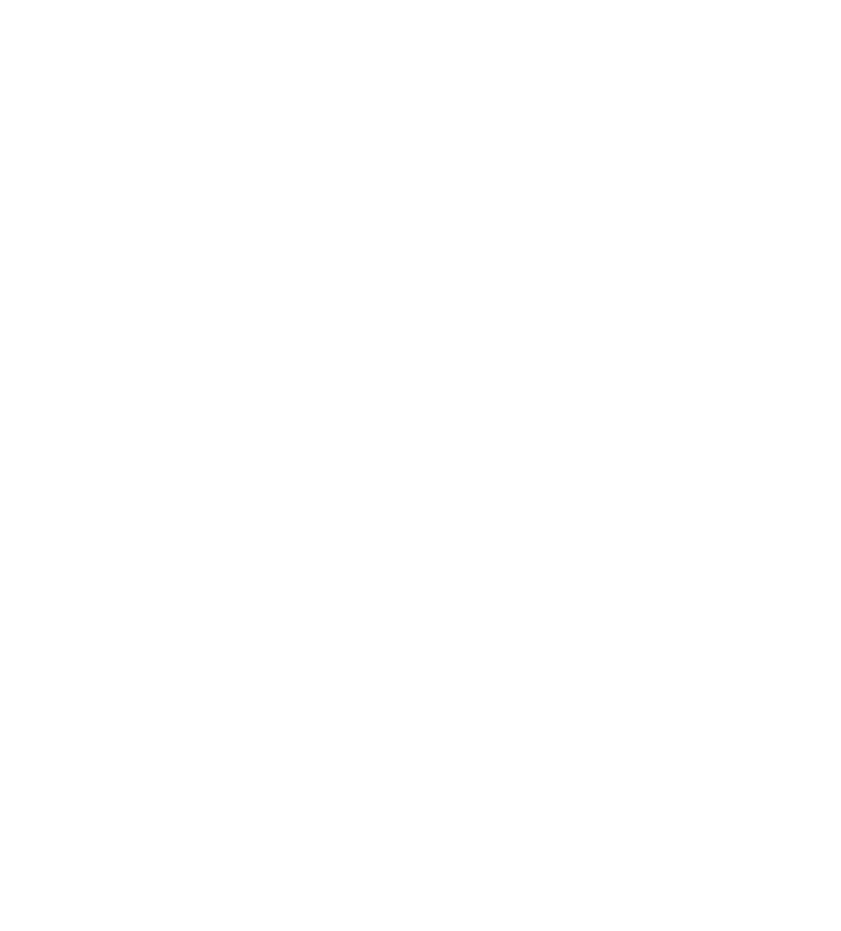
37 minute read
UMEX
Cristian Taranu is the Managing Director at UMEX. He is an experienced industry leader with a demonstrated history of working in the maritime industry and has been with the organisation since June 2018.
“In the past three years, we have focused our actions to organise a structure oriented to superior quality of services, respecting our every customer’s particular needs,” explains Taranu. “Our 350 workers are permanent employees, specialised, skilled and well trained; we can state that we have crafted a motivated and dynamic collective, respecting the working protocols, the safety procedures, the environment protection.”
In 2011, the majority stake of UMEX was acquired by an Agricultural Developer strongly present in the Romanian market, naturally, bulk cereals and fertilizers have become a key part of its activity range, which is among one of the most important port operators within the segment. For Taranu, he is clear about what sets his organisation apart from competitors and he believes that one of UMEX’s main advantages is its ability to be versatile and handle different cargo types, while performing different services to meet the company’s client’s entire logistics demands within the port. “This way, we have avoided to be restricted and interconnected to limited cargo flows, that may vary significantly and affect drastically our activity.”
Another advantage is the quality of service which is linked to the pricing policy. “A major focus of UMEX management is oriented towards the service performance, and such actions are meant to consolidate
THE FUTURE UMEX FERTILIZER TERMINAL
UMEX is constantly investing in modern technology and facilities because it aims to increase the competitiveness of its customers through increasing the standards of port operations. A vital investment of UMEX is the construction of a multifunctional warehouse for handling or storage of bulk fertilizers with a total storage of around 66,000 tonnes, divided into 10 equal compartments, two symmetrical rows of five compartments per row.
The warehouse is set to be made of reinforced concrete and will have a completely automated filling system at the upper part, with an unloading capacity from vessels of 1,200 tons/hour (2x600 tons/hour), consisting of two reversible belt conveyors with trippers, as well as an emptying system at the bottom. Each of the 10 compartments of the warehouse will have five-by-five metre access doors.
For the delivery of the cargo stored in the warehouse there will be three circuits respectively:
- The transfer of bulk cargo to ship loading bin on berth 44 to be loaded on the ship or barge with a crane equipped with grab. - Loading of bulk cargo on the truck or train. - Transfers of bulk cargo to cargo bagging facilities in bigbags. The total cost of the investment is around €18 million and is set to be completed at the end of this year.
Elica
ELICA Sweep Chain Conveyor
UNCOMPROMISING GRAIN REMOVAL
ELICA is a leading European producer of grain, seed and food handling and processing equipment. Also, it is the first manufacturer of sweep chain conveyors in Europe.
What differentiates the sweep chain conveyor from the sweep auger is that there is practically no grain left in the silo after the equipment cycle is finished. The process of emptying a silo does not require any additional manpower to shovel the grain towards the centre as it is with conventional equipment like the sweep augers.
ELICA has developed its automation, which shows the actual position of the conveyor in real-time. It helps the operators to supervise the process of emptying the bin directly from the control room. Most importantly, this proprietary software also controls the movement and the speed of both chain’s and tractor’s motors. Staging different scenarios, the automation engineers successfully built up an algorithm to automatically stop, restart or change the direction from forward to backwards if the equipment gets stuck or the pile collapsed over it.
All features of this solution now are a result of more than 10 years of research and development in that field.
ELICA’s team has more than 30 years of experience in the field of food production, seed preparation and grain processing. The company’s mission is to provide customised solutions for their clients and support them through the process - from setting up the requirements, designing the project, installing, and training to finding the right markets and solutions for managing the business.
www.elica-elevator.com

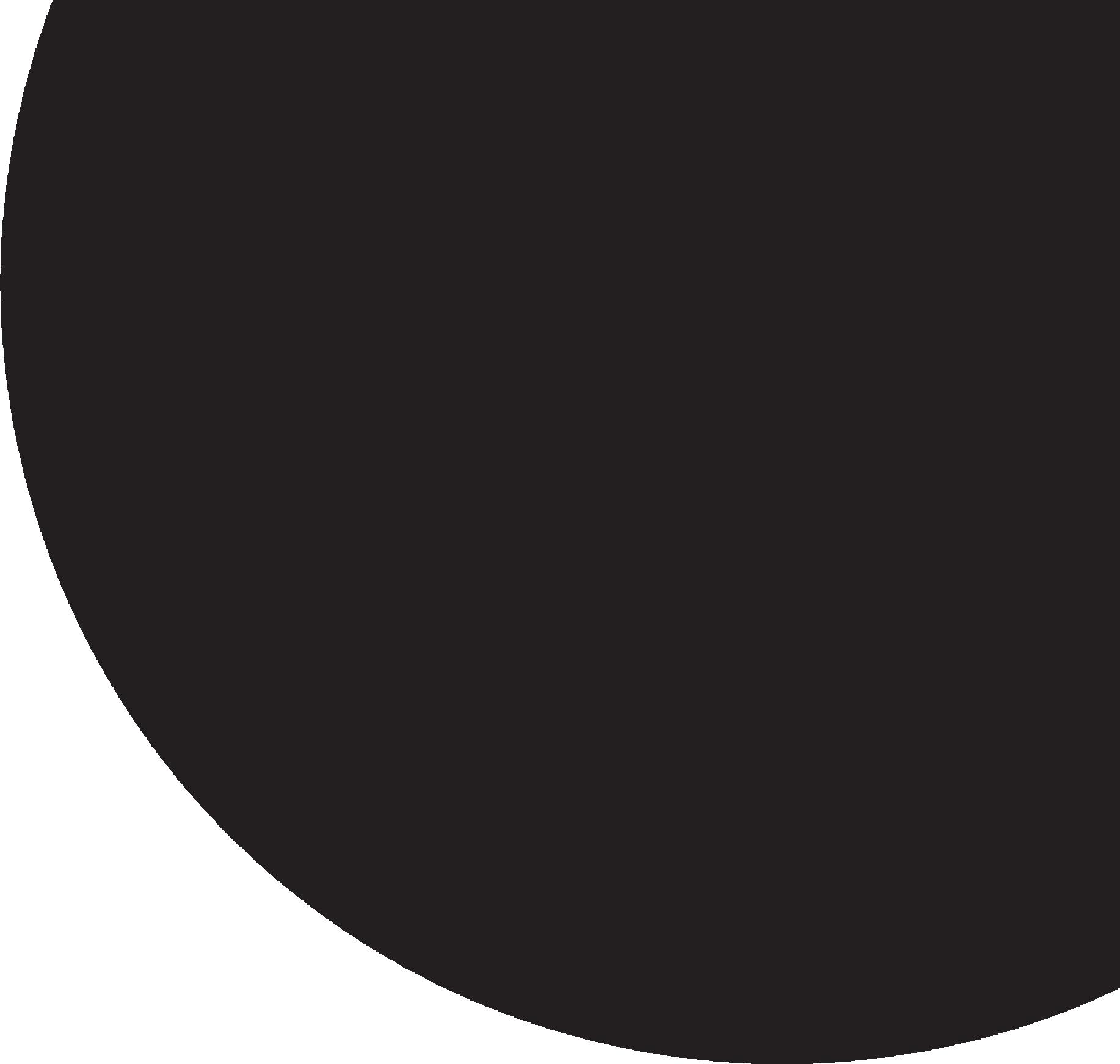
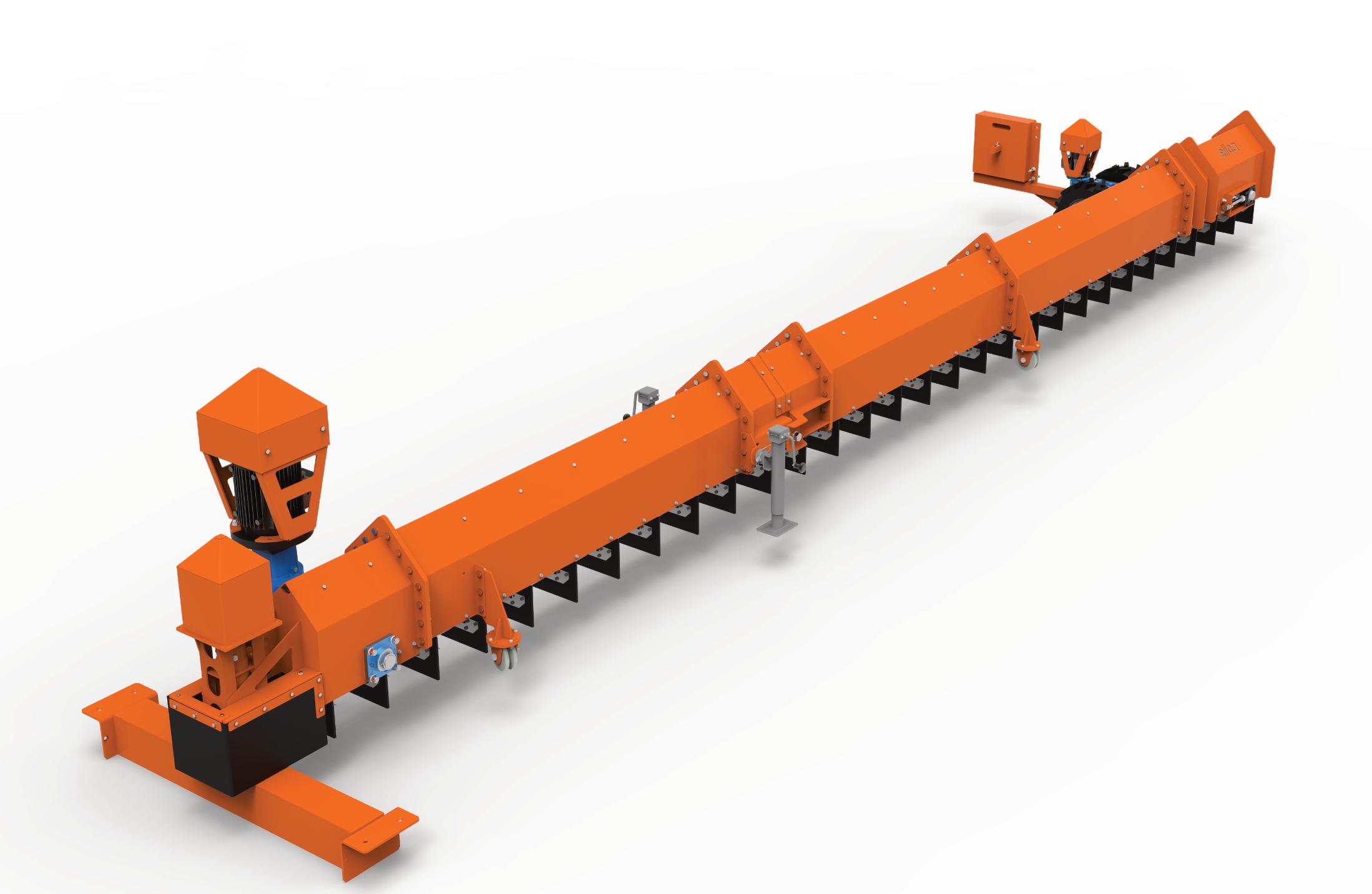

