PORTS
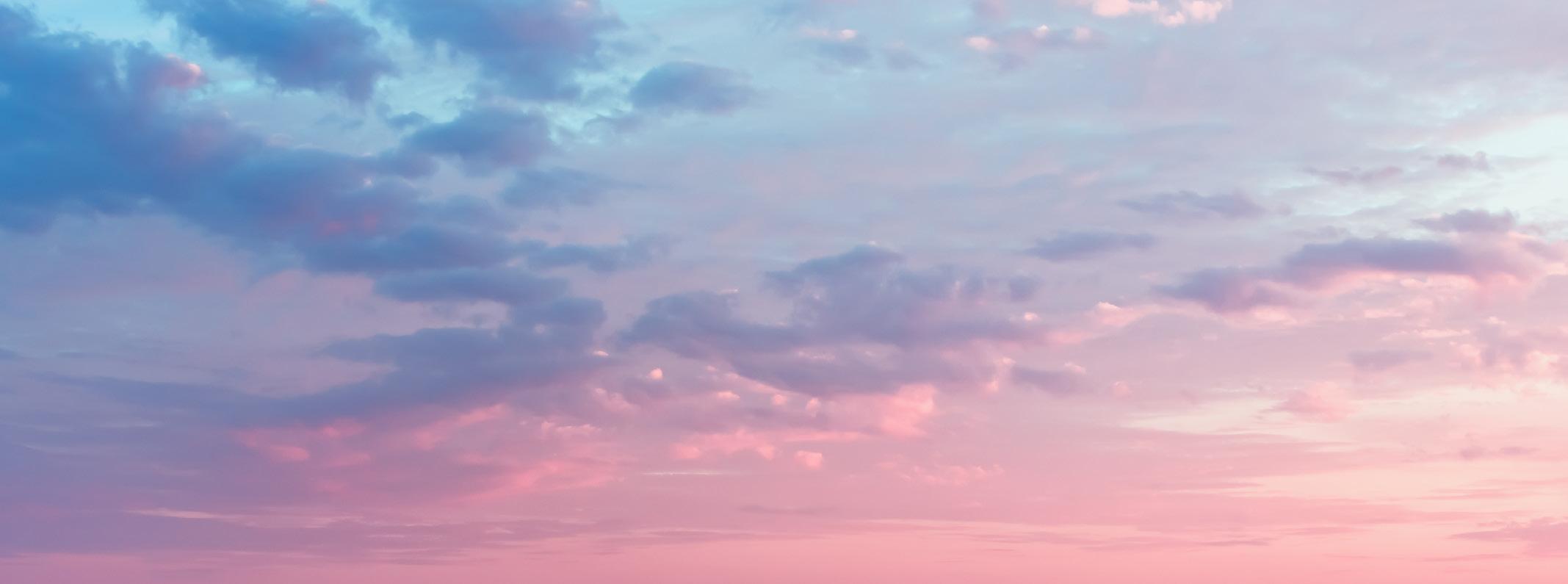

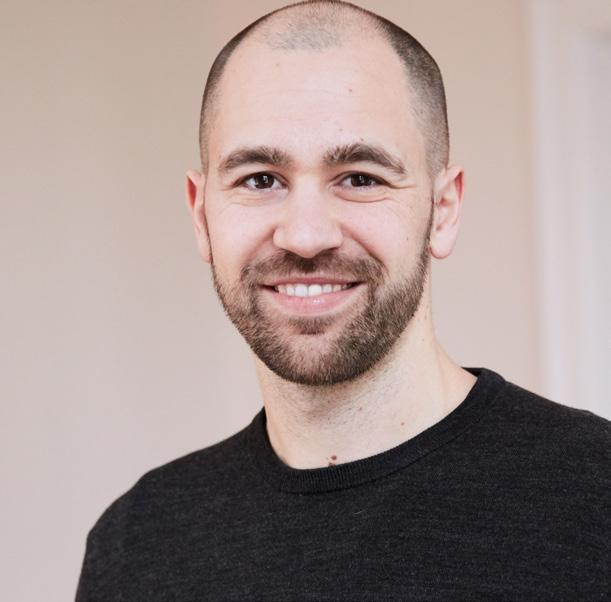
The collective voice of Australia’s ports sector as a cornerstone of the economy, tool for sustainable growth, and gateway to the rest of the world
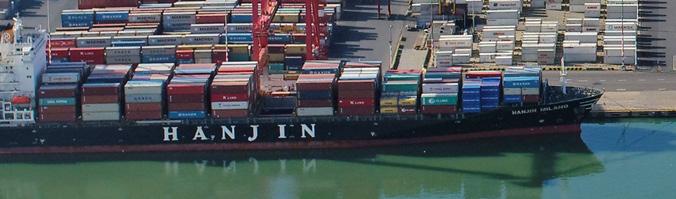
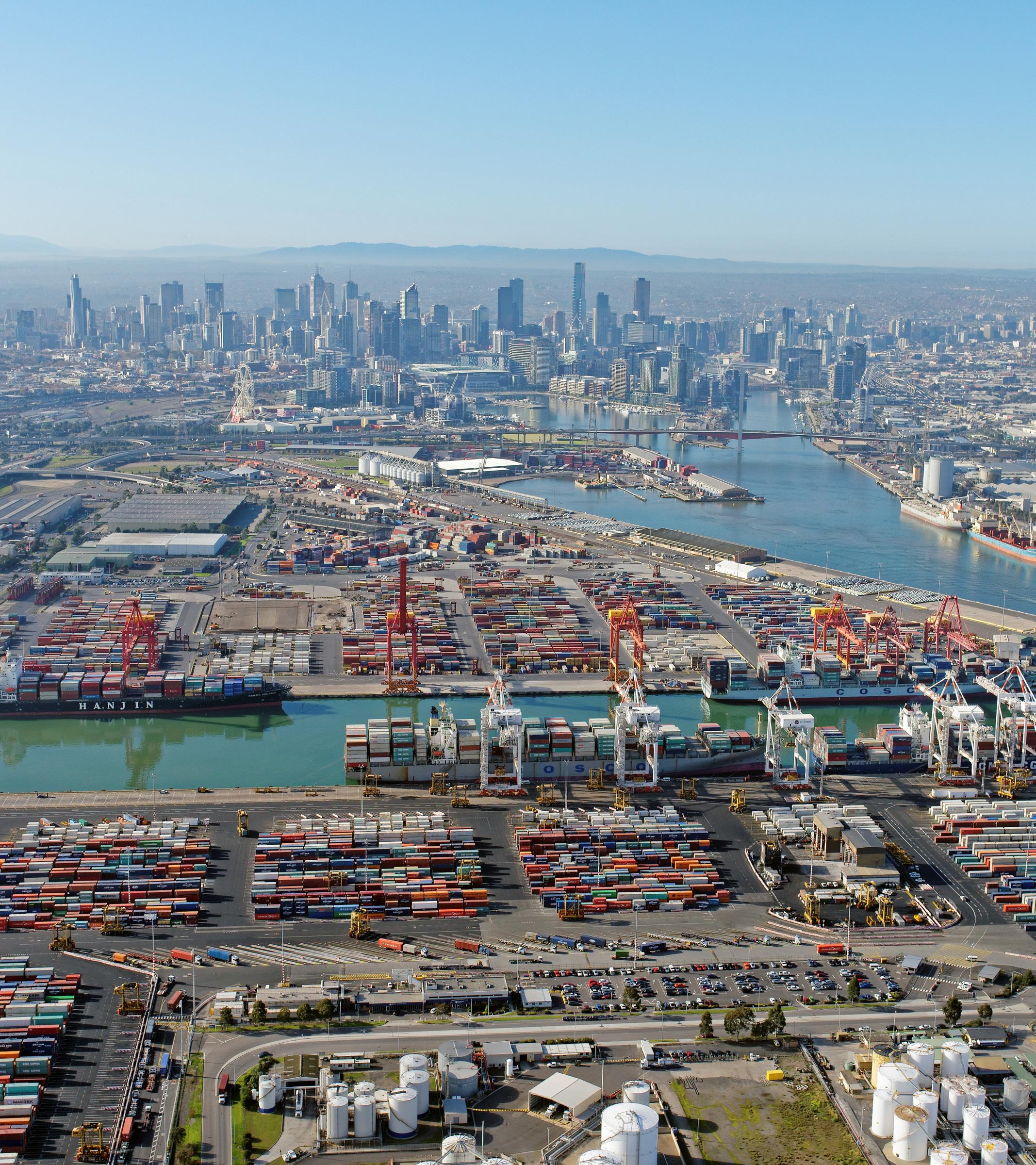
The collective voice of Australia’s ports sector as a cornerstone of the economy, tool for sustainable growth, and gateway to the rest of the world
For over a decade, our portfolio of in-house magazines has been lovingly produced, printed, and distributed to our esteemed subscribers across the globe from our headquarters in the UK.
But now we are moving with the times, adopting a digital-first approach by producing online-only publications. A major factor in this decision is to minimise our environmental footprint, reducing the carbon emissions involved in the logistics of print magazine distribution and the resources required therein.
Going forward, we will provide print orders of any magazine in-line with the requests of our featured companies, subscribers, and conference & expo partners.
Please get in touch for a print-on-demand quote or visit our website to find out more.
“We always planned that when our digital subscribers consistently accounted for 85% of our total magazine subscribers, we would cease printing our publications in-line with our environmental and sustainability goals.”
– Ben Weaver, CEO, Outlook Publishing Ltd
EDITORIAL
Editorial Director: Phoebe Harper phoebe.harper@outlookpublishing.com
Senior Editor: Marcus Kääpä marcus.kaapa@outlookpublishing.com
Editor: Jack Salter jack.salter@outlookpublishing.com
Junior Editor: Ed Budds ed.budds@outlookpublishing.com
Junior Editor: Rachel Carr rachel.carr@outlookpublishing.com
PRODUCTION
Production Director: Stephen Giles steve.giles@outlookpublishing.com
Senior Designer: Devon Collins devon.collins@outlookpublishing.com
Designer: Sophs Forte sophs.forte@outlookpublishing.com
Junior Designer: Louisa Martin louisa.martin@outlookpublishing.com
Digital Marketing Manager: Fox Tucker fox.tucker@outlookpublishing.com
Social Media Executive: Bria Clarke bria.clarke@outlookpublishing.com
Production Assistant: Megan Cooke megan.cooke@outlookpublishing.com
Web Editor: Oliver Shrouder oliver.shrouder@outlookpublishing.com
BUSINESS
CEO: Ben Weaver ben.weaver@outlookpublishing.com
Managing Director: James Mitchell james.mitchell@outlookpublishing.com
Sales Director: Nick Norris nick.norris@outlookpublishing.com
Commercial Director: Joshua Mann joshua.mann@outlookpublishing.com
HEADS OF PROJECTS
Callam Waller callam.waller@outlookpublishing.com
Deane Anderton deane.anderton@outlookpublishing.com
Eddie Clinton eddie.clinton@outlookpublishing.com
Josh Hyland josh.hyland@outlookpublishing.com
Ryan Gray ryan.gray@outlookpublishing.com
BUSINESS DEVELOPMENT DIRECTOR
Thomas Arnold thomas.arnold@outlookpublishing.com
TRAINING & DEVELOPMENT MANAGER
Marvin Iseghehi marvin.iseghehi@outlookpublishing.com
SALES AND PARTNERSHIPS MANAGER
Donovan Smith donovan.smith@outlookpublishing.com
PROJECT MANAGERS
Dennis Morales dennis.morales@outlookpublishing.com
Jordan Levey jordan.levey@outlookpublishing.com
Kierron Rose kierron.rose@outlookpublishing.com
Kyle Livingstone kyle.livingstone@outlookpublishing.com
Liam Pye liam.pye@outlookpublishing.com
Nicholas Kernan nicholas.kernan@outlookpublishing.com
Taylor Green taylor.green@outlookpublishing.com
ADMINISTRATION
Finance Director: Suzanne Welsh suzanne.welsh@outlookpublishing.com
Finance Assistant: Suzie Kittle suzie.kittle@outlookpublishing.com
Finance Assistant: Victoria McAllister victoria.mcallister@outlookpublishing.com
CONTACT
APAC Outlook
Norvic House, 29-33 Chapelfield Road
Norwich, NR2 1RP, United Kingdom
Sales: +44 (0) 1603 363 631
Editorial: +44 (0) 1603 363 655
SUBSCRIPTIONS
Tel: +44 (0) 1603 363 655 phoebe.harper@outlookpublishing.com www.apacoutlookmag.com
Like us on Facebook: facebook.com/apacoutlook Follow us on Twitter: @apac_outlook
Welcome to our 61st edition of APAC Outlook magazine. This issue, our cover star is Ports Australia - the industry association representing the proud maritime nation’s leviathan port operations. Australia’s gateways to the world and an indispensable cornerstone of the economy, we take a deep dive into the country’s maritime supply chain as it continues to drive towards a more sustainable sector championed by the collective voice setting the benchmark for industry standards.
“Our members are truly at the forefront of the debate around topical issues such as alternative fuels, automation, artificial intelligence (AI), and sustainability,” says CEO at Ports Australia, Mike Gallacher.
Elsewhere, Building Façade Group’s expert consultancy services are shaping the skylines of the island-nation of Singapore with its world-class façades.
“Working on great projects, with great people and adding value to all – this is the guiding principle in our service to clients. We help to build a better world using our skills and experience; it sounds cliché but there is no better or simpler way of explaining it,” reveals Managing Director, Sani Chang, in an exclusive interview.
In the food and beverage space, Hilton Foods remains the protein partner of choice for Asia Pacific, as we unpack its expansion and sustainability journey with regional COO, Melanie Chambers.
As always, our magazine presents a dynamic array of corporate stories showcasing businesses that are thriving in the ever-evolving industrial landscape of Asia Pacific.
We hope that you enjoy your read.
Phoebe Harper Editorial Director, Outlook PublishingTOPICAL FOCUS
18 Technology
Switching it Up a Gear
Combatting SF6 – the world’s strongest greenhouse gas
INDUSTRY SPOTLIGHTS
20 Ports Australia
Setting the benchmark for optimising assets and sustainable growth
EVENTS
196 Asia-Pacific’s International Mining Exhibition (AIMEX)
Australia’s longest-running mining event
198 Austmine
The mining innovation conference comes to Adelaide
58 SHOWCASING LEADING COMPANIES
Tell us your story and we’ll tell the world
CONSTRUCTION
60 Building Façade Group
The Face of Façade Consultancy
Technical expertise in Singapore and beyond
76 Knight Frank Malaysia
Spearheading Malaysia’s Real Estate Development
A partner of choice for project management and workplace consultancy
84 Ignite Architects
A Design for Life
Igniting a passion for architecture
92 PMDL Architecture + Design
Dynamic and Considered
Inside the mantra of a multidisciplinary design practice
MINING
132 Ravenswood Gold
A Golden Future Mining with the Queensland community in mind
146 RZ Resources
Unearthing Elemental Discovery Excavating a bold future
156 Yuxin Holdings Pty Ltd
Au Exploration
Gold production in the land Down Under MANUFACTURING
164 Seeley International
Innovative and Evaporative Proudly Australian air conditioning solutions
FOOD & BEVERAGE
100 Hilton Foods
Protein Partner of Choice
Charting regional expansion and sustainability efforts
116 Berton Vineyards
Berton Does it Better
A full bodied business, aged to perfection
124 Taco Medic
Food for the Mind, Body and Soul
Taquerias making an impact in New Zealand
LOCAL GOVERNMENT
172 Department of Transport and Main Roads (TMR)
Champions of Transport Innovation
Changes on the horizon for transport in Queensland
ENERGY & UTILITIES
182 Senversa
The Pride of Australian Versatility
Investing in people to facilitate long term growth
TECHNOLOGY
188 PNG DataCo Limited
Bridging the Communication Gap Digitally connecting Papua New Guinea
CHINA’S RE-OPENING IN the wake of the COVID-19 pandemic is tipped to create a commodity demand that will exceed levels recorded in the aftermath of the 2008 financial crisis, as observed by the Australian iron ore industry leader, Fortescue. At the annual Boao Forum for Asia, Fortescue’s Executive Chairman, Andrew Forrest, said the company was seeing “uniform demand” across China.
Fortescue entered the Chinese market in 2008 with a 180,000-metric tonne shipment of iron ore, as the nation underwent a significant stimulus programme supporting infrastructure development fuelled by commodities. Forrest said this demand is reflected in current market conditions, although the company is now dealing with a greater volume for a smaller percentage.
DBS GROUP – Southeast Asia’s largest bank – is suffering the fallout of a major outage that disrupted its digital services on Wednesday 28th March. From 08:30am to 5:45pm, users were unable to access online banking or make trades, leading to a thorough ongoing investigation. The negative impact of the outage was reflected in the company’s shares, which subsequently dropped by 1.4 percent. In an official statement, the Monetary Authority of Singapore has referred to the disruption as “unacceptable”, and that DBS Group had “fallen short of expectations”.
AMAZON WEB SERVICES
(AWS) has announced plans to invest over AUD$13 billion in its expansion across Melbourne and Sydney within the next five years. The tech giant intends to expand its existing cloud computing operations in both cities, while also progressing the conversion of its data centres to run entirely on
renewable energy.
Although AWS has been in Sydney since 2012, Melbourne is a new location and comprises the majority of the forecasted investment. The company has estimated that the overall expansion of both centres will introduce 11,000 new full-time equivalent jobs to the area, with local government welcoming the investment as a means to uplift local communities and businesses.
NEW SOUTH WALES’ newly elected premier, Chris Minns, has announced that mobile phones will be banned in public high schools during school hours. The ban, due to be imposed in term four later this year, is the culmination of a long-term election promise designed to improve children’s learning outcomes. However, several experts – including from the University of Western Sydney - have responded that phone bans do not necessarily improve academic outcomes, and
MALAYSIA and China are in the pipeline to settle disputes over the contested waters of the South China Sea. The Malaysian state news agency, Bernama, has reported that Prime Minister Anwar Ibrahim confirmed he was willing to negotiate
emphasis should be placed on using phones responsibly, rather than banning them altogether.
with Beijing if it meant that Malaysia could continue energy exploration projects within areas of the waterway where its claims overlap with China’salthough the exact locations were not specified.
At present, Beijing claims sovereignty over approximately 90 percent of the South China Sea as a strategic waterway transporting trillions of dollars’ worth of seaborne trade every year, despite overlapping claims with Malaysia, Brunei, the Philippines, Taiwan and Vietnam.
ALONGSIDE OTHER LOCAL delicacies, including whale meat and snails in a can, a vending machine in Japan is now selling black bear meat to commuters, available 24/7. Located in Tazawako Station in Akita, the machine was installed by a local restaurant – Soba Goro – who wanted to mix up its tourist food offering.
The meat is reported to come from wild bears hunted in the surrounding area. An average of 10–15 packs are sold every week and the meat costs an average of USD$17 per 250g. The Asiatic black bear is classed as an internationally vulnerable species, but Japan insists that it limits the numbers that can be hunted.
RETAIL
THANKS TO THE leading e-commerce platform’s adoption of the Google Cloud Discovery artificial intelligence (AI) solution, merchants on Shopify can enjoy advanced browsing and searching experiences. As part of four new AI innovations delivered by Google Cloud, these latest solutions are designed to enhance e-commerce sites and transform in-store shelf checking processes with more streamlined online shopping experiences for consumers.
In addition, Google Cloud has launched a new integration for Shopify’s enterprise retail solution – Commerce Components – which will introduce advanced search capabilities leveraging AI innovation.
The packaging industry – like every one of us – has to face up to climate change, pollution and scarcity. What are the challenges and how can we make our future more sustainable?
By far the biggest contributor to global warming – at more than 73 percent 1 – is energy consumption. Reducing energy use should be every organisation’s priority. It is certainly high on the agenda in the packaging industry.
According to Climate Collaborative, on average, packaging accounts for about five percent of the energy used in the life cycle of a food product,
making it a significant source of GHG emissions.
Marine waste is another huge environmental problem. The United Nations Environmental Programme (UNEP) has found that 90 percent of litter in our oceans is made up of different plastic polymers. Packaging makes up just eight percent of that total, but our industry is now moving more quickly to address this issue.
The world must also confront water scarcity. By 2025, up to 3.5 billion people might be living in areas of water stress. Without a developed water infrastructure, the only way to get them drinkable water will be
by using packaging in one form or another.
So, how is the packaging industry stepping up to these challenges? By making a drastic shift from a linear to a circular economy model. We need to acknowledge that packaging is a resource, not a waste.
By keeping it in the circular economy loop, PET plastic packaging can play a pivotal role in protecting and distributing our most precious products. This has been recognised by the Ellen MacArthur Foundation through its New Plastics Economy Global Commitment, in which Sidel is one of the signatories.
As a major supplier of packaging equipment and services, we’re working hard to help the beverage industry to become more sustainable. We’ve committed to making a bold shift to using green energy on our own production sites and are engaging with our suppliers on their sustainability journey. We committed to cut our own carbon emissions (known as Scope 1 and 2) by 30 percent by 2030 as well as help our suppliers and customers reduce theirs (Scope 3) by 25 percent in the same timeframe. We’re at our customers’ side. For example, we helped UAEbased customer Zulal make energy savings of 56 percent by moving to a new fully integrated packaging line configuration. New technology, such as our Evo-On Eco app, is enabling our customers to monitor production line energy consumption and make adjustments in real time.
Lifecycle analysis (LCA), the only scientific way to compare one material with another, shows that plastic, and PET in particular, has the best carbon footprint among materials currently available.
We are continuously working to improve packaging footprint, by following the five principles of reduce, reuse, recycle, replace and reinvent. Our new moulding technology reduces the weight of bottles, cutting down on material use as well as transport emissions.
We are providing tethered caps that stay attached to the bottle, minimising litter ahead of new European legislation. Additionally, we are leading the way in making PET bottles safely refillable, and ensuring best quality bottles even with high quantities of recycled PET.
We are also designing out waste in how bottles are labelled and packaged ready for transportation.
As for reinventing, we’re actively scouting for new bio-sourced/biobased materials.
We have to find these new sustainable solutions, because like it or not, plastic packaging is with us in the near term. Sales of packaged products in food, beverages, home and personal care are continuing to grow, especially in the APAC region. The Middle East, Africa and India are driving 4.4 percent compound annual growth in these products by 2024. The use of PET is expected to grow at 1.7 percent with packaged water leading the way with a growth of 4.2 percent. Energy drinks are performing particularly strongly in Asia. So, how can we make this future growth more sustainable?
• Reuse will come to the fore, as the industry comes up with new solutions in the different reuse schemes such as refill-on-the-go, refill-at-home, return-on-the-go and return-from-home.
• Recycled PET will become more prevalent, with the main challenges being availability, quality and price.
• New sustainable materials and easier-to-recycle solutions moving from many layers of multiple materials to one single monomaterial layer, will be on the rise.
• The way goods are packaged for transport will be very different.
We are likely to see much more cooperation between manufacturers, brand, suppliers, NGOs and, of course, end consumers. Manufacturers will be expected to take on more responsibility for waste management. More countries will be joining the 63 nations which have already enacted Extended Producer Responsibility
measures, such as product takeback schemes, deposit-refund, and waste collection and takeback guarantees. More governments will fund and create better recycling infrastructures, as well as easier, incentivised ways for consumers to recycle, such as reverse vending machines.
It will take all of these efforts to see significant improvements. If it is properly collected and recycled, PET, far from being the problem, can offer the best answer to the current sustainability challenge. By working together, we can make a true circular economy of plastics possible.
Chutima Saengow is Communications Manager for Southeast Asia and Pacific at Sidel. Based in Bangkok, Sidel is a leading provider of equipment and services solutions for packaging, beverage, food, home and personal care products, operating in over 190 countries. Find out more about Sidel’s work on sustainability and how to access its support for your business at www.sidel.com
Sources: 1 Our World in Data
From jungle beginnings to spice plantations, and now Singapore’s first gin distillery, experience the taste of the Tanglin region with co-Founder of Tanglin Gin, Charlie van Eeden
Writer: Rachel Carr
When Tanglin Gin entered the Singapore spirit market, it was a first for the drinks industry on the island country and city-state in Southeast Asia.
Materialising from the vision of four Western expats, Charlie van Eeden, Chris Box, Tim Whitefield and Andy Hodgson, Singapore’s first gin
distillery opened in 2018.
One of the co-Founders discovered a surprising revelation after a night out on a rooftop bar, where there were no local gins available. Moreover, Singapore has been connected with gin for hundreds of years.
As a global trading port and an important part of the ancient Spice
Trade Route, the spices travelled from the Far East to Europe, into the stills that created some of the UK’s bestknown gins.
With this in mind, the Tanglin Gin Distillery was developed, along with The Jungle Bar. Both are located on Dempsey Hill, a former nutmeg plantation and barracks for British
troops, in the verdant and fecund area of the Tanglin district, near the Botanic Gardens.
“The idea of the name for our brand came from one of our founders who used to live in the Tanglin neighbourhood. In the 1700s, this was where the spice plantations were located, one of which was a pepper plantation, an
ingredient we often use in our gins,” details Charlie van Eeden, co-Founder of Tanglin Gin.
Along with the name, the brand’s tiger logo is inspired by the area, hailing back to when Singapore was a dense jungle, and small villages were abandoned due to attacks from these majestic striped animals.
“The brave pushed forward as they had visions of growing spices such as sireh, pepper, nutmeg and ginger, under the waving coconut palms and secret gardens filled with lush orchids and botanicals. Tanglin Gin emerged from the same desire to pioneer, create and take a chance,” explains van Eeden.
Two historically significant buildings were repurposed to house the distillery, which includes the Tanglin Creations Lab, the gin experience centre, and The Gin Jungle which is a
retail space with a seven-metre-long gin bar.
The company recoups extra revenue with the Tanglin team offering weekend tours of the premises, so guests have the opportunity to see how the gin is made, try the results and purchase merchandise.
The location has always had a rich heritage, and now it is a place where good times and gin meet nature and the wilderness.
Since the first batch of Tanglin Gin, the quality ingredients have been inspired by the colourful flavours of Singapore, meaning that the spirit is truly unique.
To expose the optimum intensity of the flavours, the modern stainless steel still has two packs of Raschig
rings which are found below and on top of a series of glass botanical baskets.
The process, wedded to the wealth of botanicals, creates a taste which puts the international award-winning brand on the world map.
By blending Asian ingredients such as Angelica root and dendrobium orchids with a more traditional essence, many different notes are released.
Drawing on its natural surroundings, the distillery infuses its products with local botanicals, punctuated with spices sourced from around the region, such as kaffir limes, chilli, orris root, vanilla and amchoor. Although the exotic recipes are inspired by stories from all over the world, the first batch was brewed closer to home.
“Our very first gin was named the Orchid Gin, inspired by Singapore’s
national flower and its use of vanilla, an orchid of the genus Vanilla planifolia,” van Eeden informs us.
Another cornerstone product is Black Powder Gin – Tanglin’s Navy Gin, and very fitting considering Dempsey Hill’s military history. It ties in with its 58 percent alcohol by volume (ABV) navy strength, which is thought to originate from the idea that when high proof alcohol spills on gunpowder it would still light.
Expanding into the international spirit arena has been an ambition for van Eeden from the beginning.
“Seeing a bottle of Tanglin Gin on the shelf of a cocktail bar in New York City is the best feeling you can have,” he says enthusiastically.
Strategically and organically growing the company into a globally rec-
ognised brand, Tanglin Gin is looking for partners who are excited about its story and products.
“Since we are not only a brand but also a thriving cocktail bar in Singapore, we can offer more than a bottle of gin.
“I am based in Amsterdam at the moment to support our European and US exports. We are currently available in Australia, Japan, Malaysia, Hong Kong, Taiwan and the US. We will start to export to Europe this year,” he adds.
The distillery is fast approaching its fifth anniversary, and plans are underway to focus the celebrations on a new drink to pay homage to the iconic national cocktail - the Singapore Sling.
“We will launch an interesting new product, not a gin and not a liqueur, but something that will complement our offerings whilst making a great
Singapore Sling cocktail. We will also have celebrations in our Tanglin Gin Jungle throughout the month of July.”
With an endless supply of interesting cocktail recipes, the Tanglin Creations Lab invents new products every few months, such as Tanglin Triple Tangerine.
Despite the bootstrapped business being unable to escape the challenges of the COVID-19 pandemic, it was forced to navigate its own deliveries as its logistics partner stopped its operations, however, this turned out to be a positive move.
“It allowed us to meet all of our customers in person. Many of them were very happy to see us, and more importantly our gin, during lockdown. This gave us the energy we needed to keep going,” concludes van Eeden.
Tanglin Gin is going from strength to strength - sorakan to that!
As the only company to manufacture microtubers on a commercial scale, E Green Global is the start-up disrupting the global seed potato market. From lab to field, we unearth its innovative technology with CEO and Founder, Keejoon Shin Writer: Phoebe Harper
Potatoes have been a staple of global food supply for centuries. However, in the face of disruptive weather patterns, supply chain shortages and heightened import costs that are prohibitive to many developing countries, the answer to widespread potato consumption as a means to combat world food poverty, lies in agri-tech. Enter, E Green Global (EGG) - the platform tissue culture tech company utilising its plant factory platform to overcome the limitations of the current seed potato supply system. With an overriding emphasis on competitive price and productivity, EGG’s CEO and Founder, Keejoon Shin, dives into its virus-free food solution and hopes for future expansion.
• EGG will give better, faster, cheaper, and more crops to the world, helping to relieve world hunger
• EGG will expand its microtuber technology to other crops such as sweet potato, cassava, onion and garlic
• EGG is successfully working on its business in the US, China, Canada and South Korea
• EGG is willing to access new markets across the European Union, India, Russia, Africa, Central and South America
APAC Outlook (AO): Firstly, could you tell us what inspired you to start EGG? What led to the company’s foundation?
Keejoon Shin, CEO and Founder (KS): Potatoes are the only major grains that have no futures market and international trade is extremely limited, with no major grain companies entering the market. Therefore, production and local consumption are mainly carried out locally. This local production and supply of qualified seed potatoes are the key factors that determine the production yield of crops. However, most countries have no qualified seed
potato production system, except for a small number of advanced countries. These elements were the driving force behind the start-up of EGG.
AO: How can EGG’s microtubing method contribute to the global fight against world poverty and hunger?
KS: Potatoes are a very good crop with high productivity per unit area and can be a good food solution for underdeveloped countries. However, they have not been able to significantly increase potato production yet because they do not have qualified, virus-free seed potatoes. Therefore, it is possible to solve this problem by establishing a qualified microtuber (MCT) supply system locally to increase high-quality seed supply.
AO: What are the benefits involved for potato farmers?
KS: Currently, many rural farmers cannot secure high-quality seed locally due to shortage. Imported seed potatoes are too expensive to increase their margin. It is also beneficial for potato farmers because it can bring high productivity by supplying qualified seed potatoes at a low price.
AO: What makes EGG a disruptor of the Agri-Tech industry?
KS: EGG has established itself in terms of next-generation seed potatoes by commercialising MCT technology that existed only theoretically in the table tongue. MCTs can be easily traded, and transportation cost is minimal due to their small size. Also, MCT production facilities can be easily set up anywhere in the world. In the near future, farmers of the world can enjoy high-quality, virus-free seed potatoes by adopting MCT seed systems locally, which was not possible before due to local seed shortage, strict quarantine, and high transportation costs.
AO: Finally, what are your hopes for the future development of this technology? Are there any new markets that you would like to explore?
KS: We will continue to strengthen MCT responsiveness and productivity to various environmental and climate changes, while strengthening cost reduction. Ultimately, EGG will enter anywhere in the world where potatoes are needed, but we are currently entering the Middle East, Central Asia and Southeast Asia, where highquality, virus-free seed potatoes are in shortage and imported seed potatoes are expensive in a step-by-step approach according to the company’s capabilities and specific business environment.
Adding to its growing family of regional titles – EME Outlook, Africa Outlook, APAC Outlook, North America Outlook, and its sister sector title, Mining Outlook – Outlook
Publishing is proud to announce the birth of a dedicated platform for the healthcare sector. As organisations worldwide must navigate a new healthcare landscape defined by technological innovation in the wake of the COVID-19 pandemic, now is the time to showcase the strides being taken in this critical sector.
A multi-channel brand, Healthcare Outlook will bring you the positive developments driven by organisations across the healthcare industry through its various platforms. Discover exclusive content distributed through its website, online magazine, social media channels, and dispatches delivered straight to your inbox with a bi-weekly newsletter.
