70 YEARS OF COLLECTING AND RECYCLING USED COOKING OIL
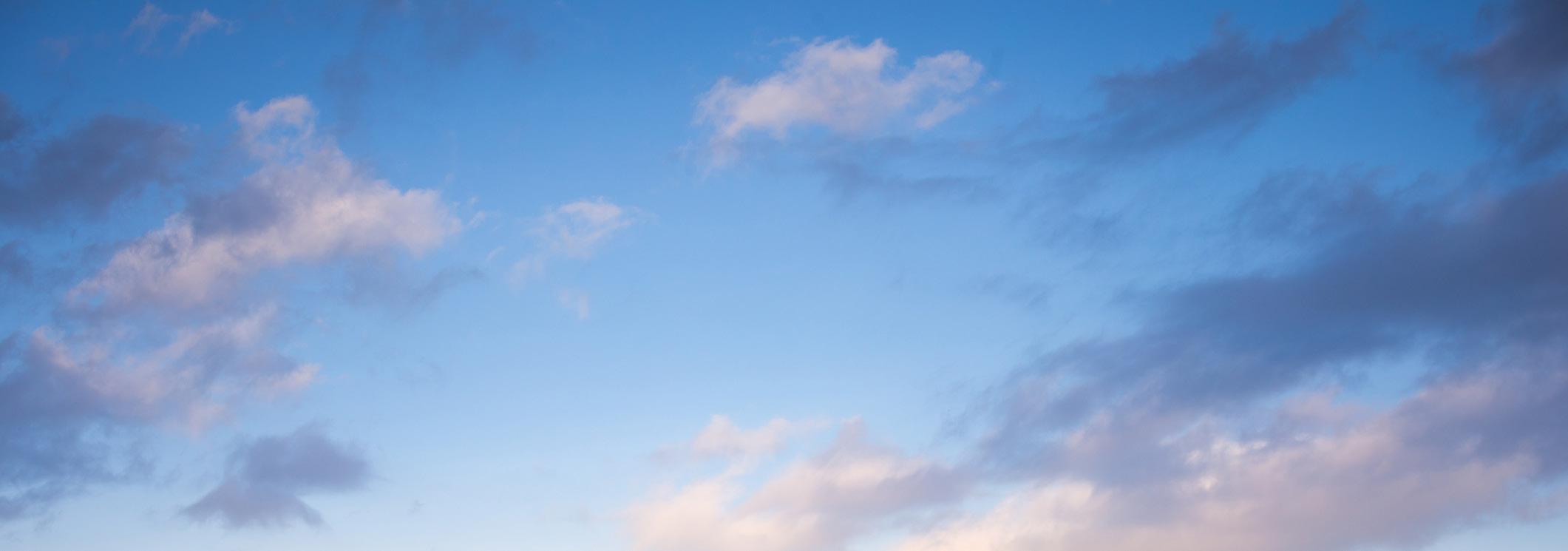

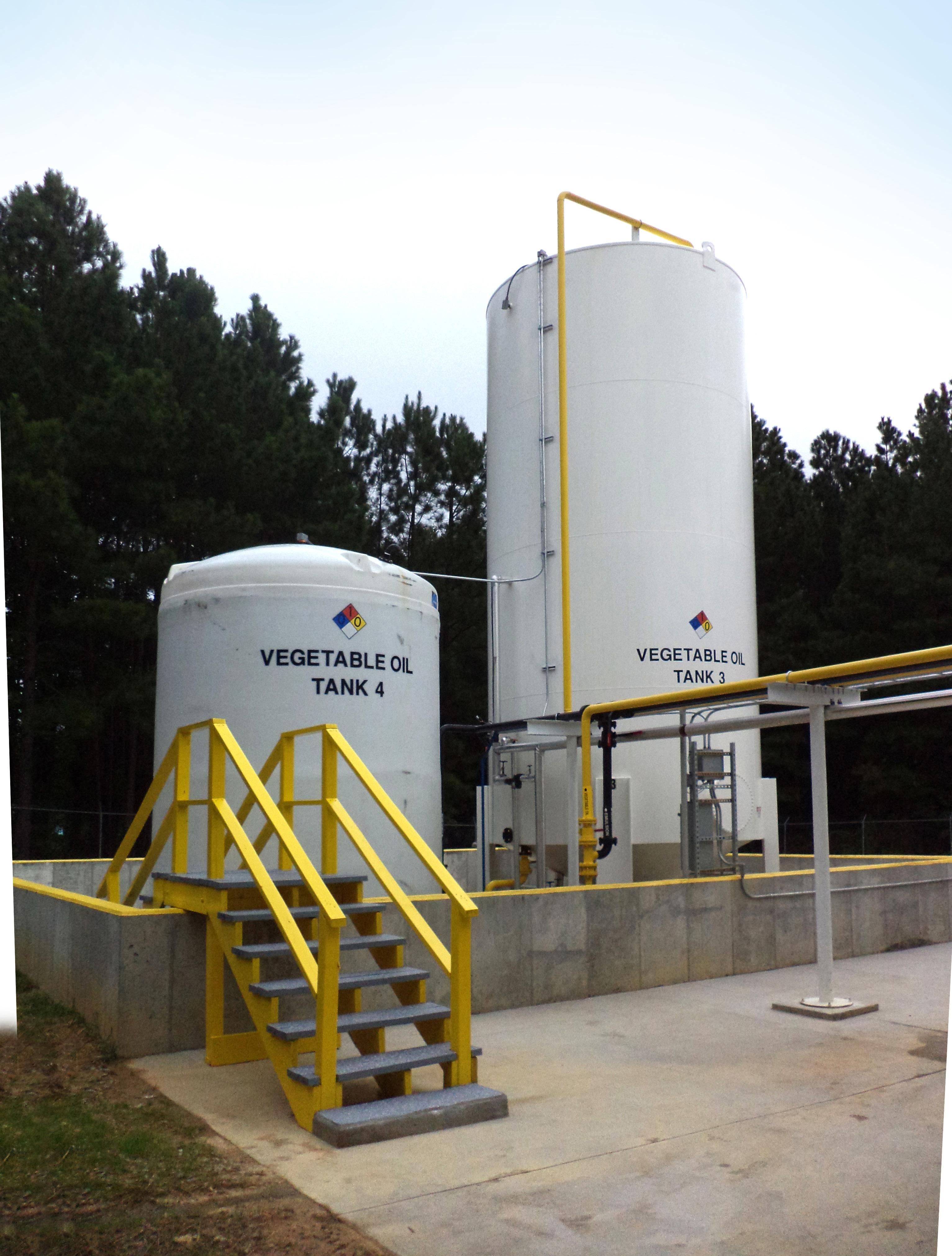
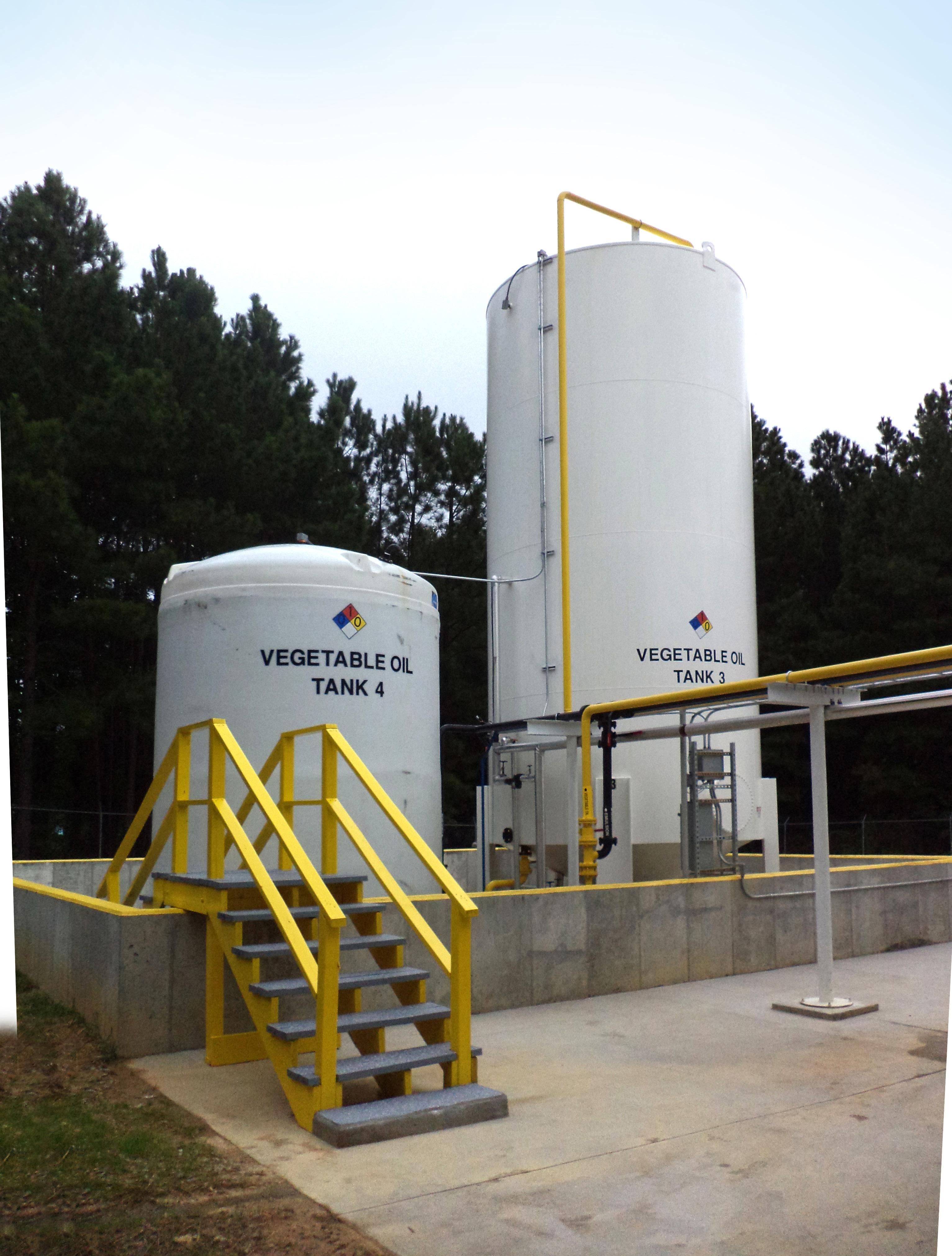
70 YEARS OF COLLECTING AND RECYCLING USED COOKING OIL
By collecting and recycling used cooking oil, Mahoney Environmental is addressing the issue of improper waste disposal. President and CEO, Dave Kimball, highlights this sustainable practice in the foodservice industry
Cooking oil waste has become a significant environmental issue in recent years, as it can have detrimental effects on the planet such as water and air pollution.
For example, used cooking oil that is poured down the drain can travel through the sewage system and make its way into rivers and oceans, polluting the water supply and causing aquatic life to perish. Equally, when cooking oil waste is sent to landfill, it can release methane, a potent greenhouse gas (GHG) that contributes to climate change.
Failure to recycle used cooking oil can therefore cause significant environmental damage, and the food supply chain would be adversely affected if the sustainability of plant and animal life was impacted.
Fortunately, there is increasing awareness of the environmentally
friendly and sustainable practice of recycling used cooking oil, which can be converted into a renewable fuel source and used in place of fossil fuels, helping to mitigate climate change and reduce GHG emissions.
“The used cooking oil collection and recycling industry is getting more and more competitive,” notes Dave Kimball, President and CEO of Mahoney Environmental (Mahoney).
“Companies are realizing the potential of how used cooking oil can
be recycled into beneficial products, so the demand for it is growing.”
Likewise, as world energy sources decline, demand is skyrocketing for renewables such as sustainable aviation fuel and renewable diesel, two of a growing list of useful products derived from used cooking oil.
