VEHICLES THAT PUSH THE LIMITS TO RECORD-BREAKING SUCCESS
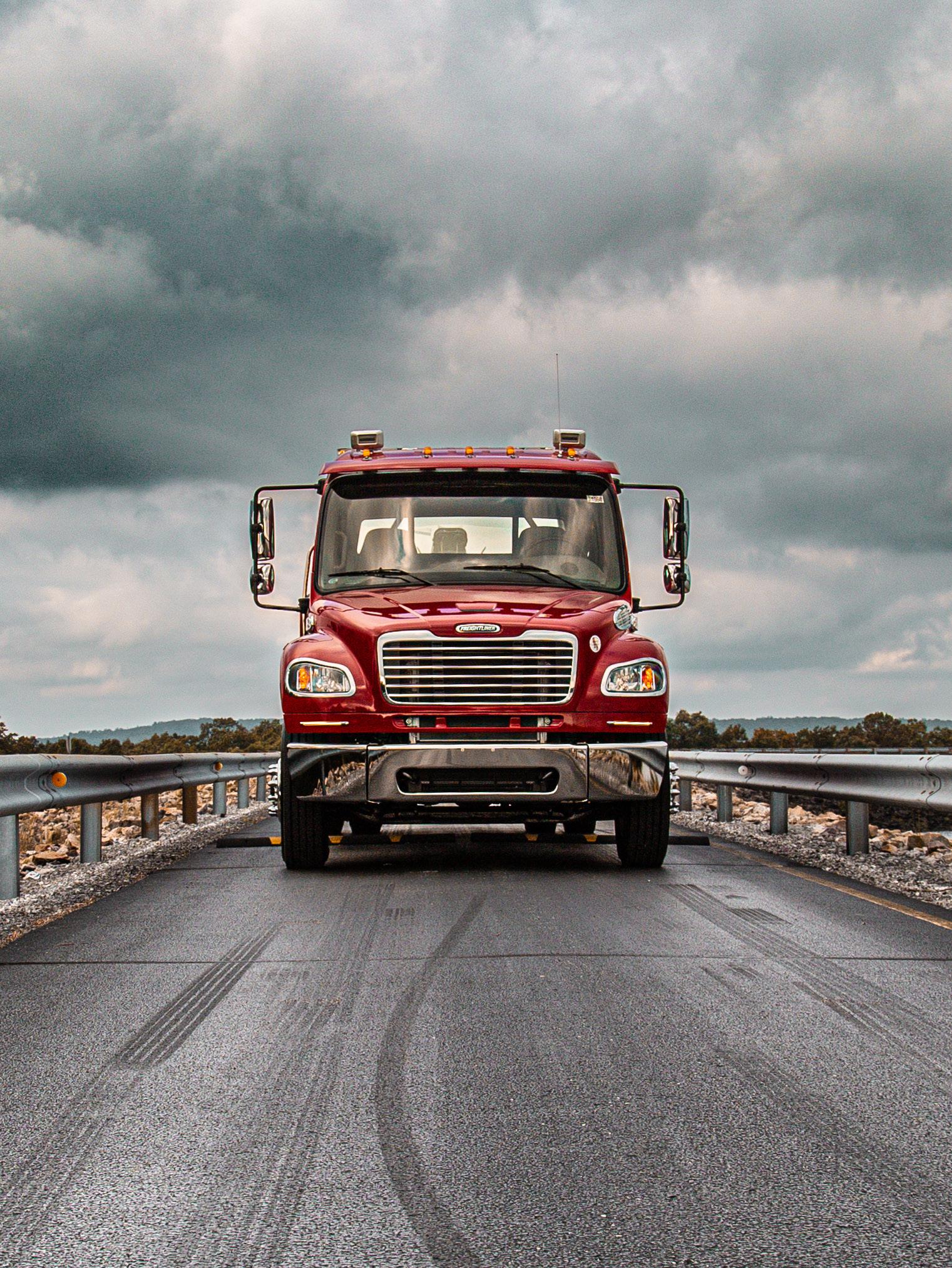
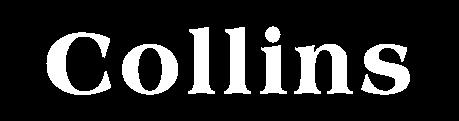
VEHICLES THAT PUSH THE LIMITS TO RECORD-BREAKING SUCCESS
With the largest portfolio of towing, recovery, and transport vehicles in the world, Miller Industries is triumphant in spearheading the global towing and recovery sector. President, Will Miller, tells us moreWriter: Lucy Pilgrim | Project Manager: Kieron Harvey
Miller Industries’ resounding success in the North American manufacturing industry stems from a founding mission of perseverance and dedication to being first in class.