Through this compelling new venture, we intend to foreground the movers and shakers of the industry. To participate as a featured company and join us in this exciting endeavour, contact one of our Project Managers today.
www.healthcare-outlook.com
Nuventura is waging war on the world’s strongest greenhouse gas - SF6 - through its unique switchgear technology. Driving towards an efficient and sustainable global power sector, Founder and CEO, Fabian Lemke, discusses plans for expansion across Asia Pacific
Writer: Phoebe HarperAPAC Outlook (AO): Could you provide us with a brief introduction to Nuventura and tell us about the company’s vision?
Fabian Lemke, CEO and Founder (FL): Nuventura was founded in 2017 with the vision of developing switchgear which would make the use of Sulphur Hexafluoride (SF6) – the world’s strongest greenhouse gas (GHG) – obsolete in the energy sector. With this goal in mind, we developed
the world’s first medium voltage (MV) gas-insulated switchgear (GIS) for the 36 kilovolt (kV) voltage range which replaces SF6 with dry air. Dry air is essentially just normal breathable air but without any moisture. As we move forward, we will continue to develop dry-air GIS for different use cases and geographical requirements. Our business model means we interact with different stakeholders in the industry. We can sell switchgear directly to end-users for projects, i.e.
renewables, but we can also enable other switchgear suppliers/EPCs and switchgear manufacturers to expand their switchgear offerings to their customers.
AO: What are the harmful impacts of SF6 gas and why do you think is it not more widely reported?
FL: As the world’s strongest GHG, SF6 has a global warming potential (GWP) of 25,200 which means that 1kg of SF6 is equivalent to 25,200kg of CO2. Annual SF6 emissions are roughly the equivalent to the yearly CO2 emissions produced by 100 million cars. And to make matters worse, in a business-asusual scenario, SF6’s use is expected to increase by 75 percent by 2030 from 2019 levels. Furthermore, though recycling of used SF6 is common, it is normally not destroyed because of the difficulty and cost associated with this destruction. Therefore, it can reasonably be expected that all SF6 that currently exists and that will be produced in the future will persist for thousands of years, whether in
GIS equipment or, ultimately, in our atmosphere. It’s for these reasons that alternatives are urgently needed.
SF6 is a topic that is not widely reported because it has highly specialised and relatively niche use cases. Until recently, electrical infrastructure and switchgear have not been topics that have excited public attention. Therefore, media has remained focused on more familiar climate topics such as methane and CO2. We hope this will change as the importance of electrical infrastructure in achieving net zero becomes better understood.
AO: In contrast, could you expand on the alternative that has been developed by Nuventura and why this is a more environmentally friendly option?
FL: Our alternative replaces SF6 as the insulating medium with dry air. A traditional MV SF6-GIS contains around 3kg of SF6 which, due to its high GWP, amounts to a CO2equivalent of 75.6t. Our solution’s insulation medium has a CO2 equivalent to zero.
Moreover, we’ve achieved this while maintaining the operational benefits traditionally associated with SF6-GIS – namely compact physical dimensions and a maintenancefree design. Therefore, it should be stressed that our climate-friendly technology does not compromise operational performance.
AO: How is Nuventura’s SF6-free GIS technology currently being applied across the Asia Pacific market? Do you see this as an attractive region for growth?
FL: We have started business activities in China and are currently developing a dry-air GIS product specifically for the Chinese market. We also have in our pipeline a number of reference projects in New Zealand. Moreover, in India, we are building a manufacturing hub for Nuventura. This is just the start of our presence in the Asia Pacific region, and I expect it to become an extremely attractive region for us.
I think this is because, right now, more than half of global energy consumption takes place across Asia Pacific, where around 85 percent comes from fossil fuels. However, 10 percent of the population across the
region still lacks access to electricity, and many more rely on traditional biomass methods, such as wood combustion, for heating and cooking.
To address these problems, as well as those posed by rapid urbanisation and industrialisation, energy demand is rising. Because of this, I believe considerable opportunities exist to avoid the long-term lock-in of energy technologies and infrastructure, such as SF6-GIS, which exacerbate the problem of climate change.
AO: Finally, what are Nuventura’s key priorities in the coming years?
FL: Our priorities for the future are to establish our first 36 kV product but also expand our product portfolio to address more switchgear use cases and different international standards. We want to do this by developing new technologies and increasing the list of our reference projects, as well as partnerships with EPCs, suppliers and switchgear manufacturers.
Moreover, we plan on further strengthening our new presence in both China and India as we develop appropriate products for the Chinese market and expand manufacturing capacity in India. Finally, we recently opened a manufacturing hall in Berlin to meet the growing demand from customers. We will appropriately expand our production capabilities, and improve processes, to supply larger volumes.
“ANNUAL SF6 EMISSIONS ARE ROUGHLY THE EQUIVALENT TO THE YEARLY CO 2 EMISSIONS PRODUCED BY 100 MILLION CARS”
– FABIAN LEMKE, FOUNDER AND CEO, NUVENTURA
As a vast island nation, Australia has a rich and varied legacy of seafaring. The country boasts a proud and diverse maritime history, ranging from the ‘deep time’ stories of its First Nations people making the first sea crossings to Southeast Asia, to the advent of formal ports postEuropean settlement, and now hosting some of the largest and most advanced shipping operations in the world as the crux of the country’s trade.
Today, a staggering 98 percent of Australia’s trade is undertaken via marine transport, with ports across Australia handling over eight million containers every single year – a figure that has doubled in the past two decades and is only set to continue rising in the years to come.
Many of Australia’s cities and towns were originally built around ports. As such, they are an integral and intrinsic component to the fabric of the nation, handling everyday consumer goods alongside the raw materials that power our world, such as energy, metals and minerals. In addition, ports facilitate the tourism sector’s reliance on cruise vessels
and are a crucial component to the national defence sector.
The country’s primary trading partners via sea – both historically and currently – consist of China, Japan, South Korea, and India. Thanks to its strategic location in the South Pacific, Australia has long been a major player in international shipping with access to significant international maritime routes, including the Strait of Malacca, the waterway connecting the Indian Ocean with the South China Sea Pacific Ocean, and the Suez Canal as a vital link for import and export trade, amongst others.
In the early years of European settlement on Australia’s shores during the late 18th century, ports often comprised little more than wooden jetties – a far cry from the highly advanced mammoth operations that can be seen today. This time gave birth to the Port of Brisbane, which today resembles Australia’s largest capital city port. It began as a river operation handling the region’s first exports of timber shipments from local pine and cedar forests during the early period of settlement, transported by raft and loaded on to sailing
First port of call in the country’s supply chain, we take a deep dive into Australia’s port sector as a cornerstone of the economy, tool for sustainable growth, and gateway to the rest of the world
Optimising container movements to improve port productivity in Australia
Artificial intelligence (AI) is the tool of the future, that is becoming integral to the way industry operates across the world. Incorporation of AI into the supply chain sector is no different.
In Australia, ports are considered to be slower at turning ships around than the average international port, and the necessity to leverage AI to improve Australian container port performance is recognised now more than ever. According to a recent inquiry report carried out by the Australian Government Productivity Commission, inefficiencies in the country’s major container ports cost the Australian economy around AUD$600 million annually, a substantial amount of money that, through improving and automating systems, could be retained and used elsewhere.
Well-functioning container ports enable goods to enter the country more swiftly than otherwise and reduce the cost of such imports. Similarly, they enable Australian exporters to compete more effectively on global markets. Efficient ports minimise the time taken for containers to pass through and the time that ships and land transport spend within the port, while ensuring that inputs are used as effectively as possible. Ports that move containers more quickly, reliably and in a costeffective manner are better performers than those that do not.
The use of AI in container movement optimisation is a significant step towards improving Australian container port performance, and one embodied by Flinders Adelaide Container Terminal (FACT) based in South Australia. Through the optimisation of container movement within container yards, FACT is able to ultimately do more with less, limiting container handling amid other streamlined improvements. The project is a perfect example of how AI can help to solve complex problems that are beyond human capacity to solve.
When it comes to AI integration, FACT has a critical partner helping to achieve the port’s logistical productivity goals - Complexica. Employing more than 100 staff across four offices, Complexica is a leading provider of AI software applications that can optimise sales, marketing, supply chain decisions, and increase container movement optimisation capabilities in the area of ports, logistics and more.
Complexica was founded upon the research of several world-renowned computer scientists and has commercialised a modularised software platform called Decision Cloud® that empowers staff across multiple business functions to make better decisions. Decision Cloud® is powered by its award-winning AI engine - Larry, the Digital
Flinders Adelaide Container Terminal in South Australia Photo Credit: Flinders Port HoldingsAnalyst® - and the company’s investors include MA Financial Group (ASX:MAF), Flinders Port Holdings and Microequities Asset Management (ASX: MAM).
Complexica has successfully delivered countless software projects and deployments, using project management methodologies that allow for ontime and on-budget delivery. Complexica has considerable experience working with some of the world’s largest companies and organisations on projects that involve large data sets, challenging optimisation and prediction requirements, and complex system integrations and operational workflows. Some of its customers include well-known names like Arnott’s, Asahi, Bunzl, DuluxGroup, Lion, Metcash, Pernod Ricard, and PFD Foods, among others.
Most Commercial-Off-The-Shelf (COTS) software applications for managing supply and demand activities are unable to handle customer-specific requirements, such as variable and calendarised constraints, negative stock values, non-linear relationships, complex business rules set in time changing data environments, and non-standard business processes and workflows, among others. Complexica understands that the only business important to customers is their business, so the company has engineered its Decision Cloud® software platform to be flexible enough to ensure that the software fits the customer’s organisations by configuring each deployment to their unique business requirements, processes, and workflows.
Complexica makes use of world-class science when it comes to decision optimisation. Scientific expertise runs across all levels of the company, and it maintains research partnerships with leading research institutions such as the University of Adelaide, RMIT, and the Polish-Japanese Institute of Information Technology.
Complexica’s central mission is to help customers, such as FACT realise measurable improvements in areas such as operational costs, forecast accuracy, asset utilisation, working capital. To that end, Complexica works with each customer to provide ongoing validation of its software and the resulting benefits.
Through Complexica, a unique combination of science, software, and business process understanding coalesce to address complex business problems, because scientific approaches such as machine learning (ML) have the potential to create value through better decisions. However, to realise this business value, these science-driven recommendations must be embedded and actioned
Complexica’s mission is to help companies become more effective in their sales and marketing and more competitive in the markets they serve, through optimised decision-making.
Complexica’s vision is to become a world leader in the practical application of AI software. As the company grows and expands, its goal is to achieve a global presence and trade on the ASX stock exchange as a publicly-listed company that represents a major part of the Australian business landscape.
within operational workflows. This requires deploying enterprise software that is tuned to a specific industry, company, and business process. Most companies excel in one or two of these areas – science, software, or business process understanding – but Complexica focuses on the combination of all three.
Leading-edge, AI-based prediction capabilities place Complexica at the forefront of business optimisation and improving port performance. Many traditional data mining and modelling methods are often less than ideal for finding non-linear relationships and counter-intuitive trends, and for analysing vast quantities of real-time data. For these reasons and others, Larry, the Digital Analyst® employs both classical and non-traditional methods, including several new branches of AI and ML. By combining different techniques, Larry, the Digital Analyst® automatically adjusts and self-validates in any timechanging environment and is especially well suited for large and fast-moving data sets.
A similar approach is used for optimisation, where multiple techniques simultaneously compete and cooperate with one another, producing superior results with respect to standard optimisation methods. Larry, the Digital Analyst® is easily linked to any objective function, can be extended to include domain-specific and user-provided algorithms and modifiers, and was named the 2018 Australian Innovation of the Year and the 2019 Australian Software Innovation of the Year.
Larry, the Digital Analyst® also hosts a range
of preconfigured AI algorithms that are tuned for specific business challenges, such as pricing, segmentation, cross-selling and up-selling, promotional planning, and demand forecasting, among others. The algorithms are constantly learning, and their performance is continuously monitored to identify and correct any unintended consequences of algorithmic bias and the timechanging environment they operate in.
Complexica’s Decision Cloud® software platform is implemented through staged and scalable deployments, rather than “big bang” implementations to minimise risk for organisations and to accelerate return on investment. All of Complexica’s software projects are quoted at a fixed price and time-line deployments, with responsibility for any cost overruns.
The company’s delivery model is based on agile principles, and Complexica strives to be responsive to customers at all stages of a project. Its business model is based on the successful use and adoption of each software deployment, making customer success, Complexica’s success. Complexica has also developed a set of standard integration APIs for its Decision Cloud® software platform for common ERP systems and platforms, as well as public data sources such as the Australian Bureau of Statistics, Bureau of Meteorology, among others.
Complexica’s Decision Cloud® software platform is deployed through Amazon Web Services (AWS). Customers benefit from the data centre and network architecture built to meet the requirements of the most security-sensitive organisations. In addition, Complexica follows best-practice security standards aligned to the globally recognised standard ISO27001. Complexica has achieved ISO27001 certification, recognising its commitment to providing customers with the highest level of
information security management. Following an extensive audit process, the certification was issued by TQCSI International, an accredited, third-party certification body providing auditing and certification of international management system standards with offices in more than 30 countries.
Complexica has significant domain-specific knowledge and expertise within a number of industry verticals, including ports and logistics, food and liquor, building materials, pharmaceuticals, wholesale and distribution, financial services, consumer goods, and retailing. The company also understands operational business challenges, processes, and workflows within these industries. Complexica’s experienced and dedicated Business and Data Analysis team brings this domain knowledge and business process understanding to every customer engagement.
Complexica is a customer-centric organisation that is focused on providing commercial outcomes by leveraging AI software. For this reason, its Business and Data Analysis team spends time with each customer to understand the operational aspects of the business and any unique elements of the challenge or business problem being addressed. From this point, a current and future state is defined, and Complexica’s Decision Cloud® software platform is configured and tuned to the future state business processes and workflows.
Many organisations have a large number of manual processes which take significant time and labour to manage. Just like Complexica’s work with FACT, these processes can be automated through approval workflows, embedded recommendations, and autonomous decision making. While streamlining processes is always a significant effort, the benefits begin accruing immediately, improving port performance into the future.
www.complexica.com
ships bound for Sydney. Elsewhere, the Port of Adelaide – now the largest port operation in Southern Australia – is generally credited as one of the country’s earliest port settlements with its origins dating back to 1836. Indeed, this historic site was the first point of contact for thousands of emigrants arriving on Australian shores by ship.
However, since these port histories are intrinsically linked to the settlement era, they can override the legacy of the occupation on these lands that pre-dates the arrival of Europeans in Australia. During the complicated and fraught era of European settlement, the exploitation of these waterside gateways paid little respect to the Traditional Owners of the land, who had long gathered in such places as locations of deep spiritual meaning –places where ancestral Indigenous Australians might hunt, camp, and fish. This legacy is now widely respected across the sector today, and can be explored through various resources such as the ‘Ports on the Indigenous Map of Australia’, an online tool developed by the leading industry body, Ports Australia.
Discoveries of natural resources such as iron ore and gold in the 19th and 20th centuries originally paved the way for the growth of ports across the country as a means to handle these exports. Now a major transport hub for
DARWIN PORT – STATISTICS
2021/22
• 248,830 - HEAD OF CATTLE EXPORTED
• 912,810 - KILOLITRES OF PETROLEUM PRODUCTS IMPORTED
• 508,883 - TONNES OF DRY BULK EXPORTED
• 6,772 - MOTOR VEHICLES IMPORTED
the resource-rich region of Western Australia (WA), the Port of Hedland originated as a jetty catering to the needs of the pastoral industry, before gold was unearthed in nearby Marble Bar. This discovery fed major extension works in 1908, culminating in the development of a railway connecting the port with the extensive gold mining operations a few years later.
Elsewhere, in the southeastern state of Victoria, the mighty Port of Melbourne traces its origins back to 1842, when the bank of the Yarra River first served as a wharf. It has since evolved to become the nation’s best connected port with comprehensive facilities designed to cater for a wide spectrum of vessels, as seen in 2016, when ER Long Beach became the largest container vessel to call at the Port of Melbourne with a capacity of nearly 7,500 twentyfoot equivalent units (TEUs).
The 19th century continued as a time of great development for the nation’s ports with significant progress in delivering an improved, robust infrastructure and the implementation of deepwater bulk facilities that would play a pivotal role during wartime.
In terms of the significance of Australia’s ports on the worldwide shipping stage, the year 1969 signifies a seminal moment. The docking of the vast Overseas Container Ltd (OCL) vessel, Encounter Bay, in Fremantle Port on the coast of WA effectively heralded the arrival of the global container revolution, with the introduction of the port’s first container terminal launched later that same year. As a result, Australia entered the realm of international carrier trade, a movement that was transforming ports across the globe as a capital-intensive model of operation handling extensive amounts of cargo from ship to shore through advanced stevedoring operations that continues to shape the sector today.
To name just a handful of the major port operations currently serving this vast nation, Australia’s northern territory hosts the Port of Darwin, so named after the famous naturalist who once visited the operation. To the east, the Port of Sydney is the trade nexus of the eastern Australian coastline, while the same can be said for Port Hedland on the western coast in WA. The Port of Adelaide is the prime shipping centre of Southern Australia, with the
The role of South Australia’s ports has never been more important, as the world’s economy rebuilds and recovers. Having a reliable network of ports to enable two-way international trade for South Australian agriculture and aquaculture farmers, the mining industry and general commerce is essential. Without growth, sustainability and development at Flinders Port Holdings (FPH), that would not occur.
FPH has undergone significant changes as it recognises the need to incorporate smart technologies to streamline logistics and movements into and out of ports, as well as improving sustainability and embracing innovation.
Led by Chief Executive Stewart Lammin, who was recently re-appointed as Ports Australia Chair, there has been a recognition that the use of increasingly-sophisticated smart technologies will be essential moving forward – and particularly at the Flinders Adelaide Container Terminal (FACT).
FACT is working to meet growing demand by introducing artificial intelligence (AI) and data-led solutions to move containers through the terminal as efficiently as possible. For the past 18 months, FPH has been working with Complexica, a leading provider of AI software applications.
Complexica and FPH are collaborating to explore how AI can optimise the manual process of moving a container through FACT, putting FACT at the forefront of container terminal innovation. The AI application pre-empts and manages key decisions linked to a container’s movement such as its contents, which berth it needs to go to, and timings linked to trucking arrivals. Using AI-based technology to rapidly collate and analyse these multiple data-points and respond represents
a step-change in container terminal management. This will enable FACT to keep well-ahead of managing growing volumes and complexities in containerised trade. The volume of containerised trade flowing through South Australia is projected to grow significantly over the next 20 years. South Australia facilitates more than AUD$25 billion in international two-way trade through its ports, and as that grows, effective movement has never been more important. To facilitate growth in container and other shipping movements, FPH has purchased equipment and machinery which has long-term sustainability benefits, including in relation to fuel efficiency. FPH recently purchased five Noell Diesel Battery Hybrid Straddle Carriers, which will be the first Konecranes Noell Diesel Battery Hybrid Straddles in the Asia Pacific region.
Fitted with a battery module that will capture power during braking and lowering, the new straddle carriers generate fuel savings of approximately 32.5 percent without compromising on performance. Over the nominal life of the straddle (approximately 50,000 operating hours), the hybrid model provides an estimated 415 tonnes of carbon dioxide reduction when measured against its comparable diesel-electric model. The five new straddles will be delivered to FACT in late 2023.
Through its use of smart technology and hybrid straddles, FPH will reduce fuel consumption while also avoiding unnecessary lifts or movements, tying innovation to sustainability and increasing efficiencies.
FACT uses three state of the art Post-Panamax cranes, delivering efficient supply chain movement. It also plays host to an in-house crane simulator training facility, further
extending its strong safety culture and allowing it to deliver greater efficiency to clients.
Sustainability is a core component of FPH’s business planning and operations, with the leadership team embedding sustainable practices across FPH from its ports to freight forwarding, logistics, warehousing and supply chain partners, on the water and on the wharves.
When it comes to the ports network in South Australia, the increasing movement of passengers cannot be overlooked. Commercial flights may have revolutionised passenger movements in the last century, almost consigning intercontinental travel via shipping to the history books, however cruising remains ever popular and is reaching new heights into and out of South Australia’s ports.
There has been a boom in the post-COVID-19 world for cruising, especially in South Australia. Known as the festival state, South Australia has a vast offering of beautiful coastlines, world-class wineries and so much more, with cruising looking set to grow exponentially.
A record 104 cruise visits are scheduled for South Australia in the 2022-23 season, a 27 percent increase on the pre-COVID-19 2018-19 season where 82 visits represented what was then a bumper season. The cruise sector represents AUD$145 million of the state’s visitor economy, bringing new faces to the state and breathing life back into the tourism, travel, hospitality and retail industries.
As container movements increase, the mining and agricultural sectors grow and tourism gathers pace, FPH has upgraded the Port Adelaide Passenger Terminal in conjunction with South Australian Tourism Commission, undergone significant
channel widening to allow for larger and wider Post-Panamax vessels, upgraded berths at Port Adelaide, and made major improvements to its Port Pirie wharf facilities, including new asphalting.
Upgrades to infrastructure have also allowed for greater collaboration with industry. FPH has begun working with the Hallett Group on its green cement project, which will significantly reduce carbon emissions within the Hallett Group’s operations. In March, Hallett Group inflated a 42-metre dome at Port Adelaide, which will be used as a green cement storage and distribution facility for wider markets.
Flinders Ports has also formed strategic relationships and begun collaborating with partners Hawsons Iron Ltd on its 20 Mtpa mine south of Broken Hill to export magnetite via Myponie Port, and Venice Energy to build a AUD$250 million LNG Import Terminal at Outer Harbor. Both of these projects are focused on sustainability.
Recognising growth is imperative to meet the increasing national and international demands on ports and logistics. FPH has embarked on several recent recruitment drives to ensure the business can service its clients and operate at optimum levels, adding to more than 700 staff currently employed across the state.
The new employees have been welcomed across the business in various departments, which will enable FPH to remain at the forefront of the Australian ports and shipping sector, leading innovation nationally, accelerating growth, and not just demonstrating resilience but growing in strength as a vital cog in the state’s economy.
southeastern Port of Melbourne providing an instrumental link in connecting Tasmania, Victoria, and New South Wales, alongside international trade.
Aside from providing indispensable logistical links in handling all manner of cargo, the traditional role of ports, and the expectations that we have of them, are changing. As Australia’s gateways to the world, ports are essential nodes for trade and are fundamental economic drivers, however the role they play as both environmental partners and members of the community is of equal importance.
Moving on to coastal shipping today, the country relies on shipping for both international trade and domestic freight movements through coastal trading. As reported by Ports Australia, coastal shipping is less than 15 percent of the volume that moves through the country’s ports, with the remainder formed of international freight (93.7 percent).
The nation’s major ports and their surrounding infrastructure are key locations for supply chains involving bulk and container facilities. Some key players include the Port of Melbourne as the major handler of the country’s container traffic, and Port Hedland in Pilbara, WA. The latter primarily handles iron ore and is the largest bulk export facility in the world. Famously both the biggest, and busiest container port across the whole of Oceania, Port of Hedland hosts over 1,500 ships every year according to Marine Insight.
Nationwide, the ports sector is a major contributor to employment and job creation. Aside from opportunities working within or around the ports themselves, most jobs across the country are in some way or another reliant on ports as a means of import/export trade. For
THE PORT OF FREMANTLE IS THE LARGEST AND BUSIEST GENERAL CARGO PORT IN WA. IT HANDLES AUD$3.6 MILLION WORTH OF TRADE EVERY HOUR, 24/7.
instance, construction, retail, fashion, manufacturing, IT, and healthcare all rely on global imports, while industries including agriculture, energy, mining and areas of manufacturing are reliant on international exports. Aside from shipping, Australia’s ports are integral to the tourism industry, with many of the country’s operations handling cruise vessels as another key component of the economy.
In light of escalating global populations and the subsequent demand for goods, the realm continues to develop at breakneck speed purely in terms of handling capacity. Indeed, both Australia’s bulk commodity exports and metropolitan container imports are forecasted to double in size with each decade. This introduces major logistical issues, involving queues for both ships and the trucks waiting to deliver or deposit cargo on land – a hurdle that rose to the fore during the COVID-19 pandemic, as with the entirety of the global shipping sector.
In the face of this demand, the nationwide ports sector must walk a fine line between the preservation of functionality and future development while remaining mindful of its effect on surrounding communities and reconciling the best interests of all parties involved. This is largely overseen by the regulatory framework applied across all Australia’s ports, set by the Australian
Port of FremantleGovernment, although port operations themselves and investment are overseen by the private sector.
With each port, state and territory governments supervise the planning of land use, not just for the ports themselves, but their surrounding lands and interconnecting network of transport systems. On a wider scale, the overarching Australian Government undertakes assessment of the ports pertaining to matters of national environmental significance or overriding issues such as safety, security, or customs measures that affect the country’s maritime obligations.
Since there are a host of players involved – including port authorities and corporations – consolidation and collaboration within the sector is key to work towards its overall betterment. One such entity that seeks to represent the multifaceted network that comprises the country’s ports sector, is Ports Australia, whose membership encompasses the full gamut of port representatives, from government owned ports, privatised operations, state
marine regulatory authorities and the Royal Australian Navy. Equally as important as connecting Australia with the rest of the world, industry bodies such as this showcase the ways in which the ports themselves connect with and support their surrounding communities.
With all of Australia’s ports strategically located in central positions – either geographically or economically speaking – they naturally occupy a major space within their surrounding communities.
In recognition of their scope and impact, many ports take an active role within their social environments through corporate social responsibility (CSR) activities that contribute to community livelihood and help to foster interaction and positive perception in a mutually beneficial manner. This might involve the port working with local schools or providing grants for educational projects and sports teams, for example.
Efficiency is key in the supply chain industry, and OneStop is leading the way towards long-term success.
As a company, we have placed emphasis on modern tools and perspectives to innovate and create new products and services that will streamline the industry. Across 2023 and beyond, OneStop will introduce advanced data smarts and machine learning capabilities into our current and future product suite and business operations. The upcoming year presents an opportunity for all of us to commit to innovation in driving progress in the supply chain. By incorporating these technologies, OneStop aims to increase efficiency, improve decision-making, and transform operations for the entire community.
“This year marks the start of an exciting time ahead for OneStop! With our commitment to future forward solutions, we are integrating stateof-the-art tech and automation capabilities, aimed at delivering value for the entire industry. We are confident in the positive impact our efforts will bring in 2023 and beyond.”
While this is an increasingly common practice across sectors and expected of many entities regardless of industry as a demonstration of responsible corporate citizenship, the particular context of Australia introduces the need for recognition of the Traditional Owners of the land on which the ports are situated, pre-dating European settlement. Indeed, it is common practice for ports to formally acknowledge the original custodians of the land on which they conduct business prior to any meeting or networking event.
Putting this respect in practice, many players in the Australian ports sector undertake projects or work with Indigenous communities, recognising the legacy of their area of operation and its Traditional Owners. This might entail reconciliation action on the understanding that engagement with Traditional Owners is a critical part of business on an acute port and local community level. It is widely understood across Australia’s maritime landscape
and marine environment that successful partnerships between both parties can foster mutual empowerment that contributes to the overall betterment of the sector. As just one example of myriad initiatives taking place across the sector, Gladstone Port Corporation
• AUD$7 BILLION OF TRADE
• 12 MILLION TONNES OF CARGO
• 1,800 REGIONAL JOBS
• 600 VESSEL VISITS
(GPC) - a multi-commodity port based in Queensland - acknowledges its location on the original lands of the First Nation peoples Bailai, Gurang, Gooreng Gooreng, Taribelang Bunda, Darumbal, Kabi Kabi and Butchulla. Consequently, an Indigenous Land Use Agreement (ILUA) has been established between GPC and the Port Curtis Coral Coast (PCCC) people, which is referred to as ‘GPC and First Nations Bailai, Gurang, Gooreng Gooreng, Taribelang Bunda People Aboriginal Corporation (RNTBC) ILUA’. This voluntary partnership ensures the responsible and respectful management of the lands and sea on which GPC does business to deliver sustainable and mutual prosperity.
This is furthered by the port’s Resources and Infrastructure Traineeship, which commenced in 2016 and is a two-year programme rotating between four key areas of the ports: marina office, building services, warehouse and parks and gardens. Once completed, trainees obtain
a Certificate II in Resources and Infrastructure Work Preparation, with the programme specifically designed to support the region’s future Aboriginal, Torres Strait Islander and Australian South Sea Islander leaders in their journey from education and training to employment and long-term career pathways. The Traineeship highlights GPC’s ongoing commitment to genuine reconciliation and equal opportunities.
Projects that work collaboratively with stakeholders to solve problems, share knowledge for the collective good and improve the community environment are an integral component of port operations.
In the context of the escalating climate crisis, the port sector, as with all industries, is embracing the transition towards a more environmentally friendly means of operation. With sustainability planning widely considered
Victoria International Container terminal (VICT) is a world leading port facility when it comes to innovations and port automation. VICT is the world’s most advanced container terminal, offering advanced automation and technologies from ship to shore. It has been a goal for the business to continue to raise the global benchmarks through delivering world-class performances for our landside and waterside services, and customer experience, to establish itself as the gateway to Victoria’s supply chain. Based outside the Westgate Bridge, VICT
offers the only accessible container terminal in Melbourne capable of handing the next generation of larger vessels connecting Victoria to the world. The location allows for quicker berthing and departures, saving time travelling up the river, allowing larger vessels to call without sailing under the bridge. The Port of Melbourne’s location is positioned just off the junction for the major freeways, so landside operators can move in all directions across Melbourne with ease.
VICT‘s parent company, International Container Terminal Services Incorporated (ICTSI), is the
largest independent port operator in the world with 34 ports across 20 countries and six continents. VICT is ICTSI’s first entry point into Australia. The innovation behind VICT’s Webb Dock East terminal is the product of ICTSI’s experience, having been at the forefront of global port management for over 35 years.
What makes VICT one of the most advanced container terminals in the world is the technology they utilise. VICT’s development delivers a leading global standard in modern container terminal design, innovation and operations, using best-proven technologies to deliver automated operations for both landside and shipside. The technology brings the equipment to life, ensuring it all runs smoothly, and our highly trained operators ensure that the machines and operation runs efficiently. Even with their automated container operation, VICT shines at its handling of break bulk and project cargo, dealing with everything from deconsolidation and over dimensional containers to heavy hook lifts.
The fully automated terminal consists of five neo-panamax sized ship-to-shore-cranes on a 660-metre (m) berth, 17 Automated Container Carriers (ACC) that transport the containers to and from the cranes to the container yard, and 20 Automated Stacking Cranes (ASC) that allow the operation to service landside and shipside operations at the same time. Along with the advanced Gate In and Out technology and block designs, VICT has built one of the most efficient terminals that benefits both sides of the supply chain.
Sustainability is a driving factor for the ICTSI group, something which factored heavily into
the design of VICT. To further develop their sustainability programme, VICT turned to community engagement to establishing positive, ongoing relationships with its neighbours. Through the VICT Community Investment fund, the terminal can positively contribute to support programmes which focus on health and education for young people within City of Port Phillip, City of Hobsons Bay, City of Maribyrnong and City of Wyndham.
Since their opening day, the goal has always remained the same; to provide a safe and reliable gateway for goods to consumers, while delivering a leading customer experience to our landside and shipside services. With the new expansion project, which includes three new yard blocks, with six new ASCs and two new neo-panamax sized ship-to-shore-cranes, whilst expanding the berth from 660m to 731m, VICT will support larger vessels and see an increased throughput to further advance the supply chain in Melbourne.
as an essential requirement for business success, ports across Australia are committed to demonstrating leadership in an operational environment to create positive change geared towards longevity and prosperity for all those involved.
With respect to carbon emissions in the transportation of commodities, port transport continues to be one of the lowest emitters in terms of efficiency compared to road transport or intermodal rail. The sector plays a major role within the wider national goal of the Australian government’s commitments of achieving the United Nation’s (UN) Sustainable Development Goals (SDGs) and adhering to the 2030 Agenda for Sustainable Development.
As a result, many ports are now officially incorporating decarbonisation into their master planning, including accounting port contributions into the Scope 3 emissions of their customers, and setting in stone their alignment with key industry initiatives, like the Sustainable Strategy Development Guidelines, as developed by Ports Australia. Aside from optimising the internal operations of the ports themselves, these nodes of transport are critical to accelerating the energy transition of the country as a whole in facilitating the implementation of renewable energy sources, with offshore wind power as the most obvious example.
Currently, as Australia is embarking on an exciting foray into offshore sites for wind power generation, ports are stepping up to the plate by bringing these projects to fruition, fulfilling a crucial logistical role in their successful construction and servicing.
