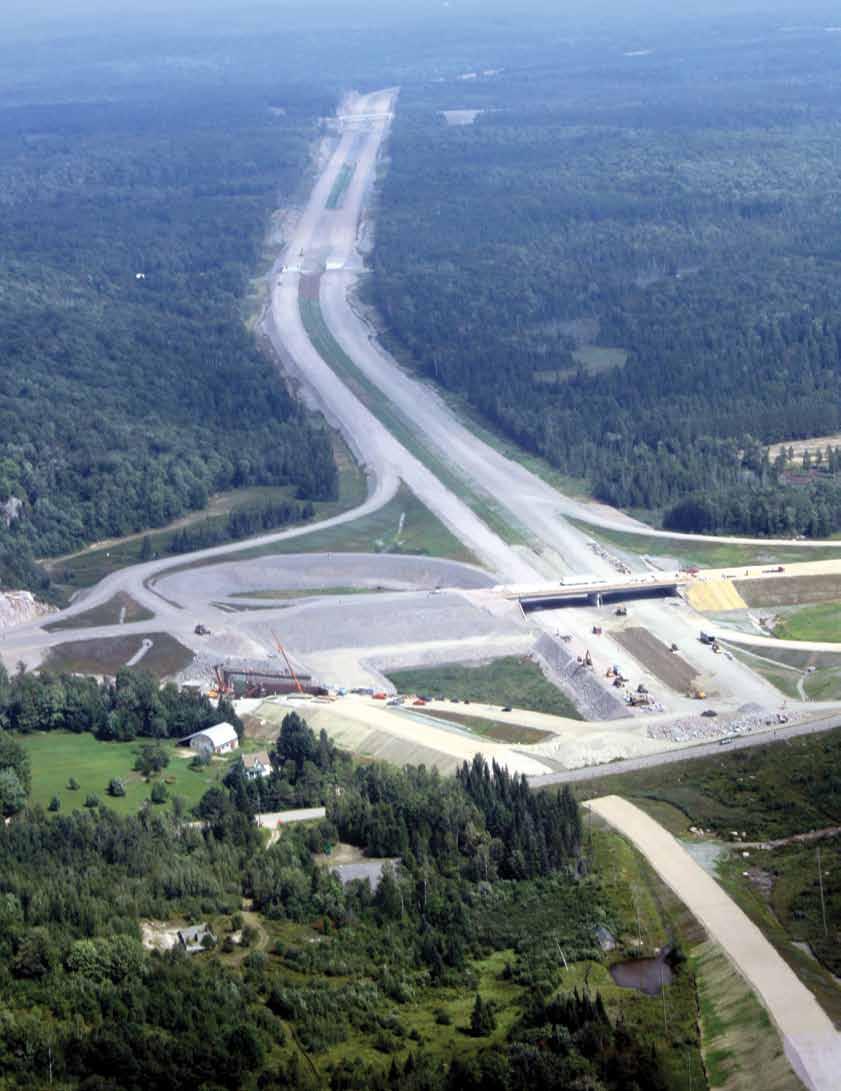
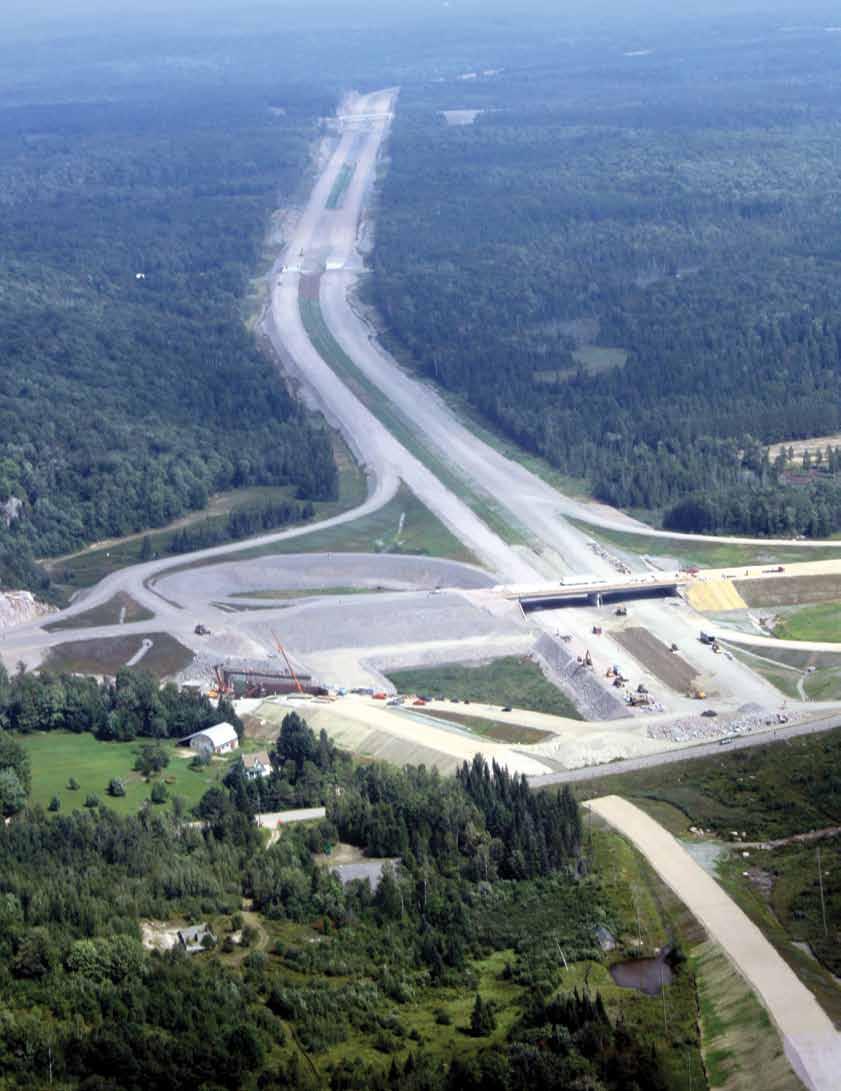
Years in the Making:
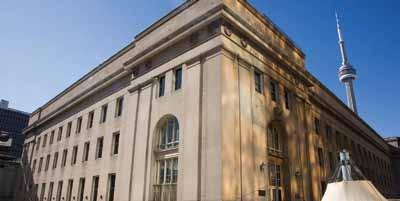
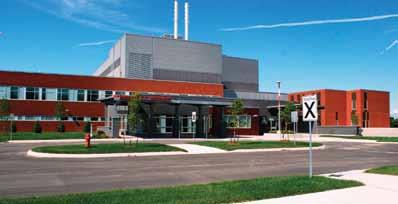
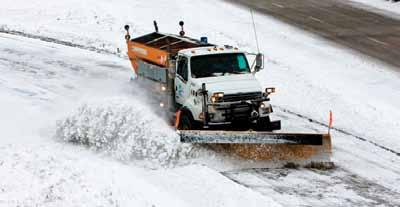
Carillion plc is one of Canada’s leading support services and construction companies. We have operations across Canada, Britain, Europe, the Middle East, North Africa and the Caribbean.
Our portfolio of award-winning work in areas vital to society includes: road, rail, health, education and regeneration, defence and commercial property. From first concept to ongoing facilities management and support services, we provide high quality, cost effective and sustainable solutions - tailored to the needs of our customers.
Roads Management
Building Construction
Integrated Facilities Management
Infrastructure Development

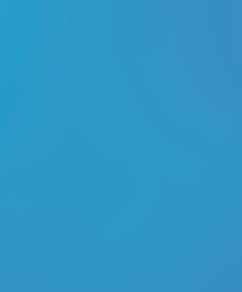

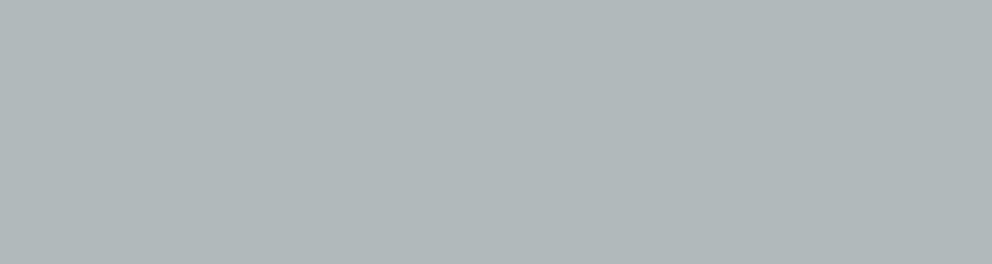

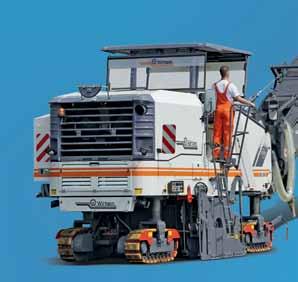
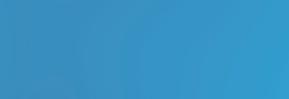
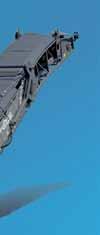


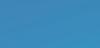
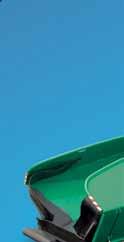

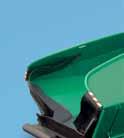
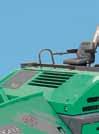
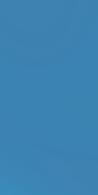
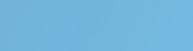





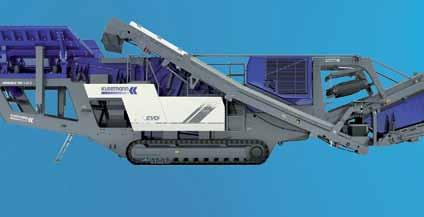

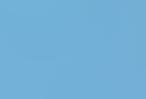


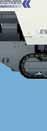
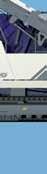
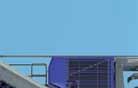



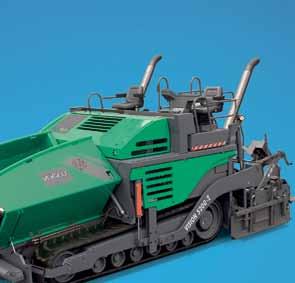
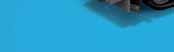


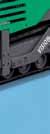












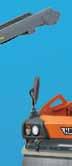
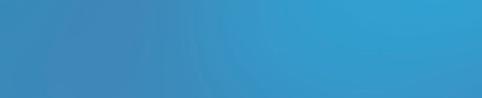
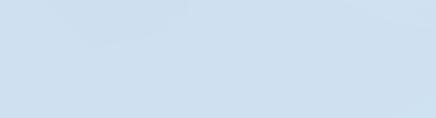


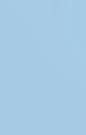
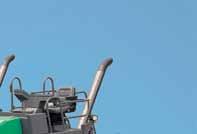
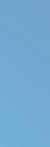


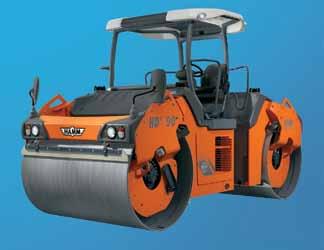
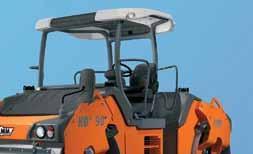




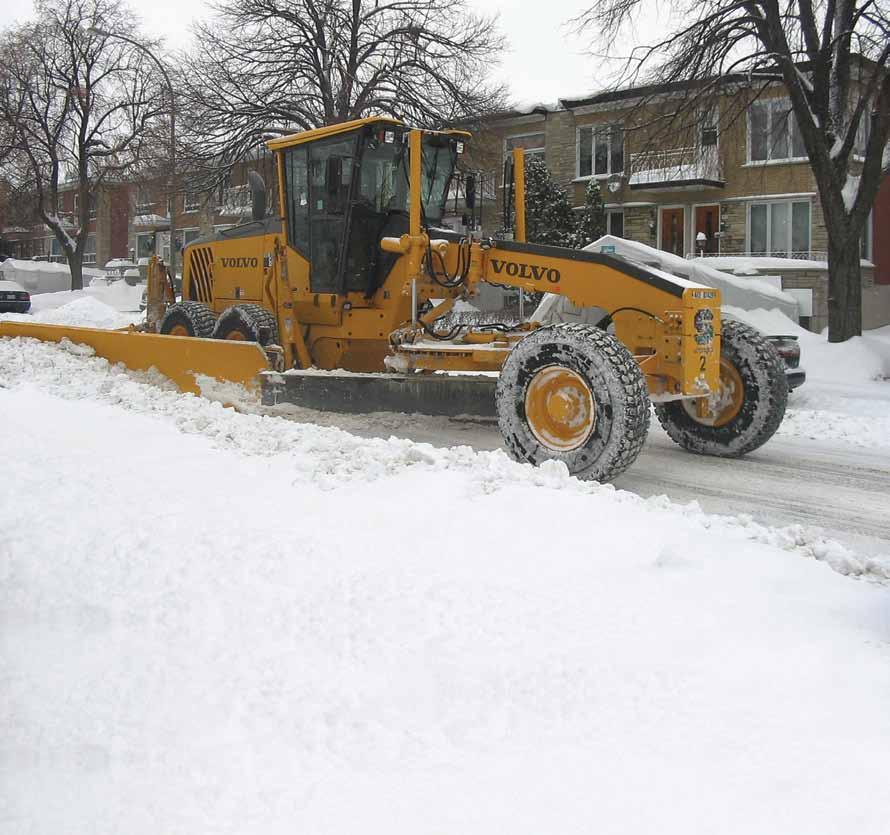
Strongco is your complete road building resource with a comprehensive range of Volvo paving, compaction, grading and milling machines, as well as construction equipment. We have everything you need for the road ahead.
Strongco’s parts and service department supports Volvo road machinery with expertly trained technicians, genuine Volvo parts and knowledgeable customer service. For more information, visit your local Strongco dealer to clear the way for progress.
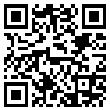

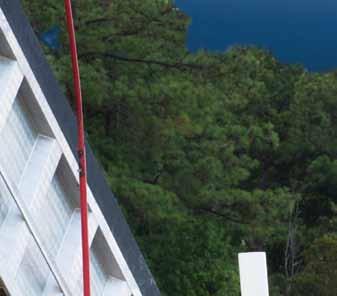
Shuttle Buggy® MTV from Roadtec:
Over 1,000 Sold Since 1988. Virtually All of Them Still in Service.
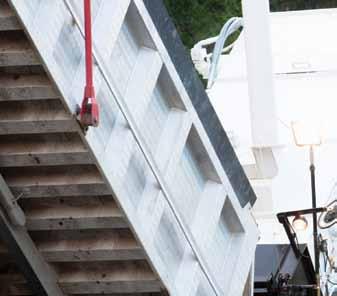

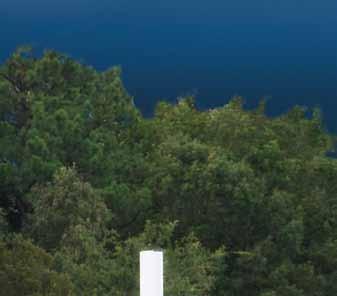

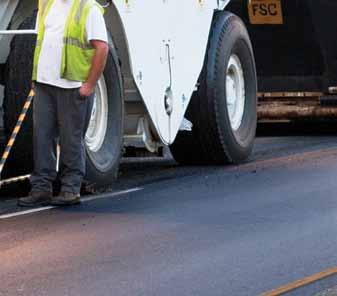
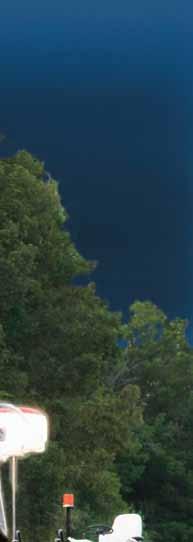
Expert, factory-direct support & rebuild service . Field service techs at your disposal 24/7. Proven performance. Units in service all over the world.
An MTV is subjected to a lot of wear. At Roadtec we’re proud to say that most of our first Shuttle Buggy MTVs remain working today. Why? Because we build them heavy-duty to start with. Then we help you perform preventive maintenance. With proper attention to wear parts and refurbishing components when needed, our machines last. And because we’re experts we can tell you exactly how much money it will cost you to protect your investment with each maintenance cycle.
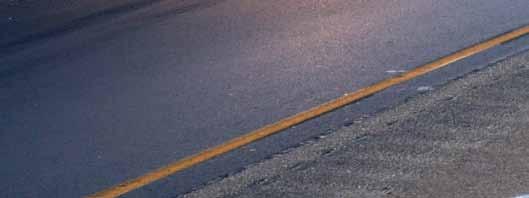
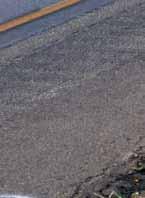
Roadtec: One step ahead with innovation, service, and expertise for Road Builders. It’s our passion. It’s all we do. Call us today!
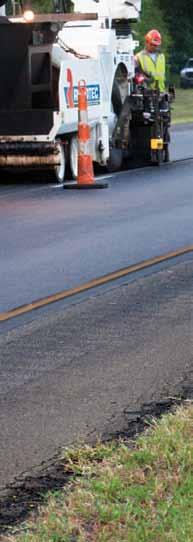
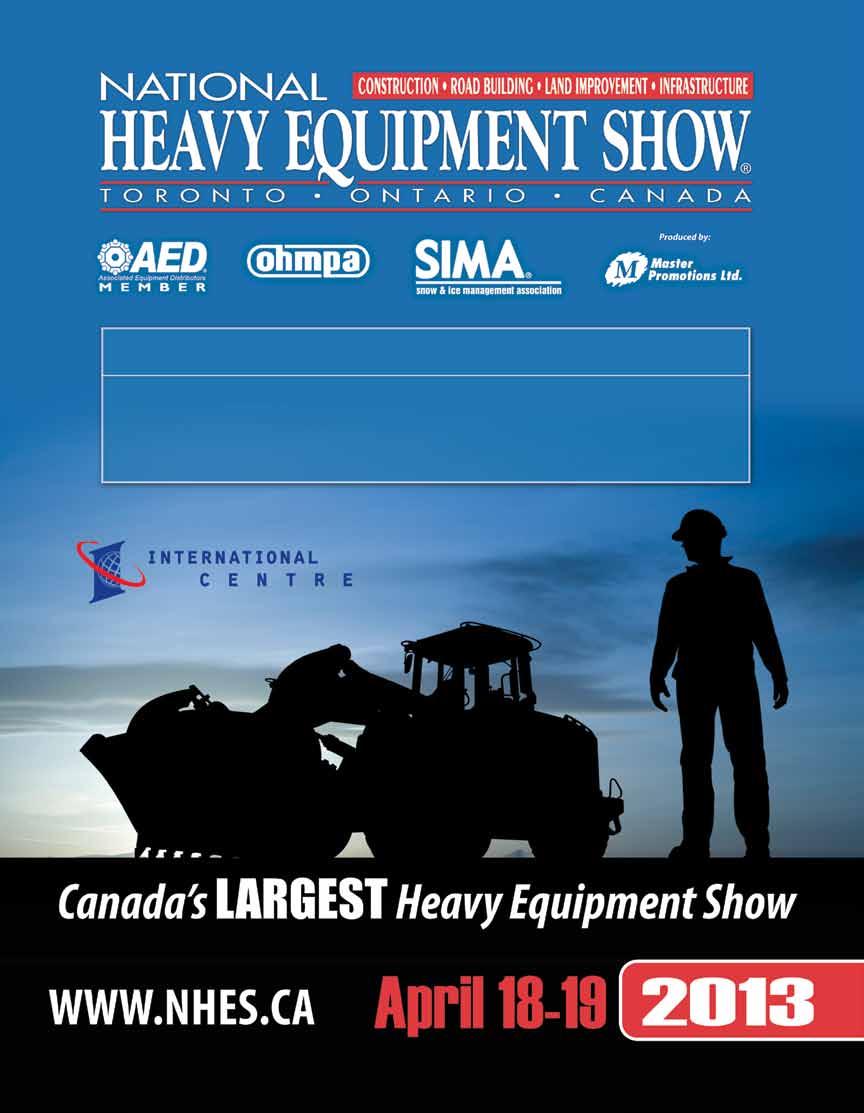
The Road Builder is published bi-annually for:
The Ontario Road Builders’ Association
365 Brunel Road, Unit 1
Mississauga, ON L4Z 1Z5
Tel: (905) 507-1107
Fax: (905) 890-8122 www.orba.org
Publisher Robert Thompson
Editor Ali Mintenko
Contributing Writer Matthew Bradford
Gary Fustey, Walter Niekamp, Ashley Privé, Jack Smith, David Tetlock
Graphic Design/Directory Specialist
Krista Zimmermann
Published by:
5255 Yonge Street, Suite 1000 Toronto, Ontario M2N 6P4
Toll Free: (866) 216-0860 ext. 229 robertt@mediaedge.ca 531 Marion Street Winnipeg, MB Canada R2J 0J9 Toll Free: (866) 201-3096 Fax: (204) 480-4420 www.mediaedgepublishing.com
President Kevin Brown
Senior Vice-President Robert Thompson
Branch Manager
Nancie Privé
All rights reserved. The contents of this publication may not be reproduced by any means, in whole or in part, without the prior written consent of the association.
Publication Mail Agreement #40787580
Return Undeliverable Items To:
Correction
In the Spring/Summer 2010 issue of The Road Builder, our Paver of the Year piece listed that K.P. Persaud was the Contract Administrator, when in fact it was Mahendra Pandya. Our apologies to Mahendra.
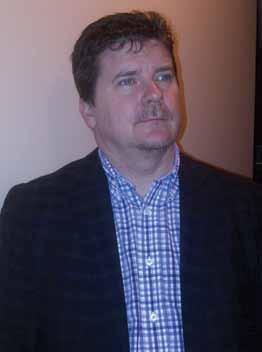
INTRODUCING GEOFF WILKINSON
ORBA welcomes new Executive Director
By Matthew Bradford
here’s a new face at ORBA’s head office in Mississauga. This June, the association welcomed Geoff Wilkinson to the team as its executive director, launching a new era of leadership for ORBA and its membership.
While relatively new to the road building industry, Wilkinson is no stranger to the transportation sector and its
major players. Prior to joining ORBA, he spent five years with the Ontario Automobile Dealer Association, working alongside key ministries and transportation stakeholders, many of whom he looks forward to working with again in his new role. This experience, in combination with his extensive association background, has equipped Wilkinson with a compre-
Canada’s Leading “SPECIALTY” Insurer
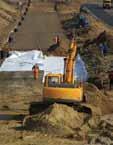
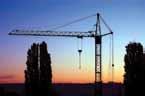
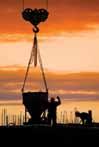
hensive suite of skills which he is eager to apply to his position at ORBA.
“(Being with ORBA) is definitely a step up in terms of my career and my involvement with many different ministries,” says Wilkinson, “When I was doing my research prior to applying, I found that ORBA is a very well respected association in terms of its relationship with the government as well as its members and stakeholders. That was definitely something that drew me to the organization, so when I saw the opportunity to join ORBA at a leadership level, I jumped at it.”
More enticing still, Wilkinson adds, was the opportunity to work directly with the industry contractors, movers and shakers, who he believes are playing a significant role in the development of the province. “One of the things I found very exciting with the position at ORBA is that while (ORBA) is an industry association, there’s also an element of social wellbeing within my role. I’m helping to build the infrastructure for the future of our children, and for me it’s very important to be advocating for that.”
Wilkinson assumed his executive director duties at a busy time for the association. Of the many projects on his radar, he says his priorities over the next few months will be to spearhead ORBA’s involvement with the ministry on the Corporate Financial Assurance Audit Services Team (CFAAST) review. “We’ve got a six-month window in which the minister has given
Like a finely-tuned race car, the International® DuraStar® is a high-performance vehicle. So if you’ve got a job to do, you can count on this truck to help you get it done. It’s the best-selling medium-duty truck for 20+ years*, a versatile, efficient performer that drivers love. An aerodynamic 3-piece hood, breakaway mirrors and one-piece grille make it easier to service. Exclusive Diamond Logic® electronics ensure safe, efficient vehicle operation. And its long-lasting, reliable Maxxforce® 7 300-hp V-8 is built on a lightweight, high-strength CGI block.
To see the DuraStar in action, go to InternationalTrucks.com/SettingThePace

