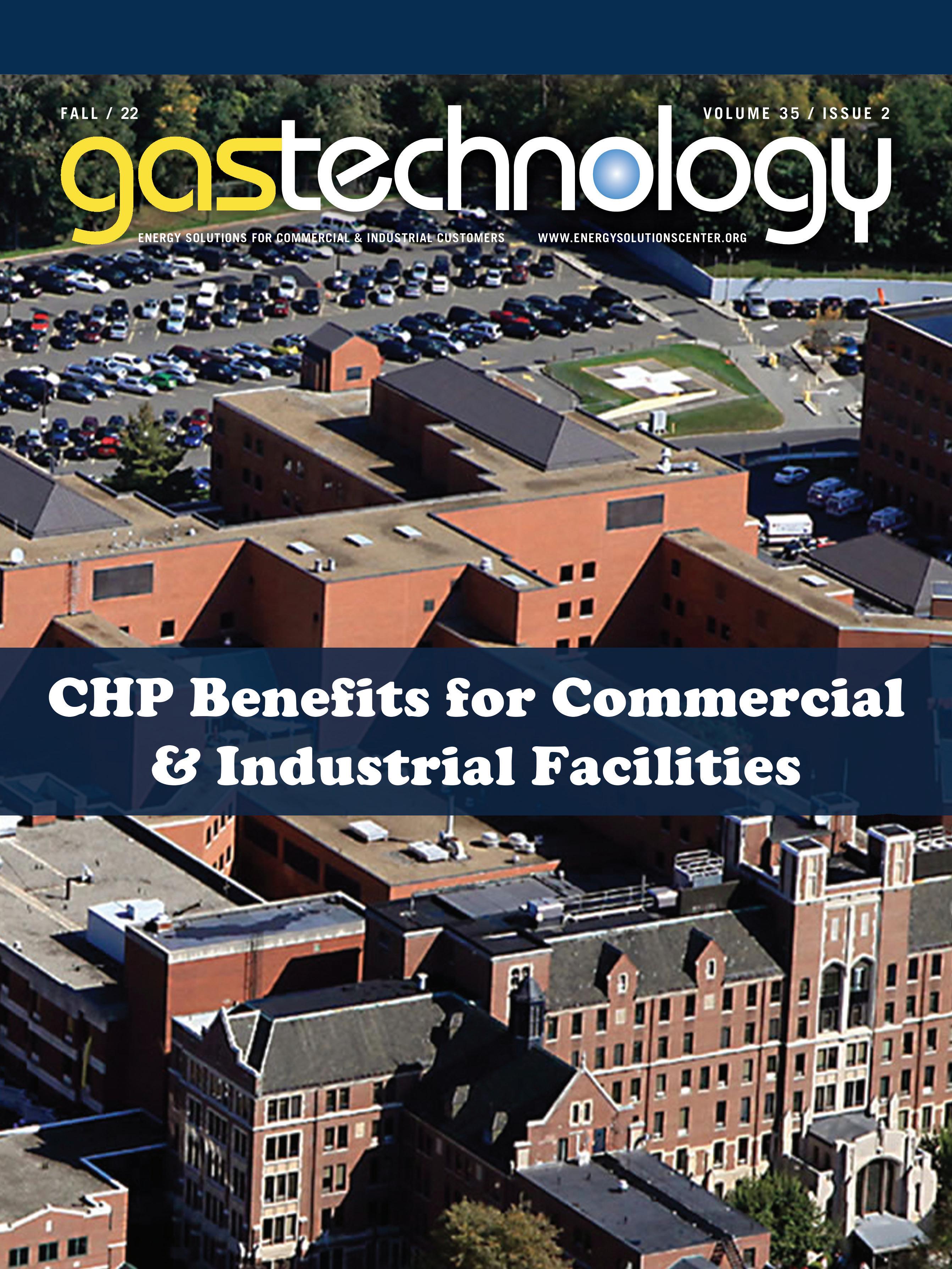
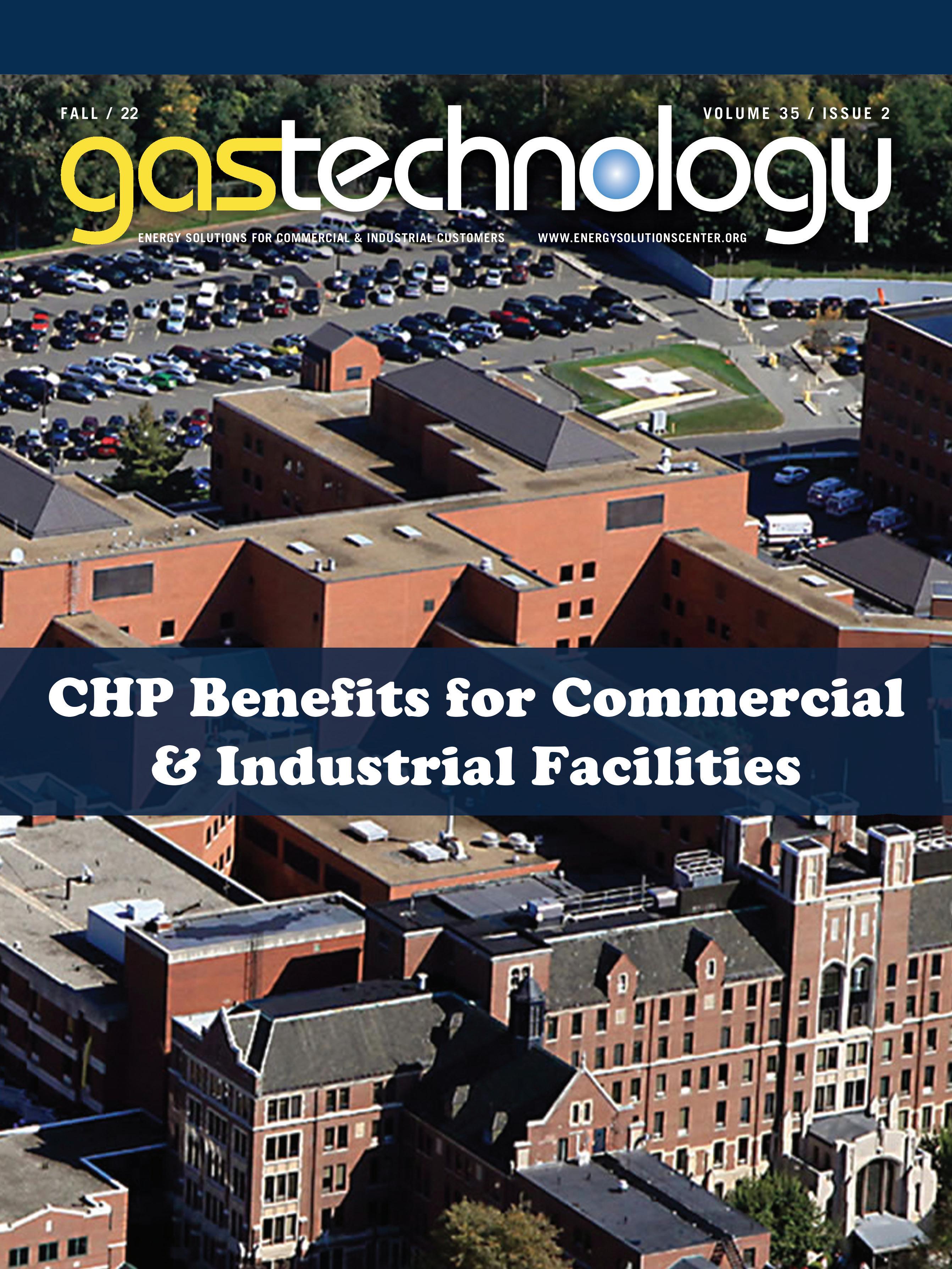
on the cover
Baystate Medical Center initiated a combined cooling heat and power (CCHP) system at their Springfield, Mass., hospital, which serves more than 800,000 people in the area.
Courtesy: Broad USA, Baystate Medical Center
inside
Gas Technology is a trademark of Energy Solutions Center Inc. and is published in cooperation with CFE Media, LLC.
Gas Technology is an educational supplement from: Energy Solutions Center Inc. 400 N. Capitol St., N.W. Washington, DC 20001
• (202) 824-7152
• www.energysolutionscenter.org
Ashley Duckman, Executive Director
Chris Vavra, Managing Editor
Comments may be directed to:
Gas Technology Editor
Plant Engineering Magazine
3010 Highland Parkway, Suite 310 Downers Grove, IL 60515
• (630) 571-4070
Printed in the USA
Energy Solutions
Center websites:
www.naturalgastechnology.org
www.energysolutionscenter.org www.understandingchp.com www.gasairconditioning.com
A3
CHP success stories for commercial & industrial facilities
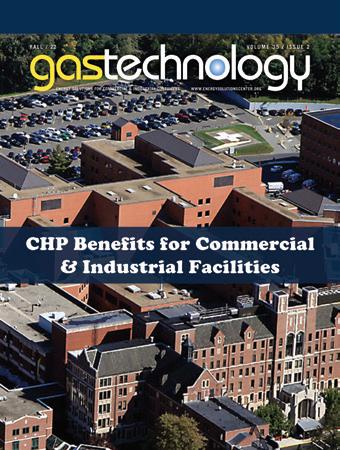
Combined heat and power (CHP) systems can help provide comfort and stability in large facilities while reducing power costs.
A6 Installing point source carbon capture on industrial sites
Carbon capture technology is a way for companies to safely remove carbon dioxide (CO2) from flue gases and the technology is getting smaller – making it more economically-viable for more companies.
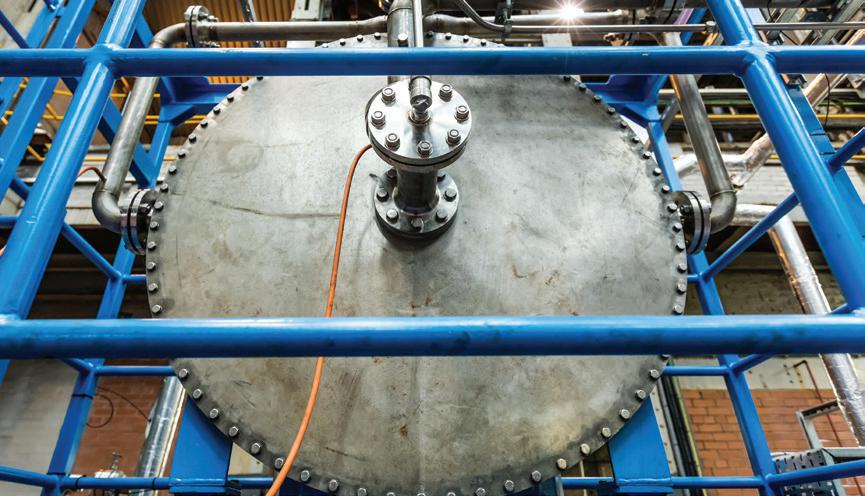
A8 Gas cooling benefits in medical and recreational facilities
Gas cooling systems can help hospitals and recreational facilities reduce their energy costs by providing reliable cooling in facilities where year-round cooling is needed.
A10 RNG benefits for fleet vehicles
Renewable natural gas (RNG) and liquefied natural gas (LNG) are being increasingly used by companies such as UPS for their fleet vehicles. Learn why.
A12 Boilers improve sustainability, energy efficiency at mushroom farm
Ostrom Mushroom Farms looked to expand their operations with a new facility that better suited their mushroom growing as well as improve their energy efficiency with three boilers that provided significant energy savings across their 43-acre facility.
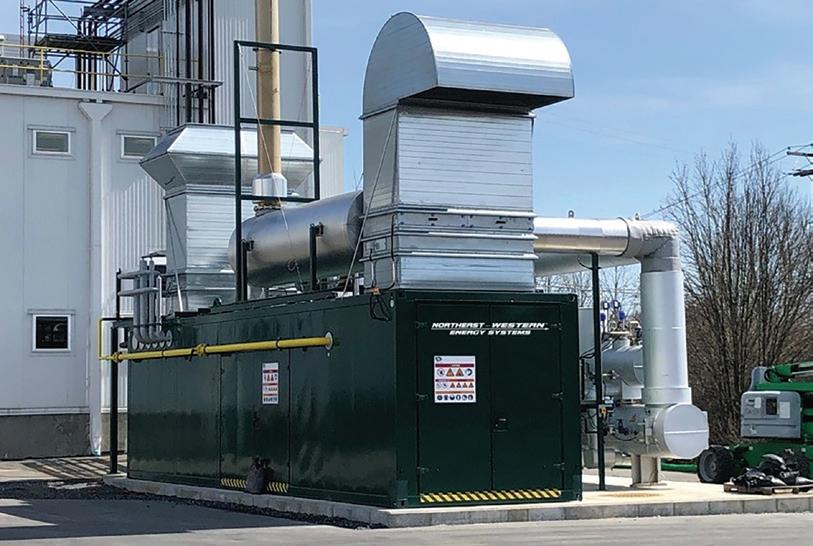
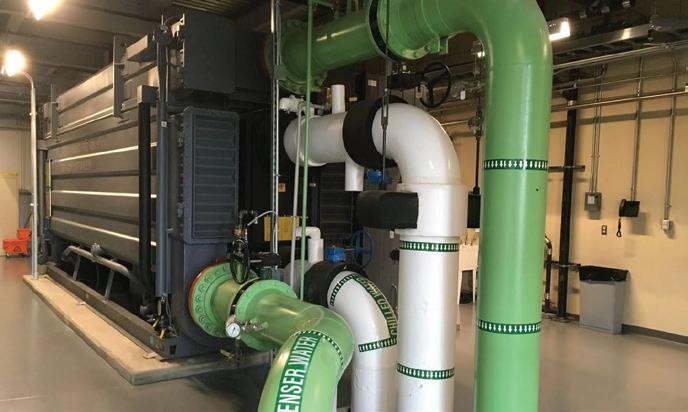
A15 Hydrogen blending demonstration with fuel cells
Companies, utilities and research institutions are investing resources into advancing hydrogen’s role in the net-zero economy. One such project involves a prestigious university in California.