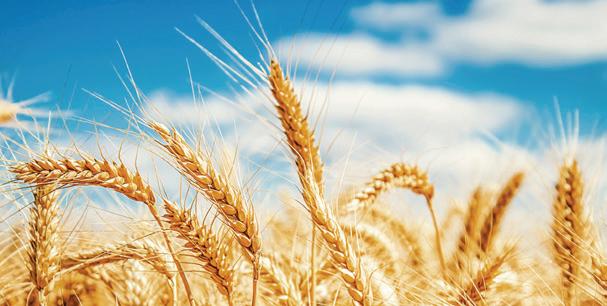
the quality protocols,” he explains. “The training of our operational and administrative staff is essential, as is the constant modernisation of the port handling equipment and storage facilities.”
One of the biggest challenges is maintaining the balance between the service quality and the pricing policy, which is influenced not only by the internal costs, but also by the volatility of the cargo flows.
“This volatility creates a competitive environment in our port activity, but that doesn’t necessarily lead to progress,” says Taranu. “Under these circumstances, our ability to balance these elements can also be considered as a strong feature of UMEX.”
UMEX possesses a diversified network of suppliers, stretching across all aspects of its activity. The company works with local and international suppliers, leading companies in their fields, capable to integrate their expertise in UMEX’s specialised environment.
“From the providers of equipment, tools, materials needed to secure our operations to builders that are shaping our vision, from maintenance specialists to survey companies that complete our services range, we seek in our partners the same values as the ones that guide our actions,” explains Taranu. “And since the supply chain performance translates into our performance, into our service quality which we value so, we are not only using some suppliers, but we are forming strong partnerships with these companies.”
UMEX operates different cargo types with different operational and storage demands. “We are in the process of equipping one of our warehouses in order to propped accommodate (intake, storage and outtake) one specific bulk cargo – soda ash for import,” says Taranu. “This is a new activity in our port,
Amspec
Amspec is the fastest growing independent Testing, Inspection and Certification provider, headquartered in Cranbury, NJ, USA has serviced the Petroleum, Chemical, Gas, Bitumen & Agricultural industries since 1986.
We have expanded to over 170 locations throughout the Continental United States, Canada, Caribbean, Europe, Asia, Africa, Middle East, Central & South America and Australia to provide the highest level of service, wherever you, the customer require it.
With more than 35 years of experience in the industry, we have the best tools to assist your business 24 hours a day, 7 days a week.
Cimbria
Cimbria is a global brand of AGCO and one of the world’s leaders in industrial processing, handling and storage of grain, seed and food, as well as animal feed, foodstuffs and other bulk products.
Cimbria works side-by-side with their customers to turn their vision into reality and beyond.
We maintain a deep connection throughout the entire process of design, engineering, manufacture, installation and service of individual machines, customized systems and complete turnkey installations.
Cimbria is a solution provider and manufacturer of custom-built products for agricultural and industrial processing within conveying, drying, processing, optical sorting and storage solutions, reflecting our customer-focus and industry expertise.
www.cimbria.com

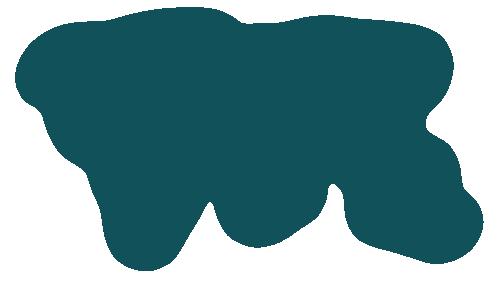


THE FUTURE UMEX GRAIN TERMINAL
UMEX’s priority is to scale the competitiveness of its customers through increasing the standards of port operations that it constantly invests in modern technology and facilities.
One of the most vital UMEX investments in the Port of Constanta is the construction of a specialised silo for the storage of bulk grains, which will improve the quality of the processes specific to the handling and storage of grains. The project is under development and is thought to be completed by the end of 2021.
The new capacity of 80,000 tonnes will consist in the construction of eight bins in the berth 38, which, together with the existing warehouse, will be able to store up to around 100,000 tonnes of bulk grain simultaneously.
The new terminal is flexible and facilitates the discharging of grain arriving in the port by any means of transport simultaneously through four independent transport lines to any of the eight storage bins. In tandem, from any bin, the cargo can be transferred at a rate of 1,500 tonnes per hour to the ship-loader that will be places on berth 38. because as markets change, some cargo flow dies, while others are born. We have seized, together with our client that proposed the cargo to us, this opportunity, forming a strong partnership which is the foundation of this particular investment.
“Another warehouse will be authorised this year in order to store Ammonium Nitrate. This particular fertilizer is classified for physicochemical hazards and specified as dangerous in the IMDG Code. In order to be allowed to store it, an exclusively dedicated warehouse must be prepared and authorised as per the regulations in order. Following the fertilizers market tendency, in the past years the presence in our port is growing. After consulting our major clients in this segment, we are confident to have started this year the procedures for the warehouse authorisation, procedures that will take up to six months, as we estimate now.”
CEMPS
For heavy and complex applications in the port of Constanta, with short execution time, Hyster forklifts are capable of excellent performance, ensuring the continuity of the logistics flow.
CEMPS is one of the few players in its domain, in Romania, that can offer a full range of equipment from 1 ton to 52 tons:
• Electric, GPL and Diesel trucks; • Warehouse equipment: pallet trucks, pallet stackers, reach trucks,
VNA; • Empty / full container handling equipment; • Equipment for special applications; • Specific attachments for various activities.
www.cemps.ro
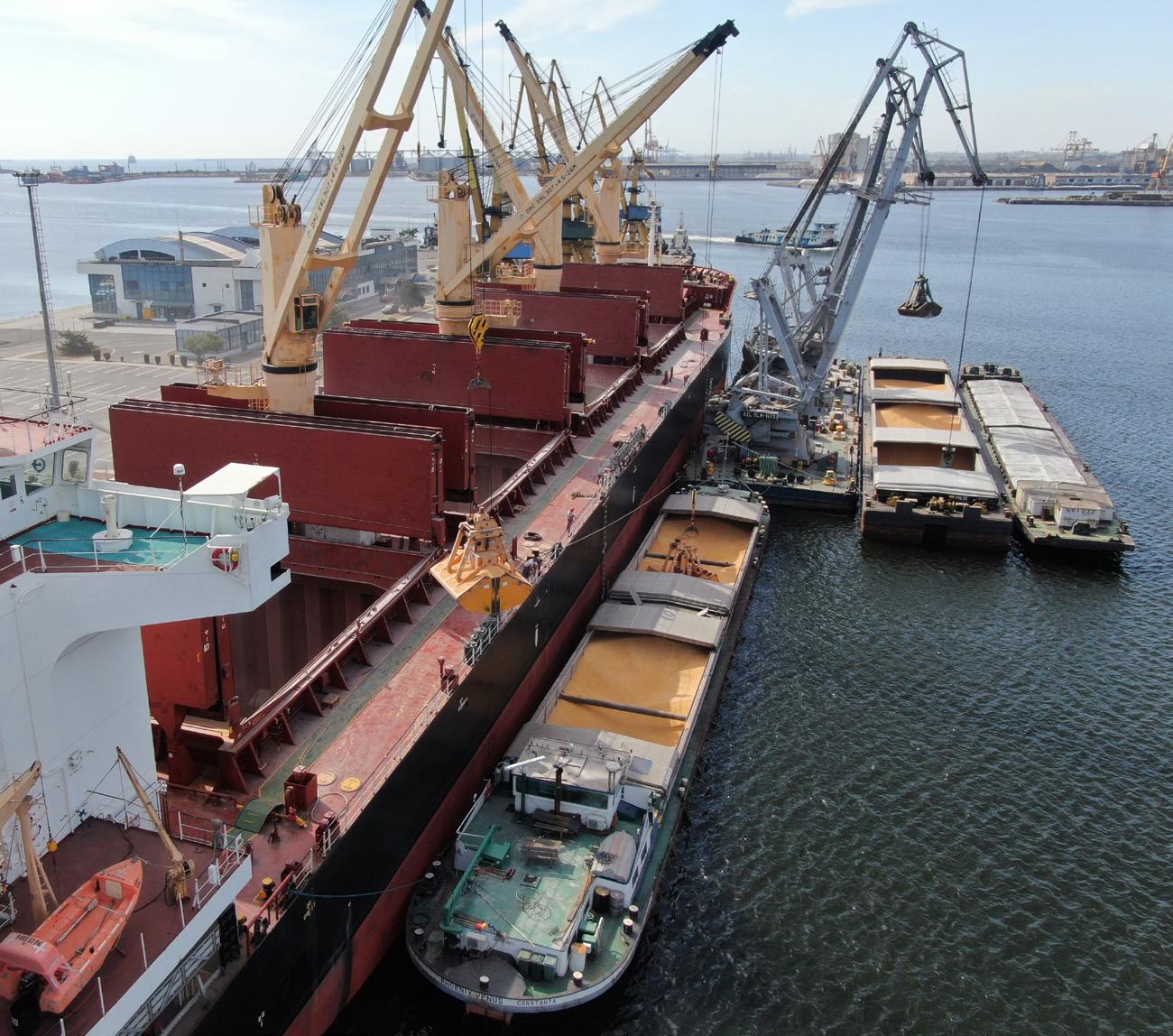
CEMPS S.A. Bd. Preciziei, Nr.3, Sector 6, 062202 Bucuresti
T (+4) 021 - 493 40 80 F (+4) 021 - 350 22 52 E office@cemps.ro
www.cemps.ro



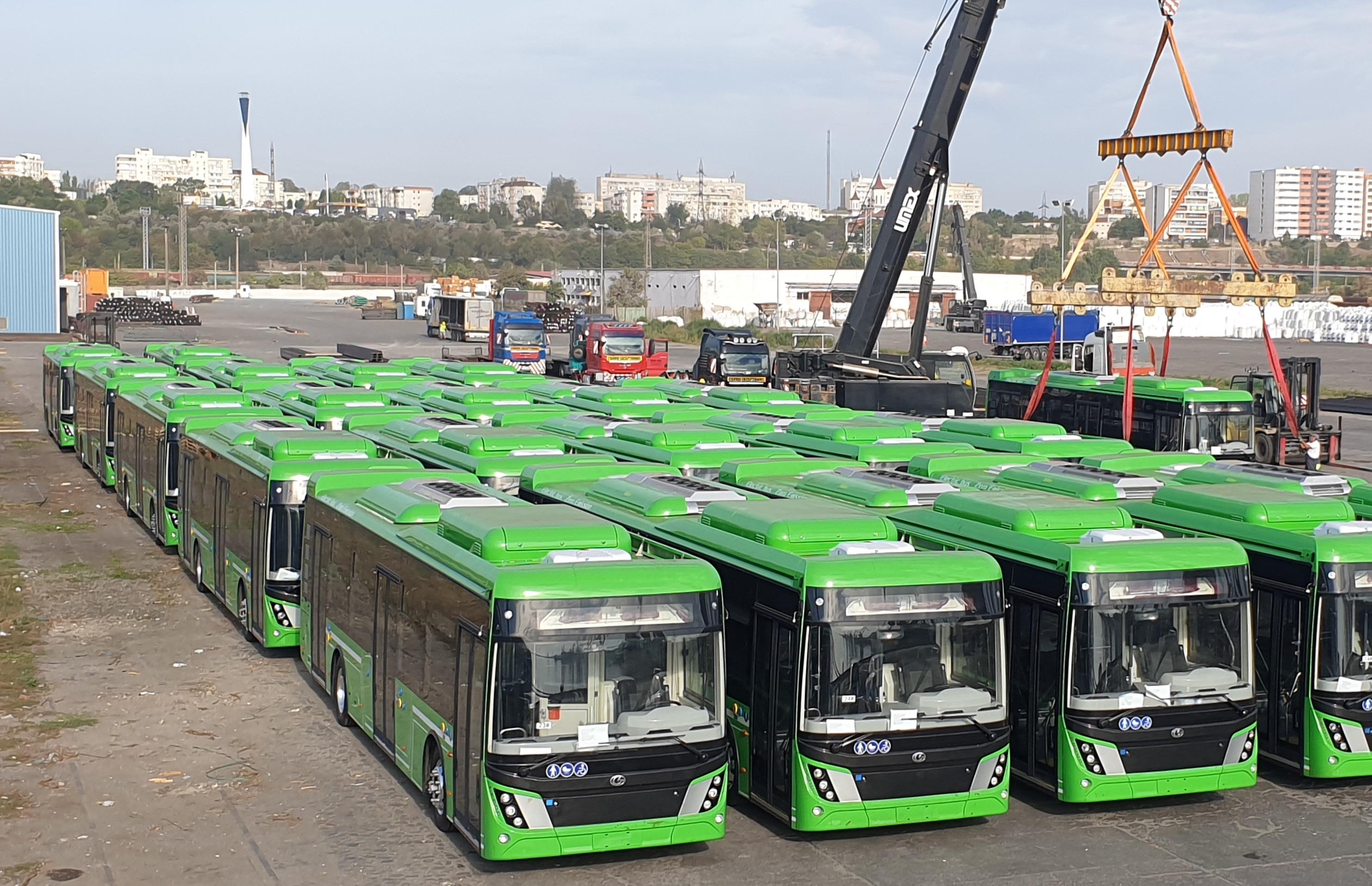
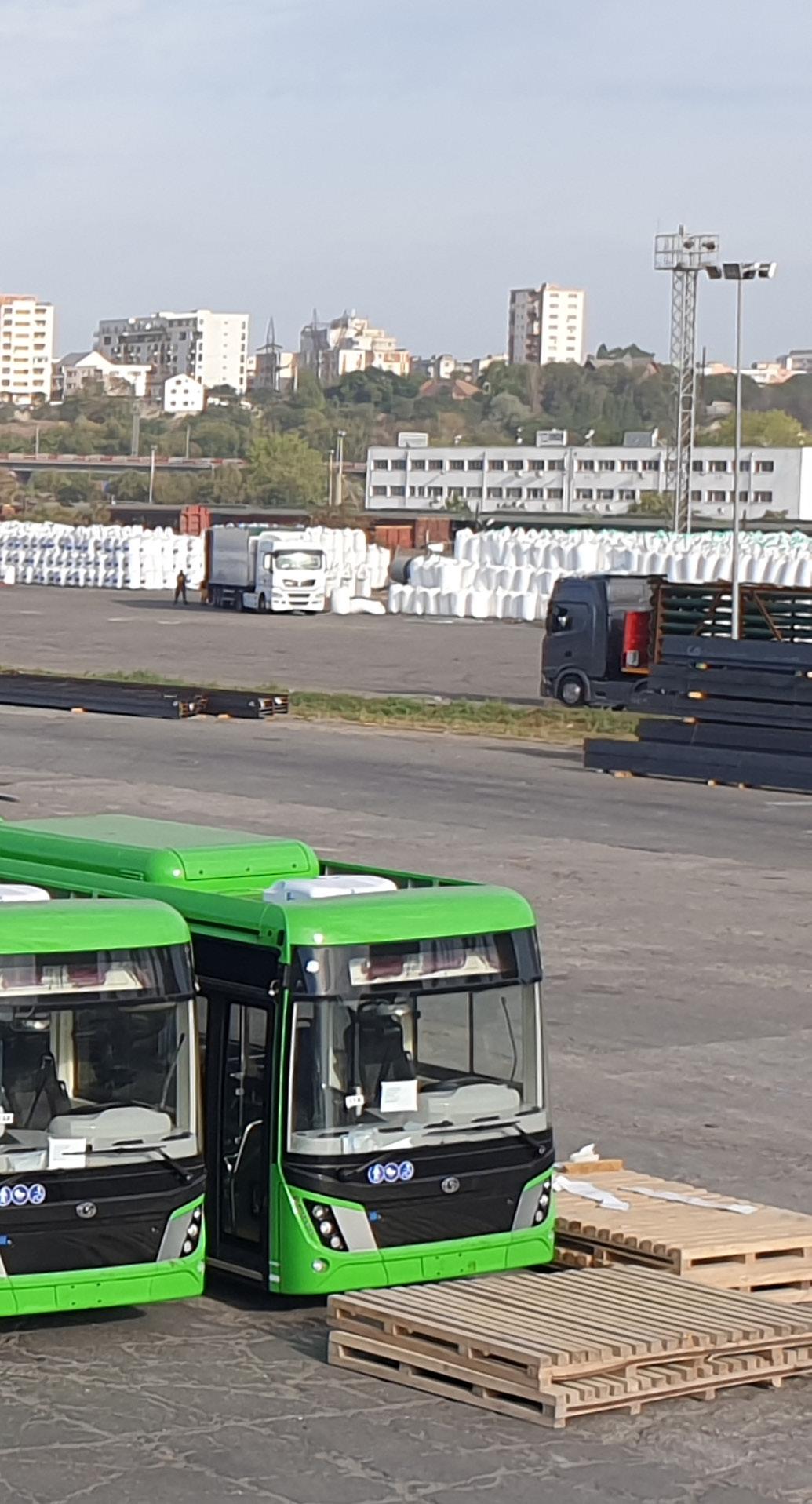
UMEX works hard to create a positive, energetic work environment for its employees, which is based on recognising and rewarding performance


