Premium data centre solutions and state of the art facilities in the Middle East
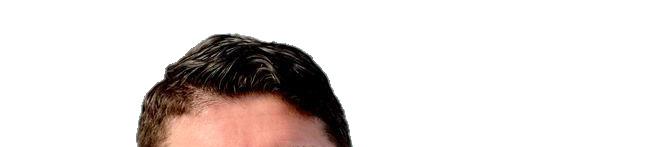
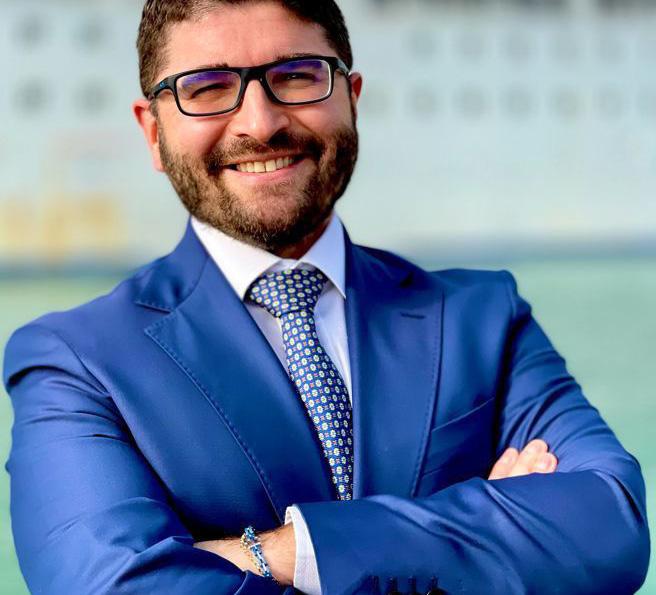
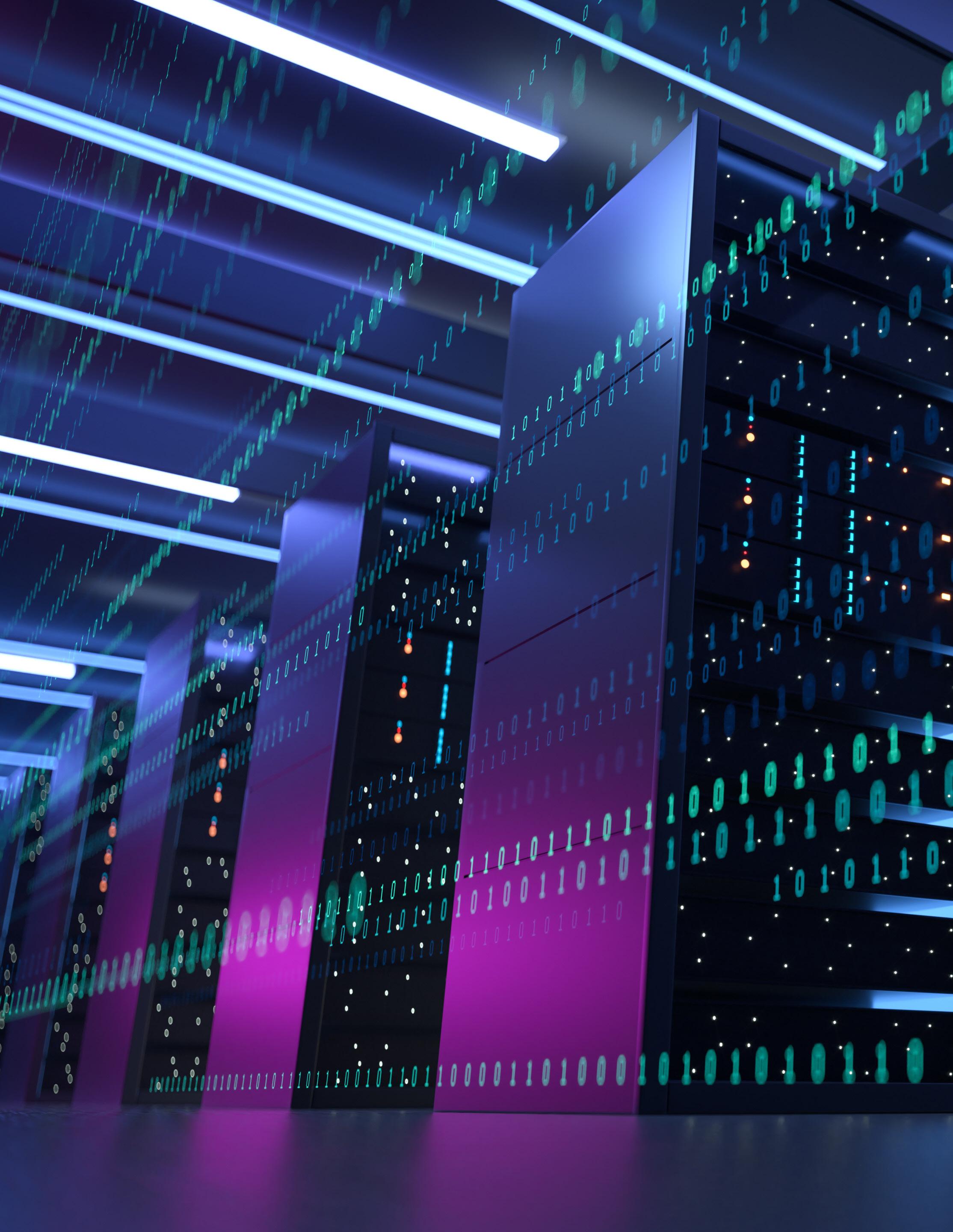
For over a decade, our portfolio of in-house magazines has been lovingly produced, printed, and distributed to our esteemed subscribers across the globe from our headquarters in the UK.
But now we are moving with the times, adopting a digital-first approach by producing online-only publications. A major factor in this decision is to minimise our environmental footprint, reducing the carbon emissions involved in the logistics of print magazine distribution and the resources required therein.
Going forward, we will provide print orders of any magazine in-line with the requests of our featured companies, subscribers, and conference & expo partners.
Please get in touch for a print-on-demand quote or visit our website to find out more.
“We always planned that when our digital subscribers consistently accounted for 85% of our total magazine subscribers, we would cease printing our publications in-line with our environmental and sustainability goals.”
– Ben Weaver, CEO, Outlook Publishing Ltd
EDITORIAL
Editorial Director: Phoebe Harper phoebe.harper@outlookpublishing.com
Senior Editor: Marcus Kääpä marcus.kaapa@outlookpublishing.com
Editor: Jack Salter jack.salter@outlookpublishing.com
Editor: Lucy Pilgrim lucy.pilgrim@outlookpublishing.com
Junior Editor: Ed Budds ed.budds@outlookpublishing.com
Junior Editor: Rachel Carr rachel.carr@outlookpublishing.com
PRODUCTION
Production Director: Stephen Giles steve.giles@outlookpublishing.com
Senior Designer: Devon Collins devon.collins@outlookpublishing.com
Designer: Sophs Forte sophs.forte@outlookpublishing.com
Junior Designer: Louisa Martin louisa.martin@outlookpublishing.com
Production Assistant: Megan Cooke megan.cooke@outlookpublishing.com
Digital Marketing Manager: Fox Tucker fox.tucker@outlookpublishing.com
Social Media Executive: Bria Clarke bria.clarke@outlookpublishing.com
Web Editor: Oliver Shrouder oliver.shrouder@outlookpublishing.com
BUSINESS
Chief Executive Officer: Ben Weaver ben.weaver@outlookpublishing.com
Managing Director: James Mitchell james.mitchell@outlookpublishing.com
Sales Director: Nick Norris nick.norris@outlookpublishing.com
Commercial Director: Joshua Mann joshua.mann@outlookpublishing.com
HEADS OF PROJECTS
Josh Hyland josh.hyland@outlookpublishing.com
Deane Anderton deane.anderton@outlookpublishing.com
Eddie Clinton eddie.clinton@outlookpublishing.com
Ryan Gray ryan.gray@outlookpublishing.com
BUSINESS DEVELOPMENT DIRECTOR
Thomas Arnold thomas.arnold@outlookpublishing.com
TRAINING & DEVELOPMENT MANAGER
Marvin Iseghehi marvin.iseghehi@outlookpublishing.com
SALES & PARTNERSHIPS MANAGER
Donovan Smith donovan.smith@outlookpublishing.com
PROJECT MANAGERS
Alfie Wilson alfie.wilson@outlookpublishing.com
Cameron Lawrence cameron.lawrence@outlookpublishing.com
Dave West dave.west@outlookpublishing.com
Dennis Morales dennis.morales@outlookpublishing.com
Jordan Levey jordan.levey@outlookpublishing.com
Kierron Rose kierron.rose@outlookpublishing.com
Kyle Livingstone kyle.livingstone@outlookpublishing.com
Nicholas Kernan nicholas.kernan@outlookpublishing.com
Liam Pye liam.pye@outlookpublishing.com
ADMINISTRATION
Finance Director: Suzanne Welsh suzanne.welsh@outlookpublishing.com
Finance Assistant: Suzie Kittle suzie.kittle@outlookpublishing.com
Finance Assistant: Victoria McAllister victoria.mcallister@outlookpublishing.com
EME OUTLOOK
Norvic House, 29-33 Chapelfield Road
Norwich, NR2 1RP, United Kingdom
Sales: +45 (0) 1603 363 631
Editorial: +45 (0) 1603 363 655
SUBSCRIPTIONS
Tel: +45 (0) 1603 363 655 phoebe.harper@outlookpublishing.com www.emeoutlookmag.com
Like us on Facebook: facebook.com/emeoutlook Follow us on Twitter: @eme_outlook
Proudly introducing our 53rd issue of EME Outlook Magazine. This edition, we’re kicking off with our cover star, Gulf Data Hub. In conversation with Chief Information Officer, Himmath Mohammed, we follow the evolutionary journey of data centres in the Middle East and dive into the company’s growing presence across the MENA region and beyond on its roadmap to 2024.
“As we grow to enjoy a global footprint, we pledge to continue being a carrier-neutral service provider. You can find a combined, cutting-edge, and market-focused set of solutions at Gulf Data Hub that are tailored to any company’s needs,” Mohammed tells us.
Elsewhere, we highlight a peerless partner in European transport, as Raben Netherlands continues to excel in delivering quality logistics services and sets out its strategic goals for 2025 in line with the wider Raben Group.
“We grow with the aim to provide better and more complete solutions for our customers,” Managing Director, Berend Jan Schuring, tells us.
Operating in an entirely different field but upholding an equally unrelenting commitment to quality, we speak with Lantmännen Unibake Romania, as the baked goods manufacturer catering to both local and international markets on its mission to deliver “billions of smiling tummies”.
Finally, be sure to take a look at our exciting range of features showcasing ground-breaking innovations alongside some of the most recognised names in industry - from the rubbish-eating aquadrone recently released into the waters of Canary Wharf, to the latest models on the market delivered by automotive icon, Mitsubishi Motors.
We hope that you enjoy your read.
Phoebe Harper Editorial Director, Outlook Publishing46 SHOWCASING LEADING COMPANIES
Tell us your story and we’ll tell the world
TECHNOLOGY
48 Gulf Data Hub
Housing the Future of Data
Premium Data-day service for the Middle East
6 NEWS
Around Europe and the Middle East in seven stories
10 EXPERT EYE
Fighting climate change with transport data
BUSINESS INSIGHTS
12 Agriculture
Grow the Best High-quality fertiliser changing modern cultivation
14 Technology
The Robot Predator with an Appetite for Waste
Introducing the WasteShark
TOPICAL FOCUS
18 Manufacturing
Stepping Up a Gear
Showcasing Mitsubishi Motors Europe’s latest development in electric vehicles and more
FOOD & BEVERAGE
64 Lantmännen Unibake
Romania
From Field to Fork State of the art baked goods, en masse
72 Salmon Evolution
Extending Ocean Potential Quality, texture, colour, taste – a new standard of salmon
MANUFACTURING
80 Marelli
Changing the Automotive Dynamic Transforming the future of mobility
26
INDUSTRY SPOTLIGHTS
26 MEDports Association
Facilitating trading port links in the Mediterranean
38 Swedish MedTech
The prerequisite for an effective healthcare system
108 EVENTS
Falcons Swoop to Success
Lift off for RAF Falcons’ 2023 season
110 THE FINAL WORD
What are your greatest motivators as a leader?
86 Vítkovice Steel
Perpetual Steel
European production of the most recyclable material in the world
86
92 Winbro Group Technologies
Vision Engineered
The fresh face of sustainable manufacturing
ENERGY & UTILITIES
SUPPLY CHAIN
56 Raben Netherlands
Establishing a Love-Freight Relationship
The peerless partner in European transport
80
98 CWP Europe
Making a Decarbonised Southeast Europe a Reality!
The renewable energy company enacting change across Serbia and beyond
CARS WITH INTERNAL combustion engines (ICEs) will continue to be built by Ferrari into the late 2030s, despite global efforts to phase out the technology.
The move towards electric vehicles (EVs) presents a steep marketing challenge for premium brands such as Ferrari, for whom the raucous roar of an ICE remains integral to its appeal and an essential part of the
company’s heritage.
A number of major markets are preparing to ban the sale of new cars with ICEs by 2023, however, the EU has since agreed to exempt cars that run exclusively on synthetic e-fuels.
Nevertheless, Ferrari plans to launch its first fully electric model in two years’ time, a design that the Italian manufacturer insists will provide a unique driving experience.
ASOS has reported large losses of £87.4 million in the six months to the end of February.
It compares to profits of £14.8 million in the same period last year, as shoppers cut back on spending and household budgets are squeezed by the rising cost of living.
SKIPTON BUILDING SOCIETY (Skipton), the UK’s fourth biggest building society, has launched a deposit-free mortgage that is specifically aimed at people currently renting.
Recognising a gap in the market, it is the first no-deposit
deal that doesn’t require the backing of a guarantor to launch in the UK since 2008.
The deal could represent a sensible option for those struggling to save for a deposit, at a time when rents are spiralling and property prices are increasing. Skipton’s 100 percent mortgage is only available to first-time buyers who have paid their rent in full, and on time, for at least 12 months.
ASOS, who announced a major restructure in October 2022, is seen as one of the poster children for the transition to online shopping and benefitted from the closure of high street stores during the COVID-19 pandemic, when shoppers – mostly younger adults – resorted to buying online.
With shops now fully reopened and customer spending power curtailed, however, the retailer has experienced very challenging trading conditions as the high street fights back postpandemic.
Europe and the Middle East in seven stories…
MICROSOFT’S USD$69 BILLION purchase of Call of Duty publisher Activision Blizzard (Activision) has been approved by EU regulators.
It comes three weeks after the UK vetoed the deal over concerns it would harm competition in the emerging cloud gaming business.
The European Commission (EC) has approved the acquisition, however, stating that Microsoft’s offer of 10-year free licensing deals – which promise access to
FOOD & BEVERAGE
PERNOD RICARD HAS stopped all exports of its international brands to Russia.
The French spirits group also plans to cease distribution of its portfolio in the country as the war in Ukraine continues, a process that is expected to take “some months” to complete.
A “limited team” will be kept in
Activision’s PC and console games for European consumers and cloud game streaming services – mean there would be fair competition in the market.
Microsoft and Activision need approval from regulatory bodies in the UK, EU and US for the takeover to go through, as it is poised to be the biggest deal in gaming history.
IN A DEAL that will test the willingness of investors, Center Parcs has been put up for sale by Brookfield.
The Canadian private equity group is seeking to raise between £4 and £5 billion for the UK holiday resort chain, which would be one of the largest real estate deals of the year.
Six holiday villages are run across the UK and Ireland by Center Parcs, offering attractions such as water parks and forest playgrounds, and attracting more than two million visitors annually to its sites.
Russia in order for Pernod Ricard, who owns international brands such as Jameson, Malibu, Beefeater and Absolut, to eventually resume business in the future. However, around 300 jobs will be lost as a result of the downsizing of local operations.
Pernod Ricard scaled back significantly on the products it sells in Russia last year following the outbreak of the conflict in Ukraine having previously derived around three percent of its sales there.
UK “staycation” businesses such as caravan and holiday parks have proven popular in recent years, as a cheaper alternative to foreign travel for consumers looking to save money at a time of economic uncertainty.
EUROPE’S MAIN BATTERY manufacturer, Northvolt, is going ahead with plans to build a factory in Germany, backed by state funding from the federal government.
Northvolt had previously indicated that it may suspend its plans for the factory and focus on the US, unless the EU matched the generous subsidies to develop green technologies provided by the Biden administration.
The project, one of the most significant flagships of the energy and transport revolution, will create thousands of green tech jobs and supply around one million EVs with high-quality battery cells annually.
The Swedish company leads just a handful of European players that are paving the way for a home-grown battery industry.
Adding to its growing family of regional titles – EME Outlook, Africa Outlook, APAC Outlook, North America Outlook, and its sister sector title, Mining Outlook – Outlook
Publishing is proud to announce the birth of a dedicated platform for the healthcare sector. As organisations worldwide must navigate a new healthcare landscape defined by technological innovation in the wake of the COVID-19 pandemic, now is the time to showcase the strides being taken in this critical sector.
A multi-channel brand, Healthcare Outlook will bring you the positive developments driven by organisations across the healthcare industry through its various platforms. Discover exclusive content distributed through its website, online magazine, social media channels, and dispatches delivered straight to your inbox with a bi-weekly newsletter.
Through this compelling new venture, we intend to foreground the movers and shakers of the industry. To participate as a featured company and join us in this exciting endeavour, contact one of our Project Managers today.
www.healthcare-outlook.com
There is absolutely no doubt that if the world is to have any hope of curbing the climate crisis, a transportation revolution is needed. According to the World Economic Forum, the transport sector is responsible for 37 percent of global CO2 emissions. In the developed world, at least, attempts to address the issue have largely focused on electrifying transport options and on getting more people onto emissionfree transport options, such as bicycles.
