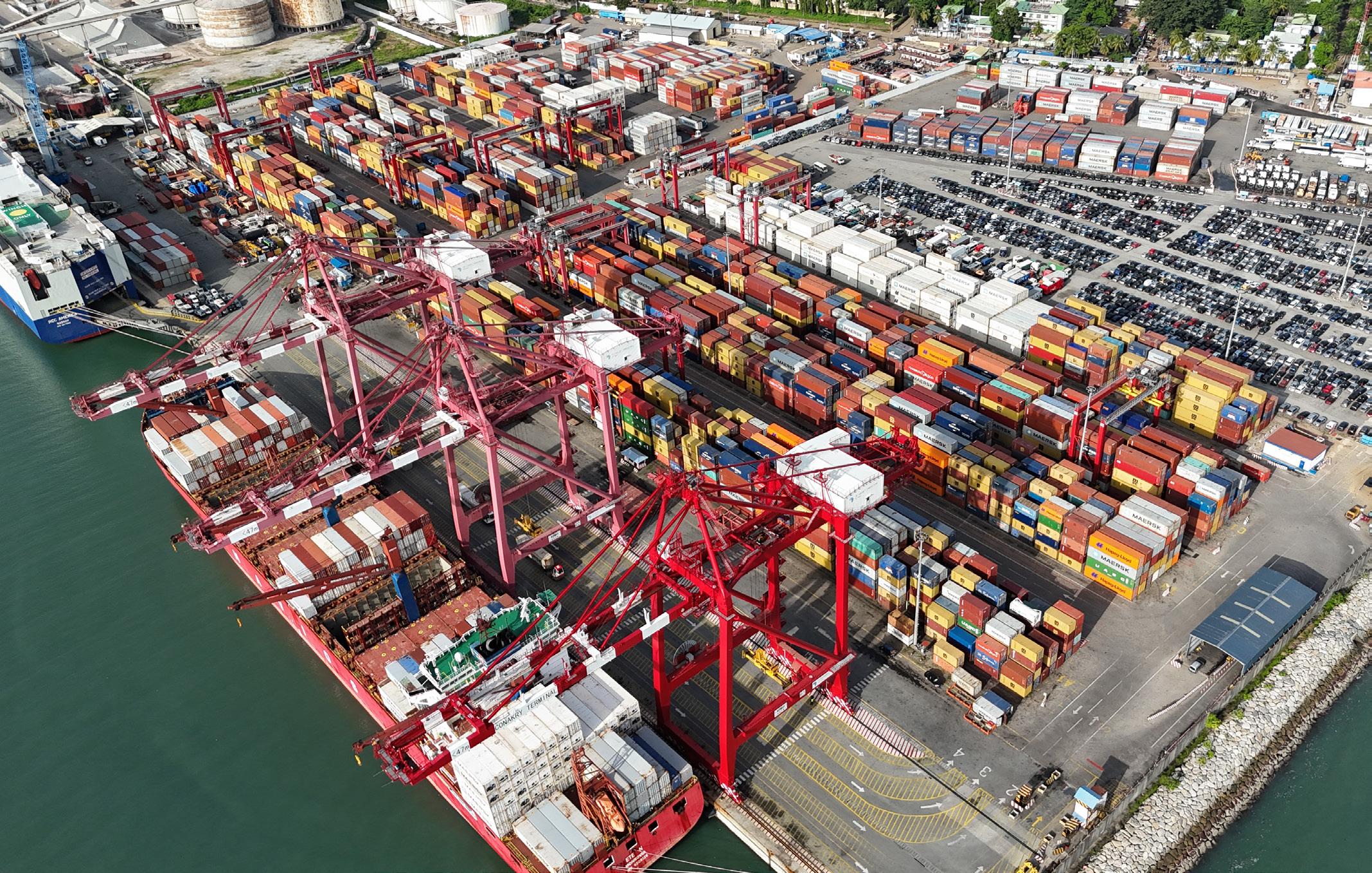
Africa Global Logistics: At the Heart of Local Economic Development in Guinea
The subsidiaries of the Africa Global Logistics (AGL) group in Guinea are important players in the provision of logistics, transport, and transit solutions in the country.
With more than 800 employees, 99 percent of whom are nationals, the company’s staff base is spread across strategic sites such as Conakry, Kamsar, and Moribaya. AGL Guinea’s Conakry Terminal, in particular, contributes to socioeconomic development by investing in the training and supervision of its local teams.
The project is part of a societal policy aimed at supporting the Guinean populations through solidarity initiatives and local development. Alongside its commitments to local content, AGL Guinea promotes the transfer of skills and creates sustainable jobs for the nation’s populations. As an organisation, AGL’s initiative in Guinea is based around the idea that the development of the local economic fabric is essential to guaranteeing longterm growth.
One of the most notable aspects of this commitment is the recent creation of a joint venture (JV) between AGL Guinea and a national transport company, which combines the in-depth expertise of the country’s transport sector with organisational solidity, making it possible to modernise and improve the efficiency of goods transportation.
Approximately 200 jobs have been created for young Guineans, serving an initial fleet of more than 60 trucks. This JV allows its clients to benefit from AGL’s international expertise and the recognised local skills of its partner to meet the needs of an increasingly demanding Guinean market.
Thanks to this successful partnership, AGL Guinea will actively involve local players in major logistics operations across key sectors such as mining, agriculture, and industry, whilst also stimulating a transport offering that takes into account the requirements of international investors.
The JV marks a new path that enriches Guinea’s logistics sector whilst also ensuring that the wealth generated remains in the national economy.

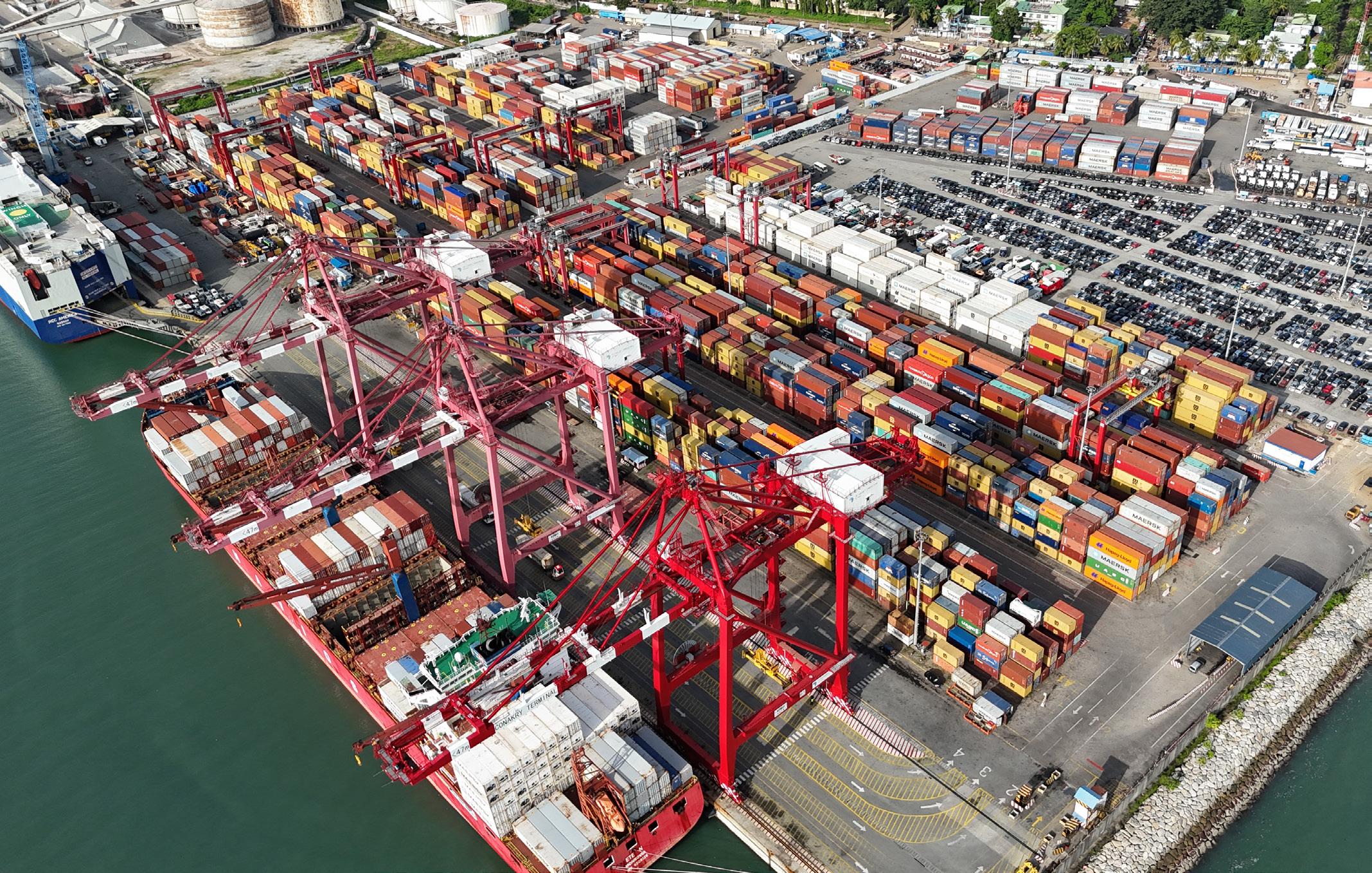
The Kagbelen Dry Port: Logistics Centre of
Excellence for Major Mining Projects
The Kagbelen dry port presents itself as a key element for strengthening Guinea’s logistics infrastructure, particularly for the industrial and mining sectors. The Kagbelen site asserts itself as a major strategic project for the economic development of Guinea, playing an essential role in expanding the country’s logistical capacities whilst increasing the efficiency of trade.
To better understand this project, we discussed with Emmanuel Masson, General Director of Conakry Terminal, a few points on Kagbelen dry port and the impact it is having on major projects.
Firstly, please could you provide a brief overview of the Kagbelen dry port.
Emmanuel Masson, General Manager of Conakry Terminal (EM): The Kagbelen dry port is an extension of the container and vehicle operations at Conakry Terminal.
Located approximately 35 kilometres from the terminal, the Kagbelen dry port operators have the opportunity to pick up or drop off their containers without having to go to the seaport, benefitting from temporary storage at a low cost. This system aims to relieve congestion at Conakry Terminal while improving the efficiency of trade and logistics activities.
Who are the target audience for the services offered by the Kagbelen dry port and what impact can it have on major projects?
EM: Dry port services are mainly intended for the mining industries, which represent a key sector of
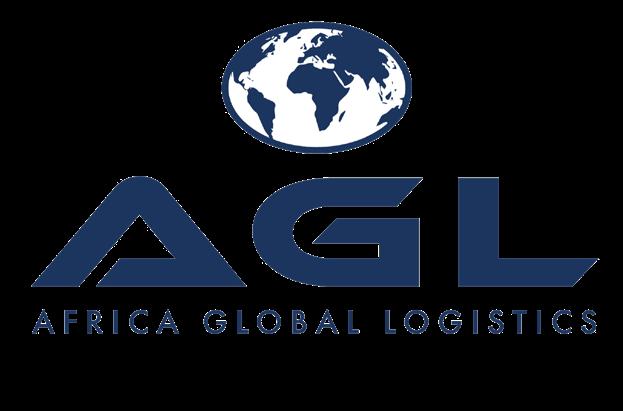
the Guinean economy, as well as companies located in the Kagbelen industrial zone. The dry port therefore makes it possible to store and manage the flow of goods, reducing pressure on the Conakry Terminal whilst facilitating transport to mining areas within the nation and other inland countries.
As key logistical support for large mining projects, the Kagbelen dry port is designed with suitable infrastructure, such as dedicated spaces for storing containers and mining equipment. Its proximity to the country’s main roads allows for the rapid movement of goods between Conakry Terminal and the mining sites, thus contributing to the competitiveness of exporting companies and the modernisation of Guinea’s infrastructure.
What does the Kagbelen dry port represent to you?
EM: The development of the Kagbelen dry port illustrates a strong commitment to optimising logistics infrastructure and supporting major economic projects in Guinea, with direct benefits for the national economy. Thanks to its vast facilities, the dry port also allows the storage and management of goods flow, thus reducing the pressure exerted on the Conakry Terminal and facilitating operations for economic operators.

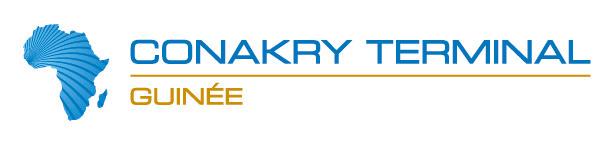
Conakry Terminal: From Performance to Economic Growth
The container terminal of the autonomous Conakry Terminal plays a crucial role in the economic transformation of Guinea, strengthening its position as a crossroads of trade in West Africa.
Thanks to major investments made by the subsidiary of AGL, the capacity and efficiency of the terminal have seen notable progress. With the extension of the quays and the acquisition of modern equipment, the Conakry Terminal is now capable of accommodating larger ships, thus increasing the competitiveness of the port on a regional scale.
The project investments are being continued to deploy a second extension of the terminal, currently being implemented, which will double its reception capacity.
This project is about preparing for the future, and the figures speak for themselves: from 269 stopovers recorded, 286,286 twenty-foot equivalent units (TEUs) were handled and 30,681 vehicles unloaded in 2023. We hope to reach 345,000 TEUs and 35,000 vehicles by the end of 2024.
Conakry Terminal is also pursuing an Operational Excellence programme that aims to optimise the management of goods flows both for the benefit of international shipowners and national and regional economic operators. This improvement in performance translates into increased fluidity of

commercial exchanges, as well as a reduction in waiting times for stranded ships. The programme will also increase the port’s attractiveness to the world’s largest shipowners, who have strengthened their service to Conakry Terminal.
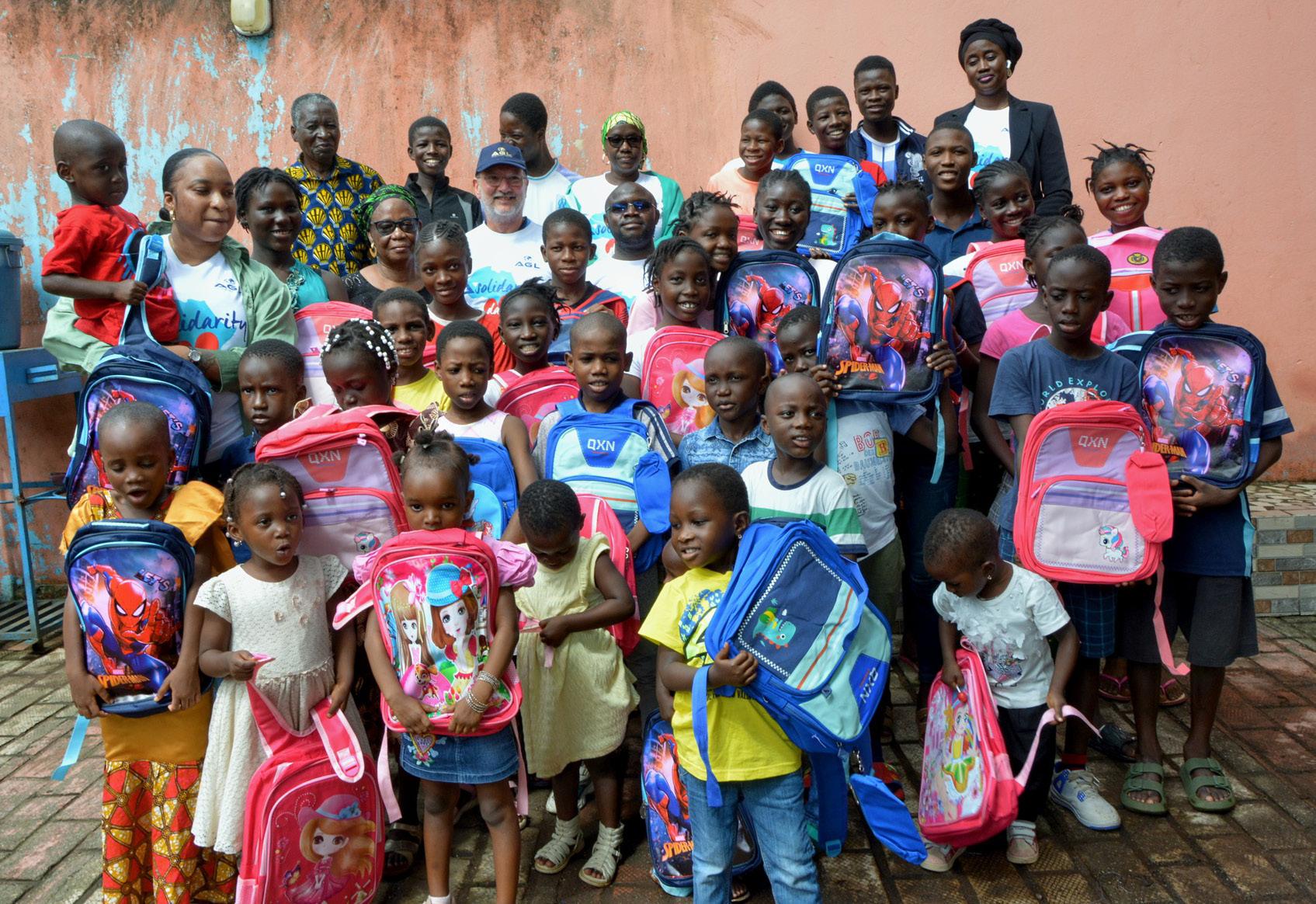
Ultimately, this allows Guinea to benefit from world-class maritime services.
The Conakry Terminal not only serves the country, but also plays a crucial role in regional connectivity, facilitating trade with landlocked countries like Mali and Burkina Faso. This regional dynamic stimulates foreign direct investment, attracted by the efficiency of the port’s infrastructure.
In addition, the development of the terminal has a significant impact on the local

