
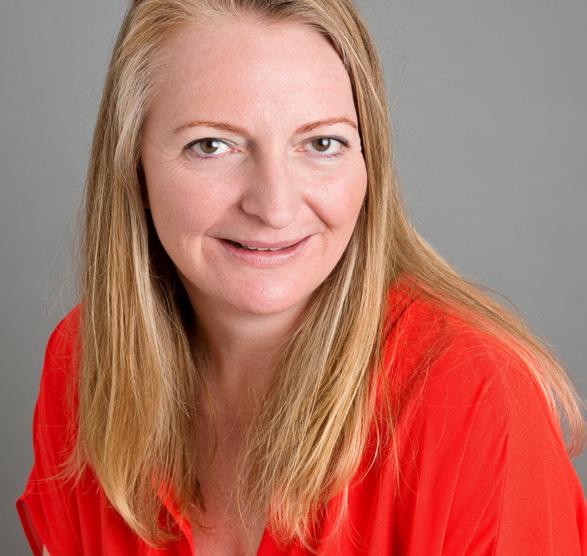
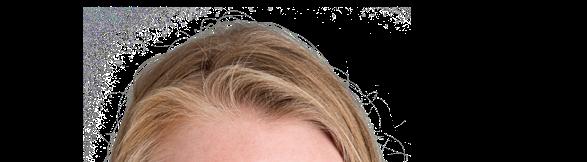
For over a decade, our portfolio of in-house magazines has been lovingly produced, printed, and distributed to our esteemed subscribers across the globe from our headquarters in the UK.
But now we are moving with the times, adopting a digital-first approach by producing online-only publications. A major factor in this decision is to minimise our environmental footprint, reducing the carbon emissions involved in the logistics of print magazine distribution and the resources required therein.
Going forward, we will provide print orders of any magazine in-line with the requests of our featured companies, subscribers, and conference & expo partners.
Please get in touch for a print-on-demand quote or visit our website to find out more.
“We always planned that when our digital subscribers consistently accounted for 85% of our total magazine subscribers, we would cease printing our publications in-line with our environmental and sustainability goals.”
– Ben Weaver, CEO, Outlook Publishing Ltd
EDITORIAL
Editorial Director: Phoebe Harper phoebe.harper@outlookpublishing.com
Senior Editor: Marcus Kääpä marcus.kaapa@outlookpublishing.com
Editor: Jack Salter jack.salter@outlookpublishing.com
Junior Editor: Ed Budds ed.budds@outlookpublishing.com
Junior Editor: Rachel Carr rachel.carr@outlookpublishing.com
PRODUCTION
Production Director: Stephen Giles steve.giles@outlookpublishing.com
Senior Designer: Devon Collins devon.collins@outlookpublishing.com
Designer: Sophs Forte sophs.forte@outlookpublishing.com
Junior Designer: Louisa Martin louisa.martin@outlookpublishing.com
Production Assistant: Megan Cooke megan.cooke@outlookpublishing.com
Digital Marketing Manager: Fox Tucker fox.tucker@outlookpublishing.com
Social Media Executive: Bria Clarke bria.clarke@outlookpublishing.com
Web Editor: Oliver Shrouder oliver.shrouder@outlookpublishing.com
BUSINESS CEO: Ben Weaver ben.weaver@outlookpublishing.com
Managing Director: James Mitchell james.mitchell@outlookpublishing.com
Sales Director: Nick Norris nick.norris@outlookpublishing.com
Regional Director: Joshua Mann joshua.mann@outlookpublishing.com
TRAINING & DEVELOPMENT MANAGER
Marvin Iseghehi marvin.Iseghehi@outlookpublishing.com
BUSINESS DEVELOPMENT DIRECTOR
Thomas Arnold thomas.arnold@outlookpublishing.com
HEADS OF PROJECTS
Callam Waller callam.waller@outlookpublishing.com
Deane Anderton deane.anderton@outlookpublishing.com
Eddie Clinton eddie.clinton@outlookpublishing.com
Josh Hyland josh.hyland@outlookpublishing.com
Ryan Gray ryan.gray@outlookpublishing.com
PROJECT MANAGERS
Olando Greenock olando.greenock@outlookpublishing.com
SALES MANAGERS
SALES & PARTNERSHIPS MANAGER
Donovan Smith donovan.smith@outlookpublishing.com
Alfie Wilson alfie.wilson@outlookpublishing.com
Krisha Canlas krisha.canlas@outlookpublishing.com
ADMINISTRATION
Finance Director: Suzanne Welsh suzanne.welsh@outlookpublishing.com
Finance Assistant: Suzie Kittle suzie.kittle@outlookpublishing.com
Finance Assistant: Victoria McAllister victoria.mcallister@outlookpublishing.com
CONTACT
Mining Outlook
First Floor, Norvic House, 29-33 Chapelfield Road Norwich, NR2 1RP, United Kingdom.
Sales: +44 (0) 1603 363 631
Editorial: +44 (0) 1603 363 655
SUBSCRIPTIONS
Tel: +44 (0) 1603 363 655
phoebe.harper@outlookpublishing.com www.mining-outlook.com
Like us on Facebook: facebook.com/miningoutlook Follow us on Twitter: @MiningOutlook
It is my pleasure to introduce the inaugural issue of Mining Outlook – a new multi-channel brand brought to you by Outlook Publishing, dedicated to foregrounding the global mining sector. As mining organisations worldwide confront unprecedented change, embracing technological innovations and incorporating critical environmental sustainability agendas, we decided that now more than ever is the time to showcase the strides being taken in this dynamic industry.
The first of our quarterly magazines does exactly that, as we take a deep dive into some major titans of industry from across the international resources sector. In South Africa, HCI Coal talks us through operations at the Palesa mine as the responsible mining company pursues growth and diversification beyond coal to remain relevant in a changing resource market.
“We need to be cognisant of the fact that coal will not be the commodity of choice in the long-term due to the environmental impacts,” shares co-CEO Pieter Terblanche.
Meanwhile, in the resource-rich territory of Brazil, we speak with the industry association driving a nation-wide responsible mining agenda in conversation with the Instituto Brasileiro de Mineração (IBRAM).
In other exclusive corporates stories, we have had the pleasure of collaborating with iconic names such as De Beers Group, Hitachi Construction Machinery Australia, Batchfire Resources and Stornoway Diamonds Canada.
Finally, be sure to check out our Industry Insights, where we highlight some of the newest developments and most exciting innovations redefining mining today.
We hope that you will join us in this exciting new venture, and enjoy your read.
Phoebe Harper Editorial Director, Outlook Publishing16 Instituto Brasileiro de Mineração (IBRAM)
Unearthing an abundance of assets in South America’s largest country
22 Wyoming Mining Association (WMA)
Inside the state’s industrial and economic lifeblood
28 Québec Mining Association (QMA)
Developing a responsible source of critical minerals
THE DEMAND FOR copper has increased to meet the green targets set out by the Paris Agreement as the metal plays a crucial role in achieving net zero.
The mining industry needs to deliver copper supplies with frequency and consistency to successfully reach carbon zero over the next 30 years. This would require
an investment of USD$23 billion per year.
The necessity for copper will continue to grow as the metal is a vital component in green technologies, from renewable energy infrastructure to electric vehicles (EVs). It is expected that demand will increase by three percent each year for the next decade.
CORA GOLD, THE West Africafocused gold explorer, is accelerating the development of its flagship Sanankoro Gold Project in southern Mali. It plans to raise at least USD$19.6 million through equitable fundraising and convertible loan notes. The company has already received binding commitments of USD$20 million.
HECLA MINING (HECLA) has reported the highest silver reserves in its 130-year history. The increase was due to discoveries at Greens Creek in Alaska and the addition of Keno Hill in Yukon.
The acquisition of Keno Hill added nearly 50 million silver ounces to Hecla’s reserve base, where two surface core drills confirmed highgrade silver mineralisation in three areas.
As silver is important in the energy transition to renewables, Hecla is in a good position with the largest silver reserve in the US, and the highest grade and largest primary silver reserve in Canada.
The shareholders continue to support the project’s development, with the largest shareholder being gold producer, Hummingbird Resources.
Cora Gold has project areas within two known gold belts in Mali and Senegal, with the former being one of Africa’s biggest gold producers, hosting companies such as Barrick Gold and B2Gold.
MINING EQUIPMENT AND services provider, Epiroc, will continue to support Roy Hill – an iron ore project in the Pilbara region of Western Australia (WA) – as it enters the final stage of its autonomous haulage system (AHS). The announcement from Epiroc, who is
SRG GLOBAL HAS secured two contracts, including a significant five-year contract, with Northern Star Resources Limited (Northern Star) at its Bronzewing Gold Mine in WA. The contracts have been valued at AUD$220 million.
The second contract, a two-year
partnering with automation specialist ASI Mining on the project, comes after a successful two-year testing phase.
The smart mine is expanding its AHS by converting its mixed fleet of conventional haul trucks to driverless operation from March. In addition, 233 modified ancillary vehicles will interact with the autonomous haul trucks to create the world’s single largest autonomous mine.
AS IT CONTINUES to diversify its global portfolio of energy assets, Idemitsu Australia has made a strategic investment in leading Australia-based lithium exploration company Red Dirt Metals.
The initial investment of AUD$5 million will give Idemitsu Australia approximately 2.3 percent of issued shares. The move is in line with plans to invest in high-growth markets such as lithium.
The proceeds from the capital raised by Red Dirt Metals will be used to progress drilling, mining studies, environmental approvals, and working capital for both the Mount Ida and Yinnetharra lithium projects.
extension of the initial agreement, is at Northern Star’s Thunderbox Operation, and Carosue Dam gold mines in WA.
The scope of services at all locations includes the provision of specialist drill and blast services, explosive management, and grade control drilling. Work at the Bronzewing has already commenced.
AFTER RECEIVING STRONG support from new and existing investors, underground drilling has commenced at Eagle Mountain Mining’s Oracle Ridge project in Arizona, with the aim of increasing copper resources. The company is delving back into the bountiful mine, where there has been no significant drilling in 25 years.
Underground drilling is expected to be more efficient than drilling from the surface. With refurbishment work on the mine recently completed, activities are being ramped up. The company will prioritise drilling aimed at upgrading existing Inferred and Indicated Resources into higher confidence Indicated and Measured Resources, respectively.
Traditionally, the mining sector has been cautious to embrace digital innovation. Frequently operating in remote locations, with poor network bandwidth, limited scalability, and challenging physical terrains, digital transformation and the long-term culture change that comes with it has often been side-lined to prioritise immediate project outputs. Accordingly, BCG’s 2021 Digital Acceleration Index (DAI) reveals that metals and mining businesses are approximately 30-40 percent less digitally mature than comparable industries, such as automotive and chemicals.
However, things now appear to be changing. Post-pandemic pressures, supply chain challenges, and economic uncertainties are causing organisations to rethink how their mining operations are performed. A renewed interest in modern digital technologies has come to the fore – not only as a means of improving efficiency and resilience at a time of economic downturn, but also to gain a
stronger long-term competitive edge over more conservative peers.
By accelerating the adoption of automation and digital capabilities to build the agile, secure, and intelligent mines of the future, businesses stand to connect and optimise the entire value chain, quickly delivering return on investment and unlocking longlasting value both below and above the ground.
The success of any mining digital transformation project is influenced by how effective the mechanisms and tools are by which data is moved from one part of the value chain to the next, especially when it comes to aggregating the gathered data to achieve a comprehensive view of how one part of mining operations affects another. Consequently, this data needs to be managed efficiently to support the planning, control, and decisionmaking that underpins the intelligent mine of the future.
Difficult decisions are made daily
by various departments, making it all too easy to operate within isolated data silos. With greater transparency around the impacts of each challenge, mine management can adapt and change course in a way that reduces disruption and maximises productivity, profitability, and predictability.
The mining sector now has an opportunity to implement single solutions that automate data gathering from various processes and facilities, using tools that detect bad data, process it in the correct context, and yield insight in a meaningful and actionable timeframe.
But the insight derived from good data is just one piece of the puzzle. Mining companies need to leverage advanced machine learning (ML) technologies to learn from and improve in the future, in order to remain agile and resilient in decades to come.
Traditional maintenance practices often fail to deliver the benchmark equipment availability, performance, and reliability required to shape the varying schedules upon which financial projections and corporate targets are based. This not only impacts quarterly profitability but can also undermine confidence in operational leadership, which
has knock-on effects on investor sentiment.
Modern prescriptive maintenance solutions are different. Utilising asset sensor data to proactively monitor equipment for imminent and future failures, the technology empowers companies to collaborate and plan around predicted downtime, rather than having to reactively muddle through it. For example, prescriptive maintenance technology can assess the health of numerous machines every few minutes, delivering insights around equipment performance to maintenance teams, often with prescriptive advice that addresses the bad actors and known issues.
Furthermore, prescriptive maintenance and artificial intelligence (AI)-powered technology is key to integrating, co-ordinating, and optimising the entire value chain, from the extraction of raw materials to the delivery of products to customers. Tailored to suit specific work environments and processes, new technologies are bringing improved operational efficiencies across the board, while also lowering costs. Not only does this help to avoid the lost revenue and profits associated with downtime, but it also gives teams more time to evaluate and prepare, allowing them to get ready for future complex challenges including meeting ambitious net zero targets, and facing increased competition and equipment maintenance costs.
Human interpretation simply isn’t capable of deriving the insights this technology delivers. The applications monitor many variables on behalf of the workers, who receive warnings to help determine which issues to prioritise.
An asset performance management (APM) approach, with integrated prescriptive maintenance capabilities, can support the mining sector in enhancing reliability, availability
and uptime while reducing the requirement and expense of redundant equipment.
Operations teams have long planned for lower availability, often installing more machines or truck fleets than they necessarily need. With the right technology, mines can achieve benchmark reliability without the need for more people, more equipment, or higher budgets. Companies can work at the required production levels, consistently delivering to the short-, medium-, and longterm plans and projections that investors and markets demand.
Mines can also implement other aspects of APM programmes to draw on data from sensors and other sources, from enterprise resource planning (ERP) systems and manufacturing execution systems (MES) to laboratory management information systems and advanced process control (APC) systems. Sourcing this data will ultimately benefit the entire value chain, as teams will have the visibility needed to identify bottlenecks, improve troubleshooting, and ensure safer and more profitable end-to-end operations.
To achieve a truly intelligent mine, the industry must now seize the opportunity to embrace and use digital optimisation technologies. Investing in the right solutions will help mining companies to improve productivity and profitability at scale, resulting in innovative new business models across the entire mining value chain.
Operators that fail to adapt, or are slow to advance on their digital transformation journey, are likely to
struggle when competing against more forward-facing businesses. Therefore, prescriptive maintenance applications are increasingly needed to bring fast, measurable results, delivering significant reductions in downtime, reducing safety risks, and ensuring the entire mining operation can meet tomorrow’s challenges with greater efficiency, transparency and agility.
Dr Jeannette McGill is Vice President and General Manager of Metals and Mining at AspenTech. As the second woman to be issued an underground blasting certificate in the Free State Province, South Africa, she brings invaluable metals and mining production experience to drive sustainable business growth.
Jeannette has a PhD from the Colorado School of Mines and in 2016 was identified as one of the Top 100 most influential women in mining globally.
Geologist, Emily King has considerable experience leading mineral exploration programmes in emerging, frontier, and post-conflict markets including Afghanistan, Libya, Algeria, Tunisia, and Mexico.
After working for the Department of Defense in collaboration with the Afghan Ministry of Mining and the US Geological Survey to digitise historical data, collect new data on 15 mineral deposits throughout Afghanistan, and execute four tenders of early stage copper and gold assets, King started her first company, Global Venture Consulting, to help natural resource companies enter emerging and frontier markets.
In 2020, she went on to found Prospector, an artificial intelligence (AI)-enabled search engine for the industry designed to help investors find and fund mining assets. Alongside her roles at Prospector and Global Venture Consulting, King also holds board level leadership positions at various organisations including Vice President (VP) of Women in Mining
Writer: Phoebe Harper
USA, Director at VVC Exploration, Director at Welsbach Technology Metals Acquisition Corp, and Director of Analog Gold. Keen to stimulate conversation around the mining industry and its future relevance, King also entertains regular guests as host of the On The Rocks podcast.
Throughout her career, she has been awarded the Medal of Merit by American Mining Hall of Fame, the Secretary of Defense Medal for Outstanding Public Service, the Global War on Terrorism Award, and a Joint Civilian Service Commendation Award. We speak with her to find out more.
Mining Outlook (MO): What led you to create Prospector? Could you tell us a bit about how the platform works?
Emily King (EK): I was walking the floor of the Prospectors & Developers Association Canada in Toronto in 2019 and had the idea for a platform and app that would allow me to search for exploration and mining projects easily – so I didn’t have to go on Sedar to find 43-101 reports! I also wanted to be able to follow companies and projects and share my findings with colleagues without everyone working from different Excel spreadsheets.
Prospector allows a user to search the world’s publicly traded TSX and ASX exploration and mining companies’ disclosure documents. It is built to work like a search engine that combs through over 10,000 projects owned by over 2,800 companies to find just the data you’re looking for, all in a simple, easy-to-use interface.
MO: Tell us more about the On the Rocks podcast?
EK: On the Rocks started as a fun way to connect with friends from the mining industry during COVID-19 –we would hop on and chat about the industry, projects, and problems or trends we saw over a cocktail. I’m a big fan of bourbon, so we tape each episode over a drink – though sometimes we’re taping early in the day so I’m stuck with coffee. I want listeners to walk away learning something about what we do in
mining, why it’s important to the world, and see that we have great adventures with cool people.
MO: Why is it so important to you to promote gender diversity and the greater education of women within the mining industry?
EK: Mining and exploration are critical to what our world is doing now and will do in the future, and I want to make sure women are a part of that. I believe it’s important to have diversity of all kinds within the industry to make sure we are incorporating all viewpoints and perspectives as we prepare to supply the world with the resources we need for the future we all want.
MO: Finally, as a mining futurist, what predictions do you see for the industry in the years ahead? How do you forecast its development over the next decade?
EK: I see the mining industry as working more closely with technology companies of all kinds, to help visionaries make the future a reality. I believe we will be critical to space exploration, deep sea exploration, as well as the development of lifechanging tools in healthcare, mobility, electrification, and analytics. We are a fundamental partner for any company looking toward the future, and I predict our industry will be more closely aligned with and integrated with those firms in the next decade as new minerals are needed and more metals are consumed to make that future possible.
“MINING AND EXPLORATION ARE CRITICAL TO WHAT OUR WORLD IS DOING NOW AND WILL DO IN THE FUTURE, AND I WANT TO MAKE SURE WOMEN ARE A PART OF THAT” – EMILY KING, FOUNDER, PROSPECTOR
The continuation of the Ukraine war and resulting sanctions which have been imposed on Russia have resulted in a violent shift in the global oil and natural gas markets, as well as major disruptions to energy supplies and agricultural resources.
Additionally, the spiralling shortages of basic supplies and dwindling reserves of precious metals are increasingly concerning Africa’s business leaders, as the effects of this scarcity continue to exacerbate multiple industries.
“The sanctions against Russia –one of the world’s largest exporters of raw materials – is causing knock-on effects that are rippling throughout many spheres of business, from the sustainability of Africa’s mining
Africa is currently experiencing great uncertainties over its base and precious metals supply. We examine whether the continent is ready to tackle this challenge
operations to the stable functioning of the manufacturing base,” details Igor Hulak, a Partner at Kearney, the leading global management
Due to foreign shipping operations being suspended, a chaotic domino effect has been triggered, causing a drastic worldwide shipping container shortage. Existing
infrastructure is currently proving insufficient as a method of handling the redirection of materials through Asia, so a broad range of industries are continuing to search for solutions.
This collection of dramatic sanctions and shutdowns looks set to continue to affect Africa’s consumers, leading to increased prices for both food and fuel.
Further adding to this tumultuous time for the industry, over the course of the last 12 months, the five base metals that Russia produces on a vast scale - nickel, aluminium, copper, iron, and zinc - have all seen dramatic increases in price.
“Nickel, which is a critical ingredient in lithium-ion batteries and essential for global energy transitions such as in Africa, is in short supply. Russian companies such as Norilsk Nickel, the world’s largest nickel producer, had
historically supplied global markets. However, the sanctions have made Russia, which accounts for roughly 10 percent of the global share of nickel, unable to meet this demand,” Hulak notes.
“This deficit in global supply presents an opportunity for African nickel producers, such as Zimbabwe and Botswana, to step in and fill the gap. However, overcoming existing inadequate export infrastructure will be a major challenge, requiring government to buy-in and a collaborative multi-sector approach. Though the challenges are formidable, Africa must find a way to seize this opportunity and emerge as a key player in the new global metals market,” he asserts. Precious metal prices have, by contrast, shown less volatility. However, as these too are crucial to the electric economy, experts are continuing to warn that price increases are still very much on the cards.
According to Hulak, market and pricing drivers are currently indicating long-term price increases for the platinum group metals. This presents a golden opportunity for South Africa, which is still the world’s largest producer of these metals, to step in and fill the supply gaps. Moreover, this is a unique opportunity for South Africa to leverage its already strong position and expand its operations in the sector to meet the escalating global demand.
“Traditionally a reliable safe-haven investment, gold (of which Russia is a major producer) is likely to see moderate price increases. This could work in favour of Africa’s gold production powerhouses like Ghana and South Africa.”
At this pivotal crossroads for
the energy transition, the major concern now is whether the market can find enough of the critical raw materials needed to support it. Apart from exacerbating the disruptions driven by the COVID-19 pandemic, these supply shocks are compounding the price pressures associated with this global shift and the resources this requires.
Supply disruptions are projected to continue to place strain on global markets, therefore some companies may need to pivot or scale down operations in order to withstand the current strains and maintain their workload.
Africa however, with its wealth of natural resources, such as many of the basic and precious metals currently facing shortages, could allow the continent to potentially leverage the opportunities surfaced by the shift towards an electric economy. By taking full advantage of these resources,
chain, and vitally, create new jobs.
To conclude, the balance in global supply will not change significantly, yet still, for some commodities, like nickel and other precious metals, price increases unfortunately look like they’re settling down for the long haul.
Igor Hulak is a Partner at Kearney, the leading business consulting and services provider predominantly responsible for supporting a multitude of clients active in the resources and energy value chain, in both the private and public sectors across the Middle East and Africa.