The company was first founded in 1990 by current Chairman, William Miller, who had the ardent belief that to be successful, a business must
have the best people, products, and distribution network.
William’s philosophy was vital for the consolidation of the towing and recovery industry in North America, dictated by abundant distribution.
This is evidenced by the swift expansion of the company’s network, as within the first year of business, William streamlined the number of
North American distributors from over 450 to 125.
“My father’s belief was that distributors are the key to our success; having the best and most profitable, solid distributors for our products makes Miller Industries successful as a whole,” opens Will Miller, son of William and President of the business.
Following the completion of
distributor consolidation in 1994, Will has gone one step further in reducing the number of Miller Industries’ distributor locations to approximately 225 worldwide, harnessing the capabilities to export to 67 different countries.
The company is proud to manufacture the largest portfolio of towing,
recovery, and transport vehicles in the world. This includes anything from 8,000 pounds (lbs) of lightduty wreckers up to 100,000 and 200,000 lbs of its largest trucks.
Its diverse network is invaluable for facilitating the company’s enviable global reach. Miller Industries boasts six world-class manufacturing facilities across three countries, with
four facilities in the US and one a piece in the UK and France.
The organization is positioned at the forefront of innovation in the towing and recovery industry, thanks to its vast product range and services that consistently break the boundaries of manufacturing.
As part of its portfolio, the company produces light, medium,
and heavy-duty wreckers, as well as rotators.
Its light-duty wreckers, known as the Vulcan 812 and the Century Express 312, are utilized throughout the industry for private property, repossession, and cater to commercial towers.
Despite the products’ trusted use throughout the field, Miller Industries is consistently improving its product designs to achieve maximum efficiency for its customers. This can be seen in its light duty lineup where it increased the rear visibility between the boom and the tailboard
that facilitates greater hook-up ability, the recently introduced hose tracking system for longer life and easier maintenance, along with giving customers more choices with several hand-held controllers and other options available.
Also notable is the Century 5130, Miller Industries’ best-performing heavy-duty wrecker with 128 inches of underlift reach. This gives users of the wrecker the ability to tow the majority of vehicles without sacrificing the maneuverability of a single axle or tandem axle unit. The product also affords customers a
highly advantageous 25-ton recovery boom and 25,000 lbs winches for a vast range of recovery and lifting applications.
Another highly significant component of Miller Industries is its rotator product, Century 1150. Seen as an industry staple, the 50-ton rotator is ideal for daily recovery tasks or more complex needs, with 360-degree continuous boom rotation.
The company is the only manufacturer of recovery equipment capable of meeting tower needs and safety, making it a highly sought-after resource in the towing and recovery sector. The rotator is also ideal for the quick clearance of congested railways, ensuring the swift recovery of vehicles.
Will Miller, President: “As most manufacturers have learned over the last two to three years, relationships are super important to ensure that your company isn’t just a sales order number.
“Since we are operating within a relatively small global industry, building generational relationships with our distribution and retail customers is essential. “Our customers, distributors, and even our employees are in their second or third generation, and we want to ensure that these relationships are passed down.
“By maintaining these relationships over the years, Miller Industries has more than doubled our number of key suppliers for key components, particularly in the hydraulic and electrical space.”
Thirdly, Miller Industries is also an industry leader in the production of light, medium, and heavy-duty carriers.
To date, it operates the largest dedicated carrier platform, comprising over 200,000 square feet (sqft), solely committed to building carriers that keep up with the demands of the industry.
One example is the 12 Series LCG™ (low center of gravity) carrier. Through a specialized patented design, it lowers by a much greater degree than conventional carriers used by competitors, whilst also offering greater stability in the transportation of taller loads.
Whilst Miller Industries thrives with the largest and most successful distribution network in North America, what differentiates the
company globally is its unmatched product quality, reputable aftersales service, and history of recordbreaking vehicles.
The notion of continuous tradition is ingrained in the company, as Miller Industries is the product of a diverse and forward-thinking sector that has cultivated some of the most wellknown machinery and vehicles of the modern era, such as the Model T Ford.
Following this, the car manufacturing sector progressed from body-on-frame construction to unibody construction in the 1960s, which can still be seen in many passenger vehicles today.
Also known as chassis frames, bodyon-frame construction is used primarily in commercial vehicles, pick-up trucks, and sports utility vehicles (SUVs), whilst most other vehicles are transferred to unibody construction.