As the topic of climate change has become an increasingly mainstream issue in the public domain, added importance has been placed on the work that Mahoney does.
“People might not know or see the connection between used cooking oil recycling and the environment, but we’re able to make the environment safer for future generations by turning a waste product into renewable fuels,” states Kimball, whose time at Mahoney has opened his eyes to the incredible things that can be done through sustainable initiatives.
Mahoney is the number one choice
for all cooking oil management needs in the US, with the goal of being the premier back-of-thehouse service provider to a variety of foodservice operators across the country.
“We are a nationwide provider, servicing over 60,000 foodservice operators across the US. Our customers range from wellmanaged independent restaurants to national chains, airports, casinos, and stadiums,” Kimball outlines.
Arrow
Blackson Arrow is a facility management and services company that provides specialized facility operations and maintenance services, as well as aviationrelated services such as airfield management, logistics, and bulk fuels facilities operations to both commercial customers and the U.S. Government. Additionally, since many of our operations are at the intersection of oil and gas, and aviation, Blackson Arrow has become a leading provider of advisory services related to sustainable aviation fuel (SAF) logistics solutions.
Founded by U.S. Air Force veteran, Mike Blackson, we are classified as a disabled veteranowned small business. The firm operates in many locations around the US, such as Littlestown, Pennsylvania; Mountain Home, Idaho; Las Vegas, Nevada; Seymour Johnson Air Force Base, North Carolina; Columbia, South Carolina and Merritt Island, Florida. The company currently has just over 100 employees.
Blackson Arrow is committed to friendly, capable, and competent service to their clients. We continuously strive to improve our processes and operations to meet the challenges of the ever-changing marketplace.
Blackson Arrow recently partnered with Mahoney Environmental Solutions (Mahoney) to provide maintenance and repair on over 20,000 of Mahoney’s used cooking oil (UCO) storage tanks installed in restaurants across the US. In addition, we also coordinate the installation of new USO storage tanks in restaurants that do not yet have Mahoney’s system installed. Our extensive facilities management expertise and network of providers across the country enable us to provide these services in a manner tailored to Mahoney’s specific needs. This project also ties in nicely with our experience with sustainable aviation fuels and their component systems across the entire SAF ecosystem. From the smallest system in a single restaurant to a large bulk fuel storage facility holding millions of barrels, we are able to provide installation, operations, and maintenance services to the entire portfolio of equipment. These systems collect millions of gallons of used cooking oil each day that is collected by Mahoney, filtered and refined as a feedstock additive to produce SAF.
For several commercial consortiums that own large bulk fuel storage facilities on or near
airports, we provide our integrated facilities management approach to these facilities that is unique from the other refuelling companies typically hired to provide bulk storage management. Coming from what the U.S. Government calls base operations services, we are able to manage the entire suite of facilities-related services, from providing reliability engineering and preventive maintenance on these complex systems to mowing the grass and even cleaning the facilities under a single contract umbrella structure.
What, for you, differentiates your business from the competition?
Blackson Arrow differentiates itself from the competition in that we are a facilities management company that also provides a variety of support services to our clients in a number of ways. For example, we have over 20 years of experience in airfield management, into-plane fueling, logistics, and bulk fuels operations and storage. This operational knowledge gives us a deep understanding of the challenges faced by clients and allows them to provide customized solutions that meet their specific needs detailed to both their infrastructure portfolio and the value chain served by that portfolio. On the facilities side, we have a team of professionals highly experienced and qualified in
maintenance engineering, reliability, and management of third-party vendors.
Could you tell us about some of the major challenges faced within the industry and then detail how these have been overcome?
Blackson Arrow has faced a number of challenges in the past, including:
• Competition: Facilities management, airfield management,
logistics, and bulk fuels operations and storage industries are exceedingly competitive. Blackson Arrow has had to compete with larger, more well-established companies in order to win contracts.
• Regulations: The government agencies that Blackson Arrow contracts with have a complex set of regulations that must be followed. Blackson Arrow has had to invest
in training and resources in order to ensure that they are compliant with all applicable regulations.