economy, particularly in terms of job creation across logistics, transport, and handling, thus contributing to the reduction of unemployment and economic development in the country.
AGL: Leaders in the Field of Logistics and Transport in Guinea
Present in Guinea since the 1990s, AGL Guinea is an essential pillar of the logistics sector that offers a range of strategic services to support the country’s trade and economic development.
Its integrated services, which cover multimodal transport (maritime, land and air), customs and administrative solutions, port logistics, as well as supply chain management, enable the company to effectively facilitate trade, both at the national and hinterland level.
With a strong commitment to sustainable development, AGL Guinea places innovation and social responsibility at the heart of its mission. Its corporate social responsibility (CSR) programme
aims to strengthen social inclusion in the country by investing in the training of local talents and implementing environmentally-friendly practices. This includes adopting green technologies and promoting multimodal transportation to reduce the company’s ecological footprint.
By supporting the creation of efficient transport corridors and participating in key infrastructure projects, such as the development of ports and rail networks, AGL actively contributes to the improvement of logistics infrastructure in Guinea.
Thanks to its expertise, the company positions itself as a key player in meeting the varied logistics needs of its customers and partners, while promoting sustainable economic growth in Guinea.
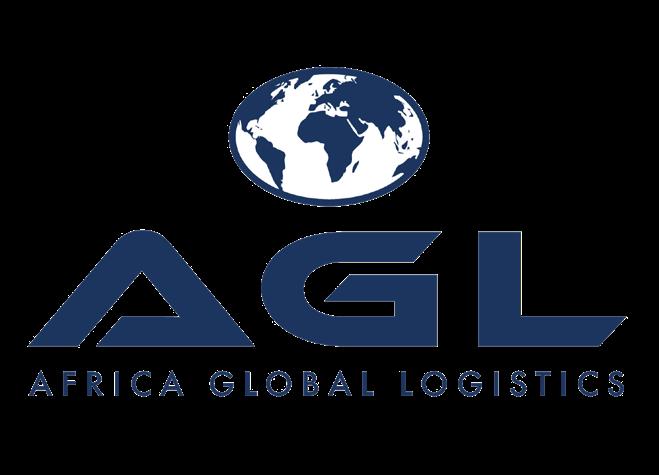
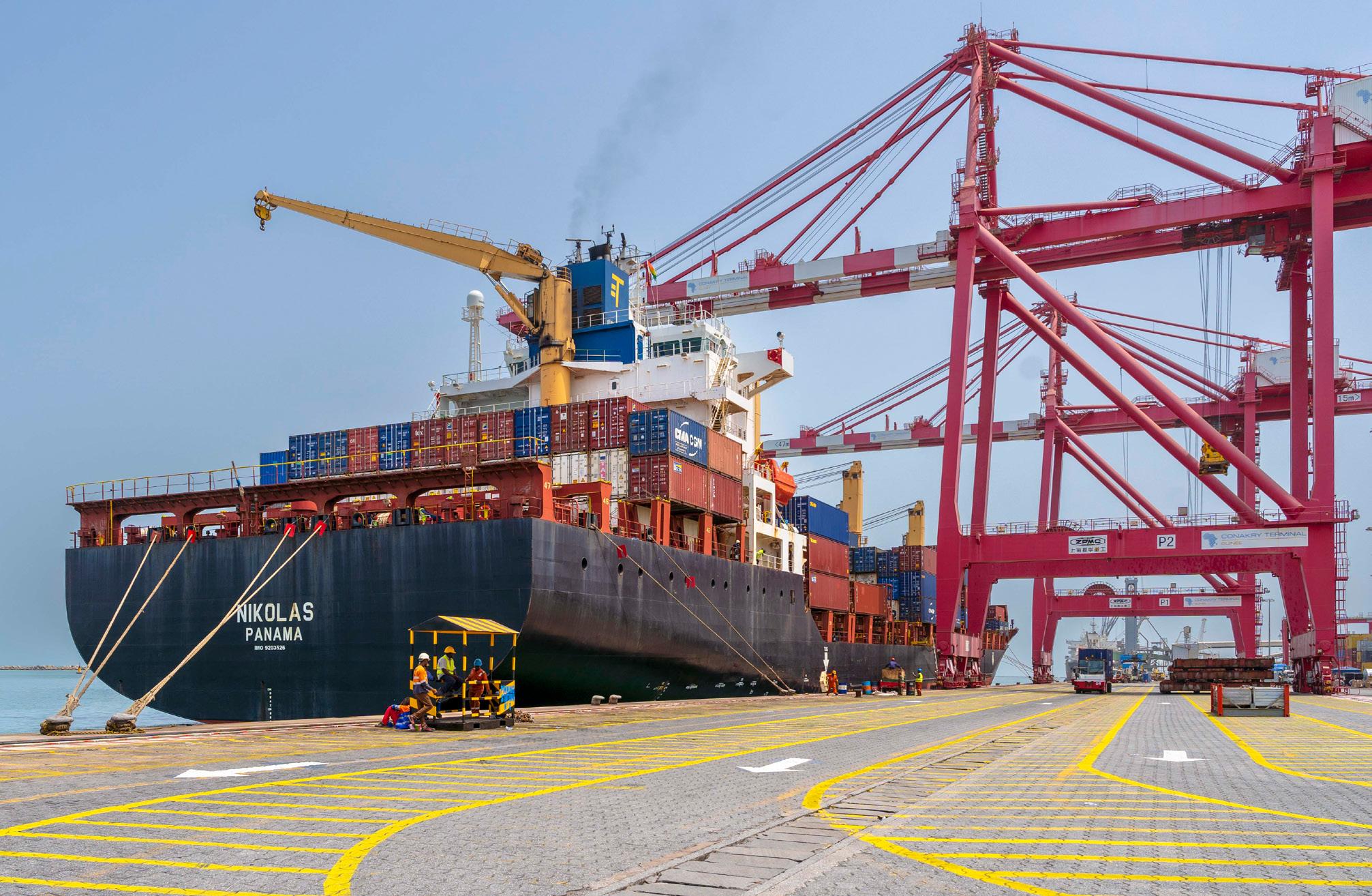
SUPPLY CHAIN OUTLOOK: HOW DID YOU BECOME INVOLVED IN THE SUPPLY CHAIN SECTOR?
Biro Diallo, Managing Director: “Before taking up my highly strategic position in Guinea’s maritime and port industry, I spent most of my career in mining and quarrying.
“My career started as a civil engineer on construction projects at Laing O’Rourke. I then found myself as Director of Mine Infrastructure at Rio Tinto Iron Ore, where I worked on the pre-feasibility and feasibility phases of the Simandou project, the largest iron deposit in the world.
“After climbing through the ranks as Director of Operations in Guinea, I was promoted to Country Director of Rio Tinto Simfer, before benefitting from the confidence of the interim President of Guinea, Mamady Doumbouya, to assume the duties of Managing Director of APC on 14th December 2021.
“I had the passion to evolve in the public sector after a great experience in the private sector. My goal was to impact the lives of disadvantaged populations and classes, and I think I made the right choice because I feel very fulfilled.”
A PLATFORM FOR PEOPLE
The Port of Conakry constitutes a “real social absorption platform,” according to Diallo, directly employing 6,000 members of staff as well as creating 15,000 indirect jobs. APC, which Diallo is responsible for leading, has 310 employees – including 164 women – with executives in various specialities such as engineers, lawyers, economists, graphic designers, and security agents.
“As soon as I took office, I initiated institutional reforms to create emulation amongst personnel and define a regulatory framework for the attributions of each workstation,” he tells us.
“The appointment criteria are competence, team spirit, and commitment. I opt for participatory management and give more responsibility to my employees for collegial management.”
Since taking office, Diallo has met
highly motivated employees who are determined to support his initiatives and contribute significantly to the outcomes obtained by the Port of Conakry.
Along with its staff, reforms that allow the port to operate 24/7 have been a catalyst for several of its recorded results.
“This has created a synergy of action across all actors, including the Port of Conakry, police, gendarmerie, customs, and even the union of carriers.
“I dare to hope that we will stay the course of reforms for the prosperity of Guinea,” concludes Diallo.
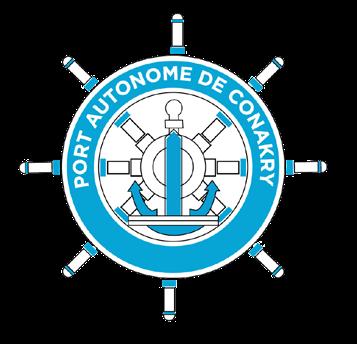
Tel: +224 626 06 08 55 info@portconakry.com www.portconakry.com
System First assists companies and partners to achieve their international market goals.
A multi-sector company for a global partnership. System First is your trusted partner for engineering solutions, and services in the fields of IT, telecommunications and digital.
Why choose System First?
• ENGINEERING COMPUTER SCIENCE
• TELECOMMUNICATIONS
• SERVICES FOR TRANSPORT COMPANIES
• DIGITALISATION
• SETTING UP AND FINANCING PROJECTS
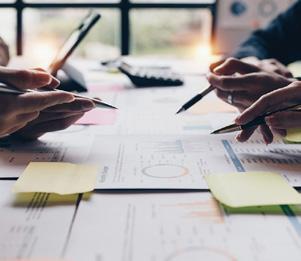
+44 7597 490249
info@systemfirst.world www.systemfirst.world
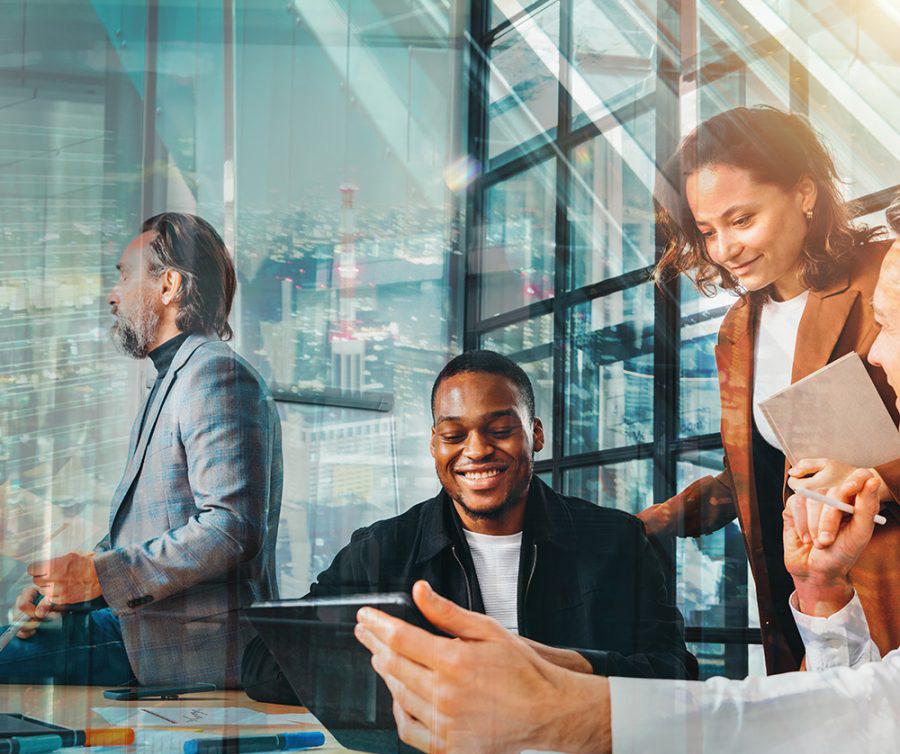
THE OCEAN CARRIER OF CHOICE
Kathleen DePrizio, Director of Marine and Terminal Operations at HMM America, tells us how the shipping agency has achieved its leading position at the forefront of the global maritime industry with a focus on innovation, expansion, and sustainability
Writer: Lucy Pilgrim
Project Manager: Poppi Burke
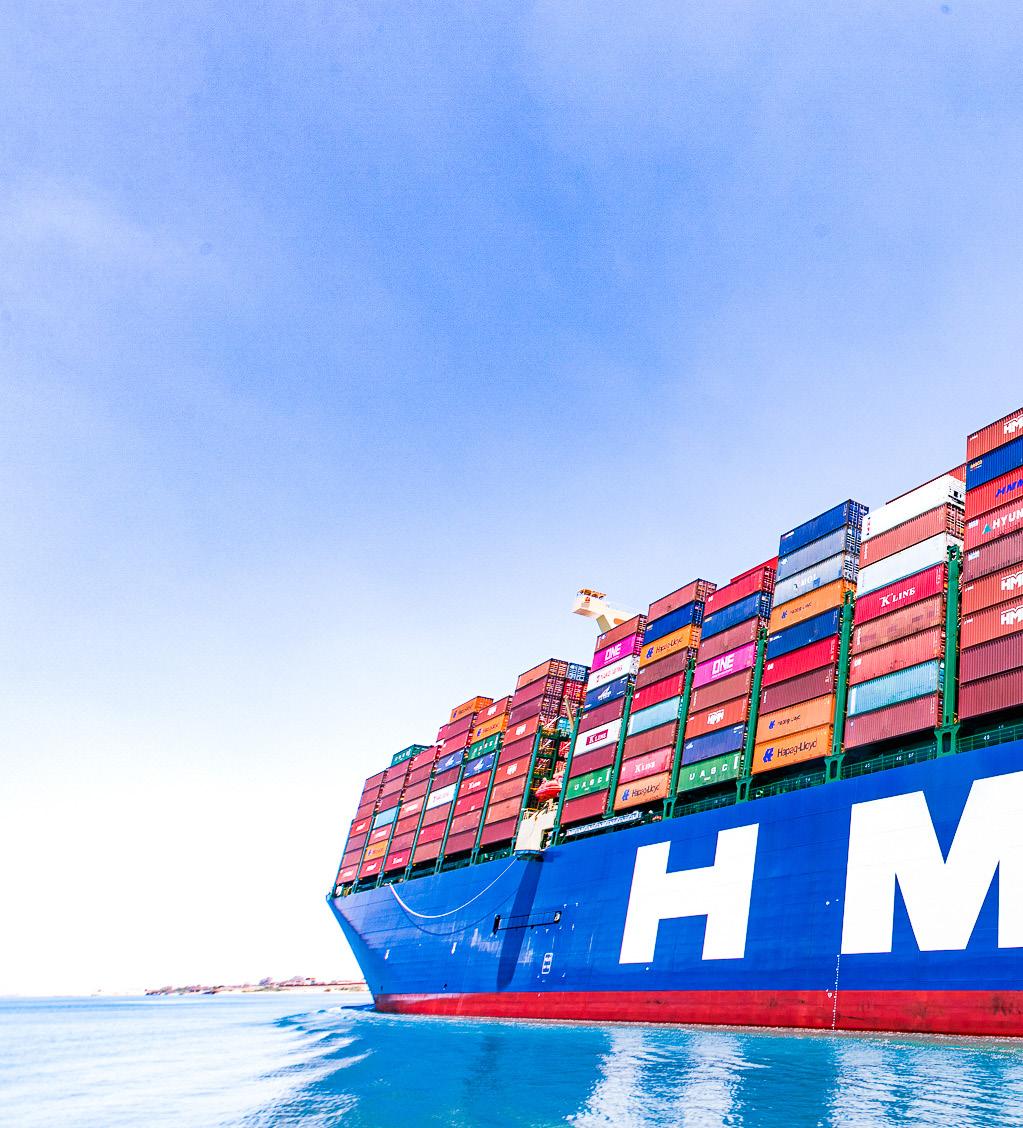
Apassion for marine shipping and transportation is an integral trait for those entering the field, which is currently under considerable strain across North America.
Kathleen DePrizio, Director of Marine and Terminal Operations at HMM America, has been in the industry for over three decades, not to mention the fact that she is the only woman in the world to hold such a role at this
time and only the second woman to ever hold this position for a carrier.
Evidently, DePrizio’s determination has carried her forward in the transportation and logistics sector from a young age.
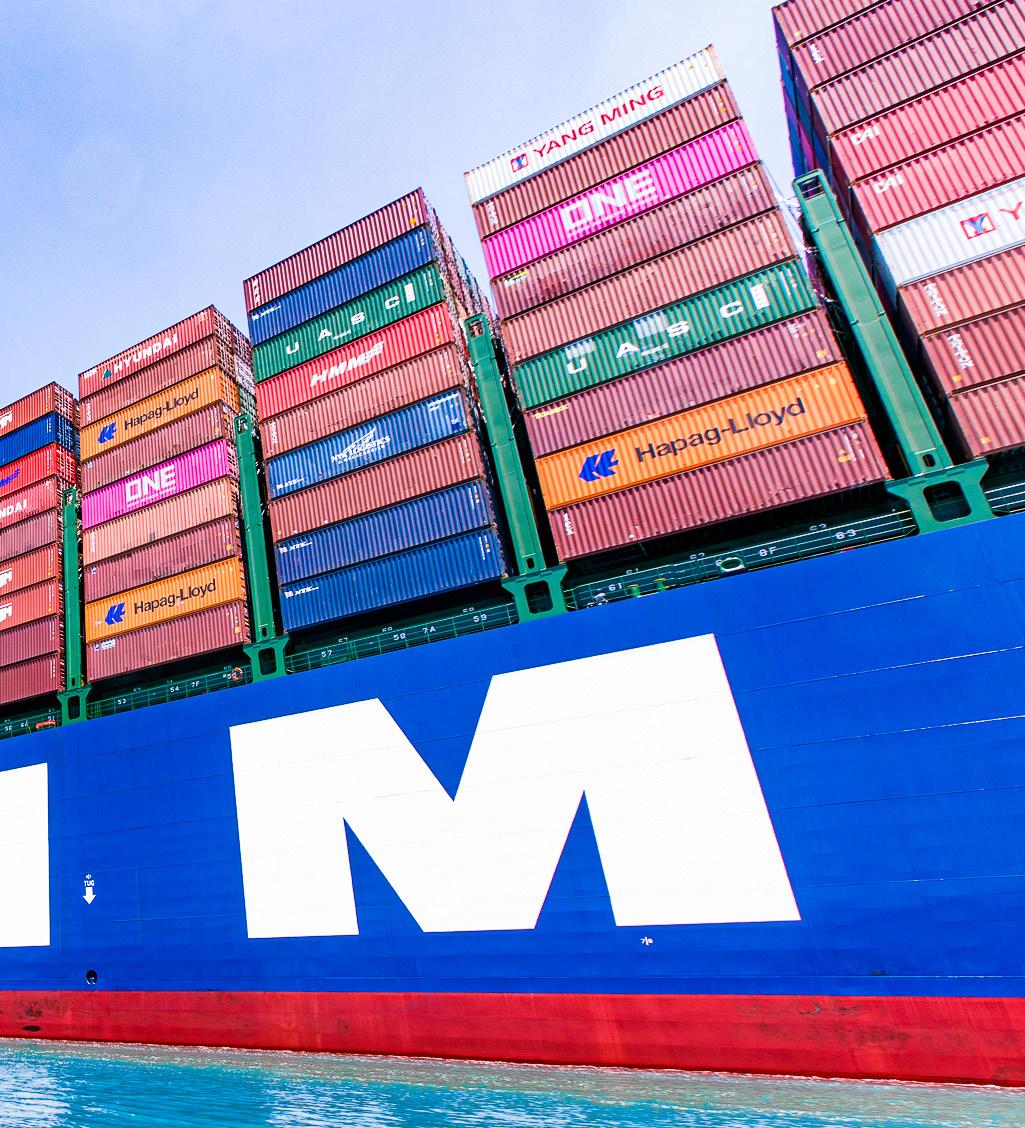
“The beginning of my career was a little different to others in the business. I was still in high school at the time and working at a gas station, but I knew I wanted something better,” she opens.
At the age of 16, she started working after school at a trucking company and went full-time following her graduation and various office administration roles, before moving on to work with a non-vessel
operating common carrier (NVOCC) in its warehouse office. While in these two positions, she found a true love for the logistics industry.
“It was exciting and there was always something happening.
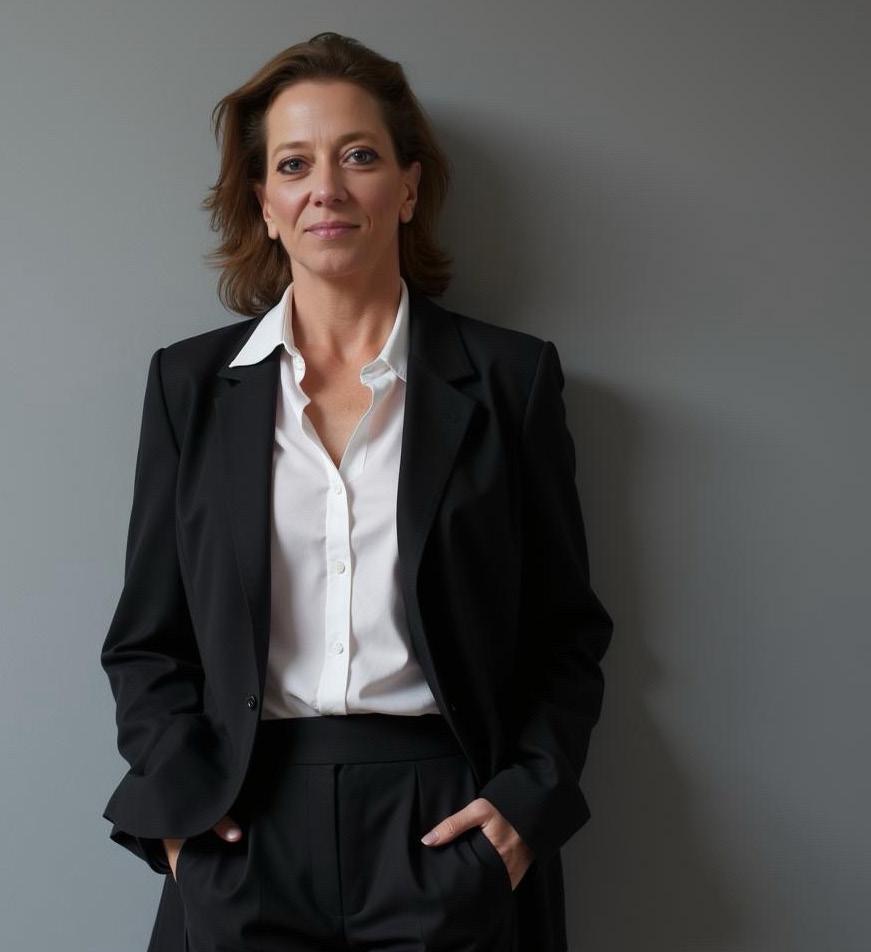
SUPPLY CHAIN OUTLOOK:
HOW DO YOU EMPOWER YOUR STAFF AND RECOGNIZE THEIR
CONTRIBUTIONS?
Kathleen DePrizio, Director of Marine and Terminal Operations:
“Our team is incredibly diverse, encompassing roles such as port captains, vessel planners, schedulers, and compliance staff. Collectively, my departments bring over 330 years of experience to the table – expertise that is essential for driving the company forward.
“Empowering our employees is non-negotiable. We hire skilled individuals for specific roles, provide thorough training, and then trust them to excel in their responsibilities every single day. Along the way, we emphasize continuous learning and professional growth, while reinforcing that safety is our top priority as an ocean carrier.
“We also make it a point to engage with and support our employees, because without their dedication and hard work, the company simply couldn’t function.”
“THE PEOPLE ARE WHAT DRIVE THIS BUSINESS TO GREATNESS EVERY DAY, AS IT IS, QUITE LITERALLY, WHAT MAKES THE WORLD MOVE”
– KATHLEEN DEPRIZIO, DIRECTOR OF MARINE AND TERMINAL OPERATIONS, HMM AMERICA
SMART SHIPPING EXPERIENCE
HMM America is a shipping agency based in Irving, Texas that operates on behalf of parent company, HMM, and oversees marine, terminal, compliance, equipment, maintenance and repair, and intermodal operations, alongside other sales and service coordination activities.
You can also learn a lot of things by talking to the people, which is one of my favourite parts of the role.”
DePrizio has subsequently had a varied career, working in freight forwarding before experiencing myriad roles with numerous ocean carriers, where her enthusiasm for the sector was ignited.
“It was a whole new world. Ports, terminals, rail roads, truckers – all of it was exciting,” she proclaims.
DePrizio was able to visit a variety of ports and terminals while working with ship captains and crews.
After being relocated to the east coast of the US, she began developing relationships with the commercial and operational teams conducting port and vessel tours.
“I got to go on ships when they were in the port, travel, and attend conferences to learn everything I could about this business, build relationships, and just thrive!”
Therefore, when the opportunity arose to take on the role of Director of Marine and Terminal Operations at HMM America, working to grow relationships with major ports and terminals across the US and Canada, DePrizio could not pass up the chance.
“I would not hold this position without the help of those that I respect and cherish. The people are what drive this business to greatness every day, as it is, quite literally, what makes the world move,” she shares.
The company offers state-of-theart ocean services across East-West and Trans-Pacific global trade routes, spanning from the US, Canada, Mexico, and South America to Asia, the Far East, and India.
“We work with almost every port and terminal in the Western Hemisphere, roughly 20 to 40 of which are in North America alone,” DePrizio points out.
HMM America’s enviable geographical presence makes it the world’s eighth largest global carrier, achieved by consistently putting the customer first and combining technology and expertise to create the ultimate smart shipping experience.
HMM America actively responds to its customers’ needs with a wide

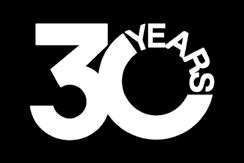
LEADING OPERATOR PORT
Experience a new era in port logistics As the leading container terminal in Mexico, we respond quickly to the changing needs of the global market, delivering exceptional quality, efficiency, and safety
Our commitment to sustainability drives us to uphold the highest environmental standards, making us your trusted partner for reliable and responsible port operations