CHP SUCCESS STORIES FOR COMMERCIAL & INDUSTRIAL FACILITIES
COMBINED HEAT AND POWER (CHP) SYSTEMS ARE PLAYING A GROWING ROLE AS A KEY SOURCE OF POWER FOR FACILITIES. By produceing electric at or near the site of use, CHP can reduce transmission and dis tribution losses therefore resulting in high efficiency, and lower energy costs. They are designed to run 24 hours a day and most systems can operate in island mode if a power grid goes down.
Their profile is getting a boost with the recent passage of the Inflation Reduction Act (IRA), which was signed in Au gust 2022, with increased tax incentives for those that install CHP systems.
“The IRA is probably the most transformative bill that CHP has ever seen,” said Aaron Tasin, vice president of operations and sales at Northeast-Western Energy Systems (NES-WES).
“We’ve gone from having a 10% tax investment credit and now it’s up to 30%. We’re finally on the same level as re newables.”
This added benefit, along with a general push toward greener energy and buildings, could help boost CHP’s poten tial profile. At the end of the day, though, it will come down to the projects and how they’re helping improve energy ef ficiency, heating and cooling in these facilities while reduc ing overall costs. There are over 4,700 sites in the U.S. alone producing almost 82,000 MW of electric with CHP.
In one case, microturbines were installed in a luxury apartment and in another, a CHP system was installed in a food and beverage facility. Both projects had unique de mands and expectations that needed to be balanced while still delivering on the project’s original purpose.
Microturbines used in luxury apartment
The Atwater Apartments complex is a 760,000-sq-ft, 54-sto ry building in the Streeterville neighborhood near the Chi cago Loop. The facility decided to upgrade their heating and cooling system because their heating costs in the winter were much higher than the cooling costs during the summer.
To accomplish this, Capstone Green Energy distributor Vergent Power Solutions was contracted in 2020 to rede
sign and convert the building from electric space heating to hot water heating. The new system featured two C65 ICHP microturbines and hydronic boilers that were tied into the existing chilled water piping system.
To ensure the microturbines would maximize their return on investment, the equipment needed to operate as close to maximum capacity as possible. The apartment building de veloped a custom operating schedule for the microturbines to maximize the heat recovery, while keeping the residents’ safety and comfort top of mind.
The CHP system was projected to save 1,360,000-kWh year. The conversion from electric heating to hot water heat ing, however, meant the energy usage would shift off tenant electricity bills and onto the building’s natural gas bill.
The microturbines are designed to minimize the environ mental footprint by reducing greenhouse gas (GHG) emis sions. Generating electric while utilizing the waste heat for space and domestic water heating generally has much lower emissions on a source to site basis.
The microturbines produced both domestic hot water and hydronic heating in the winter.
The project utilized the existing chilled water loop to run hot water to tenants in the winter. Economizer controls were added to tenant air handling equipment.
Results of the project
Replacing the older, less efficient water heaters with micro turbines and condensing boilers for domestic water heat ing, the building uses less energy and reduced carbon emis sions. To date, each microturbine has run more than 16,000 continuous hours with 99% uptime per unit. The building produces 1,138,800 kWh of electricity, which means genera tion, transmission, and distribution losses from the power grid to the building are eliminated.
Food manufacturer installs CHP system
Freshpet is a pet food manufacturer producing fresh pet food that is cooked slowly using steam and then refriger ated. They use a propriety process to produce their preserva
Combined heat and power (CHP) systems can help provide comfort and stability in large facilities while reducing power costs.
tive-free food from real meat and fresh vegetables, which includes mixing and blending of raw materials, cooking, cooling and packaging.
The process demands large amounts of steam to cook and electricity for refrigeration. Northeast-Western En ergy Systems installed a Combine Heat and Power (CHP) system at Freshpet’s Bethlehem, PA., facil ity, which is utilized to offset the electrical needs of the facility and make use of the ex haust heat from the en gine to make steam and reduce the boiler fuel consumption.
“They were look ing for sustainability, a hedge on utility rate increases, lowering their carbon footprint and doing something that would be consid ered green,” said Eric
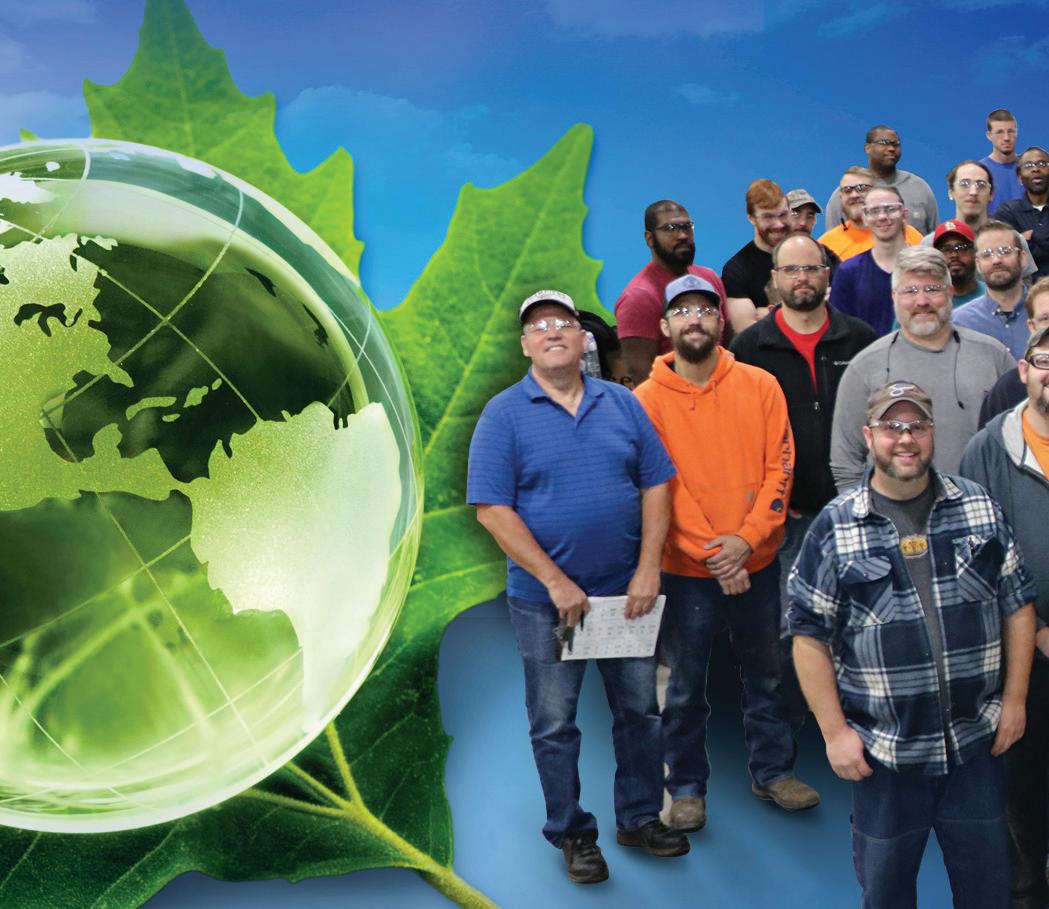
tions were particularly challenging and required sacrificing many holidays,” said Adam Masten, vice president of Engineer ing at NES-WES.
Another challenge during the instal lation process, Masten said, was the gas tie-in because their existing gas in frastructure was pressure limited. He added they could only do the cutovers during major holidays such as Easter, Thanksgiving and Christmas, which made the installation process a chal lenge. Most importantly were the safety issues because of the strict requirements necessary for food production.
“Since they are manufacturing pet food, they were concerned about any contamination from the CHP System and their product,” MacBain said.
The final installation was a success and the CHP has been able to meet the company’s demands, which are often in a state of flux.
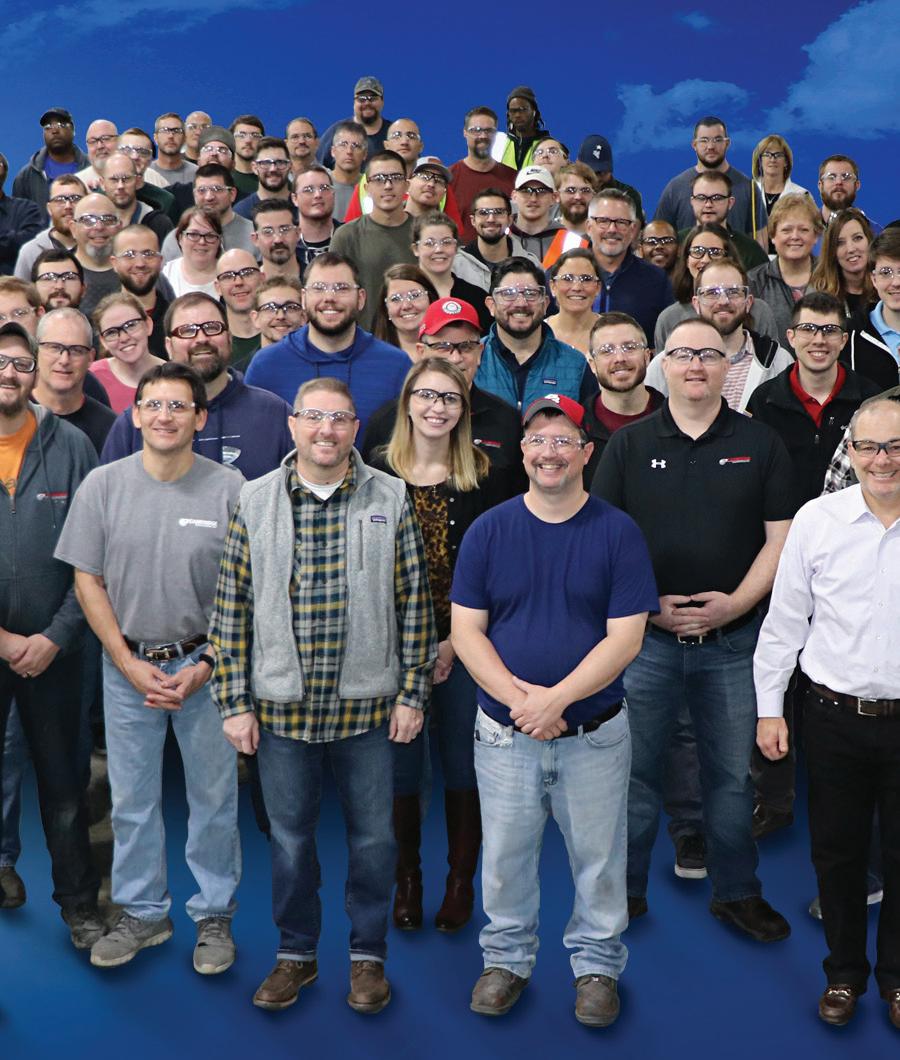
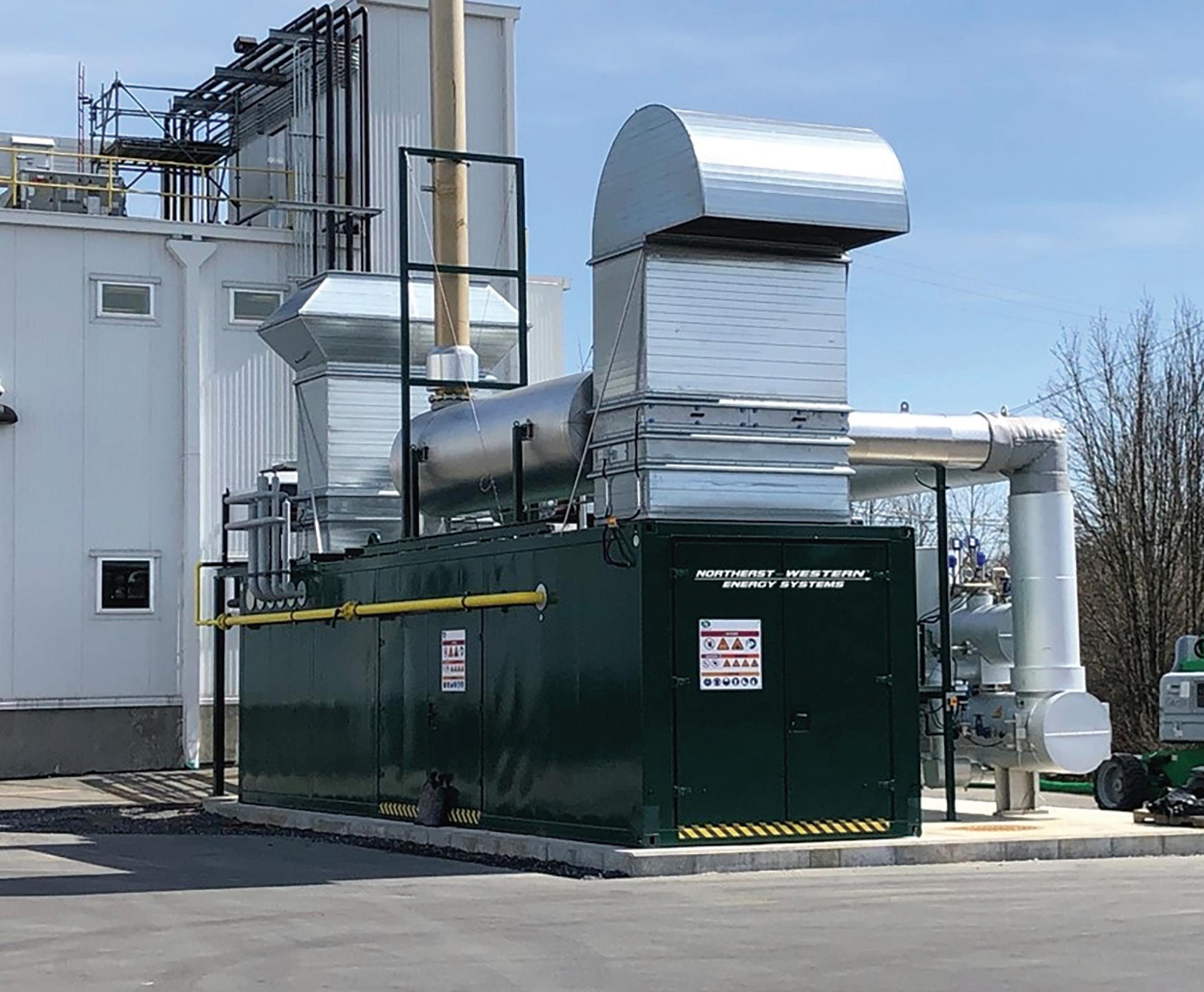
MacBain, business development at NES-WES).