Laudable as those efforts are, globally, their impact is likely to be limited. Electrifying vehicles only makes a real, tangible difference if the power they’re drawing to drive comes from renewable sources. Many of the cycling initiatives, meanwhile, are too small to make much of a difference. Even rightly celebrated initiatives, such as those in Paris and Barcelona,
will only get so many people out of their cars, especially in the short term. It will be some time, in other words, before even the world’s most cycling-friendly cities become new Amsterdams. The focus on private electric vehicles (EVs) powered by renewables and getting more people onto bicycles also ignores the reality for many people in the Majority World. In many of the world’s fastest-growing cities, which frequently have limited formal public transport infrastructure, people largely rely on their own fossilfuel-driven vehicles or informal public transport.
But it’s also those Majority World cities that show us where the real transport revolution lies. Renewablesbased EVs and cycling will play a part in a greener future for the transport sector, but right now they can’t hold a candle to what accurate, real-time traffic data can enable today.
In order to understand why that data is so important, it’s critical to understand the Majority World context. Unlike in the developed world, many Majority World cities don’t have well-established and functioning formal, subsidised public transport systems that cater to everyone. In some cases, they simply grew too fast while others simply don’t have the money to invest in public transport networks. As a result, many citizens rely on a combination of their own vehicles and informal public transport.
Unfortunately, that often means highly congested roads. The average Lagos resident, for example, spends upwards of 1,000 hours in traffic every year. In Rio de Janeiro, meanwhile, the average commute time is more than an hour each way, with families living outside the formal city boundary taking even longer to get to work or school and back.
Similar scenarios can be found in cities around the world, with every minute spent idling in traffic releasing
carbon dioxide and other greenhouse gases (GHGs) into the atmosphere. But if you could ensure that informal public transport providers were operating as efficiently as possible and spending less time idle in traffic, you’d have lower levels of emissions. The reductions might not be significant at an individual level, but when you multiply multiple daily journeys by multiple transport providers in multiple cities around the globe, the difference quickly becomes enormous.
In our experience, the best way to secure public transport efficiencies is through data. For commuters, we’re already there. In fact, we’ve found that people who use our public transport app, Rumbo, in Mexico City, Lima, and Bangkok, get 24 minutes of commuting time back every week. That’s 24 minutes less time spent in an emissions-producing vehicle. Securing similar benefits for all informal transport operators would be even more transformative - and it’s all possible when you’ve got real-time mobility data.
But that’s not the only way that data and mapping can help reduce
emissions in cities. In Sarajevo, for example, we helped engineering firm WSP with a due diligence report the city needed in support of an infrastructure investment loan from the European Bank for Reconstruction and Development (EBRD). We found over 75 percent of trips on the city’s minibuses are not completed due to a lack of available fleets. With the public transport system so unreliable, passengers often wait for up to an hour only to find the service is not running. As a result, people were increasingly choosing other modes of transport, such as private vehicles, to get around.
WhereIsMyTransport worked with a local team of data collectors to map existing public transport routes in the city, processing and validating that information using our bespoke data management platform, including checking data to ensure route names were correct, removing duplicate information, and rectifying any inconsistencies. This data provided WSP with the insight they needed, delivered as a General Transit Feed Specification (GTFS) file – the global standard format for transit data.
The due diligence report produced by WSP, informed by data from WhereIsMyTransport, helped Sarajevo Canton secure substantial investments from the EBRD and move towards a modern, reliable public transport system. Encouraging Sarajevo’s residents to travel by public
transport is expected to reduce CO2 emissions by more than 30 percent, creating a greener, more sustainable city.
That’s to say nothing of the potential benefits that can come from sharing that data with other organisations, including retailers and governments. The former can ensure that they’re closer to their target customers, meaning further reductions in emissions, while the latter can better plan where to put new infrastructure, ensuring that their resources are less likely to be wasted.
Perhaps the best part of taking this data-driven approach, however, is the fact that there are no drastic changes involved. It doesn’t require shutting off roads to drivers or building proper cycle lanes, nor does it entail the massive renewable energy investments and charging stations that will be needed for the widescale adoption of EVs.
Make no mistake, such initiatives are important and the cities that get them right will provide models for the rest of the world to follow. But an approach today that focuses on data can make a massive impact at almost no cost.
So, as we look to achieve net zero, maybe the first port-of-call shouldn’t be building bike lanes or enacting legislation to push the adoption of EVs but collecting, utilising, and sharing relevant, real-time mobility data.
Devin de Vries co-founded WhereIsMyTransport in 2008. Under his leadership as CEO the company has been recognised by the International Association of Transport, International Transport Forum, New Cities Foundation, Financial Times, WWF, and Start-Up Tel Aviv.
As an industry-leading technology company and central source of mobility and location data for emerging markets, WhereIsMyTransport’s data assets help to improve the public transport experience for consumer product users.
Devin holds a BBusSci in information systems from the University of Cape Town.
Fertilisers are critical to today’s agricultural sector. We take a look at Biota Nutri and speak to CEO, Mark Valentine, about the growing technology that is changing farming in the Netherlands and abroad
Farming is a unique and everchanging frontier. Where agriculture focuses on fieldscale produce grown at ground level, horticulture revolves around the use of greenhouses and the many technological systems that are put in place to maximise growth.
Growing technology, such as fertilisers, are key to maintaining this yield and continue to play a critical role in agricultural practices at all levels. In the Netherlands, Biota Nutri (Biota) is one such company that supplies growing technology to the European market and beyond.
“The industry is quite strong in the Netherlands, which is the second biggest exporter of agricultural products next to the US according to the government figures,” begins Mark Valentine, CEO of the company. “It is an exciting sector to work in; the Dutch are known as the de facto leaders of growing technology so the competition is high at all times, which forces you to work to the highest standards.”
Biota develops, produces and distributes organic fertilisers for agriculture and horticulture. The company is constantly conducting R&D in the field of recovering nutrients from plant-based residual streams, with the aim to create a world in which circular and organic cultivation is accessible to everyone.
Biota has three connecting business lines; the first is the manufacturing of organic fertilisers, through which the company offers a full range of fertilisers and stimulants to suit horticultural and agricultural needs; the second revolves around the company’s growing technology through which Biota advises and works with customers on bioreactors or other equipment needed for organic growing. Lastly, Biota promotes its software tool, an online calculator that helps growers switch to organic cultivation on their own schedule.
“Biota is different from other organic fertiliser companies as we make our products from plant-based waste streams, combined with our patented process to create the basis for our fertilisers,” Valentine tells us. “Our premium products are in our Low Organic NPK range of fertilisers. They’re different from the competition in that they are clear liquids that don’t block irrigation systems, provide nutrients and trace elements immediately to the plants, and also allow produce grown with Biota fertiliser to wear the vegan trademark in the stores.”
Despite being based in the Netherlands just outside of Amsterdam, Biota also has offices in Los Angeles in the US as well as Uganda and a presence in Canada, selling to around 30 countries with its main clients in North and South America.
The twin pillars of Biota’s focus are innovation and sustainability. According to Valentine, the Dutch government is introducing sustainability goals and looking to push farmers to grow more organic produce. These are positive initiatives, yet farmers require
Mark Valentine, CEO: “I was born in Manchester, UK, grew up in Nigeria, and moved to California in the early 1990s. I’ve spent most of my career as an executive for tech and medical companies but also have diverse experience with other sectors such as automotive, retail and online sales.
“I specialise in the rapid growth of operations, marketing and sales channels and how to take companies global, but I’m also an inventor and perennial entrepreneur, so I like to work with companies that make real products as much as possible. In 2017, I started working with a number of horticulture companies wanting to bring their products to
subsidies and assistance to adopt these changes successfully as the market demand is not as high, unlike in the US for example.
“The last couple of years under the COVID-19 pandemic and subsequent escalating energy prices have caused attrition in the industry and some businesses have closed, while others shut down in the winter as the cost of growing is too high,” he explains. “The long-term outlook is positive as the bio-based economy becomes a reality and even more green material developments are introduced.”
In light of this, Biota’s main mission is to reduce the use of chemical fertilisers by giving growers the tools they need to grow organically without compromising on quality and production. The use of residual flows plays a key role in this as by using residual streams, the company is turning plant waste into plant food to create a truly circular and sustainable model for growers.
“In the longer term, we aim to be integrated directly into the recycling and processing facilities to optimise the process and create other sustainable product options from the remaining biomass, such as clothes and furniture,” Valentine continues.
Biota has planned to open a US facility since 2019, with the goal of manufacturing on-site to reduce the costs and shipping delays for its US-based customers. However, with the arrival of COVID-19, the company
altered its strategy and expanded its European capacity with a new fully automated tank farm manufacturing facility that is reproducible and scalable for future locations.
“We are now in the process of working with investors to restart the US effort, and I will be spending the majority of my time in the US in 2023 as we get the project restarted,” says Valentine. “We also have a number of other projects underway, mostly collaborating with universities or groups looking to develop advanced sustainable products or solutions. One of our main challenges is price; organic products aren’t made in the same high volumes as chemical fertilisers at the moment, so the economies of scale and optimisation are still in progress.”
Yet, according to Valentine, the future of the industry is all about artificial intelligence (AI) and automation, as technology can reach a level of repeatability and accuracy that humans simply cannot match. Much like the manufacturing industry, the use of robotics and automation will continue to grow when it comes to picking and packing.
“But for the rest of this year, we hope to get the US facility started to better serve the customers in that part of the world and also reach the second stage of optimising our patented extraction process, which will enable us to control our costs and reduce risks as we grow,” concludes Valentine.
www.biota.nu
Making waves in news circles as a ground-breaking robotics innovation, the WasteShark is an aquadrone designed to remove plastics and floating debris from our waters. After launching in London’s Canary Wharf last month, we speak with the company behind its invention, RanMarine Technology, to discuss waging war against floating pollution.
EME Outlook (EO): Tell us about WasteShark’s inception and what inspired its creation?
Richard Hardiman, CEO (RH): I remember I was sat at a waterfront café in Cape Town, South Africa, and I was watching these two men taking trash out of the water using a net. I thought, there must be a more efficient way of collecting the waste, and started doodling on the back of an envelope, trying to design a better method of solving that problem. I gave myself that challenge, and kept coming back to the idea. I really had an ambition to create something and eventually settled on the idea of a robotic boat based on autonomous units constantly swimming through the water and collecting the waste. Although humans are responsible for the majority of the waste in our waters, I believe we can be deployed in far more impactful ways than simply collecting it by hand. We wanted to help solve the plastic pollution problem, with the WasteShark’s primary purpose being the collection of rubbish. But as we started developing it, we realised that the WasteShark was gathering various kinds of seaweed and algae, so we decided to use it to also collect biomass.
As these autonomous robots are swimming, we are tracking their every move, so we also thought, why don’t we use this to track data on the water itself? By adding sensors to the unit, we adapted it to become a mobile
The latest innovation from RanMarine Technology, the WasteShark is the marine drone cleaning up the world’s waterways. CEO, Richard Hardiman, tells us more
water quality data monitor, gathering information that we could pass back to our clients. This can indicate temperature changes or chemical imbalances anywhere in the water.
EO: How has the WasteShark been received since its launch?
RH: It’s been extremely well-received since we started selling them in 2019. We continue to develop it to better suit the needs of our customers, and in the last year, we have really hit our stride. It has proved to be extremely useful as a unit that can reach the smaller places where plastics and marine biomass collect. We don’t try and clean the whole football field as it were, instead we concentrate on the smaller areas where these things can get stuck. Based on the feedback we have received so far, it’s an extremely robust and practical tool to use.
EO: Could you tell us about some of your main customers?
RH: We have some major commercial clients including Disney and Universal Theme Parks, and most recently we have launched in Canary Wharf. We also work with a lot of ports – in Canada we’re in the Port of Toronto and the Port of Halifax, alongside a number of major cities in the US. Our customers are generally split between commercial interests, where
water needs to be cleaned around commercial activity, or cities that have waste management programmes that we can enter into to help clean up their waterways and canals.
EO: Could you outline your future plans for the WasteShark?
RH: My dream is to have thousands of these units floating around, monitoring and cleaning our waters while we sleep. We’re nearing the point now where we are a 24-hour operation.
We’re making major moves in the US, we’re in Israel, Africa, South Korea, and at the moment, the UK is a primary target for us.
The numbers prove that WasteShark is 85 percent more effective than other current purposebuilt mobility units. As we become a 24-hour operation, we expect that to rise to 98 percent effectiveness at cleaning water currents. Our customers are already starting to see the results, and everything that we have in our roadmap is only going to make this better.
“MY DREAM IS TO HAVE THOUSANDS OF THESE UNITS FLOATING AROUND, MONITORING AND CLEANING OUR WATERS WHILE WE SLEEP”
– RICHARD HARDIMAN, CEO, RANMARINE TECHNOLOGY
I’m extremely optimistic for the future, since our engineers have done a fantastic job in getting us closer to our nirvana of being able to clean waters all the time with minimal interference.
Although it is geared towards a slightly different market, we have
just built the MegaShark, which is 10 times the capacity of our current version. This will launch commercially later this year, and we’re incredibly excited about it. For me, it’s all about creating more robots to do a better job of cleaning our waterways.
Nowadays, it’s difficult not to spot a Mitsubishi on the road, as the iconic car manufacturer has been a titan of the automotive industry for over a century. First established in Japan, Mitsubishi Motors, like all manufacturers, has to keep pace with the latest trends and demands in the world of motoring. With a reputation for engineering innovation, the brand’s business in Europe is run by its subsidiary, Mitsubishi Motors Europe.
We speak to President and CEO, Frank Krol, about how Mitsubishi Motors Europe (Mitsubishi Motors) is combining its decades of valuable experience with the latest developments in the industry to create the cars that drivers desire.
As Mitsubishi Motors Europe pursues further growth, President and CEO, Frank Krol, discusses the ambitious developments of the automobile giant Writer: Lucy Pilgrim
EME Outlook (EO): Firstly, could you give us some historical insight into
Frank Krol, President and CEO, Mitsubishi Motors Europe (FK): Mitsubishi Motors has a long and rich heritage in manufacturing cars, building for over 100 years.
Mitsubishi Motors Corporation itself was born in 1970, having previously been a division of Mitsubishi Heavy Industries. Going back further, Mitsubishi’s first vehicle was the Model A, built as long ago as 1917. Mitsubishi Motors also has a long history in the production of 4x4 vehicles – an attribute that remains central to the Mitsubishi Motors brand today. Mitsubishi introduced Japan’s first Diesel engine (“450AD”) for use in motor vehicles in 1931, and its first 4x4 model was the PX33, built in 1937.
Mitsubishi Motors’ initial step into Europe came in 1976, when the company unveiled the Lancer at the London Motor Show. Since then, the brand has grown a strong reputation in the development of 4x4s and SUVs – such as the Pajero/Shogun/ Montero, and electric vehicles (EVs). Its first EV was a prototype over 50 years ago, and Mitsubishi Motors was the first major brand to put an EV into full series production back in 2009 with the innovative i-MiEV (Mitsubishi innovative Electric Vehicle) – and was a champion in motorsport, winning the Dakar Rally a record 12 times, as well as the World Rally Championship with the Lancer Evolution, which was also a four-wheel drive vehicle. For these reasons, Mitsubishi Motors is well known for quality, reliability, toughness and endurance, and as a pioneer, is ready to explore
new technologies and new solutions. The brand also has significant experience in small cars such as the COLT, sedans and Multi-Purpose Vehicles (MPVs), but I would say we are best known for our endeavours in the fields of 4x4s/SUVs/EVs. For example, the Outlander Plug-in Hybrid Electric Vehicle (PHEV) was the first PHEV SUV to be launched worldwide and combines all this expertise as an EV-based powertrain, with 4x4 Super All-Wheel Control all packaged in an SUV. In Europe, we are very much looking forward to launching the all-new Outlander PHEV next year.
EO: What are the most challenging elements of the business and how are you overcoming them?
FK: The automotive industry is very
dynamic and fiercely competitive, since mobility is an integral part of everybody’s lives. Therefore, the challenge for all manufacturers is how best to adapt to, and in some cases drive, the pace of change in all areas of mobility; not only the product itself and moving people from A to B, but the on-board experience, cost of ownership, services, and so on.
Besides the strong shift from combustion engines to hybrids and EVs, a key focus area is integrating people’s digital lives into the car –safely and seamlessly. As well as infotainment, there have also been significant technological advances in the area of autonomous drive or self-driving cars. All this combines to bring customers new levels of safety,
comfort and convenience. Ultimately it is a balance of how and when to introduce which technologies – this is partially regulation driven, but it is always important to focus on our customers’ needs and the solutions which will meet or exceed them in an affordable way.
All of the new technologies –from electrified powertrains to infotainment, Connected Car and autonomous drive, require extremely large R&D investments, which in some cases also carry a high cost per unit to produce - and this is where economies of scale come into play. Since 2016, Mitsubishi Motors has been a full member of the RenaultNissan-Mitsubishi Alliance (RNM Alliance), with a combined volume
of around 10 million units per year. The RNM Alliance gives Mitsubishi Motors access to, and the ability to contribute to, a variety of synergies across the board. For example, sharing platforms and components, combined purchasing, sharing of technology and joint investments in future technologies. Overall, it is a very exciting time for the automotive industry.
EO: Could you tell us more about the two new models that are currently under production?
FK: Mitsubishi Motors Europe is transitioning to a new product line-up. The entry model, the Space Star, has just been joined by the new ASX small
“MITSUBISHI MOTORS IS WELL KNOWN FOR QUALITY, RELIABILITY, TOUGHNESS AND ENDURANCE, AND AS A PIONEER, IS READY TO EXPLORE NEW TECHNOLOGIES AND NEW SOLUTIONS”
SUV that went on sale in March this year. In the compact SUV segment, we sell the Eclipse Cross PHEV, which is a 4x4 PHEV equipped with rally-bred Super All-Wheel Control technology. Later this year, we will launch the new COLT city car, which will sit between the Space Star and the ASX. Both the ASX and the COLT are based on Alliance platforms and developed for Europe, which allows us to benefit from the aforementioned synergies and offer our customers competitive products with advanced technologies. The line-up will consist of both passenger cars and SUVs featuring hybrids and Plug-in Hybrid drive trains, and of course the 4x4 Eclipse Cross PHEV.
EO: In your opinion, what continues to differentiate the company and its products from your competitors?
