OSMOFLO
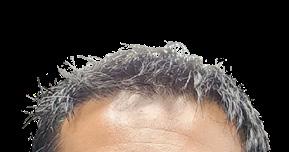
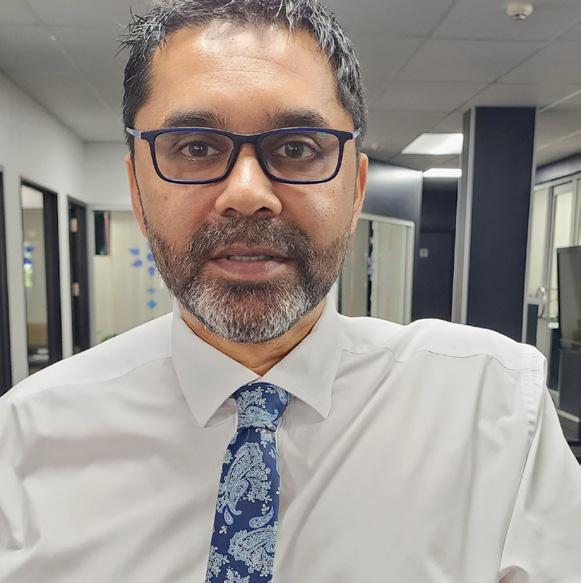
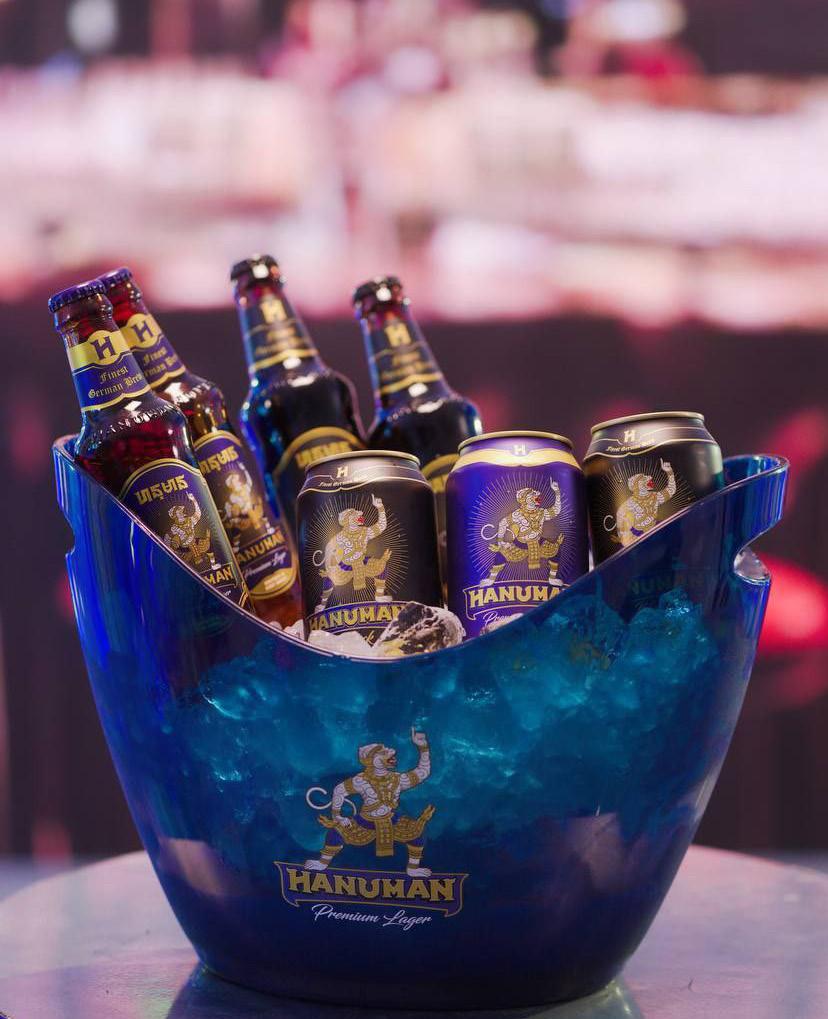
For over a decade, our portfolio of in-house magazines has been lovingly produced, printed, and distributed to our esteemed subscribers across the globe from our headquarters in the UK.
But now we are moving with the times, adopting a digital-first approach by producing online-only publications. A major factor in this decision is to minimise our environmental footprint, reducing the carbon emissions involved in the logistics of print magazine distribution and the resources required therein.
– Ben Weaver, CEO, Outlook Publishing Ltd
Going forward, we will provide print orders of any magazine in-line with the requests of our featured companies, subscribers, and conference & expo partners.
Please get in touch for a print-on-demand quote or visit our website to find out more.
Editorial Director: Phoebe Harper phoebe.harper@outlookpublishing.com
Senior Editor: Marcus Kääpä marcus.kaapa@outlookpublishing.com
Editor: Jack Salter jack.salter@outlookpublishing.com
Junior Editor: Ed Budds ed.budds@outlookpublishing.com
Junior Editor: Rachel Carr rachel.carr@outlookpublishing.com
PRODUCTION
Production Director: Stephen Giles steve.giles@outlookpublishing.com
Senior Designer: Devon Collins devon.collins@outlookpublishing.com
Designer: Matt Loudwell matt.loudwell@outlookpublishing.com
Junior Designer: Louisa Martin louisa.martin@outlookpublishing.com
Digital Marketing Manager: Fox Tucker fox.tucker@outlookpublishing.com
Social Media Executive: Bria Clarke bria.clarke@outlookpublishing.com
Production Assistant: Megan Cooke megan.cooke@outlookpublishing.com
BUSINESS
CEO: Ben Weaver ben.weaver@outlookpublishing.com
Managing Director: James Mitchell james.mitchell@outlookpublishing.com
Sales Director: Nick Norris nick.norris@outlookpublishing.com
Commercial Director: Joshua Mann joshua.mann@outlookpublishing.com
HEADS OF PROJECTS
Callam Waller callam.waller@outlookpublishing.com
Deane Anderton deane.anderton@outlookpublishing.com
Eddie Clinton eddie.clinton@outlookpublishing.com
Ryan Gray ryan.gray@outlookpublishing.com
BUSINESS DEVELOPMENT DIRECTOR
Thomas Arnold thomas.arnold@outlookpublishing.com
TRAINING & DEVELOPMENT MANAGER
Marvin Iseghehi marvin.iseghehi@outlookpublishing.com
SALES AND PARTNERSHIPS MANAGER
Donovan Smith donovan.smith@outlookpublishing.com
SALES MANAGERS
Josh Hyland josh.hyland@outlookpublishing.com Krisha Canlas krisha.canlas@outlookpublishing.com
PROJECT MANAGERS
Jordan Levey jordan.levey@outlookpublishing.com
Kierron Rose kierron.rose@outlookpublishing.com
Kyle Livingstone kyle.livingstone@outlookpublishing.com
Liam Pye liam.pye@outlookpublishing.com
Nicholas Kernan nicholas.kernan@outlookpublishing.com
Taylor Green taylor.green@outlookpublishing.com
ADMINISTRATION
Finance Director: Suzanne Welsh suzanne.welsh@outlookpublishing.com
Finance Assistant: Suzie Kittle suzie.kittle@outlookpublishing.com
Finance Assistant: Victoria McAllister victoria.mcallister@outlookpublishing.com
Office Manager: Daniel George daniel.george@outlookpublishing.com
CONTACT
APAC Outlook
Norvic House, 29-33 Chapelfield Road Norwich, NR2 1RP, United Kingdom
Sales: +44 (0) 1603 363 631
Editorial: +44 (0) 1603 363 655
SUBSCRIPTIONS
Tel: +44 (0) 1603 363 655 phoebe.harper@outlookpublishing.com www.apacoutlookmag.com
Like us on Facebook: facebook.com/apacoutlook
Follow us on Twitter: @apac_outlook
We have come a long way since stone, mud and clay. Today, our cities reach the clouds thanks to a construction industry that is constantly evolving.
COBOD International stands at the head of this futuristic industry, a world leader in 3D printing construction machines. In this most recent issue, our Topical Focus sheds a light on the company building free-form structures on demand for an evergrowing global network.
Delving further into the rapidly advancing space we look at CSC Robotic Engineering Limited (CSC ROBO), the Hong-Kong based business realising a robotic workforce. CSC ROBO’s innovation and development is seeing the construction sector advance into a realm once perceived as science fiction, utilising artificial intelligence (AI) automation in the field to boost efficiency, productivity and economic viability.
From AI and robotics to the good times we live for, our cover feature Hanuman Beverages promises the best that Cambodian beer has to offer.
“We have had great feedback internationally, so this is something we would like to really work on and ensure our brands are available outside of Cambodia for everyone to enjoy,” shares Madam Khieu Sarsileap, Founder and Chairwoman.
Hitting the premium beer segment, Hanuman Beverages is questing to become a pioneer in the beverage sector and has its sights set on growth beyond its home country competing on the global stage.
Elsewhere in this edition, Fijian Broadcasting Corporation (FBC) battles against storm winds and equally ravenous industry competition. CEO Riyaz Sayed-Khaiyum notes FBC’s dramatic rise from national radio to a fully-fledged media service and reveals the company’s challenges and developments in the field, including its efforts in disaster relief, helping to keep Fiji’s 300 islands connected.
Alongside these, you can find a selection of corporate stories from Osmoflo, Oceania Dairy, Taylor, Decmil Group, and many more.
We hope that you enjoy your read.
Phoebe Harper Editorial Director, Outlook PublishingMuraki is determined to find a suitable planet to sustain human life, and has set his sights on Mars.
To combat the Martian atmosphere of 95 percent carbon dioxide (CO2), Muraki created Hiyassy, an artificial intelligence (AI) carbon capture device when he was just 15 years old. It works by pulling in air and filtering it back out through an alkaline solution.
The red planet has been put on the back burner for now, as Muraki’s Tokyo-based company, Carbon Recovering Research Agency, is working to create an alternative fuel from CO2.
NINTENDO HAS SET new sales records with its latest Pokémon Scarlet and Pokémon Violet video games for its hybrid console, the Nintendo Switch. The industry saw an increase in profits during the COVID19 pandemic, but it is now beginning to normalise, making Nintendo’s recent hits a rare feat.
Since the global launch of the blockbusters on November 18th, 10 million units have been shifted, the highest level of sales for a game’s debut in Nintendo’s history. Consequently, shares in the company are up by 11 percent and investors are backing Nintendo due to its recent success.
INDIA’S FIRST PRIVATELY developed rocket, Vikram-S, was recently launched from the Sriharikota spaceport. Start-up Skyroot Aerospace, supported by the Indian Space Research Organisation (ISRO), has opened the sector to private companies. Up until now, the country’s space industry has been
dominated by state-run ISRO.
Founded by former ISRO engineers in 2018, Skyroot is based in the tech hub of Hyderabad, and has raised USD$68 million in funding. The rocket weighed in at 546 kilograms (kg) and reached an altitude of 89.5 kilometres (km).
India is now in the orbit of the private sector space race along with billionaires Richard Branson and Jeff Bezos.
ROO-MOVED FROM AUSTRALIA
Deliveroo Australia accounted for three percent of the company’s total gross transaction value and negatively impacted its margin, causing the company to cut costs to find profits.
The online takeaway sector is highly competitive in Australia,
prompting rival Menulog, part of Just Eat, to cut jobs just one week after Deliveroo’s withdrawal as part of its global cost reductions in the food delivery sector.
The latest drive is in Islamabad and in the high-risk districts of Punjab and Southwestern Baluchistan province, with a campaign launching in the northwest in the first week of December.
Pakistan regularly vaccinates against polio, and the country came close to eradicating the disease last year. Pakistan and Afghanistan are the only two endemic countries remaining in the drive to end polio worldwide.
TESLA IS RECALLING more than 80,000 electric cars over seatbelt and software issues.
The costly endeavour includes the imported Model S and Model X vehicles due to affected battery management systems. The imported Model 3 vehicles have also been
recalled, as well as 10,127 of the Chinese-made versions, due to potentially faulty seatbelts.
China is one of Tesla’s most important markets, and the company has a major production factory in Shanghai with a record number of sales in recent months, but Elon Musk’s company faces competition from Xpeng, Nio, and Li Auto, all releasing new cars in 2023.
CRASH AND BOOM!
While most Asian stock markets slumped, Indian stocks traded at near record highs amid growing expectations that the Reserve Bank of India will hike interest rates by a smaller margin. Despite a weakening rupee, the Indian economy is poised to be one of the best performing economies this year.
APAC Outlook Issue 59 | 7
The packaging industry – like every one of us – has to face up to climate change, pollution and scarcity. What are the challenges and how can we make our future more sustainable?
By far the biggest contributor to global warming – at more than 73 percent 1 – is energy consumption. Reducing energy use should be every organisation’s priority. It is certainly high on the agenda in the packaging industry.
According to Climate Collaborative, on average, packaging accounts for about five percent of the energy used in the life cycle of a food product,
making it a significant source of GHG emissions.
Marine waste is another huge environmental problem. The United Nations Environmental Programme (UNEP) has found that 90 percent of litter in our oceans is made up of different plastic polymers. Packaging makes up just eight percent of that total, but our industry is now moving more quickly to address this issue.
The world must also confront water scarcity. By 2025, up to 3.5 billion people might be living in areas of water stress. Without a developed water infrastructure, the only way to get them drinkable water will be
by using packaging in one form or another.
So, how is the packaging industry stepping up to these challenges? By making a drastic shift from a linear to a circular economy model. We need to acknowledge that packaging is a resource, not a waste.
By keeping it in the circular economy loop, PET plastic packaging can play a pivotal role in protecting and distributing our most precious products. This has been recognised by the Ellen MacArthur Foundation through its New Plastics Economy Global Commitment, in which Sidel is one of the signatories.
Chutima Saengow, Communications Manager for Southeast Asia and Pacific at leading services solutions provider Sidel, explores the role of PET plastic in overcoming the sustainability challenge
As a major supplier of packaging equipment and services, we’re working hard to help the beverage industry to become more sustainable. We’ve committed to making a bold shift to using green energy on our own production sites and are engaging with our suppliers on their sustainability journey. We committed to cut our own carbon emissions (known as Scope 1 and 2) by 30 percent by 2030 as well as help our suppliers and customers reduce theirs (Scope 3) by 25 percent in the same timeframe. We’re at our customers’ side. For example, we helped UAEbased customer Zulal make energy savings of 56 percent by moving to a new fully integrated packaging line configuration. New technology, such as our Evo-On Eco app, is enabling our customers to monitor production line energy consumption and make adjustments in real time.
Improving the carbon footprint of PET Lifecycle analysis (LCA), the only scientific way to compare one material with another, shows that plastic, and PET in particular, has the best carbon footprint among materials currently available.
We are continuously working to improve packaging footprint, by following the five principles of reduce, reuse, recycle, replace and reinvent. Our new moulding technology reduces the weight of bottles, cutting down on material use as well as transport emissions.
We are providing tethered caps that stay attached to the bottle, minimising litter ahead of new European legislation. Additionally, we are leading the way in making PET bottles safely refillable, and ensuring best quality bottles even with high quantities of recycled PET.
We are also designing out waste in how bottles are labelled and packaged ready for transportation.
As for reinventing, we’re actively scouting for new bio-sourced/biobased materials.
We have to find these new sustainable solutions, because like it or not, plastic packaging is with us in the near term. Sales of packaged products in food, beverages, home and personal care are continuing to grow, especially in the APAC region. The Middle East, Africa and India are driving 4.4 percent compound annual growth in these products by 2024. The use of PET is expected to grow at 1.7 percent with packaged water leading the way with a growth of 4.2 percent. Energy drinks are performing particularly strongly in Asia. So, how can we make this future growth more sustainable?
• Reuse will come to the fore, as the industry comes up with new solutions in the different reuse schemes such as refill-on-the-go, refill-at-home, return-on-the-go and return-from-home.
• Recycled PET will become more prevalent, with the main challenges being availability, quality and price.
• New sustainable materials and easier-to-recycle solutions moving from many layers of multiple materials to one single monomaterial layer, will be on the rise.
• The way goods are packaged for transport will be very different.
We are likely to see much more cooperation between manufacturers, brand, suppliers, NGOs and, of course, end consumers. Manufacturers will be expected to take on more responsibility for waste management. More countries will be joining the 63 nations which have already enacted Extended Producer Responsibility
measures, such as product takeback schemes, deposit-refund, and waste collection and takeback guarantees. More governments will fund and create better recycling infrastructures, as well as easier, incentivised ways for consumers to recycle, such as reverse vending machines.
It will take all of these efforts to see significant improvements. If it is properly collected and recycled, PET, far from being the problem, can offer the best answer to the current sustainability challenge. By working together, we can make a true circular economy of plastics possible.
Chutima Saengow is Communications Manager for Southeast Asia and Pacific at Sidel. Based in Bangkok, Sidel is a leading provider of equipment and services solutions for packaging beverage, food, home and personal care products, operating in over 190 countries. Find out more about Sidel’s work on sustainability and how to access its support for your business at www.sidel.com
Sources: 1 Our World in Data
APAC Outlook (AO): Firstly, could you introduce us to CSC ROBO and the company’s vision?
Ren, Director of
(MR): CSC ROBO is a technology and engineering company. We were founded in Hong Kong in 2019 as a subsidiary of Shun Cheong Engineering Group (SCEG) to focus on installation technology innovation and development for the construction industry. Leveraging over six decades of SCEG’s electrical and mechanical (E&M) engineering know-how, CSC ROBO contributes to the industry’s evolution with knowledge of mechanics, automation, robotics, mechatronics, vision and digital modelling.
Our vision is centred on the three pillars of automation and
CSC Robotic Engineering Limited (CSC ROBO) is a HongKong based specialist in designing robots for the construction industry. We find out more with Director of Innovation, Michael Ren
digitalisation, sustainability and environmental friendliness, and construction and process innovation.
AO: Tell us about the launch of your new product - the Df Self-Navigating Drilling Robot.
MR: This product has only just been launched in November 2022. It works similarly to our previous drilling machines, however the Df focuses exclusively on ground, as opposed to ceiling drilling.
From a technical innovation point of view, it incorporates a more sophisticated algorithm and technology to enable the machine to operate by itself. The Df simply requires an operator to input either a CAT or BIM file to indicate the locations that need to be drilled. This then creates a row that the Df travels down stop by stop – rather like a bus route. At each stop, the machine inspects the targets pre-set by the operator, and will then complete the drilling itself. With the exception of the CAT file and route definition, all operations are fully automatic. This achieves automation levels of between 50-90 percent.
AO: What role do construction robotics have to play in the industry’s future?
MR: Automation in the construction industry can improve productiv ity and transform collaboration within all the different sectors. By automating certain tasks in the construction industry, we can significantly elevate productivity, attract more highly skilled talent, conduct more efficient and timely processes and save costs in projects. The impact of construction robotics can ele vate the industry to a whole new level. They can create a humanised environment for workers to change
the existing negative impressions of the construction industry.
AO: Could you tell us more about your plans for expansion? Are there any particular markets that you have identified for future growth?
MR: Our business in Hong Kong is currently extremely active, as numerous clients are using our technologies in their projects. Therefore, we are now expanding our market and promoting our innovation outside Hong Kong. We are looking forward to joining some events and exhibitions in different countries. For example, two months ago we participated in BEX Asia in Singapore, and we are glad to hear that the feedback is quite positive. The government and many industry leaders are interested in our products since they are very unique and helpful in their country. We are open to all countries but we intend to primarily focus on markets across China, Singapore, Japan, the UK, US and Germany.
AO: Finally, what are the priorities for CSC ROBO’s development?
MR: Innovation is needed everywhere in the construction cycle. For our long-term goals, we intend to collaborate with overseas businesses and expand our target markets globally, while introducing new innovative technologies that will lead the market trends.
Although there are several focus areas, our priority is to increase productivity and efficiency. We intend to leverage different techniques to bring the construction industry to a higher level that uses less labour and provides a safer working site. In the long run, we want construction robotics to improve efficiency whilst also providing accessible ESG solutions for the industry.
In today’s corporate climate, non-financial factors are rising in significance as indicators of a company’s performance, holding greater appeal to stakeholders and influence for investors.
At the forefront of this is Environmental, Social Governance (ESG), as greater transparency is expected from companies in terms of their commitment to recognising and acting on social responsibilities, ranging from climate change to social unrest and a host of matters in between.
The maritime sector is no different, as businesses embrace ESG as a means to navigate both risk and opportunity. This comes as the call for decarbonisation in the industry grows increasingly deafening, and
RightShip takes the helm of implementing ESG strategies across the maritime industry. Charting new waters into Singapore, we speak with ESG Manager, Aishwarya Iyer
Writer: Phoebe Harperfact-based disclosure is expected from regulators, financiers, and cargo owners.
“Corporates themselves are beginning to see the benefits of transparent ESG reporting and their role in conserving marine ecosystems, reducing emissions, enhancing crew welfare and running ethical businesses,” says Aishwarya Iyer, ESG Manager for RightShip – the world’s largest third-party due diligence player.
“ESG as a discipline is well positioned to move from being an add-on or overlay to becoming a mainstream topic just like traditional financial reporting,” she continues.
Indeed, as ESG continues to be carried on a tide of acceptance and incorporation into the mainstream,
the means of reporting through ESG frameworks is becoming a uniform practice.
“ESG elements have always been important screening factors while evaluating investments or lending to offshore sectors, but in the last few years, these elements have come together in a more structured manner under ESG.”
The disclosure of ESG performance is being supported by regulatory pressure, as offshore industries are effectively screened by these standards and institutional investors and financial analysts incorporate these considerations into their valuation and risk assessments.
Established in Melbourne in 2001 under founding shareholders Rio Tinto and dry bulk charterers BHP, RightShip offers a range of products that enable shipowners, charterers, ports, terminals, financial and insurance sector players to track and benchmark their emissions performance, crew welfare and operational efficiency. By so doing, customers benefit from full visibility over the progress of sustainability goals.
“I also feel that corporates will use their ESG profiles to enhance their image and brand value, as ESG reporting provides a holistic picture of how a corporate is functioning in its
AISHWARYA IYER, ESG MANAGER, RIGHTSHIPresponsibility towards all stakeholders including the community, employees, suppliers, shareholders and of course, the environment,” adds Iyer.
Iyer herself was drawn to RightShip in recognition of the impact that ESG could have within a sector that accounts for three percent of global greenhouse gas (GHG) emissions with significant scope for progress in terms of ocean governance and an emphasis on crew welfare.
Most recently, RightShip has expanded its mission of benchmarking standards for the maritime industry by launching in Singapore. The city-state was a strategic choice, as a dynamic nexus of maritime trade home to some of the world’s largest shipping companies, with a receptive market that holds the potential for huge impact.
This is the latest in a series of moves RightShip has made to expand its footprint across in Asia, having opened representative offices in Shanghai, China in July 2021, followed by Hiroshima, Japan in November 2021.
“Singapore has continued to strengthen its presence as a leading global maritime hub and the launch of the Global Centre for Maritime Decarbonisation (August 2021) has further cemented the country’s commitment to combating climate change,” Iyer explains.
“Having a physical presence close to our customer base enables us to be on the front line of the conversation.”
The new office builds on extended collaboration with support from Singaporean organisations, including an MoU signed with the Singapore Maritime Institute to co-operate on a Maritime AI (Artificial Intelligence) Programme. The space will also act as an innovation hub to deliver zero-harm solutions for the maritime sector.
With this latest addition, RightShip offers a chance to further support decarbonisation efforts, set overall structure for ESG, and drive change in a key sector that informs global supply chains. With RightShip’s suite of solutions charting the journey to a zero-harm sector, ESG is set to become a matter of smooth sailing.
“CORPORATES THEMSELVES ARE BEGINNING TO SEE THE BENEFITS OF TRANSPARENT ESG REPORTING AND THEIR ROLE IN CONSERVING MARINE ECOSYSTEMS, REDUCING EMISSIONS, ENHANCING CREW WELFARE AND RUNNING ETHICAL BUSINESSES”
–
A start-up on an explosive trajectory, COBOD International is now the world leader in 3D printing construction machines. We explore its expanding global network with coFounder and Head of Asia Pacific, Simon Klint Bergh
The future of construction will be 3D printed. In a laborious industry faced with escalating material costs and a diminishing skilled workforce, autonomous, multifunctional construction robots are the answer.
A trailblazing innovator in this
nascent field, COBOD International (COBOD) has proven itself as a world leader in the few years since its inception in 2017. That same year, COBOD delivered Europe’s first 3D printed building in Copenhagen, and introduced the largest 3D printer in the world to Saudi Arabia just two
years later.
With an equally impressive future ahead, we delve into the pioneering start-up with co-Founder and Head of Asia Pacific, Simon Klint Bergh, as the company spreads its global network of local partners with a new venture in Indonesia.
affordable options are required due to the rising cost of materials.
Simon
Klint Bergh, co-Founderand Head
ofAsia
Pacific(SKB): COBOD stands for Construction of Buildings on Demand. In 2017, after three years of research in the sector, we realised that there weren’t any commercial companies doing 3D construction printing. Although we started as a plastics printing company, we set ourselves the goal of bringing this technology to market.
After we printed the first house in Europe near our headquarters in Denmark, everything started to take off. Today, we have regional offices in Miami, and Kuala Lumpur, Malaysia alongside our base in Denmark. We have sold just over 55 machines across the world, and we’re present through our customers in all six habitable continents.
The fact that a five-year-old scale-up can claim to be the world leader in this field because we have sold more machines than any others in the market, in fact, more than all of them combined, really speaks to the infancy of the technology.
Our focus mission is to bring this new 3D printing technology to the construction sector to innovate and change the way things are done for the better. This is why it’s so important for us to establish strategic collaborations and partnerships across the world to spread our technology.
AO: What are the key drivers for 3D construction printing?
SKB: As a young scale-up, we’re still exploring where this technology makes most sense to implement. There are four different factors that we consider when introducing 3D printing into the construction sector. Firstly, there is a huge need across the world for more housing, even in developed countries where more
A lack of skilled labour is also a major problem throughout many countries. With the increased automation our technology brings to the construction site, this problem is directly addressed.
Sustainability is another pillar - we don’t overconsume and only use the materials that we need. Our technology allows the use of new, innovative materials and our mentality is entirely based on open-sourcing materials. Basically, whatever you can extrude can be used with COBOD technology. Universities and customers are continually exploring new opportunities into materials other than concrete.
The final factor is individualism. Form freedom is appealing to most of our generation – people who want their homes to appear unique and can be a part of the design process. The form freedom enabled by our technology makes it no more expensive to build 100 different homes rather than 100 of the same, whereas conventional technology would typically appreciate that uniformity.
SKB: Our partnership with Bakrie has been in discussion for a long time. We decided to partner with them since they are a big, multi-vertical group of companies with good connections and an advanced vision of technology and how to make it viable in the market. Similarly, we work with Siam Cement Group in Thailand and KA Bina in Malaysia to help us expand our technology in those regions.
At COBOD, our focus is on continuously developing our technology to the best possible level and then finding partners for the rest. We’re not construction experts, we’re
technology experts, so we need these local partners to bring the technology to market and use their knowledge of local authority regulations and building sectors.
We have just signed the agreement with Bakrie, meaning that one of our machines will be introduced in Indonesia within the first half of 2023. Meanwhile, there are various projects soon to be delivered in Malaysia, Thailand, Japan and India.
SKB: Working with customers to refine our technology and make a better product is key for COBOD. We put a lot of emphasis on our customers succeeding, because that means that we succeed in the long run. We will continue to collaborate with them to bring the first 3D printed houses to different countries around the world.
APAC Outlook (AO): What led to COBOD’s inception and how has the company grown?
APAC OUTLOOK is a digital product aimed at boardroom and hands-on decision-makers across a wide range of industries on the continent.
With content compiled by our experienced editorial team, complemented by an in-house design and production team ensuring delivery to the highest standards, we look to promote the latest in engaging news, industry trends and success stories from the length and breadth of the Asia Pacific region. We reach an audience of 220,000 people across the continent, bridging the full range of industrial sectors: agriculture, construction, energy & utilities, finance, food & drink, healthcare, manufacturing, mining & resources, oil & gas, retail, shipping & logistics, technology and travel & tourism. In joining the leading industry heavyweights already enjoying the exposure we can provide, you can benefit from FREE coverage across our digital platforms, a FREE marketing brochure, extensive social media saturation, enhanced B2B networking opportunities, and a readymade forum to attract new investment and to grow your business.
To get involved, please contact Outlook Publishing’s Managing Director, James Mitchell, who can provide further details on how to feature your company, for FREE, in one of our upcoming editions.
Hanuman Beverages is the Cambodian drink master committed to creating best-in-class beverages that pioneer new tastes for the nation. We delve into exciting new products and continued expansion with Founder and Chairwoman, Madam Khieu Sarsileap
Cambodia has historically been heavily reliant on imported products, but gradually over the past few years more and more local beverage companies have been established to compete with international imports. Subsequently, this has allowed prices to become more competitive in the market.
“After completing my university degree in Australia, I came back to Cambodia and saw so many opportunities for qualityfocused businesses. As Cambodia has been going through a gradual re-growth stage, coupled with strong population growth, for many years I watched the beverage industry grow and whilst I had no experience in this field, it was a dream of mine to be part of it,” opens Madam Khieu Sarsileap, Founder and Chairwoman of Hanuman Beverages, reflecting on her initial attraction to the sector.
Aligning with the company mission and vision involving product innovation, premium quality produce and state of the art technology, Hanuman Beverages initially launched with a premium lager that was positioned above the present mainstream market. To be successful in this positioning, the company had to invest significantly in a great recipe that would be accepted as a premium beer. Unfortunately, doing so vastly increased the cost of beer as only the best quality hops and malt from around the world were sourced to ensure both taste and stability.