Because it’s a food and beverage fa cility, there are specific standards that have to be met regarding cleanliness and safety so the company can avoid potential recalls and other hazards. Purity standards for pet food are the same high level as human food. The sys tem had to be de veloped, particularly the steam generating capability, to meet these standards.
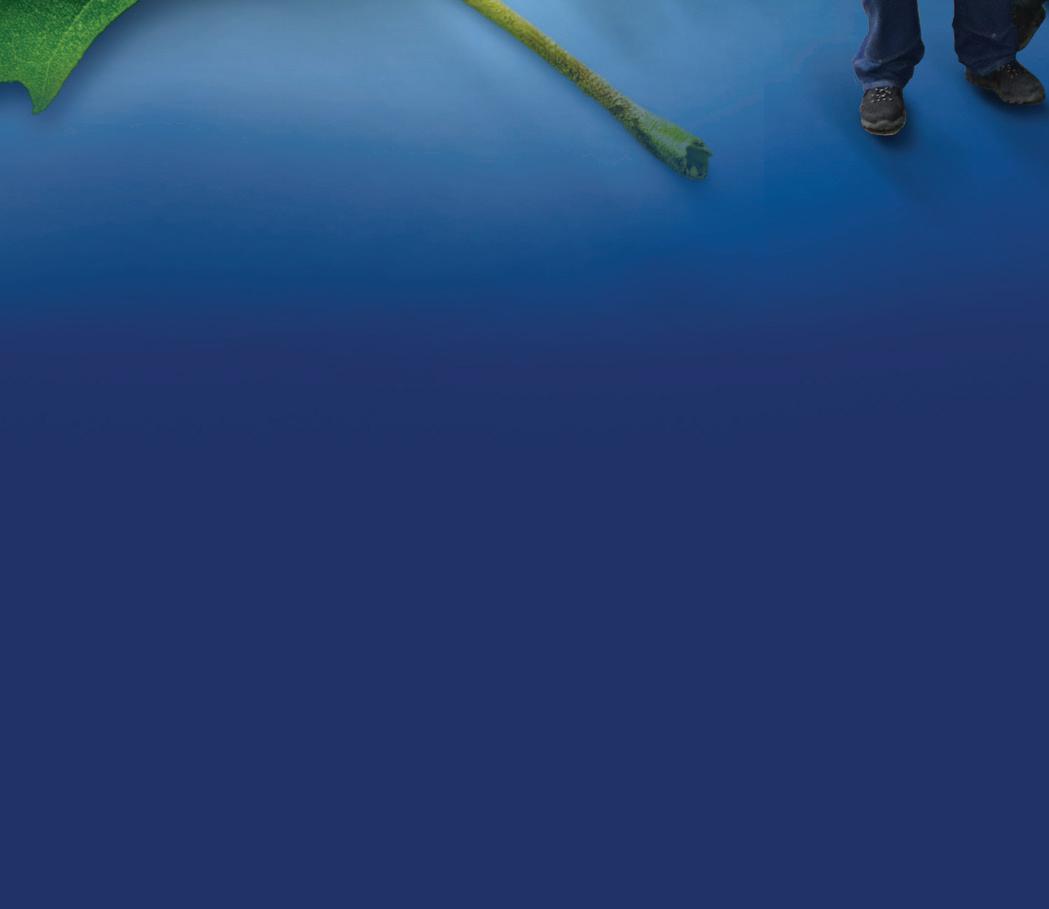
“We had to en sure during the build and for operations that strict boundar ies were maintained to keep their systems clean. The cutovers (electric, steam, feedwater, domes tic hot water) for a plant that rarely shuts down opera
“Since going into operation, the engine and related systems have functions as de signed,” said James Gibson, field service manager for NES-WES. “Since the steam is used for cooking, the amount needed changes as well as the volume and pres sure. The steam production from a CHP is meant to be consistent, so some chang es on the feedwater pump and pressure valve out of the CHP was needed.”
NES-WES, who are no strangers to these kinds of projects, were able to handle the challenges because of their experience.
Tasin said, “It really speaks to how im portant the true engineer, the guy that’s gonna stamp the system, how much they understand CHP. They’ll look for their local engineer, but they don’t nec essarily have that CHP experience.”

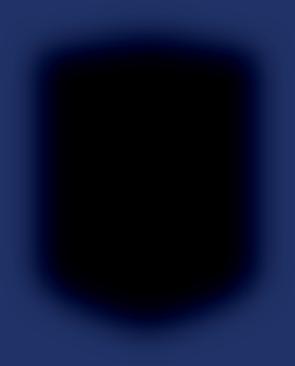
Overall CHP benefits
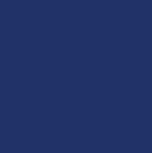

The value added by CHP technolo gies include facilitating sustainability to improving resilience and reducing costs. These benefits, coupled with the IRA legislation and a growing empha sis on efficiency and green buildings, can be attractive because if they are shown how they can provide benefit for the user by learning about their versatility.
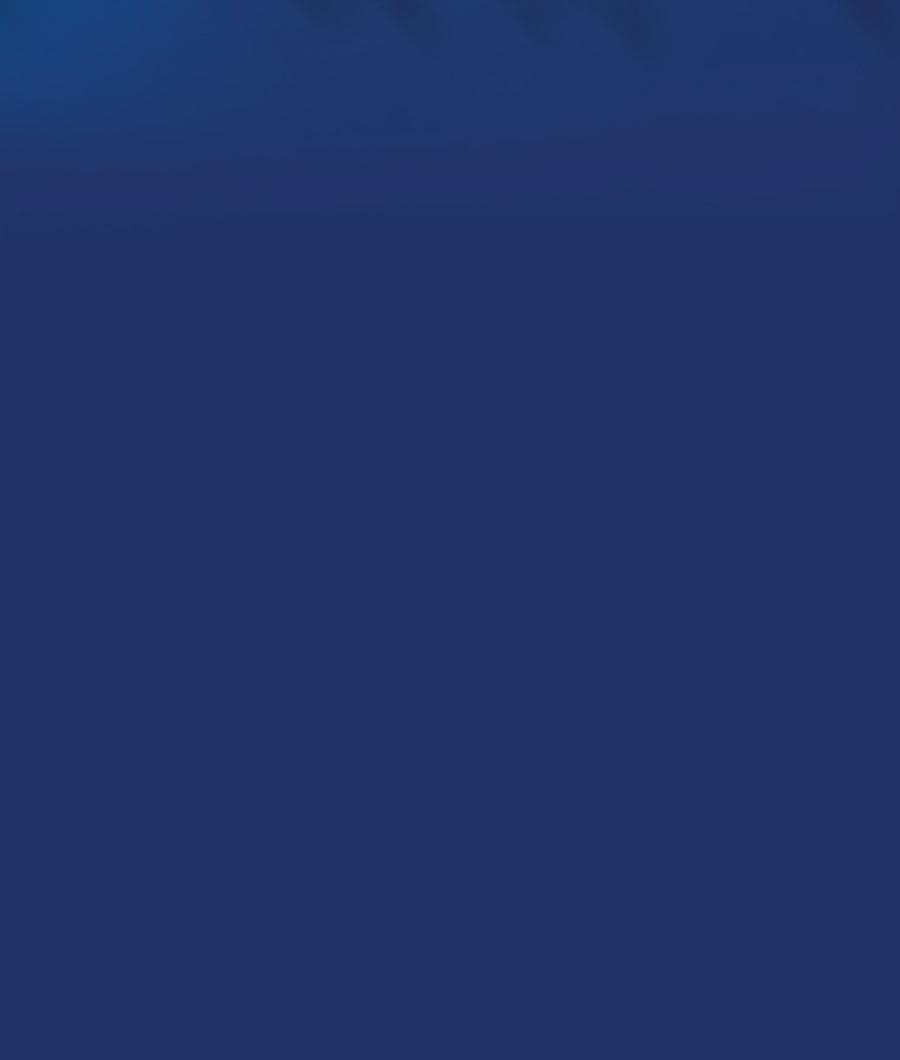
Figure
in the UK. Courtesy: CarbonClean
Installing point source carbon capture on industrial sites
Carbon capture technology is a way for companies to safely remove carbon dioxide (CO2) from flue gases and the technology is getting smaller – making it more economicallyviable for more companies.
REDUCING GREENHOUSE GAS (GHG) EMISSIONS IS A MAJOR FO CAL POINT AND CONCERN FOR IN VESTORS. As a result, companies are feel ing pressure to reduce their GHG footprint while also remaining profitable. Often, this pressure is passed onto individual indus trial facilities to reduce their GHG emissions without impacting the bottom line.
There are three decarbonization path ways that can reduce GHG emissions:
1. Fuel switching
2. Energy efficiency
3. Carbon capture
Fuel switching includes the reduction of fossil fuel use in favor of either low-carbon fuels (i.e., green hydrogen or renewable natural gas) or renewable electricity. How ever, the infrastructure for delivering lowcarbon fuels is not well developed in every jurisdiction. As such, the cost of such fuels
can be prohibitive. Furthermore, the use of coal and natural gas to generate most grid electricity in some jurisdictions means that electrifying may not result in overall emissions reduction, but “push the emis sions to the grid.
In addition to switching to expensive low-carbon fuels, or electrifying an indus trial process, fossil fuel use can be reduced via process improvements. This can include:
• Installing more efficient equipment
• Increasing heat recovery
• Taking advantage of cogeneration and trigeneration processes to deliver heat, cooling and power to industrial pro cesses.