FK: Our customers receive not only
a good quality, reliable, safe vehicle, but they all come with a five year warranty, and we are subsequently proud of the good service levels provided by our dealers. Moreover, our customers also expect a life partner in the sense that the vehicle enables our customers to explore life’s opportunities to the full, from extreme off-road adventures, to work in a pickup or a family holiday in an SUV. This spirit of adventure and exploration has been in Mitsubishi Motors’ DNA throughout its history and continues today.
EO: What do the next 12 months look like for the company in terms of new projects, future growth and other targets?
FK: This is a very exciting period for Mitsubishi Motors Europe – in addition to the launches of ASX (March this year) and COLT (to follow in the
Autumn), we will launch the all-new Outlander PHEV in 2024. With three all-new models in two years, we will have competitive vehicles in all of the core segments in the European market. Although we are a relatively small brand in Europe, these new models will lay the foundation for continued profitable growth, and a market share around the one percent mark moving forward. The Outlander PHEV, however, is more than just a new model, as our flagship brand vehicle embodies the best of Mitsubishi Motors’ design and technology, based on decades of experience in SUVs, 4x4s and EVs.
“OUR CUSTOMERS RECEIVE NOT ONLY A GOOD QUALITY, RELIABLE, SAFE VEHICLE, BUT THEY ALL COME WITH A FIVE YEAR WARRANTY, AND WE ARE SUBSEQUENTLY PROUD OF THE GOOD SERVICE LEVELS PROVIDED BY OUR DEALERS”
KROL, PRESIDENT AND CEO, MITSUBISHI MOTORS EUROPE
As a powerful force in world history, Mediterranean maritime trade has deeply impacted global traffic for millennia. We follow the ebb and flow of today’s industry with MEDports Association
Writer: Rachel Carr | Project Manager: Deane AndertonThe Mediterranean Sea translates from Latin as centre of the Earth, which is no coincidence as the waterway unites three quarters of the globe and has been an integral part of world history.
Logistically, this places Mediterranean ports in a prime position, and having served some of the past’s most powerful traders, the sea continues to be one of the busiest networks on the planet.
Presently known as the sea between the lands, and bordering 22 different countries, the Mediterranean Sea is landlocked and therefore has fewer tides. Although it is technically a “closed” sea, the Strait of Gibraltar grants traders access to the Atlantic Ocean, with an estimated 20 percent of the world’s traffic passing through annually.
The Mediterranean seaports are an important component of the global shipping network, connecting the Middle East with Asia, North Europe, Africa and the Americas, as evidenced by trading activity throughout history.
From the ancient Phoenician civilisation, which occupied the coast of the Levant and established one of the most notable maritime routes in history, to the Roman Empire and onward to the modern age, the Mediterranean has enjoyed thousands of years of sea trading.
Indeed, the Mediterranean Sea facilitated one of the most important globalisation movements in the world. The three main commodities traded were foods (olives, wine, wheat), textiles (clothes, carpets), and raw materials (copper, iron, glass), expanding the economic system of
the Mediterranean area.
Unlike the square-sailed ships with oars that were the most common historic mode of transportation, modern cargo vessels are reliant on fossil fuels. Consequently, the industry is looking to take advantage of new technologies that will help reduce carbon emissions.
In the next few years, the plan for hybrid and electric ships, advanced propulsion systems, and more efficient hull designs, will minimise the one billion tonnes of CO2 produced by the shipping industry every year.
Although container shipping is the most carbon efficient form of transporting goods, as it is less damaging than road and air, environmental concerns are not the only challenge the sector is facing.
Seaborne trade has sailed through choppy waters recently with the COVID-19 pandemic affecting the global supply chain. Home to 87 ports, the Mediterranean Sea has a crucial role in the transportation industry and has managed to remain viable for the global market.
Today, the Mediterranean is at the heart of commerce as its vast network provides a corridor for many different types of cargo and the distribution of freight, but as with other industries, advancing technology will continue to impact shipping and ports.
Optimising operations, tracking fuel consumption, minimising errors, and improving safety are some of the ways digitisation is changing the future of an industry which has been steadily progressing since the 3rd century BCE.
Tanger Med Port Complex ranks as one of the world’s best port complexes, and is viewed as one of the Mediterranean’s most essential hubs
Tanger Med Port Complex aims to develop an efficient and truly integrated port platform around the complementary activities of trans-shipment, importexport, and value-added logistics.
The complex consists of:
• Tanger Med 1 Port, which includes two container terminals, a rail terminal, a hydrocarbon terminal, a general cargo terminal, and a new vehicles terminal.
• Tanger Med 2 Port, which includes two container terminals.
• The Passenger and Ro-Ro Port, which includes the access and border inspection zones, the passenger and truck loading docks, the regulation zones, and the ferry terminal.
• The Logistics Zone.
• Tanger Med Port Centre.
In January 2010, Tanger Med Port Authority was transferred by decree-law all the missions and public prerogatives related to the management and development of Tanger Med Port Complex.
The Tanger Med Port Authority focuses its missions on the management and development of infrastructures, the coordination and animation of the port community, and guarantees the reliability and performance of services provided to the port platform’s clients.
• Construction and maintenance of the port infrastructure (dikes, dredging and docking works).
• Development of the port complex’s activities and capacities.
• Licensing authority or leading the live operation of port terminals and activities of public service nature.
• Organisation and regulation of relations and exchanges between the actors of the port community.
• Promotion of the Tanger Med Port Complex as a whole.
• A port police function through the captaincy in charge of the safety and security of the complex.
Apart from the Passenger and Ro-Ro port, the main activities of Tanger Med Port Complex are entrusted to renowned national and international private operators who, under concession contracts, invest in the superstructures and equipment of the port and provide services that meet the international standards of quality, safety and security.
Please introduce Tanger Med Port Complex, its activities, and its key figures during 2022?
Tanger Med Port Complex is a global logistics hub located on the Strait of Gibraltar, connected to over 180 worldwide ports, providing handling capacities for nine million containers, seven million passengers, 700,000 trucks, and one million vehicles.
The port enjoys a strategic geographic location, on the main East-West and North-South maritime routes, with a distribution of trans-shipment traffic for Africa, Europe, and the US. Hence, this unique position allows maritime liners to trans-ship their vessels with zero deviation and offer them competitive options to optimise transit times.
On the Mediterranean and on the Strait of Gibraltar, Tanger Med Port Complex plays a crucial role as a major container
trans-shipment platform.
Tanger Med Port Complex also serves as a maritime bridge, connecting Africa and Europe, separated with only 14 kilometres (km).
In 2022, Tanger Med Port Complex consolidated its position as the leading container port in the Mediterranean and in Africa, with 7.6 million TEUs of containers handled, an increase of six percent compared to 2021, and nearly 108 million tonnes of goods handled, an increase of six percent compared to 2021. Concurrently, we recorded close to 14,000 calls from the main maritime alliances, including 961 mega ships corresponding to an increase of 14 percent compared to last year.
What is it that makes Tanger Med Port Complex a leading port complex in Africa and the Mediterranean?
-----
• A strategic location: The port is located on the Strait of Gibraltar, the second busiest global trade route after the Strait of Malacca, with zero deviation. The strait witnesses the annual passage of 100,000 vessels, making it a crucial nodal point for global trade on maritime routes connecting East to West and North to South.
Mr Hassan Abkari, Managing Director of Tanger Med Port Authority• State of the art port facilities: The port offers state of the art infrastructure, a draft that can accommodate the world’s largest ships, and is capable of handling large capacities for container traffic, trucking, hydrocarbons, vehicles, and passengers.
• Operators’ confidence: Tanger Med Port Complex manages to develop and maintain a strong ecosystem, bringing together all stakeholders to ensure smooth and efficient port operations: harbourmaster, pilotage, terminal operations, etc. This ecosystem allows us to build trust among its clients by strengthening its partnerships with its customers, by meeting their expectations and needs daily, and continually offering high standards of productivity and competitiveness.
• Level of productivity achieved: Port terminals operate at very high levels of productivity by achieving international handling records, which is explained by a continuous increase in the skills of the teams who work daily. The digitisation initiated by the port to ensure optimised maritime calls, paperless import-export operations, efficient management of the flow of goods inside the port, the continuous traceability of operations are so many assets that make it possible to further support those achievements. Recent rankings published by World Bank and S&P Global Market Intelligence within their Container Port Performance Index report have placed Tanger Med Port Complex as the highest ranked port in the Africa/Europe region. This assessment of port efficiency is based on the number of port hours per call, starting from the time a vessel reaches the port up until it unberths and leaves the port.
• A port complex integrated with an industrial platform: Tanger Med Industrial Platform constitutes an industrial hub for more than 1,200 companies representing major industrial players from China, Japan, Europe, and America with a business volume of USD$13 billion in 2022 in various sectors such as automotive, aeronautics, logistics, textiles and trade. Backed onto the port complex, the industrial platform comprises six Activity Zones and a network of industrial and logistics parks planned according to the best international standards and benchmarks, offering competitiveness for operators, a one stop shops and world-class infrastructure.
What is the strategic part the port plays in North African trade?
-----
Tanger Med Port Complex has emerged as a global maritime and logistics hub, boasting a strategic location at the crossroads of major maritime routes for the world’s largest maritime alliances: M2, OCEAN ALLIANCE, and The Alliance. Since its inception, Tanger Med Port Complex has positioned itself as a major trans-shipment platform for intercontinental flows and distribution to Africa, which accounts for 40 percent of the container traffic handled.
The presence of major global players in the maritime, logistics, and industrial sectors is a testament to the significance of Tanger Med’s choice. Large maritime players such as Maersk, CMA-CGM, major logistics players such as DHL, CEVA Logistics, Nippon Express, DECAHTLON, and major industrial players such as Varroc, Hands Corporation, Valeo, and Marelli are in the Tanger Med industrial and port complex.
Looking ahead, what are your key priorities and ambitions for the coming year?
Commitment to strengthening its partnerships and pursuing productivity and competitiveness objectives.
Tanger Med Port Complex confirms again its leadership in the Mediterranean and Africa and consolidates its position as a key hub for global maritime alliances led respectively by Maersk Line, CMA CGM and Hapag Lloyd. With a capacity of more than nine million containers, Tanger Med Port Complex aims to integrate into the top ranking of the top 20 platforms worldwide.
Tanger Med Port Complex will keep offering excellent services to maritime lines: comprehensive infrastructure and technology, ships calling in the best conditions, excellent productivity of terminals and operators, world-class services to ships, solutions adapted to their needs (bunkering services, ship handling services etc., port call optimisation...), and finally, highly qualified harbourmaster and pilotage teams. Tanger Med Port Complex is also committed to enhancing its import-export solutions by launching dedicated zones for freight handling. This initiative aims to support the anticipated growth in freight volumes in the coming years and provide greater logistics competitiveness to operators.
At the same time, it will continue to develop as a major logistics hub, strengthening world to world flows and attracting new global operators and logisticians, particularly in Africa.
Tanger Med Port Complex will also enhance the attractiveness of the port-backed logistics area. This area developed over two hundred hectares, is home to worldrenowned logisticians and multinationals such as DHL, DACHSER, Nippon Express, Ceva Logistics, GEFCO, Adidas, TE Connectivity, Decathlon, Texla, Emirates Logistics, etc. These operators benefit from the area’s competitive advantages, its proximity to the port and its maritime connections to more than 180 ports worldwide.
As we move to a post-COVID-19 world, Tanger Med Port Complex will bolster its competitive strategic positioning in the reconfiguring of global value chains by integrating Morocco into the logistics corridors of the EuroMediterranean area.
www.tangermedport.com
MEDports Association is improving trading infrastructure by connecting the Mediterranean’s 25 port authorities. Its President, Pino Musolino, tells us how the industry is navigating the turn of the tide
EME Outlook (EO): Can you tell us about the origins of the association, its inception, and initial vision?
Pino Musolino, President (PM): MEDports Association was created by the intuition and will of the President of the Grand Port of Marseille at the time, Madame Cabau, who thought in 2017 that it was about time to give a voice and a forum to the ports of the Mediterranean.
I was President of the Ports of Venice and joined this endeavour at the beginning. In fact, on the day when the association was formally moving into its first steps at the House of the Chamber of Commerce in Marseille, I had the privilege of being the first signing party of the chart in
2018 and became Vice President of the association at its inception.
EO: How has the association developed and progressed since, and what has it achieved?
PM: Although we had to live through the COVID-19 pandemic and a year of war and instability in our first five years, it is incredible to see what has been achieved so far. We have more than 24 members, additional associated members, and the engagement of international institutions such as the Union of the Mediterranean, the EU, and the Arab League, for example, who are all a key part of the association. Moreover, there are the continuous efforts of several permanent committees - spanning different topics that have been instrumental to the association’s progression.
I would like to point out the extremely important educational value created, allowing managers and experts from all association members to exchange knowledge, best practices, and establish a strong, fruitful bond.
PM: The most significant success so far is the creation of a forum for Mediterranean ports that goes beyond political aggregations or regional institutions. In fact, we comprise ports from Europe, North Africa, and the Middle East.
We also aim to expand our presence within the next few years.
This string-free forum provides us with a dynamic and proactive space where we can discuss, analyse, assess and propose solutions to problems and issues that are common to all members, notwithstanding their geographical location.
PM: Ports are facing several challenges, from purely economic to more complex issues related to climate change, the energy transition, and the two revolutions –sustainability and digital.
All ports are aware that we are at the forefront of a major shift in business models and geopolitical changes, and ports can play a significant role in helping territories and countries get ahead with the aforementioned challenges.
In order to do so, working together, sharing experiences, assessing eventual steps back and moving together in a shared direction is fundamental. The association is the ideal place where this intellectual exchange can happen and provide significant results.
Entrusted with the role of port authority, the National Ports Agency “ANP” is responsible for ensuring the regulation of port activities and operators, in order to provide the Moroccan economy with high-performing, competitive, secure and environmentally-responsible ports.
Thanks to its strong regional anchoring and its organisational resilience, the ANP has managed to federate the entire port community around common goals. It also oversees the execution of community initiatives for the improvement and modernisation of Moroccan ports’ governance structures and processes for international commerce.
the “anp” is the national regulator, the port ecosystem federator, the catalyst for port development and the guarantor of port sustainability
regulation of port activities and operators
development and preservation of port heritage
port policing, safety, security and environmental protection
Aware of the SER challenges, and placing itself in the framework of the national environmental charter and Morocco’s adherence to a sustainable development logic, the ANP has decided to commit itself to the design and implementation of a structured SER approach, which has resulted in the signature of its SER Policy.
Aiming to ensure a long-term balanced consideration of economic, environmental, social and societal issues, this SER approach reflects the ANP’s desire to go beyond strict compliance with regulatory and contractual obligations and to pursue continuous improvement in its environmental and societal performance.
The ANP recognises the importance of innovation for the growth of the port sector and other stakeholders, which is why it has developed a “SMART PORT
plan, in partnership with the port community and the Global Alliance for Trade Facilitation.
Through this innovative approach, the ANP strives to solve the various challenges facing the port sector through the development of creative and innovative solutions, leveraging the collective intelligence of the port ecosystem.
EO: Could you tell us about the owners, operators, and service providers within your membership?
PM: Owners, operators, and service providers are the major ‘customers’ of ports, and the main stakeholders of a port’s governing bodies. Although the goal of developing trades and exchanges is the same, the way to achieve these goals can be seen differently by economic players and governing bodies.
The role of the latter is to find a way to guarantee solid economic returns, wise master planning and the development of infrastructures, while at the same time maintaining a healthy and productive relationship with cities and regional governments. Finally, granting the best use of the port areas without compromising the quality of life of the citizens living nearby or around ports is extremely important.
The so-called port-city relationship is essential to grant the success of any port development in the future. In this particular historical moment, being a port President or Director implies the capacity to deal with the interests and aims of several different stakeholders, both public and private, and being able to define a positive and productive summary of all the instances involved.
EO: What role does the association play in the growth of the region’s port and logistics sector?
PM: It does not directly enter into the prerogatives and duties of any single member. On the other hand, as a forum of discussion, the association helps to foster long-term relationships, common and shared planning and develop new forms of cooperation among its members. This sustains and allows growth and development.
Moreover, by assuring an even and consistent representation of the instances and needs of the regions of our members, we aim to place the spotlight back on the needs and dreams of Mediterranean coastal regions, which haven’t been central to the discussion in the recent past.
EO: Have you noticed any changes in the industry, particularly since the COVID-19 pandemic?
PM: It has disrupted our everyday lives and routines as individuals, and clearly COVID-19 has brought several changes in the industry. Some of the most notable examples include the incredible acceleration in the introduction of more innovations, the ‘greenisation’ of ports, and the introduction of more automatised processes.
At the same time, the disruption of global value chains caused by the COVID-19 pandemic - and to a different extent, the war in Ukraine - has brought everybody ‘back to Earth’ in regard to overstretched, and often unfeasible, supply chains. This in turn has brought some significant phenomena, such as re-shoring (the reintroduction on a national basis of parts or all of the production of certain goods), near-shoring (the shortening of supply chains to nearer regions) or friend-shoring (the location of productions or supply chain management in countries or areas where geopolitical instability can be less felt).
All of the above have an impact on our industry, the effects of which cannot be easily assessed at the moment, and neither can the long-term consequences. It must be said that now, more than in the last 40 years, port managers have to be resilient, and quick to adapt and embrace significant changes in the way we work and conceive our roles as developers and managers of areas.
EO: Which key aspects of the industry and its subsectors across the Mediterranean would you like to highlight?
PM: To quote Mr Tim Marshall, “geography matters”. Being the sea that connects Europe, Africa, the Black Sea region, and represents the trait-d’union with the Far East implies that the association is central to any process that supports the sustainable growth of several different regions of the planet.
After more than 500 years of dominating oceanic routes, this status is not yet well perceived by Mediterraneans themselves. We need to acquire an awareness of this new status, in order to accompany and sustain all the efforts that are put in place by entrepreneurs, national governments and international bodies. We need to narrow the scope of what we are doing selectively while broadening our vision and temporal perspective. We need to be surgical in the short-term solutions while long-term in the achievable goals.
EO: How do you see the industry developing over the next five years?
