
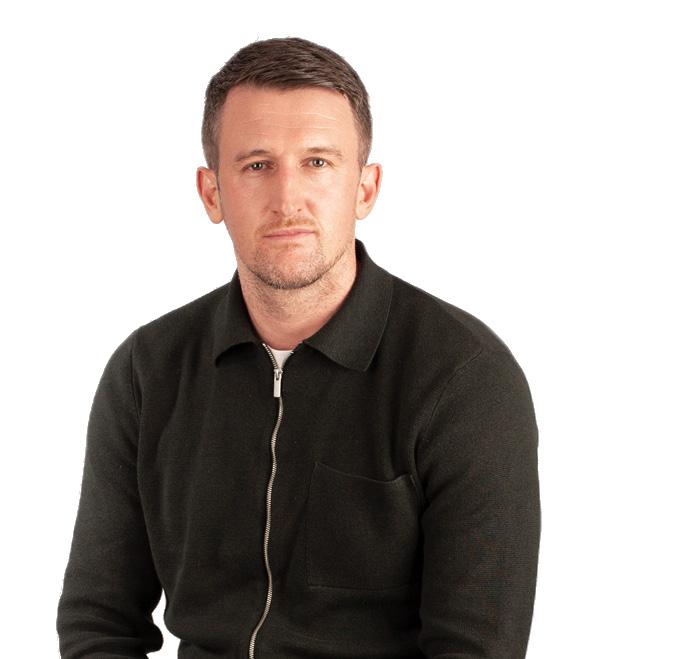
For over a decade, our portfolio of in-house magazines has been lovingly produced, printed, and distributed to our esteemed subscribers across the globe from our headquarters in the UK.
But now we are moving with the times, adopting a digital-first approach by producing online-only publications. A major factor in this decision is to minimise our environmental footprint, reducing the carbon emissions involved in the logistics of print magazine distribution and the resources required therein.
in-line with the
&
Head of Editorial: Phoebe Harper phoebe.harper@outlookpublishing.com
Senior Editor: Marcus Kääpä marcus.kaapa@outlookpublishing.com
Editor: Jack Salter jack.salter@outlookpublishing.com
Junior Editor: Ed Budds ed.budds@outlookpublishing.com
Production Director: Stephen Giles steve.giles@outlookpublishing.com
Senior Designer: Devon Collins devon.collins@outlookpublishing.com
Designer: Matt Loudwell matt.loudwell@outlookpublishing.com
Digital Marketing Manager: Fox Tucker fox.tucker@outlookpublishing.com
Chief Executive Officer: Ben Weaver ben.weaver@outlookpublishing.com
Managing Director: James Mitchell james.mitchell@outlookpublishing.com
Sales Director: Nick Norris nick.norris@outlookpublishing.com
Commercial Director: Joshua Mann joshua.mann@outlookpublishing.com
Callam Waller callam.waller@outlookpublishing.com
Deane Anderton deane.anderton@outlookpublishing.com
Eddie Clinton eddie.clinton@outlookpublishing.com
Ryan Gray ryan.gray@outlookpublishing.com
Thomas Arnold thomas.arnold@outlookpublishing.com
Marvin Iseghehi marvin.iseghehi@outlookpublishing.com
Sales & Partnerships Manager: Donovan Smith donovan.smith@outlookpublishing.com
Alfie Wilson alfie.wilson@outlookpublishing.com
Krisha Canlas krisha.canlas@outlookpublishing.com
Matt Cole-Wilkin matt.cole-wilkin@outlookpublishing.com
Nicholas Kernan nicholas.kernan@outlookpublishing.com
Liam Pye liam.pye@outlookpublishing.com
Finance Director: Suzanne Welsh suzanne.welsh@outlookpublishing.com
Finance Assistant: Suzie Kittle suzie.kittle@outlookpublishing.com
Office Manager: Daniel George daniel.george@outlookpublishing.com
EME Outlook
69-75 Thorpe Road, Norwich, Norfolk, NR1 1UA, United Kingdom.
Sales: +45 (0) 1603 363 631
Editorial: +45 (0) 1603 363 655
Tel: +45 (0) 1603 363 655
phoebe.harper@outlookpublishing.com
www.emeoutlookmag.com
Like us on Facebook: facebook.com/emeoutlook
Follow us on Twitter: @eme_outlook
In harnessing our potential to unlock and drive change, this issue centres on the power of people.
An icon of the UK’s retail landscape, we foreground Selfridges and the development of its CSR initiative
‘Project Earth’, as it combines people’s love of shopping with our need to protect the planet by establishing circular material targets.
Incorporating similar recycling schemes throughout its production processes, we speak with Fun Factory GmbH, as the German manufacturer to champion self-love and personal exploration with an inventive and industry-leading portfolio of toys designed to enhance sexual wellness for individuals and couples across the globe.
Elsewhere, ahead of Black History month in the UK, we catch up with one of the finalists of the Black British Business Awards as the ninth edition of the ceremony continues to promote racial equality and celebrate true excellence in entrepreneurial talent. With a host of inspiring finalists, these gamechanging figures act as role models within both their individual fields of expertise and in envisioning a diverse future of business that truly represents the societies in which we live.
Turning to our corporate stories, our frontrunner Milaha is a titan of the Qatari shipping industry. Combatting a prevailing talent shortage in the sector, we speak with CEO Mohammed Swidan about the company’s work in fostering and developing local talent with in-depth training initiatives for Qataris.
The same applies to industry association Wind Energy Ireland (WEI), as CEO Noel Cunniffe shares the skill training programmes available for individuals seeking a change and encouraging them to pursue an industry on the precipice of greatness.
Meanwhile, discover other fascinating insights from Lithuanian façade construction experts Staticus, data centre specialists Cyxtera Technologies, and EV manufacturers Valmet Automotive.
We hope that you enjoy your read.
Around Europe and the Middle East in seven stories
The need for verification to confront misleading ‘green’ claims
A Rising Star of the Black British Business Awards
Celebrating excellence in Black entrepreneurial talent
12 Manufacturing Fun Factory GmbH
Feeding the fantasies of the self-care generation
18 Sustainability
Changing the Way We Shop
How Selfridges’ Project Earth is reinventing retail
If you could change one thing about your industry, what would it be?
22 Wind Energy Ireland (WEI)
Fuelling the nation’s zero-carbon future
84 AUTOMA 2022
Learn the latest oil & gas industry trends
86 ADIPEC
The influential event accelerating the global energy transition
88 London Build 2022
The UK’s leading construction show
90 MECOC
Middle East Metallurgy Corrosion and Coatings Conference and Showcase
Rotating Machinery Technology and Innovation Conference and Showcase
CRAFT BEER specialist
Beavertown Brewery has been bought out by Heineken.
London-based Beavertown is the latest craft beer brewer to be taken over by the beverage industry giant. After taking a £40 million minority stake in Beavertown back in 2018, Heineken has now agreed to buy the remaining shares.
Beavertown founder Logan Plant, son of Led Zeppelin lead singer Robert Plant, will step down as boss and be replaced by Heineken veteran Jochen Van Esch.
Other UK craft brands to have been bought out in recent years include Camden Town Brewery and London Fields Brewery.
ITALIAN SUPERCAR giant Ferrari has unveiled its first-ever four-door model, a high-riding and powerful new sports car called the Purosangue.
With SUV-like proportions, the Purosangue, Italian for “thoroughbred,” is Ferrari’s first-ever production four-doored automobile.
The new model will give Ferrari’s clients a larger upscale alternative to rivals like the Porsche Cayenne when deliveries begin next year.
TENS OF thousands of passengers were affected by a French air traffic control strike last week. The strike caused Ryanair to cancel 420 flights, most of which were scheduled to fly over France, subsequently affecting 80,000 passengers.
The strike action in France is being taken by the SNCTA air traffic control union in a row over recruitment and
wages, as inflation continues to soar.
EasyJet also cut 76 flights, British Airways cancelled 22, while Air France said it would only run 45 percent of its short-haul flights.
Neal McMahon, Ryanair Operations Director, said it was “inexplicable” that thousands of European citizens and visitors “will have their travel plans unfairly disrupted”.
Despite not adhering to a traditional Ferrari shape, it will certainly still sound like a regular two-door model, powered by a 715-horsepower V12 engine.
AUTOMOTIVE Around Europe and the Middle East in seven stories…THE CHAIRMEN and management committee of dairy companies FrieslandCampina and Arla are reportedly holding initial exploratory talks over a potentially industry-changing merger. This union would result in the world’s largest dairy company.
Neither company has yet confirmed the talks, but reliable Dutch trade sources detail that negotiations have been ongoing for weeks now.
With a combined turnover of £22.7 billion, together they would become just slightly larger than Lactalis, currently the global number one for
dairy production.
The potential partnership comes as the dairy sector faces major challenges in terms of milk supply, climate requirements and financial profitability.
RETAIL
ALDI HAS overtaken Morrisons to become the fourth-largest UK supermarket for the first time in its history.
Discounters are grabbing more market share as shoppers take steps to manage their budgets. Food prices are rising quickly as energy and fuel costs soar, and the war in Ukraine continues to squeeze grain production and push up fertiliser costs.
Inflation in the UK has been rising at its fastest rate for 40 years as food prices climb with living costs eating into household budgets.
ABU DHABI’S Yas Island is set to launch a brand new metaverse in the first quarter of 2023. This ambitious project will be led by the real estate developer and investment firm Aldar Properties, and the new metaverse will allow users to buy property in the always-on virtual space.
Real estate in the metaverse
has attracted significant investor attention, with virtual real estate being sold in the form of non-fungible tokens (NFTs).
Real estate properties in the metaverse can be used for a wide range of purposes including party gatherings, NFT shows or even concerts.
THE OIL and Gas Automation and Digitalisation Congress will be held on October 17-18, 2022, in Milan, Italy, and gathers oil and gas companies, EPC contractors, drilling contractors, pipeline operators, refineries, service providers and equipment manufacturers to discuss how to unlock the full potential of innovative technologies for building smart industry.
AUTOMA 2022 is devoted to the latest innovative industry trends applicable to the whole value chain of the oil and gas industry: upstream, midstream, and downstream. The congress has been organised as a place to present case studies, exchange experience in digital transformation, and network.
With global warming dangerously close to spiralling out of control, the sustainability agenda is more crucial than ever. Companies are under heightened scrutiny and as a result, pressure to adapt and re-shape their strategies to ensure sustainability is a priority.
Recently, the NewClimate Institute in collaboration with the Carbon Market Watch released a report which found that climate pledges by 25 of the world’s largest companies are not being met.
Companies analysed in the report include Google, Amazon, IKEA, Apple and Nestlé, yet only one of the 25 corporations evaluated had a net-zero pledge with “reasonable integrity”.
These are household names who have made big pledges and have fallen short.
Whilst this is shocking, it’s not something new.
Change needs to take place from companies right at the top to those smaller and independent businesses.
The Competition and Markets
Authority reported that more than 50 percent of UK consumers are taking environmental considerations into account and increasingly seeking to shop sustainably. However, 40 percent of green claims made by companies are misleading.
Most companies have made some kind of commitment to the environment, but many have not made it explicit in terms of the products and services they sell. Consequently, key performance indicators such as brand trust, attachment and commitment
are badly impacted, and brands are at breaking point.
Using vague language such as ‘natural’, ‘organic’ or ‘eco-friendly’ to describe a product, whilst knowing that not all the ingredients are sustainably sourced, is a form of greenwashing. Alpro Almond milk, for instance, recently had an advert banned after describing the milk as being “good for the planet”.
Although Alpro argued its customers would understand the slogan was referring to the fact plant-based products do not harm the environment as much, the ASA said this claim needed to be clear and inform customers that’s the reason why the almond milk was “good for the planet”.
Fashion is another industry rife with greenwashing claims. In fact, a study by the Changing Markets Foundation likewise reviewed 12 of
the biggest British and European fashion brands, including ASOS, H&M and Zara, and found that 60 percent of the environmental claims could be classed as “unsubstantiated” and “misleading”.
Companies are under more scrutiny than ever before with the Competition and Markets Authority (CMA) set to name and shame greenwashing UK fashion firms in a crackdown on sweeping eco-friendly claims.
So why is climate change high on the agenda but greenwashing on the rise?
The reality is many brands do not know how to reach their own sustainability goals they’ve mapped out. We should also be wary of playing the blame game as many businesses have sustainable intentions but lack the resources, knowledge and support to implement these across their business.
Consumers expect retailers to share their values on climate change and this is a lot of pressure for companies who are balancing revenue and the impact of COVID-19 on operations and consumer appetite.
Business leaders know there’s a problem, but they lack the right technology to act now. Consequently, they’re stuck in the old world and in danger of becoming irrelevant.
Sustainability Communication platforms can bridge the gap by helping brands to verify, manage, and deliver their sustainable product communications at scale. Powered by AI technology, they enable brands to meet their sustainability goals and move ahead of the competition with haste.
Part of the technology behind these platforms is verification software used to verify the accuracy of documents. Using algorithms, supply chain data is used to rank and report product claims. For example, if a company made certain green claims, the verification technology could ‘verify’
if these claims were true or in fact misleading. This doesn’t just provide the customers with knowledge but allows brands to be both credible and scientifically sound.
There’s a lot of investor appetite for sustainability, therefore if companies can show they’re environmentally sound then they can unlock the potential of increased revenue and shareholder interest.
Armed with the right technology and processes, brands can put an end to greenwashing for good. However, companies need support, not only to be fully compliant in terms of sustainability regulations but to also verify and communicate these credentials to their stakeholders.
This is why sustainability communication is so vital. The World Economic Forum recently published a report on the impact that sustainable credentials can have on business models, products and company value. If brands fail to invest today, they could find themselves falling on the wrong side of authorities, and history.
Abbie Morris is CEO and co-Founder of Compare Ethics, a Sustainability Communication platform that enables brands to verify, manage and deliver their sustainable product communications at scale. Brands are verified using international product standards and a scoring system across 10 categories.
She is also a Forbes Under 30 entrepreneur and has previously worked with the United Nations and World Economic Forum.
For the ninth year in a row, the Black British Business Awards (BBBAwards) are back to celebrate the best of Black business talent across the UK.
The only premium awards programme of its kind in the UK, the BBBAwards showcases exceptional professionals and business owners from the Black community – whether senior leaders or rising stars.
As an annual ceremony, the awards are instrumental in highlighting the strength of the Black talent pipeline and promoting role models and commercial excellence across industries that showcase a more diverse representation of influential figures and substantial contributors to the UK’s economy.
Since its establishment in 2014, it has been endorsed by three Prime Ministers, the Mayor of London and global business leaders, and has come to represent a key staple in the calendar for Black History Month
in the UK. So far, the awards have showcased over 350 individuals and 80 organisations who are championing Black excellence in business.
Dedicated to talent advancement, the BBBAwards are a prestigious champion of race equality as a key priority across industries, promoting the attraction, retention, and advancement of racial and ethnic minorities in the workplace.