“The next thing we had to invest in significantly was our primary and secondary packaging design, and this was easily the hardest part. I am a bit of a perfectionist, so it took many rounds of going back and forth before I was proud enough of our final design,” recalls Madam Sarsileap.
A few months after the initial launch, Hanuman Beverages introduced another product to complement the premium lager with
the Hanuman Black beer.
“We were the first brewery to launch a commercial black beer, with all our competitors focusing on the stout segment which is very high in bitter units and not as easy to drink,” she expands.
The new black beer took a different approach and focused much more on drinkability, with an enticing roasted malt flavour. This proved to be the right approach in the stout market, where long-time brands have a strong hold on the landscape.
“We further innovated this year by becoming the first company in Cambodia to introduce a smaller bottle, launching a 250ml variety. This was a bit risky I must admit, as it is a trend that is happening around the world with smaller packaging but not something that was seen here before.”
This was followed with a different approach to distribution, with Hanuman Beverages building its own distribution network across the country with hubs in each key city, rather than being solely reliant on third parties.
About us.
For the past 18 years, Harta Packaging (a wholly owned subsidiary of OJI Holdings) has been manufacturing carton boxes for customers in Cambodia. 1. Providing good product quality with excellent services. 2. Anticipate for last minute requests which is always handled efficiently. 3. Be an essential part of customers’ business success (innovations and cost reduction).
• Corrugated boards.
• Printed and unprinted boxes.
• Food and beverage boxes.
• Garment and shoe boxes.
• Designing and manufacturing innovative prod-
“My staff are critical to my business, and I always try to place them at the heart of the company. I have the utmost respect for them and have endorsed many staff engagement initiatives, including a speak-up culture where we always value their suggestions.”
Madam Sarsileap believes that forging a meaningful connection with her staff exists as a crucial element of the company’s ongoing success.
“I treat my team professionally with great respect and work through any major issues with them, so they know they always have my prompt support anytime they need it,” she ensures.
Another key partnership that Hanuman Beverages has had to intricately develop over time is the relationship with its key supply partners.
“I can’t stress enough how important supplier relationships are for us. As we
San Miguel Yamamura Haiphong Glass Company Limited, is a joint venture glass plant between San Miguel Corporation - Philippines, Nihon Yamamura GlassJapan and HABECO - Vietnam. It is committed to maintaining quality leadership in the domestic and international glass industry and providing customers with glass containers that conform to international quality standards at a competitive cost.
smypc.com
are a new company, we must ensure our supply network trusts and wants to work with us. If we did not invest so heavily in building these strong relationships, it would be very difficult for a company like us to get supply on demand with very short notice, as is often the case when starting out,” Madam Sarsileap expands.
Therefore, whilst Hanuman Beverages is not currently the size of the big global breweries with their vast buying power, the company instead looks to invest more into longterm relationships.
As well as looking after its staff and maintaining a thriving supply chain, Hanuman Beverages understands its immense social responsibility.
“This is certainly something we take very seriously, especially in a country like Cambodia that has been re-building for so long. I firmly believe
large companies in this country have a responsibility to contribute to the community in practices outside of normal operating activities,” Madam Sarsileap elaborates.
Whilst the company is still very new, Hanuman Beverages has conducted numerous Corporate Social Responsibility (CSR) activities throughout the year.
“We have combined some of these activities with staff bonding initiatives, such as tree planting around the Angkor Ecological Park in Siem Reap and mangrove tree planting
on the coast of Kampot to support the biodiversity of the region,” she continues.
Further to this, Hanuman Beverages has recently been involved in supporting Wildlife Alliance, an international non-profit forest and wildlife conservation organisation with current programmes in Cambodia, as they have recently celebrated 20 years of activity within the nation.
“We are still very new, but this is something we take seriously and look forward to contributing more to as we continue to grow.”
To be the ‘national beverage hero’. To become the company that takes Cambodian beverages to new heights with state of the art drinks innovation.
To relentlessly create best-in-class beverages that innovate new tastes of Cambodian lifestyle.
The goal of the company is to establish the Hanuman Beverages brand as a benchmark of quality in the Cambodian beverage market. Hanuman Beverages will become the industry leader in innovation, integrity and sustainability, always ensuring its people and products represent the company in the correct Hanuman Beverages way. The company wants to become a champion of change, continually setting new standards in brewing technology, team development, sustainability and community support.
“WITH OUR PASSION, WE WILL BE SURE TO MAKE A POSITIVE MARK ON THE BEVERAGE INDUSTRY IN CAMBODIA”
APAC Outlook: You’ve made
Khieu Sarsileap, Founder
“This is an ongoing project with many of the commercial areas still under construction, however, the concept of this is to involve our community of consumers more in our company and various brands. We strongly believe in opening up for our consumers to show them what we have built and how the beer is produced, rather than being a closed-door operation. By creating more public areas, we feel people will connect more with our brands by enjoying a strong experience at the surrounding grounds of our production facility.
“On top of this, we are close to completing a large park that will allow us to host outdoor concerts and family days in a relaxed environment, which can be difficult to find with the continued development in the city. I am really looking forward to having people treat us as a destination to escape the hustle and bustle of the city.
“We have put so much effort into our design, green spaces and overall look and feel, which helps us stand out from our competitors and also makes our employees feel very proud to be working here.”
“Looking ahead, first and foremost our key target is to continue our growth trajectory in Cambodia with our two pioneer brands. We cannot take our foot off this and must keep pushing to ensure our success. We will also be working on expanding our brand portfolio here during 2023 and onwards,” details Madam Sarsileap.
Further to this, the company is also putting a key focus into building its brands internationally, and is currently searching for the best distribution partners in every potential country for each individual brand.
“We have launched into the premium beer segment, and we have had great feedback internationally, so this is something we would like to really work on and ensure our brands are available outside of Cambodia for everyone to enjoy,” Madam Sarsileap adds enthusiastically.
“As the first local company to
launch into the premium area of the industry, we have made a huge sacrifice in chasing the mainstream volume to focus on producing the best beers and building strong brands and a loyal customer base for the long-term. My vision may take a bit longer to see greater returns, but in the end, we will have the strongest brands that all Cambodians can be proud of both locally and eventually internationally as we ramp up our export markets,” she finishes.
HANUMAN BEVERAGES
Tel: +855 (0) 23 933 339 info@hanumanbeverages.com.kh https://hanumanbeverages.com.kh
use of your land to create a community centre with pub gardens, making it a tourist hotspot. Could you tell us more about this?Madam and Chairwoman:
Wide Open Agriculture is the leading regenerative food and farming company in Australia. Differentiated by its authentic and market-leading embracing of regenerative agriculture, we explore more with CEO, Jay Albany
The rise of plant-based foods is clearly more than a fad; it is a fundamental shift in consumer behaviour. Whether for environmental, animal welfare, health, or taste reasons, the demand for plant-based foods is experiencing rapid adoption worldwide.
With the rise of the conscious consumer over the last decade, this trend accelerated exponentially during the COVID-19 pandemic, a time in which food security and the relationship between food and climate change became more salient than ever.
Now, consumers are deeply considering how their buying decisions play a part in the broader world, whether through a moral or environmental lens. Using the incredible ubiquity of information readily available on the internet, consumers make intentional purchasing decisions aligned with their values. They can shape shopping habits based on a range of environmental issues like global warming, food miles, or social causes such as fair compensation, animal welfare, and supporting locally sourced food.
• Reduce all inputs – feed the soil, not the plant
• Integrated livestock – holistic farming methods including rotational grazing, which mimics natural grazing patterns for healthier food and building soil quality
• Reduce chemical fertilisers
• Reduce insecticides to zero chemical insecticides
• Fungicide free
• No feedlots
• No antibiotics
• Non-GMO
• Dedicated biodiversity and recovery zones
• Tree planting
• Use of perennial grasses
• Farm plans focused on improving utilisation and preservation of water
This means that the massive infrastructure required by the industrial food complex is exposed to a fundamental shift in consumer spending – forming the perfect climate for innovators and disruptors. Wide Open Agriculture (Wide Open) has targeted two of the largest opportunities from this structural change: the rise of plant-based foods and the advancement of regenerative agriculture, which the company believes will be the next super cycle in food, similar to what organic has been since 1990.
“What’s exciting about the rise of the conscious consumer is that it has exposed many of the problematic issues with food production, creating an opportunity for positive disruption,” opens CEO of Wide Open, Jay Albany.
Albany joined Wide Open in 2019 and launched its food brand, Dirty Clean Food, with the goal of launching a uniquely authentic food and distribution business. He envisaged a brand that stands out in a world of numbered ingredients and processed food, aiming to reimagine the way consumers, retailers, and farmers think about and interact with food.
“I joined Wide Open because I saw an opportunity to take the incredible, authentic position the company had developed in the nascent regenerative agriculture space and build a new kind of consumer food platform, while doing good for food, farmers and the planet,” he recalls.
Wide Open was founded in 2015 by Dr Ben Cole and Anthony Maslin, who were armed with nothing but a bold vision to build a business dedicated to fighting climate change through regenerative food and agriculture.
The dynamic duo understood that food waste and the food production system represent over 30 percent of carbon emissions contributing to climate change, and saw that
MBL Food & Packaging is one of Western Australia’s leading packaging providers successfully providing WA customers with quality products and professional service that matches every customer’s needs.
MBL has been proudly providing wholesale and retail services to the butchery, processing, bakery and foodservice industries for more than 70 years.
MBL continues to be a trusted household business name in WA that leads from the front, providing innovative food and packaging solutions across the WA business landscape.
Operating from its homebase in Canningvale, MBL Food & Packaging, formerly known as MBL Food Services, now has a range of over 7,000 lines selling to more than 1,500 customers. MBL’s vision is to be WA’s leading food and packaging supplier, valued for our people, partnerships and high-level performance.
MBL has recently introduced a premium flexible packaging solution partnering closely with the likes of Wide Open Agriculture supporting their future business needs to achieve their short term and long term business growth objectives. MBL’s extended flexible packaging range consists of multiple options including Thermo-Film, Lidding Films and Shrink Bags just to name a few. MBL through its growing
Ikon Pack brand, also offers an extensive range of recyclable and home compostable packaging solutions to suit all needs.
MBL is one of the industry’s most trusted suppliers, building strong, sustainable long term business partnerships across multiple business channels. Knowledge, service and innovation gives customers true confidence that they can depend on, making MBL the perfect business partner.
MBL continues to invest into the WA food and packaging industry, having recently acquired Vital Packaging and South Coast Foodservice businesses to add to its forever growing portfolio. MBL’s long standing position as a leader in the industry means that it is a brand that you can trust.
MBL will make a positive difference to your business.
JAY ALBANY, CEO: “We believe we are onto a breakthrough ingredient in the plant-based protein industry with Buntine Protein®. Our team is focused on producing from our existing facility, becoming more efficient and forming partnerships to make Buntine Protein® a global product.
“Initially, we are focused on marketing this product into the dairy alternatives space, where its high solubility and gelation properties make it a superior ingredient when compared to pea and soy. We have also been actively sampling since our production facility opened in June and expect to add multiple, large-scale strategic partners in new geographies over the next 12 months.
“For Dirty Clean Food, our aim for this year is to continue our rapid growth through geographic expansion. Dirty Clean Food Oat Milk has gained traction quickly in Southeast Asia over the last 12 months, and we expect to sell additional Dirty Clean Food products into these markets, as well as add a few new ones.”
regenerative farming was a tool that could build topsoil, improve water cycles, and increase biodiversity in Western Australia (WA). This was particularly targeted for regions like WA’s Wheatbelt, which has been significantly damaged by climate change and the rapid adoption of large-scale industrial farming practices.
They quickly teamed up with Stuart McAlpine, a well-known and experienced regenerative farmer residing in Buntine, WA.
Regenerative farming takes an industry that is a leading carbon emitter and applies practices to draw down carbon into the soil.
“We firmly believe that we will be a carbon-positive entity as we reach a greater scale and show with data that regenerative farming practices cause positive climate change,” states Albany.
“Being sustainable is simply not enough at this point, and 2050 commitments are not happening nearly fast enough. We want fundamental positive landscape change, and to provide consumers with a choice to purchase food that tastes great and is produced in an environmentally positive way,” he adds.
Dirty Clean Food is a wholly owned subsidiary of Wide Open and is the commercial arm through which the company seeks to advance regenerative agriculture.
Launched in 2019, Dirty Clean Food has grown prosperously to become the world’s leading regenerative food platform.
Magnum Flavours and Ingredients, based in Perth, Western Australia is a solution based food manufacturing organisation focused on innovation, quality and exceptional customer service. Magnum specialises in developing and manufacturing custom made food powder and liquid blends for food manufacturers and food service.
The Magnum team have worked closely with the Wide Open Agriculture team to develop several exclusive, healthy products with a compelling point of difference. Magnum is invested in the success of its client and as such looks forward to continue supporting the growth of Wide Open Agriculture and its brands. www.magnumessence.com.au
Dirty Clean Food Oat Milk is the world’s first oat milk to be both regenerative and certified carbon neutral, whilst also being the only product of its kind made from 100 percent regeneratively grown oats.
Just 18 months on from inception, Dirty Clean Food Oat Milk can now be found at 1,500 locations, with distribution across five countries, including a national range in Australia’s largest grocery chain, Woolworths, on top of a further 200 café and restaurant locations. A rapid and highly efficient delivery operation has also been created to expand Wide Open’s ever-growing presence in WA.
AGRICULTURE“BEING SUSTAINABLE IS SIMPLY NOT ENOUGH AT THIS POINT, AND 2050 COMMITMENTS ARE NOT HAPPENING NEARLY FAST ENOUGH”
– JAY ALBANY, CEO, WIDE OPEN
Today we listen and deliver the best results, on tomorrow’s innovation.
Our mission is to provide exceptional solution-based service to food manufacturers and food service clients, through a team who understands and cares about each other and the stakeholders, with a passion for creativity and focus on delivering outstanding results.
Our team of experienced food technologists can turn ideas into great tasting products.
T: +61 8 9248 1006 enquiries@magnumessence.com.au www.magnumessence.com.au
“In Perth, we essentially do 24-hour farm-to-fridge delivery for our latest products, six days per week,” Albany elaborates.
The company has initiated plans to build the first commercial oat milk factory in WA, which is expected to come online in 2023, aligned with a new recipe that uses Wide Open’s own Buntine Protein® to provide oat milk that has protein levels equivalent to dairy milk.
Buntine Protein® is an Australian sweet lupin-based protein concentrate, sold as an ingredient to food manufacturers as vegan plantbased protein. Manufactured in Wide Open’s Perth facility, it is made from regeneratively grown lupins from the Wheatbelt.
Extensively used to replace animal-based ingredients in food and beverages, Buntine Protein® possesses the potential to also create plant-based meat, dairy, baked goods, noodles, and protein supplements. Offering markedly higher solubility and gelation properties than soy and pea-based proteins, it has emerged as the current generational leader in its category.
A natural, regeneratively produced ingredient, the protein is extremely
well-aligned with the explosive trends in plant-based food production.
“What remains exciting is that lupin is such a crucial crop to WA. This product brings the original vision of the company to reality, creating value, restoring landscapes, and fostering hope in the Wheatbelt.”
“We have an incredible group of passionate people who work for Wide Open. Some are foodies, some are passionate environmentalists, and some are here for the excitement of building a growth company; I love our team,” enthuses Albany.
Being a growth company, Wide Open offers high-achieving employee opportunities for rapid career advancement.
“It’s not always about titles and salary – it’s also about the opportunity for empowerment. When people demonstrate excellence in their role, we encourage them to train their replacement and get ready to take on more responsibility,” Albany explains.
“The best possible outcome for us is that we build a committed community of curious, ambitious, and passionate people aligned with our mission.”
Wide Open builds and shapes its leaders through what the company calls the WOA Way. It is
a commitment from everyone to work on a two-week cadence, with a company-wide presentation of what was accomplished every fortnight, presented by the team leaders. This provides transparency across the business, builds community within the team, and allows Wide Open to be flexible in its goal setting.
“We must be nimble, and the twoweek goal setting and review provides a mechanism for us to take advantage of opportunities and recognise failures faster than our larger competitors in the food industry,” concludes Albany.
There is a firm belief within the entire company that this nimbleminded thinking, combined with an arsenal of innovative products, will ensure that Wide Open continues to play a key role in the expansion of regenerative agriculture, and even more vitally in combatting climate change.
Tel: 08 6202 7130
info@wideopenagriculture.com.au www.wideopenagriculture.com.au www.dirtycleanfood.com.au
“THE BEST POSSIBLE OUTCOME FOR US IS THAT WE BUILD A COMMITTED COMMUNITY OF CURIOUS, AMBITIOUS, AND PASSIONATE PEOPLE ALIGNED WITH OUR MISSION”
– JAY ALBANY, CEO, WIDE OPEN AGRICULTURE
The Kiwi Nation of New Zealand (NZ) may be small in terms of its population size, but its dairy industry has an oversized impact on the global stage.
The country is the world’s eighth largest dairy-producing nation and a major contributor to the national economy, with dairy exports earning more than twice as much as meat and forestry exports combined. Accounting for more than 30 percent of all exports from the island nation, this vital industry generates in excess of NZ$18 billion of revenue each year.
Situated within the nation’s picturesque southern farming country, Oceania Dairy Limited (Oceania Dairy) combines local community expertise with innovative talent from its parent company, Yili Group. The company boasts a proudly home-grown workforce that is given every opportunity to develop career-enhancing skills to ensure progression within the business.
“The dairy industry in NZ is thriving, and our ability to continually improve how we sustainably farm and process dairy products is keeping us at the forefront of global dairy production,” says Logan Hanifin, General Manager of Oceania Dairy.
Hanifin has a background in engineering, working for a variety of industries across the South Island of NZ, where the milk industry is intricately ingrained at the centre of
most communities.
Before becoming General Manager, Hanifin was involved initially in building the factory in 2013, progressing to take on senior management roles in engineering and operations.
“It is extremely rewarding to be leading a significant dairy company such as Oceania Dairy and to be responsible for managing the expectations and goals of our stakeholders,” he adds.
Currently employing 400 permanent staff, 50 temporary staff and myriad contractors to support the business, Oceania Dairy manufactures a wide range of value-added fast-moving consumer goods (FMCGs) specialising in both infant formula and UHT milk.
Oceania Dairy is committed to continuous improvement and staying ahead of the sustainability curve to ensure it can operate in a way that protects the planet for generations to come. With these goals in mind, the company is constantly looking to invest in further developing its already state of the art facilities and manufacturing processes to decrease its overall carbon footprint.
Throughout 2021, Oceania Dairy invested significantly
Oceania Dairy aims to provide an internationally recognised and respected source of highly valued dairy nutrition that nourishes people for a better, healthier life. We discover more with General Manager, Logan Hanifin
in a chemical recovery plant which is now successfully operating and recovering cleaning chemicals, unlocking the capability to both re-treat and reuse these substances in the manufacturing process.
Oceania Dairy has also produced an energy transition accelerator strategy, a foundational study allowing the company to plan the transition to renewable energy supplies.
“We have run trials of various types of biofuels for process heat, as well as scoping electrical infrastructure
upgrades to support emerging technology such as hightemperature heat pumps to allow full transition away from fossil fuels,” Hanifin says.
The progression to cleaner, more sustainable business practices is developing alongside a range of exciting products and expansion into new territories.
One key growth area for the Oceania Dairy product range is the registration of three infant formula brands for general trade to China, specifically produced to meet new GB standard requirements. GB standards are Chinese national standards that ensure products comply with everything from labelling to safety, usage, and more.
Similarly, Oceania Dairy recently completed China’s SAMR audit which included a significant on-site audit by MPI on behalf of SAMR. Oceania Dairy is the first company in NZ to pass this audit which is currently required for any business that wishes to sell their infant formula brands in China.
Meanwhile, the company continues to press ahead with the expansion of its whole milk and skimmed milk 1KG product portfolio into the Southeast Asian market, set to be introduced next year.
“This marks a significant achievement for our business and places us in a good strategic position for our product launches, which will begin in early 2023,” Hanifin says.
Product quality is at the core of everything Oceania Dairy does. Strict quality assurance processes wrap around the procurement of raw materials and ingredients, staff training and manufacturing processes, product testing, releasing, shipping and distribution.
“We make food for the most vulnerable population on the planet - babies. Therefore, we must have strict control over every piece of our process,” explains Hanifin.
Oceania Dairy has fashioned a robust quality management system that is validated through multiple audits including from NZ and Chinese government agencies as well as significant audits from its customers and internal audit team.
“We recently invested heavily in a state of the art laboratory to further refine our quality control, enabling full testing from end to end to be completed on-site, allowing us to control our quality from start to finish, minimising our reliance on third parties,” expands Hanifin.
This scrutiny over every level of safety-ensured decision making also includes the supply chain process. Not only does the company send its products around the globe, but it also has a significant requirement for ingredients and raw materials from all over the world that must be maintained.
“While our internal, highly talented supply team are exceptional, we cannot do it alone and this requires significant strategic collaboration with our global suppliers to ultimately deliver on our business goals and company guarantees,” Hanifin says.
“We are extremely lucky to have such valuable partners to work with us to deliver robust end-to-end supply chain management. Our key partners also worked tirelessly across the duration of the COVID-19 pandemic to keep our
“WE ARE EXTREMELY LUCKY TO HAVE SUCH VALUABLE PARTNERS TO WORK WITH US TO DELIVER ROBUST END-TO-END SUPPLY CHAIN MANAGEMENT”
– LOGAN HANIFIN, GENERAL MANAGER, OCEANIA DAIRY
supply chain moving and our products in our customers’ hands, for which we are very grateful.”
Oceania Dairy manufactures products 24/7, 365 days a year and relies on every single individual to do their bit to maintain a high standard of safety and quality management.
As Hannifin affirms, “in an industry such as ours, people are everything. We are very lucky to have such a dedicated workforce, who believe in our core values and truly understand the value they bring to our organisation.’’
With a mature strategy around growing its own talent, there are multiple examples of exceptionally talented people moving through the organisation into senior roles in management, manufacturing, supply chain, IT and engineering, or whatever role they desire as a career path.
“Our team know that our training and career development can set them on any path they wish, and they are not confined to their current roles and responsibilities. This is critical in driving an engaged, empowered and valued workforce,” Hanifin elaborates.
“For me, there are two key factors that differentiate us from our competitors, and the first is always our people. We have a unique culture that is built around quality, agility, and continuous improvement.”
This means the company’s manufacturing and sales ability is uniquely placed to pivot at the required pace to both improve processes and performance, while also responding dynamically to customer demands.
“The second is our ownership by the Yili group, the largest dairy company in Asia. This gives us significant reach in both R&D and innovation as well as sales and distribution to leverage the best value possible outcomes for NZ’s milk supply,” he tells us.
With the global demand for milk products rapidly growing, Oceania Dairy is positioned to capitalise on this surge in demand, providing confidence to both its owners and
supply partners that will result in increased profitability for farmers and owners alike.
The high concentration of existing dairy farms within a 50 kilometre radius of the Oceania site provides significant efficiencies for Oceania Dairy’s processing facility.
The local economy is strong too, with a growing population and enviable lifestyle options. Oceania Dairy is already recognised as an employer of choice in the region and plans to take active steps to maintain its favourable reputation.
“We have created a strong set of goals within our 2023 strategy, as we look to grow our people, ensure safety and deliver on sustainability improvements. Furthermore, our longer-term strategy will ensure our business is well placed to lead the industry for many years to come,” concludes Hanifin.
Historic trends show NZ farm and cow performance is continuously improving; in this way, Oceania Dairy understands the importance of responding to a changing world and seeking new and innovative ways to create competitive, resilient systems.
OCEANIA DAIRY
Tel: +6436866403 reception@oceaniadairy.co.nz www.oceaniadairy.co.nz
As a world-class designer, builder and operator of desalination projects and complete water treatment solutions, the purpose that lies at the core of Osmoflo is simple – to preserve the world’s most precious resource.
Yet the versatile nature of the company’s expansive capabilities, and the complexity of its varying technologies, are as wide-ranging and far-reaching
as the myriad waterways that carve a path across the Earth’s surface.
“Although Osmoflo specialises in membrane-based treatment technologies, it has always offered a much wider range of process, treatment and resource recovery solutions to its customers,” introduces Osmoflo’s Chief Executive Officer and Managing Director, Carmine Ciccocioppo.
These solutions encompass conventional clarification, filtration and disinfection for water treatment, and a wide range of wastewater treatment options including conventional activated sludge, membrane bioreactor (MBR), sludge dewatering and advanced recycling and reuse.
Since last speaking with Ciccocioppo in August 2021, as the company marked its 30th anniversary,
Osmoflo has continued to ride a wave of evolution through dedicated investment in innovation.
By so doing, Osmoflo has remained a key player on the global stage of water treatment solutions, thriving in a vital industry that preserves a safe water supply across locations spanning the Middle East, Asia, India, and the company’s home nation of Australia.
Today, that reach is spreading even further, as Osmoflo seeks to explore further geographic expansion into the Pacific region, the Middle East and North Africa (MENA), India and North America.
Significant investment into R&D is the lifeblood that fuels Osmoflo’s journey of continual innovation,
channelling a level of buoyancy that keeps the company both relevant and competitive.
As Osmoflo continues to strengthen its reputation and widen its capabilities beyond the traditional scope of a water treatment specialist, it is exploring a far broader range of process applications.
“Increasingly, we are looking at critical resource and mineral recovery
Osmoflo unlocks the solutions to sustainable water innovation. We follow the company’s rebranding journey and discuss future innovations with Chief Executive Officer and Managing Director, Carmine CiccocioppoWriter: Phoebe Harper | Project Manager: Nicholas Kernan
from brine streams, and utilising membranes in novel ways to help the food and beverage sector, such as whey and vinegar concentration,” expands Ciccocioppo.
CARMINE CICCOCIOPPO, CHIEF EXECUTIVE OFFICERAND
High quality and customised water treatment projects require a highly reliable partnership between all involved parties.
MANAGING DIRECTOR:“The NEOM project is an amazing ‘city of the future’ that is being funded and developed by the Kingdom of Saudi Arabia. Osmoflo is very pleased to have already delivered some of the initial ‘mission-critical’ water treatment equipment that will support the preliminary construction phases of this massive undertaking.
“Osmoflo has had an established presence in Dubai since 2011 and has subsequently progressively grown our team and expanded our activity throughout the MENA region, which has seen enormous demand for new water infrastructure. Osmoflo is pleased to have contributed to that growth by supporting a wide range of customers including power generation, public water supply and general industrial customers.
“Our aim is to continue to support NEOM during its development phases with innovative water and brine solutions and smart operations for what we hope will be many years to come.”
In keeping with this spirit of new areas of exploration, Osmoflo’s recent rebrand, which was unveiled earlier this year at the IDA 2022 World Congress in Sydney, echoes the company’s versatility and capacity to move with change. Above all, the new logo and motto of ‘a circular future for water’, champions Osmoflo’s overarching commitment to a circular economy.
“This re-branding reflects our aspiration, consistent with that of our shareholder Hitachi Zosen Corporation of Japan, to make a meaningful and fundamental contribution to the sustainable management of water across the planet, and pursue our mission of providing innovative, sustainable and value-based water solutions that contribute to a circular economy,” he affirms.
By so doing, Osmoflo clearly aligns its own ambitions with those of its customers.
“Almost without exception, our customers are looking to pursue their own respective ESG goals. This typically includes ensuring their water management is sustainable, that their waste streams are minimised or even eliminated, and that they move towards carbon neutrality within specified time frames,” outlines Ciccocioppo.
To reflects its commitment to implementing a truly sustainable water supply, Ciccocioppo highlights two particular Osmoflo projects that put circularity in action.
The first entails significant work on an ageing desalination facility for Queensland-based gas and power assets operator, Arrow Energy. The company was facing the prospect of completely replacing its ageing 12 million litres per day
GF Piping Systems understands Osmoflo’s versatility and shares its design-built application approach focusing on efficiency, quality and safety. Our joint efforts towards process automation have an integral role in the growing need for water conservation. At GF Piping Systems, we offer deep application knowledge of the entire water and chemical cycle. The process automation control loop for plastic piping systems simplifies the design, planning, and installation of multiple industrial water treatment applications.
Our partnership with Osmoflo includes a combination of technical support from concept to design, speedy delivery service during the procurement phase, installation training for fabrication and reliable products for commissioning and operation. We’re looking forward to supporting Osmoflo in many water treatment projects by providing innovative and high performance industrial thermoplastic piping systems as well as valuable support from planning to commissioning. Together we make process automation easy and are aiming to provide our customers full peace of mind.
GF Piping Systems is one of the three divisions of the Georg Fischer Corporation, founded in Switzerland in 1802. With over 65 years of experience in plastics, GF Piping Systems is dedicated to designing and manufacturing piping systems for the safe and secure transport of liquids and gases. In Australia and New Zealand, GF Piping Systems supplies a full range of plastic pipe, fittings, valves, fusion machines, process automation products and prefabrication services to the industrial and utilities market.
www.gfps.com
COULD YOU EXPAND ON YOUR WORK WITH THE DUBAI GOVERNMENT REGARDING THE NEOM PROJECT FOR A RENEWABLE SMART CITY?
By being a complete system provider, we enable our customers to design, select, install and own process automation solutions. GF Piping Systems supplies every customer not just with the highest quality parts but with an interoperable all-in-one solution. We make Process Automation easy.
Chesser Chemicals provides cleaning and sanitising products to a diverse range of industries and is a quality endorsed company that satisfies rigorous criteria of the International Standards Organisation to ISO 9001: 2015.