PM: The technological innovations that will be brought to
the industry in the next five to 10 years will change it more than those we have seen in the last 100 years. Artificial intelligence (AI), 5G, and 6G, augmented reality, the metaverse, hyperloop technology, alternative fuels, green energy production and development, and circularity in our economic models will completely change the way we make, move, and conceive goods in the world.
Ports are at the forefront of these historic turning points, and we need to be ready to face changes and handle them properly. The association, with its large numbers from different countries, can help to confront, exchange best practices, learn from different experiences and provide better tools to national and international bodies, to formulate better and more efficient policies in our fields.
EO: Are there any plans or projects in the pipeline for the association?
PM: The main aim for this first period is to provide reasons for members to join the association. In other words, to motivate and create enthusiasm around our association. We are trying to do so by creating contacts and increasing our visibility which has gone through a period of lesser activity in recent years.
The second point is to expand the number of members. Beyond the north and south bank of the Mediterranean, we need to expand to the Near East shores and, wherever possible, to the Black Sea, which is a natural extension of the Mediterranean. The association, with its non-political, technical role, can be the ideal place to discuss, develop and formulate ideas that can significantly support the creation of valuable policies across the industry.
It is an ambitious path, but also a realistic one. I am positive that with the help and support of the association and its members, expansion will be achieved. On my side, I can guarantee my unconditional and unwavering commitment.
“THE TECHNOLOGICAL INNOVATIONS THAT WILL BE BROUGHT TO THE INDUSTRY IN THE NEXT FIVE TO 10 YEARS WILL CHANGE IT MORE THAN THOSE WE HAVE SEEN IN THE LAST 100 YEARS”
– PINO MUSOLINO, PRESIDENT, MEDPORTS ASSOCIATION
Writer: Phoebe Harper | Project Manager: Bruno Kääpä
The effects of MedTech on modern healthcare are wide reaching. Across Europe, approximately one million MedTech products and services are on the market, many of which come into contact with healthcare professionals and patients every single day.
MedTech encompasses a vast technological spectrum, from advanced X-ray equipment, to something as small and effective as a stent, and behind the scenes solutions designed to streamline the administrative burden of the healthcare system by keeping digital health records.
In this ever-evolving field, Sweden continues to establish itself as a frontrunner in digitalisation and embracing innovation. This dynamic country has birthed lifechanging medical inventions, including the pacemaker, ultrasound and the beam knife to name but a few.
Today, the industry is overseen by the European Medical Technology Regulation (MDR), the governing body that regulates all MedTech products, which is also supervised by Sweden’s Medical Products Agency. Such regulation must strike a fine balance between ensuring all MedTech products on the Swedish market are both safe and effective, without stifling the freedom for innovation for which the country is known.
The current marketplace is one defined by both digitalisation and sustainability, as the two prevailing industry trends that all players must adapt to. As a peak body and trade association consolidating over 200 medical device companies, Swedish Medtech continues to champion a favourable and enabling industry climate, leveraging Sweden’s advanced knowledge to create an incubator for research, innovation, investment, and production through continued collaboration with healthcare institutions.
Positioning medical technology as a prerequisite for effective healthcare, CEO of Swedish Medtech, Anna Lefevre Skjöldebrand, dissects the industry today and the continued drive towards digitalisation and sustainability
EME Outlook (EO): Firstly, could you talk us through the origins of Swedish Medtech – when was it founded and what was its initial goal?
Anna Lefevre Skjöldebrand, CEO (ALS): Swedish Medtech was founded in 1969. At the time, it was evident how many medical device companies were encountering several issues in the market that needed to improve.
These were related to activities such as regulation and procurement. It began as a fairly small association that was trying to better understand the market for medical device companies – at the time, those companies weren’t even referred to as such since we didn’t have the legislation. It has evolved a lot since then, but originally Swedish Medtech acted as the interface between customers and medical device suppliers, in addition to dealing with matters of regulation and the marketing of products.
EO: How has Swedish Medtech evolved since that time?
ALS: Today, it is much more evident that we are an organisation working for the industry across a number of different areas. Our vision is that Sweden should be a market that is offering medical device companies the best possible climate for innovation and for introducing products.
We now have a secretariat of 11 people working within the organisation, whereas before this just consisted of a
board. Our membership is also growing. 10 years ago, we had roughly 120 members, and now we have just over 200. This growth is also challenging, since we are noticing an increasing number of mergers and acquisitions taking place in the market. As these companies continue to buy each other and join forces, we effectively lose members. As a result, we need to ensure that we are visible in how we produce value so that companies can see the benefits of our membership. This has been extremely important for us as we have grown.
EO: What is your current take on the industry across Sweden?
ALS: I find it extremely exciting. Sweden has a long history when it comes to medical devices, and it is a country that consistently scores enormously high on its innovation index in an international context. We also have a good climate for the healthcare sector to work closely with universities. We are seeing a growing number of medical
having an effect on a number of Swedish medical device companies, particularly for those who have been working with software engineers in Ukraine. We are experiencing a number of different challenges, but overall I would say that it is a healthy industry that has a very positive outlook.
EO: What are some of the major trends shaping the industry and how is the association responding to them?
ALS: The first of the two major changes we are seeing is sustainability, which is a very strong trend across Sweden and the Nordics. Secondly, the digitalisation of healthcare is also creating many new opportunities for medical device companies. We are doing a lot of work in both these areas.
device companies coming to Sweden, and it’s a strong industry.
That being said, there are challenges. These mainly relate to regulations that can make it unpredictable for companies in terms of how they put new products on the market. There are also cost issues when it comes to high inflation. Various new fees are escalating costs after COVID-19 and Russia’s war on Ukraine which are
In terms of sustainability, we are working together with our membership towards two different aims. Firstly, we want to showcase the good work that many of our members are doing today. Secondly, many of the medical device companies are small, medium or micro-sized businesses, so it’s really important that they understand the concept of sustainability and what it means for them from the beginning, since you need to be aware of this in the early stages of designing your product. As such, we are working on a lot of training in order for our members to understand the requirements in place on a global level, within the EU, and in the Swedish market. For instance, we’re arranging a sustainability conference for the first time which is aimed at medical device companies and their customers who are interested in understanding how the industry is working in the area of sustainability.
When it comes to digitalisation, this is a field we have been doing a lot of work in over the past 15 years. It’s one
“IF HEALTHCARE IS TO BECOME GREENER, BOTH ENVIRONMENTALLY SPEAKING AND IN TERMS OF SOCIAL RESPONSIBILITY, THEN IT WILL NEED TO PARTNER WITH THE MEDICAL DEVICE INDUSTRY SINCE THIS CAN ONLY BE ACHIEVED BY WORKING TOGETHER”
- ANNA LEFEVRE SKJÖLDEBRAND, CEO, SWEDISH MEDTECH
At Olympus we believe everyone should have the opportunity to live life to the full. Every day we are advancing medical technology solutions to help people everywhere fulfill their desires, their curiosity, their dreams, their ambitions, and their lives.
True to Life sits at the heart of Our Purpose of “Making people’s lives healthier, safer and more fulfilling.” For over 100 years Olympus has been pioneering innovative technologies and solutions that made the previously invisible visible and we have a
long legacy of delivering minimally invasive “see and treat” therapies that help detect, prevent and treat diseases.
Olympus collaborates with incredible professionals across the globe who are dedicated to ensuring people have the health to live fulfilling lives. Our medical technologies help them elevate the standard of care and create moments of fulfillment for all.
That is what we call True to Life.
In order to live up to Our Purpose, Olympus offers a wide range of high quality products with the newest technology. We provide solutions for General Surgery, Gastroenterology, Urology, Gynaecology, ENT, Hygiene and Preventitive Maintainance. Please have a look at our latest innovations:
Visera Elite III
A future-proof one for all system that grows with your individual needs. An endoscopic visualization platform with software upgrades designed to improve patient outcome and standardize processes.
EVIS X1
EVIS X1 represents a range of new, easy-to-use technologies that aim to revolutionize the way gastrointestinal disorders can be detected, characterized and treated.
Soltive laser
Powered by a novel energy source, the Soltive laser fragments stones relentlessly – with virtually no retropulsion - and offers precise cutting through soft tissue and state-of-the-art prostate enucleation.
thing to actually have the technology, but the difficult part that we have been focusing on is how that new technology can be implemented so that you have interoperability. Sweden has some huge advantages since we have been early in our adaption of digitalisation, but on the other side of the coin, that also means we are working with a lot of legacy software that now needs to be exchanged. In the healthcare space, these decisions can take a long time in adapting to the technology shifts that are needed. When it comes to interoperability and questions around standardisation, we are looking at how our members can ensure their systems evolve so that they’re working in the right environment. We’re also working on reimbursement issues relating to digital services and products.
Although the industry is not always seen as a selfevident partner in this area, we believe organising the future of healthcare is our most important issue to focus on. This is because big changes will need to be made if it
is to become sustainable from both a workforce and an economic perspective. We are trying to work together within Sweden in terms of our publicly financed healthcare and the various bodies that are responsible for bringing this to fruition.
“OUR VISION IS THAT SWEDEN SHOULD BE A MARKET THAT IS OFFERING MEDICAL DEVICE COMPANIES THE BEST POSSIBLE CLIMATE FOR INNOVATION AND FOR INTRODUCING PRODUCTS”
– ANNA LEFEVRE SKJÖLDEBRAND, CEO, SWEDISH MEDTECH
EO: Are there any recent or upcoming projects the association has been involved in that you would like to highlight?
ALS: For the past few years, we have been running a project that we call Innovation Accelerators. Here, we are working together to find the best ways of implementing technology and for the healthcare sector to support the uptake of new, innovative technologies. Sweden is a large country with 21 regions, but we are currently working with five of those regions, each of which has a very different approach. It’s been an extremely exciting project so far; the intended outcome is that we will try to change the system. It’s one thing to invest millions of Euros into developing a new product, but if there is no uptake, it’s not going to deliver any benefit to patients. We want to ensure that new technologies are reaching healthcare staff and patients, and that’s what this project aims to do.
EO: How would you define the outlook for the Swedish MedTech community and what are the organisation’s priorities within that future?
ALS: We are positive about the industry’s future. There will always be a role for medical devices to play in meeting healthcare needs, and I feel very secure that our companies are well-equipped to meet them. We are at a threshold now where, in order to change the healthcare systems across many countries, we need to be thinking differently. We need to invest more in technology and work in different ways to utilise the increasingly scarce resources of doctors, nurses, physiotherapists, and so on. Unfortunately, I think our systems need to be pushed a little bit further to almost crisis point before they justify making those major changes. Our industry has the potential to help the healthcare system make this transition in the best possible way before it reaches that stage. We are constantly working on making sure that we have the right regulation that ensures the products on the market are safe and effective, while simultaneously ensuring that it is not a hindrance to innovation. In addition, if healthcare is to become greener, both environmentally speaking and in terms of social responsibility, then it will need to partner with the medical device industry since this can only be achieved by working together. Finally, when it comes to the economy, we need to make sure that we are not killing our small companies at times like this when we are experiencing challenges with high costs. We are working with the Swedish market to ensure the best possible situation for our member companies in order to sell and market their products and receive the necessary reimbursement.
EME OUTLOOK is a digital product aimed at boardroom and hands-on decision-makers across a wide range of industries in Europe and the Middle East regions. With content compiled by our experienced editorial team, complemented by an in-house design and production team ensuring delivery to the highest standards, we look to promote the latest in engaging news, industry trends and success stories from the length and breadth of Europe and the Middle East.
Reaching a combined audience of more than 395,000 people, EME Outlook covers a full range of industrial sectors: agriculture, construction, energy & utilities, finance, food & drink, healthcare, manufacturing, mining & resources, oil & gas, retail, shipping & logistics, technology and travel & tourism. In joining the leading industry heavyweights already enjoying the exposure we can provide, you can benefit from FREE coverage across our digital platforms, a FREE marketing brochure, extensive social media saturation, enhanced B2B networking opportunities, and a readymade forum to attract new investment and to grow your business.
To get involved, please contact Outlook Publishing’s Managing Director, James Mitchell, who can provide further details on how to feature your company, for FREE, in one of our upcoming editions.
Gulf Data Hub offers a premium range of data centre solutions and safe storage within its state of the art facilities. We find out more from Chief Information Officer, Himmath Mohammed
Ed
Budds | Project Manager: Dennis MoralesWith initial roots stretching back to the cavernous computer rooms of the 1940s, the true boom of data centres arrived during the hectic inception of the internet era from 1997 to 2000. Collectively, companies required faster connectivity and non-stop operational capacity to deploy systems and establish a presence online.
Businesses subsequently began to construct large facilities, first called internet data centres. Flash forward and the data centres of today exist as industrial-scale operations, often using as much electricity as a small town.
A data centre is a dedicated space within a building, facility or often a group of buildings, used to house complex computer systems and associated components, such as telecommunications and storage systems.
At present, an increasingly pressing worldwide concern in the field of data is the subject of information security.
Navigating this serious issue is Gulf Data Hub, whose centres must offer a secure environment that minimises any possible downtime or outages as well as the chance of a security breach for its clients. Therefore, the complex facilities obtained by the company must maintain the highest standards to ensure the integrity and functionality of its hosted computer environment.
Having worked in the data industry for the last 20 years, gathering a wealth of experience, Himmath Mohammed, Chief Information Officer for Gulf Data Hub, has witnessed a vast transition since the company’s humble inception.
Turn back the clock to the year 2012, and this critical period for the company saw Gulf Data Hub searching and scrutinising the market
As global computing demand continues to grow exponentially in the digital intelligence era, there will be a surge in data centre construction. According to Mr. Fei, to achieve carbon neutrality, the industry must prioritise energy conservation, carbon emission reduction, and green transformation. This presents both challenges and opportunities. Drawing from its experience and industry insights, Huawei has identified the following 10 trends:
Trend 1: Low Carbon
Data centres will adopt green, lowcarbon solutions and utilise clean energy sources like photovoltaics (PV), wind, and hydropower to minimise their carbon footprint. By 2027, green power utilisation is expected to exceed 50 percent. Advanced energy conservation solutions and technologies, such as waste heat recovery, will be implemented to improve data centre energy efficiency and recovery rates.
Trend 2: Sustainability
New sustainability indicators for data centres will be introduced, including renewable energy utilisation, water usage effectiveness (WUE), carbon usage effectiveness (CUE), space usage effectiveness (SUE), grid usage effectiveness (GUE), material recovery rate, and lifetime contaminant emissions, in addition to the existing power usage effectiveness (PUE).
Trend 3: Fast Deployment
Data centres must be rapidly deployed to meet skyrocketing computing demands, with construction periods decreasing from 12 months to six months or less.
Trend 4: High Density
As chip performance and power
consumption improve, the demand for high-density data centres will increase. Cloud data centres will become mainstream, and diversified computing collaboration will become the norm. Standard power density per IT rack will increase from six to eight kilowatts (kW) to 12 to 15 kW by 2027. Power density in supercomputing and intelligent computing centres will reach 30 kW or higher.
Trend 5: Elasticity
Future data centres will be more flexible regarding upgrades, with one generation of facilities supporting power evolution over two to three generations of IT equipment. A standard design will facilitate on-demand deployment and elastic capacity expansion.
Trend 6: Prefabrication
The prefabricated and simple architecture will tackle challenges like long construction periods and complex operations and maintenance (O&M) faced by traditional data centres. In the future, a data centre building will house over 1,000 racks, and a campus will accommodate over 10,000 racks. The prefabricated design will shorten the construction period for a 1,000-rack data centre from 12 months to six months, enabling rapid delivery and on-demand deployment.
Trend 7: Storage and Backup Integration
Renewable energy and energy storage will be necessary for power-hungry data centres. The deployment of energy storage systems (ESSs) in data centres will integrate short-term backup power systems to participate in frequency regulation and peak shaving, enhancing power grid stability. Peak shaving will also improve GUE so that more IT racks can be deployed to increase revenue.
Trend 8: Distributed Cooling
A distributed cooling system uses cooling sources for each data hall and adopts a redundancy configuration as required. In the future, distributed cooling systems will gradually replace centralised cooling as the preferred solution for large data centres, due to their flexible architecture and high reliability.
Trend 9: Smart O&M
Smart O&M is crucial for enhancing data centre resource utilisation and reliability. Intelligent operations will automatically determine data centre asset statuses to maximise asset value. Intelligent maintenance will identify faults and optimise energy conservation in real time to improve O&M efficiency, achieving predictive maintenance and optimal energy efficiency.
Trend 10: Security and Trustworthiness
As digitalisation and intelligence advance, data centres will strengthen their hardware reliability, software security, system resilience, safety, privacy, and availability. Artificial intelligence (AI) technologies will implement predictive maintenance on components, devices, and systems at the hardware level. Hierarchical defence will be provided at the software level. A combination of software and hardware measures will boost data centre reliability.
Moving forward, Huawei will strengthen technological innovation to lead industry development and offer more competitive products and solutions to build a solid digital foundation for a greener, low-carbon future for the data centre industry.
for major business opportunities to invest and expand in, proving to ultimately be a pivotal and highly influential time for the future prosperity of the business.
Subsequently, the company identified data centres as one of the major fields envisioned to grow exponentially in the coming years.
Following this discovery, Gulf Data Hub hired a selection of consultants to carry out a thorough market study of these facilities and their potential, providing the company with key insights into this burgeoning market.
“Once this was done there was no looking back, as the report stated that at the time there were zero purpose-built data centres which were also carrier neutral and competed to international standards to attract major hyperscalers,” introduces Mohammed.
“This led to us setting the base goal of constructing such purposebuilt, Tier 3 certified data centres with specifications comparing directly to the European market.”
Gulf Data Hub has been growing rapidly ever since, with the company currently positioned at an operational capacity of 50 megawatts (MW), with another 120 MW of capacity already under construction.
Above all else, Gulf Data Hub is aiming to provide world-class carrier and vendor neutral data centres in the Middle East and North Africa (MENA) region. The company endeavours to maintain neutrality which will increase its customer spectrum, allowing Gulf Data Hub to become the region’s first choice facility to store companies’ mission critical equipment and information.
Since starting operations, Gulf Data Hub has consistently
innovated and looked for ways to lower the risks associated with downtime while simultaneously increasing its operational efficiency. By embracing simplicity, the company guarantees customer satisfaction with its adaptable, affordable, reliable data centre floor and apparatus space, as well as its many value-added services.
