RESTAURANT COMPANY EUROPE


With more than 75 restaurant and café locations, we pull up a table at the largest catering group in the Netherlands Peter
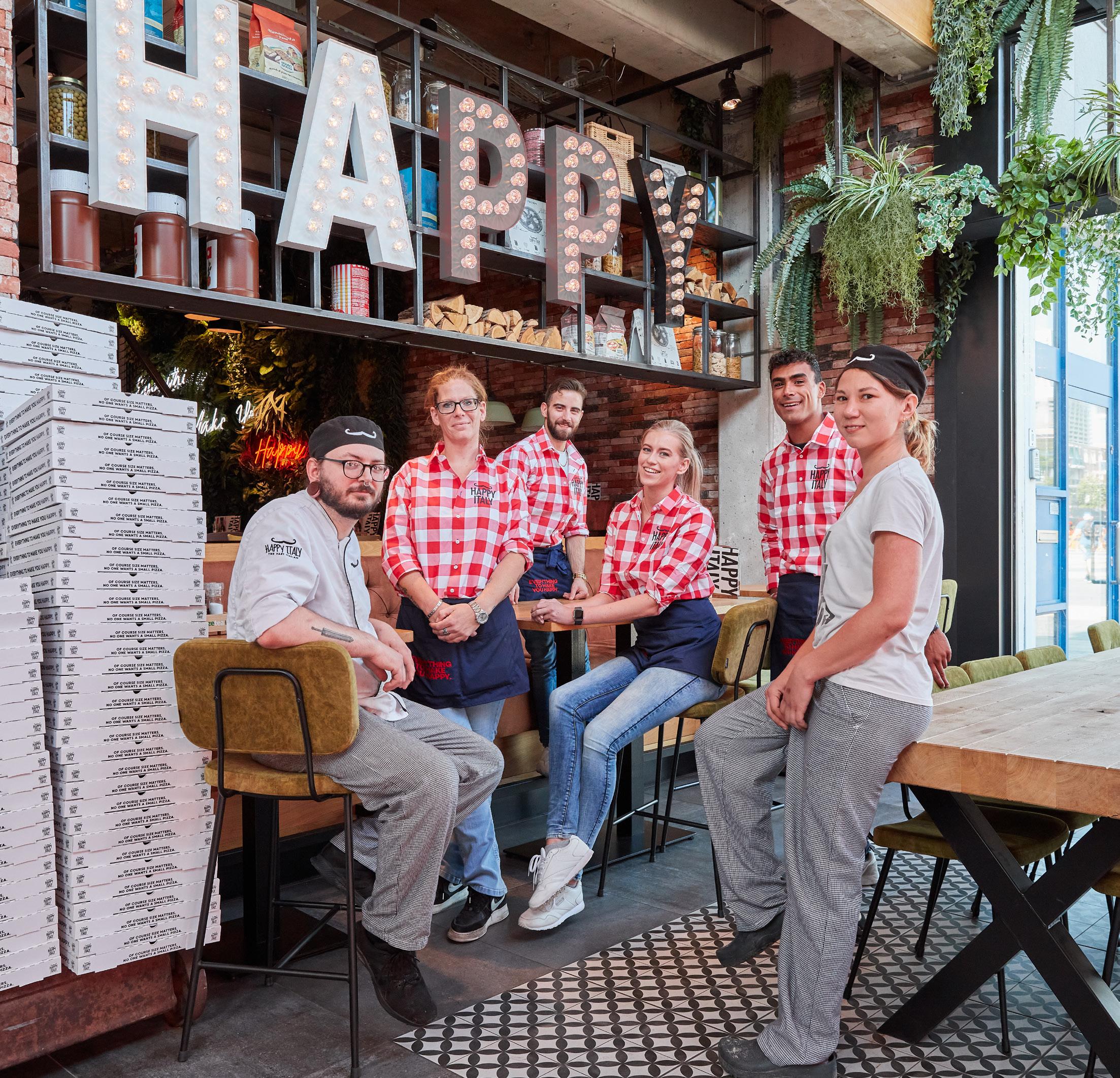
With more than 75 restaurant and café locations, we pull up a table at the largest catering group in the Netherlands Peter
For over a decade, our portfolio of in-house magazines has been lovingly produced, printed, and distributed to our esteemed subscribers across the globe from our headquarters in the UK.
But now we are moving with the times, adopting a digital-first approach by producing online-only publications. A major factor in this decision is to minimise our environmental footprint, reducing the carbon emissions involved in the logistics of print magazine distribution and the resources required therein.
Going forward, we will provide print orders of any magazine in-line with the requests of our featured companies, subscribers, and conference & expo partners.
Please get in touch for a print-on-demand quote or visit our website to find out more.
“We always planned that when our digital subscribers consistently accounted for 85% of our total magazine subscribers, we would cease printing our publications in-line with our environmental and sustainability goals.”
– Ben Weaver, CEO, Outlook Publishing Ltd
EDITORIAL
Head of Editorial: Marcus Kääpä marcus.kaapa@outlookpublishing.com
Senior Editor: Jack Salter jack.salter@outlookpublishing.com
Editor: Phoebe Harper phoebe.harper@outlookpublishing.com
Editor: Lucy Pilgrim lucy.pilgrim@outlookpublishing.com
Editor: Ed Budds ed.budds@outlookpublishing.com
Junior Editor: Rachel Carr rachel.carr@outlookpublishing.com
PRODUCTION
Production Director: Stephen Giles steve.giles@outlookpublishing.com
Senior Designer: Devon Collins devon.collins@outlookpublishing.com
Junior Designer: Louisa Martin louisa.martin@outlookpublishing.com
Production Assistant: Megan Cooke megan.cooke@outlookpublishing.com
Digital Marketing Manager: Fox Tucker fox.tucker@outlookpublishing.com
Social Media Executive: Bria Clarke bria.clarke@outlookpublishing.com
Web Editor: Oliver Shrouder oliver.shrouder@outlookpublishing.com
BUSINESS
Chief Executive Officer: Ben Weaver ben.weaver@outlookpublishing.com
Managing Director: James Mitchell james.mitchell@outlookpublishing.com
Sales Director: Nick Norris nick.norris@outlookpublishing.com
Commercial Director: Joshua Mann joshua.mann@outlookpublishing.com
HEADS OF PROJECTS
Josh Hyland josh.hyland@outlookpublishing.com
Deane Anderton deane.anderton@outlookpublishing.com
Eddie Clinton eddie.clinton@outlookpublishing.com
Ryan Gray ryan.gray@outlookpublishing.com
BUSINESS DEVELOPMENT DIRECTOR
Thomas Arnold thomas.arnold@outlookpublishing.com
TRAINING & DEVELOPMENT DIRECTOR
Marvin Iseghehi marvin.iseghehi@outlookpublishing.com
SALES & PARTNERSHIPS MANAGER
Donovan Smith donovan.smith@outlookpublishing.com
PROJECT MANAGERS
Alfie Wilson alfie.wilson@outlookpublishing.com
Cameron Lawrence cameron.lawrence@outlookpublishing.com
Dave West dave.west@outlookpublishing.com
Dennis Morales dennis.morales@outlookpublishing.com
Jordan Levey jordan.levey@outlookpublishing.com
Kierron Rose kierron.rose@outlookpublishing.com
Kyle Livingstone kyle.livingstone@outlookpublishing.com
Michaela Ferguson michaela.ferguson@outlookpublishing.com
Nicholas Kernan nicholas.kernan@outlookpublishing.com
Liam Pye liam.pye@outlookpublishing.com
ADMINISTRATION
Finance Director: Suzanne Welsh suzanne.welsh@outlookpublishing.com
Finance Assistant: Suzie Kittle suzie.kittle@outlookpublishing.com
Finance Assistant: Victoria McAllister victoria.mcallister@outlookpublishing.com
EME OUTLOOK
Norvic House, 29-33 Chapelfield Road
Norwich, NR2 1RP, United Kingdom
Sales: +45 (0) 1603 363 631
Editorial: +45 (0) 1603 363 655
SUBSCRIPTIONS Tel: +45 (0) 1603 363 655 jack.salter@outlookpublishing.com www.emeoutlookmag.com
Like us on Facebook: facebook.com/emeoutlook
Follow us on Twitter: @eme_outlook
Presenting
We kick off this month’s edition with a focus on sustenance and sustainability, from the UK-based business accelerating the energy transition via solar adoption, to the current transformation within the alternative proteins industry, bringing healthier and tastier ingredients to the market.
It is the food and beverage space that takes the spotlight with our cover feature, Restaurant Company Europe, the largest catering group in the Netherlands making digitalisation a core aspect of the business, adapting to the latest trends, and bettering the customer journey.
“It’s a privilege to be able to contribute to these experiences and great to see that guests realise, after having to deal with restrictions during the COVID-19 pandemic, that they can go out once again,” shares Sandra van Halderen, CEO of the company. “Our guests’ journey starts way in advance on our digital channels and continues via social media long after.”
Elsewhere, North Macedonian refractory manufacturer Makstil is working with European partners to transform the industry with its sustainabilitycentric mission, driving steel towards a cleaner and greener future.
“Makstil finds it extremely exciting to showcase itself as a true example of having transited towards cleaner production processes,” says Marija Dukovska-Pavlovska, General Manager. “As steel is an industry that has historically been associated with large amounts of emissions, I am very happy to say that is now in the past.”
Before you go, don’t forget to check out the latest news and industry developments with electric motor manufacturer Domel, marine interior producer MAKINEN, telecommunications service provider Farice, and many others.
We hope you enjoy your read.
Marcus Kääpä Head of Editorial, Outlook PublishingTell us your story and we’ll tell the world FOOD & BEVERAGE
38 Restaurant Company Europe
Served with a Side of Excellence
Championing creating catering concepts
56 Tim Hortons Middle East
Delivering Deliciousness to the Middle East
Always fresh, always delicious
64 Pasta Evangelists
Premium Pasta Experience A taste of Italy delivered to your door
70 Transavia
Building Farms Chick by Chick Inside Romania’s progressive poultry farms
74 Domino’s Oman Dominating the Pizza Sphere A dive into the largest pizza chain in the world
142 Schüco Middle East
Building Like There’s a Tomorrow
Innovative façade systems across the Middle East
148 Euro Mechanical
The Mechanics of Success
Facilitating development for the UAE
146
154 Emirates Beton Ready Mix
Leading the concrete sector Supplying Infrastructure Solutions
160 Synergy Construct
Pioneering Projects in the Built Environment
Shaping a new landscape
TECHNOLOGY
166 Farice
The Key to Connecting Europe
Transporting data between Iceland and the rest of the continent
174 Three
The Magic Mobile Number
Better connectivity across the UK
SUPPLY CHAIN
182 UPS Supply Chain Solutions®
The Surprise Package
Helping businesses control their supply chains
204 Belinus
The New Aesthetic of Energy Efficiency Meeting domestic solar demand with Belinus
WITH A BID to bring joy and optimism to the roads, the automobile manufacturer Fiat will no longer produce grey cars. The UK’s most popular vehicle colour does not fit the Italian brand’s way of living – la dolce vita!
The move to brighten Fiat’s image with bold colours such as Sicilia orange, rose gold, and Venezia blue, aims to inspire drivers by reminding them of beautiful Italian landscapes.
However, Fiat’s decision to terminate grey to make motorists jollier could impact UK sales for the car manufacturer. The new 600e model, an electric vehicle (EV), will be launched without the grey option.
GERMAN COMPANY BAYER AG has seen sales of its controversial weedkiller fall. Roundup was launched five decades ago and quickly became the world’s bestselling herbicide. Nonetheless, Bayer AG is now expected to take a net loss of €2 billion in Q2 due to the decrease in demand for glyphosate products. Some countries have banned herbicides containing glyphosate as the ingredient has been linked to various cancers. A spokesperson
for Bayer AG maintains Roundup’s safety while attributing the COVID-19 pandemic to the loss of profit. Furthermore, although the science is inconclusive, in 2020, Bayer AG settled many cancer-related lawsuits.
DELIVERY HERO, ONE of Europe’s biggest food delivery companies, is taking ownership of its Saudi Arabian subsidiary. The deal is valued at USD$297 million after the company bought the remaining 37 percent stake in HungerStation, which operates as Delivery Hero in Saudi Arabia.
Headquartered in Berlin, Delivery Hero will expand its presence in the Middle Eastern food delivery market after it was forced to quit the competitive sector in Germany when it lost out to Netherlands-based Just Eat. HungerStation connects more than 10,000 partners with customers, including restaurants and grocery stores, which will help build the company’s portfolio.
Around Europe and the Middle East in seven stories…
THE HEAD OF Russia’s space agency, Roscosmos, has extended the offer to participate in constructing a joint module for its planned orbital space station to Moscow’s partners in the BRICS group – Brazil, India, China and South Africa.
The Russian Orbital System (ROS) is expected to be launched in 2027 following Moscow’s decision to end its decades-long partnership with NASA and withdraw
DUBAI MADE HISTORY in 2023 by generating close to USD$850 million from the luxury property market in the first six months of the year. Residential units costing upwards of USD$10 million each saw the United Arab Emirates (UAE) city overtake London, New York and
from the ageing International Space Station (ISS). A further four modules will be dispatched into orbit between 2028 and 2030. It is hoped that the new ROS will help
necessary for future space flights to
BT IS SET to scrap up to 55,000 jobs by the end of the decade. The telecommunications giant wants to cut costs, mainly in the UK, and will replace staff with artificial intelligence (AI). Up to a fifth of the losses will be in customer services as BT has reported a 12 percent drop in profits to £1.7 billion for the financial year.
Generative AI such as ChatGPT will be used to make services faster, better and more seamless. However, whilst the advanced technologies could drive new jobs, the government’s AI task force has said it will be a challenge to protect existing British employment opportunities.
Paris for the first time. The surge in demand has led to property sales across Dubai experiencing a 17 percent growth.
Headline-making deals included the USD$111.6 million penthouse in the Bulgari Lighthouse residence on Jumeirah Bay Island. Independent real estate agency Allsopp & Allsopp has said that overseas investors are responsible for the property market’s record performance levels.
LEADING GLOBAL INVESTMENT bank and wealth management company Morgan Stanley has downgraded Israel’s sovereign credit to a “dislike stance”. This follows judiciary changes that will drastically limit the powers of the country’s Supreme Court as parliament passed the first in a series of laws sought by Prime Minister, Benjamen Netanyahu.
The recent developments have weakened the Israeli shekel, causing the currency to fall to a three-year low. In addition, the country’s stock market has lost nearly 10 percent since November, and borrowing rates have risen, with inflation remaining significantly above the Bank of Israel’s tolerance band.
Steve Haskew, Head of Sustainability and Social Leadership at Circular Computing, explains why addressing greenwashing and greenhushing needs to be a top priority for every CEO
Writer: Steve Haskew, Head of Sustainability and Social Leadership, Circular ComputingIn an age of increased environmental and sustainability pressures, businesses of all sizes are facing pressure to illustrate their green credentials. Some choose to be overt, advertising sustainability and net zero claims front and centre in their communications, while others are choosing to say nothing at all and sit back hoping it doesn’t get brought up. Yet, neither approach is likely to be the best course of action for most businesses and has led to increased policy and economic issues with greenwashing and greenhushing.
The two terms, perhaps seen as sustainability buzzwords of our era, do in fact roughly summarise where many CEOs sit on sustainability - either letting marketing teams run wild with sustainability claims, or trying to hide a dodgy underbelly from the outside world. The reality is that the wellintentioned claims of sustainability and faux efforts to become more
sustainable seen in greenwashing often fall short of the mark, and can even be equally as dangerous as doing nothing at all.
Simply put, our planet is now at a point where the term ‘green’ cannot be ‘washed’ or ‘hushed’ anymore; it needs to be rooted at the centre of all business decisions and operations. To make a real difference, prioritising the growth of the circular economy will help businesses understand how to achieve true sustainability and move beyond the smoke and mirrors tactics we see used by many today.
With eco-conscious consumers anxious to support businesses that are protecting the planet, many have turned to illusion to win over their customers. Greenwashing happens when a company makes an environmental claim unsupported
by data-driven evidence. Though the claim may have some element of truth regarding the positive effect on the environment, it likely fails to consider the true impact on the planet, and with potentially increased sales, may even do more damage than another more unsustainable product. A 2021 European Commission report found that 42 percent of green claims made by organisations were deceptive or exaggerated in some way, highlighting that this is becoming a commonplace tactic amongst many businesses. Even more recently, a report found that half of green claims used to sell products in the EU were misleading, according to the European Commission. This means oblivious consumers basing their purchase decisions on something they are told is environmentally friendly, may actually be damaging the planet more than they realise.
But as we see a crackdown on companies overly exaggerating their sustainability claims, seen in new EU anti-greenwashing legislation, there is another seriously concerning strategy in greenhushing. With businesses under fire over the credentials of
their sustainability claims, many have chosen to try and fly under the radar. Companies from industries such as tech, finance, and the engineering sectors are often choosing not to provide updates on their environmental and climate action. A report published by South Pole found that nearly one in four of the 1,200 large private companies from 12 countries that have set net zero targets are yet to publicise their progress. Given the government targets in the UK such as reaching net zero greenhouse gas emissions in England and Wales by 2050, which could add two million years of life on Earth, far too many businesses are taking the easy route out on sustainability.
For many business leaders preoccupied with the day-today running of their business, sustainability is likely something they feel is better suited to another member of the board. And while the rise of the Chief Sustainability Officer is a positive one, the need for the CEO to take on the responsibility of greening their business is more important than ever. Often, sustainability is left to the marketing team to communicate, which in order to come across better, can lead to exaggeration. The International Consumer Protection Enforcement Network analysed hundreds of websites for green claims versus the action being taken, and found that as many as 40 percent of environmentally friendly claims might be misleading customers. As a result, by leaving sustainability to other departments, CEOs are letting their brands create a false reality that they are sustainable without addressing it operationally. There are areas where the CEO can
get involved in sustainable decisions today. Reviewing procurement strategies and ensuring to work with truly sustainable suppliers is a quick win that many CEOs can start actioning right away. We see in the technology industry that CEOs are often unaware of the hardware their employees use and are unlikely to be involved in the purchasing process. Yet, when the industry has evolved to the point that second-life remanufactured laptops are certified to perform as good as or better than new, with a financial saving and at no extra cost to the environment, it seems remiss of them to not be involved in making those decisions. The rise in greenwashing and greenhushing could mean solutions like remanufacturing aren’t used or explored to their full potential. The circular economy has direct benefits to a business’ bottom line, to its genuine sustainability credentials, and to consumers and employees. Without embracing it, CEOs are at risk of adding to a false eco-reality, delaying progress and solutions to the problems at hand.
Leading sustainability from the top is key, never more so than when communicating it to the outside world. If the CEO can’t be trusted to discuss their business’ claims or actions, then why should anyone listen to the sales teams? With 65 percent of UK consumers thinking about the environmental impact of the items they buy and oneof UK workers reporting they would turn down jobs based on poor ESG commitments, making sure people understand your sustainability strategy is essential. For many business leaders, being honest and transparent about their sustainability progress is daunting, but there are ways to ensure you’re walking the
walk as well as talking the talk. Using science-based targets, such as those set out by the Science Based Targets Initiative (SBTI), will ensure robust evidence to help you avoid misleading customers and unknowingly harming the planet. As mentioned earlier, ensuring your suppliers follow these targets too is an easy way of staying across the environmental impact of your business. For example, we’ve made sure to calculate with the SBTI that for every Circular Computing remanufactured laptop, approximately 316 kilogrammes (700lb) of CO2 emissions are prevented by not buying new. For just 1,000 laptops, that is the same as taking 80 cars off the road for a year. Achieving true sustainability means business leaders leading by example, and ensuring the CEO is involved in addressing greenwashing and greenhushing will go a long way to eradicating bad practice from within the business.
As the Head of Sustainability and Social Leadership, Steve Haskew leads on defining, developing, and implementing the CSR strategy for Circular Computing. His vision is a key driver of growth across the business and ultimately looks at achieving a reduction in carbon footprint.
Whilst being at the helm of Circular Computing’s sustainability strategy, Haskew has been the driving force behind the company’s industry-first milestone, which saw the business receive the renowned BSI Kitemark certification. He is also leading on helping Circular Computing achieve other sustainability targets, including funding the planting of one million trees by March 2023 and reaching net zero carbon footprint by 2030.
MycoTechnology Inc. (MycoTechnology) is positioned at the pinnacle of the food and beverage industry, utilising the natural mushroom kingdom to create healthier food ingredients that taste delicious.
This objective has been at the core of the business from its inception in 2013, when two of the four co-founders, Alan Hahn and Pete Lumbar, each with a business background, met Brooks Kelly and Jim Langan, two scientists who were exploring the world of mushrooms from their basement, as their walls were decked with growing mushroom mycelia, the root system of fungi.
This sparked a passion project for Hahn, as his diagnosis of diabetes made him consider what foods were truly healthy and delicious, which quickly became a founding mission of the company.
“Hahn felt that if anything tasted
Writer: Lucy Pilgrimgood, then he couldn’t eat it. And it is due to the rejection of this principle that he believed there must be a way to make food that tastes good and is good for your health,” introduces Lisa Wetstone, Vice President of Marketing, Innovation and Growth Strategy at MycoTechnology.
From there, Hahn and this fellow co-founders went on to discover how a particular strain of mushroom mycelia produces an amazing mix of enzymes and molecules that can block bitterness. They quickly discovered that they could add just tiny amounts of this ingredient to dramatically change the flavour of foods and beverages for the better.
Today, based in Colorado, the company totals nearly 100 staff members. The beautiful facility features state of the art 90,000 litre fermentation tanks which grow the mycelia and provide ingredients for the Americas, Europe and Asia.
As Vice President of Marketing, Innovation and Growth Strategy at MycoTechnology Inc., Lisa Wetstone discusses the founding principles of the company and the transformation of attitudes around the alternative protein industry
The first discovery of MycoTechnology was a myceliaderived bitter blocker ingredient. Now referred to as ClearIQ™, the ingredient is used in very small quantities to improve the flavour profile of a wide range of products, enhancing positive flavours while
MycoTechnology’s FERMENTIQ™ product line uses the unique process of mycelial fermentation to unlock enhanced taste, texture, and nutrition of plant proteins. The company combines pea protein, or a complete blend of pea and rice proteins, with mushroom mycelia in its large-scale fermentation tanks to create market-leading plant-
Although the plant-based meat sector is a key part of the latest innovations in food ingredients, MycoTechnology sets itself apart from this particular space.
“We really don’t think of ourselves as a company focused on plant-based meat, and that’s just because we’re thinking about how to make food that’s healthier and tastes better across the board,” Wetstone explains.
“For us, it’s all about how you can change behaviour and how we can provide consumers with more and better options that are good for health, and something that they actually want to buy and eat, whilst supporting a sustainable system,” she adds.
Therefore, MycoTechnology is simply harnessing the power of the natural kingdom of fungi that has been seriously underutilised in the modern food system. Its team seeks to make the most of the amazing capabilities of natural mycelial fermentation, as a previously overlooked field.
Within the wider context of biotechnology (BioTech), Wetstone alludes that MycoTechnology’s platform and capabilities may expand into precision fermentation, the latest major technological innovation in our food system.
“When you talk about BioTech and the food sector, the question is usually, how do I make this economical on a large scale? With that consideration in mind, we believe that there is a huge potential for precision fermentation. Whether it’s creating small molecules and nutrients, functional ingredients, or even substitutes for animal-based products, each can be created in a more predictable and sustainable way,” she expresses.
The next wave of innovation in the plant-based movement comes in the form of altering people’s attitudes, subsequently changing behaviours and consumer habits, and significantly, giving people a reason to make those changes.
“Telling a story around health and nutrition really gives an opportunity for the industry to differentiate itself from the world of animal products.
“For decades, there has been a lot of attention around protein as a nutrient. But protein isn’t the whole story. To remedy this, do we rebrand the alternative protein movement as the holistic nutrition movement? Does it really need to be an alternative, or is it about just giving people options that work for their health and the
– LISA WETSTONE, VICE PRESIDENT OF MARKETING, INNOVATION AND GROWTH STRATEGY, MYCOTECHNOLOGY INC.planet?” questions Wetstone.
As such, MycoTechnology firmly believes that with education and time, consumers will begin to understand it is a very familiar and sustainable technology that is being engaged to create healthier food that tastes and functions a lot better.
Looking ahead, MycoTechnology is primarily focused on the global expansion of its mycelia fermentation enterprise. The company has recently acquired a strategic partnership with the Oman Investment Authority (OIA). Through this collaboration, the company is working to develop mycelia as a whole food ingredient for consumers, rather than simply using it as a tool.
Thus, alongside a greater expansion in Europe and across the globe, MycoTechnology is transforming the food and beverage industry one mushroom at a time!
(720) 897-9306
www.mycoiq.com/contact-us
www.mycoiq.com
“WE’RE WRAPPING STAINLESS STEEL AROUND NATURE, UTILISING THIS AMAZING NATURAL PHENOMENON, MUSHROOM MYCELIA, THAT IS RIGHT
BENEATH OUR FEET”
We speak to Daniel Kaminsky, President and Chairman of the Board at ELCOM Group, whose systems are helping to streamline manufacturing across Europe
Europe is renowned for its vast manufacturing industry, the complex gear behind the success of a host of sectors and businesses. Within manufacturing, it is imperative to stay up to date with the latest methods and practices to streamline operations, and this is where ELCOM Group (ELCOM) comes in.
ELCOM was founded as an electrical engineering (and later technology) company backed by knowledge and expertise in mathematics, physics, electrical engineering, and design. Since its establishment in 1990, it has delivered thousands of solutions and unique products in the fields of electrical power engineering, power electronics, and test and measurement (T&M) technology. Today, ELCOM has over 200 employees and also owns three subsidiaries.
“We supply our customers with solutions from the field of T&M technology. This is based on measuring instruments developed at ELCOM and constructed mechatronic systems, such as End of Line (EoL) testers,” introduces Daniel Kaminsky, President and Chairman of the Board.
“In these solutions and products, we apply our deep knowledge of areas such as digital signal processing, digital image processing, modern software architecture, and more. Another of our supply fields is that of devices based on power electronics, such as special power supplies used in railway infrastructure, or devices that improve the quality of electrical energy, like line conditioners for the power grid.”
ELCOM’s operations additionally envelop power quality measurement (PQM), and the company’s product portfolio currently includes a complete ecosystem for PQM in power distribution and transmission networks.
ELCOM has solutions for fixed installations in the substations of power operators and special solutions for railway substations, where a large number of outlets in heterogeneous combinations of 1f and 3f networks
need to be monitored.
“On top of this, we offer highly accurate portable Class A power quality analysers that can measure ranges of up to 500 kilohertz (kHz),” Kaminsky adds. “ELCOM’s NTS noise
and vibration measurement systems, and light measurement systems for automotive lights have become the de facto industry standard with our major customers worldwide.
“Our versatile EoL testers are used by the world’s Tier 2 automotive manufacturers. In our subsidiaries, we deal with the issue of precision cali brators and the supply of calibration stations for electricity meters, while also dealing with industrial automation and robotic applications, including 3D metal printing.”
ELCOM’S mission in T&M is to deliver turnkey solutions to its customers, helping them to become more competitive through the quality of its products.
“THERE ARE FEW FIELDS WHERE YOU CAN USE, COMBINE, AND INVENT SOLUTIONS FOR AS MANY APPLICATION AREAS AS IN T&M – NO ONE DAY IS EVER THE SAME!”
– DANIEL KAMINSKY, PRESIDENT AND CHAIRMAN OF THE BOARD, ELCOM GROUP
Based in the Czech Republic, ELCOM’s mission resonates with the country’s significant level of industrial production, a traditionally substantial contributor to its GDP. According to Kaminsky, the Czech Republic
has a great historical tie to technical fields as well as an impressive level of education relating to them. This is certainly one of the main reasons why the Czech Republic has such a high concentration of industrial production, which plays an important role in the automotive industry.
“The automotive industry in particular has an extremely short innovation cycle time, which naturally places great demands on the reliability and quality of its products,” he explains.
“This creates demands and opportunities for finding suitable testing solutions. For people who enjoy discovering and constructing new solutions, this is an ideal environment where they can fully realise their potential.”
ELCOM has a diversified portfolio of customers and key accounts, and one
Modern technology is a key element for ELCOM’s competitiveness. It is because of this that the company is implementing neural networkbased artificial intelligence (AI) elements in its noise and vibration measurement and evaluation systems.
such business segment is that of EoL testers for parameters and the quality control of production in discrete manufacturing. Noise and vibration measurement systems are sourced by global manufacturers of heating, ventilation and air conditioning (HVAC) systems in the automotive sector.
The company’s development of special software applications for the control of measuring instruments over digital buses and the associated software applications form another source of revenue. ELCOM’s major customers include ABB, Automotive Lighting, AŽD, BCS, ČEPS, ČEZ, E.ON, KOITO, Marelli, Rohde&Schwarz, RWE, SIEMENS, Varroc, VALEO, as well as many others in Europe, the US and Asia.
Modern technology is a key element for ELCOM’s competitiveness. It is because of this that the company is implementing neural networkbased artificial intelligence (AI) elements in its noise and vibration measurement and evaluation systems. Similarly, ELCOM is working on using these applications in power quality monitoring and other systems used for metering in smart grids.
“In 2023, we have quite ambitious targets in many areas,” Kaminsky tells us. “Within R&D, we plan to complete new products in the area of
measuring and analysis instruments. We are launching the world’s first billing-ready meter using low-power instrument transformer (LPIT) sensors. We anticipate completing a new laser vibration sensor, a major innovation in our NTS platform for non-destructive diagnostics and analysis of products and components containing rotating or vibrating parts.”
On the commercial front, ELCOM is working on a significant expansion of its distribution channels, where the company is establishing new partners around the world, while
paying significant attention to the continuous improvement of its environmental, social and governance (ESG) activities.
“ELCOM is ready to offer its industry services to both our existing and new business partners, and contribute to joint efforts in bringing greater satisfaction to end customers,” Kaminsky concludes.
Since its inception in 1958, Guylian has grown to become a landmark establishment in the chocolate and confectionery sector, as its iconic seashells have become synonymous with delicious luxury and indulgence. To this day, the idyllic history of the company remains a key component of its identity.
“It all started back in 1958 when Guy, a chocolatier, and Lilianne, an architect, spent their holidays as a couple at the North Sea coast. They gathered seashells on the beach, which they then took with them to
As the titan chocolatier Guylian celebrates its 65th anniversary, CEO Tom Snick tells us how the company honours its history, whilst stepping forward into a new era of confectionery extravagance
Writer: Lucy Pilgrim
Tom Snick, CEO: “I have spent my entire life in the fast-moving consumer goods (FMCG) space, starting with Unilever in deodorants. Subsequently, following my interest in the food and beverage industry, I moved to Spadel, a leading company in mineral water and soft drinks in the Benelux region. From there, I transitioned to the Italian pasta firm Barilla, also family-owned with strong values, where I had several positions in Amsterdam, Paris, Cologne, and finally Barcelona, where I was made Managing Director.
“When Guylian called me in 2020, I was immediately intrigued, given that it is a strong and iconic brand that everybody across the globe knows from their childhood. When I started at Guylian, a big transformation and turnaround was needed, and since then, we have
Sint-Niklaas – where our headquarters was established, and where the story of Guylian first started,” opens Tom Snick, CEO of the company.
The chocolate entity is the brainchild of its founders and this is reflected in the brand’s identity, with its title as a marriage of their two names. From there, it developed the first seashells made from premium Belgian chocolate, with the infamous praline filling made from 100 percent in-house roasted hazelnuts.
Following its initial success, Guylian has grown to become an international chocolate staple, exporting its iconic
seashells all over the world, both in duty-free and commercial retail.
Nowadays, the cherished brand is sold in over 100 countries and more than 70 global airports, possessing an impressive global reach.
As Guylian embraces a customer driven and modern approach, it has evolved to incorporate a more digital marketing strategy.
“Of course, a strong in-store presence is crucial for impulse categories like chocolate,” Snick acknowledges.
“However, we are currently trying to rebuild the brand image through a 360° approach, touching all relevant media that fits the target group. Television is still crucial in reaching customers, but we also understand the increasing importance of social media, public relations (PR), and influencers.”
In a further step towards incorporating positive change, Guylian envisions an environmentally friendly future.
“We are keen on becoming a frontrunner on all aspects of sustainability, as we view it as our responsibility, whilst also aligning with the increasing demand of our customers,” he tells us.
Evidently, Guylian’s environmental
practices materialise in the support of all its cocoa farmers by guaranteeing that 100 percent of its chocolate has been Fair Trade certified, allowing farmers to have a fixed price per kilogramme.