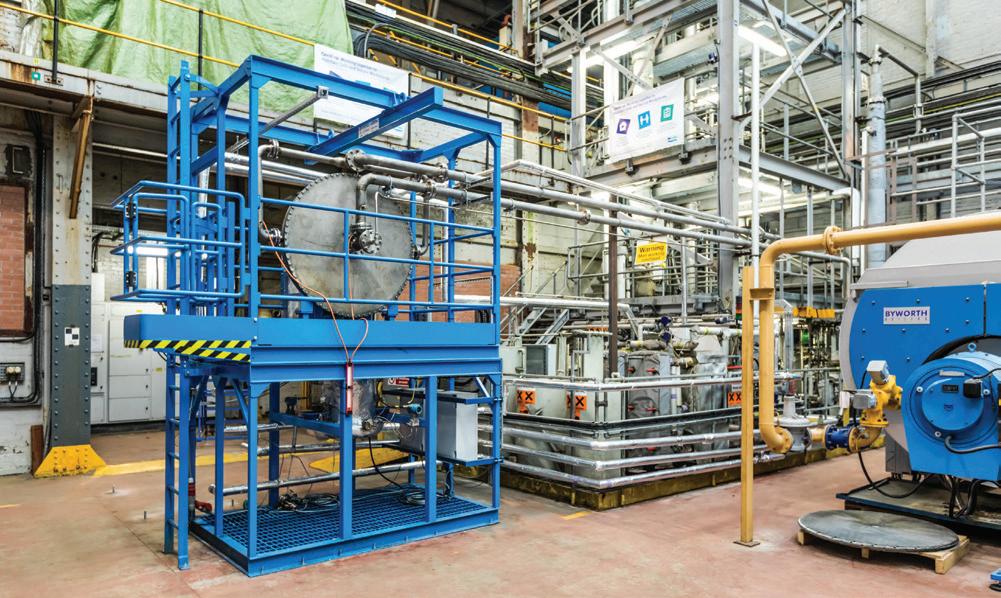
For some industrial processes, reducing energy use may be impractical or not pos sible, with existing commercially available technology.
Point source carbon capture is the pro cess of removing CO2 from flue gases, either
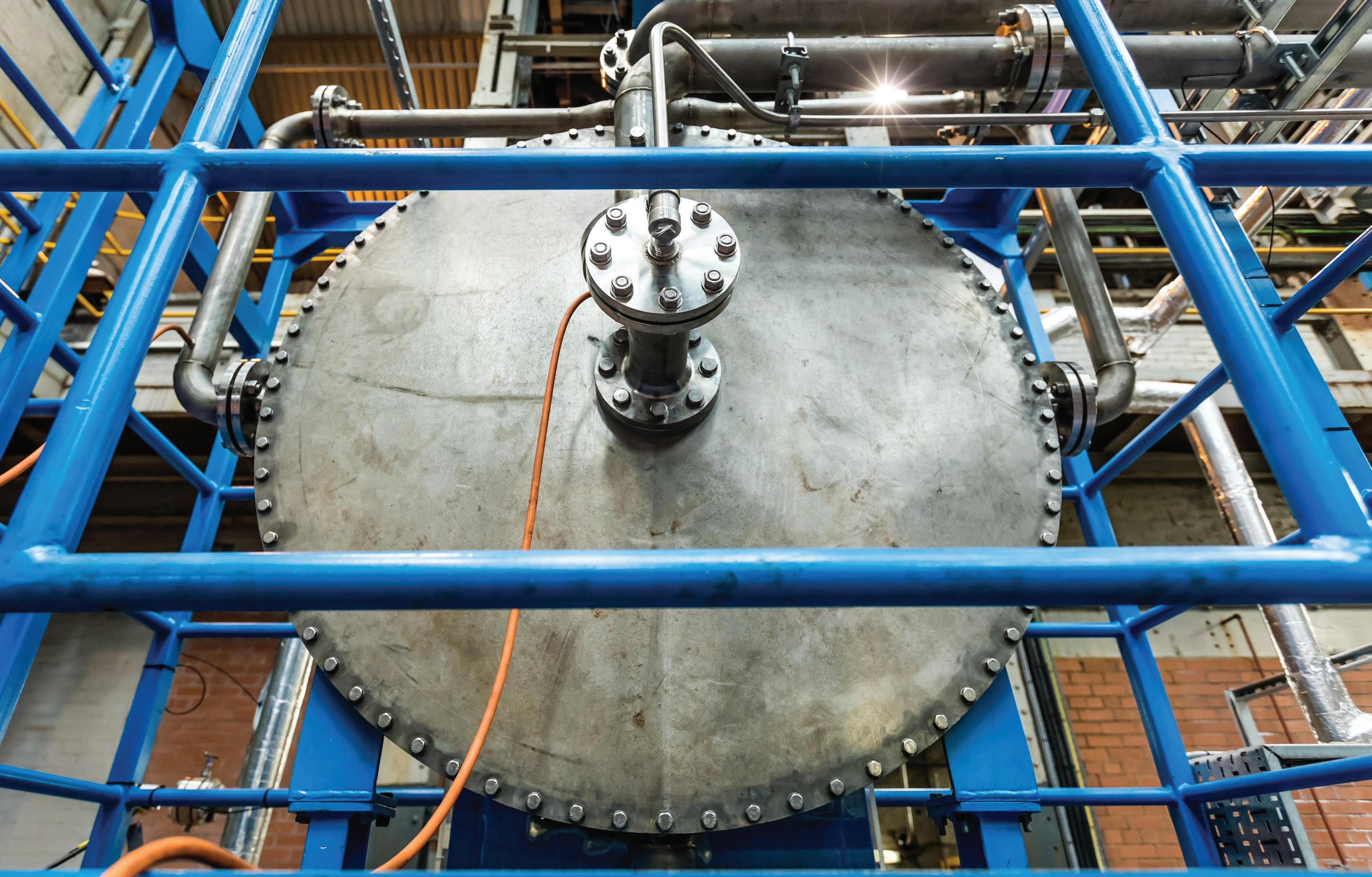
pre-combustion (or before it is used in a process) or post-combustion (or after use in a process). Post-combustion carbon capture is technically feasible for almost all indus trial facilities, given that natural gas is used in internal combustion engines, gas turbine generators or boilers. The core technical principle behind the most prevalent form of point source carbon capture (chemical ab sorption) has been proven in the field, for decades, for natural gas sweetening. Most commercially available point source carbon capture systems are large scale (> 200,000 US tons CO2 per year) and are marketed to large fossil fuel emitters or producers. These systems often require large absorption and regenerator towers to capture the CO2 from flue gas streams and remove it from the solvent. For many in dustrials with lower GHG emissions, car bon capture can be a risky solution, due to the need for large pieces of equipment and significant initial capital expenditures (CA PEX) investment.
A lack of available physical space and the high costs have both been barriers to widespread deployment of carbon capture systems. However, one original equipment manufacturer (OEM) is focused on over coming these barriers. Carbon Clean is a carbon capture solutions company head quartered in the UK that provides cost-
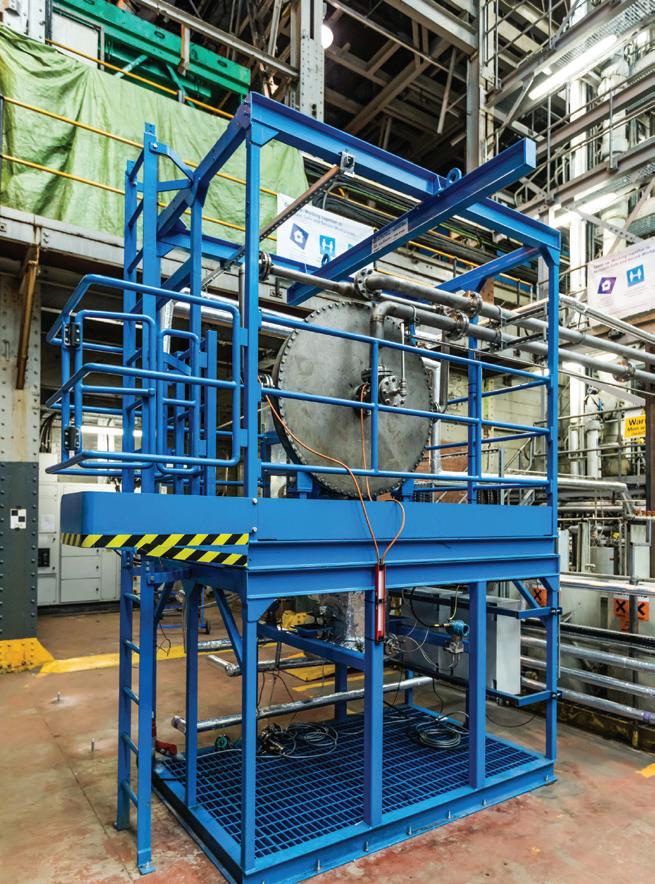
captured CO2 into soda ash which is then used in deter gent products.
effective carbon capture technologies for hard-to-abate industries such as cement, steel, energy from waste and refineries.
Its latest innovation is a fully modular carbon capture solution, CycloneCC, which has been specifically designed to reduce the physical footprint required by up to five times and the overall size of the technology by ten times – making it an ideal solution for many industries where space is at a pre mium. CycloneCC is smaller than traditional carbon capture equipment due to the use of rotating packed beds and the company’s pro prietary amine-promoted buffer salt solvent.
The technology has been successfully pi lot tested at 1 ton per day (TPD) and will be available in standardized modules of 10, 100 and 300 TPD.
It is prefabricated and skid-mounted making installation quicker (it can be in stalled in less than eight weeks) and easier.
As a fully modular technology, units can be added in line with a company’s decarbon ization ambitions and investment capacity, allowing CAPEX to be spread out over a longer period, rather than all at once.
Projects include working with CEMEX, a global leader in the building materi als industry, on deploying CycloneCC at its cement plant in Victorville, California and Rüdersdorf plant in Germany. Carbon Clean is also seeking to develop a pilot us ing CycloneCC with Chevron on a gas tur bine in San Joaquin Valley, Calif.
Carbon utilization methods
Once CO2 has been captured it must be uti lized or stored. Given that not every indus trial facility has access to a CO2 trunkline, or the suitable geology, for long-term storage, carbon utilization will be a critical activity in the post-carbon economy. For example, a project in Spain is planning to use captured CO2 in local greenhouses to boost produc tion and a project in India is converting the
While each activ ity may not qualify for CO2 reduction credits (or tax cred its for that matter) they can participate in their own carbon markets, some of which are already well established. Mineralization, for example, is one utilization pathway which can both generate CO2 reduction credits and be sold as an additive in the aggregate industry. Another utilization option is the produc tion of carbon neutral fuel. There are a few primary pathways to produce carbon-neu tral fuels using CO2 as a feedstock, including: Thermochemical conversion, electrochemi cal conversion and biochemical conversion.
Thermochemical conversion is a wellknown pathway for fuel production, and typically requires another energy carrier (e.g., hydrogen) to upgrade CO2 into a combustible fuel, such as methane. Elec trochemical Conversion is similar to ther mochemical conversion but allows for the production of other chemical feedstocks/ fuels, such as ethanol. Electrochemical con version uses electricity (potentially renew able), captured CO2, and a fuel cell to pro duce value-added chemicals.
Biological conversion of CO2 to valueadded products, such as e-fuels, is similar to other biofuel production processes such as anaerobic digestion. In one such process, a microorganism, with a specific enzyme, converts CO2 into several different chemi cals, including but not limited to: ethanol, methanol, ethylene, and even sustainable aviation fuel (with the addition of other re actants).
Cemvita Factory is an OEM that special izes in the biological conversion of CO2 into value-added products. Cemvita, which is based in Houston, focuses on offering “mi crobes-as-a-service” to potential clients who are interested in upgrading their CO2 into useful products. One notable Cemvita Fac tory project is their partnership with Oxy to convert 1.7 million tons per year of captured CO2 (from a cogeneration power plant) into 1 billion pounds per year of bioethylene.
A demonstration pilot project is being built to test this concept at a larger scale. This technology represents a promising pathway for carbon utilization.
Every industry has unique needs, but car bon capture technologies are fast developing to increasingly meet these needs and become more affordable, which remains a significant challenge. Innovation and information are the keys to the future for this technology.
MORE info
CEMVITA
Jaden Murphy, a post-carbon project en gineering coordinator for CEM Engineering, said of carbon capture’s future: “The future of carbon capture is highly dependent on the future developments in the utilization of CO2. If utilization of CO2 in manufactur ing, food and beverage production, and the mineral or metal industries is recognized, then Carbon Capture will be able to be de ployed more readily and may become ubiq uitous in the next 10 to 12 years.” GT
A combined cooling heat and power
system was
Medical Center in Springfield, Mass.
Baystate Medical Center/BROAD USA
Gas cooling benefits in medical and recreational facilities
A COMBINED COOLING HEAT AND POWER (CCHP) SYSTEM INTEGRAT
ED WITH GAS TURBINE, heat recov ery steam generator and steam chiller can provide heating, cooling and power to the medical center, realizing the energy in dependence and lower carbon emissions than grid power. While some facilities switch from heating to cooling depending on the time of year, other facilities need to provide constant cool air to meet their fa cility’s needs.
Consider the example of Baystate Medi cal Center in Springfield, Mass., which is the biggest hospital in the Baystate Health system. In another case, a mechanical CHP system that used natural gas rather than electricity was able to provide 24/7 cool ing to a newly-developed ice rink facility in suburban Boston.
Installing a CCHP at a hospital
Baystate Health initiated a $27 million CCHP plant that provides non-grid ener gy sources to critical facilities in the event of power loss during a disaster. The CCHP plant is part of the Housing & Urban De velopment (HUD) National Disaster Resil ience Competition.