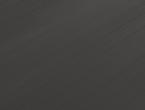
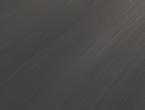
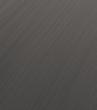
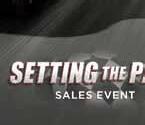
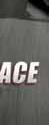
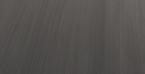

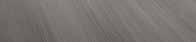
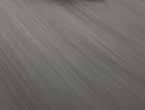
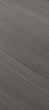
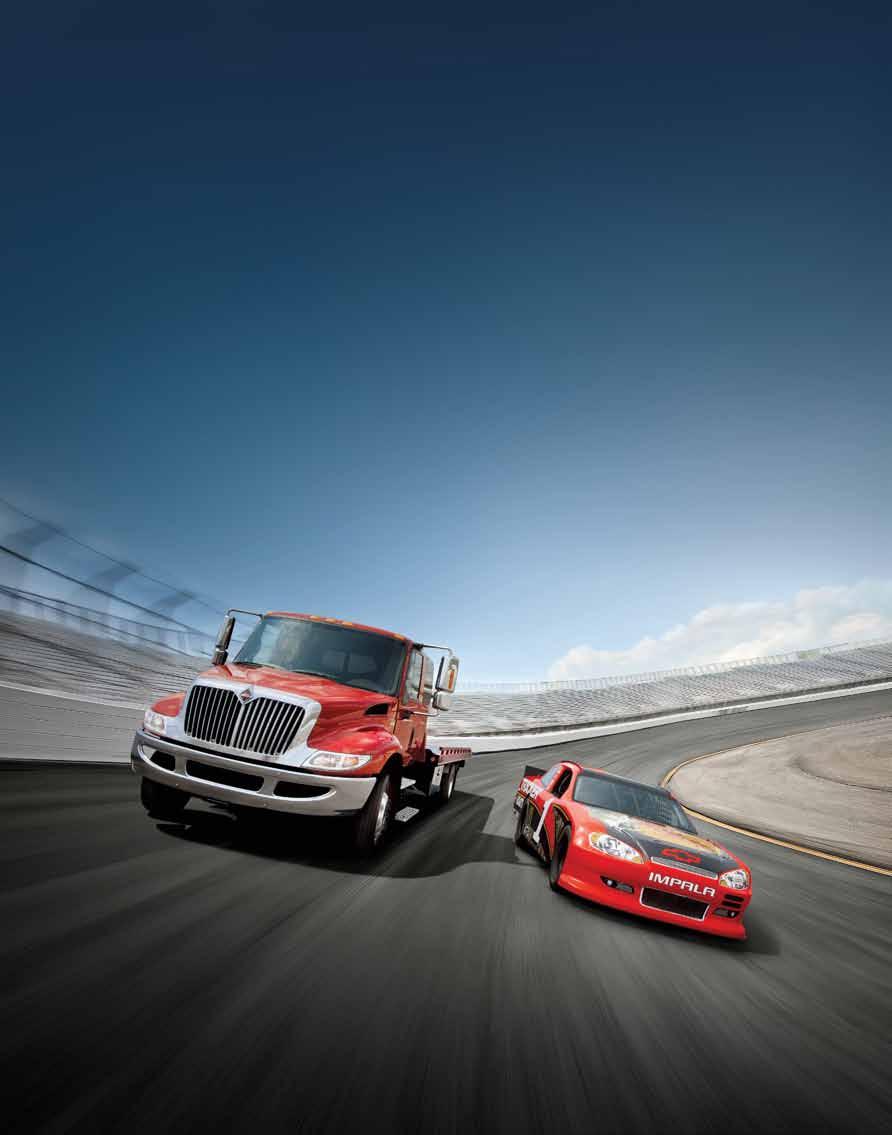
us to resolve those challenges,” says Wilkinson. “And I’d say that’s one of the most immediate areas of focus right now.”
In addition to upholding the association’s commitment to CFAAST, Wilkinson has received the go-ahead from the ORBA Board of Directors to review its strategic plan in an effort to both understand the association’s immediate goals and to apply his own perspective and ideas to its guiding blueprint.
Wilkinson is optimistic about his new role, as is ORBA, which conducted a thorough search for its new association leader following the departure of its former executive director, Rob Bradford, in August 2012.
Other priorities include working on new ways to assist contractors in municipal challenges, strengthening ORBA’s educational initiatives, and becoming acquainted with all members within ORBA’s roster.
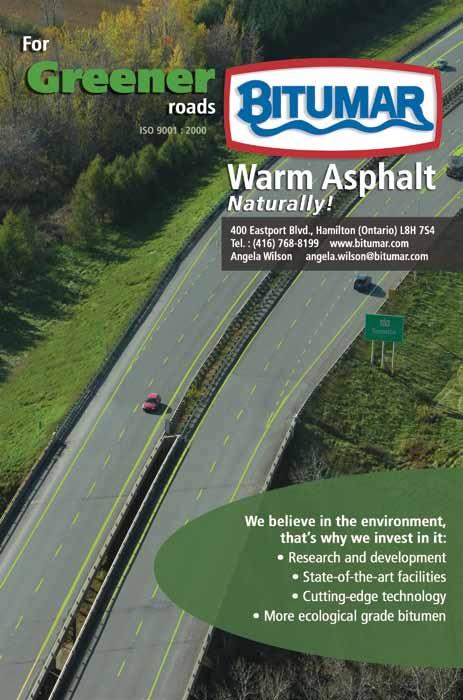
It is a packed agenda to be sure, but according to Wilkinson, he is used to accepting a challenge: “I used to have a boss that asked me every time we met, ‘Are you challenged in your role, Geoff?’ and I’d always say ‘yes,’ because… I look at challenge as opportunities. Likewise, I think with the number of challenges ORBA has in front of it, those will also lead to a number of opportunities.”
Wilkinson is optimistic about his new role, as is ORBA, which conducted a thorough search for its new association leader following the departure of its former executive director, Rob Bradford, in August 2012.
“We’re very optimistic with Geoff at the helm,” says Jim Hurst, ORBA President and VP of construction/ area maintenance contracts at Steed and Evans Ltd. “We went through a rigorous hiring process with the management committee at ORBA. We interviewed a number of good candidates and we found Geoff was the strongest. He comes with a lot of association experience, and while he might not necessarily come from a road building background, he’s learning fast and catching up really well.”
As for his outlook, Wilkinson is confident in his new role, especially with the support and commitment of ORBA’s staff at his side. “We’ve got a great team here. It’s a small team, but they’re very dedicated and very hard working,” he says.
Adds Hurst: “It goes without saying that we wish him all the best of luck in his new position, and look forward to him bringing a new perspective, new ideas and some youthful enthusiasm to the table.”
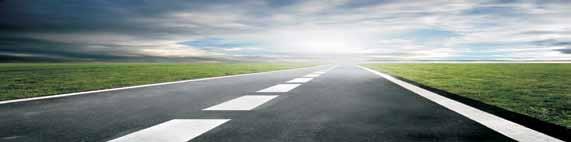
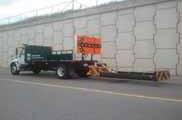
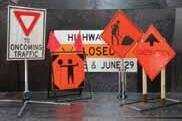

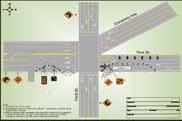
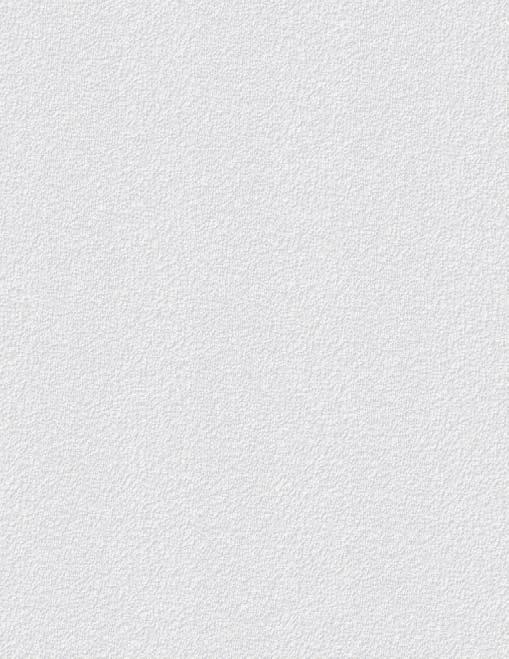

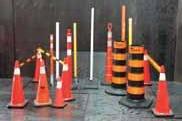
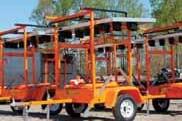
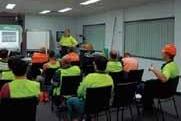
Executive Director’s Message
This past year was a very good year for ORBA with some key industry “wins.” The Honourable Bob Chiarelli struck a CFAAST Implementation Committee, which included five ORBA members and the ORBA Executive Director, to work with the MTO to resolve ORBA’s seven key issues identified within the CFAAST Report.
Other successes include:
• The passage of Bill 8 – The Ontario Underground Infrastructure Notification System Act, 2012 (formerly One Call Act)
• A 5-year extension on the use of CB radios for commercial vehicles (now lasting until 2017) – hands-free legislation
• Loosening of the rules guiding senior commercial drivers license renewal process for drivers aged 65-79
• Slowed down the implementation of the College of Trades; particularly on its ratio and compulsory certification reviews of the construction trades
• Equipment Rental Rates, including 25-40% increases for truck rental rates across the board
• Safe winter driving around snow plows “Let Us Lead the Way” campaign
• Progress on Health and Safety Issues; including a Reversing
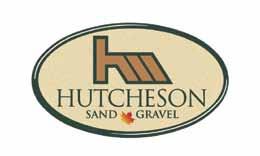
in Work Zones Best Management Practice Guide.
Despite our “wins” for 2012 there are significant challenges ahead for the industry in 2013 including advocating for:
• Continued spending on transportation infrastructure
• Abolishment or significant overhaul of the College of Trades
• A more fair-minded CVOR system for short-haul operators
• Fair, open and transparent procurement policies and process by all owners
• Improving the fairness of contract specifications
• Construction centric approach to WSIB

AFPs that are within the reach of ORBA members
This list is not exhaustive and we will continue to monitor issues and concerns as they arise.
2013 is going to be a very interesting year for provincial politics. We will be meeting with Liberal candidates in the race for the Premier’s position.
Ontarians are also anticipating an election. To this point, we will be meeting with party leaders and key MPPs from across Ontario to introduce ORBA’s issues and ask for support in addressing and resolving these issues.
We will be providing members with tools and resources to use in conversations with local MPPs outlining our positions. It will undoubtedly be a very exciting spring and summer for us working with politicians.
Geoff Wilkinson, Executive Director
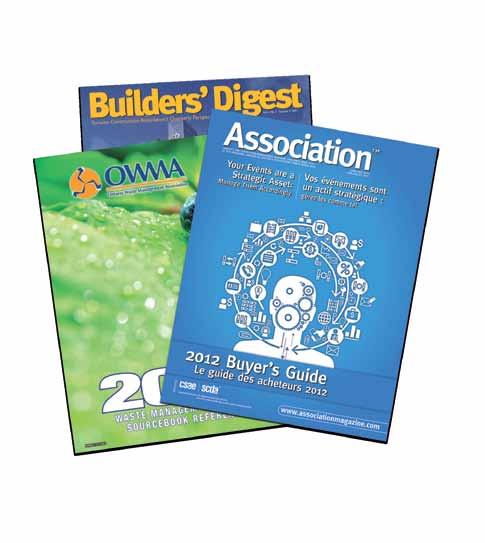

Print Digital Events Video
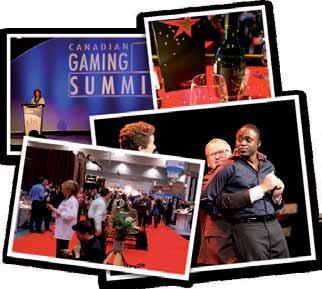
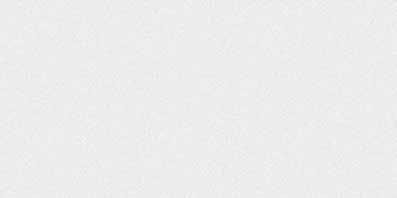
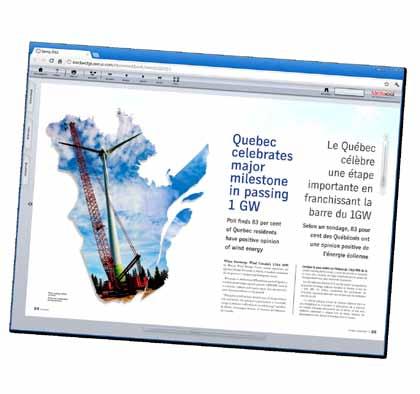
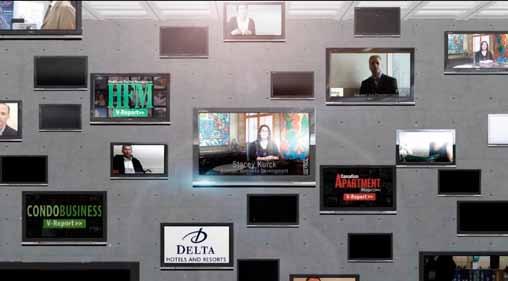
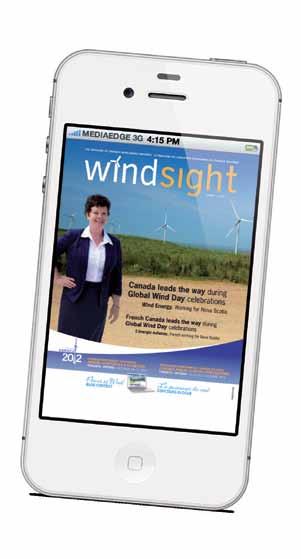
Around Queen’s Park
A Productive Year for ORBA
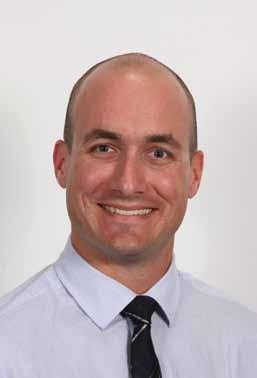
by Patrick McManus, ORBA Policy Analyst
In our last Queen’s Park update, ORBA’s own political soothsayer, Karen Renkema, identified a number of trends in the Ontario legislature that just so happen to have come to fruition over the past twelve months. In fact, her report – which foretold the byelection, increasing regulatory pressures, and greater caution from Queen’s Park in addressing the provincial debt load – led me to believe that she must have been aided by a crystal ball of some sort. Alas, after a thorough search of her office, I have returned to my desk suspicious, but empty-handed.
For those interested in politics, Ontario in 2012 has been full of inter-
esting plotlines. The “major-minority,” as Premier Dalton McGuinty has so effectively termed his government, continues to occupy the seats of power. It does so notwithstanding a turbulent year in the halls of Queen’s Park that were witness to: political brinkmanship in the form of a confidence challenge surrounding the passage Budget 2012; autumn byelections in Vaughan and Kitchener-Waterloo; and the downgrade of Ontario’s credit rating by both Moody’s and Standard & Poor’s. And after much variability on the political scene since the general election in October 2011, we head towards the year-end in much the same place as we did 12 months ago, with discussions in the media of a confidence vote surrounding Budget 2013, talk of an impending spring election and the ebb and flow of political fortunes of the three primary political parties in the province.
From the government relations’ side of the fence, operating in such a politicized environment often proves quite challenging. Acquiring and maintaining the government’s attention is a daunting task on an average day, but during a minority government, when political polls are king and show support for the Liberal, PC and NDP rising and falling like the sun, this task proves much more difficult. Nevertheless, 2012 has proven to be a productive year for ORBA’s government relations’ agenda, with success in working with the government to push forward a number of issues that have been in development over varying lengths of time. Some of these issues include Bill 8 – the Ontario Underground Infrastructure Notification
System Act, 2012; CFAAST; reform of the workplace safety and insurance system; and the ongoing issues surrounding the Ontario College of Trades, among many others.
On June 14, Bill 8, the Ontario Underground Infrastructure Notification System Act (formerly the One Call Act) received royal assent, officially establishing a not-for-profit, single-point-of-contact call system for all underground infrastructure location services in Ontario. This is a significant piece of legislation that ORBA, along with a large group of industry stakeholders and underground utility owners, had long been lobbying for. The act will allow companies to call just one number to request and obtain all necessary utility locates for any given job, at no cost. Prior to its passage, Ontario operated on a voluntary call-before-you-dig system, which required up to 13 different phone calls for infrastructure locates before any digging could occur.
The new system (which will not come fully online until June 2014) will minimize delays by mandating a fivebusiness-day limit for underground infrastructure locates. ORBA would like to congratulate and thank MPP Bob Bailey (Sarnia-Lambton) and MPP Paul Miller (Hamilton East-Stony Creek) for their bipartisan efforts in spearheading this initiative and providing their collective weight to see this issue pass into law in just a few months. Bill 8 will serve to drastically reduce the number of infrastructure strikes that occur during excavation projects across the province, making Ontario a safer place for both workers and the general public.
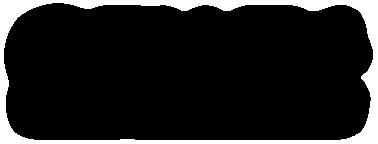
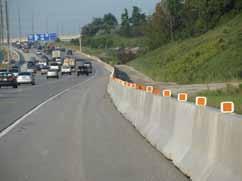
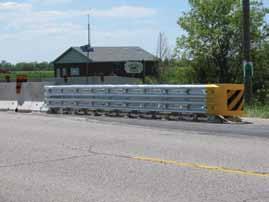

