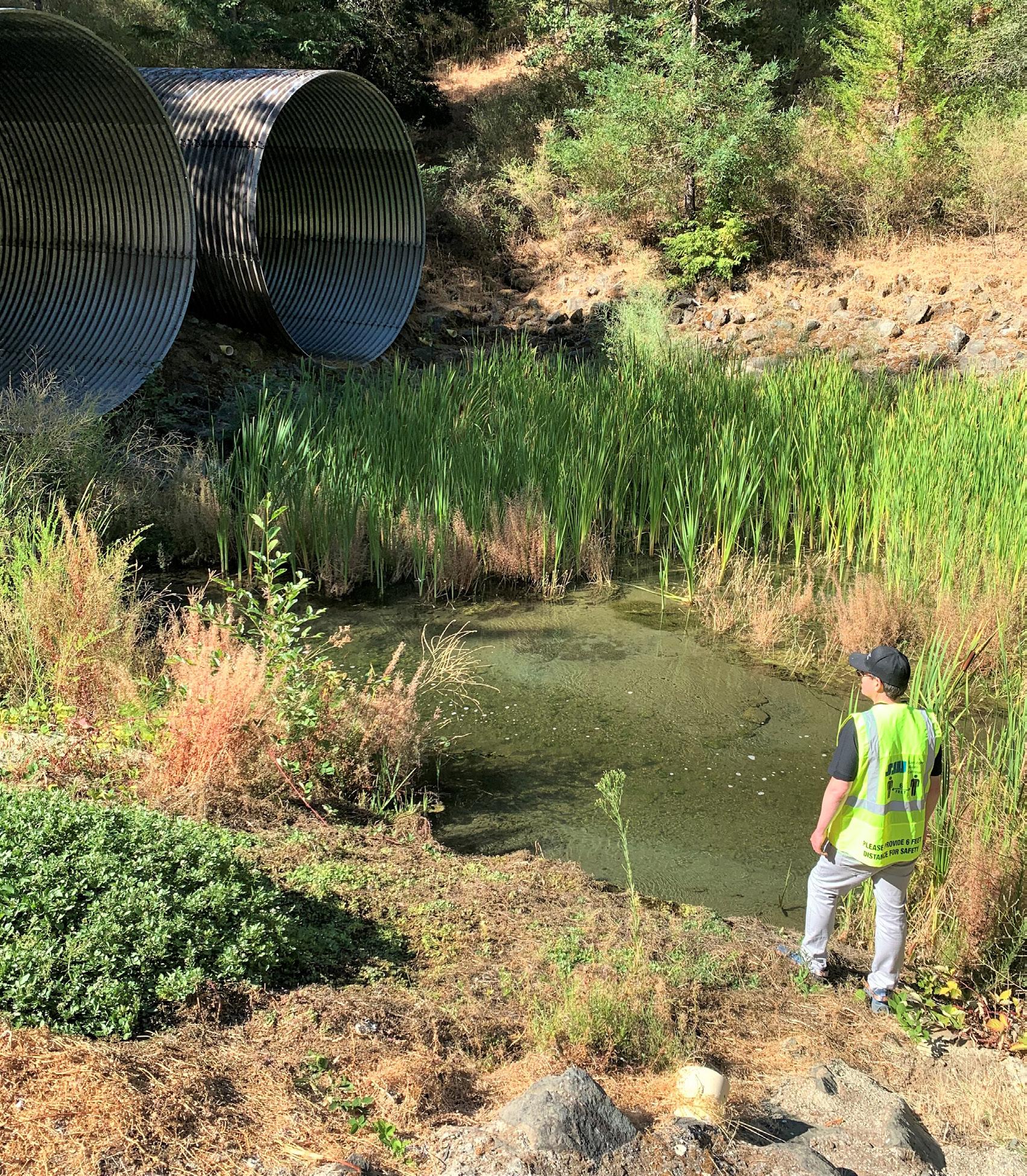
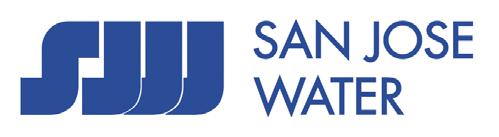
Andrew Gere tells us how San Jose Water is maximizing efficiency and conservation
Writer: Jack Salter | Project Manager: Tom McConnell
The US enjoys one of the safest water supplies in the world.