Drawing from more than 25 years of varied industry senior management and consulting experience predominantly within the industrial and energy sectors, Hulak currently provides support to energy, resources, technology and industrial companies throughout Europe, the Middle East and Africa with strategic and operational projects of national
Earlier this month, Hulak made a guest appearance speaking as an expert at Mining Indaba, the world’s largest mining investment conference, dedicated to the capitalisation and development of mining in Africa.
“THOUGH THE CHALLENGES ARE FORMIDABLE, AFRICA MUST FIND A WAY TO SEIZE THIS OPPORTUNITY AND EMERGE AS A KEY PLAYER IN THE NEW GLOBAL METALS MARKET”
– IGOR HULAK, PARTNER, KEARNEY
Electrification is expected to dramatically increase the demand for rare earth elements. Among other applications, these metals are essential for the manufacture of electric vehicles (EVs) and wind turbines.
At a time of rising geopolitical tensions, growing demand will lead to global undersupply in a market completely dominated by China, a factor which increases the vulnerability of the European market. Although no rare earth elements are currently mined in Europe, significant
Writer: Jack Salterdeposits have just been identified by LKAB in the Kiruna area of Sweden.
More than one million tonnes of rare earth oxides have been reported by the company following successful exploration, the largest known deposit of its kind in Europe.
This is good news not only for LKAB, the region and the Swedish people, but also for the continent and the climate, as it could become a significant building block for producing the raw materials that are crucial to enabling the green transition.
Swedish state-owned mining company, LKAB, has identified Europe’s largest deposit of rare earth metals, an essential building block of the green transition
Despite this landmark discovery, the road to investigating and potentially mining the Per Geijer deposit is nevertheless a long one.
LKAB plans to submit an application for an exploitation concession this year, and has already begun preparing a drift, several kilometres long, at a depth of around 700 metres in the existing Kiruna mine towards the new deposit to investigate it at depth and in detail.
The full extent of the deposit is yet to be seen by LKAB, who expect that it will take several years to investigate the deposit and the conditions for profitably and sustainably mining it.
Looking at how other permit processes have worked in the industry, it will be at least 10 to 15 years before the company can actually begin mining and delivering raw materials to the market.
According to Jan Moström, President and CEO of LKAB, permit processes must be changed to “ensure increased mining of this type of raw material in Europe. Access is today a crucial risk factor for both the competitiveness of European industry and the climate transition.”
Per Geijer has the potential to become Europe’s most important
mine for critical raw materials, and is in close proximity to LKAB’s existing operations in Kiruna.
The deposit contains up to seven times the grade of phosphorus, a critical mineral that is one of three nutrients in mineral fertilisers necessary for food production, as the orebodies that LKAB mines in Kiruna today.
Amounting to more than one million tonnes of rare earth metals in the form of rare earth oxides, the Per Geijer deposit’s assets would be sufficient to meet a large part of the EU’s future demand for manufacturing the permanent magnets needed for electric motors in EVs and wind turbines.
The Brazilian mining industry is centuries old, with the country’s first discovery of gold recorded in 1693 in the state of Minas Gerais. Despite this rich history, it has experienced the most growth in recent years. In 2021 alone, the country’s mining revenue was reported to have increased by 62 percent. Indeed, Brazil has long occupied a spot among the top five mineral producers in the world, qualifying the country’s mining industry as a dynamic force in the global arena.
While mining in Brazil is centred on metals such as iron ore, gold, copper, and aluminium, it is known as the world’s largest producer of niobium. The rare grey metal is used to make jet engines, airplane bodies, superconducting magnets, and bridges. As Brazil has the largest reserves of niobium on the planet, in 2021 the country produced 66 metric tonnes of the plentiful resource.
However, metallic mining remains the most relevant mineral activity, with the most valued commodities
As the largest country in South America, Brazil’s vast territory is rich with minerals and ores. We take a deep dive into the nation’s mining industry as a crucial element in driving the economy
being iron ore, gold and copper. In fact, iron ore accounts for almost 74 percent of the industry’s yield. Most of the minerals are concentrated in the states of Minas Gerais and Pará - an area that also produces gold and diamonds, although these quantities fluctuate from year to year.
Mining in Brazil means more than unearthing minerals, since precious and semi-precious stones are extracted from various deposits throughout the country. Geologically, Brazil is a treasure trove of gemstone deposits, including emeralds, opals, topaz, and quartz (agate, amethyst and citrine), with the rare and valuable Paraíba tourmaline as the jewel in the crown. On a smaller scale, diamonds, rubies and sapphires complete nature’s jewellery box. Other, more
quotidian resources include kaolin, phosphates, and coal. With the latter resource found in the southern states of Santa Catarina and Rio Grande do Sul, Brazil is entirely self-sufficient when it comes to harnessing energy from coal.
Known for its varied topography, 46 percent of Brazil is covered with Amazon Rainforest. Since the most biodiverse landscape on the planet is juxtaposed with one of its biggest and most profitable industries, the mines in Brazil must operate as ecologically as possible. Brazilian mining is striving to become more sustainable as the industry must reflect the expectations of both stakeholders and society by lessening the environmental impact of its processes.
Raul Jungmann, CEO of IBRAM, delves into the sustainability of the Brazilian mining industry and explores its economic and environmental future
Mining Outlook (MO): Firstly, tell us about the origins of IBRAM – what led to its creation and what is its current vision and mission?
Raul Jungmann, CEO (RJ): IBRAM was created in 1976 to defend the legitimate interests of the mining industry, as a sector that is important and influential in the performance of the national economy. It is responsible for generating fundamental currency to positively balance the country’s trade. In addition, it attracts private multi-billion-dollar investments every year to Brazil.
As an inducer of good Environmental, Social, and Governance (ESG) practices, IBRAM is aligned with sustainability. It is also ethical and transparent in its relationships with people. Through influential partner initiatives, it promotes socio-economic development, inclusivity, and general quality of life for people.
IBRAM’s actions are aimed at building a new perspective for the future of Brazilian mining, by outlining strategies, and leading the industry’s transition into an even more productive phase, with sustainability, safety and responsibility at the centre.
MO: What is your take on the mining industry in Brazil today?
RJ: Brazilian mining is a very exciting environment, as the activity will provide ores for building a more sustainable planet. The Brazilian mineral sector drives the economy and is the basis for the transformation of the industry. Ores are present in every aspect of industry, including agribusiness, and are irreplaceable and essential components for modern life and, above all, the evolution of human beings.
We act to combat unfair competition from illegal mining, which moves business with tonnes of ores – such as gold – and leaves a trail of environmental destruction, deaths, exploitation of people, tax evasion, among other crimes.
Furthermore, we seek to create a culture of national investments in mining and the establishment of mechanisms for raising funds in the capital market. Currently, few companies in the mineral sector are listed on the stock exchange in Brazil. The financial markets of Canada, Australia, and England are more prominent in the financing of mineral projects around the world, including Brazil.
Mining moves billions of reais every year, generates foreign exchange with significant exports for the positive balance of trade, but does not find support in terms of local financing. It is a situation that needs to change and IBRAM is acting in this sense.
MO: How does IBRAM encourage sustainability in the sector?
RJ: Sustainability in business is good practice in all senses for any industry, sector or company. It is a continuing presence on the global market. For sustainability to advance, whether it is in mining or any other sector, it is necessary to make the production chains aware that acting in accordance with good practice, respect for legislation and going beyond what is required, is an attitude that will gain an excellent reputation for the corporation, or the entire sector.
The mining industry has uniquely organised its own ESG Agenda and is always improving and evolving. It is a continuous sectorial effort that provokes cultural and governance change and a movement that gains strength
due to the voluntary adhesion of the companies in the sector. Those associated with IBRAM all have serious commitments to sustainability. The union of experience and knowledge provides the construction of a project that already presents practical results in the daily lives of companies.
In the case of the ESG Agenda, there are 12 areas that deserve special attention, such as safety, diversity and inclusion, the use of natural resources, energy, community relations, and impact mitigation among others. Together, we have better conditions than when we are isolated. This helps to establish goals, actions, and metrics in order to share advances with the whole of society in a transparent manner, as well as correct directions whenever necessary.
RJ: It is mining that is aligned with sustainability and ESG practices – it is ethical and transparent, inclusive and influential. This is the type of mining that IBRAM defends – a mining business that operates in full harmony with Brazilian legislation.
IBRAM works to strengthen relations between mining companies and industry professionals and suppliers, the government and society. It encourages innovation, knowledge and good practices while articulating business development opportunities for mining. It is always open to dialogue with other organisations; to listen, understand, propose, negotiate, motivate, engage and unite.
“IBRAM WORKS TO STRENGTHEN RELATIONS BETWEEN MINING COMPANIES AND INDUSTRY PROFESSIONALS AND SUPPLIERS, THE GOVERNMENT AND SOCIETY”
– RAUL JUNGMANN, CEO, IBRAM
MO: Does IBRAM have any projects or events that you would like to highlight?
RJ: In 2023, IBRAM will organise a series of events aimed at sharing news, knowledge, new practices and stimulating business in the world of the mineral sector.
We have a calendar of events with dates already set for this year:
• Diversibram – Diversity and Inclusion Week for Mining in Brazil – an online event, 28th March.
• Mining Municipalities Award in Brasilia, 31st May.
• e-MINERAÇÃO DO BRASIL, a virtual event, 4th and 5th July.
• Expo & Brazilian Mining Congress – EXPOISIBRAM, held at Belém, 29th to 31st August.
• Internacional Conference Amazon and New Economy, held at Belém, 30th and 31st August.
• Brazilian Open Pit and Underground Mine Congress –CBMINA, held at Belo Horizonte, 12th to 14th September.
In general, each IBRAM event has a range of opportunities for brand exposure actions, such as participation in podcasts, a media kit to associate brands to actions, technical lectures, short courses, sponsorship quotas, etc. More information can be found at https:// ibram.org.br/ibram-principais-eventos/
MO: Looking ahead, what are IBRAM’s main priorities for the next year?
RJ: One of the institute’s priorities is to obtain greater recognition from Brazilians, from public authorities to
citizens in general, that mining needs to be supported and encouraged in this country. It is an activity that is considered a public utility, it generates unequivocal contributions to the economy, and it is among the economic sectors that invest the most in environmental preservation. Essentially, it is a fundamental partner for the socio-environmental and economic development of Brazilians in the long term.
We are acting in this direction and the results in terms of people’s trust and respect for mining are showing, as we periodically verify when we collect public opinions. By establishing advances in this more positive perception of mining by people and authorities, we gain access to better conditions to promote the expansion of our activities. We have challenges to overcome in this regard. It is urgent to expand mineral research, since only about four percent of the territory is properly mapped.
Additionally, the country needs to create public policies that support the development of mining, such as minerals considered strategic to enable Brazil and other nations to meet the goals of the major global agendas, primarily those related to climate risks. We will only have a low-carbon economy if we can ensure a diversified and growing supply of minerals.
Tel: +55 3223 6751
ibram@ibram.org.br
ibram.org.br/en
The state of Wyoming is the powerhouse of the North American mining sector.
Blessed with a unique geology and a wealth of diverse mineral deposits, Wyoming produces raw materials for industry, energy development and a host of other sectors. Indeed, it was the potential of its vast mineral resources that led to Wyoming’s original successful campaign to gain individual statehood in the 19th century. Today, the mining industry accounts for 30 percent of annual state budget revenue.
As North America’s largest coal producer, Wyoming contributes approximately 40 percent of the nation’s coal.
However, in the current environmental context and the overwhelmingly negative perceptions surrounding the resource, federal legislation is placing this critical industry under threat.
In addition, Wyoming stands out as the leading producer of both trona – processed into natural soda ash and the state’s top international export – and bentonite. Otherwise known as ‘miracle mud’, due to its host of applications, bentonite finds myriad uses in everything from cosmetics to environmental sealants, and is primarily used as the clumping component in cat litter. Both are considered steady industries that are unlikely to diminish in relevance
and importance.
Despite the complications facing the state’s coal mining industry, unlocking the full potential of Wyoming’s unearthed resources will be instrumental in driving a renewable, low-emission future.
The US currently relies on nuclear generation for about 20 percent of its energy, and Wyoming represents the leading domestic producer of uranium. But the industry’s heyday of the 1970s is long gone. At that time, Wyoming produced 10 million lbs of uranium a year and the industry employed 5,000 people; today those figures have plummeted to an almost non-recordable level. With
nuclear holding the key to emission-free energy, and environmentally-friendly mining techniques now available using well-fields and pumping techniques, the industry is poised for a comeback.
Similarly, Wyoming boasts significant potential in rare earth minerals – the mining of which is fundamental to the development of electric vehicles (EVs) and renewable energy. The state hosts many companies currently undergoing exploration and development in this future-facing field.
Amidst fraught geopolitical tensions and the imbalance of markets towards China and Russia, the answer for Wyoming, and indeed the US, lies in domestic production.
Travis Deti, Executive Director of WMA unpacks the challenges facing the organisation today and future objectives in the face of a prohibitive legislative climate
Travis Deti Executive DirectorMining Outlook (MO): Tell us about WMA’s inception –how did it come about and what is its vision?
Travis Deti, Executive Director (TD): The Wyoming Mining Association (WMA) is the state-wide trade organisation representing all of Wyoming’s mining companies, excluding oil and gas. We represent the state’s coal and uranium mining companies, and the industrial minerals of bentonite and trona. We are the nation’s leading producer in all four of those categories. We also represent companies that are currently in the exploration and development phase for
rare earth elements and minerals, as well as gold. Our association is 65 years old, and we are a strong advocacy group for the industry in the state of Wyoming. I have been with WMA for 12 years and leading the organisation for the past five. Our goal is advocacy for Wyoming’s mining industry, and we work very closely with our state legislature and our elected officials, the governor’s office and state regulators, as well as the Wyoming congressional delegation to promote and defend it.
Wyoming is a state that is reliant on extraction. The critical revenue generated from mining supports our state and local governments, it funds our education system, and builds our highways and roads. Therefore, we remind our elected officials of the importance of keeping and defending a strong mining industry so that we can continue to run our state.
MO: Could you describe the current industry climate?
TD: We are facing some interesting times right now. At a federal level, extraction, of coal in particular, is not looked upon favourably and the government is actively pursuing measures to keep some of our materials in the ground. In all honesty, it’s tough right now in Wyoming, but the bottom
line is we need our resources, and to keep developing them.
Today, we find our largest challenge in the coal industry. As the top producer in the US, coal has traditionally been a bedrock fuel for energy production and electricity generation, and we’d like to see it stay in that mix. However, at a federal level, President Biden has made no secret of his plans to shut down all coal plants in the country and replace them with wind and solar. We fundamentally disagree with that approach, but current policy coming from Washington DC is based on keeping that resource in the ground. That’s very troubling for us, and we’re going to fight hard to continue to push our message that coal-fired generation is essential for the US. It is reliable, affordable, and an abundant resource.
On the other hand, Wyoming has plenty of opportunities in other sectors that have risen to the fore with today’s debate on climate change and global events such as the situation in Ukraine and Russia. In terms of nuclear power, we are the top domestic producer of uranium in the US, and that has been an extremely challenging environment recently. Countries such as China, Russia and Kazakhstan have flooded the market with cheap uranium and made it non-economical to produce it in the US. However, I believe that will change with the events currently taking place across the world.
If we are going to continue to have a viable nuclear generation industry, we have to start looking internally at our fuel supplies for domestic uranium. That will benefit the state of Wyoming and we’re already seeing that start to come to fruition. With global climate change and carbon dioxide emissions issues, nuclear energy really is the silver bullet. There is a lot of opportunity for Wyoming in that area - we have companies on the ground, operations in place, and we just need to follow through on it and start producing uranium domestically.
On the industrial mineral side, our natural soda ash industry is one of tremendous growth and a key economic driver. It’s very much in demand and we are seeing the trona industry expand in Wyoming. We currently produce roughly 24,000 tonnes of soda ash per year, and we expect
“WE REMIND OUR ELECTED OFFICIALS OF THE IMPORTANCE OF KEEPING AND DEFENDING A STRONG MINING INDUSTRY SO THAT WE CAN CONTINUE TO RUN OUR STATE”
– TRAVIS DETI, EXECUTIVE DIRECTOR, WMACoal mining: Dragline Operator, Powder River Basin in northeast Wyoming Uranium mining: drilling with windmills in central Wyoming Bentonite mining: pet litter processing facility, northeast Wyoming
that to increase. Our competition is mainly synthetic soda ash produced in China, however our markets are strong and we see a lot of opportunity to grow that industry in Wyoming.
Meanwhile, bentonite is unique to Wyoming and again, we are the top producer in the country. The clay of 1,000 uses, we see that industry as steady since it is an incredibly versatile and valuable resource.
Other opportunities are found in the global shift to EVs and renewables – both of which require a lot of rare earth minerals. We have one of the richest deposits of rare earth minerals in North America and we’re working on developing that. Currently, China controls about 97 percent of the global market for that industry. The US has been completely off the playing field in that sector, so we are working on building it from scratch. There is a huge opportunity out there for battery technology and expanding renewable capabilities, and you need those minerals to make it happen. The opportunity in Wyoming is tremendous right now.
Overarching everything is a major challenge which is not unique to Wyoming. It takes a lot of time to develop a new mining operation and that’s mostly due to the regulatory and permitting regimen that we must deal with both at state and federal level. The hoops that you must go through to permit and get a new mine operational are crippling. The good part is that eyes are opening in Congress, and people are gradually recognising that we need to streamline the process and make it more efficient.
MO: Has the association got any projects in the pipeline that you wish to highlight?
TD: Working very closely with our state regulatory agencies is an ongoing event – our operating sectors meet regularly with regulators to discuss where we can make effective changes in our state regulatory regimen to make our process more effective. It is in the best interests at state level to work together so that we can continue to produce, since production equals jobs and revenue. At a federal
level, we are closely in touch with our state congressional delegation to make sure our voice is heard at the table and our issues are front and centre, with the goal to boost production.
MO: Finally, are you optimistic about the future of the mining sector in Wyoming?
TD: I’m always optimistic. The fact of the matter is, the US does production better than the rest of the world. Our mining operations are by far the safest and we treat our workers right. We are conscious of our environment, and that is why our regulatory regimen is so strict, because we value our land and human rights. It does make things more challenging, but rightly so. It’s a balancing act, but the bottom line is that if you want to live the American lifestyle with the level of energy that you expect when you flick a light switch on, it comes at a price. And that is domestic production.
Tel: 307-635-0331
WMA@wyomingmining.org
www.wyomingmining.org
Avast region spanning over one-sixth of Canada’s total land area, the eastern province of Québec is blessed with a diverse bounty of mineral resources. Indeed, the area provides one-fifth of Canada’s entire mining output.
Gold, nickel, and iron ore stand out as some of its most significant resources, however, Québec is now playing an increasingly important role in the mining of critical minerals, including graphite, lithium, rare earths, zinc and apatite, with very advanced projects in graphite and lithium.
As a mature sector, Québec’s mining industry is wellreputed for its world-class best practices, particularly with regards to health and safety, and its burgeoning recognition as a diverse and inclusive field of employment. Indeed, within the past decade, Québec’s mining workforce has significantly increased its representation of both women and Indigenous communities. Between 2014 and 2020, the number of direct jobs held by each demographic within the industry increased by 42 percent and 69 percent respectively.
Combining its diverse mineral wealth with environmental awareness and social responsibility, Québec continues to prove its status on the global mining stage as a responsible mineral source. In terms of renewable energy, the sector is heavily reliant on hydroelectricity, and thanks to its continued foray into critical minerals, it will be integral in driving the energy transition and growing a domestic battery storage industry. The sector today is a hive of activity, with a multitude of innovative projects underway to reduce greenhouse gas (GHG) emissions, preserve
biodiversity, regenerate wastewater, and restore tailings sites and former mines. Currently, there are multiple mining projects in development across the region, encompassing 17 new gold mines, four new iron ore mines and 14 new projects for critical minerals.
With the government actively advancing a responsible mining agenda through the implementation of a battery strategy designed to boost both demand and investment, Québec’s mining sector is poised to energise Canada’s future.
An association born from the need to improve safety in the mines, the QMA is now advancing Québec’s responsible mining agenda. President and CEO, Josée Méthot tells us more
Mining Outlook (MO): Can you talk us through the origins of the QMA, how it came about, and its initial vision?
Josée Méthot, President and CEO (JM): The QMA was created 86 years ago. The very first general meeting that gave birth to the QMA, formerly called the “Western Québec Mine Managers Association”, was held on 19th August 1936 with the specific goal of helping to reduce the frequency of accidents in mines. The health and safety of workers was the first and major concern of this new organisation, and this is now firmly anchored within companies at every level.
JM: Over the past 86 years, in addition to health and safety, the QMA has evolved by integrating the concepts that are now essential to mining development, namely the protection of the environment, the development of harmonious community relations, human resources, good governance and innovation.
Our mission now is to promote, support and proactively develop a responsible, committed and innovative mining industry in Québec. The QMA’s vision is to be a leader and an indisputable reference for a responsible, innovative and competitive mining industry in Québec, within a sustainable development perspective.
The criteria of environmental, social and governance (ESG) are now essential in the mining sector. For this reason, all mining companies in Québec that are members of the QMA are required to join the ongoing improvement initiative known as Towards Sustainable Mining (TSM). This sustainable development programme has earned a worldwide reputation and helps companies manage key ESG risks by applying practices that go beyond the legislative and regulatory requirements.
Québec has seen a multitude of innovative projects designed to significantly reduce GHG emissions, preserve biodiversity, regenerate wastewater, and restore tailings sites and former mines.
MO: Québec’s jurisdiction scored highest in Canada in terms of investment attractiveness on the Fraser Institute. What is it that makes Québec so attractive to investors?
JM: Québec has a great variety of minerals. With our use of clean energy (hydropower) and strong regulations regarding environmental protection and our social practices in relation to local communities, in conjunction with the industry’s social and environmental practices, Québec may take its place as a responsible source of minerals.
Québec’s public policies also distinguish us from other mining jurisdictions even within Canada, as the Québec government is eager to position its mining industry on the map as a responsible source of critical minerals. For this, they have adopted a plan for the development of critical and strategic minerals and a battery strategy.
Québec has political stability, and the new mining and tax acts have been implemented for close to 10 years now, so it is widely understood by the industry.
In addition, Québec offers several tax incentive measures to support exploration activities which include deduction of exploration and development expenses, Québec’s flow-through share regime and the tax credit for resources.