Previous winners of the BBBAwards include Steven Bartlett, co-Founder of Social Chain and the latest Dragon on Dragons’ Den, Dorothy Koomson, award-winning writer, and Sir Trevor McDonald OBE.
For the third year running, J.P. Morgan will be the key partner with category sponsors including Baker McKenzie, Barclays, Bloomberg, Credit Suisse, Goldman Sachs, P&G, Tranzfar, and Wellington Management.
With the 2022 awards due to take place on the 30th September, we
Since 2014, the BBBAwards have celebrated entrepreneurial excellence among the UK’s Black professionals and business owners. We showcase one of this year’s finalists in a quickfire Q&A with Hanna Afolabi
Writer: Phoebe Harper
catch up with one of the finalists in the Rising Star for Professional Services category – Hanna Afolabi.
Afolabi is the Founder and Managing Director of Mood and Space (MAS) – a real estate business based in London. As a planning and develop ment surveyor and architect, Afolabi is passionate about the built environ ment. Aside from her work at MAS, she also occupies a host of advisory roles, including her position as a member of the Estates Gazette’s Diversity & Inclusion Content Advisory Panel and as vice chair of the University of Greenwich’s Construction, Property and Surveying Practices Industry Advisory Board. Afolabi also founded Black Women in Real Estate (BWRE) an organisation that brings together Black women in property with the intent for them to connect.
EME Outlook (EO): Firstly, congratulations on your recent nomination! What does it mean to you to be included as a finalist in this year’s BBBAwards?
Hanna Afolabi (HA): Thank you, I am very honoured to be selected as a finalist for this year’s awards. I believe that I am hard working and always push myself to do better, so it is ex tremely rewarding when my achieve ments are recognised and celebrated.
As a Black woman in the property sector, I am very much a minority, so it is also great to be highlighting success in my industry on a broader platform.
EO: What is your current take on diversity and inclusion within your industry – do you believe that there is room for improvement, particularly in terms of visibility in senior positions?
HA: The property sector is far-reach ing and touches the lives of every per
son. The world we live in is designed and built by people in my sector. Despite how impactful the industry is, it is majority white and male and is not reflective of our society.
There has been more conversation around diversity in recent years however the built environment has a long way to go to improve its diversity across every level, but more specifically at senior level. Seniority is important because this is where cultural changes take place.
EO: Could you reflect on your own experiences in the industry – has it been a challenging journey to get where you are today?
HA: I have definitely had career highs and lows! However, I have been fortunate to be surrounded by great and encouraging people through out my career. I see the challenges I have faced as learning opportunities and think of ways I can do better if presented with similar situations in the future.
In general, I am grateful for the career I have had and hope to continue to have an amazing career in the coming years with the launch of Mood and Space.
EO: Finally, what advice would you share for aspiring entrepreneurs –particularly those from traditionally marginalised or underrepresented backgrounds?
HA: Firstly, your difference is your superpower! A lot of the time we con sider being a minority as a disadvan tage but truly, if you are great at your specialism, your difference gives you a unique perspective that allows you to stand out. Embrace that and use it to your benefit.
From Play-Doh models to industry disruptors, Fun Factory is the German manufacturer delivering inventive products to enhance sexual wellness
Writer: Phoebe Harper
The global sex toy market is on an explosive trajectory.
With a valuation of over $30 billion across the global market recorded in 2021, a compound annual growth rate (CAGR) of 8.4 percent is forecasted from 2022 to 2030, as reported by Grand View Research.
The European demographic is a major contributor to this market, with traditional vibrators and dildos standing out as the most demanded products, especially across Italy, France, the UK, Denmark, and Germany. The latter is home to a toy brand of global renown – Fun Factory.
“We are the pioneers of the sex toy industry,” introduces the company’s Marketing Director Jordis Meise.
Every year, Fun Factory manufactures over 600,000 toys from its factory in Bremen, and delivers them to bedrooms across the globe.
Innovators in the field since 1996, Fun Factory was the first manufacturer to make toys with medical-grade silicone and use colourful designs in various shapes as a vibrant departure from the traditional (and not to mention, limited) models of penis-shaped toys formed from rubber in various hues of beige, and all with a distinctly strange chemical smell.
The new and exciting products that launched the company were the brainchild of Dirk Bauer and Michael Pahl, both of whom still oversee Fun Factory’s operations as CEO and Product Developer, respectively.
Ideation was sparked with a sketchpad and handfuls of Play-Doh at Bauer’s kitchen table, which led to the design of the first ever bodysafe, non-phallic, harness-compatible dildo: the Paddy Penguin.
“Back then, customers didn’t have options, especially regarding quality.
Dirk and Michael decided that they could do a lot better — and so, Fun Factory was born,” Meise tells us.
With several other ‘firsts’ under its belt, Fun Factory went on to become the first company to introduce waterproof toys and invent rechargeable vibrators. This has led to its reputation as the first high-end brand in the industry, and the first to win a mainstream design award.
“We’ve also created multiple entirely new product categories, such as rechargeable toys and pulsators (thrusting toys with patented technology),” she adds. Today, Fun Factory’s best sellers include Nos, Manta, Miss Bi, Mea, Stronic G, Limba Flex, Fun Cup, Smartballs and Share Lite.
Evolving significantly from the early days of designing on the kitchen table, Fun Factory has become a manufacturer that prides itself on not just its products, but also its ecofriendly, fair labour factory.
As a result of global lockdowns and extended periods of isolation, in many ways the COVID-19 pandemic stimulated the curiosity for sexual exploration and fuelled the worldwide demand for sex toys. Empty, idle days stuck at home became a crucible for experimentation as more couples embarked on adventurous bedroom exploits, and simply spent more time having sex.
Aside from the burgeoning social cognisance and respect for sexual wellness, self-care, and the growing universal acceptance of the LGBTQI+ community that is collectively reshaping the current sex toy market, the unique conditions of the pandemic contributed to a
At Fun Factory, this translated to a 278 percent spike in sales.
To better understand this peak, Fun Factory undertook a survey at the height of Germany’s second lockdown to analyse consumer behaviour across 1,051 newsletter subscribers. The survey attributed ‘stress relief’ as the overriding factor in demand – whether from home offices, childcare, or loneliness in isolation.
“Since the start of the first lockdown, around half of the respondents have bought new toys, and 31 percent of the respondents had even more desire for new toys in the
“More than half of the respondents (58 percent) were having as much sex as before lockdowns, whilst 15 percent were actually having sex more oftenso no strong signs of libido decrease!”
This is a company that listens to its customers, constantly working with consumer feedback to adapt and improve its product offering. This is well-evidenced by the development of one of its best-selling products –Share Lite, which will be launched B2B later this year.
“This product is the next generation of Share, which is part of our portfolio. We improved it fully based on
customer feedback,” Meise explains.
“Among negative reviews, it was always the weight and stability of the product that were criticised. As a result, Share Lite’s core is made of foam, which makes the product 22 percent lighter. We have also included an invisible hinge, which gives the product its stability and firmness.”
The idea of longevity is essential to Fun Factory – whether in the durable designs of the products themselves, or the eco-friendly manufacturing
products. Due to the convincing function of our toys, we also have an extremely low return rate in the low single-digit range.”
Environmentally speaking, the company’s carbon footprint is relatively small with all departments of the Fun Factory concentrated within one location – whether development, production, administration or shipping.
Leveraging low energy consumption machinery throughout the manufacturing process, the packaging of all Fun Factory products
practices and environmentally sustainable initiatives embraced by the company.
“At Fun Factory, the topic of sustainability has always played a role and has been reflected in the high quality of our products since day one.
“In the production of our toys, we not only rely on high-quality materials, but also on extensive, intensive functional tests to make them as durable as possible,” elaborates Meise.
“If you buy cheap, you buy twice. This is not the case with Fun Factory
is also 100 percent recyclable with plastic-free shipping. All reusable materials are then sorted, collected and sent to recycling stations across Bremen.
Recycling processes are also incorporated with the silicone used to fabricate the products. To achieve this, Fun Factory works with a partner nearby in Bremen, who takes old silicone by the tonne.
“The eco-efficiency is extremely good. For a recycling process to be meaningful and reasonable, the triad of social aspects, eco-efficiency and economy must be considered,” says Meise.
This partner has developed a chemical recycling process whereby the starting materials of silicone elastomers can be recovered. This effectively opens up completely new applications from the silicone waste –including the end product of silicone oil which has a host of industrial uses.
“In the end, of course, we are not perfect, but we are willing to learn and
“AT FUN FACTORY, THE TOPIC OF SUSTAINABILITY HAS ALWAYS PLAYED A ROLE AND HAS BEEN REFLECTED IN THE HIGH QUALITY OF OUR PRODUCTS SINCE DAY ONE”
– JORDIS MEISE, MARKETING DIRECTOR, FUN FACTORY
open to the ideas and developments that the future brings.”
With this open-minded attitude going forwards, Fun Factory has its sights set on strengthening its B2C business for the coming year.
“We are doing this to gain independence and position ourselves more strongly as a brand with customers.”
Meise also hints at pursuing an international path, using Fun Factory’s high-quality products, values, and
knowledge successfully outside of Germany, Austria, and Switzerland.
Aside from these business strategies, a major priority for Fun Factory concerns a shift in mindset, regarding society’s perception of toys. The brand’s reach is restricted, as it must confront restricted advertising regulations across major platforms. As such, Fun Factory seeks to debunk the widespread taboo around products designed to cater to sexual wellness and personal wellbeing – whether as
an individual, or a couple.
“We would like to see more tolerance towards sex toys and selflove in general because spreading the word about sexuality and especially education about pleasure and toys would make our work much easier,” Meise concludes.
“This would also allow us to communicate the positive values of acceptance and diversity towards one’s own body or sexuality, since it is these values enrich society.”
Two years into Project Earth, high-end department store chain Selfridges is zeroing in on a circular future for shopping
Writer: Jack SalterIn creating our store of tomorrow, we must commit to a fundamental shift in the way that we do business, and use the Selfridges platform for change.”
The words of Andrew Keith, Managing Director of Selfridges, embody the luxury retailer’s vision to reinvent retail, create a more sustainable future, and achieve net zero.
Underpinning the vision of Selfridges, recognised as the world’s best department store an unprecedented four times, is Project Earth.
A bold, evergreen sustainability strategy to change the way we shop, Project Earth was originally launched by Selfridges in 2020 amidst the uncertainty of the COVID-19 pandemic.
The future of retail is circular, and Project Earth builds on more than a decade of retail activism at Selfridges. From banning fur in 2005 to removing all plastic-based cosmetic glitter from its stores in 2021, sustainability is very much central to the business today.
Project Earth evolved from Project Ocean, a long-term partnership with the Zoological Society of London launched in 2011 to help protect our oceans from overfishing and plastic pollution.
Designed to apply to issues more material to Selfridges’ operations and customer experience, Project Earth aims to pioneer a new approach to business, and leverage the Selfridges platform to engage customers.
“We recognise that we need to challenge ourselves to accelerate
change, and our ambitious circular and materials targets do just that,” a statement from Keith reads.
“We don’t have all the answers, but we are committed to finding solutions through a continued imaginative approach to retail innovation. The scale of our ambitions cannot be underestimated, but we are inspired by what lies ahead and how we can bring this to life for our customers.”
Moving beyond incremental change, the intention of Project Earth is to drive genuine transformation through three key pillars: materials, models, and mindsets.
Materials matter to Selfridges, as they are responsible for a significant percentage of the company’s overall environmental impact. For this reason, Selfridges is calling for a materials
revolution to accelerate its drive towards a net zero future.
By 2025, the most environmentally impactful materials will come from certified, sustainable sources as part of a shift to a new materials culture, one in which brands and suppliers are transparent and responsible in their sourcing practices.
Everything built, bought and sold by Selfridges will also meet
environmental and ethical standards by the end of the decade, according to Project Earth, thus making both products and procurement more resilient and sustainable.
Likewise, by investing in alternative shopping models that focus on extending the life of existing products and packaging, Selfridges is putting circular at the heart of its revenue streams and customer experience.
Indeed, 45 percent of Selfridges transactions across its four stores and online will come from circular products and services by 2030.
Selfridges recognises that reducing the impact of its products and operations will only get it so far, and that it has to pioneer new business models if the company is truly going to achieve its net zero goal.
Changing the mindsets of teams, communities and customers, meanwhile, will enable Selfridges to build an inclusive retail culture that puts people and the planet first in every decision.
Together, these three pillars will contribute to the company’s commitment to achieve net zero carbon emissions by 2040, accelerated last year by Selfridges as a signatory to the Climate Pledge.
Project Earth is Selfridges’ route to achieving a sustainable future for its teams and customers, an evolving approach informed by regular assessment of its material issues and the most effective ways to address those issues.
Two years on from the proud launch
of the project, Selfridges recently shared its first Project Earth Report, detailing the progress made so far during the initiative and setting out the next steps in its plans to reinvent retail and create a sustainable future.
To meet its 2025 material com mitments, the report details how Selfridges tracked the materials coming into its business to establish a baseline volume of products. The report also notes that Selfridges’ Project Earth edit featured over 55,000 more sustainable products and accounted for more than 12 percent of all own-bought sales in 2021.
Two further material commitments have been set, namely for 50 percent of polyester and nylon used across the business and in products sold to come from certified recycled sources by 2025 and 2027, respectively.
Selfridges has also become more synonymous with circularity through pioneering new retail models and experiences, with the ‘Reselfridges’ initiative now housing all circular models and forming the backbone of the company’s future business to change the way we shop.
Sales of pre-loved items through Reselfridges have increased by an impressive 240 percent, the report reveals, whilst over 28,000 repairs have been facilitated, more than 2,000 items have been rented, and in excess of 8,000 refills have been sold by Selfridges.
Customer awareness of sustainability initiatives at Selfridges has grown exponentially in the last five years from 11 percent to 52 percent. However, research also shows that half of Selfridges customers want to make more sustainable choices but don’t know how to.
As such, to help and inspire customers, one initiative that Selfridges will offer is dedicated Project Earth appointments, to discover how to restyle existing wardrobe pieces, explore earthconscious beauty, and learn about sustainable denim.
Building on the previous two years, Selfridges’ 12-week creative scheme in Spring 2023 will creatively and collaboratively explore the ambitions of Project Earth, with a continued imaginative approach to retail innovation.
Through materials, models and mindsets, Selfridges and Project Earth are embedding and accelerating change.
With a growing offshore presence in the works and a seismic potential to reshape the energy landscape, the winds of change are in full force for Ireland’s renewable future
Writer: Phoebe Harper | Project Manager: Matt Cole-Wilkin
In an age where energy security is a growing concern, rising to the top of most national agendas, the island of Ireland is ideally located to harness an inexhaustible resource that has proven its potential to unlock a national renewable energy future.