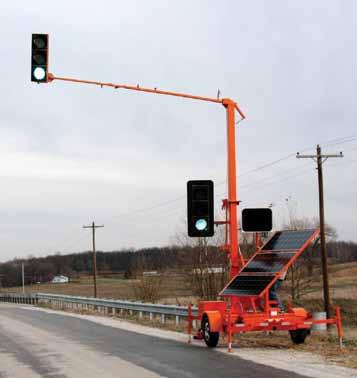
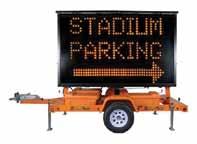






AROUND QUEEN’S PARK
In late 2010, the Ontario Ministry of Transportation (MTO) undertook an internal review of its claims and infractions processes and the administration of liquidated damages at ORBA’s behest. The CFAAST Report was the result of this review; it made a number of recommendations to improve fairness and transparency in the MTO processes. ORBA took this review process one step further, commissioning Borden Ladner Gervais LLP (BLG), a national law firm, to research best practices and first principles from across North America and further afield, based on the recommendations made in the CFAAST Report. The BLG report was delivered to Minister Bob Chiarelli and the MTO in April as supporting research for ORBA’s own recommendations.
After review of the material, Minister Chiarelli proposed the development of a joint Government of OntarioORBA Implementation Committee – made up of representatives from ORBA, Infrastructure Ontario, and the Ministries of Transportation, Infrastructure, and Finance – to navigate and consider the implementation of the CFAAST recommendations based on the material presented in the two reports. Minister Chiarelli requested
that this committee meet monthly with an eye to developing a mutually agreed upon approach to applying the recommendations before the new year.
The Workplace Safety and Insurance Board (WSIB) launched a significant modernization exercise in 2012, beginning with the publication of Funding Fairness: A Report on Ontario’s Workplace Safety and Insurance System The report was commissioned by the WSIB to make recommendations on how it should be working to address its $14.2-billion unfunded liability. Follow-up reviews of the WSIB benefits program and of its premium rate groups, rate setting and employer incentive programs were also launched in 2012. Overseeing this modernization exercise is the newly appointed Chair of the WSIB, Elizabeth Witmer, who relinquished her seat as MPP of Kitchener-Waterloo to take over this role from outgoing Chair Steve Mahoney. ORBA is working with a coalition of like-minded industry stakeholders to participate widely in the consultative process surrounding these reviews in order to ensure that our priorities and concerns are voiced and included in this review process.
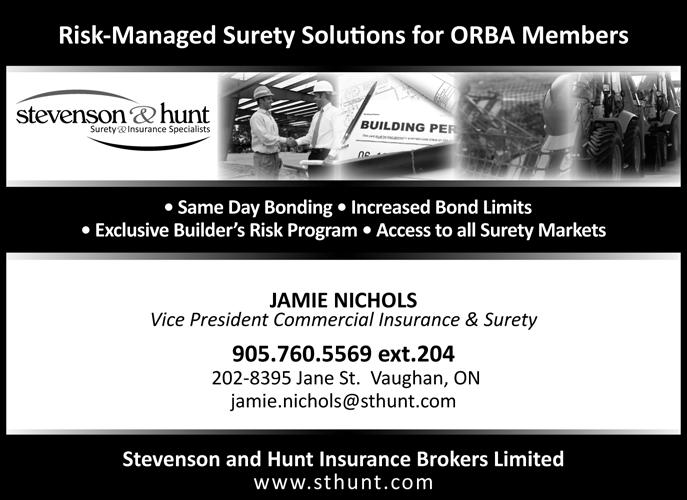
ORBA continues to address the road building industry’s concerns about the College of Trades through the Ontario Construction Employers Coalition (CEC). Our grass-roots campaign to urge the government of Ontario to shut down the College of Trades is continuing to grow, particularly following the May announcement of a new $84-million tax on Ontario’s tradespeople. The new tax is to be used to run the College, which will further tax, regulate and police tradespeople in the province, over and above the existing fees and structures in place. ORBA will continue to work through the CEC to urge the government to follow the lead of most provinces in Canada by moving away from greater regulation of the trades and towards greater flexibility and lower ratios. Visit the CEC website at www.stopthetradestax.ca for more information.
Advocating for transportation infrastructure investment will continue to be ORBA’s top priority moving forward into 2013 and beyond; however, there is a growing list of regulatory issues that impact ORBA members’ business processes and costs of delivering infrastructure projects that we must also be conscious of. We will continue to press forward with our message that Ontario needs more transportation infrastructure in order to move its economic development goals forward, while developing complementary messaging to address ongoing issues with contracts, occupational health and safety, apprenticeship reform, transportation and equipment, environmental regulations and materials specifications, among many others.
On a final note, Karen Renkema, ORBA Director of Government Relations, who normally writes this segment for Road Builder magazine, is away for the next few months celebrating the birth of her son, Everett. We at ORBA would like to send out our
heartfelt congratulations to Karen and her family on their new little addition. Enjoy your journey into parenthood and have fun!
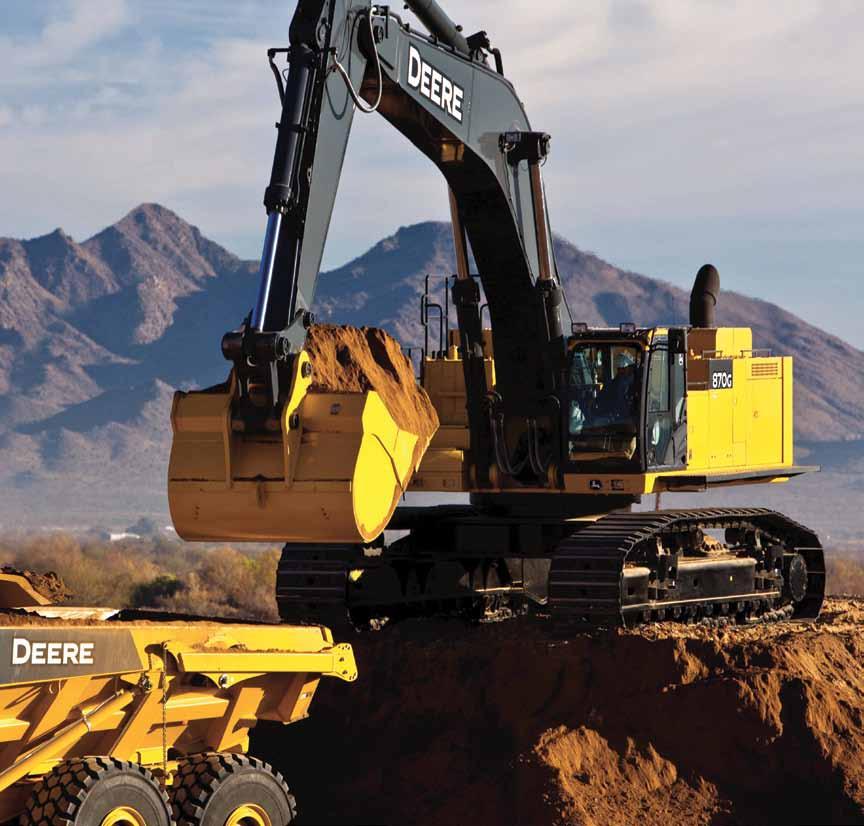
Nortrax is a proud sponsor of the Ontario Road Builders Association
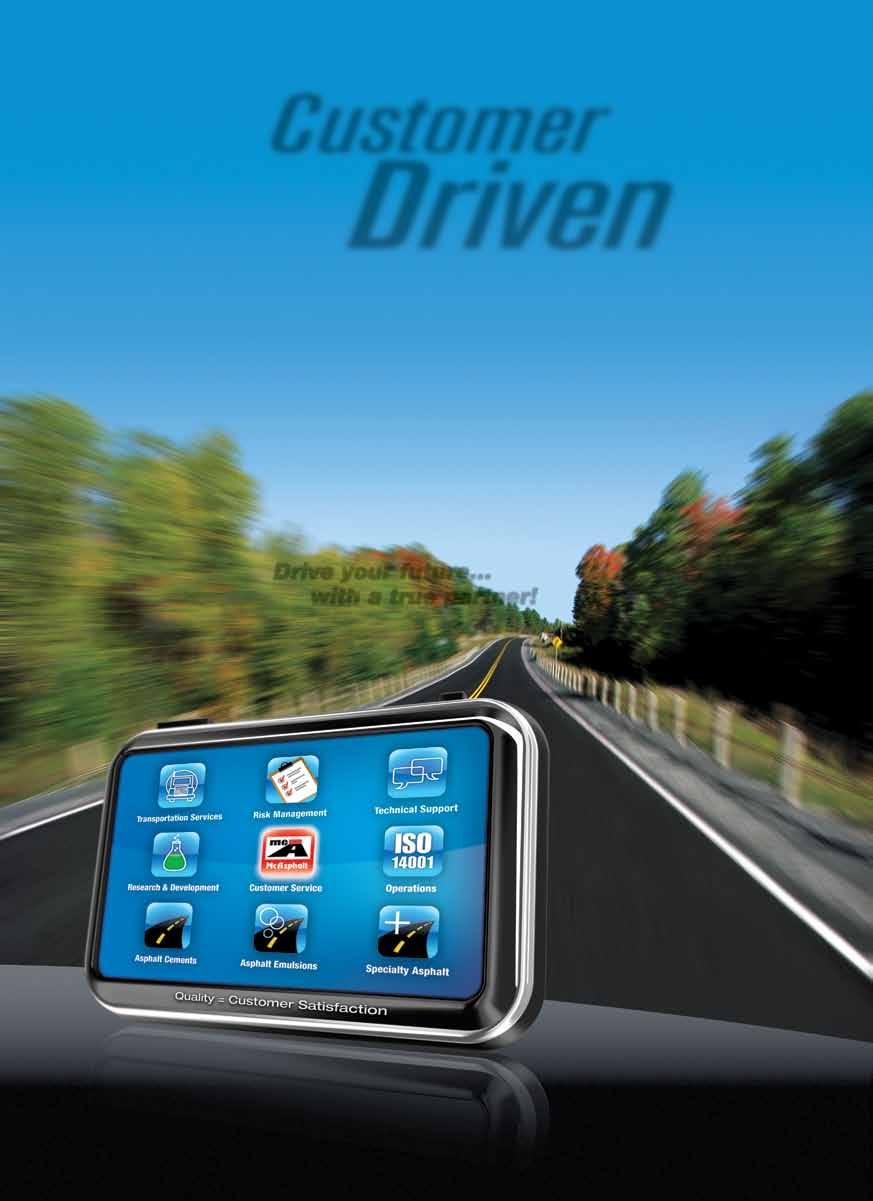
For over 40 years McAsphalt has simply been ‘Customer Driven’. Working hard to understand your business and your challenges - to be your trusted partner and advisor in today’s volatile global markets. Our people are driven by your goals and business objectives. Our customers not only count on us for quality products but also for education and training, transportation logistics, technical support and engineering services. Your demand and needs drive McAsphalt!
Drive your future… with a true partner!
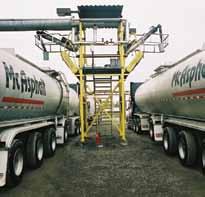


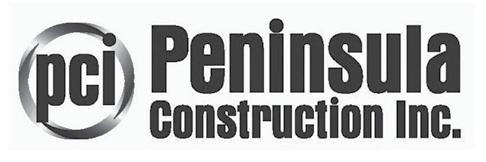
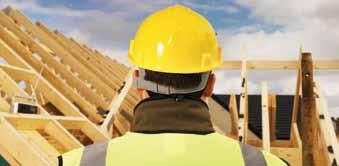

Bill 119 –Mandatory WSIB Coverage for the Construction Industry
In 2008, the government of Ontario made changes to the Workplace Safety and Insurance Act, 1997 (WSIA). This act requires all those working in the construction industry to have insurance coverage from the Workplace Safety and Insurance Board (WSIB) beginning January 1, 2013, although penalties for non-compliance will not be applied until January 1, 2014. The government’s intent behind these rule changes were threefold: to improve provincial health and safety; to level the playing field by ensuring all those working in construction are paying their fair share; and to help combat the underground economy in the construction sector.
For ORBA members, the changes to the WSIA will have a considerable impact on how you do business. The new coverage rules will require all current independent operators (IOs), sole proprietors, partners in a partnership and executive officers, who were previously exempted from coverage rules, to now register with the WSIB, report their earnings and pay premiums on reported earnings. This includes those who carry out multiple business activities in different sectors, so long as one of those activities is in construction. Below is a summary of the coverage rules that are likely to have the most impact on ORBA members.
Independent Operators
IOs in construction who presently hold a clearance certificate from the WSIB will have their status revoked
as of December 31, 2012 and will be required to re-register with the WSIB to ensure that they are appropriately covered for work in construction. Therefore, beginning in 2013 ORBA members must be diligent in requesting clearance certificates/ proof of coverage from all of their subcontractors. They will need this before they are granted entry onto your jobsites. You risk being charged with an offence under the WSIA if someone is working onsite without proper clearance/coverage.
Executive Officers
A partnership or corporation may now elect one partner/executive officer for exemption from WSIB coverage if this person does not engage in any construction work. The remaining partners/executives who have historically been exempt from coverage will now be required to register with the WSIB. Since Bill 119 was passed in 2008, ORBA has advocated strongly for the creation of a separate rate for the remaining partners/ executives who do not receive this exemption (separate from the 711 and 732 premium rates groupings). After several years of negotiation, ORBA’s efforts have proved successful, as the WSIB has agreed to create a separate rate group under Class G. This new rate group will be made akin to the legal and financial services rate group in 2013, which paid $0.21 per $100, as opposed to the 711 and 732 rate groups that paid $5.16 and $6.86 per $100 respectively, in 2012 (sole proprietors do not qualify for the special executive rate in the WSIB).
In order to receive this special rate, however, a company must specifically request it for each partner/executive. Those covered under this special rate will still be allowed to visit work sites provided they do not perform construction work.
Clearance Certificates
By issuing a clearance certificate, the WSIB is confirming that the recipient is registered and in good standing. It also means that the WSIB is waiving its right to hold a contractor liable for unpaid premiums and other costs that a subcontractor may owe the WSIB. ORBA members must ensure that they are holding on to copies of clearance certificates for a period of three years for auditing purposes. For those non-construction workers, i.e., broker truck drivers, who show up on a job site without a clearance certificate, they are available online at the WSIB website 24 hours a day, seven days a week and can be obtained in just a few short minutes.
BeRegisteredBeReady.ca
In order to accommodate these significant changes, the WSIB has launched a dedicated website (BeRegisteredBeReady.ca) to allow those who fall under these new coverage rules to register in advance of the new year. Pre-registration will be available for the remainder of 2012. Administrative practice guidelines are also available at this site to provide more details about the application of the new rules.
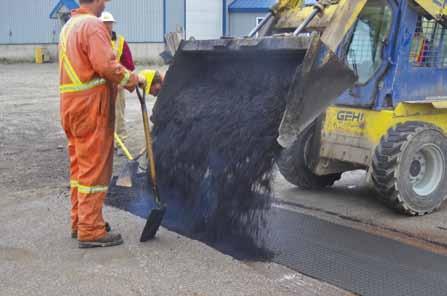
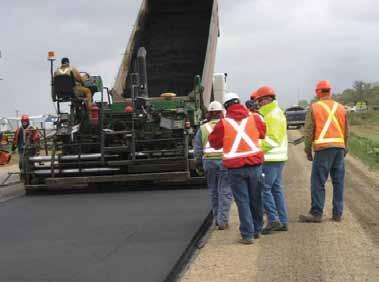
HaTelit - Geogrid Composite for Asphalt Reinforcement
• Designed to increase the service life of asphalt overlays and delay the onset of reflective cracking
• The flexible polyester geogrid has a bituminous
• HaTelit can be used directly over milled surfaces coating that creates an exceptional bond with surrounding asphalt layers
• HaTelit has a thin lightweight nonwoven fabric to make installation quicker & more economical
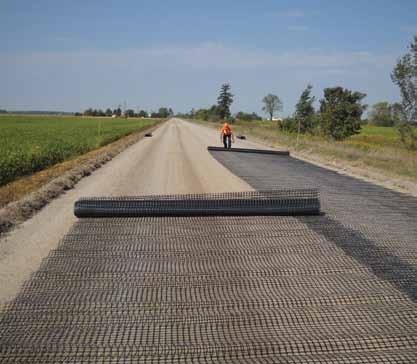
Advera WMA - Warm Mix Asphalt
With the addition of Advera WMA , asphalt mixes can be produced at temperatures 50-70 o F lower
The addition of Advera WMA to asphalt mixes allows for:
• Reduced emissions (VOC and CO2 up to 60% reduction)
• Faster opening to traffic
• Extended paving season / cold weather paving or night paving
Terra x Biaxial Geogrid for
Subgrade Improvement
• Reduce aggregate fill thickness
• Reduce sub-excavation
• Extend the service of pavement
• Reduce labour & equipment requirements
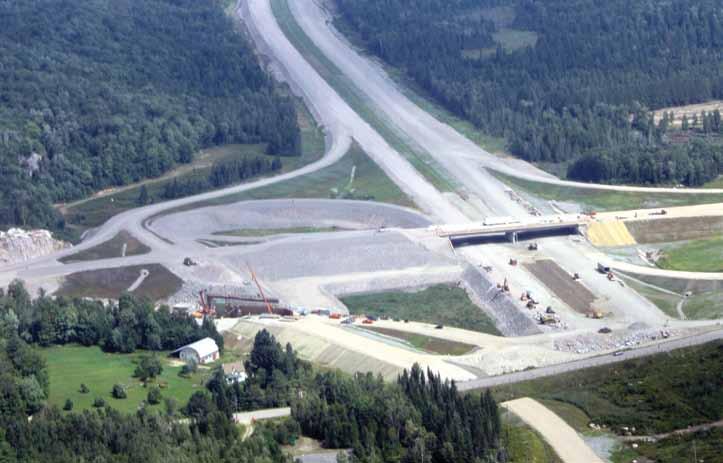
Thirty Years in the Making Northerners Celebrate Completion of Highway 11 Four-Laning
After more than 30 years since the four-laning of Highway 11 between Huntsville and North Bay first began, the project was officially capped this summer when the last 10km section between Sundridge and Burk’s Falls opened to traffic on August 8, 2012. Shortly after on September 28, contractors, regional officials from the Ministries of Transportation and Northern Mines, and local and provincial politicians attended ceremonies in North Bay to celebrate the completion.
In 2005, the Liberal government included the Highway 11 project in its new Northern Ontario Highways Strategy document and set a 2012 completion target. Hon. Rick Bartolucci, Minister of Northern Mines and Development, took a deserved moment to credit his government for finishing the northern corridor, noting, “Our government has followed through on its commitment to complete the four-laning of Highway 11 by 2012. As one of the largest undertakings ever funded through
the Northern Highways Program, our government has invested significantly in advancing safety and promoting economic development and job creation along the corridor.”
The four-laning of Highway 11 started in 1979 with a single, small project south of North Bay. It continued through the years, with its progress fluctuating according to the priorities of the governments of the day, and even coming to a standstill under the Bob Rae government in the mid 1990s. The four-laning continued through the 1980s with five major contracts tendered for the section south from Huntsville to Powassan in 1983, 1985, 1987, 1991 and 1993. Since 1995, construction has continued on 13 major contracts on the final 93km south from Powassan to Huntsville, with the program kicking into high gear around 2003.
It was also around 2003 when a similar massive four-laning project was undertaken in the west during the four-laning of Highway 69 from Parry Sound to
Sudbury. Work on Highway 69 has tracked the progress on Highway 11 over the past decade and is also into its final stages. The twin gateways to the North shared construction challenges inherent to Precambrian granite, including the multitude of lakes and rivers that requires structures and the frequent, drastic changes in elevation.
On the final projects completed this year, Teranorth Construction & Engineering Ltd. was the prime contractor for the Burk’s Falls Bypass and Carillion Canada did the work on section between Burk’s Falls and Sundridge. Carillion Canada was the contractor for the 10 km section between Burk’s Falls and Sundridge.
The logistics of Highway II have been staggering. In that final 93km stretch, the Ministry of Transportation reports there were 16 new interchanges and 54 new bridges built, primarily by ORBA members. In addition, there were 1.7 million cubic metres of rock excavation and 10.5 million cubic metres of earth excavation. Contractors crushed and
The Highway 11/123 south junction interchange
Photo by PJ Wilson
placed 4.6 million tonnes of granulars in the corridor and laid half a million tonnes of hot mix asphalt. Since 2003 the province has invested $717 million to complete the continuous four-laning and dividing of Highway 11; the bill surpasses $1 billion including work done since 1979.
Hon. Bob Chiarelli, Minister of Transportation and Minister of Infrastructure, also emphasized the economic impacts of completing the Highway 11 four-laning, saying, “The completion of the four-laning of Highway 11 is great news for Northeastern Ontario. I am pleased that our investment has finished the job for families and businesses that depend on this highway corridor.”
The northerners who will benefit from the corridor are also applauding its completion; however they are also quick to point out that it has been over 30 years in the making and therefore past due. In an article in the North Bay Nugget on August 10, Sun Media reporter Gord Young quoted North Bay and District Chamber of Commerce president John Strang as saying: “Every chamber president over the past 30-plus years has had the Highway 11 four-laning as a priority during their term.”
“It’s just hard to believe that this day has finally arrived,” said North Bay councillor, Dave Mendicino, in the same article. “There was a time when we thought it may not come.”
Mendicino was at the forefront of a relentless Highway 11 expansion lobby, first as Chamber of Commerce president and later after he was elected to Council over a decade ago.
The city’s business and elected leaders expect that completion of the new four-lane corridor will create more business opportunities for companies in the near north and more companies setting up shop. They are also looking for a boost to tourism by making the trip faster and safer. Average daily traffic on Highway 11 between Huntsville
and North Bay has reached 9,300 and rises to 11,400 daily trips (one way) in the summer. Meanwhile, the average daily truck volume, according to MTO, is 1,199.
Highway 11 was originally built in 1920 to connect southern Ontario communities to North Bay. It was pieced together by the first Minister of Highways, Frank Campbell Biggs, by linking several of the original colonization roads such as Yonge Street, Penetan-
guishene Road and the Muskoka Road. North of the Severn River roads were the jurisdiction of the Department of Northern Development and the section of Highway 11 that ran from there to North Bay was maintained by them as a very basic gravel trunk road.
Construction began on an extension of Highway 11 from North Bay to Cobalt in 1925. Today Highway 11 stretches 1,784km from Toronto to Fort Frances at the Manitoba border.
LUBE & FLUID HANDLING
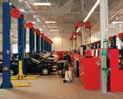
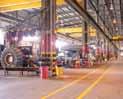
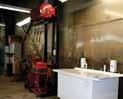