Our products are expertly designed to work in various conditions and can be tailored to meet customer requirements by implementing testing in our internal laboratory.
We design our products with the latest technology available to allow products to be tailored for maximum performance and customer satisfaction.
www.chesserchemicals.com.au
(MLD) desalination facility, first commissioned in 2008, in order to keep providing a consistent and reliable water treatment capacity for at least another 10 years.
“Instead, Osmoflo’s innovative approach facilitated a “brownfield” solution based on reusing and upgrading as many of the existing assets as possible and replacing only a limited amount of MEI equipment on a ‘like-for-like’ basis,” he explains.
Elsewhere, Osmoflo worked with Senex, an Australian producer of natural gas, who required a permanent 1.5MLD treatment facility for its coal seam gas (CSG) water. In this instance, an innovative ‘capital recycling’ solution was developed based on the company’s awareness of another client looking to divest an existing plant (that had been previously delivered by Osmoflo several years prior) that closely matched the treatment specification that Senex needed.
– CARMINE CICCOCIOPPO, CHIEF EXECUTIVE OFFICER AND MANAGING DIRECTOR, OSMOFLO“In both cases, Osmoflo’s unique and innovative approach has enabled the implementation of solutions that maximise the recycling and life extension of existing assets and significantly reduce the need for new assets and materials (and therefore the associated environmental and carbon footprint associated with those materials),” elaborates Ciccocioppo.
“All in all, a great win for circularity in the water industry!”
Aside from its focus on the circular economy, Osmoflo is also exploring further environmentally friendly solutions by continuing its foray into green hydrogen as an opportunity for new growth and diversification.
Homing in on particular areas of investment and the research taking place behind the resource, a major focus for Osmoflo’s R&D and Innovation Team concerns improving
“OUR PRIORITIES ARE ON SUPPORTING OUR EXISTING CUSTOMERS AND MARKET SECTORS TO MEET THEIR ESG GOALS, ESPECIALLY IN RELATION TO SUSTAINABLE SOURCING OF WATER, REUSE OF WASTEWATER AND MINIMISATION OF BRINE AND RESIDUALS”
and enhancing the functionality and capability of its remote monitoring and control platform, Plant Connect.
“This is part of a significant ongoing investment programme and our commitment towards R&D and innovation,” Ciccocioppo shares. The ongoing optimisation of Plant Connect is key to effectively servicing Osmoflo’s ever-increasing number of remote monitoring customers around the globe, which currently stands at over 90.
These efforts are complemented by the development of further capabilities in artificial intelligence (AI) and machine learning (ML), both of which have been proven by Osmoflo to provide tangible benefits for its customers in terms of optimised chemical and power usage whilst also significantly improving membrane life.
“Our R&D and Innovation Team
are also currently investigating novel non-membrane treatment techniques such as Controlled Hydraulic Cavitation for control of scale and removal of dissolved solids in various industrial water streams, as well as use of free radicals and LED-based UV for advanced disinfection applications,” he adds.
Finally, returning to the importance of circularity, Osmoflo continues to invest in high recovery technologies through which it can improve and refine its patented Osmoflo Brine Squeezer (OBS).
“We will work with our various industry partners to develop even higher recovery solutions based on complementary technologies such as osmotically assisted reverse osmosis (OARO) and solvent extraction,” outlines Ciccocioppo.
Leveraging technology to
implement sustainable water management that minimises waste streams and accelerates its customers’ paths towards sustainability and carbon neutrality, Osmoflo will continue to chart a course into the waters of a future circular economy, pursuing a vision that evokes endless perpetuity.
Much like the circle motif that represents the Osmoflo mission in preserving and recycling our most vital resource, it is one that will last ad infinitum
OSMOFLO
Tel: +61 8 8282 9700 marketing@osmoflo.com www.osmoflo.com
Cenergi SEA Berhad is Malaysia’s premier sustainable energy solutions company, specialising in the reduction of carbon emissions through development and investment in renewable energy and energy efficiency projects. We investigate further with GCEO, Hairol Azizi Tajudin
Against a backdrop of continuous uncertainty, from the treacherous fallout of the COVID-19 pandemic, new energy and climate policy commitments and most recently the volatile price inflation exacerbated by Russia’s invasion of Ukraine, this series of explosive circumstances has sent economic shockwaves across Southeast Asia (SEA).
Despite this, Cenergi SEA Berhad (Cenergi), continues valiantly onwards in its mission to improve the environment for a better, cleaner world.
Incorporated in 2013, Cenergi and its group of companies is an esteemed Malaysian sustainable energy solutions company, specialising in reducing carbon emissions through long-term investment in both renewable energy and energy efficiency projects.
Joining Cenergi in March 2020 as GCEO, Hairol Azizi Tajudin began his career at Sarawak Shell Berhad in 1993, later joining Malakoff in 1997. Throughout his vastly ranging 23 years of employment with Malakoff, he undertook various leadership roles as Senior Vice President, Plant Manager and Head of Departments, gathering a wealth of crucial experience to deploy in his current position.
Hairol explains how he finds it a constantly invigorating industry to be ingrained in. “All my working life I have been in the energy and utility industry,” he begins.
“Despite many global and local challenges especially during the COVID-19 period, we have increased our revenue by 40 percent every year for the last three years,” Hairol adds proudly.
“Although we have faced difficulties, we are extremely agile and very nimble in terms of matching our actions to our visions.”
The team of experts at Cenergi forms a shared community, working towards creating a more environmentally friendly and infinitely greener
world. The company’s overarching aim is to reduce carbon emissions in Malaysia and throughout Southeast Asia, through an exciting array of sustainable utility projects.
Cenergi focuses on three businesses segments, namely renewable energy, energy efficiency, and new ventures. Across these business segments, Cenergi possesses and offers a full spectrum of design, construction, technical, financing, and operational capabilities for its stakeholders.
Growing to accommodate 195 employees, Cenergi is now a diversified sustainable utility project developer and investor. Cenergi is currently the largest biogas player
in the country with a 13.9 percent market share at present while also becoming one of the main players in solar and energy efficiency projects. Realising the increase in demand for sustainable biomass fuel, Cenergi is also pioneering the premium biomass pellet business with main application as co-firing fuel in coal fired power plants.
“We are strongly committed to conducting our operations in a safe and reliable manner, reflecting the high operational standards practised by our employees. We can proudly boast 2,513,832 safe man-hours without lost time injury (LTI) recorded between August 2013 and October 2022,” Hairol acclaims.
2017
• Eco-school supply to underprivileged children at Sri Jelutung Biogas Plant.
• Providing general medical supplies, essential equipment, and social care to old people’s homes.
2018
• Sustainability school workshop with Sekolah Kebangsaan Palong 14, Negeri Sembilan.
• Communal work by Cenergi’s staff to clean the Cenergi Palong Biogas Power Plant site and its surrounding and neighbouring areas.
2019
• Beach cleaning at Port Dickson, in collaboration with The Beach School.
• Support in Sayangi Malaysiaku: Malaysia Bersih, an environmental education programme involving 120 students at Manjung District, Perak.
2020
• Food Bank Siswa Programme to help university students who were forced to remain at campus during the Movement Control Order (MCO) period due to the COVID-19 outbreak, by providing them with food/toiletries.
• Donation of personal protective equipment (PPE) to the Ministry of Health Malaysia during the COVID-19 pandemic.
• Technical visit by Environmental Management and Research Association of Malaysia (ENSEARCH), one of the biggest and earliest NGOs that focuses on environmental management and research in Malaysia, to Cenergi FJP biogas plant.
2022
• Laptop donation and sustainability workshop with Sekolah Kebangsaan Lubuk Sireh, Padang Besar, Perlis.
• Climate Action Network Southeast Asia (CANSEA) site visit to Cenergi West Biogas Plant.
AGILITY - Pivoting towards rapid change and adapting with flexibility.
INTEGRITY - Maintaining high standards of ethics, honesty and moral principles in all business conduct.
RESPECT - Achieving greater goals by acknowledging each other’s similarities and differences.
INNOVATION - Developing new ideas and converting them into realities, encouraging curiosity and a willingness to take calculated risks.
SUSTAINABILITY - Integrating sustainable developments and committing towards a safe and harmonious future for all.
KEY FIGURES
392 GWH - Electricity supplied to the National Grid Network
RM57 MIL - Savings in energy costs from energy efficiency (EE) projects 151,553 GWH - Total energy savings from EE projects
2,027,575 TONNES - Carbon savings 31 - Operational projects
VISION
• To be the premier sustainable utility company in SEA
MISSION
• 200 MW of renewable energy capacity
• RM200 million investment in energy efficiency and sustainable ventures
• 500,000 tonnes of annual CO2 emissions avoidance
GOING FULLY SUSTAINABLE
Malaysia, as one of the largest producers and exporters of palm oil products in the world, is currently working in a concerted effort to improve the sustainability aspects of this multi-billion dollar industry. It has been providing steady employment to millions of Malaysians for decades and any efforts to improve its sustainability are for the greater good. Realising this social and economic responsibility and its impacts on the country, Cenergi steps up to work together with the industry players by offering them integrated solutions for the waste coming from the midstream of this palm oil industry.
Biogas is widely recognised as one of the most attractive renewable energy resources, mainly for its various applications, as it can be used as renewable fuel in both power generation and industrial processes.
Almost all Cenergi’s biogas power plants generate renewable electricity
using biogas fuel produced from the anaerobic fermentation process of the organic contents in the Palm Oil Mill Effluent (POME), the methanerich by-product from the palm oil production process. Currently, this wastewater is being treated in a series of open ponds that allow emittance of methane, one of the most potent greenhouse gases, to the atmosphere. Cenergi helps palm oil millers to capture and monetise the methane as one of renewable energy sources.
Through a winning combination of highly experienced project management teams and thoroughly capable operations staff, Cenergi has developed the capacity to turn hazardous liabilities into green electricity for cleaner environment and sustainable palm oil industry.
“We currently oversee 21 biogas power plant projects in our portfolio across SEA, with a total generation capacity of 37.4 MW,” Hairol outlines. Alternatively, biomass is also a
Biological desulfurization of biogas or CO2 after upgrading to bio-methane (RNG)
Lowest operating expenses and highest availability of any H2S removal systems
More than 330 projects generating a total of 679 MWe in more than 40 countries
significant source of renewable electricity on a global scale and continues to play a crucial role in Cenergi’s vision to help industries, especially the utility industry, to reduce their carbon footprint.
The company’s future growth plans also include the ongoing development of premium biomass pellets for use in coal fired power plants. Cenergi developed its first pilot plant to produce this premium biomass pellet using palm oil’s empty fruit bunches (EFB), the most abundant organic solid waste coming from the palm oil mills. If left untreated in an open space, EFB degrades to produce methane that is emitted to the atmosphere.
Malaysia is blessed with yearlong sunlight and high solar irradiance, making it one of the best countries for investment in solar photovoltaic systems to harvest this free energy.
In Malaysia, solar can be regarded as a regular and dependable supply of renewable energy, thus it remains an excellent alternative to the historic reliance on fossil fuels. At present, as equipment prices are becoming affordable, infrastructure is more effective than ever and vast financing options are available, now is the time for companies such as Cenergi to capitalise and unlock the true power and potential of solar energy, an inexhaustible resource to be harnessed.
Launching headfirst into this new advancement, Cenergi has formed a joint venture with Sunseap Group, a major solar energy player in Singapore and in the ASEAN region, by incorporating Cenergi Sunseap Energy Solutions Sdn Bhd (CSES) in 2019.
With CSES acting as a catalyst, the company now expects to see a sizable increase in its solar investment and development across the key home market of Malaysia, particularly in rooftop solar leasing and large-scale solar farms.
This forms part of a proven business model for Cenergi, as the company provides cheaper and renewable alternative sources of electricity for various commercial and industrial players while simultaneously helping them to reduce their carbon footprints.
Regarding other sustainable options, hydropower is a stable and cost-effective method of generating electricity. It offers a reliable electricity supply to the grid at low operational and maintenance costs without emitting greenhouse gases.
Similarly, wind power is a readily available and sustainable source of energy making it one of the fastestgrowing green sources in the world.
“Capturing its power does not deplete our valuable natural resources and the application of wind energy in SEA has been growing tremendously in the last few years,” Hairol explains.
Cenergi is currently expanding both in its geographical reach and renewable energy asset portfolio. On a case-by-case basis, the company will evaluate investing in the development of wind power plants in SEA for both on and off-grid applications.
Cenergi has the foresight to predict potential future global shortages, and plan for appropriate response strategies.
“We are currently looking closely
“ALTHOUGH WE HAVE FACED DIFFICULTIES, WE ARE EXTREMELY AGILE AND VERY NIMBLE IN TERMS OF MATCHING OUR ACTIONS TO OUR VISION”
– HAIROL AZIZI TAJUDIN, CEO, CENERGI SEA BERHAD
into the future of water in Malaysia via water recovery projects from wastewater,” says Hairol.
Water is a basic necessity for all living things, and there is an urgent need to ensure the sustainability of clean water, something which is already an issue in some parts of the world today.
“If you look at COVID-19, there is no one, including scientists, that 15 or 20 years ago could have predicted what would happen. So, we look to anticipate these future challenges and prepare for them,” he adds.
“We will continue to monitor national water levels even though we are blessed with regular heavy rainfall at present, which makes the water tariff lower. However, we would expect the tariff to move up in the future, hence making water recovery projects more viable.”
There are many attractive qualities associated with the process of rebranding for Cenergi.
Current transition strategies are tasked with attracting more potential clients and business partners for new forms of collaboration and joint ventures. Becoming more visible among industry players and increasing market presence to better attract great talents into the company are some of the other desired outcomes for Cenergi.
From humble beginnings, the company started its business with the support of all stakeholders, including suppliers, vendors and contractors. Therefore, throughout future rebranding processes, Cenergi endeavours to treat them all as business partners who have been supporting its successful growth since the very beginning.
Establishing an ongoing, long-term healthy relationship with partners, vendors and suppliers will enhance efficiency, improve asset operations
and ultimately increase revenue.
“We forecast a promising future for all those involved in renewable energy in Malaysia as we look to achieve carbon neutrality for the country as early as 2050, the goal set by the government as the country moves towards a developed nation and low carbon society.
“We have to empower people, especially when you have a younger generation within the organisation,” Hairol continues.
Future facing, Cenergi looks towards a target of a 40 percent increase in yearly revenue in the years to come; this is alongside the ongoing mission to increase the market share of biogas from 13.9 to 25 percent within the next three to five years, while continuing to increase its market share in solar and energy
efficiency projects and becoming the main producer and exporter of premium biomass pellets.
These are ambitious targets, but Cenergi has been working hard to position itself on a springboard for continuous success and promises to continue making a significant difference in this vital period for the sustainable future of the utility industry in Malaysia and the ASEAN region.
CENERGI SEA BERHAD
Tel: +603 58850454 info@cenergi-sea.com www.cenergi-sea.com
Renewables are the energy of our vitally sustainable future.
Across Southeast Asia (SEA), solar and wind energy are rapidly growing, while energy both from biomass – including that from waste products –and hydropower remain a well-established part of SEA’s clean energy space. One key player at the centre of this industrial activity is Samaiden Group Berhad (Samaiden).
Originally established in 2013, Samaiden is principally involved in providing engineering, procurement, construction and commissioning (EPCC)
solutions for clean energyrelated businesses such as solar, biomass, biogas, energy efficiency and environmental assessment. Since 2020, the company has been listed on the Bursa Malaysia stock exchange.
Working with projects across such a broad range of environmental areas, Samaiden boasts around 85 employees from multiple disciplines including accounting and finance, business and marketing, engineering and many more fields of expertise.
“Samaiden’s mission is to provide the best clean
energy solutions by fully committing to deliver the best quality of services to the satisfaction of our customers at an affordable price,” introduces Managing Director Ir. Chow Pui Hee. “Samaiden is an EPCC solutions provider for clean energy projects that include solar photovoltaic (PV), biomass, biogas, energy efficiency etc. We have the in-house technical expertise to provide clean energy and environmental consulting services as well as operation and maintenance (O&M) services.
“At present, our company has completed the installation of more than 300 solar power projects that have successfully led to the reduction of more than 57,000kg of CO2 emissions.”
A leading player in the Malaysian clean energy space, Samaiden Group Berhad is the partner of choice in clean energy solutions. Managing Director Ir. Chow Pui Hee tells us more about solar, biomass, alternative clean energy and company growth across SEA
As part of its industry solutions, Samaiden specialises in environmental consultancy and assessment, and analysing how plans, policies, programmes and projects could affect the environment while providing its quality and personalised services.
“We provide solar O&M services tailored to your needs, maintaining system uptime and improved energy production. With our expertise and inter-capabilities, we provide end-toend services such as overseeing and managing whole plan O&M,” Ir. Chow tells us.
Ir. Chow has always worked within the environmental space, beginning her
career journey as an engineer mainly involved in specifying pumping systems for water and wastewater treatment plants.
Subsequently, Ir. Chow gained the opportunity to become involved in the design and building of wastewater treatment plants as a manager of an environmental division, a role that led her to the position she holds today.
“Throughout my career path, I have been exposed to the responsibility of managing landfill closure, providing technical advisory services of contaminated land management, solid waste and wastewater management, as well as providing environmental consulting services,” she reveals. “Eventually, I was responsible for the implementation
of several solar PV system projects during my tenure with one of my former employers.
“All these roles have given me insight into the energy and utilities EPCC space. With approximately 19 years of experience in the engineering field, clean energy and the environmental sector, I believe clean energy is one of the keys to guaranteeing a sustainable future for the planet.”
According to Ir. Chow, Malaysia is fully committed to being a key part of the global transition to becoming low-carbon, eventually evolving into a carbon-neutral nation. Based on the renewable energy (RE) roadmap, the government is targeting 31 percent RE share in the national installed capacity
mix by 2025, rising to 40 percent by 2035, and moving on to achieve full carbon neutrality by 2050.
“With these goals set, the Malaysian government has implemented various supportive policies and incentives for the growth of RE, which is further expected to drive the market,” she elaborates. “We are witnessing substantial growth in RE installations due to government support, rising awareness, as well as national targets. As part of the industry, we are dedicated to continuously educating the public on the importance of clean energy towards accomplishing the national goal.”
Samaiden has secured numerous solar farm projects under the large-scale solar (LSS) programme launched by the Malaysian government in 2019, as one of the winners of bids in the fourth round of the LSS procurement
programme (LSS4). The largest of those completed by Samaiden so far is one with a capacity of 136MWp located in the Malaysian state of Perak.
“While under the government’s LSS4 initiative, we have successfully secured four projects from different project owners with the aggregate capacity of 90MWp,” Ir. Chow says. “Apparently, there are several obstacles that we experienced prior to commencing the project construction work.
“First and foremost, it is about the funding support from financial institutions. If the profile of the owner is relatively weak then it is very likely that the financial institutions will refuse to extend the lending to that party. As such, our company might need to step in to act as their guarantor, because our track record will be the best input to convince the financial institutions to approve the borrowing from the owner.”
After resolving the issue with funding support, the following challenges will be project execution, which comprises the timeline, manpower planning, material purchase and project management. Any failure among these could potentially turn the profit to a loss. As such, vigilance when it comes to the project execution stage is a top priority for Samaiden.
“We have also been appointed by our client BTM Resources as the EPCC contractor for their 10MW biomass project, one of the largest biomass projects in the country, relying on wood chips or waste as the feeding
• IEM Award 2022
• APVIA Awards Photovoltaic Application – Enterprise 2021
• Distinguished Representative of 3rd Women in Renewables of the Year Awards 2020 – Women in Renewables Asia
• Malaysia Excellence Business Award 2018
• Star Outstanding Business Award 2018 – Best Green Initiative
• Star Outstanding Business Award 2018 – Female Entrepreneur of the Year
• Star Outstanding Business Award 2018 – Best in CSR
• Lang International Corporate Titan Awards 2018
• ASEAN Energy Awards 2017
• Star Outstanding Business Awards 2017 – Best Green Initiative
• Selangor Excellence Business Awards 2017
• Malaysia International Business Awards 2017
• SME 100 Award 2016 – Fast Moving Companies
Samaiden
stocks for the boiler system,” Ir. Chow continues. “This will be our pioneer project in the biomass industry which can allow our team to grow and strengthen our company’s profile and build up our presence in this area. Moreover, the completion of this project also will bring revenue amounting to RM115.6 million to Samaiden.”
Moving towards an increasingly sustainable future, Samaiden is focused on expanding its green development solutions and services to see the company grow and impact people’s lives, as well as the planet’s health, in a positive way. Regional expansion in SEA is one of the key objectives that Samaiden holds, and is part of its five-year plan.
“We have recently moved to Indonesia, and have plans for Cambodia at a later stage. These moves are primarily due to the
Sungrow is the world’s most bankable inverter brand with over 224 GW installed worldwide as of 2021. With a strong 25-year track record in the PV space, Sungrow products power installations in over 150 countries.
info@sungrow.cn | en.sungrowpower.com
abundant natural resources that can be detected in these two countries,” Ir. Chow explains to us. “When it comes to Indonesia specifically, sunlight is consistent yet the country’s solar industry development still remains relatively slow. In addition to that, Indonesia can also allow a biomass power plant to be built for its power supply.
“For Cambodia, one of the lucrative points for us to invest abroad is the tariff rate offered by the government. Overall, we’re pretty optimistic about our moves within SEA primarily due to geographical factors, policy, and incentives granted to us.”
As the world continues to experience severe climate change issues, Samaiden will play its role in driving green energy development. The company is not limiting itself to expanding business within SEA alone, but is also considering other regions and countries as well, while focusing on the most critical aim that is leading
in its current market.
“From our start-up as a solar EPCC contractor, we have begun to diversify our business to biomass, biogas, and energy efficiency areas,” Ir. Chow concludes. “Our future aim is to be one of the leaders in the clean energy industry, and this revenue stream shall be supplemented by the construction of power plants and investment of power plant ownership consistently.
“Lastly, we’re a company that is strongly committed to environmental, social and governance (ESG) goals. Ever since the year of our foundation, we have stuck to our pledges of driving decarbonisation and achieving a zero-carbon footprint.”
SAMAIDEN GROUP BERHAD Tel: +603-6150 7941 project@samaiden.com.my www.samaiden.com.my
REMEX Minerals Singapore Pte Ltd is contributing towards the nation’s approach towards zero waste and circular resource economy. We speak to Managing Director Venkat Patnaik about the company processing incinerator bottom ash and reducing waste on Semakau Island
Singapore is renowned as a green city. Yet, as the second-most densely populated nation on the globe, it also faces the pressing issues of limited land and large quantities of waste. However, these are two of the factors as to why Singapore is so environmentally focused and efficient at waste disposal.
With a limited landmass, Singapore turns waste into treasure and disposes minimum waste to Semakau island, the only landfill in the nation. It is only so large, meaning that smart waste disposal methods, recycling, and reusing materials emerge as not only a positive for the environment, but also a necessity for the country’s zero waste policy. It is this crucial foresight, combined with the nation’s
technological power in Southeast Asia, that makes Singapore a successful green city, and one at the top echelons of sustainability in Asia.
“What you need to take into account with Singapore is the fact that the biggest challenge remains land scarcity,” begins Venkat Patnaik, Managing Director at REMEX Minerals Singapore Pte Ltd (REMEX), addressing the elephant in the room and giving voice to a national concern that requires constant thought.
“Singapore is a land-scarce island making every inch very valuable and waste collection, reuse and disposal a critical endeavour across the country.”
REMEX is one company born from the joint need to combat waste whilst salvaging, recycling and reusing what is valuable to the environment and society.
REMEX offers solutions for the reliable disposal, processing and reuse of
raw materials contained in mineral waste. This includes the production of secondary/recycled aggregates from minerals as well as the recycling of recovered metals. In addition to the provision of appropriate disposal concepts, REMEX also offers effective services for contaminated site and land remediation, underground stowage, the operation of landfills and metal recycling.
“Mineral waste is a precious commodity - this insight gave rise to the corporate success story that is REMEX, benefitting both customers and the environment,” Patnaik says. “As a recycling company, we organise the entire mineral material cycle by processing mineral waste such as construction waste and industrial by-products, making them usable again as quality-assured secondary aggregates. As a result, REMEX has been making a relevant contribution to the protection of resources for more than four decades.
“Waste collection companies collect all this waste, before sending it to different incineration plants after removing all the unsuitable materials. The material incinerated is mostly domestic and general waste, and
WITH REGARD to sustainability, REMEX focuses on three topics: climate protection, landscape conservation and the optimisation of landfill quotas through the best possible recycling and recovery results. The environmental contribution that REMEX achieves through its activities can be quantified, particularly with regard to the production of substitute construction materials, metal recovery and land remediation.
Providing
Armed with more than 30 years of experience we own a large fleet of excavators and vehicles to support all needs of the project.
these incineration plants reduce the volume of waste while at the same time generating power.”
REMEX’s operations bring about significant positive impacts; the physical waste is reduced by approximately 75 percent in the waste incineration plants, in the form of IBA, which is in turn further processed in MRF to be potentially used for various applications like road bases and general construction, earthworks or landfill works.
This sums up the broad process
by which waste management is undertaken in Singapore today.
REMEX specialises in the recovery of metals from incinerator bottom ash (IBA) and its further application for “zero waste” goals. According to Patnaik, a substantial 15 percent of IBA is metal, making it a very valuable resource to tap into.
“IBA containing physical metal is very unstable, responsible for corrosion, and consequently loss of valuable metals. What REMEX does is recover these metals from the ashes
to be recycled and reused,” he informs us.
After recovering these metals from the ash, they are sent to various smelters based on their type, such as copper, aluminium or steel mills. This not only supports a circular economy but also helps REMEX by opening up a revenue stream that is continuous and beneficial for the environment. Yet, there is an additional benefit to the practice of metal recovery from waste ashes.
“Semakau Island is an offshore
“WE
landfill located on the eastern side of Singapore, and because it is indeed an island, space is limited as it is throughout the rest of the nation,” Patnaik explains. “Usually, these waste ashes are sent to the island, but when you look at our practice of metal recovery you realise that REMEX is reducing the overall amount of ash taken to landfill by 15 percent, accounting for the metals recovered. So, not only is it helping the environment by creating a circular resource economy, but it is also saving valuable space on the island in the process.”
IBA produced by solid waste incinerator facilities can be processed (including metal and salt removal), and once the metal is extracted, the ash can be further processed for various applications. The end result makes the ash chemically and physically stable enough to be used as aggregates in non-infrastructure buildings, such as the construction of roads, footpaths and carparks, which means that the entire process leaves nothing to waste.
“The energy from incinerators (where IBA is generated from waste)
is connected to the power grid in Singapore, the metals are smelted and reused in a circular economy, and the ash is used to contribute to building and developing the nation,” Patnaik explains.
“Another fantastic aspect of this
process is that you become selfdependant on your utilisation of ash, so there is minimal or no need to import sand. This has the potential impact of reducing construction costs across Singapore.”
With waste being recycled in such
Mineral waste is a precious commodity: this insight gave rise to a corporate success story that benefits both REMEX customers and the environment. As a recycling company, REMEX organises the entire mineral material cycle by processing mineral waste such as construction waste and industrial by-products, making them usable again as quality-assured secondary aggregates. As a result, REMEX has been making a relevant contribution to the protection of resources for more than four decades.
- Sustainable mineral management demands extensive know-how and the utmost care, requiring knowledge from various specialist areas, in particular, environmental and waste law, as well as experts with corresponding experience in the construction sector and industry.
- A performance-driven team of highly qualified employees and long-term management with extensive industry experience are the foundation of REMEX’s corporate success.
- The services provided by REMEX in the field of mineral waste are complemented by the expertise of a large number of specialised subsidiaries and associated companies. As part of the REMONDIS Group, REMEX customers benefit from a worldwide network.
a manner, Singapore stands at the forefront of a self-sustaining urban nation, helping further development and environmental goals as a zerowaste country. REMEX is part of trial projects by the National Environment Agency (NEA), Singapore.
REMEX works actively with organisations such as NEA to ensure that its own operations and end results work towards the benefit of the planet, in ways such as safeguarding and preserving the environment alongside community areas.
“We are presently undertaking a plan with NEA to develop the processed ash (new sand) into the most environmentally friendly end result possible,” Patnaik tells us. “We have taken samples of IBA after metal recovery and sent them to our facility, HEROS, in the Netherlands, for the washing process, which is used in application as a trial project.
“Here, the materials made using the processed ash are tested when
it comes to aspects such as strength and chemical properties to help to understand the suitability of the final product in various applications.”
REMEX’s European research facility helps ensure that the end result aggregates, such as those used in roads, are monitored when it comes to material endurance and cohesion, and that unwanted chemicals are removed during the process in Singapore, so as not to impact the environment that surrounds the area of infrastructure when implemented.
REMEX is continually looking for ways to improve its operations, to lead to meaner and greener activities in Singapore, and this includes increasing metal recycling from processed ash. According to Patnaik, one major inroad in this area is the potential mining of Semakau Island, and there is good reason for it.
“There are millions of tonnes of ash that have been dumped there
for many decades, as processing and reusing the ash and metal like we do today is a relatively new method of operation in the grand scheme of the island’s use as a landfill,” he says.
“So now, Singapore is looking towards the possibility of mining the cells of Semakau landfill, excavating the decades-old ash to extract the metals to reuse metal free/stable ash for different applications, thus recreating space in Semakau landfill.”
With this planned operation, Singapore will not only continue its green path of resource recycling and reuse but also begin to act on its own past, giving the waste of the past a present-day purpose.