Furthermore, to reduce its ecological footprint, the company is making strategic environmental moves to reduce its overall impact. For starters, palm oil and soy have been removed from all of its products, alongside the implementation of 100 percent recyclable packaging, as Guylian endeavours to become a fully plastic-free company and 100 percent carbon neutral.
This is further supported by smaller initiatives that include a fully electric car park and endorsing food banks in
different countries, which is part of its contribution to a better world.
Going forward, Guylian seeks to fortify its presence in its established countries, whilst simultaneously expanding its market to become the number one Belgian chocolate brand in both duty-free and relevant export markets.
+32 3 760 97 23
www.guylian.com
info@guylian.be
“IT ALL STARTED BACK IN 1958 WHEN GUY, A CHOCOLATIER, AND LILIANNE, AN ARCHITECT, SPENT THEIR HOLIDAYS AS A COUPLE AT THE NORTH SEA COAST”
– TOM SNICK, CEO, GUYLIAN
Dutch sustainable software company Solar Monkey is launching its innovative offerings across the UK, aiming to boost productivity for solar installers.
The company, which was the winner of Deloitte’s prestigious ‘Most Disruptive Innovator’ award in 2019, offers game-changing software that aims to speed up the previously lengthy and often tedious process of solar panel installations.
Solar Monkey has now landed in the UK to accelerate the energy transition after a €4 million fundraising effort and has begun launching its awardwinning software across the nation, with a mission to supercharge speed and delivery time in the solar sector, accelerating the energy transition to sustainable sources.
The bold new software that Solar Monkey has developed is based on
advanced algorithms, aerial photos and 3D models, helping installers to manage the volume of interest surrounding solar photovoltaics (PV).
At present, the UK is experiencing a vast surge in demand for solar PV, as reported recently by the clean energy company, Egg, in September 2022 who had analysed and observed enquiries for solar panels rise by 830 percent in just four months, as the technology becomes a more popular option for customers.
In a statement, Solar Monkey has declared that previously, designing and quoting for a new project could potentially take hours, with up to five separate quotes needed. Historically, this also involved an engineer doing much of the work. Solar Monkey’s process, however, takes minutes and can be carried out by a wider range of company personnel, delivering
Emerging as the brandnew phenomenon of the European energy landscape, Solar Monkey is providing innovative software for sustainable energy system providers
Writer: Ed Budds
Jan Pieter Versluijs, CEO and co-Founder, Solar Monkey
the potential for huge productivity increases for solar technology and its improved rollout.
Solar Monkey believes that by spending less time on operational processes, installers can double their output. The software that the company has developed is assured to be compatible with all major brands of panels, inverters and batteries.
By raising a considerable amount of growth capital in August 2022, Solar Monkey has been able to fund its continuing growth and accelerate its mounting impact.
“The market is ready for exponential growth – we’re helping installers make the most of it,” explains Jan Pieter Versluijs, CEO and co-Founder of Solar Monkey.
“We’ve seen tremendous growth in solar in the UK and we believe this trend will continue to accelerate as people are increasingly aware of the need to reduce CO2 emissions in response to climate change. Now, energy price rises driven by the Russo-Ukrainian War are hitting hard. The transition is well underway and increased efficiency plays a big part.”
As the next step in its evolution, the rapidly expanding firm has now appointed a UK Sales Manager and is currently involved in the meticulous process of recruiting more staff to underpin its international growth plan. In this way, the company is
stepping up the UK marketing of its digital design and quotation tools – aimed at increasing the efficiency of PV installers.
The independent, Netherlands-based business was exhibited for the first time on UK soil at the Solar and Storage live event at the NEC in Birmingham last October, generating a large trade and consumer response, as well as creating a considerable buzz within the industry.
Jasin Mahamud, who joins Solar Monkey as UK Sales Manager, brings extensive experience in software and technical sales.
“I am looking forward to helping installer clients across the UK, as I see huge market potential,” he states.
As direct evidence of this potential, installation professionals are continuing to witness unprecedented demand from customers as homes and businesses turn to rooftop electricity generation to save on fuel bills and reduce greenhouse gas (GHG) emissions, especially to try and make financially beneficial decisions during the ominous cost of living crisis. Many installers are struggling with backlogs due to this rising trend.
Solar Monkey has so far facilitated one million project designs and quotations and is being used in more than 250,000 PV systems across the Netherlands, Belgium, Spain and
Germany – saving time on designing and quoting wherever situated.
The state of the art software is fast and easy to use and integrate, even for those lacking a base level of technical knowledge. Additionally, Solar Monkey’s independence means its software is completely compatible with all the top brands of panels.
Solar Monkey offers installers clarity and security, backed by expert, real-time support. Using its services and software, installers can now accurately calculate and guarantee the clean energy production of their customers’ solar PV systems.
• Solar Monkey was founded in 2015, with the unwavering belief that smart software can accelerate solar energy adoption and that installer clients benefit from improved productivity and increased revenues.
• The firm’s R&D team has developed intuitive software enabling installers to generate a clear, accurate and appealing quote in under one minute. End users can easily review and understand the environmental and financial variables in their system.
• Solar Monkey is the number one PV installation software provider (500,000 designs a year) in the Netherlands – the leading European residential market.
CEO and co-Founder, Jan Pieter Versluijs, is among Renewable Energy World’s Solar 40 Under 40 Changemakers in the industry and has been named a Top 50 Young Talent by the Dutch business newspaper Financieel Dagblad.
Writer: Lucy Pilgrim | Project Manager: Deane Anderton
Since the first recorded form of modern biotechnology (BioTech) was conducted in 1973 with the genetic engineering of rare bacteria, the industry has catapulted to unprecedented levels. Indeed, BioTech has become paramount to modern healthcare and scientific R&D, as it permeates across many fields, including healthcare, scientific research, pharmaceuticals and tech companies.
In Europe, the BioTech industry continues to evolve through many breakthroughs, particularly in brain and neuronal therapies, which represent 50 percent of BioTech businesses in Europe.
Within Italy, there continues to be a resurgence in the aid provided by BioTech developments, as the industry works to positively serve the needs of Italian healthcare services and wider society. By the end of 2021, there was a total of 790 BioTech firms operating in the country, with R&D investment increasing by seven percent between 2019 and 2020.
The compiled impacts of the COVID-19 pandemic further highlighted a pressing need for medical research, which helped to provide the necessary tools to predict and prevent further occurrences. This is reflected by the fact that human healthcare is the largest sector active in the Italian BioTech industry, currently representing over 48 percent of the market segment.
Additionally, in line with greater climate change initiatives, Italy has witnessed an increase in industry and environmental BioTech, achieving a growth of 29 percent between 2014 and 2021, with similar growth projected in the R&D field.
With such an indispensable role, BioTech firms across the country are in need of a collaborative force and representation if the industry is to continue to flourish.
Italy’s biotechnology industry is one of the most innovative in the world, and has a major influence on the global bioeconomy. We shine a light on an evolving sector
Championing the voices of the Italian BioTech field, Assobiotec, the Italian Association for the Development of Biotechnology, part of Federchimica (Federchimica Assobiotec) facilitates a forum of discussion, leading the industry to a sustainable and safer society
Founded in 1986, Federchimica Assobiotec represents over 100 companies and science and technology parks, across the healthcare and bioeconomy sector. As a member of its Executive Committee and CEO of Geneta Science, Pierluigi Paracchi tells us how the association has developed since its founding.
EME Outlook (EO): Firstly, could you talk us through the origins of Federchimica Assobiotec and what led to its inception?
Pierluigi Paracchi, Executive Committee Member (PP): Federchimica Assobiotec is the Italian bioindustry association. Nowadays, it represents and supports not only BioTech firms, but also science and technology parks involved in the life science and bioeconomy fields.
The association brings together a variety of firms with a diverse range of applications; they all have BioTech in common as a hallmark component, which provides an engine for innovation.
Federchmica Assobiotec was first established in 1986 as part of Federchimica, the Italian Federation of the Chemical Industry. Since the beginning, its mission has been to encourage and support BioTech innovation with the ultimate goal of helping progress our country.
With the same aim, Federchimica Assobiotec is a founding member of the European Association for
Bioindustries (EuropaBio) and the International Council of Biotechnology Associations (ICBA) and, through Federchimica, the company is a founding member of the Italian National Cluster of Life Sciences (ALSISEI) and the Italian National Cluster of Circular Bioeconomy (SPRING).
As a proactive organisation, Federchimica Assobiotec is also an ongoing and active participant in the Blue Growth Cluster and Italian National AgriFood Cluster (CLAN) activities.
Image provided by UCB PharmaThe vast majority of cancer deaths are ultimately associated with metastases to the lungs and liver, which remain largely incurable — but, we believe, not for long.
BrYet has developed a therapeutic agent with unprecedented curative potential for metastases to the lung and liver. At BrYet, we believe that cancer can be treated with a new, physics-based approach, completely different from any other concept previously applied. We call it Transport Oncophysics.
The traditional view of tumours is that they are homogeneous masses of cells that proliferate uncontrollably and are resistant to pro-apoptotic stimuli. Now, we know that this view is overly simplistic. In fact, tumours are highly heterogeneous assemblies of cells that participate in constant interplay between themselves and a dynamic local microenvironment, continually changing and adapting in the process, with metastatic cancer cells being the most insidious and difficult to treat.
Current treatments often extend life expectancy by only a few months. Reduction in cancerinduced suffering is often adversely offset by the suffering caused directly by the treatments.
Throughout 30 years of research, we discovered that among the shared features of metastatic lesions are properties associated with mass transport modifications: cells, biomolecules, metabolites, nutrients, oxygen, and exogenous therapeutic agents “travel” differently through cancers and the whole body
than they do through normal tissues. These modifications take place in what are known as “biological barriers” of the body, from cancer initiation and throughout its evolution. Our research confirmed that the carcinogenesis-induced evolution of cancer-protecting biological barriers plays a dominant role in resistance. The drugs that initially work for a metastatic patient eventually start failing after some cycles of treatment, while also causing collateral damage that is disproportionate to the
therapeutic benefits, invariably leading to a tragic end. Our innovative therapeutic approach to cure metastases to the lungs and liver uniquely overcomes the issue of mass transport modifications.
We have developed “Transport Oncophysics”, the mathematical and biophysical framework for understanding cancer and how to attack it, even in the case of lung and liver lesions, enabling personalised treatment through transport biomarkers. Transport Oncophysics allows the development of unprecedented new families of cancer drugs, which surmount the cancerprotecting biological barriers of the body so that effective treatment can be delivered to cancer cells and open the way towards a potential cure for lung and liver malignancies.
Our first drug, ML-016, consists of a nanoporous silicon microparticle with a precisely defined size and shape, polymeric backbone, pH-sensitive cleavable linker, and the anthracycline chemotherapeutic agent doxorubicin. It has been proven to yield long-term, functional cures in treated animals that had devastating presentations of triple-negative breast cancer with metastases to the lung and liver. Even those that suffered relapse survived for much longer than those treated with conventional cancer therapies. ML-016 pharmacokinetic data confirmed
unprecedented selectivity for lung and liver metastases, with enhanced concentration in the target organs and drastic reduction of concentration in all other districts. No acute or followup toxicity was observed at any time after dosing up to a very high doxorubicin equivalent dose.
A Phase I clinical trial is planned for mid-2024, focused on patients with metastases to the lung and liver from different primary tumours. This includes triplenegative breast cancer, which has a low survival rate due to the lack of advanced therapies.
“Given the limited progress against metastatic cancer using traditional therapeutic strategies on primary tumours, a metastasis-focused specific and innovative therapeutic concept may represent the most effective way to cure patients,” says Lorenzo Pradella, CEO of BrYet Europe.
“If even a fraction of these results proves true for human patients, it will save many lives that otherwise would be lost. The main goal of my life is dedicated to finding a curative approach for metastatic cancer,” adds Mauro Ferrari, President and CEO of BrYet US.
A Global Presence
Metastases to the lung and liver are a major medical need with significant market potential. With a unique approach, BrYet aims to meet this challenge and provide unprecedented therapeutic benefits to patients — with a significant impact on healthcare
costs. BrYet’s proprietary technology platform can be further developed to obtain new treatments for many other diseases including vaccines.
BrYet US, Inc. operates in Houston, Texas, with a European hub in the Milan metropolitan area (BrYet Europe srl.). With a team of world-renowned experts in oncology, nanomedicine, biotechnology, semiconductor R&D and manufacturing, BrYet collaborates with top-notch institutions both in the US and Europe. We are currently scaling up ML-016 to GMP production in Italy.
Contact
BrYet Europe S.r.l. BrYetEurope.com
info@bryetpharma.com
Via Roma, n.108
Building CD1
20060 Cassina de’ Pecchi (Milan)
Italy
BrYet US, Inc. BrYetPharma.com
info.bryeteurope@bryetpharma.com
2710 Reed Road
Houston, Texas 77051 USA
#CureCancer
EO: Since inception, how has Federchimica Assobiotec developed and progressed in terms of its key objectives and the message it tries to get across?
PP: We strongly believe that Italy, through the BioTech sector, can have an instrumental impact on building a future in a sustainable way, whilst addressing the more urgent needs of civil society in the sectors of public health, environment, agriculture and food. We also believe that BioTech is a stimulus in the promotion of economic and social growth and employment opportunities.
Since our inception, we have understood the value of a vibrant and attractive ecosystem. From quality education to technology transfer, every step of the journey is fundamental to building a strong national ecosystem.
EO: What do you find most interesting about the BioTech industry in Italy currently?
PP: The Italian BioTech industry has lights and shadows. It is true that our country is recognised for its excellence in research, human capital and production. Italy is a world
leader in the number of research publications and citations per researcher. Our country shows a strong drive for innovation in areas such as biochemistry, genomics, and molecular biology.
In the meta-sector of BioTech, Italy boasts start-ups and companies that are at the height of modernisation in various fields of application, including health, through the production of new medicines, vaccines and diagnostic products, with excellent results in the export of these items. Regarding bioeconomy, BioTech is an important driver of innovation for both agricultural and industrial sectors, representing a new model to join economic growth and sustainability.
EO: On the other hand, what are the industry’s biggest challenges?
PP: Our country needs to have a clear vision for the future and must find a way to quickly untie all the knots along the journey, from the inception of an idea to its transformation into an innovative solution.
Elements that are closely connected, including training,
Lundbeck is a Danish multinational pharmaceutical company, specialising in treating diseases of the central nervous system.
The company’s main shareholder is Lundbeck Foundation, and for over 60 years it has invested in research to drive progress in neuroscience. Its funding includes the prestigious “Brain Prize” award which is worth approximately £1.3 million.
Over a century old, and headquartered in Copenhagen, Lundbeck has approximately 5,400 employees in over 50 countries.
Lundbeck has been present in Italy for almost 30 years with a commercial platform, with its presence strengthened by the production hub Lundbeck Pharmaceuticals Italy (LUPI).
R&D
Lundbeck’s R&D activity is entirely dedicated to the discovery and development of new drugs to identify and treat the mechanisms underlying brain pathologies, with sites in Denmark and the US.
Sustainability and Access to Care
Lundbeck is committed to countering the stigma towards people living with brain diseases, to contribute to the construction of a better environment where patients and caregivers are fully integrated in all aspects of life.
Currently, Lundbeck is dedicated to migraine prevention. In Italy, it is raising awareness with the ‘change your relationship with migraine’ campaign. #cambialatuarelazioneconlemicrania
“Today, more than ever before, it appears evident how the brain and its health play a fundamental role in our overall state of well-being. This is why we are committed from therapeutic and social perspectives to provide patients and their families real and concrete support in managing these diseases”
- Tiziana Mele, Managing Director - Lundbeck Italiaresearch, technology transfer, entrepreneurial skills, the creation and development of start-ups and small and medium-sized companies, production and clinical development, public-private partnerships, access, but also lean processes and reducing bureaucracy, must be able to interact in a dynamic way.
Our biggest challenge currently, however, is to create an industrial national plan for the development of our strategic sector. The news of a National Plan for Biotechnology in Italy is very recent. It was announced by Minister Adolfo Urso on 31st May this year, at our General Assembly. This is an important recognition of the strategic value of this meta-sector. We hope that it could be an opportunity to unleash the full potential of BioTech in Italy.
EO: How has the BioTech industry changed since the association’s inception?
PP: Over the last 30 years, we have seen the BioTech industry grow exponentially. The main economic data of the firms operating in this sector provide a clear picture of an industry which has withstood the crisis in all its fields of application, and not only in the traditionally countercyclical ones linked to the human health sector.
The vibrant ecosystem of small and micro BioTech firms, which complements the stable core of big companies and focuses on the development of new technologies and products, represents an 82 percent share of the total firms.
However, small and micro firms are pivotal in creating
“WE BELIEVE THAT BIOTECH REPRESENTS ONE OF THE GREATEST OPPORTUNITIES FOR THE DEVELOPMENT OF KNOWLEDGE, THE ECONOMY, AND WELL-BEING IN THE COMING DECADES”
- PIERLUIGI PARACCHI, EXECUTIVE COMMITTEE MEMBER OF FEDERCHIMICA ASSOBIOTEC AND CEO OF GENENTA SCIENCE
new jobs. Up to 65 percent of total gross job creation in 2020 can be attributed to the Innovative start-ups, as defined by the Italian policy framework, although their share in total BioTech employment in the same year was only six percent.
With reference to the distribution per field of predominant application, the human healthcare sector –“red BioTech” – still represents the majority share of Italian BioTech companies (48.5 percent). However, the industrial BioTech share of firms – “white Biotech”– increased by 29 percent between 2014 and 2021, whilst agriculture and veterinary BioTech – “green BioTech” – increased by 34.5 percent in the same period.
EO: Can you elaborate on how the COVID-19 pandemic affected the industry?
PP: The recent COVID-19 pandemic has shown how BioTech has been more than a solution to health needs. The sector has represented a key element in the geopolitical and economic strategies of the country. Vaccines, monoclonal antibodies, and diagnostics products are all BioTech solutions, and they were fundamental to overcoming COVID-19.
As reported by the BioInItaly Report 2022, the Italian BioTech industry has withstood the health crisis caused by the COVID-19 pandemic, recording only a five percent
drop in the overall 2020 turnover (less than half of the overall Italian industrial sector). In addition, the nationally controlled BioTech R&D dedicated firms increased by 30 percent in 2020, greatly increasing their turnover, particularly compared to the seven percent growth witnessed in 2019.
EO: What trends are currently transforming the BioTech industry in Italy?
PP: Italy is no different from the rest of the world in the sense that we can see some megatrends in human health, including the development of immunotherapies, advanced therapies and precision medicine, which are the key to the future of medical care.
A further fundamental point is the increasingly widespread awareness that the health of the population is strongly related to the health of our planet. Thus, the winning approach is ‘One Health’, which holistically considers the health of humans, animals and the environment.
The COVID-19 pandemic highlighted that if we want to deal effectively with the health of individuals and populations, we must also think about our planet and the better use and consumption of soil, water and air. Protecting the environment means saving ourselves.
In the pursuit of this objective, BioTech companies
• Promoting technological research and innovation, which it believes is the driving force for the nation’s economic and sustainable growth.
• Recognising, without fear of technological progress, the value of innovation, including the creation of a product.
• Providing sufficient financing for innovation.
• Attracting investment in the Italian BioTech industry, one of the few sectors where financing can yield a high possibility of returns in terms of qualified employment opportunities and the creation of added value.
represent a tool of great importance and a perspective of extreme interest. The field can make an important contribution to sustainable development, as well as an economy that respects the environment and is less dependent on fossil fuels and non-renewable resources.
EO: How do you see Federchimica Assobiotec and the BioTech industry developing over the next five years?
PP: According to the Organisation for Economic Cooperation and Development (OECD) estimates, by 2030, BioTech will have an enormous weight on the world economy: 80 percent of pharmaceutical products, 50 percent of agricultural products, and 35 percent of chemical and industrial products will be BioTech.
The acceleration in the development of BioTech today makes it possible to aim for goals that were once unimaginable, such as therapies for unmet medical needs, personalised therapies, preservation of biodiversity, plants that fight against climate change, and increasing production with less natural resources. We also hope to
work on the development of a production system based on alternative energy sources, bioproducts, and processes with no environmental impact, looking in particular at a circular bioeconomy model.
A recent study commissioned by Ernst & Young (EY) tells us that the European BioTech market will triple between now and 2028, creating value and new opportunities that Italy wants to be in the flow of.
Thus, we believe BioTech represents one of the greatest opportunities for the development of knowledge, the economy, and well-being in the coming decades.
Tel: + 39 02 34565383
assobiotec@federchimica.it
https://assobiotec.federchimica.it/en
EME OUTLOOK is a digital product aimed at boardroom and hands-on decision-makers across a wide range of industries in Europe and the Middle East regions. With content compiled by our experienced editorial team, complemented by an in-house design and production team ensuring delivery to the highest standards, we look to promote the latest in engaging news, industry trends and success stories from the length and breadth of Europe and the Middle East.
Reaching a combined audience of more than 395,000 people, EME Outlook covers a full range of industrial sectors: agriculture, construction, energy & utilities, finance, food & drink, healthcare, manufacturing, mining & resources, oil & gas, retail, shipping & logistics, technology and travel & tourism. In joining the leading industry heavyweights already enjoying the exposure we can provide, you can benefit from FREE coverage across our digital platforms, a FREE marketing brochure, extensive social media saturation, enhanced B2B networking opportunities, and a readymade forum to attract new investment and to grow your business.
To get involved, please contact Outlook Publishing’s Managing Director, James Mitchell, who can provide further details on how to feature your company, for FREE, in one of our upcoming editions.
With more than 70 restaurant and café locations, Restaurant Company Europe is the largest catering group in the Netherlands. We peruse the company’s menu for success with CEO,
Across the globe, people eat not only to nourish themselves but also to celebrate, share special moments with loved ones, as well as to experience and broaden their horizons.
“It’s a privilege to be able to contribute to these experiences and great to see that guests realise, after having to deal with restrictions during the COVID-19 pandemic, that they can go out once again,” introduces Sandra van Halderen, CEO of Restaurant Company Europe (RCE).
The vast, and forever shape-shifting food and beverage industry is never stationary, presenting copious developmental opportunities within its constant cycle of transformation and innovation.
Furthermore, the enormous restaurant industry also exists as a showcase of what’s happening in the world and how people react to it, acting as a mirror for new trends, interests, and developments. The increase in eating out, a greater focus on health, the digitalisation of the world, and the need for more social interaction between people is driving traction towards RCE restaurants.
“We also see people celebrating a night out, spending on premium products and sharing dishes more and more amongst each other. Speaking of sharing, our guests’ journey starts way in advance on our digital channels and continues via social media long after,” van Halderen adds.
In general, RCE believes that this
is an exciting year for the European food and beverage industry. After the lockdowns and restrictions of recent years, 2023 marks the full return of the foodservice sector, or at least van Halderen hopes.
“We see exciting opportunities emerging across Europe, but at the same time acknowledge the challenges when it comes to high rent prices, increasing salaries and, above all, huge inflation and the increased cost of operations,” she voices.
Today, RCE is the largest restaurant group in the Netherlands, amassing more than 70 of its own restaurants in the casual dining and fast-casual segment.
Now private equity owned, the company was created in 2020, birthed from a merger between two restaurant groups. A fast-casual formula with several restaurants throughout the Nederlands. More broadly, RCE has four distinct major variations of restaurant formulas.
Firstly, Loetje is a successful casual dining formula with 34 restaurants, starting 45 years ago in Amsterdam as a billiard café that served the traditional dish of steak in gravy with bread.
“Nowadays, Loetje is an accessible restaurant for a broad range of guests, from families and groups of friends to business guests. The steak with gravy and whitebread is still the most
ordered item on the menu, and we also serve it as a vegan dish,” van Halderen tells us.
Elsewhere, Happy Italy is a fast-casual concept with 18 large contemporary restaurants, serving large portions of high-quality fresh pizzas and pasta for low prices. Additionally, unique to this formula is that every restaurant features a large indoor playground for children, making each site family-friendly.
Another proud staple of the company is RCE’s Beers&Barrels formula, a concept with a modern restaurant and bar setting that serves a variety of beverages while also allowing guests to tap their own beers on its unique tapping tables.
“At Beers & Barrels we serve an array of cocktails and our extensive menu has a vast variety of delicious dishes, including many vegan options and beautiful dry-aged steaks across
Beuk Horeca is the leading provider of innovative foodservice and catering equipment solutions in the Netherlands and abroad. With a comprehensive range of products and services, a diverse client base, and a dedicated team of professionals, we are committed to delivering excellence in the ever-evolving foodservice and catering industry.
Beuk Horeca offers a wide array of products and services tailored to meet the unique needs of our clients. From state of the art kitchen equipment to comprehensive foodservice management, we provide end-to-end solutions for restaurants, hotels, and catering establishments. Our offerings include programmable kitchen appliances, energy-efficient equipment, kitchen design and construction, as well as ongoing support and maintenance services.
Operating throughout the Netherlands, we have established a strong presence in the catering industry. From bustling city centres to idyllic coastal towns, our services span the entire country. We have had the privilege of working with a varied range of clients, including renowned restaurant chains, luxury hotels, and prestigious catering companies. Our client base is a testament to our expertise, with long-standing relationships that reflect the trust and satisfaction of our partners.
The foodservice and catering equipment industry is undergoing a rapid transformation driven by changing consumer demands and advancements in technology. At Beuk Horeca, we are at the forefront of this evolution, constantly adapting and innovating
to stay ahead of the curve. We understand the need for efficiency, sustainability, and exceptional levels of service. As such, we embrace technological advancements, offering programmable and energyefficient equipment to enhance productivity, reduce costs, and meet the changing demands of our clients.
RCE, the owner of esteemed restaurant chains such as Loetje, Stan, Beers&Barrels, and Happy Italy, holds a special place in our journey as a company. As a key partner, RCE plays an integral role in shaping our success and reputation. Our close collaboration allows us to understand its unique requirements and deliver tailored solutions that align with its brand vision. We greatly value our relationship with RCE and the synergy we share in elevating the restaurant experience offered by its renowned establishments.
Over the years, we have collaborated with RCE on numerous projects, which have showcased our commitment to excellence and innovation. One notable project involved partnering with the iconic Loetje restaurants, where we implemented innovative foodservice and catering equipment solutions to enhance its overall efficiency, while preserving its distinctive ambience. We worked closely with RCE to understand its specific needs, resulting in a seamless integration of our cutting-edge equipment and services. These projects demonstrate our ability to deliver exceptional results and the strong bond we have forged with RCE.
Looking ahead, we are thrilled about the upcoming projects we have planned in collaboration with RCE. While we cannot disclose specific details at this time, we can assure you that these projects will continue
to redefine culinary excellence. By combining our expertise with RCE’s visionary approach, we will create unforgettable dining experiences that captivate guests and elevate their establishments to new heights.
Beyond our collaboration with RCE, Beuk Horeca is involved in various ongoing projects across the Netherlands and beyond, including the Caribbean islands. From designing and constructing kitchens for renowned restaurants to providing comprehensive catering solutions for hotels, our team is dedicated to delivering outstanding results. We leverage our expertise, industry knowledge, and attention to detail to ensure that each project is a resounding success. We have been fortunate enough to undertake several remarkable projects, including the Marriott Hotels in the Netherlands such as The Hague, as well as on Curaçao Beach where a new high-class resort is being established under the Marriott flag. Correndon is also one of Beuk Horeca’s well-respected clients in both regions. Recently, we completed a major project in the form of Sandals, a luxurious resort in Curaçao. A different significant account is Wagamama, who we have recently built several projects for in Brussels, Antwerp, and Kijkduin. Additionally, we are proud to
serve emerging concepts such as The Breakfast Club and Cannibale Royal, which are rapidly expanding. These are just a few examples as the order book is filled with more exciting opportunities.
THE IMPORTANCE OF OUR STAFF:
Our staff members are the backbone of Beuk Horeca, and we recognise the pivotal role they play in our success. We foster a culture of empowerment and continuous growth, providing our employees with opportunities to excel and contribute to our collective achievements. Through training programmes, career development initiatives, and a supportive work environment, we encourage their professional growth and ensure that they are equipped to deliver outstanding service to our valued clients.
For those considering entering the foodservice and catering equipment industry, we offer the following advice: embrace innovation, stay abreast of industry trends, and seek opportunities to learn and grow. Dedicate yourself to providing exceptional experiences, and always prioritise the needs and preferences of your clients. Cultivate strong relationships with key partners and suppliers, as collaboration and trust are essential for long-term success. Finally, never underestimate the importance of a passionate and dedicated team – they are the heart and soul of any culinary endeavour.
At Beuk Horeca, we are committed to revolutionising the culinary landscape in the Netherlands. Through our innovative solutions, strategic partnerships with RCE, and the dedication of our talented team, we continue to set new standards of excellence in the foodservice and catering equipment industry. Whether you are a restaurant owner, hotel manager, or catering professional, trust Beuk Horeca to deliver unparalleled solutions that will elevate your culinary offerings and exceed your expectations.
Contact us today and let us embark on a journey of foodservice and catering equipment excellence together.
the five locations,” she adds.
As a restaurant group, RCE operates in the middle of what the company refers to as a “high touch” environment.
“People visit our restaurants physically - there is always a large service component involved at the table, and our menus serve freshly made products. It’s a part of our industry which is generally not dominated by large brands because of the complexity of running it,” van Halderen sets out.
This high service component also
means RCE exists as an extremely people-driven organisation. Although this is the nature of its business, this attractive quality is slowly fading away in brand-dominated segments of the restaurant landscape such as delivery, convenience, and quick service restaurants (QSRs). RCE, however, endeavours to build multiple brands around this principle and continues to standardise the guest experience while still scaling operations, which remains a unique, unmatched trait in the European catering and hospitality industry. This has helped build a fantastic reputation for the company and sets RCE apart from many of its competitors.
“Our expert team that handles formula management is dedicated to the in-house development of all of our brands. This group consists of experts in brand development, strategy, concept development, menu engineering, design and food development, and is working on our brands every day,” she expands.
“To then operate these various brands by ourselves, not relying on franchisees or other operating parties, shows our expertise in managing the brand experience from A-Z.”
Furthermore, RCE’s focus on the customer journey is not only an accelerator of this process but also creates a highly guest-oriented
focus. In every step of its journey, the company aims to standardise its activities, without standardising the guest experience.
Never content with remaining
stationary, RCE is always looking to add new brands and restaurants to its already impressive portfolio of success stories. The company now possesses myriad culinary experiences all under one umbrella, with each new chain representing a fresh innovative theme, menu, and
dining environment to discover.
One such restaurant formula under the RCE umbrella is De Vooruitgang. An all-day concept in the middle of Eindhoven with a great ambience, delicious, shared dining platters and the best cocktails in town. The guests start their morning on the nice terrace with a cup of coffee, have lunch or dinner in the beautiful restaurant, and at night the tables will be set aside, as the place is transformed into a club with DJs where you can dance all night long.
Elsewhere under the RCE umbrella of brands is the Belgian Biercafé Olivier, located in an atmospheric old church, where the company serves
“ALL IN ALL, OUR CONSISTENT PERFORMANCE TOWARDS OUR GUESTS, EMPLOYEES AND OTHER STAKEHOLDERS MAKES GROWTH EASIER FOR US”
– SANDRA VAN HALDEREN, CEO, RESTAURANT COMPANY EUROPE
All restaurant formulas at RCE are defined through their specified and unique customer journeys, which exist as the starting points from where the company is working within the locations.
Starting with the base, RCE then works through the following phases of operation:
• PHASE 0
This first phase involves the initial measurement of a site with a 360-degree view and redefining the existing formula. This process also describes and records the customer journey across all elements.
• PHASE 1
This requires a description of the complete formula and summarises it in systems. This phase also requires recording operational excellence programmes and setting up all supporting RCE IT systems from recruitment and selection systems to guest journey platforms, websites, email, telephony, and the review ticket system.
• PHASE 2
Phase 2 leads a focus on quality and consistency, through the implementation and assurance of an effective operational management system. Continuous communication and internal audits are employed, as RCE also trains its own start-up team to launch new locations.
• PHASE 3
This phase involves a focus on innovating and enhancing digitalised processes. It also entails innovation for the development of new dishes such as vegetable steak, and new formats within the formula.
the tastiest beers and Flemish classics such as tender stew and warm ham with authentic local hospitality. This restaurant is the perfect place for an extensive lunch or an evening of Burgundian enjoyment.
Another popular addition to RCE’s catalogue of formulas is Café Weesper, bistro Amsterdam. This delicious drinking spot on the edge of the city allows guests to discover a French-oriented array of treats with a sprinkling of classic Amsterdam dining too.
