MOVING TOWARDS CLEANER, GREENER EUROPEAN STEEL
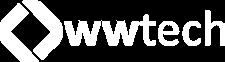


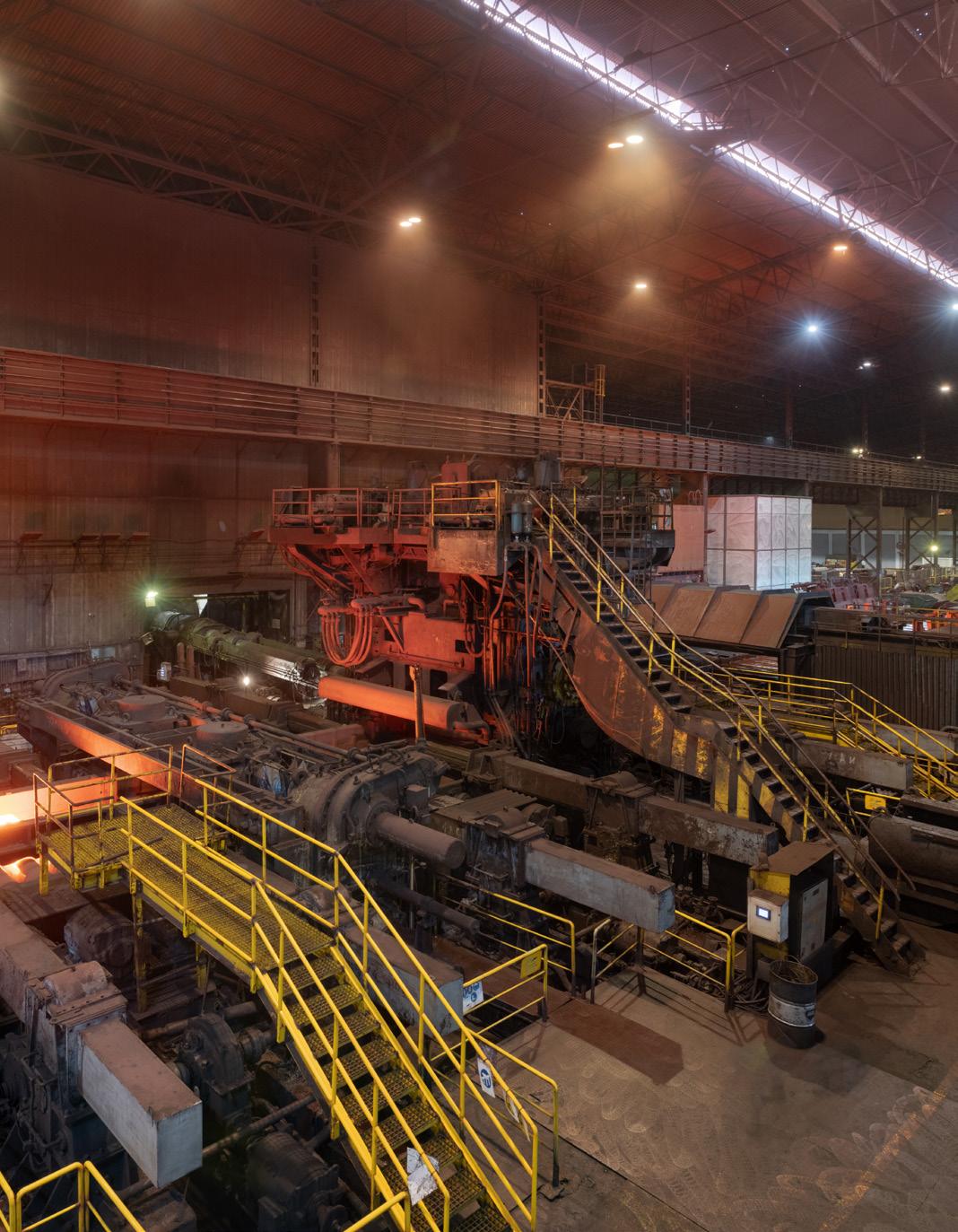
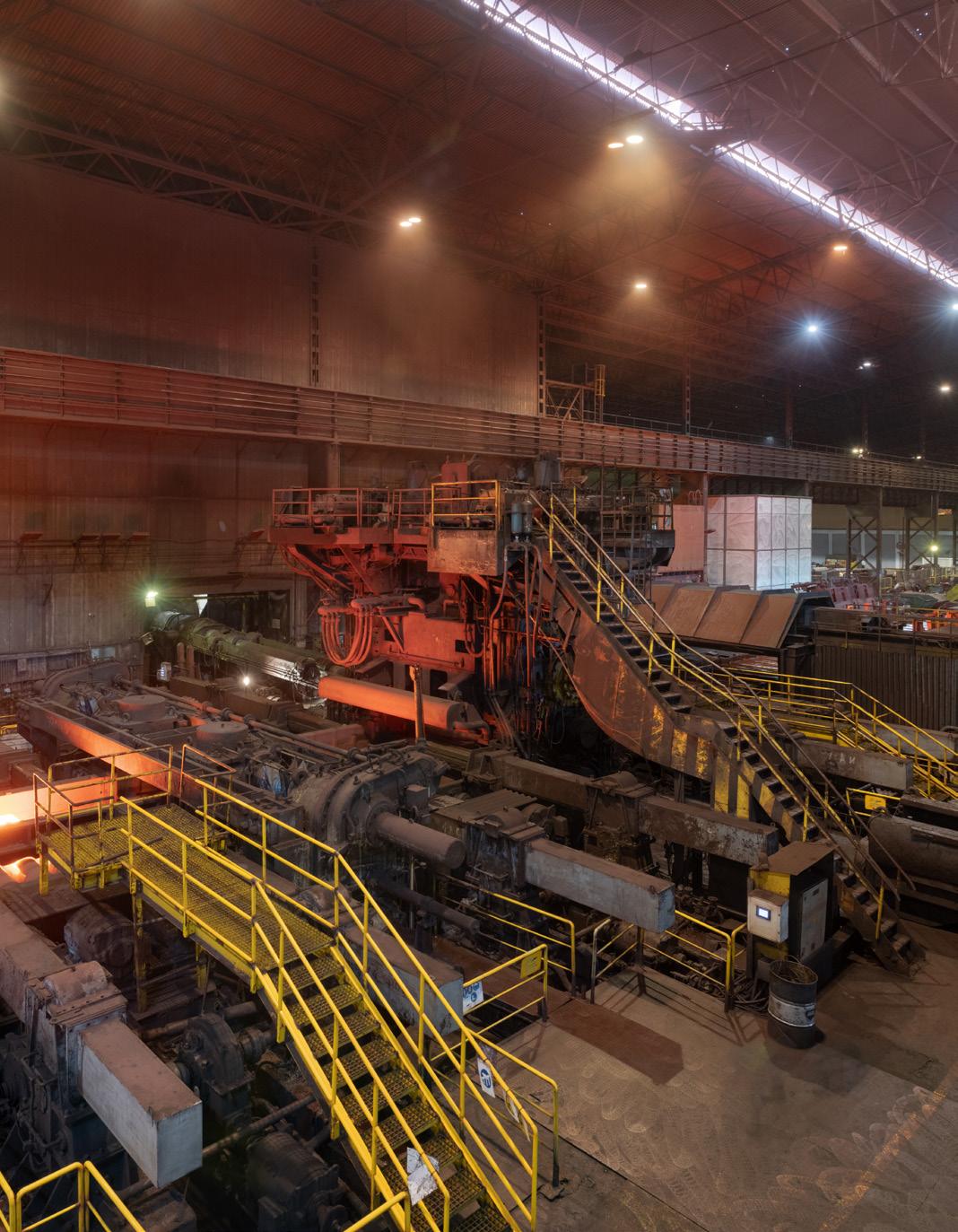
Makstil is at the forefront of environmentally friendly steel production practices. We speak to General Manager, Marija
Dukovska-Pavlovska, about industry changes and challenges in North Macedonia and beyond
Writer: Marcus Kääpä | Project Manager: Nicholas Kernan
Makstil finds it extremely exciting to showcase itself as a true example of having transited towards cleaner production processes, and we work hand in hand with the Ministry of Environment to reach our goals.”