REMEX MINERALS SINGAPORE PTE LTD
Tel: +49 211 17160-0 www.remex.de
APAC Outlook, Africa Outlook, EME Outlook and North America Outlook are digital and print publications aimed at boardroom and hands-on decision-makers, reaching an audience of more than 800,000 people around the world; spanning the full range of industrial sectors.
With original and exclusive content compiled by our experienced editorial team, we look to promote the latest in engaging news, industry trends and success stories from across the globe. Your company can join the leading industry heavyweights enjoying the free exposure we provide across our platforms with a free marketing brochure, extensive social media saturation, enhanced B2B networking opportunities, and a readymade forum to attract new investment and to help you grow your business.
Visit www.outlookpublishing.com/get-involved for details on how your company can feature for free in one of our upcoming editions.
www.outlookpublishing.com/get-involved
Building on the global success of our regional titles – APAC Outlook, Africa Outlook, EME Outlook, and North America Outlook – Outlook Publishing is proud to be launching a dedicated platform for the Mining & Resources sector.
As mining organisations worldwide confront unprecedented change, embracing technological innovations and incorporating critical environmental sustainability agendas, now more than ever is the time to showcase the strides being taken in this dynamic sector.
A multi-channel brand, Mining Outlook will bring you the positive developments driven by organisations across the global mining industry through our various platforms. Discover exclusive content distributed through our website, online magazine, social media channels, and dispatches delivered straight to your inbox with a bi-weekly newsletter.
Through this compelling new venture, we intend to foreground the movers and shakers of the industry. To participate as a featured company and join us in this exciting endeavour, contact one of our Project Managers today.
www.mining-outlook.com
Driven by a dedicated workforce and green, innovative thinking, Hitachi Construction Machinery Australia brings quality products and solutions to the Australian market. We speak to Sean Ryan, General Manager of Mining, to learn more
Australian mining is a vast and historic industry that moves with the times.
Today, the success of operations in the field comes down to the latest technology, and the calibre of the machinery involved, supplied by toptier players backed by decades in the industry.
Hitachi Construction Machinery (Australia) Pty Ltd (HCA) is a subsidiary of Hitachi Construction Machinery Co., Ltd (Japan) and part of the global Hitachi Construction Machinery Group. HCA is the exclusive distributor of Hitachi and Bell products in Australia.
“Our overall company mission is to contribute to society with superior products,” begins Sean Ryan, General Manager of Mining at
HCA, introducing HCM’s central and founding purpose that is mirrored in each of its international divisions.
“Hitachi founder Namihei Odaira’s sincere belief to “contribute to society through the development of superior, original technology and products” has been handed down from Hitachi today to form the basis of HCM’s operations around the globe. Our century-long history is one of giving shape to this mission, supporting society, and realising a more comfortable and safer world through our technologies and products - this mission is reflected in HCA.”
This mission is what stood out to Ryan upon first joining the company. He started his career as a tradesmen assistant in the early 1990’s with the previous Hitachi dealer in Australia (Marubeni, Brisbane) and after a few months, was able to start an apprenticeship with the branch as a diesel fitter. Upon receiving a trade qualification and introduction through the global dealer network, Ryan was fortunate enough to work abroad with Hitachi in the UK. After a few years, he went to university back in Brisbane and studied a Bachelor of Technology in Mechanical Engineering and subsequently continued tertiary qualifications with a Masters in Engineering Management, and Graduate Certificate in Business Administration.
“Since graduating, I have had the opportunity to work in many fields of heavy engineering such as mining with different OEMs over the last 20 years,” Ryan says. “The last seven years have been back home with HCA in the mining sales department, where I’ve since been promoted to the role of General Manager of Mining for the last six months. It is incredibly refreshing to be part of an organisation that not only talks environmental, social and governance (ESG) but actually puts it into everyday engagement with customers, employees and the community.”
HCA is committed to delivering machinery sales, parts and support to Australian customers across the mining, construction, quarry, material handling and recycling industries, through a wholly owned national branch network of 23 sites across Australia, including three remanufacturing facilities and two mining assembly facilities. With over 1,200 employees, HCA is equipped to provide 24/7 customer support and field representatives across Australia’s regions.
On top of this, being partnered with Marubeni Equipment Finance, HCA is in a position to provide in-house finance to its customers, adding an extra facet to the company’s industryleading offers.
“Our values emulate the founding spirit of Hitachi, and have been embraced with care and guided by our predecessors for over a century,” Ryan says, reinforcing the core of the company. “This spirit resonates through the way we think and operate as we collectively strive to deliver solutions that create new value globally.”
HCA’s vision is an expression of what Hitachi aims to become in the future; to achieve greater advancements, to address today’s global challenges in resources, energy
and the environment, and build a sustainable society.
In light of this, HCA has invested heavily in technology, with its product range driven by Wenco International, a wholly owned subsidiary of Hitachi, that offers an integrated suite of solutions to support the digital transformation of the mining industry. Fleet management, asset health, data analytics, and other technologies join together in the spirit of open interoperability to raise mine productivity and efficiency, lower routine costs, and establish a safe and smooth mining operation.
“Our autonomous systems for mining equipment are developing very rapidly, with solutions for our electric drive dump trucks now operating in the mining space,” Ryan adds. “On top of this, the future of operator assistance technology in excavators is well under development and on trial at different sites around the globe.”
We are focused on being a market leader In wear solutions globally.
We understand the business needs of our customers, their pain points, measures of success, and technical and performance requirements of their equipment and operations.
We utilise our unique knowledge, experience and capabilities to help our customers achieve their goals. With a focus on safety, collaboration, innovation and sustainability across all aspects of our business we deliver reliability, certainty and confidence to all our partners and stakeholders through consistent delivery of our products, services and solutions.
We specialise in solving our mining customers’ wear challenges, supporting their bulk handling and mobile equipment to operate at peak efficiency by deploying our significant experience to design, manufacture and supply high quality solutions.
EXCAVATORS - Machines guaranteed to provide world-class performance, sophisticated design and legendary reliability.
RIGID DUMP TRUCKS – HCA’s rigid dump trucks (RDT) are designed with superior hauling capabilities and industry-leading technology.
ARTICULATED DUMP TRUCKS –HCA’s articulated dump trucks (ADT) excel in productivity due to their high power-to-weight ratios and fuel efficiency.
WHEEL LOADERS - Wheel loaders are suitable for a range of applications thanks to their dynamic design and myriad optional attachments.
HCA’s success is not just down to the metals and machinery. At the heart of the company lies a team of talented and dedicated people committed to providing such industry-leading solutions, making HCA the perfect industry partner and keeping it at the forefront of the market.
For Ryan, every employee at HCA helps to build the company, and with branches across Australia, HCA offers a wide range of careers and job opportunities for those seeking to become and stay involved in the mining machinery space.
“We’re proud to be an equal opportunity employer that recruits based on merit and capabilities. We encourage and support a talent pool of diverse skills, ethnicities and genders, to create a vast culture of shared values and enriched experiences in our business,” Ryan tells us proudly.
“Along with a variety of employee benefits, HCA offers employees competitive wages and biannual discretionary bonuses to recognise positive contributions being made to the business throughout the financial year. In order to empower our people, we focus on fostering open communication and set clear expectations to provide employees with autonomy to manage their responsibilities accordingly.”
HCA provides continuous training and education to all its staff to ensure the right opportunities are given, promoting rewarding and successful careers with longevity in the business. According to Ryan, it is common for a career at HCA to start at an apprentice level, before progressing through one of the many other career path options.
HCA offers a suite of solutions for customers. This includes technology-based solutions that monitor machine performance, provide reporting and applications that can be used on mobile devices, and are available on Apple and Android phones for technical support and 24/7 nationwide customer service and support. Also available to HCA customers are premium service agreements that can provide discounts on machine servicing and other benefits.
SUPPORT – HCA’s experienced factory-trained technicians and product support representatives are on call to ensure customer machinery operates to the highest standards.
PREMIUM SERVICE AGREEMENT
– HCA’s contracts and agreements are tailored to fit customer business needs and range from maintenance and repairs to performance guarantees.
TECHNOLOGY - A suite of technology products offers equipment tracking, maintenance, daily operating information, and equipment health conditions.
HCA’s market-leading apprenticeships run in conjunction with TAFE NSW (TAFE) courses and align with the government’s Australian Apprentices Incentives Program (AAIP). The programme provides apprentices with hands-on experience and training to become heavy vehicle mobile equipment (HVME) mechanics and automotive electricians.
“These practical apprenticeship programmes are ideal for interested school students or mature-age students and are available at all major HCA branches across Australia, in every state and territory,” Ryan continues.
“The training and education strategy focuses on guiding career pathways and development to suit our staff’s needs and the requirements of the business. Course offerings include qualifications and career path options for service, parts, sales and administrative roles, with topical areas including management, supervision, technical, customer service, and business systems compliance.”
HCM offers a number of mining products and technologies in the market which customers can take advantage of in order to reduce their environmental footprint and lower their carbon emissions. The trolley truck and electric excavators are proven pieces of equipment, with HCA supplying several fleets globally,
and over 130 excavators respectively delivered into the market outside of Australia.
As well as providing environmentally friendly solutions which leverage Hitachi’s innovation and proven technology to deliver greater value to customers, HCA can convert existing fleets of trucks, trolleys and excavators to electric vehicles (EVs).
“The key to any future zero emission plans will be the infrastructure on the mine site to support electrification and any changes to mining applications, even if it’s to the detriment of production initially,” explains Ryan.
“12 months ago, I felt these were the areas which were going to hold the industry back, however we are very quickly seeing mining personnel get their heads around these requirements along with industry bodies and driving change a lot quicker than previously realised.”
Australian owned and operated business supporting the heavy earthmoving industry for over 30 years. We are proud of our commitment to safely deliver exceptional quality repairs and work closely with OEMs. Our purposebuilt facility in the NSW Hunter Valley overhaul components for Hitachi including front spindles, trailing arms, hubs, axles, boxes and specialist repairs on undercarriages from EX3600 through to EX8000 machines.
02 4932 7379 • admin@jsengineering.com.au www.jsengineering.com.au
The mining industry is already seeing the effects of climate change influence its business activities, with long-term sustainability targets now in place. As these targets and regulatory requirements approach, HCA is prioritising options to support this energy transition in the form of dynamic and static charging systems for battery dump trucks and battery/hybrid excavators.
In the immediate future, HCA will be releasing its first EX2000-7 (200tonne) excavator into the Australian market in March 2023. The model will be on display for a customer launch event at HCA’s Perth branch, where the company will also showcase the investment made at its new purposebuilt facility for mining assembly and component remanufacturing. This will align the last piece to the puzzle for the multi-million-dollar investment HCA made to support operations within the Western Australian (WA) region.
“The EX2000-7 joins the full dash seven mining excavator product range and replaces the EX19006,” Ryan notes. “Built from over 50 years of reliable hydraulic excavator history, it has the latest technologies from HCA including electronic pump regulations, updated fan speed control, regeneration valves, improved efficient cooling package and hydraulic controls all leading to 18 percent fuel saving over its previous model in this class – truly a mining machine of tomorrow.”
HITACHI CONSTRUCTION MACHINERY AUSTRALIA www.hitachicm.com.au
Parabellum International has grown impressively to become a leading emergency response and medical services provider across Australia and now the world. We speak to CEO, Navin Vij about the company’s people-centric safety mission, its services and the impressive scale of its fleet
We don’t just train emergency response; we create emergency responders. We’re in a very privileged position to genuinely save people’s lives, which means they go home to their families.”
This powerful opening statement reflects how Parabellum International (Parabellum) has worked relentlessly to claw its way into the highest echelons of the provision of emergency response, medical services, comprehensive risk management and elite training services. A true global leader in its field, Parabellum has become deeply embedded within both the onshore and offshore oil, gas, mining, defence, resources, energy, waste, construction, and government sectors. The company’s proven operational experience within high-risk and remote locations remains a global differentiator.
Dedicated to providing unrivalled emergency, medical response and risk management services across these select industries, Parabellum holds multiple long-term master services agreements supporting clients worldwide on some of the largest capital and operational projects, ensuring safe and dependable support throughout.
The company’s international exposure and long-term partnerships across a multitude of companies and projects concerning the management of risk, allow Parabellum to effectively anticipate and minimise these dangers, provide significant cost savings and simplify the on-site emergency and safety operations for its clients.
The risk management services provided by Parabellum deal flexibly with personnel, vehicles, equipment, plans, procedures and ongoing evaluation of on-site services. The company possesses unique experience in providing exclusively tailored solutions to ensure the safety of people and projects and aims to deliver “measurable value”
across the entire project life cycle so that deadlines are met safely, on time and within budget.
As a burgeoning entrepreneur from an early age, Navin Vij, CEO of Parabellum, knew his talents lay in building businesses and creating compelling careers for his people from the ground up.
“I always knew I had a business side to myself,” recalls Vij.
“Having already created businesses while I was undertaking my management and finance degree at a local university here in Perth, I built an electronics, wholesale and distribution company. It was then in 2010 I started Parabellum.
“The mining and oil and gas industries were getting a lot busier in Perth,” he continues. “There was a bit of a boom happening, so I identified an opportunity to provide some basic
Working collaboratively with Parabellum International since 2016, we have been its go-to company for all its vehicle and building signage, as well as expertly handling a vast range of general promotional displays and graphics.
We regularly prepare all of the company’s emergency response vehicles with the necessary graphics and reflective striping to ensure they not only look great, but offer a professional presence for the company and adhere to mine site requirements.
We have worked tirelessly to forge an established reputation for being reliable, able to work and thriving under pressure, while always retaining high attention to detail.
designandapply.com.au
NAVIN VIJ, CEO, PARABELLUM INTERNATIONAL: “A big part of our emergency response and safety operations is that we can transfer lifesaving learnings into day-to-day life. When we help enhance medical or emergency awareness it means we’ve contributed something that may one day help to save a life.
“For example, recently a client had attended one of our training courses for work. Sometime later, they tragically had a family member suffer a heart attack. But, because of the training they had received from us, they played a crucial role in helping to save that family member’s life.
“So, for us as a company, that’s just one of the many rewarding things that we get to do on a daily basis and really make a tangible difference in this world.”
health and safety support to companies in this sector. I was only 22 at the time, but I was willing to learn and work from the front line and I am proud to say we’re still here 12 years later.”
One of the key reasons for this longevity, and survival in what is now such a competitive industry, is that Parabellum offers a comprehensive, well-rounded and diverse array
of services, adaptable to any environment.
“If it’s firefighting, we’ve got trucks, fire stations, firefighters, firefighting equipment, and we’ll provide a full private fire service for projects or operating assets,” Vij explains.
“In the medical space, we’ve got paramedics, doctors, nurses, medical clinics, and ambulances. So, we can
supply a private, full-service delivery, that supports and protects people,” he adds.
“In training, we are a leading Registered Training Organisation dedicated to delivering best in class training exclusively to our industries. We don’t do high volume cookie cutter training courses; we specialise in providing world class training and improving our industries only!”
Elsewhere, Parabellum also delivers safety and medical care training to local communities, with the aim of leaving a lasting legacy of skill development locally after a project’s completion. This has been carried out in the Pacific Islands and Asia, as Parabellum transfers its knowledge to local populations.
“This is a very important aspect for us, not just to come in and deliver services, but to develop local skills and safety capability and improve the community that gave us a license to operate.”
Established in 2010, our highly skilled and experienced team have been creating signage and vehicle graphics for a wide range of WA businesses across a variety of industries. From fleet graphics to building signage, we ensure your brand gets noticed and meets all necessary mine-spec requirements when going to remote work sites. We are a preferred signage supplier for several companies throughout Perth, with a reputation for high quality work, meticulous attention to detail, and adhering to strict deadlines. Simply put, you can rely on us for a professional service and quality result, every time. 5 Jones Street, O’Connor WA | 1300 420 111 | sales@designandapply.com.au | designandapply.com.auVij believes that the collective skillset possessed by Parabellum is applicable and transferable across industries.
“Whether it’s government or private, there’s always risk. Everything we do in this world on a day-today basis has varying levels of risk, whether it’s driving a car to and from home, climbing a ladder, or completing major capital projects, there are always levels of risk which must be mitigated,” he explains.
Parabellum has a proven and highly successful track record of aiding the largest and most technically capable Tier 1 companies in their supply chain, not just with traditional services but by actually helping them to run entire projects, on the way to becoming an overall service delivery company.
“At present, we are building medical clinics, fire stations, administration buildings and other major infrastructure, constantly looking to
diversify sensibly,” Vij reveals.
Further to this, Parabellum has helped many companies operating in Australia for the first time, who may not be aware of the local way of working, standards, processes, or how to transition a project smoothly through a design, construction and operation phase.
When discussing the next 12 months that lie ahead for Parabellum, Vij describes an exciting and detailed vision of continued expansion for the company.
“We’ve got significant growth coming up in Australia, as well as further plans for the entire AsiaPacific region. So as the next 12, 24 and 36 months unfold, we hope to see significant expansion into Southeast Asia and the Pacific islands, and the continued development in our local markets,” he explains.
Parabellum already possesses an operating base in Singapore, upon which the company hopes to
springboard into further success across the continent. This hub will prove essential in the ability to support new emerging technologies in hydrogen, waste, and power, as well as constructing new operating bases.
Parabellum’s clients enjoy unrivalled access to the company’s esteemed fleet of emergency response and medical vehicles. This includes the option to use a range of light tankers, ambulances, fire appliances and trailers for hire, for medium- or longterm engagements, or alternatively, a custom design and build for an outright purchase.
Going above and beyond by striving to be the best the company can be, and by challenging the status quo.
Making a difference in the lives of others, each other and all those that Parabellum impacts.
Parabellum tells it like it is, even if the message is difficult to deliver; it is important to communicate what you need to hear, not what you want to hear.
Parabellum looks after all its staff and clients. The company is inclusive and respects others, with an opendoor approach.
Parabellum makes things happen; acting quickly without compromising company standards is essential, as well as thinking outside the box to solve a problem.
These highly effective vehicles can be supplied as dry hire or fully stowed, featuring all the required emergency response or medical equipment to suit capital or operational expenditure requirements and budgets.
Other models available within Parabellum’s fleet include specialist Aviation Rescue Fire Fighting (ARFF) appliances, confined space rescue and breathing apparatus trailers, and fully equipped containers and relocatable buildings.
Additionally, Parabellum continues to pursue the electrification of its fleet of vehicles. In this way, the company is aiming to transition away from the traditional diesel range and embrace hybrid technology, which brings innovation, reduced emissions, as well as renewed reliability.
Parabellum’s reputation for uncompromising quality has been hard-earned through the efforts of its
highly professional team’s devotion to craft and care. The company’s foundations are built upon a collective of high-calibre, best-in-class service professionals that act with trust and integrity at all times.
Keenly aware of the need to find people perfectly aligned with Parabellum’s core values, before joining such a specialist team, Vij tells us how it is critical to recognise key qualities and traits from the inception of a new working relationship.
“The final evaluation before we hire anyone is, do they match our culture, do they believe, and do they share our company mindset. This process has been critical in bringing the right personnel into our teams,” he expands.
He continues to tell us, “for Parabellum, having visibility, trust and sharing a collective vision has been vital to the company’s success because everyone in the team believes in what we’re doing.”
This shared responsibility and
mentality of the company culture that Parabellum works so hard to foster, aligns every level of the company to one total vision, from paramedics and firefighters on the ground to every level of management, as well as external players such as subcontractors and suppliers.
“These values are non-negotiable. No matter what level, everyone is expected to help their team – no job is too small or unimportant,” Vij concludes firmly.
“At Parabellum, we do not compromise on standards; we are steadfast in our resolve to deliver on our promise to our clients.”
Despite experiencing increasing pressure to transform our business to keep pace with rapidly evolving customer preferences, digital disruption and environmental, social and governance (ESG) issues, we are focused on pursuing long-term transactions for future business growth.”
This bold opening statement from Alvin Prasad, General Manager of Hardware Haus, reflects the fearless ambition and hunger for success in the face of adversity, that drives this essential cornerstone of the mining and construction industry across Papua New Guinea (PNG).
Hardware Haus has worked tirelessly to become the leading supplier and one-stop shop for hardware, building and mining supplies in PNG.
Ever since 1970, the mining industry has dominated PNG’s national economy. The mineral exports that contribute to this dominant sector
include the mass extraction of gold, copper, silver, nickel and cobalt.
PNG is home to a swathe of mines spread across the country, the largest of which include the Ok Tedi copper and gold mine, Porgera gold mine, Lihir gold mine, Hidden Valley gold mine, Simberi gold mine, Tolukuma gold mine, and Ramu nickel mine.
Far from smooth sailing, the mining sector continues to face a range of competing trends and the hurdles of a rapidly changing global business environment.
Against the challenging backdrop of commodity price fluctuations, miners must balance shareholder dividend expectations whilst maintaining an investment pipeline as operating costs increase.
Safety, environmental and community principles also continue to shape the mining industry in PNG as miners look to secure their licence to operate and deliver on corporate responsibilities.
We speak to Alvin Prasad, General Manager of Hardware Haus, regarding Papua New Guinea’s construction and mining retail industry and the company’s latest developments in the space
In addition to the ongoing challenges present within the global mining landscape, mining companies in PNG must deal with additional complexities, such as balancing the government’s wishes for development, the requirements of communities and resource owners, and the battle for environmental sustainability.
Despite these copious obstacles, PNG is located in a highly prospective region and the opportunity for largescale development is still significant.
The City Pharmacy Limited (CPL) Group stands proudly as PNG’s leading retailer since 1987.
Forming a crucial part of the CPL family of companies, Hardware Haus has grown to become the largest retailer within a highly competitive sector in PNG.
As the nation’s largest wholesale organisation, listed on the Port Moresby stock exchange, the company started as the City Pharmacy chain, bringing essential primary healthcare support to citizens across the nation.
CPL Group has established itself as one of PNG’s pre-eminent corporations through its strategic acquisitions of the Stop & Shop supermarket chain in Port Moresby in 2005 and similarly the Hardware Haus brand in 2009, continuing to partner with multiple brands ever since on its singular mission to bring new products and services to the people of PNG.
“Our expanded supplier network across both PNG and overseas gives us a unique competitive advantage with great pricing and a wider range for our customers,” adds Prasad.
Crucial to becoming one of the nation’s most trusted brands, the company has grown to include 13 shops nationwide.
The expansion achieved by Hardware Haus now adds up to represent a significant presence spread across PNG, including retail outlets in Port Moresby, Lae, Hagen, Goroka, Wewak, Maprik, Madang, Kavieng, Kokopo and Popondetta. This extended company footprint now sets Hardware Haus apart from its direct competitors as the brand can now be found in all major towns.
“We provide product expertise on various large to medium and smallscale projects. Hardware Haus is not just a store, it is where quality meets affordability,” Prasad tells us.
“What has been crucial for us is building a culture of trust by delivering honest feedback whilst also showing empathy at all times,” he outlines.
Elsewhere, Hardware Haus also continues to participate in carefully selected social initiatives, mainly engaging in charity work, improving its labour policies, and investing in environmentally conscious businesses to name a few.
In a world still recuperating from the traumatic effects on all industries in the wake of COVID-19, Hardware Haus is now implementing a strategic forecast and planning stage to identify and gain potential opportunities and growth despite the current global economic challenges.
The expert team at Hardware Haus is undoubtedly its greatest asset, so the company continues to invest in the growth and development of its
staff members and leaders.
Committed to building a team that does the right thing for the surrounding communities, all shareholders and above all its customers, Hardware Haus also prides itself as an equal opportunities employer.
“Whether we’re looking to start a new venture or simply collaborate with another brand in the market, we need to prove ourselves to industry veterans,” Prasad tells us.
“Open communication is fostered, and we encourage everyone to be purpose-driven by delegating responsibilities and tasks, while at the same time supporting and rewarding growth opportunities. We believe in shaping our staff; thereafter, they shape us,” he adds.
As a purpose-driven company, Hardware Haus knows how vital it is to draw on shared values and behaviours in order to bring that collective purpose to life.
To help its team members and partners do that each day, the company adheres to a strict code of ethics which represents the values and the promises made to Hardware Haus’ guests, team, stakeholders, communities and the wider CPL Group brand. It is this dedication to high standards that ensures the future looks unanimously positive for this titan of the hardware retail sector in PNG.
“OUR EXPANDED SUPPLIER NETWORK IN BOTH PNG AND OVERSEAS GIVES US A UNIQUE COMPETITIVE ADVANTAGE WITH GREAT PRICING AND A WIDER RANGE FOR OUR CUSTOMERS”
– ALVIN PRASAD, GENERAL MANAGER, HARDWARE HAUS
The mining industry today has enormous potential to transform and be part of a more sustainable future.
Historically, mining has had a less than desirable reputation, but what is often neglected is the fact that the industry is the raw material source of the majority of everyday products, materials and technologies that make modern living possible.
Mining has come a long way in rectifying its reputation, but what excites Jacob Deysel, Managing Director and CEO of Mineral Commodities (MRC), is being part of the responsible and sustainable transformation of the industry.
“The driving force for me now is about creating a legacy, and the mining industry is well-positioned to make a difference not just today, but for generations to come,” he shares.
“There is no other industry that has the potential to drive economic development, uplift host communities, or the ability to make such massive changes to ensure sustainability and responsibility, not to mention the importance of mining to sustainably source the materials required for energy systems and a low-carbon future.”
To fuel this transition, there is an urgent need to ramp up the production of critical minerals and metals.
This is one of Deysel’s biggest daily motivations, knowing that MRC can make a lasting difference where it operates, both in the communities and more broadly through supplying materials to build a sustainable future.
“I am proud to be leading MRC, as we have taken exactly this approach,” he affirms.
MRC’s mission proudly states its intent in this regard: to be a leader in the transformation of mining towards ensuring a positive contribution to a sustainable world.
“We need young leaders with progressive and outside-the-box thinking to drive the industry to support a responsible approach, and become a player towards a sustainable world.
No other industry has this much potential, and it’s extremely exciting to be part of this transition,” continues Deysel.
As a mining engineer, Deysel is extremely fortunate to have worked in several roles across a number of exciting commodities and companies in the mining industry over the past 20 years.
But MRC is unique, with established operations in both heavy minerals as well as the critical battery minerals space.
“We have excellent, world-class assets with our two operational mines, the Tormin mineral sands operation on the west coast of South Africa,
and Skaland, our graphite mine in Norway,” Deysel informs us.
“We also have an additional graphite development project in Munglinup, Western Australia (WA), and exciting exploration upside at both our existing heavy minerals and battery minerals operations,” he adds.
Tormin consists of a number of high-grade placer beach and strandline mineral sands deposits, hosting some of the richest grades of naturally occurring zircon, ilmenite, rutile, magnetite, and garnet.
The high-grade placer beach deposits at Tormin are unique due to the rate that mining areas are naturally refurbished, and the speed at which the minerals actively replenish.
Heavy minerals are regularly
replenished by new sediments from deeper waters, which occurs as a result of the naturally high dynamic nature of sediment transport processes on beaches in this area.
“Tormin employs just over 300 employees, and last year alone we contributed over ZAR400 million in local procurement expenditure in South Africa,” shares Deysel.
MRC is set apart from many of its peers in the industry by Tormin, as it has been a cashflow generative heavy mineral sands operation ever since its inception in 2015.
There is excitement around the recently announced, fully funded growth projects at Tormin, targeting both increased scale and profitability which will further strengthen performance.
“BEING PART OF THE GREEN TRANSITION AND KNOWING WE CONTRIBUTE TO MAKING THE WORLD MORE SUSTAINABLE IS CLOSE TO MY HEART”
–
MANAGING DIRECTOR AND CEO, MINERAL COMMODITIES
Skaland, meanwhile, is the only graphite mine in Scandinavia, the biggest crystalline graphite producer in Europe, and the fourth-largest producer globally outside of China.
MRC acquired Skaland Graphite AS, the owner and operator of the Skaland mine, in 2019, and the development of the Munglinup graphite project builds on this acquisition.
Just over 40 people are employed at MRC’s Skaland operations, which is a significant economic driver in the host community.
“It is a further step towards an integrated, downstream value-adding strategy, which aims to capitalise on the fast-growing demand for sustainably manufactured lithium-ion batteries,” Deysel says.
Decarbonisation is certainly one of the largest current megatrends when it comes to the battery minerals sector.
Europe, for instance, is seeing unprecedented increases in planned lithium-ion battery production capacity, driving the demand for increase graphitic anode manufacturing capacity on the continent.
pre-feasibility study in 2010 with targeted commercial production late in 2024, ramping up conservatively to between 40 and 70ktpa of anode material production,” Deysel outlines.
“Given that Europe requires between 800 and 1,000ktpa of anode material, our production will be less than 10 percent of demand, leaving significant room for growth.”
For both MRC’s heavy minerals and battery minerals divisions, funding support has recently been announced for the company’s growth strategy.
MRC is committed to being a responsible corporate citizen, implementing strategies that focus on key aspects such as health, education, and infrastructure.
Substantial initiatives are made in local communities and various programmes in order to provide practical and collaborative support, and encouragement for further growth.
“These are all initiatives that invest in our future and leave a lasting and positive impact,” Deysel says.
MRC’s engagement with communities enables people to generate and maintain sustainable livelihoods.
Not only is MRC one of very few companies with a fully permitted graphite mining operation, but Skaland is also one of the highestgrade flake graphite operations in the world, accounting for around two percent of global annual production.
“We have proven environmentally friendly anode production technology, established key partnerships, and are in the process of qualifying anode samples with customers.
“We are therefore extremely well positioned to become one of the most sustainable graphitic anode producers in Europe, to take advantage of the green transition, and to responsibly contribute to global demand for battery minerals. We will combine our world-class graphite assets in Europe and Australia to achieve economies of scale,” adds Deysel.