“Alternatively, if you prefer American style tastes and flavours, in our Ebeling formula restaurants we revive old times, recreating the feeling of the roaring twenties in New York, but in the heart of Amsterdam. With the Leidseplein within walking distance, this is one of the best places for lunch, drinks or pre-drink dining in the city,” declares van Halderen.
“The enthusiastic team at the Ebeling knows how to throw a party and provides every guest with good, affordable dishes and tasty drinks until late,” she continues.
With this impressive lineup of formulas, RCE ensures it has a restaurant for everyone, regardless of what culinary tastes its visitors are seeking.
Creating the ultimate guest experience is a quality that is ingrained deeply in the pores of RCE as a company and this remains its primary objective across all sites. Additionally, RCE strives to ensure an optimal experience for its staff as well as its customers.
From numerous company benefits, such as travel expenses and free food and beverages, RCE promotes a healthy work-life balance for all its colleagues. This is alongside plenty of career opportunities and ample development potential. RCE wants its people to grow in parallel with its company growth, sharing in its
Bidfood is the online wholesaler for the hospitality industry and total supplier in the foodservice market. From restaurant to cafeterias and from hotels to sports canteens and institutional care, we have a suitable offer for every food professional, simply ordered online and delivered to the kitchen. Thanks to our 100 percent delivery guarantee, we can call ourselves the most reliable online catering wholesaler.
bidfood.nl
collective success story.
“In addition to working on your personal development, we believe in the importance of a healthy lifestyle. We cook for our employees every day and facilitate discounts on sports subscriptions to stay fit,” adds van Halderen.
It is the firm belief of the company that it can work and grow together alongside its staff, clients and customers, savouring the glory and spoils of RCE as one large family.
In addition to working on the personal development of its people, RCE believes in the importance of encouraging an optimal, sustainable and positive way of life and therefore provides fresh meals for its employees.
“We see our staff as the best ambassadors for the company, from the scullery to the location manager, because only if you feel good about yourself and you use your talents, can we collectively get the most out of every working day together,” she elaborates.
RCE is also enthusiastic about helping its staff to further develop their talent with various internal training options.
“If you have personal growth ambitions, we offer our people the opportunity to grow into the next position. This way, they can progress within their location, but also to one of RCE’s other catering formulas or alternatively to a role in the service office.
“Within the food and beverage industry, employees are the most important value of your success. Although it is not the easiest industry to work in, I truly find it the nicest to be involved with because of the hospitality and the kind of people who work in it. It is full of very motivated individuals who are also highly dedicated and enthusiastic,” van Halderen enthuses.
Basing many crucial business decisions on key facts and figures that it has harvested through detailed analysis, RCE exists today as a modern, data-driven organisation. In this way, the company is constantly working on its own development and growth through a comprehensive data-driven approach. In general, many businesses across the vast global restaurant industry are emotionally driven, but for RCE, data is the backbone of every decision made and lays the foundation for each new direction for the company.
“Recently, we rolled out Apicbase, a purchasing, ordering and stock system with all the dishes and recipes across our formulas. Apicbase has a connection with our POS system, our finance system and our data lake,” details van Halderen.
Utilising this impressive software, RCE can easily access insights for costs of sales and price development with its suppliers, and now has the ability to analyse financial margins. These insights are combined with extensive developments in POS integration, customer data, and other data points to generate comprehensive insights throughout the entire business.
One of the other major assets for RCE is its central back office, which now allows the company to streamline customer interactions, information, and all back office facilities, resulting in a 100 percent focus on its restaurants and day-to-day
Delta Wines is a leading importer and distributor with a wide portfolio of wines, supplying over 85 million bottles of wine annually from over 21 countries to supermarkets, traditional retailers, wholesalers, the online channel and the foodservice industry. With a central role in the value chain, Delta Wines is an important strategic partner to producers and customers through a wide range of additional services including agency, advice, category management, marketing / branding, logistics and supply chain service.
Delta Wines has the ambition – in addition to a solid and healthy organic growth – to spread its presence in the European wine industry, aimed at further strengthening the connecting role between wine producer and wine selling customers. Today, Delta Wines serves its customers internationally from its own distribution centres, 30.000 m2 in the Netherlands, Poland, the Czech Republic, Belgium and most recently in Finland and Norway. Delta Wines. We love wine, we live wine!
www.deltawines.eu
We are an importer and wholesaler of wine and other beverages, providing carefully curated selections to both hospitality businesses and individuals. Our distinguishing factor is our personalized and knowledgeable customer service, as well as our D-Vine Academy which educates professionals and enthusiasts alike. Our goal is to enable everyone to enjoy wine, fine products, and the art of gastronomy. We achieve this by educating professionals, sharing our passion and wine expertise, and advising and supporting our hospitality clients so that everyone can thrive.
www.d-vine.eu
In all of RCE’s restaurants, the company has rolled out operational excellence programmes adjusted to the customer journey for each different formula. All employees are obligated to take part in full training, and this remains an ongoing project across all locations. These programmes contain the following components:
OPERATIONAL EXCELLENCE
- Predictability in all forms
WORK PROCESSES
- Clarity
- Responsibilities
SYSTEMS
- Uniformity
- Data
CAPACITY PLANNING
CONSISTENT MANAGEMENT STRUCTURE
- One management system
- Same calendars
- Universal steering information
EMPLOYEES
- Structure
- Clarity
- Expectations
SUCCESSION PLANNING
- Succession
- Scalability
operations. Procurement, IT, guest care, marketing, HR and recruitment are all activities in which RCE’s restaurants can rely on the expertise of professionals and the economies of scale of its 70 locations.
“For us as a group, we are able to innovate faster, leverage the expertise of the group, and control the customer journey even more now.”
As van Halderen affirms, RCE remains extremely reliant on statistics, numbers, and figures in its decisionmaking process.
“In comparison to other casual dining restaurants in particular, we rely on our back office to connect the right digital partners through our own digital development department. Our focus is not only on collecting and securely storing the right data, but also analysing the research with our data mining specialists and using it to back our thorough fact-based decisionmaking process,” she elaborates.
One secret to RCE’s ongoing success is its strong operational formula, which is now highly recognisable and displays the company’s array of unique selling points.
Loetje, for example, is famous for its great locations, friendly employees, the quality of the food, and of course the traditional classics on the menu. This has evolved into such a popular concept, that when RCE opens a new
Loetje restaurant it is an instant success.
“All in all, our consistent performance towards our guests, our employees and other stakeholders makes growth easier for us. If people, including investors and landlords, know what to expect, it helps you to create a stable growth path,” van Halderen affirms.
One important factor for RCE to consider within the business is whether it is important to make each new location feel unique or to embrace the tradition of staying true to the classic brand formula.
“The level of uniqueness we include in the design really varies per brand. For example, within a format like Happy Italy, we try to really bring a consistent brand experience and recognisable design into new locations,” she elaborates.
Loetje, on the other hand, leverages the specific features of the location where it is being opened. The setting, surrounding, heritage and history are captured in the design of each new store, with RCE’s designers possessing the skill to do this while maintaining the Loetje feeling and trademark atmosphere.
The colour palette, materials and furniture may be different in every new RCE location, yet visitors always feel it’s one of the company’s restaurants.
Continuing to add to its impressive
selection of sites, on the 31st March earlier this year, RCE opened a brandnew Beers&Barrels location in the centre of Amsterdam.
Ideally situated amongst what the company refers to as a ‘high traffic location’, RCE has created a draft house which caters to the need of the tourists, groups and visitors of the iconic Rembrandt Square.
“On the 6th April, we opened our 32nd Loetje facility in Vught, existing as a completely different location, right in the middle of three smaller cities in the south of the Netherlands. The nature of this location aims to draw people in from the wider area,” van Halderen confirms.
Elsewhere, on the 5th July, the company launched another restaurant in Nieuwegein, this time a Happy Italy. Situated in a food court, just off the highway and close to a residential area, this restaurant will mainly focus on the families and youngsters nearby.
“In August, September and
December of this year we will also open three more Loetje restaurants in Zeist, Maastricht and Hilversum.”
Aiming to develop the brand abroad as well as domestically, the first step in RCE’s German expansion will be with its Loetje formula.
“It is important to focus here because it is a big step for us, and we really want to do it right. You never get a second chance to make a first impression, so having the right fit for the brand is key for us.”
Looking ahead, RCE still foresees a lot of potential for new growth back home in the Netherlands, as its expansion path and development schedule fills itself, thereby creating many opportunities to chase.
For Happy Italy, van Halderen sees excellent opportunities for development in new channels like delivery, small store formats and integrated solutions. Lastly, there is always the potential for mergers and acquisitions, which may include
buying other brands or multiple locations in one action.
“The main goal right now is to hang on to our proven location strategy, upon which we base our decisions for the right formula in the right location. With this proven strategy, we can make a big impact on the results of our company,” she concludes proudly.
Tim Hortons is internationally recognised for its hearty coffee and classic Canadian cosiness. As the iconic barista branches out, CEO Hesham Almekkawi tells us how Tim Hortons Middle East is establishing its presence amongst the Gulf Cooperation Council
Writer: Lucy Pilgrim | Project Manager: Liam PyeFor nearly 60 years, Tim Hortons has been serving millions of customers with warm drinks and delightful baked goods, amongst other tantalising bites to eat.
During this time, the food and beverage icon has become known for its premium quality ingredients and serving its customers with a smile, a simple strategy that has elevated the business to global levels.
Best-known for its rich, aromatic flavours, coffee lovers all over the world have enjoyed Tim Hortons classics such as the Original Blend and the signature Iced Capp®, accompanied by a variety of inspired doughnuts including the ever-popular Timbits®.
“Our vision is to be the café of choice,” introduces CEO of Tim Hortons Middle East, Hesham Almekkawi.
“We may not have the largest number of outlets, nor exist on every corner, but we do have fresh food, quality coffee, and a cosy ambience that provides experiential moments.”
The perfect café atmosphere is guaranteed by the company’s use of superior quality products, unmatched customer service, and caring for the communities it provides for, through leadership, innovation, and strong
partnerships.
“Our restaurant chain is known for its freshly brewed coffee and baked goods, aptly demonstrated by the tag line: “Always Fresh, Always Delicious”, which rightly reflects the brand policy,” Almekkawi adds.
International adoration for Tim Hortons Middle East further stems from its intricate attention to detail, with comfortable seating and optimum light levels across each restaurant. Therefore, it is always prepared to give its customers the best possible café experience.
In 2011, the renowned Canadian brand made its way to the Middle East, opening its first café and baked goods shop in Dubai. Ten years later, Tim Hortons lovers can now enjoy the famous premium coffee, confectionary, and made to order sandwiches at food locations throughout the United Arab Emirates (UAE), the Kingdom of Saudi Arabia (KSA), Qatar, Oman, Bahrain, and soon in Kuwait, Egypt, and India.
Due to an emerging reputation as a flourishing food and beverage market, the Gulf Cooperation Council (GCC) has created a prosperous atmosphere for entrepreneurs and like-minded businesspeople to continue to invest in the region.
“The GCC constituted an attractive environment for Tim Hortons to provide developed infrastructure and a business incentive that helped the chain thrive across the country and worldwide,” Almekkawi recalls.
KSA and the UAE in particular have brought a major economic drive to the Middle East. In order to grasp this opportunity, Tim Hortons plans to expand its presence in both countries to 500 locations by 2025, taking advantage of the region’s largest two economies and growth markets.
“We plan on opening more than 200 new branches in KSA by 2024, as we are confident in its Vision 2030 blueprint; thus, we are keen to benefit from the country’s growth prospects and the progressive strategies of its wise leadership,” Almekkawi details.
With this expansion, Tim Hortons Middle East wishes to spread the welcoming nature of the company across the local community, to
facilitate connections and become an active part of each neighbourhood.
“Our expansion further solidifies the mission of offering customers comfort, refreshments, and a relaxing environment. By taking advantage of the brand’s popularity, our strategic development will ensure that Tim Hortons’ iconic coffee is accessible to those all over the GCC region,” he adds.
Being a part of each community is a major focus for Tim Hortons Middle East, as it is committed to bringing people together by empowering individuals of all diverse abilities and skills.
In correlation with this focus, and the emphasis on a welcoming, collective community, Tim Hortons Middle East has partnered with the Al Jalila Foundation in the UAE, alongside the Sanad Organisation in KSA. With both these fantastic charities, the café enterprise contributes to reducing patients’ medical bills, having a beneficial
• 1964 – Tim Horton, a Canadian hockey legend, opened the first store in Hamilton, Ontario, Canada
• 1976 – The iconic Timbits® confection is introduced
• 1999 – Iced Capp® is launched, marking a huge success
• 2000 – 2,000th Tim Hortons location opens in downtown Toronto
• 2004 – The brand’s well-loved Double Double® beverage is added to the Canadian Oxford Dictionary
• 2011 – The first Tim Hortons café opens in the Middle East
• 2017 – Tim Hortons arrives in the UK
“WE ARE PLANNING ON OPENING MORE THAN 200 NEW BRANCHES IN KSA BY 2024, AS WE ARE CONFIDENT IN ITS VISION 2030 BLUEPRINT”
– HESHAM ALMEKKAWI, CEO, TIM HORTONS MIDDLE EAST
financial impact on patients, whilst also aiding in humanitarian issues.
“This collaboration comes as part of our commitment to supporting charitable and humanitarian organisations in the UAE and KSA, fulfilling the common interest of all parties,” Almekkawi tells us.
On top of this, customers of Tim Hortons Middle East can round up their bills so that any extra money goes to charity, with 100 percent of the proceeds allocated to the Al Jalila Foundation and the Sanad Organisation. Therefore, each loyal customer can feel they are doing their bit for the local community.
“The two charity partnerships aim to fortify the means of cooperation, which are in line with the directive and mission of Tim Hortons as a brand: to mobilise community services and support societies through volunteering and joint contributions conducted by a set of charitable
initiatives and activities.”
Overall, Tim Hortons Middle East is committed to improving the quality of life for its customers as well as giving back to the communities in which it operates. This is reflected by the impressive contributions already made by the restaurant chain, raising over AED130,000 (£275,260) since the beginning of 2023.
With ambitious expansion plans on the horizon, trustworthy connections with suppliers are equally paramount to Tim Hortons Middle East’s success.
By having great suppliers, the business can improve its service to its loyal customer base, as well as its productivity and elevated market presence.
“Our success is tied to our suppliers. They provide us with what we deliver to customers, so the quality of what we receive from them is more than key,” Almekkawi affirms.
As a leading café in the Middle East and North Africa region (MENA), the company understands how important it is to react to the demands of the market and ensure long-term success.
As a result, Tim Hortons Middle East’s
main focus last year was to localise and build relationships with reliable suppliers in each market so that it could adequately adapt to a range of customer tastes. This also enabled the company to eliminate global logistical challenges, to become more flexible
“WE ARE PLANNING ON OPENING MORE THAN 200 NEW BRANCHES IN KSA BY 2024, AS WE ARE CONFIDENT IN ITS VISION 2030 BLUEPRINT”
– HESHAM ALMEKKAWI, CEO, TIM HORTONS MIDDLE EAST
and innovative with local suppliers. Additionally, through a master franchise agreement, Tim Hortons Middle East is a proud partner of the Apparel Group, a leading food and beverage entity headquartered in Dubai.
TIM HORTONS MIDDLE EAST
https://timhortonsgcc.com
From fresh recipe kits to premium takeaway meals, Pasta Evangelists delivers a taste of Italy across the UK. Chris Rennoldson, co-Founder, discusses scaling up and becoming the authority in fresh pasta
A tavola non si invecchia”. This beautiful proverb, which translates to “at the table, one does not age”, sums up the Italian approach to food.
Italians enjoy eating together with
loved ones and take their time when doing so, and the lengthy process of hand-making and consuming pasta is emblematic of this experience.
A love of pasta is therefore at the heart of Italy’s connection to food,
something that has been embraced in the UK by Pasta Evangelists.
“We have built a brand and a reputation amongst customers for quality and having novel, exciting pasta recipes,” opens co-Founder, Chris Rennoldson.
When Rennoldson started Pasta Evangelists with fellow co-Founders, Alessandro Savelli and Finn Lagun, they wanted to show that there is much more to pasta than meets the eye – a world of craftsmanship, centuries of artisanal tradition, and above all, some of Italy’s finest dishes.
Rennoldson was first introduced to Savelli in October 2016, who presented his business idea and mission to become “the authority in fresh pasta”.
“What we wanted to do was deliver an amazing, premium experience. That is important to us and has been the mission of the business from the very start,” he outlines.
Pasta Evangelists was originally founded as a direct-to-consumer, cook-at-home recipe kit business, delivering fresh handmade pasta, sauces, and garnishes across the UK.
In as little as five minutes, the company’s recipe kits transform into a 5-star pasta dish, impressing amici and delighting famiglia.
“They’re special meals because it’s something you can’t get in the supermarket. The recipe kits were a way of getting into the market quickly by sending this differentiated product to people at home,” Rennoldson says.
Whilst people were confined to their homes during the COVID-19 pandemic and resulting lockdowns, the company experienced exponential growth.
The pandemic changed the way people buy and consume which naturally had a massive impact on Pasta Evangelists, who has now served over 400,000 recipe kit customers to date.
Chris Rennoldson, co-Founder: “The advice I received from all sorts of angles was to make your hobby your job.
“Cooking was my hobby during school days, and it became my way of unwinding when I used to work in finance. It was not just a release to mark the end of the day, but also an opportunity to express my creativity. Eventually I committed to Leiths cookery school full time to learn how to be a chef and find out whether doing my hobby as a job would work for me.
“My cookery school experience ticked the idea of making my career centred around food, and set me out on my first food business ideas, ultimately leading to Pasta Evangelists. I’m hugely passionate about food, so it’s just really exciting and meaningful for me to work in a food business!”
“That was a crazy time, but it has still shaped a lot of what we see today. People have got used to the idea of home delivery, and this is one industry where a lot of new habits have stuck,” observes Rennoldson.
Pasta Evangelists also committed to serving takeaway meals just as the pandemic struck, having struggled to sell cook-at-home recipe kits on takeaway delivery platforms.
The company opened its first dedicated takeaway kitchen in March 2020 in Clapham to sell hot, freshly prepared food over the likes of Deliveroo, Uber Eats and Just Eat, and now has more than 40 of these kitchens across the country, serving over two million takeaway meals a year.
Adopting this multi-channel approach has been important for Pasta Evangelists to meet the needs of customers, as there is something for everyone.
“Trying to sell recipe kits through takeaway providers didn’t really work because that’s not what people are expecting on those platforms,” Rennoldson explains.
“A lot of restaurants had to embrace takeaway to survive the pandemic, and that’s opened up a new premium takeaway segment where we now find ourselves strongly positioned.
“Even during the cost of living crisis, many people still look for ways they can treat themselves, and we make sure it is a complete ‘premium’ experience in terms of the food, the packaging, and the way we interact with our customers,” he adds.
As Pasta Evangelists has been extremely busy growing the company during the pandemic and building its various business channels, it has now invested in its own pasta manufacturing facility in West London which is set to be the largest in the UK.
“We’ve reached a scale where there isn’t a large enough base of fresh
pasta manufacturers and producers in the UK for us to call upon,” elaborates Rennoldson.
The factory, which will be operational in the coming weeks, will allow the company to make enough fresh pasta and sauces to meet growing customer demand.
It will also enhance the quality of Pasta Evangelists’ recipes even further, something that the company is renowned for amongst customers.
“If you ask people about Pasta Evangelists, the first thing they will talk about is the quality of the food and how it’s something they can’t get elsewhere. We are a premium product, which means every single bowl of pasta we send out needs to be perfect; that quality is critical to our customers,” he emphasises.
The factory’s new pasta production lines will be difficult to replicate, therefore increasing quality to a
level that will be hard to match and bringing a significant competitive advantage to Pasta Evangelists.
“There’s a need for us to continue to improve the quality of the product, and that’s what we’re seeking to achieve with this investment.”
The rate of innovation at the company will likewise improve, thanks to the new technologies being built into the facility.
“If you are partnered with third
party suppliers, then pushing innovation through takes much longer,” notes Rennoldson.
Following on from its factory investment, Pasta Evangelists plans to grow its takeaway locations through franchising.
The company now has more than three years of experience and expertise in takeaway operations
“WE’RE ON A FANTASTIC JOURNEY TOGETHER, SO WE’RE VERY CONSCIOUS OF MAKING SURE THAT WE DON’T LOSE WHAT’S SPECIAL ABOUT BEING A PART OF THE TEAM THAT WORKS HERE”
– CHRIS RENNOLDSON, CO-FOUNDER, PASTA EVANGELISTS
since opening its first kitchen in 2020, and believes it can learn and improve by partnering with franchisees.
“We’re just starting out with franchising, which is the next evolution. The thinking is that we don’t have to own and operate every single Pasta Evangelists restaurant,” Rennoldson tells us.
“I think we’ll learn an awful lot because we’ll be partnering with people who are experts with decades of experience.”
Whilst Pasta Evangelists will benefit from the help of franchisees to grow the business further and faster, franchisees will take advantage of Pasta Evangelists brand and recipes.
Through franchising, Pasta Evangelists can be confident that it is putting the brand into safe hands.
“Once you partner with a third
party, they expect more formal operational discipline around brand guidelines, ways of working, and so on,” says Rennoldson.
This is something that has grown
organically with the business, and franchising will discipline Pasta Evangelists to document its processes more thoroughly.
“Being a scale-up, as opposed
to a start-up business, means putting together more processes, and behaving in a slightly more mature, corporate way without losing the essence, fun, speed, and entrepreneurial spirit of the company.
“We need to communicate more clearly and uniformly as we scale up, and it’s something that franchisees will expect from us,” Rennoldson acknowledges.
Equally, as Pasta Evangelists
continues to scale up, it is building a culture of togetherness across all locations and ensuring the company is a fun place to work as it expands.
“We want to create a strong set of Pasta Evangelists values and a ‘work hard, play hard’ ethic amongst our whole team. We’re on a fantastic journey together, so we’re very conscious of making sure that we don’t lose what’s special about being a part of the team that works here.”
Pasta Evangelists has also embarked on its very first restaurant venture at Harrods, in the world-famous department store’s prestigious dining hall.
The restaurant combines a modern Italian menu with the company’s signature indulgence, with exclusive dishes that celebrate the artisan quality, flavours, and traditions of authentic Italian pasta.
It goes one step further than the concession launched by Pasta Evangelists in Harrods, which first branched out the brand in 2018.
The opportunity to open a restaurant in Harrods was precisely the kind of fast, calculated risk expected of Pasta Evangelists by Barilla, the world’s largest pasta producer, who recently acquired the company.
“We started speaking to Harrods in 2021, just before shops and restaurants reopened, about a partnership to run the pasta bar,” reveals Rennoldson.
“This was not something we had entertained at the time we were going through the transaction with Barilla in late 2020. It came as a surprise, but it was exactly what Barilla wanted to see and why they partnered with us.”
The restaurant epitomises the spirit of partnership between Pasta Evangelists and Barilla, which is built upon allowing the former to move fast and make its own decisions.
“What’s been great about the partnership is it has absolutely lived that out,” Rennoldson concludes.
PASTA EVANGELISTS
Tel: 020 3514 8374
chef@pastaevangelists.com
www.pastaevangelists.com
“IF YOU ASK PEOPLE ABOUT PASTA EVANGELISTS, THE FIRST THING THEY WILL TALK ABOUT IS THE QUALITY OF THE FOOD AND HOW IT’S SOMETHING THEY CAN’T GET ELSEWHERE”
– CHRIS RENNOLDSON, CO-FOUNDER, PASTA EVANGELISTS
Since Transavia’s inception in 1991, it has continually made astute investments. Today, the company owns the most advanced vertically integrated poultry business system in Romania. However, quality products and innovation have also contributed to its success.
As the local leader in the poultry industry, the company was founded when Eng. Ioan Popa purchased a former agricultural farming cooperative for cows and transformed it into a broiler farm. Transavia then positioned itself at the forefront of the Romanian chicken meat industry in eight counties and has since become a reliable partner in the export market.
Transavia has strived to improve upon the from farm to fork mantra for healthy eating by championing its own from grain to fork process. Its integrated operation includes grain production, harvesting and accommodation for feeding chickens, breeding
and broiler farms, a meat processing plant and product distribution. The benefit of an integrated structure allows for governance over each aspect of food safety. Transavia can maintain biosecurity measures, vaccination programmes, and testing for bacteria such as salmonella at breeder farms and hatcheries. Moreover, in the feed mill, strict pest management controls the spread of disease.
With continual enforcement of all standards, it was inevitable that Transavia became the only company to have a code of conduct at the European level for the food industry. Additionally, in 2006, Transavia achieved the title of Supplier of the Royal House of Romania as well as winning other national and international awards. High-quality standards exist throughout its poultry breeding and food production processes and are therefore central to
the company’s success.
In 2011, Transavia established four vegetal farms situated within the limits of 58 localities in Transylvania to form its agricultural division, becoming the first poultry producer to provide chicken feed from its own sources.
Cultivating grains, wheat, and corn with high-performance agricultural equipment, Transavia had to extend the following phase. In 2015, the production and storage capacity of its feed mill factory was forced to increase by 70 percent.
The feed mills are provided with a fodder sterilisation system unique to Romania. Furthermore, the mixed feed fodder factory in Alba produces around 500 tonnes of feedstuff per day for Transavia farms without any contact with the external environment.
As Romania’s premier poultry product provider, Transavia is dedicated to quality and flavour with its family-run business. We tuck into the company’s processes, portfolio, and prospects
In order to avoid contamination, the 24 broiler farms are located within areas isolated from other animal farms, and there are separate rooms for each operation in Transavia’s two hatching stations. With the volume of eggs produced at the reproduction farm, the poultry is carefully selected, and their health is monitored by a sanitary veterinary laboratory.
Meat products are subsequently packaged under a controlled atmosphere and stored in the freezer or refrigerating areas from where they are distributed under the safest conditions by using vehicles from Transavia’s own fleet.
The production lines are equipped with cutting-edge technology,
• Over 2,300 employees
• Over 20 first and secondgeneration family members work at the company
• Export to over 30 countries
• €35 million invested in green energy
• 29 poultry breeding farms
• 50 million eggs produced annually
• 15 percent of the annual production of the company goes to the international market including France, Ireland, the UK, Netherlands, Hungary, Greece, Slovakia, Bulgaria, Spain, Croatia, Czech Republic, Italy, and Africa
which transforms the meat into finished products by fully automated operations.
The most recognisable brand in the Transavia portfolio is McDonald’s, but the iconic golden arches are not only associated with hamburgers and fries. Indeed, since its partnership with Transavia began in 2017, the fast-food restaurant has used around 5,000 tonnes of the company’s chicken meat.
McDonald’s has high global standards which require specific technologies, and becoming a supplier is an uncompromising process with strict rules, but Transavia has risen to the challenge.
In 2021, McDonald’s introduced a menu of superior products using 100 percent locally produced chicken. Together with Transavia, the famous eatery developed products that were an instant hit. The launch of Supreme Chicken Tenders was a collaboration that was extremely well received by the Romanian public. This was thanks to the Transavia range, Fragado, which is recognised for its high quality,
tenderness, and flavour.
This premium brand includes a range of fresh meat products which are portioned to serve individual customers and hotel, restaurant, and catering professionals. Under the Fragedo umbrella, the company has developed Fragedo Deli sub-brands, Barbecue, Marinés, and Selected Assortments, and Vin Prietenii la Tine – ready to cook specialities based on Transavia’s own recipes.
Papane, and the Papane Bistro range, offers a quick chicken fix with menus designed for active lifestyles, but also for those who want to eat healthily. State of the art technology is used to cook and freeze schnitzels, nuggets, burgers, and goujons, which also allows them to keep their taste and texture. Meanwhile, the Libertan range is natural, ethical, technologically advanced, and sustainable in terms of rearing chickens and processing the meat.
As consumers are always at the centre of Transavia’s business, its goal is to provide the best quality chicken meat, while focusing on market developments and local and international trends.
Veroniki Ecogroup is a company created in 2017 and is part of Veroniki Holding We produce food packaging using 100 percent post-consumer recycled flake materials with European Food Safety Authority (EFSA) and Food and Drug Administration (FDA) approved technology.
Transavia is committed to investing in renewable energy by adopting efficient technologies and equipment. With several projects that are already underway, this year the company will install 22,000 photovoltaic (PV) panels to produce green energy. This will eliminate the equivalent of the annual carbon emissions from 1,778 cars from the atmosphere.
The PV panels will be installed on the roofs of poultry farms and on the ground, depending on the structure of the buildings and their position in front of the sun. Currently, more than
100,000 square metres of PV panels are due to be fitted.
In addition to the PV panels, Transavia will implement two cogeneration projects with high electrical and thermal efficiency. The initiative is part of a sustainability strategy to minimise the company’s carbon footprint. By the end of next year, it should be able to produce 80 to 100 percent of the energy it needs.
To enhance the efficient use of energy, Transavia has specific measures in each operating unit. Thermal insulation of some houses and the microclimate automated
monitoring equipment in the broiler house will aid the reduction of energy consumption that the company has already made by replacing existing light fixtures with LED. Moreover, Transavia uses natural gas to produce steam that ensures technological flow to heat the chicken houses and administrative areas.
The significant reduction in carbon emissions will also have a positive economic effect as the benefits of Transavia meeting its own sustainability needs mean that the company will be protected from fluctuations in energy prices.
With 32 years of experience, Transavia continues to evolve and innovate by embracing modern technologies. However, the next step for the company is to expand international cooperation, strengthen existing partnerships, and increase exports.
veronikiecogrup.ro‘RELYING ON TRUST, CARE, AND RESPONSIBILITY, TRANSAVIA IS ABLE TO SUPPORT THE PROMISE OF WELL-MADE IN ROMANIA’ – TRANSAVIA
Domino’s Pizza (Domino’s) is the largest fast-food pizza chain in the world, standing above other giants in the industry such as Papa John’s, Pizza Hut and Little Caesars.
Writer: Marcus Kääpä | Project Manager: Liam PyeThe story of Domino’s began in 1960, when Tom and James Monaghan opened the first “DomiNick’s” store in Michigan (US). A year later, Tom traded his car to buy his brother’s share of the store and later renamed the business Domino’s Pizza, and the three dots on the company’s logo represent the three stores that Tom originally planned to open.
As the world’s leading pizza chain, Domino’s Pizza is a global name. We take a look at the company’s history, its presence in the EMENA region, and the passion for produce that drives the business forward
The business idea was simple: to deliver hot, freshly made pizzas as quickly and safely as possible, while playing an active role in the local community. Through a little-known format, now called franchising, Tom enabled other people to invest in opening their own stores.
Domino’s then expanded overseas; the company came to the UK in 1985, with the first store opening in Luton, Bedfordshire. Today, there are now over 1,200 Domino’s stores across the UK and the Republic of Ireland, with 35,000 team members delivering over 106 million freshly handcrafted pizzas a year. The expansion of Domino’s has also enveloped the Middle East, North Africa and Pakistan (MENAP).
Saudi-based Alamar Foods Company (Alamar) is a quick service restaurant (QSR) operator and the master franchisee of Domino’s, boasting more than 540 stores present in the MENAP region. For example, Domino’s Oman launched online pizza ordering in 2016 and
revolutionised the online delivery experience by launching the innovative Pizza Builder and Domino’s Tracker tools.
In the same year, Domino’s Oman launched the Domino’s Oman website, featuring the Pizza Builder which was a step forward in ordering food online, allowing customers to see their pizza come to life on the computer screen. Domino’s Tracker, meanwhile, was an innovation in food delivery, allowing customers to follow the progress of the order from the time it’s placed until they receive it.
The company also added pizza offers to the website in order to provide even more value to customers, allowing more people to get their hands on the brand’s most-loved flavours and high-quality ingredients, from chicken to beef, with a variety of vegetarian options and more. In 2020, Domino’s had 24 outlets located throughout Oman, a number that is continually increasing in order to serve more pizza lovers across the Sultanate.
• Domino’s is built on a simple, integrated business model. The company aims to deliver hot, freshly handcrafted pizza to its customers as quickly and safely as possible.
• Domino’s awards the right to operate local stores to ambitious franchise partners, who invest in setting up their own Domino’s business. This includes a programme offering current and former Domino’s colleagues the opportunity to own a store and become part of the franchisee system.
• While Domino’s is best known as a pizza delivery chain, it makes a massive chunk of its revenue by selling dough, ingredients, and toppings to other establishments.
It is due to the company’s longstanding mission that Domino’s has expanded and succeeded across multiple continents, with a passion for delivering hot, great-tasting, freshly handcrafted pizzas to customers. This relentless focus has helped Domino’s become a globally leading pizza brand in a number of countries across the world.