Alongside this ongoing development, a host of exciting projects are underway across the field that seek to manage environmental surroundings, reduce carbon emissions,
help to facilitate the clean energy transition, improve air and water quality or stimulate a circular economy.
2022 saw a major breakthrough in this area, with the announcement of the world’s first 100 percent renewable energy precinct due to be launched in Sydney Harbour. Catering to international bulk ships and cruise vessels, this is the first bulk shipping precinct of supply of shore power and the first for cruise ships in the southern hemisphere.
Shore power entails the provision of shoreside electrical power to a ship at berth whilst its main auxiliary engines are shut down, thereby reducing the air pollution emissions typically resulting from the consumption of fuel. The new precinct is anticipated to remove up to 14,000 tonnes of CO2 over a 12-month period.
An area ripe for future development – much like offshore wind - shore power promises to be a fruitful avenue that best demonstrates the results of healthy collaboration between industry and government in working towards a sustainable Australia, together.
As reflected by these commitments and endeavours in working towards shared goals, today, there is an increasing degree of inter-regional connection and collaboration between ports in Australia and surrounding countries such as New Zealand, Papua New Guinea (PNG), the Solomon Islands and the South Pacific, as they are all confronting similar conditions with respect to the climate.
With all the essentials of daily life primarily transited through a port, a healthy and efficient port system – on both sea and land - has the universal benefit of lowering the cost of living and increasing the competitiveness of the country’s exports, whilst also driving sustainable growth. They must therefore be seen as a healthy and necessary contributor for the benefit of all Australians.
We created an unrivalled level of service with a 50-year track record of paying claims.
For insurance you can depend on visit ttclub.com
leadership to sustain the port communities while fostering economic, innovative and sustainable growth.
Advancing Australia for over 100 years, Ports Australia is the national peak body representing government and privately owned ports. Its membership accounts for over 95 percent of Australia’s imports and exports.
Formed at the first interstate harbour conference in 1916, Ports Australia has provided advocacy, coordination and
Port authorities and corporations together with the Royal Australian Navy form part of its membership, along with various support service companies in the port sector. The association’s core membership consists of 21 full members from across Australia, several of which have multiple ports under the organisation, along with other associate members that are businesses related to the ports industry, representing everything from engineering to IT groups. Ports Australia itself is divided into several different working groups, ranging from accounting and human resources to communications, corporate affairs and port operations. Each group has all ports and most associate members, and they are often also attended by government officials as well.
Ports Australia’s network also comprises associate international members, including several ports across New
As the sector’s collective voice, Ports Australia is the association striving for sustainability, inter-regional connection, and promoting the longevity of quality marine assets that adhere to stringent quality and safety standards. CEO, Mike Gallacher, tells us more
Our vision is to be the global leader in port planning, operations and marine services. In 2021/22 Pilbara Ports Authority achieved a throughput of 733.1 million tonnes, worth an estimated AU$168 billion.
www.pilbaraports.com.au
feedback@pilbaraports.com.au
Zealand, PNG, the Solomon Islands and the South Pacific. With each location facing similar climate issues, this farreaching remit aims to facilitate knowledge sharing and a mutually beneficial collaborative approach whereby each country can learn from the other. Above all, Ports Australia exists as a means of support for these heavily port-reliant nations across Oceania. As such, the association is heavily involved in fulfilling an advocacy role and working closely with both state and federal governments on the primary issues and challenges facing the sector.
A major recent undertaking from Ports Australia is the Wharf Structures Condition Assessment Manual (WSCAM) - an industry-leading initiative that has been reviewed by Ports Australia’s engineering and asset management working group as a means to consolidate and implement a uniform guideline in terms of the expected standards of wharf conditions and safety requirements. Although WSCAM was officially released just last year, it has
The Manual is a recognised asset management tool to help asset owners with consistent and repeatable inspections of a wide range of asset types including but not limited to wharves, piers, jetties, walkways, breakwaters, revetments, embankments, and other fixed assets. It contains a condition inspection framework and visual assessment tool, both of which are flexible for user customisation.
The Manual has been developed to promote the use of best practice methods for the inspection and condition assessment of wharf structures. WSCAM is designed to enhance data collection efficiency and assist in moving towards a consistent approach for condition assessment of wharf structures in Australia.
“OUR MEMBERS ARE TRULY AT THE FOREFRONT OF THE DEBATE AROUND TOPICAL ISSUES SUCH AS ALTERNATIVE FUELS, AUTOMATION, AI, AND SUSTAINABILITY”
– MIKE GALLACHER, CEO, PORTS AUSTRALIA
Delivering complex and sensitive maritime operations for governments
• Vessel design and build
• Vessel operations and crewing
• Vessel repair, maintenance, and technical support
• Marine support services
• Acquisition and complex project management
• Training, education and professional development
• Fire and rescue services
• Ship charter services, logistics and operational support
• Asset and facilities management
More than 30 years’ operating in Asia Pacific, employing around 14,000 people across Australia, New Zealand, and Hong Kong. Managing more than 270 maritime assets across five waterfront locations in Australia.
become widely used across all Australian ports and port-related bodies such as local councils that may have marine or wharf assets and is available for purchase by any player in the maritime space. By setting a guideline for the maintenance of assets, involving safety standards, cost-effectiveness and a level of maintenance that will
PORT OPERATIONS – Also includes the Hydrographic/ Marine Surveyors sub-groups. Focuses on operations and navigation capabilities, management, regulation, safety, and ensuring the provisions of the National Plan for Maritime Environmental Emergencies are effectively facilitated.
ACCOUNTING, FINANCE AND GOVERNANCE - Focuses on financial, economic, taxation, legal, insurance, audit and risk, and other governance matters relevant to ports.
LOGISTICS - Focuses on logistic management and performance issues at the port, any relevant supply chain matters, and relevant regulatory issues.
INFORMATION TECHNOLOGY - Focuses on information and communications technology developments in the ports sector, its application to port operations, and any policies that govern its application at ports.
ENGINEERING - Focuses on infrastructure management and maintenance, construction and redevelopments at ports and considers the effectiveness of any overarching policies (e.g. Standards Australia) for port practitioners.
CORPORATE AFFAIRS AND COMMUNICATIONSFocuses on communications that promote ports with consideration of effective strategies and mediums, key stakeholders, brand management, drivers, and data. Also considers internal corporate communication matters.
contribute to their longevity, WSCAM is instrumental in fostering sector sustainability.
In terms of environmental sustainability, Ports Australia is key in driving this agenda across the sector having published guidelines for all relevant parties to comply with. Ports Australia recognises that sustainability is relevant to all aspects of the port business, stakeholders and along supply chains, and is taking action to support government and the ports in policies and initiatives that are sustainable.
Several such examples that seek to support the sustainable prosperity of ports across Australia and in the geographies of its associated international members include the development of industry guidelines (the Port Sustainability Strategy Development Guide), the facilitation of knowledge sharing across the industry through communities of practice and the Sustainability Hub (as a readily available online resource), and finally through the extensions of ports connections across New Zealand and the Pacific.
“WE WORK WITH THE TRADITIONAL OWNERS OF THE LAND TO IDENTIFY WAYS IN WHICH WE CAN GET NOT JUST YOUNG INDIGENOUS MEMBERS OF THE COMMUNITY INVOLVED IN THE PORTS WITH SKILLS AND ACCESS TO TRAINING, BUT ALSO THE WIDER COMMUNITY”
– MIKE GALLACHER, CEO, PORTS AUSTRALIA
Australia is a key player in the global maritime industry, with its ports and logistics sector being an integral part of the nation’s economy. The sector has been significantly impacted by the COVID-19 pandemic, causing disruptions to global and regional trade. However, Australia has shown remarkable resilience and has continued to adapt to the changing landscape of the industry.
One of the significant shifts in the industry is the increasing demand for clean energy alternatives. As the world shifts towards sustainable energy, Australia has a significant opportunity to lead the way in the production and export of LNG, green hydrogen and green ammonia. This presents a unique opportunity for Australia’s ports and logistics sector to adapt and invest in infrastructure and technologies to support the growth of these new industries.
Supply chain resilience has become a critical aspect of the ports and logistics sector, especially in the face of climate change impacts such as extreme weather events and rising sea levels. Ensuring that ports are equipped with the necessary infrastructure and technology to withstand these impacts is essential to the industry’s success. Australia’s ports have already made significant progress in this area, with many investing in renewable energy sources and implementing strategies to reduce their carbon footprint.
BMT, a leading engineering and science consultancy firm, is well-equipped to provide complex solutions to the ports and logistics sector. With over 35 years of experience in the industry, BMT has worked with some of the largest ports in the region, providing
tailored solutions to meet the specific needs of each port. The company’s expertise in the areas of sustainability, resilience, and digitalisation makes it a valuable partner to Australia’s ports and logistics sector as it continues to adapt and evolve in the face of new challenges.
Australia’s ports and logistics sector is poised for growth and transformation, with a focus on clean energy alternatives and supply chain resilience. With the right investments in infrastructure and technology, the industry can continue to adapt to the changing landscape and remain a key player in the global maritime industry. BMT’s expertise in providing complex solutions can help to ensure that Australia’s ports and logistics sector remains competitive and sustainable for years to come.
This work also translates to social sustainability, in terms of respecting local cultures and the Traditional Owners of the land, working closely with the Indigenous people of Australia. Ports Australia acknowledges the Aboriginal and Torres Strait Islander peoples of Australia and acknowledges the traditional custodians of the lands on which its ports are located. The association is committed to respecting Aboriginal and Torres Strait Islander peoples’ unique cultural and spiritual relationships to the land, waters and seas, and their rich contribution to society. This centres on healthy relationships with the local community across areas of operation, with opportunities for skills development, training and employment opportunities that are dedicated to socio-economic well-being with a respect for the land.
Fulfilling an active and essential role in Australia’s port sector, we find out more about the association today in conversation with CEO, Mike Gallacher.
APAC Outlook (AO): Could you provide us with a brief insight into the organisation’s history and Ports Australia’s membership?
Mike Gallacher, CEO (MG): The organisation has been in place for over 100 years. In fact, we celebrated our centenary in 2016, and of course there has been significant evolution during that time with ports being publicly owned and operated and the move towards the privatisation of those assets. Change is a constant in this field as ports, alongside all other areas of the supply chain, have continued to develop and professionalise. We now find ourselves in a position where the majority of our members are still publicly owned, but we also have large capital city ports primarily within the container space.
AO: What is your current take on the ports sector across Australia?
MG: A great thing we have just undergone is a public inquiry conducted on behalf of the Federal Government, looking at the ports sector. There was a lot of misunderstanding of just how the ports sector was travelling, particularly around investment and how
INDUSTRIAL RELATIONS AND HUMAN RESOURCES
- Focuses on human resources policies and practices concerning remuneration, management and negotiations of EAs/EBAs, awards (including the protection of the Port Authorities Modern Award), performance management, and changes in the industrial relations environment.
WORK HEALTH AND SAFETY - Focuses on the organisational management of health and safety of employees, contractors and visitors at ports, including incident reporting and relevant policy/legislative implications.
ENVIRONMENT, PLANNING AND SUSTAINABILITY
- Focuses on the planning and access management to the ports, environmental matters of the ports (e.g. dredging, climate change, regulatory implications) and the surrounding environment affecting the ports, and vice versa. The sustainability contingent focuses on how member ports are planning their role in the sustainable future of the Australian supply chain.
PORT SECURITY - Focuses on security management, operations and regulations at ports.
LEGAL - Focuses on the organisational management of legal matters affecting the business.
“THE MAIN THING IS THAT OUR PORTS HAVE THEIR EYES ON THE HORIZON AND BEYOND”
– MIKE GALLACHER, CEO, PORTS AUSTRALIA
Your Asia-Pacific dredging specialists.
we are keeping pace with the challenges of the global supply chain. As a result of that independent inquiry, it has become apparent that Australian ports are in a fairly healthy state with the investments that are being made for the required infrastructure and planning for the future. The main thing is that our ports have their eyes on the horizon and beyond. Some of their plans extend many years ahead, even generations ahead in fact. Our members here are truly at the forefront of the debate around topical issues such as alternative fuels, automation, artificial intelligence (AI), and sustainability. These are all fundamental to the issues that we are having here in Australia.
AO: On the topic of sustainability, could you outline some of the key ways in which the association Is working towards a more sustainable Australia? Are there any projects you would like to highlight in this regard?
MG: We started seriously talking about this several years ago, when we saw that right across the country, Australian ports had begun to embark on their sustainability journey. We identified the need for a greater understanding of where there were potential gaps in the approach that we took. So, we developed a sustainability guide to assist ports in the creation of a level playing field, in so far as the approach that they took could go above and beyond that. For us, it was about saying to our members that we are creating an environment where we are all using the same compass in terms of direction, and how far you want to go is a matter for you to decide.
CASE STUDY: NSW PORTS
NSW Ports has supported some Indigenous initiatives as part of its Community Grants Program (2021 and 2022 rounds) including:
SYDNEY CHILDREN’S HOSPITALS FOUNDATION: Its grant supports The Ngala Nanga Mai pARenT Group Program, which involves weekly art workshops at the La Perouse Aboriginal Community Health Centre. Through art making, the arts and health programme empowers young Aboriginal mothers to grow their sense of engagement and community, with a focus on improving maternal emotional and mental well-being.
WARRAWONG PUBLIC SCHOOL: This grant has been used to create a yarning circle, garden and Indigenous murals for the whole community. This includes interpretive signage to help identify plants and their usage, as well as QR codes linking to educational audio and video materials created by the students and the local community.
ENFIELD PUBLIC SCHOOL P&C ASSOCIATION: Its grant is being used to build a sensory playground and yarning circle for the school and local community to enjoy.
LA PEROUSE NETBALL CLUB: Its grant was used to increase First Nations player coaching and participation in a culturally safe learning environment within the Randwick Netball and St George Netball Associations.
The Gateway to Northern Australia is continuing to widen with the Port of Townsville undergoing continuous improvements to increase its handling capabilities and efficiencies.
With the Port of Townsville’s trade expected to treble in the coming decades, the team’s largest challenge is achieving sustainable growth that addresses the needs of more then 30 existing commodities, along with new and emerging trades, particularly in the areas of hydrogen and renewable energy.
The Port of Townsville’s General Manager of Major Projects, David McLoughlin, says the current Channel Upgrade project is on track to see larger vessels accessing the Port by late 2024.
“The Channel Upgrade is the largest infrastructure project in the Port’s 159 year history and is vital to ensuring trade, defence and cruise opportunities no longer bypass Townsville,” Mr McLoughlin says.
While the Port of Townsville is the largest multi-cargo port in Northern Australia, it had one of the narrowest shipping channels, making this project vital for future growth.
“We’ve recently celebrated the first anniversary of channel widening, with more than 1.65 million cubic metres of dredge material removed for beneficial reuse in our 62 hectare (ha) reclamation area. The reclamation, along with future stages of the Port Expansion Project, will pave the way for six new berths and associated infrastructure to accommodate existing and emerging trade opportunities.”
The Port of Townsville connects 800,000 North Australians with the rest of the world. Approximately 75 percent of the Port’s trade is conducted with Asian neighbours, allowing cargo to be transhipped anywhere in the world.
Port of Townsville Chief Operating Officer, Drew Penny, said importers were also beginning to recognise the potential for transhipping goods to Australian markets via Townsville.
“The Port of Townsville has excellent road and rail connectivity and, being only two days’ steaming time from Singapore, efficiencies are just waiting to be unlocked between Townsville and Rockhampton to the south, west to Mount Isa and the Northern Territory, and north to Cairns and the Tablelands,” Mr Penny said.
In October 2022, the Port of Townsville saw its first transhipment of motor vehicles from Japan to Port of Brisbane.
“The Port of Townsville’s motor vehicle hub has 1,700 sealed spaces for vehicle laydown, making it the ideal place to address limited capacity at other ports,” says Mr Penny.
“We are currently constructing new multi-purpose laydown areas to enhance our storage capacity for breakbulk and project cargo, as well as working with industry to make necessary supply chain adjustments that will make Townsville a more viable option for regular transhipments.”
THE PORT OF TOWNSVILLE’S CAPABILITIES INCLUDE:
• 8 berths including dedicated cruise and defence berth
• Ro-Ro and Lo-Lo facilities
• Pilotage and Towage services
• Liebherr Super Port-Panamax StS crane
• Bunker services
• Heavy-lift and project cargo
• 1.6ha wharf-adjacent cargo terminal
• Container and refrigerated cargo
• Direct-to-berth access for triple road trains
• Excellent intermodal connectivity
• Truck staging area
• Channel 11.7m deep and 92m wide (widening currently underway).
Now, we are looking at a host of projects, from decarbonisation through to noise pollution, and particularly considering emissions incentive schemes since shore power is a big issue here. We really work right across the whole board in terms of environmental issues.
AO: Can you tell us more about your recent WSCAM initiative?
MG: This has been a big area of investment for us and to our understanding, there is very little like it anywhere else in the world. What that shows is that as an organisation, we are prepared to invest in the development of technology or identifying the areas of technology that will make wharf structures last longer, but doing so in a way that they maintain safety and standards that are consistent right across the board. Commercially speaking, obviously it’s an advantage to ensure those assets last as long as they can, but this is all done through a prism of sustainability to ensure that we’re not wasting resources.
WSCAM has been launched here in Australia, but it’s also a tool that can be rolled out globally to say that if you’re running assets in the marine environment, you need to be aware of their condition, not only for the safety of your workers and those coming to your site, but also to guarantee their longevity. We are proud that we have developed such a tool. Its actual creation took place many years ago, but it has had to be revisited due to advances in technologies, including drones, and the growing understanding of alternative materials being used within
TasPorts acknowledges that prior to European occupation in 1803, Tasmania was home for millennia to the palawa Aboriginal people, belonging to nine distinct nations. The palawa were great seafarers and adventurers who were highly skilled navigators with a thorough knowledge of Tasmania’s waterways.
Indigenous maritime history was not only acknowledged but also celebrated during the recent Australian Wooden Boat Festival (Hobart - 10th February 2023). While some of the vessels showcased during the event had strong ties to Tasmania’s colonial history, Tasmania’s Indigenous maritime history was proudly celebrated when, as part of the festival opening, the Tasmanian ningher watercraft project – A Living Art Form - was launched.
A collaboration between festival organisers and Sheldon Thomas, palawa man and Indigenous canoe builder, the project celebrates Tasmania’s Indigenous maritime traditions, with the maritime environment a crucial component of the country for many Indigenous Tasmanians. A respected artist and canoe builder, Sheldon teamed up with the festival and Chris Ganabarr, yolnga man and Aboriginal youth worker, to build the largest canoe to feature along Hobart’s waterfront.
the ports. It’s not only about promoting sustainability, but also assisting ports, governments and other institutions that have structures in the marine environment. We are giving them a guideline to understand what is accepted within our sector concerning the conditions of assets.
AO: In terms of social sustainability, could you touch on why it’s important for Ports Australia to acknowledge the Aboriginal and Torres Strait Islanders peoples of Australia?
MG: We are very fortunate in that all of our ports obviously operate on traditional lands, and for many of these regional communities, it’s not just about our relationship in terms of the sustainable use of that land, but also how we can engage with the local Indigenous community to have them become more involved. This might include working with those communities with reconciliation action plans whereby we work closely with them in relation to its development, but it also involves employment opportunities as well. We work with the Traditional Owners of the land to identify ways in which we can get, not just young Indigenous members of the community involved in the ports with skills and access to training, but also the wider community. So, it’s extremely important to us. In any area that we work in, we begin by acknowledging the
NQBP’s vision of reconciliation is for an Australia that embraces and values Aboriginal and Torres Strait Islander peoples, histories and cultures, and promotes diversity, providing equitable opportunities for all Australians. It’s vital to build genuine, two-way relationships with Aboriginal and Torres Strait Islander peoples to identify real and sustainable opportunities that lead to positive outcomes for everyone.
NQBP supports Aboriginal and Torres Strait Islander businesses through economic participation strategies. The most comprehensive that has been implemented to date is with Juru Enterprise Limited (JEL), based in Bowen. This company provides land management services to NQBP at the Port of Abbot Point. NQBP and JEL have worked closely over the past 10 years to build a strong working relationship, business capability and sustainable performance.
The Australian Maritime Safety Authority is at the forefront of Australia’s ports, with our frontline staff regularly inspecting ships in our waters.
AMSA’s intelligence-led and risk-based approach to compliance uses data to focus our efforts, which is why we are putting watertight and weathertight integrity issues in the spotlight and reminding all ships entering Australian waters to ensure watertight and weathertight components are addressed as part of planned maintenance.
• Visit AMSA’s campaign hub on watertight and weathertight integrity.
• Read AMSA’s 2022 Inspections Report, including an analysis of emerging trends and risks to safety.
MSQ is responsible for:
• Providing essential maritime services such as aids to navigation and vessel traffic services, including Harbour Masters located in each of our regional ports and locations.
• Minimising vessel-sourced waste and responding to marine pollution.
• Significant compliance functions with its Maritime Enforcement Team and other Marine Officers, improving maritime safety for shipping and recreational craft through regulation and education.
• Encouraging and supporting innovation in the maritime industry.
• Maintaining key capabilities for managing maritime emergencies, ranging from shipping incidents and shipsourced pollution to high level natural disasters as, the lead agency for maritime response, with highly-trained teams ready to deploy.
“Find it, fix it, and keep your ship watertight”
Traditional Owners of the land, and the same applies to the beginning of any formal meeting that we participate in. I think that in itself is an indicator of the level of respect that we have for these communities.
AO: Looking ahead, what are some of Ports Australia’s key priorities for the immediate future?
MG: We have a fairly rigorous strategic plan in terms of the direction that we want to go. Primarily, we look at two key things. Firstly, it’s our advocacy on behalf of the ports sector nationally. As its collective voice, we need to ensure that we are building those ties with our external stakeholders.
Members of Parliament are very much a part of that external stakeholder relationship and we are now in the process of finalising the development of an organisation which has been designed to ensure that we maintain and build those relationships with our elected representatives. This applies on a local level for our members, but also at a national level so that we can discuss policy issues, whether it be environmental or commercial.
The important thing is to build those relationships early, and not in the middle of a crisis. That way, when a crisis strikes, as we saw with the COVID-19 pandemic, you have already developed that level of trust and understanding of
how the system works. That’s critical for us going forwards.
In terms of our external priorities, we are also looking to do more work with opportunities in the wider community to ensure that people are aware of what we are doing. As an example, this year I will be presenting in the Solomon Islands and later New Zealand as part of our South Pacific Members Programme; ports are one of the two critical
pieces of infrastructure, (ports and airports) that are crucial for our region’s prosperity, including Australia’s. We are encouraging Pacific nation ports to join us, share knowledge and build understanding across Oceania of the challenges that are confronting all of us with global issues such as climate change. Here, we will be addressing what we can do to assist them, and how we can help them with access to training and workplace safety. We approach this in a way that isn’t centred on a commercial perspective –we don’t do it to purely increase our membership. We are interested in their knowledge and building that level of interaction to develop a regional relationship.
Internally speaking, it’s all about making sure that we continue to deliver a quality service to our members by providing them with access to the latest information and investment in research that we possibly can. In September 2023, we will be holding a business and operations conference in Geelong, Victoria which is centred on innovation and investment through the lens of sustainability and how we can make our assets work together better, smarter and for longer, doing so in a way that brings the community’s best interests with us. A major focus of this is the investments that are being made in new energy with offshore wind turbines and what that will mean for the ports sector going forward, since we will be critical in a logistical sense. Offshore wind is the next
chapter for us and how we are going to make that happen.
We will also be looking at the issue of cybersecurity and the threat that poses to critical infrastructure such as ours. In doing so, we will be following a similar approach to how we have handled the topic of sustainability, ensuring that people understand the methodology and what practices are in place to protect all of us and protect the supply chain.
We are continuously on the go because there are so many issues that we as an organisation have to manage. Challenges will always come towards us, but the good thing is that we have undergone the aforementioned 12-month examination by an independent government body and that has confirmed that all parts of our organisational structure are performing in a healthy way. I think it’s a good sign for us going forward that we have the support of the country to get on and get the job done.
Tel: +61 02 9247 7581
info@portsaustralia.com.au
www.portsaustralia.com.au
Gladstone Ports Corporation focused on facilitating, growing and diversifying trade in a economically, environmentally and socially sustainable manner.
gpcl.com.au
Fiji Ships & Heavy Industries Limited (FSHIL), a subsidiary of FPCL, operates as a fully commercial, self-funded entity, providing slip way facilities for dry docking vessels and berthing docks at the slipway sites. FSHIL is also recognised for its other core functions of heavy industrial and engineering works.
APAC OUTLOOK is a digital product aimed at boardroom and hands-on decision-makers across a wide range of industries on the continent.
With content compiled by our experienced editorial team, complemented by an in-house design and production team ensuring delivery to the highest standards, we look to promote the latest in engaging news, industry trends and success stories from the length and breadth of the Asia Pacific region. We reach an audience of 220,000 people across the continent, bridging the full range of industrial sectors: agriculture, construction, energy & utilities, finance, food & drink, healthcare, manufacturing, mining & resources, oil & gas, retail, shipping & logistics, technology and travel & tourism.
In joining the leading industry heavyweights already enjoying the exposure we can provide, you can benefit from FREE coverage across our digital platforms, a FREE marketing brochure, extensive social media saturation, enhanced B2B networking opportunities, and a readymade forum to attract new investment and to grow your business.
To get involved, please contact Outlook Publishing’s Managing Director, James Mitchell, who can provide further details on how to feature your company, for FREE, in one of our upcoming editions.
Offering world class technical expertise, Building Façade Group’s consultancy services are expanding in Singapore and the wider region, as highlighted by Managing Director, Sani Chang
The complexity and performance demands of modern buildings are continuing to increase.
To those responsible for executing the façades of these modern buildings, it’s therefore crucial that designs are accurately validated and the intentions of the client and designers are communicated.
As one of the most important and expensive aspects of construction, the façade of a modern building can
comprise up to as much as 20 percent of construction costs.
Façades are not only the manifestation of the architect’s expectations for a building’s external appearance, but also the primary environmental modifier. Indeed, with new, more onerous energy requirements being implemented, façade designs must form part of a holistic construction strategy.
Resolving these aesthetic,
environmental, and structural issues to achieve the enclosure of habitable space, is the art of façade engineering.
It is the façade of a building that makes the internal space habitable, governed by minimum performance criteria and driven by the need to lower carbon emissions and better the energy efficiency of buildings.
The clear need for specialised engineering expertise on major construction projects is demonstrated
Jangho Construction Group Co., Ltd. (Jangho Group) is a large multinational enterprise group listed on the A-share main board of the Shanghai Stock Exchange (stock code 601886). Formerly known as Beijing Jangho Curtain Wall Co., the company was established in 1999 and is headquartered in Beijing.
With its corporate mission embodied by the ethos of, “for the living environment, health and well-being of human beings”, Jangho Group is committed to providing green building system services and high-quality medical and health services. It has two major business segments: architectural decoration, and medical and health. Sundart, Gangyuan, SLD (Steve Leung Design), Vision, etc., are world-renowned brands, with business in more than 20 countries and regions around the world. The field is at the leading level in the industry.
Jangho Group is a national high-tech enterprise, demonstrating technological innovation. It comprises the first batch of national-level intellectual property advantage enterprises, a nationally recognised enterprise technology centre, and a post-doctoral research workstation. Overall, Jangho Group comprises the top 100 private enterprises.
Glory and dreams go hand in hand, and responsibility goes with the mission. Jangho Group will always adhere to change and innovation, continue to create value for customers, shareholders, and employees, and make unremitting efforts to improve the urban living environment and enhance human health and well-being.
www.jangho.com
by the field of façade consultancy services, in which a façade’s various technological demands are managed and design requirements are met.
Offering world class technical expertise across Asia, Building Façade Group (BFG) is a specialist consulting practice with key areas of expertise in façade consultancy.
“We provide consultancy advice on how to design façades for buildings, how to procure and verify manufacturing for façade works, and conduct quality verification of façade works,” begins Managing Director, Sani Chang.
“I have always been interested in how things are put together, and this translates into how a building is assembled with the multitude of parts, technologies, purposes and concerns. It’s always great to begin with an idea and end with a beautiful building façade.”
Chang, whose career spans some 35 years, has been involved with building design consultancy in Australia, New Zealand, and now in Southeast Asia.
FAÇADES FOR NEW BUILDINGS – Bringing creative and practical solutions to new building design.
FAÇADE STRUCTURAL ENGINEERING – Structural design of cladding systems, and specialist engineering analysis of complex 3-D and lightweight façade structures.
FAÇADE CONTRACTOR REVIEW – Verification process of the façade contractor’s design.
EMBEDDING SUSTAINABILITY – Encouraging and enhancing environmental protection and improvements through façade design and specification.
TALL AND COMPLEX FAÇADES – Understanding active and passive façade systems.
FAÇADE MAINTENANCE – Studying façade access for construction, maintenance and replacement.
FAÇADE REVIVAL – Experience in conserving, upgrading and refurbishing building façades.
FAÇADE GLOBAL PROCUREMENT – Enabling clients to prepare project cost estimations with confidence and maximise value.
FAÇADE CONTRACTOR SUPPORT – Providing technical support to façade contractors.
QUALITY INSPECTIONS AND AUDITS – Diagnostic inspection of façades and reviewing works in progress.
In that time, his focus has shifted from overall building design to concentrating on the façade, and managing the whole process of achieving the best façade for each project.
BFG has likewise evolved as a company, from working in large corporate consultancy firms to a more personal, intimate practice.
“We are a small, privately owned company that is now into its 13th year in Singapore,” outlines Chang.
“The link with our clients and partners is now much closer, and of course their resulting appreciation for a job well done is more satisfying.”
Having Singapore as its base has been a real advantage for BFG, as somewhere that is renowned as a technological leader in the region.
Singapore has built a world-class, globally competitive technology industry, and continues to explore new frontiers in innovation such as cloud computing, artificial intelligence (AI), quantum computing, data analytics, and other technologies that
span multiple sectors.
Design drivers and quality concerns are also dominant in Singapore’s façade space, which together with the country’s forward facing and hardworking DNA has allowed BFG to hone its skills.
“Another benefit of being located in Singapore is its expedient infrastructure (be it connectivity or financial), and the low tax rates. All of these factors nurtured the growth of BFG,” Chang adds.
Attracting young Singaporeans to work in the sector, however, is increasingly difficult for the likes of BFG in the face of a challenging job market.
The company is nevertheless blessed with a group of skilled and experienced individuals who provide great collaboration on any façade engineering project.
“We need young blood as our senior staff have spent many years now in the façade industry, and they are ready to pass their knowledge on. Renewing and sustaining the business for another 12 years will be a real challenge.
“Working on great projects, with great people and adding value to all – this is the guiding principle in our service to clients. We help to build a better world using our skills
“THE LINK WITH OUR CLIENTS AND PARTNERS IS NOW MUCH CLOSER, AND OF COURSE THEIR RESULTING APPRECIATION FOR A JOB WELL DONE IS MORE SATISFYING”
– SANI CHANG, MANAGING DIRECTOR, BUILDING FAÇADE GROUP
Two Nine Six O Trading Pte Ltd is a reputable company that specializes in the distribution of construction materials such as sealants, specialty coatings, building expansion joint systems, fire stopping systems & solutions, fasteners, and decorative panels. They also offer an array of value-added services such as logistical support, technical services, quality assurance and checks, and after-sale services.
The company’s dedication to excellence through innovation, tech and unwavering commitment has earned them a reputation as a tru Their team of technical experts, who have extensive experience, continually explore new and innovative ways to better serve their clients.
Singapore (Headquarters)
21 Tuas West Ave S638435 +65 6267 1300 contact@t2960.com.sg
Vietnam
B05.35 RiverGate, 151-155 Ben Van Don, Ward 6, District 4, Ho Chi Minh City, Vietnam +84 126 492 1399 2960VN@t2960.com.sg
China (ShenZhen)
653, Block AB, 6th Floor Tianji Building, Tianan Digital City, No. 10 Tairan 5th Road, Tian’an Community, Shatou Street, Futian District, Shenzhen +23180306
hejun.zhao@t2960.com.sg
Indonesia (Jakarta)
Coming Soon
www.t2960.com.sg
SANI CHANG, MANAGING
DIRECTOR: “The industry in Southeast Asia right now is at an inflection point. What the COVID-19 pandemic has forced everyone to do is to reflect and reorganise.
“The end of the world somehow passed us by, and some things that were important just appear whimsical now. Starting a journey to work on an iconic, leading-edge project is always exciting, however, today it is tempered by a lot of collateral concerns.