“OUR MOTTO IS TO THINK LIKE THE CUSTOMER, TO PROVIDE A QUALITY PRODUCT THAT CAN WORK EFFICIENTLY EVERY DAY FOR THE GENERAL MOTORING PUBLIC IN A TIME OF NEED”
– WILL MILLER, PRESIDENT, MILLER INDUSTRIES
At Collins, our philosophies and priorities revolve around adding value to our customers, the industry, and our team. We seek to enrich the communities around us through safety, quality, advanced designs, personal customer service, and doing what’s right. In our nearly 40-year association with Miller Industries, we have sought to support the towing industry by providing state-of-the-art towing equipment like the Hi-Speed®Dolly, the Carrier Dolly System, truck organization and towing accessories. The history of Collins commenced with M.M. Hassell, the
father of Collins Hassell, who settled his family of eight in the small village of Bluewater, New Mexico. As a certified mechanic in the early 1930’s, Hassell senior was sought after to work on the famous Route 66 that ran 2,448 miles through eight states, (including New Mexico), from Santa Monica, California to Chicago, Illinois. Throughout his career, he was always involved in heavy equipment, logging, or trucking--in one form or another--from repairing them, to operating them, to driving them.
As was customary of the time, fathers typically passed their vocation onto their sons. All four of Hassell’s sons eventually centered their livelihoods around heavy equipment, logging, manufacturing, and long-haul trucking. Collins Hassell was extensively involved in all of these. Having logged with their father for many years in Colorado,
New Mexico, Arizona, and Oregon, Collins and his younger brother Ray Hassell identified a need for improved logging equipment. The humble beginnings of Hassell Fabrication started in 1954, in a barn behind Collins’ Ashland residence. The fledgling operation was later moved across from Ashland’s airport in Oregon, where it continues to operate today. Throughout the 1950s and 60’s, the two brothers produced advanced stakes and log bunks for the Northwest timber
industry. It was during this time that Collins left the company to his brother Ray to start another manufacturing business. Collins Manufacturing was founded in August of 1972 when Charlie Nowell partnered with Collins Hassell to develop the world’s first articulating tow-truck dolly. It had four 8” pneumatic Goodyear tires on 5” wheels, which lifted each vehicle tire off the ground. The Collins Dolly acted as both jack and dolly by means of simple leverage. By adjusting the dolly to fit around the vehicle tire with the telescopic dolly frame, a person could then use their own weight as leverage on the end of a 5’ pry bar to quickly lift a vehicle with the dolly itself. A dolly tow could be ready to go in less than a minute. In the early 1970’s, all of this was quite revolutionary. By introducing an articulating dolly that both lifted and hauled vehicles, Collins changed the towing industry forever.
1952 Collins’ First tandem-axle Truck Hi-Speed Dollies staged for shipping Tunnel Tool BoxesThat first-generation dolly set the stage that would see the design, development, and manufacturing of the first SelfLoading (SL) dollies just three years later, after which Charlie would leave for other ventures. Collins Hassell continued innovating. His years of experience in trucking, designing, and manufacturing equipment that required the hauling of tens of thousands of pounds long distances, from forest-to-mill, across rough logging roads -- was the same DNA for creating the future Collins Hi-Speed®Dolly.
Now, towed vehicles could be moved safer, easier and further with the Collins Hi-Speed®Dolly, which in the 50-plus years since, has been the preferred choice of towing professionals. As vehicles today advance in design and technology, (EVs, hybrids, all-wheel drive, electronic parking brake systems), Collins Dollies are still a critical tool that helps support and enhance the essential work that professional towing and recovery operators do to safely and effectively tow or recover vehicles. Collins Dollies support and honor these professional operators who, because of the nature of the job, often do what others can’t and go where others won’t.
“The goal is to have all our products at the highest level, in terms of safety, quality, functionality, and aesthetics. Safety truly is first and foremost ahead of everything else we do in our product designs.”
Curtis Collins Hassell, CEO & President.Hi-Speed®Dolly - The Collins Hi-Speed®Dolly has evolved significantly from the first generation in 1972 to it’s seventh generation 50 years later in 2022. Distinct features of the Collins Hi-Speed®Dolly: 1) Secondary Safety features; 2) Freeway approved--rated for both long distance and freeway/highway speeds; 3) Requires only one truck and driver to safely transport the vehicle; 4) Lightest in weight with the greatest load capacity; 5) Quickest and easiest to use with automatic locking features; 6) Widest cross rail span for larger vehicles up to 104” and a true, positivecamber center; 7) Two-Tone zinc-plated finish as standard for additional corrosion protection. The new 7th-generation G7 Hi-Speed®Dolly adds 36 advancements.