VEHICLE SERVICE FACILITIES
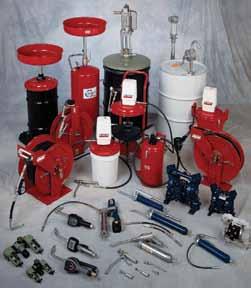

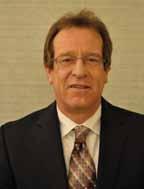
Robert Bradford bids Adieu
On August 21, ORBA members, MTO reps, industry colleagues, friends and family packed the Credit Valley Golf and Country Club in Mississauga to bid farewell to ORBA’s outgoing Executive Director, Rob Bradford.
Over 100 guests attended the afterhours event, which honoured Rob’s 17-year career with ORBA. The evening featured good food, great company and fond memories as colleagues took to the podium to thank Rob for his commitment to the road building industry, and wish him well as he transitions to working fulltime on ORBA’s Legacy Project.
“The fact that the send-off was very well attended is a credit to Rob’s reputation in the industry,” noted Jim Hurst, ORBA President. “Everyone was there to recognize his dedication to ORBA and thank him for always keeping ORBA first in mind and fighting for what was right for us.”
Taking his turn at the microphone, Rob thanked the evening’s attendees. “To say I’m overwhelmed doesn’t begin to describe how it makes me feel that you have all come out here on a weeknight in the middle of the construction season – some from very far away – to honour me like this,” he told everyone present. “Having you all here also makes it easy for me to thank all of the people who have supported me and worked with me to accomplish some of the things we achieved together for the industry.”
Rob cut his teeth on the Ontario construction scene in 1977 as the labour reporter for the Daily Commercial News, a position he acquired almost immediately after graduating from Ryerson University with a Bachelor of Applied Arts in journalism. After three years covering all corners of the construction industry, he joined the Toronto Construction Association as an assistant to its then Executive Director Cliff Bulmer, during which time he managed six trade associations. In 1982, Rob started Bradcom Ltd. to deliver association and communications services to corporate clients in the construction industry. Four years later, in 1986, he formed Construction Business Publications Inc. to publish Construction Business magazine. Rob provided contract management services to the Ontario Hot Mix Producers Association (OHMPA) and the Metropolitan Toronto Road Builders’ Association from 1984 until he became OHMPA’s first executive director in 1989. In 1996, his experience in the industry culminated in his appointment as ORBA’s executive director.
“There have been some incredibly memorable experiences and good times during my time with ORBA,” said Rob. “I’ve had the privilege of seeing nearly every province and many of the country’s cities and towns. I’ve stood at the edge of the unfinished Confederation Bridge in P.E.I., watched crews blast roads through the rock in Northern Ontario, ate pigs’ tails in Heidelberg
with the Seegmiller and Steed and Evans guys, stood at the top of the CN Tower when the Sikorsky helicopter was topping it off, and on the roof of the new SkyDome (now Rogers Centre) when nobody even knew if it would work.”
Reflecting on ORBA’s numerous successes during his time as executive director, Rob says he’s very proud to have played a key role in the creation of the Worst Road Campaign and the development of ORBA’s Road Building Academy as well as the Ontario Civil Construction Careers Institute (OCCCI). He is also pleased to have played a strong role in helping build ORBA’s influence in and contribution to the Ontario industry.
“I am proud of the role that I played and I am very proud of what ORBA has become,” said Rob. “I believe the association is well positioned for greater things in the future. I have no doubt Geoff Wilkinson will bring these new ideas and renewed focus to ORBA, and I’m sure that with his leadership the association will continue be at the forefront of change in the industry.”
In the words of Jim Hurst, ORBA President, Rob’s contribution to the industry has been critical. “(Since) I’ve been at ORBA, (Rob) has worked to get us well positioned as a strong voice to the government and a top notch reputation as an association,” said Hurst. “He’s left us in a good position.”
Rob Bradford
While the August send-off marked the end of Rob’s official tenure at ORBA, it was in no way a final stamp on his career, or even his work with the association and industry. Moving forward, Rob has embraced his new role as head researcher and author of the Legacy Project, an upcoming publication on the long and distinguished history of Ontario’s road building industry.
“The Legacy Project is a fascinating one, and I am enjoying the research and writing tremendously,” commented Rob. “It is a tremendous opportunity for me as I transition into a new stage of my life and I thank the ORBA Board and members for giving me that opportunity. I just hope that folks get as much enjoyment from reading the history of road building in Ontario as I am having in writing it.”
Operating under his new company InSite Services, Rob has spent the latter half of 2012 leading a team
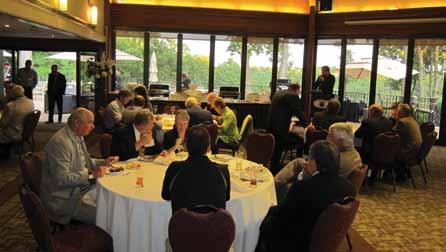
of researchers on interviews and fact-finding missions throughout the province. Says Hurst, Rob’s involvement in this key ORBA project was a natural match: “Having (Rob) on this project was a perfect fit. There’s no better person to write about our industry than a guy who’s led the association for as long as he has, and a guy with a journalistic background... I’ve got a glimpse of the first chapter and it’s looking good so far!”
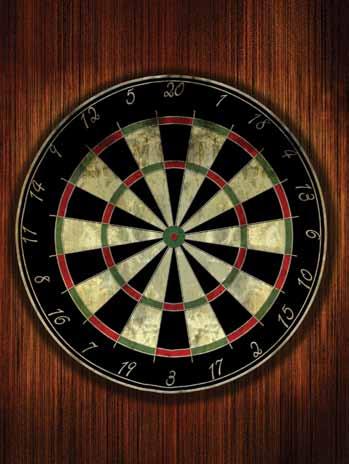
Rob is also looking forward to embarking on new adventures with wife Deanna, son Matthew, daughterin-law Marijana and new grandson Xander, not to mention getting in a few rounds of golf if his schedule allows. Still, the long-time industry veteran has no plans to retire fully. “I’m not riding off into the sunset just yet,” he says, “and I remain committed to helping ORBA and the industry in any way that I can.”
Con Cast Pipe takes accuracy to a new level. Our state-of-the-art manufacturing facilities create precast concrete products that exceed industry standards.
Products are on target every time for consistency, quality and accuracy. We combine over 20 years of innovation and leadership with state-of-the art technology to meet your target every time. We can deliver that.



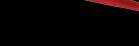



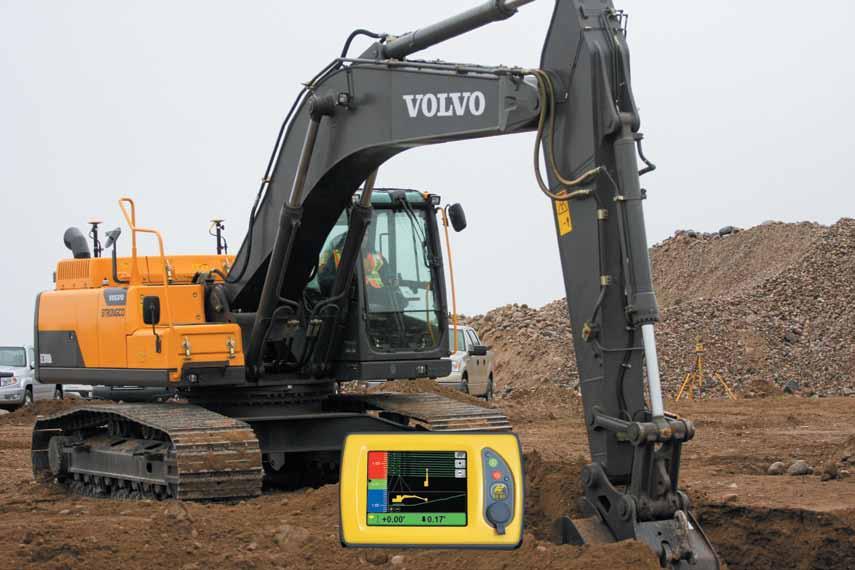

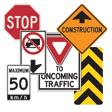
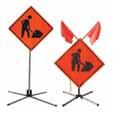
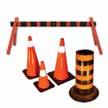

Your one stop source for comprehensive traffic control services.
Steed and Evans provides complete traffic services for a wide variety of projects, large and small, including construction and reconstruction of city streets, highway maintenance, asphalt paving and more. Our experienced team will plan and manage the process to meet your project needs so your team can comfortably focus on the work. Our services include:
• Freeway & Municipal Crews
• Crash Trucks
• Moving Operations
• Lane Closures
• Site-Specific Traffic Control Plans
Call Ken Lang at 519-650-3442 or email KLang@steedevans.on.ca for more information.
Traffic Control Services
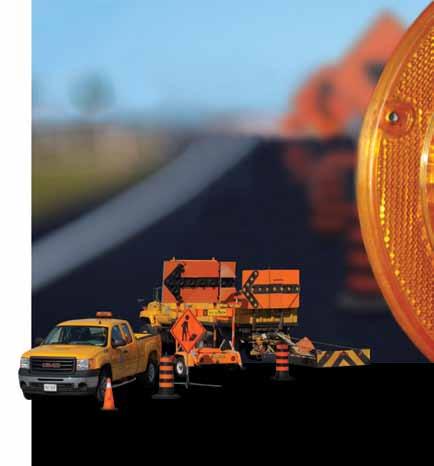

Metrolinx’s Big Move Update
In 2008, Metrolinx lifted the veil on its “Big Move,” an integrated transportation project designed to reduce commuting times and traffic congestion in the Greater Toronto and Hamilton Area (GTHA). The 25-year plan detailed a number of transportation infrastructure initiatives, including the development of 1,200 kilometres of new rapid transit lines, the doubling of transit mode share, a reduction of greenhouse gas emissions, and the placement of viable transit options within two kilometres of 75 per cent of the region’s population.
Now, four years later, Metrolinx (formerly the Greater Toronto Transportation Authority) has broken ground on a number of its Big Move plans, and its leaders are reporting success on many fronts. “Metrolinx is continuing our work
to realize the Big Move. We have $16 billion worth of projects with shovels in the ground, including priority projects like the Eglinton-Scarborough Crosstown LRT and York/ Viva Bus Rapid Transit plan,” reports Bruce McCuaig, CEO of Metrolinx.
McCuaig updated road builders on Metrolinx’s strategy at the 2012 ORBA convention. “Stakeholders like ORBA and its members will play a key role as we continue to build and plan new light rail transit and bus rapid transit routes and other improvements to the GTHA’s transportation network,” he told delegates.
Adds Leslie Woo, Vice President, Policy, Planning and Innovation for Metrolinx: “Between when we established the Big Move to now, we’ve been able to secure a significant foundational amount of funding and (we’ve) advanced quite a number of projects, particularly in the rapid transit area. So that’s very, very positive.” A review of Metrolinx’s website (www.metrolinx.com) indicates the agency is well into its ambitious project, with new components coming online at a steady pace.



Recognizing the tremendous opportunities for ORBA members from the growth in public transit infrastructure work, this year the association formalized a partnership with Metrolinx to become the official voice of the contracting sector with the provincial transit agency. The new ORBA/ Metrolinx Transit Contractors Council is the formally-recognized forum for discussion and industry consultation on Metrolinx’s procurement policy and practices, construction specifications, contracts and documents, delivery models, and other relevant issues related to Metrolinx’s civil construction capital program.
Steve Martin, Metrolinx’s Director of Administration and Contract Services, explains: “The purpose of the committee is, through discussion, to have bidders who are aware of (what) Metrolinx is, what our mandate is, and what our high-level programs are over the short term. Bidders who are better educated on our processes will be able to give us the best bids based on accurate specifications. This partnership helps Metrolinx attract multiple competitive bids with the best documents, specifications, and processes possible.”
The ORBA/Metrolinx Transit Contractors Council is comprised of senior executives from Metrolinx’s procure-
ment, finance, strategic business development and capital infrastructure groups, as well as ORBA leadership. Speaking on the association’s involvement, Martin says: “As Metrolinx continues to plan and build new transit, there will be a key role to play for stakeholders like ORBA and its members. The Big Move will see new light-rail and bus rapid transit routes, as well as other improvements, added to the region’s transportation network, and organizations like ORBA have the expertise to help us realize our vision for transit and transportation in the GTHA.”
On a broader scale, Woo notes that ORBA’s overall collaboration with Metrolinx – be it through the ORBA/Metrolinx Transit Contractors Council or general support – is integral to the success of many of the Big Move’s on-the-ground elements, specifically in providing not only the talent and resources to expand GTHA’s infrastructure, but in keeping the region’s roads in a strong state of good repair. “A lot of transit happens on the road. Our local transit, our regional transit and the buses they run on roads, and the improvements to those roads are vital to a well-functioning transportation network. This means there’s a direct vested interest in an organization like ORBA,” explains Woo.
In the meantime, Woo says the main challenge for all Big Move stakeholders going forward will be to assist Metrolinx in raising awareness for the project and, in turn, generate funding for its continued progress. “In order for us to develop a sustainable way forward, and to improve the quality of life in the region, we are all going to have to invest significantly in a sustained, long-term transportation and transit plan in this region,” says Woo. “This is an area where ORBA can really step up to the plate, along with many others who have done the same, and really raise awareness about the importance of why we need to sustain our investment.”
“There’s $16-billion that’s been invested in transportation in this region for the next seven to eight years,” continues Woo. “That’s what the government has committed to. However, there’s $34-billion still required for the remaining years, and we need to engage all stakeholders and constituencies to understand the importance of investing in our transportation network and our investment strategy.”
For its part, ORBA is optimistic about Metrolinx’s plan and impressed with the progress made in four short years. “They have a lot of projects on the go, and I’m certainly confident they’re going to meet their goals going by what I’ve seen from their senior management,” says Geoff Wilkinson, Executive Director at ORBA.
Speaking to ORBA’s commitment, Wilkinson says the association’s membership is equipped and ready to meet the demands of Metrolinx’s Big Move, as well as to partner with the agency itself to oversee mutually beneficial objectives.
“With Metrolinx, it was exciting that they approached us as an example of an association that is there to provide a resource for best practices for things like contracts, dispute resolutions, and all different areas within the tendering process. This is certainly an opportunity for members,” notes Wilkinson. “They’ve got the expertise, they’ve got the manpower, and they’re ready to build.”
Roadway Solutions...

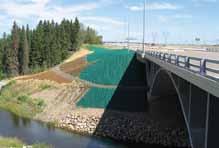
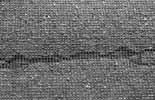

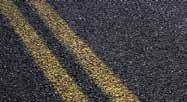
For 35 years, Nilex products have been used to build better roads by providing innovative, cost effective solutions that benefit the environment. Whether you are building over soft ground, need to strengthen a base section, improve surfacing, enhance drainage or solve a grade separation challenge, Nilex can provide an engineered design solution.
Our products simplify construction, increasing roadway life, and reduce future maintenance.
To find out more, contact us at 1.877.640.6002 or visit www.nilex.com.