The mining expertise and tradition in Québec is also first-class, with well trained workers and good working conditions. Québec has an excellent workplace health and safety record; doing business in Québec means working with people for whom health and safety are a constant concern.
Québec’s other advantages include its highly qualified workforce, which is one of the best in the world. There are Quebecers working in mines all over the world. In addition to the expertise of its workforce, Québec also has excellent training institutions for employees, many research consortia and more than 20 research chairs that help the mining industry to remain innovative. The mining sector can also count on a first-class, province-wide network of more than 4,850 suppliers.
MO: How much of a significant contribution does the mining industry make to Québec’s socio-economic development and growth?
JM: The latest study on the economic benefits generated by the mining industry in Québec, covering the year 2020, confirms the extent of its contribution to Québec’s economy and quantifies the benefits generated in terms of the jobs maintained and created, gross domestic product (GDP), state finances, and the distribution of the benefits in various regions of Québec.
The study provides concrete evidence of the role
played by the mining industry in the Québec economy. In 2020, mining industry activities in Québec amounted to CAD$12.5 billion, including CAD$11.7 billion for extraction and exploration. The contribution to Québec’s GDP has increased steadily over the period covered by the QMA’s studies on economic benefits from 2014 to 2020, and has now reached CAD$10.5 billion, an increase of 36.4 percent.
In terms of jobs, the study shows that mining in Québec supported 48,187 person-years of employment in the form of direct, indirect and induced jobs, including 15,589 person-years for residents of the Abitibi-Témiscamingue region, 7,585 for residents of the Côte-Nord region and 10,618 for residents of the Montréal and Montérégie regions. Women are increasingly present in the workforce, and the number of direct jobs held by women increased by 42 percent from 2014 to 2020. The situation is similar for workers from Indigenous communities, whose numbers increased by 69 percent over six years.
By updating the study every two years, the QMA can answer some frequently asked questions, such as: how much do governments collect from mining in Québec? The answer for 2020 is CAD$2.4 billion. In other words, mining industry activities generated important fiscal and parafiscal revenues for the two main levels of government in 2020, with a total of CAD$2.4 billion, including almost
CAD$1.8 billion for the Québec government and CAD$620 million for the Canadian government, excluding corporate income tax.
Since our first study in 2014, fiscal and parafiscal revenue for the Québec government jumped by 77.3 percent, from CAD$1.0 billion to CAD$1.8 billion. The most significant factor in this increase was mining taxes, which grew fivefold from CAD$121.1 million to CAD$631.7 million. Mining taxes now represent over 35 percent of the contribution of the mining industry to the Québec government coffers. It is important to note that our gold and iron ore mines made the most substantial contribution, accounting for almost 90 percent of total mining taxes.
“OUR MISSION NOW IS TO PROMOTE, SUPPORT AND PROACTIVELY DEVELOP A RESPONSIBLE, COMMITTED AND INNOVATIVE MINING INDUSTRY IN QUÉBEC”
– JOSÉE MÉTHOT, PRESIDENT AND CEO, QMANiobec mine
MO: What do you find most exciting, and challenging, about the mining sector in Québec?
JM: What is most exciting is the great variety of minerals found in Québec and the sector’s will to put in place best practices. The people of the industry are serious about what they do and how they do it. However, this variety is also the greatest challenge, since it is not simply one size fits all - every mineral has its own requirements and difficulties.
MO: Has the association got any projects in the pipeline that you wish to highlight?
JM: The QMA has recently changed its requirements for TSM implementation by its members. Since the QMA always strives for the highest standards in ESG, it has raised the bar for its members. I am proud of the QMA’s Board of Directors for taking this decision. Since June, our members must obtain level A for 50 percent of the TSM indicators, and if they don’t, they must produce an action plan to show what they will put in place to remedy the situation.
MO: Finally, are you optimistic about the future of the mining sector? How do you see it developing?
JM: The coming years seem promising for the mining industry, in particular thanks to the development of critical and strategic minerals which will play a leading role in the
energy transition and the battery sector in Québec. These metals offer significant potential for wealth generation in the province.
However, we need to process and transform the minerals as well as mine them. For the critical minerals, we must work on the demand side. This means a new value chain must be built, instead of only a mine, so it is difficult to secure their financing as it entails more risks. The government understands that we cannot look at the development of these mines as we do for iron ore or gold, as it is a totally different business model. Hence, the development of its battery strategy to incentivise battery manufacturers or components manufacturers to build their plants in Québec. This way they are able secure the demand for these minerals.
I am also optimistic because there are 36 mining projects currently in development in Québec and there is still a lot of activity to come. With our hydroelectricity and mining practices which are the best in the world, the Québec mining industry is well positioned to supply the planet with clean resources that meet responsible sourcing policies.
MINING OUTLOOK is a quarterly digital publication and media brand showcasing the latest innovations, industry insights and corporate stories from across the international mining and resources sector. Its world-class team collaborates with the biggest and most exciting brands to craft engaging and authoritative content for a global audience of industry players. As mining organisations worldwide confront unprecedented change, embracing technological innovations and incorporating critical environmental sustainability agendas, now more than ever is the time to showcase the strides being taken in this dynamic sector.
The expertise of our in-house design and production teams ensures delivery to the highest standards, as we look to promote the latest in engaging news, industry trends and success stories from the length and breadth of the global mining sector.
As a multi-channel brand, Mining Outlook reaches an international audience through various platforms, with exclusive content distributed through our website, online magazine, social media channels, and bi-weekly newsletter.
Through this compelling venture, we intend to foreground the movers and shakers of the industry. To participate as a featured company and join us in this exciting endeavour, contact one of our Project Managers or our Managing Director, James Mitchell, today.
HCI Coal is the responsible mining company pursuing growth and diversification across South Africa. We dig deep into operations behind the Palesa mine with co-CEO, Pieter Terblanche
Writer: Phoebe Harper
Project Manager: Joshua Mann
The demand for commodities is changing as technology evolves worldwide and we need to be able to take advantage of this shift in demand.”
Like the tectonic plates that shape our Earth’s continents and oceans, the demand for the extractive resources that power our world is shifting.
In the advent of the clean energy economy, fossil fuels continue to fulfil a vital role in keeping the lights on, but the future lies in alternate resources. Adapting to this transition is a major prospect in a heavily coal-dependent
Radian Engineering is a high-precision engineering firm with over 25-years’ experience in the mining and bulk material handling sectors. Our depth of experience means that we can provide our clients with specific and specialised solutions which require a high level of engineering expertise.
Our pursuit of excellence is driven by three core values: integrity, reliability and precision. These values govern our approach to engineering, fabrication, client and supplier relationships and our employees. We are mindful of the importance of being a responsible corporate citizen and strive to achieve this through living our values.
Contact us
country that produces over 250 million tons of coal every year, and accounts for 90 percent of the coal consumed across the entire African continent.
As a junior mining company based in South Africa (SA), HCI Coal is all too aware of this paradigm shift and is channelling the spirit of agility and diversity to maintain both relevance and competitiveness in this evolving field.
For co-CEO Pieter Terblanche, the need for HCI Coal to look and invest beyond the commodity from which the company takes its name, is a pressing challenge that it intends to meet head-on. This is particularly pertinent in a country where funding for coal projects is simply no longer available, despite SA ranking among the world’s most coal-dependent nations.
“We need to be cognisant of the fact that coal will not be the commodity of choice in the long-term due to the environmental impacts,” he says.
Consequently, HCI Coal is pursuing diversification into other, future-relevant commodities, while
preserving its proud status as a responsible mining company.
HCI Coal is 100 percent owned by Hosken Consolidated Investment (HCI), a Johannesburg Stock Exchange (JSE) listed and Level 2 Black Empowerment investment holding company. A key benefit in driving the company’s need for diversification, HCI Coal benefits as a subsidiary and contributing part of the wider holding company, which comprises a varied portfolio. The HCI Group counts a diverse array of investments across sectors, from hotel and leisure to transport, mining, clothing and properties, amongst others.
Indeed, Terblanche credits this structure as a key advantage during the recent turbulence of the COVID-19 pandemic, as HCI’s various investments reinforced the overall group against volatile and unpredictable market conditions.
“It was evident during COVID-19 that the holding company had to rely on its subsidiaries to keep it going,” he says. “It is in tough times such as this that it helps to have a diversified portfolio.”
SAFETY – Zero harm remains HCI Coal’s key safety objective at Palesa.
HEALTH – HCI Coal is committed to addressing the challenges of access to quality and affordable healthcare for its people. The health and wellness of its employees and contractors are of the utmost importance.
CLIMATE CHANGE – HCI Coal believes that the impact of climate change presents a serious challenge to society, its mining communities, and operations. It understands that urgent action is required to mitigate the local and global effects of climate change. The company remains focused on lowering its carbon footprint.
THE ENVIRONMENT – As a responsible corporate citizen, HCI Coal plays an active role in protecting and preserving the environment through initiatives aimed at reducing its carbon footprint.
COMMUNITIES – HCI Coal is committed to the empowerment of its people through investment in education, local employment, and the economic development of its host communities. The company’s Social and Labour Plan has a life cycle of 2020-2024, in which it has committed to construct low-cost houses in Region 7 and Thembisile Hani Local Municipality. Other community initiatives are supported through its Corporate Social Investment fund.
Championing a holistic vision, HCI Coal’s plans for growth fall into the wider picture of contributing to the progress of the HCI Group as a whole and to the benefit of its shareholders. Currently, HCI’s majority shareholder is the South African Clothing and Textile Workers Union – a trade union encompassing over 10,000 members.
Radian Engineering is a key partner to numerous mining companies and processing operations throughout the South African mining industry. HCI Coal is one of our longstanding mining and beneficiation partners. We have been a proud provider of mechanical and civil services including structural audits, vibrating screening equipment, structural plant, environmental and pollution control solutions, across all their plants and operations.
Radian Engineering is extensively involved in the mining operations of our broad range of clients, based on our in-depth knowledge and understanding of plant operations and the challenges faced by our mineral processing customers. Our aim is to ensure more than 95 percent production availability of the operations by providing optimally designed, manufactured, and tested equipment.
Having this level of operational experience, Radian Screens are precisely designed for our clients’ specific plant requirement. The vibrating screens are easy to operate and maintain due to the efficient design and the availability of spares and accessories.
As the original equipment manufacturer (OEM) a full range of spares and accessories are manufactured, to original specification and held in stock in our facilities throughout Southern Africa.
Due to our experience and breadth of understanding in metallurgical processing, Radian Engineering is a crucial partner to our customers in the design and construction of a new process plant. A regular service we offer is plant improvements and optimising expansions to deliver process efficiencies and increased production output.
The mining industry is a demanding sector in which Radian Engineering is renowned for integrity, reliability, and precision. In March 2022 a major mining client had an
urgent requirement for a large desliming banana screen as part of a vital plant expansion project. The standard lead time of a machine of this magnitude is 10 weeks. Due to the critical nature of this machine the client needed the screen designed, fabricated, tested, and installed within four weeks. Radian delivered exactly on time and the machine was successfully commissioned.
Radian Engineering is not only a specialist in vibrating equipment but in the entire bulk material supply chain.
Our approach to delivering turnkey projects is to provide customised complete material handling solutions which include conveying systems, crushing equipment and mobile link conveyors.
Radian Engineering’s involvement in manganese loading at the harbours has led to us becoming an industry standard in rail to port transportation with our RadianSkip for bulk loading.
We have recently embarked on a Tippler refurbishment project and 2023 will see the installation of a newly fabricated Tippler at a major export hub in South Africa.
We make use of the latest parametric 3D design software to ensure functionality, longevity and to determine the maintenance requirements of our machines. Extensive analysis of our designs is performed. These include Discrete Element Modelling (DEM), Material Flow Simulations, Finite Element Analysis (FEA), Fatigue Analysis, and Kinematic and Dynamic Simulations.
All Radian Engineering designs are managed through a product lifecycle process ensuring configuration control, traceability of the product, lifecycle maintenance which allows for accurate planning and enables cost effective management of the plant and machinery.
Radian Engineering is driven by our values of integrity, reliability and precision in all our business endeavours, and we look forward to discussing your requirements with you.
HCI Coal’s primary operations are centred on its sole operating mine –Palesa – which is located 37 kilometres (km) north of Bronkhorstspruit, and forms part of the Thembisile Hani Local Municipality, bordering the Nkangala Township within the City of Tshwane Metropolitan Municipality.
The company was originally formed in 2006, born as a joint venture with a consortium to mine coal at the Palesa site which is then sold to both local and export markets. As of financial year 2021 – 2022, the mine resumed the supply of coal to export markets on a medium-term basis.
As reported in 2022, coal accounts for a staggering 85 percent of SA’s electricity. Reflecting this dynamic, Palesa produced an initial supply of 4,653 tons of coal in the first month to Eskom – SA’s largest electricity public utility, when the mine became operational in 2009. Shortly after, in March 2010, Palesa signed an eightyear contract to supply 160,000 tons per month of coal to Eskom and in April, an additional 40,000 tons were negotiated.
“When Palesa went operational, the run-of-mine (ROM) qualities
restricted us to the energy market and we therefore entered into a longterm offtake agreement with Eskom,” Terblanche explains. A second offtake agreement followed in 2018 to supply 240,000 tons per month.
“Eskom is our majority market, and we intend to keep it that way,” he shares.
The original ROM quality that restricted HCI Coal to the energy market remains a point of focus and improvement. At present, the company is engaged in efforts to improve the quality of its product in terms of ash and sulphur content. The culmination of this endeavour is HCI Coal’s recent major investment into an FX Air Separation Plant to facilitate the continued partnership with Eskom, but with a higher quality product.
“The reason behind this investment is to secure offtake in the medium- to long-term, but also to support the principle of cleaner coal since this will reduce the level of harmful emissions at the power stations,” Terblanche elaborates. HCI Coal’s recent interest in a new solar farm facility to be built on the land surrounding the Palesa mine will also further support these efforts.
PIETER TERBLANCHE, CO-CEO: “As a responsible mining company taking into consideration the environmental impacts as well as the risk associated with power supply in the country, we made a decision to investigate the option of investing in a solar project. Palesa is situated in a rural area with a significantly high rate of unemployment, and although a solar farm would only create a limited number of jobs, it would still contribute to the local economy.
“We are in the process of securing the required environmental approvals and we expect to be in a position to begin construction in the latter part of 2023 or first quarter of 2024, depending on that process.”
A special thanks to Palesa Mine (HCI) for choosing to trust us with moving their products to various destinations. This has subsequently paved the way for other strategic partnerships like Scania SA and Afrit, where TFD has formed relations with these organisations to ensure timeously and safe delivery of Palesa’s products. We look forward to maintaining relationships we have and establishing new partnerships by learning more about the logistics industry in order to improve efficiency, reliability and being timeous.
For any enquiries
Contact: Tumelo Doone
Contact number:
072 413 0878 or 079 931 6224
Address: 378C Simunye Street, Kwa-Mhlanga 1022
Email Address: Tumelodoone@yahoo.com
Tumelodoone@yahoo.com
Fanaye Business Enterprise is a professional service provider in the transportation and plant hire business. Established in 2002, Fanaye Business Enterprise has vast experience in the relevant fields.
Our mission is to provide high quality and excellent services at a reasonably lower cost to broad based clients and to uphold the competitive standards.
Our core services include:
• Transportation of coal by road, using 34 tonne side tippers
• Supply of earth moving machinery, namely ADTs, front end loaders, graders, water bowsers, excavators and dozers
One of Fanaye’s most important aspects is putting safety first. We ensure that our employees are well orientated and educated with the useful equipment and machines to be utilised. Our monitoring systems are of high standards to make sure the safety aspects are adhered to.
For more info contact: 0822607616 / 0828961383
fanaye.online@gmail.com
The visionary behind TFD Capital Investments Pty Ltd is a young, vibrant man who defines himself as an entrepreneur and explorer. After qualifying as a Chartered Accountant (CA (SA)) he embarked on a journey of exploring the logistics industry, which was then the genesis of TFD Capital Investments Pty Ltd in South Africa. The company’s mission is striving to provide world class services to the clients by providing the highest standard of efficiency and reliability, and ensuring that all safety measures are applied. The company aims at addressing poverty and unemployment issues by employing local community members. TFD is currently based and operates in the Mpumalanga Province and employs 11 dedicated and hard-working individuals.
TFD is currently solely transporting coal from Palesa Mine to a number of Eskom Power stations, and we are operating seven trucks with the aim of growing the fleet and moving other commodities. We aim to grow the business by being active in other types of logistics like transportation of food, beverages and textiles to various destinations within and outside Mpumalanga.
Contact us
072
413 0878
Fanaye Business Enterprise has vast experience in the relevant fields.
Our mission is to provide high quality and excellent services at a reasonably lower cost to broad based clients and to uphold the competitive standards.
Our core services include:
• Transportation of coal by road, using 34 tonne side tippers
• Supply of earth moving machinery, namely: ADTs, front end loaders, graders, water bowsers, excavators and dozers
One of Fanaye’s most important aspects is putting safety first. We ensure that our employees are well orientated and educated with the useful equipment and machines to be utilised. Our monitoring systems are of high standards to make sure the safety aspects are adhered to.
Contact us 0822607616
Both undertakings will play an integral part in driving HCI Coal’s involvement in SA’s Just Energy Transition Partnership (JETP), as announced at COP26 in Glasgow, Scotland. Pledging net zero carbon emissions by 2050, the JETP seeks to address SA’s problematic status as the world’s 13th–biggest emitter of carbon by leveraging the finances of countries including the US, Germany, France and the UK, to help expedite its energy transition.
As a responsible corporate citizen, HCI Coal’s demonstrated concern for improving its environmental impact is complimented by a company-wide emphasis on social upliftment.
“It makes sense that people within the area where our business operates should benefit,” Terblanche states. “This is not just for those who are directly employed, but also their families and the communities as a whole.”
Mindset Mining Consultants is delighted with its involvement in the erection and commissioning of the air plant at HCI Coal’s Palesa mine. Having previously provided Palesa with project management services, Mindset is proud of its continued good relationship with the mine.
Mindset assisted Palesa in the daily management of the site, troubleshooting issues as they arose and keeping track of the project budget. Mindset assisted and managed the various contractors involved in bringing the air plant online and quality management of the final deliverables.
Mindset is excited to see the mine reap the benefits of this impressive technology.
www.mindsetmining.co.za
HCI Coal comprises 154 employees and 510 contractors at present, with a relatively young management team taking the helm. Across the board, there is an explicit focus on employing locally to contribute to the economic wellbeing of communities surrounding the Palesa mine.
Committed to Black Economic Empowerment (BEE), this is set in stone by the company’s social and labour plan (SLP) and reflected by HCI Coal’s tender processes, which reinforce its stance on ensuring that local black entrepreneurs are aware and benefit from the opportunities generated by its mining activities.
“When you initially start a project, you are not sure whether you are going to be able to recruit employees locally with the necessary skills and experience,” says Terblanche, which is a particular issue in a remote rural location such as Palesa.
“However, I am proud to say that more than 80 percent of our employees are from the local communities, including our contractors.”
In addition, HCI Coal uses the services of almost 50 local transport companies who are contracted to transport the coal directly to the company’s customers.
“It really is an injection for the local economy. This makes our employees proud and in turn means that the community then supports our
• Full-service mining consulting firm
• Proven experience in providing technical advice & engineering solutions
• We provide on-site project management services to keep projects on track & in budget
• We can take your prospect from concept-level to an operating mine
• We conduct evaluations that include all aspects associated with the investigation, design, economic analysis & resulting investment decision-making for a mine – both greenfields and brownfields
success,” he surmises. Furthering this community support is HCI Coal’s emphasis on creating a sustainable pipeline of talent through myriad opportunities for training and development. From learnerships for artisans at its mines to internships for top performing graduates, the company is committed to developing and nurturing local talent found within its immediate vicinity.
Moving into the years ahead, HCI Coal’s priorities are centred on continuing to create a sustainable business that looks beyond coal and works to reduce its environmental footprint.
“Our first key priority is to successfully commission and operate the FX plant in order to negotiate an extension of our current offtake agreement with Eskom or enter into a new agreement,” outlines Terblanche. “We also want to get some traction on our solar project over the course of the next 12 months.”
Simultaneously, HCI Coal will be keeping its eye on new ventures, evaluating upcoming mining projects whilst continuing to deliver to export markets and exploring other alternative markets domestically.
Regardless of these new pursuits and the changing face of global resources, HCI Coal remains steadfast in its commitments to prospecting for commodities while creating opportunities and investing in local communities.
“TO CREATE A SUSTAINABLE BUSINESS, WE NEED TO DIVERSIFY”
– PIETER TERBLANCHE, CO-CEO, HCI COAL
De Beers’ Venetia Underground Project in Limpopo, South Africa, champions the symbiotic progress of people, processes, and systems. Due to enter production in 2023, we catch up with Project Director Allan Rodel and examine what makes a mine of the future
Under the surface of South Africa’s (SA) northernmost province, work continues on what represents the single greatest investment in the country’s diamond industry in decades. Here, in Limpopo, you will find the Venetia Mine (Venetia), the largest mine in SA operated by De Beers Group (De Beers) - the iconic name that is synonymous with high-quality diamonds.
Majority-owned by the global diversified mining company Anglo American, De Beers has operated Venetia as an opencast mine since 1992 and will do so until the site reaches the end of its life. However, in 2010, the mine’s underground capacity proved difficult to ignore. With the potential to treat approximately 132 million tonnes of material containing an estimated 100 million carats and effectively extend the mine’s life to 2046, the transition below surface began. Fast forward almost a decade, and the USD$2.1 billion excavation
and build of the Venetia Underground Project (VUP) is poised to enter the first stages of production in H1 2023. For Project Director Allan Rodel, it’s an incredibly exciting time – both for what lies ahead, and what has been achieved thus far.
“In terms of underground progress, we are on track to reach operational readiness. We are undergoing a sustainable ramp-up in construction, and there are still various systems we need to put in place, including pumping systems, water management, and ventilation, but from that point of view, things are looking positive,” he outlines.
Since VUP’s inception, De Beers has adhered to an Operational Readiness Framework to guide its transition from open pit to underground, defined by the four tenets of assets, process, systems, and people. By so doing, VUP follows a holistic vision of progress, whereby no one is left behind on the journey.