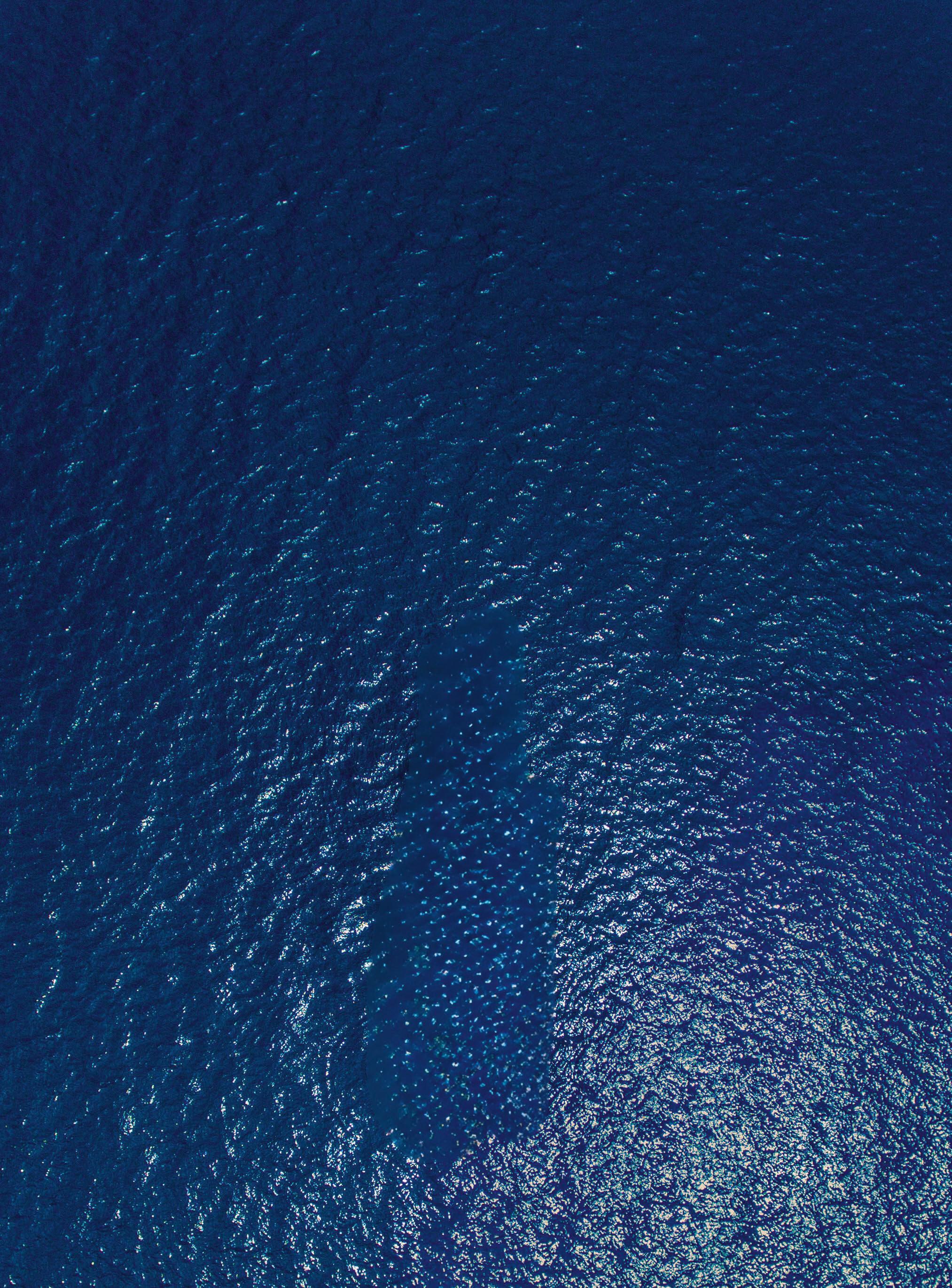
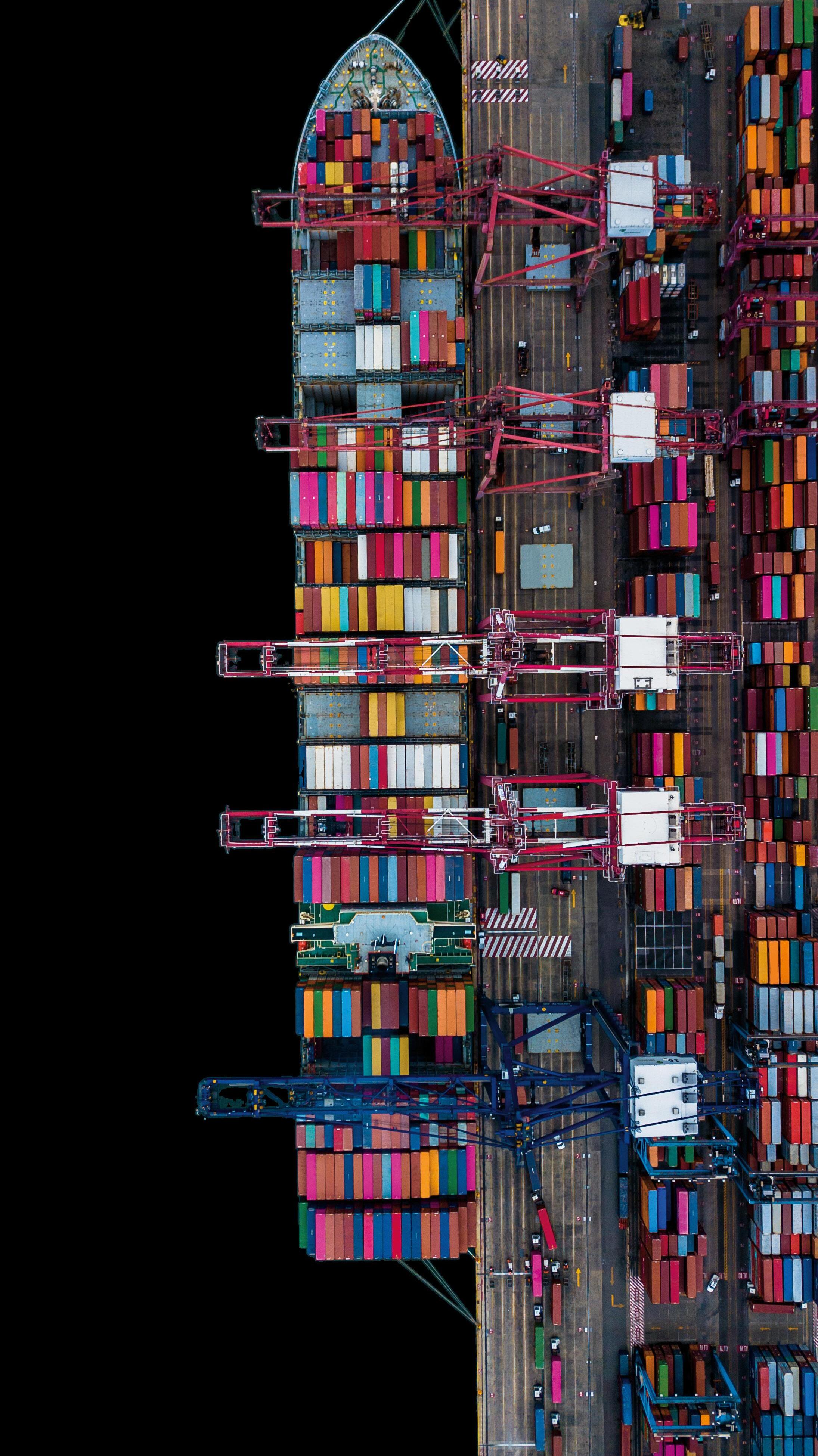
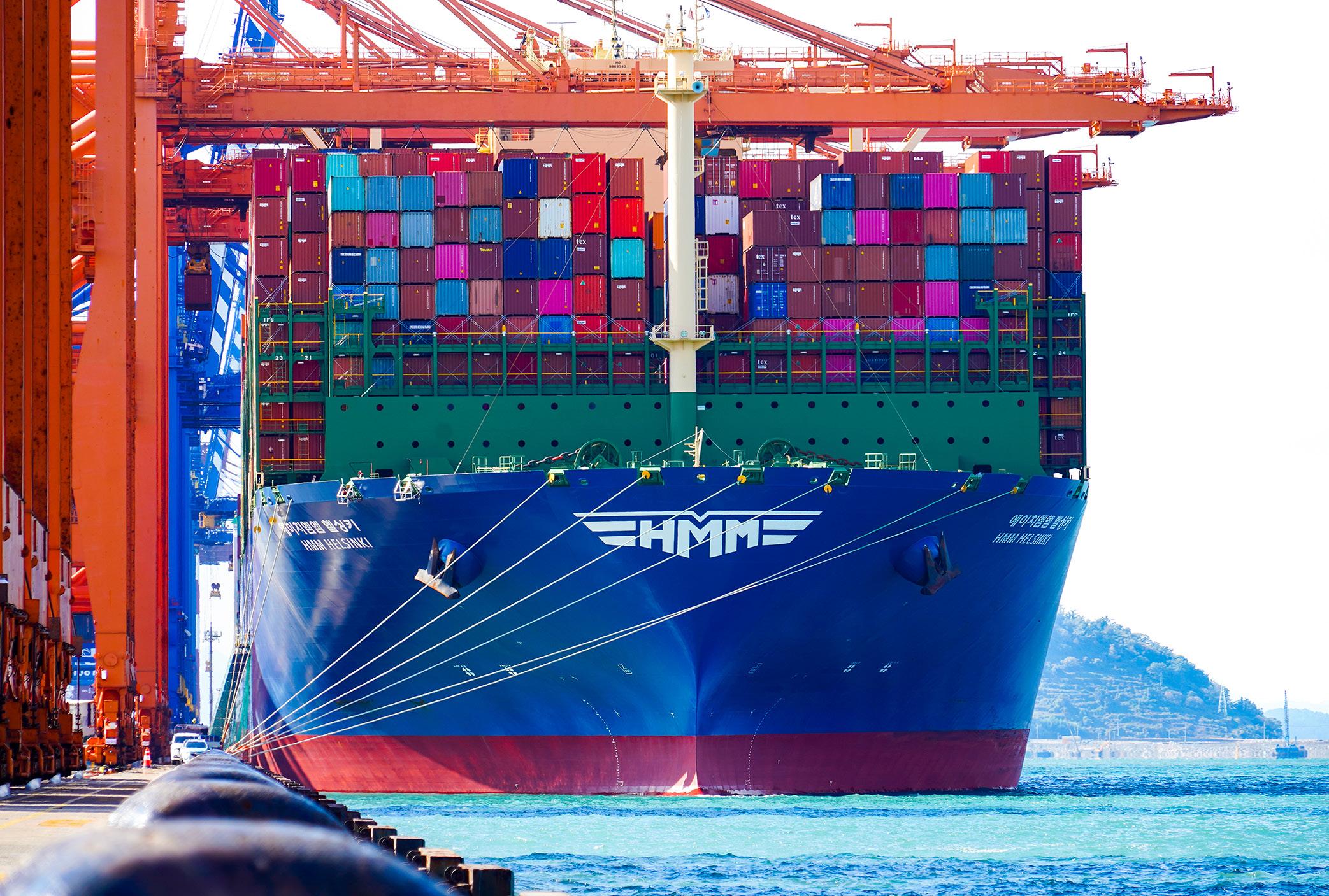
range of services, including dry, frozen, and special cargo, which are delivered through a variety of ship types, ports, and terminals.
The company likewise strives to support customer needs as they shift to a more sustainable future.
“With our green efforts, we are honing our craft and magnifying results to
make this world safer and reduce our carbon footprint,” highlights DePrizio.
As part of this objective, customers are offered HMM America’s Green Sailing Service, whereby it works with multiple port authorities and nations to create green shipping corridors.
With the aim of achieving net zero carbon emissions by 2045, the
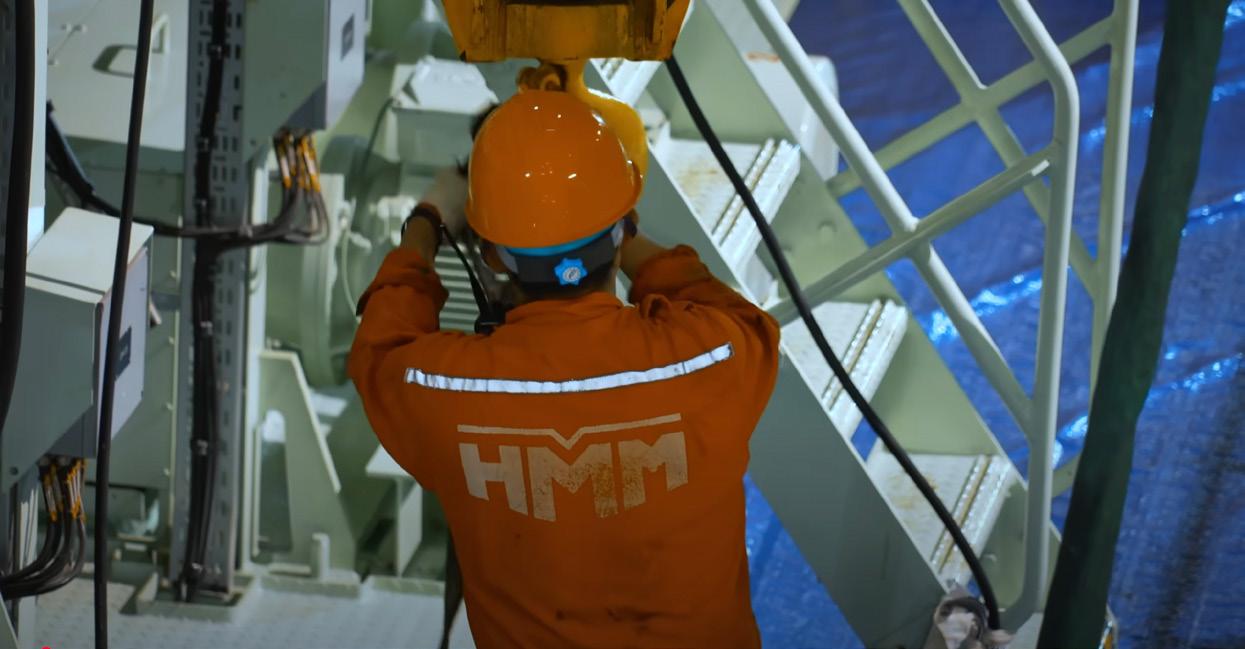
company is purposefully building ships to utilize alternative fuels and ensure it reduces the amount of greenhouse gases (GHGs) produced on the water.
HMM is taking its environmental practices one step further in South Korea, signing a memorandum of understanding (MoU) with the Korea Railroad Corporation (KORAIL) to develop of a low-carbon transportation system.
Enhancing inland rail transportation, the MoU involves utilizing domestic rail infrastructure for refrigerated cargo and establishing an Intermodal One-Stop Transportation System that connects rail and maritime freight.
HMM and KORAIL will team up to improve the efficiency of a new container yard, which the latter is scheduled to secure. From here, the project aims to build an international multimodal transport network for reefer containers.
McAllister Towing is proud to be a partner with HMM for more than 40 years servicing their vessels throughout the entire US East Coast

As such, the collaboration between the two organizations will help create an eco-friendly service by decarbonizing domestic refrigerated transportation.
Elsewhere, HMM America is also expanding its fleet and, in turn, strengthening its competitiveness.
This includes adding two 7,700 twenty-foot equivalent unit (TEU), liquefied natural gas (LNG)-powered vessels, as well as nine 9,000 TEU methanol dual fuel ships, which will be delivered in April 2025.
Worth $1.1 billion, this project is only a small part of HMM America’s strategy to expand its low-carbon fleet.
EVOLUTION ACCORDING TO INNOVATION
HMM America’s journey coincides with the innovations of its parent company, meeting bulk transportation needs for nearly 50 years.
Indeed, the company was formed
“WITH OUR GREEN EFFORTS, WE ARE HONING OUR CRAFT AND MAGNIFYING RESULTS TO MAKE THIS WORLD SAFER AND REDUCE OUR CARBON FOOTPRINT”
– KATHLEEN DEPRIZIO, DIRECTOR OF MARINE AND TERMINAL OPERATIONS, HMM AMERICA
in 1976 as a bulk carrier then known as Asia Merchant Marine. In the following two years, the company introduced bulk tramp services as well as a container service between the Far and Middle East.
The 1980s witnessed the commencement of the Asia to Middle East liner service and the introduction of many Hyundai carrier vessels, including the Hyundai No.1 and Hyundai Pacific.
After establishing a subsidiary in the US, the company then launched
its first service between the Far East, the US, and the Gulf of Mexico in 1982.
A year later, the business rebranded to Hyundai Merchant Marine and opened terminals in Los Angeles and California, while also merging with Korea Marine Transport Co., Ltd. (KMTC).
The following decade was a time of growth for the company, with a specialist service branch known as Hyundai America Shipping Agency creating an avenue for customer expansion in the US.
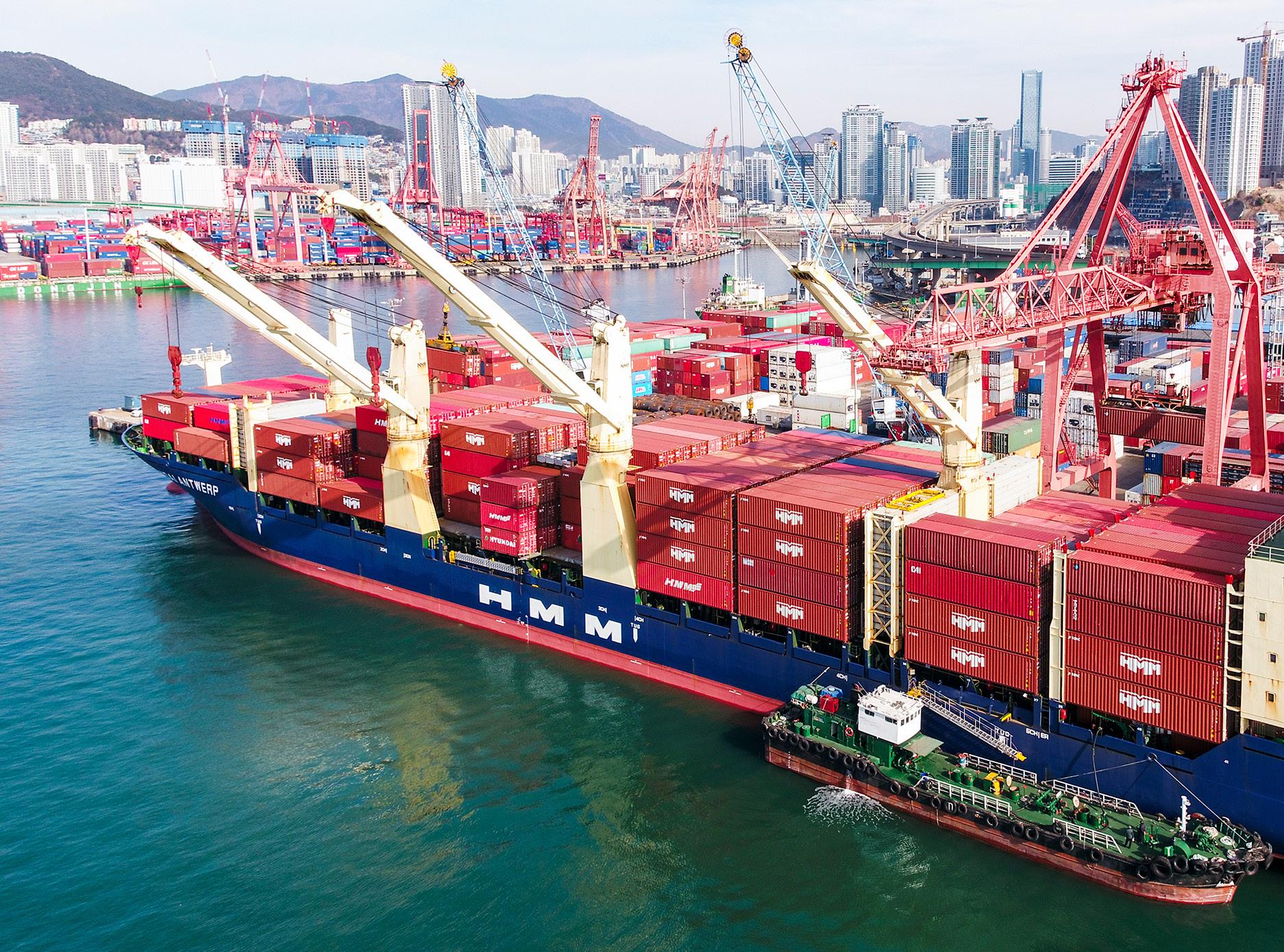
Meanwhile, it also opened branches in Thailand and China, introduced an initial public offering, and secured a terminal at the Port of Tacoma in Washington.
“Around the end of the 1990s, shipping companies began to form alliances to try and gain an advantage in a tough market. The Grand Alliance and New World Alliance were then created, with Hyundai being part of the latter when it began in 1998,” DePrizio informs.
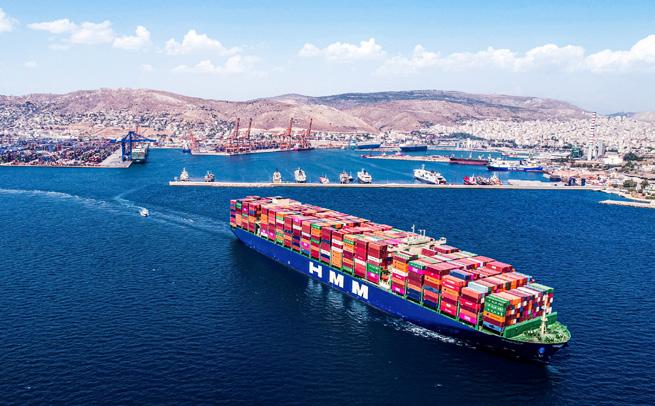
HMM AMERICA’S ENVIRONMENTAL, SOCIAL, AND GOVERNANCE (ESG) STRATEGY TIMELINE
2021 – Secured large and highly efficient container ships, improving the fleet’s energy efficiency.
2022 – Launched its ESG Management Committee, established governance for climate action, and formed the Alternative Fuels Task Force Team.
2023 – Upgraded its supply chain carbon calculator, which provides data on the company’s cargo footprint. HMM America also started a service that utilizes biofuel, established a biofuel supply chain, and launched its Green Sailing Service.
2024 – Acquired a number of global ESG evaluation ratings from reputable institutions, including CDP and EcoVadis. The company also established a GHG inventory system and introduced a standardized methodology across the organization.
2025 – Seeks to deliver methanol dual fuel vessels into its fleet.
2030 – Aims to reduce absolute GHG emissions across its operations.
2045 – Working toward achieving net zero five years ahead of regulation requirements.