Thanks to its geographic isolation in the wild waters of the Northern Atlantic, its rugged coastline and mountainous interiors, the ‘Emerald Isle’ has no shortage
of wind. Average wind speeds across the country are typically higher compared to mainland Europe, particularly in exposed northern locations where it far surpasses the minimum speed required for the economic viability of wind turbines.
As a result, Ireland has established a reputation as a world leader in leveraging wind energy to fuel its electricity sup ply, so much so that Irish Prime Minister Micheál Martin, has
referred to wind as “Ireland’s oil”. As of 2020 Ireland came second only to Denmark in terms of its wind energy use, as reported by Wind Europe.
With Ireland producing no nuclear energy, oil, or coal, wind provides a critical source in implementing national energy security. The Irish government has implemented an ambitious energy agenda, targeting an 80 percent share in renewable energy by 2030. Wind has a critical role to play
in this, as an energy source that provided 36 percent of the country’s power needs in 2020.
Yet to meet this goal, development is needed. At present, the country has just one offshore wind farm, located off the coast of County Wicklow. As such, the sector must grow significantly, particularly in the offshore field, if Ireland is to continue its path towards a net zero emissions electricity system.
Gabriel started out on his own in 1983 before officially setting up the business. The company was founded in 1989 by Gabriel O’Brien with one 15-tonne mobile crane on his books. Since then, the fleet has grown to one of the largest in Ireland, boasting over 50 cranes within its ranks. Gabriel now runs the company alongside his sons, Conor, Darragh and Bobby.
The entire fleet of cranes is kept in pristine condition, with a complete update carried out within the last three years. This commitment to keeping its equipment up to date has led to the company owning Ireland’s only Self Propelled Modular Transporter, an item that makes all the difference when it comes to lifting projects by being able to transport the massive hardware that can be needed to complete complicated works.
Gabriel O’Brien Crane Hire has a range of cranes for hire that spans from 800-tonne mobile and 11350 crawler cranes down to 3.5-tonne spider cranes that can fit in the tightest of spaces. These are used in a wide variety of onshore and offshore industries, including the construction, oil, and wind energy sectors.
The company is available 24 hours a day and offers a comprehensive service, from its free site inspection to the execution of a lift; including detailed pre-planning, fully qualified operatives, and unrivalled attention to detail. It is this thorough nature that led to the organisation being taken on to complete Cloncreen Windfarm and Lisheen 3 Windfarm as two of its recent projects alongside Clogheravaddy Windfarm in the last ten months.
Across the process of each lift, the engineering expertise of Gabriel O’Brien Crane Hire shines through. Its staff are certified in both Ireland and the UK and equipped for manual handling and working at heights, and the team has a vast knowledge of lifting across a whole range of industries. Its planning process includes full CAD drawings of how the lift will be carried out, using the most modern engineering expertise to work around wind resistance, underfoot conditions and any other factors which may influence the lift.
This all goes towards ensuring that all work is completed in the most hassle-free yet fully secure environment for its clients. Due to its detailed planning and proven track record, Gabriel O’Brien Crane Hire have been trusted with some of the most challenging projects across Ireland and the UK.
Its impeccable safety record goes together with its attention to detail in both the preparation and carrying out of all lifts. Most of the work is done before any lift takes place, with site investigation and careful planning, including RAMS (Risk Assessment Method Statements) and 3D CAD drawings being created to map out even the most complex projects in detail. All of this combines to make Gabriel O’Brien Crane Hire a company to trust with your project lifts.
The issue of grid availability is a complex one, with a lot of moving parts, intricate interactions and interdependencies. Getting power from where it is produced to where it is consumed is a challenge in itself but adding a complete shift in generation portfolio and changes in demand patterns and consumption levels brings these complexities to a whole other level.
There is no silver bullet for transforming our power system towards net zero. However, an Accelerated Decarbonisation pathway is the only game in town. Early deployment of renewable energy, as well as approaches to allow this energy access to the grid, is imperative.
The existing grid development strategy is not enough and is already incredibly ambitious in such a short timeframe. Building the level of new infrastructure required, needs urgent and unprecedented action. There are huge challenges relating to completing outages, for ongoing maintenance, connection of new renewables as well as network reinforcements. But also, there is a question of resourcing. And while waiting for grid to be delivered, we are likely to experience grid limitations in the medium term. The implementation of other technology solutions immediately to help relieve congestion is critical as well as a shift in mindset as to how the system is planned and operated to help take the best advantage of our incredible renewable energy resources.
The grid is planned, operated and managed to ensure that there is a safe and secure supply to end users. A complete paradigm shift in how we generate, transmit and use electricity is challenging against the backdrop of safety and security standards that were developed for a fundamentally different power system. While it’s important to maintain these critical standards, we must recognise that the system is changing and therefore our approach to planning and operating the network needs to also change and will require innovative and new way of thinking.
A more dynamic power system with increasing levels of renewable generation presents new operational challenges. One key aspect of this is the removal of the need for fossil fuel generators on the system for stability reasons. These fossil fuel generators offer system services that are integral to the power system and these requirements will need to be provided by other greener generators and technology types.
Policy can have such a profound impact on the evolution of the grid, what we do and how we do it. Policy (and conviction) from the top levels of Government really sets out the direction of industry and dictates investment and incentives. We need policy in place, it needs to be drastic, coordinated across all aspects of industry and most importantly, enable us in the energy sector to do what we do best, solve the problems we need to solve to get to net zero. Policy needs to be substantial and enduring to allow our System and Market Operators, our Planning Authorities and Regulators implement change at a speed that a net zero transition requires.
Alternate technologies are needed to replace some of the required functionality of conventional power stations, like frequency response and the provision of restoration services as well as inertia and voltage management.
Strategic deployment of energy storage technologies in constrained regions of the network to reduce constraint of renewable generation, by taking in excess generation during hours of constraint, will allow for additional renewable connections to be accommodated.
Power sharing can be unbalanced in parts of the transmission network, particularly following outages. Power flow control technologies can force power into parts of the network with redundant capacity, by changing circuit impedance. This in turn reduces potential overloads and allows for higher access of renewables.
Identifying overhead lines that will benefit from a capacity increase due to environmental factors such as variations in wind speed and ambient temperature, in particular in areas where grid is difficult to build, will be important. These factors can enhance the cooling effect on the overhead lines and will offer greater capacity.
The evolving power system with increasing levels of renewable generation and high levels of interconnection presents challenges and opportunities for energy markets. A transition to a new market design must reward the provision of new system requirements. For example, the rapid deployment of stored energy for congestion management and inertial support. How the market addresses challenges such as large errors in wind (and solar) generation forecasts must be established if renewables are to reach the high levels needed by 2030.
and
to
WEI is Ireland’s industry body advancing the national wind energy agenda. We speak with CEO Noel Cunniffe ahead of a seminal decade in building a zero-carbon Ireland
EME Outlook (EO): Firstly, could you briefly introduce us to WEI; when were you founded, and why?
Noel Cunniffe, CEO (NC): WEI is the largest renewable representative body on the island of Ireland, with more than 180 members. Our members are very focused on delivering onshore and offshore wind energy at the best possible value to the consumer. The organisation has been around in some shape or form for a very long time, but it’s about 30 years since the very first wind turbine was developed in Ireland, and we’ve
Noel Cunniffe, CEObeen trying to support the industry and its developments ever since.
EO: How has the association developed and progressed since its inception?
NC: It’s grown and changed hugely over time. Right now, our members represent all aspects of the entire supply chain of the wind sector, so it’s not just the companies that are developing wind farms or own wind farm assets. We have members right throughout the value chain from plan ners, to haulage companies, to people working in the banks that provide investment, to engineers and design ers, so we really are a broad church. We’re growing more and more as the industry itself evolves and develops, particularly in offshore wind energy.
Offshore wind energy is something that’s going to play a big role in Ireland, particularly towards the latter half of the decade. We’re seeing a lot more companies getting involved in that part of the sector. Areas such as ports, shipping companies and training facilities for people interested in working in wind are becoming a core part of our membership.
EO: What is your current take on Ireland’s wind energy industry? Do you find it a particularly exciting, or challenging environment to work in?
NC: It’s hugely exciting. Ireland is a world leader when it comes to the amount of onshore wind energy that we use to meet our electricity demand. It’s typically in the region of 40 percent and that was our renewable target that we needed to hit in Ireland in 2020, and we exceeded it by reaching 43 percent. For me, that was powerful because everyone will remember 2020 as the year of COVID-19 and working from home, when we were all so reliant on Teams meetings, Zoom calls and Netflix binges. To think that four times out of 10, that was powered by wind energy in Ireland is a really positive story for the sector, and it’s only the beginning. We’re going to try and get more and more of our electricity from wind energy over the next 10 years and beyond.
EO: What role does wind play in delivering a low-carbon energy future to Ireland, compared to other renewable sources?
NC: The objective that Ireland has for 2030 is to grow the amount of renewable energy we have from 40 to up to 80 percent of our supply, and wind is going to play a huge role in that. Between onshore and offshore wind, you’re probably looking at 70 percent, if not more, coming from wind energy. By 2030 there will be significantly more energy coming from onshore wind, but we’re also
going to have kickstarted a brandnew sector for Ireland in offshore wind energy. We only have one relatively small offshore wind farm in place at the moment, and over the next 10 years we’re looking to grow that to between seven to 10 large modern offshore wind farms. There’s definitely a role for all renewable sources, since the wind doesn’t blow all of the time. That’s why we need technologies like solar, battery energy storage and other types of smart technologies, but wind is going to be at the core of Ireland’s electricity supply over the next 10 years.
EO: Are there any major developments, either ongoing or in the pipeline, across the country’s wind energy industry?
NC: We carry out a survey of our members every year looking at the pipeline and developments in both on and offshore wind. It’s great to say that there are many more projects in development than our targets set for 2030. That’s important because there will be attrition throughout - some projects might not make it through the planning system. There are going
to be auctions to enable the most competitive projects that can deliver for 2030 and we are seeing a lot of progress from Government right now.
Just this year, we’re starting to see the delivery of the first onshore wind projects from a new round of auctions that started in Ireland in 2020. I can remember the day the auction results were announced in August 2020 and being excited for what that might mean.
Just a few weeks ago, I got to go to the opening of the first wind farm that came through that auction, so it was fantastic to see some of those projects actually materialise and begin contributing towards decarbonising Ireland.
On the offshore side, there’s a big milestone coming up next year when the first offshore auction will be taking place. Six different projects are going to be entering that and it will give us a good idea as to which of those projects are going to be the very first offshore wind farms developed in Ireland, hopefully in around 2028, so that they can begin providing electricity too.
Just this year, WEI is beginning to see the delivery of the first onshore wind projects from a new round of auctions that started in Ireland in 2020EO: Could you expand on WEI’s efforts in training individuals to work in the renewable energy sector and why this is so important? For instance, your partnership with Green Tech Skillnet?
NC: Green Tech Skillnet is a really important partner for us. It upskills and reskills workers that want to get into the renewable energy sector to progress and advance their career.
Every year, more than 1,000 people go on all different types of training courses ranging from how to connect a renewable project to the electricity grid, to carrying out a building energy rating in someone’s home, so it’s not just focused on wind energy.
We do training for solar, battery energy storage, hydrogen, and in the heat sector as well, so it’s a really
exciting programme that’s growing year on year.
It’s so important because one of the biggest risks that we have in delivering our targets for 2030 is a lack of trained and skilled people in the sector. It’s top of a lot of companies’ risk registers at the moment that there just isn’t enough people in the sector, so it’s crucial that we are able to bring people in through reskilling programmes.
We run a particular programme called Work in Wind that takes place twice a year where we offer an opportunity for anyone who is unemployed or wanting to get into the renewable sector to go through a series of training sessions with us. We’ve had some fantastic examples where musicians, artists
or teachers that have gone through that programme and now work for Ireland’s renewable sector, so it’s really a great time to enter the industry.
EO: Are there any upcoming events that WEI will be participating in?
NC: We run some of Ireland’s largest renewable conferences every single year. Early next year, we’ll also be running our annual conference which is our largest event of the year, where we bring people together that work on all aspects of on or offshore wind and different parts of the supply chain to share knowledge and try to progress policy in the industry as well.
We’re also very excited about our first international trade show for wind energy in Ireland which will take place in Dublin in October 2023.
EO: Finally, how do you see the future of wind energy developing across Ireland over the next few years?
NC: It’s going to be a really interesting time. Our Government has set very ambitious targets to try and hit 80 percent renewable electricity. We’re going to try and transition from 4 GW of onshore wind to up to 8 GW by 2030. At the same time, we’re trying to kickstart the offshore wind sector and get up to 7 GW by 2030 from basically a standing start. There’s a
lot to be worked through, particularly with areas that are going to need progression related to our planning system and our grid system. However, in eight years’ time we should see the vast majority of our power coming from wind energy and that’s exciting for Ireland because that will mean we have lower carbon emissions, we’ll be using much more renewable energy, we’ll be seeing lower electricity bills, and we’ll have the benefit of kickstarting a brand new economic
sector in Ireland in offshore wind energy and all of the jobs that will be created around that, particularly in coastal communities.
Tel: 00 353 45 899 341 office@windenergyireland.com www.windenergyireland.com
“IRELAND IS A WORLD LEADER WHEN IT COMES TO THE AMOUNT OF ONSHORE WIND ENERGY THAT WE USE TO MEET OUR ELECTRICITY DEMAND”
– NOEL CUNNIFFE, CEO, WEI
EME OUTLOOK is a digital product aimed at boardroom and hands-on decision-makers across a wide range of industries in Europe and the Middle East regions.
With content compiled by our experienced editorial team, complemented by an in-house design and production team ensuring delivery to the highest standards, we look to promote the latest in engaging news, industry trends and success stories from the length and breadth of Europe and the Middle East.
Reaching a combined audience of more than 395,000 people, EME Outlook covers a full range of industrial sectors: agriculture, construction, energy & utilities, finance, food & drink, healthcare, manufacturing, mining & resources, oil & gas, retail, shipping & logistics, technology and travel & tourism.
In joining the leading industry heavyweights already enjoying the exposure we can provide, you can benefit from FREE coverage across our digital platforms, a FREE marketing brochure, extensive social media saturation, enhanced B2B networking opportunities, and a readymade forum to attract new investment and to grow your business.
To get involved, please contact Outlook Publishing’s Managing Director, James Mitchell, who can provide further details on how to feature your company, for FREE, in one of our upcoming editions.
Milaha has expanded vastly into a multifaceted titan of the Qatari shipping industry. We talk to I PCEO, Eng. Mohammed Swidan, who delves into the company’s safe, reliable, and sustainable services
Writer: Ed Budds
Project Manager: Cameron Lawrence
Established back in 1957, as Qatar’s very first registered company, Milaha began its journey as a shipping agency, strategically developing over the next six decades to become one of the largest, most powerful maritime and logistics service providers in the region.