In terms of talent management, Taranu understands the importance of building a diversified and specialised business line that is based on personnel capability and performance. “We’re involved in a highly specialised industry, to create a foundation of employees that delivers the high performance aimed is not an easy task,” he says. “Especially considering that our region suffers from lack of workforce in the specialised segments: operators of equipment, equipment maintenance specialists.
“That is why we are involved in several programmes that support the professional education system, allowing the future specialists to form a practice knowledge of port working environment. And of course, within our organisation, we are supporting the evolution of each employee, providing schooling and training opportunities.”
In order to deliver the best level of service to its customers, UMEX works hard to create a positive, energetic work environment for its employees, which is based on recognising and rewarding performance. “We have generated consistent and objective methods for evaluating the employee’s performance, in order to determine the strengths, weaknesses and potential managerial gaps in the organisation. This way we’re able to determine the performance levels for each employee and act accordingly.”
With the future in mind, Taranu is clear about his plans for the coming years.
“The goals in hand are the usual ones, which we aim for every year: to secure the existing cargo flows, to attract new flows, increasing the cargo volumes handled through our terminal and expanding the turnover.
“All our actions are directed in this respect, and the quality of service is the main tool to benefit from. Referring to specific targets, we will finalise the ongoing modernisations and adaptation works for the soda warehouse, we intend to obtain the authorisation for the AN storage warehouse, we’ll advance with the construction works for the fertilizers warehouse.”
Tel: +4024 1512 493 umex@umex.ro www.umex.ro
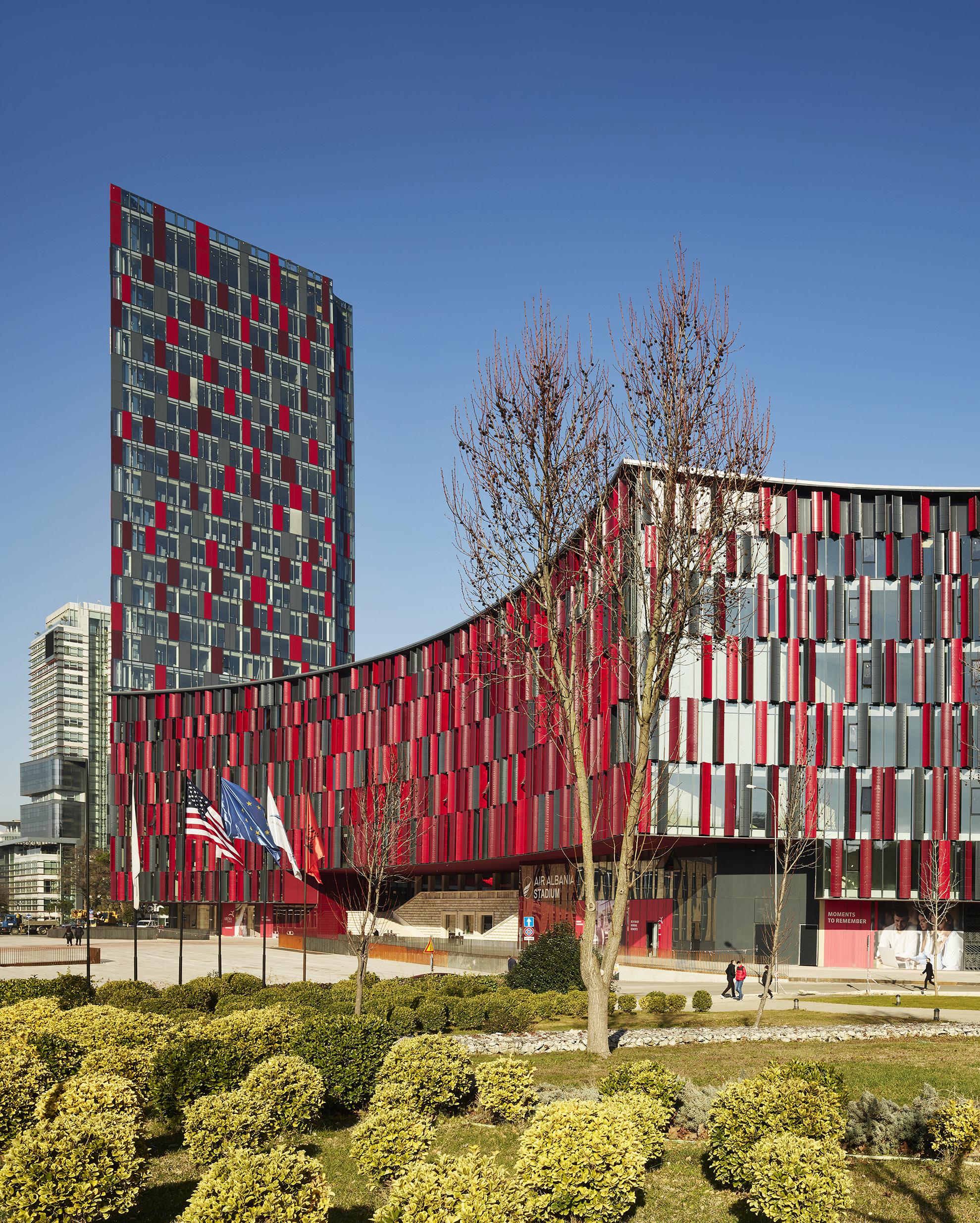
Expert Italian Architecture
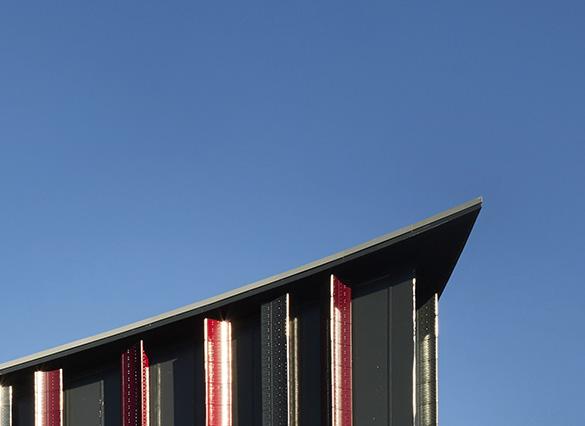
Executives at Archea Associati reflect on their organisation’s journey and the significant evolution since the studio’s founding in 1988
Writer: Sean Galea-Pace | Project Manager: Sam Love
Florence is a city renowned for its culture.
It is often regarded as a living, breathing museum and boasts a plethora of historic architecture. Famous for the Duomo, inside Florence’s cathedral and its Renaissance art, Florence attracts millions of tourists every year.