Blackson Arrow has overcome these challenges by:
• A focus on customer service: Blackson Arrow is committed to providing excellent customer service. We have a team of experienced and knowledgeable professionals dedicated to meeting the needs of their clients.
In October 2022, Blackson Arrow began a partnership with Mahoney Environmental to install and maintain over 20,000 used cooking oil (UCO) storage systems in restaurants across the US. These systems allow Mahoney to collect millions of gallons of used cooking oil each day that is then filtered and refined into a sustainable jet fuel additive used to produce SAF.
At the heart of our operation is our state of the art National Coordination Center (NCC) in Merritt Island, Florida. The NCC is to Blackson Arrow what Mission Control is to NASA. We like to say that each morning we start out with a Rubik’s Cube, and we spend the day lining up everything – maintenance, equipment, weather, technical difficulties, monitoring, and much more to keep
these systems running and our customers happy. The strength of our approach comes from a relentless focus on performance management and coordination of work activities. Using our advanced maintenance management system and relying on our years of expert facilities O&M experience, the NCC integrates and manages hundreds of vendors and technicians by providing the strategic and tactical decision-making that keeps these systems running. Here, our customer service team of dispatchers are directly responsible for the oversight and movement of our technicians and service providers.
Contact us today to learn more about how Blackson Arrow can help you reduce your carbon footprint and achieve your sustainability goals.
BLACKSON ARROW IS A LEADING PROVIDER OF SUSTAINABLE AVIATION FUEL (SAF) LOGISTICS SOLUTIONS.Investing in technology: Blackson Arrow invested in technology to improve their efficiency and productivity. This allows us to reduce costs and improve the quality of our services
As a result of these efforts, Blackson Arrow has remained a successful company in a challenging industry. We have positioned our company for continued growth in the years to come.
Here are some specific examples of how Blackson Arrow overcame challenges:
• In 2009, the economic downturn led to a decrease in government spending. Blackson Arrow responded by reducing costs and focusing on providing high-quality services. As a result, we were able to win new contracts and maintain profitability.
• In 2022, Blackson Arrow made a bold move to become the leader in sustainable aviation fuel (SAF) logistics solutions and now installs and maintains over 20,000 used cooking oil (UCO) storage systems in restaurants across the US.
What are your major future ambitions going forward and how will these goals be achieved?
Our future is all about supporting sustainable power solutions and the infrastructure associated with these upcoming changes. We are now providing support and advisory services related to SAF, electric
and battery-powered systems, and hydrogen-powered systems as the aerospace industry moves toward an ambitious goal of de-carbonizing by the year 2050. For example, in the SAF arena, both SAF blended fuels and neat SAF can use the existing bulk storage and transfer systems in place today. However, to meet the coming demand, it is likely that production facilities will have to be installed on, or close to airports and seaports that are much closer to the end user of the commodity. These are new and different systems at these locations that must be operated and maintained to support the end users. Additionally, to be truly sustainable, these systems must be powered by sustainable power, which in turn means new and different power production will also be needed in these locations. Further, the move to more battery or fuelcell-powered ground equipment and aircraft will require new and different infrastructure than what exists today. Ultimately, entirely new heavy-power systems, such as hydrogen-powered airliners and large cargo planes will replace the large fleets of fossil fuel-powered vehicles of today. This will result in extensive infrastructure evolutions in places like airports.
What does the next 12 months look like for the business?
Blackson Arrow is very excited about the next 12 months. We
believe there will be a strong continued need for specialized facilities management, ground handling, logistics support, and bulk fuels management.
Here are some of the trends that are expected to drive growth in this industry in the coming year:
• Explosive growth in aviation: Commercial aviation alone will see a near doubling of passenger and cargo numbers by 2036. What is certain is that innovations in sustainable fuel, technology, and approaches will be needed to sustain this growth.
• Expansion of drone operations and urban air mobility.
• Increased demand for training and education: As the aviation industry evolves, there is a growing demand for training and education. Businesses, like Blackson Arrow that can provide training and education solutions to the aviation industry will be well-positioned for growth.