Milaha has meticulously built a strong regional foothold in transportation and logistics, with a focus on providing integrated transport and supply chain solutions, and is supported by an expanded, modern fleet of vessels, state-of-the art equipment, modern technologies, dedicated staff and world-class partners.
The company strives to provide safe, reliable, and sustainable services and products through its strategic pillars of business, covering various key aspects of the shipping industry including warehousing and distribution, industrial and heavy equipment facility management, as well as the oil and gas sector.
The overarching vision of Milaha remains clear: to be the partner of choice in the maritime and logistics sector, with a dominant share in its home market, as well as a strong international presence. Alongside this, the company looks to deliver a sustainable level of growth to all its existing shareholders.
“We are looking to consistently deliver reliable services by focusing on safety, quality and our customers, to provide an enriching work environment, and to always live by our values,” opens I PCEO of Milaha, Eng. Mohammed Swidan.
The maritime and logistics division delivers a comprehensive range of services to some of the region’s biggest players in the oil and gas and petrochemical sectors, as well as major importers, exporters and shipping companies.
“We understand that needs don’t just change from client to client, they
also change from one day to the next. By synchronising our services, from logistics and marine transport to port services, ship repairs and complete shipping agency services, Milaha can tailor complete solutions to any requirements. The result is a simpler, more efficient and better value supply chain,” he explains.
Elsewhere, Milaha continues to serve a wide range of industry leaders in the fields of fashion, e-commerce, infrastructure, defense, health, oil and gas, heavy industries, aviation and fast-moving consumer goods (FMCG).
“By adopting a customer centric approach, we are able to build a complete understanding of our customers’ specific needs and requirements,” explains Eng. Swidan.
To serve every client in the best way possible and improve the quality of service every day.
To remain honest with all colleagues, clients and partners. It is essential to never overpromise and also to never under-deliver. Furthermore, it is important to always finish anything and everything that the company starts.
All success comes from a collective strength and the ability to work together to solve complex problems and innovate with smart solutions.
The history of Milaha is a source of pride for the company, but an eye must be kept on the future in order to leave a valuable legacy.
“Our diversified service offerings now include shipping, handling, warehousing, custom clearance, distribution, ship management and ship agency, industrial and project logistics, marine services and products, and automotive services in addition to logistic support services for the oil and gas sector,” he expands.
The freight and logistics sector in Qatar has been growing steadily over the past five years, with an estimated market value of more than USD$7.5 billion, and is expected to register an annual growth rate of more than seven percent during the 2021 – 2026 period, supported by ambitious government plans to continuously
develop the economy.
Milaha owns a dominant market share in the shipping and supply chain industry in Qatar, supported by an effective infrastructure of transport, technology, specialist staff, and supply chain partners specifically selected to consistently deliver endto-end solutions.
“The warehousing market is another key contributor to the logistics industry in Qatar, mainly supported by the retail and FMCG sectors, and recently the advanced warehousing facilities have gained a strong boost with the growth of the e-commerce sector globally,” adds Eng. Swidan.
With this in mind, the Milaha Logistics City warehouse has emerged as an integrated centre for freight logistics, warehousing facilities
and business solutions for start-up entrepreneurs and small and mediumsized enterprises (SMEs).
The state-of-the-art bonded warehouse located in Milaha Logistics City offers comprehensive services
• Establishing new trade routes and securing alternate supply sources.
• Expanding into the wellservices industry and continuing to develop and equip well stimulation vessels over the next five years.
• Expanding the company presence and service offerings in the offshore oil and gas sector, by increasing investments in Floating Storage and Offloading (FSO) units and getting more involved in the EPCI business.
• The acquisition of the new floating dock as part of a major upgrade and modernisation plan that will supplement the shiprepair and dry-docking activities, as well as catering for all vessels from both local and international markets.
with zero-duty upfront, to support global trade and e-commerce, while enhancing business efficiency and profitability.
“This dynamic sector is always vulnerable to various challenges related to HSSEQ, social, digital and economic issues, but it’s always exciting to operate in such a challenging environment that requires strategic planning, problem-solving, fleet and systems upgrading, policy updates and enhancing digitalisation,” details Eng. Swidan.
The main challenges that both the sector and Milaha currently face include decarbonisation, digitalisation, cyber-attacks, fuel price increases, and workforce and skills shortages, among others.
To directly combat the workforce shortage across the region, there is an ongoing development of the Qatari workforce through proper education and training. This is now a primary national objective designed to enhance the development march in the country.
Milaha offers a special initiative called “Alnokheda” to Qatari nationals as part of its attempts to foster and develop local talent in the business. This comprises an 18-month training and development programme that allows Qataris to demonstrate their learning along the way. Rotations,
Established in 2007, Nakilat - Keppel Offshore & Marine Limited (N-KOM) is a joint-venture between Nakilat, the world’s leading transporter of liquefied natural gas (LNG), and Keppel Offshore & Marine, the global leader in ship repair, ship conversion and construction of offshore drilling rigs.
Nakilat Keppel Offshore & Marine (N-KOM) shipyard is strategically located in the Erhama Bin Jaber Al Jalahma Shipyard complex. We are a purpose-built, modern shipyard that has achieved a five-star grading from the Five Star Occupational Health and Safety Audit conducted by the British Safety Council.
N-KOM possesses the physical capacity, state-of-the-art facilities, equipment, technical, engineering and support capabilities to conduct a wide range of marine and rig repairs, upgrades, maintenance and conversion projects as well as fabrication and industrial engineering jobs.
Our proven and growing track record in repairs and project management, safety and quality backed by consistently strong and positive client testimonials are a strong reflection of our Passion, Pride and Professionalism.
Together with our extensive network of strategic business partners including Milaha, N-KOM is able to provide a wide and enhanced range of in-house capabilities, valueadded solutions and services for our clients to meet their operational requirements and environmental regulatory standards.
N-KOM remains committed to be the Preferred Shipyard Delivering Sustainable Solutions to power local and international shipping, offshore and industrial engineering activities.
www.nkom.com.qa
Darwish Interserve Facility Management (DIFM) has come a long way, from being a subsidiary of How United in 2010 under the alliance of the Chairman Mr. Yousuf Al Darwish and CEO Mr. Abdul Rahman Al Darwish, to an independent company with world-class operations providing various services to the public and private supply chains in the State of Qatar, under the management of Mr. Mohamed Saadeh, General Manager. He was also able to usher DIFM to become one of the leading companies in the management of utilities and services in the Qatari Market.
DIFM services are based on scientific principles and practical practices, that ensure the best results in all aspects of our existing and future customers’ buildings, providing them with reassurance about the maintenance of their buildings and facilities in a manner that ensures the efficiency of its work for the duration of stay and at the lowest cost. DIFM has a professional team of highly qualified and experienced professionals in the management of facilities, services, operation and maintenance. DIFM also uses the latest technologies to provide integrated solutions for managing facilities and services at a competitive cost, and international best practices in the field of health, safety and the environment. Therefore, DIFM provides a complete package in the management of facilities and services in order to expand our business to all supply chains, including facilities and administrative buildings such as:
• Ministries and government agencies
• Banks and financial institutions
• Hospitals and medical centres
• Educational facilities such as universities, institutes and schools
• Entertainment and commercial centres and major markets
• Conference and exhibition centres
• Towers and residential communities in new cities
• Airport facilities and services
• Museums, cultural centres, hotels and marvels
• Sport facilities such as clubs, stadiums and gymnasiums
The level of satisfaction between clients and DIFM reflects the company’s vision: To provide a competitive and professional service and add value to the client’s business operations through the application of world best FM practices, innovative business solutions, with trained and motivated staff, and ultimately, understanding the client’s needs and achieving their satisfaction.
training courses, coaching, and mentoring all feature as part of this ground-breaking new scheme.
Furthermore, the internship programme at Milaha is another effective way for students to gain exposure to a real work environment and helps them to make informed decisions regarding their future employment. The target is to provide Qatari high school students with valuable, practical work experience. University and college students can also complete a mandatory work term period which is essential for their college programme. These processes represent an opportunity for the company to evaluate students and consider them for future employment, a forward-thinking strategy to secure the best possible future for Milaha.
Milaha has been providing Qatar and the region’s shipping, leisure and industrial sectors with efficient,
– ENG. MOHAMMED SWIDAN, I PCEO, MILAHA
trustworthy services for the last 30 years.
Strategically located in the south of Qatar in Mesaieed Industrial City and in proximity to the new Hamad Port, Milaha Shipyard mainly operates across four marine business sectors: offshore vessels, navy and coast guard units, yachts and commercial ships.
The shipyard occupies an area of 150,000 square metres, and operates two floating docks, one syncrolift, and extensive workshop facilities needed to perform dry-docking, maintenance and repair services for vessels.
Recently the shipyard has launched a new AC repair shed to accommodate vessels up to 50 metres. In addition to the marine sector, the shipyard also provides onshore plants repair, maintenance and shutdowns, and has major long-term contracts with oil companies.
These operations are supported by a comprehensive management system based on ISO 9001, ISO 14000 and OHSAS 18000, as well as modern processes and procedures to ensure the highest efficiency, quality and on-time commitment to all Milaha’s customers.
“OUR LONG-TERM PARTNERSHIP WITH MICROSOFT IS BUILT ON TRUST AND INNOVATION, THE KEY PILLARS OF OUR DIGITAL TRANSFORMATION JOURNEY”
Milaha works diligently to minimise the impacts on the environment associated with its operations, and to increase the sustainability of the business through the implementation of its environmental management system. This system provides the framework for carbon intensity reduction, waste and emission management, sustainability of resources, and compliance with national and international regulations.
Committed to protecting and improving the health and safety of all individuals associated with the company, Milaha imparts a safe, secure, and healthy work environment. The integration of safety principles into everyday business activities and striving to continually ensure that the company’s activities are carried out in a safe and ethical manner, is recognised by Milaha as essential to achieving health and safety excellence.
“During the COVID-19 pandemic we developed a number of initiatives such as ‘No Employee Left Behind’ to ensure our employees’ wellbeing, and to make sure our valuable staff are aware of all the health and safety procedures and measures required during the pandemic period,” continues Eng. Swidan.
“We have also signed the Neptune Declaration and worked with various stakeholders to allow crew and sea farers relief and replacement. Besides this, we also worked on strengthening our health and safety practices with strong results to date,” he adds.
“OUR PLAN FOR THE FUTURE IS TO USE THE LATEST NEW TECHNOLOGY TO SOLVE CUSTOMER PROBLEMS, CREATE A MORE SEAMLESS AND FRIENDLY EXPERIENCE AND PROVIDE MORE INSIGHT TO CUSTOMERS”
– ENG. MOHAMMED SWIDAN, I PCEO, MILAHA
Going forward, Milaha is working on building more innovative solutions for customers using existing technology. In this way, the company has experimented with dronebased survey work, remote subsea inspections, and dynamic pricing for services, among other new innovative, technological strategies.
“Our plan for the future is to use the latest new technology to solve customer problems, create a more seamless and friendly experience, and provide more insight to customers,” adds Eng. Swidan.
“Our long-term partnership with Microsoft is built on trust and innovation, the key pillars of our digital transformation journey,” he acclaims.
“We look forward to adopting new Microsoft technology tools and solutions to ensure the guaranteed security and productivity of our workforce and our technology platforms, as we strive to safeguard and develop the continuity of our services from Qatar to the world.”
This forward-thinking approach, combined with a highly efficient level of adaptability to new technology, places Milaha in an enviable industry position, prepared for inevitable shifts within the sector, and ready to pivot alongside these changes to ensure the continued excellence of service.
As is maintained in the company’s core values, the history of Milaha is a source of immense pride for the company, but a firm eye must be
kept on the future, in order to leave a valuable legacy.
“The key strengths that differentiate us from our close competitors include our reliability and diversity. In offering integrated supply chain solutions that serve a wide range of industry leaders, we can attribute our success to being a one-stop-shop for different maritime and logistics needs,” Eng. Swidan concludes proudly.
MILAHA Tel: +974 4494 9666
CorporateComms@milaha.com www.milaha.com
When it comes to navigating the often-challenging European construction industry, Staticus has taken centre stage for providing long-term value for its clients, partners and society. We catch up with CEO, Ausra Vankeviciute, on smart building concepts and construction with an environmental conscience
Writer: Ed Budds | Project Manager: Nicholas Kernan
For me personally, it’s always been all about the architecture – the art behind it, the idea of knowing what cities are going to look like in the future, and how we can make an impact upon that. It’s truly amazing and inspiring.”
It was this original allure of the construction industry that enticed Aušra Vankeviciute, CEO of Staticus, to dive headfirst into the sector in which her family was already immersed.
From humble beginnings 20 years ago as a small family-owned enterprise, which Vankeviciute was born into, her current tenure and career to date can clearly be seen as a series of natural progressions for someone born and raised in such a construction-oriented environment.
“In general, it’s very interesting to see what is happening in construction across Europe at present,” she opens enthusiastically.
“Firstly, there was the chaos of the COVID-19 pandemic which brought challenges for the supply chain and
Ausra Vankeviciute, CEOrequired adjustments. Now, with the war in Ukraine, the European market has once again been affected by a shortage of materials and prices have continuously been raised, which has happened alongside the rising costs of the energy crisis, so there have been several major hurdles to overcome in recent years,” she continues.
However, Vankeviciute remains optimistic despite these recent obstacles; “as Winston Churchill once said, never waste a good crisis!”
As a company, Staticus believes that this is the perfect time to bring about real change in the industry and improve on current issues such as sustainability. The belief is held that the entire construction sector must now all work together to find solutions for the long-term, in an industry that is forced to continuously shift and mutate in response to new challenges.
“Departing an era where most of the industry relies on Russia for gas, we can now embrace renewable energy, so we must dive deeper
into using new technologies to decrease our carbon emissions in the construction industry. I find with all these new challenges we have been encountering, that it is vital to spot the opportunities and to remain optimistic about the bright future of the industry,” offers Vankeviciute.
Through constantly developing processes, investment in R&D, and commitment to incorporating the very latest technologies, Staticus enables its clients to set new standards in aesthetics and sustainability with every project.
“We build lasting partnerships, and we ensure people always come first. We also understand what it takes to make partnerships work because we have spent 20 years building them.
Staticus delivers tailored and innovative solutions designed to fully realise the concept of the architect and the client. To do this, Staticus engages early in the process, developing prospective solutions with all stakeholders’ concept designs and consulting closely with the client. This intricate process includes:
• Early-stage consultation: early involvement allows Staticus to design energy-efficient façades, choose suitable recycled materials, and optimise panelization
• Concept design development
• Advice on the technical feasibility of the project
• Customised project solutions
• Budgeting and cost planning
“For us, long-term cooperation is always rooted in aligning different interests and knowing when and how to be flexible,” says Vankeviciute
Health and safety is the foundation of all work, culture and practices at Staticus.
“We never compromise when it comes to keeping our team, our partners, and the public safe. Respect and the continual pursuit of knowledge and excellence are also central to our culture,” she adds.