One of Archea Associati’s most important projects has been the development of New National Stadium of Albania.
The ambition was to create a contemporary monument that, through an infrastructure dedicated to sports, can enhance and scale the image and role of the Albanian capital. It is a building replacement project due to its location in the same spot where the original sports complex dedicated to athletics and football once stood, designed in the late 1930s by Florentine architect Gherardo Bosio.
The building, with the exception of the monumental entrance structure of the VIP gallery, was fully demolished and rebuilt with the aim of constructing a system able to satisfy UEFA standards to create a completely covered football complex with attached services, functions and activities which can bring the building to life every day.
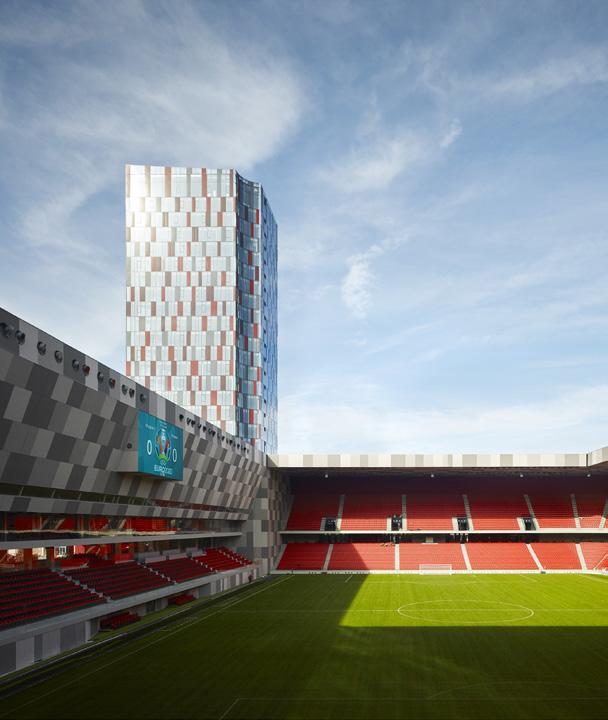
© PH. PIETRO SAVORELLI, DAMIANO VERDIANI, BENEDETTA GORI
However, also born in Florence is Archea Associati. Founded in 1988 by Laura Andreini, Marco Casamonti and Giovanni Polazzi, Archea has become an international architecture and design office, specialising in urban planning, architecture, design, interior design and graphic design. In 2001, the founders were joined by Silvia Fabi, coordinator of the firm’s project activities.
As co-founder of the Archea studio and Associate Professor of Architectural and Urban Composition at the Faculty of Architecture of the University of Florence, Andreini has witnessed and played an influential role in the company’s success over the past 30 years.
“From the very beginning, the studio has associated an intense work of in-depth analysis and critical reflection in the field of architectural design and on the themes of architecture and industrial design,” she discusses.
Archea is located on the banks of the Arno. Over the past 30 years, Archea has created or designed hundreds of projects all over the world, on almost every continent, excluding Oceania, where the company harbours ambitions to measure itself.
“This marked international trait of our work has led us to open foreign offices to be closer to customers,” says Andreini. “We work with more than 160 freelancers per assignment, and we have a large workforce for specialist investigations and technical expertise. In addition to Italy - where we have three studios, in Florence, Milan and Rome - we are also present in Sao Paulo (Brazil), Tirana (Albania), Dubai (UAE), Beijing (China).”
And Archea isn’t finished there. The company is set to open another studio in Moscow, Russia while the studio was also confirmed as the winner of the international competition for the planning and development of the new urban expansion area in the SouthEast area of Moscow.
ITALCER
The innovative eco-friendly ADVANCE® porcelain tile is suitable for both floors and walls. It is produced directly in the first and single fire at over 1200° firing and with the 40% of recycled raw materials.
Thanks to its antiviral and antibacterial properties, ADVANCE® is able to purify the environments.
In fact, after 6 hours of UV rays exposure, ADVANCE® is able to eliminate 100% of viral load and only after 15 minutes of light exposure it reduces the 90% of viral load. After 8 hours of UV rays exposure, ADVANCE® reaches a blast chilling ranging from 95% up to 100%.
Furthermore, if applied outdoors, it is able to eliminate in 3 hours the 20.7% of Nox molecules (Nitrogen Oxides). Thanks to its photocatalytic action, that activates with the presence of natural light, it allows a significant improvement of the air quality.
This new ADVANCE® technology contributes to improving the environments which surround us, even those in domestic field. In facts, once ADVANCE® comes into contact with the ceramic surface, it fights the dirt by breaking it down. In this way you will be able to reduce significantly the use of chemical detergents, as well as bad smells.
The results of the laboratory tests carried out on ADVANCE® are available on our website
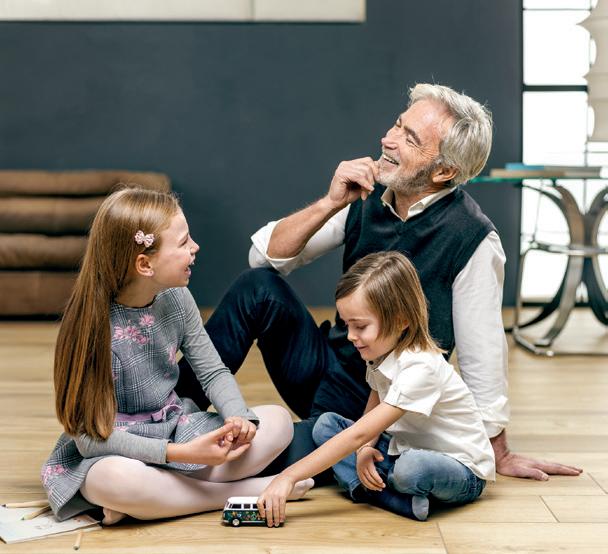
www.advanceceramic.it
Antinori Winery in the Chianti Classico, Bargino, Italy
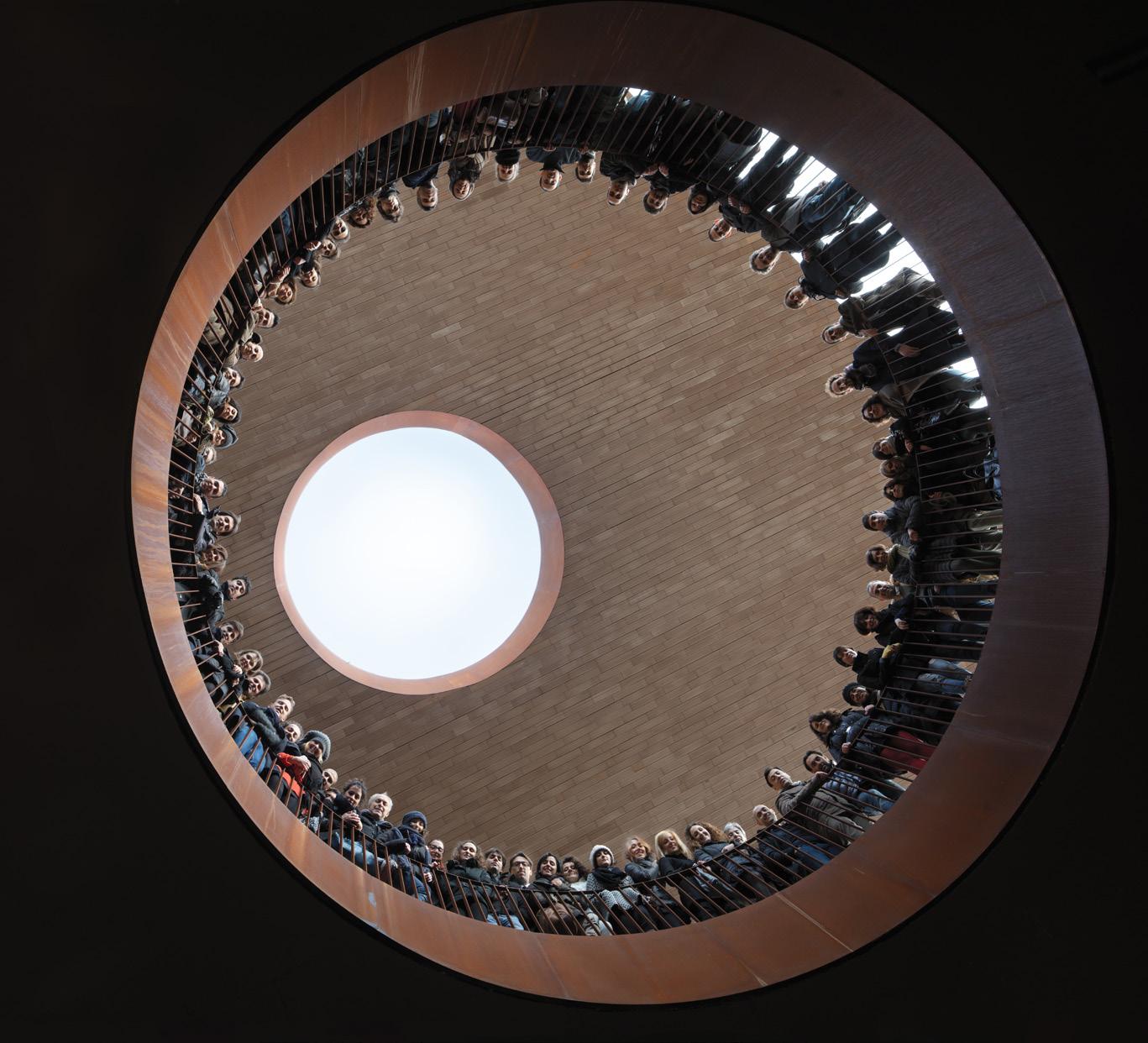
“We are proud that the Archea Associati studio from the 1980s to today, and with the same verve as then, represents the operation of Italian architecture in the world, through the creation of works that mitigate the experience of the past in the projection of the present that it is at the same time future.”
But, Andreini is adamant that Archea isn’t just an international architecture studio. She is clear about what sets her organisation apart from competitors.
“Our studio is a bearer in the world of Italian style, of the mastery of Tuscan artisans, of the brilliant Florentine acumen. Our works are permeated by all this, this spirit is manifested in the choice of materials, in the care of the colours, in the search for artistic solutions for carpenters, furniture makers, potters, bronze workers and upholsterers.
“All our work is based on the union between tradition and innovation, between the renaissance and the future,” she adds. “When we opened the studio in 1988, we hadn’t graduated. At the time, we did everything in parallel and almost unconsciously, our path was defined by simultaneously ranging between research and work in a completely natural way; we have never felt a transition between the ‘before’ linked to university life and the ‘after’ of the profession.
“There was rather a ‘continuation’ that started at university and exploded out of there. Ultimately, we could say that Archea’s profile is structured over the years through the intertwining of people and fundamental issues in which research, professional activity and theoretical reflection appear as the founding elements of a methodology in constant balance.”
Over the years, Archea has worked on a number of memorable projects, however, Andreini believes there are a few that stand out and she can remember well. “The Antinori Winery, in the heart of Tuscany, best expresses our style and our creative audacity,” she affirms. “Our signature is in the green of Chianti, which is inspired by the cuts of the Italian master of the 20th century Lucio Fontana, and illuminated by the entrepreneurial coherence of the Marquis Piero Antinori who brought his winery back to the land.”
Dedalus
© PH. PIETRO SAVORELLI
Dedalus and Archea combine their experience with the creation of a housing concept in which the comfort, wellbeing and health of the public is supported in a pervasive, non-invasive way, through advanced digital solutions.
This is the ‘House of the Future’, where Dedalus will integrate within the living environment sensory devices, components, and applications capable of supporting the comfort and wellbeing of residents and monitoring their state of health.
Solutions that will facilitate a healthy living environment which is adaptive and integrated with social services, healthcare provision, and personal care.
www.dedalus.eu
© PH. PIETRO SAVORELLI
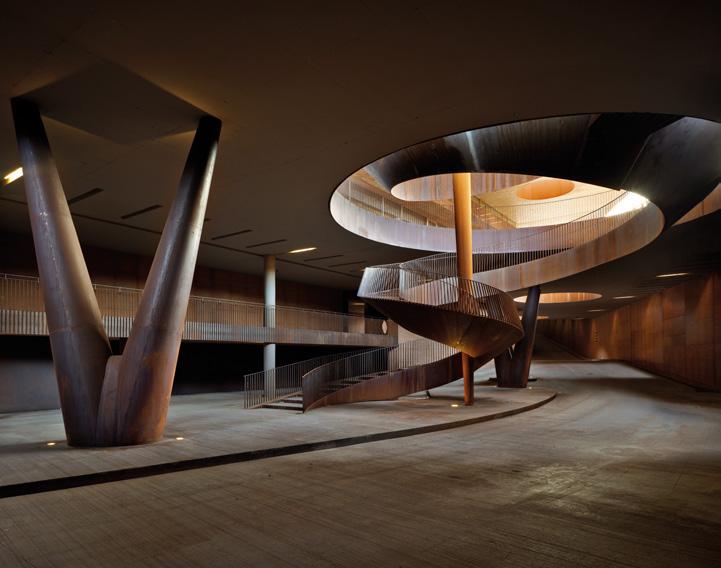
It’s clear that Archea Associati isn’t a company to rest on its laurels and is displaying no signs of slowing down. The studio is developing the Viola Park, the Training Centre of ACF Fiorentina which will become the largest sports centre in Europe. The training centre will showcase 10 sports fields, heated and with lighting as well as two mini-stadiums with 3,000 and 1,500 spectators. In addition, there will be several buildings including guesthouses, fitness areas, restaurants that are useful for hosting all teams, both male and female, as well as youth teams.
Sustainability is a key driver to Andreini and she strives to embrace a greener approach wherever possible. “A large construction of 22 hectares that unites ‘genders and generations’ in a single place, with 90 percent of the area remaining green with the autonomous ability to produce energy,” says Andreini. “The roofs will be in the valley, to collect rainwater, and will be covered with green photovoltaic panels, and inside it will be possible to circulate only with electric vehicles. It is clear that this new project will be an example of environmental sustainability.”
While sustainability is one important pillar, another is the ability to innovate and be proactive in the market. In recent years, the studio has developed a digital transformation of its offices and successfully initiated the ‘Cad to Bim’ evolution of its design techniques.
Massimo Sabatini is the General Manager of Archea Associati and over the course of his tenure at Archea, the company has started to see more of its collaborators – architects, designer, engineers, graphic designers and surveyors – invest an increasing amount in their technical specialist training by organising courses and continuous updating of programs. “This mental dynamism has allowed us to face prepared changes forced by the COVID-19 situation, starting the obligations of smart working with agility, without ever interrupting any collaboration,” explains Sabatini. “Indeed, we have also invested further in the health safety of all, creating and conducting an impressive screening activity for anyone who collaborates with us.”
Andreini believes that partnerships are vital to long-term success at Archea Associati and believes they act as a source of ‘enrichment’. Equally important are Archea’s collaborators. When the firm began to exceed the number of dozens of collaborators, Archea decided to equip itself with a manager who came from very different realities to better manage human and organisational resources. And as a result of the studio’s exponential growth, it has been a necessity.
The Veil, multi-use complex