Safety is an intrinsic thread in the cultural fabric of VUP, woven through every aspect of operation. This is embodied by the ‘2022 Safety Improvement Action Plan’, which is divided into the following key areas: leadership and governance, cultural and behavioural aspects, training and capacity, technology, risk management, performance, compliance assessment and improvement, contractor management, communication and health and wellness. Current overall progress stands at 76 percent completion of the annual plan.
The safety and culture plan incorporates the ‘Pioneering Brilliant Safety’ (PBS) framework, which commenced with a roll out in Q3 2021 in partnership with ITD and Safemap, and fulfils an essential role in establishing Venetia Mine as a safe and mature operation.
“We’ve been working with ITD
and Safemap for the past 18 months on PBS in our culture change journey. It’s an extremely validating effort in how we’re building the Venetia of tomorrow,” Rodel shares.
“It’s the safety drive I’m most excited about, and through PBS, we continually focus on various leading indicators – what are the things that didn’t happen, could have happened, or how could we have prevented them from happening,” he adds.
Key training programmes are aimed at supervisors and the teams working on the frontline of the mine’s operations, ensuring that all are equipped with the necessary skillset to perform their roles as safely as possible. Going forward, new culture change modules from ITD are set to be implemented across the Venetia Mine site.
“On a daily basis, we drive the culture of identifying things that might result in a negative outcome. You have to look for ways to make safety fresh and engaging.”
One “forward-thinking programme” that Rodel highlights as working particularly well in this respect is ‘Brothers and Sisters Keeper’ - an
on-the-spot recognition scheme launched within the past 12 months whereby individuals are incentivised for the correct culture and behaviour and for recognising their peers.
It is such initiatives that play a fundamental role in cementing VUP’s stance on prioritising its people and their safety. This is key to both talent attraction and retention, which is essential on an ambitious journey that requires significant recruitment efforts.
“We have pulled out all the stops to make sure we’re attracting the best talent,” comments Rodel, emphasising how the mine is working with different agencies and recruitment partners to entice skilled workers. As an owner-maintained mine, there is an explicit focus on localisation in recruiting people from around Limpopo.
Simultaneously, however, it is equally important to retain those who have a loyal working history at Venetia and train them to work with underground assets.
“We have many employees who have worked for us for over 30 years in our surface operations. It is rewarding to see how many want to keep working for us by transitioning to the underground,” he continues.
At the nexus of this development is the state-of-the-art Skills Development Centre, launched in 2021. A major surface project, the facility is critical in transitioning employees from open pit to underground, whilst also training new employees.
Incorporating the latest technologies, the centre is Mining Qualifications Authority (MQA) certified and boasts video walls, refuge bays, virtual reality capabilities and six simulator training modules, alongside instructor-led classroom facilities, yard training facilities, and dedicated underground skills transfer mining areas for practical experience.
Since 2019, over 130 employees have been successfully transitioned
from open pit to underground through rigorous training processes. With a fully developed training management system in place, the facility is in constant evolution to ensure up-to-date skills development for all those involved in the mine –from surface to Top of Mine (TOM) and Bottom of Mine (BOM).
Technology is a key ingredient in the change taking place across the site, as VUP follows an ambitious journey of digital transformation. Digitalisation is incorporated throughout VUP’s systems and falls within the overarching vision of establishing VUP as a mine of the future.
“It’s an extremely exciting digital journey that we’re going on,” states Rodel. “Digitalisation is the way we do business, and we have several systems employed to support this vision.”
Crucially, the technological innovation behind this transformation is encouraged to thrive in progress with people transformation, in terms of upskilling and training, to ensure cohesion and collaboration between the two.
This is evidenced by the state-ofthe-art Thoroughtec simulators for Sandvik intelligent loaders, trucks, drills and bolters installed in the training centre, and a host of other technological applications concerning skills development. This will only increase in the decade to come, as VUP’s ambitious technological development will see the site aim to
become a fully autonomous mining operation by 2027.
The Venetia Underground Technology Development Roadmap outlines that by this time, the underground operation will have established an autonomous mine production system, autonomous navigation/tramming, data analytics, 3D mine visualisation, personnel location tracking, automated asset health monitoring, and a digital operating platform.
Steps towards automation are already underway, as VUP’s first remote-operated loader undergoes safety testing at the facility in Q4 2022.
For Rodel, a series of fundamental questions lie at the core of this “forward-looking lens” regarding the application of technology - how will it affect operations, what does it mean in terms of maintenance, and does it
make business sense in light of what VUP is trying to achieve?
“The critical element of technology is that it’s got to make sense and not just implemented for the sake of it. You have to take everyone along with you on the journey of why technology is important – proving that it’s safer, more productive, and making a genuine difference.
“We have a whole series of training programmes outlining where we need to go and how this whole jigsaw puzzle fits together. Everyone must know where they are going and everyone needs to understand the “why”.”
VUP’s emphasis on bringing everyone along with the mine’s future translates not just to its employees, but also the Limpopo communities surrounding its operations, particularly the local
suppliers and service providers involved in the project who share in the site’s ambition and vision.
Here, Venetia Mine endeavours to leave a lasting positive impact that will benefit the area long after the mine’s combined open pit and underground lifespan of approximately 60 years.
“The sustainability of our business is critical to us,” introduces Supply Chain Manager Nadine Kok. “We want to ensure that we further develop the skills of our service providers
Founded in 2001, Great Nthambe Electrical Services (NES) has worked with Venetia for the past five years, providing electrical maintenance, high voltage services and electrical engineering. The business is owned by Mr. and Mrs. Nembudani, with Mr. Nembudani having worked for 16 years as an electrician in the mine.
Presently, NES holds contracts with the Musina Mine, Musina Municipality, ESCOM, SANRAL Project and Venetia – the latter of which is a contract for electrical installation worth over USD$2.8 million.
When NES encountered financial difficulties so severe that it struggled to pay its workers, Venetia stepped in to ensure that the business got back on track.
The mine continues to engage in the growth and development of NES, and its services have expanded so much that employees have increased by 25 percent since it entered a collaborative working relationship with the mine.
and contribute to the community in a way that means they’re not solely dependent on the mine’s lifespan. There’s a lot of skills development taking place both on and outside of the mine,” says Kok.
One example is the Changing Lives Forever Skills Development Programme. This came to inception after a skills shortage was identified in the labour needed to build accommodation in Musina during the construction and transition phase of the mine. As a result, VUP teamed up with BMH Africa to deliver the necessary skills training to tradespeople on mine accommodation construction projects, with excellent results. Through this project, participants are receiving valuable skills experience, literacy and health and safety training with the appropriate certifications, equipping them with the skills and
training to undertake such work anywhere in the country.
Similar initiatives also apply to small businesses, with Kok highlighting local ‘success stories’ such as electrical services contractor Great Nthambe Electrical Services, and Blue Disa – a small civils company run by Mr. Nemakonde – which has grown and evolved alongside the mine over the past decade through its Zimele Business Hub programmes and on the job coaching and mentoring by Venetia Mine employees.
“That programme has been a huge success,” says Kok. “Blue Disa went from being a 100 percent whiteowned company, to being fully owned by Mr. Nemakonde. It has since grown from 15 to 60 local employees and has allowed significant business skills development and training on the mine itself,” she elaborates.
Corporate social investment
“WE HAVE A WHOLE SERIES OF TRAINING PROGRAMMES OUTLINING WHERE WE NEED TO GO AND HOW THIS WHOLE JIGSAW PUZZLE FITS TOGETHER”
– ALLAN RODEL, PROJECT DIRECTOR, VENETIA UNDERGROUND PROJECT
contributions by all the Venetia Mine’s contractors are integral to these efforts as surrounding businesses, and in turn the communities, grow in tandem with the mine.
Returning to the idea of technology and personal development flourishing hand in hand, this is a key focus of De Beers’ partnership with the International Youth Foundation (IYF), where digitised education is making a difference for students enrolled in Technical and Vocational Education and Training (TVET) colleges.
The programme enhances course content and offers valuable work experience opportunities for those studying in institutions near Limpopo and is run in collaboration with the Department of Higher Education and Training (DHET). So far, the scheme has undertaken skills gap analysis, offered enhanced life skills training, established a private sector
engagement forum to identify early career opportunities, and has launched online lecture resources.
“We are rewriting the curriculum, adjusting training, providing digitised lectures and equipping students with the necessary life skills to prepare them for a work environment. We are digitising the whole story,” says Kok.
Indeed, earlier this year the programme received the go-ahead for digitised content to be rolled out across 50 colleges in 2022.
“It’s extremely exciting to be part of this journey and to see all the hard work paying off. We look forward to seeing the results at the end of the year,” she concludes.
Drawing to a close, Rodel returns to the vision of a mine of the future that VUP aspires to.
“It’s going to be a mine where
people will want to work – a mine that operates digitally in terms of its systems and processes, with the safest and best technology as well as trained, skilled people. It will have digitalisation at the core, using data analytics like no other mine, with corporate social investment programmes in place that genuinely make a difference.”
With all these elements combining, the future for Venetia Mine and the communities surrounding it, is sparkling.
On a trajectory of expansion, Batchfire Resources is the low-fugitive emission energy coal producer pursuing plans for Net Zero. We explore a community-centric company culture with CEO, Allan Fidock
Writer: Phoebe Harper | Project Manager: Eddie Clinton
It’s an exciting time to be in Australian coal mining.
Earlier this year, the federal government’s Resources and Energy Quarterly report forecast that Australian coal would soon become the second commodity to surpass AUD$100 billion in annual exports.
In the corridor of central Queensland’s Callide Valley, one company poised to exploit this dynamic market shift is energy coal producer, Batchfire Resources (Batchfire).
“The export market at the moment is extremely solid in terms of pricing, and is reaching historical highs,” opens CEO, Allan Fidock.
After stepping into the role just eight months ago, Fidock is set to ensure that the company is positioned to leverage these extremely favourable market conditions.
Following the discovery of bituminous coal deposits on these resource-rich lands in 1890, the Callide Mine has been in operation since 1944, before Batchfire became owners of the Callide Basin resource in November 2016.
Located 120 kilometres southwest from the Port of Gladstone, the operations of the mine are intrinsically linked to the livelihood of the Biloela township and Banana Shire as the beating heart of the local community. Batchfire is the Callide Valley’s largest employer and the mine is a catalyst for regional prosperity, driving the local economy, forming partnerships and creating a culture of local participation.
With the basin spanning over 16,000 hectares, the Batchfire tenure boasts a significant estimated resource potential of 1.07 billion tonnes of coal. Using conventional open-cut mining methods, the mine’s low-sulphur energy coal plays a significant role in domestic power generation, alumina refining, and international electricity generation.
Aside from the export segment, Batchfire’s open-cut energy coal operation is a vital source for its neighbouring power stations – Callide B and Callide C, owned by CS Energy. On an annual basis, Batchfire provides up to six million tonnes of ultralow sulphur, low fugitive emission energy coal to these power stations, helping to keep the lights on across Queensland and beyond.
These domestic markets are a crucial component of the Batchfire portfolio. While renewable sources play an increasing role in delivering Australia’s energy needs, coal remains a vital source of electrical power, providing 75 percent of Australia’s total electricity supply in 2020 alone.
“The Callide Power Stations produce just under 20 percent of the base load electrical power for the whole of Queensland,” emphasises Fidock. This equates to up to 1,525 megawatts (MW) of electricity fed into the national grid, enough to power two million homes and businesses across Eastern Australia.
• Introducing more fuel-efficient trucks and data-science led solutions to reduce overall fuel consumption.
• Using battery and solar panel systems to power communications hubs and other stationary facilities.
• Pursuing renewable energy opportunities across the Callide basin including solar and wind.
As Batchfire continues to develop its export reach, this same mission of enhancing societies with reliable power generation - and the employment opportunities and advances in education that this entails - is extending to developing countries across Asia.
“We target roughly 11 million tonnes of coal production per year, of which 4.5 million tonnes goes to export markets, while the rest is for domestic purposes,” outlines Fidock. “Aside from the Callide Power Stations, we also have another major domestic customer which we supply to in Gladstone.”
Fidock himself cut his teeth in the rewarding realm of Australian coal mining, and has long enjoyed the dynamism of such an industry.
“I grew up in rural New South Wales (NSW), when the coal mining industry was booming,” he reflects. After accepting an opportunity to join a local mining operation as a trainee surveyor, Fidock’s career path saw him climb the ranks to a managerial mining position and beyond.
Blackwoods is Australia’s largest supplier of industrial and safety products, providing end-to-end MRO solutions for an array of industries. Blackwoods supplies more than 300,000 products, including Personal Protective Equipment (PPE), safety workwear, workplace tools and equipment, industrial cleaners, lubricants, adhesives and much more.
In helping to build a better and safer Australia, Blackwoods, buys nearly 90 percent of its products from Australian organisations, and nearly a quarter of its products are Australian made. This includes products manufactured by Indigenous Australian businesses that are all Supply Nation certified. Behaving responsibly and acting with integrity is fundamental to how Blackwoods operates as a business. Blackwoods promotes and supports a rigorous sustainability agenda including a regular review of the sustainability issues that are material to the business. Blackwoods’ approach to sustainability includes assessing and managing material issues most relevant to operations such as Climate Change Resilience, Community Contributions, Ethical Sourcing, Gender Balance, Health, Safety and Wellbeing, Indigenous Diversity, People Development, Product Quality and Safety and Waste and Packaging.
The Blackwoods footprint is vast, with six distribution centres in each major Australian city, and over 50 Branches spanning cities, and rural, regional, and remote locations.
Blackwoods has earned a reputation as a leader across a vast array of industries that reflect the diversity of this nation. From snow to fire, waterways to highways, railroads to sea lanes, tilled soil to tunnels deep underground, Blackwoods is helping build a better Australia.
blackwoods.com.au
“It’s been a fantastic industry to be part of, enabling me to support my family and travel the world. From day one I was challenged, mentored and given the support that allowed me to achieve and surpass my early ambitions within the resources sector.”
1,250 families supported, directly and indirectly
42 percent of all local employment 85 percent of workforce live within Callide Valley
AUD$89.7 MILLION wages paid annually
AUD$293.4 MILLION paid for products and services annually
AUD$31.3 MILLION royalties paid to Queensland government annually
As the foundation of the company’s future objectives, maintaining credibility is crucial for both Fidock and Batchfire.
An enterprise of both drive and ambition, Batchfire prides itself on delivering its commitments. This is best evidenced by the progress of two of Batchfire’s primary goals –developing an increasing presence on the export market, and the target of reaching Net Zero by 2050.
In recent years, Batchfire’s foray into the export market has picked up speed significantly.
“A key difference that Batchfire brought when taking over the Callide Mine was to provide coal for export, since the majority of the previous owners were only concerned with domestic supply.
“The new owners have invested significantly into the mine in order to get the quantity of coal out to export. It has really given the mine a new lease of life,” he says.
Presently, Batchfire endeavours to increase its output to 11.5 million
Choose a Discovery Parks ‘home away from home’ for your next work stay
Since the company’s inception in 2004, Discovery Parks has developed a network of ‘home away from home’ properties capable of accommodating and catering for teams of workers of up to 200+ people.
First established in 2006, Biloela in Central Qld was Discovery’s first work stay property, and continues to provide accommodation services to nearby Callide mine.. Since then, Discovery’s work stay portfolio has grown to include 19 owned or managed work stay villages across Australia, offering quality accommodation and catering solutions for workforce staff.
Discovery Parks understands the unique needs of businesses operating in remote and rural areas, and our WorkStay team is committed to tailoring services that meet the needs of anyone working away from home. With that in mind, happy people are at the heart of Discovery’s work stay mission: to create a ‘home away from home’ that workers want to return to.
To ensure we deliver this at each of our properties, Discovery Parks commits to the following:
• A range of fresh, healthy meals with minimal repetition week to week.
• Regular food theme nights that utilise the strengths of our chefs to create authentic culinary experiences, including BBQs and specialty food truck nights.
• First-class recreational facilities including gymnasiums and pools.
• All the comforts of a ‘home away from home’.
• A promise to make our customer’s lives easy through every stages of their work stay rotation.
Whether you need an accommodation management team for your onsite village or you’d like to find out more about Discovery’s full Facility Management Service, Discovery Parks has the right mix of quality properties and people around Australia to help.
Next time Stay Discovery.
tonnes a year, capitalising upon the current market conditions to strengthen its position.
“The bottom line of this is simply that the more we can produce, the more coal we can send to export. We currently have plans for various options to reach 11.5 million tonnes by next year.”
It’s a major move for the company, necessitating further investment in labour and a renewed fleet of gear for operations.
“We have the equipment, and the people, but we do need more. It’s a tight labour market here at the moment, which means it can be difficult to get operators. We’re fortunate in that we have a full mix of operators and maintainers, but we need to source more to run that extra fleet,” he explains.
At the core of this movement is the premium of the Batchfire coal itself, as
a sought-after product with credible value on the global market.
“Although our coal type is quite low in typical export quality, in that it has low calorific value, it is extremely low in sulphur content which makes it keenly sought as a blend coal.”
Whilst most other coals have a sulphur level of 0.5 or 0.6, the sulphur content of Batchfire coal typically stands at 0.2. Crucially, when blended with other products, this brings down the overall sulphur content of the energy coal mix.
As the lowest fugitive emission energy coal mined anywhere in Queensland, Batchfire coal is an ideal component to fuel cleaner electricity generation across Asia Pacific, thanks to its reduced emissions and ultra-low level of inherent impurities.
The energy-efficient characteristics of the resource itself support Batchfire’s transitional energy
Mine Support Services (MSS) Is proud to be partnering with Batchfire Resources in a multi-year Mine Rehabilitation Program at Callide Mine. With shared environmental values we look forward to working together to implement the site progressive rehabilitation and closure plan, delivering positive environmental and social benefits for the Callide Valley community.
MSS are specialists in mining rehabilitation with over 30 years’ experience in mining rehabilitation.
Through every phase of the rehabilitation lifecycle, we provide turnkey solutions to achieve our client’s objectives.
Underpinning our service is a team of experienced mining professionals and environmental specialists combining best practices in science, agriculture, and bulk earthworks execution.
Our scientific approach considers every aspect of rehabilitation including landform design, earthworks modelling and optimisation, erosion and sediment control, soil chemistry, amelioration, ground preparation and seeding.
Our technical capabilities are built on innovative thinking, with constant research and development, combined with field trials to improve outcomes year after year.
Whilst what we do defines us, it is how we do it that really drives us. Everything we do revolves around the people who work for us and the people we work for. Our team values shape our business in every way. People are at our core.
Mining rehabilitation is an integral part of the mining lifecycle, and we are tremendously proud to be delivering great environmental outcomes, and to contribute to the success of Batchfire.
We are looking forward to contributing to the local community, by employing locally, purchasing locally, and supporting the community in which we are living and working.
www.minesupportservices.com.au
Drawing on over thirty years of experience MSS provide turnkey solutions to mining rehabilitation.
Our services include:
• Dozer push and bulk earthworks
• Topsoil cartage and placement
• Soil amelioration and seeding
• Erosion and sediment control
• Seed Supply
• 3D Machine Guidance and Dozer Push optimisation delivering lowest construction costs
For more on our story, visit us at www.minesupportservices.com.au
To discuss your progressive rehabilitation program requirements, contact MSS today: admin@minesupportservices.com.au Ph: 0745993401
MSS is proud to be working with Batchfire in a multiyear contract to deliver world class rehabilitation in the Callide Valley.
business model that will see the company move beyond a pure energy coal operation towards its target of Net Zero carbon emissions by 2050. A range of sustainability initiatives represent the company’s path towards this goal.
“I accept that from an external perspective it seems counterintuitive for a coal mining operation to set such an ambitious emissions target. But we see ourselves as a transitional energy company that willingly plays our part in the journey to address climate change. Our dedicated Environmental, Social and Governance (ESG) and Development Team works directly with our board to pursue opportunities for further reducing our emissions.” There are a range of innovative projects the company is participating in to reduce its environmental footprint.
“We’re currently looking into a small solar development on site, which will cover our internal use of electricity,
powering our two draglines and two coal handling plants.”
Complementing this use of renewable energy, Batchfire is also currently investigating a potential wind farm project being constructed adjacent to the mine.
“We’ve engaged with a third party regarding a project currently under development, but we’re also looking at our own opportunities within this space.
“We’ve identified a potential wind resource within the Callide Valley that we could take advantage of through such a development. Pursuing this is key to the business,” Fidock observes.
Internal improvements to operational efficiency are also being progressed, a flow on effect which includes improved emissions intensity consistent with Batchfire’s Net Zero target.
“On top of this, we are looking at a number of different things that bring smaller net reductions. This includes
We are dedicated to completing our projects safely, in full, on time and to budget. We ensure smooth delivery with minimal disruption and impact on production and asset availability. Established in 2017, Sync Lift Engineering is a privately owned and operated maintenance and engineering business group providing a broad range of services.
We offer an in depth knowledge base across all aspects of a project from the feasibility stage all the way through to commissioning, close-out and completion.
We have extensive asset expertise in the following:
• Draglines
• Electric Rope Shovels
• Coal Handling Preparation Plants
• Stacker Reclaimers
• Ship Loaders + Unloaders
• Heavy Mining Equipment including Dump Trucks, Front End Loaders, Graders and Dozers
• Fixed Plant + Process Infrastructure
• Hydraulic Excavators
We enhance the value and performance of your assets through our innovative approach. Our capabilities include structural, mechanical, piping, electrical and instrumentation, manufacturing and fabrication, and engineering disciplines.
We provide support through proactive (scheduled), reactive (breakdown) and planned major outage (shutdown) maintenance services. www.synclift.com.au
new truck fleets that have dieselelectric drive systems rather than a purely diesel-mechanical drive which reduces diesel usage,” he tells us.
“We have also installed a mine information and reporting system that enables optimised fleet movement.”
This new software-based system will be instrumental in delivering a better outcome, in terms of optimising the efficiency of the fleet in producing the same output.
“These are just some of the ways we are approaching Batchfire’s transition to that Net Zero target.”
At its heart, Batchfire is dedicated to the welfare of the communities both within and surrounding the Callide Mine. This commitment extends beyond supporting mining families and driving the local economy.
Implementing a safe, diverse, and resilient workforce is of paramount
importance to Batchfire, and is one of the most critical aspects of the company’s ESG strategy.
Indeed, the company’s perception and recognition as a socially responsible corporate citizen and the level of engagement between the mine and its people is for Fidock, one of the greater metrics used to measure Batchfire’s success.
“We’ve taken on the task of building credibility with the workforce,” he says.