“Climate change and rising costs, together with financial justification, make projects less exciting and more tedious. Of course, there is nothing wrong with being a responsible person in shaping our built environment, but we all yearn for the more outlandish, unusual and stimulating projects.”
and experience; it sounds cliché but there is no better or simpler way of explaining it,” says Chang.
BFG was involved in a number of projects in Singapore during the course of 2022.
These include Project Sprint, a life sciences and innovation campus with offices, labs, retail, and service apartments located at the Singapore Science Park (SSP), as well as the Esplanade Waterfront Theatre, and the Changi Airport expansion.
“We essentially help to dress up iconic buildings with a proper skin of glass, metal cladding, stone, pre-cast panels, mesh, and just about anything that works to enhance the building. In addition, we specify the performance of the façade system and materials to keep out water, haze, dust, heat and glare,” Chang tells us.
“At the same time, we choose
materials with durability, sustainability and easy maintenance in mind. We even have a diagnostics section that does due diligence inspections of existing buildings and condition checks of façades.”
Outside of Singapore, BFG has managed to spread its façade consultancy services over the years by establishing offices in Jakarta (Indonesia), Shanghai (China), Kuala Lumpur (Malaysia), and Bangkok (Thailand).
This has allowed the company to respond to projects within the region and follow its clients, as they make the same foray into different countries.
“Some of our projects are located in exotic cities like Hyderabad, Bangalore, Kolkata, Mandalay, Kathmandu, Colombo, Port Moresby and Surabaya,” Chang reveals.
Over the last 10 years, for example, BFG provided façade consultancy
Siderise has been serving the curtain wall façade market for over 30-years with highperformance passive fire compartmentation solutions backed by an unrivalled support service from design and engineering, to build and beyond. Protecting iconic buildings across the globe, our range of thirdparty certified perimeter fire and smoke seal systems are tested to the most stringent standards, where protection of the spandrel is needed to extend the fireresistance rating of the floor to the façade. In application, this allows our unique stone wool Lamella firestop to maintain its full performance and buy more time – valuable time.
Our Integrity. Your Designs. Safer Façades.
Discover more at siderise.com
Or get in touch today:
Siderise Asia Pacific
T: +65 963 19310
E: sideriseap@siderise.com
Siderise India
T: +91 998 700 4611
E: siderisein@siderise.com
services for RMZ Ecoworld in Bangalore, a large-scale development project offering multifaceted commercial office spaces for rent.
This work-leisure mixed asset comprises 16 towers and is an architectural marvel that stands tall amidst the pantheon of leading IT parks in Bangalore, with a range of social experience facilities alongside its sustainable design.
Façade consultancy services were also provided for the Muangthai Capital skyscraper complex in Bangkok, and Wisma Sudirman in Jakarta, a mixed-use office, residential and retail development conveniently located near the Jakarta Mass Rapid Transit (MRT) that showcases the collaboration between two BFG offices.
The project consists of a retail podium and separate office and residential towers that are approximately 68 storeys high and 300 metres tall, designed to be
a visually dramatic and towering landmark.
“It is exciting to work in the region, as different countries have different levels of maturity in their design consciousness and technology. We need to be there in order to pay proper attention to clients and their projects,” affirms Chang.
“The experience of working in Singapore and the region for the last 30 years, where the built environment changes so much and where we are so lucky to be able to contribute, is quite humbling.”
Through its involvement and growth in both Singapore and the wider region, BFG is able to share its knowledge with clients, implement new ways to design façades, and apply procurement methods that suit their requirements.
Although expansion throughout Asia is an attractive and exciting endeavour for BFG, Chang remains conscious of the limitations and wary of the pitfalls involved.
“As a privately owned company, we are limited by the availability of
“THE EXPERIENCE OF WORKING IN SINGAPORE AND THE REGION FOR THE LAST 30 YEARS, WHERE THE BUILT ENVIRONMENT CHANGES SO MUCH AND WHERE WE ARE SO LUCKY TO BE ABLE TO CONTRIBUTE, IS QUITE HUMBLING”
– SANI CHANG, MANAGING DIRECTOR, BUILDING FAÇADE GROUP
capital to expand, so even though it is appealing, we are still expanding slowly,” he informs us.
BFG’s clients throughout the region include personal building owners, developers, large architectural/ engineering consultancies, general contractors, façade contractors, and building material suppliers.
This wide variety of clients has enabled the company to understand the nuances and drivers for each specific type of client, and allows their primary concerns to be understood and identified by BFG.
“Having this universal view of the industry makes BFG more sympathetic to each client. Advising a developer where to source large curved glass works, and apprising a glass fabricator on the regional market demand for special glass are different sides of the same coin,” explains Chang.
“It is this wide ranging, holistic knowledge that BFG hopes will be its
key differentiator. Ultimately, the goal is to reach the point where our experience is respected and we are known as honest and knowledgeable to all.
“In the early days, there were some great, supportive clients that awarded us projects even as a newbie, who we are eternally grateful for,” he notes.
The COVID-19 pandemic was undoubtedly an existential juncture for BFG.
In Singapore especially, the slowdown in work, income, and lack of new projects was an immense concern, whilst managing fixed costs was incredibly challenging.
“Restructuring loans, keeping costs down, and extra capitalisation from our shareholders helped us through that period, as well as helpful subsidies from the government,” reflects Chang.
“It was a testing time, and it brought attention to our involvement in
healthcare projects. This was a sign that we are doing the right thing in building such facilities to face such an unpredictable phenomenon, and a sign for us to carry on.”
The National Centre for Infectious Diseases (NCID), for example, was completed in 2018, just in time for the pandemic response.
NCID is a 330 bed, purpose built facility designed to strengthen Singapore’s capabilities in infectious disease management and prevention, housing clinic services, public health, research, training and education, and community engagement under one overarching structure.
Benchmarked to international standards and best practices for treatment and safety, NCID better enhanced Singapore’s ability to respond effectively to infectious outbreaks such as COVID-19.
“This facility was on the front line in the fight to control COVID-19 in Singapore,” Chang says.
CSG is the largest Low-E glass manufacturer in China and a leading supplier of various glass products including float glass, tempered glass, heat strengthened glass, fritted glass, laminated glass, IGU glass, anti-reflective glass, photovoltaic and BIPV glass, and a full set of composite glass products.
Southern Glass (Thailand) Co., Ltd
Tel: 0066 0971364070
Contact Person: Robin Jiang
Email: jiangzb@csgholding.com
CSG Malaysia & Singapore Office
Tel: 0060 126509560
Contact Person: Celia Deng
Email: dengq@csgholding.com
CSG Vietnam Office
Tel: 0084 845651006
Contact Person: Jason Zhang
Email: jason@csgholding.com
CSG Indonesia Office
Tel: 0062 82298514700
Contact Person: Kane Wang
Email: kane@csgholding.com
KingZip Freeform Building Envelope Solutions enable you to fulfil design intent with total flexibility.
KingZip Linea and Infiniti are manufactured on-site, from 1 metre up to 150 metres, allowing very long sheet lengths, eliminating
the need for endlaps and speeding up construction.
KingZip systems provide advanced structural, thermal, acoustic and fire performance. Combined with interlocking seams they offer exceptional long term durability.
CSG provides both first-class glass and practical solutions.Biopolis 6, Singapore The Pearl, Thailand IFC One Saigon, Vietnam The Tower, Indonesia
Prior to the pandemic, BFG had also just finished the new Sengkang Hospital, a large regional health hub opened in August 2018 providing quality and accessible care to support the health needs of residents in north-eastern Singapore, as well as the National University Centre for Oral Health, a national speciality centre that provides a comprehensive spectrum of dental care.
“We did not give up, and were luckily rewarded with another large regional health hub, Bedok Hospital, in 2022.
“Together with a new Health Sciences Authority building, the remodelling of Changi General Hospital, and the Elective Care Centre at Singapore General Hospital (SGH), we knew we made the right decision,” states Chang.
The future of façade design consultancy is now laden with
Lee Pressed Metal Pte Ltd.
Nam Lee Pressed Metal Pte Ltd. (Nam Lee) has established itself as a one-stop specialist offering complete service in the designing, manufacturing and supplying of metal products and solutions for diverse industries in building, container shipping and infrastructure etc. It is currently one of Singapore’s leading providers of fabricated metal products and cutting edge metal solutions.
Tel: (65) 6257 5388
Email: enquiry@namlee.com.sg
automation and digitalisation.
This is naturally a great help to BFG, with buildings and façades increasingly designed using AI and digitalisation cutting down a lot of burdensome, repetitive tasks.
However, Chang recognises that the very basis of any consultancy such as BFG – to sell consultancy time –should not be forgotten.
“Having experienced staff who are in demand because of their skills and knowledge remains the core essence of any consultancy,” he emphasises.
“The future is about maintaining our
experienced staff, who must continue to amass skills and knowledge to be shared with our clients. It is still a very personal thing, and the application of automation and digitalisation will help, but it will never be the cure-all.”
Tel: 65 - 62225451
info@buildingfacadegroup.com
www.bfg-hcch.com
Combining local expertise with global connections, we dive into the premium real estate brand, Knight Frank Malaysia, with Director of Project Management, Joshua de Souza
Writer: Phoebe Harper | Project Manager: Taylor Green
The construction and real estate market across Southeast Asia is alive with activity. The region is a dynamic hub overflowing with potential and ripe for development. At the vanguard of the industry and poised to capitalise such development opportunities, stands Knight Frank Malaysia (KFM).
“We have learned so much globally on how things have been done, but in these times of innovation and with the ever-evolving technology integration within the construction industry, it makes one really appreciative of how far we have come in the advancements that we have.”
In the past 12 years that Joshua
de Souza - KFM’s Director of Project Management - has worked in this field, he has paid witness to industrychanging advancements that have shaped the evolution of the built environment. Gaining experience in Project Management after starting out as an assistant architect, it was the opportunity to both embrace and drive change across the regional industry that attracted de Souza to a young and ambitious company such as KFM.
“The opportunity to join KFM and build a department from the ground up really struck a chord with me,” he recalls fondly. “I had all these ideas of what a Project Management
department should be like and how it should be managed, so I took up the challenge and have not looked back ever since.”
With the company celebrating its 20th anniversary just last year, de Souza’s department of Project Management forms an integral part of KFM’s core competencies, within a portfolio that spans the full gamut of property services. This expertise encompasses several departments, including Valuation and Advisory, Research and Consultancy, Property Management, Office Solution and Strategy, Land and Industrial, Capital Investments, Residential Agency, Facilities Management, Project Management and Workplace Consultancy, Asset Management and International Project Marketing.
“Our main services are three pronged – advisory, transactions and management,” de Souza explains. “Through our nationwide team, we are able to provide end-to-end solutions for anything related to real estate.”
APAC OUTLOOK: CONGRATULATIONS ON REACHING YOUR 20TH ANNIVERSARY IN 2022! WHAT DOES THIS MILESTONE MEAN TO THE COMPANY AND WHAT DO YOU THINK HAS LED TO THIS CONTINUED SUCCESS?
JOSHUA DE SOUZA, DIRECTOR OF PROJECT MANAGEMENT: “This milestone shows that the company has been able to survive and thrive in a competitive marketplace over an extended period of time. So many factors are involved but if I had to choose a few, it would be due to the strong leadership team having a clear and compelling vision for the company’s future and our company culture that fosters collaboration, creativity, and employee engagement.
“Ultimately, sustained success over the long term requires a combination of strategic planning, effective execution, and a willingness to adapt to changing market conditions and customer needs. By staying attuned to these factors and consistently delivering value to stakeholders, we are able to position ourselves for long-term success and continued growth. We try our best to ‘connect people and property, perfectly’.”
Bolstering this expansive service offering is KFM’s team of over 700 employees spread across its headquarters in Kuala Lumpur and additional regional branches in Penang, Johor and Kota Kinabalu. Collectively, this translates to an unparalleled level of local expertise that marries with the world-class best practices, esteemed reputation and extensive experience of the wider Knight Frank group.
“Since we were established in 2002, we have grown to develop a strong presence both locally and globally,” says de Souza.
“We aim to provide quality service and solutions to our clients, understanding that their needs go beyond the mere promise of basic professional service.”
In seeking to truly “go beyond”, KFM is dedicated to widening its
We make your workspace a happy place.
It may not seem like it, but Intersit was founded in 1983 as an office furniture manufacturer. Back then, we only knew how to do one thing, creating simple office furniture. Not surprisingly, that’s what we mastered, furnishing workspaces for companies both big and small. Eventually, we diversified our strengths, specialising more in furniture engineering, design and creating innovation when there was none.
Today we stand at the forefront of office furnishing and workstation design that embodies our decades of expertise, our drive for sustainability, and our belief that we can shape the working environment of modern Malaysia for the better.
intersit.com.my
reach across the nation, beyond the urban destinations most typically associated with housing development. For de Souza, this explicitly local emphasis promises to be the fruitful next stage in the company’s continued trajectory of growth.
“There are still so many areas and places that need infrastructure and various upgrading projects,” he affirms. “We forget that Malaysia is not just the big cities like Kuala Lumpur, Penang or Johor Bharu - there are still many more states in the country that need developing. How this will be achieved in the next few years will be an exciting journey to be a part of.”
Continuing to develop this local network is a crucial next step in
developing its reach and allowing KFM to tap into new markets, capitalising on the burgeoning demand for real estate across the country. Within this, de Souza hints at targeting developing markets outside of the Klang Valley region.
“With a presence in more locations, the company can better serve its clients and provide more personalised and targeted services that meet their specific needs,” he shares.
“Our Managing Director, Keith Ooi
intends to elevate our premier real estate brand with his personal mantra of the ‘four Es’ – to empower, engage, embrace and expand.”
As testament to the exciting journey that the company has undertaken thus far, the past year alone has seen KFM handle its biggest projects to date. This has included working with iconic names such as DHL and retail giant, Amazon.
“WE TRY OUR BEST TO ‘CONNECT PEOPLE AND PROPERTY, PERFECTLY’”
– JOSHUA DE SOUZA, DIRECTOR OF PROJECT MANAGEMENT, KNIGHT FRANK MALAYSIA
Exsto Malaysia has grown over the past decade to become one of Singapore’s leading ergonomic solutions providers. We specialise in both contemporary and ergonomic furniture for clients who are seeking a functional design and a comfortable workplace environment.
Learn more
The former involved the development of a 70,000 square foot (sq ft) project on behalf of DHL Asia Pacific Shared Services Sdn Bhd (DHL APSSC) within the Damansara Uptown area of Petaling Jaya at Imazium – an undertaking which de Souza identifies as the KFM’s “most complicated project thus far.”
Indeed, the project involved work across multiple departments spread over several floors and two buildings, with a brief to consolidate them all into three consecutive floors in a new office, revolving around a central stairway and atrium space to allow for cross collaboration.
“We started off the programme with a workplace analysis to understand the new practices moving forward and with that constructed a change management programme to complement the move,” explains de Souza.
Added to the complex logistical
nature of the project, COVID-19 complications created a further level of challenge for KFM to navigate.
“The project team worked hard to coordinate the whole programme as we were also hit by lockdowns and other restrictions but continued to work and coordinate with multiple stakeholders and contractors to ensure a timely delivery of the project.
“On top of this, our commercial team played a crucial role to keep all project costs in check and
subsequently ended up saving the clients close to RM2 million from our initial estimates,” he observes. “Ultimately, having such understanding stakeholders and having their full trust to deliver the project made this one of our most memorable projects to date.”
Elsewhere, KFM’s work on a new Amazon (AWS) facility has involved handling state of the art fixtures and finishes, in what de Souza describes as “one of the most detail-driven
“WE HAVE LEARNT A LOT FROM OUR PEERS AND WILL CONTINUE TO TRY AND POSITION OURSELVES AS A PREFERRED PARTNER OF CHOICE FOR PROJECT MANAGEMENT AND WORKPLACE CONSULTANCY TO OUR CLIENTS AND FUTURE CLIENTS”
– JOSHUA DE SOUZA, DIRECTOR OF PROJECT MANAGEMENT, KNIGHT FRANK MALAYSIA
projects we have had to deal with.”
Although an ongoing and eventful journey, it is one that has been truly rewarding for the whole KFM team.
“Ultimately, we learnt lots from this project and I can say it was a pleasure working with some of the most intellectual and industry-savvy individuals that we have ever had to deal with on any project,” he shares.
Drawing to a close, de Souza returns to KFM’s key priority for 2023/4 of expanding operations beyond its current base.
“On the department side of things, we are continuing to look at expanding our project portfolio and diversifying into more industrial built facilities, building refurbishment works and strengthening our
workplace consultancy and change management offerings to our clients.”
In keeping pace with an everevolving industry, this notion of growth also applies to the company’s increasing use of technology and digital solutions, with the goal to enhance its digital capabilities.
“This includes developing new digital tools to enhance the client experience, and perhaps looking into virtual property tours or online property management systems,” he tells us.
In addition, KFM will remain astute to the trends that have shaped its journey thus far, increasingly developing its sustainable practices and mitigating its environmental footprint within a sector where this is now expected, and no longer a ‘nice to have’.
“As the importance of sustainability in real estate continues to grow, we aim to develop new sustainability initiatives and partner with clients to implement sustainable solutions in their properties,” de Souza affirms.
“Although we are just finding our foothold within the industry, we have learnt a lot from our peers and will continue to try and position ourselves as a preferred partner of choice for Project Management and Workplace Consultancy to our clients and future clients.”
KNIGHT FRANK MALAYSIA
Tel: 03-2289 9688
admin@my.knightfrank.com
https://www.knightfrank.com.my/
Architecture is a wonderful synergy of so many interesting threads from different industry sectors, client types and building typologies.”
Positioned prominently within this uniquely divergent landscape, is Ignite Architects (Ignite), the multidisciplinary design firm specialising in architecture, interior design, master planning and urban design.
The company excels in bringing a dynamic and innovative approach to delivering world class design solutions that are both peopleoriented and visually inspiring. With place-making at the heart of its practice, the company remains dedicated to fostering engaged and vital communities.
With over 30 years of experience to draw upon, stemming back to 1987, Ignite is now home to a team of more than 140 professionals across six design studios in Australia and New Zealand.
“The diversity of our experience and culture of craft allows us to take a fully integrated, holistic design approach to local and international projects of varying scale and complexity.” introduces Jason Marriott, Director of Ignite’s Sydney studio.
“Our scope of work includes master plans, retail and commercial buildings, workplaces and schools, hospitality and entertainment complexes, residential and hotel developments, civic and aviation buildings, and aged care and healthcare facilities.
“We don’t have a house styleour designs respond to the distinct requirements of our clients and communities.”
Remaining enthusiastic about the state of the modern-day architectural landscape, Marriott’s journey to his current role progressed parallel to an industry that has witnessed a vast transformation in terms of technology.
“I always had a passion for technical detail, paired with a strong interest in design and drawing. Eventually the
Ignite Architects’ designs forge community connections, tell cultural stories and are boldly resilient, creating spaces to be enjoyed across generations. We get the full storyWriter: Ed Budds | Project Manager: Ryan Gray
Serenity Made is a high quality supplier of all types of hospitality furniture for venue projects. Internationally recognised , Serenity Made is the go-to supplier in China for those looking for commercial quality and modern styles whilst maintaining a competitive price point.
Why Us
• Communicate your needs in fluent English.
• Products warranted for commercial use.
• Experienced in export and flexible in delivery terms.
• Able to work with you to develop bespoke products.
• Understand the quality requirements for hospitality projects.
• Small minimum order quantity with flexible terms.
Bottom line? Good quality, good price, good service!
JASON MARRIOTT, DIRECTOR, IGNITE ARCHITECTS: “The Ignite point of difference is a rigorous design process that marries creativity, functionality, and technology.
“We pride ourselves in our ability to work empathetically and collaboratively with all stakeholders, and to curate every element of a design throughout the project’s lifespan.
“Ambitious and forward thinking, we don’t hesitate to defy convention, and our clients value our ability to stay ahead of the curve and forecast future trends.
“While we are a commercial architectural practice, we believe that good design enriches the human experience and positively contributes to our collective future.
“We still see the creation of design as a craft, as place-making is at our heart, and designs should be humanistic so that they can be enjoyed across numerous generations. This approach means we don’t have a house style, with each design outcome being a response to differing needs and desires.”
combination of this led me towards architecture as a profession,” he tells us.
“It’s a career that has taken me around the world, at one point landing me in China for 13 years, working on vast mixed use and sporting projects. Seeing the profession evolve, from using drafting pens to the technologyorientated business we are in today has been an exciting experience, and looking back the evolution happened so quickly,” Mariott reminisces fondly.
Maximising usable area and yield, as land, construction, and materials become increasingly more expensive, is a key consideration across the industry.
At present, integrated mixed-use architecture and master planning is still gaining momentum as a typology, enabling more cohesive uses of land through mixed zoning combinations. This results in combinations that are
tailored to suit urban level needs while offering a higher level of user convenience and amenity, integrated lifestyle and work destinations, and more advanced sustainability solutions, as well as better commercial outcomes for investors, owners, and operators.
Standing in the shoes of the enduser, and innovating effective and user-friendly storage and amenity areas, is a key part of striking the balance for empathetic design, and commercial viability.
Flexibility and adaptable processes are critical for design responses so that they can evolve and manifest to deal with changing user needs. Ignite’s design team believes that now more than ever, technology needs to be thought of as more of an overlay that will change and can be quickly upgraded, rather than deeply embedded in a physical design.
Regarding residential spaces, ageing in place is becoming
increasingly important as a design consideration, enabling people to stay in a familiar place longer.
Additionally, the shared economy is an emerging design area that is still gaining momentum by looking at the collective synergies of like-minded people to enable co-working, co-habitation, and co-occupancy buildings.
“Fundamentally, it’s the sharing of property and space. As we leave the pandemic those operating in the shared economy have been strategizing and reimagining themselves. The idea of community sharing is disruptive and challenges the need for individual ownership, and conventional thinking, therefore this is a great opportunity for architects and designers,” Marriott elaborates.
Modern methods of construction are an area that is rapidly evolving and one that Ignite is incredibly passionate about.
“We have designed numerous buildings with prefabricated and factory-made components that include residential, schools, and resorts. These projects have deepened our understanding in this area and enabled us to develop design details specifically for these types of buildings.”
Capitalising on this deeper understanding, a project recently completed by Ignite is the Hume Street Urban Park and Through Site Connection. This forms part of the new Sydney Metro Upgrade Project by creating more
alternative inputs and thoughts, and pride ourselves on the practice of listening,” Marriott affirms.
Ignite’s suppliers in particular, have been invaluable in introducing and educating its designers regarding what is new, as well as refreshing the company’s understanding of known products and materials.
permeability within the urban fabric from one of the new metro stations. The complex and innovative methodology involved the demolition of several existing buildings, retention of a historic façade and the design of a pavilion.
Now dependant on a key selection of consultant, supplier, and manufacturer partners, maintaining these relationships has become critical to Ignite’s design work. Our studio fosters a culture of collaboration.
These partnerships bring invaluable input to projects, at times challenge the company, and keep everyone involved in the operation abreast of new technologies and products.
“Without a variety of stakeholders bringing different thoughts, opinions, and ideas to projects our design outcomes would be far less successful. We encourage
Ignite has worked on numerous projects with Serenity Made and they have always proven to be reliable and deliver quality products. Serenity regularly works to help manage budget expectations and design needs by customising products accordingly. Having the ability to adjust product materials and finishes is a real help to creating a resolved design response.
“Our people in general, at every level, are core to our design work, and we always look to build flat, multigenerational, and gender balanced teams. This helps us to blend new ideas, with proven experience so that designs are innovative yet grounded,” he expands.
Due to its now considerable level of expertise in the design field, Ignite prefers to see itself as several ‘studios of thinkers’, working towards a common goal of creating relevant and meaningful designs.
“Our business operations are as transparent as possible, and we emphasise the importance of giving professionals
“THE DIVERSITY OF OUR EXPERIENCE AND STRONG TEAM CULTURE ALLOWS US TO TAKE A FULLY INTEGRATED, HOLISTIC DESIGN APPROACH TO PROJECTS OF VARYING SCALE AND COMPLEXITY”
– JASON MARRIOTT, DIRECTOR, IGNITE ARCHITECTS
sufficient autonomy so they can express themselves through their work,” Marriott notes.
In this way, Ignite encourages its teams to communicate openly and cross-pollinate ideas, with a meeting held every Monday where business and project items are shared and developed.
“Further to this we run team-orientated design competitions and charettes with prizes to foster innovative thinking, as well as just having fun.”
Determined to adapt efficiently to a new era of technology, the entirety of Ignite’s business has become untethered from workstations and now works using laptops.
“This allows us to have a very agile team that can work from a variety of different locations – studio, home, café, or while travelling. In addition, we run the entire business through a cloudbased server to store data, giving us a more secure and flexible digital environment,” Marriott explains.
This fresh approach also enables the company to splice multiple studios together under the umbrella of a single digital ecosystem that is centrally managed.
Being a digital practice, Ignite creates its own projects as building information models, working in 3-D from the onset after broad planning decisions have been established.
Furthermore, the use of intelligent models has been proven to enable a better understanding of project issues, allowing the company’s designers to generate highly coordinated solutions and use multiple disparate teams and expertise within a single project environment.
“These models also enable us to often exploit the advantages brought by virtual reality headsets to give a better appreciation of spaces, façade expressions, and key design details,” he adds.
In the same manner in which the company has embraced new technology, Ignite will be focused on
strategic growth in areas where value can be added.
This will be achieved by continuing to invest in Ignite’s current team, while also searching for candidates that will contribute to future design and business outcomes.
“Finally, this year we are looking to expand our education and aged care offerings as these are sectors that we have a proven track record with. Our knowledge and expertise in these fields brings a depth of experience that will enable us to add considerable value moving forward,” Marriott finishes.
The best designs create solutions that respond to people, and to which people respond, and with this in mind, Ignite’s passion and unrelenting enthusiasm for innovation will continue to set them apart.
“OUR KNOWLEDGE AND EXPERTISE BRING A DEPTH OF EXPERIENCE THAT WILL ENABLE US TO ADD CONSIDERABLE VALUE MOVING FORWARD”
– JASON MARRIOTT, DIRECTOR, IGNITE ARCHITECTS
We examine a cross-section of the multidisciplinary design work carried out by PMDL Architecture + Design, with two of the company’s Practice Directors, David Morris and Vicki van Dijk
Writer: Jack Salter | Project Manager: Ryan Gray
We think before we draw.” The mindful mantra of multidisciplinary design practice, PMDL Architecture + Design (PMDL), has resonated with the Australian company since its inception in 1994.
With just under 30 years of expertise in architecture, interior design and masterplanning, PMDL enjoys an incredibly diverse portfolio in the education, retail, commercial, hospitality and leisure sectors.
More recently, the practice has expanded to once again bring its design expertise and programming acumen to high-end, boutique and multi-residential projects.
“Having a diverse set of creative disciplines means we often get to apply the full skill set to a singular project opportunity as the client’s needs evolve,” says David Morris, who is one of five Practice Directors at PMDL.
Having grown in both scale and reputation over the course of almost three decades, PMDL now employs around 70 talented members of staff across four studios in Sydney,
Melbourne, Hong Kong, and Geelong. The latter studio is a new addition to the firm, following the 2022 acquisition of another leading Australian architecture practice, McGlashan Everist. Like many businesses in the architectural industry right now, PMDL has strategically sought to build a stronger market presence with a likeminded practice.
“Our project work doesn’t necessarily reside geographically, as we share projects within the practice based upon the application of correlated expertise. For example, a designer with global hospitality experience could be residing in Melbourne and working on a 5-star resort in Macau, while a design leader in Sydney could be informing a new school masterplan in Melbourne,” outlines David.
“This concept is not new postpandemic, because it has worked successfully for our practice long beforehand. We truly have a coercive, cohesive and friendly culture of sharing and collaborating, both internally and externally.”
This collaborative culture stems from PMDL’s Practice Directors who, despite being different both as architects and humans, are bonded by an ethos of great design fused with sound decision making and ethics.
For Vicki van Dijk, another of the company’s Practice Directors with an ardent interest in viable and sustainable design solutions, it’s through extensive consultation with a clear decision-making structure that PMDL arrives at a considered and thorough brief.
“If we were to fault our overall profession, it would be on the tendency to quickly default to drawing or designing without real interrogation or exploration of the brief,” she tells us.
“We take pride in offering inspired designs and creative solutions based upon reliable and informed experience. From the outset, the need to evolve the best brief or masterplan is the precedence of best built outcomes.
“We also pride ourselves on our expertise and skills in facilitating the early design process, assisting our clients at the masterplan stage to distil and define their vision,” adds Vicki.
PMDL is likewise well-versed in managing a range of stakeholders, investigating and challenging key aspects of a brief when necessary to ultimately agree on the best or most suitable direction.
It is a skill that the practice believes
is not “given” but developed and honed over years of experience and exposure to effective masterplan management and solutions.
“PMDL invests in our team to develop these skills early on to provide them with a solid foundation to continuously build upon as they progress through their career,” Vicki shares.
“Whilst we champion our masterplanning skills, we are also immensely proud of our success in
retaining client relationships through to the design and construction of projects established within the masterplan solutions.”
With a deep understanding of the origins of the masterplan strategy, PMDL bolsters its understanding in the realisation of building designs, fostering the seed of the idea and ensuring the design intent is maintained to achieve insightful, cohesive buildings that are unique to their brief, site and context.
As such a diverse multidisciplinary design practice, there are a number of projects that best display a crosssection of the company’s work.
In Sydney, a city that is becoming truly polycentric with credible, urban spaces, PMDL recently completed William Clarke College’s Branwhite Centre, a STEAM (Science, Technology, Engineering, Art, Maths) facility providing contemporary and innovative learning environments in a state of the art building.
Representing the first stage of a considered and transformative masterplan, the Branwhite Centre is the genesis of a new architectural language and typology for the college.
It’s also a direct reflection of the college’s ambitions for teaching and learning, and there has already been a real change in the way subjects are delivered at the centre.
“The design caters to the existing student population, providing new learning spaces, a home base for two year groups, and purpose-built STEAM faculty areas,” outlines David.
“The integration of home bases and student ownership areas are a means to instil a lifelong love of learning and craft among the student population.”
Elsewhere in Australia, the masterplan for the Star of the Sea College in Melbourne has been commissioned with the aim of
determining and facilitating the staged planning for the refurbishment and redevelopment of educational spaces for the next 10 to 15 years.
Enabling the contemporary and holistic engagement of students, teachers, and the wider community, the Star of the Sea masterplan provides a new campus structure for a college that embraces new learning environments. In the first phase of the masterplan, it was imperative to enable a new east-west spine to improve the connectivity and flow of the campus.
This was achieved through a key move to open the existing impervious ground floor of the Heritage Wing, located centrally within the campus, with a generous colonnade reflecting and reinforcing the heritage of the building in a contemporary interpretation of arches and vaulted ceilings.
The Heritage Wing is now complete, and this simple move alone has instrumentally released the onceclosed campus to create a strong, open, east-west axis and connect key facilities and open spaces.
In China, meanwhile, PMDL recently completed the concept design for a Hot Springs Resort in the city of Suzhou.
The design includes a 160-room hotel, an eco-spa retreat, private lakeside residences, and features references to the “Venice of China” as the city is known for its waterways and historic architecture.
“Once again, this project encapsulates the core skillset of PMDL: masterplanning, architecture, and interior design,” says David.
It follows the completion of the Nanjing masterplan, which was delivered collaboratively between the practice’s Sydney and Hong Kong studios.
Encompassing 240,000 square metres (sqm) of commercial, hospitality and retail space, PMDL’s approach was centred around an entirely pedestrian experience.
“Vehicles are therefore taken underground immediately from
the perimeter road network,” David details. “The project shows our capability in the delivery of large and complex projects.”
This capability was also demonstrated by PMDL in nearby Cambodia, where Angkor’s T Galleria store is set within the cultural surroundings of Siem Reap and close to Angkor Wat, a UNESCO World Heritage Site.
The design proposed the adaptive reuse of an old museum complex and explores the integration of locallyinspired and derived motifs.
Working closely with the local community, PMDL developed a retail environment that is filled with cultural references in a similar vein to the Hot Springs Resort in China.
These include wall and column sandstone carvings that were
DAVID MORRIS, PRACTICE
DIRECTOR: “Our key suppliers have supported the business in both our continuing professional development (CPD) and the realisation of our building designs with innovative products that help us achieve our visions.
“At PMDL we have been fortunate to retain the role of superintendent on several of our projects, enabling us to work closely with contractors through construction to achieve economical solutions to material and buildability challenges that retain integrity and design intent.
