
THE PEERLESS PARTNER IN EUROPEAN TRANSPORT

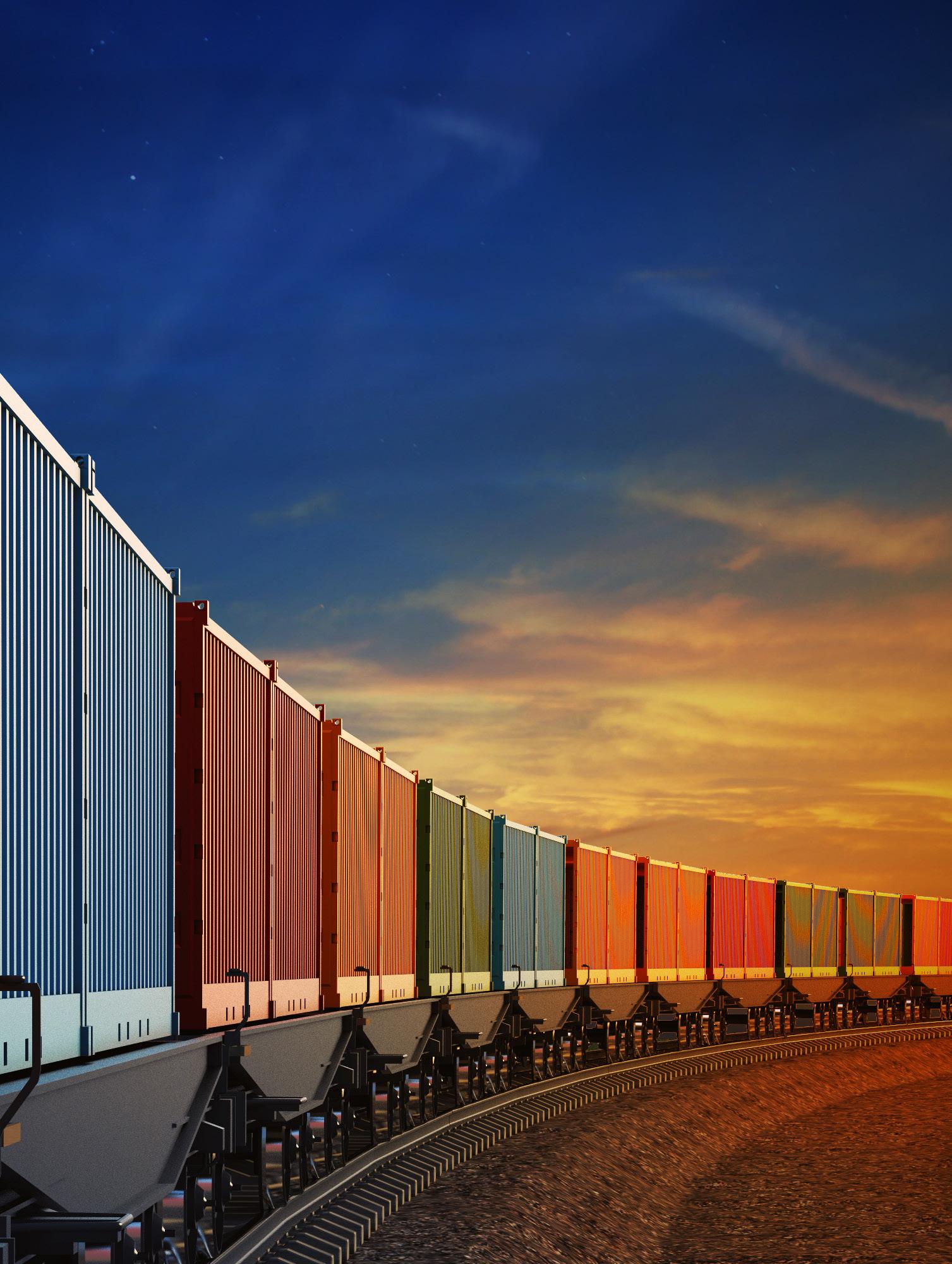
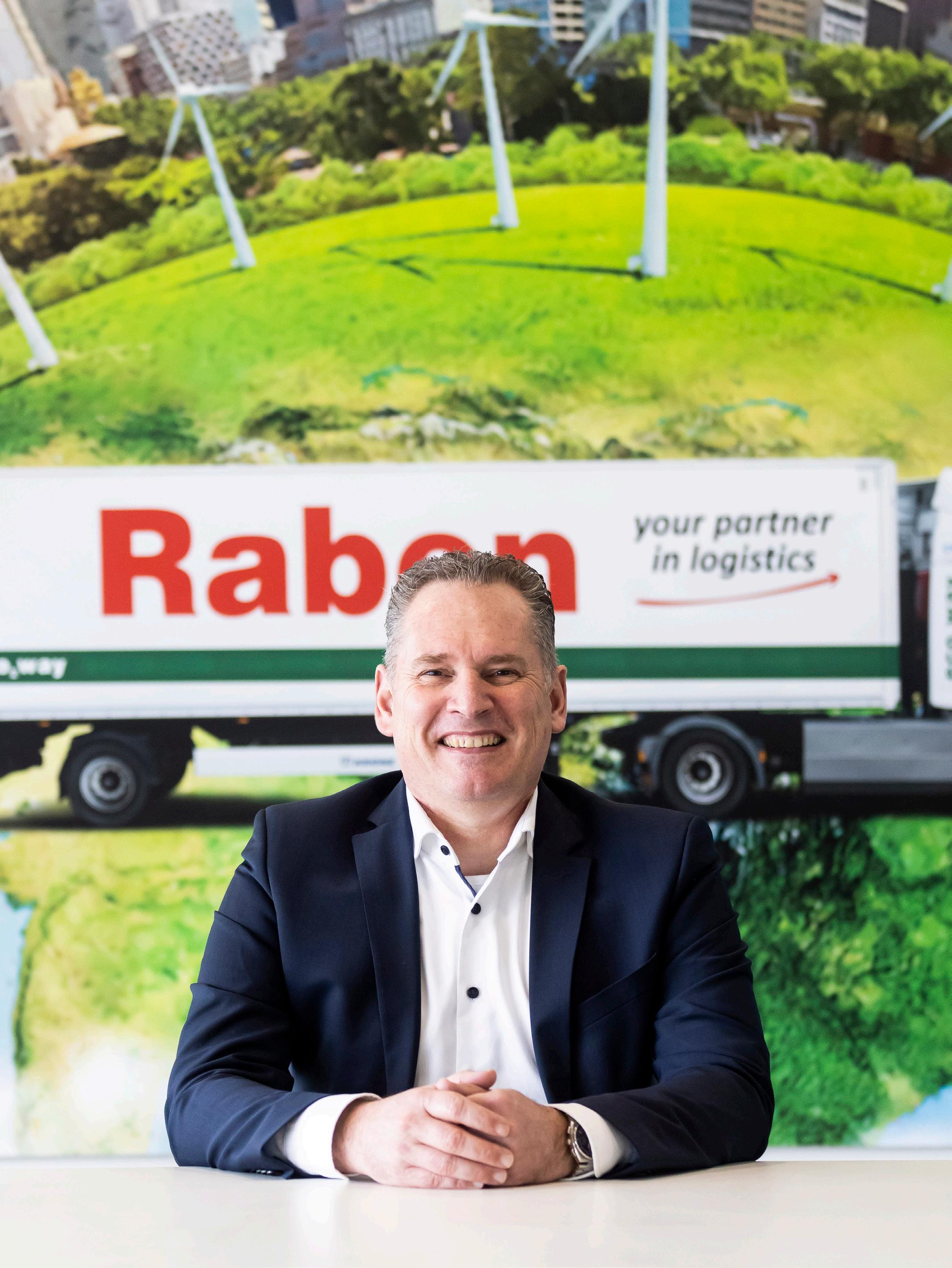
Thanks to a reliable fleet of transport and an extensive network of depots and modern warehouses across Europe, Raben Netherlands is proud to deliver the highest quality logistics services. We track the road to success with Managing Director, Berend Jan Schuring
Writer: Ed Budds | Project Manager: Cameron Lawrence
Endeavouring to form exceptional working partnerships with our clients, together we aim to satisfy the customer of our customer.”