To do this, continual engagement with employees is essential to ensure the shared goal of maintaining a safe and productive workplace that is characterised by a culture of
Butlers Yarwun Quarries, is a family owned and operated Quarry situated 12 kilometres north-west of Gladstone, QLD and has been operational since 1985.
Butlers Yarwun Quarries formed a working partnership with Batchfire Resources at Callide mine in 2021. Our mobile crushing unit produces road base for haul road maintenance, stemming aggregates for blasting operations and erosion control rock for environmental rehabilitation.
Butlers Yarwun Quarries congratulates Batchfire Resources for their vision in increasing production at Callide Mine and looks forward to an ongoing successful partnership with Batchfire Resources into the future.
www.yarwunquarries.com
challenge, courage, integrity, and commitment.
“We want to show our people what can be achieved and believe in giving them the scope and room to perform their roles.
“We are here to give them direction, show them the boundaries, and hold them to task on the individual performance of their job,” Fidock continues.
Fidock’s emphasis on this peoplecentric aspect of operations has been one of the many changes he has introduced to the company since taking over as CEO, ensuring that the people are right behind Batchfire and recognise its integrity and credibility on delivering on its commitments.
“WE’RE VERY CONSCIOUS OF OUR PLACE BOTH WITHIN THE LOCAL COMMUNITY AND THE REGION”
– ALLAN FIDOCK, CEO, BATCHFIRE RESOURCES
“It’s a new level of direction that I’ve brought to the business – there’s no rocket science behind it, it’s just the way that I do things,” he shares. “There’s always so much more that we can do, but now there’s certainly more of a sense of confidence around the workforce and the staff that we’re on the right track.”
This empowerment and motivation of employees is intrinsically linked to the support of the overall community, considering that Batchfire stands as the Callide Valley’s largest single employer and a significant contributor to the local economy.
Around 85 percent of Batchfire’s 800 full-time equivalent direct employees reside within the Callide Valley, with the company accounting for 42 percent of all local employment. This eliminates the need to rely on fly-in fly-out workers. It is a model of employment that contributes to connection within the local community, meaning that employees
do not need to spend long periods of time working away from home.
“Both as a mine and a company, we have a very close association with the township of Biloela and draw the majority of our employees from that community,” explains Fidock.
“Our social governance, our commitment to and engagement with that town is extremely strong.”
The Callide Mine has been a key source of local employment for more than 75 years, and maintaining these partnerships and supportive relationships remains a major priority for Batchfire. Working in a beneficial way with both the people and the land are the fundamental aspects of the company’s commitment to responsibly develop the resources of the Callide Basin whilst preserving the environment for future generations.
Batchfire seeks to maintain and improve its ESG credentials built on a baseline of ensuring compliance with all environmental, mining tenure
and governance approvals and requirements, including paying all necessary royalties and tax.
“We are always working to build our ESG credentials and undertaking a number of projects within this to ensure that we are environmentally maintaining our tenements as we should.”
The mine’s three active areas –Boundary Hill, Trap Gully and Dunn Creek – ensure Batchfire maintains the Callide Mine’s proud record of a reliable coal supply, local employment and business opportunities.
Batchfire recognises the First Nations Gaangalu Nation People (GNP) as the Traditional Owners and Native Title claimants over the land upon which it operates. Its relationship with the GNP helps to develop partnerships around cultural heritage management and enable access in support of the GNP maintaining connection to country.
“We are actively pursuing business
We combine true end to end solutions, local knowledge, and the most diverse product range to help keep your business running smoothly.
partnership opportunities with the GNP, alongside the increasing number of First Nations employees within our business.
“It’s extremely important to us that we are seen – and I believe that we are – as a good corporate citizen, not only for the region, but also for the state. We can always do more, but we’re very conscious of our place both within the community and the region.”
For the near future, Batchfire has its hands full with plans for increasing production levels and implementing the range of initiatives on its journey to Net Zero.
“We are investing in a new fleet of gear so that we have the best technology on site. This allows us to be more efficient, whilst also improving working conditions for our employees. After all, if you’re sat operating a truck, you’d rather be in a brand new one!”
But for Fidock, an entirely employee-centric outlook best defines Batchfire’s priorities in the years ahead, especially as the company is in the stages of recruiting more workers.
“As we are getting more and more employees on site, we want to become an employer of choice to ensure that they stay. It’s all about making people feel safe and secure, and rewarding them for their performance.”
As part of this, Batchfire is implementing extensive training and development plans at all levels. This includes supporting its frontline supervisors, to ensure that they continue to upskill and have the confidence to motivate their crews.
“Most importantly, we’re ensuring safety is a daily, ongoing priority,” Fidock adds. “We want our employees to return home uninjured each evening – perhaps just a little bit more tired than when they left for work!”
Drawing to a close, Fidock returns to the all-important notion of credibility, as the adhesive that binds the company‘s goals and ambitions with the people that can make them happen.
“We are now going through a process of looking to achieve targets that might not have been within reach previously, both in terms of production and a quality of output basis.
“We’re getting credibility with our workforce because we are achieving those targets – we’re showing that they’re not out of reach, and we are bringing them along with that journey. We want our employees to be proud of what they achieve on site.”
Tel: 07 4845 1500
callide.info@batchfire.com.au
www.batchfire.com.au
Driven by a dedicated workforce and green, innovative thinking, Hitachi Construction Machinery Australia brings quality products and solutions to the Australian market. We speak to Sean Ryan, General Manager of Mining, to learn more
Writer: Marcus Kääpä
Project Manager: Eddie Clinton
Australian mining is a vast and historic industry that moves with the times.
Today, the success of operations in the field comes down to the latest technology, and the calibre of the machinery involved, supplied by toptier players backed by decades in the industry.
Hitachi Construction Machinery (Australia) Pty Ltd (HCA) is a subsidiary of Hitachi Construction Machinery Co., Ltd (Japan) and part of the global Hitachi Construction Machinery Group. HCA is the exclusive distributor of Hitachi and Bell products in Australia.
“Our overall company mission is to contribute to society with superior products,” begins Sean Ryan, General Manager of Mining at
HCA, introducing HCM’s central and founding purpose that is mirrored in each of its international divisions.
“Hitachi founder Namihei Odaira’s sincere belief to “contribute to society through the development of superior, original technology and products” has been handed down from Hitachi today to form the basis of HCM’s operations around the globe. Our century-long history is one of giving shape to this mission, supporting society, and realising a more comfortable and safer world through our technologies and products - this mission is reflected in HCA.”
This mission is what stood out to Ryan upon first joining the company. He started his career as a tradesmen assistant in the early 1990’s with the previous Hitachi dealer in Australia (Marubeni, Brisbane) and after a few months, was able to start an apprenticeship with the branch as a diesel fitter. Upon receiving a trade qualification and introduction through the global dealer network, Ryan was fortunate enough to work abroad with Hitachi in the UK. After a few years, he went to university back in Brisbane and studied a Bachelor of Technology in Mechanical Engineering and subsequently continued tertiary qualifications with a Masters in Engineering Management, and Graduate Certificate in Business Administration.
“Since graduating, I have had the opportunity to work in many fields of heavy engineering such as mining with different OEMs over the last 20 years,” Ryan says. “The last seven years have been back home with HCA in the mining sales department, where I’ve since been promoted to the role of General Manager of Mining for the last six months. It is incredibly refreshing to be part of an organisation that not only talks environmental, social and governance (ESG) but actually puts it into everyday engagement with customers, employees and the community.”
HCA is committed to delivering machinery sales, parts and support to Australian customers across the mining, construction, quarry, material handling and recycling industries, through a wholly owned national branch network of 23 sites across Australia, including three remanufacturing facilities and two mining assembly facilities. With over 1,200 employees, HCA is equipped to provide 24/7 customer support and field representatives across Australia’s regions.
On top of this, being partnered with Marubeni Equipment Finance, HCA is in a position to provide in-house finance to its customers, adding an extra facet to the company’s industryleading offers.
“Our values emulate the founding spirit of Hitachi, and have been embraced with care and guided by our predecessors for over a century,” Ryan says, reinforcing the core of the company. “This spirit resonates through the way we think and operate as we collectively strive to deliver solutions that create new value globally.”
HCA’s vision is an expression of what Hitachi aims to become in the future; to achieve greater advancements, to address today’s global challenges in resources, energy
and the environment, and build a sustainable society.
In light of this, HCA has invested heavily in technology, with its product range driven by Wenco International, a wholly owned subsidiary of Hitachi, that offers an integrated suite of solutions to support the digital transformation of the mining industry. Fleet management, asset health, data analytics, and other technologies join together in the spirit of open interoperability to raise mine productivity and efficiency, lower routine costs, and establish a safe and smooth mining operation.
“Our autonomous systems for mining equipment are developing very rapidly, with solutions for our electric drive dump trucks now operating in the mining space,” Ryan adds. “On top of this, the future of operator assistance technology in excavators is well under development and on trial at different sites around the globe.”
We are focused on being a market leader In wear solutions globally.
We understand the business needs of our customers, their pain points, measures of success, and technical and performance requirements of their equipment and operations.
We utilise our unique knowledge, experience and capabilities to help our customers achieve their goals. With a focus on safety, collaboration, innovation and sustainability across all aspects of our business we deliver reliability, certainty and confidence to all our partners and stakeholders through consistent delivery of our products, services and solutions.
We specialise in solving our mining customers’ wear challenges, supporting their bulk handling and mobile equipment to operate at peak efficiency by deploying our significant experience to design, manufacture and supply high quality solutions.
EXCAVATORS - Machines guaranteed to provide world-class performance, sophisticated design and legendary reliability.
RIGID DUMP TRUCKS – HCA’s rigid dump trucks (RDT) are designed with superior hauling capabilities and industry-leading technology.
ARTICULATED DUMP TRUCKS –HCA’s articulated dump trucks (ADT) excel in productivity due to their high power-to-weight ratios and fuel efficiency.
WHEEL LOADERS - Wheel loaders are suitable for a range of applications thanks to their dynamic design and myriad optional attachments.
Penske Australia’s long-standing relationship with Hitachi Construction Machinery Australia is underpinned by our mutual goal of delivering excellence.
Through our range of highly efficient and powerful mtu engines, we power Hitachi equipment ensuring the delivery of superior performance with market-leading reliability and low cost of ownership.
HCA’s success is not just down to the metals and machinery. At the heart of the company lies a team of talented and dedicated people committed to providing such industry-leading solutions, making HCA the perfect industry partner and keeping it at the forefront of the market.
For Ryan, every employee at HCA helps to build the company, and with branches across Australia, HCA offers a wide range of careers and job opportunities for those seeking to become and stay involved in the mining machinery space.
“We’re proud to be an equal opportunity employer that recruits based on merit and capabilities. We encourage and support a talent pool of diverse skills, ethnicities and genders, to create a vast culture of shared values and enriched experiences in our business,” Ryan tells us proudly.
“Along with a variety of employee benefits, HCA offers employees competitive wages and biannual discretionary bonuses to recognise positive contributions being made to the business throughout the financial year. In order to empower our people, we focus on fostering open communication and set clear expectations to provide employees with autonomy to manage their responsibilities accordingly.”
HCA offers a suite of solutions for customers. This includes technology-based solutions that monitor machine performance, provide reporting and applications that can be used on mobile devices, and are available on Apple and Android phones for technical support and 24/7 nationwide customer service and support. Also available to HCA customers are premium service agreements that can provide discounts on machine servicing and other benefits.
SUPPORT – HCA’s experienced factory-trained technicians and product support representatives are on call to ensure customer machinery operates to the highest standards.
PREMIUM SERVICE AGREEMENT
– HCA’s contracts and agreements are tailored to fit customer business needs and range from maintenance and repairs to performance guarantees.
TECHNOLOGY - A suite of technology products offers equipment tracking, maintenance, daily operating information, and equipment health conditions.
HCA provides continuous training and education to all its staff to ensure the right opportunities are given, promoting rewarding and successful careers with longevity in the business. According to Ryan, it is common for a career at HCA to start at an apprentice level, before progressing through one of the many other career path options.
HCA’s market-leading apprenticeships run in conjunction with TAFE NSW (TAFE) courses and align with the government’s Australian Apprentices Incentives Program (AAIP). The programme provides apprentices with hands-on experience and training to become heavy vehicle mobile equipment (HVME) mechanics and automotive electricians.
“These practical apprenticeship programmes are ideal for interested school students or mature-age students and are available at all major HCA branches across Australia, in every state and territory,” Ryan continues.
“The training and education strategy focuses on guiding career pathways and development to suit our staff’s needs and the requirements of the business. Course offerings include qualifications and career path options for service, parts, sales and administrative roles, with topical areas including management, supervision, technical, customer service, and business systems compliance.”
HCM offers a number of mining products and technologies in the market which customers can take advantage of in order to reduce their environmental footprint and lower their carbon emissions. The trolley truck and electric excavators are proven pieces of equipment, with HCA supplying several fleets globally,
Australian owned and operated business supporting the heavy earthmoving industry for over 30 years. We are proud of our commitment to safely deliver exceptional quality repairs and work closely with OEMs. Our purposebuilt facility in the NSW Hunter Valley overhaul components for Hitachi including front spindles, trailing arms, hubs, axles, boxes and specialist repairs on undercarriages from EX3600 through to EX8000 machines.
and over 130 excavators respectively delivered into the market outside of Australia.
As well as providing environmentally friendly solutions which leverage Hitachi’s innovation and proven technology to deliver greater value to customers, HCA can convert existing fleets of trucks, trolleys and excavators to electric vehicles (EVs).
“The key to any future zero emission plans will be the infrastructure on the mine site to support electrification and any changes to mining applications, even if it’s to the detriment of production initially,” explains Ryan.
“12 months ago, I felt these were the areas which were going to hold the industry back, however we are very quickly seeing mining personnel get their heads around these requirements along with industry bodies and driving change a lot quicker than previously realised.”
The mining industry is already seeing the effects of climate change influence its business activities, with long-term sustainability targets now in place. As these targets and regulatory requirements approach, HCA is prioritising options to support this energy transition in the form of dynamic and static charging systems for battery dump trucks and battery/hybrid excavators.
In the immediate future, HCA will be releasing its first EX2000-7 (200tonne) excavator into the Australian market in March 2023. The model will be on display for a customer launch event at HCA’s Perth branch, where the company will also showcase the investment made at its new purposebuilt facility for mining assembly and component remanufacturing. This will align the last piece to the puzzle for the multi-million-dollar investment HCA made to support operations within the Western Australian (WA) region.
“The EX2000-7 joins the full dash seven mining excavator product range and replaces the EX19006,” Ryan notes. “Built from over 50 years of reliable hydraulic excavator history, it has the latest technologies from HCA including electronic pump regulations, updated fan speed control, regeneration valves, improved efficient cooling package and hydraulic controls all leading to 18 percent fuel saving over its previous model in this class – truly a mining machine of tomorrow.”
M Resources Pty Ltd. has leveraged its industry expertise and global network to become a leader in coal trading, marketing and consulting for metallurgical coal products. Founder and President, Matt Latimore digs deep into the company today
Writer: Phoebe Harper | Project Manager: Eddie Clinton
As a landmass, Australia boasts some of the largest coal resources in the world. Although an industrial and economic cornerstone, in the context of the ongoing climate crisis and exploration of alternative energy sources, coal has become a contentious issue.
Further to the shift in the global perception of coal, major geopolitical events continue to make seismic waves across the global market. This began with the demand impacts of the COVID-19 pandemic, followed by China’s imposition of a ban on
Australian coal in 2020 and most recently, the trade sanctions resulting from Russia’s invasion of Ukraine.
Regardless, for Matt Latimore, Founder and President of Brisbanebased mining, marketing, trading and investment company, M Resources Pty Ltd. (M Resources), the metallurgical coal industry is currently defined by both optimism and opportunity.
“In recent times, the coal trading industry has been an extremely exciting place,” he says. “Russia was a major supplier of metallurgical coal
to the international market, and it has been a very important role for Australia to step up and fulfil supply to our global trading partners.”
With Australia as the largest supplier of coal to the international seaborne market, M Resources is well-positioned to oversee that this demand is met, as the company markets coal from every port across Queensland, including Gladstone, the Dalrymple Bay Coal Terminal in Mackay, and Abbot Point - home to the deepwater coal port of the North Queensland Export Terminal.
“Of course, there has been a lot of volatility to deal with, but the overall demand and mid-term outlook for metallurgical coal is extremely encouraging,” observes Latimore.
With a broad remit of services, encompassing mining, marketing, trading and investment, M Resources focuses its expertise primarily on the steelmaking raw materials of metallurgical coalcoking, pulverised coal injection (PCI), iron ore and thermal coal. For almost a decade, M Resources has also handled exports of mineral sands including rutile and zircon.
In addition, the company comprises two complementary subsidiaries with MetRes (a 50-50 joint venture (JV)
between M Resources and Stanmore Resources), and M Mining - the operator of the Millennium Mine in Queensland’s upper Bowen Basin.
“We also have mining operations in Queensland near Moranbah,” adds Latimore.
Although its head offices are in Brisbane, M Resources is bolstered by a vast global network. The company’s footprint extends to regional offices in Singapore, the UK, North America and South America, and its expansion shows no sign of slowing. Indeed, 2023 is set to bring two further offices in both Japan and India.
“We have invested heavily in our global network and have strong customer relationships across the world,” shares Latimore.
SERVICES:
• Market information and strategy
• Market development
• Technical marketing consulting – coal characterisation, testing and value in use analysis
• Blending
• Specification and development
• Sourcing
• Resource evaluation
• Trading – metallurgical and thermal coal
M Resources has several existing marketing agreements in place including:
• Exclusive marketing for Stanmore Coal
• Exclusive marketing for Bowen Coking Coal
• Exclusive metallurgical coal marketing for Arcem (Mozambique)
• Exclusive marketing and sales for Allegiance Coal New Elk Mine
• Marketing for Magnum Iron Ore and Iron value-add products
• Marketing for AVF Energy hydrogen products
With an approach grounded in geology and reinforced by technical excellence, Cartledge Mining and Geotechnics (CM&G) delivers practical and innovative solutions to mining companies around the world. Based in Australia, the geotechnical consultancy is developing a global reputation of excellence through its practical yet innovative approach to mining solutions from exploration to mine closure.
CM&G Principal Tim Cartledge said focusing solely on the mining industry allows the team of geotechnical practitioners to develop a deeper understanding of the complexities across the lifecycle of mining projects for all commodity types.
“As mining specialists, the CM&G team have vast operational expertise backed by a high standard of technical knowledge in rock engineering, which means we deliver practical solutions that will keep a mine operating as efficiently and as safely as possible,” he said.
“We work in collaboration with our clients. This partnership means that the problems a mine experiences are our problems to solve.
“When challenges arise, we are there working alongside our clients as a single team to achieve the best possible outcome. We don’t hold ourselves separate from the problems and work hard to maintain safe production.”
Collectively the CM&G team has worked on projects across Great Britain, Europe, North and South America, Africa, Asia and the Pacific, establishing a proven track record for delivering solutions that work for their clients.
This experience has given CM&G’s geotechnical engineers and engineering geologists extensive hands-on experience in identifying ground-related hazards and opportunities to optimise resource extraction value.
Find out more about working with CM&G at cmandg.com.au
On top of this expansive geographic reach and portfolio of expertise, it is the people behind M Resources that are a crucial differentiator in maintaining an astute perspective on the market and responding appropriately to clients’ needs.
“We understand the markets that we cover extremely well,” he continues. “Not only this, but we understand logistics, and the technical aspects of the product we market.
“We have been building the right people around our company to be able to take advantage of identifying good assets and the right kind of companies that we want to be involved in.”
Latimore’s people philosophy is easily summed up – his clear focus is on expertise and excellence, aimed at further increasing customer assurance and confidence in the M brand.
Such entities are integrated into M Resources’ robust customer
networks, with the company adding value to each operation through the application of its unsurpassed market knowledge and industry experience.
“Building on that, we also have a team of mining professionals, meaning that when we partner with mining companies, we already have a solid understanding of the business, and so can market and represent them with a strong background in both the industry and the product,” Latimore explains.
With people as the company’s differentiating asset, M Resources continues to grow its teams, further expanding its Business Development department, and enhancing its logistics and technical capabilities. The company believes it is differentiated by its team, and its ‘go to market’ delivery capability.
Turning to ongoing projects in development, M Resources and
Atlantic Digital is a leading, Australian owned IT specialist providing expertise in the design, support and maintenance of IT networks throughout Australia and New Zealand.
With over 25 years’ experience in the mining and resources industry, we offer you a reliable partnership that can be trusted to deliver your end-toend technology solutions.
Our company foundations are firmly within the mining and resources sector where we continue to provide innovative solutions using local field personnel. In 2022, we worked closely with M Mining to deliver a rapid deployment of server infrastructure and field communication networks to the Millennium Mine and continue to support the development of their underground operations.
As with M Mining, our experience has been leveraged in modernising operations for mining companies including real-time data flow, unification of IT systems, upgrading process control and automation networks that are used across all critical systems.
Our methodology is flexible and based on the needs of our customers. The breadth of our capability in mining sector IT systems and user support, network engineering, cloud integration, procurement and licensing and cyber security is unparalleled in the industry.
We value strategic partnerships to drive innovation, deliver value, simplify IT platforms and reduce IT overhead in the business. Through the provision of reliable, quality services, our reputation as a trusted partner has grown across the resources sector. Contact us to see how we can deliver value to your business.
www.atlanticdigital.com.au
“WITH THE ENERGY CRISIS AND SUPPLY RESTRICTIONS FROM RUSSIA, WE ARE WORKING HARD ON INCREMENTAL EXPANSION TO MEET CUSTOMER NEEDS”
– MATT LATIMORE, FOUNDER AND PRESIDENT, M RESOURCES TRADING PTY LTD.
CELEBRATING 25 YEARS PROVIDING CORPORATE & FIELD IT SERIVCES TO THE MINING INDUSTRY
Our comprehensive understanding and experience in the mining sector ensures we can support and create value across mining process, applications, methods and challenges. We have locally employed field based staff throughout the Bowen Basin and Hunter Valley to provide an on-site personal approach to IT support.