Quality is a key part of this mission as Domino’s is committed to offering choice, and with thousands of combinations on its menu, customers have plenty of options. Its pizzas are made with great quality sourced ingredients, such as creamy 100 percent mozzarella, vine-ripened tomato sauce, and the company’s signature fresh dough.
As well as having great tasting pizzas, Domino’s is relentless in its pursuit when it comes to using technology, to help make its
customers’ lives that little bit easier. The company works hard to make ordering quick and easy, putting customers in control, whilst a tireless focus on innovation drives continual improvements and ensures customers are always at the heart of all the great new products that are developed.
This customer-centric focus can be seen in the accessibility and ease of the Domino’s app, able to be downloaded on mobile phones for click-and-collect or delivery, including both order tracking and an up-to-date feed of the latest deals on offer.
The Domino’s vision is a simple one - to be the favourite food delivery and collection brand, with pizza at its heart. The company’s purpose, therefore, is to deliver a better future through the food that people love. For its customers, this means going above and beyond on quality and great value. Thus, Domino’s aims to innovate and consistently deliver a
Domino’s is the largest pizza chain in the world by gross sales. As the pioneer of fast pizza delivery and the “30 minutes or less” pizza delivery concept, this iconic chain began when the Monaghan brothers started running a local pizzeria called “Dominick’s”. What began as a small-town restaurant has since expanded to 15,900 stores in more than 85 countries worldwide.
Gross sales: USD$12.2 billion+
Headquarters Location: Ann Arbor, Michigan
Year established: 1960
Founders: James and Tom Monaghan
better food experience, while bringing people together to share in their love for pizza.
People are at the core of Domino’s. For colleagues and team members, this people-centric dedication means that there are opportunities to create and develop an exciting and rewarding career at the company.
Domino’s embraces diversity and fresh thinking and celebrates individuals who bring new experiences and ways of doing things to help Domino’s continuously push boundaries to drive improvement.
For the communities Domino’s serves, this means constantly seeking ways to deliver positive change for people and the planet. The company supports its local communities and believes growth and sustainability go hand in hand. When it comes to the company’s entrepreneurs and investors, Domino’s makes decisions that support long-term growth and
is open and transparent about the progress it is making.
This attitude encapsulates the importance Domino’s places on its many international partnerships. In the Middle East, one such partnership is with the global Lactalis Group (also known as Groupe Lactalis), of which Lactilis Saudi Arabia is a key dairy product manufacturing partner of Domino’s.
The Lactalis Group is a familyowned company driven by a passion for dairy that was founded in 1933 by André Besnier in Laval, France. A global player in the production and distribution of foods that are essential for everyday wellness, such as milk, dairy products (yogurt, cream-based sauces, desserts and cheese) as well as fruit beverages, the Lactalis Group is the number one dairy company worldwide.
Lactalis Saudi Arabia is proud to provide quality and healthy dairy products locally and internationally to partners such as Domino’s through its trusted brands: Président, Galbani, Pride, Bridel, Valbreso and Yasmin. The Lactalis Group offers a wide variety of products in different forms, including cheese, cream and butter, and it is partners such as Lactilis Saudi Arabia that help to drive the likes of Domino’s Oman in the region.
Domino’s passion is built on the collective values of the company workforce, values that everybody shares at the company. These guide everyday actions across the business, from Domino’s stores through to its supply chain centres and support office.
Domino’s intends to always do the right thing when it comes to its impact of the brand, colleagues, communities, and the wider world. Because of this, the company is proud to drive forward and keep its corporate promises.
Domino’s respects and celebrates its entire team for who they are and the value each individual brings. As such, the company grabs amazing opportunities to grow, succeed and ensure that its workforce operates at its best.
On top of this, customers are at the heart of every decision and action that Domino’s takes. The company listens to customers and creates great experiences to delight them and keep them coming back for more, and it takes courage and determination to lead the field. The company’s hard-working employees are bold, entrepreneurial, and aren’t afraid to innovate and learn fast to become better every day.
Most importantly, Domino’s ensures that all of its people grow and win together, sharing big ambitions, a growth mindset, and subsequently enjoying success as part of the team.
Makstil is at the forefront of environmentally friendly steel production practices. We speak to General Manager, Marija
Dukovska-Pavlovska, about industry changes and challenges in North Macedonia and beyond
Writer: Marcus Kääpä | Project Manager: Nicholas Kernan
Makstil finds it extremely exciting to showcase itself as a true example of having transited towards cleaner production processes, and we work hand in hand with the Ministry of Environment to reach our goals.”
The words of Marija DukovskaPavlovska, General Manager at Makstil, encapsulate the active change currently being undertaken in the European steel industry.
Majority-owned by the Swiss company Duferco, Makstil is a North Macedonian regional steel industry leader with a headcount of approximately 1,000 employees that operate across two production sites,
namely the Steel Shop and the Plate Mill. Makstil’s Steel Shop consists of an electric arc furnace (EAF) to produce liquid steel, a ladle furnace for secondary refining, and three continuous casting machine lines to transform liquid steel into slabs, with the company’s production capacity amounting to more than half a million tonnes per year.
The Plate Mill makes up the production side of the business, where produced slabs are reheated in a pusher furnace and rolled into plates in a high reversing mill, levelled, then cooled on cooling beds and mechanically cut or flame cut to the ordered size.
Marija Dukovska-Pavlovska Photography ©Ekonomija i Biznis Magazine Photography ©Viktor MáchaSpeaking to Tim Saxon, Chief Marketing Officer for Resonac Graphite, we learn about the vital role of graphite electrodes in the production of steel, and how the company is shifting in a more environmentally conscious industry.
Can you briefly describe your business and how you support Makstil?
Resonac Graphite (Resonac), formerly known as Showa Denko Carbon, manufactures ultra-high power (UHP) graphite electrodes which are critical components used in the remelting of steel scrap. To produce its steel plates and slabs, Makstil owns and operates an electric arc furnace (EAF). When using an EAF to produce steel, a high-powered electric arc is used to melt and recycle steel scrap into new steel. The electricity used to melt the scrap is transferred solely through the graphite electrode. In 2022, approximately 30 percent of the world’s steel (or approximately 565.5 million metric tonnes) was produced via EAFs – making steel the most recycled material in the world.1
As of 1st January, 2023, Showa Denko Carbon officially became Resonac Graphite BU. Why the change?
We like to say, “New look. Same values.” Showa Denko Carbon has a very strong name in the global steel industry, but our parent corporation has undergone a substantial transition over the past three years. In 2023, after acquiring and completing the integration of Hitachi Chemicals, the Showa Denko Group officially became Resonac – a company whose mission is to change society through the power of chemistry. The name “Resonac” was chosen to convey the desire to RESONATE with Chemistry. Much like our business unit which
literally transforms carbon into graphite, we recognise that the world is also undergoing fundamental change. As a global community, we must place a priority on sustainability and responsibility, recognising our obligation to future generations. We know our purpose is not just to simply manufacture and sell a product. As a business unit and corporation, it is Resonac’s responsibility to co-create innovative technologies and services with partners inside and outside of our business. With these synergies, we want our combined solutions to be more than just the sum of its parts. Fortunately, the “new” steel industry provides a multitude of opportunities for co-creation.
Speaking of increased focus on sustainability in manufacturing, how do you see your business changing?
The increased focus on sustainability and environmental stewardship is having a meaningful impact on the graphite electrode industry. As mentioned earlier, recycling steel via EAF only accounts for approximately 30 percent of the world’s production, but that method of production also results in approximately 75 percent less carbon emissions than other methods of steelmaking. 2 As more steelmakers focus on sustainability, the industry is seeing a considerable increase in the construction of electric arc furnaces, which will significantly increase the demand for graphite electrodes.
Given that, how does Resonac plan to address those issues?
The graphite electrode industry, much like the steel industry, is a cyclical one. Both industries also require significant capital investment and face major threats from offshore competition – particularly by government-subsidised producers who are not required to adhere to safety or sustainability standards.
Despite these threats, Resonac has a very strong history of investment in the global EAF steelmaking industry. The company (then Showa Denko) produced its first graphite electrode in Omachi, Japan more
than 85 years ago. Over the next several decades, Resonac grew the graphite electrode business as the EAF steel industry grew. In 1988, it purchased the Ridgeville, South Carolina facility in the US, and in 2017, purchased the A Coruña Spain, Steeg Austria and Banting Malaysia facilities from SGL Carbon. Resonac is now the world’s largest manufacturer of UHP graphite electrodes with plants strategically located to meet regional demand with regional supply.
Our most recent and perhaps most exciting investment, is the acquisition of Automation (AMI), which was announced in June 2023. AMI is an industry leader in providing innovative process control and automation technology that improves customer operating efficiency. AMI’s Meltshop Division is at the forefront of EAF automation and optimisation and has the largest group of EAF specialists in the world. The Industrial Systems Division is a prominent supplier of customised automation and power control systems for steel, paper, cement, oil and gas, transportation, and mining.
As an industry leader and vital part of the EAF steelmaking supply chain, Resonac is in a unique position to use our innovative technologies, our products, and our services to help in the transition from traditional methods of steelmaking to new, safer, cleaner, more efficient, and more flexible production. While we understand that business philosophies and practices are ever-changing, we are happy that we have ongoing projects and co-creative efforts with various partners around the world.
Does this include Makstil?
Yes, of course! While both companies historically maintained a very professional “buyer/seller”
relationship in the past, Resonac’s strong partnership with Makstil was solidified during the most extensive graphite electrode crisis to date. In late 2017, after years of (ex-China) graphite electrode production rationalisation, the Chinese Blue-Sky Initiative forced the immediate stoppage of approximately 40 percent of its graphite electrode capacity.3 Almost instantly, global EAF steelmakers were left without a way to melt the steel they were dependent on producing for their survival. Even if available, prices for electrodes increased by approximately 10 times in three months, which turned out to be a small price to pay for the ability to produce product and fill customer commitments.
Needless to say, the crisis found different suppliers and different consumers negotiating various, creative ways to withstand the predicament and keep the electrode supply lines open. Some of those solutions turned out to be less advantageous in the longer term, but proved necessary for the survival of several steel businesses.
During this tumultuous time, Resonac worked diligently to develop true “win-win” partnerships that will ensure our industry not only survives… but thrives during the next crisis. The framework of these partnerships was the foundation for Resonac’s Volume Supply Partnership (VSP), which was recently renewed by Maksil, as well as our Strategic Supply Partnership (SSP). We are now excited to start “co-creating” with selected partners on a new
Optimisation Supply Partnership (OSP), but more to come on that endeavour.
Makstil has discussed some projects and ambitious plans for continued diversification and expansion in the coming years, so you are confident Resonac can help them achieve their goals?
Absolutely. Although names can change, a company’s purpose and legacy lie in its DNA. At Resonac Graphite, supporting our partners in the electric steelmaking industry is exactly what we do.
1 World Steel Association (worldsteel.org)
2 Steel Manufactures Association (steelnet.org)
3 Industry estimates
The steel plates are used for applications such as shipbuilding, pressure vessels, bridge construction, mining and industrial machinery, and windmill structures, all of which require high quality and high strength. The Plate Mill gives Makstil the opportunity to offer its clients rolled plates with various dimensional ranges adapted to their needs. This represents the company’s trademark and is recognised by Makstil’s clients across Europe.
“As steel is an industry that has historically been associated with large amounts of emissions, I am very happy to say that is now in the past. We express pride in confirming that we are causing no direct harm to the environment through our production activities, and we have clear visibility on the impact of the Carbon Border Adjustment Mechanism (CBAM),” explains Dukovska-Pavlovska.
Makstil traditionally serves its domestic regional market and neighbouring countries, such as Bulgaria, Croatia and Serbia, with the majority of its sales in the markets of the European Union (EU), which North Macedonia is foreseen to join in the next decade according to the government’s
predictions. Moreover, for DukovskaPavlovska, the market seeing the biggest growth of late is Turkey, where Makstil’s customers take advantage of the geographical proximity and availability of the company’s final production output. Makstil’s distinctive adaptability towards its clients’ needs is also recognised across the pond, as the company exports non-negligent quantities towards the US and Canadian markets. However, Makstil’s operation in the steel industry has not come without its challenges.
“The steel industry is facing particular issues linked to the availability and sourcing of the raw materials and ensuring the uninterrupted supply chain needed in our production processes. In addition, it must confront the volatility and unpredictability in terms of prices,” elaborates Dukovska-Pavlovska.
“This can create confusing ground for us, as we want to maintain optimal prices for our clients, but we also need to fulfil the various commitments that Makstil has. This includes transitioning to a more resource-efficient production process, having the least possible environmental impact, and contributing to and supporting the
Marija Dukovska-Pavlovska, General Manager: “As a female leader who has progressed throughout my career by working within organisational development, finance and human resources in various industries, being offered the opportunity to lead one of the largest steel industrial companies in our region was obviously an enormous challenge for me, not least because of the perilous and complicated times we live in.
“I intend to use my time at Makstil not only to confirm and strengthen our position as a market-leading specialised steel producer, but also to prove that a woman can successfully thrive in what is often considered a masculine work environment and serve as an example for generations of girls and young women that they too can indeed succeed in fields where their success isn’t necessarily guaranteed from the beginning.”
local communities where we operate. We also want to be at the forefront of circular economy practices, not only within the North Macedonian industry, but also regionally.”
By design, Makstil is a mini steel mill. Unlike the integrated mills that produce new steel from iron ore in a blast furnace (BF), mini steel mills such as Makstil melt, refine and recycle scrap metal by using EAF technology. By using this technology, Makstil belongs to the 30 percent of steel producers in the world leveraging this more environmentally friendly method compared to BF. Furthermore, as an active participant and supporter of the circular economy, Makstil only uses scrap metal as an input material for the production of slabs and hot rolled plates as a final product.
“Makstil is focused on saving the resources we use in our production processes (natural or otherwise). We actively support the concept of the circular economy by encouraging the rational use of secondary raw material (steel scrap) as well as the reduction, reuse, and recycling of waste,” says Dukovska-Pavlovska.
WWTECH provides its clients with a complex way of problems resolving, offering them three-dimensional coordinate measurements and a full 3D documentation. Due to accurate measuring devices FARO (Laser Tracker, Measuring Arm) WWTECH makes it is possible to carry out uniquely accurate, fast and non-contact measurements, the results of which can be analysed in a real time.
Fully functional equipment is fundamental to the company’s success. Every machine has precision elements, bearings, and a number of other parts, that enable its efficient operation. Those main elements, which ensure correct machine operation, require specific solutions in case of a breakdown. Leaks, cracks and grooves are issues that have to be eliminated to ensure proper operation.
In all undertaken activities, WWTECH gives priority to safety. The health of our staff, society, and respect for the environment are the factors which determine our whole team’s activities, and other aspects of our work, such as transportation or cooperation with a third parties.
www.wwtech.com
“All metal waste generated during the production process, and part of the refractory waste, is returned to the very same production process. The remaining waste that cannot be recycled is further selected and disposed of, to be handed over to authorised and trusted partners for their own use downstream.”
According to Dukovska-Pavlovska, any inert and non-hazardous waste, such as slag from an EAF, through the process of crushing and separating, is divided into fragments and is transformed from waste into raw material where it can be fully used as a buffer for road construction, as well as a foundation for an asphaltic or concrete pavement, cement, and various cement products.
This circular economy is designed to save natural resources and energy, creating added value and ultimately a healthier and cleaner environment with new employment opportunities. On top of this, it improves product competitiveness, focuses on positive society-wide benefits, and provides increased earnings that contribute to the sustainable development of modern civilisation and an economy fit for the challenges of the years ahead.
“At Makstil, we are proud to take the lead on these initiatives and believe we are setting an example not only for other fellow companies in our industry, but also towards those working in fields very different from our own,” Dukovska-Pavlovska adds.
“I am especially humbled by Makstil being awarded as the most environmentally friendly company,
granted by the municipality where we are based (which is also home to other heavy industry actors). The Green Agenda award from the Economic Chamber of North Macedonia further confirms Makstil’s contribution towards safeguarding the environment as well as our commitment to zero waste.”
Despite its size as a mini steel mill that produces steel plates from recycled scrap, Makstil is present in the markets of more than 40 countries and collaborates with approximately 500 customers, reaching trading destinations in several continents and meeting the needs of the most demanding clients. Makstil prides itself on offering a 45-day delivery window, with the flexibility to provide specific materials necessary for projects at the exact requested time, and answers to complicated specifications with no limitations in terms of the number of ordered pieces, dimensions, and qualities within the company’s product range.
“We are recognised for our excellent after-sales service with a prompt response time, yet one of our key features of business for clients is our dedication to practices that are more environmentally friendly,” Dukovska-Pavlovska says. “One of our leading environmental protection activities, from both a technical and financial aspect,
“MAKSTIL FINDS IT EXTREMELY EXCITING TO SHOWCASE ITSELF AS A TRUE EXAMPLE OF HAVING TRANSITED TOWARDS CLEANER PRODUCTION PROCESSES, AND WE WORK HAND IN HAND WITH THE MINISTRY OF ENVIRONMENT TO REACH OUR GOALS”
– MARIJA DUKOVSKA-PAVLOVSKA, GENERAL MANAGER, MAKSTIL
General Manager: “During the last five years, Makstil heavily invested in the field of health and safety for all its employees. Our Board of Directors and management commitment is of paramount importance for stepping up and leading the whole process by example through the top-down approach.
“Our commitment to the ISO 45001 occupational safety and health management was integrated during the last year at all levels of the company. I would like to underline that in addition to achieving the highest quality production and financial results, the company has maintained an optimal level of health and safety of our employees and improvement of the working conditions.
“We should not forget that this industry is one with a high risk, and we continuously work on process and equipment improvement to enhance workplace safety. In parallel with that, we continuously increase awareness of all employees to identify potential risks and to participate in developing countermeasures. Monitoring the trends in the industry, we are following many indicators related to health and safety, and our strategic goal fully encourages, motivates, and obliges us to be a company that has a “zero by choice” approach.”
was the installation of the Dedusting System in the Steel Plant (Filter Plant – FP) carried out back in 2015. Thanks to this investment, we succeeded in almost completely absorbing the dust particles emitted during the melting process. This dust is then packed, and we get further value from it as we collaborate with verified external partners for its collection and distribution outside Makstil.
“For more transparency with our stakeholders, Makstil continuously monitors the dust emissions in the air and on a quarterly basis publishes the results that are fewfold lower than allowed by local and EU norms. Makstil continued the practice of publicly announcing the emissions of solid particles emitted from the production chimneys during the operation of the factory, which once again confirms the company’s commitment to promoting full transparency in its business operations.”
Makstil is the first company in the country to obtain an Environment Product Declaration (EPD) for hotrolled plates. With the EPD, Makstil confirms its commitment to protect and preserve the environment
satisfy the needs of its customers in an
by continually reducing the environmental impact of its products. The declaration provides an overview of the objective, verified, and comparable environmental performance of the hot-rolled plates manufactured on the company’s production site.
The environment and employee well-being are the twin pillars of Makstil’s vision. Regarding the latter, the company has achieved significant results in employee retention and satisfaction through renewed and innovative solutions aimed at better engagement and fair reward systems and plans for its workers. Yet the
business’ operational focus is set on the continued sustainability-centric mission to help alter the industry for the good of the planet.
“Overall, the industry is dealing with different sets of specifics; regulatory, environmental, availability of raw materials, or qualified staff – you name it,” Dukovska-Pavlovska tells us. “Adjusting an entire robust steelmaking organisation with traditional business practices to new production process trends is a challenging enough activity for a female leader, especially with the new challenges regarding the transformation of production towards green steel. It is an industry environment where personal resilience and the ability to
innovate is critical to staying ahead while fully satisfying and retaining the loyalty of our clients. Nevertheless, Makstil has successfully proven that this is an achievable goal despite the challenges posed.”
Viewing itself as the frontrunner of environmental improvements in the heavy industry sector in North Macedonia, Makstil is following a vision to produce steel plates that satisfy the needs of its customers in an environmentally sustainable way, and it has already started with activities related to the decarbonisation process that it will continue moving forward.
“Decreasing greenhouse gas (GHG) emission levels requires the
introduction of some changes in all production aspects as well as delivering goods and services. In this context, Makstil has already introduced investments in renewable energy and carbon-free sources,” Dukovska-Pavlovska concludes. “We are proud of what we have achieved thus far, and we thoroughly follow the European Commission’s goals of reaching net zero by 2050.”
As the company boasts some of the most advanced equipment in the industry, CCO Peter Dijkstra discusses how Trymax Semiconductor Equipment B.V. has achieved this unique position
Amongst many titans of the manufacturing industry in the Netherlands, Trymax Semiconductor Equipment B.V. (Trymax) is the company of choice for the design, manufacture and marketing of plasmabased processing and equipment solutions. Trymax was first founded in 2003. Its name stands as a re-lettering of the Matrix plasma asher machines that are widely regarded in the industry.
“Our mission was clear, to provide service and support for European customers who depended on Matrix-like machines,” Peter Dijkstra, CCO of Trymax begins.
As time went on, the company faced new challenges; between 2007 and 2009, it realised that the ageing Matrix machines had exceeded their serviceability limits, prompting Trymax to start manufacturing its own equipment.
This signified a major transformation, as it shifted from a service-orientated provider to a cutting-edge manufacturer.
“This strategic move allowed the organisation to adapt to the evolving semiconductor landscape and stay at the forefront of technological advancements,” Dijkstra tells us.
Trymax’s headquarters, situated in Nijmegen, has an impressive total capacity of 4,200 square metres (m2), which includes a manufacturing cleanroom, a state of the art demo lab, an engineering and manufacturing area, and a logistics, storage, and technical area, with an equipment build capacity of up to 250 toolsets per year.
When situated within the wider network of facilities, Trymax is proud to be the number one European semiconductor equipment cluster, with one of the strongest supply
“Trymax is like one big family. We go above and beyond to employ a talented team of experts in the field of low-temperature plasmas, subsequently ensuring best-inclass plasma sources and solutions. Therefore, all positions are important to ensure that we supply quality performance and agreed upon equipment on time.”
- Peter Dijkstra, CCOchains. This position is bolstered by the fact that Trymax does all its final assembly and testing in-house, ensuring streamlined operations and maximum efficiency across its entire production.
The company’s service offering entails diligent plasma solutions in ashing, descumming, etching, surface preparation, and ultraviolet (UV) curing and charge erasure. To achieve this, Trymax provides an industryleading product line known as NEO, which is designed to address a wide range of applications throughout the semiconductor manufacturing process.
All platforms found in each NEO can handle two or more substrate types and sizes simultaneously without any hardware changes. Furthermore, each product has a strong focus on all types of substrate handling, catering to substrate sizes from 77 millimetres (mm) up to 330mm, with a focus on 150mm,
TES-CleanAir Systems and Airflotek are the leading supplier of standard, non-standard and custom engineered fan filter units (FFU), for semiconductor process tools, equipment front end module (EFEM), pharmaceutical restricted access barriers (RABS), Pharmaceutical battery powered transfer carts, Nuclear HEPA fan units, nuclear bag-in/bag-out HEPA filtration units, OEM memory, and various mini environment applications.
For more than 30 years in business, we have grown to be an industry leader by building strong relationships with multiple vendors, cleanroom product providers, manufacturers, and customers. These collaborations have helped to grow our knowledge base so we can identify the exact needs of our customers and find a solution that is the right fit for each unique application.
As a proud supplier to Trymax Semiconductor Equipment B.V. since 2009, our long-standing partnership proves our dedication and commitment to our mission of Reliable ProductUnmatched Service - Satisfied Customers.
For more information, please visit us at: www.tes-cleanairsystems.com and www.airflotek.com
TES-CleanAir Systems
242 W. Larch Road, Suite F Tracy, CA 95304 510-656-5333
www.tes-cleanairsystems.com
Airflotek 1075 Highway 124 Building 300, Suite 400 Hoschton, CA 30548
678-475-9800
www.airflotek.com
• Reactive Ion Etching (RIE)
• Microwave
• Dual Source (DS)
• Directly Coupled Plasma (DCP)
• Capacitively Coupled Plasma (CCP)
Depending on the number of wafers a customer prefers to run, Trymax has platforms for:
• 100 wafers per hour (single chamber system)
• 150 wafers per hour (double chamber system)
• 240 wafers per hour (four chamber system)
200mm and 300mm. Further features include platform flexibility with five different process modules, alongside a detailed system configuration based on the application specification budget.
With a global network of processing chambers, Trymax puts its burgeoning success down to the precision of its NEO products, as its equipment sets the company apart with its ability to process two different wafer sizes simultaneously. This feature proves particularly valuable in a transitioning market, such as the LED industry, in which Trymax’s
machines can process wafer sizes from 150mm to 200mm, outrunning older machines that need extensive modifications to accommodate new wafer diameters.
“By already accommodating varying wafer sizes, Trymax’s machines mitigate the risks associated with equipment reconfiguration,” elaborates Dijkstra.
“An additional feature is the machine’s automatic recognition of wafer size and the ability to handle it seamlessly, streamlining production processes and enhancing efficiency.”
At the peak of Trymax’s innovative
FIVE DIFFERENT PLASMA SOURCE TECHNOLOGIES COMMERCIALISED BY TRYMAX
“WE RECENTLY OPENED A SALES AND SERVICE OFFICE IN THE US. AS SUCH, OUR TARGET IS TO INCREASE SALES, BUT WITHOUT LOSING QUALITY, PERFORMANCE AND INNOVATION”
– PETER DIJKSTRA, CCO, TRYMAX SEMICONDUCTOR EQUIPMENT B.V.
Scope of Application:
• Photoresist stripping
• Isotropic etching
• Surface cleaning and conditioning
Typical etching rates are:
• Photo resist 5µm/min
• Silicon 3µm/min
• SiN and BPSG 1µm/min
• Thermal Oxide 250nm/min
eeplasma produces microwave plasma sources for Trymax for the photoresist strip and isotropic etching processes for semiconductor production.
• The plasma sources have a maximum power of two or three kilowatts (KW) and the plasma chamber can be equipped with quartz, ceramic or sapphire tubes.
• The plasma source is characterised by its very compact design, its high level of service friendliness and its very large process window.
solutions, it deploys a sophisticated robot arm that can be equipped with several specialised substrate gripping tools, designed for a diverse range of uses, whilst greatly advancing the organisation’s product line.
Correlating with the technical innovations of the company, Trymax is honoured to participate in a multitude of projects that facilitate a better and more sustainable future. Projects like SMART Photonics, for example, allow a much higher data exchange rate by using optical communication. This offers a vital aid to hospitals, providing significantly important components to a vast range of medical equipment.
Additionally, the power management integrated circuits (power IC) markets in each NEO have recently had a renewal, as the silicon
was replaced by short interval control (SiC) material.
“Industry leaders have made a calculation that suggests if we replace all silicon material for power applications by SiC, we can skip 880 nuclear power plants worldwide, making a huge impact,” Dijkstra informs us.
Furthermore, as a key support to the company, Trymax’s logistics supply chain is essential for streamlined operations. Receiving all components and materials on time results in shorter lead times.
“We work very closely with all our suppliers. A good example of this was during the COVID-19 pandemic when a major German customer ordered several ashing tools. We couldn’t supply all the tools on time, due to missing an essential component from a German company.
“Following our customer’s intervention, who purchased the
missing component, we managed to reduce the delayed shipping time, providing an indispensable helping hand,” he recalls.
As the year continues, Trymax is focusing on increasing its market share in the manufacturing industry. It has much to look forward to as the semiconductor sector expands its capabilities, including new UV curing technology.
To be a proactive part of the industry shift, the company brings to the fore the NEO 2000UV tool, an advanced UV curing and charge erasure system which utilises a single UV bulb. The new equipment acts as a bridge tool for two wafer diameters and is specifically designed for applications from three to eight-inch substrates, enabling greater accuracy.
Consequently, due to its highly ultra-modern technology and
influential presence in the industry, Trymax has experienced market recognition from many major automotive suppliers to the German, South Korean, North American, and Japanese car industries.
“We’re currently number one in Europe and number two in China. Additionally, we recently opened a sales and service office in the US. As such, our target is to increase sales, but without losing quality, performance and innovation,” Dijkstra closes.
From design to production: your partner for high-quality solutions.
Despite significant regional and global disruption in recent years, Metinvest Trametal has resolutely overcome adversity to remain at the forefront of steel plate manufacturing, as Managing Director, Roberto Re tells us
Writer: Jack Salter | Project Manager: Nicholas Kernan
taly is a leading industrial hub in Europe, with a high concentration of enterprises active in the construction, machinery, transport, and energy sectors.
Many leading Italian, and indeed European industrial players, are customers of Metinvest Trametal (Trametal), one of the continent’s foremost steel plate manufacturers located in San Giorgio di Nogaro.
“We serve more than 700 industrial customers, and our core sales markets are Italy and Germany, the two main steel consumption regions in Europe,” states Managing Director, Roberto Re. Founded in 1985 and part of the Metinvest Group (Metinvest) since 2008, Trametal rerolls semi-finished steel slabs into plates according to the final use requirements of various projects, such as bridges and other big structures, ships, specialised machinery, vessels for liquids and gases, and more.
The company’s steel plates have been used as the structural core for many iconic projects in Europe and beyond, namely the San Giorgio Bridge in Genoa, the sarcophagus of the Chernobyl Nuclear Power Plant in Ukraine, and the Hudson Yards Cultural Centre in New York to name a few.
Trametal’s production process comprises three main phases, the first of which preheats semi-finished steel slabs to temperatures exceeding 1,100 degrees Celsius.
The slabs are then passed through a rolling strand that consists of four vertically aligned rolling cylinders, reducing their thickness from 250-300 millimetres (mm) to just 12-100mm. This phase not only forms the plates in the required dimensions, but also guarantees the mechanical properties of the material, such as strength and toughness.
In the third and final phase, the rolled plate goes through the necessary final procedures. Additional reheating, for example, can improve the internal structure of the plate, which is especially important for use in heavy duty structures.
“Other final procedures may include levelling, surface treatment, trimming plate edges or cutting the plate into the initial shape, and various testing techniques,” adds Re.
With a state of the art production facility, the company is responsible for around five percent of total steel plate production in Europe, equating to around 550,000 tonnes per year.
However, production has been impacted by a number of disruptive regional and global events in recent years.
The onset of the COVID-19 pandemic led to the temporary halt of industrial activity in Italy, affecting Trametal’s output in Q2 2020 before the gradual reopening of the economy allowed it to recover and perform strongly in 2021.
Further significant disruption in the European steel market has since been caused by Russia’s full-scale war in Ukraine, and subsequent sanctions introduced by the EU against Russia have drastically shifted the market balance for Trametal’s products in Europe.
“More than three million tonnes of Russian finished steel was banned from the EU, and Ukrainian imports were significantly reduced due to interrupted production and the blockade of seaports,” Re explains. The spiralling energy tariffs caused by these sanctions, and supply interruptions for natural gas and crude oil, resulted in European production costs increasing by up to
30 percent.
Although energy tariffs gradually went down by early 2023, the inflationary spike is still out of control and interest rates will remain elevated in the near term.
In such conditions, credit availability is significantly restricted, especially for smaller businesses, negatively influencing the confidence of industrial buyers in terms of customer relations, steel purchasing, and the level of service.
“Our customers in downstream industries such as machine building and construction are currently living through a crisis of confidence caused by the lack of credit and geopolitical turmoil,” acknowledges Re.
“EVEN DURING THE WAR IN UKRAINE, THE COMPANY REMAINS A STRONG AND RELIABLE PARTNER FOR OUR KEY CUSTOMERS IN EUROPE”
– ROBERTO RE, MANAGING DIRECTOR, METINVEST TRAMETAL
- A constantly growing reality;
- 20 years of experience in the iron and steel industry;
- Certified UNI EN ISO 9001 IAF 17, UNI EN ISO 9001 IAF 18 and UNI EN 1090 company;
- Construction and installation of metal structures in medium-heavy carpentry;
- Assembly, disassembly and demolition of industrial plants.
www.cromes-srl.it
Information: info@cromes-srl.it
Phone: +39 030 6381678
Roberto Re, Managing Director: “Over the last five to 10 years, we have observed more of the initial processing of steel, such as large format cutting, shift from final customers upstream to intermediaries or directly to plate mills. Moreover, plates with trimmed edges are the format of choice for many customers in Europe, and we were facing a limited capacity to process the required volume of material.
“After a detailed assessment of market requirements, in 2020 we completed an investment into a new cutting centre. We have enlarged the working area of the mill, and installed an advanced high productivity plasma-cutting machine.
“The new equipment enables us to process customised plate formats including pre-worked shapes and edges for welding operations. We have also de-bottlenecked our regular edge trimming operations, allowing us to produce material according to prevailing customer requirements.”
Prior to the war, Trametal was fully integrated in the Metinvest supply chain and was getting all its core raw materials – steel slabs – from sister companies in Ukraine.