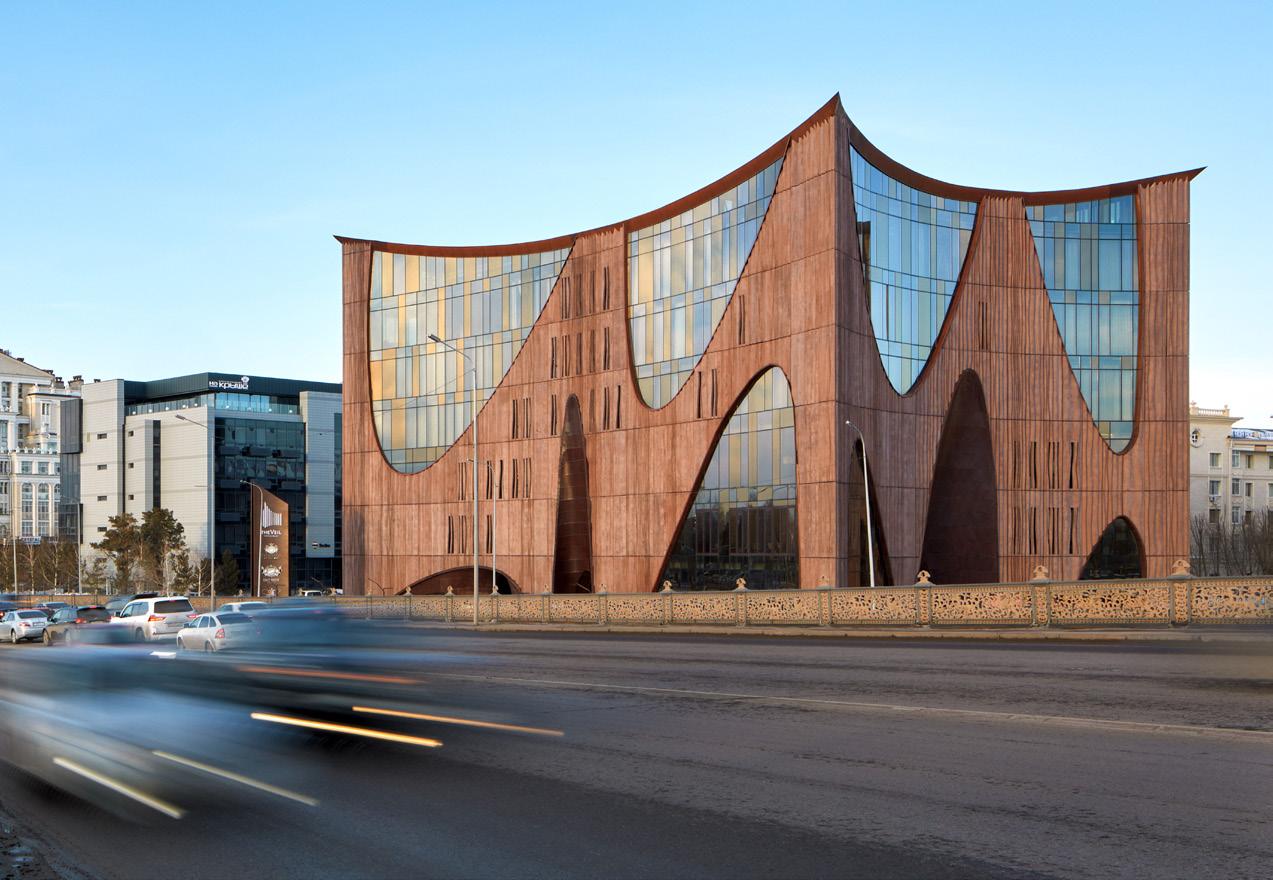

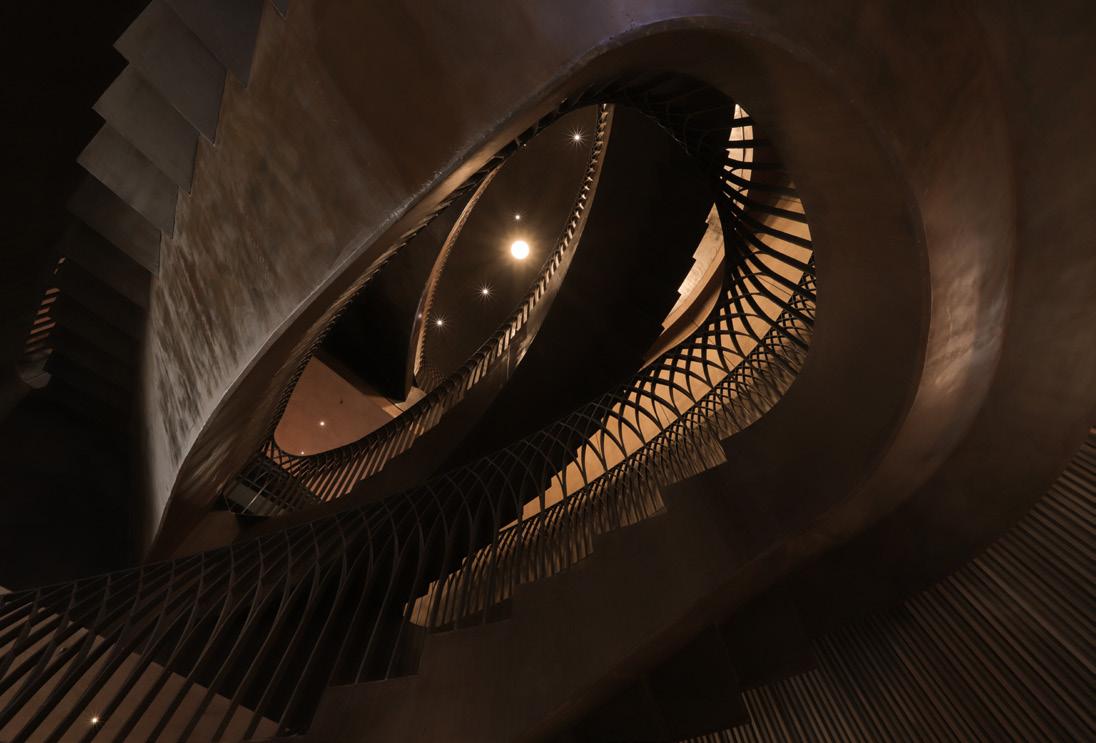
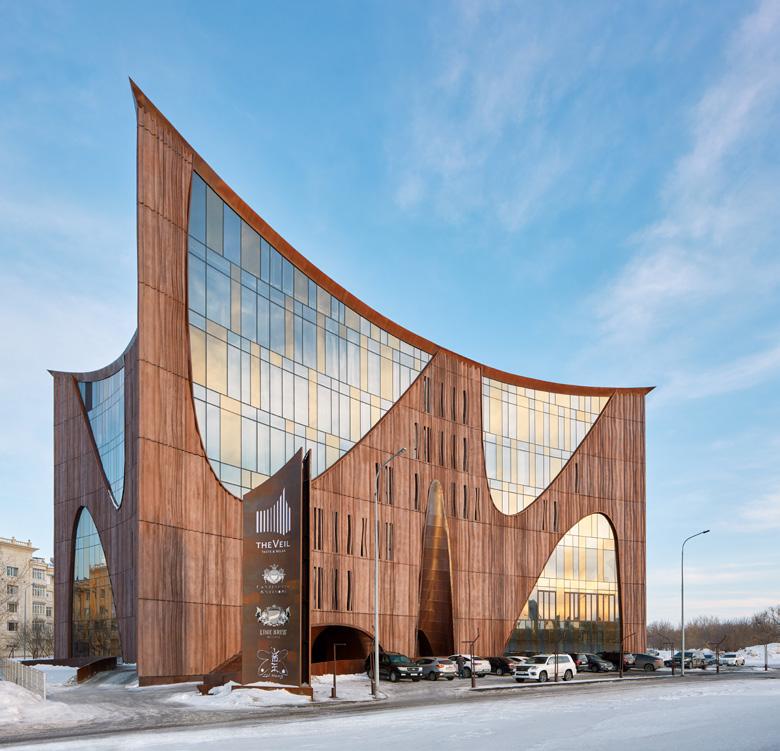
“In the last 15 months alone, we have doubled the number of collaborators and won new orders,” adds Sabatini. “We are open to foreign professionals by vocation and in addition to the many Italian collaborators we also work with American, Indian, Albanian, Iranian, Brazilian, Czech, Croatian, Peruvian, Spanish, Belgian, Chinese, Russian, Sinhalese, Vietnamese, Moldovan and Serbian professionals. The internal international front can only increase further.”
With the future in mind, Andreini is clear about what the next few years hold at Archea Associati and for architecture in general.
“The opening of the Russian headquarters and the expansion of the Chinese and Brazilian ones are at the top of our thoughts,” says Andreini. “However, we are keen to invest in research and culture and we intend to create a new centre of artistic and cultural contamination in Florence.
“We believe that architecture is a social art that must necessarily express its identity through the ability to restore a sense of belonging to the places and territories in which it will be built. Alongside this, there are other important issues that will come into play; real invention techniques expressed in the constant desire to seek a link with the figurative arts, through ever-changing forms and uses of materials.”

Tel: +39 055 538851 staff@archea.it www.archea.it/en
Constant CHANGE

With an agile approach a necessity in the market today, Osama Hamad, General Manager of Emirates Beton, discusses evolution and how his firm is embracing change at scale
Writer: Sean Galea-Pace | Project Manager: Ryan Gray
The only constant is change.” A transformation journey is never finished. The reason being is that change is ongoing and achieving success in 2021 is largely accomplished by pivoting quickly and responding to the demands of the market at will. Without embracing change, you risk remaining stagnant. And in the construction industry, you can’t afford to let this happen.
Enter Emirates Beton. As one of the leading suppliers of ready-mix concrete in UAE, the company aims to create a robust work culture that embraces innovation, change, failure, and success.
“Any successful company not only in UAE but all over the world must adapt to its environment in order to survive especially with our current market situation,” says Osama Hamad, General Manager of Emirates Beton. “It demands constant change and adaptation to the latest innovation.”
Hamad is an experienced industry professional and has worked at the organisation since February 2016. He points the influence of his family that helped him to become the person of today. “I am where I am right now because of the influence of my family, most especially my father who was into the construction field,” he explains. “He inspired me to become the person I am today.”
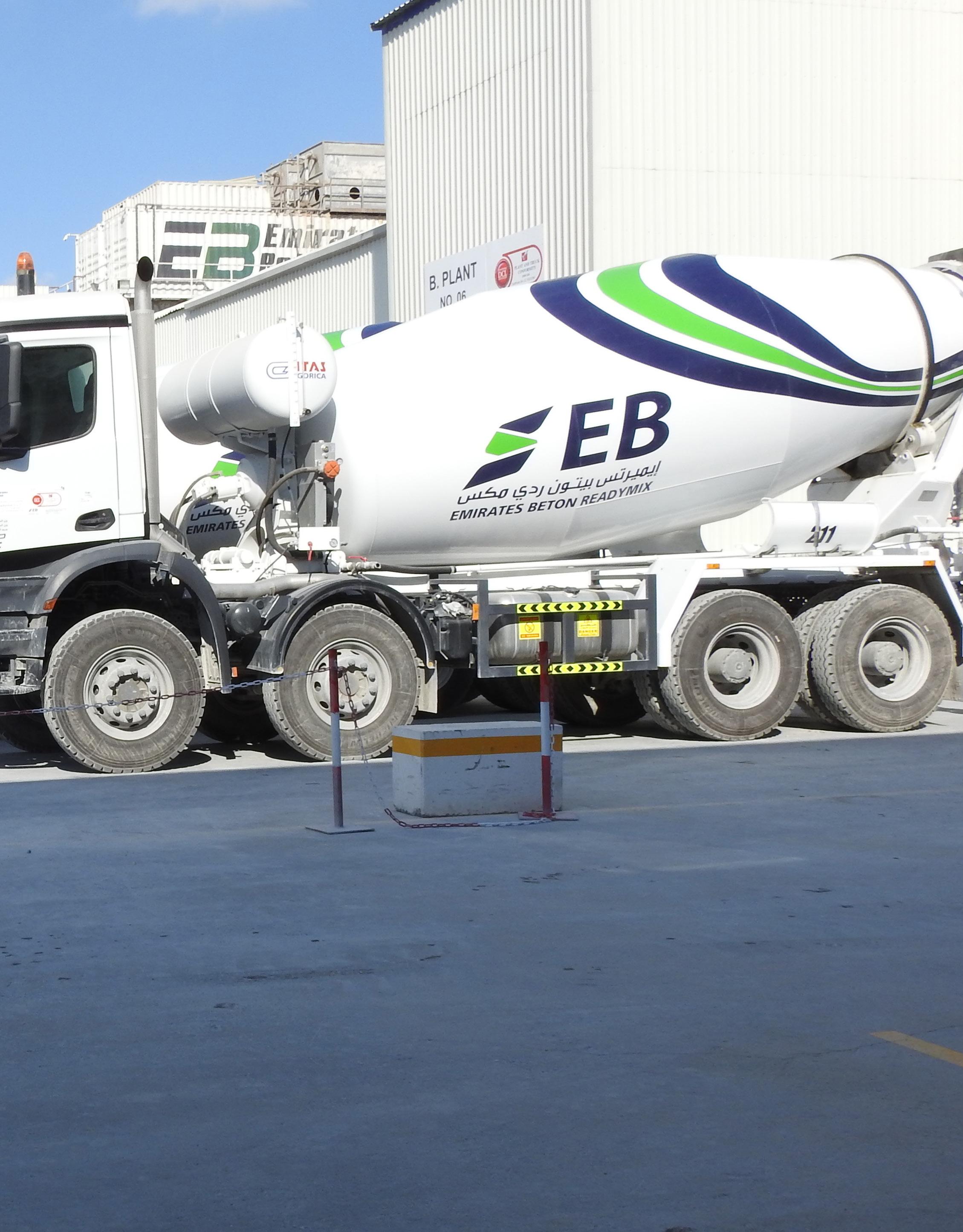
Prior to opting to join Emirates Beton, Hamad was at a crossroads and had a decision to make. Having met with Mr. Bashar Abou Mayaleh, the previous Managing Director of Emirates Beton, Hamad was offered the position of Operations Manager while also being offered a General Manager role for another ready-mix firm within the United Arab Emirates.
“Despite confusion because of two brilliant offers, I decided to join Emirates Beton without much hesitation,” recalls Hamad. “I clearly remember the words of Mr. Bashar because he asked if I am ready to take the challenge. I signed my offer letter within 30 minutes because I was aware that I could develop and grow
EMIRATES BETON: AT A GLANCE
Emirates Beton ReadyMix is a ready-mix concrete company that leads the industry in the design, production and supply of ready-mix concrete. Founded in 2008, the company is fast growing and is renowned for delivering excellent products and outstanding services.
Emirates Beton operates four batching plants in total, with two commercial plants located in Dubai. Both plants leverage the latest German technology and are fully computerised, manufactured by Liebherr and Lintec, which have a combined capacity of 480 metres per hour. Emirates Beton employs the most technologically advanced equipment and state-of-the-art machinery and fleet, which are equipped with the manufacture of a complete range of ready-mix concrete building components. All the ready-mix and aggregate trucks are equipped with a GPS tracking and quality control system.
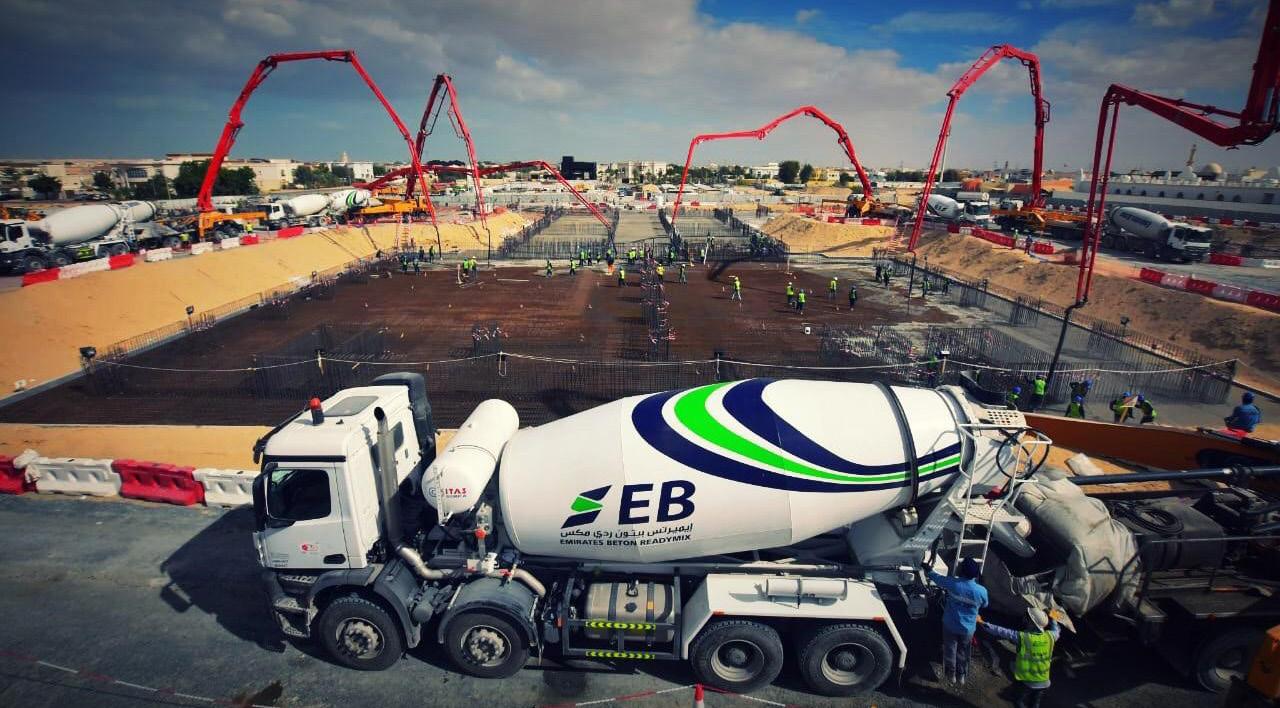
both professional and personal skills within the company.
“I knew it was going to be challenging because the firm was struggling. However, with the support of my higher management and guidance of the ASGC President and the rest of ASGC Board of Directors, we work hard to boost the production, both in quantity and quality, to put the company’s name on top of the list of ready-mix suppliers.”
“I knew I had made the right decision when I was promoted to be the General Manager within a year and recently another opportunity to be appointed as the CIC Group General Manager (EB, HPBS,HBF). Hard work, persistence and perseverance have become my guiding principles in life.”
Hamad is adamant that Emirates Beton stands out as the ready-mix company of choice in the UAE and believes the firm’s attributes act as its competitive advantage.