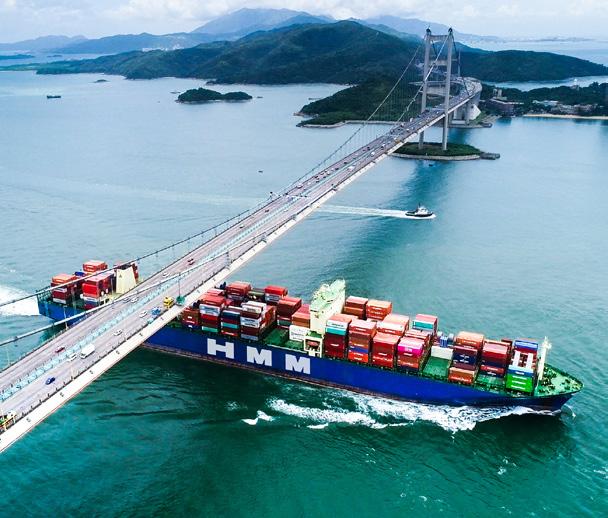
In 2010, the two alliances merged to create the G6 Alliance, which meant that Hyundai was part of the world’s largest shipping alliance.
Toward the end of the 2010s, however, the company came together with other industry players and joined 2M after departing the G6 Alliance, and then later joined THE Alliance, a global network of shipping companies.
The Hyundai Merchant Marine name was subsequently rebranded to HMM in 2020, marking a new era for the company as it continued its growth strategy.
GLOBAL LEADERS IN ECOFRIENDLY SHIPPING
As part of its ambitious expansion goals, HMM plans to spend $17.5 billion in investments over the next five years, more than half of which will facilitate new container ships and equipment.
The parent company will spend $9.5 billion on 70 new container ships as part of its sustainable growth plan, which centers around achieving net zero emissions across its container, bulk, and logistics operations.
Thus, HMM will increase its fleet to 130 vessels by 2030, meaning that it is well positioned to withstand the reorganization of global shipping alliances, strengthen its core business competitiveness, and establish a carbon-neutral ecosystem.
With HMM’s average profitability increasing by 125 percent year on year, the highest in the ocean carrier sector, the company is allocating $3.1 billion to shipping and logistics infrastructure to accommodate this rapid growth, extending its existing terminals while also acquiring new ones.
Furthermore, in line with its 2045 net zero goal, the company will spend $750 million on retrofitting ship engines, securing a supply chain for green fuels, and improving operational stability and efficiency through digitalization.
Alongside these substantial investments, HMM America’s success is also due to its work with tugs, pilots, railroads, and terminals, as well as its proactive labor force.
“These partnerships are always at the forefront of our minds. We strive to keep communication open and have healthy relationships,” DePrizio impassions.

As such, the company’s terminal contract team is consistently in contact with vendors to ensure their requirements are met, guaranteeing that vessels are serviced to the adequate standards and cater to customer needs.
Looking across the shipping horizon, there will be a joint effort across HMM America to streamline efficiencies.
“We will ensure that all team members are on board and feel the same drive to succeed, continuing on their chosen paths in this great world of transportation.”
The company strives to realize this strategy and grow its employee base and fleet to be the carrier of choice.
“I wish to be part of a great team that will lead the charge in this business to go green and set the standard for others,” closes DePrizio.
“We will be successful.”

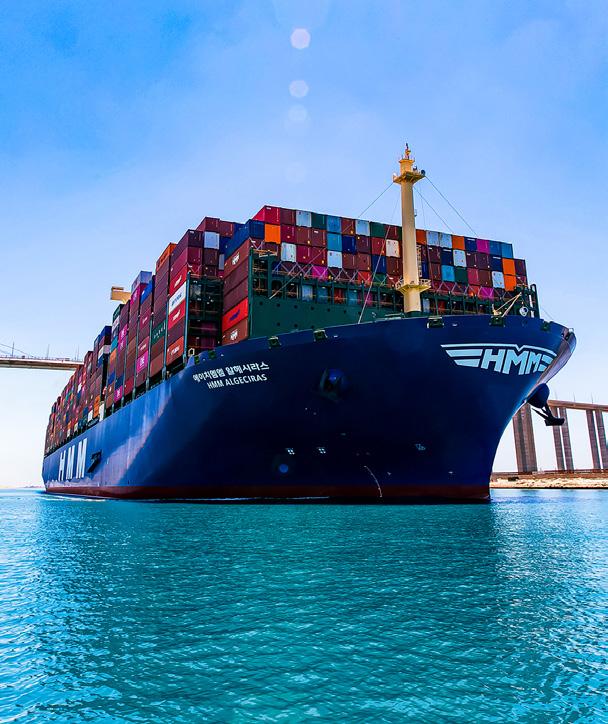
Tel: 972-501-1378
Kathleen.deprizio@hmm21.com www.hmm21.com/company.do
DRIVING SUCCESS ACROSS THE NATION
Providing passenger transportation solutions for over a century, Coach USA has established itself as a leader in the North American mobility and transportation industry. Derrick Waters, CEO, shares insights into his leadership journey, the company’s unwavering commitment to safety, and its forward-thinking plans for innovation and growth.
Writer: Lauren Kania | Project Manager: Poppi Burke

SUCCESS NATION
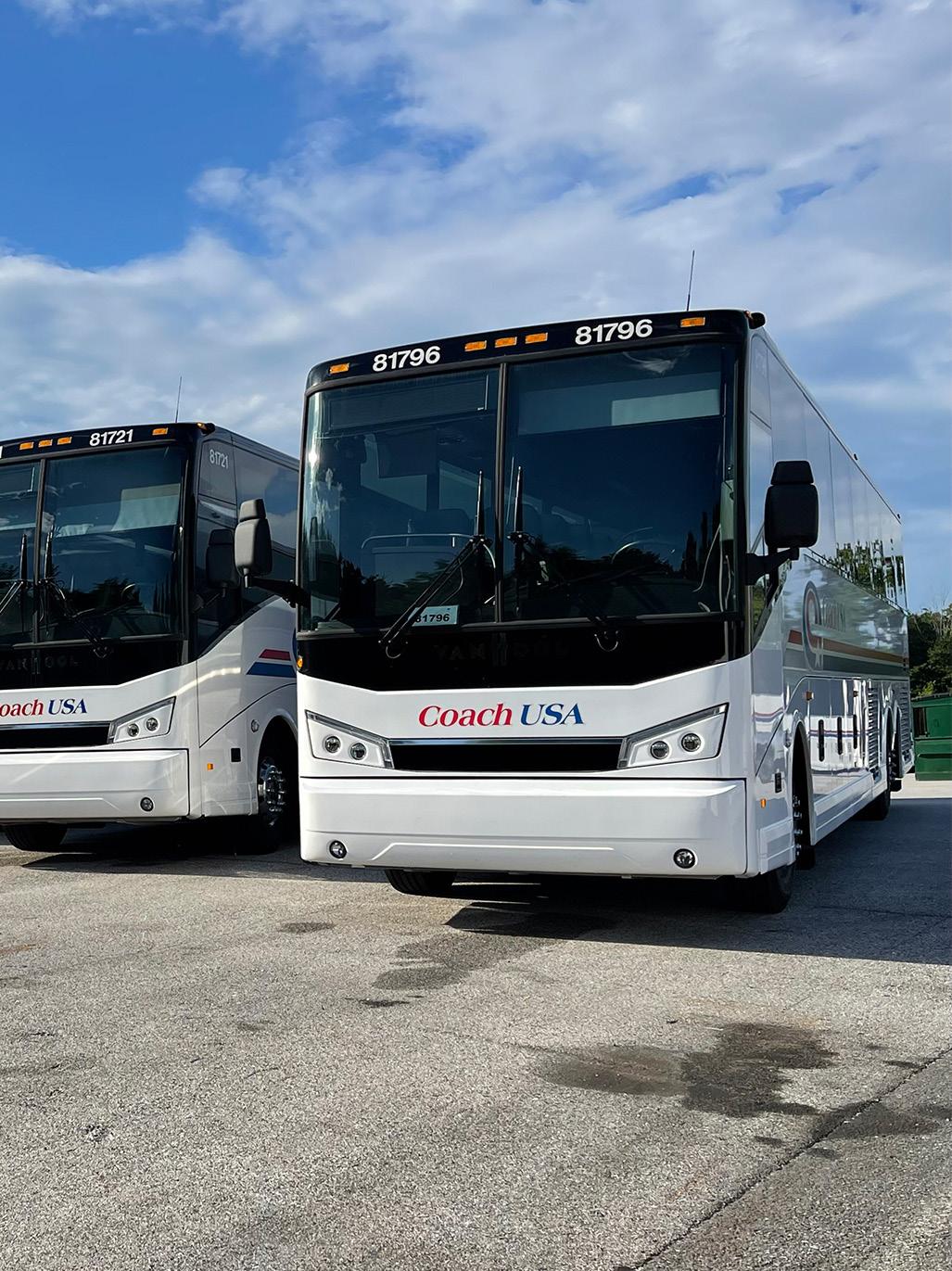
Coach USA, a leading provider of ground passenger transportation and mobility solutions in North America, has proudly delivered over 100 years of dedicated passenger transportation services.
With a network of companies that carry millions of passengers annually throughout the US and Canada, the company not only
provides transportation services but also promotes and generates wider economic growth through job creation and improved access to safe, reliable, and affordable transportation.
“Our mission is to connect people, places, and opportunities,” opens Derrick Waters, CEO of Coach USA.
“This drives our daily operations, from strategic route planning to providing accessible services in
underserved areas. By focusing on community needs and enhancing connectivity, we help individuals access vital services and opportunities while ensuring a seamless travel experience.”
Waters has built his career over 30 years in the transportation and logistics industry, including 34 years at UPS®, where he retired in 2021 as Vice President of Package Operations.

He then joined Coach USA as COO and, in 2023, became CEO, continuing his focus on innovation and operational excellence.
His passion for supply chain management stems from its critical role in driving business success and community connectivity.
“I’ve always been drawn to how the supply chain creates seamless operations and directly impacts the customer experience,” Waters explains.
In addition to his corporate roles, Waters serves as Board President of the Nate McMillan Foundation,
“WE STRIVE TO NOT JUST MEET BUT EXCEED CUSTOMER EXPECTATIONS BY DELIVERING SAFE, RELIABLE, COMFORTABLE, AND CONVENIENT TRANSPORTATION, SUPPORTED BY THE DEDICATION OF OUR PEOPLE AND OUR FOCUS ON INNOVATION”
– DERRICK WATERS, CEO, COACH USA
an organization dedicated to mentoring and empowering young men affected by fatherlessness. He is also a member of the US Department of Transportation (DOT) Human Trafficking Advisory Board, where he focuses on leveraging transportation networks to combat trafficking and support broader societal initiatives.
Waters views the supply chain industry as a consistently exciting and dynamic field, with innovations and transformations on the horizon.
“The industry is currently undergoing significant transformation. The integration of
technology, a heightened focus on sustainability, and the demand for resilience make it a dynamic space,” he says.
For transportation specifically, supply chain efficiency directly impacts service delivery and customer satisfaction, presenting challenges and growth opportunities.
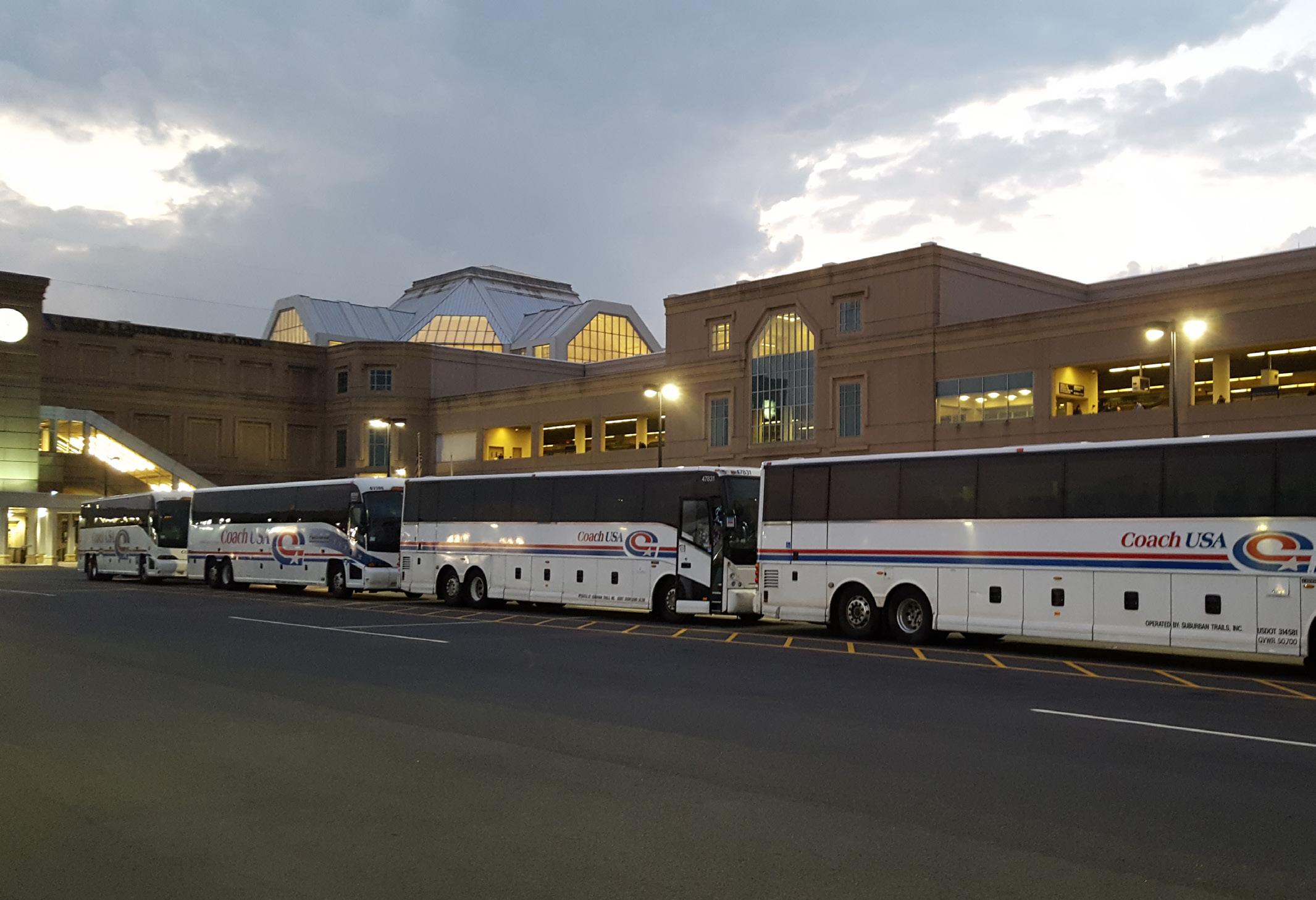
OVER A CENTURY OF INNOVATION
Coach USA and its affiliated companies are trusted business partners providing commuter and line run services, airport transfers, charter
bus rentals, tours, and many contract service solutions. Through the company’s affiliates and subsidiaries, it has been offering passenger transportation solutions for nearly 100 years.
“Coach USA has always remained committed to safety, innovation, and adaptability. From our early days of providing local bus services to becoming a leading provider of transportation solutions, we have continuously evolved to meet the changing needs of our passengers,” informs Waters.
Today, the company operates a comprehensive network connecting urban centers and rural communities, offering services such as commuter bus routes, airport shuttles, charter services, and sightseeing tours.
Additionally, it has operations in 13 locations throughout the US and Canada, alongside more than 1,700 employees and 1,100 buses.
What truly sets Coach USA apart from the rest is the company’s unwavering commitment to its mission and pillars.

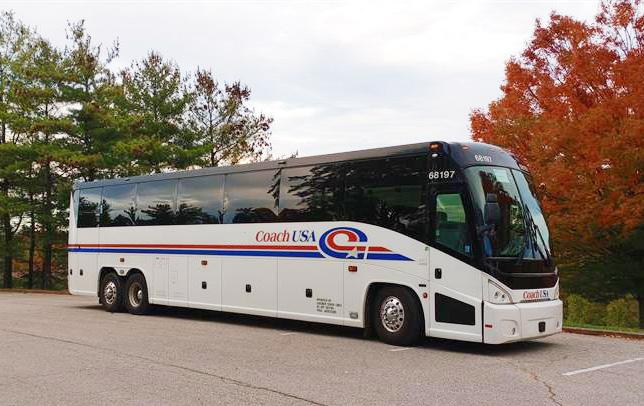
“Our mission drives every aspect of our business. We strive to not just meet but exceed customer expectations by delivering safe, reliable, comfortable, and convenient transportation, supported by the dedication of our people and our focus on innovation,” impassions Waters.
Specifically, the company highlights safety, planning, training, implementation and execution, customer-centric values, and strong community partnerships as its distinctive elements.
Effective planning underpins the company’s operational success, as it firmly believes this is essential to delivering on its service commitments.
This proactive approach enables it to anticipate challenges and adapt to changing market needs, ensuring it consistently provides seamless transportation solutions.
Equally, implementation and execution are where Coach USA turns its plans into action – whether by launching new contracts, integrating advanced technologies, or expanding its service network, the dedicated management team guarantees each initiative is executed with precision and efficiency.
Furthermore, the company tailors its services to meet the unique needs of the communities it serves, prioritizing accessibility and inclusivity.
These customer-centric values and strong community partnerships, combined with a drive for continuous improvement and technological advancement, allow Coach USA to deliver transportation solutions that truly connect people, places, and opportunities.
“Our pillars of safety, planning, training, and execution, alongside our mission-driven focus on innovation and community engagement, set us apart as a leader in passenger transportation,” declares Waters.
COMMITTED TO SAFETY
For Coach USA, safety is a top priority, setting it apart in an industry where reliability and trust are paramount.
“There are many things that we do best, but the most critical one is safety, which is at the very core of everything we do. We are dedicated to a ‘safety first, last, and always’ attitude,” emphasizes Waters.
The company adheres to rigorous safety protocols, ensuring the well-being of both passengers and employees.

COACH USA SERVICES
The company operates a wide variety of passenger transportation services, including:
• Commuter bus services
• Airport shuttle and university shuttle bus operations
• Charter bus rentals
• Bus tours
• Contract services and transportation management
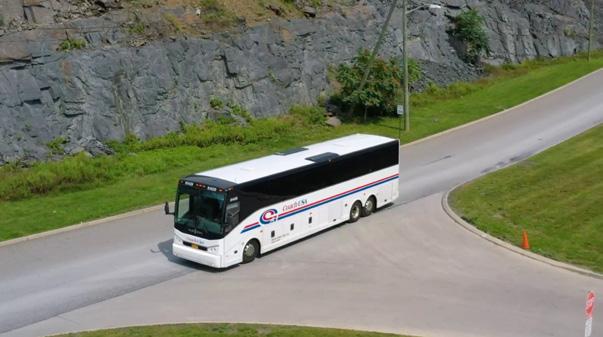
From its fleet to its facilities, safety considerations guide the company’s operations, with comprehensive training programs reinforcing a culture of safety across the organization.
The foundation of the company’s commitment to safety is embodied in its safety program and training, where new drivers undergo a minimum of 150 hours of classroom and behind-the-wheel training before they begin service. Even those with an existing commercial driver’s license are required to complete more than 90 hours of theory and practical training.
“Our driving team is one of the best-trained in the industry,” states Waters.
Serving as a cornerstone of Coach USA’s competitive edge, the company invests heavily in its people by offering extensive training that covers dispatch, fleet management, customer engagement, driver safety, and leadership development.
“By nurturing talent and fostering
diversity, we empower our employees to excel in their roles and drive the company’s success,” further expands Waters.
Equally, Coach USA also invests in new technology and innovations to ensure it remains an industry leader.
The company consistently reviews its digital touchpoints to guarantee it is offering an exceptional user experience and even provides customers peace of mind with bus tracking, allowing them to readily monitor the status of their trip in real time.
“We’ve introduced chatbots on our Coach USA and Megabus websites, which helps us to assist a much higher volume of inquiries, even outside of typical business hours, and has dramatically improved the customer experience,” prides Waters.
GOING GREEN
Partnerships are crucial to the ongoing success of Coach USA, with the company consistently leveraging
Green Energy & Environmental Consulting
Bristol Developers Inc. (BDI) Environmental Contracting & Construction Services in Denville, New Jersey
Bristol Developers Inc. (BDI) is a full-service environmental contractor in the State of New Jersey, specializing in facility environmental assessments such as SPP/SCC compliance services, general site maintenance services like oil water separators, fuel tanks and fuel distribution and management systems & waste recovery and disposal services, general underground and aboveground tank removal & installations, site assessments and site remediation services.
Helping the greater Garden State & Northern Metro area with our licensed professional contracting, our company is here to help anyone in the industrial, commercial or residential market, as well as with the environmental & petrochemicals, mining, energy, agriculture, waste management, or other adjacent industries.
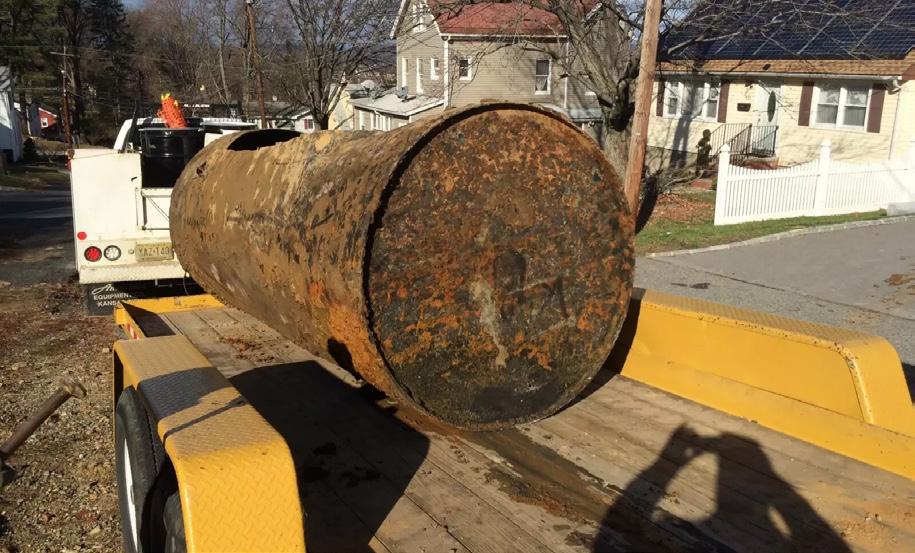
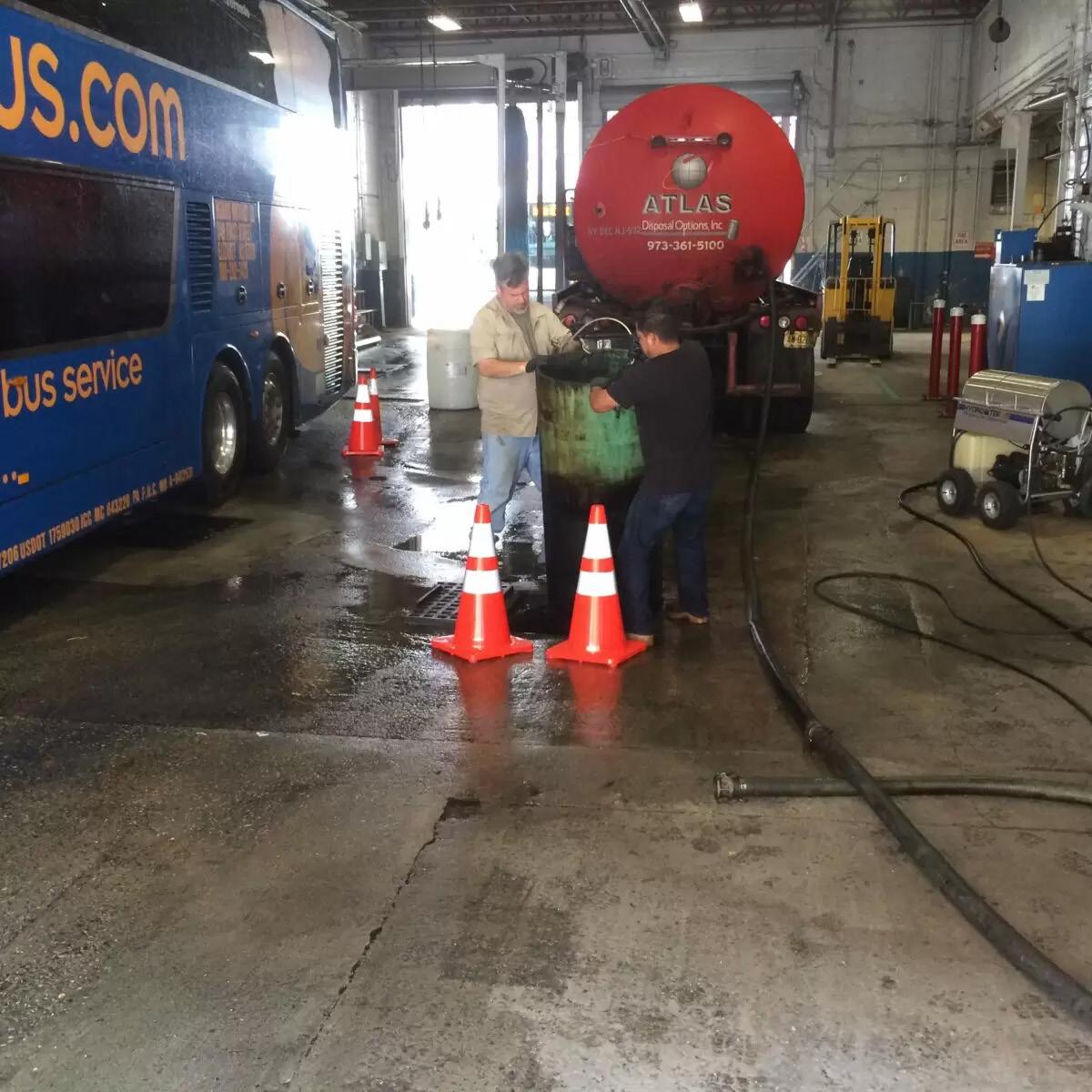
Hazardous Waste Management
BDI is dedicated to cleaning up New Jersey and surrounding states. We are a full-service environmental contractor company here to help you achieve the best possible management of hazardous waste material. Whether your site has been contaminated by a release, spill or leak, or you are cleaning up a decommissioned property from potential environmental issues on site, or you need to properly dispose of any kind of ongoing or one-time hazardous waste or soil contaminate, BDI is here to make sure it is done both safely and efficiently in compliance with all applicable regulations.
Site Investigation & Remediation
No matter what stage of the clean-up process your site is in, Bristol Developers Inc. can provide an expert environmental site assessment, removal, or remediation. From the soil to the groundwater, air, and sediment conditions, we will take a comprehensive and detailed look at your site’s environmental risks to eliminate any and all present or potential issues or concerns.