This integrated production chain meant that Metinvest was controlling the quality of products and reliability of delivery, from the extraction of raw materials (iron ore and coal) through to steelmaking and finished steel manufacturing.
Sadly, an attack on Mariupol, which is the site of Metinvest’s two key steel mills, Azovstal and Ilyich Steel, meant that Trametal lost captive slab supply of around 600,000 tonnes per year.
“We certainly plan to recover our captive slab supply, which would restore the standing of Trametal as an integrated supplier,” Re affirms.
Thanks to the exceptional resilience of Metinvest and its willingness to protect its European business, Trametal has managed to switch the
procurement of slabs from group sources in Ukraine to independent suppliers in Europe and other regions, mainly Asia and India.
After the initial period of crisis management, Trametal has thus temporarily shifted to its “standalone” business model of working as an independent reroller.
“Even during the war in Ukraine, the company remains a strong and reliable partner for our key customers in Europe.
“Maintaining our customer base through this challenging period, and providing the required level of service and product quality, has been an extraordinary achievement,” emphasises Re.
The shift in suppliers became an enormous challenge for Trametal, as the regularity and reliability of supplies had changed and the production team had to switch rapidly to new specifications compared to
Projetman
the previous 15 years.
“In the transitionary phase of the next two to five years, we may prioritise suppliers with a lower carbon footprint in order to improve our product portfolio and be economically sound once the Carbon Border Adjustment Mechanism (CBAM) comes into force in 2026.”
Despite the near-term challenges posed in particular by the war in Ukraine, Trametal sees exciting prospects for its products in the longer run due to the European Green Deal and the future transformation of industries and infrastructure.
The green transformation requires additional renewable energy equipment, such as the construction of wind farms and the dynamic growth of electric transport and its related charging infrastructure.
Finally, and most importantly, new
KeyDevelopmentSectors:
§ Steel mills
§ Integrated projects
§ Automatic warehouses
§ Rubber hoses production lines
§ Galvanic plants
§ Cranes / Lifting systems
§ Handling systems
PHONE: (+39) 035 83.24.18 | FAX: (+39) 035 83.31.26
Vat: 02427360165 | info@projetman.com | www.projetman.com
standards and regulations aiming for improved environmental footprints at the construction and utilisation phases will be introduced over the next two or three decades.
“For us, all these changes mean the emergence of new projects based on steel plates, produced to the most advanced environmental standards,” outlines Re.
As a European producer, Trametal was involved in discussing and shaping local and imported steel regulations amid the EU’s ongoing green transition.
Among other things, the company has also formally assessed its carbon footprint, which is low considering the nature of its rerolling operations, and issued its Environmental Product Declaration in 2023, which is the current industry standard in terms of footprint assessment.
The majority of the emissions embedded in Trametal’s products
currently arise from the level of steelmaking in the various regions where it now procures slabs.
“Ideally, we will strive for the usage of low-emission slabs as a feedstock in the next five years and the longer run,” Re shares.
Meanwhile, Trametal plans to consolidate in the shipbuilding and industrial infrastructure markets, where it is a leading player.
Fundamental changes have been brought to the former in the last 20 to 30 years, as the manufacturing of tankers and cargo ships has completely relocated from Europe to Asian hubs such as Japan, South Korea, and China.
However, the most lucrative highvalue segments of shipbuilding, passenger vessels, and specialised niche vessels such as Arctic explorer ships have remained in Europe.
Projetman Macchine S.r.l. operates for more than 40 years on domestic and international Markets in order to supply its customers machines and technological plants. Projetman Macchine S.r.l. stands beside the Customer in the design, development and construction of machines and technological systems, acting as a "partner" for the creation of "customer tailored" solutions. Projetman Macchine S.r.l., an Italian company specialised in the design, development and construction of machines and technological systems, has operated for more than 40 years on domestic and international markets.Roberto Re, Managing Director: “During my youth, I met perhaps the most important person in my personal and professional life, Bruno Spotorno. We were neighbours, and attended the same university where I received my engineering degree.
“After around six years of working in telecommunications, Bruno offered me the opportunity to join him at a steel company. He was looking for a young specialist with sales skills, a lot of energy, and a willingness to take on challenges, so he could dedicate himself to the technical and production side of the business.
“Initially I was not too excited about the prospect. It seemed like an “old economy”, but my curiosity convinced me to pay a visit to Trametal’s production site in late 1998. After this visit, on the back of my trust and respect for Bruno and in view of the strong support from the Malacalza family, who owned Trametal at that time, I decided to take the step.
“It was and still is a fantastic journey, even if I strongly suffered from the loss of Bruno who died in a tragic accident in December 2016, which remains my personal tragedy today.”
“Several players in Europe, such as Fincantieri Group in Italy and Meyer Weften in Germany, are dominating the global cruise ship market with long, high-value order books. These companies are among the key customers for Trametal and our strategy has always been to provide the best possible products and services to big shipyards.”
As a specialised producer of steel plates for the shipbuilding industry, Trametal is able to produce both wide (3,000mm) and thin (4-8mm) plates that are required for certain parts of ships.
Such material has to be fully certified by shipbuilding societies including DNV GL, Bureau Veritas, and Lloyd’s Register.
“Certification is a complex process of production site inspections and quality assurance for each delivered batch of material,” Re informs us.
There are also some additional customer requirements related to the
basic preparation of material before delivering it to shipyards, such as surface cleaning and painting, which the company is able to provide.
Trametal was built with niche segments such as shipbuilding in mind, and in time has become a supplier of choice for many key players in Europe.
“Over the years we added equipment and processes to fulfil the most complex requirements in the shipbuilding segment.”
The situation is similar in the industrial infrastructure market, where Trametal works with several leaders in the manufacturing of bridges and large structures in Italy and across Europe.
To guarantee the long-term reliability of industrial infrastructure projects, Trametal’s steel plates must correspond with very strict requirements in terms of dimensions, strength, and the quality of the internal structure.
In sectors such as shipbuilding, construction fabrication and specialised machinery, Trametal has demonstrated its flexibility and customer orientation over the years through a number of strategic partnerships.
Indeed, the company’s core competitive advantage is the ability to tailor its production and service to the needs of key customers.
“We are also proud to have one of the most competent sales networks among Italian producers, with specific competencies in our target industries,” adds Re.
Trametal likewise continues to upgrade its equipment in order to provide state of the art products and services to customers.
The majority of current investments
are operational rather than strategic, however, the company is always in dialogue with customers in order to assess emerging opportunities.
There is an extensive project pipeline related to the post-war reconstruction and modernisation of Metinvest assets in Ukraine, including investment in the group’s iron ore mining facilities to expand the production of direct reduced iron ore pellets, a key raw material for European green steel.
“We also plan to upgrade our steelmaking equipment in Ukraine to bring it up to date with the evolving requirements for low-emission steel in Europe,” Re says.
This ties into Trametal’s objective for the remainder of 2023, which is to ensure competitive service, quality and prices for customers in order to reach target production and profit levels.
Looking further ahead, the company expects the market climate to significantly improve on the back of economic recovery and the emergence of various steel-intensive public and private projects in Europe.
“We aim to expand our existing strategic contracts in Europe and acquire new ones, mostly in our core segments of steel construction, shipbuilding and energy, and to guarantee quality products independent of raw material market disturbances,” concludes Re.
METINVEST TRAMETAL
Tel: +39 010 576 2911
trametal@trametal.it
metinvestholding.com
trametal.metinvestholding.com
“WE CERTAINLY PLAN TO RECOVER OUR CAPTIVE SLAB SUPPLY, WHICH WOULD RESTORE THE STANDING OF TRAMETAL AS AN INTEGRATED SUPPLIER”
– ROBERTO RE, MANAGING DIRECTOR, METINVEST TRAMETAL
For almost 200 years, Höganäs Borgestad Group (Höganäs Borgestad) has mastered the design of refractories, materials highly resistant to heat and critical to a multitude of industries within the manufacturing space.
Headquartered in Sweden, the company is a small but key player in the field of refractory production, working with companies of all sizes across Europe, helping drive forward industrial sustainability practices from Nordic countries.
Höganäs Borgestad understands that designing refractories is an art that has developed through the centuries, where material composition, grain size and density are combined with precision. Meanwhile, thermal conductivity, permeability, abrasion resistance and thermal expansion are measured meticulously, as necessary for operational needs.
This is something that the company has perfected over the years. Indeed, since the industrial revolution, customers have turned to Höganäs
Borgestad for their most challenging requirements, and together with such customers, the company has developed turnkey solutions.
“Making refractory materials may seem simple, but there is much more to it; they are the result of engineering, experience, innovation and passion,” introduces Hanna Landell, Managing Director of the Production Unit at the company.
“Through close partnership with our customers, we know that cement and steel producers, along with other industries around the world that require top-notch refractories, are not actually looking for shaped or unshaped solutions. They’re looking for something else - something that will support their profitability and efficiency ambitions, and something that will deliver value longer than any other refractory.”
In light of this, customers turn to Höganäs Borgestad for turnkey solutions. Moreover, the company works closely with them all the way from design and installation to support, maintenance and beyond.
Writer: Marcus Kääpä | Project Manager: Nicholas KernanHöganäs Borgestad is a traditional Nordic producer with a main market presence in the Nordic region, but also a global presence with customers in more than 70 countries. This international market penetration has been achieved through following customers abroad to deliver global production units as the company has in the Nordics.
“It is very exciting to work in the Nordics at the moment,” says Landell. “There are so many big initiatives in various industries and all of them with a focus on reducing CO2 emissions and being fossil fuel free.”
According to Landell, the Nordics represent a small yet impactful market, in many ways driving development in the industry. Refractory technology itself is also seeing continual advancement with innovative ways being discovered that minimise the environmental impact of refractory production. Within this, there exist new materials and new technologies in order to make the refractory process more sustainable.
“In the past, refractories have sometimes been seen as commodities, but now more than ever they are being viewed as high-value products that need to be durable, high performance and green,” Landell continues.
“This sustainability-centric view is becoming increasingly important for
Hanna Landell, Managing Director - Production Unit: “The first time I encountered refractories was in 2009 during my studies. I wrote an essay at the installation company Macon, which was part of Höganäs Borgestad. Before this, I didn’t know anything about refractories.
“After my studies, I continued consulting in the company for around 18 months before I entered the steel industry. In 2016, I got the opportunity to come back to Höganäs Borgestad and the refractory industry and have been here ever since. It is a very interesting space!”
us as well as the customers we serve, and it is the direction that we – and much of the industry – is headed.”
For Landell, the refractory and manufacturing space in Europe is equally interesting as it is challenging. The steel industry, for example, is
a strong sector and one in which continual advancement and innovative initiatives are being driven forward, with its future geared towards going green and away from a reliance on fossil fuels. Of course, this then has its own impact on the refractory space; new production methods require new designs, new materials, and production adjustments, making the space full of busy developments.
“A lot is happening! We are seeing a great deal of interest regarding secondary raw materials – which can be used in manufacturing processes in place of or alongside virgin raw materials – as well as circular business models,” Landell explains.
“This level of change shows that sustainable production methods are on everybody’s agenda.”
This is an area in which the Nordics boast a foremost position, far ahead of other countries in Europe and leading the drive with their industry initiatives.
This environmental drive is showcased in Höganäs Borgestad’s own production methods. The company utilises recycled materials and applies a greener production process, for example having the option of using electricity generated by hydropower, with furnaces running on natural gas. Höganäs Borgestad has used recycled materials in the core of its products for many years now, but the company’s aim is to constantly increase the amount used and is planning investments in production equipment to increase this scope.
However, it is Höganäs Borgestad’s collaboration with its customers that sees the company make a truly greater and better impact on the environment.
“We have been working with businesses on reducing energy consumption for many years, but now there are other initiatives on top of this, and these only provide more opportunities for us to help companies make such an impact,” Landell affirms.
“Höganäs Borgestad is working on a number of projects. In the cement industry, for instance, one of our recent and ongoing projects revolves around the refractory design and linings, and this is aimed towards decarbonising the sector overall.”
In the automotive space, Höganäs Borgestad is utilising its production facility and its knowledge of materials to reduce CO2 emissions in automotive production.
Each of these kinds of developments further impacts the refractory industry, leading players such as Höganäs Borgestad to think outside of the box and seize opportunities when it comes to production development, utilising
industry knowledge to the advantage of partnering businesses and the environment.
“Höganäs Borgestad is quite a small company, but we work with a large variety of industrial players,” Landell tells us. “We can also be quite specific in our offerings when it comes to delivering customer needs and making specific developments for such clients.
“This is the strength of having R&D and production in place because we can cater to different companies of different sizes with various needs.”
Not only does Höganäs Borgestad boast professional R&D and production teams, but the company also has its installation department that tries to install the materials directly. This level of combined capability makes Höganäs Borgestad a strong partner in the market to go to, the primary advantage of being a smaller and more flexible provider.
It is because of Höganäs Borgestad’s reliability and professionalism that it has been chosen as a partner to multiple European industry players. At the end of 2021, Höganäs Borgestad made the strategic decision to cease the production of standard bricks in Sweden and instead become more specialised in the market. The company subsequently entered a partnership with German firm Refratechnik Holding GmbH (Refratechnik), revolving around sourcing those types of specialised products to Höganäs Borgestad.
Today, Höganäs Borgestad produces unshaped products, special bricks and hand-rammed products at its plant in Bjuv (Sweden) with the other bricks coming from Refratechnik, as Höganäs Borgestad is now Refratechnik’s chosen partner in the Nordic countries.
Höganäs Borgestad also cooperates on some projects
INCREASE THE PRODUCTIVITY AND COMPETITIVENESS OF OUR CUSTOMERS. OUR MAIN GOAL IS TO OPTIMISE YOUR BUSINESS AND WE STRIVE TO SET NEW INDUSTRY
“OUR VISION OF “SETTING NEW STANDARDS” MEANS THAT WE ARE SETTING THE LINE. OUR VISION IS TO OFFER THE MOST EFFECTIVE HIGH-TEMPERATURE SOLUTIONS THAT
STANDARDS”
– HÖGANÄS BORGESTAD GROUP
outside this territory. The quality of Refratechnik’s products meets high standards regarding technology and sustainability and for both companies, their combined knowledge is a strong competitive advantage.
“Refratechnik has a lot of
developments and production in Europe as well as outside of the continent, and it is also close to where we operate which is very helpful strategically,” Landell says.
“But importantly, Refratechnik already makes use of recycled
materials and has a very sustainabilitycentric approach to its operations and business, as well as innovative thinking.
“Combining our knowledge about certain industries and markets makes our partnerships very positive,
“COMBINING OUR KNOWLEDGE ABOUT CERTAIN INDUSTRIES AND MARKETS MAKES OUR PARTNERSHIPS VERY POSITIVE, EFFECTIVE AND IMPACTFUL”
– HANNA LANDELL, MANAGING DIRECTOR - PRODUCTION UNIT, HÖGANÄS BORGESTAD GROUP
effective and impactful.”
Moving ahead, Höganäs Borgestad is looking towards a green future. Sustainability is the foundation of the company’s strategy, and it hopes to launch some new products this year geared towards helping customers reduce their environmental impact. Decarbonising various industries will require innovation and investment; to do so, Höganäs Borgestad constantly challenges existing solutions in the pursuit of something better and finds new ways to solve the challenges of
today and tomorrow.
“We aim to take the next step to increase recycling and improve energy efficiency in our own production,” Landell concludes.
“We have always strived to design and produce high-value products that are durable, high-performing, and green.
“We are also looking into what we need when it comes to production facilities for continued development. Of course, this means using more secondary raw materials and
increased processing, and looking into what we can do with what we have, or if we will need to work with additional partners to achieve our vision.”
A trailblazer in the electrical motor sector, CEO Matjaz Cemazar tells us how Domel is building on its impressive repertoire to efficiently incorporate industry changes and sustainable responsibilities
Writer: Lucy Pilgrim | Project Manager: Kierron Rose
The development and supply of motors has been at the heart of the manufacturing industry for hundreds of years, as the vital mechanism exists at the core of modern technology. Domel, the Slovenian-based automotive parts company, understands the responsibilities of the manufacturing industry all too well.
With its vast repertoire of products, Domel is an established development leader in the vacuum motor market. The company has a vast presence across many commercial and residential applications, including floor care machines, gardening equipment, power tools, heating, ventilation and air conditioning (HVAC) systems, healthcare and medicine, alternative energy, and the automotive industry.
As such, Domel is renowned for its
sustainable and innovative solutions in the field of electric motors, which is supplied by its vast portfolio of products. These include universal vacuum motors, brushless direct current (DC) motors and blowers, as well as highly efficient permanent magnet synchronous motors.
With such a diverse array of applications, the company’s products find utility in cleaning technologies, industrial and laboratory settings,
medicine, automotive areas and e-mobility solutions. Thus, its motors serve a broad customer base, demonstrating Domel’s versatility and adaptability to meet different customer requirements.
In addition to its extensive product range, Domel has expanded its presence globally. Alongside its four production sites in Slovenia, the company has established manufacturing facilities in Serbia and China.
“Our global reach allows us to serve customers worldwide and collaborate as an innovative partner in R&D for cutting-edge technology,” introduces Matjaz Cemazar, CEO of Domel.
“Furthermore, the company’s presence in multiple countries solidifies our ability to cater to the evolving demands of various industries and maintains our status as a trusted and innovative partner,” he adds.
One of Domel’s greatest strengths as a global manufacturer of electric motors lies in its ability to provide end-to-end solutions.
“All core elements, including lamination, insulation, shafts, windings, and assembly, are produced in-house. This integrated approach allows for better coordination, quality control, and customisation to meet specific customer requirements,” Cemazar affirms.
Moreover, since its inception, the company has formed strategic partnerships with leading Tier 1 automotive customers, as its automotive division primarily focuses on the market sectors of electric water pumps, electric oil pumps, and electric air conditioning compressors.
With the overmolding process of advanced materials being a key part of its production operation, Domel is developing applications that can withstand a range of environmental conditions. The integration of overmolding has positioned the entity as a trendsetter in the field of electric motors, which are used for water pump and oil pump applications.
On top of this, Domel’s motors are built using state of the art tools, ensuring high efficiency, a high rate of utilisation, and adaptability to each specific application. These motors have proven to be an
excellent solution for hybrid and electric vehicles (EVs), particularly with the advancement in battery technology, increased environmental consciousness, and regulatory support for electric mobility.
As such, Domel takes pride in contributing to sustainable solutions, however, its expertise extends beyond the production of electric motors for various vehicles and industries.
Specifically, the company also manufactures a range of electronically commutated (EC) motors tailored for specific applications in gardening equipment, power tools, blowers and pumps, and HVAC systems.
Regarding the latter, the company’s EC motors power plug-in fans, axial fans, and single inlet centrifugal forward or backward curved fans. The premium energy efficient characteristic of the fans contributes significantly to the overall performance of HVAC systems, which in turn maintains good indoor air quality and heat ventilation.
“Ensuring a comfortable indoor climate in both residential and commercial buildings goes beyond luxury; it positively affects the well-being of individuals. Our HVAC system motors operate quietly and efficiently, working seamlessly around the clock if needed,” Cemazar tells us.
Customer experience aside, the EC motors reduce the operating costs of the HVAC system, resulting in them being more environmentally friendly, with improved profitability. Additionally, the new EC motors also ensure high energy savings, reduced playback time, and comply with Integrated Energy Factor (IEF) efficiency standards.
Headquartered in the municipality of Železniki, situated northwest of the capital city of Ljubljana, Domel has been a significant pillar of the community for over 70 years.
The roots of the company can be traced back to the Niko metalworking cooperative, which was founded by a group of 16 individuals in the region. The cooperative was initially named after its driver and founder, Niko Žumer, and operated by utilising machines obtained and converted from a craft workshop, focusing on the production of recording device mechanisms.
As the demand for its products grew rapidly, so did the workforce. By the end of its first year, the cooperative had already expanded to 59 members. Over time, the company’s expertise in motor manufacturing developed, enabling it to be recognised as a prominent player in the industry.
Fast forward to 1992 and the business became independent, operating under the Domel name. Consequently, last year, the company recorded revenues of €207 million, further solidifying its position as a significant player in the market.
Mersteel SSC is a leading provider of metallurgical products and services in Slovenia. We follow high standards of business, developed on the base of 127 years of experience in metallurgical business. We offer quality metal products, a variety of processing services and complex supplies of metal materials to leading partners in the automotive, construction and tool industries worldwide. The versatility of assortment and services allows our highly qualified and motivated personnel to find solutions to meet the special requirements of all customers. We gain their satisfaction, trust and loyalty with high standards regarding processes, documentation, quality and delivery.
Core programmes of our company consists of a wide selection of products:
• cold rolled programme
• hot rolled programme
• long programme (beams and sections, steels rods and bars, tubes and pipe bends)
• stainless steel and non-ferrous programme
• welding consumables
With a wide range of machine tools, our steel service centre offers the following services:
• longitudional cutting
• cross cutting
• CNC oxy-fuel and plasma cutting
• CNC milling
• band sawing
• grinding
• sand blasting
• drilling
• colouring
Elsewhere, as Domel branches out further, it has successfully developed and industrialised a central drive specifically designed for e-mountain bikes.
“This central drive exhibits exceptional power to conquer even the steepest mountain trails, with the reliability to withstand extreme downhill conditions, and efficiency to ensure a long battery charge life,” Cemazar highlights.
Such an undertaking reflects how Domel consistently searches for the latest innovations in the electric motor field. This is further signified by the identification of emerging industry trends, including gardening equipment, battery-powered tools, and e-mobility.
“The company recognises that its core competencies play a crucial role in the further development and growth of its business within these areas. As such, Domel is confident in its ability to meet the evolving demands of these sectors and contribute to their advancement,” he adds.
By focusing on these promising trends, alongside the evolving HVAC industry, Domel aims to further expand its business, enhance its market presence, and foster sustainable growth of approximately 10 percent per year.
This is despite significant disturbances faced by the electric motor industry in recent years, such as a global semiconductor shortage, trade disputes, and the COVID-19 pandemic. These disruptions have highlighted the vulnerability of complex global supply chains.
As a result, partner and supplier relationships have become even more crucial to the success of Domel’s business. By fostering a strong network, the company can guarantee a reliable source of high-quality components, enhanced supply chain resilience, optimised costs, and longterm strategic alignment.
Such factors contribute to maintaining a competitive edge, meeting customer expectations, and navigating disruptions within the electrical motors industry.
To further its commitment to creating a positive impact on the planet, Domel has implemented an environmental management system (EMS) that is ISO14001 certified. Through the EMS, Domel actively works to minimise electricity, heat and drinking water consumption, as well as reduce its greenhouse gas (GHG) emissions.
The latter will be achieved via the efficient utilisation of raw materials during the production process, as well as the introduction of measures for waste separation, collection and recycling.
In its ongoing efforts to embrace renewable energy sources, Domel also plans to construct a solar power plant at one of its locations.
“This investment aims to increase the share of renewable electricity and reduce GHG emissions associated with production activities,” Cemazar highlights.
This is further supported by publicly available sustainability reports, voluntarily prepared by Domel to
encourage transparency and accountability throughout the business. The reports showcase the company’s sustainability performance, providing stakeholders with valuable insights into its environmental and social practices.
“Domel demonstrates its commitment to innovation and ecofriendliness through its R&D activities. When developing motors, the company emphasises the optimal use of materials, state of the art technology,
high levels of energy and material efficiency, and long service life,” he adds.
In accordance with its tenacious environmental efforts, the company promotes an innovative mindset among all employees, encouraging its staff to contribute their ideas and expertise to drive progress and improve sustainability practices.
Staff remain a key focus of the company, as Domel remains employeeowned to this day.
This demonstrates a commitment to fostering shared responsibility and incentivising the workforce to contribute to its success. Therefore, with
Two upcoming projects that showcase Domel’s commitment to innovation and collaboration:
• Fifth-generation electric climate compressor: Domel is entering the fifth generation of electric climate compressors, an essential component in automotive air conditioning systems. This project signifies the company’s continuous advancements in developing efficient and reliable climate control solutions for EVs.
• Torque vectoring module for super sport EVs: Domel has initiated a new project in collaboration with two German original equipment manufacturers (OEMs) for the development of a torque vectoring module. This module is specifically designed for super sport EVs, aiming to optimise the distribution of torque to individual wheels for enhanced performance, stability, and handling.
a team of over 1,500 dedicated staff members, Domel continues to thrive as a leading manufacturer of electric motors.
What’s more, Domel recognises the importance of social responsibility and the fair treatment of employees, by proactively encouraging diversity and inclusion, whilst also supporting local communities as part of its social responsibility initiatives.
Domel greatly acknowledges that electric battery-driven power tools, as well as electric gardening equipment, are forecast with the highest growth potential. Therefore, looking ahead, the company is fully focused on these subsectors for the upcoming decade, striving to expand its market share in power tools and gardening equipment.
Such ambitions will be reached by providing higher added value through the development of more complex products. This includes incorporating software integration and connectivity features into its
product development.
“By leveraging technological advancements and connectivity capabilities, Domel aims to offer innovative and smart solutions that enhance the user experience and productivity,” Cemazar urges.
“Expanding into electric power tool applications not only allows Domel to tap into new market segments but also provides an opportunity to diversify its product portfolio and capture a larger share of the market,” he closes.
By leveraging its expertise and embracing innovation, Domel is poised to meet the evolving demands of the electric motor industry, contributing to a more sustainable and efficient future.
DOMEL
Tel: +386 4 5117 100
info@domel.com
www.domel.com
Charting its course to become the benchmark of the cruise industry by 2030, we discuss milestones and marine interior expertise with CEO of MAKINEN, Jaakko Mäkikalli
Writer: Phoebe Harper | Project Manager: Kierron Rose
When Auvo Mäkinen first started upholstering sofas in the 1960s, it may not have been obvious that the company to bear his name would become a worldclass expert in marine interiors.
However, after Mäkinen himself identified a fruitful niche in the blossoming Finnish shipbuilding industry and centred his craft on marine-grade furniture production for the country’s shipyards, that is exactly the course that MAKINEN followed, after it was officially founded in 1993 by Ismo Mäkinen.
Over its 30 years of operation, MAKINEN has become an industry name synonymous with quality, reliability, and innovation, with a rich legacy that commemorates milestone after milestone – from opening its first office in Miami, Florida in 2000 to serve the major cruise lines and develop turnkey project services, to being awarded a newbuilding contract in China in 2017 as the full interior turnkey company for Sunstone Ships’ Infinity class series of expedition vessels.
Despite its decades of experience in cabin refurbishment, newbuilding of cabins and public spaces, furniture production for cruise ships, passenger ferry companies, and shipyards, the company retains a pride in its culture and preserves the same can-do spirit and honest, down to earth attitude of
• 60,000+ refurbished cabins delivered
• 50 employees
• SIX expedition vessels delivered
• Pool of 2,000+ workers
• 25+ key subcontractors
• 60,000+ MAKINEN sofas currently sailing
its humble roots over 30 years ago. As a family-owned business whose owners are still very much actively involved in its everyday workings, this heritage creates an ethos of reliability, quality, and longevity behind the MAKINEN name.
“We are proud of our Finnish roots, and our culture of trust and quality,” opens MAKINEN’s CEO, Jaakko Mäkikalli. Indeed, Finland remains the company’s true heartland as the base for both its manufacturing unit, and a core team of 50 employees.
Complementing this local footprint, MAKINEN boasts a global network of customers across North America, Europe and Asia, and leverages an international pool of over 2,000 workers through its subcontractor relationships to bring products to fruition.
Today, MAKINEN is positioned as a full-service marine interior expert who prides itself on delivering turnkey solutions on-time, within budget, and beyond expectations.
“We take complete responsibility of the project from start to finish, including planning, resourcing,
purchasing, installation, and overall project management,” shares Mäkikalli.
“We want to be involved in the project with our customers as early as possible, including discussions around the design specifications of materials and supporting our client with potential alternatives,” he adds.
In conducting refurbishment for cabins and public spaces, MAKINEN can build new walls, floor and ceiling surfaces, refinish and refit bathrooms, reupholster soft goods and refinish fixed furniture, while also undertaking technical implementation such as HVAC, electricity and piping. Using only the finest materials and craftsmen, MAKINEN provides full turnkey deliveries of all interior works.
This comprehensive service offering is furthered by worldwide product support, spare part deliveries, and MAKINEN’s own manufacturing competencies with the production of furniture and a swathe of soft goods from headboards to textiles. Finally, the company’s newbuilding division centres on expediting new vessels and furniture production from its facilities in Finland.
At first glance, cabin doors look pretty much the same. Over the years, clear differences emerge. Antti doors stand the test of time and keep closing and opening as designed.
From a cabin manufacturer’s perspective, the most important Antti feature is that certified doors arrive exactly when and as contracted. Thanks to their flexible frame installation method, Antti doors are easy to install and perfectly fitted.
See our tips for offer request: anttimarine.fi
“We are a world-class organisation with a mission to build the best,” affirms Mäkikalli. “Regardless of the size of the project, we adhere to ‘the MAKINEN way’ of working, which means quality, agility – thanks to our lean working methods – and sustainability.”
Championing an innovative approach to marine interiors, MAKINEN upholds an unrelenting emphasis on delivering premium highquality solutions and maintaining a high level of service and support for the benefit of its customers.
With lean working methods in place to keep everything ship shape and facilitate scalability, MAKINEN utilises cabin data and design cooperation to keep projects on target, with shared tools and contractor processes to further help management. By supporting the pre-selection of materials for designers and architects,
MAKINEN ultimately reduces waste and minimises risk.
For Mäkikalli, MAKINEN’s 30-year milestone is just “business as usual”, as the company refuses to rest on its laurels in order to stay afloat on a voyage of continual improvement –the true cornerstone of MAKINEN’s ethos.
“Our culture is built on the idea of continuous improvement,” he concurs, referring to the company’s lean processes as the prime example of this focus. “We are still trying to
develop our lean system even further. We never accept that we are done and that there is nothing left to improve.”
As the fundamental basis of MAKINEN’s way of working, this lean methodology has been a crucial factor in securing the contracts that have created a sustainable and continuous workflow around the world through an esteemed roster of customers, including Azamara, Royal Caribbean International, Marella Cruises, Norwegian Cruise Line (NCL), and some of the globe’s largest shipyards to name just a few.
The concept was first conceived in 2012, when MAKINEN rose to the
“OUR CULTURE IS BUILT ON THE IDEA OF CONTINUOUS IMPROVEMENT”
– JAAKKO MÄKIKALLI, CEO, MAKINEN
challenge of developing a lean cabin refurbishment system with Porsche Consulting and Royal Caribbean Cruise Lines (RCCL).
“As the vessels were getting bigger and projects were taking longer, RCCL had started asking its contractors if other companies could perform the same tasks but in a different way to traditional cabin refurbishment,” recalls Mäkikalli.
Proving successful with more efficient throughput times for readymade cabins, MAKINEN still
adheres to this continually evolving lean system, which Mäkikalli credits as a key ingredient to the company’s reputation in the industry.
Most recently, this has resulted in MAKINEN’s foray into China for the past six years with the aforementioned newbuilding project for Sunstone Ships, whose latest vessel – Ocean Albatros – was successfully delivered in April 2023.
“Thanks to our lean concept, MAKINEN was chosen to take care of all the interior works in the series.
WHEN: January 2023
WHERE: Brest, France
SCOPE: Stateroom refurbishment (carpets, furniture reupholstering, bathroom retouch), and select public spaces
628 pax cabins and suites
17 public spaces
PROJECT SIZE: 135 workers
There have been six expedition vessels delivered thus far, with another on the horizon in the next few years,” he elaborates.
A key component of MAKINEN’s emphasis on continual improvement is the matter of environmental sustainability. As the cruise industry is increasingly placed under scrutiny for its environmental commitments, MAKINEN has long been established as a frontrunner in prioritising sustainable and responsible methods of operating.
Reflecting the company’s strategic focus to become a pioneer in the sustainable development of the marine industry, in 2015, MAKINEN became the first company in Finland to be awarded the CSR Performance Ladder Level 3 by DNV. In addition, it is ISO 9001 accredited, but despite this official recognition, MAKINEN acknowledges that there is always more to be done.
“Sustainability is a key topic for every company these days but it’s something that we are continuously working to improve beyond this certificate,” says Mäkikalli.
The company adheres to a series of social responsibility targets, including zero severe work-related injuries, 30 percent lower furniture weight in cabin renovations, and becoming carbon neutral by 2028 within Greenhouse Gas (GHG) Protocol Scopes 1 and 2.
“To improve our own sustainability targets, we are working internally through R&D and product development to focus on weight reduction for cabin furniture, since these are goals that we share with our clients,” he reveals. In addition, MAKINEN continues to explore alternative sustainable materials for soft goods, as another area that is receiving increasing attention from customers.