2012 ORBA Scholarship Awards
By Matthew Bradford
Brett Martin and Sandy Tang were recently named the recipients of ORBA’s 2012 Civil Engineering and Technology Scholarships. The annual monetary awards, established in 2010 by then ORBA President Paul Quinless, recognize exceptional high-school students entering a civil engineering course at an Ontario university or a civil technology course at an Ontario college.
Both of this year’s candidates were selected by ORBA’s Education, Training and Industry Promotion Committee from a pool of strong applicants. The selection was based on academic achievements, work and volunteer experience, and industry insight, among other criteria.
As with ORBA Scholarship recipients in the past, Martin and Tang have been invited to the 2013 ORBA Convention to be congratulated by their future colleagues and employers. If you are planning to attend, make sure to pass on your congratulations and wish them well in their future careers.
Martin’s interest in construction was sparked at young age after repeat visits to his father’s office at Miller Paving in Timmins, Ontario. Here, Martin spent much of his childhood and his teens shadowing his dad on the jobsite and soaking up all he could about the industry, its equipment and its people. Later, he went on to work for Miller Paving himself, first with a flagging job and then on a grading crew.
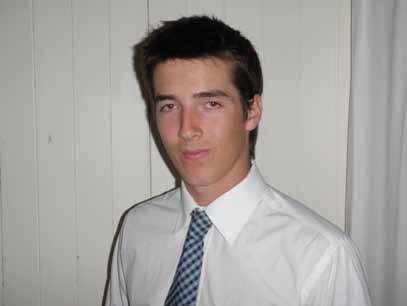
says Martin. “I hope that one day, I will be able to be a part of a successful road building team and make a difference in Ontario’s roadways.”
Martin’s natural leadership abilities have also been demonstrated at Carleton Place High School, where he actively volunteered with the girls’ hockey program, and made an impression on his teachers. “Brett exhibits a clear, strong dedication to his personal development,” noted one teacher, Craig Young, in his reference letter for Martin. “He is highly motivated and approaches his studies with purpose and resolve.”
When it came time to choosing a career path, Martin heeded the call of the industry and successfully applied to St. Lawrence College’s Civil Engineering Technology program. After a summer spent working with the Town of Carleton Place Public Works Department, he started his first year of classes at the college in September 2012.
“I cannot thank ORBA enough for this amazing scholarship,” says Martin. “This is, for sure, one of the highlights of my life so far. It encourages me to be professional with my studies and give my absolute best effort in school to impress ORBA.”
Martin adds he plans to apply the scholarship to the second half of his tuition fees, and looks forward to thanking the association in person at the 2013 ORBA Convention.
•
Tractor Rentals
• Save Capital
• Eliminate Repairs
• No Long-Term Commitment
• No Depreciation or Replacement
• Wide Variety of Late Models from 55 HP – 200 HP
• Attachments Include: Loaders, Wagons, Mowers etc.
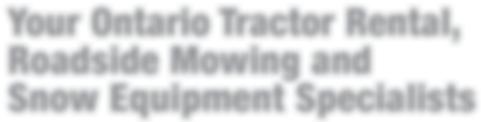
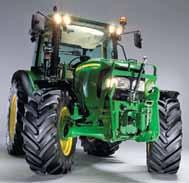
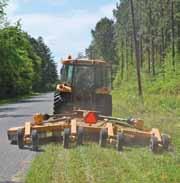
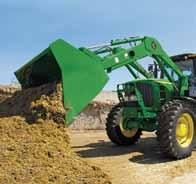
• 22' Reach with 50" HD Flail Head Capable of Handling up to 5" Brush — 50" and 60" Rotary Heads also Available
• 75" Side and Rear Flail Mowers Available
• Ideal for Mowing and Brushing along Roads, Walking Trails, Right of Ways, etc.
• Weekly and Monthly Rentals
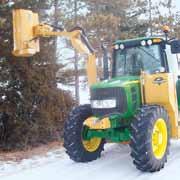

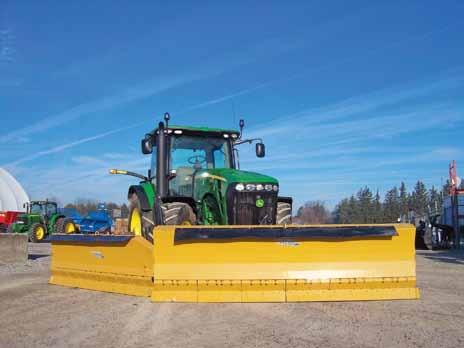

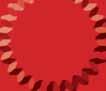

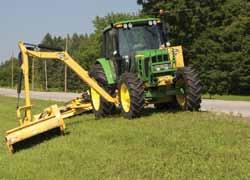
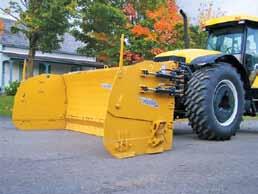
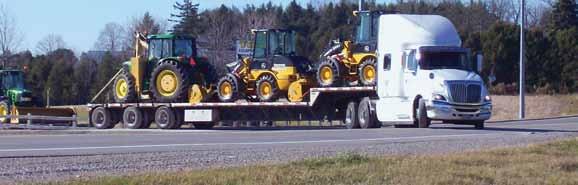
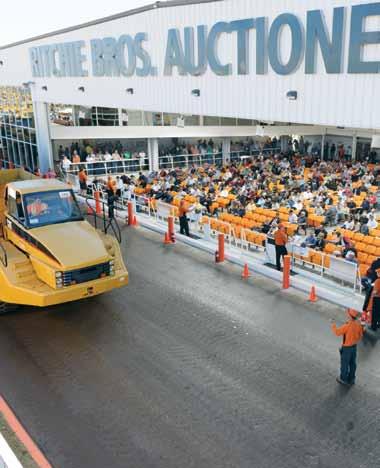
THE BEST WAY TO SELL YOUR EQUIPMENT IS TO GIVE IT SOME WELL-DESERVED ATTENTION.
THE BEST WAY TO SELL YOUR EQUIPMENT IS TO GIVE IT SOME WELL-DESERVED ATTENTION.
THE BEST WAY TO SELL YOUR EQUIPMENT IS TO GIVE IT SOME WELL-DESERVED ATTENTION.
THE BEST WAY TO SELL YOUR EQUIPMENT IS TO GIVE IT SOME WELL-DESERVED ATTENTION.
THE BEST WAY TO SELL YOUR EQUIPMENT IS TO GIVE IT SOME WELL-DESERVED ATTENTION.
Every Ritchie Bros. auction attracts a huge crowd of bidders – and there are just as many people bidding online. Add your equipment to an upcoming auction and reach interested buyers from around the world.
More bidders, better results.
THE BEST WAY TO SELL YOUR EQUIPMENT IS TO GIVE IT SOME WELL-DESERVED ATTENTION.
Call today: 1.800.357.0659
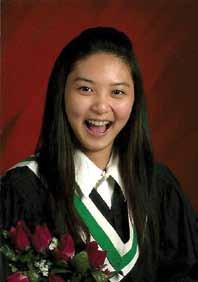
Ever since her parents introduced Sandy Tang to the world of mathematics at the age of five, she has been drawn to puzzles and professions that require a keen analytical mind. Her passion for numbers combined with her affinity for physics have helped Tang achieve great success throughout high school and earned her a spot in the University of Toronto’s Civil Engineering Program.
“I hope that in the next coming years, I will be able to offer my creativity and problem-solving skills that I have developed at University of Toronto to help improve our society,” says Tang.
Every Ritchie Bros. auction attracts a huge crowd of bidders – and there are just as many people bidding online. Add your equipment to an upcoming auction and reach interested buyers from around the world. More bidders, better results.
Call today: 1.800.357.0659
Every Ritchie Bros. auction attracts a huge crowd of bidders – and there are just as many people bidding online. Add your equipment to an upcoming auction and reach interested buyers from around the world. More bidders, better results.
Every Ritchie Bros. auction attracts a huge crowd of bidders – and there are just as many people bidding online. Add your equipment to an upcoming auction and reach interested buyers from around the world. More bidders, better results.
Every Ritchie Bros. auction attracts a huge crowd of bidders – and there are just as many people bidding online. Add your equipment to an upcoming auction and reach interested buyers from around the world. More bidders, better results.
Call today: 1.800.357.0659
rbauction.com
Call today: 1.800.357.0659
Call today: 1.800.357.0659 We’re saving a spot for you.
rbauction.com
Every Ritchie Bros. auction attracts a huge crowd of bidders – and there are just as many people bidding online. Add your equipment to an upcoming auction and reach interested buyers from around the world. More bidders, better results.
In addition to her academic success at Westlane Secondary School, Tang has also demonstrated leadership through many high-school initiatives. She was integral in planning and delivering multiple school presentations and assemblies for young men and women dealing with self-esteem, mental health and discrimination, and has been a regular participant in student art shows and a designer for her high school’s Robotic Team.
“Sandy is a dedicated student in academics and leadership aspects at school,” noted Carol Purcer, Principal of Westlane Secondary School in her reference letter for Sandy. “Sandy persistently seeks to make the world a better place in both her initiatives and the way she lives her life.”
rbauction.com
rbauction.com
rbauction.com
Call today: 1.800.357.0659
rbauction.com
Outside of school, Tang is a student of the Ontario Conservatory of Music, an active member of the Niagara Falls arts community, and a youth representative with the Niagara Region Youth Advisory Committee. Looking ahead, she is excited to be attending one of Canada’s premier universities for civil engineering, and thanks ORBA for helping her forward her career.
“I was very happy and overwhelmed when I received a call explaining that I have been selected as the recipient for this scholarship,” says Tang. “I would like to thank ORBA for providing this scholarship because it has helped with my expenses towards school. I am very grateful for this.”

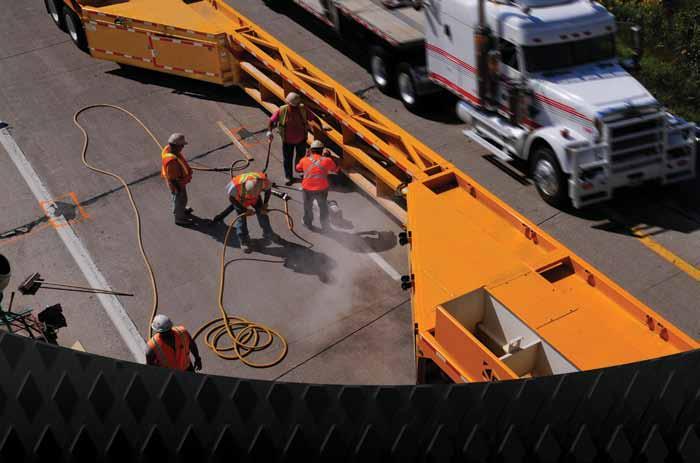
Levert Personnel Resources Inc.
By Matthew Bradford
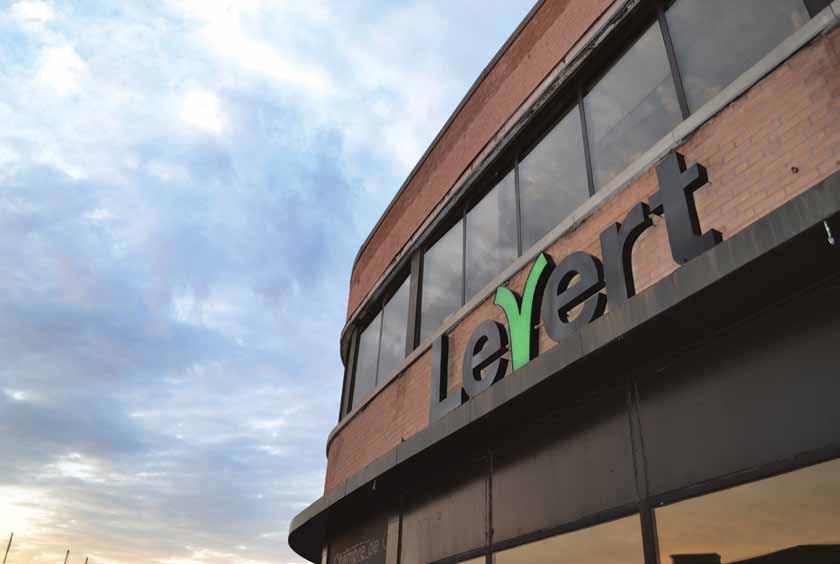
Looking for the right person for the job? Levert has you covered. For more than 25 years, Levert Personnel Resources Inc. has been supplying Canadian industries with topquality talent. This northern Ontario ORBA member is well on the road to securing its role as the province’s largest supplier of industrial personnel, and has also recently expanded its operation to the country’s East Coast.
Levert Personnel Resources began as an offshoot of the Levert Electric Powerline, which took root in Northern Ontario in 1957. Led by Wilfred E. Levert, Levert Electric Powerline carved a niche for itself in the construction industry as a specialist in electrical powerline services. In the years that followed, Levert Construction
expanded its operation to include mechanical and trades work for the bustling mining industry in the north.
In 1972, Wilfred retired, leaving son Richard to take up the reigns and develop additional areas of growth, which he did with the formation of Levert Personnel Resources Inc. in 1986. “We started seeing more of a need for industrial personnel versus construction work, so we saw an opportunity to get into that end of the business,” says Richard Levert, who has run Levert’s personnel division since it opened it doors 26 years ago.
Those first years of operation saw the company serving mainly the mining and smelting sectors, supplying a steady stream of daily and weekly labour for
various technical positions. From there, Levert Personnel Resources pushed out into surrounding industries, developing new training programs, safety initiatives and recruitment strategies along the way.
Today, Levert Personnel Resources employs over 50 employees in its Ontario offices in Sudbury, Timmins and North Bay, as well as its two recently opened offices in St. John’s, Newfoundland, and Happy Valley-Goose Bay, Labrador. In 2011, Levert placed approximately 1,500 people in multiple sectors, including mining, oil and gas, industrial, construction, and other technical trades on its ever growing client list. ”We just kept evolving,” recalls Richard Levert, “We were always chasing the industrial sector.”
That sector also includes Ontario’s road builders, who have made up the bulk of Levert Personnel Resources’ clientele over the last 10 to 15 years. From general labourers to flag attendants, traffic controllers to installers, equipment operators, and beyond, Levert Personnel Resources prides itself on being equipped with a workforce to handle any position or demand. This includes office clerical staff, which it has access to through its sister personnel company, Celebrity Staffing Inc. “We work directly for the customer,” says Levert. “When we get calls from our road building clients, we always know we’ll have ‘X’ amount of flag people or ‘X’ amount of people for a construction crew to aid them in projects.”
The search for talent is an all-year process. Business strategies for recruitment are varied, and include scouring job banks, placing local recruitment advertisements, attending job fairs, and engaging local college and university students. The company also employs social media in its search, using sites such as Facebook, LinkedIn, Monster.ca, Workopolis and Kijiji to track down talent for all company levels. It has also been known to conduct media blitzes in its effort to attract tradespeople to its roster. “We use a variety of methods to attract applicants so we have them at the ready for our customers,” says Levert. “For example, let’s say we had a request for 50 or 100 people tomorrow. We may go to the local radio or TV station, get on the air, and encourage people to come in and apply for these positions.”
In addition to relying on a mix of real world and online recruitment tactics,
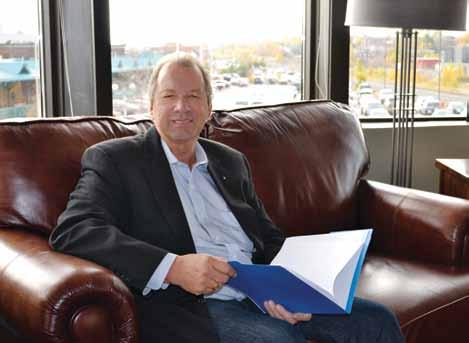
Levert, through a lucrative referral program, incentivizes current employees to find new blood. The company also takes advantage of a displaced workforce. “Our recruiters and sales staff are constantly on the lookout. If there’s a plant closing down, or there’s a mass of labour that’s not being put to use, we will go and find them and invite them to our company,” says Levert.
But while Levert Personnel Resources may cast its net wide to attract talent to the industry, it nevertheless holds every worker that comes through its doors to high company standards. To that end, it conducts a thorough pre-screening process and comprehensive employee testing using over 800 different assessments. This level of detail and due
diligence also extends to the company’s executive search services, which assist clients in filling top-level positions.
Looking at recruitment strategies, it is clear that the quality of the Levert staff is equal to – if not greater than – the quantity it provides. After all, every time it sends someone out on a job, that person is carrying the company’s reputation on the line. “These men and women are (the) daily go-between (for) us and the customer, so there needs to be a level of professionalism and respect at all times with the customer. We’re always looking for people who have safety on their minds at all times, as well as people who are dependable and hard-working individuals,” notes Levert.
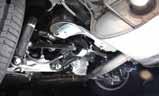

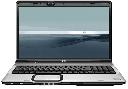
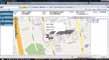





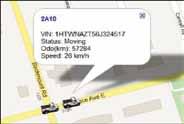


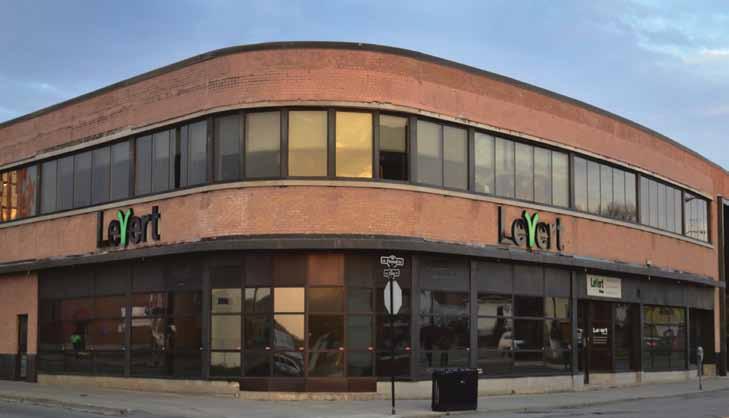
Finding the right people is just a small part of the services provided. Once new employees are through the door, Levert takes great effort to outfit them with the knowledge and training necessary to be an asset on the jobsite. In-house training programs include Workplace Hazardous Materials Information Systems (WHMIS), traffic control, and health and safety programs, while group training includes respiratory fit tests, confined space awareness, fall arrest, first aid CPR and forklift training. “We want everyone to go home to their families at the end of the day, so safety is a very, very big part of our daily routine,” says Levert on the company’s focus on health and safety awareness. “We ensure our employees are trained to the safety standards that are required, and then go beyond that.”

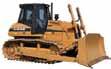
Levert Personnel Resources’ health and safety commitment includes its WorkSafe training initiatives, which help clients prepare for Workwell Core Health and Safety Audits, develop safety manuals, and create up-to-date health and safety policies, among other things. Combined, the company’s dedication to safety has resulted in one of the lowest number of lost-time accident reports in the province, with its rates slipping closer to zero with every passing year. And while Levert has received numerous business awards and accolades from the community, it is this safety record that stands as Richard Levert’s proudest achievement. “Our reward is our frequency of non-accidents,” he says. “I think that’s a testament to our business. We have a very high demand in

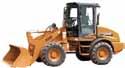

safety from both our candidates and our clients. We demand that of them.”
With the opening of their new offices in Newfoundland and Labrador, and plans to expand both their Northern and East Coast operations, Levert Personnel Resources is on an upward trajectory. But while growth is certainly on Richard Levert’s agenda, so too is maintaining a consistent level of service in all industries being served. “We are a first-class firm and we deliver first-class service. That’s who we’ve been, that’s who are are, and that’s what we want to continue to do.”
For more information on Levert Personnel Resources, visit www.levert.ca.