“Most ready-mix companies within UAE are the same,” he notes. “Most customers want value, sustainability, stability and transparency. Wherein, we ensure that we only deliver a ready-mix concrete having a value creation with a high quality of service perceived as high compared to their cost and offer stability on day-today operations. We put greater value on veracity and excellence in all our commitment, including our unparalleled dedication to service. These qualities truly define the magnitude of our company.”
Emirates Beton is actively adopting the latest trends in terms of machineries, equipment and other resources in order to progress and improve the process.
“We are proud that our company has the best and most modern system with the use of ERP and mobile applications which help our customers to have live access to their concrete order and delivery, as well as our modern GPS system for accurate tracking of our vehicles and fleets.”
Supply chain plays a prominent role in the success of most companies. Without strong and mutually beneficial supplier relationships, achieving long-term success is difficult.
“When it comes to managing our supply chain, we take the whole process with utmost importance, from supplier onboarding until delivery at customer site,” explains Hamad.
“We take pride in partnering with the best in our business. All of our strategic suppliers are aware of our business strategy, and that always ensures compliance. We engage in high-level agreements with suppliers by providing them precise, and wellplanned long-term requirements. Our data is very accurate and is extracted from our operations schedules which reflects our excellent coordination and collaboration between our departments. We have categorised all our requirements based on importance and nature. We are running multiple supply chain strategies and doing all these activities help us achieve high level of efficiency, with the right requirements being fulfilled.”