The words of Marija DukovskaPavlovska, General Manager at Makstil, encapsulate the active change currently being undertaken in the European steel industry.
Majority-owned by the Swiss company Duferco, Makstil is a North Macedonian regional steel industry leader with a headcount of approximately 1,000 employees that operate across two production sites,
namely the Steel Shop and the Plate Mill. Makstil’s Steel Shop consists of an electric arc furnace (EAF) to produce liquid steel, a ladle furnace for secondary refining, and three continuous casting machine lines to transform liquid steel into slabs, with the company’s production capacity amounting to more than half a million tonnes per year.
The Plate Mill makes up the production side of the business, where produced slabs are reheated in a pusher furnace and rolled into plates in a high reversing mill, levelled, then cooled on cooling beds and mechanically cut or flame cut to the ordered size.
Marija Dukovska-Pavlovska Photography ©Ekonomija i Biznis Magazine Photography ©Viktor MáchaSpeaking to Tim Saxon, Chief Marketing Officer for Resonac Graphite, we learn about the vital role of graphite electrodes in the production of steel, and how the company is shifting in a more environmentally conscious industry.
Can you briefly describe your business and how you support Makstil?
Resonac Graphite (Resonac), formerly known as Showa Denko Carbon, manufactures ultra-high power (UHP) graphite electrodes which are critical components used in the remelting of steel scrap. To produce its steel plates and slabs, Makstil owns and operates an electric arc furnace (EAF). When using an EAF to produce steel, a high-powered electric arc is used to melt and recycle steel scrap into new steel. The electricity used to melt the scrap is transferred solely through the graphite electrode. In 2022, approximately 30 percent of the world’s steel (or approximately 565.5 million metric tonnes) was produced via EAFs – making steel the most recycled material in the world.1
As of 1st January, 2023, Showa Denko Carbon officially became Resonac Graphite BU. Why the change?
We like to say, “New look. Same values.” Showa Denko Carbon has a very strong name in the global steel industry, but our parent corporation has undergone a substantial transition over the past three years. In 2023, after acquiring and completing the integration of Hitachi Chemicals, the Showa Denko Group officially became Resonac – a company whose mission is to change society through the power of chemistry. The name “Resonac” was chosen to convey the desire to RESONATE with Chemistry. Much like our business unit which
literally transforms carbon into graphite, we recognise that the world is also undergoing fundamental change. As a global community, we must place a priority on sustainability and responsibility, recognising our obligation to future generations. We know our purpose is not just to simply manufacture and sell a product. As a business unit and corporation, it is Resonac’s responsibility to co-create innovative technologies and services with partners inside and outside of our business. With these synergies, we want our combined solutions to be more than just the sum of its parts. Fortunately, the “new” steel industry provides a multitude of opportunities for co-creation.
Speaking of increased focus on sustainability in manufacturing, how do you see your business changing?
The increased focus on sustainability and environmental stewardship is having a meaningful impact on the graphite electrode industry. As mentioned earlier, recycling steel via EAF only accounts for approximately 30 percent of the world’s production, but that method of production also results in approximately 75 percent less carbon emissions than other methods of steelmaking. 2 As more steelmakers focus on sustainability, the industry is seeing a considerable increase in the construction of electric arc furnaces, which will significantly increase the demand for graphite electrodes.
Given that, how does Resonac plan to address those issues?
The graphite electrode industry, much like the steel industry, is a cyclical one. Both industries also require significant capital investment and face major threats from offshore competition – particularly by government-subsidised producers who are not required to adhere to safety or sustainability standards.
Despite these threats, Resonac has a very strong history of investment in the global EAF steelmaking industry. The company (then Showa Denko) produced its first graphite electrode in Omachi, Japan more
than 85 years ago. Over the next several decades, Resonac grew the graphite electrode business as the EAF steel industry grew. In 1988, it purchased the Ridgeville, South Carolina facility in the US, and in 2017, purchased the A Coruña Spain, Steeg Austria and Banting Malaysia facilities from SGL Carbon. Resonac is now the world’s largest manufacturer of UHP graphite electrodes with plants strategically located to meet regional demand with regional supply.