The existing European graphite operation at Skaland shouldn’t be underestimated, as MRC believes it can be expanded from 16 kilotons per annum (ktpa) to 25ktpa.
Equally, a definitive feasibility study completed in 2020 for the Munglinup graphite project, with an estimated production target of 52ktpa, presents a significant production upside.
“Both these deposits have significant expansion potential. We completed an anode production
MRC’s priority is on near-term cashflow generative and future growth strategies within the heavy minerals division, ahead of mediumterm future growth strategic projects in battery minerals.
“Regarding our heavy minerals division, we are in the process of finalising the extension of our operations beyond the existing beaches to target our Tormin Inland Strand deposits,” Deysel details.
“This will greatly improve our flexibility, enhance our production profile, and is due to be commissioned in Q4 2022.”
The new funds will be applied to a third primary concentration plant (PCP), increasing overall plant capacity and targeting an increase in concentrate production.
Downstream integration will also transition into higher value finished products that target enhanced profitability, whilst studies for a future bulk mining unit will target a significant increase in production profile to ensure all available minerals are mined.
The funding will also enable resource and reserve development, to support a larger production footprint.
“As far as the battery minerals division is concerned, funding will enable the development of a battery anode pilot plant, utilising Skaland and Munglinup graphite feed,” reveals Deysel.
“It de-risks our commercial-scale development of battery anodes, delivers larger qualification samples that will support and secure battery anode offtake agreements, and accelerates the development and financial investment decision of our Munglinup graphite project.”
MRC’s heavy minerals division has been instrumental in the company’s battery minerals development.
This was not by chance, either, but part of a carefully considered diversification strategy, having recognised early on that there are enormous opportunities being brought about by the decarbonisation of transport.
“Graphite specifically is being overlooked by the market. Everyone is aware of lithium and the excitement around it, however graphite makes up more than 50 percent of the active ingredients in lithium-ion batteries,” Deysel says.
“It is important to understand MRC is not simply another graphite project company. The advantage we have is the fact that we have an established operation in Europe.”
Indeed, whilst many of MRC’s competitors have permits or prospect rights in Europe, merely having a deposit or permit does not translate into a mine.
Further, not all graphite is suitable for producing anode material, there are significant barriers to entry, and Europe is relatively new to the mining space.
“There is a strong sentiment towards “not in my backyard”, so when we developed our strategy, we looked at our competitive advantages,” explains Deysel.
Aside from having an established, strategically positioned operating mine, MRC looked at scale, technology, operational capacity, and marketing.
MRC’s Munglinup project complements its diversification
Mineral Commodities is collaborating with Mitsubishi, an established market leader in the production and supply of anode materialsstrategy as it gives the company further scale, whilst developing an anode strategy moves MRC from mining into technology.
“This is where our collaboration with the Australian national science agency, CSIRO, allowed us to develop a proven, environmentally friendly anode production technology, which is now at its pilot stage.
“We are also collaborating with Mitsubishi, an established market leader in the production and supply of anode materials with extensive expertise in anode material qualification, marketing and sales,” Deysel says.
Another aspect that MRC considers is its carbon footprint. Norway has been identified as the location of its downstream anode production facilities, giving the company access to renewable energy and supporting its strong environmental, social, and governance (ESG) goals.
There are also security and supply concentration considerations, with close to 100 percent of all anode material being produced and/or supplied by China.
“With both our Skaland graphite operation in Norway and Munglinup development project in WA, located in what we consider Tier 1 locations, MRC is extremely well positioned to take advantage of the lithium-ion battery opportunity in Europe,” states Deysel.
Mining companies in the future will not be able to exist if leaders do not start to take the importance of ESG to heart.
“I am talking about real intent, not simply greenwashing the business. Our vision for MRC is to pivot the business with a strong ESG focus, engrained as part of the MRC fabric.
“This is an enormous task, but it is exciting, and I see this as a crucial part of the new era of mining,” Deysel beams.
– JACOB DEYSEL, MANAGING DIRECTOR AND CEO, MINERAL COMMODITIESMRC’s commitment to the sustainable and responsible production of critical and industrial minerals and products represent a clear intent for mining and industrial practices.
This will require strong leadership to drive a cultural shift towards accountability, a deep understanding of the environmental and socio-economic impact of the company’s operations on stakeholders, and a move towards collaboration and cooperation.
Highly focused on good corporate citizenship, whilst maintaining its focus on long-term sustainable returns for all stakeholders, MRC’s core values of zero harm, respect, integrity, innovation, and inclusion as the foundation for all its actions are unwavering.
“Repositioning the company as a diversified, sustainable and responsible producer of critical and industrial minerals lowers investment risk and is intended to attract a larger potential investor target market,” Deysel tells us.
“I do not think investors currently understand or fully appreciate MRC’s value proposition. We are a diversified
mining company with established operations in both heavy and battery minerals. As we see it, we offer investors an immediate cashflow opportunity with significant mediumterm growth potential.”
MRC’s strong focus on ESG is one of four key objectives to revive the company, unlock its potential, and make it a stronger, sustainable, consistent, and responsible company.
As well as continuing to improve its social license, empathetic of its impact on communities and achieving best practice compliance with sustainability frameworks and good corporate citizenship, MRC seeks consistently superior operational performance, and profitable growth opportunities.
“Throughout our portfolio, we will seek vertical integration, from mining and associated processing to valueadded downstream products and to profitably grow our footprint.
“This is an exciting journey we have embarked on, and I have a firm belief that MRC is a company that sets itself apart from its competitors,” Deysel concludes.
“THE DRIVING FORCE FOR ME NOW IS ABOUT CREATING A LEGACY, AND THE MINING INDUSTRY IS WELL-POSITIONED TO MAKE A DIFFERENCE NOT JUST TODAY, BUT FOR GENERATIONS TO COME”
Although it has been a challenging and difficult time in the construction industry for Australia, I believe there is significant opportunity now and in the future. We see huge potential in the four sectors in which we operate, particularly resources, energy and infrastructure.”
In 1978, Decmil Group (Decmil) was established in Western Australia (WA) as an industry partner that delivered construction and engineering services at a time of regional growth. It was not long after, in 1980, that the company was awarded its first major resources contract by salt producer Dampier Salt Limited, and its first major energy contract eight years later through Woodside Energy.
From these early days, Decmil has grown from strength to strength, building on its skills, expertise and industry recognition to undertake further contracts with key industry
Decmil Group is helping build a better Australia. We speak to CEO Rod Heale about the company’s 40 years of experience in construction and development projects for infrastructure, energy, mining, and for local communities
participants. The arrival of the millennium saw Decmil construct an accommodation camp for Apache Energy in 2003, the first of its kind for the company. The 2000s saw continued success for Decmil as it was awarded numerous government infrastructure projects, as well as contracts by the likes of Chevron, Rio Tinto, and Burrup Fertilisers. Consequently, Decmil was listed on the Australian Securities Exchange
(ASX) in 2005.
To this day, the company continues to grow and diversify, delivering projects throughout Australia with offices based in Perth, Brisbane and Melbourne.
“We have delivered integrated construction and engineering solutions for multi-disciplinary projects across the country,” comments Rod Heale, CEO of Decmil. “Outstanding project management and delivery, regardless of scale and complexity, underpin our approach to everything that we do.”
Impact Traffic and Transport Engineering are a team of highly skilled professionals with hands on, real-world experience that provide traffic engineering and design solutions on a number of major infrastructure projects.
As part of the VicConnect consortium with UGL and Arup, Decmil was awarded the major package of works by Rail Projects Victoria to deliver the Gippsland Line Upgrade as part of the Regional Rail Revival programme.
The Gippsland Line Upgrade will enable much-needed extra off-peak services such as track duplication, a crossing loop extension and second platforms at stations that will provide more opportunities for trains to pass each other. The project includes duplicating tracks, extending the Morwell crossing loop, upgrading level crossings and signalling, and second platforms. At present, the project is on track with the positive progression of the Bunyip, Longwarry and Morwell stations.
WA continues to be a region of positive growth, whilst Victoria –another key region of operation for Decmil - is currently in a transport construction boom. Indeed, over 160 major road and rail projects are currently being delivered across the state in what is being referred to as ‘Victoria’s Big Build’. Taking full advantage of this growth period, Decmil has recently completed the construction of the new Mordialloc Freeway, and is also delivering the Gippsland Line Upgrade rail projects alongside several road construction projects in the area.
“The future of the industry is looking very promising. In the eastern states of Australia, 60 wind farm projects are planned for the next five years with a total value of AUD$33 billion, and Decmil is currently delivering the Ryan Corner Wind Farm in Victoria,” Heale says.
We worked with valued partner Decmil on the Barwon Heads Road Upgrade Project and provided temporary traffic management services during tender and delivery stage, including drawings, traffic modelling and analysis. On this project, our modelling and analysis were used to support a series of road closures to complete critical civil and intersection works with a focus on minimising disruption to the community as well as minimising traffic delays.
Another major project - the Gippsland Line Upgrade Project delivered by the VicConnect Alliance -involved a series of station upgrades and track duplication between Melbourne and Traralgon, with complex traffic management interfaces. We worked in developing traffic management strategies for several work zone precincts which set the framework for how traffic would be managed during construction. Additionally, our team of Road Safety Auditors were engaged in many stages of construction to ensure the safe operation of the road network during construction.
Our difference is in our people:
• We are highly skilled with established reputations and on-the-ground experience.
• With vast experience and capabilities to deliver from start to finish, we have a unique approach that enables highly effective solutions that deliver tangible performance and safety outcomes at all levels.
impactaustralia.com.au
“According to the Department of Mines, Industry Regulation and Safety (DMIRS) mineral and petroleum industry activity review 2021 – 2022, there are also extensive future opportunities in the resources sector in WA, with AUD$57 billion-worth of projects under construction or committed already. A further AUD$87 billion of projects are in the feasibility/ pre-feasibility study stage, and exploration spending is at a record level of AUD$2.5 billion.”
In the fiscal year (FY) 2022, Decmil counted 30 different projects – either in completion or in progress – across the whole of Australia. Over the next four years, AUD$75 billion of
infrastructure projects have been announced or are currently under procurement in Victoria, WA, and Queensland in road and rail transport projects.
Decmil has also delivered a number of projects in regional Queensland for the Department of Transport and Main Roads, including various Bruce Highway upgrade projects, Warrego Highway in Chinchilla and Capricorn Highway.
ROD HEALE, CEO: “We commenced work in April of this year for the government of WA – the Department of Finance Building Management and Works - for expansion and upgrades to the Karratha Senior High School.
“The contract, scheduled to be completed in April 2023, includes the construction of a new building consisting of workshops, classrooms, teachers’ study and support services, extensions to the existing building to provide new offices, meeting rooms, reprographics and student wellness rooms, as well as refurbishment and extension of the existing metal workshop.
“Working for the community is very important to all of us at Decmil, and we are proud to be undertaking this project for Karratha Senior High School.”
Decmil’s history establishes the company as a key construction player in the Australian infrastructure space. Backed by over 40 years of experience in the sector, Decmil’s infrastructure expertise envelopes high-quality construction, fabrication and civil works across project lifecycles.
Transportation infrastructure forms a significant part of the company’s projects, each of which vary in scope and complexity. From major highways that include complex interchange designs and bridges, to extensive rail networks, Decmil’s professionalism can be seen across the country.
“We have completed various major projects for clients such as VicRoads and Major Roads Projects Victoria over the years including the Plenty Road Duplication Stage 1 and Stage 2, the Drysdale Bypass, various Princess Highway construction projects, and the Mordialloc Freeway Project,” Heale explains. “We have successfully completed a great number of projects for Main Roads Western Australia (MRWA), including the Reid Highway Upgrade (Altone to West Swan Road), the Wooroloo Great Eastern Highway Realignment, and the Roy Hill - Munjina Road bridge.”
In a joint venture with McConnell Dowell, and in partnership with Major Road Projects Victoria, Decmil delivered exceptional outcomes for the Mordialloc Project, providing many economic and social benefits for the broader community and exceeding all state requirements. This included over AUD$4.3 million Aboriginal business spending, and over 45,000 hours of employment for local Aboriginal workers.
“The project was delivered four weeks ahead of schedule while setting new industry benchmarks in sustainability and workplace mental health management,” Heale comments. “Renowned as Australia’s greenest freeway, greener materials and construction practices were used to build the project. The operation has been commended for achieving excellence in environmental outcomes with the Infrastructure Sustainability Council awarding the project with an Excellence in Environmental Outcomes Award for 2022.”
Decmil is also currently developing the Albany Ring Road, the largest infrastructure project ever undertaken
APAC
CAN YOU TELL US ABOUT THE WORK BEING UNDERTAKEN AT KARRATHA SENIOR HIGH SCHOOL?
in WA’s Great Southern region. The project, which is being constructed in two parts, will provide a freight route of 11.5 kilometres around the City of Albany for the transport of grain, fertiliser, woodchips and other goods to the Port of Albany.
The Albany Ring Road will link the existing major roads and highways radiating from Albany, bypassing urban areas and improving access to the Mirambeena Strategic Industrial Area. It will also take heavy vehicles off existing roads, reducing congestion and enhancing safety for local and tourist traffic.
“We reached a major milestone in April this year when Stage 1 of the project was successfully completed, and we are now delivering Stage 2,” Heale tells us proudly. “This project has provided some fantastic opportunities for the local region, particularly around employment and existing and emerging local businesses and suppliers who support
the project. A strategic project objective is to work with and support the local community to provide a lasting legacy. To date, 44 percent of the contract sum has been awarded to businesses within 100 kilometres of the Albany Central Business District (CBD), with 5.74 percent of total contract spending awarded to Aboriginal business.”
Supporting the community lies at the centre of Decmil’s company activities. As a people-centric company, Decmil makes sure to undertake projects that directly impact such local communities, an example of which is the Port Hedland Community Centre.
Port Hedland is in the Pilbara region in northern WA. Located approximately 1,200 kilometres north of Perth, the resources sector has remained the backbone of this remote region. Although a large part of this
comprises fly-in fly-out workers, Port Hedland’s population is anticipated to double from 15,000 at present to almost 30,000 by 2041.
To meet this demand, the town of Port Hedland is developing three critical recreational hubs to improve sporting and recreational amenities.
“The town’s Hedland Recreation Hubs initiative represents the biggest public infrastructure investment in the area in decades,” Heale informs us. “In January 2022, Decmil was awarded the contract for the Stage 1 construction of the new Port Hedland Sport and Community Hub Centre. Project works include bulk earthworks and services, the construction of the new community building, carpark, internal roads, stables refurbishment, and landscaping in the surrounding area.”
With the location of the community centre close to a horse racetrack, the work will be undertaken in three separable parts to ensure the uninterrupted running of the 2022
and 2023 horse racing seasons, therefore limiting the interruption of community activity. Decmil will complete the works during 2022 and 2023 with project completion in early 2023 ready for the upcoming horse racing season.
In August this year, Decmil commenced construction on major upgrades to North Regional TAFE (TAFE) colleges’ Pundulmurra campus. This significant project involves relocating the trade’s training activities from TAFE’s South Hedland annexe to the Pundulmurra campus,
where new workshops, classrooms and specialist training areas will be built and set up with modern, industry-relevant training equipment.
The campus will also receive a new commercial cookery training kitchen and classroom to cater for local secondary students, job seekers and career changers. Its new state of the art facilities will deliver training for a wide range of in-demand trades and specialist skill areas such as heavy automotive, heavy mobile and fixed plant, engineering trades, and commercial cookery. Extensive consultation was carried out with the local community and industries,
particularly the resources sector, throughout the planning stages of the project to ensure the new facilities are designed to meet Pilbara’s training needs.
“It is exciting for Decmil to be involved in delivering these important regional projects in the Pilbara region,” Heale tells us. “Our preference when delivering these projects is to employ people who live in the region, and to use suppliers and subcontractors from the local region. For both the Port Hedland Community Centre and TAFE approximately 70 percent of the workforce is from the local community.”
Decmil has delivered innovative solutions for a wide range of energy requirements across both the renewable energy and the oil and gas industries.
In 1988 Decmil was awarded its first major contract in the oil and gas sector, by Woodside. Since then, it has delivered construction and engineering solutions to support coal seam gas (CSG) and liquified natural gas (LNG) projects. “This includes the construction of well sites, downstream processing components, gas compressors and gas plants, non-process
infrastructure such as control rooms, substations and workshops, and accommodation facilities,” Heale explains.
“We also provide a wide range of power generation facilities to meet our clients’ demands for clean, efficient power from the sun, wind, and other sources of renewable energy. We have been involved in some of Australia’s largest solar and wind farms and have provided feasibility, engineering, project management and construction services for the renewable energy sector including solar, wind and battery.”
“WE SEE HUGE POTENTIAL IN THE FOUR SECTORS IN WHICH WE OPERATE, PARTICULARLY RESOURCES, ENERGY AND INFRASTRUCTURE”
– ROD HEALE, CEO, DECMIL GROUP
“I BELIEVE THERE IS SIGNIFICANT OPPORTUNITY IN THE INDUSTRY, NOW AND IN THE FUTURE”
– ROD HEALE, CEO, DECMIL GROUPWarradarge Windfarm
With large-scale solar growing rapidly in Australia, Decmil offers expertise in the planning, design and construction of the civil and electrical BOP works for solar energy projects. Engineering, procurement and construction (EPC) contracts that Decmil has delivered include Gullen Range Solar Farm and Sunraysia, both located in New South Wales (NSW).
Furthering the topic of renewables, wind is a resource that is poised to make a major contribution to ensuring that Australia’s future electricity grid is affordable, reliable and environmentally sustainable. As Australia is endowed with exceptional wind resources, wind energy will continue to provide substantial economic and social benefits to local and Indigenous communities across Australia.
“We have provided a range of feasibility, engineering, project management and construction services for a number of Australian wind farm projects,” Heale tells us. “Our capabilities include BOP works, civil infrastructure and electrical works as well as road construction, access roads and drainage. We provide design and construction of access roads, hardstands and wind turbine foundations, as well as electrical switch rooms, electrical reticulation and substations.”
In 2020, Decmil successfully delivered Warradarge Wind Farm and Yandin Wind Farm in WA for Vestas. Located 175 kilometres north of Perth near the town of Dandaragan, Yandin Wind Farm is one of WA’s largest wind farms, with 51 wind turbine generators. At present, Decmil is delivering BOP works for Global Power Generation’s 218-megawatt (MW) Ryan Corner Wind Farm, in a joint venture with RJE Global. Ryan Corner Wind Farm, located near Port Fairy in Victoria, comprises 52 wind turbines with a capacity of 4.2MW each.
On top of transport infrastructure, community builds, energy facilities and upgrades, a portion of Decmil’s focus is on the resources sector. Decmil has extensive experience in project delivery in this field and the company works closely with its clients to achieve unique, innovative and cost-effective solutions.
“Our capabilities within the resources sector include non-process infrastructure works, remote camp construction, earthworks, building, civil works, structural mechanical and piping, hydraulic, and electrical and instrumentation,” Heale continues.
“We are experienced in greenfield and brownfield environments and have worked in some of the most remote and harsh climatic regions around Australia.
“We understand what is required for successful project delivery in these challenging conditions and environments. With a strong local and long-term presence in many remote regions in Australia, we have established a strong reputation in regional communities.”
Over the past year, Decmil has successfully delivered the Christmas
Creek Hydrogen Refuelling Station for Fortescue Metals Group, the construction of surface water management measures on the Cloudbreak mine site for Chichester Metals Pty Ltd, and non-process infrastructure works at the Mesa A and Mesa J iron ore mines in the Pilbara region for Rio Tinto.
Decmil’s operations are gearing Australia towards the future, and one perfect example of this is the company’s activities in regard to lithium - a resource critical to batteries for all manner of industries at the centre of the green transition.
In this field, Decmil has secured a contract from Covalent Lithium Australia Pty Ltd for the design and construction of non-process infrastructure buildings for its Mount Holland Lithium Project based in WA and has also secured a contract from Talison Lithium Australia Pty Ltd to construct a Technical Services Building at its Greenbushes Lithium Operations located approximately 250 kilometres south of Perth.
“Securing these two contracts is testament to Decmil’s proven track record of successfully delivering nonprocess infrastructure construction contracts, particularly in regional areas,” Heale explains. “Importantly, this contract also strategically positions Decmil in the lithium mining and processing sector.
“With the increased demand for lithium, which is crucial for the transition to renewable energy, Decmil is well positioned to support Australia’s lithium producers and their expanding mining operations.”
Anti-government protests, the outbreak of the COVID-19 pandemic, and US-China trade tensions have severely affected the construction industry in Hong Kong.
However, the recent upheaval has only impelled S&techs, a full-service main contractor headquartered in the special administrative region, to concentrate on opportunities elsewhere.
“With the political events that have taken place here in Hong Kong, and the whole COVID-19 situation, the industry is of course challenging,” acknowledges Mike Kavanagh, COO of S&techs Hong Kong Ltd.
“It has driven us to focus on our other operating locations, for example in Singapore. We are delighted to have key members of staff now in place in
Singapore, and we have been gaining a foothold in the market there.”
Originally formed in 2000 to serve the growing international client base in Hong Kong, S&techs today has expanded across Asia Pacific (APAC) with additional offices in Tokyo, Taipei, Shenzhen, Suzhou, Shanghai, Wuhan, and Foshan, offering design and construction services throughout the region.
“We also offer construction management consulting in other APAC locations including the Philippines and South Korea, and see further opportunities for potential office locations in Malaysia, Indonesia and Vietnam, where we have key alliance partners in place to assist us in the delivery of projects for our clients,” Kavanagh adds.
To serve both local and international clients throughout APAC, S&techs has not only established a physical presence in the region but also forged alliances with other construction service providers.
For example, S&techs is an alliance partner of STO Building Group, a multi-billion dollar full service main contractor in the US with offices in Canada, the UK and Ireland.
“We are proud to be the alliance partner of STO Building Group and be in a position to service their clients in the APAC region with the same level of professional service and quality as they expect in the US, Canada and Europe,” states Kavanagh.
Though his family background was not in construction, Kavanagh held an interest in the industry from an early age.
Having started working in the
As S&techs expands across the APAC region, the company has to make sure that it implements its core values, which have been the cornerstone of its growth and success over the past 22 years.
These core values help S&techs to conquer every project and every challenge:
• Client services – Internalise the needs and goals of clients.
• Excellence – Hold high standards of quality and safety.
• Partnering – Build strong allegiances with the industry’s best.
• Relationship building – Respect local culture and communities.
• Integrity – Always deliver on promises.
• Enthusiasm – Strive for exciting and innovative solutions.
construction industry in New York City with a local heating, ventilation and air conditioning (HVAC) subcontractor, he then had the opportunity to join StructureTone, which became the STO Building Group family of companies.
A growing main contractor and construction manager at the time, joining StructureTone was a lifechanging decision for Kavanagh.
“StructureTone was focusing on the interior fit-out market in New York and other key cities, and the ownership recognised the need for a good contractor/construction manager with this specialty and focused their attention on it,” he recalls.
“This started my career in the interior fit-out and refurbishment sector, which I have been entrenched in to this day.”
In 1998, Kavanagh relocated to London as Commercial Director of StructureTone and later as Regional Director, involved in the company’s operations in Europe and subsequently Asia.
Recognising the potential opportunities in APAC, StructureTone joined forces with S&techs’ CEO, Nobuo Shigemitsu, to start the company in Hong Kong.
“From the outset, I was StructureTone’s representative on the board. I was keenly interested in S&techs, and strived to bring opportunities from our existing international clients.
“I transferred to Hong Kong in 2010, and eventually became a shareholder. Today, I am the COO of S&techs Hong Kong Ltd,” Kavanagh continues.
S&techs has grown to become one of the region’s foremost contractors, specialising in interior fit-outs and refurbishments.
Multiple projects have been completed by the company in a variety of sectors, from commercial, retail and hospitality to education,
Clestra Asia has partnered with S&techs since 2017 to deliver high-end office spaces from Japan to Singapore.
With a presence in all major Asian markets and a network of distributors spanning across South Asia, Clestra is S&techs’ partner of choice to participate in flagship office fitout projects. The relationship has intensified these last few years following their rapid expansion in Asia, with more than 15 projects completed thus far.
S&techs know they can always rely on Clestra’s expertise in modular construction and reliable contracting capabilities.
www.clestra.com
healthcare, and more.
In mainland China, S&techs offers out-of-ground design and build services primarily in the industrial/ manufacturing sector.
Offering a wide range of design and construction services, including construction manager at risk (CMAR), main contracting, design and build, and construction management consulting, S&techs performs each job with focus and dedication. The company utilises in-house capabilities and state of the art systems to assist clients from the earliest project stages, through to closeout and commissioning.
These refined, end-to-end design and construction services are second-to-none in the industry, as evidenced in 2022 when S&techs was honoured to be named Asia’s Leading Construction Service Provider of the Year at Hong Kong’s Most Outstanding Business (HKMOB) Awards.
For Kavanagh, there were a number of differentiating factors that earned S&techs this prestigious award, the first of which is its unique regional footprint.
“As a main contractor and construction manager specialising in the interior fit-out and refurbishment sector, we are the only firm to have this footprint,” he acclaims.
“Secondly, it’s our 22 years of experience in the successful delivery of key projects in multiple sectors throughout the APAC region. Last but not least, it is our hands-on professional service, and approach to being a key team member in the delivery of our projects, working alongside the client and appointed consultants.”
S&techs is proud of the diverse portfolio of fit-out and refurbishment projects that it has successfully realised for clients throughout the region over the past 22 years.
Repeat assignments from satisfied clients represent approximately 80 percent of the work undertaken annually by S&techs, who has recently
completed its second project for airport leasing company, Avolon, in Singapore.
Elsewhere in the city-state, a third project has been completed for Morningstar, an American financial services firm, with the first two having taken place in Shenzhen, China.
“We have completed the Hong Kong campus of WPP Group Plc, and have recently completed the restack of their Tokyo offices. In addition, we are working on projects for BOSE and Willis Towers Watson in Hong Kong and Tokyo, these being long-standing clients for whom we have completed multiple projects in the APAC region,” Kavanagh shares with us.
“We are also very proud to have recently completed some major fitout projects in Hong Kong, including the new BUPA offices at the quayside and the KIN Foodhall, a major food court project at Devon House in Quarry Bay.”
More than 210 dedicated members of staff are employed by S&techs, who realise that people are its greatest and most important asset.
As such, there is a significant focus on the recruitment and retention of employees, and Kavanagh is proud of the very low staff turnover rate at the company.
“AS A MAIN CONTRACTOR AND CONSTRUCTION MANAGER SPECIALISING IN THE INTERIOR FIT-OUT AND REFURBISHMENT SECTOR, WE ARE THE ONLY FIRM TO HAVE THIS FOOTPRINT”
– MIKE KAVANAGH, COO, S&TECHS HONG KONG LTD
“We provide our staff with the right environment to work in. Recently, we built state of the art offices in Hong Kong which our staff are extremely proud of,” he notifies us.
“We encourage our staff to obtain educational qualifications and organisation memberships related to the industry, and we recognise their contributions to the success of our projects. Most of all, we treat our staff with respect.”
Of equal importance to the success of S&techs’ projects are subcontractors and suppliers.
The company is therefore extremely conscious about working with the right partners, as the quality of
S&techs’ installations directly stems from their workmanship and care.
“We have long-term relationships with global glazed partition system companies, carpet and floor finish manufacturers, furniture companies, ironmongery suppliers, lighting suppliers, equipment manufacturers and so on built up over many years,” Kavanagh informs us.
For the year ahead, meanwhile, S&techs’ key priority is to build on previous successes and be able to handle a greater workload.
To this end, the company will continue to build up its employee base with qualified, talented and experienced team members.
“Additionally, we want to focus on our growing offices in the likes of Singapore, giving them as much ground support as possible and the tools and ability to grow. We also want to put more emphasis on what we see as sectors with great potential for S&techs, such as mission critical, healthcare, hotel and hospitality, and food and beverage,” Kavanagh concludes.
S&TECHS
Tel: +852 2838 8877 info@s-techs.com www.s-techs.com
Part of our strategy is to become one of the biggest players in New South Wales (NSW), but more importantly the safest and most trusted delivery partner for our clients.”
The opening gambit of George Bardas, CEO of construction and property delivery partner, Taylor, underscores the ambition that runs at the core of the company.
This is an enterprise defined by its proudly Australian heritage and one that pursues sustainable growth whilst remaining true to its concrete values as a people-centric business. These principles are the foundation of Taylor’s leading industry reputation.
“A Tier 2 contractor such as Taylor may not have the same balance sheet as some of Australia’s major Tier 1 companies, but we are a company that has the right calibre of people
and the right leadership, that delivers work safely and professionally,” he outlines.
“If we can continue to achieve this throughout NSW, that will help to progress our expansion plans.”
For Bardas, this notion of expansion and growth follows a model based on playing to the geographies the company knows best, whilst developing its portfolio and service offerings with complementary strengths.
Indeed, by concentrating its efforts in NSW, Taylor deliberately chooses to play in Australia’s largest construction market.
“Before starting to potentially expand in other states, my strategy has been to provide diversity for every type of project within NSW,” he elaborates.
By so doing, the reputation that Taylor has established on local soil naturally paves the way into new markets across Australia, nurturing a relationship with NSW partners who are likely to look to the company for future solutions.
“Growing the business here to such a level allows us to use this as a platform to expand organically in other states,” Bardas affirms. “If you satisfy all your local partners, they will give you more work in Australia.
“We want to have plenty of exposure to our clients in NSW, so that when they need a job done in Brisbane or Melbourne, it will allow us to naturally go and deliver for our clients.
“Although our expansion plans have been delayed by a year or two due to COVID-19, this is still something that we’re looking for in the future,” he continues.