Why work with Bristol Developers in NJ?
BDI is based in Morris County, Denville, NJ, an area which is known as the Hub of NJ, and we have worked with both national and international companies as part of our quality work experiences. Bristol Developers, Inc. consists of a small, seasoned team of professional environmental contracting & construction personnel with superior solutions skills offering all types of environmental, natural, cultural, and sustainable resources to help maintain and support our clients’ needs and facility operating requirements. BDI is licensed, certified, and insured to guarantee success. We stand behind all of our services and take great pride in our reputation for customer satisfaction. As a full-service environmental contractor with decades of experience and community involvement, there is no better choice for your one-stop shop for all your environmental & contracting services than Bristol Developers Inc.
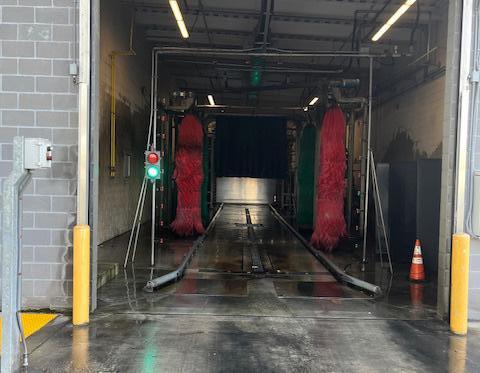
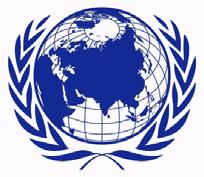

For BDI there is no job too large or too small, our NJ-based environmental contracting & construction services can travel to help anyone in need of efficient and professional assistance. Please contact us today or call (732) 558-7517 Bristol Developers Inc today.
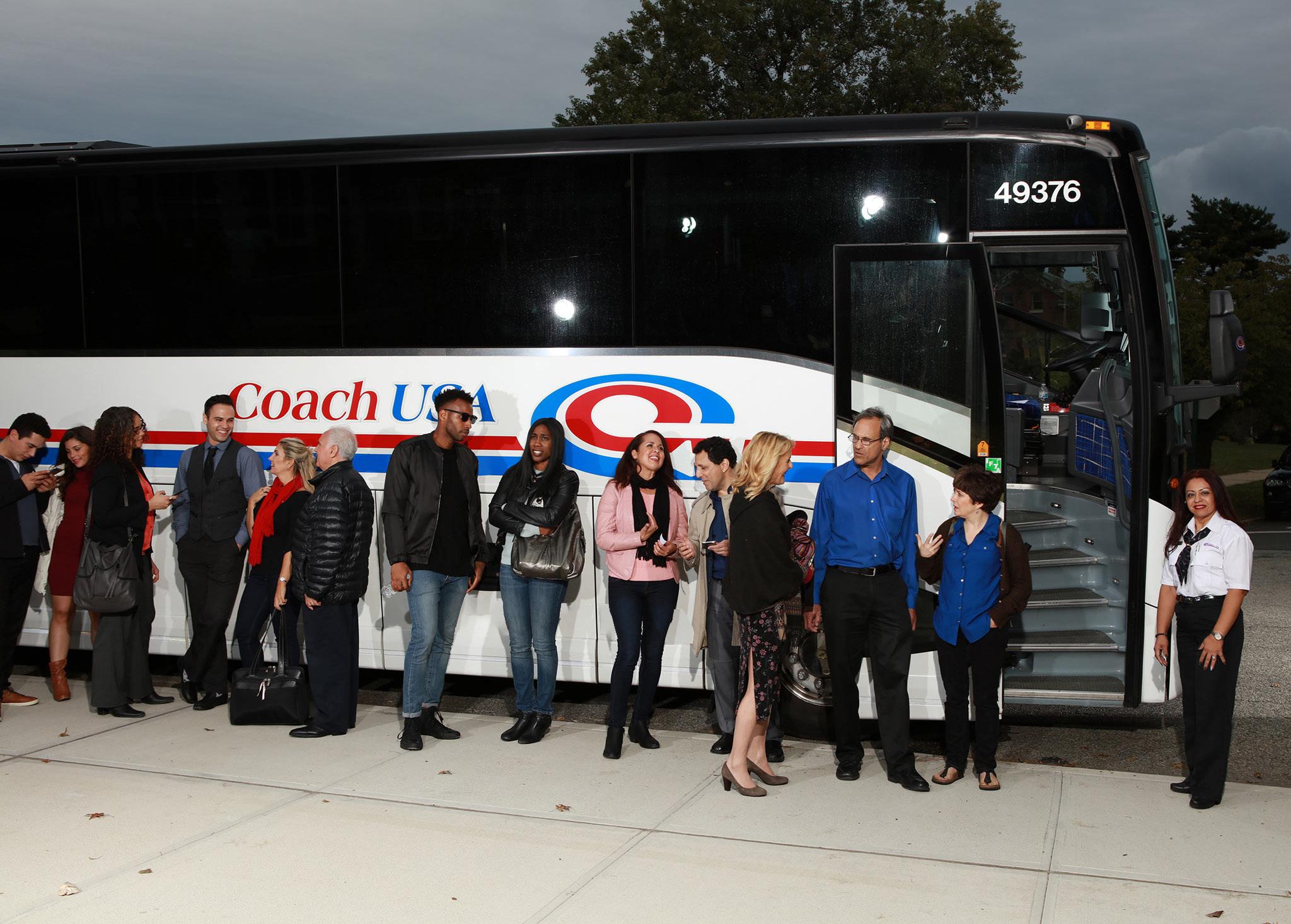
SUPPLY CHAIN OUTLOOK: HOW IMPORTANT ARE PARTNER AND SUPPLIER RELATIONSHIPS TO THE SUCCESS OF YOUR BUSINESS?
DERRICK WATERS, CEO: “Partners are essential to the success of our business, and one of our key offerings is through Megabus. We’re pivoting to position the brand as a leading retailer in the transportation industry and already have many partners actively on board.
“Partners provide the buses, but we provide advanced technology solutions, a state-of-the-art website and sales engine, and access to a nationally recognized name.
“Additionally, partners receive award-winning customer service and access to our centralized team of experts in various fields, including yield management, pricing and scheduling, marketing, e-commerce, and more.”
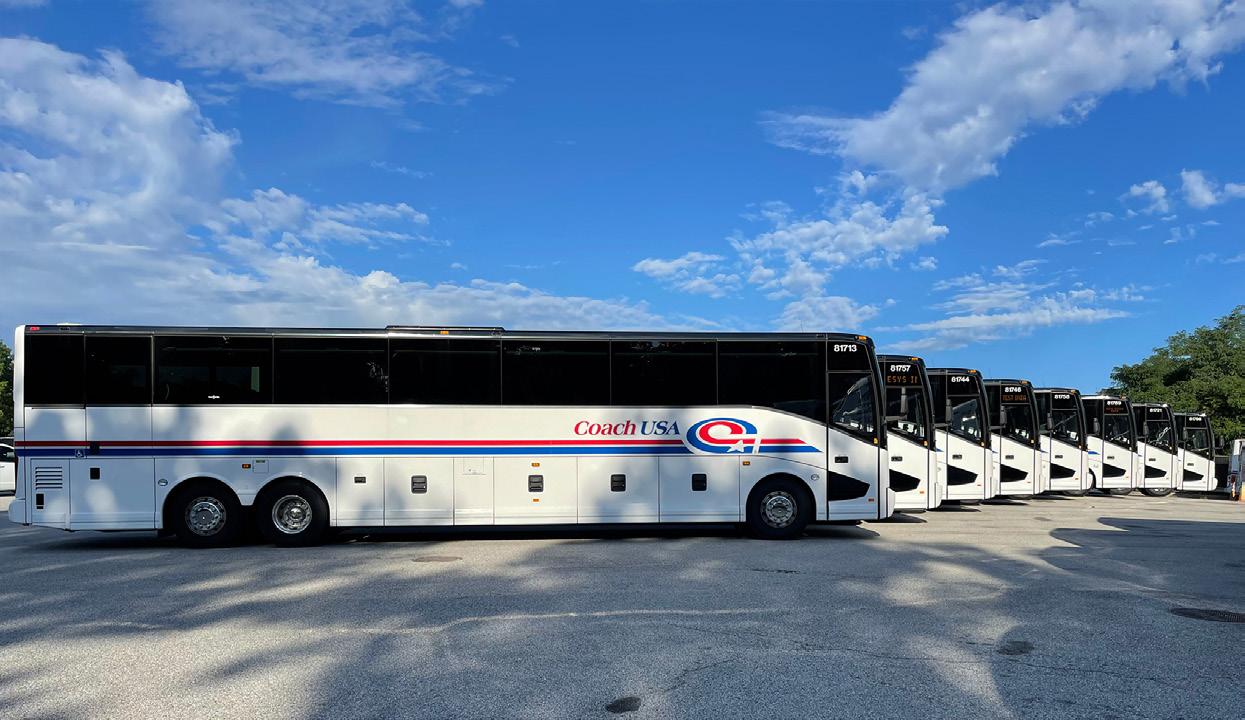
such relationships to expand its network and enhance connectivity.
A significant component of its strategy involves collaborating with smaller bus companies to link routes and streamline ticketing through shared platforms.
One such example is the company’s partnership with Transcor Data Services (TDS), allowing it to integrate real-time booking and capacity sharing with regional partners such as Peter Pan Bus Lines, Northwestern Stage Lines, and Salt Lake Express.
“These collaborations enable partner bus companies to sell tickets via our website, offering passengers broader travel options while maintaining the unique local service these companies provide,” details Waters.
“By fostering these partnerships, we’re building a more connected and efficient transportation network for the future.”
Equally as important to the

TRANSFORM YOUR DATA INTO DECISIONS WITH FLEET MANAGEMENT SOFTWARE
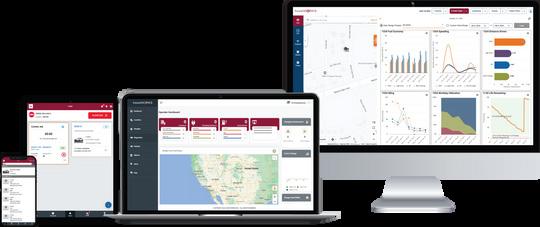
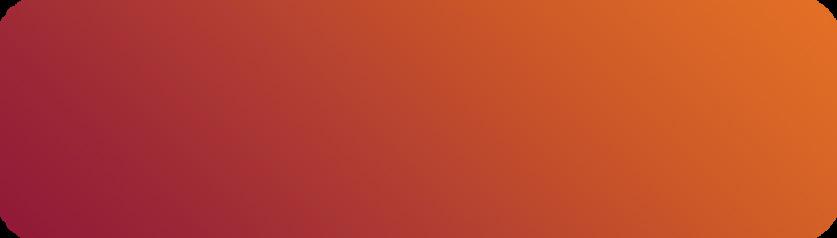
continued progression of Coach USA and the future of the industry as a whole are the company’s eco-friendly solutions, as it works to make bus travel the best alternative and green form of transportation.
In recent years, Coach USA has reduced the carbon impact of its business by 37 percent in the US and 26 percent in Canada.
This has been achieved through programs focusing on improving energy efficiency at its facilities and reducing carbon emissions from its fleet, helping customers by offering greener transportation services.
“We are actively working on sustainability through route optimization, fuel efficiency, and sustainable maintenance practices. These efforts reduce our environmental impact and position bus travel as an eco-friendly alternative to personal vehicles,” expands Waters.
As Coach USA looks ahead

to another century of success, innovation, and transportation solutions, it is focusing on key priorities such as expanding services to underserved areas, enhancing safety and operational efficiency, investing in technology and talent development, and strengthening sustainability initiatives and community partnerships.
In addition to these priorities, the company is committed to its employees’ and customers’ safety, security, and well-being.
As part of this commitment, it is striving toward Destination Zero - an international strategy to achieve zero preventable accidents and injuries. While the primary focus of Destination Zero is safety, it extends into all areas of the company’s operations, including maintenance, where the goal is to achieve zero emissions across the company’s fleet by 2050.
Coach USA is committed to being
the safest transportation company in North America. That is why the company launched its Pedestrian, Passenger, Bicyclist, and Scooter Safety Campaign (P.B.S.S.), a program specifically dedicated to eliminating passenger and traffic fatalities and serious injuries involving its fleet.
“We will also be seeking growth opportunities through partnerships from the lens of a ‘hunter’s mentality’. Cost controls and sustainability will be key to ensuring our financial health as we move forward,” concludes Waters.
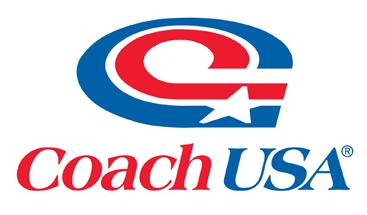
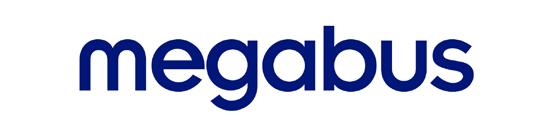
questions@coachusa.com questions@us.megabus.com www.coachusa.com us.megabus.com
FULL STEAM AHEAD
Facilitating the largest cargo operations in Mexico, Ferromex possesses an enviable fleet of locomotives and railcars that deliver the needs of the nation’s businesses, while also offering holidaygoers blissful trips around the Mexican countryside
Writer: Lucy Pilgrim | Project Manager: Scarlett Burke
The vast open plains of sandy vegetation and rugged mountain landscapes have become synonymous with Mexico and its uniquely vibrant culture.
However, the historical transportation of goods through the country’s rough terrain via carts, rivers, or even on foot proved incredibly difficult.
Yet, despite logistical adversities, the movement of cargo is ingrained in Mexico’s heritage. The pre-Hispanic era, for instance, saw Indigenous communities use carts to transport goods across carefully laid out paths, which were vital for communication and trade between communities.
Toward the beginning of the 19th century, many nations across the world were experiencing rapid industrialization, creating the early foundations of a national supply chain. Mexico was no different, as the country’s first railway opened in 1850 between Veracruz and El Molino.
This marked a turning point in the nation’s transportation capabilities and encouraged continued
government support for additional railway developments across Mexico.
Significantly, this made trade between distant regions and nations more convenient and efficient, thus creating a robust and reliable logistics network that drove the country’s industrial revolution and economic advancement.
Fast-forward 150 years and the early blueprints for cargo rail transportation have evolved into a large and complex amalgamation of state-of-the-art technologies and colossal cargo equipment.
As a result, the rail transportation of cargo has become far more expansive and methodical due to the speedier construction of tracks and containers, round-the-clock fleet management systems, and the implementation of other digital platforms that can monitor the movement of goods in real time.
At the forefront of this advanced network is Mexico’s largest cargo operator, Ferromex, whose strength and influence on the country’s logistics capabilities demonstrate just