Promising all clients a resilient environment, Gulf Data Hub creates a secure and strong ecosystem that includes hosting, disaster recovery
and workplace recovery, cloud platforms, connectivity, and core colocation.
“As we grow to enjoy a global footprint, we pledge to continue being a carrier-neutral service provider. You can find a combined, cutting-edge, and market-focused set of solutions at Gulf Data Hub that are tailored to any company’s needs,” clarifies Mohammed.
“We are a leading global provider of hybrid infrastructure that is safe, fast, and optimised for both business
“AS ONE OF OUR KEY UNIQUE FEATURES, WE HAVE A VERY FLEXIBLE DESIGN WHICH CAN ADAPT TO THE CHANGING DEMANDS OF CUSTOMERS”
– HIMMATH MOHAMMED, CHIEF INFORMATION OFFICER, GULF DATA HUB
Trane has introduced a new R1234ze chiller specifically designed to meet the stringent requirements of high temperature data centres.
LEARN MORE ABOUT US
By upholding neutrality, Gulf Data Hub wants to become a top-notch carrier and vendor-neutral data centre which will attract a wider range of clients and develop into the region’s top facility for storing businesses’ mission-critical technology.
Gulf Data Hub is committed to supporting and assisting businesses in increasing uptime and minimising operational expenses.
The company is consistently innovating and looking for ways to lower the risks associated with downtime while simultaneously increasing efficiency.
Working with integrity, prioritising the needs of the client, encouraging continuous development, and conducting business responsibly and sustainably are the cornerstones of the key values upheld by Gulf Data Hub.
and tomorrow’s digital pioneers. In this way, on a single technological platform, we combine a data centre and our selection of services,” he states proudly.
Many valuable lessons have been learnt by companies throughout a multitude of industries in the wake of the immense difficulties encountered during the COVID-19 pandemic. This is no different for Gulf Data Hub.
“We have learnt as human beings how critical our systems are and how important it is that these systems possess high availability relevant to specific locations or where data is housed,” Mohammed explains.
“People realised that they should host information with either a cloud provider that is accessible from any corner of the world, or choose to use a secure physical data centre where systems are running constantly, irrespective of the situation globally,” he continues.
This enlightenment across the industry has driven a sudden rush of new users, as more people are continuing to identify data centres as an ideal place to park their data safely.
With this increased popularity,
there comes a gigantic demand and a rush to build more data centres, especially in the MENA region where Gulf Data Hub operates.
Parallel to this, the growth of artificial intelligence (AI), machine learning (ML), and automated driverless cars, all of which are
Mr Mazen Sharaiha, Chief Operating Officerinterconnected devices, means these tools are reliant on edge computing or edge data centres.
“Analysing all these trends and the development of new technologies relating to data means it’s clear to see there is huge potential and growth in our field,” Mohammed assesses.
Mohammed explains how Gulf Data Hub’s road map for 2024 is already fixed and under execution.
“For now, we are purely a wholesale colocation provider. We build infrastructure and provide space, power and cooling to our customers,” he sets out.
However, alongside this service, Gulf Data Hub is planning to expand further into the ecosystem of data centres, particularly connectivity and cybersecurity, as the company is building several ancillary business units around its data hubs. Meanwhile,
concurrent to this, Gulf Data Hub is also interconnecting its assortment of centre locations in the Middle East, aiming to help its customers in reducing their latency.
“It is mandated that we will reach 200 MW of IT capacity and almost half of this projection is under execution already, as you can physically see the structures rising up and our projects being delivered in a physical manner.
“With each new initiative, we learn and enhance ready for our next project. We carry forward lessons learned, whether in terms of implementation, design or efficiency,” he continues.
Additionally, diversity sits top of the agenda for the future, and exists as a key government strategy and mandatory requirement in the Middle East, as businesses must now host a spread of diverse nationalities in their teams.
Dedicated to this positive
self-enhancement, Gulf Data Hub employs high levels of agility and flexibility in deploying bespoke solutions for its clients.
“As one of our key unique features, we have a very flexible design which can adapt to the changing demands of customers. Whether this is in terms of rack densities, high efficiency cooling or sustainable solutions, these services are helping our technology deployment,” Mohammed adds.
Capitalising on this ability to pivot and adapt, Gulf Data Hub is planning to expand across five new locations to reach its 2024 ambitions, securing its position as a trustworthy and dependable guardian of digital data for the modern age.
Thanks to a reliable fleet of transport and an extensive network of depots and modern warehouses across Europe, Raben Netherlands is proud to deliver the highest quality logistics services. We track the road to success with Managing Director, Berend Jan Schuring
Writer: Ed Budds | Project Manager: Cameron Lawrence
Endeavouring to form exceptional working partnerships with our clients, together we aim to satisfy the customer of our customer.”
Raben Netherlands (Raben) sits proudly as one of the 15 individual branches of the Raben Group, which specialises in road transport and contract logistics across a burgeoning multitude of locations in the Netherlands and across Europe.
“Together, we organise the best solutions to ensure all processes are as efficient as possible. At this moment, it is very important to offer a solid network with high performance
for customers,” introduces Berend Jan Schuring, the company’s Managing Director.
At present, many prominent players in the transport and logistics industry are encountering problems with selling their stock. Consequently, this means warehouses are full and the throughput is lacking the ability to roll out enough product.
In the face of this struggle currently swamping the sector, Raben recently built two extra warehouses in EttenLeur and Oss to increase its ability to store goods for both ongoing and new customers. This in turn facilitates the company’s capacity and network to
help new clients to achieve their best possible business outcomes.
Raben has almost 400 employees at present, dispersed to cater to a highly diverse client base of customers that profit from the company’s full supply chain solutions for transport and contract logistics, such as MGA Entertainment and CM Logistics.
“Transport and logistics are always an exciting world to work in as every single day is different and you continually face new challenges, but it also gives you a lot of energy if you can help your customers to deliver the right service and provide solutions for them,” Schuring sets out.
Adhering to its motto “Enginuity”, the perfect combination of engineering and ingenuity, Kässbohrer meets the needs of its customers in more than 55 countries in all sectors, including general cargo, cold chain, construction, liquid and bulk goods, and intermodal, with its unrivalled range as well as heavy and abnormal goods transportation.
Kässbohrer is unique in Europe with its competence to meet the needs of the entire tranport sector with 96 percent coverage of all needs through more than 1,000 unique products.
Founded in 1893 in Germany, Kässbohrer today is Europe’s top innovative international trailer manufacturer with an annual production capacity of 20,000 trailers, serving its European customers from multiple head offices in Germany, the Netherlands, Spain, France, Italy and Poland along with carefully selected sales partners in the UK and Nordic countries.
As of 2022, the leading semi-trailer Kässbohrer is among the overall top three choices in the Netherlands and Sweden. Kässbohrer is among the top three in tanks and silos in Germany. For heavy haulage, Kässbohrer is the market leader in low beds in Poland, and among the top three in France for platforms. With its strong local organisation, Kässbohrer is rapidly meeting its customers’ needs in Italy by doubling its sales and tripling its sales in Spain.
Not only with its robust, efficient, long life and high quality vehicles but also through its services, Kässbohrer meets the needs of its customers. Kässbohrer operates the fourth largest after sales service network in Europe with its competent certified after sales partners and carries out its spare parts operations from its manufacturing facilities as well as from France. In cooperation with leading leasing companies, Kässbohrer presents competitive financing options under K-Finance in Germany, Spain, Italy, Poland and France. Kässbohrer is continuing to develop its sales and after sales activities in the UK.
Most importantly, Kässbohrer stands out for its innovation competence, by constantly developing its products and services to meet the unmet needs of its customer. Kässbohrer prioritised collaboration with its stakeholders, foremost customers, associations, universities, research programmes as well as its premium suppliers together
in a wide R&D ecosystem to constantly advance trailer technology to take its customers to the next 125 years.
Established in 2009, Kässbohrer
R&D has completed more than 250 R&D projects and published 108 international academic articles as well as participating in European Comission backed R&D projects. As a result, in 2022 alone, Kässbohrer launched 18 new vehicles with over 50 innovations. Apart from customer satisfaction, Kässbohrer’s competence in furthering trailer technology is presented with the awards and nominations we have received, especially at the most prestigious Trailer Innovation Awards.
Kässbohrer has won the Trailer Innovation Award 2017 in the “Safety” category for its safety Bitumen tanker with electronic discharger the Trailer Innovation Award 2019 in “Chassis” category for its Novel Octagonal Frame Multifunctional Container Chassis, the Trailer Innovation Award 2021 in the “Components” category with the Multifunctional Rear Bumper RUPD-5K1, the second place winner of “Body” category with 45ft Rulo Swap Body Body, and “Smart Trailer” with Trailer Advanced Driver Assistance Systems, and the Trailer Innovation Award 2023 in the “Safety” category with its Integrity Protection Device.
As the transport sector welcomes the new European climate law, committed to at least 55 percent carbon emission reduction by 2030, an ambitious transition awaits our industry pending further legislation. In this time of transforming the transport business, Kässbohrer is equally competent in all technologies and vehicle developments to work with our customers on their unique need for transition.
Kässbohrer presents the next generation of higher capacity vehicles, including 32-metre (m) combinations already on the road in countries where the transport is permissible, in addition to our innovation award nominee 14.98m curtainsider and its unrivalled
intermodal range to support more ecofriendly intermodal transportation.
Kässbohrer is able to meet all combinations in the LHV concept, from type 1 to 5. An example is our 32m combinations used in Scandinavian countries; two semi-trailers can be combined in a single truck with our 2-axle dolly vehicle. Kässbohrer 32m Super Eco Combi (SEC) presents the highest efficiency in terms of sustainability through higher capacity in terms of two vehicles, and a mega upper structure for higher vehicle capacity as well as intermodality compatibility. Our SEC developments have recently been tested in the Netherlands with the attendance of ministers.
Kässbohrer is proudly unrivalled in the intermodal product range with it’s vehicles. Kässbohrer is the most reliable manufacturer, especially when the new EU green deal targets that 75 percent of all road traffic should switch to intermodal operations. With the entire Kässbohrer container chassis
info@kaessbohrer.com
family including award winning avmh, the lightest range of swap bodiesincluding the first ever 45ft coil swap body - and the most robust and longlasting huckepack products developed with Enginuity, we offer our customers’ the highest quality, longest lifetime as well as low TCO solutions as we are committed to meet our customers’ unique transition and the environment’s urgent needs.
Kässbohrer Dry Freight Intermodal Plywood Box K.SBT T is engineered for environmentally-friendly intermodal transportation. The vehicle is supplied with crane pockets and is suitable for e, f, g and i type railway wagons according to IRS 50596-6 as standard.
Kässbohrer Dry Freight Intermodal Plywood Box K.SBT T is robust for safety and longevity of your operations while its many options improves operational efficiency.
Dry Freight Intermodal Plywood Box stands out with its robustness through 20mm thick smooth plywood walls, 7.2 tonne forklift capacity phenol resin coated plywood floor as standard, EN 12642 Code XL certificated upper structure and KTL Coated Steel Front Panel.
Dry Freight Intermodal Plywood Box’s options are ingeniously designed to further your operational efficiency.
The optional insulated roof is coated with glass fibre reinforced polyester to protect against humidity and prolong product life, the double deck option increases the capacity to 66 euro pallets, lashing rails to improve load safety, and turtle mechanical locks increase security against theft. In order to increase the robustness of the box body, the trailer is equipped with 4mm thick and 325mm height high-quality heavy duty type steel kick plates which are welded to the chassis.
Although many of Raben’s processes are automated and the company remains confident in its IT solutions, its trusted team members must still make the key decisions.
Raben’s team plays the crucial role of supporting its clients, answering any questions and making sure that every transport link is safe, on time and serviced with a smile.
“Our international Raben network enables us to be the trusted local operator for our closest clients and an internationally established operator with transport solutions throughout the whole of Europe for the multinationals who seek the best performance,” describes Schuring.
Furthermore, Raben is connected with over 160 depots in Europe, which are all designed for a combination of groupage, part truck load and full truck load transport. Additionally, by
keeping most of its transport within its own organisation, the goods of Raben’s clients are always kept in the safe hands of the company’s people, trucks and facilities.
“We have a solid intermodal connection via rail between the Benelux region and Italy. This sustainable transport is part of the solution in reducing our CO2 emissions and we are currently piloting intermodal connections to other Raben countries, such as Poland as well,” he tells us.
The invaluable use of IT solutions helps Raben make its services accessible to the company’s valued customers. Clients can then simply request a quick price, put their order into the MyRaben system and follow their shipment with real time tracking information.
With the opening of its new cross
docking terminal in Heerlen, Raben looks to take the next step in expanding its services throughout the Benelux region. This will make the company less dependent on third parties and gives Raben more exposure in a vitally important part of its network.
Growth is always top of the agenda and remains a primary goal for the Raben Group as a whole, both within current markets and for fresh ones. “We grow with the aim to provide better and more complete solutions for our customers, and the fourth Raben depot in Heerlen is a great example of this. We were already active in Belgium and Luxembourg, with Etten-Leur as the main hub for transport to the south, but now with the opening of the Raben Heerlen depot, our trucks can enter Belgium from two directions,” affirms Schuring.
Another recent indication of the company’s expansion into new markets is the intermodal pilot between the Netherlands and Poland. “Because of the difference between regular road network and rail transport, we must adapt our solutions to a different kind of customer. We invested in new intermodal compatible trailers and now we must keep working on expanding our services even further.”
If the solutions are reliable and customers know what they can expect from the company and intermodal transport in general, Schuring is confident that they will start to find their way to Raben in great numbers.
Raben is constantly on the lookout for people with drive, entrepreneurship and who proactively face challenges and take responsibility.
“Our employees get a lot of freedom within certain boundaries, and we believe that this empowers them to come up with solutions and
really own their work,” quantifies Schuring.
A productive workforce cannot exist without a comfortable workplace, both in a physical and sociological manner.
Addressing this concern, Raben uses fully adjustable chairs, sit-stand desks, height adjustable monitors, electric pallet trucks with active suspension adjusted to the weight of the user, pallet reach trucks with a rotating workstation to prevent neck and back injuries for warehouse employees, and fully optimised truck interiors for all drivers.
“We organise events for our depots and our entire organisation, like a big barbecue in the summer. We stimulate and support our employees by encouraging participation in sporting events and every Friday we end the week together in the canteen evaluating and sharing our weekend plans,” he elaborates.
Wanting to create the safest possible environment for all its colleagues, Raben has appointed confidants who are there to address any difficulties or complaints that the employee may be having that they feel like they can’t discuss with management. Raben employees can also enjoy a range of company training platforms.
“We have an internal training platform for all the systems we use in Raben, but we also made an online training centre available in which employees
can follow classes on pretty much any subject.”
The company’s drivers are a prime example of this, receiving regular training and information sessions to keep them up to date on safe and economical driving and the best practices for unloading.
Pivotal to the company’s future prosperity and strategic growth, Raben culminates this ambition with a set of carefully measured goals for
“OUR EMPLOYEES GET A LOT OF FREEDOM WITHIN CERTAIN BOUNDARIES, AND WE BELIEVE THAT THIS EMPOWERS THEM TO COME UP WITH SOLUTIONS AND REALLY OWN THEIR WORK”
– BEREND JAN SCHURING, MANAGING DIRECTOR, RABEN NETHERLANDS
both the entire Raben Group and within the local organisation.
The Raben Group’s key goals to be achieved by 2025 include a 30 percent reduction in CO2 intensity from offices and warehouses and a 10 percent reduction from transport activities. This runs parallel to its aim of increasing the ratio of female managers from 29 percent in 2020, to 34 percent across the next two years.
On a more specific and local level, Raben’s main objective for the coming years is to fill its own network.
“We aim to make the most of every trip. By filling every trailer, we reduce CO2 emissions per kilogramme. As a result, we can offer better pricing for our customers and at the same time gain a benefit in revenue,” Schuring says.
The company is also looking to expand its warehouse capacity and services.
“With the completion of our
warehouse in Etten-Leur in 2022 and the near completion of a new warehouse in Oss this year, we are really pushing our contract logistics services to a new standard. More capacity means more available space for us to find new customers and to expand existing partnerships, but it also means that there will be more opportunities for us to improve our services,” he adds.
Elsewhere, Raben has set itself the target of increasing its Y-Z generation employees by 20 percent believing that whoever has the youth, has the future. In this way, the company aims for a sustainable organisation where people can grow together. Finding new talents and creating an environment in which they can and want to keep growing is one of the other main points of focus in the coming years.
Finally, although sea and air
transport already play pivotal roles in Raben’s operations across other countries, the Netherlands is yet to launch these solutions. Evidently there are plenty of opportunities to do so, considering the excellent geographical positioning between the harbours of Rotterdam and Antwerp and the airports of Amsterdam and Eindhoven.
This exciting scope for expansion and enhancement looks certain to catapult Raben straight to the very forefront of the transport and logistics industry.
We speak to the Managing Director of Lantmännen
Unibake Romania and Southeast Europe, Viorel Ognean, about how the company is revolutionising production of the bakery sector, across Europe and the Middle East
As a food group, grains are one of the oldest and most nutritious foods in the world. This is most greatly recognised by Lantmännen Unibake
Romania (LUR), a reputable staple of baked goods sector in Southeast Europe.
LUR’s story began in 2016, when the company acquired a state of the art bakery that was equipped to be the best-in-field. Located in the Ilfov county in Pantelimon in east Bucharest, the company manufactures the highest quality baked goods, to both local and national markets.
“Our number of direct clients increases every year. We currently cover the Romanian market, as well as exports to most European countries and the Middle East, all directly or through the Lantmännen Unibake group,” begins Viorel Ognean, Managing Director of the company.
As it stands, LUR’s well-loved and established produce includes buns for hamburgers and hotdogs, all sold fully baked and frozen. Additionally, LUR also creates fully baked buns with a longer shelf life, with different sizes, weights, and toppings, so the company’s delicious goods can be enjoyed for even longer. More recently, LUR has diversified its portfolio.
“Now, we also sell bread and pastries such as croissants, or puffs with different fillings. Currently, our assortment includes over 250 items of bread, fast food, and pastries,” Ognean says.