Baystate Health is a nonprofit, inte grated health care system headquartered in Springfield, Mass., serving more than 800,000 people. The system has four hos
Gas cooling systems can help hospitals and recreational facilities reduce their energy costs by providing reliable cooling in facilities where year-round cooling is needed.
pitals, more than 80 medical practices and 25 reference laboratories.
The trigeneration power plant is lo cated at the largest level I trauma center in western Massachusetts. The plant in cludes a 4.6-megawatt (MW) gas turbine to produce 80% of its own power, bring ing much needed relief to the stressed en ergy grid. The steam, the byproduct of the combustion associated with the spinning natural gas engine, is also used for ster ilization, to heat the hospital and drive a BROAD two-stage steam absorption chill er for summer cooling.
The CCHP system produces 80% of the electricity and 98% of the steam utilized at Baystate.
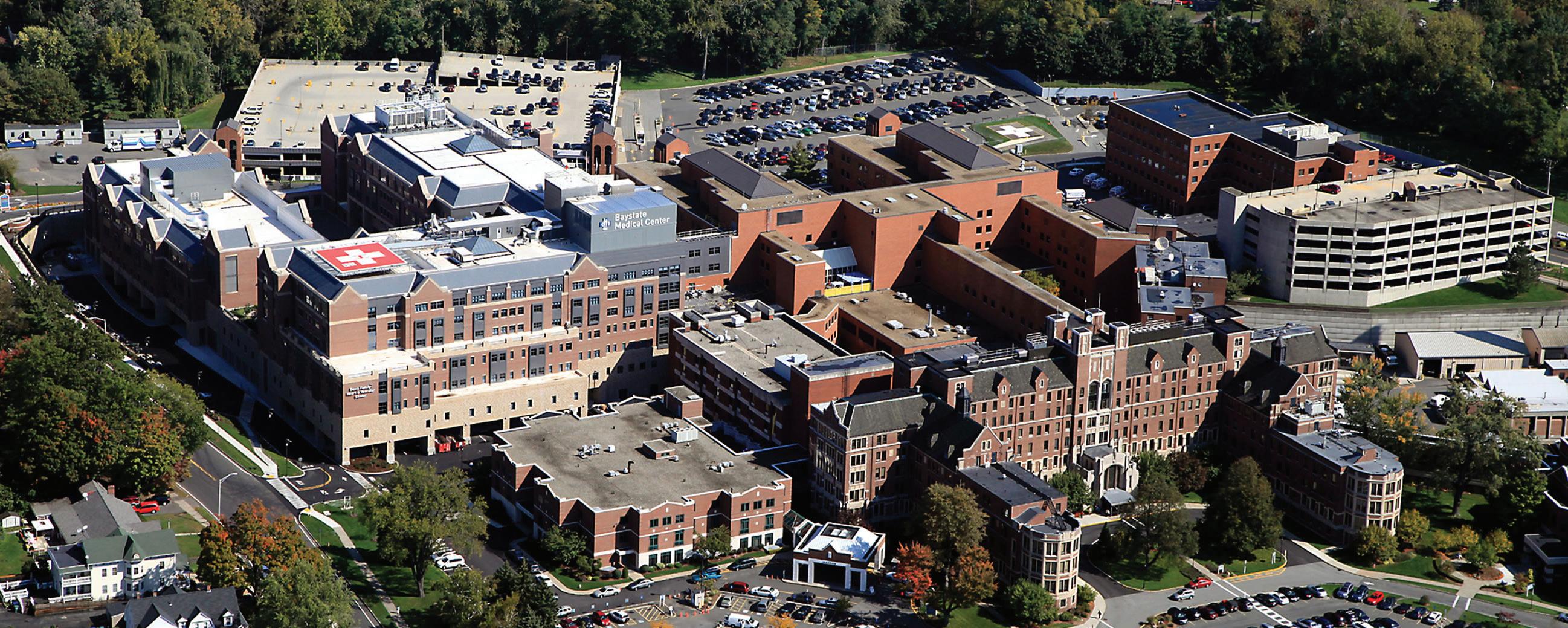
The BROAD absorption chiller uses waste heat from the trigeneration plant, increasing energy efficiency and saving more than 3,000 MWh/year electricity for cooling. In all, the CCHP system reduces annual utility costs at the hospital by al most $1.5 million.
Features include programmable logic controller (PLC) with 24/7 monitor ing, no maintenance pumps, unloading
down to 5% and proportional-integralderivative (PID) control with diagnostics to make any required fixes as minimal as possible for the operator.
The high and constant 24/7 demand of electric power, heating and cooling allows CCHP system to reduce energy costs, in crease energy efficiency and reliability, and improve environmental performance.
Mechanical CHP benefits for ice rink, cooling facilities
Maintaining championship quality ice surfaces requires precise cooling and de humidification control, which results in high energy needs. When the Skating Club of Boston relocated to a new facility in Brighton, Mass., energy efficiency was a key focus for the new facility. Tecogen provided five mechanical CHP systems for the facility.
“We have five chillers there for three sheets of ice. There’s one chiller per sheet of ice,” said Stephen Lafaille, VP of busi ness development at Tecogen Inc. “Then there’s an N+1 chiller, kind of like a re dundant chiller. The fifth chiller does
able and not have a giant pool of water out there. “
air conditioning or ice mak ing. It’s called a swing unit. Sometimes its conditioning the air above the three ice surfaces. You want the air above the ice really the right temperature and relative humidity because otherwise your boards are gonna get foggy and you could have water dripping. So you need to condition the air for the right event. Especially if you have a lot of people.”
The mechanical CHP system used for the facility operate on natural gas rather than an electric motor. Lafaille said the project was an ideal one because most of their CHP installations are retrofits. In this case, they got a new facility, which pro vided them an ideal installation because they had free rein to work with the in staller and place the chillers where they wanted for the best possible effect.
“We could design it the right way from the get-go. It was the most optimized rink we’ve done,” Lafaille said. “Every place that is using heat in this building is getting it.”
The units chosen for the facility were designed to not only maintain ice condi tions as well as air-conditioning the space above the ice, but they were designed to grab free waste heat from the chiller and use it for ice resurfacing, domestic hot water, space heating, ice pit melting and
info
regenerate their desiccant dehumidifica tion system.
Art Sutherland, president and CEO of Accent Refrigeration Systems, said, “Ice rinks by their nature consume a tremen dous amount of energy so we always try to do everything we can to reduce the oper ating costs. It’s the operating costs over the lifetime of the facility that costs a lot more than the first costs of the equipment.”
Lafaille said mechanical CHP can ben efit facilities where cooling is needed all year long. He mentioned other industries that benefit from this include manufactur ing facilities, food and beverage, hospitals and some laboratories. Any place where cooling & heating are needed simultane ously is where mechanical CHPhas the best economics.
“If you have a building that needs a lot of cooling, why not do it with natural gas? It’s more efficient from a technical standpoint.” Lafaille said.
The return on invest ment (ROI) for a mechani cal CHP is also stronger in a facility where it will con tinuously run, he said. The payback could be as little as two years.
Ice rinks, Lafaille admit ted, are a bit niche in that respect, but it does have one advantage: It’s designed to be open to the public and it gives people first-hand ex posure in a setting designed to entertain people wheth er it’s an open-skate session or a hockey match.
“It certainly helped us demonstrate that our tech nology can really be reli
That’s a message they’re trying to expound upon, par ticularly in light of the Infla tion Reduction Act, which was passed in August and has tax benefits for the CHP market as a whole. Mechani cal CHP might not be as well known, but Lafallie said the door is widening and it’s be coming more possible.
“We’ve been creating awareness that these types of systems exist,” he said. “I think a lot of people know about tradi tional cogeneration or CHP. If they un derstand their benefits, they understand there’s a cost, which might be a deterrent. We’re trying to show people there’s an other way to solving this problem. You get all the same benefits, but you actually can do it for a much lower cost, making it much more likely for an owner to make the investment.”
GT
Tecogen installed a mechanical CHP that uses natural gas rather than electricity to provide constant cooling for the Skating Club of Boston’s new facility in Brighton, Mass. Courtesy: Tecogen
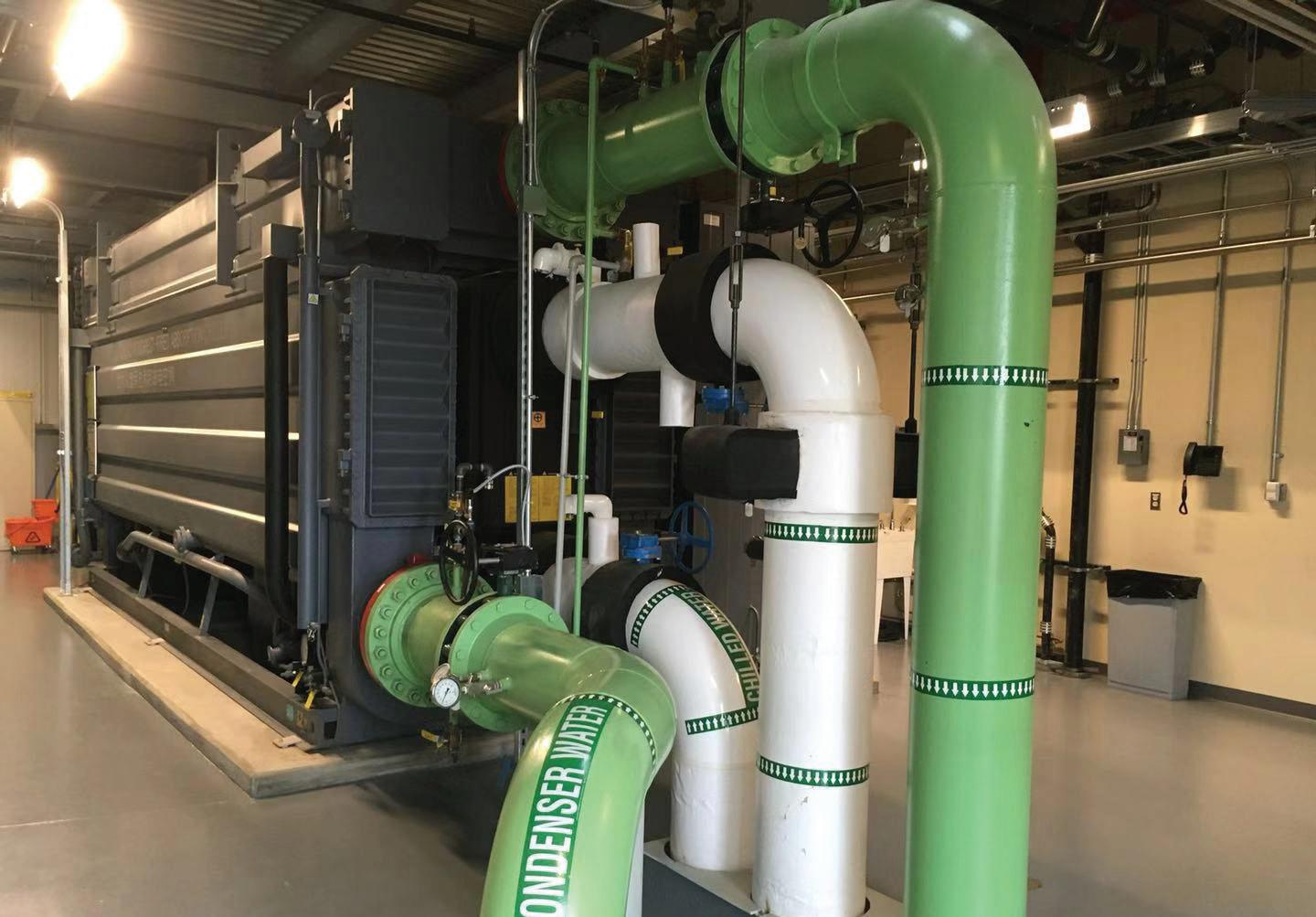
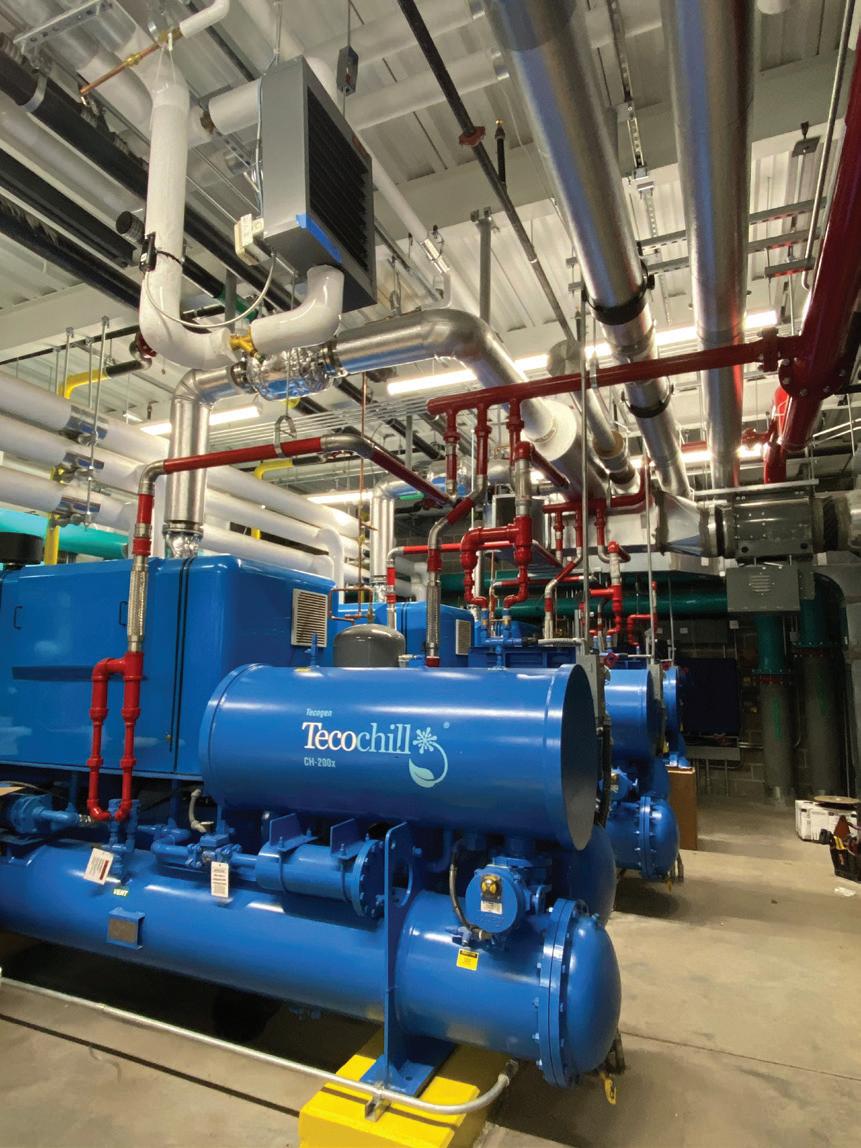
RNG benefits for fleet vehicles
Renewable natural gas (RNG) and liquefied natural gas (LNG) are being increasingly used by companies such as UPS for
RENEWABLE NATURAL GAS (RNG)
IS A BIOGAS THAT HAS BEEN UP GRADED FOR USE IN PLACE OF FOSSIL NATURAL GAS. The biogas used to produce RNG comes from a variety of sources, including municipal solid waste landfills, digesters at water resource recov ery facilities (wastewater treatment plants), livestock farms, food production facilities and organic waste management operations.