As a global operator, MAKINEN is
Marine interior images: Alexander Rudolphalso cognisant of the environmental implications of having an international network that relies heavily on flights and transport. Suppliers are carefully handpicked in accordance with the MAKINEN code of conduct which demonstrates a commitment to sustainability responsibilities.
“We are thinking more broadly in terms of our sustainability role, as we are also considering external issues such as logistics and procurement,” Mäkikalli outlines. “In the future, we would like to develop more local sourcing, both in terms of materials and the labour force to minimise the logistics involved in flying all around the world.”
With its eyes firmly on the horizon, MAKINEN has its sights set on an ambitious goal that is sure to secure the company’s legacy for the next 30 years and beyond.
“We have set a target that by 2030, MAKINEN will be the benchmark of
the cruise industry,” Mäkikalli states proudly. “Of course, many of our competitors are doing great work with similar targets, but we firmly believe that by that time, MAKINEN will be the company that everyone else should look up to.”
In terms of its more immediate focus, MAKINEN continues to receive attention following its most recent project, the CFC Renaissance, and has its hands full in delivering one final vessel for the Infinity series after establishing a level of continuity in the newbuilding market.
On a wider scale, MAKINEN, as with all other players in the marine industry, continues to navigate the uncertain waters of cruising in the aftermath of the COVID-19 pandemic. But, after two years of floating in the doldrums,
hope is finally on the forecast.
“Cruising came to a standstill during COVID-19, but cruise lines are now looking to undertake bigger projects again and the refurbishment side has started to pick back up,” Mäkikalli shares optimistically.
Once more, MAKINEN will be on hand to answer the call.
“We are working on our own resources and internal processes to make sure that we are ready to respond to the recovery that we believe is just around the corner.”
“BY 2030, MAKINEN WILL BE THE BENCHMARK OF THE CRUISE INDUSTRY”
– JAAKKO MÄKIKALLI, CEO, MAKINEN
EME Outlook, Africa Outlook, APAC Outlook, and North America Outlook and Mining Outlook are digital publications aimed at boardroom and hands-on decision-makers, reaching an audience of more than 800,000 people around the world; spanning the full range of industrial sectors.
With original and exclusive content compiled by our experienced editorial team, we look to promote the latest in engaging news, industry trends and success stories from across the globe.
Your company can join the leading industry heavyweights enjoying the free exposure we provide across our platforms with a free marketing brochure, extensive social media saturation, enhanced B2B networking opportunities, and a readymade forum to attract new investment and to help you grow your business. Visit www.outlookpublishing.com/get-involved for details on how your company can feature for free in one of our upcoming editions.
www.outlookpublishing.com/get-involved
Building on the global success of its regional titles – EME Outlook, Africa Outlook, APAC Outlook, and North America Outlook – Outlook Publishing is proud to introduce a platform dedicated to the mining and resources sector.
As mining organisations worldwide confront unprecedented change, embracing technological innovations and incorporating critical environmental sustainability agendas, now more than ever is the time to showcase the strides being taken in this dynamic sector. A multi-channel brand, Mining Outlook brings you the positive developments driven by organisations across the global mining industry through our various platforms. Discover exclusive content distributed through our website, online magazine, social media channels, and dispatches delivered straight to your inbox with a bi-weekly newsletter.
Through this compelling new venture, we foreground the movers and shakers of the industry. To participate as a featured company and join us in this exciting endeavour, contact one of our Project Managers today.
www.mining-outlook.com
The colossal construction industry in the Middle East has grown impressively to a position of enviable buoyancy in recent years. There is a plethora of vast infrastructure projects under construction throughout the United Arab Emirates (UAE) and this, combined with the numerous giga
projects underway in the Kingdom of Saudi Arabia (KSA), is spearheading a dramatic increase in the demand for high-quality aggregates.
Giga projects are infrastructure or capital project investments of such gigantic scale and ambition that they can be considered ‘once in a generation’ in terms of what they
deliver to the world and how they deliver it.
“Combined with the commencement of aggregate haulage operations with Etihad Rail, the landscape of the haulage region may change beyond recognition in the next couple of years. There is also an increased environmental
people, equipment, and world-class competencies have consistently delivered exceptional infrastructure projects over the past 33 years. We learn more from CEO, Martin McGinty
Writer: Ed Budds | Project Manager: Eddie Clinton
awareness throughout the industry which will have an impact on every aspect,” opens Martin McGinty, CEO of Western Bainoona Group (WBG).
WBG has been a cornerstone in the development of roads and infrastructure projects in the UAE, and under the country’s wise leadership, is now internationally recognised as a modern business and travel hub. This can largely be attributed to the UAE National Vision 2030, which supports strong public policies towards diversifying the nation’s economy, thus simultaneously promoting the
country’s rapid growth.
This policy has already accomplished great feats, such as the UAE’s successful bid for the Expo 2020 which was key in supporting the nation’s upward trajectory.
“We continue to invest in the most qualified, best-in-class talent to manage operations and deliver results.”
WBG’s management team is backed by a large, qualified workforce of over 4,500 employees trained to the best practices and standards, and the company’s ISO-certified
accredited management system and environment health and safety standards are what make WBG truly stand out.
“We rise above the competition because of our quality, right-time delivery, performance, reputation, price differentiation, and the fact that we are a one-stop shop.”
After graduating as a civil engineer from the University of Strathclyde in 1986, Martin immediately started working in the UK construction industry with Galliford’s, and then Balfour Beatty.
The company’s key priorities for the coming year are:
• To sustainably grow WBG through the specific targeting of upcoming tenders.
• To work with Etihad Rail in reshaping the UAE transport industry.
• To expand WBG’s footprint in Bahrain.
• To expand WBG’s footprint in KSA.
• To be the first transport company in the UAE to utilise electric vehicles (EVs) to transport aggregates.
“It was while with Balfour Beatty that I obtained my Quarry Managers certificate as we were drilling and blasting through an old quarry for the M8. Then, just under 30 years ago I had an opportunity to work in Qatar; I enjoyed the way of working in the Middle East so much that I have stayed here ever since,” he recalls.
Indeed, Martin has been working in the UAE since 1998 with some additional spells in Oman, Egypt, Bahrain, and KSA.
Steeped in a rich history of experience and success, WBG was formed in Abu Dhabi by Khalfan Mohamed Khalfan Abdulla Al Hamily and Zouheir Najem Chamandi in 1990.
“We are a company with special grade classification in roads and infrastructure. Our main office is in
Mussafah, Abu Dhabi with further branch offices in Fujairah, Dubai, Bahrain, KSA and the UK.”
Since its inception, WBG has executed numerous projects and produced and supplied aggregates and rock materials for various esteemed clients in the UAE and Bahrain.
The greatest strengths of the company today lie in the expertise of its manpower, its large fleet of specialised equipment, elite machinery and vehicles, alongside its asphalt and batching plants and operational crushers in Mahda (Oman), Ras Al Khaimah and Fujairah (UAE).
These prominent strengths have enabled WBG to participate in prestigious projects such as the Baraka Nuclear Plant, Etihad Rail, Al Wattan Road, and Sh. Zayed highway in Bahrain.
“Our main services are in the construction of roads and infrastructure, quarries and crushers, asphalt production, and logistics and transportation. Furthermore, WBG serves government authorities in charge of the development of roads and infrastructure as well as major private developers in the region,” he adds.
Despite starting as a transport company, WBG realised the demand for quality aggregates, and subsequently moved seamlessly
into the quarrying industry. As the UAE grew, the requirement for highquality construction companies also increased; WBG’s owners recognised this requirement and steered the company in the right direction.
WBG has proudly completed several iconic projects in the UAE and is particularly proud of its contribution to the execution of Al Watan Road, as this played an important part in linking major parts of the nation together.
This impressive project was executed in Ras Al Khaimah and Sharjah, eventually reaching the
outskirts of Dubai, and involved the construction of 66 kilometres (km) of new roads with extensive drilling, blasting, rock excavation, filling, and asphalting. For this assignment, WBG utilised an innovative approach where crushers, a concrete batch plant, and an asphalt plant were all installed on site.
Keen to ensure a bright future for the company, WBG plans to introduce electric trucks at the earliest possible date. Indeed, working with Emirates Motor Company-Commercial Vehicles (EMC-CV) has become a particular point of pride for the company.
“WBG values its long working
relationship with EMC-CV. We have relied on our large fleet of trucks to make deliveries over the years, and it has therefore been a contributor in the overall WBG success story.”
Elsewhere, WBG uses EMCCV’s Fleet Management Platform to measure truck productivity and drivers’ performance, whilst enhancing their driving skills.
Additionally, the company remains firmly committed to participating in initiatives to promote environmental sustainability and works in close coordination with EMC-CV to partake in the trials for electric trucks in the UAE as the first step in transforming
the entire WBG fleet.
Encouraging employees to undertake greater authority is a core belief of WBG, as the organisation actively promotes autonomy and responsibility in the workplace. Indeed, WBG sees to it that employees are provided with the necessary information, resources, equal voice, and support to contribute to the overall objectives of the business.
“Such contributions are always recognised and valued.”
As well as empowering its staff, another key relationship that WBG must nurture is the partnership it has with its network of suppliers.
“WBG considers its comprehensive supply chain to be valued as its trusted selection of partners in overall project delivery. This relationship is therefore crucial for ensuring the timely delivery of products and services and providing our clients with the best deals in the market,” he enthuses.
The key to building such relationships starts from the beginning, by choosing the right suppliers through proper due diligence and market research, maintaining regular communication throughout the delivery process, making sure all supplier payments are made on time, and providing suppliers with proper feedback to ensure continual improvement.
With a firm commitment to advancing and aiding the local community as one of its core values, engrained deep in the very fabric of the company, WBG believes that businesses have a crucial role to play in making the world a better place.
WBG’s corporate social
responsibility (CSR) strategy covers several practices, which mainly include volunteering both during environmental crises and for charitable services. Alongside this, WBG is also involved in and committed to taking part in traffic awareness campaigns, blood donations, sponsoring community sports activities, promoting the use of recycled material, providing training for undergraduates, and improving labour policies.
“This strong dedication to
CSR processes allows us to provide optimum quality in a timely and costeffective manner while ensuring that maximum care and consideration are given to society and the environment.”
Similarly, WBG is committed to offering value to its customers by assisting them to achieve their own goals while simultaneously fostering regional growth and stability.
“Our strategy is to leverage a unique bundle of services by reinforcing our local capabilities with those of our prominent local partners, in order to capture synergies for a sustainable competitive advantage,” he finishes.
With an assured, socially responsible and proven strategy for growth in place, WBG remains extremely proud of its achievements to date and is committed to continuously enhancing its capabilities to ensure it remains at the very forefront of its industry.
WESTERN BAINOONA GROUP
Tel: +97125 515 514
info@wbg.ae / contracting@wbg.ae
https://wbg.ae
high-quality window, door and façade systems made from aluminium, PVC-U and steel. Millions of Schüco products are used all over the world and meet the highest requirements of design, comfort, security and energy efficiency, making the company stand out when it comes to performance and quality, backed by an environmentally-centred mission.
Sustainable innovation is at the core of the company, and echoes throughout its many branches such as Schüco ME, bringing the best of structural design practices to the market.
Alastair Common, Technical DirectorThe Middle East is a regional treasure trove of architectural works, ranging from historic monuments to hyper-modern highrises sporting the latest systems and technologies.
With such a large industry, rapid regional growth, and the high investment in urban development,
there are a multitude of players that operate in the various sectors of the construction space bringing buildings to life.
One such player is Schüco Middle East (Schüco ME), part of the globally renowned Schüco International (Schüco). Schüco is one of the leading suppliers of
“The Middle East is one of our most important markets and is a region of impressive development at the moment,” introduces Alastair Common, Technical Director at Schüco ME. “We have expanded significantly since the end of 2020, moving our UAE headquarters to the Dubai Airport Freezone, in an office twice the size to provide more operational capacity and industry possibilities.”
The office boasts a product showroom as well as a new warehouse close by located in Sharjah International Airport Freezone, the with the warehouse marking Schüco ME out as the largest tenant in the zone.
“Our showroom is highly advantageous for us,” Common says. “Our industry is very much one where the customers like to see and test the products first hand, and so being able to offer them this opportunity is a great way to progress business and make sure they find what they are looking for. This in-person experience has a completely different impact and has been very positive for us.”
Meanwhile, Schüco ME’s warehouse covers approximately 9,000 square metres (m2) together with an employee training centre and a new Grid2Shell production facility, the latter of which is the reason Schüco ME stands ahead of many others in the industry.
We speak to Alastair Common, Technical Director at Schüco Middle East, about the company’s unique and innovative position as a leading supplier of residential and commercial façade systems from the UAE
Writer: Marcus Kääpä | Project Manager: Jordan Levey
Schüco’s Grid2Shell system is an easy-to-plan, plug-and-play modular system, with a self-supporting plug system. The high-strength, aluminiumalloy load-bearing profiles are easily connected to specially fabricated node units without complex welded joints. This self-supporting aluminium/glass construct can be used as a complete curtain wall as well as an all-glass skylight construction, depending on the project and desires of the client.
Triangular or polygonal module units can be used to create individual shapes for the building envelope, and there exists the option to have the vertical façade plane transition into the roof which gives rise to particularly unique building shapes.
What makes Schüco’s Grid2Shell system so unique, however, is that it is one of a kind in the market. Where there are comparable systems that make use of steel, there are no other industry players that utilise aluminium and the corresponding advantages.
“There are several professional and specialist fabricators that use steel systems similar to ours, and there are of course pros and cons to using either metal, but the quality that you receive from aluminium is definitely superior to what you receive from steel,” Common explains.
“The Grid2Shell system is an industry game changer and one that we take much pride in. The option of an aluminium system gives Schüco a stand-out position in the market, further helping to open the doors for customers and clients looking for a specific specialist product. It is something very unique to Schüco globally, not just our operations in the Middle East.”
The Grid2Shell system embodies the company’s innovative spirit and exists as the only system Schüco strictly produces itself (outside of its traditional supply chain), utilising a CNC machine to cut the system’s nodal elements from solid blocks of aluminium.
Alastair Common, Technical Director: “There was a definite shift for the company over the course of the COVID-19 pandemic from the commercial to the residential market. The pandemic period was very tough with a definite slowdown on commercial projects, yet fortunately, due to our portfolio of systems, we were able to remain afloat in the residential market. There were more villa projects proportionally to high-rise projects.
“After the influx of business caused by Dubai Expo 2020 (held in 2021), an expected downturn period was instead marked by a surprising continuation of project demand for Schüco ME. The UAE construction and façade market remains healthy, even with the ongoing Russia-Ukraine conflict in Europe.
“There has been a substantial influx of people to the UAE in recent years, and part of this has to do with the war in Ukraine. This has meant that the construction industry has had to respond to the growing number of people moving to the country, meaning more projects and investments for more companies.”
Due to the way the Grid2Shell system works regarding its nodal elements, designers are given the advantage of parametric freedom within the system. According to Common, Schüco has to machine the pieces at its own facilities as the exact geometry of those nodes is dictated by the company’s 3D models. These pieces are then supplied to customers in the region and internationally.
“We are seeing a lot of success from the system. Not only is it a leading offer in the market, but it also showcases Schüco’s prowess in the industry, the company’s innovation, and its ability to come up with new systems,” he continues.
“There is only so much you can do with a curtain wall or a door for example, so innovation in these areas is limited. Grid2Shell gives consultants, clients, and architects the possibility to create something parametric that is within the system, and that’s not easily achievable.”
From the winter of Norway to the sun of Middle East, from the tropical climate of Malaysia to the corrosive waves of the oceans, Jotun protects property! That’s why, the World’s Tallest Building Burj Khalifa, the Most Luxurious Hotel Burj Al Arab, the Cultural Centre of the region Louvre Museum Abu Dhabi are all protected by Jotun Powder Coatings.
Your designs come to life with Jotun architectural powder coatings, the perfect combination of aesthetics and functionality.
Specially designed for the long-lasting durability of buildings, Jotun’s architectural powder coatings are also suitable for strong UV rays, variable humidity and temperature conditions and other harsh environmental conditions.
Jotun Powder Coatings sees applicators, extruders, fabricators, architects and consultants as partners and offers tailor made solutions in the most efficient way by not just supplying powder coatings, but also assisting after sales with its dedicated sales and technical service teams.
In Middle East, India and Africa region, the market leader Jotun Powder Coatings is beautifying and protecting most of the iconic buildings and beautiful homes with the most environment friendly coating solutions.
Since 1926, Jotun is one of the leading paint manufacturers worldwide, operating in 4 segments: Marine Paints, Protective Paints, Decorative Paints and Powder Coatings, represented in more than 100 countries with 40 factories, 67 companies and more than 10.000 employees.
For more detailed information, please visit Jotun.com or reach out to us to learn more:
United
#7, Al Quoz Industrial Area
P.O.Box 51033 Dubai, UAE +971043472515 orders@jotun.ae
Saudi Arabia
Jotun Powder Coatings Saudi Arabia Co Ltd. 3078 – Industrial City 2, Ad Dammam 34326 – 6419 Saudi Arabia +966138121259 vinay.sharma@jotun.com
India
Fulcrum, A-wing , 601/602, Next to Hyatt Regency, Sahar Road, Andheri East Mumbai-400099 India +912267872100 deepak.parameswaran@jotun.com
MENA
Jotun MEIA FZ-LLC Regional Center, Dubai Science Park, Dubai, United Arab Emirates +971566820353 mohamed.ibrahim.hafez@jotun.com
Qatar
The success of Schüco’s Grid2Shell system is plain to see in its multiple projects spanning the region. One such location is Saudi Arabia, an area of focus for the company moving ahead. Schüco ME recently secured one of the largest projects in its history that is to be based in the kingdom, a huge skylight in Jeddah of around 25,000m2 that will utilise the company’s Grid2Shell system.
“This is a massive project and it represents a new kind of scope for us,” Common tells us. “We have multiple Grid2Shell projects happening in the UAE, but this project in Jeddah is by far the biggest.
“It’s a key strategic system for Schüco. The development of setting up the production facility in Sharjah was a significant investment and we don’t make that kind of investment
without a solid long-term plan. This one in Jeddah should be the first of many of these types of skylights in the Middle East.”
Saudi Arabia holds such promise for the company that Schüco ME is currently in the process of opening a regional headquarters in the country. With a full-time team based in Saudi Arabia, the company is readying itself to take advantage of the country’s short, medium, and long-term potential.
“Saudi Arabia is a very important market for us,” Common says. “There will certainly be growth in the kingdom for Schüco, especially with the amount and sizes of the projects that have been and continue to be announced. We must have boots on the ground in the kingdom itself.”
Schüco ME is also working on a 2,000m2 skylight in Abu Dhabi, having
already completed skylight projects in Dubai and Palestine, making its Grid2Shell system a real key strategic product that provides a unique selling point for the business.
Where Schüco’s Grid2Shell system is its core offer in the market, the company has also expanded to offer further products in the industry, and localised development is a key part of this.
Schüco’s international presence includes its production facilities in Germany that produce a number of the company’s standard systems. However, for Common, supplying these systems from Schüco’s German facilities, those that meet the needs of the company’s European customers, are often not suitable for clients based in the Middle East due to pricing. In the
“THE GRID2SHELL SYSTEM IS AN INDUSTRY GAME CHANGER AND ONE THAT WE TAKE MUCH PRIDE IN. THE OPTION OF AN ALUMINIUM SYSTEM GIVES SCHÜCO A STAND-OUT POSITION IN THE MARKET”
– ALASTAIR COMMON, TECHNICAL DIRECTOR, SCHÜCO MIDDLE EAST
face of this, developing systems local to the region provide huge benefits for Schüco ME and its customers.
“What’s important for us at Schüco ME, and one of the reasons we have been very successful over the years, is our local development,” he says. “In 2022, 40 percent of our annual turnover came from locally developed systems, such as unitised curtain walls, sliding doors, and balustrades. We previously had very little business in the latter, even in other company branches such as Schüco Germany, as traditionally balustrades have been too heavy and expensive for our market.”
However, the company has now been focusing on glass balustrades since the end of 2021, and Schüco ME has expanded its professional team
Schüco’s products offer sophisticated, proven system technologies combined with versatility in terms of materials, design and application options, providing security, well-being, and living in harmony with nature.
Specialist product areas include:
• Windows and fittings
• Doors and fittings
• Façades
• Sliding systems
• Sun shading systems
• Balconies and balustrades
• Security systems
• Building automation
• Surface finishes
• Building-integrated photovoltaics (BIPVs)
• Conservatories and terrace roofs
to bring on board a key member for the express purpose of focusing on the balustrade business segment. Where previously Schüco ME had zero activity in the sector, today the company offers 13 different variants of balustrade systems that range in their glass thickness and application. This gives Schüco ME a huge advantage to offer customers multiple different choices depending on their particular site, situation, location, thickness and height of the glass.
“Another advantage of this business segment is the simplicity of balustrades; we work with glass, and the projects are far simpler than a sliding door system, for example,” Common adds. “This makes our balustrades easier to carry out as there are only around half a dozen
components in this kind of system. Because of this simplicity, we are able to sell the systems to traders who can sell them on, providing continual business from that area alone which is something we cannot do with doors and windows because of their fabrication requirements and authorisation, and to make sure they are installed correctly.
“Balustrades do not have that same level of intricacy, so that was a completely new market for Schüco to dive into. In 2021 we had nothing to show regarding balustrades, and by the end of 2022 we had generated €3.5 million – a massive boost for us from something we did not have before.”
Without question, balustrades have been a critical addition to Schüco’s development over the past few years and have allowed the company to adapt to the varying demands of its client base, fulfilling their needs to successfully deliver a large number of different projects.
This recent and lucrative business segment highlights Schüco ME’s continued position as a professional and unique player in the industry, one defined by its innovative spirit to help build a better tomorrow.
Supporting the growth of the Middle East for over 40 years, Euro Mechanical is committed to innovation, in-country value and unwavering integrity. CEO, Jon Rawding, tells us more
Writer: Ed Budds
Project Manager: Jordan Levey
The Middle East, particularly the United Arab Emirates (UAE), offers a captivating growth environment for the burgeoning energy sector. Amidst the ongoing discussions surrounding the region’s ambitious energy transition, the leadership in the Middle East, specifically in the UAE, continues to adopt a pragmatic approach.
Recognising the importance of all available energy sources, the Abu Dhabi National Oil Company’s (ADNOC) Maximum Energy, Minimum Emissions initiative conveys the need to prioritise cleaner energy today while investing in renewable sources for the future.
Another significant trend that remains transformative across the region is the focus on harnessing the wealth of national talent and resources within each country. Furthermore, the UAE’s National In-Country Value (ICV) Program and Emiratisation Initiative are actively reshaping the landscape and workforce, creating new opportunities for local individuals and industries.
A pivotal and prominent player within this regional reshape is Euro Mechanical, an experienced Emirati company that has played a pivotal role in supporting the growth of Abu Dhabi’s energy sector for over 40 years.
“We take immense pride in delivering effective solutions and leveraging our expertise to benefit the entire region,” opens Jon Rawding, CEO of Euro Mechanical.
Burning bright at the core of the company’s operations is its specialised teams, which excel in construction and maintenance services.
“We offer comprehensive solutions, including fabrication, maintenance, modification, demolition, and construction of onsite packages, pressure equipment, and structural piping tailored specifically for the energy sector,” he details.
Manpower Services Division has deployed Euro Mechanical’s highly skilled and dedicated employees who have been renowned for their professionalism and strong work ethic for over 40 years. It also possesses the largest fleet of bolting and machining equipment in the UAE, ensuring its capabilities remain unmatched throughout the sector.
Through strategic partnerships, the company now facilitates the introduction of cutting-edge technologies to the region. By collaborating with sophisticated software companies and state of the art manufacturers in its field, Euro Mechanical aims to attract
companies to establish manufacturing operations in the UAE, and by doing so, contributes to the advancement of the local industry and promotes economic growth.
Committed to delivering on its promises, Euro Mechanical distinguishes itself from other companies that make similar claims and firmly believes that fostering long-term relationships is crucial for achieving success and remains vital for the company’s existence.
“In the dynamic business landscape that we operate in, every interaction holds significant value, contributing to our ongoing sustainability. We embrace a continuous learning mindset, remaining adaptable to the ever-changing environment,” Rawding affirms.
Through actively engaging with its employees, partners, and clients, Euro Mechanical has recognised the important role the company has to play and how its collective efforts contribute to the more significant cause of establishing a sustainable economy in the UAE, the wider region, and beyond.
“We perceive the world as a vast interconnected ecosystem, and in line
with this view, we seek collaboration with like-minded organisations. By becoming a trusted partner to all those who interact with us, we strive to make meaningful contributions and drive positive change,” he adds passionately.
Dedicated to upholding its commitments and acting with integrity in relation to environmental sustainability, social responsibility, and good governance practices, Euro Mechanical’s focus is now on translating its promises into concrete actions, implementing sustainable practices across its operations, and actively contributing to the well-being of its communities.
One recent achievement that Euro Mechanical points to as one of its most notable successes is the export line repair and replacement shutdown project, completed on Zirku island for
ADNOC Offshore.
Throughout this impressive project, Euro Mechanical successfully executed the comprehensive repair, replacement, and rectification of operationally critical assets, achieving exceptional results with zero lost-time incidents (LTIs) or
production downtime beyond the planned shutdown. The work also entailed mobilising, coordinating, and managing a highly skilled team of over 200 technical staff on Zirku island.
Through effective planning and efficient execution, the entire scope was completed an impressive two
weeks ahead of schedule, highlighting Euro Mechanical’s commitment to delivering projects on or ahead of time.
“Since the project’s inception, we have been actively participating in the planning, technical survey, detailed engineering, and offshore execution phases. Leveraging the expertise
of three separate Euro Mechanical businesses and collaborating with trusted subcontractors, the project was executed seamlessly, resulting in the utmost satisfaction of the end user,” Mike Purkiss, Euro Mechanical’s COO, enthuses.
Euro Mechanical’s comprehensive involvement ensured a holistic
Jon Rawding, CEO: “To fulfil our business objectives and enhance operational efficiency, we have embarked on a comprehensive digital transformation journey. This transformation aims to strengthen our cybersecurity measures and has sought to streamline our workflows and reduce reliance on paper-based processes.
“Like any transformative endeavour, we have encountered challenges along the way. Change can often be met with resistance rooted in traditional mindsets and established practices. However, our organisation fosters a culture that encourages open-mindedness and embraces change as an opportunity for growth. We remain well-positioned to address these challenges head-on by promoting a continuous improvement mindset.
“We recognise that the digital transformation journey is an ongoing process. We are committed to refining our practices and continually seeking additional opportunities to enhance our effectiveness and efficiency. Embracing emerging technologies, exploring automation possibilities, and leveraging data-driven insights are all avenues we explore to optimise our operations further.”
approach to the project, allowing for effective coordination across all aspects and disciplines. Through clear communication channels and efficient project management strategies, the company always strives to achieve outstanding outcomes, exceeding expectations and leaving the end user delighted with the results.
With an elite level of dedication, expertise, and seamless collaboration, Euro Mechanical has demonstrated its ability to successfully execute complex projects while prioritising safety, efficiency, and customer satisfaction.
“Our ownership and involvement from the project’s inception showcase our commitment to delivering comprehensive and reliable mechanical solutions,” he tells us.
In this way, Euro Mechanical continues to be a trusted partner in the industry, consistently delivering exceptional value to its clients.
Moving forward, Euro Mechanical recognises the importance of several key focus areas to drive the company’s future growth and contribute to advancing both the industry and the region.
“Firstly, we are committed to ensuring the integrity of our data and optimising project delivery processes. By implementing robust data management systems and practices, we enhance the accuracy, accessibility, and security of our information,” explains Rawding.
This empowers Euro Mechanical to make informed decisions, streamline operations, and deliver projects efficiently, meeting and exceeding client expectations.
Regarding leadership development, building a solid team is crucial for long-term success. To ensure this, Euro Mechanical invests in the development and growth of its employees, providing them with the necessary skills, knowledge, and resources to become influential leaders.
“By fostering a culture of continuous
learning and professional development, we cultivate a talented workforce capable of leading us into the future,” he adds.
Elsewhere, as the company embraces the wider energy transition, it remains determined to play a meaningful role in advancing alternative energy sources and actively seeks opportunities to support and implement renewable energy initiatives aligning with the region’s vision.
“By leveraging our expertise and collaborating with like-minded partners, we contribute to developing and adopting sustainable energy solutions.”
Looking ahead, Euro Mechanical also acknowledges the importance of diversification and exploring opportunities beyond the traditional energy sector. By adapting to new
market trends, technologies, and industry landscapes, the company looks set to place itself in a prime position to both contribute and thrive moving forward.
Through a strategic focus on these critical areas, Euro Mechanical aims to drive growth, embrace sustainability, foster leadership excellence, and expand its contribution beyond traditional energy realms. By remaining agile, proactive, and committed to its core values, the company is confident in its ability to shape a successful and impactful future.
Driven by innovation, Emirates Beton Ready Mix is an integral part of the construction industry and plays a significant role in the development of the most dynamic landmarks in the United Arab Emirates
Active in the niche highperformance concrete sector, Emirates Beton Ready Mix (Emirates Beton) has grown into one of the largest ready-mix producers in the United Arab Emirates (UAE).
Leading the industry in the design, production and supply of readymix concrete, Emirates Beton was established in 2008 by a group of people with over 20 years of experience in the industry. Today, the award-winning company boasts a reputation for high-quality products and outstanding services.
Renowned for efficiency and customised solutions, Emirates Beton has pioneering methods which undergo the most stringent material and process testing to ensure full compliance with international and approved standards.
Furthermore, the company is known for the latest technology in batching controls through computerised plants, systems monitoring, product tracking, and an in-house testing laboratory to confirm consistent quality control and frequent production testing.
As an award-winning provider of ready-mix concrete, Emirates Beton uses the latest German technology and employs the most technologically advanced equipment, operating four batching plants with two commercial plants strategically located in Dubai. With state of the art machinery and a diverse fleet of mixers and pumps, the
company manufactures a complete range of ready-mix concrete building components.
Moreover, since Emirates Beton’s inception, it has emphasised its commitment to sustainability and green initiatives, as the company is about more than just profit. Taking social responsibility into consideration is crucial to Emirates Beton’s impact on its people and the planet.
Emirates Beton’s products and services are driven by an ISO 9001 Quality Management System and follow the highest QA/QC and
HSE requirements, complying and contributing towards green building schemes, standards and codes set by LEEDS and Estidama.
Quality and planning are two of the pistons pushing the Emirates Beton engine. While the business grows through smart planning, the company stands by the certified quality of its products.
Recognising the unique characteristics of the UAE environment, Emirates Beton has a specialised range of Ultra Series™ concrete solutions that have been specifically developed for the local market.
‘INNOVATE CONCRETE SOLUTIONS HAVE BEEN RIGOROUSLY TESTED AND BEEN USED IN THE UAE FOR MANY YEARS EXCLUSIVELY WITH EMIRATES BETON’
Envirocon is a leading construction products industry leader offering concrete admixtures, surface treatments, concrete repairs, tile adhesives, grouts, bonding agents, building products, protective coating, and industrial flooring.
Envirocon focuses on providing value-added solutions for the construction industry, focusing on structural integrity, lower maintenance costs, and enhanced concrete quality. Having personnel with exceptional experience and market knowledge, we develop admixtures with enhanced workability, strength, durability, and chloride resistance. We also have high quality protective and traffic coating.
Envirocon remained committed to enhancing the standards of the industry through the development of innovative new products, process, and practices to meet the needs of all valued customers. We offer unique service and support, with experts providing assistance throughout project phases.
+971-2-5503473 | info@enviroconcp.com | Fax number: +971-2-5503474 www.enviroconcp.com
• Environmental stewardship – to instil eco-friendly awareness into the work culture, providing solutions and offering products that are not harmful to the Earth’s natural resources.
• Innovation – to propose solutions to identify, develop and deploy leading-edge technology, department programmes and process development tools.
• Integrity – to conduct business by the highest standards of professional behaviour and ethics and demonstrate a culture of transparency and honesty.
• Quality –top-quality and worldwide benchmarkable executions of projects, delivered on schedule with efficient logistics and engineering power.
• Health and safety – committed to protecting employees, partners, clients, and the communities in which it operates.
• Customer happiness – consistently performing and delivering value-added services to customers with the highest level of quality. Meeting commitments and client expectations and exceeding them on every level to deliver exceptional value.
• Dependability – ensuring Emirates Beton’s word, commitments, and promises to clients are fulfilled, as when a project is completed, the company strengthens its reputation as a trusted partner that delivers results intact.