More than 90 percent of Americans get their tap water from a network of over 148,000 public water systems, often supplied by surface or ground water, which are subject to safe drinking water standards.
In California, San Jose Water (SJW) oversees one of the most technically sophisticated urban water systems in
the US.
“SJW is the largest subsidiary of SJW Group, and serves a population of approximately one million people in the greater San Jose area with highquality, life-sustaining water,” outlines President and COO, Andrew Gere.
To ensure a high quality and reliable water supply for customers, SJW is committed to maintaining and improving its extensive water system,
which comprises more than 2,400 miles of water mains, 95 wells, 100 tanks and reservoirs, 20,000 hydrants, and 35,000 valves.
Almost $120 million is invested by SJW into its water system every year to ensure it can safely and efficiently serve customers today and into the future, especially given the current water shortages facing the Western US.
“We have water scarcity here in the West due to climate change, and we see other parts of the country facing that as well, so we have to change the way we use, store, and treat water,” emphasizes Gere.
“A big part of all this is water affordability, which is not just an SJW challenge but one that is impacting the entire industry. The technological solutions in a sense are the easy part,
Founded in the 1800s, San Jose Water has evolved to be one of the most technically sophisticated urban water systems in the US. With 230,000 service connections, the utility serves over a million residents in the greater San Jose, California metropolitan era.
To help execute on AWS migration and management in order to deliver on an all-cloud initiative, San Jose Water chose managed services from Cascadeo.
“We have a wide range of projects we’re working on, both on the cloud infrastructure side and in terms of the service we provide to the community,” said Stan Blaauw, DevOps Manager at San Jose Water. “We use AWS for both customer-facing and internal projects.”
Any San Jose Water customer, for example, can look up their address to understand the fluoride concentration in their water supply. This uses an API
call to AWS and is displayed on the public sjwater. com website. In terms of employee-facing projects, in addition to enterprise asset management software, Blaauw and his team are working to deploy a GIS application that will be available to employees both in the field and in the office. The goal is a unified experience across devices and locations.
Access to information about water mains, service lines, fire hydrants - information that can be as granular as the size of a pipe, or the year it was installed - is all critical data for San Jose Water to keep the water supply clean, compliant, and reliable. For employees who interact with this data, it increases the ability to provide exceptional customer service and better collaborate with one another, whether that is for new projects, repairs, or advanced troubleshooting.
“What we have appreciated about Cascadeo is the guidance offered in the best ways to use AWS for our
specific use cases,” said Blaauw. “When we engage with a managed service provider, we need experts. We replaced another vendor with Cascadeo, and in addition to bringing technical skills, they also communicate back to us effectively. We continue to gain knowledge just by working with them.”
As part of its commitment to drive innovation and become a cloud first organization, Blaauw said that it’s not just about a particular technology, but also cultural change. “As the company brings on new applications, they might ask me to provision a virtual machine, and I have to ask: is this something we could do instead with AWS?”
At the core of Cascadeo’s managed services practice is re-factoring applications for the public cloud, and surfacing innovation opportunities within the AWS ecosystem.
With over 100 AWS certifications, engineers have the ability to deploy AWS services which help customers move away from legacy data centers, colocation, IaaS, private clouds or any infrastructure that is incumbent on the client to maintain. When freed up from server
or VM administration, teams have more time to focus on answering the questions that are critical to their business. In addition, Cascadeo offers professional services, so IT departments are never left without the people resources to solve problems impacting the organization and their customers.
San Jose Water is an investor-owned public utility serving the greater San Jose metropolitan area with high quality water with an emphasis on exceptional customer service. By sharing these services with others, we benefit the local community, lower the cost of water operations, and improve opportunities.
Cascadeo is the cloud managed services and professional services partner that helps your organization meet internal goals like employee productivity and external goals like customer experience.
www.cascadeo.com
ANDREW GERE, PRESIDENT AND COO: “As a water utility company and as an industry, we’re absolutely tied to ESG principles. We think all those things (environmental, social, governance) are equally important.