“This was no truer than with Rohrig Construction, working on the Branwhite Centre at William Clarke College, where our combined efforts and ‘smarts’ during construction achieved a quality outcome on time and budget.”
produced by local artists – Artisans d’Angkor – as well as traditional handmade encaustic tiles.
This 8,000 sqm retail site is centred around a two-storey atrium space, with a beauty hall featured above and a luxury travel accessories area below. High in the atrium is a twisting, orange art installation entitled “Khsai Ponnareay” or “Luminous Ribbon”, which ties the store together and is visible from all angles.
PMDL’s studios worked closely to create a significant piece of artwork and a unique centrepiece for the entire development.
Like most in the industry, PMDL is implementing technology and utilising building information models (BIM) in nearly every design.
The practice has embraced the development and delivery of BIM, both as client-side managers of the modelling but also as an adept consultant to contractor-led models.
“Having multiple studios means our platforms need to offer seamless digital
modes of working,” explains Vicki.
“Our use of Revit and a bevy of technical staff offers high-end capabilities with the intimacy of a small and attentive design studio. That said, our designers remain passionate about the origins of design and conceptualisation, which starts with hand sketches, and we enjoy working with virtual reality (VR) to assist design comprehension with our clients.”
Intrigued by the constant evolution of design technology, its tools, and how they enhance and inform architecture and BIM, PMDL has
dedicated Design Leaders in each office who, in addition to project work, lead the practice’s technology research efforts.
They are supported by a BIM Manager who is responsible for the development of BIM, including all training and smart utilisation of the system across all PMDL studios.
“We value and respect the origins of good design, but remain frank and progressive in our endeavours to elevate these efforts with the appropriate technology,” Vicki says.
PMDL’s BIM team is retained from the pre-design phase to develop a BIM Management Plan specific to each project, to predict and measure performance objectives and provide multidisciplinary models.
The development of BIM in various levels of building, detailing when more or less information is required, is also being considered by PMDL, who promotes an OpenBIM approach in line with industry best practices.
“Participants in the building process are constantly challenged to deliver successful projects despite tight
Hoyt’s Luxe Lounge Barbudgets, limited human resources, accelerated schedules, and limited or conflicting information,” explains Vicki.
“Using different BIM tools, significant disciplines such as architectural, structural, and MEP (mechanical, electrical and plumbing with firefighting) models are well coordinated to ensure maximum efficiency across the documentation process, by performing collision detection and identifying the exact location of discrepancies.
“This approach makes the integration of our designs more streamlined and values interoperability, flexibility, and longterm file compatibility,” she continues.
Aside from BIM, investment in staff at every level is acknowledged as an equally important element of PMDL’s growth.
The company recently made a huge
“HAVING A DIVERSE SET OF CREATIVE DISCIPLINES MEANS WE OFTEN GET TO APPLY OUR FULL SKILL SET TO A SINGULAR PROJECT OPPORTUNITY AS THE CLIENT’S NEEDS EVOLVE”
– DAVID MORRIS, PRACTICE DIRECTOR, PMDL ARCHITECTURE + DESIGNchange to assist growth and meet the needs of its team by appointing an in-house Leader for Talent and Culture, solely engaged in the development of all employees.
“The size and complexity of the business meant we as Practice Directors could not remain closely focused on developing the team. We see this as an important investment in our staff, and remain proud that PMDL is not a hire and fire firm,” acknowledges Vicki.
“We employ people from a diverse range of backgrounds who are a good cultural fit and want to work and stay together, and aim to nurture our team’s well-being as much as their career growth.”
PMDL’s culture is reinforced by its strong design focus, and the company’s team structure has evolved to support that focus.
Specialist industry professionals have been brought in to focus on PMDL’s talent, culture, business
development, marketing, strategy, finances and operations, freeing up Practice Directors to focus on their projects, nurture clients, and build new business.
This is supported by identifying and celebrating Design Leaders in each of PMDL’s studios, to further drive creativity and innovation across all projects.
“Looking ahead, our priority remains on our team, strengthening our design focus through finding great talent and supporting our current team in reinforcing their skills and passion for design,” concludes Vicki.
PMDL ARCHITECTURE + DESIGN
Tel: (02) 8458 5500
www.pmdl.com.au
Hoyt’s Cinemas – Luxe theatre - entryFrom a new food park in New Zealand to a strategic collaboration in Singapore, we chart the latest developments in Hilton Foods’ Asia Pacific expansion and sustainability journey with regional COO,
Writer: Jack Salter | Project Manager: Kyle Livingstone
Experts in cleaning and sanitation for the food industry
Our market leading cleaning and sanitation services and solution ensures compliance with food standards required by regulators, retailers, and within specific supply chains.
We understand in-depth, the process of food safety by preventing the spread of harmful bacteria and other contaminants.
Established in 2001, Ecowize is a leading provider of cleaning and sanitation services and equipment to the food industry in Australia and New Zealand.
Since then, we have rapidly grown to the forefront, becoming the market leader in outsourced cleaning and sanitation services. We are part of the Ecowize Group, which operates in key markets around the globe, namely Australia, New Zealand, South Africa and North America.
We believe that by supporting local charities and community organisations, we can help address social issues and contribute to the betterment of the community we are servicing. Our goal is to make a meaningful impact on the lives of individuals and families, as well as the overall well-being of the community that we service.
We also believe that by participating in local initiatives that it helps us to attract and retain talented people that have similar values. A great direct example of this is our support of atWork Australia which has resulted in the Ecowize Group directly employing over 35 team members who live with a disability or are disadvantaged.
Fundamentally this involves employee personal hygiene, facility and equipment sanitation, pest control, temperature control, proper food handling, HACCP, food safety inspections and regulations. All of these practices are essential for preventing food-borne illnesses.
A trusted partnership with Hilton Food Group
Hilton Food Group (HFG) expanded to Australia and New Zealand and supplies Woolworths (Australia) and Countdown (New Zealand) stores with the highest quality protein. As a result of this expansion, HFG needed to establish local partnerships.
A key partnership for them was to find a highly experienced cleaning and sanitation company to ensure that the HFG plants located in Bunbury, Brisbane, Melbourne and Auckland would exceed the local food sanitation standards and always be audit ready.
HFG met with the Ecowize team and recognised that its +20 years of local experience combined with the following international accreditations ISO 22000 (Food Safety), ISO 9001 (Quality) and AS/NZS 4801 (Health and Safety), accredited, would be a strong foundation as a trusted partner.
Since the inception of the partnership, Ecowize has listened and worked closely to develop and implement a bespoke cleaning and sanitation programme to optimise and maximise the production up-time of HFG plants.
Even as times and tastes change, meat continues to take pride of place on plates across the world. Indeed, for millions of people, high quality meat remains the focal point of a multitude of meals and is still enjoyed as part of a healthy, mixed diet.
Not only is meat considered rich in protein, something most Australians and New Zealanders have no trouble consuming, but lean red meat especially also provides a wide variety of other nutrients including iron, zinc, and vitamins such as B12.
Meat is where it all began for Hilton Foods (Hilton), a leading meat protein and international food and supply chain service partner to retailers, global brands and the food service sector.
From humble beginnings in 1994 as a meat packing facility in Huntington, England, Hilton has become an international, diverse multi-protein food technology business. With a commitment to quality, innovation and customer satisfaction, the company has now established itself at the forefront of the Australian and New Zealand food industries.
Hilton has developed significant expertise in protein, processing and turning it into irresistible products that people buy and enjoy every day. Drawing on deep knowledge and experience, Hilton helps partners meet the broad and changing tastes of today’s market.
Having always been an ambitious entrepreneurial business, whose families at the root of its history operated primary processing slaughter and deboning facilities dating back to the 1960s, Hilton’s clear guiding principles underpin its mission to continue to be the world’s first choice protein partner.
It is these guiding principles which have led to a series of successful, if not ambitious, acquisitions and joint ventures establishing Hilton as a clear multi-protein global industry leader.
– MELANIE CHAMBERS, COOMeat is just one of five categories that Hilton operates across, along with seafood, vegan and vegetarian, easier meals, and supply chain services, serving customers in 14 countries from 24 world-class facilities worldwide and a turnover of around £3 billion.
“Our unique offering is underpinned by our category management expertise and strong environmental, social and governance (ESG) commitments throughout all the categories that we operate in on an international scale,” states Melanie Chambers, COO – Asia Pacific.
More than ever, seafood is both a staple source of protein and the focal point of exceptional dishes.
With consumer perceptions of seafood constantly shifting, freshness is paramount, as is sustainability in terms of how it’s grown, reared and caught. Hilton helps its customers meet all of these expectations with a product range that delivers convenience, variety and excitement.
Where seafood is concerned, step one is sustainability. A big part of that is using every part possible, which minimises waste and saves costs.
Hilton’s expertise and technology manage the risk and give all the
“MANUFACTURING MEAT, POULTRY AND SEAFOOD IN THE SAME FACILITY PROVIDES CUSTOMERS WITH COMMON PACKAGING FORMATS AND CONSISTENT QUALITY THAT ENGENDERS CONFIDENCE AND TRUST IN THE PRODUCT AND BRAND”
with operations in several countries, including Australia, New Zealand, Singapore, Malaysia, and Thailand.
Alsco provides uniform, washroom, and first aid rental services to various industries such as food manufacturing, mining, retail, hospitality, and food service. Alsco works closely with each customer to develop a service plan that meets their specific needs.
Alsco is committed to using high quality and sustainable products and are working towards being leaders in sustainability.
With over 130 years of experience in the industry, Alsco is the right choice for your business.
reassurances that customers expect.
Hilton’s seafood product range is global in focus and local in flavour, and includes smoked salmon, wet fish, shellfish, coated fish, and fish cakes.
Innovative meat-free foods have also been delivered by Hilton for more than 40 years, with veganism and vegetarianism going fully mainstream in recent years.
Whatever the consumer’s protein preferences, plant-based and vegetarian foods are an essential part of any offer, and Hilton delivers these fresh and frozen products to retail and food service customers.
“Our meat-free foods have helped to transform and grow the crosschannel vegan and vegetarian categories. Our Centre of Excellence delivers fresh production in local markets,” Chambers says.
As convenience is key for millions of consumers every day, Hilton’s easier meals are ready to heat or ready to eat, from straight-to-oven trays to ready meals, soups, sandwiches and wraps, reflecting both international cuisine and local tastes.
Hilton handles all consumer and retail needs across slow-cook and ready-to-cook meat, seafood, vegetarian and vegan foods. With advanced processing technology, the company can create affordable and easy solutions either for restaurants or from restaurants to enjoy at home.
Last but not least, Hilton’s supply chain consultancy services share everything the company has learned across manufacturing, sourcing, procurement and the supply chain.
Hilton’s Foods Connected platform is a cloud-based solution that gives a 360° view over supply chains, including procurement, food safety, quality, new product development and corporate social responsibility
(CSR). Real-time data enables agile decision making to minimise risks and maximise profitability, and over 150 manufacturers as well as several leading retailers already rely on it.
In Asia Pacific, Hilton operates four highly automated and technologically advanced manufacturing sites, supplying quality proteins to Woolworths and Countdown stores in the region.
The four sites employ approximately 1,600 team members operating 65 production lines, whilst 35 highly sophisticated robots pick and pack individual orders and send 5.7 million packets of meat to over
“WE LOOK FORWARD TO PROVIDING COUNTRY FOODS WITH THE INNOVATION, SUPPLY CHAIN EXCELLENCE AND TECHNICAL SERVICES FOR WHICH HILTON IS KNOWN”
– PAT MCENTEE, CEO – ASIA PACIFIC, HILTON FOODS
As a leading supplier of meat marinades, spices, and flavour concepts, we have built a reputation for excellence, producing sustainable and healthy food products both nationally and internationally.
Discover the co-manufacturing solutions you need with Berger Ingredients!
With our knowledge, expertise, state-of-the-art commercial kitchen, and a capacity of 2 million ready-made meals per annum, we’re fully equipped to handle your co-manufacturing needs.
Our unique, replicable category creation process stands out because:
We use leading technologies and food science to enable scale, but never compromise product integrity or lose focus on the families eating our food.
We conceive of, design, and deliver deliciously tasty, affordable, safe, and delightfully textured food products FAST to stay ahead of trends and define categories rather than follow.
Over decades we have developed specialist skills and processes to create products that meet the changing demands and preferences of consumers.
We are never afraid of using bold new ingredients, flavours, and cuisines.
We find partners and staff who share our values, and help them get to scale and grow with us.
MEAT – For Hilton, it’s crucial to deliver the tastiest, tenderest, and freshest meat products, helping customers meet the latest trends and expectations.
SEAFOOD – Committed to environmentally friendly and ethical fishing, Hilton sources from farms and fisheries that are continuously improving their exacting standards of quality, welfare and sustainability across a full portfolio of seafood products.
VEGAN AND VEGETARIAN – Hilton has been broadening its expertise in vegan and vegetarian proteins to deliver great-tasting and innovative products. This market-leading approach has seen the company create an ever-expanding range of meat alternatives to help meet the majority of customers’ protein needs.
EASIER MEATS – By combining a passion for innovation with culinary expertise, Hilton develops products that feed changing appetites and satisfy a hunger for something different. Its dedicated teams know exactly how to create quality products without compromising on quality or taste.
SUPPLY CHAIN SERVICES – It takes technology, talent and tenacity to get products from source to shelf and beyond. Hilton is an expert in the many services connected with the food supply chain, and supports its customers with warehouse automation, logistics and other value-adding services.
1,200 stores across Australia and New Zealand.
The company’s Australian sites are located in Bunbury (Western Australia), Heathwood (Queensland), and Truganina (Victoria), with Hilton’s latest New Zealand site located in the Auckland suburb of Wiri.
Opened in July 2021, the AUD$100 million purpose-built food park in Wiri provides a full pre-packed portfolio of more than 250 products across meat, poultry and seafood proteins, harnessing Hilton’s expertise across all of its protein categories.
The site is also complete with a fully automated warehouse store, that carries out individual store order picking for 150 Countdown stores on a daily basis. Automation in logistics has been pioneered by Hilton, driving new efficiencies in how goods are received, inspected, stored and picked.
“Our food park concept brings multiple proteins together, leveraging the combined volume to fractionalise manufacturing costs that could not be achieved in low-to-modest volume single protein facilities,” explains Chambers.
“Manufacturing meat, poultry and seafood in the same facility provides customers with common packaging formats and consistent quality that engenders confidence and trust in the product and brand.”
Three of Hilton’s Asia Pacific sites, meanwhile, now pass product pallets directly to Woolworths’ warehouses via an air bridge, reducing the need for trucks and material handling equipment (MHE).
Improving efficiency yet further is forming and slicing technology from TVI, enabling Hilton to 3D scan, weigh and mould fresh meat products.
The advantages of this worldleading technology include improved slice yields, portion control and line balancing to enable automated packaging, controlled fixed weight
How Bunzl & Hilton Foods worked together to reduce their overall plastics consumption.
Hilton Foods is one of the leading trans-Tasman suppliers of meat and added-value meat products to major supermarkets across Australia and New Zealand. Their products, all of which are palletised before leaving their premises, include red meat, poultry, sausages, fish, burgers, meatballs, kebabs, sous vide items like pulled pork and lamb shanks as well as a vegetarian and vegan line.
Finding ways to be more sustainable in the supply chain is an important part of doing business in 2023 – so with Bunzl and Hilton Foods’ mutual desire to reduce their environmental footprint and meet their sustainability goals, James Beleno, Bunzl’s National Business Development Manager in Industrial Packaging, stepped up to the challenge.
After an onsite inspection of Hilton Foods Fully Auto pallet wrappers, James made the necessary adjustments and quickly ensured a minimum 30% reduction on the film used for each pallet wrapped. “When it came to Hilton Foods, I did my homework around their machine settings, and adjusted their processes,” he says. “One of our main goals was to reduce the overall pallet wrap used to not only realise commercial savings but greatly reduce Hilton Foods’ environmental footprint.”
Due to the success, these processes were replicated across all sites in Australia and New Zealand. The film used in this process is unique to Bunzl and was developed through years of research and innovation.
Jim Rowntree, Bunzl’s Business Development Manager, says, “The benefits of this pallet wrap are not only in the significant cost reductions, but also in improving Hilton Foods environmental footprint. We can see this in the 129-tonne reduction of plastic now being used annually.” This pallet wrap is making great headway in the sustainability space with not only Hilton Foods, but other major users of this product across the country.
Need help with your sustainability goals? Then contact Bunzl at sustainability@bunzl.com.au
portions and thus fixed priced ranges for customers, and consistent presentation and portion shapes allowing for new paper packaging options.
Passionate about integrating technology and people, Hilton has dedicated technical teams that specifically support, research, and improve its technology through smart software enhancements.
“There has been a substantial push to enhance our technology stack, improve the user and supporter experience, and develop the technological aptitude of the team,” Chambers shares.
Elsewhere in the region, Hilton has
entered into a strategic collaboration with Country Foods in Singapore, providing proprietary technical solutions to the company’s manufacturing and logistics practices.
The collaboration between two highly respected and established businesses will help Country Foods to increase its product traceability efforts, execute sustainable packaging solutions, and improve efficiency.
Hilton will be trading innovative products in Singapore direct from its global manufacturing sites, including but not limited to seafood, alternate protein, slow cooked meats, and selected cuts of Australian beef, lamb and pork.
“Singapore will see protein choices
reach new levels of manufacturing and product excellence in existing sites, with ongoing joint exploration for new manufacturing and logistics opportunities in the future,” Chambers notes.
Country Foods is one of Singapore’s largest food importers, distributors and manufacturers, with a focus on innovative and sustainable food solutions. It is a wholly owned subsidiary of SATS, a leading provider of food solutions and gateway services that delights customers in over 60 locations and 14 countries, spanning Asia Pacific, the Middle East, and the UK.
SATS uses innovative food technologies and resilient supply chains to create tasty, quality food
Born 30 years ago out of a need for prepared meal solutions that actually tasted great, Flavour Makers has continued to grow and evolve through amazing innovation.
Today capability is not limited to dry blending, in fact Flavour Makers develops
Flavour Makers is the amazing Australian food company that inspires people to discover the enjoyment of food that actually tastes great!
in sustainable ways for airlines, foodservice chains, retailers, institutions and e-commerce companies.
Country Foods currently services more than 1,000 clients and 800 white label and branded products including Farmpride and Amir’s, leverages SATS’ global network to provide valuable access to markets across the region, and offers turnkey, go-to-market solutions to connect people, communities and businesses.
Commenting on the collaboration, Pat McEntee, Hilton’s CEO in the Asia Pacific region, celebrates the company’s landmark expansion into Southeast Asia.
“Hilton is well positioned to cater to the growing demand for high quality, affordable and sustainable protein products across retail and other market channels. We look forward to providing Country Foods with the innovation, supply chain excellence and technical services for which Hilton is known,” he says.
With approximately 30 percent of global emissions coming from the food system, Hilton is on an equally exciting and important journey to materially reduce emissions not only within its operations, but across its supply chain.
The company is continuously working on strategies to achieve its science-based targets across Scope 1, 2 and 3 emissions, as well as its ambitions related to resource management and consumption.
Notably, during 2022, Hilton doubled its waste recycling rates compared to the previous year, and has challenged itself to further improve this benchmark to achieve a minimum recycling rate of 60 percent of the inorganic waste generated by its facilities.
The transition to a mono-packaging structure, utilised throughout Hilton’s Asia Pacific operations, was also
classified as 100 percent recyclable by municipal kerbside recycling services in 2022.
“This classification allows up to 3,515 tonnes of plastic trays to be recycled by end users every year,” reveals Chambers.
“Furthermore, the recycling validation work completed with commercial recyclers demonstrated that plastic trays can be recycled with the plastic films still attached to them. This was an industry-first outcome which supported a further annual diversion of 3,245 tonnes of plastic film from landfill by end users.”
The implementation of circularity principles by Hilton in Asia Pacific is exemplified by the incorporation of up to 70 percent recycled materials in PET trays, and the fact that 96 percent of the packaging materials used across its operations in the region are recyclable.
As Chambers herself has been committed to carving out a career path that focuses on driving circular economies in the food and beverage industry, and dedicated to building a business that makes the future look brighter, she is naturally proud that Hilton’s Asia Pacific operations have been recognised by the Australian Packaging Covenant Organisation (APCO) with the APCO Annual Award 2022 for Highest Performing New Member.
The award recognises outstanding actions and contributions made by organisations against the packaging circularity targets set out by the Australian government.
Hilton’s crate model, for example, looks to remove cardboard in Western Australia and improve supply chain operations, whilst industrial gas conversion in Truganina to nitrogen removed the need for CO2 cooling.
“Throughout 2022 we have made significant progress in the establishment of demonstrable circularity practices in packaging,” Chambers acclaims.
“These extend beyond the formulation of packaging to reduce the use of virgin materials. We are leading the industry in the integration of an otherwise complex and diverse packaging supply chain to incorporate recyclable materials and further improve the recyclability of packaging materials.”
Managing water responsibly is also at the core of Hilton’s resource management strategy, on the understanding that water stress and scarcity is becoming a more widespread reality.
As such, the company strives to reduce water intensity in its operations and eliminate water wastage where possible.
This approach to responsible water management extends beyond the efficient and effective use of water, and also includes the use of best practice principles in wastewater management.
“Over the last several years, we have implemented various initiatives to manage the water intensity of our operations,” reveals Chambers.
“A few of these included improving our submetering and monitoring capabilities, optimising the operation of water-intensive plant and equipment such as cooling towers, and implementing various water recovery initiatives in our production lines.
“We are working on the feasibility of commissioning rainwater harvesting systems for cooling as part of our water efficiency initiatives. Subject to the outcome of our feasibility studies, we expect to implement these by the end of 2023,” she adds.
In the Asia Pacific region, Hilton has set a water use target reflective of industry best practices and is working towards more ambitious targets.
The company’s production facilities are very diverse in terms
of production throughput and processed species, presenting both exciting opportunities and challenges for Hilton to continue to improve its water efficiency and wastewater management practices.
Hilton aims to set an industry benchmark in water efficiency, and challenge itself to reduce the water intensity of its operations.
“We are committed to delivering initiatives aligned with best-practice principles, achieving our 2025 targets of improving water efficiency in our facilities by at least 10 percent from a 2018 baseline, and to continue with our resource stewardship principles,” Chambers informs us.
Hilton’s responsibilities within
the supply chain build on its environmental commitments and are a crucial element within its operations, ensuring compliance while leading the way in sustainable and ethical practices.
In Asia Pacific, the company’s supply chain operations involve sourcing raw materials, processing the meat, and delivering the final products to Woolworths and Countdown stores.
A strong emphasis is placed on quality control at every stage of the production process by Hilton, whose commitment to the concept of Chain of Responsibility (CoR) ensures that all parties involved in the supply chain have a clear understanding of their responsibilities to maintain highquality standards and comply
with regulations.
“Partner and supplier relationships are crucial to the success of Hilton’s business in Asia Pacific,” Chambers emphasises.
Indeed, the company relies on close collaboration with its suppliers to ensure a consistent supply of high-quality raw materials. Hilton also works with Woolworths and Countdown to understand their specific requirements and to develop products that meet their needs.
Effective communication and collaboration with suppliers and partners are key to ensuring the smooth operation of Hilton’s supply chain.
The company places a strong emphasis on building long-term relationships based on trust, mutual respect and shared goals, an approach that ensures Hilton can continue to deliver high quality products to Woolworths and Countdown while maintaining its position as a leading supplier of meat products in Australia and New Zealand.
With a focus on quality, innovation, and customer satisfaction, Hilton has established itself as a leading supplier of high-quality meat products.
“Our commitment to building strong relationships with suppliers and partners has helped to ensure the smooth operation of our supply chain, and Hilton’s continued success within the Australian and New Zealand food industries,” concludes Chambers.
Berton Vineyards is continuing to topple standards of wine production in Australia. We discuss sustainability, new products and how the company has managed to bottle success with Managing Director, Jamie Bennett
Writer: Ed Budds | Project Manager: Liam Pye
Wine has been the unassailable, most popular beverage of mankind for thousands of years.
Our natural fondness for this historic drink stems from its delicious flavours, underrated nutritional properties and of course not forgetting its psychotropic and intoxicating effects when consumed in excess.
No other alcoholic drink can claim to have had such a dramatic impact on society through the ages. The trade of wine between a multitude of cultures and civilisations historically opened up channels for religion and ground-breaking philosophical ideas to spread across the globe, engulfing entire regions with an enviable reputation as the new drink of choice for every occasion.
In previous eras, a thriving wine industry was also the clearest indicator of a prospering nation, as only the most developed societies could support a competitive and productive wine making operation.
Drawing on this rich and fruitful history, the Berton Vineyards (Berton) story began 25 years ago from the humblest of beginnings.
“We are still young enough to
be awed by tradition, but we also challenge ourselves by testing the boundaries of winemaking,” opens Jamie Bennett, Managing Director of Berton.
Fast forward to the present day, and the global wine industry is contending with a vast reduction in demand for product. This is simply due to policy decisions, an obstacle made all the more frustrating for companies as it is out of their direct control, therefore leaving them completely helpless to wrestle back any meaningful influence of the sector.
“I’m a great believer in market forces finding their own balance but when decision makers adversely affect your opportunities it is a hard pill to swallow,” describes Bennett.
“However, nearly every industry is dealing with its own problems, and what would work be without a few challenges? The most rewarding aspect of turning up each day is finding a solution,” he continues.
Bennett has always been involved in different manufacturing industries and having grown up in rural New South Wales (NSW), there formed a
natural affiliation with the land and being a producer of goods.
“In my first job, I spent 10 years involved in the poultry sector until the wine industry beckoned. This is where my partnership with Robert Berton
and James Ceccato began, and we have basically been tied at the hip since,” he recalls fondly.
Beginning operations in 2005 and now employing a team of 60 people, Berton’s facilities and vineyards are
Berton prides itself on being extremely water conscious, especially given its need to transport wastewater off site.
Wastewater is effectively used to spread over dry area farming land and soon it will be fully utilised for turf farming.
As wastewater is transported to dry land farming, Berton has ensured that it does not use any hazardous or toxic chemicals within the winery. An example of this is the company’s move from sodium based cleaning products to potassium based.
The potassium is readily available for plant uptake, unlike sodium which remains in the soil and can increase salinity.
located in the small town of Yenda, situated 20 kilometres northeast of Griffith, in NSW’s Riverina District.
The Riverina is distinguished from other Australian regions by the unique combination of flat plains, a hot climate and most crucially, an ample supply of water for the irrigation of crops. This combination has allowed the Riverina to develop into one of the most productive and agriculturally diverse areas of Australia. In terms of grape intake and branded sales, the production hub is now ranked prestigiously among the top 20 Australian wineries.
The winery itself was first established in 1945 and has close ties with the development of the Riverina as a major Australian viticultural area. The site now has the impressive capacity to crush and bottle approximately 20,000 tonnes of wine annually and possesses a storage capacity of 14 million litres.
Berton prides itself on being a contemporary winery with an emphasis on all that is casual, friendly and approachable in the production
and distribution of top quality wine.
“Our philosophy is to make affordable, easy drinking wines of quality, achieved through the pairing of modern technology with traditional techniques,” Bennett explains.
Testament to this philosophy, come award winning wines such as the company’s Metal Label Black Shiraz, Limited Reserve and Reserve ranges.
Over the years, Berton’s portfolio has received numerous accolades, including two Decanter Magazine awards for the 2014 Reserve Coonawarra Cabernet, which was named the best new world cabernet and the 2015 Reserve Shiraz, which was named the world’s best value Red Rhone Varietal.
“We have taken the approach of giving brands time to make their statement, and we are seeing the benefits of this approach as our brands gain traction both domestically and internationally,” elaborates Bennett.
Another particular point of pride for the company is its vineyard in High Eden, a sub-region of Eden Valley, which Bennett believes adds an element of prestige to the portfolio with 30 acres of premium fruit.
Across Australia and New Zealand, Orora Beverage (Orora) provides innovative, state of the art packaging design and manufacturing solutions to customers in the beverage industry. Working within three primary packaging solutions, Orora crafts and produces glass bottles, aluminium cans, and closures.
Orora is seen as a trusted partner for brands looking to create highquality packaging that assists in meeting their sustainability goals. With a range of infinitely recyclable products, Orora is setting a new standard for the beverage packaging industry and making a positive impact on the planet.
Orora is part of the ASX Listed company Orora Limited (ASX:ORA). Orora Limited is a global manufacturer, distributor and visual communication solutions company with more than 3,800 team members across seven countries.
Orora is known for its high-quality glass bottle packaging solutions, which are manufactured at its state of the art facility located in South Australia. Its range of glass packaging solutions includes wine, beer, cider, alcoholic ready-to-drink beverages, carbonated soft drinks, olive oil, and spirits.
In October 2022, Orora Glass opened its AUD$25 million Glass Beneficiation Plant located adjacent to its manufacturing facility in South Australia.
The plant will significantly increase the recycled content in its manufactured glass products and will deliver a number of environmental benefits, including a reduction in the amount of energy consumed and greenhouse gases emitted to manufacture glass products, a reduction in virgin materials, and a diversion of waste away from landfill.
The opening of the beneficiation plant has allowed Orora to take recycled glass from container deposit schemes and process this to create cullet, which is then used to manufacture new glass bottles at its manufacturing facility. Glass is highly regarded as a recyclable and premium option for beverage brands, as it can be recycled repeatedly without any loss of quality.
The plant has the capacity to produce a maximum of 150,000 tonnes of furnace-ready, recycled glass each year, with 100 percent of the recycled glass used by Orora to produce glass packaging for customers across the beverage industry. These benefits will advance the company toward achieving a number of its sustainability goals, including 60 percent recycled content for glass beverage containers by 2025* and net zero greenhouse gas emissions by 2050*.1
Orora is dedicated to reducing its environmental footprint and has implemented a range of initiatives to help meet its sustainability targets. This includes increasing the amount of recycled content in its products, the light-weighting of glass bottles, and increasing the use of renewable energy, all of which assists in lowering the overall greenhouse gas footprint.
As another major step in its sustainability agenda, Orora is planning to construct Australia’s first oxy-fuel furnace for its G3 furnace upgrade at Gawler.
Orora and Berton Vineyards have had a successful partnership for over a decade. Berton, a family-owned business with a remarkable team and impressive brands, has grown significantly, and Orora is proud to continue supporting its ongoing success. The partnership between the two companies is a testament to the value of strong partnerships and their shared commitment to achieving common goals.
Orora Beverage leading the way in more sustainable packaging
“Our iconic wine, The Bonsai, is made from the High Eden vineyard, and we are very proud of it,” he tells us.
“I don’t think we necessarily see ourselves as different to our competitors but we are about being faithful to our winemaking processes and producing a consistency of quality that our customers can trust.”
The development of Berton’s turf farm is a project that the company is especially satisfied with. There is a business-wide understanding of the importance of ensuring that the company’s footprint is one of enhanced sustainability and every decision Berton makes must now consider its consequences for the environmental impact.
Moving forward, Bennett sees great scope for expansion into new corners of the global wine landscape.
“It would be particularly exciting for our business to gain entry back into the Chinese market, so hopefully we come together and patch up our differences soon. The Indian and US markets also represent great opportunities as our business moves forward,” he details.
Situated within a region boasting a rich Italian migrant history, comes some wonderfully unique grape varieties that Berton is only now beginning to explore.
“We believe that these distinct varietals are perfectly aligned with our commitment to providing our
customers with a product they can rely on every time,” expands Bennett.
On top of its dedication to creativity and innovation, the one overriding belief that Berton holds close to its heart is that the partnerships that it forms with suppliers need to be the foundation of the organisation. Accordingly, many of the company’s suppliers and partners have a shareholding in the business.
“This not only gives us great confidence about tomorrow but reaffirms the commitment we are making to each other.”
“WE ARE CONSTANTLY LOOKING AT OURSELVES TO SEE WHAT WE CAN DO BETTER, BECAUSE IF YOU ARE NOT WILLING TO IMPROVE, YOU WILL BE SWALLOWED UP AND BECOME IRRELEVANT”
– JAMIE BENNETT, MANAGING DIRECTOR, BERTON VINEYARDS
As a member of Sustainable Wine Australia, Berton places a high value on its commitment to sustainability.
“We are constantly looking at ourselves to see what we can do better, because if you are not willing to improve, you will be swallowed up and become irrelevant,” Bennett affirms.
Throughout the entire business, the company continues to ask itself how it can reduce power, what systems it can make more efficient and what is a sustainable use for its secondary products. Through the implementation of these key questions, Berton will proceed forward rather than remaining stationary within an industry that is constantly evolving and morphing in imaginative new directions with a willingness to embrace innovation.