RNG has many potential applications and is being used in lieu of fossil fuels and other energy sources. One area where RNG is showing tremendous potential and benefits is with fleet vehicles. Fleet vehicles are a group of vehicles used by a group or organization. Among the most common are delivery vehicles seen on the roads in the form of Amazon, United Parcel Service (UPS) and Federal Express (FedEx). They are among the many com panies using RNG to better serve the pub lic and one company based out of India napolis is taking advantage of this.
Bringing RNG to fleet vehicles
Kinetrex started in 2013 as a subsidiary of Citizens Energy Group with two smallscale liquefied natural gas (LNG) termi nals in Indianapolis. They converted the terminals from utility to merchant facili ties and made major investments so they
could fuel trucks and sell LNG to several markets including transportation.
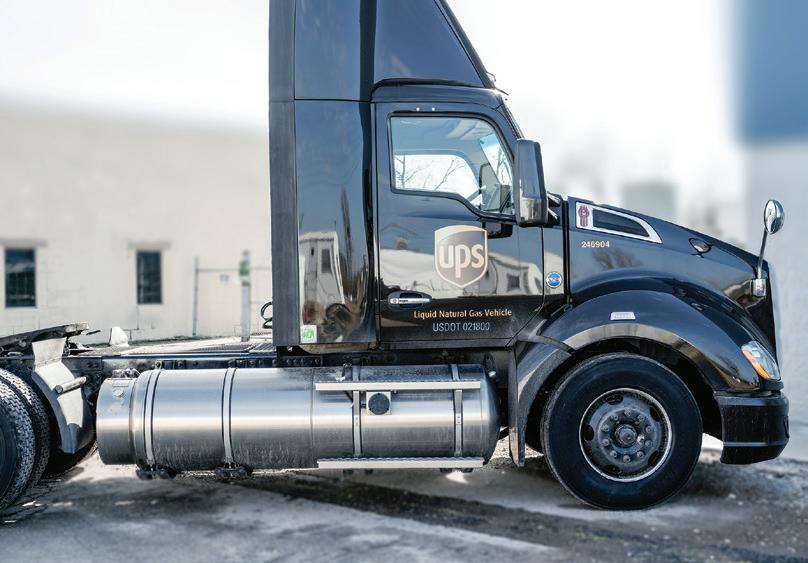
In the past couple years, Kinetrex, which was acquired by Kinder Morgan in 2021, has put a greater emphasis on help ing customers use RNG for vehicle fuel. Their centralized location in the U.S. al lows them to distribute their product all over the country and they have gained some major traction over the past several years. While Kinetrex does not receive credits, it does generate D3 renewable identification numbers (RINs) through the production of RNG, which is sold to third parties.
Casey Holsapple, vice president of busi ness development at Kinder Morgan, had been with Kinetrex since 2018 and has been a guiding voice for the company’s future and RNG plays a key role.
“From a fuel perspective, if they were running on LNG already, they are mak ing a concerted push toward RNG and they’re making concerted push to convert as many of their class 8 trucks to RNG,” he said in a video interview with Gas Technology.
This is crucial, Holsapple added, because there aren’t many LNG manufacturers out there right now. RNG has an advantage in this respect because it is flexible and can be distributed more easily.
“It’s a virtual pathway, so even though we’re making RNG in northern Indiana or at a landfill here in Indianapolis, they can use that RNG anywhere in the coun try,” Holsapple said.
For a company like UPS, this kind of return on investment (ROI) is vital.
Cummins, another Indiana-based com pany, manufactures the most popular natu ral gas engine in the country. Kinetrex has worked with Cummins on improving their technology, Holsapple said, by testing their LNG fueled engines at Cummins’ Colum bus facility.
“We actually provide LNG for their test facility so they can use that fuel as they test their LNG fueled engines,” he said. “Be tween that engine and the modifications or enhancements that have been made to the truck package itself, they’re basically interchangeable with the diesel unit from a performance perspective.”
The future of RNG
Kinetrex has had great success with their current initiatives, but Holsapple sees greater things for the company up ahead.
“We’re just scratching the surface. There are literally hundreds of potential RNG projects out there, and various studies would show that we could likely supply about 15 to 25% of the domestic natural gas market with RNG,” he said.
Kinetrex’s goal of improving the RNG market and exploiting its possibilities has led to a collaborative environment with other companies looking to expand their foothold.
“The industry is growing. It’s a very friendly industry. All the developers work really well together. It is competitive, but at the same time we’re all striving towards a goal of reducing emissions and providing support to our customers and their ESG goals in any way that we can.”
Fleet vehicles are somewhat ubiquitous in the world today and many are beginning to turn to RNG or LNG to power their vehi cles. While awareness is growing, the pub lic advertisement is a constant in our daily lives even if it remains somewhat invisible.
“Every major utility and company has a greenhouse gas reduction target in mind,” he said. “Many have announced it publicly. We are actively seeking ways to reduce the gap from where they are today and to where they want to be in 10 or 20 years. GT
Rinnai’s Commercial Portfolio Makes it Easy and Affordable to Stay in Hot Water
Rinnai offers the industry’s only 100% Sizing Guarantee along with

Turnkey Services from system design to start-up.
also has you covered with our Nationwide 24/7 Emergency Response
your business is never without reliable, unlimited hot water.
Nationwide Support and Coverage

Use Rinnai Commercial Products and enjoy
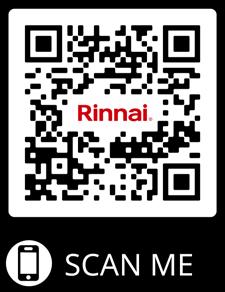

of mind that comes with these additional benefits:
Support
Rinnai National Accounts is committed to keeping your facility up and running with innovative water
Services
Design to Start-up
System Sizing Guarantee
Emergency Rapid Response
Savings
Rinnai National Accounts Worry-Free Hot Water Leasing

Savings
Lower Cost of Ownership
Maintenance
Worry-Free Hot Water Leasing Program
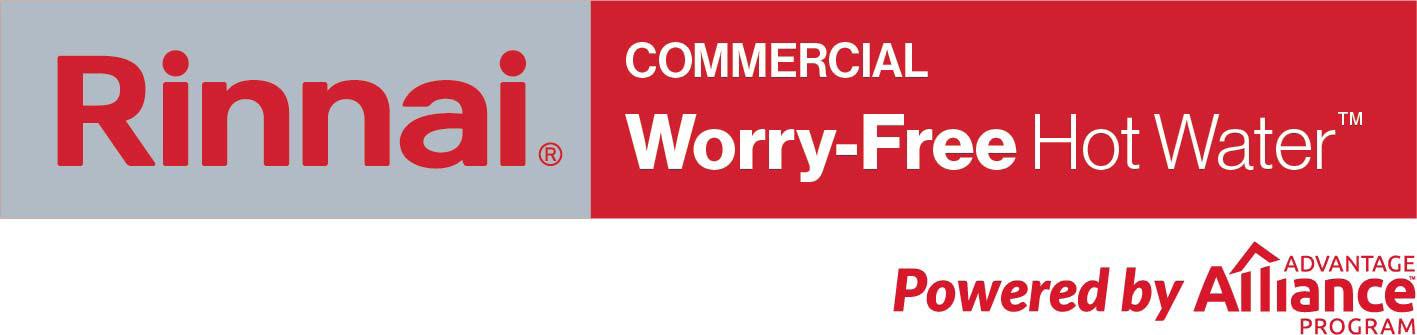
Boilers improve sustainability, energy efficiency at mushroom farm
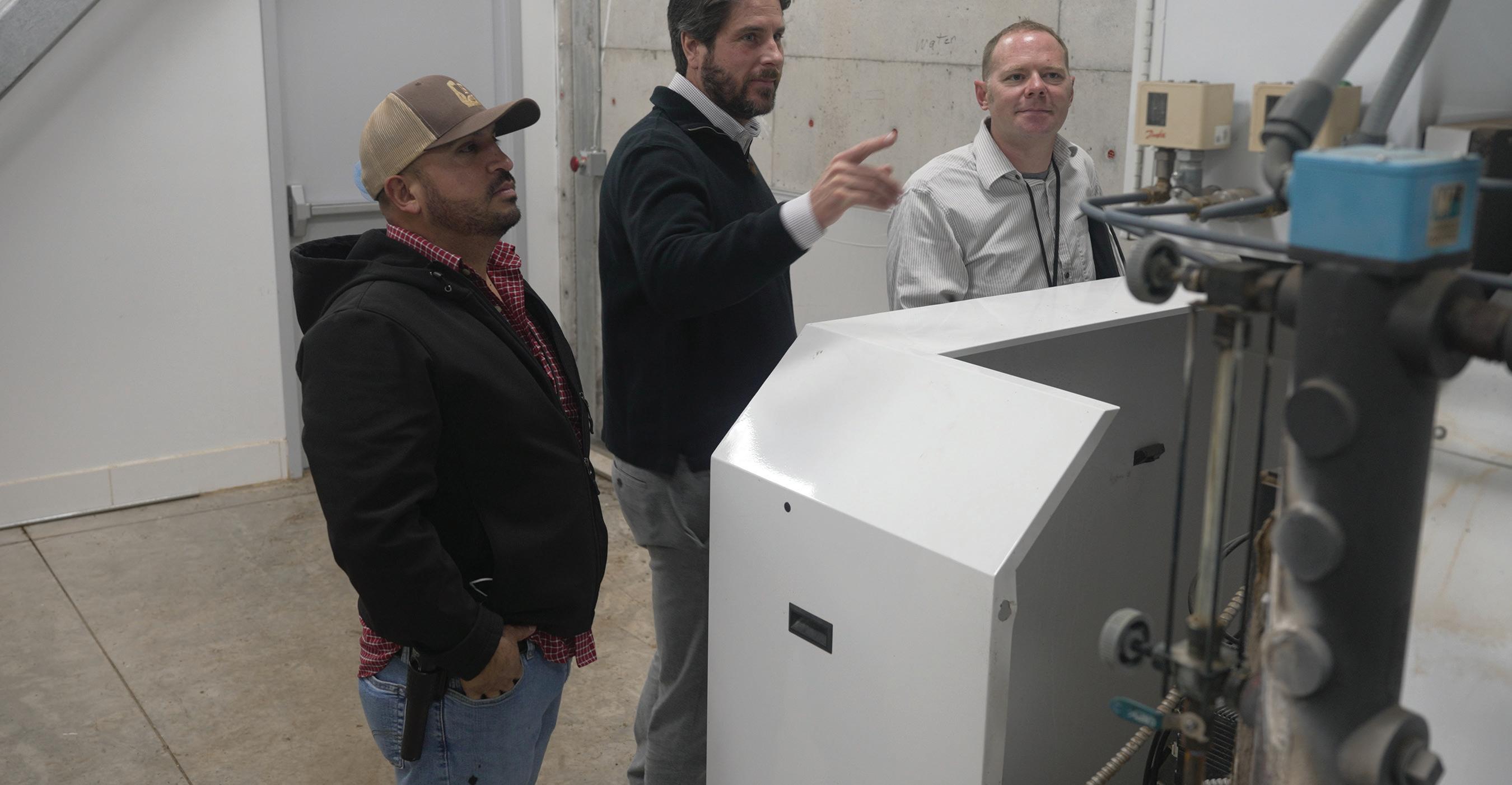
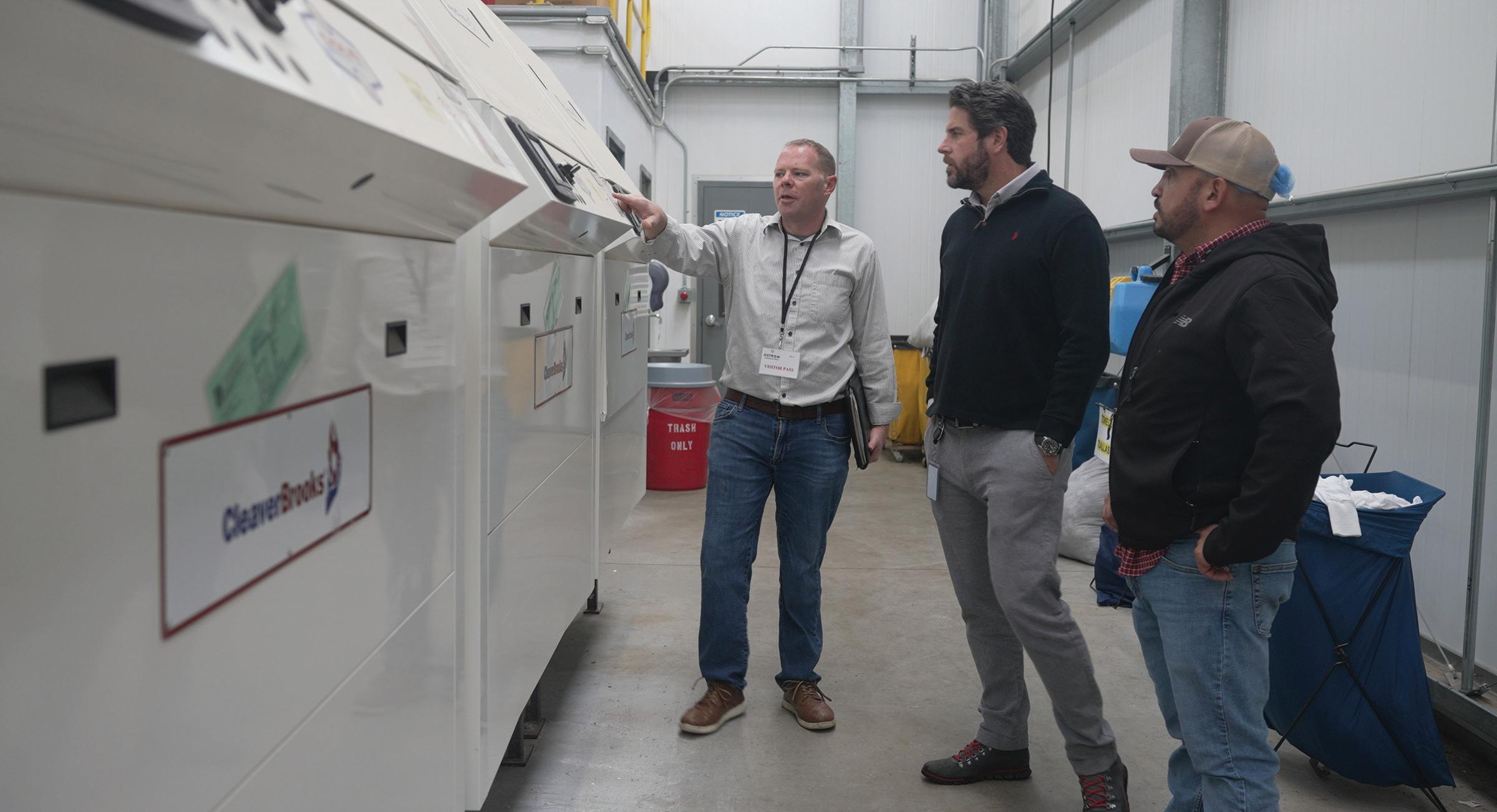