“To attract capital, we need investors, and if we are not a trusted place to invest in terms of governance where we’re transparent and well-run, then we’re sort of dead in the water. It’s the same with social and environmental initiatives, which really impact our employees, suppliers, and our standing in the communities we serve.
“We want to reduce our Stage I and Stage II greenhouse gas emissions by 50 percent by 2030 from our 2019 numbers. We’re a huge power user, and even though we’re sourcing renewable power, it needs to remain affordable for customers and not drive rates up to a level where people can’t afford water.
“I look at being strong on ESG as the baseline. We have to start there as a company in the water utility business,
but how do we implement them in such a way that consumers can still afford high quality drinking water? That’s more challenging and we’re working on those solutions.”
SJW harnesses a number of data and technology solutions to maximize water efficiency and conservation, including a Supervisory Control and Data Acquisition (SCADA) system.
SCADA is the leading US urban water management system, complete with real-time monitoring of reservoirs, pumps and water quality, including hazmat and environmental compliance.
“We use SCADA to operate and automate our distribution system. In the old days, you had an operator driving around opening and closing valves, and manually turning on pumps to make sure the tanks were full and the system was pressurized,” Gere tells us.
“Our use of mobile SCADA, which means our operators literally have a data terminal in their truck that’s updating in real-time, gives us constant system status updates. What
we’ve done to enhance that is add real-time pumping plant efficiency.”
Amid a record-breaking heatwave early in September 2022, and forecasts from the California Independent System Operator (ISO) that it would not have enough power to keep the grid up and running, SJW shed a critical 184.6 megawatts of load through its SCADA operations.
“That’s the amount of peak power we would have been operating with. SCADA makes us as efficient as we can be in terms of what’s available on the grid,” explains Gere.
Preventing water loss from underground pipelines, meanwhile, helps SJW to protect water resources and promote sustainability in the community.
Water loss prevention technologies used by SJW include acoustic leak detection sensors, which are placed on special fire hydrant caps and monitor sounds within the SJW water system, to identify any acoustic anomalies indicative of a water leak.
When acoustic anomalies are found, geographic information is automatically sent to SJW’s staff for further investigation, during which leaks are more precisely located usually with a leak correlator or highsensitivity ground microphone.
“We’ve been implementing acoustic leak detection for several years, in partnership with Echologics. We’ve now got upwards of 8,000 sensors deployed; the idea is that you have multiple sensors listening at times when there would not normally be water flow, so they develop a back ground pattern,” Gere shares.
“If they detect an anomaly, we can figure out where that leak is coming from. They help to find non-surfacing leaks with pinpoint accuracy.”
Through acoustic leak detection, SJW has reduced its year-over-year water losses by a substantial 55 million gallons.
“Every million gallons of water that we don’t leak is a million gallons of water that we don’t have to find some where else in a water-scarce state. We’re leveraging technology to make sure that the water resources we have actually make their way to customers, so it’s been really successful,” adds Gere.
After facing one of the worst droughts in US history, in 2017. San Jose Water decided its traditional approach to leak detection would no longer suffice. The company turned to Echologics®, starting with a pilot of the EchoShore®-DX leak monitoring system. After seeing success, San Jose Water adopted the permanent leak monitoring system as an integral part of its water loss control program.
Over the years, San Jose Water has used the acoustic sensors to find leaks and reduce water loss. And, it has expanded its network coverage to include a network of 8,200 leak monitoring sensors. In 2021, the company discovered 121 consumerside leaks and 108 utility-side leaks. In finding and repairing those leaks, the company saved an estimated 200 million gallons (757 million liters) of water that same calendar year – energy savings equivalent to the energy offset of 6,300 trees.
Utilities across North America use the EchoShore-DX leak monitoring system to help protect critical infrastructure, address environmental concerns, and extend pipe asset life. The EchoShore-DX product line recently extended to include both hydrant-based and new, valve-based sensors, to help utilities get coverage where they need it. Echologics is proud to serve San Jose Water and support its conservation efforts.
marketing.mueller.com/ESDXeEqually, SJW’s in-house pipe line replacement model has been enhanced and developed to predict the future performance of water mains.
SJW recognizes that partnering with Diverse Business Enterprises (DBEs) is an important part of the company’s success.
A diverse supply chain enables SJW to be more competitive, and enhances the economic vitality of the communities it serves.