In terms of looking after the future
of the business, Berton is always eyeing fresh opportunities, and its young consumers are continually searching for new and sustainable options. Innovation and a willingness to adapt to consumer trends will help position Berton in an increasingly favourable market standing within the expansive wine making landscape.
“It is incumbent upon us to meet this challenge because our goal is to introduce two to three new products to the market in the next 12 months; we aim to be a company that is prepared to not only respect the great
traditions of wine, but also be flexible enough to understand what the market desires,” Bennett concludes boldly.
BERTON VINEYARDS
Tel: +61 02 6968 1600
wine@bertonvineyards.com.au
www.bertonvineyards.com.au
“WE AIM TO BE A COMPANY THAT IS PREPARED TO NOT ONLY RESPECT THE GREAT TRADITIONS OF WINE BUT ALSO BE FLEXIBLE ENOUGH TO UNDERSTAND WHAT THE MARKET DESIRES”
– JAMIE BENNETT, MANAGING DIRECTOR, BERTON VINEYARDS
After tasting the fun, fresh and authentic tacos from the beach taqueria stalls of Puerto Escondido in Mexico, Ant Wilkins, one half of the co-founding duo at Taco Medic, decided that Queenstown needed emergency nourishment.
Wilkins took the idea to his cousin and fellow co-Founder, Robbie McGillivray, who was in the market for
Writer: Rachel Carr | Project Manager: Liam Pye
an entrepreneurial challenge.
Although he studied a diverse portfolio of business management, accounting, HR, and horticulture, McGillivray’s heart was in the hospitality industry.
“After moving to Queenstown, I was fortunate enough to work with a longtime hospitality professional, Cath Hanna, who had created and operated
many successful venues. After working under her at several different cafes, restaurants, and corporate functions, I realised my future was in hospitality,” McGillivray opens.
Hailing from a “foodie family”, the co-founders perfected their menu on friends and family while the truck was built on their front lawn.
The white van with red logos
resembled an ambulance, resulting in a menu boasting food which is “good for the mind, body and soul”; the Taco Medic moniker was therefore the obvious choice.
The idea may be rooted in Mexico, but the vibe is most definitely Queenstown, New Zealand, as community and connection play as much of a part in creating Taco Medic as its satisfying menu items.
Finding good staff was the next task, and with a clear objective in mind, the co-founders set about constructing a friendly establishment where fun was added to the fresh food element.
“We are strong believers in giving people a go, taking on employees who have the right attitude, and helping to develop their professional
maturity and leadership skills which is a really enjoyable process to be part of,” McGillivray adds.
It was from these beginnings that Taco Medic grew into the inviting succession of taquerias it is today.
As a craft taqueria, Taco Medic focuses on homemade corn tortillas and preparing all foods on the premises. With ingredients such as fresh tomato salsa, slow cooking meats, fresh fish, chipotle mayonnaise, speciality seasoning, and three types of hot sauce, it is enough to whet anyone’s appetite.
The homegrown and handcrafted elements are not the only aspects that help Taco Medic to stand out. The employees represent the ethos of the company and uphold the sociable space that McGillivray and Wilkins have nurtured.
The open kitchen policy enables and encourages chefs to talk to customers, as the tacos become the
glue of the social gathering.
“Only the kitchen experience differentiates front of house staff from chefs. Our key hiring attribute is attitude,” emphasises McGillivray.
“Of course, in key roles there needs to specific experience and qualifications, but the attitude always has to be there. Everyone needs to work together to ensure we maintain a great culture of having fun at work, working hard and getting rewarded for our efforts.”
Taco Medic’s unique selling point (USP) is that all the company’s food is gluten-free, in a country where there has been a sharp increase in coeliac disease and gluten intolerance since the 1980s.
The menu offers a variety of Mexican-inspired flavours for all taste buds, with options specific to each location.
“Having a completely gluten-free menu is an advantage, as customers often comment on how refreshing it is
not to have a limited choice. As there is a growing number of gluten issues, catering for people with an intolerance means they can order anything on the menu,” acknowledges McGillivray.
Crafting its own products allows the restaurants to know exactly what is going in the food - fresh, healthy, and most importantly delicious ingredients are the key to Taco Medic’s success.
“Tacos have not yet become as mainstream as they have in the Americas, therefore our aim is to become leaders in the market.”
The team is revolutionising how people experience quintessentially Mexican food, influenced by New Zealand’s culinary landscape.
“My co-Founder brought back some awesome local knowledge and authenticity from the shores of Puerto Escondido. If you mix that in with the Kiwi flare and fresh produce available in New Zealand, the end result is Taco Medic,” McGillivray proudly says.
Supply chain issues have affected many industries in the past few years, however Taco Medic has mostly escaped unscathed from the majority of them.
“There was a fresh corn shortage as well as potato and chicken shortages over the summer, but luckily, we were dynamic enough to come through it,” assures McGillivray.
Relationships that the company has built with suppliers over the past decade have garnered buying power. Constant communication, and good feedback are an indication of a cohesive partnership.
“We like to do business with people we get along with, and partnering with suppliers who have the same ethics and vision as us is very important.”
As a gluten-free enterprise, it would have been understandable to have some trepidation regarding procuring ingredients, especially during the
“TACOS HAVE NOT YET BECOME AS MAINSTREAM AS THEY HAVE IN THE AMERICAS, THEREFORE OUR AIM IS TO BECOME LEADERS IN THE MARKET”
– ROBBIE MCGILLIVRAY, CO-FOUNDER, TACO MEDIC
PEOPLE – whether they are employees, suppliers or customers, people are Taco Medic’s biggest assets.
PLANET – by using free range, sustainably caught, and compostable products, Taco Medic respects the environment, and is always striving to make improvements.
PALATE – passion meets craft to create the tasty tacos, by pairing handmade tortillas with fresh ingredients.
PLACE – the taquerias are an oasis where patrons can enjoy a taco, craft beer or margarita, while listening to music surrounded by people with the same ethos.
bidfood.co.nz 0800 bidfood
COVID-19 pandemic, and with the logistical interruptions plaguing industries since.
“We have a couple of speciality products, such as our flour for tortillas, and chillies, which are imported. Therefore, we maintain good communication with those suppliers and forecast weekly and monthly usage with them,” McGillivray states.
Produce is not the only commodity in short supply, as the hospitality industry is also suffering from staffing shortages.
“The customer numbers have returned to pre-COVID-19 pandemic levels, and it was a good summer season in Queenstown. It has been all hands on deck to keep the venues open, with our General Manager Glenn Peat and Director of HR Anna Lissauer also working shifts in store.”
The relaxing and jolly atmosphere of Taco Medic means that putting in a shift is more entertainment than duty.
“Hospitality is a fun industry,
especially when you create great food - it gives customers a noteworthy experience,” says McGillivray.
Taco Medic has plans to open more taquerias, create more exciting menu items, and discover new technology in the hospitality industry.
“There is a lot happening on the technology front in hospitality, so we are always keeping a finger on the pulse of what is happening,” observes McGillivray.
The company is looking forward to expanding as well as innovating. The business’ plans for new ventures are already underway with two taquerias opened in 2022 and sights set on another two this year.
“We are working on a franchise model to help Kiwis into their own business and enjoy a career in the hospitality industry, so there is plenty to look forward to,” he says enthusiastically.
Bidfood are passionate about foodservice and hospitality with a wide range of products available. We are proud to be in partnership with Taco Medic to support them with their ongoing growth and expansion.
Although the business is currently undergoing an expansion throughout New Zealand’s main centres, ambitions are stretching to other shores as business trademarks are already set up in Australia.
“We are looking for new business partners or investors who will take the next phase of expansion across New Zealand to dominate the market, then we will take our vision to Australia.”
Taco Medic aims to continue the growth of the business across New Zealand, seeking corporately owned restaurants, and is currently speaking to some franchise experts to assist with the development of the business model.
“On the successful roll out in New Zealand, we will, again, be looking for business partners and investors to take Taco Medic to the next phase of growth overseas,” he adds.
The demand for the format, food and service is evidenced in the scale of the strategic expansion plans, but
the goal does not stop there with more ideas being tested.
“We have created and trialled four different restaurants models, invested in technology for our point of sale and loyalty systems, and created a business model which is positioned for rapid expansion,” reveals McGillivray.
With a plethora of projects in the pipeline, 2023 is shaping up to be another successful year for Taco Medic.
“We will open another Auckland taqueria to finish the Auckland hub, and I have been in Wellington over the last few weeks looking at a great opportunity there, in an exciting new development in the central business district,” he shares.
“We want more Kiwis to taste our delicious food and enjoy the experience of dining at Taco Medic,” concludes McGillivray.
APAC Outlook, Africa Outlook, EME Outlook, North America Outlook and Mining Outlook are digital publications aimed at boardroom and hands-on decision-makers, reaching an audience of more than 800,000 people around the world; spanning the full range of industrial sectors.
With original and exclusive content compiled by our experienced editorial team, we look to promote the latest in engaging news, industry trends and success stories from across the globe.
Your company can join the leading industry heavyweights enjoying the free exposure we provide across our platforms with a free marketing brochure, extensive social media saturation, enhanced B2B networking opportunities, and a ready-made forum to attract new investment and to help you grow your business. Visit www.outlookpublishing.com/get-involved for details on how your company can feature for free in one of our upcoming editions.
www.outlookpublishing.com/get-involved
Building on the global success of our regional titles – APAC Outlook, Africa Outlook, EME Outlook, and North America Outlook – Outlook Publishing is proud to introduce a platform dedicated to the mining and resources sector.
As mining organisations worldwide confront unprecedented change, embracing technological innovations and incorporating critical environmental sustainability agendas, now more than ever is the time to showcase the strides being taken in this dynamic sector. A multi-channel brand, Mining Outlook brings you the positive developments driven by organisations across the global mining industry through our various platforms. Discover exclusive content distributed through our website, online magazine, social media channels, and dispatches delivered straight to your inbox with a bi-weekly newsletter.
Through this compelling new venture, we foreground the movers and shakers of the industry. To participate as a featured company and join us in this exciting endeavour, contact one of our Project Managers today.
www.mining-outlook.com
After three years of expanding operations, Ravenswood Gold is geared towards a longterm future in gold mining. We speak to CEO, Brett Fletcher, as the company celebrates the end of phase one of the project
Now that the project is established, we are looking at steady and stable operations while improving the business and growing mine activities - it is the end of the beginning stage at Ravenswood Gold.”
Gold is a distinctive and precious metal. It is unique in its combination of malleability, boiling point, conductivity and ductility, while also being prized for its evident beauty. Across the world, gold is a very real representation of wealth and, outside of trade and commerce, plays an important part in industry, such as the circuitry of computers, phones, detectors and many more modern pieces of technological hardware.
Australia is home to a huge gold mining industry, one that is embedded in its history and has been pivotal in the development of the nation. In 1851, Queensland saw the first recorded discovery of alluvial gold deposits –gold able to be extracted from water sources such as rivers and streams - at the Darling Downs, leading to a swiftly growing region of industry by the end of the decade. Today, Queensland sees multiple players bringing the region’s deeply rooted legacy of gold to the surface.
Ravenswood Gold is one such company, a gold mining and processing facility located in the town of the same name in North Queensland. Ravenswood town has a long history of mining dating back to 1868, with the modern mine operating continuously since 1987. Ravenswood Gold acquired ownership of the mine in April 2020, including around 160 permanent employees. Since then, the company has expanded its number of permanent staff to support the expanded operations and grow the gold resources.
Ravenswood Gold is a private company owned by EMR Capital (EMR) and SGX-listed Golden Energy and Resources Limited (GEAR). EMR and GEAR established a joint venture
Ravenswood Gold is committed to responsible and community-centric operations through:
- Acknowledging the Birriah people as the traditional owners of the land on which operations occur.
- Respecting the historic heritage of the town of Ravenswood and its surroundings.
- Compliance with all applicable laws, regulations, statutory obligations and agreements.
- Maintaining effective heritage management systems and practices.
- Taking all practicable steps to prevent or minimise the impacts of its operations on heritage aspects.
- Identifying and implementing opportunities to conserve or interpret local heritage.
- Ensuring all persons working on site are aware of and executing their responsibilities associated with heritage management.
- Continuous improvement of heritage management systems and practices.
- Considering community aspects and impacts in all stages of operations and development.
- Taking all practicable steps to prevent or minimise the impacts of its operations on the local community.
- Maintaining effective community and stakeholder engagement and management systems and practices.
- Compliance with the Strong and Sustainable Resource Communities Act 2017 by maintaining a principally local and regional residential or drive-in, driveout workforce.
- Working to maintain a positive and open relationship with the local community and stakeholders through effective communication.
- Ensuring the local community is kept up to date on operations and any changes that may affect them.
- Fostering sustainable social and economic initiatives through the Tourism Directions plan, supporting local organisations and providing local sponsorship opportunities.
- Sourcing local and regional supplies and services where practicable.
- Ensuring all persons working on site are aware of and executing their responsibilities associated with community aspects.
- Involving the community, employees and business partners in continuous improvement of community and stakeholder engagement and management systems and practices.
to acquire, operate and develop the Ravenswood Gold Mine which is located approximately 130 kilometres (km) south of Townsville and 90km east of Charters Towers in north-east Queensland.
For Brett Fletcher, CEO at Ravenswood Gold, this historic industry has always been familiar.
“I come from a long line of people involved in mining; I was born in New South Wales (NSW) at Broken Hill,
Eagle Drilling QLD provides specialist hard-rock drilling services across Queensland. We operate on the surface and underground, offering diamond drilling and multipurpose drilling solutions. Our clients range from large mining companies to smaller, independent prospectors.
Eagle Drilling QLD services areas between Regional QLD and surrounds. Our head office is strategically located in Charters Towers, where we have an extensive fleet, including
our own aircraft, to allow us to work across Queensland with ease.
We employ some of the best professionals in the industry – skilled, capable and experienced in all aspects of surface and underground exploration drilling. As drilling specialists, we pride ourselves in leading the industry, using the best in technology, systems and equipment to get the job done safely, on time and within budget. Learn more
a well-known mining town, and my father worked for the multinational mining giant Rio Tinto for 35 years, one of many family members on both sides who worked in the sector,” he tells us.
“Naturally, I went into the industry myself and worked at a variety of mines, from being Mine Manager at Broken Hill and working on the west coast of Tasmania as General Manager of the Rosebery operation, to working the Century Mine in Townsville (Queensland) and managing at a large zinc smelter in Hobart. I have held numerous corporate roles travelling to mines around the Pacific region and have been with the Ravenswood Gold project from day one.”
Now, Fletcher has the privilege of watching Ravenswood Gold move forward with a long and productive future. The company has undertaken significant expansion in recent years to increase production capacity. Initially, investment had been a concern due to its timing alongside the outbreak of the global COVID-19 pandemic which made way for certain challenges in the industry. However, according to Fletcher, Ravenswood Gold’s management team was very effective when it came to pandemicrelated challenges.
“Over 95 percent of Ravenswood Gold employees commute from the local region, and we partner with suppliers from North Queensland
Greenstone is a leader in the design, engineering and manufacturing of material handling solutions for the C&D recycling, concrete batching, quarrying and mining industries.
Our approach is simple. Listen to our customers and their needs, call on our years of strong industry experience and the knowledge and technical expertise of our comprehensive team of engineers, technical staff and wellrespected project managers.
The result is first-grade equipment and plant solutions brought in on time and on budget to industry leading clients who keep returning to a team they trust.
Greenstone is proud to be the company of choice for many industry leading organisations, both nationally and internationally. Our quality of work and outstanding reputation has led to some of the most recognised names in C&D recycling, concrete batching, quarrying and mining industries turning to Greenstone.
Reliability, innovation, quality and a willingness to go the extra mile, are all values that Greenstone is noted for today. We continue to grow and are proud to partner each step of the way with our clients.
Greenstone has built a well-earned reputation as the one-stop shop for making your material handling vision a reality, providing its clients with clear and transparent communication to achieve your company goals.
With its wide range of services across design and engineering, fabrication and full project management through to construction, the Greenstone team of industry experts can tailor a solution for your specific industry and company needs. We are there for you every step of the way.
Greenstone is also ISO certified, which assures the highest industry standards recognised internationally. www.greenstoneindustries.com
“WE ARE LOOKING AT STEADY AND STABLE OPERATIONS WHILE IMPROVING THE BUSINESS AND GROWING MINE ACTIVITIESIT IS THE END OF THE BEGINNING STAGE AT RAVENSWOOD GOLD”
– BRETT FLETCHER, CEO, RAVENSWOOD GOLD
Greenstone is a leader in the design, engineering and manufacturing of crushing and screening solutions for the C&D recycling, quarrying and mining industries. Our approach is simple. Listen to our customers and their needs, call on our years of strong industry experience and the know-how and technical expertise of our comprehensive team of engineers, technical staff and well-respected project managers.
The result is first-grade equipment and plant solutions brought in on time and on budget to industry leading clients who return again and again to a team they trust.
We are ISO certified, which assures the highest industry standards recognised internationally.
LEARN MORE
where possible,” Fletcher explains. “In 2022, over 70 percent of Ravenswood Gold’s procurement expenditure was spent in Queensland, with around 23 percent directly in the local region. This translates to tens of millions of dollars invested back into our local area.
“We were quite lucky in the sense that we have been able to get the
project built and operational without major disruption because we have such a local workforce - even our contractors are locals. As for the supply chain, there have been challenges in this area. However, most of our supplies are manufactured in Australia, making transportation at a time of restrictions relatively straightforward.”
Ravenswood Gold is committed to safe and sustainable operations through:
- Providing visible leadership and never walking past an unsafe condition or unsafe act.
- Continually placing the health and safety of workers as a priority over production.
- Maintaining clear and open communication lines for safety-related information between all levels of the business
- Demonstrating a commitment towards achieving an injury-free workplace.
- Involving all employees and business partners in the improvement of occupational health and safety performance, through open communication and consultation.
- Ensuring all employees and business partners are aware of their responsibility for the safety of themselves and their colleagues.
- Ensuring all individuals carry out their work safely and are provided with the resources to do so.
- Implementing risk management systems to identify, assess, monitor and control hazards in the workplace.
- Providing adequate health care to all workers and the Ravenswood community.
- Continuously aiming to improve safety-related performance.
- Meeting or exceeding all relevant legal obligations.
- Maintaining robust environmental management systems and practices.
- Complying with all applicable laws, regulations, and statutory obligations.
- Taking all practicable steps to prevent or minimise the environmental impacts of its operations.
- Managing natural resources, particularly water, in a responsible and sustainable manner.
- Considering life of mine aspects, including rehabilitation, in planning processes.
- Progressive rehabilitation of areas no longer required by the operations.
- Ensuring all persons working on site are aware of and executing their environmental responsibilities.
- Involving all employees and business partners in the continuous improvement of environmental management and performance.
- The promotion of a proactive environmental culture.
Powertx Pty Ltd specialises in the design and construction, modification and testing of high voltage electrical systems and related LV reticulation/infrastructure including earth modelling, design and testing. RPEQ design certification can be provided by our in-house engineering and engineering consultants.
Powertx fosters strong and lasting relationships with other construction industry leaders and OEM suppliers. This brings synergies and economies producing a broader scale of capabilities and resources, capturing all installation and commissioning requirements including MDR’s and critical spares.
Associated industries include:
• MV and HV Primary and Secondary Equipment Providers
• Switchroom Providers
• Civil Contractors
• Overhead Powerline Contractors
• National Electrical and Communications Association
• Energy Network Providers
Example Project
66kV METERING STATION, 66/11kV (20MVA) SUBSTATION AND 66/11kV(10MVA) SUBSTATION
As part of the mine’s HV power infrastructure upgrade, Powertx was engaged by Ravenswood Gold for the design, manufacture, and installation of three separate 66kV stations, undertaken on both greenfield and brownfield sites. The three installations consisted of:
• Design, Construct and Commission a 66kV Metering Station including the design and implementation of N.E.R compliant revenue metering.
• Design, Construct and Commission a 66/11kV 10MVA Substation including 4.5MVAR Power Factor Correction (Nolan Substation).
• Design, Construct and Commission a 66/11kV 20MVA Substation including design, installation, and commissioning of point on wave switching and Inter Substation IEC61850 GOOSE communications (ER 4 Substation).
Whilst on site, Powertx has been involved with HV protection testing and temporary HV distribution and has recently been engaged to design, construct and commission a 66/11kV 3MVA Substation to supply the Accommodation Village and Water Treatment Plant.
www.powertx.com.au
Ravenswood Gold is unique in its localisation. According to Fletcher, 95 percent of the company’s employees are locals from the region, with Ravenswood Gold’s entire employee count standing at 420 – with an additional 240 permanent contractors - where in 2020 it was 160 – proof of the mine’s expansive and productively sustainable operations.
Similarly, it is also the use of localised contractors that is helping shape Ravenswood Gold’s success. On top of major growth in its own workforce, Ravenswood Gold has seen an increase in business partnerships, which are key for the company and have been supporting its growth since its establishment.
“Our relationships provide critical
support for the project in the present and into the future, and include Cater Care, who run our village for us and the catering on site; Roc Drill, who has the production drilling contract in the pit; Orica, who support us with blasting and explosive services; Pensar, who have undertaken the civil earthwork for our Tailings Storage Facility; and SimmCo, our local earth moving contractor,” Fletcher elaborates.
“Thanks to our collective partnerships, our workforce reaches approximately 660 permanent longterm employees, and at times we have seen an additional 1,500-2,000 contractors come in to help build the project.”
Ravenswood Gold boasts productive business relationships with
During 2021 and 2022, ECG Engineering (Queensland) was proud to provide electrical design capability to the Ravenswood Gold project, located 130km south of Townsville, Queensland and owned by EMR Capital and Golden Energy and Resources Ltd.
Responsible for the electrical, instrumentation and control systems design, ECG has played a significant part in the project which involved upgrading capacity of the 5 mtpa plant by more than doubling the output to 12 mtpa.
Commissioning was completed in late 2022, with full production to start in early 2023.
www.ecg-engineering.com
A key supplier for Ravenswood Gold’s Conveyor Expansion Project, Fenner Conveyors was contracted to streamline operational processes and reduce overall down-time, with a focus on improving site efficiency.
This was done through the supply of specially engineered rollers and pulleys, alongside conveyor alignment, belt cleaners, rubber lining, and belt installation services.
Fenner is a long-standing supplier for Ravenswood Gold; from its Engineering Teams assisting with component design and system improvements, to detailed scoping and inspections from Service Teams.
From years of demonstrated performance and built trust, Fenner was also contracted to supply belt spares for the Conveyor Expansion Project featuring its impact resistance compound and carcass combination for gold mining applications: Tuff AsTM & Crows Foot Weave.
www.fenner.com.au
From our offices in Australia, The Philippines and Canada, ECG services the electrical needs of Mining, Utilities and Material Handling clients across the globe. Our electrical engineering expertise covers feasibility studies, system audits, design, project management, procurement, construction management and site support. ECG has the expertise and key staff experience to deliver Electrical and Control solutions for:
• Mining and mineral processing facilities
• Power systems, grid connections or power stations
• Non-process Infrastructure
Our guiding philosophy of engineering innovation and integrity in partnership has allowed us to develop strong and successful relationships with our mining partners.
Electrical & Controls Global
E info@ecg-engineering.com
W www.ecg-engineering.com
Engineering innovation & integrity in partnership
OUR OFFICES
PERTH - WESTERN AUSTRALIA
T +61 (0) 8 6164 3400
BRISBANE - QUEENSLAND
T +61 (0) 7 3568 8840
MANILA – THE PHILIPPINES
T +63 2 7091 7469
TORONTO – CANADA
T +1 905 206 6319
the likes of AUSENCO, the company’s engineering, procurement and construction management (EPCM) contractor, a partner who has helped design, engineer and manage the expansion project. On top of this, the company has multiple construction partners based in the Queensland area; this localisation has given Ravenswood Gold an advantage in overcoming the challenges caused by the COVID-19 period. Additionally, Ravenswood Gold’s incorporation of the latest technology has helped the company establish itself in the field, especially during a period of global challenges.
“We have this Chrysos
PhotonAssay™ machine which is a pretty unique piece of technology that helps us analyse our gold content, owned and operated by Chrysos Corporation,” Fletcher says. “All of our drill results, metallurgical samples, tests and more are now run through the high-tech machine which rapidly analyses and determines the grade of gold that’s in the pit or being processed.”
The advantage of such technology is multifaceted, including providing more accurate test results faster, and improving the overall profitability of gold mining operations through streamlining gold analysis.
Pensar challenges established thinking to deliver innovative solutions and works hand-in-hand with our clients to achieve their vision and build critical infrastructure for the future.
We customise our approach to best suit the needs of each individual project, ensuring we use leading edge solutions to deliver the best results for every client. We create clarity of purpose, alignment of all stakeholders, and ensure the safety and accountability of everyone involved across process water infrastructure, non-process water infrastructure, specialist infrastructure, electrical infrastructure and infrastructure rehabilitation.
pensar.com.au
Since 2021, Wilson Security and Ravenswood Gold have partnered to create a customised, broad security strategy.
From welcoming visitors through to asset protection and traffic and flood management, Wilson Security works closely with Ravenswood Gold, using its Integrated Security Solution Model to protect and support the northeast Queensland mining community. A national leader in security, Wilson Security is rapidly expanding and sharpening its operations across the resources sector. To learn how we can protect your future, call 1300 945 766 or email us at marketing@wilsonsecurity.com.au.
www.wilsonsecurity.com.au
Further proof of Ravenswood Gold’s success is embodied by its milestones. With the Olympics coming to Brisbane in 2032, there are exciting prospects on the horizon for the company. For example, Ravenswood Gold is proud to have commenced discussions with the Queensland government about an opportunity to provide gold for medals at the Olympics.
“Although we are currently working through this process and it may take some time, we see this as a recognition opportunity for the Birriah people, the traditional owners of the land on which we operate, who are very supportive of this as well,” Fletcher explains.
There is no doubt that there are exciting times ahead at Ravenswood Gold. While the Olympics remains a plan for the future, the company’s current activities include the opening of the expanded processing plant and new tailings storage facility expansion. This opening will showcase the company’s completion and full operation of the Buck Reef West pit mine, the completion of the process plan expansion, and the fully functional tailings storage facility.
“We are very proud to be opening
our doors to some of the many people that have helped us execute the various aspects of the Ravenswood Expansion Project since 2020,” Fletcher says. “The official opening ceremony is a way for us to thank everyone that has played a part, from our owners to our business partners, government representatives, local community and, of course, our hardworking employees.”
This marks a milestone and shows that Ravenswood Gold is a company of opportunity, supported by employees, partners and the wider community who have been paramount to the project’s success over the past three years. The ceremony will see state and federal politicians of various departments, foreign ambassadors and representatives from over 30 supplier groups gather to celebrate the completion and future prospects of the Ravenswood Gold project.
For Fletcher, the next six to 12 months will revolve around ensuring a steady and stable operation, making sure that the project is delivering on what is promised, and looking for ways to improve the business.
“We are definitely at a turning point at Ravenswood Gold,” Fletcher concludes. “We originally picked
“Our roots lie in engineering and design.”
RJE Global has a reputation for delivering innovative, client-focused solutions.
With a diverse and dynamic team of over 350 permanent employees, we can provide turnkey solutions both within Australia and internationally. We have specific expertise in the design, manufacture, fit-out, installation and commissioning of transportable switch rooms and skid mounted electrical equipment to support a large range of surface and underground mining projects.
Our unique manufacturing techniques allow for the efficient construction of high integrity transportable buildings and skid mounted structures for harsh conditions. www.rjeglobal.com
up the asset and had a very clear strategy on what needed to be built to transform the business into a longlife, low-cost, large-scale operation, looking at a production rate of around 200,000 to 250,000 ounces a year.
“There was a lot of project work to be done, but as I sit here three years later it’s fair to say we have finished that construction phase and are ramping the plant up to its new full capacity. We are going to focus on improvement: how can we achieve more production? How do we reduce costs? How can we increase the life of the mine? That is very much our medium-term focus, with the longterm being consistency and growth.”
RZ Resources explores, discovers and mines a swathe of critical minerals across the Southwest of New South Wales, Australia. Chief Operating Officer, John Costigan explores the spirit of ingenuity and sustainable responsibility alongside aspirations for vast future growth
The market for rare earth elements and critical minerals is growing exponentially in order to address the increasing demand for products and the pressing global need to drive a more sustainable future.
In Australia, the government understands the importance of critical minerals, including rare earths, and is actively supporting businesses that are entering this swiftly expanding sector.
Writer: Ed Budds | Project Manager: Eddie Clinton– David Fraser is the Founder and Managing Director of RZ Resources (previously Relentless Resources Limited), incorporating the company in 2012.
– From the outset, Fraser has worked to build a long-term, responsible business, committed to sustainable mining practices and focused on delivering value to the local communities and shareholders.
– Fraser worked for Credit Suisse where he was responsible for growing funds under management (FUM), managing high-net-worth client portfolios and facilitating investment opportunities for other banking divisions. During his tenure at Credit Suisse, Fraser was recognised with an Australian Private Banking award for his outstanding relationship management.
– As the Global Head of Distribution for one of Australia’s largest alternative investment companies, Fraser was responsible for developing and raising capital for both domestic and offshore opportunities.
– Fraser started out as the Sydney and Brisbane Director of the Office of Economic Development for the City of Brisbane, where he led investment teams in generating revenue and developing growth opportunities in industry sectors such as mining and resources, infrastructure, and advance manufacturing.
As investors seek alternatives to the fossil fuel sectors, they see immense value in the long-term opportunities presented by the critical minerals sector.
Perfectly positioned to capitalise on such possibilities is RZ Resources, a 100 percent Australian-owned emerging critical minerals producer that is focused on being a highly responsible company, mining and producing critical minerals and rare earths in the far south-western corner of New South Wales (NSW).
“We are seeing longer-term forecasts for an increasing gap between supply and demand and there is a global focus and demand from consumers for companies to prioritise environmental, social and governance (ESG). RZ Resources understands how important ESG, diversity, equity, and inclusion is to its business strategy,” says John Costigan, recently appointed Chief Operating Officer of RZ Resources.
RZ Resources has an impressive
portfolio of 10 tenements, including the flagship Copi Project, for an exploration area totalling 3,362 km2 in the mineral sands-rich region of NSW.
Growing up in regional Queensland, Costigan began forging a curiosity from an early age for all things mechanical while he and his brothers dismantled and reassembled old motorcycles. Heavily influenced by his father, his enthusiasm for science and engineering continued to grow, leading to a hugely varied career path.
“I’ve been fortunate in my career to work in technical and leadership roles in varied industries including petroleum, animal health, agricultural chemicals, minerals processing as well as mining. This variety has provided me with core skills and knowledge, allowing me to navigate a career with confidence in more senior roles later in my career,” he describes.
“It’s through some hard learned lessons, that I became an advocate of embedding ESG, sustainable development, Indigenous economic
Diamantina Laboratories was established in 1997 as a specialist mineral sands processing laboratory by Raimunda Townend, a geologist/ mineralogist now with over 51 years of international experience.
Diamantina has steadily expanded and grown into a team of skilled, dedicated professionals and technicians, based over two sites.
• High quality service
• Fast turnaround
• Accurate results
• Competitive pricing
• A modern well equipped laboratory
• Secure sample storage
FULL MINERAL PROCESSING:
• Percentage: oversize, sand, slime, and heavy mineral
• Deslime, Eg: +2mm +53 microns
• Leaving Sand: -2mm + 53 microns
• Sand fraction to HM (heavy mineral)
Magnetic separation: HS, Mag1, Mag2, NM.
MINERALOGY:
1. Qualitative:
Sachet Logging (Binocular Stereo Microscope)
2. Quantitative:
• Mineral Identification, point counting and their percentage.
• Polarising Light Microscopy and Stepping Stage point counting
• Transmitted and Reflected light.
2A. Standard:
• 600 points counting: Study for Exploration Geology
• HS, Mag, N. Mag. Head. Percentage of every mineral present
• Identifying: Opaques Eg: Oxides: Ilmenites, Rutile etc.
• Non-Opaques: Eg: Zircon, Monazite, Xenotime etc.
2B. 900 Point counting:
• Fully Quantitative study of Composites for Reserve Calculation
• HS, Mag1, Mag2, N. Mag, and Head calculation
• Results in weight percentage
empowerment and community relations. I was previously working at another sand mine in Queensland when it lost its social licence to operate, and it became obvious to me that a company needed to be trusted to resolve issues effectively with the support of its community if it was going to have a whole-of-mine life.”