Raben Netherlands (Raben) sits proudly as one of the 15 individual branches of the Raben Group, which specialises in road transport and contract logistics across a burgeoning multitude of locations in the Netherlands and across Europe.
“Together, we organise the best solutions to ensure all processes are as efficient as possible. At this moment, it is very important to offer a solid network with high performance
for customers,” introduces Berend Jan Schuring, the company’s Managing Director.
At present, many prominent players in the transport and logistics industry are encountering problems with selling their stock. Consequently, this means warehouses are full and the throughput is lacking the ability to roll out enough product.
In the face of this struggle currently swamping the sector, Raben recently built two extra warehouses in EttenLeur and Oss to increase its ability to store goods for both ongoing and new customers. This in turn facilitates the company’s capacity and network to
help new clients to achieve their best possible business outcomes.
Raben has almost 400 employees at present, dispersed to cater to a highly diverse client base of customers that profit from the company’s full supply chain solutions for transport and contract logistics, such as MGA Entertainment and CM Logistics.
“Transport and logistics are always an exciting world to work in as every single day is different and you continually face new challenges, but it also gives you a lot of energy if you can help your customers to deliver the right service and provide solutions for them,” Schuring sets out.
Adhering to its motto “Enginuity”, the perfect combination of engineering and ingenuity, Kässbohrer meets the needs of its customers in more than 55 countries in all sectors, including general cargo, cold chain, construction, liquid and bulk goods, and intermodal, with its unrivalled range as well as heavy and abnormal goods transportation.
Kässbohrer is unique in Europe with its competence to meet the needs of the entire tranport sector with 96 percent coverage of all needs through more than 1,000 unique products.
Founded in 1893 in Germany, Kässbohrer today is Europe’s top innovative international trailer manufacturer with an annual production capacity of 20,000 trailers, serving its European customers from multiple head offices in Germany, the Netherlands, Spain, France, Italy and Poland along with carefully selected sales partners in the UK and Nordic countries.
As of 2022, the leading semi-trailer Kässbohrer is among the overall top three choices in the Netherlands and Sweden. Kässbohrer is among the top three in tanks and silos in Germany. For heavy haulage, Kässbohrer is the market leader in low beds in Poland, and among the top three in France for platforms. With its strong local organisation, Kässbohrer is rapidly meeting its customers’ needs in Italy by doubling its sales and tripling its sales in Spain.
Not only with its robust, efficient, long life and high quality vehicles but also through its services, Kässbohrer meets the needs of its customers. Kässbohrer operates the fourth largest after sales service network in Europe with its competent certified after sales partners and carries out its spare parts operations from its manufacturing facilities as well as from France. In cooperation with leading leasing companies, Kässbohrer presents competitive financing options under K-Finance in Germany, Spain, Italy, Poland and France. Kässbohrer is continuing to develop its sales and after sales activities in the UK.
Most importantly, Kässbohrer stands out for its innovation competence, by constantly developing its products and services to meet the unmet needs of its customer. Kässbohrer prioritised collaboration with its stakeholders, foremost customers, associations, universities, research programmes as well as its premium suppliers together
in a wide R&D ecosystem to constantly advance trailer technology to take its customers to the next 125 years.
Established in 2009, Kässbohrer
R&D has completed more than 250 R&D projects and published 108 international academic articles as well as participating in European Comission backed R&D projects. As a result, in 2022 alone, Kässbohrer launched 18 new vehicles with over 50 innovations. Apart from customer satisfaction, Kässbohrer’s competence in furthering trailer technology is presented with the awards and nominations we have received, especially at the most prestigious Trailer Innovation Awards.
Kässbohrer has won the Trailer Innovation Award 2017 in the “Safety” category for its safety Bitumen tanker with electronic discharger the Trailer Innovation Award 2019 in “Chassis” category for its Novel Octagonal Frame Multifunctional Container Chassis, the Trailer Innovation Award 2021 in the “Components” category with the Multifunctional Rear Bumper RUPD-5K1, the second place winner of “Body” category with 45ft Rulo Swap Body Body, and “Smart Trailer” with Trailer Advanced Driver Assistance Systems, and the Trailer Innovation Award 2023 in the “Safety” category with its Integrity Protection Device.