The company is committed to continuously improving its supplier diversity program, which is designed to encourage, recruit, and utilize DBEs within the supply chain.
“Supplier diversity is really important to us. We think it’s good for our communities and makes our business stronger, so we’re very proud of that program,” Gere says.
San Jose Water trusts Grounds Control USA for all its Exterior Facility Maintenance Services. The GCUSA team of experienced professionals helps reduce high operational costs, streamline complex maintenance processes, and eliminate unnecessary work orders.
The model takes input features such as pipe attributes, diameter, material, age, length, leak data, geospatial data and hydraulic modeling, to rank pipe segments in the water system.
“Every three years, we re-rank pipes based on runs of the model. From that, we develop our water main replace ment program, and it has helped tre mendously in our reduction of water loss,” Gere acclaims.
“We’ve also added consequence of failure to the formula, i.e., how many customers would be impacted if a main fails, whether it serves a hospital or a school, what the cost would be to restore service in the event of a failure, etc.”
The combination of the leak detection program as well as the systematic pipe replacements has allowed SJW to enjoy one of the lowest non-revenue water (NRW) system in the industry. SJW’s NRW of 7.5 percent is an incredible accomplishment given the size and age of its water system.
Grounds Control USA was founded in 1986 in a small rural Georgia township located south of Atlanta. Since its humble beginnings over 30 years ago, Grounds Control USA has transformed into a managed services business that helps clients improve the quality of their landscapes, increase efficiency of their service offering, and save money. Headquartered in Charleston, SC, the Grounds Control USA team is available 24/7/365 to handle multi-location exterior needs on a local, regional and national level
Through the use of proprietary management systems, a cuttingedge software stack, vetted field partners, regional support service centers, and over 30 years of experience, Grounds Control USA can streamline exterior facility management programs to provide a consistent level of quality, limit liability and reduce overall cost. Services are available to commercial, industrial, retail, and institutional facilities in all 50 United States.
To learn more visit groundscontrolusa.net groundscontrolusa.net
SJW recently received approval from the California Public Utilities Commission to install Advanced Metering Infrastructure (AMI) throughout its service area, an innovative technology that transforms the way customers and utilities can monitor water usage.
AMI allows consumers to access an online portal or smartphone app, where they can keep track of their usage in real-time.
Water usage data is automatically and securely sent by AMI over a wireless communications network on up to an hourly basis and stored in a cloud-based system. These hourly readings provide a better understanding of the amount of water being used, and allows quick adjustments to be made as needed.
Manual meter readings are currently provided bi-monthly, which drastically reduces customers’ ability to manage their bill, conserve water, and detect
leaks.
“This is a project we’re just kicking off now; we carried out an 18-month AMI pilot in the middle of the last drought, so it was really effective,” Gere informs us.
“During this pilot, we had numerous instances where the system identified abnormal water use in the middle of the night, which would otherwise go undetected.”
AMI technology will allow both customers and SJW staff to work together to minimize water loss from leaks, improve water management, and promote equity and sustainability, resulting in cost-savings and furthering California’s ambitious water conservation goals.
Conservation technologies such as AMI are more critical than ever, with previous droughts in California having left a prolonged impact on communities and scientists predicting that climate change will only continue to affect the state’s water supply.
ICONIX Waterworks is a leading distributor of water, wastewater, civil construction, and mining products. With over 40 locations across North America, our team is dedicated to delivering the products and services you need to keep essential projects running throughout our communities.
We provide innovative water solutions by collaborating with our business partners to maximize technical expertize, reliable inventory, and localized accountability. We do this to bring real time value to the communities we all serve together. We offer an agile, expert team of trusted, technical problem solvers, providing reliable access to innovative water products and services such as gate valves, fire hydrants, service brass, ductile iron pipe and underground sewer, water and storm utilities for businesses and communities across North America.
ICONIX is proud to be part of the Deschênes Group, a family-owned business, consisting of 16 business units and growing. The Deschênes Group is committed to investing in its people and in delivering the best experience to our customers and partners.
The reality of future droughts has changed the way people think about water, as customers increasingly manage their water consumption.
“AMI will reduce our carbon footprint and greenhouse gas emissions because we won’t have people driving around every day manually reading meters. Those people will be kept in the company and put to higher and better uses, such as maintaining AMI and data handling/management,” Gere adds.