how far transportation has come.
Indeed, the company was formed from the privatization of a large percentage of state-owned railways in the late 1990s, enacted by Ernesto Zedillo, the 61st President of Mexico.
Ferromex is therefore intertwined with domestic and global cargo movement, as demonstrated by its extensive railway network spanning over 11,000 kilometers (km), industryleading capabilities, and undoubtable power and influence on today’s supply chain in Mexico and beyond.
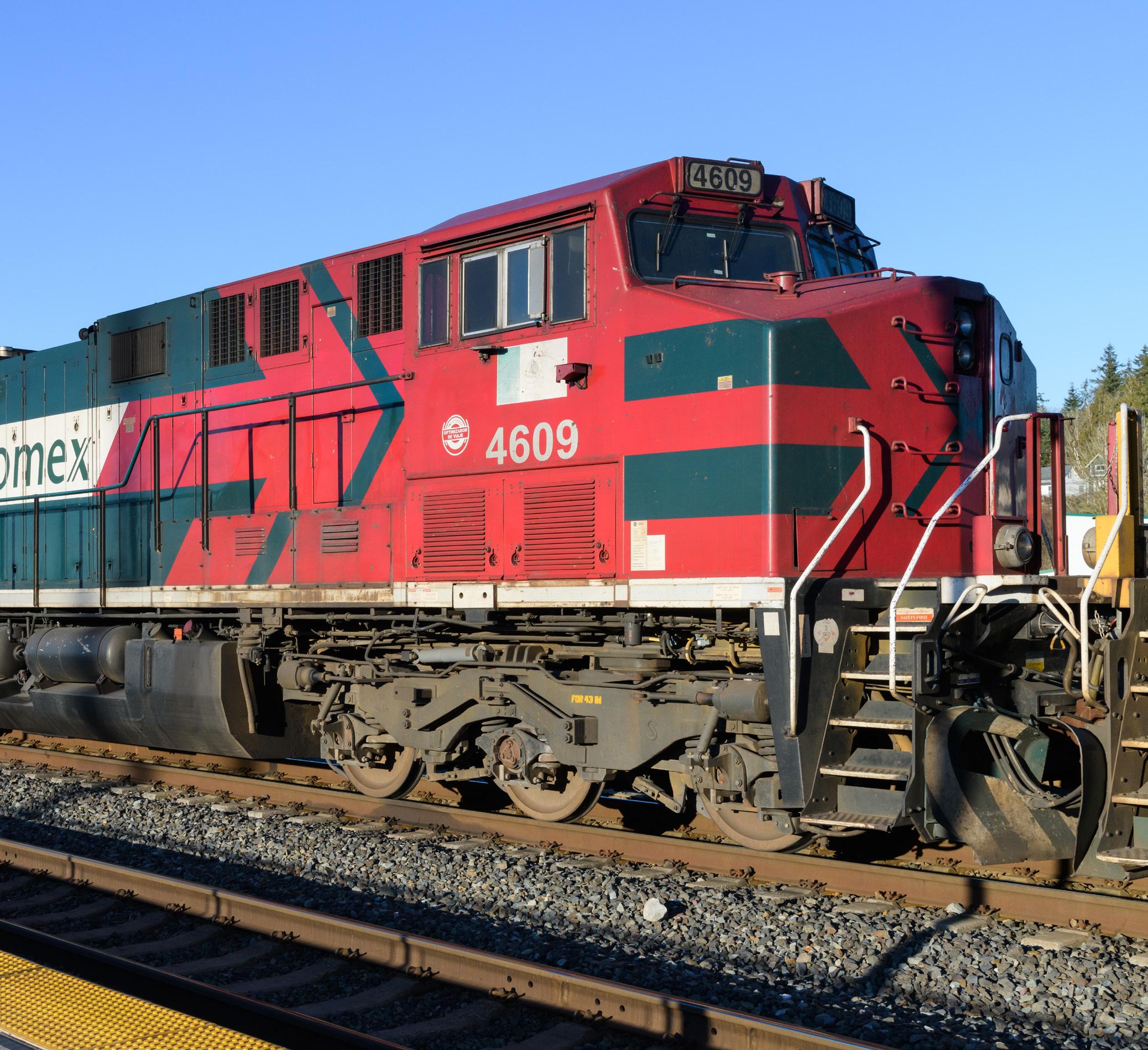
THE COMPLETE FLEET
With unmatched operational capabilities, Ferromex utilizes the immense power of over 800 locomotives and 28,000 railcars to transport whatever its clients need securely and on time.
Indeed, the company is able to transport cars, general cargo, and bulk-handling equipment, aiding its many customers with their logistics challenges.
Ferromex transports cars via three forms of equipment – Automax,
Bilevel, and Trilevel.
The former has a load capacity of 49 tons (t) and can transport 16 to 26 cars in one journey, whilst Bilevel equipment can move approximately 35t and around eight to 10 cars via two levels per cart. Trilevel equipment, meanwhile, has a similar load capacity but with the added ability to transport 12 to 15 cars across three levels.
Ferromex also offers best-in-class equipment for moving general cargo and container equipment that customers can leverage to transport a range of
products, including automotive parts, food appliances, and much more, with a total load capacity of 26t.
Intermodal platforms are then utilized to transport between 20 and 53 containers, equating to a total load capacity of 73t.
The company’s moving capabilities not only cater to vast cargo but also lighter deliveries. As such, Ferromex offers small-scale platforms to deliver loose goods, such as logs, sleepers, pipes, fences, rails, and more, equating to a capacity of 32t.
Cargo moving services are likewise offered using dry van equipment such as a covered hopper with chutes and covers for rolling cold and hot metaled sheets onto the container.
Ferromex also has the necessary fleet and logistical capabilities to transport bulk materials, in which larger-scale equipment is used to efficiently handle its customers’ biggest cargo requirements.
Alongside the covered hopper used for transporting general cargo, the company’s covered gondolas are purpose-built with cradles and covers for loading and unloading sheet rolls of various temperatures. In order to move these large volumes, this particular equipment has a load capacity of over 93t.
Moreover, Ferromex’s open-top gondolas transport a range of bulk products, such as minerals, coals, metals, scrap products, and more,
GRUPO MÉXICO
Ferromex was established as a subsidiary of Grupo México, a major Mexican conglomerate that operates the second-largest transportation division in the country.
As such, the organization spans across 24 states in Mexico, as well as operating in Texas and Florida in the US. This extensive network provides Grupo México with a vast presence throughout North America, possessing over 11,000km of track in total that seamlessly integrates with railways across the US and Canada.
Ferromex, the largest entity within the transportation division, is 74 percent owned by Grupo México, whilst Union Pacific controls the remaining 26 percent.
with a load of nearly 97t, making them a vital part of the fleet.
The company’s largest bulkhandling equipment comes in the form of hoppers. With a staggering capacity of 101t, this equipment is primarily used to transport huge quantities of agricultural products, including corn, wheat, sorghum, beans, and malt.
Agricultural products aside, hoppers are also leveraged to transport cement in bulk, catering to a number of industries.
MEETING INDUSTRY DEMAND
Ferromex’s position at the forefront of Mexican cargo logistics means that it supports a multitude of industries across the country, and North America as a whole, via nine business units.
The company’s agricultural division offers vital inputs for processing operations, aiding flour and corn mills, oilseed plants, and breweries. As a
result, the division’s customer base is far-reaching, serving businesses involved in animal feed, corn syrup, starch production, sugar mills, and much more.
Ferromex also diligently meets the needs of the country’s automotive industries, serving 70 percent of Mexico’s automotive domestic cargo, which includes some of the world’s top car brands. The company delivers goods to assembly plants used by General Motors, Ford, Chrysler, Honda, and Volkswagen, to name a few.
To cater to a wide range of models, Ferromex has strategically located terminals across the country in cities such as Hermosillo, Monterrey, Silao, Guadalajara, and Valle de Mexico. Significantly, these terminals house the largest fleet of multi-level containers, with further investment expected in the future, optimizing automotive carrier potential.
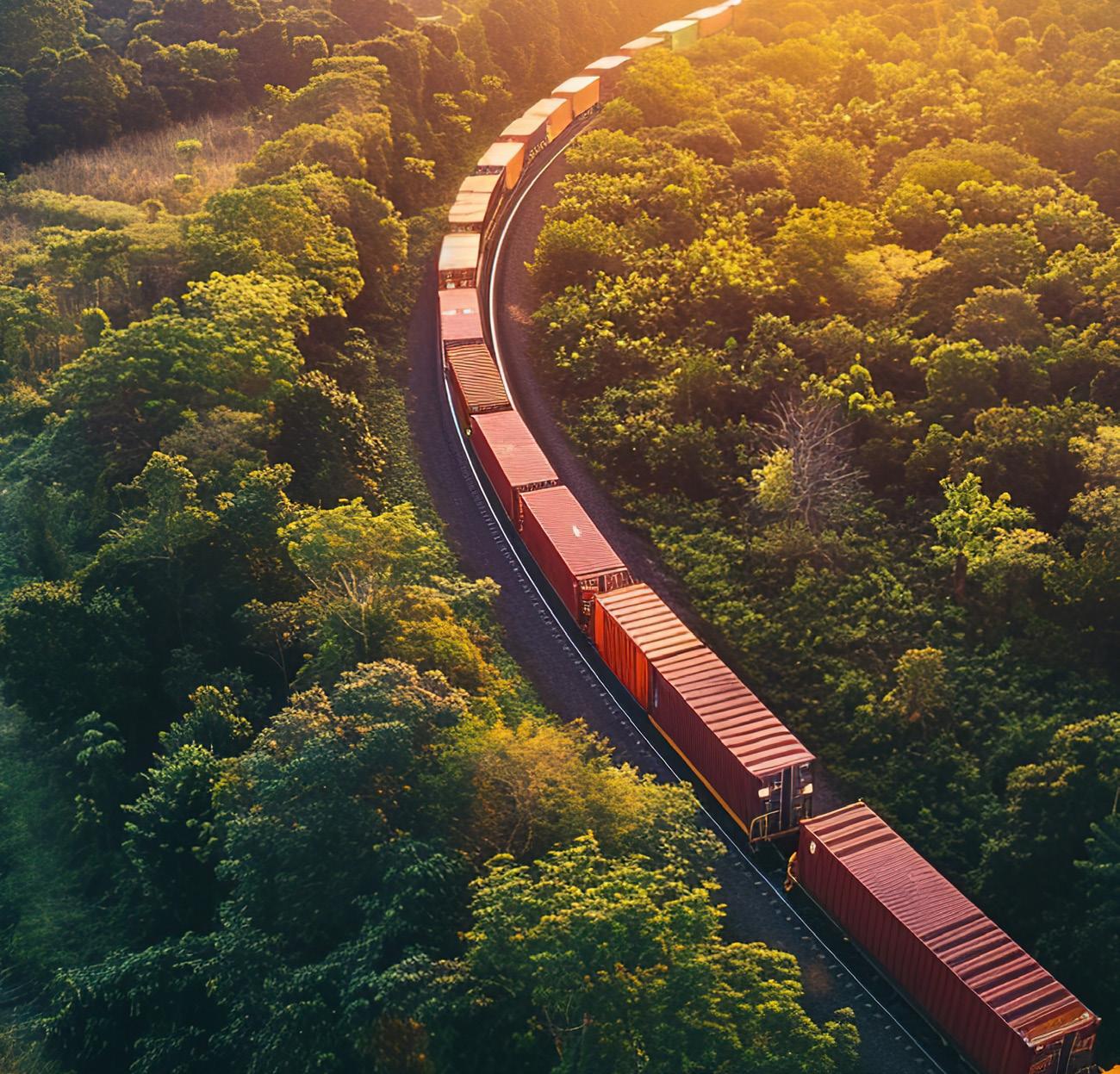
ABOUT US
For more than 50 years, ELASTÓMEROS TAZA has committed to the development, innovation, production and commercialization of thousands of proprietary polymeric formulations, thereby establishing our leadership in a wide range of products.
RAILROAD
PRESENCE
As a group, we have presence in over 30 countries worldwide with a wide web of partners and distributors to suit the needs of our global customers.
QUALITY CONTROL
Permanent QC guarantees the quality and traceability of our parts. We are certified by the Instituto Mexicano de Normalización y Certificación, A.C. and AAR The Association of American Rail Roads (M1003).
Early this century we started the manufacturing of polymeric tie plates which gave us the opportunity to start designing and manufacturing parts for entire fastening systems.
We manufacture systems such as:
• GN-115 & 136 lb/yd • ES-115 & 136 lb/yd • W-14HH 115lb/yd
• W-40HH 136 lb/yd • e clip system 115 & 136 lb/yd
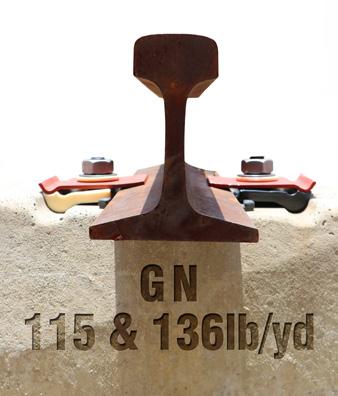
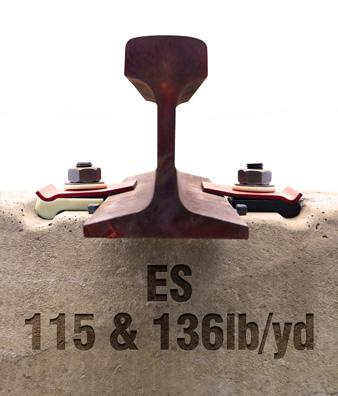