As the transport sector welcomes the new European climate law, committed to at least 55 percent carbon emission reduction by 2030, an ambitious transition awaits our industry pending further legislation. In this time of transforming the transport business, Kässbohrer is equally competent in all technologies and vehicle developments to work with our customers on their unique need for transition.
Kässbohrer presents the next generation of higher capacity vehicles, including 32-metre (m) combinations already on the road in countries where the transport is permissible, in addition to our innovation award nominee 14.98m curtainsider and its unrivalled
intermodal range to support more ecofriendly intermodal transportation.
Kässbohrer is able to meet all combinations in the LHV concept, from type 1 to 5. An example is our 32m combinations used in Scandinavian countries; two semi-trailers can be combined in a single truck with our 2-axle dolly vehicle. Kässbohrer 32m Super Eco Combi (SEC) presents the highest efficiency in terms of sustainability through higher capacity in terms of two vehicles, and a mega upper structure for higher vehicle capacity as well as intermodality compatibility. Our SEC developments have recently been tested in the Netherlands with the attendance of ministers.
Kässbohrer is proudly unrivalled in the intermodal product range with it’s vehicles. Kässbohrer is the most reliable manufacturer, especially when the new EU green deal targets that 75 percent of all road traffic should switch to intermodal operations. With the entire Kässbohrer container chassis
family including award winning avmh, the lightest range of swap bodiesincluding the first ever 45ft coil swap body - and the most robust and longlasting huckepack products developed with Enginuity, we offer our customers’ the highest quality, longest lifetime as well as low TCO solutions as we are committed to meet our customers’ unique transition and the environment’s urgent needs.
Kässbohrer Dry Freight Intermodal Plywood Box K.SBT T is engineered for environmentally-friendly intermodal transportation. The vehicle is supplied with crane pockets and is suitable for e, f, g and i type railway wagons according to IRS 50596-6 as standard.
Kässbohrer Dry Freight Intermodal Plywood Box K.SBT T is robust for safety and longevity of your operations while its many options improves operational efficiency.
Dry Freight Intermodal Plywood Box stands out with its robustness through 20mm thick smooth plywood walls, 7.2 tonne forklift capacity phenol resin coated plywood floor as standard, EN 12642 Code XL certificated upper structure and KTL Coated Steel Front Panel.
Dry Freight Intermodal Plywood Box’s options are ingeniously designed to further your operational efficiency.
The optional insulated roof is coated with glass fibre reinforced polyester to protect against humidity and prolong product life, the double deck option increases the capacity to 66 euro pallets, lashing rails to improve load safety, and turtle mechanical locks increase security against theft. In order to increase the robustness of the box body, the trailer is equipped with 4mm thick and 325mm height high-quality heavy duty type steel kick plates which are welded to the chassis.
Although many of Raben’s processes are automated and the company remains confident in its IT solutions, its trusted team members must still make the key decisions.
Raben’s team plays the crucial role of supporting its clients, answering any questions and making sure that every transport link is safe, on time and serviced with a smile.
“Our international Raben network enables us to be the trusted local operator for our closest clients and an internationally established operator with transport solutions throughout the whole of Europe for the multinationals who seek the best performance,” describes Schuring.
Furthermore, Raben is connected with over 160 depots in Europe, which are all designed for a combination of groupage, part truck load and full truck load transport. Additionally, by
keeping most of its transport within its own organisation, the goods of Raben’s clients are always kept in the safe hands of the company’s people, trucks and facilities.
“We have a solid intermodal connection via rail between the Benelux region and Italy. This sustainable transport is part of the solution in reducing our CO2 emissions and we are currently piloting intermodal connections to other Raben countries, such as Poland as well,” he tells us.
The invaluable use of IT solutions helps Raben make its services accessible to the company’s valued customers. Clients can then simply request a quick price, put their order into the MyRaben system and follow their shipment with real time tracking information.
With the opening of its new cross
docking terminal in Heerlen, Raben looks to take the next step in expanding its services throughout the Benelux region. This will make the company less dependent on third parties and gives Raben more exposure in a vitally important part of its network.