“PART OF OUR STRATEGY IS TO BECOME ONE OF THE BIGGEST PLAYERS IN NEW SOUTH WALES, IF NOT THE MOST IMPORTANT”
– GEORGE BARDAS, CEO, TAYLORGeorge Bardas,
CEO, andMark
Taylor, Managing Director and Chairman
Ergo Group are highly experienced electrical and communications contractors operating across all sectors of the construction industry in NSW.
We have built a reputation as a trusted partner renowned for a tenacious “can do” work ethic that applies professional service, practical and cost-effective solutions to all of our projects. We pride ourselves on our ability to assess risks and meet challenges
decisively to ensure that all aspects of our projects are successful.
We have a long-established relationship with Taylor, partnering on many successful projects, the latest being the Powerhouse Museum’s Discovery centre at Castle Hill. Since 2011, we have consistently delivered practical, reliable, competitive, and innovative solutions, and always seek to provide the best outcomes for our clients and the end user.
Unit 25, 17-21 Bowden Street, Alexandria, NSW 2015 | info@ergogroup.com.au | 02 9519 1179
Continuing on the topic of COVID-19, Bardas highlights how this period proved to be one of the greatest challenges faced by the global construction sector in recent history, resulting in resource scarcity, cost escalation and significant supply chain disruption. Regardless, Taylor continues to pursue its strategic goals whilst weathering the storm.
This applies in the most literal sense, since the NSW construction industry must confront the location-specific challenge of unprecedented levels of rainfall in the face of climate change.
“We have been experiencing an excessive amount of inclement
weather. We’ve had three times the amount of rain in the year that we would normally have, which means that every project has been delayed. This entails significant extra costs and time pressures, but despite all that, we are still taking on work,” says Bardas.
A significant contributor to the volume of work that Taylor is currently preoccupied with, is the development and addition of its most recent business line during a year heavily impacted by COVID-19.
Since we last spoke with Bardas in 2021, Taylor comprised four separate business units, but strategic diversification has since ensued,
culminating in the launch of Taylor’s ‘Major Projects’ division. This new unit is quickly coming to represent the jewel in Taylor’s crown.
“This division has been introduced for a number of reasons; firstly, because we aim to be taking on larger work.”
DIVISION - General Build
CLIENT - Western Parkland City Authority
LOCATION - Bringelly, NSW
STATUS - To be completed in February 2024
Western Parkland City Authority’s first building is a visionary precinct that marks the start of construction for Australia’s newest city, Bradfield City. The building includes a pilot of the new Advanced Manufacturing Research Facility.
Located within the Western Sydney Aerotropolis, the diverse, dynamic and sustainable global city precinct will unlock AUD$10 billion in private investment.
Connecting with the country is at the heart of the design, taking cues from the surrounding natural waterway and Cumberland Plans. The building will be open and welcoming, surrounded by green and open spaces where residents, workers and visitors can gather. This development is set to achieve a 6 Star Green Star rating, full Living Building Challenge certification, and a 5.5 Star NABERS Energy and Water rating. It will be energy positive, carbon neutral, water balanced, nature positive, healthy and inspiring.
Not only this, but through Major Projects, Taylor fulfils a gap in the market with an offering that is receptive both to Australia’s construction needs and the expertise of its staff. With the new business unit, Taylor retains staff that might want to pursue larger, more challenging projects, meaning they can transfer from one unit to the other and accept the challenge of embarking on an AUD$200 million job through the group that they’ve grown with professionally.
“We have recently attracted a number of senior executives and delivery staff within the market to join Taylor, which means that they need to be working on the larger projects. This is also my personal career background, working with Tier 1 organisations in senior leadership roles with access to clients in that space.
“In addition, the industry here in Australia lacks choice with the level of competency at the larger project level, so it needs more players in there,” Bardas continues.
One such recent undertaking successfully completed during the COVID-19 period is Taylor’s work on the Western Renewal Project of the iconic Sydney Opera House – a major feat comprising three separate projects falling under the Opera House’s AUD$275 million Renewal programme.
“The highlight of this project was how for the first six to eight months, the team really worked on the details of how to actually do this type of
“THE INDUSTRY HERE IN AUSTRALIA LACKS A LEVEL OF COMPETENCY AT THE LARGER PROJECT LEVEL, SO IT NEEDS MORE PLAYERS IN THERE”
– GEORGE BARDAS, CEO, TAYLOR
work, and it certainly wasn’t normal, business-as-usual conditions,” he shares.
“The planning was so good that the execution became a lot easier, despite the COVID-19 related challenges in terms of getting the stage and various other particulars from Austria. Overall, it was a fantastic job.”
In other recent developments, Taylor has completed the Gordon Quarter development for Anglicare, a significant undertaking involving the design and construction of a new three-storey, 107-bed residential aged care facility and 40 independent living units at Gordon.
LOCATION: Sydney, NSW
CLIENT: Sydney Opera House Trust
CONTRACT TYPE: Design and Construct
START DATE: July 2019
COMPLETION DATE: August 2022
DURATION: 35 months
AWARDS: Merit Award for Site Safety, Master Builders Association, 2020
The Western Renewal Project comprised three projects: the Creative Learning Centre, Entry Foyer and Concert Hall.
The project was delivered within an operational precinct under the intense scrutiny of the media, the general public and local residents. The Taylor project team worked closely with the client to manage communications surrounding the project and maintain a positive image for the site.
Taylor was appointed as a managing contractor to manage the installation of the new stage works within the Opera House and further works including refurbishment, all of which had to be done without negatively impacting on the world heritage listing of the building.
“Both clients at Anglicare and the Sydney Opera House Trust are very happy, and we consider them absolutely excellent projects. We ticked every box on those jobs and that’s what we want to do with our Major Projects business.”
This is just a sample of the myriad projects that Taylor has to its name, spanning a full and varied spectrum of contract types and sectors. The company continues to assist in the delivery of vast data centres across NSW and has recently successfully been awarded a contract on the new AMRF (Advanced Manufacturing Research Facility) - its first project in the newly constructed Bradfield City located on the doorstep of the new Western Sydney International (NancyBird Walton) Airport.
As Australia’s newest city centre, Bradfield City is poised for major development in what is set to become a cyber-secure, green and connected hub for advanced industries.
Pictured here and below: Sydney Opera House Concert Hall Renewal, Sydney Opera House Trust PHOTOGRAPHY ©DANIEL BOUD“That’s a beautiful project for us, since we are the first ones there with a lot of opportunities to follow. It was very much a strategic move for Taylor,” says Bardas.
In terms of strategic moves for the years ahead, Bardas hints at the addition of a sixth business line, purely intended as a fit-out business, further bolstering the company’s sustainability and security in the face of volatile conditions.
“We intend to introduce a pure
fit-out business, so that we can provide a fully integrated solution for new commercial buildings including fit-outs, or deliver fit-out projects which are traditionally done in the commercial space.
“This has the potential to provide us with access to major real estate investment trusts (REITs), which in turn creates opportunities for us to expand into other parts of their businesses,” he explains. “This will be an extremely good touchpoint for our clients.”
In addition, a major priority for the company concerns continually
building on its reputation and recognition as a worthy alternative to Australia’s major Tier 1 contractors, one that celebrates the connection between people and the beautiful spaces across NSW that stand as testament to the Taylor name.
TAYLOR Tel: 02 8736 9000 www.taylorau.com.au
Every day, hard-working cleaners help to keep offices, hospitals, retail stores, schools and other buildings safe and hygienic.
People have continued to prioritise cleanliness since the COVID-19 pandemic hit, highlighting the vital role of professional cleaners more than ever.
Facility services companies, such as GJK Facility Services (GJK), have played a major role in keeping COVID19 at bay, eliminating pathogens and minimising transmission in workplaces and public areas.
“We had a comprehensive pandemic plan, and through our work in the health sector, we had significant experience in infection control procedures, understood by a really strong team that works in environments which require a higher
ELIAS STAMAS, CEO: “One of the most important things that any business can do is focus on its culture, a culture that makes people feel part of something.
“We have a number of initiatives, one of which is the GJK awards which recognise people throughout the business that live and breathe our values, and we have an annual gala dinner at the end of each year to celebrate those people.
“There’s also a number of initiatives focused on not only how we make sure people can do their job well, but how they can potentially develop to become a CEO, COO or CFO one day.”
level of sterility,” opens Elias Stamas, CEO of GJK.
“In January 2020, we trained up some 160 staff in infection control, so we were able to respond to our customers’ needs immediately. With COVID-19 hitting Australia around March, we not only had cleaners that were appropriately trained, but we had the appropriate personal protective equipment (PPE), equipment and chemicals.”
Cleaning remains vital in controlling not only COVID-19, but germs in general, so workplaces need to invest in facility cleaning services to keep staff and visitors safe.
Likewise, the appearance of offices, buildings or facilities can negatively impact brand perception if their premises look dirty, have unkept grounds, or have graffiti on the walls.
With over 30 years of experience, GJK is a leading provider of facility services, providing businesses with peace of mind that their facilities are always looking their best.
“GJK currently provides soft services across Australia and New Zealand, such as commercial cleaning, restoration, maintenance, grounds, and facility support services,” Stamas informs us.
McLeod Trees is one of the largest and most respected tree arborist companies specialising in tree removal and consultancy services in Melbourne.
With a well-established and qualified management team with combined industry experience of over 75 years, together they oversee 30 staff with a diverse range of knowledge which is second to none within the aboricultural industry in Australia.
Our experience within the public and private sectors provides McLeod Trees with strong alignments and understandings for both urban tree management and government assets.
We provide first class customer service that is both cost efficient and timely. www.mcleodtrees.com.au
“We work extensively through the education space, specifically tertiary. We currently service eight universities across Australia. We’re also heavily involved in the government sector, both federal and state, and we have quite a presence in the commercial space throughout the central business districts (CBDs) of all major Australian cities.”
Services are delivered by GJK’s talented and diverse teams, who are trained, equipped and motivated to go the extra mile for customers.
As a family-owned business, people are GJK’s biggest asset, and the company looks to attract and retain the very best employees to become part of the family.
“We currently have over 2,500 employees. We’ve got a great team of people that have stayed, grown, and developed with GJK,” says Stamas.
As a family-owned business, people are GJK’s biggest asset
Indeed, many of those in senior positions have moved up the ranks, equipped with an intimate
Our solid and diverse client base is located throughout the residential suburbs of Melbourne and greater rural Victoria and includes:
• Local Private Residents
• Facility Managers
• Corporate Clients
• Public and Private Schools
• Hospitals
• Golf Courses
• Development and Construction Companies
• Local, State and Federal Government Departments
• Major Road Project Victoria (MRPV) Projects
• Level Crossing Removal Projects
Call (03) 9528 4676 or visit mcleodtrees.com.au facebook.com/McLeodTrees
understanding not only of GJK, but of customers and their businesses.
“They’re able to respond with that ability to quickly shift direction for the customer. I think that was highlighted particularly during the COVID-19 pandemic, to support our customers at the drop of a hat, but it’s true of the way we have historically operated.
“Our hypergrowth through COVID19 would not have been possible without the incredible team that we have here in the business,” Stamas recognises.
In the cleaning industry, a host of new equipment is rapidly entering the market.
Whilst nothing is more important than professional, trained cleaners who understand optimal cleaning methodologies, new technologies can make cleaning services smarter and more responsive to the end user.
For Stamas, the next few years
are going to be defining for nextgeneration solutions in the facility management (FM) space, with the Internet of Things (IoT) and robotics the stand-out technologies for their power to truly transform how commercial cleaning is delivered. These technologies provide unprecedented access to big data, to drive better decision making for a more tailored and responsive cleaning service.
“A lot of people are starting to leverage data, artificial intelligence (AI), and robotics. The lessons that are being gleaned from that data, particularly about the way spaces are used and the way people move through and interact with spaces, are really interesting,” Stamas notes.
“It allows you to consider all sorts of elements, right down to how you’re servicing that space. Are you attending the areas that are most frequently used, or where people tend to congregate the most? Can you
have a more bespoke solution which is predicated on the use of the facility?”
GJK leverages supplier relationships, many of which span more than 10 years, to access the latest machinery and technologies, including data analytics and AI robotics.
Data analytics is the most revolutionary aspect of IoT technology in cleaning. Insightful changes to how cleaning services are delivered, for example, can be made by capturing, analysing, and interpreting data.
IoT sensor technologies, meanwhile, come with advanced data analytics software, enabling cleaning companies to study trends, better understand the cleaning needs of spaces, and plan operations accordingly to make the experience of using spaces more enjoyable.
“There’s no doubt that our industry is entering the age of data and transparency. I’m interested in the
way data is used to create solutions that are true to the requirements of businesses, our customers, and end users,” Stamas tells us.
“We’ve rolled out a variety of sensors that pick up various pieces of data such as the movement of people and door openings. It brings that data
together and creates what we like to call a predictive cleaning model, which is based on the needs and uses of the building.
“Data insights are vital for intelligent decision making, and I think that it’s really starting to be embraced,” he says.
GJK delivers some key measures to drive environmentally friendly cleaning services:
GREEN PRODUCTS, EQUIPMENT AND METHODS – In consultation with customers, GJK uses green cleaning products and eco-friendly practices to reduce pollutants and improve indoor air quality, as well as low-impact equipment and chemical-free cleaning solutions where practicable.
WASTE MANAGEMENT – Assisted by waste management experts and powered by smart wastetech innovations, GJK helps customers to develop their waste management programmes with sustainability in mind.
CHEMICAL WASTE – GJK addresses the proper disposal of packaging and chemical waste with safe, responsible and sustainable waste programmes.
CONTINUOUS RESEARCH AND INNOVATION – New products and tools are actively researched and tested by GJK, to provide customers with higherquality cleaning and improved sustainability outcomes.
HOLISTIC APPROACH TO SUSTAINABILITY – A companywide approach to sustainability and reducing GJK’s environmental impact wherever possible.
AI-powered cleaning robots likewise play an increasingly important role in today’s commercial cleaning services.
GJK currently has a fleet of more than 40 vacuuming, mopping, and scrubbing robots deployed throughout Australia, which supplement rather than replace the work of cleaners.
“Robotics are nowhere near replacing human beings, but what they can do is the type of tasks that don’t require the same level of dexterity,” explains Stamas.
“While robots are cleaning floors, for instance, people are able to do more detail-oriented tasks that only a
human can do. We’re fully expecting that to continue to develop, and because there is a level of involvement for the cleaner with the robot to make sure that it’s operating efficiently and following the right mapping area, it gives cleaners the opportunity to learn new skillsets and interact with this technology.”
As sustainability becomes a major focus for businesses to achieve ambitious climate change targets, a wave of new technologies on the market has also enabled the “green cleaning” movement.
Scrutinising how office cleaning services are delivered is an obvious approach to help lower the environmental impact of businesses, who equally have a stronger focus on employee wellbeing and understand the impact of toxic cleaning chemicals on health and productivity.
GJK is pioneering sustainability in commercial cleaning, and has embraced the movement towards green cleaning practices.
“I believe we’re one of the first cleaning service providers to be carbon neutral,” Stamas acclaims.
“We’ve completely offset our Scope 1, 2, and 3 emissions, which means that any service we provide to our customers is carbon neutral. Many cleaning service providers are committing to net zero and we are all looking at ways to further reduce our environmental impact.
“That’s critical not only to us socially and consciously as a company, but also to our customers and stakeholders.”
A new sustainability framework has recently been launched by GJK, which strengthens the company’s social and environmental governance responsibilities.
Giving back to the community is part of the GJK DNA, driven by Founder and Managing Director, George Stamas, who was honoured
with an Order of Australia earlier this year in recognition of his corporate social responsibility (CSR) efforts.
For over three decades, GJK has been investing in programmes that benefit the wider community, and fostering sustainable outcomes that have a positive social impact.
GJK Giving Back, for example, is the company’s new social impact programme, designed so employees can get involved in work with charities, not-for-profits, and organisations.
“We recently launched our GJK Giving Back programme, in which we seek to support a number of charity partners through multiple avenues, not just with fiscal contributions, but also by organising employee volunteers,” Stamas elaborates.
“All of our employees get a certain amount of volunteer days, which they can allocate to a specific charity. It allows them to get involved through volunteering activities, and equally workplace giving, which is great.”
As GJK embraces both technology and sustainability, the company will continue to evolve into a multidisciplinary service provider.
To be able to offer customers endto-end solutions across the cleaning spectrum, it really comes down to two pressure points for GJK’s customers, according to Stamas.
“The first key driver is to ensure stakeholder satisfaction, making sure the tenants and end users of those facilities and buildings are happy with the space they’re using, and that they’re hygienic and safe,” he states.
“Secondly, our services must achieve the best value for money for customers. Those two overlay to produce end-to-end solutions for our customers.”
GJK FACILITY SERVICES
Tel: 1800 635 983
info@gjkfacilityservices.com.au www.gjkfacilityservices.com.au
Playing a key role in Papua New Guinea’s development for more than 40 years, Fletcher Morobe continues to deliver significant building and infrastructure projects for the nation
Fletcher Construction (Fletcher) has been an integral part of the development and modernisation of the South Pacific for more than 75 years.
A leading contractor in New Zealand (NZ) and the South Pacific with head offices in Auckland, Fletcher offers international capabilities and support matched with a deep local understanding and broad connections.
Significant national infrastructure has been planned, built, maintained and managed by Fletcher for the benefit of communities in NZ and the South Pacific.
Having undertaken its first overseas contract for Morris Hedstrom in the Samoan capital of Apia in 1946, Fletcher is now also permanently based in Papua New Guinea (PNG) as well as Fiji, Samoa and American Samoa, Tonga, Vanuatu, and the Solomon Islands.
A contract to supply and erect 342 houses in Panguana and Arawan kicked off operations in PNG for Fletcher Morobe, a wholly owned subsidiary and one of five connected businesses comprising the Fletcher family.
Fletcher Morobe established a permanent PNG office in 1984 and has since delivered a range of significant building and infrastructure projects in the country, including the Sir John Guise Stadium, Taurama Aquatic Centre, Grand Papua Hotel, National Parliament House, and Port Moresby International Airport.
Construction of TISA Rua, a new mixed use multistorey property in the capital of PNG, Port Moresby, commenced in 2020.
The Teachers Savings and Loans Society (TISA), the largest credit union in PNG, invested K82 million in the property, which can be used for commercial and residential purposes such as office spaces and top-floor
penthouses.
TISA Rua is defined by its glistening vertical fins that begin at the base of the tower and come together to form a crown at the top, a striking feature that also helps to distinguish the penthouse residential apartments from the commercial floors on lower levels.
Despite the impact of the COVID19 pandemic, construction of the 10-storey development remains on budget and is due for practical completion in Q4 2022, generating much-welcome income for TISA.
From the get-go, TISA had possible tenants in mind for this new investment, constructed by Fletcher Morobe, most of which are financial institutions, law firms and large international corporations.
Expected to be operational in February 2023, TISA believes that the full value of the building will be K151 million if and when it is fully occupied by tenants, an attractive return on this commercial property investment.
This valuation is consistent with the building life cycle of 20 years and reflects the fact that the real estate segment of the PNG economy remains attractive to long-term investors.
TISA Rua brings a new dimension to the depth of development and design of commercial complexes in the Port Moresby real estate market, providing more than 4,000 square feet of office space.
As the project contractor, Fletcher Morobe has a reputation of training and developing highly skilled Papua New Guineans, and TISA Rua has provided employment for more than 100 people, mostly from PNG.
Local job creation is key to Fletcher Morobe, whose apprentices are also locally trained and supply chain is kept as local as possible.
The Nadzab Airport Redevelopment Project (NARP) is a major
multidisciplinary engineering project comprising earthworks, drainage, water supply, sewerage, pavement, structural, electrical, mechanical and architectural works.
Located in the suburban area of Lae, the capital of Morobe Province and the second-largest city in PNG, Nadzab Airport handles the second largest amount of air passenger traffic and cargo in the country after Port Moresby International Airport.
As Nadzab Airport required large-scale improvements from both a capacity and safety perspective, the purpose of NARP is to meet the future demands of air transportation, establish it as an alternate international airport, and contribute to the gradual economic growth of PNG.
To achieve this, redevelopments at Nadzab Airport include improving airside facilities for the safe and efficient operation of larger aircraft and expanding the airport’s passenger handling capacity.
Fletcher Morobe, along with fellow contractors, have made excellent progress on the passenger terminal. It resembles the shape of a kundu drum, an emblematic symbol of PNG that appears on the country’s coat of arms.
NARP practices the highest safety and environmental standards across the entire site; this was evidenced in March 2022 when Fletcher Morobe celebrated a fantastic safety milestone, achieving 500,000 hours
of work with no lost time injuries (LTIs).
In July, Fletcher Morobe’s NARP team went on to accomplish one million hours of LTI-free work on the project, an impressive feat recognised by PNG’s National Airports Corporation (NAC).
The high safety standards that Fletcher sets out to achieve is an immense source of pride for the company, whose health and safety policy reflects its approach to ensuring a zero-harm working environment, and the fundamental belief that all work-related injuries and illnesses are preventable.
This strong focus on managing health and safety risks has earned Fletcher recognition as a leader in the field.
Caring for the places in which it operates, Fletcher has committed to reducing the impact it makes on climate change, both in New Zealand and South Pacific islands such as PNG, by achieving a 30 percent reduction in its carbon emissions by 2030.
Fletcher also looks to reduce its environmental impact by managing its impact on natural resources, local habitats and biodiversity, reducing waste, removing any hazardous materials, and managing water use and energy consumption.
NARP ensures that there is no air pollution, water pollution, waste
Barlow Industries is the flagship company of the PICSA PNG Group and specialises in rolled and merchant steel across a vast range of industries.
The company proudly services individual, corporate and wholesale customers.
Our projects with Fletcher Morobe have included providing the TISA building with structural steel fabrication and supply, the Nadzab Airport with reinforced steel to specification and the Ela Motors showroom in Lae with sufficient concrete provision.
Working closely with our project managers and key people to meet our target dates, we remain flexible to accommodate any design changes in a timely and professional manner.
www.picsa.com.pg
or soil contamination during the construction phase, and monitoring such environmental impacts remains one of the project’s top priorities.
NARP reflects Fletcher’s commitment to building a sustainable future for generations to come, focusing on the areas that are most important to its people, customers and business, and where its actions will lead to meaningful change.
In cooperation with Fletcher Morobe and other NARP contractors, engineers of the future from the PNG University of Technology (PNGUOT) were also given a tour of the project by the NAC Project Management Unit.
Students visited Nadzab Airport on a field trip in March 2022, allowing various aspects of their broad civil engineering study programme to be experienced.
These students will contribute to a vibrant future for PNG, together with Fletcher Morobe’s nation-building infrastructure projects.
Fijian Broadcasting Corporation is at the forefront of its industry, servicing the nation’s 300 islands in the face of tropical weather and equally ravenous competition. CEO Riyaz Sayed-Khaiyum tells us more about the company’s efforts to maintain the lead in the Fijian media space
The broadcasting and media industry in Fiji is surprisingly competitive, especially for a country of less than one million people! We started as a national radio service and grew to become the most popular media service in the nation, surviving the competitive industry and reaching the top in record time.”
Fiji is a nation made up of 300 separate islands home to just over 900,000 people. A much-visited destination for
holidaymakers seeking tropical leisure and adventure, the archipelago also proposes immediate challenges when it comes to establishing, maintaining and developing modern infrastructure and utilities.
The first and most obvious barrier is the South Pacific Ocean; the waters that separate the islands with unshielded open borders are vulnerable to storm winds and other dramatic weather, making infrastructure
maintenance a critical aspect of dwelling on any one isle. The second challenge that springs to mind is the rugged and often varying terrain across the islands, including forested hills and dipping valleys that are an attractive factor for the adventurer, but a struggle for those who keep Fiji connected to modern utilities.
“Aside from these, a major challenge for everyone in the broadcasting industry in Fiji is the constant flux of technology; things are moving so fast, and it is often very difficult to keep up with this rapid rate of development, especially for traditional broadcasters,” says Riyaz Sayed-Khaiyum, CEO of Fijian Broadcasting Corporation (FBC).
“Despite the relatively low population, broadcasting is exceptionally competitive. Even though we are a government-owned commercial company, we find ourselves competing with everyone in the sphere, from radio and TV stations to newspapers, magazines, mobile phone companies, billboards, cinemas and many others. This is because the name of the game is viewers, and in this respect, we have not only managed to survive, but thrive.”
Sayed-Khaiyum puts this success
down to a key aspect of FBC –adaptability. FBC has experienced and been at the centre of the everchanging technology space in Fiji, and has chosen to embrace and act on technology evolution, remaining flexible and utilising industry advantages as early as possible.
One example of this industry adaptability is FBC’s own in-house app, developed to help extend its services, not only in Fiji but across the Pacific region, substantially increasing regional awareness and publicity for FBC’s broadcasting shows and channels.
FBC has grown since its inception. Although it had just six radio stations at the time when Sayed-Khaiyum joined the company, FBC now also runs TV stations and has developed its services to cater to a wider audience. FBC has also changed its name, subtly yet significantly - from Fiji Broadcasting Corporation to Fijian Broadcasting Corporation - to reflect the whole population across its many islands.
“We still provide our six radio stations, with two being available in AM and FM format, and the other
When AVC Group first partnered with Fijian Broadcasting Corporation in 2009, this initiated what continues to be a trusted and fruitful relationship. FBC has invested heavily in technology, pushing boundaries of what’s possible and AVC has been there to power the future of broadcasting. AVC’s CEO, Simon Jackson, says, “AVC is known for its customer focused problem-solving skills and we relish the opportunity to create cutting edge tech solutions to meet FBC’s evolving needs.”
AVC first worked with FBC to supply and install world leading technology in all fifteen on-air studios, IT infrastructure and transmission networks. “Our partnership included providing all technical details for local contractors, to rebuild the studio facilities and construct buildings for FM transmitters and towers over multiple sites,” says David Broad, AVC Engineer.
As FBC’s needs have changed, AVC has been with them. Recently, FBC’s six radio stations have been upgraded and migrated to a new automation system. Despite COVID-19, FBC was able to broadcast using a mobile interface, keeping the “live and local” feel of the station. “The simplicity of the system makes it easy for presenters to concentrate on the content and let the technology do the work,” says Hayden Beetar, AVC Solutions Consultant.
The AVC-FBC relationship hasn’t stopped after installation. AVC’s 24-hour support and training plus AVC’s involvement in the move to the Walesi TV Digital platform has ensured FBC has a world class platform to broadcast their content now and into the future.
in depth solutions for broadcasters.
AVC Group is an aggregator of products that integrate to provide in depth solutions for broadcasters. With a team of highly skilled hardware engineers and software specialists, we offer support and technical consulting services and are adept in managing projects of all sizes, for large and small companies engaged in broadcast communication.
We power the future of broadcasting. sales@avc-group.net www.avc-group.net
Before: After:
RIYAZ SAYED-KHAIYUM, CEO: “I started off as a radio DJ; I worked the dawn shift on an English radio station, but I had always been interested in the news. I got this opportunity with a company in the 1990s to alternate between radio and the newsroom week by week, and I was one of the first people in Fiji to have such an arrangement with management.
“Soon after I moved into the news space full-time when I was offered a job with Fiji Television which started up in 1995, and this was where my career really began, as the company was brand new and the first of its kind in the country. It had been the largest and most viewed in Fiji at the time, and we were drawing in an audience of almost a quarter of the entire population every Sunday night when I hosted Fiji’s most popular current affair show. I worked under some really amazing people for almost 10 years, and when I finally left, I was a Senior Journalist with my own show.
“Following this, I worked in New Zealand with TVNZ and also did some radio work for four years until I applied for and became CEO of FBC – New Zealand was too cold for me anyway! I was brought on board to help fix an ailing company, and I can proudly say that we have managed to fix it. We started a national TV service from scratch, and we have also made a lot of inroads into other media fields that are very promising moving forward. I have been working at FBC coming up to 15 years in December this year.”
four FM, yet we broadcast in three languages: Fijian, Fiji Hindi, and English,” Sayed-Khaiyum tells us. “There are two stations for each language, one for young listeners and one for an older audience, and we also have our three TV stations.
“The main TV station is FBC TV, and we also offer FBC Sports which is very popular with events, for example the current World Cup, and it is also our first high-definition (HD) channel and the only HD channel in Fiji.”
FBC also boasts a digital arm, providing online news services via the company’s website and apps, an incredibly important service to a population spread across the nation’s 300 islands, who often experience varying weather and rely on up-todate news.
“About three years ago, the Fijian government decided that the country was going to invest in a digital transmission company called Walesi,
meaning “wireless” in the native iTaukei language,” says Sayed-Khaiyum. “The aim of this was to get all the TV broadcasters onto one central platform accessible by everybody. The project has been going on for the past three years, and it is aiming to be finished by the end of 2022, at which point there will be 100 percent coverage for freeto-air TV to the Fijian people.”
Walesi will provide the whole of Fiji with a total of eight channels, three of which belong to the FBC that will feature alongside a selection of private channels, a governmental channel, and one Christian channel. On top of this, FBC will be incorporating its radio stations on TV so that the national audience can switch between TV viewing and radio broadcasts.
“This is really groundbreaking, because for the first time in our country’s history, people in every corner of Fiji will be able to listen to all our radio stations,” Sayed-Khaiyum elaborates. “If any natural disaster
or heavy weather hits, like a cyclone for example, listeners will be able to flit between AM and FM and listen to broadcasts if the weather takes down one or the other.
“This is especially great news for those living on the outer-lying islands in Fiji, because we have some very remote locations with limited populations, and so it is brilliant to be able to provide them with digital and radio services even in spite of bad weather!”