• People - through supportive, approachable leaders and colleagues, the wellbeing of employees is always prioritised. This includes but is not limited to, maintaining a safe and secure workplace.
The premium range of readymix concretes is designed to give contractors, engineers, and architects increasingly flexible alternatives and sustainable solutions for their concrete needs.
These innovative concrete solutions have been rigorously tested and used in the UAE for many years, exclusively with Emirates Beton. The wide range of customised or initiated products gives customers confidence that the concrete solution they use will be suitable for any project environment and weather condition within the UAE.
With a modern enterprise resource planning (ERP) system and mobile applications, Emirates Beton helps customers have live access to their concrete orders and delivery, as well as a GPS for accurately tracking vehicles and fleets.
Over the years, Emirates Beton has been integral in completing many state of the art and iconic projects globally. This includes commercial, educational, and industrial buildings, along with low/mid/and high-rise structures,
social infrastructures, and villas.
One of the projects that Emirates Beton was proud to add to its portfolio is the Jumeirah Gate. Completed in 2021, the structure is one of Dubai’s most luxurious skyscrapers and stands 301 metres (m) above sea level.
As the preferred ready-mix provider for high-rise buildings in the UAE, with headquarters in Dubai and Abu Dhabi, Emirates Beton used 185,000 cubic metres (m3) of concrete, 75,000 m3 of which was C90 high-strength concrete, in a total of 20,210 trips, taking three years to complete.
Having recently opened a new production facility in Abu Dhabi, with approval pending for another new plant in the region, Emirates Beton has established a good customer base and continues to focus on
growth by exploring new markets and opportunities.
Indeed, projects that have the Emirates Beton stamp on them can be seen around the UAE. For example, the impressive Emirates Pavilion, the aesthetically otherworldly 54-storey Sabah Rotana Hotel in Dubai, and The Opus, located in Dubai’s Burj Khalifa neighbourhood, comprises two independent towers that come together to make a single whole in the shape of a cube.
Furthermore, Emirates Beton’s portfolio extends beyond the UAE region into Asia, Africa, and Europe, but only in design, not geographically. The imposing and striking Azerbaijan Pavilion, designed and built at Expo 2020 Dubai, and the Morocco Pavilion, designed and constructed at Expo 2020 Dubai, showcase an
ancient alternative to concrete using rammed earth.
With a wealth of experience and a host of prestigious landmarks to its name, such as the Mohammed Bin Rashid Library and Dubai International Airport expansion, plus many more, Emirates Beton remains a trusted supplier to the construction industry.
Products include shotcrete, highperformance, durable concrete, self-compacting concrete, sustainable concrete, lightweight concrete, and waterproof concrete. With state of the art production facilities, effective technology, computerised batching plants, and meticulous product tracking, Emirates Beton will generate continuous production for UAE structural development for years to come.
With a wide geographical presence, Synergy Construct remains a fixture of the construction industry as it continues to offer sustainable design and development services
As one of the top-positioned companies in the international market, Synergy Construct (Synergy) is renowned for its knowledgeable team, engineering expertise, and continuous technological investments.
Founded 22 years ago in Romania, by Savas Gunata and Huseyin Karali, Synergy is headquartered in Bucharest and has offices in five countries. Today, the company works with a plethora of clients and has successfully delivered over 100 projects.
Synergy’s portfolio, which has a proven track record, includes industrial facilities, logistics centres, energy projects, airports, hotels, retail centres, offices, medical facilities, high-rise buildings, and educational establishments.
Moreover, the operational method that Synergy frequently uses in other countries is unusual in the Hungarian construction space, as it accommodates blue-collar workers in an on-site camp facility.
This means the workforce is
available continuously without impacting the local community. At the time of this pioneering method, the COVID-19 pandemic was rife, therefore one of the benefits of the camp was a reduced impact of illness in the wider community.
Subsequently, developers who visited the site have since installed similar camp facilities.
Furthermore, over the years, Synergy has evolved into an international company with largescale projects in Hungary, Romania,
Germany, Poland, Georgia, Ukraine and Turkey for high-profile clients. It soon became the burgeoning cooperation it is now by building further turnkey design and build projects. While at times, the projects were challenging they were simultaneously rewarding.
Offering a turnkey design and construction management solution in one platform has clear benefits in terms of investment, time optimisation, design and build coordination, and having a single point of contact with one source of accountability allows for enhanced processes and communication flow, shorter time frames, and better quality control.
One of Synergy’s strengths is in civil engineering, ranging from new commercial office buildings, retail
spaces, and mixed-use development, to industrial parks and energy projects.
Undertaking complete general management, Synergy sees the project through from foundation to finish, organising the building works, selection and coordination of subcontractors with strict management of all processes.
Synergy’s in-house mechanical, electrical and plumbing (MEP)
• Present in seven countries
• Over 2,000 employees
• €12 million in equipment
• Over 100 projects worldwide
department provides assistance on design and build from preconstruction through to construction, commissioning, occupancy and warranty. The MEP system works seamlessly by integrating with existing designs for efficient and sustainable buildings.
The latest venture for Synergy is Han Spaces, which offers workspaces with special settings. Due to the full scope fit out of decorations, artwork, a podcast room, information technology (IT) equipment and audiovisual systems, people can feel the difference as soon as they sit down. The company managed to navigate the challenges of shifting client requirements by collaborating with everyone involved.
Responsible for the first Hungarian residential property to receive BREEAM certification, Synergy undertook construction work for the
SystemBau is a mixed owned Romanian-German company, founded in Ploiești in 2000, well known in the Romanian construction market as a result of numerous successful projects and various experiences, gathered in the construction of industrial and commercial steel and concrete buildings.
With more than 20 years of experience and over 200 employees, we provide comprehensive services covering the entire project lifecycle, from design to execution, with an unwavering dedication in finding optimal, technical and financial solutions.
SystemBau is one of the company members that forms DRT Group with DeRom Total as General Contractor, AluSteel Facades and TiefBau Systems, with a reputation that has been built over the years through successful execution based on quality, safety and on time delivery of our different projects.
We can:
• Design and produce both heavy and light metal structures
• Create turnkey solutions for claddings in industrial, commerciall and civil projects
• Implement fire-rated walls
• Construct industrial-scale cold freezer rooms
Our main goal is to to achieve the best results, through our strong partnerships with more than 500 satisfied clients and 70 percent returning clients with over 1,000 realised projects and five million squared metres of buildings.
a solid foundation for a strong partnership is the best way to describe our group values.
Tudo Vladimirescu Street, no.1 Berceni, Prahova, Romania•
Our in-house capabilities are:
• Professional sandblasting, coating systems
• Production capacity up to 500 tonnes per month
• Loading, handling and transportation equipment
Danubio residential complex. This high-end luxury building on the bank of the Danube River has also been recognised by the European Property Awards in the Multi-Residential Real Estate Architecture category.
Easily accessible from the historic city centre of Budapest, Danubio is a unique residence due to its location, and the first tenants will soon be able to move in as phase one is almost complete. The sustainable and environmentally friendly design is energy efficient, and the built-in technology and systems are all up to the latest standards.
Aside from Danubio, Synergy is proud to be part of Turkey’s first nuclear power plant, as it is taking the helm of the third reactor’s turbine building. The Akkuyu Nükleer Güç Santrali project is ongoing and will generate around 4.8 gigawatts
(GW) of electricity each year once completed.
Building a future as a society is a meaningful cause for Synergy, who has therefore chosen to support causes related to children in need. To this end, the company has financially secured three foster homes from S.O.S. Satele Copiilor Romania, covering homes, utilities, food, clothes, and social mothers for an entire year.
Moreover, Synergy has leveraged the Zi de Bine Association to renovate the IOMC hospital’s Paediatrics IV section and fully equip it with the necessary technology, ensuring that treatment capabilities are up to modern standards for the annual influx of over 50,000 children.
The last few years have been
• Kellogg’s – second European Pringles manufacturing facility
• Avon Cosmetics – 13,000 square metre warehouse
• Lidl – steel structure store in Romania
• Siemens – workshop, warehouse, gatehouse buildings in Turkey, and the Black Sea Transmission Network Project
• ProLogis – logistics park in Romania
• Procter & Gamble – headquarters in Romania, and a hair care products factory in Romania
challenging for the Romanian medical system; development and modernisation are therefore necessary investments, and Synergy is involved in renovating the new Cardiology Centre of the Prof. Dr Theodor Burghele Clinical Hospital.
As the budget allowed it, Synergy reached out to Asociatia HOSPICE Casa Sperantei to help children with incurable illnesses, along with Asociatia Deficientilor de Hexocinaza to care for several children with health problems, and Asociatia Noel to ensure cancer treatment for two children.
Additionally, Synergy supports Asociatia Irina Anastasia to help children with locomotor challenges, Asociatia PAVEL to assist parents whose children have been diagnosed with cancer, and finally, Asociatia Act for Tomorrow to guarantee several substantial environmental cleaning actions each year.
Furthermore, the company is an official shareholder of Happiness for Daruieste Viata, the first official
oncological hospital for children in Romania.
Supporting the medical system and providing children and their families with access to better medical services is important to Synergy.
Owing to a tenacious approach towards all projects, Synergy is set to continue along the same successful path it always has done. All performance indicators prove the company is in good professional and financial health, as customer satisfaction remains at an all-time high.
Focusing on complex and challenging projects, Synergy aims to be a game-changer in the built environment, while remaining true to the unbending values of equality, diversity, health and safety, fair practices and professional conduct, quality of work, care for the environment, and partnerships with clients.
At present, Synergy is building a fourth factory for Proctor & Gamble in Romania and has won the design and
build contract for the extension of the Nestlé Purina pet food factory.
Originally, the company was awarded the Nestlé Turul-4 project in Bük, Hungary, and work began soon after in 2021. It will eventually become Nestlé’s largest pet food production factory in Europe and will create 160 new jobs. The extension is being built within the existing functional factory and is progressing as scheduled.
As recently as last year, Synergy was also appointed as the general contractor for several of BMW Group’s new plant buildings in Debrecen, Hungary. Indeed, winning a design and build contract for a renowned international brand is a major coup for a contractor.
In terms of technological pioneering materials, uniqueness, and the overall complexity of its project scopes, Synergy has set the benchmark for the industry standard.
Writer: Lucy Pilgrim
Project Manager: Dennis Morales
Nowadays, it seems that the transference of data is what truly makes the world go round. As the lifeblood of digital global development, telecommunications (telecoms) is becoming more integral every day.
As an industry, telecoms has become the epitome of modernity with the advancement of surrounding technology.
“The industry has matured a lot over the past 30 years. We have seen the introduction of low bandwidth connections and simple voice-only handsets develop quickly into highcapacity connections to houses, businesses and handsets. We now
expect to always be connected with a high-capacity network,” introduces Thorvardur Sveinsson, CEO of Farice. “The interplay and co-development of telecoms and information technology (IT) has resulted in the rapid advancement of cloud services, which have transformed the way we live even further. In essence, cloud services are IT applications that run in data centres all over the world and are connected via high-capacity telecoms fibre links. We commonly refer to this connectivity as the internet.”
The simple transportation of the internet is facilitated by submarine cables that connect countries and
continents together, with 99 percent of internet traffic travelling beneath the ocean.
Significantly, Farice is stateowned by the Icelandic government, bringing to light the company’s strategic importance as a hub for international connectivity. As a result, Farice offers its customers highcapacity data transmission services from key network hubs in Iceland to major network hubs in Europe. This is achieved through an extensive network of both its own submarine cables and the terrestrial cables of local partners in neighbouring regions.
“The nature of our business is
to be a carrier’s carrier - that is, we sell our services primarily to carriers. Our customers are telecoms companies in Iceland, the Faroe Islands and Greenland, as well as international data centre customers hosting their IT applications in Icelandic data centres,” Sveinsson tells us.
Farice is a critical operator of telecoms infrastructure in the northwest Atlantic as the only operator of submarine cables between Iceland and Europe, which are separated by 1,500 kilometres (km) of open North Atlantic waters, giving the company a unique position in the industry.
Thorvardur Sveinsson, CEO: “Every time we invest in a new fibre cable, we work closely with local interest groups in the area to educate and support the local communities. Our approach is different between regions, which depends on how we can benefit each local community.
“Our investment in a new submarine system will always strengthen connectivity in the region. Likewise, auxiliary investment from our terrestrial partners to connect to our system will also bring benefits to the local community.”
Ireland is taking centre stage in the digital world, bridging time zones but also the massive amounts of data that traverses between New York, Dublin, London and across the globe.
Aurora Telecom, a division of Gas Networks Ireland, is a key facilitator of this connectivity through its operation of the most modern dark-fibre infrastructure in Ireland. Established in 2000, we specialise in dark fibre and colocation services and are the carrier-neutral provider of choice to the top five global content and application providers, subsea carriers, data centres and service providers.
We own and operate an extensive national backhaul fibre network, built in a ring topology of 1,250km that spans 15 counties and connects all major urban centres. This provides an ultra-high fibre count backhaul network on all routes. Our wide-reaching metro network in Dublin connects all key data centres and central business districts. We also own additional metro networks in Ennis and Shannon. The network is designed to cater for long-haul transatlantic backhaul, ensuring the best-in-class latency with minimal optical loss. The exclusive deployment of Corning G652D across the network, ensures the lowest possible fusion splice values are maintained.
Our colocation facilities have been designed to provide customers with the most secure sites to house their equipment. These facilities are spaced at a maximum of 80 km apart and have 24/7 Building Management System (BMS) monitoring to ensure business continuity of the highest level. Some of the services provided include CCTV, AC systems, DC power supply, UPS systems, generators and all ancillary systems. Since a substantial proportion of our network is located within the gas infrastructure, the Aurora Telecom network benefits from aerial and foot patrols. Our current network availability
is performing at 100 percent, but to increase the resilience of the network, we are also rolling out standby generators to increase backup power.
From dark fibre to subsea cables
Subsea cables provide the vital network that allows data travel around the globe and Ireland has become a key landing site for these highly advanced fibre optic systems. Aurora Telecom provides an advanced terrestrial network that interconnects with key submarine landing points including IRIS, AEC1, AEC2 (Havfrue), Havhingsten and Celtic Connex. Most recently, the IRIS subsea cable became ready for service and ensures a direct link from Ireland to Iceland, further diversifying the connectivity links across the country. This will potentially open the entire West Ireland region for new investment.
Our national fibre network provides the terrestrial backhaul solution from Galway to Dublin for the IRIS subsea cable system which connects from Iceland. We not only provided the connectivity from Galway to Dublin but also enabled the connectivity from its backhaul network in north Dublin city to the cable landing station in Galway Harbour.
Aurora Telecom’s network around Galway and the IRIS CLS (Cable Landing Stations), already has diverse paths from the city, connecting north to AEC1 and AEC2, south to Shannon, Limerick, and Cork (CIX), as well as direct connectivity to Dublin alongside Gas Network Ireland’s transmission pipeline. The network is modern, has ample fibre capacity and additional duct capacity to augment further fibre capacity to support natural growth or specific project requirements.
“DEVELOPING NEW SUBMARINE SYSTEMS TAKES A LONG TIME, AND THE SYSTEMS ARE COSTLY, SO GOOD AND CAREFUL PREPARATION IS NEEDED BEFORE NEW PROJECTS ARE INITIATED”
– THORVARDUR SVEINSSON, CEO, FARICE
The company operates in a small home market of 380,000 people that live an ultra-modern and digitally driven lifestyle. The cost of building and operating submarine cables has been a challenge for other operators to enter the market.
The company works with data centre partners by providing connectivity to international customers of Icelandic data centres. However, Farice is in indirect competition with other connectivity providers in the Nordic region.
Furthermore, the company recognises its responsibility as a sole provider in the country.
“We design our network for security and resilience as it is essential infrastructure for Iceland. International customers gain from the quality of the network design and operational stability.
“We also benefit from a long history of the successful operation of submarine cables in the North Atlantic,” Sveinsson comments.
When looking at Iceland’s geographical location more closely, the island is ideally positioned to be an indispensable connection hub for Greenland. As one of Greenland’s two submarine cables lands in Iceland, Farice carries the traffic onwards to Europe.
Regarding the Faroe Islands, located to the west of Iceland, the FARICE-1 cable is one of two submarine cables that connects the Faroe Islands with the rest of the world. Thus, with just a few examples, it is easy to see how the importance of the submarine cable sector is growing in correlation with the rapid development of the data centre industry in Iceland.
An additional pillar of the company’s success is certainly its employees, who stand as experts in the field of submarine fibre engineering. The employees can comprehensively work with cable manufacturing to design a cable
system for optimum performance, using the safest and most secure cable route.
“In the North Atlantic, where we sometimes have harsh weather conditions as well as a large fisheries industry, which is very important, we are very proud of that fact that we have never had any underwater faults on our submarine systems,” Sveinsson affirms.
Most recently, Farice is enjoying the success of its newest submarine fibre cable, known as IRIS, after four years in development. In service since the 1st March, the IRIS cable system lies between southwest Iceland and Galway on the west coast of Ireland. From Galway, the company connects to a key network hub in Dublin via a highly secure terrestrial fibre.
“The IRIS system is our third submarine cable system that will add diversity and dependency to our international network and bring even further security to our operation. As the main purpose of the project was to further strengthen the security of international connectivity between Iceland and Europe, we settle the cable at a new landing site in Iceland and the marine route of the new cable
Thorvardur Sveinsson, CEO: “I worked in the telecoms industry for close to 15 years before joining Farice in 2020. I was COO for Vodafone Iceland and Head of Group Development and Strategy for Iceland Telecom. Prior to that, I worked in IT and finance for 10 years.
“My interest in the telecoms industry really began in my early 20s when I decided on my graduate degree in engineering. My focus became telecoms engineering as, at the time, mobile handsets were in fast development as well as the internet, which was evolving quickly. I could see the impact that technology has on the daily lives of people as well as the development of businesses. The industry really touches people and the way we interact with each other. I found it, and still find it, a very interesting and exciting industry.”
does not cross any of the existing cables coming into the country.
“With Iceland’s digital cloud infrastructure to a large extent operating in the cloud environment from European data centres, the importance of secure connectivity cannot be understated. We also believe that the system will support Europe’s digital drive towards sustainability with the offloading of digital processing to data centres in Iceland,” Sveinsson proudly details.
In conjunction with the advancements of the IRIS system, a project currently in development
connects Ireland and Finland to Japan via the Arctic. Additionally, there are also interesting transatlantic projects that could be of great potential for the company and the connectivity of Iceland. Farice closely follows the Icelandic telecoms market and evaluates the need for potential added capacity that would require further development between Iceland and Europe.
“Developing new submarine systems takes a long time, and the systems are costly, so good and careful preparation is needed before new projects are initiated,” he states.
Overall, Farice is the vital piece of the puzzle in connecting Europe and ensuring safe passage amongst the continent. With strategic partnerships and an eye for expanding the potential of cables, Farice is the backbone of the European telecoms industry and beyond.
It has been two decades since the UK’s first 3G-only network was launched, laying its foundations as the network that was born to be different.
Three was founded in 2003 to challenge the mobile industry, and now covers 99 percent of the UK with its combined 3G and 4G network, carrying 28 percent of mobile data traffic in the country.
The average Three customer, of which there are 9.3 million, uses 3.5 times more mobile data than the industry average, and with more spectrum exclusively dedicated to 5G than any other mobile network in the UK, they also benefit from a full, outstanding experience when using the next generation of mobile technology.
Telcos can drive industry 4.0 further – through sustainability by default
Strengthening CX through real-time insights and cutting edge tech
We accelerate our clients’ NET-ZERO TRANSFORMATION whilst enabling other industries in reducing the impact across the TELCO ecosystem
We believe the FUTURE OF NETWORKS IS OPEN SOURCED AND AUTOMATED, and we lead in end-to-end open RAN, automation, digital twins and AI-enhanced network deployment capabilities
Next-generation networks – the spark of intelligence
We use DATA DRIVEN INSIGHTS for business transformation. We apply innovative technologies such as SD-WAN, Convergance, Network Slicing and analytics for B2B and B2C to deliver REVITALISED CUSTOMER EXPERIENCES
5G was launched in August 2019 by Three, who is the only operator able to meet the International Telecoms Union (ITU) 2020 standard for full 5G services.
It also lays claim to the UK’s fastest 5G network, as recognised by Ookla, which allows people to experience, share, and enjoy the everyday moments that matter and is a testament to the progress of Three’s £2 billion network and information technology (IT) infrastructure transformation.
As of July 2022, the transformation has delivered 5G mobile networking to 56 percent of the UK’s population across 3,200 sites in more than 400 locations.
This means that millions of mobile, business, and home broadband customers across more than half of the UK’s population can access superfast speeds, enabling them to
live their digital lives to the fullest and delivering on Three’s promise of providing better connectivity every day, for every customer.
The company is also upgrading its 4G network as part of the £2 billion transformation, with thousands of sites serving millions of customers already able to benefit from speeds up to 150 percent faster.
It comes as Three announced plans to completely switch off its 3G network by the end of 2024, in a move that will allow the company to focus investments and spectrum resources on further improving the 4G customer experience whilst rolling out 5G.
Amid the ongoing network and IT infrastructure transformation, another major recent announcement in June 2023 detailed the merger of Vodafone
and Three’s UK telecommunications businesses.
From day one, millions of Vodafone and Three customers in the UK will enjoy a better network experience with greater coverage and reliability at no extra cost.
The combined business will deliver up to a six-fold increase in average data speeds for customers by 2034 and invest £11 billion in the UK over 10 years to create one of Europe’s most advanced standalone 5G networks, a vote of confidence in the UK and its ambitions to be a centre for future technology.
Delivering up to £5 billion in economic benefits per year by 2030, the merger will create jobs, give all schools and hospitals in the country access to standalone 5G by the end of the decade, and support the digital transformation of businesses in the UK.
New research from Three Business in March 2023, for example, has revealed that better connectivity among small and medium-sized enterprises (SMEs) in Birmingham and Manchester would contribute an extra £3.09 billion and £2.2 billion a year respectively to the local economies.
With growth front of mind, the majority of SMEs in these two cities said their business could grow faster if they had access to better technology, whilst almost half think they could be left behind because of it.
The merger is therefore set to enable the UK to deliver its ambitions for digital and economic growth, and fully support government objectives for a world-leading digital economy.
It will also create a third operator with scale to level what is a competitive playing field and increase competition to the UK’s two leading converged operators, providing more choice in wholesale partners for mobile virtual network operators
(MVNOs).
Fixed wireless access will be offered to 82 percent of households by 2030, complementing the merger’s access to the biggest full fibre footprint in the UK.
The transaction, which is expected to close before the end of 2024 subject to regulatory and shareholder approvals, has therefore been described as great for customers, great for the country, and great for competition.
It will represent a major milestone for the two companies, who both currently lack the necessary scale on their own to earn their cost of capital.
Indeed, it has long been a challenge for Three to invest and compete, however, this merger will bring the necessary scale to deliver a bestin-class 5G network for the UK, transforming mobile services for its customers and opening up fresh opportunities for businesses across the length and breadth of the country.
As well as building a better-connected world, Three is committed to creating a more sustainable and inclusive future.
Delivering a fast and reliable network is one of three key areas that the company is focusing on to help it conscientiously deliver better connectivity, along with minimising its emissions and supporting and developing its people.
Three therefore takes its role within corporate social responsibility very seriously, as a major part of the UK’s critical infrastructure.
Whether supporting communities that need it most or nurturing a culture of belonging and respect for its diverse group of employees, every step that Three takes as a business needs to have a meaningful impact.
The latest step was taken in June 2023 as Three was listed as one of The Times Top 50 Employers for Gender Equality, the UK’s most highly
profiled and well-established listing of employers taking action and making gender equality a key part of their business strategy at all levels.
A first-time inclusion for Three on the prestigious list, it demonstrates the company’s commitment to addressing gender inequality in the workplace and shows it is taking important action.
It comes off the back of successfully narrowing Three’s gender pay gap in 2022, due to the focus on improving the gender balance across leadership roles and continued efforts to ensure pay decisions are fair and consistent.
Conscious of the value a more diverse workforce can bring to the business, Three is targeting a 50/50 gender split in leadership
Speed and reliability mean a better mobile experience, whether it’s for streaming, gaming, browsing, or video calling.
That’s why Three is continuing to improve its network by implementing cutting-edge technology, building extra 4G and 5G sites, accelerating the rollout of 5G, and phasing out 3G to bring faster download speeds, better quality streaming, and an even more reliable experience.
The company’s £2 billion network investment is well underway and will deliver better connectivity for all customers at all times. As a result, more people in more places will be able to take advantage of being on the UK’s fastest 5G network.
roles, and this latest well-deserved accolade recognises the hard work and dedication of everyone at the company to ensure gender equality is a key priority.
Equally, the company is also incredibly proud of the charitable partnerships and campaigns it has formed, particularly with Samaritans, which are having a positive impact on wider communities and the lives of customers.
A three-year charity partnership with Samaritans was announced in 2021 as the COVID-19 pandemic was having a profound impact on the UK population’s mental health.
The partnership is addressing these challenges, leveraging Three’s technology, retail stores and expertise to help more people access emotional support 24/7, 365 days a year.
Three is likewise supporting its
most vulnerable customers as part of its ongoing response to the cost of living crisis, which continues to put financial pressure on many.
With people in need of assistance more than ever, including access to affordable connectivity without restrictions, Three is committed to playing its part in the solution and launched a new social tariff through its sub-brand SMARTY in February 2023.
At £12 a month, the plan represents exceptional value for money, with unlimited data, calls and texts, and superfast 5G at no extra cost.
It is offered as a flexible monthly rolling plan which can be changed or cancelled at any time, giving customers complete control, simplicity, and value for money with no tie-in.
As it prepares to enter a new era, Three therefore continues to support the well-being and digital growth of the country.
With more than three decades at UPS® under my belt, I would say that I bleed brown!”
It was 1990 when Jeff McCorstin originally began his esteemed career at UPS®, one of the world’s largest package delivery companies, as a peak season package delivery driver.
Though UPS® is famous for delivering packages all over the planet with legendary precision, it turns out that the company also offers an unexpected wealth of services and expertise to help streamline global supply chains.
Indeed, McCorstin today has progressed to the role of President of Global Freight Forwarding at UPS Supply Chain Solutions®, the freight and logistics arm of UPS® that manages every aspect of global supply chains.
“My responsibilities continued to grow in line with our company’s direction, and it made sense to be involved with the supply chain solutions industry, where we assist customers with their global supply networks and their need for more than express small parcel delivery,” he tells us.
“It truly allows us to provide end-toend supply chain solutions on behalf of our important customers.”
The best supply chains stay in constant motion, and UPS Supply Chain Solutions® keeps them humming along by helping customers control three fundamentals: the doing, the seeing, and the optimising.
Global Freight Forwarding, overseen by McCorstin, is one of four businesses that comprise UPS Supply Chain Solutions®, along with Global Logistics and Distribution, Mail Innovations, and Coyote Logistics,
each with several of their own services and capabilities to meet the everchanging needs of customers.
Global Freight Forwarding services provided by UPS Supply Chain Solutions® are easily accessible, highly reliable, and extremely flexible for balancing speed and cost-efficiency requirements.
“Under my area of responsibility, we offer several services that support our customers’ needs, such as international air freight, North
American air freight, ocean freight, and customs brokerage,” informs McCorstin.
“With our Global Freight Forwarding solutions, we accommodate the needs and challenges that our customers come to expect.”
Within international air freight, UPS Supply Chain Solutions® stands as a top 10 air forwarder whose large global fleet and extensive carrier
partnerships ensure access to flights around the world.
From urgent, next-flight-out service to door-to-door service within one to five business days, UPS Supply Chain Solutions® has a trusted network of airline flights, charters, and strategic partners to get cargo to where it’s needed, when it’s needed, and on budget.
Serving more than 14,000 origins and destinations worldwide, this global presence and scale assists UPS Supply Chain Solutions® in acquiring
international air freight capacity. Efficiently and economically moving goods within and between the US, Canada and Puerto Rico, meanwhile, is the company’s North American air freight service.
“We have a North American air freight product which is a heavyweight next-day, second-day and third-day defined service, as well as a Trade Direct® Cross Border service offering in the US, Mexico and Canada,” McCorstin states.
In his 33-year tenure, Jeff McCorstin has had an undeniable impact at UPS®, leading supply chain strategies to improve logistics outcomes for customers around the world. Today, in his role as president of the global freight
forwarding division of UPS®, Jeff is tackling his next big ambition – bridging the data gaps that universally stunt advancements in the supply chain industry.
Jeff and his team recently selected the cloudnative data experience company, Domo, to help modernize the data strategy at UPS® and champion a new future for supply chain logistics. Jeff and Domo’s Chief Analytics Officer and SVP of Customer Success, Mark Maughan, sat down together to talk about how they plan to uplevel the UPS® customer experience and sharpen its competitive edge in a famously commoditized industry.
Mark: You have an impressive tenure in the supply chain and logistics industry. What have you learned are the most important factors to success?
Jeff: Success in this industry requires the right people, tools, technology, and processes. I’ve always leaned into tools and technology to arm our people around the world to make informed decisions. I follow a "head, heart, and hands" leadership model: being strategic, innovative, future-focused, and a complex problem-solver (head); inspiring others and fostering collaboration (heart); and delivering results, being accountable, being agile, and building effective teams (hands).
Data is the common tie between these traits and leveraging it in the complex world of supply chains is crucial. We mine it for insights, use it to predict trends, and turn it into efficiencies that give us a competitive edge. As we look ahead, our data strategy becomes increasingly vital. Machine learning and emerging technologies will be instrumental, but only with a robust data strategy in place. This understanding led us to Domo, aligning with our vision of a future where data forms our operational backbone.
Mark: Why is direct access to data importantespecially in supply chain logistics?
Jeff: Direct access to data enables us to make informed and timely decisions, resulting in better overall operational performance. It allows us to proactively identify and address bottlenecks in our customers' supply chains, working collaboratively to find solutions. Using data, we can anticipate and minimize the impact of exceptions that may arise in global supply chains.
By leveraging Domo alerts, we can promptly identify potential delays or disruptions, allowing us to take immediate action and mitigate customer impact. This not only helps us maintain efficient operations but also enables us to provide our customers with accurate delivery information. With precise delivery dates, our customers can plan their staffing resources accordingly and effectively communicate with their own customers. This immediate access to data not only bolsters our operational agility and customer service but also enhances our overall value proposition and widens our competitive advantage in the industry.
Mark: What business challenges were you trying to solve at UPS® when you started pursuing a new approach to data?
Jeff: The scale at which logistics data is siloed in this industry is a significant barrier to bringing it into the future, and I see so much potential in breaking down those walls. The complexity and fragmentation of data across systems limits our view of the full end-to-end supply chain, and the manual processes, paper-based inefficient operations, and overreliance on Excel and static rearview mirror reporting tools create bottlenecks, limit data flow and hinder decision making.
Our collaboration with Domo allows us to pull disparate systems together in a single platform and provides us with real-time dynamic data. Domo not only addresses our immediate challenges but also allows us to manage data effectively to hit our Key Performance Indicators and influence growth and innovation. By providing the right tools and empowering our teams to quickly adapt to the changing landscape, we can set new standards
for operational excellence and better serve our customers in a fast-paced industry.
Mark: What makes Domo the right provider to help you champion these changes?
Jeff: What sets Domo apart is its ability to deliver rapid time-to-value. We had been working with other BI and analytics vendors in the past, but we were not achieving the level of speed and efficiency that we needed, particularly in reporting. With Domo, we found a solution that delivered value within two weeks, while still ensuring data integrity and protection.
Because the supply chain industry typically measures project timelines in months and years, Domo’s pace is a refreshing shift, and feels like a catalyst for our journey towards "grown-up analytics." Already, this collaboration has enabled us to make data-driven decisions in real time and drive meaningful change across our entire organization –from our front-line operators to the C-Suite. Domo's solution provides the agility and flexibility we need to meet our evolving business needs. We like to manage our business by the clock and not the calendar, and Domo allows that speed and agility.
At UPS®, we are constantly searching for ways to add value while decreasing costs, and this collaboration will give us value we can pass on to our customers.
Mark: What outcomes do you expect from reinventing data strategy for Global Freight Forwarding at UPS®?
Jeff: Our ultimate goal is to create more efficiency and value for our customers, and we’re already beginning to move the needle.
For example, we’ve freed up hours of our operators’ time each day by automating processes that were historically manual. We’ve also improved our real-time decision-making capabilities through a custom-designed dashboard that drills into important data with ease. In both cases, we were enjoying the outcomes within days, compared to weeks and even months we’ve experienced with other vendors.
We’re looking forward to extending these benefits to more of our employees, and to our customers by integrating Domo into their UPS® experience. What truly sets Domo apart from our past collaborators is how easy it is for everyone to build and access business insights. Our citizen developers do not need a technology background to learn and use Domo.