Our most recent and perhaps most exciting investment, is the acquisition of Automation (AMI), which was announced in June 2023. AMI is an industry leader in providing innovative process control and automation technology that improves customer operating efficiency. AMI’s Meltshop Division is at the forefront of EAF automation and optimisation and has the largest group of EAF specialists in the world. The Industrial Systems Division is a prominent supplier of customised automation and power control systems for steel, paper, cement, oil and gas, transportation, and mining.
As an industry leader and vital part of the EAF steelmaking supply chain, Resonac is in a unique position to use our innovative technologies, our products, and our services to help in the transition from traditional methods of steelmaking to new, safer, cleaner, more efficient, and more flexible production. While we understand that business philosophies and practices are ever-changing, we are happy that we have ongoing projects and co-creative efforts with various partners around the world.
Does this include Makstil?
Yes, of course! While both companies historically maintained a very professional “buyer/seller”
relationship in the past, Resonac’s strong partnership with Makstil was solidified during the most extensive graphite electrode crisis to date. In late 2017, after years of (ex-China) graphite electrode production rationalisation, the Chinese Blue-Sky Initiative forced the immediate stoppage of approximately 40 percent of its graphite electrode capacity.3 Almost instantly, global EAF steelmakers were left without a way to melt the steel they were dependent on producing for their survival. Even if available, prices for electrodes increased by approximately 10 times in three months, which turned out to be a small price to pay for the ability to produce product and fill customer commitments.
Needless to say, the crisis found different suppliers and different consumers negotiating various, creative ways to withstand the predicament and keep the electrode supply lines open. Some of those solutions turned out to be less advantageous in the longer term, but proved necessary for the survival of several steel businesses.
During this tumultuous time, Resonac worked diligently to develop true “win-win” partnerships that will ensure our industry not only survives… but thrives during the next crisis. The framework of these partnerships was the foundation for Resonac’s Volume Supply Partnership (VSP), which was recently renewed by Maksil, as well as our Strategic Supply Partnership (SSP). We are now excited to start “co-creating” with selected partners on a new
Optimisation Supply Partnership (OSP), but more to come on that endeavour.
Makstil has discussed some projects and ambitious plans for continued diversification and expansion in the coming years, so you are confident Resonac can help them achieve their goals?
Absolutely. Although names can change, a company’s purpose and legacy lie in its DNA. At Resonac Graphite, supporting our partners in the electric steelmaking industry is exactly what we do.
1 World Steel Association (worldsteel.org)
2 Steel Manufactures Association (steelnet.org)
3 Industry estimates
The steel plates are used for applications such as shipbuilding, pressure vessels, bridge construction, mining and industrial machinery, and windmill structures, all of which require high quality and high strength. The Plate Mill gives Makstil the opportunity to offer its clients rolled plates with various dimensional ranges adapted to their needs. This represents the company’s trademark and is recognised by Makstil’s clients across Europe.
“As steel is an industry that has historically been associated with large amounts of emissions, I am very happy to say that is now in the past. We express pride in confirming that we are causing no direct harm to the environment through our production activities, and we have clear visibility on the impact of the Carbon Border Adjustment Mechanism (CBAM),” explains Dukovska-Pavlovska.
Makstil traditionally serves its domestic regional market and neighbouring countries, such as Bulgaria, Croatia and Serbia, with the majority of its sales in the markets of the European Union (EU), which North Macedonia is foreseen to join in the next decade according to the government’s
predictions. Moreover, for DukovskaPavlovska, the market seeing the biggest growth of late is Turkey, where Makstil’s customers take advantage of the geographical proximity and availability of the company’s final production output. Makstil’s distinctive adaptability towards its clients’ needs is also recognised across the pond, as the company exports non-negligent quantities towards the US and Canadian markets. However, Makstil’s operation in the steel industry has not come without its challenges.
“The steel industry is facing particular issues linked to the availability and sourcing of the raw materials and ensuring the uninterrupted supply chain needed in our production processes. In addition, it must confront the volatility and unpredictability in terms of prices,” elaborates Dukovska-Pavlovska.