“All of our buns are vegan and we do not use any ingredients or subingredients that are of animal origin, catering to more consumers through
Viorel Ognean, Managing Director: “Our colleagues enjoy a friendly and open environment, in which we treat each other with respect and consideration. We invest a lot in building and improving people’s competencies and personal leadership skills, that represent a long-term advantage for their professional and personal lives.
“Operators who want to progress have the opportunity to be trained to use more and more sophisticated equipment, which comes with an additional remuneration.
“Looking ahead to the new bakery, we have begun to strengthen our existing teams even more since 2021, both by recruiting and onboarding new colleagues, as well as through development and training programmes for potential employees.
“An example of this is the partnership in dual education that we have with the Cezar Nicolau Technological High School, through which every year we “adopt” a class of students to be qualified in the professions we need in our bakery.”
a variety of flavours and textures.”
The efficiency of LUR’s produce is achieved using a high-speed bun production line, alongside four packaging lines. Each line is automated and equipped with
multiple sensors, allowing for limited human intervention. This is further endorsed by the introduction of industrial robots, so that the entire system is digitally controlled and monitored. Thus, the manufacturing
At Kerry, we are partnering with our customers to deliver sustainable nutrition, creating products that mantain good health, while protecting people and the planet.
FOOD WASTE
Microbial, Textural, Flavour Shelf-life
NUTRITIONAL OPTIMISATION
Sugar, Salt, and Fat Reduction
CLEAN LABEL
Enzymes for Gluten Relaxions
ANIMAL DERIVED INGREDIENTS
Egg-free Solutions
What happens when sources of food waste are eliminated?
of each bun is streamlined, uniform, and to the highest hygiene and food safety standards. Subsequently, all its bun produce fully complies with the demanding requirements of their customers, as the company strives to produce the best quality, appearance, taste, and texture.
“We collaborate with fast food consumers, modern retail, gas station chains, as well as the traditional market,” Ognean explains.
The company values its 135 passionate and professional employees, who work hard to deliver the best produce every single day, much to the delight of LUR’s consumers.
LUR has steadfast values that are planted in the local culture and are projected into the wider business, which are paramount to the company’s success.
“LUR is an amazing company, embedding the Nordic (Scandinavian) culture and way of doing business, both externally and internally. We are a farmer-owned cooperative, founded in the Nordics. This combination gives
us stability because our purpose is to protect the livelihoods of people who work the land,” Ognean tells us proudly.
“There’s a very strong sense of responsibility towards our consumers and customers, that we provide high-quality, nutritive products, anchored in the local taste and texture preferences of our consumers. As a global baker, we contribute to the health and well-being of the
population, and we take our mission very seriously.”
From a sustainability perspective, LUR has a clear focus on the impacts its raw materials have on the planet. Therefore, the company is taking meaningful steps to reduce the emissions generated by its production lines.
In correlation with many other baked goods companies, an effective supply chain is vital to the success of the business. This is apparent when considering the distances that the baked goods travel, as well as the strict requirements needed for storage, transportation, and food safety and quality.
To create the best tasting buns that LUR is recognised for, the company strives to purchase local ingredients, together with spare parts, working equipment, and practically everything it needs to function. It is only a small quantity of ingredients that cannot be sourced locally, such as sesame seeds, where the company must branch out.
When sourcing its ingredients, LUR realises its responsibility to provide healthy and sustainable products.
“Our customers trust us for having a
high benchmark regarding food safety and quality, whilst being knowledgeable and in control throughout the entire chain,” Ognean assures us.
“We have a major responsibility towards our bakery supply chain, and we take our role very seriously. Currently, our country imports significant volumes of frozen bread from other European countries, while the local bakery offers the short distribution chain, with its advantages related to speed in supply, flexibility, costs, low environmental impactand so on.”
With an abundance of new investments, LUR is hoping to expand its baking portfolio and strengthen its presence in the bake-off bread and fast food sector. Once the new investments are implemented, LUR will have sufficient capacity to exceed current and future consumer needs in the entire region.
“We remain true to our global mission, to deliver high-quality products that will make people feel satisfied and happy in every corner of the world, working towards billions of
smiling tummies,” Ognean states.
Some examples of the new investments include the robotisation in the packaging area, photovoltaic (PV) panel system, as well as a heat
“WE REMAIN TRUE TO OUR GLOBAL MISSION, TO DELIVER HIGH-QUALITY PRODUCTS THAT WILL MAKE PEOPLE FEEL SATISFIED AND HAPPY IN EVERY CORNER OF THE WORLD, WORKING TOWARDS BILLIONS OF SMILING TUMMIES”
– VIOREL OGNEAN, MANAGING DIRECTOR, LANTMÄNNEN UNIBAKE ROMANIA
Viorel Ognean, Managing Director:
“In the future school year, we will get involved in the education of students attending the courses on the mechanical profile, the new class supported by us being mechanics/electricians for electrical and energy equipment. Specifically, our actions consist of offering financial support and the contribution to the development of students’ skills, through the internships. At the end of the studies, students have the opportunity to join our team, as employees.
“We support the community through partnerships with different non-governmental organisations (NGOs) in education, medical and social assistance, through financial support or through donations of products to canteens or social centres. We have an opening to support organisations or institutions that would need and
recovery and reuse system. Thus, new expansions and investments bring advancements in the efficiency of production and sustainability.
One of the most exciting projects on the horizon is a brand-new, state of the art bakery, with a greater expansion in the production lines that will be installed over the next few years. Phase 2 of the facility will further showcase LUR’s environmental commitments as well as have a positive impact on the local community. The projected total investment entails a future creation of an excess of 300 jobs to join the workforce.
“The new bakery will bring a multiple of advantages on a local level. Foremost, the range of bakery specialities will be anchored in the local profile of taste and texture, using local ingredients and will respond to the needs and expectations of Romanian consumers,” Ognean says. Although its environmental footprint has always been an important part of the company, its predominant focus for the upcoming years is sustainability, as it becomes a fundamental aspect of the organisation.
“LUR has many initiatives already in operation. We permanently optimise the packaging material dimensions and thickness, so that we do not waste resources and have a negative impact on the environment,” Ognean explains.
“Another example is that much of the volume produced is delivered in reusable crates, so we save several million carton boxes, which results in about 1,000 tonnes of carton per year.”
Significantly, the bakery also operates on 100 percent green energy, all attained from renewable energy sources, alongside PV panels. According to Ognean, these provide at least 15 percent of the energy consumption of the bakery, making a huge difference and adding towards the company’s overall
future sustainable goals as the wider Unibake organisation aspires to be net zero by 2050.
“To take our climate targets to the next level and make sure we live up to global standards, as LUR ardently contributes to Unibake’s wider sustainable goals. Signing up for SBTi (Science Based Targets Initiatives) demonstrates our clear ambition to reduce emissions in line with climate science,” Ognean tells us.
Overall, LUR endeavours to feed the nation, through high-technology, imaginative flavour strategies and evaluating all vital decisions through a sustainable lens.
Salmon Evolution is the Norwegian player at the forefront of sustainable salmon farming. We speak to CEO Trond Håkon Schaug-Pettersen about the company’s chosen hybrid flow-through technology, and its production plans moving forward
Sustainable food sources are the key to feeding a rising global population while maximising efficiency and maintaining environmental goals, a trio of factors that balance the demands of people and the planet.
Salmon Evolution aims to be one such company. A Norwegian landbased salmon farming business founded in 2017 by a group of
visionary pioneers with vast experience in the seafood industry, Salmon Evolution was established with the goal of becoming a beacon for sustainable salmon farming. Using innovative technology, Salmon Evolution is extending the ocean’s potential by transferring the best conditions offered by the sea to farm salmon on land, in a more sustainable way. The company is currently
Writer: Marcus Kääpä | Project Manager: Liam Pyetargeting a production capacity of 100,000 tonnes of head on gutted (HOG) salmon by 2032.
Through the company’s chosen hybrid flow-through (HFS) technology, which combines the benefits of both traditional and landbased aquaculture, Salmon Evolution is solving several traditional farming issues. With controlled and optimal
eliminating the challenges associated with conventional seabased farming, such as sea lice,
escapes, reducing mortality and emissions, and feed loss.
“We are becoming a part of the solution in providing the world’s growing population with more protein while reducing the impact on our shared planet,” introduces CEO Trond Håkon Schaug-Pettersen. “We are highly engaged in our mission to extend the ocean’s potential through innovative and sustainable means.”
Salmon Evolution has been listed on the main list of the Oslo Stock Exchange since 2021, and has subsequently continued to grow. The company started construction in May 2020 and has almost completed Phase 1 of its long-term development plan.
Today, Salmon Evolution numbers around 60 employees, all of whom are dedicated to achieving its progressive business and global goals.
Salmon Evolution’s first production facility is strategically located at Indre Harøy on the Norwegian west coast, which boasts unlimited access to fresh seawater, renewable energy,
established infrastructure, and an educated and experienced workforce. Phase 1 is already in operation, and the company is seeing an annual capacity of 7,900 tonnes of HOG salmon at a steady rate. Fully developed, the Indre Harøy facility will have an annual capacity of 31,500 tonnes of HOG salmon.
According to Schaug-Pettersen, the production facility was previously an abandoned quarry, and so adapting the area to suit the needs of the business has kept intrusion into nature at a minimum.
“The site had unlimited access to clean and fresh seawater, adequate electricity supplies, deepwater quays and opportunities for expansion and growth,” he details. “In addition, it was optimally positioned in terms of distance for produce to reach the market. The location for landbased farming was perfect; we have transformed an undeveloped land zone into a new and modern industrial adventure.”
Salmon Evolution has an agreement for slaughter services with Vikenco AS (Vikenco), one of the leading salmon processors in Norway, located only 10 kilometres (km) from the production site in Indre Harøy. Due to this
Plug and farm: Take your fish sludge through a high quality treatment line, from 0.3 percent dry solids to valuable biochar – all ESG supporting and bottom line positive. Blue Ocean Technology offers fish farmers, on land or at sea, a complete sludge solution that creates real resources and real value from what to date has been considered waste or unwanted discharge.
We offer flexible solutions that can easily be expanded (Plug&Farm®): Easily scalable, with very low energy signature – and minimal space requirements.
It’s a great milestone and recognition for DESMI Group to supply the entire centrifugal pumps and frequency converters package in the first project phase at Indre Harøy.
DESMI has been a supplier for the seafood sector for decades. Hydraulic energy optimalisation has been the key focus in our latest pump R&D. Long experiences in seawater applications combined with know-how in the land-based processand energy sector, we believe are important factors for the aquaculture industry in the near future.
It has been a great honour for DESMI to work closely with the EPCcontractor, Artec Aqua, and Salmon Evolution during project execution, and commissioning at Indre Harøy. E
www.desmi.com
Using Blue Ocean Technology’s dewatering and drying technology helps to lower the threshold for establishing optimal downstream systems.
We now see the contours of what this will become with technology and ingenuity facilitating sustainable opportunities. And we continue to work with purpose and great enthusiasm in collaboration with our customers who are at least as passionate about this as we are.
Land-based solutions
solutions
Dewatering: Screw presses Dryers: Blue Dryer
www.desmi.com
desmi@desmi.com
• Simple installation, operation, and maintenance
Simple installation, operation, and maintenance
• Acts as a firewall for viruses in intake water
Acts as a firewall for viruses in intake water
• Can be delivered skid mounted for super easy installation
Can be delivered skid mounted for super easy installation
• No chemicals, only UV light
No chemicals, only UV light
The DESMI pumps and systems are sold to more than 150 countries via a network of subsidiaries and distributors on six continents.
• Design to run 24 / 7 / 365
Designed to run 24 / 7 /365
• Very long intervals between maintenance
Ranges from 35 m3 to 3,500 m3 Horizontal Reverse
• High efficiency > 85% at high-flow & low-pressure conditions
Very long intervals between maintenance efficiency > 85% at high-flow & low-pressure conditions
Vertical Horizontal
proximity, there is no need to invest in subscale processing operations as Salmon Evolution’s partnership with Vikenco provides the company with a comprehensive product portfolio, full product flexibility, HOG, fillets, and portions divided into two main categories – fresh and frozen products. This gives Salmon Evolution an industrial cost level from day one.
Sustainability and innovation are two aspects of business that lay at the heart of Salmon Evolution, both of which are encapsulated by HFS technology central to the company’s farming practices. HFS represents the most suitable technology to utilise on-site, especially alongside the optimal water conditions available along the Norwegian coast and in
Salmon Evolution’s other locations worldwide.
“Our emphasis has been on creating the most natural possible environment for the salmon while avoiding the challenges we find in the sea, such as lice and disease,” SchaugPettersen says. “We have put biology first in everything we do because we want to create an environment where the salmon not only survives, but also thrives. This ensures better biology, quality, fish health and welfare, improved sustainability and, in the end, long-term profitability.”
The system itself takes in 30 to 35 percent cold and fresh water at any given time, helping to maintain fish welfare and provide control of the production environment, while the company also reuses approximately 65 to 70 percent of the water to save energy and control overall temperature. Intakes at two different water depths also provide Salmon Evolution with opportunities to optimise temperature and heating requirements.
“Each production tank is structured as a separate biological zone to reduce operational and biological
TROND HÅKON SCHAUG-PETTERSEN, CEO: “We have grown the company from only a handful of people to around 60 staff members over a period of only a couple of years. We are fortunate to be located in the heart of the aquaculture industry with very good access to competent people. Furthermore, land-based salmon farming is a merger between the farming industry and the more conventional processing industry, where both competencies are equally important to succeed.
“In addition to the significant level of farming activity in our area, there are also a number of highly advanced processing industry facilities including oil and gas refineries and alumina producers, which has enabled us to recruit a highly competent team of employees. We also see that what we represent with our vision of “extending the ocean potential” is something that appeals to people and something they want to be a part of.”
Gjøco is a Norwegian producer of thermosetting products for the construction industry. The products are mainly used for ensuring the protection and watertightness of tanks, bridges and industrial flooring. Our success is grounded in tight connections and teamwork between designer, contractor, material supplier and applicator, as well as the landlord. The good solutions comes with good planning and teamwork, especially when it comes to details.
www.gjoco.no
In 2021, PTG won a contract from Artec Aqua to supply an energy plant with a system efficiency capable of delivering 30 kW of heat for each kW input. The system efficiency is achieved by PTG supplying ultraefficient heat pumps with COP at 12. Low energy consumption will help to cut operating costs and the carbon footprint for Salmon Evolution.
The last of the six large heat pumps was delivered in August as part of the first development stage for Salmon Evolution’s land-based fish farm. Each heat pump controls the perfect temperature of a huge amount of water, up to 40,000 litres per minute.
www.ptg.no
PTGGjøco AS develops and produces innovative thermosetting plastic products, based on epoxy, polyurethane and polyurea, to withstand tough conditions.
Gjøco has outstanding expertise in polymer technology, with superior products and the ability to tailor a solution to any project. This makes your floor, deck, bridge, quay, tank, pipe, or parking garage hard-wearing, waterproof, and crack bridging at low temperatures, leaving every customer satisfied!
The PTG heat pump and energy plant for Salmon Evolution can heat water with a minimum of power. The heat pump COP is above 12, and taking the energy plant as a whole, Salmon Evolution gets 30 kilowatts back for each kilowatt it puts in.
www.ptg.no
The best solutions come from those who thrive on challenges.
risk, and wastewater treatment and sludge recycling will minimise the environmental footprint,” SchaugPettersen adds. “Waste and feed residues from production are collected and used as raw material for producing biogas or fertiliser, thereby ensuring that the whole project contributes to a circular economy.”
The Indre Harøy facility will be one of Europe’s largest fish farms on land, as it has been designed for a total annual production capacity of 31,500 tonnes of HOG salmon from its completion set for 2028. This production capacity is comparable to 10 to 15 conventional salmon farms (covering an extensive geographical area), yet the Indre Harøy location only covers around 100,000 square metres, a substantial reduction in land usage furthering the company’s sustainability-centric goals.
“We will provide around 150 million salmon portions a year for the world’s population from our flagship facility in Norway,” Schaug-Pettersen elaborates. “It is being developed in three phases, with Phase 1 providing an annual production capacity of 7,900 tonnes of HOG salmon from late 2023. Phase 2 will add another 7,900 tonnes,
with construction planned to start this year. The final phase, Phase 3, will take total production to 31,500 tonnes.
“Salmon Evolution represents a step change in salmon farming. Raising our salmon on land gives us a unique opportunity to optimise the environment so the salmon thrive and live a happy life. This results in quality the world has never seen before.”
For Salmon Evolution, operations are intended to stretch from east to west. The company has entered into a joint venture with seafood giant Dongwon Industries where the parties will develop, construct and operate a land-based salmon farming facility in South Korea with an annual production capacity of 16,800 tonnes of HOG salmon, using Salmon Evolution’s chosen HFS technology.
On top of this, the company has also initiated a process with the aim of establishing a land-based salmon farming operation in North America.
However, despite this, salmon farming can only be undertaken in specific geographical areas around the world.
“We cannot operate everywhere –we need access to waters of a certain temperature,” Schaug-Pettersen reveals. “There are places where we cannot apply this concept, but there are still a lot of locations that have the right conditions, enabling us to provide the salmon with an excellent living environment.
“We are already utilising our knowledge and experience in South Korea via our joint venture with Dongwon Industries. Together we will develop, construct, and operate a land-based salmon farming facility. As we go international, we will always do so enabled by our flagship operation at Indre Harøy. Here we are going to have the best land-based salmon farming facility in the world, in the middle of the aquaculture cluster in Norway with access to people, suppliers, competence and the full value chain.”
Through the utilisation of technology, competence, and experience from domestic projects, Salmon Evolution aims to develop projects in targeted growth markets in collaboration with local partners. The company has a clear road map towards 100,000 tonnes of production capacity by 2032, and is on track for around 25,000 tonnes of capacity by 2024.
TROND HÅKON SCHAUG-PETTERSEN, CEO: “After gaining a BSc in Economics and Business Administration from the NHH Norwegian School of Economics, I started as an investment banker at Swedbank/First Securities advising Norwegian and international companies on IPOs, equity and debt capital raisings, M&A and strategy, and continued this career for nine years.