Carrier Dolly - The Collins Carrier Dolly, (though similar in appearance to the 1st-generation highway dolly), serves a slightly different purpose. It is used on carrier or flatbed tow trucks to load and unload vehicles without risking damage by allowing the vehicle to roll on and off the deck. Prior to this, vehicles would have to be skated or dragged up onto the truck by the winch hook connected somewhere on the vehicle with a greater potential for damage, difficulty and concerned customers. In contrast, the winch hook connects to the Collins Carrier Dolly and the vehicle rides on the dollies. This also simplifies and standardizes the loading and unloading procedure no matter the vehicle—especially EVs, hybrids, vehicles with all wheel drive, and those locked up with the electronic parking brakes. The same Carrier Dolly unit, set up in a different configuration, can also be used for quickly loading and unloading motorcycles by a single operator and again, with less risk of damage to the motorcycle.
Truck Boxes - For over 30 years, Collins has designed and built an array of truck boxes: Tunnel boxes, to expand the available storage on a wrecker body, and Underbody boxes for
Loaded Log Truck outfitted with Hassell Stakes and Bunks Collins G7 Hi-Speed®Dolly Collins Hassell -- Final Dolly Build March 1984essential storage on a flatbed/carrier tow truck. These boxes have ranged in size, door styles, and materials (steel or aluminum). In each case, careful attention is given to create a robust box that holds up to the rigors of towing while refined in style to compliment the truck and body itself. The latest box project is a joint development with Jeff Cross to revamp his Streamliner Box — first made popular over 10 years ago — and is quickly recognized as the best underbody box ever built. As a manufacturer and supply partner with Miller Industries for over 40 years, Collins is committed to continuing to improve, develop, and advance our products, enhance the user experience, and keep pace with growing demand.
Today, Collins Manufacturing utilizes state-of the-art equipment and cutting-edge techniques, including CNC Fiber Laser cutting, CNC tube cutting, CNC high-precision press brakes, CNC multi-axis milling, CNC multi-axis lathe turning, automatic drilling, and machining. Our skilled craftsman in manual welding take pride in ensuring quality, while our precise repeatability in robotic welding, in-house powder coating, and world-class designs are unrivaled.
We have participated in historical and industry-recognized testing to ensure the efficacy of our products, such as the HORIBA MIRA proving grounds in the UK, the GM proving grounds in the US, as well as decades of successful in-house, and grueling real-world field testing. Collins’ partnership with Miller Industries continues across a global market with Collins supplying dealers on almost every continent, with self-loading dollies found on Miller Industries light-duty wrecker and car-carrier trucks.
“We appreciate our partners and customers and wouldn’t be around for this long without them. With our excellent team at Collins Manufacturing, who are also putting their names into a great product, we plan to be here many more decades serving our customers.”
Chris Usher, General Manager.collinsdollies.com
Collins Tunnel Boxes--Designed and Custom Built Since 1992 Collins Carrier Dollies for both Vehicles and MotorcyclesOver the years, the company has proactively reacted to changes and innovations in the sector, as it had to alter the way in which it recovers and tows a vehicle in order to stay on top of industry changes and to ensure the safety of products.
For example, Miller Industries navigated the shift in the 1990s from lightduty recovery vehicles and wreckers to car carriers and platforms by building its first dedicated carrier manufacturing facility in 1994 in Hermitage, Pennsylvania, making multiple additions to the factory over time.
Furthermore, there was a noticeable shift in light-duty wreckers from conventional wreckers of the early 2000s to auto loads – low profile crossbars that go under a vehicle to grab it by its front tires rather than using a chassis frame.
“These wreckers have hydraulic claws that reach around the tires so you can pick up half the vehicle singularly by the front or back wheels, showing a serious evolution,” Will explains.
Regarding heavy-duty products, large over-road-chassis have gotten lower to the ground and more aerodynamic as the industry has progressed, resulting in better fuel economy. Consequently, the company reduced the height of the crossbar device that comes into contact with the vehicle.
“We’ve had to make it increasingly thinner whilst retaining its strength. The crossbar is now down to five inches in height so they can
fit underneath the bumpers of commercial vehicles easily.
“This also means that we can still tow vehicles without damaging their dynamic fairings and underbody,” he adds.