New ORBA Members
TARANIS CONTRACTING GROUP

Founded in 1995, Taranis Contracting Group has come a long way from its modest roots. Debuting on the Thunder Bay construction scene as The Gravel Doctor, the company quickly expanded upon its driveway maintenance and landscaping operations to offer a vast range of construction, demolition, environmental and maintenance products and services to commercial, resident, industrial and governmental clients throughout Northern Ontario. In 2009, Taranis Contracting Group adopted its current moniker, and has since continued to foster its reputation as one of the most dynamic contractors in the Northern part of the province.
In addition to its construction services, Taranis Contracting Group’s Aggregates Division handles the compete processing, manufacturing and distribution of aggregate materials for commercial and residential construction. Its products include Hot Mix Asphalt Stone (HL2,
HL3, HL4, HL8), Superpave 12.5mm and 19.0mm, clear stone and weeping tile stone, class II, Granular B Type II, and Granular A.
Taranis Contracting Group operates out of its headquarters at 1473 Rosslyn Road, Thunder Bay, Ontario. For more information, call 807-475-5443, e-mail information@taranis.ca, or find them online at www.taranis.ca.
POWELL CONTRACTING LTD.
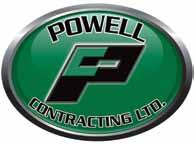
Established in 1967, Powell Contracting Ltd. provides traffic safety installation and repair services throughout Southern Ontario. Through various affiliations with a number of companies throughout the province, Powell Contracting has been able to expand its range of services. Currently they include, but are not limited to, temporary concrete barrier, guide rail, end
treatments, noise wall, ground improvement, crash cushions, ground mounted signs and overhead signs. As an added benefit to their customers, rental equipment services are also available. Hydro excavators, drilling equipment, boom trucks, cranes and crash trucks are all readily available upon request. The company also offers 24-hour emergency services.
For more information regarding Powell Contracting Ltd.’s services and capabilities, please call 905-727-2518, or visit the company online at www.powellcontracting.com.
AUSTIN POWDER
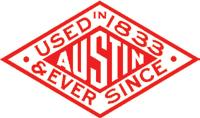
Since 1833, Austin Powder has helped clear a path for North American development through the provision of blasting products, accessories and services for quarrying, mining, construction and seismic exploration clients in Canada, the U.S. and across the globe. Austin
Powder carries a comprehensive line of detonator-sensitive and high-density molecular explosive and precision initiating systems, all designed to get the job done with the utmost attention to safety, efficiency and success.
In addition to providing industries with top-brand blasting products, Austin Powder supplies numerous services, including blasting consultation and blast design services for the quarrying industry; pre-blast testing, pre-blast simulations, blast performance monitoring and post blast profiling for construction sites; and laser profiling and blast design for the mining industry via its custom-made Austin Blasting Software (ABS), among others.
Austin Powder operates out of its main plants in McArthur, Ohio; Camden, Arkansas; Brownsville, Texas; and Valle Hermoso, Mexico. It also distributes its products in North America through 65 company-owned stores. For more
information, call 705-688-8314, or visit Austin Powder online at www.austinpowder.com.
BASF CANADA
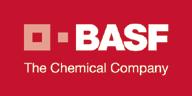
BASF – The Chemical Company is a world leader in chemical research and development for industries throughout the globe. Driven by its motto, “We create chemistry for a sustainable future,” BASF blends science and innovation to enable its clients to meet the current and future needs of their businesses, while creating a safe, healthy and sustainable future for all.
BASF’s Construction Systems division offers solutions for protection, repair, strengthening, corrosion mitigation and grouting of transportation struc-
tures. BASF also provides a wide mix of products from insulating materials, foams and sealants, refurbishment products, admixtures for anti-fire and corrosion products, and more. It also supplies concrete additives designed to enhance the stability, efficiency and flowability of concrete projects.
A full directory of BASF’s Construction Systems products and services can be found online at www.basf.com.
CANADA CULvERT
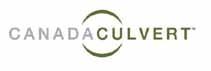
Representing the culmination of over 150 years of experiences, the newly amalgamated Canada Culvert provides water and soil management solutions for clients across the country. As a proud division of the WGI Westman Group of companies, it provides a unified
• Emergency Road Services and Rapid Clearing
• Sweepers / Magnetic Sweepers
• Pressurized Water Trucks
• Traffic Control Crash Trucks
• Loaders with Quick Attach Buckets, Clamps and Forks
• Dump Trucks and Roll-offs
• Skid Steers and Excavators
• Bulk Salt Sales
www.centennialsweeping.ca
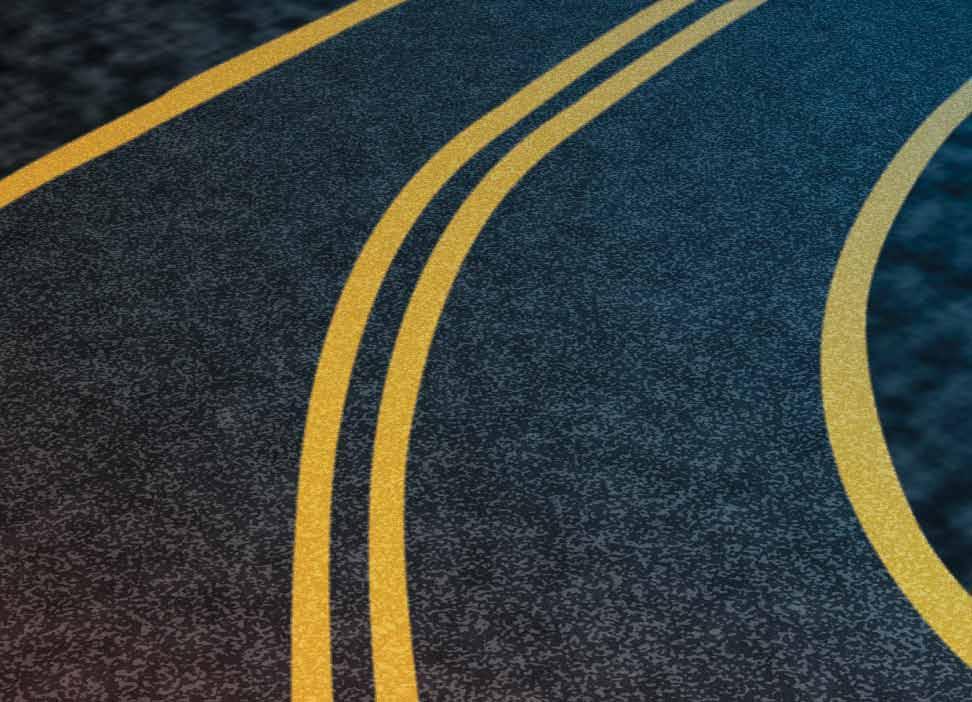
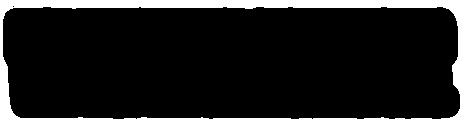
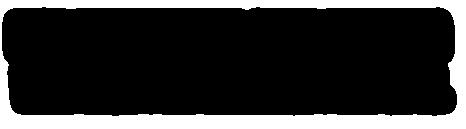
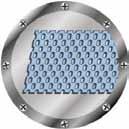
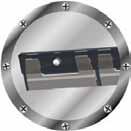
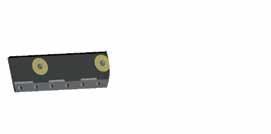
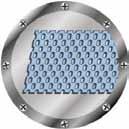
source for products and expertise designed to handle any water or soil management challenge.
Canada Culvert’s product line includes Steelcor corrugated steel pipe, HDPE pipe, geotextiles, guardrails, water control gates and environmental Beaver Stops. From pre-installation consulting to drainage assistance, product delivery and installation, Canada Culvert also stands behind each of its products with a number of services.
With offices located in key cities in British Columbia, Alberta, Saskatchewan, Manitoba and Ontario, there’s always a Canada Culvert professional close by. For more information, call Canada Culvert’s Cambridge, Ontario, office at 519-620-6000, or visit their website at www.canadaculvert.com.
G-TRAx WEAR PARTS INC.
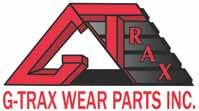
Located in Mississauga, Ontario, G-Trax Wear Parts Inc. prides itself on being an industry leader in the provision of high performance and professionally engineered aftermarket wear parts for construction equipment. G-Trax specializes in keeping its customers’ equipment on the job and in motion with a comprehensive inventory of
rubber tracks, undercarriage, tires and wheels for all equipment, big and small. This one-stop shop has the staff and services to guarantee the ultimate client experience and total satisfaction with your product.
For more information, or to speak with one of their product specialists, call 1-855-778-TRAX. G-Trax Wear Parts Inc. can also be contacted via e-mail at info@g-traxwearparts.com or online at www.g-traxwearparts.com.
hOSKIN SCIENTIFIC
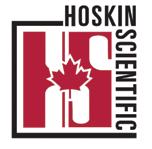
For over 50 years, Hoskin Scientific has been a supplier of testing and monitoring instrumentation to the Canadian market. With offices in Vancouver, Burlington and Montreal, the company’s customers are able to receive local sales and technical support in three major departments. Hoskin’s Materials Testing Department offers testing equipment for soil, asphalt, aggregates, concrete and cement. Their qualified sales associates focus on providing a sophisticated range of testing equipment, ensuring that accurate and consistent test results are always obtained. Their Environmental Depart-
ment provides solutions for monitoring and sampling biological and chemical parameters in the environment. Hoskin’s Instrumentation Department focuses on a wide range of products including optical camera systems, data acquisition systems, automation sensors and measurement systems.
For a complete listing of products and services, visit www.hoskin.ca. You can also contact Hoskin Scientific by phone at 905-333-5510, or by e-mail at sales@hoskin.ca.
hUTChESON SAND & GRAvEL
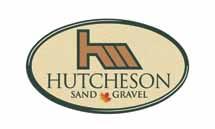
A leader in developing innovative products in the aggregate industry for over 25 years, Hutcheson Sand & Gravel mines, processes and distributes a wide range of aggregate materials for construction customers across Ontario and Quebec and the U.S. From Granular B to crushed stone, concrete sand to quarried granite, caisson (Ottawa type) sand, ballast stone and SuperPave FC1 & FC2, Hutcheson Sand & Gravel is equipped to supply Ontario road builders with the spec materials they need to get the job done. Hutcheson Sand & Gravel also supplies aggregates for land-
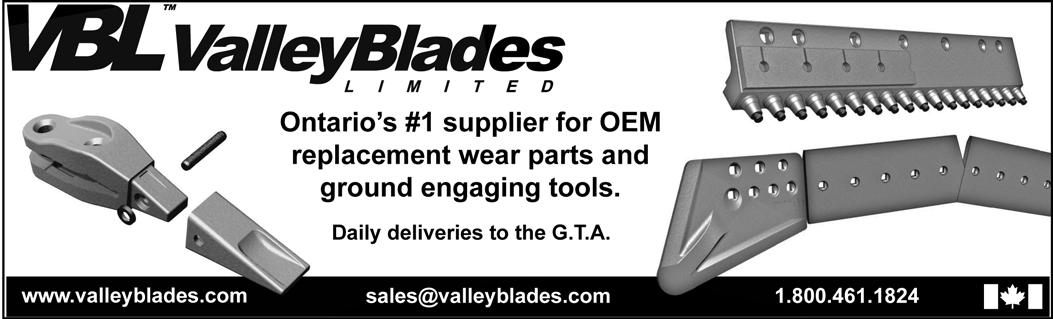
scaping and specialized sand products for a variety of applications, including golf courses, playgrounds, sports fields and water filtration.
Hutcheson Sand & Gravel is located on the southern edge of the Canadian shield in Huntsville, Ontario, putting it at a strategic advantage to best serve its Muskoka and central Ontario markets, while also distributing specialized products to southern Ontario and New York State. Its dedication to quality and industry-leading crew ensures top-tier quality and an unrivalled customer experience.
For more information, visit www.hutchesonsand.com, e-mail info@hutchesonsand.com, or call 1-800-461-5521.
SUPER SUCKER hyDRO vAC SERvICES
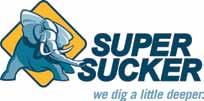
Equipped with the latest tech, the toughest equipment, and the top hydrovac crews in the business, Super Sucker Hydro Vac Service Inc. digs a little deeper when serving clients across Ontario. Whether called in for hydrovac excavation, coring, utility location, daylighting or backfill restoration, Super Sucker prides itself on its ability
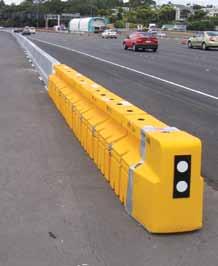
to respond quickly to any job with the utmost attention to quality, efficiency and safety.
Super Sucker’s strength comes from its reliable fleet of hydrovac units, core drilling, crane and dump/aggregates trucks, as well as its highly experienced staff who are certified and trained to tackle any situation. The company also takes its dedication to safety one step further with the addition of a full-time on-site safety auditor.
Super Sucker operates facilities in Ancaster, London and Mississauga, Ontario, and can be found online at www.supersucker.ca. Clients are also welcome to book a Super Sucker truck, or find out more about their services, by calling 1-866-227-7722 or sending an e-mail to info@supersucker.ca.
TOPLIFT ENTERPRISES
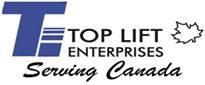
Serving industries throughout the country, TopLift Enterprises is a trusted dealer of container handling equipment. Beginning as a service-oriented business with a focus on intermodal container handling equipment, the company has expanded over the years to offer parts and service for new and pre-owned equipment for a wide range of clients.
The
Catering to construction customers specifically, TopLift Enterprises carries a full line of top brand wheel loaders, excavators and skid steers. Heavy-duty dump trucks, cranes, and other construction and material handling equipment are also available, as are any parts and access to TopLift’s comprehensive service department and expert technicians.
TopLift Enterprises operates out of its head office at 42 Pinelands Ave. in Stoney Creek, Ontario, with branch offices in Montreal and Vancouver, and satellite facilities located in Toronto and Quebec City. Its full inventory can be browsed online at www.toplift.com. For more information, call the Ontario office at 1-866-TOP-LIFT.
ThE PACE NETWORK
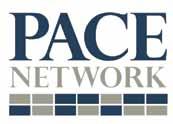
As entrepreneurs and professionals with proven industry experiences, the business experts at The Pace Network know that creating and growing a successful company requires determination and vision. Too often, the challenges that lie in a company’s way block the ultimate goal, which is to attain objectives and enjoy success. The Pace Network’s unique group of highly qualified associ-
350® Anchorless Crash Cushion
The ABSORB 350 Anchorless Crash Cushion has been engineered with the contractor in mind. The system can be easily deployed on concrete, asphalt or even dirt without ever having to pour a pad. Features like zero internal steel means no corrosion when approved de-icing agents are added for winter performance. The ABSORB 350 is available in TL-1 (50 km/h) TL-2 (70 km/h) or TL-3 (100 km/h) configurations and is approved for use by the MTO.
The ABSORB 350 Anchorless Crash Cushion has been engineered with the contractor in mind. The system can be easily deployed on concrete, asphalt or even dirt without ever having to pour a pad. Features like zero internal steel means no corrosion when approved de-icing agents are added for winter performance. The ABSORB 350 is available in TL-1 (50 km/h) TL-2 (70 km/h) or TL-3 (100 km/h) configurations and is approved for use by the MTO.
Learn more about our full line of road safety solutions in Canada at www.qmb.ca /
Learn more about our full line of road safety solutions in Canada at www.qmb.ca / +1 (905) 660-5521
The ABSORB 350® Anchorless Crash Cushion
ates work with business people from a wide variety of industries, but they have particular expertise in the construction sector. They provide advice and hands-on support across every business management category, and have helped countless entrepreneurs and executives achieve their objectives in numerous areas, including sales management and revenue growth, finance, production, operations and manufacturing, risk management, human resources and safety, marketing and packaging, and strategic planning.
The Pace Network can be found online at www.thepacenetwork.com and contacted toll free at 866-939-6444.
vIEWPOINT CONSTRUCTION SOFTWARE
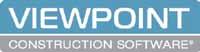
Viewpoint Construction Software is a developer and provider of software for general contractors, heavy and civil contractors, and specialty contractors within the construction industry. Its platform is built from an award-winning Microsoft. Net framework and SQL Server database with over 35 years dedicated to the construction industry. Viewpoint provides construction professionals with integrated, flexible and customizable applications for virtually all aspects of
construction management. Viewpoint’s highly adaptable V6 Software provides solutions for construction accounting, job costing, financial planning, content management, project management, financial planning, document management, equipment management, work order management, field management, risk management, and pre-qualifications. Viewpoint’s cloud computing systems also help clients reduce the risk of data loss and enhances system connectivity between the jobsite, office and anywhere the business operates. Expert product support is also provided via Viewpoint’s consulting, technical and database services.
Viewpoint Construction Software operates out of its North American headquarters in Portland, Oregon, its Canada home base in Markham, Ontario, and offices in North Carolina and Australia. A full list of its products and services can be found online at www.viewpointcs.com, or by calling 800-333-3197.
WEBTECh WIRELESS
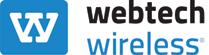
Webtech Wireless provides vehicle fleet location-based services and telematics technology. It develops, manufactures and supports end-to-end solutions
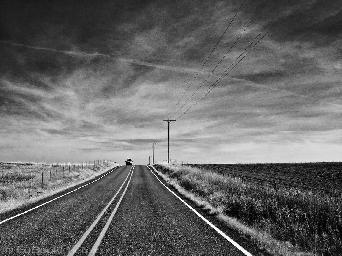
that improve the productivity, profitability, environmental compliance and safety of fleets. Its comprehensive suite of products and services includes automatic vehicle location, mapping, vehicle diagnostics, CO2 reporting, navigation, messaging and mobile resource management.
Webtech Wireless’ InterFleet solution is the leading GPS and AVL solution for government fleets in North America to efficiently manage municipal, city and Department of Transportation fleet operations. InterFleet is a full end-toend solution that uses 10-second or better reporting frequency for the realtime display of a customer’s entire fleet. InterFleet allows customers to layer their own GIS mapping information and integrate with other existing city, state or provincial systems. Equipped with comprehensive reporting capabilities, InterFleet allows fleet managers to reduce liability, reduce material usage, manage contractor compliancy, ensure minimum operating compliancy, and reduce overall operating costs.
Webtech Wireless is located online at www.webtechwireless.com, or at its Canadian office on 100-76 Stafford Street in Toronto, Ontario. The company can be contacted via e-mail at support@ webtechwireless.com, or by phone at 416-348-9991.
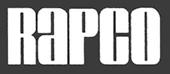
(613) 748-9762
(613) 748-7067
(613) 746-3114
(613) 566-9204
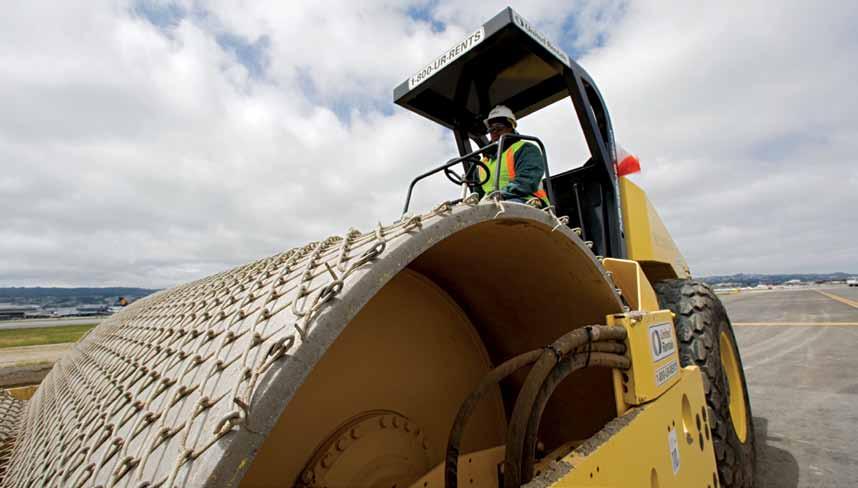
Excess Soil Update Industry promotes risk-based approach to managing excess construction materials
Stakeholders in the civil construction industry are cautiously optimistic that some clarity and common sense may soon be applied to current provincial policies concerning the management of excess construction materials. That is, while environmental stewardship remains everyone’s first priority, at issue is whether tens of millions of tonnes of excavated material must be treated as contaminated waste and hauled to landfills every year – a practice that carries huge costs and negative environmental impacts.
The Ministry of Environment’s (MOE) stance on excess soil began to change in 2009 when it started classifying the soils excavated from road building projects. Before that, the MOE had no issue with the dirt from road projects. Therefore, it wasn’t uncommon for contractors to use the material as infill in depleted aggregate quarries.
Things changed when MOE studied the composition of the dirt from civil construction projects and determined that since it didn’t meet the requirements of Table 1 of its materials classification system, it would therefore be classified as a waste. In particular, one of the MOE’s biggest concerns with soils from civil construction projects (unless from a uniquely contaminated site) is the
presence of salt, which is typically present at measurable levels on existing roads due to Ontario’s winter maintenance practices. As such, under this new waste classification, the MOE ruled it could no longer be dumped in a convenient field or used to backfill a section of a quarry, and that the only alternative is to pay the tipping fees and haul it to landfill.
The industry reacted quickly to the MOE’s changing practices in managing excess construction soils, with ORBA taking the lead under Karen Renkema, Director of Government Relations. Discussions began with the environment ministry and MTO, and the civil contracting industry also took the issue to provincial politicians, representing one of the only voices warning of the consequences of the policy shift at that time.
The Residential and Civil Construction Alliance of Ontario (RCCAO), which has led a proactive campaign to find solutions to what it calls a regulatory gap, puts the cost of Ontario’s current policies for disposing of excess soils from road building and sewer and watermain projects at between five per cent and 21 per cent of the capital costs. The regulatory gap reference reflects RRCAO’s concern that typical excess soils from civil construction projects are being
considered under the same regulatory framework as brownfields’ soils and there is no recognition of the difference. Further, in an advertisement that was slated to run this November, RCCAO explains: “Millions of dollars are being needlessly wasted because the current regulatory regime is unable to effectively introduce programs encouraging reuse of construction soil.”
RCCAO and ORBA, along with a number of industry associations and municipal representatives, have been working as a coalition with the Ministry of Environment to find appropriate ways to deal with excess construction soils. Their efforts have included the development of a best management practices document entitled, Best Management Practices for Handling Excess Construction Soils in Ontario. And while it’s clear there will never be return to the traditional “dig and dump” method of disposing of the soils from road projects wherever it is convenient, the industry is nevertheless hoping there will soon be clear and practical alternatives to simply trucking dirt to landfills.
Currently, the preferred alternative that has been promoted by ORBA and the coalition has been the re-use of excavated soils within the right-of-way of the project, because when that is
accomplished, MOE classifications of the soils are irrelevant. The Ministry of Transportation has worked actively with ORBA to establish design and construction practices that will result in excess materials being designed back into project to the maximum extent possible and ORBA is promoting the same practices for municipal civil work.
While the industry awaits the MOE’s best management practices for excess materials, the RCCAO is being a bit more proactive in pushing the process along with the release of its own commissioned, independent best management practices document in early November. It relies heavily on the British-based CL:AIRE model (Contaminated Lands: Applications in Real Environments), which sets the main objective as the responsible identification of excess soils that are non-waste at the source site and handles them based on beneficial reuse either within the project or at other acceptable receiving locations. The approach is risk-based and consistent with regulatory requirements of producing no adverse effects to the environment.
The authors of the RCCAO report describe the proposed best management practice as being based on a “transparent process that produces a Materials Management Plan (MMP) for the handling of non-waste excess soils tied to the remediation and/ or development plans for the site involved.” The BMP includes a formal excess soils tracking system, a Verification Plan (VP) and any required contingency plan components. An independent Qualified Person (QP) reviews the MMP and, if satisfied, signs a declaration confirming excess soils are not waste based. This approach encourages the beneficial reuse of excess clean soils and facilitates the further development of Soil Recycling Centres (SRCs), soil matching capability at excess soil donor/ receiver sites, and other progressive environmental initiatives in Ontario.
In an October 10 letter to Hon. Jim Bradley, Minister of Environment, and Hon. Bob Chiarelli, Minister of Transportation and Infrastructure, RCCAO Executive Director Andy Manahan said the CL:AIRE model was introduced and discussed at a stakeholder workshop September 21, and it was “clearly demonstrated to workshop participants that a practical, risk-based approach results in far less excess construction soil being deemed a ‘waste’ than is currently
the outcome under Ontario’s regulatory regime.”
“We need a responsible, workable solution, implemented on a province-wide basis,” said Marlene Yakabuski, chair of ORBA’s environment committee, adding, “The Best Management Practices proposal developed through the industry Steering Committee is a proactive and responsible response to an increasingly significant issue.”
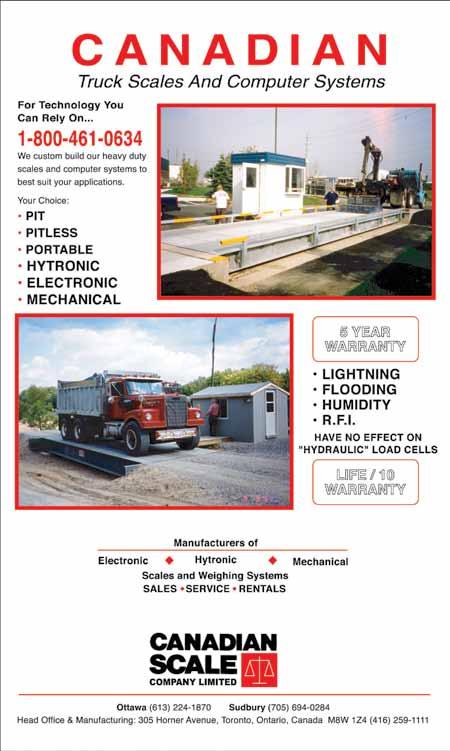
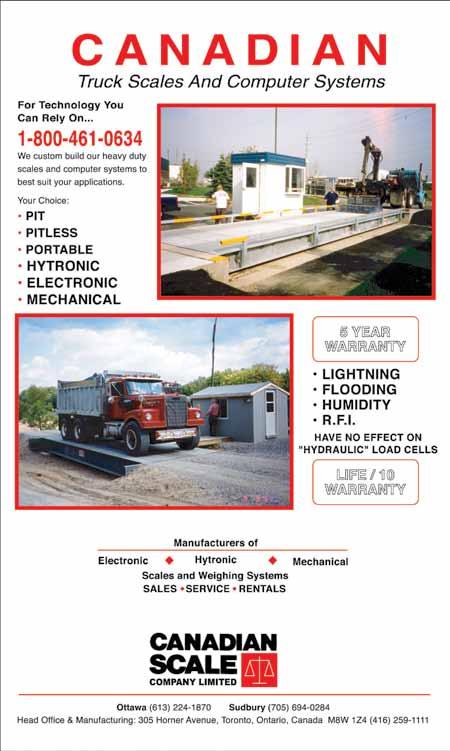
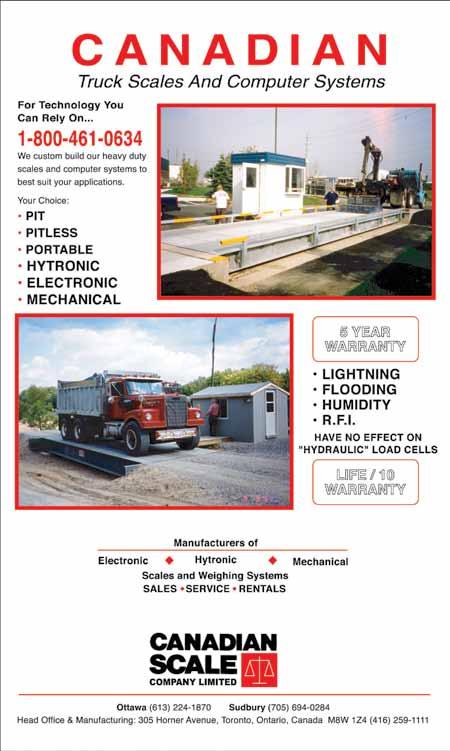
2013 Road Building Academy
By Matthew Bradford
Registration is now being accepted for ORBA’s 2013 Road Builder Academy, the seventh installment of the association’s annual industry training program. Running February 25 to March 8, 2013, out of the Mississauga Grand Banquet & Convention Centre, the program offers 10 Gold Seal accredited courses taught by professional educators, trainers, industry consultants and practitioners.
The Academy is open to all ORBA members and nonmembers, and participants who complete the courses will receive a certificate from ORBA and the Gold Seal Committee. In order to secure a space, applicants are urged to register before Monday, January 25, 2013.
The 2013 Road Building Academy features a slate of courses covering all aspects of the road building trade. They include the following:
ThE ChANGING WORKFORCE: DIvERSITy AND GENERATIONAL DIFFERENCES
February 25, 2013
Led by Patricia DeMers, Founder and President of Excel Thru Learning and Past President of the Peel/Hamilton Chapter of the Canadian Society for Training and Development, this one-day course will equip company leaders with tips and techniques for working collaboratively with all workers from all generations on the job site. From baby boomers to millennials, Patricia will examine the strengths and advantages of today’s talent, and offer effective solutions for creating a positive and productive workforce. This course is a must for foremen, managers and company leaders who want to stay on top and well-staffed in a continually evolving industry.
OCCUPATIONAL hEALTh & SAFETy DUE DILIGENCE
February 25, 2013
Keeping the jobsite safe and understanding current occupational health and safety regulations are key elements to any operation, making this an essential course for supervisors, foremen, project managers and top level executives. This highly informative course will take an in-depth look at safety topics, including current health and safety legislation; workplace responsibilities; legal liabilities, penalties, and fines; the internal responsibility system; the legal implications of
due diligence; legal accident notice obligations, Bill C-45; health and safety obligations under the Criminal Code; and more. Leading the way will be workers’ compensation specialists David Marchione, who’s current role as an Occupational Health & Safety Consultant in Gowling Lafleur Henderson LLP’s employment and labour national practice group, and past experience as a WSIB Adjudicator, will bring context and real-world experience to this vital health and safety conversation.
ThE SECRETS OF POWER NEGOTIATING
February 28, 2013
Negotiation expert Michael E. Sloopka will bring his bargaining talents and hard-won insights to this one-day course, which aims to outfit participants with the skills needed to achieve “win-win” outcomes in any situation. The Secrets of Power Negotiating will highlight the five major characteristics of a master negotiator, as well as teach valuable concepts and techniques that can be implemented in any company to improve business results, profitability, and navigate stressful day-to-day challenges. As President of Selling Solutions Inc., Michael has helped thousands of clients in a wide range of industries across Canada achieve successful negotiations, enhance corporate performances, and dramatically increase bottom lines. His strategies and teachings will set up ORBA Academy attendees to do the same in their respective organizations.
LEADERShIP SKILLS FOR CONSTRUCTION MANAGERS AND SUPERvISORS
March 7-8, 2013
For over 20 years, Monroe Porter, President of PROOF Management Consultants, has been helping business owners across the globe reach their maximum potential, and in this two-day course he will bring those lessons to ORBA Academy students. Catering to new and veteran supervisors alike, this fast-paced leadership training program will provide hands-on exercises, motivational presentations, and team-building exercises designed to teach participants advanced problem-solving and goal-setting techniques and principles. Topics will include effective communication, mind mapping, dealing with a difficult workforce, “walking the talk,” leading vs. following, and understanding the eight core values of a being a successful leader.