“From here, I joined the salmon farming industry serving for over four years as Senior Vice President of Finance and Business Development at Norwegian salmon farmer and processor Hofseth International. Thereafter, I took over as Salmon Evolution’s CFO in January 2021, and CEO from October 2022, the position I hold today.”
Norway has been a leader in providing the world with premium salmon for many decades. Since then, salmon – or in fact Norwegian salmon - has become the world’s most popular fish. With its long coastline and stable, cold temperatures, the country makes for the perfect natural salmon farming conditions, and currently, about half of all farmed salmon comes from Norway.
Norway already has an advantageous starting point with its long and proud traditions of living by and off the sea, with perfect natural conditions for salmon farming. Cold, clear waters in the fjords along its long coastline form an ideal environment where salmon thrive, and that is why Salmon Evolution is
building its flagship facility in Norway, the pinnacle of salmon farming knowledge and expertise.
“Salmon of Norwegian origin is also the most preferred among consumers, and the only origin which seems to be increasing in popularity year on year,” Schaug-Pettersen affirms. “As we see it, there is now a window of opportunity with very limited land-based competition in both Europe and abroad for the foreseeable future, and Salmon Evolution aims to be the market leader in the development of landbased salmon farming globally. With the strong platform we have at Indre Harøy, we are confident that we are in a unique position to do so.
“We have done some consumer insight and what we see is that there
is a high awareness of land-based salmon as an environmentally friendly and sustainable solution. We see a fantastic opportunity now for our land-based salmon as the market is looking for new categories, and we believe there is an open position in the market to build a new concept that really emphasises both quality and sustainability.”
The company’s first harvest has confirmed good fish health and fillet quality, firm meat texture, a vibrant and consistent red meat colour, and of course, excellent taste.
“Because we make no compromises on water quality, fish welfare or environmental responsibility, our salmon thrives better, grows better and tastes better - it’s a new standard of salmon.”
SALMON EVOLUTION
Tel: +47 46 86 00 00
post@salmone.no
www.salmonevolution.no
Writer: Jack Salter | Project Manager: Kierron Rose
Mobility – the movement of people and goods – is undergoing a transformational shift.
The future of mobility is being driven by disruptive technologies and trends such as autonomous and electric vehicles (EVs), with far-reaching implications for the way we live.
With a strong and established track record in innovation and manufacturing excellence, the mission of Marelli is
to transform the future of mobility through working with customers and partners to create a safer, greener, and better connected world.
One of the world’s leading global independent suppliers to the automotive sector, Marelli employs around 50,000 members of staff and enjoys a global footprint that includes 170 facilities and R&D centres across Europe, Asia, Africa, and the Americas.
“Marelli’s approach is based on co-creating the future of mobility with its customers, suppliers, and leading technology partners,” outlines Antonio Ferrara, President of Marelli’s Ride Dynamics division.
Serving all major carmakers at a global level and focused on advanced technologies around vehicle personality and performance, Marelli helps customers shape a unique driver experience and differentiate their vehicles of the future.
Marelli Ride Dynamics is a global player and one of several divisions that Marelli operates through, responsible for the realisation of suspension components and shock absorbers.
The company also provides advanced technologies for a range of other key automotive product areas, including automotive lighting and sensing, electronic systems, interior experience, electric and internal combustion powertrains, green technology solutions, thermal solutions, and motorsport.
Marelli Ride Dynamics in its current configuration was created in 2019, as a merger between the existing company’s shock absorber and suspension system business units, the latter of which Ferrara joined as CEO in 2014 before being appointed to lead the newly created division.
“We have the capabilities in both ‘souls’ of the division (suspension
• Development and production of chassis components with a focus on lightweighting and durability targets.
• Flexibility in the different materials selection to achieve the best cost/performance compromise (high grade steel, aluminium, composite, cast iron).
• Focus on shock absorber tuning definition to achieve customers’ requirements in terms of comfort and performance.
• Implementation of advanced technology in order to guarantee excellence in terms of quality and automation.
and shock absorbers) to develop and industrialise solutions for the customer that not only reach the requested carmaker’s expectations,
but give them added value for the final user, improving the driving experience,” he says.
The ride dynamics of a motor vehicle are determined by the forces generated by the contact between the tyre and the road surface.
Shock absorbers help to control the impact and rebound of a vehicle’s springs and suspension. Along with smoothening out bumps and vibrations, the key role of the shock absorber is to ensure the vehicle’s tyres remain in contact with the road surface at all times, ensuring the safest control and braking response.
With a deep knowledge of active and passive solutions, lightweight materials and product durability, Marelli Ride Dynamics develops solutions focused on the tuning definition in order to achieve the comfort, performance and safety requirements of customers.
“Within Marelli, the Ride Dynamics division develops a huge variety of
suspension and shock absorber solutions for a wide range of customer-oriented applications, to ensure a remarkable and safe driving experience,” Ferrara tells us.
In the suspension field, there are opportunities in e-mobility for Marelli Ride Dynamics due to the increased complexity of the chassis structural components that must sustain the new weight balance of vehicles.
“The car market is increasingly moving towards EVs and this represents a significant challenge for suppliers of underbody components such as Marelli Ride Dynamics, but also an opportunity with the technological and engineering that can be offered to customers,” observes Ferrara.
“Obviously, this requires continuous investment in R&D to
Drive results – Marelli is determined to achieve impactful and sustainable results.
Entrepreneurial – Taking the lead to invest in the future with an outside-in view.
Innovative – The company is willing to do things differently to achieve better results.
Accountable – Marelli takes responsibility for its actions and results.
Inclusive – Engaging the hearts and minds of a diverse team to achieve stretch goals.
Aware – Conscious of the impact of its behaviours and authentic in its interactions.
always be present in the market with the best and most innovative solutions.”
The challenge of remaining competitive is hugely exciting for Ferrara, and thanks to Marelli Ride Dynamics’ engineering team, considered best-in-class in such design and development, the company is improving its competitive position in the market.
The Ride Dynamics division is currently working on the evolution of its electronic shock absorbers, in order to have an even wider portfolio for its customers.
These range from the two-mode switchable damper (Dual Stage Valve) and continuous variable shock absorber (Smart Damping Control (SDC) System) to the new, sophisticated Double SDC.
“These are all “semi-active” shock absorbers, but Marelli Ride Dynamics
is also developing a “fully active” solution that enables a suspension system capable of smoothly levelling the vehicle in almost all driving conditions, obstacles, turns and road surfaces,” reveals Ferrara.
Another connected future mobility trend is the rise of Advanced Driver Assistance Systems (ADAS), which is increasing the market share and diversifying the customer base of Marelli’s electronic shock absorber technologies.
In order to optimise such investments in technology and shorten the time to market in a fast and dynamic world, it is integral for Marelli to find and develop good partners and suppliers.
“We are proactively acting on this, continuing to differentiate our supplier panel and introducing local players that are showing very high levels of quality and are ready to play in the global market,” Ferrara says.
“We are also working to take some existing technical partnerships a step forward to catch new market demands, parallel to building up new partnerships that will increase our ability to grow and diversify our customer portfolio in emerging markets, particularly China and India.”
Marelli has chosen a very clear path towards sustainability, and Marelli Ride Dynamics is developing disruptive solutions that will be capable of achieving carbon neutrality.
The division is strongly committed to achieving its ESG 2025 objectives for a more environmentally friendly product offering, through both the evolution of internal transformation processes and interaction with its main raw materials suppliers.
“We have started to develop a fully active electromechanical rotary damper suspension, an oil-free electric actuated solution providing outstanding comfort and handling for an unprecedented riding experience,” shares Ferrara.
“This active suspension solution is able to regenerate the energy it requires by capturing the vertical movement of the car caused by the asperity and roughness of the road.”
The company’s sustainable approach permeates every project under development, and in Q2 2023,
all new projects will begin from the initial concept design phase by calculating the carbon footprint involved.
Designers will have access to a database of materials and subcomponents, where they can select the best solution with the lowest carbon footprint.
“In other words, we will effectively apply a “design for sustainability” procedure,” Ferrara elaborates.
As well as aiming for the most sustainable solutions, Marelli is targeting rational production capacity utilisation and customer diversification at its various plants in the coming year.
On the product side, meanwhile, the launch of a complete and innovative
portfolio of fully active suspensions, both hydraulic and electromechanical, will be customised for different segments and vehicle needs as Marelli and its Ride Dynamics division continue to co-create the future of mobility.
“MARELLI’S APPROACH IS BASED ON CO-CREATING THE FUTURE OF MOBILITY WITH ITS CUSTOMERS, SUPPLIERS, AND LEADING TECHNOLOGY PARTNERS”
– ANTONIO FERRARA, PRESIDENT, MARELLI RIDE DYNAMICS
There are few materials as reusable as steel. We speak to Radek Strouhal, CEO of Vítkovice Steel, about the company’s commitment to quality metal production and the wider community in the Czech Republic
Steel is a unique alloy. A compound of iron combined with carbon and additional minerals, it is highly versatile as a material for construction, manufacturing and a multitude of other industries.
Historically, steel has been a defining discovery for civilisations, as both expensive to produce and made only in limited quantities. Steel was therefore saved as a luxury commodity, forged to form durable tools for specialist trades or blades for banquets and battlefields.
Today, steel cutlery is no longer reserved for lords and ladies of the court but is found as a staple of every house in Europe thanks to modern means of mass metal production. What makes steel truly special is its unlimited service life and status as the most recyclable material in the world.
Based in the Czech Republic, the promotion of steel production and reuse to help turn the globe green is exactly what Vítkovice Steel (Vítkovice) sets out to achieve.
“Throughout our whole lives we are surrounded by products which are vital for our civilisation because their properties and use are simply irreplaceable,” introduces Radek Strouhal, CEO of the company. “Such are the products that Vítkovice has been producing since the 19th century.”
Vítkovice is a leading European manufacturer of heavy plates and one of the last producers of sheet piles. Its main products are used in a wide range of industries, including construction, energy, transportation, and engineering. Vítkovice transforms steel into heavy plates, shaped cutouts and sheet pilings, which are in turn used as parts of major bridges, various buildings and high-performance machines. With two mills in the northeast city of Ostrava and employing around 850 people, Vítkovice’s mission is to provide its customers with high-quality steel products and services that meet needs and exceed expectations.
This industry-leading position is born from an extensive history in steel production. Vítkovice began in 1828 in Ostrava and continues to this day as a traditional, prominent manufacturer of hot-rolled heavy plates, sheet piles and cut shapes in Europe. Since its establishment, the company’s mission has always been to help build the country.
“The traditions and achievements of our predecessors commit us at Vítkovice to provide quality work and services for our customers,” Strouhal tells us proudly. “We connect society with quality products. For example, our heavy plates make bridges which are a focus area for us.
“Sheet piles are used for steel and bridge structures or as structures for water management and flood
Steel has a deep and rich history. Its qualities have been discovered and exploited across the globe with the oldest recordings of steel production and use being those of Anatolia (most of present-day Turkey) in approximately 1800 BCE, as well as mass steel production in China during the 3rd century CE.
This global acknowledgement of steel has also led to unique workings, methods and processes when it comes to producing, shaping and strengthening the material. There are multiple historical examples of the Bessemer Process having been used, which involves the use of blasts of air to remove impurities in molten steel.
When it comes to warfare, steel has been used as the most innovative metal for centuries, able to be morphed to form larger blades that retain their shape and durability in the heat of combat to a greater extent than iron. The versatility of steel gave rise to plate armour that reinvented feudal warfare. Japanese “jewel steel” was folded many times over and refined to create the iconic katana - the weapon of the Samurai – as well as the famous technique known as “Damascus Steel”, a form of pattern-welded steel. Knowledge of this particular technique was passed from the Middle East or India, eventually making its way as far as Scandinavia, where Vikings believed (and proved on the battlefield) that such pattern-welded swords were magic.
protection. We burn our cut shapes on the most modern equipment, which is also why they are often used for machine parts where a high level of precision is required. Quality control of products is carried out in our own accredited testing laboratories, which are equipped with the most advanced testing facilities.”
The Czech Republic has a long history of producing high-quality steel products and has a well-developed infrastructure to support the industry. The country is also strategically located in the heart of Europe, making it an ideal destination for exporting products to customers in the region and beyond. For Strouhal, the metal manufacturing industry has always been intriguing.
“I became interested in the steel industry after graduating from college with a degree in economics,” he shares. “I began working for a steel, iron and ferroalloy trading company where I quickly became CFO. After a few years I moved to help to save Tatra, the heavy vehicle manufacturer, firstly as CFO and later as CEO. After five years I got the opportunity to come to Vítkovice as CFO and now, as the CEO of a heavy plate mill, I am proud to lead a dynamic and innovative company in this exciting industry.”
SAFIN Group is an international steel supplier, providing vigorous performance, an imaginative approach, and modern technology, since 1993.
SAFIN has grown from a small group of businessmen into a successful and reliable trade and investment company. Our service includes trading, logistics, finance, insurance, and inspection.
We work with the manufacturing giants of the industry as well as newer companies, with a broad and diverse data base. Our international agents speak the local language of customers, which enables them to offer goods and services that correspond to requirements.
Owing to the extensive cooperation with our business partners in steel production, transport, insurance, and more, SAFIN offers steel products at an attractive price.
Vítkovice is constantly exploring opportunities for increasing the quality of its services, decreasing the negative impact on the environment and delivering higher value to its customers. Despite this, the company has no plans to enter new markets, but instead focuses on utilising its proximity to customers and high product range to cover all client needs with swift delivery and the highest quality.
Primarily focusing on in-house development, Vítkovice has undertaken internal upgrades such as the renewing of its lighting systems across all facilities. It is one of many actions taken by the company’s internal environmental, social and governance (ESG) team which is dedicated to improving Vítkovice’s profile in the environmental and social field.
“We recently upgraded the lighting systems across all our company facilities as part of our commitment to sustainability and reducing our environmental impact,” Strouhal says. “The new LED lighting systems are more energy-efficient and have a longer lifespan than traditional lighting, reducing our energy consumption and maintenance costs while also improving the working conditions for our employees.
“Vítkovice is also committed to sustainability and reducing its environmental impact. We are constantly exploring new ways to improve our operations, reduce our carbon footprint, and increase our value for society. We are proud to be a leader in the steel industry in this regard.”
Moving ahead into 2023 and beyond, Vítkovice’s key priorities for the coming year are to continue to improve its production capabilities and increase its efficiency and productivity. On top of this, the
company is also focusing on developing new products and services that meet the changing needs of its customers as well as expanding its presence in key markets.
“We simply focus on keeping up the pace with our customers and their needs so they can fully rely on us and our products,” Strouhal comments.
While productivity is core to the company’s focus, there is a greater aspect of the operation that Vítkovice is passionate about – people and the community sit at its heart and are the forethoughts of the business. Vítkovice keeps track of social, cultural and sporting events and is actively involved wherever needed, with employees engaged in fulfilling social responsibilities. The company’s Vítkovice Steel Foundation Fund also
helps those with social or medical needs.
“The city of Ostrava is not only the place where we work, but also where we live, and we help the people around us,” Strouhal elaborates. “We are not indifferent to what goes on in our surroundings. We care about the environment, we believe that it is important to give back to the communities where we operate, and we are committed to supporting disabled or seriously ill people in our area. Our company set up its foundation many years ago and through it, we do our best to support people to better their lives.”
“THE CITY OF OSTRAVA IS NOT ONLY THE PLACE WHERE WE WORK, BUT ALSO WHERE WE LIVE, AND WE HELP THE PEOPLE AROUND US”
– RADEK STROUHAL, CEO, VÍTKOVICE STEEL
Chris Pinciak, Vice President of Engineering and Sales, outlines the rebranding of Winbro Group Technologies as the
Writer: Jack Salter | Project Manager: David Knott
The advancement of technology through innovation has sparked renewed interest in US manufacturing.
Various high-tech manufacturers such as Tesla, Blue Origin and SpaceX, for example, have shown that this new age of manufacturing differs greatly from its predecessors.
“Advanced technology, together with clean shop floors, automation and Industry 4.0, have revolutionised manufacturing and ignited new interest in recent generations,” observes Chris Pinciak, Vice President of Engineering and Sales at Winbro Group Technologies (Winbro).
Offering an expansive range of machining technologies from high-speed electrical discharge machining (EDM) to laser micro and macro machining, Winbro leads the way in precision, non-conventional processes, providing industry-leading
productivity and high yields.
The company has a global presence spanning a triad of locations in Rock Hill (US), Shepshed (UK) and Taichung (Taiwan), with each site incorporating Winbro’s three revenue streams of contract manufacturing, systems solutions, and partner services.
“We will be expanding our offering in 2023 by creating Technology Centers at each of our sites to have a larger outreach,” reveals Pinciak, recognising the need to invest in the R&D of both Winbro and its customers.
“These will consist of a demo center, which will show our newest machine platforms for R&D, machine prototyping and customer training, as well as laser application laboratories to test cutting edge laser sources and advanced application processes.”
Pinciak has prior experience in laser
application labs, having previously worked at the Connecticut Center for Advanced Technologies during his undergraduate studies in an effort to prepare for the working world.
“Being able to focus on real world applications and helping to solve manufacturing challenges had me hooked,” he recalls.
This year marks the 50th anniversary of Winbro, who is currently going through a large, new and improved rebranding exercise.
With half a century of experience in the manufacturing of high-precision machining solutions, Winbro has established itself as a trusted expert in the industry.
Soon to have a new website and logo, the company will be reaching out to an even broader audience than it has had in the past.
EDM – Winbro’s re-engineered high speed electrical discharge machining provides substantially faster and higher precision drilling than its competitors and is vastly superior to the conventional oil dielectric process.
Laser micro – Winbro provides laser ablation, micro-machining, and high-speed micro drilling systems using short and ultrashort pulsed lasers paired with advanced scanners for precision machining.
Laser macro – Winbro’s highly flexible range of systems offers laser drilling, cutting, and welding using kilowatt power laser sources for the most advanced components and part assemblies.
Custom solutions – Winbro is able to provide bespoke custom manufacturing solutions, from the integration of its own machines into highly efficient automated cells to fully customised automation solutions.