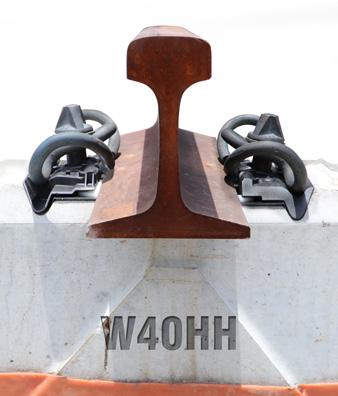

SLEEPER SOLES & PADS
TAZA POLYMER has developed engineering polymers that meet the specific needs of the railway industry, where all materials face exposure to strong impacts, severe shocks, constant friction, high abrasion and wear and a wide variety of environmental conditions. Elastomeric parts made with these polymers withstand heavy loads and protect railway infrastructure against wear from abrasion, impact and tear, among others, apart from noise, vibrations and deformation. These materials have effectively replaced both rubber and metal in countless applications, having a variety of possible applications in the infrastructure as any kind of pads for concrete sleepers, and their life time has far surpassed those of other elastomers.
Taza Polymer in its quality and development laboratory has achieved a new generation of polymers for the manufacture of sleeper soles that prevent ballast wear, which ends in puddles when the drainage system is blocked by dust caused by the friction of the sleeper with the ballast, causing very expensive periodic maintenance.
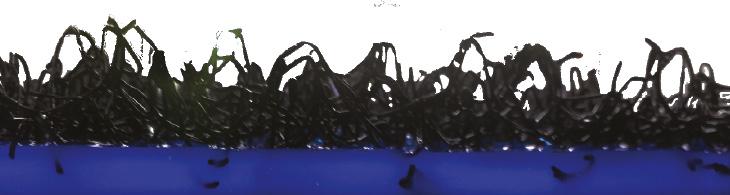
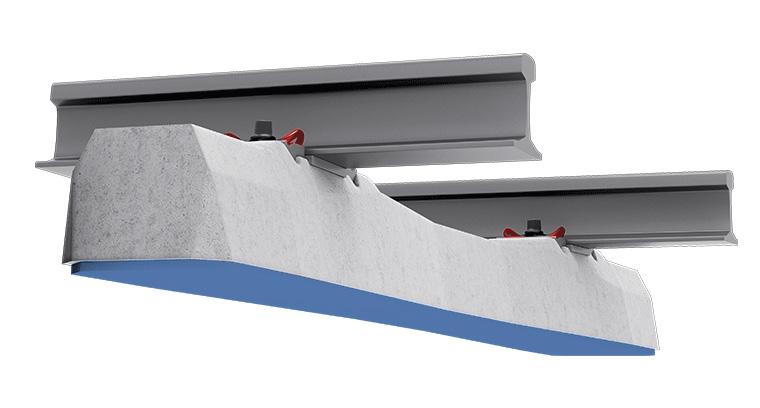
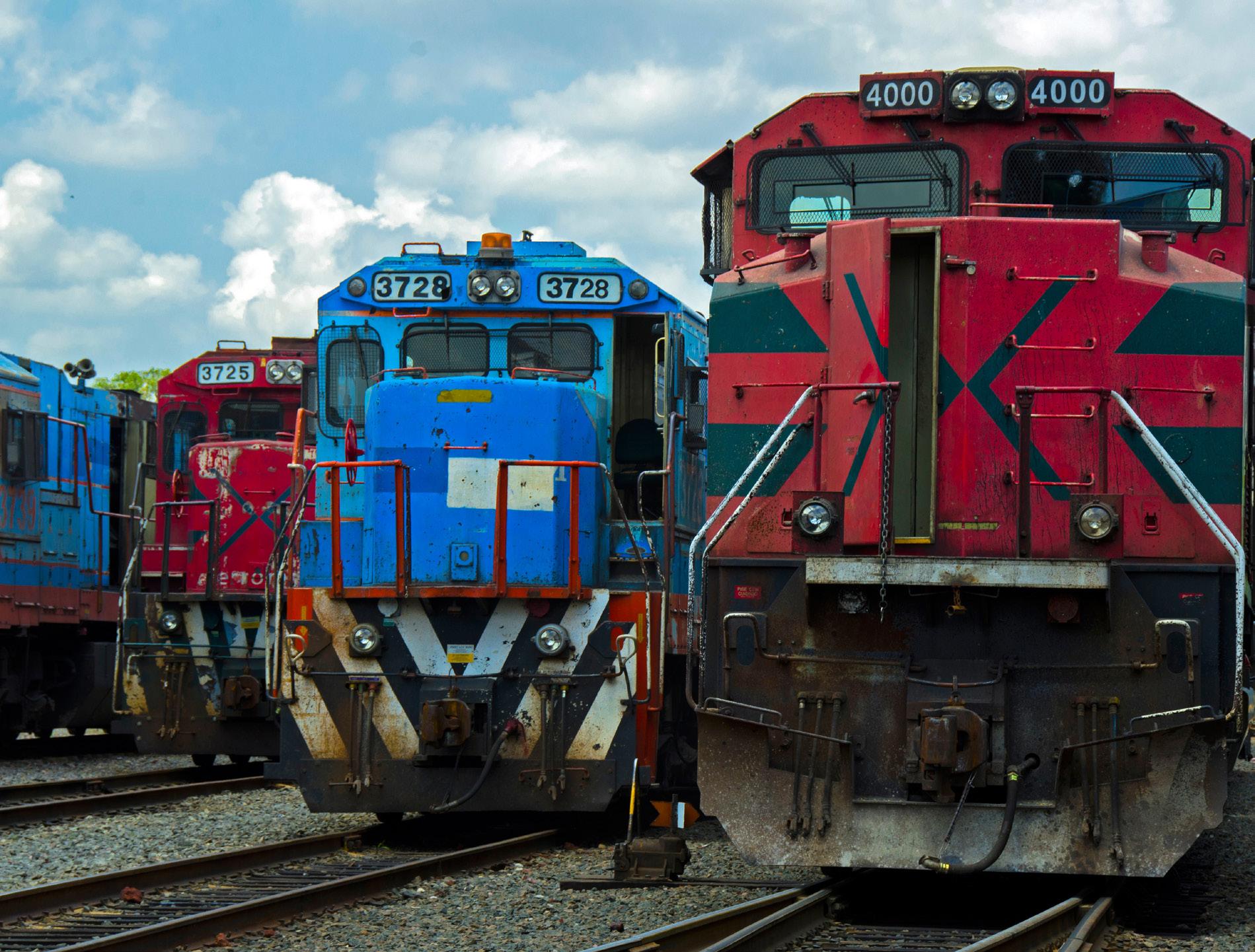
Elsewhere, the company’s impact on the industrial cement sector is felt far and wide, as it managed to move 10 million t of cement in 2022 on a national and international basis. Accordingly, Ferromex leverages the necessary high-tech fleet of cement hoppers and dry vans to transport products to their desired destination across challenging environments.
DELIVERING GOODS SECURELY
Ferromex is also committed to meeting the demands of Mexico’s oil and gas industry, transporting a range of materials including coal, diesel, oils, asphalt, liquefied petroleum gas (LPG), and more.
Additionally, the company delivers
TRADE BETWEEN MEXICO AND THE US –FACTS AND FIGURES
• Rail accounted for 12 percent of total freight between the two countries in 2022.
• In the same year, total rail trade between Mexico and the US equated to $91.4 million.
• Nuevo Laredo in Tamaulipas, Mexico, and Eagle Pass and El Paso in Texas, US are the top rail connection terminals for trade.
vital metals and minerals to the country’s many mining and steel areas, encompassing the import and export markets.
Alongside transporting everyday consumer goods for the food and beverage industry, including beer and dry goods, Ferromex also transports industrial products such as appliances, structural machinery, and packaging products using dry van delivery equipment.
On top of this, the company is dedicated to safely delivering inorganic chemical products, synthetic resins, fertilizers, petrochemicals, and other products.
Due to the highly hazardous nature of its transportation, Ferromex ensures that it acts in accordance
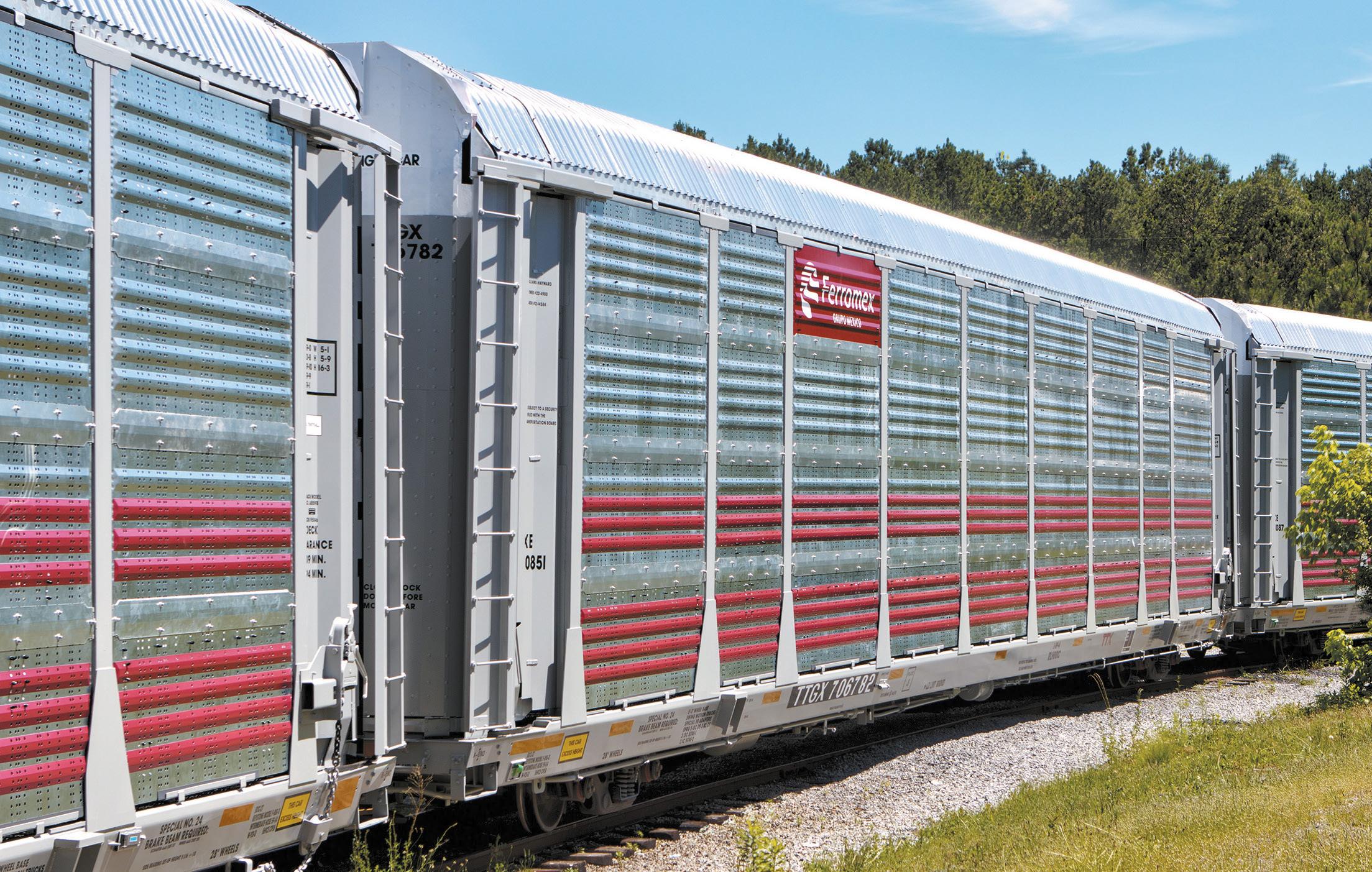
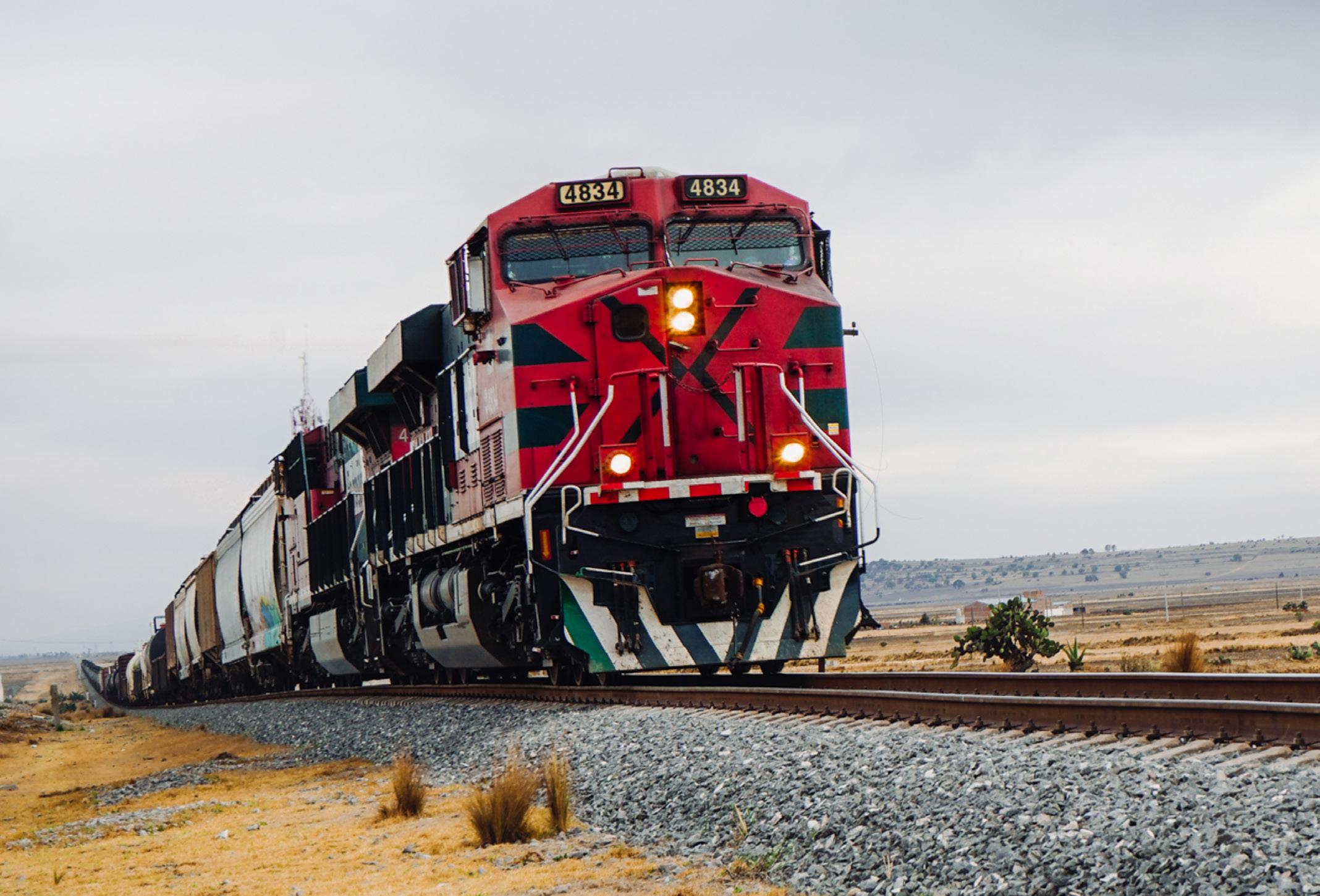
with the regulations put in place by the Secretariat of Infrastructure, Communications and Transport (SICT) and the Energy Regulation Commission, making it a highly trusted cargo operator.
In line with its sustainability commitments, Ferromex has also obtained permits from the Secretariat of Environment and Natural Resources (SEMARNAT) and the Secretariat of National Defense (SEDENA). As such, the company ensures that its activities consider the needs of both planet and country.
Overall, Ferromex transports over 8 million t of goods annually with over 400,000 containers carrying both domestic and global goods.
As timely and safe deliveries are of equal importance to the company, attentive and specialist care is consistently given to each cargo movement, organized and managed with 10 intermodal terminals across Mexico.
ONCE-IN-A-LIFETIME TRIP
From products to passengers, Ferromex also has a highly reputable tourism branch, harnessing its extensive network to create unforgettable experiences across Mexico’s beautiful landscapes through its Chepe Express and Tequila Express destination offerings.
The former took its inaugural trip in May 2018, offering passengers
FERROMEX –2024 IN NUMBERS
• 65 billion tkm
• 1.9 million cars transported
• $1.4 billion in earnings before interest, taxes, depreciation, and amortization (EBITDA).
ultimate comfort through the unique and breathtaking countryside.
Crossing an incredible 350km, passengers also have the opportunity to frequent many quaint and culturally unique towns on the journey.
Over the course of nine hours, the high-speed train travels through picturesque cities such as Los Mochis and Sinaloa before venturing up to the delights of Creel and Chihuahua, alongside Pueblos Mágicos, a truly special place that offers a plethora of festivities.
Passengers have the chance to hop off and explore any of the five stopping points before jumping back onboard to the comfort of the carriage.
With a capacity of 520 passengers across six carriages, Ferromex offers top-of-the-range facilities across its First, Executive, and Tourist Classes. Indeed, the company offers FirstClass passengers exclusive access to
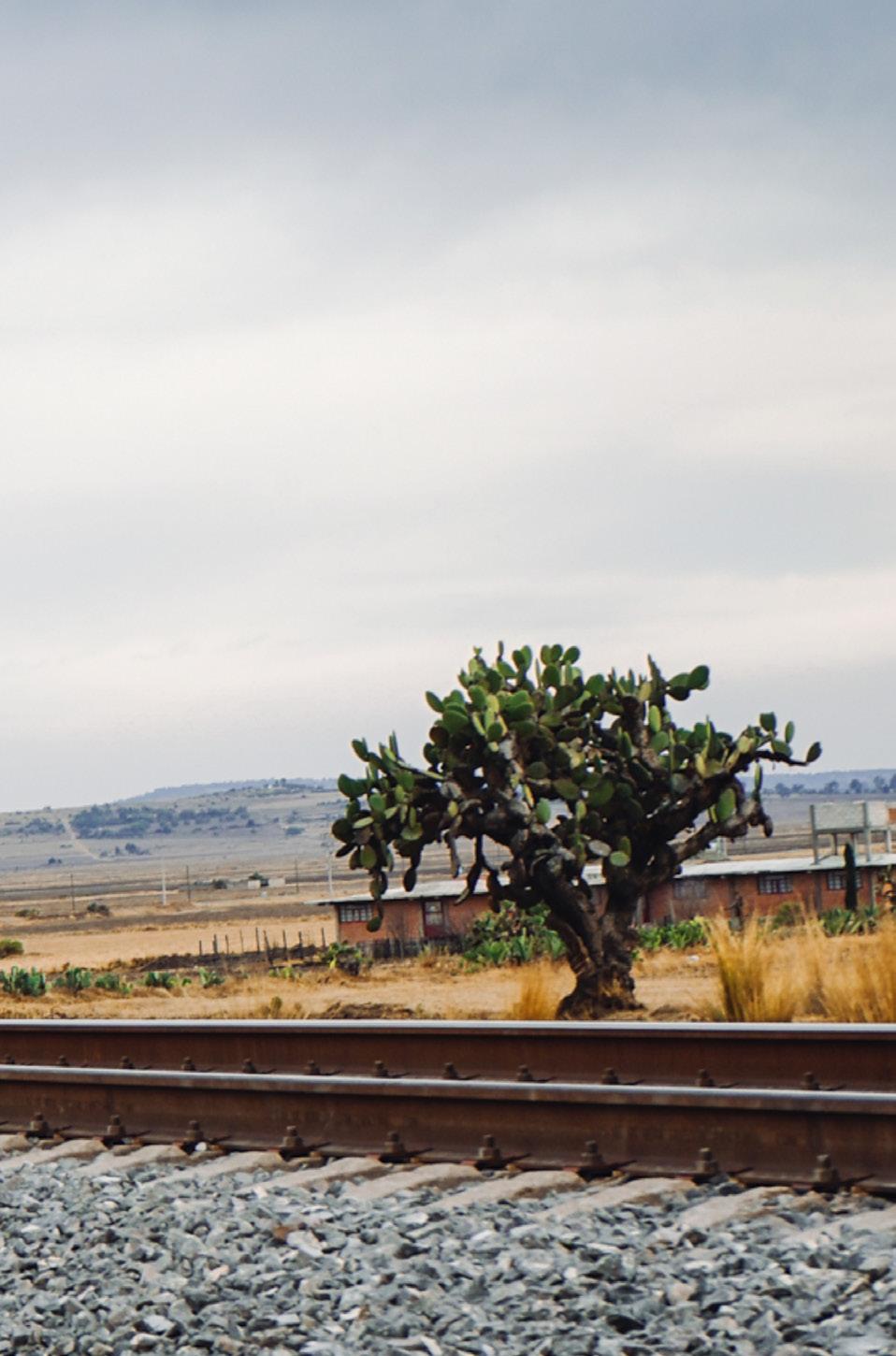
the terrace, while those in Executive Class have access to a bountiful bar.
The Chepe Express also boasts an onboard restaurant that offers authentic and local cuisine to all passengers, ensuring that each individual has the best travel experience possible.
In continuation of its tourism division, Ferromex also offers a luxurious travel experience on the Tequila Express, with guests traveling in style and sophistication from Guadalajara to the town of Tequila, a UNESCO World Heritage Site.
The company purposefully mapped out the most picturesque route, allowing passengers to make the most of the verdant agave landscape with routes only accessible via rail.
The Tequila Express, meanwhile, is a joint venture (JV) between Grupo México and the Guadalajara Chamber of Commerce in which
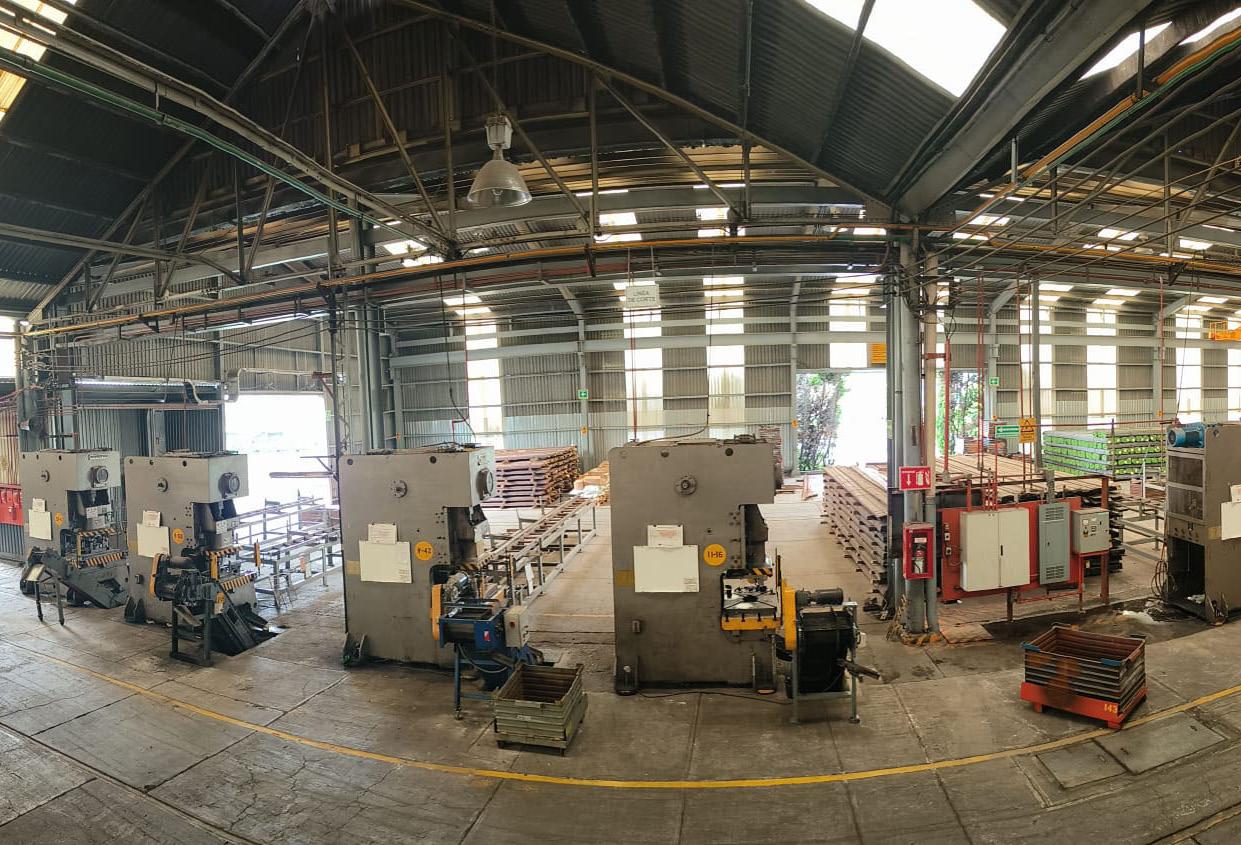
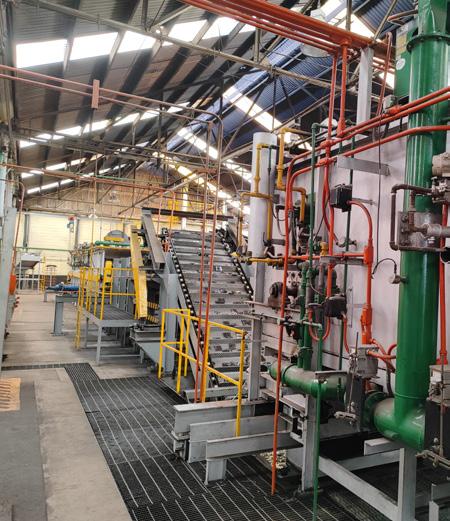
T (011-52-55) 5569-0399
F (011-52-55) 5569-9546
E ventas@nylco.com.mx www.nylco.com.mx
Ferromex offers smooth, relaxing, and safe travel to some of Jalisco’s most unforgettable activities, unmatched gastronomy, and unique terrains.
Additionally, the company’s destination offerings stand out from other rail journeys thanks to its focus on responsible tourism, utilizing one of the most sustainable forms of transportation.
Accordingly, Ferromex’s tourism division doesn’t harm the surrounding environment and allows passengers to fully immerse themselves in Tequila’s cultural heritage while preserving the beloved natural landscape.
SEAMLESS BORDER CROSSING
Looking ahead, Ferromex aims to expand its intermodal activities with a 300 percent increase over the next year.
The expansion project, known as Falcon Premium, will be completed
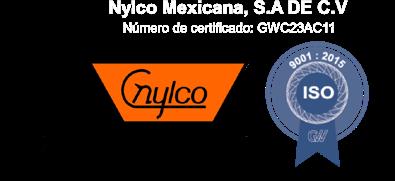
Nylco Mexicana, S.A. de C.V. is founded in 1968 answering the technical and economical necessities of the Mexican railroads and being able to develop, manufacture and test fastening accessories in accordance with international standards.
In our research and development laboratory, we can simulate service conditions, test new products, make dynamic and static tests, detect application problems and suggest select criteria of the best fastening system for customer requirements
as a JV between Union Pacific and Canadian National Railway. Established in 2023, the initiative will create a comprehensive intermodal service spanning Mexico, the US, and Canada in an unparalleled amount of time, offering clients the best connectivity across North America.
While enjoying the benefits of the direct route between Mexico and the US, Ferromex’s customers also have the advantage of reducing their greenhouse gas (GHG) contributions by transporting cargo via rail, contributing to the sustainability of the national supply chain.
Ultimately, the company has become a tenacious force that moves Mexico forward through highly advanced and secure cargo transport operations.
Thus, with the country’s largest network, influence, and industry coverage, Ferromex is on track for continued success.
Home to vast plains and diverse environments, moving goods across Western Australia (WA), the largest state in the country, requires precision and thorough efficiency. As such, WA’s heavy transport sector plays an integral role in the progression of numerous core industries, from mining to agriculture.
Providing cutting-edge logistics services since 1997, Campbell Transport has a history of innovating the bulk haulage industry and has grown to manage the biggest road-legal trucks in the world.
The company expertly oversees more than 200 top-of-the-range vehicles equipped with quad and

triple road trains, making it the largest performance-based standards (PBS) fleet, combined with a supporting plant, and specialist machinery for any load, haul, and maintenance requirements.
The WA PBS Scheme offers improved efficiency by allowing higher productivity vehicle combinations,
THE GO-TO LOGISTICS PROVIDER
We explore the ways in which Campbell Transport has evolved to provide comprehensive logistics services across the breadth of Western Australia, serving multiple industries and guaranteeing truck drivers’ safety
Writer: Lucy Pilgrim | Project Manager: Andrew Lewis
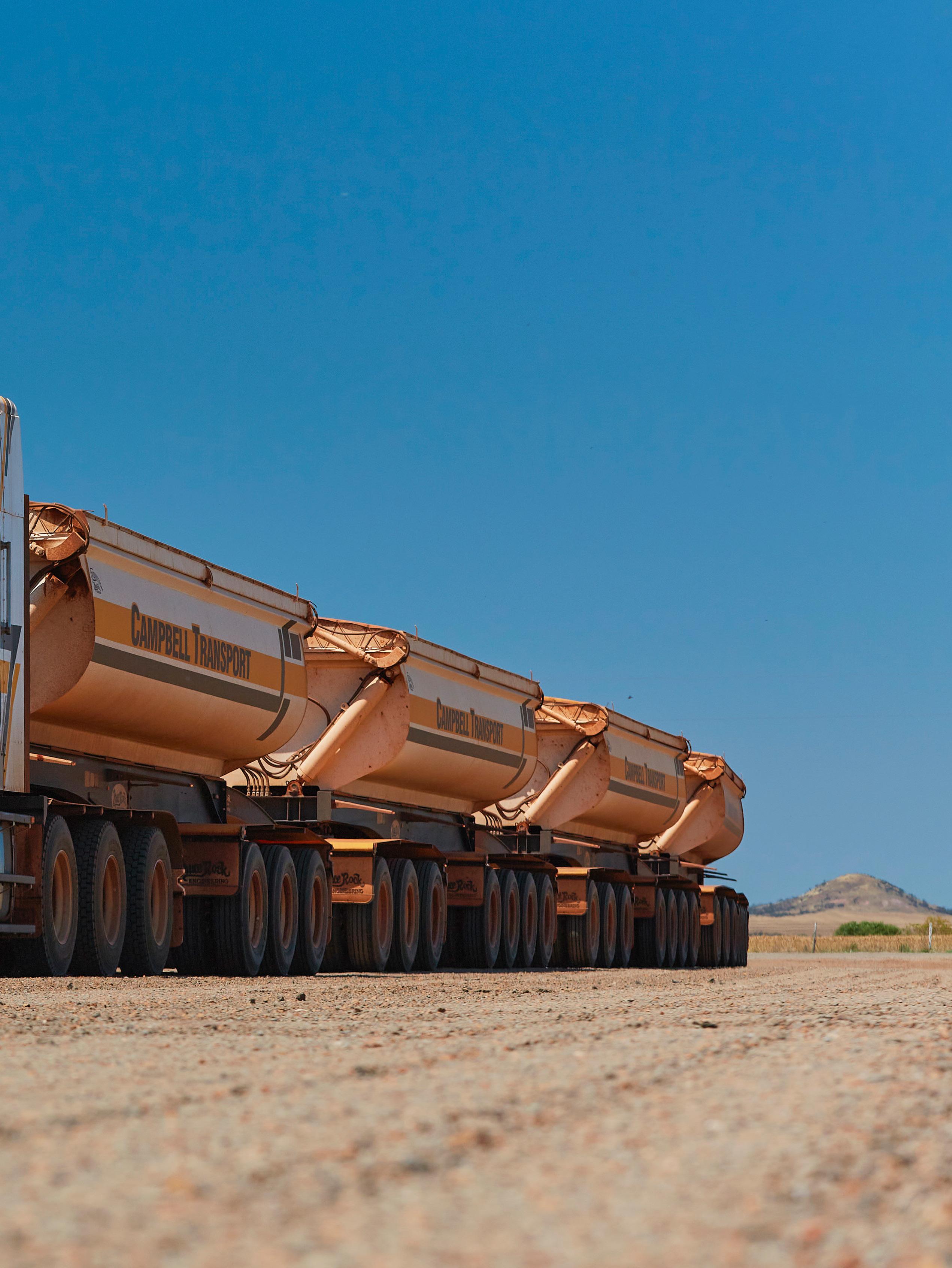
which have been assessed against stringent safety standards to operate on routes that would not typically be approved for prescriptive vehicles with the same mass and dimensions.
Thus, with an unmatched fleet, Campbell Transport is able to cover over 47,531 kilometres across WA, delivering its clients’ goods safely and
efficiently across some of the state’s most remote areas.
MEETING THE NEEDS OF MANY
Since its inception, Campbell Transport has achieved a stronghold in WA’s agricultural sector. For decades, the company has been known for its unmatched grain haulage capabilities
and its capacity to meet the needs of local farmers.
In the last 25 years, Campbell Transport has evolved to meet the changing needs of agribusinesses, initially ensuring the orderly delivery of crops before incorporating fertiliser and chemical transportation into its repertoire.
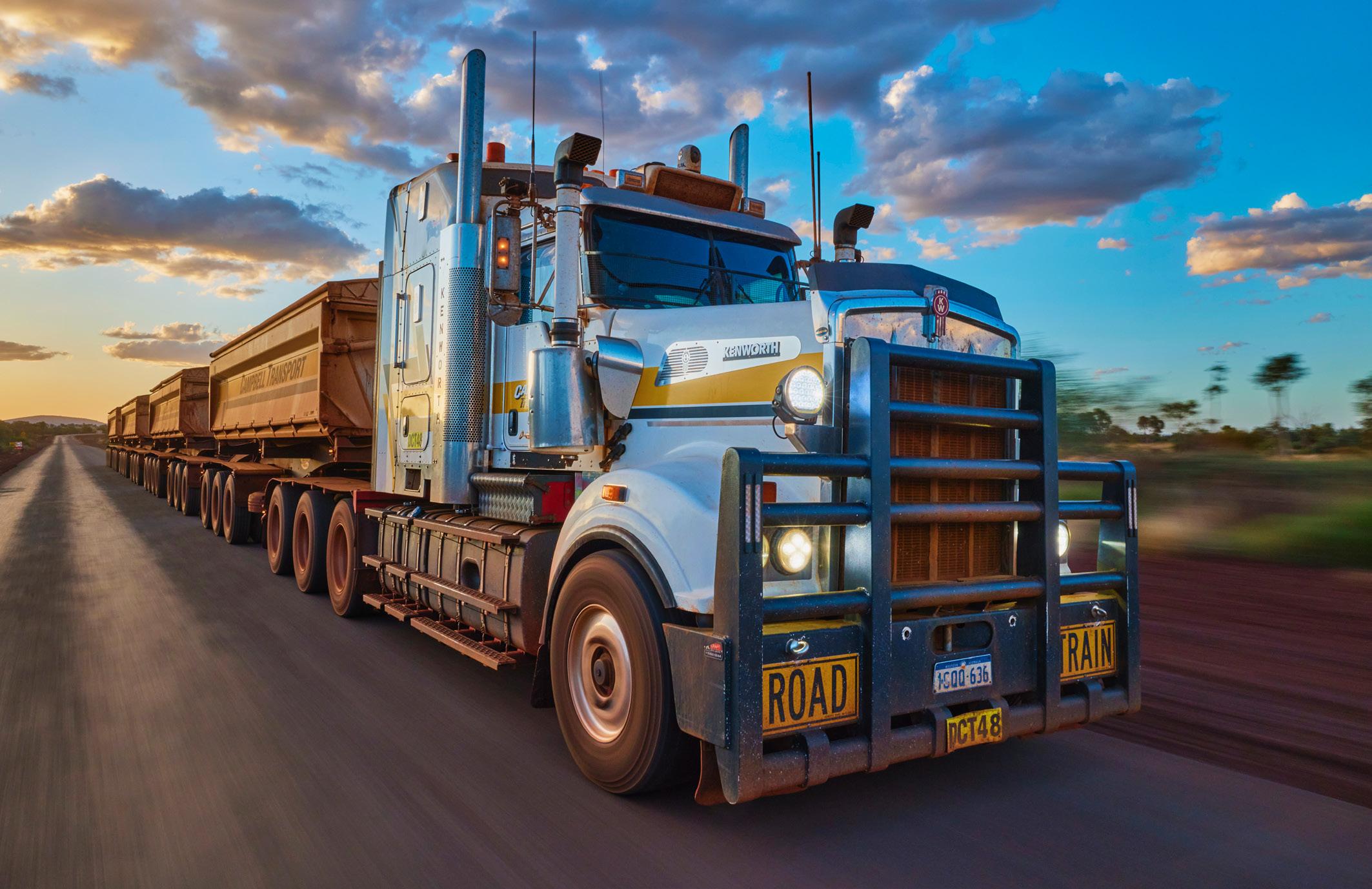
Nowadays, the company also supports the set-up and movement of sizeable agricultural machinery and complex equipment, becoming a vital aid for WA’s largest agrarian organisations.
Seven years ago, Cambell Transport entered the bulk haulage to mining market, providing both on-road and off-road services.
Subsequently, the company took the decision to accelerate its growth by branching out into more general freight operations, offering clients state-wide delivery services across a vast network of highly developed warehousing and depot facilities.
Today, Campbell Transport’s general freight division holds an admirable reputation for the seamless and safe delivery of goods. Leveraging more than 20 years of experience, the company handles a diverse range of freight, including oversized loads, using 24/7 GPS tracking. Therefore, all clients’ logistical needs are met, offering robust and dependable freight management services.
Customers can also rest assured that their products are safely stored in one of the company’s many strategically located warehouses and depots, where goods distribution is managed in an efficient and transparent manner.
Campbell Transport’s depots span WA, including Port Hedland, Perth, Geraldton, Broome, Esperance, Kalgoorlie, Bunbury, and Jerramungup, each with comprehensive warehousing and bulk solutions.
As such, the company’s allencompassing and world-class freight services expertly address business’ most complex storage and warehousing challenges.
FROM PIT TO PORT
Campbell Transport’s cutting-edge general freight and warehousing divisions are accompanied by its trusted mining services, which include drilling and blasting operations, crushing and screening, loading and hauling, and maintenance, making it front
THUNDERBIRD MINERAL SANDS PROJECT
Campbell Transport is proud to be the main carrier for the Thunderbird Mineral Sands Project (Thunderbird) in the Dampier Peninsula in the Kimberley region, WA.
Thunderbird is one of the world’s largest and highest-grade zircon mineral sand deposits, containing valuable minerals, including ilmenite, zircon, leucoxene, and rutile, extracted and exported via the Port of Broome to global markets.