Mark: How will your customers benefit from the real-time data access they’ll get through your collaboration with Domo?
Jeff: We want to provide customers with a level of unprecedented visibility and understanding of the commercial and transactional components of their relationship with UPS®. To do this, we plan to embed Domo's analytic capabilities into our existing customer-facing applications, so customers can
“We plan to embed Domo's analytic capabilities into our existing customer-facing applications, so customers can have access to real-time data and insights alongside us.”
Jeff McCorstin, UPS® President Global Freight Forwarding
have access to real-time data and insights alongside us. We want to collaborate with customers to highlight inefficiencies and ways they can drive down their transportation costs. We also want to proactively address problems in collaboration with our customers, so we can manage disruptions and provide the best customer experience.
Mark: Now that you have a new data strategy and fresh perspective on what’s possible, what excites you about the future of the supply chain and logistics industry?
Jeff: What excites me the most is the potential to transform UPS Supply Chain Solutions® and Global Freight Forwarding’s role in the logistics industry by capitalizing on our data in ways that we never thought were possible.
With Domo as our collaborator, we’ve identified numerous use cases and innovative ways to leverage data to improve our internal operational processes and capabilities as well as the supply chain experience for our customers...and for theirs. Gaining access to previously unavailable data and understanding the interrelationships enhances our operational capabilities, and also empowers us to meet the evolving needs of the industry.
As we continue to embrace technology and leverage data-driven insights, we’re shaping the future of supply chain and logistics, driving continuous improvement, and delivering unparalleled value to our customers.
To learn more visit domo.com/ups
UPS® and Domo are collaborating to reinvent the supply chain with data. By breaking down data silos and providing real-time insights, UPS® is able to make better decisions, improve efficiency, and deliver a better customer experience.
Cross Border is one of three Trade Direct® services that allow UPS Supply Chain Solutions® to meet international supply chain needs, complemented by Trade Direct® Air and Trade Direct® Ocean.
Leveraging the breadth and reliability of the UPS® global network, Trade Direct® handles freight consolidation via air, ocean and ground transportation, customs clearance, and direct delivery to multiple addresses within the destination country, all through a single source.
By consolidating individual shipments to the same destination country into just one shipment, UPS Supply Chain Solutions® can cut customs clearance times.
“One of the values of being both an asset-based provider in our small parcels business, and a
freight forwarder in our supply chain solutions business, is to offer a oneto-many solution – we call it Trade Direct®.”
“A customer can make a single shipment that has multiple recipients for final delivery; we can clear customs as a single shipment then drop it off into our small parcel network for the final recipients to receive their goods,” McCorstin elaborates.
By sea, UPS Supply Chain Solutions® is one of the world’s top nonvessel operating common carriers (NVOCCs), with contracted space allocation with major global carriers to ensure access, competitive rates, and reliability.
Ocean freight is moved across more than 2,300 shipping lanes daily by
UPS Supply Chain Solutions®, who as an experienced NVOCC provides up-to-the-minute customs expertise, visibility and communication every step of the way for those considering expanding to new markets.
The company’s value-added ocean freight services can take shipping to the next level, bolstered by strong expertise and network infrastructure around the world, and best-in-class visibility tools to provide end-to-end control.
“We support our customers at the origin with a purchase order management service. In essence, we are the eyes and ears for customers that need to consolidate multiple vendors’ projects into an ocean container but do not have people in the country,” explains McCorstin.
Having been in transportation and logistics for more than a century, UPS
Supply Chain Solutions® is likewise used to being on the front lines of customs brokerage, helping to inform and lead compliance policy, support public affairs, and ensure the best interests of both customers and the trade community are well represented.
As one of the world’s largest customs brokers, UPS Supply Chain Solutions® has close relationships with customs agencies, superior timeliness, a wide breadth of in-depth solutions, and ensures its customers’ needs are heard by not just following the rules but helping to make them.
The company also has a range of innovative multimodal services, including sea-air, rail from Asia to Europe, ocean LCL (less than container load) and preferred LCL to name a few.
These multimodal services ensure the right balance of speed and economy, as they are often less expensive than air freight yet faster
than ocean freight, making them a perfect transportation alternative.
UPS Supply Chain Solutions® has more than 115 years of transportation and logistics experience, whose global footprint, breadth of perspective, competencies, and capabilities are proven to help businesses of all sizes to deliver the right balance of speed and cost-efficiency.
But what sets the company as a whole apart is the 550,000 UPSers around the world, including more than 12,000 Global Freight Forwarding employees, that make it happen every day and exceed customer
expectations.
“Empowering our staff with the autonomy to not only bring their unique selves to work but to make decisions that will support our customers’ needs is a must.”
People are the most important asset at UPS Supply Chain Solutions®, as demonstrated by the company’s leadership model, which is designed to build a culture that retains and grows its employees.
“We have a leadership model that is all about the head, heart, and hands. The head is about strategy – can you solve complex problems? Are you innovative? Do you think outside the box?” McCorstin comments.
“WE HAVE A LEADERSHIP MODEL THAT IS ALL ABOUT THE HEAD, HEART, AND HANDS”
JEFF MCCORSTIN, PRESIDENT OF GLOBAL FREIGHT FORWARDING, UPS SUPPLY CHAIN SOLUTIONS®
Welcometo a new era of logistics excellence, where efficiency, visibility, and quality are not just goals, but a reality. At the heart of this transformation is CargoWise, a world-class logistics operations platform. It provides end-to-end visibility, shifting your operations from reactive to proactive, enabling you to reach higher, faster.
Zinnovate, as your implementation partner, is uniquely positioned to unlock the full potential of CargoWise for your business. Our deep industry knowledge and technical expertise allow us to optimize your business processes, ensuring you reach as close to optimal performance as
possible, and faster than you ever thought possible.
Our mission is simple: to improve our customers’ operations. We achieve this by harnessing the power of CargoWise to drive efficiency, standardization, and digitalization. For freight forwarders, this means streamlined operations, real-time data for quick decision-making, and improved service quality.
But what truly sets Zinnovate apart is our commitment to your success. We don’t just implement a system; we transform your business. We work closely with you, understanding your unique challenges and goals, and tailor our
approach accordingly. We’re not just a service provider; we’re your partner in this journey towards excellence. With Zinnovate and CargoWise, you’re not just adopting a new system; you’re embracing a new way of doing business. A way that’s efficient, proactive, and qualitydriven. Let Zinnovate guide you to the skies of logistics excellence. Your journey to the top starts here. Zinnovate has firmly established itself as a leading global provider at the forefront of digital transformation projects in the logistics industry. The company’s unique industry insights have been garnered from years of best practices based on actual cases
from the majority of the top 20 global forwarders. With its extensive global expert network, Zinnovate harnesses superior change management and technical know-how to deliver actionable results, guiding and empowering global logistics as they adapt to the new technological revolution.
This specialist IT and management consultancy originated from
a powerful idea and fruitful collaborations, inclusive of their team of consultants spanning 25 countries across all continents, and their key partner since 2013, WiseTechGlobal, with its flagship product, CargoWise. Having one hand on emerging exponential technologies and the other guiding their partners, teams, and clients, Zinnovate is poised to offer solutions unmatched by others.
In 2020, Zinnovate made industry history by assisting a key customer in becoming the first in the logistics world to implement their new IT system across 62 countries in a “Big Bang” worldwide go-live. By 2022, they had surpassed the 100 MSEK milestone, and their growth continues to accelerate.
Håkan Nilsson (HN), Founder & Group CEO, and Tamsin Emery (TE), Project Director, share the pride they have in the accomplished Zinnovate team, their journey to success, and the privilege of partnering with UPS®
When asked about the secret to Zinnovate’s remarkable triumph, HN confesses, “The secret ingredient? It’s our absolute passion and unwavering dedication towards serving our customers.”
TE adds, “Our success hinges on the profound respect we hold for our team. While our customers are our primary focus, we prioritize the wellbeing of our people. We believe that without our team, we are nothing. Their contributions are invaluable not only to us but also to our customers.”
On Zinnovate’s strategy for maintaining its leadership position
in the digital transformation space, TE reveals, “We invest substantial time in understanding emerging technologies and integrating them into our daily operations. We ensure our customers benefit optimally from the digital transformation landscape, aligning their needs with upcoming market trends. Our key aim while collaborating with a customer is to share our knowledge and enable them to function independently, thereby bolstering their expertise and delivering immense value.”
HN further elaborates, “In addition, we’re broadening our capabilities with cutting-edge technologies, scaling our industry-leading software as a service (SaaS) among other initiatives.”
Discussing the pillar values of the value-driven organization, TE says, “At the heart of our ethos
lies a profound appreciation for people. Our business is steered by a principle we hold dear, the Return on Competence. This mantra underscores our commitment to nurturing and valuing expertise. Honesty and integrity are not just words to us; they embody our operations, reinforcing our pledge that people truly matter to us.
One of our primary objectives when collaborating with clients is to facilitate knowledge transfer, empowering them to operate independently from us. This strategy not only fosters expertise but also builds substantial value for our clients, echoing our belief in the significance of people and competence.”
HN emphasizes, “We aspire to synergistically enhance the collective output, going beyond the sum of individual parts. This principle applies not only to human potential, where we transform high-performing individuals into synergistic teams but also to business systems, where we leverage exceptional methodologies to drive superior business performance. Our consultancy service stands unrivaled in the industry, firmly grounded in the understanding that mere aggregation of talent doesn’t guarantee a high-performing team.
“We emphasize the importance of nurturing Relationships and preserving Reputation, the twin pillars of R&R. Our dedication to forging deep, meaningful connections and protecting our hard-
earned reputation knows no bounds. Through our exceptional customer relationships and unparalleled industry expertise, we’ve built a high reputation of prestige and trust.”
When asked about Zinnovate’s approach to talent acquisition, development, and team building, HN explains, “Our focus on talent development epitomizes the Return on Competence principle. We strive to ensure our team members continually grow and find satisfaction in their growth. It’s an axiom that winners draw winners; attracting top talent to a successful team is relatively straightforward.
“Even though approximately 350 competitors are providing expert consultancy, Zinnovate leads in nine out of 10 of the largest global projects. This places us in a unique position to attract talent, offering the opportunity to work on the most challenging and exciting projects in this field. We take pride in having a substantial number of female senior expert consultants in the traditionally male-dominated intersection of Logistics, IT, and Management Consultancy. Our commitment to diversity is unwavering.”
TE elaborates, “With consultants in 25 countries, team building exercises are challenging, but we strive to unite our team whenever possible. Most of our initiatives are centered around digital connection. We distribute a regular newsletter that updates the team about ongoing projects, new developments, and customer activities, fostering a sense of unity despite geographical barriers.”
Discussing Zinnovate’s future plans, TE says, “We’re concentrating on two primary areas: team and resource expansion, and product development. While consulting is our primary area of expertise, we intend to broaden our product portfolio. We regularly observe customers struggling with tasks that lack software solutions, necessitating manual effort. Our aim in digital transformation is to bridge these gaps through product development and new applications or software creation.”
Zinnovate team at customer premise in DubaiHN adds, “Considering the fragmented state of the freight forwarding industry, I foresee a surge in mergers and acquisitions. I believe this will emerge as a crucial service area for Zinnovate to support our customers. Above all, we aim to further ignite our team’s passion and enhance their professional satisfaction.”
Addressing the partnership between UPS® and Zinnovate to maximize UPS®’s value, TE shares, “We collaborate with some partners to provide support services to UPS® , including applications and invoice processing software developed by one of our partners. We ensure comprehensive coverage, enabling UPS® to appreciate the full end-toend value.”
HN concludes, “Our collaboration with UPS® is both an honor and privilege. I’m confident that Zinnovate can deliver a competence factor to UPS®, surpassing what others can offer. However, achieving this requires strong cultural alignment between the organizations. This alignment hinges on personal chemistry, fostering productive collaborations. Zinnovate is designed to swiftly scale up to accommodate the needs of large clients like UPS® Despite UPS®’s immense size, we share a core value: people matter. This belief is not merely a marketing
strategy, and it ensures a fitting personal chemistry between UPS® and Zinnovate.”
Zinnovate’s journey is a testament to its unwavering commitment to people, competence, and customer service, reflected in its industryleading position. With a deep-rooted ethos of Return on Competence, the company has consistently proven itself as a reliable partner in navigating the vast landscape of digital transformation, even in the face of intense competition. Its dedication to understanding and integrating emerging technologies,
fostering team growth, and ensuring customer satisfaction has set a high bar in the industry. As it looks to the future, Zinnovate continues to enhance its offerings and expand its team, with an emphasis on creating valuable solutions to bridge the gap in the market and supporting its customers in the increasingly complex world of logistics and IT.
Its partnership with UPS® underscores its capacity to scale up and deliver a superior level of competence, thereby reinforcing its reputation and trust. If you want to be part of this transformative journey, contact Zinnovate, a company that is reshaping the digital landscape of the logistics industry, one project at a time.
“The heart is where I really believe my biggest strength is, and it’s all about inspirational leadership and being inclusive. Diversity, equity and inclusion (DEI) means more than just diversity of gender or race; it also means diversity of thoughts and experiences, making sure that we’re perceptive, reading the room, and making sure that we are collaborative.”
Jeff McCorstin, President of Global Freight Forwarding: “My first taste of the transportation industry came at UPS® as a peak season package driver.
“On my fourth day of the job, I received an offer from KPMG for a management consulting role. UPS® sat me down and spent 90 minutes selling me on the history, legacy, and culture of this great company. I declined the offer with KPMG and moved into management with UPS®.
“I’ve had roles in operations, industrial engineering, strategic cost, and finance
McCorstin has always believed in being a cross-functional collaborative leader, and that hearing multiple people’s opinions is the right approach.
The third and final trait that McCorstin leans into as a leader is the hands, which involves delivering results, being accountable, adapting to market conditions, and being a strong team builder.
“I like to try and keep things
and administration (F&A) across different locations within the US. I was the Air Finance Controller at our hub in Louisville, Kentucky (KY), responsible for the financial analysis of aircraft acquisitions and the Worldport facility, which led to becoming CFO for Europe, the Middle East, and Africa (EMEA).
“After this assignment, I was named President of EMEA Freight Forwarding, which began my foray into the supply chain/freight forwarding industry. Additional supply chain roles I held before my current position include Senior Vice President of Global Freight Forwarding Air and Ocean Product; President of Asia Pacific Freight Forwarding; and President of Global Customs Brokerage and Trade Advisory Services.”
straightforward with my team and how I communicate with our employees,” he affirms.
Citing his belief in the simple concepts of tools through technology, processes, and people, McCorstin informs us that UPS Supply Chain Solutions® has been investing in these three areas to make its operations more efficient through improved systems capabilities and make its operators’ jobs easier so they can focus on improving the customer experience.
“We’re building out our digital fluency and our tools through technology. It arms and empowers our frontline operations teams with good data to be able to make decisions on behalf of our customers on a real-time basis.
“It’s about providing better tools for better insights so that our employees around the world can be more proactive and make better decisions. We work with a number of providers, like The DDC Group and Domo, that are about tools through technology,” McCorstin notes.
By leveraging updated technologies, UPS Supply Chain Solutions® can better connect its systems to eliminate redundancies and streamline data transfers with customers and vendors.
Then, by taking that data to the next level through improved visualisation and data democratisation, the company makes decisions significantly closer to real-time than in the past.
“Empowering our operators with agile decision-making tools is one of our top focus areas,” reveals McCorstin.
“Our recent collaboration with Domo is taking us into the world of data democratisation, where – with the right controls and securities – we can get data to those who need it in an almost seamless manner, with speeds that we’ve never seen before.
The importance of supply chain visibility and resilience is critical for logistics service providers. Our industry-leading flagship product, CargoWise, is centralizing logistics operations on a single global database, delivering business continuity, scalability, and security.
The logistics industry is a performance-based sector. The ability to efficiently manage goods in transit is measured by crucial factors like speed, cost and accuracy.
However, in today’s increasingly complex global supply chain, meeting these metrics has become more challenging than ever before.
With shifting demands in both the business-to-business (B2B) and business-to-consumer (B2C) spaces, logistics providers must act swiftly to enhance the productivity and efficiency of their operations to meet capacity demands and overcome disruptions.
Recognizing the need for transformative solutions, many industry experts believe that the key lies in increasing digital capabilities and embracing digital practices.
Digital transformations have been ongoing in the logistics industry, but recent unpredictable pressures have accelerated the urgency for faster and more lasting implementations.
To delve deeper into this paradigm shift, we partnered with Reuters Events to conduct a comprehensive survey involving over 480 logistics and supply chain professionals worldwide.
Our objective was to gain insights into how companies perceive and drive productivity across their operations, with a particular focus
on the crucial role technology plays in achieving these goals.
Key findings from our research shed light on the challenges faced by the industry:
1. Lacking measurements of productivity makes building a case for business investment difficult. Surprisingly, more than a third (35 percent) of respondents do not measure productivity or have specific targets to benchmark success. This disconnect between recognizing the importance of productivity and setting measurable targets impedes progress.
2. The COVID-19 pandemic shifted focus from cost to value. Therefore, improved customer service and increased operational efficiency became top priorities for enhancing productivity, overshadowing more traditional financial metrics such as increased revenue and profit. This change in mindset reflects a transition towards “value over cost” sentiments in logistics and supply chain operations.
3. Technology boosts productivity. Investment in technology emerged as the primary driver of productivity, with 45 percent of respondents emphasizing its potential impact. Automation of manual tasks and real-time visibility were identified as key priorities, offering immediate and significant opportunities for efficiency gains.
4. Centralization of data for enhanced visibility is critical to long-term success. Over half of the respondents (58 percent) highlighted the challenge of relying on multiple disconnected systems across trading partners. Connectivity issues, data sharing concerns, and a lack of centralized systems hinder effective data management and productivity improvement. A single logistics platform that integrates multiple data streams can enhance visibility and facilitate the tracking and realization of productivity goals.
As demand continues to grow and evolve, so do constraints on time, money and resources. For logistics businesses to succeed in this increasingly uncertain and competitive landscape, maximizing every aspect of efficiency and productivity is crucial.
With all this in mind, there has never been a more prudent time to update digitally. And with the right investment in the right technology, you can unlock new productivity gains and meet your customers’ needs now and in the future.
Want to learn more about the link between technology and productivity? Download the report now
“It’s really exciting to see desk workers be able to see live dashboards which highlight where shipments need attention well in advance of actual problems, thus proactively enabling decision-making to avoid impacting transit times,” he adds.
The Global Freight Forwarding business at UPS Supply Chain Solutions® has evidently seen unprecedented investment in recent years, from operating systems to big data tools and even the company’s gateway network, with construction recently completed in Chicago and Frankfurt.
A continued focus on sustainability is at the forefront of the company’s investments, exemplified by the numerous electric forklifts and compressed natural gas (CNG) vehicles purchased by UPS Supply
• Ultra-cold freezer donations and in-kind vaccine deliveries to facilitate equitable distribution to remote and rural areas throughout Africa, South America, Asia, North America, and Europe, made possible by The UPS® Foundation
• Three regional 24/7 UPS® Healthcare Command Centres, dedicated to predicting and managing the global vaccine movement to ensure on-time delivery.
• Partnering with Gavi and other organisations to train and manage the ultra-cold movement of vaccines in COVID-19 Vaccines Global Access (COVAX) countries.
• Delivery of COVID-19 vaccines outside of the US, managing 4,500 movements through the UPS® network and commercial partners since the first vaccines were made available.
• Embedded UPS® logistic experts in countries including Indonesia and Malawi to fully and safely manage vaccine distribution logistics.
• Support of vaccine doses delivered via autonomous aircraft to clinics in Africa through the partnership between Zipline and Gavi
• Real-time visibility into the location of vaccines through UPS® Premier technology, which provides precise visibility into every single vaccine package.
• Supported over 130 vaccine clinical trials to date through the UPS® Healthcare subsidiary Marken, which is involved in nearly all vaccines and treatments in development today.
Goggin Warehousing is a third party logistics provider (3PL) offering storage, transportation, distribution, and logistics solutions. Simply put, we customize systems to solve complex logistical challenges.
Our priority is to make your job easier and to help your company run more effectively.
www.gogginwarehousing.com
Chain Solutions® to reduce its carbon footprint and minimise its impact on the environment.
For McCorstin, these investments are not only exciting but show customers and operators that the company is serious about moving into the future of freight forwarding.
UPS Supply Chain Solutions®, together with shareholders, customers, suppliers, communities and employees, cares deeply about sustainability.
The company’s culture centres around the values established by the founder of UPS®, Jim Casey, who believed in giving back to the community and being responsible social and environmental stewards.
“Today, we approach sustainability holistically and in alignment with our customer first, people led, innovation driven strategy,” states McCorstin. UPSers know that doing good in the world is also good for business. Thus, sustainability has always been a core value of the company, whose latest sustainability report highlights the progress it is making towards important goals that deliver good in the world, including its goal to achieve carbon neutrality across Scope 1, 2 and 3 emissions by 2050.
Another area of investment for UPS Supply Chain Solutions® is in its new, modern office spaces, which
• Year-over-year 6.9 percent decrease in Scope 1, 2, and 3 CO2e emissions.
• Added to a global fleet of alternative fuel and advanced technology vehicles.
• Purchased 162 million gallons of alternative fuels.
• Eight percent of total electricity is generated from renewable sources for its owned and leased facilities.
• Planted 28 million trees since 2012.
• Expanded the UPS® Sustainability Trailblazers employee engagement programme.
“EMPOWERING OUR OPERATORS WITH AGILE DECISION-MAKING TOOLS IS ONE OF OUR TOP FOCUS AREAS”
– JEFF MCCORSTIN,PRESIDENT OF GLOBAL FREIGHT FORWARDING, UPS SUPPLY CHAIN SOLUTIONS®
Through every peak, valley, and plateau, DDC FPO’s data-based goal driven solutions help to achieve your goals.
DDC FPO is a strategic business process outsourcing (BPO) partner for today’s leading transportation and logistics providers that enables clients to focus on core competencies and achieve their goals. As the freightfocused member company of The DDC Group – a worldwide network of BPO companies – DDC FPO is able to serve clients in over 30 languages worldwide.
Solutions include but are not limited to:
• Freight Billing
• DDC Intelligence
• Customer Care (Customer Service & Inside Sales)
• DDC Sync (Intuitive Mobile Data Capture)
• Customs Brokerage Processing
US: +1 303 674 0681 UK: +44 800 011 2750 info@ddcfpo.com www.ddcfpo.com
30+ LANGUAGES
30+ YEARS OF BPO EXCELLENCE 16+ YEARS IN FREIGHT 50% SERVING OF TODAY’S TOP CARRIERS
33 PROCESSING SHIPMENTS BETWEEN COUNTRIES
7000 TEAM MEMBERS GLOBALLY
accommodate the hybrid working environments popularised during the COVID-19 pandemic.
It was throughout the pandemic that UPS Supply Chain Solutions® also delivered equitable access to critical healthcare services, and worked tirelessly to accelerate vaccine distribution and help keep communities as safe as possible.
The staff and wide range of services played a crucial role in this, as UPS® delivered more than one billion vaccine doses by December 2021.
This impressive milestone was made possible through innovative
approaches, one-of-a-kind UPS® Premier tracking technologies, industry-leading cold chain solutions, and an expansive, sophisticated, global network providing UPS® Healthcare services to customers and communities around the world.
Not only did the global UPS® network support healthcare customers and global organisations, but it also joined in public-private partnerships to provide vaccines and cold chain expertise to hard-to-reach countries, ensuring delivery to as many people as possible.
To achieve this, UPS® Healthcare
mapped roughly 500 trade lanes to enable seamless worldwide vaccine shipments and used more than three million pounds (lbs) of dry ice to help safely move the vaccines.
“UPS® Healthcare set the global pace for COVID-19 vaccine delivery, supported by the unmatched dedication of UPSers and the company’s global logistics capabilities and expertise. Medicines derived from biologics and delivered via cutting-edge cold chain networks represent the future, and UPS® Healthcare is leading the way,” McCorstin acclaims.
Prior to the critical delivery of COVID-19 vaccines, UPS Supply Chain Solutions® was called upon to bring personal protective equipment (PPE) into the US during the pandemic.
This important role came as
“IT IS ABOUT MOVING THE WORLD FORWARD BY DELIVERING WHAT MATTERS. IF THE CUSTOMER IS HAPPY, WE ARE HAPPY!”
part of the US Government’s Project Airbridge, which was created to shorten the amount of time it takes for medical supply distributors to import PPE and other medical supplies into the country.
UPS Supply Chain Solutions® was sourced by the Federal Emergency Management Agency (FEMA) to bring PPE into the US, where supplies had depleted over recent years.
“We were a major facilitator of US bound PPE over a three-month period at the beginning of the pandemic. Our first dedicated charter flight was in the first week of April, and by the end of June, we did more than 350 dedicated charters, of which more than 200 were for Project Airbridge,” shares McCorstin.
As an order of magnitude, every one of these aircraft could handle 100 tons of PPE, which allowed the US to open up at a much faster rate than the rest of the world.
Then came the pivot to COVID-19
test kits, of which hundreds of millions were provided by UPS Supply Chain Solutions® throughout the US.
“The pandemic was the most impactful moment of my career because lives were truly at stake,” McCorstin says.
As the world has mercifully emerged from the pandemic, helping customers to navigate constant supply and demand changes in the air and ocean freight markets is paramount for UPS Supply Chain Solutions® in the coming year.
The company is focused on being the global freight forwarder of choice and will therefore also leverage UPS® Browntail air freighters to utilise
available capacity and provide better service to customers, as well as leaning into the growing healthcare industry and supporting both enterprise and small and mediumsized businesses (SMBs).
Additionally, UPS Supply Chain Solutions® will continue to help its customers to reassess their supply chains whilst building out a digitally enabled ecosystem, both operationally and from a customer input and visibility perspective.
“It is about moving the world forward by delivering what matters. If the customer is happy, we are happy!” concludes McCorstin.
Writer: Phoebe Harper | Project Manager: Thomas Arnold
Domestic demand for green energy solutions continues to escalate on a global scale. The question of how this demand is met, both responsibly and sustainably, is a quandary that many players in the energy sector must confront, and quickly.
“I believe this is one of the major global challenges in the immediate and long-term future of our world,” introduces Francis Rome, CEO at Belinus.
“We want to contribute to this challenge.”
Rome is the leading voice behind a Belgian manufacturer of solar panels and energy storage batteries, which it has been producing for home and business use since 2015. Belinus
stands out in this dynamic field as the only producer of ultra-black doubleglass IBC modules – an innovation in solar panels that combines sleek aesthetics with high-efficiency.
“IBC cells apply a distinguished idea,” explains Rome, elaborating on the science behind the modules. “Rather than placing the contacts in front of the cell, they place them on its rear side. This allows them to achieve higher efficiency due to reduced shading on the front of the cell, while at the same time, electronhole pairs generated by the absorbed light can still be collected on the rear side of the cell.”
Since their launch, these products have enjoyed high demand across Europe. Indeed, just last year,
Belinus was named as the ‘Top Brand PV 2022’ by EUPD Research – a well-established market research company headquartered in Germany.
From its head office in Thor Park, Genk (Belgium), the company operates in more than 10 countries and specialises in the research, development, and production of innovative, high-efficiency, ultrablack, double-glazed solar panels and high-quality energy storage batteries for the home and businesses.
Quality is the bedrock on which all Belinus products are manufactured and is its ultimate promise to clients.
“Quality is one of the biggest challenges in the industry. People
As the sole producer of ultra-black IBC glass-glass PV modules, Belinus is reinventing domestic demand for solar panels. We unpack its roadmap to growth and innovation with CEO, Francis Rome
these days expect this - they invest in something that they want to have on their roof for several decades, so naturally, they expect a good product that they can rely on,” says Rome.
All solar cells and solar panels produced by Belinus are manufactured in Bloomberg Tier-1 factories with an annual capacity of 2.2GW. The guarantee for
double-glass solar modules is 35 years, yet another unique selling point offered by the company.
With supply issues continuing to hamper many industries, partnerships are a key ingredient to unlocking the quality that Belinus promises to deliver.
“Supply is not always there. There is a lot of demand but not everyone can deliver, and that’s why we only choose a few good partners who are reliable and with whom we can build a relationship,” he continues.
“We at Belinus always look at our partners, who they are, what their vision and mission are, and if they have the same quality standards as us. Instead of selling to anyone, we choose who we sell to. In that way, we always have enough supply for our trustworthy partners.”
By applying this selective perspective to hand-picking carefully chosen partners, Belinus ensures autonomy and control over the level of quality it commits to delivering.
Although the company is currently pursuing further growth to meet
ever-increasing demand, Belinus remains cautious in its approach.
“Because our brand is growing and people know who we are, we get many questions from consumers as to where they can get our panels or other solar energy solutions. There are certain markets that are asking us almost daily if we will go there, but stability is the most important thing for us,” expands Rome.
“Growing in a stable and healthy manner while also standing behind our quality is essential, even if it means slower growth since quality will always be our number one focus.”
“GROWING IN A STABLE AND HEALTHY MANNER WHILE ALSO STANDING BEHIND OUR QUALITY IS ESSENTIAL, EVEN IF IT MEANS SLOWER GROWTH, SINCE QUALITY WILL ALWAYS BE OUR NUMBER ONE FOCUS”
– FRANCIS ROME, CEO, BELINUS
This quality is further guaranteed by using the opinions and feedbacks of its customers and consumers as a continual touchpoint for progress.
Rome looks back on 2022 as a year of “growth and great opportunities” for Belinus. Such pace and dynamism are set to continue, as a roadmap of growth lies ahead.
This will be fuelled by the spirit of innovation, in order to remain relevant in a competitive and everevolving field. The development of new solutions to cater to its
ever-increasing base of high-end customers is one key aspect of this continued exploration.
“Our R&D team works very hard to stay ahead towards the solar energy industry trends. Soon we will be launching the new N-type TopCon PV module series with an efficiency range up to 22.5 percent and a power range of up to 440W,” Rome tells us.
Despite these future ambitions, Rome affirms that the core priorities on which Belinus is founded will remain steadfast and unchanged.
“Our concept is all about the better home. Therefore, product quality,
guarantee terms, deliveries, and aesthetic is always our priority.”
With these values at the fore, Belinus will continue to meet the future of the solar industry head on, and paint it black.
BELINUS
Tel: +32 (0) 16 91 03 14
info@belinus.be
www.belinus.be
What advice would you give to someone considering entering your industry?
Roberto Re Managing Director, Metinvest Trametal“The global steel industry is oversupplied, and Europe is one of the hotspots of this oversupply. In order to succeed in such a market, it is essential to provide the best possible quality with a focus on growing industries. We are at the border of the new low emission steelmaking age, and it is only possible to count on future success by anticipating future regulatory requirements and expectations. “However, high quality will not be enough to prosper in the steel world. The key value driver in our market is still customer relations,
and dedication to strategic partners that drive long-term strategy and competitiveness. Long-term partnerships allow businesses to grow together and add value for both parties.”
“If you are considering entering the electric motors industry, you must first stay up to date with the latest trends and innovations to remain competitive and offer cutting-edge solutions. Additionally, it’s best to prioritise quality and reliability, whilst consistently delivering reliable and durable solutions that will earn you a strong reputation in the industry. Finally, you have to engage in open communication with your customers to understand their specific needs and provide exceptional customer service.”
“The semiconductor market is a very demanding and challenging cyclical market. You absolutely need to keep your promise and supply reliable and high up-time equipment that is supported with knowledgeable field service engineer support.”
Marija DukovskaPavlovska General Manager, Makstil“I would say be resilient, be ready to evolve personally as an industry leader, and adapt to fast-changing market needs. It is critical to get ready to challenge, and equally, to be challenged. Lastly, but most importantly, listen to your own employees, because they know the business best and are at the core of the company’s success.”
To round off each issue, we ask our contributing business leaders for their views on the same question
Adding to its growing family of regional titles – EME Outlook, Africa Outlook, APAC Outlook, North America Outlook, and its sister sector title, Mining Outlook – Outlook
Publishing is proud to announce the birth of a dedicated platform for the healthcare sector. As organisations worldwide must navigate a new healthcare landscape defined by technological innovation in the wake of the COVID-19 pandemic, now is the time to showcase the strides being taken in this critical sector.
A multi-channel brand, Healthcare Outlook will bring you the positive developments driven by organisations across the healthcare industry through its various platforms. Discover exclusive content distributed through its website, online magazine, social media channels, and dispatches delivered straight to your inbox with a bi-weekly newsletter.
Through this compelling new venture, we intend to foreground the movers and shakers of the industry. To participate as a featured company and join us in this exciting endeavour, contact one of our Project Managers today.
www.healthcare-outlook.com