It coincides with the Winbro Reimagined initiative, which is pushing the company to diversify into new industries and technologies expanding from its historic roots in the aerospace business.
“Winbro has spent the majority of the last half a century focusing on the high precision aerospace industry,” Pinciak tells us.
“We are celebrating our anniversary
with our rebranding and Winbro Reimagined initiative, culminating in a new logo and new look for the company. We appreciate our past 50 years in aerospace, but look forward to diversifying in the next 50 years.”
Winbro has since ventured into manufacturing high-precision machining solutions for various sectors, including energy, electronics and medical. Coupled with the launch
of the Winbro Reimagined initiative, the company therefore needed to elevate its branding into a more modern setting.
Thus, Winbro has spent a significant amount of time going through every detail of the rebrand, from the company culture to its future exhibition plans.
“We plan to attend more exhibitions and tradeshows to increase the exposure of the Winbro rebrand,” shares Pinciak.
With the rebrand, Winbro also wanted to incorporate environmental, social and governance (ESG) principles into its culture and day-to-day activities, to ensure it makes adequate strides for social responsibility.
“We are excited to have a new look that is more focused on a sustainable future, and have created new groups internally to help measure ESG and document areas of improvement.”
As well as rebranding and diversifying into new industries and technologies, Winbro has likewise adapted from
BOOK YOUR FREE CONSULTATION
For a free assessment on how you can improve operations and save energy and water, contact us via:
ENVIROGEN.COM
“WE ARE CELEBRATING OUR ANNIVERSARY WITH OUR REBRANDING AND WINBRO REIMAGINED INITIATIVE, CULMINATING IN A NEW LOGO AND NEW LOOK FOR THE COMPANY”
simply being a machine tool builder.
In 2006, the company added contract manufacturing as a method for its customers to outsource peak demands.
“We can offer our customers risk mitigation by producing parts for them before a capital purchase, or splitting production 80:20 with our customers to offset production demand issues,” explains Pinciak.
Since then, Winbro has significantly grown its contract manufacturing capabilities, which continue to be a great differentiator for its business model.
“We have various competitors for each of our business segments. If we focus on the machine tools segment, for example, we differentiate ourselves by using our machines for contract manufacturing,” Pinciak outlines.
This allows Winbro to increase its application knowledge and improve the machines by using them in dayto-day production, whereas many of the company’s competitors only sell machine tools.
What has remained a constant throughout the history of Winbro, however, is leveraging an engineering
mindset to solve unique, complex problems and impactful challenges.
Dedicated to overcoming challenges with innovative and efficient machining solutions, Winbro values cooperation throughout the entire manufacturing process and supports customers during the development, investment, and growth phases.
“Whether our customers need a highly specialised component or a tailored end-to-end solution, our philosophy is to provide the right solution to meet our partners’ requirements and exceed their expectations,” Pinciak states.
Winbro is a people-centric company that prides itself on exceeding expectations and having the customer’s best interests at heart. The creation of strategically placed micro offices, meanwhile, will offer localised sales and support services for customers.
“In the US, we will be creating new micro offices on the West Coast, and in the Mid-West.”
As industry experts, the company has built long-term partnerships with a proven track record of engineering its partners’ visions.
Systems solutions – At Winbro, a variety of integrated machining solutions are offered to suit the needs of customers. The company provides high reliability lifetime support for all solutions, offering flexibility with modular designs and a common platform. Winbro aims to ensure maximum productivity with an optimised footprint and integrated quality inspection.
Advanced manufacturing – As the preferred end-to-end solutions provider, Winbro has a unique offering and multiple advanced component manufacturing facilities around the world. This allows the company to develop truly innovative solutions for customers through volume manufacturing and continuous learning.
Partner support – Winbro provides comprehensive support for its partners, offering multiple services to ensure their success over the lifetime of the systems.
Winbro looks to generate partnerships with customers and suppliers for the betterment of all involved. There is proven success of this in the aerospace market, where Winbro works directly with customers on engineering and design to ensure both parties take advantage of the technology on offer.
“We endeavour to create similar relationships within the medical, semiconductor, and fuel cell markets,” informs Pinciak.
The company’s dedicated tooling facility also allows for a quick response to tooling, spares and consumables for partners to keep their systems operations, whilst Winbro’s strategic R&D hubs situated around the world are able to effectively develop new technologies as well as upgrades for its existing solutions.
In an effort to extend its partnerships, Winbro increases the life of systems and maximises the initial investment by adding these latest technologies and improvements; in doing so, Winbro will complete its main objective of introducing the rebranded company to new industries.
Along with launching the new global Technology Centers, and increasing its laser applications knowledge and experience to help support the hightech sectors it strives to enter, Winbro is set to engineer the future of sustainable manufacturing.
WINBRO GROUP TECHNOLOGIES
Tel: 803-985-9481
sales@winbrogroup.com
www.winbrogroup.com
“WE WILL BE EXPANDING OUR OFFERING IN 2023 BY CREATING TECHNOLOGY CENTERS AT EACH OF OUR SITES TO HAVE A LARGER OUTREACH”
– CHRIS PINCIAK, VICE PRESIDENT OF ENGINEERING AND SALES, WINBRO GROUP TECHNOLOGIES
CWP has the vision and capabilities to deliver the largest renewable energy portfolio in Southeast Europe. We speak to the Director of Business Development for Southeast Europe, Nikola Stamenov, about how the company addresses decarbonisation challenges.
Writer: Lucy Pilgrim | Project Manager: Jordan Levey
For Nikola Stamenov, Director of Business Development for Southeast Europe at CWP Europe (CWP), working in renewable energy development provides a purpose to both his life and career.
Despite the fact that Stamenov has had a varied career path, from working in high-end financial consultancy to overseeing the largest music and entertainment events in Europe and the Middle East, as well as the NGO sector, he has found the renewable energy industry most rewarding.
“I am a believer, and I believe that there is no more important job today than to help society completely distance itself from polluting fossil fuels. It is a matter of very existence and our own survival on this planet,” he reflects.
Stamenov’s conviction in renewable energy resources filters throughout the company, as CWP takes great pride in developing utility scale wind and solar parks across Southeast Europe (SEE), providing effective solutions to its sizeable pollution problems.
“The system has such a high dependency on poor quality lignite and coal. All that has, unfortunately, made this region become known as one of the most polluted in the world, and it is our mission at CWP to change
OF OUR VERY EXISTENCE AND SURVIVAL ON THIS PLANET”
NIKOLA STAMENOV, DIRECTOR OF BUSINESS DEVELOPMENT FOR SOUTHEAST EUROPE, CWP EUROPE
that image by providing as many green electrons to the grid system as we can, as soon as possible,” he comments.
With such an extensive portfolio, CWP is the pioneering renewable energy developer in SEE, having successfully realised some of the largest wind farms in the territory.
CWP is currently developing a six gigawatt (GW) portfolio of wind and solar projects in Serbia, Bulgaria, Romania, Montenegro, Albania, Bosnia and Herzegovina, Slovenia, Moldova, North Macedonia and Ukraine. A noteworthy case is the 600 megawatts (MW) FântâneleCogealac wind farm in Romania,
“I AM A BELIEVER, AND I BELIEVE THAT THERE IS NO MORE IMPORTANT JOB TODAY THAN TO HELP SOCIETY COMPLETELY DISTANCE ITSELF FROM POLLUTING FOSSIL FUELS. IT IS A MATTER
–
intec GOPA-International Energy Consultants GmbH is a leading independent german engineering and consulting partner in the field of energy systems. With subsidiaries on three continents and a strong network of highlyqualified experts, intec develops strategies and technological tools in order to bring or improve energy everywhere, whether developing countries and emerging markets in over 50 countries worldwide
which has been fully operational since 2012, and is still one of the largest wind farms in Europe to date. Another milestone project is the 157 MW Cibuk 1 wind farm in Serbia, that has been operational since 2019, and it is still
the largest RES project in the country. Since 2021, CWP Europe has operated as a joint venture between CWP Global, a leading global renewable energy company, and Mercuria Energy Trading, one of the
largest independent energy traders with revenue of more than USD$140 billion. Mercuria’s involvement has allowed CWP to further strengthen its leading capabilities and monetise renewable energy through innovative offtake structures.
One of CWP’s major strategic markets is the SEE nation of Serbia. As with any transitional society and market, the country can present some challenges.
Stamenov expresses, “in my opinion, the whole industry would like to see Serbia taking bolder moves to convert away from coal and fossil fuels. Nevertheless, there have been significant changes in the right direction in previous years, in both legislative and public opinion, which welcomes a greater reliance on our renewable resources.
“Among other things, Serbia is
well positioned and interconnected with neighbouring countries, and I don’t see why Serbia will not use its renewable capacities to the maximum, especially once the planned large hydro storage plants are built in the near future.
With this in mind, Serbia will have a major role in the overall energy transition of the whole SEE region, and CWP is in a great position to foster that lead. By overcoming regional difficulties, CWP can unlock SEE’s potential as the ideal spot for renewable energy development due to the region’s carbon intensive economies.
“CWP’s mission as leaders in SEE’s renewable energy sector is to
decarbonise the region by delivering the technologies, skills and services that will bridge the gap between SEE and the rest of Europe,” Stamenov details.
The company understands the importance of energy transition and possesses the vision and capabilities to deliver diverse projects that will make a decarbonised SEE a reality. CWP can identify and develop the best sites and locations for specific projects based on natural wind and solar resources.
The company can also expertly manage demanding and complex projects through their entire lifecycle. To add to this, CWP can provide impactful solutions to the high cost of electricity in the region,
develop and implement innovative business models adapted to regional specifications, and create hybrid projects that respond to market demand. Therefore, it is easy to see how CWP is having a meaningful and lasting positive impact on communities throughout the region.
Amongst the extensive portfolio that CWP has across SEE, the company has recently initiated three new renewable energy projects in Serbia: the Lederata Energy hybrid power plant, Equinox Power solar power plant, and the Vetrogon wind farm, generating 750 MW of green electricity in total. Consequently,
NIKOLA STAMENOV, DIRECTOR OF BUSINESS DEVELOPMENT FOR SOUTHEAST EUROPE: “Our 300 MW Vetrozelena wind farm is in the final stage of development and should reach ready-to-build status soon, which is our main priority for now. Another of our key targets for this year is obtaining an energy permit for our photovoltaic project Solarina, as well as reaching ready-to-build status by the end of 2023. Those would be the most important milestones this year.
“Recently, we have entered the market of Montenegro and are developing the Montechevo solar power plant, with a total installed capacity of 400 MW. Solar energy produced here will significantly contribute to Montenegro in achieving its energy goals when it comes to the share of total electricity from renewable energy sources. Accordingly, in the coming period, we will be focused on our presence in Montenegro, but at the same time we will explore and develop options in other markets across the region.”
the total capacity of development projects in Serbia has now more than doubled to 1.25 GW. CWP is therefore proud of the fact that its project portfolio in Serbia makes it the most significant renewable energy developer in the country.
When looking at each project more closely, the Vetrogon wind farm is to be installed with a maximum capacity of 450 MW. CWP is developing this renewable project in the municipalities of Srbobran and Bečej in Serbia. Furthermore, the calculated expected annual gross production of the entire wind farm is around 1,100 gigawatt hours (GWh), which is
enough to supply more than 260,000 households with green electricity. Additionally, the total production of green electricity in the Vetrogon wind farm will contribute to the reduction of CO2 emissions by a staggering 1.18 million tonnes (t) per year. Thus, CWP is a great supporter of Serbia’s energy transition goals.
Alternative projects include the Equinox Power solar power plant, which has a total installed capacity of 150 MW and is currently being developed in the Serbian municipality of Kula. The production of green electricity from the Equinox Power solar plant will reduce CO2 emissions
by 267,840t per year. Once again, this plant will have a significant impact on the area as the calculated expected annual gross production of the entire power plant is about 248 GWh, which is enough to supply more than 59,000 households with green electricity.
The Lederata Energy is another noteworthy achievement for the company, operating as a hybrid power plant project in the area of Požarevac and Veliko Gradište, Serbia. The Lederata Energy is distinct in its ability to combine both wind and solar energy sources and represents the
BULGARIA
• Wind: 900 MW
• Early Stage Developments:
160 MW
ROMANIA
• Wind: 500 MW
• Solar: 134 MW
• Early Stage Developments:
800 MW
SERBIA
• Wind: 848 MW
• Solar: 330 MW
• Early Stage Developments:
700 MW
MONTENEGRO
• Solar: 400 MW
BOSNIA AND HERZEGOVINA
• Wind: 161 MW
ALBANIA
• Early Stage Developments:
500+ MW
MOLDOVA
• Early Stage Developments:
200+ MW
UKRAINE
• Wind: 252 MW
first project of its kind implemented by CWP in Serbia. The facility will be the joint force of a 50 MW solar park, a 100 MW wind farm and an energy storage system of 10 MWh.
“Currently, the Lederata plant project is in its early development stage. We are presently focusing on observing the resources and technical design to obtain the permits, licences, and authorisations necessary to operate the plant,” shares Stamenov.
The development and construction of the Lederata Energy are planned in phases, with construction set to commence in 2025 and completion of the construction and commissioning of the plant projected for 2026. The project’s green energy production will reduce CO2 emissions by 410,400t per year, and supply enough green energy for in excess of 90,000 households on account of the 380 GWh that is produced by the plant per year.
“During the implementation of these projects, CWP will be guided by the highest international standards,
in order to contribute in the best way possible to the overall developments of the municipalities, as well as renewable energy sources in Serbia and the region,” Stamenov concludes.
Overall, CWP’s consistent expansion is an accurate demonstration of its passion for helping the SEE region develop its clean energy potential and become fully independent from fossil fuels. With the accurate renewable energy development approach of both wind and solar power projects, CWP is the one to watch in SEE’s renewable energy advancements.
Serenity Made is a high quality supplier of all types of hospitality furniture for venue projects. Internationally recognised , Serenity Made is the go-to supplier in China for those looking for commercial quality and modern styles whilst maintaining a competitive price point.
Why Us
• Communicate your needs in fluent English.
• Products warranted for commercial use.
• Experienced in export and flexible in delivery terms.
• Able to work with you to develop bespoke products.
• Understand the quality requirements for hospitality projects.
• Small minimum order quantity with flexible terms.
Bottom line? Good quality, good price, good service!
We attend the official Launch Day of the RAF Falcons’ 2023 parachute display season, kicking off with an incredible airborne performance on their home turf at RAF Brize Norton
Writer: Ed BuddsLaunching the RAF Falcons’ 2023 parachute display season in truly spectacular fashion, we watched on as the highly impressive team ignited their summer calendar of events with a breathtaking performance, streaking gracefully through the sky high above their home base of RAF Brize Norton.
Widely and rightfully recognised as the UK’s premier military parachute display team, the RAF Falcons perform their incredible mid-air manoeuvres all over Britain and Europe, with an exciting line up of
events and appearances in the diary for this summer.
Sitting proudly at the forefront of military parachuting, the Falcons are supported by a highly dedicated team of people - regulars, reserves and civil servants – all of whom play critical roles behind the scenes at every spectacular display.
Upon arrival at RAF Brize Norton, we made our way to the Officer’s Mess, which had the homely familiarity of a well-worn Sixth Form common room, and were thankfully offered copious supplies of morning
coffee to help fight back the bleary eyes of our early expedition across the country from Norwich. The Falcons were the very definition of welcoming and accommodating as they chatted amongst us, mere hours before they took to the skies.
Next, following a tour of the base and impressive training facilities where the team hone their considerable array of skills, we were treated to a chance to partake in the virtual reality parachuting simulator, an additional training tool for new recruits.
This futuristic technology placed us high amongst the clouds, able to taste a fraction of the immense adrenaline rush experienced when the Falcons launch themselves out of their aircraft. We then converged on the main airfield as we prepared for the mesmerising display.
Falling serenely towards us, the many onlookers below could not have wished for better conditions in which to witness such a stunning spectacle.
However, for the Falcons, the crystal-clear skies and dazzling sunshine only told half the story, as despite the delightful weather, wind speeds were far from optimal, pushing the boundaries of what is considered safe jumping conditions.
The team’s time-honoured red, white and blue canopies thrilled the crowd, forming a technicolour splattering across the bright blue canvas of the Oxfordshire skies above. For this season, the Falcons are proudly welcoming several new members to the team, each fulfilling a pivotal and dynamic role in the intricately choreographed displays, which demand outstanding levels of technical precision and excellent teamwork.
Staggeringly, upon negotiating a flawless landing, even in the face of such adverse wind speeds, the
tight-knit unit appeared relaxed and totally calm as they jogged over to meet the adoring hordes of onlookers, which included several nearby primary schools, members of the local press and of course the team from Outlook Publishing, as we mingled amongst the other sponsors. There was absolutely no indication
that these fearless daredevils had just descended 7,000 feet in just a matter of minutes. Indeed, looking every bit the Hollywood action heroes, straight out of a scene from Top Gun, they posed for a final team photo with a sense of irresistible and effortless cool in their pristine Falcons overalls. The 2023 season has lift off!
“My greatest motivator is working alongside people with drive. Those are the ones who give you energy. We set goals together, achieve those goals together and celebrate our successes together. When you have a team that is so connected and involved with everything a company does, it is very fulfilling to see how much we have achieved in the last 10 years
and how enthusiastic and motivated everybody is to keep growing in the next decade to come. We have faced challenges and we overcame them together. Ultimately it is our aim to be the best and the biggest logistics provider in the Benelux and Europe, but even the smallest victories mean a lot to us as a company and that’s what really drives us.”
Radek Strouhal CEO, Vítkovice Steel“As a leader, my greatest motivators are the successes of the company and the satisfaction of our customers and employees. I believe that by providing high-quality products and services and creating a positive work environment, we can achieve
our goals and continue to grow and succeed as a company. We are responsible to pass the company and society in general on to our children in better shape than we received it from our parents, and this is something I try to fulfil in my daily operations.”
Chris Pinciak Vice President of Engineering and Sales, Winbro Group Technologies“Being better than yesterday – making small incremental steps to improve the mind, body and soul.”
Are you a CEO or Director with a company story to tell?
Contact EME Outlook now!
To round off each issue, we ask our contributing business leaders for their views on the same question