It is through this cautious and effective methodology that Staticus has expertly carved out a solid industry standing as a leading façade
contractor in Northern Europe, specialising in unitised curtain wall systems.
“We now leverage a wealth of experience and our strong competencies in innovation to deliver benchmark-setting projects that maximise long-term value for our clients and society,” says Vankeviciute.
As a family-owned business that has grown and developed sustainably over a substantial period, the company understands the importance of having a long-term perspective, a key trait for securing longevity in the ultra-competitive construction industry.
Sthlm 01, SwedenWICTEC Modul air is a closed cavity system solution with a 10-year guarantee, which unites the unitised façade, dry air and solar shading systems. Therefore you receive façades, solar shading devices, dry air system, manufacture and installation by certified WICONA partners, maintenance and guarantee – all from one source.
Staticus has made commitments to looking after and preserving the natural environment of the planet. The company’s dedicated sustainability team oversees each individual project, assessing the carbon footprint of the façade’s design and production.
“We totally commit to our partners, building close and collaborative relationships with the clients and suppliers we work with. This includes taking a proactive approach to each project we work on. Our experienced team provides earlystage interventions to ensure the best possible result in terms of architectural vision, performance, and sustainability,” Vankeviciute adds.
Alongside this, the company’s endto-end value chain enables Staticus to implement genuine life cycle thinking. Furthermore, this is combined with the constantly improving environmental performance of the facilities and the plan to dedicate time and resources to developing
lower-carbon façade technologies.
“Above all else, we also commit to people. We subscribe to the very highest standards of health and safety in the industry in order to keep our team, our partners, and the public safe. Our people-first culture within the company aims to create the
conditions for every team member to develop and thrive,” she describes.
Staticus has been consistently delivering innovative, high-quality façades for two decades now, and this long-term, safety-conscious and sustainably-minded approach is what enables the company to consistently
Prisma, Sweden Okern-Portal, NorwayIn the centre of Oslo, just a stone’s throw from the offices of Schmidt Hammer Lassen Architects, stands the iconic VIA office and retail complex. The architecturally striking building complex is a new symbol of the Norwegian city, representing urban life in the metropolis. But the real highlight of the BREEAM-certified building is the innovative closed cavity façade by WICONA.
With exclusive boutiques, premium offices and parking facilities, the striking VIA building complex is a focal point of the city’s bustling business district. The building fits harmoniously into the city’s urban landscape with its fjord, numerous cultural sights and pulsing nightlife. Most of all, the remarkable architecture with shimmering curved façade helps establish VIA as the new focal point of urban life in Oslo. The design by Schmidt Hammer Lassen Architects interprets the characteristics and heights of the surrounding structures with unique architectural expression.
Sustainability was a particular focus during planning. The VIA is intended to be a pioneer in environmentally friendly construction and resource conservation. This is particularly evident in the use of recycled materials from the building that previously stood on the site. The aim was to recycle and reuse as much as possible, as Unn Hofstad, Sustainability Manager at property developer Storebrand Eiendom, explained: “It’s such a shame that perfectly good materials and products are thrown away when a building is demolished. The challenge is to use resources responsibly and keep them in the cycle.” In addition to recycling old material, the building also features a holistic energy concept that incorporates photovoltaics and green roofs.
WICONA’s WICTEC Modul air closed cavity system proved to be an ideal solution for the façade design due to the exposed inner city location with its heavy traffic, high noise pollution and high wind loads. In this special double-
shell construction, the profile system accommodates the inner glazing and the outer frame of the impact pane. The glazing technology is designed to create a cavity that is sealed off from the environment. Monitored by a cloudbased monitoring system, conditioned air with minimal overpressure is introduced into this intermediate space. This prevents moisture from the exterior or interior from entering the cavity. The sun protection designed as a Venetian blind solution also remains clean and protected within the cavity. It can be adjusted to suit the individual needs of the user, thanks to an intelligent control concept. This guarantees a pleasant room climate, optimum transparency, effective glare protection and maximum energy efficiency at all times. As part of the ventilation concept, the building is cooled passively by means of narrow ventilation flaps integrated into the windows.
Looking at the entire life cycle of the façade, the chosen solution is particularly convincing as it requires significantly less cleaning. Since the sunshade is integrated into the cavity, it is protected from the inclement weather of the coastal region. This ensures full functionality at all times. Approximately 880 closed cavity façade elements installed on the cladding of the VIA also contribute greatly to the energy efficiency and environmentally friendly construction of the building.
The closed cavity system reduces heat loss in winter and, in combination with the sun protection and automated night cooling, offers very good thermal protection in summer. WICONA’s Project Manager, Marco Theisinger explained that, “the system achieves a Ucw value of around 0.54 W/ (m2K). On top of that, the façade solution has excellent sound insulation that far exceeds the value of 39 dB required by the client. This way, the façade offers maximum user comfort over its entire life cycle, with comparatively very low maintenance costs.” The closed cavity system used on the outside of the VIA is perfectly complemented in the inner courtyard by the WICTEC EL evo element façade – a total of 1,133 elements of the highly insulating system were manufactured and installed especially for the project.
With the VIA, Oslo now has an architectural showpiece right on its famous fjord – a powerful statement for future-oriented and sustainable construction.
win and implement such impressive and benchmark-setting projects.
“We now have a very strong track record across the Northern European market and have built a reputation for going the extra mile. We have also delivered the first ever project in the region to use Closed Cavity Façade technology. And, with our R&D team working on new innovations in Internet of Things (IoT) and hybrid façades, we aim to continue leading the way in the façade industry.
“Recently our building ‘VIA vika’, in Oslo has been shortlisted in two categories at the Façade 2022 Design and Engineering Awards. The winners will be announced on the third of November 2022, and this is already a huge win for the company,” Vankeviciute acclaims.
The Staticus team and its slate of exciting developments continues to grow at record speed.
“We are currently focused on
JAGER FREIGHT LTD was formed in 2012 as a small garage, with a single van for local deliveries to residential construction sites only.
This year we are celebrating our 10th anniversary and pride ourselves as a trustworthy partner of the London construction industry. Over a decade of steady growth has allowed us to expand into an international freight forwarding company.
Jager Freight has an international haulage branch in Lithuania, warehouses in London, our own fleet (with FORS, CLOCS certificates) and a customs clearance division to help with BREXIT issues.
Our dedication to the construction industry is to provide A-Z tailored logistics solutions to our valued customers in this highly regulated sector.
entering new markets, as this year saw the company secure its first projects in Denmark and Iceland. We are also continuing to roll out agile project management, on top of working on pioneering R&D projects, and there is a lot more happening even beyond this.”
After last year’s major drive on rebranding the business, Staticus has embraced a new visual identity.
“We realised that our visual branding and company identity wasn’t keeping up with all these other key developments. It did not fit an innovative international company working on complex and cuttingedge projects, so needed upgrading,” she adds.
With this in mind, Staticus has created a new visual identity that better represents the company as it exists today. This was of course completed with one conditionthat it still reflected the reliability, high-quality standards, and, most importantly, a commitment to the long term, all of which remain key to
Over the years, our gathered knowhow from a number of delivered construction projects allows Jager Freight Ltd to form long-term partnerships with our customers and suppliers based on trust, safety, mutual understanding and always staying behind our slogan:
- to get the job done!
Unit 4, 434 London Road, Grays, RM20 4DH, UK sales@jagerfreight.com +44 (0) 203 773 1544 www.jagerfreight.com
Lexington, UK“OUR NEW VISUAL IDENTITY IS FRESH, EMPLOYING CLEAN ELEMENTS TO EFFICIENTLY COMMUNICATE HOW INNOVATIVE AND FORWARD-THINKING WE ARE”
– AUSRA VANKEVICIUTE, CEO, STATICUS
the core brand values that Staticus has worked tirelessly to establish.
“Our new visual identity is fresh, employing clean elements to efficiently communicate how innovative and forward-thinking we are, while its timeless visual language also reflects our commitment to the long term, and to our partners.”
Staticus is a truly international company and continues to expand its presence both in terms of where its team is based, and which markets it operates in. Comprising more than 600 staff members, the company has delivered or is currently working on projects in seven different countries:
Norway, Sweden, Denmark, Finland, the UK, Iceland, and Lithuania. This is in addition to Staticus’ active operations in the Netherlands, Belgium and Luxembourg.
“Our international team has seven offices at present and our headquarters and production facilities are located in Vilnius, Lithuania, with our sustainability team based in Basel, Switzerland. We also have offices in London, Vienna, Kaunas, Oslo and Stockholm, and our team members come from all four corners of the European continent.”
Creating a motivational work environment has been a key attribute to Staticus’ ongoing success. In this way, working with non-traditional structures has helped to showcase
the company’s refined qualities of adaptation and innovation.
“We are hungry, open to new possibilities, and very transparent in our way of working. Our agility to introduce new technologies is a source of great pride for the company. We see ourselves as pragmatic visionaries with the ability to stay agile, unlike many traditional construction companies, and it’s been a beautiful journey so far,” concludes Vankeviciute triumphantly.
Tel: +44 (0)660 9121260
+370
PHOTO:The world’s most renowned philosophers, from Socrates to Aristotle, have for centuries wrestled with the idea of what defines good living.
For Vita Group (Vita), good living is about what gets us up in the morning, what drives us to improve, and being progressive.
In redefining tomorrow’s urban living, Vita enables residents, colleagues, investors and local communities to have the best possible opportunities to flourish.
“Property is about more than just bricks and mortar. For brands like us that operate and run properties as well as build them, the main focus is on customer experience,” opens David Ancell, Chief Brand Officer at Vita.
“Ultimately, we are reimagining lifestyles, which is a really exciting challenge for us. We’re looking at how people live, work, play and socialise.”
David Ancell, Chief Brand OfficerFounded in 2012, Vita started out as one man’s mission to revolutionise
student accommodation in the UK.
Uninspired by characterless halls with no real attention to detail or focus on providing an environment for students to succeed, CEO Mark Stott wanted to put young academics first and give them the best possible
It began in Liverpool with Vita Student, one of five unique lifestyle brands that span life’s various stages.
“We have five core residential brands, which are Vita Student, Vita Living, House of Social, Union, and Symphony Park,” Ancell tells us.
“Today we’ve delivered 28 buildings across 16 cities, and we’re now about to expand Vita Student into Europe with our first two schemes in Barcelona.”
Having recently opened Vita’s first Spanish offices in Barcelona, to complement the company’s existing offices in the UK, Middle East and China, construction is now well underway at Vita Student Pedralbes in the Catalan capital as the business
begins its €350 million Spanish expansion programme, as part of bringing ‘the world’s best student accommodation’ to Europe.
Vita Student Pedralbes will create 274 beds and tap into Barcelona’s superb reputation for outstanding higher education on the international stage.
Indeed, the city attracts over 40,000 students from all over the world each year and has a total student population exceeding 200,000, making it the ideal place to kickstart Vita’s expansion across the continent.
“We’re focusing on Spain as our first
expansion into Europe, but after that, there are more European countries that we will be targeting,” adds Ancell.
Set to open in September 2022, the design-led Vita Student Pedralbes building will create a thriving community thanks to the very best amenities, including private study and dining rooms, a state-of-the-art gym, swimming pool, lounges and hub spaces.
“It’s really an urban oasis, as we call it. It’s next to the main university campus, it’s got extensive grounds, lots of amenities and shared spaces, and that will be our first building to open outside the UK.”
VITA STUDENT – Offering the very best student living experience. The place to ‘Begin Big’, Vita Student marries world-class amenities such as co-study suites, gyms, and private dining rooms with outstanding resident-focused services supporting wellbeing, community, and future careers.
VITA LIVING – Designed to exceed the expectations of professionals living in the city, Vita Living leads the way in urban living. High-end furnishings and best-in-class amenities extend the home to create the perfect environment for residents to thrive.
HOUSE OF SOCIAL – Providing unrivalled access to university campuses and the city, with design-led shared apartments which encourage collaboration, independence, and productivity.
UNION – Mobilising an army of young professionals and the soul of the city, Union co-living apartments make city living affordable and create shared spaces for sharing memories.
SYMPHONY PARK – With outstanding services and amenities such as wellness spas, restaurants and residents’ bars, Symphony Park is luxury senior living designed to empower the independence of its retired residents.
As a Peter Tyson client you are able to enjoy the benefits that come from a business established for over 50 years, having the highest standards of service and customer care.
We provide Audio/Visual solutions from leading brands such as Philips, Samsung, Bose, LG and many more.
Peter Tyson offer a full design, supply and installation service throughout the UK with a team of dedicated professionals.
We are delighted to be associated with Vita Group, as one of our many nationwide clients who have benefited from our bespoke commercial installation offering.
View Peter Tyson online at petertyson.co.uk or email hoteltv@petertyson.co.uk
Matrix Fitness is the commercial division of Johnson Health Tech and is one of the world’s fastest-growing commercial fitness brands with a reputation for best-in-class, innovative equipment and creative problem solving.
Following an extensive review process, Vita Group has renewed the partnership with Matrix Fitness which has existed since 2016, having partnered with them across over 20 sites and four different brands already. The latest installations include the brand-new Touch cardio range and the Virtual Training Cycles at Vita Student Cannon Park and Vita Student Cardiff opening in September 2022.
“We are delighted to be renewing this already long-lasting partnership with Vita Group,” Tony Vaughan, Strategic Key Account Manager, Matrix Fitness UK, adds.
“Across its entire portfolio, Vita Group invests in providing a luxury, premium spaces for each and every site, and we’re looking forward to continuing to support them upholding the higher level of service they are renowned for.”
No matter what your space, budget or needs, you can be sure that everything you get from Matrix will offer the same performance, functionality and durability that you’d find in the world’s finest health clubs, plus technology that makes the exercise experience just as entertaining as it is invigorating. As leaders in residential wellness, we can make your fitness centre a highlight of your offering...
Hygienic and easy to clean
Acoustic backing
Sustainable flooring
Strong and long-lasting
Elsewhere in Barcelona, Vita Student Poblenou will bring a further 349 beds once it opens in 22@district, another of the city’s student hotspots, early in 2023.
“The popular 22@district is a big regeneration area but it’s hugely vibrant, and we’ve got 349 beds being delivered there early next year. We’ve also recently secured a new site in Madrid for 588 beds, which will be delivered in 2025,” Ancell shares.
Once Vita Student Poblenou is open, Vita will directly create more than 50 new jobs in Barcelona as a result of the two developments. The company is also expected to indirectly contribute to around 750 jobs throughout Spain, as it looks to meet Barcelona’s growing demand for purpose-built student accommodation and ease existing pressures on the city’s housing stock.
Back in the UK, Ancell highlights the recently completed Circle Square mixed-use scheme in Manchester, a joint venture with property provider, Bruntwood SciTech.
Bordered by both Manchester Metropolitan University (MMU) and the University of Manchester, Circle Square is the city’s newest vibrant student neighbourhood, complete with 24/7 access to a private gym as well as movie, private dining, study and games rooms.