In a nation that is exposed to the elements and at the mercy of the open ocean, it is no surprise that one
of the greatest challenges for the panFijian community is caused by tropical weather.
In light of this eternal issue, FBC has decided to take action through its Disaster Recovery Risk (DDR) project to secure its radio, TV and digital services in preparation for any situation caused by the natural wrath of the world.
“This project was put on hold over the past few years due to the COVID-19 pandemic, however, it is being revisited in the present,” Sayed-Khaiyum explains. “The DDR project consists of renovating one of our old properties outside of the capital of Suva that contains an AM
“WE STARTED AS A NATIONAL RADIO SERVICE AND GREW TO BECOME THE MOST POPULAR MEDIA SERVICE IN THE NATION”
– RIYAZ SAYED-KHAIYUM, CEO, FIJIAN BROADCASTING CORPORATION
transmission station. We have a bit of land there, and we are going to renovate and extend the building and make it our DDR centre which will host our backup servers, as well as backup TV and radio studios in case of significant natural disasters.”
According to Sayed-Khaiyum, the DDR project aims to be completed in six months’ time, with construction starting close to the new year. The project building will also contain a sizable data centre as well as other businesses to provide additional revenue streams.
Another building project on the cards that was held up also because of the pandemic is the expansion of the FBC broadcasting house in downtown Suva.
The total building project will cover seven storeys, four of which will house FBC’s activities, an answer to the company’s continued growth and success.
“This will provide much-needed
space for both people and our services, as our current office in Suva is experiencing overcrowding, and the fact that all of our studios are located on the ground floor; if there is a flood of some kind it could cause major issues for FBC,” Sayed-Khaiyum continues.
“This is yet another perfect example of why the expansion of our main office is so necessary. Once complete, we can take all our studios up to the higher floors and reduce the risk of natural disaster impacts on our services.”
The project building will make FBC landlords to the businesses that rent out space on the floors below, adding a reliable revenue stream to the company, while giving FBC a greater foothold in the central business district in Suva, a much-desired hub in the city.
The project to increase floor space also represents a new age of media presence for the FBC. Not only will
it become a space to expand the company’s traditional services, but also allow FBC to branch into different types of media.
“We want to be Fiji’s first media academy, and we hope to work very closely with the Asia-Pacific Broadcasting Union (ABU) and the
Asia-Pacific Institute for Broadcasting Development (AIBD) to establish a media training academy where media professionals from the Pacific region can come to Fiji and use our facilities for training purposes, discussions, and help develop broadcasting services in the region,” Sayed-Khaiyum details.
RIYAZ SAYED-KHAIYUM, CEO: “There is always a set pace to be moving at, and we realise that we have to keep up because if we don’t, we will be left behind.
“As always, there is the issue of juggling and accepting change, and moving with the times, keeping our minds on technology and resources. At FBC, we pride ourselves on the fact that we can do a lot of work at a very competitive cost. For example, when we set up TV around 11 years ago, it was the biggest media project in the history of Fiji media development, and this was at the same time when the company began fixing up its AM and FM stations, as everything was in dire need of upgrades and development; even the main building and its offices needed repair.
“In the end, we managed to undertake everything for around USD$10 million, quite a feat for the level of work we carried out, and this allowed us to invest in our services, reaching over 90 percent of the Fijian population. Undertaking such work at a competitive cost allowed us to remain competitive in the industry.
“The lesson is that you have to start doing more with less so that you can stay ahead.”
The building will also house Fiji’s first studio that will have an audience capacity with around 100 seats so that FBC can begin creating content never seen produced before in the country. Gameshows, debates and team building shows are three avenues for content that such a studio opens up, and they only add more promise from both an entertainment and revenue perspective.
“This kind of development is key for the FBC to maintain its position at the head of such a competitive market moving forward.”
FIJIAN BROADCASTING CORPORATION
Tel: 331 4333 info@fbc.com.fj www.fbcnews.com.fj
APAC OUTLOOK: WHAT IS ONE OF THE MOST IMPORTANT LESSONS YOU HAVE LEARNT IN YOUR INDUSTRY?
SICE’s comprehensive roadside and back office tolling solutions are enabling smart mobility in Australia, as highlighted by Managing Director of SICE Australia and New Zealand, Manuel Gonzalez Arrojo
As Australia’s population has grown, so has congestion in its largest capital cities.
Tolling has helped to ease the country’s congestion conundrum by allowing road infrastructure to be provided earlier than traditional models of road provision.
A smart and cost-effective way to fund the highways, bridges and tunnels that keep the Australian economy moving, studies have found that toll roads make a net positive contribution to the nation’s economic wellbeing.
For commuters, meanwhile, toll roads are a safe and reliable option that reduces both travel time and vehicle operating costs.
“Tolling is an important part of our suite of services,” opens Manuel Gonzalez Arrojo, Managing Director of SICE Australia and New Zealand.
SICE, a multinational systems integration technology company, has operated in Australia since 2005, backed by more than 30 years of experience in the development of tolling systems.
Solutions offered by SICE include end-to-end conventional, multi-lane free-flow, and shadow toll systems, from roadside equipment to back office systems.
Toll systems are one of a range of SICE services in the intelligent transport systems sector, along with urban and interurban smart traffic, integrated tunnel management, public transport and environmental control of air quality or water management.
SICE’s first reference in Australia was a tolling project. SICE was part of the consortium that originally delivered the complete EastLink tolling solution, from the roadside equipment to back office systems for toll collection.
EastLink, a 39-kilometre multilane free-flow electronic toll route in
Melbourne operated by ConnectEast, is the only tollway in Australia that exceeds an average of one million toll point transactions per day.
SICE was appointed to deliver to EastLink its in-house Tolling Operational System (TOS), an operational back-office system that treats all the data collected by roadside equipment.
SICE’s TOS for EastLink was developed as a result of specific tolling needs identified by SICE in previous projects, such as Autopista Central in Santiago de Chile, where a significant amount of electronic tolling transactions needed to be converted into billable events.
“All the information collected on the road regarding how many vehicles go through the motorway, or through the different tolling points, is sent to the back office,” explains Gonzalez Arrojo. “The first step is to transform all that information into something billable. You can then price transactions depending on the time or the day, so the cost of a Monday morning commute could be different to a Saturday afternoon.
“Once the project finished, we sat down and analysed the market. The first thing we realised was that the back office system we used for EastLink was probably not going to be very cost-effective, so we started expanding our in-house back office solution,” he recalls.
As a result, SICE’s Billing and Invoicing System (BIS) was born. BIS is the commercial system component of SICE’s complete back office solution, that performs various customer account management functionalities.
BIS can be integrated with either SICE’s TOS solution or any existing host system and provides a comprehensive user interface that offers seamless access to all the information stored and processed by the system, such as customer invoices and account balances, allowing for great flexibility. Its intuitive and userfriendly web portal also provides users with the ability to interact with the system to create new accounts, consult all information assigned to their movements, pay for past trips, or request details of tolling activity.
Our collaboration with SICE through the design and development of the Westconnex Project has provided our company with many opportunities over the years.
Dallas Delta’s team is driven to work with our clients to grow our skills, develop technologies and anticipate the changing ITS communications requirements for road infrastructure in Australia.
As an Australian owned manufacturing company, we pride ourselves on designing our hardware and software locally. This allows us to support the implementation of Australian critical communications for Tunnel Maintenance Personnel, Traffic Control Operators, Emergency Services and Motorists alike. www.dallasdelta.com
“Due to our relationship with ConnectEast and after a lengthy due diligence process, in 2014, SICE signed
CONVENTIONAL TOLL – With this model, the road user pays for road use with barrier-based toll lanes at toll stations. SICE makes it easy to adapt to centralised management requirements based on standard hardware and its own software applications.
MULTI-LANE FREE-FLOW TOLL – Electronic payments are managed without interfering with traffic flow using license plate recognition and/or electronic tags.
SHADOW TOLL – For schemes where corresponding government organisations, and not real users, pay tolls to the concessionaire based on the numbers and types of vehicles driving on the roads or the availability of traffic on these roads.
OPERATIONAL BACK OFFICE (TOS) – A modular web-based software solution that performs all transaction processing functions while providing operators with all the necessary tools to review, rate, audit, monitor and control data.
COMMERCIAL BACK OFFICE (BIS) – A multi-concession and modular customer account and billing management system that allows complete integration with SICE toll solutions.
ADVANCED AUTOMATIC VEHICLE IDENTIFICATION (AAVI) – Innovative systems that provide advanced machine learning tools to optimise the automatic identification of vehicles.
Communication equipment & solutions for Major Projects. Australian designed, made & supported. www.dallasdelta.com
a new contract replace the original commercial back-office system in EastLink with our BIS solution. Having a complete back-office solution in operation with EastLink (both operational and commercial components) was a big step for us since Australia is at the forefront when it comes to multi-lane free-flow tolls,” states Gonzalez Arrojo.
SICE’s next significant step in its internal back-office development was its Advanced Automatic Vehicle Identification (AAVI) system. This module became a key tool to dramatically reduce operators’ load to manually review license plates, one of the most time-consuming activities when operating a tolling system.
SICE’s AAVI solution is based on automatic validation processes and an optimised manual review tool while incorporating fingerprinting technologies as machine learning and deep learning tools.
The AAVI module was part of the
T: +613 9387 7388 53 BARRY ROAD, CAMPBELLFIELD VIC 3061
contract SICE signed with Transport for NSW (TfNSW) in 2015 for Sydney’s iconic landmark Harbour Bridge. Together with SICE’s TOS, which was also included in the contract, both systems processed traffic transactions from Sydney’s Harbour Tunnel and Harbour Bridge.
Backed by its Australian experience, SICE entered into another contract with TfNSW in 2019, this time to provide SICE’s BIS solution.
SICE has traditionally been a systems integrator, relying on third parties to provide the roadside equipment (RSE) required to collect traffic and license plate information.
“We missed out on a couple of big projects because RSE providers began integrating upstream with their own back office technology, so it was challenging to compete,” Gonzalez Arrojo accepts.
“We strategically analysed where we were going if we wanted to really compete on tolling projects. Many tenders are split between the roadside and the back office, and I think that’s the way to go, however, some projects come as one package.”
As such, more than 10 years ago, EastLink
the company began to develop its own RSE solution implemented in the US and Europe to be complemented by SICE’s operational and commercial back office or other third-party back office toll solutions.
“SICE can now offer a whole tolling solution, from RSE to operational and commercial back offices, with everything developed in-house. Therefore, SICE’s technology is today able to manage all phases of a tolling project and operates comprehensively on numerous traffic and transport infrastructures that are used daily by thousands of drivers and operators,” Gonzalez Arrojo informs us.
SICE’s RSE solution is now in operation in the Humber Bridge in the UK, in SH-288 in Houston (Texas) and the Toll 49 Tyler Bypass in Texan Smith County, and two more projects are being delivered in Puerto Rico and Birmingham (UK); when completed, these will have an additional 50+ tolling gantries using SICE’s RSE solution.
Having also delivered TOS for TfNSW and signed a contract to provide BIS, AAVI is a highly strategic project for SICE that will also be implemented in other countries, such as New Zealand and the UK.
“We have delivered TOS, BIS, and
now our AAVI systems for TfNSW, so the three components of our tolling solution,” outlines Gonzalez Arrojo.
Elsewhere, in neighbouring New Zealand, SICE has been recently selected to provide Waka Kotahi NZ Transport Agency (Waka Kotahi) with its world-class in-house back office solution, including TOS, BIS, and AAVI.
As part of SICE’s scope for the project, the solution will be delivered under a Software-as-a-Service (SaaS) operational model and cloud-based by leveraging the company’s recent
Humber Bridge, UK Eastlink Melbourne Eastlink Melbourneexperience from the TfNSW back office system project in Sydney. SICE will provide its SaaS tolling solution for an initial period of five years, with the option to extend it up for up to 14 years.
“We really believe New Zealand has great potential when it comes to tolling and technology. Waka Kotahi selected us in June 2021 as the preferred partner for upgrading and replacing their existing back office system, and we finally signed the contract this year to deliver the three components of our tolling solution,” Gonzalez Arrojo shares.
“It’s a very strategic and significant project for us. It adds another major
reference to the large tolling projects we are already undertaking for ConnectEast and TfNSW in Australia and strengthens our relationship with Waka Kotahi, which began 10 years ago with the Waterview Tunnel,” he emphasises.
The project, which will commence operations in 2024, is also SICE’s second reference for a nationwide back office solution, following the electronic toll collection interoperability platform implemented and operated by SICE in Mexico.
Internationally, SICE is also working on another nationwide tolling project in Puerto Rico, delivering more than
30 tolling points (single gantry configuration) and the operational back-office.
“The great performance and quality of SICE’s tolling solutions and capability place us in a leading market position to offer operators and governments an end-to-end tolling solution.”
SICE AUSTRALIA
Tel: (+61) (02) 8456 7090 info@sice.com.au www.sice.com
Tyler, USA Golfo Centro, Mexico (Ecatepec)To improve living standards across the Cook Islands, high-quality and affordable information and communication technology (ICT) services are essential.
Cook Islanders at home and at work rely on a wide range of these ICT services daily, to connect with friends and family and conduct business.
For 30 years, the Cook Islands had been serviced by a single telecommunications provider. Partly owned by the government, it was responsible for delivering universal access and pricing, a unique arrangement that delivered on its objectives.
That is until 2019, when the government recognised that the Cook Islands would benefit from competition in the telecommunications services market.
“In the last few years, the telecoms sector in Cook Islands has been fully deregulated with an open market for competition,” notes Phillip Henderson, CEO of Vodafone Cook Islands.
“This means we really get to test just how good we think we are, and ultimately customer choice will determine that.”
With the passing of government legislation to open up the telecoms sector, Vodafone Cook Islands was issued with a new 15-year license to operate telecommunications networks and provide services in the South Pacific country.
Vodafone Cook Islands has a continued obligation under its current license to provide a universal service with universal pricing, and has overcome challenges such as its remote geographic location to deliver for customers.
“We offer the full product suite of telecommunications services to serve the whole nation, as part of our drive to maintain connectivity for everyone with quality services at a competitive price,” Henderson outlines.
“Our vision to provide better connectivity to the people of the Cook Islands is at the heart of
everything that we do, and we will always be motivated to expand our services and deliver the best quality we can for our people.”
With 90 employees and offices nationwide, Vodafone Cook Islands operates in what is clearly an evolving telecommunications industry, and one that presents exciting opportunities.
As technology advances, the company’s operations and services
will continue to adapt, making telecoms a very attractive and interesting space to work in.
“There are always opportunities to grow into, and unknown territories to discover in this space of work,” Henderson tells us.
“I’ve worked in this industry for over 30 years, and I haven’t grown tired of it because there’s always something new on the horizon.”
Working on the vendor side of the industry throughout his career has
provided Henderson with a much greater perspective and knowledge of the full telco domain.
A born and bred Cook Islander, Henderson has headed some significant technology rollouts in the Pacific throughout his career, including Gigabit Passive Optical Networks (GPONs) in New Caledonia and Tahiti, a fully IP-based UTMS Terrestrial Radio Access Network (UTRAN) in Vanuatu, and a pilot project for autonomous trucks used in
mines across Australia.
Vodafone Cook Islands is just as innovative in the way it uses satellite technology, to connect the islands and deliver a public switched telephone network (PTSN), mobile and broadband internet services.
“We also provide the infrastructure to transmit the main TV and radio broadcast service to all connected islands, and are resilient and adaptable to the evolving climate of technology advancements,” adds Henderson.
There has been 4G+ mobile cellular connectivity in the two most populous Cook Islands, Rarotonga and Aitutaki, since 2016.
As a result of Vodafone Cook Islands upgrading its mobile cellular network to the two islands, an impressive 92 percent of the country’s population now has access to 4G+.
To the delight of residents, the company has also recently launched a pilot project, to Manihiki, an atoll in the Northern Cook Islands, and plans to deploy 4G+ to the Southern Cook Islands in the coming year.
“As part of our Pa Enua network refresh project, in the first half of 2023 we will be upgrading the mobile network and migrating satellite services to the latest generation of the O3b mPOWER satellite constellation in a domestic hub configuration, to
take advantage of Manatua cable connectivity,” Henderson informs us.
Vodafone Cook Islands has partnered with advanced satellite bandwidth capacity provider O3b since 2013 to deliver high-speed broadband, and O3b mPOWER will deliver efficient, high-performance network communications.
Scheduled to launch in December 2022, the performance of the O3b mPOWER satellite communications system, coupled with the high-speed data connectivity of 4G+, will provide Cook Islands customers with a secure managed network that meets current requirements and has the flexibility to adapt to changing needs.
“Vodafone network connectivity for Pa Enua will be delivered over various technology platforms, the most prominent being O3b mPOWER,” confirms Henderson.
The medium Earth orbit (MEO) O3b mPOWER system will bring even more flexibility, scale, and performance to the Cook Islands, providing an equivalent experience across the entire country.
O3b mPOWER satellites have beams with smaller footprints and flexible throughputs, so each island can get its own dedicated beam to match required demands.
“To increase the maximum capacity per terminal/beam, O3b mPOWER has the flexibility to point beams directly to a wider range of internet data gateway locations,” Henderson explains.
Another feature of the O3b mPOWER constellation is that it can provide a direct connection between the islands.
Unlike the first-generation O3b services that have been operational in the Cook Islands for the last seven years, there is no requirement for an external gateway that acts as a go-between to interconnect the outer islands with Rarotonga.
“The O3b mPOWER constellation can provide both domestic and
As the leader in global content connectivity solutions, SES operates the world’s only multiorbit constellation of satellites with the unique combination of global coverage and high performance, including the commercially-proven, low-latency Medium Earth Orbit (MEO) O3b system.
O3b mPOWER is SES’s secondgeneration MEO system and will operate around 8,000 km above the earth’s surface. When fully operational in 2023, O3b mPOWER will deliver an unprecedented increase in flexibility, throughput speed and capacity, enabling the delivery of multiple gigabits-per-second of data services to customers in remote and underserved regions across Asia-Pacific.
www.ses.com
international connectivity at the same time,” Henderson shares.
“Vodafone Cook Islands has a strong partnership with O3b, and will be collaborating as new service opportunities become available. We have confidence in how the O3b service complements, extends, and protects the Manatua cable service.”
Having downsized physical hardware in its existing facilities, Vodafone Cook Islands is now opening up secure data centre capacity.
The company’s three purposebuilt data centres in Avarua, Aroa and Aitutaki ,offer a highly secure and protected environment for ICT infrastructure, which also houses critical customer data and ICT assets.
“Connectivity is provided primarily through the Manatua submarine cable system, which extends from Samoa across to French Polynesia, and at the Avarua and Aroa data centres we
Reimagine a connected world by learning more about the next-generation system, O3b mPOWER
have on-site satellite communications to the O3b constellation,” Henderson says.
“At each data centre, we are able to offer rack space or entire racks for hosting equipment, and we are happy to look at providing for specific hardware requirements. This capability is part of a concentrated Infrastructure as a Service (IaaS)
offering to our business community and government.”
Hospitality as a Service (HaaS) has also been successfully launched by Vodafone Cook Islands, in which the company takes on the ICT infrastructure of hotels.
This has been a big investment for the company, and is still to be realised with the full potential of the new BSS through Hansen Technology’s Dynamics 365 Navibilling and the features available to assist with its operations.
A few years ago, Vodafone Cook Islands embarked on lowering its carbon footprint by reducing e-waste, going paperless, utilising solar power in its operations, and investing in electric vehicles.
With the COVID-19 pandemic playing such an important role in changing the business landscape, the company is also embracing online communications and transactions.
“In addition to this, we have a recycling unit on our main office premises which allows us to collect faulty equipment returned by customers,” says Henderson.
“Last year, we purchased our own plastic shredder machine to break down these pieces of equipment, package and export them to New Zealand for recycling.”
All of the hotels’ applications are hosted on virtual machines at one of the Vodafone Cook Islands data centres, connecting hotel rooms using GPON fibre and removing active ICT components from within the facility.
“65 percent of hotel rooms are connected using HaaS, with the two largest hotels running this service for the last three years,” reveals Henderson.
“It allows hotels to focus on guest services, and leaves the challenge of maintaining high-quality telecoms and internet services to Vodafone Cook Islands.”
In the last year, the company has also finished deploying a new business support system (BSS), a major change to operations to help streamline processes and incorporate financial packaging, point of service (POS), and inventory with Vodafone Cook Islands’ customer relationship management (CRM).
Another service that is well known globally but still in its infancy in the Cook Islands is mobile money.
“Taking the lead from our sister company in Fiji, where mobile wallets are now the norm, we see this as a growth opportunity for the Cook Islands to enable those in the outer islands to access mobile money as we move towards a more efficient cashless society, particularly for the outer islands,” Henderson details.
Vodafone Cook Islands prides itself on looking after its people, as evidenced by the company’s high staff retention rate.
Staff are treated like family at Vodafone Cook Islands, as they carry the company values with pride and honour.
There is an even gender balance across the business with 50 percent of senior and executive leadership
positions occupied by women, leading to balanced decision making at all levels.
“What differentiates us from other service providers is that we have specialist, expert staff who are wellrounded across all our platforms. They are important to driving our operations forward,” Henderson emphasises.
A handful of specialist experts train new recruits on the job, and last year Vodafone Cook Islands put a number of staff members through courses at the University of the South Pacific.
Costs were covered by the company, so that employees could
undertake their studies and apply them back into their roles.
“This was a big success, and this year we witnessed these members of our staff body graduate with distinctions in their respective courses,” smiles Henderson.
“We also subscribe to LinkedIn Learning, which we have found to be a very effective learning portal for ensuring that leadership in particular is able to remain current with business thinking and practices.”
People are a key asset to Vodafone Cook Islands, and providing staff with the tools and resources to enable personal growth and development in
their role and career path is just one of the company’s strategic priorities.
“Another key priority for us in the foreseeable future is to complete the rollout of fibre to businesses and homes in Rarotonga, and continue to deliver the best services we can for our growing customer demands,” Henderson concludes.
VODAFONE COOK ISLANDS
Tel: +682 29680 info@vodafone.co.ck www.vodafone.co.ck
Founded in 1987, initially as a telephone exchange company headquartered in Qatar, Ooredoo Group is a multinational telecommunications company operating in 10 countries.
Ooredoo Maldives (Ooredoo) was launched in 2005, to digitally link businesses, locals, and tourists alike in the archipelagic nation, offering a crystal-clear connection alongside the equally pristine waters of the Indian Ocean.
The infrastructure needed to reach the inhabited and resort areas of the islands is an immense project, and a challenge that mobile operator Ooredoo has risen to. Within less than a decade it has revolutionised the telecommunications industry in the Maldives.
Ooredoo’s 400 employees are integral to its growth and success, and with this in mind it is preparing to deploy staff to all the islands. The company sees its staff as its greatest asset, and this is apparent by the amount it invests in them, with in-house training, and online courses, along with sending employees to seminars.
To celebrate 17 years of operations in the Maldives this year, Ooredoo introduced 5G to the central islands - the Greater Malé region to be precise. As well as linking fibre optics to all the islands, the company is continuously working on expanding 5G network coverage to the whole of the Maldives.
Along with 5G coverage, Ooredoo marked another first with the introduction of 5G AirFibre in 2020. As another
Telecommunications and digital services are how we stay in touch, and Ooredoo Maldives is connecting the islands with its high-speed services and IT infrastructure
example of the company providing the latest technology to enable new opportunities, AirFibre uses both wireless and direct cable connection technology to deliver the fastest available broadband services.
Among its many achievements, Ooredoo made history by launching the first ever and fastest 3G and 4G networks in the Maldives. The archipelagic nation may be the smallest country in Asia, but Ooredoo has big plans for the future of technology and communications for its inhabitants, targeting 100 percent coverage in the Maldives.
As a digital platform designed exclusively for the tourism industry, Digital Resorts by Ooredoo Business is a cloudbased solution that integrates seamlessly with existing IT infrastructure. Helping resorts transform into a digital environment, the app uses a single window to engage with guests before, during and after their stay. By giving visitors access to information about their resort and the experiences available, it will help them personalise their visit.
The app also streamlines the flow of information within the resort between staff and guests. Equally, the cloudbased tool, Digital Human Resources (HR), helps resorts simplify the management of employees and handle HR interactions on the go, including career planning, learning strategies, and recruiting. This works on a single cloud solution, which builds the collaboration of different facets of an organisation. By so doing, Ooredoo improves efficiency, which is integral to any organisation.
Ooredoo’s Digital Hub has fully integrated Quad-Play to deliver superior voice, video, internet, and TV services, built on a single gigabit fibre network. To add to the Digital Resorts portfolio, Ooredoo also has Digital Entertainment. This is a fully managed, state of the art Internet Protocol Television (IPTV) platform which offers the widest choice of HD entertainment, video-on-demand content, and in-room services. Combining all the above, Ooredoo’s Digital Resorts app is designed for a differentiated guest experience.
Elsewhere, Ooredoo has developed two e-commerce apps, offering consumers the opportunity to shop and manage money with its network. The Moolee app guides users through their shopping experience and plays an integral role in facilitating small business owners and online retailers to reach a bigger customer base. Meanwhile, the m-Faisaa mobile money app provides the convenience of making online payments. It allows users to manage utility bills, conveniently pay at the shops, and send money anywhere, all in a secure mobile wallet designed
for day-to-day transactions. In fact, the app was awarded the Excellence in Innovation in Technology Industries
Bronze Stevie award earlier this year for its services to the Maldives, while Moolee and m-Faisaa both won a silver Stevie award for Excellence in Innovation in Consumer Product and Service Industries.
Ooredoo remains committed to bringing innovative technologies to the people of the Maldives. Through the introduction of new products to its portfolio, such as Aachaa Prepaid and Post-paid, along with the extension of fixed internet coverage and the ability to access services via digital platforms, Ooredoo has enhanced business growth across the country.
Ooredoo has built a Tier 3 data centre in the Maldivian city of Hulhumalé, which is designed to be flood-resistant up to seven metres. A second data centre is currently being built as a back-up to the state of the art Ooredoo Maldives Data Centre (OMDC), which was launched to accommodate the ever-growing digitisation of businesses, creating a demand for capacity. OMDC manages the virtual infrastructure, ensuring security, connectivity, and continuity by offering end-to-end solutions for local businesses to thrive.
In addition to the data centre, work on deploying Ooredoo’s Nationwide Submarine Cable in conjunction with Huawei Marine is underway, bolstering the Maldives’ network infrastructure. This is an important investment by Ooredoo and part of its commitment to power a digital Maldives. Huawei Marine is utilising its advanced 100G technology, upgrading the Maldives to be one of the bestconnected countries across Southeast Asia.
Innovation through improved services is the future of digital technologies in the Maldives. With SuperNet, Ooredoo has a continuing commitment to its customers’ growing digital needs and to the government’s Digital Maldives initiative. The lightning fast SuperNet enables small and medium-sized enterprises (SMEs), where business models host services online, to successfully grow in the market. The fibre-optic broadband initiative
is forever expanding and has recently reached the island Kudarikilu where customers are able to access speeds of up to 100Mbps.
Ooredoo has partnered with Huawei to bring cloud services to the Maldives, distilling over 30 years of accumulated technology. One of the advantages of using Huawei Cloud is it is the only end-to-end solutions provider to supply the cloud-pipe-device approach. It is also the best way to grow enterprises with a stable, secure, and ever-improving cloud service, and affordable, inclusive artificial intelligence (AI).
Elsewhere in the world of business, Rashuphone by Ooredoo offers a reliable way to connect wirelessly with the world, making it the perfect solution for homes or small businesses. The Ooredoo Satellite Phone converts regular smartphones into satellite phones, which give customers global coverage on the go, in over 161 countries. Finally, as the only conferencing solution in the Maldives to provide a complete set of communication and collaboration tools in one package, Ooredoo Conferencing powered by StartMeeting makes it easier to stay productive anywhere, through any device.
All things considered, Ooredoo will continue to take the Maldives to the next level with its innovations in the information and communication technology industry.
Zone RV is at the forefront of the Australian towable RV industry. We take a look at the company, its various models, and how the RV is helping Australians realise their dreams of setting free on the open road
The commonplace dream of “selling shop” and riding into the sunset to travel the world is now more realised than ever before. The digital world allows us to stay connected to friends, family, work colleagues and business partners no matter where we are, be that in the middle of a Nordic forest, African plain or the Australian outback.
The reality that we can remain connected no matter the location is a true testament to the potential that we have when it comes to enabling digital work. The age of sacrificing full-time jobs and financial safety in order to travel is waning, with remote and flexible jobs becoming a norm, so much so that people are even calling into question the notion of house ownership.
For some, travel is the excitement of backpacking with limited material possessions, and a phone or laptop for online connectivity, navigation, and digital work. But for those who cannot afford the luxury of spontaneous pack-up-and-go travel, such as parents who need to think for their families, long-term adventure can now be achieved at a level that many would regard as a perfect medium between home security and comfort, and nomadism – the recreational vehicle (RV).
From its humble beginnings in Queensland in 2015, Zone RV has grown to be one of the top choices in Australia for adventure seekers to begin their eight-wheeled journey on the open road. This leading position comes down to many reasons, one of which is the advanced methods of manufacturing and production used by the company that places its RV models at the front of the market.
Zone RV incorporates technology from the aeronautical and marine industries to build lighter, stronger, and safer off-road caravans, and manufactures entirely composite
bodies and cabinetry systems to help adventurers stay below the gross combined mass (GCM) of their towable RVs. These bodies sit on a cleverly designed chassis that is also weight-conscious, and in combination with CruiseMaster suspension systems, guarantees enduring long stretches of Australian corrugations.