As demand for high quality mineral sands, specifically rutile, zircon and titanium, and rare earth elements continues to increase, RZ Resources has positioned itself optimally to deliver the Copi Project – an undertaking that has the potential to be both company and industry defining.
The Copi Mine is a globally significant resource and will help underpin the growth of Australia’s critical mineral and rare earths industry.
RZ Resources understands that the path to world-class ESG performance is paved with challenges and opportunities, particularly for a young and emerging company.
“Recently the NSW mining regulator made 22 specific allegations of environmental non-conformance which RZ accepted in an enforceable undertaking. To understand what could be done to prevent any possible future reoccurrence, we commissioned an independent auditor to uncover the root causes of the problem. The two key findings were: ineffective governance and oversight of compliance, resulting in non-compliance with legal obligations and persistence of onsite issues; and insufficient due diligence and inadequate systems to manage exploration practices and stakeholder engagement, which meant we didn’t have sufficient evidence to prove we had met our obligations. The company took immediate corrective actions to address the offences and is now building in preventive systems and governance,” says Costigan.
The founder of RZ, David Fraser, sets the tone for the company. He believes: “RZ has learned a powerful lesson that the company will be judged by its failures unless we learn from the insights gained to drive the changes needed to build a better approach to ESG.”
“I am just so impressed that the company learns from its mistakes. Today we’re proactively undertaking a gap analysis between world-best practices, our stakeholders’ expectations and our performance so we can prioritise a change programme to keep improving our ESG performance. One day I believe we will have world-leading best practices in ESG and sustainable development,” Costigan says.
Founded in 2016, in2Dredging (i2D) is an international and independent dredging consultancy based in Australia and Europe that has extensive experience in dredging and mining environments. The company provides dredging support and delivers innovative solutions to owners, contractors, engineers and suppliers. Since its inception, i2D’s commitment to quality and constant development has continued to shape its solid reputation and passion for dredging.
Although dredging and mining both excavate rock and soil, both fields are also very different. Dredging is excavating underwater using cutting and jetting techniques that are more cost-effective in marine environments. Dredging also involves a significant amount of risk since production rates vary depending on the rock and soil strength encountered.
In mining, the risk of subsurface rock is typically relatively low since the rock is first loosened by blasting. Mining projects are set up for decades and rely on custom-built mining dredgers that can be adapted to specific conditions. Since more generic dredgers are needed for the open dredging market, this requires different designs as well as a completely different mindset.
i2D has combined extensive practical field experience with academic knowledge to develop several off-the-shelf dredging tools, such as Pumps ‘n Pipelines and Estimator For
The company’s integrated management system helps ensure the highest possible quality, safety and flexibility to meet client requirements, deadlines and budgets. A handpicked multi-disciplinary team of accomplished consultants delivers cost-effective, appropriate and robust solutions backed by academic knowledge and vast field experience.
Management – i2D can manage all phases of a project, from concept to detailed design, and from tender preparation to execution, both on the owner and contractor side. Engineering – i2D’s engineers perform in-house advanced engineering that provides answers to any and all dredging challenges.
Estimating – i2D’s estimating tools are unique and state of the art, supporting them in producing appropriately defined, reliable and accurate budgets, schedules, designs and specifications.
Environment – i2D carries out marine investigations and environmental studies by identifying baseline conditions and calling attention to potential impacts and its mitigations.
Geodata Processing – i2D uses pre-invested tools to gain ground-breaking insight into dredging projects and monitor them more quickly and continuously.
R&D and Innovation – Cutting-edge research, development and innovation (RD&I) at an academic level helps provide i2D with a solid foundation to generate innovative dredging solutions.
www.in2Dredging.com
Once operational, the Copi Mine will be one of Australia’s largest mineral sands mines developed in recent decades. RZ Resources recently predicted the site to generate more than 16 megatonnes (mt) of export materials to global customers over the life of mine. With the project well underway and production expected to commence on schedule in 2026, subject to regulatory approvals, it will generate jobs for the local communities of far southwestern NSW, bringing growth and prosperity to the region.
We believe that our capability to supply final products to the market, by processing the Heavy Mineral Concentrate from the Copi Mine at our Mineral Separation Plant in Brisbane, Queensland, as a significant strategic advantage for our company.
“From this flagship project, the company will leverage the expertise and infrastructure built to further mining opportunities and as we grow
our understanding of the battery minerals and rare earth minerals sector, RZ Resources will look for downstream opportunities in that space,” Costigan elaborates.
At the centre of the company’s people-first culture, RZ Resources maintains a deep commitment to zero harm and providing a safe environment for all employees, subcontractors, visitors, and members of the public.
“We believe our greatest strength
is our people and we know that with the right team, we will deliver one of the world’s most significant critical mineral and rare earth resources projects in Australia,” details Costigan.
“At RZ Resources, we are guided by openness, honesty and twoway communication, and strive to establish a workplace where our people are empowered to live our values every day,” he continues.
There is a labour shortage in the market at present and due to the specialist nature of the industry, the greatest challenge facing the
“WE PREFER TO WORK IN PARTNERSHIP WITH OUR SUPPLIERS AND CUSTOMERS TO PRODUCE MUTUALLY BENEFICIAL OUTCOMES, SO IF THEY ARE SUCCESSFUL, THEN WE ARE”
– JOHN COSTIGAN, CHIEF OPERATING OFFICER, RZ RESOURCES
AMC consultants were an integral part of our team during the development of the Copi DFS. Their expertise in mineral sands mining, combined with their commitment to working closely with
our technical team, made a significant contribution to the success of the project. Their team was knowledgeable, experienced, and always willing to go above and beyond to ensure that our needs were met. We were particularly impressed with their ability to deliver concrete achievements with numbers attached, such as undertaking the mining component of the DFS, LG pit optimization, strategic mine plans, pit designs, coaching our junior mining engineers, and supporting budget costing for mining contractors. They also provided valuable advice on devising a mining strategy to optimize cashflow and improve NPV, as well as developing a tactical schedule approach to incorporate backfilling, reducing haulage, open areas, whilst maintaining pond length. AMC’s work was of the highest quality, and we were impressed by their level of professionalism and attention to detail throughout the project. We highly recommend AMC consultants to any mining company looking for a knowledgeable and committed partner.
www.amcconsultants.com
— John Costigan, Chief Operating Officer, RZ ResourcesCASE STUDY
company lies in recruiting the right people with the correct skillset in a market that is perilously declining in the quantity of skilled labour.
As the company continues to grow, finding professionals is becoming even more of a key priority and the wish list includes mining professionals, technicians, operations and maintenance specialists, and earthworks professionals.
“We are building a team of industry experts, who have built mines before and have decades of experience
running significant operations of this scope and size. By embedding ESG outcomes into the company’s agenda we have provided a real sense of purpose for our team,” Costigan notes.
Another key relationship that must be nurtured and developed over time, integral to every business, is that of the various components which compile to form a successful supply chain.
“Key suppliers at present include our partnering consultants who
have been selected for their technical expertise, shared values and cultural alignment. We prefer to work in partnership with our suppliers and customers to produce mutually beneficial outcomes, so if they are successful, then we are,” Costigan lays out.
RZ Resources continues to see strong demand for the high-quality critical minerals and mineral sands to be produced at the Copi Mine. Because of this, its partners and suppliers are critical to the success of every intricate rung of the entire business, and the company takes great pride in the relationships that it has built and continues to build.
“As we pursue an offtake strategy, we expect critical minerals demand will translate into additional agreements,” he tells us.
Ambitious plans for the future of the company are already in motion, as RZ Resources has developed a growth strategy to deliver jobs and economic benefits to the local community, alongside significant value to its shareholders.
“As demand increases for our sustainable and high quality critical minerals, including rutile, zircon and rare earths, RZ Resources is wellpositioned to play its part in the global economy and deliver critical
minerals and rare earths to customers worldwide from mid-2026,” Costigan acclaims.
From the outset, the RZ Resources team has built a long-term, responsible business, committed to sustainable mining practices and focused unwaveringly on delivering value to the local communities and to shareholders. An important part of maintaining this shared responsibility is ensuring the practices of First Nations peoples are respected during the construction and operation of new projects and that culturally significant sites are cared for jointly through the development of a Cultural Heritage Management Plan with Traditional Owners.
“We understand that our social licence to operate is a privilege that is earned from the community and have committed to undertaking ongoing consultations that will actively identify and mitigate any emerging issues during the project’s life. Additionally, the company is committed to providing communication openly,
honestly and in a timely manner with all stakeholders,” he adds.
A prime example of this responsible process is RZ Resources’ work on the previously mentioned Copi Project, including negotiations with Traditional Owners, the wider farming community and local towns such as Wentworth and Broken Hill.
Similarly, at RZ Resources, the entire company remains guided by openness, honesty and two-way communication, whilst striving to establish a workplace where its people are empowered to live a specific set of shared values every day.
“RZ Resources is an equal opportunity employer with a commitment
to diversity and inclusivity and we encourage professionals from all backgrounds to apply for jobs at the company. Our vision is to embed the principles of diversity, equity, and inclusiveness in our business from the start to help make us an employer of choice for our future workforce,” finishes Costigan proudly.
“RZ RESOURCES IS WELL-POSITIONED TO PLAY ITS PART IN THE GLOBAL ECONOMY AND DELIVER CRITICAL MINERALS AND RARE EARTHS TO CUSTOMERS WORLDWIDE FROM MID-2026”
– JOHN COSTIGAN, CHIEF OPERATING OFFICER, RZ RESOURCES
Yuxin Holdings Pty Ltd is a key producer and explorer of gold in the land
Down Under. We speak to Gary Goh, General Manager, about the company’s Pajingo Gold Mine and the community-centric mission that lies at its core
Despite certain challenges, the gold industry is going through an exciting and critical phase with opportunities that Yuxin Holding Pty Ltd’s (Yuxin) Pajingo Gold Mine is well-positioned to capitalise on.”
Gold has always been a source of awe. Unaffected by oxidisation and many harmful chemicals, cultures throughout history have associated gold with immortality, godhood and, by the nature of mortal aspiration, royalty. To this day, gold still carries many of these connotations and because of its relative rarity in comparison to other metals, beauty and valuable properties, is the classic representation of national wealth. Indeed, most countries across the globe hold gold reserves as insurance
against their primary currencies.
With such perpetual importance in our society, it is no surprise that there are many in the industry bringing gold to the surface; Yuxin is one such key player.
In November 2022, Yuxin acquired Pajingo Gold Mine, a mine with a longstanding history of operation dating back to the 1980s. The company owns 100 percent of the Pajingo Gold Mine operation in Northern Queensland.
Yuxin currently works with over 300 employees and contractors, and takes
pride in its work culture that promotes a positive, engaging workforce, offering career progression and training development within the mining industry.
Gary Goh, General Manager of Yuxin, has spent the majority of his career in the Australian underground hard rock mining sector with a brief stint abroad. Since his return to the country, Gary accepted the position of Group Manager of Operations and Technical Services at Minjar Gold, a company that Yuxin recently acquired, and recognises gold as a metal of key and immutable significance.
“Gold has always been a consistent source of interest due to the longterm sustainability of precious metals as well as the collective properties that make the element so unique,” Gary says. “The gold mining space is one of great activity, but despite that, it is not without its challenges.”
According to Gary, the mining industry is experiencing a significant boom whilst simultaneously undergoing difficulties in recruiting and retaining employees, with labourhire shortages and increased burnout of skilled and experienced workers in the industry. In the face of this, Yuxin offers its employees autonomy and the ability to be innovative. The company’s career progression opportunities are available to all
Yuxin is an equal employment opportunity (EEO) employer that is committed to diversity. The company’s Pajingo Gold Mine offers residential and FIFO opportunities on flexible rosters, a competitive salary, and entitlements that are above the industry award standards. Yuxin’s entitlements include bonus schemes, parental leave schemes, and EBA staff accrue 13 weeks of service leave upon completion of 10 years’ service.
The site recruits from communities in Charters Towers and the Northern Queensland region wherever possible, offering a positive worklife balance, and Yuxin supports indigenous employment, providing employment opportunities to apprentices, trainees and graduates.
Yuxin’s workplace culture embraces five core values:
staff and are truly outstanding, offering mentoring, training and development, as well as a study assistance programme to help bolster the number of skilled workers in the industry.
In order to be closer to its Pajingo Gold Mine site, Yuxin decided to set up its headquarters in Townsville (Queensland) rather than the Minjar Gold office which is located in Western Australia (WA). Yuxin also acquired NQM Gold 2 Pty Ltd (NQM), who operates the Pajingo Gold Mine in the Charters Towers region, from Minjar Gold in late 2022.
“Yuxin’s exploration strategy is to realise the full value of its extensive tenement holdings in North Queensland,” Gary elaborates. “Initially, this means focusing on targets within the mining leases, to maximise the return on capital that has been invested in the Pajingo Gold Mine infrastructure and development, and to generate revenue to fund future exploration. However, it also includes a smaller but significant commitment to identifying and testing targets beyond the mine.”
In order to achieve this, Yuxin has assembled a team of experienced exploration geologists and support personnel with a track record of discovery, both at the Pajingo Gold
Minetruck MT65
Minetruck MT65 is designed for fast productive haulage in large mining and construction operation. With smart system and robust component the Minetruck MT65 ensures productivity, reliability, operator safety and comfort along with ease of maintenance.
GARY
“As a key management staff member of an Australian company invested in by a Chinese company, managing the operations requires a unique set of skills and strategies. I have been playing a key role in bridging the communication between the board, corporate and the workforce. I believe that the key to effectively managing such a diverse workforce is to promote crosscultural understanding and respect while fostering a sense of common purpose and teamwork.
“To achieve this, I encourage open communication, promote cultural awareness, and organise cultural exchange programmes to help employees understand and appreciate each other’s cultural differences in communication. We also must ensure that key management members, both Chinese and Australian, speak the same “mining language”. Additionally, I ensure that the company’s policies and procedures comply with local laws and regulations.
“In summary, managing an international company with a blend of Chinese and Australian workers requires a sensitive and culturally aware approach. By promoting respect, understanding, teamwork, diversity, and a global mindset, I am confident that I can effectively manage the company and create a positive work environment for all employees.”
Mine and elsewhere. To support this team, Yuxin is funding exploration at levels not reached in the last 20 years; the company’s board has approved AUD$20 million in combined exploration and resource definition for 2023. In response, the exploration team are working with a local drilling contractor to increase the number of operational drill rigs on site, to achieve the estimated 50,000 metres of surface drilling to be completed this year.
As part of Yuxin’s strategic plan, the company is committed to expanding its business operations in Australia and maximising value for its stakeholders, including its dedicated staff. Yuxin’s focus on growth will not only create new opportunities for the business, but also enable it to provide additional benefits and incentives to its employees, ensuring they share in the success of the company, an aim that is communicated to all staff.
“The Pajingo Gold Mine operation is the only active mine under Yuxin at present,” Gary adds. “The
company’s procurement goal as always is to achieve the most costeffective solutions to the mine. With 62 percent of the supplier base in Queensland and the majority of them from Charters Towers, our strategy is to support the local economy, particularly small businesses, as much as we can.
“The company has the confidence to build a harmonious and ecological economic relationship with the local community. However, due to regional supply limit, a number of major mining services are sourced extensively to other states such as WA.”
For Gary, the approach to growth can vary depending on the company’s financial situation, strategic goals, and regulatory environment, however Yuxin is in a fortunate financial position thanks to its continuous outstanding operational performance.
“On top of this, the stable political environment, skilled workforce, and supportive government policies make
“WE ARE ACTIVELY SEEKING OPPORTUNITIES TO ACQUIRE OTHER MINING COMPANIES OR MINERAL DEPOSITS TO EXPAND OUR GEOGRAPHIC REACH”
– GARY GOH, GENERAL MANAGER, YUXIN HOLDINGS PTY LTD
the mining investment environment in North Queensland and the whole of Australia highly attractive to us,” he remarks. “In this way, Yuxin is able to pursue growth through a combination of approaches.”
The first of these is exploration; 2023 is the 40th year since the Pajingo Gold Mine was discovered. The mine has produced over 3.5 million ounces of gold to date, and
over two million metres of drilling have been completed, which equates to approximately AUD$245 million of drilling expenditure. Again for 2023, Yuxin has a huge exploration budget to continue its success in the region.
“We are actively seeking opportunities to acquire other mining companies or mineral deposits to expand our geographic reach,” Gary notes. “We are also open to forming
joint ventures with other companies if it benefits both parties better.
“On top of this, our operational team always pursues growth by optimising the existing operations. This involves investing in new equipment and technology to increase efficiency, reduce costs, and improve safety and environmental sustainability.”
Lastly, Yuxin is focused on
streamlining operations while remaining sustainability centric. The company has a strong willingness to invest in new technologies and infrastructure to improve sustainability for long-term success in a low-carbon economy.
“WE PRIDE OURSELVES ON EFFECTIVE PERFORMANCE MANAGEMENT SUPPORTING OUR WORKFORCE TO TRULY SUCCEED AND ACHIEVE OUR BUSINESS GOALS AND OBJECTIVES”
– GARY GOH, GENERAL MANAGER, YUXIN HOLDINGS PTY LTD
“The transition to renewable energy sources like solar farms has been seriously considered, as has engaging with manufacturers that help convert the traditional dieselpowered vehicles and equipment to the electric form,” Gary adds.
Yuxin is set to embark on an exciting year for the rest of 2023, as a 100 percent subsidiary owned by Shandong Yulong Gold (Shandong), a public company listed on the
Shanghai Stock Market. Shandong is seeking to grow and expand in both the gold mining sector and the new energy sector, and aims to become a truly international gold mining company which embraces a global vision, cultural diversity and highquality management. The acquisition of the Pajingo Gold Mine is part of this overall strategy, and Yuxin’s ultimate goal is to assist Shandong to achieve this success.
into exploration and tenement development, expanding the project’s productivity to generate better welfare for its workforce, and exploring other acquisition opportunities.
“Yuxin fosters a strong commitment to leadership, and we pride ourselves on effective performance management supporting our workforce to truly succeed and achieve our business goals and objectives.”
“This mission is challenging and exciting at the same time,” Gary reveals. “As a start, from this year, Yuxin will focus on a few key tasks, including investing more YUXIN
www.minjargold.com.au
A proudly Australian manufacturer for half a century, Seeley International’s evaporative air conditioning systems are redefining cooling. We discover this ground-breaking technology with Executive Chairman, Frank Seeley
For the first time in decades, the Australian public is keen to buy goods manufactured in their own country.
Fortune favours the brave, and there are rich rewards for those who are prepared to go after these opportunities.
One company capitalising on this strong, resurgent preference for Australian made products is Seeley International (Seeley), the country’s largest and most coveted air conditioning manufacturer.
Today, Seeley manufactures more than 80,000 products and 1.5 million components in Australia every year, sold through more than 300 independent dealerships and a worldwide network of distributors.
“We are in the process of bringing manufacturing from overseas, not only for ourselves, but also for other manufacturers, wholesalers, retailers and end users,” reveals Executive Chairman, Frank Seeley, who founded the company just over 50 years ago in 1972.
“We are very vertically integrated, making many of our own motors and virtually all of our injection moulded plastic products, components and filter materials.”
Frank is a joint shareholder in the business along with his wife, Kathy, whose role has been instrumental to the longevity and success of Seeley and its Australian cooling and heating products.
“My wife’s part in this business is critical. She has always supported the company and believed (even more than I did!) in my capability. Without her, I simply could not have done it,” he smiles.
Techtop Australia Pty Ltd, founded by well-respected Directors, Rohan Pollard and Jeff Aird, entered a joint-venture partnership in 2013 with Shanghai Top Motor Co, the largest manufacturer of aluminium electric motors in China. From humble beginnings back in 2013, Techtop Australia has grown substantially to become a significant player in the electric motor market. At the start of this business venture the path was not easy, with three employees based in a small warehouse in Rowville, Victoria, Australia. Managing Director, Rohan Pollard commented, “we had a passion to succeed, we were a jack of all trades when we started, and we attended to every aspect of the business from processing orders to packing motors for customers. On occasions we would make pallets to save money and work weekends to make sure customers’ demands were met.”
Techtop Australia’s philosophy was quite simple: provide quality products along with outstanding customer service, and go the extra mile for the customer. The first couple of years were a struggle, recalls Sales Director, Jeff Aird. “Building an unknown brand in a fickle Australian market was a huge challenge, but we could see our customer base growing at a solid rate, which gave us the drive to keep moving forward.”
In July 2014, we opened our Queensland facility with a staff of three people, doubling the workforce of Techtop Australia. It was a bold move at the time, but one that has provided great results. We followed this by opening our NSW branch in January 2016, and by July 2017
we had also established offices in both South and Western Australia, as we were becoming a national company.
During this period back in 2015, Jack Gringlas AOM joined the board of Techtop Australia as Chairman. The board comprising these three directors has knowledge of the Australian electric motor market spanning back over more than 40 years.
In addition to electric motors, Techtop Australia is proud to be the exclusive distributor of Varvel gearboxes, Motortronics soft starters and Techtop variable speed drives.
The combination of a leading motor manufacturer and Australia’s most experienced sales team provides our customers with quality products, excellent service and technical knowledge.
Techtop Australia forms part of a global organisation with Techtop’s leading partners in America, Canada, Europe and the UAE.
Techtop’s revenue shows an average growth over the past eight years of 47 percent per annum. This growth could not happen without great suppliers, our competent staff and of course our customers.
Our market strategy from the beginning was to focus on the HVAC industry, one that we knew well, and our products were a perfect fit for the industry.
Since 2016 we began supplying to Seeley International, a partnership that becomes stronger every year. We acknowledge and thank Seeley International for being part of our journey.
Despite the rising popularity of goods manufactured in Australia, Seeley nevertheless plans to build its own manufacturing facility in the US, as well as multiple smaller sites across the globe to speed up production.
Set to happen over the next three years, this will subsequently expand the business in Australia as a number of proprietary sub-assemblies are supplied to other plants.
“We’re already doing some manufacturing in the US, but that is going to increase significantly in the future,” Frank informs us.
Employing more than 500 people in Australia and overseas, Seeley dominates the Australian evaporative cooler and ducted gas heating market and is a world leader in state of the art cooling products which, in many instances, can fully replace refrigerated air conditioning with power savings of up to 80 percent.
It’s therefore no surprise that high quality air conditioners made by Seeley with Australian materials are also exported around the world, to destinations such as Europe, the UK, the Middle East, and the US.
In 2018, the company successfully completed the world’s largest order for evaporative air conditioners, resulting in around 50,000 of Seeley’s Australian made Breezair conditioners being installed in the tent city of Mina Valley, Saudi Arabia.
Evaporative air conditioners, as the name suggests, use the principles of evaporation to help cool the air. As hot and dry outside air is pumped through water-soaked cooling pads, the water evaporates and the heat in the air is absorbed, which lowers the temperature.
The bulk order provided state of the art cooling for Mecca pilgrims during their stay in the tent city, a fascinating logistical exercise involving more than 100,000 tents and houses for
BREEZAIR – Advanced technology for fixed evaporative cooling for the entire home, and the quietest running and most energy-efficient evaporative cooler on the market.
BRAEMAR – The full series of high performing and world leading heating and cooling air conditioning solutions.
COOLAIR – A range of affordable, high performance fixed evaporative air conditioning for the whole home.
CLIMATE WIZARD – Patented indirect evaporative technology that covers an exceptionally large range of flexible configurations to provide for all commercial and industrial applications.
approximately three million people.
A three year tender evaluation process saw the Breezair brand and other contenders tested on site over several months, in all conditions and seasons, including comparative tests done during a pilgrimage to assess performance under real-world conditions.
The built-in safety mechanisms, economical use of water, ease of control and compact design were critical in Breezair being successfully selected.
“We were among 900 companies asked to quote, and we understand our products were actually the most expensive, however they were without question the most effective and long lasting,” acclaims Frank.
“Through our Saudi distributor, we got those messages across to the Ministry of Hajj. We started early and were able to supply all their needs over two years without adversely affecting any of our global customers, which was a remarkable feat!”
“WE’VE BEEN WORKING ON CLIMATE WIZARD TO MAKE IT BETTER AND BETTER FOR OVER 20 YEARS, AND I BELIEVE IN ANOTHER 20 YEARS’ TIME WE WILL STILL BE IMPROVING IT”
– FRANK SEELEY, EXECUTIVE CHAIRMAN, SEELEY INTERNATIONAL
SECURED SUPPLY CHAIN. ENHANCED QUALITY. DEVELOP AND MANUFACTURE AT KEY.
Since 1951 Key has been providing innovative and cost-effective solutions to an Australian and global customer base. From sourcing raw materials, to designing, developing, and manufacturing, Key can bring ideas and products to life.
Learn more Contact us
KTI operates a significant fleet of company-owned vehicles and, in conjunction with well trusted and experienced sub-contractors, has a proud history of efficient, reliable and cost effective linehaul distribution.
www.kti.net.au
Built to withstand Australia’s hot and dry climate, Breezair is one of four brands under which Seeley’s products are sold, along with Braemar, Coolair, and Climate Wizard - the latter of which offers ground-breaking new technology throughout its wide range of models within its series of indirect evaporative air conditioning products.
Climate Wizard’s patented indirect evaporative technology delivers unparalleled levels of cooling, and
FRANK SEELEY, EXECUTIVE CHAIRMAN: “Our employees recently donated to the victims of the earthquake in Turkey and Syria.
“They donated AUD$7,500, which we matched from our charitable fund. Prior to this, they did something very similar in relation to the Ukraine crisis.
“We also have two charitable funds from which we distribute monies to various worthwhile causes that benefit the poor, hungry, sick and destitute in Australia and many countries around the world.”
has now been successfully adopted worldwide.
The technology uses a heat exchange core that provides hyperefficient cooling, generating fresh air at temperatures that can rival, or even surpass the performance of refrigerated systems which in many situations can provide 80 percent lower energy costs.
“We’ve been working on Climate Wizard to make it better and better for over 20 years, and I believe in
another 20 years’ time we will still be improving it,” Frank affirms.
“There is nothing else in the world to compare it with, and we intend to continue its development and protect every new breakthrough that we make along the way.”
At the forefront of developing ingenious, energy-efficient cooling and heating products, Climate Wizard demonstrates Seeley’s mantra – the need to innovate, automate, and accelerate like there’s no tomorrow.
“We’ve been doing these things for much of our 50 years in manufacturing, and I hope we’ll always be doing them because we know that the day we stop, is the day we’ll start to die. Innovation is not a destination, it’s a journey – a never ending journey!”
There is naturally a strong focus on R&D at Seeley, to deliver on its vision of leading the world in creating
climate control solutions which continue to be highly innovative, of premium quality, and inspirational in the delivery of energy efficiency.
Frank is an innovator himself, and as Executive Chairman, he looks after Seeley’s special R&D group, Imagineering, which continues to work on “over-the-horizon” products which outperform the competition with newer technologies.
“We’re never short of projects and its these opportunities that keep me wanting to go to work every single day,” says Frank.
“Many of my targets and goals are centred around Imagineering, to provide ever-better and cheaper heating and cooling products in Australia and throughout the world for the greater good.”
Seeley celebrated its golden jubilee in 2022, a milestone moment marking 50 years of pioneering climate control products.
“On the face of it, 50 years is only a number, however for those who have travelled the distance it’s an incredible achievement,” Frank beams.
“So many of our people have been with us for so much of the journey, that I would not for a moment take the credit for us still being here. I want to acknowledge all the wonderful people who, over the past half a century, have contributed to making Seeley the vibrant company it still is today.”
With strong supplier relationships amassed over a number of years,
Seeley, from day one, was at pains to advise its suppliers upfront about anything out of the ordinary it would be requiring.
This modus operandi has characterised the company throughout its 50 year history and has continued to pay untold dividends.
For the next 50 years, Seeley remains committed to Australian designed, made and owned air conditioning products, world leading climate control solutions, and an ongoing relevance in an everchanging world.
From being the lone woman on the team to leading an AUD$27.5 billion forward programme, Julie Mitchell has always sought ways to do things differently and better in a constantly evolving world. As Deputy Director-General for Infrastructure Management and Delivery at the Queensland Department of Transport and Main Roads, Julie discusses the state of transport, the upcoming Brisbane 2032 Olympic and Paralympic Games and how the department is partnering with industry
Writer: Julie Mitchell, Deputy Director-General, Infrastructure Management and Delivery Project
Manager: Ryan GrayIf there’s one word that describes Queensland’s transport network – it’s multidimensional. From the sandy beaches in Cairns down to the Gold Coast, to the red earth of Childers and the wheat fields in Roma and the South West, this state covers an area nearly seven times the size of Great Britain.
While Queensland’s Department of Transport and Main Roads (TMR) is responsible for a very important backbone of 33,000 kilometres (km) of state-controlled roads, this is augmented by a variety of services
and physical infrastructure from policy to school crossing supervisors.
If you’re lucky enough to live in Queensland, you might be in the Torres Strait, where we regulate marine pilotage services to protect the world heritage listed Great Barrier Reef, or you may have travelled to the west of the state to see the Muttaburrasaurus Dinosaur on our freshly sealed very rural Cramsie –Muttaburra Road? Or maybe you’ll be taking your surfboard from Broadbeach to Burleigh Heads on the Gold Coast Light Rail Stage 3 (due for
completion in 2025).
If you’re into bike riding, it’s possible you’ve used one of TMR’s cycleways or rail trails that are connecting people to places and encouraging more Queenslanders to ride their bikes. Moreover, if you’re in Queensland, it’s highly likely you’ll interact with us face-to-face over your lifetime for a driver, marine, or dangerous goods licence.
Across this broad network, TMR provides the regulatory, policy, and planning framework that keeps Queensland moving and connected.
With a workforce of around 9,500 people, I’m in awe at the range of services we deliver that contribute to making Queensland a great place to live.
Every day I learn something more about the services and infrastructure we provide.
With less than 10 years to the opening of the Brisbane 2032 Olympic and Paralympic Games, I can tell you we’re making every day until 23rd July 2032 count! Like many Queenslanders, I hope to be there at the opening ceremonies for the Brisbane 2032 Olympic and Paralympic Games. Being one of the biggest and most watched sporting events worldwide, we’re very aware of the task ahead of us.
APAC OUTLOOK: AS A REGISTERED PROFESSIONAL ENGINEER AND FELLOW OF ENGINEERS AUSTRALIA, WHAT ADVANTAGES HAS THAT TECHNICAL BACKGROUND GIVEN YOU AS A TRANSPORT LEADER?
JULIE MITCHELL, DEPUTY DIRECTOR-GENERAL, INFRASTRUCTURE MANAGEMENT AND DELIVERY: “Being a registered professional engineer has taught me the importance of technical capability in planning, design, and decision-making. In an engineering focused workplace, it has given me the credibility needed for positions I’ve held and has helped me to know what questions to ask; it’s honed my thinking and ability to evaluate risk and has taught me to actively listen, seek clarity, and enhanced my understanding.
“I’ve always valued continuous and life-long learning and how it brings value to the practical, on-the-job learnings I’ve accumulated in my career. I’ve completed a Master of Business Administration and a Master of Environmental Management in Sustainable Development and have found these both to be useful in how they have added a more strategic perspective to my approach, allowing me to identify, focus on, and explore opportunities and synergies.
“My commitment to continuous learning and my ability to be flexible has greatly benefitted me as has my respect for all professionals, valuing their input and what they bring. I’ve also encouraged the teams I’ve led to do what I have done; to look for ways to do things better and to embrace new things, to try something new and to take risks.”
However, it’s not the first significant sporting event we’ve held. Queensland had a ‘practice run’ with the Gold Coast 2018 Commonwealth Games (GC2018) but there are a couple of things that are different for 2032. Firstly, the size of the combined Brisbane 2032 Olympic and Paralympic Games are 7.5 times bigger than they were; the Paralympics alone will be bigger than GC2018.
Secondly, the duration means prolonged and significant network disruption with 30 days of competition, training and roll down, and then two weeks between the events, totalling nine weeks. We have to make sure we keep the state moving as well as deliver the games and lasting benefits.
An eye-catching mural on grain silos in Thallon, South West Queensland. Source: TMR. © The State of Queensland.This means we’re already thinking about how we provide a positive legacy. The games are a catalyst to bring forward investment to deliver great benefits, such as fully accessible transport facilities and services and a commitment to quality walking and cycling connections to venues and major public transport hubs.
Given everything we’ve experienced over the last five years, from COVID-19 to bushfires to floods, our longer-term vision is definitely agile. Queensland is unique as two thirds of the state’s population live in South East Queensland, where an additional growth of two million people is forecast in the next 20 years. Unexpectedly, our population base grew during COVID-19 as we were a destination of choice.