“Circle Square has 1,000 student beds, 683 residential apartments, 1.2 million square feet (sq ft) of office space, 100,000 sq ft of shops and restaurants, and 5.7 acres of public realm, a big green space where we hold events,” outlines Ancell.
Two 32-storey towers are also coming to St. John’s, Manchester’s newest city centre neighbourhood. Union, the co-living brand for young professionals, will create 1,676 beds with a mix of studios and sharing apartments and offer a host of fantastic amenity spaces, designed to create thriving communities.
“Union is basically a reinvention of the professional house share. The towers are being delivered across two phases; it will be a big delivery for us and the first Union brand in the UK,” Ancell informs us.
In neighbouring Cheshire, meanwhile, Vita has revealed plans for its first Symphony Park development with the mission of creating a retirement community of the highest standard.
Promising to break down the preconceptions surrounding senior living, the luxury over-65s development at Heatherley Woods will deliver 159 apartments, each featuring beautifully styled interiors, with services and amenities akin to a grand five-star hotel.
SALESUK@2TEC2.COM 2TEC2.COM The plans for the project demonstrate Symphony Park’s
Collection: Hybrid Reference: Union apartmentsthirst for premium architecture, and creating sought-after spaces with real kerb appeal that respond to their residents.
“Symphony Park, our new over-65s brand, is all about creating a best-inclass retirement living experience. The apartment scheme in Cheshire will be delivered in 2025,” Ancell reveals.
Over the last decade, Vita has evolved into an intelligence-driven platform, one that is constantly harnessing data and insights in order to inform innovation.
Data streams are continually fed into Vita’s innovation hub, the Vita Lab, where the company puts insights to the test.
Vita looks at behaviours, trends, and new technologies to shape and create new products and services, as well as evolve its existing portfolio to reflect new audiences, demands, and ways of thinking – it’s urban living reimagined and keeps the platform at
the cutting edge of tomorrow’s living.
“Every time we create a new building, we bring insights from the Vita Lab into the design and service approach. I think that’s what really separates us; we’re an end-to-end platform,” says Ancell.
“Because we’re an end-to-end platform, that allows us to learn so
much about how people live. Other developers will just sell the building once it’s built, so they never actually take those learnings.”
For example, Vita learnt through student insights that some academics didn’t want the full Vita Student experience, but a more independent lifestyle.
DAVID ANCELL, CHIEF BRAND OFFICER: “I have actually spent most of my career working in advertising and branding. I was then approached by a recruiter who said there was a property company interested in talking to me.
“I had never thought about moving into property, but when I met Mark, he explained that what they did at Vita was create branded experiences that really reinvent how people live, so that was what hooked me in.
“We’re about developing property brands around the needs of underserved tenants across different demographics, understanding their needs and lifestyles, and developing world-class branded living experiences and environments in which they can thrive.”
Symphony ParkThat gave birth to the House of Social brand, whose design-led shared apartments provide an escape from convention and a place for independent minds to belong.
“There’s a number of different innovations in our products across a whole range of areas that have been born out of the insights we’ve got from having students and professionals living with us,” Ancell states.
“We get insights from how people are interacting with our existing brands and using the buildings. We realised, for instance, that people can’t easily hold proper dinner parties and gatherings in a small studio or one bedroom flat, so we created private
dining rooms in our buildings that can be booked out and create extra space for entertainment.
“People have also said they don’t want to socialise all the time, that they want to have time to themselves, so we’ve introduced things like quietzone libraries where people can escape to,” he continues.
Over the last decade, the platform has grown considerably and continues to do so. Helping to drive that growth is Vita’s team of over 580 colleagues, from planning and design to marketing and operations.
“We’re all about developing our staff and promoting from within.
“We’ve got lots of training schemes that bring people through and develop them as individuals and professionals. For us, the treatment and development of staff is absolutely vital,” Ancell says.
On target for turnover of around £300 million this year, Ancell likewise recognises the importance of Vita’s supply chain to the company’s growth.
“The growth of our supply chain, and suppliers coming on a journey with us, is really important,” he emphasises.
Expanding into Europe and with an up-and-coming portfolio of brands, the next decade of Vita’s journey to redefine urban living is set to be as exciting as the first.
Tel: 0161 322 2255 info@vitagroup.com www.vitagroup.com
“WE GET INSIGHTS FROM HOW PEOPLE ARE INTERACTING WITH OUR EXISTING BRANDS AND USING THE BUILDINGS”
– DAVID ANCELL, CHIEF BRAND OFFICER, VITA GROUPSymphony Park
Membrane architecture is an art founded on the harmony between form and structure. Like the perfect architecture of a bird’s wing, a membrane structure is centred on both elegance and longevity, leveraging the strength and resilience of tensile stresses.
Iconic landmarks such as the O2 in London (formerly the Millennium Dome), Denver International Airport and the Khalifa International Stadium in Qatar spring to mind. All these structures have one thing in common: Taiyo Kogyo Corporation (Taiyo) - an established global leader in membrane architecture for over a century.
“I firmly believe that our longlasting success is based on the accumulation of trust and belief from our clients in our quality and commitment to executing and delivering outstanding results, achieved through the hard work and dedication of our employees and global partners,” introduces President and CEO, Yuki Nomura.
Steeped in heritage, Taiyo was originally founded in 1922 as Nomura Tent Shokai, by Nomura’s great grandfather, Kaneshige Nomura. After a turbulent period during the Second World War, the company was re-established in 1947 by the second generation of Nomura’s in its current incarnation as Taiyo Kogyo Corporation.
Following in his family’s footsteps, Nomura himself joined the company in 2008, climbing the ladder to become President of TSP Taiyo – the event planning and consulting group company of the wider Taiyo group, in 2017. It was only in March of this year that he stepped into the role of President of the wider corporation.
Celebrating a century in operation, Taiyo Kogyo Corporation is both a veteran and innovator of tensile membrane construction. Yuki Nomura, President and CEO, discusses a landmark legacy and sustainable futureWriter: Phoebe Harper | Project Manager: Ryan Gray
With wide-ranging expertise honed over its extensive legacy of operation, Taiyo specialises in the engineering, fabrication, construction and maintenance of membrane products, ranging from tensile membrane architecture to civil engineering solutions and logistic products.
“Our products are delivered to a wide variety of clients and customers, such as general contractors, architects, facility owners, event planners, government authorities, local governments, and private companies,” Nomura explains.
Complementing the corporation’s services are additional group companies, including TSP Taiyo, which specialises in event planning and consulting, and ACTIO, which manages the operation of events and facilities. In total, the entire group’s operations amount to 34 companies across the globe.
“Taiyo Kogyo Corporation has more
than 550 employees within branches and sales offices across Japan, and more than 4,500 employees within the whole Taiyo group worldwide.
“We also have global subsidiary companies in Europe (Taiyo Europe GmbH), Middle East (Taiyo Middle East LLC), USA (Birdair, Inc.), Australia (MakMax Australia), China (Shanghai Taiyo Kogyo), as well as in Cambodia, Thailand, Indonesia and Mexico,” he elaborates.
In its century of operation, Taiyo has embarked on a series of seminal undertakings and projects. With an unparalleled geographical footprint, this encompasses structures across the globe.
“We are the only company with membrane structures executed in all seven continents (including Antarctica),” states Nomura.
For Taiyo, this series of projects began with Expos, in designing and
providing the structural housing for major international exhibitions. This started in Japan in the 1970s.
“The 1970 Expo held in Osaka was one of the major turning points of our company. Taiyo was tasked with deliv ering numerous membrane structures and pavilions for the exposition.”
This included work on the USA Pavilion, which stood out as an air supported membrane structure. Taiyo’s work on this particular building blazed the trail for the development and subsequent proliferation of air dome structures across North America in the years to follow, whilst changing the widespread perception of such constructions.
“Our work at this Expo changed people’s image of membrane structures from being “temporary tents” to “permanent architecture”,” Nomura shares.
Fast forward to today, and Expos continue to represent a major avenue of work for Taiyo.
“We are looking forward to the Expo 2025 Osaka Kansai. Our company has grown through our participation in many expositions in the past and I see this as an opportunity to give back to all those who have supported us,” he says.
Other notable worldwide landmarks developed by Taiyo include the Tokyo Dome, the Yas Marina F1 racetrack structure and the Al Wasl Plaza Dome (the centrepiece of the recent Expo 2020 and the largest projection screen in the world) in the UAE, alongside the aforementioned
O2 Dome in London and the Thyssenkrupp Elevator Testower in Germany (the tallest membrane structure in the world).
Nomura also cites the development of the Madinah Haram Piazza Shading Umbrellas on the piazza of Al-Masjid an-Nabawi in Medina, Saudi Arabia as another landmark project, particularly thanks to how this work enabled Taiyo to both grow and advance its technical capabilities. A highly advanced design, the automated retractable shading umbrellas are designed to
provide a shaded area of 143,000 square metres with a high tensile strength to withstand weather conditions whilst sheltering hundreds of pilgrims worshipping underneath.
Stadiums are another major field for Taiyo, having worked on more than 120 venues worldwide, including Qatar’s Khalifa Stadium, the La Peineta Wanda Metropolitano Stadium in Spain, and the Mercedes Benz Stadium in Atlanta, Georgia, US.
Reflecting the symbiosis of form and structure evident in any membrane design, collaboration and partnerships are the foundation of any Taiyo undertaking, regardless of scale.
“The construction of any unique structure relies on the synergy between several collaborators and partners. Together, these experienced companies, each in their field of exper tise, can work towards bringing to the client excellent, reliable and durable solutions,” comments Nomura.
“OUR LONG-LASTING SUCCESS IS BASED ON THE ACCUMULATION OF TRUST AND BELIEF FROM OUR CLIENTS IN OUR QUALITY AND COMMITMENT TO EXECUTING AND DELIVERING OUTSTANDING RESULTS”
– YUKI NOMURA, PRESIDENT AND CEO, TAIYO KOGYO CORPORATION
“Among our partners, the most important ones are our clients: we ensure that we are present in every step of the life of their structures, supporting them not only during
•
•
•
•
•
•
•
•
design and execution, but also through operation, maintenance and upgrades necessary during its use.”
As a business with such significant longevity in the field, sustainability is a key concern for Taiyo in ensuring both the continued success of the company, and the durability channelled by its structures.
This also translates to an emphasis on environmental sustainability, which represents a crucial area of focus for Nomura. By its very nature, tensile membrane architecture is one of the least harmful models of construction in terms of environmental impact.
“Membrane structures have low environmental load and are highly sustainable, due to their lightweight and highly durable nature,” explains Nomura, who is also quick to highlight a host of other contributing factors that need to be considered.
“For example, controlling the carbon emissions of our production process, or the implementation of the proper evaluation of environmental assessment,” he adds. This falls into a wider concern of addressing all manner of topical issues that reflect a responsible social conscience.
“On a personal level, I believe that we must address environmental issues, and how we can better implement digital transformation into every process of the supply chain including the development of our technology and products.
“Other issues which we address include supporting the relief efforts of those affected by war and conflict, as well as solutions for global warming by applying our technology.”
Indeed, for Taiyo, advancing sus tainability and technology go hand in hand, forming a kind of circular loop whereby each field mutually compli ments and progresses the other.
For instance, the sustainability of every membrane structure requires a qualitative and quantitative level of evaluation. These results are then fed directly back into Taiyo’s R&D team for further development.
“We therefore constantly increase our investment in R&D,” Nomura tells us.
This technological research is the vital lifeblood of the entire enterprise and fuels all future endeavours, in order to maintain Taiyo’s marketleading position at the forefront of large-scale membrane architecture.
“Our R&D organisation must be adaptable to meet the needs of the latest environmental issues together with our cutting-edge technology,” he continues.
“We are the only membrane manufacturer in the world to have a laboratory which can conduct membrane evaluation as a
third-party institution.”
Taiyo’s Technical Research Center is the dynamic nexus of this activity, located adjacent to the Hirakata Factory in Osaka. As the only membrane manufacturer with ISO/ IEC17025 accreditation, the facility is fully certified in its ability to conduct testing in line with international standards.
A continuous theme for Taiyo since its inception all those years ago, is continuing to change people’s perceptions of tensile membrane structures from temporary installations to long-lasting constructions and permanent fixtures of the architectural landscape.
“In the years ahead, our structures will become more and more part of the daily life of the citizens of many countries, with new transportation,
sport, entertainment and health facilities being built by our team worldwide,” concludes Nomura.
The group has multiple projects in the pipeline to further this goal with forthcoming works at momentous global events.
Whether travelling to a major airport anywhere in the world, attending the FIFA World Cup in Qatar later this year, or even the Olympic Games in Paris 2024, Taiyo is the historic name behind these iconic constructions.
TAIYO KOGYO CORPORATION
info@taiyo-europe.com
www.taiyo-europe.com
www.taiyokogyo.co.jp
You’ve got companies not wanting to own their data centres anymore, even shutting down their corporate headquarters, and people working remotely. On the other hand, you’ve got those that may have overcorrected a little bit in the public cloud and are looking to recalibrate where their workloads run.”
At the intersection of these two macro-workload movements sits the global data centre platform, Cyxtera Technologies (Cyxtera).
Providing deeply connected and intelligently automated infrastructure, Cyxtera enables businesses around the world to scale faster, meet rising consumer expectations, and gain a competitive edge.
For experienced technology executive Holland Barry, Senior Vice President and Field CTO of Cyxtera and orator of the opening statement, the company was his first taste of data centre service provision.
“I’ve been in technology for exactly 30 years, but I’ve always been on the consumer end of the data centre industry. I’ve been in various IT roles and part of start-ups that consumed
Writer: Jack Salter Project Manager: Marvin Iseghehidata centre colocation services, so Cyxtera is my first time behind the scenes, seeing what it’s like to be on the provider side of the business,” Barry reflects.
With more than 60 data centres in over 30 markets, world-leading data centre colocation and interconnection services are provided by Cyxtera to around 2,300 customers globally, including leading enterprises, government agencies, and various service providers.
This global network of data centres offers industry-leading performance and exceptional reliability, whilst on-demand access to secure, direct and dynamic connections allow businesses to scale and accelerate growth through Cyxtera’s Digital Exchange. The Digital Exchange offers on-demand access to solutions in four main categories: compute, storage, network, and security.
“Cyxtera has built a future-ready global platform that lets you manage and monitor pretty much any aspect of the data centre experience,” explains Barry.
“We provide our customers with access to on-demand hybrid IT
Cyxtera Technologies is helping innovative enterprises to increase agility and accelerate growth. We delve into the global data centre platform with Senior Vice President and Field CTO, Holland Barry
solutions. We are very technologyfocused, more so than almost anyone else in our industry, and have built pretty much everything that’s on our core platform from the ground up.”
Being a global platform is a true differentiator for Cyxtera, who takes a wholly API-first approach to its digital infrastructure services.