Each component fitted to a Zone RV off-road caravan is carefully selected to perform superbly, have the lowest likelihood of failure, and be straightforward to repair or replace in remote locations by the company’s service partners. Zone RV’s entire range includes lithium batteries and solar panels, and these off-grid systems can be optioned to suit customer needs.
Built around endurance and reliability, Zone RV provides buyers with a vessel to achieve their dreams, while having the peace of mind of
knowing that they have invested in the best RVs on the market.
It is no surprise that 2022 has seen a substantial rise in the desire for adventure. The onset of the COVID-19 pandemic saw national lockdowns throughout the world, and Australia was no exception. Following limited social interaction and movement, there was a shift in mindset with many realising that they wanted to experience more, either domestically or abroad.
Australia is renowned for its wildlife, expansive outback, rainforests and landmarks. From Victoria’s coast, the Twelve Apostles rise like sentinels of the sea, and deep within the heart of the Australian outback, the monolith Uluru stands as a broad and flat banner of the country’s natural world. With so much within reach, who wouldn’t want to journey with home comforts and watch the sunset from the coasts and plains?
High quality, efficient and reliable 12V fridges for caravans, camping and off-grid living.
Working closely with Zone RV for many years has been a privilege for us. Our business philosophies are well aligned with a focus on high quality products and personalised customer service. It’s a great fit overall.
With over 45 years history producing low-power and alternative-power fridges for Australians, our business is built on the foundations of longterm product reliability and lifetime customer service.
If we’re going to do something, we do it properly, or not at all. Welcome to Bushman.
Enquiries to Tommy Stockdale 03 8080 9990 tom@bushman.com.au
www.bushman.com.au
The Zone RV Expedition is the company’s most adventurous model yet. The aggressive rear departure angle, shorter length and pop-top roof allow owners to tackle the toughest tracks. It is available with or without bunks and can sleep up to five.
The Zone RV Peregrine is perfect for those looking for a more manoeuvrable off-road caravan. It is only available with sleeping quarters for couples.
The Zone RV Sojourn is the company’s roomiest model and is ideally suited for those embarking on extended adventures. It is available with or without bunks and can sleep up to five.
To answer this, Zone RV offers a range of towable RVs suited to the adventurous couple or an entire family. The Sojourn is the spacious family carrier of the range, capable of housing up to five people for extended journeys, equipped with a queen-sized bed and optional double or triple bunk beds. At 8.8 metres long, the Sojourn is perfect for lengthy adventures from coast to coast, maximising home comfort with amenities common of domestic living such as a seamless kitchen with a sink, oven and bracket to hold a TV. The solar-panelled roof also allows self-sufficiency when it comes to electronics on the road, meaning no cumbersome batteries to deal with.
The Peregrine is Zone RV’s smaller, more manoeuvrable towable RV. Its size makes it the ideal option to venture offroad, where it proves advantageous to move around the wilderness. Fitted with its own kitchen, dining area, ensuite bathroom
For over 50 years, Camec has been a leading supplier to the RV industry, through our state of the art manufacturing of caravan doors, windows and cladding in Australia and by importing and distributing many leading products to the RV and marine industries. Camec is also the Australian and New Zealand distributors of Vitrifrigo fridges and Fiamma awnings.
We are proud of the lasting relationships we have built with great RV manufacturers like Zone RV.
As a national supplier to the RV Industry we continue to support all manufacturers in delivering quality, comfort and peace of mind to those looking to make anywhere home. Call your local representative to discuss how Camec can assist your business.
(07) 3710 9000 www.camec.com.au
(and shower), and queen-sized bed, it is ideal for couples seeking a singular adventure or lifestyle on the open road.
The Expedition, meanwhile, is the latest addition to the Zone RV fleet and is coming to the market soon. The most adventurous of its kind, the Expedition features a pop-top roof that creates a roomy internal space at camp, a streamlined off-road caravan on the highway, and a lower overall height to clear overhanging branches on tracks. With a larger outside kitchen, spending more time outdoors becomes a breeze.
Zone RV’s range of models not only embodies the enduring spirit required when journeying across Australia, but also a technologically advanced edge, both in material design and software applications, aspects that place them ahead of the competition in the country’s RV market.
Fit for the digital age, Zone RV’s Wi-Fi-enabled models have the option of feature control via mobile phone. Mounted wall fans, kitchen lights, and LED strip lighting with dimmer controls are three among a host of features that RV owners can tap into and activate, alter and control from a simple app, making their ideal camping environment easier to achieve than ever before, and able to be changed at a whim.
The optional Cel-Fi Go mobile Wi-Fi booster increases any available mobile signal up to 30 times and all
devices inside the caravan will benefit. Zone RV offers the Telstra unit for the best reception across Australia, boosting 3G and 4G.
The company’s towable RV models boast solar-panelled roofs that drink in the Australian sun, converting green energy to help power all of these features. Higher capacity solar arrays allow the battery banks to be replenished rapidly in peak sunshine, whilst a portable solar blanket is able to reach the sun from shaded campsites for extra solar power. The 2,000-Watt (W) 240V REDARC inverter is powerful enough to run most RV appliances, however some may require 3,000W including the optional air conditioner.
On top of this, Zone RV’s models are led by lithium – the REDARC 200Ah lithium battery bank helps ride out bad weather until full solar generation returns, perfect for spending longer periods off-grid where larger banks are ideal. The REDARC Manager 30 lithium battery charger is used in combination with a REDARC BCDC1250D charger to achieve up to 80 amps (A) charging while driving, from either solar or mains power. REDARC Manager 30 connects to the RedVision display and mobile app for effortless switching and data display.
This combined energy keeps Zone RV appliances and utilities powered up on the long haul, on road or off, such as the fridge, microwave, induction
hobs, water heater, washing machine and optional air conditioner to name a few.
Each model also comes with an awning and outdoor dining panel, with the upcoming Expedition model also featuring a BBQ slide to maximise use of the outdoors.
But Zone RV also understands that, just like any home, RV models are both a financial and emotional investment; in the area of security, Zone RV offers an optional GPS tracking system on subscription to help keep the customer’s caravan of choice monitored and safe.
When the big day comes and a customer receives their new model, the Zone RV team strives to ensure that owners enjoy the best experience during their journey. The handover day of a customer’s new Zone RV model is an exciting occasion, and the company welcomes them into its community as a Zone RV owner.
Zone RV understands that as caravan and adventure enthusiasts, handover day can be an exciting but also daunting experience. To ensure that every customer feels comfortable in their new Zone RV and has the best experience, all customers have the option to receive their new model at the stunning Hangar O.
Hangar O is a 160-acre property located just north of Gympie (Queensland), approximately just over an hour from the Zone RV showroom and factory. The Zone RV handover experience is designed to make sure every customer feels comfortable and has the opportunity to enjoy their new caravan in a relaxed environment. The experience includes a site for up to two nights at Hangar O, while customers use and learn the new features of their caravan with on-site help if necessary.
Zone RV believes that giving its customers the opportunity to relax over a two-night stay gives them the opportunity to become comfortable in a new environment before hitting the road on their next adventure.
As the world’s third-largest island country, shipping has naturally occupied a vast portion of the industry in Papua New Guinea (PNG).
Consort Express Lines (Consort) is proud to offer the most extensive shipping network in PNG, delivering routes to 16 major ports scattered across the immensely diverse island nation.
“We are a leading provider of coastal shipping across PNG, owning and operating a fleet of multipurpose vessels.
“It’s a very exciting space to be in! In the Logistics Division, we continue to professionalise and make improvements in our core offerings (like containerised liner shipping) but we’re also looking to contribute to projects like Papua LNG. A lot of logistics challenges are out there to be solved and we intend to be part of those solutions,” he enthuses passionately.
The project to which Bellamy refers, Papua LNG, is a major integrated development that is commercialising
PNG’s gas resources led by French TotalEnergies. Consort’s services include the ability to carry a wide range of cargo, such as containerised cargo, general cargo, break bulk, refrigerated cargo and project cargo. The company’s ever-expanding customer base reflects the diversity of the services that Consort offers, and spans from manufacturers and wholesalers to the resources sector, indicative of the mix of cargoes that can be carried on the geared, multipurpose ships in the fleet.
The Logistics Division, Steamships Ltd consists of Consort Express Lines, Joint Venture Port Services, EastWest Transport and Pacific Towing Marine Services (PacTow).
“Our customers can either deal with those trading entities separately (Consort for shipping, EastWest for trucking, PacTow for harbour towage and marine services, and JV Port Services for stevedoring and heavy equipment hire) or they can approach us as the Logistics Division of Steamships Ltd for a joined-up solution,” explains Bellamy.
Our Logistics Division is made up of over 2,000 staff, more than 200 trucking assets, 20 ships and tugs, and a
wealth of machinery and manpower spread around the country.
“There are lots of great players in the logistics industry in PNG – we’re all pushing each other to improve and that’s part of the fun,” he says.
As a company, Consort identifies three main differentiators which provide the building blocks to the success that has been so expertly delivered within such a competitive sector. Bellamy explains how the first crucial factor above all else, is safety.
“A LOT OF LOGISTICS CHALLENGES ARE OUT THERE TO BE SOLVED AND WE INTEND TO BE PART OF THOSE SOLUTIONS”
– THOMAS BELLAMY, COO, LOGISTICS DIVISION, STEAMSHIPS LTD
“We talk a lot about ‘Just Culture’ and ‘Felt Leadership’. ‘Just Culture’ is about making sure everyone is set up to succeed safely in the job. I use investigations of incidents and accidents to try and explain this in simple terms to my team.”
When one of the Consort team is involved in an incident or accident, the company asks a series of questions that look to understand the root cause, and Consort always asks questions of itself as an organisation and the management team before focusing on the individual.
“Most likely, if someone has been involved in an incident, we as a management team could and should have done more to prevent that from happening,” he adds.
‘Felt Leadership’ concerns Consort’s teams across the country – the ships and tugs, trucks and machines, and the promise that the company really means it when it ensures that safety always comes first.
The next key differentiator is the collective company attitude which has been carefully cultivated over many years of vital industry experience.
“We’re in the service business so we must give our customers what they need to continue to earn the right to operate. For Consort, as a PNG shipping business, the two biggest components are our schedule reliability and customer service,” continues Bellamy.
What therefore differentiates Consort is the commitment
to constantly trying to improve in those two areas.
“PNG remains a challenging operating environment for a shipping line for a whole host of reasons, so we don’t always manage to keep exactly to our schedule, but we are always striving to satisfy our customers’ expectations and where we don’t, we try to communicate clearly and early to make their life as easy as possible,” he acclaims.
Finally, the other key factor behind Consort’s ongoing success can be attributed to its breadth.
“By possessing shipping, stevedoring and trucking on the logistics side of steamships, and hotels and properties in the other divisions, we really can solve most supply chain solutions for customers.”
A major operational drive for Consort at present consists of offering its
customers a high-quality door-todoor service for containerised cargo, in both shipping and trucking.
“We’ve been working hard to integrate our operating systems for Consort, JV Port Services and EastWest to make it as easy as possible to book and deal with us. We hope to show our customers that in earnest throughout 2023,” details Bellamy.
Consort plans to continue to add new containers and other vessels to its existing fleet and must continue to scale up to keep pace with the growing demand of successful business.
“At Consort, we brought in 1,000 new build containers in 2022 – both the dry and reefer varieties – and we will be doing the same again in 2023,” he continues.
As well as these plans for expansion, Consort also brought a new vessel into its liner fleet in 2022, whilst JV
In addition to liner shipping services, Consort Express Lines provides a host of other complimentary shipping services in PNG, including:
• Door-to-door service
• Cargo consolidation and de-consolidation
• Container depot services, including storage, wash bay and container repair facilities
• Project logistics within PNG, including supply bases for the resource sector (laydown, warehousing and machinery), on application
• Charters or inducements, on application
Port Services continues to upgrade and add stevedoring and handling equipment in line with demand across the country. EastWest is growing its fleet of 150 trucks by 10 percent a year, and PacTow has upgraded its harbour towage tugs in both Port Moresby and Lae.
As well as being the largest coastal shipping line in the country, Consort is proud to employ over 200 Papua New Guinean seafarers with all-PNG crew members onboard each vessel.
Key to maintaining success for the company has been the ability to really understand its customers’ supply chain process, and then transition into helping them solve their problems.
“There can be regular supply chain issues in PNG, and we don’t always get this right, but we’re always willing to listen to our customers and
looking to improve. We have fantastic partnerships with several of our customers, deep relationships built on trust and shared learnings,” shares Bellamy.
One way to tackle these ongoing issues is through the training and empowerment of Consort’s staff.
“We aim to give our people clear direction and support them with training and the right tools to do their job well. I feel very proud to work with the team we have in our Logistics Division – we’ve got some great people,” he adds.
It’s also a two-way street with the staff at Consort, as it is with the company’s customers. It remains imperative that Consort listens to them to help them grow and develop in the ways that have been set out as targets throughout every faction of the business.
Looking ahead, Consort is aiming to grow and enhance its core offerings
and wants to be part of a logistics industry that helps make Papua LNG a success for the country.
“Alongside these ambitions, I’d like to increase the number of Papua New Guineans looking to make a career at sea. We’re working hard to attract them whilst also working with regulators and educators to make sure those coming into the industry, both male and female, have the best chance to have long and productive careers in shipping,” ends Bellamy.
CONSORT
Tel: +675 478 3000 info@consort.com.pg www.consort.com.pg
“THERE ARE LOTS OF GREAT PLAYERS IN THE LOGISTICS INDUSTRY IN PNG – WE’RE ALL PUSHING EACH OTHER TO IMPROVE AND THAT’S PART OF THE FUN”
– THOMAS BELLAMY, COO, LOGISTICS DIVISION, STEAMSHIPS LTD
Inchcape Shipping Services is the iconic name that is synonymous with the global maritime industry. A historical enterprise embracing modernity, we honour its 175th anniversary with CEO, Frank Olsen
Writer: Phoebe Harper | Project Manager: David KnottAs American astronomer Carl Sagan once said, “you have to know the past to understand the present.” Embodying this mantra within the global shipping space, is maritime giant Inchcape Shipping Services (ISS), as a company that simultaneously leverages a rich industrial heritage whilst keeping its eyes firmly on the horizon.
“Whatever curveball you might throw at us, there’s a fair chance that we’ve dealt with something similar in the past.”
In operation since 1847, our conversation with CEO at ISS, Frank Olsen, occurs as the company commemorates a major milestone in the year of its 175th anniversary.
“It doesn’t matter who you talk to in shipping, all of them will have heard about ISS and the vast majority will have done business with us,” says Olsen.
“It’s quite unique in the world we live in today that you encounter a brand which is more than 100 years old, and now we’re verging on 200.”
With an operational footprint in over 60 countries, encompassing over 2,200 ports, 245 offices, and upwards
of 3,000 employees, ISS is firmly established as a global leader in marine services and as a port agency provider.
“Wherever you are in the world, we are able to support your port call,” he continues. “We are a completely global network, and we have capabilities in all manner of port related activity for any kind of marine assets.”
Despite this versatility and the evolution that the company has undergone since its inception, the mainstay of ISS’ core services has remained unchanged over almost two centuries.
“We’re still doing the same basic things we were doing
all those years back,” observes Olsen, comparing the company to other major brands who may have been in operation for many years, but whose core business has changed dramatically in that time.
For ISS, this stands as a major competitive advantage, bolstering the brand name and reputation with credibility proven through a solid track record.
“Of course, this heritage also means that we bring to the market a tremendous amount of accumulated expertise, and a lot of the same people have stayed working with us for a long time.
Complementing its extensive geographical reach, ISS combines port agency, marine services and digital solutions with an entirely sector and activity agnostic approach.
From superyachts upwards, ISS can support any kind of vessel – whether cruise ships, navy vessels, tankers or bulk vessels and anything in between.
“It’s something we’re extremely proud of and contributes to the culture throughout the company,” Olsen continues.
We are (NSC) Navigator Shipping Company, founded in 2011 by Captain Tarek Shokri in Tripoli, to manage vessels for principals. It is run and managed by a professional team whose members have extensive experience in the shipping industry, our company’s solid work relations with the Libyan Port authorities and personnel places us above our competitions. The company strives to offer a comprehensive and constantly improving service to our principals, ensuring the safety of owners’/ charterers’ property and remaining competitive in the market.
To make our principal’s business successful and profitable.
To continuously exceed the expectations of our principals, government authorities, traders, shippers, consignees and vendors.
Our business is built around relationships with principals, government authorities, traders, shippers, consignees and vendors.
NSC emerged as one of the best if you are looking for quality shipping, marine and logistics services. Our services shine with dedication, professionalism and clients’ satisfaction. We always strive for the best as we offer a variety of service which never fails to satisfy our principals.
“Equally, it doesn’t matter what your interest in the maritime assets is. A client of ours could be involved in ship management and looking to arrange crew services, a ship owner who’s much more concerned with the actual assets, or even a cargo trader - we are happy to provide support services for all these things.”
Confronting the often volatile and unpredictable waters of the global shipping industry, ISS’ heritage and worldwide network bolster the company with resiliency learnt and honed from experience.
“The port agency market is incredibly fragmented,” Olsen comments. “There’s a handful of global companies who have about 15 percent of the market share combined, but that means that the remaining vast majority is represented by smaller local companies.
“For us, having that global network means that we can support any client wherever they require us to through the modern framework of a large multinational company.”
This in turn entails a host of advantages and additional security, in terms of stringent compliance with health and safety regulations, compliance around ABC and ethics, sound procurement practices, sanction checking and a solid environmental social governance (ESG) agenda based on industry best practices.
“We have all those crucial factors in place, and it’s something that really sets us apart,” he elaborates.
In a modern context, these capabilities can prove crucial. Throughout its rich history, ISS has witnessed various conflicts - from the two World Wars, to playing a critical role in aiding allied forces in the Middle East. Today, amid the ongoing conflict in Ukraine, ISS fulfils an equally essential role with regard to the sanctions that have been imposed against Russian entities.
“Our ability to run complete sanctions checks, and make
sure that not only the direct customer but also any kind of counter party and related parties are operating within the sanction’s regime, is extremely important.”
Clients can rely on safety in experience in ISS’ hands, as a company that has truly been through it all.
“Regardless of what you throw at us, we’ve dealt with it before,” Olsen states.
This experience both informs and differentiates the ISS approach to working with its clients, acting as an extension of the business of its maritime partners and sharing its experience entirely to their advantage.
“The other major benefit of this global network is the ability to collect data and analytics to give advice to a customer that is based on a vast number of transactions.
“It means that we can give our customers valuable, proactive insight, based on the ports they’re using, the operations they intend on doing, and the challenges they might encounter. We can guide them on how to overcome
“IT’S QUITE UNIQUE IN THE WORLD WE LIVE IN TODAY THAT YOU ENCOUNTER A BRAND WHICH IS MORE THAN 100 YEARS OLD, AND NOW WE’RE VERGING ON 200”
– FRANK OLSEN, CEO, INCHCAPE SHIPPING SERVICES
Navigator Shipping Agency is a modern Shipping Agency based in Tripoli, Libya. Since 2011, we have focused on keeping up with the adjustments and changes of the maritime world and to provide the best of maritime services for our principals by providing the most competitive prices, most accurate information and 24/7 availability with all procedures made to keep the work going under any circumstances or occurrence.
operations goes as smoothly as anywhere else as we always receive questions regarding the environment at each Libyan port. We therefore always show content at Libyan ports to give our principals peace of mind and our audience a realistic and better view on Libyan ports.
NSC is devoted to complying with all maritime laws and treaties Issued by the International Maritime Organization (IMO) and by that, the company becomes the first Libyan maritime agency to cooperate in the fight against corruption and money laundering and hold a TRACE certificate of membership since 2015.
Over the recent years
NSC has expanded its strong social responsibility presence locally and abroad with full commitment towards the needs of the Libyan government in contributing to solving legal and administrative problems whenever we were asked for, and we’ve made a good reputation between principals for this.
NSC is also the only shipping company in Libya that is taking responsibility to create graphic social media content to give the general audience and principles a view of what work at the Libyan ports is like. We provide full proof that loading / discharging
NSC is always passionate and serious about keeping up with the latest technological working tools to give extra facilitated information, more accurate times and very quick responses at anytime during the day or night on any given day to make sure our principals are satisfied and assured that their business is going well and if a problem is faced, the problem is dealt with on the spot and every time it is solved with the satisfaction of the authorities and principals.
NSC will always be flexible regarding principal requests and will always go to new heights to reach their desires or come up with a solution for any given problem.
these obstacles and avoid delays or extra costs.”
ISS is a company that takes the macro challenges facing the industry as a whole – whether it be the most recent crisis of COVID-19, the record low oil prices of 2016, or the financial crisis of 2008, just as seriously as those of its individual clients.
“Throughout all these events, we have just continued doing and delivering. We haven’t been insulated to any of them, but we’ve always come out on our feet and delivered acceptable financial performance even during the toughest of times.
“At the same time, we’ve always been able to support our clients through all the hardship that they go through too.”
“REGARDLESS
– FRANK OLSEN, CEO, INCHCAPE
2022 marks a landmark year for ISS –not just for its historic anniversary, but also because it heralds the beginning of a new chapter for the company.
“Earlier this year, we entered into new ownership,” says Olsen. “Since 2006, ISS has been owned by Dubai based investment fund Isthitmar.”
That all changed in June, when London based private equity investment firm – Epiris LLP – completed the transaction in acquiring 100 percent of the company. For Olsen, a hopeful future awaits under this new ownership.
“This gives us a lot of confidence and bullishness about the future. Now that we have access to more capital, we can accelerate some of the good things we have going,” he shares.
Within this acceleration, technology has an integral role to play in forging ISS’ future.
“We’re not a technology company and never will be, but we see technology as an enabler and a tool to more effectively capitalise on the strengths and the value generated by our global network.”
For ISS, technology has a multifaceted application. The first perspective through which the company approaches its use, is in making ISS an easy enterprise to do business with, thereby driving process optimisation to improve and advance the efficiency of its operations.
“This benefits us internally by enabling us to be more productive, but also the customer by delivering higher standards of service,” Olsen shares.
The other lens through which technology is viewed concerns the collection of essential data. This is instrumental for a port agent in creating transparency, by collecting this information, analysing it, and subsequently providing useful insight to its clients.
Adopting a model of predictive analysis, based on what has happened in the past informing what might occur in the future, this technological approach harkens back to the opening philosophy, of leveraging experience to help determine what lies ahead.
“If we get this right we will be better equipped to go proactively out to our customers and inform their port schedules, guiding their actions to avoid delays or save costs, ultimately helping them to make better decisions.
“Of course, the final positive by-product of all this, is that by increasing the efficiency of shipping, you will de facto also reduce the carbon emissions.”
Looking ahead, growth is firmly on the agenda for ISS.
“With private equity ownership, there’s a strong focus on this and we have a very clear strategy across three main segments.
“To start with there’s organic growth, doing more with our existing customers and winning new clientswhether that be through tenders or through the transactional market,” Olsen informs us.
Complementing this organic growth is a focus on ancillary and additional services, based on developing new product offerings focused in and around the port, bolstering ISS’ core portfolio with new activities.
“Our third growth pillar is inorganic, centered on acquisition and driving a positive consolidation in what’s arguably a very fragmented market,” he continues.
This third pillar is already in full effect. Just days after the recent
new ownership was announced, an acquisition has already taken place with more due to come into effect shortly.
“On 25th July we announced our acquisition of a Belgian port agency called Kennedy Hunter. Meanwhile, back in 2019, we acquired the agency division of V. Group, and both have been strategic acquisitions.”
With several other active deals in a well-advanced stage, the next few months are set to bring more acquisition announcements for ISS. But at the heart of this ambition, is a people-centric positive outlook, based on bringing together a fragmented sector.
“We want to drive positive consolidation, we don’t want to behave or to be seen as corporate raiders nor do we want to do hostile takeovers.
“We’re in the people business and we need the backing of the people within the organisations that we
buy into. We look for companies with reputations, a certain level of expertise that complements our own, and good geographic matches in areas where we are looking to accelerate our presence,” he concludes.
Despite its longstanding history, ISS is a company that refuses to stagnate, riding a tide of continual expansion and evolution and bolstered by the solid foundation of its core competencies to continually cater to the modern needs of global shipping. INCHCAPE
Tel: +44 2035 138500 enquiries@iss-shipping.com www.iss-shipping.com
7th
AUSTRALIA’S LARGEST construction, architecture and infrastructure show, Sydney Build, is back once again on the 6th and 7th March 2023.
Held at the International Convention Centre, 14 Darling Drive, the event aims to bring together all professionals in the built environment and design industry in an extremely busy two-day exhibition and conference.
The event has firmly established itself as the largest and most important trade show for the industry. This event is free to attend and merely requires a simple registration on the expo’s website to secure a spot amongst more than 40,000 pre-registered attendees.
Brought to you by Oliver Kinross, Sydney Build is part of the company’s award-winning ‘BUILD’ exhibition portfolio that extends internationally to include trade shows held throughout New York, Chicago and London.
Sydney Build 2023 will feature over 500 exhibitors and 450 speakers across nine conference stages. Alongside Sydney Build, the Sydney Infrastructure Expo and Digital Construction Australia will be co-hosted at the venue. Three major expos in one, spread across a twoday period, will showcase the latest in technological advancement and touch upon controversial topics highly prevalent within the contemporary built environment industry.
Boasting a comprehensive programme and diverse range of displays, the event’s show floor incorporates a unique format designed to stimulate business networking opportunities between attendees and exhibitors and deliver quality content for audience members in an entertaining and engaging manner. Cutting-edge seminars, sponsored networking lounges and live equipment demonstrations are just a small portion of what attendees can expect to encounter at this year’s expo.
Uniting thousands of construction experts, architects, engineers, designers, government personal and aspiring tradies is no easy task. That’s why Sydney Build Expo has themed it’s 450 top-level speakers into nine stages scattered throughout the venue’s floor. These CPD accredited presentations will encompass a wide range of exclusive industry insights, touching upon topics of interest prevalent within the field of construction and shedding light on the first-hand experience of industry professionals. Below is a list of stages occurring throughout the course of the event:
• Sydney Main Stage
• Digital Construction Stage
• Sustainability Stage
• Architecture and Design Stage
• Diversity and Inclusion Stage
• Future of Construction Stage
• Infrastructure Stage
• Climate Resilience and Safety Stage
• Skills and Wellbeing Stage
The foundation of the Sydney Build Expo has been built on providing education and training opportunities across the Australian built environment industry; therefore, Sydney Build hopes to provide guests with new perspectives and favourable circumstances for approaching this booming field. More importantly, Sydney Build hopes that its attendees can build lasting relationships within the industry to further the growth potential of Australian construction development.
For more information and to register a complimentary ticket: www.sydneybuildexpo.com marketing@sydneybuildexpo.com.au
“Believe in yourself. Being female is not a roadblock. Along with a family to raise, I have businesses to run. Therefore, be tenacious and keep your head up when confronting any new challenge. If you have a dream to do something, believe you can do it and follow through with your dream. We all make mistakes and failure is a lesson on the path to success. So don’t be afraid and back yourself.”
Sean Ryan General Manager of Mining, Hitachi Construction Machinery Australia“Work with proven companies with mature ESG, products and technologies; join crosscollaborative industry bodies, develop networks and look for opportunities for efficiency. Most industry advances come from collaborative enterprise, rather than going solo.”
Ir. Chow Pui Hee Managing Director, Samaiden Group Berhad“Agility and resilience are the two key qualities that all entrepreneurs should have. Every change is an opportunity. Be ambitious, embrace your ideas, put them into a plan, and execute it. Opportunity waits for no one.”
You need to constantly surround yourself with people who challenge you to think differently, think globally, think commercially, and think sustainably. The only constant is change. You must be comfortable pivoting and reacting to the situation at hand, whilst maintaining focus on your own core values as well as the demands of the business and its associated stakeholders.”
and there is always an opportunity. My advice is to start to build some key clients and partners that will support you to give you that base to grow your business. The “client is king” attitude of S&techs has proven successful in all markets we operate in. In addition, know the business, how to deliver, and be truthful and realistic about your capability in the responsibilities you are taking on.”
“For me, it is about truly valuing our environment, people and relationships. No matter what, you cannot succeed in an industry as big as ours on your own.
Mike KavanaghCOO, S&techs Hong Kong Ltd
“There are many options for entering the industry
Are you a CEO/Director with a company story to tell? Contact APAC Outlook now!
Logan Hanifin General Manager, Oceania Dairy
What advice would you give to an entrepreneur entering your industry?
Sarsileap, Founder and Chairwoman, Hanuman Beverages
To round off each issue, we ask our contributing business leaders for their views on the same question
Reaching an audience of over 220,000 readers, your company can take advantage of exposure in APAC Outlook with a FREE article and FREE digital brochure, as well as access to further digital-based marketing tools that could transform your business. To share in this unrivalled opportunity, contact one of our project managers today!
Complementing the production of EME Outlook, APAC Outlook, Africa Outlook and North America Outlook magazines, Outlook Publishing’s award-
winning in-house team is now utilising these same specialist production skills to offer a full and bespoke range of editorial, design and marketing services via its new Outlook Creative Services division.
For more information on how we can work with you in providing a plethora of completely flexible and customisable production services, please visit: www.outlookpublishing.com/creative-services
DESIGN:
Stephen Giles +44 (0) 1603 363 634 steve.giles@outlookpublishing.com
Devon Collins +44 (0) 1603 363 656 devon.collins@outlookpublishing.com
EDITORIAL:
Phoebe Harper +44 (0) 1603 363 655 phoebe.harper@outlookpublishing.com
Marcus Kääpä +44 (0) 1603 363 653 marcus.kaapa@outlookpublishing.com