• Managed IT Services
• Mining Applications & Technology Services
• Technology Roadmap & Planning
• Server Infrastructure & Backup
• Network Engineering
• Field Communications & Design
• Cloud Solutions & Integration
• Procurement & Licensing
• Understanding of Mining Systems & Methods
• Security Consulting
• Vendor Access Solutions
• Local, Field Based Staff
REDUCE VENDOR MANAGEMENT AND LEVERAGE OUR EXPERIENCE TO DELIVER YOUR IT SOLUTIONS AND SUPPORT
We can deliver your entire IT deparment or be part of the team.
its related entities hold strategic investments across some major forces of Australian mining. This includes a five percent equity stake in Stanmore Resources, which owns South Walker Creek, Poitrel and Isaac Plains mines and a 10 percent level of investment in Bowen Coking Coal, where M Resources both markets the coal and is a major shareholder. The latter commenced production from the Bluff Mine just last year, with the first export shipment taking place in June 2022 and Broadmeadow East Mine in January 2023.
In addition, M Mining holds 50 percent investment in the MetRes Millennium Mine and is both JV Manager and Operator. Millennium became the first mine to be operated by M Mining after it was purchased by Peabody in April 2021.
Within just six weeks of completing the mine acquisition, M Resources has been awarded AUD$460 million in contracts for auger, open-cut and underground mining at Millennium.
MATT LATIMORE, PRESIDENT AND FOUNDER: “This will be the first investment in NSW and hopefully a beachhead for M Resources’ investments there. We recently concluded 20 percent project-level equity at the Dartbrook Mine in NSW with the Australian-listed entity, Australia Pacific Coal. As owners of the project, we’re progressing a JV with that company to restart those operations and undertake the marketing. We expect that project to be up and running in the final quarter of 2023.”
Its first shipment was exported within five months of taking ownership of the mine, which was in care and maintenance with only three full-time staff.
“The plan was to extract the full economic value from the resource via auger and open-cut mining in a new pit while progressing the underground mine development with our partners PIMS Group from Mackay,” outlines Latimore.
Throughout 2022, M Resources continued to make good progress with its underground development at Millennium and mined approximately 600 thousand tonnes (kt) by open-cut.
“We have been exporting coal out of that operation for over 12 months now, and it is a fantastic achievement that fits with both our underground mining business and our coal marketing business.”
2022 proved to be a major year for the company, coinciding with Stanmore Resources’ acquisition of
MCC Group is dedicated to providing an honest, reliable and quality service to our clients. Our mission is to provide our employees with a safe and supportive work environment, where they each, individually and collectively, can dedicate themselves to providing our clients with outstanding workmanship, extraordinary service, and professional integrity.
Adam Merrick (company director) established Merrick Construction & Concrete in 2017. Within one year, the business rapidly grew into a successful company to address a growing need for proven hands-on construction, and project management of complex and major mining infrastructure including maintenance, smaller commercial, industrial projects, concrete, and civil works. In 2020, MCC Group Pty Ltd was created and took over from Merrick Construction & Concrete Pty Ltd.
Today, MCC Group Pty Ltd has a strong presence in the Australian mining and civil industries. The significant growth is due to our recognised expertise on large projects across multiple sectors.
Our services:
• Production mining
• Fixed and mobile plant maintenance
• Mine site cleaning
• Commercial and industrial construction and maintenance
• Major site access works, boom gate, culverts, intersections, and roadways
• Switchyard construction
• Ventilation fan and underground portal construction including underground concrete works
• All plumbing services
• Coal plant maintenance
• General building maintenance
• Camp maintenance
• Landscaping services
• Roadway slashing
• Polywelding
• Pit-dewatering
MCC GROUP IS A LOCALLY ESTABLISHED CONSTRUCTION AND MAINTENANCE COMPANY SERVICING THE CENTRAL HIGHLANDS REGION.
MCC GROUP
PO BOX 949, Emerald, QLD, Australia
admin@mcc.group
www.mcc.group
the BHP Mitsui coal assets at South Walker Creek, Poitrel, and Wards Well.
“This was a tremendous expansion with very good quality large-scale, low-cost mines which substantially increased production to over 10 million tonnes per annum,” Latimore tells us.
Most recently, a major development is on the horizon for M Resources with the company’s agreement to take 20 percent project interest in the Dartbrook Mine in New South Wales (NSW) with Australian Pacific Coal.
With a wealth of projects currently either underway or firmly in the pipeline, M Resources is stepping up to meet the demand expected of Australian coal, evolving and expanding in line with the global market.
“I am expecting further expansions in Queensland with all our affiliated companies. With the energy crisis and supply restrictions from Russia, we are working hard on incremental expansion to meet customer needs,” surmises Latimore.
Continually growing its investments
in mining and infrastructure, across both coal and other commodities, M Resources will direct its investment strategy towards assets and businesses where it can best add value by marketing the products generated. However, for the immediate future, Latimore’s focus for M Resources is crystal clear.
“For the year ahead, we will focus on growing our mining footprint through the Millennium operations and Dartbrook, expanding with our partners Stanmore Resources and Bowen, and increasing our global marketing network to thoroughly service the needs of our customers, partners and stakeholders.”
Drawing to a close, Latimore returns to the predictably unpredictable nature of the global trading industry as something that all companies will have to take in their stride for the years to come.
“Volatility is something that the industry is going to have to deal with even more in the future, but overall, the demand profile for metallurgical coal is strong.”
Indeed, as the Indian Government endeavours to meet its target of 300
This is the fourth time that Coal Augering Services has recovered previously inaccessible coal reserves at Mavis Downs and Millennium since 2007.
Augering has enabled a rapid re-start for M Mining, providing start-up cashflows and supporting the transition to underground mining.
Bret Leisemann, CAS Managing Director said, “we are delighted to support M Mining in successfully re-starting the mine, proud of our achievement of zero harm since starting last September, and we look forward to assisting them again as one of Queensland’s newest producers in the metallurgical coal industry.”
www.coalaugering.com
million tonnes of steel production by 2030, the global market will need to rise to meet that challenge. With Australia currently exporting between 180-185 million tonnes of metallurgical coal a year, the demand is there to be seized.
“There are not many good quality large operations coming into play in the metallurgical coal space currently, so that creates a window for entrepreneurial companies to get involved and take advantage of that opportunity,” he concludes.
Coal Augering Services offers a complete contract auger mining service, employing the highest capacity equipment and most experienced auger mining personnel in the world.
Auger mining is employed to increase reserves, accessing coal lying beyond the economic reach of conventional stripping operations at a low cost/tonne to maximise profitability and facilitate economic mine closure outcomes.
Coal Augering Services’ new generation of coal recovery augers are capable of drilling holes on angles of up to 20 degrees, with diameters ranging from 0.9m up to 1.9m, to a depth of more than 200m and augering up to 2,400 tonnes in a 12-hour operating shift. With three units available in the Bowen Basin, and one unit in Kalimantan, why not maximise your coal recovery (and profits) with highwall auger mining.
Outlook Publishing’s awardwinning in-house team is now utilising its extensive production skills to offer a full and bespoke range of editorial, design and marketing services via its new Outlook Creative Services division.
EXPERIENCED AND CUSTOMER FOCUSED ENGINEERING INNOVATION
Singleton Engineering Solutions provides engineering, drafting and visualisation services, project management and construction management services and operating site support personnel. These services include the disciplines of mechanical, electrical, civil, structural and mining engineering. Our core focus is the mining industry, specifically for mine equipment and infrastructure.
www.outlookpublishing.com/creative-services
TerraCom is an Australian-based mining resources company encompassing an impressive portfolio of operating assets and exploration projects within the national coal sectors of Australia and South Africa. We learn more about this global operation with a community-centric core from Managing Director, Danny McCarthy
Coal is a cornerstone of Australian industry. Built on the efforts of hardworking Australians across regional operations, the sector has a strong future which promises to meet all the requirements of a modern economy.
Despite the ongoing negative rhetoric concerning coal, Danny McCarthy, Managing Director of TerraCom, believes that the resource will remain at the forefront of Australian industry for a long while yet.
“Whilst alternate energy sources are discussed and strategised over, the coal industry will continue to keep the lights on in Australia and indeed around the globe until a like-for-like
DANNY MCCARTHY, MANAGING DIRECTOR: “At TerraCom, we are focused on motivating and empowering our employees, resulting in higher job satisfaction, improved work performance, and a greater commitment to the company.
“As Managing Director, I am deeply committed to making a positive difference and it is important that our vision, purpose, and values are known, understood, and lived by all employees.
“Our vision sets out what the future will look like, our purpose outlines why we exist, and our values are the fundamental shared beliefs and internal code of conduct which inform and inspire the ethics, behaviour, communication style, and culture within our company.”
energy source can eventually replace it,” he introduces.
Coal mining in Australia is a highly sophisticated and high-tech process. Continuous improvements in mining technology, occupational health and safety and environmental performance have ensured Australia’s standing as an efficient and reliable producer of high-quality, low-cost thermal and metallurgical coal for the domestic and international markets.
Regarding South Africa, TerraCom’s other major operational market, coal mining underpins the nation’s economy and is an important contributor to its success and longevity. Coal usage is integral to South Africa’s energy sector and over the course of the past decade, the nation’s public-owned utility, Eskom, announced the construction of the Medupi and Kusile coal-fired power plants to enable continued electricity supply for its people for decades to come.
Growing up in Central Queensland, McCarthy’s interest in the mining industry commenced at a young age. His father was an underground miner who transitioned to surface mines in the late 1970s, and it was this early exposure to the industry that ultimately led to McCarthy forging his own path within it.
“I was intrigued by the sheer size and complexity of the mining process,” he recalls.
Fast forward through 27 varied years in the mining, minerals processing and resources sector within Australia, and McCarthy started working with TerraCom as Chief Executive Officer in December 2018, as the company was poised to start implementing an improvement agenda focused on long-term sustainability for employees and shareholders.
Having grown significantly to now boast a global footprint, TerraCom is
CR Mining has been setting the industry standard for dragline buckets for over 35 years.
Our next-generation Hurricane dragline bucket is proven to increase productivity by up to 16 percent by shortening cycle times, reducing drag energy, and increasing machine availability through robust design.
That dragline expertise has now been applied to dragline chain and rigging.
As a long-time supplier of dragline buckets to Blair Athol mine, we were pleased to expand our relationship with our first rope-to-rope installation of dragline chain and rigging.
We know how critical dragline uptime is for open cut coal mines. That’s why we’ve invested heavily in our strong global supply chain.
The result: we were able to progress from order to installation of chain for Blair Athol within a month.
We’re also known for our legendary service. Site account managers are on site regularly and always available for help and support. From regular inspections to hands-on advice, we put our experience to work for you. The goal is to become embedded in your operations, gaining deep knowledge of your unique site conditions, maintenance practices, and operational goals.
It’s all part of our sustainable business model. We work with our customers to meet both their immediate shortterm needs and plan for the long term.
To boil it down to one question: What else can we do for you?
www.crmining.com
an Australian-based mining resources company, comprising a large portfolio of operating assets in Australia and South Africa with an impressive suite of exploration projects within the vast coal sectors of these two nations.
“We are a renowned low-cost producer focused on delivering exceptional outcomes from our highyielding diversified asset portfolio for investors,” explains McCarthy.
On a combined basis, via both direct and contractor engagement, TerraCom now employs approximately 3,600 people worldwide.
“Our people are our business, and their continued dedication allows us to consistently deliver products to our customers every day of the week, and every day is the chance to better the achievements of yesterday,” he continues.
The Australian business unit of TerraCom comprises the flagship Blair
Athol coal mine located in Clermont, Queensland, as well as a large portfolio of exploration and evaluation assets predominantly located in the Northern Galilee coal region.
The life of the Blair Athol mine is projected at more than eight years at the current run rate of 2.2 million tonnes for export, and TerraCom continues to explore several potential near-mine expansion opportunities which could see the facility utilised as a processing precinct for many decades to come.
In South Africa, TerraCom, via its 100 percent ownership of Universal Coal Plc, holds an interest in a portfolio of producing, development and exploration assets located across the nation’s major coalfields. There are currently three operational mines including the North Block Complex, New Clydesdale Colliery and Ubuntu Colliery.
Supporting TerraCom with operational technology for production and rehab.
To increase safety and productivity in both production and rehab environments, TerraCom has adopted high precision machine guidance technology on its fleet of seven dozers at the Blair Athol site in Central Queensland’s Bowen Basin.
Commissioned and supported by Position Partners, the Carlson Grade solution combines GPS positioning with an in-cab display to efficiently guide operators to work to the design in real time, reducing dependence on surveyors and rework.
In production areas, the technology ensures accurate floor levels and correct grades on ramps. For rehab, the high precision machine guidance technology is used in conjunction with 3D Data Guidance rehab optimisation software to meet all legislative requirements and community expectations.
For managers to effectively analyse and optimise operations, Carlson Command software is used for data management, productivity analysis and full design mapping with live cut, fill and elevation information available on any computer with an internet connection.
To ensure minimal downtime on machines, systems are backed by Position Partners’ comprehensive managed service, which includes full technical support via web-based remote access to machines as well as on-site visits.
www.positionpartners.com.au
“OUR MANTRA IS SIMPLE YET COMPELLING – BE BETTER THAN OUR PEERS, DELIVER RELIABLE AND CONSISTENT PRODUCTS, AND BE COST-CONSCIOUS WITH EVERY DOLLAR SPENT”
– DANNY MCCARTHY, MANAGING DIRECTOR, TERRACOM
Give operators and managers the power to mine to the design and reduce downtime. With a simple, user friendly interface that can be used across multiple machine types, Carlson Grade will increase machine productivity and profitability.
• Correct floor elevation
• Up productivity via accurate push strategies
• Reduce idle time
• Easily mine to the design
• Reduce survey cost
• Increase safety with watch and warning zones
• Track materials
• Determine accurate overhaul costs
The South African operations provide domestic quality coal to Eskom, and also supply high quality export coal to customers via the Richards Bay and Maputo coal terminals.
TerraCom currently finds itself in a unique position whereby it does not have the bureaucracy that some larger organisations in the industry have.
“We are flexible and agile, and this allows us to quickly adjust to meet the
changing demands and parameters of the market, internal business requirements and stakeholders,” McCarthy outlines.
The main ethos of the company is “we do what we say”, which is extremely important both within the organisation and when dealing with external stakeholders. TerraCom strives to maintain a high level of leadership and show accountability for everything it does, and this subsequently inspires its entire team to remain committed to goals, be attentive during all tasks, and crucially, never lose sight of
opportunities to grow.
“Our mantra is simple yet compelling – be better than our peers, deliver reliable and consistent products, and be cost-conscious with every dollar spent. There is no ‘done’ or finish line, our sights are continually honed on being better at every turn, with each interaction, every movement and motion, we aim higher and higher and higher and we do it at every chance we get,” he adds.
This is critical in building positive community relationships. Indeed, the strength and success of TerraCom, whilst founded on its people, is underpinned by long-term business partnerships with several key equipment and contracting partners.
“As part of our everyday actions, we strive for continuous improvement. We know there’s always something to learn from what we’ve done; whether that be the way we act, the choices we make, how we live out our cultural values or how we treat each other and the wider community,” McCarthy says.
“OUR PEOPLE ARE OUR BUSINESS, AND THEIR CONTINUED DEDICATION ALLOWS US TO CONSISTENTLY DELIVER PRODUCTS TO OUR CUSTOMERS EVERY DAY OF THE WEEK”
– DANNY MCCARTHY, MANAGING DIRECTOR, TERRACOM
Elsewhere, TerraCom also works cooperatively with local communities to progress its projects both in Australia and internationally, and is committed to a positive programme of engagement in every community in which it operates.
In Australia, the Blair Athol mine plays an integral part in the Clermont community. In addition to providing community group support, TerraCom has recently completed the onboarding of 16 local traineeships and is launching an apprenticeship programme providing careers in mining and skills pathways to further support the future of Clermont and the wider central highlands region.
Further to these communitybuilding initiatives, TerraCom is also a well-regarded supporter of CQ Rescue, a community-funded
rescue helicopter service based in Mackay Queensland. CQ Rescue is an instrumental service across Central and North Queensland, providing the community and stakeholders with a sustainable and supported, worldclass aeromedical and emergency helicopter rescue service available to anyone, anywhere at any time.
For the South African strand
of the business, TerraCom, via its subsidiaries, has identified education as a key area that will change the lives of the youth in the company’s host communities and will therefore continue to offer skills, training programmes, internships and funding for higher education and donations to local schools across its operations.
TerraCom transports products from its mining facilities to customers by rail, train, truck and ship. The business partners that provide the company’s supply chain services are wellestablished, reputable firms that are deeply engrained in the industry.
It is TerraCom’s preference to always work with local suppliers, in order to promote local community growth and support the availability of skilled labour, goods, and services from stakeholders near its operations in both Australia and South Africa.
The reality is, successful partnerships don’t just happen, and TerraCom recognises the genuine relationships that it has built with its customers and valuable business partners who have supported the company along the way.
“These highly reputable and established relationships emphasise accountability across all areas of our business; focusing on priorities and gauging business metrics to track and measure performance which help us to thrive, creating more value than we otherwise would,” ensures McCarthy.
Of equal importance to TerraCom is protecting the unique environment of the areas in which the company operates and managing social responsibilities with immense sincerity.
“Our commitment is being responsible to minimise our impact, to progressively rehabilitate areas disturbed during our operations, and preserve or restore the longterm health and sustainability of the environment where we operate,” McCarthy tells us.
The advancement of this rehabilitation is being completed progressively at TerraCom’s Blair Athol mine in Clermont and its South African operations, with the aim of significantly reducing rehabilitation activities at the end of the mine’s life.
The mine currently has dedicated rehabilitation equipment and resources to undertake the necessary rehabilitation works with additional support from the production dozer fleet.
It is now TerraCom’s immediate focus to continue to ensure dividends flow to shareholders and the company remains open to the right growth opportunities that pass its strict investment criteria.
“Ensuring responsible management of capital within our recently developed framework is a key focus, and our growth agenda is governed by responsible decision making for opportunities that add value to our story,” wraps up McCarthy.
The story of TerraCom is one that looks set to continue unwinding in exciting new directions and promises to deliver a highly satisfying overarching narrative for all characters involved, in line with the company’s relentless ambition for forward progress.
AJ Lucas Group is a leading player in drilling services for energy, mining and infrastructure. We take a look at the company and speak to CEO Brett Tredinnick about its services, technology integration and expansion in the mining space
(AJ Lucas). “Our coal and gas sector is buoyant, particularly metallurgical coal and coal seam gas (CSG), hence we are seeing strong demand for all types of drilling services.
Historically speaking, Australia has been built around heavy industries.
Mining in particular was an important part of trade, helping to grow early colonial communities across the country, and with abundant mineral resources it has remained a core industry unto the present day.
Yet, it is not just precious metals such as iron and gold that are mined from the Australian earth but also resources that feed into the energy industry. Access to coal and natural gas reserves, two staples of the industry, relies on drilling companies.
“The Australian drilling space is active and exciting, but it still comes with its challenges,” begins Brett Tredinnick, CEO of AJ Lucas Group
“However, the period between cycles is unpredictable and the global economic drivers are changing rapidly. Who would have predicted COVID-19, the impact it had during the height of the pandemic, and the hangover it is continuing to have on areas such as government policy, trading relationships, supply and skill shortages? Our government climate policies, planning and approval processes and mineral royalty taxes are needed to safeguard certainty for investors and companies alike.”
AJ Lucas is a specialist service provider to the energy, mining and infrastructure sectors, driven by the drilling business and significant investment in multiple shale gas licences in the UK, and is a publicly listed company on the ASX.
The business provides drilling services to the coal and CSG industries for the degasification of coal mines and the recovery and commercialisation of CSG. AJ Lucas offers exploration, production and directional drilling, drilling engineering and steering services, and well servicing.
Headquartered in Brisbane and serviced by a main workshop in Moranbah with support from a satellite facility in the Illawarra, the drilling business is strategically located within the major coal and CSG basins of Queensland and New South Wales (NSW) respectively.
“We currently have a team of around 400 people deployed across our operations, all working towards the mission of being the driller of choice for our customers,” Tredinnick tells us. “Underpinning our technical expertise and experience is the practical knowledge, application and attitude of our people. We have a passion for building relationships and providing solutions; this is the AJ Lucas difference.
“We are committed to becoming the first choice for our customers and our people. We do this by providing a safe and productive workplace where our people feel valued and can achieve their full potential. For our
customers, we develop and deliver solutions to exceed their expectations. Our values set the foundation for the way we work and the standards we expect of ourselves.”
For Tredinnick, the drilling industry is a familiar one. Tredinnick was appointed as CEO of AJ Lucas in 2020 having previously been the CEO of the drilling division and COO of the group. He has presided over the significant growth, restructuring and strategic initiatives for the Australian operations part of the business in recent years.
Prior to joining AJ Lucas, Tredinnick held various operational and project management roles with Rio Tinto Coal and BHP. He also has qualifications in Metallurgy, an MBA from the University of Queensland, and is a member of the Australian Institute of Company Directors.
“I grew up in Newcastle, NSW,
AJ Lucas operates in a highly regulated environment, requiring compliance with a broad set of standards and regulations that are driven by federal and state legislation, as well as specific standards set by industry and customers. AJ Lucas’ certified integrated Health Safety Environmental and Quality Management System provides an effective structure to achieve and maintain compliance in line with community expectations as well as providing a foundation for industry-leading performance in all aspects of its operations.
AJ Lucas’ company-wide goal is an injury-free workplace. Properly engineered plant, processes and systems of work supported by good leadership and an engaged workforce has and will continue to deliver exceptional performance. AJ Lucas understands the impact poor safety performance can have on the attainment of not only its business objectives, but also clients and other stakeholders. As such, AJ Lucas invests heavily in its people and their safety and well-being.
A responsible environmental policy supported by detailed planning applies to all of AJ Lucas’ projects, sites and related activities. The company acts in a manner that protects the environment and drives continual improvement, as well as working closely with clients to achieve the best possible environmental performance and outcomes.
The reliable performance of compressed air equipment is integral to drilling operations. More Air Group works with clients to set up an extensive preventative maintenance schedule, keeping their compressors running with minimal downtime.
Our regional locations in Mackay and Townsville allow us to respond effectively to any unforeseen breakdowns 24/7. We can provide a fast response with fully equipped service vehicles whilst our workshops house specialised tools and capabilities to perform compressor and airend overhauls and rebuilds to OEM standards.
moreair.com.au
We are a locally started and owned business, now servicing the compressed air and related products in our area of the Bowen Basin, as far as Cairns, down as far as Bundaberg and out as far as Birdsville.