“It’s an exciting four-year project. The first year is really focused on building the backbone of the radio transmission system that collects the signals from each of the meters, coalesces them, and sends them up to a data center where all the information is stored and analyzed.
“One of the things that’s really important is making sure the data accuracy is there. We’ll continue testing AMI before the system goes live to make sure customers have confidence in the technology.”
Recent droughts have made it abundantly clear that water is a finite resource.
It’s therefore also important for water providers such as SJW to team up with industry organizations to recycle wastewater, treat and disinfect it for use in irrigation and other non-potable applications, and save unrecycled water for potable uses.
SJW works in partnership with the City of San Jose, which operates the South Bay Water Recycling (SBWR) program that is designed to provide a sustainable, high-quality water supply and reduce the region’s dependence on imported water.
“Water supply is going to continue to be critical for us. We need to begin looking at how we can enhance our water supply resiliency, so we’re work ing closely with the City of San Jose to grow SBWR,” acknowledges Gere.
Though recycled water is not intended for drinking water applications, it nevertheless
significantly boosts SJW’s potable water supply by taking its place in other areas such as irrigation in public parks.
Every drop of recycled non-potable water used for irrigation purposes stretches the area’s supply of potable water even further.
“Non-potable recycled water that’s used for irrigating a park or a golf course, or used in an industrial cooling tower or data center, provides an offset of fresh potable water available for customers.”
Just last year, SJW also completed a strategic water supply assessment in which it looked at current and forecasted future demand, and is now undertaking a feasibility study for brackish groundwater desalination.
“These are generational investments that we need to make in water resources. They are not inexpensive, but when we look at the next 30 to 50 years, we think we need to be a player in that,” Gere states.
“A project of that scale may require us to use a different financing model and look for state and federal grants, or have other partners come in.”
In 2018, SJW unveiled its upgraded Montevina water treatment plant, following the completion of more than $60 million in infrastructure improvements.
This included the installation of BASF’s leading-edge ultrafiltration membrane technology to modernize the facility, clean and remove bacteria and viruses from water, and ensure it meets the highest available water
safety standards.
The plant can now treat between three and five billion gallons of water each year, serving 100,000 people during the summer months and up to 300,000 in winter.
“In California we typically get these big winter storms, and even though we have a reservoir in the water system that can hold two billion gallons, it’s relatively small for the watershed that supplies it. In a typical year, only about a third of the water would be stored, whilst the remaining two-thirds would be treated right off the creeks,” Gere says.
“WATER SUPPLY IS GOING TO CONTINUE TO BE CRITICAL FOR US. WE NEED TO BEGIN LOOKING AT HOW WE CAN ENHANCE AND GROW WATER SUPPLY OURSELVES”
– ANDREW GERE, PRESIDENT AND COO, SJW
“We pipe water down to the treatment plant from seven creek impoundments and treat it in realtime, but we were having to turn the plant off when it was about to hit its turbidity limit, so we knew that we needed to upgrade the treatment plant.
“At the same time, disinfection by-product standards were getting tougher and tougher. We had already built a microfiltration plant in 1994, the first municipal-scale membrane plant in the US, so we knew membranes were the way to go,” he continues.
Able to treat just about every storm condition, SJW has also reduced its disinfection by-products at the upgraded plant, making it a tremendous success from both a
water use efficiency and public health standpoint.
To minimize the amount of water loss during construction, SJW carried out a progressive design build in which it had a lot of input into the construction sequencing, technology and membrane selection.
Rather than destroying the old plant, which has stood next to the Lexington Reservoir since 1970, SJW repurposed a lot of the existing facilities.
“For example, we took the old filter boxes and converted them into sedimentation basins. We did some seismic reinforcing and obviously reworked a bunch of controls and pipes, but we retained the big civil structures,” Gere reveals.
SJW’s biggest investment, however, is in its people, who are easily the company’s most important asset.
“Pipes, pumps and tanks are fairly universal, but people are what make our business and our industry really special. We really focus on internal promotion and career development.
“This is an industry that you can build a career in, and we survey our employees twice a year to help us improve and make SJW a better place to work,” concludes Gere.