Another aspect Miller Industries pays close attention to is weight. It wants to ensure that its vehicles comply with all road safety standards and do not exceed the maximum weight allowance of public roads, whilst still being strong enough to efficiently tow the desired vehicle.
With continuous improvement as a hallmark of the business, the company has invested over $100 million in its manufacturing facilities globally in just over a decade, particularly in its paint capabilities and robotics, as well as developing a dedicated R&D center.
Miller Industries specifically focused on vertical integration during the COVID-19 pandemic in 2020, at a time when a lot of its competitors were slowing down production and letting staff go.
During this period, the company invested in a state-of-the-art fabrication equipment facility to begin the production of its own steel parts, growing its in-house capabilities.
Meanwhile, staff whose work had stagnated due to the decreased demand were given the opportunity to go to training centers to learn how to operate computer numerical control (CNC) machines, as well as control lasers, press brakes, plasmas, and lay mills. This contributed to the wider goal of having a functioning workforce that can efficiently operate new, highly automated, world-class fabrication equipment.
The company’s vertical integration process also included the introduction of an enterprise resource planning (ERP) system in 2019, which allowed Miller Industries to succinctly run all its worldwide facilities, streamlining
“MY FATHER’S BELIEF WAS THAT DISTRIBUTORS ARE THE KEY TO OUR SUCCESS; HAVING THE BEST AND MOST PROFITABLE, SOLID DISTRIBUTORS FOR OUR PRODUCTS MAKES MILLER INDUSTRIES SUCCESSFUL AS A WHOLE”– WILL MILLER, PRESIDENT, MILLER INDUSTRIES
operations in manufacturing, human resources (HR), accounting, and engineering.
The ERP system comprises a cloud-based piece of software called CloudSuite Automotive, created by Infor, which enabled the company to handle over a billion dollars of revenue in preparation for 2024.
“As a manufacturing organization, a solid software system allows us to expand organically and harness additional acquisitions and the future growth of Miller Industries,” Will highlights.
The company’s second phase of vertical integration in Q2 2023 witnessed the acquisition of Southern Hydraulics Cylinder (SHC). The entity had previously been a supplier; therefore, the acquisition was a natural step to progress Miller Industries into the wider manufacturing space, having more control over certain supply chain issues.
At the heart of the company lies Miller Industries’ staff base, who are continuously valued across the organization. Considered a profitsharing company, it has a strict bonus structure applicable to all employees so that each team member can take home a percentage of net profit.
Alongside company-wide financial incentivization, Miller Industries also invests in human capital and the health and safety of its employees. These standards include
climate-controlled facilities, LED lighting, and overall enhancement in the work environment.
As of last year, the company also introduced an employee family scholarship fund, into which each of the executives commits to putting $5,000 per year, a figure that the wider company then matches.
This generosity is used to facilitate 14 higher education scholarships for either the children or grandchildren of employees.
This is compounded further by the Frontline Leadership Academy, which provides tuition reimbursement to further the education of its employees. Additionally, Miller Industries also possesses an in-house welding academy where high school students and former military personnel can become skilled welders to further the productivity of its facilities.
In accordance with its commitment to employee well-being and personal development, the business strives to create an environment that is inclusive, diverse, fair, and engaged.
To meet these high standards, the company has implemented a specific diversity, equality, and inclusion (DEI) program that is consistently monitored to see how it could be improved. For example, in 2022, Miller Industries introduced an antiharassment and anti-discrimination policy as part of the program.
On top of this, the company also regularly monitors DEI metrics to
develop its minority representation, as well as having a proactive hiring process that welcomes veterans, women, and underrepresented minority groups.
At the forefront of the towing and recovery sector’s innovation, Miller Industries is immensely proud to have developed and created the Century M100 100-ton rotator. The product came into ideation in 2017 after the company identified a greater market demand for a higher capacity product.
Consequently, Miller Industries proactively created a dedicated team of engineers to develop the world’s largest rotator, setting a precedent in size and capability. Following years of testing, working to strict deadlines, and intricate efficiency and detail, the team combined all the best aspects of its most successful products, with cutting and production completed in-house.
Eventually, testing proved that the product could pick up over 200,000 lbs, marking a major turning point in the industry and cementing Miller Industries as a towing and recovery titan.
With innovation at the core of the company’s resilience, Will cites Miller Industries’ success as a simple formula.
“Our motto is to think like the customer, to provide a quality product that can work efficiently every day for the general motoring public in a time of need. This also applies to our employees, who are to focus from the top down, helping them realize they have a critical part to play in the success of the company,” he closes.