More Air Group also services and supports the drilling sector in these same areas, having spare parts in our workshops and very efficient suppliers that can get parts as needed.
Having started the business nine years ago, we have gone from four staff to 19, which incorporates, preventative maintenance systems, eight technicians with fully stocked service vehicles. 24/7 phone service for breakdowns
and was surrounded by the coal and steelmaking industries. This provided a backdrop for a seamless transition into these industries following the completion of my education in Metallurgy gained through the BHP graduate programme,” he informs us.
“I was introduced into the mining and drilling industry through a friend, and over the following two decades I have spent my time in a variety of roles within AJ Lucas, leading initiatives that have kept the company’s Australian business safe, profitable, innovative and a leader in its field. The industry has changed a lot over the years, and it continues to do so! There is a lot of technology integration happening at the moment, and we are making use of this to increase efficiency across the business.
“Rotary steerable system (RSS) and bed mapping resistivity (BMR) technology are really exciting areas for us, and the additional data collected is an important value add for our customers so they can increase their understanding of geology in and around the mining horizon. The ability to use our specialist rigs to drill further from one location whilst collecting high-resolution, deep investigation data is a compelling case for us and our customers.
“The challenge has been in communicating the large increase in possible downhole lost in hole cost. These are tools derived from oilfield
“WE HAVE A PASSION FOR BUILDING RELATIONSHIPS AND PROVIDING SOLUTIONS; THIS IS THE AJ LUCAS DIFFERENCE”
– BRETT TREDINNICK, CEO, AJ LUCAS GROUP
drilling, but they are expensive, complicated and require a significant investment to operate correctly. I expect that the discussion with our current customers will be an ongoing one as both parties gain experience in using the RSS and BMR tools.”
Technology integration is not the only area of improvement for AJ Lucas. The company has a significant number of ongoing, long-term contracts with the majority of Tier 1 mining companies, and these are a direct result of the consistently strong performance that AJ Lucas delivers.
“These will continue for the foreseeable future and deliver gas drainage, large diameter and exploration drilling,” Tredinnick explains. “Upcoming drilling projects will mostly be similar in nature, with many returning to previous customers who are ready for their next drilling programme, and we will be returning to perform CSG exploration for select customers.”
This kind of expansion directly links to AJ Lucas’ core aims and goals for the coming years. According to Tredinnick, the company is hoping to start and play a key role in underpinning the supply of the UK’s natural gas demand. Natural gas accounts for around 80 percent of the energy source used to heat homes in the UK, and according to the British Geographical Society, AJ Lucas could have approximately 33 Tcf (trillioncubic-feet) of gas, or 13 years of supply, for all of the UK’s gas needs.
Alongside this, AJ Lucas’ key priorities will be to continue to execute all operations to a high standard of safety and quality, provide high levels of customer service and work with customers to deliver their drilling programmes within the timeframes and budgets they plan for.
For Tredinnick, this kind of expansion, success and growing company potential would not be
possible without hard-working and dedicated employees.
“I’m proud of the workforce that we have, many of them have been with us for over 10 years, which speaks volumes about the culture,” he tells us. “Our leaders, both in the field and head office, are enormously experienced and that really helps to deliver the right technical outcomes for our customers whilst maintaining a safe workplace culture.”
Parabellum International has grown impressively to become a leading emergency response and medical services provider across Australia and now the world. We speak to CEO, Navin Vij about the company’s people-centric safety mission, its services and the impressive scale of its fleet
We don’t just train emergency response; we create emergency responders. We’re in a very privileged position to genuinely save people’s lives, which means they go home to their families.”
This powerful opening statement reflects how Parabellum International (Parabellum) has worked relentlessly to claw its way into the highest echelons of the provision of emergency response, medical services, comprehensive risk management and elite training services. A true global leader in its field, Parabellum has become deeply embedded within both the onshore and offshore oil, gas, mining, defence, resources, energy, waste, construction, and government sectors. The company’s proven operational experience within high-risk and remote locations remains a global differentiator.
Dedicated to providing unrivalled emergency, medical response and risk management services across these select industries, Parabellum holds multiple long-term master services agreements supporting clients worldwide on some of the largest capital and operational projects, ensuring safe and dependable support throughout.
The company’s international exposure and long-term partnerships across a multitude of companies and projects concerning the management of risk, allow Parabellum to effectively anticipate and minimise these dangers, provide significant cost savings and simplify the on-site emergency and safety operations for its clients.
The risk management services provided by Parabellum deal flexibly with personnel, vehicles, equipment, plans, procedures and ongoing evaluation of on-site services. The company possesses unique experience in providing exclusively tailored solutions to ensure the safety of people and projects and aims to deliver “measurable value”
across the entire project life cycle so that deadlines are met safely, on time and within budget.
As a burgeoning entrepreneur from an early age, Navin Vij, CEO of Parabellum, knew his talents lay in building businesses and creating compelling careers for his people from the ground up.
“I always knew I had a business side to myself,” recalls Vij.
“Having already created businesses while I was undertaking my management and finance degree at a local university here in Perth, I built an electronics, wholesale and distribution company. It was then in 2010 I started Parabellum.
“The mining and oil and gas industries were getting a lot busier in Perth,” he continues. “There was a bit of a boom happening, so I identified an opportunity to provide some basic
Working collaboratively with Parabellum International since 2016, we have been its go-to company for all its vehicle and building signage, as well as expertly handling a vast range of general promotional displays and graphics.
We regularly prepare all of the company’s emergency response vehicles with the necessary graphics and reflective striping to ensure they not only look great, but offer a professional presence for the company and adhere to mine site requirements.
We have worked tirelessly to forge an established reputation for being reliable, able to work and thriving under pressure, while always retaining high attention to detail.
designandapply.com.au
NAVIN VIJ, CEO, PARABELLUM INTERNATIONAL: “A big part of our emergency response and safety operations is that we can transfer lifesaving learnings into day-to-day life. When we help enhance medical or emergency awareness it means we’ve contributed something that may one day help to save a life.
“For example, recently a client had attended one of our training courses for work. Sometime later, they tragically had a family member suffer a heart attack. But, because of the training they had received from us, they played a crucial role in helping to save that family member’s life.
“So, for us as a company, that’s just one of the many rewarding things that we get to do on a daily basis and really make a tangible difference in this world.”
health and safety support to companies in this sector. I was only 22 at the time, but I was willing to learn and work from the front line and I am proud to say we’re still here 12 years later.”
One of the key reasons for this longevity, and survival in what is now such a competitive industry, is that Parabellum offers a comprehensive, well-rounded and diverse array
of services, adaptable to any environment.
“If it’s firefighting, we’ve got trucks, fire stations, firefighters, firefighting equipment, and we’ll provide a full private fire service for projects or operating assets,” Vij explains.
“In the medical space, we’ve got paramedics, doctors, nurses, medical clinics, and ambulances. So, we can
We are
supply a private, full-service delivery, that supports and protects people,” he adds.
“In training, we are a leading Registered Training Organisation dedicated to delivering best in class training exclusively to our industries. We don’t do high volume cookie cutter training courses; we specialise in providing world class training and improving our industries only!”
Elsewhere, Parabellum also delivers safety and medical care training to local communities, with the aim of leaving a lasting legacy of skill development locally after a project’s completion. This has been carried out in the Pacific Islands and Asia, as Parabellum transfers its knowledge to local populations.
“This is a very important aspect for us, not just to come in and deliver services, but to develop local skills and safety capability and improve the community that gave us a license to operate.”
Established in 2010, our highly skilled and experienced team have been creating signage and vehicle graphics for a wide range of WA businesses across a variety of industries. From fleet graphics to building signage, we ensure your brand gets noticed and meets all necessary mine-spec requirements when going to remote work sites. a preferred signage supplier for several companies throughout Perth, with a reputation for high quality work, meticulous attention to detail, and adhering to strict deadlines. Simply put, you can rely on us for a professional service and quality result, every time.Vij believes that the collective skillset possessed by Parabellum is applicable and transferable across industries.
“Whether it’s government or private, there’s always risk. Everything we do in this world on a day-today basis has varying levels of risk, whether it’s driving a car to and from home, climbing a ladder, or completing major capital projects, there are always levels of risk which must be mitigated,” he explains.
Parabellum has a proven and highly successful track record of aiding the largest and most technically capable Tier 1 companies in their supply chain, not just with traditional services but by actually helping them to run entire projects, on the way to becoming an overall service delivery company.
“At present, we are building medical clinics, fire stations, administration buildings and other major infrastructure, constantly looking to
diversify sensibly,” Vij reveals.
Further to this, Parabellum has helped many companies operating in Australia for the first time, who may not be aware of the local way of working, standards, processes, or how to transition a project smoothly through a design, construction and operation phase.
When discussing the next 12 months that lie ahead for Parabellum, Vij describes an exciting and detailed vision of continued expansion for the company.
“We’ve got significant growth coming up in Australia, as well as further plans for the entire AsiaPacific region. So as the next 12, 24 and 36 months unfold, we hope to see significant expansion into Southeast Asia and the Pacific islands, and the continued development in our local markets,” he explains.
Parabellum already possesses an operating base in Singapore, upon which the company hopes to
springboard into further success across the continent. This hub will prove essential in the ability to support new emerging technologies in hydrogen, waste, and power, as well as constructing new operating bases.
Parabellum’s clients enjoy unrivalled access to the company’s esteemed fleet of emergency response and medical vehicles. This includes the option to use a range of light tankers, ambulances, fire appliances and trailers for hire, for medium- or longterm engagements, or alternatively, a custom design and build for an outright purchase.
GOING ABOVE AND BEYOND
Going above and beyond by striving to be the best the company can be, and by challenging the status quo.
MAKING A DIFFERENCE
Making a difference in the lives of others, each other and all those that Parabellum impacts.
Parabellum tells it like it is, even if the message is difficult to deliver; it is important to communicate what you need to hear, not what you want to hear.
Parabellum looks after all its staff and clients. The company is inclusive and respects others, with an opendoor approach.
Parabellum makes things happen; acting quickly without compromising company standards is essential, as well as thinking outside the box to solve a problem.
These highly effective vehicles can be supplied as dry hire or fully stowed, featuring all the required emergency response or medical equipment to suit capital or operational expenditure requirements and budgets.
Other models available within Parabellum’s fleet include specialist Aviation Rescue Fire Fighting (ARFF) appliances, confined space rescue and breathing apparatus trailers, and fully equipped containers and relocatable buildings.
Additionally, Parabellum continues to pursue the electrification of its fleet of vehicles. In this way, the company is aiming to transition away from the traditional diesel range and embrace hybrid technology, which brings innovation, reduced emissions, as well as renewed reliability.
A
Parabellum’s reputation for uncompromising quality has been hard-earned through the efforts of its
highly professional team’s devotion to craft and care. The company’s foundations are built upon a collective of high-calibre, best-in-class service professionals that act with trust and integrity at all times.
Keenly aware of the need to find people perfectly aligned with Parabellum’s core values, before joining such a specialist team, Vij tells us how it is critical to recognise key qualities and traits from the inception of a new working relationship.
“The final evaluation before we hire anyone is, do they match our culture, do they believe, and do they share our company mindset. This process has been critical in bringing the right personnel into our teams,” he expands.
He continues to tell us, “for Parabellum, having visibility, trust and sharing a collective vision has been vital to the company’s success because everyone in the team believes in what we’re doing.”
This shared responsibility and
mentality of the company culture that Parabellum works so hard to foster, aligns every level of the company to one total vision, from paramedics and firefighters on the ground to every level of management, as well as external players such as subcontractors and suppliers.
“These values are non-negotiable. No matter what level, everyone is expected to help their team – no job is too small or unimportant,” Vij concludes firmly.
“At Parabellum, we do not compromise on standards; we are steadfast in our resolve to deliver on our promise to our clients.”
Gekko Systems is a global leader in mineral processing, providing fully integrated solutions to mining companies around the world. We discuss new investments and working ‘smarter together’ with General Manager of Global Sales and Solutions, Nigel Grigg
Writer: Ed Budds | Project Manager: Eddie Clinton
The Gekko Systems (Gekko) company manifesto reads, “only by embracing smart ideas together can we transform our world.”
Summarising this belief in the company tagline “smarter together”, it seems obvious that to achieve meaningful change, and to transform mining and the environment, the entire industry must collaborate. Gekko endeavours to spearhead this evolution and to deliver step-change benefits, on a global scale, through innovative mining solutions.
Having studied metallurgy at the University of Ballarat, Gekko’s General Manager of Global Sales and Solutions, Nigel Grigg had always wanted to be involved in the mining industry, as it entailed lots of opportunities to travel, both domestically and internationally.
“Directly after graduating, I was fortunate enough to assist a Canadian company to develop a small mine in Ballarat,” he begins.
“The gold in Ballarat is very coarse, and so it was challenging with the basic Carbon In Leach circuit (CIL) we had to get good gold recoveries. I introduced a gravity circuit into the circuit using an InLine Pressure Jig (IPJ) from Gekko and the recoveries dramatically improved.
“I was very impressed with the technology and the business, so when the Ballarat mine closed due to the low price of gold at the time, I asked the two founders Sandy Gray and Elizabeth Lewis-Gray if I could join them, and the rest is history.”
Having opened offices in South Africa, Brazil, Canada, Australia and Russia over the past 26 years, Gekko has developed strong capabilities in the design, manufacturing, installation and commissioning of energy-efficient mineral processing equipment and completes plants for a wide range of minerals including gold,
silver and polymetallics.
One of Gekko’s main products is the InLine Leach Reactor (ILR). Gekko’s user-friendly ILR offers superior recoveries in a proven, high-efficiency, safe and highly secure system. The ILR’s innovative design and unparalleled flexibility in gold and silver leaching chemistry provides cost and production benefits to operations across more than 40 countries around the globe.
The ILR is available as a completely automated batch model for processing high grade gravity gold concentrates. Uniquely, the unit can also be configured as a continuous model for treating high-throughput gold, silver and complex sulphide concentrates from IPJs and flotation circuits.
The IPJ is another one of Gekko’s signature products. The efficient circular IPJ design delivers 20 percent less power and consumes only 10 percent of the water required by
To maintain the passion and courage to communicate, and to improve what Gekko does and how it does it.
To respect and care for staff, family, customers and other stakeholders.
To behave with integrity at all times.
To demonstrate leadership in key global segments and Gekko’s communities.
Exhibit openness to new ideas, feedback, and personal learning.
traditional jigs. Furthermore, the low separating velocity within the unit maximises the recovery of fine mineral particles. Saving water and reducing energy helps mine operations lower their environmental impact and remain profitable. The IPJ is being used in several pre-concentration applications recovering several different minerals.
Gekko also designs and builds modular plants for given mine operations with specific requirements. The innovative core technologies and in-house process design expertise continue to produce agile and effective modular plants.
Innovation and collaboration have been integral to Gekko’s growth, not only with the products that the company has developed but also with the internal process that is followed within the organisation. As a highly vertically integrated company, Gekko performs a number of tasks such as testing, engineering, designing,
manufacturing and installing, covering a wide range of disciplines within the company.
Gekko also offers on-site performance consulting services for customers looking to optimise established process plants and achieve the highest operational performance. Its range of solutions offers value for remote and environmentally sensitive operations with high energy costs.
“Gekko uses a flexible work model with 70 to 120 staff members depending on the projects that we might be working on at the time,” Grigg tells us.
Gekko differentiates itself within the mining sector by having a genuine interest in making a significant difference in the industry. The company prides itself on investing in the R&D side of the business and viewing problems from a different perspective.
The company also invests a
considerable amount of time and resources into its staff to become agents of change and has a very nimble approach to solving problems within the mineral processing field.
“As well as our investment in people, we have a very strong focus on modular solutions, and are always looking at how to remove energy from our flowsheets in order to optimise the operating costs and lower life-ofmine capital costs,” expands Grigg.
Focusing on removing energy from the company flowsheet not only reduces the obvious issue of operating costs, but also helps Gekko and its clients towards the aim of being carbon neutral by 2030. Climate goals remain very topical at the moment, and Gekko is doing as much work as it can to remove the power required in its equipment and still achieve economic recoveries.
“We spend a lot of time looking at the liberation size of the minerals in order to determine the coarsest
Convair Engineering have been suppliers of premium products to the pneumatic bulk handling industry since 1993. These include: • AKO pneumatic pinch valves made to your specifications • Premium Australian made steel tankers and FFB aluminium tankers from Germany • CVS Siloking compressors & Gardner Denver blowers • Diesel or electric driven powerpacks • BTI pressure relief valves, check valves and fittings Convair Engineering Pty Ltd 93 Miller Street, Epping, VIC 3076 (03) 9408-7255 | sales@convair.com.aupossible size that can achieve good recoveries, in turn helping reduce crushing and grinding costs from the flow sheets,” he says.
The Carbon Scout is one of Gekko’s newer products that was developed in collaboration with the Curtin University in Western Australia (WA). The unit enables the plant operator to automatically get the carbon inventories, pH and density measurements from a single groundbased unit. This then automates the carbon transfers into each tank, ensuring that the gold solution losses are kept to a minimum. This can potentially result in thousands of dollars’ worth of extra gold being recovered by simply optimising the carbon concentrations in each of the CIL tanks.
“More recently, we have also installed an XRF sensor to determine the gold on carbon levels and as a
result, we can now automatically calculate gold in circuit measurements,” details Grigg.
These would normally be calculated manually using samples and assay data that could often take a few days to obtain. Instead, the Carbon Scout allows for these calculations to be taken every few hours. This is important for mine owners to know how much gold is in the circuit at any particular time, and can also assist the operators to determine when stripping and carbon movements are required.
“So far, we have over 10 units operating internationally, and they are providing great benefits to our clients,” he acclaims.
Located near the town of Grassy on the coast of King Island, Tasmania, Gekko has engaged with Group 6 Metals (G6M) to design, manufacture and construct the processing plant for the King Island Dolphin Project. Gekko has traditionally been very focused on the gravity gold market, and the processing flowsheet for Scheelite utilises several gravity recovery process steps; it was therefore the perfect fit for Gekko to utilise its previous experience and move into the critical mineral space.
“The flowsheet was developed by G6M in conjunction with ourselves to design a circuit that was able to recover the Scheelite at the optimum liberation size,” Grigg explains.
‘ONLY BY EMBRACING SMART IDEAS TOGETHER CAN WE TRANSFORM OUR WORLD’ – GEKKO SYSTEMS
Gekko has been able to supply key liberation equipment including bespoke milling and VSI modules to ensure that the brittle Scheelite mineral is not overground and is liberated for optimum gravity recovery. The company will now be involved in commissioning and ramping up the project for G6M, ensuring that it can start up as efficiently as possible.
Grigg tells us how Gekko believes that its “focus on liberation and gravity recovery at the coarsest possible size will be a key factor in reducing energy within the process flowsheet, and will be important as the critical mineral industry continues to be a key focus in the global market.”
As a result of the cyclical nature of the mining business, Gekko has made a large technological investment
in an alternative energy initiative called Gaia EnviroTech (Gaia). A sister company to Gekko, Gaia is all about using previously gained engineering know-how and modular systems experience in developing Anaerobic Digestion (AD) systems and composting technologies.
“The development of this wasteto-energy system is in line with our fundamental goal of reducing energy from our mineral processing systems,” Grigg explains.
Coming out of the COVID-19 pandemic, it was important for Gekko to maintain its market presence within the gold industry and continue to ensure that its key capital equipment was being utilised in the new gold plants being built. Due to the high price of gold, the company has achieved this with multiple ILR sales made over the last 12 months. Gekko was able to supply over 15 units
worldwide in the past year, marking a fantastic effort from the company collectively.
Moving forward, Gekko is directing its focus towards increasing its service offerings, getting back to travelling, visiting its global partners and improving the overall customer service.
“We are extremely focused on getting our newer products like the Carbon Scout and the OnLine Gold Analyser (OLGA) fully developed and out into the market over the course of the next year,” finishes Grigg.
Kunooz Oman Holding SAOC is unleashing the potential of mineral deposits in the Sultanate of Oman. Group CEO, Naif Al Awaid, provides an update on the company’s mining, quarrying and logistics projects
Oman has some of the world’s richest and most diverse mineral deposits.
Yet, despite a number of quarrying and mining operations being underway, mineral deposits are still relatively unearthed in the Sultanate. Mining is therefore, unsurprisingly,
one of the key focus sectors under the Omani government’s economic diversification programme, to unleash its abundant potential.
“There are a lot of untapped opportunities within the mining industry,” says Naif Al Awaid, Group CEO of Kunooz Oman Holding SAOC (KOH).
We speak with Mohsin Hani Al Bahrani – CEO - MHD ACERE, one of the largest and most successful privately owned business houses in the Gulf region
EME Outlook (EO): Firstly, could you introduce us to Mohsin Haider Darwish LLC?
Mohsin Hani Al Bahrani (MHB): The origins of Mohsin Haider Darwish LLC (MHD) date back over half a century. The family proprietary business was converted to its present form of a corporate entity in 1987. Over the decades, the company has witnessed phenomenal progress, helped by strategic planning and professional management.
MHD today is one of Oman’s leading business houses with interests spanning automotive, tyres and batteries, engineering products, leasing, education and healthcare. With our significant staff strength, we are proud to bring in some of the best global brands like Jaguar, Land Rover, McLaren, MG Motor, Hongqi, Ineos, Ashok Leyland, Ford Trucks, CMC, ABB Michelin, BF Goodrich, Riken, Weir Trio, Terex Finlay, XCMG, Mitsubishi ForkLifts, Blackline Safety, Spasciani, Britannia, Delta Fire, Zoll, Caire, Comen, Donaldson Filters, Opus, Drager cranes and many more.
EO: I understand you have 10 commercial divisions, representing hundreds of international brands. Can you provide some key details about this?
MHB: Automotive is a core business line for the company, representing some of the finest global brands in automobiles. Our automotive brands include Jaguar, Land Rover, McLaren, MG Motors, Hongqi, Jetour and Ineos.
The Commercial Vehicles and Construction Equipment Division (CVCE) represents brands like Ford Trucks, Ashok Leyland,
JMC and CMC. We offer a wide mix of commercial vehicles including models for ready mix, construction, quarrying, building material, waste management, passenger buses, freezer trucks and logistic trucks.