Growth is always top of the agenda and remains a primary goal for the Raben Group as a whole, both within current markets and for fresh ones. “We grow with the aim to provide better and more complete solutions for our customers, and the fourth Raben depot in Heerlen is a great example of this. We were already active in Belgium and Luxembourg, with Etten-Leur as the main hub for transport to the south, but now with the opening of the Raben Heerlen depot, our trucks can enter Belgium from two directions,” affirms Schuring.
Another recent indication of the company’s expansion into new markets is the intermodal pilot between the Netherlands and Poland. “Because of the difference between regular road network and rail transport, we must adapt our solutions to a different kind of customer. We invested in new intermodal compatible trailers and now we must keep working on expanding our services even further.”
If the solutions are reliable and customers know what they can expect from the company and intermodal transport in general, Schuring is confident that they will start to find their way to Raben in great numbers.
Raben is constantly on the lookout for people with drive, entrepreneurship and who proactively face challenges and take responsibility.
“Our employees get a lot of freedom within certain boundaries, and we believe that this empowers them to come up with solutions and
really own their work,” quantifies Schuring.
A productive workforce cannot exist without a comfortable workplace, both in a physical and sociological manner.
Addressing this concern, Raben uses fully adjustable chairs, sit-stand desks, height adjustable monitors, electric pallet trucks with active suspension adjusted to the weight of the user, pallet reach trucks with a rotating workstation to prevent neck and back injuries for warehouse employees, and fully optimised truck interiors for all drivers.
“We organise events for our depots and our entire organisation, like a big barbecue in the summer. We stimulate and support our employees by encouraging participation in sporting events and every Friday we end the week together in the canteen evaluating and sharing our weekend plans,” he elaborates.
Wanting to create the safest possible environment for all its colleagues, Raben has appointed confidants who are there to address any difficulties or complaints that the employee may be having that they feel like they can’t discuss with management. Raben employees can also enjoy a range of company training platforms.
“We have an internal training platform for all the systems we use in Raben, but we also made an online training centre available in which employees
can follow classes on pretty much any subject.”
The company’s drivers are a prime example of this, receiving regular training and information sessions to keep them up to date on safe and economical driving and the best practices for unloading.
Pivotal to the company’s future prosperity and strategic growth, Raben culminates this ambition with a set of carefully measured goals for
“OUR EMPLOYEES GET A LOT OF FREEDOM WITHIN CERTAIN BOUNDARIES, AND WE BELIEVE THAT THIS EMPOWERS THEM TO COME UP WITH SOLUTIONS AND REALLY OWN THEIR WORK”
– BEREND JAN SCHURING, MANAGING DIRECTOR, RABEN NETHERLANDS
both the entire Raben Group and within the local organisation.
The Raben Group’s key goals to be achieved by 2025 include a 30 percent reduction in CO2 intensity from offices and warehouses and a 10 percent reduction from transport activities. This runs parallel to its aim of increasing the ratio of female managers from 29 percent in 2020, to 34 percent across the next two years.
On a more specific and local level, Raben’s main objective for the coming years is to fill its own network.
“We aim to make the most of every trip. By filling every trailer, we reduce CO2 emissions per kilogramme. As a result, we can offer better pricing for our customers and at the same time gain a benefit in revenue,” Schuring says.
The company is also looking to expand its warehouse capacity and services.
“With the completion of our
warehouse in Etten-Leur in 2022 and the near completion of a new warehouse in Oss this year, we are really pushing our contract logistics services to a new standard. More capacity means more available space for us to find new customers and to expand existing partnerships, but it also means that there will be more opportunities for us to improve our services,” he adds.
Elsewhere, Raben has set itself the target of increasing its Y-Z generation employees by 20 percent believing that whoever has the youth, has the future. In this way, the company aims for a sustainable organisation where people can grow together. Finding new talents and creating an environment in which they can and want to keep growing is one of the other main points of focus in the coming years.
Finally, although sea and air
transport already play pivotal roles in Raben’s operations across other countries, the Netherlands is yet to launch these solutions. Evidently there are plenty of opportunities to do so, considering the excellent geographical positioning between the harbours of Rotterdam and Antwerp and the airports of Amsterdam and Eindhoven.
This exciting scope for expansion and enhancement looks certain to catapult Raben straight to the very forefront of the transport and logistics industry.