This API-first approach means clients can take advantage of futureready and extensible Cyxtera platform
features, enabling maximum flexibility, cross-platform versatility, and custom solutioning.
“We try to facilitate connections between our customers and global ecosystem of partners. If you were to take the roof off one of our data centres, you would see hundreds of customers and providers doing business with each other,” Barry says.
“It’s our job to create a fabric, an automation system to allow those people to do business together. That ecosystem is really what makes it all
As a global leader in colocation and interconnection services, Cyxtera is committed to empowering customers and partners to build sustainable businesses, minimising its own environmental footprint, fostering diverse and connected communities, and increasing trust and transparency.
ENVIRONMENTAL SUSTAINABILITY – Reduce reliance on energy-intensive resources, empower customers and partners to build sustainable businesses, and design data centres with the environment in mind.
SOCIAL IMPACT – Foster a culture of diversity and inclusion, give back to the community, and invest in employees.
GOVERNANCE – Partner with independent oversight to lead the organisation, integrate ESG across the entire corporate strategy, and strengthen governance with board diversity.
The HPE GreenLake platform powers data modernisation from edge to data centre to cloud. HPE brings a unified cloud experience to apps and data everywhere, unleashing data for companies to deliver continuous innovation to move their business forward, faster.
Cyxtera’s Global Platform empowers businesses to build their hybrid IT infrastructure through a softwaredefined platform, Digital Exchange, that offers on-demand provisioning and customisation of the elements of a traditional data centre.
Through Cyxtera Marketplace, customers access an ecosystem of solutions, such as Enterprise Bare Metal, direct cloud connect and a world of on-demand solutions offered through strategic technology service providers.
Together, HPE and Cyxtera offer a comprehensive cloud portfolio providing the outcomes you need - consumed anyway you want, wherever you want.
happen, so our API-first mindset is extremely important.”
As part of the NVIDIA DGX-Ready Data Centre Programme, many Cyxtera data centres have also been reviewed and certified as ready to meet the demands of customers implementing artificial intelligence (AI) applications, which are growing at an aggressive rate.
AI applications demand highperformance compute resources and specialised power and cooling, making it costly for enterprises to build and maintain, whilst the amount of data that needs to be managed and processed at low-latency rates is skyrocketing.
By partnering with NVIDIA, a global leader in AI hardware and software, Cyxtera ensures enterprises can deploy AI applications while avoiding many of the challenges associated with infrastructure planning, which can delay operations.
The partnership with NVIDIA is one
HPE GreenLakeof Cyxtera’s centrepiece AI initiatives, according to Barry, enabling AI workloads for NVIDIA DGX Systems customers.
“We’re also proud to be an exclusive provider within NVIDIA’s Inception programme, where they provide credits and compute resources for those who are just getting their journey started in the AI world,” he adds.
“Because we have a footprint of DGX compute systems deployed globally, premium tier Inception members can log in and get a twoweek free credit to validate their solution and carry out performance and compatibility testing, as opposed to going out and having to write a large cheque or borrowing one from someone else.”
As part of the Cyxtera ecosystem, the company is also focused on enabling the cloud service providers who are building full-service AI platforms to offer customers a
multitude of infrastructure options that fulfil their AI requirements.
“If customers need access to infrastructure, and we don’t have the right flavour or the right service on our core platform, we can easily connect them to these cloud service providers in our ecosystem who are doing AI,” Barry shares.
Cyxtera likewise works with a lot of the world’s top OEMs, like HPE, to deliver their technology within its Enterprise Bare Metal platform. Traditional HPE customers can now consume HPE-as-a-Service, for example, whilst NVIDIA customers can deploy DGX-as-a-Service.
An attractive complement to public cloud environments, the Enterprise Bare Metal platform combines the financial and operational flexibility of the cloud with the control, performance and security of enterprise-grade dedicated
infrastructure.
“If DGX is overkill for example, or might not be the right solution, it means that clients can still experience the NVIDIA platform by leveraging Cyxtera’s other OEM partners or eco system CSP partners,” Barry tells us.
Enterprise Bare Metal is an on-demand model designed to meet a broad range of workload needs. It is perfect for seamlessly extending an existing colocation environment, or rapidly expanding into new markets without the burden of capital expenditures, lengthy implementation cycles, depreciating assets, or adding to local staff.
“We describe ourselves as cloud
adjacent, and a leg of a multi-hybrid strategy which we’re seeing a lot of our customers execute on. I would even put Cyxtera in that category; we also leverage public cloud services for a certain class of workload, even though we have all the resources to run it here.
“We like to talk about ourselves in that context, so when we describe our Enterprise Bare Metal platform, we highlight why it’s different to the public cloud and why you can complement what you’re doing in the public cloud a lot of the time,” Barry outlines.
Cyxtera’s dedicated single-tenant environments are therefore the optimal venue for the workload of customers who want full control over infrastructure. At a time when most
companies have cloud-first mandates, Cyxtera ticks all the boxes.
“People are getting a little savvier around the calibration exercise of which workload is the best fit for which venue,” notes Barry.
“We’re seeing people consume a
multitude of public cloud services, and then a multitude of services from companies like ours. It’s all about that calibration with the right venues to run your workload, and we’re in the middle of those conversations.”
Another offering that Cyxtera continues to evolve and iterate on is its on-demand, single-tenant dedicated colocation cabinets.
SmartCabs come complete with built-in power and network connectivity as well as access to the Digital Exchange, accelerating time to market.
“You can think of SmartCabs as colocation on demand. These are ready-to-consume colo environments with core networking included,” Barry informs us.
“The whole idea is that you can send us your infrastructure, send us the power cord, and we’ll do the rest. You can bring that infrastructure to life without having to go through the exercise of creating a colo environment. If you have a specialised piece of equipment, you can send it to us, and we can shorten the delivery time and workload readiness for that particular piece of infrastructure.”
With SmartCabs, clients get preconfigured space and power within a Cyxtera data centre, a unified environment managed through the company’s self-service customer Command Center.
“CYXTERA HAS BUILT A FUTURE-READY GLOBAL PLATFORM THAT LETS YOU MANAGE AND MONITOR PRETTY MUCH ANY ASPECT OF THE DATA CENTRE EXPERIENCE”
– HOLLAND BARRY, SENIOR VICE PRESIDENT AND FIELD CTO, CYXTERA TECHNOLOGIES
The Cyxtera Command Center is a dedicated platform that allows infra structure to be monitored, managed, and controlled from anywhere.
With a user-friendly, mobileoptimised user interface that makes it easy to gather insights and act from any device, the Command Center allows custom reports to be created, activity to be constantly monitored, and teams to be managed with enterprise-level control and security.
Access to everything is in one place, including hardware configuration, maintenance tasks, and personnel management, which helps achieve business goals faster.
“We’re really proud of the Command Center that we’ve built, it’s something that sets us apart in the industry,” Barry acclaims.
Earlier this year, meanwhile, the company announced the newlylaunched Cyxtera Labs, a new programme that offers support and resources to accelerate customers’ innovations to market.
An encapsulation of the idea that growth can and does drive innovation, Cyxtera Labs is designed to support R&D projects by offering cost-effective, consumption-based solutions without compromising performance, control, or scale.
The programme builds off the power of Cyxtera’s Digital Exchange, to help customers connect to raw infrastructure in the form of Enterprise Bare Metal and SmartCabs.
“Cyxtera Labs is very similar to NVIDIA’s Inception programme in that it helps accelerate our customers’ prospects and ideas to market, from start-ups who maybe need a little bit of a leg up to large enterprises who may not have the budget,” states Barry.
THE LIFEBLOOD OF CYXTERA Partners are the very foundation of all these services that Cyxtera delivers to customers.
Barry describes supplier and partner relationships as the
“lifeblood” of the company. In addition to strategic partnerships with OEM partners like HPE, Barry cites the role of technology and Managed Service Providers in providing a unique, robust route to market.
“They put their extra layers of service on top, and really complete the offerings we provide as a colocation and data centre platform,” he recognises. “Cyxtera customers can then easily connect to a world of technology solutions through our Digital Exchange fabric to use on-demand, whenever they need them.”
Likewise, it goes without saying that there would be no Cyxtera without the company’s 800 or so employees.
“There is ongoing investment into educating and training staff, and we fund community outreach projects to help our employees make a difference in the community.
“We also give out what we call
Spotlight Awards that recognise employees across every functional area of the business. We’re always keeping an eye on those people who go above and beyond.
“I’m proud of the way we treat the crew here. The culture is super start-up minded, technology-focused, and we’re constantly introducing innovations and new solutions to market,” Barry smiles.
It’s thanks to the team at Cyxtera that a comprehensive portfolio of data centre and interconnection services is provided to customers globally.
CYXTERA TECHNOLOGIES
Tel: 305-537-9500
sales@cyxtera.com
www.cyxtera.com
We are at the forefront of a new age of transportation.
At the head of this frontier, electric vehicles (EVs) represent one of the most promising aspects of technological R&D in the sector for an electrified future that is better for people and the planet.
In Europe, the continental home of many internationally reputed automobile companies - BMW, Mercedes-Benz, Porsche, and Volvo to name a few –the market for EVs is vast. But for manufacturers, the space is always changing, and challenges need to be addressed.
Valmet Automotive is reshaping the way that vehicles function on roads and in industries. We speak to CEO Olaf Bongwald about the company’s innovative focus on EVs, and changing the future of mobility for the betterment of business, people and the planetWriter: Marcus Kääpä | Project Manager: Kierron Rose
“The automotive industry is at the edge of a disruptive change from combustion engines to electromobility and the technological challenges have never been bigger,” introduces Olaf Bongwald, CEO at Valmet Automotive (VA).
“First and foremost is the transformation of the industry to electromobility, in addition to digitalisation, autonomous driving and the need to design sustainable, climate-friendly mobility. Those who fail to do so may suffer from said transformation and change in the markets, and risk disappearing. For the brands in Europe, it is also a major
challenge to regain the technological leadership of China.”
Rising to such a challenge, VA takes an important role in the European EV space. VA is one of the leading European system suppliers for EVs and kinematic systems (including EV charging flaps and active spoilers) for original equipment manufacturers (OEMs) and one of the largest vehicle contract manufacturers in the world.
VA builds its strategy fully on the transformation from combustion engines to electric powertrains, with its activities divided into three primary business lines: Vehicle Contract Manufacturing (VCM),
EV Systems (EVS) and Roof and Kinematic Systems (RKS). Since its foundation in 1968, VA has produced approximately 1.8 million vehicles – for Mercedes-Benz, Saab and Porsche – at its plant in Uusikaupunki (Finland) which remains VA’s biggest plant today.
“For me personally, especially when I was young, it was a dream to run an automotive company. This dream has come true,” Bongwald tells us. “Leading an innovative company like VA in what is probably the most exciting phase in automotive history makes the task all the more interesting.”
VA operates 11 facilities in Finland, Germany and Poland, employing approximately 4,600 people.
VA currently operates three plants for the production of battery systems in Salo and Uusikaupunki in Finland and Kirchardt in Germany. In Uusikaupunki, production is under one roof for automotive manufacturing.
VA’s Roof and Kinematic systems business line runs a technology centre in Osnabrück (Germany), while production of RKS is located in Zary (Poland).
The production spectrum in battery systems ranges from 48-voltage systems to high-voltage systems and includes battery modules to complete battery systems (all cell formats).
The service portfolio in EVS covers the entire value chain:
• Concept
• Development
• Supply Chain Management
• Prototyping
• Testing and Validation
• Serial Production and Aftermarket
Ever since VA began manufacturing the well-regarded Fisker Karma –a luxury plug-in EV - in 2010, the company’s second focus has been on electric mobility beside car contract manufacturing. Proof of this is shown in VA’s new battery factory in Salo (Finland). As a system supplier, VA manufactures hundreds of thousands of 48-volt batteries every year. This is in addition to complete high-voltage battery systems for plug-in and fully EVs.
Innovation sits at the heart of VA, and has formed its spirit for more than 50 years in the industry. For Bongwald, the public discussion about the future of mobility is focused on the automotive sector.
“This comes not as a surprise; the car industry is gigantic, people love cars, and cars move society. Yet, the area of special purpose vehicles is often wrongly neglected,” he explains. “This is because the energy consumption in industries other than automotive is enormous. According to experts, greenhouse gas emissions from agriculture, forestry and fisheries amounted to over one billion tonnes of CO2 per year.
“Perhaps, as a company from Finland, we have a special sensitivity to the topic due to the strong forest industry; in any case, at the beginning there was the consideration of making a substantial contribution to reducing the CO2 emissions of forestry machines – on the one hand to enhance economic aspects, and on the other to protect the environment.”
With electrification as the leading industry trend, VA’s Modular Battery Platform offers solutions to customers of various industries with low to high production volumes. It enables OEMs to execute their electrification strategies by saving development and project costs as well as production line investments, while being able to
take full advantage of a fully proven battery system.
VA’s new Modular Power Pack is extensively tested and a safe standard battery solution for almost every possible power application, to electrify machinery and vehicles without heavy investments in R&D.
“The development of the Modular Power Pack was an opportunity to prove our capabilities as a system supplier,” Bongwald elaborates.
“It is a great success for us that Ponsse, one of the market leaders in forestry machines, relies on the battery system from VA for the Ponsse EV1 electric forestry machine concept. I am convinced that electric powertrains are the future of working machines.”
Since VA switched its focus to e-mo bility, the company has written a great success story. Despite the continued extraordinary external circumstances of the COVID-19 pandemic and
component shortages, 2021 was a year of growth for VA in all lines of business, the strongest of which was seen in its EVS business line.
“During the financial year 2021, VA’s gross sales from continuing operations increased by
Achieving the best together. This is the focus of both companies and the cornerstone for an outstanding partnership that has lasted over 10 years. The successful relationship between GTG and VALMET is based on an open, honest and critical implementation of projects at a top professional level.
GTG is very happy to have sealed the common path for further years by fixing the latest projects in 2020 and VALMET can continue to fully rely on GTG’s 40+ years of expertise in the design and manufacture of high quality sealing systems for the automotive sector.
www.gummitechnik.de
approximately 22 percent higher than the previous year, with the respective net sales from continuing operations growing by around 15.5 percent,” Bongwald tells us proudly. “Gross and net sales increased in all business lines, with the strongest growth in
GTG GummitechnikEVS. On top of this, VA’s operating profit from continuing operations increased by approximately 64 percent.”
VA achieved a new record volume in battery production in 2021 with more than 400,000 units delivered. The increase in this past and continuing volume is due to strong customer demand, the increase in production efficiency, the expansion of the battery plant in Salo, and the start of production at the Uusikaupunki battery plant.
In 2022, the production volume was continuously expanded. This makes VA a leading contract manufacturer of batteries for electromobility.
“By adding the new battery plant in Kirchardt, Germany, we further strengthen our production footprint to our battery system production network significantly,” Bongwald adds. “Small series production just started, while volume production is scheduled to commence in the near future.”