The Tyres and Batteries division offers a world-renowned range of tyre brands and tyre accessories across the Sultanate through its sub-brand Tyreplus and Michelin Truck Service Centre (MTSC) - a Michelin-owned franchise offering quality automotive products and qualified servicing at a competitive price. Our range includes world renowned brands namely Michelin, BF Goodrich, Riken, BKT, Triangle, Emrald, Federal, Three A, Constancy, Wosen & Lander. The division also offers a wide range of light and heavy-duty batteries. Trusted battery brands include NBC, Actron, Optima Batteries, Speed Mate.
MHD Leasing’s best-in-class services deliver the most innovative solutions in the field of vehicle leasing, catering not only to the needs of individual customers, but to those of corporate clients as well. MHD Leasing currently operates an extensive fleet of vehicles, providing daily, weekly, monthly, and yearly rentals to corporates, residents and visitors to Oman. Our clientele includes many governmental and highly regarded private institutions, all of whom have been loyal customers to the business.
At AutoExpert we understand that some people desire more from their vehicle, therefore we offer an extensive range of products that are designed to improve the look and performance of the
vehicle. From 4x4 accessories, car performance enhancements, car care products and solutions and a fully equipped modern workshop facility.
MHD Academy of Technical Science offers courses in Sales and Marketing, Leadership and Management, Administration, Finance, Accounting, Budgeting, Human Resources, and Health and Safety Training in Oman. The institute provides individuals and organisations across Oman with the knowledge, skills, and tools to achieve performance excellence, adapt to changing realities, and prosper in a complex and competitive world of globalisation. The institute has a wide range of unique courses, workshops, customised corporate programmes, and consultancy services to offer.
EO: What is it that differentiates MHD from the competition?
MHB: At MHD we have always looked at obstacles as stepping stones to success. This organisational ethos has helped us navigate and overcome multiple challenges. We embarked on an ambitious and aggressive campaign to enhance our network capacity, increase our team strength and elevate organisational capabilities, leading to us being recognised as among Oman’s most promising business houses.
EO: What opportunities are opening up for MHD in reliable and efficient transportation, effective communication, dependable infrastructure, better healthcare and living?
MHB: At MHD we are always seeking out the next big opportunity – be it in transportation, communication, and infrastructure, or in sectors where we have already ventures –namely healthcare products and renewable energy (RE). We see tremendous opportunities in many new fields and are always exploring our options.
EO: To leverage these opportunities, how important is your strength of legacy and spirit of ambition?
MHB: Success in itself is not a destination, but a continuous journey towards excellence. This spirit of progress, of unlocking opportunities, adding value to lives and propelling the nation ahead, is what drives MHD. That is the organisation’s legacy which has instilled a strong sense of ambition – one that is especially pertinent in these dynamic times. The respect and reputation we have earned, the lives we have touched, the growth we have inspired and above all, the inspiration provided for a young nation to keep moving forward is a living embodiment of our legacy and ambition.
Kunooz translates to “treasure” in Arabic, and KOH comprises five subsidiaries and three associates within the mining, quarrying, construction minerals, and logistics sectors.
Incorporated in 2014, KOH is 20 percent owned by Minerals Development Oman (MDO), the executive arm of the Omani government tasked with developing the mining sector in the Sultanate, with the remaining 80 percent belonging to local private investors.
MDO, which continues to build on Oman’s rich mining heritage and drive the commercialisation of prodigious mineral resources, is responsible for delivering the strategic objectives stipulated in Oman Vision 2040.
“Mining has become one of the pillars of Oman Vision 2040,” Al Awaid tells us.
According to Oman Vision 2040, a future Omani economy that
KOH SUBSIDIARIES AND ASSOCIATES - AT A GLANCE
SUBSIDIARIES:
KUNOOZ GYPSUM – Mining of gypsum
KUNOOZ GABBRO – Quarrying of gabbro
KUNOOZ MARBLE – Mining of marble
KUNOOZ LOGISTICS – Covers logistics activities
KUNOOZ READYMIX –Construction
ASSOCIATES:
MAJAN MINING – Quarrying and mining of limestone (KOH owns 35 percent)
CARMEUSE MAJAN –Manufacturing of lime (KOH owns 27 percent)
SALALAH INTERNATIONAL
GYPSUM – Selling and marketing of gypsum (KOH owns 33 percent)
embraces technology, knowledge and innovation will allow for the production of competitive products and services, with higher knowledge and technology components.
Consequently, this will contribute to developing the economy and enhancing its competitiveness in most sectors and activities, including mining.
In line with this, Oman’s significant mineral wealth needs to be commercially exploited by the likes of KOH to maximise in-country value (ICV).
Not only will this support the national economy, but it will invariably lead to further exploration activities, provide more job opportunities across Oman, and achieve prosperity for the country.
In July 2021, the Industry Development of Energy and Minerals (IDEM) unit was created by the Ministry of Energy and Minerals
(MEM) to focus on the downstream processing of minerals and ICV addition, instead of exporting unprocessed raw materials.
“We are going to focus on ICV, and there will be huge potential downstream,” states Al Awaid.
“Our focus on creating ICV within the country puts us in a good, competitive position. Competition will always be there, so we need to think regionally and internationally to give ourselves an opportunity to excel.”
Oman’s mountains host intact and exposed ophiolites, which could contain metal deposits such as copper, gold, magnesium, platinum and more.
“The geographical diversity within the region itself gives rise to a variety of different products and minerals. It’s always an exciting space where you can add value and measure it,” Al Awaid continues.
Gypsum is one mineral that holds particular promise in Oman.
The Sultanate is the world’s largest
exporter of gypsum by weight, shipping approximately nine million tonnes to ASEAN (Association of Southeast Asian Nations), Southern and Eastern African countries in 2019. The outlook continues to look positive, with demand from India and Asia predicted to grow further.
Taking Oman’s gypsum industry forward is Kunooz Gypsum, one of the company’s five wholly owned subsidiaries. The construction sector is the main end user of gypsum, which is primarily used to produce plaster of paris and plaster boards.
“Kunooz Gypsum is located in Dhofar, and we are looking into ICV on the gypsum side,” Al Awaid informs us.
To this end, two important projects
are being considered by Kunooz Gypsum, with the development of a gypsum powder and a gypsum board factory.
“With the gypsum powder factory, we can create added value for gypsum in construction and other areas of usage.”
Kunooz Gypsum is complemented in the mining and quarrying space by two further subsidiaries, Kunooz Gabbro and Kunooz Marble.
Gabbro, a dark, igneous rock formed by the cooling of molten magma trapped beneath the Earth’s surface, is a material of preference for the construction industry.
Demand in the market for crushed stone, aggregates and gravel has shown steady growth over recent years, and Kunooz Gabbro is the leading producer of high-grade gabbro for the local market in the Omani capital, Muscat.
“Kunooz Gabbro produces gabbro in different fragments and sizes, which supports the infrastructure in the Muscat area,” Al Awaid elaborates.
Al Awaid notes that Kunooz Marble was affected by the COVID19 pandemic along with Kunooz’s construction materials subsidiary, Kunooz Readymix, which is engaged in the manufacture of crushed stone and washed sand for use in the production of ready-mix concrete.
“Both Kunooz Marble and Kunooz Readymix were affected by COVID-19 due to the shutdown of construction. We are trying to revamp those areas, and see how we can enhance them,” he says.
Kunooz also owns a 35 percent share of Majan Mining, an associate engaged in the mining, crushing, and exporting of limestone. An important raw material for various industries, limestone has strong links to the construction industry, steel production, and cement manufacturing.
Limestone is processed by another associate of KOH, Carmeuse Majan, of which the company owns a 27 percent share. Carmeuse Majan calcines limestone at extremely high temperatures to obtain lime, which is used as an additive in industries such as metallurgy, environmental treatment, sewage and water treatment.
Elsewhere, KOH is exploring opportunities in dolomite and basalt, where the company has two quarries and is starting the next stage of its feasibility study. Meanwhile, KOH is looking to build up alliances with big players in the production and extraction of magnesium and other minerals.
“WE ARE GOING TO FOCUS ON ICV, AND THERE WILL BE HUGE POTENTIAL DOWNSTREAM”
– NAIF AL AWAID, GROUP CEO, KUNOOZ OMAN HOLDING SAOC– NAIF AL AWAID, GROUP CEO, KUNOOZ OMAN HOLDING SAOC
Dolomite contains around 21 percent magnesium, according to Al Awaid, which could be used in the local market or areas of manufacturing, especially the automotive sector.
“We can collaborate with the automotive, steel, and many other industries where they are using a high percentage of magnesium and other downstream minerals for different manufacturing processes,” he suggests.
Supporting KOH’s mining companies from mine to port is an expanding
fleet of prime movers and trailers owned and operated by Kunooz Logistics, who supply services to the company’s Marble, Gabbro, and Readymix subsidiaries.
Focused on bringing sustainable and cost-effective supply chain solutions, Kunooz Logistics has extensive experience in bulk and flatbed transportation as well as port operations management.
“Kunooz Logistics covers the whole of Salalah, Dhofar, Duqm as well as Sohar. It is focused on transportation, and we are currently trying to convert more opportunities in supply chain logistics,” outlines Al Awaid.
One such opportunity in logistics and supply chains that Kunooz Logistics is focusing on is cold storage warehouses, with negotiations underway with an off-taker.
The cold storage warehouse project is located in the Rusayl industrial area, and comes as Kunooz’s cold storage business continues to thrive.
“Our cold storage business today is increasing, with eight percent growth and high potential,” Al Awaid states proudly.
“Cold storage is used for food, pharmaceuticals, and because the country is growing, I believe there is a need for such facilities to be available
“IF WE CAN DIVERSIFY, WE WILL BE ABLE TO FOSTER RESILIENCE WITHIN OUR ORGANISATION, AND WITH RESILIENCE WE WILL BE ABLE TO ACHIEVE SUSTAINABILITY”
in order to enhance the products and services for the end user.
“We need to identify our end users, what the best way of reaching them is, and the mode of transportation, whether we’re talking about raw materials, finished products, or services. I think that needs to be a collaborative effort,” he adds.
The multitude of mining, quarrying and logistics projects being undertaken by KOH reflects the company’s aim to diversify its areas of activity.
“It is a privilege to be part of a team that is looking into different activities and creating diversification in our business. If we can diversify, we will be able to foster resilience within our organisation, and with resilience we will be able to achieve sustainability.”
KOH is equally focused on the environment by reducing waste and CO2 emissions, as well as participating in
corporate social responsibility (CSR) practices.
The company’s crushers and mining machines, for example, are moving to a solar operating system, whilst dust controls have been put in place to ensure that employees are working in a clean environment.
“We are trying to be a good partner with communities and local societies,” affirms Al Awaid.
Above all, KOH’s main asset is its people, whose mindset and skills are integral to what the company is aiming to achieve.
Employee safety is therefore one of the main challenges for KOH, as working in mines comes with a number of risks.
“Coming from an engineering perspective, safety is one of our high-priority key performance indicators (KPIs). If you don’t
care about your main asset, you will never reach where you want to be,” Al Awaid emphasises.
“Whether it’s the blasting, equipment, or dealing with certain types of soil and rocks, safety requires a lot of attention. I think safety in the mining sector needs to be brought to the level it’s at in the oil and gas industry.”
Away from the mines, strict safety measures have also been put in place for KOH’s drivers and operators, to help save lives on the roads.
Safety is clearly fundamental to KOH, as it aspires to be an employer of choice and continues to enhance its KPIs over the next 12 months.
Demand for diamonds aggressively rebounded to record-high levels in 2021.
Although total output volume remains below pre-pandemic levels, the production and value of diamonds compared to 2020 was up by 12 and 51 percent, respectively.
It followed significant year-over-year
declines in natural diamond production, resulting from oversupply for much of the last decade, depleting legacy mines, and a very limited number of new supply sources most recently compounded by the operational disruption and mine closures caused by COVID-19.
“In general, the increase in demand
has been driven by a number of factors, including economic growth and a rising middle class in the US and China, as well as increased marketing efforts by diamond companies,” observes the CEO of Stornoway Diamonds Canada (Stornoway), Patrick Sevigny, who has always had a keen interest in value generation.
Writer: Jack Salter | Project Manager: Olando Greenock“In addition, diamonds have become more affordable for many people due to advances in diamond production and distribution.”
While the increasing demand for diamonds is good news for the industry, it is important for companies such as Stornoway, a leading Canadian diamond producer, to meet
this demand in a responsible and sustainable manner.
This includes taking steps to minimise the environmental and social impacts of diamond mining, as well as ensuring diamonds are ethically sourced.
Stornoway has implemented a number of measures to minimise its
impact, including the use of natural gas to generate energy and the establishment of partnerships with local communities.
“We have set global industry standards in environmental and social sustainability, and are one of the only Canadian diamond companies with a comprehensive socio-economic
benefits agreement with local Aboriginal stakeholders,” reveals Sevigny.
“Moreover, both Stornoway and the Renard diamond mine are engaged in research projects to continually look for new ways to improve production and exploration processes.”
Known for producing medium-quality diamonds, production at the Renard mine commenced in 2015.
A significant contributor to the provincial economy and considered to be a responsible and sustainable operation, it is located in the remote James Bay region in north-central Quebec, one of the world’s best mining jurisdictions, and is wholly owned by Stornoway.
“Due to its isolated location, Renard has required the construction of a large number of infrastructure projects, including roads, airports, an electric power plant (natural gas gensets), housing, nursery and water treatment plant facilities,” shares Sevigny, who was born and raised in the Abitibi mining region of northwestern Quebec.
Renard is the first and only diamond mine in Quebec, one of just four diamond-producing mines in Canada, and the only one in the country that is accessible all year round by road.
As the mine is a temporary user of land that will be returned to its traditional users at the end of its lifespan, the project design has prioritised a minimal environmental footprint and progressive rehabilitation.
For those who don’t know HydroTech Mining, what would you say to them?
“HydroTech Mining develops innovative mine water management solutions. Since 2015, HydroTech Mining has been providing innovative, quality products and ongoing services to support our customers during all phases of the project. We are passionate professionals with nearly 30 years of experience serving North America and even South America!” –Cheyne Poirier, CEO
What kind of solution do you offer more specifically?
“We offer more than products! We offer the complete solution to manage mine water. Whether by submersible pumps, water clarification, pumping system up to the consulting services.” – Paul Cormier, Vice President Sales
How does HydroTech Mining stand out from its competitors?
RENARD 2 KIMBERLITE – The primary source of diamonds at the Renard mine, expected to produce the majority of the diamonds mined at the site. It extends from the surface down to an elevation of 900 metres.
RENARD 3 KIMBERLITE – The smaller ore body located 200 metres northeast of the Renard 2 kimberlite. It extends from the surface down to an elevation of 600 metres, and it is expected that exploration work will establish its presence at depth.
RENARD PROCESSING PLANT – A state of the art processing facility that is used to process the ore from the Renard 2 and Renard 3 kimberlites, equipped with advanced technology and designed to minimise environmental impacts.
RENARD INFRASTRUCTURE – The Renard diamond mine is located in an isolated region of Quebec and requires a significant amount of infrastructure in order to operate, including roads, airports and a power plant.
“We cannot speak for our competitors, but our several prizes won, and our loyal customers speak for themselves:
Laureate of the Chambre de Commerce de Val-d’Or three times:
• 2019: Export Market Development
• 2020: Export Market Development
• 2020: New business
Laureate of a Mercad’Or provincial competition:
• 2018: Regional winner
• 2022: Regional winner, Provincial winner
• 2023: Regional winner, Provincial winner? Stay tuned.” – Cheyne Poirier, CEO
Where can we find you?
“We are present across Canada and even outside. We have a branch in Mexico, and distributors in United States. Also, we participate in several trade shows like MINExpo, SME, CIM, PDAC and more!” – Paul Cormier, Vice President Sales.
HydroTech Mining is the specialist in dewatering solutions. We’re dedicated to the sale, design, and manufacture of pumping and dewatering systems for the mining industry.
Our wide range of submersible pumps and systems are designed and built for all types of operations. What’s more, exceptional service is always one of our top priorities.
Occupying just 3.1 square kilometres within a single watershed, Renard is surrounded by a network of ditches that collect all the run-off water, which is treated prior to being returned to the environment.
“Buildings have also been designed and materials selected to facilitate dismantling, recycling, and revegetation at the end of the mine’s life,” adds Sevigny.
The Renard mine has reserves that will take it to 2025, primarily sourced from the Renard 2 kimberlite which is
expected to produce the majority of diamonds mined at the site.
A project to extend the mine is now underway, which consists of deepening the ramp below the surface in order to mine the resources located between elevations of 600 and 850 metres.
A decision will be made this year on the project, and if approved, it will extend the life of the mine to 2029.
“Thereafter, the mine has additional resources in the Renard 4 and Renard 9 kimberlites that could be brought into production if diamond market conditions continue to improve. If these two kimberlites are mined, the mine life could be extended to 20352040,” Sevigny outlines.
Established in Chibougamau since 1979, Soudure GAM Chibougamau is the leader manufacturer of machined and welded parts in North-of-Québec.
The culture of the company, built on family values, has allowed for providing a personalised service in close relationship with our customers. We have a deep concern for efficiency and quality wich allows us to offer a fast and competitive service and, most importantly, respecting the targeted deadlines.
PATRICK SEVIGNY, CEO: “We know that creating strong relationships with trusted local suppliers allows us to have a reliable supply chain of materials and services that meet our high standards.
“At the same time, we prioritise paying our suppliers on time to ensure that they are consistently providing the necessary resources and services. To adequately compensate our suppliers for their efforts, we focus on delivering prompt payments and maintaining open communication on all aspects of our business.
“This allows for a level of mutual trust and respect, an atmosphere of cooperation, and ultimately, a stronger and more profitable business relationship for both our company and our suppliers.”
Completion of the Renard expansion project is Stornoway’s main priority for the coming year, and in an inflationary environment where diamond prices are expected to decline slightly and certain commodity prices are higher, it is important for the company to meet production targets in order to maintain projected profitability levels.
Hydroelectricity, meanwhile, is another potential avenue for Stornoway given the potential to substantially reduce the company’s dependence on natural gas and diesel. The water system on which
Our geographic location allows us to be at the centre of economic activity in North-of-Québec. We are, moreover, the only company to have CSA CWB 47.1 welding certification in the area.
Proud supplier of Stornoway Diamonds.
www.gamchibougamau.ca
Quebec’s numerous hydroelectric power plants are built, allowing the province to be one of the most important producers of hydroelectricity in the world, is located 120 kilometres north of the Renard mine.
Stornoway’s vision is to connect to
MINING OUTLOOK: I UNDERSTAND YOU PRIDE YOURSELVES ON PAYING SUPPLIERS ON TIME?
the provincial hydroelectric grid, an initiative that must be accomplished in partnership with the Indigenous population to benefit all parties.
“Once the Renard mine is connected to the hydro grid, the vehicle electrification phase can be undertaken. This phase consists of converting high-consumption diesel vehicles such as loaders and production trucks to battery powered vehicles, which would enable Renard to become one of the greenest diamond mines,” notes Sevigny.
The success of Stornoway depends on having a committed workforce that upholds its principles and embraces the company culture.
Stornoway offers a fulfilling career path to its employees, the majority of
whom work at Renard, and provides fair compensation and benefits that are in line with the salary range for each corresponding role.
“We give our workers rewarding opportunities for growth, recognise their accomplishments, promote and constantly hone a model corporate culture,” Sevigny emphasises.
Of the 545 full time members of staff currently employed by Stornoway, 15 percent are women and 20 percent are from Indigenous and local communities.
Stornoway collaborates with its host communities in an atmosphere of respect, openness and partnership. By keeping open lines of communication, getting to know the values and concerns of the community, and working to address those concerns, the company hopes to establish longlasting, fruitful relationships with its
Indigenous and local communities.
“We work to improve the wellbeing of our host communities’ local economies and social structures,” Sevigny elaborates.
“By creating communication procedures with the Crees (a North American Indigenous people), putting together a joint environmental monitoring committee, hiring people of the communities, and conducting business with their firms and joint ventures, we have gradually developed a trusting relationship with them.”
In 2021, 1,334 hours were devoted to the professional development of Cree employees in various functions at the surface, in the processing plant and in the underground mine, whilst more than 2,100 hours were dedicated to developing staff members from the Chibougamau and Chapais communities.
383 certificates and 347 attestations were awarded to Cree personnel as a result of this training, as well as 790 certificates to Chibougamau-Chapais employees.
A relocation policy has also been set up and promoted by Stornoway to provide employees who relocate to Chibougamau and Chapais with financial benefits.
“The objective is to attract new residents to the region and retain the Renard mine’s workforce. The policy addresses the need to build the population of Stornoway’s host communities in Chibougamau and Chapais, in addition to maintaining a stable workforce,” Sevigny tells us.
– PATRICK SEVIGNY, CEO, STORNOWAY DIAMONDS CANADAThe mining industry is diverse, and there are many different career paths that individuals can pursue, including roles in mining exploration, operations, engineering and management.
Generally, a career in the diamond mining industry may involve working in remote locations, such as the Renard mine, often in challenging and harsh environments.
“It can be physically demanding work, and individuals in the industry may be required to work long hours, including weekends and holidays,” acknowledges Sevigny.
As such, Stornoway makes sure
that it provides a vibrant, friendly, and inclusive environment at the Renard mine to alleviate the demands of mining work.
A workplace where everyone feels respected, along with maintaining a safe work environment and high environmental performance, will always be a priority at Stornoway.
STORNOWAY DIAMONDS CANADA
Tel: 1-450-616-5555
info@stornowaydiamonds.com
www.stornowaydiamonds.com
“WE WORK TO IMPROVE THE WELL-BEING OF OUR HOST COMMUNITIES’ LOCAL ECONOMIES AND SOCIAL STRUCTURES”
Building on the global success of our regional titles – Africa Outlook, APAC Outlook, EME Outlook, and North America Outlook – Outlook Publishing is proud to introduce a platform dedicated to the mining and resources sector.
As mining organisations worldwide confront unprecedented change, embracing technological innovations and incorporating critical environmental sustainability agendas, now more than ever is the time to showcase the strides being taken in this dynamic sector. A multi-channel brand, Mining Outlook brings you the positive developments driven by organisations across the global mining industry through our various platforms. Discover exclusive content distributed through our website, online magazine, social media channels, and dispatches delivered straight to your inbox with a bi-weekly newsletter.
Through this compelling new venture, we foreground the movers and shakers of the industry. To participate as a featured company and join us in this exciting endeavour, contact one of our Project Managers today.
www.mining-outlook.com