Because innovation is in our blood, Blackson Arrow is wellpositioned to capitalize on the emerging environmental trends as well as the explosive growth that will drive our industry into the future.
Around three billion gallons of used cooking oil per year is generated by restaurants, hotels, stadiums, and other venues across the US, enough to fill more than 4,500 Olympic swimming pools.
In fact, eight percent of GHG emissions are emitted by restaurant food waste, such as used cooking oil, of which large amounts are generated by the foodservice industry.
A lot of this used cooking oil currently goes to waste; however, the company’s national footprint plays an important role in attracting business from such venues to help solve their disposal problems.
Indeed, complementing Mahoney’s headquarters in Joliet, Illinois is an expansive network of processing facilities across the country, which can recycle close to 100 percent of the materials processed.
“At our Mendota facility, for example, we use basically every ounce of material we pick up, from the water
being used as fertilizer in the adjacent corn fields to the methane from the anaerobic digester fueling our facility,” shares Kimball.
With this coast-to-coast service network, the company can collect, handle, transport, and process used cooking oil, maximizing value through its transparent service programs and recycling process.
The company is building an additional two plants in Orlando and Kansas City, respectively, which will be state of the art and allow Mahoney to improve its operational efficiency.
“Several new expansion projects are on the horizon, as well as more sustainability projects. We are focused on growing the business, so we can continue to spread the word on sustainability.
“These projects allow us to do our part in making the world a better place for our children. We feel that it is our responsibility to help take care of the planet,” Kimball adds.
Mahoney’s commitment to quality begins with the collection of high-quality, used cooking oil from restaurants by highly trained specialists, using proprietary equipment designed to safely and cleanly transport the oil.
Incoming material is screened to remove contaminants before the oil is heated to remove fine particles. Mahoney then transfers the oil to its heated settling tanks, where the water and emulsion are separated from the fryer oil.
The emulsion goes through an evaporator to remove the remaining water, which goes through Mahoney’s wastewater treatment operation. Using anaerobic respiration to convert organic compounds into carbon dioxide and methane, the water is then used for organic farmland fertilizer at the Mendota location.
Oils, and any remaining solids from the emulsion, go to a centrifuge where the oils are separated out.
Since 1953, Mahoney has helped foodservice companies recycle used cooking oil and other waste forms and turn them into useful products, such as renewable diesel and sustainable aviation fuel.
Licensed by the Environmental Protection Agency (EPA), the company has thus been at the forefront of collecting and recycling used cooking oil for 70 years. This extensive experience is particularly timely, as today, government regulations surrounding the disposal of restaurant waste have never been more stringent.
Mahoney manages the entire recycling process from equipment set-up to collection and processing, right up to the finished product. The added value that the company captures from used cooking oils is then passed on to restaurants and other foodservice operators, positively impacting their bottom lines.
Mahoney’s cooking oil services don’t stop there, however, as the company also offers foodservice entities indoor and outdoor grease trap maintenance, automated equipment for collecting used cooking oil, and in select markets, fresh oil.
This unique, integrated business model enables the company to provide an unparalleled customer value proposition.
All aspects of Mahoney’s differentiated service model are supported by Neste, the world’s leading producer of sustainable aviation fuel and renewable diesel produced from waste and residue raw materials, who fully acquired the company in 2020.
By acquiring Mahoney, Neste has gained substantial access to used cooking oil, and is now working with a growing business that knows how to safely collect and pretreat it.
For Mahoney, it means joining a larger company that’s focused on creating a positive environmental impact and presents an exciting opportunity to find more ways to help the environment by turning more used cooking oil into sustainable fuels.
“I quickly learned that recycling waste cooking oil was very important in reducing emissions and that through Neste’s technology, it could become renewable diesel, sustainable aviation fuel, or even polymers,” says Kimball.
Mahoney provides the most durable, easiest-to-use, and most reliable oil waste management and recycling equipment in the foodservice industry to help with the disposal of cooking oil.