“This can create confusing ground for us, as we want to maintain optimal prices for our clients, but we also need to fulfil the various commitments that Makstil has. This includes transitioning to a more resource-efficient production process, having the least possible environmental impact, and contributing to and supporting the
Marija Dukovska-Pavlovska, General Manager: “As a female leader who has progressed throughout my career by working within organisational development, finance and human resources in various industries, being offered the opportunity to lead one of the largest steel industrial companies in our region was obviously an enormous challenge for me, not least because of the perilous and complicated times we live in.
“I intend to use my time at Makstil not only to confirm and strengthen our position as a market-leading specialised steel producer, but also to prove that a woman can successfully thrive in what is often considered a masculine work environment and serve as an example for generations of girls and young women that they too can indeed succeed in fields where their success isn’t necessarily guaranteed from the beginning.”
local communities where we operate. We also want to be at the forefront of circular economy practices, not only within the North Macedonian industry, but also regionally.”
By design, Makstil is a mini steel mill. Unlike the integrated mills that produce new steel from iron ore in a blast furnace (BF), mini steel mills such as Makstil melt, refine and recycle scrap metal by using EAF technology. By using this technology, Makstil belongs to the 30 percent of steel producers in the world leveraging this more environmentally friendly method compared to BF. Furthermore, as an active participant and supporter of the circular economy, Makstil only uses scrap metal as an input material for the production of slabs and hot rolled plates as a final product.
“Makstil is focused on saving the resources we use in our production processes (natural or otherwise). We actively support the concept of the circular economy by encouraging the rational use of secondary raw material (steel scrap) as well as the reduction, reuse, and recycling of waste,” says Dukovska-Pavlovska.
WWTECH provides its clients with a complex way of problems resolving, offering them three-dimensional coordinate measurements and a full 3D documentation. Due to accurate measuring devices FARO (Laser Tracker, Measuring Arm) WWTECH makes it is possible to carry out uniquely accurate, fast and non-contact measurements, the results of which can be analysed in a real time.
Fully functional equipment is fundamental to the company’s success. Every machine has precision elements, bearings, and a number of other parts, that enable its efficient operation. Those main elements, which ensure correct machine operation, require specific solutions in case of a breakdown. Leaks, cracks and grooves are issues that have to be eliminated to ensure proper operation.
In all undertaken activities, WWTECH gives priority to safety. The health of our staff, society, and respect for the environment are the factors which determine our whole team’s activities, and other aspects of our work, such as transportation or cooperation with a third parties.
www.wwtech.com
“All metal waste generated during the production process, and part of the refractory waste, is returned to the very same production process. The remaining waste that cannot be recycled is further selected and disposed of, to be handed over to authorised and trusted partners for their own use downstream.”
According to Dukovska-Pavlovska, any inert and non-hazardous waste, such as slag from an EAF, through the process of crushing and separating, is divided into fragments and is transformed from waste into raw material where it can be fully used as a buffer for road construction, as well as a foundation for an asphaltic or concrete pavement, cement, and various cement products.
This circular economy is designed to save natural resources and energy, creating added value and ultimately a healthier and cleaner environment with new employment opportunities. On top of this, it improves product competitiveness, focuses on positive society-wide benefits, and provides increased earnings that contribute to the sustainable development of modern civilisation and an economy fit for the challenges of the years ahead.
“At Makstil, we are proud to take the lead on these initiatives and believe we are setting an example not only for other fellow companies in our industry, but also towards those working in fields very different from our own,” Dukovska-Pavlovska adds.
“I am especially humbled by Makstil being awarded as the most environmentally friendly company,
granted by the municipality where we are based (which is also home to other heavy industry actors). The Green Agenda award from the Economic Chamber of North Macedonia further confirms Makstil’s contribution towards safeguarding the environment as well as our commitment to zero waste.”
Despite its size as a mini steel mill that produces steel plates from recycled scrap, Makstil is present in the markets of more than 40 countries and collaborates with approximately 500 customers, reaching trading destinations in several continents and meeting the needs of the most demanding clients. Makstil prides itself on offering a 45-day delivery window, with the flexibility to provide specific materials necessary for projects at the exact requested time, and answers to complicated specifications with no limitations in terms of the number of ordered pieces, dimensions, and qualities within the company’s product range.