The delivery of region-shaping infrastructure like Cross River Rail can be pivotal in shifting people to more sustainable travel modes, supporting more consolidated development, and allow for high-frequency, highcapacity links. Active transport has also increased and has a role to play in connecting people with places locally, supporting healthy and active lifestyles, and creating liveable and accessible communities in both metro and regional areas.
Rail will be the backbone of the South East’s transport network; it’s the heavy lifter for passenger movement and the cornerstone of TMR’s vision for the future. We expect more people will travel to work in Brisbane’s central business district (CBD) by rail than by any other mode and when Cross River Rail opens in 2026, further opportunities will be fully realised regarding capacity improvements.
In regional and remote areas, challenges include distance, flooding, resilience, and access to affordable transport services. Safety and connectivity are critical for the community and economy whether
moving freight more efficiently or developing tourism, and ensuring the community has access to essential services like health, education, and employment.
As for over the horizon planning, I’m reminded of a futurist who said ‘look to the sky’ when prompted about the next generation of transport
vehicles. Recently, there’s been a lot of discussion about electric autonomous vertical take-off and landing (VTOL) drones. We’re making sure we monitor this front of the innovation wave.
I didn’t expect to be dealing with passenger VTOL drones during my
Cramsie-Muttaburra Road before (above) and during sealing (below), keeping Central West Queensland communities connected. Source: TMR. © The State of Queensland. Looking south down the Gold Coast Highway from Southport towards the Gold Coast, with the light rail in view.The Waste Recycling Industry of Queensland (WRIQ) is the unified voice of waste management, recycling and materials recovery. Representing more than 90 Queensland-based operators, WRIQ engages in state-specific issues of strategic importance to achieve successful economic, social and environmental outcomes.
Infrastructure is currently enabling around 70 percent of Australia’s emissions through its construction, operation and maintenance, and use. Significant emission reductions can be achieved through the infrastructure planning and decisionmaking stages and the application of principles around resource efficiency, lifecycle assessment and the circular economy; to inform infrastructure design, and materials and technology selection.
A circular economy values resources by keeping products and materials in use for as long as possible. Queensland is increasing its use of recycled materials in road construction and resurfacing works.
Using recycled materials has the potential to deliver significant benefits including cost savings, reducing waste to landfill, protecting the environment through the reduced consumption of virgin materials, reducing greenhouse gas emissions generated by the production of new materials, as well as improving network performance.
WRIQ members are providing safe, reliable and high-quality recycled and recovered products for Queensland’s essential road infrastructure including recycled glass aggregate, crumbed rubber, reclaimed asphalt pavement material, plastics, soils, and construction and demolition waste (concrete and brick). These recovered products meet all relevant technical guidelines and material specifications.
Investment is continuing into further research to understand the opportunities for incorporating more recycled content into road infrastructure.
For more information on WRIQ and its members go to www.wriq.com.au or contact memberservices@wriq.com.au
If you would like us to bring your digital story to life with passion and purpose, visit www.outlookcs.com or email hello@outlookcs.com
The Outlook Creative Services Division provides a complete web design, build and delivery service that leverages the expertise of our in-house production team. Complementing Outlook Publishing’s portfolio of esteemed global publications, our specialist skills cater to clients around the world with a fully bespoke service.
career, so innovation in the transport industry has kept us all on our toes. Innovation plays a key role in everything we do at TMR. I’ve been an innovation champion for more than seven years now and doing things differently and better is embedded into our ethos. We need to keep innovating to stay relevant in a world that is constantly evolving.
It’s not just autonomous and connected vehicles, low carbon fuelled vehicles and drones we have our innovation lens focused on; it’s also the opportunities presented by data and data analytics. The challenges we face as a transport agency are broad; we need to be across issues as diverse as the ethics of data collection and storage.
TMR’s now working to lay the technical foundations for the next generation of smart transport infrastructure. We’re investing to prepare Queensland for connected and automated vehicles and have progressed a large scale detailed technical project and pilot trial of autonomous and connected vehicles at Ipswich.
TMR’s also progressing a roadmap for the development of traffic management systems to ‘guide’ autonomous vehicles and be fully adaptive to the current real time, on road situation. These innovations mean the future of transport is
exciting – very exciting – and the challenges and opportunities associated with emerging transport technologies are far reaching.
When I started my career as a graduate engineer with TMR over 35 years ago I certainly didn’t think I would have oversight of AUD$55 billion of transport assets with a maintenance budget alone of more than AUD$5 billion. Added to these numbers is the responsibility of leading a team of around 3,300 people who support its delivery. Pursuing a graduate position with
TMR was a purposeful move; I saw major benefits working for a large state-wide organisation that could offer me the ability to change jobs and gain experience but not have to change agencies. I knew I needed to push my boundaries and take opportunities as they arose.
A pivotal point in my career was when I was Manager of Transport Planning in the Metropolitan Region (Greater Brisbane) from 2005 for around two and a half years and absolutely loved it. It was a culmination of my earlier career experience, and I led a team of more than 100 people at a time when Brisbane was booming
– land development and transport demands were increasing, and the first South East Queensland regional plan and infrastructure programme had been released. We accomplished some unbelievable achievements and although I went on to lead bigger teams, this is one I will always proudly remember because of the amazing ‘flow’ in our combined efforts.
I was Chief Engineer for eight years which is the highest-level engineering position in TMR and meant leading and managing the Engineering
“TMR PROVIDES THE REGULATORY, POLICY, AND PLANNING FRAMEWORK THAT KEEPS QUEENSLAND MOVING AND CONNECTED. WITH A WORKFORCE OF AROUND 9,500 PEOPLE, I’M IN AWE AT THE RANGE OF SERVICES WE DELIVER THAT CONTRIBUTE TO MAKING QUEENSLAND A GREAT PLACE TO LIVE”
– JULIE MITCHELL, DEPUTY DIRECTOR-GENERAL, INFRASTRUCTURE MANAGEMENT AND DELIVERY, TMRand Technology Division with 340 professional, technical and support staff in specialist areas. This was the first time I was in a role that had an organisation-wide impact and influence and positioned me well for my role as Deputy Director-General.
Inevitably, my success and ability to ‘grow my own career’ can be attributed to a few things. All positions should be seen as opportunities; they’re key to staying relevant. If you want an opportunity, ask for it! I’ve learned resilience is not only bouncing back from setbacks but is a defining quality. Be curious, ask questions, and have personal clarity
about your goals. Who knows where it will lead you; I’ve overshot my original leadership aspirations by a few levels and learned so much on the journey.
We acknowledge there’s an industry issue in attracting more female talent and we must look at engineering as a whole. It’s still seen as a male domain; this reduces the number of women who choose to study engineering and STEM-related subjects. There’s so much research that supports diverse teams as being high performance teams.
The reality is there’s a disproportionate number of women in engineering and in TMR only 16 percent of our engineers are women (the national average is only 13 percent) so we still have a long way to go. We’re active in how we’re addressing gender diversity in engineering. TMR is formally committed through initiatives
Connecting remote communitiesMusgrave to Red Blanket (Part A) on the Peninsula Developmental Road part of the Cape York Region Package. Source: TMR. © The State of Queensland. Cross River Rail construction site at Woolloongabba as seen from the South East Arterial Road (Pacific Motorway). Source: TMR. © The State of Queensland.such as the Women in Engineering programme participation in the Engineers Australia STEM roundtable, the Engineering Link Group sponsorship to reach high school and tertiary female students to show a career path in STEM, and the Constructionarium Australia (Queensland), particularly the allfemale builds they undertake.
As a woman who has based and ultimately spent her career committed to engineering and transport in Queensland, I’m passionate about leaving a better industry than the one I entered, both now and into the future.
Like other jurisdictions and sectors, we continue to face challenges as our operating environment and community expectations change, and the sector evolves to meet both.
A key challenge is affordability –hyper escalation and cost increases lead to project re-scoping often resulting in deferral or the need to seek additional funding adding to project delays and potential price increases.
There’s also industry capacity to meet demand, where shortages of technical and delivery skills will continue to be a challenge and potentially put multi-billion-dollar projects at risk. There is potential for
this area to be unlocked longer-term with the increased uptake of STEMrelated careers by women that would significantly increase the talent pool and create greater diversity.
In saying this, there’s a lack of key professionals like Geotechnical engineers and experienced project managers and directors that come to mind, as well as the reality we’re facing of generational loss of lived experience (due to retirement) leaving us low on practical, proven experience and shared learnings creating a higher probability of
repeating previous mistakes. This is front of mind in our management meetings.
Sustainability is also a challenge and one that TMR takes very seriously. We are committed to minimising impacts on the natural environment, reducing carbon emissions, and building increased network resilience to climate change.
Queensland is a particularly climate-affected state; paradoxically it’s becoming hotter and dryer (and prone to bushfire) and intense rain events are happening more frequently. These events have affected shipping, range crossings, inland and coastal areas, and recently (March 2023) North West Queensland was significantly impacted by monsoonal flooding. We have to respond and reconnect essential access to services and markets as soon as possible and need infrastructure solutions that are not only cost effective but smart, to increase resilience to deal with these challenges.
I believe true collaboration is essential to delivering excellent outcomes.
Our industry partners continue to play a crucial role in our success and to be a preferred customer in the market has seen us move toward a more collaborative model in procurement, contracts, delivery, and culture.
Drones are being used for the inspection of infrastructure such as street light brackets on Bribie Island Bridge. Source: TMR. © The State of Queensland. The Queensland Electric Super Highway is part of TMR’s plan for the future. Here, an electric vehicle is at a charging site in Cooroy. Source: TMR. © The State of Queensland. TMR has highly skilled, diverse, and dynamic teams led by women. Source: TMR. © The State of Queensland.This is vital if we’re to continue to successfully deliver our transport infrastructure programme for Queensland. Our pipeline of construction and maintenance work from 2022–23 to 2025–26, outlines AUD$29.7 billion of investment estimated to support around 25,200 jobs.
Procurement of infrastructure has also changed; it’s historically been about employment but now our spend is a key platform to facilitate and realise social, economic, and environmental outcomes. Previously based on price, it’s now value for money that’s our focus, delivering infrastructure for the right price, not necessarily the cheapest price. It’s about what we’re getting for our investment that brings broader social and government policy outcomes, including an increase in local, small, and medium enterprise, and Indigenous business procurement spend.
COVID-19 highlighted our vulnerability and reliance on offshore supply chains for what was once available onshore. In response, we’re looking to create more resilient supply chains, investing in local manufacturing capability, and activating local supply markets of all shapes and sizes. We’ve jointly committed to demonstrated behaviours across all levels of the supply chain, including effective and visible leadership, joint ownership of outcomes, staying solutions-focused
and able to compromise, celebrating collaboration successes, and jointly pursuing technological advancements and opportunities for improvement using advancement in data.
Importantly, we’re also focused on engagement with communities and stakeholders, working with them to ensure there’s opportunities to have their say on projects that impact them both now and in the future.
The best way forward is one where we travel in the same direction, together.
www.tmr.qld.gov.au
Stemming from a bold vision to create a company with a unique and inclusive culture, Senversa attracts and retains the highest quality professionals over a broad range of disciplines. Michael Charge, Environmental Auditor and CEO recounts the recipe for success
The environmental, engineering and sustainability professional services industries in Australia and the broader APAC region currently sit at the nexus of significant market tailwinds, cruising serenely towards an optimistic future.
These services are currently experiencing remarkable growth due to several boosting market factors, such as increasing investment in infrastructure, an updated regulatory environment, and the embedding of environmental, social and governance (ESG) as a key metric of corporate performance.
There is also a rapid focus on energy
transition across all states in Australia and the region as a whole. This ambitious transition involves moving towards more sustainable means of transportation, storage and renewable energy sources, such as wind and solar. More recently, Australia is also seeing major investments in other alternative sources such as hydrogen, pumped hydro and battery storage.
Resplendently riding this wave of positivity throughout the industry is Senversa, an Australian-based environmental, sustainability, and engineering consultancy that was founded in 2009.
Starting out from a small office in Melbourne, the company now operates nationally with additional offices located in Geelong, Newcastle, Sydney, Adelaide, and Perth with over 150 staff.
“Our key premise for growth has been twofold: to create high levels of staff satisfaction and engagement, and to focus on client relationships and delivery,” sets out Michael Charge, Environmental Auditor and CEO of Senversa.
A DIVERSE SERVICE FOR ALL Senversa’s professionals are highly qualified and span a broad range
Writer: Ed Budds | Project Manager: Jordan Leveyof disciplines, which gives the collective team the ability to provide advice across a full spectrum of environmental, sustainability, and engineering services, as well as forming multidisciplinary teams to deliver focused solutions for its clients.
This extensive array of services includes approvals and environmental management, contaminated land, geotechnical engineering, civil/ environmental engineering services, digital products and services, and sustainability services.
“At our core, we thrive on providing great service to our clients who may
be facing challenging problems, whether that’s helping to solve complex operational issues or bringing together a multidisciplinary team to secure the right approvals, managing contaminated land risks, offering innovative approaches to waste management, or converting large amounts of data into valuable insights using emerging technologies and advanced analytics,” Charge tells us.
Senversa routinely undertakes strategic advisory projects across a diversified array of markets and clients, be it energy, infrastructure, waste, property, government, or
resources and mining. This has recently meant key roles on some of Australia’s most significant energy transformation and infrastructure projects, including the environmental and geotechnical investigations for Melbourne Airport’s Third Runway project (subject to government approval).
Recently, the company took some time to define what makes Senversa stand out, and subsequently identified six key factors that define the ‘Senversa Difference’: quality, delivery, partnering, striving to be the best place to work, innovation and ESG leadership.
VISION
• To be the most fulfilling workplace for quality environmental, sustainability and engineering professionals to make a positive impact
STRUCTURE OF THE FIRM
• Shareholders agreement
• Commitment to broad employee ownership
FOUNDING CULTURES
• Teaming and inclusiveness
• High quality professionals
• Great place to work
• Focus on client relationships and delivery
• Transparent, collaborative and supportive workplace
However, there remain some headwinds that businesses like Senversa continue to watch carefully with one eye trained on the horizon, particularly elements of continued economic uncertainty, the current inflationary environment and challenges around access to people.
“The industry is highly competitive, and Australia remains an attractive market for global competition, so we need to continually innovate to stay ahead of the curve.”
As a proudly employee-owned company, Senversa’s cultural values are focused on creating an exceptional working environment, fostering professional development, supporting diversity and promoting a sense of shared purpose among its staff. Employee ownership also brings a sense of challenge to contribute to the success of the company, motivating staff to compete
with big brands in the industry.
“The decision to become a 100 percent employee-owned firm was built in response to it being the best vehicle to deliver our vision and values. We wanted our firm to be around for the long term, and we wanted our staff to have a say in running the show,” Charge explains.
Starting from scratch with a clear vision and set of values allowed Senversa to communicate its approach to any new employees and shareholders.
“One unique aspect of our shared ownership model is that we actively support broad ownership, offering shareholding to less experienced staff, which is not common practice in many other employee-owned firms,” he continues.
The company’s management and board are actively engaged in the shared ownership structure to ensure transparency and
fairness.
Being a 100 percent employeeowned firm has many advantages, such as aligning the interests of the employees with those of the company, creating a strong sense of loyalty and shared purpose, and providing a stable and secure future for Senversa’s employees.
“Overall, the benefits of broadbased employee ownership far outweigh the challenges, and we believe that a clear and transparent process for share acquisition is a key factor in our success as a company,” affirms Charge.
Nowadays, companies are expected to be more accountable for their environmental and social impact, and there is a growing trend towards adopting circular economy principles to minimise waste and maximise the efficient use of resources.
Australia has also been seeing a period of updated regulatory drivers, be it policies and regulations to encourage the transition to sustainable energy sources and reduce greenhouse gas emissions, or around clarifying the roles and responsibilities when it comes to protecting the environment or the nation’s heritage.
Deeply committed to sustainability and environmental responsibility, Senversa understands that these principles are critical to its success and to the well-being of the planet. In this way, the company takes a comprehensive approach to advancing the principles of the United Nations Sustainable Development Goals (SDGs), embedded across most of its business operations.
“Our commitment to sustainability is reflected in all aspects of our business. From minimising environmental risks through sustainable practices and
technologies to achieving net zero carbon emissions, we strive to meet the expectations of our clients, the community and the environment at large,” details Charge.
Recognising that the climate crisis is an urgent issue, as a business, Senversa is Climate Active certified and committed to carbon neutrality.
Where the company has residual emissions that must be offset, it seeks local projects that also encourage co-benefits for the community and environment in which Senversa works.
As a professional services firm, the decision has been taken to scrutinise all aspects of the supply chain in this
– MICHAEL CHARGE, ENVIRONMENTALprocess, and Senversa constantly attempts to identify, assess, minimise and offset any residual emissions. Most importantly, however, the company itself is setting an example that it can use to help its clients along a similar journey of sustainability. This ongoing commitment to
sustainability goes beyond the environment, as making a positive impact is intrinsically linked to the purpose of Senversa and enshrined in its constitution.
“We believe that conducting business in a sustainable and responsible way is not only the
“ THE DECISION TO BECOME A 100 PERCENT EMPLOYEE-OWNED FIRM WAS BUILT IN RESPONSE TO IT BEING THE BEST VEHICLE TO DELIVER OUR VISION AND VALUES”
AUDITOR AND CEO, SENVERSA
right thing to do, but also critical to our operational success. Our commitments to ESG, our employees and our values and priorities are central to our operations, and we will continue to work towards creating a more sustainable future,” Charge acclaims.
At Senversa, the company is focused entirely on delivering its strategic and cultural aims.
The centre of this focus is to continue building its national presence by supporting and investing in Senversa’s growing teams, expanding strategically while keeping a close eye on managing risks.
“We’re also dedicated to integrating
technology and digital solutions across our entire business to optimise our project delivery and enhance client outcomes,” Charge adds.
Maintaining financial performance is a further priority for Senversa, as securing this will enable continual investment in the business, people, and providing premium services to its clients.
“As we continue to grow, we remain committed to maintaining and enhancing our positive culture, which is central to our vision and strategic objectives. Our goal is to foster an open, collaborative, and engaging work environment where our people feel empowered to reach their full potential,” he enthuses.
Lastly, the sustainability framework is a key part of who Senversa is as a
company, remaining fully committed to delivering positive impacts to its employees, shareholders, stakeholders and the environment.
“Whilst the company has succeeded in sustainable growth over the past decade, most importantly we have stayed true to our original vision, culture and values.”
As the world’s second largest island state, Papua New Guinea’s digital connection is growing under the guidance and determination of PNG DataCo Limited
Writer: Rachel Carr | Project Manager: Josh Hyland
Back in 1997, the ‘information superhighway’ arrived in Papua New Guinea (PNG). The new internet technology was launched by the sole carrier of communications traffic - Papua New Guinea Post and Telikom.
Today, the telecommunication sector is connecting the Pacific Island country at a steady rate. Around 25 percent of its population now has access to the internet, which is improving with the installation of the Coral Sea Cable System, the cable that links the Soloman Islands and Australia, landing at Sydney.
Key developments are continually and routinely underway, with the PIPE Pacific Cable upgraded from eight terabytes (TBs) to 12 TBs in recent
years, and the Get Connected training roll out which has boosted digital transformation.
The future of business and connection in PNG relies on information and communication technology (ICT). Recognising this critical need, PNG DataCo Limited (DataCo) is changing network opportunities one district at a time.
Created in 2014, DataCo is a stateowned entity, along with Bmobile and Telikom, providing wholesale services to the ICT industry, and mandated to build, own and operate the National Transmission Network (NTN).
Headquartered in the nation’s capital of Port Moresby, and with an aim to drive connectivity and digital solutions, DataCo provides internet
access with two data centres and is the only company with a data centre categorised as Tier 3.
With an international connection to point-of-presence (POP) in Australia, Guam, and the US, and redundant international links to Australia and Asia, the internet is primarily sourced from upstream providers through its three POPs in Sydney.
The company also manages 7,000 kilometres (km) of fibre optic network, comprising both terrestrial and submarine cables with the three international POPs, five internet gateway nodes, 15 submarine cable landing stations and 14 dense wavelength-division multiplexing (DWDM) POPs across 20 provinces.
‘COMPANY TRUSTWORTHINESS AND SERVICE RELIABILITY ARE OUR MAIN PRINCIPLES FOR CONSUMER LOYALTY’ – PNG DATACO LIMITED
The DataCo vision is to improve and expand the availability of affordable internet access to all people of PNG, by partnering with the government and surrounding communities. It ensures the company is a responsible entity championing safe and sustainable development.
• Connect my District Initiativeparamount to its core values is connecting PNG to the digital world and driving development and growth.
• Environment Safety - ensuring that local communities benefit from services in a way that the environment is safe.
• New Triplex Units - were handed over by DataCo as part of its community social responsibility initiative.
ICT has transformed the economic and social landscape of PNG in recent years. DataCo not only internally connects PNG, but it also connects the country to the world by providing core network redundancy paths through fibre loop and satellite, improving capacity and reliability, and reducing the cost of internet and data services.
DataCo operates the country’s biggest and only satellite infrastructure providing a combination of direct backbone services, redundancy and diversity services and very small aperture terminal (VSAT) hub services.
Operating an open architecture enables DataCo to provide ubiquitous connectivity supporting Broadband and point-to-point (P2P) to facilitate data, voice and video.
There are currently two internet gateways in PNG, Madang on international cables PPC-1 and Port Moresby on CS2 to Sydney, each connecting to Global Switch for PPC-1 and Paddington for CS2. Both
are managed by DataCo, although ownership is with Pipe Networks and Coral Sea Cable Company respectively.
The third internet gateway is through the O3b satellite system to Dubbo, Sydney, with a fourth gateway for Asia which will exit through Jayapura, Indonesia.
With a USD$50 million revenue growing by 18 percent year on year, and an increasing demand and capacity for digital services, the company is undergoing an evolution, and developing digital infrastructure accordingly.
The recently launched cloud technology, the implementation of the second phase of the new domestic subsea cable installation and increasing capacity on the existing cables collectively showcase the expansion of the fibre network across PNG.
Looking ahead, DataCo is expanding the fibre networking by 10,000 kilometres (km), along with building an international POP in Indonesia. The improvements are taking place with DataCo’s 110-strong
‘WE
HARD TO ENSURE A QUALITY AND SEAMLESS NETWORK EXPERIENCE FOR CUSTOMERS’
With Sunrise, we become your exclusive personal broker.
Our goal is to provide you with a personal attention to all of your needs including all lines of insurance coverage, regular reviews and a timely response in the event of a loss or claim.
We offer a full line of quality products to protect your assets, your families and your businesses financial security.
Sunrise Assurance Brokers Ltd are the existing Insurance Brokers for PNG Dataco Ltd and that Niugini Assurance Group insures two of PNG Dataco’s major policies through Sunrise Assurance Brokers.
Sunrise can offer a wide variety of insurance products and services. These products include but are not limited to: Industry Special Risks, Burglary, Business Interruption-Loss of Profits, Electronic Equipment, Construction Insurance, Corporste Travel, Fire & Perils, General Property, Glass, Goods in Transit, Machinery Breakdown, Money, Motor Vehicle Insurance, Mortgage Protection, Public Liability, Directors and Officers,
Employment Practices, Management Liability, Personal Accident, Products Recall, Professional Indemnity, Tax Probe, Workers Compensation, Cyber Risks, Householders, Landlords, Marine, Motor Vehicle, Medical, Life, Personal Accident, and Disability.
On a regular basis, we offer to meet with our clients and do an in-depth review of their insurance needs.
We do this to make sure you are getting the best protection you need at the best value possible. Call into one of our agents nationwide including FinCorp branches in:
- Port Moresby
- Goroka
- Mt Hagen
- Lae
- Kopoko
We all need insurance! Let us help you get covered. We will service all your insurance needs. Let us look after you, because no one else will do it better.
workforce, soon growing to 130 employees.
As the company is building data centres to connect the highlands of PNG, the digital divide is closing. Remote and rural areas have previously had poor connectivity due to the lack of infrastructure and difficult terrain, meaning limited access to technology for the population of the region.
However, DataCo is set to change the situation by implementing the second phase of new a domestic subsea cable installation.
One of the solutions that DataCo offers is a cloud-based, holistic service which encompasses the management of virtual machines, cloud services and resources. By DataCo’s very own definition of a virtual data centre, it is a one-stop-shop which caters to governmental needs and large enterprises on storage, optional services, security, dedicated connectivity, and disaster recovery.
Moreover, by providing cloud solutions and data centres, DataCo connects all major towns with sub-sea and land-based fibre optic cables.
The DataCo one-stop shop includes a P2P network which is an end-to-end channel carried through DataCo IP Managed Systems with the following suite of technology platforms, MPLS L2 and L3, VPLS, VXLAN< and Metro L2 connectivity.
Together with an International Ethernet Private Lease (IEPL), which can be useful for machine-to-machine connectivity, centre connectivity, offshore cloud solutions, offshore data and the extension of LAN data and voice traffic, it interconnects two offices, geographically located in different countries.
Whereas, the Secured Cloud Services include cloud storage, collaboration tools, and communication platforms which are designed with enterprise-grade security features to keep valuable data safe while using platforms and applications. Using cloud infrastructure drastically reduces capital expenditure (Capex) costs, and organisations that adopt cloud solutions find many benefits which will positively impact their business. Therefore, DataCo offers the full service to complement and emphasise its ‘Yes, you’ll be covered’ motto.
DataCo’s culture has trust as its core value, with a team in place to drive its success with teamwork as part of the company’s environment, alongside equal opportunities, empowerment and accountability. With a focus on customer and business outcomes, the vision is to improve and expand the availability of affordable internet access to the people of PNG by developing the NTN. DataCo’s mission is to develop the NTN as an efficient domestic and international telecommunication transmission network for PNG.
NTN will be available on a wholesale and non-discriminatory basis to all licenced industry operators to stimulate and foster social and economic development in PNG, and as a member of the Asia Pacific Network Information Centre (APNIC), DataCo is a trusted source for cloud services
The DataCo Secure Cloud supports ICT transformation strategy in a one cloud architecture with an enterprise-to-enterprise (E2E) solution, consequently, accelerating business innovation with full stack cloud services, ideal for companies with growing or fluctuating bandwidth demands.
Submarine fibre-optic cables are PNG’s primary international communications link, operators and internet service providers continue to use the support of satellite technology in rural areas, where development has previously been hindered by many factors, including the high cost of operating in difficult terrain.
With the government partnering with DataCo, PNG’s connection to the digital world is set to develop and grow in many ways by providing affordable ICT to the country’s education and health services alongside its business sectors.
Our company culture is founded on a commitment to continually improve and monitor the professionalism of our employees and systems. With a strong management team, and an experienced and motivated workforce, MME Wantok Ltd delivers telecommunication services for private and commercial customers. We have the capacity to undertake jobs from start to finish and provide an integrated service solutions for our customers.
Our services include:
- FIBER OPTIC HAULING – INTERNAL OR EXTERNAL (ARIEL OR UNDERGROUND);
- SPLICING SERVICES;
- RADIO INSTALLATION, MAINTENANCE AND MONITORING SERVICES;
- INSTALLATION OF POWER SYSTEM (DC/AC);
- ICT INSTALLATION AND MONITORING SERVICES;
- CONSTRUCTION OF GSM TOWERS;
- GENSET INSTALLATION AND REPAIR;
- POWER & INSTALLATION OF GENSETS & SERVICING;
- METAL FABRICATION, RIGGING & CABLING.
We boast a stable, qualified and highly experienced management team that is committed to customer and employee satisfaction. Our exposure to a broad range of telecommunication risks and solutions across the wide spectrum provides an extensive knowledge base which is utilised in formulating client specific but innovative, tailormade telecommunication solutions.
We will work closely with our clients to offer the right telecommunication solutions
www.mmewantoklimited.com
Phone: 675 74459455 / 675 75977299
Email: enquiries@mmelimited.com
Office Location: MME Wantok Limited, Murray Barracks- PNGDF HQ, Support Battalion, Supply Division Wards Road, Port Moresby, NCD, Papua New Guinea.5-7 September, 2023 | Sydney Showground, Sydney, Australia
AUSTRALIA’S LONGESTRUNNING mining event returns in September this year. Asia-Pacific’s International Mining Exhibition (AIMEX) 2023 is a destination for decision-makers, experts and suppliers determined to change the face of the mining industry through technology, collaboration and radical improvements in productivity and sustainability. With over local and international 250 exhibitors, AIMEX provides an unmatched opportunity to connect and do business with some of
the best mining suppliers from around the world. The event will also feature a free-to-attend conference, with themes including decarbonisation, technical innovation, and waste management. New at AIMEX are the Transformative Technology Pavilion, showcasing exponential technologies, such as augmented reality, virtual reality and data utilisation, and the Decarbonisation Zone, featuring smart and sustainable solutions that meet the sector’s environmental, social, and governance (ESG) obligations.
Date 5-7 September, 2023
Venue
Sydney Showground City & Country
Sydney, Australia Website aimex.com.au
Contact Email aimex@reedexhibitions.com.au
AIMEX is the destination for the mining sector to collaborate and hear from industry thought leaders. AIMEX provides an unmatched opportunity to connect and do business with some of the best mining suppliers from around the world, while sourcing solutions to boost productivity and meet sustainability goals. New at AIMEX this year are the Transformative Technology Pavilion and the Decarbonisation Zone.
6,000+ local and international suppliers
industry connections
250+ expert speakers
50+
9-11 May, 2023 | Adelaide, South Australia
JOIN US this May as we bring industry leaders, influencers, innovators and change makers to Adelaide for our world-leading mining innovation conference.
Held over three days, the event will encompass workshops, plenary sessions, Collaboration Laboratories, Meet the Miners™ and interactive breakout discussion groups. There will be plenty of networking throughout the conference, as well as the much-
anticipated Industry Leaders’ and Awards Dinner where we celebrate and recognise achievement of leading innovators in our sector.
With an expected 100+ exhibitors, Austmine 2023 will showcase the leading technologies, ground-breaking innovations and transformative solutions that are provided by the Australian METS sector.
In partnership with the South Australian Government, the Copper
Date 10-11 May, 2023
Venue
Adelaide Convention Centre
City & Country
Adelaide, South Australia
Website
austmineconference.com.au
Contact Email info@austmineconference.com.au
to the World Conference will be held in conjunction with Austmine 2023 bringing a spotlight on this key strategic mineral.
Showcasing leading technologies, ground-breaking innovations and transformative solutions set to change the future of mining, Austmine 2023 Conference & Exhibition features: 100+ Exhibitors | 1200+ Delegates | Plenery Sessions & Panels | Workshops & Networking | Collaboration Laboratories | METS Tech Talks | Meet the Miners | Industry Leaders’ Awards & Dinner | Plus more!
In partnership with the South Australian Government, Austmine is pleased to host the 2023 Copper to the World Conference. Established as a leading copper event globally, Copper to the World provides the latest insights and updates on a commodity that is essential to a sustainable future.
Principal Sponsor
“One of the most important parts of my role is people leadership. Since 2018, Hilton Foods has continued to implement and embed a companywide approach to succession and capability which supports the development of talent across the business regardless of gender or background. I am committed to people leadership and the journey of supporting our people to be the best they can be, whoever they are.”
Frank Seeley Executive Chairman, Seeley International“We do not discriminate against anyone. We employ people based on two criteria: character and work ethic. Whoever qualifies on those two measures is welcome, regardless of race, gender or creed.”
Jamie Bennett Managing Director, Berton Vineyards“To build a successful company, diversity in the workplace is crucial, especially when it comes to employee engagement. This is because
every team member—from upper management to the frontline staff — brings their own distinct backgrounds, experiences, and perspectives to the table, so workplace diversity fosters creativity and innovation. We need to create more inclusive workplace policies and educate managers about the advantages of diversity in the workplace in order to support this.”
“At PMDL, we don’t need to encourage diversity as it is simply accepted as the norm. Our endeavour to find the right fits for our practice - those with integrity that bring a broad range of experiences, skills, perspectives, and expertise - seamlessly and unassumingly builds diversity in our team. We are gender diverse but can also boast a diverse range of cultural and religious backgrounds amongst our team members, which directly aligns with the diverse range of cultural backgrounds our clients have.”
Robbie McGillivray Co-Founder, Taco Medic“Having a diverse and engaged team is one of our top priorities. We hire for passion and attitude first, to ensure we are fostering the right team culture with those team members that are positive and engaged in our brand. We also encourage them to express their personalities while at work as we are not trying to create robots who operate from scripts. Diversity and uniqueness are what assist us to create memorable experiences for our customers.”
Are you a CEO/Director with a company story to tell? Contact APAC Outlook now!
To round off each issue, we ask our contributing business leaders for their views on the same question