and centre of Campbell Transport’s activities.
Campbell Transport’s mining division is renowned for its adaptability and proactiveness, offering tailor-made and multifaceted approaches to customers’ needs. It also utilises top-of-the-range mining equipment and knowledge of the main roads’ PBS to issue its team with the necessary techniques to ensure maximum operational efficiency.
The WA PBS Scheme is also significant as it means the company can run heavier loads with specially engineered truck combinations.
For each workforce, Campbell Transport also offers on-site accommodation with comfortable facilities and amenities, ensuring that team members have a good standard of living with high-quality camp solutions.
The company’s enviable mining services lend themselves well to its turnkey pit-to-port capabilities for mining activities across WA.
To address the diverse demands of clients, Campbell Transport leverages the combined strength of state-wide bulk storage facilities, purposefully situated close to ports to maximise material transportation.
A highly knowledgeable and experienced team is also available

to clients for pre and bankable feasibility studies to maximise project capabilities and ensure specific supply chain targets are met, whilst also cementing the possibility of future projects.
On top of this, Campbell Transport also boasts a tailormade pit-toport rotating container system that centres around the loading of ore and concentrates into eco-conscious sealed containers for transportation.
The system includes a purposebuilt integrated lid that only
opens and releases a product once the material is within the ships holds.
Regarding the bulk haulage of ores, mineral sands, and other mining products, the company is capable of providing enclosed storage or directto-port deliveries for ship loading.

Leveraging the unparalleled capabilities of industry-leading equipment and a highly professional team, the safe and timely delivery of materials is a Campbell Transport guarantee, allowing clients to focus on their core mining activities.
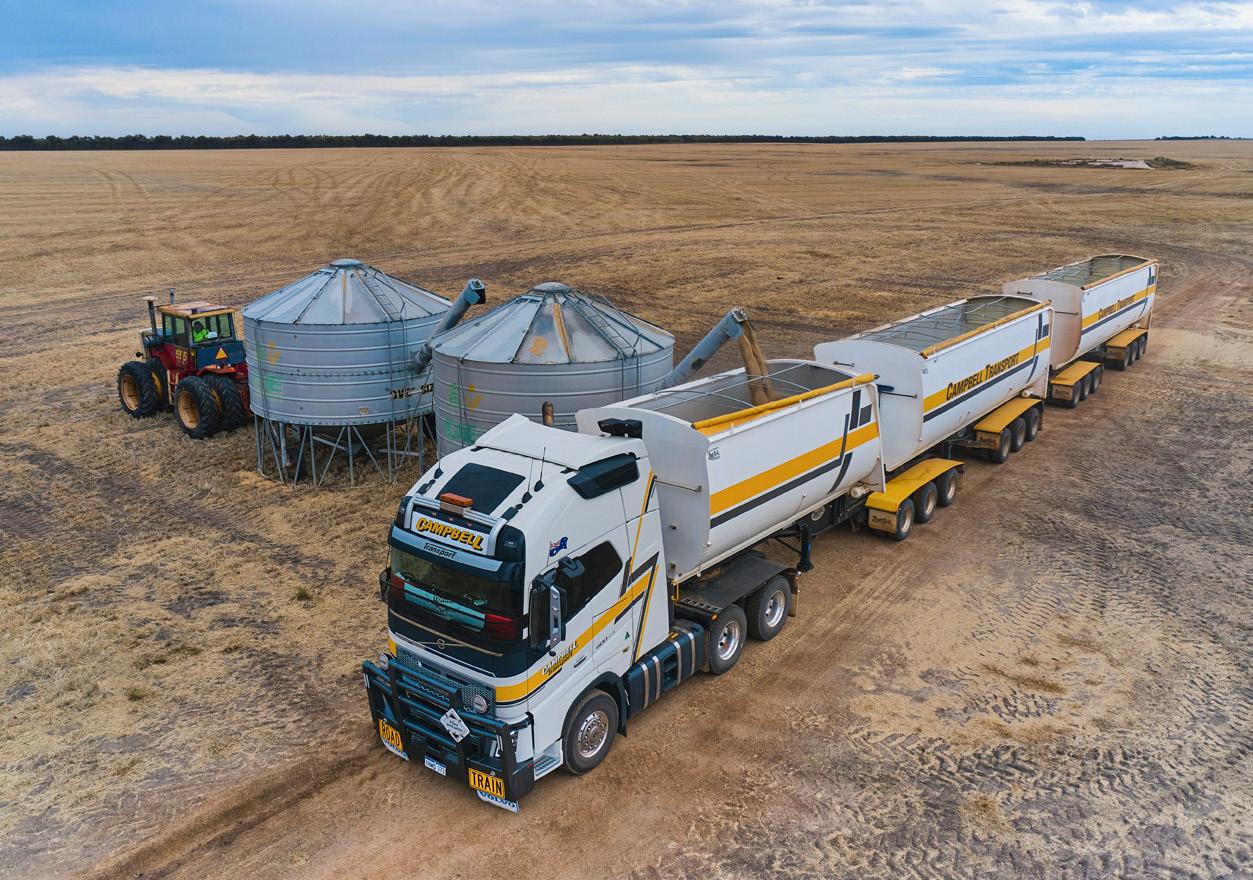
As such, the company is proud to offer end-to-end pit-to-port capabilities for mining operations in WA.
As a trusted industry partner, Campbell Transport understands the complexities involved in drill and blast, mining load and haul, crushing, haulage to port, shed storage, and ship loading. Indeed, the company’s
comprehensive solution ensures seamless coordination and efficient transportation of valuable materials from the mine site to the port.
Campbell Transport has several on-port and nearby bulk storage facilities around WA to cater for any of its current and future clients’ requirements.
COMMITTED TO SAFETY
The high supply and demand of Campbell Transport’s operations mean that its trucks are on the road 24 hours a day, leveraged by a multitude of industries.
With such an extensive and complex operative network, the company has a highly stringent set of safety protocols that have been refined to create a robust and faultless safety system, monitoring the wellbeing of drivers whilst also delivering clients’ needs.
The system comprises a range of equipment that minimises risk for truck operators, including Seeing Machines, who uses cutting-edge software such as proprietary face and eye-tracking algorithms to detect fatigue in drivers working 12 to 14-hour shifts.
This is one of the many instances of real-time in-cab intervention where the driver is told to re-focus their attention. In these cases, Campbell Transport’s 24/7 Fleet Controller Services team are notified and subsequently contact the driver to discuss their fatigue levels and provide adequate advice.
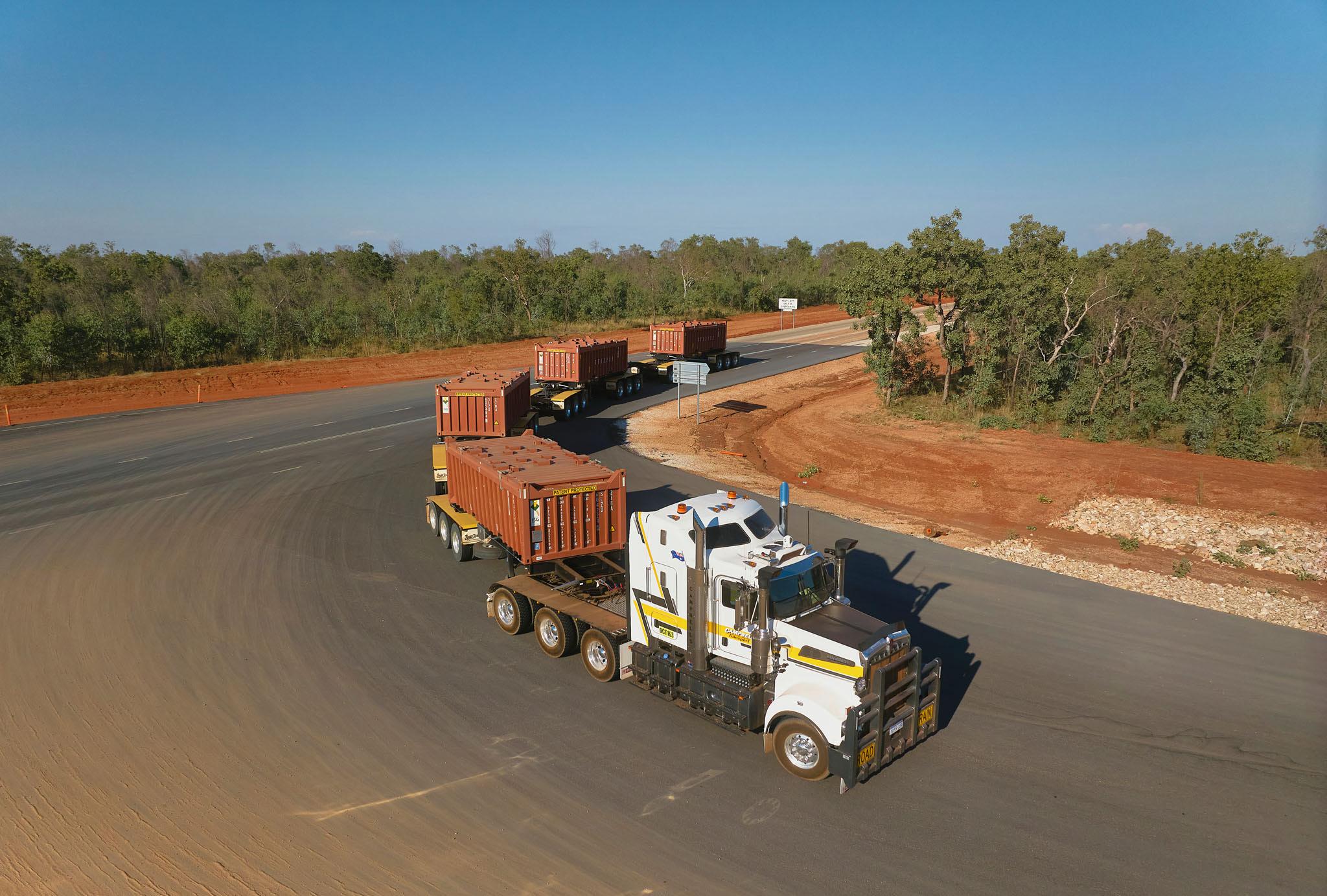
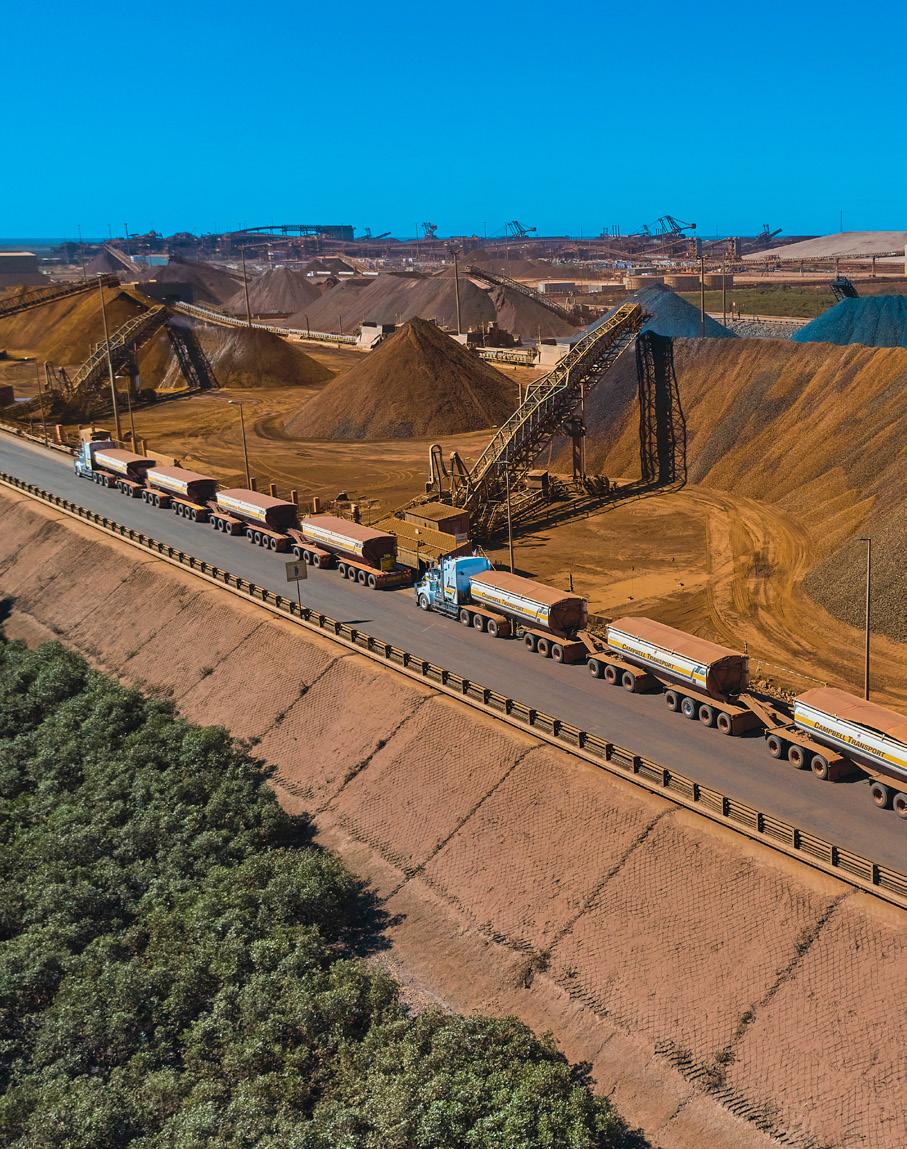
This unobtrusive process prioritises staff welfare and provides a last-ofline defence for drivers, resulting in a significant reduction in driving incidents caused by fatigue.
Drivers’ safety is also monitored by an In Vehicle Monitoring System that gathers critical information and enables around-the-clock observations. The system comprises live GPS and fatigue tracking, truck diagnostics, and the continuous recording of several footage streams.
Regarding the latter, every truck has at least five cameras, each running through an independent system. As a result, in the rare event of an incident, the company knows exactly how and where it occurred. On top of this, a thorough investigation can also be conducted on how best to prevent a reoccurrence.
Given the transportation of goods across many landscapes in WA, the company also recognises the
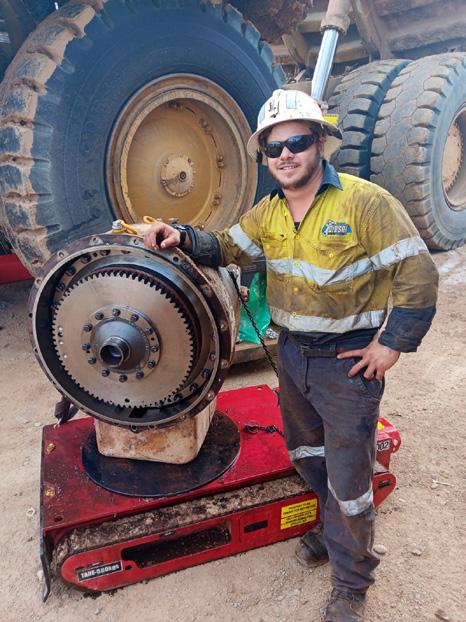
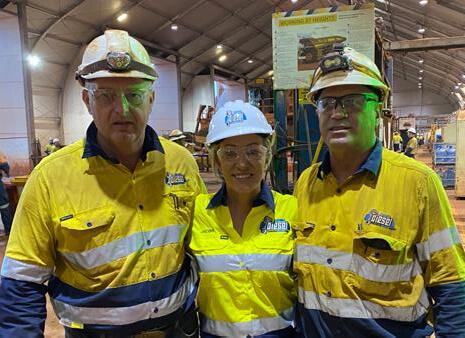
importance of the flora and fauna surrounding its operations. As such, each truck is equipped with ForwardLooking Infrared (FLIR) Thermal Imaging cameras, providing drivers with the visibility to detect heatproducing hazards such as cows, kangaroos, and camels present on the WA’s roads.
This highly-advanced software means drivers can react effectively to any potential incidents, allowing time for greater decision-making when faced with a potential hazard.
Alongside a comprehensive set of safety equipment, Campbell Transport generates regular road reports that create specialist haulage routes that are then examined by a professional safety team, who subsequently publish a detailed report for Main Roads Western Australia – a government body responsible for road access policies across the state.
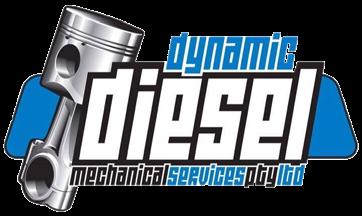
Dynamic Diesel Mechanical Services is your trusted specialist business partner for the provision of highly skilled personnel to the mining, bulk haulage, civil and rail sectors. Established in 2001, Dynamic Diesel has been immensely successful in helping our clients achieve their mission-critical projects and goals. We provide flexible services Australia-wide – whatever you need, wherever you need, we can find the workforce and the solution.
Dynamic Diesel has safety and compliance at the core of everything we do, and our competent personnel always strive for excellence in everything they do.
www.dynamic-diesel.com.au


This detailed and precise report reduces potential incidents, informing the maintenance and repair of many of WA’s arterial roads, including the Great Northern Highway, the Geraldton to Mount Magnet Road, as well as the Coolgardie-Esperance Highway.
Ultimately, Campbell Transport’s trusted and cost-effective transportation and warehousing solutions maximise the operational efficiency and profitability of clients’ projects across multiple industries, whilst also guaranteeing the safety of truck drivers and WA’s flora and fauna.
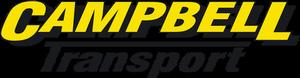
Tel: (08) 9393 9240
perth@campbelltransport.net.au
www.campbelltransport.net.au
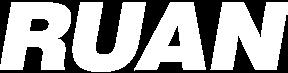
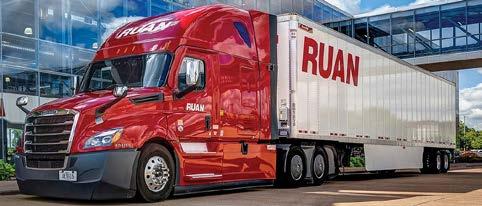
TRUCK COUNTRY IS PROUD TO SUPPORT OUR DEDICATED BUSINESS PARTNER, RUAN TRANSPORTATION. RUAN IS A DYNAMIC CUSTOMER THAT IS DEVOTED TO BEING THE BEST IN THE TRANSPORTATION INDUSTRY.
Our partnership with Truck Country began in 2015 with the acquisition of Freightliner trucks. Since then, they have been a strategic partner, providing exceptional vehicles and support. Their involvement includes driver and technician training and keeping our team proficient and up-to-date, which has been vital to our operational efficiency and overall growth.
— Brad Gehring, Ruan Transportation Vice President, Procurement & Asset Management
At Truck Country, we take a different approach to marketing trucks through our Corporate Fleet Sales program. We are not here to simply sell you trucks. We are here to build long, sustaining business partnerships. We deliver:
• Expert account management
• Dedicated uptime support
• Quality delivery process
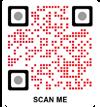

Scan to learn more about Truck Country’s Corporate Fleet Team and what we can do for your fleet.