“We are recognised for our excellent after-sales service with a prompt response time, yet one of our key features of business for clients is our dedication to practices that are more environmentally friendly,” Dukovska-Pavlovska says. “One of our leading environmental protection activities, from both a technical and financial aspect,
“MAKSTIL FINDS IT EXTREMELY EXCITING TO SHOWCASE ITSELF AS A TRUE EXAMPLE OF HAVING TRANSITED TOWARDS CLEANER PRODUCTION PROCESSES, AND WE WORK HAND IN HAND WITH THE MINISTRY OF ENVIRONMENT TO REACH OUR GOALS”
– MARIJA DUKOVSKA-PAVLOVSKA, GENERAL MANAGER, MAKSTIL
General Manager: “During the last five years, Makstil heavily invested in the field of health and safety for all its employees. Our Board of Directors and management commitment is of paramount importance for stepping up and leading the whole process by example through the top-down approach.
“Our commitment to the ISO 45001 occupational safety and health management was integrated during the last year at all levels of the company. I would like to underline that in addition to achieving the highest quality production and financial results, the company has maintained an optimal level of health and safety of our employees and improvement of the working conditions.
“We should not forget that this industry is one with a high risk, and we continuously work on process and equipment improvement to enhance workplace safety. In parallel with that, we continuously increase awareness of all employees to identify potential risks and to participate in developing countermeasures. Monitoring the trends in the industry, we are following many indicators related to health and safety, and our strategic goal fully encourages, motivates, and obliges us to be a company that has a “zero by choice” approach.”
was the installation of the Dedusting System in the Steel Plant (Filter Plant – FP) carried out back in 2015. Thanks to this investment, we succeeded in almost completely absorbing the dust particles emitted during the melting process. This dust is then packed, and we get further value from it as we collaborate with verified external partners for its collection and distribution outside Makstil.
“For more transparency with our stakeholders, Makstil continuously monitors the dust emissions in the air and on a quarterly basis publishes the results that are fewfold lower than allowed by local and EU norms. Makstil continued the practice of publicly announcing the emissions of solid particles emitted from the production chimneys during the operation of the factory, which once again confirms the company’s commitment to promoting full transparency in its business operations.”
Makstil is the first company in the country to obtain an Environment Product Declaration (EPD) for hotrolled plates. With the EPD, Makstil confirms its commitment to protect and preserve the environment
satisfy the needs of its customers in an
by continually reducing the environmental impact of its products. The declaration provides an overview of the objective, verified, and comparable environmental performance of the hot-rolled plates manufactured on the company’s production site.
The environment and employee well-being are the twin pillars of Makstil’s vision. Regarding the latter, the company has achieved significant results in employee retention and satisfaction through renewed and innovative solutions aimed at better engagement and fair reward systems and plans for its workers. Yet the
business’ operational focus is set on the continued sustainability-centric mission to help alter the industry for the good of the planet.
“Overall, the industry is dealing with different sets of specifics; regulatory, environmental, availability of raw materials, or qualified staff – you name it,” Dukovska-Pavlovska tells us. “Adjusting an entire robust steelmaking organisation with traditional business practices to new production process trends is a challenging enough activity for a female leader, especially with the new challenges regarding the transformation of production towards green steel. It is an industry environment where personal resilience and the ability to
innovate is critical to staying ahead while fully satisfying and retaining the loyalty of our clients. Nevertheless, Makstil has successfully proven that this is an achievable goal despite the challenges posed.”
Viewing itself as the frontrunner of environmental improvements in the heavy industry sector in North Macedonia, Makstil is following a vision to produce steel plates that satisfy the needs of its customers in an environmentally sustainable way, and it has already started with activities related to the decarbonisation process that it will continue moving forward.
“Decreasing greenhouse gas (GHG) emission levels requires the
introduction of some changes in all production aspects as well as delivering goods and services. In this context, Makstil has already introduced investments in renewable energy and carbon-free sources,” Dukovska-Pavlovska concludes. “We are proud of what we have achieved thus far, and we thoroughly follow the European Commission’s goals of reaching net zero by 2050.”