Ostrom Mushroom Farms looked to expand their operations with a new facility that better suited their mushroom growing as well as improve their energy efficiency with three boilers that provided significant energy savings across their 43-acre facility.
OSTROM MUSHROOM FARMS, WHICH HAS BEEN AROUND SINCE 1928, is the largest producer of mush rooms in Washington State. They sell a variety of mushrooms to consumers in the Pacific Northwest, Hawaii and Alaska.
In 2019, Ostrom decided to expand their business by moving from Olympia to a new facility in Sunnyside, Wash. The facility of fered an ideal opportunity to operate more sustainably than their previous facility.
While the company’s growth was part of the reason from the move, there were
environmental factors in play, as well. Moving their operations from Olympia to Sunnyside allowed Ostrom to be in a cli mate more conducive for growing mush rooms. Olympia, located in the Western part of Washington near Seattle, is colder and rainier. Sunny side, meanwhile, is in Eastern Washington and is in a drier, more arid climate bettersuited for growing mushrooms.
While the facility itself is indoors and climate-controlled, the environment and climate gave Ostrom the control they need as they look to improve sustainability. With help from Cascade Natural Gas Cor poration’s Commercial Incentive Program,
Ostrom had three high-efficiency condensing boiler systems installed in their Sunnyside, Wash., facility, which were designed to help them reduce overall energy costs. Images courtesy: TRC Companies/ Cascade Natural Gas Corporation
Ostrom installed three high efficiency con densing boiler systems that reduced ener gy use without harming productivity.
Sustainability is a fundamental busi ness value and Ostrom wanted equip ment that could help reduce energy use at every stage of the production process.
“Sustainability here at Ostrom is really the core of our DNA. We want to reduce our energy costs and our carbon foot print,” said Travis Wood, CEO of Ostrom Mushroom Farms. “There are critical en ergy inputs at every part of the process.”
The mushroom growing process is highly automated and reliability is essen tial; steam is generated 24/7. The boilers have an automated display that make it easy for team members to monitor tem perature and adjust as needed.
Bradey Day, program manager of TRC Companies, said installing the boilers for Ostrom was a new kind of challenge for them and Cascade, which was contracted to do the installation. They used three ClearFire ultra-high efficiency/low emis sions duel fuel natural gas and propane firing condensing hot water boilers from Cleaver-Brooks for the project. They are 96% efficiency a design pressure of 125 PSIG, which allows them to operate in tough conditions.
“For agriculture, this was new for the Cascade Natural Gas program,” he said. “It’s the first time we had incentivized
the installation of boilers spe cifically for an in door agricultural application. We had worked with farms on projects in the past, but as far as the growing process and using boilers not just as space heating, but for multiple appli cations in an agricultural facility, this was the first project.”
The three boilers amounted to almost 10 British thermal units (BTUs) for the entire 43-acre facility, which was a high for the company installing the boilers.
ing, there’s so many operational challenges in order to keep business going. You have to make adjustments and you can’t be as ef ficient as you’d like to be.”
In terms of size and scale, this was a re cord high for Cascade in a few respects.
While this was a large undertaking, there was comfort in knowing the boilers themselves would be a constant even if the project itself had some unique aspects.
While the facility itself is indoors and cli mate-controlled, the outside weather and climate gives Ostrom the control they need as they looked to improve sustainability and energy efficiency within a new facility.
“It was, I think cool for them to have a fresh start to be able to build as efficiently as possible from day one,” Day said. “Whereas when you’re retrofitting an existing build
Installing the boilers on the 43-acre prop erty showed Day and Cascade how much efficiency and savings they could gener ate in one facility.
“I think the scale of the units themselves and how efficiently they run and how this can be replicated at other properties,” Day said, noting the three installed boilers were 3.3 million British thermal units (BTUs) each. “That’s almost 10 million BTUs. Our typical project is 250,000 BTUs. The scale of the project is unique and it was cool to see how it could be used in so many different applications. Generally, boilers are used for space heating or water heating. These were used for the entire facility.”
The annual savings for Ostrom amounted to 91,980 therms per year as well as incentives for the energy savings. These savings help Ostrom can focus on growing quality, sustainably produced mushrooms rather than worrying about rising energy costs, which are becoming a growing concern throughout. GT
Superior Performance in a Compact Design
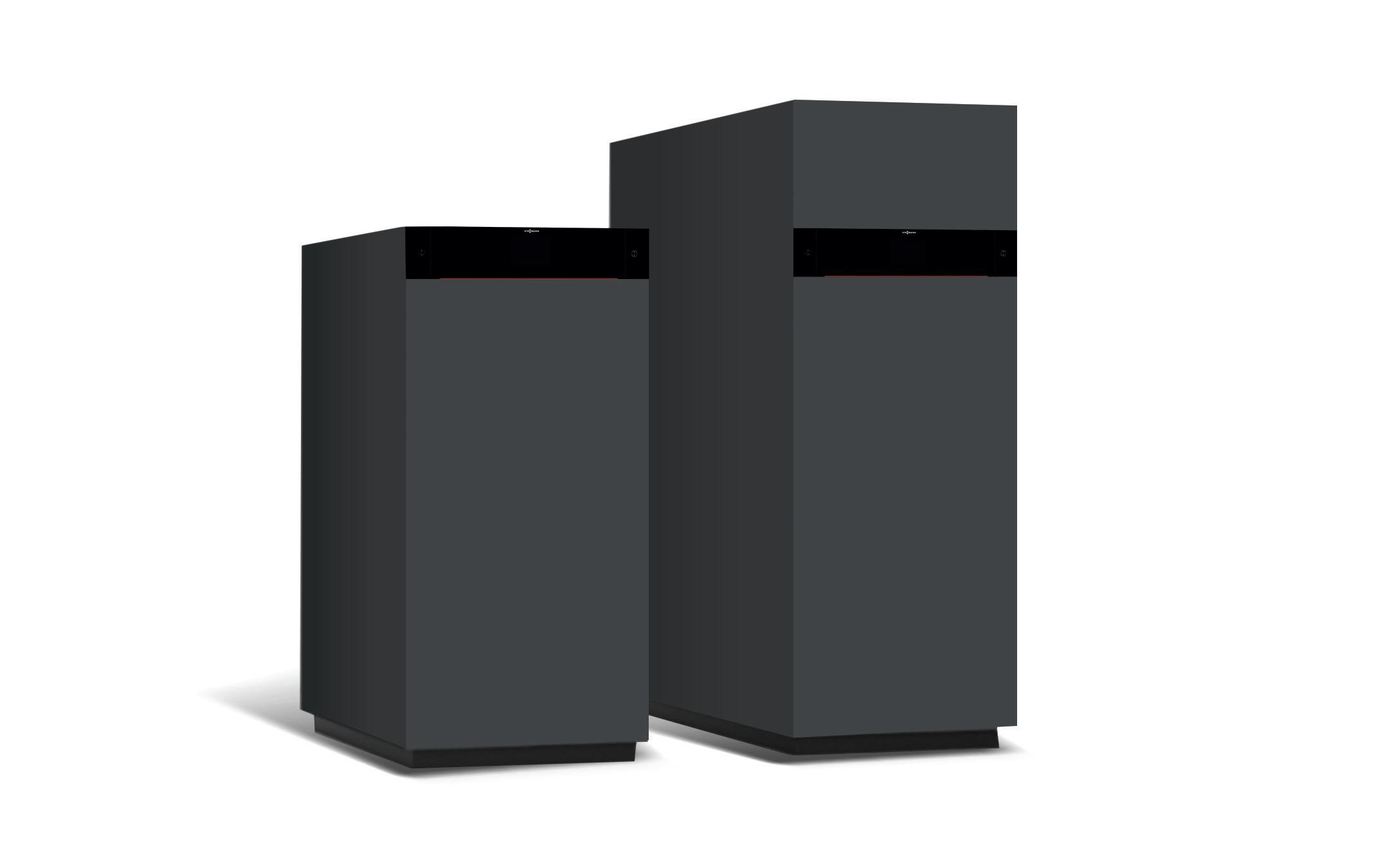
Hydrogen blending demonstration with fuel cells
Companies, utilities and research institutions are investing resources into advancing hydrogen’s role in the net-zero economy. One such project involves a prestigious university in California.