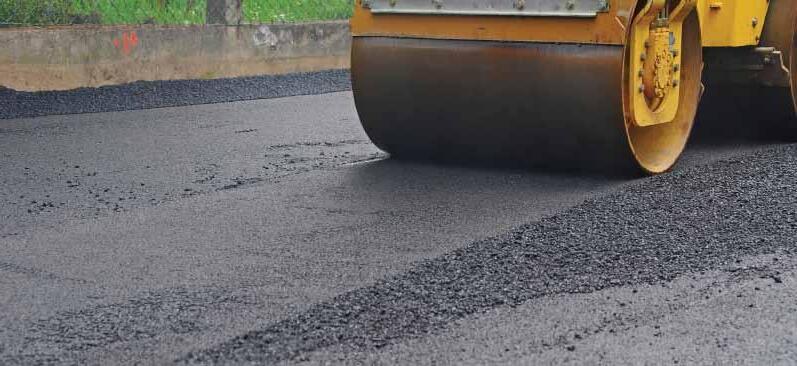

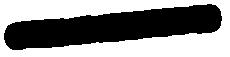
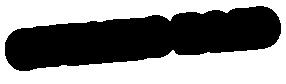


CONTRACTORS FOR MUNICIPAL & MTO PROJECTS
CENTRELINE & TRANSVERSE MARKINGS
Water Based Materials & Alkyd Based Materials
THERMO PLASTIC & METHYL METHACRYLATE
Spray, Inlaid & Overlay Methods
LINE REMOVA L
Rotary Grinding, Abrasive Blasting, Water Blasting VariousBlackout/Tape Methods
Serving Ontario Municipalities and the MTO for over 36 years.
47
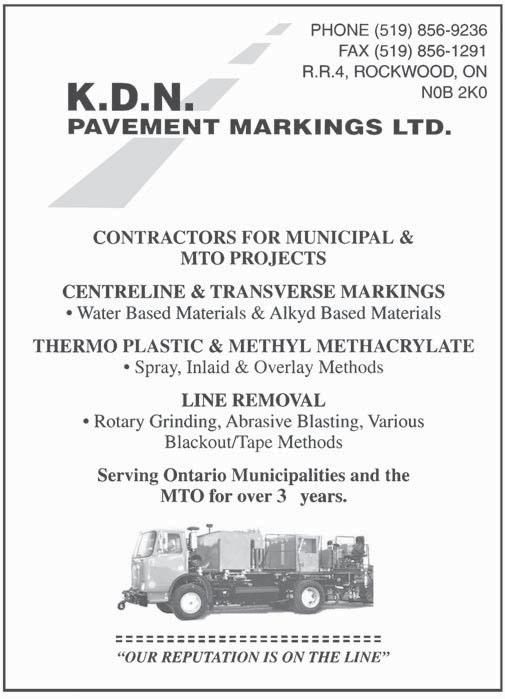
“OUR REPUTATION IS ON THE LINE”
Happy Trails
The Ontario Road Builders’ Association wishes Mike O’Connor a long, healthy and happy retirement.
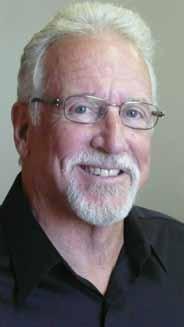
Mike O’Connor
After 15 years as CEO of Ontario Hot Mix Producers Association, Michael O’Connor has decided to retire. Over the years the hot mix asphalt industry’s journey has withstood its share of challenges, but has been paved with continual innovations that have led to vast improvements in the quality of our roads.
When Michael joined OHMPA as CEO in 1997, they began to introduce Performance Grade Asphalt Cement, the first step in the development of Superpave. Superpave optimizes
the asphalt mixture’s resistance to rutting, fatigue and low temperature cracking. For those of you that missed Michael’s retirement roast on November 22, 2012, you can imagine the types of “wise cracks” he received like those around rutting, fatigue and low temperature cracking.
In a column Michael wrote for Aggregates & Roadbuilding Magazine, he talks about all of the changes he has witnessed over the years. He talks about End Result Specifications (ERS) and perpetual pavement, green technology and reclaimed asphalt pavement (RAP). He talks about the achievements for the hot mix industry and his strong relationships with allied associations and the MTO.
The Ontario Hot Mix Producers Association has been very well served by Michael O’Connor over the past 15 years and they can attribute many of their successes to his leadership and perseverance.
Michael, on behalf of the Ontario Road Builders’ Association and our members thank you for all that you have done for OHMPA and for the hot mix industry. It has been a long, wonderful relationship we have enjoyed with you. All the best in your retirement.
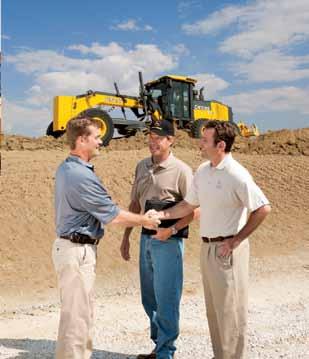
In an article for Asphaltopics Michael sums up his retirement plans “So after 47 years in the road building industry and 15 years with OHMPA, it is now time to retire... I am looking forward to more golf, more skiing, and more sailing. I want to keep on playing. I just don’t want to get up so early to do it. I am going to miss the people with whom I truly enjoy spending time.”
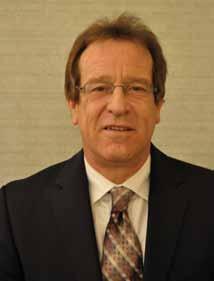
Rob Bradford
ORBA Legacy Project Update
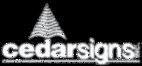

Almost four months into the year-long ORBA Legacy Project, I’m pleased to report that the book is developing nicely and on schedule. There are actually a few opening chapters on paper, and the constantly-evolving format and content are starting to become more clearly defined.




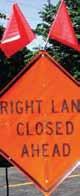
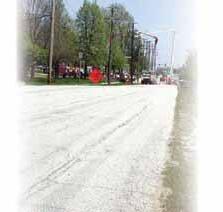
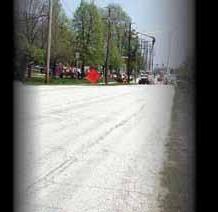




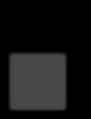

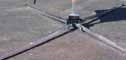
But as research on this book progresses – a book that will share the history of roads and road building in Ontario – the project is becoming bigger and bigger. Every interesting fact leads to a whole new artery of research, and the exponential nature of that process could go on indefinitely. Clearly, the challenge is not going to be what to include in the history of Ontario road building, but rather what to exclude.
The story has to begin, briefly, thousands of years ago when Aboriginal peoples trampled paths through the vast, virgin forests and did most of their travelling on the liquid highways – the province’s rivers and lakes that could take a canoe just about anywhere. Then, the first settlers came to Upper Canada in the 1700s and the concept of “roads” took on
a number of meanings for people who had to move timber to the St. Lawrence or grain to the local mill that could be 30 miles away. Water remained the preferred mode of travel for a long time. Interestingly, it appears that underfunding and neglect of roads has been a constant theme over the past 300 years. Then there were the railways that further delayed the development of roads. There are some amazing tales of what settlers went through to travel on land.
The history of how it all began in the province is about “roads” in the broader sense of the word. It encompasses the many kinds of conveyances or pathways that people, the military and commercial goods used to move from one place to another – the water highways, the old Native footpaths, the railways, the stage coaches, the toll roads, the beginnings of asphalt and concrete roads and construction tools and equipment. All are necessary to understand how we got from there to here.
And these early beginnings are well before we get to the modern history of Ontario roads, and the road building
industry as we know it today. This most recent era was sparked by the advent of the automobile in the late 1800s, but also, as you will read, by the bicyclist lobby of the time.
Over the summer, several freelance journalists and I interviewed more than 50 road builders, engineers, project managers, suppliers and others to gain their insight and personal experiences in the industry. These interviews will become an integral part of the core of the book. In some cases, these personal recollections go as far back as the 1940s, so we will be recounting the industry’s history from that point onwards in the words of the people who lived it. The interviews have also been taped and will be preserved by ORBA for posterity. We have some great stories to tell based on these interviews, and I hope that ORBA members will get half as much pleasure from reading them as I did in talking with these road building veterans.
The research has barely scratched the surface, and already the journey has been a fascinating one. Did you know that Ontarians invented plank roads? That Lieutenant-Governor John Graves Simcoe was one of the first road builders? That early settlers in the 1800s had to work 12 days a year on the roads as a civic duty?
In the rest of this space, I want to appeal to all road building contractors in Ontario to make sure that we have information about your company. We’ve collected good information from many ORBA members, but a number of companies have not responded and we would like to have any historical information, photos and documents you have about your business. We want to know where your company originates and who were the key people that built it. We want to learn about the projects you are most proud of, the projects that didn’t work out the way they should have, and how you have been impacted by technology over the years, among other things.
Important documents will be returned, but ORBA is also collecting historical materials to archive, so we would welcome your contribution of old photos and documents. This can be old labour contracts, bills of sale, invoices, advertisements, specifications, contracts, biographies or resumes of people in the industry. We are interested in all of it.
If you would like to submit any information about your company or people in the industry for consideration in compiling the Legacy Project book, please forward it directly to me at r.bradford@cogeco.ca or by mail to: Rob Bradford, Insite Services, 2523 Waterford Street, Oakville, ON, L6L 5E5.
glasvangreatdane.com glasvangreatdane.com/etnyre/ 1.888.GLASVAN

All Paved Roads Lead to Etnyre
Etnyre trailers are built to be tough, no matter what the job, or how severe the conditions.
EtnyRE BLAckhAwk PAvER
Trusted and durable Blackhawk detachable lowboys are engineered and road-tested to get the job done.
Slat-free, Lubrication-free chain belt drive system available in 3- and 4-axle configurations.
EtnyRE FALcon LivE-Bottom tRAiLER SEE it in Action At
For more information, give our specialists a call, visit us online, or drop by any of our five southern Ontario locations.1-888-GLASVAN (1-888-452-7286) 1201 Aimco Blvd. Mississauga ON L4W 2Z3 www.glasvangreatdane.com/etnyre/

Municipal Contracts: What to Look for Before the Bid
By Matthew Bradford
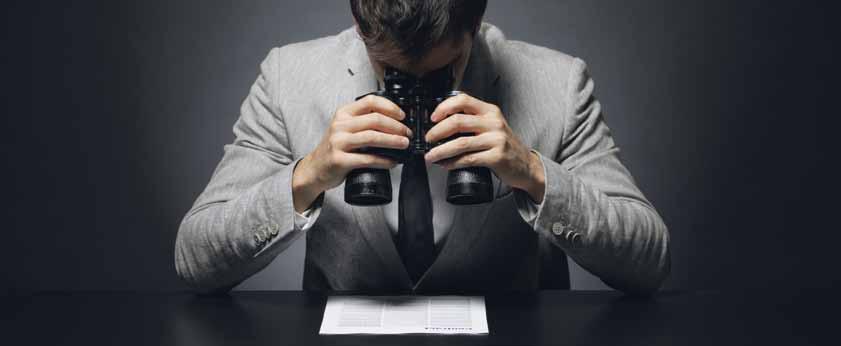
Navigating a municipal contract bid can be trying for even the most seasoned industry veterans. But between the fine print, clauses and conditions there lies great opportunity for contractors who understand what to look for in a bid, and how to get it done right.
“The private sector is about money, and the public sector is about rules and regulations. If you are filling out an RFP or tender, it’s critical to get the paperwork right,” insists Stephen Bauld, President of Purchasing Consultants International Inc.
As Canada’s leading expert on government procurement, Bauld has amassed a wealth of well-won advice for what to look for when preparing a bid. Here are the highlights:
ANSWER ThE QUESTION
No matter what the proposal is, Bauld says it’s essential for contractors to understand what the owner is asking for, and reply with exactly the type of responses they require. For example, Bauld offers, “If you’re asked how many schools you’ve worked on in Ontario, and you don’t give them three names and references in Ontario, you’re not going to get the three points. Similarly, if you list a
really nice one you did in Winnipeg, that’s great, but you’re not going to get the points because that’s not what they’re asking for.”
“Answer the exact question that they’re asking, and answer it in the most concise way possible,” he adds.
LOOK FOR OMISSIONS
A missed number or incomplete answers can be the difference between winning or losing the bid. Common mistakes to look out for are missing unit prices, omitting any sections, or submitting last minute bid changes without a signature.
As Diverse As Our Solutions


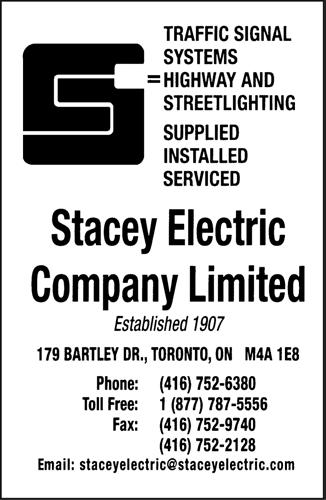
“There’s a hundred little minor mistakes that can get you disqualified,” says Bauld, explaining, “Municipalities may get five bids and they might have to disqualify three of them for some minor incident.”
Bauld explains the practice of online bidding will help to greatly reduce the number of these accidental omissions, but until everyone is logged on, it’s important to be cautious. “Eventually, everyone is going to move to e-procurement, but prior to that, someone should complete the document and then make sure there’s another set of eyes that go through it.”
IDENTIFy ThE CLAUSES
Be it a municipality, school board, hospital, or other government agency, the truth is that no two procurement documents are ever the same. As such, it’s important for contractors to pinpoint the clauses and conditions that might otherwise come back to affect their bottom line if left unchecked.
“There are sections in the document called privilege clauses, which could be extremely costly to a contractor if they don’t clearly understand the ramifications of the clauses,” notes Bauld. “For instance, municipalities will drill a couple of boar holes and then sometimes give the contractor the results. However, if a contractor then digs down 15 or 20 feet and finds old oil drums, they may find that their contract has a privilege clause that states that, as a contractor, they’re responsible for removing these hazardous materials at their own cost. A situation like that could cost the contractor the entire profit of the contract.”
UNDERSTAND ThE RISK
With municipalities moving more and more towards RFPs, the concept of who assumes the risk on a project is becoming one of the most critical factors. This in mind, Bauld cautions contractors to look closely at the bid conditions to identify where they
stand with the risk portion on the bid they submit.
“Government agencies are typically risk adverse. They want to transfer all the risks to the contractor, but what they need to understand—and what they do understand—is the more risk you transfer to the contractor, the more money they have to pay for the project. As a contractor, you have to understand what risk you’re taking on, make sure you account for it in your price, and if you’re successful,
you must be willing to honour your proposal pricing structure.”
LOOK, AND LOOK AGAIN
These are just a few areas to watch out for when setting up to place the perfect bid. Above all, Bauld urges, “The focus should be to double check, triple check, and then check again to make sure you’re covering off all your risks and that you’ve actually filled the document out in a way that they’re going to understand. Due diligence is key.”
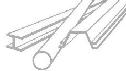
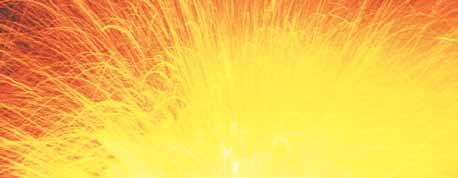
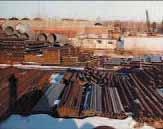