Automotive seals Special sealing systems developed for the use in household appliances High-precision elastic connecting elements for facade and window constructionOLAF BONGWALD, CEO: “VA has signed a contract regarding solar EV manufacturing with Sono Motors. The cooperation covers the manufacturing of the solar electric model Sion for a period of seven years. VA has also been nominated by Mercedes-Benz Group AG to manufacture the four-door Mercedes-AMG GT sports car. The Uusikaupunki plant will be manufacturing the four-door version of the AMG GT both as ICE and hybrid versions.
“On top of this, there are three additional developments to note: our Roof and Kinematic Systems division has been nominated by a premium OEM for an active spoiler programme for a battery EV.
“On schedule is the preparation at the Uusikaupunki plant to begin production of the Sion by Sono Motors, and the Lightyear 0 by Lightyear. This means that the two most ambitious vehicles in the field of solar EVs will be produced at VA. A decisive factor in these awards is the CO2 neutrality in production that has already been reached.
“Lastly, driven by the strong growth in our EVS division, VA was listed for the first time in 2022 in the “Top 100 Automotive Global Suppliers Ranking”, which is published annually by the trade journal Automobil Produktion in cooperation with the management consultancy Roland Berger.”
For VA, electromobility and sustainability are two sides of the same coin, and from the beginning of the company’s reach into the EV space, has remained clear in the decision to focus VA’s strategy fully on electromobility, and that this must go hand in hand with the implementation of highly ambitious sustainability targets.
“When we officially kicked off our sustainability strategy in 2019, it was clear to us that we didn’t just want to meet the customers’ requirements. We wanted to go beyond,” Bongwald says. “In our original plan, we had targeted CO2 neutrality in the group for 2024. The fact that we have already achieved this target by the start of 2022 is an outstanding achievement by our entire team.
EME Outlook: Can you tell us about any further contracts and growth aspects of the business?
“WE WANT TO BE PART OF THE SUCCESSFUL TRANSITION TOWARDS TRUE GREEN MOBILITY AND A GREENER WORLD”
– OLAF BONGWALD, CEO, VALMET AUTOMOTIVE
“Being certified CO2 neutral by the Norwegian classification society DNV CI this year is a tremendous success for our company. This means that we are a bit ahead of most competitors and one of the leaders in sustainability within the automotive industry.”
VA’s ambition is to take its place as a key player transforming the business environment, innovating new solutions, and contributing to the shift towards a zero-emission society. This year, VA launched the True Green Initiative (TGI), a programme and practical guide to accelerating green thinking and actions within VA.
This programme is also the key to ensuring competitiveness as VA responds to increasing customer, regulatory and investors demands regarding sustainability.
“Our action plan and ambitious long-term targets will continue to
secure our role as a key player for OEMs,” Bongwald tells us. “The next big thing is to implement sustainability within our supply chain. With our strategy and with our product portfolio, we want to be part of the successful transition towards true green mobility and a greener world.”
VALMET AUTOMOTIVE
www.valmet-automotive.com
October | Milan, Italy
Oil & Gas Automation and Digitalization Congress will be held on October 17-18, 2022, in Milan, Italy, and gathers oil and gas companies, EPC contractors, drilling contractors, pipeline operators, refineries, service providers and equipment manufacturers to discuss how to unlock the full potential of innovative technologies for building smart industry.
AUTOMA 2022 is devoted to the latest innovative industry trends applicable to the whole value chain of the oil and gas industry: upstream, midstream, and downstream. The congress has been organised as a place to present case-studies, exchange experience in digital transformation, and network.
AUTOMA 2022 is a closed-door
event, which means that there are only decision-makers of companies and specialists in the field of automation and digitalisation. Among the participants are representatives of TotalEnergies, Worley, MOL Group, Equinor, Petrofac, Cepsa, McDermott, TANAP, Eustream, KBR, Milazzo Refinery and TUPRAS refineries. Together they will share insights on the latest technologies and explore digitalisation strategies.
The business programme of AUTOMA 2022 is created to cover the following topics within the oil and gas industry:
• Implementing AI and ML in upstream operations
• Staying competitive in a digital world
• Impact of disruptive technologies on society
• Transportation and cybersecurity initiatives: robotics, drones
• Digital control of work as an essential tool
• Reality technologies (AR, VR, MR) for upstream
AUTOMA 2022 offers delegates several different formats of the sessions including leaders’ talks, roundtables, and a Chief Digital Officers’ opening panel in order to find out more about the latest digital projects of the oil and gas industry and how to meet companies’ needs on the journey to digital transformation.
Visit the congress website to learn more: https://sh.bgs.group/1y
HOSTED BY THE Abu Dhabi Na tional Oil Company (ADNOC), ADIPEC is the world’s most influential event for the energy industry.
ADIPEC 2022 will gather policy makers, energy CEOs and energy professionals from across the globe, to spearhead discussions focused on key global energy trends, policy formation, and geopolitical factors.
ADIPEC 2022 will accelerate the energy transition, unlock real value in a decarbonised future, showcase ground-breaking technologies and explore actionable strategies and solutions to the challenges and opportunities created by complex global energy market dynamics.
Taking place a week before COP27, ADIPEC 2022 is the global forum for leaders to reinforce strategies and commitments that will drive the industry towards reducing emissions and meeting net zero goals.
ADIPEC by the numbers:
• 150,000 energy professionals
• 140,000 gross SQM
• 2,200 exhibiting companies from across the globe
• 12,000 conference delegates
• 1,200+ conference speakers
• 350+ conference sessions
• 54 NOCs, IOCs and IEC’s
• 28 international exhibiting country pavilions
Alongside the exhibition and conferences, ADIPEC 2022 will also host four specialised industry zones that will enable the global energy industry to strengthen existing business partnerships and form new models of cross-sector collaboration to unlock and maximise value across businesses and drive future growth. These zones include:
The Offshore & Marine Zone is one of the world’s foremost meeting places for the marine transport and logistics sector to understand the latest developments in technology,
meet new buyers and develop new business opportunities with NOCs, IOCs, and IECs, service companies, EPC contractors, subsea engineering, supply chain companies and the full energy value chain. For more information, visit https://www.adipec. com/offshore-marine/
The dedicated digitalisation exhibition at ADIPEC 2022 will continue to be a global showcase of the technological solutions that can help the energy industry unlock untapped value and opportunities as digitalisation becomes more deeply integrated into all aspects of operations. For more information, visit https://www.adipec. com/digitalisation-zone/
The ADIPEC Smart Manufacturing Zone will continue to provide a unique platform for the manufacturing industry to gain insights into the energy transition and identify the challenges and opportunities for manufacturing in the drive for a net zero carbon economy. For more information, visit https://www.adipec. com/smart-manufacturing/
The newly launched Decarbonisation Zone will provide the platform for the global energy ecosystem to navigate the decarbonisation pathway. It will provide the opportunity for participants to discuss key lowcarbon technologies and the role the oil and gas sector plays in creating a foundation for the transition away from fossil fuels to cleaner energy. For more information, visit https://www. adipec.com/decarbonisation-zone/ Be a part of the conversation and shape the future of the oil, gas, and energy industry at ADIPEC 2022.
Register to attend: adipec.com/visreg
Dhabi, United Arab Emirates
Strategically taking place before
on
the industry towards
and long-term
The
Innovation
is
A taste of what’s to come at the UK’s biggest festival of construction
THE UK’S LEADING construction show returns to Olympia London’s Grand Hall on November 16th & 17th! This is going to be one major celebra tion as it opens our doors to the UK’s biggest festival of construction.
London Build is the ultimate platform for networking and connecting with thousands of seniorlevel decision-makers, buyers and influencers from across the UK’s entire built environment. Discover how you can get involved with major construction projects in the UK as you connect with industry experts and senior representatives from government, architects, major developers, housing builders, and Tier 1 contractors.
London Build plays host to eight
• 500+ inspiring speakers across eight conference stages including Future of Construction, BIM & Digital, Fire Safety, Sustainability, Diversity & Inclusion and more
• 200+ hours of CPD training and education
• The UK’s biggest festival of construction with DJs, musicians, live performances, celebrity guests, entertainment and competitions
• Meet the buyers with procurement teams exhibiting from Balfour Beatty, Skanska, Mace Dragados, BAM UK, Costain, SMP Alliance and more
• Architect’s Hub with project displays and 3D models of upcoming projects from leading architects across the UK
• The latest insights and updates on major upcoming construction projects and opportunities across the UK
• Exclusive networking events cohosted with Urbano Build, London Constructing Excellence Club, Forum for the Built Environment, The CIOB, Building People, Let’s Build, Building Equality and many more
conference stages: The Future of Construction, BIM and Digital Construction, Fire Safety, Diversity and Inclusion, Sustainability, The Skills Hub and The Built Environment Hub. Each year sees thousands of professionals attend, as they come to learn about the latest developments, innovations and case studies, from industry leaders.
Much more than just your average construction event, London Build offers a totally unique experience over the two days, featuring:
• 35,000+ registered visitors from contractors, architects, civil engineers, developers, local councils, house builders/ associations and construction professionals
• The UK’s largest networking events for Women in Construction and Diversity in Construction
• An inclusive Ambassador Programme supporting Women in Construction, Diversity in Construction and Mental Health in Construction
• 350+ exhibitors showcasing the latest services, products and innovations transforming the industry.
London Build is free to attend and promises to be two fun-filled days of high-level content, networking opportunities and endless entertainment.
Register your no-cost ticket: www. londonbuildexpo.com/eme-outlook
FROM CEOS TO engineers, The Middle East Metallurgy Corrosion and Coatings Conference & Showcase (MECOC) will bring together oil and gas leaders from every fraction of the industry. The event is scheduled to take place on November 21st - 23rd 2022 in Le Meridien Dubai, United Arab Emirates, which aims to show it self as an ideal location for the world of business and trade in the Middle East.
The conference comprises three days of valuable industry experience and knowledge exchange, featuring more than 50 sponsors and exhibitors. This is alongside a vast array of over 200 oil and gas leaders from around the globe.
Attendees will have the chance to meet new and existing clients, helping to gain a better understanding of their needs, as well as the opportunity to greatly expand your network.
This unique event gives visitors the chance to boost market exposure and promote your company, as well as build brand credibility with the extensive marketing and branding opportunities available.
Also on the agenda will be a detailed discussion on core issues within the oil and gas industry, smart and highly energised sessions and high-level networking opportunities, presentations on efficient and reliable equipment and discussions on how
to embrace the latest practices and trends in the sector. The overarching theme of the event is to collectively tackle the oil and gas digital transformation mission.
The upcoming event will also include key service providers and engineers involved in equipment design, standards, maintenance and reliability practices that evolves around the metallurgy corrosion and coating prodigy of industries in GCC by providing an all-new perspective on the technology and engineering expertise necessary to power a sustainable outcome for the industry.
This premier initiative brings together sponsors, speakers, experts, and contributing delegates to make this a truly valuable and unmissable exchange of intellectual currency and vast opportunity for anyone involved in the industry.
REGISTER NOW: Call us at +971 4 279 0800 info@aldrichme.com www.mecocmiddleeast.com
ME ROTIC IS scheduled to take place on 11th - 13th October 2022 in Dubai, United Arab Emirates to show itself as an ideal location for the world of business and trade in the Middle East. The upcoming event will gather technical experts from all over the world to discuss the latest technology related to rotating machinery for var ious sectors and to network with key industry peers. The forum will enhance communication and help in exchang ing knowledge between the major stakeholders.
At ME RoTIC 2022 be ready to witness some of the most renowned industry leaders, manufacturers,
chief engineers of oil producers, refineries, power generators and heavy industries, as they gather in this world-leading platform dedicated to rotating machinery and its innovative technology, to discover opportunities and find solutions for the current challenges within the industry.
Rotating equipment plays an important part in most operations. Critical to process plants, they are often managed separately from fixed equipment as they have different design and maintenance requirements. Rotating machinery, such as compressors, pumps, engines, generators, steam turbines, gas
turbines, turbo-expanders and more, and its technology plays a vital role in increasing productivity in today’s industrial world.
After becoming a well-established gateway for international trade, the Middle East is now recognised as an emerging market leading the way forward globally. It is a go-to destination for foreign direct investment globally, even surpassing the international market. As one of the fastest growing economies in the world, at the rate of 4.5 percent, The Middle East plays a major role in strengthening the global economy that is facing a decline, therefore making this the ideal location for such an industry-boosting event.
REGISTER NOW: Call us at +971 4 279 0800 register@aldrichme.com
www.roticmiddleeast.com
To round off each issue, we ask our contributing business leaders for their views on the same question
Yuki Nomura President and CEO, Taiyo Kogyo Corporation“I want to find a solution to bringing membrane structures to outer space. In the future, I believe that membranes have the capability of assisting construction in space and on the moon and beyond, as well as solving the problem of flying debris.”
“I would ask our industry to be more transparent and also more diverse going forward. There is a long way to go in terms of using
new technologies, and we all need to learn that without being open-minded and transparent we will not be able to bring about meaningful change. Being more open will also help the industry to become more creative.”
“I think there’s a perception that the property industry is still very traditional. Being a creative myself, I’d want to try and change the perception of our sector to attract far more people from the creative industries. Ultimately, we’re reinventing and redefining how people live, and with that the industry needs a lot of
creative thinkers. I think if you asked a lot of people in the creative industries to work for a property company, they’d probably say it’s not for them.”
“Accelerated efforts to lessen the impact on the planet with an increased focus around energy consumption, energy usage and green initiatives, and ensuring other providers are doing their part as well with a more unified approach. We have a lot of things underway, and we wish we could do them faster.”
Are you a CEO or Director with a company story to tell?
Contact EME Outlook now!
If
could change one thing about your industry, what would it be?
Now, why not tell yours? Our bi-monthly magazine EME Outlook is essential reading for business executives wanting to keep up with the latest in global news and trends affecting European and Middle Eastern businesses across all industries.
Reaching an audience of over 395,000 readers, your company can take advantage of exposure in EME Outlook with a FREE article and FREE digital brochure, as well as access to further digital and print-based marketing tools that could transform your business.
To share in this unrivalled opportunity, contact one of our project managers today!
Building on the global success of our regional titles – Africa Outlook, APAC Outlook, EME Outlook, and North America Outlook – Outlook Publishing is proud to be launching a dedicated platform for the Mining & Resources sector.
As mining organisations worldwide confront unprecedented change, embracing technological innovations and incorporating critical environmental sustainability agendas, now more than ever is the time to showcase the strides being taken in this dynamic sector.
A multi-channel brand, Mining Outlook will bring you the positive developments driven by organisations across the global mining industry through our various platforms. Discover exclusive content distributed through our website, online magazine, social media channels, and dispatches delivered straight to your inbox with a bi-weekly newsletter.
Through this compelling new venture, we intend to foreground the movers and shakers of the industry. To participate as a featured company and join us in this exciting endeavour, contact one of our Project Managers today.
www.mining-outlook.com