DOZENS OF COUNTRIES HAVE COMMITTED TO NET-ZERO EMISSIONS GOALS IN THE COMING DECADES. Hydrogen is required to reach these deep decarbonization goals. The Hydrogen Council projects that hydrogen could be 18% of global energy in 2050.
The hydrogen economy is advancing across numerous sectors in cluding power generation, transportation, industrial energy, build ing heat and power, and feedstock.
Blending Hydrogen into the Natural Gas Network at Caltech
Bloom Energy’s Solid Oxide Fuel Cells (SOFC) have been deployed in 100s of applications across healthcare, data centers, critical man ufacturing, retailers and more. The same proven fuel cell technol ogy that has powered Bloom’s natural gas fleet is being used to generate combustion-free, emissions-free and carbon-free electric ity from hydrogen. The technology enables highly efficient, distrib uted power generation.
Southern California Gas Co. (SoCalGas) is providing resilient, sus tainable solutions to customers. A number of gas utilities have in stalled fuel cells to provide clean, reliable power to various facilities.
Additionally, SoCalGas is collaborating on an initiative to generate and then blend hydrogen into the existing natural gas network at the California Institute of Technology (Caltech). The project will first gen erate hydrogen and then blend it into the university’s existing natural gas network to demonstrate how natural gas infrastructure can be de carbonized, while balancing energy supply and demand. The project is set to launch in late 2022 on the Caltech campus in Pasadena.
A collaboration will utilize Bloom Energy’s solid oxide high-tem perature electrolyzer to generate hydrogen, which will be injected into Caltech’s natural gas infrastructure. The result ing hydrogen blend will then be converted into electricity without combustion through fuel cells downstream of the SoCalGas meter, producing electricity for a portion of the university. Using grid power to make H2 from water to then put the H2 into a 40-60% efficient fuel cell to make electric does not really make sense. Its more to prove a concept for future green hydrogen.
At scale, the electrolyzer and fuel cell com bination could enable long-duration clean en
ergy storage and low-carbon distributed power generation through the gas network for businesses, residential neighborhoods, and dense urban areas. When configured as microgrids, fuel cells provide resil ient power when and where energy is needed most, protecting busi nesses, campuses or neighborhoods from widespread power outages.
“We need to pursue a diverse set of decarbonization levers,” said Maryam Brown, president, SoCalGas in a press release. “Projects like this expand and accelerate clean fuel initiatives, which will help decarbonize California faster.”
High-temperature electrolyzers produces hydrogen more efficient ly than low-temperature PEM and alkaline electrolyzers. Because it operates at high temperatures, the Electrolyzer requires less energy to break up water molecules and produce hydrogen. Electricity ac counts for nearly 80% of the cost of hydrogen from electrolysis. By using less electricity, hydrogen production becomes more economi cal and will accelerate adoption. The Electrolyzer is also designed to produce green hydrogen from 100 percent renewable power.
SoCalGas is actively engaged in more than 10 pilot projects re lated to hydrogen and also is evaluating the potential to use exist ing infrastructure for transporting hydrogen through testing and demonstration at its engineering analysis center and is collaborat ing with California’s other gas utilities and research institutions to develop a hydrogen blending standard for regulatory review.
Demonstrations provide path to commercialization
This project is a good example of corporate and education institutions coming together to further energy initiatives. By demonstrating how hydrogen can be blended with natural gas, it gives the industry a proof point in the transition to net zero. GT
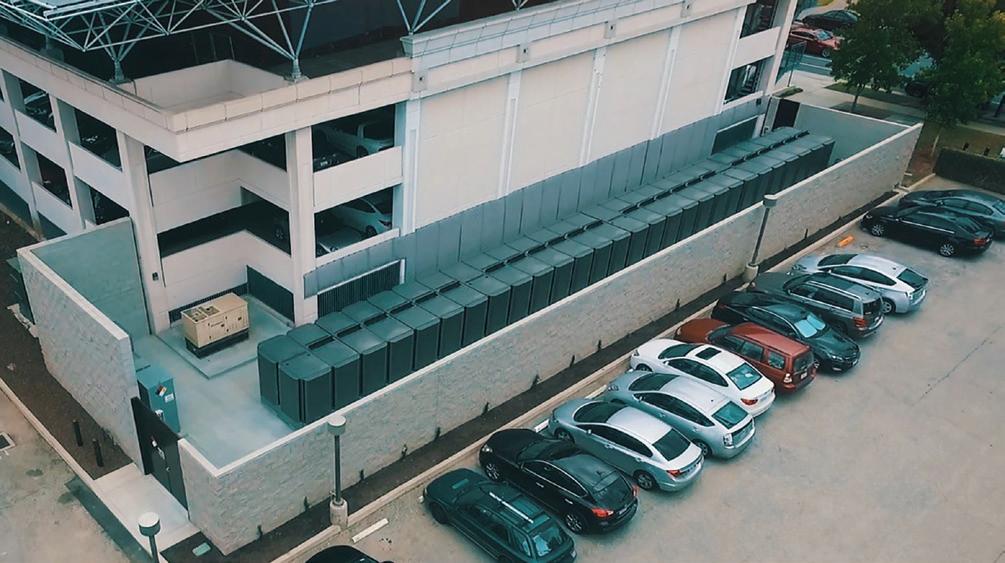
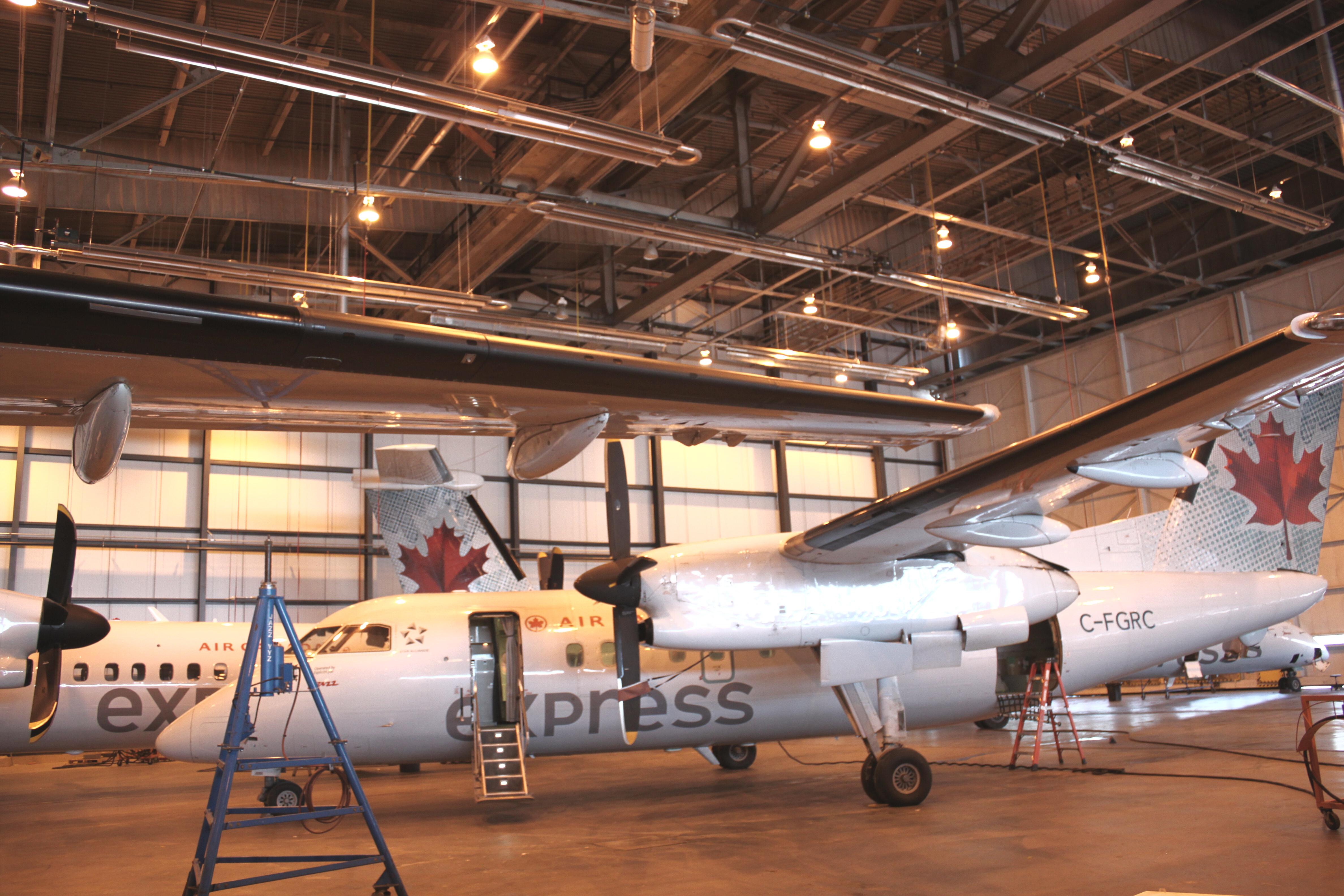

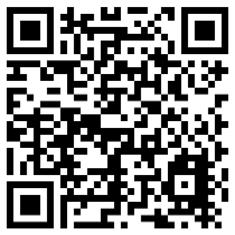
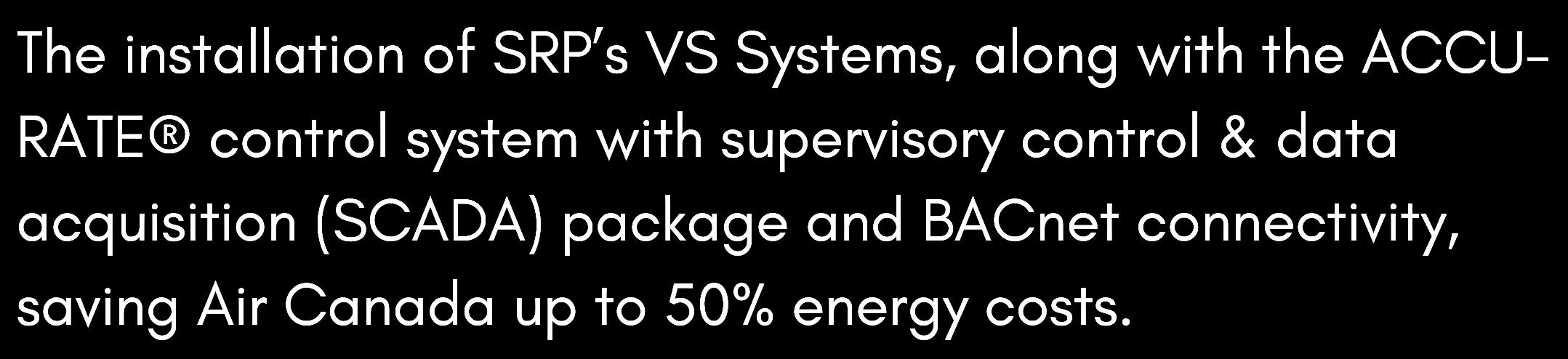


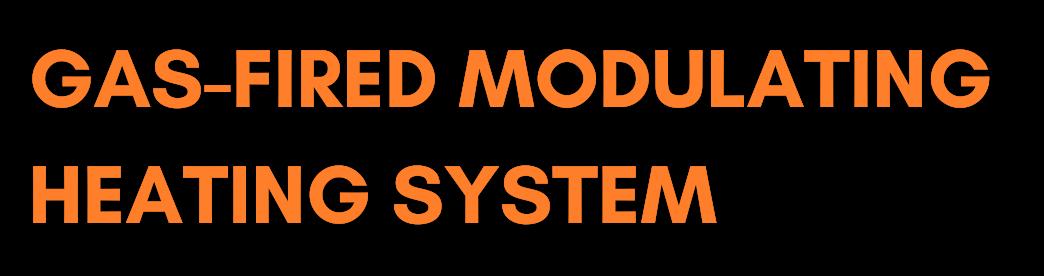
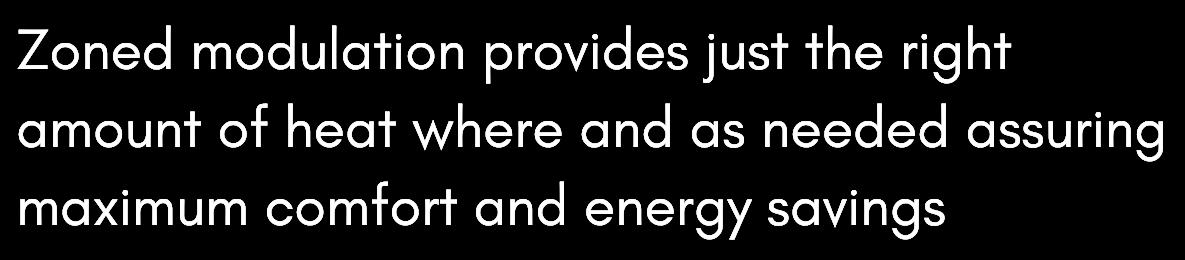