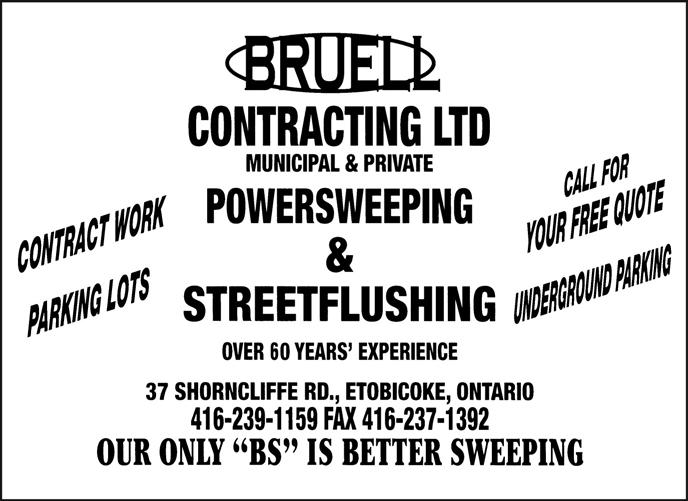
Precast Concrete Piles, Seamless, ERW & Spiral Weld Pipe Sheet Pile, Bearing Pile, WF Beams
Steel Foundation Products
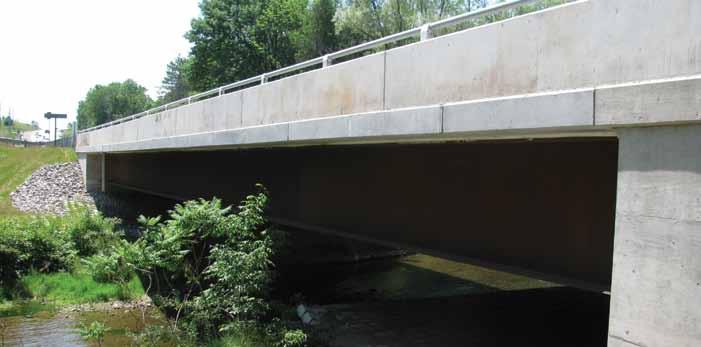
WHITEMANS CREEK BRIDGE WINS ONTARIO CONCRETE DESIGN AWARD
MTO and Delcan recognized for excellence in Structural Design Innovation
By Matthew Bradford
This fall, the Ontario Concrete Awards (OCA) Judging Committee selected the Whitemans Creek Bridge as the recipient of its 2012 Structural Design Innovation award, citing a mix of innovative design, industry-leading materials, and solid teamwork as the main reasons behind the project’s recognition.
Completed in 2011, the Brantford, Ontario, bridge was a replacement project initially designed by the Ministry of Transportation Ontario, who handed the project over for completion to Delcan Corporation. Their efforts were acknowledged by OCA’s panel of industry experts, who selected the Whitemans Creek Bridge as its Structural Design Innovation award winner for its synthesis of accelerated bridge construction (ABC), ultra high performance concrete (UHPC), and fibre reinforced polymer (FRP); the combination of which helped Delcan, the MTO, and general contractor Dufferin Construction achieve a fast completion and top-quality results.
“Our judges selected Whitemans Creek Bridge project for a number of reasons,” explains Bart Kanters, Director of Technical Services with RMCAO. “What jumped out at them most, however, was the number of
innovative techniques they applied to that project, including its fast track construction through the use of precast concrete and the application of RFP reinforcements.”
Indeed, says Kanters, a defining element of the project was its use of FRP reinforcing both in the precast components of the bridge deck and the cast-in-place components of the barrier wall. This, in combination with the application of Lafarge’s UHPC for the bridge’s joints, shear pockets, and haunches, ensured high levels of performance and durability for the new Whitemans Creek Bridge.
WhITEMANS CREEK BRIDGE
Location: Brantford, Ontario
The project was launched to replace an aging, three-span concrete T-beam structure which spanned a length of 33.5m (110 ft) and resided on the two-lane Highway 24 near Brantford. In its new form, the Whitemans Creek Bridge measures 14.5m (48 ft) in width, and is supported by a single row of steel H-piles made integral with the abutments. The structure is also composed of a 40-metre (131 ft) singlespan steel plate girder structure with a 225mm (9-inch) thick concrete deck.
Since the project required taking the entire bridge out of commission, timing was a top concern. As such,
Size: 40 m (121 feet) single span steel plate girder structured, 225mm (9 inches) thick concrete deck
Owner: Ministry of Transportation (West Region)
Engineer of Record: Delcan Corporation
General Contractor: Dufferin Construction Company, a division of Holcim (Canada) Inc.
Material Suppliers: Armtec Limited Partnership, Dufferin Construction Company, Lafarge
Additional Participants: Harris Rebar, Ironworkers Local 721, LIUNA Local 183, National Concrete Accessories

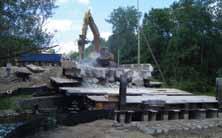

35-MPa precast concrete was used in all reinforced concrete elements, including integral abutments, with the exception of the barrier wall, which was cast-in-place once the bridge became open for traffic.
“If you’re going to take a bridge completely out of service, then you’re going to want to do it as fast as you possibly can,” says Kanters. “There wasn’t an option to do this in phase construction, so in this case precast and cast-in-place concrete was definitely the way to go.”
Reflecting on the project’s overall merits, Kanters adds that the MTO and Delcan’s design also serves as example for future bridge initiatives, noting, “It was a great project, and it was a great example of concrete’s design flexibility. We were impressed by the combination of precast, cast-in-place, and ultra high performance concrete, as it showed how all the different con crete systems can work together.”
The Ontario Concrete Awards are sponsored by association partners, and judged by a panel of representa tives from across the industry. They are handed out annually over 10 categories, with next year’s submis sions process beginning in September 2013. For more information, visit www. ontarioconcreteawards.ca.
EQUIPMENT NEEDS
For a complete listing of equipment and supply requirements, visit our website: www.contractorsrentalsupply.ca · AIR COMPRESSORS · AIR TOOLS & ACCESSORIES · AIREQUIPMENT · COMPACTIONEQUIPMENT · CONCRETEEQUIPMENT · ELECTRICTOOLS & ACCESSORIES · EXCAVATINGEQUIPMENT · FLOOREQUIPMENT · FORKLIFTS · GENERATORS · HEATERS · HIGHREACHEQUIPMENT · LADDERS · LAWN& GARDEN · LIGHTS · MATERIAL HANDLING / LIFTING · PAINTEQUIPMENT · PLUMBINGEQUIPMENT · PUMPS · SAFETYEQUIPMENT · SANDBLAST EQUIPMENT · SCAFFOLD · SHORINGEQUIPMENT · SURVEYEQUIPMENT · SWEEPERS · TRAILERS · TRENCHERS · WASHERS · WELDERS
ALSO, A FULL VARIETY OF YOUR DAILY SUPPLY REQUIREMENTS
LOCATIONS THROUGHOUT ONTARIO

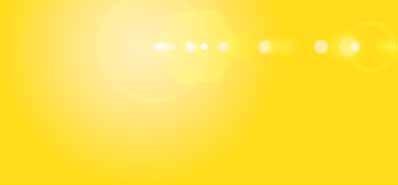
A surety solution that’s right for your business
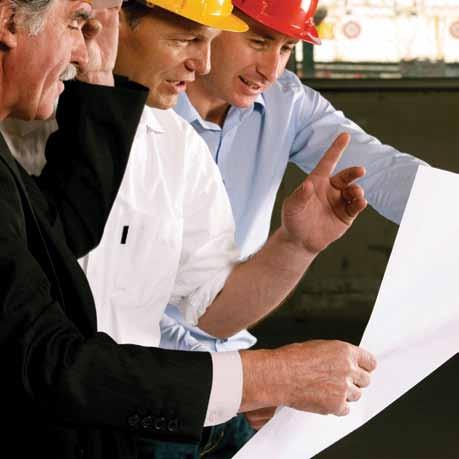




Itcanbehard to prepare foreverythingthatlife canthrowat yourbusiness.At AvivaSurety, we work hard to understand your unique needs, and offer knowledgeable business advice and a customized facility to help build your competitive advantage in the construction market.
Aviva Surety is one of Canada’s most trusted and valued surety advisors. To find out how we can arrange a surety facility for any class of business, talk to your broker today. For more information on Aviva Surety, call us at (416) 228-2488 or (416) 228-2486, or visit us at www.avivasurety.com
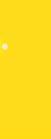
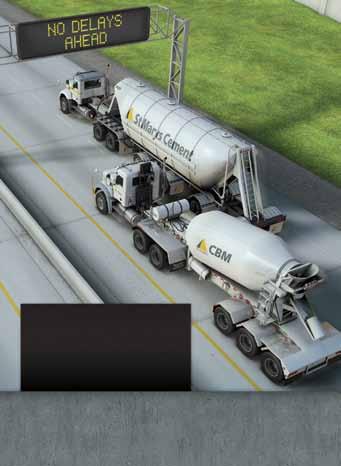

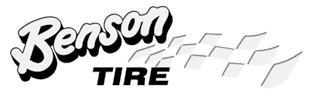
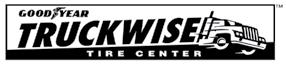
www.carillion.ca
www.centennialsweeping.ca
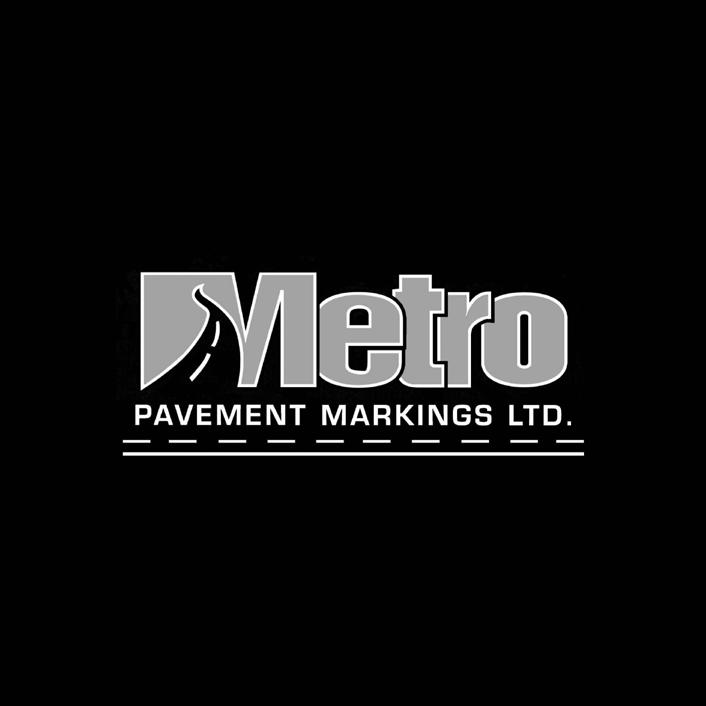
Ontario Barrier Wall Ltd.
www.ontariobw.ca
www.ontracksafety.ca
www.peninsula.ca
Peto MacCallum Ltd.
www.petomaccallum.com
Petrela, Winter & Associates
www.petrela.com
www.pipe-piling.com
www.schoonertransport.com
Building Science and Materials Engineers
Rocco Liscio, M.Eng., P.Eng. Vice-President 2051 Williams Parkway Unit 21
Brampton, Ontario L6S 5T4
Tel:(905) 792-7792
Fax: (905) 792-7829
Cell: (416) 560-7700
Email: rocco@davroc.com www.davroc.com
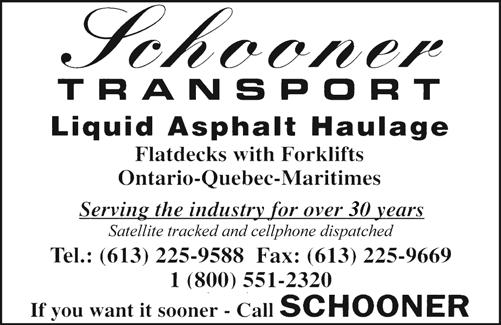

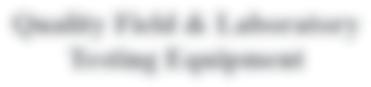
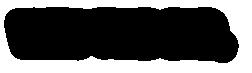

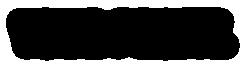
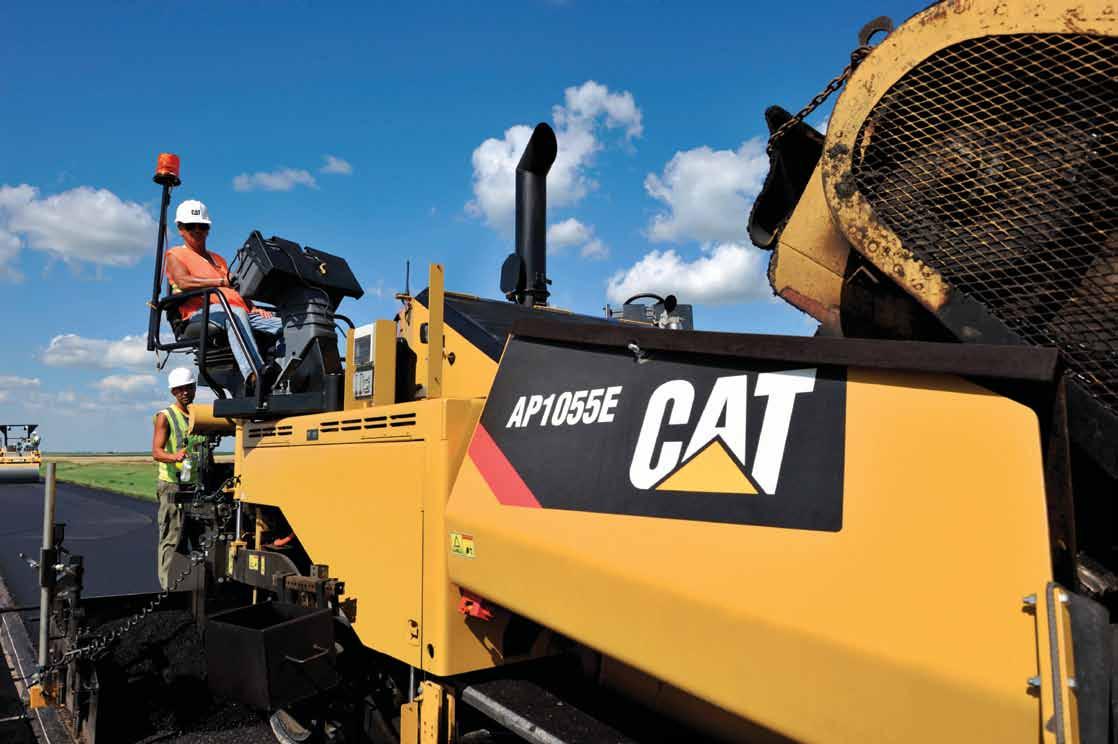
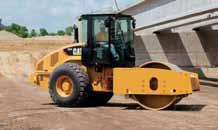
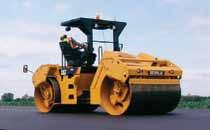
EVERYTHING HITS THAT BOTTOM LINE.
The way you bid, the equipment you put on the job, your crew's ability to make on-the-fly adjustments––everything about paving comes with a risk, or a reward. Toromont CAT can help you manage both. Toromont CAT provides the products and on-site support needed to improve your profitability. So you can bid with confidence, pave with efficiency and deliver on those nonnegotiable performance specs.
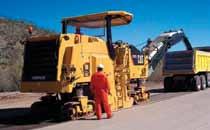
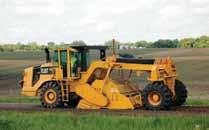
Caterpillar is committed to your success. So is Toromont CAT They are always there with financing, maintenance programs, parts and services needed to keep your equipment and crew on schedule. Or maybe ahead of it.
www.toromontcat.com
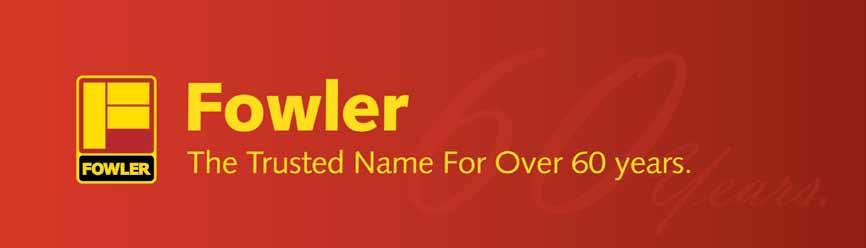
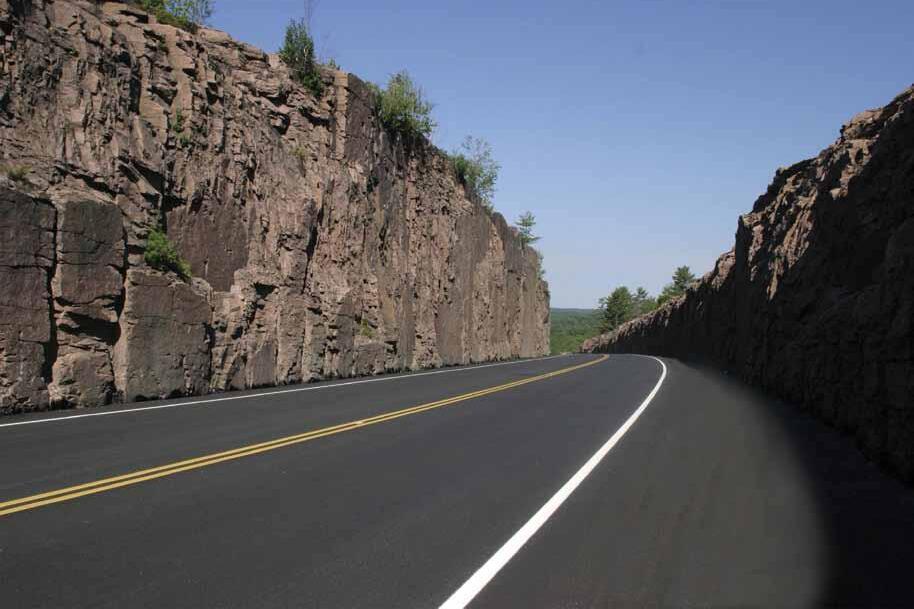
HL-1 STONE, D.F.C., S.M.A.
HL-1 STONE, D.F.C., S.M.A.
HL-1 STONE, D.F.C., S.M.A.
ASPHALT AGGREGATE SUPPLY
ASPHALT AGGREGATE SUPPLY
ASPHALT AGGREGATE SUPPLY
HL-3 MODIFIED, SP12.5FC1 & 2
HL-3 MODIFIED, SP12.5FC1 & 2
HL-3 MODIFIED, SP12.5FC1 & 2
2 QUARRIES TO SERVE YOU
2 QUARRIES TO SERVE YOU
2 QUARRIES TO SERVE YOU
HL-3 MODIFIED, SP12.5FC1 & 2
2 QUARRIES TO SERVE YOU
BRACEBRIDGE AND PARRY SOUND
BRACEBRIDGE AND PARRY SOUND
BRACEBRIDGE AND PARRY SOUND
2 QUARRIES TO SERVE YOU
BRACEBRIDGE AND PARRY SOUND
BRACEBRIDGE AND PARRY SOUND
Barrie Gravenhurst