Osama Hamad, General Manager
VISION
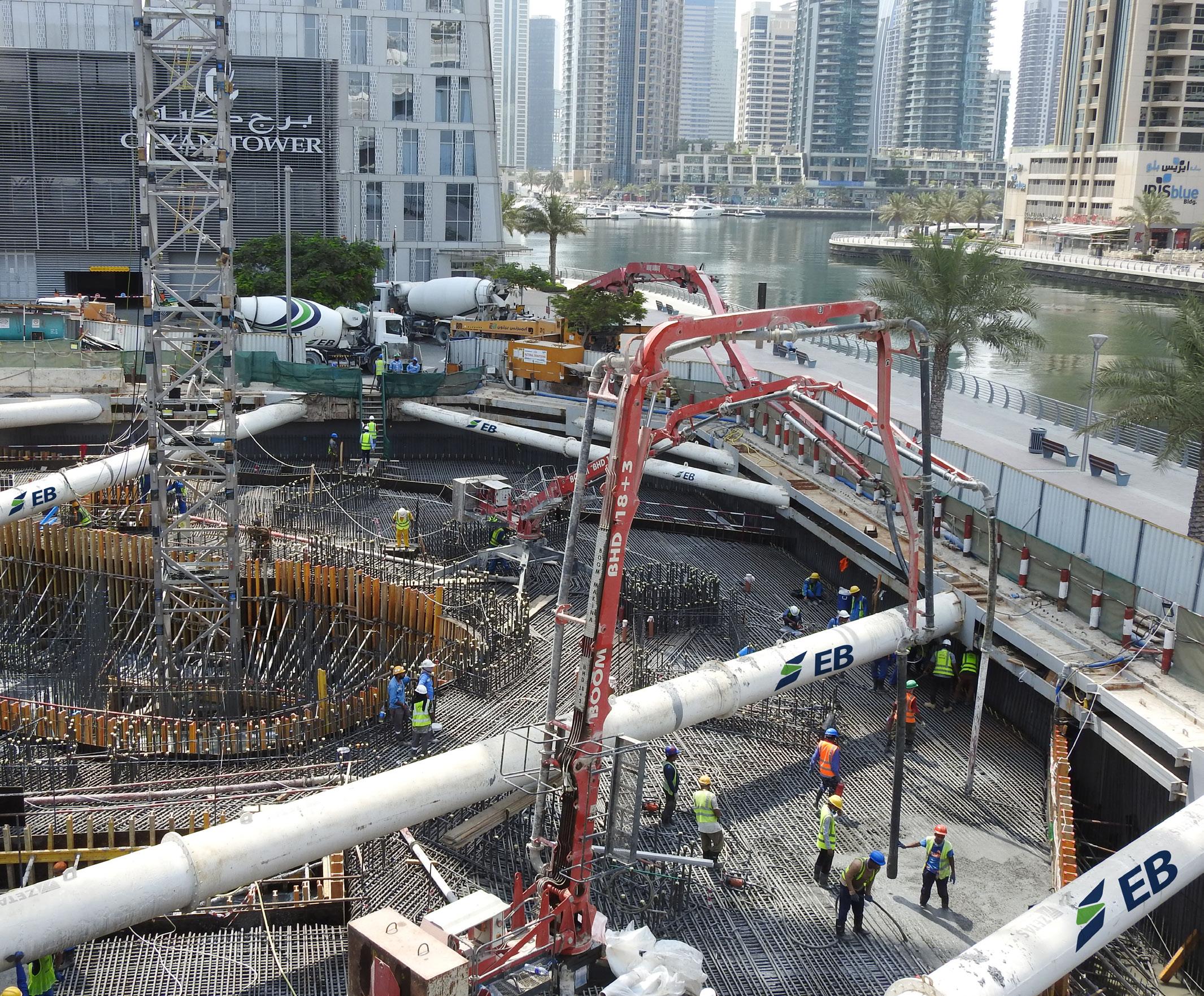
Emirates Beton aims to be the most value-creating, most specialised and advanced total concrete solutions provider within the UAE. The firm aims to have a particular emphasis on exceptional quality control, up-to-date technology and practices, and most importantly integrity in all aspects of the project, while keeping the interest of its employees and clients at heart.
MISSION
Emirates Beton has a vision to be the leader in the market by efficiently and effectively providing a comprehensive range of the highest quality concrete products, services and solutions at competitive prices while focusing on its clients’ needs and continuously enhancing products and services via safe, sustainable and innovative manufacturing practices.
To Hamad, he stresses that his organisation is more than just profit. With sustainability playing an increasingly important role in how businesses operate, Emirates Beton is committed to green.
“We are actively embracing CSR within Emirates Beton and we are proud that the company is more than just making a profit and not just simply focusing on generating revenue,” he explains. “We are socially responsible which takes into consideration the impact of our decision on the profit, our people and the planet.
“One of the ways our company has fulfilled this is by maintaining our commitment, while implementing programme-focused on the well-being of our employees, a safe work environment and participating in various activities in the UAE, while producing environmentally friendly ready-mix concrete.”
Staff are at the heart of companies across the world. For Hamad, he acknowledges how much of an influential role employees play and believes that empowering staff leads to uncapped potential of what can be achieved.
“Our employees are important assets and the backbone of the company,” he stresses. “We invest in young talented employees and really our team is back with good attitude and are autonomous – trusted to have ownership over their work and
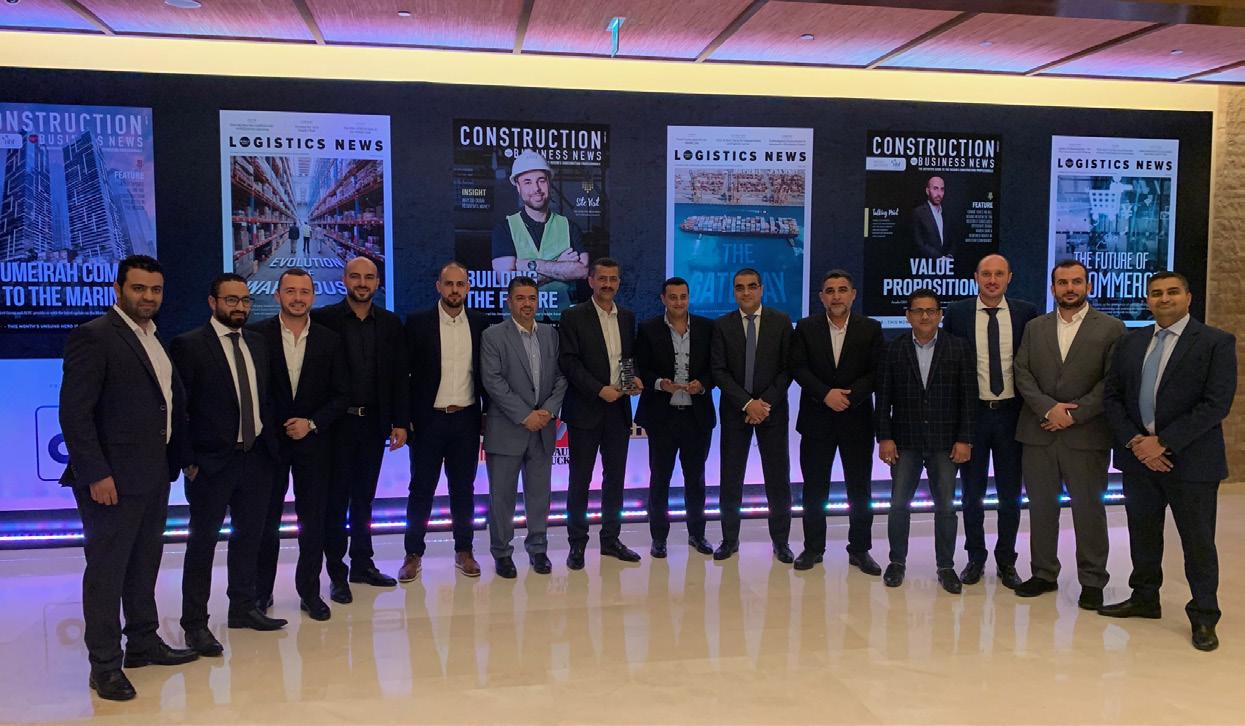
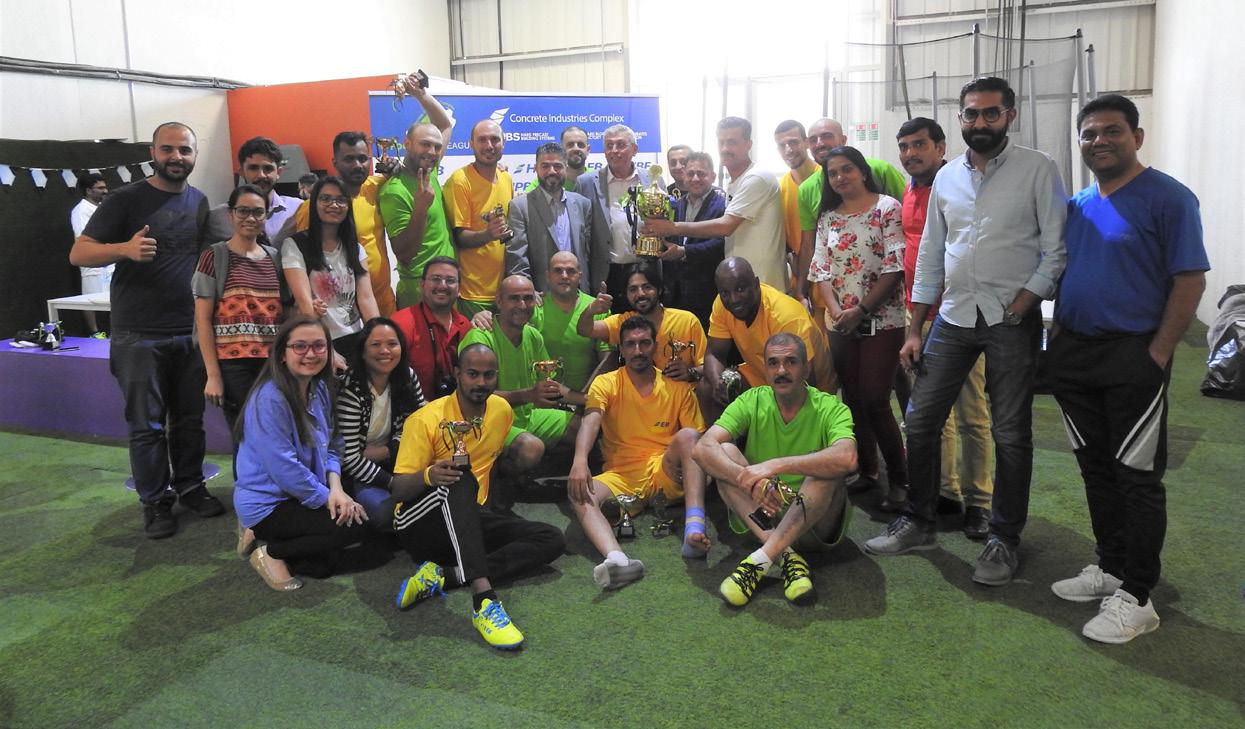
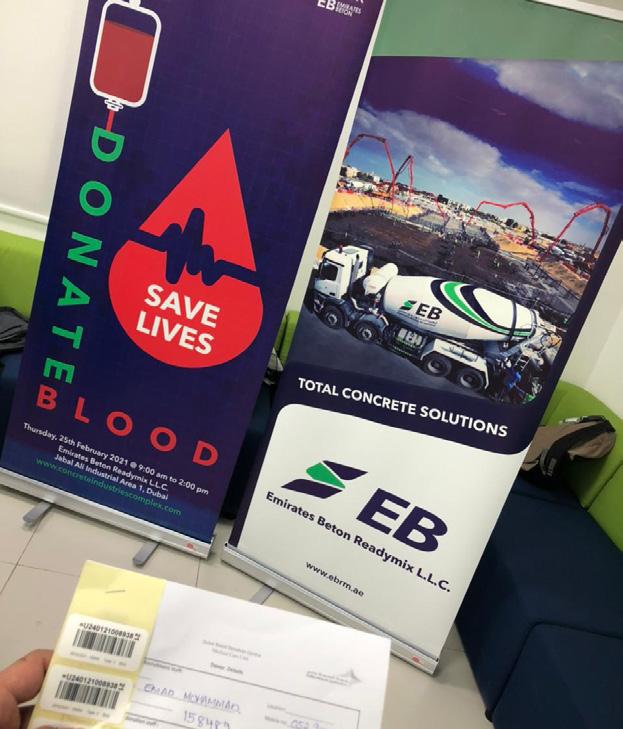
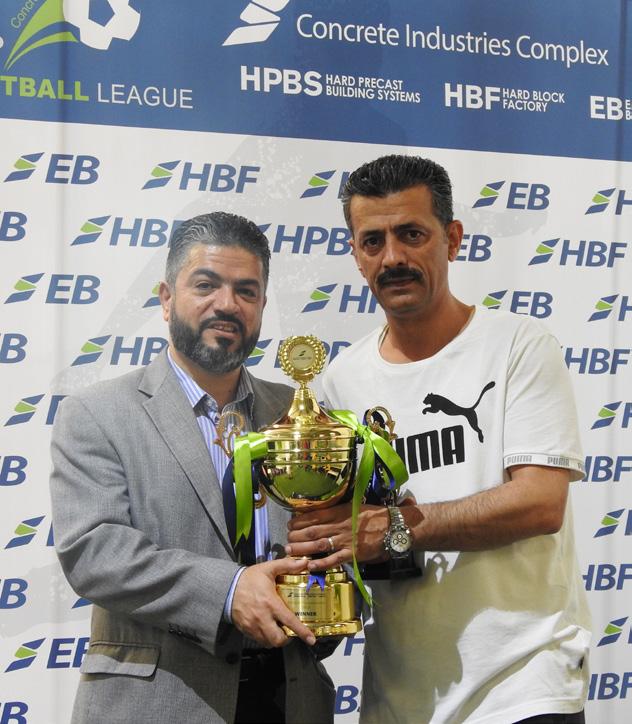
an individual capability to improve works. I always ensure that all will be empowered by setting a goal, as this will help and push them go out of their comfort zone and realise their own potential.”
Hamad believes in an ‘open door policy’ which allows for open dialogue and communication to take place to ensure all employees enjoy a healthy work/life balance, while operating with an employee development plan.
“This helps mould future leaders and provide suitable opportunities for them to shine on their field of work and appreciation to build a great company culture as well as maintaining a consistent performance of each employees,” he says. “I try to always ensure I am a friend of all employees and ensure that we will learn from each other while I create leaders for the new generation of this company.”
Looking to the future, Hamad doesn’t believe in boundaries and strives to reach unprecedented levels of success. “We will continue to reach a new high and for us the sky is the limit if there is a limit,” he sums up. “Great things in business are never done by one person, they are done by a team of people and that’s why I am very grateful to have the Concrete Industries Complex (CIC) family.”
EMIRATES BETON
Tel: 04 885 6365 info@ebrm.ae www.emiratesbeton.com
Professional Cement Production
Construction in the Middle East is a large industry. We take a look at Oman Cement Company, a key player within the cement production sector within Oman
Writer: Marcus Kääpä | Project Manager: Ryan Gray
From a large bulk and metals mining industry that backs the region with substantial raw materials, to manufacturers and multiple internationally leading architecture firms, Middle Eastern construction is a vast sector.
Within Oman especially, the bulk mining industry is impressive, with the country’s exports including gypsum, limestone, and dolomite. Oman is currently the world’s largest exporter of gypsum - approximately nine megatons (Mt) annually.
For Oman Cement Company, the procurement of these natural resources, such as limestone and gypsum, are vital to company products.
Oman Cement was established in 1978 as part of the renaissance initiated by Sultan Qaboos bin Said, and since 1983, Oman Cement has symbolised the country’s drive for self-reliance in core industries. On top of this, the company continues to be ISO 9001-2008 and ISO 140012004 certified. The company is one of many who have given a new strength to the nation’s construction industry, consolidated its efforts for infrastructure development and created resources to achieve self-sufficiency.
With a manufacturing facility operating on world class ISO 9001 certified quality management system and ISO 14001 for environment, Oman Cement’s products meet global standards in performance and quality that reflect its enduring commitment to customer satisfaction and a stronger foundation for the future.
For Oman Cement, all the raw materials required for its production are native to the land. Limestone deposits, additives, quartzophylites and ferrogenous quartzophylites are located adjacent to the plant site. Gypsum, which is used for retarding the setting of the company’s cement, is obtained from mines at Ghaba in Wilayat Adam.
Oman Cement’s three kilns and four cement grinding mills allows the flexible production of various types of cement. The process control is fully computerised and handled by highly qualified and experienced company personnel, and this total current production capacity of the company is approximately 2.4 million Mt of cement per year.
Each and every one of Oman Cement’s customers can expect a full range of professional and topquality products to meet specific requirements unique to the buyer.
Oman Cement’s products conform to the national and international standard specifications because of its centralised goal to maintain its customers’ satisfaction domestically and external to the Sultanate through
producing different cement products.
Quality control within Oman Cement is guaranteed under strict control throughout the production process, and the completed product is quality checked thoroughly and to the highest standards the company can carry out. The company’s production lines control system is operated on the hour.
Oman Cement firmly believes that customer satisfaction is the cornerstone of its business success. The company is committed to providing different types of cement products with superior quality and services. As part of the company’s ongoing efforts to provide the best possible service to its customers, Oman Cement also offers technical consultations whenever required.

OMAN CEMENT COMPANY OPERATIONS AT A GLANCE
CENTRAL LABORATORY
Oman Cement’s quality control is supported by its own central laboratory consisting of robotics, X-ray spectrometers, laser particle size analysers and computerised physical properties testing equipment providing high-tech and contemporary services across the board.
COMPUTERISED MANUFACTURING
The company’s cement manufacturing process is fully computerised. This avoids major hazards in manufacturing and requires less manpower increasing fluidity and embracing the efficiencies of automation.
POLLUTION CONTROL
Oman Cement’s manufacturing operations are environmentfriendly, as promoting the environment, especially within the company’s localised areas, is an important part of a more sustainable Oman.
QUALITY MANAGEMENT SYSTEM AND ENVIRONMENTAL MANAGEMENT SYSTEM
Oman Cement’s Quality Management System are in accordance with the Quality Assurance Procedures of ISO 9001: 2000 certification, ensuring the high-quality production and distribution of the best products the company can possibly provide.
CSR VISION
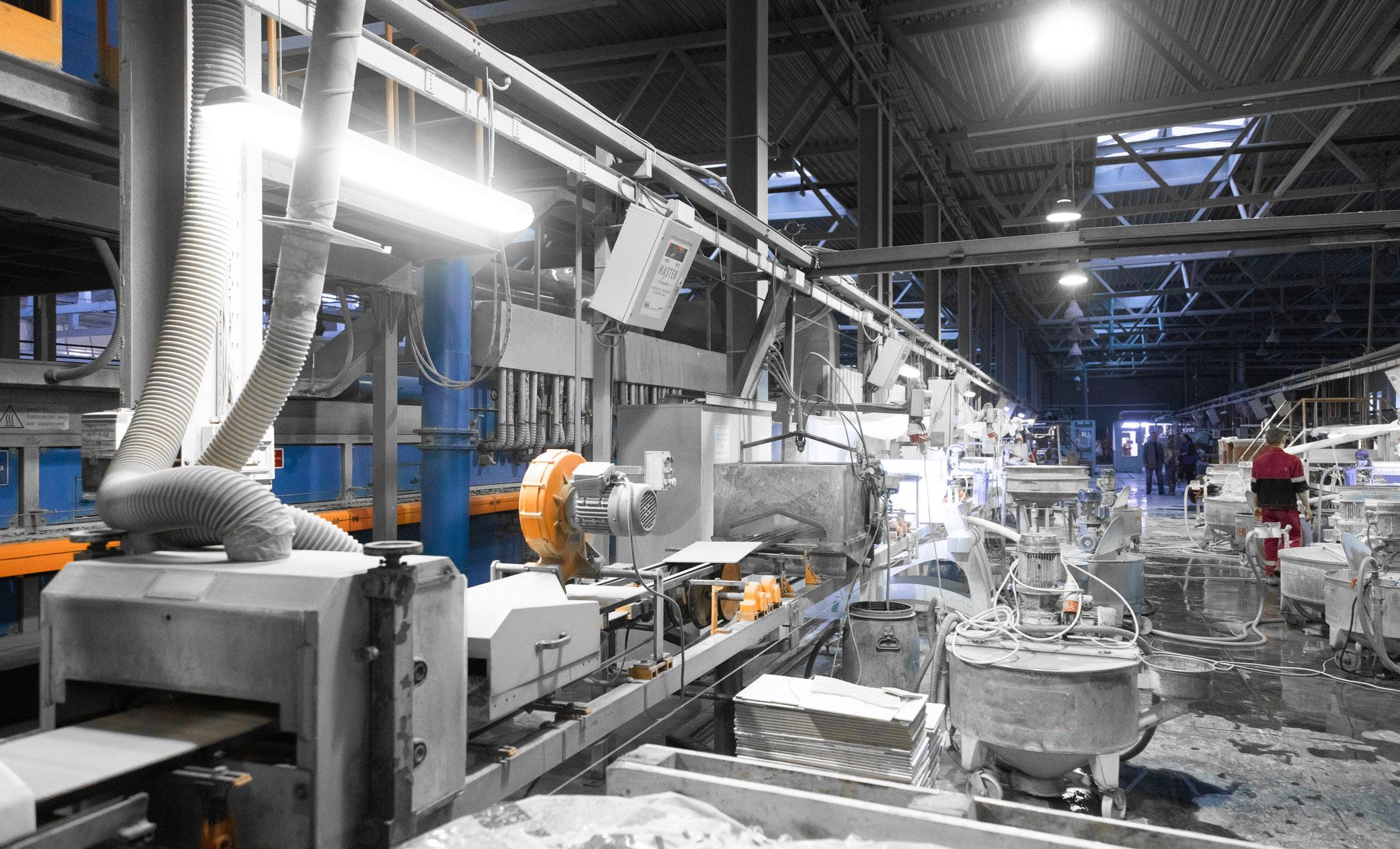
• To actively contribute to the sustainable development of the localised and national society. • As a part of CSR culture, the company is also playing a pivotal role in infrastructural development of surrounding areas, as well as reducing its emissions. Recently Oman Cement has invested more than six million
Omani rial (OR) in projects related to sustainability and the environment. • To develop sustainable technologies and products to better the wider environment. • Ensuring a safe and secure work environment for all of its employees and management teams, both on-site and within offices. • To conduct its business in an environmentally responsible manner and to protect the environment. • Ensuring the support of small and medium-sized enterprises (SME’s), female empowerment and the support of entrepreneurs local to the company’s operations. • Always honouring the commitments made between the business, customers and partners. • To support the communities in which Oman Cement operates.
CSR MISSION
• Providing the best possible service to its customers. • Delivering the highest quality product possible and to deliver on time. • Maintaining the company’s faculties and equipment in a safe, clean, and orderly manner. • Maintaining legal compliance and fostering an ethical work culture. • Oman Cement continuously seek ways to improve what it does.
Oman Cement also holds key company values that are core components to its operations from start to end result. Within these core values the company has aims and goals that reflect its optimism; Oman Cement aspires to become the number one cement manufacturing company in the nation and amongst the company of elite cement manufacturers in the Middle Eastern region.
Oman Cement is committed to meeting the needs of its customers by providing high quality products and services in an environmentally friendly manner, through a competent, inspired and motivated team whilst enriching local community and creating sustainable value to its stakeholders.
Oman Cement’s culture is born out of Omani society and culture in which employees work in a collaborative environment with management focusing on the human capital and providing
Outlook Creative Services
Outlook Publishing’s awardwinning in-house team is now utilising its extensive production skills to offer a full and bespoke range of editorial, design and marketing services via its new Outlook Creative Services division. Expand your VRM wear parts lifetime Expand your performance Expand your business
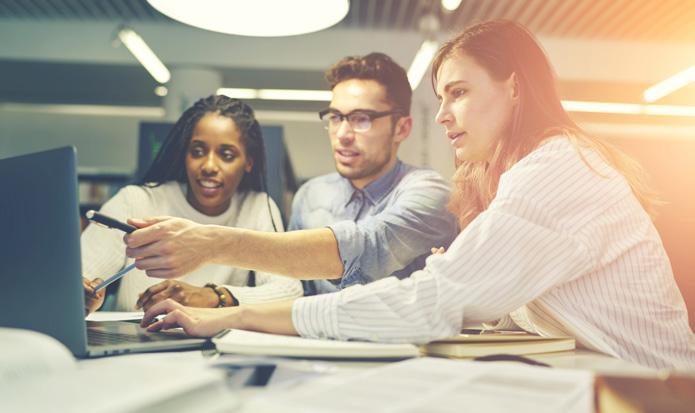