It starts with a careful assessment of the client’s kitchen operations, to design a system of cooking oil equipment that best suits their needs.
The company’s equipment can even
The fleet that Mahoney utilizes exemplifies its commitment to the environment and the removal of used cooking oil from the waste stream.
Supporting sustainability at every turn, the company’s fleet of trucks not only ensures reliable service to customers, but also supports its goal of environmental responsibility.
Mahoney strives to support the recycling efforts of its customers by operating trucks that lower its carbon footprint and have the capacity to service a greater number of customers in a shorter timeframe, built to hold more product and improve route efficiency.
be retrofitted into kitchens to help streamline used cooking oil usage and disposal.
A plethora of cooking oil equipment is offered by Mahoney, including automated systems, which are the safest, easiest, and cleanest way to manage used cooking oil.
These automated systems automate the handling of used cooking oils, so employees do not have to handle the oil manually and are a key differentiating factor between the company and its competitors.
Mahoney offers three types of automated systems, including direct connection recycling, which connects directly to the fryers.
Hot, used cooking oil is pumped from the fryer directly into their equipment, which is positioned either inside the restaurant or outside in its own storage compartment. A portable filter machine can also be used if the fryers do not have built-in
filtration capabilities.
Restaurants across the nation are legally required to recycle their cooking oil, and automated oil management systems are one of the safest ways to do so, as it eliminates the need to transfer hot oil waste to and from storage areas and then to the fryers.
“Direct connection recycling allows employees to flip a switch and dump their used cooking oil, which makes it safer for staff and eliminates slips, trips, and spills,” explains Kimball.
“Safety is one of our core values, and we feel that with our innovative automated equipment, we are able to provide a clean and hassle-free process for foodservice employees to dispose of their used cooking oil.”
Automated indoor systems are also designed and installed by Mahoney in restaurants that have enough interior floor space.
With this system, the holding tanks are installed indoors with pipelines
that run directly into the fryers.
Heated outdoor bulk containers, meanwhile, are outdoor installations that are insulated and heated to handle used cooking oil and leftover solids.
The used cooking oil is then taken to the container from the fryers using an oil shuttle or caddy. These containers filter debris from the cooking oil, whilst select indoor and outdoor containers can be installed with a remote reporting level sensor to monitor the oil levels.
In addition to automated equipment, Mahoney can help to design custom cooking oil systems based on the kitchen layout, the operation of the kitchen, and the volume of frying, with all used cooking oil handled in a clean and safe manner.
The company is therefore able to provide the piece of equipment that is most appropriate to each kitchen for
different types of customers.
“Depending on the size of the location, tank placement, and additional features to consider, we can accommodate them to create equipment that meets our customers’ needs,” says Kimball.
Almost all the cooking oil collected and recycled by Mahoney via its equipment is distributed as feedstock for sustainable aviation fuel and renewable diesel production, the former of which reduces GHG emissions by 86 percent compared to petroleum diesel.
Mahoney provides transparent reporting on the amount of used cooking oil it collects from each customer, and how much of it is transformed into renewable fuels.
“We provide this data in our Fryer Oil History Reports. This way, customers have full insight into their used cooking oil collection and recycling information,” Kimball tells us.
Focused on reaching more restaurants and providing the best customer service in the industry, the coming year is set to bring many opportunities and challenges for the company and its 500 employees across the US.
“Our employees are the backbone of our company, and together, we are focused on creating a healthier and safer planet for future generations,” concludes Kimball.
“They work hard every day, knowing they are making a positive impact on our environment, helping our restaurant partners be focused on their customers, and contributing to reducing their carbon footprint.”
We are a Commercial Plumbing, Process Piping, Heating, and Cooling contractor. We work in the Southwest portion of Washington State. We perform New construction, Remodels, Service/Maintenance and/or Replacement of Plumbing, Heating, Cooling and process Systems and equipment (Boilers, Pumps, Heat Exchangers, Air Handlers, Coils, Tanks, AC equipment, Cooling Towers, Chemical Treatment systems) Office: 253-284-0306