FOR MORE INFORMATION VISIT: www.outlookpublishing.com/creative-services
Process optimization services and products for abrasive and impact applications. vrm@magotteaux.com
www.magotteaux.com
the utmost support and care.
Oman Cement stands as one of the leading companies in the Gulf that contributes to the development of Oman’s society, all the while ensuring that it is committed to operating and growing its business in a socially responsible way for the betterment of all involved.
Oman Cement has remained socially responsible and has been voluntarily undertaken various corporate social responsibility initiatives despite there not having been any legal and statutory requirements to do so. In its commitment to CSR initiatives, Oman Cement has been making available charitable donations to Omani society though its philanthropic culture; an aspect of the company that resonates throughout every level. In addition, Oman Cement has repeatedly supported the local NGO’s initiatives in the areas of education, healthcare and environment in which it actively involves the local community in sustainable missions and activities.
Oman Cement is committed to operating and growing its business in a socially responsible way. Its vision is to grow its business whilst reducing the environmental impact of company operations and increasing its positive social impact.
On top of this, working for Oman Cement provides great opportunities for learning and development, career progression and acquiring new skills in multiple fields of industry. The company is people focused and passionate in what it does, trusting in its values of innovation, safety, integrity and collaboration.
The company believes that its employees are its main assets and in light of this offers its employees healthcare insurance and life insurance coverage, alongside individual and team educational training.
Being a part of the Oman Cement team enables employees to experience an exciting and challenging environment through which each individual can enrich their skills and increase their knowledge. Oman Cement is proud to be a member of the country that contributes to the construction of infrastructure in Oman.
Shipping SustainabilityIndustrial shipping is not commonly associated with sustainability. On a mass scale the shipping logistics sector is responsible for a large amount of varying environmental We speak to Evergas and discuss the issues including air pollution and the company’s progressive environmental and release of greenhouse gas emissions. Although not as polluting as airfreight, people-centric mission within the European with the average plane emitting 500 shipping sector grammes of CO2 per metric tonne of freight every kilometre of transporta- Writer: Marcus Kääpä | Project Manager: Nicholas Kernan tion, transport ships are still responsible for between 10 and 40 grammes of CO2 per kilometre.
Despite this, within the European region there sails a company that sits at the prow of the green shipping space.
Evergas is a Danish shipping company with roots back to 1883, wholly-owned by Greenship Gas and Jaccar Holdings. It is one of the world’s leading seaborne transporters of petrochemical gases and natural gas liquids, with a fleet of ships running on sustainable ethane gas unique in the shipping sector.
The company’s focus is to make gas transports simple and safe, and to set new standards for efficient and sustainable gas transport at sea. Evergas provides innovative and sustainable design solutions for the transportation and distribution of LNG, LPG and ethane commodities across the major areas of trade and emerging markets. With a head office in Copenhagen, Evergas also boasts offices in Singapore and Shanghai, and approximately employs more than 400 highly experienced and dedicated employees.
“The European shipping industry is definitely an exciting space to be involved within,” begins Steffen
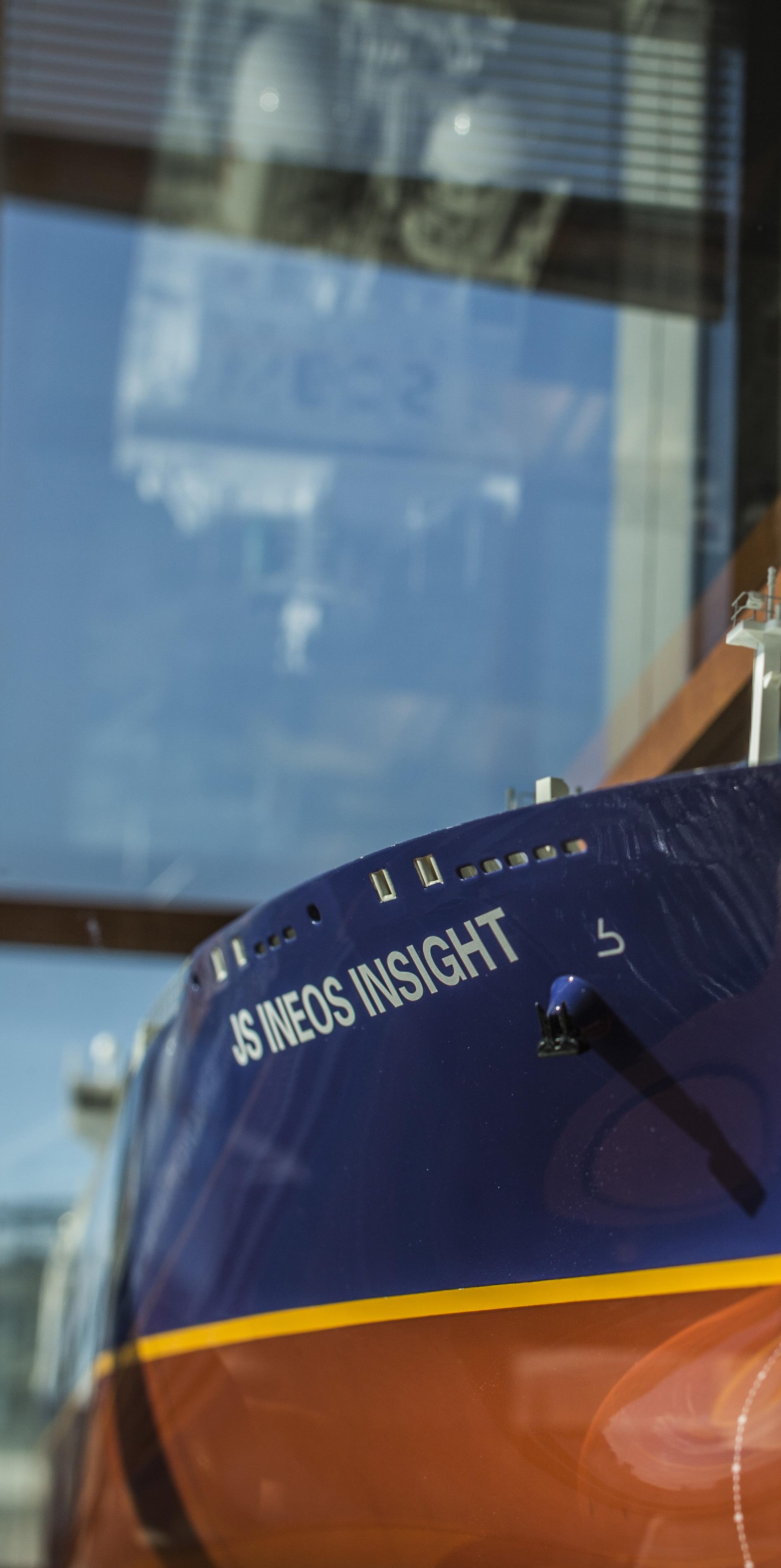
Sustainability
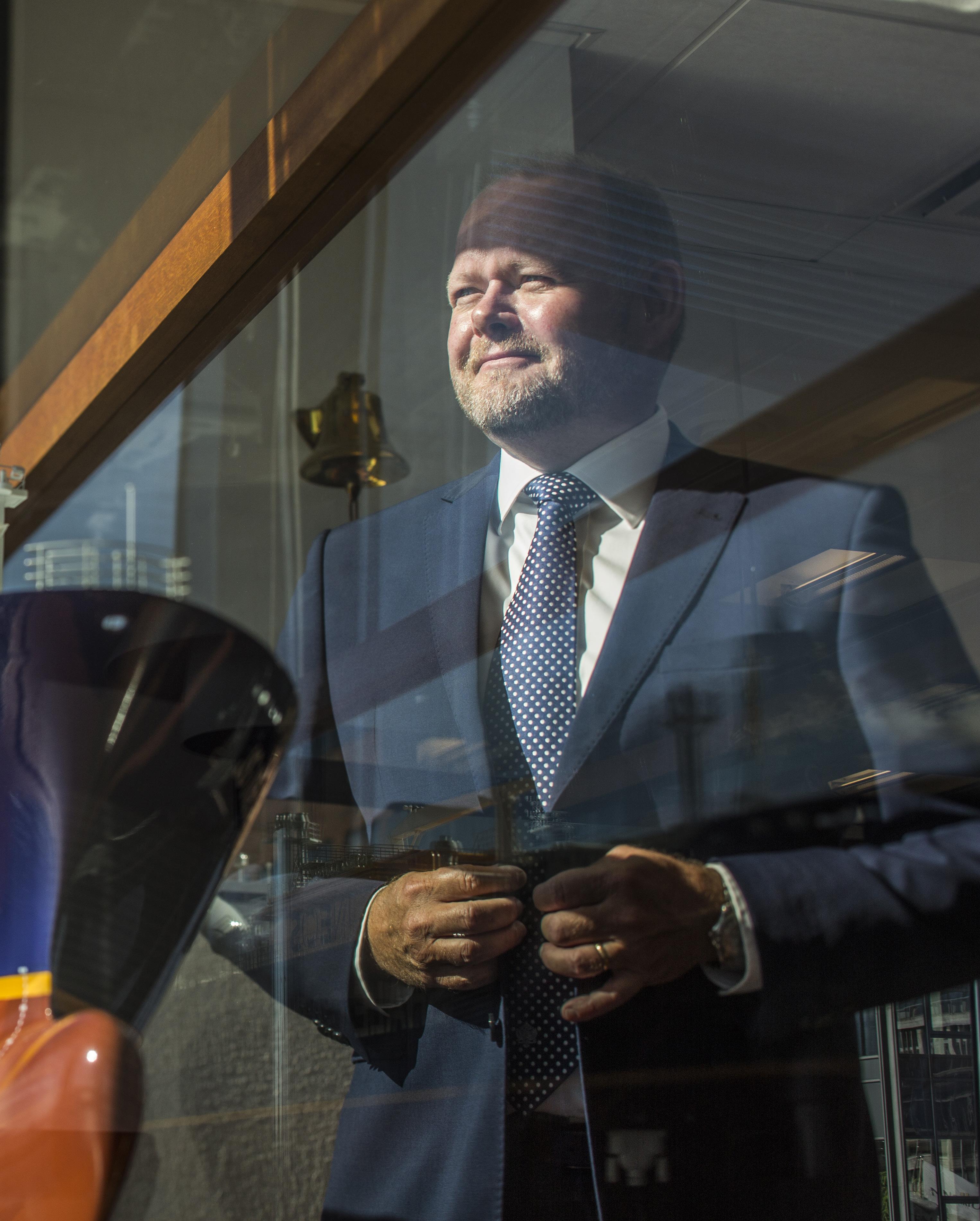